Title 7
PART 1924 APPENDIX
With slab on grade | With crawl space | With basement | |
---|---|---|---|
1. Excavation | 3 | 5 | 6 |
2. Footings, foundations columns | 8 | 8 | 11 |
3. Floor slab or framing | 6 | 4 | 4 |
4. Subflooring | 0 | 1 | 1 |
5. Wall framing, sheathing | 7 | 7 | 6 |
6. Roof and ceiling framing, sheathing | 6 | 6 | 5 |
7. Roofing | 5 | 5 | 4 |
8. Siding, exterior trim, porches | 7 | 7 | 6 |
9. Windows and exterior doors | 9 | 9 | 8 |
10. Plumbing - roughed in | 3 | 2 | 3 |
11. Sewage disposal | 1 | 1 | 1 |
12. Heating - roughed in | 1 | 1 | 1 |
13. Electrical - roughed in | 2 | 2 | 2 |
14. Insulation | 2 | 2 | 2 |
15. Dry wall or plaster | 8 | 8 | 7 |
16. Basement or porch floor, steps | 1 | 1 | 6 |
17. Heating - finished | 3 | 3 | 3 |
18. Flooring | 6 | 6 | 5 |
19. Interior carpentry, trim, doors | 6 | 6 | 5 |
20. Cabinets and counter tops | 1 | 1 | 1 |
21. Interior painting | 4 | 4 | 3 |
22. Exterior painting | 1 | 1 | 1 |
23. Plumbing - complete fixtures | 4 | 4 | 3 |
24. Electrical - complete fixtures | 1 | 1 | 1 |
25. Finish hardware | 1 | 1 | 1 |
26. Gutters and downspouts | 1 | 1 | 1 |
27. Grading, paving, landscaping | 3 | 3 | 3 |
Total | 100 | 100 | 100 |
Exhibit B to Subpart A of Part 1924 - Requirements for Modular/Panelized Housing Units
7:12.1.2.7.16.1.1.17.26 :
Exhibit B to Subpart A of Part 1924 - Requirements for Modular/Panelized Housing UnitsFor the benefit of the Agency this exhibit prescribes evaluation, acceptance, inspection and certification procedures formodular/panelized housing units proposed for use in Agency Rural Housing programs. It applies to proposed development packages provided either under a contract between an Agency borrower and a single contractor or under a conditional commitment. This exhibit also describes the use of background information available through the Department of Housing and Urban Development (HUD) for analysis of manufactured products. This exhibit also applies to the evaluation of manufactured farm service buildings in paragraph XI, below. For the purpose of this exhibit, County Supervisor and County Office also mean District Director and District Office, respectively.
I. Applicable Standards and Manuals.
A. The HUD Handbook 4950.1, Technical Suitability of Products Program Technical and Processing Procedures, must be followed by housing manufacturers to obtain acceptance of their products. Acceptance documents issued by HUD include: Structural Engineering Bulletins (SEB) on a national basis, Area Letters of Acceptance (ALA) which when accepted by all Area HUD Offices in a HUD region will, in essence, become Regional Letters of Acceptance (RLA), Truss Connector Bulletins (TCB): and, Mechanical Engineering Bulletins (MEB). These documents as well as the Use of Material Bulletins (UM) and Materials Release Bulletins (MR) are addendums to the HUD Minimum Property Standards (MPS), Under handbook guidelines, HUD also examines state agency regulations concerning design, construction and labeling of modular/panelized housing units and designates those states having procedures acceptable for use under HUD programs. Modular/panelized housing produced in these states is called Category III and is considered technically suitable for use without further structural analysis.
B. All Agency Offices should maintain a close working relationship with each HUD office in their jurisdiction to assure coordination. Any deviations in structure, materials or design from HUD acceptance documents must comply with one of the other applicable development standards.
II. Modular Housing Units that Require Factory Inspections.
Only those types which cannot be completely inspected on site are required to obtain acceptance from HUD. Those that receive acceptance will be periodically factory inspected by HUD or HUD's designated agency, usually about every 6 months.
III. Panelized Housing Units that Do Not Require Factory Inspections.
A. Housing completely assembled on the building site does not require HUD acceptance. This includes housing that is manufactured but is assembled on the site such as: Precut pieces, log wall houses, trussed roof rafters or floor trusses; open panel walls, and other types that can be completely inspected on site.
B. Housing that is assembled in local materials dealers' yards for moving to local sites and to be purchased by an Agency applicant, will be inspected during construction in the yard by the local Agency County representative. These units must be constructed according to the applicable development standard and not transported out of the local Agency County Office jurisdiction. The inspection must be recorded on Form RD 1924-12, “Inspection Report.”
IV. Manufacturer's Actions Required for Submissions to the Agency are listed in attachment 1 to this exhibit B.
V. State Agency Office Actions when Manufacturing Facilities are in its Jurisdiction. The State Office, upon receipt of manufacturer's submission, must:
A. Determine that the unit structural system has been accepted by HUD as appropriate under HUD Handbook 4950.1 requirements.
B. Review the thermal characteristics and approach of the calculations to determine actions to be taken in compliance with paragraph IV C of exhibit D of this subpart.
C. Review the proposal for compliance with § 1924.5(d)(1) of this subpart.
D. Determine that the prerequisites for consideration of acceptance by the Agency are met. The prerequisites include all of the following:
1. A current acceptance document from HUD (SEB, RLA, ALA), except for Category III housing (modular/panelized housing that does not have to have a Structural Engineering Bulletin as designated by HUD). In Category III states, the state government requirements for manufactured housing must be followed.
2. A current HUD Factory Inspection Report, Form No. 2051m, or in the case of Category III housing, a copy of the inspection report from the state government or accepted third party performing the factory inspection. Each report must be made by HUD or a HUD authorized agency, and must be no older than 6 months.
3. A letter from the manufacturer requesting a review for acceptance. Enclosed with the letter shall be all the information listed in attachment 1 to this exhibit B.
E. Issue acceptance letters to the manufacturer stating the conditions of acceptance in the format of attachment 2 to this exhibit B. The letter shall have an attachment listing all models accepted in the format of attachment 3 to this exhibit B. A copy of the acceptance letter and list of models shall be sent to each County Office in the state and, when requested by the manufacturer, to each other Agency State Office in which the product is to be marketed.
F. After initial review of a submission, maintain a master file of accepted manufacturers and models and review the file twice yearly to determine the currency of the factory inspection reports and HUD or state government acceptance documents.
G. Notify manufacturers of overdue factory inspection reports, for acceptance of documents review and updating, using the format of attachment 4 to this exhibit B. Accompanying the notification will be a temporary acceptance sheet (Attachment 3 to this exhibit B) indicating to the manufacturer that the company models have temporary acceptance for 60 days. If the manufacturer provides evidence that a review is being processed by HUD, a maximum of an additional 90 days may be granted. Otherwise, the acceptance shall terminate on the last extension date and it will be necessary for the manufacturer to resubmit as if for initial acceptance.
H. Distribute a list of added models, deleted models, or notice of deletion of any manufacturer's product to the County Offices and other State Agency Offices as necessary.
I. Issue an initial supply of Manufacturer's and Builder's Certification forms (Attachment 5 to this exhibit B) to each existing and newly accepted manufacturer. Manufacturers are to duplicate this form as necessary in their market areas.
J. Resolve any problems with the manufacturer, as reported by the County Office. Action may include coordination, Agency plant inspections or cancellation of acceptance letters when problems persist.
VI. County Office Actions:
A. When an application is received involving any of the manufacturer's products on the accepted list, the County Office Agency authorized personnel will:
1. Review the drawings and description of materials described in paragraphs A and B of attachment 1 to this exhibit B. The floor plans and elevations must be identifiable with the model listed in the accepted list issued by the State Office.
2. Require the builder/dealer or manufacturer to provide any drawings necessary to adapt the house to the site conditions where the house will be located.
3. Require site plan drawing such as those illustrated in attachments 1 and 2 to exhibit C of this subpart (available in any Agency office).
4. Inspect and identify the model delivered against the manufacturer's certification and the accepted drawings and description of materials before the unit has been set on the foundation.
5. Require the builder/dealer to certify that the work for which the builder/dealer is responsible has been erected in compliance with the applicable development standard. This certification will be completed on a copy of attachment 5 to this exhibit B, and filed in County Office case file.
6. Observe any noncompliance with the applicable development standard or with paragraphs IV and V of this exhibit B. In this respect:
a. Minor noncompliance will be resolved by the manufacturer through the builder/dealer. In cases where there is no builder/dealer, the County Office may resolve such issues with the manufacturer directly.
b. Noncompliance that cannot be resolved at the County Office level will be reported to the State Office.
7. Inspect manufactured housing according to § 1924.8(d) of this subpart.
8. Be aware that the accepted list may include many models from which loan applicants may choose. No changes from accepted model designs are permitted. The model selected by an applicant should be appropriate to the needs of that particular family in accordance with 7 CFR part 3550.
VII. Noncompliance Issues.
A. When minor issues are noted, the County Office will attempt to resolve them as described above. If they cannot be resolved locally, they will be referred to the State Office. When any issues cannot be resolved at State Office level, the National Office Program Support Staff (PSS) will be contacted for guidance.
B. The National Office PSS coordinating with HUD, will take the appropriate actions to resolve the issues reported.
C. Manufacturers and builder/dealers must be aware that if the Agency inspector finds any of the following conditions, the inspector may refuse to accept the construction until corrections have been made:
1. Evidence of noncompliance with any option of the method described in the HUD - SEB, RLA, or ALA.
2. Faulty shop fabrication, including surface defects.
3. Damage to shop fabricated items or materials due to transportation, improper storage, handling or assembly operation.
4. Unsatisfactory field or site workmanship.
VIII. Actions by Other State Offices. When a State Office receives a copy of the accepted list from the State Office in which a manufacturing plant is located, it will:
A. Maintain a file, by manufacturer, of each accepted list of models.
B. Provide copies of the accepted list of models to each County Office in the State.
C. Request a copy of the drawings, description of materials, and thermal calculations to determine compliance with the thermal requirements for the county in which the house is to be located according to exhibit D of this subpart.
D. Check to see that County Offices within the state will act as prescribed in paragraph VI of this exhibit B.
E. When two or more State Offices have different interpretations of the acceptability of a particular model, there must be an agreement between the states so that they will have the same requirements. If the states cannot agree, the National Office PSS will be consulted for guidance.
IX. Subsequent Review.
The Agency will make periodic reviews of houses, both site-built and houses manufactured offsite, to determine acceptability of the finished product. If, in the judgment of the Agency, the product has failed to perform satisfactorily, acceptance may be withdrawn. The State Director will notify the manufacturer and/or the builder/dealer of the reasons for the withdrawal no later than the time of withdrawal. Negotiations for corrections will be carried out by the County Office with the assistance of the State Office or National Office, as necessary.
X. Materials and Products Acceptance - Material Release Bulletins, Use of Materials Bulletins, Manufacturer's Instructions.
A. The Materials Release (MR) and Use of Materials Bulletins (UM) provide for the national acceptance of specific nonstandard materials and products not covered in the current HUD MPS.
B. When contractors or builders intend to use products or materials not listed as approved in the MPS, the Agency personnel reviewing or concerned with the approval of construction in which the product is to be used, will require the contractor or builder to furnish a Materials Release Bulletin or Use of Materials Bulletin on the materials or products. If the product has been accepted, the supplier should be able to obtain the bulletin for the contractor or builder from the manufacturer. These bulletins describe the products or materials limitations to use, method of installing or applying, approved type of fasteners, if used, etc. and will provide the contractor with instructions as to proper installation or application.
C. When Agency personnel are unfamiliar with any materials or products which have been accepted in the MPS, they will request the contractor or builder to furnish the manufacturer's instructions to assure that the materials or products are properly installed or applied. Any questions on any product that cannot be resolved in the County Office should be referred to the State Office. When the question cannot be resolved at the State Office level, the National Office PSS should be consulted for guidance.
XI. Manufactured Farm Service Buildings.
A. When a loan application is received that involves a manufactured building or special equipment that cannot be completely inspected on the site, the local State Land Grant University recommendations should be requested.
B. When the County Office questions the advisability of making a loan on a manufactured building, the State Office should also be consulted.
C. The State Office should review and make recommendations to the County Office. If doubt still exists, the National Office PSS should be consulted for guidance.
Attachment 1 - Required Information for Acceptance of Modular/Panelized Housing UnitsThe manufacturer or sponsor of modular/panelized housing units wishing to participate in the Agency Rural Housing programs shall submit to the Agency State Director having jurisdiction over the state in which the proposed housing is to be manufactured, two complete sets of the information listed below for evaluation. Submissions not including all the information requested will be returned.
A. Statements:
1. Name and location of organization, including titles and names of its principal officers.
2. A brief description of plant facilities.
3. Extent of intended market distribution, including a list of any other states in which units will be marketed.
4. The method of quality control during site installation.
5. A copy of the applicable current HUD Structural Engineering Bulletin (SEB), Regional Letter of Acceptance (RLA), or Area Letter of Acceptance (ALA).
6. A current factory inspection report made within 6 months by HUD or HUD authorized agency.
7. Name and address of any third party inspection agency.
8. Location of nearest assembled product for inspection.
9. Field manuals for site installation and/or set-up procedures.
10. Specifications or descriptions of materials using either Form RD 1924-2, (HUD-FHA Form 2005), “Description of Materials,” including sizes, species and grade of all building and finishing materials. All blanks should be filled and additional sheets may be attached as well as equipment manufacturer's brochures. Use an asterisk (*) to denote all items of onsite construction that will be provided by the builder-dealer. The builder-dealer must complete a form for the builder-dealer's portion of the work. Use N/A in any blank which is not applicable.
11. Names and addresses of other public and private agencies which have rendered or been asked to render a technical suitability or acceptance determination with respect to the products or structural methods employed.
12. Written certification that construction drawings and specifications conform with the applicable development standard.
13. Any other pertinent information.
14. An index of all documents submitted.
B. Working Drawings. For emphasis as to the details required for modular/panelized housing proposals, the following items are listed in addition to and in more detail than the requirements in exhibit C of this subpart. In some cases, the drawing presentation sheets may be required to be reduced to 200 mm by 266 mm (8 × 10 1/2 inches) sheet size:
1. Foundation and/or Basement Plan. This plan shall include anchorage details, exterior and interior dimensions, typical footings, wall thickness, pilaster sizes and locations, column or pier sizes and locations and girders required to support the structures. Show location of all equipment (furnace, water heater, laundry tubs, sump, etc.) floor drains, electrical outlets, electrical entrance panels, and all doors and windows or crawl space vents with all sizes indicated.
2. Floor Plans of all levels. Show square footage of each habitable room with square footage of each area of natural light and ventilation. In addition, a design sketch scaled properly to illustrate a typical furniture arrangement for all habitable levels is required to indicate intended occupancy functions of the design. A window and door schedule should also be provided indicating glazed size, sash size, and thermal conductance of each type.
3. All exterior elevations including opening and sizes; wall finish materials, flashing, finish grades intended, depth of footings when known, finish floor, ceiling heights, roof slope, location of downspouts, gutters, vents for both structural spaces and for equipment. Indicate construction joint locations and details of connections between sections, modules or components.
4. Building cross sections showing size and spaces of all framing members from lowest member (bottom of footing) to highest point of roof (ridge) plus;
(a) Type of material and method of application of all covering materials, such as subflooring, combination subflooring and underlayment, sheathing, interior and exterior finishes;
(b) Complete details including computations of trussed rafter systems with the architect/engineer's stamp of those responsible for the design.
(c) Details of insulation and vapor barrier installation and attic ventilation. If the thermal characteristics to be provided are determined according to optional method for overall structure performance allowed in exhibit D of this subpart, the submission and complete engineering calculations with all details of construction shall be sent to Administrator, Attn. PSS, U.S. Department of Agriculture, Washington, DC 20250, for analysis as prescribed in paragraph IV C of exhibit D of this subpart.
(d) Special details as necessary to show any special features of construction, including method of fabricating, erection, joining, and finishing of all elements; and
(e) Details and sections of stairways including all critical dimensions, such as, riser, run and headroom.
5. Interior elevations of kitchen cabinets and bathroom elevations with schedule of all shelf, counter-top and drawer footage. Indicate whether kitchen cabinets are to be custom made for each model or made for any model by a cabinet manufacturing company.
6. Plumbing schematics, including pipe materials, sizes and plumbing code compliance.
7. Heating plan, including heat loss of each room, is needed for heating systems, sizings and capacities, forced air, electric baseboard, or electric space heaters and, if applicable, heat gain. For forced air systems, include supply and return duct layout and location of appropriate diffusers.
8. Electrical plan, including circuit chart or diagram.
9. Any other pertinent facts or drawings that will better explain why and how certain unusual materials or structural methods are employed.
Attachment 2 John Dough Manufacturing Company, 3444 Residence Avenue, Elkton, Indiana 00051.Dear Sirs: Athough the documents submitted to this office have only received a cursory review, they appear to be in substantial compliance to qualify your firm for the type of acceptance indicated on the attached list.
The acceptance being issued is subject to this letter of conditions, compliance with HUD Handbook 4950.1 Technical Suitability of Products Program Technical and Processing Procedures, compliance with Agency) Thermal Performance Construction Standards, and compliance with the conditions set forth in the HUD acceptance document, if applicable, whose number appears on the acceptance.
The manufacturer and the authorized builder-dealer bear the responsibility of complying with the above, the exhibits submitted and the applicable development standards.
The manufacturer and/or builder-dealer also shall:
1. Provide positive identification of the modular unit by model, date of manufacture and factory in which the unit was manufactured.
2. Furnish with each home to be financed by the Agency in ___(State)___, a written certificate (Attachment 5 to this exhibit B) endorsed by the builder-dealer certifying that all requirements have been satisfied.
3. Furnish the local Agency County Supervisor with a complete set of drawings including site plans, description of materials, structural engineering bulletins when applicable in the state, and documentation relating to the manufacture, transportation, erection, and installation for each model of modular/panelized housing to be financed in the county. Electrical, plumbing and heating plans must be furnished for each model in addition to the basic drawings. Floor plans and elevation drawings may vary from those listed in attachment 1 of exhibit B to RD Instruction 1924-A to reflect each of the manufacturer's models provided they are in compliance with the applicable development standard and the Agency Thermal Performance Construction Standards and provided they have been accepted and listed in this state's approval of manufactured structures. No field alterations to the accepted models will be allowed.
4. Furnish, when required by the County Supervisor, foundation drawings (including special foundation design considerations when the unit is to be erected in seismic zones 1, 2 or 3) adapting the modular home to any unusual site conditions needing information additional to that furnished by the standard drawings.
5. Furnish the County Office with a copy of inspection reports of the manufacturing facilities immediately after the inspection reports have been completed.
6. Allow RD personnel to inspect the manufacturing facilities at any time and furnish all Agency State Offices, where acceptance has been obtained, with a copy of any Agency inspection reports immediately after the inspection reports have been completed.
7. In the event there are major changes to the submitted drawings, obtain approval under the HUD Technical Suitability of Products Program and submit verification of this approval to the County Office for listing on the state's accepted list. Any modular home shipped with major changes incorporated, without such changes on file at the County Office may be rejected.
(Add state and local requirements appropriate to this letter of conditions.)This acceptance may be subject to corrective action when deficiencies are noted in the product, field inspections, manufacturing facilities, or when there is noncompliance with the provisions of the HUD Technical Suitability of Products Program.
The inclusion of these models on the accepted list is based only on the material and structural aspects of the manufactured units. Final determination of acceptability rests with RD personnel. Other factors relating to the property in its entirety such as appraisal, location, sustained market acceptance, architectural planning and appeal, thermal qualities, mechanical and electrical equipment, etc., must be considered in the final determination.
Your cooperation in this acceptance program is appreciated.
Sincerely,
State Director Attachment 3 Date ___ File No. ___ Acceptance of Modular/Panelized Housing Units (Based on HUD Handbook 4950.1) Manufacturer: ___ Acceptance Document ___ ___ Type of Acceptance: ___ __ Regular ___ __ Temporary, Expires ___ Plant Locations: Date of Latest Plans Reviewed Date of Latest Factory Inspection Acceptance Document Review Date FmHA or its successor agency under Public Law 103-354 Instruction 1924-A, exhibit D Thermal Performance Construction Standards State Office Review (Exh. D, IV, C, 1, a or b) National Office Review (Exh. D, IV, C, 2) Maximum Winter Degree Days for State ___ Walls R ___ Glazing/Gross Wall Area Ratio ___% Ceilings R ___ Glazing ___ Pane(s) Floor R ___ Glazing ___ Pane(s) Insulated Door ___ Wood and Storm ___ Insulated Door ___ Wood and Storm ___ Models Accepted: Attachment 4 John Dough Manufacturing Company, 3444 Residence Avenue, Elktown, Indiana 00051.Dear Sirs: As set forth in acceptance letters issued by this office, acceptance of modular/panelized homes in this state is based on HUD's Technical Suitability of Products Program and the conditions stated in the acceptance letter. Your file has been reviewed and the following has been noted.
__An inspection report of your manufacturing facilities is overdue. Inspections are required twice yearly. The last inspection report on file at this office is dated ___. __Your Structural Engineering Bulletin No. __ dated __ has not been reviewed by HUD. Reviews are generally required every three years. Temporary acceptance will be considered when you provide evidence that the review documents have been submitted to HUD. __The drawings being used for the construction of your homes are not listed in your Structural Engineering Bulletins. Drawings used in the field should be those upon which the Structural Engineering Bulletin was issued. __There have been __ revisions to the development standards since ___, the date of the last drawings we have on file for your homes. It is recommended that you review the revisions to ascertain whether your drawings need to be updated.Please submit a written response and appropriate documents for the above items within __ days, or your product will be removed from the accepted list until your firm can again qualify. If you have any problems furnishing the above within the time stated, please contact this office.
We look forward to receiving the materials indicated so that your firm's listing may be continued.
Sincerely,
State Director Attachment 5 Certification by Manufacturer Delivery location of structure for component This is to certify that Model: ______, Serial # ______, manufactured ___ (date) ___, 19 _ in __ (location) ___ and being sold to ___ (name of ______ builder-dealer or borrower) has been manufactured in accordance with drawings and specifications on file in the Agency State Office and that the construction complies with applicable development standards, except as modified by HUD Acceptance Document (SEB, RLA, ALA,) NO. ______, dated ____, and in compliance with the Agency Thermal Performance Construction Standards. Date Signature of Authorized Official Title Certification by Builder-Dealer ___ (Name of builder-dealer) ___ certifies that the foundation and other on-site work has been constructed in accordance with the drawings and specifications and the above structure or component has been erected, installed or applied in compliance with the applicable development standards.It is understood that the manufacturer's certification does not relieve the builder/dealer of responsibility under the terms of the builder's warranty required by the National Housing Act.
Date Signature of Authorized Official Title [52 FR 8002, Mar. 13, 1987, as amended at 67 FR 78327, Dec. 24, 2002; 80 FR 9872, Feb. 24, 2015]Exhibit C to Subpart A of Part 1924 - Guide for Drawings and Specifications
7:12.1.2.7.16.1.1.17.27 :
Exhibit C to Subpart A of Part 1924 - Guide for Drawings and SpecificationsThis exhibit applies to all new buildings to be constructed, including all single family housing and related facilities and, as applicable, farm housing and farm service buildings.
I. GeneralThe documents recommended in this exhibit correspond with the list of exhibits in Chapter 3 of the Department of Housing and Urban Development (HUD) “Architectural Handbook for Building Single-Family Dwellings” No. 4145.2. This exhibit may be used as a public handout and shall be used as a guide for drawings and specifications to be submitted in support of any type of application involving construction of major new buildings or extensive rehabilitation, alterations or additions to existing buildings. Descriptions of work for minor alterations or repairs need pertain only to work to be done and may be in narrative form when acceptable to the County Supervisor. Complete and accurate drawings and specifications are necessary:
A. To determine the acceptability of the proposed development,
B. To determine compliance with the applicable standards and codes,
C. To prepare a cost estimate, and
D. To provide a basis for inspections and the builder's warranty.
II. Drawings for a Specific StructureDrawings for individual single dwellings shall provide at least the following:
A. Plot Plan. Refer to Example Plot Plan No. 1, attachment 1 to this exhibit C (available in any Agency office). Ratio: 1:240 (1″ = 20′) (at scale, 1″ = 20′ or 1/16″ = 1′ 0″ minimum):
1. Lot and block number.
2. Dimensions of plot and north point.
3. Dimensions of front, rear and side yards.
4. Location and dimensions of garage, carport and other accessory buildings.
5. Location and sizes of walks, driveways and approaches.
6. Location and sizes of steps, terraces, porches, fences and retaining walls.
7. Location and dimensions of easements and established setback requirements, if any.
8. Elevations at the following points: (a) first floor of dwelling and floor of garage, carport and other accessory building; (b) finish curb or crown of street at points of extension of lot lines; (c) finish grade elevation at each principal corner of structure; (d) finish grade at bottom of drainage swales at extension of each side of structure as feasible.
9. The following additional elevations, as applicable, if the topography of the site or the design of the structure is such that special grading, drainage or foundations may be necessary. Examples are irregular or steeply sloping sites, filled areas on sites, or multi-level structure designs; (a) finish and existing grade elevations at each corner of the plot; (b) existing and finish grade at each principal corner of dwelling; (c) finish grade at both sides of abrupt changes of grade such as retaining walls, slopes, etc.; (d) other elevations that may be necessary to show grading and drainage.
10. Indication of type and approximate location of drainage swales.
11. When an individual water supply and/or sewage system is proposed, drawings, specifications and other items prescribed in paragraph V of this exhibit.
B. Floor Plans.
1. Scale, 1:50 ( 1/4″ = 1′ 0″).
2. Floor plan of each floor and basement, if any. Show typical furniture locations to suggest intended use of each habitable space.
3. Plan of all attached terraces and porches, and of garage or carport.
4. If dwelling is of crawl-space type, a separate foundation plan. Slab-type foundation may be shown on sections.
5. Direction, size and spacing of all floor and ceiling framing members, girders, columns or piers.
6. Location of all partitions and indication of door sizes, and direction of door swing.
7. Location and size of all permanently installed construction and equipment such as kitchen cabinets, closets, storage shelving, plumbing fixtures, water heaters, etc. Details of kitchen cabinets may be on separate drawing.
8. Location and symbols of all electrical equipment, including switches, outlets, fixtures, etc.
9. Heating system on separate drawing, or when it may be shown clearly it may be part of the floor or basement plan showing: (a) layout of system; (b) location and size of ducts, piping, registers, radiators, etc.; (c) location of heating unit and room thermostat; (d) total calculated heat loss of dwelling including heat loss through all vertical surfaces, ceiling and floor. When a duct or piped distribution system is used, calculated heat loss of each heated space is required.
10. Cooling system, on separate drawings or, as part of heating plan, floor or basement plan showing: (a) layout of system; (b) location and size of ducts, registers, compressors, coils, etc.; (c) heat gain calculations, including estimated heat gain for each space conditioned; (d) model number and Btu capacity of equipment or units in accordance with applicable Air Conditioning and Refrigeration Institute (ARI) or American Society of Refrigerating Engineers (ASRE) Standard; (e) Btu capacity and total kilowatt (KW) input at stated local design conditions; (f) if room or zone conditioners are used, provide location, size and installation details.
C. Exterior Elevations.
1. Scale, 1:50 ( 1/4″ = 1′ 0″). Elevations, other than main elevation, which contain no special details may be drawn at 1:100 ( 1/8″ = 1′ 0″).
2. Front, rear and both side elevations, and elevations of any interior courts.
3. Windows and doors - indicate size unless separately scheduled or shown on floor plan.
4. Wall finish materials where more than one type is used.
5. Depth of wall footings, foundations, or piers, if stepped or at more than one level.
6. Finish floor lines.
7. Finish grade lines at buildings.
D. Details and Sections.
1. Section through exterior wall showing all details of construction from footings to highest point of road. Where more than one type of wall material is used, show each type. Scale 1:25 ( 3/8″ = 1′ 0″) minimum.
2. Section through any portion of dwelling where rooms are situated at various levels or where finished attic is proposed, Scale, 1:50 ( 1/4″ = 1′ 0″) minimum.
3. Section through stair wells, landings, and stairs, including headroom clearances and surrounding framing. Scale, 1:50 ( 1/4″ = 1′ 0″) minimum.
4. Details of roof trusses, if proposed, including connections and stress or test data with seal of architect or engineer responsible. Scale of connections, 1:25 ( 3/8″ = 1′ 0″) minimum.
5. Elevation and section through fireplace. Scale, 1:25 ( 3/8″ = 1′ 0″) minimum.
6. Elevations and section through kitchen cabinets, indicating shelving. Scale, 1:50 ( 1/4″ = 1′ 0″) minimum.
7. Sections and details of all critical construction points, fastening systems, anchorage methods, special structural items or special millwork. Scale as necesaary to provide information, 1:25 ( 3/8″ = 1′ 0″) minimum.
III. Master Drawings for Group StructuresDrawings for a group of structures (such as for several conditional commitments) may be submitted in lieu of drawings for each individual property when a number of applications are simultaneously submitted involving repetition of the same type structure.
A. Master plot plan shall include the following:
1. Scale which will provide the following information in a clear and legible manner.
2. North point.
3. Location and width of streets and rights-of-way.
4. Location and dimensions of all easements.
5. Dimensions of each lot.
6. Location of each dwelling on lot with basic dimensions.
7. Dimensions of front, rear and side yards.
8. Location and dimensions of garage, carports and other accessory buildings.
9. Identification of each lot by number and indication of basic plan and elevation type.
10. Location of walks, driveways and other permanent improvements.
B. Typical plot plan for each basic type dwelling may be submitted in lieu of fully detailing each lot on master plot plan, when topography and lot arrangements present no individual planning or construction problems.
1. Information not shown on the typical plot plan shall be included on the master plot plan.
2. Typical plot plans shall not be used for corner lots, lots with irregular boundaries, lots involving pronounced topographic variations or other lots where individual detailing is necessary.
3. Location of dwelling on typical lot and full dimensions.
4. Location and dimensions of all typical improvements, such as garage, carport, accessory buildings, walks, drives, steps, porches, terraces, trees, shrubs, retaining walls, fences, etc.
C. Grading may be shown on separate grading plan or on the master plot plan. Scale shall be sufficiently large to provide the following information in clear and legible manner:
1. Contours of existing grade at intervals of not more than 1.524 m (5 feet). Intervals less the 1.524 m (5 feet) may be required when indicated by the character of the topography.
2. Location of house and accessory buildings on each lot.
3. Identification of each lot by number.
4. Elevations in accordance with individual plot plan including bench mark and datum or, in lieu of finish grade elevations, contours of proposed finish grading may be submitted. Contour intervals selected shall be appropriate to the topography of the site.
5. Lot grading shall be shown by indicating protective slopes and approximate location of drainage swales.
6. Location of drainage outfall, if any drainage is not to a street.
D. Floor plans, elevations, sections and details shall be submitted for each basic plan. Alternate elevations to basic plan may be shown at scale, 1:100 ( 1/8″ = 1′ 0″).
IV. SpecificationsForm RD 1924-2, “Description of Materials,” or other acceptable and comparable descriptions of all materials forms shall be submitted with the drawings. The forms shall be completed in accordance with the instructions on Form RD 1924-2 to describe the materials to be used in the construction.
A. Form RD 1924-2 may be reproduced if size, format and printed text are identical to the current official form. When it is reproduced, the following deletions must be made:
1. All lines indicating RD form numbers or other Government agency initials and/or numbers, and
2. The United States Government Printing Office (GPO) imprint and reference number.
B. The material identification shall be in sufficient detail to fully describe the material, size, grade and when applicable, manufacturer's model or identification numbers. When necessary, additional sheets must be attached as well as manufacturer's specification sheets for equipment and/or special materials, such as aluminum siding or carpeting.
V. Individual Water Supply and Sewage Disposal SystemsWhen an individual water and/or sewage disposal system is proposed, the following additional information must be submitted:
A. Approval and recommendations of other authorities.
1. A written opinion by the health authority having jurisdiction that the site is suitable and acceptable for the proposed systems(s) and,
2. If available, a soils report from the local USDA-Soil Conservation Service and any recommendations they may have.
3. Approval of appropriate environmental control authority.
4. A signature of the health authority on the plot plan indicating approval of the design of the proposed system.
B. Plot Plan. Refer to Example Plot Plan No. 2, attachment 2 to this exhibit C (available in any Agency office).
1. Location and size of septic tank, distribution box, absorption field or bed, seepage pits and other essential parts of the sewage disposal system and distance to all individual wells, open streams or drainageways.
2. Location of well, service line and other essential parts of the water supply system and distance to other wells and/or sewage disposal systems.
3. Exact location of individual systems (water or sewage) on adjacent properties and description of system, if available.
C. Construction details of all component parts of individual water supply and sewage disposal systems shall clearly indicate material, equipment and construction. Extra sheets and drawings should be added as necessary to fully explain the proposed installation.
Exhibit D to Subpart A of Part 1924 - Thermal Performance Construction Standards
7:12.1.2.7.16.1.1.17.28 :
Exhibit D to Subpart A of Part 1924 - Thermal Performance Construction Standards I. PurposeThis exhibit prescribes thermal performance construction standards to be used in all housing loan and grant programs. These requirements shall supersede the thermal performance requirements in any of the development standards in § 1924.4(h) of this subpart.
II. PolicyAll loan or grant applications involving new construction (except for new Single Family Housing (SFH)) and all applications for conditional commitments (except for new SFH) shall have drawings and specifications prepared to comply with paragraphs IV A or C and IV D of this exhibit. All new SFH construction shall have drawing and specifications prepared to comply with paragraph IV F of this exhibit.
III. DefinitionsA. British thermal unit (Btu) means the quantity of heat required to raise the temperature of one pound (.4535 Kg.) of water by one degree Fahrenheit (F). For example, one Btu is the amount of heat needed to raise the temperature of one pound of water from 59 degrees F to 60 degrees F.
B. Glazing is the material set into a sash or door when used as a natural light source and/or for occupant's views of the outdoors.
C. “R” value, thermal resistence, is a unit of measure of the ability to resist heat flow. The higher the R value, the higher the insulating ability.
D. “U” value is the overall coefficient of heat transmission and is the combined thermal value of all the materials in a building section. U is the reciprocal of R. Thus U = 1/R or R = 1/U or 1/C where C is the thermal conductance and is the unit of measure of the rate of heat flow for the actual thickness of a material one square foot in area at a temperature of one degree Fahrenheit. The lower the U value, the higher the insulating ability.
E. Winter degree-day is a unit based on temperature difference and time. For any one day, when the mean temperature is less than 65 degrees F (18.3 degrees Celsius), there are as many degree-days as the number of degrees difference between the mean temperature for the day and 65 degrees F. The daily mean temperature is computed as half the total of the daily maximum and daily minimum temperatures.
F. CABO Model Energy Code, 1992 Edition (MEC-92) - This code sets forth the minimum energy/thermal requirements for the design of new buildings and structures or portions thereof and additions to existing buildings. The MEC is maintained by the Council of American Building Officials (CABO).
IV. Minimum RequirementsA. All multifamily dwellings to be constructed with Agency loan and/or grant funds and all repair, remodeling, or renovation work performed on single family and multifamily dwellings with Agency loan and/or grant funds shall be in conformance with the following, except as provided in paragraphs IV C 3 and IV D of this exhibit:
New Construction - Maximum U Values for Ceiling, Wall And Floor Section of Various Construction
Winter degree days 1 | Ceilings 2 | Walls | Floors 3 | Glazing 4 | Doors 5 |
---|---|---|---|---|---|
1000 or less | 0.05 | 0.08 | 0.08 | 1.13 | |
1001 to 2500 | .04 | .07 | .07 | .69 | |
2501 to 4500 | .03 | .05 | .05 | .69 | Storm door if hollow core door or if over 25% glass. |
4501 to 6000 | .03 | .05 | .05 | .47 | Storm Door. |
6001 or more | .026 | .05 | .05 | .47 | Storm Door. |
Note. U values are not adjusted for framing. Values calculated for components may be rounded. For example, a total R Value of 18.88 converts to a U value of .0529 rounded to .05.
1 Winter degree-days may be obtained from the ASHRAE Handbook; the “NAHB Insulation Manual for Homes/Apartments”; local utilities; and the National Climatic Center, Federal Building, Asheville, NC. Manuals are available from NAHB RF, Rockville, MD 20850, or NMWIA, 382 Springfield Avenue, Summit, NJ 07901. Other sources of degree day data may be used if available from a recognized authority.
2 Insulation must be continuous (i.e. no gaps) above all ceiling joists. In pitched roof construction, compression of insulation at the outside building walls is permitted to allow a 1″ ventilation space under the roof sheathing. For any loose fill insulation, a baffle must be provided. Raised trusses are not required.
3 For floors of heated spaces over unheated basements, unheated garages or unheated crawl spaces, the U value of floor section shall not exceed the value shown. A basement, crawl space, or garage shall be considered unheated unless it is provided with a positive heat supply to maintain a minimum temperature of 50 degrees F. Positive heat supply is defined by ASHRAE as “heat supplied to a space by design or by heat losses occurring from energy-consuming systems or components associated with that space.”
Where the walls of an unheated basement or crawl space are insulated in lieu of floor insulation, the total heat loss attributed to the floor from the heated area shall not exceed the heat loss calculated for floors with required insulation.
Insulation may be omitted from floors over heated basement areas or heated crawl spaces if foundation walls are insulated. The U value of foundation wall sections shall not exceed the value shown. This requirement shall include all foundation wall area, including header joist (band joist), to a point 50 percent of the distance from a finish grade to the basement floor level. Equivalent Uo configurations are acceptable.
Maximum U Values of the Foundation Wall Sections of Heated Basement Not Containing Habitable Living Area or Heated Crawl Space
Winter degree-days (65 F base) | Maximum U value | Glazing* |
---|---|---|
2500 or less | No requirement | 1.13 |
2501 to 4500 | 0.17 | 1.13 |
4501 or more | 0.10 | .69 |
* Glazing in heated basement shall be limited to 5 percent of floor area unless alternative Uo combination is documented.
4 Sliding glass doors are considered as glazing. The glazing value is for glass only. Glazing shall be limited to 15 percent of the gross area of all exterior walls enclosing heated space, except when demonstrated that the winter daily solar heat gain exceeds the heat loss and the glass area is properly screened from summer solar heat gain.
5 1 3/4 inch metal-faced door systems with rigid insulation core and durable weatherstripping providing a “U” value equivalent to a wood door with storm door and an infiltration rate no greater than .50 cfm per foot of crack length tested according to ASTM E-283 at 1.567 psf of air pressure, may be substituted for a conventional door and storm door. All doors shall be weatherstripped. Any glazed areas must be double-glazed.
Minimum R Values of Perimeter Insulation for Slabs-on-Grade
Winter degree-days (65 F base) | Minimum R values* | |
---|---|---|
Heated slab | Unheated slab | |
500 or less | 2.8 | |
1000 | 3.5 | |
2000 | 4.0 | 2.5 |
3000 | 4.8 | 2.8 |
4000 | 5.5 | 3.5 |
5000 | 6.3 | 4.2 |
6000 | 7.0 | 4.8 |
7000 | 7.8 | 5.5 |
8000 | 8.5 | 6.2 |
9000 | 9.2 | 6.8 |
10000 or greater | 10.0 | 7.5 |
* For increments between degree days shown, R values may be interpolated.
B. [Reserved]
C. Optional Standards
Housing design not in compliance with the requirements of paragraph IV A of this exhibit may be approved in accordance with the provisions of this paragraph. Requests for acceptance proposed under paragraph C 1 of this exhibit, must be approved by the State Director. Requests for acceptance of site-built housing proposed under paragraph C 2 of this exhibit must be approved by the Administrator. Requests for acceptance of manufactured housing proposed under paragraph C 2 of this exhibit may be approved by the State Director. All submissions of proposed options to the State Director or Administrator shall contain complete descriptions of materials, engineering data, test data (when U values claimed are lower than the ASHRAE Handbook of Fundamentals), and calculations to document the validity of the proposal. All data and calculations will be based upon the current edition of the ASHRAE Handbook of Fundamentals or other universally accepted data sources.
1. Overall “U” values for enveloped components. The following requirements shall be used in determining acceptable options to the requirements of paragraph IV A of this exhibit.
a. Uo (gross wall) - Total exterior wall area (opaque wall and window and door) shall have a combined thermal transmittance value (Uo value) not to exceed the values shown in attachment 1 to this exhibit D (available in any Agency office). Equation 1 in attachment 1 shall be used to determine acceptable combinations to meet the requirements.
b. Uo (gross ceiling) - Total ceiling area (opaque ceiling and skylights) shall have a combined thermal transmittance value (Uo value) not to exceed the values shown in attachment 2 to this exhibit D (available in any Agency office). Equation 2 in attachment 2 shall be used to determine acceptable combinations to meet the requirements.
2. Overall structure performance. The following requirements shall be used in determining acceptable options to the requirements of paragraph IV A of this exhibit.
a. The methodology must be cost effective to the energy user, and must not adversely affect the structural capacity, durability or safety aspects of the structure.
b. All data and calculations must show valid performance comparisons between the proposed option and a structure comparable in size, configuration, orientation and occupant usage designed in accordance with paragraph IV A. Structures may be considered for Agency loan consideration which can be shown by accepted engineering practice to have energy consumption equal to or less than those which would be attained in a representative structure utilizing the requirements of paragraph IV A.
3. Special consideration for seasonally occupied farm labor housing. The following sets forth the minimum acceptable options to the requirements of paragraph IV A of this exhibit for seasonally occupied housing serving as security for farm labor housing loans and grants.
a. When the period of occupancy does not encounter 500 or more heating degree-days (HDD) as determined by an average of the previous 10 years based upon local climatological data published by the National Oceanic and Atmospheric Administration, Environmental Data Service, the standards of paragraph IV A will not apply.
b. When the period of use exceeds 500 HDD, the 10-year average value for the period of occupancy shall be used to determine the degree to which the thermal insulation requirements of paragraph IV A shall apply.
c. If mechanical cooling is provided and the period of occupancy encounters more than 700 cooling degree-days (CDD), as determined by an average of the previous 8 years based upon local climatological data published by the same source cited in paragraph IV C3a above, the thermal insulation requirements for 1,000 and less degree-days as stated in paragraph IV A shall apply.
D. Energy efficient construction practices. This section prescribes those items of design and quality control which are necessary to guarantee the energy efficiency of homes built according to the standards of this exhibit. Also included are recommendations for extra energy efficiency in dwellings. This section does not apply to new SFH construction.
1. Infiltration. a. Requirements: All construction shall be performed in such a manner as to provide a building envelope free of excessive infiltration.
(i) Caulking and sealants. Exterior joints around windows and door frames, between wall cavities and window or door frames, between wall and foundation, between wall and roof, between wall panels, at penetrations of utility services through walls, floors and roofs, and all other openings in the exterior envelope shall be caulked, gasketed, weatherstripped, or otherwise sealed. Caulking shall be silicone rubber base or butyl rubber base, conforming to Federal Specifications TT-S-1543 and TT-S-1657 respectively, or materials demonstrating equivalent performance in resilience and durability.
(ii) Windows shall comply with ANSI 134.1, NWMA 15-2; the air infiltration rate shall not exceed 0.5 ft 3/min per ft. of sash crack.
(iii) Sliding glass doors shall comply with ANSI 134.2, NWM 15-3; the air infiltration rate shall not exceed .5 ft 3/min per square ft. of door area.
(iv) All insulation placed in open cavity walls shall be installed so that all space behind electrical switches and receptacles, plumbing, ductwork and other obstructions in the cavity are insulated as completely as possible. Insulation shall be omitted on the side facing the conditioned area; however, the vapor barrier in walls must not be cut or destroyed.
b. Recommendations: (i) Wrap outside corners of wall sheathing with 15 lb. asphalt impregnated building felt before siding application.
(ii) Utilize vestibules for entry doors, especially those facing into the direction of winter wind.
(iii) Install plumbing, mechanical and electrical components in interior partitions as much as possible. All water piping should be insulated from freezing temperatures.
2. Heating and/or Cooling Equipment. a. Requirements: All mechanical equipment for heating and/or cooling habitable space shall be designed to provide economy of operations.
(i) All space heating equipment (including fireplaces) requiring combustion air shall be sealed combustion types, or be located in a nonconditioned area (such as unheated basements) or adequate combustion air must be provided from outside the conditioned space.
(ii) All ductwork shall be designed and installed to minimize leakage. All metal to metal connections shall be mechanically joined and taped.
b. Recommendations: (i) Whenever possible, locate ductwork inside of conditioned areas in dropped ceilings, interior partitions or other similar areas.
(ii) Locate outside cooling units in areas not subject to direct sunlight or heat buildup.
3. Vapor Barrier. a. Requirements: Adequate vapor barriers must be provided adjacent to the interior finish material of the wall or other closed envelope components which do not have ventilation space on the non-conditioned side of the insulation.
(i) A vapor barrier at the inside of the wall or other closed envelope component must have a permeability (perm) rating less than that of any other material in the component and in no case have a perm rating greater than one. All vapor barriers must be sealed around all openings in the interior surface. Vapor barriers are not required in ceilings and floors. Continuous vapor barriers on ceilings, walls, and floors require adequate moisture vapor control in the conditioned space.
(ii) All vapor producing or exhaust equipment shall be ducted to the outside and equipped with dampers. This equipment includes rangehoods, bathroom exhaust fans and clothes dryers. If a dwelling design proposes the use of windows to satisfy the kitchen and/or bathroom ventilation requirements of the development standards, the incorporation of dehumidification equipment should be considered in accordance with paragraph IV D 3 b. Exhaust of any equipment shall not terminate in an attic or crawl space.
b. Recommendation: Forced air heating/cooling systems should include humidification/dehumidification systems where conditions indicate.
E. [Reserved]
F. New SFH construction. New SFH construction shall meet the requirements of CABO Model Energy Code, 1992 Edition (MEC-92).
G. New manufactured housing.
The Uo Value Zone indicated on the “Heating Certificate” for comfort heating shall be equal to or greater than the HUD Zone listed in the following table:
RHS climate zones (winter degree days) | FMHCSS (HUD code) Uo value zones |
---|---|
0-1000 | 1 |
1001-2500 | 2 |
2501-4500 | 2 |
4501-6000 | 3 |
>6000 | 3 |
If a central air conditioning system is provided by the home manufacturer, a “Comfort Cooling Certificate” must be permanently affixed to an interior surface of the unit that is readily visible. This certificate may be combined with the heating certificate on the data plate.
V. General Design Recommendations:
A. Orient homes with greatest glass area facing south with adequate overhangs to control solar gain during non-heating periods. Examples of proper roof overhangs are given in attachment 3 to this exhibit D (available in any Agency office).
B. Arrange plantings with evergreen wind buffers on north side and deciduous trees on south.
C. Whenever possible, orient entry door away from winter winds.
D. Design house with simple shape to minimize exterior wall area.
E. Minimize glass areas within constraints of required light and ventilation, applicable safety codes and other appropriate consideration.
F. Minimize the amount of paved surface adjacent to the structure where heat gain is not desirable.
VI. State Supplements: State supplements or policies will not be issued or adopted to either supplement or set requirements different from those of this exhibit without the prior written approval of the National Office.
[52 FR 8002, Mar. 13, 1987, as amended at 54 FR 6874, Feb. 15, 1989; 59 FR 43723, Aug. 25, 1994; 64 FR 48085, Sept. 2, 1999; 72 FR 70221, Dec. 11, 2007]Exhibit E to Subpart A of Part 1924 - Voluntary National Model Building Codes
7:12.1.2.7.16.1.1.17.29 :
Exhibit E to Subpart A of Part 1924 - Voluntary National Model Building CodesThe following documents address the health and safety aspects of buildings and related structures and are voluntary national model building codes as defined in § 1924.4(h)(2) of this subpart. Copies of these documents may be obtained as indicated below:
Building code | Plumbing code | Mechanical code | Electrical code |
---|---|---|---|
BOCA Basic/National Building Code 1 | BOCA Basic/National Plumbing Code 1 | BOCA Basic/National Mechanical Code 1 | National Electrical Code 5 |
Standard Building Code 2 | Standard Plumbing Code 2 | Standard Mechanical Code 2 | |
Uniform Building Code 3 | Uniform Plumbing Code 3 | Uniform Mechanical Code 3 | |
CABO One and Two Family Dwelling Code 4 |
1 Building Officials and Code Administrators International, Inc., 4051 West Flossmoor Road, Country Club Hills, Illinois 60477.
2 Southern Building Code Congress International, Inc., 900 Montclair Road, Birmingham, Alabama 35213-1206.
3 International Conference of Building Officials, 5360 South Workman Mill Road, Whittier, California 90601.
4 Council of American Building Officials, 5203 Leesburg Pike, Falls Church, Virginia 22041.
5 National Fire Protection Association, Batterymarch Park, Quincy, Massachusetts 02269.
Exhibit F to Subpart A of Part 1924 - Payment Bond
7:12.1.2.7.16.1.1.17.30 :
Exhibit F to Subpart A of Part 1924 - Payment Bond KNOW ALL PERSONS BY THESE PRESENTS: that (Name of Contractor) (Address of Contractor) a ________, (Corporation, Partnership or Individual) hereinafter called PRINCIPAL and (Name of Surety) hereinafter called SURETY, are held and firm bound unto (Name of Owner) (Address of Owner) hereinafter called OWNER and the United States of America acting through the Farmers Home Administration or its successor agency under Public Law 103-354 hereinafter referred to as GOVERNMENT, and unto all persons, firms, and corporations who or which may furnish labor, or who furnish materials to perform as described under the contract and to their successors and assigns in the total aggregate penal sum of ___, ___ Dollars ($___) in lawful money of the United States, for the payment of which sum well and truly to be made, we bind ourselves, our heirs, executors, administrators, successors, and assigns, jointly and severally, firmly by these presents. THE CONDITION OF THIS OBLIGATION is such that whereas, the PRINCIPAL entered into a certain contract with the OWNER, dated the _______ day of ________19__, a copy of which is hereto attached and made a part hereof for the construction of: NOW, THEREFORE, if the PRINCIPAL shall promptly make payment to all persons, firms, and corporations furnishing materials for or performing labor in the prosecution of the WORK provided for in such contract, and any authorized extension or modification thereof, including all amounts due for materials, lubricants, oil, gasoline, coal and coke, repairs on machinery; equipment and tools, consumed or used in connection with the construction of such WORK, and for all labor cost incurred in such WORK including that by a SUBCONTRACTOR, and to any mechanic or materialman lienholder whether it acquires its lien by operation of State or Federal law; then this obligation shall be void, otherwise to remain in full force and effect.PROVIDED, that beneficiaries or claimants hereunder shall be limited to the SUBCONTRACTORS, and persons, firms, and corporations having a direct contract with the PRINCIPAL or its SUBCONTRACTORS.
PROVIDED, FURTHER, that the said SURETY for value received hereby stipulates and agrees that no change, extension of time, alteration or addition to the terms of the contract or to the WORK to be performed thereunder or the SPECIFICATIONS accompanying the same shall in any way affect its obligation on this BOND, and it does hereby waive notice of any such change, extension of time, alteration or addition to the terms of this contract or to the WORK or to the SPECIFICATIONS.
PROVIDED, FURTHER, that no suit or action shall be commenced hereunder by any claimant: (a) Unless claimant, other than one having a direct contract with the PRINCIPAL (or with the GOVERNMENT in the event the GOVERNMENT is performing the obligations of the OWNER), shall have given written notice to any two of the following: The PRINCIPAL, the OWNER, or the SURETY above named within ninety (90) days after such claimant did or performed the last of the work or labor, or furnished the last of the materials for which said claim is made, stating with substantial accuracy the amount claimed and the name of the party to whom the materials were furnished, or for whom the work or labor was done or performed. Such notice shall be served by mailing the same by register mail or certified mail, postage prepaid, in an envelope addressed to the PRINCIPAL, OWNER, or SURETY, at any place where an office is regularly maintained for the transaction of business, or served in any manner in which legal process may be served in the state in which the aforesaid project is located, save that such service need not be made by a public officer. (b) After the expiration of one (1) year following the date of which PRINCIPAL ceased work on said CONTRACT, it being understood, however, that if any limitation embodied in the BOND is prohibited by any law controlling the construction hereof, such limitation shall be deemed to be amended so as to be equal to the minimum period of limitation permitted by such law.
PROVIDED, FURTHER, that it is expressly agreed that the BOND shall be deemed amended automatically and immediately, without formal and separate amendments hereto, upon amendment to the Contract not increasing the contract price more than 20 percent, so as to bind the PRINCIPAL and the SURETY to the full and faithful performance of the Contract as so amended. The term “Amendment”, wherever used in this BOND and whether referring to this BOND, the contract or the loan Documents shall include any alteration, addition, extension or modification of any character whatsoever.
PROVIDED, FURTHER, that no final settlement between the OWNER or GOVERNMENT and the CONTRACTOR shall abridge the right of any benficiary hereunder, whose claim may be unsatisfied.
IN WITNESS WHEREOF, this instrument is executed in [number] counterparts, each one of which shall be deemed an original, this the __ day of ___.
ATTEST:
Principal (Principal) Secretary (SEAL) By ___(s) (Address) Witness as to Principal (Address) Surety ATTEST: Witness as to Surety (Address) By Attorney-in-Fact (Address) Note.Date of BOND must not be prior to date of Contract.
If CONTRACTOR is partnership, all partners should execute BOND.
Important: Surety companies executing BONDS must appear on the Treasury Department's most current list (Circular 570 as amended) and be authorized to transact business in the state where the project is located.
Exhibit G to Subpart A of Part 1924 - Performance Bond
7:12.1.2.7.16.1.1.17.31 :
Exhibit G to Subpart A of Part 1924 - Performance Bond KNOW ALL PERSONS BY THESE PRESENTS: that (Name of Contractor) (Address of Contractor) (Corportion, Partnership, or Individual) hereinafter called PRINCIPAL, and (Name of Surety) (Address of Surety) hereinafter called SURETY, are held and firmly bound unto (Name of Owner) (Address of Owner) hereinafter called OWNER, and the United States of America acting through the Farmers Home Administration or its successor agency under Public Law 103-354 hereinafter referred to as the GOVERNMENT in the total aggregate penal sum of Dollars ($___) in lawful money of the United States, for the payment of which sum well and truly to be made, we bind ourselves, our heirs, executors, administrators, successors, and assigns, jointly and severally, firmly by these presents.THE CONDITION OF THIS OBLIGATION is such that whereas, the PRINCIPAL entered into a certain contract with the OWNER, dated the __ day of ___ 19 _, a copy of which is hereto attached and made a part hereof for the construction of:
NOW, THEREFORE, if the PRINCIPAL shall well, truly and faithfully perform its duties, all the undertakings, covenants, terms, conditions, and agreements of said contract during the original term thereof, and any extensions thereof which may be granted by the OWNER, or GOVERNMENT, with or without notice to the SURETY and during the guaranty period and if the PRINCIPAL shall satisfy all claims and demands incurred under such contract, and shall fully indemnify and save harmless the OWNER and GOVERNMENT from all costs and damages which it may suffer by reason of failure to do so, and shall reimburse and repay the OWNER and GOVERNMENT all outlay and expense which the OWNER and GOVERNMENT may incur in making good any default, then this obligation shall be void, otherwise to remain in full force and effect.
PROVIDED, FURTHER, that the liability of the PRINCIPAL AND SURETY hereunder to the GOVERNMENT shall be subject to the same limitations and defenses as may be available to them against a claim hereunder by the OWNER, provided, however, that the GOVERNMENT may, at its option, perform any obligations of the OWNER required by the contract.
PROVIDED, FURTHER, that the said SURETY, for value received hereby stipulates and agrees that no change, extension of time, alteration or addition to the terms of the contract or to WORK to be performed thereunder or the SPECIFICATIONS accompanying same shall in any way affect its obligation on this BOND, and it does hereby waive notice of any such change, extension of time, alteration or addition to the terms of the contract or to the WORK or to the SPECIFICATIONS.
PROVIDED, FURTHER, that it is expressly agreed that the BOND shall be deemed amended automatically and immediately, without formal and separate amendments hereto, upon amendment to the Contract not increasing the contract price more than 20 percent, so as to bind the PRINCIPAL and the SURETY to the full and faithful performance of the CONTRACT as so amended. The term “Amendment”, wherever used in this BOND, and whether referring to this BOND, the Contract or the Loan Documents shall include any alteration, addition, extension, or modification of any character whatsoever.
PROVIDED, FURTHER, that no final settlement between the OWNER or GOVERNMENT and the PRINCIPAL shall abridge the right of the other beneficiary hereunder, whose claim may be unsatisfied. The OWNER and GOVERNMENT are the only beneficiaries hereunder.
IN WITNESS WHEREOF, this instrument is executed in [Number] counterparts, each one of which shall be deemed an original, this the __ day of ___.
ATTEST: Principal (Principal) Secretary (SEAL) Witness as to Principal (Address) By _____(s) (Address) Surety ATTEST: Witness as to Surety (Address) By Attorney-in Fact (Address)Exhibit H to Subpart A of Part 1924 - Prohibition of Lead-Based Paints
7:12.1.2.7.16.1.1.17.32 :
Exhibit H to Subpart A of Part 1924 - Prohibition of Lead-Based Paints I. PurposeThis exhibit prescribes the methods to be used to comply with the requirements of the Lead-Based Paint Poisoning Prevention Act, Public Law 91-695, as amended, (42 U.S.C. 4801 et seq.) and the amendment to section 501 (3) of Public Law 91-695 (42 U.S.C. 4841 (3)) as amended by the National Consumer Health Information and Health Promotion Act of 1976, Public Law 94-317.
II. PolicyThe Agency shall not permit the use of lead-based paint on applicable surfaces of any housing or buildings purchased, repaired, or rehabilitated for human habitation with financial assistance provided by this agency. Paints used on applicable surfaces shall not contain more than 0.06 percent lead by weight calculated as lead metal in the total nonvolatile content of liquid paints or in the dried film of paint already applied.
III. DefinitionsA. Housing and buildings mean any house, apartment, or structure intended for human habitation. This includes any institutional structure where persons reside, such as an orphanage, boarding school, dormitory, day care center or extended care facility, college housing, domestic or migratory labor housing, hospitals, group practice facilities, community facilities, and business or industrial facilities.
B. Applicable surfaces means all interior surfaces, whether accessible or not, and those exterior surfaces which are readily accessible to children under 7 years of age, such as stairs, decks, porches, railings, windows, and doors.
C. Lead-based paint means any paint containing more than .5 of 1 percentum lead by weight, or with respect to paint manufactured after June 22, 1977, lead-based paint containing more than six one-hundredths of 1 percentum lead by weight.
IV. RequirementsA. All new housing and buildings shall comply with paragraph II of this exhibit H.
B. For all existing housing and buildings built after 1950, on which a loan is closed after July 19, 1978, the Agency requires that the applicant, borrower or tenant be notified of the potential hazard of lead-based paints, of the symptoms and treatment of lead poisoning, and of the importance and availability of maintenance and removal techniques for eliminating such hazards. This will be accomplished by providing each applicant, borrower and/or tenant with a copy of attachment 1 to this exhibit H, “Lead-based Paint Hazards, Symptoms, Treatment and Techniques for Eliminating Hazards,” available in any Agency County Office. Copies of attachment 1 may be obtained by the County Supervisor from the Finance Office, 1520 Market Street, St. Louis, MO 63103.
C. For all existing housing or buildings built before 1950 on which a loan is closed after July 19, 1978, the Agency requires that the applicant, borrower and/or tenant be notified as in paragraph IV B and a copy of attachment 2 to this exhibit H, “Caution Note on Lead-Based Paint Hazard,” available in any Agency County Office, shall be delivered to the hands of the applicant, borrowers and/or tenant.
D. For all property transfers and inventory property sales, attachments 1 and 2 to this Exhibit H (available in any Agency office) shall be handed to the purchaser by the Agency representative.
E. All inventory housing or buildings built before 1950 to be repaired, renovated, or rehabilitated shall have tests for lead content, and where found to be hazardous, shall have any interior lead-based paint removed entirely. Loose or cracked surfaces shall be cleaned down to the base surface before repainting with a paint containing not more than six one-hundredths of 1 percentum lead by weight in the total nonvolatile content of the paint or the equivalent measure of lead in the dried film of paint already applied or both. Contracting officers shall include the following provision prohibiting the use of lead-based paint in all contracts and subcontracts for construction or rehabilitation of housing or buildings:
Lead-Based Paint ProhibitionNo lead-based paint containing more than .5 of 1 percentum lead by weight (calculated as lead metal) in the total nonvolatile content of the paint, or the equivalent measure of lead in the dried film of paint already applied, or both, or with respect to paint manufactured after June 22, 1977, no lead-based paint containing more than .06 of 1 percentum lead by weight (calculated as lead metal) in the total nonvolatile content of the paint, or the equivalent measure of lead in the dried film of paint already applied, or both, shall be used in the construction or rehabilitation of residential structures under this contract or any subsequent subcontractors.
Authority: This amendment is made under provisions of 5 U.S.C. 301, 40 U.S.C. 486 (c).
Done at ________, ____ this ______ day of __________, 19__.
______________ Agency Representative V. SummarySection 401 of the Lead-Based Paint Poisoning Prevention Act as amended by the National Consumer Health Information and Health Promotion Act of 1976, Pub. L. 94-317, provides a requirement that each federal agency issue regulations and to take such other steps necessary to prohibit the use of lead-based paint on all applicable surfaces in Federal and Federally-assisted construction or rehabilitation of residential structures. The Lead-Based Paint Poisoning Prevention Act, Pub. L. 91-695, January 13, 1971, provides for grants to units of general local government in any state for the purpose of detecting and treating incidents of lead-based paint poisoning. Title II of this Act also provides for grants to the same units to identify those areas of risk including testing to detect the presence of lead-based paint on surfaces of residential housing.
Exhibit I to Subpart A of Part 1924 - Guidelines for Seasonal Farm Labor Housing
7:12.1.2.7.16.1.1.17.33 :
Exhibit I to Subpart A of Part 1924 - Guidelines for Seasonal Farm Labor Housing Section 100General - This exhibit sets forth the guidelines and minimum standards for planning and construction of new Labor Housing (LH) that will be occupied on a seasonal basis. Rehabilitation LH projects will be in substantial conformance with these guidelines and standards. A “seasonal basis” is defined as 6 months or less per year. Seasonal housing for the farmworker need not be convertible to year-round occupancy; however, the living units shall be designed for the intended type of tenant, the time of occupancy, the location, the specific site, and the planned method of operation. It is important that the design of the LH site and buildings will help to create a pleasing lifestyle which will promote human dignity and pride among its tenants.
Section 200Codes and Regulations - Compliance is required with National, state and local codes or regulations affecting design, construction, mechanical, electrical, fire prevention, sanitation, and site improvement.
Section 300 Planning300-1 Complete architectural/engineering services in accordance with this subpart will be required if an LH grant is involved or the LH loan will involve more than four individual family units, or any number of group living units, or dormitory units accommodating 20 or more persons.
300-2 Buildings and site design shall provide for a safe, secure, economical, healthful, and attractive living facility and environment suited to the needs of the domestic farm laborer and his/her family.
300-3 At least 5 percent of the individual family units in a project, or one unit, whichever is greater, and all common use facilities will be accessible to or adaptable for physically handicapped persons. This requirement may be modified if a recipient/borrower shows, through a market survey acceptable to the Agency, that a different percentage of accessible or adapatable units is more appropriate for a particular project and its service area.
Site Design301-1 General - The site design shall be arranged to utilize and preserve the favorable features and characteristics of the property and to avoid or minimize the potential harmful effect of unfavorable features. Particular attention is directed to § 1944.164 (l), (m) and (n) of subpart D of part 1944 of this chapter with reference to compliance with 7 CFR part 1970. Some of the features which must be considered are the topography, drainage, access, building orientation to sun and breezes; and advantageous features, such as vegetation, trees, good views, etc. or disadvantageous features, such as offensive odors, noxious plants, noise, dust, health hazards, etc.
301-2 Drainage - Surface and subsurface drainage systems shall be provided in accordance with the applicable development standard and subpart C of part 1924 of this chapter.
301-3 Water and Sewage Disposal - Water supply and sewage disposal installations shall comply with subpart C of part 1924 of this chapter, the applicable development standard and all governing state and local department of health requirements. Where environmentally and economically feasible, the LH facility shall connect to public water and waste disposal systems.
301-4 Electrical - Adequate electrical service shall be provided for exterior and interior lighting and for the operation of equipment.
301-5 Vehicular Access and Parking.
301-5.1 Safe and convenient all-weather roads shall be provided to connect the site and its improvements to the off-site public road.
301-5.2 All-weather drives and parking shall be provided for tenants, and for trucks and buses as needed within the site. Driveways, parking areas and walkway locations shall be in substantial conformance with the applicable development standard.
301-6 Walks:
301-6.1 Walks shall be provided for safe convenient access to all dwellings and for safe pedestrian circulation throughout the development between locations and facilities where major need for pedstrian access can be anticipated, such as laundry, parking to dwelling units, common dining rooms, etc.
301-6.2 Walkways shall be hard surface, such a concrete, asphalt, or stablized gravel, and shall be adequately drained.
301-7 Building Location:
301-7.1 Side and rear yards and distances between buildings shall conform to the applicable development standard.
301-8. Garbage and Refuse:
301-8.1 Garbage and refuse containers for individual units are required and shall be stored on durable functional racks or shall be located in a central screened area with easily cleaned surfaces. Single containers for multiple units shall be screened and in locations designed to accommodate collection vehicle functions.
301-9 Fencing:
301-9.1 Fencing used in the site design for project privacy or building security shall be harmonious in appearance with other fences and surrounding facilities which fall within the same view.
301-10 Outdoor living:
301-10.1 All public areas where pedestrian use can be anticipated after sunset shall be adequately lighted for security purposes, such as walkways to common use facilities - laundry, dining halls, building entrances, parking areas, etc.
301-11 Planting and Landscaping:
301-11.1 Planting and lawns or ground covers shall be provided as required to protect the site from erosion, control dust, for active and passive recreation areas, and provide a pleasant environment.
Building Design302-1.1 Living Units Design:
302-1.1 Individual Family Unit - One family or extended family to a unit which shall contain adequate space for living, dining, kitchen, bath and bedrooms. Multifamily type units are required whenever possible for economy of site and building construction.
a. The minimum total net living unit size shall be 400 square feet. This size assumes occupancy of four persons. Units planned for additional occupants shall include an additional 60 square feet of living area per person.
b. A living/dining area shall be provided to accommodate a table and chairs with adequate dining and circulation space for the intended number of occupants. The living/dining area should be combined with the kitchen area.
c. The kitchen shall contain a sink, cooking range and refrigerator. A minimum free countertop area of six square feet is required. A minimum of 40 square feet of shelf area is required.
d. Each bathroom shall contain adequate space and circulation for a bathtub and/or shower, water closet and lavatory. Access to the bathroom shall not be through another bedroom in dwelling units containing more than one bedroom.
e. Bedroom areas separate from living areas are required. The design of the unit shall provide a minimum of 50 square feet of sleeping area per intended occupant including storage. Housing for families with children shall have a separate bedroom or sleeping area for the adult couples. A two foot by two foot shelf with a two foot long clothes hanging rod is required for each occupant.
302-1.2 Group Living Unit - A living unit designed for the occupancy of more than one family or for separate occupancy of male and/or female groups. Common bath spaces shall be contained in the same building. Group living units for families shall have separate bedrooms for each adult couple.
a. The design of the unit shall provide for a minimum of 620 square feet of total net living area for eight persons and an additional 60 square feet for each additional occupant. Additional area shall be planned for a second bathroom when anticipated occupancy will exceed eight persons, or if it will be occupied by persons of both sexes.
b. The kitchen shall contain an adequate sink, cooking range, refrigerator, and space the size of which is commensurate with the needs of the group living unit. A minimum of free countertop area of eight square feet is required. A minimum of 50 square feet of shelf area is required.
c. Refer to paragraph 302-1.1 b for living/dining requirements.
d. Each bathroom shall contain adequate space and circulation for comfortable access to, and use of, fixtures which will include a bathtub and/or shower, water closet and lavatory. In no case shall minimum fixtures be less than that required per paragraph 302-1.3 c below.
e. Refer to paragraph 301-1.1 e for bedroom requirements.
302.1.3 Dormitory Living Unit - A building which provides common sleeping quarters for persons of the same sex and may or may not contain kitchen and/or dining facilities in the same building as the sleeping quarters.
a. The design of areas for sleeping purposes, using single beds, shall provide for not less than 72 square feet per occupant including storage.
b. The design of areas for sleeping purposes, using double bunk beds, shall provide for not less than 40 square feet per occupant. Triple bunk beds will not be allowed.
c. The design of each dormitory building must include a water closet and a bathtub or shower for each 12 occupants, and a lavatory for each 8 persons. Urinals may be substituted for men's water closets on the basis of one urinal for one water closet, up to maximum of one-third of the required water closets.
d. Adequate kitchen and dining facilities must be provided which may be in the dormitory building or detached at a distance of not more than 200 feet from the sleeping quarters. In either case, the space must contain adequate cooking ranges, refrigerators, sinks, countertop, food storage shelves, tables and chairs, and circulation space. These facilities will comply with the requirements of the “Food Service Sanitation Ordinance and Code,” part V of the “Food Service Sanitation Manual,” U.S. Public Health Service Publication 934 (1965).
302-2 Other Facilities:
302-2.1 General - Other facilities, authorized by subpart D of part 1944 of this chapter, needed by farm workers may be provided in several ways: part of a living unit, located in the project, or, with the exception of laundry facilities, available nearby.
302-2.2 Laundry Facilities - Laundry facilities shall be required on-site. Drying yards shall be provided if dryer units are not provided. The design of washing facilities shall plan for a minimum rate of one washer for each 20 occupants. One drying unit may be provided for every two washers, if automatic dryers are customarily provided for rental housing in the community. Laundry facilities shall have adequate space for loading the units, circulation, and clothes folding.
302-2.3 Office and Maintenance - An office and maintenance space shall be provided or available, commensurate with the number of living units served, and shall meet the criteria of the Agency Manual of Acceptable Practices. If necessary, the maintenance space shall have sufficient area to accommodate furniture storage.
302-2.4 Child Care Center - Where feasible, a child care center may be included to provide supervised activity and safety for children while the parents work. Supervisors and workers for such centers are sometimes enlisted on a volunteer basis and the cost borne by nonprofit associations or community organizations. Grants are sometimes available through Federal or state programs. Consequently, the design of the child care center should meet the requirements of those sources providing organizational personnel and/or financing.
302-2.5 Manager's Dwelling - If a manager's dwelling unit is to be provided as a part of the Agency loan or grant, it will meet these guidelines. However, if it is necessary to provide a year-round caretaker/manager dwelling unit with the Agency loan or grant funds, it will meet the applicable development standard.
302-2.6 Recreation - Outdoor recreation space is required and shall be commensurate with the needs of the occupants. Active and passive recreation areas will be provided which may consist of outdoor sitting areas, playfields, tot lots and play equipment.
General Requirements303-1 Materials and Construction - All materials and their installation in a LH facility shall meet the applicable development standard. Any exceptions to these requirements for materials and their installation must be obtained with the approval of the Agency National Office. Material should be selected that is durable and easily cleaned and maintained.
303-2 Fire Protection - Fire protection and egress shall be provided to comply with the applicable development standard.
303-3 Light, Ventilation, Screening - Natural light and ventilation requirements as specified in the applicable development standard shall be followed. Screening of all exterior openings is required.
303-4 Ceiling Heights - Ceiling heights of habitable rooms shall be a minimum of seven feet six inches clear, and seven feet in halls or baths in dwelling units. Public rooms shall have a minimum of eight feet clear ceiling height. Sloping ceilings shall have at least seven feet six inches for 1/2 the room with no portion less than five feet in height.
303-5 Heating and Cooling - Heating and cooling and/or air circulation equipment shall be installed as needed for the comfort of the tenants, considering the climate and time of year the facility will be in operation. Maximum feasible use of passive solar heating and cooling techniques shall be required. All equipment installed will be in accordance with the applicable development standard to protect the health and safety of occupants.
303-6 Plumbing - Plumbing materials and their installation shall meet the applicable development standard. Hot water will be required to all living units, baths, kitchens and laundry facilities.
303-7 Insulation, Thermal Standards, Winterization - Insulation will be required where either heating or cooling is provided as per paragraph 303-5 above or when climatic conditions dictate a need for insulation. Insulation Standards will comply with exhibit D, paragraph IV C 3, of this subpart, or the state insulation standards, whichever are the more stringent.
303-8 Electrical - Electrical design, equipment and installation shall comply with the requirements of the latest edition of the National Electrical Code, and the applicable development standard for materials and their installation. Individual family units may be separately metered; other types of dwelling units may be separately metered as required.
303-9 Security and Winterization - Adequate management and physical measures will be provided as necessary to protect the facility during off-season periods, including adequate heating and insulation as required.
[52 FR 8002, Mar. 13, 1987, as amended at 52 FR 19283, May 22, 1987; 58 FR 38922, July 21, 1993; 81 FR 11029, Mar. 2, 2016; 81 FR 26667, May 4, 2016]Exhibit J to Subpart A of Part 1924 - Manufactured Home Sites, Rental Projects and Subdivisions: Development, Installation and Set-Up
7:12.1.2.7.16.1.1.17.34 :
Exhibit J to Subpart A of Part 1924 - Manufactured Home Sites, Rental Projects and Subdivisions: Development, Installation and Set-Up Part A - Introduction Part B - Construction and Land Development Part C - Drawings, Specifications, Contract Documents and Other Documentation Part D - Inspection of Development Work Part A - IntroductionI. Purpose and Scope. This exhibit describes and identifies acceptable site development, installation and set-up practices and concepts for manufactured homes. It is intended for Agency field personnel, builders, developers, sponsors, and others participating in Agency housing programs.
This exhibit applies to all manufactured homes (except those referenced in exhibit B of this subpart) on scattered sites or in rental projects and subdivisions and covers the requirements for design and construction of manufactured home communities. The Agency may approve alternatives or substitutes if it finds the proposed design satisfactory for the proposed use, and if the materials, installation, device, arrangement, or method of work is at least equivalent to that prescribed in this exhibit considering quality, strength, effectiveness, durability, safety and protection of life and health.
The Agency will require satisfactory evidence to be submitted to substantiate claims made regarding the use of any proposed alternative.
II. Background. The Agency has authority to make (1) section 502 Rural Housing (RH) loans with respect to manufactured homes and lots, and (2) section 515 Rural Rental Housing (RRH) loans with respect to manufactured home rental projects.
The manufactured home must be constructed in conformance with the Federal Manufactured Home Construction and Safety Standard (FMHCSS) and be permanently attached to a site-built permanent foundation which meets or exceeds the Minimum Property Standards (MPS) for One- and Two-Family Dwellings or Model Building Codes acceptable to the Agency. The manufactured home must be permanently attached to that foundation by anchoring devices adequate to resist all loads identified in the MPS. This includes resistance to ground movements, seismic shaking, potential shearing, overturning and uplift loads caused by wind. Note that anchoring straps or cables affixed to ground anchors other than footings will not meet these requirements.
7 CFR part 1970 applies on scattered sites, in subdivisions and rental projects with regard to the development, installation and set-up of manufactured homes. To determine the level of environmental analysis required for a particular application, each manufactured home or lot involved will be considered as equivalent to one housing unit or lot. Because the development, installation and set-up of manufactured home communities, including scattered sites, rental projects, and subdivisions, differ in some requirements from conventional site and subdivision development, two of the purposes of this exhibit are to:
A. Encourage economical and orderly development of such communities and nearby areas, and
B. Promote the safety and health of residents of such communities.
Therefore, this exhibit identifies those required standards and regulations and suggested guidelines for eliminating and preventing health and safety hazards and promoting the economical and orderly development and utilization of land for planning and development of manufactured home communities. The exhibit also provides the requirements for meeting the following:
A. Resistance to Wind. Foundations and anchorages shall be designed to resist wind forces specified in American National Standards Institute (ANSI) A-58.1-1982 for the geographic area in which the manufactured home will be sited;
B. Proper Installation. The manufacturer's installation instructions provided with each manufactured home shall contain instructions for at least one site-built foundation with interior and/or perimeter supports. Agency field office personnel shall review to determine its adequacy as security for an Agency loan only, the foundation design concept for compliance with this exhibit, the Agency/MPS and any Model Building Code acceptable to the Agency in that particular geographic area; and
C. Proper Foundation Design. Manufactured homes shall be installed on a foundation system which is designed and constructed to sustain, within allowable stress and settlement limitations, all applicable loads. Any foundation and anchorage system or method of construction to be used should be analyzed in accordance with well-established principles of mechanics and structural engineering.
III. Definitions. For the purpose of this exhibit the following definitions apply:
Accessory Building or Structure.
A subordinate building or structure which is an addition to or supplements the facilities provided by a manufactured home.
Anchoring Systems. An approved system for securing the manufactured home to the ground or foundation system that will, when properly designed and installed, resist overturning and lateral movement of the home from wind forces.
Contiguous. Sharing a boundary, adjoining or adjacent. A lot or subdivision is considered to be contiguous to other lots or subdivisions if it is adjoining, touching or adjacent.
Federal manufactured Home Construction and Safety Standards (FMHCSS). A 1976 federal standard, commonly known as the HUD Standard, for the construction, design and performance of a manufactured home which meets the needs of the public including the need for quality, durability and safety. Units conforming to the FMHCSS are certified by an affixed label that reads as follows:
AS EVIDENCED BY THIS LABEL NO. ____ THE MANUFACTURER CERTIFIES TO THE BEST OF THE MANUFACTURER'S KNOWLEDGE AND BELIEF THAT THIS MANUFACTURED HOME HAS BEEN INSPECTED IN ACCORDANCE WITH THE REQUIREMENTS OF THE DEPARTMENT OF HOUSING AND URBAN DEVELOPMENT AND IS CONSTRUCTED IN CONFORMANCE WITH THE FEDERAL MANUFACTURED HOME CONSTRUCTION AND SAFETY STANDARDS IN EFFECT ON THE DATE OF MANUFACTURE. SEE DATA PLATE.
Manufactured Home. A structure which is built to the Federal Manufactured Home Construction and Safety Standards and Agency's thermal requirements. It is transportable in one or more sections, which in the traveling mode is ten body feet or more in width, and when erected on site is four hundred or more square feet, and which is built on a permanent foundation when connected to the required utilities. It is designed and constructed for permanent occupancy by a single family and contains permanent eating, cooking, sleeping and sanitary facilities. The plumbing, heating, and electrical systems are contained in the structure.
Manufactured Home Community. A parcel or contiguous parcels of land which contains two or more manufactured home sites available to the general public for occupancy. Sites and units may be for rent, or sites may be sold for residential occupancy (as in a subdivision).
Manufactured Home Rental Project. A parcel or multiple parcels of land which have been so designated and improved to contain manufactured homes with sites available for rent.
Manufactured Home Site. A designated parcel of land in a manufactured home rental project, subdivision or scattered site designed for the accommodation of a unit and its accessory structures for the exclusive use of the occupants.
Manufactured Home Subdivisions. Five or more contiguous (developed or undeveloped) lots, or building sites that meet the requirements of subpart C of part 1924 of this chapter.
Permanent Perimeter Enclosure. A permanent perimeter structural system completely enclosing the space between the floor joist of the manufactured home and the ground. If separate from the foundation system, the permanent perimeter enclosure shall be secured to the perimeter of the manufactured home, properly ventilated and accessible and constructed of materials that conform to the Agency adopted MPS requirements for foundations.
Pier Support System. Consists of footings, piers, caps, leveling spacers, or approved prefabricated load bearing devices.
Related Facilities. Any nonresidential structure or building used for rental housing related purposes.
Site-Built Permanent Foundation System. A foundation system (consisting of a combination of footings, piers, caps and shims and anchoring devices or required structural connections) which is designed and constructed to support the unit and sustain, within allowable stress and settlement limitations, all applicable loads specified in ANSI A58.1-1982. All loads shall be transferred from the manufactured home to the earth at a depth below the established frost line without exceeding the safe bearing capacity of the supporting soil.
Set-Up. The work performed and operations involved in the placement of a manufactured home on a foundation system, to include installation of accessories or appurtenances and anchoring devices, and when local regulations permit, connection of utilities, but excluding preparation of the site.
IV. Compliance with Local Regulations. These requirements do not replace site development standards established by local law, ordinances, or regulations. Whenever such local standards contain more stringent provisions than any of the site development, installation and set-up minimums of the Agency, the more stringent standards shall govern.
V. Applicable Standards, Regulations and Manuals. A. Manufactured housing to be financed by the Agency must comply with the following standards:
1. Federal Manufactured Home Construction and Safety Standards, 24 CFR part 3280, mandated by Congress under title VI of the Federal Housing and Community Development Act of 1974, except for § 3280.506, “Heat Loss,” of subpart F, “Thermal Protection,” to part 3280.
2. Foundation requirements of the Minimum Property Standards as adopted by the Agency or a Model Building Code acceptable to the Agency.
3. [Reserved]
4. Uniform Federal Accessibility Standard (UFAS).
5. ANSI A58.1-1982, Minimum Design Loads for Buildings and Other Structures.
B. Manufactured housing to be financed by the Agency shall comply with all applicable Agency regulations, including but not limited to the following:
1. Subpart C of part 1924 of this chapter, “Planning and Performing Development Work.”
2. Subpart A of part 1924, exhibit D, “Thermal Performance Construction Standards.”
3. 7 CFR part 1970.
4. 7 CFR part 3550, “Direct Single Family Housing Loans and Grants.”
5. Subpart E of part 1944, “Rural Rental Housing Loan Policies, Procedures, and Authorizations.”
The requirements of the above references have not been repeated in this exhibit. Those requirements contained above are either mandatory or minimums and every effort should be made by the applicant, builder-developer or dealer-contractor to utilize higher standards, when appropriate.
Part B - Construction and Land DevelopmentI. General Acceptability Criteria. The following criteria apply to development on scattered sites, in subdivisions and in rental project communities.
A. A manufactured home development including a site, rental project or subdivision shall be located on property designated for that use, where designations exist, by the local jurisdiction.
B. Conditions of soil, ground water level, drainage, flooding and topography shall not create hazards to the property and health or safety of the residents.
C. The finished grade elevation beneath the manufactured home or the first floor elevation of the habitable space, whichever is lower, must be above the 100-year flood elevation. This requirement applies wherever manufactured homes may be installed, not just in locations designated by the National Flood Insurance Program as areas of special flood hazards. The use of fill to accomplish this is a last resort. As is stated in EO 11988 and 7 CFR part 1970, it is the Agency's policy not to approve or fund any proposal in a 100-year floodplain area unless there is no practicable alternative to such a floodplain location.
D. Essential services such as employment centers, shopping, schools, recreation areas, police and fire protection, and garbage and trash removal shall be convenient to the development and any site, community, or subdivision must comply with the environmental review requirements in accordance with 7 CFR part 1970.
E. Manufactured home sites, rental projects and subdivisions shall not be subject to any adverse influences of adjacent land uses. An adverse influence is considered as one that is out of the acceptable level or range of a recognizable standard or where no standard exists is considered a nuisance irrespective of a site being zoned for manufactured home use. Health, safety and aesthetic consequences of location shall be carefully assessed by inspection of the site prior to selection of development. Undesirable land uses sush as deteriorated residential or commercial areas and noxious industrial properties shall be avoided to ensure compatibility. Other undesirable elements such as heavily traveled highways, airport runways, railroad, or fire hazards and other areas subject to recognizably intolerable noise levels shall be avoided.
F. The requirements for streets shall be those found in subpart C of part 1924 of this chapter.
G. The site design and development shall be in accordance with sound engineering and architectural practices and shall provide for all utilities in a manner which allows adequate, economic, safe, energy efficient and dependable systems with sufficient easements for their required installation and maintenance.
H. Utilities for each manufactured home site, rental housing project or subdivision shall be designed and installed in accordance with subpart C of part 1924 of this chapter; and the State health authority having jurisdiction, and all local laws and regulations requiring approval prior to construction.
I. Exhibit C, section V of this subpart shall be complied with by the applicant, dealer-contractor or builder-developer for manufactured home projects with individual water supply and sewage disposal systems. This exhibit shall be used by the Agency County Supervisors, District Directors, and State Directors in reviewing submissions.
J. During the planning, design, and construction of the foundation system and/or perimeter enclosure, provisions shall be made for the installation and connection of on-site water, gas, electrical and sewer systems, which are necessary for the normal operation of the manufactured home. Water and sewer system hookups shall be adequately protected from freezing.
II. Development on Scattered Sites and in Subdivisions. - A. General. Scattered sites and subdivision developments will be planned and constructed in accordance with specific requirements of this subpart, subpart C of part 1924, and 7 CFR part 1970, and the applicable Agency/MPS or Model Building Codes acceptable to the Agency. Manufactured homes for development in a manufactured home community shall:
1. Be erected with or without a basement on a site-built permanent foundation that meets or exceeds applicable requirements of the Agency/MPS for One- and Two-Family Dwellings or Model Building Codes acceptable to the Agency;
2. Be permanently attached to that foundation by anchoring devices adequate to resist all loads identified in the Agency adopted MPS (this includes resistance to ground movements, seismic shaking, potential shearing, overturning and uplift loads caused by wind, etc.);
3. Have had the towing hitch or running gear, which includes tongues, axles, brakes, wheels, lights and other parts of the chassis that operate only during transportation removed;
4. Have any crawl space beneath the manufactured home properly ventilated and enclosed by a continuous permanent perimeter enclosure. If it is not the supporting foundation, designed to resist all forces to which it may be subject without transmitting to the building superstructure movements or any effects caused by frost heave, soil settlement (consolidation), or shrinking or swelling of expansive soils; and be constructed of materials that conform to Agency adopted MPS requirements for foundations;
5. Have the manufactured home insulated to meet the energy conserving requirements contained in exhibit D of this subpart;
6. Have a manufactured home site, site improvements, and all other features of the mortgaged property not addressed by the Federal Manufactured Home Construction and Safety Standards, meet or exceed applicable requirements of this subpart and subpart C of part 1924 of this chapter, the Agency adopted MPS except paragraph 31-2.2 or a Model Building Code acceptable to the Agency;
7. Have had the manufactured unit itself braced and stiffened where necessary before it leaves the factory to eliminate racking and potential damage during transportation; and
8. Be eligible for financing in accordance with the requirements of either section 502, or section 515 of the Agency's Housing Program, for which purpose the beginning of construction will be the commencement of on-site work even though the manufactured home itself may have been produced and temporarily stored prior to the date of application for financing.
B. Site Planning and Development. The site planning and development of manufactured home scattered sites and subdivisions shall also comply with the following:
1. Arrangement of Structures and Facilities. The site, including the manufactured home, accessory structures, and all site improvements shall be harmoniously and efficiently organized in relation to topography, the shape of the plot, and the shape, size and position of the unit. Particular attention shall be paid to use, appearance and livability.
2. Adaptation to Site Assets. The manufactured home shall be fitted to the terrain with a minimum disturbance of the land. Existing trees, rock formations, and other natural site features shall be preserved to the extent practical. Favorable views or outlooks shall be emphasized by the plan.
3. Site Plan. The site plan shall provide for a desirable residential environment which is an asset to the community in which it is located.
4. Lot Size. The size of manufactured home lots (scattered sites and subdivision) shall be determined by 7 CFR part 3550 and subpart C of part 1924 of this chapter.
C. Foundation Systems, Anchoring and Set-up.
1. The foundation system shall be constructed in accordance with this subpart and one of the following: (a) The foundation system included in the manufacturer's installation instructions meeting Agency/MPS requirements, (b) the Agency/MPS 4900.1, which specifies performance requirements for foundations in section 600 “General” and paragraph 601-16 “Foundations,” or (c) an FmHA or its successor agency under Public Law 103-354 recognized model building code.
2. The manufactured home permanent foundation system shall constitute a permanent load bearing support system for the manufactured home. The manufacturer or applicant shall be permitted to design or specify the installation of a foundation system which meets Agency/MPS design requirements for foundations and the general requirements above.
3. The applicant's responsibility for proper design and installation of the permanent foundation system, anchoring and set-up shall be in accordance with § 1924.5(f)(1), of this subpart.
4. The builder/developer of the manufactured home property, for proposed construction, shall submit with the application for financing by the applicant or for a conditional commitment design calculations, details and drawings for the installation, anchorage and construction of permanent foundation and perimeter enclosure to be used.
III. Rental Housing Project Development. A. General. Manufactured housing rental developments shall be planned and constructed in accordance with requirements of subpart C of part 1924; this subpart; 7 CFR part 1970, the Agency/MPS; and the requirements of subpart E of part 1944 of this chapter.
B. Site Planning and Development. Site planning and development shall adapt to individual site conditions and the type of market to be served, reflect advances in site planning and development techniques, and be adaptable to the trends in design of the manufactured home. Site planning and development shall utilize existing terrain, trees, shrubs and rocks formations to the extent practicable. A regimental style site plan design should be avoided.
C. Foundation Systems, Anchoring and Set-up. Foundation systems, anchoring and set/ups for manufactured home rental projects (site and home) developed under Agency section 515 Rural Rental Housing program shall comply with the requirements of paragraphs II A and II C above.
IV. Accessory Structures and Related Facilities. A. General. Accessory structures and related facilities are dependent upon the manufactured home and its environment.
1. Accessory structures and related facilities shall be planned, designed and constructed in accordance with the applicable provisions of this subpart; the Agency/MPS; and local criteria of the authority having jurisdiction.
2. Accessory structures and related facilities shall be designed in a manner that will eliminate and prevent health and safety hazards and enhance the appearance of the manufactured home and its environment.
3. Accessory structures and related facilities shall not obstruct required openings for light and ventilation of the manufactured home and shall not hamper installation and utility connections of the unit.
B. Accessory Structures. 1. Accessory structures shall not include spaces for pantries, bath, toilet, laundries, closets or utility rooms.
2. Accessory structures shall be carefully designed and constructed for the convenience and comfort of the manufactured home occupant. These features significantly affect the visual appearance of the community and influence livability.
C. Related Facilities (Rental Housing Projects). 1. This includes those facilities as defined in § 1944.212(e) of subpart E of part 1944 of this chapter.
2. Related facilities built on-site must meet the Agency/MPS and subpart A of part 1924 of this chapter or other building codes approved by by the Agency.
3. Workmanship shall be of a quality equal to good standard practice. Material shall be of such kind and quality as to assure reasonable durability and economy of maintenance, all commensurate with the class of building under consideration.
4. All members and parts of the construction shall be properly designed to carry all loads imposed without detrimental effect on finish or covering materials.
5. The structure shall be adequately braced against lateral stresses and each member shall be correctly fitted and connected.
6. Adequate precautions shall be taken to protect against fire and accidents.
7. All related facilities which require accessibility to the handicapped must comply with the Uniform Federal Accessibility Standard (UFAS).
V. Fire Protection and Safety. A. The design of the site plan for each manufactured community and scattered site shall meet the fire protection and safety requirements of the local authority responsible for providing the necessary fire protection services.
B. All fire detection and alarm systems, and water supply requirements for fire protection for manufactured communities shall be in accordance with the local authority responsible for providing the necessary fire protection services.
C. Any portion of a manufactured home shall not be closer than the local separation requirements of the development standard for side to side, end to end, and end to side siting. If the exposed composite wall and roof of two or more manufactured homes are proposed to be joined they shall be without openings and constructed of materials which will provide a minimum one-hour fire rating each, or the manufactured homes are separated by a one-hour fire rated barrier designed and approved for such installation and permitted by the authority having jurisdiction.
D. Manufactured homes shall not be positioned vertically (stacked) with one over the other in whole or in part without the specific approval of the authority having jurisdiction.
Part C - Drawings, Specifications, Contract Documents and Other DocumentationI. General. Adequate site development and foundation installation drawings and specfications shall be provided by the applicant or dealer-contractor to the Agency to fully describe the construction and other development work. These documents shall be provided according to the requirements of § 1924.5(f)(1) of this subpart. Contract documents will be prepared in accordance with § 1924.6 and, in the case of multiple family housing construction and development, § 1924.13 of this subpart.
A. The documents recommended shall be used as a guide for drawings and specifications to be submitted in support of all types of loan and/or grant applications involving manufactured homes. Adequate and accurate drawings and specifications are necessary to:
1. Determine the acceptability of the physical environment and improvements,
2. Determine compliance with the applicable standards and codes,
3. Review cost estimates, and
4. Provide a basis for financing, inspections, and the warranty.
B. Detailed floor plans, drawings and specifications are not required for any manufactured home to be installed on a scattered site, in a subdivision or rental housing project. However, a schematic floor plan should be submitted by the applicant when applying for Agency financing. The unit must have an affixed label as specified in exhibit D of this subpart indicating that the unit is constructed to the Agency thermal requirements for the appropriate winter degree days. This will indicate that the manufacturer certifies that the unit has been properly inspected and it meets the Agency Thermal Performance Construction Standard.
C. For proposed construction, the builder or dealer-contractor shall submit with the loan or grant application design calculations, details and drawings for the installation, anchorage and construction of the permanent foundations and perimeter enclosure to be used. Drawings and specifications for foundation systems will be reviewed and examined by either the Agency County Supervisor, District Director, or State Architect/Engineer for foundation support locations, loads and connection requirements specified by the manufacturer as a basis for evaluating foundation compliance with the Agency/MPS or Model Building Code, and for determining design suitability for soil conditions. Drawings and specifications will also be examined by the Agency to determine compliance with all other on-site features not covered by the FMHCSS.
D. Foundation design sections and details of all critical construction points systems, anchorage methods, and structural items shall be scaled as necessary to provide all appropriate information 1:30 (3/8″ = 1′-0″) minimum.
II. Scattered Sites. Drawings for single family manufactured housing shall be submitted by the applicant in addition to the requirements of paragraph I above and the requirements of paragraphs II A and D-7 of exhibit C of this subpart.
III. Subdivisions. Subpart C of part 1924 of this chapter will be used in preparing and providing supporting documents.
IV. Rental Housing Projects. Subpart C of part 1924 of this chapter will be used in preparing and providing supporting documents.
V. Specifications. A. Form RD 424-2, “Description of Materials,” or other acceptable and comparable descriptions of all materials used for site development, foundation installation and the permanent perimeter enclosure shall be submitted with the drawings by the applicant.
B. The material identification information shall be in sufficient detail to fully describe the material, size and grade. Where necessary, additional sheets shall be attached as well as manufacturer's specification sheets for equipment and/or special materials.
Part D - Inspection of Development WorkI. General. The following policies will govern the inspection of all manufactured housing development work. This includes scattered sites, subdivisions, rental housing projects and all accessory structures and related facilities unless otherwise indicated.
II. Inspections. A. The responsibility for frequency and propose of inspections shall be in accordance with § 1924.9(b) (1), (2) and (3) of this subpart. The inspection requirements of § 1924.13 apply to the planning and conduct of construction work on all 515 housing developments that are more extensive in scope and more complex in nature than those involving an individual manufactured housing unit. The Stage 2 inspection customary for site-built housing when the building is enclosed is not required for manufactured homes.
The Stage 2 inspection for manufactured homes will be made within two working days after erection or placement on the foundation to determine compliance with accepted installation drawings and specifications for installation and set-up and to verify that the correct unit is on the site.
Stages 2 and 3 inspections for manufactured homes may be combined when authorized by the State Director.
B. The borrower will join the County Supervisor or the District Director in making periodic inspections as often as possible and always for the final inspection.
C. The borrower should be encouraged to make enough periodic visits to the site to be familiar with the progress and performance of the work in order to protect the borrower's interest. If the borrower observes or otherwise becomes aware of any fault or defect in the work or nonconformance with the contract documents, the borrower should give prompt written notice thereof to the dealer-contractor and a copy of the notice to the appropriate County Supervisor or District Director.
D. During inspection, it will generally be infeasible to determine whether a manufactured unit erected on a site was properly braced and stiffened during transportation. Inspectors should examine these units to determine that there is no obvious damage or loosening of fastenings that may have occurred during transportation. The dealer-contractor must warrant these units against such damage, which should protect the Agency's interest.
III. Warranty Plan Coverage. The warranty requirements for all development work shall be in accordance with § 1924.9(d) of this subpart and 7 CFR part 3550, subpart B.
[51 FR 41603, Nov. 18, 1986, as amended at 52 FR 19283, May 22, 1987; 53 FR 2156, Jan. 26, 1988; 67 FR 78327, Dec. 24, 2002; 81 FR 11029, Mar. 2, 2016]Exhibit K to Subpart A of Part 1924 - Classifications for Multi-Family Residential Rehabilitation Work
7:12.1.2.7.16.1.1.17.35 :
Exhibit K to Subpart A of Part 1924 - Classifications for Multi-Family Residential Rehabilitation Work I. GeneralThis exhibit distinguishes between what the Agency considers maintenance and repair work, moderate rehabilitation and substantial rehabilitation. In all cases, the building or project to be rehabilitated shall be structurally sound. The applicant shall have a structural analysis of the existing building made to determine the adequacy of all structural systems for the proposed rehabilitation.
II. DefinitionsMaintenance and Repair - Work involved in the selective replacement and general maintenance and repair of certain materials, appliances or components of an existing residential building.
Moderate Rehabilitation - All work directly involved in the rearrangement of interior space, the replacement of finish materials or components of the electrical, plumbing, heating or conveyance systems of an existing multi-family residential building. Work and improvements are considered to be more than routine maintenance and repair.
Substantial Rehabilitation - All work directly involved in the rearrangement of interior space that involves alteration of load bearing partitions and columns; the replacement of the electrical, plumbing, heating or conveyance systems; and the addition to and/or major conversion of existing multi-family residential buildings or other building structures.
Moderate rehabilitation and repair shall not be limited to building changes for cosmetic or convenience purposes. In all cases moderate rehabilitation shall involve a minimum of three (3) components of building rehabilitation listed as moderate. Unless combined with other improvements in a project that are considered to be moderate or substantial rehabilitation the items identified as maintenance and repair are considered to be cosmetic and convenience changes.
When a rehabilitation project consists of both moderate and substantial rehabilitation components, those substantial rehabilitation components shall be in accordance with the Agency's development standards and local codes and regulation requirements. Where the majority of project components of building rehabilitation are considered substantial the project shall be considered in the substantial rehabilitation category.
Those site components of rehabilitation such as landscaping, grading, drainage, fencing, parking areas, recreation areas, water and waste disposal systems, etc., whether considered either maintenance and repair, moderate rehabilitation or substantial rehabilitation shall be in accordance with the Agency's development standards for site development work; all local codes and regulation requirements; and sound engineering and architectural practices.
Any alteration of a structure listed or eligible for listing on the National Register of Historic Places may be considered either moderate or substantial rehabilitation; however, it shall conform first to the Secretary of the Interior's Standards for Rehabilitation and Guidelines for Rehabilitating Historic Buildings and then to the Agency's requirements. In cases where the Secretary of the Interior's standards cannot be met, rehabilitation will conform to the agreed upon approaches, treatments and techniques resulting from the consultation process between the Agency, the borrower, the State Historic Preservation Officer and the Advisory Council of Historic Preservation.
III. Components of Multi-Family Building RehabilitationThe components of multi-family building rehabilitation necessary and generally considered by the Agency to be either maintenance and repair, moderate rehabilitation or substantial rehabilitation include but are not limited to those listed in the following chart.
Components of Multi-Family Building Rehabilitation
Components | Maintenance and repair | Moderate rehabilitation | Substantial rehabilitation |
---|---|---|---|
Air conditioning | o | ||
Appliance replacement or repair | o | ||
Cabinet replacement or repair | o | ||
Carpeting | o | ||
Caulking | o | ||
Ceiling framing | o | ||
Clothes closets or shelving improvements | o | ||
Door repair | o | ||
Drywall repair | o | ||
Gutters and downspouts | o | ||
Hardware replacement or repair | o | ||
Kitchen cabinet improvement | o | ||
Lighting fixture replacement or repair | o | ||
Mail boxes | o | ||
Painting | o | ||
Paneling | o | ||
Partition repair | o | ||
Roof repair | o | ||
Signage | o | ||
Stair repair | o | ||
Tile work | o | ||
Wallpapering | o | ||
Window shades and curtains | o | ||
Door replacement | o | ||
Drywall replacement | o | ||
Elevator components replacement | o | ||
Exterior entrance redesign, relocation | o | ||
Finish flooring materials | o | ||
Flashing | o | ||
Furnace replacement | o | ||
Gas pipes | o | ||
Insulation | o | ||
Lath and plaster replacement | o | ||
New shingles or roof replacement | o | ||
Partition (nonbearing) replacement, or relocation | o | ||
Plumbing fixture replacement | o | ||
Pointing | o | ||
Porch and steps alterator or replacement | o | ||
Stair replacement, or relocation | o | ||
Storm windows and weatherstripping | o | ||
Subfloor material replacement | o | ||
Trim - exterior and interior | o | ||
Window replacement | o | ||
New or alteration to the: | |||
Mechanical system | o | ||
Soil pipes | o | ||
Vent pipes | o | ||
Waste pipes | o | ||
Alteration or replacement of structural components: | |||
Beams | |||
Chimneys and vents | o | ||
Columns and post | o | ||
Electrical service - replacement or new | o | ||
Elevator replacement | o | ||
Exterior walls | o | ||
Floor construction | o | ||
Footing | o | ||
Foundation wall | o | ||
Foundation waterproofing | o | ||
Interior walls | o |
Moderate repair and rehabilitation shall not be limited to building changes for cosmetic purposes. In all cases moderate rehabilitation shall involve a minimum of three (3) components of building rehabilitation listed as moderate. Unless combined with other improvements in a project that are considered to be moderate or substantial rehabilitation the items identified as maintenance and repair are considered to be cosmetic and convenience changes.
Exhibit L to Subpart A of Part 1924 - Insured 10-Year Home Warranty Plan Requirements
7:12.1.2.7.16.1.1.17.36 :
Exhibit L to Subpart A of Part 1924 - Insured 10-Year Home Warranty Plan Requirements I. PurposeIn recent years, numerous third-party home warranty plans have been developed offering new homeowners varying degrees of protection against builder default and/or major structural defects in their homes. This exhibit establishes the criteria and procedures by which a warranty plan is found acceptable for new construction of single family homes financed by the Agency. An acceptable warranty plan will:
A. Assure that the Agency borrowers receive adequate warranty coverage,
B. In certain circumstances, eliminate the requirement for the Agency personnel to make the first two construction inspections, and
C. Permit a loan up to the market value of the security (less the unpaid principal balance and past due interest of any other liens against the security), even though the Agency personnel may not have performed period inspections during construction.
II. Types of Warranty CompaniesA. An insured warranty company is underwritten by an insurance carrier, licensed to operate as an insurer by the states where the warranty company plans to operate, and has an acceptable rating from a nationally recognized rating company such as A.M. Best Company.
B. A risk retention group is an insurer which is licensed in one state and is authorized, under the Products Liability Risk Retention Act of 1981, to issue its policies in all states. This authority is not challenged by the Agency; however, there remains some question as to the legal propriety of a 10-year insured warranty insurer to be a risk-retention group. If at some future time any state insurance commission or regulatory agency challenges the legal authority of such group, the Agency will reconsider its acceptance of the group.
C. Individual state warranty plans, such as that offered by the State of New Jersey, are backed by the full faith and credit of the state government.
III. Plan RequirementsTo be considered acceptable, a warranty plan must include the following features:
A. The entire cost (fee, premium, etc.) of the coverage is prepaid and coverage automatically transfers to subsequent owners without additional cost.
B. The coverage is not cancellable by the warrantor (builder), warranty company or insurer.
C. The coverage age includes at least the following:
(1) For one year from the effective date, any defects caused by faulty workmanship of defective materials.
(2) During the second year after the effective date, the warranty continues to cover the wiring, piping and duct work of the electrical, plumbing, heating and cooling systems, plus the items in (3).
(3) During the third through the tenth years, the warranty continues to cover major structural defects. A major structural defect is actual damage to the load-bearing portion of the home including damage due to subsidence, expansion or lateral movement of the soil (excluding movement caused by flood or earthquake) which affects its load-bearing function and which vitally effects or is imminently likely to affect use of the home for residential purposes.
D. A system is provided for complaint (claims) handling which includes a conciliation and, if necessary to resolve matters in dispute, arbitration arranged by the American Arbitration Association or similar organization.
E. A construction inspection plan is required if the Agency is to eliminate the first two Agency inspections or permit a full market value loan when Agency inspections are not conducted.
IV. Information for ReviewA. Companies submitting warranty plans for a determination of acceptability must support requests with the following information.
(1) Evidence that the insured warranty company has met the applicable state licensing and/or regulatory requirements in the state in which the company plans to operate.
(2) Evidence that the insurance carrier underwriting the warranty plan is licensed to operate as an insurer in the states in which the company plans to operate and has an acceptable rating from a nationally recognized company such as A.M. Best Company.
(3) State warrenty plan agencies will provide evidence that the plan is backed by the full faith and credit of the state.
(4) A full description of the warranty plan including information on the fees, builder and home registration procedures, required construction standards, construction inspection procedures, coverage provided and claims procedures.
(5) A sample copy of the warranty information and/or policy which is provided to the homeowner.
(6) Suggested means by which Agency field offices can readily assure that the builder is a member in good standing prior to loan approval and that a warrant will be issued upon the completion of construction prior to the final release of funds.
B. Submission and Acceptance:
(1) Insured warranty companies, except those operating as risk retention groups, and state warranty plan agencies will submit their requests and supporting information to the Agency State Director in the state in which they plan to operate. State Directors will determine the acceptability of insured warranty plans and state warranty plans in their jurisdictions, notify the company or agency of the decision in writing and notify field offices by issuance of a State Supplement including the names and addresses of acceptable warranty companies and any other pertinent information.
(2) Warranty companies claiming authority as risk retention groups will submit their requests and supporting information including certification that it has complied with all requirements of the Products Liability Risk Retention Act of 1981 (Pub. L. 97-45) and information indicating the state in which it is licensed, information to the Agency National Office, Single Family Housing Processing Division. The National Office will determine the acceptability of the warranty of a risk retention group, notify the company of the decision in writing and notify field offices by issuance of an attachment to this exhibit.
V. Warranty PerformanceA. County Supervisors will report inadequate warranty performance through their District Director to the State Director. State Directors will review the situation, assist in resolving any problems and, if necessary, initiate action under subpart F of part 1942 of this chapter. State Directors will inform, by memorandum, the Director, Single Family Housing Processing Division, National Office, of any problems with warranty performance and if any debarment action is initiated.
B. State Directors will annually monitor each warranty company and/or its insurer to assure continued compliance with state licensing and/or regulatory requirements.
Attachment 1 - Acceptable Warranty CompaniesThe warranty companies listed below claim authority to act as a risk retention group under the Products Liability Risk Retention Act of 1981 and as such, to operate in all States to provide 10-year home warranties. This authority remains subject to future challenges by any State insurance commissioner or regulatory agency; however, until such challenge is made, the Agency accepts their warranty.
Name and address | Area of operation |
---|---|
Home Owners Warranty Corporation/HOW Insurance Company, 11 North Glebe Road, Arlington, Virginia 22201, (703) 516-4100 | All States. |
Home Buyers Warranty, 89 Liberty Street, Asheville, North Carolina 22801, Telephone: (704) 254-4478 | All States. |
Residential Warranty Corporation, P.O. Box 641, Harrisburg, Pennsylvania 17108-0641, Telephone: 1-800-247-1812 | All States. |
Manufactured Housing Warranty Corporation, P.O. Box 641, Harrisburg, Pennsylvania 17108-0641, Telephone: 1-800-247-1812 | All States. |
Exhibit A to Subpart C of Part 1924 [Reserved]
7:12.1.2.7.16.3.1.17.37 :
Exhibit A to Subpart C of Part 1924 [Reserved]Exhibit B to Subpart C of Part 1924 - Site Development Design Requirements
7:12.1.2.7.16.3.1.17.38 :
Exhibit B to Subpart C of Part 1924 - Site Development Design RequirementsThis exhibit prescribes site development requirements to be used in developing residential sites in all housing programs. These requirements cover only those areas which involve health and safety concerns. They are not intended to cover all aspects of site development. Applicants and developers are expected to follow local practice, as a minimum, in all areas of site development not addressed in this exhibit. When State, local, or other requirements are applicable in addition to FmHA or its successor agency under Public Law 103-354's requirements, the most stringent requirement shall apply.
Proper integration of the natural features of a site with the manmade improvements is one of the most critical aspects of residential development. Poor site planning in large scale subdivisions, rental projects and individual sites, has resulted in a loss of valuable private and public natural resources and caused economic burdens and conditions unsuitable for healthy and pleasant living. Proper site design can preserve desirable natural features of the site, minimize expenses for streets and utilities, and provide a safe and pleasant living environment.
Table of Contents I. Streets A. Types 1. Collector Streets 2. Local Streets B. Design Features 1. Emergency Access 2. Cul-de-sacs 3. Intersection Angle 4. Intersection Sight Distance C. Street Geometry 1. Definitions 2. Design Requirements D. Construction II. Walks and Steps A. Walks B. Exterior Steps Not Contiguous to Dwelling or Building 1. Flight 2. Risers and Treads 3. Landings 4. Handrails III. Grading A. Compaction B. Gradients IV. Drainage A. General 1. Collection and Disposal 2. Concentrated Flow B. Drainage Design and Flood Hazard Exposure 1. Storm Frequences 2. Street Drainage 3. Foundation Drainage C. Primary Storm Sewer 1. Pipe Size 2. Minimum Gradient 3. Easements D. Drainage Swals and Gutters 1. Design 2. Easements E. Downspouts 1. Outfall 2. Piped Drainage F. Storm Inlets and Catch Basins 1. Openings 2. Access G. Drywells V. Water Supply Systems A. Individual Water Systems 1. General 2. Well Location 3. Well Construction 4. Pumps and Equipment 5. Storage Tanks B. Community Water Systems 1. Definition 2. Design VI. Wastewater Disposal Systems A. Individual Wastewater Disposal Systems 1. General 2. Percolation Tests 3. Subsurface Absorption Systems B. Community Wastewater Disposal Systems 1. Definition 2. Design I. StreetsA. Types - 1. Collector streets. Collector streets are feeder streets which carry traffic from local streets to the major system of arterial streets and highways. They include the principal entrance streets of residential developments and streets for circulation within such developments.
2. Local streets. Local streets are minor streets used primarily for access to abutting properties. These include drives serving multi-family housing units.
B. Design Features - 1. Emergency Access. Access for fire equipment and other emergency vehicles shall be within 100 feet of main building entrances.
2. Cul-de-sacs. Cul-de-sac streets shall have a turn-around with an outside roadway diameter of at least 80 feet, and a right-of-way diameter of at least 100 feet.
3. Intersection Angle. Streets shall be laid out to intersect as nearly as possible at right angles and no street shall intersect any other street at an angle less than 75 degrees. Curb radii shall be a minimum of 20 feet for street intersections.
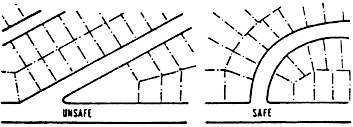
4. Intersection Sight Distance. Adequate distances must be maintained at intersections. Vehicles must be visible when within 75 feet of the centerlines of uncontrolled intersecting streets.
C. Street Geometry - 1. Definitions. The definitions in Sections I.C.1.a and I.C.1.b. apply to the requirements in Section I.C.2.
a. Terrain Classifications.
(1) Ordinary - Slope less than 8%.
(2) Rolling - Slope range of 8% to 15%.
(3) Hilly - Slope greater than 15%.
b. Development Density (Number of Lots). (Land Area minus Undeveloped Areas greater than Average Lot Size)
(1) Low - Less than 2 lots per acre.
(2) Medium - 2 to 6.0 lots per acre.
(3) High-More than six lots per acre.
2. Design Requirements. Collector streets and local streets shall comply with the requirements in tables 1 and 2 unless an exception is granted by the State Director. These requirements may need modification in localities having winter icing conditions.
Table 1 - Pavement Widths (feet)
Street type | On-street parallel parking | Development density | ||
---|---|---|---|---|
Low | Medium | High | ||
Collector | Prohibited | 26 | 32 | 36 |
Collector | No Restrictions | 36 | 36 | 40 |
Local | Prohibited | 18 | 18 | 20 |
Local | Partial, One Side 1 | 18 | 20 | 26 |
Local | Partial, One Side 1 | 22 | 26 | 32 |
Local | Total, One Side 2 | 22 | 26 | 26 |
Local | Total, Both Sides 2 | 26 | 32 | 36 |
( 1) At least one parking space per dwelling is provided off-street.
( 2) No parking spaces are provided off-street.
Table 2 - Street Design (feet)
Terrain | |||
---|---|---|---|
Ordinary | Rolling | Hilly | |
(1) Collector street: | |||
(a) Minimum centerline radius of curvature | 300 | 225 | 150 |
(b) Minimum sight distance | 250 | 200 | 150 |
(c) Minimum right-of-way width | 60 | 60 | 60 |
(2) Local Street: | |||
(a) Minimum centerline radius of curvature | 200 | 150 | 100 |
(b) Minimum sight distance | 200 | 150 | 100 |
(c) Minimum right-of-way width 1 | 50 | 50 | 50 |
( 1) For cul-de-sac streets, the minimum right-of-way width is 40 feet.
D. Construction. Street configuration and wearing surfaces must provide safe and economical access to all building sites. The design and construction of the street shall be appropriate for all anticipated traffic, climatic and soil conditions. Streets shall meet or exceed all local, county, and State requirements.
II. Walks and StepsA. Walks. Where walks are provided, they shall be located to assure a minimum vertical clearance of 7 feet from all permanent or temporary obstructions. Walks shall have a slip resistant surface.
B. Exterior Steps Not Contiguous to Dwelling or Building - 1. Flight. a. Single steps or flights of steps exceeding a vertical height of 12 feet shall not be accepted.
b. Steps shall be set back from an intersecting walk or drive a minimum of 1 foot at a retaining wall and 2 feet at slopes.
2. Risers and Treads. a. Risers shall be a maximum of 6 inches, a minimum of 3 inches and uniform throughout the flight.
b. Treads shall be a minimum of 12 inches and uniform throughout the flight.
c. Treads shall have a slip resistant surface.
d. Treads shall be pitched appropriately to ensure drainage.
3. Landings. a. Minimum length shall equal 3 feet or walk width whichever is greater.
b. A change in direction in a flight of stairs shall be accomplished only at a landing or by a winder which has a tread width at a point 18 inches from the converging end, equal to the full straight stair tread width.
4. Handrails. Stairways having a flight rise exceeding 30 inches shall have a 36 inch high handrail located on one side for stairs 5 feet or less in width and on both sides of stairways over 5 feet wide.
III. GradingA. Compaction - All fill for street or home construction shall have compaction of not less than 95 percent maximum density, as determined by proctor or other accepted testing methods. Maximum thickness of compaction layers shall be 6 inches except where compaction equipment of demonstrated capability is used under the direction of a qualified soils engineer. Earth fill used to support a building foundation shall be a controlled fill which is designed, supervised, and tested by a qualified soils engineer in accordance with good practice.
B. Gradients. Grading design shall be arranged to assure safe and convenient all-weather pedestrian and vehicular access to residential buildings and to all other necessary site facilities. Site grading shall be designed to establish building floor elevations and ground surface grades which allow drainage of surface water away from buildings and adjacent sites. Grading design shall conform with tables 3 and 4.
Table 3 - Access and Parking Gradients 1
[In percent]
Minimum | Maximum | |||
---|---|---|---|---|
Center line | Crown or cross slope | Center line | Crown or cross slope | |
Streets | 0.5 | 1.0 | 14.0 | 5.0 |
Street Intersections | 0.5 | 1.0 | 25.0 | 5.0 |
Driveways ( 3) | .05 | 1.0 | 14.0 | 5.0 |
Sidewalks ( 4): | ||||
Concrete | 0.5 | |||
Bituminous | 1.0 | |||
Building Entrances & Short Walks | 1.0 | 12.0 | 5.0 | |
Main Walks | 0.5 | 10.0 | 5.0 | |
Adjoining Steps | 2.0 | |||
Landings | 1.0 | |||
Stepped Ramp Treads | 1.0 | 2.0 | 5.0 | |
Parking | 0.5 | 5.0 | 5.0 |
1 Approximate Equivalents .5% = 1/16″ ft., 1.0 = 1/8″ ft., 2.0% = 1/4″ ft., 5.0% = 5/8″ ft., 10.0% = 1 1/4″ ft., 12.0% = 1 1/2″ ft., 21% = 2 5/8″ ft.
2 Grades approaching intersections shall not exceed 5 percent for a distance of not less than 100 feet from the centerline of the intersection.
3 Vertical transitions shall percent contact of car undercarriage of bumper with driveway surface.
4 Five percent maximum for major use by elderly tenants.
Table 4 - Slope Gradients 1
[In percent]
Minimum | Maximum | |
---|---|---|
Slope Away From Foundations: | ||
Pervious Surfaces | 2 5.0 | 3 21.0 |
Impervious Surfaces | 21.0 | 21.0 |
Pervious Surfaces: | ||
Ground Frost Area | 2.0 | |
Non-Ground Frost Areas | 41.0 | |
Impervious Surfaces | 0.5 | |
Slopes to be maintained by Machine | 333.0 |
1 See table 3, footnote (1).
2 Minimum length of 10 feet or as limited by property lines.
3 Minimum length of 4 feet.
4 The minimum is 2.0% if the annual precipitation is more than 50 inches.
A. General - 1. Collection and Disposal. Surface and subsurface drainage systems shall be provided, as appropriate, for collection and disposal of storm drainage and subsurface water. These systems shall provide for the safety and convenience of occupants. They shall protect dwellings, other improvements and useable lot areas from water damage, flooding, and erosion.
2. Concentrated Flow. Where storm drainage flow is concentrated, permanently maintained facilities shall be provided to prevent significant erosion and other damage or flooding on site or on adjacent properties.
B. Drainage Design and Flood Hazard Exposure - 1. Storm Frequency. Drainage facilities shall be designed for a 10 year storm frequency of 24-hour duration. Full potential development of all contributing areas shall be used as a basis for this determination.
2. Street Drainage. Streets shall be useable during runoff equivalent to a 10-year return frequency. Where drainage outfall is inadequate to prevent runoff equivalent to a 10-year return frequency from ponding over 6 inches deep, streets shall be made passable for local commonly used emergency vehicles during runoff equivalent to a 25-year return frequency except where an alternative access street not subject to such ponding is available.
3. Foundation Drainage. Appropriate crawl space and foundation drainage shall be provided for the removal of subsurface moisture.
C. Primary Storm Sewer - 1. Pipe Size. Pipe size for the primary storm sewer (any storm sewer or inlet lateral located in a street or other public right-of-way) shall have an inside diameter based on design analysis but not less than 15 inches. Where anticipated runoff from the five-year return frequency rainfall will not fill a 15 inch pipe, a primary storm sewer system usually is unnecessary.
2. Minimum Gradient. Minimum gradient shall be selected to provide for self-scouring of the conduit under low-flow conditions and for removal of sediments foreseeable from the drainage area.
3. Easements. Easements for storm sewers shall be a minimum of 10 feet in width.
D. Drainage Swals and Gutters - 1. Design. Paved gutters shall have a minimum grade of 0.5 percent. Paved gutters and unpaved drainage swales shall have adequate depth and width to accommodate the maximum foreseeable runoff without overflow. Swales and gutters shall be seeded, sodded, sprigged or paved as appropriate to minimize potential erosion. Side slopes shall be no steeper than 2:1.
2. Easements. Surface channels shall have an easement which is at least the width of the channel plus 10 feet.
E. Downspouts - 1. Outfall. Where downspouts are provided, they shall either be connected to an available storm sewer, provided with suitable splash blocks, or empty at acceptable locations onto paved areas so that water drains away from buildings. Downspouts shall not connect to sanitary sewers.
2. Piped Drainage. Piped roof drainage from buildings shall be connected to available storm sewers or empty at locations where no erosion or other damage will be caused.
F. Storm Inlets and Catch Basins - 1. Openings. Where inlets are accessible to small children, openings shall have one dimension limited to 6 inch access. Inlet openings in paved areas shall be designed to avoid entrapment or impedence of bicycles, baby carriages, etc.
2. Access. Access for cleaning shall be provided to all inlet boxes and catch basins.
G. Drywells - Drywells for the disposal of water from foundation drains, crawl spaces, and other small quantity sources shall be permissible where the bottom of drywells project into strata of undistributed porous soil at a level where the bottom of the drywell will be above the ground water table at its highest seasonal elevation.
V. Water Supply SystemsA. Individual Water Systems - 1. General. a. In this subpart, an individual water system is a system which serves fewer customers or connections than the lower threshold for community systems stated in the Safe Drinking Water Act.
b. The system for an individual household should be capable of delivering a sustained flow of 5 gpm. A system supplying water to multiple household shall be designed by a Professional Engineer and have sufficient capacity to serve estimated demand. A test of at least 4 hours duration shall be conducted to determine the yield and maximum drawdown for all wells developed as part of an individual water system. This test may be waived by the State Office based on the hydrologic and geologic conditions in the area.
c. Water that requires continual or repetitive treatment to be safe bacterially is not acceptable.
d. After installation, the system should be disinfected in accordance with the recommendations of the health authority. In the absence of a health authority, system cleaning and disinfection should conform with the current EPA Manual of Individual Water Supply Systems.
e. Any method for individual water supply contained herein which is not permitted by the local health authority having jurisdiction shall not be used.
2. Well Location - a. A well located within the foundation walls of a dwelling is not acceptable except in arctic and sub-arctic regions.
b. Water which comes from soil formation which may be polluted or contaminated or is fissured or creviced or which is less than 20 feet below the natural ground surface (subject to the requirements of the local health authority) is not acceptable.
c. Individual water supply systems are not acceptable for individual lots in areas where chemical soil poisoning is practiced if the overburden of soil between the ground surface and the water bearing strata is coarse-grained sand, gravel, or porous rock, or is creviced in a manner which will permit the recharge water to carry the toxicants into the zone of saturation.
d. Table 5 shall be used in establishing the minimum acceptable distances between wells and sources of pollution located on either the same or adjoining lots. These distances may be increased by either the health authority having jurisdiction or the FmHA or its successor agency under Public Law 103-354 State Director.
Table 5 - Distance From Source of Pollution
Source of pollution | Minimum horizontal distance (feet) |
---|---|
Property Line | 10 |
Septic Tank | 50 |
Absorption field | 1100 |
Seepage pit | 1100 |
Absorption Bed | 1100 |
Sewer Lines w/Permanent Watertight Joints | 10 |
Other Sewer Lines | 50 |
Chemically Poisoned Soil | 1100 |
Dry Well | 50 |
Other | ( 2) - |
Notes:
1 The horizontal distance between the sewage absorption system and the well, or the chemically poisoned soil and the well, may be reduced to 50 feet only where the ground surface is effectively separated from the water bearing formation by an extensive, continuous impervious strata of clay, hard-pan, or rock. The well shall be constructed so as to prevent the entrance of surface water and contaminants.
2 Other sources of pollution could be fuel oil or gasoline storage tanks, farm yards or chemical storage tanks, etc. The well should be separated from these sources of pollution a distance recommended by the local health authority.
3. Well Construction - a. The well shall be constructed to allow the pump to be easily placed and to function properly.
b. All drilled wells shall be provided with a sound, durable and watertight casing capable of sustaining the loads imposed. The casing shall extend from a point several feet below the water level at drawdown or from an impervious strata above the water level, to 12 inches above either the ground surface or the pump room floor. The casing shall be sealed at the upper opening.
c. Bored wells shall be lined with concrete, vitrified clay, or equivalent materials.
d. The space between the casing or liner and the wall of the well hole shall be sealed with cement grout.
e. The well casing shall not be used to convey water except under positive pressure. A separate drop pipe shall be used for suction line.
f. When sand or silt is encountered in the water-bearing formation, the well shall either be gravel packed, or a removable strainer or screen shall be installed.
g. The surface of the ground above and around the well shall be graded to drain surface water away from the well.
h. Openings in the casing, cap, or concrete cover for the entrance of pipes, pump or manholes, shall be made watertight.
i. If a breather is provided, it shall extend above the highest level to which surface water may rise. The breather shall be watertight, and the open end shall be screened and positioned to prevent entry of dust, insects and foregin objects.
4. Pumps and Equipment - a. Pumps shall be capable of delivering the volume of water required herein under normal operating pressures within the living unit. Well pump capacity shall not exceed the output of the well.
b. Pumps and equipment shall be mounted to be free of objectionable noises, vibrations, flooding, pollution, and freezing.
c. Suction lines shall terminate below maximum drawdown of the water level in the well.
d. Horizontal segments of suction line shall be placed below the frost line in a sealed casing pipe or in at least 4 inches of concrete. The distance from suction line to sources of pollution shall be not less than shown in table 5.
5. Storage Tanks - a. A system for an individual household shall include a pressure tank having a minimum capacity of 42-gallons. However, prepressured tanks and other pressurizing devices are acceptable provided that delivery between pump cycles equals or exceeds that of a 42 gallon tank. Storage capacity on a system for multiple households must be sufficient to meet estimated peak demands.
b. Tanks shall be equipped with a clean-out plug at the lowest point, and if pressurized, a suitable pressure relief valve.
c. When additional storage is necessary because the well yield will not meet the system peak demands, all nonpressurized intermediate tanks shall be designed and installed in a manner that will prevent the pollution or degradation of the water supply.
B. Community Water Systems - 1. Definition. In this subpart, a community water system is a system which meets the definition in the Safe Drinking Water Act.
2. Design. A community water system shall be designed by a qualified, professional engineer licensed in the state in which the water system will be located. Community water systems shall comply with all Federal and State laws.
VI. Wastewater Disposal SystemsEach dwelling shall be provided with a water-carried system adequate to dispose of domestic wastes in a manner which will not create a nuisance, contaminate any existing or prospective water source or water supply, or in any way endanger the public health.
A. Individual Wastewater Disposal Systems - 1. General. a. In this subpart, an individual wastewater disposal system is a sewage disposal system which serves only 1 dwelling unit.
b. When service from an acceptable public or community system is not available or feasible, and ground water and soil conditions are acceptable, an individual system may be used.
c. Each individual wastewater disposal system shall consist of a house sewer, a pretreatment unit (e.g., septic tank, individual package treatment plant), and acceptable absorption system (subsurface absorption field, seepage pit(s), or subsurface absorption bed). The system shall be designed to receive all sanitary sewage (bathrooms, kitchen and laundry) from the dwelling, but not footing or roof drainage. It shall be designed so that gases generated anywhere in the system can easily flow back to the building sewer stack.
2. Percolation Tests - a. Percolation tests are required unless a waiver is granted by the National Office. Waivers may be granted on a statewide or local basis in cases where an onsite evaluation of soils would be performed by a qualified soil technician, soil scientist, or engineer. Requests for waivers must describe the qualifications of the person evaluating the soils and discuss the criteria to be used in designing the absorption system.
b. In uniform soils one percolation test shall be made within each area proposed for an absorption system. If significant soil variations are encountered or expected, additional tests shall be made for each variation.
c. Percolation tests shall be conducted in accordance with good practice. Guidance for performing these tests is included in the EPA design manual, “Onsite Wastewater Treatment and Disposal Systems.”
3. Subsurface Absorption System - a. Where percolation rates, soil characteristics and site conditions are acceptable, an absorption system may be installed in an area which is well drained, has an acceptable slope, and is acceptable for excavation.
b. Soils with percolation rates less than 1 minute per inch may be used if the soil is replaced with a layer of loamy or fine sand at least 2 feet thick. (Refer to the EPA Design Manual, “Onsite Wastewater Treatment and Disposal System”.)
c. Soils with percolation rates greater than 60 minutes per inch are not acceptable for subsurface wastewater disposal systems.
B. Community Wastewater Disposal Systems - 1. Definition. In this subpart, a community wastewater disposal system is any wastewater disposal system which serves more than 1 dwelling unit.
2. Design. A community wastewater disposal system shall be designed by a qualified, professional engineer licensed in the state in which the system will be located.
[52 FR 19284, May 22, 1987]Exhibit C to Subpart C of Part 1924 - Checklist of Visual Exhibits and Documentation for RRH, RCH, and LH Proposals
7:12.1.2.7.16.3.1.17.39 :
Exhibit C to Subpart C of Part 1924 - Checklist of Visual Exhibits and Documentation for RRH, RCH, and LH Proposals U.S. Department of Agriculture Farmers Home Administration or its successor agency under Public Law 103-354This exhibit lists visual exhibits and documentation necessary for FmHA or its successor agency under Public Law 103-354 to properly evaluate proposed development. Intermediate consultation by the applicant, builder-developer and others hereafter referred to as the sponsor with the FmHA or its successor agency under Public Law 103-354 District or State Offices should be as frequent as necessary to reduce chances of misunderstandings and limit the amount of non-productive time and expense for all parties concerned.
I. Preapplication Submission Documents: The sponsor will submit the following information to the District Director to determine feasibility of the project and general conformance with FmHA or its successor agency under Public Law 103-354 policy:
A. Environmental review requirements. As requested by the Agency, the applicant is responsible for providing details of the project's potential impact on the human environment and historic properties, in accordance with 7 CFR part 1970. Guidance concerning the environmental review requirements is available at any Agency office or on the Agency's Web site.
B. Location Map. A general site location map of the area indicating the adjacent land zoning and uses, the present and future access roads to the site as well as the proximity to shopping, schools, churches, and major transportation facilities with note of traffic volumes. If a satisfactory map of the locality is not available, a clear and preferably scaled rough sketch map that provides the required information will be sufficient.
C. Property Survey Map. A current survey map of the project site showing the boundaries as well as all existing known features specifically including utilities, easements, access roads, floodplains, drainageways, rock outcroppings and wooded areas or specimen trees. If a current survey does not exist, the most accurate document which is available will be submitted.
D. Soils Map and Report. A complete soils map and report, including “site specific” interpretations and recommendations, from the local or county representative of the U.S. Department of Agriculture, Soil Conservation Service (SCS) Office will be included with the location and feasibility submission. A determination of whether or not any lands described in USDA Regulation 9500-3 are impacted by the proposed development should also be included. The local SCS office may provide recommendations for the development of suitable drainage and landscaping plans later in the planning process.
E. Market survey. A market survey will be submitted in accordance with the requirements of the respective loan program as indicated in part 1944, subparts D and E of this chapter.
F. Request for Exceptions. Any need for State or National Office exception(s) should be identified at this stage in the processing. Appropriate exception(s) should be requested and obtained before proceeding to the preliminary submission.
G. Other. The applicant will need to submit any additional information that may be needed as indicated in subpart D or exhibit A-7 of subpart E of part 1944 of this chapter. This may include but is not limited to:
1. Schematic design drawings showing the proposed plot plan, typical unit plans, and elevations. If available, the proposed preliminary drawings and specifications may be submitted. This would be of assistance if it is determined that the loan must receive National Office authorization.
2. Type of construction.
3. The total number of living units and the number of each type of living unit proposed.
4. Type of utilities such as water, sewer, gas, and electricity and whether each is public, community, or individually owned.
II. Application Submission Documents: After it is determined by FmHA or its successor agency under Public Law 103-354 that the project is feasible and the location conforms with the intent of the funding program, the sponsor will submit the following information to the District Director in addition to those materials submitted previously.
A. Property Survey. A survey (where 1 inch represents no more than 100 feet) of the property lot showing the exact boundaries and corners of the property accompanied by a written description of said boundaries. Also, locations of predominant features such as utilities, easements, access points, floodplains, drainageways, rock outcroppings and wooded areas or specimen trees affecting the proposed development must be included. This document shall bear the seal of a professional licensed to provide surveying services in the State in which the project will be located. This survey could be a part of item D below.
B. Topographic Map. An accurate topographic map showing existing and proposed contours with a scale compatible with the size of the project. The site shall be shown at a reasonable scale with 5-foot contour intervals. Where the site is unusually level or steep, the contour intervals may be varied accordingly.
C. Preliminary Site Plan. A line drawing, to scale, showing proposed street locations with profiles and widths, lot layouts, major drainageways, and other development planned. Preliminary sections and details shall be provided for the street construction, curbs and gutters, drainageways, and other physical improvements.
D. Preliminary Dwelling Drawings and Specifications. Drawings of the dwelling units, preliminary floor plans and specifications, elevations and sample site plans showing the placement of the individual buildings should be submitted.
E. Statement of Planning and Zoning Compliance. Local, county and State approvals as applicable. If change of zoning or variance is required, the status of the variance or change of zoning shall be documented.
F. Technical Service Contracts. Executed contracts for the professional services of an architect, engineer, land surveyor, landscape architect, site planner and/or soil engineer will be submitted as appropriate for the planning of the proposed development.
G. Utility Approvals. Statements of approval and feasibility for utility systems as follows:
1. Verification of adequate capacity and approval to tie-in with local existing water, wastewater disposal, electric, telephone, and other utility systems, as appropriate.
2. Tentative approval of local or State health authority for individual water and/or wastewater disposal systems when it is clear that central systems are unfeasible at this time. Use § 1924.108(a)(5) of this subpart when preparing information required.
H. Facility Acceptance. Evidence that the appropriate public body is willing to accept and maintain streets, common areas, lighting, fire hydrants, sidewalks, drainageways, and utilities, as appropriate, when dedicated to said body.
I. Preliminary Specifications. Outline specifications describing all the proposed materials to be used and how they are to be applied. These are only the materials used in the land development and construction of the streets, drainage, and utility work.
J. Incremental Slopes Plan. If areas of common slope are not identified elsewhere in adequate detail, this information should be provided in a separate plan.
K. Preliminary Grading Plan. This plan will indicate degree of work required to provide positive drainage of all building sites and control measures to be taken to eliminate soil erosion. Dwelling locations may be shown if they can be predetermined.
L. Other. The applicant will need to submit any additional information that may be needed as indicated in the respective loan program regulations as indicated in part 1944, subparts D and E and part 1822, subpart F of this chapter (FmHA or its successor agency under Public Law 103-354 Instruction 444.7). This may include but not be limited to:
1. A detailed trade-item cost breakdown of the project for such items as land and right-of-way, building construction, equipment, utility connections, architectural/engineering and legal fees, and both on- and off-site improvements. The cost breakdown also should show separately the items not included in the loan, such as furnishings and equipment. This trade-item cost breakdown should be updated just prior to loan approval.
2. Information on the method of construction, on the proposed contractor if a construction contract is to be negotiated and on the architectural, engineering, and legal services to be provided.
3. For all projects containing over four units the applicant will submit an Affirmative Fair Housing Marketing Plan for approval by FmHA or its successor agency under Public Law 103-354 in accordance with § 1901.203 of subpart E to part 1901 of this chapter. The Affirmative Fair Housing Marketing Plan must be prepared in a complete, meaningful, responsive and detailed manner.
4. A description and justification of any related facilities (including but not limited to workshops, community buildings, recreation center, central cooking and dining facilities, or other similar facilities to meet essential needs) to be financed wholly or in part with loan funds.
III. Technical Documents Necessary for the Obligation of Funds. All decisions regarding the conceptual design of the proposed project should be made prior to this submission. This effort is mainly to demonstrate that those agreed upon concepts have been transformed into construction documents and the necessary approvals have been granted. All items requiring revision or more detailed information as determined by the review of the preliminary submission will be resolved before the sponsor prepares the final submission. All documents shall be executed in a professional manner and shall carry the appropriate designation attesting to the professional qualifications of the architect, engineer, land surveyor or site planner. All documents will be accurately drawn at an appropriate scale.
[52 FR 19284, May 22, 1987, as amended at 56 FR 2202, Jan. 22, 1991; 81 FR 11030, Mar. 2, 2016]