Title 40
SECTION 92.114
92.114 Exhaust gas and particulate sampling and analytical system.
§ 92.114 Exhaust gas and particulate sampling and analytical system.(a) General. (1) During emission testing, the engine exhaust is routed through an exhaust duct connected to, or otherwise adjacent to the outlet of the locomotive exhaust system. Emission samples are collected as specified in paragraphs (b) and (c) of this section. Exhaust duct requirements are specified in paragraph (d) of this section.
(2) The systems described in this section are appropriate for use with locomotives or engines employing a single exhaust.
(i) For testing where the locomotive or engine has multiple exhausts all exhaust streams shall be combined into a single stream prior to sampling, except as allowed by paragraph (a)(2)(ii) of this section.
(ii) For locomotive testing where the locomotive has multiple exhaust stacks, proportional samples may be collected from each exhaust outlet instead of ducting the exhaust stacks together, provided that the CO2 concentrations in each exhaust stream are shown (either prior to testing or during testing) to be within 5 percent of each other at notch 8.
(3) All vents, including analyzer vents, bypass flow, and pressure relief vents of regulators, should be vented in such a manner to avoid endangering personnel in the immediate area.
(4) Additional components, not specified here, such as instruments, valves, solenoids, pumps, switches, and so forth, may be employed to provide additional information and coordinate the functions of the component systems, provided that their use is consistent with good engineering practice. Any variation from the specifications in this subpart including performance specifications and emission detection methods may be used only with prior approval by the Administrator.
(b) Raw exhaust sampling for gaseous emissions. (1)(i) An example of the type of sampling and analytical system which is to be used for gaseous emissions testing under this subpart is shown in Figure B114-1 of this section. All components or parts of components that are wetted by the sample or corrosive calibration gases shall be either chemically cleaned stainless steel or other inert material, for example, polytetrafluoroethylene resin. The use of “gauge savers” or “protectors” with nonreactive diaphragms to reduce dead volumes is permitted. Additional components such as instruments, valves, solenoids, pumps, switches, etc. may be employed to provide additional information and coordinate the functions of the component systems.
(ii) System components list. The following is a list of components shown in Figure B114-1 of this section by numeric identifier.
(A) Filters. Glass fiber filter paper is permitted for the fine particulate filters (F1, F2, and F3). Optional filter F4 is a coarse filter for large particulates. Filters F3 and F4 are heated filters
(B) Flowmeters. Flowmeters FL1 and FL2 indicate sample flow rates through the CO and CO2 analyzers. Flowmeters FL3, FL4, FL5, and FL6 indicate bypass flow rates.
(C) Gauges. Downstream gauges are required for any system used for testing under this subpart. Upstream gauges may be required under this subpart. Upstream gauges G1 and G2 measure the input to the CO and CO2 analyzers. Downstream gauges G3 and G4 measure the exit pressure of the CO and CO2 analyzers. If the normal operating range of the downstream gauges is less than 3 inches of water, then the downstream gauges must be capable of reading both pressure and vacuum. Gauges G3 and G4 are not necessary if the analyzers are vented directly to atmospheric pressure.
(D) Pressure gauges. P1 is a bypass pressure gauge; P2, P3, P4, and P5 are for sample or span pressure at inlet to flow control valves.
(E) Water traps. Water traps WT1 and WT2 to remove water from the sample. A water trap performing the function of WT1 is required for any system used for testing under this subpart. Chemical dryers are not an acceptable method of removing the water. Water removal by condensation is acceptable. If water is removed by condensation, the sample gas temperature or sample dew point must be monitored either within the water trap or downstream; it may not exceed 45 °F (7 °C). Means other than condensation may be used only with prior approval from the Administrator.
(F) Regulators. R1, R3, R4, and R6 are line pressure regulators to control span pressure at inlet to flow control valves; R2 and R5 are back pressure regulators to control sample pressure at inlet to flow control valves.
(G) Valves. V1, V7, V8, and V14 are selector valves to select zero or calibration gases; V2 are optional heated selector valves to purge the sample probe, perform leak checks, or to perform hang-up checks; V3 and V5 are selector valves to select sample or span gases; V4, V6, and V15 are flow control valves; V9 and V13 - heated selector valve to select sample or span gases; V10 and V12 - heated flow control valves; V11 - Selector valve to select NOX or bypass mode in the chemiluminescence analyzer; V16 - heated selector valve to perform leak checks.
(H) Pump. Sample transfer pump to transport sample to analyzers.
(I) Temperature sensor. A temperature sensor (T1) to measure the NO2 to NO converter temperature is required for any system used for testing under this subpart.
(J) Dryer. Dryers D1 and D2 to remove the water from the bypass flows to prevent condensation in flowmeters FL3, FL4, and FL6.
(2) The following requirements must be incorporated in each gaseous sampling system used for testing under this subpart:
(i) The exhaust is analyzed for gaseous emissions using analyzers meeting the specifications of § 92.109, and all analyzers must obtain the sample to be analyzed from the same sample probe, and internally split to the different analyzers.
(ii) Sample transfer lines must be heated as specified in paragraph (b)(4) of this section.
(iii) Carbon monoxide and carbon dioxide measurements must be made on a dry basis. Specific requirements for the means of drying the sample can be found in paragraph (b)(1)(ii)(E) of this section.
(iv) All NDIR analyzers must have a pressure gauge immediately downstream of the analyzer. The gauge tap must be within 2 inches of the analyzer exit port. Gauge specifications can be found in paragraph (b)(1)(ii)(C) of this section.
(v) All bypass and analyzer flows exiting the analysis system must be measured. Capillary flows such as in HFID and CL analyzers are excluded. For each NDIR analyzer with a flow meter located upstream of the analyzer, an upstream pressure gauge must be used. The gauge tap must be within 2 inches of the analyzer entrance port.
(vi) Calibration or span gases for the NOX measurement system must pass through the NO2 to NO converter.
(vii) The temperature of the NO2 to NO converter must be displayed continuously.
(3) Gaseous sample probe. (i) The gaseous emissions sample probe shall be a straight, closed end, stainless steel, multi-hole probe. The inside diameter shall not be greater than the inside diameter of the sample line by more than 0.01 inches (0.03 cm). The wall thickness of the probe shall not be greater than 0.04 inches (0.10 cm). The fitting that attaches the probe to the exhaust duct shall be as small as practical in order to minimize heat loss from the probe.
(ii) The gaseous emissions sample probe shall have a minimum of three holes in each 3 inch segment of length of the probe. The spacing of the radial planes for each hole in the probe must be such that they cover approximately equal cross-sectional areas of the exhaust duct. The angular spacing of the holes must be approximately equal. The angular spacing of any two holes in one plane may not be 180 °±20° (see section view C-C of Figure B114-2 of this section). The holes should be sized such that each has approximately the same flow. If only three holes are used in each 3 inch segment of probe length, they may not all be in the same radial plane.
(iii) The sample probe shall be so located in the center of the exhaust duct to minimize stratification, with respect to both concentration and velocity, present in the exhaust stream. The probe shall be located between two feet and five feet downstream of the locomotive exhaust outlet (or nearest practical equivalent during engine testing), and at least 1 foot upstream of the outlet of the exhaust duct to the atmosphere.
(iv) If the exhaust duct is circular in cross section, the sample probe should extend approximately radially across the exhaust duct, and approximately through the center of the duct. The sample probe must extend across at least 80 percent of the diameter of the duct.
(v) If the exhaust duct is not circular in cross section, the sample probe should extend across the exhaust duct approximately parallel to the longest sides of the duct, or along the longest axis of the duct which is not a diagonal, and through the approximate center of the duct. The sample probe must extend across at least 80 percent of the longest axis of the duct which is not a diagonal, and be approximately parallel to the longest sides of the duct.
(vi) Other sample probe designs and/or locations may be used only if demonstrated (to the Administrator's satisfaction) to provides a more representative sample.
(4) Sample transfer line(s). (i) The maximum inside diameter of the gaseous emissions sample line shall not exceed 0.52 inches (1.32 cm).
(ii) If valve V2 is used, the sample probe must connect directly to valve V2. The location of optional valve V2 may not be greater than 4 feet (1.22 m) from the exhaust duct.
(iii) The sample transport system from the engine exhaust duct to the HC analyzer and the NOX analyzer must be heated as is indicated in Figure B114-1 of this section.
(A) For diesel fueled and biodiesel fueled locomotives and engines, the wall temperature of the HC sample line must be maintained at 375 ±20 °F (191 ±11 °C). An exception is made for the first 4 feet (122 cm) of sample line from the exhaust duct. The upper temperature tolerance for this 4 foot section is waived and only the minimum temperature specification applies.
(B) For locomotives and engines using fuels other than diesel or biodiesel, the heated components in the HC sample path shall be maintained at a temperature approved by the Administrator, not exceeding 446 °F (230 °C).
(C) For all fuels, wall temperature of the NOX sample line must be maintained between 140 °F (60 °C) and 446 °F (230 °C). An exception is made for the first 4 feet (122 cm) of sample line from the exhaust duct. The upper temperature tolerance for this 4 foot section is waived and only the minimum temperature specification applies.
(D) For each component (pump, sample line section, filters, etc.) in the heated portion of the sampling system that has a separate source of power or heating element, use engineering judgment to locate the coolest portion of that component and monitor the temperature at that location. If several components are within an oven, then only the surface temperature of the component with the largest thermal mass and the oven temperature need be measured.
(c) Particulate emissions. (1)(i) Schematic drawing. An example of a sampling system which may be used for particulate emissions testing under this subpart is shown in Figure B114-3 of this section. All components or parts of components that are wetted by the samples gases upstream of the filter shall be either chemically cleaned stainless steel or other inert material, for example, polytetrafluoroethylene resin. The use of “gauge savers” or “protectors” with nonreactive diaphragms to reduce dead volumes is permitted. Additional components such as instruments, valves, solenoids, pumps, switches, etc. may be employed to provide additional information and coordinate the functions of the component systems.
(ii) The following requirements must be incorporated in each system used for testing under this subpart:
(A) All particulate filters must obtain the sample from the same sample probe located within the exhaust gas extension with internal split to the different filters.
(B) The wall temperature of the sample transport system from the probe to the dilution tunnel (excluding the first 4 feet of the particulate transfer tube) must be maintained at 375 °F to 395 °F (191 °C to 202 °C).
(2) Particulate raw sample probe. (i) The sample probe for the raw exhaust shall be a straight, closed end, stainless steel, multi-hole probe of approximately 1.25 inch (3.2 cm) diameter. The inside diameter shall not be greater than the inside diameter of the sample line by more than 0.1 inches (0.3 cm). The wall thickness of the probe shall not be greater than 0.06 inches (0.15 cm). The fitting that attaches the probe to the exhaust duct shall be as small as practical in order to minimize heat loss from the probe.
(ii) All sample collection holes in the probe shall be located so as to face away from the direction of flow of the exhaust stream or at most be tangential to the flow of the exhaust stream past the probe (see Figure B114-4 of this section). Five holes shall be located in each radial plane along the length of the probe in which sample holes are placed. The spacing of the radial planes for each set of holes in the probe must be such that they cover approximately equal cross-sectional areas of the exhaust duct. For rectangular ducts, this means that the sample hole-planes must be equidistant from each other. For circular ducts, this means that the distance between the sample hole-planes must be decreased with increasing distance from the center of the duct (see Figure B114-4 of this section).
(Note:Particulate concentrations are expected to vary to some extent as a function of the distance to the duct wall; thus each set of sample holes collects a sample that is representative of a cross-sectional disk at that approximate distance from the wall.)
The spacing between sets of sample holes along the length of the probe shall be no more than 4 inches (10 cm). The holes should be sized such that each has approximately the same flow.(iii)(A) The particulate sample probe shall be located in the exhaust duct on an axis which is directly downstream of, and parallel to the axis of the gaseous sample probe. The distance between the probes shall be between 3 inches (7.6 cm) and 6 inches (15.2 cm). Greater spacing is allowed for engine testing, where spacing of 3 inches (7.6 cm) to 6 inches (15.2 cm) is not practical.
(B) If the exhaust duct is circular in cross section, the sample probe should extend approximately radially across the exhaust duct, and approximately through the center of the duct. The sample probe must extend across at least 80 percent of the diameter of the duct.
(C) If the exhaust duct is not circular in cross section, the sample probe should extend across the exhaust duct approximately parallel to the longest sides of the duct, or along the longest axis of the duct which is not a diagonal, and through the approximate center of the duct. The sample probe must extend across at least 80 percent of the longest axis of the duct which is not a diagonal, and be approximately parallel to the longest sides of the duct.
(3) Particulate sample transfer line. (i) The maximum inside diameter of the particulate emissions sample line shall be approximately 2.5 inches (6.4 cm).
(ii) The sample transfer line shall be heated to maintain a wall temperature above 375 °F.
(4) Dilution tunnel. The flow capacity of the blower moving the mixture of sample and air through the tunnel must be sufficient to maintain the diluted sample stream at a temperature of 125 °F (51.7 °C) or less, at the sampling zone in the dilution tunnel and at the sample filter. A single measurement of diluted exhaust temperature is required. The temperature shall also be maintained as required to prevent condensation at any point in the dilution tunnel. A small negative pressure is to be maintained in the dilution tunnel by throttling at the source of the dilution air, and adjusted as necessary, sufficient to draw sample through the probe and sample transfer line. Direct sampling of the particulate material may take place (Figure B114-3 of this section) at this point.
(i)(A) The dilution tunnel shall be:
(1) Small enough in diameter to cause turbulent flow (Reynolds Number greater than 4000) and of sufficient length to cause complete mixing of the exhaust and dilution air;
(2) 4 inches (10 cm) minimum inside diameter;
(3) Constructed of electrically conductive material which does not react with the exhaust components; and
(4) Electrically grounded.
(B) The temperature of the diluted exhaust stream inside of the dilution tunnel shall be sufficient to prevent water condensation.
(C) The engine exhaust shall be directed downstream at the point where it is introduced into the dilution tunnel.
(ii) Dilution air:
(A) Shall be at a temperature of 68 °F (20 °C) or greater.
(B) May be filtered at the dilution air inlet.
(C) May be sampled to determine background particulate levels, which can then be subtracted from the values measured in the exhaust stream.
(D) Shall be sampled to determine the background concentration of CO2.
(iii) Dilute sample probe and collection system.
(A) The particulate sample probe in the dilution tunnel shall be:
(1) Installed facing upstream at a point where the dilution air and exhaust are well mixed (i.e., on the tunnel centerline, approximately 10 tunnel diameters downstream of the point where the exhaust enters the dilution tunnel).
(2) Sufficiently distant (radially) from other sampling probes so as to be free from the influence of wakes or eddies produced by the other probes.
(3) 0.5 in. (1.3 cm) minimum inside diameter.
(4) The distance from the sampling tip to the filter holder shall not be more than 40 inches (102 cm).
(5) Designed to minimize the deposition of particulate during transfer (i.e., bends should be as gradual as possible, protrusions (due to sensors, etc.) should be smooth and not sudden, etc.).
(B) The gas meters or flow instrumentation shall be located sufficiently distant from the tunnel so that the inlet gas temperature remains constant (±5 °F (±2.8 °C)). Alternately, the temperature of the sample may be monitored at the gas meter, and the measured volume corrected to standard conditions.
(C) Particulate sampling filters. (1) Fluorocarbon-coated glass fiber filters or fluorocarbon-based (membrane) filters are required.
(2) Particulate filters must have a diameter to maintain the average face velocity of the sample across the filter between 35 and 80 cm/s.
(3) The dilute exhaust will be simultaneously sampled by a pair of filters (one primary and one back-up filter) during each phase of the test. The back-up filter shall be located no more than 4 inches (10 cm) downstream of the primary filter. The primary and back-up filters shall not be in contact with each other.
(4) The recommended target loading on a primary 70-mm filter (60 mm diameter stain area) is 1.3 milligrams. Equivalent loadings (0.5 mg/1075 mm 2 stain area) shall be used as target loadings when other filter sizes are used.
(D) Diluted CO2 sample collection system. (1) The concentrations of CO2 in the dilution air and diluted exhaust are determined by pumping a sample into a sample bag (made of a nonreactive material) or directly to the analyzer, as shown in Figure B114-3 of this section.
(2) The sample probe for the diluted exhaust shall be installed facing upstream at a point where the dilution air and exhaust are well mixed (i.e., on the tunnel centerline, approximately 10 tunnel diameters downstream of the point where the exhaust enters the dilution tunnel). It shall also be sufficiently distant (radially) from other sampling probes so as to be free from the influence of any wakes or eddies produced by the other probes.
(iv) Other sample flow handling and/or measurement systems may be used if shown to yield equivalent results and if approved in advance by the Administrator. (See Appendix IV of this part for guidance.)
(d) Exhaust system. The exhaust system shall meet the following requirements:
(1) For locomotive testing, the engine exhaust shall be routed through an exhaust duct with dimensions equal to or slightly larger than the dimensions of the locomotive exhaust outlet. The exhaust duct shall be designed so as to not significantly affect exhaust backpressure.
(2) For engine testing, either a locomotive-type or a facility-type exhaust system (or a combination system) may be used. The exhaust backpressure for engine testing shall be set between 90 and 100 percent of the maximum backpressure that will result with the exhaust systems of the locomotives in which the engine will be used. Backpressure less than 90 percent of the maximum value is also allowed, provided the backpressure is within 0.07 psi of the maximum value. The facility-type exhaust system shall meet the following requirements:
(i) It must be composed of smooth ducting made of typical in-use steel or stainless steel.
(ii) If an aftertreatment system is employed, the distance from the exhaust manifold flange(s), or turbocharger outlet to any exhaust aftertreatment device shall be the same as in the locomotive configuration unless the manufacturer is able to demonstrate equivalent performance at another location.
(iii) If the exhaust system ducting from the exit of the engine exhaust manifold or turbocharger outlet to smoke meter exceeds 12 feet (3.7 m) in length, then all ducting shall be insulated consistent with good engineering practice.
(iv) For engines designed for more than one exhaust outlet to the atmosphere, a specially fabricated collection duct may be used. The collection duct should be located downstream of the in-locomotive exits to the atmosphere. Any potential increase in backpressure due to the use of a single exhaust instead of multiple exhausts may be compensated for by using larger than standard exhaust system components in the construction of the collection duct.
(e) Dilute exhaust sampling for gaseous and particulate emissions. (1) Dilution of the exhaust prior to sampling is allowed for gaseous emissions. The equipment and methods used for dilution, sampling and analysis shall comply with the requirements of 40 CFR part 1065, with the following exceptions and additional requirements:
(i) Proportional sampling and heat exchangers are not required;
(ii) Larger minimum dimensions for the dilution tunnel(s) shall be specified by the Administrator;
(iii) Other modifications may be made with written approval from the Administrator.
(2) Dilution of only a portion of the exhaust is allowed, provided that:
(i) The fraction of the total exhaust that is diluted is determined for systems that determine mass emission rates (g/hr) from the total volume of the diluted sample; or
(ii) The ratio of raw sample volume to diluted sample volume is determined for systems that determine mass emission rates (g/hr) from measured fuel flow rates.
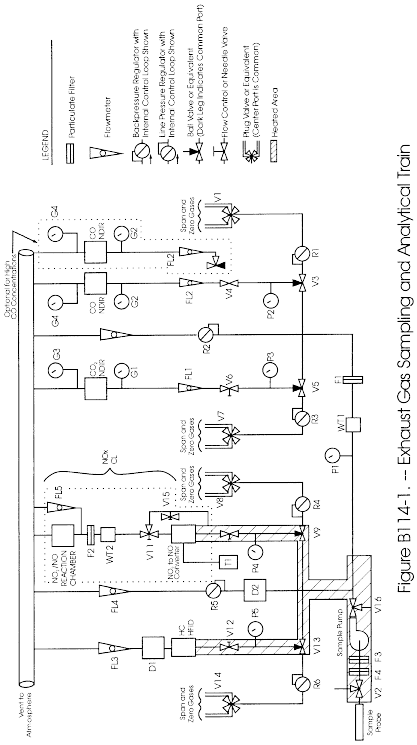
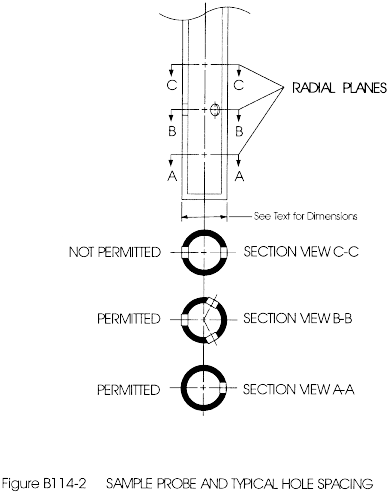
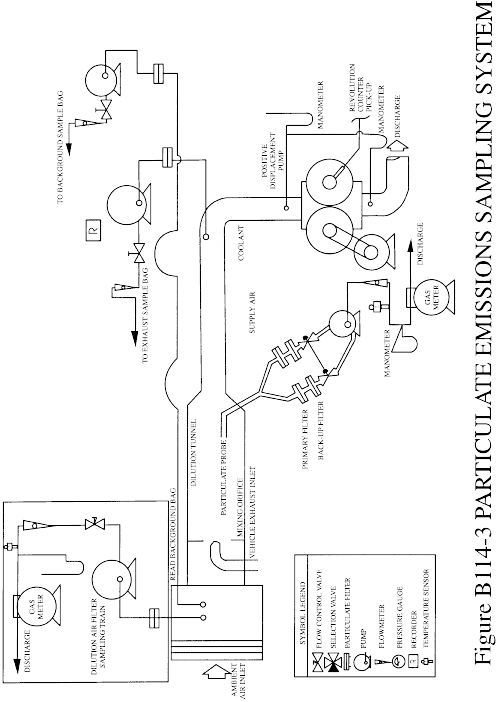
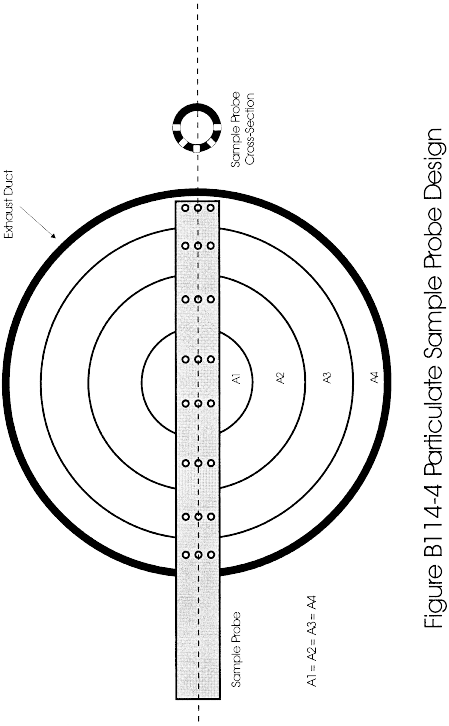