Title 40
SECTION 63.365
63.365 Test methods and procedures.
§ 63.365 Test methods and procedures.(a) Performance testing. The owner or operator of a source subject to the emissions standards in § 63.362 shall comply with the performance testing requirements in § 63.7 of subpart A of this part, according to the applicability in Table 1 of § 63.360, and in this section.
(b) Efficiency at the sterilization chamber vent. California Air Resources Board (CARB) Method 431 or the following procedures shall be used to determine the efficiency of all types of control devices used to comply with § 63.362(c), sterilization chamber vent standard.
(1) First evacuation of the sterilization chamber. These procedures shall be performed on an empty sterilization chamber, charged with a typical amount of ethylene oxide, for the duration of the first evacuation under normal operating conditions (i.e., sterilization pressure and temperature).
(i) The amount of ethylene oxide loaded into the sterilizer (Wc) shall be determined by either:
(A) Weighing the ethylene oxide gas cylinder(s) used to charge the sterilizer before and after charging. Record these weights to the nearest 45 g (0.1 lb). Multiply the total mass of gas charged by the weight percent ethylene oxide present in the gas.
(B) Installing calibrated rotameters at the sterilizer inlet and measuring flow rate and duration of sterilizer charge. Use the following equation to convert flow rate to weight of ethylene oxide:
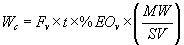
(C) Calculating the mass based on the conditions of the chamber immediately after it has been charged using the following equation:
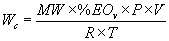
If the ethylene oxide concentration is in weight percent, use the following equation to calculate mole fraction:
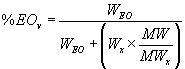
(ii) The residual mass of ethylene oxide in the sterilizer shall be determined by recording the chamber temperature, pressure, and volume after the completion of the first evacuation and using the following equation:
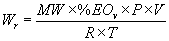
(iii) Calculate the total mass of ethylene oxide at the inlet to the control device (Wi) by subtracting the residual mass (Wr) calculated in paragraph (b)(1)(ii) of this section from the charged weight (Wc) calculated in paragraph (b)(1)(i) of this section.
(iv) The mass of ethylene oxide emitted from the control device outlet (Wo) shall be calculated by continuously monitoring the flow rate and concentration using the following procedure.
(A) Measure the flow rate through the control device exhaust continuously during the first evacuation using the procedure found in 40 CFR part 60, appendix A, Test Methods 2, 2A, 2C, or 2D, as appropriate. (Method 2D (using orifice plates or Rootstype meters) is recommended for measuring flow rates from sterilizer control devices.) Record the flow rate at 1-minute intervals throughout the test cycle, taking the first reading within 15 seconds after time zero. Time zero is defined as the moment when the pressure in the sterilizer is released. Correct the flow to standard conditions (20 °C and 101.325 kPa (68 °F and 1 atm)) and determine the flow rate for the run as outlined in the test methods listed in paragraph (b) of this section.
(B) Test Method 18 or 25A, 40 CFR part 60, appendix A (hereafter referred to as Method 18 or 25A, respectively), shall be used to measure the concentration of ethylene oxide.
(1) Prepare a graph of volumetric flow rate versus time corresponding to the period of the run cycle. Integrate the area under the curve to determine the volume.
(2) Calculate the mass of ethylene oxide by using the following equation:
Where: Wo = Mass of ethylene oxide, g (lb) C = concentration of ethylene oxide in ppmv V = volume of gas exiting the control device corrected to standard conditions, L (ft 3) 1/10 6 = correction factor LEO/10 6 LTOTAL GAS (ft 3EO/10 6 ft 3TOTAL GAS)(3) Calculate the efficiency by the equation in paragraph (b)(1)(v) of this section.
(C) [Reserved]
(v) Determine control device efficiency (% Eff) using the following equation:
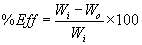
(vi) Repeat the procedures in paragraphs (b)(1) (i) through (v) of this section three times. The arithmetic average percent efficiency of the three runs shall determine the overall efficiency of the control device.
(2) [Reserved]
(c) Concentration determination. The following procedures shall be used to determine the ethylene oxide concentration.
(1) Parameter monitoring. For determining the ethylene oxide concentration required in § 63.364(e), follow the procedures in PS 8 or PS 9 in 40 CFR part 60, appendix B. Sources complying with PS 8 are exempt from the relative accuracy procedures in sections 2.4 and 3 of PS-8.
(2) Initial compliance. For determining the ethylene oxide concentration required in § 63.363(c)(2), the procedures outlined in Method 18 or Method 25 A (40 CFR part 60, appendix A) shall be used. A Method 18 or Method 25A test consists of three 1-hour runs. If using Method 25A to determine concentration, calibrate and report Method 25A instrument results using ethylene oxide as the calibration gas. The arithmetic average of the ethylene oxide concentration of the three test runs shall determine the overall outlet ethylene oxide concentration from the control device.
(d) Efficiency determination at the aeration room vent (not manifolded). The following procedures shall be used to determine the efficiency of a control device used to comply with § 63.362(d), the aeration room vent standard.
(1) Determine the concentration of ethylene oxide at the inlet and outlet of the control device using the procedures in Method 18 or 25A in 40 CFR part 60, appendix A. A test is comprised of three 1-hour runs.
(2) Determine control device efficiency (% Eff) using the following equation:
Where: % Eff = percent efficiency Wi = mass flow rate into the control device WO = mass flow rate out of the control device(3) Repeat the procedures in paragraphs (d)(1) and (2) of this section three times. The arithmetic average percent efficiency of the three runs shall determine the overall efficiency of the control device.
(e) Determination of baseline parameters for acid-water scrubbers. The procedures in this paragraph shall be used to determine the monitored parameters established in § 63.363(b), (d), or (e) for acid-water scrubbers and to monitor the parameters as established in § 63.364(b).
(1) Ethylene glycol concentration. For determining the ethylene glycol concentration, the facility owner or operator shall establish the maximum ethylene glycol concentration as the ethylene glycol concentration averaged over three test runs; the sampling and analysis procedures in ASTM D 3695-88, Standard Test Method for Volatile Alcohols in Water By Direct Aqueous-Injection Gas Chromatography, (incorporated by reference - see § 63.14) shall be used to determine the ethylene glycol concentration.
(2) Scrubber liquor tank level. For determining the scrubber liquor tank level, the sterilization facility owner or operator shall establish the maximum liquor tank level based on a single measurement of the liquor tank level during one test run.
(f) [Reserved]
(g) An owner or operator of a sterilization facility seeking to demonstrate compliance with the standards found at § 63.362(c), (d), or (e) with a control device other than an acid-water scrubber or catalytic or thermal oxidation unit shall provide to the Administrator the information requested under § 63.363(f). The owner or operator shall submit: a description of the device; test results collected in accordance with § 63.363(f) verifying the performance of the device for controlling ethylene oxide emissions to the atmosphere to the levels required by the applicable standards; the appropriate operating parameters that will be monitored; and the frequency of measuring and recording to establish continuous compliance with the standards. The monitoring plan submitted identifying the compliance monitoring is subject to the Administrator's approval. The owner or operator of the sterilization facility shall install, calibrate, operate, and maintain the monitor(s) approved by the Administrator based on the information submitted by the owner or operator. The owner or operator shall include in the information submitted to the Administrator proposed performance specifications and quality assurance procedures for their monitors. The Administrator may request further information and shall approve appropriate test methods and procedures.
(h) An owner or operator of a sterilization facility seeking to demonstrate compliance with the requirements of § 63.363 or § 63.364, with a monitoring device or procedure other than a gas chromatograph or a flame ionization analyzer, shall provide to the Administrator information describing the operation of the monitoring device or procedure and the parameter(s) that would demonstrate continuous compliance with each operating limit. The Administrator may request further information and will specify appropriate test methods and procedures.
[59 FR 62589, Dec. 6, 1994, as amended at 66 FR 55584, Nov. 2, 2001; 79 FR 11283, Feb. 27, 2014]