Title 40
SECTION 1037.565
1037.565 Transmission efficiency test.
§ 1037.565 Transmission efficiency test.This section describes a procedure for mapping transmission efficiency through a determination of transmission power loss.
(a) You may establish transmission power loss maps based on testing any number of transmission configurations within a transmission family as specified in § 1037.232. You may share data across any configurations within the family, as long as you test the transmission configuration with the lowest efficiency from the emission family. Alternatively, you may ask us to approve power loss maps for untested configurations that are analytically derived from tested configurations within the same family (see § 1037.235(h)).
(b) Prepare a transmission for testing as follows:
(1) Select a transmission with less than 500 hours of operation before testing.
(2) Mount the transmission to the dynamometer such that the geared shaft in the transmission is aligned with the input shaft from the dynamometer.
(3) Add transmission oil according to the transmission manufacturer's instructions. If the transmission manufacturer specifies multiple transmission oils, select the one with the highest viscosity at operating temperature. You may use a lower-viscosity transmission oil if we approve that as critical emission-related maintenance under § 1037.125. Fill the transmission oil to a level that represents in-use operation. You may use an external transmission oil conditioning system, as long as it does not affect measured values.
(4) Include any internal and external pumps for hydraulic fluid and lubricating oil in the test. Determine the work required to drive an external pump according to 40 CFR 1065.210.
(5) Install equipment for measuring the bulk temperature of the transmission oil in the oil sump or a similar location.
(6) If the transmission is equipped with a torque converter, lock it for all testing performed in this section.
(7) Break in the transmission using good engineering judgment. Maintain transmission oil temperature at (87 to 93) °C for automatic transmissions and transmissions having more than two friction clutches, and at (77 to 83) °C for all other transmissions. You may ask us to approve a different range of transmission oil temperatures if you have data showing that it better represents in-use operation.
(c) Measure input and output shaft speed and torque as described in 40 CFR 1065.210(b), except that you may use a magnetic or optical shaft-position detector with only one count per revolution. Use a-speed measurement system that meets an accuracy of ±0.05% of point. Use torque transducers that meet an accuracy requirement of ±0.2% of the transmission's maximum rated input torque or output torque for the selected gear ratio, for loaded test points, and ±0.1% of the transmission's maximum rated input torque for unloaded test points. Calibrate and verify measurement instruments according to 40 CFR part 1065, subpart C. Command speed and torque at a minimum of 10 Hz, and record all data, including bulk oil temperature, at a minimum of 1 Hz mean values.
(d) The test matrix consists of transmission input shaft speeds and torque setpoints meeting the following specifications for each gear tested:
(1) Include transmission input shaft speeds at the maximum rated input shaft speed, 600 r/min, and three equally spaced intermediate speeds. The intermediate speed points may be adjusted to the nearest 50 or 100 r/min.
(2) Include one loaded torque setpoint between 75% and 105% of the maximum transmission input torque and one unloaded (zero-torque) setpoint. You may test at any number of additional torque setpoints to improve accuracy. Note that GEM calculates power loss between tested or default values by linear interpolation.
(3) In the case of transmissions that automatically go into neutral when the vehicle is stopped, also perform tests at 600 r/min and 800 r/min with the transmission in neutral and the transmission output fixed at zero speed.
(e) Determine transmission torque loss using the following procedure:
(1) Maintain ambient temperature between (15 and 35) °C throughout testing. Measure ambient temperature within 1.0 m of the transmission.
(2) Maintain transmission oil temperature as described in paragraph (b)(7) of this section. You may use an external transmission oil conditioning system, as long as it does not affect measured values.
(3) Use good engineering judgment to warm up the transmission according to the transmission manufacturer's specifications.
(4) Perform unloaded transmission tests by disconnecting the transmission output shaft from the dynamometer and letting it rotate freely. If the transmission adjusts pump pressure based on whether the vehicle is moving or stopped, set up the transmission for unloaded tests to operate as if the vehicle is moving.
(5) For transmissions that have multiple configurations for a given gear ratio, such as dual-clutch transmissions that can pre-select an upshift or downshift, set the transmission to operate in the configuration with the greatest power loss. Alternatively, test in each configuration and use good engineering judgment to calculate a weighted power loss for each test point under this section based on field data that characterizes the degree of in-use operation in each configuration.
(6) Operate the transmission in the top gear at a selected torque setpoint with the input shaft speed at one of the speed setpoints for at least 10 seconds, then measure the speed and torque of the input and output shafts for at least 10 seconds. You may omit measurement of output shaft speeds if your transmission is configured is a way that does not allow slip. Calculate arithmetic mean values for all speed and torque values over each measurement period. Repeat this stabilization, measurement, and calculation for the other speed and torque setpoints from the test matrix in any sequence. Calculate power loss as described in paragraph (f) of this section based on torque and speed values at each test point.
(7) Repeat the procedure described in paragraph (e) for all gears, or for all gears down to a selected gear. GEM will use default values for any gears not tested.
(8) Perform the test sequence described in paragraphs (d)(6) and (7) of this section three times. You may do this repeat testing at any given test point before you perform measurements for the whole test matrix. Remove torque from the transmission input shaft and bring the transmission to a complete stop before each repeat measurement.
(9) You may need to perform additional testing based on a calculation of repeatability at a 95% confidence level. Make a separate repeatability calculation for the three data points at each operating condition in the test matrix. If the confidence limit is greater than 0.10% for loaded tests or greater than 0.05% for unloaded tests, perform another repeat of measurements at that operating condition and recalculate the repeatability for the whole set of test results. Continue testing until the repeatability is at or below the specified values for all operating conditions. Calculate a confidence limit representing the repeatability in establishing a 95% confidence level using the following equation:
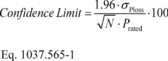

(10) Calculate mean input shaft torque, T in, mean output shaft torque, T out, mean input shaft speed, f nin, and mean output shaft speed, f nout, for each point in the test matrix using the results from all the repeat tests.
(f) Calculate the mean power loss, P loss, at each operating condition in the test matrix as follows:

(2) For each test calculate the mean power loss, P loss, as follows:
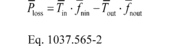

(3) For transmissions that are configured in a way that does not allow slip, you may calculate f nout based on the gear ratio using the following equation:
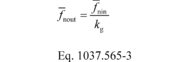
(g) Create a table showing the mean power loss,
