Appendix B to Part 80 - Test Methods for Lead in Gasoline
40:19.0.1.1.1.17.93.1.2 : Appendix B
Appendix B to Part 80 - Test Methods for Lead in Gasoline Link to
an amendment published at 85 FR 78467, Dec. 4, 2020. Method 1 -
Standard Method Test for Lead in Gasoline by Atomic Absorption
Spectrometry 1. Scope.
1.1. This method covers the determination of the total lead
content of gasoline. The procedure's calibration range is 0.010 to
0.10 gram of lead/U.S. gal. Samples above this level should be
diluted to fall within this range or a higher level calibration
standard curve must be prepared. The higher level curve must be
shown to be linear and measurement of lead at these levels must be
shown to be accurate by the analysis of control samples at a higher
level of alkyl lead content. The method compensates for variations
in gasoline composition and is independent of lead alkyl type.
2. Summary of method.
2.1 The gasoline sample is diluted with methyl isobutyl ketone
and the alkyl lead compounds are stabilized by reaction with iodine
and a quarternary ammonium salt. The lead content of the sample is
determined by atomic absorption flame spectrometry at 2833 A, using
standards prepared from reagent grade lead chloride. By the use of
this treatment, all alkyl lead compounds give identical
response.
3. Apparatus.
3.1 Atomic Absorption Spectometer, capable of scale expansion
and nebulizer adjustment, and equipped with a slot burner and
premix chamber for use with an air-acetylene flame.
3.2 Volumetric Flasks, 50-ml, 100-ml, 250-ml, and one litre
sizes.
3.3 Pipets, 2-ml, 5-ml, 10-ml, 20-ml, and 50-ml sizes.
3.4 Micropipet, 100-µl, Eppendorf type or equivalent.
4. Reagents.
4.1 Purity of Reagents - Reagent grade chemicals shall be used
in all tests. Unless otherwise indicated, it is intended that all
reagents shall conform to the specifications of the Committee on
Analytical Reagents of the American Chemical Society, where such
specifications are available. Other grades may be used, provided it
is first ascertained that the reagent is of sufficiently high
purity to permit its use without lessening the accuracy of the
determination.
4.2 Purity of Water - Unless otherwise indicated, references to
water shall be understood to mean distilled water or water of equal
purity.
4.3 Aliquat 336 (tricapryl methyl ammonium chloride).
4.4 Aliquat 336/MIBK Solution (10 percent v/v) - Dissolve and
dilute 100 ml (88.0 g) of Aliquat 336 with MIBK to one liter.
4.5 Aliquat 336/MIBK Solution (1 percent v/v) - Dissolve and
dilute 10 ml (8.8 g) of Aliquat 336 with MIBK to one liter.
4.6 Iodine Solution - Dissolve and dilute 3.0 g iodine crystals
with Toluene to 100 ml.
4.7 Lead Chloride.
4.8 Lead-Sterile Gasoline - Gasoline containing less than 0.005
g Pb/gal.
4.9 Lead, Standard Solution (5.0 g Pb/gal) - Dissolve 0.4433 g
of lead chloride (PbCl2) previously dried at 105 °C for 3 h in
about 200 ml of 10 percent Aliquat 336/MIBK solution in a 250-ml
volumetric flask. Dilute to the mark with the 10 percent Aliquat
solution, mix, and store in a brown bottle having a
polyethylene-lined cap. This solution contains 1,321 µg Pb/ml,
which is equivalent to 5.0 g Pb/gal.
4.10 Lead, Standard Solution (1.0 g Pb/gal) - By means of a
pipet, accurately transfer 50.0 ml of the 5.0 g Pb/gal solution to
a 250-ml volumetric flask, dilute to volume with 1 percent
Aliquat/MIBK solution. Store in a brown bottle having a
polyethylene-lined cap.
4.11 Lead, Standard Solutions (0.02, 0.05, and 0.10 g Pb/gal) -
Transfer accurately by means of pipets 2.0, 5.0, and 10.0 ml of the
1.0-g Pb/gal solution to 100-ml volumetric flasks; add 5.0 ml of 1
percent Aliquat 336 solution to each flask; dilute to the mark with
MIBK. Mix well and store in bottles having polyethylene-lined
caps.
4.12 Methyl Isobutyl Ketone (MIBK). (4-methyl-2-pentanone).
5. Calibration.
5.1 Preparation of Working Standards - Prepare three working
standards and a blank using the 0.02, 0.05, and 0.10-g Pb/gal
standard lead solutions described in 4.11.
5.1.1 To each of four 50-ml volumetric flasks containing 30 ml
of MIBK, add 5.0 ml of low lead standard solution and 5.0 ml of
lead-free gasoline. In the case of the blank, add only 5.0 ml of
lead-free gasoline.
5.1.2 Add immediately 0.1 ml of iodine/toluene solution by means
of the 100-µl Eppendorf pipet. Mix well. 1
1 EPA practice will be to mix well by shaking vigorously for
approximately one minute.
5.1.3 Add 5 ml of 1 percent Aliquat 336 solution and mix.
5.1.4 Dilute to volume with MIBK and mix well.
5.2 Preparation of Instrument - Optimize the atomic absorption
equipment for lead at 2833 A. Using the reagent blank, adjust the
gas mixture and the sample aspiration rate to obtain an oxidizing
flame.
5.2.1 Aspirate the 0.1-g Pb/gal working standard and adjust the
burner position to give maximum response. Some instruments require
the use of scale expansion to produce a reading of 0.150 to 0.170
for this standard.
5.2.2 Aspirate the reagent blank to zero the instrument and
check the absorbances of the three working standards for
linearity.
6. Procedure.
6.1 To a 50 ml volumetric flask containing 30 ml MIBK, add 5.0
ml of gasoline sample and mix. 2
2 The gasoline should be allowed to come to room temperature (25
°C).
6.1.1 Add 0.10 ml (100 µl) of iodine/toluene solution and allow
the mixture to react about 1 minute. 3
3 See footnote 1 of section 5.1.2.
6.1.2 Add 5.0 ml of 1 percent Aliquot 336/MIBK solution and
mix.
6.1.3 Dilute to volume with MIBK and mix.
6.2 Aspirate the samples and working standards and record the
absorbance values with frequent checks of the zero.
6.3 Any sample resulting in a peak greater than 0.05 g Pb/gal
will be run in duplicate. Samples registering greater than 0.10 g
Pb/gal should be diluted with iso-octane or unleaded fuel to fall
within the calibration range or a higher level calibration standard
curve must be prepared. The higher level curve must be shown to be
linear and measurement of lead at these levels must be shown to be
accurate by the analysis of control samples at a higher level of
alkyl lead content.
7. Calculations.
7.1 Plot the absorbance values versus concentration represented
by the working standards and read the concentrations of the samples
from the graph.
8. Precision.
8.1 The following criteria should be used for judging the
acceptability of results (95 percent confidence):
8.1.1 Repeatability - Duplicate results by the same operator
should be considered suspect if they differ by more than 0.005
g/gal.
8.1.2 Reproductibility - The results submitted by each of two
laboratories should not be considered suspect unless the two
results differ by more than 0.01 g/gal.
Method 2 - Automated Method Test for Lead in Gasoline by Atomic
Absorption Spectrometry 1. Scope and application.
1.1 This method covers the determination of the total lead
content of gasoline. The procedure's calibration range is 0.010 to
0.10 gram of lead/U.S. gal. Samples above this level should be
diluted to fall within this range or a higher level calibration
standard curve must be prepared. The higher level curve must be
shown to be linear and measurement of lead at these levels must be
shown to be accurate by the analysis of control samples at a higher
level of alkyl lead content. The method compensates for variations
in gasoline composition and is independent of lead alkyl type.
1.2 This method may be used as an alternative to the Standard
Method set forth above.
1.3 Where trade names or specific products are noted in the
method, equivalent apparatus and chemical reagents may be used.
Mention of trade names or specific products is for the assistance
of the user and does not constitute endorsement by the U.S.
Environmental Protection Agency.
2. Summary of method.
2.1 The gasoline sample is diluted with methly isobutyl ketone
(MIBK) and the alkyl lead compounds are stabilized by reacting with
iodine and a quarternary ammonium salt. An automated system is used
to perform the diluting and the chemical reactions and feed the
products to the atomic absorption spectrometer with an
air-acetylene flame.
2.2 The dilution of the gasoline with MIBK compensates for
severe non-atomic absorption, scatter from unburned carbon
containing species and matrix effects caused in part by the burning
characteristics of gasoline.
2.3 The in-situ reaction of alkyl lead in gasoline with
iodine eliminates the problem of variations in response due to
different alkyl types by leveling the response of all alkyl lead
compounds.
2.4 The addition of the quarternary ammonium salt improves
response and increases the stability of the alkyl iodide
complex.
3. Sample handling and preservation.
3.1 Samples should be collected and stored in containers which
will protect them from changes in the lead content of the gasoline
such as from loss of volatile fractions of the gasoline by
evaporation or leaching of the lead into the container or cap.
3.2 If samples have been refrigerated they should be brought to
room temperature prior to analysis.
4. Apparatus.
4.1 AutoAnalyzer system consisting of:
4.1.1 Sampler 20/hr cam, 30/hr cam.
4.1.2 Proportioning pump.
4.1.3 Lead in gas manifold.
4.1.4 Disposable test tubes.
4.1.5 Two 2-liter and one 0.5 liter Erlenmeyer solvent
displacement flasks. Alternatively, high pressure liquid
chromatography (HPLC) or syringe pumps may be used.
4.2 Atomic Absorption Spectroscopy (AAS) Detector System
consisting of:
4.2.1 Atomic absorption spectrometer.
4.2.2 10″ strip chart recorder.
4.2.3 Lead hollow cathode lamp or electrodeless discharge lamp
(EDL).
5. Reagents.
5.1 Aliquat 336/MIBK solution (10% v/v): Dissolve and dilute 100
ml (88.0 g) of Aliquat 336 (Aldrich Chemical Co., Milwaukee,
Wisconsin) with MIBK (Burdick & Jackson Lab., Inc., Muskegon,
Michigan) to one liter.
5.2 Aliquat 336/iso-octane solution (1% v/v): Dissolve and
dilute 10 ml (8.8 g) of Alquat 336 (reagent 5.1) with iso-octane to
one liter.
5.3 Iodine solution (3% w/v): Dissolve and dilute 3.0 g iodine
crystals (American Chemical Society) with toluene (Burdick &
Jackson Lab., Inc., Muskegon, Michigan) to 100 ml.
5.4 Iodine working solution (0.24% w/v): Dilute 8 ml of reagent
5.3 to 100 ml with toluene.
5.5 Methyl isobutyl ketone (MIBK) (4-methlyl-2-pentanone).
5.6 Certified unleaded gasoline (Phillips Chemical Co., Borger,
Texas) or iso-octane (Burdick & Jackson Lab, Inc., Muskegon,
Michigan).
6. Calibration standards.
6.1 Stock 5.0 g Pb/gal Standard:
Dissolve 0.4433 gram of lead chloride (PbCl2) previously dried
at 105 °C for 3 hours in 200 ml of 10% v/v Aliquat 336/MIBK
solution (reagent 5.1) in a 250 ml volumetric flask. Dilute to
volume with reagent 5.1 and store in an amber bottle.
6.2 Intermediate 1.0 g Pb/gal Standard:
Pipet 50 ml of the 5.0 g Pb/gal standard into a 250 ml
volumetric flask and dilute to volume with a 1% v/v Aliquat
336/iso-octane solution (reagent 5.2). Store in an amber
bottle.
6.3 Working 0.02, 0.05, 0.10 g Pb/gal Standards:
Pipet 2.0, 5.0, and 10.0 ml of the 1.0 g Pb/gal solution to 100
ml volumetric flasks. Add 5 ml of a 1% Aliquat 336/iso-octane
solution to each flask. Dilute to volume with iso-octane. These
solutions contain 0.02, 0.05, and 0.10 g Pb/gal in a 0.05% Aliquat
336/iso-octane solution.
7. AAS Instrumental conditions.
7.1 Lead hollow cathode lamp.
7.2 Wavelength: 283.3 nm.
7.3 Slit: 4 (0.7mm).
7.4 Range: UV.
7.5 Fuel: Acetylene (approx. 20 ml/min at 8 psi).
7.6 Oxidant: Air (approx. 65 ml/min at 31 psi).
7.7 Nebulizer: 5.2 ml/min.
7.8 Chart speed: 10 in/hr.
8. Procedures.
8.1 AAS start-up.
8.1.1 Assure that instrumental conditions have been optimized
and aligned according to Section 7 and the instrument has had
substantial time for warm-up.
8.2 Auto Analyzer start-up [see figure 1].
8.2.1 Check all pump tubing and replace as necessary. Iodine
tubing should be changed daily. All pump tubing should be replaced
after one week of use. Place the platen on the pump.
8.2.2 Withdraw any water from the sample wash cup and fill with
certified unleaded gasoline (reagent 5.6).
8.2.3 Fill the 2-liter MIBK dilution displacement Erlenmeyer
flask (reagent 5.5) and the 0.5 liter Aliquat 336/MIBK 1% v/v
(reagent 5.2) displacement flask and place the rubber stopper glass
tubing assemblies in their respective flasks.
8.2.4 Fill a 2-liter Erlenmeyer flask with distilled water. The
water will be used to displace the solvents. Therefore, place the
appropriate lines in this flask. This procedure is not relevant if
syringe pumps are used.
8.2.5 Fill the final debubbler reverse displacement 2-liter
Erlenmeyer flask with distilled water and place the rubber stopper
glass tubing assembly in the flask.
8.2.6 Place the appropriate lines for the iodine reagent
(reagent 5.4) and the wash solution (reagent 5.6) in their
respective bottles.
8.2.7 Start the pump and connect the aspiration line from the
manifold to the AAS.
8.2.8 Some initial checks to assure that the reagents are being
added are:
a. A good uniform bubble pattern.
b. Yellow color evident due to iodine in the system.
c. No surging in any tubing.
8.3 Calibration.
8.3.1 Turn the chart drive on and obtain a steady baseline.
8.3.2 Load standards and samples into sample tray.
8.3.3 Start the sampler and run the standards (Note: first check
the sample probe positioning with an empty test tube).
8.3.4 Check the linearity of calibration standards response and
slope by running a least squares fit. Check these results against
previously obtained results. They should agree within 10%.
8.3.5 If the above is in control then start the sample
analysis.
8.4 Sample Analysis.
8.4.1 To minimize gasoline vapor in the laboratory, load the
sample tray about 5-10 test tubes ahead of the sampler.
8.4.2 Record the sample number on the strip chart corresponding
to the appropriate peak.
8.4.3 Every ten samples run the high calibration standard and a
previously analyzed sample (duplicate). Also let the sampler skip
to check the baseline.
8.4.4 After an acceptable peak (within the calibration range) is
obtained, pour the excess sample from the test tube into the waste
gasoline can.
8.4.5 Any sample resulting in a peak greater than 0.05 g Pb/gal
will be run in duplicate. Samples registering greater than 0.10 g
Pb/gal should be diluted with iso-octane or unleaded fuel to fall
within the calibration range or a higher level calibration standard
curve must be prepared. The higher level curve must be shown to be
linear and measurement of lead at these levels must be shown to be
accurate by the analysis of control samples at a higher level of
alkyl lead content.
8.5 Shut Down.
8.5.1 Replace the solvent displacement flask with flasks filled
with distilled water. Also place all other lines in a beaker of
distilled water. Rinse the system with distilled water for 15
minutes.
8.5.2 Withdraw the gasoline from the wash cup and fill with
water.
8.5.3 Dispose of all solvent waste in waste glass bottles.
8.5.4 Turn the AAS off after extinguishing the flame. Also turn
the recorder and pump off. Remove the platen and release the pump
tubing.
8.5.5 Shut the acetylene off at the tank and bleed the line.
9. Quality control.
9.1 Precision.
9.1.1 All duplicate results should be considered suspect if they
differ by more than 0.005 g Pb/gal.
9.2 Accuracy.
9.2.1 All quality control standard checks should agree within
10% of the nominal value of the standard.
9.2.2 All spikes should agree within 10% of the known
addition.
10. Past quality control data.
10.1 Precision.
10.1.1 Duplicate analysis for 156 samples in a single laboratory
has resulted in an average difference of 0.00011 g Pb/gal with a
standard deviation of 0.0023.
10.1.2 Replicate analysis in a single laboratory (greater than 5
determinations) of samples at concentrations of 0.010, 0.048, and
0.085 g Pb/gal resulted in relative standard deviations of 4.2%,
3.5%, and 3.3% respectively.
10.2 Accuracy.
10.2.1 The analysis of National Bureau of Standards (NBS) lead
in reference fuel of known concentrations in a single laboratory
has resulted in found values deviating from the true value for 11
determinations of 0.0322 g Pb/gal by an average of 0.56% with a
standard deviation of 6.8%, for 15 determinations of 0.0519 g
Pb/gal by an average of −1.1% with a standard deviation of 5.8%,
and for 7 determinations of 0.0725 g Pb/gal by an average of 3.5%
with a standard deviation of 4.8%.
10.2.2 Twenty-three analyses of blind reference samples in a
single laboratory (U.S. EPA, RTP, N.C.) have resulted in found
values differing from the true value by an average of −0.0009 g
Pb/gal with a standard deviation of 0.004.
10.2.3 In a single laboratory, the average percent recovery of
108 spikes made to samples was 101% with a standard deviation of
5.6%.
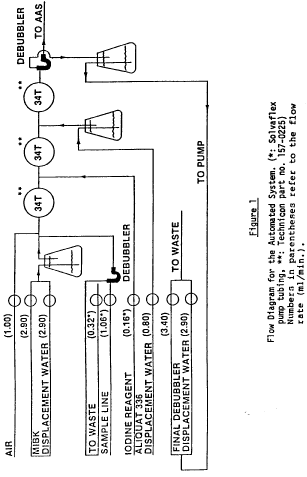
Method 3
- Test for Lead in Gasoline by X-Ray Spectrometry 1. Scope and
application.
1.1 This method covers the determination of the total lead
content of gasoline. The procedure's calibration range is 0.010 to
5.0 grams of lead/U.S. gallon. Samples above this level should be
diluted to fall within the range of 0.05 to 5.0 grams of lead/U.S.
gallon. The method compensates for variations in gasoline
composition and is independent of lead alkyl type.
1.2 This method may be used as an alternative to Method 1 -
Standard Method Test for Lead in Gasoline by Atomic Absorption
Spectrometry, or to Method 2 - Automated Method Test for Lead in
Gasoline by Atomic Absorption Spectrometry.
1.3 Where trade names or specific products are noted in the
method, equivalent apparatus and chemical reagents may be used.
Mention of trade names or specific products is for the assistance
of the user and does not constitute endorsement by the U.S.
Environmental Protection Agency.
2. Summary of method.
2.1 A portion of the gasoline sample is placed in an appropriate
holder and loaded into an X-ray spectrometer. The ratio of the net
X-ray intensity of the lead L alpha radiation to the net intensity
of the incoherently scattered tungsten L alpha radiation is
measured. The lead content is determined by reference to a linear
calibration equation which relates the lead content to the measured
ratio.
2.2 The incoherently scattered tungsten radiation is used to
compensate for variations in gasoline samples.
3. Sample handling and preservation.
3.1 Samples should be collected and stored in containers which
will protect them from changes in the lead content of the gasoline,
such as loss of volatile fractions of the gasoline by evaporation
or leaching of the lead into the container or cap.
3.2 If samples have been refrigerated they should be brought to
room temperature prior to analysis.
3.3 Gasoline is extremely flammable and should be handled
cautiously and with adequate ventilation. The vapors are harmful if
inhaled and prolonged breathing of vapors should be avoided. Skin
contact should be minimized. See precautionary statements in Annex
Al.3.
4. Apparatus.
4.1 X-ray Spectrometer, capable of exciting and measuring the
fluorescence lines mentioned in 2.1 and of being operated under the
following instrumental conditions or others giving equivalent
results: a tungsten target tube operated at 50 kV, a lithium
fluoride analyzing crystal, an air or helium optical path and a
proportional or scintillation detector.
4.2 Some manufacturers of X-ray Spectrometer units no longer
allow use of air as the beam path medium because the X-ray beam
produces ozone, which may degrade seals and electronics. In
addition, use of the equipment with liquid gasoline in close
proximity to the hot X-ray tube could pose flammability problems
with any machine in case of a rupture of the sample container.
Therefore, use of the helium alternative is recommended.
5. Reagents.
5.1 Isooctane. Isooctane is flammable and the vapors may be
harmful. See precautions in Annex Al.1.
5.2 Lead standard solution, in isooctane, toluene or a mixture
of these two solvents, containing approximately 5 gm Pb/U.S. gallon
may be prepared from a lead-in-oil concentrate such as those
prepared by Conostan (Conoco, Inc., Ponca City, Oklahoma).
Isooctane and toluene are flammable and the vapors may be harmful.
See precautionary statements in Annex Al.1 and Al.2.
6. Calibration.
6.1 Make exact dilutions with isooctane of the lead standard
solution to give solutions with concentrations of 0.01, 0.05, 0.10,
0.50, 1.0, 3.0 and 5.0 g Pb/U.S. gallon. If a more limited range is
desired as required for linearity, such range shall be covered by
at least five standard solutions approximately equally spaced and
this range shall not be exceeded by any of the samples. Place each
of the standard solutions in a sample cell using techniques
consistent with good operating practice for the spectrometer
employed. Insert the sample in the spectrometer and allow the
spectrometer atmosphere to reach equilibrium (if appropriate).
Measure the intensity of the lead L alpha peak at 1.175 angstroms,
the Compton scatter peak of the tungsten L alpha line at 1.500
angstroms and the background at 1.211 angstroms. Each measured
intensity should exceed 200,000 counts or the time of measurement
should be at least 30 seconds. The relative standard deviation of
each measurement, based on counting statistics, should be one
percent or less. The Compton scatter peak given above is for 90°
instrument geometry and should be changed for other geometries. The
Compton scatter peak (in angstroms) is found at the wavelength of
the tungsten L alpha line plus 0.024 (1-cos phi), where phi is the
angle between the incident radiation and the take-off
collimator.
6.2 For Each of the standards, as well as for an isooctane
blank, determine the net lead intensity by subtracting the
corrected background from the gross intensity. Determine the
corrected background by multiplying the intensity of the background
at 1.211 angstroms by the following ratio obtained on an isooctane
blank:
6.3 Determine the corrected lead intensity ratio, which is the
net lead intensity corrected for matrix effects by division by the
net incoherently scattered tungsten radiation. The net scattered
intensity is calculated by subtracting the background intensity at
1.211 angstroms from the gross intensity of the incoherently
scattered tungsten L alpha peak. The equation for the corrected
lead intensity ratio follows:
6.4 Obtain a linear calibration curve by performing a least
squares fit of the corrected lead intensity ratios to the standard
concentrations.
7. Procedure.
7.1 Prepare a calibration curve as described in 6. Since the
scattered tungsten radiation serves as an internal standard, the
calibration curve should serve for at least several days. Each day
the suitability of the calibration curve should be checked by
analyzing several National Bureau of Standards (NBS)
lead-in-reference-fuel standards or other suitable standards.
7.2 Determine the corrected lead intensity ratio for a sample in
the same manner as was done for the standards. The samples should
be brought to room temperature before analysis.
7.3 Determine the lead concentration of the sample from the
calibration curve. If the sample concentration is greater than 5.0
g Pb/U.S. gallon or the range calibrated for in 6.1, the sample
should be diluted so that the result is within the calibration span
of the instrument.
7.4 Quality control standards, such as NBS standard reference
materials, should be analyzed at least once every testing
session.
7.5 For each group of ten samples, a spiked sample should be
prepared by adding a known amount of lead to a sample. This known
addition should be at least 0.05 g Pb/U.S. gallon, at least 50% of
the measured lead content of the unspiked sample, and not more than
200% of the measured lead content of the unspiked sample (unless
the minimum addition of 0.05 g Pb/U.S. gallon exceeds 200%). Both
the spiked and unspiked samples should be analyzed.
8. Quality control.
8.1 The difference between duplicates should not exceed 0.005 g
Pb/U.S. gallon or a relative difference of 6%.
8.2 All quality control standard check samples should agree
within 10% of the nominal value of the standard.
8.3 All spiked samples should have a percent recovery of 100%
±10%. The percent recovery, P, is calculated as follows:
P = 100 × (A − B) / K where A = the analytical result from the
spiked sample, B = the analytical result from the unspiked sample,
and K = the known addition.
8.4 The difference between independent analyses of the same
sample in different laboratories should not exceed 0.01 g Pb/U.S.
gallon or a relative difference of 12%.
9.
Past quality control data.
9.1 Duplicate analysis for 26 samples in the range of 0.01 to
0.10 g Pb/U.S. gallon resulted in an average relative difference of
5.2% with a standard deviation of 5.4%. Duplicate analysis of 14
samples in the range 0.1 to 0.5 g Pb/U.S. gallon resulted in an
average relative difference of 2.3% with a standard deviation of
2.0. Duplicate analysis of 47 samples in the range of 0.5 to 5 g
Pb/U.S. gallon resulted in an average relative difference of 2.1%
with a standard deviation of 1.8%.
9.2 The average percent recovery for 23 spikes made to samples
in the 0.0 to 0.1 g Pb/U.S. gallon range was 103% with a standard
deviation of 3.2%. For 42 spikes made to samples in the 0.1 to 5.0
g Pb/U.S. gallon range, the average percent recovery was 102% with
a standard deviation of 4.2%.
9.3 The analysis of National Bureau of Standards
lead-in-reference-fuel standards of known concentrations in a
single laboratory has resulted in found values deviating from the
true value for 14 determinations of 0.0490 g Pb/U.S. gallon by an
average of 2.8% with a standard deviation of 6.4%, for 11
determinations of 0.065 g Pb/U.S. gallon by an average of 4.4% with
a standard deviation of 2.9%, and for 15 determinations of 1.994 g
Pb/U.S. gallon by an average of 0.3% with a standard deviation of
1.3%.
9.4 Eighteen analyses of reference samples (U.S. EPA, Research
Triangle Park, NC) have resulted in found values differing from the
true value by an average of 0.0004 g Pb/U.S. gallon with a standard
deviation of 0.004 g Pb/U.S. gallon.
Annex A1. Precautionary Statements A1.1 Isooctane Danger -
Extremely flammable. Vapors harmful if inhaled. Vapor may cause
flash fire. Keep away from heat, sparks, and open flame. Vapors are
heavier than air and may gather in low places, resulting in
explosion hazard. Keep container closed. Use adequate ventilation.
Avoid buildup of vapors. Avoid prolonged breathing of vapor or
spray mist. Avoid prolonged or repeated skin contact. A1.2 Toluene
Warning - Flammable. Vapor harmful. Keep away from heat, sparks,
and open flame. Keep container closed. Use with adequate
ventilation. Avoid breathing of vapor or spray mist. Avoid
prolonged or repeated contact with skin. A1.3 Gasoline Danger -
Extremely flammable. Vapors harmful if inhaled. Vapor may cause
flash fire. Keep away from heat, sparks, and open flame. Vapors are
heavier than air and may gather in low places, resulting in
explosion hazard. Keep container closed. Use adequate ventilation.
Avoid buildup of vapors. Avoid prolonged breathing of vapor or
spray mist. Avoid prolonged or repeated skin contact. [39 FR 24891,
July 8, 1974; 39 FR 25653, July 12, 1974; 39 FR 26287, July 18,
1974, as amended at 47 FR 765, Jan. 7, 1982; 52 FR 259, Jan. 5,
1987; 56 FR 13768, Apr. 4, 1991]