Appendix E to Part 75 - Optional NOX Emissions Estimation Protocol for Gas-Fired Peaking Units and Oil-Fired Peaking Units
40:18.0.1.1.4.10.1.1.10 : Appendix E
Appendix E to Part 75 - Optional NOX Emissions Estimation Protocol
for Gas-Fired Peaking Units and Oil-Fired Peaking Units 1.
Applicability 1.1 Unit Operation Requirements
This NOX emissions estimation procedure may be used in lieu of a
continuous NOX emission monitoring system (lb/mmBtu) for
determining the average NOX emission rate and hourly NOX rate from
gas-fired peaking units and oil-fired peaking units as defined in §
72.2 of this chapter. If a unit's operations exceed the levels
required to be a peaking unit, the owner or operator shall install
and certify a NOX-diluent continuous emission monitoring system no
later than December 31 of the following calendar year. If the
required CEMS has not been installed and certified by that date,
the owner or operator shall report the maximum potential NOX
emission rate (MER) (as defined in § 72.2 of this chapter) for each
unit operating hour, starting with the first unit operating hour
after the deadline and continuing until the CEMS has been
provisionally certified. The provision of § 75.12 apply to excepted
monitoring systems under this appendix.
1.2 Certification
1.2.1 Pursuant to the procedures in § 75.20, complete all
testing requirements to certify use of this protocol in lieu of a
NOX continuous emission monitoring system no later than the
applicable deadline specified in § 75.4. Apply to the Administrator
for certification to use this method no later than 45 days after
the completion of all certification testing. Whenever the
monitoring method is to be changed, reapply to the Administrator
for certification of the new monitoring method.
1.2.2 [Reserved]
2. Procedure 2.1 Initial Performance Testing
Use the following procedures for: measuring NOX emission rates
at heat input rate levels corresponding to different load levels;
measuring heat input rate; and plotting the correlation between
heat input rate and NOX emission rate, in order to determine the
emission rate of the unit(s). The requirements in section 6.1.2 of
appendix A to this part shall apply to any stack testing performed
to obtain O2 and NOX concentration measurements under this
appendix, either for units using the excepted methodology in this
appendix or for units using the low mass emissions excepted
methodology in § 75.19.
2.1.1 Load Selection
Establish at least four approximately equally spaced operating
load points, ranging from the maximum operating load to the minimum
operating load. Select the maximum and minimum operating load from
the operating history of the unit during the most recent two years.
(If projections indicate that the unit's maximum or minimum
operating load during the next five years will be significantly
different from the most recent two years, select the maximum and
minimum operating load based on the projected dispatched load of
the unit.) For new gas-fired peaking units or new oil-fired peaking
units, select the maximum and minimum operating load from the
expected maximum and minimum load to be dispatched to the unit in
the first five calendar years of operation.
2.1.2 NOX and O2 Concentration Measurements
Use the following procedures to measure NOX and O2 concentration
in order to determine NOX emission rate.
2.1.2.1 For boilers, select an excess O2 level for each fuel
(and, optionally, for each combination of fuels) to be combusted
that is representative for each of the four or more load levels. If
a boiler operates using a single, consistent combination of fuels
only, the testing may be performed using the combination rather
than each fuel. If a fuel is combusted only for the purpose of
testing ignition of the burners for a period of five minutes or
less per ignition test or for start-up, then the boiler NOX
emission rate does not need to be tested separately for that fuel.
Operate the boiler at a normal or conservatively high excess oxygen
level in conjunction with these tests. Measure the NOX and O2 at
each load point for each fuel or consistent fuel combination (and,
optionally, for each combination of fuels) to be combusted. Measure
the NOX and O2 concentrations according to method 7E and 3A in
appendix A of part 60 of this chapter. Use a minimum of 12 sample
points, located according to Method 1 in appendix A-1 to part 60 of
this chapter. The designated representative for the unit may also
petition the Administrator under § 75.66 to use fewer sampling
points. Such a petition shall include the proposed alternative
sampling procedure and information demonstrating that there is no
concentration stratification at the sampling location.
2.1.2.2 For stationary gas turbines, sample at a minimum of 12
points per run at each load level. Locate the sample points
according to Method 1 in appendix A-1 to part 60 of this chapter.
For each fuel or consistent combination of fuels (and, optionally,
for each combination of fuels), measure the NOX and O2
concentrations at each sampling point using methods 7E and 3A in
appendices A-4 and A-2 to part 60 of this chapter. For diesel or
dual fuel reciprocating engines, select the sampling site to be as
close as practicable to the exhaust of the engine.
2.1.2.3 Allow the unit to stabilize for a minimum of 15 minutes
(or longer if needed for the NOX and O2 readings to stabilize)
prior to commencing NOX, O2, and heat input measurements. Determine
the measurement system response time according to sections 8.2.5
and 8.2.6 of method 7E in appendix A-4 to part 60 of this chapter.
When inserting the probe into the flue gas for the first sampling
point in each traverse, sample for at least one minute plus twice
the measurement system response time (or longer, if necessary to
obtain a stable reading). For all other sampling points in each
traverse, sample for at least one minute plus the measurement
system response time (or longer, if necessary to obtain a stable
reading). Perform three test runs at each load condition and obtain
an arithmetic average of the runs for each load condition. During
each test run on a boiler, record the boiler excess oxygen level at
5 minute intervals.
2.1.3 Heat Input
Measure the total heat input (mmBtu) and heat input rate during
testing (mmBtu/hr) as follows:
2.1.3.1 When the unit is combusting fuel, measure and record the
flow of fuel consumed. Measure the flow of fuel with an in-line
flowmeter(s) and automatically record the data. If a portion of the
flow is diverted from the unit without being burned, and that
diversion occurs downstream of the fuel flowmeter, an in-line
flowmeter is required to account for the unburned fuel. Install and
calibrate in-line flow meters using the procedures and
specifications contained in sections 2.1.2, 2.1.3, 2.1.4, and 2.1.5
of appendix D of this part. Correct any gaseous fuel flow rate
measured at actual temperature and pressure to standard conditions
of 68 °F and 29.92 inches of mercury.
2.1.3.2 For liquid fuels, analyze fuel samples taken according
to the requirements of section 2.2 of appendix D of this part to
determine the heat content of the fuel. Determine heat content of
liquid or gaseous fuel in accordance with the procedures in
appendix F of this part. Calculate the heat input rate during
testing (mmBtu/hr) associated with each load condition in
accordance with equations F-19 or F-20 in appendix F of this part
and total heat input using equation E-1 of this appendix. Record
the heat input rate at each heat input/load point.
2.1.4 Emergency Fuel
The designated representative of a unit that is restricted by
its federal, State or local permit to combusting a particular fuel
only during emergencies where the primary fuel is not available may
claim an exemption from the requirements of this appendix for
testing the NOX emission rate during combustion of the emergency
fuel. To claim this exemption, the designated representative shall
include in the monitoring plan for the unit documentation that the
permit restricts use of the fuel to emergencies only. When
emergency fuel is combusted, report the maximum potential NOX
emission rate for the emergency fuel, in accordance with section
2.5.2.3 of this appendix. The designated representative shall also
provide notice under § 75.61(a)(6) for each period when the
emergency fuel is combusted.
2.1.5 Tabulation of Results
Tabulate the results of each baseline correlation test for each
fuel or, as applicable, combination of fuels, listing: time of
test, duration, operating loads, heat input rate (mmBtu/hr),
F-factors, excess oxygen levels, and NOX concentrations (ppm) on a
dry basis (at actual excess oxygen level). Convert the NOX
concentrations (ppm) to NOX emission rates (to the nearest 0.001
lb/mm/Btu) according to equation F-5 of appendix F of this part or
19-3 in method 19 of appendix A of part 60 of this chapter, as
appropriate. Calculate the NOX emission rate in lb/mmBtu for each
sampling point and determine the arithmetic average NOX emission
rate of each test run. Calculate the arithmetic average of the
boiler excess oxygen readings for each test run. Record the
arithmetic average of the three test runs as the NOX emission rate
and the boiler excess oxygen level for the heat input/load
condition.
2.1.6 Plotting of Results
Plot the tabulated results as an x-y graph for each fuel and (as
applicable) combination of fuels combusted according to the
following procedures.
2.1.6.1 Plot the heat input rate (mmBtu/hr) as the independent
(or x) variable and the NOX emission rates (lb/mmBtu) as the
dependent (or y) variable for each load point. Construct the graph
by drawing straight line segments between each load point. Draw a
horizontal line to the y-axis from the minimum heat input (load)
point.
2.1.6.2 Units that co-fire gas and oil may be tested while
firing gas only and oil only instead of testing with each
combination of fuels. In this case, construct a graph for each
fuel.
2.2 Periodic NOX Emission Rate Testing
Retest the NOX emission rate of the gas-fired peaking unit or
the oil-fired peaking unit while combusting each type of fuel (or
fuel mixture) for which a NOX emission rate versus heat input rate
correlation curve was derived, at least once every 20 calendar
quarters. If a required retest is not completed by the end of the
20th calendar quarter following the quarter of the last test, use
the missing data substitution procedures in section 2.5 of this
appendix, beginning with the first unit operating hour after the
end of the 20th calendar quarter. Continue using the missing data
procedures until the required retest has been passed. Note that
missing data substitution is fuel-specific (i.e., the use of
substitute data is required only when combusting a fuel (or fuel
mixture) for which the retesting deadline has not been met). Each
time that a new fuel-specific correlation curve is derived from
retesting, the new curve shall be used to report NOX emission rate,
beginning with the first operating hour in which the fuel is
combusted, following the completion of the retest. Notwithstanding
this requirement, for non-Acid Rain Program units that report NOX
mass emissions and heat input data only during the ozone season
under § 75.74(c), if the NOX emission rate testing is performed
outside the ozone season, the new correlation curve may be used
beginning with the first unit operating hour in the ozone season
immediately following the testing.
2.3 Other Quality Assurance/Quality Control-Related NOx Emission
Rate Testing
When the operating levels of certain parameters exceed the
limits specified below, or where the Administrator issues a notice
requesting retesting because the NOX emission rate data
availability for when the unit operates within all quality
assurance/quality control parameters in this section since the last
test is less than 90.0 percent, as calculated by the Administrator,
complete retesting of the NOX emission rate by the earlier of: (1)
30 unit operating days (as defined in § 72.2 of this chapter) or
(2) 180 calendar days after exceeding the limits or after the date
of issuance of a notice from the Administrator to re-verify the
unit's NOX emission rate. Submit test results in accordance with §
75.60 within 45 days of completing the retesting.
2.3.1 For a stationary gas turbine, select at least four
operating parameters indicative of the turbine's NOX formation
characteristics, and define in the QA plan for the unit the
acceptable ranges for these parameters at each tested load-heat
input point. The acceptable parametric ranges should be based upon
the turbine manufacturer's recommendations. Alternatively, the
owner or operator may use sound engineering judgment and operating
experience with the unit to establish the acceptable parametric
ranges, provided that the rationale for selecting these ranges is
included as part of the quality-assurance plan for the unit. If the
gas turbine uses water or steam injection for NOX control, the
water/fuel or steam/fuel ratio shall be one of these parameters.
During the NOx-heat input correlation tests, record the average
value of each parameter for each load-heat input to ensure that the
parameters are within the acceptable range. Redetermine the NOX
emission rate-heat input correlation for each fuel and (optional)
combination of fuels after continuously exceeding the acceptable
range of any of these parameters for one or more successive
operating periods totaling more than 16 unit operating hours.
2.3.2 For a diesel or dual-fuel reciprocating engine, select at
least four operating parameters indicative of the engine's NOX
formation characteristics, and define in the QA plan for the unit
the acceptable ranges for these parameters at each tested load-heat
input point. The acceptable parametric ranges should be based upon
the engine manufacturer's recommendations. Alternatively, the owner
or operator may use sound engineering judgment and operating
experience with the unit to establish the acceptable parametric
ranges, provided that the rationale for selecting these ranges is
included as part of the quality-assurance plan for the unit. Any
operating parameter critical for NOX control shall be included.
During the NOX heat-input correlation tests, record the average
value of each parameter for each load-heat input to ensure that the
parameters are within the acceptable range. Redetermine the NOX
emission rate-heat input correlation for each fuel and (optional)
combination or fuels after continuously exceeding the acceptable
range of any of these parameters for one or more successive
operating periods totaling more than 16 unit operating hours.
2.3.3 For boilers using the procedures in this appendix, the NOX
emission rate heat input correlation for each fuel and (optional)
combination of fuels shall be redetermined if the excess oxygen
level at any heat input rate (or unit operating load) continuously
exceeds by more than 2 percentage points O2 from the boiler excess
oxygen level recorded at the same operating heat input rate during
the previous NOX emission rate test for one or more successive
operating periods totaling more than 16 unit operating hours.
2.4 Procedures for Determining Hourly NOX Emission Rate
2.4.1 Record the time (hr. and min.), load (MWge or steam load
in 1000 lb/hr, or mmBtu/hr thermal output), fuel flow rate and heat
input rate (using the procedures in section 2.1.3 of this appendix)
for each hour during which the unit combusts fuel. Calculate the
total hourly heat input using equation E-1 of this appendix. Record
the heat input rate for each fuel to the nearest 0.1 mmBtu/hr.
During partial unit operating hours or during hours where more than
one fuel is combusted, heat input must be represented as an hourly
rate in mmBtu/hr, as if the fuel were combusted for the entire hour
at that rate (and not as the actual, total heat input during that
partial hour or hour) in order to ensure proper correlation with
the NOX emission rate graph.
2.4.2 Use the graph of the baseline correlation results
(appropriate for the fuel or fuel combination) to determine the NOX
emissions rate (lb/mmBtu) corresponding to the heat input rate
(mmBtu/hr). Input this correlation into the data acquisition and
handling system for the unit. Linearly interpolate to 0.1 mmBtu/hr
heat input rate and 0.001 lb/mmBtu NOX. For each type of fuel,
calculate NOX emission rate using the baseline correlation results
from the most recent test with that fuel, beginning with the date
and hour of the completion of the most recent test.
2.4.3 To determine the NOX emission rate for a unit co-firing
fuels that has not been tested for that combination of fuels,
interpolate between the NOX emission rate for each fuel as follows.
Determine the heat input rate for the hour (in mmBtu/hr) for each
fuel and select the corresponding NOX emission rate for each fuel
on the appropriate graph. (When a fuel is combusted for a partial
hour, determine the fuel usage time for each fuel and determine the
heat input rate from each fuel as if that fuel were combusted at
that rate for the entire hour in order to select the corresponding
NOX emission rate.) Calculate the total heat input to the unit in
mmBtu for the hour from all fuel combusted using Equation E-1.
Calculate a Btu-weighted average of the emission rates for all
fuels using Equation E-2 of this appendix. For each type of fuel,
calculate NOX emission rate using the baseline correlation results
from the most recent test with that fuel, beginning with the date
and hour of the completion of the most recent test.
2.4.4 For each hour, record the critical quality assurance
parameters, as identified in the monitoring plan, and as required
by section 2.3 of this appendix from the date and hour of the
completion of the most recent test for each type of fuel.
2.5 Missing Data Procedures
Provide substitute data for each unit electing to use this
alternative procedure whenever a valid quality-assured hour of NOX
emission rate data has not been obtained according to the
procedures and specifications of this appendix. For the purpose of
providing substitute data, calculate the maximum potential NOX
emission rate (as defined in § 72.2 of this chapter) for each type
of fuel combusted in the unit.
2.5.1 Use the procedures of this section whenever any of the
quality assurance/quality control parameters exceeds the limits in
section 2.3 of this appendix or whenever any of the quality
assurance/quality control parameters are not available.
2.5.2 Substitute missing NOX emission rate data using the
highest NOX emission rate tabulated during the most recent set of
baseline correlation tests for the same fuel or, if applicable,
combination of fuels, except as provided in sections 2.5.2.1,
2.5.2.2, 2.5.2.3, and 2.5.2.4 of this appendix.
2.5.2.1 If the measured heat input rate during any unit
operating hour is higher than the highest heat input rate from the
baseline correlation tests, the NOX emission rate for the hour is
considered to be missing. Provide substitute data for each such
hour, according to section 2.5.2.1.1 or 2.5.2.1.2 of this appendix,
as applicable. Either:
2.5.2.1.1 Substitute the higher of: the NOX emission rate
obtained by linear extrapolation of the correlation curve, or the
maximum potential NOX emission rate (MER) (as defined in § 72.2 of
this chapter), specific to the type of fuel being combusted. (For
fuel mixtures, substitute the highest NOX MER value for any fuel in
the mixture.) For units with NOX emission controls, the
extrapolated NOX emission rate may only be used if the controls are
documented (e.g., by parametric data) to be operating properly
during the missing data period (see section 2.5.2.2 of this
appendix); or
2.5.2.1.2 Substitute 1.25 times the highest NOX emission rate
from the baseline correlation tests for the fuel (or fuel mixture)
being combusted in the unit, not to exceed the MER for that fuel
(or mixture). For units with NOX emission controls, the option to
report 1.25 times the highest emission rate from the correlation
curve may only be used if the controls are documented (e.g., by
parametric data) to be operating properly during the missing data
period (see section 2.5.2.2 of this appendix).
2.5.2.2 For a unit with add-on NOX emission controls (e.g.,
steam or water injection, selective catalytic reduction), if, for
any unit operating hour, the emission controls are either not in
operation or if appropriate parametric data are unavailable to
ensure proper operation of the controls, the NOX emission rate for
the hour is considered to be missing. Substitute the fuel-specific
MER (as defined in § 72.2 of this chapter) for each such hour.
2.5.2.3 When emergency fuel (as defined in § 72.2) is combusted
in the unit, report the fuel-specific NOX MER for each hour that
the fuel is combusted, unless a NOX correlation curve has been
derived for the fuel.
2.5.2.4 Whenever 20 full calendar quarters have elapsed
following the quarter of the last baseline correlation test for a
particular type of fuel (or fuel mixture), without a subsequent
baseline correlation test being done for that type of fuel (or fuel
mixture), substitute the fuel-specific NOX MER (as defined in §
72.2 of this chapter) for each hour in which that fuel (or mixture)
is combusted until a new baseline correlation test for that fuel
(or mixture) has been successfully completed. For fuel mixtures,
report the highest of the individual MER values for the components
of the mixture.
2.5.3 Maintain a record indicating which data are substitute
data and the reasons for the failure to provide a valid
quality-assured hour of NOX emission rate data according to the
procedures and specifications of this appendix.
2.5.4 Substitute missing data from a fuel flowmeter using the
procedures in section 2.4.2 of appendix D to this part.
2.5.5 Substitute missing data for gross calorific value of fuel
using the procedures in sections 2.4.1 of appendix D to this
part.
3. Calculations 3.1 Heat Input
Calculate the total heat input by summing the product of heat
input rate and fuel usage time of each fuel, as in the following
equation:

Where: HT
= Total heat input of fuel flow or a combination of fuel flows to a
unit, mmBtu. HIfuel 1,2,3,...last = Heat input rate from each fuel,
in mmBtu/hr as determined using Equation F-19 or F-20 in section
5.5 of appendix F to this part, mmBtu/hr. t1,2,3....last = Fuel
usage time for each fuel (rounded up to the nearest fraction of an
hour (in equal increments that can range from one hundredth to one
quarter of an hour, at the option of the owner or operator)). 3.2
F-factors
Determine the F-factors for each fuel or combination of fuels to
be combusted according to section 3.3 of appendix F of this
part.
3.3 NOX Emission Rate 3.3.1 Conversion from Concentration to
Emission Rate
Convert the NOX concentrations (ppm) and O2 concentrations to
NOX emission rates (to the nearest 0.01 lb/mmBtu for tests
performed prior to April 1, 2000, or to the nearest 0.001 lb/mmBtu
for tests performed on and after April 1, 2000), according to the
appropriate one of the following equations: F-5 in appendix F to
this part for dry basis concentration measurements or 19-3 in
Method 19 of appendix A to part 60 of this chapter for wet basis
concentration measurements.
3.3.2 Quarterly Average NOX Emission Rate
Report the quarterly average emission rate (lb/mmBtu) as
required in subpart G of this part. Calculate the quarterly average
NOX emission rate according to equation F-9 in appendix F of this
part.
3.3.3 Annual Average NOX Emission Rate
Report the average emission rate (lb/mmBtu) for the calendar
year as required in subpart G of this part. Calculate the average
NOX emission rate according to equation F-10 in appendix F of this
part.
3.3.4 Average NOX Emission Rate During Co-firing of Fuels
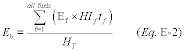
Where: Eh = NOX
emission rate for the unit for the hour, lb/mmBtu. Ef = NOX
emission rate for the unit for a given fuel at heat input rate HIf,
lb/mmBtu. HIf = Heat input rate for the hour for a given fuel,
during the fuel usage time, as determined using Equation F-19 or
F-20 in section 5.5 of appendix F to this part, mmBtu/hr. HT =
Total heat input for all fuels for the hour from Equation E-1. tf =
Fuel usage time for each fuel (rounded up to the nearest fraction
of an hour (in equal increments that can range from one hundredth
to one quarter of an hour, at the option of the owner or
operator)). Note:
For hours where a fuel is combusted for only part of the hour,
use the fuel flow rate or mass flow rate during the fuel usage
time, instead of the total fuel flow or mass flow during the hour,
when calculating heat input rate using Equation F-19 or F-20.
4. Quality Assurance/Quality Control Plan
Include a section on the NOX emission rate determination as part
of the monitoring quality assurance/quality control plan required
under § 75.21 and appendix B of this part for each gas-fired
peaking unit and each oil-fired peaking unit. In this section
present information including, but not limited to, the following:
(1) a copy of all data and results from the initial NOX emission
rate testing, including the values of quality assurance parameters
specified in section 2.3 of this appendix; (2) a copy of all data
and results from the most recent NOX emission rate load correlation
testing; (3) a copy of the recommended range of quality assurance-
and quality control-related operating parameters.
4.1 Submit a copy of the recommended range of operating
parameter values, and the range of operating parameter values
recorded during the previous NOX emission rate test that determined
the unit's NOX emission rate, along with the unit's revised
monitoring plan submitted with the certification application.
4.2 Keep records of these operating parameters for each hour of
operation in order to demonstrate that a unit is remaining within
the recommended operating range.
[58 FR 3701, Jan. 11, 1993, as amended at 60 FR 26551, May 17,
1995; 64 FR 28665, May 26, 1999; 67 FR 40473, 40474, June 12, 2002;
67 FR 53505, Aug. 16, 2002; 73 FR 4372, Jan. 24, 2008; 76 FR 17325,
Mar. 28, 2011]