Title 40
PART 60 APPENDIX B
Parameter | Specification |
---|---|
Wavelength range | 300-800 nm. |
Detector angle of view | <10°. |
Accuracy | <0.5% transmittance, NIST traceable calibration. |
You will need to use attenuators (i.e., neutral density filters) to check the daily calibration drift and calibration error of a COMS. Attenuators are designated as either primary or secondary based on how they are calibrated.
7.1 Attenuators are designated primary in one of two ways:
(1) They are calibrated by NIST; or
(2) They are calibrated on a 6-month frequency through the assignment of a luminous transmittance value in the following manner:
(i) Use a spectrophotometer meeting the specifications of section 6.3 to calibrate the required filters. Verify the spectrophotometer calibration through use of a NIST 930D Standard Reference Material (SRM). A SRM 930D consists of three neutral density glass filters and a blank, each mounted in a cuvette. The wavelengths and temperature to be used in the calibration are listed on the NIST certificate that accompanies the reported values. Determine and record a transmittance of the SRM values at the NIST wavelengths (three filters at five wavelengths each for a total of 15 determinations). Calculate a percent difference between the NIST certified values and the spectrophotometer response. At least 12 of the 15 differences (in percent) must be within ±0.5 percent of the NIST SRM values. No difference can be greater than ±1.0 percent. Recalibrate the SRM or service the spectrophotometer if the calibration results fail the criteria.
(ii) Scan the filter to be tested and the NIST blank from wavelength 380 to 780 nm, and record the spectrophotometer percent transmittance responses at 10 nm intervals. Test in this sequence: blank filter, tested filter, tested filter rotated 90 degrees in the plane of the filter, blank filter. Calculate the average transmittance at each 10 nm interval. If any pair of the tested filter transmittance values (for the same filter and wavelength) differ by more than ±0.25 percent, rescan the tested filter. If the filter fails to achieve this tolerance, do not use the filter in the calibration tests of the COMS.
(iii) Correct the tested filter transmittance values by dividing the average tested filter transmittance by the average blank filter transmittance at each 10 nm interval.
(iv) Calculate the weighted (to the response of the human eye), tested filter transmittance by multiplying the transmittance value by the corresponding response factor shown in table 1-1, to obtain the Source C Human Eye Response.
(v) Recalibrate the primary attenuators semi-annually if they are used for the required calibration error test. Recalibrate the primary attenuators annually if they are used only for calibration of secondary attenuators.
7.2 Attenuators are designated secondary if the filter calibration is done using a laboratory-based transmissometer. Conduct the secondary attenuator calibration using a laboratory-based transmissometer calibrated as follows:
(i) Use at least three primary filters of nominal luminous transmittance 50, 70 and 90 percent, calibrated as specified in section 7.1(2)(i), to calibrate the laboratory-based transmissometer. Determine and record the slope of the calibration line using linear regression through zero opacity. The slope of the calibration line must be between 0.99 and 1.01, and the laboratory-based transmissometer reading for each primary filter must not deviate by more than ±2 percent from the linear regression line. If the calibration of the laboratory-based transmissometer yields a slope or individual readings outside the specified ranges, secondary filter calibrations cannot be performed. Determine the source of the variations (either transmissometer performance or changes in the primary filters) and repeat the transmissometer calibration before proceeding with the attenuator calibration.
(ii) Immediately following the laboratory-based transmissometer calibration, insert the secondary attenuators and determine and record the percent effective opacity value per secondary attenuator from the calibration curve (linear regression line).
(iii) Recalibrate the secondary attenuators semi-annually if they are used for the required calibration error test.
8.0 What Performance Procedures Are Required To Comply With PS-1?Procedures to verify the performance of the COMS are divided into those completed by the owner or operator and those completed by the opacity monitor manufacturer.
8.1 What procedures must I follow as the Owner or Operator?
(1) You must purchase an opacity monitor that complies with ASTM D6216-12 and obtain a certificate of conformance from the opacity monitor manufacturer.
(2) You must install the opacity monitor at a location where the opacity measurements are representative of the total emissions from the affected facility. You must meet this requirement by choosing a measurement location and a light beam path as follows:
(i) Measurement Location. Select a measurement location that is (1) at least 4 duct diameters downstream from all particulate control equipment or flow disturbance, (2) at least 2 duct diameters upstream of a flow disturbance, (3) where condensed water vapor is not present, and (4) accessible in order to permit maintenance. Alternatively, you may select a measurement location specified in paragraph 8.1(2)(ii) or 8.1(2)(iii).
(ii) Light Beam Path. Select a light beam path that passes through the centroidal area of the stack or duct. Also, you must follow these additional requirements or modifications for these measurement locations:
If your measurement location is in a: | And is: | Then use a light beam path that is: |
---|---|---|
1. Straight vertical section of stack or duct | Less than 4 equivalent diameters downstream from a bend | In the plane defined by the upstream bend (see figure 1-1). |
2. Straight vertical section of stack or duct | Less than 4 equivalent diameters upstream from a bend | In the plane defined by the downstream bend (see figure 1-2). |
3. Straight vertical section of stack or duct | Less than 4 equivalent diameters downstream and is also less than 1 diameter upstream from a bend | In the plane defined by the upstream bend (see figure 1-3). |
4. Horizontal section of stack or duct | At least 4 equivalent diameters downstream from a vertical bend | In the horizontal plane that is between 1/3 and 1/2 the distance up the vertical axis from the bottom of the duct (see figure 1-4). |
5. Horizontal section of duct | Less than 4 equivalent diameters downstream from a vertical bend | In the horizontal plane that is between 1/2 and 2/3 the distance up the vertical axis from the bottom of the duct for upward flow in the vertical section, and is between 1/3 and 1/2 the distance up the vertical axis from the bottom of the duct for downward flow (figure 1-5). |
(iii) Alternative Locations and Light Beam Paths. You may select locations and light beam paths, other than those cited above, if you demonstrate, to the satisfaction of the Administrator or delegated agent, that the average opacity measured at the alternative location or path is equivalent to the opacity as measured at a location meeting the criteria of sections 8.1(2)(i) and 8.1(2)(ii). The opacity at the alternative location is considered equivalent if (1) the average opacity value measured at the alternative location is within ±10 percent of the average opacity value measured at the location meeting the installation criteria, and (2) the difference between any two average opacity values is less than 2 percent opacity (absolute). You use the following procedure to conduct this demonstration: simultaneously measure the opacities at the two locations or paths for a minimum period of time (e.g., 180-minutes) covering the range of normal operating conditions and compare the results. The opacities of the two locations or paths may be measured at different times, but must represent the same process operating conditions. You may use alternative procedures for determining acceptable locations if those procedures are approved by the Administrator.
(3) Field Audit Performance Tests. After you install the COMS, you must perform the following procedures and tests on the COMS.
(i) Optical Alignment Assessment. Verify and record that all alignment indicator devices show proper alignment. A clear indication of alignment is one that is objectively apparent relative to reference marks or conditions.
(ii) Calibration Error Check. Conduct a three-point calibration error test using three calibration attenuators that produce outlet pathlength corrected, single-pass opacity values shown in ASTM D6216-12, section 7.5. If your applicable limit is less than 10 percent opacity, use attenuators as described in ASTM D6216-12, section 7.5 for applicable standards of 10 to 19 percent opacity. Confirm the external audit device produces the proper zero value on the COMS data recorder. Separately, insert each calibration attenuators (low, mid, and high-level) into the external audit device. While inserting each attenuator, (1) ensure that the entire light beam passes through the attenuator, (2) minimize interference from reflected light, and (3) leave the attenuator in place for at least two times the shortest recording interval on the COMS data recorder. Make a total of five nonconsecutive readings for each attenuator. At the end of the test, correlate each attenuator insertion to the corresponding value from the data recorder. Subtract the single-pass calibration attenuator values corrected to the stack exit conditions from the COMS responses. Calculate the arithmetic mean difference, standard deviation, and confidence coefficient of the five measurements value using equations 1-3, 1-4, and 1-5. Calculate the calibration error as the sum of the absolute value of the mean difference and the 95 percent confidence coefficient for each of the three test attenuators using equation 1-6. Report the calibration error test results for each of the three attenuators.
(iii) System Response Time Check. Using a high-level calibration attenuator, alternately insert the filter five times and remove it from the external audit device. For each filter insertion and removal, measure the amount of time required for the COMS to display 95 percent of the step change in opacity on the COMS data recorder. For the upscale response time, measure the time from insertion to display of 95 percent of the final, steady upscale reading. For the downscale response time, measure the time from removal to display 5 percent of the initial upscale reading. Calculate the mean of the five upscale response time measurements and the mean of the five downscale response time measurements. Report both the upscale and downscale response times.
(iv) Averaging Period Calculation and Recording Check. After the calibration error check, conduct a check of the averaging period calculation (e.g., 6-minute integrated average). Consecutively insert each of the calibration error check attenuators (low, mid, and high-level) into the external audit device for a period of two times the averaging period plus 1 minute (e.g., 13 minutes for a 6-minute averaging period). Compare the path length corrected opacity value of each attenuator to the valid average value calculated by the COMS data recording device for that attenuator.
(4) Operational Test Period. Before conducting the operational testing, you must have successfully completed the field audit tests described in sections 8.1(3)(i) through 8.1(3)(iv). Then, you operate the COMS for an initial 168-hour test period while the source is operating under normal operating conditions. If normal operations contain routine source shutdowns, include the source's down periods in the 168-hour operational test period. However, you must ensure that the following minimum source operating time is included in the operational test period: (1) For a batch operation, the operational test period must include at least one full cycle of batch operation during the 168-hour period unless the batch operation is longer than 168 hours or (2) for continuous operating processes, the unit must be operating for at least 50 percent of the 168-hour period. Except during times of instrument zero and upscale calibration drift checks, you must analyze the effluent gas for opacity and produce a permanent record of the COMS output. During this period, you may not perform unscheduled maintenance, repair, or adjustment to the COMS. Automatic zero and calibration adjustments (i.e., intrinsic adjustments), made by the COMS without operator intervention or initiation, are allowable at any time. At the end of the operational test period, verify and record that the COMS optical alignment is still correct. If the test period is interrupted because of COMS failure, record the time when the failure occurred. After the failure is corrected, you restart the 168-hour period and tests from the beginning (0-hour). During the operational test period, perform the following test procedures:
(i) Zero Calibration Drift Test. At the outset of the 168-hour operational test period and at each 24-hour interval, the automatic calibration check system must initiate the simulated zero device to allow the zero drift to be determined. Record the COMS response to the simulated zero device. After each 24-hour period, subtract the COMS zero reading from the nominal value of the simulated zero device to calculate the 24-hour zero drift (ZD). At the end of the 168-hour period, calculate the arithmetic mean, standard deviation, and confidence coefficient of the 24-hour ZDs using equations 1-3, 1-4, and 1-5. Calculate the sum of the absolute value of the mean and the absolute value of the confidence coefficient using equation 1-6, and report this value as the 24-hour ZD error.
(ii) Upscale Calibration Drift Test. At each 24-hour interval after the simulated zero device value has been checked, check and record the COMS response to the upscale calibration device. After each 24-hour period, subtract the COMS upscale reading from the nominal value of the upscale calibration device to calculate the 24-hour calibration drift (CD). At the end of the 168-hour period, calculate the arithmetic mean, standard deviation, and confidence coefficient of the 24-hour CD using equations 1-3, 1-4, and 1-5. Calculate the sum of the absolute value of the mean and the absolute value of the confidence coefficient using equation 1-6, and report this value as the 24-hour CD error.
(5) Retesting. If the COMS fails to meet the specifications for the tests conducted under the operational test period, make the necessary corrections and restart the operational test period. Depending on the opinion of the enforcing agency, you may have to repeat some or all of the field audit tests.
8.2 What are the responsibilities of the Opacity Monitor Manufacturer?
You, the manufacturer, must carry out the following activities:
(1) Conduct the verification procedures for design specifications in section 6 of ASTM D6216-12.
(2) Conduct the verification procedures for performance specifications in section 7 of ASTM D6216-12.
(3) Provide to the owner or operator, a report of the opacity monitor's conformance to the design and performance specifications required in sections 6 and 7 of ASTM D6216-12 in accordance with the reporting requirements of section 9 in ASTM D6216-12.
9.0 What quality control measures are required by PS-1?Opacity monitor manufacturers must initiate a quality program following the requirements of ASTM D6216-12, section 8. The quality program must include (1) a quality system and (2) a corrective action program.
10.0 Calibration and Standardization [Reserved] 11.0 Analytical Procedure [Reserved] 12.0 What Calculations Are Needed for PS-1?12.1 Desired Attenuator Values. Calculate the desired attenuator value corrected to the emission outlet pathlength as follows:
Where: OP1 = Nominal opacity value of required low-, mid-, or high-range calibration attenuators. OP2 = Desired attenuator opacity value from ASTM D6216-12, section 7.5 at the opacity limit required by the applicable subpart. L1 = Monitoring pathlength. L2 = Emission outlet pathlength.12.2 Luminous Transmittance Value of a Filter. Calculate the luminous transmittance of a filter as follows:
Where: LT = Luminous transmittance Ti = Weighted tested filter transmittance.12.3 Arithmetic Mean. Calculate the arithmetic mean of a data set as follows:
Where:12.4 Standard Deviation. Calculate the standard deviation as follows:
Where: Sd = Standard deviation of a data set.12.5 Confidence Coefficient. Calculate the 2.5 percent error confidence coefficient (one-tailed) as follows:
Where: CC = Confidence coefficient t0.975 = t − value (see table 1-2).12.6 Calibration Error. Calculate the error (calibration error, zero drift error, and calibration drift error) as follows:
Where: Er = Error.12.7 Conversion of Opacity Values for Monitor Pathlength to Emission Outlet Pathlength. When the monitor pathlength is different from the emission outlet pathlength, use either of the following equations to convert from one basis to the other (this conversion may be automatically calculated by the monitoring system):
Where: Op1 = Opacity of the effluent based upon L1. Op2 = Opacity of the effluent based upon L2. L1 = Monitor pathlength. L2 = Emission outlet pathlength. OD1 = Optical density of the effluent based upon L1. OD2 = Optical density of the effluent based upon L2.12.8 Mean Response Wavelength. Calculate the mean of the effective spectral response curve from the individual responses at the specified wavelength values as follows:
Where: L = mean of the effective spectral response curve Li = The specified wavelength at which the response gi is calculated at 20 nm intervals. gi = The individual response value at Li. 13.0 What Specifications Does a COMS Have to Meet for Certification?A COMS must meet the following design, manufacturer's performance, and field audit performance specifications:
Note: If the initial certification of the opacity monitor occurred before November 14, 2018 using D6216-98, D6216-03, or D6216-07, it is not necessary to recertify using D6216-12.A. COMS must meet the following design, manufacturer's performance, and field audit performance specifications.
13.1 Design Specifications. The opacity monitoring equipment must comply with the design specifications of ASTM D6216-12.
13.2 Manufacturer's Performance Specifications. The opacity monitor must comply with the manufacturer's performance specifications of ASTM D6216-12.
13.3 Field Audit Performance Specifications. The installed COMS must comply with the following performance specifications:
(1) Optical Alignment. Objectively indicate proper alignment relative to reference marks (e.g., bull's-eye) or conditions.
(2) Calibration Error. The calibration error must be ≤3 percent opacity for each of the three calibration attenuators.
(3) System Response Time. The COMS upscale and downscale response times must be ≤10 seconds as measured at the COMS data recorder.
(4) Averaging Period Calculation and Recording. The COMS data recorder must average and record each calibration attenuator value to within ±2 percent opacity of the certified value of the attenuator.
(5) Operational Test Period. The COMS must be able to measure and record opacity and to perform daily calibration drift assessments for 168 hours without unscheduled maintenance, repair, or adjustment.
(6) Zero and Upscale Calibration Drift Error. The COMS zero and upscale calibration drift error must not exceed 2 percent opacity over a 24 hour period.
14.0 Pollution Prevention [Reserved] 15.0 Waste Management [Reserved] 16.0 Which references are relevant to this method?1. Experimental Statistics. Department of Commerce. National Bureau of Standards Handbook 91. Paragraph 3-3.1.4. 1963. 3-31 p.
2. Performance Specifications for Stationary Source Monitoring Systems for Gases and Visible Emissions, EPA-650/2-74-013, January 1974, U. S. Environmental Protection Agency, Research Triangle Park, NC.
3. Koontz, E.C., Walton, J. Quality Assurance Programs for Visible Emission Evaluations. Tennessee Division of Air Pollution Control. Nashville, TN. 78th Meeting of the Air Pollution Control Association. Detroit, MI. June 16-21, 1985.
4. Evaluation of Opacity CEMS Reliability and Quality Assurance Procedures. Volume 1. U. S. Environmental Protection Agency. Research Triangle Park, NC. EPA-340/1-86-009a.
5. Nimeroff, I. “Colorimetry Precision Measurement and Calibration.” NBS Special Publication 300. Volume 9. June 1972.
6. Technical Assistance Document: Performance Audit Procedures for Opacity Monitors. U. S. Environmental Protection Agency. Research Triangle Park, NC. EPA-600/8-87-025. April 1987.
7. Technical Assistance Document: Performance Audit Procedures for Opacity Monitors. U. S. Environmental Protection Agency. Research Triangle Park, NC. EPA-450/4-92-010. April 1992.
8. ASTM D6216-12: Standard Practice for Opacity Monitor Manufacturers to Certify Conformance with Design and Performance Specifications. ASTM. October 2012.
17.0 What tables and diagrams are relevant to this method?17.1 Reference Tables.
Table 1-1 - Source C, Human Eye Response Factor
Wavelength nanometers |
Weighting factor a |
Wavelength nanometers |
Weighting factor a |
---|---|---|---|
380 | 0 | 590 | 6627 |
390 | 0 | 600 | 5316 |
400 | 2 | 610 | 4176 |
410 | 9 | 620 | 3153 |
420 | 37 | 630 | 2190 |
430 | 122 | 640 | 1443 |
440 | 262 | 650 | 886 |
450 | 443 | 660 | 504 |
460 | 694 | 670 | 259 |
470 | 1058 | 680 | 134 |
480 | 1618 | 690 | 62 |
490 | 2358 | 700 | 29 |
500 | 3401 | 720 | 14 |
510 | 4833 | 720 | 6 |
520 | 6462 | 730 | 3 |
530 | 7934 | 740 | 2 |
540 | 9194 | 750 | 1 |
550 | 9832 | 760 | 1 |
560 | 9841 | 770 | 0 |
570 | 9147 | 780 | 0 |
580 | 7992 |
1 Total of weighting factors = 100,000.
Table 1-2 T Values
n a | t 0.975 | n a | t 0.975 | n a | t 0.975 |
---|---|---|---|---|---|
2 | 12.706 | 7 | 2.447 | 12 | 2.201 |
3 | 4.303 | 8 | 2.365 | 13 | 2.179 |
4 | 3.182 | 9 | 2.306 | 14 | 2.160 |
5 | 2.776 | 10 | 2.262 | 15 | 2.145 |
6 | 2.571 | 11 | 2.228 | 16 | 2.131 |
a The values in this table are already corrected for n-1 degrees of freedom. Use n equal to the number of individual values.
17.2 Diagrams.
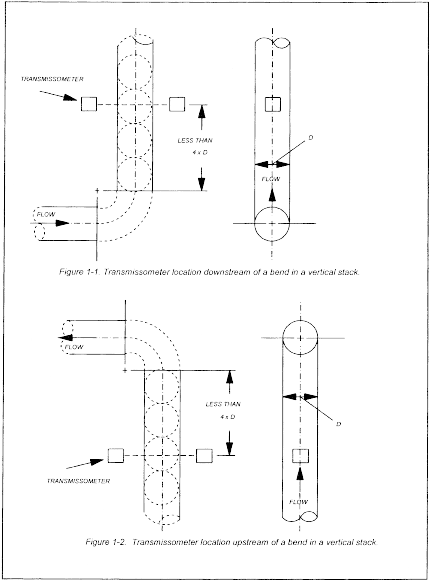
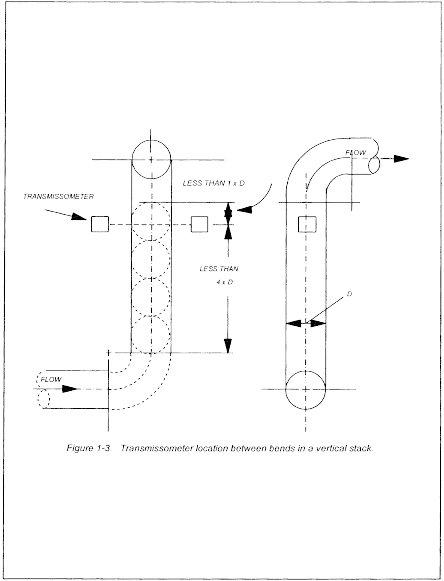
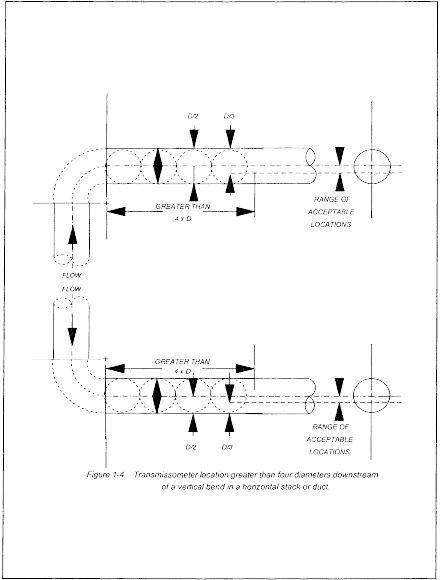
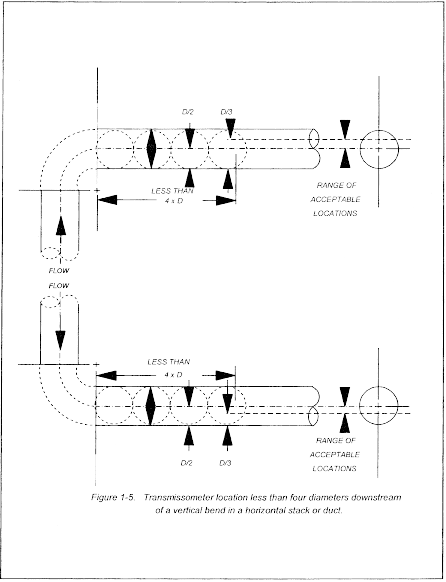
1.1 Analytes
Analyte | CAS Nos. |
---|---|
Sulfur Dioxide (SO2) | 7449-09-5 |
Nitrogen Oxides (NOX) | 10102-44-0 (NO2), 10024-97-2 (NO) |
1.2 Applicability.
1.2.1 This specification is for evaluating the acceptability of SO2 and NOX continuous emission monitoring systems (CEMS) at the time of installation or soon after and whenever specified in the regulations. The CEMS may include, for certain stationary sources, a diluent (O2 or CO2) monitor.
1.2.2 This specification is not designed to evaluate the installed CEMS performance over an extended period of time nor does it identify specific calibration techniques and other auxiliary procedures to assess the CEMS performance. The source owner or operator is responsible to calibrate, maintain, and operate the CEMS properly. The Administrator may require, under section 114 of the Act, the operator to conduct CEMS performance evaluations at other times besides the initial test to evaluate the CEMS performance. See 40 CFR Part 60, § 60.13(c).
2.0 Summary of Performance SpecificationProcedures for measuring CEMS relative accuracy and calibration drift are outlined. CEMS installation and measurement location specifications, equipment specifications, performance specifications, and data reduction procedures are included. Conformance of the CEMS with the Performance Specification is determined.
3.0 Definitions3.1 Calibration Drift (CD) means the difference in the CEMS output readings from the established reference value after a stated period of operation during which no unscheduled maintenance, repair, or adjustment took place.
3.2 Centroidal Area means a concentric area that is geometrically similar to the stack or duct cross section and is no greater than l percent of the stack or duct cross-sectional area.
3.3 Continuous Emission Monitoring System means the total equipment required for the determination of a gas concentration or emission rate. The sample interface, pollutant analyzer, diluent analyzer, and data recorder are the major subsystems of the CEMS.
3.4 Data Recorder means that portion of the CEMS that provides a permanent record of the analyzer output. The data recorder may include automatic data reduction capabilities.
3.5 Diluent Analyzer means that portion of the CEMS that senses the diluent gas (i.e., CO2 or O2) and generates an output proportional to the gas concentration.
3.6 Path CEMS means a CEMS that measures the gas concentration along a path greater than 10 percent of the equivalent diameter of the stack or duct cross section.
3.7 Point CEMS means a CEMS that measures the gas concentration either at a single point or along a path equal to or less than 10 percent of the equivalent diameter of the stack or duct cross section.
3.8 Pollutant Analyzer means that portion of the CEMS that senses the pollutant gas and generates an output proportional to the gas concentration.
3.9 Relative Accuracy (RA) means the absolute mean difference between the gas concentration or emission rate determined by the CEMS and the value determined by the reference method (RM), plus the 2.5 percent error confidence coefficient of a series of tests, divided by the mean of the RM tests or the applicable emission limit.
3.10 Sample Interface means that portion of the CEMS used for one or more of the following: sample acquisition, sample delivery, sample conditioning, or protection of the monitor from the effects of the stack effluent.
3.11 Span Value means the calibration portion of the measurement range as specified in the applicable regulation or other requirement. If the span is not specified in the applicable regulation or other requirement, then it must be a value approximately equivalent to two times the emission standard. For spans less than 500 ppm, the span value may either be rounded upward to the next highest multiple of 10 ppm, or to the next highest multiple of 100 ppm such that the equivalent emission concentration is not less than 30 percent of the selected span value.
4.0 Interferences [Reserved] 5.0 SafetyThe procedures required under this performance specification may involve hazardous materials, operations, and equipment. This performance specification may not address all of the safety problems associated with these procedures. It is the responsibility of the user to establish appropriate safety and health practices and determine the applicable regulatory limitations prior to performing these procedures. The CEMS user's manual and materials recommended by the reference method should be consulted for specific precautions to be taken.
6.0 Equipment and Supplies6.1 CEMS Equipment Specifications.
6.1.1 Data Recorder. The portion of the CEMS that provides a record of analyzer output. The data recorder may record other pertinent data such as effluent flow rates, various instrument temperatures or abnormal CEMS operation. The data recorder output range must include the full range of expected concentration values in the gas stream to be sampled including zero and span values.
6.1.2 The CEMS design should also allow the determination of calibration drift at the zero and span values. If this is not possible or practical, the design must allow these determinations to be conducted at a low-level value (zero to 20 percent of the span value) and at a value between 50 and 100 percent of the span value. In special cases, the Administrator may approve a single-point calibration drift determination.
6.2 Other equipment and supplies, as needed by the applicable reference method(s) (see section 8.4.2 of this Performance Specification), may be required.
7.0 Reagents and Standards7.1 Reference Gases, Gas Cells, or Optical Filters. As specified by the CEMS manufacturer for calibration of the CEMS (these need not be certified).
7.2 Reagents and Standards. May be required as needed by the applicable reference method(s) (see section 8.4.2 of this Performance Specification).
8.0 Performance Specification Test Procedure8.1 Installation and Measurement Location Specifications.
8.1.1 CEMS Installation. Install the CEMS at an accessible location where the pollutant concentration or emission rate measurements are directly representative or can be corrected so as to be representative of the total emissions from the affected facility or at the measurement location cross section. Then select representative measurement points or paths for monitoring in locations that the CEMS will pass the RA test (see section 8.4). If the cause of failure to meet the RA test is determined to be the measurement location and a satisfactory correction technique cannot be established, the Administrator may require the CEMS to be relocated. Suggested measurement locations and points or paths that are most likely to provide data that will meet the RA requirements are listed below.
8.1.2 CEMS Measurement Location. It is suggested that the measurement location be (1) at least two equivalent diameters downstream from the nearest control device, the point of pollutant generation, or other point at which a change in the pollutant concentration or emission rate may occur and (2) at least a half equivalent diameter upstream from the effluent exhaust or control device.
8.1.2.1 Point CEMS. It is suggested that the measurement point be (1) no less than 1.0 meter (3.3 ft) from the stack or duct wall or (2) within or centrally located over the centroidal area of the stack or duct cross section.
8.1.2.2 Path CEMS. It is suggested that the effective measurement path (1) be totally within the inner area bounded by a line 1.0 meter (3.3 ft) from the stack or duct wall, or (2) have at least 70 percent of the path within the inner 50 percent of the stack or duct cross-sectional area, or (3) be centrally located over any part of the centroidal area.
8.1.3 Reference Method Measurement Location and Traverse Points.
8.1.3.1 Select, as appropriate, an accessible RM measurement point at least two equivalent diameters downstream from the nearest control device, the point of pollutant generation, or other point at which a change in the pollutant concentration or emission rate may occur, and at least a half equivalent diameter upstream from the effluent exhaust or control device. When pollutant concentration changes are due solely to diluent leakage (e.g., air heater leakages) and pollutants and diluents are simultaneously measured at the same location, a half diameter may be used in lieu of two equivalent diameters. The CEMS and RM locations need not be the same.
8.1.3.2 Select traverse points that assure acquisition of representative samples over the stack or duct cross section. The minimum requirements are as follows: Establish a “measurement line” that passes through the centroidal area and in the direction of any expected stratification. If this line interferes with the CEMS measurements, displace the line up to 30 cm (12 in.) (or 5 percent of the equivalent diameter of the cross section, whichever is less) from the centroidal area. Locate three traverse points at 16.7, 50.0, and 83.3 percent of the measurement line. If the measurement line is longer than 2.4 meters (7.8 ft) and pollutant stratification is not expected, the three traverse points may be located on the line at 0.4, 1.2, and 2.0 meters from the stack or duct wall. This option must not be used after wet scrubbers or at points where two streams with different pollutant concentrations are combined. If stratification is suspected, the following procedure is suggested. For rectangular ducts, locate at least nine sample points in the cross section such that sample points are the centroids of similarly-shaped, equal area divisions of the cross section. Measure the pollutant concentration, and, if applicable, the diluent concentration at each point using appropriate reference methods or other appropriate instrument methods that give responses relative to pollutant concentrations. Then calculate the mean value for all sample points. For circular ducts, conduct a 12-point traverse (i.e., six points on each of the two perpendicular diameters) locating the sample points as described in 40 CFR 60, Appendix A, Method 1. Perform the measurements and calculations as described above. Determine if the mean pollutant concentration is more than 10% different from any single point. If so, the cross section is considered to be stratified, and the tester may not use the alternative traverse point locations (...0.4, 1.2, and 2.0 meters from the stack or duct wall.) but must use the three traverse points at 16.7, 50.0, and 83.3 percent of the entire measurement line. Other traverse points may be selected, provided that they can be shown to the satisfaction of the Administrator to provide a representative sample over the stack or duct cross section. Conduct all necessary RM tests within 3 cm (1.2 in.) of the traverse points, but no closer than 3 cm (1.2 in.) to the stack or duct wall.
8.2 Pretest Preparation. Install the CEMS, prepare the RM test site according to the specifications in section 8.1, and prepare the CEMS for operation according to the manufacturer's written instructions.
8.3 Calibration Drift Test Procedure.
8.3.1 CD Test Period. While the affected facility is operating, determine the magnitude of the CD once each day (at 24-hour intervals) for 7 consecutive calendar days according to the procedure given in sections 8.3.2 through 8.3.4. Alternatively, the CD test may be conducted over 7 consecutive unit operating days.
8.3.2 The purpose of the CD measurement is to verify the ability of the CEMS to conform to the established CEMS calibration used for determining the emission concentration or emission rate. Therefore, if periodic automatic or manual adjustments are made to the CEMS zero and calibration settings, conduct the CD test immediately before these adjustments, or conduct it in such a way that the CD can be determined.
8.3.3 Conduct the CD test at the two points specified in section 6.1.2. Introduce to the CEMS the reference gases, gas cells, or optical filters (these need not be certified). Record the CEMS response and subtract this value from the reference value (see example data sheet in Figure 2-1).
8.4 Relative Accuracy Test Procedure.
8.4.1 RA Test Period. Conduct the RA test according to the procedure given in sections 8.4.2 through 8.4.6 while the affected facility is operating at more than 50 percent of normal load, or as specified in an applicable subpart. The RA test may be conducted during the CD test period.
8.4.2 Reference Methods. Unless otherwise specified in an applicable subpart of the regulations, Methods 3B, 4, 6, and 7, or their approved alternatives, are the reference methods for diluent (O2 and CO2), moisture, SO2, and NOX, respectively.
8.4.3 Sampling Strategy for RM Tests. Conduct the RM tests in such a way that they will yield results representative of the emissions from the source and can be correlated to the CEMS data. It is preferable to conduct the diluent (if applicable), moisture (if needed), and pollutant measurements simultaneously. However, diluent and moisture measurements that are taken within an hour of the pollutant measurements may be used to calculate dry pollutant concentration and emission rates. In order to correlate the CEMS and RM data properly, note the beginning and end of each RM test period of each run (including the exact time of day) on the CEMS chart recordings or other permanent record of output. Use the following strategies for the RM tests:
8.4.3.1 For integrated samples (e.g., Methods 6 and Method 4), make a sample traverse of at least 21 minutes, sampling for an equal time at each traverse point (see section 8.1.3.2 for discussion of traverse points.
8.4.3.2 For grab samples (e.g., Method 7), take one sample at each traverse point, scheduling the grab samples so that they are taken simultaneously (within a 3-minute period) or at an equal interval of time apart over the span of time the CEM pollutant is measured. A test run for grab samples must be made up of at least three separate measurements.
Note:At times, CEMS RA tests are conducted during new source performance standards performance tests. In these cases, RM results obtained during CEMS RA tests may be used to determine compliance as long as the source and test conditions are consistent with the applicable regulations.
8.4.4 Number of RM Tests. Conduct a minimum of nine sets of all necessary RM test runs.
Note:More than nine sets of RM tests may be performed. If this option is chosen, a maximum of three sets of the test results may be rejected so long as the total number of test results used to determine the RA is greater than or equal to nine. However, all data must be reported, including the rejected data.
8.4.5 Correlation of RM and CEMS Data. Correlate the CEMS and the RM test data as to the time and duration by first determining from the CEMS final output (the one used for reporting) the integrated average pollutant concentration or emission rate for each pollutant RM test period. Consider system response time, if important, and confirm that the pair of results are on a consistent moisture, temperature, and diluent concentration basis. Then, compare each integrated CEMS value against the corresponding average RM value. Use the following guidelines to make these comparisons.
8.4.5.1 If the RM has an integrated sampling technique, make a direct comparison of the RM results and CEMS integrated average value.
8.4.5.2 If the RM has a grab sampling technique, first average the results from all grab samples taken during the test run, and then compare this average value against the integrated value obtained from the CEMS chart recording or output during the run. If the pollutant concentration is varying with time over the run, the arithmetic average of the CEMS value recorded at the time of each grab sample may be used.
8.4.6 Calculate the mean difference between the RM and CEMS values in the units of the emission standard, the standard deviation, the confidence coefficient, and the relative accuracy according to the procedures in section 12.0.
8.5 Reporting. At a minimum (check with the appropriate regional office, State, or Local agency for additional requirements, if any), summarize in tabular form the results of the CD tests and the RA tests or alternative RA procedure, as appropriate. Include all data sheets, calculations, charts (records of CEMS responses), cylinder gas concentration certifications, and calibration cell response certifications (if applicable) necessary to confirm that the performance of the CEMS met the performance specifications.
9.0 Quality Control [Reserved] 10.0 Calibration and Standardization [Reserved] 11.0 Analytical ProcedureSample collection and analysis are concurrent for this Performance Specification (see section 8.0). Refer to the RM for specific analytical procedures.
12.0 Calculations and Data AnalysisSummarize the results on a data sheet similar to that shown in Figure 2-2 (in section 18.0).
12.1 All data from the RM and CEMS must be on a consistent dry basis and, as applicable, on a consistent diluent basis and in the units of the emission standard. Correct the RM and CEMS data for moisture and diluent as follows:
12.1.1 Moisture Correction (as applicable). Correct each wet RM run for moisture with the corresponding Method 4 data; correct each wet CEMS run using the corresponding CEMS moisture monitor date using Equation 2-1.
12.1.2 Correction to Units of Standard (as applicable). Correct each dry RM run to the units of the emission standard with the corresponding Method 3B data; correct each dry CEMS run using the corresponding CEMS diluent monitor data as follows:
12.1.2.1 Correct to Diluent Basis. The following is an example of concentration (ppm) correction to 7% oxygen.
The following is an example of mass/gross calorific value (lbs/million Btu) correction.
lbs/MMBtu = Conc(dry) (F-factor) (20.9/20.9-%02)12.2 Arithmetic Mean. Calculate the arithmetic mean of the difference, d, of a data set as follows:
Where: n = Number of data points.12.3 Standard Deviation. Calculate the standard deviation, Sd, as follows:
12.4 Confidence Coefficient. Calculate the 2.5 percent error confidence coefficient (one-tailed), CC, as follows:
Where: t 0.975 = t-value (see Table 2-1).12.5 Relative Accuracy. Calculate the RA of a set of data as follows:
Where: |d | = Absolute value of the mean differences (from Equation 2-3). |CC| = Absolute value of the confidence coefficient (from Equation 2-3). RM = Average RM value. In cases where the average emissions for the test are less than 50 percent of the applicable standard, substitute the emission standard value in the denominator of Eq. 2-6 in place of RM. In all other cases, use RM. 13.0 Method Performance13.1 Calibration Drift Performance Specification. The CEMS calibration must not drift or deviate from the reference value of the gas cylinder, gas cell, or optical filter by more than 2.5 percent of the span value. If the CEMS includes pollutant and diluent monitors, the CD must be determined separately for each in terms of concentrations (See Performance Specification 3 for the diluent specifications), and none of the CDs may exceed the specification.
13.2 Relative Accuracy Performance Specification.
Calculate . . . | RA criteria (%) |
|
---|---|---|
If average emissions during the RATA are ≥50% of emission standard | Use Eq. 2-6, with RM in the denominator | ≤20.0 |
If average emissions during the RATA are <50% of emission standard | Use Eq. 2-6, emission standard in the denominator | ≤10.0 |
For SO2 emission standards ≤130 but ≥86 ng/J (0.30 and 0.20 lb/million Btu) | Use Eq. 2-6, emission standard in the denominator | ≤15.0 |
For SO2 emission standards <86 ng/J (0.20 lb/million Btu) | Use Eq. 2-6, emission standard in the denominator | ≤20.0 |
13.3 For instruments that use common components to measure more than one effluent gas constituent, all channels must simultaneously pass the RA requirement, unless it can be demonstrated that any adjustments made to one channel did not affect the others.
14.0 Pollution Prevention [Reserved] 15.0 Waste Management [Reserved] 16.0 Alternative ProceduresParagraphs 60.13(j)(1) and (2) of 40 CFR part 60 contain criteria for which the reference method procedure for determining relative accuracy (see section 8.4 of this Performance Specification) may be waived and the following procedure substituted.
16.1 Conduct a complete CEMS status check following the manufacturer's written instructions. The check should include operation of the light source, signal receiver, timing mechanism functions, data acquisition and data reduction functions, data recorders, mechanically operated functions (mirror movements, zero pipe operation, calibration gas valve operations, etc.), sample filters, sample line heaters, moisture traps, and other related functions of the CEMS, as applicable. All parts of the CEMS shall be functioning properly before proceeding to the alternative RA procedure.
16.2 Alternative RA Procedure.
16.2.1 Challenge each monitor (both pollutant and diluent, if applicable) with cylinder gases of known concentrations or calibration cells that produce known responses at two measurement points within the ranges shown in Table 2-2 (Section 18).
16.2.2 Use a separate cylinder gas (for point CEMS only) or calibration cell (for path CEMS or where compressed gas cylinders can not be used) for measurement points 1 and 2. Challenge the CEMS and record the responses three times at each measurement point. The Administrator may allow dilution of cylinder gas using the performance criteria in Test Method 205, 40 CFR Part 51, Appendix M. Use the average of the three responses in determining relative accuracy.
16.2.3 Operate each monitor in its normal sampling mode as nearly as possible. When using cylinder gases, pass the cylinder gas through all filters, scrubbers, conditioners, and other monitor components used during normal sampling and as much of the sampling probe as practical. When using calibration cells, the CEMS components used in the normal sampling mode should not be by-passed during the RA determination. These include light sources, lenses, detectors, and reference cells. The CEMS should be challenged at each measurement point for a sufficient period of time to assure adsorption-desorption reactions on the CEMS surfaces have stabilized.
16.2.4 Use cylinder gases that have been certified by comparison to National Institute of Standards and Technology (NIST) gaseous standard reference material (SRM) or NIST/EPA approved gas manufacturer's certified reference material (CRM) (See Reference 2 in section 17.0) following EPA Traceability Protocol Number 1 (See Reference 3 in section 17.0). As an alternative to Protocol Number 1 gases, CRM's may be used directly as alternative RA cylinder gases. A list of gas manufacturers that have prepared approved CRM's is available from EPA at the address shown in Reference 2. Procedures for preparation of CRM's are described in Reference 2.
16.2.5 Use calibration cells certified by the manufacturer to produce a known response in the CEMS. The cell certification procedure shall include determination of CEMS response produced by the calibration cell in direct comparison with measurement of gases of known concentration. This can be accomplished using SRM or CRM gases in a laboratory source simulator or through extended tests using reference methods at the CEMS location in the exhaust stack. These procedures are discussed in Reference 4 in section 17.0. The calibration cell certification procedure is subject to approval of the Administrator.
16.3 The differences between the known concentrations of the cylinder gases and the concentrations indicated by the CEMS are used to assess the accuracy of the CEMS. The calculations and limits of acceptable relative accuracy are as follows:
16.3.1 For pollutant CEMS:
Where: d = Average difference between responses and the concentration/responses (see section 16.2.2). AC = The known concentration/response of the cylinder gas or calibration cell.16.3.2 For diluent CEMS:
RA= d; ≤0.7 percent O2 or CO2, as applicable. Note:Waiver of the relative accuracy test in favor of the alternative RA procedure does not preclude the requirements to complete the CD tests nor any other requirements specified in an applicable subpart for reporting CEMS data and performing CEMS drift checks or audits.
17.0 References1. Department of Commerce. Experimental Statistics. Handbook 91. Washington, D.C. p. 3-31, paragraphs 3-3.1.4.
2. “A Procedure for Establishing Traceability of Gas Mixtures to Certain National Bureau of Standards Standard Reference Materials.” Joint publication by NBS and EPA. EPA 600/7-81-010. Available from U.S. Environmental Protection Agency, Quality Assurance Division (MD-77), Research Triangle Park, North Carolina 27711.
3. “Traceability Protocol for Establishing True Concentrations of Gases Used for Calibration and Audits of Continuous Source Emission Monitors. (Protocol Number 1).” June 1978. Protocol Number 1 is included in the Quality Assurance Handbook for Air Pollution Measurement Systems, Volume III, Stationary Source Specific Methods. EPA-600/4-77-027b. August 1977.
4. “Gaseous Continuous Emission Monitoring Systems - Performance Specification Guidelines for SO2, NOX, CO2, O2, and TRS.” EPA-450/3-82-026. Available from the U.S. EPA, Emission Measurement Center, Emission Monitoring and Data Analysis Division (MD-19), Research Triangle Park, North Carolina 27711.
18.0 Tables, Diagrams, Flowcharts, and Validation DataTable 2-1 - t-Values
n a | t0.975 | n a | t0.975 | n a | t0.975 |
---|---|---|---|---|---|
2 | 12.706 | 7 | 2.447 | 12 | 2.201 |
3 | 4.303 | 8 | 2.365 | 13 | 2.179 |
4 | 3.182 | 9 | 2.306 | 14 | 2.160 |
5 | 2.776 | 10 | 2.262 | 15 | 2.145 |
6 | 2.571 | 11 | 2.228 | 16 | 2.131 |
a The values in this table are already corrected for n−1 degrees of freedom. Use n equal to the number of individual values.
Table 2-2 - Measurement Range
Measurement point | Pollutant monitor | Diluent monitor for | |
---|---|---|---|
CO2 | O2 | ||
1 | 20-30% of span value | 5-8% by volume | 4-6% by volume. |
2 | 50-60% of span value | 10-14% by volume | 8-12% by volume. |
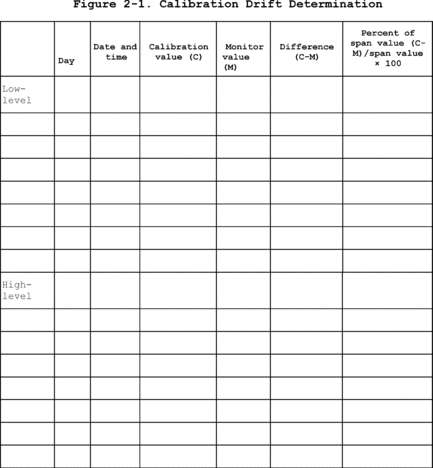
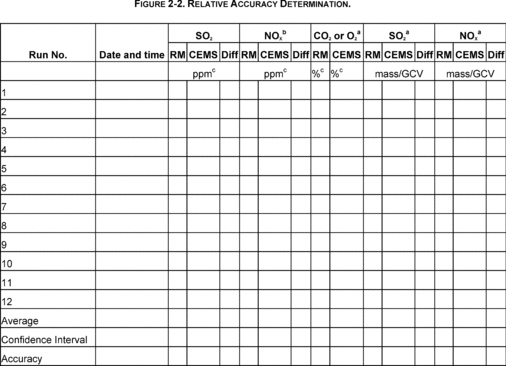
a For Steam generators.
b Average of three samples.
c Make sure that RM and CEMS data are on a consistent basis, either wet or dry.
1.1 Analytes.
Analytes | CAS No. |
---|---|
Carbon Dioxide (CO2) | 124-38-9 |
Oxygen (O2) | 7782-44-7 |
1.2 Applicability.
1.2.1 This specification is for evaluating acceptability of O2 and CO2 continuous emission monitoring systems (CEMS) at the time of installation or soon after and whenever specified in an applicable subpart of the regulations. This specification applies to O2 or CO2 monitors that are not included under Performance Specification 2 (PS 2).
1.2.2 This specification is not designed to evaluate the installed CEMS performance over an extended period of time, nor does it identify specific calibration techniques and other auxiliary procedures to assess the CEMS performance. The source owner or operator, is responsible to calibrate, maintain, and operate the CEMS properly. The Administrator may require, under section 114 of the Act, the operator to conduct CEMS performance evaluations at other times besides the initial test to evaluate the CEMS performance. See 40 CFR part 60, section 60.13(c).
1.2.3 The definitions, installation and measurement location specifications, calculations and data analysis, and references are the same as in PS 2, sections 3, 8.1, 12, and 17, respectively, and also apply to O2 and CO2 CEMS under this specification. The performance and equipment specifications and the relative accuracy (RA) test procedures for O2 and CO2 CEMS do not differ from those for SO2 and NOX CEMS (see PS 2), except as noted below.
2.0 Summary of Performance SpecificationThe RA and calibration drift (CD) tests are conducted to determine conformance of the CEMS to the specification.
3.0 DefinitionsSame as in section 3.0 of PS 2.
4.0 Interferences [Reserved] 5.0 SafetyThis performance specification may involve hazardous materials, operations, and equipment. This performance specification may not address all of the safety problems associated with its use. It is the responsibility of the user to establish appropriate safety and health practices and determine the applicable regulatory limitations prior to performing this performance specification. The CEMS users manual should be consulted for specific precautions to be taken with regard to the analytical procedures.
6.0 Equipment and SuppliesSame as section 6.0 of PS2.
7.0 Reagents and StandardsSame as section 7.0 of PS2.
8.0 Sample Collection, Preservation, Storage, and Transport8.1 Relative Accuracy Test Procedure. Sampling Strategy for reference method (RM) Tests, Correlation of RM and CEMS Data, and Number of RM Tests. Same as PS 2, sections 8.4.3, 8.4.5, and 8.4.4, respectively.
8.2 Reference Method. Unless otherwise specified in an applicable subpart of the regulations, Method 3B or other approved alternative is the RM for O2 or CO2.
9.0 Quality Control [Reserved] 10.0 Calibration and Standardization [Reserved] 11.0 Analytical ProcedureSample collection and analyses are concurrent for this performance specification (see section 8). Refer to the RM for specific analytical procedures.
12.0 Calculations and Data AnalysisCalculate the RA using equations 3-1 and 3-2. Summarize the results on a data sheet similar to that shown in Figure 2.2 of PS2.

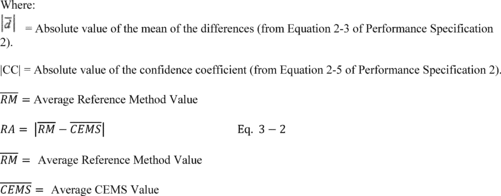
13.1 Calibration Drift Performance Specification. The CEMS calibration must not drift by more than 0.5 percent O2 or CO2 from the reference value of the gas, gas cell, or optical filter.
13.2 CEMS Relative Accuracy Performance Specification. The RA of the CEMS must be no greater than 20.0 percent of the mean value of the reference method (RM) data when calculated using equation 3-1. The results are also acceptable if the result of Equation 3-2 is less than or equal to 1.0 percent O2 (or CO2).
14.0 Pollution Prevention [Reserved] 15.0 Waste Management [Reserved] 16.0 ReferencesSame as in section 17.0 of PS 2.
17.0 Tables, Diagrams, Flowcharts, and Validation Data [Reserved] Performance Specification 4 - Specifications and Test Procedures for Carbon Monoxide Continuous Emission Monitoring Systems in Stationary Sources 1.0 Scope and Application1.1 Analytes.
Analyte | CAS No. |
---|---|
Carbon Monoxide (CO) | 630-08-0 |
1.2 Applicability.
1.2.1 This specification is for evaluating the acceptability of carbon monoxide (CO) continuous emission monitoring systems (CEMS) at the time of installation or soon after and whenever specified in an applicable subpart of the regulations. This specification was developed primarily for CEMS having span values of 1,000 ppmv CO.
1.2.2 This specification is not designed to evaluate the installed CEMS performance over an extended period of time nor does it identify specific calibration techniques and other auxiliary procedures to assess CEMS performance. The source owner or operator, is responsible to calibrate, maintain, and operate the CEMS. The Administrator may require, under section 114 of the Act, the source owner or operator to conduct CEMS performance evaluations at other times besides the initial test to evaluate the CEMS performance. See 40 CFR part 60, section 60.13(c).
1.2.3 The definitions, performance specification test procedures, calculations, and data analysis procedures for determining calibration drift (CD) and relative accuracy (RA) of Performance Specification 2 (PS 2), sections 3, 8.0, and 12, respectively, apply to this specification.
2.0 Summary of Performance SpecificationThe CD and RA tests are conducted to determine conformance of the CEMS to the specification.
3.0 DefinitionsSame as in section 3.0 of PS 2.
4.0 Interferences [Reserved] 5.0 SafetyThis performance specification may involve hazardous materials, operations, and equipment. This performance specification may not address all of the safety problems associated with its use. It is the responsibility of the user to establish appropriate safety and health practices and determine the applicable regulatory limitations prior to performing this performance specification. The CEMS users manual should be consulted for specific precautions to be taken with regard to the analytical procedures.
6.0 Equipment and SuppliesSame as section 6.0 of PS 2.
7.0 Reagents and StandardsSame as section 7.0 of PS 2.
8.0 Sample Collection, Preservation, Storage, and Transport8.1 Relative Accuracy Test Procedure. Sampling Strategy for reference method (RM) Tests, Number of RM Tests, and Correlation of RM and CEMS Data are the same as PS 2, sections 8.4.3, 8.4.4, and 8.4.5, respectively.
8.2 Reference Methods. Unless otherwise specified in an applicable subpart of the regulation, Method 10, 10A, 10B or other approved alternative are the RM for this PS.
9.0 Quality Control [Reserved] 10.0 Calibration and Standardization [Reserved] 11.0 Analytical ProcedureSample collection and analysis are concurrent for this performance specification (see section 8.0). Refer to the RM for specific analytical procedures.
12.0 Calculations and Data AnalysisSame as section 12.0 of PS 2.
13.0 Method Performance13.1 Calibration Drift. The CEMS calibration must not drift or deviate from the reference value of the calibration gas, gas cell, or optical filter by more than 5 percent of the established span value for 6 out of 7 test days (e.g., the established span value is 1000 ppm for Subpart J affected facilities).
13.2 Relative Accuracy. The RA of the CEMS must be no greater than 10 percent when the average RM value is used to calculate RA or 5 percent when the applicable emission standard is used to calculate RA.
14.0 Pollution Prevention [Reserved] 15.0 Waste Management [Reserved] 16.0 Alternative Procedures [Reserved] 17.0 References1. Ferguson, B.B., R.E. Lester, and W.J. Mitchell. Field Evaluation of Carbon Monoxide and Hydrogen Sulfide Continuous Emission Monitors at an Oil Refinery. U.S. Environmental Protection Agency. Research Triangle Park, N.C. Publication No. EPA-600/4-82-054. August 1982. 100 p.
2. “Gaseous Continuous Emission Monitoring Systems - Performance Specification Guidelines for SO2, NOX, CO2, O2, and TRS.” EPA-450/3-82-026. U.S. Environmental Protection Agency, Technical Support Division (MD-19), Research Triangle Park, NC 27711.
3. Repp, M. Evaluation of Continuous Monitors for Carbon Monoxide in Stationary Sources. U.S. Environmental Protection Agency. Research Triangle Park, N.C. Publication No. EPA-600/2-77-063. March 1977. 155 p.
4. Smith, F., D.E. Wagoner, and R.P. Donovan. Guidelines for Development of a Quality Assurance Program: Volume VIII - Determination of CO Emissions from Stationary Sources by NDIR Spectrometry. U.S. Environmental Protection Agency. Research Triangle Park, N.C. Publication No. EPA-650/4-74-005-h. February 1975. 96 p.
18.0 Tables, Diagrams, Flowcharts, and Validation DataSame as section 18.0 of PS 2.
Performance Specification 4A - Specifications and Test Procedures for Carbon Monoxide Continuous Emission Monitoring Systems in Stationary Sources 1.0 Scope and Application1.1 Analytes.
Analyte | CAS No. |
---|---|
Carbon Monoxide (CO) | 630-80-0 |
1.2 Applicability.
1.2.1 This specification is for evaluating the acceptability of carbon monoxide (CO) continuous emission monitoring systems (CEMS) at the time of installation or soon after and whenever specified in an applicable subpart of the regulations. This specification was developed primarily for CEMS that comply with low emission standards (less than 200 ppmv).
1.2.2 This specification is not designed to evaluate the installed CEMS performance over an extended period of time nor does it identify specific calibration techniques and other auxiliary procedures to assess CEMS performance. The source owner or operator is responsible to calibrate, maintain, and operate the CEMS. The Administrator may require, under section 114 of the Act, the source owner or operator to conduct CEMS performance evaluations at other times besides the initial test to evaluate CEMS performance. See 40 CFR Part 60, section 60.13(c).
1.2.3 The definitions, performance specification, test procedures, calculations and data analysis procedures for determining calibration drifts (CD) and relative accuracy (RA), of Performance Specification 2 (PS 2), sections 3, 8.0, and 12, respectively, apply to this specification.
2.0 Summary of Performance SpecificationThe CD and RA tests are conducted to determine conformance of the CEMS to the specification.
3.0 DefinitionsSame as in section 3.0 of PS 2.
4.0 Interferences [Reserved] 5.0 SafetyThis performance specification may involve hazardous materials, operations, and equipment. This performance specification may not address all of the safety problems associated with its use. It is the responsibility of the user to establish appropriate safety and health practices and determine the applicable regulatory limitations prior to performing this performance specification. The CEMS users manual should be consulted for specific precautions to be taken with regard to the analytical procedures.
6.0 Equipment and SuppliesSame as section 6.0 of PS 2 with the following additions.
6.1 Data Recorder Scale.
6.1.1 This specification is the same as section 6.1 of PS 2. The CEMS shall be capable of measuring emission levels under normal conditions and under periods of short-duration peaks of high concentrations. This dual-range capability may be met using two separate analyzers (one for each range) or by using dual-range units which have the capability of measuring both levels with a single unit. In the latter case, when the reading goes above the full-scale measurement value of the lower range, the higher-range operation shall be started automatically. The CEMS recorder range must include zero and a high-level value. Under applications of consistent low emissions, a single-range analyzer is allowed provided normal and spike emissions can be quantified. In this case, set an appropriate high-level value to include all emissions.
6.1.2 For the low-range scale of dual-range units, the high-level value shall be between 1.5 times the pollutant concentration corresponding to the emission standard level and the span value. For the high-range scale, the high-level value shall be set at 2000 ppm, as a minimum, and the range shall include the level of the span value. There shall be no concentration gap between the low-and high-range scales.
7.0 Reagents and StandardsSame as section 7.0 of PS 2.
8.0 Sample Collection, Preservation, Storage, and Transport8.1 Relative Accuracy Test Procedure. Sampling Strategy for reference method (RM) Tests, Number of RM Tests, and Correlation of RM and CEMS Data are the same as PS 2, sections 8.4.3, 8.4.4, and 8.4.5, respectively.
8.2 Reference Methods. Unless otherwise specified in an applicable subpart of the regulation, Methods 10, 10A, 10B, or other approved alternative is the RM for this PS. When evaluating nondispersive infrared CEMS using Method 10 as the RM, the alternative interference trap specified in section 16.0 of Method 10 shall be used.
8.3 Response Time Test Procedure. The response time test applies to all types of CEMS, but will generally have significance only for extractive systems. The entire system is checked with this procedure including applicable sample extraction and transport, sample conditioning, gas analyses, and data recording.
8.3.1 Introduce zero gas into the system. When the system output has stabilized (no change greater than 1 percent of full scale for 30 sec), introduce an upscale calibration gas and wait for a stable value. Record the time (upscale response time) required to reach 95 percent of the final stable value. Next, reintroduce the zero gas and wait for a stable reading before recording the response time (downscale response time). Repeat the entire procedure until you have three sets of data to determine the mean upscale and downscale response times. The slower or longer of the two means is the system response time.
8.4 Interference Check. The CEMS must be shown to be free from the effects of any interferences.
9.0 Quality Control [Reserved] 10.0 Calibration and Standardization [Reserved] 11.0 Analytical ProcedureSample collection and analysis are concurrent for this performance specification (see section 8.0). Refer to the RM for specific analytical procedures.
12.0 Calculations and Data Analysis. Same as section 12.0 of PS 2 13.0 Method Performance13.1 Calibration Drift. The CEMS calibration must not drift or deviate from the reference value of the calibration gas, gas cell, or optical filter by more than 5 percent of the established span value for 6 out of 7 test days.
13.2 Relative Accuracy. The RA of the CEMS must be no greater than 10 percent when the average RM value is used to calculate RA, 5 percent when the applicable emission standard is used to calculate RA, or within 5 ppmv when the RA is calculated as the absolute average difference between the RM and CEMS plus the 2.5 percent confidence coefficient.
13.3 Response Time. The CEMS response time shall not exceed 240 seconds to achieve 95 percent of the final stable value.
14.0 Pollution Prevention [Reserved] 15.0 Waste Management [Reserved] 16.0 Alternative Procedures16.1 Under conditions where the average CO emissions are less than 10 percent of the standard and this is verified by Method 10, a cylinder gas audit may be performed in place of the RA test to determine compliance with these limits. In this case, the cylinder gas shall contain CO in 12 percent carbon dioxide as an interference check. If this option is exercised, Method 10 must be used to verify that emission levels are less than 10 percent of the standard.
17.0 ReferencesSame as section 17 of PS 4.
18.0 Tables, Diagrams, Flowcharts, and Validation DataSame as section 18.0 of PS 2.
Performance Specification 4B - Specifications and Test Procedures for Carbon Monoxide and Oxygen Continuous Monitoring Systems in Stationary Sources a. Applicability and Principle1.1 Applicability. a. This specification is to be used for evaluating the acceptability of carbon monoxide (CO) and oxygen (O2) continuous emission monitoring systems (CEMS) at the time of or soon after installation and whenever specified in the regulations. The CEMS may include, for certain stationary sources, (a) flow monitoring equipment to allow measurement of the dry volume of stack effluent sampled, and (b) an automatic sampling system.
b. This specification is not designed to evaluate the installed CEMS' performance over an extended period of time nor does it identify specific calibration techniques and auxiliary procedures to assess the CEMS' performance. The source owner or operator, however, is responsible to properly calibrate, maintain, and operate the CEMS. To evaluate the CEMS' performance, the Administrator may require, under section 114 of the Act, the operator to conduct CEMS performance evaluations at times other than the initial test.
c. The definitions, installation and measurement location specifications, test procedures, data reduction procedures, reporting requirements, and bibliography are the same as in PS 3 (for O2) and PS 4A (for CO) except as otherwise noted below.
1.2 Principle. Installation and measurement location specifications, performance specifications, test procedures, and data reduction procedures are included in this specification. Reference method tests, calibration error tests, calibration drift tests, and interferant tests are conducted to determine conformance of the CEMS with the specification.
b. Definitions2.1 Continuous Emission Monitoring System (CEMS). This definition is the same as PS 2 section 2.1 with the following addition. A continuous monitor is one in which the sample to be analyzed passes the measurement section of the analyzer without interruption.
2.2 Response Time. The time interval between the start of a step change in the system input and when the pollutant analyzer output reaches 95 percent of the final value.
2.3 Calibration Error (CE). The difference between the concentration indicated by the CEMS and the known concentration generated by a calibration source when the entire CEMS, including the sampling interface is challenged. A CE test procedure is performed to document the accuracy and linearity of the CEMS over the entire measurement range.
3. Installation and Measurement Location Specifications3.1 The CEMS Installation and Measurement Location. This specification is the same as PS 2 section 3.1 with the following additions. Both the CO and O2 monitors should be installed at the same general location. If this is not possible, they may be installed at different locations if the effluent gases at both sample locations are not stratified and there is no in-leakage of air between sampling locations.
3.1.1 Measurement Location. Same as PS 2 section 3.1.1.
3.1.2 Point CEMS. The measurement point should be within or centrally located over the centroidal area of the stack or duct cross section.
3.1.3 Path CEMS. The effective measurement path should: (1) Have at least 70 percent of the path within the inner 50 percent of the stack or duct cross sectional area, or (2) be centrally located over any part of the centroidal area.
3.2 Reference Method (RM) Measurement Location and Traverse Points. This specification is the same as PS 2 section 3.2 with the following additions. When pollutant concentration changes are due solely to diluent leakage and CO and O2 are simultaneously measured at the same location, one half diameter may be used in place of two equivalent diameters.
3.3 Stratification Test Procedure. Stratification is defined as the difference in excess of 10 percent between the average concentration in the duct or stack and the concentration at any point more than 1.0 meter from the duct or stack wall. To determine whether effluent stratification exists, a dual probe system should be used to determine the average effluent concentration while measurements at each traverse point are being made. One probe, located at the stack or duct centroid, is used as a stationary reference point to indicate change in the effluent concentration over time. The second probe is used for sampling at the traverse points specified in Method 1 (40 CFR part 60 appendix A). The monitoring system samples sequentially at the reference and traverse points throughout the testing period for five minutes at each point.
d. Performance and Equipment Specifications4.1 Data Recorder Scale. For O2, same as specified in PS 3, except that the span must be 25 percent. The span of the O2 may be higher if the O2 concentration at the sampling point can be greater than 25 percent. For CO, same as specified in PS 4A, except that the low-range span must be 200 ppm and the high range span must be 3000 ppm. In addition, the scale for both CEMS must record all readings within a measurement range with a resolution of 0.5 percent.
4.2 Calibration Drift. For O2, same as specified in PS 3. For CO, the same as specified in PS 4A except that the CEMS calibration must not drift from the reference value of the calibration standard by more than 3 percent of the span value on either the high or low range.
4.3 Relative Accuracy (RA). For O2, same as specified in PS 3. For CO, the same as specified in PS 4A.
4.4 Calibration Error (CE). The mean difference between the CEMS and reference values at all three test points (see Table I) must be no greater than 5 percent of span value for CO monitors and 0.5 percent for O2 monitors.
4.5 Response Time. The response time for the CO or O2 monitor must not exceed 240 seconds.
e. Performance Specification Test Procedure5.1 Calibration Error Test and Response Time Test Periods. Conduct the CE and response time tests during the CD test period.
F. The CEMS Calibration Drift and Response Time Test ProceduresThe response time test procedure is given in PS 4A, and must be carried out for both the CO and O2 monitors.
7. Relative Accuracy and Calibration Error Test Procedures
7.1 Calibration Error Test Procedure. Challenge each monitor (both low and high range CO and O2) with zero gas and EPA Protocol 1 cylinder gases at three measurement points within the ranges specified in Table I.
Table I. Calibration Error Concentration Ranges
Measurement point | CO Low range (ppm) | CO High range (ppm) | O2 (%) |
---|---|---|---|
1 | 0-40 | 0-600 | 0-2 |
2 | 60-80 | 900-1200 | 8-10 |
3 | 140-160 | 2100-2400 | 14-16 |
7.1.1 Calculations. Summarize the results on a data sheet. Average the differences between the instrument response and the certified cylinder gas value for each gas. Calculate the CE results for the CO monitor according to:
CE = | d/FS | × 100 (1) Where d is the mean difference between the CEMS response and the known reference concentration, and FS is the span value. The CE for the O2 monitor is the average percent O2 difference between the O2 monitor and the certified cylinder gas value for each gas.7.2 Relative Accuracy Test Procedure. Follow the RA test procedures in PS 3 (for O2) section 3 and PS 4A (for CO) section 4.
7.3 Alternative RA Procedure. Under some operating conditions, it may not be possible to obtain meaningful results using the RA test procedure. This includes conditions where consistent, very low CO emission or low CO emissions interrupted periodically by short duration, high level spikes are observed. It may be appropriate in these circumstances to waive the RA test and substitute the following procedure.
Conduct a complete CEMS status check following the manufacturer's written instructions. The check should include operation of the light source, signal receiver, timing mechanism functions, data acquisition and data reduction functions, data recorders, mechanically operated functions, sample filters, sample line heaters, moisture traps, and other related functions of the CEMS, as applicable. All parts of the CEMS must be functioning properly before the RA requirement can be waived. The instrument must also successfully passed the CE and CD specifications. Substitution of the alternate procedure requires approval of the Regional Administrator.
8. Bibliography
1. 40 CFR Part 266, Appendix IX, section 2, “Performance Specifications for Continuous Emission Monitoring Systems.”
Performance Specification 5 - Specifications and Test Procedures for TRS Continuous Emission Monitoring Systems in Stationary Sources 1.0 Scope and Application1.1 Analytes.
Analyte | CAS No. |
---|---|
Total Reduced Sulfur (TRS) | NA |
1.2 Applicability. This specification is for evaluating the applicability of TRS continuous emission monitoring systems (CEMS) at the time of installation or soon after and whenever specified in an applicable subpart of the regulations. The CEMS may include oxygen monitors which are subject to Performance Specification 3 (PS 3).
1.3 The definitions, performance specification, test procedures, calculations and data analysis procedures for determining calibration drifts (CD) and relative accuracy (RA) of PS 2, sections 3.0, 8.0, and 12.0, respectively, apply to this specification.
2.0 Summary of Performance SpecificationThe CD and RA tests are conducted to determine conformance of the CEMS to the specification.
3.0 DefinitionsSame as in section 3.0 of PS 2.
4.0 Interferences [Reserved] 5.0 SafetyThis performance specification may involve hazardous materials, operations, and equipment. This performance specification may not address all of the safety problems associated with its use. It is the responsibility of the user to establish appropriate safety and health practices and determine the applicable regulatory limitations prior to performing this performance specification. The CEMS user's manual should be consulted for specific precautions to be taken with regard to the analytical procedures.
6.0 Equipment and SuppliesSame as section 6.0 of PS 2.
7.0 Reagents and StandardsSame as section 7.0 of PS 2.
8.0 Sample Collection, Preservation, Storage, and Transport8.1 Relative Accuracy Test Procedure. Sampling Strategy for reference method (RM) Tests, Number of RM Tests, and Correlation of RM and CEMS Data are the same as PS 2, sections 8.4.3, 8.4.4, and 8.4.5, respectively.
Note:For Method 16, a sample is made up of at least three separate injects equally spaced over time. For Method 16A, a sample is collected for at least 1 hour. For Method 16B, you must analyze a minimum of three aliquots spaced evenly over the test period.
Note:For Method 16, a sample is made up of at least three separate injects equally space over time. For Method 16A, a sample is collected for at least 1 hour.
8.2 Reference Methods. Unless otherwise specified in the applicable subpart of the regulations, Method 16, Method 16A, 16B or other approved alternative is the RM for TRS.
9.0 Quality Control [Reserved] 10.0 Calibration and Standardization [Reserved] 11.0 Analytical ProcedureSample collection and analysis are concurrent for this performance specification (see section 8.0). Refer to the reference method for specific analytical procedures.
12.0 Calculations and Data AnalysisSame as section 12.0 of PS 2.
13.0 Method Performance13.1 Calibration Drift. The CEMS detector calibration must not drift or deviate from the reference value of the calibration gas by more than 5 percent of the established span value for 6 out of 7 test days. This corresponds to 1.5 ppm drift for Subpart BB sources where the span value is 30 ppm. If the CEMS includes pollutant and diluent monitors, the CD must be determined separately for each in terms of concentrations (see PS 3 for the diluent specifications).
13.2 Relative Accuracy. The RA of the CEMS must be no greater than 20 percent when the average RM value is used to calculate RA or 10 percent when the applicable emission standard is used to calculate RA.
14.0 Pollution Prevention [Reserved] 15.0 Waste Management [Reserved] 16.0 Alternative Procedures [Reserved] 17.0 References1. Department of Commerce. Experimental Statistics, National Bureau of Standards, Handbook 91. 1963. Paragraphs 3-3.1.4, p. 3-31.
2. A Guide to the Design, Maintenance and Operation of TRS Monitoring Systems. National Council for Air and Stream Improvement Technical Bulletin No. 89. September 1977.
3. Observation of Field Performance of TRS Monitors on a Kraft Recovery Furnace. National Council for Air and Stream Improvement Technical Bulletin No. 91. January 1978.
18.0 Tables, Diagrams, Flowcharts, and Validation DataSame as section 18.0 of PS 2.
Performance Specification 6 - Specifications and Test Procedures for Continuous Emission Rate Monitoring Systems in Stationary Sources 1.0 Scope and Application1.1 Applicability. This specification is used for evaluating the acceptability of continuous emission rate monitoring systems (CERMSs).
1.2 The installation and measurement location specifications, performance specification test procedure, calculations, and data analysis procedures, of Performance Specifications (PS 2), sections 8.0 and 12, respectively, apply to this specification.
2.0 Summary of Performance SpecificationThe calibration drift (CD) and relative accuracy (RA) tests are conducted to determine conformance of the CERMS to the specification.
3.0 DefinitionsThe definitions are the same as in section 3 of PS 2, except this specification refers to the continuous emission rate monitoring system rather than the continuous emission monitoring system. The following definitions are added:
3.1 Continuous Emission Rate Monitoring System (CERMS). The total equipment required for the determining and recording the pollutant mass emission rate (in terms of mass per unit of time).
3.2 Flow Rate Sensor. That portion of the CERMS that senses the volumetric flow rate and generates an output proportional to that flow rate. The flow rate sensor shall have provisions to check the CD for each flow rate parameter that it measures individually (e.g., velocity, pressure).
4.0 Interferences [Reserved] 5.0 SafetyThis performance specification may involve hazardous materials, operations, and equipment. This performance specification may not address all of the safety problems associated with its use. It is the responsibility of the user to establish appropriate safety and health practices and determine the applicable regulatory limitations prior to performing this performance specification. The CERMS users manual should be consulted for specific precautions to be taken with regard to the analytical procedures.
6.0 Equipment and SuppliesSame as section 6.0 of PS 2.
7.0 Reagents and StandardsSame as section 7.0 of PS 2.
8.0 Sample Collection, Preservation, Storage, and Transport8.1 Calibration Drift Test Procedure.
8.1.1 The CD measurements are to verify the ability of the CERMS to conform to the established CERMS calibrations used for determining the emission rate. Therefore, if periodic automatic or manual adjustments are made to the CERMS zero and calibration settings, conduct the CD tests immediately before these adjustments, or conduct them in such a way that CD can be determined.
8.1.2 Conduct the CD tests for pollutant concentration at the two values specified in section 6.1.2 of PS 2. For other parameters that are selectively measured by the CERMS (e.g., velocity, pressure, flow rate), use two analogous values (e.g., Low: 0-20% of full scale, High: 50-100% of full scale). Introduce to the CERMS the reference signals (these need not be certified). Record the CERMS response to each and subtract this value from the respective reference value (see example data sheet in Figure 6-1).
8.2 Relative Accuracy Test Procedure.
8.2.1 Sampling Strategy for reference method (RM) Tests, Correlation of RM and CERMS Data, and Number of RM Tests are the same as PS 2, sections 8.4.3, 8.4.5, and 8.4.4, respectively. Summarize the results on a data sheet. An example is shown in Figure 6-1. The RA test may be conducted during the CD test period.
8.2.2 Reference Methods. Unless otherwise specified in the applicable subpart of the regulations, the RM for the pollutant gas is the Appendix A method that is cited for compliance test purposes, or its approved alternatives. Methods 2, 2A, 2B, 2C, or 2D, as applicable, are the RMs for the determination of volumetric flow rate.
9.0 Quality Control [Reserved] 10.0 Calibration and Standardization [Reserved] 11.0 Analytical ProcedureSame as section 11.0 of PS 2.
12.0 Calculations and Data AnalysisSame as section 12.0 of PS 2.
13.0 Method Performance13.1 Calibration Drift. Since the CERMS includes analyzers for several measurements, the CD shall be determined separately for each analyzer in terms of its specific measurement. The calibration for each analyzer associated with the measurement of flow rate shall not drift or deviate from each reference value of flow rate by more than 3 percent of the respective high-level reference value over the CD test period (e.g., seven-day) associated with the pollutant analyzer. The CD specification for each analyzer for which other PSs have been established (e.g., PS 2 for SO2 and NOX), shall be the same as in the applicable PS.
13.2 CERMS Relative Accuracy. Calculate the CERMS Relative Accuracy using Eq. 2-6 of section 12 of Performance Specification 2. The RA of the CERMS shall be no greater than 20 percent of the mean value of the RM's test data in terms of the units of the emission standard, or in cases where the average emissions for the test are less than 50 percent of the applicable standard, substitute the emission standard value in the denominator of Eq. 2-6 in place of the RM.
14.0 Pollution Prevention [Reserved] 15.0 Waste Management [Reserved] 16.0 Alternative ProceduresSame as in section 16.0 of PS 2.
17.0 References1. Brooks, E.F., E.C. Beder, C.A. Flegal, D.J. Luciani, and R. Williams. Continuous Measurement of Total Gas Flow Rate from Stationary Sources. U.S. Environmental Protection Agency. Research Triangle Park, North Carolina. Publication No. EPA-650/2-75-020. February 1975. 248 p.
18.0 Tables, Diagrams, Flowcharts, and Validation DataRun No. | Date and time | Emission rate (kg/hr) a | ||
---|---|---|---|---|
CERMS | RMs | Difference (RMs-CERMS) |
||
1 | ||||
2 | ||||
3 | ||||
4 | ||||
5 | ||||
6 | ||||
7 | ||||
8 | ||||
9 |
a The RMs and CERMS data as corrected to a consistent basis (i.e., moisture, temperature, and pressure conditions).
1.1 Analytes.
Analyte | CAS No. |
---|---|
Hydrogen Sulfide | 7783-06-4 |
1.2 Applicability.
1.2.1 This specification is to be used for evaluating the acceptability of hydrogen sulfide (H2S) continuous emission monitoring systems (CEMS) at the time of or soon after installation and whenever specified in an applicable subpart of the regulations.
1.2.2 This specification is not designed to evaluate the installed CEMS performance over an extended period of time nor does it identify specific calibration techniques and other auxiliary procedures to assess CEMS performance. The source owner or operator, however, is responsible to calibrate, maintain, and operate the CEMS. To evaluate CEMS performance, the Administrator may require, under section 114 of the Act, the source owner or operator to conduct CEMS performance evaluations at other times besides the initial test. See section 60.13(c).
2.0 SummaryCalibration drift (CD) and relative accuracy (RA) tests are conducted to determine that the CEMS conforms to the specification.
3.0 DefinitionsSame as section 3.0 of PS 2.
4.0 Interferences [Reserved] 5.0 SafetyThe procedures required under this performance specification may involve hazardous materials, operations, and equipment. This performance specification may not address all of the safety problems associated with these procedures. It is the responsibility of the user to establish appropriate safety problems associated with these procedures. It is the responsibility of the user to establish appropriate safety and health practices and determine the application regulatory limitations prior to performing these procedures. The CEMS user's manual and materials recommended by the reference method should be consulted for specific precautions to be taken.
6.0 Equipment and Supplies6.1 Instrument Zero and Span. This specification is the same as section 6.1 of PS 2.
6.2 Calibration Drift. The CEMS calibration must not drift or deviate from the reference value of the calibration gas or reference source by more than 5 percent of the established span value for 6 out of 7 test days (e.g., the established span value is 300 ppm for Subpart J fuel gas combustion devices).
6.3 Relative Accuracy. The RA of the CEMS must be no greater than 20 percent when the average reference method (RM) value is used to calculate RA or 10 percent when the applicable emission standard is used to calculate RA.
7.0 Reagents and StandardsSame as section 7.0 of PS 2.
8.0 Sample Collection, Preservation, Storage, and Transport.8.1 Installation and Measurement Location Specification. Same as section 8.1 of PS 2.
8.2 Pretest Preparation. Same as section 8.2 of PS 2.
8.3 Calibration Drift Test Procedure. Same as section 8.3 of PS 2.
8.4 Relative Accuracy Test Procedure.
8.4.1 Sampling Strategy for RM Tests, Number of RM Tests, Correlation of RM and CEMS Data, and Calculations. These are the same as that in PS-2, Sections 8.4.3 (except as specified below), 8.4.4, 8.4.5, and 8.4.6, respectively.
8.4.2 Reference Methods. Unless otherwise specified in an applicable subpart of the regulation, Methods 11, 15, and 16 may be used for the RM for this PS.
8.4.2.1 Sampling Time Per Run - Method 11. A sampling run, when Method 11 (integrated sampling) is used, shall consist of a single measurement for at least 10 minutes and 0.010 dscm (0.35 dscf). Each sample shall be taken at approximately 30-minute intervals.
8.4.2.2 Sampling Time Per Run - Methods 15 and 16. The sampling run shall consist of two injections equally spaced over a 30-minute period following the procedures described in the particular method. Note: Caution! Heater or non-approved electrical probes should not be used around explosive or flammable sources.
8.5 Reporting. Same as section 8.5 of PS 2.
9.0 Quality Control [Reserved] 10.0 Calibration and Standardizations [Reserved] 11.0 Analytical ProceduresSample Collection and analysis are concurrent for this PS (see section 8.0). Refer to the RM for specific analytical procedures.
12.0 Data Analysis and CalculationsSame as section 12.0 of PS 2.
13.0 Method Performance [Reserved] 14.0 Pollution Prevention [Reserved] 15.0 Waste Management [Reserved] 16.0 References1. U.S. Environmental Protection Agency. Standards of Performance for New Stationary Sources; Appendix B; Performance Specifications 2 and 3 for SO2, NOX, CO2, and O2 Continuous Emission Monitoring Systems; Final Rule. 48 CFR 23608. Washington, D.C. U.S. Government Printing Office. May 25, 1983.
2. U.S. Government Printing Office. Gaseous Continuous Emission Monitoring Systems - Performance Specification Guidelines for SO2, NOX, CO2, O2, and TRS. U.S. Environmental Protection Agency. Washington, D.C. EPA-450/3-82-026. October 1982. 26 p.
3. Maines, G.D., W.C. Kelly (Scott Environmental Technology, Inc.), and J.B. Homolya. Evaluation of Monitors for Measuring H2S in Refinery Gas. Prepared for the U.S. Environmental Protection Agency. Research Triangle Park, N.C. Contract No. 68-02-2707. 1978. 60 p.
4. Ferguson, B.B., R.E. Lester (Harmon Engineering and Testing), and W.J. Mitchell. Field Evaluation of Carbon Monoxide and Hydrogen Sulfide Continuous Emission Monitors at an Oil Refinery. Prepared for the U.S. Environmental Protection Agency. Research Triangle Park, N.C. Publication No. EPA-600/4-82-054. August 1982. 100 p.
5. Letter to RAMCON Environmental Corp. from Robert Kellam, December 27, 1992.
17.0 Tables, Diagrams, Flowcharts, and Validation DataSame as section 18.0 of PS 2.
Performance Specification 8 - Performance Specifications for Volatile Organic Compound Continuous Emission Monitoring Systems in Stationary Sources 1.0 Scope and Application1.1 Analytes. Volatile Organic Compounds (VOCs).
1.2 Applicability.
1.2.1 This specification is to be used for evaluating a continuous emission monitoring system (CEMS) that measures a mixture of VOC's and generates a single combined response value. The VOC detection principle may be flame ionization (FI), photoionization (PI), non-dispersive infrared absorption (NDIR), or any other detection principle that is appropriate for the VOC species present in the emission gases and that meets this performance specification. The performance specification includes procedures to evaluate the acceptability of the CEMS at the time of or soon after its installation and whenever specified in emission regulations or permits. This specification is not designed to evaluate the installed CEMS performance over an extended period of time, nor does it identify specific calibration techniques and other auxiliary procedures to assess the CEMS performance. The source owner or operator, however, is responsible to calibrate, maintain, and operate the CEMS properly. To evaluate the CEMS performance, the Administrator may require, under section 114 of the Act, the operator to conduct CEMS performance evaluations in addition to the initial test. See section 60.13(c).
1.2.2 In most emission circumstances, most VOC monitors can provide only a relative measure of the total mass or volume concentration of a mixture of organic gases, rather than an accurate quantification. This problem is removed when an emission standard is based on a total VOC measurement as obtained with a particular detection principle. In those situations where a true mass or volume VOC concentration is needed, the problem can be mitigated by using the VOC CEMS as a relative indicator of total VOC concentration if statistical analysis indicates that a sufficient margin of compliance exists for this approach to be acceptable. Otherwise, consideration can be given to calibrating the CEMS with a mixture of the same VOC's in the same proportions as they actually occur in the measured source. In those circumstances where only one organic species is present in the source, or where equal incremental amounts of each of the organic species present generate equal CEMS responses, the latter choice can be more easily achieved.
2.0 Summary of Performance Specification2.1 Calibration drift and relative accuracy tests are conducted to determine adherence of the CEMS with specifications given for those items. The performance specifications include criteria for installation and measurement location, equipment and performance, and procedures for testing and data reduction.
3.0 Definitions.Same as section 3.0 of PS 2.
4.0 Interferences [Reserved] 5.0 SafetyThe procedures required under this performance specification may involve hazardous materials, operations, and equipment. This performance specification may not address all of the safety problems associated with these procedures. It is the responsibility of the user to establish appropriate safety problems associated with these procedures. It is the responsibility of the user to establish appropriate safety and health practices and determine the application regulatory limitations prior to performing these procedures. The CEMS user's manual and materials recommended by the reference method should be consulted for specific precautions to be taken.
6.0 Equipment and Supplies6.1 VOC CEMS Selection. When possible, select a VOC CEMS with the detection principle of the reference method specified in the regulation or permit (usually either FI, NDIR, or PI). Otherwise, use knowledge of the source process chemistry, previous emission studies, or gas chromatographic analysis of the source gas to select an appropriate VOC CEMS. Exercise extreme caution in choosing and installing any CEMS in an area with explosive hazard potential.
6.2 Data Recorder Scale. Same as section 6.1 of PS 2.
7.0 Reagents and Standards [Reserved] 8.0 Sample Collection, Preservation, Storage, and Transport8.1 Installation and Measurement Location Specifications. Same as section 8.1 of PS 2.
8.2 Pretest Preparation. Same as section 8.2 of PS 2.
8.3 Calibration Drift Test Procedure. Same as section 8.3 of PS 2.
8.4 Reference Method (RM). Use the method specified in the applicable regulation or permit, or any approved alternative, as the RM.
8.5 Sampling Strategy for RM Tests, Correlation of RM and CEMS Data, and Number of RM Tests. Follow PS 2, sections 8.4.3, 8.4.5, and 8.4.4, respectively.
8.6 Reporting. Same as section 8.5 of PS 2.
9.0 Quality Control [Reserved] 10.0 Calibration and Standardization [Reserved] 11.0 Analytical ProcedureSample collection and analysis are concurrent for this PS (see section 8.0). Refer to the RM for specific analytical procedures.
12.0 Calculations and Data AnalysisSame as section 12.0 of PS 2.
13.0 Method Performance13.1 Calibration Drift. The CEMS calibration must not drift by more than 2.5 percent of the span value.
13.2 CEMS Relative Accuracy. Unless stated otherwise in the regulation or permit, the RA of the CEMS must not be greater than 20 percent of the mean value of the RM test data in terms of the units of the emission standard, or 10 percent of the applicable standard, whichever is greater.
14.0 Pollution Prevention [Reserved] 15.0 Waste Management [Reserved] 16.0 ReferencesSame as section 17.0 of PS 2.
17.0 Tables, Diagrams, Flowcharts, and Validation Data [Reserved] Performance Specification 8A - Specifications and Test Procedures for Total Hydrocarbon Continuous Monitoring Systems in Stationary Sources 1. Applicability and Principle1.1 Applicability. These performance specifications apply to hydrocarbon (HC) continuous emission monitoring systems (CEMS) installed on stationary sources. The specifications include procedures which are intended to be used to evaluate the acceptability of the CEMS at the time of its installation or whenever specified in regulations or permits. The procedures are not designed to evaluate CEMS performance over an extended period of time. The source owner or operator is responsible for the proper calibration, maintenance, and operation of the CEMS at all times.
1.2 Principle. A gas sample is extracted from the source through a heated sample line and heated filter to a flame ionization detector (FID). Results are reported as volume concentration equivalents of propane. Installation and measurement location specifications, performance and equipment specifications, test and data reduction procedures, and brief quality assurance guidelines are included in the specifications. Calibration drift, calibration error, and response time tests are conducted to determine conformance of the CEMS with the specifications.
2. Definitions2.1 Continuous Emission Monitoring System (CEMS). The total equipment used to acquire data, which includes sample extraction and transport hardware, analyzer, data recording and processing hardware, and software. The system consists of the following major subsystems:
2.1.1 Sample Interface. That portion of the system that is used for one or more of the following: Sample acquisition, sample transportation, sample conditioning, or protection of the analyzer from the effects of the stack effluent.
2.1.2 Organic Analyzer. That portion of the system that senses organic concentration and generates an output proportional to the gas concentration.
2.1.3 Data Recorder. That portion of the system that records a permanent record of the measurement values. The data recorder may include automatic data reduction capabilities.
2.2 Instrument Measurement Range. The difference between the minimum and maximum concentration that can be measured by a specific instrument. The minimum is often stated or assumed to be zero and the range expressed only as the maximum.
2.3 Span or Span Value. Full scale instrument measurement range. The span value must be documented by the CEMS manufacturer with laboratory data.
2.4 Calibration Gas. A known concentration of a gas in an appropriate diluent gas.
2.5 Calibration Drift (CD). The difference in the CEMS output readings from the established reference value after a stated period of operation during which no unscheduled maintenance, repair, or adjustment takes place. A CD test is performed to demonstrate the stability of the CEMS calibration over time.
2.6 Response Time. The time interval between the start of a step change in the system input (e.g., change of calibration gas) and the time when the data recorder displays 95 percent of the final value.
2.7 Accuracy. A measurement of agreement between a measured value and an accepted or true value, expressed as the percentage difference between the true and measured values relative to the true value. For these performance specifications, accuracy is checked by conducting a calibration error (CE) test.
2.8 Calibration Error (CE). The difference between the concentration indicated by the CEMS and the known concentration of the cylinder gas. A CE test procedure is performed to document the accuracy and linearity of the monitoring equipment over the entire measurement range.
2.9 Performance Specification Test (PST) Period. The period during which CD, CE, and response time tests are conducted.
2.10 Centroidal Area. A concentric area that is geometrically similar to the stack or duct cross section and is no greater than 1 percent of the stack or duct cross-sectional area.
3. Installation and Measurement Location Specifications3.1 CEMS Installation and Measurement Locations. The CEMS must be installed in a location in which measurements representative of the source's emissions can be obtained. The optimum location of the sample interface for the CEMS is determined by a number of factors, including ease of access for calibration and maintenance, the degree to which sample conditioning will be required, the degree to which it represents total emissions, and the degree to which it represents the combustion situation in the firebox (where applicable). The location should be as free from in-leakage influences as possible and reasonably free from severe flow disturbances. The sample location should be at least two equivalent duct diameters downstream from the nearest control device, point of pollutant generation, or other point at which a change in the pollutant concentration or emission rate occurs and at least 0.5 diameter upstream from the exhaust or control device. The equivalent duct diameter is calculated as per 40 CFR part 60, appendix A, method 1, section 2.1. If these criteria are not achievable or if the location is otherwise less than optimum, the possibility of stratification should be investigated as described in section 3.2. The measurement point must be within the centroidal area of the stack or duct cross section.
3.2 Stratification Test Procedure. Stratification is defined as a difference in excess of 10 percent between the average concentration in the duct or stack and the concentration at any point more than 1.0 meter from the duct or stack wall. To determine whether effluent stratification exists, a dual probe system should be used to determine the average effluent concentration while measurements at each traverse point are being made. One probe, located at the stack or duct centroid, is used as a stationary reference point to indicate the change in effluent concentration over time. The second probe is used for sampling at the traverse points specified in 40 CFR part 60 appendix A, method 1. The monitoring system samples sequentially at the reference and traverse points throughout the testing period for five minutes at each point.
4. CEMS Performance and Equipment SpecificationsIf this method is applied in highly explosive areas, caution and care must be exercised in choice of equipment and installation.
4.1 Flame Ionization Detector (FID) Analyzer. A heated FID analyzer capable of meeting or exceeding the requirements of these specifications. Heated systems must maintain the temperature of the sample gas between 150 °C (300 °F) and 175 °C (350 °F) throughout the system. This requires all system components such as the probe, calibration valve, filter, sample lines, pump, and the FID to be kept heated at all times such that no moisture is condensed out of the system. The essential components of the measurement system are described below:
4.1.1 Sample Probe. Stainless steel, or equivalent, to collect a gas sample from the centroidal area of the stack cross-section.
4.1.2 Sample Line. Stainless steel or Teflon tubing to transport the sample to the analyzer.
Note:Mention of trade names or specific products does not constitute endorsement by the Environmental Protection Agency.
4.1.3 Calibration Valve Assembly. A heated three-way valve assembly to direct the zero and calibration gases to the analyzer is recommended. Other methods, such as quick-connect lines, to route calibration gas to the analyzers are applicable.
4.1.4 Particulate Filter. An in-stack or out-of-stack sintered stainless steel filter is recommended if exhaust gas particulate loading is significant. An out-of-stack filter must be heated.
4.1.5 Fuel. The fuel specified by the manufacturer (e.g., 40 percent hydrogen/60 percent helium, 40 percent hydrogen/60 percent nitrogen gas mixtures, or pure hydrogen) should be used.
4.1.6 Zero Gas. High purity air with less than 0.1 parts per million by volume (ppm) HC as methane or carbon equivalent or less than 0.1 percent of the span value, whichever is greater.
4.1.7 Calibration Gases. Appropriate concentrations of propane gas (in air or nitrogen). Preparation of the calibration gases should be done according to the procedures in EPA Protocol 1. In addition, the manufacturer of the cylinder gas should provide a recommended shelf life for each calibration gas cylinder over which the concentration does not change by more than ±2 percent from the certified value.
4.2 CEMS Span Value. 100 ppm propane. The span value must be documented by the CEMS manufacturer with laboratory data.
4.3 Daily Calibration Gas Values. The owner or operator must choose calibration gas concentrations that include zero and high-level calibration values.
4.3.1 The zero level may be between zero and 0.1 ppm (zero and 0.1 percent of the span value).
4.3.2 The high-level concentration must be between 50 and 90 ppm (50 and 90 percent of the span value).
4.4 Data Recorder Scale. The strip chart recorder, computer, or digital recorder must be capable of recording all readings within the CEMS' measurement range and must have a resolution of 0.5 ppm (0.5 percent of span value).
4.5 Response Time. The response time for the CEMS must not exceed 2 minutes to achieve 95 percent of the final stable value.
4.6 Calibration Drift. The CEMS must allow the determination of CD at the zero and high-level values. The CEMS calibration response must not differ by more than ±3 ppm (±3 percent of the span value) after each 24-hour period of the 7-day test at both zero and high levels.
4.7 Calibration Error. The mean difference between the CEMS and reference values at all three test points listed below must be no greater than 5 ppm (±5 percent of the span value).
4.7.1 Zero Level. Zero to 0.1 ppm (0 to 0.1 percent of span value).
4.7.2 Mid-Level. 30 to 40 ppm (30 to 40 percent of span value).
4.7.3 High-Level. 70 to 80 ppm (70 to 80 percent of span value).
4.8 Measurement and Recording Frequency. The sample to be analyzed must pass through the measurement section of the analyzer without interruption. The detector must measure the sample concentration at least once every 15 seconds. An average emission rate must be computed and recorded at least once every 60 seconds.
4.9 Hourly Rolling Average Calculation. The CEMS must calculate every minute an hourly rolling average, which is the arithmetic mean of the 60 most recent 1-minute average values.
4.10 Retest. If the CEMS produces results within the specified criteria, the test is successful. If the CEMS does not meet one or more of the criteria, necessary corrections must be made and the performance tests repeated.
5. Performance Specification Test (PST) Periods5.1 Pretest Preparation Period. Install the CEMS, prepare the PTM test site according to the specifications in section 3, and prepare the CEMS for operation and calibration according to the manufacturer's written instructions. A pretest conditioning period similar to that of the 7-day CD test is recommended to verify the operational status of the CEMS.
5.2 Calibration Drift Test Period. While the facility is operating under normal conditions, determine the magnitude of the CD at 24-hour intervals for seven consecutive days according to the procedure given in section 6.1. All CD determinations must be made following a 24-hour period during which no unscheduled maintenance, repair, or adjustment takes place. If the combustion unit is taken out of service during the test period, record the onset and duration of the downtime and continue the CD test when the unit resumes operation.
5.3 Calibration Error Test and Response Time Test Periods. Conduct the CE and response time tests during the CD test period.
6. Performance Specification Test Procedures6.1 Relative Accuracy Test Audit (RATA) and Absolute Calibration Audits (ACA). The test procedures described in this section are in lieu of a RATA and ACA.
6.2 Calibration Drift Test.
6.2.1 Sampling Strategy. Conduct the CD test at 24-hour intervals for seven consecutive days using calibration gases at the two daily concentration levels specified in section 4.3. Introduce the two calibration gases into the sampling system as close to the sampling probe outlet as practical. The gas must pass through all CEM components used during normal sampling. If periodic automatic or manual adjustments are made to the CEMS zero and calibration settings, conduct the CD test immediately before these adjustments, or conduct it in such a way that the CD can be determined. Record the CEMS response and subtract this value from the reference (calibration gas) value. To meet the specification, none of the differences may exceed 3 percent of the span of the CEM.
6.2.2 Calculations. Summarize the results on a data sheet. An example is shown in Figure 1. Calculate the differences between the CEMS responses and the reference values.
6.3 Response Time. The entire system including sample extraction and transport, sample conditioning, gas analyses, and the data recording is checked with this procedure.
6.3.1 Introduce the calibration gases at the probe as near to the sample location as possible. Introduce the zero gas into the system. When the system output has stabilized (no change greater than 1 percent of full scale for 30 sec), switch to monitor stack effluent and wait for a stable value. Record the time (upscale response time) required to reach 95 percent of the final stable value.
6.3.2 Next, introduce a high-level calibration gas and repeat the above procedure. Repeat the entire procedure three times and determine the mean upscale and downscale response times. The longer of the two means is the system response time.
6.4 Calibration Error Test Procedure.
6.4.1 Sampling Strategy. Challenge the CEMS with zero gas and EPA Protocol 1 cylinder gases at measurement points within the ranges specified in section 4.7.
6.4.1.1 The daily calibration gases, if Protocol 1, may be used for this test.
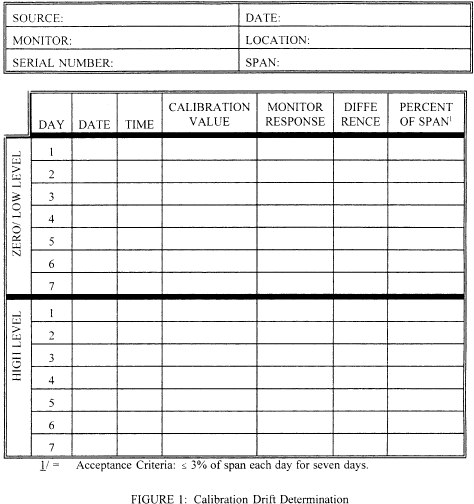
6.4.1.2 Operate the CEMS as nearly as possible in its normal sampling mode. The calibration gas should be injected into the sampling system as close to the sampling probe outlet as practical and must pass through all filters, scrubbers, conditioners, and other monitor components used during normal sampling. Challenge the CEMS three non-consecutive times at each measurement point and record the responses. The duration of each gas injection should be for a sufficient period of time to ensure that the CEMS surfaces are conditioned.
6.4.2 Calculations. Summarize the results on a data sheet. An example data sheet is shown in Figure 2. Average the differences between the instrument response and the certified cylinder gas value for each gas. Calculate three CE results according to Equation 1. No confidence coefficient is used in CE calculations.
7. EquationsCalibration Error. Calculate CE using Equation 1.

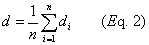
At a minimum, summarize in tabular form the results of the CD, response time, and CE test, as appropriate. Include all data sheets, calculations, CEMS data records, and cylinder gas or reference material certifications.
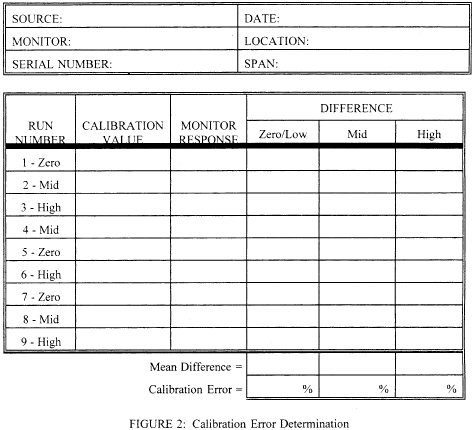
1. Measurement of Volatile Organic Compounds-Guideline Series. U.S. Environmental Protection Agency, Research Triangle Park, North Carolina, 27711, EPA-450/2-78-041, June 1978.
2. Traceability Protocol for Establishing True Concentrations of Gases Used for Calibration and Audits of Continuous Source Emission Monitors (Protocol No. 1). U.S. Environmental Protection Agency ORD/EMSL, Research Triangle Park, North Carolina, 27711, June 1978.
3. Gasoline Vapor Emission Laboratory Evaluation-Part 2. U.S. Environmental Protection Agency, OAQPS, Research Triangle Park, North Carolina, 27711, EMB Report No. 76-GAS-6, August 1975.
Performance Specification 9 - Specifications and Test Procedures for Gas Chromatographic Continuous Emission Monitoring Systems in Stationary Sources 1.0 Scope and Application1.1 Applicability. These requirements apply to continuous emission monitoring systems (CEMSs) that use gas chromatography (GC) to measure gaseous organic compound emissions. The requirements include procedures intended to evaluate the acceptability of the CEMS at the time of its installation and whenever specified in regulations or permits. Quality assurance procedures for calibrating, maintaining, and operating the CEMS properly at all times are also given in this procedure.
2.0 Summary of Performance Specification2.1 Calibration precision, calibration error, and performance audit tests are conducted to determine conformance of the CEMS with these specifications. Daily calibration and maintenance requirements are also specified.
3.0 Definitions3.1 Gas Chromatograph (GC). That portion of the system that separates and detects organic analytes and generates an output proportional to the gas concentration. The GC must be temperature controlled.
Note:The term temperature controlled refers to the ability to maintain a certain temperature around the column. Temperature-programmable GC is not required for this performance specification, as long as all other requirements for precision, linearity and accuracy listed in this performance specification are met. It should be noted that temperature programming a GC will speed up peak elution, thus allowing increased sampling frequency.
3.1.1 Column. Analytical column capable of separating the analytes of interest.
3.1.2 Detector. A detection system capable of detecting and quantifying all analytes of interest.
3.1.3 Integrator. That portion of the system that quantifies the area under a particular sample peak generated by the GC.
3.1.4 Data Recorder. A strip chart recorder, computer, or digital recorder capable of recording all readings within the instrument's calibration range.
3.2 Calibration Precision. The error between triplicate injections of each calibration standard.
4.0 Interferences [Reserved] 5.0 SafetyThe procedures required under this performance specification may involve hazardous materials, operations, and equipment. This performance specification does not purport to address all of the safety problems associated with these procedures. It is the responsibility of the user to establish appropriate safety problems associated with these procedures. It is the responsibility of the user to establish appropriate safety and health practices and determine the application regulatory limitations prior to performing these procedures. The CEMS user's manual and materials recommended by the reference method should be consulted for specific precautions to be taken.
6.0 Equipment and Supplies6.1 Presurvey Sample Analysis and GC Selection. Determine the pollutants to be monitored from the applicable regulation or permit and determine the approximate concentration of each pollutant (this information can be based on past compliance test results). Select an appropriate GC configuration to measure the organic compounds. The GC components should include a heated sample injection loop (or other sample introduction systems), separatory column, temperature-controlled oven, and detector. If the source chooses dual column and/or dual detector configurations, each column/detector is considered a separate instrument for the purpose of this performance specification and thus the procedures in this performance specification shall be carried out on each system. If this method is applied in highly explosive areas, caution should be exercised in selecting the equipment and method of installation.
6.2 Sampling System. The sampling system shall be heat traced and maintained at a minimum of 120 °C with no cold spots. All system components shall be heated, including the probe, calibration valve, sample lines, sampling loop (or sample introduction system), GC oven, and the detector block (when appropriate for the type of detector being utilized, e.g., flame ionization detector).
7.0 Reagents and Standards7.1 Calibration Gases. Obtain three concentrations of calibration gases certified by the manufacturer to be accurate to within 2 percent of the value on the label. A gas dilution system may be used to prepare the calibration gases from a high concentration certified standard if the gas dilution system meets the requirements specified in Test Method 205, 40 CFR Part 51, Appendix M. The performance test specified in Test Method 205 shall be repeated quarterly, and the results of the Method 205 test shall be included in the report. The calibration gas concentration of each target analyte shall be as follows (measured concentration is based on the presurvey concentration determined in section 6.1).
Note:If the low level calibration gas concentration falls at or below the limit of detection for the instrument for any target pollutant, a calibration gas with a concentration at 4 to 5 times the limit of detection for the instrument may be substituted for the low-level calibration gas listed in section 7.1.1.
7.1.1 Low-level. 40-60 percent of measured concentration.
7.1.2 Mid-level. 90-110 percent of measured concentration.
7.1.3 High-level. 140-160 percent of measured concentration, or select highest expected concentration.
7.2 Performance Audit Gas. Performance Audit Gas is an independent cylinder gas or cylinder gas mixture. A certified EPA audit gas shall be used, when possible. A gas mixture containing all the target compounds within the calibration range and certified by EPA's Traceability Protocol for Assay and Certification of Gaseous Calibration Standards may be used when EPA performance audit materials are not available. If a certified EPA audit gas or a traceability protocol gas is not available, use a gas manufacturer standard accurate to 2 percent.
8.0 Sample Collection, Preservation, Storage, and Transport8.1 Installation and Measurement Location Specifications. Install the CEMs in a location where the measurements are representative of the source emissions. Consider other factors, such as ease of access for calibration and maintenance purposes. The location should not be close to air in-leakages. The sampling location should be at least two equivalent duct diameters downstream from the nearest control device, point of pollutant generation, or other point at which a change in the pollutant concentration or emission rate occurs. The location should be at least 0.5 diameter upstream from the exhaust or control device. To calculate equivalent duct diameter, see section 12.2 of Method 1 (40 CFR Part 60, Appendix A). Sampling locations not conforming to the requirements in this section may be used if necessary upon approval of the Administrator.
8.2 Pretest Preparation Period. Using the procedures described in Method 18
(40 CFR Part 60, Appendix A), perform initial tests to determine GC conditions that provide good resolution and minimum analysis time for compounds of interest. Resolution interferences that may occur can be eliminated by appropriate GC column and detector choice or by shifting the retention times through changes in the column flow rate and the use of temperature programming.8.3 Seven (7)-Day Calibration Error (CE) Test Period. At the beginning of each 24-hour period, set the initial instrument set points by conducting a multi-point calibration for each compound. The multi-point calibration shall meet the requirements in sections 13.1, 13.2, and 13.3. Throughout the 24-hour period, sample and analyze the stack gas at the sampling intervals prescribed in the regulation or permit. At the end of the 24-hour period, inject the calibration gases at three concentrations for each compound in triplicate and determine the average instrument response. Determine the CE for each pollutant at each concentration using Equation 9-2. Each CE shall be ≤10 percent. Repeat this procedure six more times for a total of 7 consecutive days.
8.4 Performance Audit Test Periods. Conduct the performance audit once during the initial 7-day CE test and quarterly thereafter. Performance Audit Tests must be conducted through the entire sampling and analyzer system. Sample and analyze the EPA audit gas(es) (or the gas mixture) three times. Calculate the average instrument response. Results from the performance audit test must meet the requirements in sections 13.3 and 13.4.
8.5 Reporting. Follow the reporting requirements of the applicable regulation or permit. If the reporting requirements include the results of this performance specification, summarize in tabular form the results of the CE tests. Include all data sheets, calculations, CEMS data records, performance audit results, and calibration gas concentrations and certifications.
9.0 Quality Control [Reserved] 10.0 Calibration and Standardization10.1 Multi-Point Calibration. After initial startup of the GC, after routine maintenance or repair, or at least once per month, conduct a multi-point calibration of the GC for each target analyte. Calibration is performed at the instrument independent of the sample transport system. The multi-point calibration for each analyte shall meet the requirements in sections 13.1, 13.2, and 13.3.
10.2 Daily Calibration. Once every 24 hours, analyze the mid-level calibration standard for each analyte in triplicate. Calibration is performed at the instrument independent of the sample transport system. Calculate the average instrument response for each analyte. The average instrument response shall not vary by more than 10 percent from the certified concentration value of the cylinder for each analyte. If the difference between the analyzer response and the cylinder concentration for any target compound is greater than 10 percent, immediately inspect the instrument making any necessary adjustments, and conduct an initial multi-point calibration as described in section 10.1.
11.0 Analytical Procedure. Sample Collection and Analysis Are Concurrent for This Performance Specification (See section 8.0) 12.0 Calculations and Data Analysis12.1 Nomenclature.
Cm = average instrument response, ppm. Ca = cylinder gas value, ppm. F = Flow rate of stack gas through sampling system, in Liters/min. n = Number of measurement points. r 2 = Coefficient of determination. V = Sample system volume, in Liters, which is the volume inside the sample probe and tubing leading from the stack to the sampling loop. x = CEMS response. y = Actual value of calibration standard.12.2 Coefficient of Determination. Calculate r 2 using linear regression analysis and the average concentrations obtained at three calibration points as shown in Equation 9-1.
12.3 Calibration Error Determination. Determine the percent calibration error (CE) at each concentration for each pollutant using the following equation.
12.4 Sampling System Time Constant (T).
13.0 Method Performance13.1 Calibration Error (CE). The CEMS must allow the determination of CE at all three calibration levels. The average CEMS calibration response must not differ by more than 10 percent of calibration gas value at each level after each 24-hour period and after any triplicate calibration response check.
13.2 Calibration Precision and Linearity. For each triplicate injection at each concentration level for each target analyte, any one injection shall not deviate more than 5 percent from the average concentration measured at that level. When the CEMS response is evaluated over three concentration levels, the linear regression curve for each organic compound shall be determined using Equation 9-1 and must have an r 2 ≥0.995.
13.3 Measurement Frequency. The sample to be analyzed shall flow continuously through the sampling system. The sampling system time constant shall be ≤5 minutes or the sampling frequency specified in the applicable regulation, whichever is less. Use Equation 9-3 to determine T. The analytical system shall be capable of measuring the effluent stream at the frequency specified in the appropriate regulation or permit.
13.4 Audit Test Error. Determine the error for each average pollutant measurement using the Equation 9-2 in section 12.3. Each error shall be less than or equal to 10 percent of the cylinder gas certified value. Report the audit results including the average measured concentration, the error and the certified cylinder concentration of each pollutant as part of the reporting requirements in the appropriate regulation or permit.
14.0 Pollution Prevention [Reserved] 15.0 Waste Management [Reserved] 16.0 References [Reserved] 17.0 Tables, Diagrams, Flowcharts, and Validation Data [Reserved] Performance Specification 11 - Specifications and Test Procedures for Particulate Matter Continuous Emission Monitoring Systems at Stationary Sources 1.0 What Are the Purpose and Applicability of Performance Specification 11?The purpose of Performance Specification 11 (PS-11) is to establish the initial installation and performance procedures that are required for evaluating the acceptability of a particulate matter (PM) continuous emission monitoring system (CEMS); it is not to evaluate the ongoing performance of your PM CEMS over an extended period of time, nor to identify specific calibration techniques and auxiliary procedures to assess CEMS performance. You will find procedures for evaluating the ongoing performance of a PM CEMS in Procedure 2 of Appendix F - Quality Assurance Requirements for Particulate Matter Continuous Emission Monitoring Systems Used at Stationary Sources.
1.1 Under what conditions does PS-11 apply to my PM CEMS? The PS-11 applies to your PM CEMS if you are required by any provision of Title 40 of the Code of Federal Regulations (CFR) to install and operate PM CEMS.
1.2 When must I comply with PS-11? You must comply with PS-11 when directed by the applicable rule that requires you to install and operate a PM CEMS.
1.3 What other monitoring must I perform? To report your PM emissions in units of the emission standard, you may need to monitor additional parameters to correct the PM concentration reported by your PM CEMS. Your CEMS may include the components listed in paragraphs (1) through (3) of this section:
(1) A diluent monitor (i.e., O2, CO2, or other CEMS specified in the applicable regulation), which must meet its own performance specifications (also found in this appendix),
(2) Auxiliary monitoring equipment to allow measurement, determination, or input of the flue gas temperature, pressure, moisture content, and/or dry volume of stack effluent sampled, and
(3) An automatic sampling system. The performance of your PM CEMS and the establishment of its correlation to manual reference method measurements must be determined in units of mass concentration as measured by your PM CEMS (e.g., milligrams per actual cubic meter (mg/acm) or milligrams per dry standard cubic meter (mg/dscm)).
2.0 What Are the Basic Requirements of PS-11?The PS-11 requires you to perform initial installation and calibration procedures that confirm the acceptability of your CEMS when it is installed and placed into operation. You must develop a site-specific correlation of your PM CEMS response against manual gravimetric reference method measurements (including those made using EPA Methods 5, 5I, or 17).
2.1 What types of PM CEMS technologies are covered? Several different types of PM CEMS technologies (e.g., light scattering, Beta attenuation, etc.) can be designed with in-situ or extractive sample gas handling systems. Each PM CEMS technology and sample gas handling technology has certain site-specific advantages. You should select and install a PM CEMS that is appropriate for the flue gas conditions at your source.
2.2 How is PS-11 different from other performance specifications? The PS-11 is based on a technique of correlating PM CEMS responses relative to emission concentrations determined by the reference method. This technique is called “the correlation.” This differs from CEMS used to measure gaseous pollutants that have available calibration gases of known concentration. Because the type and characteristics of PM vary from source to source, a single PM correlation, applicable to all sources, is not possible.
2.3 How are the correlation data handled? You must carefully review your manual reference method data and your PM CEMS responses to include only valid, high-quality data. For the correlation, you must convert the manual reference method data to measurement conditions (e.g., wet or dry basis) that are consistent with your PM CEMS. Then, you must correlate the manual method and PM CEMS data in terms of the output as received from the monitor (e.g., milliamps). At the appropriate PM CEMS response specified in section 13.2 of this performance specification, you must calculate the confidence interval half range and tolerance interval half range as a percentage of the applicable PM concentration emission limit and compare the confidence interval and tolerance interval percentages with the performance criteria. Also, you must calculate the correlation coefficient and compare the correlation coefficient with the applicable performance criterion specified in section 13.2 of this performance specification.
Situations may arise where you will need two or more correlations. If you need multiple correlations, you must collect sufficient data for each correlation, and each correlation must satisfy the performance criteria specified in section 13.2 of this performance specification.
2.4 How do I design my PM CEMS correlation program? When planning your PM CEMS correlation effort, you must address each of the items in paragraphs (1) through (7) of this section to enhance the probability of success. You will find each of these elements further described in this performance specification or in the applicable reference method procedure.
(1) What type of PM CEMS should I select? You should select a PM CEMS that is appropriate for your source with technical consideration for potential factors such as interferences, site-specific configurations, installation location, flue gas conditions, PM concentration range, and other PM characteristics. You can find guidance on which technology is best suited for specific situations in our report “Current Knowledge of Particulate Matter (PM) Continuous Emission Monitoring” (PM CEMS Knowledge Document, see section 16.5).
(2) Where should I install my PM CEMS? Your PM CEMS must be installed in a location that is most representative of PM emissions, as determined by the reference method, such that the correlation between PM CEMS response and emissions determined by the reference method will meet these performance specifications. Care must be taken in selecting a location and measurement point to minimize problems due to flow disturbances, cyclonic flow, and varying PM stratification.
(3) How should I record my CEMS data? You need to ensure that your PM CEMS and data logger are set up to collect and record all normal emission levels and excursions. You must ensure that your data logger and PM CEMS have been properly programmed to accept and transfer status signals of valid monitor operation (e.g., flags for internal calibration, suspect data, or maintenance periods).
(4) What CEMS data should I review? You must review drift data daily to document proper operation. You must also ensure that any audit material is appropriate for the typical operating range of your PM CEMS.
(5) How long should I operate my PM CEMS before conducting the initial correlation test? You should allow sufficient time for your PM CEMS to operate for you to become familiar with your PM CEMS.
(i) You should observe PM CEMS response over time during normal and varying process conditions. This will ensure that your PM CEMS has been properly set up to operate at a range that is compatible with the concentrations and characteristics of PM emissions for your source. You should use this information to establish the range of operating conditions necessary to determine the correlations of PM CEMS data to manual reference method measurements over a wide operating range.
(ii) You must determine the types of process changes that will influence, on a definable and repeatable basis, flue gas PM concentrations and the resulting PM CEMS responses. You may find this period useful to make adjustments to your planned approach for operating your PM CEMS at your source. For instance, you may change the measurement range or batch sampling period to something other than those you initially planned to use.
(6) How do I conduct the initial correlation test? When conducting the initial correlation test of your PM CEMS response to PM emissions determined by the reference method, you must pay close attention to accuracy and details. Your PM CEMS must be operating properly. You must perform the manual reference method testing accurately, with attention to eliminating site-specific systemic errors. You must coordinate the timing of the manual reference method testing with the sampling cycle of your PM CEMS. You must complete a minimum of 15 manual reference method tests. You must perform the manual reference method testing over the full range of PM CEMS responses that correspond to normal operating conditions for your source and control device and will result in the widest range of emission concentrations.
(7) How should I perform the manual reference method testing? You must perform the manual reference method testing in accordance with specific rule requirements, coordinated closely with PM CEMS and process operations. It is highly recommended that you use paired trains for the manual reference method testing. You must perform the manual reference method testing over a suitable PM concentration range that corresponds to the full range of normal process and control device operating conditions. Because the manual reference method testing for this correlation test is not for compliance reporting purposes, you may conduct the reference method test runs for less than the typical minimum test run duration of 1 hour.
(8) What do I do with the manual reference method data and PM CEMS data? You must complete each of the activities in paragraphs (8)(i) through (v) of this section.
(i) Screen the manual reference method data for validity (e.g., isokinetics, leak checks), quality assurance, and quality control (e.g., outlier identification).
(ii) Screen your PM CEMS data for validity (e.g., daily drift check requirements) and quality assurance (e.g., flagged data).
(iii) Convert the manual reference method test data into measurement units (e.g., mg/acm) consistent with the measurement conditions of your PM CEMS.
(iv) Calculate the correlation equation(s) as specified in section 12.3.
(v) Calculate the correlation coefficient, confidence interval half range, and tolerance interval half range for the complete set of PM CEMS and reference method correlation data for comparison with the correlation performance criteria specified in section 13.2.
2.5 What other procedures must I perform? Before conducting the initial correlation test, you must successfully complete a 7-day drift test (See section 8.5).
3.0 What Special Definitions Apply to PS-11?3.1 “Appropriate Measurement Range of your PM CEMS” means a measurement range that is capable of recording readings over the complete range of your source's PM emission concentrations during routine operations. The appropriate range is determined during the pretest preparations as specified in section 8.4.
3.2 “Appropriate Data Range for PM CEMS Correlation” means the data range that reflects the full range of your source's PM emission concentrations recorded by your PM CEMS during the correlation test planning period or other normal operations as defined in the applicable regulations.
3.3 “Batch Sampling” means that gas is sampled on an intermittent basis and concentrated on a collection medium before intermittent analysis and follow-up reporting. Beta gauge PM CEMS are an example of batch sampling devices.
3.4 “Confidence Interval Half Range (CI)” is a statistical term and means one-half of the width of the 95 percent confidence interval around the predicted mean PM concentration (y value) calculated at the PM CEMS response value (x value) where the confidence interval is narrowest. Procedures for calculating CI are specified in section 12.3. The CI as a percent of the emission limit value (CI%) is calculated at the appropriate PM CEMS response value and must satisfy the criteria specified in section 13.2 (2).
3.5 “Continuous Emission Monitoring System (CEMS)” means all of the equipment required for determination of PM mass concentration in units of the emission standard. The sample interface, pollutant monitor, diluent monitor, other auxiliary data monitor(s), and data recorder are the major subsystems of your CEMS.
3.6 “Correlation” means the primary mathematical relationship for correlating the output from your PM CEMS to a PM concentration, as determined by the PM reference method. The correlation is expressed in the measurement units that are consistent with the measurement conditions (e.g., mg/dscm, mg/acm) of your PM CEMS.
3.7 “Correlation Coefficient (r)” means a quantitative measure of the association between your PM CEMS outputs and the reference method measurements. Equations for calculating the r value are provided in section 12.3(1)(iv) for linear correlations and in section 12.3(2)(iv) for polynomial correlations.
3.8 “Cycle Time” means the time required to complete one sampling, measurement, and reporting cycle. For a batch sampling PM CEMS, the cycle time would start when sample gas is first extracted from the stack/duct and end when the measurement of that batch sample is complete and a new result for that batch sample is produced on the data recorder.
3.9 “Data Recorder” means the portion of your CEMS that provides a permanent record of the monitor output in terms of response and status (flags). The data recorder may also provide automatic data reduction and CEMS control capabilities (see section 6.6).
3.10 “Diluent Monitor and Other Auxiliary Data Monitor(s) (if applicable)” means the portion of your CEMS that provides the diluent gas concentration (such as O2 or CO2, as specified by the applicable regulations), temperature, pressure, and/or moisture content, and generates an output proportional to the diluent gas concentration or gas property.
3.11 “Drift Check” means a check of the difference between your PM CEMS output readings and the established reference value of a reference standard or procedure after a stated period of operation during which no unscheduled maintenance, repair, or adjustment took place. The procedures used to determine drift are specific to the operating principles of your specific PM CEMS. A drift check includes both a zero drift check and an upscale drift check.
3.12 “Exponential Correlation” means an exponential equation used to define the relationship between your PM CEMS output and the reference method PM concentration, as indicated by Equation 11-37.
3.13 “Flagged Data” means data marked by your CEMS indicating that the response value(s) from one or more CEMS subsystems is suspect or invalid or that your PM CEMS is not in source-measurement operating mode.
3.14 “Linear Correlation” means a first-order mathematical relationship between your PM CEMS output and the reference method PM concentration that is linear in form, as indicated by Equation 11-3.
3.15 “Logarithmic Correlation” means a first-order mathematical relationship between the natural logarithm of your PM CEMS output and the reference method PM concentration that is linear in form, as indicated by Equation 11-34.
3.16 “Low-Emitting Source” means a source that operated at no more than 50 percent of the emission limit during the most recent performance test, and, based on the PM CEMS correlation, the daily average emissions for the source, measured in the units of the applicable emission limit, have not exceeded 50 percent of the emission limit for any day since the most recent performance test.
3.17 “Paired Trains” means two reference method trains that are used to conduct simultaneous measurements of PM concentrations. Guidance on the use of paired sampling trains can be found in the PM CEMS Knowledge Document (see section 16.5).
3.18 “Polynomial Correlation” means a second-order equation used to define the relationship between your PM CEMS output and reference method PM concentration, as indicated by Equation 11-16.
3.19 “Power Correlation” means an equation used to define a power function relationship between your PM CEMS output and the reference method concentration, as indicated by Equation 11-42.
3.20 “Reference Method” means the method defined in the applicable regulations, but commonly refers to those methods collectively known as EPA Methods 5, 5I, and 17 (for particulate matter), found in Appendix A of 40 CFR 60. Only the front half and dry filter catch portions of the reference method can be correlated to your PM CEMS output.
3.21 “Reference Standard” means a reference material or procedure that produces a known and unchanging response when presented to the pollutant monitor portion of your CEMS. You must use these standards to evaluate the overall operation of your PM CEMS, but not to develop a PM CEMS correlation.
3.22 “Response Time” means the time interval between the start of a step change in the system input and the time when the pollutant monitor output reaches 95 percent of the final value (see sections 6.5 and 13.3 for procedures and acceptance criteria).
3.23 “Sample Interface” means the portion of your CEMS used for one or more of the following: sample acquisition, sample delivery, sample conditioning, or protection of the monitor from the effects of the stack effluent.
3.24 “Sample Volume Check” means a check of the difference between your PM CEMS sample volume reading and the sample volume reference value.
3.25 “Tolerance Interval half range (TI)” means one-half of the width of the tolerance interval with upper and lower limits, within which a specified percentage of the future data population is contained with a given level of confidence, as defined by the respective tolerance interval half range equations in section 12.3(1)(iii) for linear correlations and in section 12.3(2)(iii) for polynomial correlations. The TI as a percent of the emission limit value (TI%) is calculated at the appropriate PM CEMS response value specified in section 13.2(3).
3.26 “Upscale Check Value” means the expected response to a reference standard or procedure used to check the upscale response of your PM CEMS.
3.27 “Upscale Drift (UD) Check” means a check of the difference between your PM CEMS output reading and the upscale check value.
3.28 “Zero Check Value” means the expected response to a reference standard or procedure used to check the response of your PM CEMS to particulate-free or low-particulate concentration conditions.
3.29 “Zero Drift (ZD) Check” means a check of the difference between your PM CEMS output reading and the zero check value.
3.30 “Zero Point Correlation Value” means a value added to PM CEMS correlation data to represent low or near zero PM concentration data (see section 8.6 for rationale and procedures).
4.0 Are There Any Potential Interferences for My PM CEMS?Yes, condensible water droplets or condensible acid gas aerosols (i.e., those with condensation temperatures above those specified by the reference method) at the measurement location can be interferences for your PM CEMS if the necessary precautions are not met.
4.1 Where are interferences likely to occur? Interferences may develop if your CEMS is installed downstream of a wet air pollution control system or any other conditions that produce flue gases, which, at your PM CEMS measurement point, normally or occasionally contain entrained water droplets or condensible salts before release to the atmosphere.
4.2 How do I deal with interferences? We recommend that you use a PM CEMS that extracts and heats representative samples of the flue gas for measurement to simulate results produced by the reference method for conditions such as those described in section 4.1. Independent of your PM CEMS measurement technology and extractive technique, you should have a configuration simulating the reference method to ensure that:
(1) No formation of new PM or deposition of PM occurs in sample delivery from the stack or duct; and
(2) No condensate accumulates in the sample flow measurement apparatus.
4.3 What PM CEMS measurement technologies should I use? You should use a PM CEMS measurement technology that is free of interferences from any condensible constituent in the flue gas.
5.0 What Do I Need To Know To Ensure the Safety of Persons Using PS-11?People using the procedures required under PS-11 may be exposed to hazardous materials, operations, site conditions, and equipment. This performance specification does not purport to address all of the safety issues associated with its use. It is your responsibility to establish appropriate safety and health practices and determine the applicable regulatory limitations before performing these procedures. You must consult your CEMS user's manual and other reference materials recommended by the reference method for specific precautions to be taken.
6.0 What Equipment and Supplies Do I Need?Different types of PM CEMS use different operating principles. You should select an appropriate PM CEMS based on your site-specific configurations, flue gas conditions, and PM characteristics.
(1) Your PM CEMS must sample the stack effluent continuously or, for batch sampling PM CEMS, intermittently.
(2) You must ensure that the averaging time, the number of measurements in an average, the minimum data availability, and the averaging procedure for your CEMS conform with those specified in the applicable emission regulation.
(3) Your PM CEMS must include, as a minimum, the equipment described in sections 6.1 through 6.7.
6.1 What equipment is needed for my PM CEMS's sample interface? Your PM CEMS's sample interface must be capable of delivering a representative sample of the flue gas to your PM CEMS. This subsystem may be required to heat the sample gas to avoid PM deposition or moisture condensation, provide dilution air, perform other gas conditioning to prepare the sample for analysis, or measure the sample volume or flow rate.
(1) If your PM CEMS is installed downstream of a wet air pollution control system such that the flue gases normally or occasionally contain entrained water droplets, we recommend that you select a sampling system that includes equipment to extract and heat a representative sample of the flue gas for measurement so that the pollutant monitor portion of your CEMS measures only dry PM. Heating should be sufficient to raise the temperature of the extracted flue gas above the water condensation temperature and should be maintained at all times and at all points in the sample line from where the flue gas is extracted, including the pollutant monitor and any sample flow measurement devices.
(2) You must consider the measured conditions of the sample gas stream to ensure that manual reference method test data are converted to units of PM concentration that are appropriate for the correlation calculations. Additionally, you must identify what, if any, additional auxiliary data from other monitoring and handling systems are necessary to convert your PM CEMS response into the units of the PM standard.
(3) If your PM CEMS is an extractive type and your source's flue gas volumetric flow rate varies by more than 10 percent from nominal, your PM CEMS should maintain an isokinetic sampling rate (within 10 percent of true isokinetic). If your extractive-type PM CEMS does not maintain an isokinetic sampling rate, you must use actual site-specific data or data from a similar installation to prove to us, the State, and/or local enforcement agency that isokinetic sampling is not necessary.
6.2 What type of equipment is needed for my PM CEMS? Your PM CEMS must be capable of providing an electronic output that can be correlated to the PM concentration.
(1) Your PM CEMS must be able to perform zero and upscale drift checks. You may perform these checks manually, but performing these checks automatically is preferred.
(2) We recommend that you select a PM CEMS that is capable of performing automatic diagnostic checks and sending instrument status signals (flags) to the data recorder.
(3) If your PM CEMS is an extractive type that measures the sample volume and uses the measured sample volume as part of calculating the output value, your PM CEMS must be able to perform a check of the sample volume to verify the accuracy of the sample volume measuring equipment. The sample volume check must be conducted daily and at the normal sampling rate of your PM CEMS.
6.3 What is the appropriate measurement range for my PM CEMS? Initially, your PM CEMS must be set up to measure over the expected range of your source's PM emission concentrations during routine operations. You may change the measurement range to a more appropriate range prior to correlation testing.
6.4 What if my PM CEMS does automatic range switching? Your PM CEMS may be equipped to perform automatic range switching so that it is operating in a range most sensitive to the detected concentrations. If your PM CEMS does automatic range switching, you must configure the data recorder to handle the recording of data values in multiple ranges during range-switching intervals.
6.5 What averaging time and sample intervals should be used? Your CEMS must sample the stack effluent such that the averaging time, the number of measurements in an average, the minimum sampling time, and the averaging procedure for reporting and determining compliance conform with those specified in the applicable regulation. Your PM CEMS must be designed to meet the specified response time and cycle time established in this performance specification (see section 13.3).
6.6 What type of equipment is needed for my data recorder? Your CEMS data recorder must be able to accept and record electronic signals from all the monitors associated with your PM CEMS.
(1) Your data recorder must record the signals from your PM CEMS that can be correlated to PM mass concentrations. If your PM CEMS uses multiple ranges, your data recorder must identify what range the measurement was made in and provide range-adjusted results.
(2) Your data recorder must accept and record monitor status signals (flagged data).
(3) Your data recorder must accept signals from auxiliary data monitors, as appropriate.
6.7 What other equipment and supplies might I need? You may need other supporting equipment as defined by the applicable reference method(s) (see section 7) or as specified by your CEMS manufacturer.
7.0 What Reagents and Standards Do I Need?You will need reference standards or procedures to perform the zero drift check, the upscale drift check, and the sample volume check.
7.1 What is the reference standard value for the zero drift check? You must use a zero check value that is no greater than 20 percent of the PM CEMS's response range. You must obtain documentation on the zero check value from your PM CEMS manufacturer.
7.2 What is the reference standard value for the upscale drift check? You must use an upscale check value that produces a response between 50 and 100 percent of the PM CEMS's response range. For a PM CEMS that produces output over a range of 4 mA to 20 mA, the upscale check value must produce a response in the range of 12 mA to 20 mA. You must obtain documentation on the upscale check value from your PM CEMS manufacturer.
7.3 What is the reference standard value for the sample volume check? You must use a reference standard value or procedure that produces a sample volume value equivalent to the normal sampling rate. You must obtain documentation on the sample volume value from your PM CEMS manufacturer.
8.0 What Performance Specification Test Procedure Do I Follow?You must complete each of the activities in sections 8.1 through 8.8 for your performance specification test.
8.1 How should I select and set up my equipment? You should select a PM CEMS that is appropriate for your source, giving consideration to potential factors such as flue gas conditions, interferences, site-specific configuration, installation location, PM concentration range, and other PM characteristics. Your PM CEMS must meet the equipment specifications in sections 6.1 and 6.2.
(1) You should select a PM CEMS that is appropriate for the flue gas conditions at your source. If your source's flue gas contains entrained water droplets, we recommend that your PM CEMS include a sample delivery and conditioning system that is capable of extracting and heating a representative sample.
(i) Your PM CEMS must maintain the sample at a temperature sufficient to prevent moisture condensation in the sample line before analysis of PM.
(ii) If condensible PM is an issue, we recommend that you operate your PM CEMS to maintain the sample gas temperature at the same temperature as the reference method filter.
(iii) Your PM CEMS must avoid condensation in the sample flow rate measurement lines.
(2) Some PM CEMS do not have a wide measurement range capability. Therefore, you must select a PM CEMS that is capable of measuring the full range of PM concentrations expected from your source from normal levels through the emission limit concentration.
(3) Some PM CEMS are sensitive to particle size changes, water droplets in the gas stream, particle charge, stack gas velocity changes, or other factors. Therefore, you should select a PM CEMS appropriate for the emission characteristics of your source.
(4) We recommend that you consult your PM CEMS vendor to obtain basic recommendations on the instrument capabilities and setup configuration. You are ultimately responsible for setup and operation of your PM CEMS.
8.2 Where do I install my PM CEMS? You must install your PM CEMS at an accessible location downstream of all pollution control equipment. You must perform your PM CEMS concentration measurements from a location considered representative or be able to provide data that can be corrected to be representative of the total PM emissions as determined by the manual reference method.
(1) You must select a measurement location that minimizes problems due to flow disturbances, cyclonic flow, and varying PM stratification (refer to Method 1 for guidance).
(2) If you plan to achieve higher emissions for correlation test purposes by adjusting the performance of the air pollution control device (per section 8.6(4)(i)), you must locate your PM CEMS and reference method sampling points well downstream of the control device (e.g., downstream of the induced draft fan), in order to minimize PM stratification that may be created in these cases.
8.3 How do I select the reference method measurement location and traverse points? You must follow EPA Method 1 for identifying manual reference method traverse points. Ideally, you should perform your manual reference method measurements at locations that satisfy the measurement site selection criteria specified in EPA Method 1 of at least eight duct diameters downstream and at least two duct diameters upstream of any flow disturbance. Where necessary, you may conduct testing at a location that is two diameters downstream and 0.5 diameters upstream of flow disturbances. If your location does not meet the minimum downstream and upstream requirements, you must obtain approval from us to test at your location.
8.4 What are my pretest preparation steps? You must install your CEMS and prepare the reference method test site according to the specifications in sections 8.2 and 8.3.
(1) After completing the initial field installation, we recommend that you operate your PM CEMS according to the manufacturer's instructions to familiarize yourself with its operation before you begin correlation testing.
(i) During this initial period of operation, we recommend that you conduct daily checks (zero and upscale drift and sample volume, as appropriate), and, when any check exceeds the daily specification (see section 13.1), make adjustments and perform any necessary maintenance to ensure reliable operation.
(2) When you are confident that your PM CEMS is operating properly, we recommend that you operate your CEMS over a correlation test planning period of sufficient duration to identify the full range of operating conditions and PM emissions to be used in your PM CEMS correlation test.
(i) During the correlation test planning period, you should operate the process and air pollution control equipment over the normal range of operating conditions, except when you attempt to produce higher emissions.
(ii) Your data recorder should record PM CEMS response during the full range of routine process operating conditions.
(iii) You should try to establish the relationships between operating conditions and PM CEMS response, especially those conditions that produce the highest PM CEMS response over 15-minute averaging periods, and the lowest PM CEMS response as well. The objective is to be able to reproduce the conditions for purposes of the actual correlation testing discussed in section 8.6.
(3) You must set the response range of your PM CEMS such that the instrument measures the full range of responses that correspond to the range of source operating conditions that you will implement during correlation testing.
(4) We recommend that you perform preliminary reference method testing after the correlation test planning period. During this preliminary testing, you should measure the PM emission concentration corresponding to the highest PM CEMS response observed during the full range of normal operation, when perturbing the control equipment, or as the result of PM spiking.
(5) Before performing correlation testing, you must perform a 7-day zero and upscale drift test (see section 8.5).
(6) You must not change the response range of the monitor once the response range has been set and the drift test successfully completed.
8.5 How do I perform the 7-day drift test? You must check the zero (or low-level value between 0 and 20 percent of the response range of the instrument) and upscale (between 50 and 100 percent of the instrument's response range) drift. You must perform this check at least once daily over 7 consecutive days. Your PM CEMS must quantify and record the zero and upscale measurements and the time of the measurements. If you make automatic or manual adjustments to your PM CEMS zero and upscale settings, you must conduct the drift test immediately before these adjustments, or conduct it in such a way that you can determine the amount of drift. You will find the calculation procedures for drift in section 12.1 and the acceptance criteria for allowable drift in section 13.1.
(1) What is the purpose of 7-day drift tests? The purpose of the 7-day drift test is to demonstrate that your system is capable of operating in a stable manner and maintaining its calibration for at least a 7-day period.
(2) How do I conduct the 7-day drift test? To conduct the 7-day drift test, you must determine the magnitude of the drift once each day, at 24-hour intervals, for 7 consecutive days while your source is operating normally.
(i) You must conduct the 7-day drift test at the two points specified in section 8.5. You may perform the 7-day drift tests automatically or manually by introducing to your PM CEMS suitable reference standards (these need not be certified) or by using other appropriate procedures.
(ii) You must record your PM CEMS zero and upscale response and evaluate them against the zero check value and upscale check value.
(3) When must I conduct the 7-day drift test? You must complete a valid 7-day drift test before attempting the correlation test.
8.6 How do I conduct my PM CEMS correlation test? You must conduct the correlation test according to the procedure given in paragraphs (1) through (5) of this section. If you need multiple correlations, you must conduct testing and collect at least 15 sets of reference method and PM CEMS data for calculating each separate correlation.
(1) You must use the reference method for PM (usually EPA Methods 5, 5I, or 17) that is prescribed by the applicable regulations. You may need to perform other reference methods or performance specifications (e.g., Method 3 for oxygen, Method 4 for moisture, etc.) depending on the units in which your PM CEMS reports PM concentration.
(i) We recommend that you use paired reference method trains when collecting manual PM data to identify and screen the reference method data for imprecision and bias. Procedures for checking reference method data for bias and precision can be found in the PM CEMS Knowledge Document (see section 16.5).
(ii) You may use test runs that are shorter than 60 minutes in duration (e.g., 20 or 30 minutes). You may perform your PM CEMS correlation tests during new source performance standards performance tests or other compliance tests subject to the Clean Air Act or other statutes, such as the Resource Conservation and Recovery Act. In these cases, your reference method results obtained during the PM CEMS correlation test may be used to determine compliance so long as your source and the test conditions and procedures (e.g., reference method sample run durations) are consistent with the applicable regulations and the reference method.
(iii) You must convert the reference method results to units consistent with the conditions of your PM CEMS measurements. For example, if your PM CEMS measures and reports PM emissions in the units of mass per actual volume of stack gas, you must convert your reference method results to those units (e.g., mg/acm). If your PM CEMS extracts and heats the sample gas to eliminate water droplets, then measures and reports PM emissions under those actual conditions, you must convert your reference method results to those same conditions (e.g., mg/acm at 160 °C).
(2) During each test run, you must coordinate process operations, reference method sampling, and PM CEMS operations. For example, you must ensure that the process is operating at the targeted conditions, both reference method trains are sampling simultaneously (if paired sampling trains are being used), and your PM CEMS and data logger are operating properly.
(i) You must coordinate the start and stop times of each run between the reference method sampling and PM CEMS operation. For a batch sampling PM CEMS, you must start the reference method at the same time as your PM CEMS sampling.
(ii) You must note the times for port changes (and other periods when the reference method sampling may be suspended) on the data sheets so that you can adjust your PM CEMS data accordingly, if necessary.
(iii) You must properly align the time periods for your PM CEMS and your reference method measurements to account for your PM CEMS response time.
(3) You must conduct a minimum of 15 valid runs each consisting of simultaneous PM CEMS and reference method measurement sets.
(i) You may conduct more than 15 sets of CEMS and reference method measurements. If you choose this option, you may reject certain test results so long as the total number of valid test results you use to determine the correlation is greater than or equal to 15.
(ii) You must report all data, including the rejected data.
(iii) You may reject the results of up to five test runs without explanation.
(iv) If you reject the results of more than five test runs, the basis for rejecting the results of the additional test runs must be explicitly stated in the reference method, this performance specification, Procedure 2 of appendix F, or your quality assurance plan.
(4) Simultaneous PM CEMS and reference method measurements must be performed in a manner to ensure that the range of data that will be used to establish the correlation for your PM CEMS is maximized. You must first attempt to maximize your correlation range by following the procedures described in paragraphs (4)(i) through (iv) of this section. If you cannot obtain the three levels as described in paragraphs (i) through (iv), then you must use the procedure described in section 8.6(5).
(i) You must attempt to obtain the three different levels of PM mass concentration by varying process operating conditions, varying PM control device conditions, or by means of PM spiking.
(ii) The three PM concentration levels you use in the correlation tests must be distributed over the complete operating range experienced by your source.
(iii) At least 20 percent of the minimum 15 measured data points you use should be contained in each of the following levels:
• Level 1: From no PM (zero concentration) emissions to 50 percent of the maximum PM concentration;
• Level 2: 25 to 75 percent of the maximum PM concentration; and
• Level 3: 50 to 100 percent of the maximum PM concentration.
(iv) Although the above levels overlap, you may only apply individual run data to one level.
(5) If you cannot obtain three distinct levels of PM concentration as described, you must perform correlation testing over the maximum range of PM concentrations that is practical for your PM CEMS. To ensure that the range of data used to establish the correlation for your PM CEMS is maximized, you must follow one or more of the steps in paragraphs (5)(i) through (iv) of this section.
(i) Zero point data for in-situ instruments should be obtained, to the extent possible, by removing the instrument from the stack and monitoring ambient air on a test bench.
(ii) Zero point data for extractive instruments should be obtained by removing the extractive probe from the stack and drawing in clean ambient air.
(iii) Zero point data also can be obtained by performing manual reference method measurements when the flue gas is free of PM emissions or contains very low PM concentrations (e.g., when your process is not operating, but the fans are operating or your source is combusting only natural gas).
(iv) If none of the steps in paragraphs (5)(i) through (iii) of this section are possible, you must estimate the monitor response when no PM is in the flue gas (e.g., 4 mA = 0 mg/acm).
8.7 What do I do with the initial correlation test data for my PM CEMS? You must calculate and report the results of the correlation testing, including the correlation coefficient, confidence interval, and tolerance interval for the PM CEMS response and reference method correlation data that are use to establish the correlation, as specified in section 12. You must include all data sheets, calculations, charts (records of PM CEMS responses), process data records including PM control equipment operating parameters, and reference media certifications necessary to confirm that your PM CEMS met the requirements of this performance specification. In addition, you must:
(1) Determine the integrated (arithmetic average) PM CEMS output over each reference method test period;
(2) Adjust your PM CEMS outputs and reference method test data to the same clock time (considering response time of your PM CEMS);
(3) Confirm that the reference method results are consistent with your PM CEMS response in terms of, where applicable, moisture, temperature, pressure, and diluent concentrations; and
(4) Determine whether any of the reference method test results do not meet the test method criteria.
8.8 What is the limitation on the range of my PM CEMS correlation? Although the data you collect during the correlation testing should be representative of the full range of normal operating conditions at your source, you must conduct additional correlation testing if either of the conditions specified in paragraphs (1) and (2) of this section occurs.
(1) If your source is a low-emitting source, as defined in section 3.16 of this specification, you must conduct additional correlation testing if either of the events specified in paragraphs (1)(i) or (ii) of this section occurs while your source is operating under normal conditions.
(i) Your source generates 24 consecutive hourly average PM CEMS responses that are greater than 125 percent of the highest PM CEMS response (e.g., mA reading) used for the correlation curve or are greater than the PM CEMS response that corresponds to 50 percent of the emission limit, whichever is greater, or
(ii) The cumulative hourly average PM CEMS responses generated by your source are greater than 125 percent of the highest PM CEMS response used for the correlation curve or are greater than the PM CEMS response that corresponds to 50 percent of the emission limit, whichever is greater, for more than 5 percent of your PM CEMS operating hours for the previous 30-day period.
(2) If your source is not a low-emitting source, as defined in section 3.16 of this specification, you must conduct additional correlation testing if either of the events specified in paragraph (i) or (ii) of this section occurs while your source is operating under normal conditions.
(i) Your source generates 24 consecutive hourly average PM CEMS responses that are greater than 125 percent of the highest PM CEMS response (e.g., mA reading) used for the correlation curve, or
(ii) The cumulative hourly average PM CEMS responses generated by your source are greater than 125 percent of the highest PM CEMS response used for the correlation curve for more than 5 percent of your PM CEMS operating hours for the previous 30-day period.
(3) If additional correlation testing is required, you must conduct at least three additional test runs under the conditions that caused the higher PM CEMS response.
(i) You must complete the additional testing and use the resulting new data along with the previous data to calculate a revised correlation equation within 60 days after the occurrence of the event that requires additional testing, as specified in paragraphs 8.8(1) and (2).
(4) If your source generates consecutive PM CEMS hourly responses that are greater than 125 percent of the highest PM CEMS response used to develop the correlation curve for 24 hours or for a cumulative period that amounts to more than 5 percent of the PM CEMS operating hours for the previous 30-day period, you must report the reason for the higher PM CEMS responses.
9.0 What Quality Control Measures Are Required?Quality control measures for PM CEMS are specified in 40 CFR 60, Appendix F, Procedure 2.
10.0 What Calibration and Standardization Procedures Must I Perform? [Reserved] 11.0 What Analytical Procedures Apply to This Procedure?Specific analytical procedures are outlined in the applicable reference method(s).
12.0 What Calculations and Data Analyses Are Needed?You must determine the primary relationship for correlating the output from your PM CEMS to a PM concentration, typically in units of mg/acm or mg/dscm of flue gas, using the calculations and data analysis process in sections 12.2 and 12.3. You develop the correlation by performing an appropriate regression analysis between your PM CEMS response and your reference method data.
12.1 How do I calculate upscale drift and zero drift? You must determine the difference in your PM CEMS output readings from the established reference values (zero and upscale check values) after a stated period of operation during which you performed no unscheduled maintenance, repair or adjustment.
(1) Calculate the upscale drift (UD) using Equation 11-1:

(2) Calculate the zero drift (ZD) using Equation 11-2:

(3) Summarize the results on a data sheet similar to that shown in Table 2 (see section 17).
12.2 How do I perform the regression analysis? You must couple each reference method PM concentration measurement, y, in the appropriate units, with an average PM CEMS response, x, over corresponding time periods. You must complete your PM CEMS correlation calculations using data deemed acceptable by quality control procedures identified in 40 CFR 60, Appendix F, Procedure 2.
(1) You must evaluate all flagged or suspect data produced during measurement periods and determine whether they should be excluded from your PM CEMS's average.
(2) You must assure that the reference method and PM CEMS results are on a consistent moisture, temperature, and diluent basis. You must convert the reference method PM concentration measurements (dry standard conditions) to the units of your PM CEMS measurement conditions. The conditions of your PM CEMS measurement are monitor-specific. You must obtain from your PM CEMS vendor or instrument manufacturer the conditions and units of measurement for your PM CEMS.
(i) If your sample gas contains entrained water droplets and your PM CEMS is an extractive system that measures at actual conditions (i.e., wet basis), you must use the measured moisture content determined from the impinger analysis when converting your reference method PM data to PM CEMS conditions; do not use the moisture content calculated from a psychrometric chart based on saturated conditions.
12.3 How do I determine my PM CEMS correlation? To predict PM concentrations from PM CEMS responses, you must use the calculation method of least squares presented in paragraphs (1) through (5) of this section. When performing the calculations, each reference method PM concentration measurement must be treated as a discrete data point; if using paired sampling trains, do not average reference method data pairs for any test run.
This performance specification describes procedures for evaluating five types of correlation models: linear, polynomial, logarithmic, exponential, and power. Procedures for selecting the most appropriate correlation model are presented in section 12.4 of this specification.
(1) How do I evaluate a linear correlation for my correlation test data? To evaluate a linear correlation, follow the procedures described in paragraphs (1)(i) through (iv) of this section.
(i) Calculate the linear correlation equation, which gives the predicted PM concentration () as a function of the PM CEMS response (x), as indicated by Equation 11-3:
Where: y = the predicted PM concentration, b0 = the intercept for the correlation curve, as calculated using Equation 11-4, b1 = the slope of the correlation curve, as calculated using Equation 11-6, and x = the PM CEMS response value.Calculate the y intercept (b0) of the correlation curve using Equation 11-4:
Where: x = the mean value of the PM CEMS response data, as calculated using Equation 11-5, and y = the mean value of the PM concentration data, as calculated using Equation 11-5: Where: xi = the PM CEMS response value for run i, yi = the PM concentration value for run i, and n = the number of data points.Calculate the slope (b1) of the correlation curve using Equation 11-6:
Where: Sxx, Sxy = as calculated using Equation 11-7:(ii) Calculate the half range of the 95 percent confidence interval (CI) for the predicted PM concentration () at the mean value of x, using Equation 11-8:
Where: CI = the half range of the 95 percent confidence interval for the predicted PM concentration at the mean x value, tdf,1-a/2 = the value for the t statistic provided in Table 1 for df = (n - 2), and SL = the scatter or deviation of values about the correlation curve, which is determined using Equation 11-9: Calculate the confidence interval half range for the predicted PM concentration () at the mean x value as a percentage of the emission limit (CI%) using Equation 11-10: Where: CI = the half range of the 95 percent confidence interval for the predicted PM concentration at the mean x value, and EL = PM emission limit, as described in section 13.2.(iii) Calculate the half range of the tolerance interval (TI) for the predicted PM concentration () at the mean x value using Equation 11-11:
Where: TI = the half range of the tolerance interval for the predicted PM concentration () at the mean x value, kT = as calculated using Equation 11-12, and SL = as calculated using Equation 11-9: Where: n′ = the number of test runs (n), un′ = the tolerance factor for 75 percent coverage at 95 percent confidence provided in Table 1 for df = (n−2), and vdf = the value from Table 1 for df = (n−2).Calculate the half range of the tolerance interval for the predicted PM concentration () at the mean x value as a percentage of the emission limit (TI%) using Equation 11-13:
Where: TI = the half range of the tolerance interval for the predicted PM concentration () at the mean x value, and EL = PM emission limit, as described in section 13.2.(iv) Calculate the linear correlation coefficient (r) using Equation 11-14:
Where: SL = as calculated using Equation 11-9, and Sy = as calculated using Equation 11-15:(2) How do I evaluate a polynomial correlation for my correlation test data? To evaluate a polynomial correlation, follow the procedures described in paragraphs (2)(i) through (iv) of this section.
(i) Calculate the polynomial correlation equation, which is indicated by Equation 11-16, using Equations 11-17 through 11-22:
Where: = the PM CEMS concentration predicted by the polynomial correlation equation, and b0, b1, b2 = the coefficients determined from the solution to the matrix equation Ab = B Where: Where: Xi = the PM CEMS response for run i, Yi = the reference method PM concentration for run i, and n = the number of test runs.Calculate the polynomial correlation curve coefficients (b0, b1, and b2) using Equations 11-19 through 11-21, respectively:
Where:(ii) Calculate the 95 percent confidence interval half range (CI) by first calculating the C coefficients (Co to C5) using Equations 11-23 and 11-24:
Where: Calculate Δ using Equation 11-25 for each x value: Determine the x value that corresponds to the minimum value of Δ (Δmin). Determine the scatter or deviation of values about the polynomial correlation curve (SP) using Equation 11-26: Calculate the half range of the 95 percent confidence interval (CI) for the predicted PM concentration () at the x value that corresponds to Δmin using Equation 11-27: Where: df = (n-3), and tdf = as listed in Table 1 (see section 17). Calculate the half range of the 95 percent confidence interval for the predicted PM concentration at the x value that corresponds to Δmin as a percentage of the emission limit (CI%) using Equation 11-28: Where: CI = the half range of the 95 percent confidence interval for the predicted PM concentration at the x value that corresponds to Δmin, and EL = PM emission limit, as described in section 13.2.(iii) Calculate the tolerance interval half range (TI) for the predicted PM concentration at the x value that corresponds to Δmin, as indicated in Equation 11-29 for the polynomial correlation, using Equations 11-30 and 11-31:
Where: un′ = the value indicated in Table 1 for df = (n′-3), and vdf = the value indicated in Table 1 for df = (n′ - 3). Calculate the tolerance interval half range for the predicted PM concentration at the x value that corresponds to Δmin as a percentage of the emission limit (TI%) using Equation 11-32: Where: TI = the tolerance interval half range for the predicted PM concentration at the x value that corresponds to Δmin, and EL = PM emission limit, as described in section 13.2.(iv) Calculate the polynomial correlation coefficient (r) using Equation 11-33:
Where: SP = as calculated using Equation 11-26, and Sy = as calculated using Equation 11-15.(3) How do I evaluate a logarithmic correlation for my correlation test data? To evaluate a logarithmic correlation, which has the form indicated by Equation 11-34, follow the procedures described in paragraphs (3)(i) through (iii) of this section.
(i) Perform a logarithmic transformation of each PM CEMS response value (x values) using Equation 11-35:
Where: xi′ = is the transformed value of xi, and Ln(xi) = the natural logarithm of the PM CEMS response for run i.(ii) Using the values for xi′ in place of the values for xi, perform the same procedures used to develop the linear correlation equation described in paragraph (1)(i) of this section. The resulting equation has the form indicated by Equation 11-36:
Where: x′ = the natural logarithm of the PM CEMS response, and the variables , b0, and b1 are as defined in paragraph (1)(i) of this section.(iii) Using the values for xi′ in place of the values for xi, calculate the confidence interval half range at the mean x′ value as a percentage of the emission limit (CI%), the tolerance interval half range at the mean x′ value as a percentage of the emission limit (TI%), and the correlation coefficient (r) using the procedures described in paragraphs (1)(ii) through (iv) of this section.
(4) How do I evaluate an exponential correlation for my correlation test data? To evaluate an exponential correlation, which has the form indicated by Equation 11-37, follow the procedures described in paragraphs (4)(i) through (v) of this section:
(i) Perform a logarithmic transformation of each PM concentration measurement (y values) using Equation 11-38:
Where: y′i = is the transformed value of yi, and Ln(yi) = the natural logarithm of the PM concentration measurement for run i.(ii) Using the values for y′i in place of the values for yi, perform the same procedures used to develop the linear correlation equation described in paragraph (1)(i) of this section. The resulting equation will have the form indicated by Equation 11-39.
Where: ′ = the predicted log PM concentration value, b′0 = the natural logarithm of b0, and the variables b0, b1, and x are as defined in paragraph (1)(i) of this section.(iii) Using the values for y″i in place of the values for yi, calculate the half range of the 95 percent confidence interval (CI′), as described in paragraph (1)(ii) of this section for CI. Note that CI′ is on the log scale. Next, calculate the upper and lower 95 percent confidence limits for the mean value y′ using Equations 11-40 and 11-41:



(iv) Using the values for y′i in place of the values for yi, calculate the half range tolerance interval (TI′), as described in paragraph (1)(iii) of this section for TI. Note that TI′ is on the log scale. Next, calculate the half range tolerance limits for the mean value y′ using Equations 11-43 and 11-44:



(v) Using the values for y″ i in place of the values for yi, calculate the correlation coefficient (r) using the procedure described in paragraph (1)(iv) of this section.
(5) How do I evaluate a power correlation for my correlation test data? To evaluate a power correlation, which has the form indicated by Equation 11-46, follow the procedures described in paragraphs (5)(i) through (v) of this section.

(i) Perform logarithmic transformations of each PM CEMS response (x values) and each PM concentration measurement (y values) using Equations 11-35 and 11-38, respectively.
(ii) Using the values for x″i in place of the values for xi, and the values for y″i in place of the values for yi, perform the same procedures used to develop the linear correlation equation described in paragraph (1)(i) of this section. The resulting equation will have the form indicated by Equation 11-47:

(iii) Using the same procedure described for exponential models in paragraph (4)(iii) of this section, calculate the half range of the 95 percent confidence interval for the predicted PM concentration corresponding to the mean value of x′ as a percentage of the emission limit.
(iv) Using the same procedure described for exponential models in paragraph (4)(iv) of this section, calculate the tolerance interval half range for the predicted PM concentration corresponding to the mean value of x′ as a percentage of the emission limit.
(v) Using the values for y′i in place of the values for yi, calculate the correlation coefficient (r) using the procedure described in paragraph (1)(iv) of this section.
Note: PS-11 does not address the application of correlation equations to calculate PM emission concentrations using PM CEMS response data during normal operations of a PM CEMS. However, we will provide guidance on the use of specific correlation models (i.e., logarithmic, exponential, and power models) to calculate PM concentrations in an operating PM CEMS in situations when the PM CEMS response values are equal to or less than zero, and the correlation model is undefined.
12.4 Which correlation model should I use? Follow the procedures described in paragraphs (1) through (4) of this section to determine which correlation model you should use.
(1) For each correlation model that you develop using the procedures described in section 12.3 of this specification, compare the confidence interval half range percentage, tolerance interval half range percentage, and correlation coefficient to the performance criteria specified in section 13.2 of this specification. You can use the linear, logarithmic, exponential, or power correlation model if the model satisfies all of the performance criteria specified in section 13.2 of this specification. However, to use the polynomial model you first must check that the polynomial correlation curve satisfies the criteria for minimum and maximum values specified in paragraph (3) of this section.
(2) If you develop more than one correlation curve that satisfy the performance criteria specified in section 13.2 of this specification, you should use the correlation curve with the greatest correlation coefficient. If the polynomial model has the greatest correlation coefficient, you first must check that the polynomial correlation curve satisfies the criteria for minimum and maximum values specified in paragraph (3) of this section.
(3) You can use the polynomial model that you develop using the procedures described in section 12.3(2) if the model satisfies the performance criteria specified in section 13.2 of this specification, and the minimum or maximum value of the polynomial correlation curve does not occur within the expanded data range. The minimum or maximum value of the polynomial correlation curve is the point where the slope of the curve equals zero. To determine if the minimum or maximum value occurs within the expanded data range, follow the procedure described in paragraphs (3)(i) through (iv) of this section.
(i) Determine if your polynomial correlation curve has a minimum or maximum point by comparing the polynomial coefficient b2 to zero. If b2 is less than zero, the curve has a maximum value. If b2 is greater than zero, the curve has a minimum value. (Note: If b2 equals zero, the correlation curve is linear.)
(ii) Calculate the minimum value using Equation 11-48.
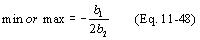
(iii) If your polynomial correlation curve has a minimum point, you must compare the minimum value to the minimum PM CEMS response used to develop the correlation curve. If the correlation curve minimum value is less than or equal to the minimum PM CEMS response value, you can use the polynomial correlation curve, provided the correlation curve also satisfies all of the performance criteria specified in section 13.2 of this specification. If the correlation curve minimum value is greater than the minimum PM CEMS response value, you cannot use the polynomial correlation curve to predict PM concentrations.
(iv) If your polynomial correlation curve has a maximum, the maximum value must be greater than the allowable extrapolation limit. If your source is not a low-emitting source, as defined in section 3.16 of this specification, the allowable extrapolation limit is 125 percent of the highest PM CEMS response used to develop the correlation curve. If your source is a low-emitting source, the allowable extrapolation limit is 125 percent of the highest PM CEMS response used to develop the correlation curve or the PM CEMS response that corresponds to 50 percent of the emission limit, whichever is greater. If the polynomial correlation curve maximum value is greater than the extrapolation limit, and the correlation curve satisfies all of the performance criteria specified in section 13.2 of this specification, you can use the polynomial correlation curve to predict PM concentrations. If the correlation curve maximum value is less than the extrapolation limit, you cannot use the polynomial correlation curve to predict PM concentrations.
(4) You may petition the Administrator for alternative solutions or sampling recommendations if the correlation models described in section 12.3 of this specification do not satisfy the performance criteria specified in section 13.2 of this specification.
13.0 What Are the Performance Criteria for My PM CEMS?You must evaluate your PM CEMS based on the 7-day drift check, the accuracy of the correlation, and the sampling periods and cycle/response time.
13.1 What is the 7-day drift check performance specification? Your daily PM CEMS internal drift checks must demonstrate that the daily drift of your PM CEMS does not deviate from the value of the reference light, optical filter, Beta attenuation signal, or other technology-suitable reference standard by more than 2 percent of the response range. If your CEMS includes diluent and/or auxiliary monitors (for temperature, pressure, and/or moisture) that are employed as a necessary part of this performance specification, you must determine the calibration drift separately for each ancillary monitor in terms of its respective output (see the appropriate performance specification for the diluent CEMS specification). None of the calibration drifts may exceed their individual specification.
13.2 What performance criteria must my PM CEMS correlation satisfy? Your PM CEMS correlation must meet each of the minimum specifications in paragraphs (1), (2), and (3) of this section. Before confidence and tolerance interval half range percentage calculations are made, you must convert the emission limit to the appropriate units of your PM CEMS measurement conditions using the average of emissions gas property values (e.g., diluent concentration, temperature, pressure, and moisture) measured during the correlation test.
(1) The correlation coefficient must satisfy the criterion specified in paragraph (1)(i) or (ii), whichever applies.
(i) If your source is not a low-emitting source, as defined in section 3.16 of this specification, the correlation coefficient (r) must be greater than or equal to 0.85.
(ii) If your source is a low-emitting source, as defined in section 3.16 of this specification, the correlation coefficient (r) must be greater than or equal to 0.75.
(2) The confidence interval half range must satisfy the applicable criterion specified in paragraph (2)(i), (ii), or (iii) of this section, based on the type of correlation model.
(i) For linear or logarithmic correlations, the 95 percent confidence interval half range at the mean PM CEMS response value from the correlation test must be within 10 percent of the PM emission limit value specified in the applicable regulation. Therefore, the CI% calculated using Equation 11-10 must be less than or equal to 10 percent.
(ii) For polynomial correlations, the 95 percent confidence interval half range at the PM CEMS response value from the correlation test that corresponds to the minimum value for Δ must be within 10 percent of the PM emission limit value specified in the applicable regulation. Therefore, the CI% calculated using Equation 11-28 must be less than or equal to 10 percent.
(iii) For exponential or power correlations, the 95 percent confidence interval half range at the mean of the logarithm of the PM CEMS response values from the correlation test must be within 10 percent of the PM emission limit value specified in the applicable regulation. Therefore, the CI% calculated using Equation 11-10 must be less than or equal to 10 percent.
(3) The tolerance interval half range must satisfy the applicable criterion specified in paragraph (3)(i), (ii), or (iii) of this section, based on the type of correlation model.
(i) For linear or logarithmic correlations, the half range tolerance interval with 95 percent confidence and 75 percent coverage at the mean PM CEMS response value from the correlation test must be within 25 percent of the PM emission limit value specified in the applicable regulation. Therefore, the TI% calculated using Equation 11-13 must be less than or equal to 25 percent.
(ii) For polynomial correlations, the half range tolerance interval with 95 percent confidence and 75 percent coverage at the PM CEMS response value from the correlation test that corresponds to the minimum value for Δ must be within 25 percent of the PM emission limit value specified in the applicable regulation. Therefore, the TI% calculated using Equation 11-32 must be less than or equal to 25 percent.
(iii) For exponential or power correlations, the half range tolerance interval with 95 percent confidence and 75 percent coverage at the mean of the logarithm of the PM CEMS response values from the correlation test must be within 25 percent of the PM emission limit value specified in the applicable regulation. Therefore, the TI% calculated using Equation 11-13 must be less than or equal to 25 percent.
13.3 What are the sampling periods and cycle/response time? You must document and maintain the response time and any changes in the response time following installation.
(1) If you have a batch sampling PM CEMS, you must evaluate the limits presented in paragraphs (1)(i) and (ii) of this section.
(i) The response time of your PM CEMS, which is equivalent to the cycle time, must be no longer than 15 minutes. In addition, the delay between the end of the sampling time and reporting of the sample analysis must be no greater than 3 minutes. You must document any changes in the response time following installation.
(ii) The sampling time of your PM CEMS must be no less than 30 percent of the cycle time. If you have a batch sampling PM CEMS, sampling must be continuous except during pauses when the collected pollutant on the capture media is being analyzed and the next capture medium starts collecting a new sample.
13.4 What PM compliance monitoring must I do? You must report your CEMS measurements in the units of the standard expressed in the regulations (e.g., mg/dscm @ 7 percent oxygen, pounds per million Btu (lb/mmBtu), etc.). You may need to install auxiliary data monitoring equipment to convert the units reported by your PM CEMS into units of the PM emission standard.
14.0 Pollution Prevention [Reserved] 15.0 Waste Management [Reserved] 16.0 Which References Are Relevant to This Performance Specification?16.1 Technical Guidance Document: Compliance Assurance Monitoring. U.S. Environmental Protection Agency Office of Air Quality Planning and Standards Emission Measurement Center. August 1998.
16.2 40 CFR 60, Appendix B, “Performance Specification 2 - Specifications and Test Procedures for SO2, and NOX, Continuous Emission Monitoring Systems in Stationary Sources.”
16.3 40 CFR 60, Appendix B, “Performance Specification 1 - Specification and Test Procedures for Opacity Continuous Emission Monitoring Systems in Stationary Sources.”
16.4 40 CFR 60, Appendix A, “Method 1 - Sample and Velocity Traverses for Stationary Sources.”
16.5 “Current Knowledge of Particulate Matter (PM) Continuous Emission Monitoring.” EPA-454/R-00-039. U.S. Environmental Protection Agency, Research Triangle Park, NC. September 2000.
16.6 40 CFR 266, Appendix IX, section 2, “Performance Specifications for Continuous Emission Monitoring Systems.”
16.7 ISO 10155, “Stationary Source Emissions - Automated Monitoring of Mass Concentrations of Particles: Performance Characteristics, Test Procedures, and Specifications.” American National Standards Institute, New York City. 1995.
16.8 Snedecor, George W. and Cochran, William G. (1989), Statistical Methods, Eighth Edition, Iowa State University Press.
16.9 Wallis, W. A. (1951) “Tolerance Intervals for Linear Regression,” in Second Berkeley Symposium on Mathematical Statistics and Probability, ed. J. Neyman, Berkeley: University of California Press, pp. 43-51.
17.0 What Reference Tables and Validation Data Are Relevant to PS-11?Use the information in Table 1 for determining the confidence and tolerance interval half ranges. Use Table 2 to record your 7-day drift test data.
Table 1 - Factors for Calculation of Confidence and Tolerance Interval Half Ranges
df | Student's t, tdf | Tolerance interval with 75% coverage and 95% confidence level | ||
---|---|---|---|---|
vdf (95%) | un′ (75%) | kT | ||
3 | 3.182 | 2.920 | 1.266 | 3.697 |
4 | 2.776 | 2.372 | 1.247 | 2.958 |
5 | 2.571 | 2.089 | 1.233 | 2.576 |
6 | 2.447 | 1.915 | 1.223 | 2.342 |
7 | 2.365 | 1.797 | 1.214 | 2.183 |
8 | 2.306 | 1.711 | 1.208 | 2.067 |
9 | 2.262 | 1.645 | 1.203 | 1.979 |
10 | 2.228 | 1.593 | 1.198 | 1.909 |
11 | 2.201 | 1.551 | 1.195 | 1.853 |
12 | 2.179 | 1.515 | 1.192 | 1.806 |
13 | 2.160 | 1.485 | 1.189 | 1.766 |
14 | 2.145 | 1.460 | 1.186 | 1.732 |
15 | 2.131 | 1.437 | 1.184 | 1.702 |
16 | 2.120 | 1.418 | 1.182 | 1.676 |
17 | 2.110 | 1.400 | 1.181 | 1.653 |
18 | 2.101 | 1.384 | 1.179 | 1.633 |
19 | 2.093 | 1.370 | 1.178 | 1.614 |
20 | 2.086 | 1.358 | 1.177 | 1.597 |
21 | 2.080 | 1.346 | 1.175 | 1.582 |
22 | 2.074 | 1.335 | 1.174 | 1.568 |
23 | 2.069 | 1.326 | 1.173 | 1.555 |
24 | 2.064 | 1.316 | 1.172 | 1.544 |
25 | 2.060 | 1.308 | 1.172 | 1.533 |
26 | 2.056 | 1.300 | 1.171 | 1.522 |
27 | 2.052 | 1.293 | 1.170 | 1.513 |
28 | 2.048 | 1.286 | 1.170 | 1.504 |
29 | 2.045 | 1.280 | 1.169 | 1.496 |
30 | 2.042 | 1.274 | 1.168 | 1.488 |
31 | 2.040 | 1.268 | 1.168 | 1.481 |
32 | 2.037 | 1.263 | 1.167 | 1.474 |
33 | 2.035 | 1.258 | 1.167 | 1.467 |
34 | 2.032 | 1.253 | 1.166 | 1.461 |
35 | 2.030 | 1.248 | 1.166 | 1.455 |
36 | 2.028 | 1.244 | 1.165 | 1.450 |
37 | 2.026 | 1.240 | 1.165 | 1.444 |
38 | 2.024 | 1.236 | 1.165 | 1.439 |
39 | 2.023 | 1.232 | 1.164 | 1.435 |
40 | 2.021 | 1.228 | 1.164 | 1.430 |
41 | 2.020 | 1.225 | 1.164 | 1.425 |
42 | 2.018 | 1.222 | 1.163 | 1.421 |
43 | 2.017 | 1.218 | 1.163 | 1.417 |
44 | 2.015 | 1.215 | 1.163 | 1.413 |
45 | 2.014 | 1.212 | 1.163 | 1.410 |
46 | 2.013 | 1.210 | 1.162 | 1.406 |
47 | 2.012 | 1.207 | 1.162 | 1.403 |
48 | 2.011 | 1.204 | 1.162 | 1.399 |
49 | 2.010 | 1.202 | 1.162 | 1.396 |
50 | 2.009 | 1.199 | 1.161 | 1.393 |
51 | 2.008 | 1.197 | 1.161 | 1.390 |
52 | 2.007 | 1.195 | 1.161 | 1.387 |
53 | 2.006 | 1.192 | 1.161 | 1.384 |
54 | 2.005 | 1.190 | 1.161 | 1.381 |
55 | 2.004 | 1.188 | 1.160 | 1.379 |
56 | 2.003 | 1.186 | 1.160 | 1.376 |
57 | 2.002 | 1.184 | 1.160 | 1.374 |
58 | 2.002 | 1.182 | 1.160 | 1.371 |
59 | 2.001 | 1.180 | 1.160 | 1.369 |
60 | 2.000 | 1.179 | 1.160 | 1.367 |
References 16.8 (t values) and 16.9 (vdf and un′ values).
Table 2 - 7-Day Drift Test Data
Zero drift day # | Date and time |
Zero check value (RL) |
PM CEMS response (RCEMS) |
Difference (RCEMS−RL) |
Zero drift ((RCEMS−RL) /RU) × 100 |
---|---|---|---|---|---|
1 | |||||
2 | |||||
3 | |||||
4 | |||||
5 | |||||
6 | |||||
7 |
Upscale drift day # | Date and time |
Upscale check value (RU) |
PM CEMS response (RCEMS) |
Difference (RCEMS−RU) |
Upscale drift ((RCEMS−RU)/RU) × 100% |
---|---|---|---|---|---|
1 | |||||
2 | |||||
3 | |||||
4 | |||||
5 | |||||
6 | |||||
7 |
1.1 Analyte. The analyte measured by these procedures and specifications is total vapor phase mercury (Hg) in the flue gas, which represents the sum of elemental Hg (Hg°, CAS Number 7439-97-6) and oxidized forms of gaseous Hg (Hg+2), in concentration units of micrograms per cubic meter (µg/m 3).
1.2 Applicability.
1.2.1 This specification is for evaluating the acceptability of total vapor phase Hg continuous emission monitoring systems (CEMS) installed at stationary sources at the time of or soon after installation and whenever specified in the regulations. The Hg CEMS must be capable of measuring the total concentration in µg/m 3 of vapor phase Hg, regardless of speciation, and recording that concentration at standard conditions on a wet or dry basis. These specifications do not address measurement of particle bound Hg.
1.2.2 This specification is not designed to evaluate an installed CEMS's performance over an extended period of time nor does it identify specific calibration techniques and auxiliary procedures to assess the CEMS's performance. The source owner or operator, however, is responsible to calibrate, maintain, and operate the CEMS properly. The Administrator may require, under section 114 of the Clean Air Act, the operator to conduct CEMS performance evaluations at other times besides the initial performance evaluation test. See §§ 60.13(c) and 63.8(e)(1).
1.2.3 Mercury monitoring approaches not entirely suited to these specifications may be approvable under the alternative monitoring or alternative test method provisions of § 60.13(i) and § 63.8(f) or § 60.8(b)(3) and § 63.7(f), respectively.
2.0 Summary of Performance SpecificationProcedures for determining CEMS relative accuracy, linearity, and calibration drift are outlined. CEMS installation and measurement location specifications, data reduction procedures, and performance criteria are included.
3.0 Definitions3.1 Continuous Emission Monitoring System (CEMS) means the total equipment required to measure a pollutant concentration. The system generally consists of the following three major subsystems:
3.2 Sample Interface means that portion of the CEMS used for one or more of the following: sample acquisition, sample transport, sample conditioning, and protection of the monitor from the effects of the stack effluent.
3.3 Hg Analyzer means that portion of the Hg CEMS that measures the total vapor phase Hg mass concentration and generates a proportional output.
3.4 Data Recorder means that portion of the CEMS that provides a permanent electronic record of the analyzer output. The data recorder may provide automatic data reduction and CEMS control capabilities.
3.5 Span Value means the measurement range as specified in the applicable regulation or other requirement. If the span is not specified in the applicable regulation or other requirement, then it must be a value approximately equivalent to two times the emission standard. Unless otherwise specified, the span value may be rounded up to the nearest multiple of 10.
3.6 Measurement Error Test means a test procedure in which the accuracy of the concentrations measured by a CEMS at three or more points over its measurement range is evaluated using reference gases. For Hg CEMS, elemental and oxidized Hg (Hg 0 and mercuric chloride, HgCl2) gas standards of known concentration are used for this procedure.
3.7 Measurement Error (ME) means the absolute value of the difference between the concentration indicated by the CEMS and the known concentration of a reference gas, expressed as a percentage of the span value, when the entire CEMS, including the sampling interface, is challenged.
3.8 Calibration Drift (CD) means the absolute value of the difference between the CEMS output response and either an upscale Hg reference gas or a zero-level Hg reference gas, expressed as a percentage of the span value, when the entire CEMS, including the sampling interface, is challenged after a stated period of operation during which no unscheduled maintenance or repair took place.
3.9 Relative Accuracy Test Procedure means a test procedure consisting of at least nine test runs, in which the accuracy of the concentrations measured by a CEMS is evaluated by comparison against concurrent measurements made with a reference method (RM). Relative accuracy tests repeated on a regular, on-going basis are referred to as relative accuracy test audits or RATAs.
3.10 Relative Accuracy (RA) means the absolute mean difference between the pollutant concentrations determined by the CEMS and the values determined by the RM plus the 2.5 percent error confidence coefficient of a series of tests divided by the mean of the RM tests. Alternatively, for sources with an average RM concentration less than 5.0 micrograms per standard cubic meter (µg/scm), the RA may be expressed as the absolute value of the difference between the mean CEMS and RM values.
4.0 Interferences [Reserved] 5.0 SafetyThe procedures required under this performance specification may involve hazardous materials, operations, and equipment. This performance specification may not address all of the safety problems associated with these procedures. It is the responsibility of the user to establish appropriate safety and health practices and determine the applicable regulatory limitations prior to performing these procedures. The CEMS user's manual and materials recommended by the RM should be consulted for specific precautions to be taken.
6.0 Equipment and Supplies6.1 CEMS Equipment Specifications.
6.1.1 Data Recorder Scale. The Hg CEMS data recorder output range must include the full range of expected Hg concentration values in the gas stream to be sampled including zero and the span value.
6.1.2 The Hg CEMS design should also provide for the determination of CD and ME at a zero value (zero to 20 percent of the span value) and at upscale values (between 50 and 100 percent of the span value). The Hg CEMS must be constructed to permit the introduction of known concentrations of Hg and HgCl2 separately into the sampling system of the CEMS immediately preceding the sample extraction filtration system such that the entire CEMS can be challenged.
6.2 Reference Gas Delivery System. The reference gas delivery system must be designed so that the flowrate exceeds the sampling system flow requirements of the CEMS and that the gas is delivered to the CEMS at atmospheric pressure.
6.3 Other equipment and supplies, as needed by the reference method used for the Relative Accuracy Test Procedure. See section 8.6.2.
7.0 Reagents and Standards7.1 Reference Gases. Reference gas standards are required for both elemental and oxidized Hg (Hg and mercuric chloride, HgCl2). The use of National Institute of Standards and Technology (NIST)-traceable standards and reagents is required. The following gas concentrations are required.
7.1.1 Zero-level. 0 to 20 percent of the span value.
7.1.2 Mid-level. 50 to 60 percent of the span value.
7.1.3 High-level. 80 to 100 percent of the span value.
7.2 Reference gas standards may also be required for the reference methods. See section 8.6.2.
8.0 Performance Specification Test Procedure8.1 Installation and Measurement Location Specifications.
8.1.1 CEMS Installation. Install the CEMS at an accessible location downstream of all pollution control equipment. Place the probe outlet or other sampling interface at a point or location in the stack (or vent) representative of the stack gas concentration of Hg. Since the Hg CEMS sample system normally extracts gas from a single point in the stack, a location that has been shown to be free of stratification for Hg or, alternatively, SO2 is recommended. If the cause of failure to meet the RA test requirement is determined to be the measurement location and a satisfactory correction technique cannot be established, the Administrator may require the CEMS to be relocated. Measurement locations and points or paths that are most likely to provide data that will meet the RA requirements are described in sections 8.1.2 and 8.1.3 below.
8.1.2 Measurement Location. The measurement location should be (1) at least two equivalent diameters downstream of the nearest control device, point of pollutant generation or other point at which a change of pollutant concentration may occur, and (2) at least half an equivalent diameter upstream from the effluent exhaust. The equivalent duct diameter is calculated according to Method 1 in appendix A-1 to this part.
8.1.3 Hg CEMS Sample Extraction Point. Use a sample extraction point either (1) no less than 1.0 meter from the stack or duct wall, or (2) within the centroidal velocity traverse area of the stack or duct cross section. This does not apply to cross-stack, in-situ measurement systems.
8.2 Measurement Error (ME) Test Procedure. Sequentially inject each of at least three elemental Hg reference gases (zero, mid-level, and high level, as defined in section 7.1), three times each for a total of nine injections. Inject the gases in such a manner that the entire CEMS is challenged. Do not inject the same gas concentration twice in succession. At each reference gas concentration, determine the average of the three CEMS responses and subtract the average response from the reference gas value. Calculate the measurement error (ME) using Equation 12-1 by expressing the absolute value of the difference between the average CEMS response (A) and the reference gas value (R) as a percentage of the span (see example data sheet in Figure 12A-1). For each elemental Hg reference gas, the absolute value of the difference between the CEMS response and the reference value must not exceed 5 percent of the span value. If this specification is not met, identify and correct the problem before proceeding. Repeat the measurement error test procedure using oxidized Hg reference gases. For each oxidized Hg reference gas, the absolute value of the difference between the CEMS response and the reference value shall not exceed 10 percent of the span value. If this specification is not met, identify and correct the problem before proceeding.
8.3 Seven-Day Calibration Drift (CD) Test Procedure.
8.3.1 CD Test Period. While the affected facility is operating normally, or as specified in an applicable regulation, determine the magnitude of the CD once each day (at 24-hour intervals, to the extent practicable) for 7 consecutive unit operating days according to the procedures in sections 8.3.2 and 8.3.3. The 7 consecutive unit operating days need not be 7 consecutive calendar days. Use either Hg° or HgCl2 standards for this test.
8.3.2 The purpose of the CD measurement is to verify the ability of the CEMS to conform to the established CEMS response used for determining emission concentrations or emission rates. Therefore, if periodic automatic or manual adjustments are made to the CEMS zero and upscale response settings, conduct the CD test immediately before these adjustments, or conduct it in such a way that the CD can be determined.
8.3.3 Conduct the CD test using the zero gas specified and either the mid-level or high-level gas as specified in section 7.1. Sequentially introduce the reference gases to the CEMS at the sampling system of the CEMS immediately preceding the sample extraction filtration system. Record the CEMS response (A) for each reference gas and, using Equation 12A-2, subtract the corresponding reference value (R) from the CEMS value, and express the absolute value of the difference as a percentage of the span value (see also example data sheet in Figure 12A-2). For each reference gas, the absolute value of the difference between the CEMS response and the reference value must not exceed 5 percent of the span value. If these specifications are not met, identify and correct the problem before proceeding.
8.4 Relative Accuracy (RA) Test Procedure.
8.4.1 RA Test Period. Conduct the RA test according to the procedure given in sections 8.4.2 through 8.4.6 while the affected facility is operating normally, or as specified in an applicable subpart. The RA test may be conducted during the CD test period.
8.4.2 Reference Methods (RM). Unless otherwise specified in an applicable subpart of the regulations, use Method 29, Method 30A, or Method 30B in appendix A-8 to this part or American Society of Testing and Materials (ASTM) Method D6784-02 (incorporated by reference, see § 60.17) as the RM for Hg concentration. For Method 29 and ASTM Method D6784-02 only, the filterable portion of the sample need not be included when making comparisons to the CEMS results. When Method 29, Method 30B, or ASTM D6784-02 is used, conduct the RM test runs with paired or duplicate sampling systems and use the average of the vapor phase Hg concentrations measured by the two trains. When Method 30A is used, paired sampling systems are not required. If the RM and CEMS measure on a different moisture basis, data derived with Method 4 in appendix A-3 to this part must also be obtained during the RA test.
8.4.3 Sampling Strategy for RM Tests. Conduct the RM tests in such a way that they will yield results representative of the emissions from the source and can be compared to the CEMS data. The RM and CEMS locations need not be immediately adjacent. Locate the RM measurement points in accordance with section 8.1.3 of Performance Specification 2 (PS 2) in this appendix. It is preferable to conduct moisture measurements (if needed) and Hg measurements simultaneously, although moisture measurements that are taken within an hour of the Hg measurements may be used to adjust the Hg concentrations to a consistent moisture basis. In order to correlate the CEMS and RM data properly, note the beginning and end of each RM test period for each paired RM run (including the exact time of day) on the CEMS chart recordings or other permanent record of output.
8.4.4 Number and Length of RM Test Runs. Conduct a minimum of nine RM test runs. When Method 29, Method 30B, or ASTM D6784-02 is used, only test runs for which the paired RM trains meet the relative deviation criteria (RD) of this PS must be used in the RA calculations. In addition, for Method 29 and ASTM D6784-02, use a minimum sample time of 2 hours and for Methods 30A and 30B use a minimum sample time of 30 minutes.
Note:More than nine sets of RM test runs may be performed. If this option is chosen, RM test run results may be excluded so long as the total number of RM test run results used to determine the CEMS RA is greater than or equal to nine. However, all data must be reported including the excluded test run data.
8.4.5 Correlation of RM and CEMS Data. Correlate the CEMS and the RM test data as to the time and duration by first determining from the CEMS final output (the one used for reporting) the integrated average pollutant concentration for each RM test period. Consider system response time, if important, and confirm that the results are on a consistent moisture basis with the RM test. Then, compare each integrated CEMS value against the corresponding RM value. When Method 29, Method 30B, or ASTM D6784-02 is used, compare each CEMS value against the corresponding average of the paired RM values.
8.4.6 Paired RM Outliers.
8.4.6.1 When Method 29, Method 30B, or ASTM D6784-02 is used, outliers are identified through the determination of relative deviation (RD) of the paired RM tests. Data that do not meet the RD criteria must be flagged as a data quality problem and may not be used in the calculation of RA. The primary reason for performing paired RM sampling is to ensure the quality of the RM data. The percent RD of paired data is the parameter used to quantify data quality. Determine RD for paired data points as follows:
Where: Ca and Cb are the Hg concentration values determined from the paired samples.8.4.6.2 The minimum performance criteria for RM Hg data is that RD for any data pair must be ≤10 percent as long as the mean Hg concentration is greater than 1.0 µg/m 3. If the mean Hg concentration is less than or equal to 1.0 µg/m 3, the RD must be ≤20 percent or ≤0.2 µg/m 3 absolute difference. Pairs of RM data exceeding these RD criteria should be eliminated from the data set used to develop a Hg CEMS correlation or to assess CEMS RA.
8.4.7 Calculate the mean difference between the RM and CEMS values in the units of micrograms per cubic meter (µg/m 3), the standard deviation, the confidence coefficient, and the RA according to the procedures in section 12.0.
8.5 Reporting. At a minimum (check with the appropriate EPA Regional Office, State or local Agency for additional requirements, if any), summarize in tabular form the results of the CD tests, the linearity tests, and the RA test or alternative RA procedure, as appropriate. Include all data sheets, calculations, charts (records of CEMS responses), reference gas concentration certifications, and any other information necessary to confirm that the CEMS meets the performance criteria.
9.0 Quality Control [Reserved] 10.0 Calibration and Standardization [Reserved] 11.0 Analytical ProcedureFor Method 30A, sample collection and analysis are concurrent. For the other RM, post-run sample analyses are performed. Refer to the RM employed for specific analytical procedures.
12.0 Calculations and Data AnalysisCalculate and summarize the RA test results on a data sheet similar to Figure 12A-3.
12.1 Consistent Basis. All data from the RM and CEMS must be compared in units of micrograms per standard cubic meter (µg/scm), on a consistent and identified moisture basis. The values must be standardized to 20 °C, 760 mm Hg.
12.1.1 Moisture Correction (as applicable). If the RM and CEMS measure Hg on a different moisture basis, they will need to be corrected to a consistent basis. Use Equation 12A-4a to correct data from a wet basis to a dry basis.
Use Equation 12A-4b to correct data from a dry basis to a wet basis.
Where: Bws is the moisture content of the flue gas from Method 4, expressed as a decimal fraction (e.g., for 8.0 percent H2O, Bws= 0.08).12.2 Arithmetic Mean. Calculate d , the arithmetic mean of the differences (di) of a data set as follows:
Where: n = Number of data points.12.3 Standard Deviation. Calculate the standard deviation, Sd, as follows:
12.3 Confidence Coefficient (CC). Calculate the 2.5 percent error confidence coefficient (one-tailed), CC, as follows:
12.4 Relative Accuracy. Calculate the RA of a set of data as follows:
Where: |d | = Absolute value of the mean of the differences (from Equation 12A-5) |CC| = Absolute value of the confidence coefficient (from Equation 12A-7) RM = Average reference method value 13.0 Method Performance13.1 Measurement Error (ME). For Hg 0, the ME must not exceed 5 percent of the span value at the zero-, mid-, and high-level reference gas concentrations. For HgCl2, the ME must not exceed 10 percent of the span value at the zero-, mid-, and high-level reference gas concentrations.
13.2 Calibration Drift (CD). The CD must not exceed 5 percent of the span value on any of the 7 days of the CD test.
13.3 Relative Accuracy (RA). The RA of the CEMS must be no greater than 20 percent of the mean value of the RM test data in terms of units of µg/scm. Alternatively, if the mean RM is less than 5.0 µg/scm, the results are acceptable if the absolute value of the difference between the mean RM and CEMS values does not exceed 1.0 µg/scm.
14.0 Pollution Prevention [Reserved] 15.0 Waste Management [Reserved] 16.0 Alternative Procedures [Reserved] 17.0 Bibliography17.1 40 CFR part 60, appendix B, “Performance Specification 2 - Specifications and Test Procedures for SO2 and NOX Continuous Emission Monitoring Systems in Stationary Sources.”
17.2 40 CFR part 60, appendix A, “Method 29 - Determination of Metals Emissions from Stationary Sources.”
17.3 40 CFR part 60, appendix A, “Method 30A - Determination of Total Vapor Phase Mercury Emissions From Stationary Sources (Instrumental Analyzer Procedure).
17.4 40 CFR part 60, appendix A, “Method 30B - Determination of Total Vapor Phase Mercury Emissions From Coal-Fired Combustion Sources Using Carbon Sorbent Traps.”
17.5 ASTM Method D6784-02, “Standard Test Method for Elemental, Oxidized, Particle-Bound and Total Mercury in Flue Gas Generated from Coal-Fired Stationary Sources (Ontario Hydro Method).”
18.0 Tables and FiguresTable 12A-1 - T-Values
n a | t0.975 | n a | t0.975 | n a | t0.975 |
---|---|---|---|---|---|
2 | 12.706 | 7 | 2.447 | 12 | 2.201 |
3 | 4.303 | 8 | 2.365 | 13 | 2.179 |
4 | 3.182 | 9 | 2.306 | 14 | 2.160 |
5 | 2.776 | 10 | 2.262 | 15 | 2.145 |
6 | 2.571 | 11 | 2.228 | 16 | 2.131 |
a The values in this table are already corrected for n-1 degrees of freedom. Use n equal to the number of individual values.
Figure 12A-1 - ME Determination
Date | Time | Reference gas value (µg/m 3) |
CEMS measured value (µg/m 3) |
Absolute difference (µg/m 3) |
ME (% of span value) |
|
---|---|---|---|---|---|---|
Zero level | ||||||
Average | ||||||
Mid level | ||||||
Average | ||||||
High level | ||||||
Average |
Figure 12A-2 - 7-Day Calibration Drift Determination
Date | Time | Reference gas value (µg/m 3) |
CEMS measured value (µg/m 3) |
Absolute difference (µg/m 3) |
CD (% of span value) |
|
---|---|---|---|---|---|---|
Zero level | ||||||
Upscale (Mid or High) |
||||||
Figure 12A-3 - Relative Accuracy Test Data
Run No. | Date | Begin time | End time | RM value (µg/m 3) | CEMS value (µg/m 3) | Difference (µg/m 3) |
Run used? (Yes/No) | RD 1 |
---|---|---|---|---|---|---|---|---|
1 | ||||||||
2 | ||||||||
3 | ||||||||
4 | ||||||||
5 | ||||||||
6 | ||||||||
7 | ||||||||
8 | ||||||||
9 | ||||||||
10 | ||||||||
11 | ||||||||
12 | ||||||||
Average Values | ||||||||
Arithmetic Mean Difference: | ||||||||
Standard Deviation: | ||||||||
Confidence Coefficient: | ||||||||
T-Value: | ||||||||
% Relative Accuracy: | ||||||||
| (RM)avg − (CEMS)avg | : |
1 Calculate the RD only if paired samples are taken using RM 30B, RM 29, or ASTM 6784-08. Express RD as a percentage or, for very low RM concentrations (≤1.0 µg/m 3), as the absolute difference between Ca and Cb.
The purpose of Performance Specification 12B (PS 12B) is to establish performance benchmarks for, and to evaluate the acceptability of, sorbent trap monitoring systems used to monitor total vapor-phase mercury (Hg) emissions in stationary source flue gas streams. These monitoring systems involve continuous repetitive in-stack sampling using paired sorbent media traps with periodic analysis of the time-integrated samples. Persons using PS 12B should have a thorough working knowledge of Methods 1, 2, 3, 4, 5 and 30B in appendices A-1 through A-3 and A-8 to this part.
1.1 Analyte. The analyte measured by these procedures and specifications is total vapor phase Hg in the flue gas, which represents the sum of elemental Hg (Hg 0, CAS Number 7439-97-6) and gaseous forms of oxidized Hg (i.e., Hg+2) in mass concentration units of micrograms per dry standard cubic meter (µg/dscm).
1.2 Applicability1.2.1 These procedures are only intended for use under relatively low particulate conditions (e.g., monitoring after all pollution control devices). This specification is for evaluating the acceptability of total vapor phase Hg sorbent trap monitoring systems installed at stationary sources at the time of, or soon after, installation and whenever specified in the regulations. The Hg monitoring system must be capable of measuring the total concentration of vapor phase Hg (regardless of speciation), in units of µg/dscm.
1.2.2 This specification contains routine procedures and specifications designed to evaluate an installed sorbent trap monitoring system's performance over time; Procedure 5 of appendix F to this part contains additional procedures and specifications which may be required for long term operation. In addition, the source owner or operator is responsible to calibrate, maintain, and operate the monitoring system properly. The Administrator may require the owner or operator, under section 114 of the Clean Air Act, to conduct performance evaluations at other times besides the initial test to evaluate the CEMS performance. See § 60.13(c) and 63.8(e)(1).
2.0 PrincipleKnown volumes of flue gas are continuously extracted from a stack or duct through paired, in-stack, pre-spiked sorbent media traps at appropriate nominal flow rates. The sorbent traps in the sampling system are periodically exchanged with new ones, prepared for analysis as needed, and analyzed by any technique that can meet the performance criteria. For quality-assurance purposes, a section of each sorbent trap is spiked with Hg 0 prior to sampling. Following sampling, this section is analyzed separately and a specified minimum percentage of the spike must be recovered. Paired train sampling is required to determine method precision.
3.0 Definitions3.1 Sorbent Trap Monitoring System means the total equipment required for the collection of gaseous Hg samples using paired three-partition sorbent traps.
3.2 Relative Accuracy Test Procedure means a test procedure consisting of at least nine runs, in which the accuracy of the total vapor phase Hg concentrations measured by the sorbent trap monitoring system is evaluated by comparison against concurrent measurements made with a reference method (RM). Relative accuracy tests repeated on a regular, on-going basis are referred to as relative accuracy test audits or RATAs.
3.3 Relative Accuracy (RA) means the absolute mean difference between the pollutant (Hg) concentrations determined by the sorbent trap monitoring system and the values determined by the reference method (RM) plus the 2.5 percent error confidence coefficient of a series of tests divided by the mean of the RM tests. Alternatively, for low concentration sources, the RA may be expressed as the absolute value of the difference between the mean sorbent trap monitoring system and RM values.
3.4 Relative Deviation (RD) means the absolute difference of the Hg concentration values obtained with a pair of sorbent traps divided by the sum of those concentrations, expressed as a percentage. RD is used to assess the precision of the sorbent trap monitoring system.
3.5 Spike Recovery means the mass of Hg recovered from the spiked trap section, expressed as a percentage of the amount spiked. Spike recovery is used to assess sample matrix interference.
4.0 Interferences [Reserved] 5.0 SafetyThe procedures required under this performance specification may involve hazardous materials, operations, and equipment. This performance specification may not address all of the safety problems associated with these procedures. It is the responsibility of the user to establish appropriate safety and health practices and determine the applicable regulatory limitations prior to performing these procedures.
6.0 Equipment and Supplies6.1 Sorbent Trap Monitoring System Equipment Specifications.
6.1.1 Monitoring System. The equipment described in Method 30B in appendix A-8 to this part must be used to continuously sample for Hg emissions, with the substitution of three-section traps in place of two-section traps, as described below. A typical sorbent trap monitoring system is shown in Figure 12B-1.
6.1.2 Three-Section Sorbent Traps. The sorbent media used to collect Hg must be configured in traps with three distinct and identical segments or sections, connected in series, to be separately analyzed. section 1 is designated for primary capture of gaseous Hg. section 2 is designated as a backup section for determination of vapor-phase Hg breakthrough. section 3 is designated for quality assurance/quality control (QA/QC) purposes. section 3 must be spiked with a known amount of gaseous Hg 0 prior to sampling and later analyzed to determine the spike (and hence sample) recovery efficiency.
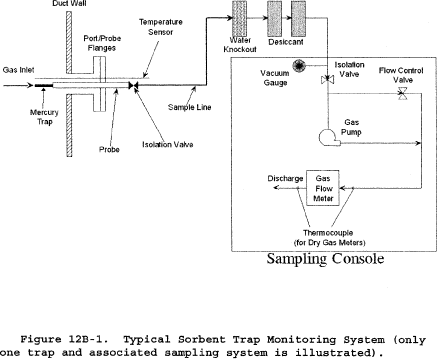
6.1.3 Gaseous Hg 0 Sorbent Trap Spiking System. A known mass of gaseous Hg 0 must be spiked onto section 3 of each sorbent trap prior to sampling. Any approach capable of quantitatively delivering known masses of Hg 0 onto sorbent traps is acceptable. Several technologies or devices are available to meet this objective. Their practicality is a function of Hg mass spike levels. For low levels, NIST-certified or NIST-traceable gas generators or tanks may be suitable, but will likely require long preparation times. A more practical, alternative system, capable of delivering almost any mass required, employs NIST-certified or NIST-traceable Hg salt solutions (e.g., Hg(NO3)2). With this system, an aliquot of known volume and concentration is added to a reaction vessel containing a reducing agent (e.g., stannous chloride); the Hg salt solution is reduced to Hg 0 and purged onto section 3 of the sorbent trap by using an impinger sparging system.
6.1.4 Sample Analysis Equipment. Any analytical system capable of quantitatively recovering and quantifying total gaseous Hg from sorbent media is acceptable provided that the analysis can meet the performance criteria in Table 12B-1 in section 9 of this performance specification. Candidate recovery techniques include leaching, digestion, and thermal desorption. Candidate analytical techniques include ultraviolet atomic fluorescence (UV AF); ultraviolet atomic absorption (UV AA), with and without gold trapping; and in-situ X-ray fluorescence (XRF).
7.0 Reagents and StandardsOnly NIST-certified or NIST-traceable calibration gas standards and reagents must be used for the tests and procedures required under this performance specification. The sorbent media may be any collection material (e.g., carbon, chemically treated filter, etc.) capable of quantitatively capturing and recovering for subsequent analysis, all gaseous forms of Hg in the emissions from the intended application. Selection of the sorbent media must be based on the material's ability to achieve the performance criteria contained in this method as well as the sorbent's vapor phase Hg capture efficiency for the emissions matrix and the expected sampling duration at the test site.
8.0 Performance Specification Test Procedure8.1 Installation and Measurement Location Specifications.
8.1.1 Selection of Monitoring Site. Sampling site information should be obtained in accordance with Method 1 in appendix A-1 to this part. Place the probe inlet at a point or location in the stack (or vent) downstream of all pollution control equipment and representative of the stack gas concentration of Hg. A location that has been shown to be free of stratification for Hg or, alternatively, SO2 is recommended. An estimation of the expected stack Hg concentration is required to establish a target sample flow rate, total gas sample volume, and the mass of Hg 0 to be spiked onto section 3 of each sorbent trap.
8.1.2 Pre-sampling Spiking of Sorbent Traps. Based on the estimated Hg concentration in the stack, the target sample rate and the target sampling duration, calculate the expected mass loading for section 1 of each sorbent trap (see section 12.1 of this performance specification). The pre-sampling spike to be added to section 3 of each sorbent trap must be within ±50 percent of the expected section 1 mass loading. Spike section 3 of each sorbent trap at this level, as described in section 6.1.3 of this performance specification. For each sorbent trap, keep a record of the mass of Hg 0 added to section 3. This record must include, at a minimum, the identification number of the trap, the date and time of the spike, the name of the analyst performing the procedure, the method of spiking, the mass of Hg 0 added to section 3 of the trap (µg), and the supporting calculations.
8.1.3 Pre-monitoring Leak Check. Perform a leak check with the sorbent traps in place in the sampling system. Draw a vacuum in each sample train. Adjust the vacuum in each sample train to ∼15″ Hg. Use the gas flow meter to determine leak rate. The leakage rate must not exceed 4 percent of the target sampling rate. Once the leak check passes this criterion, carefully release the vacuum in the sample train, then seal the sorbent trap inlet until the probe is ready for insertion into the stack or duct.
8.1.4 Determination of Flue Gas Characteristics. Determine or measure the flue gas measurement environment characteristics (gas temperature, static pressure, gas velocity, stack moisture, etc.) in order to determine ancillary requirements such as probe heating requirements (if any), sampling rate, proportional sampling conditions, moisture management, etc.
8.2 Monitoring.
8.2.1 System Preparation and Initial Data Recording. Remove the plug from the end of each sorbent trap and store each plug in a clean sorbent trap storage container. Remove the stack or duct port cap and insert the probe(s) with the inlet(s) aligned perpendicular to the stack gas flow. Secure the probe(s) and ensure that no leakage occurs between the duct and environment. Record initial data including the sorbent trap ID, start time, starting gas flow meter readings, initial temperatures, set points, and any other appropriate information.
8.2.2 Flow Rate Control. Set the initial sample flow rate at the target value from section 8.1.1 of this performance specification. Then, for every operating hour during the sampling period, record the date and time, the sample flow rate, the gas flow meter reading, the stack temperature (if needed), the flow meter temperatures (if needed), temperatures of heated equipment such as the vacuum lines and the probes (if heated), and the sampling system vacuum readings. Also, record the stack gas flow rate and the ratio of the stack gas flow rate to the sample flow rate. Adjust the sampling flow rate to maintain proportional sampling, i.e., keep the ratio of the stack gas flow rate to sample flow rate within ±25 percent of the reference ratio from the first hour of the data collection period (see section 12.2 of this performance specification). The sample flow rate through a sorbent trap monitoring system during any hour (or portion of an hour) that the unit is not operating must be zero.
8.2.3 Stack Gas Moisture Determination. If data from the sorbent trap monitoring system will be used to calculate Hg mass emissions, determine the stack gas moisture content using a continuous moisture monitoring system or other means acceptable to the Administrator, such as the ones described in § 75.11(b) of this chapter. Alternatively, for combustion of coal, wood, or natural gas in boilers only, a default moisture percentage from § 75.11(b) of this chapter may be used.
8.2.4 Essential Operating Data. Obtain and record any essential operating data for the facility during the test period, e.g., the barometric pressure for correcting the sample volume measured by a dry gas meter to standard conditions. At the end of the data collection period, record the final gas flow meter reading and the final values of all other essential parameters.
8.2.5 Post-monitoring Leak Check. When the monitoring period is completed, turn off the sample pump, remove the probe/sorbent trap from the port and carefully re-plug the end of each sorbent trap. Perform a leak check with the sorbent traps in place, at the maximum vacuum reached during the monitoring period. Use the same general approach described in section 8.1.3 of this performance specification. Record the leakage rate and vacuum. The leakage rate must not exceed 4 percent of the average sampling rate for the monitoring period. Following the leak check, carefully release the vacuum in the sample train.
8.2.6 Sample Recovery. Recover each sampled sorbent trap by removing it from the probe and seal both ends. Wipe any deposited material from the outside of the sorbent trap. Place the sorbent trap into an appropriate sample storage container and store/preserve it in an appropriate manner.
8.2.7 Sample Preservation, Storage, and Transport. While the performance criteria of this approach provide for verification of appropriate sample handling, it is still important that the user consider, determine, and plan for suitable sample preservation, storage, transport, and holding times for these measurements. Therefore, procedures in recognized voluntary consensus standards such as those in ASTM D6911-03 “Standard Guide for Packaging and Shipping Environmental Samples for Laboratory Analysis” should be followed for all samples.
8.2.8 Sample Custody. Proper procedures and documentation for sample chain of custody are critical to ensuring data integrity. Chain of custody procedures in recognized voluntary consensus standards such as those in ASTM D4840-99 “Standard Guide for Sample Chain-of-Custody Procedures” should be followed for all samples (including field samples and blanks).
8.3 Relative Accuracy (RA) Test Procedure
8.3.1 For the initial certification of a sorbent trap monitoring system, a RA Test is required. Follow the basic RA test procedures and calculation methodology described in sections 8.4.1 through 8.4.7 and 12.4 of PS 12A in this appendix, replacing the term “CEMS” with “sorbent trap monitoring system”.
8.3.2 Special Considerations. The type of sorbent material used in the traps must be the same as that used for daily operation of the monitoring system; however, the size of the traps used for the RA test may be smaller than the traps used for daily operation of the system. Spike the third section of each sorbent trap with elemental Hg, as described in section 8.1.2 of this performance specification. Install a new pair of sorbent traps prior to each test run. For each run, the sorbent trap data must be validated according to the quality assurance criteria in Table 12B-1 in section 9.0, below.
8.3.3 Acceptance Criteria. The RA of the sorbent trap monitoring system must be no greater than 20 percent of the mean value of the RM test data in terms of units of µg/scm. Alternatively, if the RM concentration is less than or equal to 5.0 µg/scm, then the RA results are acceptable if the absolute difference between the means of the RM and sorbent trap monitoring system values does not exceed 1.0 µg/scm.
9.0 Quality Assurance and Quality Control (QA/QC)Table 12B-1 summarizes the QA/QC performance criteria that are used to validate the Hg emissions data from a sorbent trap monitoring system. Failure to achieve these performance criteria will result in invalidation of Hg emissions data, except where otherwise noted.
Table 12B-1 - QA/QC Criteria for Sorbent Trap Monitoring Systems
QA/QC test or specification |
Acceptance criteria | Frequency | Consequences if not met |
---|---|---|---|
Pre-test leak check | ≤4% of target sampling rate | Prior to monitoring | Monitoring must not commence until the leak check is passed. |
Post-test leak check | ≤4% of average sampling rate | After monitoring | Invalidate the data from the paired traps or, if certain conditions are met, report adjusted data from a single trap (see Section 12.8.3). |
Ratio of stack gas flow rate to sample flow rate | No more than 5% of the hourly ratios or 5 hourly ratios (whichever is less restrictive) may deviate from the reference ratio by more than ±25% | Every hour throughout monitoring period | Invalidate the data from the paired traps or, if certain conditions are met, report adjusted data from a single trap (see Section 12.8.3). |
Sorbent trap section 2 breakthrough | ≤5% of Section 1 Hg mass ≤10% of Section 1 Hg mass if average Hg concentration is ≤0.5 µg/scm |
Every sample | Invalidate the data from the paired traps or, if certain conditions are met, report adjusted data from a single trap (see Section 12.8.3). |
No criterion when Hg concentration for trap less than 10% of the applicable emission limit (must meet all other QA/QC specifications) | |||
Paired sorbent trap agreement | ≤10% Relative Deviation (RD)
if the average concentration is > 1.0 µg/m 3 ≤20% RD if the average concentration is ≤1.0 µg/m 3 |
Every sample | Either invalidate the data from the paired traps or report the results from the trap with the higher Hg concentration. |
Results also acceptable if absolute difference between concentrations from paired traps is ≤ 0.03 µg/m 3 | |||
Spike Recovery Study | Average recovery between 85% and 115% for each of the 3 spike concentration levels | Prior to analyzing field samples and prior to use of new sorbent media | Field samples must not be analyzed until the percent recovery criteria have been met. |
Multipoint analyzer calibration | Each analyzer reading within ±10% of true value and r 2 ≥ 0.99 | On the day of analysis, before analyzing any samples | Recalibrate until successful. |
Analysis of independent calibration standard | Within ±10% of true value | Following daily calibration, prior to analyzing field samples | Recalibrate and repeat independent standard analysis until successful. |
Spike recovery from section 3 of both sorbent traps | 75-125% of spike amount | Every sample | Invalidate the data from the paired traps or, if certain conditions are met, report adjusted data from a single trap (see Section 12.8.3). |
Relative Accuracy | RA ≤ 20.0% of RM mean value; or if RM mean value ≤5.0 µg/scm, absolute difference between RM and sorbent trap monitoring system mean values ≤1.0 µg/scm | RA specification must be met for initial certification | Data from the system are invalid until a RA test is passed. |
Gas flow meter calibration | An initial calibration factor (Y) has been determined at 3 settings; for mass flow meters, initial calibration with stack gas has been performed. For subsequent calibrations, Y within ±5% of average value from the most recent 3-point calibration | At 3 settings prior to initial use and at least quarterly at one setting thereafter | Recalibrate meter at 3 settings to determine a new value of Y. |
Temperature sensor calibration | Absolute temperature measured by sensor within ±1.5% of a reference sensor | Prior to initial use and at least quarterly thereafter | Recalibrate; sensor may not be used until specification is met. |
Barometer calibration | Absolute pressure measured by instrument within ±10 mm Hg of reading with a NIST-traceable barometer | Prior to initial use and at least quarterly thereafter | Recalibrate; instrument may not be used until specification is met. |
10.1 Gaseous and Liquid Standards. Only NIST certified or NIST-traceable calibration standards (i.e., calibration gases, solutions, etc.) must be used for the spiking and analytical procedures in this performance specification.
10.2 Gas Flow Meter Calibration. The manufacturer or supplier of the gas flow meter should perform all necessary set-up, testing, programming, etc., and should provide the end user with any necessary instructions, to ensure that the meter will give an accurate readout of dry gas volume in standard cubic meters for the particular field application.
10.2.1 Initial Calibration. Prior to its initial use, a calibration of the flow meter must be performed. The initial calibration may be done by the manufacturer, by the equipment supplier, or by the end user. If the flow meter is volumetric in nature (e.g., a dry gas meter), the manufacturer, equipment supplier, or end user may perform a direct volumetric calibration using any gas. For a mass flow meter, the manufacturer, equipment supplier, or end user may calibrate the meter using a bottled gas mixture containing 12 ±0.5% CO2, 7 ±0.5% O2, and balance N2, or these same gases in proportions more representative of the expected stack gas composition. Mass flow meters may also be initially calibrated on-site, using actual stack gas.
10.2.1.1 Initial Calibration Procedures. Determine an average calibration factor (Y) for the gas flow meter, by calibrating it at three sample flow rate settings covering the range of sample flow rates at which the sorbent trap monitoring system typically operates. Either the procedures in section 10.3.1 of Method 5 in appendix A-3 to this part or the procedures in section 16 of Method 5 in appendix A-3 to this part may be followed. If a dry gas meter is being calibrated, use at least five revolutions of the meter at each flow rate.
10.2.1.2 Alternative Initial Calibration Procedures. Alternatively, the initial calibration of the gas flow meter may be performed using a reference gas flow meter (RGFM). The RGFM may be either: (1) A wet test meter calibrated according to section 10.3.1 of Method 5 in appendix A-3 to this part; (2) A gas flow metering device calibrated at multiple flow rates using the procedures in section 16 of Method 5 in appendix A-3 to this part; or (3) A NIST-traceable calibration device capable of measuring volumetric flow to an accuracy of 1 percent. To calibrate the gas flow meter using the RGFM, proceed as follows: While the sorbent trap monitoring system is sampling the actual stack gas or a compressed gas mixture that simulates the stack gas composition (as applicable), connect the RGFM to the discharge of the system. Care should be taken to minimize the dead volume between the sample flow meter being tested and the RGFM. Concurrently measure dry gas volume with the RGFM and the flow meter being calibrated for a minimum of 10 minutes at each of three flow rates covering the typical range of operation of the sorbent trap monitoring system. For each 10-minute (or longer) data collection period, record the total sample volume, in units of dry standard cubic meters (dscm), measured by the RGFM and the gas flow meter being tested.
10.2.1.3 Initial Calibration Factor. Calculate an individual calibration factor Yi at each tested flow rate from section 10.2.1.1 or 10.2.1.2 of this performance specification (as applicable), by taking the ratio of the reference sample volume to the sample volume recorded by the gas flow meter. Average the three Yi values, to determine Y, the calibration factor for the flow meter. Each of the three individual values of Yi must be within ±0.02 of Y. Except as otherwise provided in sections 10.2.1.4 and 10.2.1.5 of this performance specification, use the average Y value from the three level calibration to adjust all subsequent gas volume measurements made with the gas flow meter.
10.2.2 Initial On-Site Calibration Check. For a mass flow meter that was initially calibrated using a compressed gas mixture, an on-site calibration check must be performed before using the flow meter to provide data. While sampling stack gas, check the calibration of the flow meter at one intermediate flow rate typical of normal operation of the monitoring system. Follow the basic procedures in section 10.2.1.1 or 10.2.1.2 of this performance specification. If the onsite calibration check shows that the value of Yi, the calibration factor at the tested flow rate, differs by more than 5 percent from the value of Y obtained in the initial calibration of the meter, repeat the full 3-level calibration of the meter using stack gas to determine a new value of Y, and apply the new Y value to all subsequent gas volume measurements made with the gas flow meter.
10.2.3 Ongoing Quality Control. Recalibrate the gas flow meter quarterly at one intermediate flow rate setting representative of normal operation of the monitoring system. Follow the basic procedures in section 10.2.1.1 or 10.2.1.2 of this performance specification. If a quarterly recalibration shows that the value of Yi, the calibration factor at the tested flow rate, differs from the current value of Y by more than 5 percent, repeat the full 3-level calibration of the meter to determine a new value of Y, and apply the new Y value to all subsequent gas volume measurements made with the gas flow meter.
10.3 Calibration of Thermocouples and Other Temperature Sensors. Use the procedures and criteria in section 10.3 of Method 2 in appendix A-1 to this part to calibrate in-stack temperature sensors and thermocouples. Calibrations must be performed prior to initial use and at least quarterly thereafter. At each calibration point, the absolute temperature measured by the temperature sensor must agree to within ±1.5 percent of the temperature measured with the reference sensor, otherwise the sensor may not continue to be used.
10.4 Barometer Calibration. Calibrate the barometer against another barometer that has a NIST-traceable calibration. This calibration must be performed prior to initial use and at least quarterly thereafter. At each calibration point, the absolute pressure measured by the barometer must agree to within ±10 mm Hg of the pressure measured by the NIST-traceable barometer, otherwise the barometer may not continue to be used.
10.5 Calibration of Other Sensors and Gauges. Calibrate all other sensors and gauges according to the procedures specified by the instrument manufacturer(s).
10.6 Analytical System Calibration. See section 11.1 of this performance specification.
11.0 Analytical ProceduresThe analysis of the Hg samples may be conducted using any instrument or technology capable of quantifying total Hg from the sorbent media and meeting the performance criteria in section 9 of this performance specification.
11.1 Analyzer System Calibration. Perform a multipoint calibration of the analyzer at three or more upscale points over the desired quantitative range (multiple calibration ranges must be calibrated, if necessary). The field samples analyzed must fall within a calibrated, quantitative range and meet the necessary performance criteria. For samples that are suitable for aliquotting, a series of dilutions may be needed to ensure that the samples fall within a calibrated range. However, for sorbent media samples that are consumed during analysis (e.g., thermal desorption techniques), extra care must be taken to ensure that the analytical system is appropriately calibrated prior to sample analysis. The calibration curve range(s) should be determined based on the anticipated level of Hg mass on the sorbent media. Knowledge of estimated stack Hg concentrations and total sample volume may be required prior to analysis. The calibration curve for use with the various analytical techniques (e.g., UV AA, UV AF, and XRF) can be generated by directly introducing standard solutions into the analyzer or by spiking the standards onto the sorbent media and then introducing into the analyzer after preparing the sorbent/standard according to the particular analytical technique. For each calibration curve, the value of the square of the linear correlation coefficient, i.e., r 2, must be ≥0.99, and the analyzer response must be within ±10 percent of reference value at each upscale calibration point. Calibrations must be performed on the day of the analysis, before analyzing any of the samples. Following calibration, an independently prepared standard (not from same calibration stock solution) must be analyzed. The measured value of the independently prepared standard must be within ±10 percent of the expected value.
11.2 Sample Preparation. Carefully separate the three sections of each sorbent trap. Combine for analysis all materials associated with each section, i.e., any supporting substrate that the sample gas passes through prior to entering a media section (e.g., glass wool, polyurethane foam, etc.) must be analyzed with that segment.
11.3 Spike Recovery Study. Before analyzing any field samples, the laboratory must demonstrate the ability to recover and quantify Hg from the sorbent media by performing the following spike recovery study for sorbent media traps spiked with elemental mercury. Using the procedures described in sections 6.2 and 12.1 of this performance specification, spike the third section of nine sorbent traps with gaseous Hg 0, i.e., three traps at each of three different mass loadings, representing the range of masses anticipated in the field samples. This will yield a 3 × 3 sample matrix. Prepare and analyze the third section of each spiked trap, using the techniques that will be used to prepare and analyze the field samples. The average recovery for each spike concentration must be between 85 and 115 percent. If multiple types of sorbent media are to be analyzed, a separate spike recovery study is required for each sorbent material. If multiple ranges are calibrated, a separate spike recovery study is required for each range.
11.4 Field Sample Analyses. Analyze the sorbent trap samples following the same procedures that were used for conducting the spike recovery study. The three sections of each sorbent trap must be analyzed separately (i.e., section 1, then section 2, then section 3). Quantify the total mass of Hg for each section based on analytical system response and the calibration curve from section 11.1 of this performance specification. Determine the spike recovery from sorbent trap section 3. The spike recovery must be no less than 75 percent and no greater than 125 percent. To report the final Hg mass for each trap, add together the Hg masses collected in trap sections 1 and 2.
12.0 Calculations, Data Reduction, and Data Analysis12.1 Calculation of Pre-Sampling Spiking Level. Determine sorbent trap section 3 spiking level using estimates of the stack Hg concentration, the target sample flow rate, and the expected monitoring period. Calculate Mexp, the expected Hg mass that will be collected in section 1 of the trap, using Equation 12B-1. The pre-sampling spike must be within ±50 percent of this mass.
Where: Mexp = Expected sample mass (µg) Qs = Sample flow rate (L/min) ts = Expected monitoring period (min) Cest = Estimated Hg concentration in stack gas (µg/m 3) 10−3 = Conversion factor (m 3/L) Example calculation:For an estimated stack Hg concentration of 5 µg/m 3, a target sample rate of 0.30 L/min, and a monitoring period of 5 days: Mexp = (0.30 L/min)(1440 min/day)(5 days)(10−3 m 3/L)(5 µg/m 3) = 10.8 µgA pre-sampling spike of 10.8 µg ±50 percent is, therefore, appropriate.
12.2 Calculations for Flow-Proportional Sampling. For the first hour of the data collection period, determine the reference ratio of the stack gas volumetric flow rate to the sample flow rate, as follows:
Where: Rref = Reference ratio of hourly stack gas flow rate to hourly sample flow rate Qref = Average stack gas volumetric flow rate for first hour of collection period (scfh) Fref = Average sample flow rate for first hour of the collection period, in appropriate units (e.g., liters/min, cc/min, dscm/min) K = Power of ten multiplier, to keep the value of Rref between 1 and 100. The appropriate K value will depend on the selected units of measure for the sample flow rate.Then, for each subsequent hour of the data collection period, calculate ratio of the stack gas flow rate to the sample flow rate using Equation 12B-3:
Where: Rh = Ratio of hourly stack gas flow rate to hourly sample flow rate Qh = Average stack gas volumetric flow rate for the hour (scfh) Fh = Average sample flow rate for the hour, in appropriate units (e.g., liters/min, cc/min, dscm/min) K = Power of ten multiplier, to keep the value of Rh between 1 and 100. The appropriate K value will depend on the selected units of measure for the sample flow rate and the range of expected stack gas flow rates.Maintain the value of Rh within ±25 percent of Rref throughout the data collection period.
12.3 Calculation of Spike Recovery. Calculate the percent recovery of each section 3 spike, as follows:
Where: %R = Percentage recovery of the pre-sampling spike M3 = Mass of Hg recovered from section 3 of the sorbent trap, (µg) Ms = Calculated Hg mass of the pre-sampling spike, from section 8.1.2 of this performance specification, (µg)12.4 Calculation of Breakthrough. Calculate the percent breakthrough to the second section of the sorbent trap, as follows:
Where: %B = Percent breakthrough M2 = Mass of Hg recovered from section 2 of the sorbent trap, (µg) M1 = Mass of Hg recovered from section 1 of the sorbent trap, (µg)12.5 Calculation of Hg Concentration. Calculate the Hg concentration for each sorbent trap, using the following equation:
Where: C = Concentration of Hg for the collection period, (µg/dscm) M* = Total mass of Hg recovered from sections 1 and 2 of the sorbent trap, (µg) Vt = Total volume of dry gas metered during the collection period, (dscm). For the purposes of this performance specification, standard temperature and pressure are defined as 20 °C and 760 mm Hg, respectively.12.6 Calculation of Paired Trap Agreement. Calculate the relative deviation (RD) between the Hg concentrations measured with the paired sorbent traps:
Where: RD = Relative deviation between the Hg concentrations from traps “a” and “b” (percent) Ca = Concentration of Hg for the collection period, for sorbent trap “a” (µg/dscm) Cb = Concentration of Hg for the collection period, for sorbent trap “b” (µg/dscm)12.7 Calculation of Relative Accuracy. Calculate the relative accuracy as described in section 12.4 of PS 12A in this appendix.
12.8 Data Reduction. Typical monitoring periods for normal, day-to-day operation of a sorbent trap monitoring system range from about 24 hours to 168 hours. For the required RA tests of the system, smaller sorbent traps are often used, and the “monitoring period” or time per run is considerably shorter (e.g., 1 hour or less). Generally speaking, to validate sorbent trap monitoring system data, the acceptance criteria for the following five QC specifications in Table 12B-1 above must be met for both traps: (a) the post-monitoring leak check; (b) the ratio of stack gas flow rate to sample flow rate; (c) section 2 breakthrough; (d) paired trap agreement; and (e) section 3 spike recovery.
12.8.1 For routine day-to-day operation of a sorbent trap monitoring system, when both traps meet the acceptance criteria for all five QC specifications, the two measured Hg concentrations must be averaged arithmetically and the average value must be applied to each hour of the data collection period.
12.8.2 To validate a RA test run, both traps must meet the acceptance criteria for all five QC specifications. However, as specified in section 12.8.3 below, for routine day-to-day operation of the monitoring system, a monitoring period may, in certain instances, be validated based on the results from one trap.
12.8.3 For the routine, day-to-day operation of the monitoring system, when one of the two sorbent trap samples or sampling systems either: (a) Fails the post-monitoring leak check; or (b) has excessive section 2 breakthrough; or (c) fails to maintain the proper stack flow-to-sample flow ratio; or (d) fails to achieve the required section 3 spike recovery; or (e) is lost, broken, or damaged, provided that the other trap meets the acceptance criteria for all four of these QC specifications, the Hg concentration measured by the valid trap may be multiplied by a factor of 1.111 and then used for reporting purposes. Further, if both traps meet the acceptance criteria for all four of these QC specifications, but the acceptance criterion for paired trap agreement is not met, the owner or operator may report the higher of the two Hg concentrations measured by the traps, in lieu of invalidating the data from the paired traps.
12.8.4 Whenever the data from a pair of sorbent traps must be invalidated and no quality-assured data from a certified backup Hg monitoring system or Hg reference method are available to cover the hours in the data collection period, treat those hours in the manner specified in the applicable regulation (i.e., use missing data substitution procedures or count the hours as monitoring system down time, as appropriate).
13.0 Monitoring System PerformanceThese monitoring criteria and procedures have been successfully applied to coal-fired utility boilers (including units with post-combustion emission controls), having vapor-phase Hg concentrations ranging from 0.03 µg/dscm to approximately 100 µg/dscm.
14.0 Pollution Prevention [Reserved] 15.0 Waste Management [Reserved] 16.0 Alternative Procedures [Reserved] 17.0 Bibliography17.1 40 CFR Part 60, Appendix B, “Performance Specification 2 - Specifications and Test Procedures for SO2 and NOX Continuous Emission Monitoring Systems in Stationary Sources.”
17.2 40 CFR Part 60, Appendix B, “Performance Specification 12A - Specifications and Test Procedures for Total Vapor Phase Mercury Continuous Emission Monitoring Systems in Stationary Sources.”
Performance Specification 15 - Performance Specification for Extractive FTIR Continuous Emissions Monitor Systems in Stationary Sources 1.0 Scope and Application1.1 Analytes. This performance specification is applicable for measuring all hazardous air pollutants (HAPs) which absorb in the infrared region and can be quantified using Fourier Transform Infrared Spectroscopy (FTIR), as long as the performance criteria of this performance specification are met. This specification is to be used for evaluating FTIR continuous emission monitoring systems for measuring HAPs regulated under Title III of the 1990 Clean Air Act Amendments. This specification also applies to the use of FTIR CEMs for measuring other volatile organic or inorganic species.
1.2 Applicability. A source which can demonstrate that the extractive FTIR system meets the criteria of this performance specification for each regulated pollutant may use the FTIR system to continuously monitor for the regulated pollutants.
2.0 Summary of Performance SpecificationFor compound-specific sampling requirements refer to FTIR sampling methods (e.g., reference 1). For data reduction procedures and requirements refer to the EPA FTIR Protocol (reference 2), hereafter referred to as the “FTIR Protocol.” This specification describes sampling and analytical procedures for quality assurance. The infrared spectrum of any absorbing compound provides a distinct signature. The infrared spectrum of a mixture contains the superimposed spectra of each mixture component. Thus, an FTIR CEM provides the capability to continuously measure multiple components in a sample using a single analyzer. The number of compounds that can be speciated in a single spectrum depends, in practice, on the specific compounds present and the test conditions.
3.0 DefinitionsFor a list of definitions related to FTIR spectroscopy refer to Appendix A of the FTIR Protocol. Unless otherwise specified, spectroscopic terms, symbols and equations in this performance specification are taken from the FTIR Protocol or from documents cited in the Protocol. Additional definitions are given below.
3.1 FTIR Continuous Emission Monitoring System (FTIR CEM).
3.1.1 FTIR System. Instrument to measure spectra in the mid-infrared spectral region (500 to 4000 cm−1). It contains an infrared source, interferometer, sample gas containment cell, infrared detector, and computer. The interferometer consists of a beam splitter that divides the beam into two paths, one path a fixed distance and the other a variable distance. The computer is equipped with software to run the interferometer and store the raw digitized signal from the detector (interferogram). The software performs the mathematical conversion (the Fourier transform) of the interferogram into a spectrum showing the frequency dependent sample absorbance. All spectral data can be stored on computer media.
3.1.2 Gas Cell. A gas containment cell that can be evacuated. It contains the sample as the infrared beam passes from the interferometer, through the sample, and to the detector. The gas cell may have multi-pass mirrors depending on the required detection limit(s) for the application.
3.1.3 Sampling System. Equipment used to extract sample from the test location and transport the gas to the FTIR analyzer. Sampling system components include probe, heated line, heated non-reactive pump, gas distribution manifold and valves, flow measurement devices and any sample conditioning systems.
3.2 Reference CEM. An FTIR CEM, with sampling system, that can be used for comparison measurements.
3.3 Infrared Band (also Absorbance Band or Band). Collection of lines arising from rotational transitions superimposed on a vibrational transition. An infrared absorbance band is analyzed to determine the analyte concentration.
3.4 Sample Analysis. Interpreting infrared band shapes, frequencies, and intensities to obtain sample component concentrations. This is usually performed by a software routine using a classical least squares (cls), partial least squares (pls), or K- or P- matrix method.
3.5 (Target) Analyte. A compound whose measurement is required, usually to some established limit of detection and analytical uncertainty.
3.6 Interferant. A compound in the sample matrix whose infrared spectrum overlaps at least part of an analyte spectrum complicating the analyte measurement. The interferant may not prevent the analyte measurement, but could increase the analytical uncertainty in the measured concentration. Reference spectra of interferants are used to distinguish the interferant bands from the analyte bands. An interferant for one analyte may not be an interferant for other analytes.
3.7 Reference Spectrum. Infrared spectra of an analyte, or interferant, prepared under controlled, documented, and reproducible laboratory conditions (see section 4.6 of the FTIR Protocol). A suitable library of reference spectra can be used to measure target analytes in gas samples.
3.8 Calibration Spectrum. Infrared spectrum of a compound suitable for characterizing the FTIR instrument configuration (Section 4.5 in the FTIR Protocol).
3.9 One hundred percent line. A double beam transmittance spectrum obtained by combining two successive background single beam spectra. Ideally, this line is equal to 100 percent transmittance (or zero absorbance) at every point in the spectrum. The zero absorbance line is used to measure the RMS noise of the system.
3.10 Background Deviation. Any deviation (from 100 percent) in the one hundred percent line (or from zero absorbance). Deviations greater than ±5 percent in any analytical region are unacceptable. Such deviations indicate a change in the instrument throughput relative to the single-beam background.
3.11 Batch Sampling. A gas cell is alternately filled and evacuated. A Spectrum of each filled cell (one discreet sample) is collected and saved.
3.12 Continuous Sampling. Sample is continuously flowing through a gas cell. Spectra of the flowing sample are collected at regular intervals.
3.13 Continuous Operation. In continuous operation an FTIR CEM system, without user intervention, samples flue gas, records spectra of samples, saves the spectra to a disk, analyzes the spectra for the target analytes, and prints concentrations of target analytes to a computer file. User intervention is permitted for initial set-up of sampling system, initial calibrations, and periodic maintenance.
3.14 Sampling Time. In batch sampling - the time required to fill the cell with flue gas. In continuous sampling - the time required to collect the infrared spectrum of the sample gas.
3.15 PPM-Meters. Sample concentration expressed as the concentration-path length product, ppm (molar) concentration multiplied by the path length of the FTIR gas cell. Expressing concentration in these units provides a way to directly compare measurements made using systems with different optical configurations. Another useful expression is (ppm-meters)/K, where K is the absolute temperature of the sample in the gas cell.
3.16 CEM Measurement Time Constant. The Time Constant (TC, minutes for one cell volume to flow through the cell) determines the minimum interval for complete removal of an analyte from the FTIR cell. It depends on the sampling rate (Rs in Lpm), the FTIR cell volume (Vcell in L) and the chemical and physical properties of an analyte.
For example, if the sample flow rate (through the FTIR cell) is 5 Lpm and the cell volume is 7 liters, then TC is equal to 1.4 minutes (0.71 cell volumes per minute). This performance specification defines 5 * TC as the minimum interval between independent samples.3.17 Independent Measurement. Two independent measurements are spectra of two independent samples. Two independent samples are separated by, at least 5 cell volumes. The interval between independent measurements depends on the cell volume and the sample flow rate (through the cell). There is no mixing of gas between two independent samples. Alternatively, estimate the analyte residence time empirically: (1) Fill cell to ambient pressure with a (known analyte concentration) gas standard, (2) measure the spectrum of the gas standard, (3) purge the cell with zero gas at the sampling rate and collect a spectrum every minute until the analyte standard is no longer detected spectroscopically. If the measured time corresponds to less than 5 cell volumes, use 5 * TC as the minimum interval between independent measurements. If the measured time is greater than 5 * TC, then use this time as the minimum interval between independent measurements.
3.18 Test Condition. A period of sampling where all process, and sampling conditions, and emissions remain constant and during which a single sampling technique and a single analytical program are used. One Run may include results for more than one test condition. Constant emissions means that the composition of the emissions remains approximately stable so that a single analytical program is suitable for analyzing all of the sample spectra. A greater than two-fold change in analyte or interferant concentrations or the appearance of additional compounds in the emissions, may constitute a new test condition and may require modification of the analytical program.
3.19 Run. A single Run consists of spectra (one spectrum each) of at least 10 independent samples over a minimum of one hour. The concentration results from the spectra can be averaged together to give a run average for each analyte measured in the test run.
4.0 InterferencesSeveral compounds, including water, carbon monoxide, and carbon dioxide, are known interferences in the infrared region in which the FTIR instrument operates. Follow the procedures in the FTIR protocol for subtracting or otherwise dealing with these and other interferences.
5.0 SafetyThe procedures required under this performance specification may involve hazardous materials, operations, and equipment. This performance specification may not address all of the safety problems associated with these procedures. It is the responsibility of the user to establish appropriate safety and health practices and determine the applicable regulatory limitations prior to performing these procedures. The CEMS users manual and materials recommended by this performance specification should be consulted for specific precautions to be taken.
6.0 Equipment and Supplies6.1 Installation of sampling equipment should follow requirements of FTIR test Methods such as references 1 and 3 and the EPA FTIR Protocol (reference 2). Select test points where the gas stream composition is representative of the process emissions. If comparing to a reference method, the probe tips for the FTIR CEM and the RM should be positioned close together using the same sample port if possible.
6.2 FTIR Specifications. The FTIR CEM must be equipped with reference spectra bracketing the range of path length-concentrations (absorbance intensities) to be measured for each analyte. The effective concentration range of the analyzer can be adjusted by changing the path length of the gas cell or by diluting the sample. The optical configuration of the FTIR system must be such that maximum absorbance of any target analyte is no greater than 1.0 and the minimum absorbance of any target analyte is at least 10 times the RMSD noise in the analytical region. For example, if the measured RMSD in an analytical region is equal to 10−3, then the peak analyte absorbance is required to be at least 0.01. Adequate measurement of all of the target analytes may require changing path lengths during a run, conducting separate runs for different analytes, diluting the sample, or using more than one gas cell.
6.3 Data Storage Requirements. The system must have sufficient capacity to store all data collected in one week of routine sampling. Data must be stored to a write-protected medium, such as write-once-read-many (WORM) optical storage medium or to a password protected remote storage location. A back-up copy of all data can be temporarily saved to the computer hard drive. The following items must be stored during testing.
• At least one sample interferogram per sampling Run or one interferogram per hour, whichever is greater. This assumes that no sampling or analytical conditions have changed during the run.
• All sample absorbance spectra (about 12 per hr, 288 per day).
• All background spectra and interferograms (variable, but about 5 per day).
• All CTS spectra and interferograms (at least 2 each 24 hour period).
• Documentation showing a record of resolution, path length, apodization, sampling time, sampling conditions, and test conditions for all sample, CTS, calibration, and background spectra.
Using a resolution of 0.5 cm−1, with analytical range of 3500 cm−1, assuming about 65 Kbytes per spectrum and 130 Kb per interferogram, the storage requirement is about 164 Mb for one week of continuous sampling. Lower spectral resolution requires less storage capacity. All of the above data must be stored for at least two weeks. After two weeks, storage requirements include: (1) all analytical results (calculated concentrations), (2) at least 1 sample spectrum with corresponding background and sample interferograms for each test condition, (3) CTS and calibration spectra with at least one interferogram for CTS and all interferograms for calibrations, (4) a record of analytical input used to produce results, and (5) all other documentation. These data must be stored according to the requirements of the applicable regulation.
7.0 Reagents and Standards [Reserved] 8.0 Sample Collection, Preservation, Storage, and Transport [Reserved] 9.0 Quality ControlThese procedures shall be used for periodic quarterly or semiannual QA/QC checks on the operation of the FTIR CEM. Some procedures test only the analytical program and are not intended as a test of the sampling system.
9.1 Audit Sample. This can serve as a check on both the sampling system and the analytical program.
9.1.1 Sample Requirements. The audit sample can be a mixture or a single component. It must contain target analyte(s) at approximately the expected flue gas concentration(s). If possible, each mixture component concentration should be NIST traceable (±2 percent accuracy). If a cylinder mixture standard(s) cannot be obtained, then, alternatively, a gas phase standard can be generated from a condensed phase analyte sample. Audit sample contents and concentrations are not revealed to the FTIR CEM operator until after successful completion of procedures in 5.3.2.
9.1.2 Test Procedure. Spike the audit sample using the analyte spike procedure in section 11. The audit sample is measured directly by the FTIR system (undiluted) and then spiked into the effluent at a known dilution ratio. Measure a series of spiked and unspiked samples using the same procedures as those used to analyze the stack gas. Analyze the results using sections 12.1 and 12.2. The measured concentration of each analyte must be within ±5 percent of the expected concentration (plus the uncertainty), i.e., the calculated correction factor must be within 0.93 and 1.07 for an audit with an analyte uncertainty of ±2 percent.
9.2 Audit Spectra. Audit spectra can be used to test the analytical program of the FTIR CEM, but provide no test of the sampling system.
9.2.1 Definition and Requirements. Audit spectra are absorbance spectra that; (1) have been well characterized, and (2) contain absorbance bands of target analyte(s) and potential interferants at intensities equivalent to what is expected in the source effluent. Audit spectra are provided by the administrator without identifying information. Methods of preparing Audit spectra include; (1) mathematically adding sample spectra or adding reference and interferant spectra, (2) obtaining sample spectra of mixtures prepared in the laboratory, or (3) they may be sample spectra collected previously at a similar source. In the last case it must be demonstrated that the analytical results are correct and reproducible. A record associated with each Audit spectrum documents its method of preparation. The documentation must be sufficient to enable an independent analyst to reproduce the Audit spectra.
9.2.2 Test Procedure. Audit spectra concentrations are measured using the FTIR CEM analytical program. Analytical results must be within ±5 percent of the certified audit concentration for each analyte (plus the uncertainty in the audit concentration). If the condition is not met, demonstrate how the audit spectra are unrepresentative of the sample spectra. If the audit spectra are representative, modify the FTIR CEM analytical program until the test requirement is met. Use the new analytical program in subsequent FTIR CEM analyses of effluent samples.
9.3 Submit Spectra For Independent Analysis. This procedure tests only the analytical program and not the FTIR CEM sampling system. The analyst can submit FTIR CEM spectra for independent analysis by EPA. Requirements for submission include; (1) three representative absorbance spectra (and stored interferograms) for each test period to be reviewed, (2) corresponding CTS spectra, (3) corresponding background spectra and interferograms, (4) spectra of associated spiked samples if applicable, and (5) analytical results for these sample spectra. The analyst will also submit documentation of process times and conditions, sampling conditions associated with each spectrum, file names and sampling times, method of analysis and reference spectra used, optical configuration of FTIR CEM including cell path length and temperature, spectral resolution and apodization used for every spectrum. Independent analysis can also be performed on site in conjunction with the FTIR CEM sampling and analysis. Sample spectra are stored on the independent analytical system as they are collected by the FTIR CEM system. The FTIR CEM and the independent analyses are then performed separately. The two analyses will agree to within ±120 percent for each analyte using the procedure in section 12.3. This assumes both analytical routines have properly accounted for differences in optical path length, resolution, and temperature between the sample spectra and the reference spectra.
10.0 Calibration and Standardization10.1 Calibration Transfer Standards. For CTS requirements see section 4.5 of the FTIR Protocol. A well characterized absorbance band in the CTS gas is used to measure the path length and line resolution of the instrument. The CTS measurements made at the beginning of every 24 hour period must agree to within ±5 percent after correction for differences in pressure.
Verify that the frequency response of the instrument and CTS absorbance intensity are correct by comparing to other CTS spectra or by referring to the literature.
10.2 Analyte Calibration. If EPA library reference spectra are not available, use calibration standards to prepare reference spectra according to section 6 of the FTIR Protocol. A suitable set of analyte reference data includes spectra of at least 2 independent samples at each of at least 2 different concentrations. The concentrations bracket a range that includes the expected analyte absorbance intensities. The linear fit of the reference analyte band areas must have a fractional calibration uncertainty (FCU in Appendix F of the FTIR Protocol) of no greater than 10 percent. For requirements of analyte standards refer to section 4.6 of the FTIR Protocol.
10.3 System Calibration. The calibration standard is introduced at a point on the sampling probe. The sampling system is purged with the calibration standard to verify that the absorbance measured in this way is equal to the absorbance in the analyte calibration. Note that the system calibration gives no indication of the ability of the sampling system to transport the target analyte(s) under the test conditions.
10.4 Analyte Spike. The target analyte(s) is spiked at the outlet of the sampling probe, upstream of the particulate filter, and combined with effluent at a ratio of about 1 part spike to 9 parts effluent. The measured absorbance of the spike is compared to the expected absorbance of the spike plus the analyte concentration already in the effluent. This measures sampling system bias, if any, as distinguished from analyzer bias. It is important that spiked sample pass through all of the sampling system components before analysis.
10.5 Signal-to-Noise Ratio (S/N). The measure of S/N in this performance specification is the root-mean-square (RMS) noise level as given in Appendix C of the FTIR Protocol. The RMS noise level of a contiguous segment of a spectrum is defined as the RMS difference (RMSD) between the n contiguous absorbance values (Ai) which form the segment and the mean value (AM) of that segment.
A decrease in the S/N may indicate a loss in optical throughput, or detector or interferometer malfunction.10.6 Background Deviation. The 100 percent baseline must be between 95 and 105 percent transmittance (absorbance of 0.02 to −0.02) in every analytical region. When background deviation exceeds this range, a new background spectrum must be collected using nitrogen or other zero gas.
10.7 Detector Linearity. Measure the background and CTS at three instrument aperture settings; one at the aperture setting to be used in the testing, and one each at settings one half and twice the test aperture setting. Compare the three CTS spectra. CTS band areas should agree to within the uncertainty of the cylinder standard. If test aperture is the maximum aperture, collect CTS spectrum at maximum aperture, then close the aperture to reduce the IR through-put by half. Collect a second background and CTS at the smaller aperture setting and compare the spectra as above. Instead of changing the aperture neutral density filters can be used to attenuate the infrared beam. Set up the FTIR system as it will be used in the test measurements. Collect a CTS spectrum. Use a neutral density filter to attenuate the infrared beam (either immediately after the source or the interferometer) to approximately 1/2 its original intensity. Collect a second CTS spectrum. Use another filter to attenuate the infrared beam to approximately 1/4 its original intensity. Collect a third background and CTS spectrum. Compare the CTS spectra as above. Another check on linearity is to observe the single beam background in frequency regions where the optical configuration is known to have a zero response. Verify that the detector response is “flat” and equal to zero in these regions. If detector response is not linear, decrease aperture, or attenuate the infrared beam. Repeat the linearity check until system passes the requirement.
11.0 Analytical Procedure11.1 Initial Certification. First, perform the evaluation procedures in section 6.0 of the FTIR Protocol. The performance of an FTIR CEM can be certified upon installation using EPA Method 301 type validation (40 CFR, Part 63, Appendix A), or by comparison to a reference Method if one exists for the target analyte(s). Details of each procedure are given below. Validation testing is used for initial certification upon installation of a new system. Subsequent performance checks can be performed with more limited analyte spiking. Performance of the analytical program is checked initially, and periodically as required by EPA, by analyzing audit spectra or audit gases.
11.1.1 Validation. Use EPA Method 301 type sampling (reference 4, section 5.3 of Method 301) to validate the FTIR CEM for measuring the target analytes. The analyte spike procedure is as follows: (1) a known concentration of analyte is mixed with a known concentration of a non-reactive tracer gas, (2) the undiluted spike gas is sent directly to the FTIR cell and a spectrum of this sample is collected, (3) pre-heat the spiked gas to at least the sample line temperature, (4) introduce spike gas at the back of the sample probe upstream of the particulate filter, (5) spiked effluent is carried through all sampling components downstream of the probe, (6) spike at a ratio of roughly 1 part spike to 9 parts flue gas (or more dilute), (7) the spike-to-flue gas ratio is estimated by comparing the spike flow to the total sample flow, and (8) the spike ratio is verified by comparing the tracer concentration in spiked flue gas to the tracer concentration in undiluted spike gas. The analyte flue gas concentration is unimportant as long as the spiked component can be measured and the sample matrix (including interferences) is similar to its composition under test conditions. Validation can be performed using a single FTIR CEM analyzing sample spectra collected sequentially. Since flue gas analyte (unspiked) concentrations can vary, it is recommended that two separate sampling lines (and pumps) are used; one line to carry unspiked flue gas and the other line to carry spiked flue gas. Even with two sampling lines the variation in unspiked concentration may be fast compared to the interval between consecutive measurements. Alternatively, two FTIR CEMs can be operated side-by-side, one measuring spiked sample, the other unspiked sample. In this arrangement spiked and unspiked measurements can be synchronized to minimize the affect of temporal variation in the unspiked analyte concentration. In either sampling arrangement, the interval between measured concentrations used in the statistical analysis should be, at least, 5 cell volumes (5 * TC in equation 1). A validation run consists of, at least, 24 independent analytical results, 12 spiked and 12 unspiked samples. See section 3.17 for definition of an “independent” analytical result. The results are analyzed using sections 12.1 and 12.2 to determine if the measurements passed the validation requirements. Several analytes can be spiked and measured in the same sampling run, but a separate statistical analysis is performed for each analyte. In lieu of 24 independent measurements, averaged results can be used in the statistical analysis. In this procedure, a series of consecutive spiked measurements are combined over a sampling period to give a single average result. The related unspiked measurements are averaged in the same way. The minimum 12 spiked and 12 unspiked result averages are obtained by averaging measurements over subsequent sampling periods of equal duration. The averaged results are grouped together and statistically analyzed using section 12.2.
11.1.1.1 Validation with a Single Analyzer and Sampling Line. If one sampling line is used, connect the sampling system components and purge the entire sampling system and cell with at least 10 cell volumes of sample gas. Begin sampling by collecting spectra of 2 independent unspiked samples. Introduce the spike gas into the back of the probe, upstream of the particulate filter. Allow 10 cell volumes of spiked flue gas to purge the cell and sampling system. Collect spectra of 2 independent spiked samples. Turn off the spike flow and allow 10 cell volumes of unspiked flue gas to purge the FTIR cell and sampling system. Repeat this procedure 6 times until the 24 samples are collected. Spiked and unspiked samples can also be measured in groups of 4 instead of in pairs. Analyze the results using sections 12.1 and 12.2. If the statistical analysis passes the validation criteria, then the validation is completed. If the results do not pass the validation, the cause may be that temporal variations in the analyte sample gas concentration are fast relative to the interval between measurements. The difficulty may be avoided by: (1) Averaging the measurements over long sampling periods and using the averaged results in the statistical analysis, (2) modifying the sampling system to reduce TC by, for example, using a smaller volume cell or increasing the sample flow rate, (3) using two sample lines (4) use two analyzers to perform synchronized measurements. This performance specification permits modifications in the sampling system to minimize TC if the other requirements of the validation sampling procedure are met.
11.1.1.2 Validation With a Single Analyzer and Two Sampling Lines. An alternative sampling procedure uses two separate sample lines, one carrying spiked flue gas, the other carrying unspiked gas. A valve in the gas distribution manifold allows the operator to choose either sample. A short heated line connects the FTIR cell to the 3-way valve in the manifold. Both sampling lines are continuously purged. Each sample line has a rotameter and a bypass vent line after the rotameter, immediately upstream of the valve, so that the spike and unspiked sample flows can each be continuously monitored. Begin sampling by collecting spectra of 2 independent unspiked samples. Turn the sampling valve to close off the unspiked gas flow and allow the spiked flue gas to enter the FTIR cell. Isolate and evacuate the cell and fill with the spiked sample to ambient pressure. (While the evacuated cell is filling, prevent air leaks into the cell by making sure that the spike sample rotameter always indicates that a portion of the flow is directed out the by-pass vent.) Open the cell outlet valve to allow spiked sample to continuously flow through the cell. Measure spectra of 2 independent spiked samples. Repeat this procedure until at least 24 samples are collected.
11.1.1.3 Synchronized Measurements With Two Analyzers. Use two FTIR analyzers, each with its own cell, to perform synchronized spiked and unspiked measurements. If possible, use a similar optical configuration for both systems. The optical configurations are compared by measuring the same CTS gas with both analyzers. Each FTIR system uses its own sampling system including a separate sampling probe and sampling line. A common gas distribution manifold can be used if the samples are never mixed. One sampling system and analyzer measures spiked effluent. The other sampling system and analyzer measures unspiked flue gas. The two systems are synchronized so that each measures spectra at approximately the same times. The sample flow rates are also synchronized so that both sampling rates are approximately the same (TC1 ∼ TC2 in equation 1). Start both systems at the same time. Collect spectra of at least 12 independent samples with each (spiked and unspiked) system to obtain the minimum 24 measurements. Analyze the analytical results using sections 12.1 and 12.2. Run averages can be used in the statistical analysis instead of individual measurements.
11.1.1.4 Compare to a Reference Method (RM). Obtain EPA approval that the method qualifies as an RM for the analyte(s) and the source to be tested. Follow the published procedures for the RM in preparing and setting up equipment and sampling system, performing measurements, and reporting results. Since FTIR CEMS have multicomponent capability, it is possible to perform more than one RM simultaneously, one for each target analyte. Conduct at least 9 runs where the FTIR CEM and the RM are sampling simultaneously. Each Run is at least 30 minutes long and consists of spectra of at least 5 independent FTIR CEM samples and the corresponding RM measurements. If more than 9 runs are conducted, the analyst may eliminate up to 3 runs from the analysis if at least 9 runs are used.
11.1.1.4.1 RMs Using Integrated Sampling. Perform the RM and FTIR CEM sampling simultaneously. The FTIR CEM can measure spectra as frequently as the analyst chooses (and should obtain measurements as frequently as possible) provided that the measurements include spectra of at least 5 independent measurements every 30 minutes. Concentration results from all of the FTIR CEM spectra within a run may be averaged for use in the statistical comparison even if all of the measurements are not independent. When averaging the FTIR CEM concentrations within a run, it is permitted to exclude some measurements from the average provided the minimum of 5 independent measurements every 30 minutes are included: The Run average of the FTIR CEM measurements depends on both the sample flow rate and the measurement frequency (MF). The run average of the RM using the integrated sampling method depends primarily on its sampling rate. If the target analyte concentration fluctuates significantly, the contribution to the run average of a large fluctuation depends on the sampling rate and measurement frequency, and on the duration and magnitude of the fluctuation. It is, therefore, important to carefully select the sampling rate for both the FTIR CEM and the RM and the measurement frequency for the FTIR CEM. The minimum of 9 run averages can be compared according to the relative accuracy test procedure in Performance Specification 2 for SO2 and NOX CEMs (40 CFR, Part 60, App. B).
11.1.1.4.2 RMs Using a Grab Sampling Technique. Synchronize the RM and FTIR CEM measurements as closely as possible. For a grab sampling RM, record the volume collected and the exact sampling period for each sample. Synchronize the FTIR CEM so that the FTIR measures a spectrum of a similar cell volume at the same time as the RM grab sample was collected. Measure at least five independent samples with both the FTIR CEM and the RM for each of the minimum nine runs. Compare the run concentration averages by using the relative accuracy analysis procedure in Performance Specification 2 of appendix B of 40 CFR part 60.
11.1.1.4.3 Continuous Emission Monitors as RMs. If the RM is a CEM, synchronize the sampling flow rates of the RM and the FTIR CEM. Each run is at least 1 hour long and consists of at least 10 FTIR CEM measurements and the corresponding 10 RM measurements (or averages). For the statistical comparison, use the relative accuracy analysis procedure in Performance Specification 2 of appendix B of 40 CFR part 60. If the RM time constant is < 1/2 the FTIR CEM time constant, brief fluctuations in analyte concentrations that are not adequately measured with the slower FTIR CEM time constant can be excluded from the run average along with the corresponding RM measurements. However, the FTIR CEM run average must still include at least 10 measurements over a 1-hour period.
12.0 Calculations and Data Analysis12.1 Spike Dilution Ratio, Expected Concentration. The Method 301 bias is calculated as follows.
Where: B = Bias at the spike level Sm = Mean of the observed spiked sample concentrations Mm = Mean of the observed unspiked sample concentrations CS = Expected value of the spiked concentration.The CS is determined by comparing the SF6 tracer concentration in undiluted spike gas to the SF6 tracer concentrations in the spiked samples;
The expected concentration (CS) is the measured concentration of the analyte in undiluted spike gas divided by the dilution factor Where: [anal]dir = The analyte concentration in undiluted spike gas measured directly by filling the FTIR cell with the spike gas. If the bias is statistically significant (Section 12.2), Method 301 requires that a correction factor, CF, be multiplied by the analytical results, and that 0.7 ≤CF ≤1.3.12.2 Statistical Analysis of Validation Measurements. Arrange the independent measurements (or measurement averages) as in Table 1. More than 12 pairs of measurements can be analyzed. The statistical analysis follows EPA Method 301, section 6.3. section 12.1 of this performance specification shows the calculations for the bias, expected spike concentration, and correction factor. This section shows the determination of the statistical significance of the bias. Determine the statistical significance of the bias at the 95 percent confidence level by calculating the t-value for the set of measurements. First, calculate the differences, di, for each pair of spiked and each pair of unspiked measurements. Then calculate the standard deviation of the spiked pairs of measurements.
Where: di = The differences between pairs of spiked measurements. SDs = The standard deviation in the di values. n = The number of spiked pairs, 2n = 12 for the minimum of 12 spiked and 12 unspiked measurements. Calculate the relative standard deviation, RSD, using SDs and the mean of the spiked concentrations, Sm. The RSD must be ≤50%. Repeat the calculations in equations 7 and 8 to determine SDu and RSD, respectively, for the unspiked samples. Calculate the standard deviation of the mean using SDs and SDu from equation 7. The t-statistic is calculated as follows to test the bias for statistical significance; where the bias, B, and the correction factor, CF, are given in section 12.1. For 11 degrees of freedom, and a one-tailed distribution, Method 301 requires that t ≤2.201. If the t-statistic indicates the bias is statistically significant, then analytical measurements must be multiplied by the correction factor. There is no limitation on the number of measurements, but there must be at least 12 independent spiked and 12 independent unspiked measurements. Refer to the t-distribution (Table 2) at the 95 percent confidence level and appropriate degrees of freedom for the critical t-value. 13.0 Method Performance [Reserved] 14.0 Pollution Prevention [Reserved] 15.0 Waste Management [Reserved] 16.0 References1. Method 318, 40 CFR, Part 63, Appendix A (Draft), “Measurement of Gaseous Formaldehyde, Phenol and Methanol Emissions by FTIR Spectroscopy,” EPA Contract No. 68D20163, Work Assignment 2-18, February, 1995.
2. “EPA Protocol for the Use of Extractive Fourier Transform Infrared (FTIR) Spectrometry in Analyses of Gaseous Emissions from Stationary Industrial Sources,” February, 1995.
3. “Measurement of Gaseous Organic and Inorganic Emissions by Extractive FTIR Spectroscopy,” EPA Contract No. 68-D2-0165, Work Assignment 3-08.
4. “Method 301 - Field Validation of Pollutant Measurement Methods from Various Waste Media,” 40 CFR 63, App A.
17.0 Tables, Diagrams, Flowcharts, and Validation DataTable 1 - Arrangement of Validation Measurements for Statistical Analysis
Measurement (or average) |
Time | Spiked (ppm) |
di spiked | Unspiked (ppm) |
di unspiked |
---|---|---|---|---|---|
1 | S1 | U1 | |||
2 | S2 | S2−S1 | U2 | U2−U1 | |
3 | S3 | U3 | |||
4 | S4 | S4−S3 | U4 | U4−U3 | |
5 | S5 | U5 | |||
6 | S6 | S6−S5 | U6 | U6−U5 | |
7 | S7 | U7 | |||
8 | S8 | S8−S7 | U8 | U8−U7 | |
9 | S9 | U9 | |||
10 | S10 | S10−S9 | U10 | U10−U9 | |
11 | S11 | U11 | |||
12 | S12 | S12−S11 | U12 | U12−U11 | |
Average −> | Sm | Mm |
Table 2 - t = Values
n−1 a | t−value | n−1 a | t−value | n−1 a | t−value | n−1 a | t−value |
---|---|---|---|---|---|---|---|
11 | 2.201 | 17 | 2.110 | 23 | 2.069 | 29 | 2.045 |
12 | 2.179 | 18 | 2.101 | 24 | 2.064 | 30 | 2.042 |
13 | 2.160 | 19 | 2.093 | 25 | 2.060 | 40 | 2.021 |
14 | 2.145 | 20 | 2.086 | 26 | 2.056 | 60 | 2.000 |
15 | 2.131 | 21 | 2.080 | 27 | 2.052 | 120 | 1.980 |
16 | 2.120 | 22 | 2.074 | 28 | 2.048 | 8 | 1.960 |
a n is the number of independent pairs of measurements (a pair consists of one spiked and its corresponding unspiked measurement). Either discreet (independent) measurements in a single run, or run averages can be used.
1.1 Does this performance specification apply to me? If you, the source owner or operator, intend to use (with any necessary approvals) a predictive emission monitoring system (PEMS) to show compliance with your emission limitation under 40 CFR 60, 61, or 63, you must use the procedures in this performance specification (PS) to determine whether your PEMS is acceptable for use in demonstrating compliance with applicable requirements. Use these procedures to certify your PEMS after initial installation and periodically thereafter to ensure the PEMS is operating properly. If your PEMS contains a diluent (O2 or CO2) measuring component and your emissions limitation is in units that require a diluent measurement (e.g. lbs/mm Btu), the diluent component must be tested as well. These specifications apply to PEMS that are installed under 40 CFR 60, 61, and 63 after the effective date of this performance specification. These specifications do not apply to parametric monitoring systems, these are covered under PS-17.
1.1.1 How do I certify my PEMS after it is installed? PEMS must pass a relative accuracy (RA) test and accompanying statistical tests in the initial certification test to be acceptable for use in demonstrating compliance with applicable requirements. Ongoing quality assurance tests also must be conducted to ensure the PEMS is operating properly. An ongoing sensor evaluation procedure must be in place before the PEMS certification is complete. The amount of testing and data validation that is required depends upon the regulatory needs, i.e., whether precise quantification of emissions will be needed or whether indication of exceedances of some regulatory threshold will suffice. Performance criteria are more rigorous for PEMS used in determining continual compliance with an emission limit than those used to measure excess emissions. You must perform the initial certification test on your PEMS before reporting any PEMS data as quality-assured.
1.1.2 Is other testing required after certification? After you initially certify your PEMS, you must pass additional periodic performance checks to ensure the long-term quality of data. These periodic checks are listed in the table in section 9. You are always responsible for properly maintaining and operating your PEMS.
2.0 Summary of Performance SpecificationThe following performance tests are required in addition to other equipment and measurement location requirements.
2.1 Initial PEMS Certification.
2.1.1 Excess Emissions PEMS. For a PEMS that is used for excess emission reporting, the owner or operator must perform a minimum 9-run, 3-level (3 runs at each level) RA test (see section 8.2).
2.1.2 Compliance PEMS. For a PEMS that is used for continual compliance standards, the owner or operator must perform a minimum 27-run, 3-level (9 runs at each level) RA test (see section 8.2). Additionally, the data must be evaluated for bias and by F-test and correlation analysis.
2.2 Periodic Quality Assurance (QA) Assessments. Owners and operators of all PEMS are required to conduct quarterly relative accuracy audits (RAA) and yearly relative accuracy test audits (RATA) to assess ongoing PEMS operation. The frequency of these periodic assessments may be shortened by successful operation during a prior year.
3.0 DefinitionsThe following definitions apply:
3.1 Centroidal Area means that area in the center of the stack (or duct) comprising no more than 1 percent of the stack cross-sectional area and having the same geometric shape as the stack.
3.2 Data Recorder means the equipment that provides a permanent record of the PEMS output. The data recorder may include automatic data reduction capabilities and may include electronic data records, paper records, or a combination of electronic data and paper records.
3.3 Defective sensor means a sensor that is responsible for PEMS malfunction or that operates outside the approved operating envelope. A defective sensor may be functioning properly, but because it is operating outside the approved operating envelope, the resulting predicted emission is not validated.
3.4 Diluent PEMS means the total equipment required to predict a diluent gas concentration or emission rate.
3.5 Operating envelope means the defined range of a parameter input that is established during PEMS development. Emission data generated from parameter inputs that are beyond the operating envelope are not considered quality assured and are therefore unacceptable.
3.6 PEMS means all of the equipment required to predict an emission concentration or emission rate. The system may consist of any of the following major subsystems: sensors and sensor interfaces, emission model, algorithm, or equation that uses process data to generate an output that is proportional to the emission concentration or emission rate, diluent emission model, data recorder, and sensor evaluation system. Systems that use fewer than 3 variables do not qualify as PEMS unless the system has been specifically approved by the Administrator for use as a PEMS. A PEMS may predict emissions data that are corrected for diluent if the relative accuracy and relevant QA tests are passed in the emission units corrected for diluent. Parametric monitoring systems that serve as indicators of compliance and have parametric limits but do not predict emissions to comply with an emissions limit are not included in this definition.
3.7 PEMS training means the process of developing or confirming the operation of the PEMS against a reference method under specified conditions.
3.8 Quarter means a quarter of a calendar year in which there are at least 168 unit operating hours.
3.9 Reconciled Process Data means substitute data that are generated by a sensor evaluation system to replace that of a failed sensor. Reconciled process data may not be used without approval from the Administrator.
3.10 Relative Accuracy means the accuracy of the PEMS when compared to a reference method (RM) at the source. The RA is the average difference between the pollutant PEMS and RM data for a specified number of comparison runs plus a 2.5 percent confidence coefficient, divided by the average of the RM tests. For a diluent PEMS, the RA may be expressed as a percentage of absolute difference between the PEMS and RM. Alternative specifications are given for units that have very low emissions.
3.11 Relative Accuracy Audit means a quarterly audit of the PEMS against a portable analyzer meeting the requirements of ASTM D6522-00 or a RM for a specified number of runs. A RM may be used in place of the portable analyzer for the RAA.
3.12 Relative Accuracy Test Audit means a RA test that is performed at least once every four calendar quarters after the initial certification test while the PEMS is operating at the normal operating level.
3.13 Reference Value means a PEMS baseline value that may be established by RM testing under conditions when all sensors are functioning properly. This reference value may then be used in the sensor evaluation system or in adjusting new sensors.
3.14 Sensor Evaluation System means the equipment or procedure used to periodically assess the quality of sensor input data. This system may be a sub-model that periodically cross-checks sensor inputs among themselves or any other procedure that checks sensor integrity at least daily (when operated for more than one hour in any calendar day).
3.15 Sensors and Sensor Interface means the equipment that measures the process input signals and transports them to the emission prediction system.
4.0 Interferences [Reserved] 5.0 Safety [Reserved] 6.0 Equipment and Supplies6.1 PEMS Design. You must detail the design of your PEMS and make this available in reports and for on-site inspection. You must also establish the following, as applicable:
6.1.1 Number of Input Parameters. An acceptable PEMS will normally use three or more input parameters. You must obtain the Administrator's permission on a case-by-case basis if you desire to use a PEMS having fewer than three input parameters.
6.1.2 Parameter Operating Envelopes. Before you evaluate your PEMS through the certification test, you must specify the input parameters your PEMS uses, define their range of minimum and maximum values (operating envelope), and demonstrate the integrity of the parameter operating envelope using graphs and data from the PEMS development process, vendor information, or engineering calculations, as appropriate. If you operate the PEMS beyond these envelopes at any time after the certification test, the data generated during this condition will not be acceptable for use in demonstrating compliance with applicable requirements. If these parameter operating envelopes are not clearly defined and supported by development data, the PEMS operation will be limited to the range of parameter inputs encountered during the certification test until the PEMS has a new operating envelope established.
6.1.3 Source-Specific Operating Conditions. Identify any source-specific operating conditions, such as fuel type, that affect the output of your PEMS. You may only use the PEMS under the source-specific operating conditions it was certified for.
6.1.4 Ambient Conditions. You must explain whether and how ambient conditions and seasonal changes affect your PEMS. Some parameters such as absolute ambient humidity cannot be manipulated during a test. The effect of ambient conditions such as humidity on the pollutant concentration must be determined and this effect extrapolated to include future anticipated conditions. Seasonal changes and their effects on the PEMS must be evaluated unless you can show that such effects are negligible.
6.1.5 PEMS Principle of Operation. If your PEMS is developed on the basis of known physical principles, you must identify the specific physical assumptions or mathematical manipulations that support its operation. If your PEMS is developed on the basis of linear or nonlinear regression analysis, you must make available the paired data (preferably in graphic form) used to develop or train the model.
6.1.6 Data Recorder Scale. If you are not using a digital recorder, you must choose a recorder scale that accurately captures the desired range of potential emissions. The lower limit of your data recorder's range must be no greater than 20 percent of the applicable emission standard (if subject to an emission standard). The upper limit of your data recorder's range must be determined using the following table. If you obtain approval first, you may use other lower and upper recorder limits.
If PEMS is measuring. . . | And if. . . | Then your upper limit. . . |
---|---|---|
Uncontrolled emissions, such as NOX at the stack of a natural gas-fired boiler | No other regulation sets an upper limit for the data recorder's range | Must be 1.25 to 2 times the average potential emission level |
Uncontrolled emissions, such as NOX at the stack of a natural gas-fired boiler | Another regulation sets an upper limit for the data recorder's range | Must follow the other regulation |
Controlled emissions | Must be 1.5 to 2.0 times concentration of the emission standard that applies to your emission unit | |
Continual compliance emissions for an applicable regulation | Must be 1.1 to 1.5 times the concentration of the emission standard that applies to your emission unit |
6.1.7 Sensor Location and Repair. We recommend you install sensors in an accessible location in order to perform repairs and replacements. Permanently-installed platforms or ladders may not be needed. If you install sensors in an area that is not accessible, you may be required to shut down the emissions unit to repair or replace a sensor. Conduct a new RATA after replacing a sensor that supplies a critical PEMS parameter if the new sensor provides a different output or scaling or changes the historical training dataset of the PEMS. Replacement of a non-critical sensor that does not cause an impact in the accuracy of the PEMS does not trigger a RATA. All sensors must be calibrated as often as needed but at least as often as recommended by the manufacturers.
6.1.8 Sensor Evaluation System. Your PEMS must be designed to perform automatic or manual determination of defective sensors on at least a daily basis. This sensor evaluation system may consist of a sensor validation sub-model, a comparison of redundant sensors, a spot check of sensor input readings at a reference value, operation, or emission level, or other procedure that detects faulty or failed sensors. Some sensor evaluation systems generate substitute values (reconciled data) that are used when a sensor is perceived to have failed. You must obtain prior approval before using reconciled data.
6.1.9 Parameter Envelope Exceedances. Your PEMS must include a plan to detect and notify the operator of parameter envelope exceedances. Emission data collected outside the ranges of the sensor envelopes will not be considered quality assured.
6.2 Recordkeeping. All valid data recorded by the PEMS must be used to calculate the emission value.
7.0 Reagents and Standards [Reserved] 8.0 Sample Collection, Preservation, Storage, and Transport8.1 Initial Certification. Use the following procedure to certify your PEMS. Complete all PEMS training before the certification begins.
8.2 Relative Accuracy Test.
8.2.1 Reference Methods. Unless otherwise specified in the applicable regulations, you must use the test methods in appendix A of this part for the RM test. Conduct the RM tests at three operating levels. The RM tests shall be performed at a low-load (or production) level between the minimum safe, stable load and 50 percent of the maximum level load, at the mid-load level (an intermediary level between the low and high levels), and at a high-load level between 80 percent and the maximum load. Alternatively, if practicable, you may test at three levels of the key operating parameter (e.g. selected based on a covariance analysis between each parameter and the PEMS output) equally spaced within the normal range of the parameter.
8.2.2 Number of RM Tests for Excess Emission PEMS. For PEMS used for excess emission reporting, conduct at least the following number of RM tests at the following key parameter operating levels:
(1) Three at a low level.
(2) Three at a mid level.
(3) Three at a high level.
You may choose to perform more than nine total RM tests. If you perform more than nine tests, you may reject a maximum of three tests as long as the total number of test results used to determine the RA is nine or greater and each operating level has at least three tests. You must report all data, including the rejected data.
8.2.3 Number of RM Tests for Continual Compliance PEMS. For PEMS used to determine compliance, conduct at least the following number of RM tests at the following key parameter operating levels:
(1) Nine at a low level.
(2) Nine at a mid level.
(3) Nine at a high level.
You may choose to perform more than 9 RM runs at each operating level. If you perform more than 9 runs, you may reject a maximum of three runs per level as long as the total number of runs used to determine the RA at each operating level is 9 or greater.
8.2.4 Reference Method Measurement Location. Select an accessible measurement point for the RM that will ensure you measure emissions representatively. Ensure the location is at least two equivalent stack diameters downstream and half an equivalent diameter upstream from the nearest flow disturbance such as the control device, point of pollutant generation, or other place where the pollutant concentration or emission rate can change. You may use a half diameter downstream instead of the two diameters if you meet both of the following conditions:
(1) Changes in the pollutant concentration are caused solely by diluent leakage, such as leaks from air heaters.
(2) You measure pollutants and diluents simultaneously at the same locations.
8.2.5 Traverse Points. Select traverse points that ensure representative samples. Conduct all RM tests within 3 cm of each selected traverse point but no closer than 3 cm to the stack or duct wall. The minimum requirement for traverse points are as follows:
(1) Establish a measurement line across the stack that passes through the center and in the direction of any expected stratification.
(2) Locate a minimum of three traverse points on the line at 16.7, 50.0, and 83.3 percent of the stack inside diameter.
(3) Alternatively, if the stack inside diameter is greater than 2.4 meters, you may locate the three traverse points on the line at 0.4, 1.2, and 2.0 meters from the stack or duct wall. You may not use this alternative option after wet scrubbers or at points where two streams with different pollutant concentrations are combined. You may select different traverse points if you demonstrate and provide verification that it provides a representative sample. You may also use the traverse point specifications given the RM.
8.2.6 Relative Accuracy Procedure. Perform the number of RA tests at the levels required in sections 8.2.2 and 8.2.3. For integrated samples (e.g., Method 3A or 7E), make a sample traverse of at least 21 minutes, sampling for 7 minutes at each traverse point. For grab samples (e.g., Method 3 or 7), take one sample at each traverse point, scheduling the grab samples so that they are taken simultaneously (within a 3-minute period) or at an equal interval of time apart over a 21-minute period. A test run for grab samples must be made up of at least three separate measurements. Where multiple fuels are used in the monitored unit and the fuel type affects the predicted emissions, determine a RA for each fuel unless the effects of the alternative fuel on predicted emissions or diluent were addressed in the model training process. The unit may only use fuels that have been evaluated this way.
8.2.7 Correlation of RM and PEMS Data. Mark the beginning and end of each RM test run (including the exact time of day) on the permanent record of PEMS output. Correlate the PEMS and the RM test data by the time and duration using the following steps:
A. Determine the integrated pollutant concentration for the PEMS for each corresponding RM test period.
B. Consider system response time, if important, and confirm that the pair of results is on a consistent moisture, temperature, and diluent concentration basis.
C. Compare each average PEMS value to the corresponding average RM value. Use the following guidelines to make these comparisons.
If . . . | Then . . . | And then . . . |
---|---|---|
The RM has an instrumental or integrated non-instrumental sampling technique | Directly compare RM and PEMS results | |
The RM has a grab sampling technique | Average the results from all grab samples taken during the test run. The test run must include ≥3 separate grab measurements | Compare this average RM result with the PEMS result obtained during the run. |
Use the paired PEMS and RM data and the equations in section 12.2 to calculate the RA in the units of the applicable emission standard. For this 3-level RA test, calculate the RA at each operation level.
8.3 Statistical Tests for PEMS that are Used for Continual Compliance. In addition to the RA determination, evaluate the paired RA and PEMS data using the following statistical tests.
8.3.1 Bias Test. From the RA data taken at the mid-level, determine if a bias exists between the RM and PEMS. Use the equations in section 12.3.1.
8.3.2 F-test. Perform a separate F-test for the RA paired data from each operating level to determine if the RM and PEMS variances differ by more than might be expected from chance. Use the equations in section 12.3.2.
8.3.3 Correlation Analysis. Perform a correlation analysis using the RA paired data from all operating levels combined to determine how well the RM and PEMS correlate. Use the equations in section 12.3.3. The correlation is waived if the process cannot be varied to produce a concentration change sufficient for a successful correlation test because of its technical design. In such cases, should a subsequent RATA identify a variation in the RM measured values by more than 30 percent, the waiver will not apply, and a correlation analysis test must be performed at the next RATA.
8.4 Reporting. Summarize in tabular form the results of the RA and statistical tests. Include all data sheets, calculations, and charts (records of PEMS responses) necessary to verify that your PEMS meets the performance specifications. Include in the report the documentation used to establish your PEMS parameter envelopes.
8.5 Reevaluating Your PEMS After a Failed Test, Change in Operations, or Change in Critical PEMS Parameter. After initial certification, if your PEMS fails to pass a quarterly RAA or yearly RATA, or if changes occur or are made that could result in a significant change in the emission rate (e.g., turbine aging, process modification, new process operating modes, or changes to emission controls), your PEMS must be recertified using the tests and procedures in section 8.1. For example, if you initially developed your PEMS for the emissions unit operating at 80-100 percent of its range, you would have performed the initial test under these conditions. Later, if you wanted to operate the emission unit at 50-100 percent of its range, you must conduct another RA test and statistical tests, as applicable, to verify that the new conditions of 50-100 percent of range are functional. These tests must demonstrate that your PEMS provides acceptable data when operating in the new range or with the new critical PEMS parameter(s). The requirements of section 8.1 must be completed by the earlier of 60 unit operating days or 180 calendar days after the failed RATA or after the change that caused a significant change in emission rate.
9.0 Quality ControlYou must incorporate a QA plan beyond the initial PEMS certification test to verify that your system is generating quality-assured data. The QA plan must include the components of this section.
9.1 QA/QC Summary. Conduct the applicable ongoing tests listed below.
Ongoing Quality Assurance Tests
Test | PEMS regulatory purpose |
Acceptability | Frequency |
---|---|---|---|
Sensor Evaluation | All | Daily. | |
RAA | Compliance | 3-test avg ≤10% of simultaneous analyzer or RM average | Each quarter except quarter when RATA performed. |
RATA | All | Same as for RA in Sec. 13.1 | Yearly in quarter when RAA not performed. |
Bias Correction | All | If davg ≤ |cc| | Bias test passed (no correction factor needed). |
PEMS Training | All | If Fcritical ≥F r ≥0.8 |
Optional after initial and subsequent RATAs. |
Sensor Evaluation Alert Test (optional) | All | See Section 6.1.8 | After each PEMS training. |
9.2 Daily Sensor Evaluation Check. Your sensor evaluation system must check the integrity of each PEMS input at least daily.
9.3 Quarterly Relative Accuracy Audits. In the first year of operation after the initial certification, perform a RAA consisting of at least three 30-minute portable analyzer or RM determinations each quarter a RATA is not performed. To conduct a RAA, follow the procedures in Section 8.2 for the relative accuracy test, except that only three sets of measurement data are required, and the statistical tests are not required. The average of the three or more portable analyzer or RM determinations must not exceed the limits given in Section 13.5. Report the data from all sets of measurement data. If a PEMS passes all quarterly RAAs in the first year and also passes the subsequent yearly RATA in the second year, you may elect to perform a single mid-year RAA in the second year in place of the quarterly RAAs. This option may be repeated, but only until the PEMS fails either a mid-year RAA or a yearly RATA. When such a failure occurs, you must resume quarterly RAAs in the quarter following the failure and continue conducting quarterly RAAs until the PEMS successfully passes both a year of quarterly RAAs and a subsequent RATA.
9.4 Yearly Relative Accuracy Test. Perform a minimum 9-run RATA at the normal operating level on a yearly basis in the quarter that the RAA is not performed. The statistical tests in Section 8.3 are not required for the yearly RATA.
10.0 Calibration and Standardization [Reserved] 11.0 Analytical Procedure [Reserved] 12.0 Calculations and Data Analysis 12.1 Nomenclature B = PEMS bias adjustment factor. cc = Confidence coefficient. di = Difference between each RM and PEMS run. d = Arithmetic mean of differences for all runs. ei = Individual measurement provided by the PEMS or RM at a particular level. em = Mean of the PEMS or RM measurements at a particular level. ep = Individual measurement provided by the PEMS. ev = Individual measurement provided by the RM. F = Calculated F-value. n = Number of RM runs. PEMSi = Individual measurement provided by the PEMS. PEMSiAdjusted = Individual measurement provided by the PEMS adjusted for bias. PEMS = Mean of the values provided by the PEMS at the normal operating range during the bias test. r = Coefficient of correlation. RA = Relative accuracy. RAA = Relative accuracy audit. RM = Average RM value (or in the case of the RAA, the average portable analyzer value). In cases where the average emissions for the test are less than 50 percent of the applicable standard, substitute the emission standard value here in place of the average RM value. Sd = Standard deviation of differences. S 2 = Variance of your PEMS or RM. t0.025 = t-value for a one-sided, 97.5 percent confidence interval (see Table 16-1).12.2 Relative Accuracy Calculations. Calculate the mean of the RM values. Calculate the differences between the pairs of observations for the RM and the PEMS output sets. Finally, calculate the mean of the differences, standard deviation, confidence coefficient, and PEMS RA, using Equations 16-1, 16-2, 16-3, and 16-4, respectively. For compliance PEMS, calculate the RA at each test level. The PEMS must pass the RA criterion at each test level.
12.2.1 Arithmetic Mean. Calculate the arithmetic mean of the differences between paired RM and PEMS observations using Equation 16-1.
12.2.2 Standard Deviation. Calculate the standard deviation of the differences using Equation 16-2 (positive square root).
12.2.3 Confidence Coefficient. Calculate the confidence coefficient using Equation 16-3 and Table 16-1 for n−1 degrees of freedom.
12.2.4 Relative Accuracy. Calculate the RA of your data using Equation 16-4.
12.3 Compliance PEMS Statistical Tests. If your PEMS will be used for continual compliance purposes, conduct the following tests using the information obtained during the RA tests. For the pollutant measurements at any one test level, if the mean value of the RM is less than either 10 ppm or 5 percent of the emission standard, all statistical tests are waived at that specific test level. For diluent measurements at any one test level, if the mean value of the RM is less than 3 percent of span, all statistical tests are waived for that specific test level.
12.3.1 Bias Test. Conduct a bias test to determine if your PEMS is biased relative to the RM. Determine the PEMS bias by comparing the confidence coefficient obtained from Equation 16-3 to the arithmetic mean of the differences determined in Equation 16-1. If the arithmetic mean of the differences (d ) is greater than the absolute value of the confidence coefficient (cc), your PEMS must incorporate a bias factor to adjust future PEMS values as in Equation 16-5.
Where:12.3.2 F-test. Conduct an F-test for each of the three RA data sets collected at different test levels. Calculate the variances of the PEMS and the RM using Equation 16-6.
Determine if the variance of the PEMS data is significantly different from that of the RM data at each level by calculating the F-value using Equation 16-7. Compare the calculated F-value with the critical value of F at the 95 percent confidence level with n-1 degrees of freedom. The critical value is obtained from Table 16-2 or a similar table for F-distribution. If the calculated F-value is greater than the critical value at any level, your proposed PEMS is unacceptable. For pollutant PEMS measurements, if the standard deviation of the RM is less than either 3 percent of the span or 5 ppm, use a RM standard deviation of either 5 ppm or 3 percent of span. For diluent PEMS measurements, if the standard deviation of the reference method is less than 3 percent of span, use a RM standard deviation of 3 percent of span.12.3.3 Correlation Analysis. Calculate the correlation coefficient either manually using Eq. 16-8, on a graph, or by computer using all of the paired data points from all operating levels. Your PEMS correlation must be 0.8 or greater to be acceptable. If during the initial certification test, your PEMS data are determined to be auto-correlated according to the procedures in 40 CFR 75.41(b)(2), or if the signal-to-noise ratio of the data is less than 4, then the correlation analysis is permanently waived.
12.4 Relative Accuracy Audit. Calculate the quarterly RAA using Equation 16-9.

13.1 PEMS Relative Accuracy. The RA must not exceed 10 percent if the PEMS measurements are greater than 100 ppm or 0.2 lbs/mm Btu. The RA must not exceed 20 percent if the PEMS measurements are between 100 ppm (or 0.2 lb/mm Btu) and 10 ppm (or 0.05 lb/mm Btu). For measurements below 10 ppm, the absolute mean difference between the PEMS measurements and the RM measurements must not exceed 2 pppm. For diluent PEMS, an alternative criterion of ±1 percent absolute difference between the PEMS and RM may be used if less stringent.
13.2 PEMS Bias. Your PEMS data is considered biased and must be adjusted if the arithmetic mean (d) is greater than the absolute value of the confidence coefficient (cc) in Equations 16.1 and 16.3. In such cases, a bias factor must be used to correct your PEMS data.
13.3 PEMS Variance. Your calculated F-value must not be greater than the critical F-value at the 95-percent confidence level for your PEMS to be acceptable.
13.4 PEMS Correlation. Your calculated r-value must be greater than or equal to 0.8 for your PEMS to be acceptable.
13.5 Relative Accuracy Audits. The average of the three portable analyzer or RM determinations must not differ from the simultaneous PEMS average value by more than 10 percent of the analyzer or RM for concentrations greater than 100 ppm or 20 percent for concentrations between 100 and 20 ppm, or the test is failed. For measurements at 20 ppm or less, this difference must not exceed 2 ppm for a pollutant PEMS and 1 percent absolute for a diluents PEMS.
14.0 Pollution Prevention [Reserved] 15.0 Waste Management [Reserved] 16.0 References [Reserved] 17.0 Tables, Diagrams, Flowcharts, and Validation DataTable 16-1 - t-Values for One-sided, 97.5 Percent Confidence Intervals for Selected Sample Sizes *
n−1 * | t-value | n−1 | t-value |
---|---|---|---|
1 | 12.706 | 15 | 2.131 |
2 | 4.303 | 16 | 2.120 |
3 | 3.182 | 17 | 2.110 |
4 | 2.776 | 18 | 2.101 |
5 | 2.571 | 19 | 2.093 |
6 | 2.447 | 20 | 2.086 |
7 | 2.365 | 21 | 2.080 |
8 | 2.306 | 22 | 2.074 |
9 | 2.262 | 23 | 2.069 |
10 | 2.228 | 24 | 2.064 |
11 | 2.201 | 25 | 2.060 |
12 | 2.179 | 26 | 2.056 |
13 | 2.160 | 27 | 2.052 |
14 | 2.145 | >28 | t-Table |
* The value n is the number of RM runs; n−1 equals the degrees of freedom.
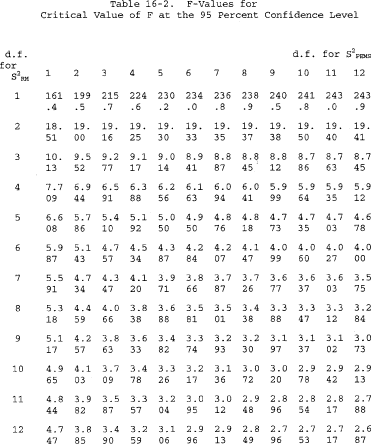
1.1 Analyte. This performance specification (PS) is applicable for measuring gaseous concentrations of hydrogen chloride (HCl), CAS: 7647-01-0, on a continuous basis in the units of the applicable standard or in units that can be converted to units of the applicable standard(s).
1.2 Applicability.
1.2.1 This specification is used to evaluate the acceptability of HCl continuous emission monitoring systems (CEMS) at the time of installation or soon after and whenever specified in the regulations. The specification includes requirements for initial acceptance including instrument accuracy and stability assessments and use of audit samples if they are available.
1.2.2 The Administrator may require the operator, under section 114 of the Clean Air Act, to conduct CEMS performance evaluations at other times besides the initial test to evaluate the CEMS performance. See 40 CFR part 60, §§ 60.13(c) and 63.8(e)(1).
1.2.3 A source that demonstrates their CEMS meets the criteria of this PS may use the system to continuously monitor gaseous HCl under any regulation or permit that requires compliance with this PS. If your CEMS is capable of reporting the HCl concentration in the units of the applicable standard, no additional CEMS components are necessary. If your CEMS does not report concentrations in the units of the existing standard, then other CEMS components (e.g., oxygen (O2), temperature, stack gas flow, moisture and pressure) may be necessary to convert the units reported by your CEMS to the units of the standard.
1.2.4 These specification test results are intended to be valid for the life of the system. As a result, the HCl measurement system must be tested and operated in a configuration consistent with the configuration that will be used for ongoing continuous emissions monitoring.
1.2.5 Substantive changes to the system configuration require retesting according to this PS. Examples of such conditions include, but are not limited to: major changes in dilution ratio (for dilution based systems); changes in sample conditioning and transport, if used, such as filtering device design or materials; changes in probe design or configuration and changes in materials of construction. Changes consistent with instrument manufacturer upgrade that fall under manufacturer's certification do not require additional field verification. Manufacturer's upgrades require recertification by the manufacturer for those requirements allowed by this PS, including interference, level of detection (LOD), and light intensity qualification.
1.2.6 This specification is not designed to evaluate the ongoing CEMS performance nor does it identify specific calibration techniques and auxiliary procedures to assess CEMS performance over an extended period of time. The requirements in appendix F, Procedure 6 are designed to provide a way to assess CEMS performance over an extended period of time. The source owner or operator is responsible to calibrate, maintain, and operate the CEMS properly.
2.0 Summary of Performance Specification2.1 This specification covers the procedures that each CEMS must meet during the performance evaluation test. Installation and measurement location specifications, data reduction procedures, and performance criteria are included.
2.2 The technology used to measure gaseous HCl must provide a distinct response and address any appropriate interference correction(s). It must accurately measure gaseous HCl in a representative sample (path or point sampling) of stack effluent.
2.3 The relative accuracy (RA) must be established against a reference method (RM) (e.g., Method 26A, Method 320, ASTM International (ASTM) D6348-12, including mandatory annexes, or Method 321 for Portland cement plants as specified by the applicable regulation or, if not specified, as appropriate for the source concentration and category). Method 26 may be approved as a RM by the Administrator on a case-by-case basis if not otherwise allowed or denied in an applicable regulation.
2.4 A standard addition (SA) procedure using a reference standard is included in appendix A to this performance specification for use in verifying LOD. For extractive CEMS, where the SA is done by dynamic spiking (DS), the appendix A procedure is allowed as an option for assessing calibration drift and is also referenced by Procedure 6 of appendix F to this part for ongoing quality control tests.
3.0 Definitions3.1 Beam attenuation is the reduction in electromagnetic radiation (light) throughput from the maximum beam intensity experienced during site specific CEMS operation.
3.2 Beam intensity is the electromagnetic radiation (light) throughput for an IP-CEMS instrument measured following manufacturers specifications.
3.3 Calibration cell means a gas containment cell used with cross stack or integrated path (IP) CEMS for calibration and to perform many of the test procedures required by this performance specification. The cell may be a removable sealed cell or an evacuated and/or purged cell capable of exchanging reference and other calibration gases as well as zero gas standards. When charged, it contains a known concentration of HCl and/or interference gases. The calibration cell is filled with zero gas or removed from the optical path during stack gas measurement.
3.4 Calibration drift (CD) means the absolute value of the difference between the CEMS output response and an upscale reference gas or a zero-level gas, expressed as a percentage of the span value, when the CEMS is challenged after a stated period of operation during which no unscheduled adjustments, maintenance or repairs took place.
3.5 Centroidal area means a central area that is geometrically similar to the stack or duct cross section and is no greater than 10 percent of the stack or duct cross-sectional area.
3.6 Continuous Emission Monitoring System (CEMS) means the total equipment required to measure the pollutant concentration or emission rate continuously. The system generally consists of the following three major subsystems:
3.6.1 Sample interface means that portion of the CEMS used for one or more of the following: Sample acquisition, sample transport, sample conditioning, defining the optical measurement path, and protection of the monitor from the effects of the stack effluent.
3.6.2 HCl analyzer means that portion of the HCl CEMS that measures the total vapor phase HCl concentration and generates a proportional output.
3.6.3 Data recorder means that portion of the CEMS that provides a permanent electronic record of the analyzer output. The data recorder may record other pertinent data such as effluent flow rates, various instrument temperatures or abnormal CEMS operation. The data recorder may also include automatic data reduction capabilities and CEMS control capabilities.
3.7 Diluent gas means a major gaseous constituent in a gaseous pollutant mixture. For combustion sources, either carbon dioxide (CO2) or oxygen (O2) or a combination of these two gases are the major gaseous diluents of interest.
3.8 Dynamic spiking (DS) means the procedure where a known concentration of HCl gas is injected into the probe sample gas stream for extractive CEMS at a known flow rate to assess the performance of the measurement system in the presence of potential interference from the flue gas sample matrix.
3.9 Independent measurement(s) means the series of CEMS data values taken during sample gas analysis separated by two times the procedure specific response time (RT) of the CEMS.
3.10 Integrated path CEMS (IP-CEMS) means an in-situ CEMS that measures the gas concentration along an optical path in the stack or duct cross section.
3.11 Interference means a compound or material in the sample matrix other than HCl whose characteristics may bias the CEMS measurement (positively or negatively). The interference may not prevent the sample measurement, but could increase the analytical uncertainty in the measured HCl concentration through reaction with HCl or by changing the electronic signal generated during HCl measurement.
3.12 Interference test means the test to detect CEMS responses to interferences that are not adequately accounted for in the calibration procedure and may cause measurement bias.
3.13 Level of detection (LOD) means the lowest level of pollutant that the CEMS can detect in the presence of the source gas matrix interferents with 99 percent confidence.
3.14 Liquid evaporative standard means a reference gas produced by vaporizing National Institute of Standards and Technology (NIST) traceable liquid standards of known HCl concentration and quantitatively diluting the resultant vapor with a carrier gas.
3.15 Measurement error (ME) is the mean difference between the concentration measured by the CEMS and the known concentration of a reference gas standard, divided by the span, when the entire CEMS, including the sampling interface, is challenged.
3.16 Optical path means the route light travels from the light source to the receiver used to make sample measurements.
3.17 Path length means, for an extractive optical CEMS, the distance in meters of the optical path within a gas measurement cell. For an IP-CEMS, path length means the distance in meters of the optical path that passes through the source gas in the stack or duct.
3.18 Point CEMS means a CEMS that measures the source gas concentration, either at a single point at the sampling probe tip or over a path length for IP-CEMS less than 10 percent of the equivalent diameter of the stack or duct cross section.
3.19 Stack pressure measurement device means a NIST-traceable gauge or monitor that measures absolute pressure and conforms to the design requirements of ASME B40.100-2010, “Pressure Gauges and Gauge Attachments” (incorporated by reference - see § 60.17).
3.20 Reference gas standard means a NIST-traceable gas standard containing a known concentration of HCl certified in accordance with an EPA traceability protocol in section 7.1 of this PS.
3.21 Relative accuracy (RA) means the absolute mean difference between the gas concentration or the emission rate determined by the CEMS and the value determined by the RM, plus the confidence coefficient of a series of nine test runs, divided by the average of the RM or the applicable emission standard.
3.22 Response time (RT) means the time it takes for the measurement system, while operating normally at its target sample flow rate, dilution ratio, or data collection rate to respond to a known step change in gas concentration, either from a low- or zero-level to a high-level gas concentration or from a high-level to a low or zero-level gas concentration, and to read 95 percent of the change to the stable instrument response. There may be several RTs for an instrument related to different functions or procedures (e.g., DS, LOD, and ME).
3.23 Span value means an HCl concentration approximately equal to two times the concentration equivalent to the emission standard unless otherwise specified in the applicable regulation, permit or other requirement. Unless otherwise specified, the span may be rounded up to the nearest multiple of 5.
3.24 Standard addition means the addition of known amounts of HCl gas (either statically or dynamically) to the actual measurement path or measured sample gas stream.
3.25 Zero gas means a gas or liquid with an HCl concentration that is below the LOD of the measurement system.
4.0 InterferencesSample gas interferences will vary depending on the instrument or technology used to make the measurement. Interferences must be evaluated through the interference test in this PS. Several compounds including carbon dioxide (CO2), carbon monoxide (CO), formaldehyde (CH2O), methane (CH4), and water (H2O) are potential optical interferences with certain types of HCl monitoring technology. Ammonia is a potential chemical interference with HCl.
5.0 SafetyThe procedures required under this PS may involve hazardous materials, operations, and equipment. This PS may not address all of the safety issues associated with these procedures. It is the responsibility of the user to establish appropriate safety and health practices and determine the applicable regulatory limitations prior to performing these procedures. The CEMS user's manual and materials recommended by the RM should be consulted for specific precautions to be taken.
6.0 Equipment and SuppliesEquipment and supplies for CEMS will vary depending on the measurement technology and equipment vendors. This section provides a description of the equipment and supplies typically found in one or more types of CEMS.
6.1 Sample Extraction System. The portion of an extractive CEMS that collects and transports the sample to the pressure regulation and sample conditioning module. The extraction system must deliver a representative sample to the measurement instrument. The sample extraction system typically consists of a sample probe and a heated umbilical line.
6.2 Sample Conditioning Module. The portion of an extractive CEMS that removes particulate matter and moisture from the gas stream and provides a sample gas stream to the CEMS analysis module or analyzer. You must keep the particle-free gas sample above the dew point temperature of its components.
6.3 HClAnalyzer. The portion of the CEMS that detects, quantifies and generates an output proportional to the sample gas HCl concentration.
6.4 System Controller. The portion of the CEMS that provides control of the analyzer and other sub-systems (e.g., sample extraction, sample conditioning, reference gas) as necessary for continuous operation and periodic maintenance/QC activities.
6.5 Data Recorder. The portion of the CEMS that provides a record of analyzer output. The data recorder may record other pertinent data such as effluent flow rates, various instrument temperatures or abnormal CEMS operation. The data recorder output range must include the full range of expected HCl concentration values in the gas stream to be sampled including zero and span value.
6.6 Reference Gas System(s). Gas handling system(s) needed to introduce reference and other gases into the measurement system. For extractive CEMS, the system must be able to introduce gas flow sufficient to flood the sampling probe and prevent entry of gas from the effluent stream. For IP-CEMS, the system must be able to introduce a known concentration of HCl, at known cell length, pressure and temperature, into the optical path used to measure HCl gas concentration.
6.7 Moisture Measurement System. If correction of the measured HCl emissions for moisture is required, you must install, operate, maintain, and quality assure a continuous moisture monitoring system for measuring and recording the moisture content of the flue gases. The following continuous moisture monitoring systems are acceptable: An FTIR system validated according to Method 301 or section 13.0 of Method 320 in appendix A to part 63 of this chapter; a continuous moisture sensor; an oxygen analyzer (or analyzers) capable of measuring O2 both on a wet basis and on a dry basis; a stack temperature sensor and a moisture look-up table, i.e., a psychrometric chart (for saturated gas streams following wet scrubbers or other demonstrably saturated gas streams, only); or other continuous moisture measurement methods approved by the Administrator. Alternatively, for any type of fuel, you may determine an appropriate site-specific default moisture value (or values), using measurements made with Method 4 - Determination of Moisture Content In Stack Gases, in appendix A-3 to of this part. If this option is selected, the site-specific moisture default value(s) must represent the fuel(s) or fuel blends that are combusted in the unit during normal, stable operation, and must account for any distinct difference(s) in the stack gas moisture content associated with different process operating conditions. At least nine Method 4 runs are required for determining each site-specific default moisture percentage. Calculate each site-specific default moisture value by taking the arithmetic average of the Method 4 runs. Each site-specific moisture default value shall be updated whenever the current value is non-representative, due to changes in unit or process operation, but in any event no less frequently than annually.
7.0 Reagents and Standards7.1 Reference Gases. Reference gases (e.g., cylinder gases or liquid evaporative standards) used to meet the requirements of this PS must be NIST certified or NIST-traceable and vendor certified to ±5.0 percent accuracy. HCl cylinder gases must be certified according to Reference 5 in section 16 of this PS through a documented unbroken chain of comparisons each contributing to the reported uncertainty. Liquid evaporative standards must be certified using the gravimetrically-based procedures of the latest version of the EPA Traceability Protocol for Qualification and Certification of Evaporative HCl Gas Standards and Humidification of HCl Gas Standards from Cylinders (see EPA-HQ-OAR-2013-0696-0026.pdf).
7.2 Cylinder gas and/or liquid evaporative standards must be used within their certification periods.
7.3 High concentration cylinder gas or liquid evaporative HCl standards may be diluted for use in this specification. You must document the quantitative introduction of HCl standards into the system using Method 205, found in 40 CFR part 51, appendix M, or other procedure approved by the Administrator.
8.0 CEMS Measurement Location Specifications and Pretest Preparation8.1 Prior to the start of your initial PS tests, you must ensure that the CEMS is installed according to the manufacturer's specifications and the requirements in this section. You may use either point or IP sampling technology.
8.2 CEMS Installation. Install the CEMS at an accessible location where the pollutant concentration or emission rate measurements are directly representative of the HCl emissions or can be corrected so as to be representative of the total emissions from the affected facility. The CEMS need not be installed at the same location as the relative accuracy test location. If you fail the RA requirements in this specification due to the CEMS measurement location and a satisfactory correction technique cannot be established, the Administrator may require the CEMS to be relocated.
8.2.1 Single point sample gas extraction should be (1) no less than 1.0 m (3.3 ft.) from the stack or duct wall or (2) within the centroidal area of the stack or duct cross section.
8.2.2 IP-CEMS measurements should (1) be conducted totally within the inner area bounded by a line 1.0 m (3.3 ft.) from the stack or duct wall, (2) have at least 70 percent of the path within the inner 50 percent of the stack or duct cross-sectional area, or (3) be located over any part of the centroidal area.
8.2.2.1 You must measure the IP-CEMS path length from the inner flange of the sampling ports or the inner end of the instrument insertion into the stack cavity using a laser tape measure, mechanical measurement tape, or similar device accurate to ±1.5 mm (0.059 in).
8.2.2.2 You must ensure that any purge flow used to protect IP-CEMS instrument windows from stack gas does not alter the measurement path length. Purge flow of less than or equal to 10 percent of the gas velocity in the duct meets this requirement.
8.2.3 CEMS and Data Recorder Scale Check. After CEMS installation, record and document the measurement range of the HCl CEMS. The CEMS operating range and the range of the data recording device must encompass all potential and expected HCl concentrations, including the concentration equivalent to the applicable emission limit and the span value.
9.0 Quality Control [Reserved] 10.0 Calibration and Standardization [Reserved] 11.0 Performance Specification Test ProcedureAfter completing the CEMS installation, setup and calibration, you must complete the PS test procedures in this section. You must perform the following procedures and meet the performance requirements for the initial demonstration of your CEMS:
a. Interference Test;
b. Beam Intensity Test (IP-CEMS only);
c. Temperature Verification Procedure (IP-CEMS only);
d. Pressure Verification Procedure (IP-CEMS only);
e. Level of Detection Determination;
f. Response Time Test;
g. Measurement Error Test;
h. Calibration Drift Test; and
i. Relative Accuracy Test.
11.1 Interference Test11.1.1 Prior to its initial use in the field, you must demonstrate that your monitoring system meets the performance requirements of the interference test in section 13.5 to verify that the candidate system measures HCl accurately in the presence of common interferences in emission matrices.
11.1.2 Your interference test must be conducted in a controlled environment. The equipment you test for interference must include the combination of the analyzer, related analysis software, and any sample conditioning equipment (e.g., dilution module, moisture removal equipment or other interferent scrubber) used to control interferents.
11.1.3 If you own multiple measurement systems with components of the same make and model numbers, you need only perform this interference test on one analyzer and associated interference conditioning equipment combination. You may also rely on an interference test conducted by the manufacturer or a continuous measurement system integrator on a system having components of the same make and model(s) of the system that you use.
11.1.4 Perform the interference check using an HCl reference gas concentration of approximately five times the LOD.
11.1.5 Introduce the interference test gases listed in Table 1 in section 17.0 of this PS to the analyzer/conditioning system separately or in any combination. The interference test gases need not be of reference gas quality.
11.1.5.1 For extractive CEMS, the interference test gases may be introduced directly into the inlet to the analyzer/conditioning system after the probe extension coupling.
11.1.5.2 For IP-CEMS, the interference test gases may be added with the HCl in a calibration cell or separately in a temperature-controlled cell. The effective concentration of the gas in the cell must meet the requirements in Table 1 corrected for absolute pressure, temperature and the nominal stack sampling path length of the CEMS.
11.1.6 The interference test must be performed by combining an HCl reference gas with each interference test gas (or gas mixture). You must measure the baseline HCl response, followed by the response after adding the interference test gas(es) while maintaining a constant HCl concentration. You must perform each interference gas injection and evaluation in triplicate.
Note:The baseline HCl gas may include interference gases at concentrations typical of ambient air (e.g., 21 percent O2, 400 parts per million (ppm) CO2, 2 percent H2O), but these concentrations must be brought to the concentrations listed in Table 1 when their interference effects are being evaluated.
11.1.7 You should document the gas volume/rate, temperature, and pressure used to conduct the interference test. A gas blending system or manifold may be used.
11.1.8 Ensure the duration of each interference test is sufficient to condition the HCl measurement system surfaces before a stable measurement is obtained.
11.1.9 Measure the HCl response of the analyzer/sample conditioning system combination to the test gases in ppmv. Record the responses and determine the overall interference response using Table 2 in section 17.0.
11.1.10 For each interference gas (or mixture), calculate the mean difference (ΔMCavg) between the measurement system responses with and without the interference test gas(es) using Equation 1 in section 12.2. Summarize the results following the format contained in Table 2 in section 17.
11.1.11 Calculate the percent interference (I) for the gas runs using Equation 2 in section 12.2.
11.1.12 The total interference response (i.e., the sum of the interference responses of all tested gaseous components) must not exceed the criteria set forth in section 13.5 of this PS.
11.2 Beam Intensity Test for IP-CEMS11.2.1 For IP-CEMS, you must establish the tolerance of your system to beam intensity attenuation.
11.2.1.1 Your beam intensity test may be conducted in either a controlled environment or on-site during initial setup and demonstration of your CEMS.
11.2.1.2 If you have multiple measurement systems with components of the same make and model numbers, you need only perform this attenuation check on one system and you may also rely on an attenuation test conducted by the manufacturer on a system having components of the same make and model(s) of the system that you use.
11.2.2 Insert one or more neutral density filter(s) or otherwise attenuate the beam intensity by a known percentage (e.g., 90 percent of the beam intensity).
11.2.3 Perform a high-level HCl reference gas measurement.
11.2.4 Record and report the attenuated beam intensity, the measured HCl calibration gas concentration at full beam intensity, the measured HCl gas concentration with attenuated beam intensity, and the percent difference between the two HCl measurements with and without attenuation of the beam intensity. The percent difference must not exceed the criteria set forth in section 13.6 of this PS.
11.2.5 In the future, you may not operate your IP-CEMS at a beam intensity lower than that established based on the attenuation used during this test. However, you may repeat the test to establish a lower beam intensity limit or level.
11.3 Temperature Measurement Verification Procedure for IP-CEMS11.3.1 Any measurement instrument or device that is used as a reference in verification of temperature measurement must have an accuracy that is traceable to NIST.
11.3.2 You must verify the temperature sensor used in IP-CEMS measurements on-site as part of the initial installation and verification procedures.
11.3.3 Comparison to Calibrated Temperature Measurement Device.
11.3.3.1 Place the sensor of a calibrated temperature reference device adjacent to the sensor used to measure stack temperature for your IP-CEMS. The calibrated temperature reference device must satisfy the accuracy requirements specified in Table 3 of this PS. The calibrated temperature reference device must also have a range equal to or greater than the range of your IP-CEMS temperature sensor.
11.3.3.2 Allow sufficient time for the response of the calibrated temperature reference device to reach equilibrium. With the process and control device operating under normal conditions, concurrently record the temperatures measured by your IP-CEMS system (Mt) and the calibrated temperature reference device (Vt). You must meet the accuracy requirements specified in section 13.7 of this PS.
11.3.3.3 If your IP-CEMS temperature sensor does not satisfy the accuracy requirement of this PS, check all system components and take any corrective action that is necessary to achieve the required minimum accuracy. Repeat this verification procedure until the accuracy requirement of this specification is satisfied.
11.4 Pressure Measurement Verification Procedure for IP-CEMS11.4.1 For stack pressure measurement verification, you must select a NIST-traceable gauge or monitor that conforms to the design requirements of ASME B40.100-2010, “Pressure Gauges and Gauge Attachments,” (incorporated by reference - see § 60.17) as a reference device.
11.4.2 As an alternative for a calibrated pressure reference device with NIST-traceable accuracy, you may use a water-in-glass U-tube manometer to verify your IP-CEMS pressure measurement equipment, provided there is also an accurate measurement of absolute atmospheric pressure at the manometer location.
11.4.3 Allow sufficient time for the response of the reference pressure measurement device to reach equilibrium. With the process and control device operating under normal conditions, concurrently record the pressures measured by your IP-CEMS system (MP) and the pressure reference device (Vp). You must meet the accuracy requirements specified in section 13.8 of this PS.
11.4.4 If your IP-CEMS pressure sensor does not satisfy the accuracy requirement of this PS, check all system components and take any corrective action that is necessary to achieve the required minimum accuracy. Repeat this verification procedure until the accuracy requirement of this specification is satisfied.
11.5 Level of Detection Determination11.5.1 You must determine the minimum amount of HCl that can be detected above the background in a representative gas matrix.
11.5.2 You must perform the LOD determination in a controlled environment such as a laboratory or manufacturer's facility.
11.5.3 You must add interference gases listed in Table 1 of this PS to a constant concentration of HCl reference gas.
11.5.3.1 You may not use an effective reference HCl gas concentration greater than five times the estimated instrument LOD.
11.5.3.2 For extractive CEMS, inject the HCl and interferents described in section 11.1.5 directly into the inlet to the analyzer.
11.5.3.3 For IP-CEMS, the HCl and interference test gases may be added to a calibration cell or separately in a temperature-controlled cell that is part of the measurement path. The effective concentration of the gas in the cell must meet the requirements in Table 1 corrected for absolute pressure, temperature and the nominal stack sampling path length of the CEMS.
11.5.4 Collect seven or more consecutive measurements separated by twice the RT (described in section 11.6) to determine the LOD.
11.5.5 Calculate the standard deviation of the measured values and define the LOD as three times the standard deviation of these measurements.
11.5.5.1 The LOD for extractive units must be determined and reported in ppmv.
11.5.5.2 The LOD for IP units must be determined and reported on a ppm-meter basis and the site- or installation-specific LOD must be calculated based on the actual measurement path length and gas density of the emissions at the specific site installation in ppmv.
11.5.6 You must verify the controlled environment LOD of section 11.5.2 of this PS for your CEMS during initial setup and field certification testing. You must use the SA procedure in appendix A of this PS with the following exceptions:
11.5.6.1 For the LOD verification in the field, you must make three independent SA measurements spiking the native source concentration by no more than three times the controlled environment LOD concentration determined in section 11.5.5.
11.5.6.2 For extractive CEMS, you must perform the SA as a dynamic spike by passing the spiked source gas sample through all filters, scrubbers, conditioners and other monitoring system components used during normal sampling, and as much of the sampling probe as practical. For IP-CEMS, you must perform the SA procedure by adding or passing a known concentration reference gas into a calibration cell in the optical path of the CEMS; you must also include the source measurement optical path while performing the SA measurement.
11.5.6.3 The amount detected, or standard addition response (SAR), is based on the average difference of the native HCl concentration in the stack or duct relative to the native stack concentration plus the SA. You must be able to detect the effective spike addition (ESA) above the native HCl present in the stack gas matrix. For extractive CEMS, the ESA is calculated using Equation A7 in appendix A of this PS. For IP-CEMS, the ESA is calculated as Ci,eff using Equation 4 of this PS.
11.5.6.4 For extractive CEMS, calculate the SAR using Equation A4 in appendix A of this PS. For IP-CEMS, calculate the SAR using Equation A8.
11.5.6.5 If your system LOD field verification does not demonstrate a SAR greater than or equal to your initial controlled environment LOD, you must increase the SA concentration incrementally and repeat the field verification procedure until the SAR is equal to or greater than LOD. The site-specific standard addition detection level (SADL) is equal to the standard addition needed to achieve the acceptable SAR, and SADL replaces the controlled environment LOD. For extractive CEMS, the SADL is calculated as the ESA using Equation A7 in appendix A of this PS. For IP-CEMS, the SADL is the SA calculated using Equation A8 in appendix A of this PS. As described in section 13.1 of this PS, the LOD or the SADL that replaces an LOD must be less than 20 percent of the applicable emission limit.
11.6 Response Time Determination. You must determine ME-, LOD- and SA-RT11.6.1 For ME- or LOD-RT, start the upscale RT determination by injecting zero gas into the measurement system as required by the procedures in section 11.7 or 11.5, respectively. You may use humidified zero gas. For standard addition RT, start the upscale RT determination by measuring the native stack gas concentration of HCl.
11.6.1.1 For extractive CEMS measuring ME- or LOD-RT, the output has stabilized when there is no change greater than 1.0 percent of full scale for 30 seconds.
11.6.1.2 For standard addition RT that includes the stack gas matrix the final stable response may continue to vary by more than 1 percent, but may be considered stable if the variability is random and not continuously rising or falling.
11.6.2 When the CEMS output has stabilized, record the response in ppmv and introduce an upscale (high level) or spike reference gas as required by the relevant procedure.
11.6.3 Record the time (upscale RT) required to reach 95 percent of the change to the final stable value.
11.6.4 Next, for ME or LOD RT, reintroduce the zero gas and record the time required to reach 95 percent of the change to the stable instrument response at the zero gas reading. For SA RT, introduce zero gas to the IP-CEMS cell or stop the spike gas flow to the extractive CEMS as required by the specified procedure and record the time required to reach 95 percent of the change to the stable instrument response of the native gas reading. This time is the downscale RT.
(Note: For CEMS that perform a series of operations (purge, blow back, sample integration, analyze, etc.), you must start adding reference or zero gas immediately after these procedures are complete.)
11.6.5 Repeat the entire procedure until you have three sets of data, then determine the mean upscale and mean downscale RTs for each relevant procedure. Report the greater of the average upscale or average downscale RTs as the RT for the system.
11.7 Measurement Error (ME) Test11.7.1 On the same day and as close in time as practicable to when the ME test is conducted, perform and meet requirements for a calibration drift (CD) test using a zero gas as used in the Seven-Day Drift Test (see section 11.8) and document and report the results. To meet this requirement, the ME test may be conducted during the Seven-Day CD Test.
11.7.2 Extractive CEMS ME Test.
11.7.2.1 Introduce reference gases to the CEMS probe, prior to the sample conditioning and filtration system.
11.7.2.2 Measure three upscale HCl reference gas concentrations in the range shown in Table 4 of this PS.
11.7.2.3 Introduce the gases into the sampling probe with sufficient flow rate to replace the entire source gas sample.
11.7.2.4 Continue to add the reference gas until the response is stable as evidenced when the difference between two consecutive measurements is less than the LOD or within five percent of each other.
11.7.2.5 Make triplicate measurements for each reference gas for a total of nine measurements. Introduce different reference gas concentrations in any order but do not introduce the same gas concentration twice in succession.
11.7.2.6 At each reference gas concentration, determine the average of the three CEMS responses (MCl). Calculate the ME using Equation 3A in section 12.3.
11.7.2.7 If you desire to determine the system RT during this test, you must inject zero gas immediately before and after each injection of the high-level gas standard.
11.7.2.8 For non-dilution systems, you may adjust the system to maintain the correct flow rate at the analyzer during the test, but you may not make adjustments for any other purpose. For dilution systems, you must operate the measurement system at the appropriate dilution ratio during all system ME checks, and you may make only the adjustments necessary to maintain the proper ratio.
11.7.3 IP-CEMS ME Test.
11.7.3.1 Conduct a 3-level system ME test by individually adding the known concentrations of HCl reference gases into a calibration cell of known volume, temperature, pressure and path length.
Note: The optical path used for IP-CEMS ME checks must include the native HCl measurement path. You must also collect native stack concentration HCl measurements before and after each HCl standard measurement. Bracketing HCl reference gas measurements with native stack HCl measurements must be used in the calculations in Equation 5 in section 12.4.2 to correct the upscale measurements for stack gas HCl concentration changes.
11.7.3.2 Introduce HCl reference gas into your calibration cell in a range of concentrations that produce responses equivalent to the source concentrations shown in Table 4 of this PS for your path length.
11.7.3.3 Make triplicate measurements for each reference gas standard for a total of nine measurements. Introduce different calibration concentrations in any order but do not introduce the same reference gas concentration twice in succession.
11.7.3.4 You must calculate the effective concentration (Ci,eff) of the HCl reference gas equivalent to the stack concentration by correcting for calibration cell temperature, pressure, path length, line strength factor (LSF) and, if necessary, the native stack gas HCl concentration using Equation 4 in section 12.0.
11.7.3.5 You may use the LSF provided by your instrument manufacturer or determine an instrument-specific LSF as a function of temperature using a heated gas cell and equivalent concentrations (Ci,eff) between 50 and 150 percent of the emission limit.
11.7.3.6 At each reference gas concentration, average the three independent CEMS measurement responses corrected for native HCl stack concentration. Calculate the ME using Equation 6A in section 12.4.3.
11.7.4 You may use Figure 1 in section 17.0 to record and report your ME test results.
11.7.5 If the ME specification in section 13.3 is not met for all three reference gas concentrations, take corrective action and repeat the test until an acceptable 3-level ME test is achieved.
11.8 Seven-Day Calibration Drift (CD) Test11.8.1 The CD Test Period. Prior to the start of the RA tests, you must perform a seven-day CD test. The purpose of the seven-day CD test is to verify the ability of the CEMS to maintain calibration for each of seven consecutive unit operating days as specified in section 11.8.5 of this PS.
11.8.2 The CD tests must be performed using the zero gas and mid-level reference gas standards as defined in Table 4 of this PS.
11.8.3 Conduct the CD test on each day during continuous operation of the CEMS and normal facility operations following the procedures in section 11.7 of this PS, except that the zero gas and mid-level gas need only be introduced to the measurement system once each.
11.8.4 If periodic automatic or manual adjustments are made to the CEMS zero and upscale response factor settings, conduct the CD test immediately before these adjustments.
Note:Automatic signal or mathematical processing of all measurement data to determine emission results may be performed throughout the entire CD process.
11.8.5 Determine the magnitude of the CD at approximately 24-hour intervals, for 7 consecutive unit operating days. The 7 consecutive unit operating days need not be 7 consecutive calendar days.
11.8.6 Record the CEMS response for single measurements of zero gas and mid-level reference gas. You may use Figure 2 in section 17 of this PS to record and report the results of your 7-day CD test.
11.8.6.1 For extractive CEMS, calculate the CD using Equation 3B in section 12.3. Report the absolute value of the differences as a percentage of the span value.
11.8.6.2 For IP-CEMS, you must include the source measurement optical path while performing the upscale CD measurement; you may exclude the source measurement optical path when determining the zero gas concentration. Calculate the CD for IP CEMS using equations 4, 5, 6B, and 7 in section 12.4.
11.8.7 The zero-level and mid-level CD for each day must be less than 5.0 percent of the span value as specified in section 13.2 of this PS. You must meet this criterion for 7 consecutive operating days.
11.8.8 Dynamic Spiking Option for Seven-Day CD Test. For extractive CEMS, you have the option to conduct a mid-level dynamic spiking procedure for each of the 7 days in lieu of the mid-level reference gas injection described in sections 11.8.2 and 11.8.3. If this option is selected, the daily zero CD check is still required.
11.8.8.1 To conduct each of the seven daily mid-level dynamic spikes, you must use the DS procedure described in appendix A of this PS using a single spike of the mid-level reference gas (see Table 4).
11.8.8.2 You must perform the dynamic spike procedure by passing the spiked source gas sample through all filters, scrubbers, conditioners and other monitoring system components used during normal sampling, and as much of the sampling probe as practical.
11.8.8.3 Calculate the mid-level CD as a percent of span using Equation A6 of appendix A to this PS and calculate the zero drift using Equation 3B in section 12.3. Record and report the results as described in sections 11.8.6 and 11.8.7.
11.9 Relative Accuracy Test11.9.1 Unless otherwise specified in an applicable regulation, use Method 26A in 40 CFR part 60, appendix A-8, Method 320 in 40 CFR part 63, appendix A, or ASTM D6348-12 including all annexes, as applicable, as the RMs for HCl measurement. Obtain and analyze RM audit samples, if they are available, concurrently with RM test samples according to the same procedure specified for performance tests in the general provisions of the applicable part. If Method 26 is not specified in an applicable subpart of the regulations, you may request approval to use Method 26 in appendix A-8 to this part as the RM on a site-specific basis under §§ 63.7(f) or 60.8(b). Other RMs for moisture, O2, etc., may be necessary. Conduct the RM tests in such a way that they will yield results representative of the emissions from the source and can be compared to the CEMS data.
11.9.1.1 When Method 26A is used as the RM, you must sample sufficient gas to reach three times your method detection limit for Method 26A in 40 CFR part 60, appendix A-8, or for a minimum of one hour, whichever is greater.
11.9.1.2 When Method 320 or Method 321, both found in 40 CFR part 63, appendix A, or ASTM D6348-12, are used as the RM, you must collect gas samples that are at stack conditions (hot and wet) and you must traverse as required in section 11.9.3.
11.9.2 Conduct the diluent (if applicable), moisture (if needed), and pollutant measurements simultaneously. However, diluent and moisture measurements that are taken within an hour of the pollutant measurements may be used to calculate dry pollutant concentration and emission rates.
11.9.3 Reference Method Measurement Location and Traverse Point(s) Selection.
11.9.3.1 Measurement Location. Select, as appropriate, an accessible RM measurement location at least two equivalent diameters downstream from the nearest control device, point of pollutant generation, or other point at which a change in the pollutant concentration or emission rate may occur, and at least one half equivalent diameter upstream from the effluent exhaust or a control device. When pollutant concentration changes are due solely to diluent leakage (e.g., air heater leakages) and pollutants and diluents are simultaneously measured at the same location, a half diameter may be used in lieu of two equivalent diameters. The equivalent duct diameter is calculated according to Method 1 in appendix A-1 to this part. The CEMS and RM sampling locations need not be the same.
11.9.3.2 Traverse Point Selection. Select traverse points that assure acquisition of representative RM samples over the stack or duct cross section according to one of the following options: (a) sample at twelve traverse points located according to section 11.3 of Method 1 in appendix A-1 to this part, (b) sample at 6 Method 1 traverse points according to section 6.5.6(b)(1) of appendix A to part 75 of this chapter, or (c) sample at three points on a measurement line (“3-point long line”) that passes through the centroidal area of the duct in the direction of any potential stratification. If this line interferes with the CEMS measurements, you may displace the line up to 20 cm (12 in.) or 5.0 percent of the equivalent diameter of the cross section, whichever is less, from the centroidal area. Locate the three traverse points at 16.7, 50.0, and 83.3 percent of the measurement line. Alternatively, you may conduct a stratification test following the procedures in sections 11.9.3.2.1 through 11.9.3.2.4 to justify sampling at a single point or three points located on the measurement line at 0.4, 1.2, and 2.0 m from the stack wall (“3-point short line”). Stratification testing must be conducted at the sampling location to be used for the RM measurements during the RA test and must be made during normal facility operating conditions. You must evaluate the stratification by measuring the gas on the same moisture basis as the HCl CEMS (wet or dry). Stratification testing must be repeated for each RA test program to justify single point or “3-point short line” sampling.
11.9.3.2.1 Use a probe of appropriate length to measure the HCl concentration or an alternative analyte, as described in this section, using 12 traverse points located according to section 11.3 of Method 1 in appendix A-1 to 40 CFR part 60 for a circular stack or nine points at the centroids of similarly-shaped, equal area divisions of the cross section of a rectangular stack.
11.9.3.2.2 You may substitute a stratification test for SO2 for the HCl stratification test. If you select this option, you must follow the test procedures in Method 6C of appendix A-4 to 40 CFR part 60 or Method 320 of appendix A of 40 CFR part 63.
11.9.3.2.3 Calculate the mean measured concentration for all sampling points (MNavg).
11.9.3.2.4 Calculate the percent stratification (St) of each traverse point using Equation 8 in section 12.5.
11.9.3.2.5 The gas stream is considered to be unstratified and you may perform the RA testing at a single point that most closely matches the mean if the concentration at each traverse point differs from the mean concentration for all traverse points by: (a) No more than 5.0 percent of the mean concentration; or (b) 0.2 ppm (for HCl) or 3 ppm (for SO2) absolute, whichever is less restrictive.
11.9.3.2.6 If the criterion for single point sampling (5.0 percent, 0.2 ppm for HCl or 3 ppm for SO2 are not met, but the concentration at each traverse point differs from the mean concentration for all traverse points by no more than 10.0 percent of the mean, the gas stream is considered to be minimally stratified, and you may take RA samples using the “3-point short line”. Alternatively, you may use the 3-point short line if each traverse point differs from the mean value by no more than 0.4 ppm (for HCl) or 5 ppm (for SO2).
11.9.3.2.7 If the concentration at any traverse point differs from the mean concentration by more than 10 percent, the gas stream is considered stratified and you must sample using one of the options in section 11.9.3.2 above.
11.9.3.3 Conduct all necessary RM tests within 3 cm (1.2 in.) of the traverse points, but no closer than 3 cm (1.2 in.) to the stack or duct wall.
11.9.4 In order to correlate the CEMS and RM data properly, record the beginning and end of each RM run (including the time of day in hours, minutes, and seconds) using a clock synchronized with the CEM clock used to create a permanent time record with the CEMS output.
11.9.5 You must conduct the RATA during representative process and control operating conditions or as specified in an applicable regulation, permit or subpart.
11.9.6 Conduct a minimum of nine RM test runs. NOTE: More than nine RM test runs may be performed. If this option is chosen, up to three test run results may be excluded so long as the total number of test run results used to determine the CEMS RA is greater than or equal to nine. However, all data must be reported including the excluded test runs.
11.9.7 Analyze the results from the RM test runs using Equations 9-14 in section 12.6. Calculate the RA between the CEMS results and the RM.
11.10 Record Keeping and Reporting11.10.1 For systems that use a liquid evaporative standard generator to deliver HCl reference gas standards, record supporting data for these devices, including liquid feed calibrations, liquid standard concentration(s) and NIST-traceability, feed rate and gas flow calibrations for all diluent and HCl gas flows. All calibrations must include a stated uncertainty, and the combined uncertainty of the delivered HCl reference gas concentration must be calculated and reported.
11.10.2 Record the results of the CD test, the RT test, the ME test, the RA test, and for IP-CEMS, the results of the beam intensity, temperature and pressure verification procedures. Also keep records of the RM and CEMS field data, calculations, and reference gas certifications necessary to confirm that the performance of the CEMS met the performance specifications.
11.10.3 For systems that use Method 205 to prepare HCl reference gas standards, record results of Method 205 performance test field evaluation, reference gas certifications, and gas dilution system calibration.
11.10.4 Record the LOD for the CEMS. For extractive CEMS, record the LOD in ppmv. For IP-CEMS, record the LOD on a ppm-meter basis along with a calculation of the installation specific LOD in ppmv. For both CEMS types, you must also record the field verified SADL.
11.10.5 Record the results of the interference test.
11.10.6 Report the results of all certification tests to the appropriate regulatory agency (or agencies), in hardcopy and/or electronic format, as required by the applicable regulation or permit.
12.0 Calculations and Data Analysis 12.1 Nomenclature Ci = Zero or HCl reference gas concentration used for test i (ppmv); Ci,eff = Equivalent concentration of the reference gas value, Ci, at the specified conditions (ppmv); CC = Confidence coefficient (ppmv); CDextractive = Calibration drift for extractive CEMS (percent); CDIP = Calibration drift for IP-CEMS (percent); CD0 = Calibration drift at zero HCl concentrations for an IP-CEMS (percent); davg = Mean difference between CEMS response and the reference gas (ppmv); di = Difference of CEMS response and the RM value (ppmv); I = Total interference from major matrix stack gases, (percent); LSF = Line strength factor for IP-CEMS instrument specific correction for temperature and gas matrix effects derived from the HITRAN and/or manufacturer specific database (unitless); ΔMCavg = Average of the 3 absolute values of the difference between the measured HCl calibration gas concentrations with and without interference from selected stack gases (ppmv); MCi = Measured HCl reference gas concentration i (ppmv); MCi = Average of the measured HCl reference gas concentration i (ppmv); MCint = Measured HCl concentration of the HCl reference gas plus the individual or combined interference gases (ppmv); MEextractive = Measurement error for extractive CEMS (percent); MEIP = Measurement error for IP-CEMS (percent); MNavg = Average concentration at all sampling points (ppmv); MNbi = Measured native concentration bracketing each calibration check measurement (ppmv); MNi = Measured native concentration for test or run I (ppmv); n = Number of measurements in an average value; Pstack = Absolute stack pressure (mm Hg) Preference = Absolute pressure of the calibration cell for IP-CEMS (mm Hg) PLCell = Path length of IP-CEMS calibration cell (m); PLStack = Path length of IP-CEMS stack optical path (m); RA = Relative accuracy of CEMS compared to a RM (percent); RMi = RM concentration for test run i (ppmv); RMavg = Mean measured RM value (ppmv); S = Span value (ppmv); Sd = Standard deviation of the differences (ppmv); Sti = Stratification at traverse point i (percent); SADL = Standard addition detection level (ppmv); t0.975 = One-sided t-value at the 97.5th percentile obtained from Table 5 in section 17.0 for n-1 measurements; Treference = Temperature of the calibration cell for IP-CEMS (degrees Kelvin); Tstack = Temperature of the stack at the monitoring location for IP-CEM (degrees Kelvin).12.2 Calculate the difference between the measured HCl concentration with and without interferents for each interference gas (or mixture) for your CEMS as:

Calculate the total percent interference as:

12.2.1 Calculate the equivalent concentration Ci,eff using Equation 4:



12.4.1 Calculate the equivalent concentration Ci,eff using Equation 4:

12.4.2 Calculate the average native concentration before and after each calibration check measurement as:

12.4.3 Calculate the ME or CD at concentration i for an IP-CEM as:
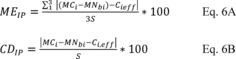

12.4.4 Calculate the zero CD as a percent of span for an IP-CEMS as:


12.6.1 Determine the CEMS final integrated minute average pollutant concentration or emission rate for each RM test period. Consider system RT, if important, and confirm that the results have been corrected to the same moisture, temperature and diluent concentration basis.
12.6.2 When Method 26A (or if approved for use, Method 26), found in 40 CFR part 60, appendix A-8 of this part, is used as the RM, compare each CEMS integrated average value against the corresponding RM value for identical test periods. Make these comparisons on the same basis (e.g., wet, dry, ppmv, or units of the standard). To convert results generate by Method 26A or 26 in mg/DSCM to ppmv, use the conversion factor 0.662 ppm/(mg/DSCM).
12.6.3 If the RM is Method 320 or Method 321, found in 40 CFR part 63, appendix A, or ASTM D6348-12, make a direct comparison of the average RM results and CEMS average value for identical test periods.
12.6.4 For each test run, calculate the arithmetic difference of the RM and CEMS results using Equation 9.

12.6.5 Calculate the standard deviation of the differences (Sd) of the CEMS measured and RM results using Equation 10.

12.6.6 Calculate the confidence coefficient (CC) for the RATA using Equation 11.

12.6.7 Calculate the mean difference (davg) between the RM and CEMS values in the units of ppmv or the emission standard using Equation 12.

12.6.8 Calculate the average RM value using Equation 13.

12.6.9 Calculate RA of the CEMS using Equation 14.

13.1 Level of Detection. You may not use a CEMS whose LOD or SADL is greater than 20 percent of the applicable regulatory limit or other action level for the intended use of the data.
13.2 Calibration Drift. The zero- and mid-level calibration drift for the CEMS must not exceed 5.0 percent of the span value for 7 consecutive operating days.
13.3 Measurement Error. The ME must be less than or equal to 5.0 percent of the span value at the low-, mid-, and high-level reference gas concentrations.
13.4 Relative Accuracy. Unless otherwise specified in an applicable regulation or permit, the RA of the CEMS, whether calculated in units of HCl concentration or in units of the emission standard, must be less than or equal to 20.0 percent of the RM when RMavg is used in the denominator of Equation 14.
13.4.1 In cases where the RA is calculated on a concentration (ppmv) basis, if the average RM emission level for the test is less than 75 percent of the HCl concentration equivalent to the emission standard, you may substitute the HCl concentration equivalent to the standard in the denominator of Equation 14 in place of RMavg.
13.4.2 Similarly, if the RA is calculated in units of the emission standard and the HCl emission level measured by the RMs is less than 75 percent of the emission standard, you may substitute the emission standard in the denominator of Equation 14 in place of RMavg.
13.4.3 The alternative calculated RA in paragraph 13.4.1 or 13.4.2 must be less than or equal to 15.0 percent.
13.5 Interference Test.
13.5.1 The sum of the interference response(s) from Equation 2 must not be greater than 2.5 percent of the calibration span or ±3.0 percent of the equivalent HCl concentration used for the interference test, whichever is less restrictive. The results are also acceptable if the sum of the interference response(s) does not exceed six times the LOD or 0.5 ppmv for a calibration span of 5 to 10 ppm, or 0.2 ppmv for a calibration span of less than 5 ppmv.
13.6 IP-CEMS Beam Intensity Test. For IP-CEMS, the percent difference between the measured concentration with and without attenuation of the light source must not exceed ±3.0 percent.
13.7 IP-CEMS Temperature Measurement Verification. Your temperature sensor satisfies the accuracy required if the absolute relative difference between measured value of stack temperature (Mt) and the temperature value from the calibrated temperature reference device (Vt) is ≤1.0 percent or if the absolute difference between Mt and Vt is ≤2.8 °C (5.0 °F), whichever is less restrictive.
13.8 IP-CEMS Pressure Sensor Measurement Verification. Your pressure sensor satisfies the accuracy required if the absolute relative difference between the measured value of stack pressure (MP) and the pressure value from the calibrated pressure reference device (VP) is ≤5.0 percent or if the absolute difference between Mp and VP is ≤0.12 kilopascals (0.5 inches of water column), whichever is less restrictive.
14.0 Pollution Prevention [Reserved] 15.0 Waste Management [Reserved] 16.0 Bibliography1. Method 318 - Extractive FTIR Method for the Measurement of Emissions From the Mineral Wool and Wool Fiberglass Industries, 40 CFR, part 63, subpart HHHHHHH, appendix A.
2. “EPA Protocol for the Use of Extractive Fourier Transform Infrared (FTIR) Spectrometry in Analyses of Gaseous Emissions from Stationary Industrial Sources,” February, 1995.
3. “Measurement of Gaseous Organic and Inorganic Emissions by Extractive FTIR Spectroscopy,” EPA Contract No. 68-D2-0165, Work Assignment 3-08.
4. “Method 301 - Field Validation of Pollutant Measurement Methods from Various Waste Media,” 40 CFR part 63, appendix A.
5. EPA Traceability Protocol for Assay and Certification of Gaseous Calibration Standards, U.S. Environmental Protection Agency office of Research and Development, EPA/600/R-12/531, May 2012.
17.0 Tables, Diagrams, Flowcharts, and Validation DataTable 1 - Interference Test Gas Concentrations
Potential interferent gas 1 | Approximate concentration (balance N2) |
---|---|
CO2 | 15% ± 1% CO2. 2 |
CO | 100 ± 20 ppm. |
CH2O | 20 ± 5 ppm. |
CH4 | 100 ± 20 ppm. |
NH3 | 10 ± 5 ppm (extractive CEMS only). |
NO | 250 ± 50 ppm. |
SO2 | 200 ± 20 ppm. |
O2 | 3% ± 1% O2. 2 |
H2O | 10% ± 1% H2O. 2 |
N2 | Balance. 2 |
1 Any of these specific gases can be tested at a lower level if the manufacturer has provided reliable means for limiting or scrubbing that gas to a specified level in CEMS field installations.
2 Gases for short path IP cell interference tests cannot be added above 100 percent stack equivalent concentration. Add these gases at the indicated percentages to make up the remaining cell volume.
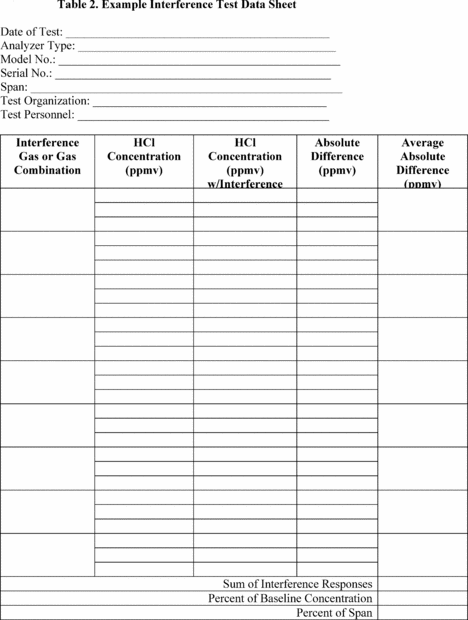
Table 3 - Design Standards for Temperature Sensors
If the sensor is a . . . | You can use the following design standards as guidance in selecting a sensor for your IP-CEMS |
---|---|
1. Thermocouple | a. ASTM E235-88 (1996), “Specification for Thermocouples, Sheathed, Type K, for Nuclear or Other High-Reliability Applications.” |
b. ASTM E585/E585M-04, “Specification for Compacted Mineral-Insulated, Metal-Sheathed, Base Metal Thermocouple Cable.” | |
c. ASTM E608/E608M-06, “Specification for Mineral-Insulated, Metal-Sheathed Base Metal Thermocouples.” | |
d. ASTM E696-07, “Specification for Tungsten-Rhenium Alloy Thermocouple Wire.” | |
e. ASTM E1129/E1129M-98 (2002), “Standard Specification for Thermocouple Connectors.” | |
f. ASTM E1159-98 (2003), “Specification for Thermocouple Materials, Platinum-Rhodium Alloys, and Platinum.” | |
g. ISA-MC96.1-1982, “Temperature Measurement Thermocouples.” | |
2. Resistance temperature detector | ASTM E1137/E1137M-04, “Standard Specification for Industrial Platinum Resistance Thermometers.” |
Table 4 - Performance Specification Test Zero and Reference Gas Ranges
Test | Units | HCl Zero and Reference Gas Concentrations in Terms of Percent of Span a | Section | |||
---|---|---|---|---|---|---|
Zero | Low Level | Mid Level | High Level | |||
Calibration Drift | % of Span | <LOD | NA | 50-60 b | NA | 11.8 |
Measurement Error | % of Span | NA | 20-30 | 50-60 | 80-100 | 11.7 |
a Reference gas concentration must be NIST traceable. (see section 7.1)
b Mid-level is required. For DS calibration drift option, choose a concentration that yields a value in this range at the analyzer.
Table 5 - Student's t-Values
n-1 a | t-value | n-1 a | t-value | n-1 a | t-value |
---|---|---|---|---|---|
1 | 12.71 | 11 | 2.201 | 21 | 2.080 |
2 | 4.303 | 12 | 2.179 | 22 | 2.074 |
3 | 3.182 | 13 | 2.160 | 23 | 2.069 |
4 | 2.776 | 14 | 2.145 | 24 | 2.064 |
5 | 2.571 | 15 | 2.131 | 25 | 2.060 |
6 | 2.447 | 16 | 2.120 | 26 | 2.056 |
7 | 2.365 | 17 | 2.110 | 27 | 2.052 |
8 | 2.306 | 18 | 2.101 | 28 | 2.048 |
9 | 2.262 | 19 | 2.093 | 29 | 2.045 |
10 | 2.228 | 20 | 2.086 | 30 | 2.042 |
a The value n is the number of independent pairs of measurements. Either discrete (independent) measurements in a single run, or run averages can be used.
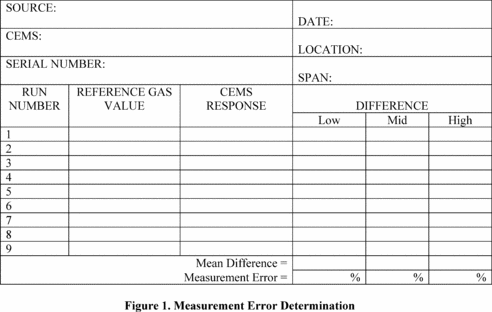
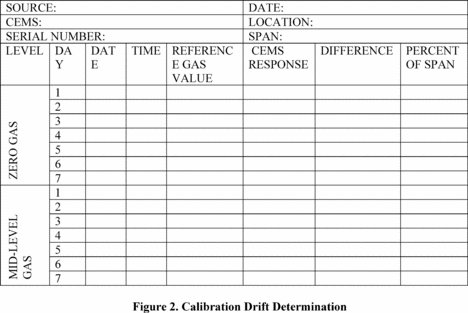
1.1 This appendix to Performance Specification (PS) 18 describes the procedure and performance requirements for standard addition (SA) as a quality check for hydrogen chloride (HCl) continuous emission monitoring systems (CEMS).
1.2 This appendix is applicable to quality checks of both extractive and integrated path (IP) technologies used to measure HCl emissions.
1.3 For extractive CEMS, this procedure must be used, as a level of detection (LOD) verification of all field-installed CEMS. Additionally, it is allowed by Procedure 6 in appendix F to this part as an alternative to upscale calibration drift (CD) tests, cylinder gas audits and relative accuracy audits (RAAs), and may be used for quality assurance purposes under other applicable regulations or permits that require HCl monitoring.
1.4 For IP-CEMS, this procedure must be used as a LOD verification of all field-installed CEMS.
2.0 Summary of the Appendix for Standard AdditionAs used here, SA is a gas phase method of standard additions (either static or dynamic) used to verify the accuracy of CEMS measurements in the presence of the sample matrix. For extractive CEMS, it consists of spiking a known quantity of HCl dynamically into the measurement system as an addition to the native HCl and the native source gas matrix. For IP-CEMS, this procedure consists of introducing a known quantity of HCl into the optical path that also includes the native source gas.
3.0 Definitions. (See PS-18 and Procedure 6 of Appendix F to Part 60 for the Definitions Used in This Appendix.) 4.0 Interferences. Interferences are discussed in PS-18, section 4.05.0 Safety. The procedures required under this appendix may involve hazardous materials, operations and equipment. This procedure may not address all of the safety problems associated with these procedures. You as the facility or operator must establish appropriate safety and health practices and determine the applicable regulatory limitations prior to performing these procedures. As the CEMS user, you should consult instrument operation manuals, material safety data sheets, compressed gas safety requirements, and other Occupational Safety and Health Administration regulations for specific precautions to be taken.
6.0 Equipment and Supplies. An example of equipment and supplies is described in section 6 of PS-18.
7.0 Reagents and Standards. SA materials must meet the requirements defined for reference gases in section 7 of PS-18 to perform this procedure with the following exception. You may use gases certified by the gas vendor to ±5 percent to perform the daily calibration drift assessment in section 4.1 of Procedure 6 in appendix F of this part.
Note:For extractive CEMS the concentrations of reference gases required for SA are likely to be significantly higher than the concentration of reference gases associated with PS-18 requirements.
8.0 Standard Addition and Dynamic Spiking Procedure. The standard addition procedure consists of measuring the native source gas concentration, addition of reference gas, and measurement of the resulting SA elevated source gas concentration. For extractive CEMS, HCl is spiked dynamically and thus, one must account for the dilution of sample gas from the addition of the HCl reference gas. For IP-CEMS, standard addition of an HCl reference gas is made by either adding an HCl reference gas to a flow through cell or inserting a sealed reference gas cell into the measurement path of the CEMS. The enclosed cell or a fixed cell must contain an HCl concentration that accounts for the difference in path length of the cell used for SA relative to the measurement path.
8.1 SA Concentration and Measurement Replicates.
8.1.1 You must inject HCl gas to create a measured concentration based on the requirements of the particular performance test (e.g., LOD verification, CD, DSA).
8.1.2 Each dynamic spike (DS) or standard addition (SA) replicate consists of a measurement of the source emissions concentration of HCl (native stack concentration) with and without the addition of HCl. With a single CEMS, you must alternate the measurement of the native and SA-elevated source gas so that each measurement of SA-elevated source gas is immediately preceded and followed by a measurement of native stack gas. Introduce the SA gases in such a manner that the entire CEMS is challenged. Alternatively, you may use an independent continuous HCl monitor to measure the native source concentration before and after each standard addition as described in section 8.1.4.
8.1.3 Unless specified otherwise by an applicable rule, your SA-elevated concentration may not exceed 100 percent of span when the SA and native HCl concentration are combined.
8.1.4 As an alternative to making background measurements pre- and post-SA, you may use an independent continuous HCl monitor as a temporary unit to measure native stack HCl concentration while simultaneously using the CEMS to measure the SA-elevated source concentration. If you use an independent continuous HCl monitor you must make one concurrent background or native HCl measurement using both the installed CEMS and the independent continuous HCl monitor, immediately before the SA procedure in section 8.2 or 8.3 begins, to confirm that the independent monitoring system measures the same background concentration as the CEMS being qualified with this PS.
8.2 SA Procedure for Extractive CEMS (Dynamic Spiking)
8.2.1 Your HCl spike addition must not alter the total volumetric sample system flow rate or basic dilution ratio of your CEMS (if applicable).
8.2.2 Your spike gas flow rate must not contribute more than 10 percent of the total volumetric flow rate through the CEMS.
8.2.3 You must determine a dilution factor (DF) or relative concentration of HCl for each dynamic spike. Calibrated, NIST-traceable flow meters accurate to within 2.0 percent or highly accurate tracer gas measurements are required to make the necessary DF determinations at the accuracy required for this PS. Calibrated, NIST-traceable flow meters (e.g., venturi, orifice) accurate to within 2.0 percent should be recertified against an NIST-traceable flow meter annually. Note: Since the spiking mass balance calculation is directly dependent on the accuracy of the DF determination, the accuracy of measurements required to determine the total volumetric gas flow rate, spike gas flow rate, or tracer gas standard addition concentration is critical to your ability to accurately perform the DS procedure and calculate the results.
8.2.4 You must monitor and record the total sampling system flow rate and sample dilution factor (DF) for the spiking and stack gas sampling systems to ensure they are known and do not change during the spiking procedure. Record all data on a data sheet similar to Table A1 in section 13 of this appendix.
8.2.4.1 You may either measure the spike gas flow and the total flow with calibrated flow meters capable of NIST traceable accuracy to ±2.0 percent or calculate the flow using a stable tracer gas included in your spike gas standard.
8.2.4.2 If you use flow measurements to determine the spike dilution, then use Equation A1 in section 11.2.1 of this appendix to calculate the DF. Determination of the spike dilution requires measurement of HCl spike flow (Qspike) and total flow through the CEM sampling system (Qprobe).
8.2.4.3 If your CEMS is capable of measuring an independent stable tracer gas, you may use a spike gas that includes the tracer to determine the DF using Equation A2 or A3 (sections 11.2.2 and 11.2.3 of this appendix) depending on whether the tracer gas is also present in the native source emissions.
8.2.4.4 For extractive CEMS, you must correct the background measurements of HCl for the dilution caused by the addition of the spike gas standard. For spiking systems that alternate between addition of HCl and zero gas at a constant DF, the background measurements between spikes will not be equal to the native source concentration.
8.2.5 Begin by collecting unspiked sample measurements of HCl. You must use the average of two unspiked sample measurements as your pre-spike background.
Note:Measurements should agree within 5.0 percent or three times the level of detection to avoid biasing the spike results.
8.2.5.1 Introduce the HCl gas spike into the permanent CEMS probe, upstream of the particulate filter or sample conditioning system and as close to the sampling inlet as practical.
8.2.5.2 Maintain the HCl gas spike for at least twice the DS response time of your CEMS or until the consecutive measurements agree within 5.0 percent. Collect two independent measurements of the native plus spiked HCl concentration.
8.2.5.3 Stop the flow of spike gas for at least twice the DS response time of your CEMS or until the consecutive measurements agree within 5.0 percent. Collect two independent measurements of the native HCl concentration.
8.2.6 Repeat the collection of sample measurements in section 8.2.5 until you have data for each spike concentration including a final set of unspiked sample measurements according to section 8.2.5.3.
8.2.7 Verify that the CEMS responded as expected for each spike gas injection, and that the data quality is not impacted by large shifts in the native source concentration. Discard and repeat any spike injections as necessary to generate a complete set of the required replicate spike measurements.
8.2.8 Calculate the standard addition response (SAR) for extractive CEMS, using Equation A4 in section 11.2, of this appendix.
8.2.9 If the DS results do not meet the specifications for the appropriate performance test in PS-18 or Procedure 6 of appendix F of this part, you must take corrective action and repeat the DS procedure.
8.3 SA Procedure for IP-CEMS (Static Spiking).
8.3.1 For IP-CEMS, you must make measurements of native source gas HCl concentration and an HCl standard addition using a calibration cell added to the optical measurement path.
8.3.2 Introduce zero gas into a calibration cell located in the optical measurement path of the instrument. Continue to flush the zero gas into the cell for at least the SA response time of your CEMS or until two consecutive measurements taken are within 5.0 percent, then collect two independent measurements. Alternatively you may measure native concentrations without the calibration cell in the optical path.
8.3.3 Introduce the HCl spike gas into the calibration cell. Continue to flush the spike gas into the cell for at least the SA response time of your CEMS or until two consecutive measurements taken are within 5.0 percent of one another. Then collect two independent measurements of the SA addition to the native concentration. Alternatively you may insert a sealed calibration cell, containing HCl at the appropriate concentration, into the optical path to measure the SA addition to the native concentration.
8.3.4 Repeat the collection of SA-elevated and native HCl measurements in sections 8.3.2 and 8.3.3 until you have data for each SA concentration. Then, make a final native HCl measurement. The measured concentrations must be corrected for calibration cell and stack temperature, pressure and stack measurement path length.
8.3.5 Calculate the standard addition response (SAR) for an IP-CEMS, using Equation A8 in section 11.3 of this appendix.
8.3.6 If the SA results do not meet the specifications for the appropriate performance test in PS-18 or Procedure 6 of appendix F of this part, you must take corrective action and repeat the SA procedure.
9.0 Quality Control [Reserved] 10.0 Calibration and Standardization [Reserved]11.0 Calculations and Data Analysis. Calculate the SA response for each measurement and its associated native HCl measurement(s), using equations in this section. (Note: For cases where the emission standard is expressed in units of lb/MMBtu or corrected to a specified O2 or CO2 concentration, an absolute accuracy specification based on a span at stack conditions may be calculated using the average concentration and applicable conversion factors. The appropriate procedures for use in cases where a percent removal standard is more restrictive than the emission standard are the same as in 40 CFR part 60, PS-2, sections 12 and 13.)
11.1 Nomenclature.
Cspike = Actual HCl reference gas concentration spiked (e.g., bottle or reference gas concentration) ppmv; Ctracer spiked = Tracer gas concentration injected with spike gas (“reference concentration”) ppmv; DF = Spiked gas dilution factor; DSCD = Calibration drift determined using DS procedure (percent); DSE = Dynamic spike error (ppmv); ESA = Effective spike addition (ppmv); MCSA = Measured SA-elevated source gas concentration (ppmv); MCspiked = Measured HCl reference gas concentration i (ppmv); MCnative = Average measured concentration of the native HCl (ppmv); Mnative tracer = Measured tracer gas concentration present in native effluent gas (ppmv); Mspiked tracer = Measured diluted tracer gas concentration in a spiked sample (ppmv); Qspike = Flow rate of the dynamic spike gas (Lpm); Qprobe = Average total stack sample flow through the system (Lpm); S = Span (ppmv); SAR = Standard addition response (ppmv)11.2 Calculating Dynamic Spike Response and Error for Extractive CEMS.
11.2.1 If you determine your spike DF using spike gas and stack sample flow measurements, calculate the DF using equation A1:

11.2.2 If you determine your spike DF using an independent stable tracer gas that is not present in the native source emissions, calculate the DF for DS using equation A2:

11.2.3 If you determine your spike dilution factor using an independent stable tracer that is present in the native source emissions, calculate the dilution factor for dynamic spiking using equation A3:

11.2.4 Calculate the SA response using Equation A4:

11.2.5 Calculate the DS error using Equation A5.

11.2.6 Calculating CD using DS. When using the DS option for determining mid-level CD, calculate the CD as a percent of span using equation A6:

11.2.7 The effective spike addition (ESA) is the expected increase in the measured concentration as a result of injecting a spike. Calculate ESA using Equation A7:

11.3 Standard Addition Response for IP-CEMS. If you use an IP-CEMS and a calibration cell, calculate the SA response using Equation A8.

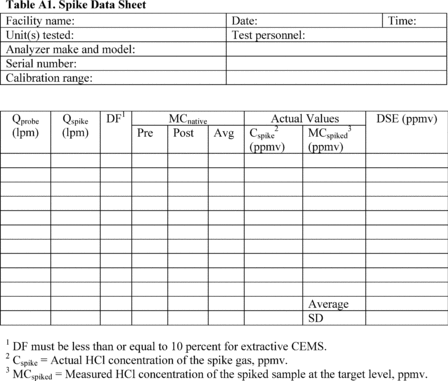