Title 40
PART 60 APPENDIX
Monitoring frequency per subpart a | Detection sensitivity level |
---|---|
Bi-Monthly | 60 |
Semi-Quarterly | 85 |
Monthly | 100 |
a When this alternative work practice is used to identify leaking equipment, the owner or operator must choose one of the monitoring frequencies listed in this table in lieu of the monitoring frequency specified in the applicable subpart. Bi-monthly means every other month. Semi-quarterly means twice per quarter. Monthly means once per month.
Table 1 to Subpart Cb of Part 60 - Nitrogen Oxides Guidelines for Designated Facilities
40:7.0.1.1.1.6.1.11.2 :
Table 1 to Subpart Cb of Part 60 - Nitrogen Oxides Guidelines for Designated FacilitiesMunicipal waste combustor technology | Before April 28, 2009, nitrogen oxides emission limit (parts per million by volume) a |
On and after April 28,
2009, nitrogen oxides emission limit (parts per million by volume) a |
---|---|---|
Mass burn waterwall | 205 | 205. |
Mass burn rotary waterwall | 250 | 210. |
Refuse-derived fuel combustor | 250 | 250. |
Fluidized bed combustor | 180 | 180. |
Mass burn refractory combustors | No limit | No limit. |
a Corrected to 7 percent oxygen, dry basis.
Table 2 to Subpart Cb of Part 60 - Nitrogen Oxides Limits for Existing Designated Facilities Included in an Emissions Averaging Plan at a Municipal Waste Combustor Plant b
40:7.0.1.1.1.6.1.11.3 :
Table 2 to Subpart Cb of Part 60 - Nitrogen Oxides Limits for Existing Designated Facilities Included in an Emissions Averaging Plan at a Municipal Waste Combustor Plant bMunicipal waste combustor technology | Before April 28, 2009, nitrogen oxides emission limit (parts per million by volume) b |
On and after April 28,
2009, nitrogen oxides emission limit (parts per million by volume) a |
---|---|---|
Mass burn waterwall | 185 | 185 |
Mass burn rotary waterwall | 220 | 190 |
Refuse-derived fuel combustor | 230 | 230 |
Fluidized bed combustor | 165 | 165 |
a Mass burn refractory municipal waste combustors and other MWC technologies not listed above may not be included in an emissions averaging plan.
b Corrected to 7 percent oxygen, dry basis.
Table 3 to Subpart Cb of Part 60 - Municipal Waste Combustor Operating Guidelines
40:7.0.1.1.1.6.1.11.4 :
Table 3 to Subpart Cb of Part 60 - Municipal Waste Combustor Operating GuidelinesMunicipal waste combustor technology | Carbon monoxide emissions levels (parts per million by volume) a | Averaging time (hrs) b |
---|---|---|
Mass burn waterwall | 100 | 4 |
Mass burn refractory | 100 | 4 |
Mass burn rotary refractory | 100 | 24 |
Mass burn rotary waterwall | 250 | 24 |
Modular starved air | 50 | 4 |
Modular excess air | 50 | 4 |
Refuse-derived fuel stoker | 200 | 24 |
Fluidized bed, mixed fuel (wood/refuse-derived fuel) | 200 | c 24 |
Bubbling fluidized bed combustor | 100 | 4 |
Circulating fluidized bed combustor | 100 | 4 |
Pulverized coal/refuse-derived fuel mixed fuel-fired combustor | 150 | 4 |
Spreader stoker coal/refuse-derived fuel mixed fuel-fired combustor | 200 | 24 |
Semi-suspension refuse-derived fuel-fired combustor/wet refuse-derived fuel process conversion | 250 | c 24 |
Spreader stoker fixed floor refuse-derived fuel-fired combustor/100 percent coal capable | 250 | c 24 |
a Measured at the combustor outlet in conjunction with a measurement of oxygen concentration, corrected to 7 percent oxygen, dry basis. Calculated as an arithmetic average.
b Averaging times are 4-hour or 24-hour block averages.
c 24-hour block average, geometric mean.
Table 1A to Subpart Ce of Part 60 - Emissions Limits for Small, Medium, and Large HMIWI at Designated Facilities as Defined in § 60.32e(a)(1)
40:7.0.1.1.1.9.1.11.5 :
Table 1A to Subpart Ce of Part 60 - Emissions Limits for Small, Medium, and Large HMIWI at Designated Facilities as Defined in § 60.32e(a)(1)Pollutant | Units (7 percent oxygen, dry basis) | Emissions limits | Averaging time 1 | Method for demonstrating compliance 2 | ||
---|---|---|---|---|---|---|
HMIWI size | ||||||
Small | Medium | Large | ||||
Particulate matter | Milligrams per dry standard cubic meter (mg/dscm) (grains per dry standard cubic foot (gr/dscf)) | 115 (0.05) | 69 (0.03) | 34 (0.015) | 3-run average (1-hour minimum sample time per run) | EPA Reference Method 5 of appendix A-3 of part 60, or EPA Reference Method 26A or 29 of appendix A-8 of part 60. |
Carbon monoxide | Parts per million by volume (ppmv) | 40 | 40 | 40 | 3-run average (1-hour minimum sample time per run) | EPA Reference Method 10 or 10B of appendix A-4 of part 60. |
Dioxins/furans | Nanograms per dry standard cubic meter total dioxins/furans (ng/dscm) (grains per billion dry standard cubic feet (gr/10 9 dscf)) or ng/dscm TEQ (gr/10 9 dscf) | 125 (55) or 2.3 (1.0) | 125 (55) or 2.3 (1.0) | 125 (55) or 2.3 (1.0) | 3-run average (4-hour minimum sample time per run) | EPA Reference Method 23 of appendix A-7 of part 60. |
Hydrogen chloride | ppmv or percent reduction | 100 or 93% | 100 or 93% | 100 or 93% | 3-run average (1-hour minimum sample time per run) | EPA Reference Method 26 or 26A of appendix A-8 of part 60. |
Sulfur dioxide | ppmv | 55 | 55 | 55 | 3-run average (1-hour minimum sample time per run) | EPA Reference Method 6 or 6C of appendix A-4 of part 60. |
Nitrogen oxides | ppmv | 250 | 250 | 250 | 3-run average (1-hour minimum sample time per run) | EPA Reference Method 7 or 7E of appendix A-4 of part 60. |
Lead | mg/dscm (grains per thousand dry standard cubic feet (gr/10 3 dscf)) or percent reduction | 1.2 (0.52) or 70% | 1.2 (0.52) or 70% | 1.2 (0.52) or 70% | 3-run average (1-hour minimum sample time per run) | EPA Reference Method 29 of appendix A-8 of part 60. |
Cadmium | mg/dscm (gr/10 3 dscf) or percent reduction | 0.16 (0.07) or 65% | 0.16 (0.07) or 65% | 0.16 (0.07) or 65% | 3-run average (1-hour minimum sample time per run) | EPA Reference Method 29 of appendix A-8 of part 60. |
Mercury | mg/dscm (gr/10 3 dscf) or percent reduction | 0.55 (0.24) or 85% | 0.55 (0.24) or 85% | 0.55 (0.24) or 85% | 3-run average (1-hour minimum sample time per run) | EPA Reference Method 29 of appendix A-8 of part 60. |
1 Except as allowed under § 60.56c(c) for HMIWI equipped with CEMS.
2 Does not include CEMS and approved alternative non-EPA test methods allowed under § 60.56c(b).
Table 1B to Subpart Ce of Part 60 - Emissions Limits for Small, Medium, and Large HMIWI at Designated Facilities as Defined in § 60.32e(a)(1) and (a)(2)
40:7.0.1.1.1.9.1.11.6 :
Table 1B to Subpart Ce of Part 60 - Emissions Limits for Small, Medium, and Large HMIWI at Designated Facilities as Defined in § 60.32e(a)(1) and (a)(2)Pollutant | Units (7 percent oxygen, dry basis) |
Emissions limits | Averaging time 1 | Method for demonstrating compliance 2 | ||
---|---|---|---|---|---|---|
HMIWI size | ||||||
Small | Medium | Large | ||||
Particulate matter | Milligrams per dry standard cubic meter (mg/dscm) (grains per dry standard cubic foot (gr/dscf)) | 66 (0.029) | 46 (0.020) | 25 (0.011) | 3-run average (1-hour minimum sample time per run) | EPA Reference Method 5 of appendix A-3 of part 60, or EPA Reference Method 26A or 29 of appendix A-8 of part 60. |
Carbon monoxide | Parts per million by volume (ppmv) | 20 | 5.5 | 11 | 3-run average (1-hour minimum sample time per run) | EPA Reference Method 10 or 10B of appendix A-4 of part 60. |
Dioxins/furans | Nanograms per dry standard cubic meter total dioxins/furans (ng/dscm) (grains per billion dry standard cubic feet (gr/10 9 dscf)) or ng/dscm TEQ (gr/10 9 dscf) | 16 (7.0) or 0.013 (0.0057) | 0.85 (0.37) or 0.020 (0.0087) | 9.3 (4.1) or 0.054 (0.024) | 3-run average (4-hour minimum sample time per run) | EPA Reference Method 23 of appendix A-7 of part 60. |
Hydrogen chloride | ppmv | 44 | 7.7 | 6.6 | 3-run average (1-hour minimum sample time per run) | EPA Reference Method 26 or 26A of appendix A-8 of part 60. |
Sulfur dioxide | ppmv | 4.2 | 4.2 | 9.0 | 3-run average (1-hour minimum sample time per run) | EPA Reference Method 6 or 6C of appendix A-4 of part 60. |
Nitrogen oxides | ppmv | 190 | 190 | 140 | 3-run average (1-hour minimum sample time per run) | EPA Reference Method 7 or 7E of appendix A-4 of part 60. |
Lead | mg/dscm (grains per thousand dry standard cubic feet (gr/10 3 dscf)) | 0.31 (0.14) | 0.018 (0.0079) | 0.036 (0.016) | 3-run average (1-hour minimum sample time per run) | EPA Reference Method 29 of appendix A-8 of part 60. |
Cadmium | mg/dscm (gr/10 3 dscf) | 0.017 (0.0074) | 0.013 (0.0057) | 0.0092 (0.0040) | 3-run average (1-hour minimum sample time per run) | EPA Reference Method 29 of appendix A-8 of part 60. |
Mercury | mg/dscm (gr/10 3 dscf) | 0.014 (0.0061) | 0.025 (0.011) | 0.018 (0.0079) | 3-run average (1-hour minimum sample time per run) | EPA Reference Method 29 of appendix A-8 of part 60. |
1 Except as allowed under § 60.56c(c) for HMIWI equipped with CEMS.
2 Does not include CEMS and approved alternative non-EPA test methods allowed under § 60.56c(b).
Table 2A to Subpart Ce of Part 60 - Emissions Limits for Small HMIWI Which Meet the Criteria Under § 60.33e(b)(1)
40:7.0.1.1.1.9.1.11.7 :
Table 2A to Subpart Ce of Part 60 - Emissions Limits for Small HMIWI Which Meet the Criteria Under § 60.33e(b)(1)Pollutant | Units (7 percent oxygen, dry basis) |
HMIWI emissions limits | Averaging time 1 | Method for demonstrating compliance 2 |
---|---|---|---|---|
Particulate matter | mg/dscm (gr/dscf) | 197 (0.086) | 3-run average (1-hour minimum sample time per run) | EPA Reference Method 5 of appendix A-3 of part 60, or EPA Reference Method 26A or 29 of appendix A-8 of part 60. |
Carbon monoxide | ppmv | 40 | 3-run average (1-hour minimum sample time per run) | EPA Reference Method 10 or 10B of appendix A-4 of part 60. |
Dioxins/furans | ng/dscm total dioxins/furans (gr/10 9 dscf) or ng/dscm TEQ (gr/10 9 dscf) | 800 (350) or 15 (6.6) | 3-run average (4-hour minimum sample time per run) | EPA Reference Method 23 of appendix A-7 of part 60. |
Hydrogen chloride | ppmv | 3,100 | 3-run average (1-hour minimum sample time per run) | EPA Reference Method 26 or 26A of appendix A-8 of part 60. |
Sulfur dioxide | ppmv | 55 | 3-run average (1-hour minimum sample time per run) | EPA Reference Method 6 or 6C of appendix A-4 of part 60. |
Nitrogen oxides | ppmv | 250 | 3-run average (1-hour minimum sample time per run) | EPA Reference Method 7 or 7E of appendix A-4 of part 60. |
Lead | mg/dscm (gr/10 3 dscf) | 10 (4.4) | 3-run average (1-hour minimum sample time per run) | EPA Reference Method 29 of appendix A-8 of part 60. |
Cadmium | mg/dscm (gr/10 3 dscf) | 4 (1.7) | 3-run average (1-hour minimum sample time per run) | EPA Reference Method 29 of appendix A-8 of part 60. |
Mercury | mg/dscm (gr/10 3 dscf) | 7.5 (3.3) | 3-run average (1-hour minimum sample time per run) | EPA Reference Method 29 of appendix A-8 of part 60. |
1 Except as allowed under § 60.56c(c) for HMIWI equipped with CEMS.
2 Does not include CEMS and approved alternative non-EPA test methods allowed under § 60.56c(b).
Table 2B to Subpart Ce of Part 60 - Emissions Limits for Small HMIWI Which Meet the Criteria Under § 60.33e(b)(2)
40:7.0.1.1.1.9.1.11.8 :
Table 2B to Subpart Ce of Part 60 - Emissions Limits for Small HMIWI Which Meet the Criteria Under § 60.33e(b)(2)Pollutant | Units (7 percent oxygen, dry basis) |
HMIWI Emissions limits | Averaging time 1 | Method for demonstrating compliance 2 |
---|---|---|---|---|
Particulate matter | mg/dscm (gr/dscf) | 87 (0.038) | 3-run average (1-hour minimum sample time per run) | EPA Reference Method 5 of appendix A-3 of part 60, or EPA Reference Method 26A or 29 of appendix A-8 of part 60. |
Carbon monoxide | ppmv | 20 | 3-run average (1-hour minimum sample time per run) | EPA Reference Method 10 or 10B of appendix A-4 of part 60. |
Dioxins/furans | ng/dscm total dioxins/furans (gr/10 9 dscf) or ng/dscm TEQ (gr/10 9 dscf) | 240 (100) or 5.1 (2.2) | 3-run average (4-hour minimum sample time per run) | EPA Reference Method 23 of appendix A-7 of part 60. |
Hydrogen chloride | ppmv | 810 | 3-run average (1-hour minimum sample time per run) | EPA Reference Method 26 or 26A of appendix A-8 of part 60. |
Sulfur dioxide | ppmv | 55 | 3-run average (1-hour minimum sample time per run) | EPA Reference Method 6 or 6C of appendix A-4 of part 60. |
Nitrogen oxides | ppmv | 130 | 3-run average (1-hour minimum sample time per run) | EPA Reference Method 7 or 7E of appendix A-4 of part 60. |
Lead | mg/dscm (gr/10 3 dscf) | 0.50 (0.22) | 3-run average (1-hour minimum sample time per run) | EPA Reference Method 29 of appendix A-8 of part 60. |
Cadmium | mg/dscm (gr/10 3 dscf) | 0.11 (0.048) | 3-run average (1-hour minimum sample time per run) | EPA Reference Method 29 of appendix A-8 of part 60. |
Mercury | mg/dscm (gr/10 3 dscf) | 0.0051 (0.0022) | 3-run average (1-hour minimum sample time per run) | EPA Reference Method 29 of appendix A-8 of part 60. |
1 Except as allowed under § 60.56c(c) for HMIWI equipped with CEMS.
2 Does not include CEMS and approved alternative non-EPA test methods allowed under § 60.56c(b).
Table 1A to Subpart Ec of Part 60 - Emissions Limits for Small, Medium, and Large HMIWI at Affected Facilities as Defined in § 60.50c(a)(1) and (2)
40:7.0.1.1.1.18.1.10.9 :
Table 1A to Subpart Ec of Part 60 - Emissions Limits for Small, Medium, and Large HMIWI at Affected Facilities as Defined in § 60.50c(a)(1) and (2)Pollutant | Units (7 percent oxygen, dry basis) | Emissions limits | Averaging time 1 | Method for demonstrating compliance 2 |
||
---|---|---|---|---|---|---|
HMIWI size | ||||||
Small | Medium | Large | ||||
Particulate matter | Milligrams per dry standard cubic meter (grains per dry standard cubic foot) | 69 (0.03) | 34 (0.015) | 34 (0.015) | 3-run average (1-hour minimum sample time per run) | EPA Reference Method 5 of appendix A-3 of part 60, or EPA Reference Method M 26A or 29 of appendix A-8 of part 60. |
Carbon monoxide | Parts per million by volume | 40 | 40 | 40 | 3-run average (1-hour minimum sample time per run) | EPA Reference Method 10 or 10B of appendix A-4 of part 60. |
Dioxins/furans | Nanograms per dry standard cubic meter total dioxins/furans (grains per billion dry standard cubic feet) or nanograms per dry standard cubic meter TEQ (grains per billion dry standard cubic feet) | 125 (55) or 2.3 (1.0) | 25 (11) or 0.6 (0.26) | 25 (11) or 0.6 (0.26) | 3-run average (4-hour minimum sample time per run) | EPA Reference Method 23 of appendix A-7 of part 60. |
Hydrogen chloride | Parts per million by volume or percent reduction | 15 or 99% | 15 or 99% | 15 or 99% | 3-run average (1-hour minimum sample time per run) | EPA Reference Method 26 or 26A of appendix A-8 of part 60. |
Sulfur dioxide | Parts per million by volume | 55 | 55 | 55 | 3-run average (1-hour minimum sample time per run) | EPA Reference Method 6 or 6C of appendix A-4 of part 60. |
Nitrogen oxides | Parts per million by volume | 250 | 250 | 250 | 3-run average (1-hour minimum sample time per run) | EPA Reference Method 7 or 7E of appendix A-4 of part 60. |
Lead | Milligrams per dry standard cubic meter (grains per thousand dry standard cubic feet) or percent reduction | 1.2 (0.52) or 70% | 0.07 (0.03) or 98% | 0.07 (0.03) or 98% | 3-run average (1-hour minimum sample time per run) | EPA Reference Method 29 of appendix A-8 of part 60. |
Cadmium | Milligrams per dry standard cubic meter (grains per thousand dry standard cubic feet) or percent reduction | 0.16 (0.07) or 65% | 0.04 (0.02) or 90% | 0.04 (0.02) or 90% | 3-run average (1-hour minimum sample time per run) | EPA Reference Method 29 of appendix A-8 of part 60. |
Mercury | Milligrams per dry standard cubic meter (grains per thousand dry standard cubic feet) or percent reduction | 0.55 (0.24) or 85% | 0.55 (0.24) or 85% | 0.55 (0.24) or 85% | 3-run average (1-hour minimum sample time per run) | EPA Reference Method 29 of appendix A-8 of part 60. |
1 Except as allowed under § 60.56c(c) for HMIWI equipped with CEMS.
2 Does not include CEMS and approved alternative non-EPA test methods allowed under § 60.56c(b).
Table 1B to Subpart Ec of Part 60 - Emissions Limits for Small, Medium, and Large HMIWI at Affected Facilities as Defined in § 60.50c(a)(3) and (4)
40:7.0.1.1.1.18.1.10.10 :
Table 1B to Subpart Ec of Part 60 - Emissions Limits for Small, Medium, and Large HMIWI at Affected Facilities as Defined in § 60.50c(a)(3) and (4)Pollutant | Units (7 percent oxygen, dry basis) |
Emissions limits | Averaging time 1 | Method for demonstrating compliance 2 |
||
---|---|---|---|---|---|---|
HMIWI size | ||||||
Small | Medium | Large | ||||
Particulate matter | Milligrams per dry standard cubic meter (grains per dry standard cubic foot) | 66 (0.029) | 22 (0.0095) | 18 (0.0080) | 3-run average (1-hour minimum sample time per run) | EPA Reference Method 5 of appendix A-3 of part 60, or EPA Reference Method M 26A or 29 of appendix A-8 of part 60. |
Carbon monoxide | Parts per million by volume | 20 | 1.8 | 11 | 3-run average (1-hour minimum sample time per run) | EPA Reference Method 10 or 10B of appendix A-4 of part 60. |
Dioxins/furans | Nanograms per dry standard cubic meter total dioxins/furans (grains per billion dry standard cubic feet) or nanograms per dry standard cubic meter TEQ (grains per billion dry standard cubic feet) | 16 (7.0) or 0.013 (0.0057) | 0.47 (0.21) or 0.014 (0.0061) | 9.3 (4.1) or 0.035 (0.015) | 3-run average (4-hour minimum sample time per run) | EPA Reference Method 23 of appendix A-7 of part 60. |
Hydrogen chloride | Parts per million by volume | 15 | 7.7 | 5.1 | 3-run average (1-hour minimum sample time per run) | EPA Reference Method 26 or 26A of appendix A-8 of part 60. |
Sulfur dioxide | Parts per million by volume | 1.4 | 1.4 | 8.1 | 3-run average (1-hour minimum sample time per run) | EPA Reference Method 6 or 6C of appendix A-4 of part 60. |
Nitrogen oxides | Parts per million by volume | 67 | 67 | 140 | 3-run average (1-hour minimum sample time per run) | EPA Reference Method 7 or 7E of appendix A-4 of part 60. |
Lead | Milligrams per dry standard cubic meter (grains per thousand dry standard cubic feet) | 0.31 (0.14) | 0.018 (0.0079) | 0.00069 (0.00030) | 3-run average (1-hour minimum sample time per run) | EPA Reference Method 29 of appendix A-8 of part 60. |
Cadmium | Milligrams per dry standard cubic meter (grains per thousand dry standard cubic feet) | 0.017 (0.0074) | 0.0098 (0.0043) | 0.00013 (0.000057) | 3-run average (1-hour minimum sample time per run) | EPA Reference Method 29 of appendix A-8 of part 60. |
Mercury | Milligrams per dry standard cubic meter (grains per thousand dry standard cubic feet) | 0.014 (0.0061) | 0.0035 (0.0015) | 0.0013 (0.00057) | 3-run average (1-hour minimum sample time per run) | EPA Reference Method 29 of appendix A-8 of part 60. |
1 Except as allowed under § 60.56c(c) for HMIWI equipped with CEMS.
2 Does not include CEMS and approved alternative non-EPA test methods allowed under § 60.56c(b).
Table 2 to Subpart Ec of Part 60 - Toxic Equivalency Factors
40:7.0.1.1.1.18.1.10.11 :
Table 2 to Subpart Ec of Part 60 - Toxic Equivalency FactorsDioxin/furan congener | Toxic equivalency factor |
---|---|
2,3,7,8-tetrachlorinated dibenzo-p-dioxin | 1 |
1,2,3,7,8-pentachlorinated dibenzo-p-dioxin | 0.5 |
1,2,3,4,7,8-hexachlorinated dibenzo-p-dioxin | 0.1 |
1,2,3,7,8,9-hexachlorinated dibenzo-p-dioxin | 0.1 |
1,2,3,6,7,8-hexachlorinated dibenzo-p-dioxin | 0.1 |
1,2,3,4,6,7,8-heptachlorinated dibenzo-p-dioxin | 0.01 |
octachlorinated dibenzo-p-dioxin | 0.001 |
2,3,7,8-tetrachlorinated dibenzofuran | 0.1 |
2,3,4,7,8-pentachlorinated dibenzofuran | 0.5 |
1,2,3,7,8-pentachlorinated dibenzofuran | 0.05 |
1,2,3,4,7,8-hexachlorinated dibenzofuran | 0.1 |
1,2,3,6,7,8-hexachlorinated dibenzofuran | 0.1 |
1,2,3,7,8,9-hexachlorinated dibenzofuran | 0.1 |
2,3,4,6,7,8-hexachlorinated dibenzofuran | 0.1 |
1,2,3,4,6,7,8-heptachlorinated dibenzofuran | 0.01 |
1,2,3,4,7,8,9-heptachlorinated dibenzofuran | 0.01 |
Octachlorinated dibenzofuran | 0.001 |
Table 3 to Subpart Ec of Part 60 - Operating Parameters To Be Monitored and Minimum Measurement and Recording Frequencies
40:7.0.1.1.1.18.1.10.12 :
Table 3 to Subpart Ec of Part 60 - Operating Parameters To Be Monitored and Minimum Measurement and Recording FrequenciesOperating parameters to be monitored | Minimum frequency | Control system | |||
---|---|---|---|---|---|
Data measurement | Data recording | Dry scrubber followed by fabric filter | Wet scrubber | Dry scrubber followed by fabric filter and wet scrubber | |
Maximum operating parameters: | |||||
Maximum charge rate | Continuous | 1 × hour | ✔ | ✔ | ✔ |
Maximum fabric filter inlet temperature | Continuous | 1 × minute | ✔ | ✔ | |
Maximum flue gas temperature | Continuous | 1 × minute | ✔ | ✔ | |
Minimum operating parameters: | |||||
Minimum secondary chamber temperature | Continuous | 1 × minute | ✔ | ✔ | ✔ |
Minimum dioxin/furan sorbent flow rate | Hourly | 1 × hour | ✔ | ✔ | |
Minimum HCI sorbent flow rate | Hourly | 1 × hour | ✔ | ✔ | |
Minimum mercury (Hg) sorbent flow rate | Hourly | 1 × hour | ✔ | ✔ | |
Minimum pressure drop across the wet scrubber or minimum horsepower or amperage to wet scrubber | Continuous | 1 × minute | ✔ | ✔ | |
Minimum scrubber liquor flow rate | Continuous | 1 × minute | ✔ | ✔ | |
Minimum scrubber liquor pH | Continuous | 1 × minute | ✔ | ✔ |
Table 1 to Subpart Ja of Part 60 - Molar Exhaust Volumes and Molar Heat Content of Fuel Gas Constituents
40:7.0.1.1.1.25.1.11.13 :
Table 1 to Subpart Ja of Part 60 - Molar Exhaust Volumes and Molar Heat Content of Fuel Gas ConstituentsConstituent | MEV a dscf/mol |
MHC b Btu/mol |
---|---|---|
Methane (CH4) | 7.29 | 842 |
Ethane (C2H6) | 12.96 | 1,475 |
Hydrogen (H2) | 1.61 | 269 |
Ethene (C2H4) | 11.34 | 1,335 |
Propane (C3H8) | 18.62 | 2,100 |
Propene (C3H6) | 17.02 | 1,947 |
Butane (C4H10) | 24.30 | 2,717 |
Butene (C4H8) | 22.69 | 2,558 |
Inerts | 0.85 | 0 |
a MEV = molar exhaust volume, dry standard cubic feet per gram-mole (dscf/g-mol) at standard conditions of 68 °F and 1 atmosphere.
b MHC = molar heat content (higher heating value basis), Btu per gram-mole (Btu/g-mol).
Table 1 to Subpart OOO of Part 60 - Exceptions to Applicability of Subpart A to Subpart OOO
40:8.0.1.1.1.17.163.8.1 :
Table 1 to Subpart OOO of Part 60 - Exceptions to Applicability of Subpart A to Subpart OOOSubpart A reference | Applies to subpart OOO |
Explanation |
---|---|---|
60.4, Address | Yes | Except in § 60.4(a) and (b) submittals need not be submitted to both the EPA Region and delegated State authority (§ 60.676(k)). |
60.7, Notification and recordkeeping | Yes | Except in (a)(1) notification of the date construction or reconstruction commenced (§ 60.676(h)). |
Also, except in (a)(6) performance tests involving only Method 9 (40 CFR part 60, appendix A-4) require a 7-day advance notification instead of 30 days (§ 60.675(g)). | ||
60.8, Performance tests | Yes | Except in (d) performance tests involving only Method 9 (40 CFR part 60, appendix A-4) require a 7-day advance notification instead of 30 days (§ 60.675(g)). |
60.11, Compliance with standards and maintenance requirements | Yes | Except in (b) under certain conditions (§§ 60.675(c)), Method 9 (40 CFR part 60, appendix A-4) observation is reduced from 3 hours to 30 minutes for fugitive emissions. |
60.18, General control device | No | Flares will not be used to comply with the emission limits. |
Table 2 to Subpart OOO of Part 60 - Stack Emission Limits for Affected Facilities With Capture Systems
40:8.0.1.1.1.17.163.8.2 :
Table 2 to Subpart OOO of Part 60 - Stack Emission Limits for Affected Facilities With Capture SystemsFor * * * | The owner or operator must meet a PM limit of * * * | And the owner or operator must meet an opacity limit of * * * | The owner or operator must demonstrate compliance with these limits by conducting * * * |
---|---|---|---|
Affected facilities (as defined in §§ 60.670 and 60.671) that commenced construction, modification, or reconstruction after August 31, 1983 but before April 22, 2008 | 0.05 g/dscm (0.022 gr/dscf) a | 7 percent for dry control devices b | An initial performance test
according to § 60.8 of this part and § 60.675 of this subpart;
and Monitoring of wet scrubber parameters according to § 60.674(a) and § 60.676(c), (d), and (e). |
Affected facilities (as defined in §§ 60.670 and 60.671) that commence construction, modification, or reconstruction on or after April 22, 2008 | 0.032 g/dscm (0.014 gr/dscf) a | Not applicable (except for
individual enclosed storage bins) 7 percent for dry control devices on individual enclosed storage bins |
An initial performance test
according to § 60.8 of this part and § 60.675 of this subpart;
and Monitoring of wet scrubber parameters according to § 60.674(a) and § 60.676(c), (d), and (e); and |
Monitoring of baghouses according to § 60.674(c), (d), or (e) and § 60.676(b). |
a Exceptions to the PM limit apply for individual enclosed storage bins and other equipment. See § 60.672(d) through (f).
b The stack opacity limit and associated opacity testing requirements do not apply for affected facilities using wet scrubbers.
Table 3 to Subpart OOO of Part 60 - Fugitive Emission Limits
40:8.0.1.1.1.17.163.8.3 :
Table 3 to Subpart OOO of Part 60 - Fugitive Emission LimitsFor * * * | The owner or operator must meet the following fugitive emissions limit for grinding mills, screening operations, bucket elevators, transfer points on belt conveyors, bagging operations, storage bins, enclosed truck or railcar loading stations or from any other affected facility (as defined in §§ 60.670 and 60.671) * * * | The owner or operator must meet the following fugitive emissions limit for crushers at which a capture system is not used * * * | The owner or operator must demonstrate compliance with these limits by conducting * * * |
---|---|---|---|
Affected facilities (as defined in §§ 60.670 and 60.671) that commenced construction, modification, or reconstruction after August 31, 1983 but before April 22, 2008 | 10 percent opacity | 15 percent opacity | An initial performance test according to § 60.11 of this part and § 60.675 of this subpart. |
Affected facilities (as defined in §§ 60.670 and 60.671) that commence construction, modification, or reconstruction on or after April 22, 2008 | 7 percent opacity | 12 percent opacity | An initial performance test
according to § 60.11 of this part and § 60.675 of this subpart;
and Periodic inspections of water sprays according to § 60.674(b) and § 60.676(b); and |
A repeat performance test according to § 60.11 of this part and § 60.675 of this subpart within 5 years from the previous performance test for fugitive emissions from affected facilities without water sprays. Affected facilities controlled by water carryover from upstream water sprays that are inspected according to the requirements in §§ 60.674(b) and 60.676(b) are exempt from this 5-year repeat testing requirement. |
Table 1 to Subpart AAAA of Part 60 - Emission Limits for New Small Municipal Waste Combustion Units
40:8.0.1.1.1.28.179.95.4 :
Table 1 to Subpart AAAA of Part 60 - Emission Limits for New Small Municipal Waste Combustion UnitsFor the following pollutants | You must meet the following emission limits a |
Using the following averaging times |
And determine compliance by the following methods |
---|---|---|---|
1. Organics | |||
Dioxins/Furans (total mass basis) | 13 nanograms per dry standard cubic meter | 3-run average (minimum run duration is 4 hours) | Stack test. |
2. Metals: | |||
Cadmium | 0.020 milligrams per dry standard cubic meter | 3-run average (run duration specified in test method) | Stack test. |
Lead | 0.20 milligrams per dry standard cubic meter | 3-run average (run duration specified in test method) | Stack test. |
Mercury | 0.080 milligrams per dry standard cubic meter or 85 percent reduction of potential mercury emissions | 3-run average (run duration specified in test method) | Stack test. |
Opacity | 10 percent | Thirty 6-minute averages | Stack test. |
Particulate Matter | 24 milligrams per dry standard cubic meter | 3-run average (run duration specified in test method) | Stack test. |
3. Acid Gases: | |||
Hydrogen Chloride | 25 parts per million by dry volume or 95 percent reduction of potential hydrogen chloride emissions | 3-run average (minimum run duration is 1 hour) | Stack test |
Nitrogen Oxides (Class I units) b | 150 (180 for 1st year of operation) parts per million by dry volume | 24-hour daily block arithmetic average concentration | Continuous emission monitoring system. |
Nitrogen Oxides (Class II units) c | 500 parts per million by dry volume | See footnote d | See footnote d |
Sulfur Dioxide | 30 parts per million by dry volume or 80 percent reduction of potential sulfur dioxide emissions | 24-hour daily block geometric average concentration or percent reduction | Continuous monitoring emission system. |
4. Other: | |||
Fugitive Ash | Visible emissions for no more than 5 percent of hourly observation period | Three 1-hour observation periods | Visible emission test. |
a All emission limits (except for opacity) are measured at 7 percent oxygen.
b Class I units mean small municipal waste combustion units subject to this subpart that are located at municipal waste combustion plants with an aggregate plant combustion capacity more than 250 tons per day of municipal solid waste. See § 60.1465 for definitions.
c Class II units mean small municipal waste combustion units subject to this subpart that are located at municipal waste combustion plants with an aggregate plant combustion capacity no more than 250 tons per day of municipal solid waste. See § 60.1465 for definitions.
d No monitoring, testing, recordkeeping, or reporting is required to demonstrate compliance with the nitrogen oxides limit for Class II units.
Table 2 to Subpart AAAA of Part 60 - Carbon Monoxide Emission Limits for New Small Municipal Waste Combustion Units
40:8.0.1.1.1.28.179.95.5 :
Table 2 to Subpart AAAA of Part 60 - Carbon Monoxide Emission Limits for New Small Municipal Waste Combustion UnitsFor the following municipal waste combustion units | You must meet the
following carbon monoxide limits a |
Using the following averaging times b |
---|---|---|
1. Fluidized-bed | 100 parts per million by dry volume | 4-hour. |
2. Fluidized bed, mixed fuel, (wood/refuse-derived fuel) | 200 parts per million by dry volume | 24-hour. c |
3. Mass burn rotary refractory | 100 parts per million by dry volume | 4-hour. |
4. Mass burn rotary waterwall | 100 parts per million by dry volume | 24-hour. |
5. Mass burn waterwall and refractory | 100 parts per million by dry volume | 4-hour. |
6. Mixed fuel-fired (pulverized coal/refuse-derived fuel) | 150 parts per million by dry volume | 4-hour. |
7. Modular starved-air and excess air | 50 parts per million by dry volume | 4-hour. |
8. Spreader stoker, mixed fuel-fired (coal/refuse-derived fuel) | 150 parts per million by dry volume | 24-hour daily. |
9. Stoker, refuse-derived fuel | 150 parts per million by dry volume | 24-hour daily. |
a All limits (except for opacity) are measured at 7 percent oxygen. Compliance is determined by continuous emission monitoring systems.
b Block averages, arithmetic mean. See § 60.1465 for definitions.
c 24-hour block average, geometric mean. See § 60.1465 for definitions.
Table 3 to Subpart AAAA of Part 60 - Requirements for Validating Continuous Emission Monitoring Systems (CEMS)
40:8.0.1.1.1.28.179.95.6 :
Table 3 to Subpart AAAA of Part 60 - Requirements for Validating Continuous Emission Monitoring Systems (CEMS)For the following continuous emission monitoring systems | Use the following methods in appendix A of this part to validate pollutant concentration levels | Use the following methods in appendix A of this part to measure oxygen (or carbon dioxide) |
---|---|---|
1. Nitrogen Oxides (Class I units only) a | Method 7, 7A, 7B, 7C, 7D, or 7E | Method 3 or 3A. |
2. Sulfur Dioxide | Method 6 or 6C | Method 3 or 3A. |
3. Carbon Monoxide | Method 10, 10A, or 10B | Method 3 or 3A. |
a Class I units mean small municipal waste combustion units subject to this subpart that are located at municipal waste combustion plants with an aggregate plant combustion capacity more than 250 tons per day of municipal solid waste. See § 60.1465 for definitions.
Table 4 to Subpart AAAA of Part 60 - Requirements for Continuous Emission Monitoring Systems (CEMS)
40:8.0.1.1.1.28.179.95.7 :
Table 4 to Subpart AAAA of Part 60 - Requirements for Continuous Emission Monitoring Systems (CEMS)For the following pollutants | Use the following span values for your CEMS | Use the following performance specifications in appendix B of this part for your CEMS | If needed to meet minimum data requirements, use the following alternate methods in appendix A of this part to collect data |
---|---|---|---|
1. Opacity | 100 percent opacity | P.S. 1 | Method 9. |
2. Nitrogen Oxides (Class I units only) a | Control device outlet: 125 percent of the maximum expected hourly potential nitrogen oxides emissions of the municipal waste combustion unit | P.S. 2 | Method 7E. |
3. Sulfur Dioxide | Inlet to control device: 125 percent of the maximum expected sulfur dioxide emissions of the municipal waste combustion unit. Control device outlet: 50 percent of the maximum expected hourly potential sulfur dioxide emissions of the municipal waste combustion unit | P.S. 2 | Method 6C. |
4. Carbon Monoxide | 125 percent of the maximum expected hourly potential carbon with monoxide emissions of the municipal waste combustion unit | P.S. 4A | Method 10 alternative interference trap. |
5. Oxygen or Carbon Dioxide | 25 percent oxygen or 25 percent carbon dioxide | P.S. 3 | Method 3A or 3B. |
a Class I units mean small municipal waste combustion units subject to this subpart that are located at municipal waste combustion plants with an aggregate plant combustion capacity more than 250 tons per day of municipal solid waste. See § 60.1465 for definitions.
Table 5 to Subpart AAAA of Part 60 - Requirements for Stack Tests
40:8.0.1.1.1.28.179.95.8 :
Table 5 to Subpart AAAA of Part 60 - Requirements for Stack TestsTo measure the following pollutants | Use the following methods in appendix A of this part to determine the sampling location | Use the methods in appendix A of this part to measure pollutant concentration | Also note the following additional information |
---|---|---|---|
1. Organics: | |||
Dioxins/Furans | Method 1 | Method 23 a | The minimum sampling time must be 4 hours per test run while the municipal waste combustion unit is operating at full load. |
2. Metals: | |||
Cadmium | Method 1 | Method 29 a | Compliance testing must be performed while the municipal waste combustion unit is operating at full load. |
Lead | Method 1 | Method 29 a | Compliance testing must be performed while the municipal waste combustion unit is operating at full load. |
Mercury | Method 1 | Method 29 a | Compliance testing must be performed while the municipal waste combustion unit is operating at full load. |
Opacity | Method 9 | Method 9 | Use Method 9 to determine compliance with opacity limit. 3-hour observation period (thirty 6-minute averages). |
Particulate Matter | Method 1 | Method 5 a | The minimum sample Matter volume must be 1.0 cubic meters. The probe and filter holder heating systems in the sample train must be set to provide a gas temperature no greater than 160 ±14 °C. The minimum sampling time is 1 hour. |
3. Acid Gases: b | |||
Hydrogen Chloride | Method 1 | Method 26 or 26A a | Test runs must be at least 1 hour long while the municipal waste combustion unit is operating at full load. |
4. Other: b | |||
Fugitive Ash | Not applicable | Method 22 (visible emissions) | The three 1-hour observation period must include periods when the facility transfers fugitive ash from the municipal waste combustion unit to the area where the fugitive ash is stored or loaded into containers or trucks. |
a Must simultaneously measure oxygen (or carbon dioxide) using Method 3A or 3B in appendix A of this part.
b Use CEMS to test sulfur dioxide, nitrogen oxide, and carbon monoxide. Stack tests are not required except for quality assurance requirements in appendix F of this part.
Table 1 to Subpart BBBB of Part 60 - Model Rule - Compliance Schedules and Increments of Progress
40:8.0.1.1.1.29.195.90.9 :
Table 1 to Subpart BBBB of Part 60 - Model Rule - Compliance Schedules and Increments of ProgressAffected units | Increment 1 (Submit final control plan) | Increment 2 (Award contracts) | Increment 3 (Begin onsite construction) | Increment 4 (Complete onsite construction) | Increment 5 (Final compliance) |
---|---|---|---|---|---|
1. All Class I units a b | (Dates to be specified in State plan) | (Dates to be specified in State plan) | (Dates to be specified in State plan) | (Dates to be specified in State plan) | (Dates to be specified in State plan). c d |
2. All Class II units a e | (Dates to be specified in State plan) | Not applicable | Not applicable | Not applicable | (Dates to be specified in State plan). c |
a Plant specific schedules can be used at the discretion of the State.
b Class I units mean small municipal waste combustion units subject to this subpart that are located at municipal waste combustion plants with an aggregate plant combustion capacity greater than 250 tons per day of municipal solid waste. See § 60.1940 for definitions.
c The date can be no later than 3 years after the effective date of State plan approval or December 6, 2005.
d For Class I units that began construction, reconstruction, or modification after June 26, 1987, comply with the dioxins/furans and mercury limits by the later of two dates:
1. One year after the effective date of State plan approval.
2. One year after the issuance of a revised construction or operation permit, if a permit modification is required.
3. Final compliance with the dioxins/furans limits must be achieved no later than December 6, 2005, even if the date one year after the issuance of a revised construction or operation permit is after December 6, 2005.
e Class II units mean all small municipal combustion units subject to this subpart that are located at municipal waste combustion plants with aggregate plant combustion capacity less than or equal to 250 tons per day of municipal solid waste. See § 60.1940 for definitions.
Table 2 to Subpart BBBB of Part 60 - Model Rule - Class I Emission Limits for Existing Small Municipal Waste Combustion Units a
40:8.0.1.1.1.29.195.90.10 :
Table 2 to Subpart BBBB of Part 60 - Model Rule - Class I Emission Limits for Existing Small Municipal Waste Combustion Units aFor the following pollutants | You must meet the following emission limits b | Using the following averaging times | And determine compliance by the following methods |
---|---|---|---|
1. Organics: | |||
Dioxins/Furans (total mass basis) | 30 nanograms per dry standard cubic meter for municipal waste combustion units that do not employ an electrostatic precipitator-based emission control system -or- | 3-run average (minimum run duration is 4 hours) | Stack test. |
60 nanograms per dry standard cubic meter for municipal waste combustion units that employ an electrostatic precipitator-based emission control system | |||
2. Metals: | |||
Cadmium | 0.040 milligrams per dry standard cubic meter | 3-run average (run duration specified in test method) | Stack test. |
Lead | 0.490 milligrams per dry standard cubic meter | 3-run average (run duration specified in test method) | Stack test. |
Mercury | 0.080 milligrams per dry standard cubic meter | 3-run average (run duration specified in test method) | Stack test. |
85 percent reduction of potential mercury emissions | |||
Opacity | 10 percent | Thirty 6-minute averages | Stack test. |
Particulate Matter | 27 milligrams per dry standard cubic meter | 3-run average (run duration specified in test method) | Stack test. |
3. Acid Gases: | |||
Hydrogen Chloride | 31 parts per million by dry volume 95 percent reduction of potential hydrogen chloride emissions | 3-run average (minimum run duration is 1 hour) | Stack test. |
Sulfur Dioxide | 31 parts per million by dry volume 75 percent reduction of potential sulfur dioxide emissions | 24-hour daily block geometric average concentration percent reduction | Continuous emission monitoring system. |
4. Other: | |||
Fugitive Ash | Visible emissions for no more than 5 percent of hourly observation period | Three 1-hour observation periods | Visible emission test. |
a Class I units mean small municipal waste combustion units subject to this subpart that are located at municipal waste combustion plants with an aggregate plant combustion capacity greater than 250 tons per day of municipal solid waste. See § 60.1940 for definitions.
b All emission limits (except for opacity) are measured at 7 percent oxygen.
Table 3 to Subpart BBBB of Part 60 - Model Rule - Class I Nitrogen Oxides Emission Limits for Existing Small Municipal Waste Combustion Units a b c
40:8.0.1.1.1.29.195.90.11 :
Table 3 to Subpart BBBB of Part 60 - Model Rule - Class I Nitrogen Oxides Emission Limits for Existing Small Municipal Waste Combustion Units a b cMunicipal waste combustion technology | Limits for class I municipal waste combustion units |
---|---|
1. Mass burn waterwall | 200 parts per million by dry volume. |
2. Mass burn rotary waterwall | 170 parts per million by dry volume. |
3. Refuse-derived fuel | 250 parts per million by dry volume. |
4. Fluidized bed | 220 parts per million by dry volume. |
5. Mass burn refractory | 350 parts per million by dry volume. |
6. Modular excess air | 190 parts per million by dry volume. |
7. Modular starved air | 380 parts per million by dry volume. |
a Class I units mean small municipal waste combustion units subject to this subpart that are located at municipal waste combustion plants with an aggregate plant combustion capacity greater than 250 tons per day of municipal solid waste. See § 60.1940 for definitions.
b Nitrogen oxides limits are measured at 7 percent oxygen.
c All limits are 24-hour daily block arithmetic average concentration. Compliance is determined for Class I units by continuous emission monitoring systems.
Table 4 to Subpart BBBB of Part 60 - Model Rule - Class II Emission Limits for Existing Small Municipal Waste Combustion Unit a
40:8.0.1.1.1.29.195.90.12 :
Table 4 to Subpart BBBB of Part 60 - Model Rule - Class II Emission Limits for Existing Small Municipal Waste Combustion Unit aFor the following pollutants | You must meet the following emission following determine limits b | Using the following averaging times | And determine compliance by the following methods |
---|---|---|---|
1. Organics: | |||
Dioxins/Furans (total mass basis) | 125 nanorgrams per dry standard cubic meter | 3-run average (minimum run duration is 4 hours) | Stack test. |
2. Metals: | |||
Cadmium | 0.10 milligrams per dry standard cubic meter | 3-run average (run duration specified in test method) | Stack test. |
Lead | 1.6 milligrams per dry standard cubic meter | 3-run average (run duration specified in test method) | Stack test. |
Mercury | 0.080 milligrams per dry standard cubic meter | 3-run average (run duration specified in test method) | Stack test. |
85 percent reduction of potential mercury emissions | |||
Opacity | 10 percent | Thirty 6-minute average | Stack test. |
Particulate Matter | 70 milligrams per dry standard cubic meter | 3-run average (run duration specified in test method) | Stack test. |
3. Acid Gases: | |||
Hydrogen Chloride | 250 parts per million by volume -or- | 3-run average (minimum run duration is 1 hour) | Stack test. |
50 percent reduction of potential hydrogen chloride emissions | |||
Sulfur Dioxide | 77 parts per million by dry
volume -or- 50 percent reduction of potential sulfur dioxides emissions |
24-hour daily block geometric average concentration -or- percent reduction | Continuous emission monitoring system. |
4. Other: | |||
Fugitive Ash | Visible emissions for no more than 5 percent of hourly observation period | Three 1-hour observation periods | Visible emission test. |
a Class II units mean all small municipal combustion units subject to this subpart that are located at municipal waste combustion plants with aggregate plant combustion capacity less than or equal to 250 tons per day of municipal solid waste. See § 60.1940 for definitions.
b All emission limits (except for opacity) are measured at 7 percent oxygen.
c No monitoring, testing, recordkeeping or reporting is required to demonstrate compliance with the nitrogen oxides limit for Class II units.
Table 5 to Subpart BBBB of Part 60 - Model Rule - Carbon Monoxide Emission Limits for Existing Small Municipal Waste Combustion Units
40:8.0.1.1.1.29.195.90.13 :
Table 5 to Subpart BBBB of Part 60 - Model Rule - Carbon Monoxide Emission Limits for Existing Small Municipal Waste Combustion UnitsFor the following municipal waste combustion units | You must meet the following carbon monoxide limits a | Using the following averaging times b |
---|---|---|
1. Fluidized bed | 100 parts per million by dry volume | 4-hour. |
2. Fluidized bed, mixed fuel, (wood/refuse-derived fuel) | 200 parts per million by dry volume | 24-hour c. |
3. Mass burn rotary refractory | 100 parts per million by dry volume | 4-hour. |
4. Mass burn rotary waterwall | 250 parts per million by dry volume | 24-hour. |
5. Mass burn waterwall and refractory | 100 parts per million by dry volume | 4-hour. |
6. Mixed fuel-fired, (pulverized coal/refuse-derived fuel) | 150 parts per million by dry volume | 4-hour. |
7. Modular starved-air and excess air | 50 parts per million by dry volume | 4-hour. |
8. Spreader stoker, mixed fuel-fired (coal/refuse-derived fuel) | 200 parts per million by dry volume | 24-hour daily. |
9. Stoker, refuse-derived fuel | 200 parts per million by dry volume | 24-hour daily. |
a All emission limits (except for opacity) are measured at 7 percent oxygen. Compliance is determined by continuous emission monitoring systems.
b Block averages, arithmetic mean. See § 60.1940 for definitions.
c 24-hour block average, geometric mean.
Table 6 to Subpart BBBB of Part 60 - Model Rule - Requirements for Validating Continuous Emission Monitoring Systems (CEMS)
40:8.0.1.1.1.29.195.90.14 :
Table 6 to Subpart BBBB of Part 60 - Model Rule - Requirements for Validating Continuous Emission Monitoring Systems (CEMS)For the following continuous emission monitoring systems | Use the following methods in appendix A of this part to validate poollutant concentratin levels | Use the following methods in appendix A of this part to measure oxygen (or carbon dioxide) |
---|---|---|
1. Nitrogen Oxides (Class I units only) a | Method 7, 7A, 7B,7C, 7D, or 7E | Method 3 or 3A. |
2. Sulfur Dioxide | Method 6 or 6C | Method 3 or 3A. |
3. Carbon Monoxide | Method 10, 10A, or 10B | Method 3 or 3A. |
a Class I units mean small municipal waste combustion units subject to this subpart that are located at municipal waste combustion plants with an aggregate plant combustion capacity greater than 250 tons per day of municipal solid waste. See § 60.1940 for definitions.
Table 7 to Subpart BBBB of Part 60 - Model Rule - Requirements for Continuous Emission Monitoring Systems (CEMS)
40:8.0.1.1.1.29.195.90.15 :
Table 7 to Subpart BBBB of Part 60 - Model Rule - Requirements for Continuous Emission Monitoring Systems (CEMS)For the following pollutants | Use the following span values for CEMS | Use the following performance specifications in appendix B of this part for your CEMS | If needed to meet minimum data requirements, use the following alternate methods in appendix A of this part to collect data |
---|---|---|---|
1. Opacity | 100 percent opacity | P.S. 1 | Method 9. |
2. Nitrogen Oxides (Class I units only) | Control device outlet: 125 percent of the maximum expected hourly potential nitrogen oxides emissions of the municipal waste combustion unit | P.S. 2 | Method 7E. |
3. Sulfur Dioxide | Inlet to control device: 125 percent of the maximum expected hourly potential sulfur dioxide emissions of the municipal waste combustion unit | P.S. 2 | Method 6C. |
Control device outlet: 50 percent of the maximum expected hourly potential sulfur dioxide emissions of the municipal waste combustion unit | |||
4. Carbon Monoxide | 125 percent of the maximum expected hourly potential carbon monoxide emissions of the municipal waste combustion unit | P.S. 4A | Method 10 with alternative interference trap. |
5. Oxygen or Carbon Dioxide | 25 percent oxygen or 25 percent carbon dioxide | P.S. 3 | Method 3A or 3B. |
Table 8 to Subpart BBBB of Part 60 - Model Rule - Requirements for Stack Tests
40:8.0.1.1.1.29.195.90.16 :
Table 8 to Subpart BBBB of Part 60 - Model Rule - Requirements for Stack TestsTo measure the following pollutants | Use the following methods in appendix A of this part to determine the sampling location | Use the following methods in appendix A of this part to measure pollutant concentration | Also note the following additional information |
---|---|---|---|
1. Organics | |||
Dioxins/Furans | Method 1 | Method 23 a | The minimum sampling time must be 4 hours per test run while the municipal waste combustion unit is operating at full load. |
2. Metals | |||
Cadmium | Method 1 | Method 29 a | Compliance testing must be performed while the municipal waste combustion unit is operating at full load. |
Lead | Method 1 | Method 29 a | Compliance testing must be performed while the municipal waste combustion unit is operating at full load. |
Mercury | Method 1 | Method 29 a | Compliance testing must be performed while the municipal waste combustion unit is operating at full load. |
Opacity | Method 9 | Method 9 | Use Method 9 to determine compliance with opacity limits. 3-hour observation period (thirty 6-minute averages). |
Particulate Matter | Method 1 | Method 5 or 29 | The minimum sample volume must be 1.0 cubic meters. The probe and filter holder heating systems in the sample train must be set to provide a gas temperature no greater than 160 ±14 °C. The minimum sampling time is 1 hour. |
3. Acid Gases b | |||
Hydrogen Chloride | Method 1 | Method 26 or 26A a | Test runs must be at least 1 hour long while the municipal waste combustion unit is operating at full load. |
4. Other b | |||
Fugitive Ash | Not applicable | Method 22 (visible emissions) | The three 1-hour observation period must include periods when the facility transfers fugitive ash from the municipal waste combustion unit to the area where the fugitive ash is stored or loaded into containers or trucks. |
a Must simultaneously measure oxygen (or carbon dioxide) using Method 3A or 3B in appendix A of this part.
b Use CEMS to test sulfur dioxide, nitrogen oxide, and carbon monoxide. Stack tests are not required except for quality assurance requirements in appendix F of this part.
Table 1 to Subpart CCCC of Part 60 - Emission Limitations for Incinerators for Which Construction is Commenced After November 30, 1999, But no Later Than June 4, 2010, or for Which Modification or Reconstruction is Commenced on or After June 1, 2001, But no Later Than August 7, 2013
40:8.0.1.1.1.30.209.56.17 :
Table 1 to Subpart CCCC of Part 60 - Emission Limitations for Incinerators for Which Construction is Commenced After November 30, 1999, But no Later Than June 4, 2010, or for Which Modification or Reconstruction is Commenced on or After June 1, 2001, But no Later Than August 7, 2013For the air pollutant | You must meet this emission limitation 1 |
Using this averaging time 2 | And determining
compliance using this method 2 |
---|---|---|---|
Cadmium | 0.004 milligrams per dry standard cubic meter | 3-run average (1 hour minimum sample time per run) | Performance test (Method 29 of appendix A of this part). |
Carbon monoxide | 157 parts per million by dry volume | 3-run average (1 hour minimum sample time per run) | Performance test (Method 10 at 40 CFR part 60, appendix A-4). |
Dioxin/Furan (toxic equivalency basis) | 0.41 nanograms per dry standard cubic meter | 3-run average (collect a minimum volume of 4 dry standard cubic meters per run) | Performance test (Method 23 of appendix A-7 of this part). |
Hydrogen chloride | 62 parts per million by dry volume | 3-run average (For Method 26, collect a minimum volume of 120 liters per run. For Method 26A, collect a minimum volume of 1 dry standard cubic meter per run) | Performance test (Method 26 or 26A at 40 CFR part 60, appendix A-8). |
Lead | 0.04 milligrams per dry standard cubic meter | 3-run average (1 hour minimum sample time per run) | Performance test (Method 29 of appendix A of this part). |
Mercury | 0.47 milligrams per dry standard cubic meter | 3-run average (1 hour minimum sample time per run) | Performance test (Method 29 of appendix A of this part). |
Nitrogen oxides | 388 parts per million by dry volume | 3-run average (for Method 7E, 1 hour minimum sample time per run) | Performance test (Method 7 or 7E at 40 CFR part 60, appendix A-4). |
Opacity | 10 percent | 6-minute averages | Performance test (Method 9 of appendix A of this part). |
Particulate matter | 70 milligrams per dry standard cubic meter | 3-run average (1 hour minimum sample time per run) | Performance test (Method 5 or 29 of appendix A of this part). |
Sulfur dioxide | 20 parts per million by dry volume | 3-run average (For Method 6, collect a minimum volume of 20 liters per run. For Method 6C, collect sample for a minimum duration of 1 hour per run) | Performance test (Method 6 or 6C at 40 CFR part 60, appendix A-4). |
1 All emission limitations (except for opacity) are measured at 7 percent oxygen, dry basis at standard conditions.
2 In lieu of performance testing, you may use a CEMS or, for mercury, an integrated sorbent trap monitoring system, to demonstrate initial and continuing compliance with an emissions limit, as long as you comply with the CEMS or integrated sorbent trap monitoring system requirements applicable to the specific pollutant in §§ 60.2145 and 60.2165. As prescribed in § 60.2145(u), if you use a CEMS or an integrated sorbent trap monitoring system to demonstrate compliance with an emissions limit, your averaging time is a 30-day rolling average of 1-hour arithmetic average emission concentrations.
Table 2 to Subpart CCCC of Part 60 - Operating Limits for Wet Scrubbers
40:8.0.1.1.1.30.209.56.18 :
Table 2 to Subpart CCCC of Part 60 - Operating Limits for Wet ScrubbersFor these operating parameters | You must establish these operating limits | And monitoring using these minimum frequencies | ||
---|---|---|---|---|
Data measurement | Data recording | Averaging time | ||
Charge rate | Maximum charge rate | Continuous | Every hour | Daily (batch units) 3-hour rolling (continuous and intermittent units). 1 |
Pressure drop across the wet scrubber or amperage to wet scrubber | Minimum pressure drop or amperage | Continuous | Every 15 minutes | 3-hour rolling. 1 |
Scrubber liquor flow rate | Minimum flow rate | Continuous | Every 15 minutes | 3-hour rolling. 1 |
Scrubber liquor pH | Minimum pH | Continuous | Every 15 minutes | 3-hour rolling. 1 |
1 Calculated each hour as the average of the previous 3 operating hours.
Table 3 to Subpart CCCC of Part 60 - Toxic Equivalency Factors
40:8.0.1.1.1.30.209.56.19 :
Table 3 to Subpart CCCC of Part 60 - Toxic Equivalency FactorsDioxin/furan congener | Toxic equivalency factor |
---|---|
2,3,7,8-tetrachlorinated dibenzo-p-dioxin | 1 |
1,2,3,7,8-pentachlorinated dibenzo-p-dioxin | 0.5 |
1,2,3,4,7,8-hexachlorinated dibenzo-p-dioxin | 0.1 |
1,2,3,7,8,9-hexachlorinated dibenzo-p-dioxin | 0.1 |
1,2,3,6,7,8-hexachlorinated dibenzo-p-dioxin | 0.1 |
1,2,3,4,6,7,8-heptachlorinated dibenzo-p-dioxin | 0.01 |
octachlorinated dibenzo-p-dioxin | 0.001 |
2,3,7,8-tetrachlorinated dibenzofuran | 0.1 |
2,3,4,7,8-pentachlorinated dibenzofuran | 0.5 |
1,2,3,7,8-pentachlorinated dibenzofuran | 0.05 |
1,2,3,4,7,8-hexachlorinated dibenzofuran | 0.1 |
1,2,3,6,7,8-hexachlorinated dibenzofuran | 0.1 |
1,2,3,7,8,9-hexachlorinated dibenzofuran | 0.1 |
2,3,4,6,7,8-hexachlorinated dibenzofuran | 0.1 |
1,2,3,4,6,7,8-heptachlorinated dibenzofuran | 0.01 |
1,2,3,4,7,8,9-heptachlorinated dibenzofuran | 0.01 |
octachlorinated dibenzofuran | 0.001 |
Table 4 to Subpart CCCC of Part 60 - Summary of Reporting Requirements 1
40:8.0.1.1.1.30.209.56.20 :
Table 4 to Subpart CCCC of Part 60 - Summary of Reporting Requirements 1Report | Due date | Contents | Reference |
---|---|---|---|
Preconstruction report | Prior to commencing construction | • Statement of intent to construct | § 60.2190. |
• Anticipated date of
commencement of construction • Documentation for siting requirements • Waste management plan • Anticipated date of initial startup |
|||
Startup notification | Prior to initial startup | • Type of waste to be burned | § 60.2195. |
• Maximum design waste burning
capacity • Anticipated maximum charge rate • If applicable, the petition for site-specific operating limits |
|||
Initial test report | No later than 60 days following the initial performance test | • Complete test report for the
initial performance test • The values for the site-specific operating limits |
§ 60.2200. |
• Installation of bag leak detection system for fabric filter | |||
Annual report | No later than 12 months following the submission of the initial test report. Subsequent reports are to be submitted no more than 12 months following the previous report | • Name and address • Statement and signature by responsible official • Date of report • Values for the operating limits |
§§ 60.2205 and 60.2210. |
• Highest recorded 3-hour
average and the lowest 3-hour average, as applicable, (or 30-day
average, if applicable) for each operating parameter recorded for
the calendar year being reported • For each performance test conducted during the reporting period, if any performance test is conducted, the process unit(s) tested, the pollutant(s) tested, and the date that such performance test was conducted • If a performance test was not conducted during the reporting period, a statement that the requirements of § 60.2155(a) were met • Documentation of periods when all qualified CISWI operators were unavailable for more than 8 hours but less than 2 weeks • If you are conducting performance tests once every 3 years consistent with § 60.2155(a), the date of the last 2 performance tests, a comparison of the emission level you achieved in the last 2 performance tests to the 75 percent emission limit threshold required in § 60.2155(a) and a statement as to whether there have been any operational changes since the last performance test that could increase emissions • Any malfunction, deviation, or continuous monitoring system out of control periods information as specified in § 60.2210(k) through (o) |
|||
Emission limitation or operating limit deviation report | By August 1 of that year for data collected during the first half of the calendar year. By February 1 of the following year for data collected during the second half of the calendar year | • Dates and times of
deviation • Averaged and recorded data for those dates • Duration and causes of each deviation and the corrective actions taken • Copy of operating limit monitoring data and, if any performance test was conducted that documents emission levels, the process unit(s) tested, the pollutant(s) tested, and the date that such performance test was conducted |
§ 60.2215 and 60.2220. |
• Dates, times and causes for monitor downtime incidents | |||
Qualified operator deviation notification | Within 10 days of deviation | • Statement of cause of
deviation • Description of efforts to have an accessible qualified operator |
§ 60.2225(a)(1). |
• The date a qualified operator will be accessible | |||
Qualified operator deviation status report | Every 4 weeks following deviation | • Description of efforts to have an accessible qualified operator | § 60.2225(a)(2). |
• The date a qualified
operator will be accessible • Request for approval to continue operation |
|||
Qualified operator deviation notification of resumed operation | Prior to resuming operation | • Notification that you are resuming operation | § 60.2225(b). |
1 This table is only a summary, see the referenced sections of the rule for the complete requirements.
Table 5 to Subpart CCCC of Part 60 - Emission Limitations for Incinerators That Commenced Construction After June 4, 2010, or That Commenced Reconstruction or Modification After August 7, 2013
40:8.0.1.1.1.30.209.56.21 :
Table 5 to Subpart CCCC of Part 60 - Emission Limitations for Incinerators That Commenced Construction After June 4, 2010, or That Commenced Reconstruction or Modification After August 7, 2013For the air pollutant | You must meet this emission limitation 1 | Using this averaging time 2 | And determining compliance
using this method 2 |
---|---|---|---|
Cadmium | 0.0023 milligrams per dry standard cubic meter | 3-run average (collect a minimum volume of 4 dry standard cubic meter per run) | Performance test (Method 29 at 40 CFR part 60, appendix A-8 of this part). Use ICPMS for the analytical finish. |
Carbon monoxide | 17 parts per million by dry volume | 3-run average (1 hour minimum sample time per run) | Performance test (Method 10 at 40 CFR part 60, appendix A-4). |
Dioxin/furan (Total Mass Basis) | 0.58 nanograms per dry standard cubic meter | 3-run average (collect a minimum volume of 4 dry standard cubic meters per run) | Performance test (Method 23 at 40 CFR part 60, appendix A-7). |
Dioxin/furan (toxic equivalency basis) | 0.13 nanograms per dry standard cubic meter | 3-run average (collect a minimum volume of 4 dry standard cubic meter per run) | Performance test (Method 23 at 40 CFR part 60, appendix A-7). |
Fugitive ash | Visible emissions for no more than 5 percent of the hourly observation period | Three 1-hour observation periods | Visible emission test (Method 22 at 40 CFR part 60, appendix A-7). |
Hydrogen chloride | 0.091 parts per million by dry volume | 3-run average (For Method 26, collect a minimum volume of 360 liters per run. For Method 26A, collect a minimum volume of 3 dry standard cubic meters per run) | Performance test (Method 26 or 26A at 40 CFR part 60, appendix A-8). |
Lead | 0.015 milligrams per dry standard cubic meter | 3-run average (collect a minimum volume of 4 dry standard cubic meters per run) | Performance test (Method 29 of appendix A-8 at 40 CFR part 60). Use ICPMS for the analytical finish. |
Mercury | 0.00084 milligrams per dry standard cubic meter | 3-run average (collect enough volume to meet a detection limit data quality objective of 0.03 ug/dry standard cubic meter) | Performance test (Method 29 or 30B at 40 CFR part 60, appendix A-8) or ASTM D6784-02 (Reapproved 2008). 3 |
Nitrogen oxides | 23 parts per million dry volume | 3-run average (for Method 7E, 1 hour minimum sample time per run) | Performance test (Method 7 or 7E at 40 CFR part 60, appendix A-4). |
Particulate matter (filterable) | 18 milligrams per dry standard cubic meter | 3-run average (collect a minimum volume of 2 dry standard cubic meters per run) | Performance test (Method 5 or 29 at 40 CFR part 60, appendix A-3 or appendix A-8 at 40 CFR part 60). |
Sulfur dioxide | 11 parts per million dry volume | 3-run average (1 hour minimum sample time per run) | Performance test (Method 6 or 6C at 40 CFR part 60, appendix A-4). |
1 All emission limitations are measured at 7 percent oxygen, dry basis at standard conditions. For dioxins/furans, you must meet either the Total Mass Limit or the toxic equivalency basis limit.
2 In lieu of performance testing, you may use a CEMS or, for mercury, an integrated sorbent trap monitoring system to demonstrate initial and continuing compliance with an emissions limit, as long as you comply with the CEMS or integrated sorbent trap monitoring system requirements applicable to the specific pollutant in §§ 60.2145 and 60.2165. As prescribed in § 60.2145(u), if you use a CEMS or an integrated sorbent trap monitoring system to demonstrate compliance with an emissions limit, your averaging time is a 30-day rolling average of 1-hour arithmetic average emission concentrations.
3 Incorporated by reference, see § 60.17.
Table 6 to Subpart CCCC of Part 60 - Emission Limitations for Energy Recovery Units That Commenced Construction After June 4, 2010, or That Commenced Reconstruction or Modification After August 7, 2013
40:8.0.1.1.1.30.209.56.22 :
Table 6 to Subpart CCCC of Part 60 - Emission Limitations for Energy Recovery Units That Commenced Construction After June 4, 2010, or That Commenced Reconstruction or Modification After August 7, 2013For the air pollutant | You must meet this emission limitation 1 | Using this averaging time 2 | And determining compliance using this method 2 | |
---|---|---|---|---|
Liquid/gas | Solids | |||
Cadmium | 0.023 milligrams per dry standard cubic meter | Biomass - 0.0014 milligrams per dry standard cubic meter. Coal - 0.0017 milligrams per dry standard cubic meter | 3-run average (collect a minimum volume of 4 dry standard cubic meters per run) | Performance test (Method 29 at 40 CFR part 60, appendix A-8). Use ICPMS for the analytical finish. |
Carbon monoxide | 35 parts per million dry volume | Biomass - 240 parts per million dry volume. Coal - 95 parts per million dry volume | 3-run average (1 hour minimum sample time per run) | Performance test (Method 10 at 40 CFR part 60, appendix A-4). |
Dioxin/furans (Total Mass Basis) | No Total Mass Basis limit, must meet the toxic equivalency basis limit below | Biomass - 0.52 nanograms per dry standard cubic meter. Coal - 5.1 nanograms per dry standard cubic meter | 3-run average (collect a minimum volume of 4 dry standard cubic meters) | Performance test (Method 23 at 40 CFR part 60, appendix A-7). |
Dioxins/furans (toxic equivalency basis) | 0.093 nanograms per dry standard cubic meter | Biomass - 0.076 nanograms per dry standard cubic meter. 3 Coal - 0.075 nanograms per dry standard cubic meter | 3-run average (collect a minimum volume of 4 dry standard cubic meters per run) | Performance test (Method 23 of appendix A-7 of this part). |
Fugitive ash | Visible emissions for no more than 5 percent of the hourly observation period | Three 1-hour observation periods | Visible emission test (Method 22 at 40 CFR part 60, appendix A-7) | Fugitive ash. |
Hydrogen chloride | 14 parts per million dry volume | Biomass - 0.20 parts per million dry volume. Coal - 58 parts per million dry volume | 3-run average (For Method 26, collect a minimum volume of 360 liters per run. For Method 26A, collect a minimum volume of 3 dry standard cubic meters per run) | Performance test (Method 26 or 26A at 40 CFR part 60, appendix A-8). |
Lead | 0.096 milligrams per dry standard cubic meter | Biomass - 0.014 milligrams per dry standard cubic meter. Coal - 0.057 milligrams per dry standard cubic meter | 3-run average (collect a minimum volume of 4 dry standard cubic meters per run) | Performance test (Method 29 at 40 CFR part 60, appendix A-8). Use ICPMS for the analytical finish. |
Mercury | 0.00056 milligrams per dry standard cubic meter | Biomass - 0.0022 milligrams per dry standard cubic meter. Coal - 0.013 milligrams per dry standard cubic meter | 3-run average (collect enough volume to meet an in-stack detection limit data quality objective of 0.03 ug/dscm) | Performance test (Method 29 or 30B at 40 CFR part 60, appendix A-8) or ASTM D6784-02 (Reapproved 2008). 3 |
Nitrogen oxides | 76 parts per million dry volume | Biomass - 290 parts per million dry volume. Coal - 460 parts per million dry volume | 3-run average (for Method 7E, 1 hour minimum sample time per run) | Performance test (Method 7 or 7E at 40 CFR part 60, appendix A-4). |
Particulate matter (filterable) | 110 milligrams per dry standard cubic meter | Biomass - 5.1 milligrams per dry standard cubic meter. Coal - 130 milligrams per dry standard cubic meter | 3-run average (collect a minimum volume of 1 dry standard cubic meter per run) | Performance test (Method 5 or 29 at 40 CFR part 60, appendix A-3 or appendix A-8). |
Sulfur dioxide | 720 parts per million dry volume | Biomass - 7.3 parts per million dry volume. Coal - 850 parts per million dry volume | 3-run average (for Method 6, collect a minimum of 60 liters, for Method 6C, 1 hour minimum sample time per run) | Performance test (Method 6 or 6C at 40 CFR part 60, appendix A-4). |
1 All emission limitations are measured at 7 percent oxygen, dry basis at standard conditions. For dioxins/furans, you must meet either the Total Mass Basis limit or the toxic equivalency basis limit.
2 In lieu of performance testing, you may use a CEMS or, for mercury, an integrated sorbent trap monitoring system to demonstrate initial and continuing compliance with an emissions limit, as long as you comply with the CEMS or integrated sorbent trap monitoring system requirements applicable to the specific pollutant in §§ 60.2145 and 60.2165. As prescribed in § 60.2145(u), if you use a CEMS or an integrated sorbent trap monitoring system to demonstrate compliance with an emissions limit, your averaging time is a 30-day rolling average of 1-hour arithmetic average emission concentrations.
3 Incorporated by reference, see § 60.17.
Table 7 to Subpart CCCC of Part 60 - Emission Limitations for Waste-Burning Kilns That Commenced Construction After June 4, 2010, or Reconstruction or Modification After August 7, 2013
40:8.0.1.1.1.30.209.56.23 :
Table 7 to Subpart CCCC of Part 60 - Emission Limitations for Waste-Burning Kilns That Commenced Construction After June 4, 2010, or Reconstruction or Modification After August 7, 2013For the air pollutant | You must meet this emission limitation 1 | Using this averaging time 2 | And determining compliance using this method 2, 3 |
---|---|---|---|
Cadmium | 0.0014 milligrams per dry standard cubic meter | 3-run average (collect a minimum volume of 4 dry standard cubic meters per run) | Performance test (Method 29 at 40 CFR part 60, appendix A-8). Use ICPMS for the analytical finish. |
Carbon monoxide | 90 (long kilns)/190 (preheater/precalciner) parts per million dry volume | 3-run average (1 hour minimum sample time per run) | Performance test (Method 10 at 40 CFR part 60, appendix A-4). |
Dioxins/furans (total mass basis) | 0.51 nanograms per dry standard cubic meter | 3-run average (collect a minimum volume of 4 dry standard cubic meters per run) | Performance test (Method 23 at 40 CFR part 60, appendix A-7). |
Dioxins/furans (toxic equivalency basis) | 0.075 nanograms per dry standard cubic meter | 3-run average (collect a minimum volume of 4 dry standard cubic meters) | Performance test (Method 23 at 40 CFR part 60, appendix A-7). |
Hydrogen chloride | 3.0 parts per million dry volume | 3-run average (1 hour minimum sample time per run) or 30-day rolling average if HCl CEMS is being used | If a wet scrubber or dry scrubber is used, performance test (Method 321 at 40 CFR part 63, appendix A). If a wet scrubber or dry scrubber is not used, HCl CEMS as specified in § 60.2145(j). |
Lead | 0.014 milligrams per dry standard cubic meter | 3-run average (collect a minimum volume of 4 dry standard cubic meters) | Performance test (Method 29 at 40 CFR part 60, appendix A-8). Use ICPMS for the analytical finish. |
Mercury | 0.0037 milligrams per dry standard cubic meter. Or 21 pounds/million tons of clinker 3 | 30-day rolling average | Mercury CEMS or integrated sorbent trap monitoring system (performance specification 12A or 12B, respectively, of appendix B and procedure 5 of appendix F of this part), as specified in § 60.2145(j). |
Nitrogen oxides | 200 parts per million dry volume | 30-day rolling average | Nitrogen oxides CEMS (performance specification 2 of appendix B and procedure 1 of appendix F of this part). |
Particulate matter (filterable) | 4.9 milligrams per dry standard cubic meter | 3-run average (collect a minimum volume of 2 dry standard cubic meters) | Performance test (Method 5 or 29 at 40 CFR part 60, appendix A-3 or appendix-8). |
Sulfur dioxide | 28 parts per million dry volume | 30-day rolling average | Sulfur dioxide CEMS (performance specification 2 of appendix B and procedure 1 of appendix F of this part). |
1 All emission limitations are measured at 7 percent oxygen (except for CEMS and integrated sorbent trap monitoring system data during startup and shutdown), dry basis at standard conditions. For dioxins/furans, you must meet either the Total Mass Basis limit or the toxic equivalency basis limit.
2 In lieu of performance testing, you may use a CEMS or, for mercury, an integrated sorbent trap monitoring system, to demonstrate initial and continuing compliance with an emissions limit, as long as you comply with the CEMS or integrated sorbent trap monitoring system requirements applicable to the specific pollutant in §§ 60.2145 and 60.2165. As prescribed in § 60.2145(u), if you use a CEMS or integrated sorbent trap monitoring system to demonstrate compliance with an emissions limit, your averaging time is a 30-day rolling average of 1-hour arithmetic average emission concentrations.
3 Alkali bypass and in-line coal mill stacks are subject to performance testing only, as specified in § 60.2145(y)(3). They are not subject to the CEMS, integrated sorbent trap monitoring system, or CPMS requirements that otherwise may apply to the main kiln exhaust.
Table 8 to Subpart CCCC of Part 60 - Emission Limitations for Small, Remote Incinerators That Commenced Construction After June 4, 2010, or That Commenced Reconstruction or Modification After August 7, 2013
40:8.0.1.1.1.30.209.56.24 :
Table 8 to Subpart CCCC of Part 60 - Emission Limitations for Small, Remote Incinerators That Commenced Construction After June 4, 2010, or That Commenced Reconstruction or Modification After August 7, 2013For the air pollutant | You must meet this emission limitation 1 |
Using this averaging time 2 | And determining
compliance using this method 2 |
---|---|---|---|
Cadmium | 0.67 milligrams per dry standard cubic meter | 3-run average (collect a minimum volume of 1 dry standard cubic meters per run) | Performance test (Method 29 at 40 CFR part 60, appendix A-8). |
Carbon monoxide | 13 parts per million dry volume | 3-run average (1 hour minimum sample time per run) | Performance test (Method 10 at 40 CFR part 60, appendix A-4). |
Dioxins/furans (total mass basis) | 1,800 nanograms per dry standard cubic meter | 3-run average (collect a minimum volume of 1 dry standard cubic meters per run) | Performance test (Method 23 at 40 CFR part 60, appendix A-7). |
Dioxins/furans (toxic equivalency basis) | 31 nanograms per dry standard cubic meter | 3-run average (collect a minimum volume of 1 dry standard cubic meters) | Performance test (Method 23 at 40 CFR part 60, appendix A-7). |
Fugitive ash | Visible emissions for no more than 5 percent of the hourly observation period | Three 1-hour observation periods | Visible emissions test (Method 22 at 40 CFR part 60, appendix A-7). |
Hydrogen chloride | 200 parts per million by dry volume | 3-run average (For Method 26, collect a minimum volume of 60 liters per run. For Method 26A, collect a minimum volume of 1 dry standard cubic meter per run) | Performance test (Method 26 or 26A at 40 CFR part 60, appendix A-8). |
Lead | 2.0 milligrams per dry standard cubic meter | 3-run average (collect a minimum volume of 1 dry standard cubic meters) | Performance test (Method 29 at 40 CFR part 60, appendix A-8). Use ICPMS for the analytical finish. |
Mercury | 0.0035 milligrams per dry standard cubic meter | 3-run average (For Method 29 and ASTM D6784-02 (Reapproved 2008) 2, collect a minimum volume of 2 dry standard cubic meters per run. For Method 30B, collect a minimum volume as specified in Method 30B at 40 CFR part 60, appendix A) | Performance test (Method 29 or 30B at 40 CFR part 60, appendix A-8) or ASTM D6784-02 (Reapproved 2008). 3 |
Nitrogen oxides | 170 parts per million dry volume | 3-run average (for Method 7E, 1 hour minimum sample time per run) | Performance test (Method 7 or 7E at 40 CFR part 60, appendix A-4). |
Particulate matter (filterable) | 270 milligrams per dry standard cubic meter | 3-run average (collect a minimum volume of 1 dry standard cubic meters) | Performance test (Method 5 or 29 at 40 CFR part 60, appendix A-3 or appendix A-8). |
Sulfur dioxide | 1.2 parts per million dry volume | 3-run average (1 hour minimum sample time per run) | Performance test (Method 6 or 6c at 40 CFR part 60, appendix A-4). |
1 All emission limitations are measured at 7 percent oxygen, dry basis at standard conditions. For dioxins/furans, you must meet either the Total Mass Basis limit or the toxic equivalency basis limit.
2 In lieu of performance testing, you may use a CEMS or, for mercury, an integrated sorbent trap monitoring system to demonstrate initial and continuing compliance with an emissions limit, as long as you comply with the CEMS or integrated sorbent trap monitoring system requirements applicable to the specific pollutant in §§ 60.2145 and 60.2165. As prescribed in § 60.2145(u), if you use a CEMS or an integrated sorbent trap monitoring system to demonstrate compliance with an emissions limit, your averaging time is a 30-day rolling average of 1-hour arithmetic average emission concentrations.
3 Incorporated by reference, see § 60.17.
Table 1 to Subpart DDDD of Part 60 - Model Rule - Increments of Progress and Compliance Schedules
40:8.0.1.1.1.31.224.80.25 :
Table 1 to Subpart DDDD of Part 60 - Model Rule - Increments of Progress and Compliance SchedulesComply with these increments of progress | By these dates 1 |
---|---|
Increment 1-Submit final control plan | (Dates to be specified in state plan). |
Increment 2-Final compliance | (Dates to be specified in state plan). 2 |
1 Site-specific schedules can be used at the discretion of the state.
2 The date can be no later than 3 years after the effective date of state plan approval or December 1, 2005 for CISWIs that commenced construction on or before November 30, 1999. The date can be no later than 3 years after the effective date of approval of a revised state plan or February 7, 2018, for CISWIs that commenced construction on or before June 4, 2010.
Table 2 to Subpart DDDD of Part 60 - Model Rule - Emission Limitations That Apply to Incinerators Before [Date To Be Specified in State Plan] 1
40:8.0.1.1.1.31.224.80.26 :
Table 2 to Subpart DDDD of Part 60 - Model Rule - Emission Limitations That Apply to Incinerators Before [Date To Be Specified in State Plan] 1For the air pollutant | You must meet this emission limitation 2 |
Using this averaging time 3 | And determining compliance using this method 3 |
---|---|---|---|
Cadmium | 0.004 milligrams per dry standard cubic meter | 3-run average (1 hour minimum sample time per run) | Performance test (Method 29 of appendix A of this part). |
Carbon monoxide | 157 parts per million by dry volume | 3-run average (1 hour minimum sample time per run) | Performance test (Method 10, 10A, or 10B, of appendix A of this part). |
Dioxins/furans (toxic equivalency basis) | 0.41 nanograms per dry standard cubic meter | 3-run average (1 hour minimum sample time per run) | Performance test (Method 23 of appendix A of this part). |
Hydrogen chloride | 62 parts per million by dry volume | 3-run average (For Method 26, collect a minimum volume of 120 liters per run. For Method 26A, collect a minimum volume of 1 dry standard cubic meter per run) | Performance test (Method 26 or 26A at 40 CFR part 60, appendix A-8). |
Lead | 0.04 milligrams per dry standard cubic meter | 3-run average (1 hour minimum sample time per run) | Performance test (Method 29 of appendix A of this part). |
Mercury | 0.47 milligrams per dry standard cubic meter | 3-run average (1 hour minimum sample time per run) | Performance test (Method 29 or 30B at 40 CFR part 60, appendix A-8) or ASTM D6784-02 (Reapproved 2008). 4 |
Opacity | 10 percent | Three 1-hour blocks consisting of ten 6-minute average opacity values | Performance test (Method 9 at 40 CFR part 60, appendix A-4). |
Nitrogen oxides | 388 parts per million by dry volume | 3-run average (1 hour minimum sample time per run) | Performance test (Methods 7 or 7E at 40 CFR part 60, appendix A-4). |
Particulate matter | 70 milligrams per dry standard cubic meter | 3-run average (1 hour minimum sample time per run) | Performance test (Method 5 or 29 of appendix A of this part). |
Sulfur dioxide | 20 parts per million by dry volume | 3-run average (1 hour minimum sample time per run) | Performance test (Method 6 or 6c of appendix A of this part). |
1 Applies only to incinerators subject to the CISWI standards through a state plan or the Federal plan prior to June 4, 2010. The date specified in the state plan can be no later than 3 years after the effective date of approval of a revised state plan or February 7, 2018.
2 All emission limitations (except for opacity) are measured at 7 percent oxygen, dry basis at standard conditions.
3 In lieu of performance testing, you may use a CEMS or, for mercury, an integrated sorbent trap monitoring system, to demonstrate initial and continuing compliance with an emissions limit, as long as you comply with the CEMS or integrated sorbent trap monitoring system requirements applicable to the specific pollutant in §§ 60.2710 and 60.2730. As prescribed in § 60.2710(u), if you use a CEMS or integrated sorbent trap monitoring system to demonstrate compliance with an emissions limit, your averaging time is a 30-day rolling average of 1-hour arithmetic average emission concentrations.
4 Incorporated by reference, see § 60.17.
Table 3 to Subpart DDDD of Part 60 - Model Rule - Operating Limits for Wet Scrubbers
40:8.0.1.1.1.31.224.80.27 :
Table 3 to Subpart DDDD of Part 60 - Model Rule - Operating Limits for Wet ScrubbersFor these
operating parameters |
You must establish these operating limits | And monitor using these minimum frequencies | ||
---|---|---|---|---|
Data measurement |
Data recording |
Averaging time | ||
Charge rate | Maximum charge rate | Continuous | Every hour | Daily (batch units). 3-hour rolling (continuous and intermittent units). 1 |
Pressure drop across the wet scrubber or amperage to wet scrubber | Minimum pressure drop or amperage | Continuous | Every 15 minutes | 3-hour rolling. 1 |
Scrubber liquor flow rate | Minimum flow rate | Continuous | Every 15 minutes | 3-hour rolling. 1 |
Scrubber liquor pH | Minimum pH | Continuous | Every 15 minutes | 3-hour rolling. 1 |
1 Calculated each hour as the average of the previous 3 operating hours.
Table 4 to Subpart DDDD of Part 60 - Model Rule - Toxic Equivalency Factors
40:8.0.1.1.1.31.224.80.28 :
Table 4 to Subpart DDDD of Part 60 - Model Rule - Toxic Equivalency FactorsDioxin/furan isomer | Toxic equivalency factor |
---|---|
2,3,7,8-tetrachlorinated dibenzo-p-dioxin | 1 |
1,2,3,7,8-pentachlorinated dibenzo-p-dioxin | 0.5 |
1,2,3,4,7,8-hexachlorinated dibenzo-p-dioxin | 0.1 |
1,2,3,7,8,9-hexachlorinated dibenzo-p-dioxin | 0.1 |
1,2,3,6,7,8-hexachlorinated dibenzo-p-dioxin | 0.1 |
1,2,3,4,6,7,8-heptachlorinated dibenzo-p-dioxin | 0.01 |
octachlorinated dibenzo-p-dioxin | 0.001 |
2,3,7,8-tetrachlorinated dibenzofuran | 0.1 |
2,3,4,7,8-pentachlorinated dibenzofuran | 0.5 |
1,2,3,7,8-pentachlorinated dibenzofuran | 0.05 |
1,2,3,4,7,8-hexachlorinated dibenzofuran | 0.1 |
1,2,3,6,7,8-hexachlorinated dibenzofuran | 0.1 |
1,2,3,7,8,9-hexachlorinated dibenzofuran | 0.1 |
2,3,4,6,7,8-hexachlorinated dibenzofuran | 0.1 |
1,2,3,4,6,7,8-heptachlorinated dibenzofuran | 0.01 |
1,2,3,4,7,8,9-heptachlorinated dibenzofuran | 0.01 |
octachlorinated dibenzofuran | 0.001 |
Table 5 to Subpart DDDD of Part 60 - Model Rule - Summary of Reporting Requirements 1
40:8.0.1.1.1.31.224.80.29 :
Table 5 to Subpart DDDD of Part 60 - Model Rule - Summary of Reporting Requirements 1Report | Due date | Contents | Reference |
---|---|---|---|
Waste Management Plan | No later than the date specified in table 1 for submittal of the final control plan | • Waste management plan | § 60.2755. |
Initial Test Report | No later than 60 days following the initial performance test | • Complete test report for the
initial performance test • The values for the site-specific operating limits • Installation of bag leak detection systems for fabric filters |
§ 60.2760. |
Annual report | No later than 12 months following the submission of the initial test report. Subsequent reports are to be submitted no more than 12 months following the previous report | • Name and address • Statement and signature by responsible official • Date of report • Values for the operating limits • Highest recorded 3-hour average and the lowest 3-hour average, as applicable, (or 30-day average, if applicable) for each operating parameter recorded for the calendar year being reported • If a performance test was conducted during the reporting period, the results of the test • If a performance test was not conducted during the reporting period, a statement that the requirements of § 60.2720(a) were met • Documentation of periods when all qualified CISWI operators were unavailable for more than 8 hours but less than 2 weeks • If you are conducting performance tests once every 3 years consistent with § 60.2720(a), the date of the last 2 performance tests, a comparison of the emission level you achieved in the last 2 performance tests to the 75 percent emission limit threshold required in § 60.2720(a) and a statement as to whether there have been any operational changes since the last performance test that could increase emissions • Any malfunction, deviation, or continuous monitoring system out of control periods information as specified in § 60.2770(k) through (o) • Fuel input information for energy recovery unit subcategory verification as specified in § 60.2770(p) |
§§ 60.2765 and 60.2770. |
Emission limitation or operating limit deviation report | By August 1 of that year for data collected during the first half of the calendar year. By February 1 of the following year for data collected during the second half of the calendar year | • Dates and times of
deviation • Averaged and recorded data for those dates • Duration and causes of each deviation and the corrective actions taken • Copy of operating limit monitoring data and any test reports • Dates, times and causes for monitor downtime incidents |
§ 60.2775 and 60.2780. |
Qualified Operator Deviation Notification | Within 10 days of deviation | • Statement of cause of
deviation • Description of efforts to have an accessible qualified operator • The date a qualified operator will be accessible |
§ 60.2785(a)(1). |
Qualified Operator Deviation Status Report | Every 4 weeks following deviation | • Description of efforts to
have an accessible qualified operator • The date a qualified operator will be accessible • Request for approval to continue operation |
§ 60.2785(a)(2). |
Qualified Operator Deviation Notification of Resumed Operation | Prior to resuming operation | • Notification that you are resuming operation | § 60.2785(b). |
1 This table is only a summary, see the referenced sections of the rule for the complete requirements.
Table 6 to Subpart DDDD of Part 60 - Model Rule - Emission Limitations That Apply to Incinerators on and After [Date To Be Specified in State Plan] 1
40:8.0.1.1.1.31.224.80.30 :
Table 6 to Subpart DDDD of Part 60 - Model Rule - Emission Limitations That Apply to Incinerators on and After [Date To Be Specified in State Plan] 1For the air pollutant | You must meet this emission limitation 2 |
Using this averaging time 3 | And determining compliance using this method 3 |
---|---|---|---|
Cadmium | 0.0026 milligrams per dry standard cubic meter | 3-run average (collect a minimum volume of 2 dry standard cubic meters) | Performance test (Method 29 at 40 CFR part 60, appendix A-8). Use ICPMS for the analytical finish. |
Carbon monoxide | 17 parts per million dry volume | 3-run average (1 hour minimum sample time per run) | Performance test (Method 10 at 40 CFR part 60, appendix A-4). |
Dioxins/furans (total mass basis) | 4.6 nanograms per dry standard cubic meter | 3-run average (collect a minimum volume of 2 dry standard cubic meters) | Performance test (Method 23 at 40 CFR part 60, appendix A-7). |
Dioxins/furans (toxic equivalency basis) | 0.13 nanograms per dry standard cubic meter | 3-run average (collect a minimum volume of 2 dry standard cubic meters) | Performance test (Method 23 at 40 CFR part 60, appendix A-7). |
Hydrogen chloride | 29 parts per million dry volume | 3-run average (For Method 26, collect a minimum volume of 60 liters per run. For Method 26A, collect a minimum volume of 1 dry standard cubic meter per run) | Performance test (Method 26 or 26A at 40 CFR part 60, appendix A-8). |
Lead | 0.015 milligrams per dry standard cubic meter | 3-run average (collect a minimum volume of 2 dry standard cubic meters) | Performance test (Method 29 at 40 CFR part 60, appendix A-8). Use ICPMS for the analytical finish. |
Mercury | 0.0048 milligrams per dry standard cubic meter | 3-run average (For Method 29 an ASTM D6784-02 (Reapproved 2008), 4 collect a minimum volume of 2 dry standard cubic meters per run. For Method 30B, collect a minimum sample as specified in Method 30B at 40 CFR part 60, appendix A) | Performance test (Method 29 or 30B at 40 CFR part 60, appendix A-8) or ASTM D6784-02 (Reapproved 2008). 4 |
Nitrogen oxides | 53 parts per million dry volume | 3-run average (for Method 7E, 1 hour minimum sample time per run) | Performance test (Method 7 or 7E at 40 CFR part 60, appendix A-4). |
Particulate matter filterable | 34 milligrams per dry standard cubic meter | 3-run average (collect a minimum volume of 1 dry standard cubic meter) | Performance test (Method 5 or 29 at 40 CFR part 60, appendix A-3 or appendix A-8). |
Sulfur dioxide | 11 parts per million dry volume | 3-run average (1 hour minimum sample time per run) | Performance test (Method 6 or 6c at 40 CFR part 60, appendix A-4). |
Fugitive ash | Visible emissions for no more than 5% of the hourly observation period | Three 1-hour observation periods | Visible emission test (Method 22 at 40 CFR part 60, appendix A-7). |
1 The date specified in the state plan can be no later than 3 years after the effective date of approval of a revised state plan or February 7, 2018.
2 All emission limitations are measured at 7 percent oxygen, dry basis at standard conditions. For dioxins/furans, you must meet either the total mass basis limit or the toxic equivalency basis limit.
3 In lieu of performance testing, you may use a CEMS or, for mercury, an integrated sorbent trap monitoring system, to demonstrate initial and continuing compliance with an emissions limit, as long as you comply with the CEMS or integrated sorbent trap monitoring system requirements applicable to the specific pollutant in §§ 60.2710 and 60.2730. As prescribed in § 60.2710(u), if you use a CEMS or integrated sorbent trap monitoring system to demonstrate compliance with an emissions limit, your averaging time is a 30-day rolling average of 1-hour arithmetic average emission concentrations.
4 Incorporated by reference, see § 60.17.
Table 7 to Subpart DDDD of Part 60 - Model Rule - Emission Limitations That Apply to Energy Recovery Units After May 20, 2011
40:8.0.1.1.1.31.224.80.31 :
Table 7 to Subpart DDDD of Part 60 - Model Rule - Emission Limitations That Apply to Energy Recovery Units After May 20, 2011[Date to be specified in state plan] 1
For the air pollutant | You must meet this emission limitation 2 | Using this averaging time 3 | And determining compliance using this method 3 | |
---|---|---|---|---|
Liquid/gas | Solids | |||
Cadmium | 0.023 milligrams per dry standard cubic meter | Biomass - 0.0014 milligrams per dry standard cubic meter. Coal - 0.0017 milligrams per dry standard cubic meter | 3-run average (collect a minimum volume of 2 dry standard cubic meters) | Performance test (Method 29 at 40 CFR part 60, appendix A-8). Use ICPMS for the analytical finish. |
Carbon monoxide | 35 parts per million dry volume | Biomass - 260 parts per million dry volume. Coal - 95 parts per million dry volume | 3-run average (1 hour minimum sample time per run) | Performance test (Method 10 at 40 CFR part 60, appendix A-4). |
Dioxins/furans (total mass basis) | 2.9 nanograms per dry standard cubic meter | Biomass - 0.52 nanograms per dry standard cubic meter. Coal - 5.1 nanograms per dry standard cubic meter | 3-run average (collect a minimum volume of 4 dry standard cubic meter) | Performance test (Method 23 at 40 CFR part 60, appendix A-7). |
Dioxins/furans (toxic equivalency basis) | 0.32 nanograms per dry standard cubic meter | Biomass - 0.12 nanograms per dry standard cubic meter. Coal - 0.075 nanograms per dry standard cubic meter | 3-run average (collect a minimum volume of 4 dry standard cubic meters) | Performance test (Method 23 at 40 CFR part 60, appendix A-7). |
Hydrogen chloride | 14 parts per million dry volume | Biomass - 0.20 parts per million dry volume. Coal - 58 parts per million dry volume | 3-run average (for Method 26, collect a minimum of 120 liters; for Method 26A, collect a minimum volume of 1 dry standard cubic meter) | Performance test (Method 26 or 26A at 40 CFR part 60, appendix A-8). |
Lead | 0.096 milligrams per dry standard cubic meter | Biomass - 0.014 milligrams per dry standard cubic meter. Coal - 0.057 milligrams per dry standard cubic meter | 3-run average (collect a minimum volume of 2 dry standard cubic meters) | Performance test (Method 29 at 40 CFR part 60, appendix A-8). Use ICPMS for the analytical finish. |
Mercury | 0.0024 milligrams per dry standard cubic meter | Biomass - 0.0022 milligrams per dry standard cubic meter. Coal - 0.013 milligrams per dry standard cubic meter | 3-run average (For Method 29 and ASTM D6784-02 (Reapproved 2008) 4, collect a minimum volume of 2 dry standard cubic meters per run. For Method 30B, collect a minimum sample as specified in Method 30B at 40 CFR part 60, appendix A) | Performance test (Method 29 or 30B at 40 CFR part 60, appendix A-8) or ASTM D6784-02 (Reapproved 2008). 4 |
Nitrogen oxides | 76 parts per million dry volume | Biomass - 290 parts per million dry volume. Coal - 460 parts per million dry volume | 3-run average (for Method 7E, 1 hour minimum sample time per run) | Performance test (Method 7 or 7E at 40 CFR part 60, appendix A-4). |
Particulate matter filterable | 110 milligrams per dry standard cubic meter | Biomass - 11 milligrams per dry standard cubic meter. Coal - 130 milligrams per dry standard cubic meter | 3-run average (collect a minimum volume of 1 dry standard cubic meter) | Performance test (Method 5 or 29 at 40 CFR part 60, appendix A-3 or appendix A-8). |
Sulfur dioxide | 720 parts per million dry volume | Biomass - 7.3 parts per million dry volume. Coal - 850 parts per million dry volume | 3-run average (1 hour minimum sample time per run) | Performance test (Method 6 or 6c at 40 CFR part 60, appendix A-4). |
Fugitive ash | Visible emissions for no more than 5 percent of the hourly observation period | Visible emissions for no more than 5 percent of the hourly observation period | Three 1-hour observation periods | Visible emission test (Method 22 at 40 CFR part 60, appendix A-7). |
1 The date specified in the state plan can be no later than 3 years after the effective date of approval of a revised state plan or February 7, 2018.
2 All emission limitations (except for opacity) are measured at 7 percent oxygen, dry basis at standard conditions. For dioxins/furans, you must meet either the total mass basis limit or the toxic equivalency basis limit.
3 In lieu of performance testing, you may use a CEMS or, for mercury, an integrated sorbent trap monitoring system, to demonstrate initial and continuing compliance with an emissions limit, as long as you comply with the CEMS or integrated sorbent trap monitoring system requirements applicable to the specific pollutant in §§ 60.2710 and 60.2730. As prescribed in § 60.2710(u), if you use a CEMS or integrated sorbent trap monitoring system to demonstrate compliance with an emissions limit, your averaging time is a 30-day rolling average of 1-hour arithmetic average emission concentrations.
4 Incorporated by reference, see § 60.17.
Table 8 to Subpart DDDD of Part 60 - Model Rule - Emission Limitations That Apply to Waste-Burning Kilns After May 20, 2011
40:8.0.1.1.1.31.224.80.32 :
Table 8 to Subpart DDDD of Part 60 - Model Rule - Emission Limitations That Apply to Waste-Burning Kilns After May 20, 2011[Date to be specified in state plan] 1
For the air pollutant | You must meet this emission limitation 2 | Using this averaging time 3 | And determining compliance using this method 3 4 |
---|---|---|---|
Cadmium | 0.0014 milligrams per dry standard cubic meter | 3-run average (collect a minimum volume of 2 dry standard cubic meters) | Performance test (Method 29 at 40 CFR part 60, appendix A-8). |
Carbon monoxide | 110 (long kilns)/790 (preheater/precalciner) parts per million dry volume | 3-run average (1 hour minimum sample time per run) | Performance test (Method 10 at 40 CFR part 60, appendix A-4). |
Dioxins/furans (total mass basis) | 1.3 nanograms per dry standard cubic meter | 3-run average (collect a minimum volume of 4 dry standard cubic meters) | Performance test (Method 23 at 40 CFR part 60, appendix A-7). |
Dioxins/furans (toxic equivalency basis) | 0.075 nanograms per dry standard cubic meter | 3-run average (collect a minimum volume of 4 dry standard cubic meters) | Performance test (Method 23 at 40 CFR part 60, appendix A-7). |
Hydrogen chloride | 3.0 parts per million dry volume | 3-run average (collect a minimum volume of 1 dry standard cubic meter), or 30-day rolling average if HCl CEMS is being used | If a wet scrubber or dry scrubber is used, performance test (Method 321 at 40 CFR part 63, appendix A of this part). If a wet scrubber or dry scrubber is not used, HCl CEMS as specified in § 60.2710(j). |
Lead | 0.014 milligrams per dry standard cubic meter | 3-run average (collect a minimum volume of 2 dry standard cubic meters) | Performance test (Method 29 at 40 CFR part 60, appendix A-8). |
Mercury | 0.011 milligrams per dry standard cubic meter. Or 58 pounds/million tons of clinker | 30-day rolling average | Mercury CEMS or integrated sorbent trap monitoring system (performance specification 12A or 12B, respectively, of appendix B and procedure 5 of appendix F of this part), as specified in § 60.2710(j). |
Nitrogen oxides | 630 parts per million dry volume | 3-run average (for Method 7E, 1 hour minimum sample time per run) | Performance test (Method 7 or 7E at 40 CFR part 60, appendix A-4). |
Particulate matter filterable | 13.5 milligrams per dry standard cubic meter | 3-run average (collect a minimum volume of 1 dry standard cubic meter) | Performance test (Method 5 or 29 at 40 CFR part 60, appendix A-3 or appendix-8). |
Sulfur dioxide | 600 parts per million dry volume | 3-run average (for Method 6, collect a minimum of 20 liters; for Method 6C, 1 hour minimum sample time per run) | Performance test (Method 6 or 6c at 40 CFR part 60, appendix A-4). |
1 The date specified in the state plan can be no later than 3 years after the effective date of approval of a revised state plan or February 7, 2018.
2 All emission limitations are measured at 7 percent oxygen (except for CEMS and integrated sorbent trap monitoring system data during startup and shutdown), dry basis at standard conditions. For dioxins/furans, you must meet either the total mass basis limit or the toxic equivalency basis limit.
3 In lieu of performance testing, you may use a CEMS or, for mercury, an integrated sorbent trap monitoring system, to demonstrate initial and continuing compliance with an emissions limit, as long as you comply with the CEMS or integrated sorbent trap monitoring system requirements applicable to the specific pollutant in §§ 60.2710 and 60.2730. As prescribed in § 60.2710(u), if you use a CEMS or integrated sorbent trap monitoring system to demonstrate compliance with an emissions limit, your averaging time is a 30-day rolling average of 1-hour arithmetic average emission concentrations.
4 Alkali bypass and in-line coal mill stacks are subject to performance testing only, as specified in § 60.2710(y)(3). They are not subject to the CEMS, integrated sorbent trap monitoring system, or CPMS requirements that otherwise may apply to the main kiln exhaust.
Table 9 to Subpart DDDD of Part 60 - Model Rule - Emission Limitations That Apply to Small, Remote Incinerators After May 20, 2011 [Date To Be Specified in State Plan] 1
40:8.0.1.1.1.31.224.80.33 :
Table 9 to Subpart DDDD of Part 60 - Model Rule - Emission Limitations That Apply to Small, Remote Incinerators After May 20, 2011 [Date To Be Specified in State Plan] 1For the air pollutant | You must meet this emission limitation 2 |
Using this averaging time 3 | And determining compliance using this method 3 |
---|---|---|---|
Cadmium | 0.95 milligrams per dry standard cubic meter | 3-run average (collect a minimum volume of 1 dry standard cubic meters per run) | Performance test (Method 29 at 40 CFR part 60, appendix A-8). |
Carbon monoxide | 64 parts per million dry volume | 3-run average (1 hour minimum sample time per run) | Performance test (Method 10 at 40 CFR part 60, appendix A-4). |
Dioxins/furans (total mass basis) | 4,400 nanograms per dry standard cubic meter | 3-run average (collect a minimum volume of 1 dry standard cubic meters per run) | Performance test (Method 23 at 40 CFR part 60, appendix A-7). |
Dioxins/furans (toxic equivalency basis) | 180 nanograms per dry standard cubic meter | 3-run average (collect a minimum volume of 1 dry standard cubic meters) | Performance test (Method 23 at 40 CFR part 60, appendix A-7). |
Fugitive ash | Visible emissions for no more than 5 percent of the hourly observation period | Three 1-hour observation periods | Visible emissions test (Method 22 at 40 CFR part 60, appendix A-7). |
Hydrogen chloride | 300 parts per million dry volume | 3-run average (For Method 26, collect a minimum volume of 120 liters per run. For Method 26A, collect a minimum volume of 1 dry standard cubic meter per run) | Performance test (Method 26 or 26A at 40 CFR part 60, appendix A-8). |
Lead | 2.1 milligrams per dry standard cubic meter | 3-run average (collect a minimum volume of 1 dry standard cubic meters) | Performance test (Method 29 at 40 CFR part 60, appendix A-8). Use ICPMS for the analytical finish. |
Mercury | 0.0053 milligrams per dry standard cubic meter | 3-run average (For Method 29 and ASTM D6784-02 (Reapproved 2008), 3 collect a minimum volume of 2 dry standard cubic meters per run. For Method 30B, collect a minimum sample as specified in Method 30B at 40 CFR part 60, appendix A) | Performance test (Method 29 or 30B at 40 CFR part 60, appendix A-8) or ASTM D6784-02 (Reapproved 2008). 4 |
Nitrogen oxides | 190 parts per million dry volume | 3-run average (for Method 7E, 1 hour minimum sample time per run) | Performance test (Method 7 or 7E at 40 CFR part 60, appendix A-4). |
Particulate matter (filterable) | 270 milligrams per dry standard cubic meter | 3-run average (collect a minimum volume of 1 dry standard cubic meters) | Performance test (Method 5 or 29 at 40 CFR part 60, appendix A-3 or appendix A-8). |
Sulfur dioxide | 150 parts per million dry volume | 3-run average (for Method 6, collect a minimum of 20 liters per run; for Method 6C, 1 hour minimum sample time per run) | Performance test (Method 6 or 6c at 40 CFR part 60, appendix A-4). |
1 The date specified in the state plan can be no later than 3 years after the effective date of approval of a revised state plan or February 7, 2018.
2 All emission limitations (except for opacity) are measured at 7 percent oxygen, dry basis at standard conditions. For dioxins/furans, you must meet either the total mass basis limit or the toxic equivalency basis limit.
3 In lieu of performance testing, you may use a CEMS or, for mercury, an integrated sorbent trap monitoring system, to demonstrate initial and continuing compliance with an emissions limit, as long as you comply with the CEMS or integrated sorbent trap monitoring system requirements applicable to the specific pollutant in §§ 60.2710 and 60.2730. As prescribed in § 60.2710(u), if you use a CEMS or integrated sorbent trap monitoring system to demonstrate compliance with an emissions limit, your averaging time is a 30-day rolling average of 1-hour arithmetic average emission concentrations.
4 Incorporated by reference, see § 60.17.
Table 1 to Subpart EEEE of Part 60 - Emission Limitations
40:8.0.1.1.1.32.240.65.34 :
Table 1 to Subpart EEEE of Part 60 - Emission LimitationsAs stated in § 60.2915, you must comply with the following:
For the air pollutant | You must meet this
emission limitation a |
Using this averaging time | And determining compliance using this method |
---|---|---|---|
1. Cadmium | 18 micrograms per dry standard cubic meter | 3-run average (1 hour minimum sample time per run) | Method 29 of appendix A of this part. |
2. Carbon monoxide | 40 parts per million by dry volume | 3-run average (1 hour minimum sample time per run during performance test), and 12-hour rolling averages measured using CEMS. b | Method 10, 10A, or 10B of appendix A of this part and CEMS. |
3. Dioxins/furans (total basis) | 33 nanograms per dry standard cubic meter | 3-run average (1 hour minimum sample meter time per run) | Method 23 of appendix A of this part. |
4. Hydrogen chloride | 15 parts per million by dry volume | 3-run average (1 hour minimum sample time per run) | Method 26A of appendix A of this part. |
5. Lead | 226 micrograms per dry standard cubic meter | 3-run average (1 hour minimum sample time per run) | Method 29 of appendix A of this part. |
6. Mercury | 74 micrograms per dry standard cubic meter | 3-run average (1 hour minimum sample time per run) | Method 29 of appendix A of this part. |
7. Opacity | 10 percent | 6-minute average (observe over three 1-hour test runs; i.e., thirty 6-minute averages) | Method 9 of appendix A of this part. |
8. Oxides of nitrogen | 103 parts per million by dry volume | 3-run average (1 hour minimum sample time per run) | Method 7, 7A, 7C, 7D, or 7E of appendix A of this part, or ANSI/ASME PTC 19.10-1981 (IBR, see § 60.17(h)) in lieu of Methods 7 and 7C only. |
9. Particulate matter | 0.013 grains per dry standard cubic foot | 3-run average (1 hour minimum sample time per run) | Method 5 or 29 of appendix A of this part. |
10. Sulfur dioxide | 3.1 parts per million by dry volume | 3-run average (1 hour minimum sample time per run) | Method 6 or 6C of appendix A of this part, or ANSI/ASME PTC 19.10-1981 (IBR, see § 60.17(h)) in lieu of Method 6 only. |
a All emission limitations (except for opacity) are measured at 7 percent oxygen, dry basis at standard conditions.
b Calculated each hour as the average of the previous 12 operating hours.
Table 2 to Subpart EEEE of Part 60 - Operating Limits for Incinerators and Wet Scrubbers
40:8.0.1.1.1.32.240.65.35 :
Table 2 to Subpart EEEE of Part 60 - Operating Limits for Incinerators and Wet ScrubbersAs stated in § 60.2916, you must comply with the following:
For these
operating parameters |
You must establish these operating limits | And monitoring using these minimum frequencies | ||
---|---|---|---|---|
Data measurement | Data recording | Averaging time | ||
1. Charge rate | Maximum charge rate | Continuous | Every hour | Daily for batch units. 3-hour rolling for continuous and intermittent units a. |
2. Pressure drop across the wet scrubber or amperage to wet scrubber | Minimum pressure drop or amperage | Continuous | Every 15 minutes | 3-hour rolling a. |
3. Scrubber liquor flow rate | Minimum flow rate | Continuous | Every 15 minutes | 3-hour rolling a. |
4. Scrubber liquor pH | Minimum pH | Continuous | Every 15 minutes | 3-hour rolling a. |
a Calculated each hour as the average of the previous 3 operating hours.
Table 3 to Subpart EEEE of Part 60 - Requirements for Continuous Emission Monitoring Systems (CEMS)
40:8.0.1.1.1.32.240.65.36 :
Table 3 to Subpart EEEE of Part 60 - Requirements for Continuous Emission Monitoring Systems (CEMS)As stated in § 60.2940, you must comply with the following:
For the following pollutants |
Use the following span values for your CEMS | Use the following performance specifications (P.S.) in appendix B of this part for your CEMS | If needed to meet minimum data requirements, use the following alternate methods in appendix A of this part to collect data |
---|---|---|---|
1. Carbon Monoxide | 125 percent of the maximum hourly potential carbon monoxide emissions of the waste combustion unit | P.S.4A | Method 10. |
2. Oxygen | 25 percent oxygen | P.S.3 | Method 3A or 3B, or ANSI/ASME PTC 19.10-1981 (IBR, see § 60.17(h)) in lieu of Method 3B only. |
Table 4 to Subpart EEEE of Part 60 - Summary of Reporting Requirements
40:8.0.1.1.1.32.240.65.37 :
Table 4 to Subpart EEEE of Part 60 - Summary of Reporting RequirementsAs stated in § 60.2951, you must comply with the following:
Report | Due date | Contents | Reference |
---|---|---|---|
1. Preconstruction report | a. Prior to commencing construction | i. Statement of intent to
construct; ii. Anticipated date of commencement of onstruction; |
§ 60.2952. § 60.2952. |
iii. Documentation for siting requirements; | § 60.2952. | ||
iv. Waste management plan; and | § 60.2952. | ||
v. Anticipated date of initial startup. | § 60.2952. | ||
2. Startup notification | a. Prior to initial startup | i. Types of waste to be
burned; ii. Maximum design waste burning capacity; |
§ 60.2953. § 60.2953. |
iii. Anticipated maximum charge rate; | § 60.2953. | ||
iv. If applicable, the petition for site-specific operating limits; and | § 60.2953. | ||
v. Anticipated date of initial startup. | § 60.2953. | ||
3. Initial test report | a. No later than 60 days following the initial performance test | i. Complete test report for
the initial performance test; and ii. The values for the site-specific operating limits |
§ 60.2954. § 60.2954. |
4. Annual report | a. No later than 12 months following the submission of the initial test report. Subsequent reports are to be submitted no more than 12 months following the previous report | i. Company Name and
address; ii. Statement and signature by the owner or operator; iii. Date of report; iv. Values for the operating limits; v. If no deviations or malfunctions were reported, a statement that no deviations occurred during the reporting period; |
§§ 60.2955 and 60.2956. §§ 60.2955 and 60.2956. §§ 60.2955 and 60.2956. §§ 60.2955 and 60.2956. §§ 60.2955 and 60.2956. |
vi. Highest and lowest recorded 12-hour averages, as applicable, for carbon monoxide emissions and highest and lowest recorded 3-hour averages, as applicable, for each operating parameter recorded for the calendar year being reported; | §§ 60.2955 and 60.2956. | ||
vii. Information for deviations or malfunctions recorded under § 60.2949(b)(6) and (c) through (e); | §§ 60.2955 and 60.2956. | ||
viii. If a performance test was conducted during the reporting period, the results of the test; | §§ 60.2955 and 60.2956. | ||
ix. If a performance test was not conducted during the reporting period, a statement that the requirements of § 60.2934 (a) or (b) were met; and | §§ 60.2955 and 60.2956. | ||
x. Documentation of periods when all qualified OSWI unit operators were unavailable for more than 12 hours but less than 2 weeks. | §§ 60.2955 and 60.2956. | ||
5. Emission limitation or operating limit deviation report | a. By August 1 of that year for data collected during the first half of the calendar year. By February 1 of the following year for data collected during the second half of the calendar year | i. Dates and times of
deviation; ii. Averaged and recorded data for those dates; iii. Duration and causes of each deviation and the corrective actions taken; iv. Copy of operating limit monitoring data and any test reports; v. Dates, times, and causes for monitor downtimes incidents; vi. Whether each deviation occurred during a period of startup, shutdown, or malfunction; and |
§§ 60.2957 and 60.2958. §§ 60.2957 and 60.2958. §§ 60.2957 and 60.2958. §§ 60.2957 and 60.2958. §§ 60.2957 and 60.2958. §§ 60.2957 and 60.2958. |
vii. Dates, times, and durations of any bypass of the control device. | §§ 60.2957 and 60.2958. | ||
6. Qualified operator deviation notification | a. Within 10 days of deviation | i. Statement of cause of
deviation; ii. Description of efforts to have an accessible qualified operator; and |
§ 60.2959(a)(1). § 60.2959(a)(1) |
iii. The date a qualified operator will be accessible | § 60.2959(a)(1). | ||
7. Qualified operation deviation status report | a. Every 4 weeks following deviation | i. Description of efforts to
have an accessible qualified operator; ii. The date a qualified operator will be accessible; and |
§ 60.2959(a)(2). § 60.2959(a)(2). |
iii. Request to continue operation | § 60.2959(a)(2). | ||
8. Qualified operator deviation notification of resumed operation | a. Prior to resuming operation | i. Notification that you are resuming operation | § 60.2959(b). |
Note: This table is only a summary, see the referenced sections of the rule for the complete requirements.
Table 1 to Subpart FFFF of Part 60 - Model Rule - Compliance Schedule
40:8.0.1.1.1.33.257.76.38 :
Table 1 to Subpart FFFF of Part 60 - Model Rule - Compliance ScheduleAs stated in § 60.3000, you must comply with the following:
Complete this action | By this date a |
---|---|
Final compliance b | (Dates to be specified in State plan) c. |
a Site-specific schedules can be used at the discretion of the State.
b Final compliance means that you complete all process changes and retrofit of control devices so that, when the incineration unit is brought on line, all process changes and air pollution control devices necessary to meet the emission limitations operate as designed.
c The date can be no later than 3 years after the effective date of State plan approval or December 16, 2010, whichever is earlier.
Table 2 to Subpart FFFF of Part 60 - Model Rule - Emission Limitations
40:8.0.1.1.1.33.257.76.39 :
Table 2 to Subpart FFFF of Part 60 - Model Rule - Emission LimitationsAs stated in § 60.3022, you must comply with the following:
For the air pollutant | You must meet this emission limitation a | Using this averaging time | And determining compliance
using this method |
---|---|---|---|
1. Cadmium | 18 micrograms per dry standard cubic meter | 3-run average (1 hour minimum sample time per run) | Method 29 of appendix A of this part. |
2. Carbon monoxide | 40 parts per million by dry volume | 3-run average (1 hour minimum sample time per run during performance test), and 12-hour rolling averages measured using CEMS b | Method 10, 10A, or 10B of appendix A of this part and CEMS. |
3. Dioxins/furans (total basis) | 33 nanograms per dry standard cubic meter | 3-run average (1 hour minimum sample time per run) | Method 23 of appendix A of this part. |
4. Hydrogen chloride | 15 parts per million by dry volume | 3-run average (1 hour minimum sample time per run) | Method 26A of appendix A of this part. |
5. Lead | 226 micrograms per dry standard cubic meter | 3-run average (1 hour minimum sample time per run) | Method 29 of appendix A of this part. |
6. Mercury | 74 micrograms per dry standard cubic meter | 3-run average (1 hour minimum sample time per run) | Method 29 of appendix A of this part. |
7. Opacity | 10 percent | 6-minute average (observe over three 1-hour test runs; i.e., thirty 6-minute averages) | Method 9 of appendix A of this part. |
8. Oxides of nitrogen | 103 parts per million by dry volume | 3-run average (1 hour minimum sample time per run) | Method 7, 7A, 7C, 7D, or 7E of appendix A of this part, or ANSI/ASME PTC 19.10-1981 (IBR, see § 60.17(h)) in lieu of Methods 7 and 7C only. |
9. Particulate matter | 0.013 grains per dry standard cubic foot | 3-run average (1 hour minimum sample time per run) | Method 5 or 29 of appendix A of this part. |
10. Sulfur dioxide | 3.1 parts per million by dry volume | 3-run average (1 hour minimum sample time per run) | Method 6 or 6C of appendix A of this part, or ANSI/ASME PTC 19.10-1981 (IBR, see § 60.17(h)) in lieu of Method 6 only. |
a All emission limitations (except for opacity) are measured at 7 percent oxygen, dry basis at standard conditions.
b Calculated each hour as the average of the previous 12 operating hours.
Table 3 to Subpart FFFF of Part 60 - Model Rule - Operating Limits for Incinerators and Wet Scrubbers
40:8.0.1.1.1.33.257.76.40 :
Table 3 to Subpart FFFF of Part 60 - Model Rule - Operating Limits for Incinerators and Wet ScrubbersAs stated in § 60.3023, you must comply with the following:
For these operating parameters | You must establish operating limits | And monitoring using these minimum frequencies | ||
---|---|---|---|---|
Data measurement | Data recording | Averaging time | ||
1. Charge rate | Maximum charge rate | Continuous | Every hour | Daily for batch units. 3-hour rolling for continuous and intermittent units. a |
2. Pressure drop across the wet scrubber or amperage to wet scrubber | Minimum pressure drop or amperage | Continuous | Every 15 minutes | 3-hour rolling. a |
3. Scrubber liquor flow rate | Minimum flow rate | Continuous | Every 15 minutes | 3-hour rolling. a |
4. Scrubber liquor pH | Minimum pH | Continuous | Every 15 minutes | 3-hour rolling. a |
a Calculated each hour as the average of the previous 3 operating hours.
Table 4 to Subpart FFFF of Part 60 - Model Rule - Requirements for Continuous Emission Monitoring Systems (CEMS)
40:8.0.1.1.1.33.257.76.41 :
Table 4 to Subpart FFFF of Part 60 - Model Rule - Requirements for Continuous Emission Monitoring Systems (CEMS)As stated in § 60.3039, you must comply with the following:
For the following pollutants | Use the following span values for your CEMS | Use the following performance specifications (P.S.) in appendix B of this part for your CEMS | If needed to meet minimum data requirements, use the following alternate methods in appendix A of this part to collect data |
---|---|---|---|
1. Carbon Monoxide | 125 percent of the maximum hourly potential carbon monoxide emissions of the waste combustion unit | P.S.4A | Method 10. |
2. Oxygen | 25 percent oxygen | P.S.3 | Method 3A or 3B, or ANSI/ASME PTC 19.10-1981 (IBR, see § 60.17(h)) in lieu of Method 3B only. |
Table 5 to Subpart FFFF of Part 60 - Model Rule - Summary of Reporting Requirements
40:8.0.1.1.1.33.257.76.42 :
Table 5 to Subpart FFFF of Part 60 - Model Rule - Summary of Reporting RequirementsAs stated in § 60.3048, you must comply with the following:
Report | Due date | Contents | Reference |
---|---|---|---|
1. Initial test report | a. No later than 60 days following the initial performance test | i. Complete test report for the initial performance test; and | § 60.3049. |
ii. The values for the site-specific operating limits | § 60.3049. | ||
2. Waste management plan | a. No later than 60 days following the initial performance test | i. Reduction or separation of recyclable materials; and | §§ 60.3010 through 60.3012. |
ii. Identification of additional waste management measures and how they will be implemented | §§ 60.3010 through 60.3012. | ||
3. Annual Report | a. No later than 12 months following the submission of the initial test report. Subsequent reports are to be submitted no more than 12 months following the previous report | i. Company Name and address; | §§ 60.3050 and 60.3051. |
ii. Statement and signature by the owner or operator; | §§ 60.3050 and 60.3051. | ||
iii. Date of report; | §§ 60.3050 and 60.3051. | ||
iv. Values for the operation limits; | §§ 60.3050 and 60.3051. | ||
v. If no deviations or malfunctions were reported, a statement that no deviations occurred during the reporting period; | §§ 60.3050 and 60.3051. | ||
vi. Highest and lowest recorded 12-hour averages, as applicable, for carbon monoxide emissions and highest and lowest recorded 3-hour averages, as applicable, for each operating parameter recorded for the calendar year being reported; | §§ 60.3050 and 60.3051. | ||
vii. Information for deviations or malfunctions recorded under § 60.2949(b)(6) and (c) through (e); | §§ 60.3050 and 60.3051. | ||
viii. If a performance test was conducted during the reporting period, the results of the test; | §§ 60.3050 and 60.3051. | ||
ix. If a performance test was not conducted during the reporting period, a statement that the requirements of § 60.2934(a) or (b) were met; and | §§ 60.3050 and 60.3051. | ||
x. Documentation of periods when all qualified OSWI unit operators were unavailable for more than 12 hours but less than 2 weeks | §§ 60.3050 and 60.3051. | ||
4. Emission limitation or operating limit deviation report | a. By August 1 of that year for data collected during the first half of the calendar year. By February 1 of the following year for data collected during the second half of the calendar year | i. Dates and times of deviation; | §§ 60.3052 and 60.3053. |
ii. Averaged and recorded data for those dates; | §§ 60.3052 and 60.3053. | ||
iii. Duration and causes of each deviation and the corrective actions taken. | §§ 60.3052 and 60.3053. | ||
iv. Copy of operating limit monitoring data and any test reports; | §§ 60.3052 and 60.3053. | ||
v. Dates, times, and causes for monitor downtime incidents; | §§ 60.3052 and 60.3053. | ||
vi. Whether each deviation occurred during a period of startup, shutdown, or malfunction; and | §§ 60.3052 and 60.3053. | ||
vii. Dates, times, and duration of any bypass of the control device | §§ 60.3052 and 60.3053. | ||
5. Qualified operator deviation notification | a. Within 10 days of deviation | i. Statement of cause of deviation; | § 60.3054(a)(1). |
ii. Description of efforts to have an accessible qualified operator; and | § 60.3054(a)(1). | ||
iii. The date a qualified operator will be accessible | § 60.3054(a)(1). | ||
6. Qualified operation deviation status report | a. Every 4 weeks following deviation | i. Description of efforts to have an accessible qualified operator; | § 60.3054(a)(2). |
ii. The date a qualified operator will be accessible; and | § 60.3054(a)(2). | ||
iii. Request to continue operation | § 60.3054(a)(2). | ||
7. Qualified operator deviation notification of resumed operation | a. Prior to resuming operation | i. Notification that you are resuming operation | § 60.3054(b). |
Note: This table is only a summary, see the referenced sections of the rule for the complete requirements.
Table 1 to Subpart IIII of Part 60 - Emission Standards for Stationary Pre-2007 Model Year Engines With a Displacement of <10 Liters per Cylinder and 2007-2010 Model Year Engines >2,237 KW (3,000 HP) and With a Displacement of <10 Liters per Cylinder
40:8.0.1.1.1.35.268.21.43 :
Table 1 to Subpart IIII of Part 60 - Emission Standards for Stationary Pre-2007 Model Year Engines With a Displacement of <10 Liters per Cylinder and 2007-2010 Model Year Engines >2,237 KW (3,000 HP) and With a Displacement of <10 Liters per Cylinder[As stated in §§ 60.4201(b), 60.4202(b), 60.4204(a), and 60.4205(a), you must comply with the following emission standards]
Maximum engine power | Emission standards for stationary pre-2007 model year engines with a displacement of <10 liters per cylinder and 2007-2010 model year engines >2,237 KW (3,000 HP) and with a displacement of <10 liters per cylinder in g/KW-hr (g/HP-hr) | ||||
---|---|---|---|---|---|
NMHC + NOX | HC | NOX | CO | PM | |
KW<8 (HP<11) | 10.5 (7.8) | 8.0 (6.0) | 1.0 (0.75) | ||
8≤KW<19 (11≤HP<25) | 9.5 (7.1) | 6.6 (4.9) | 0.80 (0.60) | ||
19≤KW<37 (25≤HP<50) | 9.5 (7.1) | 5.5 (4.1) | 0.80 (0.60) | ||
37≤KW<56 (50≤HP<75) | 9.2 (6.9) | ||||
56≤KW<75 (75≤HP<100) | 9.2 (6.9) | ||||
75≤KW<130 (100≤HP<175) | 9.2 (6.9) | ||||
130≤KW<225 (175≤HP<300) | 1.3 (1.0) | 9.2 (6.9) | 11.4 (8.5) | 0.54 (0.40) | |
225≤KW<450 (300≤HP<600) | 1.3 (1.0) | 9.2 (6.9) | 11.4 (8.5) | 0.54 (0.40) | |
450≤KW≤560 (600≤HP≤750) | 1.3 (1.0) | 9.2 (6.9) | 11.4 (8.5) | 0.54 (0.40) | |
KW>560 (HP>750) | 1.3 (1.0) | 9.2 (6.9) | 11.4 (8.5) | 0.54 (0.40) |
Table 2 to Subpart IIII of Part 60 - Emission Standards for 2008 Model Year and Later Emergency Stationary CI ICE <37 KW (50 HP) With a Displacement of <10 Liters per Cylinder
40:8.0.1.1.1.35.268.21.44 :
Table 2 to Subpart IIII of Part 60 - Emission Standards for 2008 Model Year and Later Emergency Stationary CI ICE <37 KW (50 HP) With a Displacement of <10 Liters per Cylinder[As stated in § 60.4202(a)(1), you must comply with the following emission standards]
Engine power | Emission standards for 2008 model year and later emergency stationary CI ICE <37 KW (50 HP) with a displacement of <10 liters per cylinder in g/KW-hr (g/HP-hr) | |||
---|---|---|---|---|
Model year(s) | NOX + NMHC | CO | PM | |
KW<8 (HP<11) | 2008 + | 7.5 (5.6) | 8.0 (6.0) | 0.40 (0.30) |
8≤KW<19 (11≤HP<25) | 2008 + | 7.5 (5.6) | 6.6 (4.9) | 0.40 (0.30) |
19≤KW<37 (25≤HP<50) | 2008 + | 7.5 (5.6) | 5.5 (4.1) | 0.30 (0.22) |
Table 3 to Subpart IIII of Part 60 - Certification Requirements for Stationary Fire Pump Engines
40:8.0.1.1.1.35.268.21.45 :
Table 3 to Subpart IIII of Part 60 - Certification Requirements for Stationary Fire Pump EnginesAs stated in § 60.4202(d), you must certify new stationary fire pump engines beginning with the following model years:
Engine power |
Starting model year engine
manufacturers must certify new stationary fire pump engines according to § 60.4202(d) 1 |
---|---|
KW<75 (HP<100) |
2011 |
75≤KW<130 (100≤HP<175) |
2010 |
130≤KW≤560 (175≤HP≤750) |
2009 |
KW>560 (HP>750) |
2008 |
1Manufacturers of fire pump stationary CI ICE with a maximum engine power greater than or equal to 37 kW (50 HP) and less than 450 KW (600 HP) and a rated speed of greater than 2,650 revolutions per minute (rpm) are not required to certify such engines until three model years following the model year indicated in this Table 3 for engines in the applicable engine power category.
Table 4 to Subpart IIII of Part 60 - Emission Standards for Stationary Fire Pump Engines
40:8.0.1.1.1.35.268.21.46 :
Table 4 to Subpart IIII of Part 60 - Emission Standards for Stationary Fire Pump Engines[As stated in §§ 60.4202(d) and 60.4205(c), you must comply with the following emission standards for stationary fire pump engines]
Maximum engine power | Model year(s) | NMHC + NOX | CO | PM |
---|---|---|---|---|
KW<8 (HP<11) | 2010 and earlier | 10.5 (7.8) | 8.0 (6.0) | 1.0 (0.75) |
2011 + | 7.5 (5.6) | 0.40 (0.30) | ||
8≤KW<19 (11≤HP<25) | 2010 and earlier | 9.5 (7.1) | 6.6 (4.9) | 0.80 (0.60) |
2011 + | 7.5 (5.6) | 0.40 (0.30) | ||
19≤KW<37 (25≤HP<50) | 2010 and earlier | 9.5 (7.1) | 5.5 (4.1) | 0.80 (0.60) |
2011 + | 7.5 (5.6) | 0.30 (0.22) | ||
37≤KW<56 (50≤HP<75) | 2010 and earlier | 10.5 (7.8) | 5.0 (3.7) | 0.80 (0.60) |
2011 + 1 | 4.7 (3.5) | 0.40 (0.30) | ||
56≤KW<75 (75≤HP<100) | 2010 and earlier | 10.5 (7.8) | 5.0 (3.7) | 0.80 (0.60) |
2011 + 1 | 4.7 (3.5) | 0.40 (0.30) | ||
75≤KW<130 (100≤HP<175) | 2009 and earlier | 10.5 (7.8) | 5.0 (3.7) | 0.80 (0.60) |
2010 + 2 | 4.0 (3.0) | 0.30 (0.22) | ||
130≤KW<225 (175≤HP<300) | 2008 and earlier | 10.5 (7.8) | 3.5 (2.6) | 0.54 (0.40) |
2009 + 3 | 4.0 (3.0) | 0.20 (0.15) | ||
225≤KW<450 (300≤HP<600) | 2008 and earlier | 10.5 (7.8) | 3.5 (2.6) | 0.54 (0.40) |
2009 + 3 | 4.0 (3.0) | 0.20 (0.15) | ||
450≤KW≤560 (600≤HP≤750) | 2008 and earlier | 10.5 (7.8) | 3.5 (2.6) | 0.54 (0.40) |
2009 + | 4.0 (3.0) | 0.20 (0.15) | ||
KW>560 (HP>750) | 2007 and earlier | 10.5 (7.8) | 3.5 (2.6) | 0.54 (0.40) |
2008 + | 6.4 (4.8) | 0.20 (0.15) |
1 For model years 2011-2013, manufacturers, owners and operators of fire pump stationary CI ICE in this engine power category with a rated speed of greater than 2,650 revolutions per minute (rpm) may comply with the emission limitations for 2010 model year engines.
2 For model years 2010-2012, manufacturers, owners and operators of fire pump stationary CI ICE in this engine power category with a rated speed of greater than 2,650 rpm may comply with the emission limitations for 2009 model year engines.
3 In model years 2009-2011, manufacturers of fire pump stationary CI ICE in this engine power category with a rated speed of greater than 2,650 rpm may comply with the emission limitations for 2008 model year engines.
Table 5 to Subpart IIII of Part 60 - Labeling and Recordkeeping Requirements for New Stationary Emergency Engines
40:8.0.1.1.1.35.268.21.47 :
Table 5 to Subpart IIII of Part 60 - Labeling and Recordkeeping Requirements for New Stationary Emergency Engines[You must comply with the labeling requirements in § 60.4210(f) and the recordkeeping requirements in § 60.4214(b) for new emergency stationary CI ICE beginning in the following model years:]
Engine power | Starting model year |
---|---|
19≤KW<56 (25≤HP<75) | 2013 |
56≤KW<130 (75≤HP<175) | 2012 |
KW≥130 (HP≥175) | 2011 |
Table 6 to Subpart IIII of Part 60 - Optional 3-Mode Test Cycle for Stationary Fire Pump Engines
40:8.0.1.1.1.35.268.21.48 :
Table 6 to Subpart IIII of Part 60 - Optional 3-Mode Test Cycle for Stationary Fire Pump Engines[As stated in § 60.4210(g), manufacturers of fire pump engines may use the following test cycle for testing fire pump engines:]
Mode No. | Engine speed 1 | Torque (percent) 2 |
Weighting factors |
---|---|---|---|
1 | Rated | 100 | 0.30 |
2 | Rated | 75 | 0.50 |
3 | Rated | 50 | 0.20 |
1 Engine speed: ±2 percent of point.
2 Torque: NFPA certified nameplate HP for 100 percent point. All points should be ±2 percent of engine percent load value.
Table 7 to Subpart IIII of Part 60 - Requirements for Performance Tests for Stationary CI ICE With a Displacement of ≥30 Liters per Cylinder
40:8.0.1.1.1.35.268.21.49 :
Table 7 to Subpart IIII of Part 60 - Requirements for Performance Tests for Stationary CI ICE With a Displacement of ≥30 Liters per CylinderAs stated in § 60.4213, you must comply with the following requirements for performance tests for stationary CI ICE with a displacement of ≥30 liters per cylinder:
Each | Complying with the requirement to | You must | Using | According to the following requirements |
---|---|---|---|---|
1. Stationary CI internal combustion engine with a displacement of ≥ 30 liters per cylinder | a. Reduce NOX emissions by 90 percent or more; | i. Select the sampling port location and number/location of traverse points at the inlet and outlet of the control device; | (a) For NOX, O2, and moisture measurement, ducts ≤6 inches in diameter may be sampled at a single point located at the duct centroid and ducts >6 and ≤12 inches in diameter may be sampled at 3 traverse points located at 16.7, 50.0, and 83.3% of the measurement line ('3-point long line'). If the duct is >12 inches in diameter and the sampling port location meets the two and half-diameter criterion of Section 11.1.1 of Method 1 of 40 CFR part 60, appendix A-1, the duct may be sampled at '3-point long line'; otherwise, conduct the stratification testing and select sampling points according to Section 8.1.2 of Method 7E of 40 CFR part 60, appendix A-4. | |
ii. Measure O2 at the inlet and outlet of the control device; | (1) Method 3, 3A, or 3B of 40 CFR part 60, appendix A-2 | (b) Measurements to determine O2 concentration must be made at the same time as the measurements for NOX concentration. | ||
iii. If necessary, measure moisture content at the inlet and outlet of the control device; and | (2) Method 4 of 40 CFR part 60, appendix A-3, Method 320 of 40 CFR part 63, appendix A, or ASTM D 6348-03 (incorporated by reference, see § 60.17) | (c) Measurements to determine moisture content must be made at the same time as the measurements for NOX concentration. | ||
iv. Measure NOX at the inlet and outlet of the control device. | (3) Method 7E of 40 CFR part 60, appendix A-4, Method 320 of 40 CFR part 63, appendix A, or ASTM D 6348-03 (incorporated by reference, see § 60.17) | (d) NOX concentration must be at 15 percent O2, dry basis. Results of this test consist of the average of the three 1-hour or longer runs. | ||
b. Limit the concentration of NOX in the stationary CI internal combustion engine exhaust. | i. Select the sampling port location and number/location of traverse points at the exhaust of the stationary internal combustion engine; | (a) For NOX, O2, and moisture measurement, ducts ≤6 inches in diameter may be sampled at a single point located at the duct centroid and ducts >6 and ≤12 inches in diameter may be sampled at 3 traverse points located at 16.7, 50.0, and 83.3% of the measurement line ('3-point long line'). If the duct is >12 inches in diameter and the sampling port location meets the two and half-diameter criterion of Section 11.1.1 of Method 1 of 40 CFR part 60, appendix A-1, the duct may be sampled at '3-point long line'; otherwise, conduct the stratification testing and select sampling points according to Section 8.1.2 of Method 7E of 40 CFR part 60, appendix A-4. | ||
ii. Determine the O2 concentration of the stationary internal combustion engine exhaust at the sampling port location; | (1) Method 3, 3A, or 3B of 40 CFR part 60, appendix A-2 | (b) Measurements to determine O2 concentration must be made at the same time as the measurement for NOX concentration. | ||
iii. If necessary, measure moisture content of the stationary internal combustion engine exhaust at the sampling port location; and | (2) Method 4 of 40 CFR part 60, appendix A-3, Method 320 of 40 CFR part 63, appendix A, or ASTM D 6348-03 (incorporated by reference, see § 60.17) | (c) Measurements to determine moisture content must be made at the same time as the measurement for NOX concentration. | ||
iv. Measure NOX at the exhaust of the stationary internal combustion engine; if using a control device, the sampling site must be located at the outlet of the control device. | (3) Method 7E of 40 CFR part 60, appendix A-4, Method 320 of 40 CFR part 63, appendix A, or ASTM D 6348-03 (incorporated by reference, see § 60.17) | (d) NOX concentration must be at 15 percent O2, dry basis. Results of this test consist of the average of the three 1-hour or longer runs. | ||
c. Reduce PM emissions by 60 percent or more | i. Select the sampling port location and the number of traverse points; | (1) Method 1 or 1A of 40 CFR part 60, appendix A-1 | (a) Sampling sites must be located at the inlet and outlet of the control device. | |
ii. Measure O2 at the inlet and outlet of the control device; | (2) Method 3, 3A, or 3B of 40 CFR part 60, appendix A-2 | (b) Measurements to determine O2 concentration must be made at the same time as the measurements for PM concentration. | ||
iii. If necessary, measure moisture content at the inlet and outlet of the control device; and | (3) Method 4 of 40 CFR part 60, appendix A-3 | (c) Measurements to determine and moisture content must be made at the same time as the measurements for PM concentration. | ||
iv. Measure PM at the inlet and outlet of the control device. | (4) Method 5 of 40 CFR part 60, appendix A-3 | (d) PM concentration must be at 15 percent O2, dry basis. Results of this test consist of the average of the three 1-hour or longer runs. | ||
d. Limit the concentration of PM in the stationary CI internal combustion engine exhaust | i. Select the sampling port location and the number of traverse points; | (1) Method 1 or 1A of 40 CFR part 60, appendix A-1 | (a) If using a control device, the sampling site must be located at the outlet of the control device. | |
ii. Determine the O2 concentration of the stationary internal combustion engine exhaust at the sampling port location; | (2) Method 3, 3A, or 3B of 40 CFR part 60, appendix A-2 | (b) Measurements to determine O2 concentration must be made at the same time as the measurements for PM concentration. | ||
iii. If necessary, measure moisture content of the stationary internal combustion engine exhaust at the sampling port location; and | (3) Method 4 of 40 CFR part 60, appendix A-3 | (c) Measurements to determine moisture content must be made at the same time as the measurements for PM concentration. | ||
iv. Measure PM at the exhaust of the stationary internal combustion engine. | (4) Method 5 of 40 CFR part 60, appendix A-3 | (d) PM concentration must be at 15 percent O2, dry basis. Results of this test consist of the average of the three 1-hour or longer runs. |
Table 8 to Subpart IIII of Part 60 - Applicability of General Provisions to Subpart IIII
40:8.0.1.1.1.35.268.21.50 :
Table 8 to Subpart IIII of Part 60 - Applicability of General Provisions to Subpart IIII[As stated in § 60.4218, you must comply with the following applicable General Provisions:]
General Provisions citation |
Subject of citation | Applies to subpart |
Explanation |
---|---|---|---|
§ 60.1 | General applicability of the General Provisions | Yes | |
§ 60.2 | Definitions | Yes | Additional terms defined in § 60.4219. |
§ 60.3 | Units and abbreviations | Yes | |
§ 60.4 | Address | Yes | |
§ 60.5 | Determination of construction or modification | Yes | |
§ 60.6 | Review of plans | Yes | |
§ 60.7 | Notification and Recordkeeping | Yes | Except that § 60.7 only applies as specified in § 60.4214(a). |
§ 60.8 | Performance tests | Yes | Except that § 60.8 only applies to stationary CI ICE with a displacement of (≥30 liters per cylinder and engines that are not certified. |
§ 60.9 | Availability of information | Yes | |
§ 60.10 | State Authority | Yes | |
§ 60.11 | Compliance with standards and maintenance requirements | No | Requirements are specified in subpart IIII. |
§ 60.12 | Circumvention | Yes | |
§ 60.13 | Monitoring requirements | Yes | Except that § 60.13 only applies to stationary CI ICE with a displacement of (≥30 liters per cylinder. |
§ 60.14 | Modification | Yes | |
§ 60.15 | Reconstruction | Yes | |
§ 60.16 | Priority list | Yes | |
§ 60.17 | Incorporations by reference | Yes | |
§ 60.18 | General control device requirements | No | |
§ 60.19 | General notification and reporting requirements | Yes |
Table 1 to Subpart JJJJ of Part 60 - NOX, CO, and VOC Emission Standards for Stationary Non-Emergency SI Engines ≥100 HP (Except Gasoline and Rich Burn LPG), Stationary SI Landfill/Digester Gas Engines, and Stationary Emergency Engines >25 HP
40:8.0.1.1.1.36.279.20.51 :
Table 1 to Subpart JJJJ of Part 60 - NOX, CO, and VOC Emission Standards for Stationary Non-Emergency SI Engines ≥100 HP (Except Gasoline and Rich Burn LPG), Stationary SI Landfill/Digester Gas Engines, and Stationary Emergency Engines >25 HPEngine type and fuel |
Maximum engine power |
Manufacture date |
Emission standards a | |||||
---|---|---|---|---|---|---|---|---|
g/HP-hr | ppmvd at 15% O2 | |||||||
NOX | CO | VOC d | NOX | CO | VOC d | |||
Non-Emergency SI Natural Gas b and Non-Emergency SI Lean Burn LPG b | 100≤HP<500 | 7/1/2008 | 2.0 | 4.0 | 1.0 | 160 | 540 | 86 |
1/1/2011 | 1.0 | 2.0 | 0.7 | 82 | 270 | 60 | ||
Non-Emergency SI Lean Burn Natural Gas and LPG | 500≤HP<1,350 | 1/1/2008 | 2.0 | 4.0 | 1.0 | 160 | 540 | 86 |
7/1/2010 | 1.0 | 2.0 | 0.7 | 82 | 270 | 60 | ||
Non-Emergency SI Natural Gas and Non-Emergency SI Lean Burn LPG (except lean burn 500≤HP<1,350) | HP≥500 | 7/1/2007 | 2.0 | 4.0 | 1.0 | 160 | 540 | 86 |
HP≥500 | 7/1/2010 | 1.0 | 2.0 | 0.7 | 82 | 270 | 60 | |
Landfill/Digester Gas (except lean burn 500≤HP<1,350) | HP<500 | 7/1/2008 | 3.0 | 5.0 | 1.0 | 220 | 610 | 80 |
1/1/2011 | 2.0 | 5.0 | 1.0 | 150 | 610 | 80 | ||
HP≥500 | 7/1/2007 | 3.0 | 5.0 | 1.0 | 220 | 610 | 80 | |
7/1/2010 | 2.0 | 5.0 | 1.0 | 150 | 610 | 80 | ||
Landfill/Digester Gas Lean Burn | 500≤HP<1,350 | 1/1/2008 | 3.0 | 5.0 | 1.0 | 220 | 610 | 80 |
7/1/2010 | 2.0 | 5.0 | 1.0 | 150 | 610 | 80 | ||
Emergency | 25<HP<130 | 1/1/2009 | c 10 | 387 | N/A | N/A | N/A | N/A |
HP≥130 | 2.0 | 4.0 | 1.0 | 160 | 540 | 86 |
a Owners and operators of stationary non-certified SI engines may choose to comply with the emission standards in units of either g/HP-hr or ppmvd at 15 percent O2.
b Owners and operators of new or reconstructed non-emergency lean burn SI stationary engines with a site rating of greater than or equal to 250 brake HP located at a major source that are meeting the requirements of 40 CFR part 63, subpart ZZZZ, Table 2a do not have to comply with the CO emission standards of Table 1 of this subpart.
c The emission standards applicable to emergency engines between 25 HP and 130 HP are in terms of NOX + HC.
d For purposes of this subpart, when calculating emissions of volatile organic compounds, emissions of formaldehyde should not be included.
Table 2 to Subpart JJJJ of Part 60 - Requirements for Performance Tests
40:8.0.1.1.1.36.279.20.52 :
Table 2 to Subpart JJJJ of Part 60 - Requirements for Performance TestsAs stated in § 60.4244, you must comply with the following requirements for performance tests within 10 percent of 100 percent peak (or the highest achievable) load].
For each | Complying with the requirement to |
You must | Using | According to the
following requirements |
---|---|---|---|---|
1. Stationary SI internal combustion engine demonstrating compliance according to § 60.4244 | a. Limit the concentration of NOX in the stationary SI internal combustion engine exhaust | i. Select the sampling port location and the number/location of traverse points at the exhaust of the stationary internal combustion engine; | (1) Method 1 or 1A of 40 CFR part 60, appendix A-1, if measuring flow rate | (a) Alternatively, for NOX, O2, and moisture measurement, ducts ≤6 inches in diameter may be sampled at a single point located at the duct centroid and ducts >6 and ≤12 inches in diameter may be sampled at 3 traverse points located at 16.7, 50.0, and 83.3% of the measurement line (`3-point long line'). If the duct is >12 inches in diameter and the sampling port location meets the two and half-diameter criterion of Section 11.1.1 of Method 1 of 40 CFR part 60, Appendix A, the duct may be sampled at `3-point long line'; otherwise, conduct the stratification testing and select sampling points according to Section 8.1.2 of Method 7E of 40 CFR part 60, Appendix A. |
ii. Determine the O2 concentration of the stationary internal combustion engine exhaust at the sampling port location; | (2) Method 3, 3A, or 3B b of 40 CFR part 60, appendix A-2 or ASTM Method D6522-00 (Reapproved 2005) a d | (b) Measurements to determine O2 concentration must be made at the same time as the measurements for NOX concentration. | ||
iii. If necessary, determine the exhaust flowrate of the stationary internal combustion engine exhaust; | (3) Method 2 or 2C of 40 CFR part 60, appendix A-1 or Method 19 of 40 CFR part 60, appendix A-7 | (c) Measurements to determine the exhaust flowrate must be made (1) at the same time as the measurement for NOX concentration or, alternatively (2) according to the option in Section 11.1.2 of Method 1A of 40 CFR part 60, Appendix A-1, if applicable. | ||
iv. If necessary, measure moisture content of the stationary internal combustion engine exhaust at the sampling port location; and | (4) Method 4 of 40 CFR part 60, appendix A-3, Method 320 of 40 CFR part 63, appendix A, e or ASTM Method D6348-03 d e | (d) Measurements to determine moisture must be made at the same time as the measurement for NOX concentration. | ||
v. Measure NOX at the exhaust of the stationary internal combustion engine; if using a control device, the sampling site must be located at the outlet of the control device | (5) Method 7E of 40 CFR part 60, appendix A-4, ASTM Method D6522-00 (Reapproved 2005),a d Method 320 of 40 CFR part 63, appendix A, e or ASTM Method D6348-03 d e | (e) Results of this test consist of the average of the three 1-hour or longer runs. | ||
b. Limit the concentration of CO in the stationary SI internal combustion engine exhaust | i. Select the sampling port location and the number/location of traverse points at the exhaust of the stationary internal combustion engine; | (1) Method 1 or 1A of 40 CFR part 60, appendix A-1, if measuring flow rate | (a) Alternatively, for CO, O2, and moisture measurement, ducts ≤6 inches in diameter may be sampled at a single point located at the duct centroid and ducts >6 and ≤12 inches in diameter may be sampled at 3 traverse points located at 16.7, 50.0, and 83.3% of the measurement line (`3-point long line'). If the duct is >12 inches in diameter and the sampling port location meets the two and half-diameter criterion of Section 11.1.1 of Method 1 of 40 CFR part 60, Appendix A, the duct may be sampled at `3-point long line'; otherwise, conduct the stratification testing and select sampling points according to Section 8.1.2 of Method 7E of 40 CFR part 60, Appendix A. | |
ii. Determine the O2 concentration of the stationary internal combustion engine exhaust at the sampling port location; | (2) Method 3, 3A, or 3B b of 40 CFR part 60, appendix A-2 or ASTM Method D6522-00 (Reapproved 2005) a d | (b) Measurements to determine O2 concentration must be made at the same time as the measurements for CO concentration. | ||
iii. If necessary, determine the exhaust flowrate of the stationary internal combustion engine exhaust; | (3) Method 2 or 2C of 40 CFR 60, appendix A-1 or Method 19 of 40 CFR part 60, appendix A-7 | (c) Measurements to determine the exhaust flowrate must be made (1) at the same time as the measurement for CO concentration or, alternatively (2) according to the option in Section 11.1.2 of Method 1A of 40 CFR part 60, Appendix A-1, if applicable. | ||
iv. If necessary, measure moisture content of the stationary internal combustion engine exhaust at the sampling port location; and | (4) Method 4 of 40 CFR part 60, appendix A-3, Method 320 of 40 CFR part 63, appendix A, e or ASTM Method D6348-03 d e | (d) Measurements to determine moisture must be made at the same time as the measurement for CO concentration. | ||
v. Measure CO at the exhaust of the stationary internal combustion engine; if using a control device, the sampling site must be located at the outlet of the control device | (5) Method 10 of 40 CFR part 60, appendix A4, ASTM Method D6522-00 (Reapproved 2005),a d e Method 320 of 40 CFR part 63, appendix A, e or ASTM Method D6348-03 d e | (e) Results of this test consist of the average of the three 1-hour or longer runs. | ||
c. Limit the concentration of VOC in the stationary SI internal combustion engine exhaust | i. Select the sampling port location and the number/location of traverse points at the exhaust of the stationary internal combustion engine; | (1) Method 1 or 1A of 40 CFR part 60, appendix A-1, if measuring flow rate | (a) Alternatively, for VOC, O2, and moisture measurement, ducts ≤6 inches in diameter may be sampled at a single point located at the duct centroid and ducts >6 and ≤12 inches in diameter may be sampled at 3 traverse points located at 16.7, 50.0, and 83.3% of the measurement line (`3-point long line'). If the duct is >12 inches in diameter and the sampling port location meets the two and half-diameter criterion of Section 11.1.1 of Method 1 of 40 CFR part 60, Appendix A, the duct may be sampled at `3-point long line'; otherwise, conduct the stratification testing and select sampling points according to Section 8.1.2 of Method 7E of 40 CFR part 60, Appendix A. | |
ii. Determine the O2 concentration of the stationary internal combustion engine exhaust at the sampling port location; | (2) Method 3, 3A, or 3B b of 40 CFR part 60, appendix A-2 or ASTM Method D6522-00 (Reapproved 2005) a d | (b) Measurements to determine O2 concentration must be made at the same time as the measurements for VOC concentration. | ||
iii. If necessary, determine the exhaust flowrate of the stationary internal combustion engine exhaust; | (3) Method 2 or 2C of 40 CFR 60, appendix A-1 or Method 19 of 40 CFR part 60, appendix A-7 | (c) Measurements to determine the exhaust flowrate must be made (1) at the same time as the measurement for VOC concentration or, alternatively (2) according to the option in Section 11.1.2 of Method 1A of 40 CFR part 60, Appendix A-1, if applicable. | ||
iv. If necessary, measure moisture content of the stationary internal combustion engine exhaust at the sampling port location; and | (4) Method 4 of 40 CFR part 60, appendix A-3, Method 320 of 40 CFR part 63, appendix A, e or ASTM Method D6348-03 d e | (d) Measurements to determine moisture must be made at the same time as the measurement for VOC concentration. | ||
v. Measure VOC at the exhaust of the stationary internal combustion engine; if using a control device, the sampling site must be located at the outlet of the control device | (5) Methods 25A and 18 of 40 CFR part 60, appendices A-6 and A-7, Method 25A with the use of a hydrocarbon cutter as described in 40 CFR 1065.265, Method 18 of 40 CFR part 60, appendix A-6,c e Method 320 of 40 CFR part 63, appendix A, e or ASTM Method D6348-03 d e | (e) Results of this test consist of the average of the three 1-hour or longer runs. |
a Also, you may petition the Administrator for approval to use alternative methods for portable analyzer.
b You may use ASME PTC 19.10-1981, Flue and Exhaust Gas Analyses, for measuring the O2 content of the exhaust gas as an alternative to EPA Method 3B. AMSE PTC 19.10-1981 incorporated by reference, see 40 CFR 60.17
c You may use EPA Method 18 of 40 CFR part 60, appendix A-6, provided that you conduct an adequate pre-survey test prior to the emissions test, such as the one described in OTM 11 on EPA's website (http://www.epa.gov/ttn/emc/prelim/otm11.pdf).
d Incorporated by reference; see 40 CFR 60.17.
e You must meet the requirements in § 60.4245(d).
Table 3 to Subpart JJJJ of Part 60 - Applicability of General Provisions to Subpart JJJJ
40:8.0.1.1.1.36.279.20.53 :
Table 3 to Subpart JJJJ of Part 60 - Applicability of General Provisions to Subpart JJJJ[As stated in § 60.4246, you must comply with the following applicable General Provisions]
General provisions citation | Subject of citation | Applies to subpart | Explanation |
---|---|---|---|
§ 60.1 | General applicability of the General Provisions | Yes | |
§ 60.2 | Definitions | Yes | Additional terms defined in § 60.4248. |
§ 60.3 | Units and abbreviations | Yes | |
§ 60.4 | Address | Yes | |
§ 60.5 | Determination of construction or modification | Yes | |
§ 60.6 | Review of plans | Yes | |
§ 60.7 | Notification and Recordkeeping | Yes | Except that § 60.7 only applies as specified in § 60.4245. |
§ 60.8 | Performance tests | Yes | Except that § 60.8 only applies to owners and operators who are subject to performance testing in subpart JJJJ. |
§ 60.9 | Availability of information | Yes | |
§ 60.10 | State Authority | Yes | |
§ 60.11 | Compliance with standards and maintenance requirements | Yes | Requirements are specified in subpart JJJJ. |
§ 60.12 | Circumvention | Yes | |
§ 60.13 | Monitoring requirements | No | |
§ 60.14 | Modification | Yes | |
§ 60.15 | Reconstruction | Yes | |
§ 60.16 | Priority list | Yes | |
§ 60.17 | Incorporations by reference | Yes | |
§ 60.18 | General control device requirements | No | |
§ 60.19 | General notification and reporting requirements | Yes |
Table 4 to Subpart JJJJ of Part 60 - Applicability of Mobile Source Provisions for Manufacturers Participating in the Voluntary Certification Program and Certifying Stationary SI ICE to Emission Standards in Table 1 of Subpart JJJJ
40:8.0.1.1.1.36.279.20.54 :
Table 4 to Subpart JJJJ of Part 60 - Applicability of Mobile Source Provisions for Manufacturers Participating in the Voluntary Certification Program and Certifying Stationary SI ICE to Emission Standards in Table 1 of Subpart JJJJ[As stated in § 60.4247, you must comply with the following applicable mobile source provisions if you are a manufacturer participating in the voluntary certification program and certifying stationary SI ICE to emission standards in Table 1 of subpart JJJJ]
Mobile source provisions citation | Subject of citation | Applies to subpart | Explanation |
---|---|---|---|
1048 subpart A | Overview and Applicability | Yes | |
1048 subpart B | Emission Standards and Related Requirements | Yes | Except for the specific sections below. |
1048.101 | Exhaust Emission Standards | No | |
1048.105 | Evaporative Emission Standards | No | |
1048.110 | Diagnosing Malfunctions | No | |
1048.140 | Certifying Blue Sky Series Engines | No | |
1048.145 | Interim Provisions | No | |
1048 subpart C | Certifying Engine Families | Yes | Except for the specific sections below. |
1048.205(b) | AECD reporting | Yes | |
1048.205(c) | OBD Requirements | No | |
1048.205(n) | Deterioration Factors | Yes | Except as indicated in 60.4247(c). |
1048.205(p)(1) | Deterioration Factor Discussion | Yes | |
1048.205(p)(2) | Liquid Fuels as they require | No | |
1048.240(b)(c)(d) | Deterioration Factors | Yes | |
1048 subpart D | Testing Production-Line Engines | Yes | |
1048 subpart E | Testing In-Use Engines | No | |
1048 subpart F | Test Procedures | Yes | |
1065.5(a)(4) | Raw sampling (refers reader back to the specific emissions regulation for guidance) | Yes | |
1048 subpart G | Compliance Provisions | Yes | |
1048 subpart H | Reserved | ||
1048 subpart I | Definitions and Other Reference Information | Yes | |
1048 appendix I and II | Yes | ||
1065 (all subparts) | Engine Testing Procedures | Yes | Except for the specific section below. |
1065.715 | Test Fuel Specifications for Natural Gas | No | |
1068 (all subparts) | General Compliance Provisions for Nonroad Programs | Yes | Except for the specific sections below. |
1068.245 | Hardship Provisions for Unusual Circumstances | No | |
1068.250 | Hardship Provisions for Small-Volume Manufacturers | No | |
1068.255 | Hardship Provisions for Equipment Manufacturers and Secondary Engine Manufacturers | No |
Table 1 to Subpart KKKK of Part 60 - Nitrogen Oxide Emission Limits for New Stationary Combustion Turbines
40:8.0.1.1.1.37.287.27.55 :
Table 1 to Subpart KKKK of Part 60 - Nitrogen Oxide Emission Limits for New Stationary Combustion TurbinesCombustion turbine type | Combustion turbine heat input
at peak load (HHV) |
NOX emission standard |
---|---|---|
New turbine firing natural gas, electric generating | ≤ 50 MMBtu/h | 42 ppm at 15 percent O2 or 290 ng/J of useful output (2.3 lb/MWh). |
New turbine firing natural gas, mechanical drive | ≤ 50 MMBtu/h | 100 ppm at 15 percent O2 or 690 ng/J of useful output (5.5 lb/MWh). |
New turbine firing natural gas | > 50 MMBtu/h and ≤ 850 MMBtu/h | 25 ppm at 15 percent O2 or 150 ng/J of useful output (1.2 lb/MWh). |
New, modified, or reconstructed turbine firing natural gas | > 850 MMBtu/h | 15 ppm at 15 percent O2 or 54 ng/J of useful output (0.43 lb/MWh) |
New turbine firing fuels other than natural gas, electric generating | ≤ 50 MMBtu/h | 96 ppm at 15 percent O2 or 700 ng/J of useful output (5.5 lb/MWh). |
New turbine firing fuels other than natural gas, mechanical drive | ≤ 50 MMBtu/h | 150 ppm at 15 percent O2 or 1,100 ng/J of useful output (8.7 lb/MWh). |
New turbine firing fuels other than natural gas | > 50 MMBtu/h and ≤ 850 MMBtu/h | 74 ppm at 15 percent O2 or 460 ng/J of useful output (3.6 lb/MWh). |
New, modified, or reconstructed turbine firing fuels other than natural gas | > 850 MMBtu/h | 42 ppm at 15 percent O2 or 160 ng/J of useful output (1.3 lb/MWh). |
Modified or reconstructed turbine | ≤ 50 MMBtu/h | 150 ppm at 15 percent O2 or 1,100 ng/J of useful output (8.7 lb/MWh). |
Modified or reconstructed turbine firing natural gas | > 50 MMBtu/h and ≤ 850 MMBtu/h | 42 ppm at 15 percent O2 or 250 ng/J of useful output (2.0 lb/MWh). |
Modified or reconstructed turbine firing fuels other than natural gas | > 50 MMBtu/h and ≤ 850 MMBtu/h | 96 ppm at 15 percent O2 or 590 ng/J of useful output (4.7 lb/MWh). |
Turbines located north of the Arctic Circle (latitude 66.5 degrees north), turbines operating at less than 75 percent of peak load, modified and reconstructed offshore turbines, and turbine operating at temperatures less than 0 °F | ≤ 30 MW output | 150 ppm at 15 percent O2 or 1,100 ng/J of useful output (8.7 lb/MWh). |
Turbines located north of the Arctic Circle (latitude 66.5 degrees north), turbines operating at less than 75 percent of peak load, modified and reconstructed offshore turbines, and turbine operating at temperatures less than 0 °F | > 30 MW output | 96 ppm at 15 percent O2 or 590 ng/J of useful output (4.7 lb/MWh). |
Heat recovery units operating independent of the combustion turbine | All sizes | 54 ppm at 15 percent O2 or 110 ng/J of useful output (0.86 lb/MWh). |
Table 1 to Subpart LLLL of Part 60 - Emission Limits and Standards for New Fluidized Bed Sewage Sludge Incineration Units
40:8.0.1.1.1.38.298.37.56 :
Table 1 to Subpart LLLL of Part 60 - Emission Limits and Standards for New Fluidized Bed Sewage Sludge Incineration UnitsFor the air pollutant | You must meet this emission limit a | Using these averaging methods and minimum sampling volumes or durations |
And determining compliance using this method |
---|---|---|---|
Particulate matter | 9.6 milligrams per dry standard cubic meter | 3-run average (collect a minimum volume of 1 dry standard cubic meters per run) | Performance test (Method 5 at 40 CFR part 60, appendix A-3; Method 26A or Method 29 at 40 CFR part 60, appendix A-8). |
Hydrogen chloride | 0.24 parts per million by dry volume | 3-run average (Collect a minimum volume of 1 dry standard cubic meters per run) | Performance test (Method 26A at 40 CFR part 60, appendix A-8). |
Carbon monoxide | 27 parts per million by dry volume | 24-hour block average (using 1-hour averages of data). For determining compliance with the carbon monoxide concentration limit using carbon monoxide CEMS, the correction to 7 percent oxygen does not apply during periods of startup or shutdown. Use the measured carbon monoxide concentration without correcting for oxygen concentration in averaging with other carbon monoxide concentrations (corrected to 7 percent oxygen) to determine the 24-hour average value | Continuous emissions monitoring system. (Performance Specification 4B of this part, using a low-range span of 100 ppm and a high-range span of 1000 ppm, and a RA of 0.5 ppm instead of 5 ppm specified in section 13.2. For the cylinder gas audit of Procedure 1, ±15% or 0.5 whichever is greater). |
Dioxins/furans
(total mass basis); or Dioxins/furans (toxic equivalency basis) b |
0.013 nanograms per dry
standard cubic meter (total mass basis); or 0.0044 nanograms per dry standard cubic meter (toxic equivalency basis) |
3-run average (collect a minimum volume of 3 dry standard cubic meters per run) | Performance test (Method 23 at 40 CFR part 60, appendix A-7). |
Mercury | 0.0010 milligrams per dry standard cubic meter | 3-run average (For Method 29 and ASTM D6784-02 (Reapproved 2008), c collect a minimum volume of 3 dry standard cubic meters per run. For Method 30B, collect a minimum sample as specified in Method 30B at 40 CFR part 60, appendix A-8) | Performance test (Method 29 at 40 CFR part 60, appendix A-8; Method 30B at 40 CFR part 60, appendix A-8; or ASTM D6784-02 (Reapproved 2008). c |
Oxides of nitrogen | 30 parts per million by dry volume | 3-run average (Collect sample for a minimum duration of one hour per run) | Performance test (Method 7 or 7E at 40 CFR part 60, appendix A-4). |
Sulfur dioxide | 5.3 parts per million by dry volume | 3-run average (For Method 6, collect a minimum volume of 100 liters per run. For Method 6C, sample for a minimum duration of one hour per run) | Performance test (Method 6 or 6C at 40 CFR part 40, appendix A-4; or ANSI/ASME PTC 19.10-1981. c |
Cadmium | 0.0011 milligrams per dry standard cubic meter | 3-run average (collect a minimum volume of 1 dry standard cubic meters per run) | Performance test (Method 29 at 40 CFR part 60, appendix A-8). Use GFAAS or ICP/MS for the analytical finish. |
Lead | 0.00062 milligrams per dry standard cubic meter | 3-run average (collect a minimum volume of 3 dry standard cubic meters per run) | Performance test (Method 29 at 40 CFR part 60, appendix A-8. Use GFAAS or ICP/MS for the analytical finish. |
Fugitive emissions from ash handling | Visible emissions of combustion ash from an ash conveying system (including conveyor transfer points) for no more than 5 percent of the hourly observation period | Three 1-hour observation periods | Visible emission test (Method 22 of appendix A-7 of this part). |
a All emission limits are measured at 7 percent oxygen, dry basis at standard conditions.
b You have the option to comply with either the dioxin/furan emission limit on a total mass basis or the dioxin/furan emission limit on a toxic equivalency basis.
c Incorporated by reference, see § 60.17.
Table 2 to Subpart LLLL of Part 60 - Emission Limits and Standards for New Multiple Hearth Sewage Sludge Incineration Units
40:8.0.1.1.1.38.298.37.57 :
Table 2 to Subpart LLLL of Part 60 - Emission Limits and Standards for New Multiple Hearth Sewage Sludge Incineration UnitsFor the air pollutant | You must meet this emission limit a | Using these averaging methods and minimum sampling volumes or durations | And determining compliance using this method |
---|---|---|---|
Particulate matter | 60 milligrams per dry standard cubic meter | 3-run average (collect a minimum volume of 0.75 dry standard cubic meters per run) | Performance test (Method 5 at 40 CFR part 60, appendix A-3; Method 26A or Method 29 at 40 CFR part 60, appendix A-8). |
Hydrogen chloride | 1.2 parts per million by dry volume | 3-run average (For Method 26, collect a minimum volume of 200 liters per run. For Method 26A, collect a minimum volume of 1 dry standard cubic meters per run) | Performance test (Method 26 or 26A at 40 CFR part 60, appendix A-8). |
Carbon monoxide | 52 parts per million by dry volume | 24-hour block average (using 1-hour averages of data) | Continuous emissions monitoring system. (Performance Specification 4B of this part, using a low-range span of 100 ppm and a high-range span of 1000 ppm, and a relative accuracy of 0.5 ppm instead of 5 ppm specified in section 13.2. For the cylinder gas audit of Procedure 1, ±15% or 0.5 whichever is greater). |
Dioxins/furans
(total mass basis); or Dioxins/furans (toxic equivalency basis) b |
0.045 nanograms per dry
standard cubic meter (total mass basis); or 0.0022 nanograms per dry standard cubic meter (toxic equivalency basis) |
3-run average (collect a minimum volume of 3 dry standard cubic meters per run) | Performance test (Method 23 at 40 CFR part 60, appendix A-7). |
Mercury | 0.15 milligrams per dry standard cubic meter | 3-run average (For Method 29 and ASTM D6784-02 (Reapproved 2008), c collect a minimum volume of 1 dry standard cubic meters per run. For Method 30B, collect a minimum sample as specified in Method 30B at 40 CFR part 60, appendix A-8) | Performance test (Method 29 at 40 CFR part 60, appendix A-8; Method 30B at 40 CFR part 60, appendix A-8; or ASTM D6784-02 (Reapproved 2008). c |
Oxides of nitrogen | 210 parts per million by dry volume | 3-run average (Collect sample for a minimum duration of one hour per run) | Performance test (Method 7 or 7E at 40 CFR part 60, appendix A-4). |
Sulfur dioxide | 26 parts per million by dry volume | 3-run average (For Method 6, collect a minimum volume of 200 liters per run. For Method 6C, collect sample for a minimum duration of one hour per run) | Performance test (Method 6 or 6C at 40 CFR part 40, appendix A-4; or ANSI/ASME PTC 19.10-1981. c |
Cadmium | 0.0024 milligrams per dry standard cubic meter | 3-run average (collect a minimum volume of 1 dry standard cubic meters per run) | Performance test (Method 29 at 40 CFR part 60, appendix A-8). Use GFAAS or ICP/MS for the analytical finish. |
Lead | 0.0035 milligrams per dry standard cubic meter | 3-run average (collect a minimum volume of 1 dry standard cubic meters per run) | Performance test (Method 29 at 40 CFR part 60, appendix A-8. Use GFAAS or ICP/MS for the analytical finish. |
Fugitive emissions from ash handling | Visible emissions of combustion ash from an ash conveying system (including conveyor transfer points) for no more than 5 percent of the hourly observation period | Three 1-hour observation periods | Visible emission test (Method 22 of appendix A-7 of this part). |
a All emission limits are measured at 7 percent oxygen, dry basis at standard conditions.
b You have the option to comply with either the dioxin/furan emission limit on a total mass basis or the dioxin/furan emission limit on a toxic equivalency basis.
c Incorporated by reference, see § 60.17.
Table 3 to Subpart LLLL of Part 60 - Operating Parameters for New Sewage Sludge Incineration Units a
40:8.0.1.1.1.38.298.37.58 :
Table 3 to Subpart LLLL of Part 60 - Operating Parameters for New Sewage Sludge Incineration Units aFor these operating parameters | You must establish these operating limits | And monitor using these minimum frequencies | ||
---|---|---|---|---|
Data measurement | Data recording b |
Data averaging period for compliance |
||
All sewage sludge incineration units | ||||
Combustion chamber operating temperature or afterburner temperature | Minimum combustion chamber operating temperature or afterburner temperature | Continuous | Every 15 minutes | 12-hour block. |
Fugitive emissions from ash handling | Site-specific operating requirements | Not applicable | Not applicable | Not applicable. |
Scrubber | ||||
Pressure drop across each wet scrubber | Minimum pressure drop | Continuous | Every 15 minutes | 12-hour block. |
Scrubber liquid flow rate | Minimum flow rate | Continuous | Every 15 minutes | 12-hour block. |
Scrubber liquid pH | Minimum pH | Continuous | Every 15 minutes | 3-hour block. |
Fabric Filter | ||||
Alarm time of the bag leak detection system alarm | Maximum alarm time of the bag leak detection system alarm (this operating limit is provided in § 60.4850 and is not established on a site-specific basis). | |||
Electrostatic precipitator | ||||
Secondary voltage of the electrostatic precipitator collection plates | Minimum power input to the electrostatic precipitator collection plates | Continuous | Hourly | 12-hour block. |
Secondary amperage of the electrostatic precipitator collection plates | ||||
Effluent water flow rate at the outlet of the electrostatic precipitator | Minimum effluent water flow rate at the outlet of the electrostatic precipitator | Hourly | Hourly | 12-hour block. |
Activated carbon injection | ||||
Mercury sorbent injection rate | Minimum mercury sorbent injection rate | Hourly | Hourly | 12-hour block. |
Dioxin/furan sorbent injection rate | Minimum dioxin/furan sorbent injection rate | |||
Carrier gas flow rate or carrier gas pressure drop | Minimum carrier gas flow rate or minimum carrier gas pressure drop | Continuous | Every 15 minutes | 12-hour block. |
a As specified in § 60.4870, you may use a continuous emissions monitoring system or continuous automated sampling system in lieu of establishing certain operating limits.
b This recording time refers to the minimum frequency that the continuous monitor or other measuring device initially records data. For all data recorded every 15 minutes, you must calculate hourly arithmetic averages. For all parameters, you use hourly averages to calculate the 12-hour or 3-hour block average specified in this table for demonstrating compliance. You maintain records of 1-hour averages.
Table 4 to Subpart LLLL of Part 60 - Toxic Equivalency Factors
40:8.0.1.1.1.38.298.37.59 :
Table 4 to Subpart LLLL of Part 60 - Toxic Equivalency FactorsDioxin/furan isomer | Toxic equivalency factor |
---|---|
2,3,7,8-tetrachlorinated dibenzo-p-dioxin | 1 |
1,2,3,7,8-pentachlorinated dibenzo-p-dioxin | 1 |
1,2,3,4,7,8-hexachlorinated dibenzo-p-dioxin | 0.1 |
1,2,3,7,8,9-hexachlorinated dibenzo-p-dioxin | 0.1 |
1,2,3,6,7,8-hexachlorinated dibenzo-p-dioxin | 0.1 |
1,2,3,4,6,7,8-heptachlorinated dibenzo-p-dioxin | 0.01 |
octachlorinated dibenzo-p-dioxin | 0.0003 |
2,3,7,8-tetrachlorinated dibenzofuran | 0.1 |
2,3,4,7,8-pentachlorinated dibenzofuran | 0.3 |
1,2,3,7,8-pentachlorinated dibenzofuran | 0.03 |
1,2,3,4,7,8-hexachlorinated dibenzofuran | 0.1 |
1,2,3,6,7,8-hexachlorinated dibenzofuran | 0.1 |
1,2,3,7,8,9-hexachlorinated dibenzofuran | 0.1 |
2,3,4,6,7,8-hexachlorinated dibenzofuran | 0.1 |
1,2,3,4,6,7,8-heptachlorinated dibenzofuran | 0.01 |
1,2,3,4,7,8,9-heptachlorinated dibenzofuran | 0.01 |
octachlorinated dibenzofuran | 0.0003 |
Table 5 to Subpart LLLL of Part 60 - Summary of Reporting Requirements for New Sewage Sludge Incineration Units a
40:8.0.1.1.1.38.298.37.60 :
Table 5 to Subpart LLLL of Part 60 - Summary of Reporting Requirements for New Sewage Sludge Incineration Units aReport | Due date | Contents | Reference |
---|---|---|---|
Notification of construction | Prior to commencing construction | 1. Statement of intent to
construct 2. Anticipated date of commencement of construction. 3. Documentation for siting requirements. 4. Anticipated date of initial startup. |
§ 60.4915(a). |
Notification of initial startup | Prior to initial startup | 1. Maximum design dry sewage
sludge burning capacity 2. Anticipated and permitted maximum feed rate. 3. If applicable, the petition for site-specific operating limits. 4. Anticipated date of initial startup. 5. Site-specific monitoring plan. 6. The site-specific monitoring plan for your ash handling system. |
§ 60.4915(b). |
Initial compliance report | No later than 60 days following the initial performance test | 1. Company name and
address 2. Statement by a responsible official, with that official's name, title, and signature, certifying the accuracy of the content of the report. 3. Date of report. 4. Complete test report for the initial performance test. 5. Results of CMS b performance evaluation. 6. The values for the site-specific operating limits and the calculations and methods, as applicable, used to establish each operating limit. 7. Documentation of installation of bag leak detection system for fabric filter. 8. Results of initial air pollution control device inspection, including a description of repairs. |
§ 60.4915(c). |
Annual compliance report | No later than 12 months following the submission of the initial compliance report; subsequent reports are to be submitted no more than 12 months following the previous report | 1. Company name and
address 2. Statement and signature by responsible official. 3. Date and beginning and ending dates of report. 4. If a performance test was conducted during the reporting period, the results of the test, including any new operating limits and associated calculations and the type of activated carbon used, if applicable. 5. For each pollutant and operating parameter recorded using a CMS, the highest recorded 3-hour average and the lowest recorded 3-hour average, as applicable. 6. If no deviations from emission limits, emission standards, or operating limits occurred, a statement that no deviations occurred. 7. If a fabric filter is used, the date, time, and duration of alarms. 8. If a performance evaluation of a CMS was conducted, the results, including any new operating limits and their associated calculations. 9. If you met the requirements of § 60.4885(a)(3) and did not conduct a performance test, include the dates of the last three performance tests, a comparison to the 50 percent emission limit threshold of the emission level achieved in the last three performance tests, and a statement as to whether there have been any process changes. 10. Documentation of periods when all qualified SSI unit operators were unavailable for more than 8 hours but less than 2 weeks. 11. Results of annual pollutions control device inspections, including description of repairs. 12. If there were no periods during which your CMSs had malfunctions, a statement that there were no periods during which your CMSs had malfunctions. 13. If there were no periods during which your CMSs were out of control, a statement that there were no periods during which your CMSs were out of control. 14. If there were no operator training deviations, a statement that there were no such deviations. 15. Information on monitoring plan revisions, including a copy of any revised monitoring plan. |
§§ 60.4915(d). |
Deviation report (deviations from emission limits, emission standards, or operating limits, as specified in § 60.4915(e)(1)) | By August 1 of a calendar year for data collected during the first half of the calendar year; by February 1 of a calendar year for data collected during the second half of the calendar year | If using a CMS: 1. Company
name and address 2. Statement by a responsible official. 3. The calendar dates and times your unit deviated from the emission limits or operating limits. 4. The averaged and recorded data for those dates. 5. Duration and cause of each deviation. 6. Dates, times, and causes for monitor downtime incidents. 7. A copy of the operating parameter monitoring data during each deviation and any test report that documents the emission levels. 8. For periods of CMS malfunction or when a CMS was out of control, you must include the information specified in § 60.4915(e)(3)(viii). If not using a CMS: 1. Company name and address 2. Statement by a responsible official. 3. The total operating time of each affected SSI. 4. The calendar dates and times your unit deviated from the emission limits, emission standard, or operating limits. 5. The averaged and recorded data for those dates. 6. Duration and cause of each deviation. 7. A copy of any performance test report that showed a deviation from the emission limits or standards. 8. A brief description of any malfunction, a description of actions taken during the malfunction to minimize emissions, and corrective action taken. |
§ 60.4915(e). |
Notification of qualified operator deviation (if all qualified operators are not accessible for 2 weeks or more) | Within 10 days of deviation | 1. Statement of cause of
deviation 2. Description of actions taken to ensure that a qualified operator will be available 3. The date when a qualified operator will be accessible. |
§ 60.4915(f). |
Notification of status of qualified operator deviation | Every 4 weeks following notification of deviation | 1. Description of actions
taken to ensure that a qualified operator is accessible 2. The date when you anticipate that a qualified operator will be accessible. 3. Request for approval to continue operation. |
§ 60.4915(f). |
Notification of resumed operation following shutdown (due to qualified operator deviation and as specified in § 60.4835(b)(2)(i) | Within 5 days of obtaining a qualified operator and resuming operation | 1. Notification that you have obtained a qualified operator and are resuming operation | § 60.4915(f). |
Notification of a force majeure | As soon as practicable following the date you first knew, or through due diligence should have known that the event may cause or caused a delay in conducting a performance test beyond the regulatory deadline; the notification must occur before the performance test deadline unless the initial force majeure or a subsequent force majeure event delays the notice, and in such cases, the notification must occur as soon as practicable | 1. Description of the force
majeure event 2. Rationale for attributing the delay in conducting the performance test beyond the regulatory deadline to the force majeure. 3. Description of the measures taken or to be taken to minimize the delay. 4. Identification of the date by which you propose to conduct the performance test. |
§ 60.4915(g). |
Notification of intent to start or stop use of a CMS | 1 month before starting or stopping use of a CMS | 1. Intent to start or stop use of a CMS | § 60.4915(h). |
Notification of intent to conduct a performance test | At least 30 days prior to the performance test | 1. Intent to conduct a performance test to comply with this subpart | |
Notification of intent to conduct a rescheduled performance test | At least 7 days prior to the date of a rescheduled performance test | 1. Intent to conduct a rescheduled performance test to comply with this subpart |
a This table is only a summary, see the referenced sections of the rule for the complete requirements.
b CMS means continuous monitoring system.
Table 1 to Subpart MMMM of Part 60 - Model Rule - Increments of Progress and Compliance Schedules for Existing Sewage Sludge Incineration Units
40:8.0.1.1.1.39.310.53.61 :
Table 1 to Subpart MMMM of Part 60 - Model Rule - Increments of Progress and Compliance Schedules for Existing Sewage Sludge Incineration UnitsComply with these increments of progress | By these dates a |
---|---|
Increment 1 - Submit final control plan | (Dates to be specified in state plan) |
Increment 2 - Final compliance | (Dates to be specified in state plan) b |
a Site-specific schedules can be used at the discretion of the state.
b The date can be no later than 3 years after the effective date of state plan approval or March 21, 2016 for SSI units that commenced construction on or before October 14, 2010.
Table 2 to Subpart MMMM of Part 60 - Model Rule - Emission Limits and Standards for Existing Fluidized Bed Sewage Sludge Incineration Units
40:8.0.1.1.1.39.310.53.62 :
Table 2 to Subpart MMMM of Part 60 - Model Rule - Emission Limits and Standards for Existing Fluidized Bed Sewage Sludge Incineration UnitsFor the air pollutant | You must meet this emission limit a | Using these averaging methods
and minimum sampling volumes or durations |
And determining compliance using this method |
---|---|---|---|
Particulate matter | 18 milligrams per dry standard cubic meter | 3-run average (collect a minimum volume of 1 dry standard cubic meters sample per run) | Performance test (Method 5 at 40 CFR part 60, appendix A-3; Method 26A or Method 29 at 40 CFR part 60, appendix A-8). |
Hydrogen chloride | 0.51 parts per million by dry volume | 3-run average (Collect a minimum volume of 1 dry standard cubic meters per run) | Performance test (Method 26A at 40 CFR part 60, appendix A-8). |
Carbon monoxide | 64 parts per million by dry volume | 3-run average (collect sample for a minimum duration of one hour per run) | Performance test (Method 10, 10A, or 10B at 40 CFR part 60, appendix A-4). |
Dioxins/furans
(total mass basis); or Dioxins/furans (toxic equivalency basis) b |
1.2 nanograms per dry standard
cubic meter (total mass basis); or 0.10 nanograms per dry standard cubic meter (toxic equivalency basis) |
3-run average (collect a minimum volume of 1 dry standard cubic meters per run) | Performance test (Method 23 at 40 CFR part 60, appendix A-7). |
Mercury | 0.037 milligrams per dry standard cubic meter | 3-run average (For Method 29 and ASTM D6784-02 (Reapproved 2008) c, collect a minimum volume of 1 dry standard cubic meters per run. For Method 30B, collect a minimum sample as specified in Method 30B at 40 CFR part 60, appendix A-8) | Performance test (Method 29 at 40 CFR part 60, appendix A-8; Method 30B at 40 CFR part 60, appendix A-8; or ASTM D6784-02 (Reapproved 2008). c |
Oxides of nitrogen | 150 parts per million by dry volume | 3-run average (Collect sample for a minimum duration of one hour per run) | Performance test (Method 7 or 7E at 40 CFR part 60, appendix A-4). |
Sulfur dioxide | 15 parts per million by dry volume | 3-run average (For Method 6, collect a minimum volume of 60 liters per run. For Method 6C, collect sample for a minimum duration of one hour per run) | Performance test (Method 6 or 6C at 40 CFR part 40, appendix A-4; or ANSI/ASME PTC-19.10-1981. c |
Cadmium | 0.0016 milligrams per dry standard cubic meter | 3-run average (collect a minimum volume of 1 dry standard cubic meters per run) | Performance test (Method 29 at 40 CFR part 60, appendix A-8). Use GFAAS or ICP/MS for the analytical finish. |
Lead | 0.0074 milligrams per dry standard cubic meter | 3-run average (collect a minimum volume of 1 dry standard cubic meters sample per run) | Performance test (Method 29 at 40 CFR part 60, appendix A-8. Use GFAAS or ICP/MS for the analytical finish. |
Fugitive emissions from ash handling | Visible emissions of combustion ash from an ash conveying system (including conveyor transfer points) for no more than 5 percent of the hourly observation period | Three 1-hour observation periods | Visible emission test (Method 22 of appendix A-7 of this part). |
a All emission limits are measured at 7 percent oxygen, dry basis at standard conditions.
b You have the option to comply with either the dioxin/furan emission limit on a total mass basis or the dioxin/furan emission limit on a toxic equivalency basis.
c Incorporated by reference, see § 60.17.
Table 3 to Subpart MMMM of Part 60 - Model Rule - Emission Limits and Standards for Existing Multiple Hearth Sewage Sludge Incineration Units
40:8.0.1.1.1.39.310.53.63 :
Table 3 to Subpart MMMM of Part 60 - Model Rule - Emission Limits and Standards for Existing Multiple Hearth Sewage Sludge Incineration UnitsFor the air pollutant | You must meet this emission limit a | Using these averaging methods
and minimum sampling volumes or durations |
And determining compliance
using this method |
---|---|---|---|
Particulate matter | 80 milligrams per dry standard cubic meter | 3-run average (collect a minimum volume of 0.75 dry standard cubic meters per run) | Performance test (Method 5 at 40 CFR part 60, appendix A-3; Method 26A or Method 29 at 40 CFR part 60, appendix A-8). |
Hydrogen chloride | 1.2 parts per million by dry volume | 3-run average (For Method 26, collect a minimum volume of 200 liters per run. For Method 26A, collect a minimum volume of 1 dry standard cubic meters per run) | Performance test (Method 26 or 26A at 40 CFR part 60, appendix A-8). |
Carbon monoxide | 3,800 parts per million by dry volume | 3-run average (collect sample for a minimum duration of one hour per run) | Performance test (Method 10, 10A, or 10B at 40 CFR part 60, appendix A-4). |
Dioxins/furans (total mass basis) | 5.0 nanograms per dry standard cubic meter; or | 3-run average (collect a minimum volume of 1 dry standard cubic meters per run) | Performance test (Method 23 at 40 CFR part 60, appendix A-7). |
Dioxins/furans (toxic equivalency basis) b | 0.32 nanograms per dry standard cubic meter | ||
Mercury | 0.28 milligrams per dry standard cubic meter | 3-run average (For Method 29 and ASTM D6784-02 (Reapproved 2008), c collect a minimum volume of 1 dry standard cubic meters per run. For Method 30B, collect a minimum sample as specified in Method 30B at 40 CFR part 60, appendix A-8) | Performance test (Method 29 at 40 CFR part 60, appendix A-8; Method 30B at 40 CFR part 60, appendix A-8; or ASTM D6784-02 (Reapproved 2008)). c |
Oxides of nitrogen | 220 parts per million by dry volume | 3-run average (Collect sample for a minimum duration of one hour per run) | Performance test (Method 7 or 7E at 40 CFR part 60, appendix A-4). |
Sulfur dioxide | 26 parts per million by dry volume | 3-run average (For Method 6, collect a minimum volume of 200 liters per run. For Method 6C, collect sample for a minimum duration of one hour per run) | Performance test (Method 6 or 6C at 40 CFR part 40, appendix A-4; or ANSI/ASME PTC 19.10-1981). c |
Cadmium | 0.095 milligrams per dry standard cubic meter | 3-run average (collect a minimum volume of 1 dry standard cubic meters per run) | Performance test (Method 29 at 40 CFR part 60, appendix A-8). |
Lead | 0.30 milligrams per dry standard cubic meter | 3-run average (collect a minimum volume of 1 dry standard cubic meters per run) | Performance test (Method 29 at 40 CFR part 60, appendix A-8). |
Fugitive emissions from ash handling | Visible emissions of combustion ash from an ash conveying system (including conveyor transfer points) for no more than 5 percent of the hourly observation period | Three 1-hour observation periods | Visible emission test (Method 22 of appendix A-7 of this part). |
a All emission limits are measured at 7 percent oxygen, dry basis at standard conditions.
b You have the option to comply with either the dioxin/furan emission limit on a total mass basis or the dioxin/furan emission limit on a toxic equivalency basis.
c Incorporated by reference, see § 60.17.
Table 4 to Subpart MMMM of Part 60 - Model Rule - Operating Parameters for Existing Sewage Sludge Incineration Units a
40:8.0.1.1.1.39.310.53.64 :
Table 4 to Subpart MMMM of Part 60 - Model Rule - Operating Parameters for Existing Sewage Sludge Incineration Units aFor these operating parameters | You must establish these operating limits | And monitor using these minimum frequencies | ||
---|---|---|---|---|
Data measurement | Data recording b | Data averaging period for compliance |
||
All sewage sludge incineration units | ||||
Combustion chamber operating temperature (not required if afterburner temperature is monitored) | Minimum combustion chamber operating temperature or afterburner temperature | Continuous | Every 15 minutes | 12-hour block. |
Fugitive emissions from ash handling | Site-specific operating requirements | Not applicable | No applicable | Not applicable. |
Scrubber | ||||
Pressure drop across each wet scrubber | Minimum pressure drop | Continuous | Every 15 minutes | 12-hour block. |
Scrubber liquid flow rate | Minimum flow rate | Continuous | Every 15 minutes | 12-hour block. |
Scrubber liquid pH | Minimum pH | Continuous | Every 15 minutes | 3-hour block. |
Fabric Filter | ||||
Alarm time of the bag leak detection system alarm | Maximum alarm time of the bag leak detection system alarm (this operating limit is provided in § 60.4850 and is not established on a site-specific basis) | |||
Electrostatic precipitator | ||||
Secondary voltage of the electrostatic precipitator collection plates | Minimum power input to the electrostatic precipitator collection plates | Continuous | Hourly | 12-hour block. |
Secondary amperage of the electrostatic precipitator collection plates | ||||
Effluent water flow rate at the outlet of the electrostatic precipitator | Minimum effluent water flow rate at the outlet of the electrostatic precipitator | Hourly | Hourly | 12-hour block. |
Activated carbon injection | ||||
Mercury sorbent injection rate | Minimum mercury sorbent injection rate | Hourly | Hourly | 12-hour block. |
Dioxin/furan sorbent injection rate | Minimum dioxin/furan sorbent injection rate | |||
Carrier gas flow rate or carrier gas pressure drop | Minimum carrier gas flow rate or minimum carrier gas pressure drop | Continuous | Every 15 minutes | 12-hour block. |
Afterburner | ||||
Temperature of the afterburner combustion chamber | Minimum temperature of the afterburner combustion chamber | Continuous | Every 15 minutes | 12-hour block. |
a As specified in § 60.5190, you may use a continuous emissions monitoring system or continuous automated sampling system in lieu of establishing certain operating limits.
b This recording time refers to the minimum frequency that the continuous monitor or other measuring device initially records data. For all data recorded every 15 minutes, you must calculate hourly arithmetic averages. For all parameters, you use hourly averages to calculate the 12-hour or 3-hour block average specified in this table for demonstrating compliance. You maintain records of 1-hour averages.
Table 5 to Subpart MMMM of Part 60 - Model Rule - Toxic Equivalency Factors
40:8.0.1.1.1.39.310.53.65 :
Table 5 to Subpart MMMM of Part 60 - Model Rule - Toxic Equivalency FactorsDioxin/furan isomer | Toxic equivalency factor |
---|---|
2,3,7,8-tetrachlorinated dibenzo-p-dioxin | 1 |
1,2,3,7,8-pentachlorinated dibenzo-p-dioxin | 1 |
1,2,3,4,7,8-hexachlorinated dibenzo-p-dioxin | 0.1 |
1,2,3,7,8,9-hexachlorinated dibenzo-p-dioxin | 0.1 |
1,2,3,6,7,8-hexachlorinated dibenzo-p-dioxin | 0.1 |
1,2,3,4,6,7,8-heptachlorinated dibenzo-p-dioxin | 0.01 |
octachlorinated dibenzo-p-dioxin | 0.0003 |
2,3,7,8-tetrachlorinated dibenzofuran | 0.1 |
2,3,4,7,8-pentachlorinated dibenzofuran | 0.3 |
1,2,3,7,8-pentachlorinated dibenzofuran | 0.03 |
1,2,3,4,7,8-hexachlorinated dibenzofuran | 0.1 |
1,2,3,6,7,8-hexachlorinated dibenzofuran | 0.1 |
1,2,3,7,8,9-hexachlorinated dibenzofuran | 0.1 |
2,3,4,6,7,8-hexachlorinated dibenzofuran | 0.1 |
1,2,3,4,6,7,8-heptachlorinated dibenzofuran | 0.01 |
1,2,3,4,7,8,9-heptachlorinated dibenzofuran | 0.01 |
octachlorinated dibenzofuran | 0.0003 |
Table 6 to Subpart MMMM of Part 60 - Model Rule - Summary of Reporting Requirements for Existing Sewage Sludge Incineration Units a
40:8.0.1.1.1.39.310.53.66 :
Table 6 to Subpart MMMM of Part 60 - Model Rule - Summary of Reporting Requirements for Existing Sewage Sludge Incineration Units aReport | Due date | Contents | Reference |
---|---|---|---|
Increments of progress report | No later than 10 business days after the compliance date for the increment | 1. Final control plan
including air pollution control device descriptions, process
changes, type of waste to be burned, and the maximum design sewage
sludge burning capacity 2. Notification of any failure to meet an increment of progress. 3. Notification of any closure. |
§ 60.5235(a). |
Initial compliance report | No later than 60 days following the initial performance test | 1. Company name and
address 2. Statement by a responsible official, with that official's name, title, and signature, certifying the accuracy of the content of the report |
§ 60.5235(b). |
3. Date of report | |||
4. Complete test report for the initial performance test | |||
5. Results of CMS b performance evaluation | |||
6. The values for the site-specific operating limits and the calculations and methods used to establish each operating limit | |||
7. Documentation of installation of bag leak detection system for fabric filter | |||
8. Results of initial air pollution control device inspection, including a description of repairs | |||
9. The site-specific monitoring plan required under § 60.5200 | |||
10. The site-specific monitoring plan for your ash handling system required under § 60.5200 | |||
Annual compliance report | No later than 12 months following the submission of the initial compliance report; subsequent reports are to be submitted no more than 12 months following the previous report | 1. Company name and
address 2. Statement and signature by responsible official. 3. Date and beginning and ending dates of report. 4. If a performance test was conducted during the reporting period, the results of the test, including any new operating limits and associated calculations and the type of activated carbon used, if applicable. |
§ 60.5235(c). |
5. For each pollutant and operating parameter recorded using a CMS, the highest recorded 3-hour average and the lowest recorded 3-hour average, as applicable | |||
6. If no deviations from emission limits, emission standards, or operating limits occurred, a statement that no deviations occurred | |||
7. If a fabric filter is used, the date, time, and duration of alarms | |||
8. If a performance evaluation of a CMS was conducted, the results, including any new operating limits and their associated calculations | |||
9. If you met the requirements of § 60.5205(a)(3) and did not conduct a performance test, include the dates of the last three performance tests, a comparison to the 50 percent emission limit threshold of the emission level achieved in the last three performance tests, and a statement as to whether there have been any process changes | |||
10. Documentation of periods when all qualified SSI unit operators were unavailable for more than 8 hours but less than 2 weeks | |||
11. Results of annual pollutions control device inspections, including description of repairs | |||
12. If there were no periods during which your CMSs had malfunctions, a statement that there were no periods during which your CMSs had malfunctions | |||
13. If there were no periods during which your CMSs were out of control, a statement that there were no periods during which your CMSs were out of control | |||
14. If there were no operator training deviations, a statement that there were no such deviations | |||
15. Information on monitoring plan revisions, including a copy of any revised monitoring plan | |||
Deviation report (deviations from emission limits, emission standards, or operating limits, as specified in § 60.5235(e)(1)) | By August 1 of a calendar year for data collected during the first half of the calendar year; by February 1 of a calendar year for data collected during the second half of the calendar year | If using a CMS: 1. Company name and address. 2. Statement by a responsible official. 3. The calendar dates and times your unit deviated from the emission limits or operating limits. 4. The averaged and recorded data for those dates. 5. Duration and cause of each deviation. |
§ 60.5235(d). |
6. Dates, times, and causes for monitor downtime incidents | |||
7. A copy of the operating parameter monitoring data during each deviation and any test report that documents the emission levels | |||
8. For periods of CMS malfunction or when a CMS was out of control, you must include the information specified in § 60.5235(d)(3)(viii) | |||
If not using a CMS: | |||
1. Company name and address | |||
2. Statement by a responsible official | |||
3. The total operating time of each affected SSI | |||
4. The calendar dates and times your unit deviated from the emission limits, emission standard, or operating limits | |||
5. The averaged and recorded data for those dates | |||
6. Duration and cause of each deviation | |||
7. A copy of any performance test report that showed a deviation from the emission limits or standards | |||
8. A brief description of any malfunction, a description of actions taken during the malfunction to minimize emissions, and corrective action taken | |||
Notification of qualified operator deviation (if all qualified operators are not accessible for 2 weeks or more) | Within 10 days of deviation | 1. Statement of cause of
deviation 2. Description of actions taken to ensure that a qualified operator will be available. 3. The date when a qualified operator will be accessible. |
§ 60.5235(e). |
Notification of status of qualified operator deviation | Every 4 weeks following notification of deviation | 1. Description of actions
taken to ensure that a qualified operator is accessible 2. The date when you anticipate that a qualified operator will be accessible. 3. Request for approval to continue operation. |
§ 60.5235(e). |
Notification of resumed operation following shutdown (due to qualified operator deviation and as specified in § 60.5155(b)(2)(i) | Within five days of obtaining a qualified operator and resuming operation | 1. Notification that you have obtained a qualified operator and are resuming operation | § 60.5235(e). |
Notification of a force majeure | As soon as practicable following the date you first knew, or through due diligence should have known that the event may cause or caused a delay in conducting a performance test beyond the regulatory deadline; the notification must occur before the performance test deadline unless the initial force majeure or a subsequent force majeure event delays the notice, and in such cases, the notification must occur as soon as practicable | 1. Description of the force
majeure event 2. Rationale for attributing the delay in conducting the performance test beyond the regulatory deadline to the force majeure 3. Description of the measures taken or to be taken to minimize the delay. 4. Identification of the date by which you propose to conduct the performance test. |
§ 60.5235(f). |
Notification of intent to start or stop use of a CMS | 1 month before starting or stopping use of a CMS | 1. Intent to start or stop use of a CMS | § 60.5235(g). |
Notification of intent to conduct a performance test | At least 30 days prior to the performance test | 1. Intent to conduct a performance test to comply with this subpart | |
Notification of intent to conduct a rescheduled performance test | At least 7 days prior to the date of a rescheduled performance test | 1. Intent to conduct a rescheduled performance test to comply with this subpart |
a This table is only a summary, see the referenced sections of the rule for the complete requirements.
b CMS means continuous monitoring system.
Table 1 to Subpart OOOO of Part 60 - Required Minimum Initial SO2 Emission Reduction Efficiency (Zi)
40:8.0.1.1.1.41.310.29.67 :
Table 1 to Subpart OOOO of Part 60 - Required Minimum Initial SO2 Emission Reduction Efficiency (Zi)H2S content of acid gas (Y), % | Sulfur feed rate (X), LT/D | |||
---|---|---|---|---|
2.0 ≤ X ≤ 5.0 | 5.0 < X ≤ 15.0 | 15.0 < X ≤ 300.0 | X > 300.0 | |
Y ≥ 50 | 79.0 | 88.51X 0.0101Y 0.0125 or 99.9, whichever is smaller. | ||
20 ≤ Y < 50 | 79.0 | 88.51X 0.0101Y 0.0125 or 97.9, whichever is smaller | 97.9 | |
10 ≤ Y < 20 | 79.0 | 88.51X 0.0101Y 0.0125 or 93.5, whichever is smaller | 93.5 | 93.5 |
Y < 10 | 79.0 | 79.0 | 79.0 | 79.0 |
Table 2 to Subpart OOOO of Part 60 - Required Minimum SO2 Emission Reduction Efficiency (Zc)
40:8.0.1.1.1.41.310.29.68 :
Table 2 to Subpart OOOO of Part 60 - Required Minimum SO2 Emission Reduction Efficiency (Zc)H2S content of acid gas (Y), % | Sulfur feed rate (X), LT/D | |||
---|---|---|---|---|
2.0 ≤ X ≤ 5.0 | 5.0 < X ≤ 15.0 | 15.0 < X ≤ 300.0 | X > 300.0 | |
Y ≥ 50 | 74.0 | 85.35X 0.0144Y 0.0128 or 99.9, whichever is smaller. | ||
20 ≤ Y < 50 | 74.0 | 85.35X 0.0144Y 0.0128 or 97.5, whichever is smaller | 97.5 | |
10 ≤ Y < 20 | 74.0 | 85.35X 0.0144Y 0.0128 or 90.8, whichever is smaller | 90.8 | 90.8 |
Y < 10 | 74.0 | 74.0 | 74.0 | 74.0 |
X = The sulfur feed rate from the sweetening unit (i.e., the H2S in the acid gas), expressed as sulfur, Mg/D(LT/D), rounded to one decimal place.
Y = The sulfur content of the acid gas from the sweetening unit, expressed as mole percent H2S (dry basis) rounded to one decimal place.
Z = The minimum required sulfur dioxide (SO2) emission reduction efficiency, expressed as percent carried to one decimal place. Zi refers to the reduction efficiency required at the initial performance test. Zc refers to the reduction efficiency required on a continuous basis after compliance with Zi has been demonstrated.
Table 3 to Subpart OOOO of Part 60 - Applicability of General Provisions to Subpart OOOO
40:8.0.1.1.1.41.310.29.69 :
Table 3 to Subpart OOOO of Part 60 - Applicability of General Provisions to Subpart OOOOAs stated in § 60.5425, you must comply with the following applicable General Provisions:
General provisions citation |
Subject of citation | Applies to subpart? |
Explanation |
---|---|---|---|
§ 60.1 | General applicability of the General Provisions | Yes. | |
§ 60.2 | Definitions | Yes | Additional terms defined in § 60.5430. |
§ 60.3 | Units and abbreviations | Yes. | |
§ 60.4 | Address | Yes. | |
§ 60.5 | Determination of construction or modification | Yes. | |
§ 60.6 | Review of plans | Yes. | |
§ 60.7 | Notification and record keeping | Yes | Except that § 60.7 only applies as specified in § 60.5420(a). |
§ 60.8 | Performance tests | Yes | Performance testing is required for control devices used on storage vessels and centrifugal compressors. |
§ 60.9 | Availability of information | Yes. | |
§ 60.10 | State authority | Yes. | |
§ 60.11 | Compliance with standards and maintenance requirements | No | Requirements are specified in subpart OOOO. |
§ 60.12 | Circumvention | Yes. | |
§ 60.13 | Monitoring requirements | Yes | Continuous monitors are required for storage vessels. |
§ 60.14 | Modification | Yes. | |
§ 60.15 | Reconstruction | Yes. | Except that § 60.15(d) does not apply to gas wells, pneumatic controllers, centrifugal compressors, reciprocating compressors or storage vessels. |
§ 60.16 | Priority list | Yes. | |
§ 60.17 | Incorporations by reference | Yes. | |
§ 60.18 | General control device requirements | Yes | Except that the period of visible emissions shall not exceed a total of 1 minute during any 15-minute period instead of 5 minutes during any 2 consecutive hours as required in § 60.18(c). |
§ 60.19 | General notification and reporting requirement | Yes. |
Table 1 to Subpart OOOOa of Part 60 - Required Minimum Initial SO2 Emission Reduction Efficiency (Zi)
40:8.0.1.1.1.42.310.35.70 :
Table 1 to Subpart OOOOa of Part 60 - Required Minimum Initial SO2 Emission Reduction Efficiency (Zi)H2S content of acid gas (Y), % | Sulfur feed rate (X), LT/D | |||
---|---|---|---|---|
2.0 < X < 5.0 | 5.0 < X < 15.0 | 15.0 < X < 300.0 | X > 300.0 | |
Y > 50 | 79.0 | 88.51X 0.0101Y 0.0125 or 99.9, whichever is smaller. | ||
20 < Y < 50 | 79.0 | 88.51X 0.0101Y 0.0125 or 97.9, whichever is smaller | 97.9 | |
10 < Y < 20 | 79.0 | 88.51X 0.0101Y 0.0125 or 93.5, whichever is smaller | 93.5 | 93.5 |
Y < 10 | 79.0 | 79.0 | 79.0 | 79.0 |
Table 2 to Subpart OOOOa of Part 60 - Required Minimum SO2 Emission Reduction Efficiency (Zc)
40:8.0.1.1.1.42.310.35.71 :
Table 2 to Subpart OOOOa of Part 60 - Required Minimum SO2 Emission Reduction Efficiency (Zc)H2S content of acid gas (Y), % | Sulfur feed rate (X), LT/D | |||
---|---|---|---|---|
2.0 < X < 5.0 | 5.0 < X < 15.0 | 15.0 < X < 300.0 | X > 300.0 | |
Y > 50 | 74.0 | 85.35X 0.0144Y 0.0128 or 99.9, whichever is smaller. | ||
20 < Y < 50 | 74.0 | 85.35X 0.0144Y 0.0128 or 97.5, whichever is smaller | 97.5 | |
10 < Y < 20 | 74.0 | 85.35X 0.0144Y 0.0128 or 90.8, whichever is smaller | 90.8 | 90.8 |
Y < 10 | 74.0 | 74.0 | 74.0 | 74.0 |
X = The sulfur feed rate from the sweetening unit (i.e., the H2S in the acid gas), expressed as sulfur, Mg/D(LT/D), rounded to one decimal place.
Y = The sulfur content of the acid gas from the sweetening unit, expressed as mole percent H2S (dry basis) rounded to one decimal place.
Z = The minimum required sulfur dioxide (SO2) emission reduction efficiency, expressed as percent carried to one decimal place. Zi refers to the reduction efficiency required at the initial performance test. Zc refers to the reduction efficiency required on a continuous basis after compliance with Zi has been demonstrated.
As stated in § 60.5425a, you must comply with the following applicable General Provisions:
Table 3 to Subpart OOOOa of Part 60 - Applicability of General Provisions to Subpart OOOOa
40:8.0.1.1.1.42.310.35.72 :
Table 3 to Subpart OOOOa of Part 60 - Applicability of General Provisions to Subpart OOOOaGeneral provisions citation |
Subject of citation | Applies to subpart? | Explanation |
---|---|---|---|
§ 60.1 | General applicability of the General Provisions | Yes | |
§ 60.2 | Definitions | Yes | Additional terms defined in § 60.5430a. |
§ 60.3 | Units and abbreviations | Yes | |
§ 60.4 | Address | Yes | |
§ 60.5 | Determination of construction or modification | Yes | |
§ 60.6 | Review of plans | Yes | |
§ 60.7 | Notification and record keeping | Yes | Except that § 60.7 only applies as specified in § 60.5420a(a). |
§ 60.8 | Performance tests | Yes | Except that the format of performance test reports is described in § 60.5420a(b). Performance testing is required for control devices used on storage vessels, centrifugal compressors, and pneumatic pumps, except that performance testing is not required for a control device used solely on pneumatic pump(s). |
§ 60.9 | Availability of information | Yes | |
§ 60.10 | State authority | Yes | |
§ 60.11 | Compliance with standards and maintenance requirements | No | Requirements are specified in subpart OOOOa. |
§ 60.12 | Circumvention | Yes | |
§ 60.13 | Monitoring requirements | Yes | Continuous monitors are required for storage vessels. |
§ 60.14 | Modification | Yes | To the extent any provision in § 60.14 conflicts with specific provisions in subpart OOOOa, it is superseded by subpart OOOOa provisions. |
§ 60.15 | Reconstruction | Yes | Except that § 60.15(d) does not apply to wells, pneumatic controllers, pneumatic pumps, centrifugal compressors, reciprocating compressors, storage vessels, or the collection of fugitive emissions components at a well site or the collection of fugitive emissions components at a compressor station. |
§ 60.16 | Priority list | Yes | |
§ 60.17 | Incorporations by reference | Yes | |
§ 60.18 | General control device and work practice requirements | Yes | |
§ 60.19 | General notification and reporting requirement | Yes |
Table 1 of Subpart TTTT of Part 60 - CO2 Emission Standards for Affected Steam Generating Units and Integrated Gasification Combined Cycle Facilities That Commenced Construction After January 8, 2014 and Reconstruction or Modification After June 18, 2014
40:8.0.1.1.1.45.316.15.73 :
Table 1 of Subpart TTTT of Part 60 - CO2 Emission Standards for Affected Steam Generating Units and Integrated Gasification Combined Cycle Facilities That Commenced Construction After January 8, 2014 and Reconstruction or Modification After June 18, 2014[Note: Numerical values of 1,000 or greater have a minimum of 3 significant figures and numerical values of less than 1,000 have a minimum of 2 significant figures]
Affected EGU | CO2 Emission standard |
---|---|
Newly constructed steam generating unit or integrated gasification combined cycle (IGCC) | 640 kg CO2/MWh of gross energy output (1,400 lb CO2/MWh). |
Reconstructed steam generating unit or IGCC that has base load rating of 2,100 GJ/h (2,000 MMBtu/h) or less | 910 kg of CO2 per MWh of gross energy output (2,000 lb CO2/MWh). |
Reconstructed steam generating unit or IGCC that has a base load rating greater than 2,100 GJ/h (2,000 MMBtu/h) | 820 kg of CO2 per MWh of gross energy output (1,800 lb CO2/MWh). |
Modified steam generating unit or IGCC | A unit-specific emission limit determined by the unit's best historical annual CO2 emission rate (from 2002 to the date of the modification); the emission limit will be no lower than: |
1. 1,800 lb CO2/MWh-gross for units with a base load rating greater than 2,000 MMBtu/h; or | |
2. 2,000 lb CO2/MWh-gross for units with a base load rating of 2,000 MMBtu/h or less. |
Table 2 of Subpart TTTT of Part 60 - CO2 Emission Standards for Affected Stationary Combustion Turbines That Commenced Construction After January 8, 2014 and Reconstruction After June 18, 2014 (Net Energy Output-Based Standards Applicable as Approved by the Administrator)
40:8.0.1.1.1.45.316.15.74 :
Table 2 of Subpart TTTT of Part 60 - CO2 Emission Standards for Affected Stationary Combustion Turbines That Commenced Construction After January 8, 2014 and Reconstruction After June 18, 2014 (Net Energy Output-Based Standards Applicable as Approved by the Administrator)[Note: Numerical values of 1,000 or greater have a minimum of 3 significant figures and numerical values of less than 1,000 have a minimum of 2 significant figures]
Affected EGU | CO2 Emission standard |
---|---|
Newly constructed or reconstructed stationary combustion turbine that supplies more than its design efficiency or 50 percent, whichever is less, times its potential electric output as net-electric sales on both a 12-operating month and a 3-year rolling average basis and combusts more than 90% natural gas on a heat input basis on a 12-operating-month rolling average basis | 450 kg of CO2 per MWh of gross
energy output (1,000 lb CO2/MWh); or 470 kilograms (kg) of CO2 per megawatt-hour (MWh) of net energy output (1,030 lb/MWh). |
Newly constructed or reconstructed stationary combustion turbine that supplies its design efficiency or 50 percent, whichever is less, times its potential electric output or less as net-electric sales on either a 12-operating month or a 3-year rolling average basis and combusts more than 90% natural gas on a heat input basis on a 12-operating-month rolling average basis | 50 kg CO2 per gigajoule (GJ) of heat input (120 lb CO2/MMBtu). |
Newly constructed and reconstructed stationary combustion turbine that combusts 90% or less natural gas on a heat input basis on a 12-operating-month rolling average basis | 50 kg CO2/GJ of heat input (120 lb/MMBtu) to 69 kg CO2/GJ of heat input (160 lb/MMBtu) as determined by the procedures in § 60.5525. |
Table 3 to Subpart TTTT of Part 60 - Applicability of Subpart A of Part 60 (General Provisions) to Subpart TTTT
40:8.0.1.1.1.45.316.15.75 :
Table 3 to Subpart TTTT of Part 60 - Applicability of Subpart A of Part 60 (General Provisions) to Subpart TTTTGeneral provisions citation |
Subject of citation | Applies to subpart TTTT | Explanation |
---|---|---|---|
§ 60.1 | Applicability | Yes | |
§ 60.2 | Definitions | Yes | Additional terms defined in § 60.5580. |
§ 60.3 | Units and Abbreviations | Yes | |
§ 60.4 | Address | Yes | Does not apply to information reported electronically through ECMPS. Duplicate submittals are not required. |
§ 60.5 | Determination of construction or modification | Yes | |
§ 60.6 | Review of plans | Yes | |
§ 60.7 | Notification and Recordkeeping | Yes | Only the requirements to submit the notifications in § 60.7(a)(1) and (3) and to keep records of malfunctions in § 60.7(b), if applicable. |
§ 60.8 | Performance tests | No | |
§ 60.9 | Availability of Information | Yes | |
§ 60.10 | State authority | Yes | |
§ 60.11 | Compliance with standards and maintenance requirements | No | |
§ 60.12 | Circumvention | Yes | |
§ 60.13 | Monitoring requirements | No | All monitoring is done according to part 75. |
§ 60.14 | Modification | Yes (steam generating units
and IGCC facilities) No (stationary combustion turbines) |
|
§ 60.15 | Reconstruction | Yes | |
§ 60.16 | Priority list | No | |
§ 60.17 | Incorporations by reference | Yes | |
§ 60.18 | General control device requirements | No | |
§ 60.19 | General notification and reporting requirements | Yes | Does not apply to notifications under § 75.61 or to information reported through ECMPS. |
Appendix A-1 to Part 60 - Test Methods 1 through 2F
40:9.0.1.1.1.0.1.1.1 : Appendix A
Appendix A-1 to Part 60 - Test Methods 1 through 2F Method 1 - Sample and velocity traverses for stationary sources Method 1A - Sample and velocity traverses for stationary sources with small stacks or ducts Method 2 - Determination of stack gas velocity and volumetric flow rate (Type S pitot tube) Method 2A - Direct measurement of gas volume through pipes and small ducts Method 2B - Determination of exhaust gas volume flow rate from gasoline vapor incinerators Method 2C - Determination of gas velocity and volumetric flow rate in small stacks or ducts (standard pitot tube) Method 2D - Measurement of gas volume flow rates in small pipes and ducts Method 2E - Determination of landfill gas production flow rate Method 2F - Determination of Stack Gas Velocity and Volumetric Flow Rate With Three-Dimensional ProbesThe test methods in this appendix are referred to in § 60.8 (Performance Tests) and § 60.11 (Compliance With Standards and Maintenance Requirements) of 40 CFR part 60, subpart A (General Provisions). Specific uses of these test methods are described in the standards of performance contained in the subparts, beginning with Subpart D.
Within each standard of performance, a section title “Test Methods and Procedures” is provided to: (1) Identify the test methods to be used as reference methods to the facility subject to the respective standard and (2) identify any special instructions or conditions to be followed when applying a method to the respective facility. Such instructions (for example, establish sampling rates, volumes, or temperatures) are to be used either in addition to, or as a substitute for procedures in a test method. Similarly, for sources subject to emission monitoring requirements, specific instructions pertaining to any use of a test method as a reference method are provided in the subpart or in appendix B.
Inclusion of methods in this appendix is not intended as an endorsement or denial of their applicability to sources that are not subject to standards of performance. The methods are potentially applicable to other sources; however, applicability should be confirmed by careful and appropriate evaluation of the conditions prevalent at such sources.
The approach followed in the formulation of the test methods involves specifications for equipment, procedures, and performance. In concept, a performance specification approach would be preferable in all methods because this allows the greatest flexibility to the user. In practice, however, this approach is impractical in most cases because performance specifications cannot be established. Most of the methods described herein, therefore, involve specific equipment specifications and procedures, and only a few methods in this appendix rely on performance criteria.
Minor changes in the test methods should not necessarily affect the validity of the results and it is recognized that alternative and equivalent methods exist. section 60.8 provides authority for the Administrator to specify or approve (1) equivalent methods, (2) alternative methods, and (3) minor changes in the methodology of the test methods. It should be clearly understood that unless otherwise identified all such methods and changes must have prior approval of the Administrator. An owner employing such methods or deviations from the test methods without obtaining prior approval does so at the risk of subsequent disapproval and retesting with approved methods.
Within the test methods, certain specific equipment or procedures are recognized as being acceptable or potentially acceptable and are specifically identified in the methods. The items identified as acceptable options may be used without approval but must be identified in the test report. The potentially approvable options are cited as “subject to the approval of the Administrator” or as “or equivalent.” Such potentially approvable techniques or alternatives may be used at the discretion of the owner without prior approval. However, detailed descriptions for applying these potentially approvable techniques or alternatives are not provided in the test methods. Also, the potentially approvable options are not necessarily acceptable in all applications. Therefore, an owner electing to use such potentially approvable techniques or alternatives is responsible for: (1) assuring that the techniques or alternatives are in fact applicable and are properly executed; (2) including a written description of the alternative method in the test report (the written method must be clear and must be capable of being performed without additional instruction, and the degree of detail should be similar to the detail contained in the test methods); and (3) providing any rationale or supporting data necessary to show the validity of the alternative in the particular application. Failure to meet these requirements can result in the Administrator's disapproval of the alternative.
Method 1 - Sample and Velocity Traverses for Stationary Sources Note:This method does not include all of the specifications (e.g., equipment and supplies) and procedures (e.g., sampling) essential to its performance. Some material is incorporated by reference from other methods in this part. Therefore, to obtain reliable results, persons using this method should have a thorough knowledge of at least the following additional test method: Method 2.
1.0 Scope and Application1.1 Measured Parameters. The purpose of the method is to provide guidance for the selection of sampling ports and traverse points at which sampling for air pollutants will be performed pursuant to regulations set forth in this part. Two procedures are presented: a simplified procedure, and an alternative procedure (see section 11.5). The magnitude of cyclonic flow of effluent gas in a stack or duct is the only parameter quantitatively measured in the simplified procedure.
1.2 Applicability. This method is applicable to gas streams flowing in ducts, stacks, and flues. This method cannot be used when: (1) the flow is cyclonic or swirling; or (2) a stack is smaller than 0.30 meter (12 in.) in diameter, or 0.071 m 2 (113 in. 2) in cross-sectional area. The simplified procedure cannot be used when the measurement site is less than two stack or duct diameters downstream or less than a half diameter upstream from a flow disturbance.
1.3 Data Quality Objectives. Adherence to the requirements of this method will enhance the quality of the data obtained from air pollutant sampling methods.
Note:The requirements of this method must be considered before construction of a new facility from which emissions are to be measured; failure to do so may require subsequent alterations to the stack or deviation from the standard procedure. Cases involving variants are subject to approval by the Administrator.
2.0 Summary of Method2.1 This method is designed to aid in the representative measurement of pollutant emissions and/or total volumetric flow rate from a stationary source. A measurement site where the effluent stream is flowing in a known direction is selected, and the cross-section of the stack is divided into a number of equal areas. Traverse points are then located within each of these equal areas.
3.0 Definitions [Reserved] 4.0 Interferences [Reserved] 5.0 Safety5.1 Disclaimer. This method may involve hazardous materials, operations, and equipment. This test method may not address all of the safety problems associated with its use. It is the responsibility of the user of this test method to establish appropriate safety and health practices and determine the applicability of regulatory limitations prior to performing this test method.
6.0 Equipment and Supplies.6.1 Apparatus. The apparatus described below is required only when utilizing the alternative site selection procedure described in section 11.5 of this method.
6.1.1 Directional Probe. Any directional probe, such as United Sensor Type DA Three-Dimensional Directional Probe, capable of measuring both the pitch and yaw angles of gas flows is acceptable. Before using the probe, assign an identification number to the directional probe, and permanently mark or engrave the number on the body of the probe. The pressure holes of directional probes are susceptible to plugging when used in particulate-laden gas streams. Therefore, a procedure for cleaning the pressure holes by “back-purging” with pressurized air is required.
6.1.2 Differential Pressure Gauges. Inclined manometers, U-tube manometers, or other differential pressure gauges (e.g., magnehelic gauges) that meet the specifications described in Method 2, section 6.2.
Note:If the differential pressure gauge produces both negative and positive readings, then both negative and positive pressure readings shall be calibrated at a minimum of three points as specified in Method 2, section 6.2.
7.0 Reagents and Standards [Reserved] 8.0 Sample Collection, Preservation, Storage, and Transport [Reserved] 9.0 Quality Control [Reserved] 10.0 Calibration and Standardization [Reserved] 11.0 Procedure11.1 Selection of Measurement Site.
11.1.1 Sampling and/or velocity measurements are performed at a site located at least eight stack or duct diameters downstream and two diameters upstream from any flow disturbance such as a bend, expansion, or contraction in the stack, or from a visible flame. If necessary, an alternative location may be selected, at a position at least two stack or duct diameters downstream and a half diameter upstream from any flow disturbance.
11.1.2 An alternative procedure is available for determining the acceptability of a measurement location not meeting the criteria above. This procedure described in section 11.5 allows for the determination of gas flow angles at the sampling points and comparison of the measured results with acceptability criteria.
11.2 Determining the Number of Traverse Points.
11.2.1 Particulate Traverses.
11.2.1.1 When the eight- and two-diameter criterion can be met, the minimum number of traverse points shall be: (1) twelve, for circular or rectangular stacks with diameters (or equivalent diameters) greater than 0.61 meter (24 in.); (2) eight, for circular stacks with diameters between 0.30 and 0.61 meter (12 and 24 in.); and (3) nine, for rectangular stacks with equivalent diameters between 0.30 and 0.61 meter (12 and 24 in.).
11.2.1.2 When the eight- and two-diameter criterion cannot be met, the minimum number of traverse points is determined from Figure 1-1. Before referring to the figure, however, determine the distances from the measurement site to the nearest upstream and downstream disturbances, and divide each distance by the stack diameter or equivalent diameter, to determine the distance in terms of the number of duct diameters. Then, determine from Figure 1-1 the minimum number of traverse points that corresponds:
(1) To the number of duct diameters upstream; and
(2) To the number of diameters downstream. Select the higher of the two minimum numbers of traverse points, or a greater value, so that for circular stacks, the number is a multiple of 4, and for rectangular stacks, the number is one of those shown in Table 1-1.
11.2.2 Velocity (Non-Particulate) Traverses. When velocity or volumetric flow rate is to be determined (but not particulate matter), the same procedure as that used for particulate traverses (Section 11.2.1) is followed, except that Figure 1-2 may be used instead of Figure 1-1.
11.3 Cross-Sectional Layout and Location of Traverse Points.
11.3.1 Circular Stacks.
11.3.1.1 Locate the traverse points on two perpendicular diameters according to Table 1-2 and the example shown in Figure 1-3. Any equation (see examples in References 2 and 3 in section 16.0) that gives the same values as those in Table 1-2 may be used in lieu of Table 1-2.
11.3.1.2 For particulate traverses, one of the diameters must coincide with the plane containing the greatest expected concentration variation (e.g., after bends); one diameter shall be congruent to the direction of the bend. This requirement becomes less critical as the distance from the disturbance increases; therefore, other diameter locations may be used, subject to the approval of the Administrator.
11.3.1.3 In addition, for elliptical stacks having unequal perpendicular diameters, separate traverse points shall be calculated and located along each diameter. To determine the cross-sectional area of the elliptical stack, use the following equation:
Square Area = D1 × D2 × 0.7854 Where: D1 = Stack diameter 1 D2 = Stack diameter 211.3.1.4 In addition, for stacks having diameters greater than 0.61 m (24 in.), no traverse points shall be within 2.5 centimeters (1.00 in.) of the stack walls; and for stack diameters equal to or less than 0.61 m (24 in.), no traverse points shall be located within 1.3 cm (0.50 in.) of the stack walls. To meet these criteria, observe the procedures given below.
11.3.2 Stacks With Diameters Greater Than 0.61 m (24 in.).
11.3.2.1 When any of the traverse points as located in section 11.3.1 fall within 2.5 cm (1.0 in.) of the stack walls, relocate them away from the stack walls to: (1) a distance of 2.5 cm (1.0 in.); or (2) a distance equal to the nozzle inside diameter, whichever is larger. These relocated traverse points (on each end of a diameter) shall be the “adjusted” traverse points.
11.3.2.2 Whenever two successive traverse points are combined to form a single adjusted traverse point, treat the adjusted point as two separate traverse points, both in the sampling and/or velocity measurement procedure, and in recording of the data.
11.3.3 Stacks With Diameters Equal To or Less Than 0.61 m (24 in.). Follow the procedure in section 11.3.1.1, noting only that any “adjusted” points should be relocated away from the stack walls to: (1) a distance of 1.3 cm (0.50 in.); or (2) a distance equal to the nozzle inside diameter, whichever is larger.
11.3.4 Rectangular Stacks.
11.3.4.1 Determine the number of traverse points as explained in sections 11.1 and 11.2 of this method. From Table 1-1, determine the grid configuration. Divide the stack cross-section into as many equal rectangular elemental areas as traverse points, and then locate a traverse point at the centroid of each equal area according to the example in Figure 1-4.
11.3.4.2 To use more than the minimum number of traverse points, expand the “minimum number of traverse points” matrix (see Table 1-1) by adding the extra traverse points along one or the other or both legs of the matrix; the final matrix need not be balanced. For example, if a 4 × 3 “minimum number of points” matrix were expanded to 36 points, the final matrix could be 9 × 4 or 12 × 3, and would not necessarily have to be 6 × 6. After constructing the final matrix, divide the stack cross-section into as many equal rectangular, elemental areas as traverse points, and locate a traverse point at the centroid of each equal area.
11.3.4.3 The situation of traverse points being too close to the stack walls is not expected to arise with rectangular stacks. If this problem should ever arise, the Administrator must be contacted for resolution of the matter.
11.4 Verification of Absence of Cyclonic Flow.
11.4.1 In most stationary sources, the direction of stack gas flow is essentially parallel to the stack walls. However, cyclonic flow may exist (1) after such devices as cyclones and inertial demisters following venturi scrubbers, or (2) in stacks having tangential inlets or other duct configurations which tend to induce swirling; in these instances, the presence or absence of cyclonic flow at the sampling location must be determined. The following techniques are acceptable for this determination.
11.4.2 Level and zero the manometer. Connect a Type S pitot tube to the manometer and leak-check system. Position the Type S pitot tube at each traverse point, in succession, so that the planes of the face openings of the pitot tube are perpendicular to the stack cross-sectional plane; when the Type S pitot tube is in this position, it is at “0° reference.” Note the differential pressure (Δp) reading at each traverse point. If a null (zero) pitot reading is obtained at 0° reference at a given traverse point, an acceptable flow condition exists at that point. If the pitot reading is not zero at 0° reference, rotate the pitot tube (up to ±90° yaw angle), until a null reading is obtained. Carefully determine and record the value of the rotation angle (α) to the nearest degree. After the null technique has been applied at each traverse point, calculate the average of the absolute values of α; assign α values of 0° to those points for which no rotation was required, and include these in the overall average. If the average value of α is greater than 20°, the overall flow condition in the stack is unacceptable, and alternative methodology, subject to the approval of the Administrator, must be used to perform accurate sample and velocity traverses.
11.5 The alternative site selection procedure may be used to determine the rotation angles in lieu of the procedure outlined in section 11.4.
11.5.1 Alternative Measurement Site Selection Procedure. This alternative applies to sources where measurement locations are less than 2 equivalent or duct diameters downstream or less than one-half duct diameter upstream from a flow disturbance. The alternative should be limited to ducts larger than 24 in. in diameter where blockage and wall effects are minimal. A directional flow-sensing probe is used to measure pitch and yaw angles of the gas flow at 40 or more traverse points; the resultant angle is calculated and compared with acceptable criteria for mean and standard deviation.
Note:Both the pitch and yaw angles are measured from a line passing through the traverse point and parallel to the stack axis. The pitch angle is the angle of the gas flow component in the plane that INCLUDES the traverse line and is parallel to the stack axis. The yaw angle is the angle of the gas flow component in the plane PERPENDICULAR to the traverse line at the traverse point and is measured from the line passing through the traverse point and parallel to the stack axis.
11.5.2 Traverse Points. Use a minimum of 40 traverse points for circular ducts and 42 points for rectangular ducts for the gas flow angle determinations. Follow the procedure outlined in section 11.3 and Table 1-1 or 1-2 for the location and layout of the traverse points. If the measurement location is determined to be acceptable according to the criteria in this alternative procedure, use the same traverse point number and locations for sampling and velocity measurements.
11.5.3 Measurement Procedure.
11.5.3.1 Prepare the directional probe and differential pressure gauges as recommended by the manufacturer. Capillary tubing or surge tanks may be used to dampen pressure fluctuations. It is recommended, but not required, that a pretest leak check be conducted. To perform a leak check, pressurize or use suction on the impact opening until a reading of at least 7.6 cm (3 in.) H2O registers on the differential pressure gauge, then plug the impact opening. The pressure of a leak-free system will remain stable for at least 15 seconds.
11.5.3.2 Level and zero the manometers. Since the manometer level and zero may drift because of vibrations and temperature changes, periodically check the level and zero during the traverse.
11.5.3.3 Position the probe at the appropriate locations in the gas stream, and rotate until zero deflection is indicated for the yaw angle pressure gauge. Determine and record the yaw angle. Record the pressure gauge readings for the pitch angle, and determine the pitch angle from the calibration curve. Repeat this procedure for each traverse point. Complete a “back-purge” of the pressure lines and the impact openings prior to measurements of each traverse point.
11.5.3.4 A post-test check as described in section 11.5.3.1 is required. If the criteria for a leak-free system are not met, repair the equipment, and repeat the flow angle measurements.
11.5.4 Calibration. Use a flow system as described in sections 10.1.2.1 and 10.1.2.2 of Method 2. In addition, the flow system shall have the capacity to generate two test-section velocities: one between 365 and 730 m/min (1,200 and 2,400 ft/min) and one between 730 and 1,100 m/min (2,400 and 3,600 ft/min).
11.5.4.1 Cut two entry ports in the test section. The axes through the entry ports shall be perpendicular to each other and intersect in the centroid of the test section. The ports should be elongated slots parallel to the axis of the test section and of sufficient length to allow measurement of pitch angles while maintaining the pitot head position at the test-section centroid. To facilitate alignment of the directional probe during calibration, the test section should be constructed of plexiglass or some other transparent material. All calibration measurements should be made at the same point in the test section, preferably at the centroid of the test section.
11.5.4.2 To ensure that the gas flow is parallel to the central axis of the test section, follow the procedure outlined in section 11.4 for cyclonic flow determination to measure the gas flow angles at the centroid of the test section from two test ports located 90° apart. The gas flow angle measured in each port must be ±2° of 0°. Straightening vanes should be installed, if necessary, to meet this criterion.
11.5.4.3 Pitch Angle Calibration. Perform a calibration traverse according to the manufacturer's recommended protocol in 5° increments for angles from −60° to + 60° at one velocity in each of the two ranges specified above. Average the pressure ratio values obtained for each angle in the two flow ranges, and plot a calibration curve with the average values of the pressure ratio (or other suitable measurement factor as recommended by the manufacturer) versus the pitch angle. Draw a smooth line through the data points. Plot also the data values for each traverse point. Determine the differences between the measured data values and the angle from the calibration curve at the same pressure ratio. The difference at each comparison must be within 2° for angles between 0° and 40° and within 3° for angles between 40° and 60°.
11.5.4.4 Yaw Angle Calibration. Mark the three-dimensional probe to allow the determination of the yaw position of the probe. This is usually a line extending the length of the probe and aligned with the impact opening. To determine the accuracy of measurements of the yaw angle, only the zero or null position need be calibrated as follows: Place the directional probe in the test section, and rotate the probe until the zero position is found. With a protractor or other angle measuring device, measure the angle indicated by the yaw angle indicator on the three-dimensional probe. This should be within 2° of 0°. Repeat this measurement for any other points along the length of the pitot where yaw angle measurements could be read in order to account for variations in the pitot markings used to indicate pitot head positions.
12.0 Data Analysis and Calculations12.1 Nomenclature.
L = length. n = total number of traverse points. Pi = pitch angle at traverse point i, degree. Ravg = average resultant angle, degree. Ri = resultant angle at traverse point i, degree. Sd = standard deviation, degree. W = width. Yi = yaw angle at traverse point i, degree.12.2 For a rectangular cross section, an equivalent diameter (De) shall be calculated using the following equation, to determine the upstream and downstream distances:
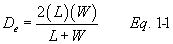
12.3 If use of the alternative site selection procedure (Section 11.5 of this method) is required, perform the following calculations using the equations below: the resultant angle at each traverse point, the average resultant angle, and the standard deviation. Complete the calculations retaining at least one extra significant figure beyond that of the acquired data. Round the values after the final calculations.
12.3.1 Calculate the resultant angle at each traverse point:

12.3.2 Calculate the average resultant for the measurements:
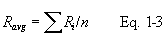
12.3.3 Calculate the standard deviations:
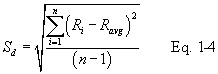
12.3.4 Acceptability Criteria. The measurement location is acceptable if Ravg ≤20° and Sd ≤10°.
13.0 Method Performance [Reserved] 14.0 Pollution Prevention [Reserved] 15.0 Waste Management [Reserved] 16.0 References1. Determining Dust Concentration in a Gas Stream, ASME Performance Test Code No. 27. New York. 1957.
2. DeVorkin, Howard, et al. Air Pollution Source Testing Manual. Air Pollution Control District. Los Angeles, CA. November 1963.
3. Methods for Determining of Velocity, Volume, Dust and Mist Content of Gases. Western Precipitation Division of Joy Manufacturing Co. Los Angeles, CA. Bulletin WP-50. 1968.
4. Standard Method for Sampling Stacks for Particulate Matter. In: 1971 Book of ASTM Standards, Part 23. ASTM Designation D 2928-71. Philadelphia, PA. 1971.
5. Hanson, H.A., et al. Particulate Sampling Strategies for Large Power Plants Including Nonuniform Flow. USEPA, ORD, ESRL, Research Triangle Park, NC. EPA-600/2-76-170. June 1976.
6. Entropy Environmentalists, Inc. Determination of the Optimum Number of Sampling Points: An Analysis of Method 1 Criteria. Environmental Protection Agency. Research Triangle Park, NC. EPA Contract No. 68-01-3172, Task 7.
7. Hanson, H.A., R.J. Davini, J.K. Morgan, and A.A. Iversen. Particulate Sampling Strategies for Large Power Plants Including Nonuniform Flow. USEPA, Research Triangle Park, NC. Publication No. EPA-600/2-76-170. June 1976. 350 pp.
8. Brooks, E.F., and R.L. Williams. Flow and Gas Sampling Manual. U.S. Environmental Protection Agency. Research Triangle Park, NC. Publication No. EPA-600/2-76-203. July 1976. 93 pp.
9. Entropy Environmentalists, Inc. Traverse Point Study. EPA Contract No. 68-02-3172. June 1977. 19 pp.
10. Brown, J. and K. Yu. Test Report: Particulate Sampling Strategy in Circular Ducts. Emission Measurement Branch. U.S. Environmental Protection Agency, Research Triangle Park, NC 27711. July 31, 1980. 12 pp.
11. Hawksley, P.G.W., S. Badzioch, and J.H. Blackett. Measurement of Solids in Flue Gases. Leatherhead, England, The British Coal Utilisation Research Association. 1961. pp. 129-133.
12. Knapp, K.T. The Number of Sampling Points Needed for Representative Source Sampling. In: Proceedings of the Fourth National Conference on Energy and Environment. Theodore, L. et al. (ed). Dayton, Dayton section of the American Institute of Chemical Engineers. October 3-7, 1976. pp. 563-568.
13. Smith, W.S. and D.J. Grove. A Proposed Extension of EPA Method 1 Criteria. Pollution Engineering. XV (8):36-37. August 1983.
14. Gerhart, P.M. and M.J. Dorsey. Investigation of Field Test Procedures for Large Fans. University of Akron. Akron, OH. (EPRI Contract CS-1651). Final Report (RP-1649-5). December 1980.
15. Smith, W.S. and D.J. Grove. A New Look at Isokinetic Sampling - Theory and Applications. Source Evaluation Society Newsletter. VIII (3):19-24. August 1983.
17.0 Tables, Diagrams, Flowcharts, and Validation Data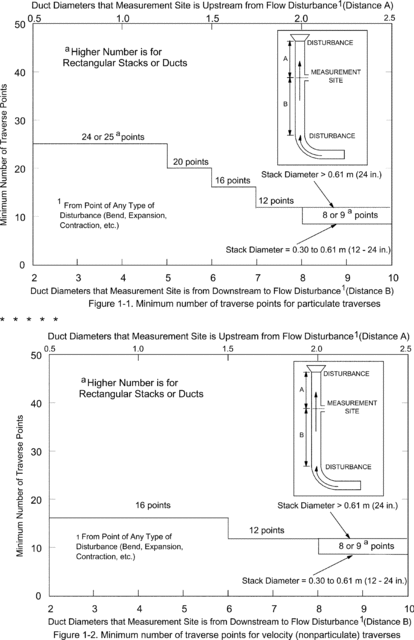
Table 1-1 Cross-Section Layout for Rectangular Stacks
Number of tranverse points layout | Matrix |
---|---|
9 | 3 × 3 |
12 | 4 × 3 |
16 | 4 × 4 |
20 | 5 × 4 |
25 | 5 × 5 |
30 | 6 × 5 |
36 | 6 × 6 |
42 | 7 × 6 |
49 | 7 × 7 |
Table 1-2 - Location of Traverse Points in Circular Stacks
[Percent of stack diameter from inside wall to tranverse point]
Traverse point number on a diameter |
Number of traverse points on a diameter | |||||||||||
---|---|---|---|---|---|---|---|---|---|---|---|---|
2 | 4 | 6 | 8 | 10 | 12 | 14 | 16 | 18 | 20 | 22 | 24 | |
1 | 14.6 | 6.7 | 4.4 | 3.2 | 2.6 | 2.1 | 1.8 | 1.6 | 1.4 | 1.3 | 1.1 | 1.1 |
2 | 85.4 | 25.0 | 14.6 | 10.5 | 8.2 | 6.7 | 5.7 | 4.9 | 4.4 | 3.9 | 3.5 | 3.2 |
3 | 75.0 | 29.6 | 19.4 | 14.6 | 11.8 | 9.9 | 8.5 | 7.5 | 6.7 | 6.0 | 5.5 | |
4 | 93.3 | 70.4 | 32.3 | 22.6 | 17.7 | 14.6 | 12.5 | 10.9 | 9.7 | 8.7 | 7.9 | |
5 | 85.4 | 67.7 | 34.2 | 25.0 | 20.1 | 16.9 | 14.6 | 12.9 | 11.6 | 10.5 | ||
6 | 95.6 | 80.6 | 65.8 | 35.6 | 26.9 | 22.0 | 18.8 | 16.5 | 14.6 | 13.2 | ||
7 | 89.5 | 77.4 | 64.4 | 36.6 | 28.3 | 23.6 | 20.4 | 18.0 | 16.1 | |||
8 | 96.8 | 85.4 | 75.0 | 63.4 | 37.5 | 29.6 | 25.0 | 21.8 | 19.4 | |||
9 | 91.8 | 82.3 | 73.1 | 62.5 | 38.2 | 30.6 | 26.2 | 23.0 | ||||
10 | 97.4 | 88.2 | 79.9 | 71.7 | 61.8 | 38.8 | 31.5 | 27.2 | ||||
11 | 93.3 | 85.4 | 78.0 | 70.4 | 61.2 | 39.3 | 32.3 | |||||
12 | 97.9 | 90.1 | 83.1 | 76.4 | 69.4 | 60.7 | 39.8 | |||||
13 | 94.3 | 87.5 | 81.2 | 75.0 | 68.5 | 60.2 | ||||||
14 | 98.2 | 91.5 | 85.4 | 79.6 | 73.8 | 67.7 | ||||||
15 | 95.1 | 89.1 | 83.5 | 78.2 | 72.8 | |||||||
16 | 98.4 | 92.5 | 87.1 | 82.0 | 77.0 | |||||||
17 | 95.6 | 90.3 | 85.4 | 80.6 | ||||||||
18 | 98.6 | 93.3 | 88.4 | 83.9 | ||||||||
19 | 96.1 | 91.3 | 86.8 | |||||||||
20 | 98.7 | 94.0 | 89.5 | |||||||||
21 | 96.5 | 92.1 | ||||||||||
22 | 98.9 | 94.5 | ||||||||||
23 | 96.8 | |||||||||||
24 | 99.9 |
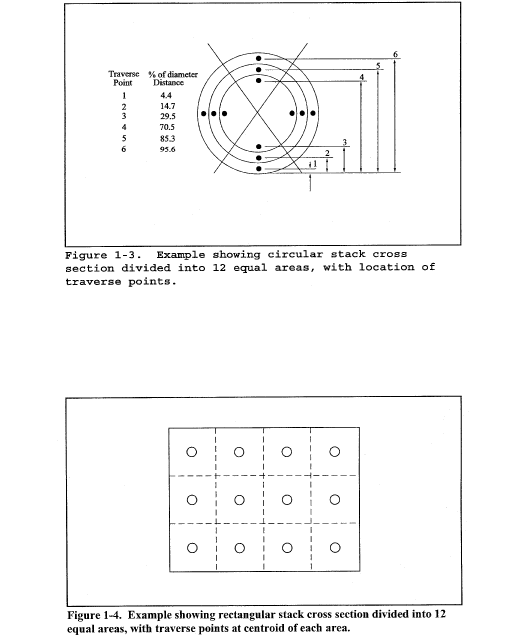
This method does not include all of the specifications (e.g., equipment and supplies) and procedures (e.g., sampling) essential to its performance. Some material is incorporated by reference from other methods in this part. Therefore, to obtain reliable results, persons using this method should have a thorough knowledge of at least the following additional test method: Method 1.
1.0 Scope and Application1.1 Measured Parameters. The purpose of the method is to provide guidance for the selection of sampling ports and traverse points at which sampling for air pollutants will be performed pursuant to regulations set forth in this part.
1.2 Applicability. The applicability and principle of this method are identical to Method 1, except its applicability is limited to stacks or ducts. This method is applicable to flowing gas streams in ducts, stacks, and flues of less than about 0.30 meter (12 in.) in diameter, or 0.071 m 2 (113 in. 2) in cross-sectional area, but equal to or greater than about 0.10 meter (4 in.) in diameter, or 0.0081 m 2 (12.57 in. 2) in cross-sectional area. This method cannot be used when the flow is cyclonic or swirling.
1.3 Data Quality Objectives. Adherence to the requirements of this method will enhance the quality of the data obtained from air pollutant sampling methods.
2.0 Summary of Method2.1 The method is designed to aid in the representative measurement of pollutant emissions and/or total volumetric flow rate from a stationary source. A measurement site or a pair of measurement sites where the effluent stream is flowing in a known direction is (are) selected. The cross-section of the stack is divided into a number of equal areas. Traverse points are then located within each of these equal areas.
2.2 In these small diameter stacks or ducts, the conventional Method 5 stack assembly (consisting of a Type S pitot tube attached to a sampling probe, equipped with a nozzle and thermocouple) blocks a significant portion of the cross-section of the duct and causes inaccurate measurements. Therefore, for particulate matter (PM) sampling in small stacks or ducts, the gas velocity is measured using a standard pitot tube downstream of the actual emission sampling site. The straight run of duct between the PM sampling and velocity measurement sites allows the flow profile, temporarily disturbed by the presence of the sampling probe, to redevelop and stabilize.
3.0 Definitions [Reserved] 4.0 Interferences [Reserved] 5.0 Safety5.1 Disclaimer. This method may involve hazardous materials, operations, and equipment. This test method may not address all of the safety problems associated with its use. It is the responsibility of the user of this test method to establish appropriate safety and health practices and determine the applicability of regulatory limitations prior to performing this test method.
6.0 Equipment and Supplies [Reserved] 7.0 Reagents and Standards [Reserved] 8.0 Sample Collection, Preservation, Storage, and Transport [Reserved] 9.0 Quality Control [Reserved] 10.0 Calibration and Standardization [Reserved] 11.0 Procedure11.1 Selection of Measurement Site.
11.1.1 Particulate Measurements - Steady or Unsteady Flow. Select a particulate measurement site located preferably at least eight equivalent stack or duct diameters downstream and 10 equivalent diameters upstream from any flow disturbances such as bends, expansions, or contractions in the stack, or from a visible flame. Next, locate the velocity measurement site eight equivalent diameters downstream of the particulate measurement site (see Figure 1A-1). If such locations are not available, select an alternative particulate measurement location at least two equivalent stack or duct diameters downstream and two and one-half diameters upstream from any flow disturbance. Then, locate the velocity measurement site two equivalent diameters downstream from the particulate measurement site. (See section 12.2 of Method 1 for calculating equivalent diameters for a rectangular cross-section.)
11.1.2 PM Sampling (Steady Flow) or Velocity (Steady or Unsteady Flow) Measurements. For PM sampling when the volumetric flow rate in a duct is constant with respect to time, section 11.1.1 of Method 1 may be followed, with the PM sampling and velocity measurement performed at one location. To demonstrate that the flow rate is constant (within 10 percent) when PM measurements are made, perform complete velocity traverses before and after the PM sampling run, and calculate the deviation of the flow rate derived after the PM sampling run from the one derived before the PM sampling run. The PM sampling run is acceptable if the deviation does not exceed 10 percent.
11.2 Determining the Number of Traverse Points.
11.2.1 Particulate Measurements (Steady or Unsteady Flow). Use Figure 1-1 of Method 1 to determine the number of traverse points to use at both the velocity measurement and PM sampling locations. Before referring to the figure, however, determine the distances between both the velocity measurement and PM sampling sites to the nearest upstream and downstream disturbances. Then divide each distance by the stack diameter or equivalent diameter to express the distances in terms of the number of duct diameters. Then, determine the number of traverse points from Figure 1-1 of Method 1 corresponding to each of these four distances. Choose the highest of the four numbers of traverse points (or a greater number) so that, for circular ducts the number is a multiple of four; and for rectangular ducts, the number is one of those shown in Table 1-1 of Method 1. When the optimum duct diameter location criteria can be satisfied, the minimum number of traverse points required is eight for circular ducts and nine for rectangular ducts.
11.2.2 PM Sampling (Steady Flow) or only Velocity (Non-Particulate) Measurements. Use Figure 1-2 of Method 1 to determine number of traverse points, following the same procedure used for PM sampling as described in section 11.2.1 of Method 1. When the optimum duct diameter location criteria can be satisfied, the minimum number of traverse points required is eight for circular ducts and nine for rectangular ducts.
11.3 Cross-sectional Layout, Location of Traverse Points, and Verification of the Absence of Cyclonic Flow. Same as Method 1, sections 11.3 and 11.4, respectively.
12.0 Data Analysis and Calculations [Reserved] 13.0 Method Performance [Reserved] 14.0 Pollution Prevention [Reserved] 15.0 Waste Management [Reserved] 16.0 ReferencesSame as Method 1, section 16.0, References 1 through 6, with the addition of the following:
1. Vollaro, Robert F. Recommended Procedure for Sample Traverses in Ducts Smaller Than 12 Inches in Diameter. U.S. Environmental Protection Agency, Emission Measurement Branch, Research Triangle Park, North Carolina. January 1977.
17.0 Tables, Diagrams, Flowcharts, and Validation Data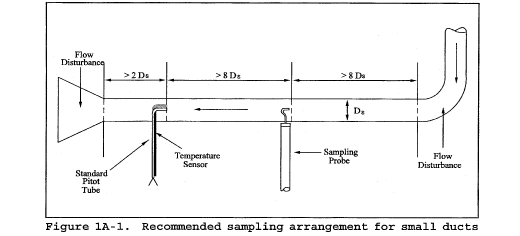
This method does not include all of the specifications (e.g., equipment and supplies) and procedures (e.g., sampling) essential to its performance. Some material is incorporated by reference from other methods in this part. Therefore, to obtain reliable results, persons using this method should have a thorough knowledge of at least the following additional test method: Method 1.
1.0 Scope and Application.1.1 This method is applicable for the determination of the average velocity and the volumetric flow rate of a gas stream.
1.2 This method is not applicable at measurement sites that fail to meet the criteria of Method 1, section 11.1. Also, the method cannot be used for direct measurement in cyclonic or swirling gas streams; section 11.4 of Method 1 shows how to determine cyclonic or swirling flow conditions. When unacceptable conditions exist, alternative procedures, subject to the approval of the Administrator, must be employed to produce accurate flow rate determinations. Examples of such alternative procedures are: (1) to install straightening vanes; (2) to calculate the total volumetric flow rate stoichiometrically, or (3) to move to another measurement site at which the flow is acceptable.
1.3 Data Quality Objectives. Adherence to the requirements of this method will enhance the quality of the data obtained from air pollutant sampling methods.
2.0 Summary of Method.2.1 The average gas velocity in a stack is determined from the gas density and from measurement of the average velocity head with a Type S (Stausscheibe or reverse type) pitot tube.
3.0 Definitions [Reserved] 4.0 Interferences [Reserved] 5.0 Safety5.1 Disclaimer. This method may involve hazardous materials, operations, and equipment. This test method may not address all of the safety problems associated with its use. It is the responsibility of the user of this test method to establish appropriate safety and health practices and determine the applicability of regulatory limitations prior to performing this test method.
6.0 Equipment and SuppliesSpecifications for the apparatus are given below. Any other apparatus that has been demonstrated (subject to approval of the Administrator) to be capable of meeting the specifications will be considered acceptable.
6.1 Type S Pitot Tube.
6.1.1 Pitot tube made of metal tubing (e.g., stainless steel) as shown in Figure 2-1. It is recommended that the external tubing diameter (dimension Dt, Figure 2-2b) be between 0.48 and 0.95 cm ( 3/16 and 3/8 inch). There shall be an equal distance from the base of each leg of the pitot tube to its face-opening plane (dimensions PA and PB, Figure 2-2b); it is recommended that this distance be between 1.05 and 1.50 times the external tubing diameter. The face openings of the pitot tube shall, preferably, be aligned as shown in Figure 2-2; however, slight misalignments of the openings are permissible (see Figure 2-3).
6.1.2 The Type S pitot tube shall have a known coefficient, determined as outlined in section 10.0. An identification number shall be assigned to the pitot tube; this number shall be permanently marked or engraved on the body of the tube. A standard pitot tube may be used instead of a Type S, provided that it meets the specifications of sections 6.7 and 10.2. Note, however, that the static and impact pressure holes of standard pitot tubes are susceptible to plugging in particulate-laden gas streams. Therefore, whenever a standard pitot tube is used to perform a traverse, adequate proof must be furnished that the openings of the pitot tube have not plugged up during the traverse period. This can be accomplished by comparing the velocity head (Δp) measurement recorded at a selected traverse point (readable Δp value) with a second Δp measurement recorded after “back purging” with pressurized air to clean the impact and static holes of the standard pitot tube. If the before and after Δp measurements are within 5 percent, then the traverse data are acceptable. Otherwise, the data should be rejected and the traverse measurements redone. Note that the selected traverse point should be one that demonstrates a readable Δp value. If “back purging” at regular intervals is part of a routine procedure, then comparative Δp measurements shall be conducted as above for the last two traverse points that exhibit suitable Δp measurements.
6.2 Differential Pressure Gauge. An inclined manometer or equivalent device. Most sampling trains are equipped with a 10 in. (water column) inclined-vertical manometer, having 0.01 in. H20 divisions on the 0 to 1 in. inclined scale, and 0.1 in. H20 divisions on the 1 to 10 in. vertical scale. This type of manometer (or other gauge of equivalent sensitivity) is satisfactory for the measurement of Δp values as low as 1.27 mm (0.05 in.) H20. However, a differential pressure gauge of greater sensitivity shall be used (subject to the approval of the Administrator), if any of the following is found to be true: (1) the arithmetic average of all Δp readings at the traverse points in the stack is less than 1.27 mm (0.05 in.) H20; (2) for traverses of 12 or more points, more than 10 percent of the individual Δp readings are below 1.27 mm (0.05 in.) H20; or (3) for traverses of fewer than 12 points, more than one Δp reading is below 1.27 mm (0.05 in.) H20. Reference 18 (see section 17.0) describes commercially available instrumentation for the measurement of low-range gas velocities.
6.2.1 As an alternative to criteria (1) through (3) above, Equation 2-1 (Section 12.2) may be used to determine the necessity of using a more sensitive differential pressure gauge. If T is greater than 1.05, the velocity head data are unacceptable and a more sensitive differential pressure gauge must be used.
Note:If differential pressure gauges other than inclined manometers are used (e.g., magnehelic gauges), their calibration must be checked after each test series. To check the calibration of a differential pressure gauge, compare Δp readings of the gauge with those of a gauge-oil manometer at a minimum of three points, approximately representing the range of Δp values in the stack. If, at each point, the values of Δp as read by the differential pressure gauge and gauge-oil manometer agree to within 5 percent, the differential pressure gauge shall be considered to be in proper calibration. Otherwise, the test series shall either be voided, or procedures to adjust the measured Δp values and final results shall be used, subject to the approval of the Administrator.
6.3 Temperature Sensor. A thermocouple, liquid-filled bulb thermometer, bimetallic thermometer, mercury-in-glass thermometer, or other gauge capable of measuring temperatures to within 1.5 percent of the minimum absolute stack temperature. The temperature sensor shall be attached to the pitot tube such that the sensor tip does not touch any metal; the gauge shall be in an interference-free arrangement with respect to the pitot tube face openings (see Figure 2-1 and Figure 2-4). Alternative positions may be used if the pitot tube-temperature gauge system is calibrated according to the procedure of section 10.0. Provided that a difference of not more than 1 percent in the average velocity measurement is introduced, the temperature gauge need not be attached to the pitot tube. This alternative is subject to the approval of the Administrator.
6.4 Pressure Probe and Gauge. A piezometer tube and mercury- or water-filled U-tube manometer capable of measuring stack pressure to within 2.5 mm (0.1 in.) Hg. The static tap of a standard type pitot tube or one leg of a Type S pitot tube with the face opening planes positioned parallel to the gas flow may also be used as the pressure probe.
6.5 Barometer. A mercury, aneroid, or other barometer capable of measuring atmospheric pressure to within 2.54 mm (0.1 in.) Hg.
Note:The barometric pressure reading may be obtained from a nearby National Weather Service station. In this case, the station value (which is the absolute barometric pressure) shall be requested and an adjustment for elevation differences between the weather station and sampling point shall be made at a rate of minus 2.5 mm (0.1 in.) Hg per 30 m (100 ft) elevation increase or plus 2.5 mm (0.1 in.) Hg per 30 m (100 ft.) for elevation decrease.
6.6 Gas Density Determination Equipment. Method 3 equipment, if needed (see section 8.6), to determine the stack gas dry molecular weight, and Method 4 (reference method) or Method 5 equipment for moisture content determination. Other methods may be used subject to approval of the Administrator.
6.7 Calibration Pitot Tube. Calibration of the Type S pitot tube requires a standard pitot tube for a reference. When calibration of the Type S pitot tube is necessary (see Section 10.1), a standard pitot tube shall be used for a reference. The standard pitot tube shall, preferably, have a known coefficient, obtained directly from the National Institute of Standards and Technology (NIST), Gaithersburg, MD 20899, (301) 975-2002; or by calibration against another standard pitot tube with a NIST-traceable coefficient. Alternatively, a standard pitot tube designed according to the criteria given in sections 6.7.1 through 6.7.5 below and illustrated in Figure 2-5 (see also References 7, 8, and 17 in section 17.0) may be used. Pitot tubes designed according to these specifications will have baseline coefficients of 0.99 ±0.01.
6.7.1 Standard Pitot Design.
6.7.1.1 Hemispherical (shown in Figure 2-5), ellipsoidal, or conical tip.
6.7.1.2 A minimum of six diameters straight run (based upon D, the external diameter of the tube) between the tip and the static pressure holes.
6.7.1.3 A minimum of eight diameters straight run between the static pressure holes and the centerline of the external tube, following the 90° bend.
6.7.1.4 Static pressure holes of equal size (approximately 0.1 D), equally spaced in a piezometer ring configuration.
6.7.1.5 90° bend, with curved or mitered junction.
6.8 Differential Pressure Gauge for Type S Pitot Tube Calibration. An inclined manometer or equivalent. If the single-velocity calibration technique is employed (see section 10.1.2.3), the calibration differential pressure gauge shall be readable to the nearest 0.127 mm (0.005 in.) H20. For multivelocity calibrations, the gauge shall be readable to the nearest 0.127 mm (0.005 in.) H20 for Δp values between 1.27 and 25.4 mm (0.05 and 1.00 in.) H20, and to the nearest 1.27 mm (0.05 in.) H20 for Δp values above 25.4 mm (1.00 in.) H20. A special, more sensitive gauge will be required to read Δp values below 1.27 mm (0.05 in.) H20 (see Reference 18 in section 16.0).
7.0 Reagents and Standards [Reserved] 8.0 Sample Collection and Analysis8.1 Set up the apparatus as shown in Figure 2-1. Capillary tubing or surge tanks installed between the manometer and pitot tube may be used to dampen ΔP fluctuations. It is recommended, but not required, that a pretest leak-check be conducted as follows: (1) blow through the pitot impact opening until at least 7.6 cm (3.0 in.) H2O velocity head registers on the manometer; then, close off the impact opening. The pressure shall remain stable (±2.5 mm H2O, ±0.10 in. H2O) for at least 15 seconds; (2) do the same for the static pressure side, except using suction to obtain the minimum of 7.6 cm (3.0 in.) H2O. Other leak-check procedures, subject to the approval of the Administrator, may be used.
8.2 Level and zero the manometer. Because the manometer level and zero may drift due to vibrations and temperature changes, make periodic checks during the traverse (at least once per hour). Record all necessary data on a form similar to that shown in Figure 2-6.
8.3 Measure the velocity head and temperature at the traverse points specified by Method 1. Ensure that the proper differential pressure gauge is being used for the range of Δp values encountered (see section 6.2). If it is necessary to change to a more sensitive gauge, do so, and remeasure the Δp and temperature readings at each traverse point. Conduct a post-test leak-check (mandatory), as described in section 8.1 above, to validate the traverse run.
8.4 Measure the static pressure in the stack. One reading is usually adequate.
8.5 Determine the atmospheric pressure.
8.6 Determine the stack gas dry molecular weight. For combustion processes or processes that emit essentially CO2, O2, CO, and N2, use Method 3. For processes emitting essentially air, an analysis need not be conducted; use a dry molecular weight of 29.0. For other processes, other methods, subject to the approval of the Administrator, must be used.
8.7 Obtain the moisture content from Method 4 (reference method, or equivalent) or from Method 5.
8.8 Determine the cross-sectional area of the stack or duct at the sampling location. Whenever possible, physically measure the stack dimensions rather than using blueprints. Do not assume that stack diameters are equal. Measure each diameter distance to verify its dimensions.
9.0 Quality ControlSection | Quality control measure | Effect |
---|---|---|
10.1-10.4 | Sampling equipment calibration | Ensure accurate measurement of stack gas flow rate, sample volume. |
10.1 Type S Pitot Tube. Before its initial use, carefully examine the Type S pitot tube top, side, and end views to verify that the face openings of the tube are aligned within the specifications illustrated in Figures 2-2 and 2-3. The pitot tube shall not be used if it fails to meet these alignment specifications. After verifying the face opening alignment, measure and record the following dimensions of the pitot tube: (a) the external tubing diameter (dimension Dt, Figure 2-2b); and (b) the base-to-opening plane distances (dimensions PA and PB, Figure 2-2b). If Dt is between 0.48 and 0.95 cm 3/16 and 3/8 in.), and if PA and PB are equal and between 1.05 and 1.50 Dt, there are two possible options: (1) the pitot tube may be calibrated according to the procedure outlined in sections 10.1.2 through 10.1.5, or (2) a baseline (isolated tube) coefficient value of 0.84 may be assigned to the pitot tube. Note, however, that if the pitot tube is part of an assembly, calibration may still be required, despite knowledge of the baseline coefficient value (see section 10.1.1). If Dt, PA, and PB are outside the specified limits, the pitot tube must be calibrated as outlined in sections 10.1.2 through 10.1.5.
10.1.1 Type S Pitot Tube Assemblies. During sample and velocity traverses, the isolated Type S pitot tube is not always used; in many instances, the pitot tube is used in combination with other source-sampling components (e.g., thermocouple, sampling probe, nozzle) as part of an “assembly.” The presence of other sampling components can sometimes affect the baseline value of the Type S pitot tube coefficient (Reference 9 in section 17.0); therefore, an assigned (or otherwise known) baseline coefficient value may or may not be valid for a given assembly. The baseline and assembly coefficient values will be identical only when the relative placement of the components in the assembly is such that aerodynamic interference effects are eliminated. Figures 2-4, 2-7, and 2-8 illustrate interference-free component arrangements for Type S pitot tubes having external tubing diameters between 0.48 and 0.95 cm ( 3/16 and 3/8 in.). Type S pitot tube assemblies that fail to meet any or all of the specifications of Figures 2-4, 2-7, and 2-8 shall be calibrated according to the procedure outlined in sections 10.1.2 through 10.1.5, and prior to calibration, the values of the intercomponent spacings (pitot-nozzle, pitot-thermocouple, pitot-probe sheath) shall be measured and recorded.
Note:Do not use a Type S pitot tube assembly that is constructed such that the impact pressure opening plane of the pitot tube is below the entry plane of the nozzle (see Figure 2-7B).
10.1.2 Calibration Setup. If the Type S pitot tube is to be calibrated, one leg of the tube shall be permanently marked A, and the other, B. Calibration shall be performed in a flow system having the following essential design features:
10.1.2.1 The flowing gas stream must be confined to a duct of definite cross-sectional area, either circular or rectangular. For circular cross sections, the minimum duct diameter shall be 30.48 cm (12 in.); for rectangular cross sections, the width (shorter side) shall be at least 25.4 cm (10 in.).
10.1.2.2 The cross-sectional area of the calibration duct must be constant over a distance of 10 or more duct diameters. For a rectangular cross section, use an equivalent diameter, calculated according to Equation 2-2 (see section 12.3), to determine the number of duct diameters. To ensure the presence of stable, fully developed flow patterns at the calibration site, or “test section,” the site must be located at least eight diameters downstream and two diameters upstream from the nearest disturbances.
Note:The eight- and two-diameter criteria are not absolute; other test section locations may be used (subject to approval of the Administrator), provided that the flow at the test site has been demonstrated to be or found stable and parallel to the duct axis.
10.1.2.3 The flow system shall have the capacity to generate a test-section velocity around 910 m/min (3,000 ft/min). This velocity must be constant with time to guarantee constant and steady flow during the entire period of calibration. A centrifugal fan is recommended for this purpose, as no flow rate adjustment for back pressure of the fan is allowed during the calibration process. Note that Type S pitot tube coefficients obtained by single-velocity calibration at 910 m/min (3,000 ft/min) will generally be valid to ±3 percent for the measurement of velocities above 300 m/min (1,000 ft/min) and to ±6 percent for the measurement of velocities between 180 and 300 m/min (600 and 1,000 ft/min). If a more precise correlation between the pitot tube coefficient (Cp) and velocity is desired, the flow system should have the capacity to generate at least four distinct, time-invariant test-section velocities covering the velocity range from 180 to 1,500 m/min (600 to 5,000 ft/min), and calibration data shall be taken at regular velocity intervals over this range (see References 9 and 14 in section 17.0 for details).
10.1.2.4 Two entry ports, one for each of the standard and Type S pitot tubes, shall be cut in the test section. The standard pitot entry port shall be located slightly downstream of the Type S port, so that the standard and Type S impact openings will lie in the same cross-sectional plane during calibration. To facilitate alignment of the pitot tubes during calibration, it is advisable that the test section be constructed of Plexiglas TM or some other transparent material.
10.1.3 Calibration Procedure. Note that this procedure is a general one and must not be used without first referring to the special considerations presented in section 10.1.5. Note also that this procedure applies only to single-velocity calibration. To obtain calibration data for the A and B sides of the Type S pitot tube, proceed as follows:
10.1.3.1 Make sure that the manometer is properly filled and that the oil is free from contamination and is of the proper density. Inspect and leak-check all pitot lines; repair or replace if necessary.
10.1.3.2 Level and zero the manometer. Switch on the fan, and allow the flow to stabilize. Seal the Type S pitot tube entry port.
10.1.3.3 Ensure that the manometer is level and zeroed. Position the standard pitot tube at the calibration point (determined as outlined in section 10.1.5.1), and align the tube so that its tip is pointed directly into the flow. Particular care should be taken in aligning the tube to avoid yaw and pitch angles. Make sure that the entry port surrounding the tube is properly sealed.
10.1.3.4 Read Δpstd, and record its value in a data table similar to the one shown in Figure 2-9. Remove the standard pitot tube from the duct, and disconnect it from the manometer. Seal the standard entry port. Make no adjustment to the fan speed or other wind tunnel volumetric flow control device between this reading and the corresponding Type S pitot reading.
10.1.3.5 Connect the Type S pitot tube to the manometer and leak-check. Open the Type S tube entry port. Check the manometer level and zero. Insert and align the Type S pitot tube so that its A side impact opening is at the same point as was the standard pitot tube and is pointed directly into the flow. Make sure that the entry port surrounding the tube is properly sealed.
10.1.3.6 Read Δps, and enter its value in the data table. Remove the Type S pitot tube from the duct, and disconnect it from the manometer.
10.1.3.7 Repeat Steps 10.1.3.3 through 10.1.3.6 until three pairs of Δp readings have been obtained for the A side of the Type S pitot tube, with all the paired observations conducted at a constant fan speed (no changes to fan velocity between observed readings).
10.1.3.8 Repeat Steps 10.1.3.3 through 10.1.3.7 for the B side of the Type S pitot tube.
10.1.3.9 Perform calculations as described in section 12.4. Use the Type S pitot tube only if the values of σA and σB are less than or equal to 0.01 and if the absolute value of the difference between C p(A) and C p(B) is 0.01 or less.
10.1.4 Special Considerations.
10.1.4.1 Selection of Calibration Point.
10.1.4.1.1 When an isolated Type S pitot tube is calibrated, select a calibration point at or near the center of the duct, and follow the procedures outlined in section 10.1.3. The Type S pitot coefficients measured or calculated, (i.e., C p(A) and C p(B)) will be valid, so long as either: (1) the isolated pitot tube is used; or (2) the pitot tube is used with other components (nozzle, thermocouple, sample probe) in an arrangement that is free from aerodynamic interference effects (see Figures 2-4, 2-7, and 2-8).
10.1.4.1.2 For Type S pitot tube-thermocouple combinations (without probe assembly), select a calibration point at or near the center of the duct, and follow the procedures outlined in section 10.1.3. The coefficients so obtained will be valid so long as the pitot tube-thermocouple combination is used by itself or with other components in an interference-free arrangement (Figures 2-4, 2-7, and 2-8).
10.1.4.1.3 For Type S pitot tube combinations with complete probe assemblies, the calibration point should be located at or near the center of the duct; however, insertion of a probe sheath into a small duct may cause significant cross-sectional area interference and blockage and yield incorrect coefficient values (Reference 9 in section 17.0). Therefore, to minimize the blockage effect, the calibration point may be a few inches off-center if necessary, but no closer to the outer wall of the wind tunnel than 4 inches. The maximum allowable blockage, as determined by a projected-area model of the probe sheath, is 2 percent or less of the duct cross-sectional area (Figure 2-10a). If the pitot and/or probe assembly blocks more than 2 percent of the cross-sectional area at an insertion point only 4 inches inside the wind tunnel, the diameter of the wind tunnel must be increased.
10.1.4.2 For those probe assemblies in which pitot tube-nozzle interference is a factor (i.e., those in which the pitot-nozzle separation distance fails to meet the specifications illustrated in Figure 2-7A), the value of Cp(s) depends upon the amount of free space between the tube and nozzle and, therefore, is a function of nozzle size. In these instances, separate calibrations shall be performed with each of the commonly used nozzle sizes in place. Note that the single-velocity calibration technique is acceptable for this purpose, even though the larger nozzle sizes (>0.635 cm or 1/4 in.) are not ordinarily used for isokinetic sampling at velocities around 910 m/min (3,000 ft/min), which is the calibration velocity. Note also that it is not necessary to draw an isokinetic sample during calibration (see Reference 19 in section 17.0).
10.1.4.3 For a probe assembly constructed such that its pitot tube is always used in the same orientation, only one side of the pitot tube needs to be calibrated (the side which will face the flow). The pitot tube must still meet the alignment specifications of Figure 2-2 or 2-3, however, and must have an average deviation (σ) value of 0.01 or less (see section 12.4.4).
10.1.5 Field Use and Recalibration.
10.1.5.1 Field Use.
10.1.5.1.1 When a Type S pitot tube (isolated or in an assembly) is used in the field, the appropriate coefficient value (whether assigned or obtained by calibration) shall be used to perform velocity calculations. For calibrated Type S pitot tubes, the A side coefficient shall be used when the A side of the tube faces the flow, and the B side coefficient shall be used when the B side faces the flow. Alternatively, the arithmetic average of the A and B side coefficient values may be used, irrespective of which side faces the flow.
10.1.5.1.2 When a probe assembly is used to sample a small duct, 30.5 to 91.4 cm (12 to 36 in.) in diameter, the probe sheath sometimes blocks a significant part of the duct cross-section, causing a reduction in the effective value of Cp(s). Consult Reference 9 (see section 17.0) for details. Conventional pitot-sampling probe assemblies are not recommended for use in ducts having inside diameters smaller than 30.5 cm (12 in.) (see Reference 16 in section 17.0).
10.1.5.2 Recalibration.
10.1.5.2.1 Isolated Pitot Tubes. After each field use, the pitot tube shall be carefully reexamined in top, side, and end views. If the pitot face openings are still aligned within the specifications illustrated in Figure 2-2 and Figure 2-3, it can be assumed that the baseline coefficient of the pitot tube has not changed. If, however, the tube has been damaged to the extent that it no longer meets the specifications of Figure 2-2 and Figure 2-3, the damage shall either be repaired to restore proper alignment of the face openings, or the tube shall be discarded.
10.1.5.2.2 Pitot Tube Assemblies. After each field use, check the face opening alignment of the pitot tube, as in section 10.1.5.2.1. Also, remeasure the intercomponent spacings of the assembly. If the intercomponent spacings have not changed and the face opening alignment is acceptable, it can be assumed that the coefficient of the assembly has not changed. If the face opening alignment is no longer within the specifications of Figure 2-2 and Figure 2-3, either repair the damage or replace the pitot tube (calibrating the new assembly, if necessary). If the intercomponent spacings have changed, restore the original spacings, or recalibrate the assembly.
10.2 Standard Pitot Tube (if applicable). If a standard pitot tube is used for the velocity traverse, the tube shall be constructed according to the criteria of section 6.7 and shall be assigned a baseline coefficient value of 0.99. If the standard pitot tube is used as part of an assembly, the tube shall be in an interference-free arrangement (subject to the approval of the Administrator).
10.3 Temperature Sensors.
10.3.1 After each field use, calibrate dial thermometers, liquid-filled bulb thermometers, thermocouple-potentiometer systems, and other sensors at a temperature within 10 percent of the average absolute stack temperature. For temperatures up to 405 °C (761 °F), use an ASTM mercury-in-glass reference thermometer, or equivalent, as a reference. Alternatively, either a reference thermocouple and potentiometer (calibrated against NIST standards) or thermometric fixed points (e.g., ice bath and boiling water, corrected for barometric pressure) may be used. For temperatures above 405 °C (761 °F), use a reference thermocouple-potentiometer system calibrated against NIST standards or an alternative reference, subject to the approval of the Administrator.
10.3.2 The temperature data recorded in the field shall be considered valid. If, during calibration, the absolute temperature measured with the sensor being calibrated and the reference sensor agree within 1.5 percent, the temperature data taken in the field shall be considered valid. Otherwise, the pollutant emission test shall either be considered invalid or adjustments (if appropriate) of the test results shall be made, subject to the approval of the Administrator.
10.4 Barometer. Calibrate the barometer used against a mercury barometer or NIST-traceable barometer prior to each field test.
11.0 Analytical ProcedureSample collection and analysis are concurrent for this method (see section 8.0).
12.0 Data Analysis and CalculationsCarry out calculations, retaining at least one extra significant figure beyond that of the acquired data. Round off figures after final calculation.
12.1 Nomenclature.
A = Cross-sectional area of stack, m 2 (ft 2). Bws = Water vapor in the gas stream (from Method 4 (reference method) or Method 5), proportion by volume. Cp = Pitot tube coefficient, dimensionless. Cp(s) = Type S pitot tube coefficient, dimensionless. Cp(std) = Standard pitot tube coefficient; use 0.99 if the coefficient is unknown and the tube is designed according to the criteria of sections 6.7.1 to 6.7.5 of this method. De = Equivalent diameter. K = 0.127 mm H2O (metric units). 0.005 in. H2O (English units). Kp = Velocity equation constant. L = Length. Md = Molecular weight of stack gas, dry basis (see section 8.6), g/g-mole (lb/lb-mole). Ms = Molecular weight of stack gas, wet basis, g/g-mole (lb/lb-mole). n = Total number of traverse points. Pbar = Barometric pressure at measurement site, mm Hg (in. Hg). Pg = Stack static pressure, mm Hg (in. Hg). Ps = Absolute stack pressure (Pbar + Pg), mm Hg (in. Hg), Pstd = Standard absolute pressure, 760 mm Hg (29.92 in. Hg). Qsd = Dry volumetric stack gas flow rate corrected to standard conditions, dscm/hr (dscf/hr). T = Sensitivity factor for differential pressure gauges. Ts(abavg) = Average absolute stack temperature, °K (°R). = 273 + Ts for metric units, = 460 + Ts for English units. Ts = Stack temperature, °C (°F). = 273 + Ts for metric units, = 460 + Ts for English units. Tstd = Standard absolute temperature, 293 °K (528 °R). Vs = Average stack gas velocity, m/sec (ft/sec). W = Width. Δp = Velocity head of stack gas, mm H2O (in. H20). Δpi = Individual velocity head reading at traverse point “i”, mm (in.) H2O. Δpstd = Velocity head measured by the standard pitot tube, cm (in.) H2O. Δps = Velocity head measured by the Type S pitot tube, cm (in.) H2O. 3600 = Conversion Factor, sec/hr. 18.0 = Molecular weight of water, g/g-mole (lb/lb-mole).12.2 Calculate T as follows:
12.3 Calculate De as follows:
12.4 Calibration of Type S Pitot Tube.
12.4.1 For each of the six pairs of Δp readings (i.e., three from side A and three from side B) obtained in section 10.1.3, calculate the value of the Type S pitot tube coefficient according to Equation 2-3:
12.4.2 Calculate C p(A), the mean A-side coefficient, and C p(B), the mean B-side coefficient. Calculate the difference between these two average values.
12.4.3 Calculate the deviation of each of the three A-side values of Cp(s) from C p(A), and the deviation of each of the three B-side values of Cp(s) from C p(B), using Equation 2-4:
12.4.4 Calculate σ the average deviation from the mean, for both the A and B sides of the pitot tube. Use Equation 2-5:
12.5 Molecular Weight of Stack Gas.
12.6 Average Stack Gas Velocity.
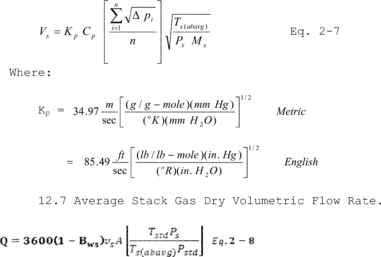
12.7 Average Stack Gas Dry Volumetric Flow Rate.

1. Mark, L.S. Mechanical Engineers' Handbook. New York. McGraw-Hill Book Co., Inc. 1951.
2. Perry, J.H., ed. Chemical Engineers' Handbook. New York. McGraw-Hill Book Co., Inc. 1960.
3. Shigehara, R.T., W.F. Todd, and W.S. Smith. Significance of Errors in Stack Sampling Measurements. U.S. Environmental Protection Agency, Research Triangle Park, N.C. (Presented at the Annual Meeting of the Air Pollution Control Association, St. Louis, MO., June 14-19, 1970).
4. Standard Method for Sampling Stacks for Particulate Matter. In: 1971 Book of ASTM Standards, Part 23. Philadelphia, PA. 1971. ASTM Designation D 2928-71.
5. Vennard, J.K. Elementary Fluid Mechanics. New York. John Wiley and Sons, Inc. 1947.
6. Fluid Meters - Their Theory and Application. American Society of Mechanical Engineers, New York, N.Y. 1959.
7. ASHRAE Handbook of Fundamentals. 1972. p. 208.
8. Annual Book of ASTM Standards, Part 26. 1974. p. 648.
9. Vollaro, R.F. Guidelines for Type S Pitot Tube Calibration. U.S. Environmental Protection Agency, Research Triangle Park, N.C. (Presented at 1st Annual Meeting, Source Evaluation Society, Dayton, OH, September 18, 1975.)
10. Vollaro, R.F. A Type S Pitot Tube Calibration Study. U.S. Environmental Protection Agency, Emission Measurement Branch, Research Triangle Park, N.C. July 1974.
11. Vollaro, R.F. The Effects of Impact Opening Misalignment on the Value of the Type S Pitot Tube Coefficient. U.S. Environmental Protection Agency, Emission Measurement Branch, Research Triangle Park, NC. October 1976.
12. Vollaro, R.F. Establishment of a Baseline Coefficient Value for Properly Constructed Type S Pitot Tubes. U.S. Environmental Protection Agency, Emission Measurement Branch, Research Triangle Park, NC. November 1976.
13. Vollaro, R.F. An Evaluation of Single-Velocity Calibration Technique as a Means of Determining Type S Pitot Tube Coefficients. U.S. Environmental Protection Agency, Emission Measurement Branch, Research Triangle Park, NC. August 1975.
14. Vollaro, R.F. The Use of Type S Pitot Tubes for the Measurement of Low Velocities. U.S. Environmental Protection Agency, Emission Measurement Branch, Research Triangle Park, NC. November 1976.
15. Smith, Marvin L. Velocity Calibration of EPA Type Source Sampling Probe. United Technologies Corporation, Pratt and Whitney Aircraft Division, East Hartford, CT. 1975.
16. Vollaro, R.F. Recommended Procedure for Sample Traverses in Ducts Smaller than 12 Inches in Diameter. U.S. Environmental Protection Agency, Emission Measurement Branch, Research Triangle Park, NC. November 1976.
17. Ower, E. and R.C. Pankhurst. The Measurement of Air Flow, 4th Ed. London, Pergamon Press. 1966.
18. Vollaro, R.F. A Survey of Commercially Available Instrumentation for the Measurement of Low-Range Gas Velocities. U.S. Environmental Protection Agency, Emission Measurement Branch, Research Triangle Park, NC. November 1976. (Unpublished Paper).
19. Gnyp, A.W., et al. An Experimental Investigation of the Effect of Pitot Tube-Sampling Probe Configurations on the Magnitude of the S Type Pitot Tube Coefficient for Commercially Available Source Sampling Probes. Prepared by the University of Windsor for the Ministry of the Environment, Toronto, Canada. February 1975.
17.0 Tables, Diagrams, Flowcharts, and Validation Data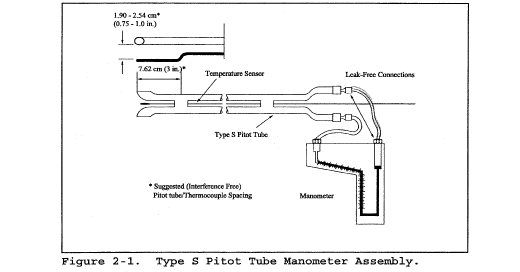
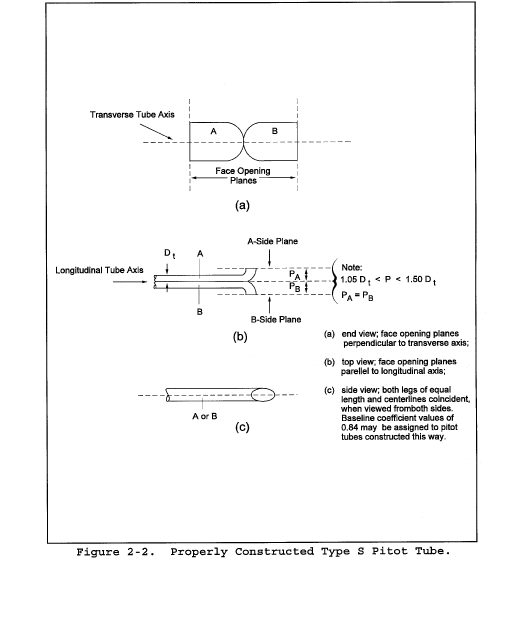
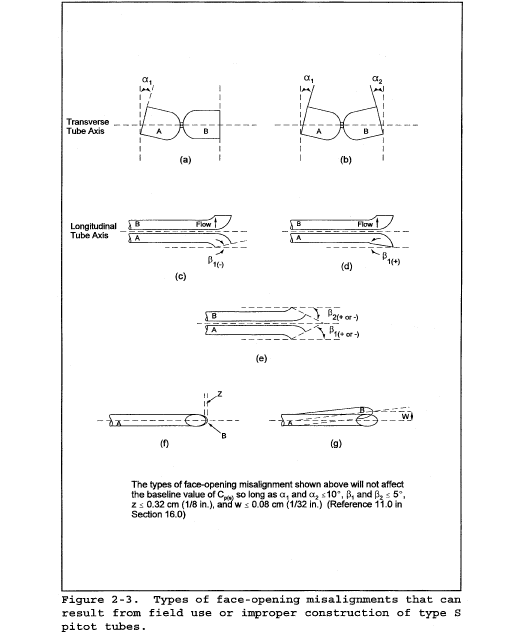
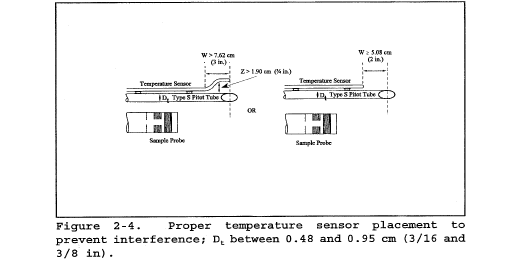
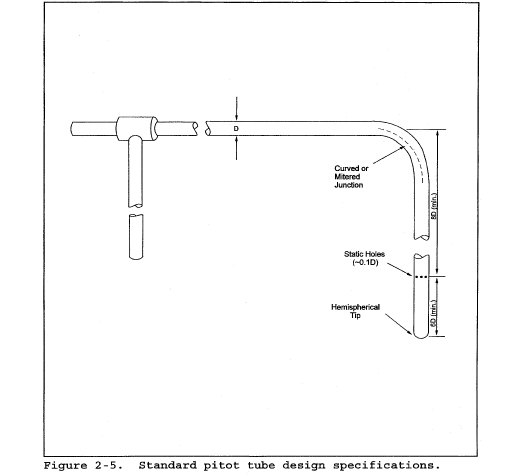
Traverse Pt. No. |
Vel. Hd., Δp mm (in.) H2O |
Stack temperature |
Pg mm Hg (in. Hg) |
(Δp) 1/2 | |
---|---|---|---|---|---|
Ts, °C ( °F) |
Ts, °K (°R) |
||||
Average(1) |
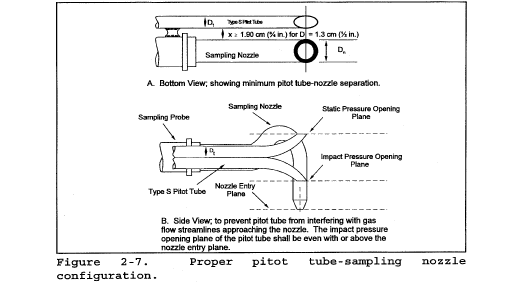
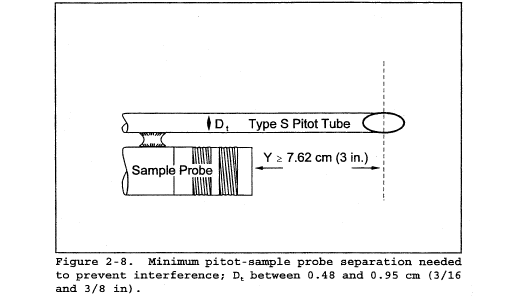
“A” Side Calibration
Run No. | ΔPstd cm H2O (in H2O) |
ΔP(s) cm H2O (in H2O) |
Cp(s) | Deviation Cp(s) - Cp(A) |
---|---|---|---|---|
1 | ||||
2 | ||||
3 | ||||
Cp, avg (SIDE A) |
“B” Side Calibration
Run No. | ΔPstd cm H2O (in H2O) |
ΔP(s) cm H2O (in H2O) |
Cp(s) | Deviation Cp(s) - Cp(B) |
---|---|---|---|---|
1 | ||||
2 | ||||
3 | ||||
Cp, avg (SIDE B) |
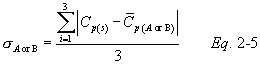
*Must be less than or equal to 0.01
Figure 2-9. Pitot Tube Calibration Data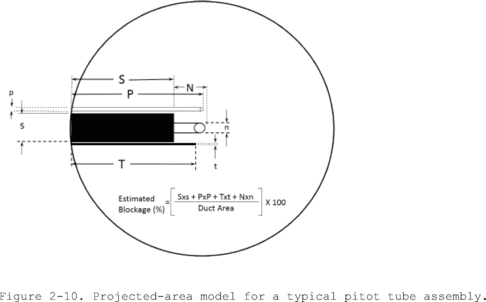
This method does not include all of the specifications (e.g., equipment and supplies) and procedures (e.g., sampling) essential to its performance. Some material is incorporated by reference from other methods in this part. Therefore, to obtain reliable results, persons using this method should have a thorough knowledge of at least the following additional test methods: Method 1, Method 2.
1.0 Scope and Application1.1 This method is applicable for the determination of gas flow rates in pipes and small ducts, either in-line or at exhaust positions, within the temperature range of 0 to 50 °C (32 to 122 °F).
1.2 Data Quality Objectives. Adherence to the requirements of this method will enhance the quality of the data obtained from air pollutant sampling methods.
2.0 Summary of Method2.1 A gas volume meter is used to measure gas volume directly. Temperature and pressure measurements are made to allow correction of the volume to standard conditions.
3.0 Definitions [Reserved] 4.0 Interferences [Reserved] 5.0 Safety5.1 Disclaimer. This method may involve hazardous materials, operations, and equipment. This test method may not address all of the safety problems associated with its use. It is the responsibility of the user of this test method to establish appropriate safety and health practices and determine the applicability of regulatory limitations prior to performing this test method.
6.0 Equipment and SuppliesSpecifications for the apparatus are given below. Any other apparatus that has been demonstrated (subject to approval of the Administrator) to be capable of meeting the specifications will be considered acceptable.
6.1 Gas Volume Meter. A positive displacement meter, turbine meter, or other direct measuring device capable of measuring volume to within 2 percent. The meter shall be equipped with a temperature sensor (accurate to within ±2 percent of the minimum absolute temperature) and a pressure gauge (accurate to within ±2.5 mm Hg). The manufacturer's recommended capacity of the meter shall be sufficient for the expected maximum and minimum flow rates for the sampling conditions. Temperature, pressure, corrosive characteristics, and pipe size are factors necessary to consider in selecting a suitable gas meter.
6.2 Barometer. A mercury, aneroid, or other barometer capable of measuring atmospheric pressure to within ±2.5 mm Hg.
Note:In many cases, the barometric reading may be obtained from a nearby National Weather Service station, in which case the station value (which is the absolute barometric pressure) shall be requested and an adjustment for elevation differences between the weather station and sampling point shall be applied at a rate of minus 2.5 mm (0.1 in.) Hg per 30 m (100 ft) elevation increase or vice versa for elevation decrease.
6.3 Stopwatch. Capable of measurement to within 1 second.
7.0 Reagents and Standards [Reserved] 8.0 Sample Collection and Analysis8.1 Installation. As there are numerous types of pipes and small ducts that may be subject to volume measurement, it would be difficult to describe all possible installation schemes. In general, flange fittings should be used for all connections wherever possible. Gaskets or other seal materials should be used to assure leak-tight connections. The volume meter should be located so as to avoid severe vibrations and other factors that may affect the meter calibration.
8.2 Leak Test.
8.2.1 A volume meter installed at a location under positive pressure may be leak-checked at the meter connections by using a liquid leak detector solution containing a surfactant. Apply a small amount of the solution to the connections. If a leak exists, bubbles will form, and the leak must be corrected.
8.2.2 A volume meter installed at a location under negative pressure is very difficult to test for leaks without blocking flow at the inlet of the line and watching for meter movement. If this procedure is not possible, visually check all connections to assure leak-tight seals.
8.3 Volume Measurement.
8.3.1 For sources with continuous, steady emission flow rates, record the initial meter volume reading, meter temperature(s), meter pressure, and start the stopwatch. Throughout the test period, record the meter temperatures and pressures so that average values can be determined. At the end of the test, stop the timer, and record the elapsed time, the final volume reading, meter temperature, and pressure. Record the barometric pressure at the beginning and end of the test run. Record the data on a table similar to that shown in Figure 2A-1.
8.3.2 For sources with noncontinuous, non-steady emission flow rates, use the procedure in section 8.3.1 with the addition of the following: Record all the meter parameters and the start and stop times corresponding to each process cyclical or noncontinuous event.
9.0 Quality ControlSection | Quality control measure | Effect |
---|---|---|
10.1-10.4 | Sampling equipment calibration | Ensure accurate measurement of stack gas flow rate, sample volume. |
10.1 Volume Meter.
10.1.1 The volume meter is calibrated against a standard reference meter prior to its initial use in the field. The reference meter is a spirometer or liquid displacement meter with a capacity consistent with that of the test meter.
10.1.2 Alternatively, a calibrated, standard pitot may be used as the reference meter in conjunction with a wind tunnel assembly. Attach the test meter to the wind tunnel so that the total flow passes through the test meter. For each calibration run, conduct a 4-point traverse along one stack diameter at a position at least eight diameters of straight tunnel downstream and two diameters upstream of any bend, inlet, or air mover. Determine the traverse point locations as specified in Method 1. Calculate the reference volume using the velocity values following the procedure in Method 2, the wind tunnel cross-sectional area, and the run time.
10.1.3 Set up the test meter in a configuration similar to that used in the field installation (i.e., in relation to the flow moving device). Connect the temperature sensor and pressure gauge as they are to be used in the field. Connect the reference meter at the inlet of the flow line, if appropriate for the meter, and begin gas flow through the system to condition the meters. During this conditioning operation, check the system for leaks.
10.1.4 The calibration shall be performed during at least three different flow rates. The calibration flow rates shall be about 0.3, 0.6, and 0.9 times the rated maximum flow rate of the test meter.
10.1.5 For each calibration run, the data to be collected include: reference meter initial and final volume readings, the test meter initial and final volume reading, meter average temperature and pressure, barometric pressure, and run time. Repeat the runs at each flow rate at least three times.
10.1.6 Calculate the test meter calibration coefficient as indicated in section 12.2.
10.1.7 Compare the three Ym values at each of the flow rates tested and determine the maximum and minimum values. The difference between the maximum and minimum values at each flow rate should be no greater than 0.030. Extra runs may be required to complete this requirement. If this specification cannot be met in six successive runs, the test meter is not suitable for use. In addition, the meter coefficients should be between 0.95 and 1.05. If these specifications are met at all the flow rates, average all the Ym values from runs meeting the specifications to obtain an average meter calibration coefficient, Ym.
10.1.8 The procedure above shall be performed at least once for each volume meter. Thereafter, an abbreviated calibration check shall be completed following each field test. The calibration of the volume meter shall be checked with the meter pressure set at the average value encountered during the field test. Three calibration checks (runs) shall be performed using this average flow rate value. Calculate the average value of the calibration factor. If the calibration has changed by more than 5 percent, recalibrate the meter over the full range of flow as described above.
Note:If the volume meter calibration coefficient values obtained before and after a test series differ by more than 5 percent, the test series shall either be voided, or calculations for the test series shall be performed using whichever meter coefficient value (i.e., before or after) gives the greater value of pollutant emission rate.
10.2 Temperature Sensor. After each test series, check the temperature sensor at ambient temperature. Use an American Society for Testing and Materials (ASTM) mercury-in-glass reference thermometer, or equivalent, as a reference. If the sensor being checked agrees within 2 percent (absolute temperature) of the reference, the temperature data collected in the field shall be considered valid. Otherwise, the test data shall be considered invalid or adjustments of the results shall be made, subject to the approval of the Administrator.
10.3 Barometer. Calibrate the barometer used against a mercury barometer or NIST-traceable barometer prior to the field test.
11.0 Analytical ProcedureSample collection and analysis are concurrent for this method (see section 8.0).
12.0 Data Analysis and CalculationsCarry out calculations, retaining at least one extra decimal figure beyond that of the acquired data. Round off figures after final calculation.
12.1 Nomenclature.
f = Final reading. i = Initial reading. Pbar = Barometric pressure, mm Hg. Pg = Average static pressure in volume meter, mm Hg. Qs = Gas flow rate, m 3/min, standard conditions. s = Standard conditions, 20 °C and 760 mm Hg. Tr = Reference meter average temperature, °K (°R). Tm = Test meter average temperature, °K (°R). Vr = Reference meter volume reading, m 3. Vm = Test meter volume reading, m 3. Ym = Test meter calibration coefficient, dimensionless. θ = Elapsed test period time, min.12.2 Test Meter Calibration Coefficient.

12.3 Volume.
12.4 Gas Flow Rate.
13.0 Method Performance [Reserved] 14.0 Pollution Prevention [Reserved] 15.0 Waste Management [Reserved] 16.0 References1. Rom, Jerome J. Maintenance, Calibration, and Operation of Isokinetic Source Sampling Equipment. U.S. Environmental Protection Agency, Research Triangle Park, NC. Publication No. APTD-0576. March 1972.
2. Wortman, Martin, R. Vollaro, and P.R. Westlin. Dry Gas Volume Meter Calibrations. Source Evaluation Society Newsletter. Vol. 2, No. 2. May 1977.
3. Westlin, P.R., and R.T. Shigehara. Procedure for Calibrating and Using Dry Gas Volume Meters as Calibration Standards. Source Evaluation Society Newsletter. Vol. 3, No. 1. February 1978.
17.0 Tables, Diagrams, Flowcharts, and Validation Data [Reserved] Method 2B - Determination of Exhaust Gas Volume Flow Rate From Gasoline Vapor Incinerators Note:This method does not include all of the specifications (e.g., equipment and supplies) and procedures (e.g., sampling and analytical) essential to its performance. Some material is incorporated by reference from other methods in this part. Therefore, to obtain reliable results, persons using this method should also have a thorough knowledge of at least the following additional test methods: Method 1, Method 2, Method 2A, Method 10, Method 25A, Method 25B.
1.0 Scope and Application1.1 This method is applicable for the determination of exhaust volume flow rate from incinerators that process gasoline vapors consisting primarily of alkanes, alkenes, and/or arenes (aromatic hydrocarbons). It is assumed that the amount of auxiliary fuel is negligible.
1.2 Data Quality Objectives. Adherence to the requirements of this method will enhance the quality of the data obtained from air pollutant sampling methods.
2.0 Summary of Method2.1 Organic carbon concentration and volume flow rate are measured at the incinerator inlet using either Method 25A or Method 25B and Method 2A, respectively. Organic carbon, carbon dioxide (CO2), and carbon monoxide (CO) concentrations are measured at the outlet using either Method 25A or Method 25B and Method 10, respectively. The ratio of total carbon at the incinerator inlet and outlet is multiplied by the inlet volume to determine the exhaust volume flow rate.
3.0 DefinitionsSame as section 3.0 of Method 10 and Method 25A.
4.0 InterferencesSame as section 4.0 of Method 10.
5.0 Safety5.1 This method may involve hazardous materials, operations, and equipment. This test method may not address all of the safety problems associated with its use. It is the responsibility of the user of this test method to establish appropriate safety and health practices and determine the applicability of regulatory limitations prior to performing this test method.
6.0 Equipment and SuppliesSame as section 6.0 of Method 2A, Method 10, and Method 25A and/or Method 25B as applicable, with the addition of the following:
6.1 This analyzer must meet the specifications set forth in section 6.1.2 of Method 10, except that the span shall be 15 percent CO2 by volume.
7.0 Reagents and StandardsSame as section 7.0 of Method 10 and Method 25A, with the following addition and exceptions:
7.1 Carbon Dioxide Analyzer Calibration. CO2 gases meeting the specifications set forth in section 7 of Method 6C are required.
7.2 Hydrocarbon Analyzer Calibration. Methane shall not be used as a calibration gas when performing this method.
7.3 Fuel Gas. If Method 25B is used to measure the organic carbon concentrations at both the inlet and exhaust, no fuel gas is required.
8.0 Sample Collection and Analysis8.1 Pre-test Procedures. Perform all pre-test procedures (e.g., system performance checks, leak checks) necessary to determine gas volume flow rate and organic carbon concentration in the vapor line to the incinerator inlet and to determine organic carbon, carbon monoxide, and carbon dioxide concentrations at the incinerator exhaust, as outlined in Method 2A, Method 10, and Method 25A and/or Method 25B as applicable.
8.2 Sampling. At the beginning of the test period, record the initial parameters for the inlet volume meter according to the procedures in Method 2A and mark all of the recorder strip charts to indicate the start of the test. Conduct sampling and analysis as outlined in Method 2A, Method 10, and Method 25A and/or Method 25B as applicable. Continue recording inlet organic and exhaust CO2, CO, and organic concentrations throughout the test. During periods of process interruption and halting of gas flow, stop the timer and mark the recorder strip charts so that data from this interruption are not included in the calculations. At the end of the test period, record the final parameters for the inlet volume meter and mark the end on all of the recorder strip charts.
8.3 Post-test Procedures. Perform all post-test procedures (e.g., drift tests, leak checks), as outlined in Method 2A, Method 10, and Method 25A and/or Method 25B as applicable.
9.0 Quality ControlSame as section 9.0 of Method 2A, Method 10, and Method 25A.
10.0 Calibration and StandardizationSame as section 10.0 of Method 2A, Method 10, and Method 25A.
Note:If a manifold system is used for the exhaust analyzers, all the analyzers and sample pumps must be operating when the analyzer calibrations are performed.
10.1 If an analyzer output does not meet the specifications of the method, invalidate the test data for the period. Alternatively, calculate the exhaust volume results using initial calibration data and using final calibration data and report both resulting volumes. Then, for emissions calculations, use the volume measurement resulting in the greatest emission rate or concentration.
11.0 Analytical ProcedureSample collection and analysis are concurrent for this method (see section 8.0).
12.0 Data Analysis and CalculationsCarry out the calculations, retaining at least one extra decimal figure beyond that of the acquired data. Round off figures after the final calculation.
12.1 Nomenclature.
COe = Mean carbon monoxide concentration in system exhaust, ppm. (CO2)a = Ambient carbon dioxide concentration, ppm (if not measured during the test period, may be assumed to equal the global monthly mean CO2 concentration posted at http://www.esrl.noaa.gov/gmd/ccgg/trends/global.html#global_data). (CO2)e = Mean carbon dioxide concentration in system exhaust, ppm. HCe = Mean organic concentration in system exhaust as defined by the calibration gas, ppm. Hci = Mean organic concentration in system inlet as defined by the calibration gas, ppm. Ke = Hydrocarbon calibration gas factor for the exhaust hydrocarbon analyzer, unitless [equal to the number of carbon atoms per molecule of the gas used to calibrate the analyzer (2 for ethane, 3 for propane, etc.)]. Ki = Hydrocarbon calibration gas factor for the inlet hydrocarbon analyzer, unitless. Ves = Exhaust gas volume, m 3. Vis = Inlet gas volume, m 3. Qes = Exhaust gas volume flow rate, m 3/min. Qis = Inlet gas volume flow rate, m 3/min.θ = Sample run time, min.
S = Standard conditions: 20 °C, 760 mm Hg.
12.2 Concentrations. Determine mean concentrations of inlet organics, outlet CO2, outlet CO, and outlet organics according to the procedures in the respective methods and the analyzers' calibration curves, and for the time intervals specified in the applicable regulations.
12.3 Exhaust Gas Volume. Calculate the exhaust gas volume as follows:
12.4 Exhaust Gas Volume Flow Rate. Calculate the exhaust gas volume flow rate as follows:
13.0 Method Performance [Reserved] 14.0 Pollution Prevention [Reserved] 15.0 Waste Management [Reserved] 16.0 ReferencesSame as section 16.0 of Method 2A, Method 10, and Method 25A.
17.0 Tables, Diagrams, Flowcharts, and Validation Data [Reserved] Method 2C - Determination of Gas Velocity and Volumetric Flow Rate in Small Stacks or Ducts (Standard Pitot Tube) Note:This method does not include all of the specifications (e.g., equipment and supplies) and procedures (e.g., sampling) essential to its performance. Some material is incorporated by reference from other methods in this part. Therefore, to obtain reliable results, persons using this method should also have a thorough knowledge of at least the following additional test methods: Method 1, Method 2.
1.0 Scope and Application1.1 This method is applicable for the determination of average velocity and volumetric flow rate of gas streams in small stacks or ducts. Limits on the applicability of this method are identical to those set forth in Method 2, section 1.0, except that this method is limited to stationary source stacks or ducts less than about 0.30 meter (12 in.) in diameter, or 0.071 m 2 (113 in. 2) in cross-sectional area, but equal to or greater than about 0.10 meter (4 in.) in diameter, or 0.0081 m 2 (12.57 in. 2) in cross-sectional area.
1.2 Data Quality Objectives. Adherence to the requirements of this method will enhance the quality of the data obtained from air pollutant sampling methods.
2.0 Summary of Method2.1 The average gas velocity in a stack or duct is determined from the gas density and from measurement of velocity heads with a standard pitot tube.
3.0 Definitions [Reserved] 4.0 Interferences [Reserved] 5.0 Safety5.1 This method may involve hazardous materials, operations, and equipment. This test method may not address all of the safety problems associated with its use. It is the responsibility of the user of this test method to establish appropriate safety and health practices and determine the applicability of regulatory limitations prior to performing this test method.
6.0 Equipment and SuppliesSame as Method 2, section 6.0, with the exception of the following:
6.1 Standard Pitot Tube (instead of Type S). A standard pitot tube which meets the specifications of section 6.7 of Method 2. Use a coefficient of 0.99 unless it is calibrated against another standard pitot tube with a NIST-traceable coefficient (see section 10.2 of Method 2).
6.2 Alternative Pitot Tube. A modified hemispherical-nosed pitot tube (see Figure 2C-1), which features a shortened stem and enlarged impact and static pressure holes. Use a coefficient of 0.99 unless it is calibrated as mentioned in section 6.1 above. This pitot tube is useful in particulate liquid droplet-laden gas streams when a “back purge” is ineffective.
7.0 Reagents and Standards [Reserved] 8.0 Sample Collection and Analysis8.1 Follow the general procedures in section 8.0 of Method 2, except conduct the measurements at the traverse points specified in Method 1A. The static and impact pressure holes of standard pitot tubes are susceptible to plugging in particulate-laden gas streams. Therefore, adequate proof that the openings of the pitot tube have not plugged during the traverse period must be furnished; this can be done by taking the velocity head (Δp) heading at the final traverse point, cleaning out the impact and static holes of the standard pitot tube by “back-purging” with pressurized air, and then taking another Δp reading. If the Δp readings made before and after the air purge are the same (within ±5 percent) the traverse is acceptable. Otherwise, reject the run. Note that if the Δp at the final traverse point is unsuitably low, another point may be selected. If “back purging” at regular intervals is part of the procedure, then take comparative Δp readings, as above, for the last two back purges at which suitably high Δp readings are observed.
9.0 Quality ControlSection | Quality control measure | Effect |
---|---|---|
10.0 | Sampling equipment calibration | Ensure accurate measurement of stack gas velocity head. |
Same as Method 2, sections 10.2 through 10.4.
11.0 Analytical ProcedureSample collection and analysis are concurrent for this method (see section 8.0).
12.0 Calculations and Data AnalysisSame as Method 2, section 12.0.
13.0 Method Performance [Reserved] 14.0 Pollution Prevention [Reserved] 15.0 Waste Management [Reserved] 16.0 ReferencesSame as Method 2, section 16.0.
17.0 Tables, Diagrams, Flowcharts, and Validation Data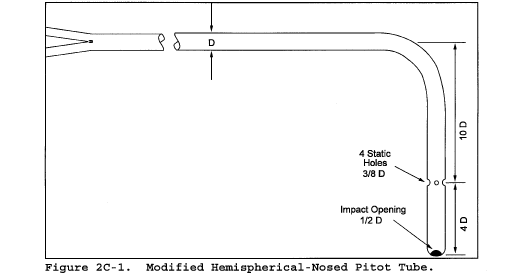
This method does not include all of the specifications (e.g., equipment and supplies) and procedures (e.g., sampling) essential to its performance. Some material is incorporated by reference from other methods in this part. Therefore, to obtain reliable results, persons using this method should also have a thorough knowledge of at least the following additional test methods: Method 1, Method 2, and Method 2A.
1.0 Scope and Application1.1 This method is applicable for the determination of the volumetric flow rates of gas streams in small pipes and ducts. It can be applied to intermittent or variable gas flows only with particular caution.
1.2 Data Quality Objectives. Adherence to the requirements of this method will enhance the quality of the data obtained from air pollutant sampling methods.
2.0 Summary of Method2.1 All the gas flow in the pipe or duct is directed through a rotameter, orifice plate or similar device to measure flow rate or pressure drop. The device has been previously calibrated in a manner that insures its proper calibration for the gas being measured. Absolute temperature and pressure measurements are made to allow correction of volumetric flow rates to standard conditions.
3.0 Definitions [Reserved] 4.0 Interferences [Reserved] 5.0 Safety5.1 This method may involve hazardous materials, operations, and equipment. This test method may not address all of the safety problems associated with its use. It is the responsibility of the user of this test method to establish appropriate safety and health practices and determine the applicability of regulatory limitations prior to performing this test method.
6.0 Equipment and SuppliesSpecifications for the apparatus are given below. Any other apparatus that has been demonstrated (subject to approval of the Administrator) to be capable of meeting the specifications will be considered acceptable.
6.1 Gas Metering Rate or Flow Element Device. A rotameter, orifice plate, or other volume rate or pressure drop measuring device capable of measuring the stack flow rate to within ±5 percent. The metering device shall be equipped with a temperature gauge accurate to within ±2 percent of the minimum absolute stack temperature and a pressure gauge (accurate to within ±5 mm Hg). The capacity of the metering device shall be sufficient for the expected maximum and minimum flow rates at the stack gas conditions. The magnitude and variability of stack gas flow rate, molecular weight, temperature, pressure, dewpoint, and corrosive characteristics, and pipe or duct size are factors to consider in choosing a suitable metering device.
6.2 Barometer. Same as Method 2, section 6.5.
6.3 Stopwatch. Capable of measurement to within 1 second.
7.0 Reagents and Standards [Reserved] 8.0 Sample Collection and Analysis8.1 Installation and Leak Check. Same as Method 2A, sections 8.1 and 8.2, respectively.
8.2 Volume Rate Measurement.
8.2.1 Continuous, Steady Flow. At least once an hour, record the metering device flow rate or pressure drop reading, and the metering device temperature and pressure. Make a minimum of 12 equally spaced readings of each parameter during the test period. Record the barometric pressure at the beginning and end of the test period. Record the data on a table similar to that shown in Figure 2D-1.
8.2.2 Noncontinuous and Nonsteady Flow. Use volume rate devices with particular caution. Calibration will be affected by variation in stack gas temperature, pressure and molecular weight. Use the procedure in section 8.2.1 with the addition of the following: Record all the metering device parameters on a time interval frequency sufficient to adequately profile each process cyclical or noncontinuous event. A multichannel continuous recorder may be used.
9.0 Quality ControlSection | Quality control measure | Effect |
---|---|---|
10.0 | Sampling equipment calibration | Ensure accurate measurement of stack gas flow rate or sample volume. |
Same as Method 2A, section 10.0, with the following exception:
10.1 Gas Metering Device. Same as Method 2A, section 10.1, except calibrate the metering device with the principle stack gas to be measured (examples: air, nitrogen) against a standard reference meter. A calibrated dry gas meter is an acceptable reference meter. Ideally, calibrate the metering device in the field with the actual gas to be metered. For metering devices that have a volume rate readout, calculate the test metering device calibration coefficient, Ym, for each run shown in Equation 2D-2 section 12.3.
10.2 For metering devices that do not have a volume rate readout, refer to the manufacturer's instructions to calculate the Vm2 corresponding to each Vr.
10.3 Temperature Gauge. Use the procedure and specifications in Method 2A, section 10.2. Perform the calibration at a temperature that approximates field test conditions.
10.4 Barometer. Calibrate the barometer used against a mercury barometer or NIST-traceable barometer prior to the field test.
11.0 Analytical Procedure.Sample collection and analysis are concurrent for this method (see section 8.0).
12.0 Data Analysis and Calculations12.1 Nomenclature.
Pbar = Barometric pressure, mm Hg (in. Hg). Pm = Test meter average static pressure, mm Hg (in. Hg). Qr = Reference meter volume flow rate reading, m 3/min (ft 3/min). Qm = Test meter volume flow rate reading, m 3/min (ft 3/min). Tr = Absolute reference meter average temperature, °K (°R). Tm = Absolute test meter average temperature, °K (°R). Kl = 0.3855 °K/mm Hg for metric units, = 17.65 °R/in. Hg for English units.12.2 Gas Flow Rate.
12.3 Test Meter Device Calibration Coefficient. Calculation for testing metering device calibration coefficient, Ym.
13.0 Method Performance [Reserved] 14.0 Pollution Prevention [Reserved] 15.0 Waste Management [Reserved] 16.0 References1. Spink, L.K. Principles and Practice of Flowmeter Engineering. The Foxboro Company. Foxboro, MA. 1967.
2. Benedict, R.P. Fundamentals of Temperature, Pressure, and Flow Measurements. John Wiley & Sons, Inc. New York, NY. 1969.
3. Orifice Metering of Natural Gas. American Gas Association. Arlington, VA. Report No. 3. March 1978. 88 pp.
17.0 Tables, Diagrams, Flowcharts, and Validation Data Plant Date Run No. Sample location Barometric pressure (mm Hg): Start Finish Operators Metering device No. Calibration coefficient Calibration gas Date to recalibrateTime | Flow rate reading |
Static
Pressure [mm Hg (in. Hg)] |
Temperature | |
---|---|---|---|---|
°C (°F) | °K (°R) | |||
Average |
This method does not include all of the specifications (e.g., equipment and supplies) and procedures (e.g., sampling and analytical) essential to its performance. Some material is incorporated by reference from other methods in this part. Therefore, to obtain reliable results, persons using this method should also have a thorough knowledge of at least the following additional test methods: Methods 2 and 3C.
1.0 Scope and Application1.1 Applicability. This method applies to the measurement of landfill gas (LFG) production flow rate from municipal solid waste landfills and is used to calculate the flow rate of nonmethane organic compounds (NMOC) from landfills.
1.2 Data Quality Objectives. Adherence to the requirements of this method will enhance the quality of the data obtained from air pollutant sampling methods.
2.0 Summary of Method2.1 Extraction wells are installed either in a cluster of three or at five dispersed locations in the landfill. A blower is used to extract LFG from the landfill. LFG composition, landfill pressures, and orifice pressure differentials from the wells are measured and the landfill gas production flow rate is calculated.
3.0 Definitions [Reserved] 4.0 Interferences [Reserved] 5.0 Safety5.1 Since this method is complex, only experienced personnel should perform the test. Landfill gas contains methane, therefore explosive mixtures may exist at or near the landfill. It is advisable to take appropriate safety precautions when testing landfills, such as refraining from smoking and installing explosion-proof equipment.
6.0 Equipment and Supplies6.1 Well Drilling Rig. Capable of boring a 0.61 m (24 in.) diameter hole into the landfill to a minimum of 75 percent of the landfill depth. The depth of the well shall not extend to the bottom of the landfill or the liquid level.
6.2 Gravel. No fines. Gravel diameter should be appreciably larger than perforations stated in sections 6.10 and 8.2.
6.3 Bentonite.
6.4 Backfill Material. Clay, soil, and sandy loam have been found to be acceptable.
6.5 Extraction Well Pipe. Minimum diameter of 3 in., constructed of polyvinyl chloride (PVC), high density polyethylene (HDPE), fiberglass, stainless steel, or other suitable nonporous material capable of transporting landfill gas.
6.6 Above Ground Well Assembly. Valve capable of adjusting gas flow, such as a gate, ball, or butterfly valve; sampling ports at the well head and outlet; and a flow measuring device, such as an in-line orifice meter or pitot tube. A schematic of the aboveground well head assembly is shown in Figure 2E-1.
6.7 Cap. Constructed of PVC or HDPE.
6.8 Header Piping. Constructed of PVC or HDPE.
6.9 Auger. Capable of boring a 0.15-to 0.23-m (6-to 9-in.) diameter hole to a depth equal to the top of the perforated section of the extraction well, for pressure probe installation.
6.10 Pressure Probe. Constructed of PVC or stainless steel (316), 0.025-m (1-in.). Schedule 40 pipe. Perforate the bottom two-thirds. A minimum requirement for perforations is slots or holes with an open area equivalent to four 0.006-m ( 1/4-in.) diameter holes spaced 90° apart every 0.15 m (6 in.).
6.11 Blower and Flare Assembly. Explosion-proof blower, capable of extracting LFG at a flow rate of 8.5 m 3/min (300 ft 3/min), a water knockout, and flare or incinerator.
6.12 Standard Pitot Tube and Differential Pressure Gauge for Flow Rate Calibration with Standard Pitot. Same as Method 2, sections 6.7 and 6.8.
6.13 Orifice Meter. Orifice plate, pressure tabs, and pressure measuring device to measure the LFG flow rate.
6.14 Barometer. Same as Method 4, section 6.1.5.
6.15 Differential Pressure Gauge. Water-filled U-tube manometer or equivalent, capable of measuring within 0.02 mm Hg (0.01 in. H2O), for measuring the pressure of the pressure probes.
7.0 Reagents and Standards. Not Applicable 8.0 Sample Collection, Preservation, Storage, and Transport8.1 Placement of Extraction Wells. The landfill owner or operator may install a single cluster of three extraction wells in a test area or space five equal-volume wells over the landfill. The cluster wells are recommended but may be used only if the composition, age of the refuse, and the landfill depth of the test area can be determined.
8.1.1 Cluster Wells. Consult landfill site records for the age of the refuse, depth, and composition of various sections of the landfill. Select an area near the perimeter of the landfill with a depth equal to or greater than the average depth of the landfill and with the average age of the refuse between 2 and 10 years old. Avoid areas known to contain nondecomposable materials, such as concrete and asbestos. Locate the cluster wells as shown in Figure 2E-2.
8.1.1.1 The age of the refuse in a test area will not be uniform, so calculate a weighted average age of the refuse as shown in section 12.2.
8.1.2 Equal Volume Wells. Divide the sections of the landfill that are at least 2 years old into five areas representing equal volumes. Locate an extraction well near the center of each area.
8.2 Installation of Extraction Wells. Use a well drilling rig to dig a 0.6 m (24 in.) diameter hole in the landfill to a minimum of 75 percent of the landfill depth, not to extend to the bottom of the landfill or the liquid level. Perforate the bottom two thirds of the extraction well pipe. A minimum requirement for perforations is holes or slots with an open area equivalent to 0.01-m (0.5-in.) diameter holes spaced 90° apart every 0.1 to 0.2 m (4 to 8 in.). Place the extraction well in the center of the hole and backfill with gravel to a level 0.30 m (1 ft) above the perforated section. Add a layer of backfill material 1.2 m (4 ft) thick. Add a layer of bentonite 0.9 m (3 ft) thick, and backfill the remainder of the hole with cover material or material equal in permeability to the existing cover material. The specifications for extraction well installation are shown in Figure 2E-3.
8.3 Pressure Probes. Shallow pressure probes are used in the check for infiltration of air into the landfill, and deep pressure probes are use to determine the radius of influence. Locate pressure probes along three radial arms approximately 120° apart at distances of 3, 15, 30, and 45 m (10, 50, 100, and 150 ft) from the extraction well. The tester has the option of locating additional pressure probes at distances every 15 m (50 feet) beyond 45 m (150 ft). Example placements of probes are shown in Figure 2E-4. The 15-, 30-, and 45-m, (50-, 100-, and 150-ft) probes from each well, and any additional probes located along the three radial arms (deep probes), shall extend to a depth equal to the top of the perforated section of the extraction wells. All other probes (shallow probes) shall extend to a depth equal to half the depth of the deep probes.
8.3.1 Use an auger to dig a hole, 0.15- to 0.23-m (6-to 9-in.) in diameter, for each pressure probe. Perforate the bottom two thirds of the pressure probe. A minimum requirement for perforations is holes or slots with an open area equivalent to four 0.006-m (0.25-in.) diameter holes spaced 90° apart every 0.15 m (6 in.). Place the pressure probe in the center of the hole and backfill with gravel to a level 0.30 m (1 ft) above the perforated section. Add a layer of backfill material at least 1.2 m (4 ft) thick. Add a layer of bentonite at least 0.3 m (1 ft) thick, and backfill the remainder of the hole with cover material or material equal in permeability to the existing cover material. The specifications for pressure probe installation are shown in Figure 2E-5.
8.4 LFG Flow Rate Measurement. Place the flow measurement device, such as an orifice meter, as shown in Figure 2E-1. Attach the wells to the blower and flare assembly. The individual wells may be ducted to a common header so that a single blower, flare assembly, and flow meter may be used. Use the procedures in section 10.1 to calibrate the flow meter.
8.5 Leak-Check. A leak-check of the above ground system is required for accurate flow rate measurements and for safety. Sample LFG at the well head sample port and at the outlet sample port. Use Method 3C to determine nitrogen (N2) concentrations. Determine the difference between the well head and outlet N2 concentrations using the formula in section 12.3. The system passes the leak-check if the difference is less than 10,000 ppmv.
8.6 Static Testing. Close the control valves on the well heads during static testing. Measure the gauge pressure (Pg) at each deep pressure probe and the barometric pressure (Pbar) every 8 hours (hr) for 3 days. Convert the gauge pressure of each deep pressure probe to absolute pressure using the equation in section 12.4. Record as Pi (initial absolute pressure).
8.6.1 For each probe, average all of the 8-hr deep pressure probe readings (Pi) and record as Pia (average absolute pressure). Pia is used in section 8.7.5 to determine the maximum radius of influence.
8.6.2 Measure the static flow rate of each well once during static testing.
8.7 Short-Term Testing. The purpose of short-term testing is to determine the maximum vacuum that can be applied to the wells without infiltration of ambient air into the landfill. The short-term testing is performed on one well at a time. Burn all LFG with a flare or incinerator.
8.7.1 Use the blower to extract LFG from a single well at a rate at least twice the static flow rate of the respective well measured in section 8.6.2. If using a single blower and flare assembly and a common header system, close the control valve on the wells not being measured. Allow 24 hr for the system to stabilize at this flow rate.
8.7.2 Test for infiltration of air into the landfill by measuring the gauge pressures of the shallow pressure probes and using Method 3C to determine the LFG N2 concentration. If the LFG N2 concentration is less than 5 percent and all of the shallow probes have a positive gauge pressure, increase the blower vacuum by 3.7 mm Hg (2 in. H2O), wait 24 hr, and repeat the tests for infiltration. Continue the above steps of increasing blower vacuum by 3.7 mm Hg (2 in. H2O), waiting 24 hr, and testing for infiltration until the concentration of N2 exceeds 5 percent or any of the shallow probes have a negative gauge pressure. When this occurs,reduce the blower vacuum to the maximum setting at which the N2 concentration was less than 5 percent and the gauge pressures of the shallow probes are positive.
8.7.3 At this blower vacuum, measure atmospheric pressure (Pbar) every 8 hr for 24 hr, and record the LFG flow rate (Qs) and the probe gauge pressures (Pf) for all of the probes. Convert the gauge pressures of the deep probes to absolute pressures for each 8-hr reading at Qs as shown in section 12.4.
8.7.4 For each probe, average the 8-hr deep pressure probe absolute pressure readings and record as Pfa (the final average absolute pressure).
8.7.5 For each probe, compare the initial average pressure (Pia) from section 8.6.1 to the final average pressure (Pfa). Determine the furthermost point from the well head along each radial arm where Pfa ≤Pia. This distance is the maximum radius of influence (Rm), which is the distance from the well affected by the vacuum. Average these values to determine the average maximum radius of influence (Rma).
8.7.6 Calculate the depth (Dst) affected by the extraction well during the short term test as shown in section 12.6. If the computed value of Dst exceeds the depth of the landfill, set Dst equal to the landfill depth.
8.7.7 Calculate the void volume (V) for the extraction well as shown in section 12.7.
8.7.8 Repeat the procedures in section 8.7 for each well.
8.8 Calculate the total void volume of the test wells (Vv) by summing the void volumes (V) of each well.
8.9 Long-Term Testing. The purpose of long-term testing is to extract two void volumes of LFG from the extraction wells. Use the blower to extract LFG from the wells. If a single Blower and flare assembly and common header system are used, open all control valves and set the blower vacuum equal to the highest stabilized blower vacuum demonstrated by any individual well in section 8.7. Every 8 hr, sample the LFG from the well head sample port, measure the gauge pressures of the shallow pressure probes, the blower vacuum, the LFG flow rate, and use the criteria for infiltration in section 8.7.2 and Method 3C to test for infiltration. If infiltration is detected, do not reduce the blower vacuum, instead reduce the LFG flow rate from the well by adjusting the control valve on the well head. Adjust each affected well individually. Continue until the equivalent of two total void volumes (Vv) have been extracted, or until Vt = 2Vv.
8.9.1 Calculate Vt, the total volume of LFG extracted from the wells, as shown in section 12.8.
8.9.2 Record the final stabilized flow rate as Qf and the gauge pressure for each deep probe. If, during the long term testing, the flow rate does not stabilize, calculate Qf by averaging the last 10 recorded flow rates.
8.9.3 For each deep probe, convert each gauge pressure to absolute pressure as in section 12.4. Average these values and record as Psa. For each probe, compare Pia to Psa. Determine the furthermost point from the well head along each radial arm where Psa ≤Pia. This distance is the stabilized radius of influence. Average these values to determine the average stabilized radius of influence (Rsa).
8.10 Determine the NMOC mass emission rate using the procedures in section 12.9 through 12.15.
9.0 Quality Control9.1 Miscellaneous Quality Control Measures.
Section | Quality control measure | Effect |
---|---|---|
10.1 | LFG flow rate meter calibration | Ensures accurate measurement of LFG flow rate and sample volume |
10.1 LFG Flow Rate Meter (Orifice) Calibration Procedure. Locate a standard pitot tube in line with an orifice meter. Use the procedures in section 8, 12.5, 12.6, and 12.7 of Method 2 to determine the average dry gas volumetric flow rate for at least five flow rates that bracket the expected LFG flow rates, except in section 8.1, use a standard pitot tube rather than a Type S pitot tube. Method 3C may be used to determine the dry molecular weight. It may be necessary to calibrate more than one orifice meter in order to bracket the LFG flow rates. Construct a calibration curve by plotting the pressure drops across the orifice meter for each flow rate versus the average dry gas volumetric flow rate in m 3/min of the gas.
11.0 Procedures [Reserved] 12.0 Data Analysis and Calculations12.1 Nomenclature.
A = Age of landfill, yr. Aavg = Average age of the refuse tested, yr. Ai = Age of refuse in the ith fraction, yr. Ar = Acceptance rate, Mg/yr. CNMOC = NMOC concentration, ppmv as hexane (CNMOC = Ct/6). Co = Concentration of N2 at the outlet, ppmv. Ct = NMOC concentration, ppmv (carbon equivalent) from Method 25C. Cw = Concentration of N2 at the wellhead, ppmv. D = Depth affected by the test wells, m. Dst = Depth affected by the test wells in the short-term test, m. e = Base number for natural logarithms (2.718). f = Fraction of decomposable refuse in the landfill. fi = Fraction of the refuse in the ith section. k = Landfill gas generation constant, yr−1. Lo = Methane generation potential, m 3/Mg. Lo′ = Revised methane generation potential to account for the amount of nondecomposable material in the landfill, m 3/Mg. Mi = Mass of refuse in the ith section, Mg. Mr = Mass of decomposable refuse affected by the test well, Mg. Pbar = Atmospheric pressure, mm Hg. Pf = Final absolute pressure of the deep pressure probes during short-term testing, mm Hg. Pfa = Average final absolute pressure of the deep pressure probes during short-term testing, mm Hg. Pgf = final gauge pressure of the deep pressure probes, mm Hg. Pgi = Initial gauge pressure of the deep pressure probes, mm Hg. Pi = Initial absolute pressure of the deep pressure probes during static testing, mm Hg. Pia = Average initial absolute pressure of the deep pressure probes during static testing, mm Hg. Ps = Final absolute pressure of the deep pressure probes during long-term testing, mm Hg. Psa = Average final absolute pressure of the deep pressure probes during long-term testing, mm Hg. Qf = Final stabilized flow rate, m 3/min. Qi = LFG flow rate measured at orifice meter during the ith interval, m 3/min. Qs = Maximum LFG flow rate at each well determined by short-term test, m 3/min. Qt = NMOC mass emission rate, m 3/min. Rm = Maximum radius of influence, m. Rma = Average maximum radius of influence, m. Rs = Stabilized radius of influence for an individual well, m. Rsa = Average stabilized radius of influence, m. ti = Age of section i, yr. tt = Total time of long-term testing, yr. tvi = Time of the ith interval (usually 8), hr. V = Void volume of test well, m 3. Vr = Volume of refuse affected by the test well, m 3. Vt = Total volume of refuse affected by the long-term testing, m 3. Vv = Total void volume affected by test wells, m 3. WD = Well depth, m. ρ = Refuse density, Mg/m 3 (Assume 0.64 Mg/m 3 if data are unavailable).12.2 Use the following equation to calculate a weighted average age of landfill refuse.
12.3 Use the following equation to determine the difference in N2 concentrations (ppmv) at the well head and outlet location.
12.4 Use the following equation to convert the gauge pressure (Pg) of each initial deep pressure probe to absolute pressure (Pi).
12.5 Use the following equation to convert the gauge pressures of the deep probes to absolute pressures for each 8-hr reading at Qs.
12.6 Use the following equation to calculate the depth (Dst) affected by the extraction well during the short-term test.
12.7 Use the following equation to calculate the void volume for the extraction well (V).
12.8 Use the following equation to calculate Vt, the total volume of LFG extracted from the wells.
12.9 Use the following equation to calculate the depth affected by the test well. If using cluster wells, use the average depth of the wells for WD. If the value of D is greater than the depth of the landfill, set D equal to the landfill depth.
12.10 Use the following equation to calculate the volume of refuse affected by the test well.
12.11 Use the following equation to calculate the mass affected by the test well.
12.12 Modify Lo to account for the nondecomposable refuse in the landfill.
12.13 In the following equation, solve for k (landfill gas generation constant) by iteration. A suggested procedure is to select a value for k, calculate the left side of the equation, and if not equal to zero, select another value for k. Continue this process until the left hand side of the equation equals zero, ±0.001.
12.14 Use the following equation to determine landfill NMOC mass emission rate if the yearly acceptance rate of refuse has been consistent (10 percent) over the life of the landfill.
12.15 Use the following equation to determine landfill NMOC mass emission rate if the acceptance rate has not been consistent over the life of the landfill.
13.0 Method Performance [Reserved] 14.0 Pollution Prevention [Reserved] 15.0 Waste Management [Reserved] 16.0 References1. Same as Method 2, Appendix A, 40 CFR Part 60.
2. Emcon Associates, Methane Generation and Recovery from Landfills. Ann Arbor Science, 1982.
3. The Johns Hopkins University, Brown Station Road Landfill Gas Resource Assessment, Volume 1: Field Testing and Gas Recovery Projections. Laurel, Maryland: October 1982.
4. Mandeville and Associates, Procedure Manual for Landfill Gases Emission Testing.
5. Letter and attachments from Briggum, S., Waste Management of North America, to Thorneloe, S., EPA. Response to July 28, 1988 request for additional information. August 18, 1988.
6. Letter and attachments from Briggum, S., Waste Management of North America, to Wyatt, S., EPA. Response to December 7, 1988 request for additional information. January 16, 1989.
17.0 Tables, Diagrams, Flowcharts, and Validation Data Method 2F - Determination of Stack Gas Velocity And Volumetric Flow Rate With Three-Dimensional Probes Note:This method does not include all of the specifications (e.g., equipment and supplies) and procedures (e.g., sampling) essential to its performance. Some material has been incorporated from other methods in this part. Therefore, to obtain reliable results, those using this method should have a thorough knowledge of at least the following additional test methods: Methods 1, 2, 3 or 3A, and 4.
1.0 Scope and Application 1.1 This method is applicable for the determination of yaw angle, pitch angle, axial velocity and the volumetric flow rate of a gas stream in a stack or duct using a three-dimensional (3-D) probe. This method may be used only when the average stack or duct gas velocity is greater than or equal to 20 ft/sec. When the above condition cannot be met, alternative procedures, approved by the Administrator, U.S. Environmental Protection Agency, shall be used to make accurate flow rate determinations. 2.0 Summary of Method2.1 A 3-D probe is used to determine the velocity pressure and the yaw and pitch angles of the flow velocity vector in a stack or duct. The method determines the yaw angle directly by rotating the probe to null the pressure across a pair of symmetrically placed ports on the probe head. The pitch angle is calculated using probe-specific calibration curves. From these values and a determination of the stack gas density, the average axial velocity of the stack gas is calculated. The average gas volumetric flow rate in the stack or duct is then determined from the average axial velocity.
3.0 Definitions3.1. Angle-measuring Device Rotational Offset (RADO). The rotational position of an angle-measuring device relative to the reference scribe line, as determined during the pre-test rotational position check described in section 8.3.
3.2 Axial Velocity. The velocity vector parallel to the axis of the stack or duct that accounts for the yaw and pitch angle components of gas flow. The term “axial” is used herein to indicate that the velocity and volumetric flow rate results account for the measured yaw and pitch components of flow at each measurement point.
3.3 Calibration Pitot Tube. The standard (Prandtl type) pitot tube used as a reference when calibrating a 3-D probe under this method.
3.4 Field Test. A set of measurements conducted at a specific unit or exhaust stack/duct to satisfy the applicable regulation (e.g., a three-run boiler performance test, a single-or multiple-load nine-run relative accuracy test).
3.5 Full Scale of Pressure-measuring Device. Full scale refers to the upper limit of the measurement range displayed by the device. For bi-directional pressure gauges, full scale includes the entire pressure range from the lowest negative value to the highest positive value on the pressure scale.
3.6 Main probe. Refers to the probe head and that section of probe sheath directly attached to the probe head. The main probe sheath is distinguished from probe extensions, which are sections of sheath added onto the main probe to extend its reach.
3.7 “May,” “Must,” “Shall,” “Should,” and the imperative form of verbs.
3.7.1 “May” is used to indicate that a provision of this method is optional.
3.7.2 “Must,” “Shall,” and the imperative form of verbs (such as “record” or “enter”) are used to indicate that a provision of this method is mandatory.
3.7.3 “Should” is used to indicate that a provision of this method is not mandatory, but is highly recommended as good practice.
3.8 Method 1. Refers to 40 CFR part 60, appendix A, “Method 1 - Sample and velocity traverses for stationary sources.”
3.9 Method 2. Refers to 40 CFR part 60, appendix A, “Method 2 - Determination of stack gas velocity and volumetric flow rate (Type S pitot tube).”
3.10 Method 2G. Refers to 40 CFR part 60, appendix A, “Method 2G - Determination of stack gas velocity and volumetric flow rate with two-dimensional probes.”
3.11 Nominal Velocity. Refers to a wind tunnel velocity setting that approximates the actual wind tunnel velocity to within ±1.5 m/sec (±5 ft/sec).
3.12 Pitch Angle. The angle between the axis of the stack or duct and the pitch component of flow, i.e., the component of the total velocity vector in a plane defined by the traverse line and the axis of the stack or duct. (Figure 2F-1 illustrates the “pitch plane.”) From the standpoint of a tester facing a test port in a vertical stack, the pitch component of flow is the vector of flow moving from the center of the stack toward or away from that test port. The pitch angle is the angle described by this pitch component of flow and the vertical axis of the stack.
3.13 Readability. For the purposes of this method, readability for an analog measurement device is one half of the smallest scale division. For a digital measurement device, it is the number of decimals displayed by the device.
3.14 Reference Scribe Line. A line permanently inscribed on the main probe sheath (in accordance with section 6.1.6.1) to serve as a reference mark for determining yaw angles.
3.15 Reference Scribe Line Rotational Offset (RSLO). The rotational position of a probe's reference scribe line relative to the probe's yaw-null position, as determined during the yaw angle calibration described in section 10.5.
3.16 Response Time. The time required for the measurement system to fully respond to a change from zero differential pressure and ambient temperature to the stable stack or duct pressure and temperature readings at a traverse point.
3.17 Tested Probe. A 3-D probe that is being calibrated.
3.18 Three-dimensional (3-D) Probe. A directional probe used to determine the velocity pressure and yaw and pitch angles in a flowing gas stream.
3.19 Traverse Line. A diameter or axis extending across a stack or duct on which measurements of differential pressure and flow angles are made.
3.20 Wind Tunnel Calibration Location. A point, line, area, or volume within the wind tunnel test section at, along, or within which probes are calibrated. At a particular wind tunnel velocity setting, the average velocity pressures at specified points at, along, or within the calibration location shall vary by no more than 2 percent or 0.3 mm H2O (0.01 in. H2O), whichever is less restrictive, from the average velocity pressure at the calibration pitot tube location. Air flow at this location shall be axial, i.e., yaw and pitch angles within ±3°. Compliance with these flow criteria shall be demonstrated by performing the procedures prescribed in sections 10.1.1 and 10.1.2. For circular tunnels, no part of the calibration location may be closer to the tunnel wall than 10.2 cm (4 in.) or 25 percent of the tunnel diameter, whichever is farther from the wall. For elliptical or rectangular tunnels, no part of the calibration location may be closer to the tunnel wall than 10.2 cm (4 in.) or 25 percent of the applicable cross-sectional axis, whichever is farther from the wall.
3.21 Wind Tunnel with Documented Axial Flow. A wind tunnel facility documented as meeting the provisions of sections 10.1.1 (velocity pressure cross-check) and 10.1.2 (axial flow verification) using the procedures described in these sections or alternative procedures determined to be technically equivalent.
3.22 Yaw Angle. The angle between the axis of the stack or duct and the yaw component of flow, i.e., the component of the total velocity vector in a plane perpendicular to the traverse line at a particular traverse point. (Figure 2F-1 illustrates the “yaw plane.”) From the standpoint of a tester facing a test port in a vertical stack, the yaw component of flow is the vector of flow moving to the left or right from the center of the stack as viewed by the tester. (This is sometimes referred to as “vortex flow,” i.e., flow around the centerline of a stack or duct.) The yaw angle is the angle described by this yaw component of flow and the vertical axis of the stack. The algebraic sign convention is illustrated in Figure 2F-2.
3.23 Yaw Nulling. A procedure in which a probe is rotated about its axis in a stack or duct until a zero differential pressure reading (“yaw null”) is obtained. When a 3-D probe is yaw-nulled, its impact pressure port (P1) faces directly into the direction of flow in the stack or duct and the differential pressure between pressure ports P2 and P3 is zero.
4.0 Interferences [Reserved] 5.0 Safety5.1 This test method may involve hazardous operations and the use of hazardous materials or equipment. This method does not purport to address all of the safety problems associated with its use. It is the responsibility of the user to establish and implement appropriate safety and health practices and to determine the applicability of regulatory limitations before using this test method.
6.0 Equipment and Supplies6.1 Three-dimensional Probes. The 3-D probes as specified in subsections 6.1.1 through 6.1.3 below qualify for use based on comprehensive wind tunnel and field studies involving both inter-and intra-probe comparisons by multiple test teams. Other types of probes shall not be used unless approved by the Administrator. Each 3-D probe shall have a unique identification number or code permanently marked on the main probe sheath. The minimum recommended diameter of the sensing head of any probe used under this method is 2.5 cm (1 in.). Each probe shall be calibrated prior to use according to the procedures in section 10. Manufacturer-supplied calibration data shall be used as example information only, except when the manufacturer calibrates the 3-D probe as specified in section 10 and provides complete documentation.
6.1.1 Five-hole prism-shaped probe. This type of probe consists of five pressure taps in the flat facets of a prism-shaped sensing head. The pressure taps are numbered 1 through 5, with the pressures measured at each hole referred to as P1, P2, P3, P4, and P5, respectively. Figure 2F-3 is an illustration of the placement of pressure taps on a commonly available five-hole prism-shaped probe, the 2.5-cm (1-in.) DAT probe. (Note: Mention of trade names or specific products does not constitute endorsement by the U.S. Environmental Protection Agency.) The numbering arrangement for the prism-shaped sensing head presented in Figure 2F-3 shall be followed for correct operation of the probe. A brief description of the probe measurements involved is as follows: the differential pressure P2-P3 is used to yaw null the probe and determine the yaw angle; the differential pressure P4-P5 is a function of pitch angle; and the differential pressure P1-P2 is a function of total velocity.
6.1.2 Five-hole spherical probe. This type of probe consists of five pressure taps in a spherical sensing head. As with the prism-shaped probe, the pressure taps are numbered 1 through 5, with the pressures measured at each hole referred to as P1, P2, P3, P4, and P5, respectively. However, the P4 and P5 pressure taps are in the reverse location from their respective positions on the prism-shaped probe head. The differential pressure P2-P3 is used to yaw null the probe and determine the yaw angle; the differential pressure P4-P5 is a function of pitch angle; and the differential pressure P1-P2 is a function of total velocity. A diagram of a typical spherical probe sensing head is presented in Figure 2F-4. Typical probe dimensions are indicated in the illustration.
6.1.3 A manual 3-D probe refers to a five-hole prism-shaped or spherical probe that is positioned at individual traverse points and yaw nulled manually by an operator. An automated 3-D probe refers to a system that uses a computer-controlled motorized mechanism to position the five-hole prism-shaped or spherical head at individual traverse points and perform yaw angle determinations.
6.1.4 Other three-dimensional probes. [Reserved]
6.1.5 Probe sheath. The probe shaft shall include an outer sheath to: (1) provide a surface for inscribing a permanent reference scribe line, (2) accommodate attachment of an angle-measuring device to the probe shaft, and (3) facilitate precise rotational movement of the probe for determining yaw angles. The sheath shall be rigidly attached to the probe assembly and shall enclose all pressure lines from the probe head to the farthest position away from the probe head where an angle-measuring device may be attached during use in the field. The sheath of the fully assembled probe shall be sufficiently rigid and straight at all rotational positions such that, when one end of the probe shaft is held in a horizontal position, the fully extended probe meets the horizontal straightness specifications indicated in section 8.2 below.
6.1.6 Scribe lines.
6.1.6.1 Reference scribe line. A permanent line, no greater than 1.6 mm (1/16 in.) in width, shall be inscribed on each manual probe that will be used to determine yaw angles of flow. This line shall be placed on the main probe sheath in accordance with the procedures described in section 10.4 and is used as a reference position for installation of the yaw angle-measuring device on the probe. At the discretion of the tester, the scribe line may be a single line segment placed at a particular position on the probe sheath (e.g., near the probe head), multiple line segments placed at various locations along the length of the probe sheath (e.g., at every position where a yaw angle-measuring device may be mounted), or a single continuous line extending along the full length of the probe sheath.
6.1.6.2 Scribe line on probe extensions. A permanent line may also be inscribed on any probe extension that will be attached to the main probe in performing field testing. This allows a yaw angle-measuring device mounted on the extension to be readily aligned with the reference scribe line on the main probe sheath.
6.1.6.3 Alignment specifications. This specification shall be met separately, using the procedures in section 10.4.1, on the main probe and on each probe extension. The rotational position of the scribe line or scribe line segments on the main probe or any probe extension must not vary by more than 2°. That is, the difference between the minimum and maximum of all of the rotational angles that are measured along the full length of the main probe or the probe extension must not exceed 2°.
6.1.7 Probe and system characteristics to ensure horizontal stability.
6.1.7.1 For manual probes, it is recommended that the effective length of the probe (coupled with a probe extension, if necessary) be at least 0.9 m (3 ft.) longer than the farthest traverse point mark on the probe shaft away from the probe head. The operator should maintain the probe's horizontal stability when it is fully inserted into the stack or duct. If a shorter probe is used, the probe should be inserted through a bushing sleeve, similar to the one shown in Figure 2F-5, that is installed on the test port; such a bushing shall fit snugly around the probe and be secured to the stack or duct entry port in such a manner as to maintain the probe's horizontal stability when fully inserted into the stack or duct.
6.1.7.2 An automated system that includes an external probe casing with a transport system shall have a mechanism for maintaining horizontal stability comparable to that obtained by manual probes following the provisions of this method. The automated probe assembly shall also be constructed to maintain the alignment and position of the pressure ports during sampling at each traverse point. The design of the probe casing and transport system shall allow the probe to be removed from the stack or duct and checked through direct physical measurement for angular position and insertion depth.
6.1.8 The tubing that is used to connect the probe and the pressure-measuring device should have an inside diameter of at least 3.2 mm (1/8 in.), to reduce the time required for pressure equilibration, and should be as short as practicable.
6.2 Yaw Angle-measuring Device. One of the following devices shall be used for measurement of the yaw angle of flow.
6.2.1 Digital inclinometer. This refers to a digital device capable of measuring and displaying the rotational position of the probe to within ±1°. The device shall be able to be locked into position on the probe sheath or probe extension, so that it indicates the probe's rotational position throughout the test. A rotational position collar block that can be attached to the probe sheath (similar to the collar shown in Figure 2F-6) may be required to lock the digital inclinometer into position on the probe sheath.
6.2.2 Protractor wheel and pointer assembly. This apparatus, similar to that shown in Figure 2F-7, consists of the following components.
6.2.2.1 A protractor wheel that can be attached to a port opening and set in a fixed rotational position to indicate the yaw angle position of the probe's scribe line relative to the longitudinal axis of the stack or duct. The protractor wheel must have a measurement ring on its face that is no less than 17.8 cm (7 in.) in diameter, shall be able to be rotated to any angle and then locked into position on the stack or duct port, and shall indicate angles to a resolution of 1°.
6.2.2.2 A pointer assembly that includes an indicator needle mounted on a collar that can slide over the probe sheath and be locked into a fixed rotational position on the probe sheath. The pointer needle shall be of sufficient length, rigidity, and sharpness to allow the tester to determine the probe's angular position to within 1° from the markings on the protractor wheel. Corresponding to the position of the pointer, the collar must have a scribe line to be used in aligning the pointer with the scribe line on the probe sheath.
6.2.3 Other yaw angle-measuring devices. Other angle-measuring devices with a manufacturer's specified precision of 1° or better may be used, if approved by the Administrator.
6.3 Probe Supports and Stabilization Devices. When probes are used for determining flow angles, the probe head should be kept in a stable horizontal position. For probes longer than 3.0 m (10 ft.), the section of the probe that extends outside the test port shall be secured. Three alternative devices are suggested for maintaining the horizontal position and stability of the probe shaft during flow angle determinations and velocity pressure measurements: (1) Monorails installed above each port, (2) probe stands on which the probe shaft may be rested, or (3) bushing sleeves of sufficient length secured to the test ports to maintain probes in a horizontal position. Comparable provisions shall be made to ensure that automated systems maintain the horizontal position of the probe in the stack or duct. The physical characteristics of each test platform may dictate the most suitable type of stabilization device. Thus, the choice of a specific stabilization device is left to the judgment of the testers.
6.4 Differential Pressure Gauges. The pressure (ΔP) measuring devices used during wind tunnel calibrations and field testing shall be either electronic manometers (e.g., pressure transducers), fluid manometers, or mechanical pressure gauges (e.g., MagnehelicΔ gauges). Use of electronic manometers is recommended. Under low velocity conditions, use of electronic manometers may be necessary to obtain acceptable measurements.
6.4.1 Differential pressure-measuring device. This refers to a device capable of measuring pressure differentials and having a readability of ±1 percent of full scale. The device shall be capable of accurately measuring the maximum expected pressure differential. Such devices are used to determine the following pressure measurements: velocity pressure, static pressure, yaw-null pressure, and pitch-angle pressure. For an inclined-vertical manometer, the readability specification of ±1 percent shall be met separately using the respective full-scale upper limits of the inclined and vertical portions of the scales. To the extent practicable, the device shall be selected such that most of the pressure readings are between 10 and 90 percent of the device's full-scale measurement range (as defined in section 3.5). Typical velocity pressure (P1-P2) ranges for both the prism-shaped probe and the spherical probe are 0 to 1.3 cm H2O (0 to 0.5 in. H2O), 0 to 5.1 cm H2O (0 to 2 in. H2O), and 0 to 12.7 cm H2O (0 to 5 in. H2O). The pitch angle (P4-P5) pressure range is typically −6.4 to + 6.4 mm H2O (−0.25 to + 0.25 in. H2O) or −12.7 to + 12.7 mm H2O (−0.5 to + 0.5 in. H2O) for the prism-shaped probe, and −12.7 to + 12.7 mm H2O (−0.5 to + 0.5 in. H2O) or −5.1 to + 5.1 cm H2O (−2 to + 2 in. H2O) for the spherical probe. The pressure range for the yaw null (P2-P3) readings is typically −12.7 to + 12.7 mm H2O (−0.5 to + 0.5 in. H2O) for both probe types. In addition, pressure-measuring devices should be selected such that the zero does not drift by more than 5 percent of the average expected pressure readings to be encountered during the field test. This is particularly important under low pressure conditions.
6.4.2 Gauge used for yaw nulling. The differential pressure-measuring device chosen for yaw nulling the probe during the wind tunnel calibrations and field testing shall be bi-directional, i.e., capable of reading both positive and negative differential pressures. If a mechanical, bi-directional pressure gauge is chosen, it shall have a full-scale range no greater than 2.6 cm H2O (1 in. H2O) [i.e., −1.3 to + 1.3 cm H2O (−0.5 in. to + 0.5 in.)].
6.4.3 Devices for calibrating differential pressure-measuring devices. A precision manometer (e.g., a U-tube, inclined, or inclined-vertical manometer, or micromanometer) or NIST (National Institute of Standards and Technology) traceable pressure source shall be used for calibrating differential pressure-measuring devices. The device shall be maintained under laboratory conditions or in a similar protected environment (e.g., a climate-controlled trailer). It shall not be used in field tests. The precision manometer shall have a scale gradation of 0.3 mm H2O (0.01 in. H2O), or less, in the range of 0 to 5.1 cm H2O (0 to 2 in. H2O) and 2.5 mm H2O (0.1 in. H2O), or less, in the range of 5.1 to 25.4 cm H2O (2 to 10 in. H2O). The manometer shall have manufacturer's documentation that it meets an accuracy specification of at least 0.5 percent of full scale. The NIST-traceable pressure source shall be recertified annually.
6.4.4 Devices used for post-test calibration check. A precision manometer meeting the specifications in section 6.4.3, a pressure-measuring device or pressure source with a documented calibration traceable to NIST, or an equivalent device approved by the Administrator shall be used for the post-test calibration check. The pressure-measuring device shall have a readability equivalent to or greater than the tested device. The pressure source shall be capable of generating pressures between 50 and 90 percent of the range of the tested device and known to within ±1 percent of the full scale of the tested device. The pressure source shall be recertified annually.
6.5 Data Display and Capture Devices. Electronic manometers (if used) shall be coupled with a data display device (such as a digital panel meter, personal computer display, or strip chart) that allows the tester to observe and validate the pressure measurements taken during testing. They shall also be connected to a data recorder (such as a data logger or a personal computer with data capture software) that has the ability to compute and retain the appropriate average value at each traverse point, identified by collection time and traverse point.
6.6 Temperature Gauges. For field tests, a thermocouple or resistance temperature detector (RTD) capable of measuring temperature to within ±3 °C (±5 °F) of the stack or duct temperature shall be used. The thermocouple shall be attached to the probe such that the sensor tip does not touch any metal and is located on the opposite side of the probe head from the pressure ports so as not to interfere with the gas flow around the probe head. The position of the thermocouple relative to the pressure port face openings shall be in the same configuration as used for the probe calibrations in the wind tunnel. Temperature gauges used for wind tunnel calibrations shall be capable of measuring temperature to within ±0.6 °C (±1 °F) of the temperature of the flowing gas stream in the wind tunnel.
6.7 Stack or Duct Static Pressure Measurement. The pressure-measuring device used with the probe shall be as specified in section 6.4 of this method. The static tap of a standard (Prandtl type) pitot tube or one leg of a Type S pitot tube with the face opening planes positioned parallel to the gas flow may be used for this measurement. Also acceptable is the pressure differential reading of P1-Pbar from a five-hole prism-shaped probe (e.g., Type DA or DAT probe) with the P1 pressure port face opening positioned parallel to the gas flow in the same manner as the Type S probe. However, the spherical probe, as specified in section 6.1.2, is unable to provide this measurement and shall not be used to take static pressure measurements. Static pressure measurement is further described in section 8.11.
6.8 Barometer. Same as Method 2, section 2.5.
6.9 Gas Density Determination Equipment. Method 3 or 3A shall be used to determine the dry molecular weight of the stack gas. Method 4 shall be used for moisture content determination and computation of stack gas wet molecular weight. Other methods may be used, if approved by the Administrator.
6.10 Calibration Pitot Tube. Same as Method 2, section 2.7.
6.11 Wind Tunnel for Probe Calibration. Wind tunnels used to calibrate velocity probes must meet the following design specifications.
6.11.1 Test section cross-sectional area. The flowing gas stream shall be confined within a circular, rectangular, or elliptical duct. The cross-sectional area of the tunnel must be large enough to ensure fully developed flow in the presence of both the calibration pitot tube and the tested probe. The calibration site, or “test section,” of the wind tunnel shall have a minimum diameter of 30.5 cm (12 in.) for circular or elliptical duct cross-sections or a minimum width of 30.5 cm (12 in.) on the shorter side for rectangular cross-sections. Wind tunnels shall meet the probe blockage provisions of this section and the qualification requirements prescribed in section 10.1. The projected area of the portion of the probe head, shaft, and attached devices inside the wind tunnel during calibration shall represent no more than 4 percent of the cross-sectional area of the tunnel. The projected area shall include the combined area of the calibration pitot tube and the tested probe if both probes are placed simultaneously in the same cross-sectional plane in the wind tunnel, or the larger projected area of the two probes if they are placed alternately in the wind tunnel.
6.11.2 Velocity range and stability. The wind tunnel should be capable of maintaining velocities between 6.1 m/sec and 30.5 m/sec (20 ft/sec and 100 ft/sec). The wind tunnel shall produce fully developed flow patterns that are stable and parallel to the axis of the duct in the test section.
6.11.3 Flow profile at the calibration location. The wind tunnel shall provide axial flow within the test section calibration location (as defined in section 3.20). Yaw and pitch angles in the calibration location shall be within ±3° of 0°. The procedure for determining that this requirement has been met is described in section 10.1.2.
6.11.4 Entry ports in the wind tunnel test section.
6.11.4.1 Port for tested probe. A port shall be constructed for the tested probe. The port should have an elongated slot parallel to the axis of the duct at the test section. The elongated slot should be of sufficient length to allow attaining all the pitch angles at which the probe will be calibrated for use in the field. To facilitate alignment of the probe during calibration, the test section should include a window constructed of a transparent material to allow the tested probe to be viewed. This port shall be located to allow the head of the tested probe to be positioned within the calibration location (as defined in section 3.20) at all pitch angle settings.
6.11.4.2 Port for verification of axial flow. Depending on the equipment selected to conduct the axial flow verification prescribed in section 10.1.2, a second port, located 90° from the entry port for the tested probe, may be needed to allow verification that the gas flow is parallel to the central axis of the test section. This port should be located and constructed so as to allow one of the probes described in section 10.1.2.2 to access the same test point(s) that are accessible from the port described in section 6.11.4.1.
6.11.4.3 Port for calibration pitot tube. The calibration pitot tube shall be used in the port for the tested probe or a separate entry port. In either case, all measurements with the calibration pitot tube shall be made at the same point within the wind tunnel over the course of a probe calibration. The measurement point for the calibration pitot tube shall meet the same specifications for distance from the wall and for axial flow as described in section 3.20 for the wind tunnel calibration location.
6.11.5 Pitch angle protractor plate. A protractor plate shall be attached directly under the port used with the tested probe and set in a fixed position to indicate the pitch angle position of the probe relative to the longitudinal axis of the wind tunnel duct (similar to Figure 2F-8). The protractor plate shall indicate angles in 5° increments with a minimum resolution of ±2°. The tested probe shall be able to be locked into position at the desired pitch angle delineated on the protractor. The probe head position shall be maintained within the calibration location (as defined in section 3.20) in the test section of the wind tunnel during all tests across the range of pitch angles.
7.0 Reagents and Standards [Reserved] 8.0 Sample Collection and Analysis8.1 Equipment Inspection and Set-Up
8.1.1 All probes, differential pressure-measuring devices, yaw angle-measuring devices, thermocouples, and barometers shall have a current, valid calibration before being used in a field test. (See sections 10.3.3, 10.3.4, and 10.5 through10.10 for the applicable calibration requirements.)
8.1.2 Before each field use of a 3-D probe, perform a visual inspection to verify the physical condition of the probe head according to the procedures in section 10.2. Record the inspection results on a form similar to Table 2F-1. If there is visible damage to the 3-D probe, the probe shall not be used until it is recalibrated.
8.1.3 After verifying that the physical condition of the probe head is acceptable, set up the apparatus using lengths of flexible tubing that are as short as practicable. Surge tanks installed between the probe and pressure-measuring device may be used to dampen pressure fluctuations provided that an adequate measurement response time (see section 8.8) is maintained.
8.2 Horizontal Straightness Check. A horizontal straightness check shall be performed before the start of each field test, except as otherwise specified in this section. Secure the fully assembled probe (including the probe head and all probe shaft extensions) in a horizontal position using a stationary support at a point along the probe shaft approximating the location of the stack or duct entry port when the probe is sampling at the farthest traverse point from the stack or duct wall. The probe shall be rotated to detect bends. Use an angle-measuring device or trigonometry to determine the bend or sag between the probe head and the secured end. (See Figure 2F-9.) Probes that are bent or sag by more than 5° shall not be used. Although this check does not apply when the probe is used for a vertical traverse, care should be taken to avoid the use of bent probes when conducting vertical traverses. If the probe is constructed of a rigid steel material and consists of a main probe without probe extensions, this check need only be performed before the initial field use of the probe, when the probe is recalibrated, when a change is made to the design or material of the probe assembly, and when the probe becomes bent. With such probes, a visual inspection shall be made of the fully assembled probe before each field test to determine if a bend is visible. The probe shall be rotated to detect bends. The inspection results shall be documented in the field test report. If a bend in the probe is visible, the horizontal straightness check shall be performed before the probe is used.
8.3 Rotational Position Check. Before each field test, and each time an extension is added to the probe during a field test, a rotational position check shall be performed on all manually operated probes (except as noted in section 8.3.5, below) to ensure that, throughout testing, the angle-measuring device is either: aligned to within ±1° of the rotational position of the reference scribe line; or is affixed to the probe such that the rotational offset of the device from the reference scribe line is known to within ±1°. This check shall consist of direct measurements of the rotational positions of the reference scribe line and angle-measuring device sufficient to verify that these specifications are met. Annex A in section 18 of this method gives recommended procedures for performing the rotational position check, and Table 2F-2 gives an example data form. Procedures other than those recommended in Annex A in section 18 may be used, provided they demonstrate whether the alignment specification is met and are explained in detail in the field test report.
8.3.1 Angle-measuring device rotational offset. The tester shall maintain a record of the angle-measuring device rotational offset, RADO, as defined in section 3.1. Note that RADO is assigned a value of 0° when the angle-measuring device is aligned to within ±1° of the rotational position of the reference scribe line. The RADO shall be used to determine the yaw angle of flow in accordance with section 8.9.4.
8.3.2 Sign of angle-measuring device rotational offset. The sign of RADO is positive when the angle-measuring device (as viewed from the “tail” end of the probe) is positioned in a clockwise direction from the reference scribe line and negative when the device is positioned in a counterclockwise direction from the reference scribe line.
8.3.3 Angle-measuring devices that can be independently adjusted (e.g., by means of a set screw), after being locked into position on the probe sheath, may be used. However, the RADO must also take into account this adjustment.
8.3.4 Post-test check. If probe extensions remain attached to the main probe throughout the field test, the rotational position check shall be repeated, at a minimum, at the completion of the field test to ensure that the angle-measuring device has remained within ±2° of its rotational position established prior to testing. At the discretion of the tester, additional checks may be conducted after completion of testing at any sample port or after any test run. If the ±2° specification is not met, all measurements made since the last successful rotational position check must be repeated. section 18.1.1.3 of Annex A provides an example procedure for performing the post-test check.
8.3.5 Exceptions.
8.3.5.1 A rotational position check need not be performed if, for measurements taken at all velocity traverse points, the yaw angle-measuring device is mounted and aligned directly on the reference scribe line specified in sections 6.1.6.1 and 6.1.6.3 and no independent adjustments, as described in section 8.3.3, are made to the device's rotational position.
8.3.5.2 If extensions are detached and re-attached to the probe during a field test, a rotational position check need only be performed the first time an extension is added to the probe, rather than each time the extension is re-attached, if the probe extension is designed to be locked into a mechanically fixed rotational position (e.g., through use of interlocking grooves) that can re-establish the initial rotational position to within ±1°.
8.4 Leak Checks. A pre-test leak check shall be conducted before each field test. A post-test check shall be performed at the end of the field test, but additional leak checks may be conducted after any test run or group of test runs. The post-test check may also serve as the pre-test check for the next group of test runs. If any leak check is failed, all runs since the last passed leak check are invalid. While performing the leak check procedures, also check each pressure device's responsiveness to the changes in pressure.
8.4.1 To perform the leak check, pressurize the probe's P1 pressure port until at least 7.6 cm H2O (3 in. H2O) pressure, or a pressure corresponding to approximately 75 percent of the pressure-measuring device's measurement scale, whichever is less, registers on the device; then, close off the pressure port. The pressure shall remain stable [±2.5 mm H2O (±0.10 in. H2O)] for at least 15 seconds. Check the P2, P3, P4, and P5 pressure ports in the same fashion. Other leak-check procedures may be used, if approved by the Administrator.
8.5 Zeroing the Differential Pressure-measuring Device. Zero each differential pressure-measuring device, including the device used for yaw nulling, before each field test. At a minimum, check the zero after each field test. A zero check may also be performed after any test run or group of test runs. For fluid manometers and mechanical pressure gauges (e.g., MagnehelicΔ gauges), the zero reading shall not deviate from zero by more than ±0.8 mm H2O (±0.03 in. H2O) or one minor scale division, whichever is greater, between checks. For electronic manometers, the zero reading shall not deviate from zero between checks by more than: ±0.3 mm H2O (±0.01 in. H2O), for full scales less than or equal to 5.1 cm H2O (2.0 in. H2O); or ±0.8 mm H2O (±0.03 in. H2O), for full scales greater than 5.1 cm H2O (2.0 in. H2O). (Note: If negative zero drift is not directly readable, estimate the reading based on the position of the gauge oil in the manometer or of the needle on the pressure gauge.) In addition, for all pressure-measuring devices except those used exclusively for yaw nulling, the zero reading shall not deviate from zero by more than 5 percent of the average measured differential pressure at any distinct process condition or load level. If any zero check is failed at a specific process condition or load level, all runs conducted at that process condition or load level since the last passed zero check are invalid.
8.6 Traverse Point Verification. The number and location of the traverse points shall be selected based on Method 1 guidelines. The stack or duct diameter and port nipple lengths, including any extension of the port nipples into stack or duct, shall be verified the first time the test is performed; retain and use this information for subsequent field tests, updating it as required. Physically measure the stack or duct dimensions or use a calibrated laser device; do not use engineering drawings of the stack or duct. The probe length necessary to reach each traverse point shall be recorded to within ±6.4 mm (±1/4 in.) and, for manual probes, marked on the probe sheath. In determining these lengths, the tester shall take into account both the distance that the port flange projects outside of the stack and the depth that any port nipple extends into the gas stream. The resulting point positions shall reflect the true distances from the inside wall of the stack or duct, so that when the tester aligns any of the markings with the outside face of the stack port, the probe's impact port shall be located at the appropriate distance from the inside wall for the respective Method 1 traverse point. Before beginning testing at a particular location, an out-of-stack or duct verification shall be performed on each probe that will be used to ensure that these position markings are correct. The distances measured during the verification must agree with the previously calculated distances to within ±1/4 in. For manual probes, the traverse point positions shall be verified by measuring the distance of each mark from the probe's P1 pressure port. A comparable out-of-stack test shall be performed on automated probe systems. The probe shall be extended to each of the prescribed traverse point positions. Then, the accuracy of the positioning for each traverse point shall be verified by measuring the distance between the port flange and the probe's P1 pressure port.
8.7 Probe Installation. Insert the probe into the test port. A solid material shall be used to seal the port.
8.8 System Response Time. Determine the response time of the probe measurement system. Insert and position the “cold” probe (at ambient temperature and pressure) at any Method 1 traverse point. Read and record the probe's P1-P2 differential pressure, temperature, and elapsed time at 15-second intervals until stable readings for both pressure and temperature are achieved. The response time is the longer of these two elapsed times. Record the response time.
8.9 Sampling.
8.9.1 Yaw angle measurement protocol. With manual probes, yaw angle measurements may be obtained in two alternative ways during the field test, either by using a yaw angle-measuring device (e.g., digital inclinometer) affixed to the probe, or using a protractor wheel and pointer assembly. For horizontal traversing, either approach may be used. For vertical traversing, i.e., when measuring from on top or into the bottom of a horizontal duct, only the protractor wheel and pointer assembly may be used. With automated probes, curve-fitting protocols may be used to obtain yaw-angle measurements.
8.9.1.1 If a yaw angle-measuring device affixed to the probe is to be used, lock the device on the probe sheath, aligning it either on the reference scribe line or in the rotational offset position established under section 8.3.1.
8.9.1.2 If a protractor wheel and pointer assembly is to be used, follow the procedures in Annex B of this method.
8.9.1.3 Other yaw angle-determination procedures. If approved by the Administrator, other procedures for determining yaw angle may be used, provided that they are verified in a wind tunnel to be able to perform the yaw angle calibration procedure as described in section 10.5.
8.9.2 Sampling strategy. At each traverse point, first yaw-null the probe, as described in section 8.9.3, below. Then, with the probe oriented into the direction of flow, measure and record the yaw angle, the differential pressures and the temperature at the traverse point, after stable readings are achieved, in accordance with sections 8.9.4 and 8.9.5. At the start of testing in each port (i.e., after a probe has been inserted into the flue gas stream), allow at least the response time to elapse before beginning to take measurements at the first traverse point accessed from that port. Provided that the probe is not removed from the flue gas stream, measurements may be taken at subsequent traverse points accessed from the same test port without waiting again for the response time to elapse.
8.9.3 Yaw-nulling procedure. In preparation for yaw angle determination, the probe must first be yaw nulled. After positioning the probe at the appropriate traverse point, perform the following procedures.
8.9.3.1 Rotate the probe until a null differential pressure reading (the difference in pressures across the P2 and P3 pressure ports is zero, i.e., P2 = P3) is indicated by the yaw angle pressure gauge. Read and record the angle displayed by the angle-measuring device.
8.9.3.2 Sign of the measured angle. The angle displayed on the angle-measuring device is considered positive when the probe's impact pressure port (as viewed from the “tail” end of the probe) is oriented in a clockwise rotational position relative to the stack or duct axis and is considered negative when the probe's impact pressure port is oriented in a counterclockwise rotational position (see Figure 2F-10).
8.9.4 Yaw angle determination. After performing the yaw-nulling procedure in section 8.9.3, determine the yaw angle of flow according to one of the following procedures. Special care must be observed to take into account the signs of the recorded angle and all offsets.
8.9.4.1 Direct-reading. If all rotational offsets are zero or if the angle-measuring device rotational offset (RADO) determined in section 8.3 exactly compensates for the scribe line rotational offset (RSLO) determined in section 10.5, then the magnitude of the yaw angle is equal to the displayed angle-measuring device reading from section 8.9.3.1. The algebraic sign of the yaw angle is determined in accordance with section 8.9.3.2.
Note:Under certain circumstances (e.g., testing of horizontal ducts), a 90° adjustment to the angle-measuring device readings may be necessary to obtain the correct yaw angles.
8.9.4.2 Compensation for rotational offsets during data reduction. When the angle-measuring device rotational offset does not compensate for reference scribe line rotational offset, the following procedure shall be used to determine the yaw angle:
(a) Enter the reading indicated by the angle-measuring device from section 8.9.3.1.
(b) Associate the proper algebraic sign from section 8.9.3.2 with the reading in step (a).
(c) Subtract the reference scribe line rotational offset, RSLO, from the reading in step (b).
(d) Subtract the angle-measuring device rotational offset, RADO, if any, from the result obtained in step (c).
(e) The final result obtained in step (d) is the yaw angle of flow.
Note:It may be necessary to first apply a 90° adjustment to the reading in step (a), in order to obtain the correct yaw angle.
8.9.4.3 Record the yaw angle measurements on a form similar to Table 2F-3.
8.9.5 Velocity determination. Maintain the probe rotational position established during the yaw angle determination. Then, begin recording the pressure-measuring device readings for the impact pressure (P1-P2) and pitch angle pressure (P4-P5). These pressure measurements shall be taken over a sampling period of sufficiently long duration to ensure representative readings at each traverse point. If the pressure measurements are determined from visual readings of the pressure device or display, allow sufficient time to observe the pulsation in the readings to obtain a sight-weighted average, which is then recorded manually. If an automated data acquisition system (e.g., data logger, computer-based data recorder, strip chart recorder) is used to record the pressure measurements, obtain an integrated average of all pressure readings at the traverse point. Stack or duct gas temperature measurements shall be recorded, at a minimum, once at each traverse point. Record all necessary data as shown in the example field data form (Table 2F-3).
8.9.6 Alignment check. For manually operated probes, after the required yaw angle and differential pressure and temperature measurements have been made at each traverse point, verify (e.g., by visual inspection) that the yaw angle-measuring device has remained in proper alignment with the reference scribe line or with the rotational offset position established in section 8.3. If, for a particular traverse point, the angle-measuring device is found to be in proper alignment, proceed to the next traverse point; otherwise, re-align the device and repeat the angle and differential pressure measurements at the traverse point. In the course of a traverse, if a mark used to properly align the angle-measuring device (e.g., as described in section 18.1.1.1) cannot be located, re-establish the alignment mark before proceeding with the traverse.
8.10 Probe Plugging. Periodically check for plugging of the pressure ports by observing the responses on pressure differential readouts. Plugging causes erratic results or sluggish responses. Rotate the probe to determine whether the readouts respond in the expected direction. If plugging is detected, correct the problem and repeat the affected measurements.
8.11 Static Pressure. Measure the static pressure in the stack or duct using the equipment described in section 6.7.
8.11.1 If a Type DA or DAT probe is used for this measurement, position the probe at or between any traverse point(s) and rotate the probe until a null differential pressure reading is obtained at P2-P3. Rotate the probe 90°. Disconnect the P2 pressure side of the probe and read the pressure P1-Pbar and record as the static pressure. (Note: The spherical probe, specified in section 6.1.2, is unable to provide this measurement and shall not be used to take static pressure measurements.)
8.11.2 If a Type S probe is used for this measurement, position the probe at or between any traverse point(s) and rotate the probe until a null differential pressure reading is obtained. Disconnect the tubing from one of the pressure ports; read and record the ΔP. For pressure devices with one-directional scales, if a deflection in the positive direction is noted with the negative side disconnected, then the static pressure is positive. Likewise, if a deflection in the positive direction is noted with the positive side disconnected, then the static pressure is negative.
8.12 Atmospheric Pressure. Determine the atmospheric pressure at the sampling elevation during each test run following the procedure described in section 2.5 of Method 2.
8.13 Molecular Weight. Determine the stack gas dry molecular weight. For combustion processes or processes that emit essentially CO2, O2, CO, and N2, use Method 3 or 3A. For processes emitting essentially air, an analysis need not be conducted; use a dry molecular weight of 29.0. Other methods may be used, if approved by the Administrator.
8.14 Moisture. Determine the moisture content of the stack gas using Method 4 or equivalent.
8.15 Data Recording and Calculations. Record all required data on a form similar to Table 2F-3.
8.15.1 Selection of appropriate calibration curves. Choose the appropriate pair of F1 and F2 versus pitch angle calibration curves, created as described in section 10.6.
8.15.2 Pitch angle derivation. Use the appropriate calculation procedures in section 12.2 to find the pitch angle ratios that are applicable at each traverse point. Then, find the pitch angles corresponding to these pitch angle ratios on the “F1 versus pitch angle” curve for the probe.
8.15.3 Velocity calibration coefficient derivation. Use the pitch angle obtained following the procedures described in section 8.15.2 to find the corresponding velocity calibration coefficients from the “F2 versus pitch angle” calibration curve for the probe.
8.15.4 Calculations. Calculate the axial velocity at each traverse point using the equations presented in section 12.2 to account for the yaw and pitch angles of flow. Calculate the test run average stack gas velocity by finding the arithmetic average of the point velocity results in accordance with sections 12.3 and 12.4, and calculate the stack gas volumetric flow rate in accordance with section 12.5 or 12.6, as applicable.
9.0 Quality Control9.1 Quality Control Activities. In conjunction with the yaw angle determination and the pressure and temperature measurements specified in section 8.9, the following quality control checks should be performed.
9.1.1 Range of the differential pressure gauge. In accordance with the specifications in section 6.4, ensure that the proper differential pressure gauge is being used for the range of ΔP values encountered. If it is necessary to change to a more sensitive gauge, replace the gauge with a gauge calibrated according to section 10.3.3, perform the leak check described in section 8.4 and the zero check described in section 8.5, and repeat the differential pressure and temperature readings at each traverse point.
9.1.2 Horizontal stability check. For horizontal traverses of a stack or duct, visually check that the probe shaft is maintained in a horizontal position prior to taking a pressure reading. Periodically, during a test run, the probe's horizontal stability should be verified by placing a carpenter's level, a digital inclinometer, or other angle-measuring device on the portion of the probe sheath that extends outside of the test port. A comparable check should be performed by automated systems.
10.0 Calibration10.1 Wind Tunnel Qualification Checks. To qualify for use in calibrating probes, a wind tunnel shall have the design features specified in section 6.11 and satisfy the following qualification criteria. The velocity pressure cross-check in section 10.1.1 and axial flow verification in section 10.1.2 shall be performed before the initial use of the wind tunnel and repeated immediately after any alteration occurs in the wind tunnel's configuration, fans, interior surfaces, straightening vanes, controls, or other properties that could reasonably be expected to alter the flow pattern or velocity stability in the tunnel. The owner or operator of a wind tunnel used to calibrate probes according to this method shall maintain records documenting that the wind tunnel meets the requirements of sections 10.1.1 and 10.1.2 and shall provide these records to the Administrator upon request.
10.1.1 Velocity pressure cross-check. To verify that the wind tunnel produces the same velocity at the tested probe head as at the calibration pitot tube impact port, perform the following cross-check. Take three differential pressure measurements at the fixed calibration pitot tube location, using the calibration pitot tube specified in section 6.10, and take three measurements with the calibration pitot tube at the wind tunnel calibration location, as defined in section 3.20. Alternate the measurements between the two positions. Perform this procedure at the lowest and highest velocity settings at which the probes will be calibrated. Record the values on a form similar to Table 2F-4. At each velocity setting, the average velocity pressure obtained at the wind tunnel calibration location shall be within ±2 percent or 2.5 mm H2O (0.01 in. H2O), whichever is less restrictive, of the average velocity pressure obtained at the fixed calibration pitot tube location. This comparative check shall be performed at 2.5-cm (1-in.), or smaller, intervals across the full length, width, and depth (if applicable) of the wind tunnel calibration location. If the criteria are not met at every tested point, the wind tunnel calibration location must be redefined, so that acceptable results are obtained at every point. Include the results of the velocity pressure cross-check in the calibration data section of the field test report. (See section 16.1.4.)
10.1.2 Axial flow verification. The following procedures shall be performed to demonstrate that there is fully developed axial flow within the calibration location and at the calibration pitot tube location. Two testing options are available to conduct this check.
10.1.2.1 Using a calibrated 3-D probe. A 3-D probe that has been previously calibrated in a wind tunnel with documented axial flow (as defined in section 3.21) may be used to conduct this check. Insert the calibrated 3-D probe into the wind tunnel test section using the tested probe port. Following the procedures in sections 8.9 and 12.2 of this method, determine the yaw and pitch angles at all the point(s) in the test section where the velocity pressure cross-check, as specified in section 10.1.1, is performed. This includes all the points in the calibration location and the point where the calibration pitot tube will be located. Determine the yaw and pitch angles at each point. Repeat these measurements at the highest and lowest velocities at which the probes will be calibrated. Record the values on a form similar to Table 2F-5. Each measured yaw and pitch angle shall be within ±3° of 0°. Exceeding the limits indicates unacceptable flow in the test section. Until the problem is corrected and acceptable flow is verified by repetition of this procedure, the wind tunnel shall not be used for calibration of probes. Include the results of the axial flow verification in the calibration data section of the field test report. (See section 16.1.4.)
10.1.2.2 Using alternative probes. Axial flow verification may be performed using an uncalibrated prism-shaped 3-D probe (e.g., DA or DAT probe) or an uncalibrated wedge probe. (Figure 2F-11 illustrates a typical wedge probe.) This approach requires use of two ports: the tested probe port and a second port located 90° from the tested probe port. Each port shall provide access to all the points within the wind tunnel test section where the velocity pressure cross-check, as specified in section 10.1.1, is conducted. The probe setup shall include establishing a reference yaw-null position on the probe sheath to serve as the location for installing the angle-measuring device. Physical design features of the DA, DAT, and wedge probes are relied on to determine the reference position. For the DA or DAT probe, this reference position can be determined by setting a digital inclinometer on the flat facet where the P1 pressure port is located and then identifying the rotational position on the probe sheath where a second angle-measuring device would give the same angle reading. The reference position on a wedge probe shaft can be determined either geometrically or by placing a digital inclinometer on each side of the wedge and rotating the probe until equivalent readings are obtained. With the latter approach, the reference position is the rotational position on the probe sheath where an angle-measuring device would give a reading of 0°. After installing the angle-measuring device in the reference yaw-null position on the probe sheath, determine the yaw angle from the tested port. Repeat this measurement using the 90° offset port, which provides the pitch angle of flow. Determine the yaw and pitch angles at all the point(s) in the test section where the velocity pressure cross-check, as specified in section 10.1.1, is performed. This includes all the points in the wind tunnel calibration location and the point where the calibration pitot tube will be located. Perform this check at the highest and lowest velocities at which the probes will be calibrated. Record the values on a form similar to Table 2F-5. Each measured yaw and pitch angle shall be within ±3° of 0°. Exceeding the limits indicates unacceptable flow in the test section. Until the problem is corrected and acceptable flow is verified by repetition of this procedure, the wind tunnel shall not be used for calibration of probes. Include the results in the probe calibration report.
10.1.3 Wind tunnel audits.
10.1.3.1 Procedure. Upon the request of the Administrator, the owner or operator of a wind tunnel shall calibrate a 3-D audit probe in accordance with the procedures described in sections 10.3 through 10.6. The calibration shall be performed at two velocities and over a pitch angle range that encompasses the velocities and pitch angles typically used for this method at the facility. The resulting calibration data and curves shall be submitted to the Agency in an audit test report. These results shall be compared by the Agency to reference calibrations of the audit probe at the same velocity and pitch angle settings obtained at two different wind tunnels.
10.1.3.2 Acceptance criteria. The audited tunnel's calibration is acceptable if all of the following conditions are satisfied at each velocity and pitch setting for the reference calibration obtained from at least one of the wind tunnels. For pitch angle settings between −15° and + 15°, no velocity calibration coefficient (i.e., F2) may differ from the corresponding reference value by more than 3 percent. For pitch angle settings outside of this range (i.e., less than −15° and greater than + 15°), no velocity calibration coefficient may differ by more than 5 percent from the corresponding reference value. If the acceptance criteria are not met, the audited wind tunnel shall not be used to calibrate probes for use under this method until the problems are resolved and acceptable results are obtained upon completion of a subsequent audit.
10.2 Probe Inspection. Before each calibration of a 3-D probe, carefully examine the physical condition of the probe head. Particular attention shall be paid to the edges of the pressure ports and the surfaces surrounding these ports. Any dents, scratches, or asymmetries on the edges of the pressure ports and any scratches or indentations on the surfaces surrounding the pressure ports shall be noted because of the potential effect on the probe's pressure readings. If the probe has been previously calibrated, compare the current condition of the probe's pressure ports and surfaces to the results of the inspection performed during the probe's most recent wind tunnel calibration. Record the results of this inspection on a form and in diagrams similar to Table 2F-1. The information in Table 2F-1 will be used as the basis for comparison during the probe head inspections performed before each subsequent field use.
10.3 Pre-Calibration Procedures. Prior to calibration, a scribe line shall have been placed on the probe in accordance with section 10.4. The yaw angle and velocity calibration procedures shall not begin until the pre-test requirements in sections 10.3.1 through 10.3.4 have been met.
10.3.1 Perform the horizontal straightness check described in section 8.2 on the probe assembly that will be calibrated in the wind tunnel.
10.3.2 Perform a leak check in accordance with section 8.4.
10.3.3 Except as noted in section 10.3.3.3, calibrate all differential pressure-measuring devices to be used in the probe calibrations, using the following procedures. At a minimum, calibrate these devices on each day that probe calibrations are performed.
10.3.3.1 Procedure. Before each wind tunnel use, all differential pressure-measuring devices shall be calibrated against the reference device specified in section 6.4.3 using a common pressure source. Perform the calibration at three reference pressures representing 30, 60, and 90 percent of the full-scale range of the pressure-measuring device being calibrated. For an inclined-vertical manometer, perform separate calibrations on the inclined and vertical portions of the measurement scale, considering each portion of the scale to be a separate full-scale range. [For example, for a manometer with a 0- to 2.5-cm H2O (0- to 1-in. H2O) inclined scale and a 2.5- to 12.7-cm H2O (1- to 5-in. H2O) vertical scale, calibrate the inclined portion at 7.6, 15.2, and 22.9 mm H2O (0.3, 0.6, and 0.9 in. H2O), and calibrate the vertical portion at 3.8, 7.6, and 11.4 cm H2O (1.5, 3.0, and 4.5 in. H2O).] Alternatively, for the vertical portion of the scale, use three evenly spaced reference pressures, one of which is equal to or higher than the highest differential pressure expected in field applications.
10.3.3.2 Acceptance criteria. At each pressure setting, the two pressure readings made using the reference device and the pressure-measuring device being calibrated shall agree to within ±2 percent of full scale of the device being calibrated or 0.5 mm H2O (0.02 in. H2O), whichever is less restrictive. For an inclined-vertical manometer, these requirements shall be met separately using the respective full-scale upper limits of the inclined and vertical portions of the scale. Differential pressure-measuring devices not meeting the #2 percent of full scale or 0.5 mm H2O (0.02 in. H2O) calibration requirement shall not be used.
10.3.3.3 Exceptions. Any precision manometer that meets the specifications for a reference device in section 6.4.3 and that is not used for field testing does not require calibration, but must be leveled and zeroed before each wind tunnel use. Any pressure device used exclusively for yaw nulling does not require calibration, but shall be checked for responsiveness to rotation of the probe prior to each wind tunnel use.
10.3.4 Calibrate digital inclinometers on each day of wind tunnel or field testing (prior to beginning testing) using the following procedures. Calibrate the inclinometer according to the manufacturer's calibration procedures. In addition, use a triangular block (illustrated in Figure 2F-12) with a known angle, θ independently determined using a protractor or equivalent device, between two adjacent sides to verify the inclinometer readings.
Note:If other angle-measuring devices meeting the provisions of section 6.2.3 are used in place of a digital inclinometer, comparable calibration procedures shall be performed on such devices.)
Secure the triangular block in a fixed position. Place the inclinometer on one side of the block (side A) to measure the angle of inclination (R1). Repeat this measurement on the adjacent side of the block (side B) using the inclinometer to obtain a second angle reading (R2). The difference of the sum of the two readings from 180° (i.e., 180° −R1 −R2) shall be within ±2° of the known angle, Θ10.4 Placement of Reference Scribe Line. Prior to the first calibration of a probe, a line shall be permanently inscribed on the main probe sheath to serve as a reference mark for determining yaw angles. Annex C in section 18 of this method gives a guideline for placement of the reference scribe line.
10.4.1 This reference scribe line shall meet the specifications in sections 6.1.6.1 and 6.1.6.3 of this method. To verify that the alignment specification in section 6.1.6.3 is met, secure the probe in a horizontal position and measure the rotational angle of each scribe line and scribe line segment using an angle-measuring device that meets the specifications in section 6.2.1 or 6.2.3. For any scribe line that is longer than 30.5 cm (12 in.), check the line's rotational position at 30.5-cm (12-in.) intervals. For each line segment that is 30.5 cm (12 in.) or less in length, check the rotational position at the two endpoints of the segment. To meet the alignment specification in section 6.1.6.3, the minimum and maximum of all of the rotational angles that are measured along the full length of the main probe must not differ by more than 2°.
Note:A short reference scribe line segment [e.g., 15.2 cm (6 in.) or less in length] meeting the alignment specifications in section 6.1.6.3 is fully acceptable under this method. See section 18.1.1.1 of Annex A for an example of a probe marking procedure, suitable for use with a short reference scribe line.
10.4.2 The scribe line should be placed on the probe first and then its offset from the yaw-null position established (as specified in section 10.5). The rotational position of the reference scribe line relative to the yaw-null position of the probe, as determined by the yaw angle calibration procedure in section 10.5, is defined as the reference scribe line rotational offset, RSLO. The reference scribe line rotational offset shall be recorded and retained as part of the probe's calibration record.
10.4.3 Scribe line for automated probes. A scribe line may not be necessary for an automated probe system if a reference rotational position of the probe is built into the probe system design. For such systems, a “flat” (or comparable, clearly identifiable physical characteristic) should be provided on the probe casing or flange plate to ensure that the reference position of the probe assembly remains in a vertical or horizontal position. The rotational offset of the flat (or comparable, clearly identifiable physical characteristic) needed to orient the reference position of the probe assembly shall be recorded and maintained as part of the automated probe system's specifications.
10.5 Yaw Angle Calibration Procedure. For each probe used to measure yaw angles with this method, a calibration procedure shall be performed in a wind tunnel meeting the specifications in section 10.1 to determine the rotational position of the reference scribe line relative to the probe's yaw-null position. This procedure shall be performed on the main probe with all devices that will be attached to the main probe in the field [such as thermocouples or resistance temperature detectors (RTDs)] that may affect the flow around the probe head. Probe shaft extensions that do not affect flow around the probe head need not be attached during calibration. At a minimum, this procedure shall include the following steps.
10.5.1 Align and lock the angle-measuring device on the reference scribe line. If a marking procedure (such as that described in section 18.1.1.1) is used, align the angle-measuring device on a mark within ±1° of the rotational position of the reference scribe line. Lock the angle-measuring device onto the probe sheath at this position.
10.5.2 Zero the pressure-measuring device used for yaw nulling.
10.5.3 Insert the probe assembly into the wind tunnel through the entry port, positioning the probe's impact port at the calibration location. Check the responsiveness of the pressure-measurement device to probe rotation, taking corrective action if the response is unacceptable.
10.5.4 Ensure that the probe is in a horizontal position, using a carpenter's level.
10.5.5 Rotate the probe either clockwise or counterclockwise until a yaw null (P2 = P3) is obtained.
10.5.6 Use the reading displayed by the angle-measuring device at the yaw-null position to determine the magnitude of the reference scribe line rotational offset, RSLO, as defined in section 3.15. Annex D in section 18 of this method provides a recommended procedure for determining the magnitude of RSLO with a digital inclinometer and a second procedure for determining the magnitude of RSLO with a protractor wheel and pointer device. Table 2F-6 presents an example data form and Table 2F-7 is a look-up table with the recommended procedure. Procedures other than those recommended in Annex D in section 18 may be used, if they can determine RSLO to within ±1° and are explained in detail in the field test report. The algebraic sign of RSLO will either be positive, if the rotational position of the reference scribe line (as viewed from the “tail” end of the probe) is clockwise, or negative, if counterclockwise with respect to the probe's yaw-null position. (This is illustrated in Figure 2F-13.)
10.5.7 The steps in sections 10.5.3 through 10.5.6 shall be performed twice at each of the velocities at which the probe will be calibrated (in accordance with section 10.6). Record the values of RSLO.
10.5.8 The average of all of the RSLO values shall be documented as the reference scribe line rotational offset for the probe.
10.5.9 Use of reference scribe line offset. The reference scribe line rotational offset shall be used to determine the yaw angle of flow in accordance with section 8.9.4.
10.6 Pitch Angle and Velocity Pressure Calibrations. Use the procedures in sections 10.6.1 through 10.6.16 to generate an appropriate set (or sets) of pitch angle and velocity pressure calibration curves for each probe. The calibration procedure shall be performed on the main probe and all devices that will be attached to the main probe in the field (e.g., thermocouple or RTDs) that may affect the flow around the probe head. Probe shaft extensions that do not affect flow around the probe head need not be attached during calibration. (Note: If a sampling nozzle is part of the assembly, a wind tunnel demonstration shall be performed that shows the probe's ability to measure velocity and yaw null is not impaired when the nozzle is drawing a sample.) The calibration procedure involves generating two calibration curves, F1 versus pitch angle and F2 versus pitch angle. To generate these two curves, F1 and F2 shall be derived using Equations 2F-1 and 2F-2, below. Table 2F-8 provides an example wind tunnel calibration data sheet, used to log the measurements needed to derive these two calibration curves.
10.6.1 Calibration velocities. The tester may calibrate the probe at two nominal wind tunnel velocity settings of 18.3 m/sec and 27.4 m/sec (60 ft/sec and 90 ft/sec) and average the results of these calibrations, as described in section 10.6.16.1, in order to generate a set of calibration curves. If this option is selected, this single set of calibration curves may be used for all field applications over the entire velocity range allowed by the method. Alternatively, the tester may customize the probe calibration for a particular field test application (or for a series of applications), based on the expected average velocity(ies) at the test site(s). If this option is selected, generate each set of calibration curves by calibrating the probe at two nominal wind tunnel velocity settings, at least one of which is greater than or equal to the expected average velocity(ies) for the field application(s), and average the results as described in section 10.6.16.1. Whichever calibration option is selected, the probe calibration coefficients (F2 values) obtained at the two nominal calibration velocities shall, for the same pitch angle setting, meet the conditions specified in section 10.6.16.
10.6.2 Pitch angle calibration curve (F1 versus pitch angle). The pitch angle calibration involves generating a calibration curve of calculated F1 values versus tested pitch angles, where F1 is the ratio of the pitch pressure to the velocity pressure, i.e.,
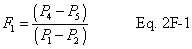
10.6.3 Velocity calibration curve (F2 versus pitch angle). The velocity calibration involves generating a calibration curve of the 3-D probe's F2 coefficient against the tested pitch angles, where
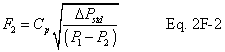
10.6.4 Connect the tested probe and calibration pitot probe to their respective pressure-measuring devices. Zero the pressure-measuring devices. Inspect and leak-check all pitot lines; repair or replace, if necessary. Turn on the fan, and allow the wind tunnel air flow to stabilize at the first of the two selected nominal velocity settings.
10.6.5 Position the calibration pitot tube at its measurement location (determined as outlined in section 6.11.4.3), and align the tube so that its tip is pointed directly into the flow. Ensure that the entry port surrounding the tube is properly sealed. The calibration pitot tube may either remain in the wind tunnel throughout the calibration, or be removed from the wind tunnel while measurements are taken with the probe being calibrated.
10.6.6 Set up the pitch protractor plate on the tested probe's entry port to establish the pitch angle positions of the probe to within ±2°.
10.6.7 Check the zero setting of each pressure-measuring device.
10.6.8 Insert the tested probe into the wind tunnel and align it so that its P1 pressure port is pointed directly into the flow and is positioned within the calibration location (as defined in section 3.20). Secure the probe at the 0° pitch angle position. Ensure that the entry port surrounding the probe is properly sealed.
10.6.9 Read the differential pressure from the calibration pitot tube (ΔPstd), and record its value. Read the barometric pressure to within ±2.5 mm Hg (±0.1 in. Hg) and the temperature in the wind tunnel to within 0.6 °C (1 °F). Record these values on a data form similar to Table 2F-8.
10.6.10 After the tested probe's differential pressure gauges have had sufficient time to stabilize, yaw null the probe, then obtain differential pressure readings for (P1-P2) and (P4-P5). Record the yaw angle and differential pressure readings. After taking these readings, ensure that the tested probe has remained at the yaw-null position.
10.6.11 Either take paired differential pressure measurements with both the calibration pitot tube and tested probe (according to sections 10.6.9 and 10.6.10) or take readings only with the tested probe (according to section 10.6.10) in 5° increments over the pitch-angle range for which the probe is to be calibrated. The calibration pitch-angle range shall be symmetric around 0° and shall exceed the largest pitch angle expected in the field by 5°. At a minimum, probes shall be calibrated over the range of −15° to + 15°. If paired calibration pitot tube and tested probe measurements are not taken at each pitch angle setting, the differential pressure from the calibration pitot tube shall be read, at a minimum, before taking the tested probe's differential pressure reading at the first pitch angle setting and after taking the tested probe's differential pressure readings at the last pitch angle setting in each replicate.
10.6.12 Perform a second replicate of the procedures in sections 10.6.5 through 10.6.11 at the same nominal velocity setting.
10.6.13 For each replicate, calculate the F1 and F2 values at each pitch angle. At each pitch angle, calculate the percent difference between the two F2 values using Equation 2F-3.

If the percent difference is less than or equal to 2 percent, calculate an average F1 value and an average F2 value at that pitch angle. If the percent difference is greater than 2 percent and less than or equal to 5 percent, perform a third repetition at that angle and calculate an average F1 value and an average F2 value using all three repetitions. If the percent difference is greater than 5 percent, perform four additional repetitions at that angle and calculate an average F1 value and an average F2 value using all six repetitions. When additional repetitions are required at any pitch angle, move the probe by at least 5° and then return to the specified pitch angle before taking the next measurement. Record the average values on a form similar to Table 2F-9.
10.6.14 Repeat the calibration procedures in sections 10.6.5 through 10.6.13 at the second selected nominal wind tunnel velocity setting.
10.6.15 Velocity drift check. The following check shall be performed, except when paired calibration pitot tube and tested probe pressure measurements are taken at each pitch angle setting. At each velocity setting, calculate the percent difference between consecutive differential pressure measurements made with the calibration pitot tube. If a measurement differs from the previous measurement by more than 2 percent or 0.25 mm H2O (0.01 in. H2O), whichever is less restrictive, the calibration data collected between these calibration pitot tube measurements may not be used, and the measurements shall be repeated.
10.6.16 Compare the averaged F2 coefficients obtained from the calibrations at the two selected nominal velocities, as follows. At each pitch angle setting, use Equation 2F-3 to calculate the difference between the corresponding average F2 values at the two calibration velocities. At each pitch angle in the −15° to + 15° range, the percent difference between the average F2 values shall not exceed 3.0 percent. For pitch angles outside this range (i.e., less than −15°0 and greater than + 15°), the percent difference shall not exceed 5.0 percent.
10.6.16.1 If the applicable specification in section 10.6.16 is met at each pitch angle setting, average the results obtained at the two nominal calibration velocities to produce a calibration record of F1 and F2 at each pitch angle tested. Record these values on a form similar to Table 2F-9. From these values, generate one calibration curve representing F1 versus pitch angle and a second curve representing F2 versus pitch angle. Computer spreadsheet programs may be used to graph the calibration data and to develop polynomial equations that can be used to calculate pitch angles and axial velocities.
10.6.16.2 If the applicable specification in section 10.6.16 is exceeded at any pitch angle setting, the probe shall not be used unless: (1) the calibration is repeated at that pitch angle and acceptable results are obtained or (2) values of F1 and F2 are obtained at two nominal velocities for which the specifications in section 10.6.16 are met across the entire pitch angle range.
10.7 Recalibration. Recalibrate the probe using the procedures in section 10 either within 12 months of its first field use after its most recent calibration or after 10 field tests (as defined in section 3.4), whichever occurs later. In addition, whenever there is visible damage to the 3-D head, the probe shall be recalibrated before it is used again.
10.8 Calibration of pressure-measuring devices used in field tests. Before its initial use in a field test, calibrate each pressure-measuring device (except those used exclusively for yaw nulling) using the three-point calibration procedure described in section 10.3.3. The device shall be recalibrated according to the procedure in section 10.3.3 no later than 90 days after its first field use following its most recent calibration. At the discretion of the tester, more frequent calibrations (e.g., after a field test) may be performed. No adjustments, other than adjustments to the zero setting, shall be made to the device between calibrations.
10.8.1 Post-test calibration check. A single-point calibration check shall be performed on each pressure-measuring device after completion of each field test. At the discretion of the tester, more frequent single-point calibration checks (e.g., after one or more field test runs) may be performed. It is recommended that the post-test check be performed before leaving the field test site. The check shall be performed at a pressure between 50 and 90 percent of full scale by taking a common pressure reading with the tested device and a reference pressure-measuring device (as described in section 6.4.4) or by challenging the tested device with a reference pressure source (as described in section 6.4.4) or by performing an equivalent check using a reference device approved by the Administrator.
10.8.2 Acceptance criterion. At the selected pressure setting, the pressure readings made using the reference device and the tested device shall agree to within 3 percent of full scale of the tested device or 0.8 mm H2O (0.03 in. H2O), whichever is less restrictive. If this specification is met, the test data collected during the field test are valid. If the specification is not met, all test data collected since the last successful calibration or calibration check are invalid and shall be repeated using a pressure-measuring device with a current, valid calibration. Any device that fails the calibration check shall not be used in a field test until a successful recalibration is performed according to the procedures in section 10.3.3.
10.9 Temperature Gauges. Same as Method 2, section 4.3. The alternative thermocouple calibration procedures outlined in Emission Measurement Center (EMC) Approved Alternative Method (ALT-011) “Alternative Method 2 Thermocouple Calibration Procedure” may be performed. Temperature gauges shall be calibrated no more than 30 days prior to the start of a field test or series of field tests and recalibrated no more than 30 days after completion of a field test or series of field tests.
10.10 Barometer. Same as Method 2, section 4.4. The barometer shall be calibrated no more than 30 days prior to the start of a field test or series of field tests.
11.0 Analytical ProcedureSample collection and analysis are concurrent for this method (see section 8.0).
12.0 Data Analysis and CalculationsThese calculations use the measured yaw angle, derived pitch angle, and the differential pressure and temperature measurements at individual traverse points to derive the axial flue gas velocity (va(i)) at each of those points. The axial velocity values at all traverse points that comprise a full stack or duct traverse are then averaged to obtain the average axial flue gas velocity (va (avg)). Round off figures only in the final calculation of reported values.
12.1 Nomenclature
A = Cross-sectional area of stack or duct, m 2 (ft 2). Bws = Water vapor in the gas stream (from Method 4 or alternative), proportion by volume. Kp Conversion factor (a constant),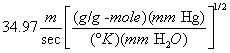
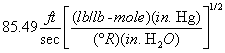

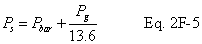


12.2 Traverse Point Velocity Calculations. Perform the following calculations from the measurements obtained at each traverse point.
12.2.1 Selection of calibration curves. Select calibration curves as described in section 10.6.1.
12.2.2 Traverse point pitch angle ratio. Use Equation 2F-1, as described in section 10.6.2, to calculate the pitch angle ratio, F1(i), at each traverse point.
12.2.3 Pitch angle. Use the pitch angle ratio, F1(i), to derive the pitch angle, θp(i), at traverse point i from the F1 versus pitch angle calibration curve generated under section 10.6.16.1.
12.2.4 Velocity calibration coefficient. Use the pitch angle, θp(i), to obtain the probe velocity calibration coefficient, F2(i), at traverse point i from the “velocity pressure calibration curve,” i.e., the F2 versus pitch angle calibration curve generated under section 10.6.16.1.
12.2.5 Axial velocity. Use the following equation to calculate the axial velocity, va(i), from the differential pressure (P1-P2)i and yaw angle, θy(i), measured at traverse point i and the previously calculated values for the velocity calibration coefficient, F2(i), absolute stack or duct standard temperature, Ts(i), absolute stack or duct pressure, Ps, molecular weight, Ms, and pitch angle, “θp(i).

12.2.6 Handling multiple measurements at a traverse point. For pressure or temperature devices that take multiple measurements at a traverse point, the multiple measurements (or where applicable, their square roots) may first be averaged and the resulting average values used in the equations above. Alternatively, the individual measurements may be used in the equations above and the resulting multiple calculated values may then be averaged to obtain a single traverse point value. With either approach, all of the individual measurements recorded at a traverse point must be used in calculating the applicable traverse point value.
12.3 Average Axial Velocity in Stack or Duct. Use the reported traverse point axial velocity in the following equation.
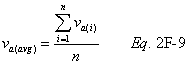
12.4 Acceptability of Results. The test results are acceptable and the calculated value of va(avg) may be reported as the average axial velocity for the test run if the conditions in either section 12.4.1 or 12.4.2 are met.
12.4.1 The calibration curves were generated at nominal velocities of 18.3 m/sec and 27.4 m/sec (60 ft/sec and 90 ft/sec).
12.4.2 The calibration curves were generated at nominal velocities other than 18.3 m/sec and 27.4 m/sec (60 ft/sec and 90 ft/sec), and the value of va(avg) obtained using Equation 2F-9 is less than or equal to at least one of the nominal velocities used to derive the F1 and F2 calibration curves.
12.4.3 If the conditions in neither section 12.4.1 nor section 12.4.2 are met, the test results obtained in Equation 2F-9 are not acceptable, and the steps in sections 12.2 and 12.3 must be repeated using a set of F1 and F2 calibration curves that satisfies the conditions specified in section 12.4.1 or 12.4.2.
12.5 Average Gas Wet Volumetric Flow Rate in Stack or Duct. Use the following equation to compute the average volumetric flow rate on a wet basis.

12.6 Average Gas Dry Volumetric Flow Rate in Stack or Duct. Use the following equation to compute the average volumetric flow rate on a dry basis.

16.1 Field Test Reports. Field test reports shall be submitted to the Agency according to applicable regulatory requirements. Field test reports should, at a minimum, include the following elements.
16.1.1 Description of the source. This should include the name and location of the test site, descriptions of the process tested, a description of the combustion source, an accurate diagram of stack or duct cross-sectional area at the test site showing the dimensions of the stack or duct, the location of the test ports, and traverse point locations and identification numbers or codes. It should also include a description and diagram of the stack or duct layout, showing the distance of the test location from the nearest upstream and downstream disturbances and all structural elements (including breachings, baffles, fans, straighteners, etc.) affecting the flow pattern. If the source and test location descriptions have been previously submitted to the Agency in a document (e.g., a monitoring plan or test plan), referencing the document in lieu of including this information in the field test report is acceptable.
16.1.2 Field test procedures. These should include a description of test equipment and test procedures. Testing conventions, such as traverse point numbering and measurement sequence (e.g., sampling from center to wall, or wall to center), should be clearly stated. Test port identification and directional reference for each test port should be included on the appropriate field test data sheets.
16.1.3 Field test data.
16.1.3.1 Summary of results. This summary should include the dates and times of testing and the average axial gas velocity and the average flue gas volumetric flow results for each run and tested condition.
16.1.3.2 Test data. The following values for each traverse point should be recorded and reported:
(a) P1-P2 and P4-P5 differential pressures
(b) Stack or duct gas temperature at traverse point i (ts(i))
(c) Absolute stack or duct gas temperature at traverse point i (Ts(i))
(d) Yaw angle at each traverse point i (θy(i))
(e) Pitch angle at each traverse point i (θp(i))
(f) Stack or duct gas axial velocity at traverse point i (va(i))
16.1.3.3 The following values should be reported once per run:
(a) Water vapor in the gas stream (from Method 4 or alternative), proportion by volume (Bws), measured at the frequency specified in the applicable regulation
(b) Molecular weight of stack or duct gas, dry basis (Md)
(c) Molecular weight of stack or duct gas, wet basis (Ms)
(d) Stack or duct static pressure (Pg)
(e) Absolute stack or duct pressure (Ps)
(f) Carbon dioxide concentration in the flue gas, dry basis ( 0/0d CO2)
(g) Oxygen concentration in the flue gas, dry basis ( 0/0d O2)
(h) Average axial stack or duct gas velocity (va(avg)) across all traverse points
(i) Gas volumetric flow rate corrected to standard conditions, dry or wet basis as required by the applicable regulation (Qsd or Qsw)
16.1.3.4 The following should be reported once per complete set of test runs:(a) Cross-sectional area of stack or duct at the test location (A)
(b) Measurement system response time (sec)
(c) Barometric pressure at measurement site (Pbar)
16.1.4 Calibration data. The field test report should include calibration data for all probes and test equipment used in the field test. At a minimum, the probe calibration data reported to the Agency should include the following:
(a) Date of calibration
(b) Probe type
(c) Probe identification number(s) or code(s)
(d) Probe inspection sheets
(e) Pressure measurements and intermediate calculations of F1 and F2 at each pitch angle used to obtain calibration curves in accordance with section 10.6 of this method
(f) Calibration curves (in graphic or equation format) obtained in accordance with sections 10.6.11 of this method
(g) Description and diagram of wind tunnel used for the calibration, including dimensions of cross-sectional area and position and size of the test section
(h) Documentation of wind tunnel qualification tests performed in accordance with section 10.1 of this method
16.1.5 Quality Assurance. Specific quality assurance and quality control procedures used during the test should be described.
17.0 Bibliography(1) 40 CFR Part 60, Appendix A, Method 1 - Sample and velocity traverses for stationary sources.
(2) 40 CFR Part 60, Appendix A, Method 2H - Determination of stack gas velocity taking into account velocity decay near the stack wall.
(3) 40 CFR Part 60, Appendix A, Method 2 - Determination of stack gas velocity and volumetric flow rate (Type S pitot tube).
(4) 40 CFR Part 60, Appendix A, Method 3 - Gas analysis for carbon dioxide, oxygen, excess air, and dry molecular weight.
(5) 40 CFR Part 60, Appendix A, Method 3A - Determination of oxygen and carbon dioxide concentrations in emissions from stationary sources (instrumental analyzer procedure).
(6) 40 CFR Part 60, Appendix A, Method 4 - Determination of moisture content in stack gases.
(7) Emission Measurement Center (EMC) Approved Alternative Method (ALT-011) “Alternative Method 2 Thermocouple Calibration Procedure.”
(8) Electric Power Research Institute, Interim Report EPRI TR-106698, “Flue Gas Flow Rate Measurement Errors,” June 1996.
(9) Electric Power Research Institute, Final Report EPRI TR-108110, “Evaluation of Heat Rate Discrepancy from Continuous Emission Monitoring Systems,” August 1997.
(10) Fossil Energy Research Corporation, Final Report, “Velocity Probe Tests in Non-axial Flow Fields,” November 1998, Prepared for the U.S. Environmental Protection Agency.
(11) Fossil Energy Research Corporation, “Additional Swirl Tunnel Tests: E-DAT and T-DAT Probes,” February 24, 1999, Technical Memorandum Prepared for U.S. Environmental Protection Agency, P.O. No. 7W-1193-NALX.
(12) Massachusetts Institute of Technology, Report WBWT-TR-1317, “Calibration of Eight Wind Speed Probes Over a Reynolds Number Range of 46,000 to 725,000 Per Foot, Text and Summary Plots,” Plus appendices, October 15, 1998, Prepared for The Cadmus Group, Inc.
(13) National Institute of Standards and Technology, Special Publication 250, “NIST Calibration Services Users Guide 1991,” Revised October 1991, U.S. Department of Commerce, p. 2.
(14) National Institute of Standards and Technology, 1998, “Report of Special Test of Air Speed Instrumentation, Four Prandtl Probes, Four S-Type Probes, Four French Probes, Four Modified Kiel Probes,” Prepared for the U.S. Environmental Protection Agency under IAG #DW13938432-01-0.
(15) National Institute of Standards and Technology, 1998, “Report of Special Test of Air Speed Instrumentation, Five Autoprobes,” Prepared for the U.S. Environmental Protection Agency under IAG #DW13938432-01-0.
(16) National Institute of Standards and Technology, 1998, “Report of Special Test of Air Speed Instrumentation, Eight Spherical Probes,” Prepared for the U.S. Environmental Protection Agency under IAG #DW13938432-01-0.
(17) National Institute of Standards and Technology, 1998, “Report of Special Test of Air Speed Instrumentation, Four DAT Probes,” Prepared for the U.S. Environmental Protection Agency under IAG #DW13938432-01-0.
(18) Norfleet, S.K., “An Evaluation of Wall Effects on Stack Flow Velocities and Related Overestimation Bias in EPA's Stack Flow Reference Methods,” EPRI CEMS User's Group Meeting, New Orleans, Louisiana, May 13-15, 1998.
(19) Page, J.J., E.A. Potts, and R.T. Shigehara, “3-D Pitot Tube Calibration Study,” EPA Contract No. 68-D1-0009, Work Assignment No. I-121, March 11, 1993.
(20) Shigehara, R.T., W.F. Todd, and W.S. Smith, “Significance of Errors in Stack Sampling Measurements,” Presented at the Annual Meeting of the Air Pollution Control Association, St. Louis, Missouri, June 14-19, 1970.
(21) The Cadmus Group, Inc., May 1999, “EPA Flow Reference Method Testing and Analysis: Findings Report,” EPA/430-R-99-009.
(22) The Cadmus Group, Inc., 1998, “EPA Flow Reference Method Testing and Analysis: Data Report, Texas Utilities, DeCordova Steam Electric Station, Volume I: Test Description and Appendix A (Data Distribution Package),” EPA/430-R-98-015a.
(23) The Cadmus Group, Inc., 1998, “EPA Flow Reference Method Testing and Analysis: Data Report, Texas Utilities, Lake Hubbard Steam Electric Station, Volume I: Test Description and Appendix A (Data Distribution Package),” EPA/430-R-98-017a.
(24) The Cadmus Group, Inc., 1998, “EPA Flow Reference Method Testing and Analysis: Data Report, Pennsylvania Electric Co., G.P.U. Genco Homer City Station: Unit 1, Volume I: Test Description and Appendix A (Data Distribution Package),” EPA/430-R-98-018a.
(25) The Cadmus Group, Inc., 1997, “EPA Flow Reference Method Testing and Analysis: Wind Tunnel Experimental Results,” EPA/430-R-97-013.
18.0 AnnexesAnnex A, C, and D describe recommended procedures for meeting certain provisions in sections 8.3, 10.4, and 10.5 of this method. Annex B describes procedures to be followed when using the protractor wheel and pointer assembly to measure yaw angles, as provided under section 8.9.1.
18.1 Annex A - Rotational Position Check. The following are recommended procedures that may be used to satisfy the rotational position check requirements of section 8.3 of this method and to determine the angle-measuring device rotational offset RADO.
18.1.1 Rotational position check with probe outside stack. Where physical constraints at the sampling location allow full assembly of the probe outside the stack and insertion into the test port, the following procedures should be performed before the start of testing. Two angle-measuring devices that meet the specifications in section 6.2.1 or 6.2.3 are required for the rotational position check. An angle measuring device whose position can be independently adjusted (e.g., by means of a set screw) after being locked into position on the probe sheath shall not be used for this check unless the independent adjustment is set so that the device performs exactly like a device without the capability for independent adjustment. That is, when aligned on the probe such a device must give the same reading as a device that does not have the capability of being independently adjusted. With the fully assembled probe (including probe shaft extensions, if any) secured in a horizontal position, affix one yaw angle-measuring device to the probe sheath and lock it into position on the reference scribe line specified in section 6.1.6.1. Position the second angle-measuring device using the procedure in section 18.1.1.1 or 18.1.1.2.
18.1.1.1 Marking procedure. The procedures in this section should be performed at each location on the fully assembled probe where the yaw angle-measuring device will be mounted during the velocity traverse. Place the second yaw angle-measuring device on the main probe sheath (or extension) at the position where a yaw angle will be measured during the velocity traverse. Adjust the position of the second angle-measuring device until it indicates the same angle (±1°) as the reference device, and affix the second device to the probe sheath (or extension). Record the angles indicated by the two angle-measuring devices on a form similar to Table 2F-2. In this position, the second angle-measuring device is considered to be properly positioned for yaw angle measurement. Make a mark, no wider than 1.6 mm (1/16 in.), on the probe sheath (or extension), such that the yaw angle-measuring device can be re-affixed at this same properly aligned position during the velocity traverse.
18.1.1.2 Procedure for probe extensions with scribe lines. If, during a velocity traverse the angle-measuring device will be affixed to a probe extension having a scribe line as specified in section 6.1.6.2, the following procedure may be used to align the extension's scribe line with the reference scribe line instead of marking the extension as described in section 18.1.1.1. Attach the probe extension to the main probe. Align and lock the second angle-measuring device on the probe extension's scribe line. Then, rotate the extension until both measuring devices indicate the same angle (±1°). Lock the extension at this rotational position. Record the angles indicated by the two angle-measuring devices on a form similar to Table 2F-2. An angle-measuring device may be aligned at any position on this scribe line during the velocity traverse, if the scribe line meets the alignment specification in section 6.1.6.3.
18.1.1.3 Post-test rotational position check. If the fully assembled probe includes one or more extensions, the following check should be performed immediately after the completion of a velocity traverse. At the discretion of the tester, additional checks may be conducted after completion of testing at any sample port. Without altering the alignment of any of the components of the probe assembly used in the velocity traverse, secure the fully assembled probe in a horizontal position. Affix an angle-measuring device at the reference scribe line specified in section 6.1.6.1. Use the other angle-measuring device to check the angle at each location where the device was checked prior to testing. Record the readings from the two angle-measuring devices.
18.1.2 Rotational position check with probe in stack. This section applies only to probes that, due to physical constraints, cannot be inserted into the test port as fully assembled with all necessary extensions needed to reach the inner-most traverse point(s).
18.1.2.1 Perform the out-of-stack procedure in section 18.1.1 on the main probe and any attached extensions that will be initially inserted into the test port.
18.1.2.2 Use the following procedures to perform additional rotational position check(s) with the probe in the stack, each time a probe extension is added. Two angle-measuring devices are required. The first of these is the device that was used to measure yaw angles at the preceding traverse point, left in its properly aligned measurement position. The second angle-measuring device is positioned on the added probe extension. Use the applicable procedures in section 18.1.1.1 or 18.1.1.2 to align, adjust, lock, and mark (if necessary) the position of the second angle-measuring device to within ±1° of the first device. Record the readings of the two devices on a form similar to Table 2F-2.
18.1.2.3 The procedure in section 18.1.2.2 should be performed at the first port where measurements are taken. The procedure should be repeated each time a probe extension is re-attached at a subsequent port, unless the probe extensions are designed to be locked into a mechanically fixed rotational position (e.g., through use of interlocking grooves), which can be reproduced from port to port as specified in section 8.3.5.2.
18.2 Annex B - Angle Measurement Protocol for Protractor Wheel and Pointer Device. The following procedure shall be used when a protractor wheel and pointer assembly, such as the one described in section 6.2.2 and illustrated in Figure 2F-7 is used to measure the yaw angle of flow. With each move to a new traverse point, unlock, re-align, and re-lock the probe, angle-pointer collar, and protractor wheel to each other. At each such move, particular attention is required to ensure that the scribe line on the angle pointer collar is either aligned with the reference scribe line on the main probe sheath or is at the rotational offset position established under section 8.3.1. The procedure consists of the following steps:
18.2.1 Affix a protractor wheel to the entry port for the test probe in the stack or duct.
18.2.2 Orient the protractor wheel so that the 0° mark corresponds to the longitudinal axis of the stack or duct. For stacks, vertical ducts, or ports on the side of horizontal ducts, use a digital inclinometer meeting the specifications in section 6.2.1 to locate the 0° orientation. For ports on the top or bottom of horizontal ducts, identify the longitudinal axis at each test port and permanently mark the duct to indicate the 0° orientation. Once the protractor wheel is properly aligned, lock it into position on the test port.
18.2.3 Move the pointer assembly along the probe sheath to the position needed to take measurements at the first traverse point. Align the scribe line on the pointer collar with the reference scribe line or at the rotational offset position established under section 8.3.1. Maintaining this rotational alignment, lock the pointer device onto the probe sheath. Insert the probe into the entry port to the depth needed to take measurements at the first traverse point.
18.2.4 Perform the yaw angle determination as specified in sections 8.9.3 and 8.9.4 and record the angle as shown by the pointer on the protractor wheel. Then, take velocity pressure and temperature measurements in accordance with the procedure in section 8.9.5. Perform the alignment check described in section 8.9.6.
18.2.5 After taking velocity pressure measurements at that traverse point, unlock the probe from the collar and slide the probe through the collar to the depth needed to reach the next traverse point.
18.2.6 Align the scribe line on the pointer collar with the reference scribe line on the main probe or at the rotational offset position established under section 8.3.1. Lock the collar onto the probe.
18.2.7 Repeat the steps in sections 18.2.4 through 18.2.6 at the remaining traverse points accessed from the current stack or duct entry port.
18.2.8 After completing the measurement at the last traverse point accessed from a port, verify that the orientation of the protractor wheel on the test port has not changed over the course of the traverse at that port. For stacks, vertical ducts, or ports on the side of horizontal ducts, use a digital inclinometer meeting the specifications in section 6.2.1 to check the rotational position of the 0° mark on the protractor wheel. For ports on the top or bottom of horizontal ducts, observe the alignment of the angle wheel 0° mark relative to the permanent 0° mark on the duct at that test port. If these observed comparisons exceed ±2° of 0°, all angle and pressure measurements taken at that port since the protractor wheel was last locked into position on the port shall be repeated.
18.2.9 Move to the next stack or duct entry port and repeat the steps in sections 18.2.1 through 18.2.8.
18.3 Annex C - Guideline for Reference Scribe Line Placement. Use of the following guideline is recommended to satisfy the requirements of section 10.4 of this method. The rotational position of the reference scribe line should be either 90° or 180° from the probe's impact pressure port.
18.4 Annex D - Determination of Reference Scribe Line Rotational Offset. The following procedures are recommended for determining the magnitude and sign of a probe's reference scribe line rotational offset, RSLO. Separate procedures are provided for two types of angle-measuring devices: digital inclinometers and protractor wheel and pointer assemblies.
18.4.1 Perform the following procedures on the main probe with all devices that will be attached to the main probe in the field [such as thermocouples or resistance temperature detectors (RTDs)] that may affect the flow around the probe head. Probe shaft extensions that do not affect flow around the probe head need not be attached during calibration.
18.4.2 The procedures below assume that the wind tunnel duct used for probe calibration is horizontal and that the flow in the calibration wind tunnel is axial as determined by the axial flow verification check described in section 10.1.2. Angle-measuring devices are assumed to display angles in alternating 0° to 90° and 90° to 0° intervals. If angle-measuring devices with other readout conventions are used or if other calibration wind tunnel duct configurations are used, make the appropriate calculational corrections.
18.4.2.1 Position the angle-measuring device in accordance with one of the following procedures.
18.4.2.1.1 If using a digital inclinometer, affix the calibrated digital inclinometer to the probe. If the digital inclinometer can be independently adjusted after being locked into position on the probe sheath (e.g., by means of a set screw), the independent adjustment must be set so that the device performs exactly like a device without the capability for independent adjustment. That is, when aligned on the probe the device must give the same readings as a device that does not have the capability of being independently adjusted. Either align it directly on the reference scribe line or on a mark aligned with the scribe line determined according to the procedures in section 18.1.1.1. Maintaining this rotational alignment, lock the digital inclinometer onto the probe sheath.
18.4.2.1.2 If using a protractor wheel and pointer device, orient the protractor wheel on the test port so that the 0° mark is aligned with the longitudinal axis of the wind tunnel duct. Maintaining this alignment, lock the wheel into place on the wind tunnel test port. Align the scribe line on the pointer collar with the reference scribe line or with a mark aligned with the reference scribe line, as determined under section 18.1.1.1. Maintaining this rotational alignment, lock the pointer device onto the probe sheath.
18.4.2.2 Zero the pressure-measuring device used for yaw nulling.
18.4.2.3 Insert the probe assembly into the wind tunnel through the entry port, positioning the probe's impact port at the calibration location. Check the responsiveness of the pressure-measuring device to probe rotation, taking corrective action if the response is unacceptable.
18.4.2.4 Ensure that the probe is in a horizontal position using a carpenter's level.
18.4.2.5 Rotate the probe either clockwise or counterclockwise until a yaw null (P2 = P3) is obtained.
18.4.2.6 Read and record the value of θnull, the angle indicated by the angle-measuring device at the yaw-null position. Record the angle reading on a form similar to Table 2F-6. Do not associate an algebraic sign with this reading.
18.4.2.7 Determine the magnitude and algebraic sign of the reference scribe line rotational offset, RSLO. The magnitude of RSLO will be equal to either θnull or (90°−θnull), depending on the angle-measuring device used. (See Table 2F-7 for a summary.) The algebraic sign of RSLO will either be positive, if the rotational position of the reference scribe line is clockwise, or negative, if counterclockwise with respect to the probe's yaw-null position. Figure 2F-13 illustrates how the magnitude and sign of RSLO are determined.
18.4.2.8 Perform the steps in sections 18.4.2.3 through 18.4.2.7 twice at each of the two calibration velocities selected for the probe under section 10.6. Record the values of RSLO in a form similar to Table 2F-6.
18.4.2.9 The average of all RSLO values is the reference scribe line rotational offset for the probe.
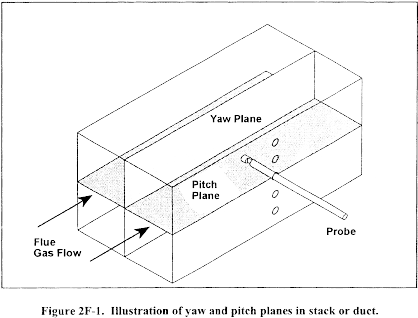

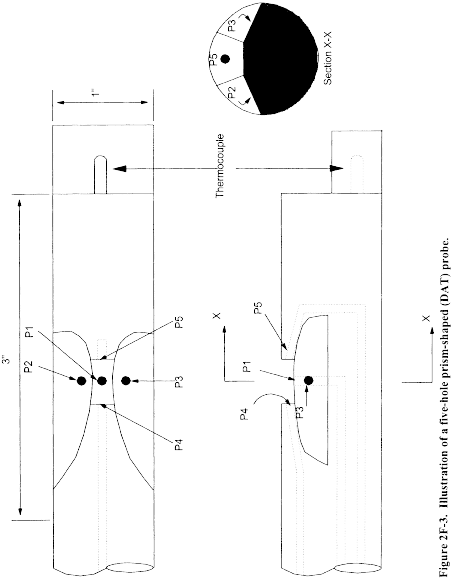
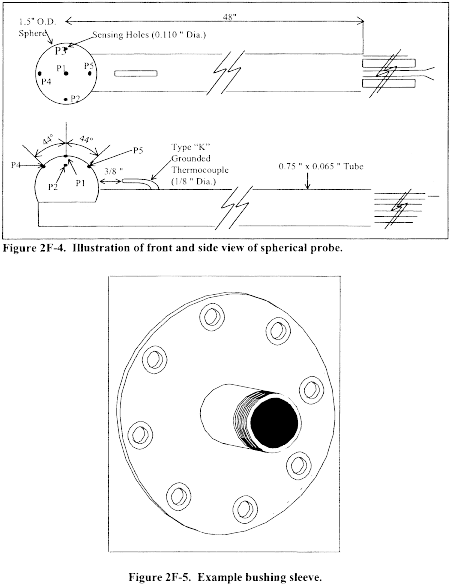
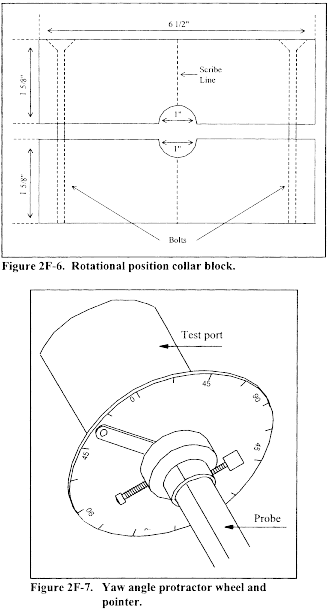
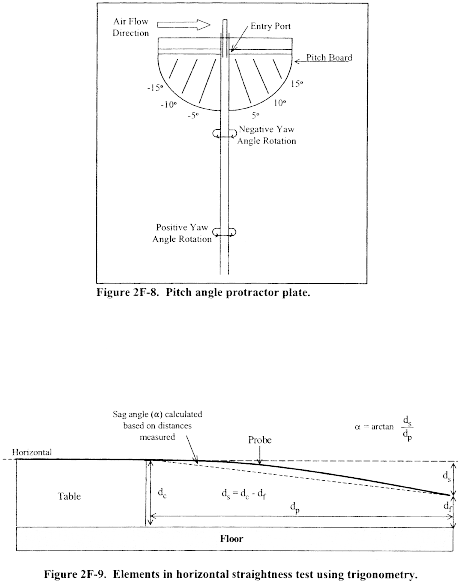
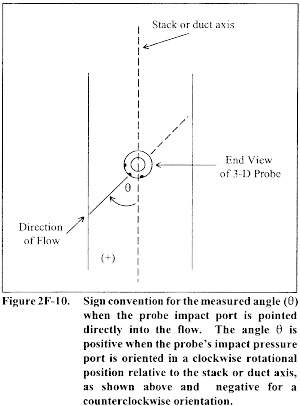
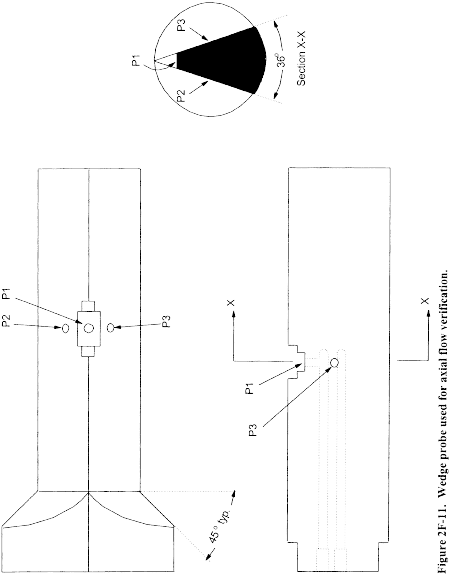
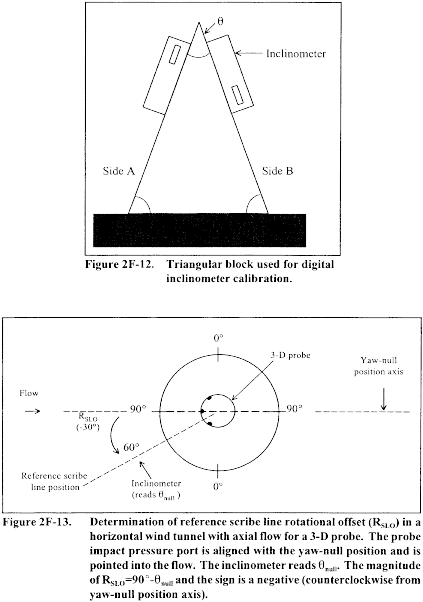
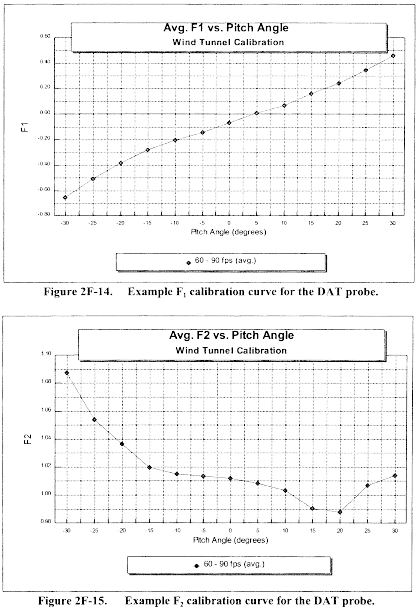
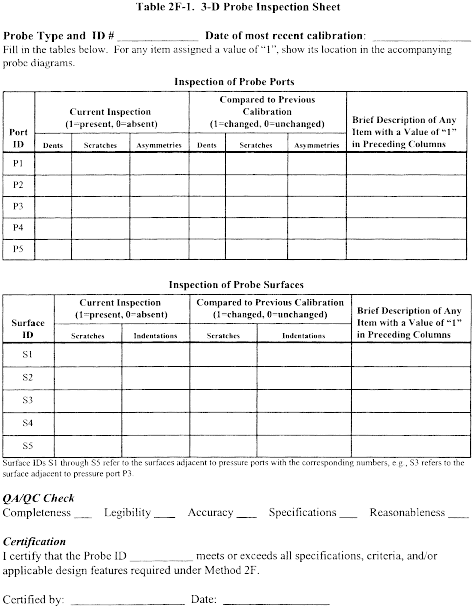
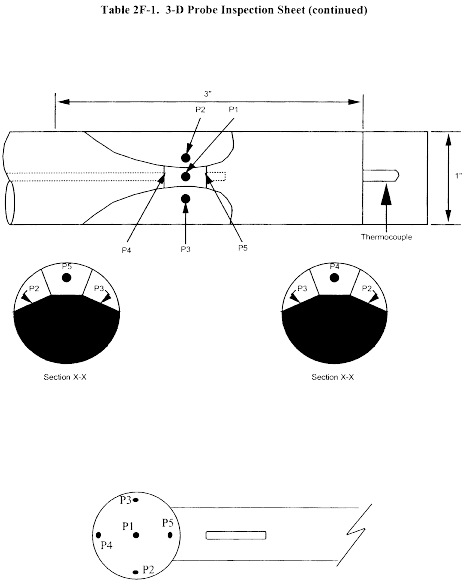
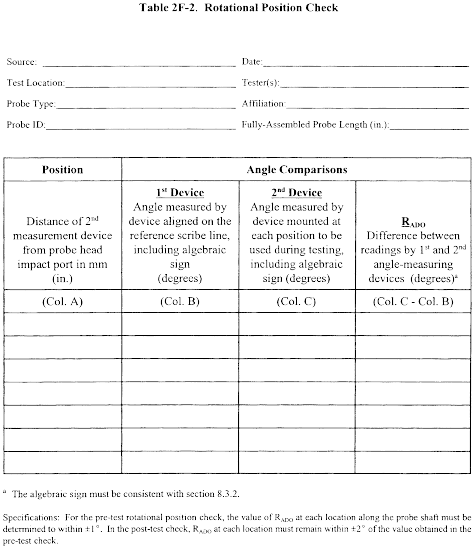
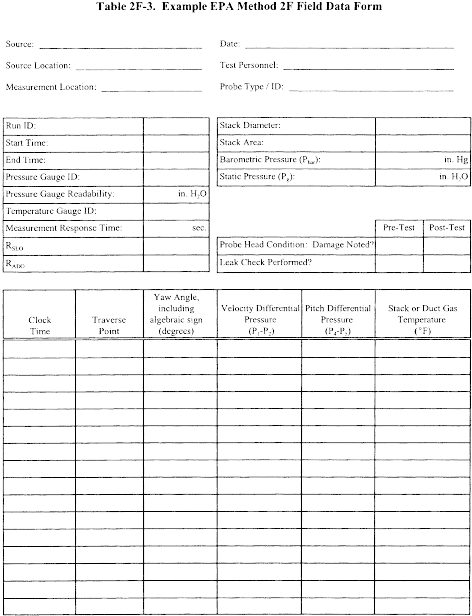
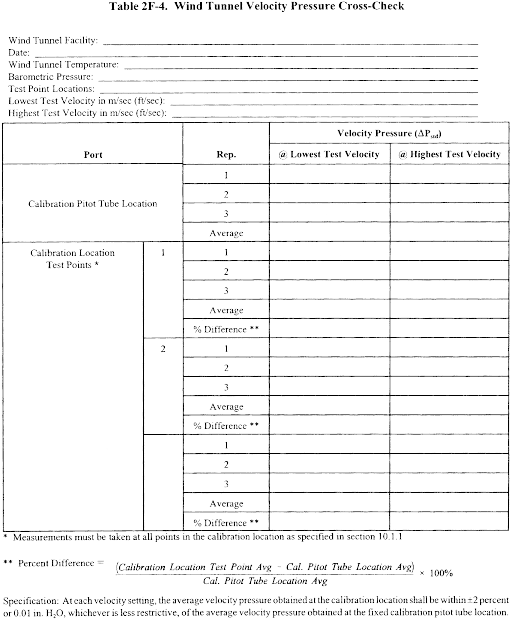
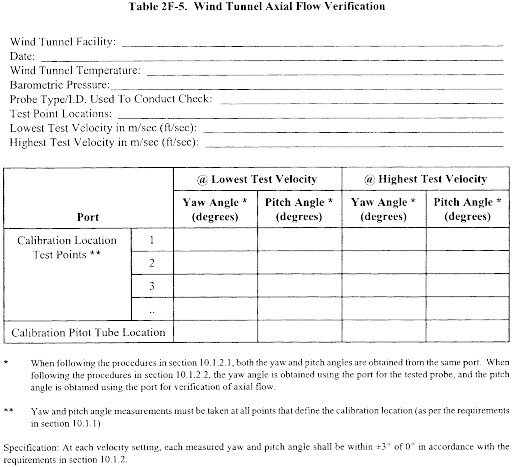
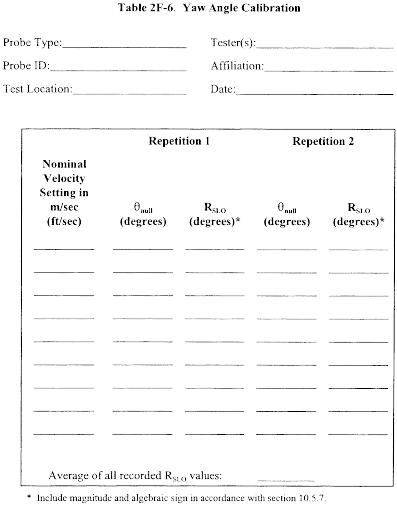
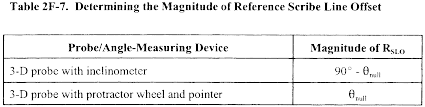
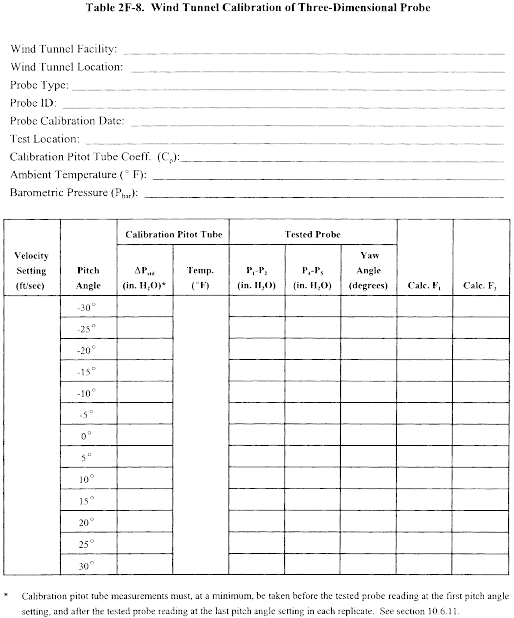
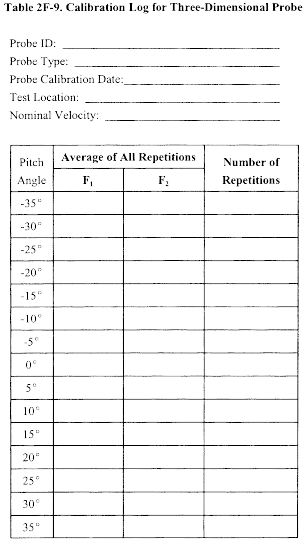
Appendix A-2 to Part 60 - Test Methods 2G through 3C
40:9.0.1.1.1.0.1.1.2 : Appendix A
Appendix A-2 to Part 60 - Test Methods 2G through 3C Method 2G - Determination of Stack Gas Velocity and Volumetric Flow Rate With Two-Dimensional Probes Method 2H - Determination of Stack Gas Velocity Taking Into Account Velocity Decay Near the Stack Wall Method 3 - Gas analysis for the determination of dry molecular weight Method 3A - Determination of Oxygen and Carbon Dioxide Concentrations in Emissions From Stationary Sources (Instrumental Analyzer Procedure) Method 3B - Gas analysis for the determination of emission rate correction factor or excess air Method 3C - Determination of carbon dioxide, methane, nitrogen, and oxygen from stationary sourcesThe test methods in this appendix are referred to in § 60.8 (Performance Tests) and § 60.11 (Compliance With Standards and Maintenance Requirements) of 40 CFR part 60, subpart A (General Provisions). Specific uses of these test methods are described in the standards of performance contained in the subparts, beginning with Subpart D.
Within each standard of performance, a section title “Test Methods and Procedures” is provided to: (1) Identify the test methods to be used as reference methods to the facility subject to the respective standard and (2) identify any special instructions or conditions to be followed when applying a method to the respective facility. Such instructions (for example, establish sampling rates, volumes, or temperatures) are to be used either in addition to, or as a substitute for procedures in a test method. Similarly, for sources subject to emission monitoring requirements, specific instructions pertaining to any use of a test method as a reference method are provided in the subpart or in Appendix B.
Inclusion of methods in this appendix is not intended as an endorsement or denial of their applicability to sources that are not subject to standards of performance. The methods are potentially applicable to other sources; however, applicability should be confirmed by careful and appropriate evaluation of the conditions prevalent at such sources.
The approach followed in the formulation of the test methods involves specifications for equipment, procedures, and performance. In concept, a performance specification approach would be preferable in all methods because this allows the greatest flexibility to the user. In practice, however, this approach is impractical in most cases because performance specifications cannot be established. Most of the methods described herein, therefore, involve specific equipment specifications and procedures, and only a few methods in this appendix rely on performance criteria.
Minor changes in the test methods should not necessarily affect the validity of the results and it is recognized that alternative and equivalent methods exist. section 60.8 provides authority for the Administrator to specify or approve (1) equivalent methods, (2) alternative methods, and (3) minor changes in the methodology of the test methods. It should be clearly understood that unless otherwise identified all such methods and changes must have prior approval of the Administrator. An owner employing such methods or deviations from the test methods without obtaining prior approval does so at the risk of subsequent disapproval and retesting with approved methods.
Within the test methods, certain specific equipment or procedures are recognized as being acceptable or potentially acceptable and are specifically identified in the methods. The items identified as acceptable options may be used without approval but must be identified in the test report. The potentially approvable options are cited as “subject to the approval of the Administrator” or as “or equivalent.” Such potentially approvable techniques or alternatives may be used at the discretion of the owner without prior approval. However, detailed descriptions for applying these potentially approvable techniques or alternatives are not provided in the test methods. Also, the potentially approvable options are not necessarily acceptable in all applications. Therefore, an owner electing to use such potentially approvable techniques or alternatives is responsible for: (1) assuring that the techniques or alternatives are in fact applicable and are properly executed; (2) including a written description of the alternative method in the test report (the written method must be clear and must be capable of being performed without additional instruction, and the degree of detail should be similar to the detail contained in the test methods); and (3) providing any rationale or supporting data necessary to show the validity of the alternative in the particular application. Failure to meet these requirements can result in the Administrator's disapproval of the alternative.
Method 2G - Determination of Stack Gas Velocity and Volumetric Flow Rate With Two-Dimensional Probes Note:This method does not include all of the specifications (e.g., equipment and supplies) and procedures (e.g., sampling) essential to its performance. Some material has been incorporated from other methods in this part. Therefore, to obtain reliable results, those using this method should have a thorough knowledge of at least the following additional test methods: Methods 1, 2, 3 or 3A, and 4.
1.0 Scope and Application1.1 This method is applicable for the determination of yaw angle, near-axial velocity, and the volumetric flow rate of a gas stream in a stack or duct using a two-dimensional (2-D) probe.
2.0 Summary of Method 2.1 A 2-D probe is used to measure the velocity pressure and the yaw angle of the flow velocity vector in a stack or duct. Alternatively, these measurements may be made by operating one of the three-dimensional (3-D) probes described in Method 2F, in yaw determination mode only. From these measurements and a determination of the stack gas density, the average near-axial velocity of the stack gas is calculated. The near-axial velocity accounts for the yaw, but not the pitch, component of flow. The average gas volumetric flow rate in the stack or duct is then determined from the average near-axial velocity. 3.0 Definitions3.1. Angle-measuring Device Rotational Offset (RADO). The rotational position of an angle-measuring device relative to the reference scribe line, as determined during the pre-test rotational position check described in section 8.3.
3.2 Calibration Pitot Tube. The standard (Prandtl type) pitot tube used as a reference when calibrating a probe under this method.
3.3 Field Test. A set of measurements conducted at a specific unit or exhaust stack/duct to satisfy the applicable regulation (e.g., a three-run boiler performance test, a single-or multiple-load nine-run relative accuracy test).
3.4 Full Scale of Pressure-measuring Device. Full scale refers to the upper limit of the measurement range displayed by the device. For bi-directional pressure gauges, full scale includes the entire pressure range from the lowest negative value to the highest positive value on the pressure scale.
3.5 Main probe. Refers to the probe head and that section of probe sheath directly attached to the probe head. The main probe sheath is distinguished from probe extensions, which are sections of sheath added onto the main probe to extend its reach.
3.6 “May,” “Must,” “Shall,” “Should,” and the imperative form of verbs.
3.6.1 “May” is used to indicate that a provision of this method is optional.
3.6.2 “Must,” “Shall,” and the imperative form of verbs (such as “record” or “enter”) are used to indicate that a provision of this method is mandatory.
3.6.3 “Should” is used to indicate that a provision of this method is not mandatory, but is highly recommended as good practice.
3.7 Method 1. Refers to 40 CFR part 60, appendix A, “Method 1 - Sample and velocity traverses for stationary sources.”
3.8 Method 2. Refers to 40 CFR part 60, appendix A, “Method 2 - Determination of stack gas velocity and volumetric flow rate (Type S pitot tube).”
3.9 Method 2F. Refers to 40 CFR part 60, appendix A, “Method 2F - Determination of stack gas velocity and volumetric flow rate with three-dimensional probes.”
3.10 Near-axial Velocity. The velocity vector parallel to the axis of the stack or duct that accounts for the yaw angle component of gas flow. The term “near-axial” is used herein to indicate that the velocity and volumetric flow rate results account for the measured yaw angle component of flow at each measurement point.
3.11 Nominal Velocity. Refers to a wind tunnel velocity setting that approximates the actual wind tunnel velocity to within ±1.5 m/sec (±5 ft/sec).
3.12 Pitch Angle. The angle between the axis of the stack or duct and the pitch component of flow, i.e., the component of the total velocity vector in a plane defined by the traverse line and the axis of the stack or duct. (Figure 2G-1 illustrates the “pitch plane.”) From the standpoint of a tester facing a test port in a vertical stack, the pitch component of flow is the vector of flow moving from the center of the stack toward or away from that test port. The pitch angle is the angle described by this pitch component of flow and the vertical axis of the stack.
3.13 Readability. For the purposes of this method, readability for an analog measurement device is one half of the smallest scale division. For a digital measurement device, it is the number of decimals displayed by the device.
3.14 Reference Scribe Line. A line permanently inscribed on the main probe sheath (in accordance with section 6.1.5.1) to serve as a reference mark for determining yaw angles.
3.15 Reference Scribe Line Rotational Offset (RSLO). The rotational position of a probe's reference scribe line relative to the probe's yaw-null position, as determined during the yaw angle calibration described in section 10.5.
3.16 Response Time. The time required for the measurement system to fully respond to a change from zero differential pressure and ambient temperature to the stable stack or duct pressure and temperature readings at a traverse point.
3.17 Tested Probe. A probe that is being calibrated.
3.18 Three-dimensional (3-D) Probe. A directional probe used to determine the velocity pressure and the yaw and pitch angles in a flowing gas stream.
3.19 Two-dimensional (2-D) Probe. A directional probe used to measure velocity pressure and yaw angle in a flowing gas stream.
3.20 Traverse Line. A diameter or axis extending across a stack or duct on which measurements of velocity pressure and flow angles are made.
3.21 Wind Tunnel Calibration Location. A point, line, area, or volume within the wind tunnel test section at, along, or within which probes are calibrated. At a particular wind tunnel velocity setting, the average velocity pressures at specified points at, along, or within the calibration location shall vary by no more than 2 percent or 0.3 mm H20 (0.01 in. H2O), whichever is less restrictive, from the average velocity pressure at the calibration pitot tube location. Air flow at this location shall be axial, i.e., yaw and pitch angles within ±3° of 0°. Compliance with these flow criteria shall be demonstrated by performing the procedures prescribed in sections 10.1.1 and 10.1.2. For circular tunnels, no part of the calibration location may be closer to the tunnel wall than 10.2 cm (4 in.) or 25 percent of the tunnel diameter, whichever is farther from the wall. For elliptical or rectangular tunnels, no part of the calibration location may be closer to the tunnel wall than 10.2 cm (4 in.) or 25 percent of the applicable cross-sectional axis, whichever is farther from the wall.
3.22 Wind Tunnel with Documented Axial Flow. A wind tunnel facility documented as meeting the provisions of sections 10.1.1 (velocity pressure cross-check) and 10.1.2 (axial flow verification) using the procedures described in these sections or alternative procedures determined to be technically equivalent.
3.23 Yaw Angle. The angle between the axis of the stack or duct and the yaw component of flow, i.e., the component of the total velocity vector in a plane perpendicular to the traverse line at a particular traverse point. (Figure 2G-1 illustrates the “yaw plane.”) From the standpoint of a tester facing a test port in a vertical stack, the yaw component of flow is the vector of flow moving to the left or right from the center of the stack as viewed by the tester. (This is sometimes referred to as “vortex flow,” i.e., flow around the centerline of a stack or duct.) The yaw angle is the angle described by this yaw component of flow and the vertical axis of the stack. The algebraic sign convention is illustrated in Figure 2G-2.
3.24 Yaw Nulling. A procedure in which a Type-S pitot tube or a 3-D probe is rotated about its axis in a stack or duct until a zero differential pressure reading (“yaw null”) is obtained. When a Type S probe is yaw-nulled, the rotational position of its impact port is 90° from the direction of flow in the stack or duct and the ΔP reading is zero. When a 3-D probe is yaw-nulled, its impact pressure port (P1) faces directly into the direction of flow in the stack or duct and the differential pressure between pressure ports P2 and P3 is zero.
4.0 Interferences [Reserved] 5.0 Safety5.1 This test method may involve hazardous operations and the use of hazardous materials or equipment. This method does not purport to address all of the safety problems associated with its use. It is the responsibility of the user to establish and implement appropriate safety and health practices and to determine the applicability of regulatory limitations before using this test method.
6.0 Equipment and Supplies6.1 Two-dimensional Probes. Probes that provide both the velocity pressure and the yaw angle of the flow vector in a stack or duct, as listed in sections 6.1.1 and 6.1.2, qualify for use based on comprehensive wind tunnel and field studies involving both inter-and intra-probe comparisons by multiple test teams. Each 2-D probe shall have a unique identification number or code permanently marked on the main probe sheath. Each probe shall be calibrated prior to use according to the procedures in section 10. Manufacturer-supplied calibration data shall be used as example information only, except when the manufacturer calibrates the probe as specified in section 10 and provides complete documentation.
6.1.1 Type S (Stausscheibe or reverse type) pitot tube. This is the same as specified in Method 2, section 2.1, except for the following additional specifications that enable the pitot tube to accurately determine the yaw component of flow. For the purposes of this method, the external diameter of the tubing used to construct the Type S pitot tube (dimension Dt in Figure 2-2 of Method 2) shall be no less than 9.5 mm (3/8 in.). The pitot tube shall also meet the following alignment specifications. The angles α1, α2, β1, and β2, as shown in Method 2, Figure 2-3, shall not exceed ±2°. The dimensions w and z, shown in Method 2, Figure 2-3 shall not exceed 0.5 mm (0.02 in.).
6.1.1.1 Manual Type S probe. This refers to a Type S probe that is positioned at individual traverse points and yaw nulled manually by an operator.
6.1.1.2 Automated Type S probe. This refers to a system that uses a computer-controlled motorized mechanism to position the Type S pitot head at individual traverse points and perform yaw angle determinations.
6.1.2 Three-dimensional probes used in 2-D mode. A 3-D probe, as specified in sections 6.1.1 through 6.1.3 of Method 2F, may, for the purposes of this method, be used in a two-dimensional mode (i.e., measuring yaw angle, but not pitch angle). When the 3-D probe is used as a 2-D probe, only the velocity pressure and yaw-null pressure are obtained using the pressure taps referred to as P1, P2, and P3. The differential pressure P1-P2 is a function of total velocity and corresponds to the ΔP obtained using the Type S probe. The differential pressure P2-P3 is used to yaw null the probe and determine the yaw angle. The differential pressure P4-P5, which is a function of pitch angle, is not measured when the 3-D probe is used in 2-D mode.
6.1.3 Other probes. [Reserved]
6.1.4 Probe sheath. The probe shaft shall include an outer sheath to: (1) provide a surface for inscribing a permanent reference scribe line, (2) accommodate attachment of an angle-measuring device to the probe shaft, and (3) facilitate precise rotational movement of the probe for determining yaw angles. The sheath shall be rigidly attached to the probe assembly and shall enclose all pressure lines from the probe head to the farthest position away from the probe head where an angle-measuring device may be attached during use in the field. The sheath of the fully assembled probe shall be sufficiently rigid and straight at all rotational positions such that, when one end of the probe shaft is held in a horizontal position, the fully extended probe meets the horizontal straightness specifications indicated in section 8.2 below.
6.1.5 Scribe lines.
6.1.5.1 Reference scribe line. A permanent line, no greater than 1.6 mm (1/16 in.) in width, shall be inscribed on each manual probe that will be used to determine yaw angles of flow. This line shall be placed on the main probe sheath in accordance with the procedures described in section 10.4 and is used as a reference position for installation of the yaw angle-measuring device on the probe. At the discretion of the tester, the scribe line may be a single line segment placed at a particular position on the probe sheath (e.g., near the probe head), multiple line segments placed at various locations along the length of the probe sheath (e.g., at every position where a yaw angle-measuring device may be mounted), or a single continuous line extending along the full length of the probe sheath.
6.1.5.2 Scribe line on probe extensions. A permanent line may also be inscribed on any probe extension that will be attached to the main probe in performing field testing. This allows a yaw angle-measuring device mounted on the extension to be readily aligned with the reference scribe line on the main probe sheath.
6.1.5.3 Alignment specifications. This specification shall be met separately, using the procedures in section 10.4.1, on the main probe and on each probe extension. The rotational position of the scribe line or scribe line segments on the main probe or any probe extension must not vary by more than 2°. That is, the difference between the minimum and maximum of all of the rotational angles that are measured along the full length of the main probe or the probe extension must not exceed 2°.
6.1.6 Probe and system characteristics to ensure horizontal stability.
6.1.6.1 For manual probes, it is recommended that the effective length of the probe (coupled with a probe extension, if necessary) be at least 0.9 m (3 ft.) longer than the farthest traverse point mark on the probe shaft away from the probe head. The operator should maintain the probe's horizontal stability when it is fully inserted into the stack or duct. If a shorter probe is used, the probe should be inserted through a bushing sleeve, similar to the one shown in Figure 2G-3, that is installed on the test port; such a bushing shall fit snugly around the probe and be secured to the stack or duct entry port in such a manner as to maintain the probe's horizontal stability when fully inserted into the stack or duct.
6.1.6.2 An automated system that includes an external probe casing with a transport system shall have a mechanism for maintaining horizontal stability comparable to that obtained by manual probes following the provisions of this method. The automated probe assembly shall also be constructed to maintain the alignment and position of the pressure ports during sampling at each traverse point. The design of the probe casing and transport system shall allow the probe to be removed from the stack or duct and checked through direct physical measurement for angular position and insertion depth.
6.1.7 The tubing that is used to connect the probe and the pressure-measuring device should have an inside diameter of at least 3.2 mm ( 1/8 in.), to reduce the time required for pressure equilibration, and should be as short as practicable.
6.1.8 If a detachable probe head without a sheath [e.g., a pitot tube, typically 15.2 to 30.5 cm (6 to 12 in.) in length] is coupled with a probe sheath and calibrated in a wind tunnel in accordance with the yaw angle calibration procedure in section 10.5, the probe head shall remain attached to the probe sheath during field testing in the same configuration and orientation as calibrated. Once the detachable probe head is uncoupled or re-oriented, the yaw angle calibration of the probe is no longer valid and must be repeated before using the probe in subsequent field tests.
6.2 Yaw Angle-measuring Device. One of the following devices shall be used for measurement of the yaw angle of flow.
6.2.1 Digital inclinometer. This refers to a digital device capable of measuring and displaying the rotational position of the probe to within ±1°. The device shall be able to be locked into position on the probe sheath or probe extension, so that it indicates the probe's rotational position throughout the test. A rotational position collar block that can be attached to the probe sheath (similar to the collar shown in Figure 2G-4) may be required to lock the digital inclinometer into position on the probe sheath.
6.2.2 Protractor wheel and pointer assembly. This apparatus, similar to that shown in Figure 2G-5, consists of the following components.
6.2.2.1 A protractor wheel that can be attached to a port opening and set in a fixed rotational position to indicate the yaw angle position of the probe's scribe line relative to the longitudinal axis of the stack or duct. The protractor wheel must have a measurement ring on its face that is no less than 17.8 cm (7 in.) in diameter, shall be able to be rotated to any angle and then locked into position on the stack or duct test port, and shall indicate angles to a resolution of 1°.
6.2.2.2 A pointer assembly that includes an indicator needle mounted on a collar that can slide over the probe sheath and be locked into a fixed rotational position on the probe sheath. The pointer needle shall be of sufficient length, rigidity, and sharpness to allow the tester to determine the probe's angular position to within 1° from the markings on the protractor wheel. Corresponding to the position of the pointer, the collar must have a scribe line to be used in aligning the pointer with the scribe line on the probe sheath.
6.2.3 Other yaw angle-measuring devices. Other angle-measuring devices with a manufacturer's specified precision of 1° or better may be used, if approved by the Administrator.
6.3 Probe Supports and Stabilization Devices. When probes are used for determining flow angles, the probe head should be kept in a stable horizontal position. For probes longer than 3.0 m (10 ft.), the section of the probe that extends outside the test port shall be secured. Three alternative devices are suggested for maintaining the horizontal position and stability of the probe shaft during flow angle determinations and velocity pressure measurements: (1) monorails installed above each port, (2) probe stands on which the probe shaft may be rested, or (3) bushing sleeves of sufficient length secured to the test ports to maintain probes in a horizontal position. Comparable provisions shall be made to ensure that automated systems maintain the horizontal position of the probe in the stack or duct. The physical characteristics of each test platform may dictate the most suitable type of stabilization device. Thus, the choice of a specific stabilization device is left to the judgement of the testers.
6.4 Differential Pressure Gauges. The velocity pressure (ΔP) measuring devices used during wind tunnel calibrations and field testing shall be either electronic manometers (e.g., pressure transducers), fluid manometers, or mechanical pressure gauges (e.g., MagnehelicΔ gauges). Use of electronic manometers is recommended. Under low velocity conditions, use of electronic manometers may be necessary to obtain acceptable measurements.
6.4.1 Differential pressure-measuring device. This refers to a device capable of measuring pressure differentials and having a readability of ±1 percent of full scale. The device shall be capable of accurately measuring the maximum expected pressure differential. Such devices are used to determine the following pressure measurements: velocity pressure, static pressure, and yaw-null pressure. For an inclined-vertical manometer, the readability specification of ±1 percent shall be met separately using the respective full-scale upper limits of the inclined anvertical portions of the scales. To the extent practicable, the device shall be selected such that most of the pressure readings are between 10 and 90 percent of the device's full-scale measurement range (as defined in section 3.4). In addition, pressure-measuring devices should be selected such that the zero does not drift by more than 5 percent of the average expected pressure readings to be encountered during the field test. This is particularly important under low pressure conditions.
6.4.2 Gauge used for yaw nulling. The differential pressure-measuring device chosen for yaw nulling the probe during the wind tunnel calibrations and field testing shall be bi-directional, i.e., capable of reading both positive and negative differential pressures. If a mechanical, bi-directional pressure gauge is chosen, it shall have a full-scale range no greater than 2.6 cm (i.e., −1.3 to + 1.3 cm) [1 in. H2O (i.e., −0.5 in. to + 0.5 in.)].
6.4.3 Devices for calibrating differential pressure-measuring devices. A precision manometer (e.g., a U-tube, inclined, or inclined-vertical manometer, or micromanometer) or NIST (National Institute of Standards and Technology) traceable pressure source shall be used for calibrating differential pressure-measuring devices. The device shall be maintained under laboratory conditions or in a similar protected environment (e.g., a climate-controlled trailer). It shall not be used in field tests. The precision manometer shall have a scale gradation of 0.3 mm H2O (0.01 in. H2O), or less, in the range of 0 to 5.1 cm H2O (0 to 2 in. H2O) and 2.5 mm H2O (0.1 in. H2O), or less, in the range of 5.1 to 25.4 cm H2O (2 to 10 in. H2O). The manometer shall have manufacturer's documentation that it meets an accuracy specification of at least 0.5 percent of full scale. The NIST-traceable pressure source shall be recertified annually.
6.4.4 Devices used for post-test calibration check. A precision manometer meeting the specifications in section 6.4.3, a pressure-measuring device or pressure source with a documented calibration traceable to NIST, or an equivalent device approved by the Administrator shall be used for the post-test calibration check. The pressure-measuring device shall have a readability equivalent to or greater than the tested device. The pressure source shall be capable of generating pressures between 50 and 90 percent of the range of the tested device and known to within ±1 percent of the full scale of the tested device. The pressure source shall be recertified annually.
6.5 Data Display and Capture Devices. Electronic manometers (if used) shall be coupled with a data display device (such as a digital panel meter, personal computer display, or strip chart) that allows the tester to observe and validate the pressure measurements taken during testing. They shall also be connected to a data recorder (such as a data logger or a personal computer with data capture software) that has the ability to compute and retain the appropriate average value at each traverse point, identified by collection time and traverse point.
6.6 Temperature Gauges. For field tests, a thermocouple or resistance temperature detector (RTD) capable of measuring temperature to within ±3 °C (±5 °F) of the stack or duct temperature shall be used. The thermocouple shall be attached to the probe such that the sensor tip does not touch any metal. The position of the thermocouple relative to the pressure port face openings shall be in the same configuration as used for the probe calibrations in the wind tunnel. Temperature gauges used for wind tunnel calibrations shall be capable of measuring temperature to within ±0.6 °C (±1 °F) of the temperature of the flowing gas stream in the wind tunnel.
6.7 Stack or Duct Static Pressure Measurement. The pressure-measuring device used with the probe shall be as specified in section 6.4 of this method. The static tap of a standard (Prandtl type) pitot tube or one leg of a Type S pitot tube with the face opening planes positioned parallel to the gas flow may be used for this measurement. Also acceptable is the pressure differential reading of P1-Pbar from a five-hole prism-shaped 3-D probe, as specified in section 6.1.1 of Method 2F (such as the Type DA or DAT probe), with the P1 pressure port face opening positioned parallel to the gas flow in the same manner as the Type S probe. However, the 3-D spherical probe, as specified in section 6.1.2 of Method 2F, is unable to provide this measurement and shall not be used to take static pressure measurements. Static pressure measurement is further described in section 8.11.
6.8 Barometer. Same as Method 2, section 2.5.
6.9 Gas Density Determination Equipment. Method 3 or 3A shall be used to determine the dry molecular weight of the stack or duct gas. Method 4 shall be used for moisture content determination and computation of stack or duct gas wet molecular weight. Other methods may be used, if approved by the Administrator.
6.10 Calibration Pitot Tube. Same as Method 2, section 2.7.
6.11 Wind Tunnel for Probe Calibration. Wind tunnels used to calibrate velocity probes must meet the following design specifications.
6.11.1 Test section cross-sectional area. The flowing gas stream shall be confined within a circular, rectangular, or elliptical duct. The cross-sectional area of the tunnel must be large enough to ensure fully developed flow in the presence of both the calibration pitot tube and the tested probe. The calibration site, or “test section,” of the wind tunnel shall have a minimum diameter of 30.5 cm (12 in.) for circular or elliptical duct cross-sections or a minimum width of 30.5 cm (12 in.) on the shorter side for rectangular cross-sections. Wind tunnels shall meet the probe blockage provisions of this section and the qualification requirements prescribed in section 10.1. The projected area of the portion of the probe head, shaft, and attached devices inside the wind tunnel during calibration shall represent no more than 2 percent of the cross-sectional area of the tunnel. If the pitot and/or probe assembly blocks more than 2 percent of the cross-sectional area at an insertion point only 4 inches inside the wind tunnel, the diameter of the wind tunnel must be increased.
6.11.2 Velocity range and stability. The wind tunnel should be capable of achieving and maintaining a constant and steady velocity between 6.1 m/sec and 30.5 m/sec (20 ft/sec and 100 ft/sec) for the entire calibration period for each selected calibration velocity. The wind tunnel shall produce fully developed flow patterns that are stable and parallel to the axis of the duct in the test section.
6.11.3 Flow profile at the calibration location. The wind tunnel shall provide axial flow within the test section calibration location (as defined in section 3.21). Yaw and pitch angles in the calibration location shall be within ±3° of 0°. The procedure for determining that this requirement has been met is described in section 10.1.2.
6.11.4 Entry ports in the wind tunnel test section.
6.11.4.1 Port for tested probe. A port shall be constructed for the tested probe. This port shall be located to allow the head of the tested probe to be positioned within the wind tunnel calibration location (as defined in section 3.21). The tested probe shall be able to be locked into the 0° pitch angle position. To facilitate alignment of the probe during calibration, the test section should include a window constructed of a transparent material to allow the tested probe to be viewed.
6.11.4.2 Port for verification of axial flow. Depending on the equipment selected to conduct the axial flow verification prescribed in section 10.1.2, a second port, located 90° from the entry port for the tested probe, may be needed to allow verification that the gas flow is parallel to the central axis of the test section. This port should be located and constructed so as to allow one of the probes described in section 10.1.2.2 to access the same test point(s) that are accessible from the port described in section 6.11.4.1.
6.11.4.3 Port for calibration pitot tube. The calibration pitot tube shall be used in the port for the tested probe or in a separate entry port. In either case, all measurements with the calibration pitot tube shall be made at the same point within the wind tunnel over the course of a probe calibration. The measurement point for the calibration pitot tube shall meet the same specifications for distance from the wall and for axial flow as described in section 3.21 for the wind tunnel calibration location.
7.0 Reagents and Standards [Reserved] 8.0 Sample Collection and Analysis8.1 Equipment Inspection and Set Up
8.1.1 All 2-D and 3-D probes, differential pressure-measuring devices, yaw angle-measuring devices, thermocouples, and barometers shall have a current, valid calibration before being used in a field test. (See sections 10.3.3, 10.3.4, and 10.5 through 10.10 for the applicable calibration requirements.)
8.1.2 Before each field use of a Type S probe, perform a visual inspection to verify the physical condition of the pitot tube. Record the results of the inspection. If the face openings are noticeably misaligned or there is visible damage to the face openings, the probe shall not be used until repaired, the dimensional specifications verified (according to the procedures in section 10.2.1), and the probe recalibrated.
8.1.3 Before each field use of a 3-D probe, perform a visual inspection to verify the physical condition of the probe head according to the procedures in section 10.2 of Method 2F. Record the inspection results on a form similar to Table 2F-1 presented in Method 2F. If there is visible damage to the 3-D probe, the probe shall not be used until it is recalibrated.
8.1.4 After verifying that the physical condition of the probe head is acceptable, set up the apparatus using lengths of flexible tubing that are as short as practicable. Surge tanks installed between the probe and pressure-measuring device may be used to dampen pressure fluctuations provided that an adequate measurement system response time (see section 8.8) is maintained.
8.2 Horizontal Straightness Check. A horizontal straightness check shall be performed before the start of each field test, except as otherwise specified in this section. Secure the fully assembled probe (including the probe head and all probe shaft extensions) in a horizontal position using a stationary support at a point along the probe shaft approximating the location of the stack or duct entry port when the probe is sampling at the farthest traverse point from the stack or duct wall. The probe shall be rotated to detect bends. Use an angle-measuring device or trigonometry to determine the bend or sag between the probe head and the secured end. (See Figure 2G-6.) Probes that are bent or sag by more than 5° shall not be used. Although this check does not apply when the probe is used for a vertical traverse, care should be taken to avoid the use of bent probes when conducting vertical traverses. If the probe is constructed of a rigid steel material and consists of a main probe without probe extensions, this check need only be performed before the initial field use of the probe, when the probe is recalibrated, when a change is made to the design or material of the probe assembly, and when the probe becomes bent. With such probes, a visual inspection shall be made of the fully assembled probe before each field test to determine if a bend is visible. The probe shall be rotated to detect bends. The inspection results shall be documented in the field test report. If a bend in the probe is visible, the horizontal straightness check shall be performed before the probe is used.
8.3 Rotational Position Check. Before each field test, and each time an extension is added to the probe during a field test, a rotational position check shall be performed on all manually operated probes (except as noted in section 8.3.5 below) to ensure that, throughout testing, the angle-measuring device is either: aligned to within ±1° of the rotational position of the reference scribe line; or is affixed to the probe such that the rotational offset of the device from the reference scribe line is known to within ±1°. This check shall consist of direct measurements of the rotational positions of the reference scribe line and angle-measuring device sufficient to verify that these specifications are met. Annex A in section 18 of this method gives recommended procedures for performing the rotational position check, and Table 2G-2 gives an example data form. Procedures other than those recommended in Annex A in section 18 may be used, provided they demonstrate whether the alignment specification is met and are explained in detail in the field test report.
8.3.1 Angle-measuring device rotational offset. The tester shall maintain a record of the angle-measuring device rotational offset, RADO, as defined in section 3.1. Note that RADO is assigned a value of 0° when the angle-measuring device is aligned to within ±1° of the rotational position of the reference scribe line. The RADO shall be used to determine the yaw angle of flow in accordance with section 8.9.4.
8.3.2 Sign of angle-measuring device rotational offset. The sign of RADO is positive when the angle-measuring device (as viewed from the “tail” end of the probe) is positioned in a clockwise direction from the reference scribe line and negative when the device is positioned in a counterclockwise direction from the reference scribe line.
8.3.3 Angle-measuring devices that can be independently adjusted (e.g., by means of a set screw), after being locked into position on the probe sheath, may be used. However, the RADO must also take into account this adjustment.
8.3.4 Post-test check. If probe extensions remain attached to the main probe throughout the field test, the rotational position check shall be repeated, at a minimum, at the completion of the field test to ensure that the angle-measuring device has remained within ±2° of its rotational position established prior to testing. At the discretion of the tester, additional checks may be conducted after completion of testing at any sample port or after any test run. If the ±2° specification is not met, all measurements made since the last successful rotational position check must be repeated. section 18.1.1.3 of Annex A provides an example procedure for performing the post-test check.
8.3.5 Exceptions.
8.3.5.1 A rotational position check need not be performed if, for measurements taken at all velocity traverse points, the yaw angle-measuring device is mounted and aligned directly on the reference scribe line specified in sections 6.1.5.1 and 6.1.5.3 and no independent adjustments, as described in section 8.3.3, are made to device's rotational position.
8.3.5.2 If extensions are detached and re-attached to the probe during a field test, a rotational position check need only be performed the first time an extension is added to the probe, rather than each time the extension is re-attached, if the probe extension is designed to be locked into a mechanically fixed rotational position (e.g., through the use of interlocking grooves), that can re-establish the initial rotational position to within ±1°.
8.4 Leak Checks. A pre-test leak check shall be conducted before each field test. A post-test check shall be performed at the end of the field test, but additional leak checks may be conducted after any test run or group of test runs. The post-test check may also serve as the pre-test check for the next group of test runs. If any leak check is failed, all runs since the last passed leak check are invalid. While performing the leak check procedures, also check each pressure device's responsiveness to changes in pressure.
8.4.1 To perform the leak check on a Type S pitot tube, pressurize the pitot impact opening until at least 7.6 cm H2O (3 in. H2O) velocity pressure, or a pressure corresponding to approximately 75 percent of the pressure device's measurement scale, whichever is less, registers on the pressure device; then, close off the impact opening. The pressure shall remain stable (±2.5 mm H2O, ±0.10 in. H2O) for at least 15 seconds. Repeat this procedure for the static pressure side, except use suction to obtain the required pressure. Other leak-check procedures may be used, if approved by the Administrator.
8.4.2 To perform the leak check on a 3-D probe, pressurize the probe's impact (P1) opening until at least 7.6 cm H2O (3 in. H2O) velocity pressure, or a pressure corresponding to approximately 75 percent of the pressure device's measurement scale, whichever is less, registers on the pressure device; then, close off the impact opening. The pressure shall remain stable (±2.5 mm H2O, ±0.10 in. H2O) for at least 15 seconds. Check the P2 and P3 pressure ports in the same fashion. Other leak-check procedures may be used, if approved by the Administrator.
8.5 Zeroing the Differential Pressure-measuring Device. Zero each differential pressure-measuring device, including the device used for yaw nulling, before each field test. At a minimum, check the zero after each field test. A zero check may also be performed after any test run or group of test runs. For fluid manometers and mechanical pressure gauges (e.g., MagnehelicΔ gauges), the zero reading shall not deviate from zero by more than ±0.8 mm H2O (±0.03 in. H2O) or one minor scale division, whichever is greater, between checks. For electronic manometers, the zero reading shall not deviate from zero between checks by more than: ±0.3 mm H2O (±0.01 in. H2O), for full scales less than or equal to 5.1 cm H2O (2.0 in. H2O); or ±0.8 mm H2O (±0.03 in. H2O), for full scales greater than 5.1 cm H2O (2.0 in. H2O). (Note: If negative zero drift is not directly readable, estimate the reading based on the position of the gauge oil in the manometer or of the needle on the pressure gauge.) In addition, for all pressure-measuring devices except those used exclusively for yaw nulling, the zero reading shall not deviate from zero by more than 5 percent of the average measured differential pressure at any distinct process condition or load level. If any zero check is failed at a specific process condition or load level, all runs conducted at that process condition or load level since the last passed zero check are invalid.
8.6 Traverse Point Verification. The number and location of the traverse points shall be selected based on Method 1 guidelines. The stack or duct diameter and port nipple lengths, including any extension of the port nipples into the stack or duct, shall be verified the first time the test is performed; retain and use this information for subsequent field tests, updating it as required. Physically measure the stack or duct dimensions or use a calibrated laser device; do not use engineering drawings of the stack or duct. The probe length necessary to reach each traverse point shall be recorded to within ±6.4 mm (± 1/4 in.) and, for manual probes, marked on the probe sheath. In determining these lengths, the tester shall take into account both the distance that the port flange projects outside of the stack and the depth that any port nipple extends into the gas stream. The resulting point positions shall reflect the true distances from the inside wall of the stack or duct, so that when the tester aligns any of the markings with the outside face of the stack port, the probe's impact port shall be located at the appropriate distance from the inside wall for the respective Method 1 traverse point. Before beginning testing at a particular location, an out-of-stack or duct verification shall be performed on each probe that will be used to ensure that these position markings are correct. The distances measured during the verification must agree with the previously calculated distances to within ± 1/4 in. For manual probes, the traverse point positions shall be verified by measuring the distance of each mark from the probe's impact pressure port (the P1 port for a 3-D probe). A comparable out-of-stack test shall be performed on automated probe systems. The probe shall be extended to each of the prescribed traverse point positions. Then, the accuracy of the positioning for each traverse point shall be verified by measuring the distance between the port flange and the probe's impact pressure port.
8.7 Probe Installation. Insert the probe into the test port. A solid material shall be used to seal the port.
8.8 System Response Time. Determine the response time of the probe measurement system. Insert and position the “cold” probe (at ambient temperature and pressure) at any Method 1 traverse point. Read and record the probe differential pressure, temperature, and elapsed time at 15-second intervals until stable readings for both pressure and temperature are achieved. The response time is the longer of these two elapsed times. Record the response time.
8.9 Sampling.
8.9.1 Yaw angle measurement protocol. With manual probes, yaw angle measurements may be obtained in two alternative ways during the field test, either by using a yaw angle-measuring device (e.g., digital inclinometer) affixed to the probe, or using a protractor wheel and pointer assembly. For horizontal traversing, either approach may be used. For vertical traversing, i.e., when measuring from on top or into the bottom of a horizontal duct, only the protractor wheel and pointer assembly may be used. With automated probes, curve-fitting protocols may be used to obtain yaw-angle measurements.
8.9.1.1 If a yaw angle-measuring device affixed to the probe is to be used, lock the device on the probe sheath, aligning it either on the reference scribe line or in the rotational offset position established under section 8.3.1.
8.9.1.2 If a protractor wheel and pointer assembly is to be used, follow the procedures in Annex B of this method.
8.9.1.3 Curve-fitting procedures. Curve-fitting routines sweep through a range of yaw angles to create curves correlating pressure to yaw position. To find the zero yaw position and the yaw angle of flow, the curve found in the stack is computationally compared to a similar curve that was previously generated under controlled conditions in a wind tunnel. A probe system that uses a curve-fitting routine for determining the yaw-null position of the probe head may be used, provided that it is verified in a wind tunnel to be able to determine the yaw angle of flow to within ±1°.
8.9.1.4 Other yaw angle determination procedures. If approved by the Administrator, other procedures for determining yaw angle may be used, provided that they are verified in a wind tunnel to be able to perform the yaw angle calibration procedure as described in section 10.5.
8.9.2 Sampling strategy. At each traverse point, first yaw-null the probe, as described in section 8.9.3, below. Then, with the probe oriented into the direction of flow, measure and record the yaw angle, the differential pressure and the temperature at the traverse point, after stable readings are achieved, in accordance with sections 8.9.4 and 8.9.5. At the start of testing in each port (i.e., after a probe has been inserted into the flue gas stream), allow at least the response time to elapse before beginning to take measurements at the first traverse point accessed from that port. Provided that the probe is not removed from the flue gas stream, measurements may be taken at subsequent traverse points accessed from the same test port without waiting again for the response time to elapse.
8.9.3 Yaw-nulling procedure. In preparation for yaw angle determination, the probe must first be yaw nulled. After positioning the probe at the appropriate traverse point, perform the following procedures.
8.9.3.1 For Type S probes, rotate the probe until a null differential pressure reading is obtained. The direction of the probe rotation shall be such that the thermocouple is located downstream of the probe pressure ports at the yaw-null position. Rotate the probe 90° back from the yaw-null position to orient the impact pressure port into the direction of flow. Read and record the angle displayed by the angle-measuring device.
8.9.3.2 For 3-D probes, rotate the probe until a null differential pressure reading (the difference in pressures across the P2 and P3 pressure ports is zero, i.e., P2 = P3) is indicated by the yaw angle pressure gauge. Read and record the angle displayed by the angle-measuring device.
8.9.3.3 Sign of the measured angle. The angle displayed on the angle-measuring device is considered positive when the probe's impact pressure port (as viewed from the “tail” end of the probe) is oriented in a clockwise rotational position relative to the stack or duct axis and is considered negative when the probe's impact pressure port is oriented in a counterclockwise rotational position (see Figure 2G-7).
8.9.4 Yaw angle determination. After performing the applicable yaw-nulling procedure in section 8.9.3, determine the yaw angle of flow according to one of the following procedures. Special care must be observed to take into account the signs of the recorded angle reading and all offsets.
8.9.4.1 Direct-reading. If all rotational offsets are zero or if the angle-measuring device rotational offset (RADO) determined in section 8.3 exactly compensates for the scribe line rotational offset (RSLO) determined in section 10.5, then the magnitude of the yaw angle is equal to the displayed angle-measuring device reading from section 8.9.3.1 or 8.9.3.2. The algebraic sign of the yaw angle is determined in accordance with section 8.9.3.3. [Note: Under certain circumstances (e.g., testing of horizontal ducts) a 90° adjustment to the angle-measuring device readings may be necessary to obtain the correct yaw angles.]
8.9.4.2 Compensation for rotational offsets during data reduction. When the angle-measuring device rotational offset does not compensate for reference scribe line rotational offset, the following procedure shall be used to determine the yaw angle:
(a) Enter the reading indicated by the angle-measuring device from section 8.9.3.1 or 8.9.3.2.
(b) Associate the proper algebraic sign from section 8.9.3.3 with the reading in step (a).
(c) Subtract the reference scribe line rotational offset, RSLO, from the reading in step (b).
(d) Subtract the angle-measuring device rotational offset, RADO, if any, from the result obtained in step (c).
(e) The final result obtained in step (d) is the yaw angle of flow.
Note:It may be necessary to first apply a 90° adjustment to the reading in step (a), in order to obtain the correct yaw angle.
8.9.4.3 Record the yaw angle measurements on a form similar to Table 2G-3.
8.9.5 Impact velocity determination. Maintain the probe rotational position established during the yaw angle determination. Then, begin recording the pressure-measuring device readings. These pressure measurements shall be taken over a sampling period of sufficiently long duration to ensure representative readings at each traverse point. If the pressure measurements are determined from visual readings of the pressure device or display, allow sufficient time to observe the pulsation in the readings to obtain a sight-weighted average, which is then recorded manually. If an automated data acquisition system (e.g., data logger, computer-based data recorder, strip chart recorder) is used to record the pressure measurements, obtain an integrated average of all pressure readings at the traverse point. Stack or duct gas temperature measurements shall be recorded, at a minimum, once at each traverse point. Record all necessary data as shown in the example field data form (Table 2G-3).
8.9.6 Alignment check. For manually operated probes, after the required yaw angle and differential pressure and temperature measurements have been made at each traverse point, verify (e.g., by visual inspection) that the yaw angle-measuring device has remained in proper alignment with the reference scribe line or with the rotational offset position established in section 8.3. If, for a particular traverse point, the angle-measuring device is found to be in proper alignment, proceed to the next traverse point; otherwise, re-align the device and repeat the angle and differential pressure measurements at the traverse point. In the course of a traverse, if a mark used to properly align the angle-measuring device (e.g., as described in section 18.1.1.1) cannot be located, re-establish the alignment mark before proceeding with the traverse.
8.10 Probe Plugging. Periodically check for plugging of the pressure ports by observing the responses on the pressure differential readouts. Plugging causes erratic results or sluggish responses. Rotate the probe to determine whether the readouts respond in the expected direction. If plugging is detected, correct the problem and repeat the affected measurements.
8.11 Static Pressure. Measure the static pressure in the stack or duct using the equipment described in section 6.7.
8.11.1 If a Type S probe is used for this measurement, position the probe at or between any traverse point(s) and rotate the probe until a null differential pressure reading is obtained. Disconnect the tubing from one of the pressure ports; read and record the ΔP. For pressure devices with one-directional scales, if a deflection in the positive direction is noted with the negative side disconnected, then the static pressure is positive. Likewise, if a deflection in the positive direction is noted with the positive side disconnected, then the static pressure is negative.
8.11.2 If a 3-D probe is used for this measurement, position the probe at or between any traverse point(s) and rotate the probe until a null differential pressure reading is obtained at P2-P3. Rotate the probe 90°. Disconnect the P2 pressure side of the probe and read the pressure P1-Pbar and record as the static pressure. (Note: The spherical probe, specified in section 6.1.2 of Method 2F, is unable to provide this measurement and shall not be used to take static pressure measurements.)
8.12 Atmospheric Pressure. Determine the atmospheric pressure at the sampling elevation during each test run following the procedure described in section 2.5 of Method 2.
8.13 Molecular Weight. Determine the stack or duct gas dry molecular weight. For combustion processes or processes that emit essentially CO2, O2, CO, and N2, use Method 3 or 3A. For processes emitting essentially air, an analysis need not be conducted; use a dry molecular weight of 29.0. Other methods may be used, if approved by the Administrator.
8.14 Moisture. Determine the moisture content of the stack gas using Method 4 or equivalent.
8.15 Data Recording and Calculations. Record all required data on a form similar to Table 2G-3.
8.15.1 2-D probe calibration coefficient. When a Type S pitot tube is used in the field, the appropriate calibration coefficient as determined in section 10.6 shall be used to perform velocity calculations. For calibrated Type S pitot tubes, the A-side coefficient shall be used when the A-side of the tube faces the flow, and the B-side coefficient shall be used when the B-side faces the flow.
8.15.2 3-D calibration coefficient. When a 3-D probe is used to collect data with this method, follow the provisions for the calibration of 3-D probes in section 10.6 of Method 2F to obtain the appropriate velocity calibration coefficient (F2 as derived using Equation 2F-2 in Method 2F) corresponding to a pitch angle position of 0°.
8.15.3 Calculations. Calculate the yaw-adjusted velocity at each traverse point using the equations presented in section 12.2. Calculate the test run average stack gas velocity by finding the arithmetic average of the point velocity results in accordance with sections 12.3 and 12.4, and calculate the stack gas volumetric flow rate in accordance with section 12.5 or 12.6, as applicable.
9.0 Quality Control9.1 Quality Control Activities. In conjunction with the yaw angle determination and the pressure and temperature measurements specified in section 8.9, the following quality control checks should be performed.
9.1.1 Range of the differential pressure gauge. In accordance with the specifications in section 6.4, ensure that the proper differential pressure gauge is being used for the range of ΔP values encountered. If it is necessary to change to a more sensitive gauge, replace the gauge with a gauge calibrated according to section 10.3.3, perform the leak check described in section 8.4 and the zero check described in section 8.5, and repeat the differential pressure and temperature readings at each traverse point.
9.1.2 Horizontal stability check. For horizontal traverses of a stack or duct, visually check that the probe shaft is maintained in a horizontal position prior to taking a pressure reading. Periodically, during a test run, the probe's horizontal stability should be verified by placing a carpenter's level, a digital inclinometer, or other angle-measuring device on the portion of the probe sheath that extends outside of the test port. A comparable check should be performed by automated systems.
10.0 Calibration10.1 Wind Tunnel Qualification Checks. To qualify for use in calibrating probes, a wind tunnel shall have the design features specified in section 6.11 and satisfy the following qualification criteria. The velocity pressure cross-check in section 10.1.1 and axial flow verification in section 10.1.2 shall be performed before the initial use of the wind tunnel and repeated immediately after any alteration occurs in the wind tunnel's configuration, fans, interior surfaces, straightening vanes, controls, or other properties that could reasonably be expected to alter the flow pattern or velocity stability in the tunnel. The owner or operator of a wind tunnel used to calibrate probes according to this method shall maintain records documenting that the wind tunnel meets the requirements of sections 10.1.1 and 10.1.2 and shall provide these records to the Administrator upon request.
10.1.1 Velocity pressure cross-check. To verify that the wind tunnel produces the same velocity at the tested probe head as at the calibration pitot tube impact port, perform the following cross-check. Take three differential pressure measurements at the fixed calibration pitot tube location, using the calibration pitot tube specified in section 6.10, and take three measurements with the calibration pitot tube at the wind tunnel calibration location, as defined in section 3.21. Alternate the measurements between the two positions. Perform this procedure at the lowest and highest velocity settings at which the probes will be calibrated. Record the values on a form similar to Table 2G-4. At each velocity setting, the average velocity pressure obtained at the wind tunnel calibration location shall be within ±2 percent or 2.5 mm H2O (0.01 in. H2O), whichever is less restrictive, of the average velocity pressure obtained at the fixed calibration pitot tube location. This comparative check shall be performed at 2.5-cm (1-in.), or smaller, intervals across the full length, width, and depth (if applicable) of the wind tunnel calibration location. If the criteria are not met at every tested point, the wind tunnel calibration location must be redefined, so that acceptable results are obtained at every point. Include the results of the velocity pressure cross-check in the calibration data section of the field test report. (See section 16.1.4.)
10.1.2 Axial flow verification. The following procedures shall be performed to demonstrate that there is fully developed axial flow within the wind tunnel calibration location and at the calibration pitot tube location. Two options are available to conduct this check.
10.1.2.1 Using a calibrated 3-D probe. A probe that has been previously calibrated in a wind tunnel with documented axial flow (as defined in section 3.22) may be used to conduct this check. Insert the calibrated 3-D probe into the wind tunnel test section using the tested probe port. Following the procedures in sections 8.9 and 12.2 of Method 2F, determine the yaw and pitch angles at all the point(s) in the test section where the velocity pressure cross-check, as specified in section 10.1.1, is performed. This includes all the points in the calibration location and the point where the calibration pitot tube will be located. Determine the yaw and pitch angles at each point. Repeat these measurements at the highest and lowest velocities at which the probes will be calibrated. Record the values on a form similar to Table 2G-5. Each measured yaw and pitch angle shall be within ±3° of 0°. Exceeding the limits indicates unacceptable flow in the test section. Until the problem is corrected and acceptable flow is verified by repetition of this procedure, the wind tunnel shall not be used for calibration of probes. Include the results of the axial flow verification in the calibration data section of the field test report. (See section 16.1.4.)
10.1.2.2 Using alternative probes. Axial flow verification may be performed using an uncalibrated prism-shaped 3-D probe (e.g., DA or DAT probe) or an uncalibrated wedge probe. (Figure 2G-8 illustrates a typical wedge probe.) This approach requires use of two ports: the tested probe port and a second port located 90° from the tested probe port. Each port shall provide access to all the points within the wind tunnel test section where the velocity pressure cross-check, as specified in section 10.1.1, is conducted. The probe setup shall include establishing a reference yaw-null position on the probe sheath to serve as the location for installing the angle-measuring device. Physical design features of the DA, DAT, and wedge probes are relied on to determine the reference position. For the DA or DAT probe, this reference position can be determined by setting a digital inclinometer on the flat facet where the P1 pressure port is located and then identifying the rotational position on the probe sheath where a second angle-measuring device would give the same angle reading. The reference position on a wedge probe shaft can be determined either geometrically or by placing a digital inclinometer on each side of the wedge and rotating the probe until equivalent readings are obtained. With the latter approach, the reference position is the rotational position on the probe sheath where an angle-measuring device would give a reading of 0°. After installation of the angle-measuring device in the reference yaw-null position on the probe sheath, determine the yaw angle from the tested port. Repeat this measurement using the 90° offset port, which provides the pitch angle of flow. Determine the yaw and pitch angles at all the point(s) in the test section where the velocity pressure cross-check, as specified in section 10.1.1, is performed. This includes all the points in the wind tunnel calibration location and the point where the calibration pitot tube will be located. Perform this check at the highest and lowest velocities at which the probes will be calibrated. Record the values on a form similar to Table 2G-5. Each measured yaw and pitch angle shall be within ±3° of 0°. Exceeding the limits indicates unacceptable flow in the test section. Until the problem is corrected and acceptable flow is verified by repetition of this procedure, the wind tunnel shall not be used for calibration of probes. Include the results in the probe calibration report.
10.1.3 Wind tunnel audits.
10.1.3.1 Procedure. Upon the request of the Administrator, the owner or operator of a wind tunnel shall calibrate a 2-D audit probe in accordance with the procedures described in sections 10.3 through 10.6. The calibration shall be performed at two velocities that encompass the velocities typically used for this method at the facility. The resulting calibration data shall be submitted to the Agency in an audit test report. These results shall be compared by the Agency to reference calibrations of the audit probe at the same velocity settings obtained at two different wind tunnels.
10.1.3.2 Acceptance criterion. The audited tunnel's calibration coefficient is acceptable if it is within ±3 percent of the reference calibrations obtained at each velocity setting by one (or both) of the wind tunnels. If the acceptance criterion is not met at each calibration velocity setting, the audited wind tunnel shall not be used to calibrate probes for use under this method until the problems are resolved and acceptable results are obtained upon completion of a subsequent audit.
10.2 Probe Inspection.
10.2.1 Type S probe. Before each calibration of a Type S probe, verify that one leg of the tube is permanently marked A, and the other, B. Carefully examine the pitot tube from the top, side, and ends. Measure the angles (α1, α2, β1, and β2) and the dimensions (w and z) illustrated in Figures 2-2 and 2-3 in Method 2. Also measure the dimension A, as shown in the diagram in Table 2G-1, and the external tubing diameter (dimension Dt, Figure 2-2b in Method 2). For the purposes of this method, Dt shall be no less than 9.5 mm ( 3/8 in.). The base-to-opening plane distances PA and PB in Figure 2-3 of Method 2 shall be equal, and the dimension A in Table 2G-1 should be between 2.10Dt and 3.00Dt. Record the inspection findings and probe measurements on a form similar to Table CD2-1 of the “Quality Assurance Handbook for Air Pollution Measurement Systems: Volume III, Stationary Source-Specific Methods” (EPA/600/R-94/038c, September 1994). For reference, this form is reproduced herein as Table 2G-1. The pitot tube shall not be used under this method if it fails to meet the specifications in this section and the alignment specifications in section 6.1.1. All Type S probes used to collect data with this method shall be calibrated according to the procedures outlined in sections 10.3 through 10.6 below. During calibration, each Type S pitot tube shall be configured in the same manner as used, or planned to be used, during the field test, including all components in the probe assembly (e.g., thermocouple, probe sheath, sampling nozzle). Probe shaft extensions that do not affect flow around the probe head need not be attached during calibration.
10.2.2 3-D probe. If a 3-D probe is used to collect data with this method, perform the pre-calibration inspection according to procedures in Method 2F, section 10.2.
10.3 Pre-Calibration Procedures. Prior to calibration, a scribe line shall have been placed on the probe in accordance with section 10.4. The yaw angle and velocity calibration procedures shall not begin until the pre-test requirements in sections 10.3.1 through 10.3.4 have been met.
10.3.1 Perform the horizontal straightness check described in section 8.2 on the probe assembly that will be calibrated in the wind tunnel.
10.3.2 Perform a leak check in accordance with section 8.4.
10.3.3 Except as noted in section 10.3.3.3, calibrate all differential pressure-measuring devices to be used in the probe calibrations, using the following procedures. At a minimum, calibrate these devices on each day that probe calibrations are performed.
10.3.3.1 Procedure. Before each wind tunnel use, all differential pressure-measuring devices shall be calibrated against the reference device specified in section 6.4.3 using a common pressure source. Perform the calibration at three reference pressures representing 30, 60, and 90 percent of the full-scale range of the pressure-measuring device being calibrated. For an inclined-vertical manometer, perform separate calibrations on the inclined and vertical portions of the measurement scale, considering each portion of the scale to be a separate full-scale range. [For example, for a manometer with a 0-to 2.5-cm H2O (0-to 1-in. H2O) inclined scale and a 2.5-to 12.7-cm H2O (1-to 5-in. H2O) vertical scale, calibrate the inclined portion at 7.6, 15.2, and 22.9 mm H2O (0.3, 0.6, and 0.9 in. H2O), and calibrate the vertical portion at 3.8, 7.6, and 11.4 cm H2O (1.5, 3.0, and 4.5 in. H2O).] Alternatively, for the vertical portion of the scale, use three evenly spaced reference pressures, one of which is equal to or higher than the highest differential pressure expected in field applications.
10.3.3.2 Acceptance criteria. At each pressure setting, the two pressure readings made using the reference device and the pressure-measuring device being calibrated shall agree to within ±2 percent of full scale of the device being calibrated or 0.5 mm H2O (0.02 in. H2O), whichever is less restrictive. For an inclined-vertical manometer, these requirements shall be met separately using the respective full-scale upper limits of the inclined and vertical portions of the scale. Differential pressure-measuring devices not meeting the ±2 percent of full scale or 0.5 mm H2O (0.02 in. H2O) calibration requirement shall not be used.
10.3.3.3 Exceptions. Any precision manometer that meets the specifications for a reference device in section 6.4.3 and that is not used for field testing does not require calibration, but must be leveled and zeroed before each wind tunnel use. Any pressure device used exclusively for yaw nulling does not require calibration, but shall be checked for responsiveness to rotation of the probe prior to each wind tunnel use.
10.3.4 Calibrate digital inclinometers on each day of wind tunnel or field testing (prior to beginning testing) using the following procedures. Calibrate the inclinometer according to the manufacturer's calibration procedures. In addition, use a triangular block (illustrated in Figure 2G-9) with a known angle θ, independently determined using a protractor or equivalent device, between two adjacent sides to verify the inclinometer readings. (Note: If other angle-measuring devices meeting the provisions of section 6.2.3 are used in place of a digital inclinometer, comparable calibration procedures shall be performed on such devices.) Secure the triangular block in a fixed position. Place the inclinometer on one side of the block (side A) to measure the angle of inclination (R1). Repeat this measurement on the adjacent side of the block (side B) using the inclinometer to obtain a second angle reading (R2). The difference of the sum of the two readings from 180° (i.e., 180°-R1-R2) shall be within ±2° of the known angle, θ.
10.4 Placement of Reference Scribe Line. Prior to the first calibration of a probe, a line shall be permanently inscribed on the main probe sheath to serve as a reference mark for determining yaw angles. Annex C in section 18 of this method gives a guideline for placement of the reference scribe line.
10.4.1 This reference scribe line shall meet the specifications in sections 6.1.5.1 and 6.1.5.3 of this method. To verify that the alignment specification in section 6.1.5.3 is met, secure the probe in a horizontal position and measure the rotational angle of each scribe line and scribe line segment using an angle-measuring device that meets the specifications in section 6.2.1 or 6.2.3. For any scribe line that is longer than 30.5 cm (12 in.), check the line's rotational position at 30.5-cm (12-in.) intervals. For each line segment that is 12 in. or less in length, check the rotational position at the two endpoints of the segment. To meet the alignment specification in section 6.1.5.3, the minimum and maximum of all of the rotational angles that are measured along the full length of main probe must not differ by more than 2°. (Note: A short reference scribe line segment [e.g., 15.2 cm (6 in.) or less in length] meeting the alignment specifications in section 6.1.5.3 is fully acceptable under this method. See section 18.1.1.1 of Annex A for an example of a probe marking procedure, suitable for use with a short reference scribe line.)
10.4.2 The scribe line should be placed on the probe first and then its offset from the yaw-null position established (as specified in section 10.5). The rotational position of the reference scribe line relative to the yaw-null position of the probe, as determined by the yaw angle calibration procedure in section 10.5, is the reference scribe line rotational offset, RSLO. The reference scribe line rotational offset shall be recorded and retained as part of the probe's calibration record.
10.4.3 Scribe line for automated probes. A scribe line may not be necessary for an automated probe system if a reference rotational position of the probe is built into the probe system design. For such systems, a “flat” (or comparable, clearly identifiable physical characteristic) should be provided on the probe casing or flange plate to ensure that the reference position of the probe assembly remains in a vertical or horizontal position. The rotational offset of the flat (or comparable, clearly identifiable physical characteristic) needed to orient the reference position of the probe assembly shall be recorded and maintained as part of the automated probe system's specifications.
10.5 Yaw Angle Calibration Procedure. For each probe used to measure yaw angles with this method, a calibration procedure shall be performed in a wind tunnel meeting the specifications in section 10.1 to determine the rotational position of the reference scribe line relative to the probe's yaw-null position. This procedure shall be performed on the main probe with all devices that will be attached to the main probe in the field [such as thermocouples, resistance temperature detectors (RTDs), or sampling nozzles] that may affect the flow around the probe head. Probe shaft extensions that do not affect flow around the probe head need not be attached during calibration. At a minimum, this procedure shall include the following steps.
10.5.1 Align and lock the angle-measuring device on the reference scribe line. If a marking procedure (such as described in section 18.1.1.1) is used, align the angle-measuring device on a mark within ±1° of the rotational position of the reference scribe line. Lock the angle-measuring device onto the probe sheath at this position.
10.5.2 Zero the pressure-measuring device used for yaw nulling.
10.5.3 Insert the probe assembly into the wind tunnel through the entry port, positioning the probe's impact port at the calibration location. Check the responsiveness of the pressure-measurement device to probe rotation, taking corrective action if the response is unacceptable.
10.5.4 Ensure that the probe is in a horizontal position, using a carpenter's level.
10.5.5 Rotate the probe either clockwise or counterclockwise until a yaw null [zero ΔP for a Type S probe or zero (P2-P3) for a 3-D probe] is obtained. If using a Type S probe with an attached thermocouple, the direction of the probe rotation shall be such that the thermocouple is located downstream of the probe pressure ports at the yaw-null position.
10.5.6 Use the reading displayed by the angle-measuring device at the yaw-null position to determine the magnitude of the reference scribe line rotational offset, RSLO, as defined in section 3.15. Annex D in section 18 of this method gives a recommended procedure for determining the magnitude of RSLO with a digital inclinometer and a second procedure for determining the magnitude of RSLO with a protractor wheel and pointer device. Table 2G-6 gives an example data form and Table 2G-7 is a look-up table with the recommended procedure. Procedures other than those recommended in Annex D in section 18 may be used, if they can determine RSLO to within 1° and are explained in detail in the field test report. The algebraic sign of RSLO will either be positive if the rotational position of the reference scribe line (as viewed from the “tail” end of the probe) is clockwise, or negative, if counterclockwise with respect to the probe's yaw-null position. (This is illustrated in Figure 2G-10.)
10.5.7 The steps in sections 10.5.3 through 10.5.6 shall be performed twice at each of the velocities at which the probe will be calibrated (in accordance with section 10.6). Record the values of RSLO.
10.5.8 The average of all of the RSLO values shall be documented as the reference scribe line rotational offset for the probe.
10.5.9 Use of reference scribe line offset. The reference scribe line rotational offset shall be used to determine the yaw angle of flow in accordance with section 8.9.4.
10.6 Velocity Calibration Procedure. When a 3-D probe is used under this method, follow the provisions for the calibration of 3-D probes in section 10.6 of Method 2F to obtain the necessary velocity calibration coefficients (F2 as derived using Equation 2F-2 in Method 2F) corresponding to a pitch angle position of 0°. The following procedure applies to Type S probes. This procedure shall be performed on the main probe and all devices that will be attached to the main probe in the field (e.g., thermocouples, RTDs, sampling nozzles) that may affect the flow around the probe head. Probe shaft extensions that do not affect flow around the probe head need not be attached during calibration. (Note: If a sampling nozzle is part of the assembly, two additional requirements must be satisfied before proceeding. The distance between the nozzle and the pitot tube shall meet the minimum spacing requirement prescribed in Method 2, and a wind tunnel demonstration shall be performed that shows the probe's ability to yaw null is not impaired when the nozzle is drawing sample.) To obtain velocity calibration coefficient(s) for the tested probe, proceed as follows.
10.6.1 Calibration velocities. The tester may calibrate the probe at two nominal wind tunnel velocity settings of 18.3 m/sec and 27.4 m/sec (60 ft/sec and 90 ft/sec) and average the results of these calibrations, as described in sections 10.6.12 through 10.6.14, in order to generate the calibration coefficient, Cp. If this option is selected, this calibration coefficient may be used for all field applications where the velocities are 9.1 m/sec (30 ft/sec) or greater. Alternatively, the tester may customize the probe calibration for a particular field test application (or for a series of applications), based on the expected average velocity(ies) at the test site(s). If this option is selected, generate the calibration coefficients by calibrating the probe at two nominal wind tunnel velocity settings, one of which is less than or equal to and the other greater than or equal to the expected average velocity(ies) for the field application(s), and average the results as described in sections 10.6.12 through 10.6.14. Whichever calibration option is selected, the probe calibration coefficient(s) obtained at the two nominal calibration velocities shall meet the conditions specified in sections 10.6.12 through 10.6.14.
10.6.2 Connect the tested probe and calibration pitot tube to their respective pressure-measuring devices. Zero the pressure-measuring devices. Inspect and leak-check all pitot lines; repair or replace them, if necessary. Turn on the fan, and allow the wind tunnel air flow to stabilize at the first of the selected nominal velocity settings.
10.6.3 Position the calibration pitot tube at its measurement location (determined as outlined in section 6.11.4.3), and align the tube so that its tip is pointed directly into the flow. Ensure that the entry port surrounding the tube is properly sealed. The calibration pitot tube may either remain in the wind tunnel throughout the calibration, or be removed from the wind tunnel while measurements are taken with the probe being calibrated.
10.6.4 Check the zero setting of each pressure-measuring device.
10.6.5 Insert the tested probe into the wind tunnel and align it so that the designated pressure port (e.g., either the A-side or B-side of a Type S probe) is pointed directly into the flow and is positioned within the wind tunnel calibration location (as defined in section 3.21). Secure the probe at the 0° pitch angle position. Ensure that the entry port surrounding the probe is properly sealed.
10.6.6 Read the differential pressure from the calibration pitot tube (ΔPstd), and record its value. Read the barometric pressure to within ±2.5 mm Hg (±0.1 in. Hg) and the temperature in the wind tunnel to within 0.6 °C (1 °F). Record these values on a data form similar to Table 2G-8. Record the rotational speed of the fan or indicator of wind tunnel velocity control (damper setting, variac rheostat, etc.) and make no adjustment to fan speed or wind tunnel velocity control between this observation and the Type S probe reading.
10.6.7 After the tested probe's differential pressure gauges have had sufficient time to stabilize, yaw null the probe (and then rotate it back 90° for Type S probes), then obtain the differential pressure reading (ΔP). Record the yaw angle and differential pressure readings.
10.6.8 Take paired differential pressure measurements with the calibration pitot tube and tested probe (according to sections 10.6.6 and 10.6.7). The paired measurements in each replicate can be made either simultaneously (i.e., with both probes in the wind tunnel) or by alternating the measurements of the two probes (i.e., with only one probe at a time in the wind tunnel). Adjustments made to the fan speed or other changes to the system designed to change the air flow velocity of the wind tunnel between observation of the calibration pitot tube (ΔPstd) and the Type S pitot tube invalidates the reading and the observation must be repeated.
10.6.9 Repeat the steps in sections 10.6.6 through 10.6.8 at the same nominal velocity setting until three pairs of ΔP readings have been obtained from the calibration pitot tube and the tested probe.
10.6.10 Repeat the steps in sections 10.6.6 through 10.6.9 above for the A-side and B-side of the Type S pitot tube. For a probe assembly constructed such that its pitot tube is always used in the same orientation, only one side of the pitot tube need be calibrated (the side that will face the flow). However, the pitot tube must still meet the alignment and dimension specifications in section 6.1.1 and must have an average deviation (σ) value of 0.01 or less as provided in section 10.6.12.4.
10.6.11 Repeat the calibration procedures in sections 10.6.6 through 10.6.10 at the second selected nominal wind tunnel velocity setting.
10.6.12 Perform the following calculations separately on the A-side and B-side values.
10.6.12.1 Calculate a Cp value for each of the three replicates performed at the lower velocity setting where the calibrations were performed using Equation 2-2 in section 4.1.4 of Method 2.
10.6.12.2 Calculate the arithmetic average, Cp(avg-low), of the three Cp values.
10.6.12.3 Calculate the deviation of each of the three individual values of Cp from the A-side average Cp(avg-low) value using Equation 2-3 in Method 2.
10.6.12.4 Calculate the average deviation (σ) of the three individual Cp values from Cp(avg-low) using Equation 2-4 in Method 2. Use the Type S pitot tube only if the values of σ (side A) and σ (side B) are less than or equal to 0.01. If both A-side and B-side calibration coefficients are calculated, the absolute value of the difference between Cp(avg-low) (side A) and Cp(avg-low) (side B) must not exceed 0.01.
10.6.13 Repeat the calculations in section 10.6.12 using the data obtained at the higher velocity setting to derive the arithmetic Cp values at the higher velocity setting, Cp(avg-high), and to determine whether the conditions in 10.6.12.4 are met by both the A-side and B-side calibrations at this velocity setting.
10.6.14 Use equation 2G-1 to calculate the percent difference of the averaged Cp values at the two calibration velocities.

10.6.15 If the two nominal velocities used in the calibration were 18.3 and 27.4 m/sec (60 and 90 ft/sec), the average Cp from section 10.6.14 is applicable to all velocities 9.1 m/sec (30 ft/sec) or greater. If two other nominal velocities were used in the calibration, the resulting average Cp value shall be applicable only in situations where the velocity calculated using the calibration coefficient is neither less than the lower nominal velocity nor greater than the higher nominal velocity.
10.7 Recalibration. Recalibrate the probe using the procedures in section 10 either within 12 months of its first field use after its most recent calibration or after 10 field tests (as defined in section 3.3), whichever occurs later. In addition, whenever there is visible damage to the probe head, the probe shall be recalibrated before it is used again.
10.8 Calibration of pressure-measuring devices used in the field. Before its initial use in a field test, calibrate each pressure-measuring device (except those used exclusively for yaw nulling) using the three-point calibration procedure described in section 10.3.3. The device shall be recalibrated according to the procedure in section 10.3.3 no later than 90 days after its first field use following its most recent calibration. At the discretion of the tester, more frequent calibrations (e.g., after a field test) may be performed. No adjustments, other than adjustments to the zero setting, shall be made to the device between calibrations.
10.8.1 Post-test calibration check. A single-point calibration check shall be performed on each pressure-measuring device after completion of each field test. At the discretion of the tester, more frequent single-point calibration checks (e.g., after one or more field test runs) may be performed. It is recommended that the post-test check be performed before leaving the field test site. The check shall be performed at a pressure between 50 and 90 percent of full scale by taking a common pressure reading with the tested probe and a reference pressure-measuring device (as described in section 6.4.4) or by challenging the tested device with a reference pressure source (as described in section 6.4.4) or by performing an equivalent check using a reference device approved by the Administrator.
10.8.2 Acceptance criterion. At the selected pressure setting, the pressure readings made using the reference device and the tested device shall agree to within ±3 percent of full scale of the tested device or 0.8 mm H2O (0.03 in. H2O), whichever is less restrictive. If this specification is met, the test data collected during the field test are valid. If the specification is not met, all test data collected since the last successful calibration or calibration check are invalid and shall be repeated using a pressure-measuring device with a current, valid calibration. Any device that fails the calibration check shall not be used in a field test until a successful recalibration is performed according to the procedures in section 10.3.3.
10.9 Temperature Gauges. Same as Method 2, section 4.3. The alternative thermocouple calibration procedures outlined in Emission Measurement Center (EMC) Approved Alternative Method (ALT-011) “Alternative Method 2 Thermocouple Calibration Procedure” may be performed. Temperature gauges shall be calibrated no more than 30 days prior to the start of a field test or series of field tests and recalibrated no more than 30 days after completion of a field test or series of field tests.
10.10 Barometer. Same as Method 2, section 4.4. The barometer shall be calibrated no more than 30 days prior to the start of a field test or series of field tests.
11.0 Analytical ProcedureSample collection and analysis are concurrent for this method (see section 8.0).
12.0 Data Analysis and CalculationsThese calculations use the measured yaw angle and the differential pressure and temperature measurements at individual traverse points to derive the near-axial flue gas velocity (va(i)) at each of those points. The near-axial velocity values at all traverse points that comprise a full stack or duct traverse are then averaged to obtain the average near-axial stack or duct gas velocity (va(avg)).
12.1 Nomenclature A = Cross-sectional area of stack or duct at the test port location, m 2 (ft 2). Bws = Water vapor in the gas stream (from Method 4 or alternative), proportion by volume. Cp = Pitot tube calibration coefficient, dimensionless. F2(i) = 3-D probe velocity coefficient at 0 pitch, applicable at traverse point i. Kp = Pitot tube constant,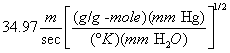
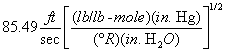

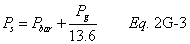


12.2 Traverse Point Velocity Calculations. Perform the following calculations from the measurements obtained at each traverse point.
12.2.1 Selection of calibration coefficient. Select the calibration coefficient as described in section 10.6.1.
12.2.2 Near-axial traverse point velocity. When using a Type S probe, use the following equation to calculate the traverse point near-axial velocity (va(i)) from the differential pressure (ΔPi), yaw angle (θy(i)), absolute stack or duct standard temperature (Ts(i)) measured at traverse point i, the absolute stack or duct pressure (Ps), and molecular weight (Ms).


12.2.3 Handling multiple measurements at a traverse point. For pressure or temperature devices that take multiple measurements at a traverse point, the multiple measurements (or where applicable, their square roots) may first be averaged and the resulting average values used in the equations above. Alternatively, the individual measurements may be used in the equations above and the resulting calculated values may then be averaged to obtain a single traverse point value. With either approach, all of the individual measurements recorded at a traverse point must be used in calculating the applicable traverse point value.
12.3 Average Near-Axial Velocity in Stack or Duct. Use the reported traverse point near-axial velocity in the following equation.
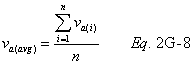
12.4 Acceptability of Results. The acceptability provisions in section 12.4 of Method 2F apply to 3-D probes used under Method 2G. The following provisions apply to Type S probes. For Type S probes, the test results are acceptable and the calculated value of va(avg) may be reported as the average near-axial velocity for the test run if the conditions in either section 12.4.1 or 12.4.2 are met.
12.4.1 The average calibration coefficient Cp used in Equation 2G-6 was generated at nominal velocities of 18.3 and 27.4 m/sec (60 and 90 ft/sec) and the value of va(avg) calculated using Equation 2G-8 is greater than or equal to 9.1 m/sec (30 ft/sec).
12.4.2 The average calibration coefficient Cp used in Equation 2G-6 was generated at nominal velocities other than 18.3 or 27.4 m/sec (60 or 90 ft/sec) and the value of va(avg) calculated using Equation 2G-8 is greater than or equal to the lower nominal velocity and less than or equal to the higher nominal velocity used to derive the average Cp.
12.4.3 If the conditions in neither section 12.4.1 nor section 12.4.2 are met, the test results obtained from Equation 2G-8 are not acceptable, and the steps in sections 12.2 and 12.3 must be repeated using an average calibration coefficient Cp that satisfies the conditions in section 12.4.1 or 12.4.2.
12.5 Average Gas Volumetric Flow Rate in Stack or Duct (Wet Basis). Use the following equation to compute the average volumetric flow rate on a wet basis.

12.6 Average Gas Volumetric Flow Rate in Stack or Duct (Dry Basis). Use the following equation to compute the average volumetric flow rate on a dry basis.

16.1 Field Test Reports. Field test reports shall be submitted to the Agency according to applicable regulatory requirements. Field test reports should, at a minimum, include the following elements.
16.1.1 Description of the source. This should include the name and location of the test site, descriptions of the process tested, a description of the combustion source, an accurate diagram of stack or duct cross-sectional area at the test site showing the dimensions of the stack or duct, the location of the test ports, and traverse point locations and identification numbers or codes. It should also include a description and diagram of the stack or duct layout, showing the distance of the test location from the nearest upstream and downstream disturbances and all structural elements (including breachings, baffles, fans, straighteners, etc.) affecting the flow pattern. If the source and test location descriptions have been previously submitted to the Agency in a document (e.g., a monitoring plan or test plan), referencing the document in lieu of including this information in the field test report is acceptable.
16.1.2 Field test procedures. These should include a description of test equipment and test procedures. Testing conventions, such as traverse point numbering and measurement sequence (e.g., sampling from center to wall, or wall to center), should be clearly stated. Test port identification and directional reference for each test port should be included on the appropriate field test data sheets.
16.1.3 Field test data.
16.1.3.1 Summary of results. This summary should include the dates and times of testing, and the average near-axial gas velocity and the average flue gas volumetric flow results for each run and tested condition.
16.1.3.2 Test data. The following values for each traverse point should be recorded and reported:
(a) Differential pressure at traverse point i (ΔPi)
(b) Stack or duct temperature at traverse point i (ts(i))
(c) Absolute stack or duct temperature at traverse point i (Ts(i))
(d) Yaw angle at traverse point i (θy(i))
(e) Stack gas near-axial velocity at traverse point i (va(i))
16.1.3.3 The following values should be reported once per run:
(a) Water vapor in the gas stream (from Method 4 or alternative), proportion by volume (Bws), measured at the frequency specified in the applicable regulation
(b) Molecular weight of stack or duct gas, dry basis (Md)
(c) Molecular weight of stack or duct gas, wet basis (Ms)
(d) Stack or duct static pressure (Pg)
(e) Absolute stack or duct pressure (Ps)
(f) Carbon dioxide concentration in the flue gas, dry basis (%d CO2)
(g) Oxygen concentration in the flue gas, dry basis (%d O2)
(h) Average near-axial stack or duct gas velocity (va(avg)) across all traverse points
(i) Gas volumetric flow rate corrected to standard conditions, dry or wet basis as required by the applicable regulation (Qsd or Qsw)
16.1.3.4 The following should be reported once per complete set of test runs:
(a) Cross-sectional area of stack or duct at the test location (A)
(b) Pitot tube calibration coefficient (Cp)
(c) Measurement system response time (sec)
(d) Barometric pressure at measurement site (Pbar)
16.1.4 Calibration data. The field test report should include calibration data for all probes and test equipment used in the field test. At a minimum, the probe calibration data reported to the Agency should include the following:
(a) Date of calibration
(b) Probe type
(c) Probe identification number(s) or code(s)
(d) Probe inspection sheets
(e) Pressure measurements and calculations used to obtain calibration coefficients in accordance with section 10.6 of this method
(f) Description and diagram of wind tunnel used for the calibration, including dimensions of cross-sectional area and position and size of the test section
(g) Documentation of wind tunnel qualification tests performed in accordance with section 10.1 of this method
16.1.5 Quality assurance. Specific quality assurance and quality control procedures used during the test should be described.
17.0 Bibliography.(1) 40 CFR Part 60, Appendix A, Method 1 - Sample and velocity traverses for stationary sources.
(2) 40 CFR Part 60, Appendix A, Method 2 - Determination of stack gas velocity and volumetric flow rate (Type S pitot tube) .
(3) 40 CFR Part 60, Appendix A, Method 2F - Determination of stack gas velocity and volumetric flow rate with three-dimensional probes.
(4) 40 CFR Part 60, Appendix A, Method 2H - Determination of stack gas velocity taking into account velocity decay near the stack wall.
(5) 40 CFR Part 60, Appendix A, Method 3 - Gas analysis for carbon dioxide, oxygen, excess air, and dry molecular weight.
(6) 40 CFR Part 60, Appendix A, Method 3A - Determination of oxygen and carbon dioxide concentrations in emissions from stationary sources (instrumental analyzer procedure).
(7) 40 CFR Part 60, Appendix A, Method 4 - Determination of moisture content in stack gases.
(8) Emission Measurement Center (EMC) Approved Alternative Method (ALT-011) “Alternative Method 2 Thermocouple Calibration Procedure.”
(9) Electric Power Research Institute, Interim Report EPRI TR-106698, “Flue Gas Flow Rate Measurement Errors,” June 1996.
(10) Electric Power Research Institute, Final Report EPRI TR-108110, “Evaluation of Heat Rate Discrepancy from Continuous Emission Monitoring Systems,” August 1997.
(11) Fossil Energy Research Corporation, Final Report, “Velocity Probe Tests in Non-axial Flow Fields,” November 1998, Prepared for the U.S. Environmental Protection Agency.
(12) Fossil Energy Research Corporation, “Additional Swirl Tunnel Tests: E-DAT and T-DAT Probes,” February 24, 1999, Technical Memorandum Prepared for U.S. Environmental Protection Agency, P.O. No. 7W-1193-NALX.
(13) Massachusetts Institute of Technology, Report WBWT-TR-1317, “Calibration of Eight Wind Speed Probes Over a Reynolds Number Range of 46,000 to 725,000 Per Foot, Text and Summary Plots,” Plus appendices, October 15, 1998, Prepared for The Cadmus Group, Inc.
(14) National Institute of Standards and Technology, Special Publication 250, “NIST Calibration Services Users Guide 1991,” Revised October 1991, U.S. Department of Commerce, p. 2.
(15) National Institute of Standards and Technology, 1998, “Report of Special Test of Air Speed Instrumentation, Four Prandtl Probes, Four S-Type Probes, Four French Probes, Four Modified Kiel Probes,” Prepared for the U.S. Environmental Protection Agency under IAG #DW13938432-01-0.
(16) National Institute of Standards and Technology, 1998, “Report of Special Test of Air Speed In-strumentation, Five Autoprobes,” Prepared for the U.S. Environmental Protection Agency under IAG #DW13938432-01-0.
(17) National Institute of Standards and Technology, 1998, “Report of Special Test of Air Speed Instrumentation, Eight Spherical Probes,” Prepared for the U.S. Environmental Protection Agency under IAG #DW13938432-01-0.
(18) National Institute of Standards and Technology, 1998, “Report of Special Test of Air Speed Instrumentation, Four DAT Probes, “ Prepared for the U.S. Environmental Protection Agency under IAG #DW13938432-01-0.
(19) Norfleet, S.K., “An Evaluation of Wall Effects on Stack Flow Velocities and Related Overestimation Bias in EPA's Stack Flow Reference Methods,” EPRI CEMS User's Group Meeting, New Orleans, Louisiana, May 13-15, 1998.
(20) Page, J.J., E.A. Potts, and R.T. Shigehara, “3-D Pitot Tube Calibration Study,” EPA Contract No. 68D10009, Work Assignment No. I-121, March 11, 1993.
(21) Shigehara, R.T., W.F. Todd, and W.S. Smith, “Significance of Errors in Stack Sampling Measurements,” Presented at the Annual Meeting of the Air Pollution Control Association, St. Louis, Missouri, June 1419, 1970.
(22) The Cadmus Group, Inc., May 1999, “EPA Flow Reference Method Testing and Analysis: Findings Report,” EPA/430-R-99-009.
(23) The Cadmus Group, Inc., 1998, “EPA Flow Reference Method Testing and Analysis: Data Report, Texas Utilities, DeCordova Steam Electric Station, Volume I: Test Description and Appendix A (Data Distribution Package),” EPA/430-R-98-015a.
(24) The Cadmus Group, Inc., 1998, “EPA Flow Reference Method Testing and Analysis: Data Report, Texas Utilities, Lake Hubbard Steam Electric Station, Volume I: Test Description and Appendix A (Data Distribution Package),” EPA/430-R-98-017a.
(25) The Cadmus Group, Inc., 1998, “EPA Flow Reference Method Testing and Analysis: Data Report, Pennsylvania Electric Co., G.P.U. Genco Homer City Station: Unit 1, Volume I: Test Description and Appendix A (Data Distribution Package),” EPA/430-R-98-018a.
(26) The Cadmus Group, Inc., 1997, “EPA Flow Reference Method Testing and Analysis: Wind Tunnel Experimental Results,” EPA/430-R-97-013.
18.0 AnnexesAnnex A, C, and D describe recommended procedures for meeting certain provisions in sections 8.3, 10.4, and 10.5 of this method. Annex B describes procedures to be followed when using the protractor wheel and pointer assembly to measure yaw angles, as provided under section 8.9.1.
18.1 Annex A - Rotational Position Check. The following are recommended procedures that may be used to satisfy the rotational position check requirements of section 8.3 of this method and to determine the angle-measuring device rotational offset (RADO).
18.1.1 Rotational position check with probe outside stack. Where physical constraints at the sampling location allow full assembly of the probe outside the stack and insertion into the test port, the following procedures should be performed before the start of testing. Two angle-measuring devices that meet the specifications in section 6.2.1 or 6.2.3 are required for the rotational position check. An angle measuring device whose position can be independently adjusted (e.g., by means of a set screw) after being locked into position on the probe sheath shall not be used for this check unless the independent adjustment is set so that the device performs exactly like a device without the capability for independent adjustment. That is, when aligned on the probe such a device must give the same reading as a device that does not have the capability of being independently adjusted. With the fully assembled probe (including probe shaft extensions, if any) secured in a horizontal position, affix one yaw angle-measuring device to the probe sheath and lock it into position on the reference scribe line specified in section 6.1.5.1. Position the second angle-measuring device using the procedure in section 18.1.1.1 or 18.1.1.2.
18.1.1.1 Marking procedure. The procedures in this section should be performed at each location on the fully assembled probe where the yaw angle-measuring device will be mounted during the velocity traverse. Place the second yaw angle-measuring device on the main probe sheath (or extension) at the position where a yaw angle will be measured during the velocity traverse. Adjust the position of the second angle-measuring device until it indicates the same angle (±1°) as the reference device, and affix the second device to the probe sheath (or extension). Record the angles indicated by the two angle-measuring devices on a form similar to table 2G-2. In this position, the second angle-measuring device is considered to be properly positioned for yaw angle measurement. Make a mark, no wider than 1.6 mm ( 1/16 in.), on the probe sheath (or extension), such that the yaw angle-measuring device can be re-affixed at this same properly aligned position during the velocity traverse.
18.1.1.2 Procedure for probe extensions with scribe lines. If, during a velocity traverse the angle-measuring device will be affixed to a probe extension having a scribe line as specified in section 6.1.5.2, the following procedure may be used to align the extension's scribe line with the reference scribe line instead of marking the extension as described in section 18.1.1.1. Attach the probe extension to the main probe. Align and lock the second angle-measuring device on the probe extension's scribe line. Then, rotate the extension until both measuring devices indicate the same angle (±1°). Lock the extension at this rotational position. Record the angles indicated by the two angle-measuring devices on a form similar to table 2G-2. An angle-measuring device may be aligned at any position on this scribe line during the velocity traverse, if the scribe line meets the alignment specification in section 6.1.5.3.
18.1.1.3 Post-test rotational position check. If the fully assembled probe includes one or more extensions, the following check should be performed immediately after the completion of a velocity traverse. At the discretion of the tester, additional checks may be conducted after completion of testing at any sample port. Without altering the alignment of any of the components of the probe assembly used in the velocity traverse, secure the fully assembled probe in a horizontal position. Affix an angle-measuring device at the reference scribe line specified in section 6.1.5.1. Use the other angle-measuring device to check the angle at each location where the device was checked prior to testing. Record the readings from the two angle-measuring devices.
18.1.2 Rotational position check with probe in stack. This section applies only to probes that, due to physical constraints, cannot be inserted into the test port as fully assembled with all necessary extensions needed to reach the inner-most traverse point(s).
18.1.2.1 Perform the out-of-stack procedure in section 18.1.1 on the main probe and any attached extensions that will be initially inserted into the test port.
18.1.2.2 Use the following procedures to perform additional rotational position check(s) with the probe in the stack, each time a probe extension is added. Two angle-measuring devices are required. The first of these is the device that was used to measure yaw angles at the preceding traverse point, left in its properly aligned measurement position. The second angle-measuring device is positioned on the added probe extension. Use the applicable procedures in section 18.1.1.1 or 18.1.1.2 to align, adjust, lock, and mark (if necessary) the position of the second angle-measuring device to within ±1° of the first device. Record the readings of the two devices on a form similar to Table 2G-2.
18.1.2.3 The procedure in section 18.1.2.2 should be performed at the first port where measurements are taken. The procedure should be repeated each time a probe extension is re-attached at a subsequent port, unless the probe extensions are designed to be locked into a mechanically fixed rotational position (e.g., through use of interlocking grooves), which can be reproduced from port to port as specified in section 8.3.5.2.
18.2 Annex B - Angle Measurement Protocol for Protractor Wheel and Pointer Device. The following procedure shall be used when a protractor wheel and pointer assembly, such as the one described in section 6.2.2 and illustrated in Figure 2G-5 is used to measure the yaw angle of flow. With each move to a new traverse point, unlock, re-align, and re-lock the probe, angle-pointer collar, and protractor wheel to each other. At each such move, particular attention is required to ensure that the scribe line on the angle pointer collar is either aligned with the reference scribe line on the main probe sheath or is at the rotational offset position established under section 8.3.1. The procedure consists of the following steps:
18.2.1 Affix a protractor wheel to the entry port for the test probe in the stack or duct.
18.2.2 Orient the protractor wheel so that the 0° mark corresponds to the longitudinal axis of the stack or duct. For stacks, vertical ducts, or ports on the side of horizontal ducts, use a digital inclinometer meeting the specifications in section 6.2.1 to locate the 0° orientation. For ports on the top or bottom of horizontal ducts, identify the longitudinal axis at each test port and permanently mark the duct to indicate the 0° orientation. Once the protractor wheel is properly aligned, lock it into position on the test port.
18.2.3 Move the pointer assembly along the probe sheath to the position needed to take measurements at the first traverse point. Align the scribe line on the pointer collar with the reference scribe line or at the rotational offset position established under section 8.3.1. Maintaining this rotational alignment, lock the pointer device onto the probe sheath. Insert the probe into the entry port to the depth needed to take measurements at the first traverse point.
18.2.4 Perform the yaw angle determination as specified in sections 8.9.3 and 8.9.4 and record the angle as shown by the pointer on the protractor wheel. Then, take velocity pressure and temperature measurements in accordance with the procedure in section 8.9.5. Perform the alignment check described in section 8.9.6.
18.2.5 After taking velocity pressure measurements at that traverse point, unlock the probe from the collar and slide the probe through the collar to the depth needed to reach the next traverse point.
18.2.6 Align the scribe line on the pointer collar with the reference scribe line on the main probe or at the rotational offset position established under section 8.3.1. Lock the collar onto the probe.
18.2.7 Repeat the steps in sections 18.2.4 through 18.2.6 at the remaining traverse points accessed from the current stack or duct entry port.
18.2.8 After completing the measurement at the last traverse point accessed from a port, verify that the orientation of the protractor wheel on the test port has not changed over the course of the traverse at that port. For stacks, vertical ducts, or ports on the side of horizontal ducts, use a digital inclinometer meeting the specifications in section 6.2.1 to check the rotational position of the 0° mark on the protractor wheel. For ports on the top or bottom of horizontal ducts, observe the alignment of the angle wheel 0° mark relative to the permanent 0° mark on the duct at that test port. If these observed comparisons exceed ±2° of 0°, all angle and pressure measurements taken at that port since the protractor wheel was last locked into position on the port shall be repeated.
18.2.9 Move to the next stack or duct entry port and repeat the steps in sections 18.2.1 through 18.2.8.
18.3 Annex C - Guideline for Reference Scribe Line Placement. Use of the following guideline is recommended to satisfy the requirements of section 10.4 of this method. The rotational position of the reference scribe line should be either 90° or 180° from the probe's impact pressure port. For Type-S probes, place separate scribe lines, on opposite sides of the probe sheath, if both the A and B sides of the pitot tube are to be used for yaw angle measurements.
18.4 Annex D - Determination of Reference Scribe Line Rotational Offset. The following procedures are recommended for determining the magnitude and sign of a probe's reference scribe line rotational offset, RSLO. Separate procedures are provided for two types of angle-measuring devices: digital inclinometers and protractor wheel and pointer assemblies.
18.4.1 Perform the following procedures on the main probe with all devices that will be attached to the main probe in the field [such as thermocouples, resistance temperature detectors (RTDs), or sampling nozzles] that may affect the flow around the probe head. Probe shaft extensions that do not affect flow around the probe head need not be attached during calibration.
18.4.2 The procedures below assume that the wind tunnel duct used for probe calibration is horizontal and that the flow in the calibration wind tunnel is axial as determined by the axial flow verification check described in section 10.1.2. Angle-measuring devices are assumed to display angles in alternating 0° to 90° and 90° to 0° intervals. If angle-measuring devices with other readout conventions are used or if other calibration wind tunnel duct configurations are used, make the appropriate calculational corrections. For Type-S probes, calibrate the A-side and B-sides separately, using the appropriate scribe line (see section 18.3, above), if both the A and B sides of the pitot tube are to be used for yaw angle determinations.
18.4.2.1 Position the angle-measuring device in accordance with one of the following procedures.
18.4.2.1.1 If using a digital inclinometer, affix the calibrated digital inclinometer to the probe. If the digital inclinometer can be independently adjusted after being locked into position on the probe sheath (e.g., by means of a set screw), the independent adjustment must be set so that the device performs exactly like a device without the capability for independent adjustment. That is, when aligned on the probe the device must give the same readings as a device that does not have the capability of being independently adjusted. Either align it directly on the reference scribe line or on a mark aligned with the scribe line determined according to the procedures in section 18.1.1.1. Maintaining this rotational alignment, lock the digital inclinometer onto the probe sheath.
18.4.2.1.2 If using a protractor wheel and pointer device, orient the protractor wheel on the test port so that the 0° mark is aligned with the longitudinal axis of the wind tunnel duct. Maintaining this alignment, lock the wheel into place on the wind tunnel test port. Align the scribe line on the pointer collar with the reference scribe line or with a mark aligned with the reference scribe line, as determined under section 18.1.1.1. Maintaining this rotational alignment, lock the pointer device onto the probe sheath.
18.4.2.2 Zero the pressure-measuring device used for yaw nulling.
18.4.2.3 Insert the probe assembly into the wind tunnel through the entry port, positioning the probe's impact port at the calibration location. Check the responsiveness of the pressure-measuring device to probe rotation, taking corrective action if the response is unacceptable.
18.4.2.4 Ensure that the probe is in a horizontal position using a carpenter's level.
18.4.2.5 Rotate the probe either clockwise or counterclockwise until a yaw null [zero ΔP for a Type S probe or zero (P2-P3) for a 3-D probe] is obtained. If using a Type S probe with an attached thermocouple, the direction of the probe rotation shall be such that the thermocouple is located downstream of the probe pressure ports at the yaw-null position.
18.4.2.6 Read and record the value of θnull, the angle indicated by the angle-measuring device at the yaw-null position. Record the angle reading on a form similar to Table 2G-6. Do not associate an algebraic sign with this reading.
18.4.2.7 Determine the magnitude and algebraic sign of the reference scribe line rotational offset, RSLO. The magnitude of RSLO will be equal to either θnull or (90°−θnull), depending on the type of probe being calibrated and the type of angle-measuring device used. (See Table 2G-7 for a summary.) The algebraic sign of RSLO will either be positive if the rotational position of the reference scribe line is clockwise or negative if counterclockwise with respect to the probe's yaw-null position. Figure 2G-10 illustrates how the magnitude and sign of RSLO are determined.
18.4.2.8 Perform the steps in sections 18.3.2.3 through 18.3.2.7 twice at each of the two calibration velocities selected for the probe under section 10.6. Record the values of RSLO in a form similar to Table 2G-6.
18.4.2.9 The average of all RSLO values is the reference scribe line rotational offset for the probe.
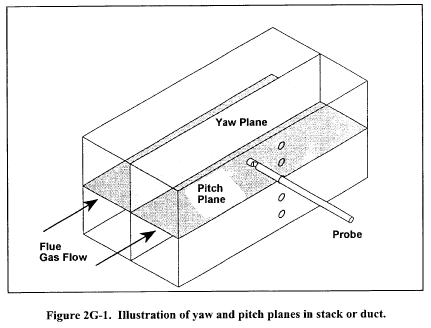
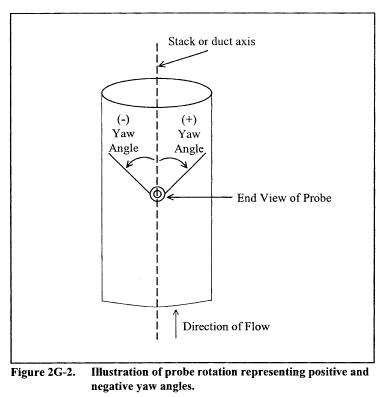
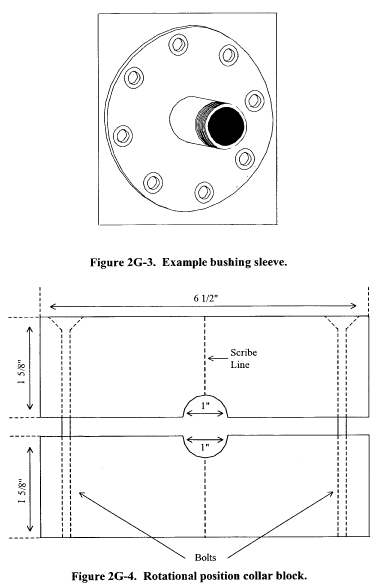
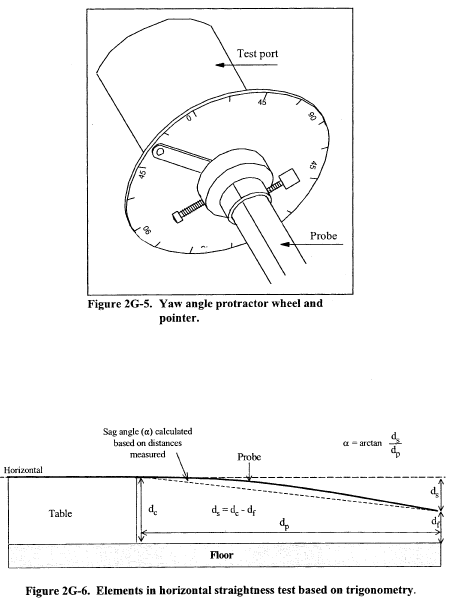
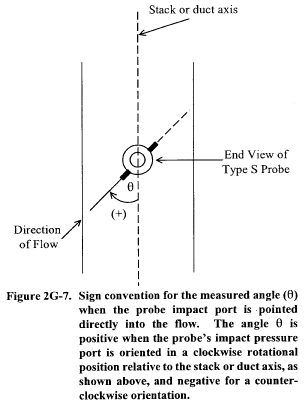
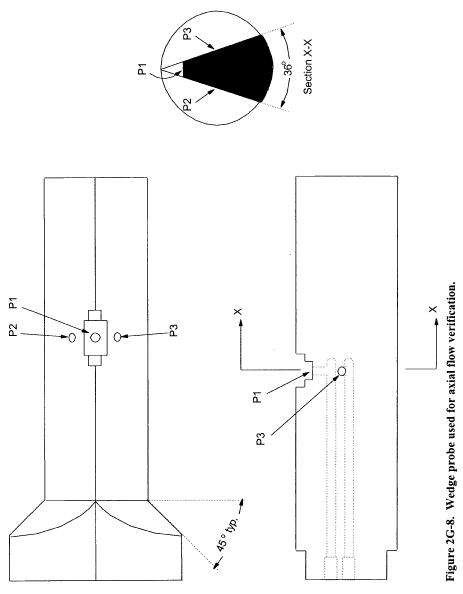
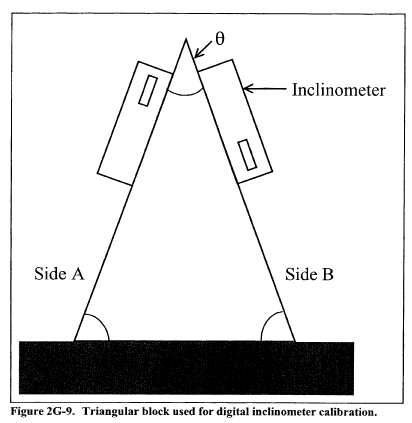
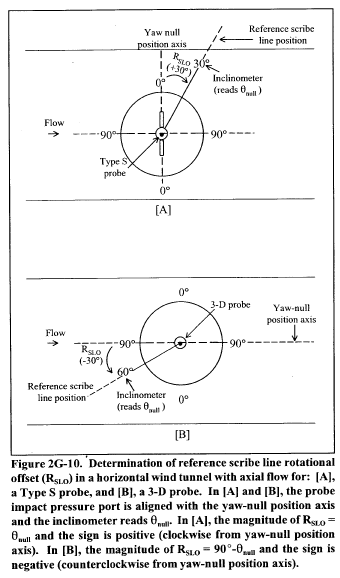
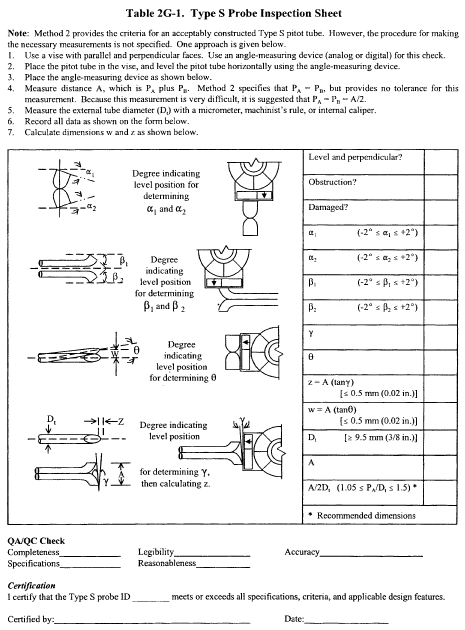
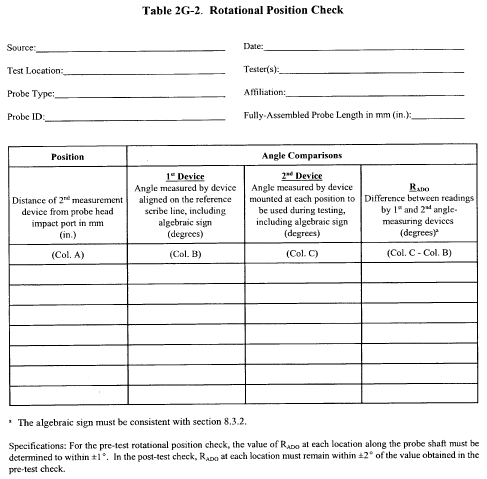
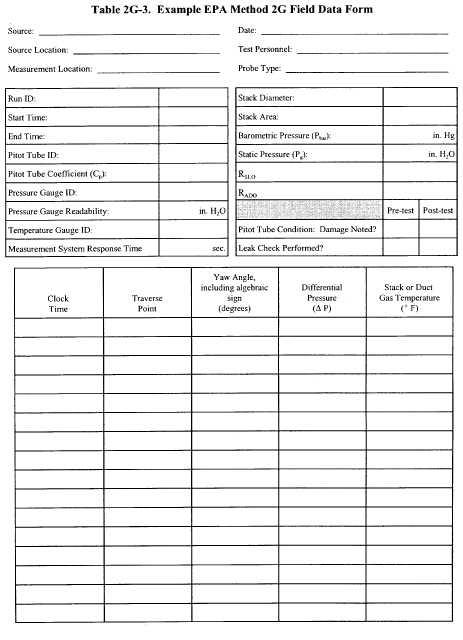
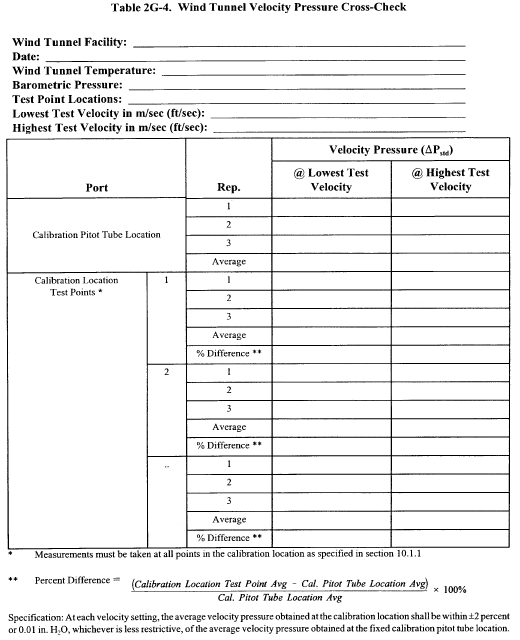
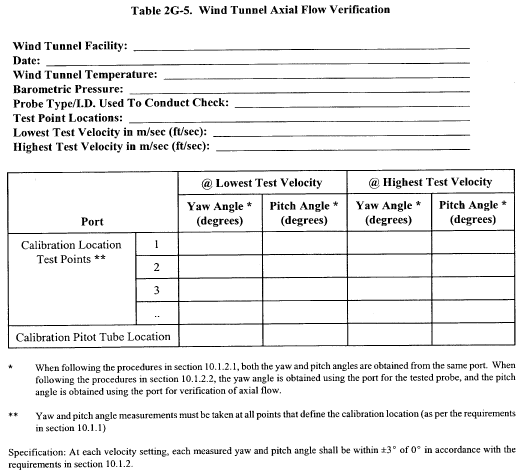
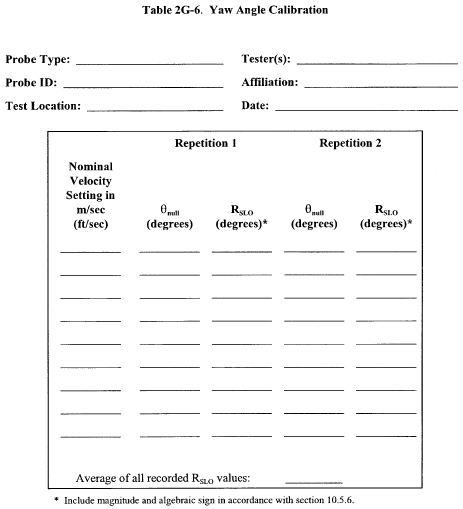
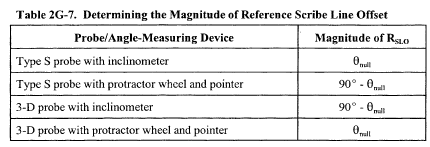
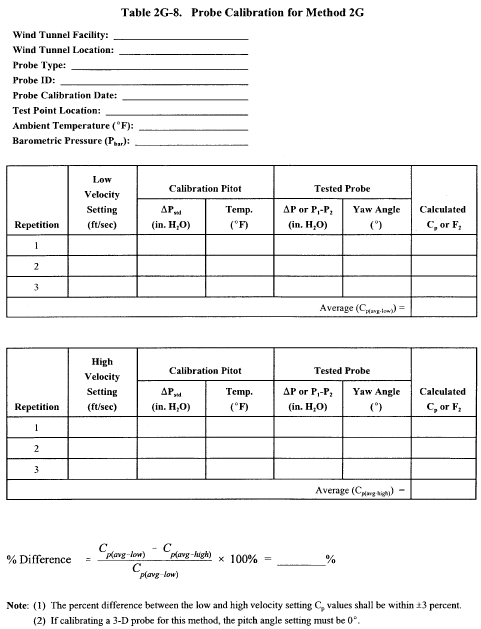
1.1 This method is applicable in conjunction with Methods 2, 2F, and 2G (40 CFR Part 60, Appendix A) to account for velocity decay near the wall in circular stacks and ducts.
1.2 This method is not applicable for testing stacks and ducts less than 3.3 ft (1.0 m) in diameter.
1.3 Data Quality Objectives. Adherence to the requirements of this method will enhance the quality of the data obtained from air pollutant sampling methods.
2.0 Summary of Method2.1 A wall effects adjustment factor is determined. It is used to adjust the average stack gas velocity obtained under Method 2, 2F, or 2G of this appendix to take into account velocity decay near the stack or duct wall.
2.2 The method contains two possible procedures: a calculational approach which derives an adjustment factor from velocity measurements and a default procedure which assigns a generic adjustment factor based on the construction of the stack or duct.
2.2.1 The calculational procedure derives a wall effects adjustment factor from velocity measurements taken using Method 2, 2F, or 2G at 16 (or more) traverse points specified under Method 1 of this appendix and a total of eight (or more) wall effects traverse points specified under this method. The calculational procedure based on velocity measurements is not applicable for horizontal circular ducts where build-up of particulate matter or other material in the bottom of the duct is present.
2.2.2 A default wall effects adjustment factor of 0.9900 for brick and mortar stacks and 0.9950 for all other types of stacks and ducts may be used without taking wall effects measurements in a stack or duct.
2.3 When the calculational procedure is conducted as part of a relative accuracy test audit (RATA) or other multiple-run test procedure, the wall effects adjustment factor derived from a single traverse (i.e., single RATA run) may be applied to all runs of the same RATA without repeating the wall effects measurements. Alternatively, wall effects adjustment factors may be derived for several traverses and an average wall effects adjustment factor applied to all runs of the same RATA.
3.0 Definitions.3.1 Complete wall effects traverse means a traverse in which measurements are taken at drem (see section 3.3) and at 1-in. intervals in each of the four Method 1 equal-area sectors closest to the wall, beginning not farther than 4 in. (10.2 cm) from the wall and extending either (1) across the entire width of the Method 1 equal-area sector or (2) for stacks or ducts where this width exceeds 12 in. (30.5 cm) (i.e., stacks or ducts greater than or equal to 15.6 ft [4.8 m] in diameter), to a distance of not less than 12 in. (30.5 cm) from the wall. Note: Because this method specifies that measurements must be taken at whole number multiples of 1 in. from a stack or duct wall, for clarity numerical quantities in this method are expressed in English units followed by metric units in parentheses. To enhance readability, hyphenated terms such as “1-in. intervals” or “1-in. incremented,” are expressed in English units only.
3.2 dlast Depending on context, dlast means either (1) the distance from the wall of the last 1-in. incremented wall effects traverse point or (2) the traverse point located at that distance (see Figure 2H-2).
3.3 drem Depending on context, drem means either (1) the distance from the wall of the centroid of the area between dlast and the interior edge of the Method 1 equal-area sector closest to the wall or (2) the traverse point located at that distance (see Figure 2H-2).
3.4 “May,” “Must,” “Shall,” “Should,” and the imperative form of verbs.
3.4.1 “May” is used to indicate that a provision of this method is optional.
3.4.2 “Must,” “Shall,” and the imperative form of verbs (such as “record” or “enter”) are used to indicate that a provision of this method is mandatory.
3.4.3 “Should” is used to indicate that a provision of this method is not mandatory but is highly recommended as good practice.
3.5 Method 1 refers to 40 CFR part 60, appendix A, “Method 1 - Sample and velocity traverses for stationary sources.”
3.6 Method 1 exterior equal-area sector and Method 1 equal-area sector closest to the wall mean any one of the four equal-area sectors that are closest to the wall for a circular stack or duct laid out in accordance with section 2.3.1 of Method 1 (see Figure 2H-1).
3.7 Method 1 interior equal-area sector means any of the equal-area sectors other than the Method 1 exterior equal-area sectors (as defined in section 3.6) for a circular stack or duct laid out in accordance with section 2.3.1 of Method 1 (see Figure 2H-1).
3.8 Method 1 traverse point and Method 1 equal-area traverse point mean a traverse point located at the centroid of an equal-area sector of a circular stack laid out in accordance with section 2.3.1 of Method 1.
3.9 Method 2 refers to 40 CFR part 60, appendix A, “Method 2 - Determination of stack gas velocity and volumetric flow rate (Type S pitot tube).”
3.10 Method 2F refers to 40 CFR part 60, appendix A, “Method 2F - Determination of stack gas velocity and volumetric flow rate with three-dimensional probes.”
3.11 Method 2G refers to 40 CFR part 60, appendix A, “Method 2G - Determination of stack gas velocity and volumetric flow rate with two-dimensional probes.”
3.12 1-in. incremented wall effects traverse point means any of the wall effects traverse points that are located at 1-in. intervals, i.e., traverse points d1 through dlast (see Figure 2H-2).
3.13 Partial wall effects traverse means a traverse in which measurements are taken at fewer than the number of traverse points required for a “complete wall effects traverse” (as defined in section 3.1), but are taken at a minimum of two traverse points in each Method 1 equal-area sector closest to the wall, as specified in section 8.2.2.
3.14 Relative accuracy test audit (RATA) is a field test procedure performed in a stack or duct in which a series of concurrent measurements of the same stack gas stream is taken by a reference method and an installed monitoring system. A RATA usually consists of series of 9 to 12 sets of such concurrent measurements, each of which is referred to as a RATA run. In a volumetric flow RATA, each reference method run consists of a complete traverse of the stack or duct.
3.15 Wall effects-unadjusted average velocity means the average stack gas velocity, not accounting for velocity decay near the wall, as determined in accordance with Method 2, 2F, or 2G for a Method 1 traverse consisting of 16 or more points.
3.16 Wall effects-adjusted average velocity means the average stack gas velocity, taking into account velocity decay near the wall, as calculated from measurements at 16 or more Method 1 traverse points and at the additional wall effects traverse points specified in this method.
3.17 Wall effects traverse point means a traverse point located in accordance with sections 8.2.2 or 8.2.3 of this method.
4.0 Interferences [Reserved] 5.0 Safety5.1 This method may involve hazardous materials, operations, and equipment. This method does not purport to address all of the health and safety considerations associated with its use. It is the responsibility of the user of this method to establish appropriate health and safety practices and to determine the applicability of occupational health and safety regulatory requirements prior to performing this method.
6.0 Equipment and Supplies6.1 The provisions pertaining to equipment and supplies in the method that is used to take the traverse point measurements (i.e., Method 2, 2F, or 2G) are applicable under this method.
7.0 Reagents and Standards [Reserved] 8.0 Sample Collection and Analysis8.1 Default Wall Effects Adjustment Factors. A default wall effects adjustment factor of 0.9900 for brick and mortar stacks and 0.9950 for all other types of stacks and ducts may be used without conducting the following procedures.
8.2 Traverse Point Locations. Determine the location of the Method 1 traverse points in accordance with section 8.2.1 and the location of the traverse points for either a partial wall effects traverse in accordance with section 8.2.2 or a complete wall effects traverse in accordance with section 8.2.3.
8.2.1 Method 1 equal-area traverse point locations. Determine the location of the Method 1 equal-area traverse points for a traverse consisting of 16 or more points using Table 1-2 (Location of Traverse Points in Circular Stacks) of Method 1.
8.2.2 Partial wall effects traverse. For a partial wall effects traverse, measurements must be taken at a minimum of the following two wall effects traverse point locations in all four Method 1 equal-area sectors closest to the wall: (1) 1 in. (2.5 cm) from the wall (except as provided in section 8.2.2.1) and (2) drem, as determined using Equation 2H-1 or 2H-2 (see section 8.2.2.2).
8.2.2.1 If the probe cannot be positioned at 1 in. (2.5 cm) from the wall (e.g., because of insufficient room to withdraw the probe shaft) or if velocity pressure cannot be detected at 1 in. (2.5 cm) from the wall (for any reason other than build-up of particulate matter in the bottom of a duct), take measurements at the 1-in. incremented wall effects traverse point closest to the wall where the probe can be positioned and velocity pressure can be detected.
8.2.2.2 Calculate the distance of drem from the wall to within ± 1/4 in. (6.4 mm) using Equation 2H-1 or Equation 2H-2 (for a 16-point traverse).


8.2.2.3 Measurements may be taken at any number of additional wall effects traverse points, with the following provisions.
(a) dlast must not be closer to the center of the stack or duct than the distance of the interior edge (boundary), db, of the Method 1 equal-area sector closest to the wall (see Figure 2H-2 or 2H-3). That is,
Where: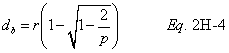
(b) Each point must be located at a distance that is a whole number (e.g., 1, 2, 3) multiple of 1 in. (2.5 cm).
(c) Points do not have to be located at consecutive 1-in. intervals. That is, one or more 1-in. incremented points may be skipped. For example, it would be acceptable for points to be located at 1 in. (2.5 cm), 3 in. (7.6 cm), 5 in. (12.7 cm), dlast, and drem; or at 1 in. (2.5 cm), 2 in. (5.1 cm), 4 in. (10.2 cm), 7 in. (17.8 cm), dlast, and drem. Follow the instructions in section 8.7.1.2 of this method for recording results for wall effects traverse points that are skipped. It should be noted that the full extent of velocity decay may not be accounted for if measurements are not taken at all 1-in. incremented points close to the wall.
8.2.3 Complete wall effects traverse. For a complete wall effects traverse, measurements must be taken at the following points in all four Method 1 equal-area sectors closest to the wall.
(a) The 1-in. incremented wall effects traverse point closest to the wall where the probe can be positioned and velocity can be detected, but no farther than 4 in. (10.2 cm) from the wall.
(b) Every subsequent 1-in. incremented wall effects traverse point out to the interior edge of the Method 1 equal-area sector or to 12 in. (30.5 cm) from the wall, whichever comes first. Note: In stacks or ducts with diameters greater than 15.6 ft (4.8 m) the interior edge of the Method 1 equal-area sector is farther from the wall than 12 in. (30.5 cm).
(c) drem, as determined using Equation 2H-1 or 2H-2 (as applicable). Note: For a complete traverse of a stack or duct with a diameter less than 16.5 ft (5.0 m), the distance between drem and dlast is less than or equal to 1/2 in. (12.7 mm). As discussed in section 8.2.4.2, when the distance between drem and dlast is less than or equal to 1/2 in. (12.7 mm), the velocity measured at dlast may be used for drem. Thus, it is not necessary to calculate the distance of drem or to take measurements at drem when conducting a complete traverse of a stack or duct with a diameter less than 16.5 ft (5.0 m).
8.2.4 Special considerations. The following special considerations apply when the distance between traverse points is less than or equal to 1/2 in. (12.7 mm).
8.2.4.1 A wall effects traverse point and the Method 1 traverse point. If the distance between a wall effects traverse point and the Method 1 traverse point is less than or equal to 1/2 in. (12.7 mm), taking measurements at both points is allowed but not required or recommended; if measurements are taken at only one point, take the measurements at the point that is farther from the wall and use the velocity obtained at that point as the value for both points (see sections 8.2.3 and 9.2 for related requirements).
8.2.4.2 drem and dlast. If the distance between drem and dlast is less than or equal to 1/2 in. (12.7 mm), taking measurements at drem is allowed but not required or recommended; if measurements are not taken at drem, the measured velocity value at dlast must be used as the value for both dlast and drem.
8.3 Traverse Point Sampling Order and Probe Selection. Determine the sampling order of the Method 1 and wall effects traverse points and select the appropriate probe for the measurements, taking into account the following considerations.
8.3.1 Traverse points on any radius may be sampled in either direction (i.e., from the wall toward the center of the stack or duct, or vice versa).
8.3.2 To reduce the likelihood of velocity variations during the time of the traverse and the attendant potential impact on the wall effects-adjusted and unadjusted average velocities, the following provisions of this method shall be met.
8.3.2.1 Each complete set of Method 1 and wall effects traverse points accessed from the same port shall be sampled without interruption. Unless traverses are performed simultaneously in all ports using separate probes at each port, this provision disallows first sampling all Method 1 points at all ports and then sampling all the wall effects points.
8.3.2.2 The entire integrated Method 1 and wall effects traverse across all test ports shall be as short as practicable, consistent with the measurement system response time (see section 8.4.1.1) and sampling (see section 8.4.1.2) provisions of this method.
8.3.3 It is recommended but not required that in each Method 1 equal-area sector closest to the wall, the Method 1 equal-area traverse point should be sampled in sequence between the adjacent wall effects traverse points. For example, for the traverse point configuration shown in Figure 2H-2, it is recommended that the Method 1 equal-area traverse point be sampled between dlast and drem. In this example, if the traverse is conducted from the wall toward the center of the stack or duct, it is recommended that measurements be taken at points in the following order: d1, d2, dlast, the Method 1 traverse point, drem, and then at the traverse points in the three Method 1 interior equal-area sectors.
8.3.4 The same type of probe must be used to take measurements at all Method 1 and wall effects traverse points. However, different copies of the same type of probe may be used at different ports (e.g., Type S probe 1 at port A, Type S probe 2 at port B) or at different traverse points accessed from a particular port (e.g., Type S probe 1 for Method 1 interior traverse points accessed from port A, Type S probe 2 for wall effects traverse points and the Method 1 exterior traverse point accessed from port A). The identification number of the probe used to obtain measurements at each traverse point must be recorded.
8.4 Measurements at Method 1 and Wall Effects Traverse Points. Conduct measurements at Method 1 and wall effects traverse points in accordance with Method 2, 2F, or 2G and in accordance with the provisions of the following subsections (some of which are included in Methods 2F and 2G but not in Method 2), which are particularly important for wall effects testing.
8.4.1 Probe residence time at wall effects traverse points. Due to the steep temperature and pressure gradients that can occur close to the wall, it is very important for the probe residence time (i.e., the total time spent at a traverse point) to be long enough to ensure collection of representative temperature and pressure measurements. The provisions of Methods 2F and 2G in the following subsections shall be observed.
8.4.1.1 System response time. Determine the response time of each probe measurement system by inserting and positioning the “cold” probe (at ambient temperature and pressure) at any Method 1 traverse point. Read and record the probe differential pressure, temperature, and elapsed time at 15-second intervals until stable readings for both pressure and temperature are achieved. The response time is the longer of these two elapsed times. Record the response time.
8.4.1.2 Sampling. At the start of testing in each port (i.e., after a probe has been inserted into the stack gas stream), allow at least the response time to elapse before beginning to take measurements at the first traverse point accessed from that port. Provided that the probe is not removed from the stack gas stream, measurements may be taken at subsequent traverse points accessed from the same test port without waiting again for the response time to elapse.
8.4.2 Temperature measurement for wall effects traverse points. Either (1) take temperature measurements at each wall effects traverse point in accordance with the applicable provisions of Method 2, 2F, or 2G; or (2) use the temperature measurement at the Method 1 traverse point closest to the wall as the temperature measurement for all the wall effects traverse points in the corresponding equal-area sector.
8.4.3 Non-detectable velocity pressure at wall effects traverse points. If the probe cannot be positioned at a wall effects traverse point or if no velocity pressure can be detected at a wall effects point, measurements shall be taken at the first subsequent wall effects traverse point farther from the wall where velocity can be detected. Follow the instructions in section 8.7.1.2 of this method for recording results for wall effects traverse points where velocity pressure cannot be detected. It should be noted that the full extent of velocity decay may not be accounted for if measurements are not taken at the 1-in. incremented wall effects traverse points closest to the wall.
8.5 Data Recording. For each wall effects and Method 1 traverse point where measurements are taken, record all pressure, temperature, and attendant measurements prescribed in section 3 of Method 2 or section 8.0 of Method 2F or 2G, as applicable.
8.6 Point Velocity Calculation. For each wall effects and Method 1 traverse point, calculate the point velocity value (vi) in accordance with sections 12.1 and 12.2 of Method 2F for tests using Method 2F and in accordance with sections 12.1 and 12.2 of Method 2G for tests using Method 2 and Method 2G. (Note that the term (vi) in this method corresponds to the term (va(i)) in Methods 2F and 2G.) When the equations in the indicated sections of Method 2G are used in deriving point velocity values for Method 2 tests, set the value of the yaw angles appearing in the equations to 0°.
8.7 Tabulating Calculated Point Velocity Values for Wall Effects Traverse Points. Enter the following values in a hardcopy or electronic form similar to Form 2H-1 (for 16-point Method 1 traverses) or Form 2H-2 (for Method 1 traverses consisting of more than 16 points). A separate form must be completed for each of the four Method 1 equal-area sectors that are closest to the wall.
(a) Port ID (e.g., A, B, C, or D)
(b) Probe type
(c) Probe ID
(d) Stack or duct diameter in ft (m) (determined in accordance with section 8.6 of Method 2F or Method 2G)
(e) Stack or duct radius in in. (cm)
(f) Distance from the wall of wall effects traverse points at 1-in. intervals, in ascending order starting with 1 in. (2.5 cm) (column A of Form 2H-1 or 2H-2)
(g) Point velocity values (vd) for 1-in. incremented traverse points (see section 8.7.1), including dlast (see section 8.7.2)
(h) Point velocity value (vdrem) at drem (see section 8.7.3).
8.7.1 Point velocity values at wall effects traverse points other than dlast. For every 1-in. incremented wall effects traverse point other than dlast, enter in column B of Form 2H-1 or 2H-2 either the velocity measured at the point (see section 8.7.1.1) or the velocity measured at the first subsequent traverse point farther from the wall (see section 8.7.1.2). A velocity value must be entered in column B of Form 2H-1 or 2H-2 for every 1-in. incremented traverse point from d1 (representing the wall effects traverse point 1 in. [2.5 cm] from the wall) to dlast.
8.7.1.1 For wall effects traverse points where the probe can be positioned and velocity pressure can be detected, enter the value obtained in accordance with section 8.6.
8.7.1.2 For wall effects traverse points that were skipped [see section 8.2.2.3(c)] and for points where the probe cannot be positioned or where no velocity pressure can be detected, enter the value obtained at the first subsequent traverse point farther from the wall where velocity pressure was detected and measured and follow the entered value with a “flag,” such as the notation “NM,” to indicate that “no measurements” were actually taken at this point.
8.7.2 Point velocity value at dlast. For dlast, enter in column B of Form 2H-1 or 2H-2 the measured value obtained in accordance with section 8.6.
8.7.3 Point velocity value (vdrem) at drem. Enter the point velocity value obtained at drem in column G of row 4a in Form 2H-1 or 2H-2. If the distance between drem and dlast is less than or equal to 1/2 in. (12.7 mm), the measured velocity value at dlast may be used as the value at drem (see section 8.2.4.2).
9.0 Quality Control.9.1 Particulate Matter Build-up in Horizontal Ducts. Wall effects testing of horizontal circular ducts should be conducted only if build-up of particulate matter or other material in the bottom of the duct is not present.
9.2 Verifying Traverse Point Distances. In taking measurements at wall effects traverse points, it is very important for the probe impact pressure port to be positioned as close as practicable to the traverse point locations in the gas stream. For this reason, before beginning wall effects testing, it is important to calculate and record the traverse point positions that will be marked on each probe for each port, taking into account the distance that each port nipple (or probe mounting flange for automated probes) extends out of the stack and any extension of the port nipple (or mounting flange) into the gas stream. To ensure that traverse point positions are properly identified, the following procedures should be performed on each probe used.
9.2.1 Manual probes. Mark the probe insertion distance of the wall effects and Method 1 traverse points on the probe sheath so that when a mark is aligned with the outside face of the stack port, the probe impact port is located at the calculated distance of the traverse point from the stack inside wall. The use of different colored marks is recommended for designating the wall effects and Method 1 traverse points. Before the first use of each probe, check to ensure that the distance of each mark from the center of the probe impact pressure port agrees with the previously calculated traverse point positions to within ± 1/4 in. (6.4 mm).
9.2.2 Automated probe systems. For automated probe systems that mechanically position the probe head at prescribed traverse point positions, activate the system with the probe assemblies removed from the test ports and sequentially extend the probes to the programmed location of each wall effects traverse point and the Method 1 traverse points. Measure the distance between the center of the probe impact pressure port and the inside of the probe assembly mounting flange for each traverse point. The measured distances must agree with the previously calculated traverse point positions to within ± 1/4 in. (6.4 mm).
9.3 Probe Installation. Properly sealing the port area is particularly important in taking measurements at wall effects traverse points. For testing involving manual probes, the area between the probe sheath and the port should be sealed with a tightly fitting flexible seal made of an appropriate material such as heavy cloth so that leakage is minimized. For automated probe systems, the probe assembly mounting flange area should be checked to verify that there is no leakage.
9.4 Velocity Stability. This method should be performed only when the average gas velocity in the stack or duct is relatively constant over the duration of the test. If the average gas velocity changes significantly during the course of a wall effects test, the test results should be discarded.
10.0 Calibration10.1 The calibration coefficient(s) or curves obtained under Method 2, 2F, or 2G and used to perform the Method 1 traverse are applicable under this method.
11.0 Analytical Procedure11.1 Sample collection and analysis are concurrent for this method (see section 8).
12.0 Data Analysis and Calculations12.1 The following calculations shall be performed to obtain a wall effects adjustment factor (WAF) from (1) the wall effects-unadjusted average velocity (T4avg), (2) the replacement velocity (v ej) for each of the four Method 1 sectors closest to the wall, and (3) the average stack gas velocity that accounts for velocity decay near the wall (v avg).
12.2 Nomenclature. The following terms are listed in the order in which they appear in Equations 2H-5 through 2H-21.
vavg = the average stack gas velocity, unadjusted for wall effects, actual ft/sec (m/sec); vii = stack gas point velocity value at Method 1 interior equal-area sectors, actual ft/sec (m/sec); vej = stack gas point velocity value, unadjusted for wall effects, at Method 1 exterior equal-area sectors, actual ft/sec (m/sec); i = index of Method 1 interior equal-area traverse points; j = index of Method 1 exterior equal-area traverse points; n = total number of traverse points in the Method 1 traverse; vdecd = the wall effects decay velocity for a sub-sector located between the traverse points at distances d−1 (in metric units, d−2.5) and d from the wall, actual ft/sec (m/sec); vd = the measured stack gas velocity at distance d from the wall, actual ft/sec (m/sec); Note: v0 = 0; d = the distance of a 1-in. incremented wall effects traverse point from the wall, for traverse points d1 through dlast, in. (cm); Ad = the cross-sectional area of a sub-sector located between the traverse points at distances d−1 (in metric units, d−2.5) and d from the wall, in. 2 (cm 2) ( e.g., sub-sector A2 shown in Figures 2H-3 and 2H-4); r = the stack or duct radius, in. (cm); Qd = the stack gas volumetric flow rate for a sub-sector located between the traverse points at distances d−1 (in metric units, d−2.5) and d from the wall, actual ft-in. 2/sec (m-cm 2/sec); Qd1→dlast = the total stack gas volumetric flow rate for all sub-sectors located between the wall and dlast, actual ft-in. 2/sec (m-cm 2/sec); dlast = the distance from the wall of the last 1-in. incremented wall effects traverse point, in. (cm); Adrem = the cross-sectional area of the sub-sector located between dlast and the interior edge of the Method 1 equal-area sector closest to the wall, in. 2 (cm 2) (see Figure 2H-4); p = the number of Method 1 traverse points per diameter, p≥8 (e.g., for a 16-point traverse, p = 8); drem = the distance from the wall of the centroid of the area between dlast and the interior edge of the Method 1 equal-area sector closest to the wall, in. (cm); Qdrem = the total stack gas volumetric flow rate for the sub-sector located between dlast and the interior edge of the Method 1 equal-area sector closest to the wall, actual ft-in. 2/sec (m-cm 2/sec); vdrem = the measured stack gas velocity at distance drem from the wall, actual ft/sec (m/sec); QT = the total stack gas volumetric flow rate for the Method 1 equal-area sector closest to the wall, actual ft-in. 2/sec (m-cm 2/sec); v ej = the replacement stack gas velocity for the Method 1 equal-area sector closest to the wall, i.e., the stack gas point velocity value, adjusted for wall effects, for the j th Method 1 equal-area sector closest to the wall, actual ft/sec (m/sec); v avg = the average stack gas velocity that accounts for velocity decay near the wall, actual ft/sec (m/sec); WAF = the wall effects adjustment factor derived from vavg and v avg for a single traverse, dimensionless; v final = the final wall effects-adjusted average stack gas velocity that replaces the unadjusted average stack gas velocity obtained using Method 2, 2F, or 2G for a field test consisting of a single traverse, actual ft/sec (m/sec); W A F = the wall effects adjustment factor that is applied to the average velocity, unadjusted for wall effects, in order to obtain the final wall effects-adjusted stack gas velocity, v final or, v final(k), dimensionless; v final(k) = the final wall effects-adjusted average stack gas velocity that replaces the unadjusted average stack gas velocity obtained using Method 2, 2F, or 2G on run k of a RATA or other multiple-run field test procedure, actual ft/sec (m/sec); vavg(k) = the average stack gas velocity, obtained on run k of a RATA or other multiple-run procedure, unadjusted for velocity decay near the wall, actual ft/sec (m/sec); k=index of runs in a RATA or other multiple-run procedure.12.3 Calculate the average stack gas velocity that does not account for velocity decay near the wall (vavg) using Equation 2H-5.
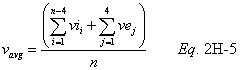
For a 16-point traverse, Equation 2H-5 may be written as follows:
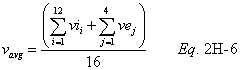
12.4 Calculate the replacement velocity, v ej, for each of the four Method 1 equal-area sectors closest to the wall using the procedures described in sections 12.4.1 through 12.4.8. Forms 2H-1 and 2H-2 provide sample tables that may be used in either hardcopy or spreadsheet format to perform the calculations described in sections 12.4.1 through 12.4.8. Forms 2H-3 and 2H-4 provide examples of Form 2H-1 filled in for partial and complete wall effects traverses.
12.4.1 Calculate the average velocity (designated the “decay velocity,” vdecd) for each sub-sector located between the wall and dlast (see Figure 2H-3) using Equation 2H-7.
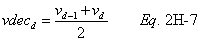
12.4.2 Calculate the cross-sectional area between the wall and the first 1-in. incremented wall effects traverse point and between successive 1-in. incremented wall effects traverse points, from the wall to dlast (see Figure 2H-3), using Equation 2H-8.

12.4.3 Calculate the volumetric flow through each cross-sectional area derived in section 12.4.2 by multiplying the values of vdecd, derived according to section 12.4.1, by the cross-sectional areas derived in section 12.4.2 using Equation 2H-9.

12.4.4 Calculate the total volumetric flow through all sub-sectors located between the wall and dlast, using Equation 2H-10.
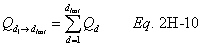
12.4.5 Calculate the cross-sectional area of the sub-sector located between dlast and the interior edge of the Method 1 equal-area sector (e.g., sub-sector Adrem shown in Figures 2H-3 and 2H-4) using Equation 2H-11.


12.4.6 Calculate the volumetric flow for the sub-sector located between dlast and the interior edge of the Method 1 equal-area sector, using Equation 2H-13.

12.4.7 Calculate the total volumetric flow for the Method 1 equal-area sector closest to the wall, using Equation 2H-14.

12.4.8 Calculate the wall effects-adjusted replacement velocity value for the Method 1 equal-area sector closest to the wall, using Equation 2H-15.
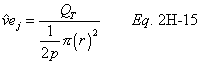
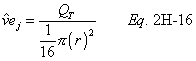
12.5 Calculate the wall effects-adjusted average velocity, v avg, by replacing the four values of vej shown in Equation 2H-5 with the four wall effects-adjusted replacement velocity values,v ej, calculated according to section 12.4.8, using Equation 2H-17.
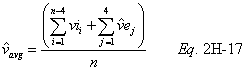
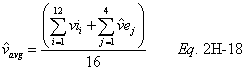
12.6 Calculate the wall effects adjustment factor, WAF, using Equation 2H-19.
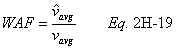
12.6.1 Partial wall effects traverse. If a partial wall effects traverse (see section 8.2.2) is conducted, the value obtained from Equation 2H-19 is acceptable and may be reported as the wall effects adjustment factor provided that the value is greater than or equal to 0.9800. If the value is less than 0.9800, it shall not be used and a wall effects adjustment factor of 0.9800 may be used instead.
12.6.2 Complete wall effects traverse. If a complete wall effects traverse (see section 8.2.3) is conducted, the value obtained from Equation 2H-19 is acceptable and may be reported as the wall effects adjustment factor provided that the value is greater than or equal to 0.9700. If the value is less than 0.9700, it shall not be used and a wall effects adjustment factor of 0.9700 may be used instead. If the wall effects adjustment factor for a particular stack or duct is less than 0.9700, the tester may (1) repeat the wall effects test, taking measurements at more Method 1 traverse points and (2) recalculate the wall effects adjustment factor from these measurements, in an attempt to obtain a wall effects adjustment factor that meets the 0.9700 specification and completely characterizes the wall effects.
12.7 Applying a Wall Effects Adjustment Factor. A default wall effects adjustment factor, as specified in section 8.1, or a calculated wall effects adjustment factor meeting the requirements of section 12.6.1 or 12.6.2 may be used to adjust the average stack gas velocity obtained using Methods 2, 2F, or 2G to take into account velocity decay near the wall of circular stacks or ducts. Default wall effects adjustment factors specified in section 8.1 and calculated wall effects adjustment factors that meet the requirements of section 12.6.1 and 12.6.2 are summarized in Table 2H-2.
12.7.1 Single-run tests. Calculate the final wall effects-adjusted average stack gas velocity for field tests consisting of a single traverse using Equation 2H-20.

12.7.2 RATA or other multiple run test procedure. Calculate the final wall effects-adjusted average stack gas velocity for any run k of a RATA or other multiple-run procedure using Equation 2H-21.

12.8 Calculating Volumetric Flow Using Final Wall Effects-Adjusted Average Velocity Value. To obtain a stack gas flow rate that accounts for velocity decay near the wall of circular stacks or ducts, replace vs in Equation 2-10 in Method 2, or va(avg) in Equations 2F-10 and 2F-11 in Method 2F, or va(avg) in Equations 2G-9 and 2G-10 in Method 2G with one of the following.
12.8.1 For single-run test procedures, use the final wall effects-adjusted average stack gas velocity, v final, calculated according to Equation 2H-20.
12.8.2 For RATA and other multiple run test procedures, use the final wall effects-adjusted average stack gas velocity, v final(k), calculated according to Equation 2H-21.
13.0 Method Performance [Reserved] 14.0 Pollution Prevention [Reserved] 15.0 Waste Management [Reserved] 16.0 Reporting16.1 Field Test Reports. Field test reports shall be submitted to the Agency according to the applicable regulatory requirements. When Method 2H is performed in conjunction with Method 2, 2F, or 2G to derive a wall effects adjustment factor, a single consolidated Method 2H/2F (or 2H/2G) field test report should be prepared. At a minimum, the consolidated field test report should contain (1) all of the general information, and data for Method 1 points, specified in section 16.0 of Method 2F (when Method 2H is used in conjunction with Method 2F) or section 16.0 of Method 2G (when Method 2H is used in conjunction with Method 2 or 2G) and (2) the additional general information, and data for Method 1 points and wall effects points, specified in this section (some of which are included in section 16.0 of Methods 2F and 2G and are repeated in this section to ensure complete reporting for wall effects testing).
16.1.1 Description of the source and site. The field test report should include the descriptive information specified in section 16.1.1 of Method 2F (when using Method 2F) or 2G (when using either Method 2 or 2G). It should also include a description of the stack or duct's construction material along with the diagram showing the dimensions of the stack or duct at the test port elevation prescribed in Methods 2F and 2G. The diagram should indicate the location of all wall effects traverse points where measurements were taken as well as the Method 1 traverse points. The diagram should provide a unique identification number for each wall effects and Method 1 traverse point, its distance from the wall, and its location relative to the probe entry ports.
16.1.2 Field test forms. The field test report should include a copy of Form 2H-1, 2H-2, or an equivalent for each Method 1 exterior equal-area sector.
16.1.3 Field test data. The field test report should include the following data for the Method 1 and wall effects traverse.
16.1.3.1 Data for each traverse point. The field test report should include the values specified in section 16.1.3.2 of Method 2F (when using Method 2F) or 2G (when using either Method 2 or 2G) for each Method 1 and wall effects traverse point. The provisions of section 8.4.2 of Method 2H apply to the temperature measurements reported for wall effects traverse points. For each wall effects and Method 1 traverse point, the following values should also be included in the field test report.
(a) Traverse point identification number for each Method 1 and wall effects traverse point.
(b) Probe type.
(c) Probe identification number.
(d) Probe velocity calibration coefficient (i.e., Cp when Method 2 or 2G is used; F2 when Method 2F is used).
For each Method 1 traverse point in an exterior equal-area sector, the following additional value should be included.
(e) Calculated replacement velocity, v ej, accounting for wall effects.
16.1.3.2 Data for each run. The values specified in section 16.1.3.3 of Method 2F (when using Method 2F) or 2G (when using either Method 2 or 2G) should be included in the field test report once for each run. The provisions of section 12.8 of Method 2H apply for calculating the reported gas volumetric flow rate. In addition, the following Method 2H run values should also be included in the field test report.
(a) Average velocity for run, accounting for wall effects, v avg.
(b) Wall effects adjustment factor derived from a test run, WAF.
16.1.3.3 Data for a complete set of runs. The values specified in section 16.1.3.4 of Method 2F (when using Method 2F) or 2G (when using either Method 2 or 2G) should be included in the field test report once for each complete set of runs. In addition, the field test report should include the wall effects adjustment factor, W A F , that is applied in accordance with section 12.7.1 or 12.7.2 to obtain the final wall effects-adjusted average stack gas velocity v final or v final(k).
16.1.4 Quality assurance and control. Quality assurance and control procedures, specifically tailored to wall effects testing, should be described.
16.2 Reporting a Default Wall Effects Adjustment Factor. When a default wall effects adjustment factor is used in accordance with section 8.1 of this method, its value and a description of the stack or duct's construction material should be reported in lieu of submitting a test report.
17.0 References.(1) 40 CFR Part 60, Appendix A, Method 1 - Sample and velocity traverses for stationary sources.
(2) 40 CFR Part 60, Appendix A, Method 2 - Determination of stack gas velocity and volumetric flow rate (Type S pitot tube).
(3) 40 CFR Part 60, Appendix A, Method 2F - Determination of stack gas velocity and volumetric flow rate with three-dimensional probes.
(4) 40 CFR Part 60, Appendix A, Method 2G - Determination of stack gas velocity and volumetric flow rate with two-dimensional probes.
(5) 40 CFR Part 60, Appendix A, Method 3 - Gas analysis for carbon dioxide, oxygen, excess air, and dry molecular weight.
(6) 40 CFR Part 60, Appendix A, Method 3A - Determination of oxygen and carbon dioxide concentrations in emissions from stationary sources (instrumental analyzer procedure).
(7) 40 CFR Part 60, Appendix A, Method 4 - Determination of moisture content in stack gases.
(8) Emission Measurement Center (EMC) Approved Alternative Method (ALT-011) “Alternative Method 2 Thermocouple Calibration Procedure.”
(9) The Cadmus Group, Inc., 1998, “EPA Flow Reference Method Testing and Analysis: Data Report, Texas Utilities, DeCordova Steam Electric Station, Volume I: Test Description and Appendix A (Data Distribution Package),” EPA/430-R-98-015a.
(10) The Cadmus Group, Inc., 1998, “EPA Flow Reference Method Testing and Analysis: Data Report, Texas Utilities, Lake Hubbard Steam Electric Station, Volume I: Test Description and Appendix A (Data Distribution Package),” EPA/430-R-98-017a.
(11) The Cadmus Group, Inc., 1998, “EPA Flow Reference Method Testing and Analysis: Data Report, Pennsylvania Electric Co., G.P.U. Genco Homer City Station: Unit 1, Volume I: Test Description and Appendix A (Data Distribution Package),” EPA/430-R-98-018a.
(12) The Cadmus Group, Inc., May 1999, “EPA Flow Reference Method Testing and Analysis: Findings Report,” EPA/430-R-99-009.
(13) The Cadmus Group, Inc., 1997, “EPA Flow Reference Method Testing and Analysis: Wind Tunnel Experimental Results,” EPA/430-R-97-013.
(14) National Institute of Standards and Technology, 1998, “Report of Special Test of Air Speed Instrumentation, Four Prandtl Probes, Four S-Type Probes, Four French Probes, Four Modified Kiel Probes,” Prepared for the U.S. Environmental Protection Agency under IAG No. DW13938432-01-0.
(15) National Institute of Standards and Technology, 1998, “Report of Special Test of Air Speed Instrumentation, Five Autoprobes,” Prepared for the U.S. Environmental Protection Agency under IAG No. DW13938432-01-0.
(16) National Institute of Standards and Technology, 1998, “Report of Special Test of Air Speed Instrumentation, Eight Spherical Probes,” Prepared for the U.S. Environmental Protection Agency under IAG No. DW13938432-01-0.
(17) National Institute of Standards and Technology, 1998, “Report of Special Test of Air Speed Instrumentation, Four DAT Probes,” Prepared for the U.S. Environmental Protection Agency under IAG No. DW13938432-01-0.
(18) Massachusetts Institute of Technology (MIT), 1998, “Calibration of Eight Wind Speed Probes Over a Reynolds Number Range of 46,000 to 725,000 per Foot, Text and Summary Plots,” Plus Appendices, WBWT-TR-1317, Prepared for The Cadmus Group, Inc., under EPA Contract 68-W6-0050, Work Assignment 0007AA-3.
(19) Fossil Energy Research Corporation, Final Report, “Velocity Probe Tests in Non-axial Flow Fields,” November 1998, Prepared for the U.S. Environmental Protection Agency.
(20) Fossil Energy Research Corporation, “Additional Swirl Tunnel Tests: E-DAT and T-DAT Probes,” February 24, 1999, Technical Memorandum Prepared for U.S. Environmental Protection Agency, P.O. No. 7W-1193-NALX.
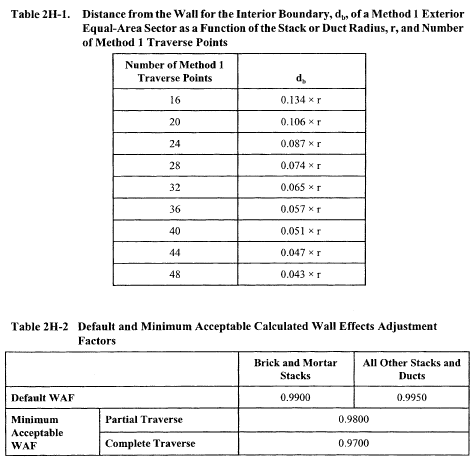
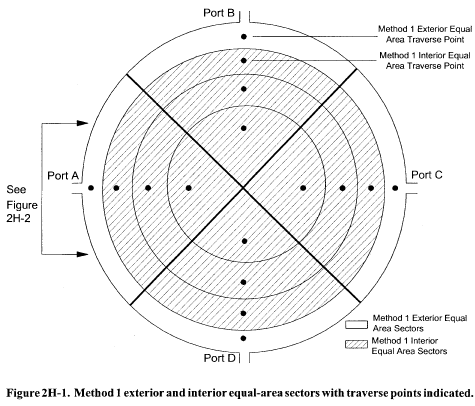
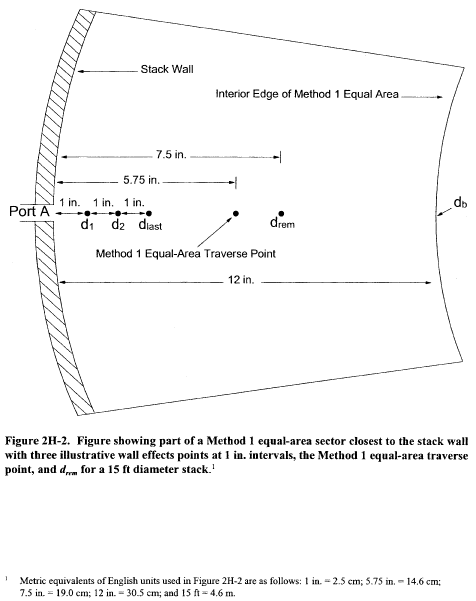
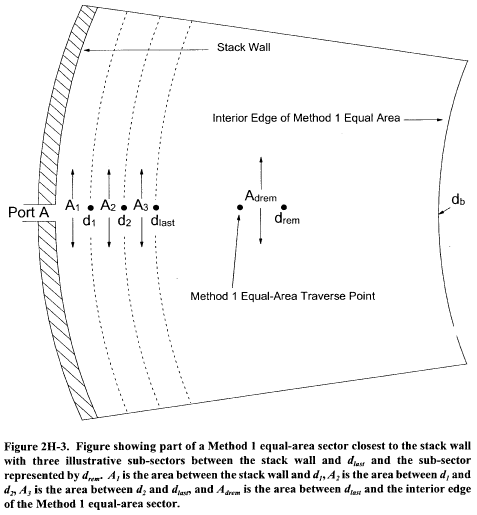
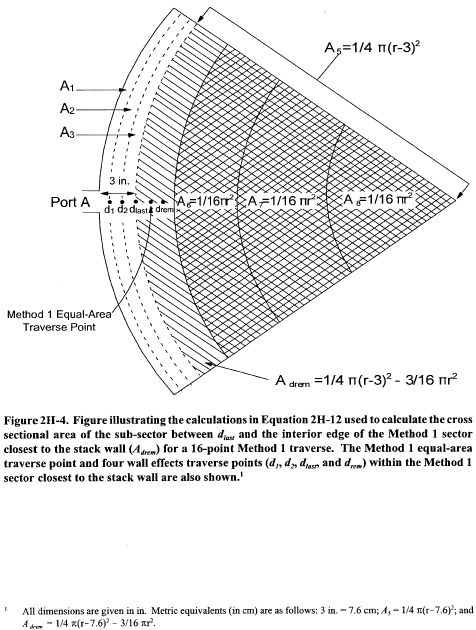
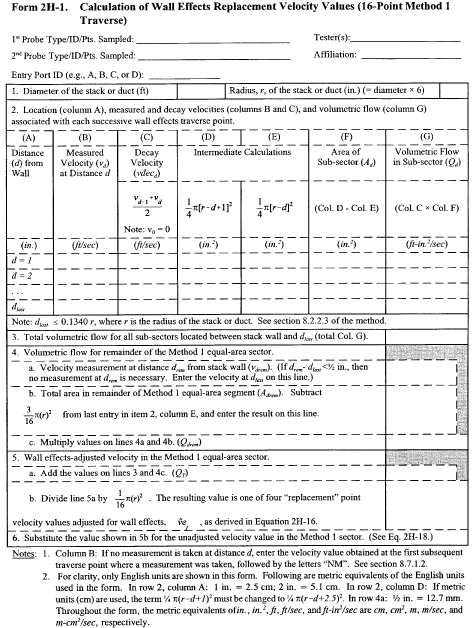
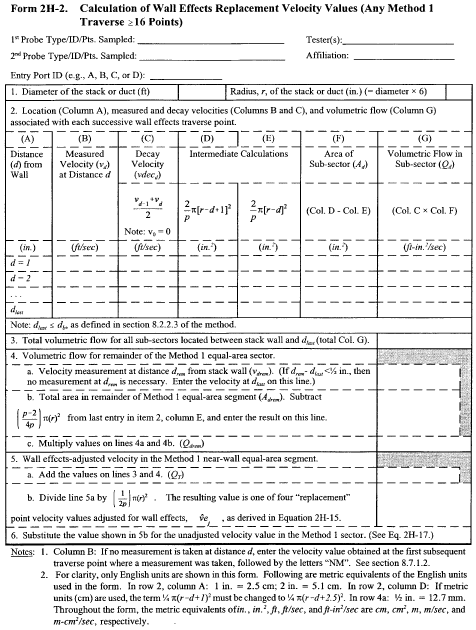
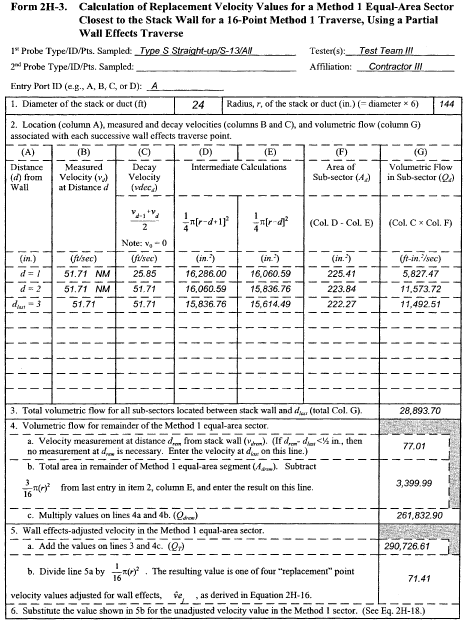
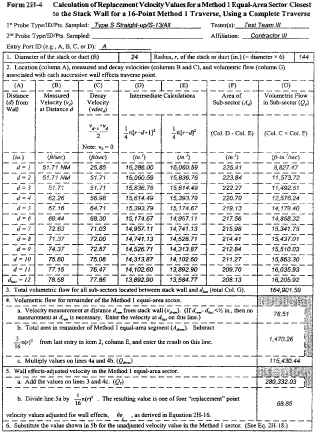
This method does not include all of the specifications (e.g., equipment and supplies) and procedures (e.g., sampling) essential to its performance. Some material is incorporated by reference from other methods in this part. Therefore, to obtain reliable results, persons using this method should also have a thorough knowledge of Method 1.
1.0 Scope and Application1.1 Analytes.
Analytes | CAS No. | Sensitivity |
---|---|---|
Oxygen (O2) | 7782-44-7 | 2,000 ppmv. |
Nitrogen (N2) | 7727-37-9 | N/A. |
Carbon dioxide (CO2) | 124-38-9 | 2,000 ppmv. |
Carbon monoxide (CO) | 630-08-0 | N/A. |
1.2 Applicability. This method is applicable for the determination of CO2 and O2 concentrations and dry molecular weight of a sample from an effluent gas stream of a fossil-fuel combustion process or other process.
1.3 Other methods, as well as modifications to the procedure described herein, are also applicable for all of the above determinations. Examples of specific methods and modifications include: (1) A multi-point grab sampling method using an Orsat analyzer to analyze the individual grab sample obtained at each point; (2) a method for measuring either CO2 or O2 and using stoichiometric calculations to determine dry molecular weight; and (3) assigning a value of 30.0 for dry molecular weight, in lieu of actual measurements, for processes burning natural gas, coal, or oil. These methods and modifications may be used, but are subject to the approval of the Administrator. The method may also be applicable to other processes where it has been determined that compounds other than CO2, O2, carbon monoxide (CO), and nitrogen (N2) are not present in concentrations sufficient to affect the results.
1.4 Data Quality Objectives. Adherence to the requirements of this method will enhance the quality of the data obtained from air pollutant sampling methods.
2.0 Summary of Method2.1 A gas sample is extracted from a stack by one of the following methods: (1) single-point, grab sampling; (2) single-point, integrated sampling; or (3) multi-point, integrated sampling. The gas sample is analyzed for percent CO2 and percent O2. For dry molecular weight determination, either an Orsat or a Fyrite analyzer may be used for the analysis.
3.0 Definitions [Reserved] 4.0 Interferences4.1 Several compounds can interfere, to varying degrees, with the results of Orsat or Fyrite analyses. Compounds that interfere with CO2 concentration measurement include acid gases (e.g., sulfur dioxide, hydrogen chloride); compounds that interfere with O2 concentration measurement include unsaturated hydrocarbons (e.g., acetone, acetylene), nitrous oxide, and ammonia. Ammonia reacts chemically with the O2 absorbing solution, and when present in the effluent gas stream must be removed before analysis.
5.0 Safety5.1 Disclaimer. This method may involve hazardous materials, operations, and equipment. This test method may not address all of the safety problems associated with its use. It is the responsibility of the user of this test method to establish appropriate safety and health practices and determine the applicability of regulatory limitations prior to performing this test method.
5.2 Corrosive Reagents.
5.2.1 A typical Orsat analyzer requires four reagents: a gas-confining solution, CO2 absorbent, O2 absorbent, and CO absorbent. These reagents may contain potassium hydroxide, sodium hydroxide, cuprous chloride, cuprous sulfate, alkaline pyrogallic acid, and/or chromous chloride. Follow manufacturer's operating instructions and observe all warning labels for reagent use.
5.2.2 A typical Fyrite analyzer contains zinc chloride, hydrochloric acid, and either potassium hydroxide or chromous chloride. Follow manufacturer's operating instructions and observe all warning labels for reagent use.
6.0 Equipment and Supplies Note:As an alternative to the sampling apparatus and systems described herein, other sampling systems (e.g., liquid displacement) may be used, provided such systems are capable of obtaining a representative sample and maintaining a constant sampling rate, and are, otherwise, capable of yielding acceptable results. Use of such systems is subject to the approval of the Administrator.
6.1 Grab Sampling (See Figure 3-1).
6.1.1 Probe. Stainless steel or borosilicate glass tubing equipped with an in-stack or out-of-stack filter to remove particulate matter (a plug of glass wool is satisfactory for this purpose). Any other materials, resistant to temperature at sampling conditions and inert to all components of the gas stream, may be used for the probe. Examples of such materials may include aluminum, copper, quartz glass, and Teflon.
6.1.2 Pump. A one-way squeeze bulb, or equivalent, to transport the gas sample to the analyzer.
6.2 Integrated Sampling (Figure 3-2).
6.2.1 Probe. Same as in section 6.1.1.
6.2.2 Condenser. An air-cooled or water-cooled condenser, or other condenser no greater than 250 ml that will not remove O2, CO2, CO, and N2, to remove excess moisture which would interfere with the operation of the pump and flowmeter.
6.2.3 Valve. A needle valve, to adjust sample gas flow rate.
6.2.4 Pump. A leak-free, diaphragm-type pump, or equivalent, to transport sample gas to the flexible bag. Install a small surge tank between the pump and rate meter to eliminate the pulsation effect of the diaphragm pump on the rate meter.
6.2.5 Rate Meter. A rotameter, or equivalent, capable of measuring flow rate to ±2 percent of the selected flow rate. A flow rate range of 500 to 1000 ml/min is suggested.
6.2.6 Flexible Bag. Any leak-free plastic (e.g., Tedlar, Mylar, Teflon) or plastic-coated aluminum (e.g., aluminized Mylar) bag, or equivalent, having a capacity consistent with the selected flow rate and duration of the test run. A capacity in the range of 55 to 90 liters (1.9 to 3.2 ft 3) is suggested. To leak-check the bag, connect it to a water manometer, and pressurize the bag to 5 to 10 cm H2O (2 to 4 in. H2O). Allow to stand for 10 minutes. Any displacement in the water manometer indicates a leak. An alternative leak-check method is to pressurize the bag to 5 to 10 cm (2 to 4 in.) H2O and allow to stand overnight. A deflated bag indicates a leak.
6.2.7 Pressure Gauge. A water-filled U-tube manometer, or equivalent, of about 30 cm (12 in.), for the flexible bag leak-check.
6.2.8 Vacuum Gauge. A mercury manometer, or equivalent, of at least 760 mm (30 in.) Hg, for the sampling train leak-check.
6.3 Analysis. An Orsat or Fyrite type combustion gas analyzer.
7.0 Reagents and Standards7.1 Reagents. As specified by the Orsat or Fyrite-type combustion analyzer manufacturer.
7.2 Standards. Two standard gas mixtures, traceable to National Institute of Standards and Technology (NIST) standards, to be used in auditing the accuracy of the analyzer and the analyzer operator technique:
7.2.1. Gas cylinder containing 2 to 4 percent O2 and 14 to 18 percent CO2.
7.2.2. Gas cylinder containing 2 to 4 percent CO2 and about 15 percent O2.
8.0 Sample Collection, Preservation, Storage, and Transport8.1 Single Point, Grab Sampling Procedure.
8.1.1 The sampling point in the duct shall either be at the centroid of the cross section or at a point no closer to the walls than 1.0 m (3.3 ft), unless otherwise specified by the Administrator.
8.1.2 Set up the equipment as shown in Figure 3-1, making sure all connections ahead of the analyzer are tight. If an Orsat analyzer is used, it is recommended that the analyzer be leak-checked by following the procedure in section 11.5; however, the leak-check is optional.
8.1.3 Place the probe in the stack, with the tip of the probe positioned at the sampling point. Purge the sampling line long enough to allow at least five exchanges. Draw a sample into the analyzer, and immediately analyze it for percent CO2 and percent O2 according to section 11.2.
8.2 Single-Point, Integrated Sampling Procedure.
8.2.1 The sampling point in the duct shall be located as specified in section 8.1.1.
8.2.2 Leak-check (optional) the flexible bag as in section 6.2.6. Set up the equipment as shown in Figure 3-2. Just before sampling, leak-check (optional) the train by placing a vacuum gauge at the condenser inlet, pulling a vacuum of at least 250 mm Hg (10 in. Hg), plugging the outlet at the quick disconnect, and then turning off the pump. The vacuum should remain stable for at least 0.5 minute. Evacuate the flexible bag. Connect the probe, and place it in the stack, with the tip of the probe positioned at the sampling point. Purge the sampling line. Next, connect the bag, and make sure that all connections are tight.
8.2.3 Sample Collection. Sample at a constant rate (±10 percent). The sampling run should be simultaneous with, and for the same total length of time as, the pollutant emission rate determination. Collection of at least 28 liters (1.0 ft 3) of sample gas is recommended; however, smaller volumes may be collected, if desired.
8.2.4 Obtain one integrated flue gas sample during each pollutant emission rate determination. Within 8 hours after the sample is taken, analyze it for percent CO2 and percent O2 using either an Orsat analyzer or a Fyrite type combustion gas analyzer according to section 11.3.
Note:When using an Orsat analyzer, periodic Fyrite readings may be taken to verify/confirm the results obtained from the Orsat.
8.3 Multi-Point, Integrated Sampling Procedure.
8.3.1 Unless otherwise specified in an applicable regulation, or by the Administrator, a minimum of eight traverse points shall be used for circular stacks having diameters less than 0.61 m (24 in.), a minimum of nine shall be used for rectangular stacks having equivalent diameters less than 0.61 m (24 in.), and a minimum of 12 traverse points shall be used for all other cases. The traverse points shall be located according to Method 1.
8.3.2 Follow the procedures outlined in sections 8.2.2 through 8.2.4, except for the following: Traverse all sampling points, and sample at each point for an equal length of time. Record sampling data as shown in Figure 3-3.
9.0 Quality ControlSection | Quality control measure | Effect |
---|---|---|
8.2 | Use of Fyrite to confirm Orsat results | Ensures the accurate measurement of CO2 and O2. |
10.1 | Periodic audit of analyzer and operator technique | Ensures that the analyzer is operating properly and that the operator performs the sampling procedure correctly and accurately. |
11.3 | Replicable analyses of integrated samples | Minimizes experimental error. |
10.1 Analyzer. The analyzer and analyzer operator's technique should be audited periodically as follows: take a sample from a manifold containing a known mixture of CO2 and O2, and analyze according to the procedure in section 11.3. Repeat this procedure until the measured concentration of three consecutive samples agrees with the stated value ±0.5 percent. If necessary, take corrective action, as specified in the analyzer users manual.
10.2 Rotameter. The rotameter need not be calibrated, but should be cleaned and maintained according to the manufacturer's instruction.
11.0 Analytical Procedure11.1 Maintenance. The Orsat or Fyrite-type analyzer should be maintained and operated according to the manufacturers specifications.
11.2 Grab Sample Analysis. Use either an Orsat analyzer or a Fyrite-type combustion gas analyzer to measure O2 and CO2 concentration for dry molecular weight determination, using procedures as specified in the analyzer user's manual. If an Orsat analyzer is used, it is recommended that the Orsat leak-check, described in section 11.5, be performed before this determination; however, the check is optional. Calculate the dry molecular weight as indicated in section 12.0. Repeat the sampling, analysis, and calculation procedures until the dry molecular weights of any three grab samples differ from their mean by no more than 0.3 g/g-mole (0.3 lb/lb-mole). Average these three molecular weights, and report the results to the nearest 0.1 g/g-mole (0.1 lb/lb-mole).
11.3 Integrated Sample Analysis. Use either an Orsat analyzer or a Fyrite-type combustion gas analyzer to measure O2 and CO2 concentration for dry molecular weight determination, using procedures as specified in the analyzer user's manual. If an Orsat analyzer is used, it is recommended that the Orsat leak-check, described in section 11.5, be performed before this determination; however, the check is optional. Calculate the dry molecular weight as indicated in section 12.0. Repeat the analysis and calculation procedures until the individual dry molecular weights for any three analyses differ from their mean by no more than 0.3 g/g-mole (0.3 lb/lb-mole). Average these three molecular weights, and report the results to the nearest 0.1 g/g-mole (0.1 lb/lb-mole).
11.4 Standardization. A periodic check of the reagents and of operator technique should be conducted at least once every three series of test runs as outlined in section 10.1.
11.5 Leak-Check Procedure for Orsat Analyzer. Moving an Orsat analyzer frequently causes it to leak. Therefore, an Orsat analyzer should be thoroughly leak-checked on site before the flue gas sample is introduced into it. The procedure for leak-checking an Orsat analyzer is as follows:
11.5.1 Bring the liquid level in each pipette up to the reference mark on the capillary tubing, and then close the pipette stopcock.
11.5.2 Raise the leveling bulb sufficiently to bring the confining liquid meniscus onto the graduated portion of the burette, and then close the manifold stopcock.
11.5.3 Record the meniscus position.
11.5.4 Observe the meniscus in the burette and the liquid level in the pipette for movement over the next 4 minutes.
11.5.5 For the Orsat analyzer to pass the leak-check, two conditions must be met:
11.5.5.1 The liquid level in each pipette must not fall below the bottom of the capillary tubing during this 4-minute interval.
11.5.5.2 The meniscus in the burette must not change by more than 0.2 ml during this 4-minute interval.
11.5.6 If the analyzer fails the leak-check procedure, check all rubber connections and stopcocks to determine whether they might be the cause of the leak. Disassemble, clean, and regrease any leaking stopcocks. Replace leaking rubber connections. After the analyzer is reassembled, repeat the leak-check procedure.
12.0 Calculations and Data Analysis12.1 Nomenclature.
Md = Dry molecular weight, g/g-mole (lb/lb-mole). %CO2 = Percent CO2 by volume, dry basis. %O2 = Percent O2 by volume, dry basis. %CO = Percent CO by volume, dry basis. %N2 = Percent N2 by volume, dry basis. 0.280 = Molecular weight of N2 or CO, divided by 100. 0.320 = Molecular weight of O2 divided by 100. 0.440 = Molecular weight of CO2 divided by 100.12.2 Nitrogen, Carbon Monoxide Concentration. Determine the percentage of the gas that is N2 and CO by subtracting the sum of the percent CO2 and percent O2 from 100 percent.
12.3 Dry Molecular Weight. Use Equation 3-1 to calculate the dry molecular weight of the stack gas.
Note:The above Equation 3-1 does not consider the effect on calculated dry molecular weight of argon in the effluent gas. The concentration of argon, with a molecular weight of 39.9, in ambient air is about 0.9 percent. A negative error of approximately 0.4 percent is introduced. The tester may choose to include argon in the analysis using procedures subject to approval of the Administrator.
13.0 Method Performance [Reserved] 14.0 Pollution Prevention [Reserved] 15.0 Waste Management [Reserved] 16.0 References1. Altshuller, A.P. Storage of Gases and Vapors in Plastic Bags. International Journal of Air and Water Pollution. 6:75-81. 1963.
2. Conner, William D. and J.S. Nader. Air Sampling with Plastic Bags. Journal of the American Industrial Hygiene Association. 25:291-297. 1964.
3. Burrell Manual for Gas Analysts, Seventh edition. Burrell Corporation, 2223 Fifth Avenue, Pittsburgh, PA. 15219. 1951.
4. Mitchell, W.J. and M.R. Midgett. Field Reliability of the Orsat Analyzer. Journal of Air Pollution Control Association. 26:491-495. May 1976.
5. Shigehara, R.T., R.M. Neulicht, and W.S. Smith. Validating Orsat Analysis Data from Fossil Fuel-Fired Units. Stack Sampling News. 4(2):21-26. August 1976.
17.0 Tables, Diagrams, Flowcharts, and Validation Data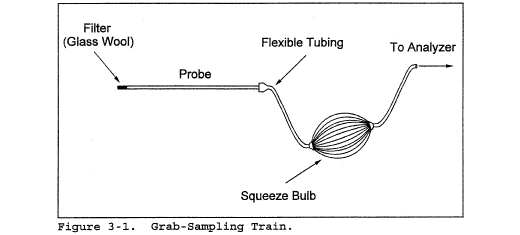
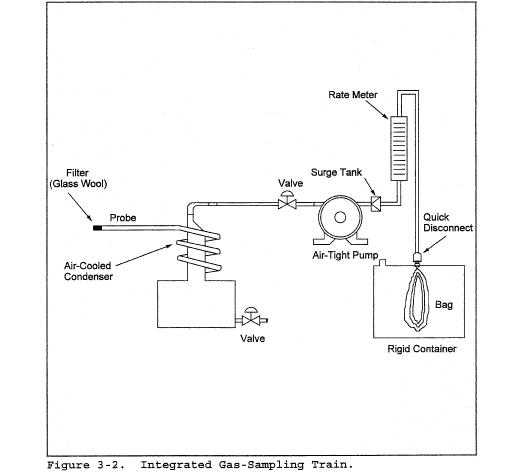
Time | Traverse point | Q (liter/min) | % Deviation a |
---|---|---|---|
Average |
a % Dev.=[(Q−Qavg)/Qavg] × 100 (Must be ≤±10%)
Method 3A is a procedure for measuring oxygen (O2) and carbon dioxide (CO2) in stationary source emissions using a continuous instrumental analyzer. Quality assurance and quality control requirements are included to assure that you, the tester, collect data of known quality. You must document your adherence to these specific requirements for equipment, supplies, sample collection and analysis, calculations, and data analysis.
This method does not completely describe all equipment, supplies, and sampling and analytical procedures you will need but refers to other methods for some of the details. Therefore, to obtain reliable results, you should also have a thorough knowledge of these additional test methods which are found in appendix A to this part:
(a) Method 1 - Sample and Velocity Traverses for Stationary Sources.
(b) Method 3 - Gas Analysis for the Determination of Molecular Weight.
(c) Method 4 - Determination of Moisture Content in Stack Gases.
(d) Method 7E - Determination of Nitrogen Oxides Emissions from Stationary Sources (Instrumental Analyzer Procedure).
1.1 Analytes. What does this method determine? This method measures the concentration of oxygen and carbon dioxide.
Analyte | CAS No. | Sensitivity |
---|---|---|
Oxygen (O2) | 7782-44-7 | Typically <2% of Calibration Span. |
Carbon dioxide (CO2) | 124-38-9 | Typically <2% of Calibration Span. |
1.2 Applicability. When is this method required? The use of Method 3A may be required by specific New Source Performance Standards, Clean Air Marketing rules, State Implementation Plans and permits, where measurements of O2 and CO2 concentrations in stationary source emissions must be made, either to determine compliance with an applicable emission standard or to conduct performance testing of a continuous emission monitoring system (CEMS). Other regulations may also require the use of Method 3A.
1.3 Data Quality Objectives. How good must my collected data be? Refer to section 1.3 of Method 7E.
2.0 Summary of MethodIn this method, you continuously or intermittently sample the effluent gas and convey the sample to an analyzer that measures the concentration of O2 or CO2. You must meet the performance requirements of this method to validate your data.
3.0 DefinitionsRefer to section 3.0 of Method 7E for the applicable definitions.
4.0 Interferences [Reserved] 5.0 SafetyRefer to section 5.0 of Method 7E.
6.0 Equipment and SuppliesFigure 7E-1 in Method 7E is a schematic diagram of an acceptable measurement system.
6.1 What do I need for the measurement system? The components of the measurement system are described (as applicable) in sections 6.1 and 6.2 of Method 7E, except that the analyzer described in section 6.2 of this method must be used instead of the analyzer described in Method 7E. You must follow the noted specifications in section 6.1 of Method 7E except that the requirements to use stainless steel, Teflon, or non-reactive glass filters do not apply. Also, a heated sample line is not required to transport dry gases or for systems that measure the O2 or CO2 concentration on a dry basis, provided that the system is not also being used to concurrently measure SO2 and/or NOX.
6.2 What analyzer must I use? You must use an analyzer that continuously measures O2 or CO2 in the gas stream and meets the specifications in section 13.0.
7.0 Reagents and Standards7.1 Calibration Gas. What calibration gases do I need? Refer to Section 7.1 of Method 7E for the calibration gas requirements. Example calibration gas mixtures are listed below. Pre-cleaned or scrubbed air may be used for the O2 high-calibration gas provided it does not contain other gases that interfere with the O2 measurement.
(a) CO2 in Nitrogen (N2).
(b) CO2/SO2 gas mixture in N2.
(c) O2/SO2 gas mixture in N2.
(d) O2/CO2/SO2 gas mixture in N2.
(e) CO2/NOX gas mixture in N2.
(f) CO2/SO2/NOX gas mixture in N2.
The tests for analyzer calibration error and system bias require high-, mid-, and low-level gases.
7.2 Interference Check. What reagents do I need for the interference check? Potential interferences may vary among available analyzers. Table 7E-3 of Method 7E lists a number of gases that should be considered in conducting the interference test.
8.0 Sample Collection, Preservation, Storage, and Transport8.1 Sampling Site and Sampling Points. You must follow the procedures of section 8.1 of Method 7E to determine the appropriate sampling points, unless you are using Method 3A only to determine the stack gas molecular weight and for no other purpose. In that case, you may use single-point integrated sampling as described in section 8.2.1 of Method 3. If the stratification test provisions in section 8.1.2 of Method 7E are used to reduce the number of required sampling points, the alternative acceptance criterion for 3-point sampling will be ±0.5 percent CO2 or O2, and the alternative acceptance criterion for single-point sampling will be ±0.3 percent CO2 or O2. In that case, you may use single-point integrated sampling as described in section 8.2.1 of Method 3.
8.2 Initial Measurement System Performance Tests. You must follow the procedures in section 8.2 of Method 7E. If a dilution-type measurement system is used, the special considerations in section 8.3 of Method 7E apply.
8.3 Interference Check. The O2 or CO2 analyzer must be documented to show that interference effects to not exceed 2.5 percent of the calibration span. The interference test in section 8.2.7 of Method 7E is a procedure that may be used to show this. The effects of all potential interferences at the concentrations encountered during testing must be addressed and documented. This testing and documentation may be done by the instrument manufacturer.
8.4 Sample Collection. You must follow the procedures in section 8.4 of Method 7E.
8.5 Post-Run System Bias Check and Drift Assessment. You must follow the procedures in section 8.5 of Method 7E.
9.0 Quality ControlFollow quality control procedures in section 9.0 of Method 7E.
10.0 Calibration and StandardizationFollow the procedures for calibration and standardization in section 10.0 of Method 7E.
11.0 Analytical ProceduresBecause sample collection and analysis are performed together (see section 8), additional discussion of the analytical procedure is not necessary.
12.0 Calculations and Data AnalysisYou must follow the applicable procedures for calculations and data analysis in section 12.0 of Method 7E, substituting percent O2 and percent CO2 for ppmv of NOX as appropriate.
13.0 Method PerformanceThe specifications for the applicable performance checks are the same as in section 13.0 of Method 7E except for the alternative specifications for system bias, drift, and calibration error. In these alternative specifications, replace the term “0.5 ppmv” with the term “0.5 percent O2” or “0.5 percent CO2” (as applicable).
14.0 Pollution Prevention [Reserved] 15.0 Waste Management [Reserved] 16.0 Alternative Procedures [Reserved] 17.0 References1. “EPA Traceability Protocol for Assay and Certification of Gaseous Calibration Standards” September 1997 as amended, EPA-600/R-97/121.
18.0 Tables, Diagrams, Flowcharts, and Validation DataRefer to section 18.0 of Method 7E.
Method 3B - Gas Analysis for the Determination of Emission Rate Correction Factor or Excess Air Note:This method does not include all of the specifications (e.g., equipment and supplies) and procedures (e.g., sampling) essential to its performance. Some material is incorporated by reference from other methods in this part. Therefore, to obtain reliable results, persons using this method should have a thorough knowledge of at least the following additional test methods: Method 1 and 3.
1.0 Scope and Application1.1 Analytes.
Analyte | CAS No. | Sensitivity |
---|---|---|
Oxygen (O2) | 7782-44-7 | 2,000 ppmv. |
Carbon Dioxide (CO2) | 124-38-9 | 2,000 ppmv. |
Carbon Monoxide (CO) | 630-08-0 | N/A. |
1.2 Applicability. This method is applicable for the determination of O2, CO2, and CO concentrations in the effluent from fossil-fuel combustion processes for use in excess air or emission rate correction factor calculations. Where compounds other than CO2, O2, CO, and nitrogen (N2) are present in concentrations sufficient to affect the results, the calculation procedures presented in this method must be modified, subject to the approval of the Administrator.
1.3 Other methods, as well as modifications to the procedure described herein, are also applicable for all of the above determinations. Examples of specific methods and modifications include: (1) A multi-point sampling method using an Orsat analyzer to analyze individual grab samples obtained at each point, and (2) a method using CO2 or O2 and stoichiometric calculations to determine excess air. These methods and modifications may be used, but are subject to the approval of the Administrator.
1.4 Data Quality Objectives. Adherence to the requirements of this method will enhance the quality of the data obtained from air pollutant sampling methods.
2.0 Summary of Method2.1 A gas sample is extracted from a stack by one of the following methods: (1) Single-point, grab sampling; (2) single-point, integrated sampling; or (3) multi-point, integrated sampling. The gas sample is analyzed for percent CO2, percent O2, and, if necessary, percent CO using an Orsat combustion gas analyzer.
3.0 Definitions [Reserved] 4.0 Interferences4.1 Several compounds can interfere, to varying degrees, with the results of Orsat analyses. Compounds that interfere with CO2 concentration measurement include acid gases (e.g., sulfur dioxide, hydrogen chloride); compounds that interfere with O2 concentration measurement include unsaturated hydrocarbons (e.g., acetone, acetylene), nitrous oxide, and ammonia. Ammonia reacts chemically with the O2 absorbing solution, and when present in the effluent gas stream must be removed before analysis.
5.0 Safety5.1 Disclaimer. This method may involve hazardous materials, operations, and equipment. This test method may not address all of the safety problems associated with its use. It is the responsibility of the user of this test method to establish appropriate safety and health practices and determine the applicability of regulatory limitations prior to performing this test method.
5.2 Corrosive Reagents. A typical Orsat analyzer requires four reagents: a gas-confining solution, CO2 absorbent, O2 absorbent, and CO absorbent. These reagents may contain potassium hydroxide, sodium hydroxide, cuprous chloride, cuprous sulfate, alkaline pyrogallic acid, and/or chromous chloride. Follow manufacturer's operating instructions and observe all warning labels for reagent use.
6.0 Equipment and Supplies Note:As an alternative to the sampling apparatus and systems described herein, other sampling systems (e.g., liquid displacement) may be used, provided such systems are capable of obtaining a representative sample and maintaining a constant sampling rate, and are, otherwise, capable of yielding acceptable results. Use of such systems is subject to the approval of the Administrator.
6.1 Grab Sampling and Integrated Sampling. Same as in sections 6.1 and 6.2, respectively for Method 3.
6.2 Analysis. An Orsat analyzer only. For low CO2 (less than 4.0 percent) or high O2 (greater than 15.0 percent) concentrations, the measuring burette of the Orsat must have at least 0.1 percent subdivisions. For Orsat maintenance and operation procedures, follow the instructions recommended by the manufacturer, unless otherwise specified herein.
7.0 Reagents and Standards7.1 Reagents. Same as in Method 3, section 7.1.
7.2 Standards. Same as in Method 3, section 7.2.
8.0 Sample Collection, Preservation, Storage, and Transport Note:Each of the three procedures below shall be used only when specified in an applicable subpart of the standards. The use of these procedures for other purposes must have specific prior approval of the Administrator. A Fyrite-type combustion gas analyzer is not acceptable for excess air or emission rate correction factor determinations, unless approved by the Administrator. If both percent CO2 and percent O2 are measured, the analytical results of any of the three procedures given below may also be used for calculating the dry molecular weight (see Method 3).
8.1 Single-Point, Grab Sampling and Analytical Procedure.
8.1.1 The sampling point in the duct shall either be at the centroid of the cross section or at a point no closer to the walls than 1.0 m (3.3 ft), unless otherwise specified by the Administrator.
8.1.2 Set up the equipment as shown in Figure 3-1 of Method 3, making sure all connections ahead of the analyzer are tight. Leak-check the Orsat analyzer according to the procedure described in section 11.5 of Method 3. This leak-check is mandatory.
8.1.3 Place the probe in the stack, with the tip of the probe positioned at the sampling point; purge the sampling line long enough to allow at least five exchanges. Draw a sample into the analyzer. For emission rate correction factor determinations, immediately analyze the sample for percent CO2 or percent O2, as outlined in section 11.2. For excess air determination, immediately analyze the sample for percent CO2, O2, and CO, as outlined in section 11.2, and calculate excess air as outlined in section 12.2.
8.1.4 After the analysis is completed, leak-check (mandatory) the Orsat analyzer once again, as described in section 11.5 of Method 3. For the results of the analysis to be valid, the Orsat analyzer must pass this leak-test before and after the analysis.
8.2 Single-Point, Integrated Sampling and Analytical Procedure.
8.2.1 The sampling point in the duct shall be located as specified in section 8.1.1.
8.2.2 Leak-check (mandatory) the flexible bag as in section 6.2.6 of Method 3. Set up the equipment as shown in Figure 3-2 of Method 3. Just before sampling, leak-check (mandatory) the train by placing a vacuum gauge at the condenser inlet, pulling a vacuum of at least 250 mm Hg (10 in. Hg), plugging the outlet at the quick disconnect, and then turning off the pump. The vacuum should remain stable for at least 0.5 minute. Evacuate the flexible bag. Connect the probe, and place it in the stack, with the tip of the probe positioned at the sampling point; purge the sampling line. Next, connect the bag, and make sure that all connections are tight.
8.2.3 Sample at a constant rate, or as specified by the Administrator. The sampling run must be simultaneous with, and for the same total length of time as, the pollutant emission rate determination. Collect at least 28 liters (1.0 ft 3) of sample gas. Smaller volumes may be collected, subject to approval of the Administrator.
8.2.4 Obtain one integrated flue gas sample during each pollutant emission rate determination. For emission rate correction factor determination, analyze the sample within 4 hours after it is taken for percent CO2 or percent O2 (as outlined in section 11.2).
8.3 Multi-Point, Integrated Sampling and Analytical Procedure.
8.3.1 Unless otherwise specified in an applicable regulation, or by the Administrator, a minimum of eight traverse points shall be used for circular stacks having diameters less than 0.61 m (24 in.), a minimum of nine shall be used for rectangular stacks having equivalent diameters less than 0.61 m (24 in.), and a minimum of 12 traverse points shall be used for all other cases. The traverse points shall be located according to Method 1.
8.3.2 Follow the procedures outlined in sections 8.2.2 through 8.2.4, except for the following: Traverse all sampling points, and sample at each point for an equal length of time. Record sampling data as shown in Figure 3-3 of Method 3.
9.0 Quality Control9.1 Data Validation Using Fuel Factor. Although in most instances, only CO2 or O2 measurement is required, it is recommended that both CO2 and O2 be measured to provide a check on the quality of the data. The data validation procedure of section 12.3 is suggested.
Note:Since this method for validating the CO2 and O2 analyses is based on combustion of organic and fossil fuels and dilution of the gas stream with air, this method does not apply to sources that (1) remove CO2 or O2 through processes other than combustion, (2) add O2 (e.g., oxygen enrichment) and N2 in proportions different from that of air, (3) add CO2 (e.g., cement or lime kilns), or (4) have no fuel factor, FO, values obtainable (e.g., extremely variable waste mixtures). This method validates the measured proportions of CO2 and O2 for fuel type, but the method does not detect sample dilution resulting from leaks during or after sample collection. The method is applicable for samples collected downstream of most lime or limestone flue-gas desulfurization units as the CO2 added or removed from the gas stream is not significant in relation to the total CO2 concentration. The CO2 concentrations from other types of scrubbers using only water or basic slurry can be significantly affected and would render the fuel factor check minimally useful.
10.0 Calibration and Standardization10.1 Analyzer. The analyzer and analyzer operator technique should be audited periodically as follows: take a sample from a manifold containing a known mixture of CO2 and O2, and analyze according to the procedure in section 11.3. Repeat this procedure until the measured concentration of three consecutive samples agrees with the stated value ±0.5 percent. If necessary, take corrective action, as specified in the analyzer users manual.
10.2 Rotameter. The rotameter need not be calibrated, but should be cleaned and maintained according to the manufacturer's instruction.
11.0 Analytical Procedure11.1 Maintenance. The Orsat analyzer should be maintained according to the manufacturers specifications.
11.2 Grab Sample Analysis. To ensure complete absorption of the CO2, O2, or if applicable, CO, make repeated passes through each absorbing solution until two consecutive readings are the same. Several passes (three or four) should be made between readings. (If constant readings cannot be obtained after three consecutive readings, replace the absorbing solution.) Although in most cases, only CO2 or O2 concentration is required, it is recommended that both CO2 and O2 be measured, and that the procedure in section 12.3 be used to validate the analytical data.
Note:Since this single-point, grab sampling and analytical procedure is normally conducted in conjunction with a single-point, grab sampling and analytical procedure for a pollutant, only one analysis is ordinarily conducted. Therefore, great care must be taken to obtain a valid sample and analysis.
11.3 Integrated Sample Analysis. The Orsat analyzer must be leak-checked (see section 11.5 of Method 3) before the analysis. If excess air is desired, proceed as follows: (1) within 4 hours after the sample is taken, analyze it (as in sections 11.3.1 through 11.3.3) for percent CO2, O2, and CO; (2) determine the percentage of the gas that is N2 by subtracting the sum of the percent CO2, percent O2, and percent CO from 100 percent; and (3) calculate percent excess air, as outlined in section 12.2.
11.3.1 To ensure complete absorption of the CO2, O2, or if applicable, CO, follow the procedure described in section 11.2.
Note:Although in most instances only CO2 or O2 is required, it is recommended that both CO2 and O2 be measured, and that the procedures in section 12.3 be used to validate the analytical data.
11.3.2 Repeat the analysis until the following criteria are met:
11.3.2.1 For percent CO2, repeat the analytical procedure until the results of any three analyses differ by no more than (a) 0.3 percent by volume when CO2 is greater than 4.0 percent or (b) 0.2 percent by volume when CO2 is less than or equal to 4.0 percent. Average three acceptable values of percent CO2, and report the results to the nearest 0.2 percent.
11.3.2.2 For percent O2, repeat the analytical procedure until the results of any three analyses differ by no more than (a) 0.3 percent by volume when O2 is less than 15.0 percent or (b) 0.2 percent by volume when O2 is greater than or equal to 15.0 percent. Average the three acceptable values of percent O2, and report the results to the nearest 0.1 percent.
11.3.2.3 For percent CO, repeat the analytical procedure until the results of any three analyses differ by no more than 0.3 percent. Average the three acceptable values of percent CO, and report the results to the nearest 0.1 percent.
11.3.3 After the analysis is completed, leak-check (mandatory) the Orsat analyzer once again, as described in section 11.5 of Method 3. For the results of the analysis to be valid, the Orsat analyzer must pass this leak-test before and after the analysis.
11.4 Standardization. A periodic check of the reagents and of operator technique should be conducted at least once every three series of test runs as indicated in section 10.1.
12.0 Calculations and Data Analysis12.1 Nomenclature. Same as section 12.1 of Method 3 with the addition of the following:
%EA = Percent excess air. 0.264 = Ratio of O2 to N2 in air, v/v.12.2 Percent Excess Air. Determine the percentage of the gas that is N2 by subtracting the sum of the percent CO2, percent CO, and percent O2 from 100 percent. Calculate the percent excess air (if applicable) by substituting the appropriate values of percent O2, CO, and N2 into Equation 3B-1.
Note:The equation above assumes that ambient air is used as the source of O2 and that the fuel does not contain appreciable amounts of N2 (as do coke oven or blast furnace gases). For those cases when appreciable amounts of N2 are present (coal, oil, and natural gas do not contain appreciable amounts of N2) or when oxygen enrichment is used, alternative methods, subject to approval of the Administrator, are required.
12.3 Data Validation When Both CO2 and O2 Are Measured.
12.3.1 Fuel Factor, Fo. Calculate the fuel factor (if applicable) using Equation 3B-2:
Where: %O2 = Percent O2 by volume, dry basis. %CO2 = Percent CO2 by volume, dry basis. 20.9 = Percent O2 by volume in ambient air.If CO is present in quantities measurable by this method, adjust the O2 and CO2 values using Equations 3B-3 and 3B-4 before performing the calculation for Fo:
Where: %CO = Percent CO by volume, dry basis.12.3.2 Compare the calculated Fo factor with the expected Fo values. Table 3B-1 in section 17.0 may be used in establishing acceptable ranges for the expected Fo if the fuel being burned is known. When fuels are burned in combinations, calculate the combined fuel Fd and Fc factors (as defined in Method 19, section 12.2) according to the procedure in Method 19, sections 12.2 and 12.3. Then calculate the Fo factor according to Equation 3B-5.
12.3.3 Calculated Fo values, beyond the acceptable ranges shown in this table, should be investigated before accepting the test results. For example, the strength of the solutions in the gas analyzer and the analyzing technique should be checked by sampling and analyzing a known concentration, such as air; the fuel factor should be reviewed and verified. An acceptability range of ±12 percent is appropriate for the Fo factor of mixed fuels with variable fuel ratios. The level of the emission rate relative to the compliance level should be considered in determining if a retest is appropriate; i.e., if the measured emissions are much lower or much greater than the compliance limit, repetition of the test would not significantly change the compliance status of the source and would be unnecessarily time consuming and costly.
13.0 Method Performance [Reserved] 14.0 Pollution Prevention [Reserved] 15.0 Waste Management [Reserved] 16.0 ReferencesSame as Method 3, section 16.0.
17.0 Tables, Diagrams, Flowcharts, and Validation DataTable 3B-1 - Fo Factors for Selected Fuels
Fuel type | Fo range |
---|---|
Coal: | |
Anthracite and lignite | 1.016-1.130 |
Bituminous | 1.083-1.230 |
Oil: | |
Distillate | 1.260-1.413 |
Residual | 1.210-1.370 |
Gas: | |
Natural | 1.600-1.836 |
Propane | 1.434-1.586 |
Butane | 1.405-1.553 |
Wood | 1.000-1.120 |
Wood bark | 1.003-1.130 |
1.1 Applicability. This method applies to the analysis of carbon dioxide (CO2), methane (CH4), nitrogen (N2), and oxygen (O2) in samples from municipal solid waste landfills and other sources when specified in an applicable subpart.
1.2 Principle. A portion of the sample is injected into a gas chromatograph (GC) and the CO2, CH4, N2, and O2 concentrations are determined by using a thermal conductivity detector (TCD) and integrator.
2. Range and Sensitivity2.1 Range. The range of this method depends upon the concentration of samples. The analytical range of TCD's is generally between approximately 10 ppmv and the upper percent range.
2.2 Sensitivity. The sensitivity limit for a compound is defined as the minimum detectable concentration of that compound, or the concentration that produces a signal-to-noise ratio of three to one. For CO2, CH4, N2, and O2, the sensitivity limit is in the low ppmv range.
3. InterferencesSince the TCD exhibits universal response and detects all gas components except the carrier, interferences may occur. Choosing the appropriate GC or shifting the retention times by changing the column flow rate may help to eliminate resolution interferences.
To assure consistent detector response, helium is used to prepare calibration gases. Frequent exposure to samples or carrier gas containing oxygen may gradually destroy filaments.
4. Apparatus4.1 Gas Chromatograph. GC having at least the following components:
4.1.1 Separation Column. Appropriate column(s) to resolve CO2, CH4, N2, O2, and other gas components that may be present in the sample.
4.1.2 Sample Loop. Teflon or stainless steel tubing of the appropriate diameter.
Note:Mention of trade names or specific products does not constitute endorsement or recommendation by the U. S. Environmental Protection Agency.
4.1.3 Conditioning System. To maintain the column and sample loop at constant temperature.
4.1.4 Thermal Conductivity Detector.
4.2 Recorder. Recorder with linear strip chart. Electronic integrator (optional) is recommended.
4.3 Teflon Tubing. Diameter and length determined by connection requirements of cylinder regulators and the GC.
4.4 Regulators. To control gas cylinder pressures and flow rates.
4.5 Adsorption Tubes. Applicable traps to remove any O2 from the carrier gas.
5. Reagents5.1 Calibration and Linearity Gases. Standard cylinder gas mixtures for each compound of interest with at least three concentration levels spanning the range of suspected sample concentrations. The calibration gases shall be prepared in helium.
5.2 Carrier Gas. Helium, high-purity.
6. Analysis6.1 Sample Collection. Use the sample collection procedures described in Methods 3 or 25C to collect a sample of landfill gas (LFG).
6.2 Preparation of GC. Before putting the GC analyzer into routine operation, optimize the operational conditions according to the manufacturer's specifications to provide good resolution and minimum analysis time. Establish the appropriate carrier gas flow and set the detector sample and reference cell flow rates at exactly the same levels. Adjust the column and detector temperatures to the recommended levels. Allow sufficient time for temperature stabilization. This may typically require 1 hour for each change in temperature.
6.3 Analyzer Linearity Check and Calibration. Perform this test before sample analysis.
6.3.1 Using the gas mixtures in section 5.1, verify the detector linearity over the range of suspected sample concentrations with at least three concentrations per compound of interest. This initial check may also serve as the initial instrument calibration.
6.3.2 You may extend the use of the analyzer calibration by performing a single-point calibration verification. Calibration verifications shall be performed by triplicate injections of a single-point standard gas. The concentration of the single-point calibration must either be at the midpoint of the calibration curve or at approximately the source emission concentration measured during operation of the analyzer.
6.3.3 Triplicate injections must agree within 5 percent of their mean, and the average calibration verification point must agree within 10 percent of the initial calibration response factor. If these calibration verification criteria are not met, the initial calibration described in section 6.3.1, using at least three concentrations, must be repeated before analysis of samples can continue.
6.3.4 For each instrument calibration, record the carrier and detector flow rates, detector filament and block temperatures, attenuation factor, injection time, chart speed, sample loop volume, and component concentrations.
6.3.5 Plot a linear regression of the standard concentrations versus area values to obtain the response factor of each compound. Alternatively, response factors of uncorrected component concentrations (wet basis) may be generated using instrumental integration.
Note:Peak height may be used instead of peak area throughout this method.
6.4 Sample Analysis. Purge the sample loop with sample, and allow to come to atmospheric pressure before each injection. Analyze each sample in duplicate, and calculate the average sample area (A). The results are acceptable when the peak areas for two consecutive injections agree within 5 percent of their average. If they do not agree, run additional samples until consistent area data are obtained. Determine the tank sample concentrations according to section 7.2.
7. CalculationsCarry out calculations retaining at least one extra decimal figure beyond that of the acquired data. Round off results only after the final calculation.
7.1 Nomenclature.
Bw = Moisture content in the sample, fraction. CN2 = Measured N2 concentration (by Method 3C), fraction. CN2Corr = Measured N2 concentration corrected only for dilution, fraction. Ct = Calculated NMOC concentration, ppmv C equivalent. Ctm = Measured NMOC concentration, ppmv C equivalent. Pb = Barometric pressure, mm Hg. Pt = Gas sample tank pressure after sampling, but before pressurizing, mm Hg absolute. Ptf = Final gas sample tank pressure after pressurizing, mm Hg absolute. Pti = Gas sample tank pressure after evacuation, mm Hg absolute. Pw = Vapor pressure of H2O (from Table 25C-1), mm Hg. r = Total number of analyzer injections of sample tank during analysis (where j = injection number, 1 . . . r). R = Mean calibration response factor for specific sample component, area/ppm. Tt = Sample tank temperature at completion of sampling, °K. Tti = Sample tank temperature before sampling, °K. Ttf = Sample tank temperature after pressurizing, °K.7.2 Concentration of Sample Components. Calculate C for each compound using Equations 3C-1 and 3C-2. Use the temperature and barometric pressure at the sampling site to calculate Bw. If the sample was diluted with helium using the procedures in Method 25C, use Equation 3C-3 to calculate the concentration.
7.3 Measured N2 Concentration Correction. Calculate the reported N2 correction for Method 25-C using Eq. 3C-4. If oxygen is determined in place of N2, substitute the oxygen concentration for the nitrogen concentration in the equation.
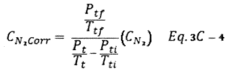
1. McNair, H.M., and E.J. Bonnelli. Basic Gas Chromatography. Consolidated Printers, Berkeley, CA. 1969.
[36 FR 24877, Dec. 23, 1971] Editorial Note:For Federal Register citations affecting appendix A-2 to part 60, see the List of CFR sections Affected, which appears in the Finding Aids section of the printed volume and at www.govinfo.gov.Appendix A-3 to Part 60 - Test Methods 4 through 5I
40:9.0.1.1.1.0.1.1.3 : Appendix A
Appendix A-3 to Part 60 - Test Methods 4 through 5I Method 4 - Determination of moisture content in stack gases Method 5 - Determination of particulate matter emissions from stationary sources Method 5A - Determination of particulate matter emissions from the asphalt processing and asphalt roofing industry Method 5B - Determination of nonsulfuric acid particulate matter emissions from stationary sources Method 5C [Reserved] Method 5D - Determination of particulate matter emissions from positive pressure fabric filters Method 5E - Determination of particulate matter emissions from the wool fiberglass insulation manufacturing industry Method 5F - Determination of nonsulfate particulate matter emissions from stationary sources Method 5G - Determination of particulate matter emissions from wood heaters (dilution tunnel sampling location) Method 5H - Determination of particulate emissions from wood heaters from a stack location Method 5I - Determination of Low Level Particulate Matter Emissions From Stationary SourcesThe test methods in this appendix are referred to in § 60.8 (Performance Tests) and § 60.11 (Compliance With Standards and Maintenance Requirements) of 40 CFR part 60, subpart A (General Provisions). Specific uses of these test methods are described in the standards of performance contained in the subparts, beginning with Subpart D.
Within each standard of performance, a section title “Test Methods and Procedures” is provided to: (1) Identify the test methods to be used as reference methods to the facility subject to the respective standard and (2) identify any special instructions or conditions to be followed when applying a method to the respective facility. Such instructions (for example, establish sampling rates, volumes, or temperatures) are to be used either in addition to, or as a substitute for procedures in a test method. Similarly, for sources subject to emission monitoring requirements, specific instructions pertaining to any use of a test method as a reference method are provided in the subpart or in Appendix B.
Inclusion of methods in this appendix is not intended as an endorsement or denial of their applicability to sources that are not subject to standards of performance. The methods are potentially applicable to other sources; however, applicability should be confirmed by careful and appropriate evaluation of the conditions prevalent at such sources.
The approach followed in the formulation of the test methods involves specifications for equipment, procedures, and performance. In concept, a performance specification approach would be preferable in all methods because this allows the greatest flexibility to the user. In practice, however, this approach is impractical in most cases because performance specifications cannot be established. Most of the methods described herein, therefore, involve specific equipment specifications and procedures, and only a few methods in this appendix rely on performance criteria.
Minor changes in the test methods should not necessarily affect the validity of the results and it is recognized that alternative and equivalent methods exist. section 60.8 provides authority for the Administrator to specify or approve (1) equivalent methods, (2) alternative methods, and (3) minor changes in the methodology of the test methods. It should be clearly understood that unless otherwise identified all such methods and changes must have prior approval of the Administrator. An owner employing such methods or deviations from the test methods without obtaining prior approval does so at the risk of subsequent disapproval and retesting with approved methods.
Within the test methods, certain specific equipment or procedures are recognized as being acceptable or potentially acceptable and are specifically identified in the methods. The items identified as acceptable options may be used without approval but must be identified in the test report. The potentially approvable options are cited as “subject to the approval of the Administrator” or as “or equivalent.” Such potentially approvable techniques or alternatives may be used at the discretion of the owner without prior approval. However, detailed descriptions for applying these potentially approvable techniques or alternatives are not provided in the test methods. Also, the potentially approvable options are not necessarily acceptable in all applications. Therefore, an owner electing to use such potentially approvable techniques or alternatives is responsible for: (1) assuring that the techniques or alternatives are in fact applicable and are properly executed; (2) including a written description of the alternative method in the test report (the written method must be clear and must be capable of being performed without additional instruction, and the degree of detail should be similar to the detail contained in the test methods); and (3) providing any rationale or supporting data necessary to show the validity of the alternative in the particular application. Failure to meet these requirements can result in the Administrator's disapproval of the alternative.
Method 4 - Determination of Moisture Content in Stack Gases Note:This method does not include all the specifications (e.g., equipment and supplies) and procedures (e.g., sampling) essential to its performance. Some material is incorporated by reference from other methods in this part. Therefore, to obtain reliable results, persons using this method should have a thorough knowledge of at least the following additional test methods: Method 1, Method 5, and Method 6.
1.0 Scope and Application1.1 Analytes.
Analyte | CAS No. | Sensitivity |
---|---|---|
Water vapor (H2O) | 7732-18-5 | N/A |
1.2 Applicability. This method is applicable for the determination of the moisture content of stack gas.
1.3 Data Quality Objectives. Adherence to the requirements of this method will enhance the quality of the data obtained from air pollutant sampling methods.
2.0 Summary of Method2.1 A gas sample is extracted at a constant rate from the source; moisture is removed from the sample stream and determined gravimetrically.
2.2 The method contains two possible procedures: a reference method and an approximation method.
2.2.1 The reference method is used for accurate determinations of moisture content (such as are needed to calculate emission data). The approximation method, provides estimates of percent moisture to aid in setting isokinetic sampling rates prior to a pollutant emission measurement run. The approximation method described herein is only a suggested approach; alternative means for approximating the moisture content (e.g., drying tubes, wet bulb-dry bulb techniques, condensation techniques, stoichiometric calculations, previous experience, etc.) are also acceptable.
2.2.2 The reference method is often conducted simultaneously with a pollutant emission measurement run. When it is, calculation of percent isokinetic, pollutant emission rate, etc., for the run shall be based upon the results of the reference method or its equivalent. These calculations shall not be based upon the results of the approximation method, unless the approximation method is shown, to the satisfaction of the Administrator, to be capable of yielding results within one percent H2O of the reference method.
3.0 Definitions [Reserved] 4.0 Interferences4.1 The moisture content of saturated gas streams or streams that contain water droplets, as measured by the reference method, may be positively biased. Therefore, when these conditions exist or are suspected, a second determination of the moisture content shall be made simultaneously with the reference method, as follows: Assume that the gas stream is saturated. Attach a temperature sensor [capable of measuring to ±1 °C (2 °F)] to the reference method probe. Measure the stack gas temperature at each traverse point (see section 8.1.1.1) during the reference method traverse, and calculate the average stack gas temperature. Next, determine the moisture percentage, either by: (1) Using a psychrometric chart and making appropriate corrections if the stack pressure is different from that of the chart, or (2) using saturation vapor pressure tables. In cases where the psychrometric chart or the saturation vapor pressure tables are not applicable (based on evaluation of the process), alternative methods, subject to the approval of the Administrator, shall be used.
5.0 Safety5.1 Disclaimer. This method may involve hazardous materials, operations, and equipment. This test method may not address all of the safety problems associated with its use. It is the responsibility of the user of this test method to establish appropriate safety and health practices and determine the applicability of regulatory limitations prior to performing this test method.
6.0 Equipment and Supplies6.1 Reference Method. A schematic of the sampling train used in this reference method is shown in Figure 4-1.
6.1.1 Probe. Stainless steel or glass tubing, sufficiently heated to prevent water condensation, and equipped with a filter, either in-stack (e.g., a plug of glass wool inserted into the end of the probe) or heated out-of-stack (e.g., as described in Method 5), to remove particulate matter. When stack conditions permit, other metals or plastic tubing may be used for the probe, subject to the approval of the Administrator.
6.1.2 Condenser. Same as Method 5, section 6.1.1.8.
6.1.3 Cooling System. An ice bath container, crushed ice, and water (or equivalent), to aid in condensing moisture.
6.1.4 Metering System. Same as in Method 5, section 6.1.1.9, except do not use sampling systems designed for flow rates higher than 0.0283 m 3/min (1.0 cfm). Other metering systems, capable of maintaining a constant sampling rate to within 10 percent and determining sample gas volume to within 2 percent, may be used, subject to the approval of the Administrator.
6.1.5 Barometer and Balance. Same as Method 5, sections 6.1.2 and 6.2.5, respectively.
6.2. Approximation Method. A schematic of the sampling train used in this approximation method is shown in Figure 4-2.
6.2.1 Probe. Same as section 6.1.1.
6.2.2 Condenser. Two midget impingers, each with 30-ml capacity, or equivalent.
6.2.3 Cooling System. Ice bath container, crushed ice, and water, to aid in condensing moisture in impingers.
6.2.4 Drying Tube. Tube packed with new or regenerated 6- to 16-mesh indicating-type silica gel (or equivalent desiccant), to dry the sample gas and to protect the meter and pump.
6.2.5 Valve. Needle valve, to regulate the sample gas flow rate.
6.2.6 Pump. Leak-free, diaphragm type, or equivalent, to pull the gas sample through the train.
6.2.7 Volume Meter. Dry gas meter, sufficiently accurate to measure the sample volume to within 2 percent, and calibrated over the range of flow rates and conditions actually encountered during sampling.
6.2.8 Rate Meter. Rotameter, or equivalent, to measure the flow range from 0 to 3 liters/min (0 to 0.11 cfm).
6.2.9 Graduated Cylinder. 25-ml.
6.2.10 Barometer. Same as Method 5, section 6.1.2.
6.2.11 Vacuum Gauge. At least 760-mm (30-in.) Hg gauge, to be used for the sampling leak check.
7.0 Reagents and Standards [Reserved] 8.0 Sample Collection, Preservation, Transport, and Storage8.1 Reference Method. The following procedure is intended for a condenser system (such as the impinger system described in section 6.1.1.8 of Method 5) incorporating volumetric analysis to measure the condensed moisture, and silica gel and gravimetric analysis to measure the moisture leaving the condenser.
8.1.1 Preliminary Determinations.
8.1.1.1 Unless otherwise specified by the Administrator, a minimum of eight traverse points shall be used for circular stacks having diameters less than 0.61 m (24 in.), a minimum of nine points shall be used for rectangular stacks having equivalent diameters less than 0.61 m (24 in.), and a minimum of twelve traverse points shall be used in all other cases. The traverse points shall be located according to Method 1. The use of fewer points is subject to the approval of the Administrator. Select a suitable probe and probe length such that all traverse points can be sampled. Consider sampling from opposite sides of the stack (four total sampling ports) for large stacks, to permit use of shorter probe lengths. Mark the probe with heat resistant tape or by some other method to denote the proper distance into the stack or duct for each sampling point.
8.1.1.2 Select a total sampling time such that a minimum total gas volume of 0.60 scm (21 scf) will be collected, at a rate no greater than 0.021 m 3/min (0.75 cfm). When both moisture content and pollutant emission rate are to be determined, the moisture determination shall be simultaneous with, and for the same total length of time as, the pollutant emission rate run, unless otherwise specified in an applicable subpart of the standards.
8.1.2 Preparation of Sampling Train.
8.1.2.1 Transfer water into the first two impingers, leave the third impinger empty and add silica gel to the fourth impinger. Weigh the impingers before sampling and record the weight to the nearest 0.5g at a minimum.
8.1.2.2 Set up the sampling train as shown in Figure 4-1. Turn on the probe heater and (if applicable) the filter heating system to temperatures of approximately 120 °C (248 °F), to prevent water condensation ahead of the condenser. Allow time for the temperatures to stabilize. Place crushed ice and water in the ice bath container.
8.1.3 Leak-Check Procedures.
8.1.3.1 Metering System. Same as Method 5, section 8.4.1.
8.1.3.2 Sampling Train. Disconnect the probe from the first impinger or (if applicable) from the filter holder. Plug the inlet to the first impinger (or filter holder), and pull a 380 mm (15 in.) Hg vacuum. A lower vacuum may be used, provided that it is not exceeded during the test. A leakage rate in excess of 4 percent of the average sampling rate or 0.00057 m 3/min (0.020 cfm), whichever is less, is unacceptable. Following the leak check, reconnect the probe to the sampling train.
8.1.4 Sampling Train Operation. During the sampling run, maintain a sampling rate within 10 percent of constant rate, or as specified by the Administrator. For each run, record the data required on a data sheet similar to that shown in Figure 4-3. Be sure to record the dry gas meter reading at the beginning and end of each sampling time increment and whenever sampling is halted. Take other appropriate readings at each sample point at least once during each time increment.
Note:When Method 4 is used concurrently with an isokinetic method (e.g., Method 5) the sampling rate should be maintained at isokinetic conditions rather than 10 percent of constant rate.
8.1.4.1 To begin sampling, position the probe tip at the first traverse point. Immediately start the pump, and adjust the flow to the desired rate. Traverse the cross section, sampling at each traverse point for an equal length of time. Add more ice and, if necessary, salt to maintain a temperature of less than 20 °C (68 °F) at the silica gel outlet.
8.1.4.2 At the end of the sample run, close the coarse adjust valve, remove the probe and nozzle from the stack, turn off the pump, record the final DGM meter reading, and conduct a post-test leak check, as outlined in section 8.1.3.4.
8.2 Approximation Method.
Note:The approximation method described below is presented only as a suggested method (see section 2.0).
8.2.1 Place exactly 5 ml water in each impinger. Leak check the sampling train as follows: Temporarily insert a vacuum gauge at or near the probe inlet. Then, plug the probe inlet and pull a vacuum of at least 250 mm (10 in.) Hg. Note the time rate of change of the dry gas meter dial; alternatively, a rotameter (0 to 40 ml/min) may be temporarily attached to the dry gas meter outlet to determine the leakage rate. A leak rate not in excess of 2 percent of the average sampling rate is acceptable.
Note:Release the probe inlet plug slowly before turning off the pump.
8.2.2 Connect the probe, insert it into the stack, and sample at a constant rate of 2 liters/min (0.071 cfm). Continue sampling until the dry gas meter registers about 30 liters (1.1 ft 3) or until visible liquid droplets are carried over from the first impinger to the second. Record temperature, pressure, and dry gas meter readings as indicated by Figure 4-4.
9.0 Quality Control9.1 Miscellaneous Quality Control Measures.
Section | Quality control measure | Effect |
---|---|---|
Section 8.1.3.2.2 | Leak rate of the sampling system cannot exceed four percent of the average sampling rate or 0.00057 m 3/min (0.020 cfm) | Ensures the accuracy of the volume of gas sampled. (Reference Method). |
Section 8.2.1 | Leak rate of the sampling system cannot exceed two percent of the average sampling rate | Ensures the accuracy of the volume of gas sampled. (Approximation Method). |
9.2 Volume Metering System Checks. Same as Method 5, section 9.2.
10.0 Calibration and Standardization Note:Maintain a laboratory log of all calibrations.
10.1 Reference Method. Calibrate the metering system, temperature sensors, and barometer according to Method 5, sections 10.3, 10.5, and 10.6, respectively.
10.2 Approximation Method. Calibrate the metering system and the barometer according to Method 6, section 10.1 and Method 5, section 10.6, respectively.
10.3 Field Balance Calibration Check. Check the calibration of the balance used to weigh impingers with a weight that is at least 500g or within 50g of a loaded impinger. The weight must be ASTM E617-13 “Standard Specification for Laboratory Weights and Precision Mass Standards” (incorporated by reference-see 40 CFR 60.17) Class 6 (or better). Daily, before use, the field balance must measure the weight within ± 0.5g of the certified mass. If the daily balance calibration check fails, perform corrective measures and repeat the check before using balance.
11.0 Analytical Procedure11.1 Reference Method. Weigh the impingers after sampling and record the difference in weight to the nearest 0.5 g at a minimum. Determine the increase in weight of the silica gel (or silica gel plus impinger) to the nearest 0.5 g at a minimum. Record this information (see example data sheet, Figure 4-5), and calculate the moisture content, as described in section 12.0.
11.2 Approximation Method. Weigh the contents of the two impingers, and measure the weight to the nearest 0.5 g.
12.0 Data Analysis and CalculationsCarry out the following calculations, retaining at least one extra significant figure beyond that of the acquired data. Round off figures after final calculation.
12.1 Reference Method.
12.1.1 Nomenclature.
Bws = Proportion of water vapor, by volume, in the gas stream.
Mw = Molecular weight of water, 18.015 g/g-mole (18.015 lb/lb-mole).
Pm = Absolute pressure (for this method, same as barometric pressure) at the dry gas meter, mm Hg (in. Hg).
Pstd = Standard absolute pressure, 760 mm Hg (29.92 in. Hg).
R = Ideal gas constant, 0.06236 (mm Hg)(m 3)/(g-mole)(°K) for metric units and 21.85 (in. Hg)(ft 3)/(lb-mole) (°R) for English units.
Tm = Absolute temperature at meter, °K (°R).
Tstd = Standard absolute temperature, 293.15 °K (527.67 °R).
Vf = Final weight of condenser water plus impinger, g.
Vi = Initial weight, if any, of condenser water plus impinger, g.
Vm = Dry gas volume measured by dry gas meter, dcm (dcf).
Vm(std) = Dry gas volume measured by the dry gas meter, corrected to standard conditions, dscm (dscf).
Vwc(std) = Volume of water vapor condensed, corrected to standard conditions, scm (scf).
Vwsg(std) = Volume of water vapor collected in silica gel, corrected to standard conditions, scm (scf).
Wf = Final weight of silica gel or silica gel plus impinger, g.
Wi = Initial weight of silica gel or silica gel plus impinger, g.
Y = Dry gas meter calibration factor.
ΔVm = Incremental dry gas volume measured by dry gas meter at each traverse point, dcm (dcf).
12.1.2 Volume of Water Vapor Condensed.

12.1.3
K3 = 0.001335 m 3/g for metric units, = 0.04716 ft 3/g for English units.12.1.4 Sample Gas Volume.
Where: K4 = 0.3855 °K/mm Hg for metric units, = 17.64 °R/in. Hg for English units. Note:If the post-test leak rate (Section 8.1.4.2) exceeds the allowable rate, correct the value of Vm in Equation 4-3, as described in section 12.3 of Method 5.
12.1.5 Moisture Content.
12.1.6 Verification of Constant Sampling Rate. For each time increment, determine the ΔVm. Calculate the average. If the value for any time increment differs from the average by more than 10 percent, reject the results, and repeat the run.
12.1.7 In saturated or moisture droplet-laden gas streams, two calculations of the moisture content of the stack gas shall be made, one using a value based upon the saturated conditions (see section 4.1), and another based upon the results of the impinger analysis. The lower of these two values of Bws shall be considered correct.
12.2 Approximation Method. The approximation method presented is designed to estimate the moisture in the stack gas; therefore, other data, which are only necessary for accurate moisture determinations, are not collected. The following equations adequately estimate the moisture content for the purpose of determining isokinetic sampling rate settings.
12.2.1 Nomenclature.
Bwm = Approximate proportion by volume of water vapor in the gas stream leaving the second impinger, 0.025.
Bws = Water vapor in the gas stream, proportion by volume.
Mw = Molecular weight of water, 18.015 g/g-mole (18.015 lb/lb-mole).
Pm = Absolute pressure (for this method, same as barometric pressure) at the dry gas meter, mm Hg (in. Hg).
Pstd = Standard absolute pressure, 760 mm Hg (29.92 in. Hg).
R = Ideal gas constant, 0.06236 [(mm Hg)(m 3)]/[(g-mole)(K)] for metric units and 21.85 [(in. Hg)(ft 3)]/[(lb-mole)(°R)] for English units.
Tm = Absolute temperature at meter, °K (°R).
Tstd = Standard absolute temperature, 293.15 °K (527.67 °R).
Vf = Final weight of condenser water plus impinger, g.
Vi = Initial weight, if any, of condenser water plus impinger, g.
Vm = Dry gas volume measured by dry gas meter, dcm (dcf).
Vm(std) = Dry gas volume measured by dry gas meter, corrected to standard conditions, dscm (dscf).
Vwc(std) = Volume of water vapor condensed, corrected to standard conditions, scm (scf).
Y = Dry gas meter calibration factor.
12.2.2 Volume of Water Vapor Collected.

K5 = 0.001335 m 3/g for metric units,
= 0.04716 ft 3/g for English units.
12.2.3 Sample Gas Volume.
Where: K6 = 0.3855 °K/mm Hg for metric units, = 17.64 °R/in. Hg for English units.12.2.4 Approximate Moisture Content.
12.2.5 Using F-factors to determine approximate moisture for estimating moisture content where no wet scrubber is being used, for the purpose of determining isokinetic sampling rate settings with no fuel sample, is acceptable using the average Fc or Fd factor from Method 19 (see Method 19, section 12.3.1). If this option is selected, calculate the approximate moisture as follows:
Bws = BH + BA+ BF Where: BA = Mole Fraction of moisture in the ambient air.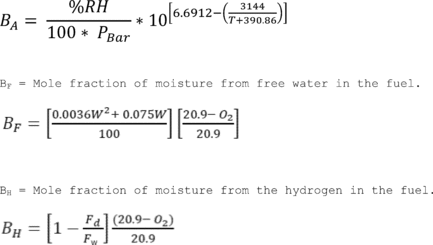
Btu (scm/J). See Table 19-2 in Method 19.
Fw = Volume of wet combustion components per unit of heat content at 0 percent oxygen, wet.scf/10 6 Btu (scm/J). See Table 19-2 in Method 19.
%RH = Percent relative humidity (calibrated hygrometer acceptable), percent. PBar = Barometric pressure, in. Hg. T = Ambient temperature, °F. W = Percent free water by weight, percent. O2 = Percent oxygen in stack gas, dry basis, percent. 13.0 Method Performance [Reserved] 14.0 Pollution Prevention [Reserved] 15.0 Waste Management [Reserved] 16.0 Alternative Procedures16.1 The procedure described in Method 5 for determining moisture content is an acceptable alternative to Method 4.
16.2 The procedures in Method 6A for determining moisture is an acceptable alternative to Method 4.
16.3 Method 320 is an acceptable alternative to Method 4 for determining moisture.
16.4 Using F-factors to determine moisture is an acceptable alternative to Method 4 for a combustion stack not using a scrubber, and where a fuel sample is taken during the test run and analyzed for development of an Fd factor (see Method 19, section 12.3.2), and where stack O2 content is measured by Method 3A or 3B during each test run. If this option is selected, calculate the moisture content as follows:
Bws = BH + BA + BF Where: BA = Mole fraction of moisture in the ambient air.
Values of BA should be between 0.00 and 0.06 with common values being about 0.015.
BF = Mole fraction of moisture from free water in the fuel.
Free water in fuel is minimal for distillate oil and gases, such as propane and natural gas, so this step may be omitted for those fuels.
BH = Mole fraction of moisture from the hydrogen in the fuel.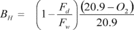
1. Air Pollution Engineering Manual (Second Edition). Danielson, J.A. (ed.). U.S. Environmental Protection Agency, Office of Air Quality Planning and Standards. Research Triangle Park, NC. Publication No. AP-40. 1973.
2. Devorkin, Howard, et al. Air Pollution Source Testing Manual. Air Pollution Control District, Los Angeles, CA. November 1963.
3. Methods for Determination of Velocity, Volume, Dust and Mist Content of Gases. Western Precipitation Division of Joy Manufacturing Co. Los Angeles, CA. Bulletin WP-50. 1968.
18.0 Tables, Diagrams, Flowcharts, and Validation Data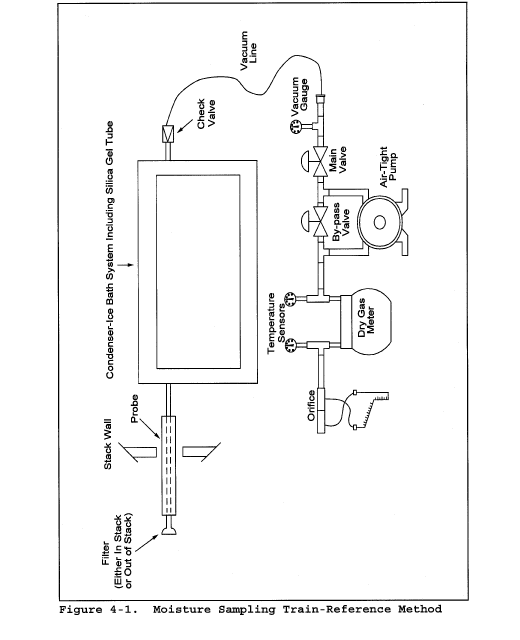
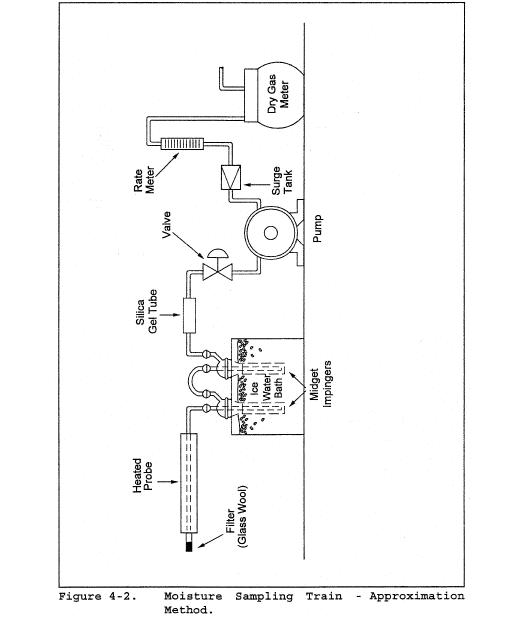
Schematic of Stack Cross section
Traverse Pt. No. | Sampling time (Δ), min |
Stack temperature °C ( °F) |
Pressure differential across orifice meter ΔH mm (in.) H2O |
Meter reading gas sample volume m 3 (ft 3) |
ΔVm m 3 (ft 3) | Gas sample temperature at dry gas meter |
Temperature of gas leaving condenser or last impinger °C ( °F) |
|
---|---|---|---|---|---|---|---|---|
Inlet Tmin °C ( °F) |
Outlet Tmout °C ( °F) |
|||||||
Average |


This method does not include all of the specifications (e.g., equipment and supplies) and procedures (e.g., sampling and analytical) essential to its performance. Some material is incorporated by reference from other methods in this part. Therefore, to obtain reliable results, persons using this method should have a thorough knowledge of at least the following additional test methods: Method 1, Method 2, Method 3.
1.0 Scope and Application1.1 Analyte. Particulate matter (PM). No CAS number assigned.
1.2 Applicability. This method is applicable for the determination of PM emissions from stationary sources.
1.3 Data Quality Objectives. Adherence to the requirements of this method will enhance the quality of the data obtained from air pollutant sampling methods.
2.0 Summary of MethodParticulate matter is withdrawn isokinetically from the source and collected on a glass fiber filter maintained at a temperature of 120 ±14 °C (248 ±25 °F) or such other temperature as specified by an applicable subpart of the standards or approved by the Administrator for a particular application. The PM mass, which includes any material that condenses at or above the filtration temperature, is determined gravimetrically after the removal of uncombined water.
3.0 Definitions [Reserved] 4.0 Interferences [Reserved] 5.0 Safety5.1 Disclaimer. This method may involve hazardous materials, operations, and equipment. This test method may not address all of the safety problems associated with its use. It is the responsibility of the user of this test method to establish appropriate safety and health practices and to determine the applicability of regulatory limitations prior to performing this test method.
6.0 Equipment and Supplies6.1 Sample Collection. The following items are required for sample collection:
6.1.1 Sampling Train. A schematic of the sampling train used in this method is shown in Figure 5-1 in section 18.0. Complete construction details are given in APTD-0581 (Reference 2 in section 17.0); commercial models of this train are also available. For changes from APTD-0581 and for allowable modifications of the train shown in Figure 5-1, see the following subsections.
Note:The operating and maintenance procedures for the sampling train are described in APTD-0576 (Reference 3 in section 17.0). Since correct usage is important in obtaining valid results, all users should read APTD-0576 and adopt the operating and maintenance procedures outlined in it, unless otherwise specified herein.
6.1.1.1 Probe Nozzle. Stainless steel (316) or glass with a sharp, tapered leading edge. The angle of taper shall be ≤30°, and the taper shall be on the outside to preserve a constant internal diameter. The probe nozzle shall be of the button-hook or elbow design, unless otherwise specified by the Administrator. If made of stainless steel, the nozzle shall be constructed from seamless tubing. Other materials of construction may be used, subject to the approval of the Administrator. A range of nozzle sizes suitable for isokinetic sampling should be available. Typical nozzle sizes range from 0.32 to 1.27 cm ( 1/8 to 1/2 in) inside diameter (ID) in increments of 0.16 cm ( 1/16 in). Larger nozzles sizes are also available if higher volume sampling trains are used. Each nozzle shall be calibrated, according to the procedures outlined in section 10.1.
6.1.1.2 Probe Liner. Borosilicate or quartz glass tubing with a heating system capable of maintaining a probe gas temperature during sampling of 120 ±14 °C (248 ±25 °F), or such other temperature as specified by an applicable subpart of the standards or as approved by the Administrator for a particular application. Since the actual temperature at the outlet of the probe is not usually monitored during sampling, probes constructed according to APTD-0581 and utilizing the calibration curves of APTD-0576 (or calibrated according to the procedure outlined in APTD-0576) will be considered acceptable. Either borosilicate or quartz glass probe liners may be used for stack temperatures up to about 480 °C (900 °F); quartz glass liners shall be used for temperatures between 480 and 900 °C (900 and 1,650 °F). Both types of liners may be used at higher temperatures than specified for short periods of time, subject to the approval of the Administrator. The softening temperature for borosilicate glass is 820 °C (1500 °F), and for quartz glass it is 1500 °C (2700 °F). Whenever practical, every effort should be made to use borosilicate or quartz glass probe liners. Alternatively, metal liners (e.g., 316 stainless steel, Incoloy 825 or other corrosion resistant metals) made of seamless tubing may be used, subject to the approval of the Administrator.
6.1.1.3 Pitot Tube. Type S, as described in section 6.1 of Method 2, or other device approved by the Administrator. The pitot tube shall be attached to the probe (as shown in Figure 5-1) to allow constant monitoring of the stack gas velocity. The impact (high pressure) opening plane of the pitot tube shall be even with or above the nozzle entry plane (see Method 2, Figure 2-7) during sampling. The Type S pitot tube assembly shall have a known coefficient, determined as outlined in section 10.0 of Method 2.
6.1.1.4 Differential Pressure Gauge. Inclined manometer or equivalent device (two), as described in section 6.2 of Method 2. One manometer shall be used for velocity head (Δp) readings, and the other, for orifice differential pressure readings.
6.1.1.5 Filter Holder. Borosilicate glass, with a glass or Teflon frit filter support and a silicone rubber gasket. Other materials of construction (e.g., stainless steel or Viton) may be used, subject to the approval of the Administrator. The holder design shall provide a positive seal against leakage from the outside or around the filter. The holder shall be attached immediately at the outlet of the probe (or cyclone, if used).
6.1.1.6 Filter Heating System. Any heating system capable of monitoring and maintaining temperature around the filter shall be used to ensure the sample gas temperature exiting the filter of 120 ±14 °C (248 ±25 °F) during sampling or such other temperature as specified by an applicable subpart of the standards or approved by the Administrator for a particular application. The monitoring and regulation of the temperature around the filter may be done with the filter temperature sensor or another temperature sensor.
6.1.1.7 Filter Temperature Sensor. A temperature sensor capable of measuring temperature to within ±3 °C (5.4 °F) shall be installed so that the sensing tip of the temperature sensor is in direct contact with the sample gas exiting the filter. The sensing tip of the sensor may be encased in glass, Teflon, or metal and must protrude at least 1/2 in. into the sample gas exiting the filter. The filter temperature sensor must be monitored and recorded during sampling to ensure a sample gas temperature exiting the filter of 120 ±14 °C (248 ±25 °F), or such other temperature as specified by an applicable subpart of the standards or approved by the Administrator for a particular application.
6.1.1.8 Condenser. The following system shall be used to determine the stack gas moisture content: Four impingers connected in series with leak-free ground glass fittings or any similar leak-free noncontaminating fittings. The first, third, and fourth impingers shall be of the Greenburg-Smith design, modified by replacing the tip with a 1.3 cm ( 1/2 in.) ID glass tube extending to about 1.3 cm ( 1/2 in.) from the bottom of the flask. The second impinger shall be of the Greenburg-Smith design with the standard tip. Modifications (e.g., using flexible connections between the impingers, using materials other than glass, or using flexible vacuum lines to connect the filter holder to the condenser) may be used, subject to the approval of the Administrator. The first and second impingers shall contain known quantities of water (Section 8.3.1), the third shall be empty, and the fourth shall contain a known weight of silica gel, or equivalent desiccant. A temperature sensor, capable of measuring temperature to within 1 °C (2 °F) shall be placed at the outlet of the fourth impinger for monitoring purposes. Alternatively, any system that cools the sample gas stream and allows measurement of the water condensed and moisture leaving the condenser, each to within 0.5 g may be used, subject to the approval of the Administrator. An acceptable technique involves the measurement of condensed water either gravimetrically and the determination of the moisture leaving the condenser by: (1) Monitoring the temperature and pressure at the exit of the condenser and using Dalton's law of partial pressures; or (2) passing the sample gas stream through a tared silica gel (or equivalent desiccant) trap with exit gases kept below 20 °C (68 °F) and determining the weight gain. If means other than silica gel are used to determine the amount of moisture leaving the condenser, it is recommended that silica gel (or equivalent) still be used between the condenser system and pump to prevent moisture condensation in the pump and metering devices and to avoid the need to make corrections for moisture in the metered volume.
Note:If a determination of the PM collected in the impingers is desired in addition to moisture content, the impinger system described above shall be used, without modification. Individual States or control agencies requiring this information shall be contacted as to the sample recovery and analysis of the impinger contents.
6.1.1.9 Metering System. Vacuum gauge, leak-free pump, calibrated temperature sensors, dry gas meter (DGM) capable of measuring volume to within 2 percent, and related equipment, as shown in Figure 5-1. Other metering systems capable of maintaining sampling rates within 10 percent of isokinetic and of determining sample volumes to within 2 percent may be used, subject to the approval of the Administrator. When the metering system is used in conjunction with a pitot tube, the system shall allow periodic checks of isokinetic rates. The average DGM temperature for use in the calculations of section 12.0 may be obtained by averaging the two temperature sensors located at the inlet and outlet of the DGM as shown in Figure 5-3 or alternatively from a single temperature sensor located at the immediate outlet of the DGM or the plenum of the DGM.
6.1.1.10 Sampling trains utilizing metering systems designed for higher flow rates than that described in APTD-0581 or APTD-0576 may be used provided that the specifications of this method are met.
6.1.2 Barometer. Mercury, aneroid, or other barometer capable of measuring atmospheric pressure to within 2.5 mm Hg (0.1 in.).
Note:The barometric pressure reading may be obtained from a nearby National Weather Service station. In this case, the station value (which is the absolute barometric pressure) shall be requested and an adjustment for elevation differences between the weather station and sampling point shall be made at a rate of minus 2.5 mm Hg (0.1 in.) per 30 m (100 ft) elevation increase or plus 2.5 mm Hg (0.1 in) per 30 m (100 ft) elevation decrease.
6.1.3 Gas Density Determination Equipment. Temperature sensor and pressure gauge, as described in sections 6.3 and 6.4 of Method 2, and gas analyzer, if necessary, as described in Method 3. The temperature sensor shall, preferably, be permanently attached to the pitot tube or sampling probe in a fixed configuration, such that the tip of the sensor extends beyond the leading edge of the probe sheath and does not touch any metal. Alternatively, the sensor may be attached just prior to use in the field. Note, however, that if the temperature sensor is attached in the field, the sensor must be placed in an interference-free arrangement with respect to the Type S pitot tube openings (see Method 2, Figure 2-4). As a second alternative, if a difference of not more than 1 percent in the average velocity measurement is to be introduced, the temperature sensor need not be attached to the probe or pitot tube. (This alternative is subject to the approval of the Administrator.)
6.2 Sample Recovery. The following items are required for sample recovery:
6.2.1 Probe-Liner and Probe-Nozzle Brushes. Nylon bristle brushes with stainless steel wire handles. The probe brush shall have extensions (at least as long as the probe) constructed of stainless steel, Nylon, Teflon, or similarly inert material. The brushes shall be properly sized and shaped to brush out the probe liner and nozzle.
6.2.2 Wash Bottles. Two Glass wash bottles are recommended. Alternatively, polyethylene wash bottles may be used. It is recommended that acetone not be stored in polyethylene bottles for longer than a month.
6.2.3 Glass Sample Storage Containers. Chemically resistant, borosilicate glass bottles, for acetone washes, 500 ml or 1000 ml. Screw cap liners shall either be rubber-backed Teflon or shall be constructed so as to be leak-free and resistant to chemical attack by acetone. (Narrow mouth glass bottles have been found to be less prone to leakage.) Alternatively, polyethylene bottles may be used.
6.2.4 Petri dishes. For filter samples; glass, polystyrene, or polyethylene, unless otherwise specified by the Administrator.
6.2.5 Balance. To measure condensed water to within 0.5 g at a minimum.
6.2.6 Plastic Storage Containers. Air-tight containers to store silica gel.
6.2.7 Funnel and Rubber Policeman. To aid in transfer of silica gel to container; not necessary if silica gel is weighed in the field.
6.2.8 Funnel. Glass or polyethylene, to aid in sample recovery.
6.3 Sample Analysis. The following equipment is required for sample analysis:
6.3.1 Glass Weighing Dishes.
6.3.2 Desiccator.
6.3.3 Analytical Balance. To measure to within 0.1 mg.
6.3.4 Balance. To measure to within 0.5 g.
6.3.5 Beakers. 250 ml.
6.3.6 Hygrometer. To measure the relative humidity of the laboratory environment.
6.3.7 Temperature Sensor. To measure the temperature of the laboratory environment.
7.0 Reagents and Standards7.1 Sample Collection. The following reagents are required for sample collection:
7.1.1 Filters. Glass fiber filters, without organic binder, exhibiting at least 99.95 percent efficiency (<0.05 percent penetration) on 0.3 micron dioctyl phthalate smoke particles. The filter efficiency test shall be conducted in accordance with ASTM Method D 2986-71, 78, or 95a (incorporated by reference - see § 60.17). Test data from the supplier's quality control program are sufficient for this purpose. In sources containing SO2 or SO3, the filter material must be of a type that is unreactive to SO2 or SO3. Reference 10 in section 17.0 may be used to select the appropriate filter.
7.1.2 Silica Gel. Indicating type, 6 to 16 mesh. If previously used, dry at 175 °C (350 °F) for 2 hours. New silica gel may be used as received. Alternatively, other types of desiccants (equivalent or better) may be used, subject to the approval of the Administrator.
7.1.3 Water. When analysis of the material caught in the impingers is required, deionized distilled water [to conform to ASTM D1193-77 or 91 Type 3 (incorporated by reference - see § 60.17)] with at least <0.001 percent residue shall be used or as specified in the applicable method requiring analysis of the water. Run reagent blanks prior to field use to eliminate a high blank on test samples.
7.1.4 Crushed Ice.
7.2 Sample Recovery. Acetone, reagent grade, ≤0.001 percent residue, in glass bottles, is required. Acetone from metal containers generally has a high residue blank and should not be used. Sometimes, suppliers transfer acetone to glass bottles from metal containers; thus, acetone blanks shall be run prior to field use and only acetone with low blank values (≤0.001 percent) shall be used. In no case shall a blank value of greater than 0.001 percent of the weight of acetone used be subtracted from the sample weight.
7.3 Sample Analysis. The following reagents are required for sample analysis:
7.3.1 Acetone. Same as in section 7.2.
7.3.2 Desiccant. Anhydrous calcium sulfate, indicating type. Alternatively, other types of desiccants may be used, subject to the approval of the Administrator.
8.0 Sample Collection, Preservation, Storage, and Transport8.1 Pretest Preparation. It is suggested that sampling equipment be maintained according to the procedures described in APTD-0576. Alternative mercury-free thermometers may be used if the thermometers are at a minimum equivalent in terms of performance or suitably effective for the specific temperature measurement application.
8.1.1 Place 200 to 300 g of silica gel in each of several air-tight containers. Weigh each container, including silica gel, to the nearest 0.5 g, and record this weight. As an alternative, the silica gel need not be preweighed, but may be weighed directly in its impinger or sampling holder just prior to train assembly.
8.1.2 Check filters visually against light for irregularities, flaws, or pinhole leaks. Label filters of the proper diameter on the back side near the edge using numbering machine ink. As an alternative, label the shipping containers (glass, polystyrene or polyethylene petri dishes), and keep each filter in its identified container at all times except during sampling.
8.1.3 Desiccate the filters at 20 ±5.6 °C (68 ±10 °F) and ambient pressure for at least 24 hours. Weigh each filter (or filter and shipping container) at intervals of at least 6 hours to a constant weight (i.e., ≤0.5 mg change from previous weighing). Record results to the nearest 0.1 mg. During each weighing, the period for which the filter is exposed to the laboratory atmosphere shall be less than 2 minutes. Alternatively (unless otherwise specified by the Administrator), the filters may be oven dried at 105 °C (220 °F) for 2 to 3 hours, desiccated for 2 hours, and weighed. Procedures other than those described, which account for relative humidity effects, may be used, subject to the approval of the Administrator.
8.2 Preliminary Determinations.
8.2.1 Select the sampling site and the minimum number of sampling points according to Method 1 or as specified by the Administrator. Determine the stack pressure, temperature, and the range of velocity heads using Method 2; it is recommended that a leak check of the pitot lines (see Method 2, section 8.1) be performed. Determine the moisture content using Approximation Method 4 or its alternatives for the purpose of making isokinetic sampling rate settings. Determine the stack gas dry molecular weight, as described in Method 2, section 8.6; if integrated Method 3 sampling is used for molecular weight determination, the integrated bag sample shall be taken simultaneously with, and for the same total length of time as, the particulate sample run.
8.2.2 Select a nozzle size based on the range of velocity heads, such that it is not necessary to change the nozzle size in order to maintain isokinetic sampling rates. During the run, do not change the nozzle size. Ensure that the proper differential pressure gauge is chosen for the range of velocity heads encountered (see section 8.3 of Method 2).
8.2.3 Select a suitable probe liner and probe length such that all traverse points can be sampled. For large stacks, consider sampling from opposite sides of the stack to reduce the required probe length.
8.2.4 Select a total sampling time greater than or equal to the minimum total sampling time specified in the test procedures for the specific industry such that (l) the sampling time per point is not less than 2 minutes (or some greater time interval as specified by the Administrator), and (2) the sample volume taken (corrected to standard conditions) will exceed the required minimum total gas sample volume. The latter is based on an approximate average sampling rate.
8.2.5 The sampling time at each point shall be the same. It is recommended that the number of minutes sampled at each point be an integer or an integer plus one-half minute, in order to avoid timekeeping errors.
8.2.6 In some circumstances (e.g., batch cycles) it may be necessary to sample for shorter times at the traverse points and to obtain smaller gas sample volumes. In these cases, the Administrator's approval must first be obtained.
8.3 Preparation of Sampling Train.
8.3.1 During preparation and assembly of the sampling train, keep all openings where contamination can occur covered until just prior to assembly or until sampling is about to begin. Place 100 ml of water in each of the first two impingers, leave the third impinger empty, and transfer approximately 200 to 300 g of preweighed silica gel from its container to the fourth impinger. More silica gel may be used, but care should be taken to ensure that it is not entrained and carried out from the impinger during sampling. Place the container in a clean place for later use in the sample recovery. Alternatively, the weight of the silica gel plus impinger may be determined to the nearest 0.5 g and recorded.
8.3.2 Using a tweezer or clean disposable surgical gloves, place a labeled (identified) and weighed filter in the filter holder. Be sure that the filter is properly centered and the gasket properly placed so as to prevent the sample gas stream from circumventing the filter. Check the filter for tears after assembly is completed.
8.3.3 When glass probe liners are used, install the selected nozzle using a Viton A O-ring when stack temperatures are less than 260 °C (500 °F) or a heat-resistant string gasket when temperatures are higher. See APTD-0576 for details. Other connecting systems using either 316 stainless steel or Teflon ferrules may be used. When metal liners are used, install the nozzle as discussed above or by a leak-free direct mechanical connection. Mark the probe with heat resistant tape or by some other method to denote the proper distance into the stack or duct for each sampling point.
8.3.4 Set up the train as shown in Figure 5-1 ensuring that the connections are leak-tight. Subject to the approval of the Administrator, a glass cyclone may be used between the probe and filter holder when the total particulate catch is expected to exceed 100 mg or when water droplets are present in the stack gas.
8.3.5 Place crushed ice around the impingers.
8.4 Leak-Check Procedures.
8.4.1 Leak Check of Metering System Shown in Figure 5-1. That portion of the sampling train from the pump to the orifice meter should be leak-checked prior to initial use and after each shipment. Leakage after the pump will result in less volume being recorded than is actually sampled. The following procedure is suggested (see Figure 5-2): Close the main valve on the meter box. Insert a one-hole rubber stopper with rubber tubing attached into the orifice exhaust pipe. Disconnect and vent the low side of the orifice manometer. Close off the low side orifice tap. Pressurize the system to 13 to 18 cm (5 to 7 in.) water column by blowing into the rubber tubing. Pinch off the tubing, and observe the manometer for one minute. A loss of pressure on the manometer indicates a leak in the meter box; leaks, if present, must be corrected.
8.4.2 Pretest Leak Check. A pretest leak check of the sampling train is recommended, but not required. If the pretest leak check is conducted, the following procedure should be used.
8.4.2.1 After the sampling train has been assembled, turn on and set the filter and probe heating systems to the desired operating temperatures. Allow time for the temperatures to stabilize. If a Viton A O-ring or other leak-free connection is used in assembling the probe nozzle to the probe liner, leak-check the train at the sampling site by plugging the nozzle and pulling a 380 mm (15 in.) Hg vacuum.
Note:A lower vacuum may be used, provided that it is not exceeded during the test.
8.4.2.2 If a heat-resistant string is used, do not connect the probe to the train during the leak check. Instead, leak-check the train by first plugging the inlet to the filter holder (cyclone, if applicable) and pulling a 380 mm (15 in.) Hg vacuum (see note in section 8.4.2.1). Then connect the probe to the train, and leak-check at approximately 25 mm (1 in.) Hg vacuum; alternatively, the probe may be leak-checked with the rest of the sampling train, in one step, at 380 mm (15 in.) Hg vacuum. Leakage rates in excess of 4 percent of the average sampling rate or 0.00057 m 3/min (0.020 cfm), whichever is less, are unacceptable.
8.4.2.3 The following leak-check instructions for the sampling train described in APTD-0576 and APTD-0581 may be helpful. Start the pump with the bypass valve fully open and the coarse adjust valve completely closed. Partially open the coarse adjust valve, and slowly close the bypass valve until the desired vacuum is reached. Do not reverse the direction of the bypass valve, as this will cause water to back up into the filter holder. If the desired vacuum is exceeded, either leak-check at this higher vacuum, or end the leak check and start over.
8.4.2.4 When the leak check is completed, first slowly remove the plug from the inlet to the probe, filter holder, or cyclone (if applicable), and immediately turn off the vacuum pump. This prevents the water in the impingers from being forced backward into the filter holder and the silica gel from being entrained backward into the third impinger.
8.4.3 Leak Checks During Sample Run. If, during the sampling run, a component (e.g., filter assembly or impinger) change becomes necessary, a leak check shall be conducted immediately before the change is made. The leak check shall be done according to the procedure outlined in section 8.4.2 above, except that it shall be done at a vacuum equal to or greater than the maximum value recorded up to that point in the test. If the leakage rate is found to be no greater than 0.00057 m 3/min (0.020 cfm) or 4 percent of the average sampling rate (whichever is less), the results are acceptable, and no correction will need to be applied to the total volume of dry gas metered; if, however, a higher leakage rate is obtained, either record the leakage rate and plan to correct the sample volume as shown in section 12.3 of this method, or void the sample run.
Note:Immediately after component changes, leak checks are optional. If such leak checks are done, the procedure outlined in section 8.4.2 above should be used.
8.4.4 Post-Test Leak Check. A leak check of the sampling train is mandatory at the conclusion of each sampling run. The leak check shall be performed in accordance with the procedures outlined in section 8.4.2, except that it shall be conducted at a vacuum equal to or greater than the maximum value reached during the sampling run. If the leakage rate is found to be no greater than 0.00057 m 3 min (0.020 cfm) or 4 percent of the average sampling rate (whichever is less), the results are acceptable, and no correction need be applied to the total volume of dry gas metered. If, however, a higher leakage rate is obtained, either record the leakage rate and correct the sample volume as shown in section 12.3 of this method, or void the sampling run.
8.5 Sampling Train Operation. During the sampling run, maintain an isokinetic sampling rate (within 10 percent of true isokinetic unless otherwise specified by the Administrator) and a sample gas temperature through the filter of 120 ±14 °C (248 ±25 °F) or such other temperature as specified by an applicable subpart of the standards or approved by the Administrator.
8.5.1 For each run, record the data required on a data sheet such as the one shown in Figure 5-3. Be sure to record the initial DGM reading. Record the DGM readings at the beginning and end of each sampling time increment, when changes in flow rates are made, before and after each leak check, and when sampling is halted. Take other readings indicated by Figure 5-3 at least once at each sample point during each time increment and additional readings when significant changes (20 percent variation in velocity head readings) necessitate additional adjustments in flow rate. Level and zero the manometer. Because the manometer level and zero may drift due to vibrations and temperature changes, make periodic checks during the traverse.
8.5.2 Clean the portholes prior to the test run to minimize the chance of collecting deposited material. To begin sampling, verify that the filter and probe heating systems are up to temperature, remove the nozzle cap, verify that the pitot tube and probe are properly positioned. Position the nozzle at the first traverse point with the tip pointing directly into the gas stream. Immediately start the pump, and adjust the flow to isokinetic conditions. Nomographs are available which aid in the rapid adjustment of the isokinetic sampling rate without excessive computations. These nomographs are designed for use when the Type S pitot tube coefficient (Cp) is 0.85 ±0.02, and the stack gas equivalent density [dry molecular weight (Md)] is equal to 29 ±4. APTD-0576 details the procedure for using the nomographs. If Cp and Md are outside the above stated ranges, do not use the nomographs unless appropriate steps (see Reference 7 in section 17.0) are taken to compensate for the deviations.
8.5.3 When the stack is under significant negative pressure (i.e., height of impinger stem), take care to close the coarse adjust valve before inserting the probe into the stack to prevent water from backing into the filter holder. If necessary, the pump may be turned on with the coarse adjust valve closed.
8.5.4 When the probe is in position, block off the openings around the probe and porthole to prevent unrepresentative dilution of the gas stream.
8.5.5 Traverse the stack cross-section, as required by Method 1 or as specified by the Administrator, being careful not to bump the probe nozzle into the stack walls when sampling near the walls or when removing or inserting the probe through the portholes; this minimizes the chance of extracting deposited material.
8.5.6 During the test run, make periodic adjustments to keep the temperature around the filter holder at the proper level to maintain the sample gas temperature exiting the filter; add more ice and, if necessary, salt to maintain a temperature of less than 20 °C (68 °F) at the condenser/silica gel outlet. Also, periodically check the level and zero of the manometer.
8.5.7 If the pressure drop across the filter becomes too high, making isokinetic sampling difficult to maintain, the filter may be replaced in the midst of the sample run. It is recommended that another complete filter assembly be used rather than attempting to change the filter itself. Before a new filter assembly is installed, conduct a leak check (see section 8.4.3). The total PM weight shall include the summation of the filter assembly catches.
8.5.8 A single train shall be used for the entire sample run, except in cases where simultaneous sampling is required in two or more separate ducts or at two or more different locations within the same duct, or in cases where equipment failure necessitates a change of trains. In all other situations, the use of two or more trains will be subject to the approval of the Administrator.
Note:When two or more trains are used, separate analyses of the front-half and (if applicable) impinger catches from each train shall be performed, unless identical nozzle sizes were used on all trains, in which case, the front-half catches from the individual trains may be combined (as may the impinger catches) and one analysis of front-half catch and one analysis of impinger catch may be performed. Consult with the Administrator for details concerning the calculation of results when two or more trains are used.
8.5.9 At the end of the sample run, close the coarse adjust valve, remove the probe and nozzle from the stack, turn off the pump, record the final DGM meter reading, and conduct a post-test leak check, as outlined in section 8.4.4. Also, leak-check the pitot lines as described in Method 2, section 8.1. The lines must pass this leak check, in order to validate the velocity head data.
8.6 Calculation of Percent Isokinetic. Calculate percent isokinetic (see Calculations, section 12.11) to determine whether the run was valid or another test run should be made. If there was difficulty in maintaining isokinetic rates because of source conditions, consult with the Administrator for possible variance on the isokinetic rates.
8.7 Sample Recovery.
8.7.1 Proper cleanup procedure begins as soon as the probe is removed from the stack at the end of the sampling period. Allow the probe to cool.
8.7.2 When the probe can be safely handled, wipe off all external PM near the tip of the probe nozzle, and place a cap over it to prevent losing or gaining PM. Do not cap off the probe tip tightly while the sampling train is cooling down. This would create a vacuum in the filter holder, thereby drawing water from the impingers into the filter holder.
8.7.3 Before moving the sample train to the cleanup site, remove the probe from the sample train and cap the open outlet of the probe. Be careful not to lose any condensate that might be present. Cap the filter inlet where the probe was fastened. Remove the umbilical cord from the last impinger, and cap the impinger. If a flexible line is used between the first impinger or condenser and the filter holder, disconnect the line at the filter holder, and let any condensed water or liquid drain into the impingers or condenser. Cap off the filter holder outlet and impinger inlet. Either ground-glass stoppers, plastic caps, or serum caps may be used to close these openings.
8.7.4 Transfer the probe and filter-impinger assembly to the cleanup area. This area should be clean and protected from the wind so that the chances of contaminating or losing the sample will be minimized.
8.7.5 Save a portion of the acetone used for cleanup as a blank. From each storage container of acetone used for cleanup, save 200 ml and place in a glass sample container labeled “acetone blank.” To minimize any particulate contamination, rinse the wash bottle prior to filling from the tested container.
8.7.6 Inspect the train prior to and during disassembly, and note any abnormal conditions. Treat the samples as follows:
8.7.6.1 Container No. 1. Carefully remove the filter from the filter holder, and place it in its identified petri dish container. Use a pair of tweezers and/or clean disposable surgical gloves to handle the filter. If it is necessary to fold the filter, do so such that the PM cake is inside the fold. Using a dry Nylon bristle brush and/or a sharp-edged blade, carefully transfer to the petri dish any PM and/or filter fibers that adhere to the filter holder gasket. Seal the container.
8.7.6.2 Container No. 2. Taking care to see that dust on the outside of the probe or other exterior surfaces does not get into the sample, quantitatively recover PM or any condensate from the probe nozzle, probe fitting, probe liner, and front half of the filter holder by washing these components with acetone and placing the wash in a glass container. Deionized distilled water may be used instead of acetone when approved by the Administrator and shall be used when specified by the Administrator. In these cases, save a water blank, and follow the Administrator's directions on analysis. Perform the acetone rinse as follows:
8.7.6.2.1 Carefully remove the probe nozzle. Clean the inside surface by rinsing with acetone from a wash bottle and brushing with a Nylon bristle brush. Brush until the acetone rinse shows no visible particles, after which make a final rinse of the inside surface with acetone.
8.7.6.2.2 Brush and rinse the inside parts of the fitting with acetone in a similar way until no visible particles remain.
8.7.6.2.3 Rinse the probe liner with acetone by tilting and rotating the probe while squirting acetone into its upper end so that all inside surfaces will be wetted with acetone. Let the acetone drain from the lower end into the sample container. A funnel (glass or polyethylene) may be used to aid in transferring liquid washes to the container. Follow the acetone rinse with a probe brush. Hold the probe in an inclined position, squirt acetone into the upper end as the probe brush is being pushed with a twisting action through the probe; hold a sample container underneath the lower end of the probe, and catch any acetone and particulate matter that is brushed from the probe. Run the brush through the probe three times or more until no visible PM is carried out with the acetone or until none remains in the probe liner on visual inspection. With stainless steel or other metal probes, run the brush through in the above prescribed manner at least six times since metal probes have small crevices in which particulate matter can be entrapped. Rinse the brush with acetone, and quantitatively collect these washings in the sample container. After the brushing, make a final acetone rinse of the probe.
8.7.6.2.4 It is recommended that two people clean the probe to minimize sample losses. Between sampling runs, keep brushes clean and protected from contamination.
8.7.6.2.5 Clean the inside of the front half of the filter holder by rubbing the surfaces with a Nylon bristle brush and rinsing with acetone. Rinse each surface three times or more if needed to remove visible particulate. Make a final rinse of the brush and filter holder. Carefully rinse out the glass cyclone, also (if applicable). After all acetone washings and particulate matter have been collected in the sample container, tighten the lid on the sample container so that acetone will not leak out when it is shipped to the laboratory. Mark the height of the fluid level to allow determination of whether leakage occurred during transport. Label the container to clearly identify its contents.
8.7.6.3 Container No. 3. Note the color of the indicating silica gel to determine whether it has been completely spent, and make a notation of its condition. Transfer the silica gel from the fourth impinger to its original container, and seal. A funnel may make it easier to pour the silica gel without spilling. A rubber policeman may be used as an aid in removing the silica gel from the impinger. It is not necessary to remove the small amount of dust particles that may adhere to the impinger wall and are difficult to remove. Since the gain in weight is to be used for moisture calculations, do not use any water or other liquids to transfer the silica gel. If a balance is available in the field, follow the procedure for Container No. 3 in section 11.2.3.
8.7.6.4 Impinger Water. Treat the impingers as follows: Make a notation of any color or film in the liquid catch. Measure the liquid that is in the first three impingers by weighing it to within 0.5 g at a minimum by using a balance. Record the weight of liquid present. This information is required to calculate the moisture content of the effluent gas. Discard the liquid after measuring and recording the weight, unless analysis of the impinger catch is required (see Note, section 6.1.1.8). If a different type of condenser is used, measure the amount of moisture condensed gravimetrically.
8.8 Sample Transport. Whenever possible, containers should be shipped in such a way that they remain upright at all times.
9.0 Quality Control9.1 Miscellaneous Quality Control Measures.
Section | Quality control measure | Effect |
---|---|---|
8.4, 10.1-10.6 | Sampling equipment leak check and calibration | Ensures accurate measurement of stack gas flow rate, sample volume. |
9.2 Volume Metering System Checks. The following procedures are suggested to check the volume metering system calibration values at the field test site prior to sample collection. These procedures are optional.
9.2.1 Meter Orifice Check. Using the calibration data obtained during the calibration procedure described in section 10.3, determine the ΔH@ for the metering system orifice. The ΔH@ is the orifice pressure differential in units of in. H2O that correlates to 0.75 cfm of air at 528 °R and 29.92 in. Hg. The ΔH@ is calculated as follows:
Where: ΔH = Average pressure differential across the orifice meter, in. H2O. Tm = Absolute average DGM temperature, °R. Pbar = Barometric pressure, in. Hg. θ = Total sampling time, min. Y = DGM calibration factor, dimensionless. Vm = Volume of gas sample as measured by DGM, dcf. 0.0319 = (0.0567 in. Hg/°R) (0.75 cfm) 29.2.1.1 Before beginning the field test (a set of three runs usually constitutes a field test), operate the metering system (i.e., pump, volume meter, and orifice) at the ΔH@ pressure differential for 10 minutes. Record the volume collected, the DGM temperature, and the barometric pressure. Calculate a DGM calibration check value, Yc, as follows:
where: Yc = DGM calibration check value, dimensionless. 10 = Run time, min.9.2.1.2 Compare the Yc value with the dry gas meter calibration factor Y to determine that: 0.97Y <Yc <1.03Y. If the Yc value is not within this range, the volume metering system should be investigated before beginning the test.
9.2.2 Calibrated Critical Orifice. A critical orifice, calibrated against a wet test meter or spirometer and designed to be inserted at the inlet of the sampling meter box, may be used as a check by following the procedure of section 16.2.
10.0 Calibration and Standardization Note:Maintain a laboratory log of all calibrations.
10.1 Probe Nozzle. Probe nozzles shall be calibrated before their initial use in the field. Using a micrometer, measure the ID of the nozzle to the nearest 0.025 mm (0.001 in.). Make three separate measurements using different diameters each time, and obtain the average of the measurements. The difference between the high and low numbers shall not exceed 0.1 mm (0.004 in.). When nozzles become nicked, dented, or corroded, they shall be reshaped, sharpened, and recalibrated before use. Each nozzle shall be permanently and uniquely identified.
10.2 Pitot Tube Assembly. The Type S pitot tube assembly shall be calibrated according to the procedure outlined in section 10.1 of Method 2.
10.3 Metering System.
10.3.1 Calibration Prior to Use. Before its initial use in the field, the metering system shall be calibrated as follows: Connect the metering system inlet to the outlet of a wet test meter that is accurate to within 1 percent. Refer to Figure 5-4. The wet test meter should have a capacity of 30 liters/rev (1 ft 3/rev). A spirometer of 400 liters (14 ft 3) or more capacity, or equivalent, may be used for this calibration, although a wet test meter is usually more practical. The wet test meter should be periodically calibrated with a spirometer or a liquid displacement meter to ensure the accuracy of the wet test meter. Spirometers or wet test meters of other sizes may be used, provided that the specified accuracies of the procedure are maintained. Run the metering system pump for about 15 minutes with the orifice manometer indicating a median reading as expected in field use to allow the pump to warm up and to permit the interior surface of the wet test meter to be thoroughly wetted. Then, at each of a minimum of three orifice manometer settings, pass an exact quantity of gas through the wet test meter and note the gas volume indicated by the DGM. Also note the barometric pressure and the temperatures of the wet test meter, the inlet of the DGM, and the outlet of the DGM. Select the highest and lowest orifice settings to bracket the expected field operating range of the orifice. Use a minimum volume of 0.14 m 3 (5 ft 3) at all orifice settings. Record all the data on a form similar to Figure 5-5 and calculate Y, the DGM calibration factor, and ΔH , the orifice calibration factor, at each orifice setting as shown on Figure 5-5. Allowable tolerances for individual Y and ΔH values are given in Figure 5-5. Use the average of the Y values in the calculations in section 12.0.
10.3.1.1 Before calibrating the metering system, it is suggested that a leak check be conducted. For metering systems having diaphragm pumps, the normal leak-check procedure will not detect leakages within the pump. For these cases the following leak-check procedure is suggested: make a 10-minute calibration run at 0.00057 m 3/min (0.020 cfm). At the end of the run, take the difference of the measured wet test meter and DGM volumes. Divide the difference by 10 to get the leak rate. The leak rate should not exceed 0.00057 m 3/min (0.020 cfm).
10.3.2 Calibration After Use. After each field use, the calibration of the metering system shall be checked by performing three calibration runs at a single, intermediate orifice setting (based on the previous field test), with the vacuum set at the maximum value reached during the test series. To adjust the vacuum, insert a valve between the wet test meter and the inlet of the metering system. Calculate the average value of the DGM calibration factor. If the value has changed by more than 5 percent, recalibrate the meter over the full range of orifice settings, as detailed in section 10.3.1.
Note:Alternative procedures (e.g., rechecking the orifice meter coefficient) may be used, subject to the approval of the Administrator.
10.3.3 Acceptable Variation in Calibration Check. If the DGM coefficient values obtained before and after a test series differ by more than 5 percent, the test series shall either be voided, or calculations for the test series shall be performed using whichever meter coefficient value (i.e., before or after) gives the lower value of total sample volume.
10.4 Probe Heater Calibration. Use a heat source to generate air heated to selected temperatures that approximate those expected to occur in the sources to be sampled. Pass this air through the probe at a typical sample flow rate while measuring the probe inlet and outlet temperatures at various probe heater settings. For each air temperature generated, construct a graph of probe heating system setting versus probe outlet temperature. The procedure outlined in APTD-0576 can also be used. Probes constructed according to APTD-0581 need not be calibrated if the calibration curves in APTD-0576 are used. Also, probes with outlet temperature monitoring capabilities do not require calibration.
Note:The probe heating system shall be calibrated before its initial use in the field.
10.5 Temperature Sensors. Use the procedure in Section 10.3 of Method 2 to calibrate in-stack temperature sensors. Dial thermometers, such as are used for the DGM and condenser outlet, shall be calibrated against mercury-in-glass thermometers. An alternative mercury-free NIST-traceable thermometer may be used if the thermometer is, at a minimum, equivalent in terms of performance or suitably effective for the specific temperature measurement application. As an alternative, the following single-point calibration procedure may be used. After each test run series, check the accuracy (and, hence, the calibration) of each thermocouple system at ambient temperature, or any other temperature, within the range specified by the manufacturer, using a reference thermometer (either ASTM reference thermometer or a thermometer that has been calibrated against an ASTM reference thermometer). The temperatures of the thermocouple and reference thermometers shall agree to within ±2 °F.
10.6 Barometer. Calibrate against a mercury barometer or NIST-traceable barometer prior to the field test. Alternatively, barometric pressure may be obtained from a weather report that has been adjusted for the test point (on the stack) elevation.
10.7 Field Balance Calibration Check. Check the calibration of the balance used to weigh impingers with a weight that is at least 500g or within 50g of a loaded impinger. The weight must be ASTM E617-13 “Standard Specification for Laboratory Weights and Precision Mass Standards” (incorporated by reference - see 40 CFR 60.17) Class 6 (or better). Daily before use, the field balance must measure the weight within ±0.5g of the certified mass. If the daily balance calibration check fails, perform corrective measures and repeat the check before using balance.
10.8 Analytical Balance Calibration. Perform a multipoint calibration (at least five points spanning the operational range) of the analytical balance before the first use, and semiannually thereafter. The calibration of the analytical balance must be conducted using ASTM E617-13 “Standard Specification for Laboratory Weights and Precision Mass Standards” (incorporated by reference - see 40 CFR 60.17) Class 2 (or better) tolerance weights. Audit the balance each day it is used for gravimetric measurements by weighing at least one ASTM E617-13 Class 2 tolerance (or better) calibration weight that corresponds to 50 to 150 percent of the weight of one filter or between 1g and 5g. If the scale cannot reproduce the value of the calibration weight to within 0.5 mg of the certified mass, perform corrective measures, and conduct the multipoint calibration before use.
11.0 Analytical Procedure11.1 Record the data required on a sheet such as the one shown in Figure 5-6.
11.2 Handle each sample container as follows:
11.2.1 Container No. 1. Leave the contents in the shipping container or transfer the filter and any loose PM from the sample container to a tared weighing container. Desiccate for 24 hours in a desiccator containing anhydrous calcium sulfate. Weigh to a constant weight, and report the results to the nearest 0.1 mg. For the purposes of this section, the term “constant weight” means a difference of no more than 0.5 mg or 1 percent of total weight less tare weight, whichever is greater, between two consecutive weighings, with no less than 6 hours of desiccation time between weighings. Alternatively, the sample may be oven dried at 104 °C (220 °F) for 2 to 3 hours, cooled in the desiccator, and weighed to a constant weight, unless otherwise specified by the Administrator. The sample may be oven dried at 104 °C (220 °F) for 2 to 3 hours. Once the sample has cooled, weigh the sample, and use this weight as a final weight.
11.2.2 Container No. 2. Note the level of liquid in the container, and confirm on the analysis sheet whether leakage occurred during transport. If a noticeable amount of leakage has occurred, either void the sample or use methods, subject to the approval of the Administrator, to correct the final results. Measure the liquid in this container either volumetrically to ±1 ml or gravimetrically to ±0.5 g. Transfer the contents to a tared 250 ml beaker, and evaporate to dryness at ambient temperature and pressure. Desiccate for 24 hours, and weigh to a constant weight. Report the results to the nearest 0.1 mg.
11.2.3 Container No. 3. Weigh the spent silica gel (or silica gel plus impinger) to the nearest 0.5 g using a balance. This step may be conducted in the field.
11.2.4 Acetone Blank Container. Measure the acetone in this container either volumetrically or gravimetrically. Transfer the acetone to a tared 250 ml beaker, and evaporate to dryness at ambient temperature and pressure. Desiccate for 24 hours, and weigh to a constant weight. Report the results to the nearest 0.1 mg.
Note:The contents of Container No. 2 as well as the acetone blank container may be evaporated at temperatures higher than ambient. If evaporation is done at an elevated temperature, the temperature must be below the boiling point of the solvent; also, to prevent “bumping,” the evaporation process must be closely supervised, and the contents of the beaker must be swirled occasionally to maintain an even temperature. Use extreme care, as acetone is highly flammable and has a low flash point.
12.0 Data Analysis and CalculationsCarry out calculations, retaining at least one extra significant figure beyond that of the acquired data. Round off figures after the final calculation. Other forms of the equations may be used, provided that they give equivalent results.
12.1 Nomenclature.
An = Cross-sectional area of nozzle, m 2 (ft 2).
Bws = Water vapor in the gas stream, proportion by volume.
Ca = Acetone blank residue concentration, mg/mg.
cs = Concentration of particulate matter in stack gas, dry basis, corrected to standard conditions, g/dscm (gr/dscf).
I = Percent of isokinetic sampling.
L1 = Individual leakage rate observed during the leak-check conducted prior to the first component change, m 3/min (ft 3/min)
La = Maximum acceptable leakage rate for either a pretest leak-check or for a leak-check following a component change; equal to 0.00057 m 3/min (0.020 cfm) or 4 percent of the average sampling rate, whichever is less.
Li = Individual leakage rate observed during the leak-check conducted prior to the “i th” component change (i = 1, 2, 3 . . . n), m 3/min (cfm).
Lp = Leakage rate observed during the post-test leak-check, m 3/min (cfm).
ma = Mass of residue of acetone after evaporation, mg.
mn = Total amount of particulate matter collected, mg.
Mw = Molecular weight of water, 18.015 g/g-mole (18.015 lb/lb-mole).
Pbar = Barometric pressure at the sampling site, mm Hg (in. Hg).
Ps = Absolute stack gas pressure, mm Hg (in. Hg).
Pstd = Standard absolute pressure, 760 mm Hg (29.92 in. Hg).
R = Ideal gas constant, 0.06236 ((mm Hg)(m 3))/((K)(g-mole)) {21.85 ((in. Hg) (ft 3))/((°R) (lb-mole))}.
Tm = Absolute average DGM temperature (see Figure 5-3), K (°R).
Ts = Absolute average stack gas temperature (see Figure 5-3), K (°R).
Tstd = Standard absolute temperature, 293.15 K (527.67 °R).
Va = Volume of acetone blank, ml.
Vaw = Volume of acetone used in wash, ml.
V1c = Total volume of liquid collected in impingers and silica gel (see Figure 5-6), g.
Vm = Volume of gas sample as measured by dry gas meter, dcm (dcf).
Vm(std) = Volume of gas sample measured by the dry gas meter, corrected to standard conditions, dscm (dscf).
Vw(std) = Volume of water vapor in the gas sample, corrected to standard conditions, scm (scf).
Vs = Stack gas velocity, calculated by Method 2, Equation 2-7, using data obtained from Method 5, m/sec (ft/sec).
Wa = Weight of residue in acetone wash, mg.
Y = Dry gas meter calibration factor.
ΔH = Average pressure differential across the orifice meter (see Figure 5-4), mm H2O (in. H2O).
ρa = Density of acetone, mg/ml (see label on bottle).
θ = Total sampling time, min.
θ1 = Sampling time interval, from the beginning of a run until the first component change, min.
θi = Sampling time interval, between two successive component changes, beginning with the interval between the first and second changes, min.
θp = Sampling time interval, from the final (nth) component change until the end of the sampling run, min.
13.6 = Specific gravity of mercury.
60 = Sec/min.
100 = Conversion to percent.
12.2 Average Dry Gas Meter Temperature and Average Orifice Pressure Drop. See data sheet (Figure 5-3).
12.3
K1 = 0.38572 °K/mm Hg for metric units, = 17.636 °R/in. Hg for English units.
12.4 Volume of Water Vapor Condensed

12.5 Moisture Content.
Note:In saturated or water droplet-laden gas streams, two calculations of the moisture content of the stack gas shall be made, one from the impinger analysis (Equation 5-3), and a second from the assumption of saturated conditions. The lower of the two values of Bws shall be considered correct. The procedure for determining the moisture content based upon the assumption of saturated conditions is given in section 4.0 of Method 4. For the purposes of this method, the average stack gas temperature from Figure 5-3 may be used to make this determination, provided that the accuracy of the in-stack temperature sensor is ±1 °C (2 °F).
12.6 Acetone Blank Concentration.
12.7 Acetone Wash Blank.
12.8 Total Particulate Weight. Determine the total particulate matter catch from the sum of the weights obtained from Containers 1 and 2 less the acetone blank (see Figure 5-6).
Note:In no case shall a blank value of greater than 0.001 percent of the weight of acetone used be subtracted from the sample weight. Refer to section 8.5.8 to assist in calculation of results involving two or more filter assemblies or two or more sampling trains.
12.9 Particulate Concentration.
Where: K3 = 0.001 g/mg for metric units. = 0.0154 gr/mg for English units.12.10 Conversion Factors:
From | To | Multiply by |
---|---|---|
ft 3 | m 3 | 0.02832 |
gr | mg | 64.80004 |
gr/ft 3 | mg/m 3 | 2288.4 |
mg | g | 0.001 |
gr | lb | 1.429 × 10−4 |
12.11 Isokinetic Variation.
12.11.1
Where: K4 = 0.003456 ((mm Hg)(m 3))/((ml)(°K)) for metric units, = 0.002668 ((in. Hg)(ft 3))/((ml)(°R)) for English units.12.11.2
Where: K5 = 4.3209 for metric units, = 0.09450 for English units.12.11.3 Acceptable Results. If 90 percent ≤I ≤110 percent, the results are acceptable. If the PM results are low in comparison to the standard, and “I” is over 110 percent or less than 90 percent, the Administrator may opt to accept the results. Reference 4 in section 17.0 may be used to make acceptability judgments. If “I” is judged to be unacceptable, reject the results, and repeat the sampling run.
12.12 Stack Gas Velocity and Volumetric Flow Rate. Calculate the average stack gas velocity and volumetric flow rate, if needed, using data obtained in this method and the equations in sections 12.3 and 12.4 of Method 2.
13.0 Method Performance [Reserved] 14.0 Pollution Prevention [Reserved] 15.0 Waste Management [Reserved] 16.0 Alternative Procedures16.1 Dry Gas Meter as a Calibration Standard. A DGM may be used as a calibration standard for volume measurements in place of the wet test meter specified in section 10.3, provided that it is calibrated initially and recalibrated periodically as follows:
16.1.1 Standard Dry Gas Meter Calibration.
16.1.1.1. The DGM to be calibrated and used as a secondary reference meter should be of high quality and have an appropriately sized capacity (e.g., 3 liters/rev (0.1 ft 3/rev)). A spirometer (400 liters (14 ft 3) or more capacity), or equivalent, may be used for this calibration, although a wet test meter is usually more practical. The wet test meter should have a capacity of 30 liters/rev (1 ft 3/rev) and capable of measuring volume to within 1.0 percent. Wet test meters should be checked against a spirometer or a liquid displacement meter to ensure the accuracy of the wet test meter. Spirometers or wet test meters of other sizes may be used, provided that the specified accuracies of the procedure are maintained.
16.1.1.2 Set up the components as shown in Figure 5-7. A spirometer, or equivalent, may be used in place of the wet test meter in the system. Run the pump for at least 5 minutes at a flow rate of about 10 liters/min (0.35 cfm) to condition the interior surface of the wet test meter. The pressure drop indicated by the manometer at the inlet side of the DGM should be minimized (no greater than 100 mm H2O (4 in. H2O) at a flow rate of 30 liters/min (1 cfm)). This can be accomplished by using large diameter tubing connections and straight pipe fittings.
16.1.1.3 Collect the data as shown in the example data sheet (see Figure 5-8). Make triplicate runs at each of the flow rates and at no less than five different flow rates. The range of flow rates should be between 10 and 34 liters/min (0.35 and 1.2 cfm) or over the expected operating range.
16.1.1.4
Where: K1 = 0.38572 °K/mm Hg for metric units, = 17.636 °R/in. Hg for English units. Tadj = 273.15 °C for metric units = 459.67 °F for English units.16.1.1.5 Compare the three Yds values at each of the flow rates and determine the maximum and minimum values. The difference between the maximum and minimum values at each flow rate should be no greater than 0.030. Extra sets of triplicate runs may be made in order to complete this requirement. In addition, the meter coefficients should be between 0.95 and 1.05. If these specifications cannot be met in three sets of successive triplicate runs, the meter is not suitable as a calibration standard and should not be used as such. If these specifications are met, average the three Yds values at each flow rate resulting in no less than five average meter coefficients, Yds.
16.1.1.6 Prepare a curve of meter coefficient, Yds, versus flow rate, Q, for the DGM. This curve shall be used as a reference when the meter is used to calibrate other DGMs and to determine whether recalibration is required.
16.1.2 Standard Dry Gas Meter Recalibration.
16.1.2.1 Recalibrate the standard DGM against a wet test meter or spirometer annually or after every 200 hours of operation, whichever comes first. This requirement is valid provided the standard DGM is kept in a laboratory and, if transported, cared for as any other laboratory instrument. Abuse to the standard meter may cause a change in the calibration and will require more frequent recalibrations.
16.1.2.2 As an alternative to full recalibration, a two-point calibration check may be made. Follow the same procedure and equipment arrangement as for a full recalibration, but run the meter at only two flow rates [suggested rates are 14 and 30 liters/min (0.5 and 1.0 cfm)]. Calculate the meter coefficients for these two points, and compare the values with the meter calibration curve. If the two coefficients are within 1.5 percent of the calibration curve values at the same flow rates, the meter need not be recalibrated until the next date for a recalibration check.
16.2 Critical Orifices As Calibration Standards. Critical orifices may be used as calibration standards in place of the wet test meter specified in section 16.1, provided that they are selected, calibrated, and used as follows:
16.2.1 Selection of Critical Orifices.
16.2.1.1 The procedure that follows describes the use of hypodermic needles or stainless steel needle tubings which have been found suitable for use as critical orifices. Other materials and critical orifice designs may be used provided the orifices act as true critical orifices (i.e., a critical vacuum can be obtained, as described in section 16.2.2.2.3). Select five critical orifices that are appropriately sized to cover the range of flow rates between 10 and 34 liters/min (0.35 and 1.2 cfm) or the expected operating range. Two of the critical orifices should bracket the expected operating range. A minimum of three critical orifices will be needed to calibrate a Method 5 DGM; the other two critical orifices can serve as spares and provide better selection for bracketing the range of operating flow rates. The needle sizes and tubing lengths shown in Table 5-1 in section 18.0 give the approximate flow rates.
16.2.1.2 These needles can be adapted to a Method 5 type sampling train as follows: Insert a serum bottle stopper, 13 by 20 mm sleeve type, into a 1/2-inch Swagelok (or equivalent) quick connect. Insert the needle into the stopper as shown in Figure 5-9.
16.2.2 Critical Orifice Calibration. The procedure described in this section uses the Method 5 meter box configuration with a DGM as described in section 6.1.1.9 to calibrate the critical orifices. Other schemes may be used, subject to the approval of the Administrator.
16.2.2.1 Calibration of Meter Box. The critical orifices must be calibrated in the same configuration as they will be used (i.e., there should be no connections to the inlet of the orifice).
16.2.2.1.1 Before calibrating the meter box, leak check the system as follows: Fully open the coarse adjust valve, and completely close the by-pass valve. Plug the inlet. Then turn on the pump, and determine whether there is any leakage. The leakage rate shall be zero (i.e., no detectable movement of the DGM dial shall be seen for 1 minute).
16.2.2.1.2 Check also for leakages in that portion of the sampling train between the pump and the orifice meter. See section 8.4.1 for the procedure; make any corrections, if necessary. If leakage is detected, check for cracked gaskets, loose fittings, worn O-rings, etc., and make the necessary repairs.
16.2.2.1.3 After determining that the meter box is leakless, calibrate the meter box according to the procedure given in section 10.3. Make sure that the wet test meter meets the requirements stated in section 16.1.1.1. Check the water level in the wet test meter. Record the DGM calibration factor, Y.
16.2.2.2 Calibration of Critical Orifices. Set up the apparatus as shown in Figure 5-10.
16.2.2.2.1 Allow a warm-up time of 15 minutes. This step is important to equilibrate the temperature conditions through the DGM.
16.2.2.2.2 Leak check the system as in section 16.2.2.1.1. The leakage rate shall be zero.
16.2.2.2.3 Before calibrating the critical orifice, determine its suitability and the appropriate operating vacuum as follows: Turn on the pump, fully open the coarse adjust valve, and adjust the by-pass valve to give a vacuum reading corresponding to about half of atmospheric pressure. Observe the meter box orifice manometer reading, ΔH. Slowly increase the vacuum reading until a stable reading is obtained on the meter box orifice manometer. Record the critical vacuum for each orifice. Orifices that do not reach a critical value shall not be used.
16.2.2.2.4 Obtain the barometric pressure using a barometer as described in section 6.1.2. Record the barometric pressure, Pbar, in mm Hg (in. Hg).
16.2.2.2.5 Conduct duplicate runs at a vacuum of 25 to 50 mm Hg (1 to 2 in. Hg) above the critical vacuum. The runs shall be at least 5 minutes each. The DGM volume readings shall be in increments of complete revolutions of the DGM. As a guideline, the times should not differ by more than 3.0 seconds (this includes allowance for changes in the DGM temperatures) to achieve ±0.5 percent in K′ (see Eq. 5-11). Record the information listed in Figure 5-11.
16.2.2.2.6 Calculate K′ using Equation 5-11.
Where: K′ = Critical orifice coefficient, [m 3)(°K) 1/2]/ [(mm Hg)(min)] {[(ft 3)(°R) 1/2)] [(in. Hg)(min)]. Tamb = Absolute ambient temperature, °K (°R).Calculate the arithmetic mean of the K′ values. The individual K' values should not differ by more than ±0.5 percent from the mean value.
16.2.3 Using the Critical Orifices as Calibration Standards.
16.2.3.1 Record the barometric pressure.
16.2.3.2 Calibrate the metering system according to the procedure outlined in section 16.2.2. Record the information listed in Figure 5-12.
16.2.3.3
Where: K1 = 0.38572 °K/mm Hg for metric units, = 17.636 °R/in. Hg for English units.16.2.3.4 Average the DGM calibration values for each of the flow rates. The calibration factor, Y, at each of the flow rates should not differ by more than ±2 percent from the average.
16.2.3.5 To determine the need for recalibrating the critical orifices, compare the DGM Y factors obtained from two adjacent orifices each time a DGM is calibrated; for example, when checking orifice 13/2.5, use orifices 12/10.2 and 13/5.1. If any critical orifice yields a DGM Y factor differing by more than 2 percent from the others, recalibrate the critical orifice according to section 16.2.2.
16.3 Alternative Post-Test Metering System Calibration. The following procedure may be used as an alternative to the post-test calibration described in Section 10.3.2. This alternative procedure does not detect leakages between the inlet of the metering system and the dry gas meter. Therefore, two steps must be included to make it an equivalent alternative:
(1) The metering system must pass the post-test leak-check from either the inlet of the sampling train or the inlet of the metering system. Therefore, if the train fails the former leak-check, another leak-check from the inlet of the metering system must be conducted;
(2) The metering system must pass the leak-check of that portion of the train from the pump to the orifice meter as described in Section 8.4.1.
16.3.1 After each test run, do the following:
16.3.1.1 Ensure that the metering system has passed the post-test leak-check. If not, conduct a leak-check of the metering system from its inlet.
16.3.1.2 Conduct the leak-check of that portion of the train from the pump to the orifice meter as described in Section 10.3.1.1.
16.3.1.3 Calculate Yqa for each test run using the following equation:

16.3.2 After each test run series, do the following:
16.3.2.1 Average the three or more Yqa's obtained from the test run series and compare this average Yqa with the dry gas meter calibration factor Y. The average Yqa must be within 5 percent of Y.
16.3.2.2 If the average Yqa does not meet the 5 percent criterion, recalibrate the meter over the full range of orifice settings as detailed in Section 10.3.1. Then follow the procedure in Section 10.3.3.
17.0 References.1. Addendum to Specifications for Incinerator Testing at Federal Facilities. PHS, NCAPC. December 6, 1967.
2. Martin, Robert M. Construction Details of Isokinetic Source-Sampling Equipment. Environmental Protection Agency. Research Triangle Park, NC. APTD-0581. April 1971.
3. Rom, Jerome J. Maintenance, Calibration, and Operation of Isokinetic Source Sampling Equipment. Environmental Protection Agency. Research Triangle Park, NC. APTD-0576. March 1972.
4. Smith, W.S., R.T. Shigehara, and W.F. Todd. A Method of Interpreting Stack Sampling Data. Paper Presented at the 63rd Annual Meeting of the Air Pollution Control Association, St. Louis, MO. June 14-19, 1970.
5. Smith, W.S., et al. Stack Gas Sampling Improved and Simplified With New Equipment. APCA Paper No. 67-119. 1967.
6. Specifications for Incinerator Testing at Federal Facilities. PHS, NCAPC. 1967.
7. Shigehara, R.T. Adjustment in the EPA Nomograph for Different Pitot Tube Coefficients and Dry Molecular Weights. Stack Sampling News 2:4-11. October 1974.
8. Vollaro, R.F. A Survey of Commercially Available Instrumentation for the Measurement of Low-Range Gas Velocities. U.S. Environmental Protection Agency, Emission Measurement Branch. Research Triangle Park, NC. November 1976 (unpublished paper).
9. Annual Book of ASTM Standards. Part 26. Gaseous Fuels; Coal and Coke; Atmospheric Analysis. American Society for Testing and Materials. Philadelphia, PA. 1974. pp. 617-622.
10. Felix, L.G., G.I. Clinard, G.E. Lacy, and J.D. McCain. Inertial Cascade Impactor Substrate Media for Flue Gas Sampling. U.S. Environmental Protection Agency. Research Triangle Park, NC 27711. Publication No. EPA-600/7-77-060. June 1977. 83 pp.
11. Westlin, P.R. and R.T. Shigehara. Procedure for Calibrating and Using Dry Gas Volume Meters as Calibration Standards. Source Evaluation Society Newsletter. 3(1):17-30. February 1978.
12. Lodge, J.P., Jr., J.B. Pate, B.E. Ammons, and G.A. Swanson. The Use of Hypodermic Needles as Critical Orifices in Air Sampling. J. Air Pollution Control Association. 16:197-200. 1966.
13. Shigehara, Roger T., P.G. Royals, and E.W. Steward. “Alternative Method 5 Post-Test Calibration.” Entropy Incorporated, Research Triangle Park, NC 27709.
18.0 Tables, Diagrams, Flowcharts, and Validation DataTable 5-1 Flor Rates for Various needle Sizes and Tube Lengths
Gauge/cm | Flow rate liters/min. |
Gauge/cm | Flow rate liters/min. |
---|---|---|---|
12/7.6 | 32.56 | 14/2.5 | 19.54 |
12/10.2 | 30.02 | 14/5.1 | 17.27 |
13/2.5 | 25.77 | 14/7.6 | 16.14 |
13/5.1 | 23.50 | 15/3.2 | 14.16 |
13/7.6 | 22.37 | 15/7.6 | 11.61 |
13/10.2 | 20.67 | 15/10.2 | 10.48 |
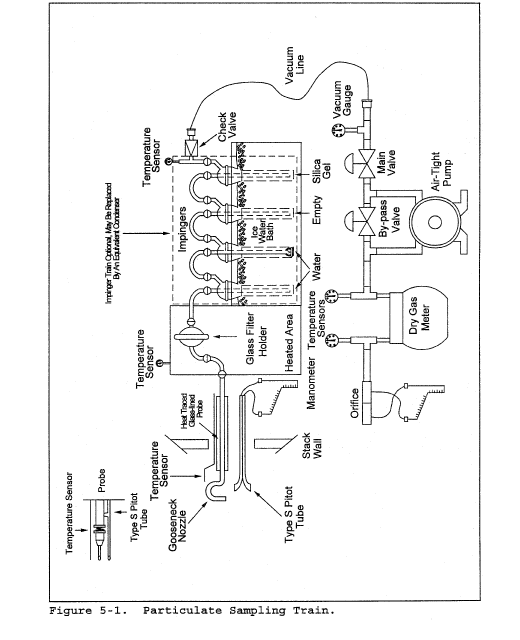
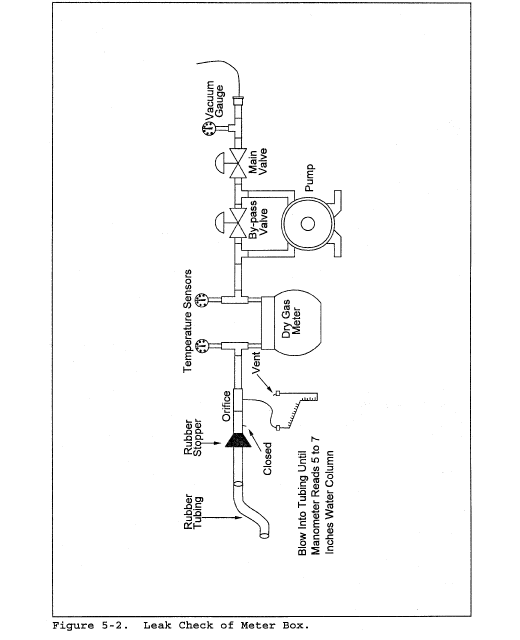
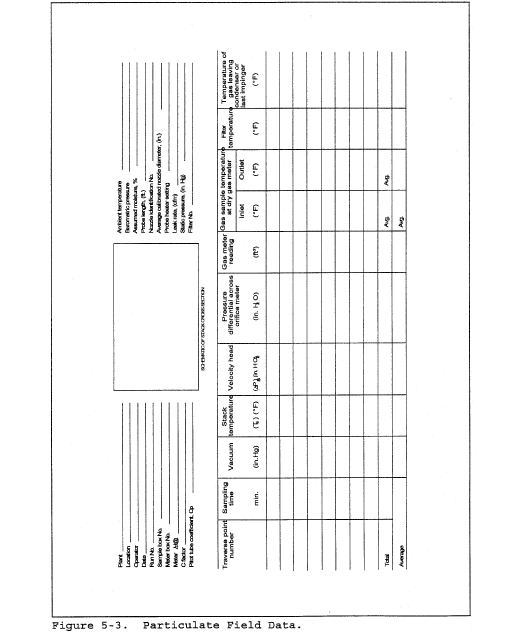
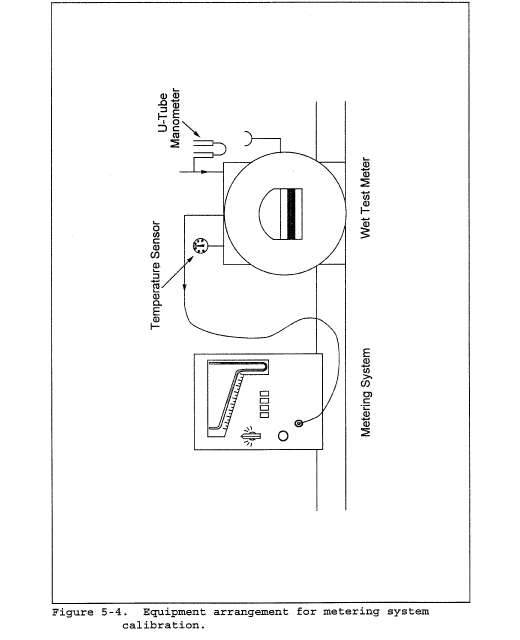
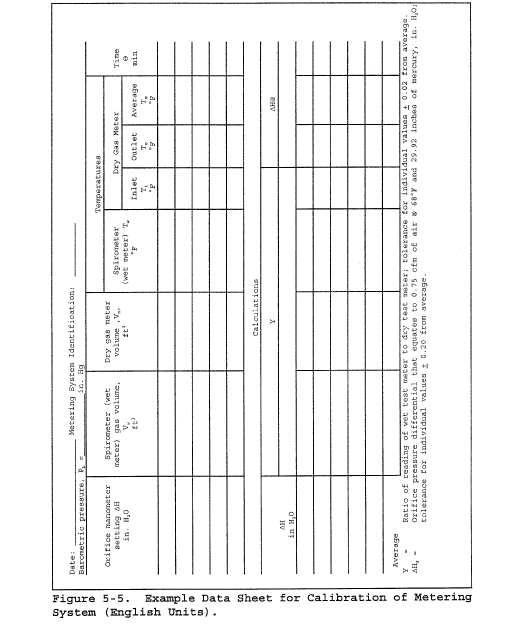

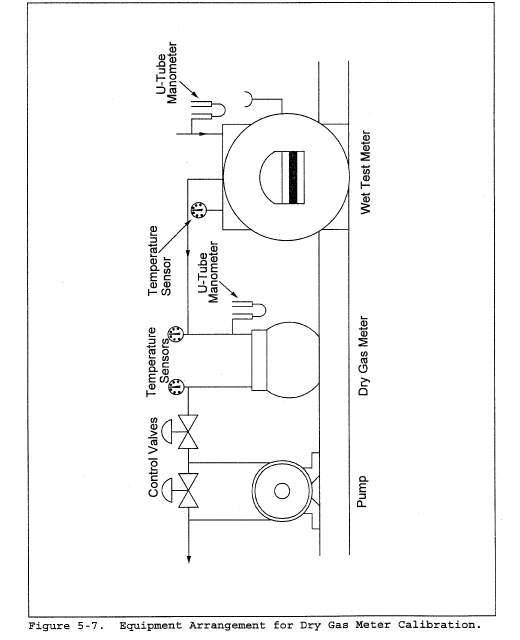
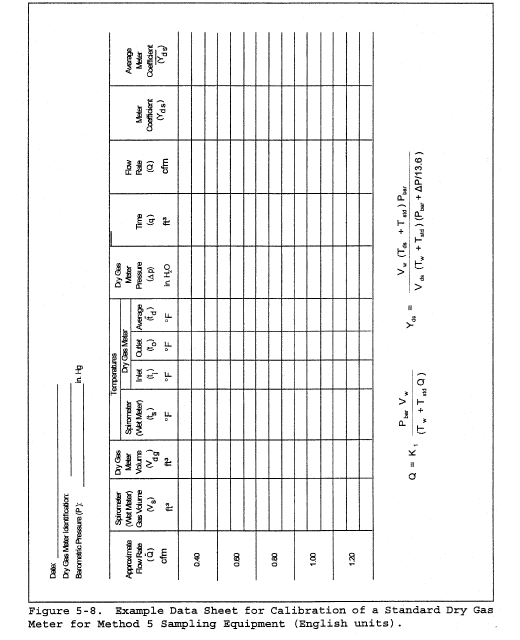
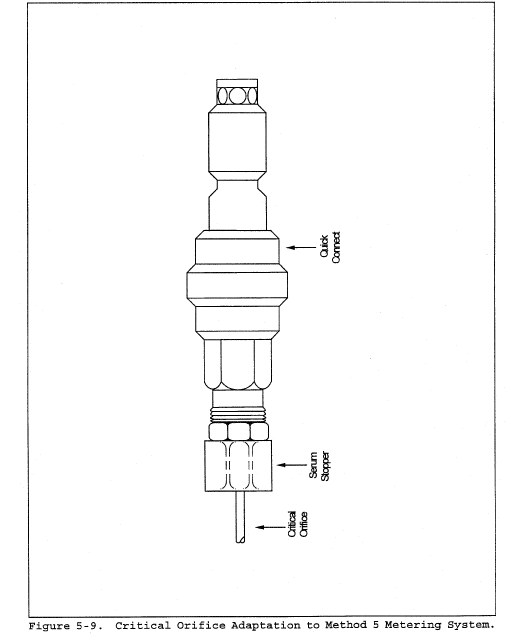
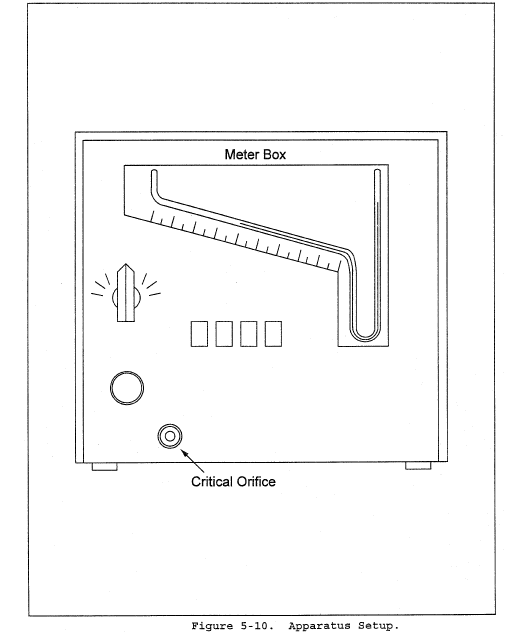
Dry gas meter | Run No. | ||
---|---|---|---|
1 | 2 | ||
Final reading | m 3 (ft 3) | ||
Initial reading | m 3 (ft 3) | ||
Difference, V m | m 3 (ft 3) | ||
Inlet/Outlet | |||
Temperatures: | °C ( °F) | / | / |
Initial | °C ( °F) | / | / |
Final | min/sec | / | / |
Av. Temeperature, t m | min | ||
Time, θ | |||
Orifice man. rdg., ΔH | mm (in.) H 2 | ||
Bar. pressure, P bar | mm (in.) Hg | ||
Ambient temperature, tamb | mm (in.) Hg | ||
Pump vacuum | |||
K′ factor | |||
Average |
Dry gas meter | Run No. | ||
---|---|---|---|
1 | 2 | ||
Final reading | m 3 (ft 3) | ||
Initial reading | m 3 (ft 3) | ||
Difference, Vm | m 3 (ft 3) | ||
Inlet/outlet temperatures | °C ( °F) | / | / |
Initial | °C ( °F) | / | / |
Final | °C ( °F) | ||
Avg. Temperature, tm | min/sec | / | / |
Time, θ | min | ||
Orifice man. rdg., ΔH | min | ||
Bar. pressure, Pbar | mm (in.) H2O | ||
Ambient temperature, tamb | mm (in.) Hg | ||
Pump vacuum | °C ( °F) | ||
Vm(std) | mm (in.) Hg | ||
Vcr(std) | m 3 (ft 3) | ||
DGM cal. factor, Y | m 3 (ft 3) |
This method does not include all of the specifications (e.g., equipment and supplies) and procedures (e.g., sampling and analytical) essential to its performance. Some material is incorporated by reference from other methods in this part. Therefore, to obtain reliable results, persons using this method should have a thorough knowledge of at least the following additional test methods: Method 1, Method 2, Method 3, and Method 5.
1.0 Scope and Applications1.1 Analyte. Particulate matter (PM). No CAS number assigned.
1.2 Applicability. This method is applicable for the determination of PM emissions from asphalt roofing industry process saturators, blowing stills, and other sources as specified in the regulations.
1.3 Data Quality Objectives. Adherence to the requirements of this method will enhance the quality of the data obtained from air pollutant sampling methods.
2.0 Summary of MethodParticulate matter is withdrawn isokinetically from the source and collected on a glass fiber filter maintained at a temperature of 42 ±10 °C (108 ±18 °F). The PM mass, which includes any material that condenses at or above the filtration temperature, is determined gravimetrically after the removal of uncombined water.
3.0 Definitions [Reserved] 4.0 Interferences [Reserved] 5.0 Safety5.1 Disclaimer. This method may involve hazardous materials, operations, and equipment. This test method may not address all of the safety problems associated with its use. It is the responsibility of the user of this test method to establish appropriate safety and health practices and to determine the applicability of regulatory limitations prior to performing this test method.
6.0 Equipment and Supplies6.1 Sample Collection. Same as Method 5, section 6.1, with the following exceptions and additions:
6.1.1 Probe Liner. Same as Method 5, section 6.1.1.2, with the note that at high stack gas temperatures greater than 250 °C (480 °F), water-cooled probes may be required to control the probe exit temperature to 42 ±10 °C (108 ±18 °F).
6.1.2 Precollector Cyclone. Borosilicate glass following the construction details shown in Air Pollution Technical Document (APTD)-0581, “Construction Details of Isokinetic Source-Sampling Equipment” (Reference 2 in Method 5, section 17.0).
Note:The cyclone shall be used when the stack gas moisture is greater than 10 percent, and shall not be used otherwise.
6.1.3 Filter Heating System. Any heating (or cooling) system capable of maintaining a sample gas temperature at the exit end of the filter holder during sampling at 42 ±10 °C (108 ±18 °F).
6.2 Sample Recovery. The following items are required for sample recovery:
6.2.1 Probe-Liner and Probe-Nozzle Brushes, Graduated Cylinder and/or Balance, Plastic Storage Containers, and Funnel and Rubber Policeman. Same as in Method 5, sections 6.2.1, 6.2.5, 6.2.6, and 6.2.7, respectively.
6.2.2 Wash Bottles. Glass.
6.2.3 Sample Storage Containers. Chemically resistant 500-ml or 1,000-ml borosilicate glass bottles, with rubber-backed Teflon screw cap liners or caps that are constructed so as to be leak-free, and resistant to chemical attack by 1,1,1-trichloroethane (TCE). (Narrow-mouth glass bottles have been found to be less prone to leakage.)
6.2.4 Petri Dishes. Glass, unless otherwise specified by the Administrator.
6.2.5 Funnel. Glass.
6.3 Sample Analysis. Same as Method 5, section 6.3, with the following additions:
6.3.1 Beakers. Glass, 250-ml and 500-ml.
6.3.2 Separatory Funnel. 100-ml or greater.
7.0. Reagents and Standards7.1 Sample Collection. The following reagents are required for sample collection:
7.1.1 Filters, Silica Gel, Water, and Crushed Ice. Same as in Method 5, sections 7.1.1, 7.1.2, 7.1.3, and 7.1.4, respectively.
7.1.2 Stopcock Grease. TCE-insoluble, heat-stable grease (if needed). This is not necessary if screw-on connectors with Teflon sleeves, or similar, are used.
7.2 Sample Recovery. Reagent grade TCE, ≤0.001 percent residue and stored in glass bottles. Run TCE blanks before field use, and use only TCE with low blank values (≤0.001 percent). In no case shall a blank value of greater than 0.001 percent of the weight of TCE used be subtracted from the sample weight.
7.3 Analysis. Two reagents are required for the analysis:
7.3.1 TCE. Same as in section 7.2.
7.3.2 Desiccant. Same as in Method 5, section 7.3.2.
8.0. Sample Collection, Preservation, Storage, and Transport8.1 Pretest Preparation. Unless otherwise specified, maintain and calibrate all components according to the procedure described in APTD-0576, “Maintenance, Calibration, and Operation of Isokinetic Source-Sampling Equipment” (Reference 3 in Method 5, Section 17.0). Alternative mercury-free thermometers may be used if the thermometers are, at a minimum, equivalent in terms of performance or suitably effective for the specific temperature measurement application.
8.1.1 Prepare probe liners and sampling nozzles as needed for use. Thoroughly clean each component with soap and water followed by a minimum of three TCE rinses. Use the probe and nozzle brushes during at least one of the TCE rinses (refer to section 8.7 for rinsing techniques). Cap or seal the open ends of the probe liners and nozzles to prevent contamination during shipping.
8.1.2 Prepare silica gel portions and glass filters as specified in Method 5, section 8.1.
8.2 Preliminary Determinations. Select the sampling site, probe nozzle, and probe length as specified in Method 5, section 8.2. Select a total sampling time greater than or equal to the minimum total sampling time specified in the “Test Methods and Procedures” section of the applicable subpart of the regulations. Follow the guidelines outlined in Method 5, section 8.2 for sampling time per point and total sample volume collected.
8.3 Preparation of Sampling Train. Prepare the sampling train as specified in Method 5, section 8.3, with the addition of the precollector cyclone, if used, between the probe and filter holder. The temperature of the precollector cyclone, if used, should be maintained in the same range as that of the filter, i.e., 42 ±10 °C (108 ±18 °F). Use no stopcock grease on ground glass joints unless grease is insoluble in TCE.
8.4 Leak-Check Procedures. Same as Method 5, section 8.4.
8.5 Sampling Train Operation. Operate the sampling train as described in Method 5, section 8.5, except maintain the temperature of the gas exiting the filter holder at 42 ±10 °C (108 ±18 °F).
8.6 Calculation of Percent Isokinetic. Same as Method 5, section 8.6.
8.7 Sample Recovery. Same as Method 5, section 8.7.1 through 8.7.6.1, with the addition of the following:
8.7.1 Container No. 2 (Probe to Filter Holder).
8.7.1.1 Taking care to see that material on the outside of the probe or other exterior surfaces does not get into the sample, quantitatively recover PM or any condensate from the probe nozzle, probe fitting, probe liner, precollector cyclone and collector flask (if used), and front half of the filter holder by washing these components with TCE and placing the wash in a glass container. Carefully measure the total amount of TCE used in the rinses. Perform the TCE rinses as described in Method 5, section 8.7.6.2, using TCE instead of acetone.
8.7.1.2 Brush and rinse the inside of the cyclone, cyclone collection flask, and the front half of the filter holder. Brush and rinse each surface three times or more, if necessary, to remove visible PM.
8.7.2 Container No. 3 (Silica Gel). Same as in Method 5, section 8.7.6.3.
8.7.3 Impinger Water. Same as Method 5, section 8.7.6.4.
8.8 Blank. Save a portion of the TCE used for cleanup as a blank. Take 200 ml of this TCE directly from the wash bottle being used, and place it in a glass sample container labeled “TCE Blank.”
9.0 Quality Control9.1 Miscellaneous Quality Control Measures.
Section | Quality control measure | Effect |
---|---|---|
8.4, 10.0 | Sampling equipment leak check and calibration | Ensures accurate measurement of stack gas flow rate, sample volume. |
9.2 A quality control (QC) check of the volume metering system at the field site is suggested before collecting the sample. Use the procedure outlined in Method 5, section 9.2.
10.0 Calibration and StandardizationSame as Method 5, section 10.0.
11.0 Analytical Procedures11.1 Analysis. Record the data required on a sheet such as the one shown in Figure 5A-1. Handle each sample container as follows:
11.1.1 Container No. 1 (Filter). Transfer the filter from the sample container to a tared glass weighing dish, and desiccate for 24 hours in a desiccator containing anhydrous calcium sulfate. Rinse Container No. 1 with a measured amount of TCE, and analyze this rinse with the contents of Container No. 2. Weigh the filter to a constant weight. For the purpose of this analysis, the term “constant weight” means a difference of no more than 10 percent of the net filter weight or 2 mg (whichever is greater) between two consecutive weighings made 24 hours apart. Report the “final weight” to the nearest 0.1 mg as the average of these two values.
11.1.2 Container No. 2 (Probe to Filter Holder).
11.1.2.1 Before adding the rinse from Container No. 1 to Container No. 2, note the level of liquid in Container No. 2, and confirm on the analysis sheet whether leakage occurred during transport. If noticeable leakage occurred, either void the sample or take steps, subject to the approval of the Administrator, to correct the final results.
11.1.2.2 Add the rinse from Container No. 1 to Container No. 2 and measure the liquid in this container either volumetrically to ±1 ml or gravimetrically to ±0.5 g. Check to see whether there is any appreciable quantity of condensed water present in the TCE rinse (look for a boundary layer or phase separation). If the volume of condensed water appears larger than 5 ml, separate the oil-TCE fraction from the water fraction using a separatory funnel. Measure the volume of the water phase to the nearest ml; adjust the stack gas moisture content, if necessary (see sections 12.3 and 12.4). Next, extract the water phase with several 25-ml portions of TCE until, by visual observation, the TCE does not remove any additional organic material. Transfer the remaining water fraction to a tared beaker and evaporate to dryness at 93 °C (200 °F), desiccate for 24 hours, and weigh to the nearest 0.1 mg.
11.1.2.3 Treat the total TCE fraction (including TCE from the filter container rinse and water phase extractions) as follows: Transfer the TCE and oil to a tared beaker, and evaporate at ambient temperature and pressure. The evaporation of TCE from the solution may take several days. Do not desiccate the sample until the solution reaches an apparent constant volume or until the odor of TCE is not detected. When it appears that the TCE has evaporated, desiccate the sample, and weigh it at 24-hour intervals to obtain a “constant weight” (as defined for Container No. 1 above). The “total weight” for Container No. 2 is the sum of the evaporated PM weight of the TCE-oil and water phase fractions. Report the results to the nearest 0.1 mg.
11.1.3 Container No. 3 (Silica Gel). This step may be conducted in the field. Weigh the spent silica gel (or silica gel plus impinger) to the nearest 0.5 g using a balance.
11.1.4 “TCE Blank” Container. Measure TCE in this container either volumetrically or gravimetrically. Transfer the TCE to a tared 250-ml beaker, and evaporate to dryness at ambient temperature and pressure. Desiccate for 24 hours, and weigh to a constant weight. Report the results to the nearest 0.1 mg.
Note:In order to facilitate the evaporation of TCE liquid samples, these samples may be dried in a controlled temperature oven at temperatures up to 38 °C (100 °F) until the liquid is evaporated.
12.0 Data Analysis and CalculationsCarry out calculations, retaining at least one extra significant figure beyond that of the acquired data. Round off figures after the final calculation. Other forms of the equations may be used as long as they give equivalent results.
12.1 Nomenclature. Same as Method 5, section 12.1, with the following additions:
Ct = TCE blank residue concentration, mg/g. mt = Mass of residue of TCE blank after evaporation, mg. Vpc = Volume of water collected in precollector, ml. Vt = Volume of TCE blank, ml. Vtw = Volume of TCE used in wash, ml. Wt = Weight of residue in TCE wash, mg. ρt = Density of TCE (see label on bottle), g/ml.12.2 Dry Gas Meter Temperature, Orifice Pressure Drop, and Dry Gas Volume. Same as Method 5, sections 12.2 and 12.3, except use data obtained in performing this test.
12.3 Volume of Water Vapor.
Where: K2 = 0.001333 m 3/ml for metric units. = 0.04706 ft 3/ml for English units.12.4 Moisture Content.
Note:In saturated or water droplet-laden gas streams, two calculations of the moisture content of the stack gas shall be made, one from the impinger and precollector analysis (Equations 5A-1 and 5A-2) and a second from the assumption of saturated conditions. The lower of the two values of moisture content shall be considered correct. The procedure for determining the moisture content based upon assumption of saturated conditions is given in section 4.0 of Method 4. For the purpose of this method, the average stack gas temperature from Figure 5-3 of Method 5 may be used to make this determination, provided that the accuracy of the in-stack temperature sensor is within 1 °C (2 °F).
12.5 TCE Blank Concentration.
Note:In no case shall a blank value of greater than 0.001 percent of the weight of TCE used be subtracted from the sample weight.
12.6 TCE Wash Blank.
12.7 Total PM Weight. Determine the total PM catch from the sum of the weights obtained from Containers 1 and 2, less the TCE blank.
12.8 PM Concentration.
Where: K3 = 0.001 g/mg for metric units = 0.0154 gr/mg for English units12.9 Isokinetic Variation. Same as in Method 5, section 12.11.
13.0 Method Performance [Reserved] 14.0 Pollution Prevention [Reserved] 15.0 Waste Management [Reserved] 16.0 ReferencesSame as Method 5, section 17.0.
17.0 Tables, Diagrams, Flowcharts, and Validation Data Plant Date Run No. Filter No. Amount liquid lost during transport Acetone blank volume, m1 Acetone blank concentration, mg/mg (Equation 5-4) Acetone wash blank, mg (Equation 5-5)Container number | Weight of particulate collected, mg | ||
---|---|---|---|
Final weight | Tare weight | Weight gain | |
1. | |||
2. | |||
Total: | |||
Less acetone blank | |||
Weight of particulate matter |
Volume of liquid water collected | ||
---|---|---|
Impinger volume, ml |
Silica gel weight, g |
|
Final | ||
Initial | ||
Liquid collected | ||
Total volume collected | g* ml |
* Convert weight of water to volume by dividing total weight increase by density of water (1 g/ml).
This method does not include all of the specifications (e.g., equipment and supplies) and procedures (e.g., sampling and analytical) essential to its performance. Some material is incorporated by reference from other methods in this part. Therefore, to obtain reliable results, persons using this method should have a thorough knowledge of at least the following additional test methods: Method 1, Method 2, Method 3, Method 5.
1.0 Scope and Application1.1 Analyte. Nonsulfuric acid particulate matter. No CAS number assigned.
1.2 Applicability. This method is determining applicable for the determination of nonsulfuric acid particulate matter from stationary sources, only where specified by an applicable subpart of the regulations or where approved by the Administrator for a particular application.
1.3 Data Quality Objectives. Adherence to the requirements of this method will enhance the quality of the data obtained from air pollutant sampling methods.
2.0 Summary of MethodParticulate matter is withdrawn isokinetically from the source and collected on a glass fiber filter maintained at a temperature of 160 ±14 °C (320 ±25 °F). The collected sample is then heated in an oven at 160 °C (320 °F) for 6 hours to volatilize any condensed sulfuric acid that may have been collected, and the nonsulfuric acid particulate mass is determined gravimetrically.
3.0 Definitions [Reserved] 4.0 Interferences [Reserved] 5.0 Safety5.1 Disclaimer. This method may involve hazardous materials, operations, and equipment. This test method may not address all of the safety problems associated with its use. It is the responsibility of the user of this test method to establish appropriate safety and health practices and to determine the applicability of regulatory limitations prior to performing this test method.
6.0 Equipment and SuppliesSame as Method 5, section 6.0, with the following addition and exceptions:
6.1 Sample Collection. The probe liner heating system and filter heating system must be capable of maintaining a sample gas temperature of 160 ±14 °C (320 ±25 °F).
6.2 Sample Preparation. An oven is required for drying the sample.
7.0 Reagents and StandardsSame as Method 5, section 7.0.
8.0 Sample Collection, Preservation, Storage, and Transport.Same as Method 5, with the exception of the following:
8.1 Initial Filter Tare. Oven dry the filter at 160 ±5 °C (320 ±10 °F) for 2 to 3 hours, cool in a desiccator for 2 hours, and weigh. Desiccate to constant weight to obtain the initial tare weight. Use the applicable specifications and techniques of section 8.1.3 of Method 5 for this determination.
8.2 Probe and Filter Temperatures. Maintain the probe outlet and filter temperatures at 160 ±14 °C (320 ±25 °F).
9.0 Quality ControlSame as Method 5, section 9.0.
10.0 Calibration and StandardizationSame as Method 5, section 10.0.
11.0 Analytical Procedure11.1 Record and report the data required on a sheet such as the one shown in Figure 5B-1.
11.2 Handle each sample container as follows:
11.2.1 Container No. 1. Leave the contents in the shipping container or transfer the filter and any loose PM from the sample container to a tared non-reactive oven-proof container. Oven dry the filter sample at a temperature of 160 ±5 °C (320 ±9 °F) for 6 hours. Cool in a desiccator for 2 hours, and weigh to constant weight. Report the results to the nearest 0.1 mg. For the purposes of this section, the term “constant weight” means a difference of no more than 0.5 mg or 1 percent of total weight less tare weight, whichever is greater, between two consecutive weighings, with no less than 6 hours of desiccation time between weighings.
11.2.2 Container No. 2. Note the level of liquid in the container, and confirm on the analysis sheet whether leakage occurred during transport. If a noticeable amount of leakage has occurred, either void the sample or use methods, subject to the approval of the Administrator, to correct the final results. Measure the liquid in this container either volumetrically to ±1 ml or gravimetrically to ±0.5 g. Transfer the contents to a tared 250 ml beaker, and evaporate to dryness at ambient temperature and pressure. Then oven dry the probe sample at a temperature of 160 ±5 °C (320 ±9 °F) for 6 hours. Cool in a desiccator for 2 hours, and weigh to constant weight. Report the results to the nearest 0.1 mg.
11.2.3 Container No. 3. Weigh the spent silica gel (or silica gel plus impinger) to the nearest 0.5 g using a balance. This step may be conducted in the field.
11.2.4 Acetone Blank Container. Measure the acetone in this container either volumetrically or gravimetrically. Transfer the acetone to a tared 250 ml beaker, and evaporate to dryness at ambient temperature and pressure. Desiccate for 24 hours, and weigh to a constant weight. Report the results to the nearest 0.1 mg.
Note: The contents of Container No. 2 as well as the acetone blank container may be evaporated at temperatures higher than ambient. If evaporation is done at an elevated temperature, the temperature must be below the boiling point of the solvent; also, to prevent “bumping,” the evaporation process must be closely supervised, and the contents of the beaker must be swirled occasionally to maintain an even temperature. Use extreme care, as acetone is highly flammable and has a low flash point.
12.0 Data Analysis and CalculationsSame as in Method 5, section 12.0.
13.0 Method Performance [Reserved] 14.0 Pollution Prevention [Reserved] 15.0 Waste Management [Reserved] 16.0 ReferencesSame as Method 5, section 17.0.
17.0 Tables, Diagrams, Flowcharts, and Validation DataContainer number | Weight of particulate collected, mg | ||
---|---|---|---|
Final weight | Tare weight | Weight gain | |
1. | |||
2. | |||
Total: | |||
Less acetone blank | |||
Weight of particulate matter |
Volume of liquid water collected | ||
---|---|---|
Impinger volume, | Silica gel weight, | |
ml | g | |
Final | ||
Initial | ||
Liquid collected | ||
Total volume collected | g* ml |
* Convert weight of water to volume by dividing total weight increase by density of water (1 g/ml).
This method does not include all of the specifications (e.g., equipment and supplies) and procedures (e.g., sampling and analytical) essential to its performance. Some material is incorporated by reference from other methods in this part. Therefore, to obtain reliable results, persons using this method should have a thorough knowledge of at least the following additional test methods: Method 1, Method 2, Method 3, Method 5, Method 17.
1.0 Scope and Application1.1 Analyte. Particulate matter (PM). No CAS number assigned.
1.2 Applicability.
1.2.1 This method is applicable for the determination of PM emissions from positive pressure fabric filters. Emissions are determined in terms of concentration (mg/m 3 or gr/ft 3) and emission rate (kg/hr or lb/hr).
1.2.2 The General Provisions of 40 CFR part 60, § 60.8(e), require that the owner or operator of an affected facility shall provide performance testing facilities. Such performance testing facilities include sampling ports, safe sampling platforms, safe access to sampling sites, and utilities for testing. It is intended that affected facilities also provide sampling locations that meet the specification for adequate stack length and minimal flow disturbances as described in Method 1. Provisions for testing are often overlooked factors in designing fabric filters or are extremely costly. The purpose of this procedure is to identify appropriate alternative locations and procedures for sampling the emissions from positive pressure fabric filters. The requirements that the affected facility owner or operator provide adequate access to performance testing facilities remain in effect.
1.3 Data Quality Objectives. Adherence to the requirements of this method will enhance the quality of the data obtained from air pollutant sampling methods.
2.0 Summary of Method2.1 Particulate matter is withdrawn isokinetically from the source and collected on a glass fiber filter maintained at a temperature at or above the exhaust gas temperature up to a nominal 120 °C (248 ±25 °F). The particulate mass, which includes any material that condenses at or above the filtration temperature, is determined gravimetrically after the removal of uncombined water.
3.0 Definitions [Reserved] 4.0 Interferences [Reserved] 5.0 Safety5.1 Disclaimer. This method may involve hazardous materials, operations, and equipment. This test method may not address all of the safety problems associated with its use. It is the responsibility of the user to establish appropriate safety and health practices and to determine the applicability of regulatory limitations prior to performing this test method.
6.0 Equipment and SuppliesSame as section 6.0 of either Method 5 or Method 17.
7.0 Reagents and StandardsSame as section 7.0 of either Method 5 or Method 17.
8.0 Sample Collection, Preservation, Storage, and TransportSame section 8.0 of either Method 5 or Method 17, except replace section 8.2.1 of Method 5 with the following:
8.1 Determination of Measurement Site. The configuration of positive pressure fabric filter structures frequently are not amenable to emission testing according to the requirements of Method 1. Following are several alternatives for determining measurement sites for positive pressure fabric filters.
8.1.1 Stacks Meeting Method 1 Criteria. Use a measurement site as specified in Method 1, section 11.1.
8.1.2 Short Stacks Not Meeting Method 1 Criteria. Use stack extensions and the procedures in Method 1. Alternatively, use flow straightening vanes of the “egg-crate” type (see Figure 5D-1). Locate the measurement site downstream of the straightening vanes at a distance equal to or greater than two times the average equivalent diameter of the vane openings and at least one-half of the overall stack diameter upstream of the stack outlet.
8.1.3 Roof Monitor or Monovent. (See Figure 5D-2). For a positive pressure fabric filter equipped with a peaked roof monitor, ridge vent, or other type of monovent, use a measurement site at the base of the monovent. Examples of such locations are shown in Figure 5D-2. The measurement site must be upstream of any exhaust point (e.g., louvered vent).
8.1.4 Compartment Housing. Sample immediately downstream of the filter bags directly above the tops of the bags as shown in the examples in Figure 5D-2. Depending on the housing design, use sampling ports in the housing walls or locate the sampling equipment within the compartment housing.
8.2 Determination of Number and Location of Traverse Points. Locate the traverse points according to Method 1, section 11.3. Because a performance test consists of at least three test runs and because of the varied configurations of positive pressure fabric filters, there are several schemes by which the number of traverse points can be determined and the three test runs can be conducted.
8.2.1 Single Stacks Meeting Method 1 Criteria. Select the number of traverse points according to Method 1. Sample all traverse points for each test run.
8.2.2 Other Single Measurement Sites. For a roof monitor or monovent, single compartment housing, or other stack not meeting Method 1 criteria, use at least 24 traverse points. For example, for a rectangular measurement site, such as a monovent, use a balanced 5 × 5 traverse point matrix. Sample all traverse points for each test run.
8.2.3 Multiple Measurement Sites. Sampling from two or more stacks or measurement sites may be combined for a test run, provided the following guidelines are met:
8.2.3.1 All measurement sites up to 12 must be sampled. For more than 12 measurement sites, conduct sampling on at least 12 sites or 50 percent of the sites, whichever is greater. The measurement sites sampled should be evenly, or nearly evenly, distributed among the available sites; if not, all sites are to be sampled.
8.2.3.2 The same number of measurement sites must be sampled for each test run.
8.2.3.3 The minimum number of traverse points per test run is 24. An exception to the 24-point minimum would be a test combining the sampling from two stacks meeting Method 1 criteria for acceptable stack length, and Method 1 specifies fewer than 12 points per site.
8.2.3.4 As long as the 24 traverse points per test run criterion is met, the number of traverse points per measurement site may be reduced to eight.
8.2.3.5 Alternatively, conduct a test run for each measurement site individually using the criteria in section 8.2.1 or 8.2.2 to determine the number of traverse points. Each test run shall count toward the total of three required for a performance test. If more than three measurement sites are sampled, the number of traverse points per measurement site may be reduced to eight as long as at least 72 traverse points are sampled for all the tests.
8.2.3.6 The following examples demonstrate the procedures for sampling multiple measurement sites.
8.2.3.6.1 Example 1: A source with nine circular measurement sites of equal areas may be tested as follows: For each test run, traverse three measurement sites using four points per diameter (eight points per measurement site). In this manner, test run number 1 will include sampling from sites 1,2, and 3; run 2 will include samples from sites 4, 5, and 6; and run 3 will include sites 7, 8, and 9. Each test area may consist of a separate test of each measurement site using eight points. Use the results from all nine tests in determining the emission average.
8.2.3.6.2 Example 2: A source with 30 rectangular measurement sites of equal areas may be tested as follows: For each of the three test runs, traverse five measurement sites using a 3 × 3 matrix of traverse points for each site. In order to distribute the sampling evenly over all the available measurement sites while sampling only 50 percent of the sites, number the sites consecutively from 1 to 30 and sample all the even numbered (or odd numbered) sites. Alternatively, conduct a separate test of each of 15 measurement sites using section 8.2.1 or 8.2.2 to determine the number and location of traverse points, as appropriate.
8.2.3.6.3 Example 3: A source with two measurement sites of equal areas may be tested as follows: For each test of three test runs, traverse both measurement sites, using section 8.2.3 in determining the number of traverse points. Alternatively, conduct two full emission test runs for each measurement site using the criteria in section 8.2.1 or 8.2.2 to determine the number of traverse points.
8.2.3.7 Other test schemes, such as random determination of traverse points for a large number of measurement sites, may be used with prior approval from the Administrator.
8.3 Velocity Determination.
8.3.1 The velocities of exhaust gases from positive pressure baghouses are often too low to measure accurately with the type S pitot tube specified in Method 2 (i.e., velocity head <1.3 mm H2O (0.05 in. H2O)). For these conditions, measure the gas flow rate at the fabric filter inlet following the procedures outlined in Method 2. Calculate the average gas velocity at the measurement site as shown in section 12.2 and use this average velocity in determining and maintaining isokinetic sampling rates.
8.3.2 Velocity determinations to determine and maintain isokinetic rates at measurement sites with gas velocities within the range measurable with the type S pitot tube (i.e., velocity head greater than 1.3 mm H2O (0.05 in. H2O)) shall be conducted according to the procedures outlined in Method 2.
8.4 Sampling. Follow the procedures specified in sections 8.1 through 8.6 of Method 5 or sections 8.1 through 8.25 in Method 17 with the exceptions as noted above.
8.5 Sample Recovery. Follow the procedures specified in section 8.7 of Method 5 or section 8.2 of Method 17.
9.0 Quality Control9.1 Miscellaneous Quality Control Measures.
Section | Quality control measure | Effect |
---|---|---|
8.0, 10.0 | Sampling equipment leak check and calibration | Ensures accurate measurement of stack gas flow rate, sample volume. |
9.2 Volume Metering System Checks. Same as Method 5, section 9.2.
10.0 Calibration and StandardizationSame as section 10.0 of either Method 5 or Method 17.
11.0 Analytical ProcedureSame as section 11.0 of either Method 5 or Method 17.
12.0 Data Analysis and CalculationsSame as section 12.0 of either Method 5 or Method 17 with the following exceptions:
12.1 Nomenclature.
Ao = Measurement site(s) total cross-sectional area, m 2 (ft 2). C or Cavg = Average concentration of PM for all n runs, mg/scm (gr/scf). Qi = Inlet gas volume flow rate, m 3/sec (ft 3/sec). mi = Mass collected for run i of n, mg (gr). To = Average temperature of gas at measurement site, °K (°R). Ti = Average temperature of gas at inlet, °K (°R). Voli = Sample volume collected for run i of n, scm (scf). v = Average gas velocity at the measurement site(s), m/s (ft/s) Qo = Total baghouse exhaust volumetric flow rate, m 3/sec (ft 3/sec). Qd = Dilution air flow rate, m 3/sec (ft 3/sec). Tamb = Ambient Temperature, (°K).12.2 Average Gas Velocity. When following section 8.3.1, calculate the average gas velocity at the measurement site as follows:
12.3 Volumetric Flow Rate. Total volumetric flow rate may be determined as follows:
12.4 Dilution Air Flow Rate.
12.5 Average PM Concentration. For multiple measurement sites, calculate the average PM concentration as follows:
13.0 Method Performance [Reserved] 14.0 Pollution Prevention [Reserved] 15.0 Waste Management [Reserved] 16.0 ReferencesSame as Method 5, section 17.0.
17.0 Tables, Diagrams, Flowcharts, and Validation Data Method 5E - Determination of Particulate Matter Emissions From the Wool Fiberglass Insulation Manufacturing Industry Note:This method does not include all of the specifications (e.g., equipment and supplies) and procedures (e.g., sampling and analytical) essential to its performance. Some material is incorporated by reference from other methods in this part. Therefore, to obtain reliable results, persons using this method should have a thorough knowledge of at least the following additional test methods: Method 1, Method 2, Method 3, and Method 5.
1.0 Scope and Applications1.1 Analyte. Particulate matter (PM). No CAS number assigned.
1.2 Applicability. This method is applicable for the determination of PM emissions from wool fiberglass insulation manufacturing sources.
2.0 Summary of MethodParticulate matter is withdrawn isokinetically from the source and is collected either on a glass fiber filter maintained at a temperature in the range of 120 ±14 °C (248 ±25 °F) and in impingers in solutions of 0.1 N sodium hydroxide (NaOH). The filtered particulate mass, which includes any material that condenses at or above the filtration temperature, is determined gravimetrically after the removal of uncombined water. The condensed PM collected in the impinger solutions is determined as total organic carbon (TOC) using a nondispersive infrared type of analyzer. The sum of the filtered PM mass and the condensed PM is reported as the total PM mass.
3.0 Definitions [Reserved] 4.0 Interferences [Reserved] 5.0 Safety5.1 Disclaimer. This method may involve hazardous materials, operations, and equipment. This test method may not address all of the safety problems associated with its use. It is the responsibility of the user of this test method to establish appropriate safety and health practices and to determine the applicability of regulatory limitations prior to performing this test method.
5.2 Corrosive Reagents. The following reagents are hazardous. Personal protective equipment and safe procedures are useful in preventing chemical splashes. If contact occurs, immediately flush with copious amounts of water at least 15 minutes. Remove clothing under shower and decontaminate. Treat residual chemical burn as thermal burn.
5.2.1 Hydrochloric Acid (HCl). Highly toxic. Vapors are highly irritating to eyes, skin, nose, and lungs, causing severe damage. May cause bronchitis, pneumonia, or edema of lungs. Exposure to concentrations of 0.13 to 0.2 percent in air can be lethal in minutes. Will react with metals, producing hydrogen.
5.2.2 Sodium Hydroxide (NaOH). Causes severe damage to eye tissues and to skin. Inhalation causes irritation to nose, throat, and lungs. Reacts exothermically with limited amounts of water.
6.0 Equipment and Supplies6.1 Sample Collection. Same as Method 5, section 6.1, with the exception of the following:
6.1.1 Probe Liner. Same as described in section 6.1.1.2 of Method 5 except use only borosilicate or quartz glass liners.
6.1.2 Filter Holder. Same as described in section 6.1.1.5 of Method 5 with the addition of a leak-tight connection in the rear half of the filter holder designed for insertion of a temperature sensor used for measuring the sample gas exit temperature.
6.2 Sample Recovery. Same as Method 5, section 6.2, except three wash bottles are needed instead of two and only glass storage bottles and funnels may be used.
6.3 Sample Analysis. Same as Method 5, section 6.3, with the additional equipment for TOC analysis as described below:
6.3.1 Sample Blender or Homogenizer. Waring type or ultrasonic.
6.3.2 Magnetic Stirrer.
6.3.3 Hypodermic Syringe. 0- to 100-µl capacity.
6.3.4 Total Organic Carbon Analyzer. Rosemount Model 2100A analyzer or equivalent and a recorder.
6.3.5 Beaker. 30-ml.
6.3.6 Water Bath. Temperature controlled.
6.3.7 Volumetric Flasks. 1000-ml and 500-ml.
7.0 Reagents and StandardsUnless otherwise indicated, it is intended that all reagents conform to the specifications established by the Committee on Analytical Reagents of the American Chemical Society, where such specifications are available; otherwise, use the best available grade.
7.1 Sample Collection. Same as Method 5, section 7.1, with the addition of 0.1 N NaOH (Dissolve 4 g of NaOH in water and dilute to 1 liter).
7.2 Sample Recovery. Same as Method 5, section 7.2, with the addition of the following:
7.2.1 Water. Deionized distilled to conform to ASTM Specification D 1193-77 or 91 Type 3 (incorporated by reference - see § 60.17). The potassium permanganate (KMnO4) test for oxidizable organic matter may be omitted when high concentrations of organic matter are not expected to be present.
7.2.2 Sodium Hydroxide. Same as described in section 7.1.
7.3 Sample Analysis. Same as Method 5, section 7.3, with the addition of the following:
7.3.1 Carbon Dioxide-Free Water. Distilled or deionized water that has been freshly boiled for 15 minutes and cooled to room temperature while preventing exposure to ambient air by using a cover vented with an Ascarite tube.
7.3.2 Hydrochloric Acid. HCl, concentrated, with a dropper.
7.3.3 Organic Carbon Stock Solution. Dissolve 2.1254 g of dried potassium biphthalate (HOOCC6H4COOK) in CO2-free water, and dilute to 1 liter in a volumetric flask. This solution contains 1000 mg/L organic carbon.
7.3.4 Inorganic Carbon Stock Solution. Dissolve 4.404 g anhydrous sodium carbonate (Na2CO3.) in about 500 ml of CO2-free water in a 1-liter volumetric flask. Add 3.497 g anhydrous sodium bicarbonate (NaHCO3) to the flask, and dilute to 1 liter with CO2 -free water. This solution contains 1000 mg/L inorganic carbon.
7.3.5 Oxygen Gas. CO2 -free.
8.0 Sample Collection, Preservation, Storage, and Transport8.1 Pretest Preparation and Preliminary Determinations. Same as Method 5, sections 8.1 and 8.2, respectively.
8.2 Preparation of Sampling Train. Same as Method 5, section 8.3, except that 0.1 N NaOH is used in place of water in the impingers. The volumes of the solutions are the same as in Method 5.
8.3 Leak-Check Procedures, Sampling Train Operation, Calculation of Percent Isokinetic. Same as Method 5, sections 8.4 through 8.6, respectively.
8.4 Sample Recovery. Same as Method 5, sections 8.7.1 through 8.7.4, with the addition of the following:
8.4.1 Save portions of the water, acetone, and 0.1 N NaOH used for cleanup as blanks. Take 200 ml of each liquid directly from the wash bottles being used, and place in glass sample containers labeled “water blank,” “acetone blank,” and “NaOH blank,” respectively.
8.4.2 Inspect the train prior to and during disassembly, and note any abnormal conditions. Treat the samples as follows:
8.4.2.1 Container No. 1. Same as Method 5, section 8.7.6.1.
8.4.2.2 Container No. 2. Use water to rinse the sample nozzle, probe, and front half of the filter holder three times in the manner described in section 8.7.6.2 of Method 5 except that no brushing is done. Put all the water wash in one container, seal, and label.
8.4.2.3 Container No. 3. Rinse and brush the sample nozzle, probe, and front half of the filter holder with acetone as described for Container No. 2 in section 8.7.6.2 of Method 5.
8.4.2.4 Container No. 4. Place the contents of the silica gel impinger in its original container as described for Container No. 3 in section 8.7.6.3 of Method 5.
8.4.2.5 Container No. 5. Measure the liquid in the first three impingers and record the volume or weight as described for the Impinger Water in section 8.7.6.4 of Method 5. Do not discard this liquid, but place it in a sample container using a glass funnel to aid in the transfer from the impingers or graduated cylinder (if used) to the sample container. Rinse each impinger thoroughly with 0.1 N NaOH three times, as well as the graduated cylinder (if used) and the funnel, and put these rinsings in the same sample container. Seal the container and label to clearly identify its contents.
8.5 Sample Transport. Whenever possible, containers should be shipped in such a way that they remain upright at all times.
9.0 Quality Control.9.1 Miscellaneous Quality Control Measures.
Section | Quality control measure | Effect |
---|---|---|
8.3, 10.0 | Sampling equipment leak-check and calibration | Ensures accurate measurement of stack gas flow rate, sample volume. |
10.1.2, 11.2.5.3 | Repetitive analyses | Ensures precise measurement of total carbon and inorganic carbon concentration of samples, blank, and standards. |
10.1.4 | TOC analyzer calibration | Ensures linearity of analyzer response to standards. |
9.2 Volume Metering System Checks. Same as Method 5, section 9.2.
10.0 Calibration and StandardizationSame as Method 5, section 10.0, with the addition of the following procedures for calibrating the total organic carbon analyzer:
10.1 Preparation of Organic Carbon Standard Curve.
10.1.1 Add 10 ml, 20 ml, 30 ml, 40 ml, and 50 ml of the organic carbon stock solution to a series of five 1000-ml volumetric flasks. Add 30 ml, 40 ml, and 50 ml of the same solution to a series of three 500-ml volumetric flasks. Dilute the contents of each flask to the mark using CO2-free water. These flasks contain 10, 20, 30, 40, 50, 60, 80, and 100 mg/L organic carbon, respectively.
10.1.2 Use a hypodermic syringe to withdraw a 20- to 50-µl aliquot from the 10 mg/L standard solution and inject it into the total carbon port of the analyzer. Measure the peak height. Repeat the injections until three consecutive peaks are obtained within 10 percent of their arithmetic mean. Repeat this procedure for the remaining organic carbon standard solutions.
10.1.3 Calculate the corrected peak height for each standard by deducting the blank correction (see section 11.2.5.3) as follows:
Where: A = Peak height of standard or sample, mm or other appropriate unit. B = Peak height of blank, mm or other appropriate unit.10.1.4 Prepare a linear regression plot of the arithmetic mean of the three consecutive peak heights obtained for each standard solution against the concentration of that solution. Calculate the calibration factor as the inverse of the slope of this curve. If the product of the arithmetic mean peak height for any standard solution and the calibration factor differs from the actual concentration by more than 5 percent, remake and reanalyze that standard.
10.2 Preparation of Inorganic Carbon Standard Curve. Repeat the procedures outlined in sections 10.1.1 through 10.1.4, substituting the inorganic carbon stock solution for the organic carbon stock solution, and the inorganic carbon port of the analyzer for the total carbon port.
11.0 Analytical Procedure11.1 Record the data required on a sheet such as the one shown in Figure 5-6 of Method 5.
11.2 Handle each sample container as follows:
11.2.1 Container No. 1. Same as Method 5, section 11.2.1, except that the filters must be dried at 20 ±6 °C (68 ±10 °F) and ambient pressure.
11.2.2 Containers No. 2 and No. 3. Same as Method 5, section 11.2.2, except that evaporation of the samples must be at 20 ±6 °C (68 ±10 °F) and ambient pressure.
11.2.3 Container No. 4. Same as Method 5, section 11.2.3.
11.2.4 “Water Blank” and “Acetone Blank” Containers. Determine the water and acetone blank values following the procedures for the “Acetone Blank” container in section 11.2.4 of Method 5. Evaporate the samples at ambient temperature (20 ±6 °C (68 ±10 °F)) and pressure.
11.2.5 Container No. 5. For the determination of total organic carbon, perform two analyses on successive identical samples, i.e., total carbon and inorganic carbon. The desired quantity is the difference between the two values obtained. Both analyses are based on conversion of sample carbon into carbon dioxide for measurement by a nondispersive infrared analyzer. Results of analyses register as peaks on a strip chart recorder.
11.2.5.1 The principal differences between the operating parameters for the two channels involve the combustion tube packing material and temperature. In the total carbon channel, a high temperature (950 °C (1740 °F)) furnace heats a Hastelloy combustion tube packed with cobalt oxide-impregnated asbestos fiber. The oxygen in the carrier gas, the elevated temperature, and the catalytic effect of the packing result in oxidation of both organic and inorganic carbonaceous material to CO2, and steam. In the inorganic carbon channel, a low temperature (150 °C (300 °F)) furnace heats a glass tube containing quartz chips wetted with 85 percent phosphoric acid. The acid liberates CO2 and steam from inorganic carbonates. The operating temperature is below that required to oxidize organic matter. Follow the manufacturer's instructions for assembly, testing, calibration, and operation of the analyzer.
11.2.5.2 As samples collected in 0.1 N NaOH often contain a high measure of inorganic carbon that inhibits repeatable determinations of TOC, sample pretreatment is necessary. Measure and record the liquid volume of each sample (or impinger contents). If the sample contains solids or immiscible liquid matter, homogenize the sample with a blender or ultrasonics until satisfactory repeatability is obtained. Transfer a representative portion of 10 to 15 ml to a 30-ml beaker, and acidify with about 2 drops of concentrated HCl to a pH of 2 or less. Warm the acidified sample at 50 °C (120 °F) in a water bath for 15 minutes.
11.2.5.3 While stirring the sample with a magnetic stirrer, use a hypodermic syringe to withdraw a 20-to 50-µ1 aliquot from the beaker. Analyze the sample for total carbon and calculate its corrected mean peak height according to the procedures outlined in sections 10.1.2 and 10.1.3. Similarly analyze an aliquot of the sample for inorganic carbon. Repeat the analyses for all the samples and for the 0.1 N NaOH blank.
11.2.5.4 Ascertain the total carbon and inorganic carbon concentrations (CTC and CIC, respectively) of each sample and blank by comparing the corrected mean peak heights for each sample and blank to the appropriate standard curve.
Note:If samples must be diluted for analysis, apply an appropriate dilution factor.
12.0 Data Analysis and CalculationsSame as Method 5, section 12.0, with the addition of the following:
12.1 Nomenclature.
Cc = Concentration of condensed particulate matter in stack gas, gas dry basis, corrected to standard conditions, g/dscm (gr/dscf). CIC = Concentration of condensed TOC in the liquid sample, from section 11.2.5, mg/L. Ct = Total particulate concentration, dry basis, corrected to standard conditions, g/dscm (gr/dscf). CTC = Concentration of condensed TOC in the liquid sample, from section 11.2.5, mg/L. CTOC = Concentration of condensed TOC in the liquid sample, mg/L. mTOC = Mass of condensed TOC collected in the impingers, mg. Vm(std) = Volume of gas sample measured by the dry gas meter, corrected to standard conditions, from section 12.3 of Method 5, dscm (dscf). Vs = Total volume of liquid sample, ml.12.2 Concentration of Condensed TOC in Liquid Sample.
12.3 Mass of Condensed TOC Collected.
Where: 0.001 = Liters per milliliter.12.4 Concentration of Condensed Particulate Material.
Where: K4 = 0.001 g/mg for metric units. = 0.0154 gr/mg for English units.12.5 Total Particulate Concentration.
13.0 Method Performance [Reserved] 14.0 Pollution Prevention [Reserved] 15.0 Waste Management [Reserved] 16.0 Alternative Procedures16.1 Total Organic Carbon Analyzer. Tekmar-Dohrmann analyzers using the single injection technique may be used as an alternative to Rosemount Model 2100A analyzers.
17.0 References.Same as section 17.0 of Method 5, with the addition of the following:
1. American Public Health Association, American Water Works Association, Water Pollution Control Federation. Standard Methods for the Examination of Water and Wastewater. Fifteenth Edition. Washington, D.C. 1980.
18.0 Tables, Diagrams, Flowcharts, and Validation Data [Reserved] Method 5F - Determination of Nonsulfate Particulate Matter Emissions From Stationary Sources Note:This method does not include all of the specifications (e.g., equipment and supplies) and procedures (e.g., sampling and analytical) essential to its performance. Some material is incorporated by reference from other methods in this part. Therefore, to obtain reliable results, persons using this method should have a thorough knowledge of at least the following additional test methods: Method 1, Method 2, Method 3, and Method 5.
1.0 Scope and Applications1.1 Analyte. Nonsulfate particulate matter (PM). No CAS number assigned.
1.2 Applicability. This method is applicable for the determination of nonsulfate PM emissions from stationary sources. Use of this method must be specified by an applicable subpart of the standards, or approved by the Administrator for a particular application.
1.3 Data Quality Objectives. Adherence to the requirements of this method will enhance the quality of the data obtained from air pollutant sampling methods.
2.0 Summary of MethodParticulate matter is withdrawn isokinetically from the source and collected on a filter maintained at a temperature in the range 160 ±14 °C (320 ±25 °F). The collected sample is extracted with water. A portion of the extract is analyzed for sulfate content by ion chromatography. The remainder is neutralized with ammonium hydroxide (NH4OH), dried, and weighed. The weight of sulfate in the sample is calculated as ammonium sulfate ((NH4)2SO4), and is subtracted from the total particulate weight; the result is reported as nonsulfate particulate matter.
3.0 Definitions [Reserved] 4.0 Interferences [Reserved] 5.0 Safety5.1 Disclaimer. This method may involve hazardous materials, operations, and equipment. This test method may not address all of the safety problems associated with its use. It is the responsibility of the user of this test method to establish appropriate safety and health practices and to determine the applicability of regulatory limitations prior to performing this test method.
6.0 Equipment and Supplies6.1 Sample Collection and Recovery. Same as Method 5, sections 6.1 and 6.2, respectively.
6.2 Sample Analysis. Same as Method 5, section 6.3, with the addition of the following:
6.2.1 Erlenmeyer Flasks. 125-ml, with ground glass joints.
6.2.2 Air Condenser. With ground glass joint compatible with the Erlenmeyer flasks.
6.2.3 Beakers. 600-ml.
6.2.4 Volumetric Flasks. 1-liter, 500-ml (one for each sample), 200-ml, and 50-ml (one for each sample and standard).
6.2.5 Pipet. 5-ml (one for each sample and standard).
6.2.6 Ion Chromatograph. The ion chromatograph should have at least the following components.
6.2.6.1 Columns. An anion separation column or other column capable of resolving the sulfate ion from other species present and a standard anion suppressor column. Suppressor columns are produced as proprietary items; however, one can be produced in the laboratory using the resin available from BioRad Company, 32nd and Griffin Streets, Richmond, California. Other systems which do not use suppressor columns may also be used.
6.2.6.2 Pump. Capable of maintaining a steady flow as required by the system.
6.2.6.3 Flow Gauges. Capable of measuring the specified system flow rate.
6.2.6.4 Conductivity Detector.
6.2.6.5 Recorder. Compatible with the output voltage range of the detector.
7.0 Reagents and StandardsUnless otherwise indicated, it is intended that all reagents conform to the specifications established by the Committee on Analytical Reagents of the American Chemical Society, where such specifications are available; otherwise, use the best available grade.
7.1 Sample Collection. Same as Method 5, section 7.1.
7.2 Sample Recovery. Same as Method 5, section 7.2, with the addition of the following:
7.2.1 Water. Deionized distilled, to conform to ASTM D 1193-77 or 91 Type 3 (incorporated by reference - see § 60.17). The potassium permanganate (KMnO4) test for oxidizable organic matter may be omitted when high concentrations of organic matter are not expected to be present.
7.3 Analysis. Same as Method 5, section 7.3, with the addition of the following:
7.3.1 Water. Same as in section 7.2.1.
7.3.2 Stock Standard Solution, 1 mg (NH4)2SO4/ml. Dry an adequate amount of primary standard grade ammonium sulfate ((NH4)2SO4) at 105 to 110 °C (220 to 230 °F) for a minimum of 2 hours before preparing the standard solution. Then dissolve exactly 1.000 g of dried (NH4)2SO4 in water in a 1-liter volumetric flask, and dilute to 1 liter. Mix well.
7.3.3 Working Standard Solution, 25 µg (NH4)2SO4/ml. Pipet 5 ml of the stock standard solution into a 200-ml volumetric flask. Dilute to 200 ml with water.
7.3.4 Eluent Solution. Weigh 1.018 g of sodium carbonate (Na2CO3) and 1.008 g of sodium bicarbonate (NaHCO3), and dissolve in 4 liters of water. This solution is 0.0024 M Na2CO3/0.003 M NaHCO3. Other eluents appropriate to the column type and capable of resolving sulfate ion from other species present may be used.
7.3.5 Ammonium Hydroxide. Concentrated, 14.8 M.
7.3.6 Phenolphthalein Indicator. 3,3-Bis(4-hydroxyphenyl)-1-(3H)-isobenzo-furanone. Dissolve 0.05 g in 50 ml of ethanol and 50 ml of water.
8.0 Sample Collection, Preservation, Storage, and TransportSame as Method 5, section 8.0, with the exception of the following:
8.1 Sampling Train Operation. Same as Method 5, section 8.5, except that the probe outlet and filter temperatures shall be maintained at 160 ±14 °C (320 ±25 °F).
8.2 Sample Recovery. Same as Method 5, section 8.7, except that the recovery solvent shall be water instead of acetone, and a clean filter from the same lot as those used during testing shall be saved for analysis as a blank.
9.0 Quality Control9.1 Miscellaneous Quality Control Measures
Section | Quality control measure | Effect |
---|---|---|
8.3, 10.0 | Sampling equipment leak check and calibration | Ensures accurate measurement of stack gas flow rate, sample volume. |
10.1.2, 11.2.5.3 | Repetitive analyses | Ensures precise measurement of total carbon and inorganic carbon concentration of samples, blank, and standards. |
9.2 Volume Metering System Checks. Same as Method 5, section 9.2.
10.0 Calibration and StandardizationSame as Method 5, section 10.0, with the addition of the following:
10.1 Determination of Ion Chromatograph Calibration Factor S. Prepare a series of five standards by adding 1.0, 2.0, 4.0, 6.0, and 10.0 ml of working standard solution (25 µg/ml) to a series of five 50-ml volumetric flasks. (The standard masses will equal 25, 50, 100, 150, and 250 µg.) Dilute each flask to the mark with water, and mix well. Analyze each standard according to the chromatograph manufacturer's instructions. Take peak height measurements with symmetrical peaks; in all other cases, calculate peak areas. Prepare or calculate a linear regression plot of the standard masses in µg (x-axis) versus their responses (y-axis). From this line, or equation, determine the slope and calculate its reciprocal which is the calibration factor, S. If any point deviates from the line by more than 7 percent of the concentration at that point, remake and reanalyze that standard. This deviation can be determined by multiplying S times the response for each standard. The resultant concentrations must not differ by more than 7 percent from each known standard mass (i.e., 25, 50, 100, 150, and 250 µg).
10.2 Conductivity Detector. Calibrate according to manufacturer's specifications prior to initial use.
11.0 Analytical Procedure11.1 Sample Extraction.
11.1.1 Note on the analytical data sheet, the level of the liquid in the container, and whether any sample was lost during shipment. If a noticeable amount of leakage has occurred, either void the sample or use methods, subject to the approval of the Administrator, to correct the final results.
11.1.2 Cut the filter into small pieces, and place it in a 125-ml Erlenmeyer flask with a ground glass joint equipped with an air condenser. Rinse the shipping container with water, and pour the rinse into the flask. Add additional water to the flask until it contains about 75 ml, and place the flask on a hot plate. Gently reflux the contents for 6 to 8 hours. Cool the solution, and transfer it to a 500-ml volumetric flask. Rinse the Erlenmeyer flask with water, and transfer the rinsings to the volumetric flask including the pieces of filter.
11.1.3 Transfer the probe rinse to the same 500-ml volumetric flask with the filter sample. Rinse the sample bottle with water, and add the rinsings to the volumetric flask. Dilute the contents of the flask to the mark with water.
11.1.4 Allow the contents of the flask to settle until all solid material is at the bottom of the flask. If necessary, remove and centrifuge a portion of the sample.
11.1.5 Repeat the procedures outlined in sections 11.1.1 through 11.1.4 for each sample and for the filter blank.
11.2 Sulfate (SO4) Analysis.
11.2.1 Prepare a standard calibration curve according to the procedures outlined in section 10.1.
11.2.2 Pipet 5 ml of the sample into a 50-ml volumetric flask, and dilute to 50 ml with water. (Alternatively, eluent solution may be used instead of water in all sample, standard, and blank dilutions.) Analyze the set of standards followed by the set of samples, including the filter blank, using the same injection volume used for the standards.
11.2.3 Repeat the analyses of the standards and the samples, with the standard set being done last. The two peak height or peak area responses for each sample must agree within 5 percent of their arithmetic mean for the analysis to be valid. Perform this analysis sequence on the same day. Dilute any sample and the blank with equal volumes of water if the concentration exceeds that of the highest standard.
11.2.4 Document each sample chromatogram by listing the following analytical parameters: injection point, injection volume, sulfate retention time, flow rate, detector sensitivity setting, and recorder chart speed.
11.3 Sample Residue.
11.3.1 Transfer the remaining contents of the volumetric flask to a tared 600-ml beaker or similar container. Rinse the volumetric flask with water, and add the rinsings to the tared beaker. Make certain that all particulate matter is transferred to the beaker. Evaporate the water in an oven at 105 °C (220 °F) until only about 100 ml of water remains. Remove the beakers from the oven, and allow them to cool.
11.3.2 After the beakers have cooled, add five drops of phenolphthalein indicator, and then add concentrated ammonium hydroxide until the solution turns pink. Return the samples to the oven at 105 °C (220 °F), and evaporate the samples to dryness. Cool the samples in a desiccator, and weigh the samples to constant weight.
12.0 Data Analysis and CalculationsSame as Method 5, section 12.0, with the addition of the following:
12.1 Nomenclature.
CW = Water blank residue concentration, mg/ml. F = Dilution factor (required only if sample dilution was needed to reduce the concentration into the range of calibration). HS = Arithmetic mean response of duplicate sample analyses, mm for height or mm2 for area. Hb = Arithmetic mean response of duplicate filter blank analyses, mm for height or mm2 for area. mb = Mass of beaker used to dry sample, mg. mf = Mass of sample filter, mg. mn = Mass of nonsulfate particulate matter in the sample as collected, mg. ms = Mass of ammonium sulfate in the sample as collected, mg. mt = Mass of beaker, filter, and dried sample, mg. mw = Mass of residue after evaporation of water blank, mg. S = Calibration factor, µg/mm. Vb = Volume of water blank, ml. VS = Volume of sample collected, 500 ml.12.2 Water Blank Concentration.
12.3 Mass of Ammonium Sulfate.
Where: 100 = Aliquot factor, 495 ml/5 ml 1000 = Constant, µg/mg12.4 Mass of Nonsulfate Particulate Matter.
13.0 Method Performance [Reserved] 14.0 Pollution Prevention [Reserved] 15.0 Waste Management [Reserved] 16.0 Alternative Procedures16.1 The following procedure may be used as an alternative to the procedure in section 11.0
16.1.1 Apparatus. Same as for Method 6, sections 6.3.3 to 6.3.6 with the following additions.
16.1.1.1 Beakers. 250-ml, one for each sample, and 600-ml.
16.1.1.2 Oven. Capable of maintaining temperatures of 75 ±5 °C (167 ±9 °F) and 105 ±5 °C (221 ±9 °F).
16.1.1.3 Buchner Funnel.
16.1.1.4 Glass Columns. 25-mm × 305-mm (1-in. × 12-in.) with Teflon stopcock.
16.1.1.5 Volumetric Flasks. 50-ml and 500-ml, one set for each sample, and 100-ml, 200-ml, and 1000-ml.
16.1.1.6 Pipettes. Two 20-ml and one 200-ml, one set for each sample, and 5-ml.
16.1.1.7 Filter Flasks. 500-ml.
16.1.1.8 Polyethylene Bottle. 500-ml, one for each sample.
16.1.2 Reagents. Same as Method 6, sections 7.3.2 to 7.3.5 with the following additions:
16.1.2.1 Water, Ammonium Hydroxide, and Phenolphthalein. Same as sections 7.2.1, 7.3.5, and 7.3.6 of this method, respectively.
16.1.2.2 Filter. Glass fiber to fit Buchner funnel.
16.1.2.3 Hydrochloric Acid (HCl), 1 m. Add 8.3 ml of concentrated HCl (12 M) to 50 ml of water in a 100-ml volumetric flask. Dilute to 100 ml with water.
16.1.2.4 Glass Wool.
16.1.2.5 Ion Exchange Resin. Strong cation exchange resin, hydrogen form, analytical grade.
16.1.2.6 pH Paper. Range of 1 to 7.
16.1.3 Analysis.
16.1.3.1 Ion Exchange Column Preparation. Slurry the resin with 1 M HCl in a 250-ml beaker, and allow to stand overnight. Place 2.5 cm (1 in.) of glass wool in the bottom of the glass column. Rinse the slurried resin twice with water. Resuspend the resin in water, and pour sufficient resin into the column to make a bed 5.1 cm (2 in.) deep. Do not allow air bubbles to become entrapped in the resin or glass wool to avoid channeling, which may produce erratic results. If necessary, stir the resin with a glass rod to remove air bubbles, after the column has been prepared, never let the liquid level fall below the top of the upper glass wool plug. Place a 2.5-cm (1-in.) plug of glass wool on top of the resin. Rinse the column with water until the eluate gives a pH of 5 or greater as measured with pH paper.
16.1.3.2 Sample Extraction. Followup the procedure given in section 11.1.3 except do not dilute the sample to 500 ml.
16.1.3.3 Sample Residue.
16.1.3.3.1 Place at least one clean glass filter for each sample in a Buchner funnel, and rinse the filters with water. Remove the filters from the funnel, and dry them in an oven at 105 ±5 °C (221 ±9 °F); then cool in a desiccator. Weigh each filter to constant weight according to the procedure in Method 5, section 11.0. Record the weight of each filter to the nearest 0.1 mg.
16.1.3.3.2 Assemble the vacuum filter apparatus, and place one of the clean, tared glass fiber filters in the Buchner funnel. Decant the liquid portion of the extracted sample (Section 16.1.3.2) through the tared glass fiber filter into a clean, dry, 500-ml filter flask. Rinse all the particulate matter remaining in the volumetric flask onto the glass fiber filter with water. Rinse the particulate matter with additional water. Transfer the filtrate to a 500-ml volumetric flask, and dilute to 500 ml with water. Dry the filter overnight at 105 ±5 °C (221 ±9 °F), cool in a desiccator, and weigh to the nearest 0.1 mg.
16.1.3.3.3 Dry a 250-ml beaker at 75 ±5 °C (167 ±9 °F), and cool in a desiccator; then weigh to constant weight to the nearest 0.1 mg. Pipette 200 ml of the filtrate that was saved into a tared 250-ml beaker; add five drops of phenolphthalein indicator and sufficient concentrated ammonium hydroxide to turn the solution pink. Carefully evaporate the contents of the beaker to dryness at 75 ±5 °C (167 ±9 °F). Check for dryness every 30 minutes. Do not continue to bake the sample once it has dried. Cool the sample in a desiccator, and weigh to constant weight to the nearest 0.1 mg.
16.1.3.4 Sulfate Analysis. Adjust the flow rate through the ion exchange column to 3 ml/min. Pipette a 20-ml aliquot of the filtrate onto the top of the ion exchange column, and collect the eluate in a 50-ml volumetric flask. Rinse the column with two 15-ml portions of water. Stop collection of the eluate when the volume in the flask reaches 50-ml. Pipette a 20-ml aliquot of the eluate into a 250-ml Erlenmeyer flask, add 80 ml of 100 percent isopropanol and two to four drops of thorin indicator, and titrate to a pink end point using 0.0100 N barium perchlorate. Repeat and average the titration volumes. Run a blank with each series of samples. Replicate titrations must agree within 1 percent or 0.2 ml, whichever is larger. Perform the ion exchange and titration procedures on duplicate portions of the filtrate. Results should agree within 5 percent. Regenerate or replace the ion exchange resin after 20 sample aliquots have been analyzed or if the end point of the titration becomes unclear.
Note:Protect the 0.0100 N barium perchlorate solution from evaporation at all times.
16.1.3.5 Blank Determination. Begin with a sample of water of the same volume as the samples being processed and carry it through the analysis steps described in sections 16.1.3.3 and 16.1.3.4. A blank value larger than 5 mg should not be subtracted from the final particulate matter mass. Causes for large blank values should be investigated and any problems resolved before proceeding with further analyses.
16.1.4 Calibration. Calibrate the barium perchlorate solutions as in Method 6, section 10.5.
16.1.5 Calculations.
16.1.5.1 Nomenclature. Same as section 12.1 with the following additions:
ma = Mass of clean analytical filter, mg. md = Mass of dissolved particulate matter, mg. me = Mass of beaker and dissolved particulate matter after evaporation of filtrate, mg. mp = Mass of insoluble particulate matter, mg. mr = Mass of analytical filter, sample filter, and insoluble particulate matter, mg. mbk = Mass of nonsulfate particulate matter in blank sample, mg. mn = Mass of nonsulfate particulate matter, mg. ms = Mass of Ammonium sulfate, mg. N = Normality of Ba(ClO4) titrant, meq/ml. Va = Volume of aliquot taken for titration, 20 ml. Vc = Volume of titrant used for titration blank, ml. Vd = Volume of filtrate evaporated, 200 ml. Ve = Volume of eluate collected, 50 ml. Vf = Volume of extracted sample, 500 ml. Vi = Volume of filtrate added to ion exchange column, 20 ml. Vt = Volume of Ba(C104)2 titrant, ml. W = Equivalent weight of ammonium sulfate, 66.07 mg/meq.16.1.5.2 Mass of Insoluble Particulate Matter.
16.1.5.3 Mass of Dissolved Particulate Matter.
16.1.5.4 Mass of Ammonium Sulfate.
16.1.5.5 Mass of Nonsulfate Particulate Matter.
17.0 ReferencesSame as Method 5, section 17.0, with the addition of the following:
1. Mulik, J.D. and E. Sawicki. Ion Chromatographic Analysis of Environmental Pollutants. Ann Arbor, Ann Arbor Science Publishers, Inc. Vol. 2, 1979.
2. Sawicki, E., J.D. Mulik, and E. Wittgenstein. Ion Chromatographic Analysis of Environmental Pollutants. Ann Arbor, Ann Arbor Science Publishers, Inc. Vol. 1. 1978.
3. Siemer, D.D. Separation of Chloride and Bromide from Complex Matrices Prior to Ion Chromatographic Determination. Analytical Chemistry 52(12): 1874-1877. October 1980.
4. Small, H., T.S. Stevens, and W.C. Bauman. Novel Ion Exchange Chromatographic Method Using Conductimetric Determination. Analytical Chemistry. 47(11):1801. 1975.
18.0 Tables, Diagrams, Flowcharts, and Validation Data [Reserved] Method 5G - Determination of Particulate Matter Emissions From Wood Heaters (Dilution Tunnel Sampling Location) Note:This method does not include all of the specifications (e.g., equipment and supplies) and procedures (e.g., sampling and analytical) essential to its performance. Some material is incorporated by reference from other methods in this part. Therefore, to obtain reliable results, persons using this method should have a thorough knowledge of at least the following additional test methods: Method 1, Method 2, Method 3, Method 4, Method 5, Method 5H, and Method 28.
1.0 Scope and Application1.1 Analyte. Particulate matter (PM). No CAS number assigned.
1.2 Applicability. This method is applicable for the determination of PM emissions from wood heaters.
1.3 Data Quality Objectives. Adherence to the requirements of this method will enhance the quality of the data obtained from air pollutant sampling methods.
2.0 Summary of Method2.1 The exhaust from a wood heater is collected with a total collection hood, and is combined with ambient dilution air. Particulate matter is withdrawn proportionally from a single point in a sampling tunnel, and is collected on two glass fiber filters in series. The filters are maintained at a temperature of no greater than 32 °C (90 °F). The particulate mass is determined gravimetrically after the removal of uncombined water.
2.2 There are three sampling train approaches described in this method: (1) One dual-filter dry sampling train operated at about 0.015 m 3/min (0.5 cfm), (2) One dual-filter plus impingers sampling train operated at about 0.015 m 3/min (0.5 cfm), and (3) two dual-filter dry sampling trains operated simultaneously at any flow rate. Options (2) and (3) are referenced in section 16.0 of this method. The dual-filter dry sampling train equipment and operation, option (1), are described in detail in this method.
3.0 Definitions [Reserved] 4.0 Interferences [Reserved] 5.0 Safety5.1 Disclaimer. This method may involve hazardous materials, operations, and equipment. This test method may not address all of the safety problems associated with its use. It is the responsibility of the user of this test method to establish appropriate safety and health practices and to determine the applicability of regulatory limitations prior to performing this test method.
6.0 Equipment and Supplies6.1 Sample Collection. The following items are required for sample collection:
6.1.1 Sampling Train. The sampling train configuration is shown in Figure 5G-1 and consists of the following components:
6.1.1.1 Probe. Stainless steel (e.g., 316 or grade more corrosion resistant) or glass about 9.5 mm ( 3/8 in.) I.D., 0.6 m (24 in.) in length. If made of stainless steel, the probe shall be constructed from seamless tubing.
6.1.1.2 Pitot Tube. Type S, as described in section 6.1 of Method 2. The Type S pitot tube assembly shall have a known coefficient, determined as outlined in Method 2, section 10. Alternatively, a standard pitot may be used as described in Method 2, section 6.1.2.
6.1.1.3 Differential Pressure Gauge. Inclined manometer or equivalent device, as described in Method 2, section 6.2. One manometer shall be used for velocity head (Δp) readings and another (optional) for orifice differential pressure readings (ΔH).
6.1.1.4 Filter Holders. Two each made of borosilicate glass, stainless steel, or Teflon, with a glass frit or stainless steel filter support and a silicone rubber, Teflon, or Viton gasket. The holder design shall provide a positive seal against leakage from the outside or around the filters. The filter holders shall be placed in series with the backup filter holder located 25 to 100 mm (1 to 4 in.) downstream from the primary filter holder. The filter holder shall be capable of holding a filter with a 100 mm (4 in.) diameter, except as noted in section 16.
6.1.1.5 Filter Temperature Monitoring System. A temperature sensor capable of measuring temperature to within ±3 °C (±5 °F). The sensor shall be installed at the exit side of the front filter holder so that the sensing tip of the temperature sensor is in direct contact with the sample gas or in a thermowell as shown in Figure 5G-1. The temperature sensor shall comply with the calibration specifications in Method 2, section 10.3. Alternatively, the sensing tip of the temperature sensor may be installed at the inlet side of the front filter holder.
6.1.1.6 Dryer. Any system capable of removing water from the sample gas to less than 1.5 percent moisture (volume percent) prior to the metering system. The system shall include a temperature sensor for demonstrating that sample gas temperature exiting the dryer is less than 20 °C (68 °F).
6.1.1.7 Metering System. Same as Method 5, section 6.1.1.9.
6.1.2 Barometer. Same as Method 5, section 6.1.2.
6.1.3 Dilution Tunnel Gas Temperature Measurement. A temperature sensor capable of measuring temperature to within ±3 °C (±5 °F).
6.1.4 Dilution Tunnel. The dilution tunnel apparatus is shown in Figure 5G-2 and consists of the following components:
6.1.4.1 Hood. Constructed of steel with a minimum diameter of 0.3 m (1 ft) on the large end and a standard 0.15 to 0.3 m (0.5 to 1 ft) coupling capable of connecting to standard 0.15 to 0.3 m (0.5 to 1 ft) stove pipe on the small end.
6.1.4.2 90° Elbows. Steel 90° elbows, 0.15 to 0.3 m (0.5 to 1 ft) in diameter for connecting mixing duct, straight duct and optional damper assembly. There shall be at least two 90° elbows upstream of the sampling section (see Figure 5G-2).
6.1.4.3 Straight Duct. Steel, 0.15 to 0.3 m (0.5 to 1 ft) in diameter to provide the ducting for the dilution apparatus upstream of the sampling section. Steel duct, 0.15 m (0.5 ft) in diameter shall be used for the sampling section. In the sampling section, at least 1.2 m (4 ft) downstream of the elbow, shall be two holes (velocity traverse ports) at 90° to each other of sufficient size to allow entry of the pitot for traverse measurements. At least 1.2 m (4 ft) downstream of the velocity traverse ports, shall be one hole (sampling port) of sufficient size to allow entry of the sampling probe. Ducts of larger diameter may be used for the sampling section, provided the specifications for minimum gas velocity and the dilution rate range shown in section 8 are maintained. The length of duct from the hood inlet to the sampling ports shall not exceed 9.1 m (30 ft).
6.1.4.4 Mixing Baffles. Steel semicircles (two) attached at 90° to the duct axis on opposite sides of the duct midway between the two elbows upstream of sampling section. The space between the baffles shall be about 0.3 m (1 ft).
6.1.4.5 Blower. Squirrel cage or other fan capable of extracting gas from the dilution tunnel of sufficient flow to maintain the velocity and dilution rate specifications in section 8 and exhausting the gas to the atmosphere.
6.2 Sample Recovery. The following items are required for sample recovery: probe brushes, wash bottles, sample storage containers, petri dishes, and funnel. Same as Method 5, sections 6.2.1 through 6.2.4, and 6.2.8, respectively.
6.3 Sample Analysis. The following items are required for sample analysis: glass weighing dishes, desiccator, analytical balance, beakers (250-ml or smaller), hygrometer, and temperature sensor. Same as Method 5, sections 6.3.1 through 6.3.3 and 6.3.5 through 6.3.7, respectively.
7.0 Reagents and Standards7.1 Sample Collection. The following reagents are required for sample collection:
7.1.1 Filters. Glass fiber filters with a minimum diameter of 100 mm (4 in.), without organic binder, exhibiting at least 99.95 percent efficiency (<0.05 percent penetration) on 0.3-micron dioctyl phthalate smoke particles. Gelman A/E 61631 has been found acceptable for this purpose.
7.1.2 Stopcock Grease. Same as Method 5, section 7.1.5. 7.2 Sample Recovery. Acetone-reagent grade, same as Method 5, section 7.2.
7.3 Sample Analysis. Two reagents are required for the sample analysis:
7.3.1 Acetone. Same as in section 7.2.
7.3.2 Desiccant. Anhydrous calcium sulfate, calcium chloride, or silica gel, indicating type.
8.0 Sample Collection, Preservation, Transport, and Storage8.1 Dilution Tunnel Assembly and Cleaning. A schematic of a dilution tunnel is shown in Figure 5G-2. The dilution tunnel dimensions and other features are described in section 6.1.4. Assemble the dilution tunnel, sealing joints and seams to prevent air leakage. Clean the dilution tunnel with an appropriately sized wire chimney brush before each certification test.
8.2 Draft Determination. Prepare the wood heater as in Method 28, section 6.2.1. Locate the dilution tunnel hood centrally over the wood heater stack exhaust. Operate the dilution tunnel blower at the flow rate to be used during the test run. Measure the draft imposed on the wood heater by the dilution tunnel (i.e., the difference in draft measured with and without the dilution tunnel operating) as described in Method 28, section 6.2.3. Adjust the distance between the top of the wood heater stack exhaust and the dilution tunnel hood so that the dilution tunnel induced draft is less than 1.25 Pa (0.005 in. H2O). Have no fire in the wood heater, close the wood heater doors, and open fully the air supply controls during this check and adjustment.
8.3 Pretest Ignition. Same as Method 28, section 8.7.
8.4 Smoke Capture. During the pretest ignition period, operate the dilution tunnel and visually monitor the wood heater stack exhaust. Operate the wood heater with the doors closed and determine that 100 percent of the exhaust gas is collected by the dilution tunnel hood. If less than 100 percent of the wood heater exhaust gas is collected, adjust the distance between the wood heater stack and the dilution tunnel hood until no visible exhaust gas is escaping. Stop the pretest ignition period, and repeat the draft determination procedure described in section 8.2.
8.5 Velocity Measurements. During the pretest ignition period, conduct a velocity traverse to identify the point of average velocity. This single point shall be used for measuring velocity during the test run.
8.5.1 Velocity Traverse. Measure the diameter of the duct at the velocity traverse port location through both ports. Calculate the duct area using the average of the two diameters. A pretest leak-check of pitot lines as in Method 2, section 8.1, is recommended. Place the calibrated pitot tube at the centroid of the stack in either of the velocity traverse ports. Adjust the damper or similar device on the blower inlet until the velocity indicated by the pitot is approximately 220 m/min (720 ft/min). Continue to read the Δp and temperature until the velocity has remained constant (less than 5 percent change) for 1 minute. Once a constant velocity is obtained at the centroid of the duct, perform a velocity traverse as outlined in Method 2, section 8.3 using four points per traverse as outlined in Method 1. Measure the Δp and tunnel temperature at each traverse point and record the readings. Calculate the total gas flow rate using calculations contained in Method 2, section 12. Verify that the flow rate is 4 ±0.40 dscm/min (140 ±14 dscf/min); if not, readjust the damper, and repeat the velocity traverse. The moisture may be assumed to be 4 percent (100 percent relative humidity at 85 °F). Direct moisture measurements (e.g., according to Method 4) are also permissible.
Note:If burn rates exceed 3 kg/hr (6.6 lb/hr), dilution tunnel duct flow rates greater than 4 dscm/min (140 dscfm) and sampling section duct diameters larger than 150 mm (6 in.) are allowed. If larger ducts or flow rates are used, the sampling section velocity shall be at least 220 m/min (720 fpm). In order to ensure measurable particulate mass catch, it is recommended that the ratio of the average mass flow rate in the dilution tunnel to the average fuel burn rate be less than 150:1 if larger duct sizes or flow rates are used.
8.5.2 Testing Velocity Measurements. After obtaining velocity traverse results that meet the flow rate requirements, choose a point of average velocity and place the pitot and temperature sensor at that location in the duct. Alternatively, locate the pitot and the temperature sensor at the duct centroid and calculate a velocity correction factor for the centroidal position. Mount the pitot to ensure no movement during the test run and seal the port holes to prevent any air leakage. Align the pitot opening to be parallel with the duct axis at the measurement point. Check that this condition is maintained during the test run (about 30-minute intervals). Monitor the temperature and velocity during the pretest ignition period to ensure that the proper flow rate is maintained. Make adjustments to the dilution tunnel flow rate as necessary.
8.6 Pretest Preparation. Same as Method 5, section 8.1.
8.7 Preparation of Sampling Train. During preparation and assembly of the sampling train, keep all openings where contamination can occur covered until just prior to assembly or until sampling is about to begin.
Using a tweezer or clean disposable surgical gloves, place one labeled (identified) and weighed filter in each of the filter holders. Be sure that each filter is properly centered and that the gasket is properly placed so as to prevent the sample gas stream from circumventing the filter. Check each filter for tears after assembly is completed.
Mark the probe with heat resistant tape or by some other method to denote the proper distance into the stack or duct. Set up the train as shown in Figure 5G-1.
8.8 Leak-Check Procedures.
8.8.1 Leak-Check of Metering System Shown in Figure 5G-1. That portion of the sampling train from the pump to the orifice meter shall be leak-checked prior to initial use and after each certification or audit test. Leakage after the pump will result in less volume being recorded than is actually sampled. Use the procedure described in Method 5, section 8.4.1. Similar leak-checks shall be conducted for other types of metering systems (i.e., without orifice meters).
8.8.2 Pretest Leak-Check. A pretest leak-check of the sampling train is recommended, but not required. If the pretest leak check is conducted, the procedures outlined in Method 5, section 8.4.2 should be used. A vacuum of 130 mm Hg (5 in. Hg) may be used instead of 380 mm Hg (15 in. Hg).
8.8.3 Post-Test Leak-Check. A leak-check of the sampling train is mandatory at the conclusion of each test run. The leak-check shall be performed in accordance with the procedures outlined in Method 5, section 8.4.2. A vacuum of 130 mm Hg (5 in. Hg) or the highest vacuum measured during the test run, whichever is greater, may be used instead of 380 mm Hg (15 in. Hg).
8.9 Preliminary Determinations. Determine the pressure, temperature and the average velocity of the tunnel gases as in section 8.5. Moisture content of diluted tunnel gases is assumed to be 4 percent for making flow rate calculations; the moisture content may be measured directly as in Method 4.
8.10 Sampling Train Operation. Position the probe inlet at the stack centroid, and block off the openings around the probe and porthole to prevent unrepresentative dilution of the gas stream. Be careful not to bump the probe into the stack wall when removing or inserting the probe through the porthole; this minimizes the chance of extracting deposited material.
8.10.1 Begin sampling at the start of the test run as defined in Method 28, section 8.8.1. During the test run, maintain a sample flow rate proportional to the dilution tunnel flow rate (within 10 percent of the initial proportionality ratio) and a filter holder temperature of no greater than 32 °C (90 °F). The initial sample flow rate shall be approximately 0.015 m 3/min (0.5 cfm).
8.10.2 For each test run, record the data required on a data sheet such as the one shown in Figure 5G-3. Be sure to record the initial dry gas meter reading. Record the dry gas meter readings at the beginning and end of each sampling time increment and when sampling is halted. Take other readings as indicated on Figure 5G-3 at least once each 10 minutes during the test run. Since the manometer level and zero may drift because of vibrations and temperature changes, make periodic checks during the test run.
8.10.3 For the purposes of proportional sampling rate determinations, data from calibrated flow rate devices, such as glass rotameters, may be used in lieu of incremental dry gas meter readings. Proportional rate calculation procedures must be revised, but acceptability limits remain the same.
8.10.4 During the test run, make periodic adjustments to keep the temperature between (or upstream of) the filters at the proper level. Do not change sampling trains during the test run.
8.10.5 At the end of the test run (see Method 28, section 6.4.6), turn off the coarse adjust valve, remove the probe from the stack, turn off the pump, record the final dry gas meter reading, and conduct a post-test leak-check, as outlined in section 8.8.2. Also, leak-check the pitot lines as described in Method 2, section 8.1; the lines must pass this leak-check in order to validate the velocity head data.
8.11 Calculation of Proportional Sampling Rate. Calculate percent proportionality (see section 12.7) to determine whether the run was valid or another test run should be made.
8.12 Sample Recovery. Same as Method 5, section 8.7, with the exception of the following:
8.12.1 An acetone blank volume of about 50-ml or more may be used.
8.12.2 Treat the samples as follows:
8.12.2.1 Container Nos. 1 and 1A. Treat the two filters according to the procedures outlined in Method 5, section 8.7.6.1. The filters may be stored either in a single container or in separate containers. Use the sum of the filter tare weights to determine the sample mass collected.
8.12.2.3 Container No. 2.
8.12.2.3.1 Taking care to see that dust on the outside of the probe or other exterior surfaces does not get into the sample, quantitatively recover particulate matter or any condensate from the probe and filter holders by washing and brushing these components with acetone and placing the wash in a labeled glass container. At least three cycles of brushing and rinsing are required.
8.12.2.3.2 Between sampling runs, keep brushes clean and protected from contamination.
8.12.2.3.3 After all acetone washings and particulate matter have been collected in the sample containers, tighten the lids on the sample containers so that the acetone will not leak out when transferred to the laboratory weighing area. Mark the height of the fluid levels to determine whether leakage occurs during transport. Label the containers clearly to identify contents.
8.13 Sample Transport. Whenever possible, containers should be shipped in such a way that they remain upright at all times.
Note:Requirements for capping and transport of sample containers are not applicable if sample recovery and analysis occur in the same room.
9.0 Quality Control9.1 Miscellaneous Quality Control Measures.
Section | Quality control measure | Effect |
---|---|---|
8.8, 10.1-10.4 | Sampling equipment leak check and calibration | Ensures accurate measurement of stack gas flow rate, sample volume. |
10.5 | Analytical balance calibration | Ensure accurate and precise measurement of collected particulate. |
16.2.5 | Simultaneous, dual-train sample collection | Ensure precision of measured particulate concentration. |
9.2 Volume Metering System Checks. Same as Method 5, section 9.2.
10.0 Calibration and Standardization Note:Maintain a laboratory record of all calibrations.
10.1 Pitot Tube. The Type S pitot tube assembly shall be calibrated according to the procedure outlined in Method 2, section 10.1, prior to the first certification test and checked semiannually, thereafter. A standard pitot need not be calibrated but shall be inspected and cleaned, if necessary, prior to each certification test.
10.2 Volume Metering System.
10.2.1 Initial and Periodic Calibration. Before its initial use and at least semiannually thereafter, calibrate the volume metering system as described in Method 5, section 10.3.1, except that the wet test meter with a capacity of 3.0 liters/rev (0.1 ft 3/rev) may be used. Other liquid displacement systems accurate to within ±1 percent, may be used as calibration standards.
Note:Procedures and equipment specified in Method 5, section 16.0, for alternative calibration standards, including calibrated dry gas meters and critical orifices, are allowed for calibrating the dry gas meter in the sampling train. A dry gas meter used as a calibration standard shall be recalibrated at least once annually.
10.2.2 Calibration After Use. After each certification or audit test (four or more test runs conducted on a wood heater at the four burn rates specified in Method 28), check calibration of the metering system by performing three calibration runs at a single, intermediate flow rate as described in Method 5, section 10.3.2.
Note:Procedures and equipment specified in Method 5, section 16.0, for alternative calibration standards are allowed for the post-test dry gas meter calibration check.
10.2.3 Acceptable Variation in Calibration. If the dry gas meter coefficient values obtained before and after a certification test differ by more than 5 percent, the certification test shall either be voided and repeated, or calculations for the certification test shall be performed using whichever meter coefficient value (i.e., before or after) gives the lower value of total sample volume.
10.3 Temperature Sensors. Use the procedure in Method 2, section 10.3, to calibrate temperature sensors before the first certification or audit test and at least semiannually, thereafter.
10.4 Barometer. Calibrate against a mercury barometer before the first certification test and at least semiannually, thereafter. If a mercury barometer is used, no calibration is necessary. Follow the manufacturer's instructions for operation.
10.5 Analytical Balance. Perform a multipoint calibration (at least five points spanning the operational range) of the analytical balance before the first certification test and semiannually, thereafter. Before each certification test, audit the balance by weighing at least one calibration weight (class F) that corresponds to 50 to 150 percent of the weight of one filter. If the scale cannot reproduce the value of the calibration weight to within 0.1 mg, conduct the multipoint calibration before use.
11.0 Analytical Procedure11.1 Record the data required on a sheet such as the one shown in Figure 5G-4. Use the same analytical balance for determining tare weights and final sample weights.
11.2 Handle each sample container as follows:
11.2.1 Container Nos. 1 and 1A. Treat the two filters according to the procedures outlined in Method 5, section 11.2.1.
11.2.2 Container No. 2. Same as Method 5, section 11.2.2, except that the beaker may be smaller than 250 ml.
11.2.3 Acetone Blank Container. Same as Method 5, section 11.2.4, except that the beaker may be smaller than 250 ml.
12.0 Data Analysis and CalculationsCarry out calculations, retaining at least one extra significant figure beyond that of the acquired data. Round off figures after the final calculation. Other forms of the equations may be used as long as they give equivalent results.
12.1 Nomenclature.
Bws = Water vapor in the gas stream, proportion by volume (assumed to be 0.04). cs = Concentration of particulate matter in stack gas, dry basis, corrected to standard conditions, g/dscm (gr/dscf). E = Particulate emission rate, g/hr (lb/hr). Eadj = Adjusted particulate emission rate, g/hr (lb/hr). La = Maximum acceptable leakage rate for either a pretest or post-test leak-check, equal to 0.00057 m 3/min (0.020 cfm) or 4 percent of the average sampling rate, whichever is less. Lp = Leakage rate observed during the post-test leak-check, m 3/min (cfm). ma = Mass of residue of acetone blank after evaporation, mg. maw = Mass of residue from acetone wash after evaporation, mg. mn = Total amount of particulate matter collected, mg. Mw = Molecular weight of water, 18.0 g/g-mole (18.0 lb/lb-mole). Pbar = Barometric pressure at the sampling site, mm Hg (in. Hg). PR = Percent of proportional sampling rate. Ps = Absolute gas pressure in dilution tunnel, mm Hg (in. Hg). Pstd = Standard absolute pressure, 760 mm Hg (29.92 in. Hg). Qsd = Average gas flow rate in dilution tunnel, calculated as in Method 2, Equation 2-8, dscm/hr (dscf/hr). Tm = Absolute average dry gas meter temperature (see Figure 5G-3), °K (°R). Tmi = Absolute average dry gas meter temperature during each 10-minute interval, i, of the test run, °K (°R). Ts = Absolute average gas temperature in the dilution tunnel (see Figure 5G-3), °K (°R). Tsi = Absolute average gas temperature in the dilution tunnel during each 10 minute interval, i, of the test run, °K (°R). Tstd = Standard absolute temperature, 293 °K (528 °R). Va = Volume of acetone blank, ml. Vaw = Volume of acetone used in wash, ml. Vm = Volume of gas sample as measured by dry gas meter, dcm (dcf). Vmi = Volume of gas sample as measured by dry gas meter during each 10-minute interval, i, of the test run, dcm. Vm(std) = Volume of gas sample measured by the dry gas meter, corrected to standard conditions, dscm (dscf). Vs = Average gas velocity in the dilution tunnel, calculated by Method 2, Equation 2-7, m/sec (ft/sec). The dilution tunnel dry gas molecular weight may be assumed to be 29 g/g mole (lb/lb mole). Vsi = Average gas velocity in dilution tunnel during each 10-minute interval, i, of the test run, calculated by Method 2, Equation 2-7, m/sec (ft/sec). Y = Dry gas meter calibration factor. ΔH = Average pressure differential across the orifice meter, if used (see Figure 5G-2), mm H 2O (in. H 2O). U = Total sampling time, min. 10 = 10 minutes, length of first sampling period. 13.6 = Specific gravity of mercury. 100 = Conversion to percent.12.2 Dry Gas Volume. Same as Method 5, section 12.2, except that component changes are not allowable.
12.3 Solvent Wash Blank.
12.4 Total Particulate Weight. Determine the total particulate catch, mn, from the sum of the weights obtained from Container Nos. 1, 1A, and 2, less the acetone blank (see Figure 5G-4).
12.5 Particulate Concentration.
Where: K2 = 0.001 g/mg for metric units. = 0.0154 gr/mg for English units.12.6 Particulate Emission Rate.
Note:Particulate emission rate results produced using the sampling train described in section 6 and shown in Figure 5G-1 shall be adjusted for reporting purposes by the following method adjustment factor:
Where: K3 = constant, 1.82 for metric units. = constant, 0.643 for English units.12.7 Proportional Rate Variation. Calculate PR for each 10-minute interval, i, of the test run.
Alternate calculation procedures for proportional rate variation may be used if other sample flow rate data (e.g., orifice flow meters or rotameters) are monitored to maintain proportional sampling rates. The proportional rate variations shall be calculated for each 10-minute interval by comparing the stack to nozzle velocity ratio for each 10-minute interval to the average stack to nozzle velocity ratio for the test run. Proportional rate variation may be calculated for intervals shorter than 10 minutes with appropriate revisions to Equation 5G-5. If no more than 10 percent of the PR values for all the intervals exceed 90 percent ≤PR ≤110 percent, and if no PR value for any interval exceeds 80 percent ≤PR ≤120 percent, the results are acceptable. If the PR values for the test run are judged to be unacceptable, report the test run emission results, but do not include the results in calculating the weighted average emission rate, and repeat the test run.
13.0 Method Performance [Reserved] 14.0 Pollution Prevention [Reserved] 15.0 Waste Management [Reserved] 16.0 Alternative Procedures16.1 Method 5H Sampling Train. The sampling train and sample collection, recovery, and analysis procedures described in Method 5H, sections 6.1.1, 7.1, 7.2, 8.1, 8.10, 8.11, and 11.0, respectively, may be used in lieu of similar sections in Method 5G. Operation of the Method 5H sampling train in the dilution tunnel is as described in section 8.10 of this method. Filter temperatures and condenser conditions are as described in Method 5H. No adjustment to the measured particulate matter emission rate (Equation 5G-4, section 12.6) is to be applied to the particulate emission rate measured by this alternative method.
16.2 Dual Sampling Trains. Two sampling trains may be operated simultaneously at sample flow rates other than that specified in section 8.10, provided that the following specifications are met.
16.2.1 Sampling Train. The sampling train configuration shall be the same as specified in section 6.1.1, except the probe, filter, and filter holder need not be the same sizes as specified in the applicable sections. Filter holders of plastic materials such as Nalgene or polycarbonate materials may be used (the Gelman 1119 filter holder has been found suitable for this purpose). With such materials, it is recommended that solvents not be used in sample recovery. The filter face velocity shall not exceed 150 mm/sec (30 ft/min) during the test run. The dry gas meter shall be calibrated for the same flow rate range as encountered during the test runs. Two separate, complete sampling trains are required for each test run.
16.2.2 Probe Location. Locate the two probes in the dilution tunnel at the same level (see section 6.1.4.3). Two sample ports are necessary. Locate the probe inlets within the 50 mm (2 in.) diameter centroidal area of the dilution tunnel no closer than 25 mm (1 in.) apart.
16.2.3 Sampling Train Operation. Operate the sampling trains as specified in section 8.10, maintaining proportional sampling rates and starting and stopping the two sampling trains simultaneously. The pitot values as described in section 8.5.2 shall be used to adjust sampling rates in both sampling trains.
16.2.4 Recovery and Analysis of Sample. Recover and analyze the samples from the two sampling trains separately, as specified in sections 8.12 and 11.0, respectively.
16.2.4.1 For this alternative procedure, the probe and filter holder assembly may be weighed without sample recovery (use no solvents) described above in order to determine the sample weight gains. For this approach, weigh the clean, dry probe and filter holder assembly upstream of the front filter (without filters) to the nearest 0.1 mg to establish the tare weights. The filter holder section between the front and second filter need not be weighed. At the end of the test run, carefully clean the outside of the probe, cap the ends, and identify the sample (label). Remove the filters from the filter holder assemblies as described for container Nos. 1 and 1A in section 8.12.2.1. Reassemble the filter holder assembly, cap the ends, identify the sample (label), and transfer all the samples to the laboratory weighing area for final weighing. Requirements for capping and transport of sample containers are not applicable if sample recovery and analysis occur in the same room.
16.2.4.2 For this alternative procedure, filters may be weighed directly without a petri dish. If the probe and filter holder assembly are to be weighed to determine the sample weight, rinse the probe with acetone to remove moisture before desiccating prior to the test run. Following the test run, transport the probe and filter holder to the desiccator, and uncap the openings of the probe and the filter holder assembly. Desiccate for 24 hours and weigh to a constant weight. Report the results to the nearest 0.1 mg.
16.2.5 Calculations. Calculate an emission rate (Section 12.6) for the sample from each sampling train separately and determine the average emission rate for the two values. The two emission rates shall not differ by more than 7.5 percent from the average emission rate, or 7.5 percent of the weighted average emission rate limit in the applicable subpart of the regulations, whichever is greater. If this specification is not met, the results are unacceptable. Report the results, but do not include the results in calculating the weighted average emission rate. Repeat the test run until acceptable results are achieved, report the average emission rate for the acceptable test run, and use the average in calculating the weighted average emission rate.
17.0 ReferencesSame as Method 5, section 17.0, References 1 through 11, with the addition of the following:
1. Oregon Department of Environmental Quality. Standard Method for Measuring the Emissions and Efficiencies of Woodstoves. June 8, 1984. Pursuant to Oregon Administrative Rules Chapter 340, Division 21.
2. American Society for Testing and Materials. Proposed Test Methods for Heating Performance and Emissions of Residential Wood-fired Closed Combustion-Chamber Heating Appliances. E-6 Proposal P 180. August 1986.
18.0 Tables, Diagrams, Flowcharts, and Validation Data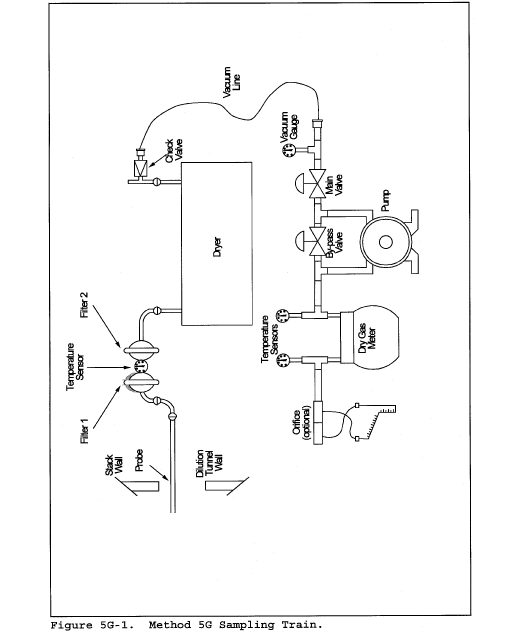
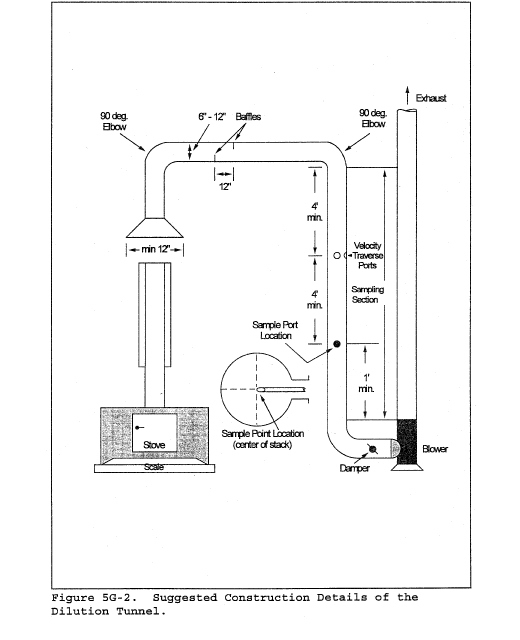
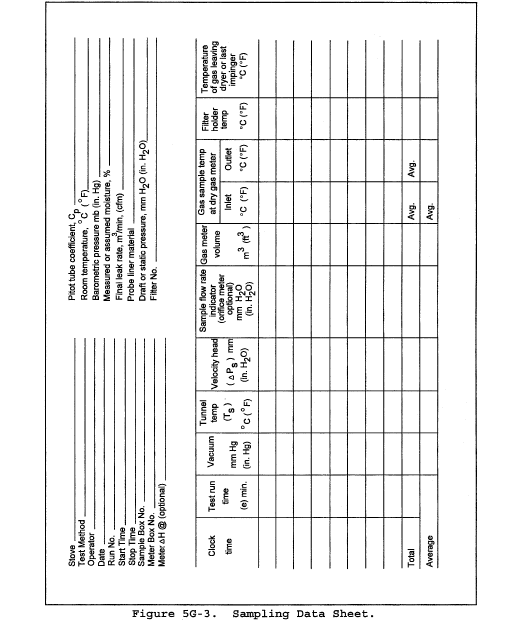
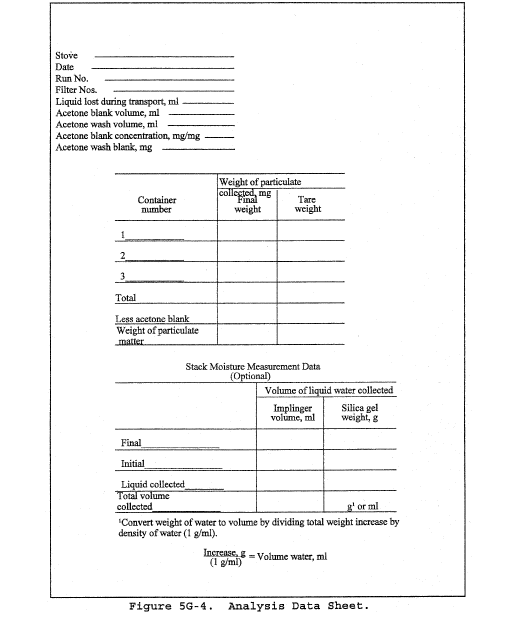
This method does not include all of the specifications (e.g., equipment and supplies) and procedures (e.g., sampling and analytical) essential to its performance. Some material is incorporated by reference from other methods in this part. Therefore, to obtain reliable results, persons using this method should have a thorough knowledge of at least the following additional test methods: Method 2, Method 3, Method 5, Method 5G, Method 6, Method 6C, Method 16A, and Method 28.
1.0 Scope and Application1.1 Analyte. Particulate matter (PM). No CAS number assigned.
1.2 Applicability. This method is applicable for the determination of PM and condensible emissions from wood heaters.
1.3 Data Quality Objectives. Adherence to the requirements of this method will enhance the quality of the data obtained from air pollutant sampling methods.
2.0 Summary of Method2.1 Particulate matter is withdrawn proportionally from the wood heater exhaust and is collected on two glass fiber filters separated by impingers immersed in an ice water bath. The first filter is maintained at a temperature of no greater than 120 °C (248 °F). The second filter and the impinger system are cooled such that the temperature of the gas exiting the second filter is no greater than 20 °C (68 °F). The particulate mass collected in the probe, on the filters, and in the impingers is determined gravimetrically after the removal of uncombined water.
3.0 DefinitionsSame as in Method 6C, section 3.0.
4.0 Interferences [Reserved] 5.0 Safety5.1 Disclaimer. This method may involve hazardous materials, operations, and equipment. This test method may not address all of the safety problems associated with its use. It is the responsibility of the user of this test method to establish appropriate safety and health practices and to determine the applicability of regulatory limitations prior to performing this test method.
6.0 Equipment and Supplies6.1 Sample Collection. The following items are required for sample collection:
6.1.1 Sampling Train. The sampling train configuration is shown in Figure 5H-1. Same as Method 5, section 6.1.1, with the exception of the following:
6.1.1.1 Probe Nozzle. The nozzle is optional; a straight sampling probe without a nozzle is an acceptable alternative.
6.1.1.2 Probe Liner. Same as Method 5, section 6.1.1.2, except that the maximum length of the sample probe shall be 0.6 m (2 ft) and probe heating is optional.
6.1.1.3 Filter Holders. Two each of borosilicate glass, with a glass frit or stainless steel filter support and a silicone rubber, Teflon, or Viton gasket. The holder design shall provide a positive seal against leakage from the outside or around the filter. The front filter holder shall be attached immediately at the outlet of the probe and prior to the first impinger. The second filter holder shall be attached on the outlet of the third impinger and prior to the inlet of the fourth (silica gel) impinger.
6.1.2 Barometer. Same as Method 5, section 6.2.
6.1.3 Stack Gas Flow Rate Measurement System. A schematic of an example test system is shown in Figure 5H-2. The flow rate measurement system consists of the following components:
6.1.3.1 Sample Probe. A glass or stainless steel sampling probe.
6.1.3.2 Gas Conditioning System. A high density filter to remove particulate matter and a condenser capable of lowering the dew point of the gas to less than 5 °C (40 °F). Desiccant, such as Drierite, may be used to dry the sample gas. Do not use silica gel.
6.1.3.3 Pump. An inert (e.g., Teflon or stainless steel heads) sampling pump capable of delivering more than the total amount of sample required in the manufacturer's instructions for the individual instruments. A means of controlling the analyzer flow rate and a device for determining proper sample flow rate (e.g., precision rotameter, pressure gauge downstream of all flow controls) shall be provided at the analyzer. The requirements for measuring and controlling the analyzer flow rate are not applicable if data are presented that demonstrate that the analyzer is insensitive to flow variations over the range encountered during the test.
6.1.3.4 Carbon Monoxide (CO) Analyzer. Any analyzer capable of providing a measure of CO in the range of 0 to 10 percent by volume at least once every 10 minutes.
6.1.3.5 Carbon Dioxide (CO2) Analyzer. Any analyzer capable of providing a measure of CO2 in the range of 0 to 25 percent by volume at least once every 10 minutes.
Note:Analyzers with ranges less than those specified above may be used provided actual concentrations do not exceed the range of the analyzer.
6.1.3.6 Manifold. A sampling tube capable of delivering the sample gas to two analyzers and handling an excess of the total amount used by the analyzers. The excess gas is exhausted through a separate port.
6.1.3.7 Recorders (optional). To provide a permanent record of the analyzer outputs.
6.1.4 Proportional Gas Flow Rate System. To monitor stack flow rate changes and provide a measurement that can be used to adjust and maintain particulate sampling flow rates proportional to the stack gas flow rate. A schematic of the proportional flow rate system is shown in Figure 5H-2 and consists of the following components:
6.1.4.1 Tracer Gas Injection System. To inject a known concentration of sulfur dioxide (SO2) into the flue. The tracer gas injection system consists of a cylinder of SO2, a gas cylinder regulator, a stainless steel needle valve or flow controller, a nonreactive (stainless steel and glass) rotameter, and an injection loop to disperse the SO2 evenly in the flue.
6.1.4.2 Sample Probe. A glass or stainless steel sampling probe.
6.1.4.3 Gas Conditioning System. A combustor as described in Method 16A, sections 6.1.5 and 6.1.6, followed by a high density filter to remove particulate matter, and a condenser capable of lowering the dew point of the gas to less than 5 °C (40 °F). Desiccant, such as Drierite, may be used to dry the sample gas. Do not use silica gel.
6.1.4.4 Pump. Same as described in section 6.1.3.3.
6.1.4.5 SO2 Analyzer. Any analyzer capable of providing a measure of the SO2 concentration in the range of 0 to 1,000 ppm by volume (or other range necessary to measure the SO2 concentration) at least once every 10 minutes.
6.1.4.6 Recorder (optional). To provide a permanent record of the analyzer outputs.
Note:Other tracer gas systems, including helium gas systems, are acceptable for determination of instantaneous proportional sampling rates.
6.2 Sample Recovery. Same as Method 5, section 6.2.
6.3 Sample Analysis. Same as Method 5, section 6.3, with the addition of the following:
6.3.1 Separatory Funnel. Glass or Teflon, 500-ml or greater.
7.0 Reagents and Standards7.1 Sample Collection. Same as Method 5, section 7.1, including deionized distilled water.
7.2 Sample Recovery. Same as Method 5, section 7.2.
7.3 Sample Analysis. The following reagents and standards are required for sample analysis:
7.3.1 Acetone. Same as Method 5 section 7.2.
7.3.2 Dichloromethane (Methylene Chloride). Reagent grade, <0.001 percent residue in glass bottles.
7.3.3 Desiccant. Anhydrous calcium sulfate, calcium chloride, or silica gel, indicating type.
7.3.4 Cylinder Gases. For the purposes of this procedure, span value is defined as the upper limit of the range specified for each analyzer as described in section 6.1.3.4 or 6.1.3.5. If an analyzer with a range different from that specified in this method is used, the span value shall be equal to the upper limit of the range for the analyzer used (see note in section 6.1.3.5).
7.3.4.1 Calibration Gases. The calibration gases for the CO2, CO, and SO2 analyzers shall be CO2 in nitrogen (N2), CO in N2, and SO2 in N2, respectively. CO2 and CO calibration gases may be combined in a single cylinder. Use three calibration gases as specified in Method 6C, sections 7.2.1 through 7.2.3.
7.3.4.2 SO2 Injection Gas. A known concentration of SO2 in N2. The concentration must be at least 2 percent SO2 with a maximum of 100 percent SO2.
8.0 Sample Collection, Preservation, Transport, and Storage8.1 Pretest Preparation. Same as Method 5, section 8.1.
8.2 Calibration Gas and SO2 Injection Gas Concentration Verification, Sampling System Bias Check, Response Time Test, and Zero and Calibration Drift Tests. Same as Method 6C, sections 8.2.1, 8.2.3, 8.2.4, and 8.5, respectively, except that for verification of CO and CO2 gas concentrations, substitute Method 3 for Method 6.
8.3 Preliminary Determinations.
8.3.1 Sampling Location. The sampling location for the particulate sampling probe shall be 2.45 ±0.15 m (8 ±0.5 ft) above the platform upon which the wood heater is placed (i.e., the top of the scale).
8.3.2 Sampling Probe and Nozzle. Select a nozzle, if used, sized for the range of velocity heads, such that it is not necessary to change the nozzle size in order to maintain proportional sampling rates. During the run, do not change the nozzle size. Select a suitable probe liner and probe length to effect minimum blockage.
8.4 Preparation of Particulate Sampling Train. Same as Method 5, section 8.3, with the exception of the following:
8.4.1 The train should be assembled as shown in Figure 5H-1.
8.4.2 A glass cyclone may not be used between the probe and filter holder.
8.5 Leak-Check Procedures.
8.5.1 Leak-Check of Metering System Shown in Figure 5H-1. That portion of the sampling train from the pump to the orifice meter shall be leak-checked after each certification or audit test. Use the procedure described in Method 5, section 8.4.1.
8.5.2 Pretest Leak-Check. A pretest leak-check of the sampling train is recommended, but not required. If the pretest leak-check is conducted, the procedures outlined in Method 5, section 8.5.2 should be used. A vacuum of 130 mm Hg (5 in. Hg) may be used instead of 380 mm Hg (15 in. Hg).
8.5.2 Leak-Checks During Sample Run. If, during the sampling run, a component (e.g., filter assembly or impinger) change becomes necessary, conduct a leak-check as described in Method 5, section 8.4.3.
8.5.3 Post-Test Leak-Check. A leak-check is mandatory at the conclusion of each sampling run. The leak-check shall be performed in accordance with the procedures outlined in Method 5, section 8.4.4, except that a vacuum of 130 mm Hg (5 in. Hg) or the greatest vacuum measured during the test run, whichever is greater, may be used instead of 380 mm Hg (15 in. Hg).
8.6 Tracer Gas Procedure. A schematic of the tracer gas injection and sampling systems is shown in Figure 5H-2.
8.6.1 SO2 Injection Probe. Install the SO2 injection probe and dispersion loop in the stack at a location 2.9 ±0.15 m (9.5 ±0.5 ft) above the sampling platform.
8.6.2 SO2 Sampling Probe. Install the SO2 sampling probe at the centroid of the stack at a location 4.1 ±0.15 m (13.5 ±0.5 ft) above the sampling platform.
8.7 Flow Rate Measurement System. A schematic of the flow rate measurement system is shown in Figure 5H-2. Locate the flow rate measurement sampling probe at the centroid of the stack at a location 2.3 ±0.3 m (7.5 ±1 ft) above the sampling platform.
8.8 Tracer Gas Procedure. Within 1 minute after closing the wood heater door at the start of the test run (as defined in Method 28, section 8.8.1), meter a known concentration of SO2 tracer gas at a constant flow rate into the wood heater stack. Monitor the SO2 concentration in the stack, and record the SO2 concentrations at 10-minute intervals or more often. Adjust the particulate sampling flow rate proportionally to the SO2 concentration changes using Equation 5H-6 (e.g., the SO2 concentration at the first 10-minute reading is measured to be 100 ppm; the next 10 minute SO2 concentration is measured to be 75 ppm: the particulate sample flow rate is adjusted from the initial 0.15 cfm to 0.20 cfm). A check for proportional rate variation shall be made at the completion of the test run using Equation 5H-10.
8.9 Volumetric Flow Rate Procedure. Apply stoichiometric relationships to the wood combustion process in determining the exhaust gas flow rate as follows:
8.9.1 Test Fuel Charge Weight. Record the test fuel charge weight (wet) as specified in Method 28, section 8.8.2. The wood is assumed to have the following weight percent composition: 51 percent carbon, 7.3 percent hydrogen, 41 percent oxygen. Record the wood moisture for each fuel charge as described in Method 28, section 8.6.5. The ash is assumed to have negligible effect on associated C, H, and O concentrations after the test burn.
8.9.2 Measured Values. Record the CO and CO2 concentrations in the stack on a dry basis every 10 minutes during the test run or more often. Average these values for the test run. Use as a mole fraction (e.g., 10 percent CO2 is recorded as 0.10) in the calculations to express total flow (see Equation 5H-6).
8.10 Sampling Train Operation.
8.10.1 For each run, record the data required on a data sheet such as the one shown in Figure 5H-3. Be sure to record the initial dry gas meter reading. Record the dry gas meter readings at the beginning and end of each sampling time increment, when changes in flow rates are made, before and after each leak-check, and when sampling is halted. Take other readings as indicated on Figure 5H-3 at least once each 10 minutes during the test run.
8.10.2 Remove the nozzle cap, verify that the filter and probe heating systems are up to temperature, and that the probe is properly positioned. Position the nozzle, if used, facing into gas stream, or the probe tip in the 50 mm (2 in.) centroidal area of the stack.
8.10.3 Be careful not to bump the probe tip into the stack wall when removing or inserting the probe through the porthole; this minimizes the chance of extracting deposited material.
8.10.4 When the probe is in position, block off the openings around the probe and porthole to prevent unrepresentative dilution of the gas stream.
8.10.5 Begin sampling at the start of the test run as defined in Method 28, section 8.8.1, start the sample pump, and adjust the sample flow rate to between 0.003 and 0.014 m 3/min (0.1 and 0.5 cfm). Adjust the sample flow rate proportionally to the stack gas flow during the test run according to the procedures outlined in section 8. Maintain a proportional sampling rate (within 10 percent of the desired value) and a filter holder temperature no greater than 120 °C (248 °F).
8.10.6 During the test run, make periodic adjustments to keep the temperature around the filter holder at the proper level. Add more ice to the impinger box and, if necessary, salt to maintain a temperature of less than 20 °C (68 °F) at the condenser/silica gel outlet.
8.10.7 If the pressure drop across the filter becomes too high, making proportional sampling difficult to maintain, either filter may be replaced during a sample run. It is recommended that another complete filter assembly be used rather than attempting to change the filter itself. Before a new filter assembly is installed, conduct a leak-check (see section 8.5.2). The total particulate weight shall include the summation of all filter assembly catches. The total time for changing sample train components shall not exceed 10 minutes. No more than one component change is allowed for any test run.
8.10.8 At the end of the test run, turn off the coarse adjust valve, remove the probe and nozzle from the stack, turn off the pump, record the final dry gas meter reading, and conduct a post-test leak-check, as outlined in section 8.5.3.
8.11 Sample Recovery. Same as Method 5, section 8.7, with the exception of the following:
8.11.1 Blanks. The volume of the acetone blank may be about 50-ml, rather than 200-ml; a 200-ml water blank shall also be saved for analysis.
8.11.2 Samples.
8.11.2.1 Container Nos. 1 and 1A. Treat the two filters according to the procedures outlined in Method 5, section 8.7.6.1. The filters may be stored either in a single container or in separate containers.
8.11.2.2 Container No. 2. Same as Method 5, section 8.7.6.2, except that the container should not be sealed until the impinger rinse solution is added (see section 8.10.2.4).
8.11.2.3 Container No. 3. Treat the impingers as follows: Measure the liquid which is in the first three impingers to within 1-ml by using a graduated cylinder or by weighing it to within 0.5 g by using a balance (if one is available). Record the volume or weight of liquid present. This information is required to calculate the moisture content of the effluent gas. Transfer the water from the first, second, and third impingers to a glass container. Tighten the lid on the sample container so that water will not leak out.
8.11.2.4 Rinse impingers and graduated cylinder, if used, with acetone three times or more. Avoid direct contact between the acetone and any stopcock grease or collection of any stopcock grease in the rinse solutions. Add these rinse solutions to sample Container No. 2.
8.11.2.5 Container No. 4. Same as Method 5, section 8.7.6.3
8.12 Sample Transport. Whenever possible, containers should be transferred in such a way that they remain upright at all times.
Note:Requirements for capping and transport of sample containers are not applicable if sample recovery and analysis occur in the same room.
9.0 Quality Control9.1 Miscellaneous Quality Control Measures.
Section | Quality control measure | Effect |
---|---|---|
8.2 | Sampling system bias check | Ensures that bias introduced by measurement system, minus analyzer, is no greater than 3 percent of span. |
8.2 | Analyzer zero and calibration drift tests | Ensures that bias introduced by drift in the measurement system output during the run is no greater than 3 percent of span. |
8.5, 10.1, 12.13 | Sampling equipment leak-check and calibration; proportional sampling rate verification | Ensures accurate measurement of stack gas flow rate, sample volume. |
10.1 | Analytical balance calibration | Ensure accurate and precise measurement of collected particulate. |
10.3 | Analyzer calibration error check | Ensures that bias introduced by analyzer calibration error is no greater than 2 percent of span. |
9.2 Volume Metering System Checks. Same as Method 5, section 9.2.
10.0 Calibration and Standardization Note:Maintain a laboratory record of all calibrations.
10.1 Volume Metering System, Temperature Sensors, Barometer, and Analytical Balance. Same as Method 5G, sections 10.2 through 10.5, respectively.
10.2 SO2 Injection Rotameter. Calibrate the SO2 injection rotameter system with a soap film flowmeter or similar direct volume measuring device with an accuracy of 2 percent. Operate the rotameter at a single reading for at least three calibration runs for 10 minutes each. When three consecutive calibration flow rates agree within 5 percent, average the three flow rates, mark the rotameter at the calibrated setting, and use the calibration flow rate as the SO2 injection flow rate during the test run. Repeat the rotameter calibration before the first certification test and semiannually thereafter.
10.3. Gas Analyzers. Same as Method 6C, section 10.0.
10.4 Field Balance Calibration Check. Check the calibration of the balance used to weigh impingers with a weight that is at least 500g or within 50g of a loaded impinger. The weight must be ASTM E617-13 “Standard Specification for Laboratory Weights and Precision Mass Standards” (incorporated by reference - see 40 CFR 60.17) Class 6 (or better). Daily before use, the field balance must measure the weight within ± 0.5g of the certified mass. If the daily balance calibration check fails, perform corrective measures and repeat the check before using balance.
10.5 Analytical Balance Calibration. Perform a multipoint calibration (at least five points spanning the operational range) of the analytical balance before the first use, and semiannually thereafter. The calibration of the analytical balance must be conducted using ASTM E617-13 “Standard Specification for Laboratory Weights and Precision Mass Standards” (incorporated by reference - see 40 CFR 60.17) Class 2 (or better) tolerance weights. Audit the balance each day it is used for gravimetric measurements by weighing at least one ASTM E617-13 Class 2 tolerance (or better) calibration weight that corresponds to 50 to 150 percent of the weight of one filter or between 1g and 5g. If the scale cannot reproduce the value of the calibration weight to within 0.5 mg of the certified mass, perform corrective measures, and conduct the multipoint calibration before use.
11.0 Analytical Procedure11.1 Record the data required on a sheet such as the one shown in Figure 5H-4.
11.2 Handle each sample container as follows:
11.2.1 Container Nos. 1 and 1A. Treat the two filters according to the procedures outlined in Method 5, section 11.2.1.
11.2.2 Container No. 2. Same as Method 5, section 11.2.2, except that the beaker may be smaller than 250-ml.
11.2.3 Container No. 3. Note the level of liquid in the container and confirm on the analysis sheet whether leakage occurred during transport. If a noticeable amount of leakage has occurred, either void the sample or use methods, subject to the approval of the Administrator, to correct the final results. Determination of sample leakage is not applicable if sample recovery and analysis occur in the same room. Measure the liquid in this container either volumetrically to within 1-ml or gravimetrically to within 0.5 g. Transfer the contents to a 500-ml or larger separatory funnel. Rinse the container with water, and add to the separatory funnel. Add 25-ml of dichloromethane to the separatory funnel, stopper and vigorously shake 1 minute, let separate and transfer the dichloromethane (lower layer) into a tared beaker or evaporating dish. Repeat twice more. It is necessary to rinse Container No. 3 with dichloromethane. This rinse is added to the impinger extract container. Transfer the remaining water from the separatory funnel to a tared beaker or evaporating dish and evaporate to dryness at 104 °C (220 °F). Desiccate and weigh to a constant weight. Evaporate the combined impinger water extracts at ambient temperature and pressure. Desiccate and weigh to a constant weight. Report both results to the nearest 0.1 mg.
11.2.4 Container No. 4. Weigh the spent silica gel (or silica gel plus impinger) to the nearest 0.5 g using a balance.
11.2.5 Acetone Blank Container. Same as Method 5, section 11.2.4, except that the beaker may be smaller than 250 ml.
11.2.6 Dichloromethane Blank Container. Treat the same as the acetone blank.
11.2.7 Water Blank Container. Transfer the water to a tared 250 ml beaker and evaporate to dryness at 104 °C (220 °F). Desiccate and weigh to a constant weight.
12.0 Data Analysis and CalculationsCarry out calculations, retaining at least one extra significant figure beyond that of the acquired data. Round off figures after the final calculation. Other forms of the equations may be used as long as they give equivalent results.
12.1 Nomenclature.
A = Sample flow rate adjustment factor. BR = Dry wood burn rate, kg/hr (lb/hr), from Method 28, Section 8.3. Bws = Water vapor in the gas stream, proportion by volume. Ci = Tracer gas concentration at inlet, ppmv. Co = Tracer gas concentration at outlet, ppmv. Cs = Concentration of particulate matter in stack gas, dry basis, corrected to standard conditions, g/dscm (g/dscf). E = Particulate emission rate, g/hr (lb/hr). ΔH = Average pressure differential across the orifice meter (see Figure 5H-1), mm H2O (in. H2O). La = Maximum acceptable leakage rate for either a post-test leak-check or for a leak-check following a component change; equal to 0.00057 cmm (0.020 cfm) or 4 percent of the average sampling rate, whichever is less. L1 = Individual leakage rate observed during the leak-check conducted before a component change, cmm (cfm). Lp = Leakage rate observed during the post-test leak-check, cmm (cfm). mn = Total amount of particulate matter collected, mg. Ma = Mass of residue of solvent after evaporation, mg. NC = Grams of carbon/gram of dry fuel (lb/lb), equal to 0.0425. NT = Total dry moles of exhaust gas/kg of dry wood burned, g-moles/kg (lb-moles/lb). PR = Percent of proportional sampling rate. Pbar = Barometric pressure at the sampling site, mm Hg (in.Hg). Pstd = Standard absolute pressure, 760 mm Hg (29.92 in.Hg). Qi = Gas volumetric flow rate at inlet, cfm (l/min). Qo = Gas volumetric flow rate at outlet, cfm (l/min).12.2 Average Dry Gas Meter Temperature and Average Orifice Pressure Drop. See data sheet (Figure 5H-3).
12.3 Dry Gas Volume. Same as Method 5, section 12.3.
12.4 Volume of Water Vapor.
Where: K2 = 0.001333 m 3/ml for metric units. K2 = 0.04707 ft 3/ml for English units.12.5 Moisture Content.
12.6 Solvent Wash Blank.
12.7 Total Particulate Weight. Determine the total particulate catch from the sum of the weights obtained from containers 1, 2, 3, and 4 less the appropriate solvent blanks (see Figure 5H-4).
Note:Refer to Method 5, section 8.5 to assist in calculation of results involving two filter assemblies.
12.8 Particulate Concentration.
12.9 Sample Flow Rate Adjustment.
12.10 Carbon Balance for Total Moles of Exhaust Gas (dry)/kg of Wood Burned in the Exhaust Gas.
Where: K3 = 1000 g/kg for metric units. K3 = 1.0 lb/lb for English units. Note:The NOX/SOX portion of the gas is assumed to be negligible.
12.11 Total Stack Gas Flow Rate.
Where: K4 = 0.02406 dscm/g-mole for metric units. K4 = 384.8 dscf/lb-mole for English units.12.12 Particulate Emission Rate.
12.13 Proportional Rate Variation. Calculate PR for each 10-minute interval, i, of the test run.
12.14 Acceptable Results. If no more than 15 percent of the PR values for all the intervals fall outside the range 90 percent ≤PR ≤110 percent, and if no PR value for any interval falls outside the range 75 ≤PR ≤125 percent, the results are acceptable. If the PR values for the test runs are judged to be unacceptable, report the test run emission results, but do not include the test run results in calculating the weighted average emission rate, and repeat the test.
12.15 Alternative Tracer Gas Flow Rate Determination.

This gives Q for a single instance only. Repeated multiple determinations are needed to track temporal variations. Very small variations in Qi, Ci, or Co may give very large variations in Qo.
13.0 Method Performance [Reserved] 14.0 Pollution Prevention [Reserved] 15.0 Waste Management [Reserved] 16.0 Alternative Procedures16.1 Alternative Stack Gas Volumetric Flow Rate Determination (Tracer Gas).
16.1.1 Apparatus.
16.1.1.1 Tracer Gas Injector System. This is to inject a known concentration of tracer gas into the stack. This system consists of a cylinder of tracer gas, a gas cylinder regulator, a stainless steel needle valve or a flow controller, a nonreactive (stainless steel or glass) rotameter, and an injection loop to disperse the tracer gas evenly in the stack.
16.1.1.2 Tracer Gas Probe. A glass or stainless steel sampling probe.
16.1.1.3 Gas Conditioning System. A gas conditioning system is suitable for delivering a cleaned sample to the analyzer consisting of a filter to remove particulate and a condenser capable of lowering the dew point of the sample gas to less than 5 °C (40 °F). A desiccant such as anhydrous calcium sulfate may be used to dry the sample gas. Desiccants which react or absorb tracer gas or stack gas may not be used, e.g. silica gel absorbs CO2.
16.1.1.4 Pump. An inert (i.e., stainless steel or Teflon head) pump to deliver more than the total sample required by the manufacturer's specifications for the analyzer used to measure the downstream tracer gas concentration.
16.1.1.5 Gas Analyzer. A gas analyzer is any analyzer capable of measuring the tracer gas concentration in the range necessary at least every 10 minutes. A means of controlling the analyzer flow rate and a device for determining proper sample flow rate shall be provided unless data is provided to show that the analyzer is insensitive to flow variations over the range encountered during the test. The gas analyzer needs to meet or exceed the following performance specifications:
Linearity | ±1 percent of full scale. |
Calibration Error | ≤2 percent of span. |
Response Time | ≤10 seconds. |
Zero Drift (24 hour) | ≤2 percent of full scale. |
Span Drift (24 hour) | ≤2 percent of full scale. |
Resolution | ≤0.5 percent of span. |
16.1.1.6 Recorder (optional). To provide a permanent record of the analyzer output.
16.1.2 Reagents.
16.1.2.1 Tracer Gas. The tracer gas is sulfur hexafluoride in an appropriate concentration for accurate analyzer measurement or pure sulfur dioxide. The gas used must be nonreactive with the stack effluent and give minimal (<3 percent) interference to measurement by the gas analyzer.
16.1.3 Procedure. Select upstream and downstream locations in the stack or duct for introducing the tracer gas and delivering the sampled gas to the analyzer. The inlet location should be 8 or more duct diameters beyond any upstream flow disturbance. The outlet should be 8 or more undisturbed duct diameters from the inlet and 2 or more duct diameters from the duct exit. After installing the apparatus, meter a known concentration of the tracer gas into the stack at the inlet location. Use the gas sample probe and analyzer to show that no stratification of the tracer gas is found in the stack at the measurement locations. Monitor the tracer gas concentration from the outlet location and record the concentration at 10-minute intervals or more often at the option of the tester. A minimum of three measured intervals is recommended to determine the stack gas volumetric flow rate. Other statistical procedures may be applied for complete flow characterization and additional QA/QC.
17.0 ReferencesSame as Method 5G, section 17.0.
18.0 Tables, Diagrams, Flowcharts, and Validation Data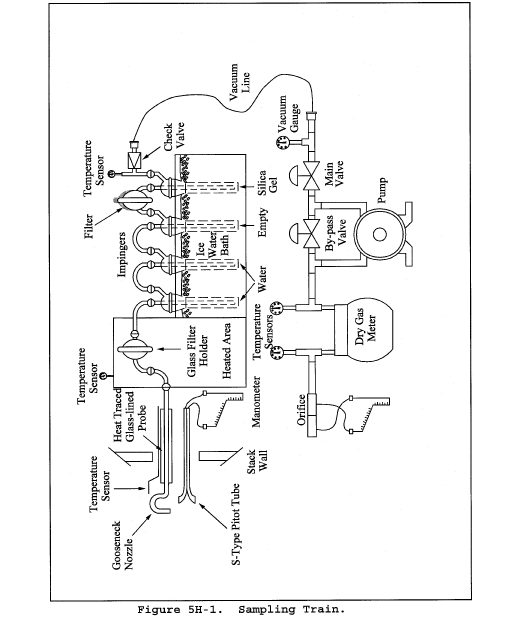
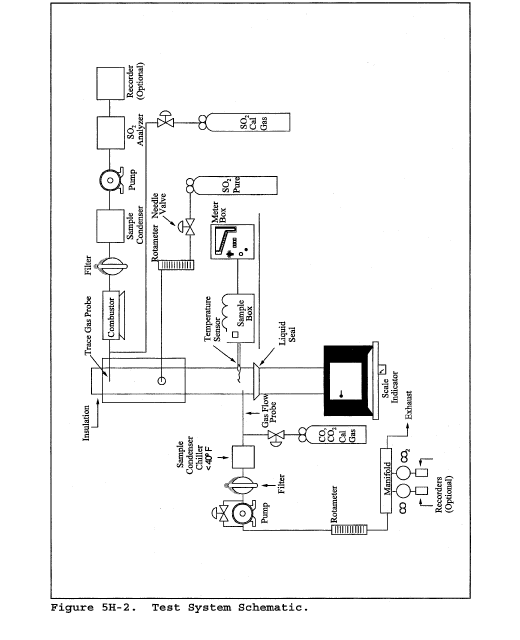
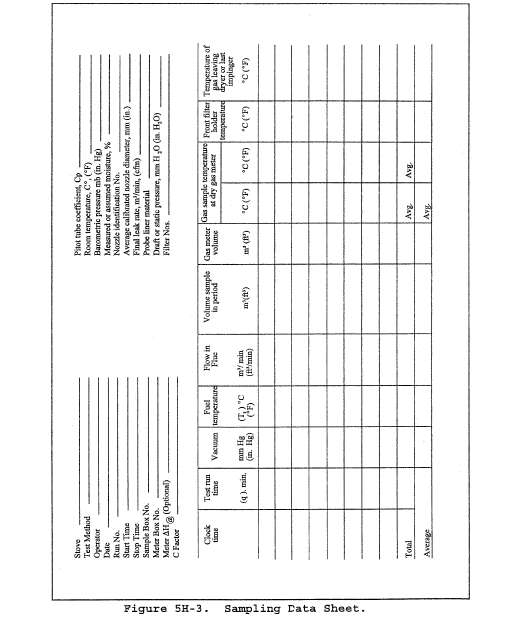
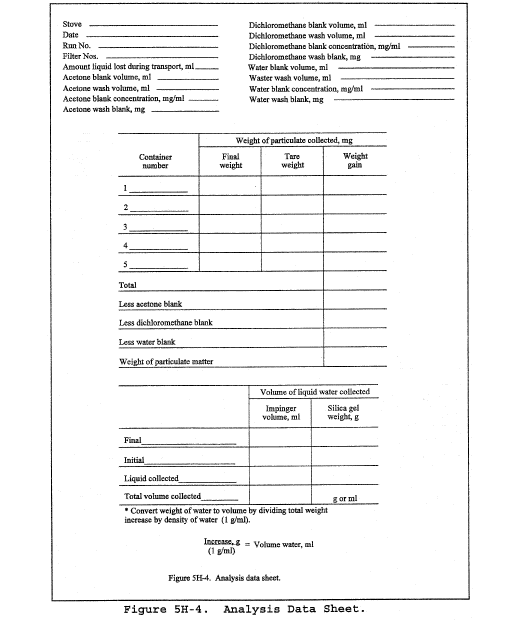
This method does not include all of the specifications (e.g., equipment and supplies) and procedures (e.g., sampling and analytical) essential to its performance. Certain information is contained in other EPA procedures found in this part. Therefore, to obtain reliable results, persons using this method should have experience with and a thorough knowledge of the following Methods: Methods 1, 2, 3, 4 and 5.
1. Scope and Application.1.1 Analyte. Particulate matter (PM). No CAS number assigned.
1.2 Applicability. This method is applicable for the determination of low level particulate matter (PM) emissions from stationary sources. The method is most effective for total PM catches of 50 mg or less. This method was initially developed for performing correlation of manual PM measurements to PM continuous emission monitoring systems (CEMS), however it is also useful for other low particulate concentration applications.
1.3 Data Quality Objectives. Adherence to the requirements of this method will enhance the quality of the data obtained from air pollutant sampling methods. Method 5I requires the use of paired trains. Acceptance criteria for the identification of data quality outliers from the paired trains are provided in section 12.2 of this Method.
2. Summary of Method.2.1. Description. The system setup and operation is essentially identical to Method 5. Particulate is withdrawn isokinetically from the source and collected on a 47 mm glass fiber filter maintained at a temperature of 120 ±14 °C (248 ±25 °F). The PM mass is determined by gravimetric analysis after the removal of uncombined water. Specific measures in this procedure designed to improve system performance at low particulate levels include:
1. Improved sample handling procedures 2 Light weight sample filter assembly 3. Use of low residue grade acetone Accuracy is improved through the minimization of systemic errors associated with sample handling and weighing procedures. High purity reagents, all glass, grease free, sample train components, and light weight filter assemblies and beakers, each contribute to the overall objective of improved precision and accuracy at low particulate concentrations.2.2 Paired Trains. This method must be performed using a paired train configuration. These trains may be operated as co-located trains (to trains operating collecting from one port) or as simultaneous trains (separate trains operating from different ports at the same time). Procedures for calculating precision of the paired trains are provided in section 12.
2.3 Detection Limit. a. Typical detection limit for manual particulate testing is 0.5 mg. This mass is also cited as the accepted weight variability limit in determination of “constant weight” as cited in section 8.1.2 of this Method. EPA has performed studies to provide guidance on minimum PM catch. The minimum detection limit (MDL) is the minimum concentration or amount of an analyte that can be determined with a specified degree of confidence to be different from zero. We have defined the minimum or target catch as a concentration or amount sufficiently larger than the MDL to ensure that the results are reliable and repeatable. The particulate matter catch is the product of the average particulate matter concentration on a mass per volume basis and the volume of gas collected by the sample train. The tester can generally control the volume of gas collected by increasing the sampling time or to a lesser extent by increasing the rate at which sample is collected. If the tester has a reasonable estimate of the PM concentration from the source, the tester can ensure that the target catch is collected by sampling the appropriate gas volume.
b. However, if the source has a very low particulate matter concentration in the stack, the volume of gas sampled may need to be very large which leads to unacceptably long sampling times. When determining compliance with an emission limit, EPA guidance has been that the tester does not always have to collect the target catch. Instead, we have suggested that the tester sample enough stack gas, that if the source were exactly at the level of the emission standard, the sample catch would equal the target catch. Thus, if at the end of the test the catch were smaller than the target, we could still conclude that the source is in compliance though we might not know the exact emission level. This volume of gas becomes a target volume that can be translated into a target sampling time by assuming an average sampling rate. Because the MDL forms the basis for our guidance on target sampling times, EPA has conducted a systematic laboratory study to define what is the MDL for Method 5 and determined the Method to have a calculated practical quantitation limit (PQL) of 3 mg of PM and an MDL of 1 mg.
c. Based on these results, the EPA has concluded that for PM testing, the target catch must be no less than 3 mg. Those sample catches between 1 mg and 3 mg are between the detection limit and the limit of quantitation. If a tester uses the target catch to estimate a target sampling time that results in sample catches that are less than 3 mg, you should not automatically reject the results. If the tester calculated the target sampling time as described above by assuming that the source was at the level of the emission limit, the results would still be valid for determining that the source was in compliance. For purposes other than determining compliance, results should be divided into two categories - those that fall between 3 mg and 1 mg and those that are below 1 mg. A sample catch between 1 and 3 mg may be used for such purposes as calculating emission rates with the understanding that the resulting emission rates can have a high degree of uncertainty. Results of less than 1 mg should not be used for calculating emission rates or pollutant concentrations.
d. When collecting small catches such as 3 mg, bias becomes an important issue. Source testers must use extreme caution to reach the PQL of 3 mg by assuring that sampling probes are very clean (perhaps confirmed by low blank weights) before use in the field. They should also use low tare weight sample containers, and establish a well-controlled balance room to weigh the samples.
3. Definitions.3.1 Light Weight Filter Housing. A smaller housing that allows the entire filtering system to be weighed before and after sample collection. (See. 6.1.3)
3.2 Paired Train. Sample systems trains may be operated as co-located trains (two sample probes attached to each other in the same port) or as simultaneous trains (two separate trains operating from different ports at the same time).
4. Interferences.a. There are numerous potential interferents that may be encountered during performance of Method 5I sampling and analyses. This Method should be considered more sensitive to the normal interferents typically encountered during particulate testing because of the low level concentrations of the flue gas stream being sampled.
b. Care must be taken to minimize field contamination, especially to the filter housing since the entire unit is weighed (not just the filter media). Care must also be taken to ensure that no sample is lost during the sampling process (such as during port changes, removal of the filter assemblies from the probes, etc.).
c. Balance room conditions are a source of concern for analysis of the low level samples. Relative humidity, ambient temperatures variations, air draft, vibrations and even barometric pressure can affect consistent reproducible measurements of the sample media. Ideally, the same analyst who performs the tare weights should perform the final weights to minimize the effects of procedural differences specific to the analysts.
d. Attention must also be provided to weighing artifacts caused by electrostatic charges which may have to be discharged or neutralized prior to sample analysis. Static charge can affect consistent and reliable gravimetric readings in low humidity environments. Method 5I recommends a relative humidity of less than 50 percent in the weighing room environment used for sample analyses. However, lower humidity may be encountered or required to address sample precision problems. Low humidity conditions can increase the effects of static charge.
e. Other interferences associated with typical Method 5 testing (sulfates, acid gases, etc.) are also applicable to Method 5I.
5. Safety.Disclaimer. This method may involve hazardous materials, operations, and equipment. This test method may not address all of the safety concerns associated with its use. It is the responsibility of the user to establish appropriate safety and health practices and to determine the applicability and observe all regulatory limitations before using this method.
6. Equipment and Supplies.6.1 Sample Collection Equipment and Supplies. The sample train is nearly identical in configuration to the train depicted in Figure 5-1 of Method 5. The primary difference in the sample trains is the lightweight Method 5I filter assembly that attaches directly to the exit to the probe. Other exceptions and additions specific to Method 5I include:
6.1.1 Probe Nozzle. Same as Method 5, with the exception that it must be constructed of borosilicate or quartz glass tubing.
6.1.2 Probe Liner. Same as Method 5, with the exception that it must be constructed of borosilicate or quartz glass tubing.
6.1.3 Filter Holder. The filter holder is constructed of borosilicate or quartz glass front cover designed to hold a 47-mm glass fiber filter, with a wafer thin stainless steel (SS) filter support, a silicone rubber or Viton O-ring, and Teflon tape seal. This holder design will provide a positive seal against leakage from the outside or around the filter. The filter holder assembly fits into a SS filter holder and attaches directly to the outlet of the probe. The tare weight of the filter, borosilicate or quartz glass holder, SS filter support, O-ring and Teflon tape seal generally will not exceed approximately 35 grams. The filter holder is designed to use a 47-mm glass fiber filter meeting the quality criteria in of Method 5. These units are commercially available from several source testing equipment vendors. Once the filter holder has been assembled, desiccated and tared, protect it from external sources of contamination by covering the front socket with a ground glass plug. Secure the plug with an impinger clamp or other item that will ensure a leak-free fitting.
6.2 Sample Recovery Equipment and Supplies. Same as Method 5, with the following exceptions:
6.2.1 Probe-Liner and Probe-Nozzle Brushes. Teflon or nylon bristle brushes with stainless steel wire handles, should be used to clean the probe. The probe brush must have extensions (at least as long as the probe) of Teflon, nylon or similarly inert material. The brushes must be properly sized and shaped for brushing out the probe liner and nozzle.
6.2.2 Wash Bottles. Two Teflon wash bottles are recommended however, polyethylene wash bottles may be used at the option of the tester. Acetone should not be stored in polyethylene bottles for longer than one month.
6.2.3 Filter Assembly Transport. A system should be employed to minimize contamination of the filter assemblies during transport to and from the field test location. A carrying case or packet with clean compartments of sufficient size to accommodate each filter assembly can be used. This system should have an air tight seal to further minimize contamination during transport to and from the field.
6.3 Analysis Equipment and Supplies. Same as Method 5, with the following exception:
6.3.1 Lightweight Beaker Liner. Teflon or other lightweight beaker liners are used for the analysis of the probe and nozzle rinses. These light weight liners are used in place of the borosilicate glass beakers typically used for the Method 5 weighings in order to improve sample analytical precision.
6.3.2 Anti-static Treatment. Commercially available gaseous anti-static rinses are recommended for low humidity situations that contribute to static charge problems.
7. Reagents and Standards.7.1 Sampling Reagents. The reagents used in sampling are the same as Method 5 with the following exceptions:
7.1.1 Filters. The quality specifications for the filters are identical to those cited for Method 5. The only difference is the filter diameter of 47 millimeters.
7.1.2 Stopcock Grease. Stopcock grease cannot be used with this sampling train. We recommend that the sampling train be assembled with glass joints containing O-ring seals or screw-on connectors, or similar.
7.1.3 Acetone. Low residue type acetone, ≤0.001 percent residue, purchased in glass bottles is used for the recovery of particulate matter from the probe and nozzle. Acetone from metal containers generally has a high residue blank and should not be used. Sometimes, suppliers transfer acetone to glass bottles from metal containers; thus, acetone blanks must be run prior to field use and only acetone with low blank values (≤0.001 percent residue, as specified by the manufacturer) must be used. Acetone blank correction is not allowed for this method; therefore, it is critical that high purity reagents be purchased and verified prior to use.
7.1.4 Gloves. Disposable, powder-free, latex surgical gloves, or their equivalent are used at all times when handling the filter housings or performing sample recovery.
7.2 Standards. There are no applicable standards commercially available for Method 5I analyses.
8. Sample Collection, Preservation, Storage, and Transport.8.1 Pretest Preparation. Same as Method 5 with several exceptions specific to filter assembly and weighing.
8.1.1 Filter Assembly. Uniquely identify each filter support before loading filters into the holder assembly. This can be done with an engraving tool or a permanent marker. Use powder free latex surgical gloves whenever handling the filter holder assemblies. Place the O-ring on the back of the filter housing in the O-ring groove. Place a 47 mm glass fiber filter on the O-ring with the face down. Place a stainless steel filter holder against the back of the filter. Carefully wrap 5 mm ( 1/4 inch) wide Teflon” tape one timearound the outside of the filter holder overlapping the stainless steel filter support by approximately 2.5 mm ( 1/8 inch). Gently brush the Teflon tape down on the back of the stainless steel filter support. Store the filter assemblies in their transport case until time for weighing or field use.
8.1.2 Filter Weighing Procedures. a. Desiccate the entire filter holder assemblies at 20 ±5.6 °C (68 ±10 °F) and ambient pressure for at least 24 hours. Weigh at intervals of at least 6 hours to a constant weight, i.e., 0.5 mg change from previous weighing. Record the results to the nearest 0.1 mg. During each weighing, the filter holder assemblies must not be exposed to the laboratory atmosphere for a period greater than 2 minutes and a relative humidity above 50 percent. Lower relative humidity may be required in order to improve analytical precision. However, low humidity conditions increase static charge to the sample media.
b. Alternatively (unless otherwise specified by the Administrator), the filters holder assemblies may be oven dried at 105 °C (220 °F) for a minimum of 2 hours, desiccated for 2 hours, and weighed. The procedure used for the tare weigh must also be used for the final weight determination.
c. Experience has shown that weighing uncertainties are not only related to the balance performance but to the entire weighing procedure. Therefore, before performing any measurement, establish and follow standard operating procedures, taking into account the sampling equipment and filters to be used.
8.2 Preliminary Determinations. Select the sampling site, traverse points, probe nozzle, and probe length as specified in Method 5.
8.3 Preparation of Sampling Train. Same as Method 5, section 8.3, with the following exception: During preparation and assembly of the sampling train, keep all openings where contamination can occur covered until justbefore assembly or until sampling is about to begin. Using gloves, place a labeled (identified) and weighed filter holder assembly into the stainless steel holder. Then place this whole unit in the Method 5 hot box, and attach it to the probe. Do not use stopcock grease.
8.4 Leak-Check Procedures. Same as Method 5.
8.5 Sampling Train Operation.
8.5.1. Operation. Operate the sampling train in a manner consistent with those described in Methods 1, 2, 4 and 5 in terms of the number of sample points and minimum time per point. The sample rate and total gas volume should be adjusted based on estimated grain loading of the source being characterized. The total sampling time must be a function of the estimated mass of particulate to be collected for the run. Targeted mass to be collected in a typical Method 5I sample train should be on the order of 10 to 20 mg. Method 5I is most appropriate for total collected masses of less than 50 milligrams, however, there is not an exact particulate loading cutoff, and it is likely that some runs may exceed 50 mg. Exceeding 50 mg (or less than 10 mg) for the sample mass does not necessarily justify invalidating a sample run if all other Method criteria are met.
8.5.2 Paired Train. This Method requires PM samples be collected with paired trains.
8.5.2.1 It is important that the systems be operated truly simultaneously. This implies that both sample systems start and stop at the same times. This also means that if one sample system is stopped during the run, the other sample systems must also be stopped until the cause has been corrected.
8.5.2.2 Care should be taken to maintain the filter box temperature of the paired trains as close as possible to the Method required temperature of 120 ±14 °C (248 ±25 °F). If separate ovens are being used for simultaneously operated trains, it is recommended that the oven temperature of each train be maintained within ±14 °C (±25 °F) of each other.
8.5.2.3 The nozzles for paired trains need not be identically sized.
8.5.2.4 Co-located sample nozzles must be within the same plane perpendicular to the gas flow. Co-located nozzles and pitot assemblies should be within a 6.0 cm × 6.0 cm square (as cited for a quadruple train in Reference Method 301).
8.5.3 Duplicate gas samples for molecular weight determination need not be collected.
8.6 Sample Recovery. Same as Method 5 with several exceptions specific to the filter housing.
8.6.1 Before moving the sampling train to the cleanup site, remove the probe from the train and seal the nozzle inlet and outlet of the probe. Be careful not to lose any condensate that might be present. Cap the filter inlet using a standard ground glass plug and secure the cap with an impinger clamp. Remove the umbilical cord from the last impinger and cap the impinger. If a flexible line is used between the first impinger condenser and the filter holder, disconnect the line at the filter holder and let any condensed water or liquid drain into the impingers or condenser.
8.6.2 Transfer the probe and filter-impinger assembly to the cleanup area. This area must be clean and protected from the wind so that the possibility of losing any of the sample will be minimized.
8.6.3 Inspect the train prior to and during disassembly and note any abnormal conditions such as particulate color, filter loading, impinger liquid color, etc.
8.6.4 Container No. 1, Filter Assembly. Carefully remove the cooled filter holder assembly from the Method 5 hot box and place it in the transport case. Use a pair of clean gloves to handle the filter holder assembly.
8.6.5 Container No. 2, Probe Nozzle and Probe Liner Rinse. Rinse the probe and nozzle components with acetone. Be certain that the probe and nozzle brushes have been thoroughly rinsed prior to use as they can be a source of contamination.
8.6.6 All Other Train Components. (Impingers) Same as Method 5.
8.7 Sample Storage and Transport. Whenever possible, containers should be shipped in such a way that they remain upright at all times. All appropriate dangerous goods shipping requirements must be observed since acetone is a flammable liquid.
9. Quality Control.9.1 Miscellaneous Field Quality Control Measures.
9.1.1 A quality control (QC) check of the volume metering system at the field site is suggested before collecting the sample using the procedures in Method 5, section 4.4.1.
9.1.2 All other quality control checks outlined in Methods 1, 2, 4 and 5 also apply to Method 5I. This includes procedures such as leak-checks, equipment calibration checks, and independent checks of field data sheets for reasonableness and completeness.
9.2 Quality Control Samples.
9.2.1 Required QC Sample. A laboratory reagent blank must be collected and analyzed for each lot of acetone used for a field program to confirm that it is of suitable purity. The particulate samples cannot be blank corrected.
9.2.2 Recommended QC Samples. These samples may be collected and archived for future analyses.
9.2.2.1 A field reagent blank is a recommended QC sample collected from a portion of the acetone used for cleanup of the probe and nozzle. Take 100 ml of this acetone directly from the wash bottle being used and place it in a glass sample container labeled “field acetone reagent blank.” At least one field reagent blank is recommended for every five runs completed. The field reagent blank samples demonstrate the purity of the acetone was maintained throughout the program.
9.2.2.2 A field bias blank train is a recommended QC sample. This sample is collected by recovering a probe and filter assembly that has been assembled, taken to the sample location, leak checked, heated, allowed to sit at the sample location for a similar duration of time as a regular sample run, leak-checked again, and then recovered in the same manner as a regular sample. Field bias blanks are not a Method requirement, however, they are recommended and are very useful for identifying sources of contamination in emission testing samples. Field bias blank train results greater than 5 times the method detection limit may be considered problematic.
10. Calibration and Standardization Same as Method 5, section 5.10.1 Field Balance Calibration Check. Check the calibration of the balance used to weigh impingers with a weight that is at least 500g or within 50g of a loaded impinger. The weight must be ASTM E617-13 “Standard Specification for Laboratory Weights and Precision Mass Standards” (incorporated by reference - see 40 CFR 60.17) Class 6 (or better). Daily, before use, the field balance must measure the weight within ±0.5g of the certified mass. If the daily balance calibration check fails, perform corrective measures and repeat the check before using balance.
10.2 Analytical Balance Calibration. Perform a multipoint calibration (at least five points spanning the operational range) of the analytical balance before the first use, and semiannually thereafter. The calibration of the analytical balance must be conducted using ASTM E617-13 “Standard Specification for Laboratory Weights and Precision Mass Standards” (incorporated by reference - see 40 CFR 60.17) Class 2 (or better) tolerance weights. Audit the balance each day it is used for gravimetric measurements by weighing at least one ASTM E617-13 Class 2 tolerance (or better) calibration weight that corresponds to 50 to 150 percent of the weight of one filter or between 1g and 5g. If the scale cannot reproduce the value of the calibration weight to within 0.5 mg of the certified mass, perform corrective measures and conduct the multipoint calibration before use.
11. Analytical Procedures.11.1 Analysis. Same as Method 5, sections 11.1-11.2.4, with the following exceptions:
11.1.1 Container No. 1. Same as Method 5, section 11.2.1, with the following exception: Use disposable gloves to remove each of the filter holder assemblies from the desiccator, transport container, or sample oven (after appropriate cooling).
11.1.2 Container No. 2. Same as Method 5, section 11.2.2, with the following exception: It is recommended that the contents of Container No. 2 be transferred to a 250 ml beaker with a Teflon liner or similar container that has a minimal tare weight before bringing to dryness.
12. Data Analysis and Calculations.12.1 Particulate Emissions. The analytical results cannot be blank corrected for residual acetone found in any of the blanks. All other sample calculations are identical to Method 5.
12.2 Paired Trains Outliers. a. Outliers are identified through the determination of precision and any systemic bias of the paired trains. Data that do not meet this criteria should be flagged as a data quality problem. The primary reason for performing dual train sampling is to generate information to quantify the precision of the Reference Method data. The relative standard deviation (RSD) of paired data is the parameter used to quantify data precision. RSD for two simultaneously gathered data points is determined according to:

b. A minimum precision criteria for Reference Method PM data is that RSD for any data pair must be less than 10% as long as the mean PM concentration is greater than 10 mg/dscm. If the mean PM concentration is less than 10 mg/dscm higher RSD values are acceptable. At mean PM concentration of 1 mg/dscm acceptable RSD for paired trains is 25%. Between 1 and 10 mg/dscm acceptable RSD criteria should be linearly scaled from 25% to 10%. Pairs of manual method data exceeding these RSD criteria should be eliminated from the data set used to develop a PM CEMS correlation or to assess RCA. If the mean PM concentration is less than 1 mg/dscm, RSD does not apply and the mean result is acceptable.
13. Method Performance [Reserved] 14. Pollution Prevention [Reserved] 15. Waste Management [Reserved]16. Alternative Procedures. Same as Method 5.
17. Bibliography. Same as Method 5.
18. Tables, Diagrams, Flowcharts and Validation Data. Figure 5I-1 is a schematic of the sample train.
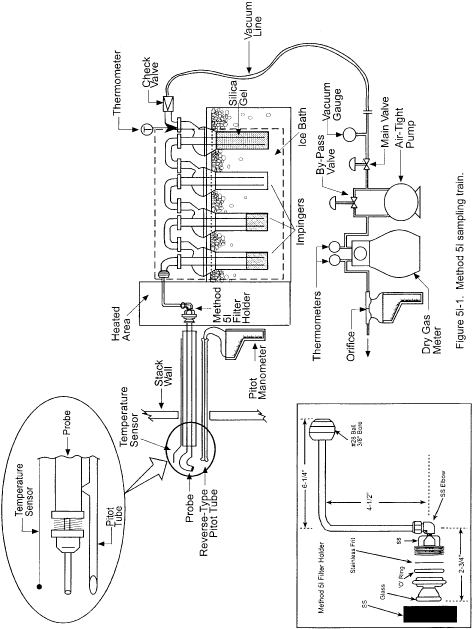
Appendix A-4 to Part 60 - Test Methods 6 through 10B
40:9.0.1.1.1.0.1.1.4 : Appendix A
Appendix A-4 to Part 60 - Test Methods 6 through 10B Method 6 - Determination of sulfur dioxide emissions from stationary sources Method 6A - Determination of sulfur dioxide, moisture, and carbon dioxide emissions from fossil fuel combustion sources Method 6B - Determination of sulfur dioxide and carbon dioxide daily average emissions from fossil fuel combustion sources Method 6C - Determination of Sulfur Dioxide Emissions From Stationary Sources (Instrumental Analyzer Procedure) Method 7 - Determination of nitrogen oxide emissions from stationary sources Method 7A - Determination of nitrogen oxide emissions from stationary sources - Ion chromatographic method Method 7B - Determination of nitrogen oxide emissions from stationary sources (Ultraviolet spectrophotometry) Method 7C - Determination of nitrogen oxide emissions from stationary sources - Alkaline-permanganate/colorimetric method Method 7D - Determination of nitrogen oxide emissions from stationary sources - Alkaline-permanganate/ion chromatographic method Method 7E - Determination of Nitrogen Oxides Emissions From Stationary Sources (Instrumental Analyzer Procedure) Method 8 - Determination of sulfuric acid mist and sulfur dioxide emissions from stationary sources Method 9 - Visual determination of the opacity of emissions from stationary sources Alternate method 1 - Determination of the opacity of emissions from stationary sources remotely by lidar Method 10 - Determination of carbon monoxide emissions from stationary sources Method 10A - Determination of carbon monoxide emissions in certifying continuous emission monitoring systems at petroleum refineries Method 10B - Determination of carbon monoxide emissions from stationary sourcesThe test methods in this appendix are referred to in § 60.8 (Performance Tests) and § 60.11 (Compliance With Standards and Maintenance Requirements) of 40 CFR part 60, subpart A (General Provisions). Specific uses of these test methods are described in the standards of performance contained in the subparts, beginning with Subpart D.
Within each standard of performance, a section title “Test Methods and Procedures” is provided to: (1) Identify the test methods to be used as reference methods to the facility subject to the respective standard and (2) identify any special instructions or conditions to be followed when applying a method to the respective facility. Such instructions (for example, establish sampling rates, volumes, or temperatures) are to be used either in addition to, or as a substitute for procedures in a test method. Similarly, for sources subject to emission monitoring requirements, specific instructions pertaining to any use of a test method as a reference method are provided in the subpart or in Appendix B.
Inclusion of methods in this appendix is not intended as an endorsement or denial of their applicability to sources that are not subject to standards of performance. The methods are potentially applicable to other sources; however, applicability should be confirmed by careful and appropriate evaluation of the conditions prevalent at such sources.
The approach followed in the formulation of the test methods involves specifications for equipment, procedures, and performance. In concept, a performance specification approach would be preferable in all methods because this allows the greatest flexibility to the user. In practice, however, this approach is impractical in most cases because performance specifications cannot be established. Most of the methods described herein, therefore, involve specific equipment specifications and procedures, and only a few methods in this appendix rely on performance criteria.
Minor changes in the test methods should not necessarily affect the validity of the results and it is recognized that alternative and equivalent methods exist. section 60.8 provides authority for the Administrator to specify or approve (1) equivalent methods, (2) alternative methods, and (3) minor changes in the methodology of the test methods. It should be clearly understood that unless otherwise identified all such methods and changes must have prior approval of the Administrator. An owner employing such methods or deviations from the test methods without obtaining prior approval does so at the risk of subsequent disapproval and retesting with approved methods.
Within the test methods, certain specific equipment or procedures are recognized as being acceptable or potentially acceptable and are specifically identified in the methods. The items identified as acceptable options may be used without approval but must be identified in the test report. The potentially approvable options are cited as “subject to the approval of the Administrator” or as “or equivalent.” Such potentially approvable techniques or alternatives may be used at the discretion of the owner without prior approval. However, detailed descriptions for applying these potentially approvable techniques or alternatives are not provided in the test methods. Also, the potentially approvable options are not necessarily acceptable in all applications. Therefore, an owner electing to use such potentially approvable techniques or alternatives is responsible for: (1) assuring that the techniques or alternatives are in fact applicable and are properly executed; (2) including a written description of the alternative method in the test report (the written method must be clear and must be capable of being performed without additional instruction, and the degree of detail should be similar to the detail contained in the test methods); and (3) providing any rationale or supporting data necessary to show the validity of the alternative in the particular application. Failure to meet these requirements can result in the Administrator's disapproval of the alternative.
Method 6 - Determination of Sulfur Dioxide Emissions From Stationary Sources Note:This method does not include all of the specifications (e.g., equipment and supplies) and procedures (e.g., sampling and analytical) essential to its performance. Some material is incorporated by reference from other methods in this part. Therefore, to obtain reliable results, persons using this method should have a thorough knowledge of at least the following additional test methods: Method 1, Method 2, Method 3, Method 5, and Method 8.
1.0 Scope and Application1.1 Analytes.
Analyte | CAS No. | Sensitivity |
---|---|---|
SO2 | 7449-09-5 | 3.4 mg SO2/m 3 (2.12 × 10)−7 lb/ft 3 |
1.2 Applicability. This method applies to the measurement of sulfur dioxide (SO2) emissions from stationary sources.
1.3 Data Quality Objectives. Adherence to the requirements of this method will enhance the quality of the data obtained from air pollutant sampling methods.
2.0 Summary of Method2.1 A gas sample is extracted from the sampling point in the stack. The SO2 and the sulfur trioxide, including those fractions in any sulfur acid mist, are separated. The SO2 fraction is measured by the barium-thorin titration method.
3.0 Definitions [Reserved] 4.0 Interferences4.1 Free Ammonia. Free ammonia interferes with this method by reacting with SO2 to form particulate sulfite and by reacting with the indicator. If free ammonia is present (this can be determined by knowledge of the process and/or noticing white particulate matter in the probe and isopropanol bubbler), alternative methods, subject to the approval of the Administrator are required. One approved alternative is listed in Reference 13 of section 17.0.
4.2 Water-Soluble Cations and Fluorides. The cations and fluorides are removed by a glass wool filter and an isopropanol bubbler; therefore, they do not affect the SO2 analysis. When samples are collected from a gas stream with high concentrations of metallic fumes (i.e., very fine cation aerosols) a high-efficiency glass fiber filter must be used in place of the glass wool plug (i.e., the one in the probe) to remove the cation interferent.
5.0 Safety5.1 Disclaimer. This method may involve hazardous materials, operations, and equipment. This test method may not address all of the safety problems associated with its use. It is the responsibility of the user to establish appropriate safety and health practices and determine the applicability of regulatory limitations before performing this test method.
5.2 Corrosive reagents. The following reagents are hazardous. Personal protective equipment and safe procedures are useful in preventing chemical splashes. If contact occurs, immediately flush with copious amounts of water for at least 15 minutes. Remove clothing under shower and decontaminate. Treat residual chemical burns as thermal burns.
5.2.1 Hydrogen Peroxide (H2O2). Irritating to eyes, skin, nose, and lungs. 30% H2O2 is a strong oxidizing agent. Avoid contact with skin, eyes, and combustible material. Wear gloves when handling.
5.2.2 Sodium Hydroxide (NaOH). Causes severe damage to eyes and skin. Inhalation causes irritation to nose, throat, and lungs. Reacts exothermically with limited amounts of water.
5.2.3 Sulfuric Acid (H2SO4). Rapidly destructive to body tissue. Will cause third degree burns. Eye damage may result in blindness. Inhalation may be fatal from spasm of the larynx, usually within 30 minutes. May cause lung tissue damage with edema. 1 mg/m 3 for 8 hours will cause lung damage or, in higher concentrations, death. Provide ventilation to limit inhalation. Reacts violently with metals and organics.
6.0 Equipment and Supplies6.1 Sample Collection. The following items are required for sample collection:
6.1.1 Sampling Train. A schematic of the sampling train is shown in Figure 6-1. The sampling equipment described in Method 8 may be substituted in place of the midget impinger equipment of Method 6. However, the Method 8 train must be modified to include a heated filter between the probe and isopropanol impinger, and the operation of the sampling train and sample analysis must be at the flow rates and solution volumes defined in Method 8. Alternatively, SO2 may be determined simultaneously with particulate matter and moisture determinations by either (1) replacing the water in a Method 5 impinger system with a 3 percent H2O2 solution, or (2) replacing the Method 5 water impinger system with a Method 8 isopropanol-filter-H2O2 system. The analysis for SO2 must be consistent with the procedure of Method 8. The Method 6 sampling train consists of the following components:
6.1.1.1 Probe. Borosilicate glass or stainless steel (other materials of construction may be used, subject to the approval of the Administrator), approximately 6 mm (0.25 in.) inside diameter, with a heating system to prevent water condensation and a filter (either in-stack or heated out-of-stack) to remove particulate matter, including sulfuric acid mist. A plug of glass wool is a satisfactory filter.
6.1.1.2 Bubbler and Impingers. One midget bubbler with medium-coarse glass frit and borosilicate or quartz glass wool packed in top (see Figure 6-1) to prevent sulfuric acid mist carryover, and three 30-ml midget impingers. The midget bubbler and midget impingers must be connected in series with leak-free glass connectors. Silicone grease may be used, if necessary, to prevent leakage. A midget impinger may be used in place of the midget bubbler.
Note:Other collection absorbers and flow rates may be used, subject to the approval of the Administrator, but the collection efficiency must be shown to be at least 99 percent for each test run and must be documented in the report. If the efficiency is found to be acceptable after a series of three tests, further documentation is not required. To conduct the efficiency test, an extra absorber must be added and analyzed separately. This extra absorber must not contain more than 1 percent of the total SO2.
6.1.1.3 Glass Wool. Borosilicate or quartz.
6.1.1.4 Stopcock Grease. Acetone-insoluble, heat-stable silicone grease may be used, if necessary.
6.1.1.5 Temperature Sensor. Dial thermometer, or equivalent, to measure temperature of gas leaving impinger train to within 1 °C (2 °F).
6.1.1.6 Drying Tube. Tube packed with 6- to 16- mesh indicating-type silica gel, or equivalent, to dry the gas sample and to protect the meter and pump. If silica gel is previously used, dry at 177 °C (350 °F) for 2 hours. New silica gel may be used as received. Alternatively, other types of desiccants (equivalent or better) may be used, subject to the approval of the Administrator.
6.1.1.7 Valve. Needle valve, to regulate sample gas flow rate.
6.1.1.8 Pump. Leak-free diaphragm pump, or equivalent, to pull gas through the train. Install a small surge tank between the pump and rate meter to negate the pulsation effect of the diaphragm pump on the rate meter.
6.1.1.9 Rate Meter. Rotameter, or equivalent, capable of measuring flow rate to within 2 percent of the selected flow rate of about 1 liter/min (0.035 cfm).
6.1.1.10 Volume Meter. Dry gas meter (DGM), sufficiently accurate to measure the sample volume to within 2 percent, calibrated at the selected flow rate and conditions actually encountered during sampling, and equipped with a temperature sensor (dial thermometer, or equivalent) capable of measuring temperature accurately to within 3 °C (5.4 °F). A critical orifice may be used in place of the DGM specified in this section provided that it is selected, calibrated, and used as specified in section 16.0.
6.1.2 Barometer. Mercury, aneroid, or other barometer capable of measuring atmospheric pressure to within 2.5 mm Hg (0.1 in. Hg). See the note in Method 5, section 6.1.2.
6.1.3 Vacuum Gauge and Rotameter. At least 760-mm Hg (30-in. Hg) gauge and 0- to 40-ml/min rotameter, to be used for leak-check of the sampling train.
6.2 Sample Recovery. The following items are needed for sample recovery:
6.2.1 Wash Bottles. Two polyethylene or glass bottles, 500-ml.
6.2.2 Storage Bottles. Polyethylene bottles, 100-ml, to store impinger samples (one per sample).
6.3 Sample Analysis. The following equipment is needed for sample analysis:
6.3.1 Pipettes. Volumetric type, 5-ml, 20-ml (one needed per sample), and 25-ml sizes.
6.3.2 Volumetric Flasks. 100-ml size (one per sample) and 1000-ml size.
6.3.3 Burettes. 5- and 50-ml sizes.
6.3.4 Erlenmeyer Flasks. 250-ml size (one for each sample, blank, and standard).
6.3.5 Dropping Bottle. 125-ml size, to add indicator.
6.3.6 Graduated Cylinder. 100-ml size.
6.3.7 Spectrophotometer. To measure absorbance at 352 nm.
7.0 Reagents and Standards Note:Unless otherwise indicated, all reagents must conform to the specifications established by the Committee on Analytical Reagents of the American Chemical Society. Where such specifications are not available, use the best available grade.
7.1 Sample Collection. The following reagents are required for sample collection:
7.1.1 Water. Deionized distilled to conform to ASTM Specification D 1193-77 or 91 Type 3 (incorporated by reference - see § 60.17). The KMnO4 test for oxidizable organic matter may be omitted when high concentrations of organic matter are not expected to be present.
7.1.2 Isopropanol, 80 Percent by Volume. Mix 80 ml of isopropanol with 20 ml of water.
7.1.2.1 Check each lot of isopropanol for peroxide impurities as follows: Shake 10 ml of isopropanol with 10 ml of freshly prepared 10 percent potassium iodide solution. Prepare a blank by similarly treating 10 ml of water. After 1 minute, read the absorbance at 352 nm on a spectrophotometer using a 1-cm path length. If absorbance exceeds 0.1, reject alcohol for use.
7.1.2.2 Peroxides may be removed from isopropanol by redistilling or by passage through a column of activated alumina; however, reagent grade isopropanol with suitably low peroxide levels may be obtained from commercial sources. Rejection of contaminated lots may, therefore, be a more efficient procedure.
7.1.3 Hydrogen Peroxide (H2O2), 3 Percent by Volume. Add 10 ml of 30 percent H2O2 to 90 ml of water. Prepare fresh daily.
7.1.4 Potassium Iodide Solution, 10 Percent Weight by Volume (w/v). Dissolve 10.0 g of KI in water, and dilute to 100 ml. Prepare when needed.
7.2 Sample Recovery. The following reagents are required for sample recovery:
7.2.1 Water. Same as in section 7.1.1.
7.2.2 Isopropanol, 80 Percent by Volume. Same as in section 7.1.2.
7.3 Sample Analysis. The following reagents and standards are required for sample analysis:
7.3.1 Water. Same as in section 7.1.1.
7.3.2 Isopropanol, 100 Percent.
7.3.3 Thorin Indicator. 1-(o-arsonophenylazo)-2-naphthol-3,6-disulfonic acid, disodium salt, or equivalent. Dissolve 0.20 g in 100 ml of water.
7.3.4 Barium Standard Solution, 0.0100 N. Dissolve 1.95 g of barium perchlorate trihydrate [Ba(ClO4)2 3H2O] in 200 ml water, and dilute to 1 liter with isopropanol. Alternatively, 1.22 g of barium chloride dihydrate [BaCl2 2H2O] may be used instead of the barium perchlorate trihydrate. Standardize as in section 10.5.
7.3.5 Sulfuric Acid Standard, 0.0100 N. Purchase or standardize to ±0.0002 N against 0.0100 N NaOH which has previously been standardized against potassium acid phthalate (primary standard grade).
8.0 Sample Collection, Preservation, Storage and Transport8.1 Preparation of Sampling Train. Measure 15 ml of 80 percent isopropanol into the midget bubbler and 15 ml of 3 percent H2O2 into each of the first two midget impingers. Leave the final midget impinger dry. Assemble the train as shown in Figure 6-1. Adjust the probe heater to a temperature sufficient to prevent water condensation. Place crushed ice and water around the impingers.
8.2 Sampling Train Leak-Check Procedure. A leak-check prior to the sampling run is recommended, but not required. A leak-check after the sampling run is mandatory. The leak-check procedure is as follows:
8.2.1 Temporarily attach a suitable (e.g., 0- to 40- ml/min) rotameter to the outlet of the DGM, and place a vacuum gauge at or near the probe inlet. Plug the probe inlet, pull a vacuum of at least 250 mm Hg (10 in. Hg), and note the flow rate as indicated by the rotameter. A leakage rate in excess of 2 percent of the average sampling rate is not acceptable.
Note:Carefully (i.e., slowly) release the probe inlet plug before turning off the pump.
8.2.2 It is suggested (not mandatory) that the pump be leak-checked separately, either prior to or after the sampling run. To leak-check the pump, proceed as follows: Disconnect the drying tube from the probe-impinger assembly. Place a vacuum gauge at the inlet to either the drying tube or the pump, pull a vacuum of 250 mm Hg (10 in. Hg), plug or pinch off the outlet of the flow meter, and then turn off the pump. The vacuum should remain stable for at least 30 seconds.
If performed prior to the sampling run, the pump leak-check shall precede the leak-check of the sampling train described immediately above; if performed after the sampling run, the pump leak-check shall follow the sampling train leak-check.
8.2.3 Other leak-check procedures may be used, subject to the approval of the Administrator.
8.3 Sample Collection.
8.3.1 Record the initial DGM reading and barometric pressure. To begin sampling, position the tip of the probe at the sampling point, connect the probe to the bubbler, and start the pump. Adjust the sample flow to a constant rate of approximately 1.0 liter/min as indicated by the rate meter. Maintain this constant rate (±10 percent) during the entire sampling run.
8.3.2 Take readings (DGM volume, temperatures at DGM and at impinger outlet, and rate meter flow rate) at least every 5 minutes. Add more ice during the run to keep the temperature of the gases leaving the last impinger at 20 °C (68 °F) or less.
8.3.3 At the conclusion of each run, turn off the pump, remove the probe from the stack, and record the final readings. Conduct a leak-check as described in section 8.2. (This leak-check is mandatory.) If a leak is detected, void the test run or use procedures acceptable to the Administrator to adjust the sample volume for the leakage.
8.3.4 Drain the ice bath, and purge the remaining part of the train by drawing clean ambient air through the system for 15 minutes at the sampling rate. Clean ambient air can be provided by passing air through a charcoal filter or through an extra midget impinger containing 15 ml of 3 percent H2O2. Alternatively, ambient air without purification may be used.
8.4 Sample Recovery. Disconnect the impingers after purging. Discard the contents of the midget bubbler. Pour the contents of the midget impingers into a leak-free polyethylene bottle for shipment. Rinse the three midget impingers and the connecting tubes with water, and add the rinse to the same storage container. Mark the fluid level. Seal and identify the sample container.
9.0 Quality ControlSection | Quality control measure | Effect |
---|---|---|
7.1.2 | Isopropanol check | Ensure acceptable level of peroxide impurities in isopropanol. |
8.2, 10.1-10.4 | Sampling equipment leak-check and calibration | Ensure accurate measurement of stack gas flow rate, sample volume. |
10.5 | Barium standard solution standardization | Ensure precision of normality determination |
11.2.3 | Replicate titrations | Ensure precision of titration determinations. |
10.1 Volume Metering System.
10.1.1 Initial Calibration.
10.1.1.1 Before its initial use in the field, leak-check the metering system (drying tube, needle valve, pump, rate meter, and DGM) as follows: Place a vacuum gauge at the inlet to the drying tube and pull a vacuum of 250 mm Hg (10 in. Hg). Plug or pinch off the outlet of the flow meter, and then turn off the pump. The vacuum must remain stable for at least 30 seconds. Carefully release the vacuum gauge before releasing the flow meter end.
10.1.1.2 Remove the drying tube, and calibrate the metering system (at the sampling flow rate specified by the method) as follows: Connect an appropriately sized wet-test meter (e.g., 1 liter per revolution) to the inlet of the needle valve. Make three independent calibration runs, using at least five revolutions of the DGM per run. Calculate the calibration factor Y (wet-test meter calibration volume divided by the DGM volume, both volumes adjusted to the same reference temperature and pressure) for each run, and average the results (Yi). If any Y-value deviates by more than 2 percent from (Yi), the metering system is unacceptable for use. If the metering system is acceptable, use (Yi) as the calibration factor for subsequent test runs.
10.1.2 Post-Test Calibration Check. After each field test series, conduct a calibration check using the procedures outlined in section 10.1.1.2, except that three or more revolutions of the DGM may be used, and only two independent runs need be made. If the average of the two post-test calibration factors does not deviate by more than 5 percent from Yi, then Yi is accepted as the DGM calibration factor (Y), which is used in Equation 6-1 to calculate collected sample volume (see section 12.2). If the deviation is more than 5 percent, recalibrate the metering system as in section 10.1.1, and determine a post-test calibration factor (Yf). Compare Yi and Yf; the smaller of the two factors is accepted as the DGM calibration factor. If recalibration indicates that the metering system is unacceptable for use, either void the test run or use methods, subject to the approval of the Administrator, to determine an acceptable value for the collected sample volume.
10.1.3 DGM as a Calibration Standard. A DGM may be used as a calibration standard for volume measurements in place of the wet-test meter specified in section 10.1.1.2, provided that it is calibrated initially and recalibrated periodically according to the same procedures outlined in Method 5, section 10.3 with the following exceptions: (a) the DGM is calibrated against a wet-test meter having a capacity of 1 liter/rev (0.035 ft 3/rev) or 3 liters/rev (0.1 ft 3/rev) and having the capability of measuring volume to within 1 percent; (b) the DGM is calibrated at 1 liter/min (0.035 cfm); and (c) the meter box of the Method 6 sampling train is calibrated at the same flow rate.
10.2 Temperature Sensors. Calibrate against mercury-in-glass thermometers. An alternative mercury-free thermometer may be used if the thermometer is, at a minimum, equivalent in terms of performance or suitably effective for the specific temperature measurement application.
10.3 Rate Meter. The rate meter need not be calibrated, but should be cleaned and maintained according to the manufacturer's instructions.
10.4 Barometer. Calibrate against a mercury barometer or NIST-traceable barometer prior to the field test.
10.5 Barium Standard Solution. Standardize the barium perchlorate or chloride solution against 25 ml of standard sulfuric acid to which 100 ml of 100 percent isopropanol has been added. Run duplicate analyses. Calculate the normality using the average of duplicate analyses where the titrations agree within 1 percent or 0.2 ml, whichever is larger.
11.0 Analytical Procedure11.1 Sample Loss Check. Note level of liquid in container and confirm whether any sample was lost during shipment; note this finding on the analytical data sheet. If a noticeable amount of leakage has occurred, either void the sample or use methods, subject to the approval of the Administrator, to correct the final results.
11.2 Sample Analysis.
11.2.1 Transfer the contents of the storage container to a 100-ml volumetric flask, dilute to exactly 100 ml with water, and mix the diluted sample.
11.2.2 Pipette a 20-ml aliquot of the diluted sample into a 250-ml Erlenmeyer flask and add 80 ml of 100 percent isopropanol plus two to four drops of thorin indicator. While stirring the solution, titrate to a pink endpoint using 0.0100 N barium standard solution.
11.2.3 Repeat the procedures in section 11.2.2, and average the titration volumes. Run a blank with each series of samples. Replicate titrations must agree within 1 percent or 0.2 ml, whichever is larger.
Note:Protect the 0.0100 N barium standard solution from evaporation at all times.
12.0 Data Analysis and CalculationsCarry out calculations, retaining at least one extra significant figure beyond that of the acquired data. Round off figures after final calculation.
12.1 Nomenclature CSO2 = Concentration of SO2, dry basis, corrected to standard conditions, mg/dscm (lb/dscf). N = Normality of barium standard titrant, meq/ml. Pbar = Barometric pressure, mm Hg (in. Hg). Pstd = Standard absolute pressure, 760 mm Hg (29.92 in. Hg). Tm = Average DGM absolute temperature, °K (°R). Tstd = Standard absolute temperature, 293 °K (528 °R). Va = Volume of sample aliquot titrated, ml. Vm = Dry gas volume as measured by the DGM, dcm (dcf). Vm(std) = Dry gas volume measured by the DGM, corrected to standard conditions, dscm (dscf). Vsoln = Total volume of solution in which the SO2 sample is contained, 100 ml. Vt = Volume of barium standard titrant used for the sample (average of replicate titration), ml. Vtb = Volume of barium standard titrant used for the blank, ml. Y = DGM calibration factor.12.2 Dry Sample Gas Volume, Corrected to Standard Conditions.
Where: K1 = 0.3855 °K/mm Hg for metric units, K1 = 17.65 °R/in. Hg for English units.12.3 SO2 Concentration.
Where: K2 = 32.03 mg SO2/meq for metric units, K2 = 7.061 × 10−5 lb SO2/meq for English units. 13.0 Method Performance13.1 Range. The minimum detectable limit of the method has been determined to be 3.4 mg SO2/m 3 (2.12 × 10−7 lb/ft 3). Although no upper limit has been established, tests have shown that concentrations as high as 80,000 mg/m 3 (0.005 lb/ft 3) of SO2 can be collected efficiently at a rate of 1.0 liter/min (0.035 cfm) for 20 minutes in two midget impingers, each containing 15 ml of 3 percent H2O2. Based on theoretical calculations, the upper concentration limit in a 20 liter (0.7 ft 3) sample is about 93,300 mg/m 3 (0.00583 lb/ft 3).
14.0 Pollution Prevention [Reserved] 15.0 Waste Management [Reserved] 16.0 Alternative Procedures16.1 Nomenclature. Same as section 12.1, with the following additions:
Bwa = Water vapor in ambient air, proportion by volume. Ma = Molecular weight of the ambient air saturated at impinger temperature, g/g-mole (lb/lb-mole). Ms = Molecular weight of the sample gas saturated at impinger temperature, g/g-mole (lb/lb-mole). Pc = Inlet vacuum reading obtained during the calibration run, mm Hg (in. Hg). Psr = Inlet vacuum reading obtained during the sampling run, mm Hg (in. Hg). Q std = Volumetric flow rate through critical orifice, scm/min (scf/min). Qstd = Average flow rate of pre-test and post-test calibration runs, scm/min (scf/min). Tamb = Ambient absolute temperature of air, °K (°R). Vsb = Volume of gas as measured by the soap bubble meter, m 3 (ft 3).Vsb(std) = Volume of gas as measured by the soap bubble meter, corrected to standard conditions, scm (scf).
θ = Soap bubble travel time, min. θs = Time, min.16.2 Critical Orifices for Volume and Rate Measurements. A critical orifice may be used in place of the DGM specified in section 6.1.1.10, provided that it is selected, calibrated, and used as follows:
16.2.1 Preparation of Sampling Train. Assemble the sampling train as shown in Figure 6-2. The rate meter and surge tank are optional but are recommended in order to detect changes in the flow rate.
Note:The critical orifices can be adapted to a Method 6 type sampling train as follows: Insert sleeve type, serum bottle stoppers into two reducing unions. Insert the needle into the stoppers as shown in Figure 6-3.
16.2.2 Selection of Critical Orifices.
16.2.2.1 The procedure that follows describes the use of hypodermic needles and stainless steel needle tubings, which have been found suitable for use as critical orifices. Other materials and critical orifice designs may be used provided the orifices act as true critical orifices, (i.e., a critical vacuum can be obtained) as described in this section. Select a critical orifice that is sized to operate at the desired flow rate. The needle sizes and tubing lengths shown in Table 6-1 give the following approximate flow rates.
16.2.2.2 Determine the suitability and the appropriate operating vacuum of the critical orifice as follows: If applicable, temporarily attach a rate meter and surge tank to the outlet of the sampling train, if said equipment is not present (see section 16.2.1). Turn on the pump and adjust the valve to give an outlet vacuum reading corresponding to about half of the atmospheric pressure. Observe the rate meter reading. Slowly increase the vacuum until a stable reading is obtained on the rate meter. Record the critical vacuum, which is the outlet vacuum when the rate meter first reaches a stable value. Orifices that do not reach a critical value must not be used.
16.2.3 Field Procedures.
16.2.3.1 Leak-Check Procedure. A leak-check before the sampling run is recommended, but not required. The leak-check procedure is as follows: Temporarily attach a suitable (e.g., 0-40 ml/min) rotameter and surge tank, or a soap bubble meter and surge tank to the outlet of the pump. Plug the probe inlet, pull an outlet vacuum of at least 250 mm Hg (10 in. Hg), and note the flow rate as indicated by the rotameter or bubble meter. A leakage rate in excess of 2 percent of the average sampling rate (Q std) is not acceptable. Carefully release the probe inlet plug before turning off the pump.
16.2.3.2 Moisture Determination. At the sampling location, prior to testing, determine the percent moisture of the ambient air using the wet and dry bulb temperatures or, if appropriate, a relative humidity meter.
16.2.3.3 Critical Orifice Calibration. At the sampling location, prior to testing, calibrate the entire sampling train (i.e., determine the flow rate of the sampling train when operated at critical conditions). Attach a 500-ml soap bubble meter to the inlet of the probe, and operate the sampling train at an outlet vacuum of 25 to 50 mm Hg (1 to 2 in. Hg) above the critical vacuum. Record the information listed in Figure 6-4. Calculate the standard volume of air measured by the soap bubble meter and the volumetric flow rate using the equations below:
16.2.3.4 Sampling.
16.2.3.4.1 Operate the sampling train for sample collection at the same vacuum used during the calibration run. Start the watch and pump simultaneously. Take readings (temperature, rate meter, inlet vacuum, and outlet vacuum) at least every 5 minutes. At the end of the sampling run, stop the watch and pump simultaneously.
16.2.3.4.2 Conduct a post-test calibration run using the calibration procedure outlined in section 16.2.3.3. If the Qstd obtained before and after the test differ by more than 5 percent, void the test run; if not, calculate the volume of the gas measured with the critical orifice using Equation 6-6 as follows:
16.2.3.4.3 If the percent difference between the molecular weight of the ambient air at saturated conditions and the sample gas is more that ±3 percent, then the molecular weight of the gas sample must be considered in the calculations using the following equation:
Note:A post-test leak-check is not necessary because the post-test calibration run results will indicate whether there is any leakage.
16.2.3.4.4 Drain the ice bath, and purge the sampling train using the procedure described in section 8.3.4.
16.3 Elimination of Ammonia Interference. The following alternative procedures must be used in addition to those specified in the method when sampling at sources having ammonia emissions.
16.3.1 Sampling. The probe shall be maintained at 275 °C (527 °F) and equipped with a high-efficiency in-stack filter (glass fiber) to remove particulate matter. The filter material shall be unreactive to SO2. Whatman 934AH (formerly Reeve Angel 934AH) filters treated as described in Reference 10 in section 17.0 of Method 5 is an example of a filter that has been shown to work. Where alkaline particulate matter and condensed moisture are present in the gas stream, the filter shall be heated above the moisture dew point but below 225 °C (437 °F).
16.3.2 Sample Recovery. Recover the sample according to section 8.4 except for discarding the contents of the midget bubbler. Add the bubbler contents, including the rinsings of the bubbler with water, to a separate polyethylene bottle from the rest of the sample. Under normal testing conditions where sulfur trioxide will not be present significantly, the tester may opt to delete the midget bubbler from the sampling train. If an approximation of the sulfur trioxide concentration is desired, transfer the contents of the midget bubbler to a separate polyethylene bottle.
16.3.3 Sample Analysis. Follow the procedures in sections 11.1 and 11.2, except add 0.5 ml of 0.1 N HCl to the Erlenmeyer flask and mix before adding the indicator. The following analysis procedure may be used for an approximation of the sulfur trioxide concentration. The accuracy of the calculated concentration will depend upon the ammonia to SO2 ratio and the level of oxygen present in the gas stream. A fraction of the SO2 will be counted as sulfur trioxide as the ammonia to SO2 ratio and the sample oxygen content increases. Generally, when this ratio is 1 or less and the oxygen content is in the range of 5 percent, less than 10 percent of the SO2 will be counted as sulfur trioxide. Analyze the peroxide and isopropanol sample portions separately. Analyze the peroxide portion as described above. Sulfur trioxide is determined by difference using sequential titration of the isopropanol portion of the sample. Transfer the contents of the isopropanol storage container to a 100-ml volumetric flask, and dilute to exactly 100 ml with water. Pipette a 20-ml aliquot of this solution into a 250-ml Erlenmeyer flask, add 0.5 ml of 0.1 N HCl, 80 ml of 100 percent isopropanol, and two to four drops of thorin indicator. Titrate to a pink endpoint using 0.0100 N barium perchlorate. Repeat and average the titration volumes that agree within 1 percent or 0.2 ml, whichever is larger. Use this volume in Equation 6-2 to determine the sulfur trioxide concentration. From the flask containing the remainder of the isopropanol sample, determine the fraction of SO2 collected in the bubbler by pipetting 20-ml aliquots into 250-ml Erlenmeyer flasks. Add 5 ml of 3 percent H2O2, 100 ml of 100 percent isopropanol, and two to four drips of thorin indicator, and titrate as before. From this titration volume, subtract the titrant volume determined for sulfur trioxide, and add the titrant volume determined for the peroxide portion. This final volume constitutes Vt, the volume of barium perchlorate used for the SO2 sample.
17.0 References1. Atmospheric Emissions from Sulfuric Acid Manufacturing Processes. U.S. DHEW, PHS, Division of Air Pollution. Public Health Service Publication No. 999-AP-13. Cincinnati, OH. 1965.
2. Corbett, P.F. The Determination of SO2 and SO3 in Flue Gases. Journal of the Institute of Fuel. 24:237-243. 1961.
3. Matty, R.E., and E.K. Diehl. Measuring Flue-Gas SO2 and SO3. Power. 101:94-97. November 1957.
4. Patton, W.F., and J.A. Brink, Jr. New Equipment and Techniques for Sampling Chemical Process Gases. J. Air Pollution Control Association. 13:162. 1963.
5. Rom, J.J. Maintenance, Calibration, and Operation of Isokinetic Source Sampling Equipment. Office of Air Programs, U.S. Environmental Protection Agency. Research Triangle Park, NC. APTD-0576. March 1972.
6. Hamil, H.F., and D.E. Camann. Collaborative Study of Method for the Determination of Sulfur Dioxide Emissions from Stationary Sources (Fossil-Fuel Fired Steam Generators). U.S. Environmental Protection Agency, Research Triangle Park, NC. EPA-650/4-74-024. December 1973.
7. Annual Book of ASTM Standards. Part 31; Water, Atmospheric Analysis. American Society for Testing and Materials. Philadelphia, PA. 1974. pp. 40-42.
8. Knoll, J.E., and M.R. Midgett. The Application of EPA Method 6 to High Sulfur Dioxide Concentrations. U.S. Environmental Protection Agency. Research Triangle Park, NC. EPA-600/4-76-038. July 1976.
9. Westlin, P.R., and R.T. Shigehara. Procedure for Calibrating and Using Dry Gas Volume Meters as Calibration Standards. Source Evaluation Society Newsletter. 3(1):17-30. February 1978.
10. Yu, K.K. Evaluation of Moisture Effect on Dry Gas Meter Calibration. Source Evaluation Society Newsletter. 5(1):24-28. February 1980.
11. Lodge, J.P., Jr., et al. The Use of Hypodermic Needles as Critical Orifices in Air Sampling. J. Air Pollution Control Association. 16:197-200. 1966.
12. Shigehara, R.T., and C.B. Sorrell. Using Critical Orifices as Method 5 CalibrationStandards. Source Evaluation Society Newsletter. 10:4-15. August 1985.
13. Curtis, F., Analysis of Method 6 Samples in the Presence of Ammonia. Source Evaluation Society Newsletter. 13(1):9-15 February 1988.
18.0 Tables, Diagrams, Flowcharts and Validation DataTable 6-1 - Approximate Flow Rates for Various Needle Sizes
Needle size (gauge) |
Needle length (cm) |
Flow rate (ml/min) |
---|---|---|
21 | 7.6 | 1,100 |
22 | 2.9 | 1,000 |
22 | 3.8 | 900 |
23 | 3.8 | 500 |
23 | 5.1 | 450 |
24 | 3.2 | 400 |
This method does not include all of the specifications (e.g., equipment and supplies) and procedures (e.g., sampling and analytical) essential to its performance. Some material is incorporated by reference from other methods in this part. Therefore, to obtain reliable results, persons using this method should have a thorough knowledge of at least the following additional test methods: Method 1, Method 2, Method 3, Method 5, Method 6, and Method 19.
1.0 Scope and Application1.1 Analytes.
Analyte | CAS No. | Sensitivity |
---|---|---|
SO2 | 7449-09-05 | 3.4 mg SO2/m 3 (2.12 × 10−7 lb/ft 3) |
CO2 | 124-38-9 | N/A |
H2O | 7732-18-5 | N/A |
1.2 Applicability. This method is applicable for the determination of sulfur dioxide (SO2) emissions from fossil fuel combustion sources in terms of concentration (mg/dscm or lb/dscf) and in terms of emission rate (ng/J or lb/10 6 Btu) and for the determination of carbon dioxide (CO2) concentration (percent). Moisture content (percent), if desired, may also be determined by this method.
1.3 Data Quality Objectives. Adherence to the requirements of this method will enhance the quality of the data obtained from air pollutant sampling methods.
2.0 Summary of Method2.1 A gas sample is extracted from a sampling point in the stack. The SO2 and the sulfur trioxide, including those fractions in any sulfur acid mist, are separated. The SO2 fraction is measured by the barium-thorin titration method. Moisture and CO2 fractions are collected in the same sampling train, and are determined gravimetrically.
3.0 Definitions [Reserved] 4.0 InterferencesSame as Method 6, section 4.0.
5.0 Safety5.1 Disclaimer. This method may involve hazardous materials, operations, and equipment. This test method may not address all of the safety problems associated with its use. It is the responsibility of the user to establish appropriate safety and health practices and determine the applicability of regulatory limitations prior to performing this test method.
5.2 Corrosive reagents. Same as Method 6, section 5.2.
6.0 Equipment and Supplies6.1 Sample Collection. Same as Method 6, section 6.1, with the exception of the following:
6.1.1 Sampling Train. A schematic of the sampling train used in this method is shown in Figure 6A-1.
6.1.1.1 Impingers and Bubblers. Two 30 = ml midget impingers with a 1 = mm restricted tip and two 30 = ml midget bubblers with unrestricted tips. Other types of impingers and bubblers (e.g., Mae West for SO2 collection and rigid cylinders containing Drierite for moisture absorbers), may be used with proper attention to reagent volumes and levels, subject to the approval of the Administrator.
6.1.1.2 CO2 Absorber. A sealable rigid cylinder or bottle with an inside diameter between 30 and 90 mm , a length between 125 and 250 mm, and appropriate connections at both ends. The filter may be a separate heated unit or may be within the heated portion of the probe. If the filter is within the sampling probe, the filter should not be within 15 cm of the probe inlet or any unheated section of the probe, such as the connection to the first bubbler. The probe and filter should be heated to at least 20 °C (68 °F) above the source temperature, but not greater than 120 °C (248 °F). The filter temperature (i.e., the sample gas temperature) should be monitored to assure the desired temperature is maintained. A heated Teflon connector may be used to connect the filter holder or probe to the first impinger.
Note:For applications downstream of wet scrubbers, a heated out-of-stack filter (either borosilicate glass wool or glass fiber mat) is necessary.
6.2 Sample Recovery. Same as Method 6, section 6.2.
6.3 Sample Analysis. Same as Method 6, section 6.3, with the addition of a balance to measure within 0.05 g.
7.0 Reagents and Standards Note:Unless otherwise indicated, all reagents must conform to the specifications established by the Committee on Analytical Reagents of the American Chemical Society. Where such specifications are not available, use the best available grade.
7.1 Sample Collection. Same as Method 6, section 7.1, with the addition of the following:
7.1.1 Drierite. Anhydrous calcium sulfate (CaSO4) desiccant, 8 mesh, indicating type is recommended.
Note:Do not use silica gel or similar desiccant in this application.
7.1.2 CO2 Absorbing Material. Ascarite II. Sodium hydroxide-coated silica, 8- to 20-mesh.
7.2 Sample Recovery and Analysis. Same as Method 6, sections 7.2 and 7.3, respectively.
8.0 Sample Collection, Preservation, Transport, and Storage8.1 Preparation of Sampling Train.
8.1.1 Measure 15 ml of 80 percent isopropanol into the first midget bubbler and 15 ml of 3 percent hydrogen peroxide into each of the two midget impingers (the second and third vessels in the train) as described in Method 6, section 8.1. Insert the glass wool into the top of the isopropanol bubbler as shown in Figure 6A-1. Place about 25 g of Drierite into the second midget bubbler (the fourth vessel in the train). Clean the outside of the bubblers and impingers and allow the vessels to reach room temperature. Weigh the four vessels simultaneously to the nearest 0.1 g, and record this initial weight (mwi).
8.1.2 With one end of the CO2 absorber sealed, place glass wool into the cylinder to a depth of about 1 cm (0.5 in.). Place about 150 g of CO2 absorbing material in the cylinder on top of the glass wool, and fill the remaining space in the cylinder with glass wool. Assemble the cylinder as shown in figure 6A-2. With the cylinder in a horizontal position, rotate it around the horizontal axis. The CO2 absorbing material should remain in position during the rotation, and no open spaces or channels should be formed. If necessary, pack more glass wool into the cylinder to make the CO2 absorbing material stable. Clean the outside of the cylinder of loose dirt and moisture and allow the cylinder to reach room temperature. Weigh the cylinder to the nearest 0.1 g, and record this initial weight (mai).
8.1.3 Assemble the train as shown in figure 6A-1. Adjust the probe heater to a temperature sufficient to prevent condensation (see note in section 6.1). Place crushed ice and water around the impingers and bubblers. Mount the CO2 absorber outside the water bath in a vertical flow position with the sample gas inlet at the bottom. Flexible tubing (e.g., Tygon) may be used to connect the last SO2 absorbing impinger to the moisture absorber and to connect the moisture absorber to the CO2 absorber. A second, smaller CO2 absorber containing Ascarite II may be added in-line downstream of the primary CO2 absorber as a breakthrough indicator. Ascarite II turns white when CO2 is absorbed.
8.2 Sampling Train Leak-Check Procedure and Sample Collection. Same as Method 6, sections 8.2 and 8.3, respectively.
8.3 Sample Recovery.
8.3.1 Moisture Measurement. Disconnect the isopropanol bubbler, the SO2 impingers, and the moisture absorber from the sample train. Allow about 10 minutes for them to reach room temperature, clean the outside of loose dirt and moisture, and weigh them simultaneously in the same manner as in section 8.1. Record this final weight (mwf).
8.3.2 Peroxide Solution. Discard the contents of the isopropanol bubbler and pour the contents of the midget impingers into a leak-free polyethylene bottle for shipping. Rinse the two midget impingers and connecting tubes with water, and add the washing to the same storage container.
8.3.3 CO2 Absorber. Allow the CO2 absorber to warm to room temperature (about 10 minutes), clean the outside of loose dirt and moisture, and weigh to the nearest 0.1 g in the same manner as in section 8.1. Record this final weight (maf). Discard used Ascarite II material.
9.0 Quality ControlSame as Method 6, section 9.0.
10.0 Calibration and StandardizationSame as Method 6, section 10.0.
11.0 Analytical Procedure11.1 Sample Analysis. The sample analysis procedure for SO2 is the same as that specified in Method 6, section 11.0.
12.0 Data Analysis and CalculationsSame as Method 6, section 12.0, with the addition of the following:
12.1 Nomenclature.
Cw = Concentration of moisture, percent. CCO2 = Concentration of CO2, dry basis, percent. ESO2 = Emission rate of SO2, ng/J (lb/10 6 Btu). FC = Carbon F-factor from Method 19 for the fuel burned, dscm/J (dscf/10 6 Btu). mwi = Initial weight of impingers, bubblers, and moisture absorber, g. mwf = Final weight of impingers, bubblers, and moisture absorber, g. mai = Initial weight of CO2 absorber, g. maf = Final weight of CO2 absorber, g. mSO2 = Mass of SO2 collected, mg. VCO2(std) = Equivalent volume of CO2 collected at standard conditions, dscm (dscf). Vw(std) = Equivalent volume of moisture collected at standard conditions, scm (scf).12.2 CO2 Volume Collected, Corrected to Standard Conditions.
Where: K3 = Equivalent volume of gaseous CO2 at standard conditions, 5.467 × 10−4 dscm/g (1.930 × 10−2 dscf/g).12.3 Moisture Volume Collected, Corrected to Standard Conditions.
Where: K4 = Equivalent volume of water vapor at standard conditions, 1.336 × 10−3 scm/g (4.717 × 10−2 scf/g).12.4 SO2 Concentration.
Where: K2 = 32.03 mg SO2/meq. SO2 (7.061 × 10−5 lb SO2/meq. SO2)12.5 CO2 Concentration.
12.6 Moisture Concentration.
13.0 Method Performance13.1 Range and Precision. The minimum detectable limit and the upper limit for the measurement of SO2 are the same as for Method 6. For a 20-liter sample, this method has a precision of ±0.5 percent CO2 for concentrations between 2.5 and 25 percent CO2 and ±1.0 percent moisture for moisture concentrations greater than 5 percent.
14.0 Pollution Prevention [Reserved] 15.0 Waste Management [Reserved] 16.0 Alternative MethodsIf the only emission measurement desired is in terms of emission rate of SO2 (ng/J or lb/10 6 Btu), an abbreviated procedure may be used. The differences between the above procedure and the abbreviated procedure are described below.
16.1 Sampling Train. The sampling train is the same as that shown in Figure 6A-1 and as described in section 6.1, except that the dry gas meter is not needed.
16.2 Preparation of the Sampling Train. Follow the same procedure as in section 8.1, except do not weigh the isopropanol bubbler, the SO2 absorbing impingers, or the moisture absorber.
16.3 Sampling Train Leak-Check Procedure and Sample Collection. Leak-check and operate the sampling train as described in section 8.2, except that dry gas meter readings, barometric pressure, and dry gas meter temperatures need not be recorded during sampling.
16.4 Sample Recovery. Follow the procedure in section 8.3, except do not weigh the isopropanol bubbler, the SO2 absorbing impingers, or the moisture absorber.
16.5 Sample Analysis. Analysis of the peroxide solution is the same as that described in section 11.1.
16.6 Calculations.
16.6.1 SO2 Collected.
Where: K2 = 32.03 mg SO2/meq. SO2 K2 = 7.061 × 10−5 lb SO2/meq. SO216.6.2 Sulfur Dioxide Emission Rate.
Where: K5 = 1.829 × 10 9 mg/dscm K2 = 0.1142 lb/dscf 17.0 ReferencesSame as Method 6, section 17.0, References 1 through 8, with the addition of the following:
1. Stanley, Jon and P.R. Westlin. An Alternate Method for Stack Gas Moisture Determination. Source Evaluation Society Newsletter. 3(4). November 1978.
2. Whittle, Richard N. and P.R. Westlin. Air Pollution Test Report: Development and Evaluation of an Intermittent Integrated SO2/CO2 Emission Sampling Procedure. Environmental Protection Agency, Emission Standard and Engineering Division, Emission Measurement Branch. Research Triangle Park, NC. December 1979. 14 pp.
18.0 Tables, Diagrams, Flowcharts, and Validation Data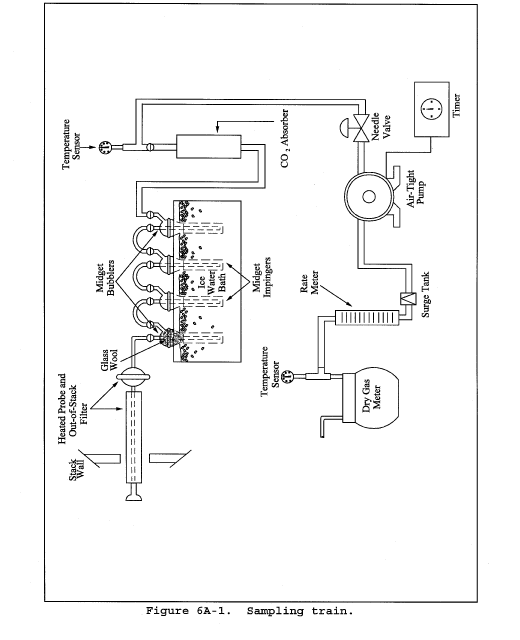
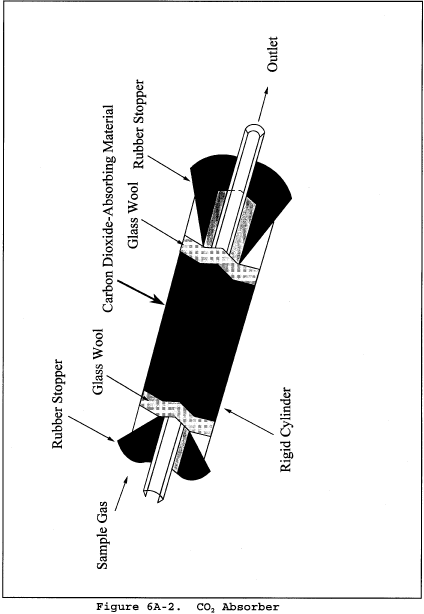
This method does not include all of the specifications (e.g., equipment and supplies) and procedures (e.g., sampling and analytical) essential to its performance. Some material is incorporated by reference from other methods in this part. Therefore, to obtain reliable results, persons using this method should have a thorough knowledge of at least the following additional test methods: Method 1, Method 2, Method 3, Method 5, Method 6, and Method 6A.
1.0 Scope and Application1.1 Analytes.
Analyte | CAS No. | Sensitivity |
---|---|---|
Sulfur dioxide (SO2) | 7449-09-05 | 3.4 mg SO2/m 3 (2.12 × 10−7 lb/ft 3) |
Carbon dioxide (CO2) | 124-38-9 | N/A |
1.2 Applicability. This method is applicable for the determination of SO2 emissions from combustion sources in terms of concentration (ng/dscm or lb/dscf) and emission rate (ng/J or lb/10 6 Btu), and for the determination of CO2 concentration (percent) on a daily (24 hours) basis.
1.3 Data Quality Objectives. Adherence to the requirements of this method will enhance the quality of the data obtained from air pollutant sampling methods.
2.0 Summary of Method2.1 A gas sample is extracted from the sampling point in the stack intermittently over a 24-hour or other specified time period. The SO2 fraction is measured by the barium-thorin titration method. Moisture and CO2 fractions are collected in the same sampling train, and are determined gravimetrically.
3.0 Definitions [Reserved] 4.0 InterferencesSame as Method 6, section 4.0.
5.0 Safety5.1 Disclaimer. This method may involve hazardous materials, operations, and equipment. This test method may not address all of the safety problems associated with its use. It is the responsibility of the user to establish appropriate safety and health practices and determine the applicability of regulatory limitations prior to performing this test method.
5.2 Corrosive Reagents. Same as Method 6, section 5.2.
6.0 Equipment and SuppliesSame as Method 6A, section 6.0, with the following exceptions and additions:
6.1 The isopropanol bubbler is not used. An empty bubbler for the collection of liquid droplets, that does not allow direct contact between the collected liquid and the gas sample, may be included in the sampling train.
6.2 For intermittent operation, include an industrial timer-switch designed to operate in the “on” position at least 2 minutes continuously and “off” the remaining period over a repeating cycle. The cycle of operation is designated in the applicable regulation. At a minimum, the sampling operation should include at least 12, equal, evenly-spaced periods per 24 hours.
6.3 Stainless steel sampling probes, type 316, are not recommended for use with Method 6B because of potential sample contamination due to corrosion. Glass probes or other types of stainless steel, e.g., Hasteloy or Carpenter 20, are recommended for long-term use.
Note:For applications downstream of wet scrubbers, a heated out-of-stack filter (either borosilicate glass wool or glass fiber mat) is necessary. Probe and filter heating systems capable of maintaining a sample gas temperature of between 20 and 120 °C (68 and 248 °F) at the filter are also required in these cases. The electric supply for these heating systems should be continuous and separate from the timed operation of the sample pump.
7.0 Reagents and StandardsSame as Method 6A, section 7.0, with the following exceptions:
7.1 Isopropanol is not used for sampling.
7.2 The hydrogen peroxide absorbing solution shall be diluted to no less than 6 percent by volume, instead of 3 percent as specified in Methods 6 and 6A.
7.3 If the Method 6B sampling train is to be operated in a low sample flow condition (less than 100 ml/min or 0.21 ft 3/hr), molecular sieve material may be substituted for Ascarite II as the CO2 absorbing material. The recommended molecular sieve material is Union Carbide 1/16 inch pellets, 5 A°, or equivalent. Molecular sieve material need not be discarded following the sampling run, provided that it is regenerated as per the manufacturer's instruction. Use of molecular sieve material at flow rates higher than 100 ml/min (0.21 ft 3/hr) may cause erroneous CO2 results.
8.0 Sample Collection, Preservation, Transport, and Storage8.1 Preparation of Sampling Train. Same as Method 6A, section 8.1, with the addition of the following:
8.1.1 The sampling train is assembled as shown in Figure 6A-1 of Method 6A, except that the isopropanol bubbler is not included.
8.1.2 Adjust the timer-switch to operate in the “on” position from 2 to 4 minutes on a 2-hour repeating cycle or other cycle specified in the applicable regulation. Other timer sequences may be used with the restriction that the total sample volume collected is between 25 and 60 liters (0.9 and 2.1 ft 3) for the amounts of sampling reagents prescribed in this method.
8.1.3 Add cold water to the tank until the impingers and bubblers are covered at least two-thirds of their length. The impingers and bubbler tank must be covered and protected from intense heat and direct sunlight. If freezing conditions exist, the impinger solution and the water bath must be protected.
Note:Sampling may be conducted continuously if a low flow-rate sample pump [20 to 40 ml/min (0.04 to 0.08 ft 3/hr) for the reagent volumes described in this method] is used. If sampling is continuous, the timer-switch is not necessary. In addition, if the sample pump is designed for constant rate sampling, the rate meter may be deleted. The total gas volume collected should be between 25 and 60 liters (0.9 and 2.1 ft 3) for the amounts of sampling reagents prescribed in this method.
8.2 Sampling Train Leak-Check Procedure. Same as Method 6, section 8.2.
8.3 Sample Collection.
8.3.1 The probe and filter (either in-stack, out-of-stack, or both) must be heated to a temperature sufficient to prevent water condensation.
8.3.2 Record the initial dry gas meter reading. To begin sampling, position the tip of the probe at the sampling point, connect the probe to the first impinger (or filter), and start the timer and the sample pump. Adjust the sample flow to a constant rate of approximately 1.0 liter/min (0.035 cfm) as indicated by the rotameter. Observe the operation of the timer, and determine that it is operating as intended (i.e., the timer is in the “on” position for the desired period, and the cycle repeats as required).
8.3.3 One time between 9 a.m. and 11 a.m. during the 24-hour sampling period, record the dry gas meter temperature (Tm) and the barometric pressure (P(bar)).
8.3.4 At the conclusion of the run, turn off the timer and the sample pump, remove the probe from the stack, and record the final gas meter volume reading. Conduct a leak-check as described in section 8.2. If a leak is found, void the test run or use procedures acceptable to the Administrator to adjust the sample volume for leakage. Repeat the steps in sections 8.3.1 to 8.3.4 for successive runs.
8.4 Sample Recovery. The procedures for sample recovery (moisture measurement, peroxide solution, and CO2 absorber) are the same as those in Method 6A, section 8.3.
9.0 Quality ControlSame as Method 6, section 9.0., with the exception of the isopropanol-check.
10.0 Calibration and StandardizationSame as Method 6, section 10.0, with the addition of the following:
10.1 Periodic Calibration Check. After 30 days of operation of the test train, conduct a calibration check according to the same procedures as the post-test calibration check (Method 6, section 10.1.2). If the deviation between initial and periodic calibration factors exceeds 5 percent, use the smaller of the two factors in calculations for the preceding 30 days of data, but use the most recent calibration factor for succeeding test runs.
11.0 Analytical Procedures11.1 Sample Loss Check and Analysis. Same as Method 6, sections 11.1 and 11.2, respectively.
12.0 Data Analysis and CalculationsSame as Method 6A, section 12.0, except that Pbar and Tm correspond to the values recorded in section 8.3.3 of this method. The values are as follows:
Pbar = Initial barometric pressure for the test period, mm Hg. Tm = Absolute meter temperature for the test period, °K. 13.0 Method Performance13.1 Range.
13.1.1 Sulfur Dioxide. Same as Method 6.
13.1.2 Carbon Dioxide. Not determined.
13.2 Repeatability and Reproducibility. EPA-sponsored collaborative studies were undertaken to determine the magnitude of repeatability and reproducibility achievable by qualified testers following the procedures in this method. The results of the studies evolve from 145 field tests including comparisons with Methods 3 and 6. For measurements of emission rates from wet, flue gas desulfurization units in (ng/J), the repeatability (intra-laboratory precision) is 8.0 percent and the reproducibility (inter-laboratory precision) is 11.1 percent.
14.0 Pollution Prevention [Reserved] 15.0 Waste Management [Reserved] 16.0 Alternative MethodsSame as Method 6A, section 16.0, except that the timer is needed and is operated as outlined in this method.
17.0 ReferencesSame as Method 6A, section 17.0, with the addition of the following:
1. Butler, Frank E., et. al. The Collaborative Test of Method 6B: Twenty-Four-Hour Analysis of SO2 and CO2. JAPCA. Vol. 33, No. 10. October 1983.
18.0 Tables, Diagrams, Flowcharts, and Validation Data [Reserved] Method 6C - Determination of Sulfur Dioxide Emissions From Stationary Sources (Instrumental Analyzer Procedure) 1.0 Scope and Application What is Method 6C?Method 6C is a procedure for measuring sulfur dioxide (SO2) in stationary source emissions using a continuous instrumental analyzer. Quality assurance and quality control requirements are included to assure that you, the tester, collect data of known quality. You must document your adherence to these specific requirements for equipment, supplies, sample collection and analysis, calculations, and data analysis.
This method does not completely describe all equipment, supplies, and sampling and analytical procedures you will need but refers to other methods for some of the details. Therefore, to obtain reliable results, you should also have a thorough knowledge of these additional test methods which are found in appendix A to this part:
(a) Method 1 - Sample and Velocity Traverses for Stationary Sources.
(b) Method 4 - Determination of Moisture Content in Stack Gases.
(c) Method 6 - Determination of Sulfur Dioxide Emissions from Stationary Sources.
(d) Method 7E - Determination of Nitrogen Oxides Emissions from Stationary Sources (Instrumental Analyzer Procedure).
1.1 Analytes. What does this method determine? This method measures the concentration of sulfur dioxide.
Analyte | CAS No. | Sensitivity |
---|---|---|
SO2 | 7446-09-5 | Typically <2% of Calibration Span. |
1.2 Applicability. When is this method required? The use of Method 6C may be required by specific New Source Performance Standards, Clean Air Marketing rules, State Implementation Plans, and permits where SO2 concentrations in stationary source emissions must be measured, either to determine compliance with an applicable emission standard or to conduct performance testing of a continuous emission monitoring system (CEMS). Other regulations may also require the use of Method 6C.
1.3 Data Quality Objectives. How good must my collected data be? Refer to section 1.3 of Method 7E.
2.0 Summary of MethodIn this method, you continuously sample the effluent gas and convey the sample to an analyzer that measures the concentration of SO2. You must meet the performance requirements of this method to validate your data.
3.0 DefinitionsRefer to section 3.0 of Method 7E for the applicable definitions.
4.0 InterferencesRefer to Section 4.0 of Method 7E.
5.0 SafetyRefer to section 5.0 of Method 7E.
6.0 Equipment and SuppliesFigure 7E-1 of Method 7E is a schematic diagram of an acceptable measurement system.
6.1 What do I need for the measurement system? The essential components of the measurement system are the same as those in sections 6.1 and 6.2 of Method 7E, except that the SO2 analyzer described in section 6.2 of this method must be used instead of the analyzer described in section 6.2 of Method 7E. You must follow the noted specifications in section 6.1 of Method 7E.
6.2 What analyzer must I use? You may use an instrument that uses an ultraviolet, non-dispersive infrared, fluorescence, or other detection principle to continuously measure SO2 in the gas stream and meets the performance specifications in section 13.0. The low-range and dual-range analyzer provisions in sections 6.2.8.1 and 6.2.8.2 of Method 7E apply.
7.0 Reagents and Standards7.1 Calibration Gas. What calibration gases do I need? Refer to section 7.1 of Method 7E for the calibration gas requirements. Example calibration gas mixtures are listed below.
(a) SO2 in nitrogen (N2).
(b) SO2 in air.
(c) SO2 and CO2 in N2.
(d) SO2 andO2 in N2.
(e) SO2/CO2/O2 gas mixture in N2.
(f) CO2/NOX gas mixture in N2.
(g) CO2/SO2/NOX gas mixture in N2.
7.2 Interference Check. What additional reagents do I need for the interference check? The test gases for the interference check are listed in Table 7E-3 of Method 7E. For the alternative interference check, you must use the reagents described in section 7.0 of Method 6.
8.0 Sample Collection, Preservation, Storage, and Transport8.1 Sampling Site and Sampling Points. You must follow the procedures of section 8.1 of Method 7E.
8.2 Initial Measurement System Performance Tests. You must follow the procedures in section 8.2 of Method 7E. If a dilution-type measurement system is used, the special considerations in section 8.3 of Method 7E also apply.
8.3 Interference Check. You must follow the procedures of section 8.2.7 of Method 7E to conduct an interference check, substituting SO2 for NOX as the method pollutant. For dilution-type measurement systems, you must use the alternative interference check procedure in section 16 and a co-located, unmodified Method 6 sampling train.
8.4 Sample Collection. You must follow the procedures of section 8.4 of Method 7E.
8.5 Post-Run System Bias Check and Drift Assessment. You must follow the procedures of section 8.5 of Method 7E.
9.0 Quality ControlFollow quality control procedures in section 9.0 of Method 7E.
10.0 Calibration and StandardizationFollow the procedures for calibration and standardization in section 10.0 of Method 7E.
11.0 Analytical ProceduresBecause sample collection and analysis are performed together (see section 8), additional discussion of the analytical procedure is not necessary.
12.0 Calculations and Data AnalysisYou must follow the applicable procedures for calculations and data analysis in section 12.0 of Method 7E as applicable, substituting SO2 for NOX as appropriate.
13.0 Method Performance13.1 The specifications for the applicable performance checks are the same as in section 13.0 of Method 7E.
13.2 Alternative Interference Check. The results are acceptable if the difference between the Method 6C result and the modified Method 6 result is less than 7.0 percent of the Method 6 result for each of the three test runs. For the purposes of comparison, the Method 6 and 6C results must be expressed in the same units of measure.
14.0 Pollution Prevention [Reserved] 15.0 Waste Management [Reserved] 16.0 Alternative Procedures16.1 Alternative Interference Check. You may perform an alternative interference check consisting of at least three comparison runs between Method 6C and Method 6. This check validates the Method 6C results at each particular source category (type of facility) where the check is performed. When testing under conditions of low concentrations (<15 ppm), this alternative interference check is not allowed.
Note:The procedure described below applies to non-dilution sampling systems only. If this alternative interference check is used for a dilution sampling system, use a standard Method 6 sampling train and extract the sample directly from the exhaust stream at points collocated with the Method 6C sample probe.
a. Build the modified Method 6 sampling train (flow control valve, two midget impingers containing 3 percent hydrogen peroxide, and dry gas meter) shown in Figure 6C-1. Connect the sampling train to the sample bypass discharge vent. Record the dry gas meter reading before you begin sampling. Simultaneously collect modified Method 6 and Method 6C samples. Open the flow control valve in the modified Method 6 train as you begin to sample with Method 6C. Adjust the Method 6 sampling rate to 1 liter per minute (.10 percent). The sampling time per run must be the same as for Method 6 plus twice the average measurement system response time. If your modified Method 6 train does not include a pump, you risk biasing the results high if you over-pressurize the midget impingers and cause a leak. You can reduce this risk by cautiously increasing the flow rate as sampling begins.
b. After completing a run, record the final dry gas meter reading, meter temperature, and barometric pressure. Recover and analyze the contents of the midget impingers using the procedures in Method 6. Determine the average gas concentration reported by Method 6C for the run.
17.0 References1. “EPA Traceability Protocol for Assay and Certification of Gaseous Calibration Standards” September 1997 as amended, EPA-600/R-97/121
18.0 Tables, Diagrams, Flowcharts, and Validation Data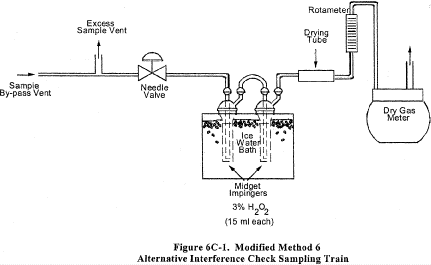
This method does not include all of the specifications (e.g., equipment and supplies) and procedures (e.g., sampling and analytical) essential to its performance. Some material is incorporated by reference from other methods in this part. Therefore, to obtain reliable results, persons using this method should have a thorough knowledge of at least the following additional test methods: Method 1 and Method 5.
1.0 Scope and Application1.1 Analytes.
Analyte | CAS No. | Sensitivity |
---|---|---|
Nitrogen oxides (NOX), as NO2, including: | ||
Nitric oxide (NO) | 10102-43-9 | |
Nitrogen dioxide (NO2) | 10102-44-0 | 2-400 mg/dscm |
1.2 Applicability. This method is applicable for the measurement of nitrogen oxides (NOX) emitted from stationary sources.
1.3 Data Quality Objectives. Adherence to the requirements of this method will enhance the quality of the data obtained from air pollutant sample methods.
2.0 Summary of MethodA grab sample is collected in an evacuated flask containing a dilute sulfuric acid-hydrogen peroxide absorbing solution, and the nitrogen oxides, except nitrous oxide, are measured colorimetrically using the phenoldisulfonic acid (PDS) procedure.
3.0 Definitions [Reserved] 4.0 InterferencesBiased results have been observed when sampling under conditions of high sulfur dioxide concentrations. At or above 2100 ppm SO2, use five times the H2O2 concentration of the Method 7 absorbing solution. Laboratory tests have shown that high concentrations of SO2 (about 2100 ppm) cause low results in Method 7 and 7A. Increasing the H2O2 concentration to five times the original concentration eliminates this bias. However, when no SO2 is present, increasing the concentration by five times results in a low bias.
5.0 Safety5.1 Disclaimer. This method may involve hazardous materials, operations, and equipment. This test method may not address all of the safety problems associated with its use. It is the responsibility of the user to establish appropriate safety and health practices and to determine the applicability of regulatory limitations prior to performing this test method.
5.2 Corrosive Reagents. The following reagents are hazardous. Personal protective equipment and safe procedures are useful in preventing chemical splashes. If contact occurs, immediately flush with copious amounts of water for at least 15 minutes. Remove clothing under shower and decontaminate. Treat residual chemical burns as thermal burns.
5.2.1 Hydrogen Peroxide (H2O2). Irritating to eyes, skin, nose, and lungs.
5.2.2 Phenoldisulfonic Acid. Irritating to eyes and skin.
5.2.3 Sodium Hydroxide (NaOH). Causes severe damage to eyes and skin. Inhalation causes irritation to nose, throat, and lungs. Reacts exothermically with limited amounts of water.
5.2.4 Sulfuric Acid (H2SO4). Rapidly destructive to body tissue. Will cause third degree burns. Eye damage may result in blindness. Inhalation may be fatal from spasm of the larynx, usually within 30 minutes. May cause lung tissue damage with edema. 1 mg/m 3 for 8 hours will cause lung damage or, in higher concentrations, death. Provide ventilation to limit inhalation. Reacts violently with metals and organics.
5.2.5 Phenol. Poisonous and caustic. Do not handle with bare hands as it is absorbed through the skin.
6.0 Equipment and Supplies6.1 Sample Collection. A schematic of the sampling train used in performing this method is shown in Figure 7-1. Other grab sampling systems or equipment, capable of measuring sample volume to within 2.0 percent and collecting a sufficient sample volume to allow analytical reproducibility to within 5 percent, will be considered acceptable alternatives, subject to the approval of the Administrator. The following items are required for sample collection:
6.1.1 Probe. Borosilicate glass tubing, sufficiently heated to prevent water condensation and equipped with an in-stack or heated out-of-stack filter to remove particulate matter (a plug of glass wool is satisfactory for this purpose). Stainless steel or Teflon tubing may also be used for the probe. Heating is not necessary if the probe remains dry during the purging period.
6.1.2 Collection Flask. Two-liter borosilicate, round bottom flask, with short neck and 24/40 standard taper opening, protected against implosion or breakage.
6.1.3 Flask Valve. T-bore stopcock connected to a 24/40 standard taper joint.
6.1.4 Temperature Gauge. Dial-type thermometer, or other temperature gauge, capable of measuring 1 °C (2 °F) intervals from −5 to 50 °C (23 to 122 °F).
6.1.5 Vacuum Line. Tubing capable of withstanding a vacuum of 75 mm (3 in.) Hg absolute pressure, with “T” connection and T-bore stopcock.
6.1.6 Vacuum Gauge. U-tube manometer, 1 meter (39 in.), with 1 mm (0.04 in.) divisions, or other gauge capable of measuring pressure to within 2.5 mm (0.10 in.) Hg.
6.1.7 Pump. Capable of evacuating the collection flask to a pressure equal to or less than 75 mm (3 in.) Hg absolute.
6.1.8 Squeeze Bulb. One-way.
6.1.9 Volumetric Pipette. 25-ml.
6.1.10 Stopcock and Ground Joint Grease. A high-vacuum, high-temperature chlorofluorocarbon grease is required. Halocarbon 25-5S has been found to be effective.
6.1.11 Barometer. Mercury, aneroid, or other barometer capable of measuring atmospheric pressure to within 2.5 mm (0.1 in.) Hg. See note in Method 5, section 6.1.2.
6.2 Sample Recovery. The following items are required for sample recovery:
6.2.1 Graduated Cylinder. 50-ml with 1 ml divisions.
6.2.2 Storage Containers. Leak-free polyethylene bottles.
6.2.3 Wash Bottle. Polyethylene or glass.
6.2.4 Glass Stirring Rod.
6.2.5 Test Paper for Indicating pH. To cover the pH range of 7 to 14.
6.3 Analysis. The following items are required for analysis:
6.3.1 Volumetric Pipettes. Two 1-ml, two 2-ml, one 3-ml, one 4-ml, two 10-ml, and one 25-ml for each sample and standard.
6.3.2 Porcelain Evaporating Dishes. 175- to 250-ml capacity with lip for pouring, one for each sample and each standard. The Coors No. 45006 (shallowform, 195-ml) has been found to be satisfactory. Alternatively, polymethyl pentene beakers (Nalge No. 1203, 150-ml), or glass beakers (150-ml) may be used. When glass beakers are used, etching of the beakers may cause solid matter to be present in the analytical step; the solids should be removed by filtration.
6.3.3 Steam Bath. Low-temperature ovens or thermostatically controlled hot plates kept below 70 °C (160 °F) are acceptable alternatives.
6.3.4 Dropping Pipette or Dropper. Three required.
6.3.5 Polyethylene Policeman. One for each sample and each standard.
6.3.6 Graduated Cylinder. 100-ml with 1-ml divisions.
6.3.7 Volumetric Flasks. 50-ml (one for each sample and each standard), 100-ml (one for each sample and each standard, and one for the working standard KNO3 solution), and 1000-ml (one).
6.3.8 Spectrophotometer. To measure at 410 nm.
6.3.9 Graduated Pipette. 10-ml with 0.1-ml divisions.
6.3.10 Test Paper for Indicating pH. To cover the pH range of 7 to 14.
6.3.11 Analytical Balance. To measure to within 0.1 mg.
7.0 Reagents and StandardsUnless otherwise indicated, it is intended that all reagents conform to the specifications established by the Committee on Analytical Reagents of the American Chemical Society, where such specifications are available; otherwise, use the best available grade.
7.1 Sample Collection. The following reagents are required for sampling:
7.1.1 Water. Deionized distilled to conform to ASTM D 1193-77 or 91 Type 3 (incorporated by reference - see § 60.17). The KMnO4 test for oxidizable organic matter may be omitted when high concentrations of organic matter are not expected to be present.
7.1.2 Absorbing Solution. Cautiously add 2.8 ml concentrated H2SO4 to a 1-liter flask partially filled with water. Mix well, and add 6 ml of 3 percent hydrogen peroxide, freshly prepared from 30 percent hydrogen peroxide solution. Dilute to 1 liter of water and mix well. The absorbing solution should be used within 1 week of its preparation. Do not expose to extreme heat or direct sunlight.
7.2 Sample Recovery. The following reagents are required for sample recovery:
7.2.1 Water. Same as in 7.1.1.
7.2.2 Sodium Hydroxide, 1 N. Dissolve 40 g NaOH in water, and dilute to 1 liter.
7.3 Analysis. The following reagents and standards are required for analysis:
7.3.1 Water. Same as in 7.1.1.
7.3.2 Fuming Sulfuric Acid. 15 to 18 percent by weight free sulfur trioxide. HANDLE WITH CAUTION.
7.3.3 Phenol. White solid.
7.3.4 Sulfuric Acid. Concentrated, 95 percent minimum assay.
7.3.5 Potassium Nitrate (KNO3). Dried at 105 to 110 °C (221 to 230 °F) for a minimum of 2 hours just prior to preparation of standard solution.
7.3.6 Standard KNO3 Solution. Dissolve exactly 2.198 g of dried KNO3 in water, and dilute to 1 liter with water in a 1000-ml volumetric flask.
7.3.7 Working Standard KNO3 Solution. Dilute 10 ml of the standard solution to 100 ml with water. One ml of the working standard solution is equivalent to 100 µg nitrogen dioxide (NO2).
7.3.8 Phenoldisulfonic Acid Solution. Dissolve 25 g of pure white phenol solid in 150 ml concentrated sulfuric acid on a steam bath. Cool, add 75 ml fuming sulfuric acid (15 to 18 percent by weight free sulfur trioxide - HANDLE WITH CAUTION), and heat at 100 °C (212 °F) for 2 hours. Store in a dark, stoppered bottle.
7.3.9 Concentrated Ammonium Hydroxide.
8.0 Sample Collection, Preservation, Storage and Transport8.1 Sample Collection.
8.1.1 Flask Volume. The volume of the collection flask and flask valve combination must be known prior to sampling. Assemble the flask and flask valve, and fill with water to the stopcock. Measure the volume of water to ±10 ml. Record this volume on the flask.
8.1.2 Pipette 25 ml of absorbing solution into a sample flask, retaining a sufficient quantity for use in preparing the calibration standards. Insert the flask valve stopper into the flask with the valve in the “purge” position. Assemble the sampling train as shown in Figure 7-1, and place the probe at the sampling point. Make sure that all fittings are tight and leak-free, and that all ground glass joints have been greased properly with a high-vacuum, high temperature chlorofluorocarbon-based stopcock grease. Turn the flask valve and the pump valve to their “evacuate” positions. Evacuate the flask to 75 mm (3 in.) Hg absolute pressure, or less. Evacuation to a pressure approaching the vapor pressure of water at the existing temperature is desirable. Turn the pump valve to its “vent” position, and turn off the pump. Check for leakage by observing the manometer for any pressure fluctuation. (Any variation greater than 10 mm (0.4 in.) Hg over a period of 1 minute is not acceptable, and the flask is not to be used until the leakage problem is corrected. Pressure in the flask is not to exceed 75 mm (3 in.) Hg absolute at the time sampling is commenced.) Record the volume of the flask and valve (Vf), the flask temperature (Ti), and the barometric pressure. Turn the flask valve counterclockwise to its “purge” position, and do the same with the pump valve. Purge the probe and the vacuum tube using the squeeze bulb. If condensation occurs in the probe and the flask valve area, heat the probe, and purge until the condensation disappears. Next, turn the pump valve to its “vent” position. Turn the flask valve clockwise to its “evacuate” position, and record the difference in the mercury levels in the manometer. The absolute internal pressure in the flask (Pi) is equal to the barometric pressure less the manometer reading. Immediately turn the flask valve to the “sample” position, and permit the gas to enter the flask until pressures in the flask and sample line (i.e., duct, stack) are equal. This will usually require about 15 seconds; a longer period indicates a plug in the probe, which must be corrected before sampling is continued. After collecting the sample, turn the flask valve to its “purge” position, and disconnect the flask from the sampling train.
8.1.3 Shake the flask for at least 5 minutes.
8.1.4 If the gas being sampled contains insufficient oxygen for the conversion of NO to NO2 (e.g., an applicable subpart of the standards may require taking a sample of a calibration gas mixture of NO in N2), then introduce oxygen into the flask to permit this conversion. Oxygen may be introduced into the flask by one of three methods: (1) Before evacuating the sampling flask, flush with pure cylinder oxygen, then evacuate flask to 75 mm (3 in.) Hg absolute pressure or less; or (2) inject oxygen into the flask after sampling; or (3) terminate sampling with a minimum of 50 mm (2 in.) Hg vacuum remaining in the flask, record this final pressure, and then vent the flask to the atmosphere until the flask pressure is almost equal to atmospheric pressure.
8.2 Sample Recovery. Let the flask sit for a minimum of 16 hours, and then shake the contents for 2 minutes.
8.2.1 Connect the flask to a mercury filled U-tube manometer. Open the valve from the flask to the manometer, and record the flask temperature (Tf), the barometric pressure, and the difference between the mercury levels in the manometer. The absolute internal pressure in the flask (Pf) is the barometric pressure less the manometer reading. Transfer the contents of the flask to a leak-free polyethylene bottle. Rinse the flask twice with 5 ml portions of water, and add the rinse water to the bottle. Adjust the pH to between 9 and 12 by adding 1 N NaOH, dropwise (about 25 to 35 drops). Check the pH by dipping a stirring rod into the solution and then touching the rod to the pH test paper. Remove as little material as possible during this step. Mark the height of the liquid level so that the container can be checked for leakage after transport. Label the container to identify clearly its contents. Seal the container for shipping.
9.0 Quality ControlSection | Quality control measure | Effect |
---|---|---|
10.1 | Spectrophotometer calibration | Ensure linearity of spectrophotometer response to standards. |
10.1 Spectrophotometer.
10.1.1 Optimum Wavelength Determination.
10.1.1.1 Calibrate the wavelength scale of the spectrophotometer every 6 months. The calibration may be accomplished by using an energy source with an intense line emission such as a mercury lamp, or by using a series of glass filters spanning the measuring range of the spectrophotometer. Calibration materials are available commercially and from the National Institute of Standards and Technology. Specific details on the use of such materials should be supplied by the vendor; general information about calibration techniques can be obtained from general reference books on analytical chemistry. The wavelength scale of the spectrophotometer must read correctly within 5 nm at all calibration points; otherwise, repair and recalibrate the spectrophotometer. Once the wavelength scale of the spectrophotometer is in proper calibration, use 410 nm as the optimum wavelength for the measurement of the absorbance of the standards and samples.
10.1.1.2 Alternatively, a scanning procedure may be employed to determine the proper measuring wavelength. If the instrument is a double-beam spectrophotometer, scan the spectrum between 400 and 415 nm using a 200 µg NO2 standard solution in the sample cell and a blank solution in the reference cell. If a peak does not occur, the spectrophotometer is probably malfunctioning and should be repaired. When a peak is obtained within the 400 to 415 nm range, the wavelength at which this peak occurs shall be the optimum wavelength for the measurement of absorbance of both the standards and the samples. For a single-beam spectrophotometer, follow the scanning procedure described above, except scan separately the blank and standard solutions. The optimum wavelength shall be the wavelength at which the maximum difference in absorbance between the standard and the blank occurs.
10.1.2 Determination of Spectrophotometer Calibration Factor Kc. Add 0 ml, 2.0 ml, 4.0 ml, 6.0 ml, and 8.0 ml of the KNO3 working standard solution (1 ml = 100 µg NO2) to a series of five 50-ml volumetric flasks. To each flask, add 25 ml of absorbing solution and 10 ml water. Add 1 N NaOH to each flask until the pH is between 9 and 12 (about 25 to 35 drops). Dilute to the mark with water. Mix thoroughly, and pipette a 25-ml aliquot of each solution into a separate porcelain evaporating dish. Beginning with the evaporation step, follow the analysis procedure of section 11.2 until the solution has been transferred to the 100-ml volumetric flask and diluted to the mark. Measure the absorbance of each solution at the optimum wavelength as determined in section 10.1.1. This calibration procedure must be repeated on each day that samples are analyzed. Calculate the spectrophotometer calibration factor as shown in section 12.2.
10.1.3 Spectrophotometer Calibration Quality Control. Multiply the absorbance value obtained for each standard by the Kc factor (reciprocal of the least squares slope) to determine the distance each calibration point lies from the theoretical calibration line. The difference between the calculated concentration values and the actual concentrations (i.e., 100, 200, 300, and 400 µg NO2) should be less than 7 percent for all standards.
10.2 Barometer. Calibrate against a mercury barometer or NIST-traceable barometer prior to the field test.
10.3 Temperature Gauge. Calibrate dial thermometers against mercury-in-glass thermometers. An alternative mercury-free thermometer may be used if the thermometer is, at a minimum, equivalent in terms of performance or suitably effective for the specific temperature measurement application.
10.4 Vacuum Gauge. Calibrate mechanical gauges, if used, against a mercury manometer such as that specified in section 6.1.6.
10.5 Analytical Balance. Calibrate against standard weights.
11.0 Analytical Procedures11.1 Sample Loss Check. Note the level of the liquid in the container, and confirm whether any sample was lost during shipment. Note this on the analytical data sheet. If a noticeable amount of leakage has occurred, either void the sample or use methods, subject to the approval of the Administrator, to correct the final results.
11.2 Sample Preparation. Immediately prior to analysis, transfer the contents of the shipping container to a 50 ml volumetric flask, and rinse the container twice with 5 ml portions of water. Add the rinse water to the flask, and dilute to mark with water; mix thoroughly. Pipette a 25-ml aliquot into the porcelain evaporating dish. Return any unused portion of the sample to the polyethylene storage bottle. Evaporate the 25-ml aliquot to dryness on a steam bath, and allow to cool. Add 2 ml phenoldisulfonic acid solution to the dried residue, and triturate thoroughly with a polyethylene policeman. Make sure the solution contacts all the residue. Add 1 ml water and 4 drops of concentrated sulfuric acid. Heat the solution on a steam bath for 3 minutes with occasional stirring. Allow the solution to cool, add 20 ml water, mix well by stirring, and add concentrated ammonium hydroxide, dropwise, with constant stirring, until the pH is 10 (as determined by pH paper). If the sample contains solids, these must be removed by filtration (centrifugation is an acceptable alternative, subject to the approval of the Administrator) as follows: Filter through Whatman No. 41 filter paper into a 100-ml volumetric flask. Rinse the evaporating dish with three 5-ml portions of water. Filter these three rinses. Wash the filter with at least three 15-ml portions of water. Add the filter washings to the contents of the volumetric flask, and dilute to the mark with water. If solids are absent, the solution can be transferred directly to the 100-ml volumetric flask and diluted to the mark with water.
11.3 Sample Analysis. Mix the contents of the flask thoroughly, and measure the absorbance at the optimum wavelength used for the standards (section 10.1.1), using the blank solution as a zero reference. Dilute the sample and the blank with equal volumes of water if the absorbance exceeds A4, the absorbance of the 400-µg NO2 standard (see section 10.1.3).
12.0 Data Analysis and CalculationsCarry out the calculations, retaining at least one extra significant figure beyond that of the acquired data. Round off figures after final calculations.
12.1 12.1 Nomenclature
A = Absorbance of sample. A1 = Absorbance of the 100-µg NO2 standard. A2 = Absorbance of the 200-µg NO2 standard. A3 = Absorbance of the 300-µg NO2 standard. A4 = Absorbance of the 400-µg NO2 standard. C = Concentration of NOX as NO2, dry basis, corrected to standard conditions, mg/dsm 3 (lb/dscf). F = Dilution factor (i.e., 25/5, 25/10, etc., required only if sample dilution was needed to reduce the absorbance into the range of the calibration). Kc = Spectrophotometer calibration factor. M = Mass of NOX as NO2 in gas sample, µg. Pf = Final absolute pressure of flask, mm Hg (in. Hg). Pi = Initial absolute pressure of flask, mm Hg (in. Hg). Pstd = Standard absolute pressure, 760 mm Hg (29.92 in. Hg). Tf = Final absolute temperature of flask, °K (°R). Ti = Initial absolute temperature of flask, °K (°R). Tstd = Standard absolute temperature, 293 °K (528°R). Vsc = Sample volume at standard conditions (dry basis), ml. Vf = Volume of flask and valve, ml. Va = Volume of absorbing solution, 25 ml.12.2 Spectrophotometer Calibration Factor.
12.3 Sample Volume, Dry Basis, Corrected to Standard Conditions.
Where: K1 = 0.3858 °K/mm Hg for metric units, K1 = 17.65 °R/in. Hg for English units.12.4 Total µg NO2 per sample.
Where: 2 = 50/25, the aliquot factor. Note:If other than a 25-ml aliquot is used for analysis, the factor 2 must be replaced by a corresponding factor.
12.5 Sample Concentration, Dry Basis, Corrected to Standard Conditions.
Where: K2 = 10 3 (mg/m 3)/(µg/ml) for metric units, K2 = 6.242 × 10−5 (lb/scf)/(µg/ml) for English units. 13.0 Method Performance13.1 Range. The analytical range of the method has been determined to be 2 to 400 milligrams NOX (as NO2) per dry standard cubic meter, without having to dilute the sample.
14.0 Pollution Prevention [Reserved] 15.0 Waste Management [Reserved] 16.0 References1. Standard Methods of Chemical Analysis. 6th ed. New York, D. Van Nostrand Co., Inc. 1962. Vol. 1, pp. 329-330.
2. Standard Method of Test for Oxides of Nitrogen in Gaseous Combustion Products (Phenoldisulfonic Acid Procedure). In: 1968 Book of ASTM Standards, Part 26. Philadelphia, PA. 1968. ASTM Designation D 1608-60, pp. 725-729.
3. Jacob, M.B. The Chemical Analysis of Air Pollutants. New York. Interscience Publishers, Inc. 1960. Vol. 10, pp. 351-356.
4. Beatty, R.L., L.B. Berger, and H.H. Schrenk. Determination of Oxides of Nitrogen by the Phenoldisulfonic Acid Method. Bureau of Mines, U.S. Dept. of Interior. R.I. 3687. February 1943.
5. Hamil, H.F. and D.E. Camann. Collaborative Study of Method for the Determination of Nitrogen Oxide Emissions from Stationary Sources (Fossil Fuel-Fired Steam Generators). Southwest Research Institute Report for Environmental Protection Agency. Research Triangle Park, NC. October 5, 1973.
6. Hamil, H.F. and R.E. Thomas. Collaborative Study of Method for the Determination of Nitrogen Oxide Emissions from Stationary Sources (Nitric Acid Plants). Southwest Research Institute Report for Environmental Protection Agency. Research Triangle Park, NC. May 8, 1974.
7. Stack Sampling Safety Manual (Draft). U.S. Environmental Protection Agency, Office of Air Quality Planning and Standards, Research Triangle Park, NC. September 1978.
17.0 Tables, Diagrams, Flowcharts, and Validation Data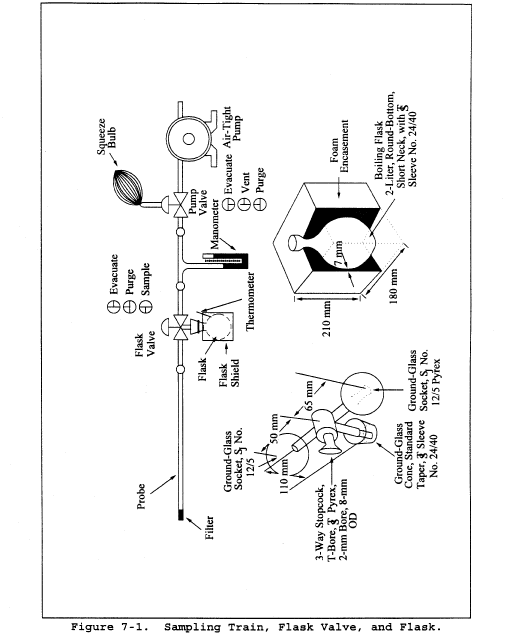
This method does not include all of the specifications (e.g., equipment and supplies) and procedures (e.g., sampling and analytical) essential to its performance. Some material is incorporated by reference from other methods in this part. Therefore, to obtain reliable results, persons using this method should have a thorough knowledge of at least the following additional test methods: Method 1, Method 3, Method 5, and Method 7.
1.0 Scope and Application1.1 Analytes.
Analyte | CAS No. | Sensitivity |
---|---|---|
Nitrogen oxides (NOX), as NO2, including: | ||
Nitric oxide (NO) | 10102-43-9 | |
Nitrogen dioxide (NO2) | 10102-44-0 | 65-655 ppmv |
1.2 Applicability. This method is applicable for the determination of NOX emissions from stationary sources.
1.3 Data Quality Objectives. Adherence to the requirements of this method will enhance the quality of the data obtained from air pollutant sampling methods.
2.0 Summary of MethodA grab sample is collected in an evacuated flask containing a dilute sulfuric acid-hydrogen peroxide absorbing solution. The nitrogen oxides, excluding nitrous oxide (N2O), are oxidized to nitrate and measured by ion chromatography.
3.0 Definitions [Reserved] 4.0 InterferencesBiased results have been observed when sampling under conditions of high sulfur dioxide concentrations. At or above 2100 ppm SO2, use five times the H2O2 concentration of the Method 7 absorbing solution. Laboratory tests have shown that high concentrations of SO2 (about 2100 ppm) cause low results in Method 7 and 7A. Increasing the H2O2 concentration to five times the original concentration eliminates this bias. However, when no SO2 is present, increasing the concentration by five times results in a low bias.
5.0 Safety5.1 This method may involve hazardous materials, operations, and equipment. This test method may not address all of the safety problems associated with its use. It is the responsibility of the user of this test method to establish appropriate safety and health practices and to determine the applicability of regulatory limitations prior to performing this test method.
5.2 Corrosive reagents. The following reagents are hazardous. Personal protective equipment and safe procedures are useful in preventing chemical splashes. If contact occurs, immediately flush with copious amounts of water at least 15 minutes. Remove clothing under shower and decontaminate. Treat residual chemical burns as thermal burns.
5.2.1 Hydrogen Peroxide (H2O2). Irritating to eyes, skin, nose, and lungs.
5.2.2 Sulfuric Acid (H2SO4). Rapidly destructive to body tissue. Will cause third degree burns. Eye damage may result in blindness. Inhalation may be fatal from spasm of the larynx, usually within 30 minutes. May cause lung tissue damage with edema. 3 mg/m 3 will cause lung damage in uninitiated. 1 mg/m 3 for 8 hours will cause lung damage or, in higher concentrations, death. Provide ventilation to limit inhalation. Reacts violently with metals and organics.
6.0 Equipment and Supplies6.1 Sample Collection. Same as in Method 7, section 6.1.
6.2 Sample Recovery. Same as in Method 7, section 6.2, except the stirring rod and pH paper are not needed.
6.3 Analysis. For the analysis, the following equipment and supplies are required. Alternative instrumentation and procedures will be allowed provided the calibration precision requirement in section 10.1.2 can be met.
6.3.1 Volumetric Pipets. Class A;1-, 2-, 4-, 5-ml (two for the set of standards and one per sample), 6-, 10-, and graduated 5-ml sizes.
6.3.2 Volumetric Flasks. 50-ml (two per sample and one per standard), 200-ml, and 1-liter sizes.
6.3.3 Analytical Balance. To measure to within 0.1 mg.
6.3.4 Ion Chromatograph. The ion chromatograph should have at least the following components:
6.3.4.1 Columns. An anion separation or other column capable of resolving the nitrate ion from sulfate and other species present and a standard anion suppressor column (optional). Suppressor columns are produced as proprietary items; however, one can be produced in the laboratory using the resin available from BioRad Company, 32nd and Griffin Streets, Richmond, California. Peak resolution can be optimized by varying the eluent strength or column flow rate, or by experimenting with alternative columns that may offer more efficient separation. When using guard columns with the stronger reagent to protect the separation column, the analyst should allow rest periods between injection intervals to purge possible sulfate buildup in the guard column.
6.3.4.2 Pump. Capable of maintaining a steady flow as required by the system.
6.3.4.3 Flow Gauges. Capable of measuring the specified system flow rate.
6.3.4.4 Conductivity Detector.
6.3.4.5 Recorder. Compatible with the output voltage range of the detector.
7.0 Reagents and StandardsUnless otherwise indicated, it is intended that all reagents conform to the specifications established by the Committee on Analytical Reagents of the American Chemical Society, where such specifications are available; otherwise, use the best available grade.
7.1 Sample Collection. Same as Method 7, section 7.1.
7.2 Sample Recovery. Same as Method 7, section 7.1.1.
7.3 Analysis. The following reagents and standards are required for analysis:
7.3.1 Water. Same as Method 7, section 7.1.1.
7.3.2 Stock Standard Solution, 1 mg NO2/ml. Dry an adequate amount of sodium nitrate (NaNO3) at 105 to 110 °C (221 to 230 °F) for a minimum of 2 hours just before preparing the standard solution. Then dissolve exactly 1.847 g of dried NaNO3 in water, and dilute to l liter in a volumetric flask. Mix well. This solution is stable for 1 month and should not be used beyond this time.
7.3.3 Working Standard Solution, 25 µg/ml. Dilute 5 ml of the standard solution to 200 ml with water in a volumetric flask, and mix well.
7.3.4 Eluent Solution. Weigh 1.018 g of sodium carbonate (Na2CO3) and 1.008 g of sodium bicarbonate (NaHCO3), and dissolve in 4 liters of water. This solution is 0.0024 M Na2CO3/0.003 M NaHCO3. Other eluents appropriate to the column type and capable of resolving nitrate ion from sulfate and other species present may be used.
8.0 Sample Collection, Preservation, Storage, and Transport8.1 Sampling. Same as in Method 7, section 8.1.
8.2 Sample Recovery. Same as in Method 7, section 8.2, except delete the steps on adjusting and checking the pH of the sample. Do not store the samples more than 4 days between collection and analysis.
9.0 Quality ControlSection | Quality control measure | Effect |
---|---|---|
10.1 | Ion chromatographn calibration | Ensure linearity of ion chromatograph response to standards. |
10.1 Ion Chromatograph.
10.1.1 Determination of Ion Chromatograph Calibration Factor S. Prepare a series of five standards by adding 1.0, 2.0, 4.0, 6.0, and 10.0 ml of working standard solution (25 µg/ml) to a series of five 50-ml volumetric flasks. (The standard masses will equal 25, 50, 100, 150, and 250 µg.) Dilute each flask to the mark with water, and mix well. Analyze with the samples as described in section 11.2, and subtract the blank from each value. Prepare or calculate a linear regression plot of the standard masses in µg (x-axis) versus their peak height responses in millimeters (y-axis). (Take peak height measurements with symmetrical peaks; in all other cases, calculate peak areas.) From this curve, or equation, determine the slope, and calculate its reciprocal to denote as the calibration factor, S.
10.1.2 Ion Chromatograph Calibration Quality Control. If any point on the calibration curve deviates from the line by more than 7 percent of the concentration at that point, remake and reanalyze that standard. This deviation can be determined by multiplying S times the peak height response for each standard. The resultant concentrations must not differ by more than 7 percent from each known standard mass (i.e., 25, 50, 100, 150, and 250 µg).
10.2 Conductivity Detector. Calibrate according to manufacturer's specifications prior to initial use.
10.3 Barometer. Calibrate against a mercury barometer.
10.4 Temperature Gauge. Calibrate dial thermometers against mercury-in-glass thermometers. An alternative mercury-free thermometer may be used if the thermometer is, at a minimum, equivalent in terms of performance or suitably effective for the specific temperature measurement application.
10.5 Vacuum Gauge. Calibrate mechanical gauges, if used, against a mercury manometer such as that specified in section 6.1.6 of Method 7.
10.6 Analytical Balance. Calibrate against standard weights.
11.0 Analytical Procedures11.1 Sample Preparation.
11.1.1 Note on the analytical data sheet, the level of the liquid in the container, and whether any sample was lost during shipment. If a noticeable amount of leakage has occurred, either void the sample or use methods, subject to the approval of the Administrator, to correct the final results. Immediately before analysis, transfer the contents of the shipping container to a 50-ml volumetric flask, and rinse the container twice with 5 ml portions of water. Add the rinse water to the flask, and dilute to the mark with water. Mix thoroughly.
11.1.2 Pipet a 5-ml aliquot of the sample into a 50-ml volumetric flask, and dilute to the mark with water. Mix thoroughly. For each set of determinations, prepare a reagent blank by diluting 5 ml of absorbing solution to 50 ml with water. (Alternatively, eluent solution may be used instead of water in all sample, standard, and blank dilutions.)
11.2 Analysis.
11.2.1 Prepare a standard calibration curve according to section 10.1.1. Analyze the set of standards followed by the set of samples using the same injection volume for both standards and samples. Repeat this analysis sequence followed by a final analysis of the standard set. Average the results. The two sample values must agree within 5 percent of their mean for the analysis to be valid. Perform this duplicate analysis sequence on the same day. Dilute any sample and the blank with equal volumes of water if the concentration exceeds that of the highest standard.
11.2.2 Document each sample chromatogram by listing the following analytical parameters: injection point, injection volume, nitrate and sulfate retention times, flow rate, detector sensitivity setting, and recorder chart speed.
12.0 Data Analysis and CalculationsCarry out the calculations, retaining at least one extra significant figure beyond that of the acquired data. Round off figures after final calculations.
12.1 Sample Volume. Calculate the sample volume Vsc (in ml), on a dry basis, corrected to standard conditions, using Equation 7-2 of Method 7.
12.2 Sample Concentration of NOX as NO2.
12.2.1 Calculate the sample concentration C (in mg/dscm) as follows:
Where: H = Sample peak height, mm. S = Calibration factor, µg/mm. F = Dilution factor (required only if sample dilution was needed to reduce the concentration into the range of calibration), dimensionless. 10 4 = 1:10 dilution times conversion factor of: (mg/10 3 µg)(10 6 ml/m 3).12.2.2 If desired, the concentration of NO2 may be calculated as ppm NO2 at standard conditions as follows:
Where: 0.5228 = ml/mg NO2. 13.0 Method Performance13.1 Range. The analytical range of the method is from 125 to 1250 mg NOX/m 3 as NO2 (65 to 655 ppmv), and higher concentrations may be analyzed by diluting the sample. The lower detection limit is approximately 19 mg/m 3 (10 ppmv), but may vary among instruments.
14.0 Pollution Prevention [Reserved] 15.0 Waste Management [Reserved] 16.0 References1. Mulik, J.D., and E. Sawicki. Ion Chromatographic Analysis of Environmental Pollutants. Ann Arbor, Ann Arbor Science Publishers, Inc. Vol. 2, 1979.
2. Sawicki, E., J.D. Mulik, and E. Wittgenstein. Ion Chromatographic Analysis of Environmental Pollutants. Ann Arbor, Ann Arbor Science Publishers, Inc. Vol. 1. 1978.
3. Siemer, D.D. Separation of Chloride and Bromide from Complex Matrices Prior to Ion Chromatographic Determination. Anal. Chem. 52(12):1874-1877. October 1980.
4. Small, H., T.S. Stevens, and W.C. Bauman. Novel Ion Exchange Chromatographic Method Using Conductimetric Determination. Anal. Chem. 47(11):1801. 1975.
5. Yu, K.K., and P.R. Westlin. Evaluation of Reference Method 7 Flask Reaction Time. Source Evaluation Society Newsletter. 4(4). November 1979. 10 pp.
6. Stack Sampling Safety Manual (Draft). U.S. Environmental Protection Agency, Office of Air Quality Planning and Standard, Research Triangle Park, NC. September 1978.
17.0 Tables, Diagrams, Flowcharts, and Validation Data [Reserved] Method 7B - Determination of Nitrogen Oxide Emissions From Stationary Sources (Ultraviolet Spectrophotometric Method) Note:This method does not include all of the specifications (e.g., equipment and supplies) and procedures (e.g., sampling and analytical) essential to its performance. Some material is incorporated by reference from other methods in this part. Therefore, to obtain reliable results, persons using this method should have a thorough knowledge of at least the following additional test methods: Method 1, Method 5, and Method 7.
1.0 Scope and Application1.1 Analytes.
Analyte | CAS No. | Sensitivity |
---|---|---|
Nitrogen oxides (NOX), as NO2, including: | ||
Nitric oxide (NO) | 10102-43-9 | |
Nitrogen dioxide (NO2) | 10102-44-0 | 30-786 ppmv |
1.2 Applicability. This method is applicable for the determination of NOX emissions from nitric acid plants.
1.3 Data Quality Objectives. Adherence to the requirements of this method will enhance the quality of the data obtained from air pollutant sampling methods.
2.0 Summary of Method2.1 A grab sample is collected in an evacuated flask containing a dilute sulfuric acid-hydrogen peroxide absorbing solution; the NOX, excluding nitrous oxide (N2O), are measured by ultraviolet spectrophotometry.
3.0 Definition [Reserved] 4.0 Interferences [Reserved] 5.0 Safety5.1 This method may involve hazardous materials, operations, and equipment. This test method may not address all of the safety problems associated with its use. It is the responsibility of the user of this test method to establish appropriate safety and health practices and to determine the applicability of regulatory limitations prior to performing this test method.
5.2 Corrosive reagents. The following reagents are hazardous. Personal protective equipment and safe procedures are useful in preventing chemical splashes. If contact occurs, immediately flush with copious amounts of water at least 15 minutes. Remove clothing under shower and decontaminate. Treat residual chemical burn as thermal burn.
5.2.1 Hydrogen Peroxide (H2O2). Irritating to eyes, skin, nose, and lungs.
5.2.2 Sodium Hydroxide (NaOH). Causes severe damage to eyes and skin. Inhalation causes irritation to nose, throat, and lungs. Reacts exothermically with limited amounts of water.
5.2.3 Sulfuric Acid (H2SO4). Rapidly destructive to body tissue. Will cause third degree burns. Eye damage may result in blindness. Inhalation may be fatal from spasm of the larynx, usually within 30 minutes. May cause lung tissue damage with edema. 3 mg/m 3 will cause lung damage in uninitiated. 1 mg/m 3 for 8 hours will cause lung damage or, in higher concentrations, death. Provide ventilation to limit inhalation. Reacts violently with metals and organics.
6.0 Equipment and Supplies6.1 Sample Collection. Same as Method 7, section 6.1.
6.2 Sample Recovery. The following items are required for sample recovery:
6.2.1 Wash Bottle. Polyethylene or glass.
6.2.2 Volumetric Flasks. 100-ml (one for each sample).
6.3 Analysis. The following items are required for analysis:
6.3.1 Volumetric Pipettes. 5-, 10-, 15-, and 20-ml to make standards and sample dilutions.
6.3.2 Volumetric Flasks. 1000- and 100-ml for preparing standards and dilution of samples.
6.3.3 Spectrophotometer. To measure ultraviolet absorbance at 210 nm.
6.3.4 Analytical Balance. To measure to within 0.1 mg.
7.0 Reagents and Standards Note:Unless otherwise indicated, all reagents are to conform to the specifications established by the Committee on Analytical Reagents of the American Chemical Society, where such specifications are available. Otherwise, use the best available grade.
7.1 Sample Collection. Same as Method 7, section 7.1. It is important that the amount of hydrogen peroxide in the absorbing solution not be increased. Higher concentrations of peroxide may interfere with sample analysis.
7.2 Sample Recovery. Same as Method 7, section 7.2.
7.3 Analysis. Same as Method 7, sections 7.3.1, 7.3.3, and 7.3.4, with the addition of the following:
7.3.1 Working Standard KNO3 Solution. Dilute 10 ml of the standard solution to 1000 ml with water. One milliliter of the working standard is equivalent to 10 µg NO2.
8.0 Sample Collection, Preservation, Storage, and Transport8.1 Sample Collection. Same as Method 7, section 8.1.
8.2 Sample Recovery.
8.2.1 Let the flask sit for a minimum of 16 hours, and then shake the contents for 2 minutes.
8.2.2 Connect the flask to a mercury filled U-tube manometer. Open the valve from the flask to the manometer, and record the flask temperature (Tf), the barometric pressure, and the difference between the mercury levels in the manometer. The absolute internal pressure in the flask (Pf) is the barometric pressure less the manometer reading.
8.2.3 Transfer the contents of the flask to a leak-free wash bottle. Rinse the flask three times with 10-ml portions of water, and add to the bottle. Mark the height of the liquid level so that the container can be checked for leakage after transport. Label the container to identify clearly its contents. Seal the container for shipping.
9.0 Quality ControlSection | Quality control measure | Effect |
---|---|---|
10.1 | Spectrophotometer calibration | Ensures linearity of spectrophotometer response to standards. |
Same as Method 7, sections 10.2 through 10.5, with the addition of the following:
10.1 Determination of Spectrophotometer Standard Curve. Add 0 ml, 5 ml, 10 ml, 15 ml, and 20 ml of the KNO3 working standard solution (1 ml = 10 µg NO2) to a series of five 100-ml volumetric flasks. To each flask, add 5 ml of absorbing solution. Dilute to the mark with water. The resulting solutions contain 0.0, 50, 100, 150, and 200 µg NO2, respectively. Measure the absorbance by ultraviolet spectrophotometry at 210 nm, using the blank as a zero reference. Prepare a standard curve plotting absorbance vs. µg NO2.
Note:If other than a 20-ml aliquot of sample is used for analysis, then the amount of absorbing solution in the blank and standards must be adjusted such that the same amount of absorbing solution is in the blank and standards as is in the aliquot of sample used.
10.1.1 Calculate the spectrophotometer calibration factor as follows:
Where: Mi = Mass of NO2 in standard i, µg. Ai = Absorbance of NO2 standard i. n = Total number of calibration standards.10.1.2 For the set of calibration standards specified here, Equation 7B-1 simplifies to the following:
10.2 Spectrophotometer Calibration Quality Control. Multiply the absorbance value obtained for each standard by the Kc factor (reciprocal of the least squares slope) to determine the distance each calibration point lies from the theoretical calibration line. The difference between the calculated concentration values and the actual concentrations (i.e., 50, 100, 150, and 200 µg NO2) should be less than 7 percent for all standards.
11.0 Analytical Procedures11.1 Sample Loss Check. Note the level of the liquid in the container, and confirm whether any sample was lost during shipment. Note this on the analytical data sheet. If a noticeable amount of leakage has occurred, either void the sample or use methods, subject to the approval of the Administrator, to correct the final results.
11.2 Sample Preparation. Immediately prior to analysis, transfer the contents of the shipping container to a 100-ml volumetric flask, and rinse the container twice with 5-ml portions of water. Add the rinse water to the flask, and dilute to mark with water.
11.3 Sample Analysis. Mix the contents of the flask thoroughly and pipette a 20 ml-aliquot of sample into a 100-ml volumetric flask. Dilute to the mark with water. Using the blank as zero reference, read the absorbance of the sample at 210 nm.
11.4 Audit Sample Analysis. Same as Method 7, section 11.4, except that a set of audit samples must be analyzed with each set of compliance samples or once per analysis day, or once per week when averaging continuous samples.
12.0 Data Analysis and CalculationsSame as Method 7, section 12.0, except replace section 12.3 with the following:
12.1 Total µg NO2 Per Sample.
Where: 5 = 100/20, the aliquot factor. Note:If other than a 20-ml aliquot is used for analysis, the factor 5 must be replaced by a corresponding factor.
13.0 Method Performance13.1 Range. The analytical range of the method as outlined has been determined to be 57 to 1500 milligrams NOX (as NO2) per dry standard cubic meter, or 30 to 786 parts per million by volume (ppmv) NOX.
14.0 Pollution Prevention [Reserved] 15.0 Waste Management [Reserved] 16.0 References1. National Institute for Occupational Safety and Health. Recommendations for Occupational Exposure to Nitric Acid. In: Occupational Safety and Health Reporter. Washington, D.C. Bureau of National Affairs, Inc. 1976. p. 149.
2. Rennie, P.J., A.M. Sumner, and F.B. Basketter. Determination of Nitrate in Raw, Potable, and Waste Waters by Ultraviolet Spectrophotometry. Analyst. 104:837. September 1979.
17.0 Tables, Diagrams, Flowcharts, and Validation Data [Reserved] Method 7C - Determination of Nitrogen Oxide Emissions From Stationary Sources (Alkaline Permanganate/Colorimetric Method) Note:This method does not include all of the specifications (e.g., equipment and supplies) and procedures (e.g., sampling and analytical) essential to its performance. Some material is incorporated by reference from other methods in this part. Therefore, to obtain reliable results, persons using this method should have a thorough knowledge of at least the following additional test methods: Method 1, Method 3, Method 6 and Method 7.
1.0 Scope and Application1.1 Analytes.
Analyte | CAS no. | Sensitivity |
---|---|---|
Nitrogen oxides (NOX), as NO2, including: | ||
Nitric oxide (NO) | 10102-43-9 | |
Nitrogen dioxide (NO2) | 10102-44-07 | ppmv |
1.2 Applicability. This method applies to the measurement of NOX emissions from fossil-fuel fired steam generators, electric utility plants, nitric acid plants, or other sources as specified in the regulations.
1.3 Data Quality Objectives. Adherence to the requirements of this method will enhance the quality of the data obtained from air pollutant sampling methods.
2.0 Summary of MethodAn integrated gas sample is extracted from the stack and passed through impingers containing an alkaline potassium permanganate solution; NOX (NO + NO2) emissions are oxidized to NO2 and NO3. Then NO3−is reduced to NO2−with cadmium, and the NO2−is analyzed colorimetrically.
3.0 Definitions [Reserved] 4.0 InterferencesPossible interferents are sulfur dioxides (SO2) and ammonia (NH3).
4.1 High concentrations of SO2 could interfere because SO2 consumes MnO4 (as does NOX) and, therefore, could reduce the NOX collection efficiency. However, when sampling emissions from a coal-fired electric utility plant burning 2.1 percent sulfur coal with no control of SO2 emissions, collection efficiency was not reduced. In fact, calculations show that sampling 3000 ppm SO2 will reduce the MnO4 concentration by only 5 percent if all the SO2 is consumed in the first impinger.
4.2 Ammonia (NH3) is slowly oxidized to NO3− by the absorbing solution. At 100 ppm NH3 in the gas stream, an interference of 6 ppm NOX (11 mg NO2/m 3) was observed when the sample was analyzed 10 days after collection. Therefore, the method may not be applicable to plants using NH3 injection to control NOX emissions unless means are taken to correct the results. An equation has been developed to allow quantification of the interference and is discussed in Reference 5 of section 16.0.
5.0 Safety5.1 Disclaimer. This method may involve hazardous materials, operations, and equipment. This test method may not address all of the safety problems associated with its use. It is the responsibility of the user of this test method to establish appropriate safety and health practices and to determine the applicability of regulatory limitations prior to performing this test method.
5.2 Corrosive Reagents. The following reagents are hazardous. Personal protective equipment and safe procedures are useful in preventing chemical splashes. If contact occurs, immediately flush with copious amounts of water for at least 15 minutes. Remove clothing under shower and decontaminate. Treat residual chemical burns as thermal burns.
5.2.1 Hydrochloric Acid (HCl). Highly toxic and corrosive. Causes severe damage to skin. Vapors are highly irritating to eyes, skin, nose, and lungs, causing severe damage. May cause bronchitis, pneumonia, or edema of lungs. Exposure to vapor concentrations of 0.13 to 0.2 percent can be lethal in minutes. Will react with metals, producing hydrogen.
5.2.2 Oxalic Acid (COOH)2. Poisonous. Irritating to eyes, skin, nose, and throat.
5.2.3 Sodium Hydroxide (NaOH). Causes severe damage to eye tissues and to skin. Inhalation causes irritation to nose, throat, and lungs. Reacts exothermically with small amounts of water.
5.2.4 Potassium Permanganate (KMnO4). Caustic, strong oxidizer. Avoid bodily contact with.
6.0 Equipment and Supplies6.1 Sample Collection and Sample Recovery. A schematic of the Method 7C sampling train is shown in Figure 7C-1, and component parts are discussed below. Alternative apparatus and procedures are allowed provided acceptable accuracy and precision can be demonstrated to the satisfaction of the Administrator.
6.1.1 Probe. Borosilicate glass tubing, sufficiently heated to prevent water condensation and equipped with an in-stack or heated out-of-stack filter to remove particulate matter (a plug of glass wool is satisfactory for this purpose). Stainless steel or Teflon tubing may also be used for the probe.
6.1.2 Impingers. Three restricted-orifice glass impingers, having the specifications given in Figure 7C-2, are required for each sampling train. The impingers must be connected in series with leak-free glass connectors. Stopcock grease may be used, if necessary, to prevent leakage. (The impingers can be fabricated by a glass blower if not available commercially.)
6.1.3 Glass Wool, Stopcock Grease, Drying Tube, Valve, Pump, Barometer, and Vacuum Gauge and Rotameter. Same as in Method 6, sections 6.1.1.3, 6.1.1.4, 6.1.1.6, 6.1.1.7, 6.1.1.8, 6.1.2, and 6.1.3, respectively.
6.1.4 Rate Meter. Rotameter, or equivalent, accurate to within 2 percent at the selected flow rate of between 400 and 500 ml/min (0.014 to 0.018 cfm). For rotameters, a range of 0 to 1 liter/min (0 to 0.035 cfm) is recommended.
6.1.5 Volume Meter. Dry gas meter (DGM) capable of measuring the sample volume under the sampling conditions of 400 to 500 ml/min (0.014 to 0.018 cfm) for 60 minutes within an accuracy of 2 percent.
6.1.6 Filter. To remove NOX from ambient air, prepared by adding 20 g of 5-angstrom molecular sieve to a cylindrical tube (e.g., a polyethylene drying tube).
6.1.7 Polyethylene Bottles. 1-liter, for sample recovery.
6.1.8 Funnel and Stirring Rods. For sample recovery.
6.2 Sample Preparation and Analysis.
6.2.1 Hot Plate. Stirring type with 50- by 10-mm Teflon-coated stirring bars.
6.2.2 Beakers. 400-, 600-, and 1000-ml capacities.
6.2.3 Filtering Flask. 500-ml capacity with side arm.
6.2.4 Buchner Funnel. 75-mm ID, with spout equipped with a 13-mm ID by 90-mm long piece of Teflon tubing to minimize possibility of aspirating sample solution during filtration.
6.2.5 Filter Paper. Whatman GF/C, 7.0-cm diameter.
6.2.6 Stirring Rods.
6.2.7 Volumetric Flasks. 100-, 200- or 250-, 500-, and 1000-ml capacity.
6.2.8 Watch Glasses. To cover 600- and 1000-ml beakers.
6.2.9 Graduated Cylinders. 50- and 250-ml capacities.
6.2.10 Pipettes. Class A.
6.2.11 pH Meter. To measure pH from 0.5 to 12.0.
6.2.12 Burette. 50-ml with a micrometer type stopcock. (The stopcock is Catalog No. 8225-t-05, Ace Glass, Inc., Post Office Box 996, Louisville, Kentucky 50201.) Place a glass wool plug in bottom of burette. Cut off burette at a height of 43 cm (17 in.) from the top of plug, and have a blower attach a glass funnel to top of burette such that the diameter of the burette remains essentially unchanged. Other means of attaching the funnel are acceptable.
6.2.13 Glass Funnel. 75-mm ID at the top.
6.2.14 Spectrophotometer. Capable of measuring absorbance at 540 nm; 1-cm cells are adequate.
6.2.15 Metal Thermometers. Bimetallic thermometers, range 0 to 150 °C (32 to 300 °F).
6.2.16 Culture Tubes. 20-by 150-mm, Kimax No. 45048.
6.2.17 Parafilm “M.” Obtained from American Can Company, Greenwich, Connecticut 06830.
6.2.18 CO2 Measurement Equipment. Same as in Method 3, section 6.0.
7.0 Reagents and StandardsUnless otherwise indicated, it is intended that all reagents conform to the specifications established by the Committee on Analytical Reagents of the American Chemical Society, where such specifications are available; otherwise, use the best available grade.
7.1 Sample Collection.
7.1.1 Water. Deionized distilled to conform to ASTM Specification D 1193-77 or 91 Type 3 (incorporated by reference - see § 60.17).
7.1.2 Potassium Permanganate, 4.0 Percent (w/w), Sodium Hydroxide, 2.0 Percent (w/w) solution (KMnO4/NaOH solution). Dissolve 40.0 g of KMnO4 and 20.0 g of NaOH in 940 ml of water.
7.2 Sample Preparation and Analysis.
7.2.1 Water. Same as in section 7.1.1.
7.2.2 Oxalic Acid Solution. Dissolve 48 g of oxalic acid [(COOH)2·2H2O] in water, and dilute to 500 ml. Do not heat the solution.
7.2.3 Sodium Hydroxide, 0.5 N. Dissolve 20 g of NaOH in water, and dilute to 1 liter.
7.2.4 Sodium Hydroxide, 10 N. Dissolve 40 g of NaOH in water, and dilute to 100 ml.
7.2.5 Ethylenediamine Tetraacetic Acid (EDTA) Solution, 6.5 percent (w/v). Dissolve 6.5 g of EDTA (disodium salt) in water, and dilute to 100 ml. Dissolution is best accomplished by using a magnetic stirrer.
7.2.6 Column Rinse Solution. Add 20 ml of 6.5 percent EDTA solution to 960 ml of water, and adjust the pH to between 11.7 and 12.0 with 0.5 N NaOH.
7.2.7 Hydrochloric Acid (HCl), 2 N. Add 86 ml of concentrated HCl to a 500 ml-volumetric flask containing water, dilute to volume, and mix well. Store in a glass-stoppered bottle.
7.2.8 Sulfanilamide Solution. Add 20 g of sulfanilamide (melting point 165 to 167 °C (329 to 333 °F)) to 700 ml of water. Add, with mixing, 50 ml concentrated phosphoric acid (85 percent), and dilute to 1000 ml. This solution is stable for at least 1 month, if refrigerated.
7.2.9 N-(1-Naphthyl)-Ethylenediamine Dihydrochloride (NEDA) Solution. Dissolve 0.5 g of NEDA in 500 ml of water. An aqueous solution should have one absorption peak at 320 nm over the range of 260 to 400 nm. NEDA that shows more than one absorption peak over this range is impure and should not be used. This solution is stable for at least 1 month if protected from light and refrigerated.
7.2.10 Cadmium. Obtained from Matheson Coleman and Bell, 2909 Highland Avenue, Norwood, Ohio 45212, as EM Laboratories Catalog No. 2001. Prepare by rinsing in 2 N HCl for 5 minutes until the color is silver-grey. Then rinse the cadmium with water until the rinsings are neutral when tested with pH paper. CAUTION: H2 is liberated during preparation. Prepare in an exhaust hood away from any flame or combustion source.
7.2.11 Sodium Nitrite (NaNO2) Standard Solution, Nominal Concentration, 1000 µg NO2−/ml. Desiccate NaNO2 overnight. Accurately weigh 1.4 to 1.6 g of NaNO2 (assay of 97 percent NaNO2 or greater), dissolve in water, and dilute to 1 liter. Calculate the exact NO2-concentration using Equation 7C-1 in section 12.2. This solution is stable for at least 6 months under laboratory conditions.
7.2.12 Potassium Nitrate (KNO3) Standard Solution. Dry KNO3 at 110 °C (230 °F) for 2 hours, and cool in a desiccator. Accurately weigh 9 to 10 g of KNO3 to within 0.1 mg, dissolve in water, and dilute to 1 liter. Calculate the exact NO3− concentration using Equation 7C-2 in section 12.3. This solution is stable for 2 months without preservative under laboratory conditions.
7.2.13 Spiking Solution. Pipette 7 ml of the KNO3 standard into a 100-ml volumetric flask, and dilute to volume.
7.2.14 Blank Solution. Dissolve 2.4 g of KMnO4 and 1.2 g of NaOH in 96 ml of water. Alternatively, dilute 60 ml of KMnO4/NaOH solution to 100 ml.
8.0 Sample Collection, Preservation, Storage, and Transport8.1 Preparation of Sampling Train. Add 200 ml of KMnO4/NaOH solution (Section 7.1.2) to each of three impingers, and assemble the train as shown in Figure 7C-1. Adjust the probe heater to a temperature sufficient to prevent water condensation.
8.2 Leak-Checks. Same as in Method 6, section 8.2.
8.3 Sample Collection.
8.3.1 Record the initial DGM reading and barometric pressure. Determine the sampling point or points according to the appropriate regulations (e.g., § 60.46(b)(5) of 40 CFR Part 60). Position the tip of the probe at the sampling point, connect the probe to the first impinger, and start the pump. Adjust the sample flow to a value between 400 and 500 ml/min (0.014 and 0.018 cfm). CAUTION: DO NOT EXCEED THESE FLOW RATES. Once adjusted, maintain a constant flow rate during the entire sampling run. Sample for 60 minutes. For relative accuracy (RA) testing of continuous emission monitors, the minimum sampling time is 1 hour, sampling 20 minutes at each traverse point.
Note:When the SO2 concentration is greater than 1200 ppm, the sampling time may have to be reduced to 30 minutes to eliminate plugging of the impinger orifice with MnO2. For RA tests with SO2 greater than 1200 ppm, sample for 30 minutes (10 minutes at each point).
8.3.2 Record the DGM temperature, and check the flow rate at least every 5 minutes. At the conclusion of each run, turn off the pump, remove the probe from the stack, and record the final readings. Divide the sample volume by the sampling time to determine the average flow rate. Conduct the mandatory post-test leak-check. If a leak is found, void the test run, or use procedures acceptable to the Administrator to adjust the sample volume for the leakage.
8.4 CO2 Measurement. During sampling, measure the CO2 content of the stack gas near the sampling point using Method 3. The single-point grab sampling procedure is adequate, provided the measurements are made at least three times (near the start, midway, and before the end of a run), and the average CO2 concentration is computed. The Orsat or Fyrite analyzer may be used for this analysis.
8.5 Sample Recovery. Disconnect the impingers. Pour the contents of the impingers into a 1-liter polyethylene bottle using a funnel and a stirring rod (or other means) to prevent spillage. Complete the quantitative transfer by rinsing the impingers and connecting tubes with water until the rinsings are clear to light pink, and add the rinsings to the bottle. Mix the sample, and mark the solution level. Seal and identify the sample container.
9.0 Quality ControlSection | Quality control measure | Effect |
---|---|---|
8.2, 10.1-10.3 | Sampling equipment leak-check and calibration | Ensure accurate measurement of sample volume. |
10.4 | Spectrophotometer calibration | Ensure linearity of spectrophotometer response to standards |
11.3 | Spiked sample analysis. | Ensure reduction efficiency of column. |
10.1 Volume Metering System. Same as Method 6, section 10.1. For detailed instructions on carrying out these calibrations, it is suggested that section 3.5.2 of Reference 4 of section 16.0 be consulted.
10.2 Temperature Sensors and Barometer. Same as in Method 6, sections 10.2 and 10.4, respectively.
10.3 Check of Rate Meter Calibration Accuracy (Optional). Disconnect the probe from the first impinger, and connect the filter. Start the pump, and adjust the rate meter to read between 400 and 500 ml/min (0.014 and 0.018 cfm). After the flow rate has stabilized, start measuring the volume sampled, as recorded by the dry gas meter and the sampling time. Collect enough volume to measure accurately the flow rate. Then calculate the flow rate. This average flow rate must be less than 500 ml/min (0.018 cfm) for the sample to be valid; therefore, it is recommended that the flow rate be checked as above prior to each test.
10.4 Spectrophotometer.
10.4.1 Dilute 5.0 ml of the NaNO2 standard solution to 200 ml with water. This solution nominally contains 25 µg NO2−/ml. Use this solution to prepare calibration standards to cover the range of 0.25 to 3.00 µg NO2−/ml. Prepare a minimum of three standards each for the linear and slightly nonlinear (described below) range of the curve. Use pipettes for all additions.
10.4.2 Measure the absorbance of the standards and a water blank as instructed in section 11.5. Plot the net absorbance vs. µg NO2−/ml. Draw a smooth curve through the points. The curve should be linear up to an absorbance of approximately 1.2 with a slope of approximately 0.53 absorbance units/µg NO2−/ml. The curve should pass through the origin. The curve is slightly nonlinear from an absorbance of 1.2 to 1.6.
11.0 Analytical Procedures11.1 Sample Stability. Collected samples are stable for at least four weeks; thus, analysis must occur within 4 weeks of collection.
11.2 Sample Preparation.
11.2.1 Prepare a cadmium reduction column as follows: Fill the burette with water. Add freshly prepared cadmium slowly, with tapping, until no further settling occurs. The height of the cadmium column should be 39 cm (15 in). When not in use, store the column under rinse solution.
Note:The column should not contain any bands of cadmium fines. This may occur if regenerated cadmium is used and will greatly reduce the column lifetime.
11.2.2 Note the level of liquid in the sample container, and determine whether any sample was lost during shipment. If a noticeable amount of leakage has occurred, the volume lost can be determined from the difference between initial and final solution levels, and this value can then be used to correct the analytical result. Quantitatively transfer the contents to a 1-liter volumetric flask, and dilute to volume.
11.2.3 Take a 100-ml aliquot of the sample and blank (unexposed KMnO4/NaOH) solutions, and transfer to 400-ml beakers containing magnetic stirring bars. Using a pH meter, add concentrated H2SO4 with stirring until a pH of 0.7 is obtained. Allow the solutions to stand for 15 minutes. Cover the beakers with watch glasses, and bring the temperature of the solutions to 50 °C (122 °F). Keep the temperature below 60 °C (140 °F). Dissolve 4.8 g of oxalic acid in a minimum volume of water, approximately 50 ml, at room temperature. Do not heat the solution. Add this solution slowly, in increments, until the KMnO4 solution becomes colorless. If the color is not completely removed, prepare some more of the above oxalic acid solution, and add until a colorless solution is obtained. Add an excess of oxalic acid by dissolving 1.6 g of oxalic acid in 50 ml of water, and add 6 ml of this solution to the colorless solution. If suspended matter is present, add concentrated H2SO4 until a clear solution is obtained.
11.2.4 Allow the samples to cool to near room temperature, being sure that the samples are still clear. Adjust the pH to between 11.7 and 12.0 with 10 N NaOH. Quantitatively transfer the mixture to a Buchner funnel containing GF/C filter paper, and filter the precipitate. Filter the mixture into a 500-ml filtering flask. Wash the solid material four times with water. When filtration is complete, wash the Teflon tubing, quantitatively transfer the filtrate to a 500-ml volumetric flask, and dilute to volume. The samples are now ready for cadmium reduction. Pipette a 50-ml aliquot of the sample into a 150-ml beaker, and add a magnetic stirring bar. Pipette in 1.0 ml of 6.5 percent EDTA solution, and mix.
11.3 Determine the correct stopcock setting to establish a flow rate of 7 to 9 ml/min of column rinse solution through the cadmium reduction column. Use a 50-ml graduated cylinder to collect and measure the solution volume. After the last of the rinse solution has passed from the funnel into the burette, but before air entrapment can occur, start adding the sample, and collect it in a 250-ml graduated cylinder. Complete the quantitative transfer of the sample to the column as the sample passes through the column. After the last of the sample has passed from the funnel into the burette, start adding 60 ml of column rinse solution, and collect the rinse solution until the solution just disappears from the funnel. Quantitatively transfer the sample to a 200-ml volumetric flask (a 250-ml flask may be required), and dilute to volume. The samples are now ready for NO2-analysis.
Note:Two spiked samples should be run with every group of samples passed through the column. To do this, prepare two additional 50-ml aliquots of the sample suspected to have the highest NO2-concentration, and add 1 ml of the spiking solution to these aliquots. If the spike recovery or column efficiency (see section 12.2) is below 95 percent, prepare a new column, and repeat the cadmium reduction.
11.5 Sample Analysis. Pipette 10 ml of sample into a culture tube. Pipette in 10 ml of sulfanilamide solution and 1.4 ml of NEDA solution. Cover the culture tube with parafilm, and mix the solution. Prepare a blank in the same manner using the sample from treatment of the unexposed KMnO4/NaOH solution. Also, prepare a calibration standard to check the slope of the calibration curve. After a 10-minute color development interval, measure the absorbance at 540 nm against water. Read µg NO2−/ml from the calibration curve. If the absorbance is greater than that of the highest calibration standard, use less than 10 ml of sample, and repeat the analysis. Determine the NO2−concentration using the calibration curve obtained in section 10.4.
Note:Some test tubes give a high blank NO2− value but culture tubes do not.
11.6 Audit Sample Analysis. Same as in Method 7, section 11.4.
12.0 Data Analysis and CalculationsCarry out calculations, retaining at least one extra significant figure beyond that of the acquired data. Round off figures after final calculation.
12.1 Nomenclature.
B = Analysis of blank, µg NO2−/ml. C = Concentration of NOX as NO2, dry basis, mg/dsm 3. E = Column efficiency, dimensionless K2 = 10−3 mg/µg. m = Mass of NOX, as NO2, in sample, µg. Pbar = Barometric pressure, mm Hg (in. Hg). Pstd = Standard absolute pressure, 760 mm Hg (29.92 in. Hg). s = Concentration of spiking solution, µg NO3/ml. S = Analysis of sample, µg NO2−/ml. Tm = Average dry gas meter absolute temperature, °K. Tstd = Standard absolute temperature, 293 °K (528 °R). Vm(std) = Dry gas volume measured by the dry gas meter, corrected to standard conditions, dscm (dscf). Vm = Dry gas volume as measured by the dry gas meter, scm (scf). x = Analysis of spiked sample, µg NO2−/ml. X = Correction factor for CO2 collection = 100/(100 − %CO2(V/V)). y = Analysis of unspiked sample, µg NO2−/ml. Y = Dry gas meter calibration factor. 1.0 ppm NO = 1.247 mg NO/m 3 at STP. 1.0 ppm NO2 = 1.912 mg NO2/m 3 at STP. 1 ft 3 = 2.832 × 10−2 m 3.12.2 NO2 Concentration. Calculate the NO2 concentration of the solution (see section 7.2.11) using the following equation:
12.3 NO3 Concentration. Calculate the NO3 concentration of the KNO3 solution (see section 7.2.12) using the following equation:
12.4 Sample Volume, Dry Basis, Corrected to Standard Conditions.
Where: K1 = 0.3855 °K/mm Hg for metric units. K1 = 17.65 °R/in. Hg for English units.12.5 Efficiency of Cadmium Reduction Column. Calculate this value as follows:
Where: 200 = Final volume of sample and blank after passing through the column, ml. 1.0 = Volume of spiking solution added, ml. 46.01=µg NO2−/µmole. 62.01=µg NO3−/µmole.12.6 Total µg NO2.
Where: 500 = Total volume of prepared sample, ml. 50 = Aliquot of prepared sample processed through cadmium column, ml. 100 = Aliquot of KMnO4/NaOH solution, ml. 1000 = Total volume of KMnO4/NaOH solution, ml.12.7 Sample Concentration.
13.0 Method Performance13.1 Precision. The intra-laboratory relative standard deviation for a single measurement is 2.8 and 2.9 percent at 201 and 268 ppm NOX, respectively.
13.2 Bias. The method does not exhibit any bias relative to Method 7.
13.3 Range. The lower detectable limit is 13 mg NOX/m 3, as NO2 (7 ppm NOX) when sampling at 500 ml/min for 1 hour. No upper limit has been established; however, when using the recommended sampling conditions, the method has been found to collect NOX emissions quantitatively up to 1782 mg NOX/m 3, as NO2 (932 ppm NOX).
14.0 Pollution Prevention [Reserved] 15.0 Waste Management [Reserved] 16.0 References1. Margeson, J.H., W.J. Mitchell, J.C. Suggs, and M.R. Midgett. Integrated Sampling and Analysis Methods for Determining NOX Emissions at Electric Utility Plants. U.S. Environmental Protection Agency, Research Triangle Park, NC. Journal of the Air Pollution Control Association. 32:1210-1215. 1982.
2. Memorandum and attachment from J.H. Margeson, Source Branch, Quality Assurance Division, Environmental Monitoring Systems Laboratory, to The Record, EPA. March 30, 1983. NH3 Interference in Methods 7C and 7D.
3. Margeson, J.H., J.C. Suggs, and M.R. Midgett. Reduction of Nitrate to Nitrite with Cadmium. Anal. Chem. 52:1955-57. 1980.
4. Quality Assurance Handbook for Air Pollution Measurement Systems. Volume III - Stationary Source Specific Methods. U.S. Environmental Protection Agency. Research Triangle Park, NC. Publication No. EPA-600/4-77-027b. August 1977.
5. Margeson, J.H., et al. An Integrated Method for Determining NOX Emissions at Nitric Acid Plants. Analytical Chemistry. 47 (11):1801. 1975.
17.0 Tables, Diagrams, Flowcharts, and Validation Data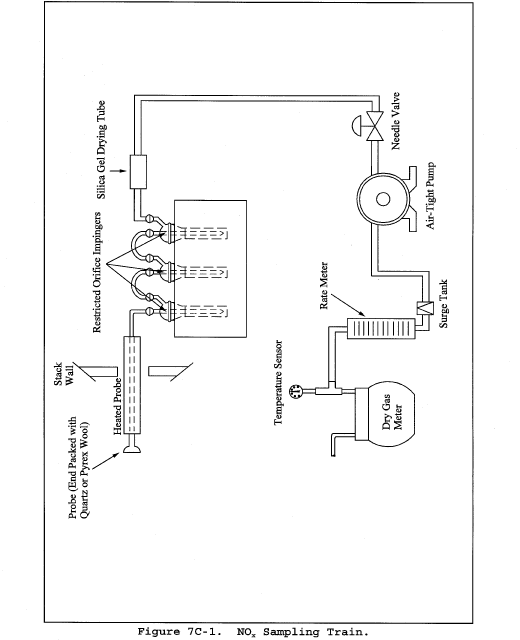
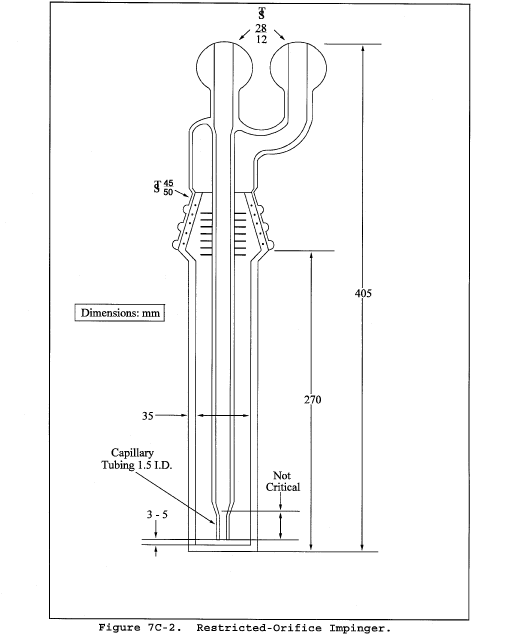
This method is not inclusive with respect to specifications (e.g., equipment and supplies) and procedures (e.g., sampling and analytical) essential to its performance. Some material is incorporated by reference from other methods in this part. Therefore, to obtain reliable results, persons using this method should have a thorough knowledge of at least the following additional test methods: Method 1, Method 3, Method 6, Method 7, and Method 7C.
1.0 Scope and Application1.1 Analytes.
Analyte | CAS No. | Sensitivity |
---|---|---|
Nitrogen oxides (NOX), as NO2, including: | ||
Nitric oxide (NO) | 10102-43-9 | |
Nitrogen dioxide (NO2) | 10102-44-0 | 7 ppmv |
1.2 Applicability. This method applies to the measurement of NOX emissions from fossil-fuel fired steam generators, electric utility plants, nitric acid plants, or other sources as specified in the regulations.
1.3 Data Quality Objectives. Adherence to the requirements of this method will enhance the quality of the data obtained from air pollutant sampling methods.
2.0 Summary of MethodAn integrated gas sample is extracted from the stack and passed through impingers containing an alkaline-potassium permanganate solution; NOX (NO + NO2) emissions are oxidized to NO3−. Then NO3− is analyzed by ion chromatography.
3.0 Definitions [Reserved] 4.0 InterferencesSame as in Method 7C, section 4.0.
5.0 Safety5.1 Disclaimer. This method may involve hazardous materials, operations, and equipment. This test method may not address all of the safety problems associated with its use. It is the responsibility of the user of this test method to establish appropriate safety and health practices and to determine the applicability of regulatory limitations prior to performing this test method.
5.2 Corrosive reagents. The following reagents are hazardous. Personal protective equipment and safe procedures are useful in preventing chemical splashes. If contact occurs, immediately flush with copious amounts of water for at least 15 minutes. Remove clothing under shower and decontaminate. Treat residual chemical burns as thermal burns.
5.2.1 Hydrogen Peroxide (H2O2). Irritating to eyes, skin, nose, and lungs. 30% H2O2 is a strong oxidizing agent; avoid contact with skin, eyes, and combustible material. Wear gloves when handling.
5.2.2 Sodium Hydroxide (NaOH). Causes severe damage to eye tissues and to skin. Inhalation causes irritation to nose, throat, and lungs. Reacts exothermically with limited amounts of water.
5.2.3 Potassium Permanganate (KMnO4). Caustic, strong oxidizer. Avoid bodily contact with.
6.0 Equipment and Supplies6.1 Sample Collection and Sample Recovery. Same as Method 7C, section 6.1. A schematic of the sampling train used in performing this method is shown in Figure 7C-1 of Method 7C.
6.2 Sample Preparation and Analysis.
6.2.1 Magnetic Stirrer. With 25- by 10-mm Teflon-coated stirring bars.
6.2.2 Filtering Flask. 500-ml capacity with sidearm.
6.2.3 Buchner Funnel. 75-mm ID, with spout equipped with a 13-mm ID by 90-mm long piece of Teflon tubing to minimize possibility of aspirating sample solution during filtration.
6.2.4 Filter Paper. Whatman GF/C, 7.0-cm diameter.
6.2.5 Stirring Rods.
6.2.6 Volumetric Flask. 250-ml.
6.2.7 Pipettes. Class A.
6.2.8 Erlenmeyer Flasks. 250-ml.
6.2.9 Ion Chromatograph. Equipped with an anion separator column to separate NO3−, H3 + suppressor, and necessary auxiliary equipment. Nonsuppressed and other forms of ion chromatography may also be used provided that adequate resolution of NO3− is obtained. The system must also be able to resolve and detect NO2−.
7.0 Reagents and Standards Note:Unless otherwise indicated, it is intended that all reagents conform to the specifications established by the Committee on Analytical Reagents of the American Chemical Society, where such specifications are available; otherwise, use the best available grade.
7.1 Sample Collection.
7.1.1 Water. Deionized distilled to conform to ASTM specification D 1193-77 or 91 Type 3 (incorporated by reference - see § 60.17).
7.1.2 Potassium Permanganate, 4.0 Percent (w/w), Sodium Hydroxide, 2.0 Percent (w/w). Dissolve 40.0 g of KMnO4 and 20.0 g of NaOH in 940 ml of water.
7.2 Sample Preparation and Analysis.
7.2.1 Water. Same as in section 7.1.1.
7.2.2 Hydrogen Peroxide (H2O2), 5 Percent. Dilute 30 percent H2O2 1:5 (v/v) with water.
7.2.3 Blank Solution. Dissolve 2.4 g of KMnO4 and 1.2 g of NaOH in 96 ml of water. Alternatively, dilute 60 ml of KMnO4/NaOH solution to 100 ml.
7.2.4 KNO3 Standard Solution. Dry KNO3 at 110 °C for 2 hours, and cool in a desiccator. Accurately weigh 9 to 10 g of KNO3 to within 0.1 mg, dissolve in water, and dilute to 1 liter. Calculate the exact NO3− concentration using Equation 7D-1 in section 12.2. This solution is stable for 2 months without preservative under laboratory conditions.
7.2.5 Eluent, 0.003 M NaHCO3/0.0024 M Na2CO3. Dissolve 1.008 g NaHCO3 and 1.018 g Na2CO3 in water, and dilute to 4 liters. Other eluents capable of resolving nitrate ion from sulfate and other species present may be used.
8.0 Sample Collection, Preservation, Transport, and Storage.8.1 Sampling. Same as in Method 7C, section 8.1.
8.2 Sample Recovery. Same as in Method 7C, section 8.2.
8.3 Sample Preparation for Analysis.
Note:Samples must be analyzed within 28 days of collection.
8.3.1 Note the level of liquid in the sample container, and determine whether any sample was lost during shipment. If a noticeable amount of leakage has occurred, the volume lost can be determined from the difference between initial and final solution levels, and this value can then be used to correct the analytical result. Quantitatively transfer the contents to a 1-liter volumetric flask, and dilute to volume.
8.3.2 Sample preparation can be started 36 hours after collection. This time is necessary to ensure that all NO2− is converted to NO3− in the collection solution. Take a 50-ml aliquot of the sample and blank, and transfer to 250-ml Erlenmeyer flasks. Add a magnetic stirring bar. Adjust the stirring rate to as fast a rate as possible without loss of solution. Add 5 percent H2O2 in increments of approximately 5 ml using a 5-ml pipette. When the KMnO4 color appears to have been removed, allow the precipitate to settle, and examine the supernatant liquid. If the liquid is clear, the H2O2 addition is complete. If the KMnO4 color persists, add more H2O2, with stirring, until the supernatant liquid is clear.
Note:The faster the stirring rate, the less volume of H2O2 that will be required to remove the KMnO4.) Quantitatively transfer the mixture to a Buchner funnel containing GF/C filter paper, and filter the precipitate. The spout of the Buchner funnel should be equipped with a 13-mm ID by 90-mm long piece of Teflon tubing. This modification minimizes the possibility of aspirating sample solution during filtration. Filter the mixture into a 500-ml filtering flask. Wash the solid material four times with water. When filtration is complete, wash the Teflon tubing, quantitatively transfer the filtrate to a 250-ml volumetric flask, and dilute to volume. The sample and blank are now ready for NO3−analysis.
9.0 Quality ControlSection | Quality control measure | Effect |
---|---|---|
8.2, 10.1-10.3 | Sampling equipment leak-check and calibration | Ensure accurate measurement of sample volume. |
10.4 | Spectrophotometer calibration | Ensure linearity of spectrophotometer response to standards. |
11.3 | Spiked sample analysis | Ensure reduction efficiency of column. |
10.1 Dry Gas Meter (DGM) System.
10.1.1 Initial Calibration. Same as in Method 6, section 10.1.1. For detailed instructions on carrying out this calibration, it is suggested that section 3.5.2 of Citation 4 in section 16.0 of Method 7C be consulted.
10.1.2 Post-Test Calibration Check. Same as in Method 6, section 10.1.2.
10.2 Thermometers for DGM and Barometer. Same as in Method 6, sections 10.2 and 10.4, respectively.
10.3 Ion Chromatograph.
10.3.1 Dilute a given volume (1.0 ml or greater) of the KNO3 standard solution to a convenient volume with water, and use this solution to prepare calibration standards. Prepare at least four standards to cover the range of the samples being analyzed. Use pipettes for all additions. Run standards as instructed in section 11.2. Determine peak height or area, and plot the individual values versus concentration in µg NO3−/ml.
10.3.2 Do not force the curve through zero. Draw a smooth curve through the points. The curve should be linear. With the linear curve, use linear regression to determine the calibration equation.
11.0 Analytical Procedures11.1 The following chromatographic conditions are recommended: 0.003 M NaHCO3/0.0024 Na2CO3 eluent solution (Section 7.2.5), full scale range, 3 µMHO; sample loop, 0.5 ml; flow rate, 2.5 ml/min. These conditions should give a NO3− retention time of approximately 15 minutes (Figure 7D-1).
11.2 Establish a stable baseline. Inject a sample of water, and determine whether any NO3− appears in the chromatogram. If NO3− is present, repeat the water load/injection procedure approximately five times; then re-inject a water sample and observe the chromatogram. When no NO3− is present, the instrument is ready for use. Inject calibration standards. Then inject samples and a blank. Repeat the injection of the calibration standards (to compensate for any drift in response of the instrument). Measure the NO3− peak height or peak area, and determine the sample concentration from the calibration curve.
12.0 Data Analysis and CalculationsCarry out calculations, retaining at least one extra significant figure beyond that of the acquired data. Round off figures after final calculation.
12.1 Nomenclature. Same as in Method 7C, section 12.1.
12.2 NO3− concentration. Calculate the NO3− concentration in the KNO3 standard solution (see section 7.2.4) using the following equation:
12.3 Sample Volume, Dry Basis, Corrected to Standard Conditions. Same as in Method 7C, section 12.4.
12.4 Total µg NO2 Per Sample.
Where: 250 = Volume of prepared sample, ml. 1000 = Total volume of KMnO4 solution, ml. 50 = Aliquot of KMnO4/NaOH solution, ml. 46.01 = Molecular weight of NO3−. 62.01 = Molecular weight of NO3−.12.5 Sample Concentration. Same as in Method 7C, section 12.7.
13.0 Method Performance13.1 Precision. The intra-laboratory relative standard deviation for a single measurement is approximately 6 percent at 200 to 270 ppm NOX.
13.2 Bias. The method does not exhibit any bias relative to Method 7.
13.3 Range. The lower detectable limit is similar to that of Method 7C. No upper limit has been established; however, when using the recommended sampling conditions, the method has been found to collect NOX emissions quantitatively up to 1782 mg NOX/m 3, as NO2 (932 ppm NOX).
14.0 Pollution Prevention [Reserved] 15.0 Waste Management [Reserved] 16.0 ReferencesSame as Method 7C, section 16.0, References 1, 2, 4, and 5.
17.0 Tables, Diagrams, Flowcharts, and Validation Data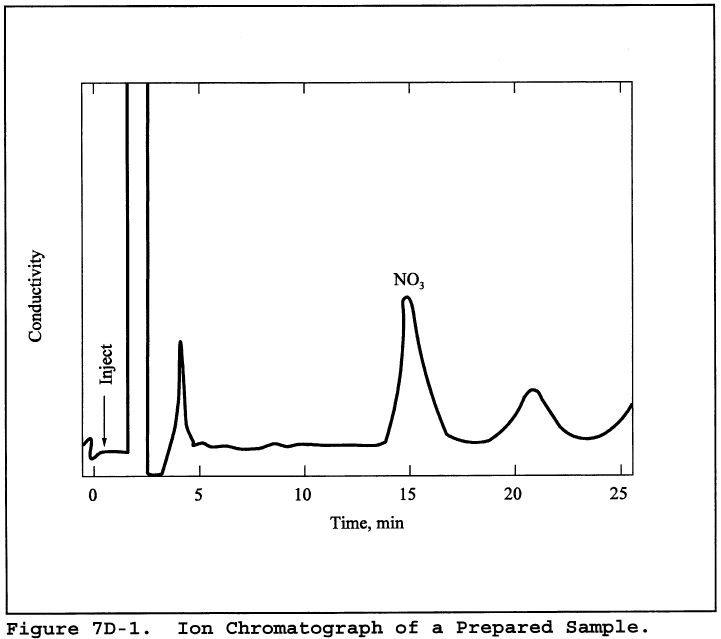
Method 7E is a procedure for measuring nitrogen oxides (NOX) in stationary source emissions using a continuous instrumental analyzer. Quality assurance and quality control requirements are included to assure that you, the tester, collect data of known quality. You must document your adherence to these specific requirements for equipment, supplies, sample collection and analysis, calculations, and data analysis. This method does not completely describe all equipment, supplies, and sampling and analytical procedures you will need but refers to other methods for some of the details. Therefore, to obtain reliable results, you should also have a thorough knowledge of these additional test methods which are found in appendix A to this part:
(a) Method 1 - Sample and Velocity Traverses for Stationary Sources.
(b) Method 4 - Determination of Moisture Content in Stack Gases.
1.1 Analytes. What does this method determine? This method measures the concentration of nitrogen oxides as NO2.
Analyte | CAS No. | Sensitivity |
---|---|---|
Nitric oxide (NO) | 10102-43-9 | Typically <2% of |
Nitrogen dioxide (NO2) | 10102-44-0 | Calibration Span. |
1.2 Applicability. When is this method required? The use of Method 7E may be required by specific New Source Performance Standards, Clean Air Marketing rules, State Implementation Plans, and permits where measurement of NOX concentrations in stationary source emissions is required, either to determine compliance with an applicable emissions standard or to conduct performance testing of a continuous monitoring system (CEMS). Other regulations may also require the use of Method 7E.
1.3 Data Quality Objectives (DQO). How good must my collected data be? Method 7E is designed to provide high-quality data for determining compliance with Federal and State emission standards and for relative accuracy testing of CEMS. In these and other applications, the principal objective is to ensure the accuracy of the data at the actual emission levels encountered. To meet this objective, the use of EPA traceability protocol calibration gases and measurement system performance tests are required.
1.4 Data Quality Assessment for Low Emitters. Is performance relief granted when testing low-emission units? Yes. For low-emitting sources, there are alternative performance specifications for analyzer calibration error, system bias, drift, and response time. Also, the alternative dynamic spiking procedure in section 16 may provide performance relief for certain low-emitting units.
2.0 Summary of MethodIn this method, a sample of the effluent gas is continuously sampled and conveyed to the analyzer for measuring the concentration of NOX. You may measure NO and NO2 separately or simultaneously together but, for the purposes of this method, NOX is the sum of NO and NO2. You must meet the performance requirements of this method to validate your data.
3.0 Definitions3.1 Analyzer Calibration Error, for non-dilution systems, means the difference between the manufacturer certified concentration of a calibration gas and the measured concentration of the same gas when it is introduced into the analyzer in direct calibration mode.
3.2 Calibration Curve means the relationship between an analyzer's response to the injection of a series of calibration gases and the actual concentrations of those gases.
3.3 Calibration Gas means the gas mixture containing NOX at a known concentration and produced and certified in accordance with “EPA Traceability Protocol for Assay and Certification of Gaseous Calibration Standards,” September 1997, as amended August 25, 1999, EPA-600/R-97/121 or more recent updates. The tests for analyzer calibration error, drift, and system bias require the use of calibration gas prepared according to this protocol. If a zero gas is used for the low-level gas, it must meet the requirements under the definition for “zero air material” in 40 CFR 72.2 in place of being prepared by the traceability protocol.
3.3.1 Low-Level Gas means a calibration gas with a concentration that is less than 20 percent of the calibration span and may be a zero gas.
3.3.2 Mid-Level Gas means a calibration gas with a concentration that is 40 to 60 percent of the calibration span.
3.3.3 High-Level Gas means a calibration gas with a concentration that is equal to the calibration span.
3.4 Calibration Span means the upper limit of the analyzer's calibration that is set by the choice of high-level calibration gas. No valid run average concentration may exceed the calibration span. To the extent practicable, the measured emissions should be between 20 to 100 percent of the selected calibration span. This may not be practicable in some cases of low-concentration measurements or testing for compliance with an emission limit when emissions are substantially less than the limit. In such cases, calibration spans that are practicable to achieving the data quality objectives without being excessively high should be chosen.
3.5 Centroidal Area means the central area of the stack or duct that is no greater than 1 percent of the stack or duct cross section. This area has the same geometric shape as the stack or duct.
3.6 Converter Efficiency Gas means a calibration gas with a known NO or NO2 concentration and of Traceability Protocol quality.
3.7 Data Recorder means the equipment that permanently records the concentrations reported by the analyzer.
3.8 Direct Calibration Mode means introducing the calibration gases directly into the analyzer (or into the assembled measurement system at a point downstream of all sample conditioning equipment) according to manufacturer's recommended calibration procedure. This mode of calibration applies to non-dilution-type measurement systems.
3.9 Drift means the difference between the pre- and post-run system bias (or system calibration error) checks at a specific calibration gas concentration level (i.e. low-, mid- or high-).
3.10 Gas Analyzer means the equipment that senses the gas being measured and generates an output proportional to its concentration.
3.11 Interference Check means the test to detect analyzer responses to compounds other than the compound of interest, usually a gas present in the measured gas stream, that is not adequately accounted for in the calibration procedure and may cause measurement bias.
3.12 Low-Concentration Analyzer means any analyzer that operates with a calibration span of 20 ppm NOX or lower. Each analyzer model used routinely to measure low NOX concentrations must pass a manufacturer's stability test (MST). An MST subjects the analyzer to a range of line voltages and temperatures that reflect potential field conditions to demonstrate its stability following procedures similar to those provided in 40 CFR 53.23. Ambient-level analyzers are exempt from the MST requirements of section 16.3. A copy of this information must be included in each test report. Table 7E-5 lists the criteria to be met.
3.13 Measurement System means all of the equipment used to determine the NOX concentration. The measurement system comprises six major subsystems: Sample acquisition, sample transport, sample conditioning, calibration gas manifold, gas analyzer, and data recorder.
3.14 Response Time means the time it takes the measurement system to respond to a change in gas concentration occurring at the sampling point when the system is operating normally at its target sample flow rate or dilution ratio.
3.15 Run means a series of gas samples taken successively from the stack or duct. A test normally consists of a specific number of runs.
3.16 System Bias means the difference between a calibration gas measured in direct calibration mode and in system calibration mode. System bias is determined before and after each run at the low- and mid- or high-concentration levels. For dilution-type systems, pre- and post-run system calibration error is measured rather than system bias.
3.17 System Calibration Error applies to dilution-type systems and means the difference between the measured concentration of low-, mid-, or high-level calibration gas and the certified concentration for each gas when introduced in system calibration mode. For dilution-type systems, a 3-point system calibration error test is conducted in lieu of the analyzer calibration error test, and 2-point system calibration error tests are conducted in lieu of system bias tests.
3.18 System Calibration Mode means introducing the calibration gases into the measurement system at the probe, upstream of the filter and all sample conditioning components.
3.19 Test refers to the series of runs required by the applicable regulation.
4.0 InterferencesNote that interferences may vary among instruments and that instrument-specific interferences must be evaluated through the interference test.
5.0 SafetyWhat safety measures should I consider when using this method? This method may require you to work with hazardous materials and in hazardous conditions. We encourage you to establish safety procedures before using the method. Among other precautions, you should become familiar with the safety recommendations in the gas analyzer user's manual. Occupational Safety and Health Administration (OSHA) regulations concerning cylinder and noxious gases may apply. Nitric oxide and NO2 are toxic and dangerous gases. Nitric oxide is immediately converted to NO2 upon reaction with air. Nitrogen dioxide is a highly poisonous and insidious gas. Inflammation of the lungs from exposure may cause only slight pain or pass unnoticed, but the resulting edema several days later may cause death. A concentration of 100 ppm is dangerous for even a short exposure, and 200 ppm may be fatal. Calibration gases must be handled with utmost care and with adequate ventilation. Emission-level exposure to these gases should be avoided.
6.0 Equipment and SuppliesThe performance criteria in this method will be met or exceeded if you are properly using equipment designed for this application.
6.1 What do I need for the measurement system? You may use any equipment and supplies meeting the following specifications:
(1) Sampling system components that are not evaluated in the system bias or system calibration error test must be glass, Teflon, or stainless steel. Other materials are potentially acceptable, subject to approval by the Administrator.
(2) The interference, calibration error, and system bias criteria must be met.
(3) Sample flow rate must be maintained within 10 percent of the flow rate at which the system response time was measured.
(4) All system components (excluding sample conditioning components, if used) must maintain the sample temperature above the moisture dew point. Ensure minimal contact between any condensate and the sample gas. Section 6.2 provides example equipment specifications for a NOX measurement system. Figure 7E-1 is a diagram of an example dry-basis measurement system that is likely to meet the method requirements and is provided as guidance. For wet-basis systems, you may use alternative equipment and supplies as needed (some of which are described in Section 6.2), provided that the measurement system meets the applicable performance specifications of this method.
6.2 Measurement System Components
6.2.1 Sample Probe. Glass, stainless steel, or other approved material, of sufficient length to traverse the sample points.
6.2.2 Particulate Filter. An in-stack or out-of-stack filter. The filter must be made of material that is non-reactive to the gas being sampled. The filter media for out-of-stack filters must be included in the system bias test. The particulate filter requirement may be waived in applications where no significant particulate matter is expected (e.g., for emission testing of a combustion turbine firing natural gas).
6.2.3 Sample Line. The sample line from the probe to the conditioning system/sample pump should be made of Teflon or other material that does not absorb or otherwise alter the sample gas. For a dry-basis measurement system (as shown in Figure 7E-1), the temperature of the sample line must be maintained at a sufficiently high level to prevent condensation before the sample conditioning components. For wet-basis measurement systems, the temperature of the sample line must be maintained at a sufficiently high level to prevent condensation before the analyzer.
6.2.4 Conditioning Equipment. For dry basis measurements, a condenser, dryer or other suitable device is required to remove moisture continuously from the sample gas. Any equipment needed to heat the probe or sample line to avoid condensation prior to the sample conditioning component is also required.
For wet basis systems, you must keep the sample above its dew point either by: (1) Heating the sample line and all sample transport components up to the inlet of the analyzer (and, for hot-wet extractive systems, also heating the analyzer) or (2) by diluting the sample prior to analysis using a dilution probe system. The components required to do either of the above are considered to be conditioning equipment.
6.2.5 Sampling Pump. For systems similar to the one shown in Figure 7E-1, a leak-free pump is needed to pull the sample gas through the system at a flow rate sufficient to minimize the response time of the measurement system. The pump may be constructed of any material that is non-reactive to the gas being sampled. For dilution-type measurement systems, an ejector pump (eductor) is used to create a vacuum that draws the sample through a critical orifice at a constant rate.
6.2.6 Calibration Gas Manifold. Prepare a system to allow the introduction of calibration gases either directly to the gas analyzer in direct calibration mode or into the measurement system, at the probe, in system calibration mode, or both, depending upon the type of system used. In system calibration mode, the system should be able to flood the sampling probe and vent excess gas. Alternatively, calibration gases may be introduced at the calibration valve following the probe. Maintain a constant pressure in the gas manifold. For in-stack dilution-type systems, a gas dilution subsystem is required to transport large volumes of purified air to the sample probe and a probe controller is needed to maintain the proper dilution ratio.
6.2.7 Sample Gas Manifold. For the type of system shown in Figure 7E-1, the sample gas manifold diverts a portion of the sample to the analyzer, delivering the remainder to the by-pass discharge vent. The manifold should also be able to introduce calibration gases directly to the analyzer (except for dilution-type systems). The manifold must be made of material that is non-reactive to the gas sampled or the calibration gas and be configured to safely discharge the bypass gas.
6.2.8 NOX Analyzer. An instrument that continuously measures NOX in the gas stream and meets the applicable specifications in section 13.0. An analyzer that operates on the principle of chemiluminescence with an NO2 to NO converter is one example of an analyzer that has been used successfully in the past. Analyzers operating on other principles may also be used provided the performance criteria in section 13.0 are met.
6.2.8.1 Dual Range Analyzers. For certain applications, a wide range of gas concentrations may be encountered, necessitating the use of two measurement ranges. Dual-range analyzers are readily available for these applications. These analyzers are often equipped with automated range-switching capability, so that when readings exceed the full-scale of the low measurement range, they are recorded on the high range. As an alternative to using a dual-range analyzer, you may use two segments of a single, large measurement scale to serve as the low and high ranges. In all cases, when two ranges are used, you must quality-assure both ranges using the proper sets of calibration gases. You must also meet the interference, calibration error, system bias, and drift checks. However, we caution that when you use two segments of a large measurement scale for dual range purposes, it may be difficult to meet the performance specifications on the low range due to signal-to-noise ratio considerations.
6.2.8.2 Low Concentration Analyzer. When an analyzer is routinely calibrated with a calibration span of 20 ppmv or less, the manufacturer's stability test (MST) is required. See Table 7E-5 for test parameters.
6.2.9 Data Recording. A strip chart recorder, computerized data acquisition system, digital recorder, or data logger for recording measurement data may be used.
7.0 Reagents and Standards7.1 Calibration Gas. What calibration gases do I need? Your calibration gas must be NO in N2 and certified (or recertified) within an uncertainty of 2.0 percent in accordance with “EPA Traceability Protocol for Assay and Certification of Gaseous Calibration Standards” September 1997, as amended August 25, 1999, EPA-600/R-97/121. Blended gases meeting the Traceability Protocol are allowed if the additional gas components are shown not to interfere with the analysis. If a zero gas is used for the low-level gas, it must meet the requirements under the definition for “zero air material” in 40 CFR 72.2. The calibration gas must not be used after its expiration date. Except for applications under part 75 of this chapter, it is acceptable to prepare calibration gas mixtures from EPA Traceability Protocol gases in accordance with Method 205 in appendix M to part 51 of this chapter. For part 75 applications, the use of Method 205 is subject to the approval of the Administrator. The goal and recommendation for selecting calibration gases is to bracket the sample concentrations. The following calibration gas concentrations are required:
7.1.1 High-Level Gas. This concentration is chosen to set the calibration span as defined in Section 3.4.
7.1.2 Mid-Level Gas. 40 to 60 percent of the calibration span.
7.1.3 Low-Level Gas. Less than 20 percent of the calibration span.
7.1.4 Converter Efficiency Gas. What reagents do I need for the converter efficiency test? The converter efficiency gas is a manufacturer-certified gas with a concentration sufficient to show NO2 conversion at the concentrations encountered in the source. A test gas concentration in the 40 to 60 ppm range is suggested, but other concentrations may be more appropriate to specific sources. For the test described in section 8.2.4.1, NO2 is required. For the alternative converter efficiency tests in section 16.2, NO is required.
7.2 Interference Check. What reagents do I need for the interference check? Use the appropriate test gases listed in Table 7E-3 or others not listed that can potentially interfere (as indicated by the test facility type, instrument manufacturer, etc.) to conduct the interference check. These gases should be manufacturer certified but do not have to be prepared by the EPA traceability protocol.
8.0 Sample Collection, Preservation, Storage, and Transport Emission Test ProcedureSince you are allowed to choose different options to comply with some of the performance criteria, it is your responsibility to identify the specific options you have chosen, to document that the performance criteria for that option have been met, and to identify any deviations from the method.
8.1 What sampling site and sampling points do I select?
8.1.1 Unless otherwise specified in an applicable regulation or by the Administrator, when this method is used to determine compliance with an emission standard, conduct a stratification test as described in section 8.1.2 to determine the sampling traverse points to be used. For performance testing of continuous emission monitoring systems, follow the sampling site selection and traverse point layout procedures described in the appropriate performance specification or applicable regulation (e.g., Performance Specification 2 in appendix B to this part).
8.1.2 Determination of Stratification. Perform a stratification test at each test site to determine the appropriate number of sample traverse points. If testing for multiple pollutants or diluents at the same site, a stratification test using only one pollutant or diluent satisfies this requirement. A stratification test is not required for small stacks that are less than 4 inches in diameter. To test for stratification, use a probe of appropriate length to measure the NOX (or pollutant of interest) concentration at 12 traverse points located according to Table 1-1 or Table 1-2 of Method 1. Alternatively, you may measure at three points on a line passing through the centroidal area. Space the three points at 16.7, 50.0, and 83.3 percent of the measurement line. Sample for a minimum of twice the system response time (see section 8.2.6) at each traverse point. Calculate the individual point and mean NOX concentrations. If the concentration at each traverse point differs from the mean concentration for all traverse points by no more than: ±5.0 percent of the mean concentration; or ±0.5 ppm (whichever is less restrictive), the gas stream is considered unstratified, and you may collect samples from a single point that most closely matches the mean. If the 5.0 percent or 0.5 ppm criterion is not met, but the concentration at each traverse point differs from the mean concentration for all traverse points by not more than: ±10.0 percent of the mean concentration; or ±1.0 ppm (whichever is less restrictive), the gas stream is considered to be minimally stratified and you may take samples from three points. Space the three points at 16.7, 50.0, and 83.3 percent of the measurement line. Alternatively, if a 12-point stratification test was performed and the emissions were shown to be minimally stratified (all points within ± 10.0 percent of their mean or within ±1.0 ppm), and if the stack diameter (or equivalent diameter, for a rectangular stack or duct) is greater than 2.4 meters (7.8 ft), then you may use 3-point sampling and locate the three points along the measurement line exhibiting the highest average concentration during the stratification test at 0.4, 1.2 and 2.0 meters from the stack or duct wall. If the gas stream is found to be stratified because the 10.0 percent or 1.0 ppm criterion for a 3-point test is not met, locate 12 traverse points for the test in accordance with Table 1-1 or Table 1-2 of Method 1.
8.2 Initial Measurement System Performance Tests. What initial performance criteria must my system meet before I begin collecting samples? Before measuring emissions, perform the following procedures:
(a) Calibration gas verification,
(b) Measurement system preparation,
(c) Calibration error test,
(d) NO2 to NO conversion efficiency test, if applicable,
(e) System bias check,
(f) System response time test, and
(g) Interference check
8.2.1 Calibration Gas Verification. How must I verify the concentrations of my calibration gases? Obtain a certificate from the gas manufacturer documenting the quality of the gas. Confirm that the manufacturer certification is complete and current. Ensure that your calibration gas certifications have not expired. This documentation should be available on-site for inspection. To the extent practicable, select a high-level gas concentration that will result in the measured emissions being between 20 and 100 percent of the calibration span.
8.2.2 Measurement System Preparation. How do I prepare my measurement system? Assemble, prepare, and precondition the measurement system according to your standard operating procedure. Adjust the system to achieve the correct sampling rate or dilution ratio (as applicable).
8.2.3 Calibration Error Test. How do I confirm my analyzer calibration is correct? After you have assembled, prepared and calibrated your sampling system and analyzer, you must conduct a 3-point analyzer calibration error test (or a 3-point system calibration error test for dilution systems) before the first run and again after any failed system bias test (or 2-point system calibration error test for dilution systems) or failed drift test. Introduce the low-, mid-, and high-level calibration gases sequentially. For non-dilution-type measurement systems, introduce the gases in direct calibration mode. For dilution-type measurement systems, introduce the gases in system calibration mode.
(1) For non-dilution systems, you may adjust the system to maintain the correct flow rate at the analyzer during the test, but you may not make adjustments for any other purpose. For dilution systems, you must operate the measurement system at the appropriate dilution ratio during all system calibration error checks, and may make only the adjustments necessary to maintain the proper ratio.
(2) Record the analyzer's response to each calibration gas on a form similar to Table 7E-1. For each calibration gas, calculate the analyzer calibration error using Equation 7E-1 in section 12.2 or the system calibration error using Equation 7E-3 in section 12.4 (as applicable). The calibration error specification in section 13.1 must be met for the low-, mid-, and high-level gases. If the calibration error specification is not met, take corrective action and repeat the test until an acceptable 3-point calibration is achieved.
8.2.4 NO2 to NO Conversion Efficiency Test. Before or after each field test, you must conduct an NO2 to NO conversion efficiency test if your system converts NO2 to NO before analyzing for NOX. You may risk testing multiple facilities before performing this test provided you pass this test at the conclusion of the final facility test. A failed final conversion efficiency test in this case will invalidate all tests performed subsequent to the test in which the converter efficiency test was passed. Follow the procedures in section 8.2.4.1, or 8.2.4.2. If desired, the converter efficiency factor derived from this test may be used to correct the test results for converter efficiency if the NO2 fraction in the measured test gas is known. Use Equation 7E-8 in section 12.8 for this correction.
8.2.4.1 Introduce NO2 converter efficiency gas to the analyzer in direct calibration mode and record the NOX concentration displayed by the analyzer. Calculate the converter efficiency using Equation 7E-7 in section 12.7. The specification for converter efficiency in section 13.5 must be met. The user is cautioned that state-of-the-art NO2 calibration gases may have limited shelf lives, and this could affect the ability to pass the 90-percent conversion efficiency requirement.
8.2.4.2 Alternatively, either of the procedures for determining conversion efficiency using NO in section 16.2 may be used.
8.2.5 Initial System Bias and System Calibration Error Checks. Before sampling begins, determine whether the high-level or mid-level calibration gas best approximates the emissions and use it as the upscale gas. Introduce the upscale gas at the probe upstream of all sample conditioning components in system calibration mode. Record the time it takes for the measured concentration to increase to a value that is at least 95 percent or within 0.5 ppm (whichever is less restrictive) of a stable response for both the low-level and upscale gases. Continue to observe the gas concentration reading until it has reached a final, stable value. Record this value on a form similar to Table 7E-2.
(1) Next, introduce the low-level gas in system calibration mode and record the time required for the concentration response to decrease to a value that is within 5.0 percent or 0.5 ppm (whichever is less restrictive) of the certified low-range gas concentration. If the low-level gas is a zero gas, use the procedures described above and observe the change in concentration until the response is 0.5 ppm or 5.0 percent of the upscale gas concentration (whichever is less restrictive).
(2) Continue to observe the low-level gas reading until it has reached a final, stable value and record the result on a form similar to Table 7E-2. Operate the measurement system at the normal sampling rate during all system bias checks. Make only the adjustments necessary to achieve proper calibration gas flow rates at the analyzer.
(3) From these data, calculate the measurement system response time (see section 8.2.6) and then calculate the initial system bias using Equation 7E-2 in section 12.3. For dilution systems, calculate the system calibration error in lieu of system bias using equation 7E-3 in section 12.4. See section 13.2 for acceptable performance criteria for system bias and system calibration error. If the initial system bias (or system calibration error) specification is not met, take corrective action. Then, you must repeat the applicable calibration error test from section 8.2.3 and the initial system bias (or 2-point system calibration error) check until acceptable results are achieved, after which you may begin sampling.
(Note: For dilution-type systems, data from the 3-point system calibration error test described in section 8.2.3 may be used to meet the initial 2-point system calibration error test requirement of this section, if the calibration gases were injected as described in this section, and if response time data were recorded).
8.2.6 Measurement System Response Time. As described in section 8.2.5, you must determine the measurement system response time during the initial system bias (or 2-point system calibration error) check. Observe the times required to achieve 95 percent of a stable response for both the low-level and upscale gases. The longer interval is the response time.
8.2.7 Interference Check. Conduct an interference response test of the gas analyzer prior to its initial use in the field. If you have multiple analyzers of the same make and model, you need only perform this alternative interference check on one analyzer. You may also meet the interference check requirement if the instrument manufacturer performs this or a similar check on an analyzer of the same make and model of the analyzer that you use and provides you with documented results.
(1) You may introduce the appropriate interference test gases (that are potentially encountered during a test; see examples in Table 7E-3) into the analyzer separately or as mixtures. Test the analyzer with the interference gas alone at the highest concentration expected at a test source and again with the interference gas and NOX at a representative NOX test concentration. For analyzers measuring NOX greater than 20 ppm, use a calibration gas with a NOX concentration of 80 to 100 ppm and set this concentration equal to the calibration span. For analyzers measuring less than 20 ppm NOX, select an NO concentration for the calibration span that reflects the emission levels at the sources to be tested, and perform the interference check at that level. Measure the total interference response of the analyzer to these gases in ppmv. Record the responses and determine the interference using Table 7E-4. The specification in section 13.4 must be met.
(2) A copy of this data, including the date completed and signed certification, must be available for inspection at the test site and included with each test report. This interference test is valid for the life of the instrument unless major analytical components (e.g., the detector) are replaced with different model parts. If major components are replaced with different model parts, the interference gas check must be repeated before returning the analyzer to service. If major components are replaced, the interference gas check must be repeated before returning the analyzer to service. The tester must ensure that any specific technology, equipment, or procedures that are intended to remove interference effects are operating properly during testing.
8.3 Dilution-Type Systems - Special Considerations. When a dilution-type measurement system is used, there are three important considerations that must be taken into account to ensure the quality of the emissions data. First, the critical orifice size and dilution ratio must be selected properly so that the sample dew point will be below the sample line and analyzer temperatures. Second, a high-quality, accurate probe controller must be used to maintain the dilution ratio during the test. The probe controller should be capable of monitoring the dilution air pressure, eductor vacuum, and sample flow rates. Third, differences between the molecular weight of calibration gas mixtures and the stack gas molecular weight must be addressed because these can affect the dilution ratio and introduce measurement bias.
8.4 Sample Collection.
(1) Position the probe at the first sampling point. Purge the system for at least two times the response time before recording any data. Then, traverse all required sampling points, sampling at each point for an equal length of time and maintaining the appropriate sample flow rate or dilution ratio (as applicable). You must record at least one valid data point per minute during the test run.
(2) Each time the probe is removed from the stack and replaced, you must recondition the sampling system for at least two times the system response time prior to your next recording. If the average of any run exceeds the calibration span value, that run is invalid.
(3) You may satisfy the multipoint traverse requirement by sampling sequentially using a single-hole probe or a multi-hole probe designed to sample at the prescribed points with a flow within 10 percent of mean flow rate. Notwithstanding, for applications under part 75 of this chapter, the use of multi-hole probes is subject to the approval of the Administrator.
8.5 Post-Run System Bias Check and Drift Assessment.
How do I confirm that each sample I collect is valid? After each run, repeat the system bias check or 2-point system calibration error check (for dilution systems) to validate the run. Do not make adjustments to the measurement system (other than to maintain the target sampling rate or dilution ratio) between the end of the run and the completion of the post-run system bias or system calibration error check. Note that for all post-run system bias or 2-point system calibration error checks, you may inject the low-level gas first and the upscale gas last, or vice-versa. If conducting a relative accuracy test or relative accuracy test audit, consisting of nine runs or more, you may risk sampling for up to three runs before performing the post-run bias or system calibration error check provided you pass this test at the conclusion of the group of three runs. A failed post-run bias or system calibration error check in this case will invalidate all runs subsequent to the last passed check. When conducting a performance or compliance test, you must perform a post-run system bias or system calibration error check after each individual test run.
(1) If you do not pass the post-run system bias (or system calibration error) check, then the run is invalid. You must diagnose and fix the problem and pass another calibration error test (Section 8.2.3) and system bias (or 2-point system calibration error) check (Section 8.2.5) before repeating the run. Record the system bias (or system calibration error) results on a form similar to Table 7E-2.
(2) After each run, calculate the low-level and upscale drift, using Equation 7E-4 in section 12.5. If the post-run low- and upscale bias (or 2-point system calibration error) checks are passed, but the low-or upscale drift exceeds the specification in section 13.3, the run data are valid, but a 3-point calibration error test and a system bias (or 2-point system calibration error) check must be performed and passed before any more test runs are done.
(3) For dilution systems, data from a 3-point system calibration error test may be used to met the pre-run 2-point system calibration error requirement for the first run in a test sequence. Also, the post-run bias (or 2-point calibration error) check data may be used as the pre-run data for the next run in the test sequence at the discretion of the tester.
8.6 Alternative Interference and System Bias Checks (Dynamic Spike Procedure). If I want to use the dynamic spike procedure to validate my data, what procedure should I follow? Except for applications under part 75 of this chapter, you may use the dynamic spiking procedure and requirements provided in section 16.1 during each test as an alternative to the interference check and the pre- and post-run system bias checks. The calibration error test is still required under this option. Use of the dynamic spiking procedure for Part 75 applications is subject to the approval of the Administrator.
8.7 Moisture correction. You must determine the moisture content of the flue gas and correct the measured gas concentrations to a dry basis using Method 4 or other appropriate methods, subject to the approval of the Administrator, when the moisture basis (wet or dry) of the measurements made with this method is different from the moisture basis of either: (1) The applicable emissions limit; or (2) the CEMS being evaluated for relative accuracy. Moisture correction is also required if the applicable limit is in lb/mmBtu and the moisture basis of the Method 7E NOX analyzer is different from the moisture basis of the Method 3A diluent gas (CO2 or O2) analyzer.
9.0 Quality Control What quality control measures must I take?The following table is a summary of the mandatory, suggested, and alternative quality assurance and quality control measures and the associated frequency and acceptance criteria. All of the QC data, along with the sample run data, must be documented and included in the test report.
Summary Table of AQ/QC
Status | Process or element | QA/QC specification | Acceptance criteria | Checking frequency |
---|---|---|---|---|
S | Identify Data User | Regulatory Agency or other primary end user of data | Before designing test. | |
S | Analyzer Design | Analyzer resolution or sensitivity | <2.0% of full-scale range | Manufacturer design. |
M | Interference gas check | Sum of responses ≤2.5% of calibration span Alternatively, sum of responses: | ||
≤0.5 ppmv for calibration spans of 5 to 10 ppmv | ||||
≤0.2 ppmv for calibration spans <5 ppmv | ||||
See Table 7E-3 | ||||
M | Calibration Gases | Traceability protocol (G1, G2) | Valid certificate required Uncertainty ≤2.0% of tag value | |
M | High-level gas | Equal to the calibration span | Each test. | |
M | Mid-level gas | 40 to 60% of calibration span | Each test. | |
M | Low-level gas | <20% of calibration span | Each test. | |
S | Data Recorder Design | Data resolution | ≤0.5% of full-scale range | Manufacturer design. |
S | Sample Extraction | Probe material | SS or quartz if stack >500 °F | East test. |
M | Sample Extraction | Probe, filter and sample line temperature | For dry-basis analyzers, keep sample above the dew point by heating, prior to sample conditioning | Each run. |
For wet-basis analyzers, keep sample above dew point at all times, by heating or dilution | ||||
S | Sample Extraction | Calibration valve material | SS | Each test. |
S | Sample Extraction | Sample pump material | Inert to sample constituents | Each test. |
S | Sample Extraction | Manifolding material | Inert to sample constituents | Each test. |
S | Moisture Removal | Equipment efficiency | <5% target compound removal | Verified through system bias check. |
S | Particulate Removal | Filter inertness | Pass system bias check | Each bias check. |
M | Analyzer & Calibration Gas Performance | Analyzer calibration error (of 3-point system calibration error for dilution systems) | Within ±2.0 percent of the calibration span of the analyzer for the low-, mid-, and high-level calibration gases | Before initial run and after a failed system bias test or drift test. |
Alternative specification: ≤0.5 ppmv absolute difference | ||||
M | System Performance | System bias (or pre- and post-run 2-point system calibration error for dilution (Systems) | Within ±5.0% of the analyzer calibration span for low-sacle and upscale calibration gases | Before and after each run. |
Alternative specification: ≤0.5 ppmv absolute difference | ||||
M | System Performance | System response time | Determines minimum sampling time per point | During initial sampling system bias test. |
M | System Performance | Drift | ≤3.0% of calibration span for low-level and mid- or high-level gases | After each test run. |
Alternative specification: ≤0.5 ppmv absolute difference | ||||
M | System Performance | NO2-NO conversion efficiency | ≥90% of certified test gas concentration | Before or after each test. |
M | System Performance | Purge time | ≥2 times system response time | Before starting the first run and when probe is removed from and re-inserted into the stack. |
M | System Performance | Minimum sample time at each point | Two times the system response time | Each sample point. |
M | System Performance | Stable sample flow rate (surrogate for maintaining system response time) | Within 10% of flow rate established during system response time check | Each run. |
M | Sample Point Selection | Stratification test | All points within: | Prior to first run. |
±5% of mean for 1-point sampling | ||||
±10% of mean for 3-point | ||||
Alternatively, all points within: | ||||
±0.5 ppm of mean for 1-point sampling | ||||
±1.0 ppm of mean for 3-point sampling | ||||
A | Multiple sample points simultaneously | No. of openings in probe | Multi-hole probe with verifiable constant flow through all holes within 10% of mean flow rate (requires Administrative approval for Part 75) | Each run. |
M | Data Recording | Frequency | ≤1 minute average | During run. |
S | Data Parameters | Sample concentration range | All 1-minute averages within calibration span | Each run. |
M | Date Parameters | Average concentration for the run | Run average ≤calibration span | Each run. |
S = Suggest.
M = Mandatory.
A = Alternative.
Agency.
(1) The initial 3-point calibration error test as described in section 8.2.3 and the system bias (or system calibration error) checks described in section 8.2.5 are required and must meet the specifications in section 13 before you start the test. Make all necessary adjustments to calibrate the gas analyzer and data recorder. Then, after the test commences, the system bias or system calibration error checks described in section 8.5 are required before and after each run. Your analyzer must be calibrated for all species of NOX that it detects. Analyzers that measure NO and NO2 separately without using a converter must be calibrated with both NO and NO2.
(2) You must include a copy of the manufacturer's certification of the calibration gases used in the testing as part of the test report. This certification must include the 13 documentation requirements in the EPA Traceability Protocol For Assay and Certification of Gaseous Calibration Standards, September 1997, as amended August 25, 1999. When Method 205 is used to produce diluted calibration gases, you must document that the specifications for the gas dilution system are met for the test. You must also include the date of the most recent dilution system calibration against flow standards and the name of the person or manufacturer who carried out the calibration in the test report.
11.0 Analytical ProceduresBecause sample collection and analysis are performed together (see section 8), additional discussion of the analytical procedure is not necessary.
12.0 Calculations and Data AnalysisYou must follow the procedures for calculations and data analysis listed in this section.
12.1 Nomenclature. The terms used in the equations are defined as follows:
ACE = Analyzer calibration error, percent of calibration span. BWS = Moisture content of sample gas as measured by Method 4 or other approved method, percent/100. CAvg = Average unadjusted gas concentration indicated by data recorder for the test run, ppmv. CD = Pollutant concentration adjusted to dry conditions, ppmv. CDir = Measured concentration of a calibration gas (low, mid, or high) when introduced in direct calibration mode, ppmv. CGas = Average effluent gas concentration adjusted for bias, ppmv. CM = Average of initial and final system calibration bias (or 2-point system calibration error) check responses for the upscale calibration gas, ppmv. CMA = Actual concentration of the upscale calibration gas, ppmv. CNative = NOX concentration in the stack gas as calculated in section 12.6, ppmv. CO = Average of the initial and final system calibration bias (or 2-point system calibration error) check responses from the low-level (or zero) calibration gas, ppmv. COA = Actual concentration of the low-level calibration gas, ppmv. CS = Measured concentration of a calibration gas (low, mid, or high) when introduced in system calibration mode, ppmv. CSS = Concentration of NOX measured in the spiked sample, ppmv. CSpike = Concentration of NOX in the undiluted spike gas, ppmv. CCalc = Calculated concentration of NOX in the spike gas diluted in the sample, ppmv. CV = Manufacturer certified concentration of a calibration gas (low, mid, or high), ppmv. CW = Pollutant concentration measured under moist sample conditions, wet basis, ppmv. CS = Calibration span, ppmv. D = Drift assessment, percent of calibration span. DF = Dilution system dilution factor or spike gas dilution factor, dimensionless. EffNO2 = NO2 to NO converter efficiency, percent. NOXCorr = The NOX concentration corrected for the converter efficiency, ppmv. NOXFinal = The final NOX concentration observed during the converter efficiency test in section 16.2.2, ppmv. NOXPeak = The highest NOX concentration observed during the converter efficiency test in section 16.2.2, ppmv. QSpike = Flow rate of spike gas introduced in system calibration mode, L/min. QTotal = Total sample flow rate during the spike test, L/min. R = Spike recovery, percent. SB = System bias, percent of calibration span. SBi = Pre-run system bias, percent of calibration span. SBfinal = Post-run system bias, percent of calibration span. SCE = System calibration error, percent of calibration span. SCEi = Pre-run system calibration error, percent of calibration span. SCEFinal = Post-run system calibration error, percent of calibration span.12.2 Analyzer Calibration Error. For non-dilution systems, use Equation 7E-1 to calculate the analyzer calibration error for the low-, mid-, and high-level calibration gases.

12.3 System Bias. For non-dilution systems, use Equation 7E-2 to calculate the system bias separately for the low-level and upscale calibration gases.

12.4 System Calibration Error. Use Equation 7E-3 to calculate the system calibration error for dilution systems. Equation 7E-3 applies to both the initial 3-point system calibration error test and the subsequent 2-point calibration error checks between test runs. In this equation, the term “Cs” refers to the diluted calibration gas concentration measured by the analyzer.
12.5 Drift Assessment. Use Equation 7E-4 to separately calculate the low-level and upscale drift over each test run. For dilution systems, replace “SBfinal” and “SBi” with “SCEfinal” and “SCEi”, respectively, to calculate and evaluate drift.

12.6 Effluent Gas Concentration. For each test run, calculate Cavg, the arithmetic average of all valid NOX concentration values (e.g., 1-minute averages). Then adjust the value of Cavg for bias using Equation 7E-5a if you use a non-zero gas as your low-level calibration gas, or Equation 7E-5b if you use a zero gas as your low-level calibration gas.
12.7 NO2 - NO Conversion Efficiency. If the NOX converter efficiency test described in section 8.2.4.1 is performed, calculate the efficiency using Equation 7E-7.
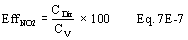
12.8 NO2 - NO Conversion Efficiency Correction. If desired, calculate the total NOX concentration with a correction for converter efficiency using Equation 7E-8.

12.9 Alternative NO2 Converter Efficiency. If the alternative procedure of section 16.2.2 is used, determine the NOX concentration decrease from NOXPeak after the minimum 30-minute test interval using Equation 7E-9. This decrease from NOXPeak must meet the requirement in section 13.5 for the converter to be acceptable.
12.10 Moisture Correction. Use Equation 7E-10 if your measurements need to be corrected to a dry basis.
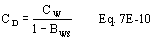
12.11 Calculated Spike Gas Concentration and Spike Recovery for the Example Alternative Dynamic Spiking Procedure in section 16.1.3. Use Equation 7E-11 to determine the calculated spike gas concentration. Use Equation 7E-12 to calculate the spike recovery.
13.0 Method Performance13.1 Calibration Error. This specification is applicable to both the analyzer calibration error and the 3-point system calibration error tests described in section 8.2.3. At each calibration gas level (low, mid, and high) the calibration error must either be within ±2.0 percent of the calibration span. Alternatively, the results are acceptable if |Cdir − Cv| or |Cs−Cv| (as applicable) is ≤0.5 ppmv.
13.2 System Bias. This specification is applicable to both the system bias and 2-point system calibration error tests described in section 8.2.5 and 8.5. The pre- and post-run system bias (or system calibration error) must be within ±5.0 percent of the calibration span for the low-level and upscale calibration gases. Alternatively, the results are acceptable if | Cs −Cdir | is ≤0.5 ppmv or if | Cs− Cv | is ≤0.5 ppmv (as applicable).
13.3 Drift. For each run, the low-level and upscale drift must be less than or equal to 3.0 percent of the calibration span. The drift is also acceptable if the pre- and post-run bias (or the pre- and post-run system calibration error) responses do not differ by more than 0.5 ppmv at each gas concentration (i.e. | Cs post-run− Cs pre-run | ≤0.5 ppmv).
13.4 Interference Check. The total interference response (i.e., the sum of the interference responses of all tested gaseous components) must not be greater than 2.50 percent of the calibration span for the analyzer tested. In summing the interferences, use the larger of the absolute values obtained for the interferent tested with and without the pollutant present. The results are also acceptable if the sum of the responses does not exceed 0.5 ppmv for a calibration span of 5 to 10 ppmv, or 0.2 ppmv for a calibration span <5 ppmv.
13.5 NO2 to NO Conversion Efficiency Test (as applicable). The NO2 to NO conversion efficiency, calculated according to Equation 7E-7, must be greater than or equal to 90 percent. The alternative conversion efficiency check, described in section 16.2.2 and calculated according to Equation 7E-9, must not result in a decrease from NOXPeak by more than 2.0 percent.
13.6 Alternative Dynamic Spike Procedure. Recoveries of both pre-test spikes and post-test spikes must be within 100 ±10 percent. If the absolute difference between the calculated spike value and measured spike value is equal to or less than 0.20 ppmv, then the requirements of the ADSC are met.
14.0 Pollution Prevention [Reserved] 15.0 Waste Management [Reserved] 16.0 Alternative Procedures16.1 Dynamic Spike Procedure. Except for applications under part 75 of this chapter, you may use a dynamic spiking procedure to validate your test data for a specific test matrix in place of the interference check and pre- and post-run system bias checks. For part 75 applications, use of this procedure is subject to the approval of the Administrator. Best results are obtained for this procedure when source emissions are steady and not varying. Fluctuating emissions may render this alternative procedure difficult to pass. To use this alternative, you must meet the following requirements.
16.1.1 Procedure Documentation. You must detail the procedure you followed in the test report, including how the spike was measured, added, verified during the run, and calculated after the test.
16.1.2 Spiking Procedure Requirements. The spikes must be prepared from EPA Traceability Protocol gases. Your procedure must be designed to spike field samples at two target levels both before and after the test. Your target spike levels should bracket the average sample NOX concentrations. The higher target concentration must be less than the calibration span. You must collect at least 5 data points for each target concentration. The spiking procedure must be performed before the first run and repeated after the last run of the test program.
16.1.3 Example Spiking Procedure. Determine the NO concentration needed to generate concentrations that are 50 and 150 percent of the anticipated NOX concentration in the stack at the total sampling flow rate while keeping the spike flow rate at or below 10 percent of this total. Use a mass flow meter (accurate within 2.0 percent) to generate these NO spike gas concentrations at a constant flow rate. Use Equation 7E-11 in section 12.11 to determine the calculated spike concentration in the collected sample.
(1) Prepare the measurement system and conduct the analyzer calibration error test as described in sections 8.2.2 and 8.2.3. Following the sampling procedures in section 8.1, determine the stack NOX concentration and use this concentration as the average stack concentration (Cavg) for the first spike level, or if desired, for both pre-test spike levels. Introduce the first level spike gas into the system in system calibration mode and begin sample collection. Wait for at least two times the system response time before measuring the spiked sample concentration. Then record at least five successive 1-minute averages of the spiked sample gas. Monitor the spike gas flow rate and maintain at the determined addition rate. Average the five 1-minute averages and determine the spike recovery using Equation 7E-12. Repeat this procedure for the other pre-test spike level. The recovery at each level must be within the limits in section 13.6 before proceeding with the test.
(2) Conduct the number of runs required for the test. Then repeat the above procedure for the post-test spike evaluation. The last run of the test may serve as the average stack concentration for the post-test spike test calculations. The results of the post-test spikes must meet the limits in section 13.6.
16.2 Alternative NO2 to NO Conversion Efficiency Procedures. You may use either of the following procedures to determine converter efficiency in place of the procedure in section 8.2.4.1.
16.2.1 The procedure for determining conversion efficiency using NO in 40 CFR 86.123-78.
16.2.2 Bag Procedure. Perform the analyzer calibration error test to document the calibration (both NO and NOX modes, as applicable). Fill a Tedlar or equivalent bag approximately half full with either ambient air, pure oxygen, or an oxygen standard gas with at least 19.5 percent by volume oxygen content. Fill the remainder of the bag with mid- to high-level NO in N2 (or other appropriate concentration) calibration gas. (Note that the concentration of the NO standard should be sufficiently high enough for the diluted concentration to be easily and accurately measured on the scale used. The size of the bag should be large enough to accommodate the procedure and time required. Verify through the manufacturer that the Tedlar alternative is suitable for NO and make this verifed information available for inspection.)
(1) Immediately attach the bag to the inlet of the NOX analyzer (or external converter if used). In the case of a dilution-system, introduce the gas at a point upstream of the dilution assembly. Measure the NOX concentration for a period of 30 minutes. If the NOX concentration drops more than 2 percent absolute from the peak value observed, then the NO2 converter has failed to meet the criteria of this test. Take corrective action. The highest NOX value observed is considered to be NOXPeak. The final NOX value observed is considered to be NOXfinal.
(2) [Reserved]
16.3 Manufacturer's Stability Test. A manufacturer's stability test is required for all analyzers that routinely measure emissions below 20 ppmv and is optional but recommended for other analyzers. This test evaluates each analyzer model by subjecting it to the tests listed in Table 7E-5 following procedures similar to those in 40 CFR 53.23 for thermal stability and insensitivity to supply voltage variations. If the analyzer will be used under temperature conditions that are outside the test conditions in Table B-4 of Part 53.23, alternative test temperatures that better reflect the analyzer field environment should be used. Alternative procedures or documentation that establish the analyzer's stability over the appropriate line voltages and temperatures are acceptable.
17.0 References1. “ERA Traceability Protocol for Assay and Certification of Gaseous Calibration Standards” September 1997 as amended, ERA-600/R-97/121.
18.0 Tables, Diagrams, Flowcharts, and Validation Data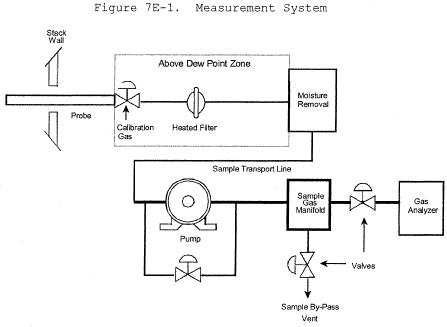
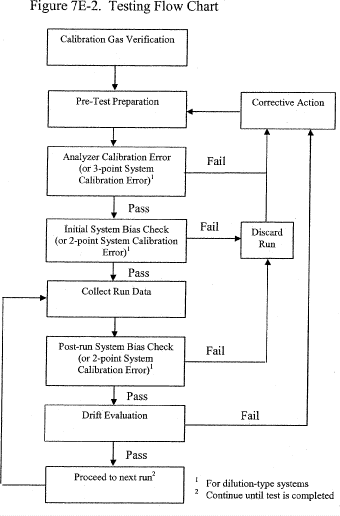
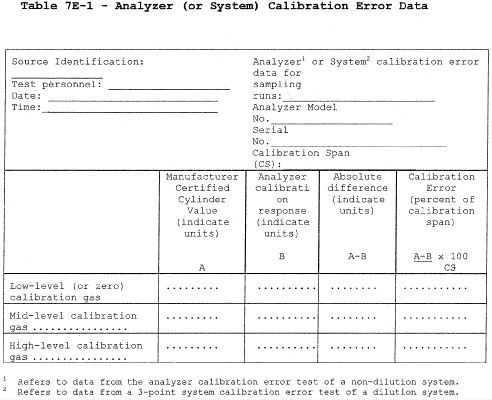
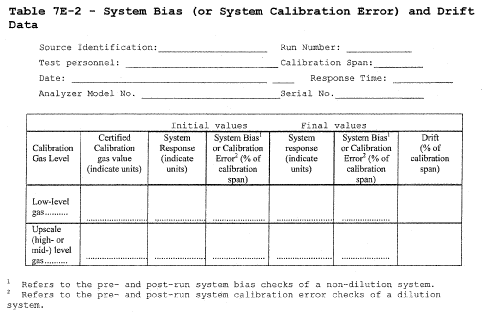
Table 7E-3 - Example Interference Check Gas Concentrations
Potential interferent gas 1 | Concentrations 2 sample conditioning type | |
---|---|---|
Hot wet | Dried | |
CO2 | 5 and 15% | 5 and 15% |
H2O | 25% | 1% |
NO | 15 ppmv | 15 ppmv |
NO2 | 15 ppmv | 15 ppmv |
N2O | 10 ppmv | 10 ppmv |
CO | 50 ppmv | 50 ppmv |
NH3 | 10 ppmv | 10 ppmv |
CH4 | 50 ppmv | 50 ppmv |
SO2 | 20 ppmv | 20 ppmv |
H2 | 50 ppmv | 50 ppmv |
HCl | 10 ppmv | 10 ppmv |
1 Any applicable gas may be eliminated or tested at a reduced level if the manufacturer has provided reliable means for limiting or scrubbing that gas to a specified level.
2 As practicable, gas concentrations should be the highest expected at test sites.
Test gas type | Concentration (ppm) |
Analyzer response |
---|---|---|
Sum of Responses | ||
% of Calibration Span |
Table 7E-5 - Manufacturer Stability Test
Test description | Acceptance criteria (note 1) |
---|---|
Thermal Stability | Temperature range when drift does not exceed 3.0% of analyzer range over a 12-hour run when measured with NOX present @ 80% of calibration span. |
Fault Conditions | Identify conditions which, when they occur, result in performance which is not in compliance with the Manufacturer's Stability Test criteria. These are to be indicated visually or electrically to alert the operator of the problem. |
Insensitivity to Supply Voltage Variations | ±10.0% (or manufacturers alternative) variation from nominal voltage must produce a drift of ≤2.0% of calibration span for either zero or concentration ≥80% NOX present. |
Analyzer Calibration Error | For a low-, medium-, and high-calibration gas, the difference between the manufacturer certified value and the analyzer response in direct calibration mode, no more than 2.0% of calibration span. |
Note 1: If the instrument is to be used as a Low Range analyzer, all tests must be performed at a calibration span of 20 ppm or less.
This method does not include all of the specifications (e.g., equipment and supplies) and procedures (e.g., sampling and analytical) essential to its performance. Some material is incorporated by reference from other methods in this part. Therefore, to obtain reliable results, persons using this method should have a thorough knowledge of at least the following additional test methods: Method 1, Method 2, Method 3, Method 5, and Method 6.
1.0 Scope and Application1.1 Analytes.
Analyte | CAS No. | Sensitivity |
---|---|---|
Sulfuric acid, including: Sulfuric acid (H2SO4) mist, Sulfur trioxide (SO3) | 7664-93-9, 7449-11-9 | 0.05 mg/m 3 (0.03 × 10−7 lb/ft 3). |
Sulfur dioxide (SO2) | 7449-09-5 | 1.2 mg/m 3 (3 × 10−9 lb/ft 3). |
1.2 Applicability. This method is applicable for the determination of H2SO4 (including H2SO4 mist and SO3) and gaseous SO2 emissions from stationary sources.
Note:Filterable particulate matter may be determined along with H2SO4 and SO2 (subject to the approval of the Administrator) by inserting a heated glass fiber filter between the probe and isopropanol impinger (see section 6.1.1 of Method 6). If this option is chosen, particulate analysis is gravimetric only; sulfuric acid is not determined separately.
1.3 Data Quality Objectives. Adherence to the requirements of this method will enhance the quality of the data obtained from air pollutant sampling methods.
2.0 Summary of MethodA gas sample is extracted isokinetically from the stack. The H2SO4 and the SO2 are separated, and both fractions are measured separately by the barium-thorin titration method.
3.0 Definitions [Reserved] 4.0 Interferences4.1 Possible interfering agents of this method are fluorides, free ammonia, and dimethyl aniline. If any of these interfering agents is present (this can be determined by knowledge of the process), alternative methods, subject to the approval of the Administrator, are required.
5.0 Safety5.1 Disclaimer. This method may involve hazardous materials, operations, and equipment. This test method may not address all of the safety problems associated with its use. It is the responsibility of the user of this test method to establish appropriate safety and health practices and determine the applicability of regulatory limitations prior to performing this test method.
5.2 Corrosive reagents. Same as Method 6, section 5.2.
6.0 Equipment and Supplies6.1 Sample Collection. Same as Method 5, section 6.1, with the following additions and exceptions:
6.1.1 Sampling Train. A schematic of the sampling train used in this method is shown in Figure 8-1; it is similar to the Method 5 sampling train, except that the filter position is different, and the filter holder does not have to be heated. See Method 5, section 6.1.1, for details and guidelines on operation and maintenance.
6.1.1.1 Probe Nozzle. Borosilicate or quartz glass with a sharp, tapered leading edge and coupled to the probe liner using a polytetrafluoroethylene (PTFE) or glass-lined union (e.g., fused silica, Slico, or equivalent). When the stack temperature exceeds 210 °C (410 °F), a leak-free ground glass fitting or other leak free, non-contaminating fitting must be used to couple the nozzle to the probe liner. It is also acceptable to use a one-piece glass nozzle/liner assembly. The angle of the taper shall be ≤30°, and the taper shall be on the outside to preserve a constant internal diameter. The probe nozzle shall be of the button-hook or elbow design, unless otherwise specified by the Administrator. Other materials of construction may be used, subject to the approval of the Administrator. A range of nozzle sizes suitable for isokinetic sampling should be available. Typical nozzle sizes range from 0.32 to 1.27 cm ( 1/8 to 1/2 in) inside diameter (ID) in increments of 0.16 cm ( 1/16 in). Larger nozzles sizes are also available if higher volume sampling trains are used.
6.1.1.2 Probe Liner. Borosilicate or quartz glass, with a heating system to prevent visible condensation during sampling. Do not use metal probe liners.
6.1.1.3 Filter Holder. Borosilicate glass, with a glass frit filter support and a silicone rubber gasket. Other gasket materials (e.g., Teflon or Viton) may be used, subject to the approval of the Administrator. The holder design shall provide a positive seal against leakage from the outside or around the filter. The filter holder shall be placed between the first and second impingers. Do not heat the filter holder.
6.1.1.4 Impingers. Four, of the Greenburg-Smith design, as shown in Figure 8-1. The first and third impingers must have standard tips. The second and fourth impingers must be modified by replacing the insert with an approximately 13-mm ( 1/2-in.) ID glass tube, having an unconstricted tip located 13 mm ( 1/2 in.) from the bottom of the impinger. Similar collection systems, subject to the approval of the Administrator, may be used.
6.1.1.5 Temperature Sensor. Thermometer, or equivalent, to measure the temperature of the gas leaving the impinger train to within 1 °C (2 °F).
6.2 Sample Recovery. The following items are required for sample recovery:
6.2.1 Wash Bottles. Two polyethylene or glass bottles, 500-ml.
6.2.2 Graduated Cylinders. Two graduated cylinders (volumetric flasks may be used), 250-ml, 1-liter.
6.2.3 Storage Bottles. Leak-free polyethylene bottles, 1-liter size (two for each sampling run).
6.2.4 Trip Balance. 500-g capacity, to measure to ±0.5 g (necessary only if a moisture content analysis is to be done).
6.3 Analysis. The following items are required for sample analysis:
6.3.1 Pipettes. Volumetric 10-ml, 100-ml.
6.3.2 Burette. 50-ml.
6.3.3 Erlenmeyer Flask. 250-ml (one for each sample, blank, and standard).
6.3.4 Graduated Cylinder. 100-ml.
6.3.5 Dropping Bottle. To add indicator solution, 125-ml size.
7.0 Reagents and Standards Note:Unless otherwise indicated, all reagents are to conform to the specifications established by the Committee on Analytical Reagents of the American Chemical Society, where such specifications are available. Otherwise, use the best available grade.
7.1 Sample Collection. The following reagents are required for sample collection:
7.1.1 Filters and Silica Gel. Same as in Method 5, sections 7.1.1 and 7.1.2, respectively.
7.1.2 Water. Same as in Method 6, section 7.1.1.
7.1.3 Isopropanol, 80 Percent by Volume. Mix 800 ml of isopropanol with 200 ml of water.
Note:Check for peroxide impurities using the procedure outlined in Method 6, section 7.1.2.1.
7.1.4 Hydrogen Peroxide (H 2O 2), 3 Percent by Volume. Dilute 100 ml of 30 percent H2O2) to 1 liter with water. Prepare fresh daily.
7.1.5 Crushed Ice.
7.2 Sample Recovery. The reagents and standards required for sample recovery are:
7.2.1 Water. Same as in section 7.1.2.
7.2.2 Isopropanol, 80 Percent. Same as in section 7.1.3.
7.3 Sample Analysis. Same as Method 6, section 7.3.
8.0 Sample Collection, Preservation, Storage, and Transport8.1 Pretest Preparation. Same as Method 5, section 8.1, except that filters should be inspected but need not be desiccated, weighed, or identified. If the effluent gas can be considered dry (i.e., moisture-free), the silica gel need not be weighed.
8.2 Preliminary Determinations. Same as Method 5, section 8.2.
8.3 Preparation of Sampling Train. Same as Method 5, section 8.3, with the following exceptions:
8.3.1 Use Figure 8-1 instead of Figure 5-1.
8.3.2 Replace the second sentence of Method 5, section 8.3.1 with: Place 100 ml of 80 percent isopropanol in the first impinger, 100 ml of 3 percent H2O2 in both the second and third impingers; retain a portion of each reagent for use as a blank solution. Place about 200 g of silica gel in the fourth impinger.
8.3.3 Ignore any other statements in section 8.3 of Method 5 that are obviously not applicable to the performance of Method 8.
Note:If moisture content is to be determined by impinger analysis, weigh each of the first three impingers (plus absorbing solution) to the nearest 0.5 g, and record these weights. Weigh also the silica gel (or silica gel plus container) to the nearest 0.5 g, and record.)
8.4 Metering System Leak-Check Procedure. Same as Method 5, section 8.4.1.
8.5 Pretest Leak-Check Procedure. Follow the basic procedure in Method 5, section 8.4.2, noting that the probe heater shall be adjusted to the minimum temperature required to prevent condensation, and also that verbage such as “* * * plugging the inlet to the filter holder * * * ” found in section 8.4.2.2 of Method 5 shall be replaced by “ * * * plugging the inlet to the first impinger * * * ”. The pretest leak-check is recommended, but is not required.
8.6 Sampling Train Operation. Follow the basic procedures in Method 5, section 8.5, in conjunction with the following special instructions:
8.6.1 Record the data on a sheet similar to that shown in Figure 8-2 (alternatively, Figure 5-2 in Method 5 may be used). The sampling rate shall not exceed 0.030 m 3/min (1.0 cfm) during the run. Periodically during the test, observe the connecting line between the probe and first impinger for signs of condensation. If condensation does occur, adjust the probe heater setting upward to the minimum temperature required to prevent condensation. If component changes become necessary during a run, a leak-check shall be performed immediately before each change, according to the procedure outlined in section 8.4.3 of Method 5 (with appropriate modifications, as mentioned in section 8.5 of this method); record all leak rates. If the leakage rate(s) exceeds the specified rate, the tester shall either void the run or plan to correct the sample volume as outlined in section 12.3 of Method 5. Leak-checks immediately after component changes are recommended, but not required. If these leak-checks are performed, the procedure in section 8.4.2 of Method 5 (with appropriate modifications) shall be used.
8.6.2 After turning off the pump and recording the final readings at the conclusion of each run, remove the probe from the stack. Conduct a post-test (mandatory) leak-check as outlined in section 8.4.4 of Method 5 (with appropriate modifications), and record the leak rate. If the post-test leakage rate exceeds the specified acceptable rate, either correct the sample volume, as outlined in section 12.3 of Method 5, or void the run.
8.6.3 Drain the ice bath and, with the probe disconnected, purge the remaining part of the train by drawing clean ambient air through the system for 15 minutes at the average flow rate used for sampling.
Note:Clean ambient air can be provided by passing air through a charcoal filter. Alternatively, ambient air (without cleaning) may be used.
8.7 Calculation of Percent Isokinetic. Same as Method 5, section 8.6.
8.8 Sample Recovery. Proper cleanup procedure begins as soon as the probe is removed from the stack at the end of the sampling period. Allow the probe to cool. Treat the samples as follows:
8.8.1 Container No. 1.
8.8.1.1 If a moisture content analysis is to be performed, clean and weigh the first impinger (plus contents) to the nearest 0.5 g, and record this weight.
8.8.1.2 Transfer the contents of the first impinger to a 250-ml graduated cylinder. Rinse the probe, first impinger, all connecting glassware before the filter, and the front half of the filter holder with 80 percent isopropanol. Add the isopropanol rinse solution to the cylinder. Dilute the contents of the cylinder to 225 ml with 80 percent isopropanol, and transfer the cylinder contents to the storage container. Rinse the cylinder with 25 ml of 80 percent isopropanol, and transfer the rinse to the storage container. Add the filter to the solution in the storage container and mix. Seal the container to protect the solution against evaporation. Mark the level of liquid on the container, and identify the sample container.
8.8.2 Container No. 2.
8.8.2.1 If a moisture content analysis is to be performed, clean and weigh the second and third impingers (plus contents) to the nearest 0.5 g, and record the weights. Also, weigh the spent silica gel (or silica gel plus impinger) to the nearest 0.5 g, and record the weight.
8.8.2.2 Transfer the solutions from the second and third impingers to a 1-liter graduated cylinder. Rinse all connecting glassware (including back half of filter holder) between the filter and silica gel impinger with water, and add this rinse water to the cylinder. Dilute the contents of the cylinder to 950 ml with water. Transfer the solution to a storage container. Rinse the cylinder with 50 ml of water, and transfer the rinse to the storage container. Mark the level of liquid on the container. Seal and identify the sample container.
9.0 Quality Control9.1 Miscellaneous Quality Control Measures.
Section | Quality control measure | Effect |
---|---|---|
7.1.3 | Isopropanol check | Ensure acceptable level of peroxide impurities in isopropanol. |
8.4, 8.5, 10.1 | Sampling equipment leak-check and calibration | Ensure accurate measurement of stack gas flow rate, sample volume. |
10.2 | Barium standard solution standardization | Ensure normality determination. |
11.2 | Replicate titrations | Ensure precision of titration determinations. |
9.2 Volume Metering System Checks. Same as Method 5, section 9.2.
10.0 Calibration and Standardization10.1 Sampling Equipment. Same as Method 5, section 10.0.
10.2 Barium Standard Solution. Same as Method 6, section 10.5.
11.0 Analytical Procedure11.1. Sample Loss. Same as Method 6, section 11.1.
11.2. Sample Analysis.
11.2.1 Container No. 1. Shake the container holding the isopropanol solution and the filter. If the filter breaks up, allow the fragments to settle for a few minutes before removing a sample aliquot. Pipette a 100-ml aliquot of this solution into a 250-ml Erlenmeyer flask, add 2 to 4 drops of thorin indicator, and titrate to a pink endpoint using 0.0100 N barium standard solution. Repeat the titration with a second aliquot of sample, and average the titration values. Replicate titrations must agree within 1 percent or 0.2 ml, whichever is greater.
11.2.2 Container No. 2. Thoroughly mix the solution in the container holding the contents of the second and third impingers. Pipette a 10-ml aliquot of sample into a 250-ml Erlenmeyer flask. Add 40 ml of isopropanol, 2 to 4 drops of thorin indicator, and titrate to a pink endpoint using 0.0100 N barium standard solution. Repeat the titration with a second aliquot of sample, and average the titration values. Replicate titrations must agree within 1 percent or 0.2 ml, whichever is greater.
11.2.3 Blanks. Prepare blanks by adding 2 to 4 drops of thorin indicator to 100 ml of 80 percent isopropanol. Titrate the blanks in the same manner as the samples.
12.0 Data Analysis and CalculationsCarry out calculations retaining at least one extra significant figure beyond that of the acquired data. Round off figures after final calculation.
12.1 Nomenclature. Same as Method 5, section 12.1, with the following additions and exceptions:
CH2SO4 = Sulfuric acid (including SO3) concentration, g/dscm (lb/dscf). CSO2 = Sulfur dioxide concentration, g/dscm (lb/dscf). N = Normality of barium perchlorate titrant, meq/ml. Va = Volume of sample aliquot titrated, 100 ml for H2SO4 and 10 ml for SO2. Vsoln = Total volume of solution in which the sample is contained, 1000 ml for the SO2 sample and 250 ml for the H2SO4 sample. Vt = Volume of barium standard solution titrant used for the sample, ml. Vtb = Volume of barium standard solution titrant used for the blank, ml.12.2 Average Dry Gas Meter Temperature and Average Orifice Pressure Drop. See data sheet (Figure 8-2).
12.3 Dry Gas Volume. Same as Method 5, section 12.3.
12.4 Volume of Water Vapor Condensed and Moisture Content. Calculate the volume of water vapor using Equation 5-2 of Method 5; the weight of water collected in the impingers and silica gel can be converted directly to milliliters (the specific gravity of water is 1 g/ml). Calculate the moisture content of the stack gas (Bws) using Equation 5-3 of Method 5. The note in section 12.5 of Method 5 also applies to this method. Note that if the effluent gas stream can be considered dry, the volume of water vapor and moisture content need not be calculated.
12.5 Sulfuric Acid Mist (Including SO3) Concentration.
Where: K3 = 0.04904 g/meq for metric units, K3 = 1.081 × 10−4 lb/meq for English units.12.6 Sulfur Dioxide Concentration.
Where: K4 = 0.03203 g/meq for metric units, K4 = 7.061 × 10−5 lb/meq for English units.12.7 Isokinetic Variation. Same as Method 5, section 12.11.
12.8 Stack Gas Velocity and Volumetric Flow Rate. Calculate the average stack gas velocity and volumetric flow rate, if needed, using data obtained in this method and the equations in sections 12.6 and 12.7 of Method 2.
13.0 Method Performance13.1 Analytical Range. Collaborative tests have shown that the minimum detectable limits of the method are 0.06 mg/m 3 (4 × 10−9 lb/ft 3) for H2SO4 and 1.2 mg/m 3 (74 × 10−9 lb/ft 3) for SO2. No upper limits have been established. Based on theoretical calculations for 200 ml of 3 percent H2O2 solution, the upper concentration limit for SO2 in a 1.0 m 3 (35.3 ft 3) gas sample is about 12,000 mg/m 3 (7.7 × 10−4 lb/ft 3). The upper limit can be extended by increasing the quantity of peroxide solution in the impingers.
14.0 Pollution Prevention [Reserved] 15.0 Waste Management [Reserved] 16.0 ReferencesSame as section 17.0 of Methods 5 and 6.
17.0 Tables, Diagrams, Flowcharts, and Validation Data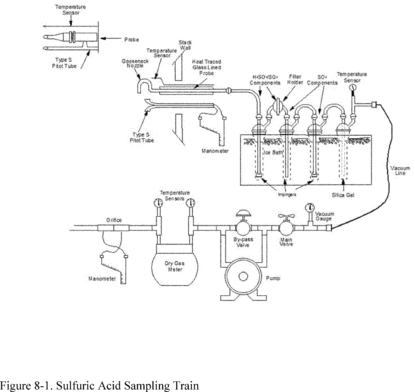
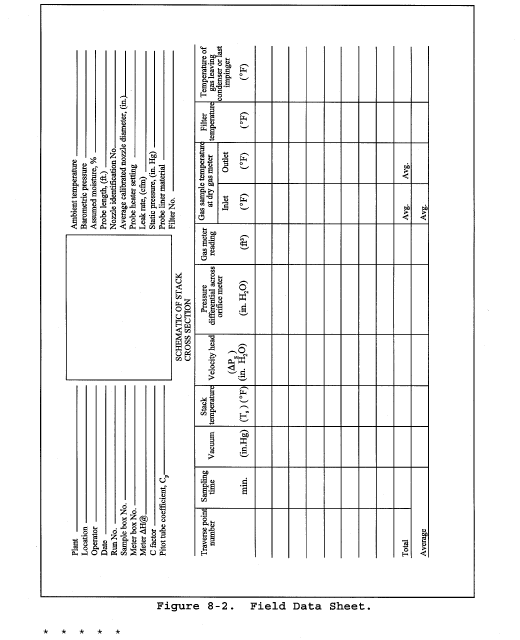
Many stationary sources discharge visible emissions into the atmosphere; these emissions are usually in the shape of a plume. This method involves the determination of plume opacity by qualified observers. The method includes procedures for the training and certification of observers, and procedures to be used in the field for determination of plume opacity. The appearance of a plume as viewed by an observer depends upon a number of variables, some of which may be controllable and some of which may not be controllable in the field. Variables which can be controlled to an extent to which they no longer exert a significant influence upon plume appearance include: Angle of the observer with respect to the plume; angle of the observer with respect to the sun; point of observation of attached and detached steam plume; and angle of the observer with respect to a plume emitted from a rectangular stack with a large length to width ratio. The method includes specific criteria applicable to these variables.
Other variables which may not be controllable in the field are luminescence and color contrast between the plume and the background against which the plume is viewed. These variables exert an influence upon the appearance of a plume as viewed by an observer, and can affect the ability of the observer to accurately assign opacity values to the observed plume. Studies of the theory of plume opacity and field studies have demonstrated that a plume is most visible and presents the greatest apparent opacity when viewed against a contrasting background. It follows from this, and is confirmed by field trials, that the opacity of a plume, viewed under conditions where a contrasting background is present can be assigned with the greatest degree of accuracy. However, the potential for a positive error is also the greatest when a plume is viewed under such contrasting conditions. Under conditions presenting a less contrasting background, the apparent opacity of a plume is less and approaches zero as the color and luminescence contrast decrease toward zero. As a result, significant negative bias and negative errors can be made when a plume is viewed under less contrasting conditions. A negative bias decreases rather than increases the possibility that a plant operator will be cited for a violation of opacity standards due to observer error.
Studies have been undertaken to determine the magnitude of positive errors which can be made by qualified observers while reading plumes under contrasting conditions and using the procedures set forth in this method. The results of these studies (field trials) which involve a total of 769 sets of 25 readings each are as follows:
(1) For black plumes (133 sets at a smoke generator), 100 percent of the sets were read with a positive error 1 of less than 7.5 percent opacity; 99 percent were read with a positive error of less than 5 percent opacity.
1 For a set, positive error = average opacity determined by observers' 25 observations - average opacity determined from transmissometer's 25 recordings.
(2) For white plumes (170 sets at a smoke generator, 168 sets at a coal-fired power plant, 298 sets at a sulfuric acid plant), 99 percent of the sets were read with a positive error of less than 7.5 percent opacity; 95 percent were read with a positive error of less than 5 percent opacity.
The positive observational error associated with an average of twenty-five readings is therefore established. The accuracy of the method must be taken into account when determining possible violations of applicable opacity standards.
1. Principle and Applicability1.1 Principle. The opacity of emissions from stationary sources is determined visually by a qualified observer.
1.2 Applicability. This method is applicable for the determination of the opacity of emissions from stationary sources pursuant to § 60.11(b) and for qualifying observers for visually determining opacity of emissions.
2. ProceduresThe observer qualified in accordance with section 3 of this method shall use the following procedures for visually determining the opacity of emissions:
2.1 Position. The qualified observer shall stand at a distance sufficient to provide a clear view of the emissions with the sun oriented in the 140° sector to his back. Consistent with maintaining the above requirement, the observer shall, as much as possible, make his observations from a position such that his line of vision is approximately perpendicular to the plume direction, and when observing opacity of emissions from rectangular outlets (e.g., roof monitors, open baghouses, noncircular stacks), approximately perpendicular to the longer axis of the outlet. The observer's line of sight should not include more than one plume at a time when multiple stacks are involved, and in any case the observer should make his observations with his line of sight perpendicular to the longer axis of such a set of multiple stacks (e.g., stub stacks on baghouses).
2.2 Field Records. The observer shall record the name of the plant, emission location, type facility, observer's name and affiliation, a sketch of the observer's position relative to the source, and the date on a field data sheet (Figure 9-1). The time, estimated distance to the emission location, approximate wind direction, estimated wind speed, description of the sky condition (presence and color of clouds), and plume background are recorded on a field data sheet at the time opacity readings are initiated and completed.
2.3 Observations. Opacity observations shall be made at the point of greatest opacity in that portion of the plume where condensed water vapor is not present. The observer shall not look continuously at the plume, but instead shall observe the plume momentarily at 15-second intervals.
2.3.1 Attached Steam Plumes. When condensed water vapor is present within the plume as it emerges from the emission outlet, opacity observations shall be made beyond the point in the plume at which condensed water vapor is no longer visible. The observer shall record the approximate distance from the emission outlet to the point in the plume at which the observations are made.
2.3.2 Detached Steam Plume. When water vapor in the plume condenses and becomes visible at a distinct distance from the emission outlet, the opacity of emissions should be evaluated at the emission outlet prior to the condensation of water vapor and the formation of the steam plume.
2.4 Recording Observations. Opacity observations shall be recorded to the nearest 5 percent at 15-second intervals on an observational record sheet. (See Figure 9-2 for an example.) A minimum of 24 observations shall be recorded. Each momentary observation recorded shall be deemed to represent the average opacity of emissions for a 15-second period.
2.5 Data Reduction. Opacity shall be determined as an average of 24 consecutive observations recorded at 15-second intervals. Divide the observations recorded on the record sheet into sets of 24 consecutive observations. A set is composed of any 24 consecutive observations. Sets need not be consecutive in time and in no case shall two sets overlap. For each set of 24 observations, calculate the average by summing the opacity of the 24 observations and dividing this sum by 24. If an applicable standard specifies an averaging time requiring more than 24 observations, calculate the average for all observations made during the specified time period. Record the average opacity on a record sheet. (See Figure 9-1 for an example.)
3. Qualifications and Testing3.1 Certification Requirements. To receive certification as a qualified observer, a candidate must be tested and demonstrate the ability to assign opacity readings in 5 percent increments to 25 different black plumes and 25 different white plumes, with an error not to exceed 15 percent opacity on any one reading and an average error not to exceed 7.5 percent opacity in each category. Candidates shall be tested according to the procedures described in section 3.2. Smoke generators used pursuant to section 3.2 shall be equipped with a smoke meter which meets the requirements of section 3.3.
The certification shall be valid for a period of 6 months, at which time the qualification procedure must be repeated by any observer in order to retain certification.
3.2 Certification Procedure. The certification test consists of showing the candidate a complete run of 50 plumes - 25 black plumes and 25 white plumes - generated by a smoke generator. Plumes within each set of 25 black and 25 white runs shall be presented in random order. The candidate assigns an opacity value to each plume and records his observation on a suitable form. At the completion of each run of 50 readings, the score of the candidate is determined. If a candidate fails to qualify, the complete run of 50 readings must be repeated in any retest. The smoke test may be administered as part of a smoke school or training program, and may be preceded by training or familiarization runs of the smoke generator during which candidates are shown black and white plumes of known opacity.
3.3 Smoke Generator Specifications. Any smoke generator used for the purposes of section 3.2 shall be equipped with a smoke meter installed to measure opacity across the diameter of the smoke generator stack. The smoke meter output shall display instack opacity based upon a pathlength equal to the stack exit diameter, on a full 0 to 100 percent chart recorder scale. The smoke meter optical design and performance shall meet the specifications shown in Table 9-1. The smoke meter shall be calibrated as prescribed in section 3.3.1 prior to the conduct of each smoke reading test. At the completion of each test, the zero and span drift shall be checked and if the drift exceeds ±1 percent opacity, the condition shall be corrected prior to conducting any subsequent test runs. The smoke meter shall be demonstrated, at the time of installation, to meet the specifications listed in Table 9-1. This demonstration shall be repeated following any subsequent repair or replacement of the photocell or associated electronic circuitry including the chart recorder or output meter, or every 6 months, whichever occurs first.
Table 9-1 - Smoke Meter Design and Performance Specifications
Parameter | Specification |
---|---|
a. Light source | Incandescent lamp operated at nominal rated voltage. |
b. Spectral response of photocell | Photopic (daylight spectral response of the human eye - Citation 3). |
c. Angle of view | 15° maximum total angle. |
d. Angle of projection | 15° maximum total angle. |
e. Calibration error | ±3% opacity, maximum. |
f. Zero and span drift | ±1% opacity, 30 minutes. |
g. Response time | 5 seconds. |
3.3.1 Calibration. The smoke meter is calibrated after allowing a minimum of 30 minutes warmup by alternately producing simulated opacity of 0 percent and 100 percent. When stable response at 0 percent or 100 percent is noted, the smoke meter is adjusted to produce an output of 0 percent or 100 percent, as appropriate. This calibration shall be repeated until stable 0 percent and 100 percent readings are produced without adjustment. Simulated 0 percent and 100 percent opacity values may be produced by alternately switching the power to the light source on and off while the smoke generator is not producing smoke.
3.3.2 Smoke Meter Evaluation. The smoke meter design and performance are to be evaluated as follows:
3.3.2.1 Light Source. Verify from manufacturer's data and from voltage measurements made at the lamp, as installed, that the lamp is operated within ±5 percent of the nominal rated voltage.
3.3.2.2 Spectral Response of Photocell. Verify from manufacturer's data that the photocell has a photopic response; i.e., the spectral sensitivity of the cell shall closely approximate the standard spectral-luminosity curve for photopic vision which is referenced in (b) of Table 9-1.
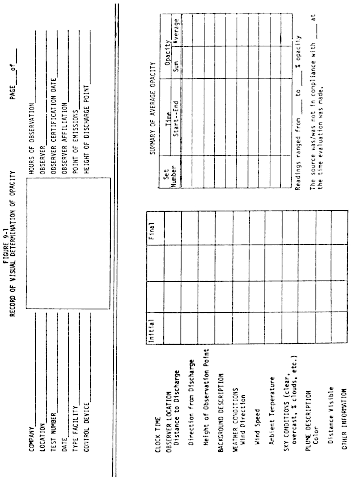
Figure 9-2 - Observation Record
Page __ of __
Company | Observer | |
Location | Type facility | |
Test Number | Point of emissions | |
Date |
Hr. | Min. | Seconds | Steam plume (check if applicable) | Comments | ||||
---|---|---|---|---|---|---|---|---|
0 | 15 | 30 | 45 | Attached | Detached | |||
0 | ||||||||
1 | ||||||||
2 | ||||||||
3 | ||||||||
4 | ||||||||
5 | ||||||||
6 | ||||||||
7 | ||||||||
8 | ||||||||
9 | ||||||||
10 | ||||||||
11 | ||||||||
12 | ||||||||
13 | ||||||||
14 | ||||||||
15 | ||||||||
16 | ||||||||
17 | ||||||||
18 | ||||||||
19 | ||||||||
20 | ||||||||
21 | ||||||||
22 | ||||||||
23 | ||||||||
24 | ||||||||
25 | ||||||||
26 | ||||||||
27 | ||||||||
28 | ||||||||
29 |
Figure 9-2 - Observation Record (Continued)
Page __ of __
Company | Observer | |
Location | Type facility | |
Test Number | Point of emissions | |
Date |
Hr. | Min. | Seconds | Steam plume (check if applicable) | Comments | ||||
---|---|---|---|---|---|---|---|---|
0 | 15 | 30 | 45 | Attached | Detached | |||
30 | ||||||||
31 | ||||||||
32 | ||||||||
33 | ||||||||
34 | ||||||||
35 | ||||||||
36 | ||||||||
37 | ||||||||
38 | ||||||||
39 | ||||||||
40 | ||||||||
41 | ||||||||
42 | ||||||||
43 | ||||||||
44 | ||||||||
45 | ||||||||
46 | ||||||||
47 | ||||||||
48 | ||||||||
49 | ||||||||
50 | ||||||||
51 | ||||||||
52 | ||||||||
53 | ||||||||
54 | ||||||||
55 | ||||||||
56 | ||||||||
57 | ||||||||
58 | ||||||||
59 |
3.3.2.3 Angle of View. Check construction geometry to ensure that the total angle of view of the smoke plume, as seen by the photocell, does not exceed 15°. The total angle of view may be calculated from: θ = 2 tan−1d/2L, where θ = total angle of view; d = the sum of the photocell diameter + the diameter of the limiting aperture; and L = the distance from the photocell to the limiting aperture. The limiting aperture is the point in the path between the photocell and the smoke plume where the angle of view is most restricted. In smoke generator smoke meters this is normally an orifice plate.
3.3.2.4 Angle of Projection. Check construction geometry to ensure that the total angle of projection of the lamp on the smoke plume does not exceed 15°. The total angle of projection may be calculated from: θ = 2 tan−1d/2L, where θ = total angle of projection; d = the sum of the length of the lamp filament + the diameter of the limiting aperture; and L = the distance from the lamp to the limiting aperture.
3.3.2.5 Calibration Error. Using neutral-density filters of known opacity, check the error between the actual response and the theoretical linear response of the smoke meter. This check is accomplished by first calibrating the smoke meter according to 3.3.1 and then inserting a series of three neutral-density filters of nominal opacity of 20, 50, and 75 percent in the smoke meter pathlength. Filters calibrated within ±2 percent shall be used. Care should be taken when inserting the filters to prevent stray light from affecting the meter. Make a total of five nonconsecutive readings for each filter. The maximum error on any one reading shall be 3 percent opacity.
3.3.2.6 Zero and Span Drift. Determine the zero and span drift by calibrating and operating the smoke generator in a normal manner over a 1-hour period. The drift is measured by checking the zero and span at the end of this period.
3.3.2.7 Response Time. Determine the response time by producing the series of five simulated 0 percent and 100 percent opacity values and observing the time required to reach stable response. Opacity values of 0 percent and 100 percent may be simulated by alternately switching the power to the light source off and on while the smoke generator is not operating.
4. Bibliography1. Air Pollution Control District Rules and Regulations, Los Angeles County Air Pollution Control District, Regulation IV, Prohibitions, Rule 50.
2. Weisburd, Melvin I., Field Operations and Enforcement Manual for Air, U.S. Environmental Protection Agency, Research Triangle Park, NC. APTD-1100, August 1972, pp. 4.1-4.36.
3. Condon, E.U., and Odishaw, H., Handbook of Physics, McGraw-Hill Co., New York, NY, 1958, Table 3.1, p. 6-52.
Alternate Method 1 - Determination of the Opacity of Emissions From Stationary Sources Remotely by LidarThis alternate method provides the quantitative determination of the opacity of an emissions plume remotely by a mobile lidar system (laser radar; Light Detection and Ranging). The method includes procedures for the calibration of the lidar and procedures to be used in the field for the lidar determination of plume opacity. The lidar is used to measure plume opacity during either day or nighttime hours because it contains its own pulsed light source or transmitter. The operation of the lidar is not dependent upon ambient lighting conditions (light, dark, sunny or cloudy).
The lidar mechanism or technique is applicable to measuring plume opacity at numerous wavelengths of laser radiation. However, the performance evaluation and calibration test results given in support of this method apply only to a lidar that employs a ruby (red light) laser [Reference 5.1].
1. Principle and Applicability1.1 Principle. The opacity of visible emissions from stationary sources (stacks, roof vents, etc.) is measured remotely by a mobile lidar (laser radar).
1.2 Applicability. This method is applicable for the remote measurement of the opacity of visible emissions from stationary sources during both nighttime and daylight conditions, pursuant to 40 CFR § 60.11(b). It is also applicable for the calibration and performance verification of the mobile lidar for the measurement of the opacity of emissions. A performance/design specification for a basic lidar system is also incorporated into this method.
1.3 Definitions.
Azimuth angle: The angle in the horizontal plane that designates where the laser beam is pointed. It is measured from an arbitrary fixed reference line in that plane.
Backscatter: The scattering of laser light in a direction opposite to that of the incident laser beam due to reflection from particulates along the beam's atmospheric path which may include a smoke plume.
Backscatter signal: The general term for the lidar return signal which results from laser light being backscattered by atmospheric and smoke plume particulates.
Convergence distance: The distance from the lidar to the point of overlap of the lidar receiver's field-of-view and the laser beam.
Elevation angle: The angle of inclination of the laser beam referenced to the horizontal plane.
Far region: The region of the atmosphere's path along the lidar line-of-sight beyond or behind the plume being measured.
Lidar: Acronym for Light Detection and Ranging.
Lidar range: The range or distance from the lidar to a point of interest along the lidar line-of-sight.
Near region: The region of the atmospheric path along the lidar line-of-sight between the lidar's convergence distance and the plume being measured.
Opacity: One minus the optical transmittance of a smoke plume, screen target, etc.
Pick interval: The time or range intervals in the lidar backscatter signal whose minimum average amplitude is used to calculate opacity. Two pick intervals are required, one in the near region and one in the far region.
Plume: The plume being measured by lidar.
Plume signal: The backscatter signal resulting from the laser light pulse passing through a plume.
1/R 2Correction: The correction made for the systematic decrease in lidar backscatter signal amplitude with range.
Reference signal: The backscatter signal resulting from the laser light pulse passing through ambient air.
Sample interval: The time period between successive samples for a digital signal or between successive measurements for an analog signal.
Signal spike: An abrupt, momentary increase and decrease in signal amplitude.
Source: The source being tested by lidar.
Time reference: The time (to) when the laser pulse emerges from the laser, used as the reference in all lidar time or range measurements.
2. ProceduresThe mobile lidar calibrated in accordance with Paragraph 3 of this method shall use the following procedures for remotely measuring the opacity of stationary source emissions:
2.1 Lidar Position. The lidar shall be positioned at a distance from the plume sufficient to provide an unobstructed view of the source emissions. The plume must be at a range of at least 50 meters or three consecutive pick intervals (whichever is greater) from the lidar's transmitter/receiver convergence distance along the line-of-sight. The maximum effective opacity measurement distance of the lidar is a function of local atmospheric conditions, laser beam diameter, and plume diameter. The test position of the lidar shall be selected so that the diameter of the laser beam at the measurement point within the plume shall be no larger than three-fourths the plume diameter. The beam diameter is calculated by Equation (AM1-1):
D(lidar) = A + Rφ≤0.75 D(Plume) (AM1-1) Where: D(Plume) = diameter of the plume (cm), φ = laser beam divergence measured in radians R = range from the lidar to the source (cm) D(Lidar) = diameter of the laser beam at range R (cm), A = diameter of the laser beam or pulse where it leaves the laser. The lidar range, R, is obtained by aiming and firing the laser at the emissions source structure immediately below the outlet. The range value is then determined from the backscatter signal which consists of a signal spike (return from source structure) and the atmospheric backscatter signal [Reference 5.1]. This backscatter signal should be recorded.When there is more than one source of emissions in the immediate vicinity of the plume, the lidar shall be positioned so that the laser beam passes through only a single plume, free from any interference of the other plumes for a minimum of 50 meters or three consecutive pick intervals (whichever is greater) in each region before and beyond the plume along the line-of-sight (determined from the backscatter signals). The lidar shall initially be positioned so that its line-of-sight is approximately perpendicular to the plume.
When measuring the opacity of emissions from rectangular outlets (e.g., roof monitors, open baghouses, noncircular stacks, etc.), the lidar shall be placed in a position so that its line-of-sight is approximately perpendicular to the longer (major) axis of the outlet.
2.2 Lidar Operational Restrictions. The lidar receiver shall not be aimed within an angle of ±15° (cone angle) of the sun.
This method shall not be used to make opacity measurements if thunderstorms, snowstorms, hail storms, high wind, high-ambient dust levels, fog or other atmospheric conditions cause the reference signals to consistently exceed the limits specified in section 2.3.
2.3 Reference Signal Requirements. Once placed in its proper position for opacity measurement, the laser is aimed and fired with the line-of-sight near the outlet height and rotated horizontally to a position clear of the source structure and the associated plume. The backscatter signal obtained from this position is called the ambient-air or reference signal. The lidar operator shall inspect this signal [Section V of Reference 5.1] to: (1) determine if the lidar line-of-sight is free from interference from other plumes and from physical obstructions such as cables, power lines, etc., for a minimum of 50 meters or three consecutive pick intervals (whichever is greater) in each region before and beyond the plume, and (2) obtain a qualitative measure of the homogeneity of the ambient air by noting any signal spikes.
Should there be any signal spikes on the reference signal within a minimum of 50 meters or three consecutive pick intervals (whichever is greater) in each region before and beyond the plume, the laser shall be fired three more times and the operator shall inspect the reference signals on the display. If the spike(s) remains, the azimuth angle shall be changed and the above procedures conducted again. If the spike(s) disappears in all three reference signals, the lidar line-of-sight is acceptable if there is shot-to-shot consistency and there is no interference from other plumes.
Shot-to-shot consistency of a series of reference signals over a period of twenty seconds is verified in either of two ways. (1) The lidar operator shall observe the reference signal amplitudes. For shot-to-shot consistency the ratio of Rf to Rn [amplitudes of the near and far region pick intervals (Section 2.6.1)] shall vary by not more than ±6% between shots; or (2) the lidar operator shall accept any one of the reference signals and treat the other two as plume signals; then the opacity for each of the subsequent reference signals is calculated (Equation AM1-2). For shot-to-shot consistency, the opacity values shall be within ±3% of 0% opacity and the associated So values less than or equal to 8% (full scale) [Section 2.6].
If a set of reference signals fails to meet the requirements of this section, then all plume signals [Section 2.4] from the last set of acceptable reference signals to the failed set shall be discarded.
2.3.1 Initial and Final Reference Signals. Three reference signals shall be obtained within a 90-second time period prior to any data run. A final set of three reference signals shall be obtained within three (3) minutes after the completion of the same data run.
2.3.2 Temporal Criterion for Additional Reference Signals. An additional set of reference signals shall be obtained during a data run if there is a change in wind direction or plume drift of 30° or more from the direction that was prevalent when the last set of reference signals was obtained. An additional set of reference signals shall also be obtained if there is an increase in value of SIn (near region standard deviation, Equation AM1-5) or SIf (far region standard deviation, Equation AM1-6) that is greater than 6% (full scale) over the respective values calculated from the immediately previous plume signal, and this increase in value remains for 30 seconds or longer. An additional set of reference signals shall also be obtained if there is a change in amplitude in either the near or the far region of the plume signal, that is greater than 6% of the near signal amplitude and this change in amplitude remains for 30 seconds or more.
2.4 Plume Signal Requirements. Once properly aimed, the lidar is placed in operation with the nominal pulse or firing rate of six pulses/minute (1 pulse/10 seconds). The lidar operator shall observe the plume backscatter signals to determine the need for additional reference signals as required by section 2.3.2. The plume signals are recorded from lidar start to stop and are called a data run. The length of a data run is determined by operator discretion. Short-term stops of the lidar to record additional reference signals do not constitute the end of a data run if plume signals are resumed within 90 seconds after the reference signals have been recorded, and the total stop or interrupt time does not exceed 3 minutes.
2.4.1 Non-hydrated Plumes. The laser shall be aimed at the region of the plume which displays the greatest opacity. The lidar operator must visually verify that the laser is aimed clearly above the source exit structure.
2.4.2 Hydrated Plumes. The lidar will be used to measure the opacity of hydrated or so-called steam plumes. As listed in the reference method, there are two types, i.e., attached and detached steam plumes.
2.4.2.1 Attached Steam Plumes. When condensed water vapor is present within a plume, lidar opacity measurements shall be made at a point within the residual plume where the condensed water vapor is no longer visible. The laser shall be aimed into the most dense region (region of highest opacity) of the residual plume.
During daylight hours the lidar operator locates the most dense portion of the residual plume visually. During nighttime hours a high-intensity spotlight, night vision scope, or low light level TV, etc., can be used as an aid to locate the residual plume. If visual determination is ineffective, the lidar may be used to locate the most dense region of the residual plume by repeatedly measuring opacity, along the longitudinal axis or center of the plume from the emissions outlet to a point just beyond the steam plume. The lidar operator should also observe color differences and plume reflectivity to ensure that the lidar is aimed completely within the residual plume. If the operator does not obtain a clear indication of the location of the residual plume, this method shall not be used.
Once the region of highest opacity of the residual plume has been located, aiming adjustments shall be made to the laser line-of-sight to correct for the following: movement to the region of highest opacity out of the lidar line-of-sight (away from the laser beam) for more than 15 seconds, expansion of the steam plume (air temperature lowers and/or relative humidity increases) so that it just begins to encroach on the field-of-view of the lidar's optical telescope receiver, or a decrease in the size of the steam plume (air temperature higher and/or relative humidity decreases) so that regions within the residual plume whose opacity is higher than the one being monitored, are present.
2.4.2.2 Detached Steam Plumes. When the water vapor in a hydrated plume condenses and becomes visible at a finite distance from the stack or source emissions outlet, the opacity of the emissions shall be measured in the region of the plume clearly above the emissions outlet and below condensation of the water vapor.
During daylight hours the lidar operators can visually determine if the steam plume is detached from the stack outlet. During nighttime hours a high-intensity spotlight, night vision scope, low light level TV, etc., can be used as an aid in determining if the steam plume is detached. If visual determination is ineffective, the lidar may be used to determine if the steam plume is detached by repeatedly measuring plume opacity from the outlet to the steam plume along the plume's longitudinal axis or center line. The lidar operator should also observe color differences and plume reflectivity to detect a detached plume. If the operator does not obtain a clear indication of the location of the detached plume, this method shall not be used to make opacity measurements between the outlet and the detached plume.
Once the determination of a detached steam plume has been confirmed, the laser shall be aimed into the region of highest opacity in the plume between the outlet and the formation of the steam plume. Aiming adjustments shall be made to the lidar's line-of-sight within the plume to correct for changes in the location of the most dense region of the plume due to changes in wind direction and speed or if the detached steam plume moves closer to the source outlet encroaching on the most dense region of the plume. If the detached steam plume should move too close to the source outlet for the lidar to make interference-free opacity measurements, this method shall not be used.
2.5 Field Records. In addition to the recording recommendations listed in other sections of this method the following records should be maintained. Each plume measured should be uniquely identified. The name of the facility, type of facility, emission source type, geographic location of the lidar with respect to the plume, and plume characteristics should be recorded. The date of the test, the time period that a source was monitored, the time (to the nearest second) of each opacity measurement, and the sample interval should also be recorded. The wind speed, wind direction, air temperature, relative humidity, visibility (measured at the lidar's position), and cloud cover should be recorded at the beginning and end of each time period for a given source. A small sketch depicting the location of the laser beam within the plume should be recorded.
If a detached or attached steam plume is present at the emissions source, this fact should be recorded. Figures AM1-I and AM1-II are examples of logbook forms that may be used to record this type of data. Magnetic tape or paper tape may also be used to record data.
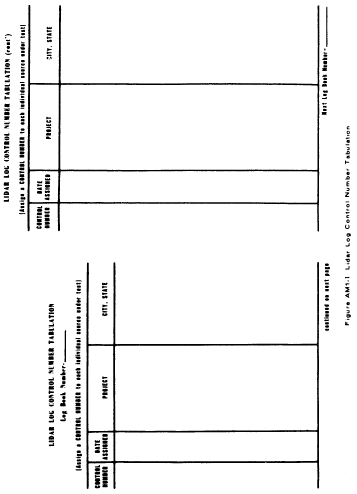
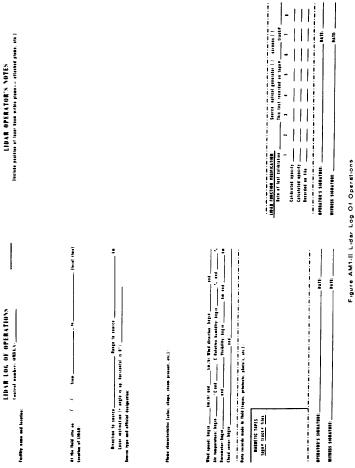

2.6 Opacity Calculation and Data Analysis. Referring to the reference signal and plume signal in Figure AM1-III, the measured opacity (Op) in percent for each lidar measurement is calculated using Equation AM1-2. (Op = 1−Tp; Tp is the plume transmittance.)
Where: In = near-region pick interval signal amplitude, plume signal, 1/R 2 corrected, If = far-region pick interval signal amplitude, plume signal, 1/R 2 corrected, Rn = near-region pick interval signal amplitude, reference signal, 1/R 2 corrected, and Rf = far-region pick interval signal amplitude, reference signal, 1/R 2 corrected.The 1/R 2 correction to the plume and reference signal amplitudes is made by multiplying the amplitude for each successive sample interval from the time reference, by the square of the lidar time (or range) associated with that sample interval [Reference 5.1].
The first step in selecting the pick intervals for Equation AM1-2 is to divide the plume signal amplitude by the reference signal amplitude at the same respective ranges to obtain a “normalized” signal. The pick intervals selected using this normalized signal, are a minimum of 15 m (100 nanoseconds) in length and consist of at least 5 contiguous sample intervals. In addition, the following criteria, listed in order of importance, govern pick interval selection. (1) The intervals shall be in a region of the normalized signal where the reference signal meets the requirements of section 2.3 and is everywhere greater than zero. (2) The intervals (near and far) with the minimum average amplitude are chosen. (3) If more than one interval with the same minimum average amplitude is found, the interval closest to the plume is chosen. (4) The standard deviation, So, for the calculated opacity shall be 8% or less. (So is calculated by Equation AM1-7).
If So is greater than 8%, then the far pick interval shall be changed to the next interval of minimal average amplitude. If So is still greater than 8%, then this procedure is repeated for the far pick interval. This procedure may be repeated once again for the near pick interval, but if So remains greater than 8%, the plume signal shall be discarded.
The reference signal pick intervals, Rn and Rf, must be chosen over the same time interval as the plume signal pick intervals, In and If, respectively [Figure AM1-III]. Other methods of selecting pick intervals may be used if they give equivalent results. Field-oriented examples of pick interval selection are available in Reference 5.1.
The average amplitudes for each of the pick intervals, In, If, Rn, Rf, shall be calculated by averaging the respective individual amplitudes of the sample intervals from the plume signal and the associated reference signal each corrected for 1/R 2. The amplitude of In shall be calculated according to Equation (AM-3).
Where: Ini = the amplitude of the ith sample interval (near-region), Σ = sum of the individual amplitudes for the sample intervals, m = number of sample intervals in the pick interval, and In = average amplitude of the near-region pick interval.Similarly, the amplitudes for If, Rn, and Rf are calculated with the three expressions in Equation (AM1-4).
The standard deviation, SIn, of the set of amplitudes for the near-region pick interval, In, shall be calculated using Equation (AM1-5).
Similarly, the standard deviations SIf, SRn, and SRf are calculated with the three expressions in Equation (AM1-6).
The standard deviation, So, for each associated opacity value, Op, shall be calculated using Equation (AM1-7).The calculated values of In, If, Rn, Rf, SIn, SIf, SRn, SRf, Op, and So should be recorded. Any plume signal with an So greater than 8% shall be discarded.
2.6.1 Azimuth Angle Correction. If the azimuth angle correction to opacity specified in this section is performed, then the elevation angle correction specified in section 2.6.2 shall not be performed. When opacity is measured in the residual region of an attached steam plume, and the lidar line-of-sight is not perpendicular to the plume, it may be necessary to correct the opacity measured by the lidar to obtain the opacity that would be measured on a path perpendicular to the plume. The following method, or any other method which produces equivalent results, shall be used to determine the need for a correction, to calculate the correction, and to document the point within the plume at which the opacity was measured.
Figure AM1-IV(b) shows the geometry of the opacity correction. L′ is the path through the plume along which the opacity measurement is made. P′ is the path perpendicular to the plume at the same point. The angle ε is the angle between L′ and the plume center line. The angle (π/2-ε), is the angle between the L′ and P′. The measured opacity, Op, measured along the path L′ shall be corrected to obtain the corrected opacity, Opc, for the path P′, using Equation (AM1-8).
The correction in Equation (AM1-8) shall be performed if the inequality in Equation (AM1-9) is true.Figure AM1-IV(a) shows the geometry used to calculate ε and the position in the plume at which the lidar measurement is made. This analysis assumes that for a given lidar measurement, the range from the lidar to the plume, the elevation angle of the lidar from the horizontal plane, and the azimuth angle of the lidar from an arbitrary fixed reference in the horizontal plane can all be obtained directly.
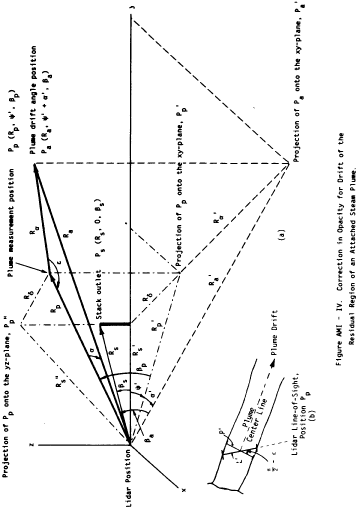
The correction angle ε shall be determined using Equation AM1-10.
*Obtained directly from lidar. These values should be recorded.
Where: α = Cos−1 (Cosβp Cosβa Cosα′ + Sinβp Sinβa), and Rθ = (Rp2 + Ra2 − 2 Rp Ra Cosα) 1/2R≤, the distance from the source to the opacity measurement point projected in the horizontal plane, shall be determined using Equation AM1-11.
Where: R′s = Rs Cos βs, and R′p = Rp Cos βp. In the special case where the plume centerline at the opacity measurement point is horizontal, parallel to the ground, Equation AM1-12 may be used to determine ε instead of Equation AM1-10. Where: R″s = (R′ 2s + Rp 2Sin 2βp)1/2. If the angle ε is such that ε≤30° or ε ≥150°, the azimuth angle correction shall not be performed and the associated opacity value shall be discarded.2.6.2 Elevation Angle Correction. An individual lidar-measured opacity, Op, shall be corrected for elevation angle if the laser elevation or inclination angle, βp [Figure AM1-V], is greater than or equal to the value calculated in Equation AM1-13.
The measured opacity, Op, along the lidar path L, is adjusted to obtain the corrected opacity, Opc, for the actual plume (horizontal) path, P, by using Equation (AM1-14). Where: βp = lidar elevation or inclination angle, Op = measured opacity along path L, and Opc = corrected opacity for the actual plume thickness P.The values for βp, Op and Opc should be recorded.
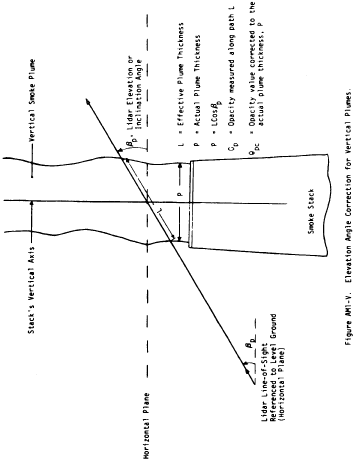
2.6.3 Determination of Actual Plume Opacity. Actual opacity of the plume shall be determined by Equation AM1-15.
2.6.4 Calculation of Average Actual Plume Opacity. The average of the actual plume opacity, Opa, shall be calculated as the average of the consecutive individual actual opacity values, Opa, by Equation AM1-16.
Where: (Opa)k = the kth actual opacity value in an averaging interval containing n opacity values; k is a summing index. Σ = the sum of the individual actual opacity values. n = the number of individual actual opacity values contained in the averaging interval. Opa = average actual opacity calculated over the averaging interval. 3. Lidar Performance VerificationThe lidar shall be subjected to two types of performance verifications that shall be performed in the field. The annual calibration, conducted at least once a year, shall be used to directly verify operation and performance of the entire lidar system. The routine verification, conducted for each emission source measured, shall be used to insure proper performance of the optical receiver and associated electronics.
3.1 Annual Calibration Procedures. Either a plume from a smoke generator or screen targets shall be used to conduct this calibration.
If the screen target method is selected, five screens shall be fabricated by placing an opaque mesh material over a narrow frame (wood, metal extrusion, etc.). The screen shall have a surface area of at least one square meter. The screen material should be chosen for precise optical opacities of about 10, 20, 40, 60, and 80%. Opacity of each target shall be optically determined and should be recorded. If a smoke generator plume is selected, it shall meet the requirements of section 3.3 of Reference Method 9. This calibration shall be performed in the field during calm (as practical) atmospheric conditions. The lidar shall be positioned in accordance with section 2.1.
The screen targets must be placed perpendicular to and coincident with the lidar line-of-sight at sufficient height above the ground (suggest about 30 ft) to avoid ground-level dust contamination. Reference signals shall be obtained just prior to conducting the calibration test.
The lidar shall be aimed through the center of the plume within 1 stack diameter of the exit, or through the geometric center of the screen target selected. The lidar shall be set in operation for a 6-minute data run at a nominal pulse rate of 1 pulse every 10 seconds. Each backscatter return signal and each respective opacity value obtained from the smoke generator transmissometer, shall be obtained in temporal coincidence. The data shall be analyzed and reduced in accordance with section 2.6 of this method. This calibration shall be performed for 0% (clean air), and at least five other opacities (nominally 10, 20, 40, 60, and 80%).
The average of the lidar opacity values obtained during a 6-minute calibration run shall be calculated and should be recorded. Also the average of the opacity values obtained from the smoke generator transmissometer for the same 6-minute run shall be calculated and should be recorded.
Alternate calibration procedures that do not meet the above requirements but produce equivalent results may be used.
3.2 Routine Verification Procedures. Either one of two techniques shall be used to conduct this verification. It shall be performed at least once every 4 hours for each emission source measured. The following parameters shall be directly verified.
1) The opacity value of 0% plus a minimum of 5 (nominally 10, 20, 40, 60, and 80%) opacity values shall be verified through the PMT detector and data processing electronics.
2) The zero-signal level (receiver signal with no optical signal from the source present) shall be inspected to insure that no spurious noise is present in the signal. With the entire lidar receiver and analog/digital electronics turned on and adjusted for normal operating performance, the following procedures shall be used for Techniques 1 and 2, respectively.
3.2.1 Procedure for Technique 1. This test shall be performed with no ambient or stray light reaching the PMT detector. The narrow band filter (694.3 nanometers peak) shall be removed from its position in front of the PMT detector. Neutral density filters of nominal opacities of 10, 20, 40, 60, and 80% shall be used. The recommended test configuration is depicted in Figure AM1-VI.
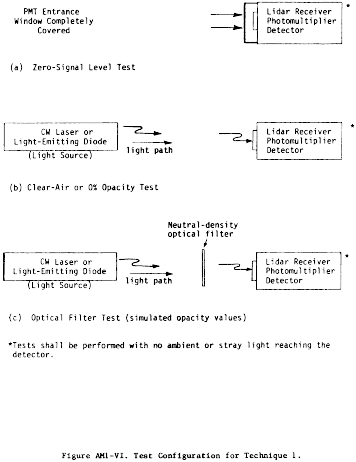
The zero-signal level shall be measured and should be recorded, as indicated in Figure AM1-VI(a). This simulated clear-air or 0% opacity value shall be tested in using the selected light source depicted in Figure AM1-VI(b).
The light source either shall be a continuous wave (CW) laser with the beam mechanically chopped or a light emitting diode controlled with a pulse generator (rectangular pulse). (A laser beam may have to be attenuated so as not to saturate the PMT detector). This signal level shall be measured and should be recorded. The opacity value is calculated by taking two pick intervals [Section 2.6] about 1 microsecond apart in time and using Equation (AM1-2) setting the ratio Rn/Rf = 1. This calculated value should be recorded.
The simulated clear-air signal level is also employed in the optical test using the neutral density filters. Using the test configuration in Figure AM1-VI(c), each neutral density filter shall be separately placed into the light path from the light source to the PMT detector. The signal level shall be measured and should be recorded. The opacity value for each filter is calculated by taking the signal level for that respective filter (If), dividing it by the 0% opacity signal level (In) and performing the remainder of the calculation by Equation (AM1-2) with Rn/Rf = 1. The calculated opacity value for each filter should be recorded.
The neutral density filters used for Technique 1 shall be calibrated for actual opacity with accuracy of ±2% or better. This calibration shall be done monthly while the filters are in use and the calibrated values should be recorded.
3.2.2 Procedure for Technique 2. An optical generator (built-in calibration mechanism) that contains a light-emitting diode (red light for a lidar containing a ruby laser) is used. By injecting an optical signal into the lidar receiver immediately ahead of the PMT detector, a backscatter signal is simulated. With the entire lidar receiver electronics turned on and adjusted for normal operating performance, the optical generator is turned on and the simulation signal (corrected for 1/R 2) is selected with no plume spike signal and with the opacity value equal to 0%. This simulated clear-air atmospheric return signal is displayed on the system's video display. The lidar operator then makes any fine adjustments that may be necessary to maintain the system's normal operating range.
The opacity values of 0% and the other five values are selected one at a time in any order. The simulated return signal data should be recorded. The opacity value shall be calculated. This measurement/calculation shall be performed at least three times for each selected opacity value. While the order is not important, each of the opacity values from the optical generator shall be verified. The calibrated optical generator opacity value for each selection should be recorded.
The optical generator used for Technique 2 shall be calibrated for actual opacity with an accuracy of ±1% or better. This calibration shall be done monthly while the generator is in use and calibrated value should be recorded.
Alternate verification procedures that do not meet the above requirements but produce equivalent results may be used.
3.3 Deviation. The permissible error for the annual calibration and routine verification are:
3.3.1 Annual Calibration Deviation.
3.3.1.1 Smoke Generator. If the lidar-measured average opacity for each data run is not within ±5% (full scale) of the respective smoke generator's average opacity over the range of 0% through 80%, then the lidar shall be considered out of calibration.
3.3.1.2 Screens. If the lidar-measured average opacity for each data run is not within ±3% (full scale) of the laboratory-determined opacity for each respective simulation screen target over the range of 0% through 80%, then the lidar shall be considered out of calibration.
3.3.2 Routine Verification Error. If the lidar-measured average opacity for each neutral density filter (Technique 1) or optical generator selection (Technique 2) is not within ±3% (full scale) of the respective laboratory calibration value then the lidar shall be considered non-operational.
4. Performance/Design Specification for Basic Lidar System4.1 Lidar Design Specification. The essential components of the basic lidar system are a pulsed laser (transmitter), optical receiver, detector, signal processor, recorder, and an aiming device that is used in aiming the lidar transmitter and receiver. Figure AM1-VII shows a functional block diagram of a basic lidar system.
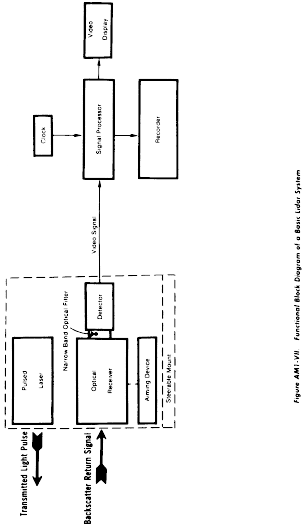
4.2 Performance Evaluation Tests. The owner of a lidar system shall subject such a lidar system to the performance verification tests described in section 3, prior to first use of this method. The annual calibration shall be performed for three separate, complete runs and the results of each should be recorded. The requirements of section 3.3.1 must be fulfilled for each of the three runs.
Once the conditions of the annual calibration are fulfilled the lidar shall be subjected to the routine verification for three separate complete runs. The requirements of section 3.3.2 must be fulfilled for each of the three runs and the results should be recorded. The Administrator may request that the results of the performance evaluation be submitted for review.
5. References5.1 The Use of Lidar for Emissions Source Opacity Determination, U.S. Environmental Protection Agency, National Enforcement Investigations Center, Denver, CO. EPA-330/1-79-003-R, Arthur W. Dybdahl, current edition [NTIS No. PB81-246662].
5.2 Field Evaluation of Mobile Lidar for the Measurement of Smoke Plume Opacity, U.S. Environmental Protection Agency, National Enforcement Investigations Center, Denver, CO. EPA/NEIC-TS-128, February 1976.
5.3 Remote Measurement of Smoke Plume Transmittance Using Lidar, C. S. Cook, G. W. Bethke, W. D. Conner (EPA/RTP). Applied Optics 11, pg 1742. August 1972.
5.4 Lidar Studies of Stack Plumes in Rural and Urban Environments, EPA-650/4-73-002, October 1973.
5.5 American National Standard for the Safe Use of Lasers ANSI Z 136.1-176, March 8, 1976.
5.6 U.S. Army Technical Manual TB MED 279, Control of Hazards to Health from Laser Radiation, February 1969.
5.7 Laser Institute of America Laser Safety Manual, 4th Edition.
5.8 U.S. Department of Health, Education and Welfare, Regulations for the Administration and Enforcement of the Radiation Control for Health and Safety Act of 1968, January 1976.
5.9 Laser Safety Handbook, Alex Mallow, Leon Chabot, Van Nostrand Reinhold Co., 1978.
Method 10 - Determination of Carbon Monoxide Emissions From Stationary Sources (Instrumental Analyzer Procedure) 1.0 Scope and Application What is Method 10?Method 10 is a procedure for measuring carbon monoxide (CO) in stationary source emissions using a continuous instrumental analyzer. Quality assurance and quality control requirements are included to assure that you, the tester, collect data of known quality. You must document your adherence to these specific requirements for equipment, supplies, sample collection and analysis, calculations, and data analysis. This method does not completely describe all equipment, supplies, and sampling and analytical procedures you will need but refers to other methods for some of the details. Therefore, to obtain reliable results, you should also have a thorough knowledge of these additional test methods which are found in appendix A to this part:
(a) Method 1 - Sample and Velocity Traverses for Stationary Sources.
(b) Method 4 - Determination of Moisture Content in Stack Gases.
(c) Method 7E - Determination of Nitrogen Oxides Emissions from Stationary Sources (Instrumental Analyzer Procedure).
1.1 Analytes. What does this method determine? This method measures the concentration of carbon monoxide.
Analyte | CAS No. | Sensitivity |
---|---|---|
CO | 630-08-0 | Typically <2% of Calibration Span. |
1.2 Applicability. When is this method required? The use of Method 10 may be required by specific New Source Performance Standards, State Implementation Plans, and permits where CO concentrations in stationary source emissions must be measured, either to determine compliance with an applicable emission standard or to conduct performance testing of a continuous emission monitoring system (CEMS). Other regulations may also require the use of Method 10.
1.3 Data Quality Objectives. Refer to section 1.3 of Method 7E.
2.0 Summary of MethodIn this method, you continuously or intermittently sample the effluent gas and convey the sample to an analyzer that measures the concentration of CO. You must meet the performance requirements of this method to validate your data.
3.0 DefinitionsRefer to section 3.0 of Method 7E for the applicable definitions.
4.0 InterferencesSubstances having a strong absorption of infrared energy may interfere to some extent in some analyzers. Instrumental correction may be used to compensate for the interference. You may also use silica gel and ascarite traps to eliminate the interferences. If this option is used, correct the measured gas volume for the carbon dioxide (CO2) removed in the trap.
5.0 SafetyRefer to section 5.0 of Method 7E.
6.0 Equipment and Supplies What do I need for the measurement system?6.1 Continuous Sampling. Figure 7E-1 of Method 7E is a schematic diagram of an acceptable measurement system. The components are the same as those in sections 6.1 and 6.2 of Method 7E, except that the CO analyzer described in section 6.2 of this method must be used instead of the analyzer described in section 6.2 of Method 7E. You must follow the noted specifications in section 6.1 of Method 7E except that the requirements to use stainless steel, Teflon, or non-reactive glass filters do not apply. Also, a heated sample line is not required to transport dry gases or for systems that measure the CO concentration on a dry basis.
6.2 Integrated Sampling.
6.2.1 Air-Cooled Condenser or Equivalent. To remove any excess moisture.
6.2.2 Valve. Needle valve, or equivalent, to adjust flow rate.
6.2.3 Pump. Leak-free diaphragm type, or equivalent, to transport gas.
6.2.4 Rate Meter. Rotameter, or equivalent, to measure a flow range from 0 to 1.0 liter per minute (0.035 cfm).
6.2.5 Flexible Bag. Tedlar, or equivalent, with a capacity of 60 to 90 liters (2 to 3 ft 3). (Verify through the manufacturer that the Tedlar alternative is suitable for CO and make this verified information available for inspection.) Leak-test the bag in the laboratory before using by evacuating with a pump followed by a dry gas meter. When the evacuation is complete, there should be no flow through the meter.
6.2.6 Sample Tank. Stainless steel or aluminum tank equipped with a pressure indicator with a minimum volume of 4 liters.
6.3 What analyzer must I use? You must use an instrument that continuously measures CO in the gas stream and meets the specifications in section 13.0. The dual-range analyzer provisions in section 6.2.8.1 of Method 7E apply.
7.0 Reagents and Standards7.1 Calibration Gas. What calibration gases do I need? Refer to section 7.1 of Method 7E for the calibration gas requirements.
7.2 Interference Check. What additional reagents do I need for the interference check? Use the appropriate test gases listed in Table 7E-3 of Method 7E (i.e., potential interferents, as identified by the instrument manufacturer) to conduct the interference check.
8.0 Sample Collection, Preservation, Storage, and Transport Emission Test Procedure8.1 Sampling Site and Sampling Points. You must follow section 8.1 of Method 7E.
8.2 Initial Measurement System Performance Tests. You must follow the procedures in section 8.2 of Method 7E. If a dilution-type measurement system is used, the special considerations in section 8.3 of Method 7E also apply.
8.3 Interference Check. You must follow the procedures of section 8.2.7 of Method 7E.
8.4 Sample Collection.
8.4.1 Continuous Sampling. You must follow the procedures of section 8.4 of Method 7E.
8.4.2 Integrated Sampling. Evacuate the flexible bag or sample tank. Set up the equipment as shown in Figure 10-1 with the bag disconnected. Place the probe in the stack and purge the sampling line. Connect the bag, making sure that all connections are leak-free. Sample at a rate proportional to the stack velocity. If needed, the CO2 content of the gas may be determined by using the Method 3 integrated sample procedures, or by weighing an ascarite CO2 removal tube used and computing CO2 concentration from the gas volume sampled and the weight gain of the tube. Data may be recorded on a form similar to Table 10-1. If a sample tank is used for sample collection, follow procedures similar to those in sections 8.1.2, 8.2.3, 8.3, and 12.4 of Method 25 as appropriate to prepare the tank, conduct the sampling, and correct the measured sample concentration.
8.5 Post-Run System Bias Check, Drift Assessment, and Alternative Dynamic Spike Procedure. You must follow the procedures in sections 8.5 and 8.6 of Method 7E.
9.0 Quality ControlFollow the quality control procedures in section 9.0 of Method 7E.
10.0 Calibration and StandardizationFollow the procedures for calibration and standardization in section 10.0 of Method 7E.
11.0 Analytical ProceduresBecause sample collection and analysis are performed together (see section 8), additional discussion of the analytical procedure is not necessary.
12.0 Calculations and Data AnalysisYou must follow the procedures for calculations and data analysis in section 12.0 of Method 7E, as applicable, substituting CO for NOX as applicable.
12.1 Concentration Correction for CO2 Removal. Correct the CO concentration for CO2 removal (if applicable) using Eq. 10-1.
Where: CAvg = Average gas concentration for the test run, ppm. CCO stack = Average unadjusted stack gas CO concentration indicated by the data recorder for the test run, ppmv. FCO2 = Volume fraction of CO2 in the sample, i.e., percent CO2 from Orsat analysis divided by 100. 13.0 Method PerformanceThe specifications for analyzer calibration error, system bias, drift, interference check, and alternative dynamic spike procedure are the same as in section 13.0 of Method 7E.
14.0 Pollution Prevention [Reserved] 15.0 Waste Management [Reserved] 16.0 Alternative ProceduresThe dynamic spike procedure and the manufacturer stability test are the same as in sections 16.1 and 16.3 of Method 7E
17.0 References1. “EPA Traceability Protocol for Assay and Certification of Gaseous Calibration Standards - September 1997 as amended, EPA-600/R-97/121
18.0 Tables, Diagrams, Flowcharts, and Validation Data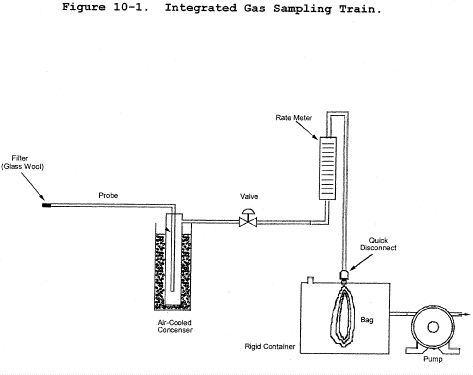
Table 10-1 - Field Data
[Integrated sampling]
Location: Date: | ||
Test: Operator: | ||
Clock Time | Rotameter Reading liters/min (cfm) | Comments |
This method does not include all of the specifications (e.g., equipment and supplies) and procedures (e.g., sampling and analytical) essential to its performance. Some material is incorporated by reference from other methods in this part. Therefore, to obtain reliable results, persons using this method should have a thorough knowledge of at least the following additional test methods: Method 1, Method 4, and Method 5.
1.0 Scope and Application1.1 Analytes.
Analyte | CAS No. | Sensitivity |
---|---|---|
Carbon monoxide (CO) | 630-08-0 | 3 ppmv |
1.2 Applicability. This method is applicable for the determination of CO emissions at petroleum refineries. This method serves as the reference method in the relative accuracy test for nondispersive infrared (NDIR) CO continuous emission monitoring systems (CEMS) that are required to be installed in petroleum refineries on fluid catalytic cracking unit catalyst regenerators (§ 60.105(a)(2) of this part).
1.3 Data Quality Objectives. Adherence to the requirements of this method will enhance the quality of the data obtained from air pollutant sampling methods.
2.0 Summary of MethodAn integrated gas sample is extracted from the stack, passed through an alkaline permanganate solution to remove sulfur oxides and nitrogen oxides, and collected in a Tedlar or equivalent bag. (Verify through the manufacturer that the Tedlar alternative is suitable for NO and make this verified information available for inspection.) The CO concentration in the sample is measured spectrophotometrically using the reaction of CO with p-sulfaminobenzoic acid.
3.0 Definitions [Reserved] 4.0 InterferencesSulfur oxides, nitric oxide, and other acid gases interfere with the colorimetric reaction. They are removed by passing the sampled gas through an alkaline potassium permanganate scrubbing solution. Carbon dioxide (CO2) does not interfere, but, because it is removed by the scrubbing solution, its concentration must be measured independently and an appropriate volume correction made to the sampled gas.
5.0 Safety5.1 Disclaimer. This method may involve hazardous materials, operations, and equipment. This test method may not address all of the safety problems associated with its use. It is the responsibility of the user of this test method to establish appropriate safety and health practices and determine the applicability of regulatory limitations prior to performing this test method. The analyzer users manual should be consulted for specific precautions to be taken with regard to the analytical procedure.
5.2 Corrosive reagents. The following reagents are hazardous. Personal protective equipment and safe procedures are useful in preventing chemical splashes. If contact occurs, immediately flush with copious amounts of water for at least 15 minutes. Remove clothing under shower and decontaminate. Treat residual chemical burns as thermal burns.
5.2.1 Sodium Hydroxide (NaOH). Causes severe damage to eyes and skin. Inhalation causes irritation to nose, throat, and lungs. Reacts exothermically with limited amounts of water.
6.0 Equipment and Supplies6.1 Sample Collection. The sampling train shown in Figure 10A-1 is required for sample collection. Component parts are described below:
6.1.1 Probe. Stainless steel, sheathed Pyrex glass, or equivalent, equipped with a glass wool plug to remove particulate matter.
6.1.2 Sample Conditioning System. Three Greenburg-Smith impingers connected in series with leak-free connections.
6.1.3 Pump. Leak-free pump with stainless steel and Teflon parts to transport sample at a flow rate of 300 ml/min (0.01 ft 3/min) to the flexible bag.
6.1.4 Surge Tank. Installed between the pump and the rate meter to eliminate the pulsation effect of the pump on the rate meter.
6.1.5 Rate Meter. Rotameter, or equivalent, to measure flow rate at 300 ml/min (0.01 ft 3/min). Calibrate according to section 10.2.
6.1.6 Flexible Bag. Tedlar, or equivalent, with a capacity of 10 liters (0.35 ft 3) and equipped with a sealing quick-connect plug. The bag must be leak-free according to section 8.1. For protection, it is recommended that the bag be enclosed within a rigid container.
6.1.7 Sample Tank. Stainless steel or aluminum tank equipped with a pressure indicator with a minimum volume of 10 liters.
6.1.8 Valves. Stainless-steel needle valve to adjust flow rate, and stainless-steel 3-way valve, or equivalent.
6.1.9 CO2 Analyzer. Fyrite, or equivalent, to measure CO2 concentration to within 0.5 percent.
6.1.10 Volume Meter. Dry gas meter, capable of measuring the sample volume under calibration conditions of 300 ml/min (0.01 ft 3/min) for 10 minutes.
6.1.11 Pressure Gauge. A water filled U-tube manometer, or equivalent, of about 30 cm (12 in.) to leak-check the flexible bag.
6.2 Sample Analysis.
6.2.1 Spectrophotometer. Single- or double-beam to measure absorbance at 425 and 600 nm. Slit width should not exceed 20 nm.
6.2.2 Spectrophotometer Cells. 1-cm pathlength.
6.2.3 Vacuum Gauge. U-tube mercury manometer, 1 meter (39 in.), with 1-mm divisions, or other gauge capable of measuring pressure to within 1 mm Hg.
6.2.4 Pump. Capable of evacuating the gas reaction bulb to a pressure equal to or less than 40 mm Hg absolute, equipped with coarse and fine flow control valves.
6.2.5 Barometer. Mercury, aneroid, or other barometer capable of measuring atmospheric pressure to within 1 mm Hg.
6.2.6 Reaction Bulbs. Pyrex glass, 100-ml with Teflon stopcock (Figure 10A-2), leak-free at 40 mm Hg, designed so that 10 ml of the colorimetric reagent can be added and removed easily and accurately. Commercially available gas sample bulbs such as Supelco Catalog No. 2-2161 may also be used.
6.2.7 Manifold. Stainless steel, with connections for three reaction bulbs and the appropriate connections for the manometer and sampling bag as shown in Figure 10A-3.
6.2.8 Pipets. Class A, 10-ml size.
6.2.9 Shaker Table. Reciprocating-stroke type such as Eberbach Corporation, Model 6015. A rocking arm or rotary-motion type shaker may also be used. The shaker must be large enough to accommodate at least six gas sample bulbs simultaneously. It may be necessary to construct a table top extension for most commercial shakers to provide sufficient space for the needed bulbs (Figure 10A-4).
6.2.10 Valve. Stainless steel shut-off valve.
6.2.11 Analytical Balance. Capable of weighing to 0.1 mg.
7.0 Reagents and StandardsUnless otherwise indicated, all reagents shall conform to the specifications established by the Committee on Analytical Reagents of the American Chemical Society, where such specifications are available; otherwise, the best available grade shall be used.
7.1 Sample Collection.
7.1.1 Water. Deionized distilled, to conform to ASTM D 1193-77 or 91, Type 3 (incorporated by reference - see § 60.17). If high concentrations of organic matter are not expected to be present, the potassium permanganate test for oxidizable organic matter may be omitted.
7.1.2 Alkaline Permanganate Solution, 0.25 M KMnO4/1.5 M Sodium Hydroxide (NaOH). Dissolve 40 g KMnO4 and 60 g NaOH in approximately 900 ml water, cool, and dilute to 1 liter.
7.2 Sample Analysis.
7.2.1 Water. Same as in section 7.1.1.
7.2.2 1 M Sodium Hydroxide Solution. Dissolve 40 g NaOH in approximately 900 ml of water, cool, and dilute to 1 liter.
7.2.3 0.1 M NaOH Solution. Dilute 50 ml of the 1 M NaOH solution prepared in section 7.2.2 to 500 ml.
7.2.4 0.1 M Silver Nitrate (AgNO3) Solution. Dissolve 8.5 g AgNO3 in water, and dilute to 500 ml.
7.2.5 0.1 M Para-Sulfaminobenzoic Acid (p-SABA) Solution. Dissolve 10.0 g p-SABA in 0.1 M NaOH, and dilute to 500 ml with 0.1 M NaOH.
7.2.6 Colorimetric Solution. To a flask, add 100 ml of 0.1 M p-SABA solution and 100 ml of 0.1 M AgNO3 solution. Mix, and add 50 ml of 1 M NaOH with shaking. The resultant solution should be clear and colorless. This solution is acceptable for use for a period of 2 days.
7.2.7 Standard Gas Mixtures. Traceable to National Institute of Standards and Technology (NIST) standards and containing between 50 and 1000 ppm CO in nitrogen. At least two concentrations are needed to span each calibration range used (Section 10.3). The calibration gases must be certified by the manufacturer to be within 2 percent of the specified concentrations.
8.0 Sample Collection, Preservation, Storage, and Transport8.1 Sample Bag or Tank Leak-Checks. While a leak-check is required after bag or sample tank use, it should also be done before the bag or sample tank is used for sample collection. The tank should be leak-checked according to the procedure specified in section 8.1.2 of Method 25. The bag should be leak-checked in the inflated and deflated condition according to the following procedure:
8.1.1 Connect the bag to a water manometer, and pressurize the bag to 5 to 10 cm H2O (2 to 4 in H2O). Allow the bag to stand for 60 minutes. Any displacement in the water manometer indicates a leak.
8.1.2 Evacuate the bag with a leakless pump that is connected to the downstream side of a flow indicating device such as a 0- to 100-ml/min rotameter or an impinger containing water. When the bag is completely evacuated, no flow should be evident if the bag is leak-free.
8.2 Sample Collection.
8.2.1 Evacuate and leak check the sample bag or tank as specified in section 8.1. Assemble the apparatus as shown in Figure 10A-1. Loosely pack glass wool in the tip of the probe. Place 400 ml of alkaline permanganate solution in the first two impingers and 250 ml in the third. Connect the pump to the third impinger, and follow this with the surge tank, rate meter, and 3-way valve. Do not connect the bag or sample tank to the system at this time.
8.2.2 Leak-check the sampling system by plugging the probe inlet, opening the 3-way valve, and pulling a vacuum of approximately 250 mm Hg on the system while observing the rate meter for flow. If flow is indicated on the rate meter, do not proceed further until the leak is found and corrected.
8.2.3 Purge the system with sample gas by inserting the probe into the stack and drawing the sample gas through the system at 300 ml/min ±10 percent for 5 minutes. Connect the evacuated bag or sample tank to the system, record the starting time, and sample at a rate of 300 ml/min for 30 minutes, or until the bag is nearly full, or the sample tank reaches ambient pressure. Record the sampling time, the barometric pressure, and the ambient temperature. Purge the system as described above immediately before each sample.
8.2.4 The scrubbing solution is adequate for removing sulfur oxides and nitrogen oxides from 50 liters (1.8 ft 3) of stack gas when the concentration of each is less than 1,000 ppm and the CO2 concentration is less than 15 percent. Replace the scrubber solution after every fifth sample.
8.3 Carbon Dioxide Measurement. Measure the CO2 content in the stack to the nearest 0.5 percent each time a CO sample is collected. A simultaneous grab sample analyzed by the Fyrite analyzer is acceptable.
9.0 Quality Control9.1 Miscellaneous Quality Control Measures.
Section | Quality control measure | Effect |
---|---|---|
8.1 | Sampling equipment leak-checks and calibration | Ensure accuracy and precision of sampling measurements. |
10.3 | Spectrophotometer calibration | Ensure linearity of spectrophotometer response to standards. |
9.2 Volume Metering System Checks. Same as Method 5, section 9.2.
10.0 Calibration and Standardization Note:Maintain a laboratory log of all calibrations.
10.1 Gas Bulb Calibration. Weigh the empty bulb to the nearest 0.1 g. Fill the bulb to the stopcock with water, and again weigh to the nearest 0.1 g. Subtract the tare weight, and calculate the volume in liters to three significant figures using the density of water at the measurement temperature. Record the volume on the bulb. Alternatively, mark an identification number on the bulb, and record the volume in a notebook.
10.2 Rate Meter Calibration. Assemble the system as shown in Figure 10A-1 (the impingers may be removed), and attach a volume meter to the probe inlet. Set the rotameter at 300 ml/min, record the volume meter reading, start the pump, and pull ambient air through the system for 10 minutes. Record the final volume meter reading. Repeat the procedure and average the results to determine the volume of gas that passed through the system.
10.3 Spectrophotometer Calibration Curve.
10.3.1 Collect the standards as described in section 8.2. Prepare at least two sets of three bulbs as standards to span the 0 to 400 or 400 to 1000 ppm range. If any samples span both concentration ranges, prepare a calibration curve for each range using separate reagent blanks. Prepare a set of three bulbs containing colorimetric reagent but no CO to serve as a reagent blank. Analyze each standard and blank according to the sample analysis procedure of section 11.0 Reject the standard set where any of the individual bulb absorbances differs from the set mean by more than 10 percent.
10.3.2 Calculate the average absorbance for each set (3 bulbs) of standards using Equation 10A-1 and Table 10A-1. Construct a graph of average absorbance for each standard against its corresponding concentration. Draw a smooth curve through the points. The curve should be linear over the two concentration ranges discussed in section 13.3.
11.0 Analytical Procedure11.1 Assemble the system shown in Figure 10A-3, and record the information required in Table 10A-1 as it is obtained. Pipet 10.0 ml of the colorimetric reagent into each gas reaction bulb, and attach the bulbs to the system. Open the stopcocks to the reaction bulbs, but leave the valve to the bag closed. Turn on the pump, fully open the coarse-adjust flow valve, and slowly open the fine-adjust valve until the pressure is reduced to at least 40 mm Hg. Now close the coarse adjust valve, and observe the manometer to be certain that the system is leak-free. Wait a minimum of 2 minutes. If the pressure has increased less than 1 mm Hg, proceed as described below. If a leak is present, find and correct it before proceeding further.
11.2 Record the vacuum pressure (Pv) to the nearest 1 mm Hg, and close the reaction bulb stopcocks. Open the bag valve, and allow the system to come to atmospheric pressure. Close the bag valve, open the pump coarse adjust valve, and evacuate the system again. Repeat this fill/evacuation procedure at least twice to flush the manifold completely. Close the pump coarse adjust valve, open the bag valve, and let the system fill to atmospheric pressure. Open the stopcocks to the reaction bulbs, and let the entire system come to atmospheric pressure. Close the bulb stopcocks, remove the bulbs, record the room temperature and barometric pressure (Pbar, to nearest mm Hg), and place the bulbs on the shaker table with their main axis either parallel to or perpendicular to the plane of the table top. Purge the bulb-filling system with ambient air for several minutes between samples. Shake the samples for exactly 2 hours.
11.3 Immediately after shaking, measure the absorbance (A) of each bulb sample at 425 nm if the concentration is less than or equal to 400 ppm CO or at 600 nm if the concentration is above 400 ppm.
Note:This may be accomplished with multiple bulb sets by sequentially collecting sets and adding to the shaker at staggered intervals, followed by sequentially removing sets from the shaker for absorbance measurement after the two-hour designated intervals have elapsed.
11.4 Use a small portion of the sample to rinse a spectrophotometer cell several times before taking an aliquot for analysis. If one cell is used to analyze multiple samples, rinse the cell with deionized distilled water several times between samples. Prepare and analyze standards and a reagent blank as described in section 10.3. Use water as the reference. Reject the analysis if the blank absorbance is greater than 0.1. All conditions should be the same for analysis of samples and standards. Measure the absorbances as soon as possible after shaking is completed.
11.5 Determine the CO concentration of each bag sample using the calibration curve for the appropriate concentration range as discussed in section 10.3.
12.0 Calculations and Data AnalysisCarry out calculations retaining at least one extra decimal figure beyond that of the acquired data. Round off figures after final calculation.
12.1 Nomenclature.
A = Sample absorbance, uncorrected for the reagent blank. Ar = Absorbance of the reagent blank. As = Average sample absorbance per liter, units/liter. Bw = Moisture content in the bag sample. C = CO concentration in the stack gas, dry basis, ppm. Cb = CO concentration of the bag sample, dry basis, ppm. Cg = CO concentration from the calibration curve, ppm. F = Volume fraction of CO2 in the stack. n = Number of reaction bulbs used per bag sample. Pb = Barometric pressure, mm Hg. Pv = Residual pressure in the sample bulb after evacuation, mm Hg. Pw = Vapor pressure of H2O in the bag (from Table 10A-2), mm Hg. Vb = Volume of the sample bulb, liters. Vr = Volume of reagent added to the sample bulb, 0.0100 liter.12.2 Average Sample Absorbance per Liter. Calculate As for each gas bulb using Equation 10A-1, and record the value in Table 10A-1. Calculate the average As for each bag sample, and compare the three values to the average. If any single value differs by more than 10 percent from the average, reject this value, and calculate a new average using the two remaining values.
Note:A and Ar must be at the same wavelength.
12.3 CO Concentration in the Bag. Calculate Cb using Equations 10A-2 and 10A-3. If condensate is visible in the bag, calculate Bw using Table 10A-2 and the temperature and barometric pressure in the analysis room. If condensate is not visible, calculate Bw using the temperature and barometric pressure at the sampling site.
12.4 CO Concentration in the Stack.
13.0 Method Performance13.1 Precision. The estimated intralaboratory standard deviation of the method is 3 percent of the mean for gas samples analyzed in duplicate in the concentration range of 39 to 412 ppm. The interlaboratory precision has not been established.
13.2 Accuracy. The method contains no significant biases when compared to an NDIR analyzer calibrated with NIST standards.
13.3 Range. Approximately 3 to 1800 ppm CO. Samples having concentrations below 400 ppm are analyzed at 425 nm, and samples having concentrations above 400 ppm are analyzed at 600 nm.
13.4 Sensitivity. The detection limit is 3 ppmv based on a change in concentration equal to three times the standard deviation of the reagent blank solution.
13.5 Stability. The individual components of the colorimetric reagent are stable for at least one month. The colorimetric reagent must be used within two days after preparation to avoid excessive blank correction. The samples in the bag should be stable for at least one week if the bags are leak-free.
14.0 Pollution Prevention [Reserved] 15.0 Waste Management [Reserved] 16.0 References1. Butler, F.E., J.E. Knoll, and M.R. Midgett. Development and Evaluation of Methods for Determining Carbon Monoxide Emissions. U.S. Environmental Protection Agency, Research Triangle Park, N.C. June 1985. 33 pp.
2. Ferguson, B.B., R.E. Lester, and W.J. Mitchell. Field Evaluation of Carbon Monoxide and Hydrogen Sulfide Continuous Emission Monitors at an Oil Refinery. U.S. Environmental Protection Agency, Research Triangle Park, N.C. Publication No. EPA-600/4-82-054. August 1982. 100 pp.
3. Lambert, J.L., and R.E. Weins. Induced Colorimetric Method for Carbon Monoxide. Analytical Chemistry. 46(7):929-930. June 1974.
4. Levaggi, D.A., and M. Feldstein. The Colorimetric Determination of Low Concentrations of Carbon Monoxide. Industrial Hygiene Journal. 25:64-66. January-February 1964.
5. Repp, M. Evaluation of Continuous Monitors For Carbon Monoxide in Stationary Sources. U.S. Environmental Protection Agency. Research Triangle Park, N.C. Publication No. EPA-600/2-77-063. March 1977. 155 pp.
6. Smith, F., D.E. Wagoner, and R.P. Donovan. Guidelines for Development of a Quality Assurance Program: Volume VIII - Determination of CO Emissions from Stationary Sources by NDIR Spectrometry. U.S. Environmental Protection Agency. Research Triangle Park, N.C. Publication No. EPA-650/4-74-005-h. February 1975. 96 pp.
17.0 Tables, Diagrams, Flowcharts, and Validation DataTable 10A-1 - Data Recording Sheet for Samples Analyzed in Triplicate
Sample No./type |
Room temp °C |
Stack %CO2 |
Bulb No. |
Bulb vol. liters |
Reagent vol. in bulb, liter |
Partial pressure of gas in bulb, mm Hg |
Pb, mm Hg |
Shaking time, min |
Abs versus water |
A-Ar | As | Avg As |
---|---|---|---|---|---|---|---|---|---|---|---|---|
blank | ||||||||||||
Std. 1 | ||||||||||||
Std. 2 | ||||||||||||
Sample 1 | ||||||||||||
Sample 2 | ||||||||||||
Sample 3 |
Table 10A-2 - Moisture Correction
Temperature °C | Vapor pressure of H2O, mm Hg |
Temperature °C | Vapor pressure of H2, mm Hg |
---|---|---|---|
4 | 6.1 | 18 | 15.5 |
6 | 7.0 | 20 | 17.5 |
8 | 8.0 | 22 | 19.8 |
10 | 9.2 | 24 | 22.4 |
12 | 10.5 | 26 | 25.2 |
14 | 12.0 | 28 | 28.3 |
16 | 13.6 | 30 | 31.8 |
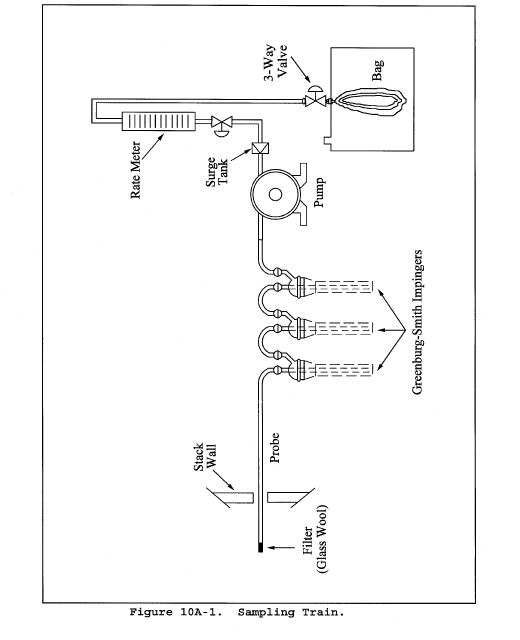
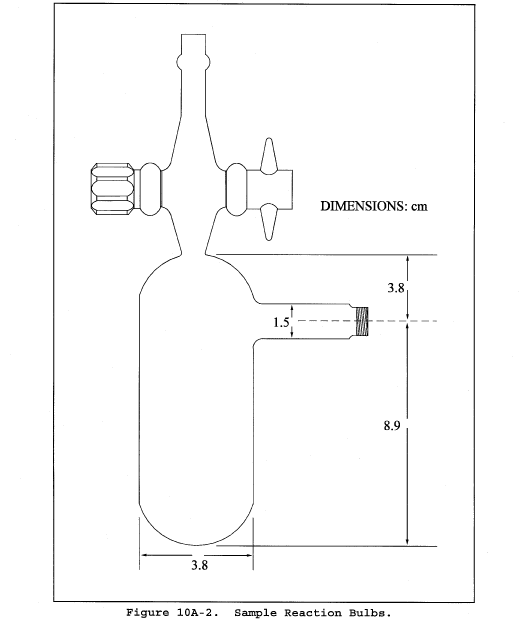
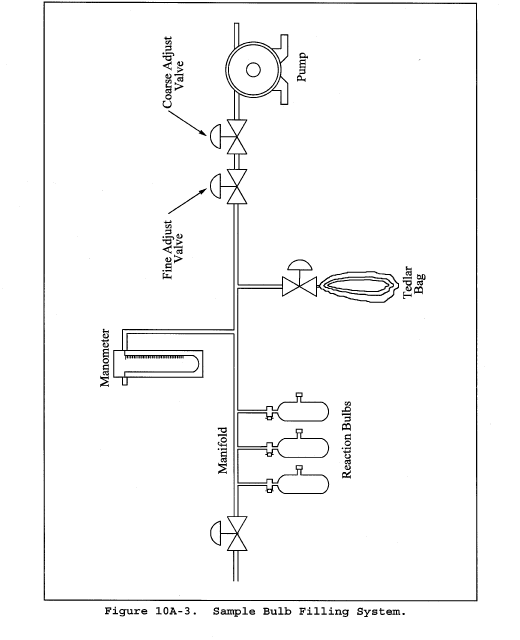
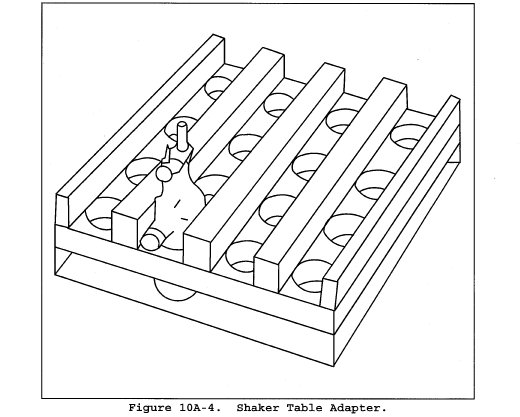
This method is not inclusive with respect to specifications (e.g., equipment and supplies) and procedures (e.g., sampling and analytical) essential to its performance. Some material is incorporated by reference from other methods in this part. Therefore, to obtain reliable results, persons using this method should have a thorough knowledge of at least the following additional test methods: Method 1, Method 4, Method 10A, and Method 25.
1.0 Scope and Application1.1 Analytes.
Analyte | CAS No. | Sensitivity |
---|---|---|
Carbon monoxide (CO) | 630-08-0 | Not determined. |
1.2 Applicability. This method applies to the measurement of CO emissions at petroleum refineries and from other sources when specified in an applicable subpart of the regulations.
1.3 Data Quality Objectives. Adherence to the requirements of this method will enhance the quality of the data obtained from air pollutant sampling methods.
2.0 Summary of Method2.1 An integrated gas sample is extracted from the sampling point, passed through a conditioning system to remove interferences, and collected in a Tedlar or equivalent bag. (Verify through the manufacturer that the Tedlar alternative is suitable for NO and make this verifying information available for inspection.) The CO is separated from the sample by gas chromatography (GC) and catalytically reduced to methane (CH4) which is determined by flame ionization detection (FID). The analytical portion of this method is identical to applicable sections in Method 25 detailing CO measurement.
3.0 Definitions [Reserved] 4.0 Interferences4.1 Carbon dioxide (CO2) and organics potentially can interfere with the analysis. Most of the CO2 is removed from the sample by the alkaline permanganate conditioning system; any residual CO2 and organics are separated from the CO by GC.
5.0 Safety5.1 Disclaimer. This method may involve hazardous materials, operations, and equipment. This test method may not address all of the safety problems associated with its use. It is the responsibility of the user of this test method to establish appropriate safety and health practices and determine the applicability of regulatory limitations prior to performing this test method. The analyzer users manual should be consulted for specific precautions concerning the analytical procedure.
6.0 Equipment and Supplies6.1 Sample Collection. Same as in Method 10A, section 6.1 (paragraphs 6.1.1 through 6.1.11).
6.2 Sample Analysis. A GC/FID analyzer, capable of quantifying CO in the sample and consisting of at least the following major components, is required for sample analysis. [Alternatively, complete Method 25 analytical systems (Method 25, section 6.3) are acceptable alternatives when calibrated for CO and operated in accordance with the Method 25 analytical procedures (Method 25, section 11.0).]
6.2.1 Separation Column. A column capable of separating CO from CO2 and organic compounds that may be present. A 3.2-mm ( 1/8-in.) OD stainless steel column packed with 1.7 m (5.5 ft.) of 60/80 mesh Carbosieve S-II (available from Supelco) has been used successfully for this purpose.
6.2.2 Reduction Catalyst. Same as in Method 25, section 6.3.1.2.
6.2.3 Sample Injection System. Same as in Method 25, Section 6.3.1.4, equipped to accept a sample line from the bag.
6.2.4 Flame Ionization Detector. Meeting the linearity specifications of section 10.3 and having a minimal instrument range of 10 to 1,000 ppm CO.
6.2.5 Data Recording System. Analog strip chart recorder or digital integration system, compatible with the FID, for permanently recording the analytical results.
7.0 Reagents and Standards7.1 Sample Collection. Same as in Method 10A, section 7.1.
7.2 Sample Analysis.
7.2.1 Carrier, Fuel, and Combustion Gases. Same as in Method 25, sections 7.2.1, 7.2.2, and 7.2.3, respectively.
7.2.2 Calibration Gases. Three standard gases with nominal CO concentrations of 20, 200, and 1,000 ppm CO in nitrogen. The calibration gases shall be certified by the manufacturer to be ±2 percent of the specified concentrations.
7.2.3 Reduction Catalyst Efficiency Check Calibration Gas. Standard CH4 gas with a nominal concentration of 1,000 ppm in air.
8.0 Sample Collection, Preservation, Storage, and TransportSame as in Method 10A, section 8.0.
9.0 Quality ControlSection | Quality control measure | Effect |
---|---|---|
8.0 | Sample bag/sampling system leak-checks | Ensures that negative bias introduced through leakage is minimized. |
10.1 | Carrier gas blank check | Ensures that positive bias introduced by contamination of carrier gas is less than 5 ppmv. |
10.2 | Reduction catalyst efficiency check | Ensures that negative bias introduced by inefficient reduction catalyst is less than 5 percent. |
10.3 | Analyzer calibration | Ensures linearity of analyzer response to standards. |
11.2 | Triplicate sample analyses | Ensures precision of analytical results. |
10.1 Carrier Gas Blank Check. Analyze each new tank of carrier gas with the GC analyzer according to section 11.2 to check for contamination. The corresponding concentration must be less than 5 ppm for the tank to be acceptable for use.
10.2 Reduction Catalyst Efficiency Check. Prior to initial use, the reduction catalyst shall be tested for reduction efficiency. With the heated reduction catalyst bypassed, make triplicate injections of the 1,000 ppm CH4 gas (Section 7.2.3) to calibrate the analyzer. Repeat the procedure using 1,000 ppm CO gas (Section 7.2.2) with the catalyst in operation. The reduction catalyst operation is acceptable if the CO response is within 5 percent of the certified gas value.
10.3 Analyzer Calibration. Perform this test before the system is first placed into operation. With the reduction catalyst in operation, conduct a linearity check of the analyzer using the standards specified in section 7.2.2. Make triplicate injections of each calibration gas, and then calculate the average response factor (area/ppm) for each gas, as well as the overall mean of the response factor values. The instrument linearity is acceptable if the average response factor of each calibration gas is within 2.5 percent of the overall mean value and if the relative standard deviation (calculated in section 12.8 of Method 25) for each set of triplicate injections is less than 2 percent. Record the overall mean of the response factor values as the calibration response factor (R).
11.0 Analytical Procedure11.1 Preparation for Analysis. Before putting the GC analyzer into routine operation, conduct the calibration procedures listed in section 10.0. Establish an appropriate carrier flow rate and detector temperature for the specific instrument used.
11.2 Sample Analysis. Purge the sample loop with sample, and then inject the sample. Analyze each sample in triplicate, and calculate the average sample area (A). Determine the bag CO concentration according to section 12.2.
12.0 Calculations and Data AnalysisCarry out calculations retaining at least one extra significant figure beyond that of the acquired data. Round off results only after the final calculation.
12.1 Nomenclature.
A = Average sample area. Bw = Moisture content in the bag sample, fraction. C = CO concentration in the stack gas, dry basis, ppm. Cb = CO concentration in the bag sample, dry basis, ppm. F = Volume fraction of CO2 in the stack, fraction. Pbar = Barometric pressure, mm Hg. Pw = Vapor pressure of the H2O in the bag (from Table 10A-2, Method 10A), mm Hg. R = Mean calibration response factor, area/ppm.12.2 CO Concentration in the Bag. Calculate Cb using Equations 10B-1 and 10B-2. If condensate is visible in the bag, calculate Bw using Table 10A-2 of Method 10A and the temperature and barometric pressure in the analysis room. If condensate is not visible, calculate Bw using the temperature and barometric pressure at the sampling site.
12.3 CO Concentration in the Stack
13.0 Method Performance [Reserved] 14.0 Pollution Prevention [Reserved] 15.0 Waste Management [Reserved] 16.0 ReferencesSame as in Method 25, section 16.0, with the addition of the following:
1. Butler, F.E, J.E. Knoll, and M.R. Midgett. Development and Evaluation of Methods for Determining Carbon Monoxide Emissions. Quality Assurance Division, Environmental Monitoring Systems Laboratory, U.S. Environmental Protection Agency, Research Triangle Park, NC. June 1985. 33 pp.
17.0 Tables, Diagrams, Flowcharts, and Validation Data [Reserved] [36 FR 24877, Dec. 23, 1971] Editorial Note:For Federal Register citations affecting appendix A-4 to part 60, see the List of CFR sections Affected, which appears in the Finding Aids section of the printed volume and at www.govinfo.gov.Appendix A-5 to Part 60 - Test Methods 11 through 15A
40:9.0.1.1.1.0.1.1.5 : Appendix A
Appendix A-5 to Part 60 - Test Methods 11 through 15A Method 11 - Determination of hydrogen sulfide content of fuel gas streams in petroleum refineries Method 12 - Determination of inorganic lead emissions from stationary sources Method 13A - Determination of total fluoride emissions from stationary sources - SPADNS zirconium lake method Method 13B - Determination of total fluoride emissions from stationary sources - Specific ion electrode method Method 14 - Determination of fluoride emissions from potroom roof monitors for primary aluminum plants Method 14A - Determination of Total Fluoride Emissions from Selected Sources at Primary Aluminum Production Facilities Method 15 - Determination of hydrogen sulfide, carbonyl sulfide, and carbon disulfide emissions from stationary sources Method 15A - Determination of total reduced sulfur emissions from sulfur recovery plants in petroleum refineriesThe test methods in this appendix are referred to in § 60.8 (Performance Tests) and § 60.11 (Compliance With Standards and Maintenance Requirements) of 40 CFR part 60, subpart A (General Provisions). Specific uses of these test methods are described in the standards of performance contained in the subparts, beginning with Subpart D.
Within each standard of performance, a section title “Test Methods and Procedures” is provided to: (1) Identify the test methods to be used as reference methods to the facility subject to the respective standard and (2) identify any special instructions or conditions to be followed when applying a method to the respective facility. Such instructions (for example, establish sampling rates, volumes, or temperatures) are to be used either in addition to, or as a substitute for procedures in a test method. Similarly, for sources subject to emission monitoring requirements, specific instructions pertaining to any use of a test method as a reference method are provided in the subpart or in Appendix B.
Inclusion of methods in this appendix is not intended as an endorsement or denial of their applicability to sources that are not subject to standards of performance. The methods are potentially applicable to other sources; however, applicability should be confirmed by careful and appropriate evaluation of the conditions prevalent at such sources.
The approach followed in the formulation of the test methods involves specifications for equipment, procedures, and performance. In concept, a performance specification approach would be preferable in all methods because this allows the greatest flexibility to the user. In practice, however, this approach is impractical in most cases because performance specifications cannot be established. Most of the methods described herein, therefore, involve specific equipment specifications and procedures, and only a few methods in this appendix rely on performance criteria.
Minor changes in the test methods should not necessarily affect the validity of the results and it is recognized that alternative and equivalent methods exist. section 60.8 provides authority for the Administrator to specify or approve (1) equivalent methods, (2) alternative methods, and (3) minor changes in the methodology of the test methods. It should be clearly understood that unless otherwise identified all such methods and changes must have prior approval of the Administrator. An owner employing such methods or deviations from the test methods without obtaining prior approval does so at the risk of subsequent disapproval and retesting with approved methods.
Within the test methods, certain specific equipment or procedures are recognized as being acceptable or potentially acceptable and are specifically identified in the methods. The items identified as acceptable options may be used without approval but must be identified in the test report. The potentially approvable options are cited as “subject to the approval of the Administrator” or as “or equivalent.” Such potentially approvable techniques or alternatives may be used at the discretion of the owner without prior approval. However, detailed descriptions for applying these potentially approvable techniques or alternatives are not provided in the test methods. Also, the potentially approvable options are not necessarily acceptable in all applications. Therefore, an owner electing to use such potentially approvable techniques or alternatives is responsible for: (1) assuring that the techniques or alternatives are in fact applicable and are properly executed; (2) including a written description of the alternative method in the test report (the written method must be clear and must be capable of being performed without additional instruction, and the degree of detail should be similar to the detail contained in the test methods); and (3) providing any rationale or supporting data necessary to show the validity of the alternative in the particular application. Failure to meet these requirements can result in the Administrator's disapproval of the alternative.
Method 11 - Determination of Hydrogen Sulfide Content of Fuel Gas Streams in Petroleum Refineries 1.0 Scope and Application1.1 Analytes.
Analyte | CAS No. | Sensitivity |
---|---|---|
Hydrogen sulfide (H2S) | 7783-06-4 | 8 mg/m 3 - 740 mg/m 3, (6 ppm - 520 ppm). |
1.2 Applicability. This method is applicable for the determination of the H2S content of fuel gas streams at petroleum refineries.
1.3 Data Quality Objectives. Adherence to the requirements of this method will enhance the quality of the data obtained from air pollutant sampling methods.
2.0 Summary of Method2.1 A sample is extracted from a source and passed through a series of midget impingers containing a cadmium sulfate (CdSO4) solution; H2S is absorbed, forming cadmium sulfide (CdS). The latter compound is then measured iodometrically.
3.0 Definitions [Reserved] 4.0 Interferences4.1 Any compound that reduces iodine (I2) or oxidizes the iodide ion will interfere in this procedure, provided it is collected in the CdSO4 impingers. Sulfur dioxide in concentrations of up to 2,600 mg/m 3 is removed with an impinger containing a hydrogen peroxide (H2O2) solution. Thiols precipitate with H2S. In the absence of H2S, only traces of thiols are collected. When methane-and ethane-thiols at a total level of 300 mg/m 3 are present in addition to H2S, the results vary from 2 percent low at an H2S concentration of 400 mg/m 3 to 14 percent high at an H2S concentration of 100 mg/m 3. Carbonyl sulfide at a concentration of 20 percent does not interfere. Certain carbonyl-containing compounds react with iodine and produce recurring end points. However, acetaldehyde and acetone at concentrations of 1 and 3 percent, respectively, do not interfere.
4.2 Entrained H2O2 produces a negative interference equivalent to 100 percent of that of an equimolar quantity of H2S. Avoid the ejection of H2O2 into the CdSO4 impingers.
5.0 Safety5.1 Disclaimer. This method may involve hazardous materials, operations, and equipment. This test method may not address all of the safety problems associated with its use. It is the responsibility of the user of this test method to establish appropriate safety and health practices and determine the applicability of regulatory limitations prior to performing this test method.
5.2 Corrosive reagents. The following reagents are hazardous. Personal protective equipment and safe procedures are useful in preventing chemical splashes. If contact occurs, immediately flush with copious amounts of water for at least 15 minutes. Remove clothing under shower and decontaminate. Treat residual chemical burns as thermal burns.
5.2.1 Hydrogen Peroxide. Irritating to eyes, skin, nose, and lungs. 30% H2O2 is a strong oxidizing agent. Avoid contact with skin, eyes, and combustible material. Wear gloves when handling.
5.2.2 Hydrochloric Acid. Highly toxic. Vapors are highly irritating to eyes, skin, nose, and lungs, causing severe damage. May cause bronchitis, pneumonia, or edema of lungs. Exposure to concentrations of 0.13 to 0.2 percent can be lethal in minutes. Will react with metals, producing hydrogen.
6.0 Equipment and Supplies6.1 Sample Collection. The following items are needed for sample collection:
6.1.1 Sampling Line. Teflon tubing, 6- to 7- mm ( 1/4-in.) ID, to connect the sampling train to the sampling valve.
6.1.2 Impingers. Five midget impingers, each with 30-ml capacity. The internal diameter of the impinger tip must be 1 mm ±0.05 mm. The impinger tip must be positioned 4 to 6 mm from the bottom of the impinger.
6.1.3 Tubing. Glass or Teflon connecting tubing for the impingers.
6.1.4 Ice Water Bath. To maintain absorbing solution at a low temperature.
6.1.5 Drying Tube. Tube packed with 6- to 16- mesh indicating-type silica gel, or equivalent, to dry the gas sample and protect the meter and pump. If the silica gel has been used previously, dry at 175 °C (350 °F) for 2 hours. New silica gel may be used as received. Alternatively, other types of desiccants (equivalent or better) may be used, subject to approval of the Administrator.
Note:Do not use more than 30 g of silica gel. Silica gel adsorbs gases such as propane from the fuel gas stream, and use of excessive amounts of silica gel could result in errors in the determination of sample volume.
6.1.6 Sampling Valve. Needle valve, or equivalent, to adjust gas flow rate. Stainless steel or other corrosion-resistant material.
6.1.7 Volume Meter. Dry gas meter (DGM), sufficiently accurate to measure the sample volume within 2 percent, calibrated at the selected flow rate (about 1.0 liter/min) and conditions actually encountered during sampling. The meter shall be equipped with a temperature sensor (dial thermometer or equivalent) capable of measuring temperature to within 3 °C (5.4 °F). The gas meter should have a petcock, or equivalent, on the outlet connector which can be closed during the leak-check. Gas volume for one revolution of the meter must not be more than 10 liters.
6.1.8 Rate Meter. Rotameter, or equivalent, to measure flow rates in the range from 0.5 to 2 liters/min (1 to 4 ft 3/hr).
6.1.9 Graduated Cylinder. 25-ml size.
6.1.10 Barometer. Mercury, aneroid, or other barometer capable of measuring atmospheric pressure to within 2.5 mm Hg (0.1 in. Hg). In many cases, the barometric reading may be obtained from a nearby National Weather Service station, in which case, the station value (which is the absolute barometric pressure) shall be requested and an adjustment for elevation differences between the weather station and the sampling point shall be applied at a rate of minus 2.5 mm Hg (0.1 in Hg) per 30 m (100 ft) elevation increase or vice-versa for elevation decrease.
6.1.11 U-tube Manometer. 0-; to 30-cm water column, for leak-check procedure.
6.1.12 Rubber Squeeze Bulb. To pressurize train for leak-check.
6.1.13 Tee, Pinchclamp, and Connecting Tubing. For leak-check.
6.1.14 Pump. Diaphragm pump, or equivalent. Insert a small surge tank between the pump and rate meter to minimize the pulsation effect of the diaphragm pump on the rate meter. The pump is used for the air purge at the end of the sample run; the pump is not ordinarily used during sampling, because fuel gas streams are usually sufficiently pressurized to force sample gas through the train at the required flow rate. The pump need not be leak-free unless it is used for sampling.
6.1.15 Needle Valve or Critical Orifice. To set air purge flow to 1 liter/min.
6.1.16 Tube Packed with Active Carbon. To filter air during purge.
6.1.17 Volumetric Flask. One 1000-ml.
6.1.18 Volumetric Pipette. One 15-ml.
6.1.19 Pressure-Reduction Regulator. Depending on the sampling stream pressure, a pressure-reduction regulator may be needed to reduce the pressure of the gas stream entering the Teflon sample line to a safe level.
6.1.20 Cold Trap. If condensed water or amine is present in the sample stream, a corrosion-resistant cold trap shall be used immediately after the sample tap. The trap shall not be operated below 0 °C (32 °F) to avoid condensation of C3 or C4 hydrocarbons.
6.2 Sample Recovery. The following items are needed for sample recovery:
6.2.1 Sample Container. Iodine flask, glass-stoppered, 500-ml size.
6.2.2 Volumetric Pipette. One 50-ml.
6.2.3 Graduated Cylinders. One each 25- and 250-ml.
6.2.4 Erlenmeyer Flasks. 125-ml.
6.2.5 Wash Bottle.
6.2.6 Volumetric Flasks. Three 1000-ml.
6.3 Sample Analysis. The following items are needed for sample analysis:
6.3.1 Flask. Glass-stoppered iodine flask, 500-ml.
6.3.2 Burette. 50-ml.
6.3.3 Erlenmeyer Flask. 125-ml.
6.3.4 Volumetric Pipettes. One 25-ml; two each 50- and 100-ml.
6.3.5 Volumetric Flasks. One 1000-ml; two 500-ml.
6.3.6 Graduated Cylinders. One each 10- and 100-ml.
7.0 Reagents and Standards Note:Unless otherwise indicated, it is intended that all reagents conform to the specifications established by the Committee on Analytical Reagents of the American Chemical Society, where such specifications are available. Otherwise, use the best available grade.
7.1 Sample Collection. The following reagents are required for sample collection:
7.1.1 CdSO4 Absorbing Solution. Dissolve 41 g of 3CdSO48H2O and 15 ml of 0.1 M sulfuric acid in a 1-liter volumetric flask that contains approximately 3/4 liter of water. Dilute to volume with deionized, distilled water. Mix thoroughly. The pH should be 3 ±0.1. Add 10 drops of Dow-Corning Antifoam B. Shake well before use. This solution is stable for at least one month. If Antifoam B is not used, a more labor-intensive sample recovery procedure is required (see section 11.2).
7.1.2 Hydrogen Peroxide, 3 Percent. Dilute 30 percent H2O2 to 3 percent as needed. Prepare fresh daily.
7.1.3 Water. Deionized distilled to conform to ASTM D 1193-77 or 91, Type 3 (incorporated by reference - see § 60.17). The KMnO4 test for oxidizable organic matter may be omitted when high concentrations of organic matter are not expected to be present.
7.2 Sample Recovery. The following reagents are needed for sample recovery:
7.2.1 Water. Same as section 7.1.3.
7.2.2 Hydrochloric Acid (HCl) Solution, 3 M. Add 240 ml of concentrated HCl (specific gravity 1.19) to 500 ml of water in a 1-liter volumetric flask. Dilute to 1 liter with water. Mix thoroughly.
7.2.3 Iodine (I2) Solution, 0.1 N. Dissolve 24 g of potassium iodide (KI) in 30 ml of water. Add 12.7 g of resublimed iodine (I2) to the KI solution. Shake the mixture until the I2 is completely dissolved. If possible, let the solution stand overnight in the dark. Slowly dilute the solution to 1 liter with water, with swirling. Filter the solution if it is cloudy. Store solution in a brown-glass reagent bottle.
7.2.4 Standard I2 Solution, 0.01 N. Pipette 100.0 ml of the 0.1 N iodine solution into a 1-liter volumetric flask, and dilute to volume with water. Standardize daily as in section 10.2.1. This solution must be protected from light. Reagent bottles and flasks must be kept tightly stoppered.
7.3 Sample Analysis. The following reagents and standards are needed for sample analysis:
7.3.1 Water. Same as in section 7.1.3.
7.3.2 Standard Sodium Thiosulfate Solution, 0.1 N. Dissolve 24.8 g of sodium thiosulfate pentahydrate (Na2S2O3·5H2O) or 15.8 g of anhydrous sodium thiosulfate (Na2S2O3) in 1 liter of water, and add 0.01 g of anhydrous sodium carbonate (Na2CO3) and 0.4 ml of chloroform (CHCl3) to stabilize. Mix thoroughly by shaking or by aerating with nitrogen for approximately 15 minutes, and store in a glass-stoppered, reagent bottle. Standardize as in section 10.2.2.
7.3.3 Standard Sodium Thiosulfate Solution, 0.01 N. Pipette 50.0 ml of the standard 0.1 N Na2S2O3 solution into a volumetric flask, and dilute to 500 ml with water.
Note:A 0.01 N phenylarsine oxide (C6H5AsO) solution may be prepared instead of 0.01 N Na2S2O3 (see section 7.3.4).
7.3.4 Standard Phenylarsine Oxide Solution, 0.01 N. Dissolve 1.80 g of (C6H5AsO) in 150 ml of 0.3 N sodium hydroxide. After settling, decant 140 ml of this solution into 800 ml of water. Bring the solution to pH 6-7 with 6 N HCl, and dilute to 1 liter with water. Standardize as in section 10.2.3.
7.3.5 Starch Indicator Solution. Suspend 10 g of soluble starch in 100 ml of water, and add 15 g of potassium hydroxide (KOH) pellets. Stir until dissolved, dilute with 900 ml of water, and let stand for 1 hour. Neutralize the alkali with concentrated HCl, using an indicator paper similar to Alkacid test ribbon, then add 2 ml of glacial acetic acid as a preservative.
Note:Test starch indicator solution for decomposition by titrating with 0.01 N I2 solution, 4 ml of starch solution in 200 ml of water that contains 1 g of KI. If more than 4 drops of the 0.01 N I2 solution are required to obtain the blue color, a fresh solution must be prepared.
8.0 Sample Collection, Preservation, Storage, and Transport8.1 Sampling Train Preparation. Assemble the sampling train as shown in Figure 11-1, connecting the five midget impingers in series. Place 15 ml of 3 percent H2O2 solution in the first impinger. Leave the second impinger empty. Place 15 ml of the CdSO4 solution in the third, fourth, and fifth impingers. Place the impinger assembly in an ice water bath container, and place water and crushed ice around the impingers. Add more ice during the run, if needed.
8.2 Leak-Check Procedure.
8.2.1 Connect the rubber bulb and manometer to the first impinger, as shown in Figure 11-1. Close the petcock on the DGM outlet. Pressurize the train to 25 cm water with the bulb, and close off the tubing connected to the rubber bulb. The train must hold 25 cm water pressure with not more than a 1 cm drop in pressure in a 1-minute interval. Stopcock grease is acceptable for sealing ground glass joints.
8.2.2 If the pump is used for sampling, it is recommended, but not required, that the pump be leak-checked separately, either prior to or after the sampling run. To leak-check the pump, proceed as follows: Disconnect the drying tube from the impinger assembly. Place a vacuum gauge at the inlet to either the drying tube or the pump, pull a vacuum of 250 mm Hg (10 in. Hg), plug or pinch off the outlet of the flow meter, and then turn off the pump. The vacuum should remain stable for at least 30 seconds. If performed prior to the sampling run, the pump leak-check should precede the leak-check of the sampling train described immediately above; if performed after the sampling run, the pump leak-check should follow the sampling train leak-check.
8.3 Purge the connecting line between the sampling valve and the first impinger by disconnecting the line from the first impinger, opening the sampling valve, and allowing process gas to flow through the line for one to two minutes. Then, close the sampling valve, and reconnect the line to the impinger train. Open the petcock on the dry gas meter outlet. Record the initial DGM reading.
8.4 Open the sampling valve, and then adjust the valve to obtain a rate of approximately 1 liter/min (0.035 cfm). Maintain a constant (±10 percent) flow rate during the test. Record the DGM temperature.
8.5 Sample for at least 10 minutes. At the end of the sampling time, close the sampling valve, and record the final volume and temperature readings. Conduct a leak-check as described in Section 8.2. A yellow color in the final cadmium sulfate impinger indicates depletion of the absorbing solution. An additional cadmium sulfate impinger should be added for subsequent samples and the sample with yellow color in the final impinger should be voided.
8.6 Disconnect the impinger train from the sampling line. Connect the charcoal tube and the pump as shown in Figure 11-1. Purge the train [at a rate of 1 liter/min (0.035 ft 3/min)] with clean ambient air for 15 minutes to ensure that all H2S is removed from the H2O2. For sample recovery, cap the open ends, and remove the impinger train to a clean area that is away from sources of heat. The area should be well lighted, but not exposed to direct sunlight.
8.7 Sample Recovery.
8.7.1 Discard the contents of the H2O2 impinger. Carefully rinse with water the contents of the third, fourth, and fifth impingers into a 500-ml iodine flask.
Note:The impingers normally have only a thin film of CdS remaining after a water rinse. If Antifoam B was not used or if significant quantities of yellow CdS remain in the impingers, the alternative recovery procedure in section 11.2 must be used.
8.7.2 Proceed to section 11 for the analysis.
9.0 Quality ControlSection | Quality control measure | Effect |
---|---|---|
8.2, 10.1 | Sampling equipment leak-check and calibration | Ensure accurate measurement of sample volume. |
11.2 | Replicate titrations of blanks | Ensure precision of titration determinations. |
Maintain a log of all calibrations.
10.1 Calibration. Calibrate the sample collection equipment as follows.
10.1.1 Dry Gas Meter.
10.1.1.1 Initial Calibration. The DGM shall be calibrated before its initial use in the field. Proceed as follows: First, assemble the following components in series: Drying tube, needle valve, pump, rotameter, and DGM. Then, leak-check the metering system as follows: Place a vacuum gauge (at least 760 mm Hg) at the inlet to the drying tube, and pull a vacuum of 250 mm Hg (10 in. Hg); plug or pinch off the outlet of the flow meter, and then turn off the pump. The vacuum shall remain stable for at least 30 seconds. Carefully release the vacuum gauge before releasing the flow meter end. Next, calibrate the DGM (at the sampling flow rate specified by the method) as follows: Connect an appropriately sized wet-test meter (e.g., 1 liter per revolution) to the inlet of the drying tube. Make three independent calibration runs, using at least five revolutions of the DGM per run. Calculate the calibration factor, Y (wet-test meter calibration volume divided by the DGM volume, both volumes adjusted to the same reference temperature and pressure), for each run, and average the results. If any Y value deviates by more than 2 percent from the average, the DGM is unacceptable for use. Otherwise, use the average as the calibration factor for subsequent test runs.
10.1.1.2 Post-Test Calibration Check. After each field test series, conduct a calibration check as in section 10.1.1.1, above, except for the following two variations: (a) three or more revolutions of the DGM may be used and (b) only two independent runs need be made. If the calibration factor does not deviate by more than 5 percent from the initial calibration factor (determined in section 10.1.1.1), then the DGM volumes obtained during the test series are acceptable. If the calibration factor deviates by more than 5 percent, recalibrate the DGM as in section 10.1.1.1, and for the calculations, use the calibration factor (initial or recalibration) that yields the lower gas volume for each test run.
10.1.2 Temperature Sensors. Calibrate against mercury-in-glass thermometers. An alternative mercury-free thermometer may be used if the thermometer is at a minimum equivalent in terms of performance or suitably effective for the specific temperature measurement application.
10.1.3 Rate Meter. The rate meter need not be calibrated, but should be cleaned and maintained according to the manufacturer's instructions.
10.1.4 Barometer. Calibrate against a mercury barometer.
10.2 Standardization.
10.2.1 Iodine Solution Standardization. Standardize the 0.01 N I2 solution daily as follows: Pipette 25 ml of the I2 solution into a 125-ml Erlenmeyer flask. Add 2 ml of 3 M HCl. Titrate rapidly with standard 0.01 N Na2S2O3 solution or with 0.01 N C6H5AsO until the solution is light yellow, using gentle mixing. Add four drops of starch indicator solution, and continue titrating slowly until the blue color just disappears. Record the volume of Na2S2O3 solution used, VSI, or the volume of C6H5AsO solution used, VAI, in ml. Repeat until replicate values agree within 0.05 ml. Average the replicate titration values which agree within 0.05 ml, and calculate the exact normality of the I2 solution using Equation 11-3. Repeat the standardization daily.
10.2.2 Sodium Thiosulfate Solution Standardization. Standardize the 0.1 N Na2S2O3 solution as follows: Oven-dry potassium dichromate (K2Cr2O7) at 180 to 200 °C (360 to 390 °F). To the nearest milligram, weigh 2 g of the dichromate (W). Transfer the dichromate to a 500-ml volumetric flask, dissolve in water, and dilute to exactly 500 ml. In a 500-ml iodine flask, dissolve approximately 3 g of KI in 45 ml of water, then add 10 ml of 3 M HCl solution. Pipette 50 ml of the dichromate solution into this mixture. Gently swirl the contents of the flask once, and allow it to stand in the dark for 5 minutes. Dilute the solution with 100 to 200 ml of water, washing down the sides of the flask with part of the water. Titrate with 0.1 N Na2S2O3 until the solution is light yellow. Add 4 ml of starch indicator and continue titrating slowly to a green end point. Record the volume of Na2S2O3 solution used, VS, in ml. Repeat until replicate values agree within 0.05 ml. Calculate the normality using Equation 11-1. Repeat the standardization each week or after each test series, whichever time is shorter.
10.2.3 Phenylarsine Oxide Solution Standardization. Standardize the 0.01 N C6H5AsO (if applicable) as follows: Oven-dry K2Cr2O7 at 180 to 200 °C (360 to 390 °F). To the nearest milligram, weigh 2 g of the dichromate (W). Transfer the dichromate to a 500-ml volumetric flask, dissolve in water, and dilute to exactly 500 ml. In a 500-ml iodine flask, dissolve approximately 0.3 g of KI in 45 ml of water, then add 10 ml of 3 M HCl. Pipette 5 ml of the dichromate solution into the iodine flask. Gently swirl the contents of the flask once, and allow it to stand in the dark for 5 minutes. Dilute the solution with 100 to 200 ml of water, washing down the sides of the flask with part of the water. Titrate with 0.01 N C6H5AsO until the solution is light yellow. Add 4 ml of starch indicator, and continue titrating slowly to a green end point. Record the volume of C6H5AsO used, VA, in ml. Repeat until replicate analyses agree within 0.05 ml. Calculate the normality using Equation 11-2. Repeat the standardization each week or after each test series, whichever time is shorter.
11.0 Analytical ProcedureConduct the titration analyses in a clean area away from direct sunlight.
11.1 Pipette exactly 50 ml of 0.01 N I2 solution into a 125-ml Erlenmeyer flask. Add 10 ml of 3 M HCl to the solution. Quantitatively rinse the acidified I2 into the iodine flask. Stopper the flask immediately, and shake briefly.
11.2 Use these alternative procedures if Antifoam B was not used or if significant quantities of yellow CdS remain in the impingers. Extract the remaining CdS from the third, fourth, and fifth impingers using the acidified I2 solution. Immediately after pouring the acidified I2 into an impinger, stopper it and shake for a few moments, then transfer the liquid to the iodine flask. Do not transfer any rinse portion from one impinger to another; transfer it directly to the iodine flask. Once the acidified I2 solution has been poured into any glassware containing CdS, the container must be tightly stoppered at all times except when adding more solution, and this must be done as quickly and carefully as possible. After adding any acidified I2 solution to the iodine flask, allow a few minutes for absorption of the H2S before adding any further rinses. Repeat the I2 extraction until all CdS is removed from the impingers. Extract that part of the connecting glassware that contains visible CdS. Quantitatively rinse all the I2 from the impingers, connectors, and the beaker into the iodine flask using water. Stopper the flask and shake briefly.
11.3 Allow the iodine flask to stand about 30 minutes in the dark for absorption of the H2S into the I2, then complete the titration analysis as outlined in sections 11.5 and 11.6.
Note:Iodine evaporates from acidified I2 solutions. Samples to which acidified I2 has been added may not be stored, but must be analyzed in the time schedule stated above.
11.4 Prepare a blank by adding 45 ml of CdSO4 absorbing solution to an iodine flask. Pipette exactly 50 ml of 0.01 N I2 solution into a 125-ml Erlenmeyer flask. Add 10 ml of 3 M HCl. Stopper the flask, shake briefly, let stand 30 minutes in the dark, and titrate with the samples.
Note:The blank must be handled by exactly the same procedure as that used for the samples.
11.5 Using 0.01 N Na2S2O3 solution (or 0.01 N C6H5AsO, if applicable), rapidly titrate each sample in an iodine flask using gentle mixing, until solution is light yellow. Add 4 ml of starch indicator solution, and continue titrating slowly until the blue color just disappears. Record the volume of Na2S2O3 solution used, VTT, or the volume of C6H5AsO solution used, VAT, in ml.
11.6 Titrate the blanks in the same manner as the samples. Run blanks each day until replicate values agree within 0.05 ml. Average the replicate titration values which agree within 0.05 ml.
12.0 Data Analysis and CalculationsCarry out calculations, retaining at least one extra significant figure beyond that of the acquired data. Round off figures only after the final calculation.
12.1 Nomenclature.
CH2S = Concentration of H2S at standard conditions, mg/dscm. NA = Normality of standard C6H5AsO solution, g-eq/liter. NI = Normality of standard I2 solution, g-eq/liter. NS = Normality of standard (≃0.1 N) Na2S2O3 solution, g-eq/liter. NT = Normality of standard (≃0.01 N) Na2S2O3 solution, assumed to be 0.1 NS, g-eq/liter. Pbar = Barometric pressure at the sampling site, mm Hg. Pstd = Standard absolute pressure, 760 mm Hg. Tm = Average DGM temperature, °K. Tstd = Standard absolute temperature, 293 °K. VA = Volume of C6H5AsO solution used for standardization, ml. VAI = Volume of standard C6H5AsO solution used for titration analysis, ml. VI = Volume of standard I2 solution used for standardization, ml. VIT = Volume of standard I2 solution used for titration analysis, normally 50 ml. Vm = Volume of gas sample at meter conditions, liters. Vm(std) = Volume of gas sample at standard conditions, liters. VSI = Volume of “0.1 N Na2S2O3 solution used for standardization, ml. VT = Volume of standard (≃0.01 N) Na2S2O3 solution used in standardizing iodine solution (see section 10.2.1), ml. VTT = Volume of standard (∼0.01 N) Na2S2O3 solution used for titration analysis, ml. W = Weight of K2Cr2O7 used to standardize Na2s2O3 or C6H5AsO solutions, as applicable (see sections 10.2.2 and 10.2.3), g. Y = DGM calibration factor.12.2 Normality of the Standard (≃0.1 N) Sodium Thiosulfate Solution.
Where: 2.039 = Conversion factor = (6 g-eq I2/mole K2Cr2O7) (1,000 ml/liter)/(294.2 g K2Cr2O7/mole) (10 aliquot factor)12.3 Normality of Standard Phenylarsine Oxide Solution (if applicable).
Where: 0.2039 = Conversion factor. = (6 g-eq I2/mole K2Cr2O7) (1,000 ml/liter)/(294.2 g K2Cr2O7/mole) (100 aliquot factor)12.4 Normality of Standard Iodine Solution.
Note:If C6H5AsO is used instead of Na2S2O3, replace NT and VT in Equation 11-3 with NA and VAS, respectively (see sections 10.2.1 and 10.2.3).
12.5 Dry Gas Volume. Correct the sample volume measured by the DGM to standard conditions (20 °C and 760 mm Hg).
12.6 Concentration of H2S. Calculate the concentration of H2S in the gas stream at standard conditions using Equation 11-5:
Where: 17.04 × 10 3 = Conversion factor = (34.07 g/mole H2S) (1,000 liters/m 3) (1,000mg/g)/(1,000 ml/liter) (2H2S eq/mole) Note:If C6H5AsO is used instead of NaS22O3, replace NA and VAT in Equation 11-5 with NA and VAT, respectively (see sections 11.5 and 10.2.3).
13.0 Method Performance13.1 Precision. Collaborative testing has shown the intra-laboratory precision to be 2.2 percent and the inter-laboratory precision to be 5 percent.
13.2 Bias. The method bias was shown to be −4.8 percent when only H2S was present. In the presence of the interferences cited in section 4.0, the bias was positive at low H2S concentration and negative at higher concentrations. At 230 mg H2S/m 3, the level of the compliance standard, the bias was + 2.7 percent. Thiols had no effect on the precision.
14.0 Pollution Prevention [Reserved] 15.0 Waste Management [Reserved] 16.0 References1. Determination of Hydrogen Sulfide, Ammoniacal Cadmium Chloride Method. API Method 772-54. In: Manual on Disposal of Refinery Wastes, Vol. V: Sampling and Analysis of Waste Gases and Particulate Matter. American Petroleum Institute, Washington, D.C. 1954.
2. Tentative Method of Determination of Hydrogen Sulfide and Mercaptan Sulfur in Natural Gas. Natural Gas Processors Association, Tulsa, OK. NGPA Publication No. 2265-65. 1965.
3. Knoll, J.D., and M.R. Midgett. Determination of Hydrogen Sulfide in Refinery Fuel Gases. Environmental Monitoring Series, Office of Research and Development, USEPA. Research Triangle Park, NC 27711. EPA 600/4-77-007.
4. Scheil, G.W., and M.C. Sharp. Standardization of Method 11 at a Petroleum Refinery. Midwest Research Institute Draft Report for USEPA. Office of Research and Development. Research Triangle Park, NC 27711. EPA Contract No. 68-02-1098. August 1976. EPA 600/4-77-088a (Volume 1) and EPA 600/4-77-088b (Volume 2).
17.0 Tables, Diagrams, Flowcharts, and Validation Data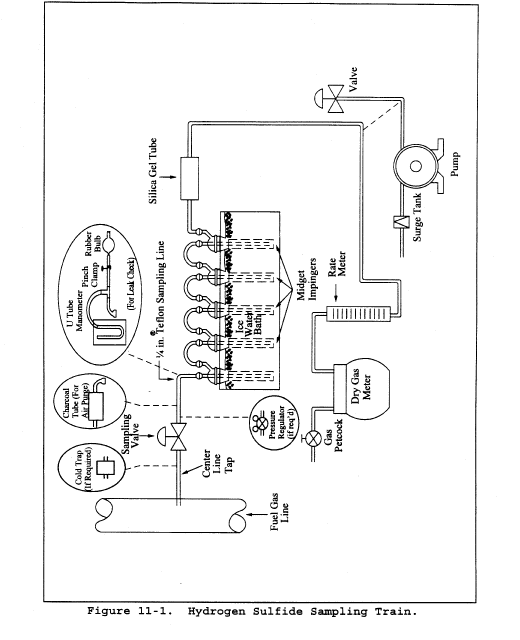
This method does not include all of the specifications (e.g., equipment and supplies) and procedures (e.g., sampling and analytical) essential to its performance. Some material is incorporated by reference from other methods in this part. Therefore, to obtain reliable results, persons using this method should have a thorough knowledge of at least the following additional test methods: Method 1, Method 2, Method 3, and Method 5.
1.0 Scope and Application1.1 Analytes.
Analyte | CAS No. | Sensitivity |
---|---|---|
Inorganic Lead Compounds as lead (Pb) | 7439-92-1 | see section 13.3. |
1.2 Applicability. This method is applicable for the determination of inorganic lead emissions from stationary sources, only as specified in an applicable subpart of the regulations.
1.3 Data Quality Objectives. Adherence to the requirements of this method will enhance the quality of the data obtained from air pollutant sampling methods.
2.0 Summary of Method2.1 Particulate and gaseous Pb emissions are withdrawn isokinetically from the source and are collected on a filter and in dilute nitric acid. The collected samples are digested in acid solution and are analyzed by atomic absorption spectrophotometry using an air/acetylene flame.
3.0 Definitions [Reserved] 4.0 Interferences4.1 Copper. High concentrations of copper may interfere with the analysis of Pb at 217.0 nm. This interference can be avoided by analyzing the samples at 283.3 nm.
4.2 Matrix Effects. Analysis for Pb by flame atomic absorption spectrophotometry is sensitive to the chemical composition and to the physical properties (e.g., viscosity, pH) of the sample. The analytical procedure requires the use of the Method of Standard Additions to check for these matrix effects, and requires sample analysis using the Method of Standard Additions if significant matrix effects are found to be present.
5.0 Safety5.1 Disclaimer. This method may involve hazardous materials, operations, and equipment. This test method may not address all of the safety problems associated with its use. It is the responsibility of the user of this test method to establish appropriate safety and health practices and to determine the applicability of regulatory limitations prior to performing this test method.
5.2 Corrosive Reagents. The following reagents are hazardous. Personal protective equipment and safe procedures are useful in preventing chemical splashes. If contact occurs, immediately flush with copious amounts of water at least 15 minutes. Remove clothing under shower and decontaminate. Treat residual chemical burn as thermal burn.
5.2.1 Hydrogen Peroxide (H2O2). Irritating to eyes, skin, nose, and lungs.
5.2.2 Nitric Acid (HNO3). Highly corrosive to eyes, skin, nose, and lungs. Vapors cause bronchitis, pneumonia, or edema of lungs. Reaction to inhalation may be delayed as long as 30 hours and still be fatal. Provide ventilation to limit exposure. Strong oxidizer. Hazardous reaction may occur with organic materials such as solvents.
6.0 Equipment and Supplies6.1 Sample Collection. A schematic of the sampling train used in performing this method is shown in Figure 12-1 in section 18.0; it is similar to the Method 5 train. The following items are needed for sample collection:
6.1.1 Probe Nozzle, Probe Liner, Pitot Tube, Differential Pressure Gauge, Filter Holder, Filter Heating System, Temperature Sensor, Metering System, Barometer, and Gas Density Determination Equipment. Same as Method 5, sections 6.1.1.1 through 6.1.1.7, 6.1.1.9, 6.1.2, and 6.1.3, respectively.
6.1.2 Impingers. Four impingers connected in series with leak-free ground glass fittings or any similar leak-free noncontaminating fittings are needed. For the first, third, and fourth impingers, use the Greenburg-Smith design, modified by replacing the tip with a 1.3 cm ( 1/2 in.) ID glass tube extending to about 1.3 cm ( 1/2 in.) from the bottom of the flask. For the second impinger, use the Greenburg-Smith design with the standard tip.
6.1.3 Temperature Sensor. Place a temperature sensor, capable of measuring temperature to within 1 °C (2 °F) at the outlet of the fourth impinger for monitoring purposes.
6.2 Sample Recovery. The following items are needed for sample recovery:
6.2.1 Probe-Liner and Probe-Nozzle Brushes, Petri Dishes, Graduated Cylinder and/or Balance, Plastic Storage Containers, and Funnel and Rubber Policeman. Same as Method 5, sections 6.2.1 and 6.2.4 through 6.2.7, respectively.
6.2.2 Wash Bottles. Glass (2).
6.2.3 Sample Storage Containers. Chemically resistant, borosilicate glass bottles, for 0.1 N nitric acid (HNO3) impinger and probe solutions and washes, 1000-ml. Use screw-cap liners that are either rubber-backed Teflon or leak-free and resistant to chemical attack by 0.1 N HNO3. (Narrow mouth glass bottles have been found to be less prone to leakage.)
6.2.4 Funnel. Glass, to aid in sample recovery.
6.3 Sample Analysis. The following items are needed for sample analysis:
6.3.1 Atomic Absorption Spectrophotometer. With lead hollow cathode lamp and burner for air/acetylene flame.
6.3.2 Hot Plate.
6.3.3 Erlenmeyer Flasks. 125-ml, 24/40 standard taper.
6.3.4 Membrane Filters. Millipore SCWPO 4700, or equivalent.
6.3.5 Filtration Apparatus. Millipore vacuum filtration unit, or equivalent, for use with the above membrane filter.
6.3.6 Volumetric Flasks. 100-ml, 250-ml, and 1000-ml.
7.0 Reagents and Standards Note:Unless otherwise indicated, it is intended that all reagents conform to the specifications established by the Committee on Analytical Reagents of the American Chemical Society, where such specifications are available; otherwise, use the best available grade.
7.1 Sample Collection. The following reagents are needed for sample collection:
7.1.1 Filter. Gelman Spectro Grade, Reeve Angel 934 AH, MSA 1106 BH, all with lot assay for Pb, or other high-purity glass fiber filters, without organic binder, exhibiting at least 99.95 percent efficiency (<0.05 percent penetration) on 0.3 micron dioctyl phthalate smoke particles. Conduct the filter efficiency test using ASTM D 2986-71, 78, or 95a (incorporated by reference - see § 60.17) or use test data from the supplier's quality control program.
7.1.2 Silica Gel and Crushed Ice. Same as Method 5, sections 7.1.2 and 7.1.4, respectively.
7.1.3 Water. Deionized distilled, to conform to ASTM D 1193-77 or 91, Type 3 (incorporated by reference - see § 60.17). If high concentrations of organic matter are not expected to be present, the potassium permanganate test for oxidizable organic matter may be omitted.
7.1.4 Nitric Acid, 0.1 N. Dilute 6.5 ml of concentrated HNO3 to 1 liter with water. (It may be desirable to run blanks before field use to eliminate a high blank on test samples.)
7.2 Sample Recovery. 0.1 N HNO3 (Same as in section 7.1.4 above).
7.3 Sample Analysis. The following reagents and standards are needed for sample analysis:
7.3.1 Water. Same as in section 7.1.3.
7.3.2 Nitric Acid, Concentrated.
7.3.3 Nitric Acid, 50 Percent (v/v). Dilute 500 ml of concentrated HNO3 to 1 liter with water.
7.3.4 Stock Lead Standard Solution, 1000 µg Pb/ml. Dissolve 0.1598 g of lead nitrate [Pb(NO3)2] in about 60 ml water, add 2 ml concentrated HNO3, and dilute to 100 ml with water.
7.3.5 Working Lead Standards. Pipet 0.0, 1.0, 2.0, 3.0, 4.0, and 5.0 ml of the stock lead standard solution (Section 7.3.4) into 250-ml volumetric flasks. Add 5 ml of concentrated HNO3 to each flask, and dilute to volume with water. These working standards contain 0.0, 4.0, 8.0, 12.0, 16.0, and 20.0 µg Pb/ml, respectively. Prepare, as needed, additional standards at other concentrations in a similar manner.
7.3.6 Air. Suitable quality for atomic absorption spectrophotometry.
7.3.7 Acetylene. Suitable quality for atomic absorption spectrophotometry.
7.3.8 Hydrogen Peroxide, 3 Percent (v/v). Dilute 10 ml of 30 percent H2O2 to 100 ml with water.
8.0 Sample Collection, Preservation, Storage, and Transport8.1 Pretest Preparation. Follow the same general procedure given in Method 5, section 8.1, except that the filter need not be weighed.
8.2 Preliminary Determinations. Follow the same general procedure given in Method 5, section 8.2.
8.3 Preparation of Sampling Train. Follow the same general procedure given in Method 5, section 8.3, except place 100 ml of 0.1 N HNO3 (instead of water) in each of the first two impingers. As in Method 5, leave the third impinger empty and transfer approximately 200 to 300 g of preweighed silica gel from its container to the fourth impinger. Set up the train as shown in Figure 12-1.
8.4 Leak-Check Procedures. Same as Method 5, section 8.4.
8.5 Sampling Train Operation. Same as Method 5, section 8.5.
8.6 Calculation of Percent Isokinetic. Same as Method 5, section 8.6.
8.7 Sample Recovery. Same as Method 5, sections 8.7.1 through 8.7.6.1, with the addition of the following:
8.7.1 Container No. 2 (Probe).
8.7.1.1 Taking care that dust on the outside of the probe or other exterior surfaces does not get into the sample, quantitatively recover sample matter and any condensate from the probe nozzle, probe fitting, probe liner, and front half of the filter holder by washing these components with 0.1 N HNO3 and placing the wash into a glass sample storage container. Measure and record (to the nearest 2 ml) the total amount of 0.1 N HNO3 used for these rinses. Perform the 0.1 N HNO3 rinses as follows:
8.7.1.2 Carefully remove the probe nozzle, and rinse the inside surfaces with 0.1 N HNO3 from a wash bottle while brushing with a stainless steel, Nylon-bristle brush. Brush until the 0.1 N HNO3 rinse shows no visible particles, then make a final rinse of the inside surface with 0.1 N HNO3.
8.7.1.3 Brush and rinse with 0.1 N HNO3 the inside parts of the Swagelok fitting in a similar way until no visible particles remain.
8.7.1.4 Rinse the probe liner with 0.1 N HNO3. While rotating the probe so that all inside surfaces will be rinsed with 0.1 N HNO3, tilt the probe, and squirt 0.1 N HNO3 into its upper end. Let the 0.1 N HNO3 drain from the lower end into the sample container. A glass funnel may be used to aid in transferring liquid washes to the container. Follow the rinse with a probe brush. Hold the probe in an inclined position, squirt 0.1 N HNO3 into the upper end of the probe as the probe brush is being pushed with a twisting action through the probe; hold the sample container underneath the lower end of the probe, and catch any 0.1 N HNO3 and sample matter that is brushed from the probe. Run the brush through the probe three times or more until no visible sample matter is carried out with the 0.1 N HNO3 and none remains on the probe liner on visual inspection. With stainless steel or other metal probes, run the brush through in the above prescribed manner at least six times, since metal probes have small crevices in which sample matter can be entrapped. Rinse the brush with 0.1 N HNO3, and quantitatively collect these washings in the sample container. After the brushing, make a final rinse of the probe as described above.
8.7.1.5 It is recommended that two people clean the probe to minimize loss of sample. Between sampling runs, keep brushes clean and protected from contamination.
8.7.1.6 Brush and rinse with 0.1 N HNO3 the inside of the front half of the filter holder. Brush and rinse each surface three times or more, if needed, to remove visible sample matter. Make a final rinse of the brush and filter holder. After all 0.1 N HNO3 washings and sample matter are collected in the sample container, tighten the lid on the sample container so that the fluid will not leak out when it is shipped to the laboratory. Mark the height of the fluid level to determine whether leakage occurs during transport. Label the container to identify its contents clearly.
8.7.2 Container No. 3 (Silica Gel). Note the color of the indicating silica gel to determine if it has been completely spent, and make a notation of its condition. Transfer the silica gel from the fourth impinger to the original container, and seal. A funnel may be used to pour the silica gel from the impinger and a rubber policeman may be used to remove the silica gel from the impinger. It is not necessary to remove the small amount of particles that may adhere to the walls and are difficult to remove. Since the gain in weight is to be used for moisture calculations, do not use any water or other liquids to transfer the silica gel. If a balance is available in the field, follow the procedure for Container No. 3 in section 11.4.2.
8.7.3 Container No. 4 (Impingers). Due to the large quantity of liquid involved, the impinger solutions may be placed in several containers. Clean each of the first three impingers and connecting glassware in the following manner:
8.7.3.1 Cap the impinger ball joints.
8.7.3.2. Rotate and agitate each impinger, so that the impinger contents might serve as a rinse solution.
8.7.3.3 Treat the impingers as follows: Make a notation of any color or film in the liquid catch. Measure the liquid that is in the first three impingers by weighing it to within 0.5 g at a minimum by using a balance. Record the weight of liquid present. The liquid weight is needed, along with the silica gel data, to calculate the stack gas moisture content (see Method 5, Figure 5-6).
8.7.3.4. Transfer the contents to Container No. 4.
Note:In sections 8.7.3.5 and 8.7.3.6, measure and record the total amount of 0.1 N HNO3 used for rinsing.
8.7.3.5. Pour approximately 30 ml of 0.1 N HNO3 into each of the first three impingers and agitate the impingers. Drain the 0.1 N HNO3 through the outlet arm of each impinger into Container No. 4. Repeat this operation a second time; inspect the impingers for any abnormal conditions.
8.7.3.6 Rinse the insides of each piece of connecting glassware for the impingers twice with 0.1 N HNO3; transfer this rinse into Container No. 4. Do not rinse or brush the glass-fritted filter support. Mark the height of the fluid level to determine whether leakage occurs during transport. Label the container to identify its contents clearly.
8.8 Blanks.
8.8.1 Nitric Acid. Save 200 ml of the 0.1 N HNO3 used for sampling and cleanup as a blank. Take the solution directly from the bottle being used and place into a glass sample container labeled “0.1 N HNO3 blank.”
8.8.2 Filter. Save two filters from each lot of filters used in sampling. Place these filters in a container labeled “filter blank.”
9.0 Quality Control9.1 Miscellaneous Quality Control Measures.
Section | Quality control measure | Effect |
---|---|---|
8.4, 10.1 | Sampling equipment leak-checks and calibration | Ensure accuracy and precision of sampling measurements. |
10.2 | Spectrophotometer calibration | Ensure linearity of spectrophotometer response to standards. |
11.5 | Check for matrix effects | Eliminate matrix effects. |
9.2 Volume Metering System Checks. Same as Method 5, section 9.2.
10.0 Calibration and Standardizations Note:Maintain a laboratory log of all calibrations.
10.1 Sampling Equipment. Same as Method 5, section 10.0.
10.2 Spectrophotometer.
10.2.1 Measure the absorbance of the standard solutions using the instrument settings recommended by the spectrophotometer manufacturer. Repeat until good agreement (±3 percent) is obtained between two consecutive readings. Plot the absorbance (y-axis) versus concentration in µg Pb/ml (x-axis). Draw or compute a straight line through the linear portion of the curve. Do not force the calibration curve through zero, but if the curve does not pass through the origin or at least lie closer to the origin than ±0.003 absorbance units, check for incorrectly prepared standards and for curvature in the calibration curve.
10.2.2 To determine stability of the calibration curve, run a blank and a standard after every five samples, and recalibrate as necessary.
11.0 Analytical Procedures11.1 Sample Loss Check. Prior to analysis, check the liquid level in Containers Number 2 and Number 4. Note on the analytical data sheet whether leakage occurred during transport. If a noticeable amount of leakage occurred, either void the sample or take steps, subject to the approval of the Administrator, to adjust the final results.
11.2 Sample Preparation.
11.2.1 Container No. 1 (Filter). Cut the filter into strips and transfer the strips and all loose particulate matter into a 125-ml Erlenmeyer flask. Rinse the petri dish with 10 ml of 50 percent HNO3 to ensure a quantitative transfer, and add to the flask.
Note:If the total volume required in section 11.2.3 is expected to exceed 80 ml, use a 250-ml flask in place of the 125-ml flask.
11.2.2 Containers No. 2 and No. 4 (Probe and Impingers). Combine the contents of Containers No. 2 and No. 4, and evaporate to dryness on a hot plate.
11.2.3 Sample Extraction for Lead.
11.2.3.1 Based on the approximate stack gas particulate concentration and the total volume of stack gas sampled, estimate the total weight of particulate sample collected. Next, transfer the residue from Containers No. 2 and No. 4 to the 125-ml Erlenmeyer flask that contains the sampling filter using a rubber policeman and 10 ml of 50 percent HNO3 for every 100 mg of sample collected in the train or a minimum of 30 ml of 50 percent HNO3, whichever is larger.
11.2.3.2 Place the Erlenmeyer flask on a hot plate, and heat with periodic stirring for 30 minutes at a temperature just below boiling. If the sample volume falls below 15 ml, add more 50 percent HNO3. Add 10 ml of 3 percent H2O2, and continue heating for 10 minutes. Add 50 ml of hot (80 °C, 176 °F) water, and heat for 20 minutes. Remove the flask from the hot plate, and allow to cool. Filter the sample through a Millipore membrane filter, or equivalent, and transfer the filtrate to a 250-ml volumetric flask. Dilute to volume with water.
11.2.4 Filter Blank. Cut each filter into strips, and place each filter in a separate 125-ml Erlenmeyer flask. Add 15 ml of 50 percent HNO3, and treat as described in section 11.2.3 using 10 ml of 3 percent H2O2 and 50 ml of hot water. Filter and dilute to a total volume of 100 ml using water.
11.2.5 Nitric Acid Blank, 0.1 N. Take the entire 200 ml of 0.1 N HNO3 to dryness on a steam bath, add 15 ml of 50 percent HNO3, and treat as described in section 11.2.3 using 10 ml of 3 percent H202 and 50 ml of hot water. Dilute to a total volume of 100 ml using water.
11.3 Spectrophotometer Preparation. Turn on the power; set the wavelength, slit width, and lamp current; and adjust the background corrector as instructed by the manufacturer's manual for the particular atomic absorption spectrophotometer. Adjust the burner and flame characteristics as necessary.
11.4 Analysis.
11.4.1 Lead Determination. Calibrate the spectrophotometer as outlined in section 10.2, and determine the absorbance for each source sample, the filter blank, and 0.1 N HNO3 blank. Analyze each sample three times in this manner. Make appropriate dilutions, as needed, to bring all sample Pb concentrations into the linear absorbance range of the spectrophotometer. Because instruments vary between manufacturers, no detailed operating instructions will be given here. Instead, the instructions provided with the particular instrument should be followed. If the Pb concentration of a sample is at the low end of the calibration curve and high accuracy is required, the sample can be taken to dryness on a hot plate and the residue dissolved in the appropriate volume of water to bring it into the optimum range of the calibration curve.
11.4.2 Container No. 3 (Silica Gel). This step may be conducted in the field. Weigh the spent silica gel (or silica gel plus impinger) to the nearest 0.5 g; record this weight.
11.5 Check for Matrix Effects. Use the Method of Standard Additions as follows to check at least one sample from each source for matrix effects on the Pb results:
11.5.1 Add or spike an equal volume of standard solution to an aliquot of the sample solution.
11.5.2 Measure the absorbance of the resulting solution and the absorbance of an aliquot of unspiked sample.
11.5.3 Calculate the Pb concentration Cm in µg/ml of the sample solution using Equation 12-1 in section 12.5.
Volume corrections will not be required if the solutions as analyzed have been made to the same final volume. Therefore, Cm and Ca represent Pb concentration before dilutions.
Method of Standard Additions procedures described on pages 9-4 and 9-5 of the section entitled “General Information” of the Perkin Elmer Corporation Atomic Absorption Spectrophotometry Manual, Number 303-0152 (Reference 1 in section 17.0) may also be used. In any event, if the results of the Method of Standard Additions procedure used on the single source sample do not agree to within ±5 percent of the value obtained by the routine atomic absorption analysis, then reanalyze all samples from the source using the Method of Standard Additions procedure.
12.0 Data Analysis and Calculations12.1 Nomenclature.
Am = Absorbance of the sample solution.
An = Cross-sectional area of nozzle, m 2 (ft 2).
At = Absorbance of the spiked sample solution.
Bws = Water in the gas stream, proportion by volume.
Ca = Lead concentration in standard solution, µg/ml.
Cm = Lead concentration in sample solution analyzed during check for matrix effects, µg/ml.
Cs = Lead concentration in stack gas, dry basis, converted to standard conditions, mg/dscm (gr/dscf).
I = Percent of isokinetic sampling.
L1 = Individual leakage rate observed during the leak-check conducted prior to the first component change, m 3/min (ft 3/min).
La = Maximum acceptable leakage rate for either a pretest leak-check or for a leak-check following a component change; equal to 0.00057 m 3/min (0.020 cfm) or 4 percent of the average sampling rate, whichever is less.
Li = Individual leakage rate observed during the leak-check conducted prior to the “ith” component change (i = 1, 2, 3 * * * n), m 3/min (cfm).
Lp = Leakage rate observed during the post-test leak-check, m 3/min (cfm).
mt = Total weight of lead collected in the sample, µg.
Mw = Molecular weight of water, 18.0 g/g-mole (18.0 lb/lb-mole).
Pbar = Barometric pressure at the sampling site, mm Hg (in. Hg).
Ps = Absolute stack gas pressure, mm Hg (in. Hg).
Pstd = Standard absolute pressure, 760 mm Hg (29.92 in. Hg).
R = Ideal gas constant, 0.06236 [(mm Hg) (m 3)]/[(°K) (g-mole)] {21.85 [(in. Hg) (ft 3)]/[(°R) (lb-mole)]}.
Tm = Absolute average dry gas meter temperature (see Figure 5-3 of Method 5), °K (°R).
Tstd = Standard absolute temperature, 293 °K (528 °R).
vs = Stack gas velocity, m/sec (ft/sec).
Vm = Volume of gas sample as measured by the dry gas meter, dry basis, m 3 (ft 3).
Vm(std) = Volume of gas sample as measured by the dry gas meter, corrected to standard conditions, m 3 (ft 3).
Vw(std) = Volume of water vapor collected in the sampling train, corrected to standard conditions, m 3 (ft 3).
Y = Dry gas meter calibration factor.
ΔH = Average pressure differential across the orifice meter (see Figure 5-3 of Method 5), mm H2O (in. H2O).
θ = Total sampling time, min.
θl = Sampling time interval, from the beginning of a run until the first component change, min.
θi = Sampling time interval, between two successive component changes, beginning with the interval between the first and second changes, min.
θp = Sampling time interval, from the final (nth) component change until the end of the sampling run, min.
12.2 Average Dry Gas Meter Temperatures (Tm) and Average Orifice Pressure Drop (ΔH). See data sheet (Figure 5-3 of Method 5).
12.3 Dry Gas Volume, Volume of Water Vapor Condensed, and Moisture Content. Using data obtained in this test, calculate Vm(std), Vw(std), and Bws according to the procedures outlined in Method 5, sections 12.3 through 12.5.
12.4 Total Lead in Source Sample. For each source sample, correct the average absorbance for the contribution of the filter blank and the 0.1 N HNO3 blank. Use the calibration curve and this corrected absorbance to determine the Pb concentration in the sample aspirated into the spectrophotometer. Calculate the total Pb content mt (in µg) in the original source sample; correct for all the dilutions that were made to bring the Pb concentration of the sample into the linear range of the spectrophotometer.
12.5 Sample Lead Concentration. Calculate the Pb concentration of the sample using the following equation:
12.6 Lead Concentration. Calculate the stack gas Pb concentration Cs using Equation 12-2:
Where: K3 = 0.001 mg/µg for metric units. = 1.54 × 10−5 gr/µg for English units12.7 Stack Gas Velocity and Volumetric Flow Rate. Calculate the average stack gas velocity and volumetric flow rate using data obtained in this method and the equations in sections 12.2 and 12.3 of Method 2.
12.8 Isokinetic Variation. Same as Method 5, section 12.11.
13.0 Method Performance13.1 Precision. The within-laboratory precision, as measured by the coefficient of variation, ranges from 0.2 to 9.5 percent relative to a run-mean concentration. These values were based on tests conducted at a gray iron foundry, a lead storage battery manufacturing plant, a secondary lead smelter, and a lead recovery furnace of an alkyl lead manufacturing plant. The concentrations encountered during these tests ranged from 0.61 to 123.3 mg Pb/m 3.
13.2 Analytical Range. For a minimum analytical accuracy of ±10 percent, the lower limit of the range is 100 µg. The upper limit can be extended considerably by dilution.
13.3 Analytical Sensitivity. Typical sensitivities for a 1-percent change in absorption (0.0044 absorbance units) are 0.2 and 0.5 µg Pb/ml for the 217.0 and 283.3 nm lines, respectively.
14.0 Pollution Prevention [Reserved] 15.0 Waste Management [Reserved] 16.0 Alternative Procedures16.1 Simultaneous Determination of Particulate Matter and Lead Emissions. Method 12 may be used to simultaneously determine Pb and particulate matter provided:
(1) A glass fiber filter with a low Pb background is used and this filter is checked, desiccated and weighed per section 8.1 of Method 5,
(2) An acetone rinse, as specified by Method 5, sections 7.2 and 8.7.6.2, is used to remove particulate matter from the probe and inside of the filter holder prior to and kept separate from the 0.1 N HNO3 rinse of the same components,
(3) The recovered filter, the acetone rinse, and an acetone blank (Method 5, section 7.2) are subjected to the gravimetric analysis of Method 5, sections 6.3 and 11.0 prior to the analysis for Pb as described below, and
(4) The entire train contents, including the 0.1 N HNO3 impingers, filter, acetone and 0.1 N HNO3 probe rinses are treated and analyzed for Pb as described in sections 8.0 and 11.0 of this method.
16.2 Filter Location. A filter may be used between the third and fourth impingers provided the filter is included in the analysis for Pb.
16.3 In-Stack Filter. An in-stack filter may be used provided: (1) A glass-lined probe and at least two impingers, each containing 100 ml of 0.1 N HNO3 after the in-stack filter, are used and (2) the probe and impinger contents are recovered and analyzed for Pb. Recover sample from the nozzle with acetone if a particulate analysis is to be made as described in section 16.1 of this method.
16.4 Inductively Coupled Plasma-Atomic Emission Spectrometry (ICP-AES) Analysis. ICP-AES may be used as an alternative to atomic absorption analysis provided the following conditions are met:
16.4.1 Sample collection/recovery, sample loss check, and sample preparation procedures are as defined in sections 8.0, 11.1, and 11.2, respectively, of this method.
16.4.2 Analysis shall be conducted following Method 6010D of SW-846 (incorporated by reference, see § 60.17). The limit of detection for the ICP-AES must be demonstrated according to section 15.0 of Method 301 in appendix A of part 63 of this chapter and must be no greater than one-third of the applicable emission limit. Perform a check for matrix effects according to section 11.5 of this method.
16.5 Inductively Coupled Plasma-Mass Spectrometry (ICP-MS) Analysis. ICP-MS may be used as an alternative to atomic absorption analysis provided the following conditions are met:
16.5.1 Sample collection/recovery, sample loss check, and sample preparation procedures are as defined in sections 8.0, 11.1, and 11.2, respectively of this method.
16.5.2 Analysis shall be conducted following Method 6020B of SW-846 (incorporated by reference, see § 60.17). The limit of detection for the ICP-MS must be demonstrated according to section 15.0 of Method 301 in appendix A to part 63 of this chapter and must be no greater than one-third of the applicable emission limit. Use the multipoint calibration curve option in section 10.4 of Method 6020B and perform a check for matrix effects according to section 11.5 of this method.
17.0 ReferencesSame as Method 5, section 17.0, References 2, 3, 4, 5, and 7, with the addition of the following:
1. Perkin Elmer Corporation. Analytical Methods for Atomic Absorption Spectrophotometry. Norwalk, Connecticut. September 1976.
2. American Society for Testing and Materials. Annual Book of ASTM Standards, Part 31: Water, Atmospheric Analysis. Philadelphia, PA 1974. p. 40-42.
3. Kelin, R., and C. Hach. Standard Additions - Uses and Limitations in Spectrophotometric Analysis. Amer. Lab. 9:21-27. 1977.
4. Mitchell, W.J., and M.R. Midgett. Determining Inorganic and Alkyl Lead Emissions from Stationary Sources. U.S. Environmental Protection Agency. Emission Monitoring and Support Laboratory. Research Triangle Park, NC. (Presented at National APCA Meeting, Houston. June 26, 1978).
18.0 Tables, Diagrams, Flowcharts, and Validation Data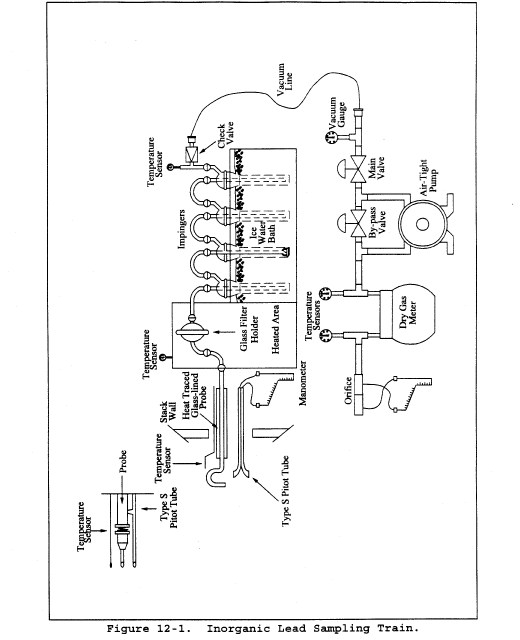
This method does not include all of the specifications (e.g., equipment and supplies) and procedures (e.g., sampling and analytical) essential to its performance. Some material is incorporated by reference from other methods in this part. Therefore, to obtain reliable results, persons using this method should have a thorough knowledge of at least the following additional test methods: Method 1, Method 2, Method 3, and Method 5.
1.0 Scope and Application1.1 Analytes.
Analyte | CAS No. | Sensitivity |
---|---|---|
Total fluorides as Fluorine | 7782-41-4 | Not determined. |
1.2 Applicability. This method is applicable for the determination of fluoride (F−) emissions from sources as specified in the regulations. It does not measure fluorocarbons, such as Freons.
1.3 Data Quality Objectives. Adherence to the requirements of this method will enhance the quality of the data obtained from air pollutant sampling methods.
2.0 SummaryGaseous and particulate F− are withdrawn isokinetically from the source and collected in water and on a filter. The total F− is then determined by the SPADNS Zirconium Lake Colorimetric method.
3.0 Definitions [Reserved] 4.0 Interferences4.1 Chloride. Large quantities of chloride will interfere with the analysis, but this interference can be prevented by adding silver sulfate into the distillation flask (see section 11.3). If chloride ion is present, it may be easier to use the specific ion electrode method of analysis (Method 13B).
4.2 Grease. Grease on sample-exposed surfaces may cause low F− results due to adsorption.
5.0 Safety5.1 Disclaimer. This method may involve hazardous materials, operations, and equipment. This test method may not address all of the safety problems associated with its use. It is the responsibility of the user of this test method to establish appropriate safety and health practices and to determine the applicability of regulatory limitations prior to performing this test method.
5.2 Corrosive Reagents. The following reagents are hazardous. Personal protective equipment and safe procedures are useful in preventing chemical splashes. If contact occurs, immediately flush with copious amounts of water at least 15 minutes. Remove clothing under shower and decontaminate. Treat residual chemical burn as thermal burn.
5.2.1 Hydrochloric Acid (HCl). Highly toxic. Vapors are highly irritating to eyes, skin, nose, and lungs, causing severe damage. May cause bronchitis, pneumonia, or edema of lungs. Exposure to concentrations of 0.13 to 0.2 percent can be lethal in minutes. Will react with metals, producing hydrogen.
5.2.2 Sodium Hydroxide (NaOH). Causes severe damage to eye tissues and to skin. Inhalation causes irritation to nose, throat, and lungs. Reacts exothermically with limited amounts of water.
5.2.3 Sulfuric Acid (H2SO4). Rapidly destructive to body tissue. Will cause third degree burns. Eye damage may result in blindness. Inhalation may be fatal from spasm of the larynx, usually within 30 minutes. May cause lung tissue damage with edema. 1 mg/m 3 for 8 hours will cause lung damage or, in higher concentrations, death. Provide ventilation to limit inhalation. Reacts violently with metals and organics.
6.0 Equipment and Supplies6.1 Sample Collection. A schematic of the sampling train used in performing this method is shown in Figure 13A-1; it is similar to the Method 5 sampling train except that the filter position is interchangeable. The sampling train consists of the following components:
6.1.1 Probe Nozzle, Pitot Tube, Differential Pressure Gauge, Filter Heating System, Temperature Sensor, Metering System, Barometer, and Gas Density Determination Equipment. Same as Method 5, sections 6.1.1.1, 6.1.1.3 through 6.1.1.7, 6.1.1.9, 6.1.2, and 6.1.3, respectively. The filter heating system and temperature sensor are needed only when moisture condensation is a problem.
6.1.2 Probe Liner. Borosilicate glass or 316 stainless steel. When the filter is located immediately after the probe, a probe heating system may be used to prevent filter plugging resulting from moisture condensation, but the temperature in the probe shall not be allowed to exceed 120 ±14 °C (248 ±25 °F).
6.1.3 Filter Holder. With positive seal against leakage from the outside or around the filter. If the filter is located between the probe and first impinger, use borosilicate glass or stainless steel with a 20-mesh stainless steel screen filter support and a silicone rubber gasket; do not use a glass frit or a sintered metal filter support. If the filter is located between the third and fourth impingers, borosilicate glass with a glass frit filter support and a silicone rubber gasket may be used. Other materials of construction may be used, subject to the approval of the Administrator.
6.1.4 Impingers. Four impingers connected as shown in Figure 13A-1 with ground-glass (or equivalent), vacuum-tight fittings. For the first, third, and fourth impingers, use the Greenburg-Smith design, modified by replacing the tip with a 1.3-cm ( 1/2 in.) ID glass tube extending to 1.3 cm ( 1/2 in.) from the bottom of the flask. For the second impinger, use a Greenburg-Smith impinger with the standard tip. Modifications (e.g., flexible connections between the impingers or materials other than glass) may be used, subject to the approval of the Administrator. Place a temperature sensor, capable of measuring temperature to within 1 °C (2 °F), at the outlet of the fourth impinger for monitoring purposes.
6.2 Sample Recovery. The following items are needed for sample recovery:
6.2.1 Probe-liner and Probe-Nozzle Brushes, Wash Bottles, Graduated Cylinder and/or Balance, Plastic Storage Containers, Funnel and Rubber Policeman, and Funnel. Same as Method 5, sections 6.2.1, 6.2.2 and 6.2.5 to 6.2.8, respectively.
6.2.2 Sample Storage Container. Wide-mouth, high-density polyethylene bottles for impinger water samples, 1 liter.
6.3 Sample Preparation and Analysis. The following items are needed for sample preparation and analysis:
6.3.1 Distillation Apparatus. Glass distillation apparatus assembled as shown in Figure 13A-2.
6.3.2 Bunsen Burner.
6.3.3 Electric Muffle Furnace. Capable of heating to 600 °C (1100 °F).
6.3.4 Crucibles. Nickel, 75- to 100-ml.
6.3.5 Beakers. 500-ml and 1500-ml.
6.3.6 Volumetric Flasks. 50-ml.
6.3.7 Erlenmeyer Flasks or Plastic Bottles. 500-ml.
6.3.8 Constant Temperature Bath. Capable of maintaining a constant temperature of ±1.0 °C at room temperature conditions.
6.3.9 Balance. 300-g capacity, to measure to ±0.5 g.
6.3.10 Spectrophotometer. Instrument that measures absorbance at 570 nm and provides at least a 1-cm light path.
6.3.11 Spectrophotometer Cells. 1-cm path length.
7.0 Reagents and StandardsUnless otherwise indicated, all reagents are to conform to the specifications established by the Committee on Analytical Reagents of the American Chemical Society, where such specifications are available. Otherwise, use the best available grade.
7.1 Sample Collection. The following reagents are needed for sample collection:
7.1.1 Filters.
7.1.1.1 If the filter is located between the third and fourth impingers, use a Whatman No. 1 filter, or equivalent, sized to fit the filter holder.
7.1.1.2 If the filter is located between the probe and first impinger, use any suitable medium (e.g., paper, organic membrane) that can withstand prolonged exposure to temperatures up to 135 °C (275 °F), and has at least 95 percent collection efficiency (<5 percent penetration) for 0.3 µm dioctyl phthalate smoke particles. Conduct the filter efficiency test before the test series, using ASTM D 2986-71, 78, or 95a (incorporated by reference - see § 60.17), or use test data from the supplier's quality control program. The filter must also have a low F− blank value (<0.015 mg F−/cm 2 of filter area). Before the test series, determine the average F− blank value of at least three filters (from the lot to be used for sampling) using the applicable procedures described in sections 8.3 and 8.4 of this method. In general, glass fiber filters have high and/or variable F− blank values, and will not be acceptable for use.
7.1.2 Water. Deionized distilled, to conform to ASTM D 1193-77 or 91, Type 3 (incorporated by reference - see § 60.17). If high concentrations of organic matter are not expected to be present, the potassium permanganate test for oxidizable organic matter may be deleted.
7.1.3 Silica Gel, Crushed Ice, and Stopcock Grease. Same as Method 5, sections 7.1.2, 7.1.4, and 7.1.5, respectively.
7.2 Sample Recovery. Water, as described in section 7.1.2, is needed for sample recovery.
7.3 Sample Preparation and Analysis. The following reagents and standards are needed for sample preparation and analysis:
7.3.1 Calcium Oxide (CaO). Certified grade containing 0.005 percent F− or less.
7.3.2 Phenolphthalein Indicator. Dissolve 0.1 g of phenolphthalein in a mixture of 50 ml of 90 percent ethanol and 50 ml of water.
7.3.3 Silver Sulfate (Ag2SO4).
7.3.4 Sodium Hydroxide (NaOH), Pellets.
7.3.5 Sulfuric Acid (H2SO4), Concentrated.
7.3.6 Sulfuric Acid, 25 Percent (v/v). Mix 1 part of concentrated H2SO4 with 3 parts of water.
7.3.7 Filters. Whatman No. 541, or equivalent.
7.3.8 Hydrochloric Acid (HCl), Concentrated.
7.3.9 Water. Same as in section 7.1.2.
7.3.10 Fluoride Standard Solution, 0.01 mg F−/ml. Dry approximately 0.5 g of sodium fluoride (NaF) in an oven at 110 °C (230 °F) for at least 2 hours. Dissolve 0.2210 g of NaF in 1 liter of water. Dilute 100 ml of this solution to 1 liter with water.
7.3.11 SPADNS Solution [4,5 Dihydroxyl-3-(p-Sulfophenylazo)-2,7-Naphthalene-Disulfonic Acid Trisodium Salt]. Dissolve 0.960 ±0.010 g of SPADNS reagent in 500 ml water. If stored in a well-sealed bottle protected from the sunlight, this solution is stable for at least 1 month.
7.3.12 Spectrophotometer Zero Reference Solution. Add 10 ml of SPADNS solution to 100 ml water, and acidify with a solution prepared by diluting 7 ml of concentrated HCl to 10 ml with deionized, distilled water. Prepare daily.
7.3.13 SPADNS Mixed Reagent. Dissolve 0.135 ±0.005 g of zirconyl chloride octahydrate (ZrOCl2 8H2O) in 25 ml of water. Add 350 ml of concentrated HCl, and dilute to 500 ml with deionized, distilled water. Mix equal volumes of this solution and SPADNS solution to form a single reagent. This reagent is stable for at least 2 months.
8.0 Sample Collection, Preservation, Storage, and Transport8.1 Pretest Preparation. Follow the general procedure given in Method 5, section 8.1, except that the filter need not be weighed.
8.2 Preliminary Determinations. Follow the general procedure given in Method 5, section 8.2, except that the nozzle size must be selected such that isokinetic sampling rates below 28 liters/min (1.0 cfm) can be maintained.
8.3 Preparation of Sampling Train. Follow the general procedure given in Method 5, section 8.3, except for the following variation: Assemble the train as shown in Figure 13A-1 with the filter between the third and fourth impingers. Alternatively, if a 20-mesh stainless steel screen is used for the filter support, the filter may be placed between the probe and first impinger. A filter heating system to prevent moisture condensation may be used, but shall not allow the temperature to exceed 120 ±14 °C (248 ±25 °F). Record the filter location on the data sheet (see section 8.5).
8.4 Leak-Check Procedures. Follow the leak-check procedures given in Method 5, section 8.4.
8.5 Sampling Train Operation. Follow the general procedure given in Method 5, section 8.5, keeping the filter and probe temperatures (if applicable) at 120 ±14 °C (248 ±25 °F) and isokinetic sampling rates below 28 liters/min (1.0 cfm). For each run, record the data required on a data sheet such as the one shown in Method 5, Figure 5-3.
8.6 Sample Recovery. Proper cleanup procedure begins as soon as the probe is removed from the stack at the end of the sampling period. Allow the probe to cool.
8.6.1 When the probe can be safely handled, wipe off all external particulate matter near the tip of the probe nozzle, and place a cap over it to keep from losing part of the sample. Do not cap off the probe tip tightly while the sampling train is cooling down as this would create a vacuum in the filter holder, thus drawing water from the impingers into the filter holder.
8.6.2 Before moving the sample train to the cleanup site, remove the probe from the sample train, wipe off any silicone grease, and cap the open outlet of the probe. Be careful not to lose any condensate that might be present. Remove the filter assembly, wipe off any silicone grease from the filter holder inlet, and cap this inlet. Remove the umbilical cord from the last impinger, and cap the impinger. After wiping off any silicone grease, cap off the filter holder outlet and any open impinger inlets and outlets. Ground-glass stoppers, plastic caps, or serum caps may be used to close these openings.
8.6.3 Transfer the probe and filter-impinger assembly to the cleanup area. This area should be clean and protected from the wind so that the chances of contaminating or losing the sample will be minimized.
8.6.4 Inspect the train prior to and during disassembly, and note any abnormal conditions. Treat the samples as follows:
8.6.4.1 Container No. 1 (Probe, Filter, and Impinger Catches).
8.6.4.1.1 Using a graduated cylinder, measure to the nearest ml, and record the volume of the water in the first three impingers; include any condensate in the probe in this determination. Transfer the impinger water from the graduated cylinder into a polyethylene container. Add the filter to this container. (The filter may be handled separately using procedures subject to the Administrator's approval.) Taking care that dust on the outside of the probe or other exterior surfaces does not get into the sample, clean all sample-exposed surfaces (including the probe nozzle, probe fitting, probe liner, first three impingers, impinger connectors, and filter holder) with water. Use less than 500 ml for the entire wash. Add the washings to the sample container. Perform the water rinses as follows:
8.6.4.1.2 Carefully remove the probe nozzle and rinse the inside surface with water from a wash bottle. Brush with a Nylon bristle brush, and rinse until the rinse shows no visible particles, after which make a final rinse of the inside surface. Brush and rinse the inside parts of the Swagelok fitting with water in a similar way.
8.6.4.1.3 Rinse the probe liner with water. While squirting the water into the upper end of the probe, tilt and rotate the probe so that all inside surfaces will be wetted with water. Let the water drain from the lower end into the sample container. A funnel (glass or polyethylene) may be used to aid in transferring the liquid washes to the container. Follow the rinse with a probe brush. Hold the probe in an inclined position, and squirt water into the upper end as the probe brush is being pushed with a twisting action through the probe. Hold the sample container underneath the lower end of the probe, and catch any water and particulate matter that is brushed from the probe. Run the brush through the probe three times or more. With stainless steel or other metal probes, run the brush through in the above prescribed manner at least six times since metal probes have small crevices in which particulate matter can be entrapped. Rinse the brush with water, and quantitatively collect these washings in the sample container. After the brushing, make a final rinse of the probe as described above.
8.6.4.1.4 It is recommended that two people clean the probe to minimize sample losses. Between sampling runs, keep brushes clean and protected from contamination.
8.6.4.1.5 Rinse the inside surface of each of the first three impingers (and connecting glassware) three separate times. Use a small portion of water for each rinse, and brush each sample-exposed surface with a Nylon bristle brush, to ensure recovery of fine particulate matter. Make a final rinse of each surface and of the brush.
8.6.4.1.6 After ensuring that all joints have been wiped clean of the silicone grease, brush and rinse with water the inside of the filter holder (front-half only, if filter is positioned between the third and fourth impingers). Brush and rinse each surface three times or more if needed. Make a final rinse of the brush and filter holder.
8.6.4.1.7 After all water washings and particulate matter have been collected in the sample container, tighten the lid so that water will not leak out when it is shipped to the laboratory. Mark the height of the fluid level to transport. Label the container clearly to identify its contents.
8.6.4.2 Container No. 2 (Sample Blank). Prepare a blank by placing an unused filter in a polyethylene container and adding a volume of water equal to the total volume in Container No. 1. Process the blank in the same manner as for Container No. 1.
8.6.4.3 Container No. 3 (Silica Gel). Note the color of the indicating silica gel to determine whether it has been completely spent, and make a notation of its condition. Transfer the silica gel from the fourth impinger to its original container, and seal. A funnel may be used to pour the silica gel and a rubber policeman to remove the silica gel from the impinger. It is not necessary to remove the small amount of dust particles that may adhere to the impinger wall and are difficult to remove. Since the gain in weight is to be used for moisture calculations, do not use any water or other liquids to transfer the silica gel. If a balance is available in the field, follow the analytical procedure for Container No. 3 in section 11.4.2.
9.0 Quality Control9.1 Miscellaneous Quality Control Measures.
Section | Quality control measure | Effect |
---|---|---|
8.4, 10.1 | Sampling equipment leak-check and calibration | Ensure accurate measurement of stack gas flow rate and sample volume. |
10.2 | Spectrophotometer calibration | Evaluate analytical technique, preparation of standards. |
11.3.3 | Interference/recovery efficiency check during distillation | Minimize negative effects of used acid. |
9.2 Volume Metering System Checks. Same as Method 5, section 9.2.
10.0 Calibration and Standardization Note:Maintain a laboratory log of all calibrations.
10.1 Sampling Equipment. Calibrate the probe nozzle, pitot tube, metering system, probe heater, temperature sensors, and barometer according to the procedures outlined in Method 5, sections 10.1 through 10.6. Conduct the leak-check of the metering system according to the procedures outlined in Method 5, section 8.4.1.
10.2 Spectrophotometer.
10.2.1 Prepare the blank standard by adding 10 ml of SPADNS mixed reagent to 50 ml of water.
10.2.2 Accurately prepare a series of standards from the 0.01 mg F−/ml standard fluoride solution (Section 7.3.10) by diluting 0, 2, 4, 6, 8, 10, 12, and 14 ml to 100 ml with deionized, distilled water. Pipet 50 ml from each solution, and transfer each to a separate 100-ml beaker. Then add 10 ml of SPADNS mixed reagent (Section 7.3.13) to each. These standards will contain 0, 10, 20, 30, 40, 50, 60, and 70 µg F−(0 to 1.4 µg/ml), respectively.
10.2.3 After mixing, place the blank and calibration standards in a constant temperature bath for 30 minutes before reading the absorbance with the spectrophotometer. Adjust all samples to this same temperature before analyzing.
10.2.4 With the spectrophotometer at 570 nm, use the blank standard to set the absorbance to zero. Determine the absorbance of the standards.
10.2.5 Prepare a calibration curve by plotting µg F−/50 ml versus absorbance on linear graph paper. Prepare the standard curve initially and thereafter whenever the SPADNS mixed reagent is newly made. Also, run a calibration standard with each set of samples and, if it differs from the calibration curve by more than ±2 percent, prepare a new standard curve.
11.0 Analytical Procedures11.1 Sample Loss Check. Note the liquid levels in Containers No. 1 and No. 2, determine whether leakage occurred during transport, and note this finding on the analytical data sheet. If noticeable leakage has occurred, either void the sample or use methods, subject to the approval of the Administrator, to correct the final results.
11.2 Sample Preparation. Treat the contents of each sample container as described below:
11.2.1 Container No. 1 (Probe, Filter, and Impinger Catches). Filter this container's contents, including the sampling filter, through Whatman No. 541 filter paper, or equivalent, into a 1500-ml beaker.
11.2.1.1 If the filtrate volume exceeds 900 ml, make the filtrate basic (red to phenolphthalein) with NaOH, and evaporate to less than 900 ml.
11.2.1.2 Place the filtered material (including sampling filter) in a nickel crucible, add a few ml of water, and macerate the filters with a glass rod.
11.2.1.2.1 Add 100 mg CaO to the crucible, and mix the contents thoroughly to form a slurry. Add two drops of phenolphthalein indicator. Place the crucible in a hood under infrared lamps or on a hot plate at low heat. Evaporate the water completely. During the evaporation of the water, keep the slurry basic (red to phenolphthalein) to avoid loss of F−. If the indicator turns colorless (acidic) during the evaporation, add CaO until the color turns red again.
11.2.1.2.2 After evaporation of the water, place the crucible on a hot plate under a hood, and slowly increase the temperature until the Whatman No. 541 and sampling filters char. It may take several hours to char the filters completely.
11.2.1.2.3 Place the crucible in a cold muffle furnace. Gradually (to prevent smoking) increase the temperature to 600 °C (1100 °F), and maintain this temperature until the contents are reduced to an ash. Remove the crucible from the furnace, and allow to cool.
11.2.1.2.4 Add approximately 4 g of crushed NaOH to the crucible, and mix. Return the crucible to the muffle furnace, and fuse the sample for 10 minutes at 600 °C.
11.2.1.2.5 Remove the sample from the furnace, and cool to ambient temperature. Using several rinsings of warm water, transfer the contents of the crucible to the beaker containing the filtrate. To ensure complete sample removal, rinse finally with two 20-ml portions of 25 percent H2SO4, and carefully add to the beaker. Mix well, and transfer to a 1-liter volumetric flask. Dilute to volume with water, and mix thoroughly. Allow any undissolved solids to settle.
11.2.2 Container No. 2 (Sample Blank). Treat in the same manner as described in section 11.2.1 above.
11.2.3 Adjustment of Acid/Water Ratio in Distillation Flask. Place 400 ml of water in the distillation flask, and add 200 ml of concentrated H2SO4. Add some soft glass beads and several small pieces of broken glass tubing, and assemble the apparatus as shown in Figure 13A-2. Heat the flask until it reaches a temperature of 175 °C (347 °F) to adjust the acid/water ratio for subsequent distillations. Discard the distillate.
Caution: Use a protective shield when carrying out this procedure. Observe standard precautions when mixing H2SO4 with water. Slowly add the acid to the flask with constant swirling.
11.3 Distillation.
11.3.1 Cool the contents of the distillation flask to below 80 °C (180 °F). Pipet an aliquot of sample containing less than 10.0 mg F− directly into the distillation flask, and add water to make a total volume of 220 ml added to the distillation flask. (To estimate the appropriate aliquot size, select an aliquot of the solution, and treat as described in section 11.4.1. This will be an approximation of the F− content because of possible interfering ions.)
Note:If the sample contains chloride, add 5 mg of Ag2SO4 to the flask for every mg of chloride.
11.3.2 Place a 250-ml volumetric flask at the condenser exit. Heat the flask as rapidly as possible with a Bunsen burner, and collect all the distillate up to 175 °C (347 °F). During heatup, play the burner flame up and down the side of the flask to prevent bumping. Conduct the distillation as rapidly as possible (15 minutes or less). Slow distillations have been found to produce low F− recoveries. Be careful not to exceed 175 °C (347 °F) to avoid causing H2SO4 to distill over. If F− distillation in the mg range is to be followed by a distillation in the fractional mg range, add 220 ml of water and distill it over as in the acid adjustment step to remove residual F− from the distillation system.
11.3.3 The acid in the distillation flask may be used until there is carry-over of interferences or poor F− recovery. Check for interference and for recovery efficiency every tenth distillation using a water blank and a standard solution. Change the acid whenever the F− recovery is less than 90 percent or the blank value exceeds 0.1 µg/ml.
11.4 Sample Analysis.
11.4.1 Containers No. 1 and No. 2.
11.4.1.1 After distilling suitable aliquots from Containers No. 1 and No. 2 according to section 11.3, dilute the distillate in the volumetric flasks to exactly 250 ml with water, and mix thoroughly. Pipet a suitable aliquot of each sample distillate (containing 10 to 40 µg F−/ml) into a beaker, and dilute to 50 ml with water. Use the same aliquot size for the blank. Add 10 ml of SPADNS mixed reagent (Section 7.3.13), and mix thoroughly.
11.4.1.2 After mixing, place the sample in a constant-temperature bath containing the standard solutions for 30 minutes before reading the absorbance on the spectrophotometer.
Note:After the sample and colorimetric reagent are mixed, the color formed is stable for approximately 2 hours. Also, a 3 °C (5.4 °F) temperature difference between the sample and standard solutions produces an error of approximately 0.005 mg F−/liter. To avoid this error, the absorbencies of the sample and standard solutions must be measured at the same temperature.
11.4.1.3 Set the spectrophotometer to zero absorbance at 570 nm with the zero reference solution (Section 7.3.12), and check the spectrophotometer calibration with the standard solution (Section 7.3.10). Determine the absorbance of the samples, and determine the concentration from the calibration curve. If the concentration does not fall within the range of the calibration curve, repeat the procedure using a different size aliquot.
11.4.2 Container No. 3 (Silica Gel). Weigh the spent silica gel (or silica gel plus impinger) to the nearest 0.5 g using a balance. This step may be conducted in the field.
12.0 Data Analysis and CalculationsCarry out calculations, retaining at least one extra significant figure beyond that of the acquired data. Round off figures after final calculation. Other forms of the equations may be used, provided that they yield equivalent results.
12.1 Nomenclature.
Ad = Aliquot of distillate taken for color development, ml. At = Aliquot of total sample added to still, ml. Bws = Water vapor in the gas stream, portion by volume. Cs = Concentration of F− in stack gas, mg/dscm (gr/dscf). Fc = F− concentration from the calibration curve, µg. Ft = Total F− in sample, mg. Tm = Absolute average dry gas meter (DGM) temperature (see Figure 5-3 of Method 5), °K (°R). Ts = Absolute average stack gas temperature (see Figure 5-3 of Method 5), °K (°R). Vd = Volume of distillate as diluted, ml. Vm(std) = Volume of gas sample as measured by DGM at standard conditions, dscm (dscf). Vt = Total volume of F− sample, after final dilution, ml. Vw(std) = Volume of water vapor in the gas sample at standard conditions, scm (scf)12.2 Average DGM Temperature and Average Orifice Pressure Drop (see Figure 5-3 of Method 5).
12.3 Dry Gas Volume. Calculate Vm(std), and adjust for leakage, if necessary, using Equation 5-1 of Method 5.
12.4 Volume of Water Vapor and Moisture Content. Calculate Vw(std) and Bws from the data obtained in this method. Use Equations 5-2 and 5-3 of Method 5.
12.5 Total Fluoride in Sample. Calculate the amount of F− in the sample using the following equation:
Where: K = 10−3 mg/µg (metric units) = 1.54 × 10−5 gr/µg (English units)12.6 Fluoride Concentration in Stack Gas. Determine the F− concentration in the stack gas using the following equation:
12.7 Isokinetic Variation. Same as Method 5, section 12.11.
13.0 Method PerformanceThe following estimates are based on a collaborative test done at a primary aluminum smelter. In the test, six laboratories each sampled the stack simultaneously using two sampling trains for a total of 12 samples per sampling run. Fluoride concentrations encountered during the test ranged from 0.1 to 1.4 mg F−/m 3.
13.1 Precision. The intra- and inter-laboratory standard deviations, which include sampling and analysis errors, were 0.044 mg F−/m 3 with 60 degrees of freedom and 0.064 mg F−/m 3 with five degrees of freedom, respectively.
13.2 Bias. The collaborative test did not find any bias in the analytical method.
13.3 Range. The range of this method is 0 to 1.4 µg F−/ml.
14.0 Pollution Prevention [Reserved] 15.0 Waste Management [Reserved] 16.0 Alternative Procedures16.1 Compliance with ASTM D 3270-73T, 80, 91, or 95 (incorporated by reference - see § 60.17) “Analysis of Fluoride Content of the Atmosphere and Plant Tissues (Semiautomated Method) is an acceptable alternative for the requirements specified in sections 11.2, 11.3, and 11.4.1 when applied to suitable aliquots of Containers 1 and 2 samples.
17.0 References1. Bellack, Ervin. Simplified Fluoride Distillation Method. J. of the American Water Works Association. 50:5306. 1958.
2. Mitchell, W.J., J.C. Suggs, and F.J. Bergman. Collaborative Study of EPA Method 13A and Method 13B. Publication No. EPA-300/4-77-050. U.S. Environmental Protection Agency, Research Triangle Park, NC. December 1977.
3. Mitchell, W.J., and M.R. Midgett. Adequacy of Sampling Trains and Analytical Procedures Used for Fluoride. Atm. Environ. 10:865-872. 1976.
18.0 Tables, Diagrams, Flowcharts, and Validation Data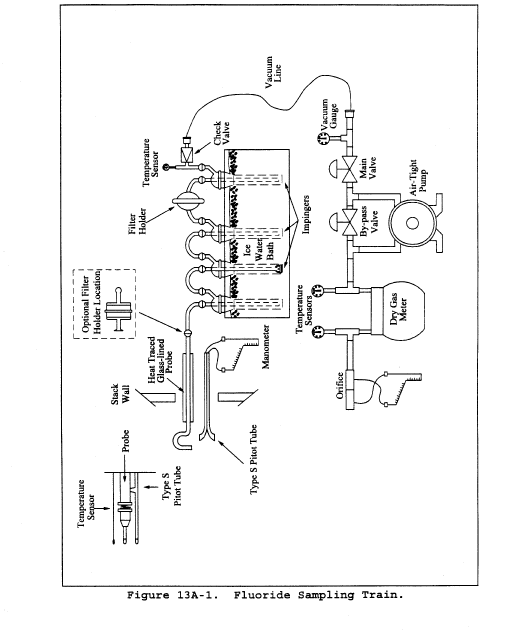
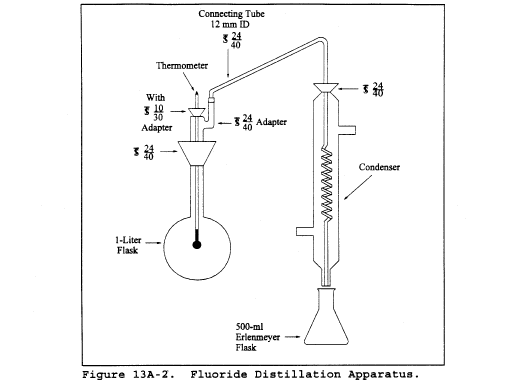
This method does not include all of the specifications (e.g., equipment and supplies) and procedures (e.g., sampling and analytical) essential to its performance. Some material is incorporated by reference from other methods in this part. Therefore, to obtain reliable results, persons using this method should have a thorough knowledge of at least the following additional test methods: Method 1, Method 2, Method 3, Method 5, and Method 13A.
1.0 Scope and Application1.1 Analytes.
Analyte | CAS No. | Sensitivity |
---|---|---|
Total fluorides as Fluorine | 7782-41-4 | Not determined. |
1.2 Applicability. This method is applicable for the determination of fluoride (F−) emissions from sources as specified in the regulations. It does not measure fluorocarbons, such as Freons.
1.3 Data Quality Objectives. Adherence to the requirements of this method will enhance the quality of the data obtained from air pollutant sampling methods.
2.0 SummaryGaseous and particulate F− are withdrawn isokinetically from the source and collected in water and on a filter. The total F− is then determined by the specific ion electrode method.
3.0 Definitions [Reserved] 4.0 InterferencesGrease on sample-exposed surfaces may cause low F− results because of adsorption.
5.0 Safety5.1 Disclaimer. This method may involve hazardous materials, operations, and equipment. This test method does not purport to address all of the safety problems associated with its use. It is the responsibility of the user of this test method to establish appropriate safety and health practices and to determine the applicability of regulatory limitations prior to performing this test method.
5.2 Corrosive Reagents. The following reagents are hazardous. Personal protective equipment and safe procedures are useful in preventing chemical splashes. If contact occurs, immediately flush with copious amounts of water at least 15 minutes. Remove clothing under shower and decontaminate. Treat residual chemical burn as thermal burn.
5.2.1 Sodium Hydroxide (NaOH). Causes severe damage to eye tissues and to skin. Inhalation causes irritation to nose, throat, and lungs. Reacts exothermically with limited amounts of water.
5.2.2 Sulfuric Acid (H2SO4). Rapidly destructive to body tissue. Will cause third degree burns. Eye damage may result in blindness. Inhalation may be fatal from spasm of the larynx, usually within 30 minutes. May cause lung tissue damage with edema. 1 mg/m 3 for 8 hours will cause lung damage or, in higher concentrations, death. Provide ventilation to limit inhalation. Reacts violently with metals and organics.
6.0 Equipment and Supplies6.1 Sample Collection and Sample Recovery. Same as Method 13A, sections 6.1 and 6.2, respectively.
6.2 Sample Preparation and Analysis. The following items are required for sample preparation and analysis:
6.2.1 Distillation Apparatus, Bunsen Burner, Electric Muffle Furnace, Crucibles, Beakers, Volumetric Flasks, Erlenmeyer Flasks or Plastic Bottles, Constant Temperature Bath, and Balance. Same as Method 13A, sections 6.3.1 to 6.3.9, respectively.
6.2.2 Fluoride Ion Activity Sensing Electrode.
6.2.3 Reference Electrode. Single junction, sleeve type.
6.2.4 Electrometer. A pH meter with millivolt-scale capable of ±0.1-mv resolution, or a specific ion meter made specifically for specific ion electrode use.
6.2.5 Magnetic Stirrer and Tetrafluoroethylene (TFE) Fluorocarbon-Coated Stirring Bars.
6.2.6 Beakers. Polyethylene, 100-ml.
7.0 Reagents and StandardsUnless otherwise indicated, all reagents are to conform to the specifications established by the Committee on Analytical Reagents of the American Chemical Society, where such specifications are available. Otherwise, use the best available grade.
7.1 Sample Collection and Sample Recovery. Same as Method 13A, sections 7.1 and 7.2, respectively.
7.2 Sample Preparation and Analysis. The following reagents and standards are required for sample analysis:
7.2.1 Calcium Oxide (CaO). Certified grade containing 0.005 percent F− or less.
7.2.2 Phenolphthalein Indicator. Dissolve 0.1 g phenolphthalein in a mixture of 50 ml of 90 percent ethanol and 50 ml water.
7.2.3 Sodium Hydroxide (NaOH), Pellets.
7.2.4 Sulfuric Acid (H2SO4), Concentrated.
7.2.5 Filters. Whatman No. 541, or equivalent.
7.2.6 Water. Same as section 7.1.2 of Method 13A.
7.2.7 Sodium Hydroxide, 5 M. Dissolve 20 g of NaOH in 100 ml of water.
7.2.8 Sulfuric Acid, 25 Percent (v/v). Mix 1 part of concentrated H2SO4 with 3 parts of water.
7.2.9 Total Ionic Strength Adjustment Buffer (TISAB). Place approximately 500 ml of water in a 1-liter beaker. Add 57 ml of glacial acetic acid, 58 g of sodium chloride, and 4 g of cyclohexylene dinitrilo tetraacetic acid. Stir to dissolve. Place the beaker in a water bath and cool to 20 °C (68 °F). Slowly add 5 M NaOH to the solution, measuring the pH continuously with a calibrated pH/reference electrode pair, until the pH is 5.3. Pour into a 1-liter volumetric flask, and dilute to volume with deionized, distilled water. Commercially prepared TISAB may be substituted for the above.
7.2.10 Fluoride Standard Solution, 0.1 M. Oven dry approximately 10 g of sodium fluoride (NaF) for a minimum of 2 hours at 110 °C (230 °F), and store in a desiccator. Then add 4.2 g of NaF to a 1-liter volumetric flask, and add enough water to dissolve. Dilute to volume with water.
8.0 Sample Collection, Preservation, Storage, and TransportSame as Method 13A, section 8.0.
9.0 Quality Control9.1 Miscellaneous Quality Control Measures.
Section | Quality control measure | Effect |
---|---|---|
8.0, 10.1 | Sampling equipment leak-check and calibration | Ensure accurate measurement of stack gas flow rate and sample volume. |
10.2 | Fluoride electrode | Evaluate analytical technique, preparation of standards. |
11.1 | Interference/recovery efficiency-check during distillation | Minimize negative effects of used acid. |
9.2 Volume Metering System Checks. Same as Method 5, section 9.2.
10.0 Calibration and Standardizations Note:Maintain a laboratory log of all calibrations.
10.1 Sampling Equipment. Same as Method 13A, section 10.1.
10.2 Fluoride Electrode. Prepare fluoride standardizing solutions by serial dilution of the 0.1 M fluoride standard solution. Pipet 10 ml of 0.1 M fluoride standard solution into a 100-ml volumetric flask, and make up to the mark with water for a 10−2 M standard solution. Use 10 ml of 10−2 M solution to make a 10−3 M solution in the same manner. Repeat the dilution procedure, and make 10−4 and 10−5 M solutions.
10.2.1 Pipet 50 ml of each standard into a separate beaker. Add 50 ml of TISAB to each beaker. Place the electrode in the most dilute standard solution. When a steady millivolt reading is obtained, plot the value on the linear axis of semilog graph paper versus concentration on the log axis. Plot the nominal value for concentration of the standard on the log axis, (e.g., when 50 ml of 10−2 M standard is diluted with 50 ml of TISAB, the concentration is still designated “10−2 M”).
10.2.2 Between measurements, soak the fluoride sensing electrode in water for 30 seconds, and then remove and blot dry. Analyze the standards going from dilute to concentrated standards. A straight-line calibration curve will be obtained, with nominal concentrations of 10−4, 10−3, 10−2, 10−1 fluoride molarity on the log axis plotted versus electrode potential (in mv) on the linear scale. Some electrodes may be slightly nonlinear between 10−5 and 10−4 M. If this occurs, use additional standards between these two concentrations.
10.2.3 Calibrate the fluoride electrode daily, and check it hourly. Prepare fresh fluoride standardizing solutions daily (10−2 M or less). Store fluoride standardizing solutions in polyethylene or polypropylene containers.
Note:Certain specific ion meters have been designed specifically for fluoride electrode use and give a direct readout of fluoride ion concentration. These meters may be used in lieu of calibration curves for fluoride measurements over a narrow concentration ranges. Calibrate the meter according to the manufacturer's instructions.
11.0 Analytical Procedures11.1 Sample Loss Check, Sample Preparation, and Distillation. Same as Method 13A, sections 11.1 through 11.3, except that the note following section 11.3.1 is not applicable.
11.2 Analysis.
11.2.1 Containers No. 1 and No. 2. Distill suitable aliquots from Containers No. 1 and No. 2. Dilute the distillate in the volumetric flasks to exactly 250 ml with water, and mix thoroughly. Pipet a 25-ml aliquot from each of the distillate into separate beakers. Add an equal volume of TISAB, and mix. The sample should be at the same temperature as the calibration standards when measurements are made. If ambient laboratory temperature fluctuates more than ±2 °C from the temperature at which the calibration standards were measured, condition samples and standards in a constant-temperature bath before measurement. Stir the sample with a magnetic stirrer during measurement to minimize electrode response time. If the stirrer generates enough heat to change solution temperature, place a piece of temperature insulating material, such as cork, between the stirrer and the beaker. Hold dilute samples (below 10−4 M fluoride ion content) in polyethylene beakers during measurement.
11.2.2 Insert the fluoride and reference electrodes into the solution. When a steady millivolt reading is obtained, record it. This may take several minutes. Determine concentration from the calibration curve. Between electrode measurements, rinse the electrode with water.
11.2.3 Container No. 3 (Silica Gel). Same as in Method 13A, section 11.4.2.
12.0 Data Analysis and CalculationsCarry out calculations, retaining at least one extra significant figure beyond that of the acquired data. Round off figures after final calculation.
12.1 Nomenclature. Same as Method 13A, section 12.1, with the addition of the following:
M = F− concentration from calibration curve, molarity.12.2 Average DGM Temperature and Average Orifice Pressure Drop, Dry Gas Volume, Volume of Water Vapor and Moisture Content, Fluoride Concentration in Stack Gas, and Isokinetic Variation. Same as Method 13A, sections 12.2 to 12.4, 12.6, and 12.7, respectively.
12.3 Total Fluoride in Sample. Calculate the amount of F− in the sample using Equation 13B-1:
Where: K = 19 [(mg·l)/(mole·ml)] (metric units) = 0.292 [(gr·l)/(mole·ml)] (English units) 13.0 Method PerformanceThe following estimates are based on a collaborative test done at a primary aluminum smelter. In the test, six laboratories each sampled the stack simultaneously using two sampling trains for a total of 12 samples per sampling run. Fluoride concentrations encountered during the test ranged from 0.1 to 1.4 mg F−/m 3.
13.1 Precision. The intra-laboratory and inter-laboratory standard deviations, which include sampling and analysis errors, are 0.037 mg F−/m 3 with 60 degrees of freedom and 0.056 mg F−/m 3 with five degrees of freedom, respectively.
13.2 Bias. The collaborative test did not find any bias in the analytical method.
13.3 Range. The range of this method is 0.02 to 2,000 µg F−/ml; however, measurements of less than 0.1 µg F−/ml require extra care.
14.0 Pollution Prevention [Reserved] 15.0 Waste Management [Reserved] 16.0 Alternative Procedures16.1 Compliance with ASTM D 3270-73T, 91, 95 “Analysis for Fluoride Content of the Atmosphere and Plant Tissues (Semiautomated Method)” is an acceptable alternative for the distillation and analysis requirements specified in sections 11.1 and 11.2 when applied to suitable aliquots of Containers 1 and 2 samples.
17.0 ReferencesSame as Method 13A, section 16.0, References 1 and 2, with the following addition:
1. MacLeod, Kathryn E., and Howard L. Crist. Comparison of the SPADNS-Zirconium Lake and Specific Ion Electrode Methods of Fluoride Determination in Stack Emission Samples. Analytical Chemistry. 45:1272-1273. 1973.
18.0 Tables, Diagrams, Flowcharts, and Validation Data [Reserved] Method 14 - Determination of Fluoride Emissions From Potroom Roof Monitors for Primary Aluminum Plants Note:This method does not include all of the specifications (e.g., equipment and supplies) and procedures (e.g., sampling and analytical) essential to its performance. Some material is incorporated by reference from other methods in this part. Therefore, to obtain reliable results, persons using this method should have a thorough knowledge of at least the following additional test methods: Method 1, Method 2, Method 3, Method 5, Method 13A, and Method 13B.
1.0 Scope and Application1.1 Analytes.
Analyte | CAS No. | Sensitivity |
---|---|---|
Total fluorides as Fluorine | 7782-41-4 | Not determined. |
1.2 Applicability. This method is applicable for the determination of fluoride emissions from roof monitors at primary aluminum reduction plant potroom groups.
1.3 Data Quality Objectives. Adherence to the requirements of this method will enhance the quality of the data obtained from air pollutant sampling methods.
2.0 Summary of Method2.1 Gaseous and particulate fluoride roof monitor emissions are drawn into a permanent sampling manifold through several large nozzles. The sample is transported from the sampling manifold to ground level through a duct. The fluoride content of the gas in the duct is determined using either Method 13A or Method 13B. Effluent velocity and volumetric flow rate are determined using anemometers located in the roof monitor.
3.0 DefinitionsPotroom means a building unit which houses a group of electrolytic cells in which aluminum is produced.
Potroom group means an uncontrolled potroom, a potroom which is controlled individually, or a group of potrooms or potroom segments ducted to a common control system.
Roof monitor means that portion of the roof of a potroom where gases not captured at the cell exit from the potroom.
4.0 InterferencesSame as section 4.0 of either Method 13A or Method 13B, with the addition of the following:
4.1 Magnetic Field Effects. Anemometer readings can be affected by potroom magnetic field effects. section 6.1 provides for minimization of this interference through proper shielding or encasement of anemometer components.
5.0 Safety5.1 Disclaimer. This method may involve hazardous materials, operations, and equipment. This test method may not address all of the safety problems associated with its use. It is the responsibility of the user of this test method to establish appropriate safety and health practices and to determine the applicability of regulatory limitations prior to performing this test method.
5.2 Corrosive Reagents. Same as section 5.2 of either Method 13A or Method 13B.
6.0 Equipment and SuppliesSame as section 6.0 of either Method 13A or Method 13B, as applicable, with the addition of the following:
6.1 Velocity Measurement Apparatus.
6.1.1 Anemometer Specifications. Propeller anemometers, or equivalent. Each anemometer shall meet the following specifications:
6.1.1.1 Its propeller shall be made of polystyrene, or similar material of uniform density. To ensure uniformity of performance among propellers, it is desirable that all propellers be made from the same mold.
6.1.1.2 The propeller shall be properly balanced, to optimize performance.
6.1.1.3 When the anemometer is mounted horizontally, its threshold velocity shall not exceed 15 m/min (50 ft/min).
6.1.1.4 The measurement range of the anemometer shall extend to at least 600 m/min (2,000 ft/min).
6.1.1.5 The anemometer shall be able to withstand prolonged exposure to dusty and corrosive environments; one way of achieving this is to purge the bearings of the anemometer continuously with filtered air during operation.
6.1.1.6 All anemometer components shall be properly shielded or encased, such that the performance of the anemometer is uninfluenced by potroom magnetic field effects.
6.1.1.7 A known relationship shall exist between the electrical output signal from the anemometer generator and the propeller shaft rpm (see section 10.2.1). Anemometers having other types of output signals (e.g., optical) may be used, subject to the approval of the Administrator. If other types of anemometers are used, there must be a known relationship between output signal and shaft rpm (see section 10.2.2).
6.1.1.8 Each anemometer shall be equipped with a suitable readout system (see section 6.1.3).
6.1.2 Anemometer Installation Requirements.
6.1.2.1 Single, Isolated Potroom. If the affected facility consists of a single, isolated potroom (or potroom segment), install at least one anemometer for every 85 m (280 ft) of roof monitor length. If the length of the roof monitor divided by 85 m (280 ft) is not a whole number, round the fraction to the nearest whole number to determine the number of anemometers needed. For monitors that are less than 130 m (430 ft) in length, use at least two anemometers. Divide the monitor cross-section into as many equal areas as anemometers, and locate an anemometer at the centroid of each equal area. See exception in section 6.1.2.3.
6.1.2.2 Two or More Potrooms. If the affected facility consists of two or more potrooms (or potroom segments) ducted to a common control device, install anemometers in each potroom (or segment) that contains a sampling manifold. Install at least one anemometer for every 85 m (280 ft) of roof monitor length of the potroom (or segment). If the potroom (or segment) length divided by 85 m (280 ft) is not a whole number, round the fraction to the nearest whole number to determine the number of anemometers needed. If the potroom (or segment) length is less than 130 m (430 ft), use at least two anemometers. Divide the potroom (or segment) monitor cross-section into as many equal areas as anemometers, and locate an anemometer at the centroid of each equal area. See exception in section 6.1.2.3.
6.1.2.3 Placement of Anemometer at the Center of Manifold. At least one anemometer shall be installed in the immediate vicinity (i.e., within 10 m (33 ft)) of the center of the manifold (see section 6.2.1). For its placement in relation to the width of the monitor, there are two alternatives. The first is to make a velocity traverse of the width of the roof monitor where an anemometer is to be placed and install the anemometer at a point of average velocity along this traverse. The traverse may be made with any suitable low velocity measuring device, and shall be made during normal process operating conditions. The second alternative is to install the anemometer half-way across the width of the roof monitor. In this latter case, the velocity traverse need not be conducted.
6.1.3 Recorders. Recorders that are equipped with suitable auxiliary equipment (e.g., transducers) for converting the output signal from each anemometer to a continuous recording of air flow velocity or to an integrated measure of volumetric flowrate shall be used. A suitable recorder is one that allows the output signal from the propeller anemometer to be read to within 1 percent when the velocity is between 100 and 120 m/min (330 and 390 ft/min). For the purpose of recording velocity, “continuous” shall mean one readout per 15-minute or shorter time interval. A constant amount of time shall elapse between readings. Volumetric flow rate may be determined by an electrical count of anemometer revolutions. The recorders or counters shall permit identification of the velocities or flowrates measured by each individual anemometer.
6.1.4 Pitot Tube. Standard-type pitot tube, as described in section 6.7 of Method 2, and having a coefficient of 0.99 ±0.01.
6.1.5 Pitot Tube (Optional). Isolated, Type S pitot, as described in section 6.1 of Method 2, and having a known coefficient, determined as outlined in section 4.1 of Method 2.
6.1.6 Differential Pressure Gauge. Inclined manometer, or equivalent, as described in section 6.1.2 of Method 2.
6.2 Roof Monitor Air Sampling System.
6.2.1 Manifold System and Ductwork. A minimum of one manifold system shall be installed for each potroom group. The manifold system and ductwork shall meet the following specifications:
6.2.1.1 The manifold system and connecting duct shall be permanently installed to draw an air sample from the roof monitor to ground level. A typical installation of a duct for drawing a sample from a roof monitor to ground level is shown in Figure 14-1 in section 17.0. A plan of a manifold system that is located in a roof monitor is shown in Figure 14-2. These drawings represent a typical installation for a generalized roof monitor. The dimensions on these figures may be altered slightly to make the manifold system fit into a particular roof monitor, but the general configuration shall be followed.
6.2.1.2 There shall be eight nozzles, each having a diameter of 0.40 to 0.50 m.
6.2.1.3 The length of the manifold system from the first nozzle to the eighth shall be 35 m (115 ft) or eight percent of the length of the potroom (or potroom segment) roof monitor, whichever is greater. Deviation from this requirement is subject to the approval of the Administrator.
6.2.1.4 The duct leading from the roof monitor manifold system shall be round with a diameter of 0.30 to 0.40 m (1.0 to 1.3 ft). All connections in the ductwork shall be leak-free.
6.2.1.5 As shown in Figure 14-2, each of the sample legs of the manifold shall have a device, such as a blast gate or valve, to enable adjustment of the flow into each sample nozzle.
6.2.1.6 The manifold system shall be located in the immediate vicinity of one of the propeller anemometers (see section 8.1.1.4) and as close as possible to the midsection of the potroom (or potroom segment). Avoid locating the manifold system near the end of a potroom or in a section where the aluminum reduction pot arrangement is not typical of the rest of the potroom (or potroom segment). The sample nozzles shall be centered in the throat of the roof monitor (see Figure 14-1).
6.2.1.7 All sample-exposed surfaces within the nozzles, manifold, and sample duct shall be constructed with 316 stainless steel. Alternatively, aluminum may be used if a new ductwork is conditioned with fluoride-laden roof monitor air for a period of six weeks before initial testing. Other materials of construction may be used if it is demonstrated through comparative testing, to the satisfaction of the Administrator, that there is no loss of fluorides in the system.
6.2.1.8 Two sample ports shall be located in a vertical section of the duct between the roof monitor and the exhaust fan (see section 6.2.2). The sample ports shall be at least 10 duct diameters downstream and three diameters upstream from any flow disturbance such as a bend or contraction. The two sample ports shall be situated 90° apart. One of the sample ports shall be situated so that the duct can be traversed in the plane of the nearest upstream duct bend.
6.2.2 Exhaust Fan. An industrial fan or blower shall be attached to the sample duct at ground level (see Figure 14-1). This exhaust fan shall have a capacity such that a large enough volume of air can be pulled through the ductwork to maintain an isokinetic sampling rate in all the sample nozzles for all flow rates normally encountered in the roof monitor. The exhaust fan volumetric flow rate shall be adjustable so that the roof monitor gases can be drawn isokinetically into the sample nozzles. This control of flow may be achieved by a damper on the inlet to the exhauster or by any other workable method.
6.3 Temperature Measurement Apparatus. To monitor and record the temperature of the roof monitor effluent gas, and consisting of the following:
6.3.1 Temperature Sensor. A temperature sensor shall be installed in the roof monitor near the sample duct. The temperature sensor shall conform to the specifications outlined in Method 2, section 6.3.
6.3.2 Signal Transducer. Transducer, to change the temperature sensor voltage output to a temperature readout.
6.3.3 Thermocouple Wire. To reach from roof monitor to signal transducer and recorder.
6.3.4 Recorder. Suitable recorder to monitor the output from the thermocouple signal transducer.
7.0 Reagents and StandardsSame as section 7.0 of either Method 13A or Method 13B, as applicable.
8.0 Sample Collection, Preservation, Storage, and Transport8.1 Roof Monitor Velocity Determination.
8.1.1 Velocity Estimate(s) for Setting Isokinetic Flow. To assist in setting isokinetic flow in the manifold sample nozzles, the anticipated average velocity in the section of the roof monitor containing the sampling manifold shall be estimated before each test run. Any convenient means to make this estimate may be used (e.g., the velocity indicated by the anemometer in the section of the roof monitor containing the sampling manifold may be continuously monitored during the 24-hour period before the test run). If there is question as to whether a single estimate of average velocity is adequate for an entire test run (e.g., if velocities are anticipated to be significantly different during different potroom operations), the test run may be divided into two or more “sub-runs,” and a different estimated average velocity may be used for each sub-run (see section 8.4.2).
8.1.2 Velocity Determination During a Test Run. During the actual test run, record the velocity or volumetric flowrate readings of each propeller anemometer in the roof monitor. Readings shall be taken from each anemometer at equal time intervals of 15 minutes or less (or continuously).
8.2 Temperature Recording. Record the temperature of the roof monitor effluent gases at least once every 2 hours during the test run.
8.3 Pretest Ductwork Conditioning. During the 24-hour period immediately preceding the test run, turn on the exhaust fan, and draw roof monitor air through the manifold system and ductwork. Adjust the fan to draw a volumetric flow through the duct such that the velocity of gas entering the manifold nozzles approximates the average velocity of the air exiting the roof monitor in the vicinity of the sampling manifold.
8.4 Manifold Isokinetic Sample Rate Adjustment(s).
8.4.1 Initial Adjustment. Before the test run (or first sub-run, if applicable; see sections 8.1.1 and 8.4.2), adjust the fan such that air enters the manifold sample nozzles at a velocity equal to the appropriate estimated average velocity determined under section 8.1.1. Use Equation 14-1 (Section 12.2.2) to determine the correct stream velocity needed in the duct at the sampling location, in order for sample gas to be drawn isokinetically into the manifold nozzles. Next, verify that the correct stream velocity has been achieved, by performing a pitot tube traverse of the sample duct (using either a standard or Type S pitot tube); use the procedure outlined in Method 2.
8.4.2 Adjustments During Run. If the test run is divided into two or more “sub-runs” (see section 8.1.1), additional isokinetic rate adjustment(s) may become necessary during the run. Any such adjustment shall be made just before the start of a sub-run, using the procedure outlined in section 8.4.1 above.
Note:Isokinetic rate adjustments are not permissible during a sub-run.
8.5 Pretest Preparation, Preliminary Determinations, Preparation of Sampling Train, Leak-Check Procedures, Sampling Train Operation, and Sample Recovery. Same as Method 13A, sections 8.1 through 8.6, with the exception of the following:
8.5.1 A single train shall be used for the entire sampling run. Alternatively, if two or more sub-runs are performed, a separate train may be used for each sub-run; note, however, that if this option is chosen, the area of the sampling nozzle shall be the same (±2 percent) for each train. If the test run is divided into sub-runs, a complete traverse of the duct shall be performed during each sub-run.
8.5.2 Time Per Run. Each test run shall last 8 hours or more; if more than one run is to be performed, all runs shall be of approximately the same (±10 percent) length. If questions exist as to the representativeness of an 8-hour test, a longer period should be selected. Conduct each run during a period when all normal operations are performed underneath the sampling manifold. For most recently-constructed plants, 24 hours are required for all potroom operations and events to occur in the area beneath the sampling manifold. During the test period, all pots in the potroom group shall be operated such that emissions are representative of normal operating conditions in the potroom group.
9.0 Quality Control9.1 Miscellaneous Quality Control Measures.
Section | Quality Control Measure | Effect |
---|---|---|
8.0, 10.0 | Sampling equipment leak-check and calibration | Ensure accurate measurement of gas flow rate in duct and of sample volume. |
10.3, 10.4 | Initial and periodic performance checks of roof monitor effluent gas characterization apparatus | Ensure accurate and precise measurement of roof monitor effluent gas temperature and flow rate. |
11.0 | Interference/recovery efficiency check during distillation | Minimize negative effects of used acid. |
9.2 Volume Metering System Checks. Same as Method 5, section 9.2.
10.0 Calibration and StandardizationSame as section 10.0 of either Method 13A or Method 13B, as applicable, with the addition of the following:
10.1 Manifold Intake Nozzles. The manifold intake nozzles shall be calibrated when the manifold system is installed or, alternatively, the manifold may be preassembled and the nozzles calibrated on the ground prior to installation. The following procedures shall be observed:
10.1.1 Adjust the exhaust fan to draw a volumetric flow rate (refer to Equation 14-1) such that the entrance velocity into each manifold nozzle approximates the average effluent velocity in the roof monitor.
10.1.2 Measure the velocity of the air entering each nozzle by inserting a standard pitot tube into a 2.5 cm or less diameter hole (see Figure 14-2) located in the manifold between each blast gate (or valve) and nozzle. Note that a standard pitot tube is used, rather than a type S, to eliminate possible velocity measurement errors due to cross-section blockage in the small (0.13 m diameter) manifold leg ducts. The pitot tube tip shall be positioned at the center of each manifold leg duct. Take care to ensure that there is no leakage around the pitot tube, which could affect the indicated velocity in the manifold leg.
10.1.3 If the velocity of air being drawn into each nozzle is not the same, open or close each blast gate (or valve) until the velocity in each nozzle is the same. Fasten each blast gate (or valve) so that it will remain in position, and close the pitot port holes.
10.2 Initial Calibration of Propeller Anemometers.
10.2.1 Anemometers that meet the specifications outlined in section 6.1.1 need not be calibrated, provided that a reference performance curve relating anemometer signal output to air velocity (covering the velocity range of interest) is available from the manufacturer. If a reference performance curve is not available from the manufacturer, such a curve shall be generated.
For the purpose of this method, a “reference” performance curve is defined as one that has been derived from primary standard calibration data, with the anemometer mounted vertically. “Primary standard” data are obtainable by: (a) direct calibration of one or more of the anemometers by the National Institute of Standards and Technology (NIST); (b) NIST-traceable calibration; or (c) Calibration by direct measurement of fundamental parameters such as length and time (e.g., by moving the anemometers through still air at measured rates of speed, and recording the output signals).
10.2.2 Anemometers having output signals other than electrical (e.g., optical) may be used, subject to the approval of the Administrator. If other types of anemometers are used, a reference performance curve shall be generated, using procedures subject to the approval of the Administrator.
10.2.3 The reference performance curve shall be derived from at least the following three points: 60 ±15, 900 ±100, and 1800 ±100 rpm.
10.3 Initial Performance Checks. Conduct these checks within 60 days before the first performance test.
10.3.1 Anemometers. A performance-check shall be conducted as outlined in sections 10.3.1.1 through 10.3.1.3. Alternatively, any other suitable method that takes into account the signal output, propeller condition, and threshold velocity of the anemometer may be used, subject to the approval of the Administrator.
10.3.1.1 Check the signal output of the anemometer by using an accurate rpm generator (see Figure 14-3) or synchronous motors to spin the propeller shaft at each of the three rpm settings described in section 10.2.3, and measuring the output signal at each setting. If, at each setting, the output signal is within 5 percent of the manufacturer's value, the anemometer can be used. If the anemometer performance is unsatisfactory, the anemometer shall either be replaced or repaired.
10.3.1.2 Check the propeller condition, by visually inspecting the propeller, making note of any significant damage or warpage; damaged or deformed propellers shall be replaced.
10.3.1.3 Check the anemometer threshold velocity as follows: With the anemometer mounted as shown in Figure 14-4(A), fasten a known weight (a straight-pin will suffice) to the anemometer propeller at a fixed distance from the center of the propeller shaft. This will generate a known torque; for example, a 0.1-g weight, placed 10 cm from the center of the shaft, will generate a torque of 1.0 g-cm. If the known torque causes the propeller to rotate downward, approximately 90° [see Figure 14-4(B)], then the known torque is greater than or equal to the starting torque; if the propeller fails to rotate approximately 90°, the known torque is less than the starting torque. By trying different combinations of weight and distance, the starting torque of a particular anemometer can be satisfactorily estimated. Once an estimate of the starting torque has been obtained, the threshold velocity of the anemometer (for horizontal mounting) can be estimated from a graph such as Figure 14-5 (obtained from the manufacturer). If the horizontal threshold velocity is acceptable [<15 m/min (50 ft/min), when this technique is used], the anemometer can be used. If the threshold velocity of an anemometer is found to be unacceptably high, the anemometer shall either be replaced or repaired.
10.3.2 Recorders and Counters. Check the calibration of each recorder and counter (see section 6.1.2) at a minimum of three points, approximately spanning the expected range of velocities. Use the calibration procedures recommended by the manufacturer, or other suitable procedures (subject to the approval of the Administrator). If a recorder or counter is found to be out of calibration by an average amount greater than 5 percent for the three calibration points, replace or repair the system; otherwise, the system can be used.
10.3.3 Temperature Measurement Apparatus. Check the calibration of the Temperature Measurement Apparatus, using the procedures outlined in section 10.3 of Method 2, at temperatures of 0, 100, and 150 °C (32, 212, and 302 °F). If the calibration is off by more than 5 °C (9 °F) at any of the temperatures, repair or replace the apparatus; otherwise, the apparatus can be used.
10.4 Periodic Performance Checks. Repeat the procedures outlined in section 10.3 no more than 12 months after the initial performance checks. If the above systems pass the performance checks (i.e., if no repair or replacement of any component is necessary), continue with the performance checks on a 12-month interval basis. However, if any of the above systems fail the performance checks, repair or replace the system(s) that failed, and conduct the periodic performance checks on a 3-month interval basis, until sufficient information (to the satisfaction of the Administrator) is obtained to establish a modified performance check schedule and calculation procedure.
Note:If any of the above systems fails the 12-month periodic performance checks, the data for the past year need not be recalculated.
11.0 Analytical ProceduresSame as section 11.0 of either Method 13A or Method 13B.
12.0 Data Analysis and CalculationsSame as section 12.0 of either Method 13A or Method 13B, as applicable, with the following additions and exceptions:
12.1 Nomenclature.
A = Roof monitor open area, m 2 (ft 2). Bws = Water vapor in the gas stream, portion by volume. Cs = Average fluoride concentration in roof monitor air, mg F/dscm (gr/dscf). Dd = Diameter of duct at sampling location, m (ft). Dn = Diameter of a roof monitor manifold nozzle, m (ft). F = Emission Rate multiplication factor, dimensionless. Ft = Total fluoride mass collected during a particular sub-run (from Equation 13A-1 of Method 13A or Equation 13B-1 of Method 13B), mg F− (gr F−). Md = Mole fraction of dry gas, dimensionless. Prm = Pressure in the roof monitor; equal to barometric pressure for this application. Qsd = Average volumetric flow from roof monitor at standard conditions on a dry basis, m 3/min. Trm = Average roof monitor temperature (from section 8.2), °C ( °F). Vd = Desired velocity in duct at sampling location, m/sec. Vm = Anticipated average velocity (from section 8.1.1) in sampling duct, m/sec. Vmt = Arithmetic mean roof monitor effluent gas velocity, m/sec. Vs = Actual average velocity in the sampling duct (from Equation 2-9 of Method 2 and data obtained from Method 13A or 13B), m/sec.12.2 Isokinetic Sampling Check.
12.2.1 Calculate the arithmetic mean of the roof monitor effluent gas velocity readings (vm) as measured by the anemometer in the section of the roof monitor containing the sampling manifold. If two or more sub-runs have been performed, the average velocity for each sub-run may be calculated separately.
12.2.2 Calculate the expected average velocity (vd) in the duct, corresponding to each value of vm obtained under section 12.2.1, using Equation 14-1.
Where: 8 = number of required manifold nozzles. 60 = sec/min.12.2.3 Calculate the actual average velocity (vs) in the sampling duct for each run or sub-run according to Equation 2-9 of Method 2, using data obtained during sampling (Section 8.0 of Method 13A).
12.2.4 Express each vs value from section 12.2.3 as a percentage of the corresponding vd value from section 12.2.2.
12.2.4.1 If vs is less than or equal to 120 percent of vd, the results are acceptable (note that in cases where the above calculations have been performed for each sub-run, the results are acceptable if the average percentage for all sub-runs is less than or equal to 120 percent).
12.2.4.2 If vs is more than 120 percent of vd, multiply the reported emission rate by the following factor:
12.3 Average Velocity of Roof Monitor Effluent Gas. Calculate the arithmetic mean roof monitor effluent gas velocity (vmt) using all the velocity or volumetric flow readings from section 8.1.2.
12.4 Average Temperature of Roof Monitor Effluent Gas. Calculate the arithmetic mean roof monitor effluent gas temperature (Tm) using all the temperature readings recorded in section 8.2.
12.5 Concentration of Fluorides in Roof Monitor Effluent Gas.
12.5.1 If a single sampling train was used throughout the run, calculate the average fluoride concentration for the roof monitor using Equation 13A-2 of Method 13A.
12.5.2 If two or more sampling trains were used (i.e., one per sub-run), calculate the average fluoride concentration for the run using Equation 14-3:
Where: n = Total number of sub-runs.12.6 Mole Fraction of Dry Gas.
12.7 Average Volumetric Flow Rate of Roof Monitor Effluent Gas. Calculate the arithmetic mean volumetric flow rate of the roof monitor effluent gases using Equation 14-5.
Where: K1 = 0.3858 K/mm Hg for metric units, = 17.64 °R/in. Hg for English units. 13.0 Method Performance [Reserved] 14.0 Pollution Prevention [Reserved] 15.0 Waste Management [Reserved] 16.0 ReferencesSame as section 16.0 of either Method 13A or Method 13B, as applicable, with the addition of the following:
1. Shigehara, R.T. A Guideline for Evaluating Compliance Test Results (Isokinetic Sampling Rate Criterion). U.S. Environmental Protection Agency, Emission Measurement Branch, Research Triangle Park, NC. August 1977.
17.0 Tables, Diagrams, Flowcharts, and Validation Data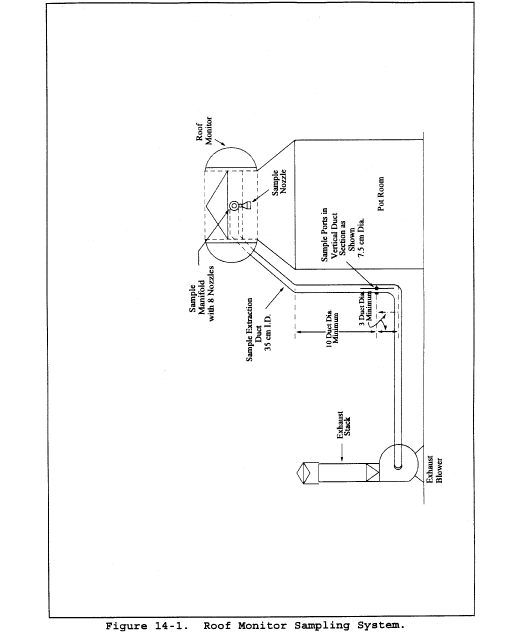
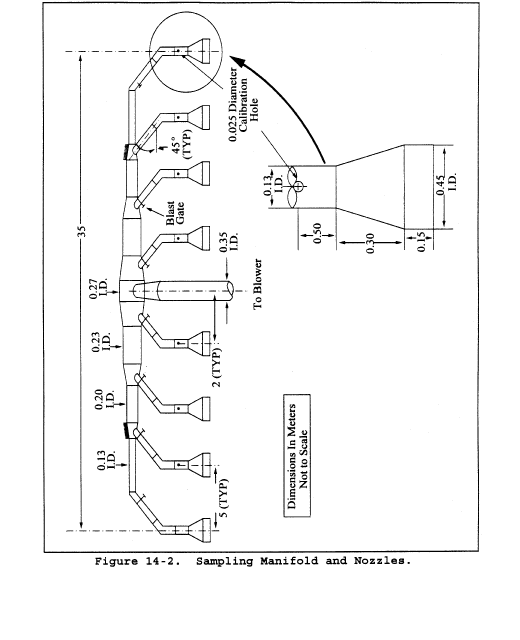
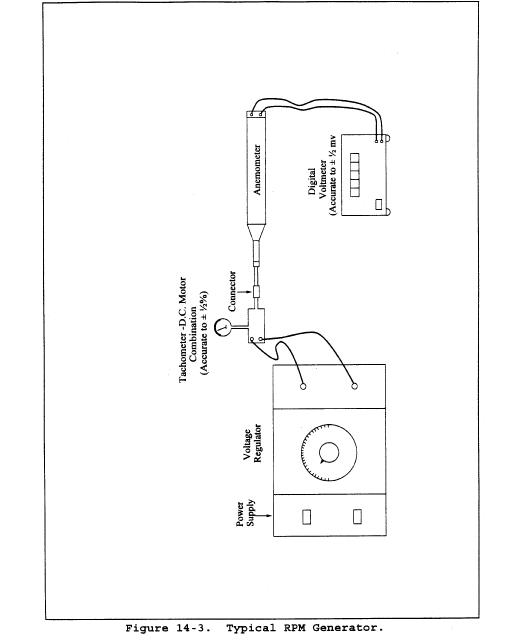
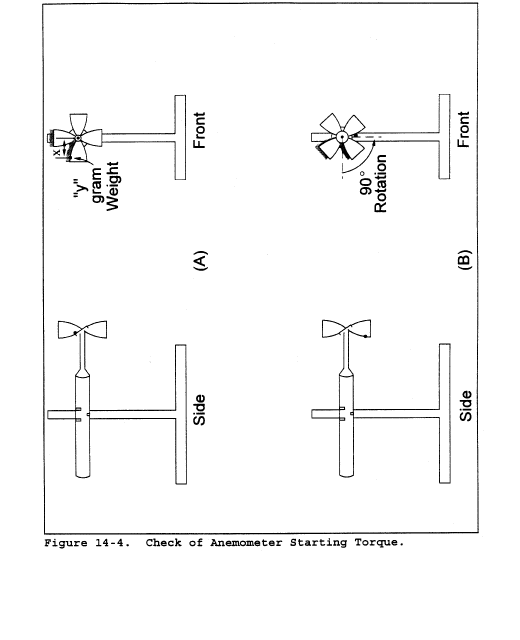
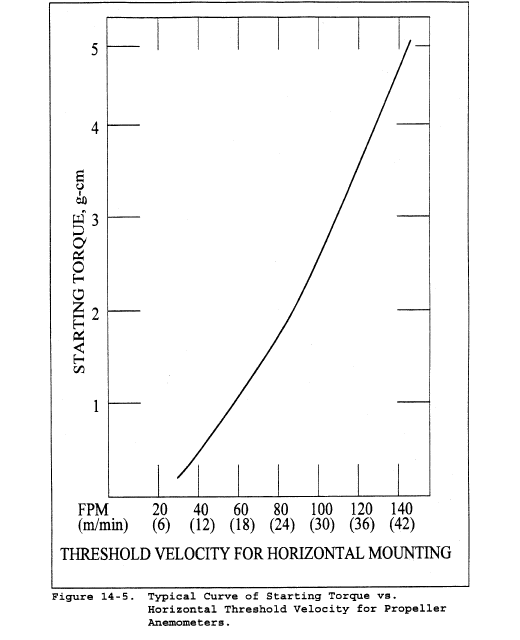
This method does not include all the specifications (e.g., equipment and supplies) and procedures (e.g., sampling) essential to its performance. Some material is incorporated by reference from other methods in this part. Therefore, to obtain reliable results, persons using this method should have a thorough knowledge of at least the following additional test methods: Method 5, Methods 13A and 13B, and Method 14 of this appendix.
1.0 Scope and Application1.1 Analytes.
Analyte | CAS No. | Sensitivity |
---|---|---|
Total fluorides | None assigned | Not determined. |
Includes hydrogen fluoride | 007664-39-3 | Not determined. |
1.2 Applicability. This method is applicable for the determination of total fluorides (TF) emissions from sources specified in the applicable regulation. This method was developed by consensus with the Aluminum Association and the U.S. Environmental Protection Agency (EPA).
2.0 Summary of Method2.1 Total fluorides, in the form of solid and gaseous fluorides, are withdrawn from the ascending air stream inside of an aluminum reduction potroom and, prior to exiting the potroom roof monitor, into a specific cassette arrangement. The cassettes are connected by tubing to flowmeters and a manifold system that allows for the equal distribution of volume pulled through each cassette, and finally to a dry gas meter. The cassettes have a specific internal arrangement of one unaltered cellulose filter and support pad in the first section of the cassette for solid fluoride retention and two cellulose filters with support pads that are impregnated with sodium formate for the chemical absorption of gaseous fluorides in the following two sections of the cassette. A minimum of eight cassettes shall be used for a potline and shall be strategically located at equal intervals across the potroom roof so as to encompass a minimum of 8 percent of the total length of the potroom. A greater number of cassettes may be used should the regulated facility choose to do so. The mass flow rate of pollutants is determined with anemometers and temperature sensing devices located immediately below the opening of the roof monitor and spaced evenly within the cassette group.
3.0 Definitions3.1 Cassette. A segmented, styrene acrylonitrile cassette configuration with three separate segments and a base, for the purpose of this method, to capture and retain fluoride from potroom gases.
3.2 Cassette arrangement. The cassettes, tubing, manifold system, flowmeters, dry gas meter, and any other related equipment associated with the actual extraction of the sample gas stream.
3.3 Cassette group. That section of the potroom roof monitor where a distinct group of cassettes is located.
3.4 Potline. A single, discrete group of electrolytic reduction cells electrically connected in series, in which alumina is reduced to form aluminum.
3.5 Potroom. A building unit that houses a group of electrolytic reduction cells in which aluminum is produced.
3.6 Potroom group. An uncontrolled potroom, a potroom that is controlled individually, or a group of potrooms or potroom segments ducted to a common primary control system.
3.7 Primary control system. The equipment used to capture the gases and particulate matter generated during the reduction process and the emission control device(s) used to remove pollutants prior to discharge of the cleaned gas to the atmosphere.
3.8 Roof monitor. That portion of the roof of a potroom building where gases, not captured at the cell, exit from the potroom.
3.9 Total fluorides (TF). Elemental fluorine and all fluoride compounds as measured by Methods 13A or 13B of this appendix or by an approved alternative method.
4.0 Interferences and Known Limitations4.1 There are two principal categories of limitations that must be addressed when using this method. The first category is sampling bias and the second is analytical bias. Biases in sampling can occur when there is an insufficient number of cassettes located along the roof monitor of a potroom or if the distribution of those cassettes is spatially unequal. Known sampling biases also can occur when there are leaks within the cassette arrangement and if anemometers and temperature devices are not providing accurate data. Applicable instruments must be properly calibrated to avoid sampling bias. Analytical biases can occur when instrumentation is not calibrated or fails calibration and the instrument is used out of proper calibration. Additionally, biases can occur in the laboratory if fusion crucibles retain residual fluorides over lengthy periods of use. This condition could result in falsely elevated fluoride values. Maintaining a clean work environment in the laboratory is crucial to producing accurate values.
4.2 Biases during sampling can be avoided by properly spacing the appropriate number of cassettes along the roof monitor, conducting leak checks of the cassette arrangement, calibrating the dry gas meter every 30 days, verifying the accuracy of individual flowmeters (so that there is no more than 5 percent difference in the volume pulled between any two flowmeters), and calibrating or replacing anemometers and temperature sensing devices as necessary to maintain true data generation.
4.3 Analytical biases can be avoided by calibrating instruments according to the manufacturer's specifications prior to conducting any analyses, by performing internal and external audits of up to 10 percent of all samples analyzed, and by rotating individual crucibles as the “blank” crucible to detect any potential residual fluoride carry-over to samples. Should any contamination be discovered in the blank crucible, the crucible shall be thoroughly cleaned to remove any detected residual fluorides and a “blank” analysis conducted again to evaluate the effectiveness of the cleaning. The crucible shall remain in service as long as no detectable residual fluorides are present.
5.0 Safety5.1 This method may involve the handling of hazardous materials in the analytical phase. This method does not purport to address all of the potential safety hazards associated with its use. It is the responsibility of the user to establish appropriate safety and health practices and determine the applicability of regulatory limitations prior to performing this test method.
5.2 Corrosive reagents. The following reagents are hazardous. Personal protective equipment and safe procedures are useful in preventing chemical splashes. If contact occurs, immediately flush with copious amounts of water for at least 15 minutes. Remove clothing under shower and decontaminate. Treat residual chemical burn as thermal burn.
5.3 Sodium Hydroxide (NaOH). Causes severe damage to eyes and skin. Inhalation causes irritation to nose, throat, and lungs. Reacts exothermically with limited amounts of water.
5.4 Perchloric Acid (HClO4). Corrosive to eyes, skin, nose, and throat. Provide ventilation to limit exposure. Very strong oxidizer. Keep separate from water and oxidizable materials to prevent vigorous evolution of heat, spontaneous combustion, or explosion. Heat solutions containing HClO4 only in hoods specifically designed for HClO4.
6.0 Equipment and Supplies6.1 Sampling.
6.1.1 Cassette arrangement. The cassette itself is a three-piece, styrene acrylonitrile cassette unit (a Gelman Sciences product), 37 millimeter (mm), with plastic connectors. In the first section (the intake section), an untreated Gelman Sciences 37 mm, 0.8 micrometer (µm) DM-800 metricel membrane filter and cellulose support pad, or equivalent, is situated. In the second and third segments of the cassette there is placed one each of Gelman Sciences 37 mm, 5 µm GLA-5000 low-ash PVC filter with a cellulose support pad or equivalent product. Each of these two filters and support pads shall have been immersed in a solution of 10 percent sodium formate (volume/volume in an ethyl alcohol solution). The impregnated pads shall be placed in the cassette segments while still wet and heated at 50 °C (122 °F) until the pad is completely dry. It is important to check for a proper fit of the filter and support pad to the cassette segment to ensure that there are no areas where gases could bypass the filter. Once all of the cassette segments have been prepared, the cassette shall be assembled and a plastic plug shall be inserted into the exhaust hole of the cassette. Prior to placing the cassette into service, the space between each segment shall be taped with an appropriately durable tape to prevent the infiltration of gases through the points of connection, and an aluminum nozzle shall be inserted into the intake hole of the cassette. The aluminum nozzle shall have a short section of tubing placed over the opening of the nozzle, with the tubing plugged to prevent dust from entering the nozzle and to prepare the nozzle for the cassette arrangement leak check. An alternate nozzle type can be used if historical results or scientific demonstration of applicability can be shown.
6.1.2 Anemometers and temperature sensing devices. To calculate the mass flow rate of TF from the roof monitor under standard conditions, anemometers that meet the specifications in section 2.1.1 in Method 14 of this appendix or an equivalent device yielding equivalent information shall be used. A recording mechanism capable of accurately recording the exit gas temperature at least every 2 hours shall be used.
6.1.3 Barometer. To correct the volumetric flow from the potline roof monitor to standard conditions, a mercury (Hg), aneroid, or other barometer capable of measuring atmospheric pressure to within 2.5 mm [0.1 inch (in)] Hg shall be used.
Note:The barometric reading may be obtained from a nearby National Weather Service Station. In this case, the station value (which is absolute barometric pressure) shall be requested and an adjustment for elevation differences between the weather station and the sampling point shall be made at a rate of minus 2.5 mm (0.1 in) Hg per 30 meters (m) [100 feet (ft)] elevation increase or plus 2.5 mm (0.1 in) Hg per 30 m (100 ft) elevation decrease.
6.2 Sample recovery.
6.2.1 Hot plate.
6.2.2 Muffle furnace.
6.2.3 Nickel crucible.
6.2.4 Stirring rod. Teflon.
6.2.5 Volumetric flask. 50-milliliter (ml).
6.2.6 Plastic vial. 50-ml.
6.3 Analysis.
6.3.1 Primary analytical method. An automated analyzer having the following components or equivalent: a multichannel proportioning pump, multiposition sampler, voltage stabilizer, colorimeter, instrument recording device, microdistillation apparatus, flexible Teflon ® heating bath, vacuum pump, pulse suppressers and an air flow system.
6.3.2 Secondary analytical method. Specific Ion Electrode (SIE).
7.0 Reagents and Standards7.1 Water. Deionized distilled to conform to ASTM Specification D 1193-77, Type 3 (incorporated by reference in § 60.17(a)(22) of this part). The KMnO4 test for oxidizable organic matter may be omitted when high concentrations of organic matter are not expected to be present.
7.2 Calcium oxide.
7.3 Sodium hydroxide (NaOH). Pellets.
7.4 Perchloric acid (HClO4). Mix 1:1 with water. Sulfuric acid (H2SO4) may be used in place of HClO4.
7.5 Audit samples. The audit samples discussed in section 9.1 shall be prepared from reagent grade, water soluble stock reagents, or purchased as an aqueous solution from a commercial supplier. If the audit stock solution is purchased from a commercial supplier, the standard solution must be accompanied by a certificate of analysis or an equivalent proof of fluoride concentration.
8.0 Sample Collection and Analysis8.1 Preparing cassette arrangement for sampling. The cassettes are initially connected to flexible tubing. The tubing is connected to flowmeters and a manifold system. The manifold system is connected to a dry gas meter (Research Appliance Company model 201009 or equivalent). The length of tubing is managed by pneumatically or electrically operated hoists located in the roof monitor, and the travel of the tubing is controlled by encasing the tubing in aluminum conduit. The tubing is lowered for cassette insertion by operating a control box at floor level. Once the cassette has been securely inserted into the tubing and the leak check performed, the tubing and cassette are raised to the roof monitor level using the floor level control box. Arrangements similar to the one described are acceptable if the scientific sample collection principles are followed.
8.2 Test run sampling period. A test run shall comprise a minimum of a 24-hour sampling event encompassing at least eight cassettes per potline (or four cassettes per potroom group). Monthly compliance shall be based on three test runs during the month. Test runs of greater than 24 hours are allowed; however, three such runs shall be conducted during the month.
8.3 Leak-check procedures.
8.3.1 Pretest leak check. A pretest leak-check is recommended; however, it is not required. To perform a pretest leak-check after the cassettes have been inserted into the tubing, isolate the cassette to be leak-checked by turning the valves on the manifold to stop all flows to the other sampling points connected to the manifold and meter. The cassette, with the plugged tubing section securing the intake of the nozzle, is subjected to the highest vacuum expected during the run. If no leaks are detected, the tubing plug can be briefly removed as the dry gas meter is rapidly turned off.
8.3.2 Post-test leak check. A leak check is required at the conclusion of each test run for each cassette. The leak check shall be performed in accordance with the procedure outlined in section 8.3.1 of this method except that it shall be performed at a vacuum greater than the maximum vacuum reached during the test run. If the leakage rate is found to be no greater than 4 percent of the average sampling rate, the results are acceptable. If the leakage rate is greater than 4 percent of the average sampling rate, either record the leakage rate and correct the sampling volume as discussed in section 12.4 of this method or void the test run if the minimum number of cassettes were used. If the number of cassettes used was greater than the minimum required, discard the leaking cassette and use the remaining cassettes for the emission determination.
8.3.3 Anemometers and temperature sensing device placement. Install the recording mechanism to record the exit gas temperature. Anemometers shall be installed as required in section 6.1.2 of Method 14 of this appendix, except replace the word “manifold” with “cassette group” in section 6.1.2.3. These two different instruments shall be located near each other along the roof monitor. See conceptual configurations in Figures 14A-1, 14A-2, and 14A-3 of this method. Fewer temperature devices than anemometers may be used if at least one temperature device is located within the span of the cassette group. Other anemometer location siting scenarios may be acceptable as long as the exit velocity of the roof monitor gases is representative of the entire section of the potline being sampled.
8.4 Sampling. The actual sample run shall begin with the removal of the tubing and plug from the cassette nozzle. Each cassette is then raised to the roof monitor area, the dry gas meter is turned on, and the flowmeters are set to the calibration point, which allows an equal volume of sampled gas to enter each cassette. The dry gas meter shall be set to a range suitable for the specific potroom type being sampled that will yield valid data known from previous experience or a range determined by the use of the calculation in section 12 of this method. Parameters related to the test run that shall be recorded, either during the test run or after the test run if recording devices are used, include: anemometer data, roof monitor exit gas temperature, dry gas meter temperature, dry gas meter volume, and barometric pressure. At the conclusion of the test run, the cassettes shall be lowered, the dry gas meter turned off, and the volume registered on the dry gas meter recorded. The post-test leak check procedures described in section 8.3.2 of this method shall be performed. All data relevant to the test shall be recorded on a field data sheet and maintained on file.
8.5 Sample recovery.
8.5.1 The cassettes shall be brought to the laboratory with the intake nozzle contents protected with the section of plugged tubing previously described. The exterior of cassettes shall carefully be wiped free of any dust or debris, making sure that any falling dust or debris does not present a potential laboratory contamination problem.
8.5.2 Carefully remove all tape from the cassettes and remove the initial filter, support pad, and all loose solids from the first (intake) section of the cassette. Fold the filter and support pad several times and, along with all loose solids removed from the interior of the first section of the cassette, place them into a nickel crucible. Using water, wash the interior of the nozzle into the same nickel crucible. Add 0.1 gram (g) [±0.1 milligram (mg)] of calcium oxide and a sufficient amount of water to make a loose slurry. Mix the contents of the crucible thoroughly with a Teflon” stirring rod. After rinsing any adhering residue from the stirring rod back into the crucible, place the crucible on a hot plate or in a muffle furnace until all liquid is evaporated and allow the mixture to gradually char for 1 hour.
8.5.3 Transfer the crucible to a cold muffle furnace and ash at 600 °C (1,112 °F). Remove the crucible after the ashing phase and, after the crucible cools, add 3.0 g (±0.1 g) of NaOH pellets. Place this mixture in a muffle furnace at 600 °C (1,112 °F) for 3 minutes. Remove the crucible and roll the melt so as to reach all of the ash with the molten NaOH. Let the melt cool to room temperature. Add 10 to 15 ml of water to the crucible and place it on a hot plate at a low temperature setting until the melt is soft or suspended. Transfer the contents of the crucible to a 50-ml volumetric flask. Rinse the crucible with 20 ml of 1:1 perchloric acid or 20 ml of 1:1 sulfuric acid in two (2) 10 ml portions. Pour the acid rinse slowly into the volumetric flask and swirl the flask after each addition. Cool to room temperature. The product of this procedure is particulate fluorides.
8.5.4 Gaseous fluorides can be isolated for analysis by folding the gaseous fluoride filters and support pads to approximately 1/4 of their original size and placing them in a 50-ml plastic vial. To the vial add exactly 10 ml of water and leach the sample for a minimum of 1 hour. The leachate from this process yields the gaseous fluorides for analysis.
9.0 Quality Control9.1 Laboratory auditing. Laboratory audits of specific and known concentrations of fluoride shall be submitted to the laboratory with each group of samples submitted for analysis. An auditor shall prepare and present the audit samples as a “blind” evaluation of laboratory performance with each group of samples submitted to the laboratory. The audits shall be prepared to represent concentrations of fluoride that could be expected to be in the low, medium and high range of actual results. Average recoveries of all three audits must equal 90 to 110 percent for acceptable results; otherwise, the laboratory must investigate procedures and instruments for potential problems.
Note:The analytical procedure allows for the analysis of individual or combined filters and pads from the cassettes provided that equal volumes (±10 percent) are sampled through each cassette.
10.0 Calibrations10.1 Equipment evaluations. To ensure the integrity of this method, periodic calibrations and equipment replacements are necessary.
10.1.1 Metering system. At 30-day intervals the metering system shall be calibrated. Connect the metering system inlet to the outlet of a wet test meter that is accurate to 1 percent. Refer to Figure 5-4 of Method 5 of this appendix. The wet-test meter shall have a capacity of 30 liters/revolution [1 cubic foot (ft 3)/revolution]. A spirometer of 400 liters (14 ft 3) or more capacity, or equivalent, may be used for calibration; however, a wet-test meter is usually more practical. The wet-test meter shall be periodically tested with a spirometer or a liquid displacement meter to ensure the accuracy. Spirometers or wet-test meters of other sizes may be used, provided that the specified accuracies of the procedure are maintained. Run the metering system pump for about 15 min. with the orifice manometer indicating a median reading as expected in field use to allow the pump to warm up and to thoroughly wet the interior of the wet-test meter. Then, at each of a minimum of three orifice manometer settings, pass an exact quantity of gas through the wet-test meter and record the volume indicated by the dry gas meter. Also record the barometric pressure, the temperatures of the wet test meter, the inlet temperatures of the dry gas meter, and the temperatures of the outlet of the dry gas meter. Record all calibration data on a form similar to the one shown in Figure 5-5 of Method 5 of this appendix and calculate Y, the dry gas meter calibration factor, and ΔH@, the orifice calibration factor at each orifice setting. Allowable tolerances for Y and ΔH@ are given in Figure 5-6 of Method 5 of this appendix. Allowable tolerances for Y and ΔH@ are given in Figure 5-5 of Method 5 of this appendix.
10.1.2 Estimating volumes for initial test runs. For a facility's initial test runs, the regulated facility must have a target or desired volume of gases to be sampled and a target range of volumes to use during the calibration of the dry gas meter. Use Equations 14A-1 and 14A-2 in section 12 of this method to derive the target dry gas meter volume (Fv) for these purposes.
10.1.3 Calibration of anemometers and temperature sensing devices. If the standard anemometers in Method 14 of this appendix are used, the calibration and integrity evaluations in sections 10.3.1.1 through 10.3.1.3 of Method 14 of this appendix shall be used as well as the recording device described in section 2.1.3 of Method 14. The calibrations or complete change-outs of anemometers shall take place at a minimum of once per year. The temperature sensing and recording devices shall be calibrated according to the manufacturer's specifications.
10.1.4 Calibration of flowmeters. The calibration of flowmeters is necessary to ensure that an equal volume of sampled gas is entering each of the individual cassettes and that no large differences, which could possibly bias the sample, exist between the cassettes.
10.1.4.1 Variable area, 65 mm flowmeters or equivalent shall be used. These flowmeters can be mounted on a common base for convenience. These flowmeters shall be calibrated by attaching a prepared cassette, complete with filters and pads, to the flowmeter and then to the system manifold. This manifold is an aluminum cylinder with valved inlets for connections to the flowmeters/cassettes and one outlet to a dry gas meter. The connection is then made to the wet-test meter and finally to a dry gas meter. All connections are made with tubing.
10.1.4.2 Turn the dry gas meter on for 15 min. in preparation for the calibration. Turn the dry gas meter off and plug the intake hole of the cassette. Turn the dry gas meter back on to evaluate the entire system for leaks. If the dry gas meter shows a leakage rate of less than 0.02 ft 3/min at 10 in. of Hg vacuum as noted on the dry gas meter, the system is acceptable to further calibration.
10.1.4.3 With the dry gas meter turned on and the flow indicator ball at a selected flow rate, record the exact amount of gas pulled through the flowmeter by taking measurements from the wet test meter after exactly 10 min. Record the room temperature and barometric pressure. Conduct this test for all flowmeters in the system with all flowmeters set at the same indicator ball reading. When all flowmeters have gone through the procedure above, correct the volume pulled through each flowmeter to standard conditions. The acceptable difference between the highest and lowest flowmeter rate is 5 percent. Should one or more flowmeters be outside of the acceptable limit of 5 percent, repeat the calibration procedure at a lower or higher indicator ball reading until all flowmeters show no more than 5 percent difference among them.
10.1.4.4 This flowmeter calibration shall be conducted at least once per year.
10.1.5 Miscellaneous equipment calibrations. Miscellaneous equipment used such as an automatic recorder/ printer used to measure dry gas meter temperatures shall be calibrated according to the manufacturer's specifications in order to maintain the accuracy of the equipment.
11.0 Analytical Procedure11.1 The preferred primary analytical determination of the individual isolated samples or the combined particulate and gaseous samples shall be performed by an automated methodology. The analytical method for this technology shall be based on the manufacturer's instructions for equipment operation and shall also include the analysis of five standards with concentrations in the expected range of the actual samples. The results of the analysis of the five standards shall have a coefficient of correlation of at least 0.99. A check standard shall be analyzed as the last sample of the group to determine if instrument drift has occurred. The acceptable result for the check standard is 95 to 105 percent of the standard's true value.
11.2 The secondary analytical method shall be by specific ion electrode if the samples are distilled or if a TISAB IV buffer is used to eliminate aluminum interferences. Five standards with concentrations in the expected range of the actual samples shall be analyzed, and a coefficient of correlation of at least 0.99 is the minimum acceptable limit for linearity. An exception for this limit for linearity is a condition when low-level standards in the range of 0.01 to 0.48 µg fluoride/ml are analyzed. In this situation, a minimum coefficient of correlation of 0.97 is required. TISAB II shall be used for low-level analyses.
12.0 Data Analysis and Calculations12.1 Carry out calculations, retaining at least one extra decimal point beyond that of the acquired data. Round off values after the final calculation. Other forms of calculations may be used as long as they give equivalent results.
12.2 Estimating volumes for initial test runs.


12.2.1 Example calculation. Assume that the typical emission rate (Re) is 1.0 lb TF/ton of aluminum, the typical roof vent gas exit velocity (Vr) is 250 ft/min, the typical production rate (Rp) is 0.10 ton/min, the known open area for the roof monitor (Ar) is 8,700 ft 2, and the desired (analytically optimum) mass of TF per cassette is 1,500 µg. First calculate the concentration of TF per cassette (Fe) in µg/ft 3 using Equation 14A-2. Then calculate the desired volume of gas to be sampled (Fv) using Equation 14A-1.


This is a total of 575.40 ft 3 for eight cassettes or 71.925 ft 3/cassette.
12.3 Calculations of TF emissions from field and laboratory data that would yield a production related emission rate can be calculated as follows:
12.3.1 Obtain a standard cubic feet (scf) value for the volume pulled through the dry gas meter for all cassettes by using the field and calibration data and Equation 5-1 of Method 5 of this appendix.
12.3.2 Derive the average quantity of TF per cassette (in µg TF/cassette) by adding all laboratory data for all cassettes and dividing this value by the total number of cassettes used. Divide this average TF value by the corrected dry gas meter volume for each cassette; this value then becomes TFstd (µg/ft 3).
12.3.3 Calculate the production-based emission rate (Re) in lb/ton using Equation 14A-5.

12.3.4 As an example calculation, assume eight cassettes located in a potline were used to sample for 72 hours during the run. The analysis of all eight cassettes yielded a total of 3,000 µg of TF. The dry gas meter volume was corrected to yield a total of 75 scf per cassette, which yields a value for TFstd of 3,000/75 = 5 µg/ft 3. The open area of the roof monitor for the potline (Ar) is 17,400 ft 2. The exit velocity of the roof monitor gases (Vr) is 250 ft/min. The production rate of aluminum over the previous 720 hours was 5,000 tons, which is 6.94 tons/hr or 0.116 ton/min (Rp). Substituting these values into Equation 14A-5 yields:

12.4 Corrections to volumes due to leakage. Should the post-test leak check leakage rate exceed 4 percent as described in section 8.3.2 of this method, correct the volume as detailed in Case I in section 6.3 of Method 5 of this appendix.

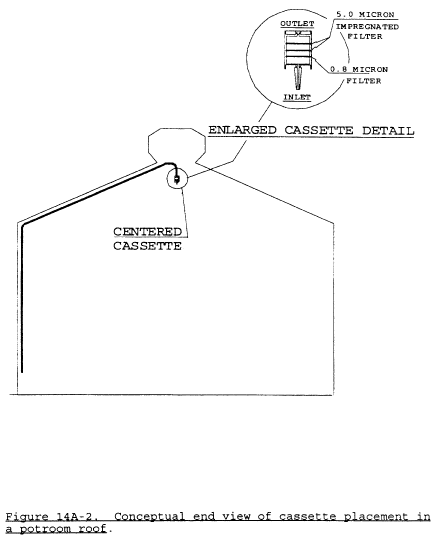
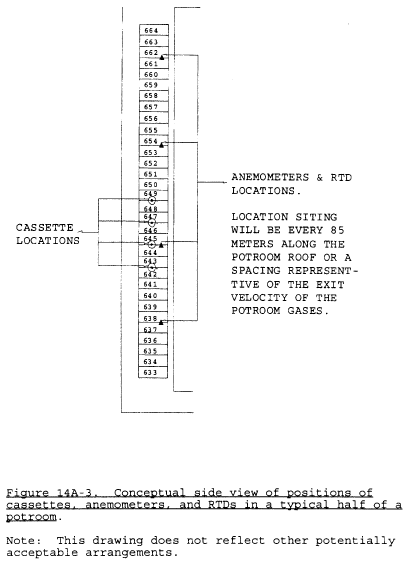
This method is not inclusive with respect to specifications (e.g., equipment and supplies) and procedures (e.g., sampling and analytical) essential to its performance. Some material is incorporated by reference from other methods in this part. Therefore, to obtain reliable results, persons using this method should have a thorough knowledge of gas chromatography techniques.
1.0 Scope and Application1.1 Analytes.
Analyte | CAS No. | Sensitivity (See Sec 13.2) |
---|---|---|
Carbon disulfide [CS2] | 75-15-0 | 0.5 ppmv |
Carbonyl sulfide [COS] | 463-58-1 | 0.5 ppmv |
Hydrogen sulfide [H2S] | 7783-06-4 | 0.5 ppmv |
1.2 Applicability.
1.2.1 This method applies to the determination of emissions of reduced sulfur compounds from tail gas control units of sulfur recovery plants, H2S in fuel gas for fuel gas combustion devices, and where specified in other applicable subparts of the regulations.
1.2.2 The method described below uses the principle of gas chromatographic (GC) separation and flame photometric detection (FPD). Since there are many systems or sets of operating conditions that represent useable methods for determining sulfur emissions, all systems which employ this principle, but differ only in details of equipment and operation, may be used as alternative methods, provided that the calibration precision and sample-line loss criteria are met.
1.3 Data Quality Objectives. Adherence to the requirements of this method will enhance the quality of the data obtained from air pollutant sampling methods.
2.0 Summary of Method2.1 A gas sample is extracted from the emission source and diluted with clean dry air (if necessary). An aliquot of the diluted sample is then analyzed for CS2, COS, and H2S by GC/FPD.
3.0 Definitions [Reserved] 4.0 Interferences4.1 Moisture Condensation. Moisture condensation in the sample delivery system, the analytical column, or the FPD burner block can cause losses or interferences. This potential is eliminated by heating the probe, filter box, and connections, and by maintaining the SO2 scrubber in an ice water bath. Moisture is removed in the SO2 scrubber and heating the sample beyond this point is not necessary provided the ambient temperature is above 0 °C (32 °F). Alternatively, moisture may be eliminated by heating the sample line, and by conditioning the sample with dry dilution air to lower its dew point below the operating temperature of the GC/FPD analytical system prior to analysis.
4.2 Carbon Monoxide (CO) and Carbon Dioxide (CO2). CO and CO2 have substantial desensitizing effects on the FPD even after 9:1 dilution. (Acceptable systems must demonstrate that they have eliminated this interference by some procedure such as eluting CO and CO2 before any of the sulfur compounds to be measured.) Compliance with this requirement can be demonstrated by submitting chromatograms of calibration gases with and without CO2 in the diluent gas. The CO2 level should be approximately 10 percent for the case with CO2 present. The two chromatograms should show agreement within the precision limits of section 13.3.
4.3 Elemental Sulfur. The condensation of sulfur vapor in the sampling system can lead to blockage of the particulate filter. This problem can be minimized by observing the filter for buildup and changing as needed.
4.4 Sulfur Dioxide (SO2). SO2 is not a specific interferent but may be present in such large amounts that it cannot be effectively separated from the other compounds of interest. The SO2 scrubber described in section 6.1.3 will effectively remove SO2 from the sample.
4.5 Alkali Mist. Alkali mist in the emissions of some control devices may cause a rapid increase in the SO2 scrubber pH, resulting in low sample recoveries. Replacing the SO2 scrubber contents after each run will minimize the chances of interference in these cases.
5.0 Safety5.1 Disclaimer. This method may involve hazardous materials, operations, and equipment. This test method may not address all of the safety problems associated with its use. It is the responsibility of the user of this test to establish appropriate safety and health practices and determine the applicability of regulatory limitations to performing this test.
6.0 Equipment and Supplies6.1 Sample Collection. See Figure 15-1. The sampling train component parts are discussed in the following sections:
6.1.1 Probe. The probe shall be made of Teflon or Teflon-lined stainless steel and heated to prevent moisture condensation. It shall be designed to allow calibration gas to enter the probe at or near the sample point entry. Any portion of the probe that contacts the stack gas must be heated to prevent moisture condensation. The probe described in section 6.1.1 of Method 16A having a nozzle directed away from the gas stream is recommended for sources having particulate or mist emissions. Where very high stack temperatures prohibit the use of Teflon probe components, glass or quartz-lined probes may serve as substitutes.
6.1.2 Particulate Filter. 50-mm Teflon filter holder and a 1- to 2-micron porosity Teflon filter (available through Savillex Corporation, 5325 Highway 101, Minnetonka, Minnesota 55343). The filter holder must be maintained in a hot box at a temperature of at least 120 °C (248 °F).
6.1.3 SO2 Scrubber. Three 300-ml Teflon segment impingers connected in series with flexible, thick-walled, Teflon tubing. (Impinger parts and tubing available through Savillex.) The first two impingers contain 100 ml of citrate buffer, and the third impinger is initially dry. The tip of the tube inserted into the solution should be constricted to less than 3-mm ( 1/8-in.) ID and should be immersed to a depth of at least 50 cm (2 in.). Immerse the impingers in an ice water bath and maintain near 0 °C. The scrubber solution will normally last for a 3-hour run before needing replacement. This will depend upon the effects of moisture and particulate matter on the solution strength and pH. Connections between the probe, particulate filter, and SO2 scrubber shall be made of Teflon and as short in length as possible. All portions of the probe, particulate filter, and connections prior to the SO2 scrubber (or alternative point of moisture removal) shall be maintained at a temperature of at least 120 °C (248 °F).
6.1.4 Sample Line. Teflon, no greater than 13-mm ( 1/2-in.) ID. Alternative materials, such as virgin Nylon, may be used provided the line-loss test is acceptable.
6.1.5 Sample Pump. The sample pump shall be a leakless Teflon-coated diaphragm type or equivalent.
6.2 Analysis. The following items are needed for sample analysis:
6.2.1 Dilution System. The dilution system must be constructed such that all sample contacts are made of Teflon, glass, or stainless steel. It must be capable of approximately a 9:1 dilution of the sample.
6.2.2 Gas Chromatograph (see Figure 15-2). The gas chromatograph must have at least the following components:
6.2.2.1 Oven. Capable of maintaining the separation column at the proper operating temperature ±1 °C.
6.2.2.2 Temperature Gauge. To monitor column oven, detector, and exhaust temperature ±1 °C.
6.2.2.3 Flow System. Gas metering system to measure sample, fuel, combustion gas, and carrier gas flows.
6.2.2.4 Flame Photometric Detector.
6.2.2.4.1 Electrometer. Capable of full scale amplification of linear ranges of 10−9 to 10−4 amperes full scale.
6.2.2.4.2 Power Supply. Capable of delivering up to 750 volts.
6.2.2.5 Recorder. Compatible with the output voltage range of the electrometer.
6.2.2.6 Rotary Gas Valves. Multiport Teflon-lined valves equipped with sample loop. Sample loop volumes shall be chosen to provide the needed analytical range. Teflon tubing and fittings shall be used throughout to present an inert surface for sample gas. The GC shall be calibrated with the sample loop used for sample analysis.
6.2.2.7 GC Columns. The column system must be demonstrated to be capable of resolving three major reduced sulfur compounds: H2S, COS, and CS2. To demonstrate that adequate resolution has been achieved, a chromatogram of a calibration gas containing all three reduced sulfur compounds in the concentration range of the applicable standard must be submitted. Adequate resolution will be defined as base line separation of adjacent peaks when the amplifier attenuation is set so that the smaller peak is at least 50 percent of full scale. Base line separation is defined as a return to zero (±5 percent) in the interval between peaks. Systems not meeting this criteria may be considered alternate methods subject to the approval of the Administrator.
6.3 Calibration System (See Figure 15-3). The calibration system must contain the following components:
6.3.1 Flow System. To measure air flow over permeation tubes within 2 percent. Each flowmeter shall be calibrated after each complete test series with a wet-test meter. If the flow measuring device differs from the wet-test meter by more than 5 percent, the completed test shall be discarded. Alternatively, use the flow data that will yield the lowest flow measurement. Calibration with a wet-test meter before a test is optional. Flow over the permeation device may also be determined using a soap bubble flowmeter.
6.3.2 Constant Temperature Bath. Device capable of maintaining the permeation tubes at the calibration temperature within 0.1 °C.
6.3.3 Temperature Sensor. Thermometer or equivalent to monitor bath temperature within 0.1 °C.
7.0 Reagents and Standards7.1 Fuel. Hydrogen gas (H2). Prepurified grade or better.
7.2 Combustion Gas. Oxygen (O2) or air, research purity or better.
7.3 Carrier Gas. Prepurified grade or better.
7.4 Diluent. Air containing less than 0.5 ppmv total sulfur compounds and less than 10 ppmv each of moisture and total hydrocarbons.
7.5 Calibration Gases.
7.5.1 Permeation Devices. One each of H2S, COS, and CS2, gravimetrically calibrated and certified at some convenient operating temperature. These tubes consist of hermetically sealed FEP Teflon tubing in which a liquified gaseous substance is enclosed. The enclosed gas permeates through the tubing wall at a constant rate. When the temperature is constant, calibration gases covering a wide range of known concentrations can be generated by varying and accurately measuring the flow rate of diluent gas passing over the tubes. These calibration gases are used to calibrate the GC/FPD system and the dilution system.
7.5.2 Cylinder Gases. Cylinder gases may be used as alternatives to permeation devices. The gases must be traceable to a primary standard (such as permeation tubes) and not used beyond the certification expiration date.
7.6 Citrate Buffer. Dissolve 300 g of potassium citrate and 41 g of anhydrous citric acid in 1 liter of water. Alternatively, 284 g of sodium citrate may be substituted for the potassium citrate. Adjust the pH to between 5.4 and 5.6 with potassium citrate or citric acid, as required.
8.0 Sample Collection, Preservation, Transport, and Storage
8.1 Pretest Procedures. After the complete measurement system has been set up at the site and deemed to be operational, the following procedures should be completed before sampling is initiated. These procedures are not required, but would be helpful in preventing any problem which might occur later to invalidate the entire test.
8.1.1 Leak-Check. Appropriate leak-check procedures should be employed to verify the integrity of all components, sample lines, and connections. The following procedure is suggested: For components upstream of the sample pump, attach the probe end of the sample line to a manometer or vacuum gauge, start the pump and pull a vacuum greater than 50 mm (2 in.) Hg, close off the pump outlet, and then stop the pump and ascertain that there is no leak for 1 minute. For components after the pump, apply a slight positive pressure and check for leaks by applying a liquid (detergent in water, for example) at each joint. Bubbling indicates the presence of a leak. As an alternative to the initial leak-test, the sample line loss test described in section 8.3.1 may be performed to verify the integrity of components.
8.1.2 System Performance. Since the complete system is calibrated at the beginning and end of each day of testing, the precise calibration of each component is not critical. However, these components should be verified to operate properly. This verification can be performed by observing the response of flowmeters or of the GC output to changes in flow rates or calibration gas concentrations, respectively, and ascertaining the response to be within predicted limits. If any component or the complete system fails to respond in a normal and predictable manner, the source of the discrepancy should be identified and corrected before proceeding.
8.2 Sample Collection and Analysis
8.2.1 After performing the calibration procedures outlined in section 10.0, insert the sampling probe into the test port ensuring that no dilution air enters the stack through the port. Begin sampling and dilute the sample approximately 9:1 using the dilution system. Note that the precise dilution factor is the one determined in section 10.4. Condition the entire system with sample for a minimum of 15 minutes before beginning the analysis. Inject aliquots of the sample into the GC/FPD analyzer for analysis. Determine the concentration of each reduced sulfur compound directly from the calibration curves or from the equation for the least-squares line.
8.2.2 If reductions in sample concentrations are observed during a sample run that cannot be explained by process conditions, the sampling must be interrupted to determine if the probe or filter is clogged with particulate matter. If either is found to be clogged, the test must be stopped and the results up to that point discarded. Testing may resume after cleaning or replacing the probe and filter. After each run, the probe and filter shall be inspected and, if necessary, replaced.
8.2.3 A sample run is composed of 16 individual analyses (injects) performed over a period of not less than 3 hours or more than 6 hours.
8.3 Post-Test Procedures.
8.3.1 Sample Line Loss. A known concentration of H2S at the level of the applicable standard, ±20 percent, must be introduced into the sampling system at the opening of the probe in sufficient quantities to ensure that there is an excess of sample which must be vented to the atmosphere. The sample must be transported through the entire sampling system to the measurement system in the same manner as the emission samples. The resulting measured concentration is compared to the known value to determine the sampling system loss. For sampling losses greater than 20 percent, the previous sample run is not valid. Sampling losses of 0-20 percent must be corrected by dividing the resulting sample concentration by the fraction of recovery. The known gas sample may be calibration gas as described in section 7.5. Alternatively, cylinder gas containing H2S mixed in nitrogen and verified according to section 7.1.4 of Method 16A may be used. The optional pretest procedures provide a good guideline for determining if there are leaks in the sampling system.
8.3.2 Determination of Calibration Drift. After each run, or after a series of runs made within a 24-hour period, perform a partial recalibration using the procedures in section 10.0. Only H2S (or other permeant) need be used to recalibrate the GC/FPD analysis system and the dilution system. Partial recalibration may be performed at the midlevel calibration gas concentration or at a concentration measured in the samples but not less than the lowest calibration standard used in the initial calibration. Compare the calibration curves obtained after the runs to the calibration curves obtained under section 10.3. The calibration drift should not exceed the limits set forth in section 13.4. If the drift exceeds this limit, the intervening run or runs should be considered invalid. As an option, the calibration data set that gives the highest sample values may be chosen by the tester.
9.0 Quality ControlSection | Quality control measure | Effect |
---|---|---|
8.3.1 | Sample line loss check | Ensures that uncorrected negative bias introduced by sample loss is no greater than 20 percent, and provides for correction of bias of 20 percent or less. |
8.3.2 | Calibration drift test | Ensures that bias introduced by drift in the measurement system output during the run is no greater than 5 percent. |
10.0 | Analytical calibration | Ensures precision of analytical results within 5 percent. |
Prior to any sampling run, calibrate the system using the following procedures. (If more than one run is performed during any 24-hour period, a calibration need not be performed prior to the second and any subsequent runs. However, the calibration drift must be determined as prescribed in section 8.3.2 after the last run is made within the 24-hour period.)
Note:This section outlines steps to be followed for use of the GC/FPD and the dilution system. The calibration procedure does not include detailed instructions because the operation of these systems is complex, and it requires an understanding of the individual system being used. Each system should include a written operating manual describing in detail the operating procedures associated with each component in the measurement system. In addition, the operator should be familiar with the operating principles of the components, particularly the GC/FPD. The references in section 16.0 are recommended for review for this purpose.
10.1 Calibration Gas Permeation Tube Preparation.
10.1.1 Insert the permeation tubes into the tube chamber. Check the bath temperature to assure agreement with the calibration temperature of the tubes within 0.1 °C. Allow 24 hours for the tubes to equilibrate. Alternatively, equilibration may be verified by injecting samples of calibration gas at 1-hour intervals. The permeation tubes can be assumed to have reached equilibrium when consecutive hourly samples agree within 5 percent of their mean.
10.1.2 Vary the amount of air flowing over the tubes to produce the desired concentrations for calibrating the analytical and dilution systems. The air flow across the tubes must at all times exceed the flow requirement of the analytical systems. The concentration in ppmv generated by a tube containing a specific permeant can be calculated using Equation 15-1 in section 12.2.
10.2 Calibration of Analytical System. Generate a series of three or more known concentrations spanning the linear range of the FPD (approximately 0.5 to 10 ppmv for a 1-ml sample) for each of the three major sulfur compounds. Bypassing the dilution system, inject these standards into the GC/FPD and monitor the responses until three consecutive injections for each concentration agree within 5 percent of their mean. Failure to attain this precision indicates a problem in the calibration or analytical system. Any such problem must be identified and corrected before proceeding.
10.3 Calibration Curves. Plot the GC/FPD response in current (amperes) versus their causative concentrations in ppmv on log-log coordinate graph paper for each sulfur compound. Alternatively, a least-squares equation may be generated from the calibration data using concentrations versus the appropriate instrument response units.
10.4 Calibration of Dilution System. Generate a known concentration of H2S using the permeation tube system. Adjust the flow rate of diluent air for the first dilution stage so that the desired level of dilution is approximated. Inject the diluted calibration gas into the GC/FPD system until the results of three consecutive injections for each dilution agree within 5 percent of their mean. Failure to attain this precision in this step is an indication of a problem in the dilution system. Any such problem must be identified and corrected before proceeding. Using the calibration data for H2S (developed under section 10.3), determine the diluted calibration gas concentration in ppmv. Then calculate the dilution factor as the ratio of the calibration gas concentration before dilution to the diluted calibration gas concentration determined under this section. Repeat this procedure for each stage of dilution required. Alternatively, the GC/FPD system may be calibrated by generating a series of three or more concentrations of each sulfur compound and diluting these samples before injecting them into the GC/FPD system. These data will then serve as the calibration data for the unknown samples and a separate determination of the dilution factor will not be necessary. However, the precision requirements are still applicable.
11.0 Analytical ProcedureSample collection and analysis are concurrent for this method (see section 8.0).
12.0 Data Analysis and Calculations12.1 Nomenclature.
C = Concentration of permeant produced, ppmv. COS = Carbonyl sulfide concentration, ppmv. CS2 = Carbon disulfide concentration, ppmv. d = Dilution factor, dimensionless. H2S = Hydrogen sulfide concentration, ppmv. K = 24.04 L/g mole. (Gas constant at 20 °C and 760 mm Hg) L = Flow rate, L/min, of air over permeant 20 °C, 760 mm Hg. M = Molecular weight of the permeant, g/g-mole. N = Number of analyses performed. Pr = Permeation rate of the tube, µg/min.12.2 Permeant Concentration. Calculate the concentration generated by a tube containing a specific permeant (see section 10.1) using the following equation:
12.3 Calculation of SO2 Equivalent. SO2 equivalent will be determined for each analysis made by summing the concentrations of each reduced sulfur compound resolved during the given analysis. The SO2 equivalent is expressed as SO2 in ppmv.
12.4 Average SO2 Equivalent. This is determined using the following equation. Systems that do not remove moisture from the sample but condition the gas to prevent condensation must correct the average SO2 equivalent for the fraction of water vapor present. This is not done under applications where the emission standard is not specified on a dry basis.
Where: Avg SO2 equivalent = Average SO2 equivalent in ppmv, dry basis. Average SO2 equivalent i = SO2 in ppmv as determined by Equation 15-2. 13.0 Method Performance13.1 Range. Coupled with a GC system using a 1-ml sample size, the maximum limit of the FPD for each sulfur compound is approximately 10 ppmv. It may be necessary to dilute samples from sulfur recovery plants a hundredfold (99:1), resulting in an upper limit of about 1000 ppmv for each compound.
13.2 Sensitivity. The minimum detectable concentration of the FPD is also dependent on sample size and would be about 0.5 ppmv for a 1-ml sample.
13.3 Calibration Precision. A series of three consecutive injections of the same calibration gas, at any dilution, shall produce results which do not vary by more than 5 percent from the mean of the three injections.
13.4 Calibration Drift. The calibration drift determined from the mean of three injections made at the beginning and end of any run or series of runs within a 24-hour period shall not exceed 5 percent.
14.0 Pollution Prevention [Reserved] 15.0 Waste Management [Reserved] 16.0 References.1. O'Keeffe, A.E., and G.C. Ortman. “Primary Standards for Trace Gas Analysis.” Anal. Chem. 38,760. 1966.
2. Stevens, R.K., A.E. O'Keeffe, and G.C. Ortman. “Absolute Calibration of a Flame Photometric Detector to Volatile Sulfur Compounds at Sub-Part-Per-Million Levels.” Environmental Science and Technology 3:7. July 1969.
3. Mulik, J.D., R.K. Stevens, and R. Baumgardner. “An Analytical System Designed to Measure Multiple Malodorous Compounds Related to Kraft Mill Activities.” Presented at the 12th Conference on Methods in Air Pollution and Industrial Hygiene Studies, University of Southern California, Los Angeles, CA, April 6-8, 1971.
4. Devonald, R.H., R.S. Serenius, and A.D. McIntyre. “Evaluation of the Flame Photometric Detector for Analysis of Sulfur Compounds.” Pulp and Paper Magazine of Canada, 73,3. March 1972.
5. Grimley, K.W., W.S. Smith, and R.M. Martin. “The Use of a Dynamic Dilution System in the Conditioning of Stack Gases for Automated Analysis by a Mobile Sampling Van.” Presented at the 63rd Annual APCA Meeting in St. Louis, MO. June 14-19, 1970.
6. General Reference. Standard Methods of Chemical Analysis Volume III-A and III-B: Instrumental Analysis. Sixth Edition. Van Nostrand Reinhold Co.
17.0 Tables, Diagrams, Flowcharts, and Validation Data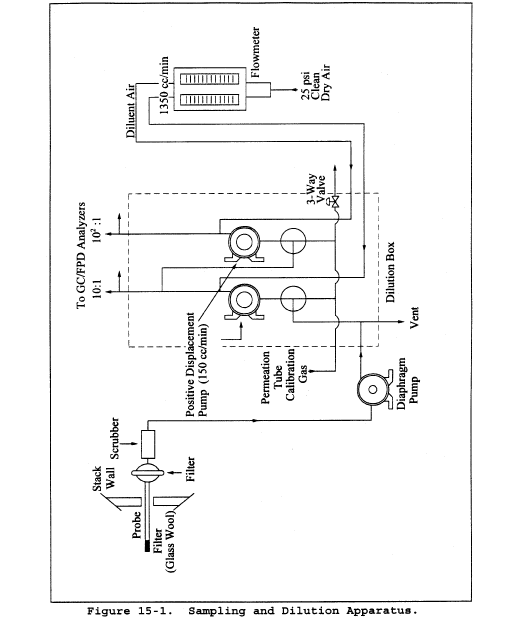
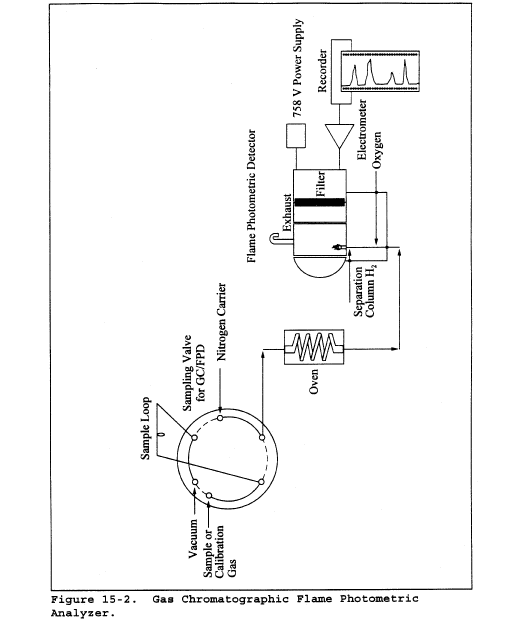
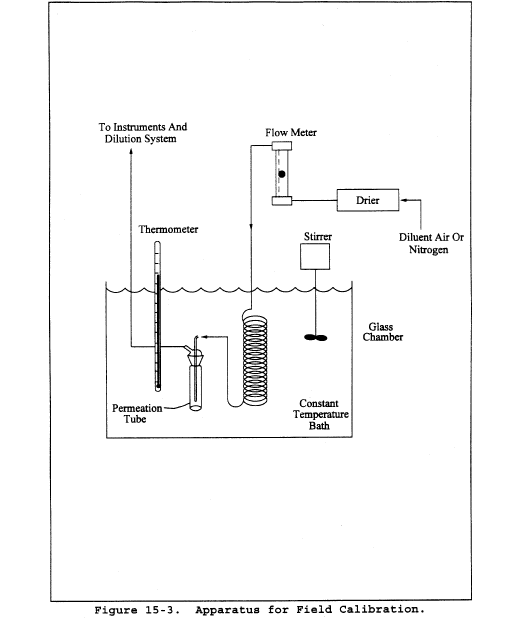
This method does not include all of the specifications (e.g., equipment and supplies) and procedures (e.g., sampling and analytical) essential to its performance. Some material is incorporated by reference from other methods in this part. Therefore, to obtain reliable results, persons using this method should have a thorough knowledge of at least the following additional test methods: Method 1, Method 6, Method 15, and Method 16A.
1.0 Scope and Application1.1 Analytes.
Analyte | CAS No. | Sensitivity |
---|---|---|
Reduced sulfur compounds | None assigned | Not determined. |
1.2 Applicability. This method is applicable for the determination of emissions of reduced sulfur compounds from sulfur recovery plants where the emissions are in a reducing atmosphere, such as in Stretford units.
1.3 Data Quality Objectives. Adherence to the requirements of this method will enhance the quality of the data obtained from air pollutant sampling methods.
2.0 Summary of Method2.1 An integrated gas sample is extracted from the stack, and combustion air is added to the oxygen (O2)-deficient gas at a known rate. The reduced sulfur compounds [including carbon disulfide (CS2), carbonyl sulfide (COS), and hydrogen sulfide (H2S)] are thermally oxidized to sulfur dioxide (SO2), which is then collected in hydrogen peroxide as sulfate ion and analyzed according to the Method 6 barium-thorin titration procedure.
3.0 Definitions [Reserved] 4.0 Interferences4.1 Reduced sulfur compounds, other than CS2, COS, and H2S, that are present in the emissions will also be oxidized to SO2, causing a positive bias relative to emission standards that limit only the three compounds listed above. For example, thiophene has been identified in emissions from a Stretford unit and produced a positive bias of 30 percent in the Method 15A result. However, these biases may not affect the outcome of the test at units where emissions are low relative to the standard.
4.2 Calcium and aluminum have been shown to interfere in the Method 6 titration procedure. Since these metals have been identified in particulate matter emissions from Stretford units, a Teflon filter is required to minimize this interference.
4.3 Dilution of the hydrogen peroxide (H2O2) absorbing solution can potentially reduce collection efficiency, causing a negative bias. When used to sample emissions containing 7 percent moisture or less, the midget impingers have sufficient volume to contain the condensate collected during sampling. Dilution of the H2O2 does not affect the collection of SO2. At higher moisture contents, the potassium citrate-citric acid buffer system used with Method 16A should be used to collect the condensate.
5.0 Safety5.1 Disclaimer. This method may involve hazardous materials, operations, and equipment. This test method may not address all of the safety problems associated with its use. It is the responsibility of the user of this test method to establish appropriate safety and health practices and determine the applicability of regulatory limitations prior to performing this test method.
5.2 Corrosive reagents. The following reagents are hazardous. Personal protective equipment and safe procedures are useful in preventing chemical splashes. If contact occurs, immediately flush with copious amounts of water for at least 15 minutes. Remove clothing under shower and decontaminate. Treat residual chemical burns as thermal burns.
5.2.1 Hydrogen Peroxide (H2O2). Irritating to eyes, skin, nose, and lungs.
5.2.2 Sodium Hydroxide (NaOH). Causes severe damage to eyes and skin. Inhalation causes irritation to nose, throat, and lungs. Reacts exothermically with limited amounts of water.
5.2.3 Sulfuric Acid (H2SO4). Rapidly destructive to body tissue. Will cause third degree burns. Eye damage may result in blindness. Inhalation may be fatal from spasm of the larynx, usually within 30 minutes. May cause lung tissue damage with edema. 3 mg/m 3 will cause lung damage in uninitiated. 1 mg/m 3 for 8 hours will cause lung damage or, in higher concentrations, death. Provide ventilation to limit inhalation. Reacts violently with metals and organics.
6.0 Equipment and Supplies6.1 Sample Collection. The sampling train used in performing this method is shown in Figure 15A-1, and component parts are discussed below. Modifications to this sampling train are acceptable provided that the system performance check is met.
6.1.1 Probe. 6.4-mm ( 1/4-in.) OD Teflon tubing sequentially wrapped with heat-resistant fiber strips, a rubberized heating tape (with a plug at one end), and heat-resistant adhesive tape. A flexible thermocouple or some other suitable temperature-measuring device shall be placed between the Teflon tubing and the fiber strips so that the temperature can be monitored. The probe should be sheathed in stainless steel to provide in-stack rigidity. A series of bored-out stainless steel fittings placed at the front of the sheath will prevent flue gas from entering between the probe and sheath. The sampling probe is depicted in Figure 15A-2.
6.1.2 Particulate Filter. A 50-mm Teflon filter holder and a 1- to 2-mm porosity Teflon filter (available through Savillex Corporation, 5325 Highway 101, Minnetonka, Minnesota 55345). The filter holder must be maintained in a hot box at a temperature high enough to prevent condensation.
6.1.3 Combustion Air Delivery System. As shown in the schematic diagram in Figure 15A-3. The rate meter should be selected to measure an air flow rate of 0.5 liter/min (0.02 ft 3/min).
6.1.4 Combustion Tube. Quartz glass tubing with an expanded combustion chamber 2.54 cm (1 in.) in diameter and at least 30.5 cm (12 in.) long. The tube ends should have an outside diameter of 0.6 cm ( 1/4 in.) and be at least 15.3 cm (6 in.) long. This length is necessary to maintain the quartz-glass connector near ambient temperature and thereby avoid leaks. Alternatively, the outlet may be constructed with a 90 degree glass elbow and socket that would fit directly onto the inlet of the first peroxide impinger.
6.1.5 Furnace. Of sufficient size to enclose the combustion tube. The furnace must have a temperature regulator capable of maintaining the temperature at 1100 ±50 °C (2,012 ±90 °F). The furnace operating temperature must be checked with a thermocouple to ensure accuracy. Lindberg furnaces have been found to be satisfactory.
6.1.6 Peroxide Impingers, Stopcock Grease, Temperature Sensor, Drying Tube, Valve, Pump, and Barometer. Same as in Method 6, sections 6.1.1.2, 6.1.1.4, 6.1.1.5, 6.1.1.6, 6.1.1.7, 6.1.1.8, and 6.1.2, respectively, except that the midget bubbler of Method 6, section 6.1.1.2 is not required.
6.1.7 Vacuum Gauge and Rate Meter. At least 760 mm Hg (30 in. Hg) gauge and rotameter, or equivalent, capable of measuring flow rate to ±5 percent of the selected flow rate and calibrated as in section 10.2.
6.1.8 Volume Meter. Dry gas meter capable of measuring the sample volume under the particular sampling conditions with an accuracy of 2 percent.
6.1.9 U-tube manometer. To measure the pressure at the exit of the combustion gas dry gas meter.
6.2 Sample Recovery and Analysis. Same as Method 6, sections 6.2 and 6.3, except a 10-ml buret with 0.05-ml graduations is required for titrant volumes of less than 10.0 ml, and the spectrophotometer is not needed.
7.0 Reagents and Standards Note:Unless otherwise indicated, all reagents must conform to the specifications established by the Committee on Analytical Reagents of the American Chemical Society. When such specifications are not available, the best available grade shall be used.
7.1 Sample Collection. The following reagents and standards are required for sample analysis:
7.1.1 Water. Same as Method 6, section 7.1.1.
7.1.2 Hydrogen Peroxide (H2O2), 3 Percent by Volume. Same as Method 6, section 7.1.3 (40 ml is needed per sample).
7.1.3 Recovery Check Gas. Carbonyl sulfide in nitrogen [100 parts per million by volume (ppmv) or greater, if necessary] in an aluminum cylinder. Concentration certified by the manufacturer with an accuracy of ±2 percent or better, or verified by gas chromatography where the instrument is calibrated with a COS permeation tube.
7.1.4 Combustion Gas. Air, contained in a gas cylinder equipped with a two-stage regulator. The gas shall contain less than 50 ppb of reduced sulfur compounds and less than 10 ppm total hydrocarbons.
7.2 Sample Recovery and Analysis. Same as Method 6, sections 7.2 and 7.3.
8.0 Sample Collection, Preservation, Storage, and Transport8.1 Preparation of Sampling Train. For the Method 6 part of the train, measure 20 ml of 3 percent H2O2 into the first and second midget impingers. Leave the third midget impinger empty and add silica gel to the fourth impinger. Alternatively, a silica gel drying tube may be used in place of the fourth impinger. Place crushed ice and water around all impingers. Maintain the oxidation furnace at 1100 ±50 °C (2,012 ±90 °F) to ensure 100 percent oxidation of COS. Maintain the probe and filter temperatures at a high enough level (no visible condensation) to prevent moisture condensation and monitor the temperatures with a thermocouple.
8.2 Leak-Check Procedure. Assemble the sampling train and leak-check as described in Method 6, section 8.2. Include the combustion air delivery system from the needle valve forward in the leak-check.
8.3 Sample Collection. Adjust the pressure on the second stage of the regulator on the combustion air cylinder to 10 psig. Adjust the combustion air flow rate to 0.5 ±0.05 L/min (1.1 ±0.1 ft 3/hr) before injecting combustion air into the sampling train. Then inject combustion air into the sampling train, start the sample pump, and open the stack sample gas valve. Carry out these three operations within 15 to 30 seconds to avoid pressurizing the sampling train. Adjust the total sample flow rate to 2.0 ±0.2 L/min (4.2 ±0.4 ft 3/hr). These flow rates produce an O2 concentration of 5.0 percent in the stack gas, which must be maintained constantly to allow oxidation of reduced sulfur compounds to SO2. Adjust these flow rates during sampling as necessary. Monitor and record the combustion air manometer reading at regular intervals during the sampling period. Sample for 1 or 3 hours. At the end of sampling, turn off the sample pump and combustion air simultaneously (within 30 seconds of each other). All other procedures are the same as in Method 6, section 8.3, except that the sampling train should not be purged. After collecting the sample, remove the probe from the stack and conduct a leak-check according to the procedures outlined in section 8.2 of Method 6 (mandatory). After each 3-hour test run (or after three 1-hour samples), conduct one system performance check (see section 8.5). After this system performance check and before the next test run, it is recommended that the probe be rinsed and brushed and the filter replaced.
Note:In Method 15, a test run is composed of 16 individual analyses (injects) performed over a period of not less than 3 hours or more than 6 hours. For Method 15A to be consistent with Method 15, the following may be used to obtain a test run: (1) Collect three 60-minute samples or (2) collect one 3-hour sample. (Three test runs constitute a test.)
8.4 Sample Recovery. Recover the hydrogen peroxide-containing impingers as detailed in Method 6, section 8.4.
8.5 System Performance Check.
8.5.1 A system performance check is done (1) to validate the sampling train components and procedure (before testing, optional) and (2) to validate a test run (after a run, mandatory). Perform a check in the field before testing consisting of at least two samples (optional), and perform an additional check after each 3-hour run or after three 1-hour samples (mandatory).
8.5.2 The checks involve sampling a known concentration of COS and comparing the analyzed concentration with the known concentration. Mix the recovery gas with N2 as shown in Figure 15A-4 if dilution is required. Adjust the flow rates to generate a COS concentration in the range of the stack gas or within 20 percent of the applicable standard at a total flow rate of at least 2.5 L/min (5.3 ft 3/hr). Use Equation 15A-4 (see section 12.5) to calculate the concentration of recovery gas generated. Calibrate the flow rate from both sources with a soap bubble flow tube so that the diluted concentration of COS can be accurately calculated. Collect 30-minute samples, and analyze in the same manner as the emission samples. Collect the samples through the probe of the sampling train using a manifold or some other suitable device that will ensure extraction of a representative sample.
8.5.3 The recovery check must be performed in the field before replacing the particulate filter and before cleaning the probe. A sample recovery of 100 ±20 percent must be obtained for the data to be valid and should be reported with the emission data, but should not be used to correct the data. However, if the performance check results do not affect the compliance or noncompliance status of the affected facility, the Administrator may decide to accept the results of the compliance test. Use Equation 15A-5 (see section 12.6) to calculate the recovery efficiency.
9.0 Quality ControlSection | Quality control measure | Effect |
---|---|---|
8.5 | System performance check | Ensures validity of sampling train components and analytical procedure. |
8.2, 10.0 | Sampling equipment leak-check and calibration | Ensures accurate measurement of stack gas flow rate, sample volume. |
10.0 | Barium standard solution standardization | Ensures precision of normality determination. |
11.1 | Replicate titrations | Ensures precision of titration determinations. |
10.1 Metering System, Temperature Sensors, Barometer, and Barium Perchlorate Solution. Same as Method 6, sections 10.1, 10.2, 10.4, and 10.5, respectively.
10.2 Rate Meter. Calibrate with a bubble flow tube.
11.0 Analytical Procedure11.1 Sample Loss Check and Sample Analysis. Same as Method 6, sections 11.1 and 11.2.
12.0 Data Analysis and CalculationsIn the calculations, retain at least one extra decimal figure beyond that of the acquired data. Round off figures after final calculations.
12.1 Nomenclature.
CCOS = Concentration of COS recovery gas, ppm. CRG(act) = Actual concentration of recovery check gas (after dilution), ppm. CRG(m) = Measured concentration of recovery check gas generated, ppm. CRS = Concentration of reduced sulfur compounds as SO2, dry basis, corrected to standard conditions, ppm. N = Normality of barium perchlorate titrant, milliequivalents/ml. Pbar = Barometric pressure at exit orifice of the dry gas meter, mm Hg. Pstd = Standard absolute pressure, 760 mm Hg. QCOS = Flow rate of COS recovery gas, liters/min. QN = Flow rate of diluent N2, liters/min. R = Recovery efficiency for the system performance check, percent. Tm = Average dry gas meter absolute temperature, °K. Tstd = Standard absolute temperature, 293 °K. Va = Volume of sample aliquot titrated, ml. Vms = Dry gas volume as measured by the sample train dry gas meter, liters. Vmc = Dry gas volume as measured by the combustion air dry gas meter, liters. Vms(std) = Dry gas volume measured by the sample train dry gas meter, corrected to standard conditions, liters. Vmc(std) = Dry gas volume measured by the combustion air dry gas meter, corrected to standard conditions, liters. Vsoln = Total volume of solution in which the sulfur dioxide sample is contained, 100 ml. Vt = Volume of barium perchlorate titrant used for the sample (average of replicate titrations), ml. Vtb = Volume of barium perchlorate titrant used for the blank, ml. Y = Calibration factor for sampling train dry gas meter. Yc = Calibration factor for combustion air dry gas meter. 32.03 = Equivalent weight of sulfur dioxide, mg/meq.12.2 Dry Sample Gas Volume, Corrected to Standard Conditions.
Where: K1 = 0.3855 °K/mm Hg for metric units, = 17.65 °R/in. Hg for English units.12.3 Combustion Air Gas Volume, corrected to Standard Conditions.
Note:Correct Pbar for the average pressure of the manometer during the sampling period.
12.4 Concentration of reduced sulfur compounds as ppm SO2.
Where:12.5 Concentration of Generated Recovery Gas.
12.6 Recovery Efficiency for the System Performance Check.
13.0 Method Performance13.1 Analytical Range. The lower detectable limit is 0.1 ppmv when sampling at 2 lpm for 3 hours or 0.3 ppmv when sampling at 2 lpm for 1 hour. The upper concentration limit of the method exceeds concentrations of reduced sulfur compounds generally encountered in sulfur recovery plants.
13.2 Precision. Relative standard deviations of 2.8 and 6.9 percent have been obtained when sampling a stream with a reduced sulfur compound concentration of 41 ppmv as SO2 for 1 and 3 hours, respectively.
13.3 Bias. No analytical bias has been identified. However, results obtained with this method are likely to contain a positive bias relative to emission regulations due to the presence of nonregulated sulfur compounds (that are present in petroleum) in the emissions. The magnitude of this bias varies accordingly, and has not been quantified.
14.0 Pollution Prevention [Reserved] 15.0 Waste Management [Reserved] 16.0 References1. American Society for Testing and Materials Annual Book of ASTM Standards. Part 31: Water, Atmospheric Analysis. Philadelphia, Pennsylvania. 1974. pp. 40-42.
2. Blosser, R.O., H.S. Oglesby, and A.K. Jain. A Study of Alternate SO2 Scrubber Designs Used for TRS Monitoring. National Council of the Paper Industry for Air and Stream Improvement, Inc., New York, New York. Special Report 77-05. July 1977.
3. Curtis, F., and G.D. McAlister. Development and Evaluation of an Oxidation/Method 6 TRS Emission Sampling Procedure. Emission Measurement Branch, Emission Standards and Engineering Division, U.S. Environmental Protection Agency, Research Triangle Park, North Carolina. February 1980.
4. Gellman, I. A Laboratory and Field Study of Reduced Sulfur Sampling and Monitoring Systems. National Council of the Paper Industry for Air and Stream Improvement, Inc., New York, New York. Atmospheric Quality Improvement Technical Bulletin No. 81. October 1975.
5. Margeson, J.H., et al. A Manual Method for TRS Determination. Journal of Air Pollution Control Association. 35:1280-1286. December 1985.
17.0 Tables, Diagrams, Flowcharts, and Validation Data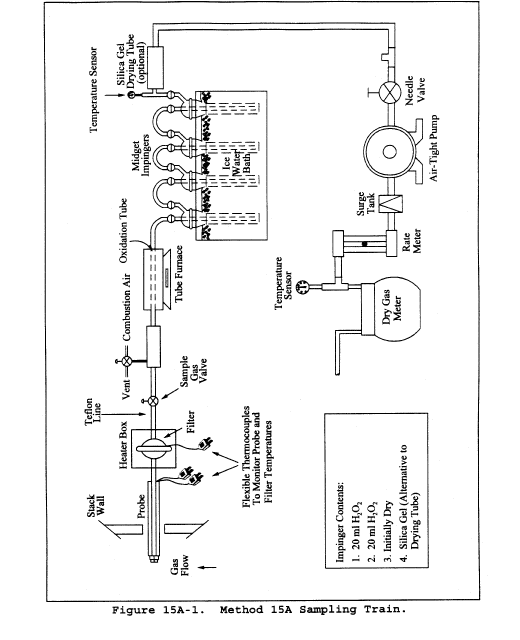
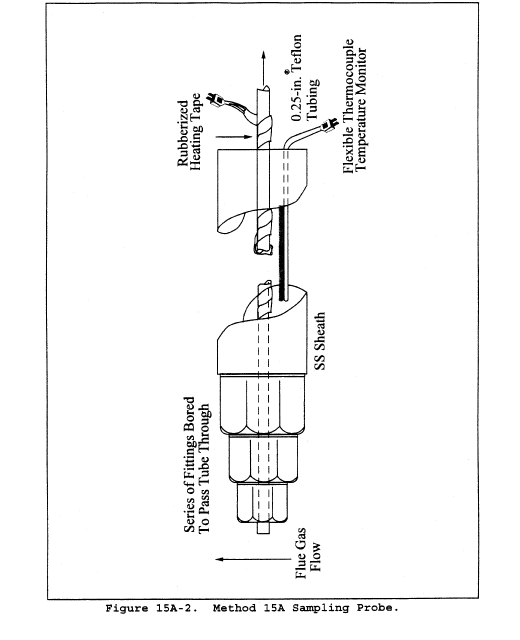
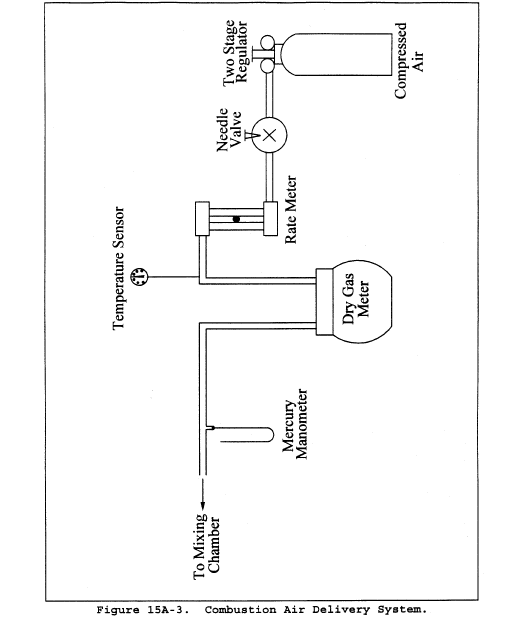
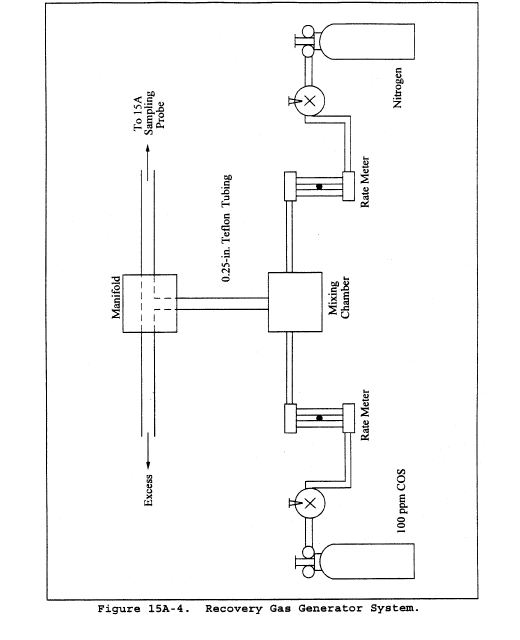
Appendix A-6 to Part 60 - Test Methods 16 through 18
40:9.0.1.1.1.0.1.1.6 : Appendix A
Appendix A-6 to Part 60 - Test Methods 16 through 18 Method 16 - Semicontinuous determination of sulfur emissions from stationary sources Method 16A - Determination of total reduced sulfur emissions from stationary sources (impinger technique) Method 16B - Determination of total reduced sulfur emissions from stationary sources Method 16C - Determination of Total Reduced Sulfur Emissions From Stationary Sources Method 17 - Determination of particulate emissions from stationary sources (in-stack filtration method) Method 18 - Measurement of gaseous organic compound emissions by gas chromatographyThe test methods in this appendix are referred to in § 60.8 (Performance Tests) and § 60.11 (Compliance With Standards and Maintenance Requirements) of 40 CFR part 60, subpart A (General Provisions). Specific uses of these test methods are described in the standards of performance contained in the subparts, beginning with Subpart D.
Within each standard of performance, a section title “Test Methods and Procedures” is provided to: (1) Identify the test methods to be used as reference methods to the facility subject to the respective standard and (2) identify any special instructions or conditions to be followed when applying a method to the respective facility. Such instructions (for example, establish sampling rates, volumes, or temperatures) are to be used either in addition to, or as a substitute for procedures in a test method. Similarly, for sources subject to emission monitoring requirements, specific instructions pertaining to any use of a test method as a reference method are provided in the subpart or in Appendix B.
Inclusion of methods in this appendix is not intended as an endorsement or denial of their applicability to sources that are not subject to standards of performance. The methods are potentially applicable to other sources; however, applicability should be confirmed by careful and appropriate evaluation of the conditions prevalent at such sources.
The approach followed in the formulation of the test methods involves specifications for equipment, procedures, and performance. In concept, a performance specification approach would be preferable in all methods because this allows the greatest flexibility to the user. In practice, however, this approach is impractical in most cases because performance specifications cannot be established. Most of the methods described herein, therefore, involve specific equipment specifications and procedures, and only a few methods in this appendix rely on performance criteria.
Minor changes in the test methods should not necessarily affect the validity of the results and it is recognized that alternative and equivalent methods exist. section 60.8 provides authority for the Administrator to specify or approve (1) equivalent methods, (2) alternative methods, and (3) minor changes in the methodology of the test methods. It should be clearly understood that unless otherwise identified all such methods and changes must have prior approval of the Administrator. An owner employing such methods or deviations from the test methods without obtaining prior approval does so at the risk of subsequent disapproval and retesting with approved methods.
Within the test methods, certain specific equipment or procedures are recognized as being acceptable or potentially acceptable and are specifically identified in the methods. The items identified as acceptable options may be used without approval but must be identified in the test report. The potentially approvable options are cited as “subject to the approval of the Administrator” or as “or equivalent.” Such potentially approvable techniques or alternatives may be used at the discretion of the owner without prior approval. However, detailed descriptions for applying these potentially approvable techniques or alternatives are not provided in the test methods. Also, the potentially approvable options are not necessarily acceptable in all applications. Therefore, an owner electing to use such potentially approvable techniques or alternatives is responsible for: (1) assuring that the techniques or alternatives are in fact applicable and are properly executed; (2) including a written description of the alternative method in the test report (the written method must be clear and must be capable of being performed without additional instruction, and the degree of detail should be similar to the detail contained in the test methods); and (3) providing any rationale or supporting data necessary to show the validity of the alternative in the particular application. Failure to meet these requirements can result in the Administrator's disapproval of the alternative.
Method 16 - Semicontinuous Determination of Sulfur Emissions From Stationary Sources Note:This method does not include all of the specifications (e.g., equipment and supplies) and procedures (e.g., sampling and analytical) essential to its performance. Some material is incorporated by reference from other methods in this part. Therefore, to obtain reliable results, persons using this method should have a thorough knowledge of at least the following additional test methods: Method 1, Method 4, Method 15, and Method 16A.
1.0 Scope and Application1.1 Analytes.
Analyte | CAS No. | Sensitivity |
---|---|---|
Dimethyl disulfide [(CH3)2S2] | 62-49-20 | 50 ppb. |
Dimethyl sulfide [(CH3)2S] | 75-18-3 | 50 ppb. |
Hydrogen sulfide [H2S] | 7783-06-4 | 50 ppb. |
Methyl mercaptan [CH4S] | 74-93-1 | 50 ppb. |
1.2 Applicability. This method is applicable for the determination of total reduced sulfur (TRS) compounds from recovery furnaces, lime kilns, and smelt dissolving tanks at kraft pulp mills and fuel gas combustion devices at petroleum refineries.
Note:The method described below uses the principle of gas chromatographic (GC) separation and flame photometric detection (FPD). Since there are many systems or sets of operating conditions that represent useable methods of determining sulfur emissions, all systems which employ this principle, but differ only in details of equipment and operation, may be used as alternative methods, provided that the calibration precision and sample line loss criteria are met.
1.3 Data Quality Objectives. Adherence to the requirements of this method will enhance the quality of the data obtained from air pollutant sampling methods.
2.0 Summary of Method2.1 A gas sample is extracted from the emission source and an aliquot is analyzed for hydrogen sulfide (H2S), methyl mercaptan (MeSH), dimethyl sulfide (DMS), and dimethyl disulfide (DMDS) by GC/FPD. These four compounds are known collectively as TRS.
3.0 Definitions [Reserved] 4.0 Interferences4.1 Moisture. Moisture condensation in the sample delivery system, the analytical column, or the FPD burner block can cause losses or interferences. This is prevented by maintaining the probe, filter box, and connections at a temperature of at least 120 °C (248 °F). Moisture is removed in the SO2 scrubber and heating the sample beyond this point is not necessary when the ambient temperature is above 0 °C (32 °F). Alternatively, moisture may be eliminated by heating the sample line, and by conditioning the sample with dry dilution air to lower its dew point below the operating temperature of the GC/FPD analytical system prior to analysis.
4.2 Carbon Monoxide (CO) and Carbon Dioxide (CO2). CO and CO2 have a substantial desensitizing effect on the flame photometric detector even after dilution. Acceptable systems must demonstrate that they have eliminated this interference by some procedure such as eluting these compounds before any of the compounds to be measured. Compliance with this requirement can be demonstrated by submitting chromatograms of calibration gases with and without CO2 in the diluent gas. The CO2 level should be approximately 10 percent for the case with CO2 present. The two chromatograms should show agreement within the precision limits of section 10.2.
4.3 Particulate Matter. Particulate matter in gas samples can cause interference by eventual clogging of the analytical system. This interference is eliminated by using the Teflon filter after the probe.
4.4 Sulfur Dioxide (SO2). Sulfur dioxide is not a specific interferant but may be present in such large amounts that it cannot effectively be separated from the other compounds of interest. The SO2 scrubber described in section 6.1.3 will effectively remove SO2 from the sample.
5.0 Safety5.1 Disclaimer. This method may involve hazardous materials, operations, and equipment. This test method may not address all of the safety problems associated with its use. It is the responsibility of the user of this test method to establish appropriate safety and health practices and determine the applicability of regulatory limitations prior to performing this test method.
5.2 Hydrogen Sulfide. A flammable, poisonous gas with the odor of rotten eggs. H2S is extremely hazardous and can cause collapse, coma, and death within a few seconds of one or two inhalations at sufficient concentrations. Low concentrations irritate the mucous membranes and may cause nausea, dizziness, and headache after exposure.
6.0 Equipment and Supplies6.1. Sample Collection. The following items are needed for sample collection.
6.1.1 Probe. Teflon or Teflon-lined stainless steel. The probe must be heated to prevent moisture condensation. It must be designed to allow calibration gas to enter the probe at or near the sample point entry. Any portion of the probe that contacts the stack gas must be heated to prevent moisture condensation. Figure 16-1 illustrates the probe used in lime kilns and other sources where significant amounts of particulate matter are present. The probe is designed with the deflector shield placed between the sample and the gas inlet holes to reduce clogging of the filter and possible adsorption of sample gas. As an alternative, the probe described in section 6.1.1 of Method 16A having a nozzle directed away from the gas stream may be used at sources having significant amounts of particulate matter.
6.1.2 Particulate Filter. 50-mm Teflon filter holder and a 1- to 2-micron porosity Teflon filter (available through Savillex Corporation, 5325 Highway 101, Minnetonka, Minnesota 55343). The filter holder must be maintained in a hot box at a temperature of at least 120 °C (248 °F).
6.1.3 SO2 Scrubber. Three 300-ml Teflon segmented impingers connected in series with flexible, thick-walled, Teflon tubing. (Impinger parts and tubing available through Savillex.) The first two impingers contain 100 ml of citrate buffer and the third impinger is initially dry. The tip of the tube inserted into the solution should be constricted to less than 3 mm ( 1/8 in.) ID and should be immersed to a depth of at least 5 cm (2 in.). Immerse the impingers in an ice water bath and maintain near 0 °C (32 °F). The scrubber solution will normally last for a 3-hour run before needing replacement. This will depend upon the effects of moisture and particulate matter on the solution strength and pH. Connections between the probe, particulate filter, and SO2 scrubber must be made of Teflon and as short in length as possible. All portions of the probe, particulate filter, and connections prior to the SO2 scrubber (or alternative point of moisture removal) must be maintained at a temperature of at least 120 °C (248 °F).
6.1.4 Sample Line. Teflon, no greater than 1.3 cm ( 1/2 in.) ID. Alternative materials, such as virgin Nylon, may be used provided the line loss test is acceptable.
6.1.5 Sample Pump. The sample pump must be a leakless Teflon-coated diaphragm type or equivalent.
6.2 Analysis. The following items are needed for sample analysis:
6.2.1 Dilution System. Needed only for high sample concentrations. The dilution system must be constructed such that all sample contacts are made of Teflon, glass, or stainless steel.
6.2.2 Gas Chromatograph. The gas chromatograph must have at least the following components:
6.2.2.1 Oven. Capable of maintaining the separation column at the proper operating temperature ±1 °C (2 °F).
6.2.2.2 Temperature Gauge. To monitor column oven, detector, and exhaust temperature ±1 °C (2 °F).
6.2.2.3 Flow System. Gas metering system to measure sample, fuel, combustion gas, and carrier gas flows.
6.2.2.4 Flame Photometric Detector.
6.2.2.4.1 Electrometer. Capable of full scale amplification of linear ranges of 10−9 to 10−4 amperes full scale.
6.2.2.4.2 Power Supply. Capable of delivering up to 750 volts.
6.2.2.4.3 Recorder. Compatible with the output voltage range of the electrometer.
6.2.2.4.4 Rotary Gas Valves. Multiport Teflon-lined valves equipped with sample loop. Sample loop volumes must be chosen to provide the needed analytical range. Teflon tubing and fittings must be used throughout to present an inert surface for sample gas. The gas chromatograph must be calibrated with the sample loop used for sample analysis.
6.2.3 Gas Chromatogram Columns. The column system must be demonstrated to be capable of resolving the four major reduced sulfur compounds: H2S, MeSH, DMS, and DMDS. It must also demonstrate freedom from known interferences. To demonstrate that adequate resolution has been achieved, submit a chromatogram of a calibration gas containing all four of the TRS compounds in the concentration range of the applicable standard. Adequate resolution will be defined as base line separation of adjacent peaks when the amplifier attenuation is set so that the smaller peak is at least 50 percent of full scale. Baseline separation is defined as a return to zero ±5 percent in the interval between peaks. Systems not meeting this criteria may be considered alternate methods subject to the approval of the Administrator.
6.3 Calibration. A calibration system, containing the following components, is required (see Figure 16-2).
6.3.1 Tube Chamber. Chamber of glass or Teflon of sufficient dimensions to house permeation tubes.
6.3.2 Flow System. To measure air flow over permeation tubes at ±2 percent. Flow over the permeation device may also be determined using a soap bubble flowmeter.
6.3.3 Constant Temperature Bath. Device capable of maintaining the permeation tubes at the calibration temperature within 0.1 °C (0.2 °F).
6.3.4 Temperature Gauge. Thermometer or equivalent to monitor bath temperature within 1 °C (2 °F).
7.0 Reagents and Standards7.1 Fuel. Hydrogen (H2), prepurified grade or better.
7.2 Combustion Gas. Oxygen (O2) or air, research purity or better.
7.3 Carrier Gas. Prepurified grade or better.
7.4 Diluent (if required). Air containing less than 50 ppb total sulfur compounds and less than 10 ppmv each of moisture and total hydrocarbons.
7.5 Calibration Gases
7.5.1 Permeation tubes, one each of H2S, MeSH, DMS, and DMDS, gravimetrically calibrated and certified at some convenient operating temperature. These tubes consist of hermetically sealed FEP Teflon tubing in which a liquified gaseous substance is enclosed. The enclosed gas permeates through the tubing wall at a constant rate. When the temperature is constant, calibration gases covering a wide range of known concentrations can be generated by varying and accurately measuring the flow rate of diluent gas passing over the tubes. These calibration gases are used to calibrate the GC/FPD system and the dilution system.
7.5.2 Cylinder Gases. Cylinder gases may be used as alternatives to permeation devices. The gases must be traceable to a primary standard (such as permeation tubes) and not used beyond the certification expiration date.
7.6 Citrate Buffer and Sample Line Loss Gas. Same as Method 15, sections 7.6 and 7.7.
8.0 Sample Collection, Preservation, Storage, and TransportSame as Method 15, section 8.0, except that the references to the dilution system may not be applicable.
9.0 Quality ControlSection | Quality control measure | Effect |
---|---|---|
8.0 | Sample line loss check | Ensures that uncorrected negative bias introduced by sample loss is no greater than 20 percent, and provides for correction of bias of 20 percent or less. |
8.0 | Calibration drift test | Ensures that bias introduced by drift in the measurement system output during the run is no greater than 5 percent. |
10.0 | Analytical calibration | Ensures precision of analytical results within 5 percent. |
Same as Method 15, section 10.0, with the following addition and exceptions:
10.1 Use the four compounds that comprise TRS instead of the three reduced sulfur compounds measured by Method 15.
10.2 Flow Meter. Calibration before each test run is recommended, but not required; calibration following each test series is mandatory. Calibrate each flow meter after each complete test series with a wet-test meter. If the flow measuring device differs from the wet-test meter by 5 percent or more, the completed test runs must be voided. Alternatively, the flow data that yield the lower flow measurement may be used. Flow over the permeation device may also be determined using a soap bubble flowmeter.
11.0 Analytical ProcedureSample collection and analysis are concurrent for this method (see section 8.0).
12.0 Data Analysis and Calculations12.1 Concentration of Reduced Sulfur Compounds. Calculate the average concentration of each of the four analytes (i.e., DMDS, DMS, H2S, and MeSH) over the sample run (specified in section 8.2 of Method 15 as 16 injections).
Where: Si = Concentration of any reduced sulfur compound from the i th sample injection, ppm. C = Average concentration of any one of the reduced sulfur compounds for the entire run, ppm. N = Number of injections in any run period.12.2 TRS Concentration. Using Equation 16-2, calculate the TRS concentration for each sample run.
Where: CTRS = TRS concentration, ppmv. CH2S = Hydrogen sulfide concentration, ppmv. CMeSH = Methyl mercaptan concentration, ppmv. CDMS = Dimethyl sulfide concentration, ppmv. CDMDS = Dimethyl disulfide concentration, ppmv. d = Dilution factor, dimensionless.12.3 Average TRS Concentration. Calculate the average TRS concentration for all sample runs performed.
Where: Average TRS = Average total reduced sulfur in ppm. TRSi = Total reduced sulfur in ppm as determined by Equation 16-2. N = Number of samples. Bwo = Fraction of volume of water vapor in the gas stream as determined by Method 4 - Determination of Moisture in Stack Gases. 13.0 Method Performance13.1 Analytical Range. The analytical range will vary with the sample loop size. Typically, the analytical range may extend from 0.1 to 100 ppmv using 10- to 0.1-ml sample loop sizes. This eliminates the need for sample dilution in most cases.
13.2 Sensitivity. Using the 10-ml sample size, the minimum detectable concentration is approximately 50 ppb.
14.0 Pollution Prevention [Reserved] 15.0 Waste Management [Reserved] 16.0 References1. O'Keeffe, A.E., and G.C. Ortman. “Primary Standards for Trace Gas Analysis.” Analytical Chemical Journal, 38,76. 1966.
2. Stevens, R.K., A.E. O'Keeffe, and G.C. Ortman. “Absolute Calibration of a Flame Photometric Detector to Volatile Sulfur Compounds at Sub-Part-Per-Million Levels.” Environmental Science and Technology, 3:7. July 1969.
3. Mulik, J.D., R.K. Stevens, and R. Baumgardner. “An Analytical System Designed to Measure Multiple Malodorous Compounds Related to Kraft Mill Activities.” Presented at the 12th Conference on Methods in Air Pollution and Industrial Hygiene Studies, University of Southern California, Los Angeles, CA. April 6-8, 1971.
4. Devonald, R.H., R.S. Serenius, and A.D. McIntyre. “Evaluation of the Flame Photometric Detector for Analysis of Sulfur Compounds.” Pulp and Paper Magazine of Canada, 73,3. March 1972.
5. Grimley, K.W., W.S. Smith, and R.M. Martin. “The Use of a Dynamic Dilution System in the Conditioning of Stack Gases for Automated Analysis by a Mobile Sampling Van.” Presented at the 63rd Annual APCA Meeting, St. Louis, MO. June 14-19, 1970.
6. General Reference. Standard Methods of Chemical Analysis, Volumes III-A and III-B Instrumental Methods. Sixth Edition. Van Nostrand Reinhold Co.
17.0 Tables, Diagrams, Flowcharts, and Validation Data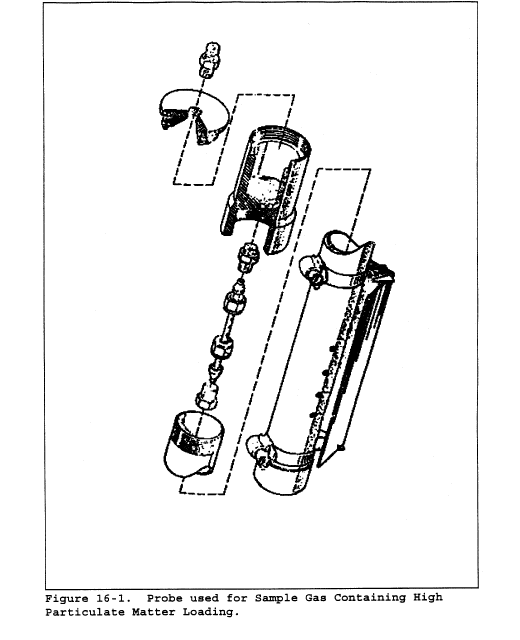
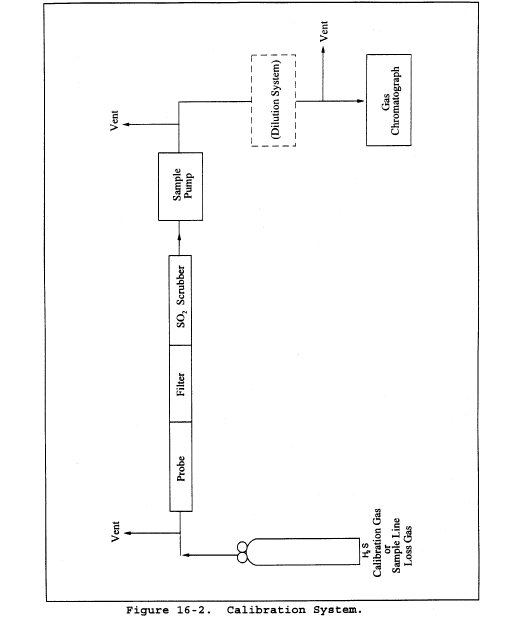
This method does not include all of the specifications (e.g., equipment and supplies) and procedures (e.g., sampling and analytical) essential to its performance. Some material is incorporated by reference from other methods in this part. Therefore, to obtain reliable results, persons using this method should have a thorough knowledge of at least the following additional test methods: Method 1, Method 6, and Method 16.
1.0 Scope and Application1.1 Analytes.
Analyte | CAS No. | Sensitivity |
---|---|---|
Total reduced sulfur (TRS) including: | N/A | See section 13.1. |
Dimethyl disulfide [(CH3)2S2] | 62-49-20 | |
Dimethyl sulfide [(CH3)2S] | 75-18-3 | |
Hydrogen sulfide [H2S] | 7783-06-4 | |
Methyl mercaptan [CH4S] | 74-93-1 | |
Reduced sulfur (RS) including: | N/A | |
H2S | 7783-06-4 | |
Carbonyl sulfide [COS] | 463-58-1 | |
Carbon disulfide [CS2] | 75-15-0 | |
Reported as: Sulfur dioxide (SO2) | 7449-09-5 |
1.2 Applicability. This method is applicable for the determination of TRS emissions from recovery boilers, lime kilns, and smelt dissolving tanks at kraft pulp mills, reduced sulfur compounds (H2S, carbonyl sulfide, and carbon disulfide) from sulfur recovery units at onshore natural gas processing facilities, and from other sources when specified in an applicable subpart of the regulations. The flue gas must contain at least 1 percent oxygen for complete oxidation of all TRS to SO2. Note: If sources other than kraft pulp mills experience low oxygen levels in the emissions, the method results may be biased low.
1.3 Data Quality Objectives. Adherence to the requirements of this method will enhance the quality of the data obtained from air pollutant sampling methods.
2.0 Summary of Method2.1 An integrated gas sample is extracted from the stack. SO2 is removed selectively from the sample using a citrate buffer solution. TRS compounds are then thermally oxidized to SO2, collected in hydrogen peroxide as sulfate, and analyzed by the Method 6 barium-thorin titration procedure.
3.0 Definitions [Reserved] 4.0 Interferences4.1 Reduced sulfur compounds other than those regulated by the emission standards, if present, may be measured by this method. Therefore, carbonyl sulfide, which is partially oxidized to SO2 and may be present in a lime kiln exit stack, would be a positive interferant.
4.2 Particulate matter from the lime kiln stack gas (primarily calcium carbonate) can cause a negative bias if it is allowed to enter the citrate scrubber; the particulate matter will cause the pH to rise and H2S to be absorbed prior to oxidation. Furthermore, if the calcium carbonate enters the hydrogen peroxide impingers, the calcium will precipitate sulfate ion. Proper use of the particulate filter described in section 6.1.3 will eliminate this interference.
5.0 Safety5.1 Disclaimer. This method may involve hazardous materials, operations, and equipment. This test method may not address all of the safety problems associated with its use. It is the responsibility of the user of this test method to establish appropriate safety and health practices and determine the applicability of regulatory limitations prior to performing this test method.
5.2 Corrosive reagents. The following reagents are hazardous. Personal protective equipment and safe procedures are useful in preventing chemical splashes. If contact occurs, immediately flush with copious amounts of water for at least 15 minutes. Remove clothing under shower and decontaminate. Treat residual chemical burns as thermal burns.
5.2.1 Hydrogen Peroxide (H2O2). Irritating to eyes, skin, nose, and lungs.
5.2.2 Sodium Hydroxide (NaOH). Causes severe damage to eyes and skin. Inhalation causes irritation to nose, throat, and lungs. Reacts exothermically with limited amounts of water.
5.2.3 Sulfuric Acid (H2SO4). Rapidly destructive to body tissue. Will cause third degree burns. Eye damage may result in blindness. Inhalation may be fatal from spasm of the larynx, usually within 30 minutes. May cause lung tissue damage with edema. 3 mg/m 3 will cause lung damage in uninitiated. 1 mg/m 3 for 8 hours will cause lung damage or, in higher concentrations, death. Provide ventilation to limit inhalation. Reacts violently with metals and organics.
5.3 Hydrogen Sulfide (H2S). A flammable, poisonous gas with the odor of rotten eggs. H2S is extremely hazardous and can cause collapse, coma, and death within a few seconds of one or two inhalations at sufficient concentrations. Low concentrations irritate the mucous membranes and may cause nausea, dizziness, and headache after exposure.
6.0 Equipment and Supplies6.1 Sample Collection. The sampling train is shown in Figure 16A-1 and component parts are discussed below. Modifications to this sampling train are acceptable provided the system performance check is met (see section 8.5).
6.1.1 Probe. Teflon tubing, 6.4-mm ( 1/4-in.) diameter, sequentially wrapped with heat-resistant fiber strips, a rubberized heat tape (plug at one end), and heat-resistant adhesive tape. A flexible thermocouple or other suitable temperature measuring device should be placed between the Teflon tubing and the fiber strips so that the temperature can be monitored to prevent softening of the probe. The probe should be sheathed in stainless steel to provide in-stack rigidity. A series of bored-out stainless steel fittings placed at the front of the sheath will prevent moisture and particulate from entering between the probe and sheath. A 6.4-mm ( 1/4-in.) Teflon elbow (bored out) should be attached to the inlet of the probe, and a 2.54 cm (1 in.) piece of Teflon tubing should be attached at the open end of the elbow to permit the opening of the probe to be turned away from the particulate stream; this will reduce the amount of particulate drawn into the sampling train. The probe is depicted in Figure 16A-2.
6.1.2 Probe Brush. Nylon bristle brush with handle inserted into a 3.2-mm ( 1/8-in.) Teflon tubing. The Teflon tubing should be long enough to pass the brush through the length of the probe.
6.1.3 Particulate Filter. 50-mm Teflon filter holder and a 1- to 2-µm porosity, Teflon filter (available through Savillex Corporation, 5325 Highway 101, Minnetonka, Minnesota 55343). The filter holder must be maintained in a hot box at a temperature sufficient to prevent moisture condensation. A temperature of 121 °C (250 °F) was found to be sufficient when testing a lime kiln under sub-freezing ambient conditions.
6.1.4 SO2 Scrubber. Three 300-ml Teflon segmented impingers connected in series with flexible, thick-walled, Teflon tubing. (Impinger parts and tubing available through Savillex.) The first two impingers contain 100 ml of citrate buffer and the third impinger is initially dry. The tip of the tube inserted into the solution should be constricted to less than 3 mm ( 1/8-in.) ID and should be immersed to a depth of at least 5 cm (2 in.).
6.1.5 Combustion Tube. Quartz glass tubing with an expanded combustion chamber 2.54 cm (1 in.) in diameter and at least 30.5 cm (12 in.) long. The tube ends should have an outside diameter of 0.6 cm ( 1/4 in.) and be at least 15.3 cm (6 in.) long. This length is necessary to maintain the quartz-glass connector near ambient temperature and thereby avoid leaks. Alternatively, the outlet may be constructed with a 90-degree glass elbow and socket that would fit directly onto the inlet of the first peroxide impinger.
6.1.6 Furnace. A furnace of sufficient size to enclose the combustion chamber of the combustion tube with a temperature regulator capable of maintaining the temperature at 800 ±100 °C (1472 ±180 °F). The furnace operating temperature should be checked with a thermocouple to ensure accuracy.
6.1.7 Peroxide Impingers, Stopcock Grease, Temperature Sensor, Drying Tube, Valve, Pump, and Barometer. Same as Method 6, sections 6.1.1.2, 6.1.1.4, 6.1.1.5, 6.1.1.6, 6.1.1.7, 6.1.1.8, and 6.1.2, respectively, except that the midget bubbler of Method 6, section 6.1.1.2 is not required.
6.1.8 Vacuum Gauge. At least 760 mm Hg (30 in. Hg) gauge.
6.1.9 Rate Meter. Rotameter, or equivalent, accurate to within 5 percent at the selected flow rate of approximately 2 liters/min (4.2 ft 3/hr).
6.1.10 Volume Meter. Dry gas meter capable of measuring the sample volume under the sampling conditions of 2 liters/min (4.2 ft 3/hr) with an accuracy of 2 percent.
6.2 Sample Recovery. Polyethylene Bottles, 250-ml (one per sample).
6.3 Sample Preparation and Analysis. Same as Method 6, section 6.3, except a 10-ml buret with 0.05-ml graduations is required, and the spectrophotometer is not needed.
7.0 Reagents and Standards Note:Unless otherwise indicated, all reagents must conform to the specifications established by the Committee on Analytical Reagents of the American Chemical Society. When such specifications are not available, the best available grade must be used.
7.1 Sample Collection. The following reagents are required for sample analysis:
7.1.1 Water. Same as in Method 6, section 7.1.1.
7.1.2 Citrate Buffer. Dissolve 300 g of potassium citrate (or 284 g of sodium citrate) and 41 g of anhydrous citric acid in 1 liter of water (200 ml is needed per test). Adjust the pH to between 5.4 and 5.6 with potassium citrate or citric acid, as required.
7.1.3 Hydrogen Peroxide, 3 percent. Same as in Method 6, section 7.1.3 (40 ml is needed per sample).
7.1.4 Recovery Check Gas. Hydrogen sulfide (100 ppmv or less) in nitrogen, stored in aluminum cylinders. Verify the concentration by Method 11 or by gas chromatography where the instrument is calibrated with an H2S permeation tube as described below. For Method 11, the relative standard deviation should not exceed 5 percent on at least three 20-minute runs.
Note:Alternatively, hydrogen sulfide recovery gas generated from a permeation device gravimetrically calibrated and certified at some convenient operating temperature may be used. The permeation rate of the device must be such that at a dilution gas flow rate of 3 liters/min (6.4 ft 3/hr), an H2S concentration in the range of the stack gas or within 20 percent of the standard can be generated.
7.1.5 Combustion Gas. Gas containing less than 50 ppb reduced sulfur compounds and less than 10 ppmv total hydrocarbons. The gas may be generated from a clean-air system that purifies ambient air and consists of the following components: Diaphragm pump, silica gel drying tube, activated charcoal tube, and flow rate measuring device. Flow from a compressed air cylinder is also acceptable.
7.2 Sample Recovery and Analysis. Same as Method 6, sections 7.2.1 and 7.3, respectively.
8.0 Sample Collection, Preservation, Storage, and Transport8.1 Preparation of Sampling Train.
8.1.1 For the SO2 scrubber, measure 100 ml of citrate buffer into the first and second impingers; leave the third impinger empty. Immerse the impingers in an ice bath, and locate them as close as possible to the filter heat box. The connecting tubing should be free of loops. Maintain the probe and filter temperatures sufficiently high to prevent moisture condensation, and monitor with a suitable temperature sensor.
8.1.2 For the Method 6 part of the train, measure 20 ml of 3 percent hydrogen peroxide into the first and second midget impingers. Leave the third midget impinger empty, and place silica gel in the fourth midget impinger. Alternatively, a silica gel drying tube may be used in place of the fourth impinger. Maintain the oxidation furnace at 800 ±100 °C (1472 ±180 °F). Place crushed ice and water around all impingers.
8.2 Citrate Scrubber Conditioning Procedure. Condition the citrate buffer scrubbing solution by pulling stack gas through the Teflon impingers and bypassing all other sampling train components. A purge rate of 2 liters/min for 10 minutes has been found to be sufficient to obtain equilibrium. After the citrate scrubber has been conditioned, assemble the sampling train, and conduct (optional) a leak-check as described in Method 6, section 8.2.
8.3 Sample Collection. Same as in Method 6, section 8.3, except the sampling rate is 2 liters/min (±10 percent) for 1 or 3 hours. After the sample is collected, remove the probe from the stack, and conduct (mandatory) a post-test leak-check as described in Method 6, section 8.2. The 15-minute purge of the train following collection should not be performed. After each 3-hour test run (or after three 1-hour samples), conduct one system performance check (see section 8.5) to determine the reduced sulfur recovery efficiency through the sampling train. After this system performance check and before the next test run, rinse and brush the probe with water, replace the filter, and change the citrate scrubber (optional but recommended).
Note:In Method 16, a test run is composed of 16 individual analyses (injects) performed over a period of not less than 3 hours or more than 6 hours. For Method 16A to be consistent with Method 16, the following may be used to obtain a test run: (1) collect three 60-minute samples or (2) collect one 3-hour sample. (Three test runs constitute a test.)
8.4 Sample Recovery. Disconnect the impingers. Quantitatively transfer the contents of the midget impingers of the Method 6 part of the train into a leak-free polyethylene bottle for shipment. Rinse the three midget impingers and the connecting tubes with water and add the washings to the same storage container. Mark the fluid level. Seal and identify the sample container.
8.5 System Performance Check.
8.5.1 A system performance check is done (1) to validate the sampling train components and procedure (prior to testing; optional) and (2) to validate a test run (after a run). Perform a check in the field prior to testing consisting of at least two samples (optional), and perform an additional check after each 3 hour run or after three 1-hour samples (mandatory).
8.5.2 The checks involve sampling a known concentration of H2S and comparing the analyzed concentration with the known concentration. Mix the H2S recovery check gas (Section 7.1.4) and combustion gas in a dilution system such as that shown in Figure 16A-3. Adjust the flow rates to generate an H2S concentration in the range of the stack gas or within 20 percent of the applicable standard and an oxygen concentration greater than 1 percent at a total flow rate of at least 2.5 liters/min (5.3 ft 3/hr). Use Equation 16A-3 to calculate the concentration of recovery gas generated. Calibrate the flow rate from both sources with a soap bubble flow meter so that the diluted concentration of H2S can be accurately calculated.
8.5.3 Collect 30-minute samples, and analyze in the same manner as the emission samples. Collect the sample through the probe of the sampling train using a manifold or some other suitable device that will ensure extraction of a representative sample.
8.5.4 The recovery check must be performed in the field prior to replacing the SO2 scrubber and particulate filter and before the probe is cleaned. Use Equation 16A-4 (see section 12.5) to calculate the recovery efficiency. Report the recovery efficiency with the emission data; do not correct the emission data for the recovery efficiency. A sample recovery of 100 ±20 percent must be obtained for the emission data to be valid. However, if the recovery efficiency is not in the 100 ±20 percent range but the results do not affect the compliance or noncompliance status of the affected facility, the Administrator may decide to accept the results of the compliance test.
9.0 Quality ControlSection | Quality control measure | Effect |
---|---|---|
8.5 | System performance check | Ensure validity of sampling train components and analytical procedure. |
8.2, 10.0 | Sampling equipment leak-check and calibration | Ensure accurate measurement of stack gas flow rate, sample volume. |
10.0 | Barium standard solution standardization | Ensure precision of normality determination. |
11.1 | Replicate titrations | Ensure precision of titration determinations. |
Same as Method 6, section 10.0.
11.0 Analytical Procedure11.1 Sample Loss Check and Sample Analysis. Same as Method 6, sections 11.1 and 11.2, respectively, with the following exception: for 1-hour sampling, take a 40-ml aliquot, add 160 ml of 100 percent isopropanol and four drops of thorin.
12.0 Data Analysis and CalculationsIn the calculations, at least one extra decimal figure should be retained beyond that of the acquired data. Figures should be rounded off after final calculations.
12.1 Nomenclature.
CTRS = Concentration of TRS as SO2, dry basis corrected to standard conditions, ppmv. CRG(act) = Actual concentration of recovery check gas (after dilution), ppm. CRG(m) = Measured concentration of recovery check gas generated, ppm. CH2S = Verified concentration of H2S recovery gas. N = Normality of barium perchlorate titrant, milliequivalents/ml. Pbar = Barometric pressure at exit orifice of the dry gas meter, mm Hg (in. Hg). Pstd = Standard absolute pressure, 760 mm Hg (29.92 in. Hg). QH2S = Calibrated flow rate of H2S recovery gas, liters/min. QCG = Calibrated flow rate of combustion gas, liters/min. R = Recovery efficiency for the system performance check, percent. Tm = Average dry gas meter absolute temperature, °K (°R). Tstd = Standard absolute temperature, 293 °K (528 °R). Va = Volume of sample aliquot titrated, ml. Vm = Dry gas volume as measured by the dry gas meter, liters (dcf). Vm(std) = Dry gas volume measured by the dry gas meter, corrected to standard conditions, liters (dscf). Vsoln = Total volume of solution in which the sulfur dioxide sample is contained, 100 ml. Vt = Volume of barium perchlorate titrant used for the sample, ml (average of replicate titrations). Vtb = Volume of barium perchlorate titrant used for the blank, ml. Y = Dry gas meter calibration factor. 32.03 = Equivalent weight of sulfur dioxide, mg/meq.12.2 Dry Sample Gas Volume, Corrected to Standard Conditions.
Where: K1 = 0.3855 °K/mm Hg for metric units, = 17.65 °R/in. Hg for English units.12.3 Concentration of TRS as ppm SO2.
Where:12.4 Concentration of Recovery Gas Generated in the System Performance Check.
12.5 Recovery Efficiency for the System Performance Check.
13.0 Method Performance13.1 Analytical Range. The lower detectable limit is 0.1 ppmv SO2 when sampling at 2 liters/min (4.2 ft 3/hr) for 3 hours or 0.3 ppmv when sampling at 2 liters/min (4.2 ft 3/hr) for 1 hour. The upper concentration limit of the method exceeds the TRS levels generally encountered at kraft pulp mills.
13.2 Precision. Relative standard deviations of 2.0 and 2.6 percent were obtained when sampling a recovery boiler for 1 and 3 hours, respectively.
13.3 Bias.
13.3.1 No bias was found in Method 16A relative to Method 16 in a separate study at a recovery boiler.
13.3.2 Comparison of Method 16A with Method 16 at a lime kiln indicated that there was no bias in Method 16A. However, instability of the source emissions adversely affected the comparison. The precision of Method 16A at the lime kiln was similar to that obtained at the recovery boiler (Section 13.2.1).
13.3.3 Relative standard deviations of 2.7 and 7.7 percent have been obtained for system performance checks.
14.0 Pollution Prevention [Reserved] 15.0 Waste Management [Reserved] 16.0 Alternative ProceduresAs an alternative to the procedures specified in section 7.1.4, the following procedure may be used to verify the H2S concentration of the recovery check gas.
16.1 Summary. The H2S is collected from the calibration gas cylinder and is absorbed in zinc acetate solution to form zinc sulfide. The latter compound is then measured iodometrically.
16.2 Range. The procedure has been examined in the range of 5 to 1500 ppmv.
16.3 Interferences. There are no known interferences to this procedure when used to analyze cylinder gases containing H2S in nitrogen.
16.4 Precision and Bias. Laboratory tests have shown a relative standard deviation of less than 3 percent. The procedure showed no bias when compared to a gas chromatographic method that used gravimetrically certified permeation tubes for calibration.
16.5 Equipment and Supplies.
16.5.1 Sampling Apparatus. The sampling train is shown in Figure 16A-4. Its component parts are discussed in sections 16.5.1.1 through 16.5.2.
16.5.1.1 Sampling Line. Teflon tubing ( 1/4-in.) to connect the cylinder regulator to the sampling valve.
16.5.1.2 Needle Valve. Stainless steel or Teflon needle valve to control the flow rate of gases to the impingers.
16.5.1.3 Impingers. Three impingers of approximately 100-ml capacity, constructed to permit the addition of reagents through the gas inlet stem. The impingers shall be connected in series with leak-free glass or Teflon connectors. The impinger bottoms have a standard 24/25 ground-glass fitting. The stems are from standard 6.4-mm ( 1/4-in.) ball joint midget impingers, custom lengthened by about 1 in. When fitted together, the stem end should be approximately 1.27 cm ( 1/2 in.) from the bottom (Southern Scientific, Inc., Micanopy, Florida: Set Number S6962-048). The third in-line impinger acts as a drop-out bottle.
16.5.1.4 Drying Tube, Rate Meter, and Barometer. Same as Method 11, sections 6.1.5, 6.1.8, and 6.1.10, respectively.
16.5.1.5 Cylinder Gas Regulator. Stainless steel, to reduce the pressure of the gas stream entering the Teflon sampling line to a safe level.
16.5.1.6 Soap Bubble Meter. Calibrated for 100 and 500 ml, or two separate bubble meters.
16.5.1.7 Critical Orifice. For volume and rate measurements. The critical orifice may be fabricated according to section 16.7.3 and must be calibrated as specified in section 16.12.4.
16.5.1.8 Graduated Cylinder. 50-ml size.
16.5.1.9 Volumetric Flask. 1-liter size.
16.5.1.10 Volumetric Pipette. 15-ml size.
16.5.1.11 Vacuum Gauge. Minimum 20 in. Hg capacity.
16.5.1.12 Stopwatch.
16.5.2 Sample Recovery and Analysis.
16.5.2.1 Erlenmeyer Flasks. 125- and 250-ml sizes.
16.5.2.2 Pipettes. 2-, 10-, 20-, and 100-ml volumetric.
16.5.2.3 Burette. 50-ml size.
16.5.2.4 Volumetric Flask. 1-liter size.
16.5.2.5 Graduated Cylinder. 50-ml size.
16.5.2.6 Wash Bottle.
16.5.2.7 Stirring Plate and Bars.
16.6 Reagents and Standards. Unless otherwise indicated, all reagents must conform to the specifications established by the Committee on Analytical Reagents of the American Chemical Society, where such specifications are available. Otherwise, use the best available grade.
16.6.1 Water. Same as Method 11, section 7.1.3.
16.6.2 Zinc Acetate Absorbing Solution. Dissolve 20 g zinc acetate in water, and dilute to 1 liter.
16.6.3 Potassium Bi-iodate [KH(IO3)2] Solution, Standard 0.100 N. Dissolve 3.249 g anhydrous KH(IO3)2 in water, and dilute to 1 liter.
16.6.4 Sodium Thiosulfate (Na2S2O3) Solution, Standard 0.1 N. Same as Method 11, section 7.3.2. Standardize according to section 16.12.2.
16.6.5 Na2S2O3 Solution, Standard 0.01 N. Pipette 100.0 ml of 0.1 N Na2S2O3 solution into a 1-liter volumetric flask, and dilute to the mark with water.
16.6.6 Iodine Solution, 0.1 N. Same as Method 11, section 7.2.3.
16.6.7 Standard Iodine Solution, 0.01 N. Same as in Method 11, section 7.2.4. Standardize according to section 16.12.3.
16.6.8 Hydrochloric Acid (HCl) Solution, 10 Percent by Weight. Add 230 ml concentrated HCl (specific gravity 1.19) to 770 ml water.
16.6.9 Starch Indicator Solution. To 5 g starch (potato, arrowroot, or soluble), add a little cold water, and grind in a mortar to a thin paste. Pour into 1 liter of boiling water, stir, and let settle overnight. Use the clear supernatant. Preserve with 1.25 g salicylic acid, 4 g zinc chloride, or a combination of 4 g sodium propionate and 2 g sodium azide per liter of starch solution. Some commercial starch substitutes are satisfactory.
16.7 Pre-test Procedures.
16.7.1 Selection of Gas Sample Volumes. This procedure has been validated for estimating the volume of cylinder gas sample needed when the H2S concentration is in the range of 5 to 1500 ppmv. The sample volume ranges were selected in order to ensure a 35 to 60 percent consumption of the 20 ml of 0.01 N iodine (thus ensuring a 0.01 N Na2S2O3 titer of approximately 7 to 12 ml). The sample volumes for various H2S concentrations can be estimated by dividing the approximate ppm-liters desired for a given concentration range by the H2S concentration stated by the manufacturer. For example, for analyzing a cylinder gas containing approximately 10 ppmv H2S, the optimum sample volume is 65 liters (650 ppm-liters/10 ppmv). For analyzing a cylinder gas containing approximately 1000 ppmv H2S, the optimum sample volume is 1 liter (1000 ppm-liters/1000 ppmv).
Approximate cylinder gas H2S concentration (ppmv) | Approximate ppm-liters desired |
---|---|
5 to <30 | 650 |
30 to <500 | 800 |
500 to <1500 | 1000 |
16.7.2 Critical Orifice Flow Rate Selection. The following table shows the ranges of sample flow rates that are desirable in order to ensure capture of H2S in the impinger solution. Slight deviations from these ranges will not have an impact on measured concentrations.
Cylinder gas H2S concentration (ppmv) | Critical orifice flow rate (ml/min) |
---|---|
5 to 50 ppmv | 1500 ±500 |
50 to 250 ppmv | 500 ±250 |
250 to <1000 ppmv | 200 ±50 |
>1000 ppmv | 75 ±25 |
16.7.3 Critical Orifice Fabrication. Critical orifice of desired flow rates may be fabricated by selecting an orifice tube of desired length and connecting 1/16-in. × 1/4-in. (0.16 cm × 0.64 cm) reducing fittings to both ends. The inside diameters and lengths of orifice tubes needed to obtain specific flow rates are shown below.
Tube (in. OD) |
Tube (in. ID) |
Length (in.) |
Flowrate (ml/min) |
Altech Catalog No. |
---|---|---|---|---|
1/16 | 0.007 | 1.2 | 85 | 301430 |
1/16 | 0.01 | 3.2 | 215 | 300530 |
1/16 | 0.01 | 1.2 | 350 | 300530 |
1/16 | 0.02 | 1.2 | 1400 | 300230 |
16.7.4 Determination of Critical Orifice Approximate Flow Rate. Connect the critical orifice to the sampling system as shown in Figure 16A-4 but without the H2S cylinder. Connect a rotameter in the line to the first impinger. Turn on the pump, and adjust the valve to give a reading of about half atmospheric pressure. Observe the rotameter reading. Slowly increase the vacuum until a stable flow rate is reached, and record this as the critical vacuum. The measured flow rate indicates the expected critical flow rate of the orifice. If this flow rate is in the range shown in section 16.7.2, proceed with the critical orifice calibration according to section 16.12.4.
16.7.5 Determination of Approximate Sampling Time. Determine the approximate sampling time for a cylinder of known concentration. Use the optimum sample volume obtained in section 16.7.1.
16.8 Sample Collection.
16.8.1 Connect the Teflon tubing, Teflon tee, and rotameter to the flow control needle valve as shown in Figure 16A-4. Vent the rotameter to an exhaust hood. Plug the open end of the tee. Five to 10 minutes prior to sampling, open the cylinder valve while keeping the flow control needle valve closed. Adjust the delivery pressure to 20 psi. Open the needle valve slowly until the rotameter shows a flow rate approximately 50 to 100 ml above the flow rate of the critical orifice being used in the system.
16.8.2 Place 50 ml of zinc acetate solution in two of the impingers, connect them and the empty third impinger (dropout bottle) and the rest of the equipment as shown in Figure 16A-4. Make sure the ground-glass fittings are tight. The impingers can be easily stabilized by using a small cardboard box in which three holes have been cut, to act as a holder. Connect the Teflon sample line to the first impinger. Cover the impingers with a dark cloth or piece of plastic to protect the absorbing solution from light during sampling.
16.8.3 Record the temperature and barometric pressure. Note the gas flow rate through the rotameter. Open the closed end of the tee. Connect the sampling tube to the tee, ensuring a tight connection. Start the sampling pump and stopwatch simultaneously. Note the decrease in flow rate through the excess flow rotameter. This decrease should equal the known flow rate of the critical orifice being used. Continue sampling for the period determined in section 16.7.5.
16.8.4 When sampling is complete, turn off the pump and stopwatch. Disconnect the sampling line from the tee and plug it. Close the needle valve followed by the cylinder valve. Record the sampling time.
16.9 Blank Analysis. While the sample is being collected, run a blank as follows: To a 250-ml Erlenmeyer flask, add 100 ml of zinc acetate solution, 20.0 ml of 0.01 N iodine solution, and 2 ml HCl solution. Titrate, while stirring, with 0.01 N Na2S2O3 until the solution is light yellow. Add starch, and continue titrating until the blue color disappears. Analyze a blank with each sample, as the blank titer has been observed to change over the course of a day.
Note:Iodine titration of zinc acetate solutions is difficult to perform because the solution turns slightly white in color near the end point, and the disappearance of the blue color is hard to recognize. In addition, a blue color may reappear in the solution about 30 to 45 seconds after the titration endpoint is reached. This should not be taken to mean the original endpoint was in error. It is recommended that persons conducting this test perform several titrations to be able to correctly identify the endpoint. The importance of this should be recognized because the results of this analytical procedure are extremely sensitive to errors in titration.
16.10 Sample Analysis. Sample treatment is similar to the blank treatment. Before detaching the stems from the bottoms of the impingers, add 20.0 ml of 0.01 N iodine solution through the stems of the impingers holding the zinc acetate solution, dividing it between the two (add about 15 ml to the first impinger and the rest to the second). Add 2 ml HCl solution through the stems, dividing it as with the iodine. Disconnect the sampling line, and store the impingers for 30 minutes. At the end of 30 minutes, rinse the impinger stems into the impinger bottoms. Titrate the impinger contents with 0.01 N Na2S2O3. Do not transfer the contents of the impinger to a flask because this may result in a loss of iodine and cause a positive bias.
16.11 Post-test Orifice Calibration. Conduct a post-test critical orifice calibration run using the calibration procedures outlined in section 16.12.4. If the Qstd obtained before and after the test differs by more than 5 percent, void the sample; if not, proceed to perform the calculations.
16.12 Calibrations and Standardizations.
16.12.1 Rotameter and Barometer. Same as Method 11, sections 10.1.3 and 10.1.4.
16.12.2 Na2S2O3 Solution, 0.1 N. Standardize the 0.1 N Na2S2O3 solution as follows: To 80 ml water, stirring constantly, add 1 ml concentrated H2SO4, 10.0 ml of 0.100 N KH(IO3)2 and 1 g potassium iodide. Titrate immediately with 0.1 N Na2S2O3 until the solution is light yellow. Add 3 ml starch solution, and titrate until the blue color just disappears. Repeat the titration until replicate analyses agree within 0.05 ml. Take the average volume of Na2S2O3 consumed to calculate the normality to three decimal figures using Equation 16A-5.
16.12.3 Iodine Solution, 0.01 N. Standardize the 0.01 N iodine solution as follows: Pipet 20.0 ml of 0.01 N iodine solution into a 125-ml Erlenmeyer flask. Titrate with standard 0.01 N Na2S2O3 solution until the solution is light yellow. Add 3 ml starch solution, and continue titrating until the blue color just disappears. If the normality of the iodine tested is not 0.010, add a few ml of 0.1 N iodine solution if it is low, or a few ml of water if it is high, and standardize again. Repeat the titration until replicate values agree within 0.05 ml. Take the average volume to calculate the normality to three decimal figures using Equation 16A-6.
16.12.4 Critical Orifice. Calibrate the critical orifice using the sampling train shown in Figure 16A-4 but without the H2S cylinder and vent rotameter. Connect the soap bubble meter to the Teflon line that is connected to the first impinger. Turn on the pump, and adjust the needle valve until the vacuum is higher than the critical vacuum determined in section 16.7.4. Record the time required for gas flow to equal the soap bubble meter volume (use the 100-ml soap bubble meter for gas flow rates below 100 ml/min, otherwise use the 500-ml soap bubble meter). Make three runs, and record the data listed in Table 16A-1. Use these data to calculate the volumetric flow rate of the orifice.
16.13 Calculations.
16.13.1 Nomenclature.
Bwa = Fraction of water vapor in ambient air during orifice calibration. CH2S = H2S concentration in cylinder gas, ppmv. Ma = Molecular weight of ambient air saturated at impinger temperature, g/g-mole. Ms = Molecular weight of sample gas (nitrogen) saturated at impinger temperature, g/g-mole. Note:(For tests carried out in a laboratory where the impinger temperature is 25 °C, Ma = 28.5 g/g-mole and Ms = 27.7 g/g-mole.)
NI = Normality of standard iodine solution (0.01 N), g-eq/liter. NT = Normality of standard Na2S2O3 solution (0.01 N), g-eq/liter. Pbar = Barometric pressure, mm Hg. Pstd = Standard absolute pressure, 760 mm Hg. Qstd = Average volumetric flow rate through critical orifice, liters/min. Tamb = Absolute ambient temperature, °K. Tstd = Standard absolute temperature, 293 °K. θs = Sampling time, min. θsb = Time for soap bubble meter flow rate measurement, min. Vm(std) = Sample gas volume measured by the critical orifice, corrected to standard conditions, liters. Vsb = Volume of gas as measured by the soap bubble meter, ml. Vsb(std) = Volume of gas as measured by the soap bubble meter, corrected to standard conditions, liters. VI = Volume of standard iodine solution (0.01 N) used, ml. VT = Volume of standard Na2S2O3 solution (0.01 N) used, ml. VTB = Volume of standard Na2S2O3 solution (0.01 N) used for the blank, ml.16.13.2 Normality of Standard Na2S2O3 Solution (0.1 N).
16.13.3 Normality of Standard Iodine Solution (0.01 N).
16.13.4 Sample Gas Volume.
16.13.5 Concentration of H2S in the Gas Cylinder.
17.0 References1. American Public Health Association, American Water Works Association, and Water Pollution Control Federation. Standard Methods for the Examination of Water and Wastewater. Washington, DC. American Public Health Association. 1975. pp. 316-317.
2. American Society for Testing and Materials. Annual Book of ASTM Standards. Part 31: Water, Atmospheric Analysis. Philadelphia, PA. 1974. pp. 40-42.
3. Blosser, R.O. A Study of TRS Measurement Methods. National Council of the Paper Industry for Air and Stream Improvement, Inc., New York, NY. Technical Bulletin No. 434. May 1984. 14 pp.
4. Blosser, R.O., H.S. Oglesby, and A.K. Jain. A Study of Alternate SO2 Scrubber Designs Used for TRS Monitoring. A Special Report by the National Council of the Paper Industry for Air and Stream Improvement, Inc., New York, NY. July 1977.
5. Curtis, F., and G.D. McAlister. Development and Evaluation of an Oxidation/Method 6 TRS Emission Sampling Procedure. Emission Measurement Branch, Emission Standards and Engineering Division, U.S. Environmental Protection Agency, Research Triangle Park, NC 27711. February 1980.
6. Gellman, I. A Laboratory and Field Study of Reduced Sulfur Sampling and Monitoring Systems. National Council of the Paper Industry for Air and Stream Improvement, Inc., New York, NY. Atmospheric Quality Improvement Technical Bulletin No. 81. October 1975.
7. Margeson, J.H., J.E. Knoll, and M.R. Midgett. A Manual Method for TRS Determination. Source Branch, Quality Assurance Division, U.S. Environmental Protection Agency, Research Triangle Park, NC 27711.
8. National Council of the Paper Industry for Air and Stream Improvement. An Investigation of H2S and SO2. Calibration Cylinder Gas Stability and Their Standardization Using Wet Chemical Techniques. Special Report 76-06. New York, NY. August 1976.
9. National Council of the Paper Industry for Air and Stream Improvement. Wet Chemical Method for Determining the H2S Concentration of Calibration Cylinder Gases. Technical Bulletin Number 450. New York, NY. January 1985. 23 pp.
10. National Council of the Paper Industry for Air and Stream Improvement. Modified Wet Chemical Method for Determining the H2S Concentration of Calibration Cylinder Gases. Draft Report. New York, NY. March 1987. 29 pp.
18.0 Tables, Diagrams, Flowcharts, and Validation Data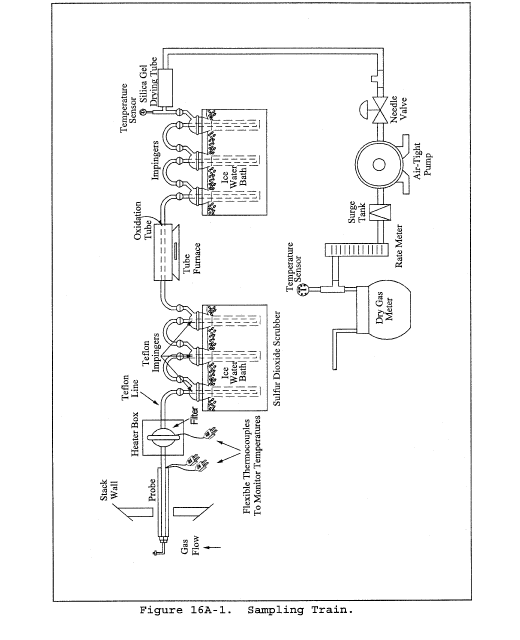
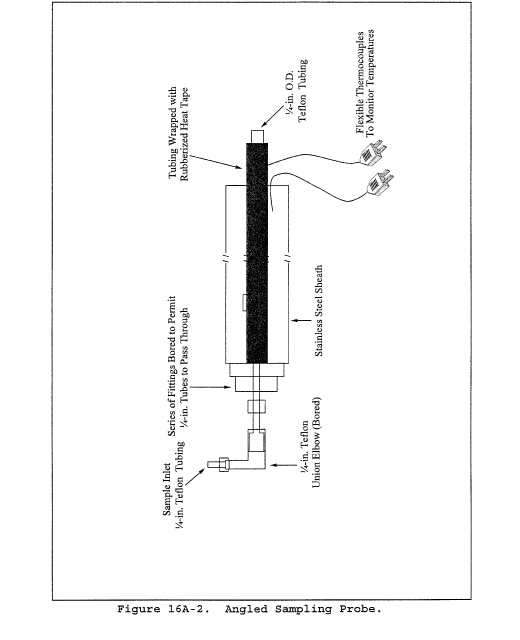

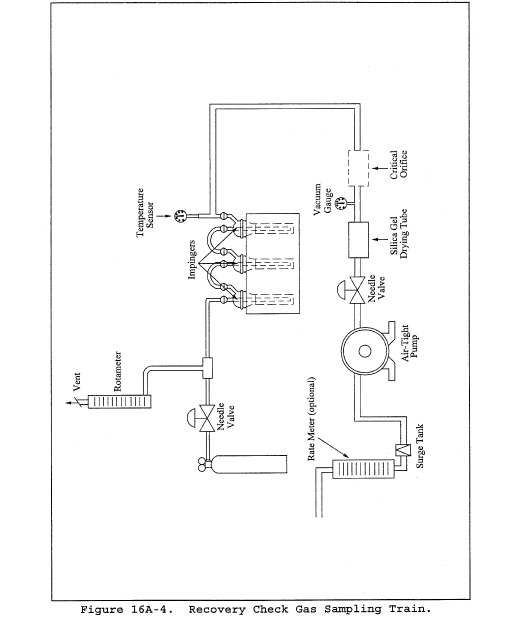
This method does not include all of the specifications (e.g., equipment and supplies) and procedures (e.g., sampling and analytical) essential to its performance. Some material is incorporated by reference from other methods in this part. Therefore, to obtain reliable results, persons using this method should have a knowledge of at least the following additional test methods: Method 6C, Method 16, and Method 16A.
1.0 Scope and Application1.1 Analytes.
Analyte | CAS No. |
---|---|
Total reduced sulfur (TRS) including: | N/A |
Dimethyl disulfide (DMDS), [(CH3)2S2] | 62-49-20 |
Dimethyl sulfide (DMS), [(CH3)2S] | 75-18-3 |
Hydrogen sulfide (H2S) | 7783-06-4 |
Methyl mercaptan (MeSH), [CH4S] | 74-93-1 |
Reported as: Sulfur dioxide (SO2) | 7449-09-5 |
1.2 Applicability. This method is applicable for determining TRS emissions from recovery furnaces (boilers), lime kilns, and smelt dissolving tanks at kraft pulp mills, and from other sources when specified in an applicable subpart of the regulations. The flue gas must contain at least 1 percent oxygen for complete oxidation of all TRS to SO2.
1.3 Data Quality Objectives. Adherence to the requirements of this method will enhance the quality of the data obtained from air pollutant sampling methods.
2.0 Summary of Method2.1 A gas sample is extracted from the stack. The SO2 is removed selectively from the sample using a citrate buffer solution. The TRS compounds are then thermally oxidized to SO2 and analyzed as SO2 by gas chromatography (GC) using flame photometric detection (FPD).
3.0 Definitions [Reserved] 4.0 Interferences4.1 Reduced sulfur compounds other than those regulated by the emission standards, if present, may be measured by this method. Therefore, carbonyl sulfide, which is partially oxidized to SO2 and may be present in a lime kiln exit stack, would be a positive interferant.
4.2 Particulate matter from the lime kiln stack gas (primarily calcium carbonate) can cause a negative bias if it is allowed to enter the citrate scrubber; the particulate matter will cause the pH to rise and H2S to be absorbed before oxidation. Proper use of the particulate filter, described in section 6.1.3 of Method 16A, will eliminate this interference.
4.3 Carbon monoxide (CO) and carbon dioxide (CO2) have substantial desensitizing effects on the FPD even after dilution. Acceptable systems must demonstrate that they have eliminated this interference by some procedure such as eluting these compounds before the SO2. Compliance with this requirement can be demonstrated by submitting chromatograms of calibration gases with and without CO2 in diluent gas. The CO2 level should be approximately 10 percent for the case with CO2 present. The two chromatograms should show agreement within the precision limits of section 13.0.
5.0 Safety5.1 Disclaimer. This method may involve hazardous materials, operations, and equipment. This test method may not address all of the safety problems associated with its use. It is the responsibility of the user of this test method to establish appropriate safety and health practices and determine the applicability of regulatory limitations prior to performing this test method.
5.2 Hydrogen Sulfide (H2S). A flammable, poisonous gas with the odor of rotten eggs. H2S is extremely hazardous and can cause collapse, coma, and death within a few seconds of one or two inhalations at sufficient concentrations. Low concentrations irritate the mucous membranes and may cause nausea, dizziness, and headache after exposure.
6.0 Equipment and Supplies6.1 Sample Collection. The sampling train is shown in Figure 16B-1. Modifications to the apparatus are accepted provided the system performance check in section 8.3.1 is met.
6.1.1 Probe, Probe Brush, Particulate Filter, SO2 Scrubber, Combustion Tube, and Furnace. Same as in Method 16A, sections 6.1.1 to 6.1.6.
6.1.2 Sampling Pump. Leakless Teflon-coated diaphragm type or equivalent.
6.2 Analysis.
6.2.1 Dilution System (optional), Gas Chromatograph, Oven, Temperature Gauges, Flow System, Flame Photometric Detector, Electrometer, Power Supply, Recorder, Calibration System, Tube Chamber, Flow System, and Constant Temperature Bath. Same as in Method 16, sections 6.2.1, 6.2.2, and 6.3.
6.2.2 Gas Chromatograph Columns. Same as in Method 16, section 6.2.3. Other columns with demonstrated ability to resolve SO2 and be free from known interferences are acceptable alternatives. Single column systems such as a 7-ft Carbsorb B HT 100 column have been found satisfactory in resolving SO2 from CO2.
7.0 Reagents and StandardsSame as in Method 16, section 7.0, except for the following:
7.1 Calibration Gas. SO2 permeation tube gravimetrically calibrated and certified at some convenient operating temperature. These tubes consist of hermetically sealed FEP Teflon tubing in which a liquefied gaseous substance is enclosed. The enclosed gas permeates through the tubing wall at a constant rate. When the temperature is constant, calibration gases covering a wide range of known concentrations can be generated by varying and accurately measuring the flow rate of diluent gas passing over the tubes. In place of SO2 permeation tubes, cylinder gases containing SO2 in nitrogen may be used for calibration. The cylinder gas concentration must be verified according to section 8.2.1 of Method 6C. The calibration gas is used to calibrate the GC/FPD system and the dilution system.
7.2 Recovery Check Gas.
7.2.1 Hydrogen sulfide [100 parts per million by volume (ppmv) or less] in nitrogen, stored in aluminum cylinders. Verify the concentration by Method 11, the procedure discussed in section 16.0 of Method 16A, or gas chromatography where the instrument is calibrated with an H2S permeation tube as described below. For the wet-chemical methods, the standard deviation should not exceed 5 percent on at least three 20-minute runs.
7.2.2 Hydrogen sulfide recovery gas generated from a permeation device gravimetrically calibrated and certified at some convenient operation temperature may be used. The permeation rate of the device must be such that at a dilution gas flow rate of 3 liters/min (64 ft 3/hr), an H2S concentration in the range of the stack gas or within 20 percent of the emission standard can be generated.
7.3 Combustion Gas. Gas containing less than 50 ppbv reduced sulfur compounds and less than 10 ppmv total hydrocarbons. The gas may be generated from a clean-air system that purifies ambient air and consists of the following components: diaphragm pump, silica gel drying tube, activated charcoal tube, and flow rate measuring device. Gas from a compressed air cylinder is also acceptable.
8.0 Sample Collection, Preservation, Storage, and Transport8.1 Pretest Procedures. Same as in Method 15, section 8.1.
8.2 Sample Collection. Before any source sampling is performed, conduct a system performance check as detailed in section 8.3.1 to validate the sampling train components and procedures. Although this test is optional, it would significantly reduce the possibility of rejecting tests as a result of failing the post-test performance check. At the completion of the pretest system performance check, insert the sampling probe into the test port making certain that no dilution air enters the stack though the port. Condition the entire system with sample for a minimum of 15 minutes before beginning analysis. If the sample is diluted, determine the dilution factor as in section 10.4 of Method 15.
8.3. Post-Test Procedures
8.3.1 System Performance Check. Same as in Method 16A, section 8.5. A sufficient number of sample injections should be made so that the precision requirements of section 13.2 are satisfied.
8.3.2 Determination of Calibration Drift. Same as in Method 15, section 8.3.2.
9.0 Quality ControlSection | Quality control measure | Effect |
---|---|---|
8.2, 8.3 | System performance check | Ensure validity of sampling train components and analytical procedure. |
8.1 | Sampling equipment leak-check and calibration | Ensure accurate measurement of stack gas flow rate, sample volume. |
10.0 | Analytical calibration | Ensure precision of analytical results within 5 percent. |
Same as in Method 16, section 10, except SO2 is used instead of H2S.
11.0 Analytical Procedure11.1 Analysis. Inject aliquots of the sample into the GC/FPD analyzer for analysis. Determine the concentration of SO2 directly from the calibration curves or from the equation for the least-squares line.
11.2 Perform analysis of a minimum of three aliquots or one every 15 minutes, whichever is greater, spaced evenly over the test period.
12.0 Data Analysis and Calculations
12.1 Nomenclature. CSO2 = Sulfur dioxide concentration, ppmv. CTRS = Total reduced sulfur concentration as determined by Equation 16B-1, ppmv. d = Dilution factor, dimensionless. N = Number of samples.12.2 SO2 Concentration. Determine the concentration of SO2, CSO2, directly from the calibration curves. Alternatively, the concentration may be calculated using the equation for the least-squares line.
12.3 TRS Concentration.
12.4 Average TRS Concentration
13.0 Method Performance.13.1 Range and Sensitivity. Coupled with a GC using a 1-ml sample size, the maximum limit of the FPD for SO2 is approximately 10 ppmv. This limit is extended by diluting the sample gas before analysis or by reducing the sample aliquot size. For sources with emission levels between 10 and 100 ppm, the measuring range can be best extended by reducing the sample size.
13.2 GC/FPD Calibration and Precision. A series of three consecutive injections of the sample calibration gas, at any dilution, must produce results which do not vary by more than 5 percent from the mean of the three injections.
13.3 Calibration Drift. The calibration drift determined from the mean of the three injections made at the beginning and end of any run or series of runs within a 24-hour period must not exceed 5 percent.
13.4 System Calibration Accuracy. Losses through the sample transport system must be measured and a correction factor developed to adjust the calibration accuracy to 100 percent.
13.5 Field tests between this method and Method 16A showed an average difference of less than 4.0 percent. This difference was not determined to be significant.
14.0 Pollution Prevention [Reserved] 15.0 Waste Management [Reserved] 16.0 References1. Same as in Method 16, section 16.0.
2. National Council of the Paper Industry for Air and Stream Improvement, Inc, A Study of TRS Measurement Methods. Technical Bulletin No. 434. New York, NY. May 1984. 12p.
3. Margeson, J.H., J.E. Knoll, and M.R. Midgett. A Manual Method for TRS Determination. Draft available from the authors. Source Branch, Quality Assurance Division, U.S. Environmental Protection Agency, Research Triangle Park, NC 27711.
17.0 Tables, Diagrams, Flowcharts, and Validation Data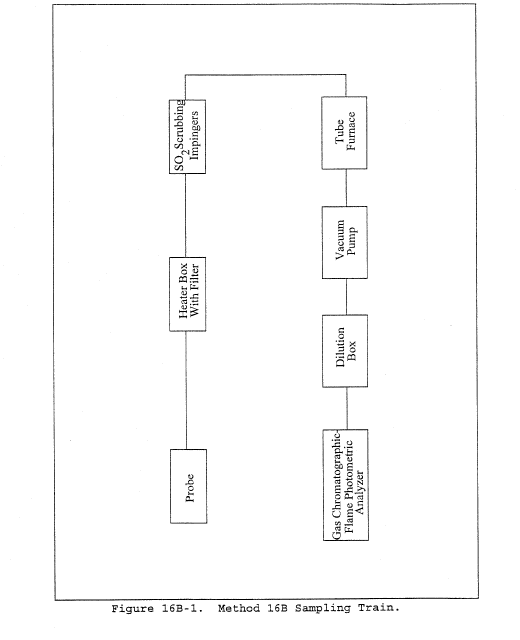
Method 16C is a procedure for measuring total reduced sulfur (TRS) in stationary source emissions using a continuous instrumental analyzer. Quality assurance and quality control requirements are included to assure that you, the tester, collect data of known quality. You must document your adherence to these specific requirements for equipment, supplies, sample collection and analysis, calculations, and data analysis. This method does not completely describe all equipment, supplies, and sampling and analytical procedures you will need but refers to other methods for some of the details. Therefore, to obtain reliable results, you should also have a thorough knowledge of these additional test methods which are found in appendix A to this part:
(a) Method 6C - Determination of Sulfur Dioxide Emissions from Stationary Sources (Instrumental Analyzer Procedure)
(b) Method 7E - Determination of Nitrogen Oxides Emissions from Stationary Sources (Instrumental Analyzer Procedure)
(c) Method 16A - Determination of Total Reduced Sulfur Emissions from Stationary Sources (Impinger Technique)
1.1 Analytes. What does Method 16C determine?
Analyte | CAS No. |
---|---|
Total reduced sulfur including: | N/A |
Dimethyl disulfide (DMDS), [(CH3)2S2] | 62-49-20 |
Dimethyl sulfide (DMS), [(CH3)2S] | 75-18-3 |
Hydrogen sulfide (H2S) | 7783-06-4 |
Methyl mercaptan (MeSH), (CH4S) | 74-93-1 |
Reported as: Sulfur dioxide (SO2) | 7449-09-5 |
1.2 Applicability. This method is applicable for determining TRS emissions from recovery furnaces (boilers), lime kilns, and smelt dissolving tanks at kraft pulp mills, and from other sources when specified in an applicable subpart of the regulations.
1.3 Data Quality Objectives. Adherence to the requirements described in Method 16C will enhance the quality of the data obtained.
2.0 Summary of Method2.1 An integrated gas sample is extracted from the stack. The SO2 is removed selectively from the sample using a citrate buffer solution. The TRS compounds are then thermally oxidized to SO2 and determined as SO2 by an instrumental analyzer. This method is a combination of the sampling procedures of Method 16A and the analytical procedures of Method 6C (referenced in Method 7E), with minor modifications to facilitate their use together.
3.0 DefinitionsAnalyzer calibration error, Calibration curve, Calibration gas, Low-level gas, Mid-level gas, High-level gas, Calibration drift, Calibration span, Data recorder, Direct calibration mode, Gas analyzer, Interference check, Measurement system, Response time, Run, System calibration mode, System performance check, and Test are the same as used in Methods 16A and 6C.
4.0 Interferences4.1 Reduced sulfur compounds other than those defined as TRS, if present, may be measured by this method. Compounds like carbonyl sulfide, which is partially oxidized to SO2 and may be present in a lime kiln exit stack, would be a positive interferent. Interferences may vary among instruments, and instrument-specific interferences must be evaluated through the interference check.
4.2 Particulate matter from the lime kiln stack gas (primarily calcium carbonate) can cause a negative bias if it is allowed to enter the citrate scrubber; the particulate matter will cause the pH to rise and H2S to be absorbed before oxidation. Proper use of the particulate filter, described in section 6.1.3 of Method 16A, will eliminate this interference.
5.0 Safety5.1 Disclaimer. This method may involve hazardous materials, operations, and equipment. This test method may not address all of the safety problems associated with its use. It is the responsibility of the user to establish appropriate safety and health practices before performing this test method.
5.2 Hydrogen Sulfide. Hydrogen sulfide is a flammable, poisonous gas with the odor of rotten eggs. Hydrogen sulfide is extremely hazardous and can cause collapse, coma, and death within a few seconds of one or two inhalations at sufficient concentrations. Low concentrations irritate the mucous membranes and may cause nausea, dizziness, and headache after exposure. It is the responsibility of the user of this test method to establish appropriate safety and health practices.
6.0 Equipment and Supplies What do I need for the measurement system?The measurement system is similar to those applicable components in Methods 16A and 6C. Modifications to the apparatus are accepted provided the performance criteria in section 13.0 are met.
6.1 Probe. Teflon tubing, 6.4-mm ( 1/4 in.) diameter, sequentially wrapped with heat-resistant fiber strips, a rubberized heat tape (plug at one end), and heat-resistant adhesive tape. A flexible thermocouple or other suitable temperature measuring device must be placed between the Teflon tubing and the fiber strips so that the temperature can be monitored to prevent softening of the probe. The probe must be sheathed in stainless steel to provide in-stack rigidity. A series of bored-out stainless steel fittings placed at the front of the sheath will prevent moisture and particulate from entering between the probe and sheath. A 6.4-mm ( 1/4 in.) Teflon elbow (bored out) must be attached to the inlet of the probe, and a 2.54 cm (1 in.) piece of Teflon tubing must be attached at the open end of the elbow to permit the opening of the probe to be turned away from the particulate stream; this will reduce the amount of particulate drawn into the sampling train. The probe is depicted in Figure 16A-2 of Method 16A.
6.2 Probe Brush. Nylon bristle brush with handle inserted into a 3.2-mm ( 1/8 in.) Teflon tubing. The Teflon tubing should be long enough to pass the brush through the length of the probe.
6.3 Particulate Filter. 50-mm Teflon filter holder and a 1- to 2-µm porosity, Teflon filter (may be available through Savillex Corporation, 5325 Highway 101, Minnetonka, Minnesota 55343, or other suppliers of filters). The filter holder must be maintained in a hot box at a temperature sufficient to prevent moisture condensation. A temperature of 121 °C (250 °F) was found to be sufficient when testing a lime kiln under sub-freezing ambient conditions.
6.4 SO2 Scrubber. Three 300-ml Teflon segmented impingers connected in series with flexible, thick-walled, Teflon tubing. (Impinger parts and tubing may be available through Savillex or other suppliers.) The first two impingers contain 100 ml of citrate buffer, and the third impinger is initially dry. The tip of the tube inserted into the solution should be constricted to less than 3 mm ( 1/8 in.) ID and should be immersed to a depth of at least 5 cm (2 in.).
6.5 Combustion Tube. Quartz glass tubing with an expanded combustion chamber 2.54 cm (1 in.) in diameter and at least 30.5 cm (12 in.) long. The tube ends should have an outside diameter of 0.6 cm ( 1/4 in.) and be at least 15.3 cm (6 in.) long. This length is necessary to maintain the quartz-glass connector near ambient temperature and thereby avoid leaks. Alternative combustion tubes are acceptable provided they are shown to combust TRS at concentrations encountered during tests.
6.6 Furnace. A furnace of sufficient size to enclose the combustion chamber of the combustion tube with a temperature regulator capable of maintaining the temperature at 800 ±100 °C (1472 ±180 °F). The furnace operating temperature should be checked with a thermocouple to ensure accuracy.
6.7 Sampling Pump. A leak-free pump is required to pull the sample gas through the system at a flow rate sufficient to minimize the response time of the measurement system and must be constructed of material that is non-reactive to the gas it contacts. For dilution-type measurement systems, an eductor pump may be used to create a vacuum that draws the sample through a critical orifice at a constant rate.
6.8 Calibration Gas Manifold. The calibration gas manifold must allow the introduction of calibration gases either directly to the gas analyzer in direct calibration mode or into the measurement system, at the probe, in system calibration mode, or both, depending upon the type of system used. In system calibration mode, the system must be able to flood the sampling probe and vent excess gas. Alternatively, calibration gases may be introduced at the calibration valve following the probe. Maintain a constant pressure in the gas manifold. For in-stack dilution-type systems, a gas dilution subsystem is required to transport large volumes of purified air to the sample probe, and a probe controller is needed to maintain the proper dilution ratio.
6.9 Sample Gas Manifold. The sample gas manifold diverts a portion of the sample to the analyzer, delivering the remainder to the by-pass discharge vent. The manifold should also be able to introduce calibration gases directly to the analyzer. The manifold must be made of material that is non-reactive to SO2 and be configured to safely discharge the bypass gas.
6.10 SO2 Analyzer. You must use an instrument that uses an ultraviolet, non-dispersive infrared, fluorescence, or other detection principle to continuously measure SO2 in the gas stream provided it meets the performance specifications in section 13.0.
6.11 Data Recording. A strip chart recorder, computerized data acquisition system, digital recorder, or data logger for recording measurement data must be used.
7.0 Reagents and Standards Note:Unless otherwise indicated, all reagents must conform to the specifications established by the Committee on Analytical Reagents of the American Chemical Society. When such specifications are not available, the best available grade must be used.
7.1 Water. Deionized distilled water must conform to ASTM Specification D 1193-77 or 91 Type 3 (incorporated by reference - see § 60.17). The KMnO4 test for oxidizable organic matter may be omitted when high concentrations of organic matter are not expected to be present.
7.2 Citrate Buffer. Dissolve 300 g of potassium citrate (or 284 g of sodium citrate) and 41 g of anhydrous citric acid in 1 liter of water (200 ml is needed per test). Adjust the pH to between 5.4 and 5.6 with potassium citrate or citric acid, as required.
7.3 Calibration Gas. Refer to section 7.1 of Method 7E (as applicable) for the calibration gas requirements. Example calibration gas mixtures are listed below.
(a) SO2 in nitrogen (N2).
(b) SO2 in air.
(c) SO2 and carbon dioxide (CO2) in N2.
(d) SO2 and oxygen (O2) in N2.
(e) SO2/CO2/O2 gas mixture in N2.
(f) CO2/NOX gas mixture in N2.
(g) CO2/SO2/NOX gas mixture in N2.
For fluorescence-based analyzers, the O2 and CO2 concentrations of the calibration gases as introduced to the analyzer must be within 1.0 percent (absolute) O2 and 1.0 percent (absolute) CO2 of the O2 and CO2 concentrations of the effluent samples as introduced to the analyzer. Alternatively, for fluorescence-based analyzers, use calibration blends of SO2 in air and the nomographs provided by the vendor to determine the quenching correction factor (the effluent O2 and CO2 concentrations must be known). This requirement does not apply to ambient-level fluorescence analyzers that are used in conjunction with sample dilution systems. Alternatively, H2S in O2 or air may be used to calibrate the analyzer through the tube furnace.7.4 System Performance Check Gas. You must use H2S (100 ppmv or less) stored in aluminum cylinders with the concentration certified by the manufacturer. Hydrogen sulfide in nitrogen is more stable than H2S in air, but air may be used as the balance gas.
Note:Alternatively, H2S recovery gas generated from a permeation device gravimetrically calibrated and certified at some convenient operating temperature may be used. The permeation rate of the device must be such that at the appropriate dilution gas flow rate, an H2S concentration can be generated in the range of the stack gas or within 20 percent of the emission standard.
7.5 Interference Check. Examples of test gases for the interference check are listed in Table 7E-3 of Method 7E.
8.0 Sample Collection, Preservation, Storage, and Transport8.1 Pre-sampling Tests. Before measuring emissions, perform the following procedures:
(a) Calibration gas verification,
(b) Calibration error test,
(c) System performance check,
(d) Verification that the interference check has been satisfied.
8.1.1 Calibration Gas Verification. Obtain a certificate from the gas manufacturer documenting the quality of the gas. Confirm that the manufacturer certification is complete and current. Ensure that your calibration gas certifications have not expired. This documentation should be available on-site for inspection. To the extent practicable, select a high-level gas concentration that will result in the measured emissions being between 20 and 100 percent of the calibration span.
8.1.2 Analyzer Calibration Error Test. After you have assembled, prepared, and calibrated your sampling system and analyzer, you must conduct a 3-point analyzer calibration error test before the first run and again after any failed system performance check or failed drift test to ensure the calibration is acceptable. Introduce the low-, mid-, and high-level calibration gases sequentially to the analyzer in direct calibration mode. For each calibration gas, calculate the analyzer calibration error using Equation 16C-1 in section 12.2. The calibration error for the low-, mid-, and high-level gases must not exceed 5.0 percent or 0.5 ppmv. If the calibration error specification is not met, take corrective action and repeat the test until an acceptable 3-point calibration is achieved.
8.1.3 System Performance Check. A system performance check is done (1) to validate the sampling train components and procedure (prior to testing), and (2) to validate a test run (after a run). You must conduct a performance check in the field prior to testing, and after each 3-hour run or after three 1-hour runs. A performance check consists of sampling and analyzing a known concentration of H2S (system performance check gas) and comparing the analyzed concentration to the known concentration. To conduct the system performance check, mix the system performance check gas (Section 7.4) and ambient air, that has been conditioned to remove moisture and sulfur-containing gases, in a dilution system such as that shown in Figure 16A-3 of Method 16A. Alternatively, ultra-high purity (UHP) grade air may be used. Adjust the gas flow rates to generate an H2S concentration in the range of the stack gas or within 20 percent of the applicable standard and an oxygen concentration greater than 1 percent at a total flow rate of at least 2.5 liters/min (5.3 ft3/hr). Use Equation 16A-3 from Method 16A to calculate the concentration of system performance check gas generated. Calibrate the flow rate from both gas sources with a soap bubble flow meter so that the diluted concentration of H2S can be accurately calculated. Alternatively, mass flow controllers with documented calibrations may be used if UHP grade air is being used. Sample duration should be sufficiently long to ensure a stable response from the analyzer. Analyze in the same manner as the emission samples. Collect the sample through the probe of the sampling train using a manifold or other suitable device that will ensure extraction of a representative sample. The TRS sample concentration measured between system performance checks is corrected by the average of the pre- and post-system performance checks.
8.1.4 Interference Check. Same as in Method 7E, section 8.2.7.
8.2 Measurement System Preparation.
8.2.1 For the SO2 scrubber, measure 100 ml of citrate buffer into the first and second impingers; leave the third impinger empty. Immerse the impingers in an ice bath, and locate them as close as possible to the filter heat box. The connecting tubing should be free of loops. Maintain the probe and filter temperatures sufficiently high to prevent moisture condensation, and monitor with a suitable temperature sensor. Prepare the oxidation furnace and maintain at 800 ±100 °C (1472 ±180 °F).
8.2.2 Citrate Scrubber Conditioning Procedure. Condition the citrate buffer scrubbing solution by pulling stack gas through the Teflon impingers as described in section 8.4.1.
8.3 Pretest Procedures. After the complete measurement system has been set up at the site and deemed to be operational, the following procedures must be completed before sampling is initiated.
8.3.1 Leak-Check. Appropriate leak-check procedures must be employed to verify the integrity of all components, sample lines, and connections. For components upstream of the sample pump, attach the probe end of the sample line to a manometer or vacuum gauge, start the pump and pull a vacuum greater than 50 mm (2 in.) Hg, close off the pump outlet, and then stop the pump and ascertain that there is no leak for 1 minute. For components after the pump, apply a slight positive pressure and check for leaks by applying a liquid (detergent in water, for example) at each joint. Bubbling indicates the presence of a leak.
8.3.2 Initial System Performance Check. A system performance check using the test gas (Section 7.4) is performed prior to testing to validate the sampling train components and procedure.
8.4 Sample Collection and Analysis.
8.4.1 After performing the required pretest procedures described in section 8.1, insert the sampling probe into the test port ensuring that no dilution air enters the stack through the port. Condition the sampling system and citrate buffer solution for a minimum of 15 minutes before beginning analysis. Begin sampling and analysis. A source test consists of three test runs. A test run shall consist of a single sample collected over a 3-hour period or three separate 1-hour samples collected over a period not to exceed six hours.
8.5 Post-Run Evaluations.
8.5.1 System Performance Check. Perform a post-run system performance check before replacing the citrate buffer solution and particulate filter and before the probe is cleaned. The check results must not exceed the 100 ±20 percent limit set forth in section 13.2. If this limit is exceeded, the intervening run is considered invalid. However, if the recovery efficiency is not in the 100 ±20 percent range, but the results do not affect the compliance or noncompliance status of the affected facility, the Administrator may decide to accept the results of the compliance test.
8.5.2 Calibration Drift. After a run or series of runs, not to exceed a 24-hour period after initial calibration, perform a calibration drift test using a calibration gas (preferably the level that best approximates the sample concentration) in direct calibration mode. This drift must not differ from the initial calibration error percent by more than 3.0 percent or 0.5 ppm. If the drift exceeds this limit, the intervening run or runs are considered valid, but a new analyzer calibration error test must be performed and passed before continuing sampling.
9.0 Quality ControlSection | Quality control measure | Effect |
---|---|---|
8.1.2 | Analyzer calibration error test | Establishes initial calibration accuracy within 5.0%. |
8.1.3, 8.5.1 | System performance check | Ensures accuracy of sampling/analytical procedure to 100 ±20%. |
8.5.2 | Calibration drift test | Ensures calibration drift is within 3.0%. |
8.1.4 | Interference check | Checks for analytical interferences. |
8.3 | Sampling equipment leak-check | Ensures accurate measurement of sample gas flow rate, sample volume. |
10.1 Calibrate the system using the gases described in section 7.3. Perform the initial 3-point calibration error test as described in section 8.1.2 before you start the test. The specification in section 13 must be met. Conduct an initial system performance test described in section 8.1.3 as well before the test to validate the sampling components and procedures before sampling. After the test commences, a system performance check is required after each run. You must include a copy of the manufacturer's certification of the calibration gases used in the testing as part of the test report. This certification must include the 13 documentation requirements in the EPA Traceability Protocol for Assay and Certification of Gaseous Calibration Standards, September 1997, as amended August 25, 1999.
11.0 Analytical ProcedureBecause sample collection and analysis are performed together (see section 8.0), additional discussion of the analytical procedure is not necessary.
12.0 Calculations and Data Analysis12.1 Nomenclature.
ACE = Analyzer calibration error, percent of calibration span. CD = Calibration drift, percent. CDir = Measured concentration of a calibration gas (low, mid, or high) when introduced in direct calibration mode, ppmv. CH2S = Concentration of the system performance check gas, ppmv H2S. CS = Measured concentration of the system performance gas when introduced in system calibration mode, ppmv H2S. CV = Manufacturer certified concentration of a calibration gas (low, mid, or high), ppmv SO2. CSO2 = Unadjusted sample SO2 concentration, ppmv. CTRS = Total reduced sulfur concentration corrected for system performance, ppmv. CS = Calibration span, ppmv. DF = Dilution system (if used) dilution factor, dimensionless. SP = System performance, percent.12.2 Analyzer Calibration Error. For non-dilution systems, use Equation 16C-1 to calculate the analyzer calibration error for the low-, mid-, and high-level calibration gases.

12.3 System Performance Check. Use Equation 16C-2 to calculate the system performance.

12.4 Calibration Drift. Use Equation 16C-3 to calculate the calibration drift at a single concentration level after a run or series of runs (not to exceed a 24-hr period) from initial calibration. Compare the single-level calibration gas error (ACEn) to the original error obtained for that gas in the initial analyzer calibration error test (ACEi).

12.5 TRS Concentration as SO2. For each sample or test run, calculate the arithmetic average of SO2 concentration values (e.g., 1-minute averages). Then calculate the sample TRS concentration by adjusting the average value of CSO2 for system performance using Equation 16C-4.
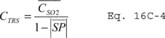
13.1 Analyzer Calibration Error. At each calibration gas level (low, mid, and high), the calibration error must either not exceed 5.0 percent of the calibration span or |CDir−Cv| must be ≤0.5 ppmv.
13.2 System Performance. Each system performance check must not deviate from the system performance gas concentration by more than 20 percent. Alternatively, the results are acceptable if |Cs−CH2S| is ≤0.5 ppmv.
13.3 Calibration Drift. The calibration drift at the end of any run or series of runs within a 24-hour period must not differ by more than 3.0 percent from the original ACE at the test concentration level or |ACEi−ACEn| must not exceed 0.5 ppmv.
13.4 Interference Check. For the analyzer, the total interference response (i.e., the sum of the interference responses of all tested gaseous components) must not be greater than 2.5 percent of the calibration span. Any interference is also acceptable if the sum of the responses does not exceed 0.5 ppmv for a calibration span of 5 to 10 ppmv, or 0.2 ppmv for a calibration span <5 ppmv.
14.0 Pollution Prevention [Reserved] 15.0 Waste Management [Reserved] 16.0 References 1. The references are the same as in section 16.0 of Method 16, section 17.0 of Method 16A, and section 17.0 of Method 6C. 2. National Council of the Paper Industry for Air and Stream Improvement, Inc,. A Study of TRS Measurement Methods. Technical Bulletin No. 434. New York, NY. May 1984. 12p. 3. Margeson, J.H., J.E. Knoll, and M.R. Midgett. A Manual Method for TRS Determination. Draft available from the authors. Source Branch, Quality Assurance Division, U.S. Environmental Protection Agency, Research Triangle Park, NC 27711. 17.0 Tables, Diagrams, Flowcharts, and Validation Data [Reserved] Method 17 - Determination of Particulate Matter Emissions From Stationary Sources Note:This method does not include all of the specifications (e.g., equipment and supplies) and procedures (e.g., sampling and analytical) essential to its performance. Some material is incorporated by reference from other methods in this part. Therefore, to obtain reliable results, persons using this method should have a thorough knowledge of at least the following additional test methods: Method 1, Method 2, Method 3, Method 5.
1.0 Scope and Application1.1 Analyte. Particulate matter (PM). No CAS number assigned.
Note:Particulate matter is not an absolute quantity. It is a function of temperature and pressure. Therefore, to prevent variability in PM emission regulations and/or associated test methods, the temperature and pressure at which PM is to be measured must be carefully defined. Of the two variables (i.e., temperature and pressure), temperature has the greater effect upon the amount of PM in an effluent gas stream; in most stationary source categories, the effect of pressure appears to be negligible. In Method 5, 120 °C (248 °F) is established as a nominal reference temperature. Thus, where Method 5 is specified in an applicable subpart of the standard, PM is defined with respect to temperature. In order to maintain a collection temperature of 120 °C (248 °F), Method 5 employs a heated glass sample probe and a heated filter holder. This equipment is somewhat cumbersome and requires care in its operation. Therefore, where PM concentrations (over the normal range of temperature associated with a specified source category) are known to be independent of temperature, it is desirable to eliminate the glass probe and the heating systems, and to sample at stack temperature.
1.2 Applicability. This method is applicable for the determination of PM emissions, where PM concentrations are known to be independent of temperature over the normal range of temperatures characteristic of emissions from a specified source category. It is intended to be used only when specified by an applicable subpart of the standards, and only within the applicable temperature limits (if specified), or when otherwise approved by the Administrator. This method is not applicable to stacks that contain liquid droplets or are saturated with water vapor. In addition, this method shall not be used as written if the projected cross-sectional area of the probe extension-filter holder assembly covers more than 5 percent of the stack cross-sectional area (see section 8.1.2).
1.3 Data Quality Objectives. Adherence to the requirements of this method will enhance the quality of the data obtained from air pollutant sampling methods.
2.0 Summary of Method2.1 Particulate matter is withdrawn isokinetically from the source and collected on a glass fiber filter maintained at stack temperature. The PM mass is determined gravimetrically after the removal of uncombined water.
3.0 DefinitionsSame as Method 5, section 3.0.
4.0 Interferences [Reserved] 5.0 Safety5.1 Disclaimer. This method may involve hazardous materials, operations, and equipment. This test method may not address all of the safety problems associated with its use. It is the responsibility of the user of this test method to establish appropriate safety and health practices and determine the applicability of regulatory limitations prior to performing this test method.
6.0 Equipment and Supplies6.1 Sampling Train. A schematic of the sampling train used in this method is shown in Figure 17-1. The sampling train components and operation and maintenance are very similar to Method 5, which should be consulted for details.
6.1.1 Probe Nozzle, Differential Pressure Gauge, Metering System, Barometer, Gas Density Determination Equipment. Same as in Method 5, sections 6.1.1, 6.1.4, 6.1.8, 6.1.9, and 6.1.10, respectively.
6.1.2 Filter Holder. The in-stack filter holder shall be constructed of borosilicate or quartz glass, or stainless steel. If a gasket is used, it shall be made of silicone rubber, Teflon, or stainless steel. Other holder and gasket materials may be used, subject to the approval of the Administrator. The filter holder shall be designed to provide a positive seal against leakage from the outside or around the filter.
6.1.3 Probe Extension. Any suitable rigid probe extension may be used after the filter holder.
6.1.4 Pitot Tube. Same as in Method 5, section 6.1.3.
6.1.4.1 It is recommended (1) that the pitot tube have a known baseline coefficient, determined as outlined in section 10 of Method 2; and (2) that this known coefficient be preserved by placing the pitot tube in an interference-free arrangement with respect to the sampling nozzle, filter holder, and temperature sensor (see Figure 17-1). Note that the 1.9 cm ( 3/4-in.) free-space between the nozzle and pitot tube shown in Figure 17-1, is based on a 1.3 cm ( 1/2-in.) ID nozzle. If the sampling train is designed for sampling at higher flow rates than that described in APTD-0581, thus necessitating the use of larger sized nozzles, the free-space shall be 1.9 cm ( 3/4-in.) with the largest sized nozzle in place.
6.1.4.2 Source-sampling assemblies that do not meet the minimum spacing requirements of Figure 17-1 (or the equivalent of these requirements, e.g., Figure 2-4 of Method 2) may be used; however, the pitot tube coefficients of such assemblies shall be determined by calibration, using methods subject to the approval of the Administrator.
6.1.5 Condenser. It is recommended that the impinger system or alternatives described in Method 5 be used to determine the moisture content of the stack gas. Flexible tubing may be used between the probe extension and condenser. Long tubing lengths may affect the moisture determination.
6.2 Sample Recovery. Probe-liner and probe-nozzle brushes, wash bottles, glass sample storage containers, petri dishes, graduated cylinder and/or balance, plastic storage containers, funnel and rubber policeman, funnel. Same as in Method 5, sections 6.2.1 through 6.2.8, respectively.
6.3 Sample Analysis. Glass weighing dishes, desiccator, analytical balance, balance, beakers, hygrometer, temperature sensor. Same as in Method 5, sections 6.3.1 through 6.3.7, respectively.
7.0 Reagents and Standards7.1 Sampling. Filters, silica gel, water, crushed ice, stopcock grease. Same as in Method 5, sections 7.1.1, 7.1.2, 7.1.3, 7.1.4, and 7.1.5, respectively. Thimble glass fiber filters may also be used.
7.2 Sample Recovery. Acetone (reagent grade). Same as in Method 5, section 7.2.
7.3 Sample Analysis. Acetone and Desiccant. Same as in Method 5, sections 7.3.1 and 7.3.2, respectively.
8.0 Sample Collection, Preservation, Storage, and Transport8.1 Sampling.
8.1.1 Pretest Preparation. Same as in Method 5, section 8.1.1.
8.1.2 Preliminary Determinations. Same as in Method 5, section 8.1.2, except as follows: Make a projected-area model of the probe extension-filter holder assembly, with the pitot tube face openings positioned along the centerline of the stack, as shown in Figure 17-2. Calculate the estimated cross-section blockage, as shown in Figure 17-2. If the blockage exceeds 5 percent of the duct cross sectional area, the tester has the following options exist: (1) a suitable out-of-stack filtration method may be used instead of in-stack filtration; or (2) a special in-stack arrangement, in which the sampling and velocity measurement sites are separate, may be used; for details concerning this approach, consult with the Administrator (see also Reference 1 in section 17.0). Select a probe extension length such that all traverse points can be sampled. For large stacks, consider sampling from opposite sides of the stack to reduce the length of probes.
8.1.3 Preparation of Sampling Train. Same as in Method 5, section 8.1.3, except the following: Using a tweezer or clean disposable surgical gloves, place a labeled (identified) and weighed filter in the filter holder. Be sure that the filter is properly centered and the gasket properly placed so as not to allow the sample gas stream to circumvent the filter. Check filter for tears after assembly is completed. Mark the probe extension with heat resistant tape or by some other method to denote the proper distance into the stack or duct for each sampling point. Assemble the train as in Figure 17-1, using a very light coat of silicone grease on all ground glass joints and greasing only the outer portion (see APTD-0576) to avoid possibility of contamination by the silicone grease. Place crushed ice around the impingers.
8.1.4 Leak-Check Procedures. Same as in Method 5, section 8.1.4, except that the filter holder is inserted into the stack during the sampling train leak-check. To do this, plug the inlet to the probe nozzle with a material that will be able to withstand the stack temperature. Insert the filter holder into the stack and wait approximately 5 minutes (or longer, if necessary) to allow the system to come to equilibrium with the temperature of the stack gas stream.
8.1.5 Sampling Train Operation. The operation is the same as in Method 5. Use a data sheet such as the one shown in Figure 5-3 of Method 5, except that the filter holder temperature is not recorded.
8.1.6 Calculation of Percent Isokinetic. Same as in Method 5, section 12.11.
8.2 Sample Recovery.
8.2.1 Proper cleanup procedure begins as soon as the probe extension assembly is removed from the stack at the end of the sampling period. Allow the assembly to cool.
8.2.2 When the assembly can be safely handled, wipe off all external particulate matter near the tip of the probe nozzle and place a cap over it to prevent losing or gaining particulate matter. Do not cap off the probe tip tightly while the sampling train is cooling down as this would create a vacuum in the filter holder, forcing condenser water backward.
8.2.3 Before moving the sample train to the cleanup site, disconnect the filter holder-probe nozzle assembly from the probe extension; cap the open inlet of the probe extension. Be careful not to lose any condensate, if present. Remove the umbilical cord from the condenser outlet and cap the outlet. If a flexible line is used between the first impinger (or condenser) and the probe extension, disconnect the line at the probe extension and let any condensed water or liquid drain into the impingers or condenser. Disconnect the probe extension from the condenser; cap the probe extension outlet. After wiping off the silicone grease, cap off the condenser inlet. Ground glass stoppers, plastic caps, or serum caps (whichever are appropriate) may be used to close these openings.
8.2.4 Transfer both the filter holder-probe nozzle assembly and the condenser to the cleanup area. This area should be clean and protected from the wind so that the chances of contaminating or losing the sample will be minimized.
8.2.5 Save a portion of the acetone used for cleanup as a blank. Take 200 ml of this acetone from the wash bottle being used and place it in a glass sample container labeled “acetone blank.” Inspect the train prior to and during disassembly and not any abnormal conditions. Treat the sample as discussed in Method 5, section 8.2.
9.0 Quality Control [Reserved] 10.0 Calibration and StandardizationThe calibrations of the probe nozzle, pitot tube, metering system, temperature sensors, and barometer are the same as in Method 5, sections 10.1 through 10.3, 10.5, and 10.6, respectively.
11.0 Analytical ProcedureSame as in Method 5, section 11.0. Analytical data should be recorded on a form similar to that shown in Figure 5-6 of Method 5.
12.0 Data Analysis and Calculations.Same as in Method 5, section 12.0.
13.0 Method Performance [Reserved] 14.0 Pollution Prevention [Reserved] 15.0 Waste Management [Reserved] 16.0 Alternative ProceduresSame as in Method 5, section 16.0.
17.0 ReferencesSame as in Method 5, section 17.0, with the addition of the following:
1. Vollaro, R.F. Recommended Procedure for Sample Traverses in Ducts Smaller than 12 Inches in Diameter. U.S. Environmental Protection Agency, Emission Measurement Branch. Research Triangle Park, NC. November 1976.
18.0 Tables, Diagrams, Flowcharts, and Validation Data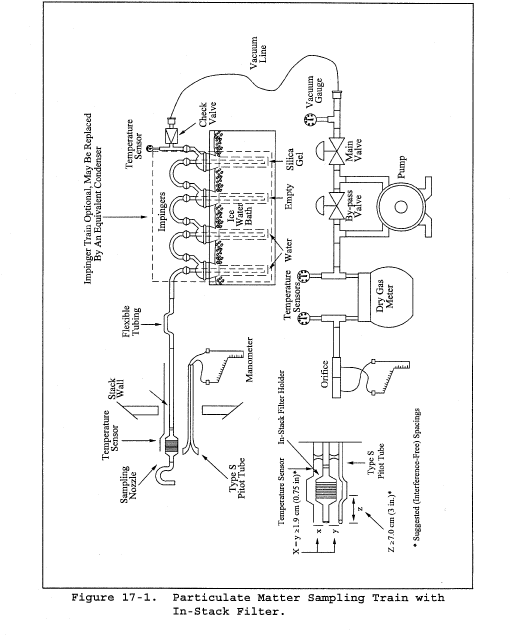
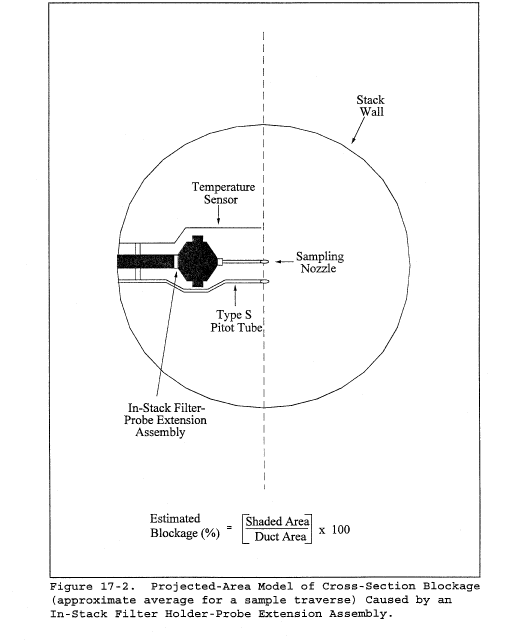
This method is not inclusive with respect to specifications (e.g., equipment and supplies) and procedures (e.g., sampling and analytical) essential to its performance. Some material is incorporated by reference from other methods in this part. Therefore, to obtain reliable results, persons using this method should have a thorough knowledge of at least the following additional test methods: Method 1, Method 2, Method 3.
Note:This method should not be attempted by persons unfamiliar with the performance characteristics of gas chromatography, nor by those persons who are unfamiliar with source sampling. Particular care should be exercised in the area of safety concerning choice of equipment and operation in potentially explosive atmospheres.
1.0 Scope and Application1.1 Analyte. Total gaseous organic compounds.
1.2 Applicability.
1.2.1 This method is designed to measure gaseous organics emitted from an industrial source. While designed for ppm level sources, some detectors are quite capable of detecting compounds at ambient levels, e.g., ECD, ELCD, and helium ionization detectors. Some other types of detectors are evolving such that the sensitivity and applicability may well be in the ppb range in only a few years.
1.2.2 This method will not determine compounds that (1) are polymeric (high molecular weight), (2) can polymerize before analysis, or (3) have very low vapor pressures at stack or instrument conditions.
1.3 Range. The lower range of this method is determined by the sampling system; adsorbents may be used to concentrate the sample, thus lowering the limit of detection below the 1 part per million (ppm) typically achievable with direct interface or bag sampling. The upper limit is governed by GC detector saturation or column overloading; the upper range can be extended by dilution of sample with an inert gas or by using smaller volume gas sampling loops. The upper limit can also be governed by condensation of higher boiling compounds.
1.4 Sensitivity. The sensitivity limit for a compound is defined as the minimum detectable concentration of that compound, or the concentration that produces a signal-to-noise ratio of three to one. The minimum detectable concentration is determined during the presurvey calibration for each compound.
2.0 Summary of MethodThe major organic components of a gas mixture are separated by gas chromatography (GC) and individually quantified by flame ionization, photoionization, electron capture, or other appropriate detection principles. The retention times of each separated component are compared with those of known compounds under identical conditions. Therefore, the analyst confirms the identity and approximate concentrations of the organic emission components beforehand. With this information, the analyst then prepares or purchases commercially available standard mixtures to calibrate the GC under conditions identical to those of the samples. The analyst also determines the need for sample dilution to avoid detector saturation, gas stream filtration to eliminate particulate matter, and prevention of moisture condensation.
3.0 Definitions [Reserved] 4.0 Interferences4.1 Resolution interferences that may occur can be eliminated by appropriate GC column and detector choice or by shifting the retention times through changes in the column flow rate and the use of temperature programming.
4.2 The analytical system is demonstrated to be essentially free from contaminants by periodically analyzing blanks that consist of hydrocarbon-free air or nitrogen.
4.3 Sample cross-contamination that occurs when high-level and low-level samples or standards are analyzed alternately is best dealt with by thorough purging of the GC sample loop between samples.
4.4 To assure consistent detector response, calibration gases are contained in dry air. To adjust gaseous organic concentrations when water vapor is present in the sample, water vapor concentrations are determined for those samples, and a correction factor is applied.
4.5 The gas chromatograph run time must be sufficient to clear all eluting peaks from the column before proceeding to the next run (in order to prevent sample carryover).
5.0 Safety5.1 Disclaimer. This method may involve hazardous materials, operations, and equipment. This test method may not address all of the safety problems associated with its use. It is the responsibility of the user of this test method to establish appropriate safety and health practices and determine the applicability of regulatory limitations prior to performing this test method. The analyzer users manual should be consulted for specific precautions to be taken with regard to the analytical procedure.
6.0 Equipment and Supplies6.1 Equipment needed for the presurvey sampling procedure can be found in section 16.1.1.
6.2 Equipment needed for the integrated bag sampling and analysis procedure can be found in section 8.2.1.1.1.
6.3 Equipment needed for direct interface sampling and analysis can be found in section 8.2.2.1.
6.4 Equipment needed for the dilution interface sampling and analysis can be found in section 8.2.3.1.
6.5 Equipment needed for adsorbent tube sampling and analysis can be found in section 8.2.4.1.
7.0 Reagents and Standards7.1 Reagents needed for the presurvey sampling procedure can be found in section 16.1.2.
8.0 Sample Collection, Preservation, Storage, and Transport8.2 Final Sampling and Analysis Procedure. Considering safety (flame hazards) and the source conditions, select an appropriate sampling and analysis procedure (Section 8.2.1, 8.2.2, 8.2.3 or 8.2.4). In situations where a hydrogen flame is a hazard and no intrinsically safe GC is suitable, use the flexible bag collection technique or an adsorption technique.
8.2.1 Integrated Bag Sampling and Analysis.
8.2.1.1 Evacuated Container Sampling Procedure. In this procedure, the bags are filled by evacuating the rigid air-tight container holding the bags. Use a field sample data sheet as shown in Figure 18-10. Collect triplicate samples from each sample location.
8.2.1.1.1 Apparatus.
8.2.1.1.1.1 Probe. Stainless steel, Pyrex glass, or Teflon tubing probe, according to the duct temperature, with Teflon tubing of sufficient length to connect to the sample bag. Use stainless steel or Teflon unions to connect probe and sample line.
8.2.1.1.1.2 Quick Connects. Male (2) and female (2) of stainless steel construction.
8.2.1.1.1.3 Needle Valve. To control gas flow.
8.2.1.1.1.4 Pump. Leakless Teflon-coated diaphragm-type pump or equivalent. To deliver at least 1 liter/min.
8.2.1.1.1.5 Charcoal Adsorption Tube. Tube filled with activated charcoal, with glass wool plugs at each end, to adsorb organic vapors.
8.2.1.1.1.6 Flowmeter. 0 to 500-ml flow range; with manufacturer's calibration curve.
8.2.1.1.2 Sampling Procedure. To obtain a sample, assemble the sample train as shown in Figure 18-9. Leak-check both the bag and the container. Connect the vacuum line from the needle valve to the Teflon sample line from the probe. Place the end of the probe at the centroid of the stack or at a point no closer to the walls than 1 in., and start the pump. Set the flow rate so that the final volume of the sample is approximately 80 percent of the bag capacity. After allowing sufficient time to purge the line several times, connect the vacuum line to the bag, and evacuate until the rotameter indicates no flow. Then position the sample and vacuum lines for sampling, and begin the actual sampling, keeping the rate proportional to the stack velocity. As a precaution, direct the gas exiting the rotameter away from sampling personnel. At the end of the sample period, shut off the pump, disconnect the sample line from the bag, and disconnect the vacuum line from the bag container. Record the source temperature, barometric pressure, ambient temperature, sampling flow rate, and initial and final sampling time on the data sheet shown in Figure 18-10. Protect the bag and its container from sunlight. Record the time lapsed between sample collection and analysis, and then conduct the recovery procedure in Section 8.4.2.
8.2.1.2 Direct Pump Sampling Procedure. Follow 8.2.1.1, except place the pump and needle valve between the probe and the bag. Use a pump and needle valve constructed of inert material not affected by the stack gas. Leak-check the system, and then purge with stack gas before connecting to the previously evacuated bag.
8.2.1.3 Explosion Risk Area Bag Sampling Procedure. Follow 8.2.1.1 except replace the pump with another evacuated can (see Figure 18-9a). Use this method whenever there is a possibility of an explosion due to pumps, heated probes, or other flame producing equipment.
8.2.1.4 Other Modified Bag Sampling Procedures. In the event that condensation is observed in the bag while collecting the sample and a direct interface system cannot be used, heat the bag during collection and maintain it at a suitably elevated temperature during all subsequent operations. (Note: Take care to leak-check the system prior to the dilutions so as not to create a potentially explosive atmosphere.) As an alternative, collect the sample gas, and simultaneously dilute it in the bag.
8.2.1.4.1 First Alternative Procedure. Heat the box containing the sample bag to 120 °C (±5 °C). Then transport the bag as rapidly as possible to the analytical area while maintaining the heating, or cover the box with an insulating blanket. In the analytical area, keep the box heated to 120 °C (±5 °C) until analysis. Be sure that the method of heating the box and the control for the heating circuit are compatible with the safety restrictions required in each area.
8.2.1.4.2 Second Alternative Procedure. Prefill the bag with a known quantity of inert gas. Meter the inert gas into the bag according to the procedure for the preparation of gas concentration standards of volatile liquid materials (Section 10.1.2.2), but eliminate the midget impinger section. Take the partly filled bag to the source, and meter the source gas into the bag through heated sampling lines and a heated flowmeter, or Teflon positive displacement pump. Verify the dilution factors before sampling each bag through dilution and analysis of gases of known concentration.
8.2.1.5 Analysis of Bag Samples.
8.2.1.5.1 Apparatus. Same as section 8.1. A minimum of three gas standards are required.
8.2.1.5.2 Procedure.
8.2.1.5.2.1 Establish proper GC operating conditions as described in section 10.2, and record all data listed in Figure 18-7. Prepare the GC so that gas can be drawn through the sample valve. Flush the sample loop with calibration gas mixture, and activate the valve (sample pressure at the inlet to the GC introduction valve should be similar during calibration as during actual sample analysis). Obtain at least three chromatograms for the mixture. The results are acceptable when the peak areas for the three injections agree to within 5 percent of their average. If they do not agree, run additional samples or correct the analytical techniques until this requirement is met. Then analyze the other two calibration mixtures in the same manner. Prepare a calibration curve as described in section 10.2.
8.2.1.5.2.2 Analyze the three source gas samples by connecting each bag to the sampling valve with a piece of Teflon tubing identified with that bag. Analyze each bag sample three times. Record the data in Figure 18-11. If certain items do not apply, use the notation “N.A.” If the bag has been maintained at an elevated temperature as described in section 8.2.1.4, determine the stack gas water content by Method 4. After all samples have been analyzed, repeat the analysis of the mid-level calibration gas for each compound. Compare the average response factor of the pre- and post-test analysis for each compound. If they differ by >5percent, analyze the other calibration gas levels for that compound, and prepare a calibration curve using all the pre- and post-test calibration gas mixture values. If the two response factor averages (pre-and post-test) differ by less than 5 percent from their mean value, the tester has the option of using only the pre-test calibration curve to generate the concentration values.
8.2.1.6 Determination of Bag Water Vapor Content. Measure the ambient temperature and barometric pressure near the bag. From a water saturation vapor pressure table, determine and record the water vapor content of the bag as a decimal figure. (Assume the relative humidity to be 100 percent unless a lesser value is known.) If the bag has been maintained at an elevated temperature as described in section 8.2.1.4, determine the stack gas water content by Method 4.
8.2.1.8 Emission Calculations. From the calibration curve described in section 8.2.1.5, select the value of Cs that corresponds to the peak area. Calculate the concentration Cc in ppm, dry basis, of each organic in the sample using Equation 18-5 in section 12.6.
8.2.2 Direct Interface Sampling and Analysis Procedure. The direct interface procedure can be used provided that the moisture content of the gas does not interfere with the analysis procedure, the physical requirements of the equipment can be met at the site, and the source gas concentration falls within the linear range of the detector. Adhere to all safety requirements with this method.
8.2.2.1 Apparatus.
8.2.2.1.1 Probe. Constructed of stainless steel, Pyrex glass, or Teflon tubing as dictated by duct temperature and reactivity of target compounds. A filter or glass wool plug may be needed if particulate is present in the stack gas. If necessary, heat the probe with heating tape or a special heating unit capable of maintaining a temperature greater than 110 °C.
8.2.2.1.2 Sample Lines. 6.4-mm OD (or other diameter as needed) Teflon lines, heat-traced to prevent condensation of material (greater than 110 °C).
8.2.2.1.3 Quick Connects. To connect sample line to gas sampling valve on GC instrument and to pump unit used to withdraw source gas. Use a quick connect or equivalent on the cylinder or bag containing calibration gas to allow connection of the calibration gas to the gas sampling valve.
8.2.2.1.4 Thermocouple Readout Device. Potentiometer or digital thermometer, to measure source temperature and probe temperature.
8.2.2.1.5 Heated Gas Sampling Valve. Of two-position, six-port design, to allow sample loop to be purged with source gas or to direct source gas into the GC instrument.
8.2.2.1.6 Needle Valve. To control gas sampling rate from the source.
8.2.2.1.7 Pump. Leakless Teflon-coated diaphragm-type pump or equivalent, capable of at least 1 liter/minute sampling rate.
8.2.2.1.8 Flowmeter. Of suitable range to measure sampling rate.
8.2.2.1.9 Charcoal Adsorber. To adsorb organic vapor vented from the source to prevent exposure of personnel to source gas.
8.2.2.1.10 Gas Cylinders. Carrier gas, oxygen and fuel as needed to run GC and detector.
8.2.2.1.11 Gas Chromatograph. Capable of being moved into the field, with detector, heated gas sampling valve, column required to complete separation of desired components, and option for temperature programming.
8.2.2.1.12 Recorder/Integrator. To record results.
8.2.2.2 Procedure. Calibrate the GC using the procedures in section 8.2.1.5.2.1. To obtain a stack gas sample, assemble the sampling system as shown in Figure 18-12. Make sure all connections are tight. Turn on the probe and sample line heaters. As the temperature of the probe and heated line approaches the target temperature as indicated on the thermocouple readout device, control the heating to maintain a temperature greater than 110 °C. Conduct a 3-point calibration of the GC by analyzing each gas mixture in triplicate. Generate a calibration curve. Place the inlet of the probe at the centroid of the duct, or at a point no closer to the walls than 1 m, and draw source gas into the probe, heated line, and sample loop. After thorough flushing, analyze the stack gas sample using the same conditions as for the calibration gas mixture. For each run, sample, analyze, and record five consecutive samples. A test consists of three runs (five samples per run times three runs, for a total of fifteen samples). After all samples have been analyzed, repeat the analysis of the mid-level calibration gas for each compound. For each calibration standard, compare the pre- and post-test average response factors (RF) for each compound. If the two calibration RF values (pre- and post-analysis) differ by more than 5 percent from their mean value, then analyze the other calibration gas levels for that compound and determine the stack gas sample concentrations by comparison to both calibration curves (this is done by preparing a calibration curve using all the pre- and post-test calibration gas mixture values.) If the two calibration RF values differ by less than 5 percent from their mean value, the tester has the option of using only the pre-test calibration curve to generate the concentration values. Record this calibration data and the other required data on the data sheet shown in Figure 18-11, deleting the dilution gas information.
Note:Take care to draw all samples and calibration mixtures through the sample loop at the same pressure.
8.2.2.3 Determination of Stack Gas Moisture Content. Use Method 4 to measure the stack gas moisture content.
8.2.2.5 Emission Calculations. Same as section 8.2.1.8.
8.2.3 Dilution Interface Sampling and Analysis Procedure. Source samples that contain a high concentration of organic materials may require dilution prior to analysis to prevent saturating the GC detector. The apparatus required for this direct interface procedure is basically the same as that described in the section 8.2.2, except a dilution system is added between the heated sample line and the gas sampling valve. The apparatus is arranged so that either a 10:1 or 100:1 dilution of the source gas can be directed to the chromatograph. A pump of larger capacity is also required, and this pump must be heated and placed in the system between the sample line and the dilution apparatus.
8.2.3.1 Apparatus. The equipment required in addition to that specified for the direct interface system is as follows:
8.2.3.1.1 Sample Pump. Leakless Teflon-coated diaphragm-type that can withstand being heated to 120 °C and deliver 1.5 liters/minute.
8.2.3.1.2 Dilution Pumps. Two Model A-150 Komhyr Teflon positive displacement type delivering 150 cc/minute, or equivalent. As an option, calibrated flowmeters can be used in conjunction with Teflon-coated diaphragm pumps.
8.2.3.1.3 Valves. Two Teflon three-way valves, suitable for connecting to Teflon tubing.
8.2.3.1.4 Flowmeters. Two, for measurement of diluent gas.
8.2.3.1.5 Diluent Gas with Cylinders and Regulators. Gas can be nitrogen or clean dry air, depending on the nature of the source gases.
8.2.3.1.6 Heated Box. Suitable for being heated to 120 °C, to contain the three pumps, three-way valves, and associated connections. The box should be equipped with quick connect fittings to facilitate connection of: (1) the heated sample line from the probe, (2) the gas sampling valve, (3) the calibration gas mixtures, and (4) diluent gas lines. A schematic diagram of the components and connections is shown in Figure 18-13. The heated box shown in Figure 18-13 is designed to receive a heated line from the probe. An optional design is to build a probe unit that attaches directly to the heated box. In this way, the heated box contains the controls for the probe heaters, or, if the box is placed against the duct being sampled, it may be possible to eliminate the probe heaters. In either case, a heated Teflon line is used to connect the heated box to the gas sampling valve on the chromatograph.
Note:Care must be taken to leak-check the system prior to the dilutions so as not to create a potentially explosive atmosphere.
8.2.3.2 Procedure.
8.2.3.2.1 Assemble the apparatus by connecting the heated box, shown in Figure 18-13, between the heated sample line from the probe and the gas sampling valve on the chromatograph. Vent the source gas from the gas sampling valve directly to the charcoal filter, eliminating the pump and rotameter. Heat the sample probe, sample line, and heated box. Insert the probe and source thermocouple at the centroid of the duct, or to a point no closer to the walls than 1 m. Measure the source temperature, and adjust all heating units to a temperature 0 to 3 °C above this temperature. If this temperature is above the safe operating temperature of the Teflon components, adjust the heating to maintain a temperature high enough to prevent condensation of water and organic compounds (greater than 110 °C). Calibrate the GC through the dilution system by following the procedures in section 8.2.1.5.2.1. Determine the concentration of the diluted calibration gas using the dilution factor and the certified concentration of the calibration gas. Record the pertinent data on the data sheet shown in Figure 18-11.
8.2.3.2.2 Once the dilution system and GC operations are satisfactory, proceed with the analysis of source gas, maintaining the same dilution settings as used for the standards.
8.2.3.2.3 Analyze the audit samples using either the dilution system, or directly connect to the gas sampling valve as required. Record all data and report the results to the audit supervisor.
8.2.3.3 Determination of Stack Gas Moisture Content. Same as section 8.2.2.3.
8.2.3.4 Quality Assurance. Same as section 8.2.2.4.
8.2.3.5 Emission Calculations. Same as section 8.2.2.5, with the dilution factor applied.
8.2.4 Adsorption Tube Procedure. Any commercially available adsorbent is allowed for the purposes of this method, as long as the recovery study criteria in section 8.4.3 are met. Help in choosing the adsorbent may be found by calling the distributor, or the tester may refer to National Institute for Occupational Safety and Health (NIOSH) methods for the particular organics to be sampled. For some adsorbents, the principal interferent will be water vapor. If water vapor is thought to be a problem, the tester may place a midget impinger in an ice bath before the adsorbent tubes. If this option is chosen, the water catch in the midget impinger shall be analyzed for the target compounds. Also, the spike for the recovery study (in section 8.4.3) shall be conducted in both the midget impinger and the adsorbent tubes. The combined recovery (add the recovered amount in the impinger and the adsorbent tubes to calculate R) shall then meet the criteria in section 8.4.3.
Note:Post-test leak-checks are not allowed for this technique since this can result in sample contamination.
8.2.4.1 Additional Apparatus. The following items (or equivalent) are suggested.
8.2.4.1.1 Probe. Borosilicate glass or stainless steel, approximately 6-mm ID, with a heating system if water condensation is a problem, and a filter (either in-stack or out-of-stack, heated to stack temperature) to remove particulate matter. In most instances, a plug of glass wool is a satisfactory filter.
8.2.4.1.2 Flexible Tubing. To connect probe to adsorption tubes. Use a material that exhibits minimal sample adsorption.
8.2.4.1.3 Leakless Sample Pump. Flow controlled, constant rate pump, with a set of limiting (sonic) orifices.
8.2.4.1.4 Bubble-Tube Flowmeter. Volume accuracy within 1 percent, to calibrate pump.
8.2.4.1.5 Stopwatch. To time sampling and pump rate calibration.
8.2.4.1.6 Adsorption Tubes. Precleaned adsorbent, with mass of adsorbent to be determined by calculating breakthrough volume and expected concentration in the stack.
8.2.4.1.7 Barometer. Accurate to 5 mm Hg, to measure atmospheric pressure during sampling and pump calibration.
8.2.4.1.8 Rotameter. O to 100 cc/min, to detect changes in flow rate during sampling.
8.2.4.2 Sampling and Analysis.
8.2.4.2.1 Calibrate the pump and limiting orifice flow rate through adsorption tubes with the bubble tube flowmeter before sampling. The sample system can be operated as a “recirculating loop” for this operation. Record the ambient temperature and barometric pressure. Then, during sampling, use the rotameter to verify that the pump and orifice sampling rate remains constant.
8.2.4.2.2 Use a sample probe, if required, to obtain the sample at the centroid of the duct or at a point no closer to the walls than 1 m. Minimize the length of flexible tubing between the probe and adsorption tubes. Several adsorption tubes can be connected in series, if the extra adsorptive capacity is needed. Adsorption tubes should be maintained vertically during the test in order to prevent channeling. Provide the gas sample to the sample system at a pressure sufficient for the limiting orifice to function as a sonic orifice. Record the total time and sample flow rate (or the number of pump strokes), the barometric pressure, and ambient temperature. Obtain a total sample volume commensurate with the expected concentration(s) of the volatile organic(s) present and recommended sample loading factors (weight sample per weight adsorption media). Laboratory tests prior to actual sampling may be necessary to predetermine this volume. If water vapor is present in the sample at concentrations above 2 to 3 percent, the adsorptive capacity may be severely reduced. Operate the gas chromatograph according to the manufacturer's instructions. After establishing optimum conditions, verify and document these conditions during all operations. Calibrate the instrument and then analyze the emission samples.
8.2.4.3 Standards and Calibration. If using thermal desorption, obtain calibration gases using the procedures in section 10.1. If using solvent extraction, prepare liquid standards in the desorption solvent. Use a minimum of three different standards; select the concentrations to bracket the expected average sample concentration. Perform the calibration before and after each day's sample analyses using the procedures in section 8.2.1.5.2.1.
8.2.4.4 Quality Assurance.
8.2.4.4.1 Determine the recovery efficiency of the pollutants of interest according to section 8.4.3.
8.2.4.4.2 Determination of Sample Collection Efficiency (Optional). If sample breakthrough is thought to be a problem, a routine procedure for determining breakthrough is to analyze the primary and backup portions of the adsorption tubes separately. If the backup portion exceeds 10 percent of the total amount (primary and back-up), it is usually a sign of sample breakthrough. For the purposes of this method, only the recovery efficiency value (Section 8.4.3) is used to determine the appropriateness of the sampling and analytical procedure.
8.2.4.4.3 Volume Flow Rate Checks. Perform this check immediately after sampling with all sampling train components in place. Use the bubble-tube flowmeter to measure the pump volume flow rate with the orifice used in the test sampling, and record the result. If it has changed by more than 5 but less than 20 percent, calculate an average flow rate for the test. If the flow rate has changed by more than 20 percent, recalibrate the pump and repeat the sampling.
8.2.4.4.4 Calculations. Correct all sample volumes to standard conditions. If a sample dilution system has been used, multiply the results by the appropriate dilution ratio. Correct all results according to the applicable procedure in section 8.4.3. Report results as ppm by volume, dry basis.
8.3 Reporting of Results. At the completion of the field analysis portion of the study, ensure that the data sheets shown in Figure 18-11 have been completed. Summarize this data on the data sheets shown in Figure 18-15.
8.4 Recovery Study. After conducting the presurvey and identifying all of the pollutants of interest, conduct the appropriate recovery study during the test based on the sampling system chosen for the compounds of interest.
8.4.1 Recovery Study for Direct Interface or Dilution Interface Sampling. If the procedures in section 8.2.2 or 8.2.3 are to be used to analyze the stack gas, conduct the calibration procedure as stated in section 8.2.2.2 or 8.2.3.2, as appropriate. Upon successful completion of the appropriate calibration procedure, attach the mid-level calibration gas for at least one target compound to the inlet of the probe or as close as possible to the inlet of the probe, but before the filter. Repeat the calibration procedure by sampling and analyzing the mid-level calibration gas through the entire sampling and analytical system in triplicate. The mean of the calibration gas response sampled through the probe shall be within 10 percent of the analyzer response. If the difference in the two means is greater than 10 percent, check for leaks throughout the sampling system and repeat the analysis of the standard through the sampling system until this criterion is met.
8.4.2 Recovery Study for Bag Sampling.
8.4.2.1 Follow the procedures for the bag sampling and analysis in section 8.2.1. After analyzing all three bag samples, choose one of the bag samples and tag this bag as the spiked bag. Spike the chosen bag sample with a known mixture (gaseous or liquid) of all of the target pollutants. The theoretical concentration, in ppm, of each spiked compound in the bag shall be 40 to 60 percent of the average concentration measured in the three bag samples. If a target compound was not detected in the bag samples, the concentration of that compound to be spiked shall be 5 times the limit of detection for that compound. Store the spiked bag for the same period of time as the bag samples collected in the field. After the appropriate storage time has passed, analyze the spiked bag three times. Calculate the average fraction recovered (R) of each spiked target compound with the equation in section 12.7.
8.4.2.2 For the bag sampling technique to be considered valid for a compound, 0.70 ≤R ≤1.30. If the R value does not meet this criterion for a target compound, the sampling technique is not acceptable for that compound, and therefore another sampling technique shall be evaluated for acceptance (by repeating the recovery study with another sampling technique). Report the R value in the test report and correct all field measurements with the calculated R value for that compound by using the equation in section 12.8.
8.4.3 Recovery Study for Adsorption Tube Sampling. If following the adsorption tube procedure in section 8.2.4, conduct a recovery study of the compounds of interest during the actual field test. Set up two identical sampling trains. Collocate the two sampling probes in the stack. The probes shall be placed in the same horizontal plane, where the first probe tip is 2.5 cm from the outside edge of the other. One of the sampling trains shall be designated the spiked train and the other the unspiked train. Spike all of the compounds of interest (in gaseous or liquid form) onto the adsorbent tube(s) in the spiked train before sampling. The mass of each spiked compound shall be 40 to 60 percent of the mass expected to be collected with the unspiked train. Sample the stack gas into the two trains simultaneously. Analyze the adsorbents from the two trains utilizing identical analytical procedures and instrumentation. Determine the fraction of spiked compound recovered (R) using the equations in section 12.9.
8.4.3.1 Repeat the procedure in section 8.4.3 twice more, for a total of three runs. In order for the adsorbent tube sampling and analytical procedure to be acceptable for a compound, 0.70≤R≤1.30 (R in this case is the average of three runs). If the average R value does not meet this criterion for a target compound, the sampling technique is not acceptable for that compound, and therefore another sampling technique shall be evaluated for acceptance (by repeating the recovery study with another sampling technique). Report the R value in the test report and correct all field measurements with the calculated R value for that compound by using the equation in section 12.8.
9.0 Quality Control9.1 Miscellaneous Quality Control Measures
Section | Quality control measure | Effect |
---|---|---|
8.4.1 | Recovery study for direct interface or dilution interface sampling | Ensure that there are no significant leaks in the sampling system. |
8.4.2 | Recovery study for bag sampling | Demonstrate that proper sampling/analysis procedures were selected. |
8.4.3 | Recovery study for adsorption tube sampling | Demonstrate that proper sampling/analysis procedures were selected. |
10.1 Calibration Standards. Obtain calibration gas standards for each target compound to be analyzed. Commercial cylinder gases certified by the manufacturer to be accurate to within 1 percent of the certified label value are preferable, although cylinder gases certified by the manufacturer to 2 percent accuracy are allowed. Another option allowed by this method is for the tester to obtain high concentration certified cylinder gases and then use a dilution system meeting the requirements of Test Method 205, 40 CFR Part 51, Appendix M to make multi-level calibration gas standards. Prepare or obtain enough calibration standards so that there are three different concentrations of each organic compound expected to be measured in the source sample. For each organic compound, select those concentrations that bracket the concentrations expected in the source samples. A calibration standard may contain more than one organic compound. If samples are collected in adsorbent tubes and extracted using solvent extraction, prepare or obtain standards in the same solvent used for the sample extraction procedure. Verify the stability of all standards for the time periods they are used.
10.2 Preparation of Calibration Curves.
10.2.1 Establish proper GC conditions, then flush the sampling loop for 30 seconds. Allow the sample loop pressure to equilibrate to atmospheric pressure, and activate the injection valve. Record the standard concentration, attenuator factor, injection time, chart speed, retention time, peak area, sample loop temperature, column temperature, and carrier gas flow rate. Analyze each standard in triplicate.
10.2.2 Repeat this procedure for each standard. Prepare a graphical plot of concentration (Cs) versus the calibration area values. Perform a regression analysis, and draw the least square line.
11.0 Analytical Procedures11.1 Analysis Development
11.1.1 Selection of GC Parameters
11.1.1.1 Column Choice. Based on the initial contact with plant personnel concerning the plant process and the anticipated emissions, choose a column that provides good resolution and rapid analysis time. The choice of an appropriate column can be aided by a literature search, contact with manufacturers of GC columns, and discussion with personnel at the emission source.
Note:Most column manufacturers keep excellent records on their products. Their technical service departments may be able to recommend appropriate columns and detector type for separating the anticipated compounds, and they may be able to provide information on interferences, optimum operating conditions, and column limitations. Plants with analytical laboratories may be able to provide information on their analytical procedures.
11.1.1.2 Preliminary GC Adjustment. Using the standards and column obtained in section 11.1.1.1, perform initial tests to determine appropriate GC conditions that provide good resolution and minimum analysis time for the compounds of interest.
11.1.1.3 Preparation of Presurvey Samples. If the samples were collected on an adsorbent, extract the sample as recommended by the manufacturer for removal of the compounds with a solvent suitable to the type of GC analysis. Prepare other samples in an appropriate manner.
11.1.1.4 Presurvey Sample Analysis.
11.1.1.4.1 Before analysis, heat the presurvey sample to the duct temperature to vaporize any condensed material. Analyze the samples by the GC procedure, and compare the retention times against those of the calibration samples that contain the components expected to be in the stream. If any compounds cannot be identified with certainty by this procedure, identify them by other means such as GC/mass spectroscopy (GC/MS) or GC/infrared techniques. A GC/MS system is recommended.
11.1.1.4.2 Use the GC conditions determined by the procedure of section 11.1.1.2 for the first injection. Vary the GC parameters during subsequent injections to determine the optimum settings. Once the optimum settings have been determined, perform repeat injections of the sample to determine the retention time of each compound. To inject a sample, draw sample through the loop at a constant rate (100 ml/min for 30 seconds). Be careful not to pressurize the gas in the loop. Turn off the pump and allow the gas in the sample loop to come to ambient pressure. Activate the sample valve, and record injection time, loop temperature, column temperature, carrier flow rate, chart speed, and attenuator setting. Calculate the retention time of each peak using the distance from injection to the peak maximum divided by the chart speed. Retention times should be repeatable within 0.5 seconds.
11.1.1.4.3 If the concentrations are too high for appropriate detector response, a smaller sample loop or dilutions may be used for gas samples, and, for liquid samples, dilution with solvent is appropriate. Use the standard curves (Section 10.2) to obtain an estimate of the concentrations.
11.1.1.4.4 Identify all peaks by comparing the known retention times of compounds expected to be in the retention times of peaks in the sample. Identify any remaining unidentified peaks which have areas larger than 5 percent of the total using a GC/MS, or estimation of possible compounds by their retention times compared to known compounds, with confirmation by further GC analysis.
12.0 Data Analysis and Calculations12.1 Nomenclature.
Bws = Water vapor content of the bag sample or stack gas, proportion by volume. Cs = Concentration of the organic from the calibration curve, ppm. Gv = Gas volume or organic compound injected, ml. Lv = Liquid volume of organic injected, µl. M = Molecular weight of organic, g/g-mole. ms = Total mass of compound measured on adsorbent with spiked train (µg). mu = Total mass of compound measured on adsorbent with unspiked train (µg). mv = Mass per volume of spiked compound measured (µg/L). Pi = Barometric or absolute sample loop pressure at time of sample analysis, mm Hg. Pm = Absolute pressure of dry gas meter, mm Hg. Pr = Reference pressure, the barometric pressure or absolute sample loop pressure recorded during calibration, mm Hg. Ps = Absolute pressure of syringe before injection, mm Hg. qc = Flow rate of the calibration gas to be diluted. qc1 = Flow rate of the calibration gas to be diluted in stage 1. qc2 = Flow rate of the calibration gas to be diluted in stage 2. qd = Diluent gas flow rate. qd1 = Flow rate of diluent gas in stage 1. qd2 = Flow rate of diluent gas in stage 2. s = Theoretical concentration (ppm) of spiked target compound in the bag. S = Theoretical mass of compound spiked onto adsorbent in spiked train (µg). t = Measured average concentration (ppm) of target compound and source sample (analysis results subsequent to bag spiking) Ti = Sample loop temperature at the time of sample analysis, °K. Tm = Absolute temperature of dry gas meter, °K. Ts = Absolute temperature of syringe before injection, °K. u = Source sample average concentration (ppm) of target compound in the bag (analysis results before bag spiking). Vm = Gas volume indicated by dry gas meter, liters. vs = volume of stack gas sampled with spiked train (L). vu = volume of stack gas sampled with unspiked train (L). X = Mole or volume fraction of the organic in the calibration gas to be diluted. Y = Dry gas meter calibration factor, dimensionless. µl = Liquid organic density as determined, g/ml. 24.055 = Ideal gas molar volume at 293 °K and 760 mm Hg, liters/g-mole. 1000 = Conversion factor, ml/liter. 10 6 = Conversion to ppm.12.2 Calculate the concentration, Cs, in ppm using the following equation:
12.3 Calculate the concentration, Cs, in ppm of the organic in the final gas mixture using the following equation:
12.4 Calculate each organic standard concentration, Cs, in ppm using the following equation:
12.5 Calculate each organic standard concentration, Cs, in ppm using the following equation:
12.6 Calculate the concentration, Cc, in ppm, dry basis, of each organic is the sample using the following equation:
12.7 Calculate the average fraction recovered (R) of each spiked target compound using the following equation:
12.8 Correct all field measurements with the calculated R value for that compound using the following equation:
12.9 Determine the mass per volume of spiked compound measured using the following equation:
12.10 Calculate the fraction of spiked compound recovered, R, using the following equation:
13.0 Method Performance13.1 Since a potential sample may contain a variety of compounds from various sources, a specific precision limit for the analysis of field samples is impractical. Precision in the range of 5 to 10 percent relative standard deviation (RSD) is typical for gas chromatographic techniques, but an experienced GC operator with a reliable instrument can readily achieve 5 percent RSD. For this method, the following combined GC/operator values are required.
(a) Precision. Triplicate analyses of calibration standards fall within 5 percent of their mean value.
(b) Recovery. After developing an appropriate sampling and analytical system for the pollutants of interest, conduct the procedure in section 8.4. Conduct the appropriate recovery study in section 8.4 at each sampling point where the method is being applied. Submit the data and results of the recovery procedure with the reporting of results under section 8.3.
14.0 Pollution Prevention [Reserved] 15.0 Waste Management [Reserved] 16.0 Alternative Procedures16.1 Optional Presurvey and Presurvey Sampling.
Note:Presurvey screening is optional. Presurvey sampling should be conducted for sources where the target pollutants are not known from previous tests and/or process knowledge.
Perform a presurvey for each source to be tested. Refer to Figure 18-1. Some of the information can be collected from literature surveys and source personnel. Collect gas samples that can be analyzed to confirm the identities and approximate concentrations of the organic emissions.
16.1.1 Apparatus. This apparatus list also applies to sections 8.2 and 11.
16.1.1.1 Teflon Tubing. (Mention of trade names or specific products does not constitute endorsement by the U.S. Environmental Protection Agency.) Diameter and length determined by connection requirements of cylinder regulators and the GC. Additional tubing is necessary to connect the GC sample loop to the sample.
16.1.1.2 Gas Chromatograph. GC with suitable detector, columns, temperature-controlled sample loop and valve assembly, and temperature programmable oven, if necessary. The GC shall achieve sensitivity requirements for the compounds under study.
16.1.1.3 Pump. Capable of pumping 100 ml/min. For flushing sample loop.
16.1.1.4 Flow Meter. To measure flow rates.
16.1.1.5 Regulators. Used on gas cylinders for GC and for cylinder standards.
16.1.1.6 Recorder. Recorder with linear strip chart is minimum acceptable. Integrator (optional) is recommended.
16.1.1.7 Syringes. 0.5-ml, 1.0- and 10-microliter size, calibrated, maximum accuracy (gas tight) for preparing calibration standards. Other appropriate sizes can be used.
16.1.1.8 Tubing Fittings. To plumb GC and gas cylinders.
16.1.1.9 Septa. For syringe injections.
16.1.1.10 Glass Jars. If necessary, clean, colored glass jars with Teflon-lined lids for condensate sample collection. Size depends on volume of condensate.
16.1.1.11 Soap Film Flowmeter. To determine flow rates.
16.1.1.12 Flexible Bags. Tedlar or equivalent, 10- and 50-liter capacity, for preparation of standards. (Verify through the manufacturer that the Tedlar alternative is suitable for the compound of interest and make this verifying information available for inspection.)
16.1.1.13 Dry Gas Meter with Temperature and Pressure Gauges. Accurate to ±2 percent, for preparation of gas standards.
16.1.1.14 Midget Impinger/Hot Plate Assembly. For preparation of gas standards.
16.1.1.15 Sample Flasks. For presurvey samples, must have gas-tight seals.
16.1.1.16 Adsorption Tubes. If necessary, blank tubes filled with necessary adsorbent (charcoal, Tenax, XAD-2, etc.) for presurvey samples.
16.1.1.17 Personnel Sampling Pump. Calibrated, for collecting adsorbent tube presurvey samples.
16.1.1.18 Dilution System. Calibrated, the dilution system is to be constructed following the specifications of an acceptable method.
16.1.1.19 Sample Probes. Pyrex or stainless steel, of sufficient length to reach centroid of stack, or a point no closer to the walls than 1 m.
16.1.1.20 Barometer. To measure barometric pressure.
16.1.2 Reagents.
16.1.2.1 Water. Deionized distilled.
16.1.2.2 Methylene chloride.
16.1.2.3 Calibration Gases. A series of standards prepared for every compound of interest.
16.1.2.4 Organic Compound Solutions. Pure (99.9 percent), or as pure as can reasonably be obtained, liquid samples of all the organic compounds needed to prepare calibration standards.
16.1.2.5 Extraction Solvents. For extraction of adsorbent tube samples in preparation for analysis.
16.1.2.6 Fuel. As recommended by the manufacturer for operation of the GC.
16.1.2.7 Carrier Gas. Hydrocarbon free, as recommended by the manufacturer for operation of the detector and compatibility with the column.
16.1.2.8 Zero Gas. Hydrocarbon free air or nitrogen, to be used for dilutions, blank preparation, and standard preparation.
16.1.3 Sampling.
16.1.3.1 Collection of Samples with Glass Sampling Flasks. Presurvey samples may be collected in precleaned 250-ml double-ended glass sampling flasks. Teflon stopcocks, without grease, are preferred. Flasks should be cleaned as follows: Remove the stopcocks from both ends of the flasks, and wipe the parts to remove any grease. Clean the stopcocks, barrels, and receivers with methylene chloride (or other non-target pollutant solvent, or heat and humidified air). Clean all glass ports with a soap solution, then rinse with tap and deionized distilled water. Place the flask in a cool glass annealing furnace, and apply heat up to 500 °C. Maintain at this temperature for 1 hour. After this time period, shut off and open the furnace to allow the flask to cool. Return the stopcocks to the flask receivers. Purge the assembly with high-purity nitrogen for 2 to 5 minutes. Close off the stopcocks after purging to maintain a slight positive nitrogen pressure. Secure the stopcocks with tape. Presurvey samples can be obtained either by drawing the gases into the previously evacuated flask or by drawing the gases into and purging the flask with a rubber suction bulb.
16.1.3.1.1 Evacuated Flask Procedure. Use a high-vacuum pump to evacuate the flask to the capacity of the pump; then close off the stopcock leading to the pump. Attach a 6-mm outside diameter (OD) glass tee to the flask inlet with a short piece of Teflon tubing. Select a 6-mm OD borosilicate sampling probe, enlarged at one end to a 12-mm OD and of sufficient length to reach the centroid of the duct to be sampled. Insert a glass wool plug in the enlarged end of the probe to remove particulate matter. Attach the other end of the probe to the tee with a short piece of Teflon tubing. Connect a rubber suction bulb to the third leg of the tee. Place the filter end of the probe at the centroid of the duct, and purge the probe with the rubber suction bulb. After the probe is completely purged and filled with duct gases, open the stopcock to the grab flask until the pressure in the flask reaches duct pressure. Close off the stopcock, and remove the probe from the duct. Remove the tee from the flask and tape the stopcocks to prevent leaks during shipment. Measure and record the duct temperature and pressure.
16.1.3.1.2 Purged Flask Procedure. Attach one end of the sampling flask to a rubber suction bulb. Attach the other end to a 6-mm OD glass probe as described in section 8.3.3.1.1. Place the filter end of the probe at the centroid of the duct, or at a point no closer to the walls than 1 m, and apply suction with the bulb to completely purge the probe and flask. After the flask has been purged, close off the stopcock near the suction bulb, and then close off the stopcock near the probe. Remove the probe from the duct, and disconnect both the probe and suction bulb. Tape the stopcocks to prevent leakage during shipment. Measure and record the duct temperature and pressure.
16.1.3.2 Flexible Bag Procedure. Any leak-free plastic (e.g., Tedlar, Mylar, Teflon) or plastic-coated aluminum (e.g., aluminized Mylar) bag, or equivalent, can be used to obtain the pre-survey sample. Use new bags, and leak-check them before field use. In addition, check the bag before use for contamination by filling it with nitrogen or air and analyzing the gas by GC at high sensitivity. Experience indicates that it is desirable to allow the inert gas to remain in the bag about 24 hours or longer to check for desorption of organics from the bag. Follow the leak-check and sample collection procedures given in Section 8.2.1.
16.1.3.3 Determination of Moisture Content. For combustion or water-controlled processes, obtain the moisture content from plant personnel or by measurement during the presurvey. If the source is below 59 °C, measure the wet bulb and dry bulb temperatures, and calculate the moisture content using a psychrometric chart. At higher temperatures, use Method 4 to determine the moisture content.
16.1.4 Determination of Static Pressure. Obtain the static pressure from the plant personnel or measurement. If a type S pitot tube and an inclined manometer are used, take care to align the pitot tube 90° from the direction of the flow. Disconnect one of the tubes to the manometer, and read the static pressure; note whether the reading is positive or negative.
16.1.5 Collection of Presurvey Samples with Adsorption Tube. Follow section 8.2.4 for presurvey sampling.
17.0 References1. American Society for Testing and Materials. C1 Through C5 Hydrocarbons in the Atmosphere by Gas Chromatography. ASTM D 2820-72, Part 23. Philadelphia, Pa. 23:950-958. 1973.
2. Corazon, V.V. Methodology for Collecting and Analyzing Organic Air Pollutants. U.S. Environmental Protection Agency. Research Triangle Park, N.C. Publication No. EPA-600/2-79-042. February 1979.
3. Dravnieks, A., B.K. Krotoszynski, J. Whitfield, A. O'Donnell, and T. Burgwald. Environmental Science and Technology. 5(12):1200-1222. 1971.
4. Eggertsen, F.T., and F.M. Nelsen. Gas Chromatographic Analysis of Engine Exhaust and Atmosphere. Analytical Chemistry. 30(6): 1040-1043. 1958.
5. Feairheller, W.R., P.J. Marn, D.H. Harris, and D.L. Harris. Technical Manual for Process Sampling Strategies for Organic Materials. U.S. Environmental Protection Agency. Research Triangle Park, N.C. Publication No. EPA 600/2-76-122. April 1976. 172 p.
6. Federal Register, 39 FR 9319-9323. 1974.
7. Federal Register, 39 FR 32857-32860. 1974.
8. Federal Register, 23069-23072 and 23076-23090. 1976.
9. Federal Register, 46569-46571. 1976.
10. Federal Register, 41771-41776. 1977.
11. Fishbein, L. Chromatography of Environmental Hazards, Volume II. Elesevier Scientific Publishing Company. New York, N.Y. 1973.
12. Hamersma, J.W., S.L. Reynolds, and R.F. Maddalone. EPA/IERL-RTP Procedures Manual: Level 1 Environmental Assessment. U.S. Environmental Protection Agency. Research Triangle Park, N.C. Publication No. EPA 600/276-160a. June 1976. 130 p.
13. Harris, J.C., M.J. Hayes, P.L. Levins, and D.B. Lindsay. EPA/IERL-RTP Procedures for Level 2 Sampling and Analysis of Organic Materials. U.S. Environmental Protection Agency. Research Triangle Park, N.C. Publication No. EPA 600/7-79-033. February 1979. 154 p.
14. Harris, W.E., H.W. Habgood. Programmed Temperature Gas Chromatography. John Wiley and Sons, Inc. New York. 1966.
15. Intersociety Committee. Methods of Air Sampling and Analysis. American Health Association. Washington, D.C. 1972.
16. Jones, P.W., R.D. Grammer, P.E. Strup, and T.B. Stanford. Environmental Science and Technology. 10:806-810. 1976.
17. McNair Han Bunelli, E.J. Basic Gas Chromatography. Consolidated Printers. Berkeley. 1969.
18. Nelson, G.O. Controlled Test Atmospheres, Principles and Techniques. Ann Arbor. Ann Arbor Science Publishers. 1971. 247 p.
19. NIOSH Manual of Analytical Methods, Volumes 1, 2, 3, 4, 5, 6, 7. U.S. Department of Health and Human Services, National Institute for Occupational Safety and Health. Center for Disease Control. 4676 Columbia Parkway, Cincinnati, Ohio 45226. April 1977 - August 1981. May be available from the Superintendent of Documents, Government Printing Office, Washington, D.C. 20402. Stock Number/Price:
Volume 1 - O17-033-00267-3/$13 Volume 2 - O17-033-00260-6/$11 Volume 3 - O17-033-00261-4/$14 Volume 4 - O17-033-00317-3/$7.25 Volume 5 - O17-033-00349-1/$10 Volume 6 - O17-033-00369-6/$9 Volume 7 - O17-033-00396-5/$7 Prices subject to change. Foreign orders add 25 percent.20. Schuetzle, D., T.J. Prater, and S.R. Ruddell. Sampling and Analysis of Emissions from Stationary Sources; I. Odor and Total Hydrocarbons. Journal of the Air Pollution Control Association. 25(9): 925-932. 1975.
21. Snyder, A.D., F.N. Hodgson, M.A. Kemmer and J.R. McKendree. Utility of Solid Sorbents for Sampling Organic Emissions from Stationary Sources. U.S. Environmental Protection Agency. Research Triangle Park, N.C. Publication No. EPA 600/2-76-201. July 1976. 71 p.
22. Tentative Method for Continuous Analysis of Total Hydrocarbons in the Atmosphere. Intersociety Committee, American Public Health Association. Washington, D.C. 1972. p. 184-186.
23. Zwerg, G. CRC Handbook of Chromatography, Volumes I and II. Sherma, Joseph (ed.). CRC Press. Cleveland. 1972.
18.0 Tables, Diagrams, Flowcharts, and Validation Data I. Name of company Date Address Contracts Phone Process to be sampled Duct or vent to be sampled II. Process description Raw material Products Operating cycle Check: Batch ____ Continuous ____ Cyclic ____ Timing of batch or cycle Best time to test III. Sampling site A. Description Site decription Duct shape and size Material Wall thickness ____ inches Upstream distance ____ inches ____ diameter Downstream distance ____ inches ____ diameter Size of port Size of access area Hazards ____ Ambient temp. ____ °F B. Properties of gas stream Temperature ____ °C ____ °F, Data source ____ Velocity ____, Data source ____ Static pressure ____ inches H2O, Data source ____ Moisture content ____%, Data source ____ Particulate content ____, Data source____ Gaseous components N2 ____ % Hydrocarbons ____ ppm O2 ____% ____ CO ____ % ____ ____ CO2 ____ % ____ ____ SO2 ____ % ____ ____ Hydrocarbon components ____ ____ ppm ____ ____ ppm ____ ____ ppm ____ ____ ppm ____ ____ ppm ____ ____ ppm C. Sampling considerations Location to set up GC Special hazards to be considered Power available at duct Power available for GC Plant safety requirements Vehicle traffic rules Plant entry requirements Security agreements Potential problems D. Site diagrams. (Attach additional sheets if required). Figure 18-1. Preliminary Survey Data Sheet Components to be analyzed and Expected concentration Suggested chromatographic column Column flow rate _ ml/min Head pressure ____ mm Hg Column temperature: Isothermal ____ °C, Programmed from ____ °C to ____ °C at ____ °C/min Injection port/sample loop temperature ____ °C Detector temperature ____ °C Detector flow rates: Hydrogen ____ ml/min., head pressure ____ mm Hg, Air/Oxygen ____ ml/min., head pressure ____ mm Hg. Chart speed ____ inches/minute Compound data: Compound and Retention time and Attenuation Figure 18-2. Chromatographic Conditions Data SheetFigure 18-3. Preparation of Standards in Tedlar or Tedlar-Equlivalent Bags and Calibration Curve
Standards | |||
---|---|---|---|
Mixture #1 | Mixture #2 | Mixture #3 | |
Standards Preparation Data: | |||
Organic: | |||
Bag number or identification | |||
Dry gas meter calibration factor | |||
Final meter reading (liters) | |||
Initial meter reading (liters) | |||
Metered volume (liters) | |||
Average meter temperature (°K) | |||
Average meter pressure, gauge (mm Hg) | |||
Average atmospheric perssure (mm Hg) | |||
Average meter pressure, absolute (mm Hg) | |||
Syringe temperature (°K) (see section 10.1.2.1) | |||
Syringe pressure, absolute (mm Hg) (see section 10.1.2.1) | |||
Volume of gas in syringe (ml) (Section 10.1.2.1) | |||
Density of liquid organic (g/ml) (Section 10.1.2.1) | |||
Volume of liquid in syringe (ml) (Section 10.1.2.1) | |||
GC Operating Conditions: | |||
Sample loop volume (ml) | |||
Sample loop temperature ( °C) | |||
Carrier gas flow rate (ml/min) | |||
Column temperature: | |||
Initial ( °C) | |||
Rate change ( °C/min) | |||
Final ( °C) | |||
Organic Peak Identification and Calculated Concentrations: | |||
Injection time (24 hour clock) | |||
Distance to peak (cm) | |||
Chart speed (cm/min) | |||
Organic retention time (min) | |||
Attenuation factor | |||
Peak height (mm) | |||
Peak area (mm2) | |||
Peak area * attenuation factor (mm2) | |||
Calculated concentration (ppm) (Equation 18-3 or 18-4) |
Plot peak area * attenuation factor against calculated concentration to obtain calibration curve.
Flowmeter
Reading (as marked) | Temp. (°K) | Pressure (absolute) |
---|---|---|
Calibration Device
Time (min) | Gas volume a | Flow rate b |
---|---|---|
a Vol. of gas may be measured in milliliters, liters or cubic feet.
b Convert to standard conditions (20 °C and 760 mm Hg). Plot flowmeter reading against flow rate (standard conditions), and draw a smooth curve. If the flowmeter being calibrated is a rotameter or other flow device that is viscosity dependent, it may be necessary to generate a “family” of calibration curves that cover the operating pressure and temperature ranges of the flowmeter. While the following technique should be verified before application, it may be possible to calculate flow rate reading for rotameters at standard conditions Qstd as follows:
Flow rate (laboratory conditions) | Flow rate (STD conditions) |
---|---|
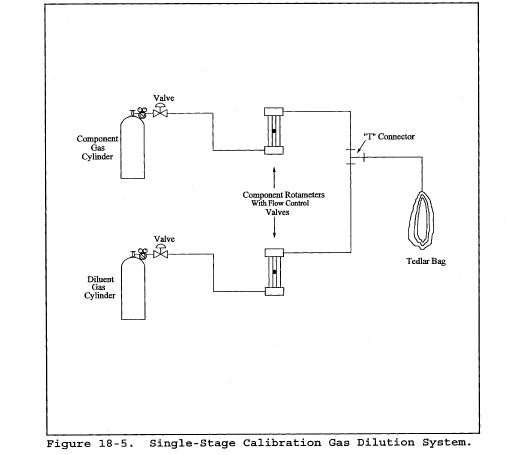
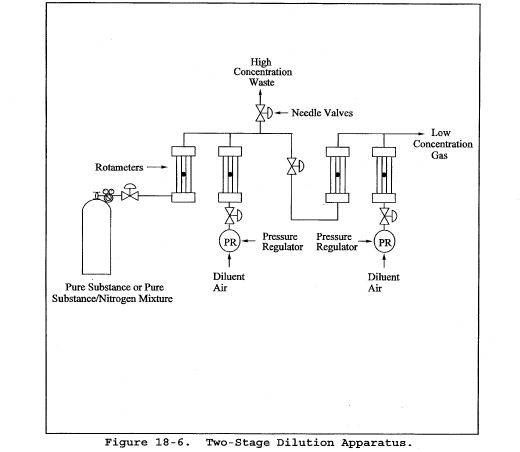
Preparation of Standards by Dilution of Cylinder Standard
[Cylinder Standard: Organic ____ Certified Concentration ____ ppm]
Standards preparation data: | Date: | ||
---|---|---|---|
Mixture 1 | Mixture 2 | Mixture 3 | |
Stage 1: | |||
Standard gas flowmeter reading | |||
Diluent gas flowmeter reading | |||
Laboratory temperature (°K) | |||
Barometric pressure (mm Hg) | |||
Flowmeter gage pressure (mm Hg) | |||
Flow rate cylinder gas at standard conditions (ml/min) | |||
Flow rate diluent gas at standard conditions (ml/min) | |||
Calculated concentration (ppm) | |||
Stage 2 (if used): | |||
Standard gas flowmeter reading | |||
Diluent gas flowmeter reading | |||
Flow rate Stage 1 gas at standard conditions (ml/min) | |||
Flow rate diluent gas at standard conditions | |||
Calculated concentration (ppm) | |||
GC Operating Conditions: | |||
Sample loop volume (ml) | |||
Sample loop temperature ( °C) | |||
Carrier gas flow rate (ml/min) | |||
Column temperature: | |||
Initial ( °C) | |||
Program rate ( °C/min) | |||
Final ( °C) | |||
Organic Peak Identification and Calculated Concentrations: | |||
Injection time (24-hour clock) | |||
Distance to peak (cm) | |||
Chart speed (cm/min) | |||
Retention time (min) | |||
Attenuation factor | |||
Peak area (mm 2) | |||
Peak area *attenuation factor |
Plot peak area *attenuation factor against calculated concentration to obtain calibration curve.
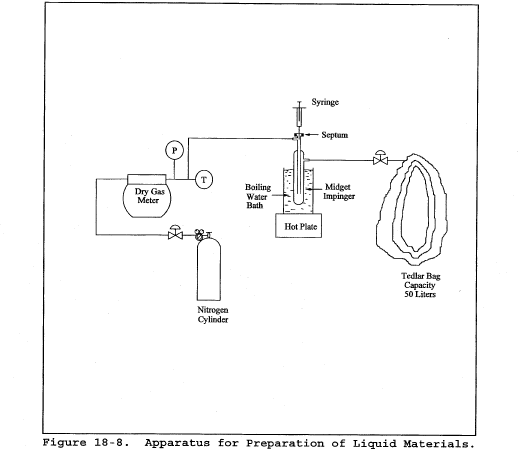
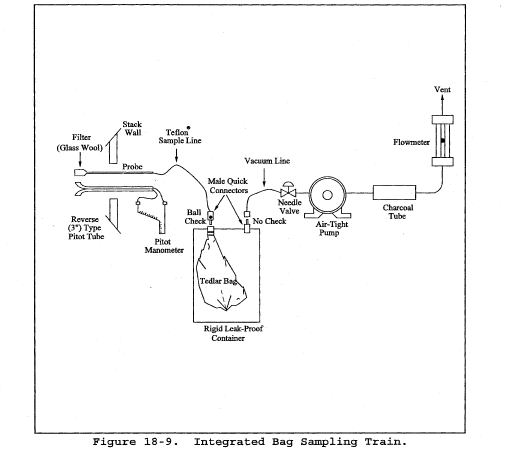
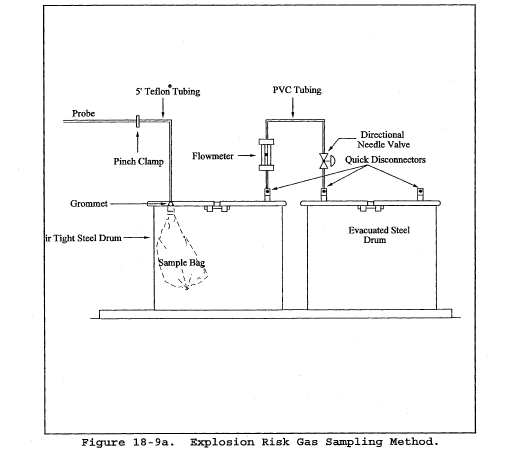
Plant____ Date____ Site____
Sample 1 | Sample 2 | Sample 3 | |
---|---|---|---|
Source temperature ( °C) | |||
Barometric pressure (mm Hg) | |||
Ambient temperature ( °C) | |||
Sample flow rate (appr.) | |||
Bag number | |||
Start time | |||
Finish time |
Plant _________ Date ________ Location ____________
1. General information: | |
Source temperature ( °C) | |
Probe temperature ( °C) | |
Ambient temperature ( °C) | |
Atmospheric pressure (mm) | |
Source pressure (′Hg) | |
Absolute source pressure (mm) | |
Sampling rate (liter/min) | |
Sample loop volume (ml) | |
Sample loop temperature ( °C) | |
Columnar temperature: | |
Initial ( °C) time (min) | |
Program rate ( °C/min) | |
Final ( °C)/time (min) | |
Carrier gas flow rate (ml/min) | |
Detector temperature ( °C) | |
Injection time (24-hour basis) | |
Chart Speed (mm/min) | |
Dilution gas flow rate (ml/min) | |
Dilution gas used (symbol) | |
Dilution ratio |
2. Field Analysis Data - Calibration Gas
2. [Run No. ____ Time ______]
Components | Area | Attenuation | A × A Factor | Conc._ (ppm) |
---|---|---|---|---|
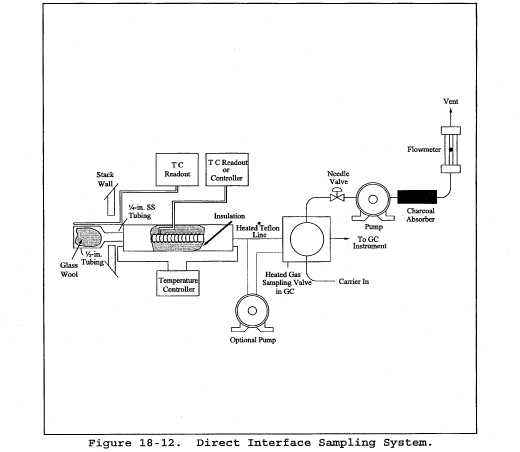
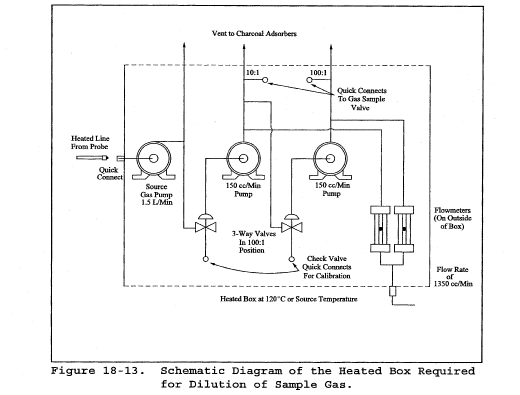
Gaseous Organic Sampling and Analysis Check List
[Respond with initials or number as appropriate]
Date | ||
---|---|---|
1. Presurvey data: | ||
A. Grab sample collected | □ | ___ |
B. Grab sample analyzed for composition | □ | ___ |
Method GC | □ | ___ |
GC/MS | □ | ___ |
Other | □ | ___ |
C. GC-FID analysis performed | □ | ___ |
2. Laboratory calibration data: | ||
A. Calibration curves prepared | □ | ___ |
Number of components | □ | ___ |
Number of concentrations/component (3 required) | □ | ___ |
B. Audit samples (optional): | ||
Analysis completed | □ | ___ |
Verified for concentration | □ | ___ |
OK obtained for field work | □ | ___ |
3. Sampling procedures: | ||
A. Method: | ||
Bag sample | □ | ___ |
Direct interface | □ | ___ |
Dilution interface | □ | ___ |
B. Number of samples collected | □ | ___ |
4. Field Analysis: | ||
A. Total hydrocarbon analysis performed | □ | ___ |
B. Calibration curve prepared | □ | ___ |
Number of components | □ | ___ |
Number of concentrations per component (3 required) | □ | ___ |
Gaseous Organic Sampling and Analysis Check List (Respond With Initials or Number as Appropriate)
1. Pre-survey data | Date |
A. Grab sample collected | ____ |
B. Grab sample analyzed for composition | ____ |
Method GC | ____ |
GC/MS | ____ |
Other____________ | ____ |
C. GC-FID analysis performed | ____ |
2. Laboratory calibration curves prepared | ____ |
A. Number of components | ____ |
B. Number of concentrations per component (3 required) | ____ |
C. OK obtained for field work | ____ |
3. Sampling procedures | |
A. Method | |
Bag sample | ____ |
Direct interface | ____ |
Dilution interface | ____ |
B. Number of samples collected | ____ |
4. Field Analysis | |
A. Total hydrocarbon analysis performed | ____ |
B. Calibration curve prepared | ____ |
Number of components | ____ |
Number of concentrations per component (3 required) | ____ |
Appendix A-7 to Part 60 - Test Methods 19 through 25E
40:9.0.1.1.1.0.1.1.7 : Appendix A
Appendix A-7 to Part 60 - Test Methods 19 through 25E Method 19 - Determination of sulfur dioxide removal efficiency and particulate, sulfur dioxide and nitrogen oxides emission rates Method 20 - Determination of nitrogen oxides, sulfur dioxide, and diluent emissions from stationary gas turbines Method 21 - Determination of volatile organic compound leaks Method 22 - Visual determination of fugitive emissions from material sources and smoke emissions from flares Method 23 - Determination of Polychlorinated Dibenzo-p-Dioxins and Polychlorinated Dibenzofurans From Stationary Sources Method 24 - Determination of volatile matter content, water content, density, volume solids, and weight solids of surface coatings Method 24A - Determination of volatile matter content and density of printing inks and related coatings Method 25 - Determination of total gaseous nonmethane organic emissions as carbon Method 25A - Determination of total gaseous organic concentration using a flame ionization analyzer Method 25B - Determination of total gaseous organic concentration using a nondispersive infrared analyzer Method 25C - Determination of nonmethane organic compounds (NMOC) in MSW landfill gases Method 25D - Determination of the Volatile Organic Concentration of Waste Samples Method 25E - Determination of Vapor Phase Organic Concentration in Waste SamplesThe test methods in this appendix are referred to in § 60.8 (Performance Tests) and § 60.11 (Compliance With Standards and Maintenance Requirements) of 40 CFR part 60, subpart A (General Provisions). Specific uses of these test methods are described in the standards of performance contained in the subparts, beginning with Subpart D.
Within each standard of performance, a section title “Test Methods and Procedures” is provided to: (1) Identify the test methods to be used as reference methods to the facility subject to the respective standard and (2) identify any special instructions or conditions to be followed when applying a method to the respective facility. Such instructions (for example, establish sampling rates, volumes, or temperatures) are to be used either in addition to, or as a substitute for procedures in a test method. Similarly, for sources subject to emission monitoring requirements, specific instructions pertaining to any use of a test method as a reference method are provided in the subpart or in Appendix B.
Inclusion of methods in this appendix is not intended as an endorsement or denial of their applicability to sources that are not subject to standards of performance. The methods are potentially applicable to other sources; however, applicability should be confirmed by careful and appropriate evaluation of the conditions prevalent at such sources.
The approach followed in the formulation of the test methods involves specifications for equipment, procedures, and performance. In concept, a performance specification approach would be preferable in all methods because this allows the greatest flexibility to the user. In practice, however, this approach is impractical in most cases because performance specifications cannot be established. Most of the methods described herein, therefore, involve specific equipment specifications and procedures, and only a few methods in this appendix rely on performance criteria.
Minor changes in the test methods should not necessarily affect the validity of the results and it is recognized that alternative and equivalent methods exist. section 60.8 provides authority for the Administrator to specify or approve (1) equivalent methods, (2) alternative methods, and (3) minor changes in the methodology of the test methods. It should be clearly understood that unless otherwise identified all such methods and changes must have prior approval of the Administrator. An owner employing such methods or deviations from the test methods without obtaining prior approval does so at the risk of subsequent disapproval and retesting with approved methods.
Within the test methods, certain specific equipment or procedures are recognized as being acceptable or potentially acceptable and are specifically identified in the methods. The items identified as acceptable options may be used without approval but must be identified in the test report. The potentially approvable options are cited as “subject to the approval of the Administrator” or as “or equivalent.” Such potentially approvable techniques or alternatives may be used at the discretion of the owner without prior approval. However, detailed descriptions for applying these potentially approvable techniques or alternatives are not provided in the test methods. Also, the potentially approvable options are not necessarily acceptable in all applications. Therefore, an owner electing to use such potentially approvable techniques or alternatives is responsible for: (1) assuring that the techniques or alternatives are in fact applicable and are properly executed; (2) including a written description of the alternative method in the test report (the written method must be clear and must be capable of being performed without additional instruction, and the degree of detail should be similar to the detail contained in the test methods); and (3) providing any rationale or supporting data necessary to show the validity of the alternative in the particular application. Failure to meet these requirements can result in the Administrator's disapproval of the alternative.
Method 19 - Determination of Sulfur Dioxide Removal Efficiency and Particulate Matter, Sulfur Dioxide, and Nitrogen Oxide Emission Rates 1.0 Scope and Application1.1 Analytes. This method provides data reduction procedures relating to the following pollutants, but does not include any sample collection or analysis procedures.
Analyte | CAS No. | Sensitivity |
---|---|---|
Nitrogen oxides (NOX), including: | ||
Nitric oxide (NO) | 10102-43-9 | N/A |
Nitrogen dioxide (NO2) | 10102-44-0 | |
Particulate matter (PM) | None assigned | N/A |
Sulfur dioxide (SO2) | 7499-09-05 | N/A |
1.2 Applicability. Where specified by an applicable subpart of the regulations, this method is applicable for the determination of (a) PM, SO2, and NOX emission rates; (b) sulfur removal efficiencies of fuel pretreatment and SO2 control devices; and (c) overall reduction of potential SO2 emissions.
2.0 Summary of Method2.1 Emission Rates. Oxygen (O2) or carbon dioxide (CO2) concentrations and appropriate F factors (ratios of combustion gas volumes to heat inputs) are used to calculate pollutant emission rates from pollutant concentrations.
2.2 Sulfur Reduction Efficiency and SO2 Removal Efficiency. An overall SO2 emission reduction efficiency is computed from the efficiency of fuel pretreatment systems, where applicable, and the efficiency of SO2 control devices.
2.2.1 The sulfur removal efficiency of a fuel pretreatment system is determined by fuel sampling and analysis of the sulfur and heat contents of the fuel before and after the pretreatment system.
2.2.2 The SO2 removal efficiency of a control device is determined by measuring the SO2 rates before and after the control device.
2.2.2.1 The inlet rates to SO2 control systems (or, when SO2 control systems are not used, SO2 emission rates to the atmosphere) are determined by fuel sampling and analysis.
3.0 Definitions [Reserved] 4.0 Interferences [Reserved] 5.0 Safety [Reserved] 6.0 Equipment and Supplies [Reserved] 7.0 Reagents and Standards [Reserved] 8.0 Sample Collection, Preservation, Storage, and Transport [Reserved] 9.0 Quality Control [Reserved] 10.0 Calibration and Standardization [Reserved] 11.0 Analytical Procedures [Reserved] 12.0 Data Analysis and Calculations12.1 Nomenclature
Bwa = Moisture fraction of ambient air, percent. Bws = Moisture fraction of effluent gas, percent. %C = Concentration of carbon from an ultimate analysis of fuel, weight percent. Cd = Pollutant concentration, dry basis, ng/scm (lb/scf) %CO2d,%CO2w = Concentration of carbon dioxide on a dry and wet basis, respectively, percent. Cw = Pollutant concentration, wet basis, ng/scm (lb/scf). D = Number of sampling periods during the performance test period. E = Pollutant emission rate, ng/J (lb/million Btu). Ea = Average pollutant rate for the specified performance test period, ng/J (lb/million Btu). Eao, Eai = Average pollutant rate of the control device, outlet and inlet, respectively, for the performance test period, ng/J (lb/million Btu). Ebi = Pollutant rate from the steam generating unit, ng/J (lb/million Btu) Ebo = Pollutant emission rate from the steam generating unit, ng/J (lb/million Btu). Eci = Pollutant rate in combined effluent, ng/J (lb/million Btu). Eco = Pollutant emission rate in combined effluent, ng/J (lb/million Btu). Ed = Average pollutant rate for each sampling period (e.g., 24-hr Method 6B sample or 24-hr fuel sample) or for each fuel lot (e.g., amount of fuel bunkered), ng/J (lb/million Btu). Edi = Average inlet SO2 rate for each sampling period d, ng/J (lb/million Btu) Eg = Pollutant rate from gas turbine, ng/J (lb/million Btu). Ega = Daily geometric average pollutant rate, ng/J (lbs/million Btu) or ppm corrected to 7 percent O2. Ejo,Eji = Matched pair hourly arithmetic average pollutant rate, outlet and inlet, respectively, ng/J (lb/million Btu) or ppm corrected to 7 percent O2. Eh = Hourly average pollutant, ng/J (lb/million Btu). Ehj = Hourly arithmetic average pollutant rate for hour “j,” ng/J (lb/million Btu) or ppm corrected to 7 percent O2. EXP = Natural logarithmic base (2.718) raised to the value enclosed by brackets. Fd, Fw, Fc = Volumes of combustion components per unit of heat content, scm/J (scf/million Btu). GCV = Gross calorific value of the fuel consistent with the ultimate analysis, kJ/kg (Btu/lb). GCVp, GCVr = Gross calorific value for the product and raw fuel lots, respectively, dry basis, kJ/kg (Btu/lb). %H = Concentration of hydrogen from an ultimate analysis of fuel, weight percent. H = Total number of operating hours for which pollutant rates are determined in the performance test period. Hb = Heat input rate to the steam generating unit from fuels fired in the steam generating unit, J/hr (million Btu/hr). Hg = Heat input rate to gas turbine from all fuels fired in the gas turbine, J/hr (million Btu/hr). %H2O = Concentration of water from an ultimate analysis of fuel, weight percent. Hr = Total numbers of hours in the performance test period (e.g., 720 hours for 30-day performance test period). K = Conversion factor, 10−5 (kJ/J)/(%) [106 Btu/million Btu]. Kc = (9.57 scm/kg)/% [(1.53 scf/lb)/%]. Kcc = (2.0 scm/kg)/% [(0.321 scf/lb)/%]. Khd = (22.7 scm/kg)/% [(3.64 scf/lb)/%]. Khw = (34.74 scm/kg)/% [(5.57 scf/lb)/%]. Kn = (0.86 scm/kg)/% [(0.14 scf/lb)/%]. Ko = (2.85 scm/kg)/% [(0.46 scf/lb)/%]. Ks = (3.54 scm/kg)/% [(0.57 scf/lb)/%]. Kw = (1.30 scm/kg)/% [(0.21 scf/lb)/%]. ln = Natural log of indicated value. Lp,Lr = Weight of the product and raw fuel lots, respectively, metric ton (ton). %N = Concentration of nitrogen from an ultimate analysis of fuel, weight percent. N = Number of fuel lots during the averaging period. n = Number of fuels being burned in combination. nd = Number of operating hours of the affected facility within the performance test period for each Ed determined. nt = Total number of hourly averages for which paired inlet and outlet pollutant rates are available within the 24-hr midnight to midnight daily period. %O = Concentration of oxygen from an ultimate analysis of fuel, weight percent. %O2d, %O2w = Concentration of oxygen on a dry and wet basis, respectively, percent. Ps = Potential SO2 emissions, percent. %Rf = SO2 removal efficiency from fuel pretreatment, percent. %Rg = SO2 removal efficiency of the control device, percent. %Rga = Daily geometric average percent reduction. %Ro = Overall SO2 reduction, percent. %S = Sulfur content of as-fired fuel lot, dry basis, weight percent. Se = Standard deviation of the hourly average pollutant rates for each performance test period, ng/J (lb/million Btu). %Sf = Concentration of sulfur from an ultimate analysis of fuel, weight percent. Si = Standard deviation of the hourly average inlet pollutant rates for each performance test period, ng/J (lb/million Btu). So = Standard deviation of the hourly average emission rates for each performance test period, ng/J (lb/million Btu). %Sp, %Sr = Sulfur content of the product and raw fuel lots respectively, dry basis, weight percent. t0.95 = Values shown in Table 19-3 for the indicated number of data points n. Xk = Fraction of total heat input from each type of fuel k.12.2 Emission Rates of PM, SO2, and NOX. Select from the following sections the applicable procedure to compute the PM, SO2, or NOX emission rate (E) in ng/J (lb/million Btu). The pollutant concentration must be in ng/scm (lb/scf) and the F factor must be in scm/J (scf/million Btu). If the pollutant concentration (C) is not in the appropriate units, use Table 19-1 in section 17.0 to make the proper conversion. An F factor is the ratio of the gas volume of the products of combustion to the heat content of the fuel. The dry F factor (Fd) includes all components of combustion less water, the wet F factor (Fw) includes all components of combustion, and the carbon F factor (Fc) includes only carbon dioxide.
Note:Since Fw factors include water resulting only from the combustion of hydrogen in the fuel, the procedures using Fw factors are not applicable for computing E from steam generating units with wet scrubbers or with other processes that add water (e.g., steam injection).
12.2.1 Oxygen-Based F Factor, Dry Basis. When measurements are on a dry basis for both O (%O2d) and pollutant (Cd) concentrations, use the following equation:
12.2.2 Oxygen-Based F Factor, Wet Basis. When measurements are on a wet basis for both O2 (%O2w) and pollutant (Cw) concentrations, use either of the following:
12.2.2.1 If the moisture fraction of ambient air (Bwa) is measured:
Instead of actual measurement, Bwa may be estimated according to the procedure below.
Note:The estimates are selected to ensure that negative errors will not be larger than −1.5 percent. However, positive errors, or over-estimation of emissions by as much as 5 percent may be introduced depending upon the geographic location of the facility and the associated range of ambient moisture.
12.2.2.1.1 Bwa = 0.027. This value may be used at any location at all times.
12.2.2.1.2 Bwa = Highest monthly average of Bwa that occurred within the previous calendar year at the nearest Weather Service Station. This value shall be determined annually and may be used as an estimate for the entire current calendar year.
12.2.2.1.3 Bwa = Highest daily average of Bwa that occurred within a calendar month at the nearest Weather Service Station, calculated from the data from the past 3 years. This value shall be computed for each month and may be used as an estimate for the current respective calendar month.
12.2.2.2 If the moisture fraction (Bws) of the effluent gas is measured:
12.2.3 Oxygen-Based F Factor, Dry/Wet Basis.
12.2.3.1 When the pollutant concentration is measured on a wet basis (Cw) and O2 concentration is measured on a dry basis (%O2d), use the following equation:
12.2.3.2 When the pollutant concentration is measured on a dry basis (Cd) and the O2 concentration is measured on a wet basis (%O2w), use the following equation:
12.2.4 Carbon Dioxide-Based F Factor, Dry Basis. When measurements are on a dry basis for both CO2 (%CO2d) and pollutant (Cd) concentrations, use the following equation:
12.2.5 Carbon Dioxide-Based F Factor, Wet Basis. When measurements are on a wet basis for both CO2 (%CO2w) and pollutant (Cw) concentrations, use the following equation:
12.2.6 Carbon Dioxide-Based F Factor, Dry/Wet Basis.
12.2.6.1 When the pollutant concentration is measured on a wet basis (Cw) and CO2 concentration is measured on a dry basis (%CO2d), use the following equation:
12.2.6.2 When the pollutant concentration is measured on a dry basis (Cd) and CO2 concentration is measured on a wet basis (%CO2w), use the following equation:
12.2.7 Direct-Fired Reheat Fuel Burning. The effect of direct-fired reheat fuel burning (for the purpose of raising the temperature of the exhaust effluent from wet scrubbers to above the moisture dew-point) on emission rates will be less than 1.0 percent and, therefore, may be ignored.
12.2.8 Combined Cycle-Gas Turbine Systems. For gas turbine-steam generator combined cycle systems, determine the emissions from the steam generating unit or the percent reduction in potential SO2 emissions as follows:
12.2.8.1 Compute the emission rate from the steam generating unit using the following equation:
12.2.8.1.1 Use the test methods and procedures section of 40 CFR Part 60, Subpart GG to obtain Eco and Eg. Do not use Fw factors for determining Eg or Eco. If an SO2 control device is used, measure Eco after the control device.
12.2.8.1.2 Suitable methods shall be used to determine the heat input rates to the steam generating units (Hb) and the gas turbine (Hg).
12.2.8.2 If a control device is used, compute the percent of potential SO2 emissions (Ps) using the following equations:
Note:Use the test methods and procedures section of Subpart GG to obtain Eci and Eg. Do not use Fw factors for determining Eg or Eci.
12.3 F Factors. Use an average F factor according to section 12.3.1 or determine an applicable F factor according to section 12.3.2. If combined fuels are fired, prorate the applicable F factors using the procedure in section 12.3.3.
12.3.1 Average F Factors. Average F factors (Fd, Fw, or Fc) from Table 19-2 in section 17.0 may be used.
12.3.2 Determined F Factors. If the fuel burned is not listed in Table 19-2 or if the owner or operator chooses to determine an F factor rather than use the values in Table 19-2, use the procedure below:
12.3.2.1 Equations. Use the equations below, as appropriate, to compute the F factors:
Note:Omit the %H2O term in the equations for Fw if %H and %O include the unavailable hydrogen and oxygen in the form of H2O.)
12.3.2.2 Use applicable sampling procedures in section 12.5.2.1 or 12.5.2.2 to obtain samples for analyses.
12.3.2.3 Use ASTM D 3176-74 or 89 (all cited ASTM standards are incorporated by reference - see § 60.17) for ultimate analysis of the fuel.
12.3.2.4 Use applicable methods in section 12.5.2.1 or 12.5.2.2 to determine the heat content of solid or liquid fuels. For gaseous fuels, use ASTM D 1826-77 or 94 (incorporated by reference - see § 60.17) to determine the heat content.
12.3.3 F Factors for Combination of Fuels. If combinations of fuels are burned, use the following equations, as applicable unless otherwise specified in an applicable subpart:
12.4 Determination of Average Pollutant Rates.
12.4.1 Average Pollutant Rates from Hourly Values. When hourly average pollutant rates (Eh), inlet or outlet, are obtained (e.g., CEMS values), compute the average pollutant rate (Ea) for the performance test period (e.g., 30 days) specified in the applicable regulation using the following equation:
12.4.2 Average Pollutant Rates from Other than Hourly Averages. When pollutant rates are determined from measured values representing longer than 1-hour periods (e.g., daily fuel sampling and analyses or Method 6B values), or when pollutant rates are determined from combinations of 1-hour and longer than 1-hour periods (e.g., CEMS and Method 6B values), compute the average pollutant rate (Ea) for the performance test period (e.g., 30 days) specified in the applicable regulation using the following equation:
12.4.3 Daily Geometric Average Pollutant Rates from Hourly Values. The geometric average pollutant rate (Ega) is computed using the following equation:
12.5 Determination of Overall Reduction in Potential Sulfur Dioxide Emission.
12.5.1 Overall Percent Reduction. Compute the overall percent SO2 reduction (%Ro) using the following equation:
12.5.2 Pretreatment Removal Efficiency (Optional). Compute the SO2 removal efficiency from fuel pretreatment (%Rf) for the averaging period (e.g., 90 days) as specified in the applicable regulation using the following equation:
Note:In calculating %Rf, include %S and GCV values for all fuel lots that are not pretreated and are used during the averaging period.
12.5.2.1 Solid Fossil (Including Waste) Fuel/Sampling and Analysis.
Note:For the purposes of this method, raw fuel (coal or oil) is the fuel delivered to the desulfurization (pretreatment) facility. For oil, the input oil to the oil desulfurization process (e.g., hydrotreatment) is considered to be the raw fuel.
12.5.2.1.1 Sample Increment Collection. Use ASTM D 2234-76, 96, 97a, or 98 (incorporated by reference - see § 60.17), Type I, Conditions A, B, or C, and systematic spacing. As used in this method, systematic spacing is intended to include evenly spaced increments in time or increments based on equal weights of coal passing the collection area. As a minimum, determine the number and weight of increments required per gross sample representing each coal lot according to Table 2 or Paragraph 7.1.5.2 of ASTM D 2234. Collect one gross sample for each lot of raw coal and one gross sample for each lot of product coal.
12.5.2.1.2 ASTM Lot Size. For the purpose of section 12.5.2 (fuel pretreatment), the lot size of product coal is the weight of product coal from one type of raw coal. The lot size of raw coal is the weight of raw coal used to produce one lot of product coal. Typically, the lot size is the weight of coal processed in a 1-day (24-hour) period. If more than one type of coal is treated and produced in 1 day, then gross samples must be collected and analyzed for each type of coal. A coal lot size equaling the 90-day quarterly fuel quantity for a steam generating unit may be used if representative sampling can be conducted for each raw coal and product coal.
Note:Alternative definitions of lot sizes may be used, subject to prior approval of the Administrator.
12.5.2.1.3 Gross Sample Analysis. Use ASTM D 2013-72 or 86 to prepare the sample, ASTM D 3177-75 or 89 or ASTM D 4239-85, 94, or 97 to determine sulfur content (%S), ASTM D 3173-73 or 87 to determine moisture content, and ASTM D 2015-77 (Reapproved 1978) or 96, D 3286-85 or 96, or D 5865-98 or 10 to determine gross calorific value (GCV) (all standards cited are incorporated by reference - see § 60.17 for acceptable versions of the standards) on a dry basis for each gross sample.
12.5.2.2 Liquid Fossil Fuel-Sampling and Analysis. See Note under section 12.5.2.1.
12.5.2.2.1 Sample Collection. Follow the procedures for continuous sampling in ASTM D 270 or D 4177-95 (incorporated by reference - see § 60.17) for each gross sample from each fuel lot.
12.5.2.2.2 Lot Size. For the purpose of section 12.5.2 (fuel pretreatment), the lot size of a product oil is the weight of product oil from one pretreatment facility and intended as one shipment (ship load, barge load, etc.). The lot size of raw oil is the weight of each crude liquid fuel type used to produce a lot of product oil.
Note:Alternative definitions of lot sizes may be used, subject to prior approval of the Administrator.
12.5.2.2.3 Sample Analysis. Use ASTM D 129-64, 78, or 95, ASTM D 1552-83 or 95, or ASTM D 4057-81 or 95 to determine the sulfur content (%S) and ASTM D 240-76 or 92 (all standards cited are incorporated by reference - see § 60.17) to determine the GCV of each gross sample. These values may be assumed to be on a dry basis. The owner or operator of an affected facility may elect to determine the GCV by sampling the oil combusted on the first steam generating unit operating day of each calendar month and then using the lowest GCV value of the three GCV values per quarter for the GCV of all oil combusted in that calendar quarter.
12.5.2.3 Use appropriate procedures, subject to the approval of the Administrator, to determine the fraction of total mass input derived from each type of fuel.
12.5.3 Control Device Removal Efficiency. Compute the percent removal efficiency (%Rg) of the control device using the following equation:
12.5.3.1 Use continuous emission monitoring systems or test methods, as appropriate, to determine the outlet SO2 rates and, if appropriate, the inlet SO2 rates. The rates may be determined as hourly (Eh) or other sampling period averages (Ed). Then, compute the average pollutant rates for the performance test period (Eao and Eai) using the procedures in section 12.4.
12.5.3.2 As an alternative, as-fired fuel sampling and analysis may be used to determine inlet SO2 rates as follows:
12.5.3.2.1 Compute the average inlet SO2 rate (Edi) for each sampling period using the following equation:
Where: After calculating Edi, use the procedures in section 12.4 to determine the average inlet SO2 rate for the performance test period (Eai).12.5.3.2.2 Collect the fuel samples from a location in the fuel handling system that provides a sample representative of the fuel bunkered or consumed during a steam generating unit operating day. For the purpose of as-fired fuel sampling under section 12.5.3.2 or section 12.6, the lot size for coal is the weight of coal bunkered or consumed during each steam generating unit operating day. The lot size for oil is the weight of oil supplied to the “day” tank or consumed during each steam generating unit operating day. For reporting and calculation purposes, the gross sample shall be identified with the calendar day on which sampling began. For steam generating unit operating days when a coal-fired steam generating unit is operated without coal being added to the bunkers, the coal analysis from the previous “as bunkered” coal sample shall be used until coal is bunkered again. For steam generating unit operating days when an oil-fired steam generating unit is operated without oil being added to the oil “day” tank, the oil analysis from the previous day shall be used until the “day” tank is filled again. Alternative definitions of fuel lot size may be used, subject to prior approval of the Administrator.
12.5.3.2.3 Use ASTM procedures specified in section 12.5.2.1 or 12.5.2.2 to determine %S and GCV.
12.5.4 Daily Geometric Average Percent Reduction from Hourly Values. The geometric average percent reduction (%Rga) is computed using the following equation:
Note:The calculation includes only paired data sets (hourly average) for the inlet and outlet pollutant measurements.
12.6 Sulfur Retention Credit for Compliance Fuel. If fuel sampling and analysis procedures in section 12.5.2.1 are being used to determine average SO2 emission rates (Eas) to the atmosphere from a coal-fired steam generating unit when there is no SO2 control device, the following equation may be used to adjust the emission rate for sulfur retention credits (no credits are allowed for oil-fired systems) (Edi) for each sampling period using the following equation:
Where:After calculating Edi, use the procedures in section 12.4.2 to determine the average SO2 emission rate to the atmosphere for the performance test period (Eao).
12.7 Determination of Compliance When Minimum Data Requirement Is Not Met.
12.7.1 Adjusted Emission Rates and Control Device Removal Efficiency. When the minimum data requirement is not met, the Administrator may use the following adjusted emission rates or control device removal efficiencies to determine compliance with the applicable standards.
12.7.1.1 Emission Rate. Compliance with the emission rate standard may be determined by using the lower confidence limit of the emission rate (Eao*) as follows:
12.7.1.2 Control Device Removal Efficiency. Compliance with the overall emission reduction (%Ro) may be determined by using the lower confidence limit of the emission rate (Eao*) and the upper confidence limit of the inlet pollutant rate (Eai*) in calculating the control device removal efficiency (%Rg) as follows:
12.7.2 Standard Deviation of Hourly Average Pollutant Rates. Compute the standard deviation (Se) of the hourly average pollutant rates using the following equation:
Equation 19-19 through 19-31 may be used to compute the standard deviation for both the outlet (So) and, if applicable, inlet (Si) pollutant rates.
13.0 Method Performance [Reserved] 14.0 Pollution Prevention [Reserved] 15.0 Waste Management [Reserved] 16.0 References [Reserved] 17.0 Tables, Diagrams, Flowcharts, and Validation DataTable 19-1 - Conversion Factors for Concentration
From | To | Multiply by |
---|---|---|
g/scm | ng/scm | 10 9 |
mg/scm | ng/scm | 10 6 |
lb/scf | ng/scm | 1.602 × 10 13 |
ppm SO2 | ng/scm | 2.66 × 10 6 |
ppm NOX | ng/scm | 1.912 × 10 6 |
ppm SO2 | lb/scf | 1.660 × 10−7 |
ppm NOX | lb/scf | 1.194 × 10−7 |
Table 19-2 - F Factors for Various Fuels 1
Fuel Type | Fd | Fw | Fc | |||
---|---|---|---|---|---|---|
dscm/J | dscf/10 6 Btu | wscm/J | wscf/10 6 Btu | scm/J | scf/10 6 Btu | |
Coal: | ||||||
Anthracite 2 | 2.71 × 10−7 | 10,100 | 2.83 × 10−7 | 10,540 | 0.530 × 10−7 | 1,970 |
Bituminus 2 | 2.63 × 10−7 | 9,780 | 2.86 × 10−7 | 10,640 | 0.484 × 10−7 | 1,800 |
Lignite | 2.65 × 10−7 | 9,860 | 3.21 × 10−7 | 11,950 | 0.513 × 10−7 | 1,910 |
Oil 3 | 2.47 × 10−7 | 9,190 | 2.77 × 10−7 | 10,320 | 0.383 × 10−7 | 1,420 |
Gas: | ||||||
Natural | 2.34 × 10−7 | 8,710 | 2.85 × 10−7 | 10,610 | 0.287 × 10−7 | 1,040 |
Propane | 2.34 × 10−7 | 8,710 | 2.74 × 10−7 | 10,200 | 0.321 × 10−7 | 1,190 |
Butane | 2.34 × 10−7 | 8,710 | 2.79 × 10−7 | 10,390 | 0.337 × 10−7 | 1,250 |
Wood | 2.48 × 10−7 | 9,240 | 0.492 × 10−7 | 1,830 | ||
Wood Bark | 2.58 × 10−7 | 9,600 | 0.516 × 10−7 | 1,920 | ||
Municipal | 2.57 × 10−7 | 9,570 | 0.488 × 10−7 | 1,820 | ||
Solid Waste |
1 Determined at standard conditions: 20 °C (68 °F) and 760 mm Hg (29.92 in Hg)
2 As classified according to ASTM D 388.
3 Crude, residual, or distillate.
Table 19-3 - Values for T0.95*
n 1 | t0.95 | n 1 | t0.95 | n 1 | t0.95 |
---|---|---|---|---|---|
2 | 6.31 | 8 | 1.89 | 22-26 | 1.71 |
3 | 2.42 | 9 | 1.86 | 27-31 | 1.70 |
4 | 2.35 | 10 | 1.83 | 32-51 | 1.68 |
5 | 2.13 | 11 | 1.81 | 52-91 | 1.67 |
6 | 2.02 | 12-16 | 1.77 | 92-151 | 1.66 |
7 | 1.94 | 17-21 | 1.73 | 152 or more | 1.65 |
1The values of this table are corrected for n-1 degrees of freedom. Use n equal to the number (H) of hourly average data points.
Method 20 contains the details you must follow when using an instrumental analyzer to determine concentrations of nitrogen oxides, oxygen, carbon dioxide, and sulfur dioxide in the emissions from stationary gas turbines. This method follows the specific instructions for equipment and performance requirements, supplies, sample collection and analysis, calculations, and data analysis in the methods listed in section 2.0.
1.1 Analytes. What does this method determine?
Analyte | CAS No. | Sensitivity |
---|---|---|
Nitrogen oxides (NOX) as nitrogen dioxide: | 10102-43-9 | Typically <2% of Calibration Span. |
Nitric oxide (NO) | 10102-44-0 | |
Nitrogen dioxide NO2 | ||
Diluent oxygen (O2) or carbon dioxide (CO2) | Typically <2% of Calibration Span. | |
Sulfur dioxide (SOX) | 7446-09-5 | Typically <2% of Calibration Span. |
1.2 Applicability. When is this method required? The use of Method 20 may be required by specific New Source Performance Standards, Clean Air Marketing rules, and State Implementation Plans and permits where measuring SO2, NOX, CO2, and/or O2 concentrations in stationary gas turbines emissions are required. Other regulations may also require its use.
1.3 Data Quality Objectives. How good must my collected data be? Refer to section 1.3 of Method 7E.
2.0 Summary of MethodIn this method, NOX, O2 (or CO2), and SOX are measured using the following methods found in appendix A to this part:
(a) Method 1 - Sample and Velocity Traverses for Stationary Sources.
(b) Method 3A - Determination of Oxygen and Carbon Dioxide Emissions From Stationary Sources (Instrumental Analyzer Procedure).
(c) Method 6C - Determination of Sulfur Dioxide Emissions From Stationary Sources (Instrumental Analyzer Procedure).
(d) Method 7E - Determination of Nitrogen Oxides Emissions From Stationary Sources (Instrumental Analyzer Procedure).
(e) Method 19 - Determination of Sulfur Dioxide Removal Efficiency and Particulate Matter, Sulfur Dioxide, and Nitrogen Oxide Emission Rates.
3.0 DefinitionsRefer to section 3.0 of Method 7E for the applicable definitions.
4.0 InterferencesRefer to section 4.0 of Methods 3A, 6C, and 7E as applicable.
5.0 SafetyRefer to section 5.0 of Method 7E.
6.0 Equipment and SuppliesThe measurement system design is shown in Figure 7E-1 of Method 7E. Refer to the appropriate methods listed in section 2.0 for equipment and supplies.
7.0 Reagents and StandardsRefer to the appropriate methods listed in section 2.0 for reagents and standards.
8.0 Sample Collection, Preservation, Storage, and Transport8.1 Sampling Site and Sampling Points. Follow the procedures of section 8.1 of Method 7E. For the stratification test in section 8.1.2, determine the diluent-corrected pollutant concentration at each traverse point.
8.2 Initial Measurement System Performance Tests. You must refer to the appropriate methods listed in section 2.0 for the measurement system performance tests as applicable.
8.3 Interference Check. You must follow the procedures in section 8.3 of Method 3A or 6C, or section 8.2.7 of Method 7E (as appropriate).
8.4 Sample Collection. You must follow the procedures of section 8.4 of the appropriate methods listed in section 2.0. A test run must have a duration of at least 21 minutes.
8.5 Post-Run System Bias Check, Drift Assessment, and Alternative Dynamic Spike Procedure. You must follow the procedures of sections 8.5 and 8.6 of the appropriate methods listed in section 2.0. A test run must have a duration of at least 21 minutes.
9.0 Quality ControlFollow quality control procedures in section 9.0 of Method 7E.
10.0 Calibration and StandardizationFollow the procedures for calibration and standardization in section 10.0 of Method 7E.
11.0 Analytical ProceduresBecause sample collection and analysis are performed together (see section 8), additional discussion of the analytical procedure is not necessary.
12.0 Calculations and Data AnalysisYou must follow the procedures for calculations and data analysis in section 12.0 of the appropriate method listed in section 2.0. Follow the procedures in section 12.0 of Method 19 for calculating fuel-specific F factors, diluent-corrected pollutant concentrations, and emission rates.
13.0 Method PerformanceThe specifications for the applicable performance checks are the same as in section 13.0 of Method 7E.
14.0 Pollution Prevention [Reserved] 15.0 Waste Management [Reserved] 16.0 Alternative ProceduresRefer to section 16.0 of the appropriate method listed in section 2.0 for alternative procedures.
17.0 ReferencesRefer to section 17.0 of the appropriate method listed in section 2.0 for references.
18.0 Tables, Diagrams, Flowcharts, and Validation DataRefer to section 18.0 of the appropriate method listed in section 2.0 for tables, diagrams, flowcharts, and validation data.
Method 21 - Determination of Volatile Organic Compound Leaks 1.0 Scope and Application1.1 Analytes.
Analyte | CAS No. |
---|---|
Volatile Organic Compounds (VOC) | No CAS number assigned. |
1.2 Scope. This method is applicable for the determination of VOC leaks from process equipment. These sources include, but are not limited to, valves, flanges and other connections, pumps and compressors, pressure relief devices, process drains, open-ended valves, pump and compressor seal system degassing vents, accumulator vessel vents, agitator seals, and access door seals.
1.3 Data Quality Objectives. Adherence to the requirements of this method will enhance the quality of the data obtained from air pollutant sampling methods.
2.0 Summary of Method2.1 A portable instrument is used to detect VOC leaks from individual sources. The instrument detector type is not specified, but it must meet the specifications and performance criteria contained in section 6.0. A leak definition concentration based on a reference compound is specified in each applicable regulation. This method is intended to locate and classify leaks only, and is not to be used as a direct measure of mass emission rate from individual sources.
3.0 Definitions3.1 Calibration gas means the VOC compound used to adjust the instrument meter reading to a known value. The calibration gas is usually the reference compound at a known concentration approximately equal to the leak definition concentration.
3.2 Calibration precision means the degree of agreement between measurements of the same known value, expressed as the relative percentage of the average difference between the meter readings and the known concentration to the known concentration.
3.3 Leak definition concentration means the local VOC concentration at the surface of a leak source that indicates that a VOC emission (leak) is present. The leak definition is an instrument meter reading based on a reference compound.
3.4 No detectable emission means a local VOC concentration at the surface of a leak source, adjusted for local VOC ambient concentration, that is less than 2.5 percent of the specified leak definition concentration. that indicates that a VOC emission (leak) is not present.
3.5 Reference compound means the VOC species selected as the instrument calibration basis for specification of the leak definition concentration. (For example, if a leak definition concentration is 10,000 ppm as methane, then any source emission that results in a local concentration that yields a meter reading of 10,000 on an instrument meter calibrated with methane would be classified as a leak. In this example, the leak definition concentration is 10,000 ppm and the reference compound is methane.)
3.6 Response factor means the ratio of the known concentration of a VOC compound to the observed meter reading when measured using an instrument calibrated with the reference compound specified in the applicable regulation.
3.7 Response time means the time interval from a step change in VOC concentration at the input of the sampling system to the time at which 90 percent of the corresponding final value is reached as displayed on the instrument readout meter.
4.0 Interferences [Reserved] 5.0 Safety5.1 Disclaimer. This method may involve hazardous materials, operations, and equipment. This test method may not address all of the safety problems associated with its use. It is the responsibility of the user of this test method to establish appropriate safety and health practices and determine the applicability of regulatory limitations prior to performing this test method.
5.2 Hazardous Pollutants. Several of the compounds, leaks of which may be determined by this method, may be irritating or corrosive to tissues (e.g., heptane) or may be toxic (e.g., benzene, methyl alcohol). Nearly all are fire hazards. Compounds in emissions should be determined through familiarity with the source. Appropriate precautions can be found in reference documents, such as reference No. 4 in section 16.0.
6.0 Equipment and SuppliesA VOC monitoring instrument meeting the following specifications is required:
6.1 The VOC instrument detector shall respond to the compounds being processed. Detector types that may meet this requirement include, but are not limited to, catalytic oxidation, flame ionization, infrared absorption, and photoionization.
6.2 The instrument shall be capable of measuring the leak definition concentration specified in the regulation.
6.3 The scale of the instrument meter shall be readable to ±2.5 percent of the specified leak definition concentration.
6.4 The instrument shall be equipped with an electrically driven pump to ensure that a sample is provided to the detector at a constant flow rate. The nominal sample flow rate, as measured at the sample probe tip, shall be 0.10 to 3.0 l/min (0.004 to 0.1 ft 3/min) when the probe is fitted with a glass wool plug or filter that may be used to prevent plugging of the instrument.
6.5 The instrument shall be equipped with a probe or probe extension or sampling not to exceed 6.4 mm ( 1/4 in) in outside diameter, with a single end opening for admission of sample.
6.6 The instrument shall be intrinsically safe for operation in explosive atmospheres as defined by the National Electrical Code by the National Fire Prevention Association or other applicable regulatory code for operation in any explosive atmospheres that may be encountered in its use. The instrument shall, at a minimum, be intrinsically safe for Class 1, Division 1 conditions, and/or Class 2, Division 1 conditions, as appropriate, as defined by the example code. The instrument shall not be operated with any safety device, such as an exhaust flame arrestor, removed.
7.0 Reagents and Standards7.1 Two gas mixtures are required for instrument calibration and performance evaluation:
7.1.1 Zero Gas. Air, less than 10 parts per million by volume (ppmv) VOC.
7.1.2 Calibration Gas. For each organic species that is to be measured during individual source surveys, obtain or prepare a known standard in air at a concentration approximately equal to the applicable leak definition specified in the regulation.
7.2 Cylinder Gases. If cylinder calibration gas mixtures are used, they must be analyzed and certified by the manufacturer to be within 2 percent accuracy, and a shelf life must be specified. Cylinder standards must be either reanalyzed or replaced at the end of the specified shelf life.
7.3 Prepared Gases. Calibration gases may be prepared by the user according to any accepted gaseous preparation procedure that will yield a mixture accurate to within 2 percent. Prepared standards must be replaced each day of use unless it is demonstrated that degradation does not occur during storage.
7.4 Mixtures with non-Reference Compound Gases. Calibrations may be performed using a compound other than the reference compound. In this case, a conversion factor must be determined for the alternative compound such that the resulting meter readings during source surveys can be converted to reference compound results.
8.0 Sample Collection, Preservation, Storage, and Transport8.1 Instrument Performance Evaluation. Assemble and start up the instrument according to the manufacturer's instructions for recommended warmup period and preliminary adjustments.
8.1.1 Response Factor. A response factor must be determined for each compound that is to be measured, either by testing or from reference sources. The response factor tests are required before placing the analyzer into service, but do not have to be repeated at subsequent intervals.
8.1.1.1 Calibrate the instrument with the reference compound as specified in the applicable regulation. Introduce the calibration gas mixture to the analyzer and record the observed meter reading. Introduce zero gas until a stable reading is obtained. Make a total of three measurements by alternating between the calibration gas and zero gas. Calculate the response factor for each repetition and the average response factor.
8.1.1.2 The instrument response factors for each of the individual VOC to be measured shall be less than 10 unless otherwise specified in the applicable regulation. When no instrument is available that meets this specification when calibrated with the reference VOC specified in the applicable regulation, the available instrument may be calibrated with one of the VOC to be measured, or any other VOC, so long as the instrument then has a response factor of less than 10 for each of the individual VOC to be measured.
8.1.1.3 Alternatively, if response factors have been published for the compounds of interest for the instrument or detector type, the response factor determination is not required, and existing results may be referenced. Examples of published response factors for flame ionization and catalytic oxidation detectors are included in References 1-3 of section 17.0.
8.1.2 Calibration Precision. The calibration precision test must be completed prior to placing the analyzer into service and at subsequent 3-month intervals or at the next use, whichever is later.
8.1.2.1 Make a total of three measurements by alternately using zero gas and the specified calibration gas. Record the meter readings. Calculate the average algebraic difference between the meter readings and the known value. Divide this average difference by the known calibration value and multiply by 100 to express the resulting calibration precision as a percentage.
8.1.2.2 The calibration precision shall be equal to or less than 10 percent of the calibration gas value.
8.1.3 Response Time. The response time test is required before placing the instrument into service. If a modification to the sample pumping system or flow configuration is made that would change the response time, a new test is required before further use.
8.1.3.1 Introduce zero gas into the instrument sample probe. When the meter reading has stabilized, switch quickly to the specified calibration gas. After switching, measure the time required to attain 90 percent of the final stable reading. Perform this test sequence three times and record the results. Calculate the average response time.
8.1.3.2 The instrument response time shall be equal to or less than 30 seconds. The instrument pump, dilution probe (if any), sample probe, and probe filter that will be used during testing shall all be in place during the response time determination.
8.2 Instrument Calibration. Calibrate the VOC monitoring instrument according to section 10.0.
8.3 Individual Source Surveys.
8.3.1 Type I - Leak Definition Based on Concentration. Place the probe inlet at the surface of the component interface where leakage could occur. Move the probe along the interface periphery while observing the instrument readout. If an increased meter reading is observed, slowly sample the interface where leakage is indicated until the maximum meter reading is obtained. Leave the probe inlet at this maximum reading location for approximately two times the instrument response time. If the maximum observed meter reading is greater than the leak definition in the applicable regulation, record and report the results as specified in the regulation reporting requirements. Examples of the application of this general technique to specific equipment types are:
8.3.1.1 Valves. The most common source of leaks from valves is the seal between the stem and housing. Place the probe at the interface where the stem exits the packing gland and sample the stem circumference. Also, place the probe at the interface of the packing gland take-up flange seat and sample the periphery. In addition, survey valve housings of multipart assembly at the surface of all interfaces where a leak could occur.
8.3.1.2 Flanges and Other Connections. For welded flanges, place the probe at the outer edge of the flange-gasket interface and sample the circumference of the flange. Sample other types of nonpermanent joints (such as threaded connections) with a similar traverse.
8.3.1.3 Pumps and Compressors. Conduct a circumferential traverse at the outer surface of the pump or compressor shaft and seal interface. If the source is a rotating shaft, position the probe inlet within 1 cm of the shaft-seal interface for the survey. If the housing configuration prevents a complete traverse of the shaft periphery, sample all accessible portions. Sample all other joints on the pump or compressor housing where leakage could occur.
8.3.1.4 Pressure Relief Devices. The configuration of most pressure relief devices prevents sampling at the sealing seat interface. For those devices equipped with an enclosed extension, or horn, place the probe inlet at approximately the center of the exhaust area to the atmosphere.
8.3.1.5 Process Drains. For open drains, place the probe inlet at approximately the center of the area open to the atmosphere. For covered drains, place the probe at the surface of the cover interface and conduct a peripheral traverse.
8.3.1.6 Open-ended Lines or Valves. Place the probe inlet at approximately the center of the opening to the atmosphere.
8.3.1.7 Seal System Degassing Vents and Accumulator Vents. Place the probe inlet at approximately the center of the opening to the atmosphere.
8.3.1.8 Access door seals. Place the probe inlet at the surface of the door seal interface and conduct a peripheral traverse.
8.3.2 Type II - “No Detectable Emission”. Determine the local ambient VOC concentration around the source by moving the probe randomly upwind and downwind at a distance of one to two meters from the source. If an interference exists with this determination due to a nearby emission or leak, the local ambient concentration may be determined at distances closer to the source, but in no case shall the distance be less than 25 centimeters. Then move the probe inlet to the surface of the source and determine the concentration as outlined in section 8.3.1. The difference between these concentrations determines whether there are no detectable emissions. Record and report the results as specified by the regulation. For those cases where the regulation requires a specific device installation, or that specified vents be ducted or piped to a control device, the existence of these conditions shall be visually confirmed. When the regulation also requires that no detectable emissions exist, visual observations and sampling surveys are required. Examples of this technique are:
8.3.2.1 Pump or Compressor Seals. If applicable, determine the type of shaft seal. Perform a survey of the local area ambient VOC concentration and determine if detectable emissions exist as described in section 8.3.2.
8.3.2.2 Seal System Degassing Vents, Accumulator Vessel Vents, Pressure Relief Devices. If applicable, observe whether or not the applicable ducting or piping exists. Also, determine if any sources exist in the ducting or piping where emissions could occur upstream of the control device. If the required ducting or piping exists and there are no sources where the emissions could be vented to the atmosphere upstream of the control device, then it is presumed that no detectable emissions are present. If there are sources in the ducting or piping where emissions could be vented or sources where leaks could occur, the sampling surveys described in section 8.3.2 shall be used to determine if detectable emissions exist.
8.3.3 Alternative Screening Procedure.
8.3.3.1 A screening procedure based on the formation of bubbles in a soap solution that is sprayed on a potential leak source may be used for those sources that do not have continuously moving parts, that do not have surface temperatures greater than the boiling point or less than the freezing point of the soap solution, that do not have open areas to the atmosphere that the soap solution cannot bridge, or that do not exhibit evidence of liquid leakage. Sources that have these conditions present must be surveyed using the instrument technique of section 8.3.1 or 8.3.2.
8.3.3.2 Spray a soap solution over all potential leak sources. The soap solution may be a commercially available leak detection solution or may be prepared using concentrated detergent and water. A pressure sprayer or squeeze bottle may be used to dispense the solution. Observe the potential leak sites to determine if any bubbles are formed. If no bubbles are observed, the source is presumed to have no detectable emissions or leaks as applicable. If any bubbles are observed, the instrument techniques of section 8.3.1 or 8.3.2 shall be used to determine if a leak exists, or if the source has detectable emissions, as applicable.
9.0 Quality ControlSection | Quality control measure | Effect |
---|---|---|
8.1.2 | Instrument calibration precision check | Ensure precision and accuracy, respectively, of instrument response to standard. |
10.0 | Instrument calibration |
10.1 Calibrate the VOC monitoring instrument as follows. After the appropriate warmup period and zero internal calibration procedure, introduce the calibration gas into the instrument sample probe. Adjust the instrument meter readout to correspond to the calibration gas value.
Note:If the meter readout cannot be adjusted to the proper value, a malfunction of the analyzer is indicated and corrective actions are necessary before use.
11.0 Analytical Procedures [Reserved] 12.0 Data Analyses and Calculations [Reserved] 13.0 Method Performance [Reserved] 14.0 Pollution Prevention [Reserved] 15.0 Waste Management [Reserved] 16.0 References1. Dubose, D.A., and G.E. Harris. Response Factors of VOC Analyzers at a Meter Reading of 10,000 ppmv for Selected Organic Compounds. U.S. Environmental Protection Agency, Research Triangle Park, NC. Publication No. EPA 600/2-81051. September 1981.
2. Brown, G.E., et al. Response Factors of VOC Analyzers Calibrated with Methane for Selected Organic Compounds. U.S. Environmental Protection Agency, Research Triangle Park, NC. Publication No. EPA 600/2-81-022. May 1981.
3. DuBose, D.A. et al. Response of Portable VOC Analyzers to Chemical Mixtures. U.S. Environmental Protection Agency, Research Triangle Park, NC. Publication No. EPA 600/2-81-110. September 1981.
4. Handbook of Hazardous Materials: Fire, Safety, Health. Alliance of American Insurers. Schaumberg, IL. 1983.
17.0 Tables, Diagrams, Flowcharts, and Validation Data [Reserved] Method 22 - Visual Determination of Fugitive Emissions From Material Sources and Smoke Emissions From Flares Note:This method is not inclusive with respect to observer certification. Some material is incorporated by reference from Method 9.
1.0 Scope and ApplicationThis method is applicable for the determination of the frequency of fugitive emissions from stationary sources, only as specified in an applicable subpart of the regulations. This method also is applicable for the determination of the frequency of visible smoke emissions from flares.
2.0 Summary of Method2.1 Fugitive emissions produced during material processing, handling, and transfer operations or smoke emissions from flares are visually determined by an observer without the aid of instruments.
2.2 This method is used also to determine visible smoke emissions from flares used for combustion of waste process materials.
2.3 This method determines the amount of time that visible emissions occur during the observation period (i.e., the accumulated emission time). This method does not require that the opacity of emissions be determined. Since this procedure requires only the determination of whether visible emissions occur and does not require the determination of opacity levels, observer certification according to the procedures of Method 9 is not required. However, it is necessary that the observer is knowledgeable with respect to the general procedures for determining the presence of visible emissions. At a minimum, the observer must be trained and knowledgeable regarding the effects of background contrast, ambient lighting, observer position relative to lighting, wind, and the presence of uncombined water (condensing water vapor) on the visibility of emissions. This training is to be obtained from written materials found in References 1 and 2 or from the lecture portion of the Method 9 certification course.
3.0 Definitions3.1 Emission frequency means the percentage of time that emissions are visible during the observation period.
3.2 Emission time means the accumulated amount of time that emissions are visible during the observation period.
3.3 Fugitive emissions means emissions generated by an affected facility which is not collected by a capture system and is released to the atmosphere. This includes emissions that (1) escape capture by process equipment exhaust hoods; (2) are emitted during material transfer; (3) are emitted from buildings housing material processing or handling equipment; or (4) are emitted directly from process equipment.
3.4 Observation period means the accumulated time period during which observations are conducted, not to be less than the period specified in the applicable regulation.
3.5 Smoke emissions means a pollutant generated by combustion in a flare and occurring immediately downstream of the flame. Smoke occurring within the flame, but not downstream of the flame, is not considered a smoke emission.
4.0 Interferences4.1 Occasionally, fugitive emissions from sources other than the affected facility (e.g., road dust) may prevent a clear view of the affected facility. This may particularly be a problem during periods of high wind. If the view of the potential emission points is obscured to such a degree that the observer questions the validity of continuing observations, then the observations shall be terminated, and the observer shall clearly note this fact on the data form.
5.0 Safety5.1 Disclaimer. This method may involve hazardous materials, operations, and equipment. This test method may not address all of the safety problems associated with its use. It is the responsibility of the user of this test method to establish appropriate safety and health practices and determine the applicability of regulatory limitations prior to performing this test method.
6.0 Equipment6.1 Stopwatches (two). Accumulative type with unit divisions of at least 0.5 seconds.
6.2 Light Meter. Light meter capable of measuring illuminance in the 50 to 200 lux range, required for indoor observations only.
7.0 Reagents and Supplies [Reserved] 8.0 Sample Collection, Preservation, Storage, and Transfer [Reserved] 9.0 Quality Control [Reserved] 10.0 Calibration and Standardization [Reserved] 11.0 Analytical Procedure11.1 Selection of Observation Location. Survey the affected facility, or the building or structure housing the process to be observed, and determine the locations of potential emissions. If the affected facility is located inside a building, determine an observation location that is consistent with the requirements of the applicable regulation (i.e., outside observation of emissions escaping the building/structure or inside observation of emissions directly emitted from the affected facility process unit). Then select a position that enables a clear view of the potential emission point(s) of the affected facility or of the building or structure housing the affected facility, as appropriate for the applicable subpart. A position at least 4.6 m (15 feet), but not more than 400 m (0.25 miles), from the emission source is recommended. For outdoor locations, select a position where the sunlight is not shining directly in the observer's eyes.
11.2 Field Records.
11.2.1 Outdoor Location. Record the following information on the field data sheet (Figure 22-1): Company name, industry, process unit, observer's name, observer's affiliation, and date. Record also the estimated wind speed, wind direction, and sky condition. Sketch the process unit being observed, and note the observer location relative to the source and the sun. Indicate the potential and actual emission points on the sketch. Alternatively, digital photography as described in section 11.2.3 may be used for a subset of the recordkeeping requirements of this section.
11.2.2 Indoor Location. Record the following information on the field data sheet (Figure 22-2): Company name, industry, process unit, observer's name, observer's affiliation, and date. Record as appropriate the type, location, and intensity of lighting on the data sheet. Sketch the process unit being observed, and note the observer location relative to the source. Indicate the potential and actual fugitive emission points on the sketch. Alternatively, digital photography as described in section 11.2.3 may be used for a subset of the recordkeeping requirements of this section.
11.2.3 Digital Photographic Records. Digital photographs, annotated or unaltered, may be used to record and report sky conditions, observer's location relative to the source, observer's location relative to the sun, process unit being observed, potential emission points and actual emission points for the requirements in sections 11.2.1 and 11.2.2. The image must have the proper lighting, field of view and depth of field to properly distinguish the sky condition (if applicable), process unit, potential emission point and actual emission point. At least one digital photograph must be from the point of the view of the observer. The photograph(s) representing the environmental conditions including the sky conditions and the position of the sun relative to the observer and the emission point must be taken within a reasonable time of the observation (i.e., 15 minutes). When observations are taken from exactly the same observation point on a routine basis (i.e., daily) and as long as there are no modifications to the units depicted, only a single photograph each is necessary to document the observer's location relative to the emissions source, the process unit being observed, and the location of potential and actual emission points. Any photographs altered or annotated must be retained in an unaltered format for recordkeeping purposes.
11.3 Indoor Lighting Requirements. For indoor locations, use a light meter to measure the level of illumination at a location as close to the emission source(s) as is feasible. An illumination of greater than 100 lux (10 foot candles) is considered necessary for proper application of this method.
11.4 Observations.
11.4.1 Procedure. Record the clock time when observations begin. Use one stopwatch to monitor the duration of the observation period. Start this stopwatch when the observation period begins. If the observation period is divided into two or more segments by process shutdowns or observer rest breaks (see section 11.4.3), stop the stopwatch when a break begins and restart the stopwatch without resetting it when the break ends. Stop the stopwatch at the end of the observation period. The accumulated time indicated by this stopwatch is the duration of observation period. When the observation period is completed, record the clock time. During the observation period, continuously watch the emission source. Upon observing an emission (condensed water vapor is not considered an emission), start the second accumulative stopwatch; stop the watch when the emission stops. Continue this procedure for the entire observation period. The accumulated elapsed time on this stopwatch is the total time emissions were visible during the observation period (i.e., the emission time.)
11.4.2 Observation Period. Choose an observation period of sufficient length to meet the requirements for determining compliance with the emission standard in the applicable subpart of the regulations. When the length of the observation period is specifically stated in the applicable subpart, it may not be necessary to observe the source for this entire period if the emission time required to indicate noncompliance (based on the specified observation period) is observed in a shorter time period. In other words, if the regulation prohibits emissions for more than 6 minutes in any hour, then observations may (optional) be stopped after an emission time of 6 minutes is exceeded. Similarly, when the regulation is expressed as an emission frequency and the regulation prohibits emissions for greater than 10 percent of the time in any hour, then observations may (optional) be terminated after 6 minutes of emission are observed since 6 minutes is 10 percent of an hour. In any case, the observation period shall not be less than 6 minutes in duration. In some cases, the process operation may be intermittent or cyclic. In such cases, it may be convenient for the observation period to coincide with the length of the process cycle.
11.4.3 Observer Rest Breaks. Do not observe emissions continuously for a period of more than 15 to 20 minutes without taking a rest break. For sources requiring observation periods of greater than 20 minutes, the observer shall take a break of not less than 5 minutes and not more than 10 minutes after every 15 to 20 minutes of observation. If continuous observations are desired for extended time periods, two observers can alternate between making observations and taking breaks.
11.5 Recording Observations. Record the accumulated time of the observation period on the data sheet as the observation period duration. Record the accumulated time emissions were observed on the data sheet as the emission time. Record the clock time the observation period began and ended, as well as the clock time any observer breaks began and ended.
12.0 Data Analysis and CalculationsIf the applicable subpart requires that the emission rate be expressed as an emission frequency (in percent), determine this value as follows: Divide the accumulated emission time (in seconds) by the duration of the observation period (in seconds) or by any minimum observation period required in the applicable subpart, if the actual observation period is less than the required period, and multiply this quotient by 100.
13.0 Method Performance [Reserved] 14.0 Pollution Prevention [Reserved] 15.0 Waste Management [Reserved] 16.0 References1. Missan, R., and A. Stein. Guidelines for Evaluation of Visible Emissions Certification, Field Procedures, Legal Aspects, and Background Material. EPA Publication No. EPA-340/1-75-007. April 1975.
2. Wohlschlegel, P., and D.E. Wagoner. Guideline for Development of a Quality Assurance Program: Volume IX - Visual Determination of Opacity Emissions from Stationary Sources. EPA Publication No. EPA-650/4-74-005i. November 1975.
17.0 Tables, Diagrams, Flowcharts, and Validation Data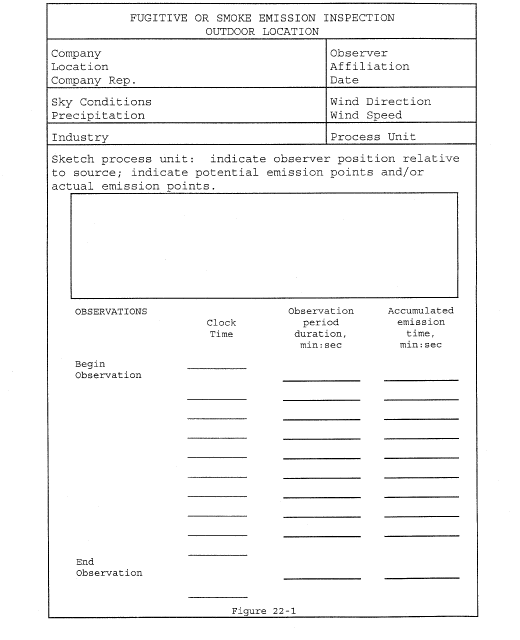
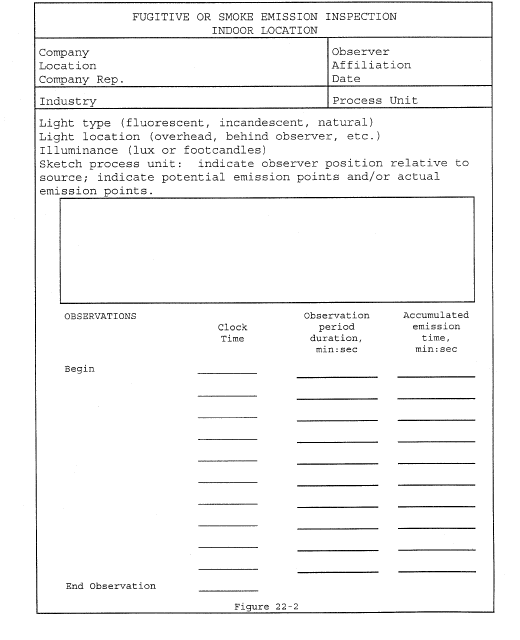
1.1 Applicability. This method is applicable to the determination of polychlorinated dibenzo-p-dioxins (PCDD's) and polychlorinated dibenzofurans (PCDF's) from stationary sources.
1.2 Principle. A sample is withdrawn from the gas stream isokinetically and collected in the sample probe, on a glass fiber filter, and on a packed column of adsorbent material. The sample cannot be separated into a particle vapor fraction. The PCDD's and PCDF's are extracted from the sample, separated by high resolution gas chromatography, and measured by high resolution mass spectrometry.
2. Apparatus2.1 Sampling. A schematic of the sampling train used in this method is shown in Figure 23-1. Sealing greases may not be used in assembling the train. The train is identical to that described in section 2.1 of Method 5 of this appendix with the following additions:
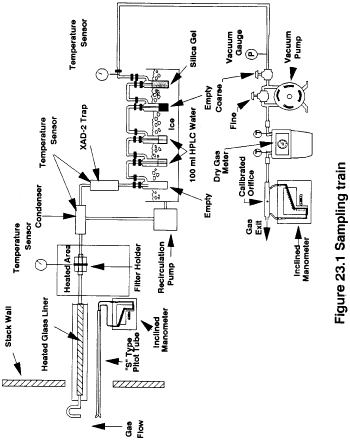
2.1.1 Nozzle. The nozzle shall be made of nickel, nickel-plated stainless steel, quartz, or borosilicate glass.
2.1.2 Sample Transfer Lines. The sample transfer lines, if needed, shall be heat traced, heavy walled TFE ( 1/2 in. OD with 1/8 in. wall) with connecting fittings that are capable of forming leak-free, vacuum-tight connections without using sealing greases. The line shall be as short as possible and must be maintained at 120 °C.
2.1.1 Filter Support. Teflon or Teflon-coated wire.
2.1.2 Condenser. Glass, coil type with compatible fittings. A schematic diagram is shown in Figure 23-2.
2.1.3 Water Bath. Thermostatically controlled to maintain the gas temperature exiting the condenser at <20 °C (68 °F).
2.1.4 Adsorbent Module. Glass container to hold the solid adsorbent. A shematic diagram is shown in Figure 23-2. Other physical configurations of the resin trap/condenser assembly are acceptable. The connecting fittings shall form leak-free, vacuum tight seals. No sealant greases shall be used in the sampling train. A coarse glass frit is included to retain the adsorbent.
2.2 Sample Recovery.
2.2.1 Fitting Caps. Ground glass, Teflon tape, or aluminum foil (Section 2.2.6) to cap off the sample exposed sections of the train.
2.2.2 Wash Bottles. Teflon, 500-ml.
2.2.3 Probe-Liner Probe-Nozzle, and Filter-Holder Brushes. Inert bristle brushes with precleaned stainless steel or Teflon handles. The probe brush shall have extensions of stainless steel or Teflon, at least as long as the probe. The brushes shall be properly sized and shaped to brush out the nozzle, probe liner, and transfer line, if used.
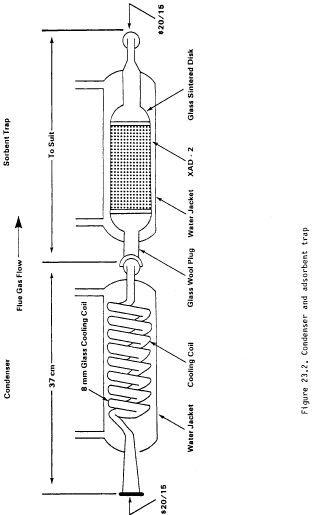
2.2.4 Filter Storage Container. Sealed filter holder, wide-mouth amber glass jar with Teflon-lined cap, or glass petri dish.
2.2.5 Balance. Triple beam.
2.2.6 Aluminum Foil. Heavy duty, hexane-rinsed.
2.2.7 Storage Container. Air-tight container to store silica gel.
2.2.8 Graduated Cylinder. Glass, 250-ml with 2-ml graduation.
2.2.9 Glass Sample Storage Container. Amber glass bottle for sample glassware washes, 500- or 1000-ml, with leak free Teflon-lined caps.
2.3 Analysis.
2.3.1 Sample Container. 125- and 250-ml flint glass bottles with Teflon-lined caps.
2.3.2 Test Tube. Glass.
2.3.3 Soxhlet Extraction Apparatus. Capable of holding 43 × 123 mm extraction thimbles.
2.3.4 Extraction Thimble. Glass, precleaned cellulosic, or glass fiber.
2.3.5 Pasteur Pipettes. For preparing liquid chromatographic columns.
2.3.6 Reacti-vials. Amber glass, 2-ml, silanized prior to use.
2.3.7 Rotary Evaporator. Buchi/Brinkman RF-121 or equivalent.
2.3.8 Nitrogen Evaporative Concentrator. N-Evap Analytical Evaporator Model III or equivalent.
2.3.9 Separatory Funnels. Glass, 2-liter.
2.3.10 Gas Chromatograph. Consisting of the following components:
2.3.10.1 Oven. Capable of maintaining the separation column at the proper operating temperature ±°C and performing programmed increases in temperature at rates of at least 40 °C/min.
2.3.10.2 Temperature Gauge. To monitor column oven, detector, and exhaust temperatures ±1 °C.
2.3.10.3 Flow System. Gas metering system to measure sample, fuel, combustion gas, and carrier gas flows.
2.3.10.4 Capillary Columns. A fused silica column, 60 × 0.25 mm inside diameter (ID), coated with DB-5 and a fused silica column, 30 m × 0.25 mm ID coated with DB-225. Other column systems may be used provided that the user is able to demonstrate using calibration and performance checks that the column system is able to meet the specifications of section 6.1.2.2.
2.3.11 Mass Spectrometer. Capable of routine operation at a resolution of 1:10000 with a stability of ±5 ppm.
2.3.12 Data System. Compatible with the mass spectrometer and capable of monitoring at least five groups of 25 ions.
2.3.13 Analytical Balance. To measure within 0.1 mg.
3. Reagents3.1 Sampling.
3.1.1 Filters. Glass fiber filters, without organic binder, exhibiting at least 99.95 percent efficiency (<0.05 percent penetration) on 0.3-micron dioctyl phthalate smoke particles. The filter efficiency test shall be conducted in accordance with ASTM Standard Method D 2986-71 (Reapproved 1978) (incorporated by reference - see § 60.17).
3.1.1.1 Precleaning. All filters shall be cleaned before their initial use. Place a glass extraction thimble and 1 g of silica gel and a plug of glass wool into a Soxhlet apparatus, charge the apparatus with toluene, and reflux for a minimum of 3 hours. Remove the toluene and discard it, but retain the silica gel. Place no more than 50 filters in the thimble onto the silica gel bed and top with the cleaned glass wool. Charge the Soxhlet with toluene and reflux for 16 hours. After extraction, allow the Soxhlet to cool, remove the filters, and dry them under a clean N2 stream. Store the filters in a glass petri dish sealed with Teflon tape.
3.1.2 Adsorbent Resin. Amberlite XAD-2 resin. Thoroughly cleaned before initial use.
3.1.2.1 Cleaning Procedure. This procedure may be carried out in a giant Soxhlet extractor. An all-glass filter thimble containing an extra-course frit is used for extraction of XAD-2. The frit is recessed 10-15 mm above a crenelated ring at the bottom of the thimble to facilitate drainage. The resin must be carefully retained in the extractor cup with a glass wool plug and a stainless steel ring because it floats on methylene chloride. This process involves sequential extraction in the following order.
Solvent | Procedure |
---|---|
Water | Initial rinse: Place resin in a beaker, rinse once with water, and discard. Fill with water a second time, let stand overnight, and discard. |
Water | Extract with water for 8 hours. |
Methanol | Extract for 22 hours. |
Methylene Chloride | Extract for 22 hours. |
Toluene | Extract for 22 hours. |
3.1.2.2 Drying.
3.1.2.2.1 Drying Column. Pyrex pipe, 10.2 cm ID by 0.6 m long, with suitable retainers.
3.1.2.2.2 Procedure. The adsorbent must be dried with clean inert gas. Liquid nitrogen from a standard commercial liquid nitrogen cylinder has proven to be a reliable source of large volumes of gas free from organic contaminants. Connect the liquid nitrogen cylinder to the column by a length of cleaned copper tubing, 0.95 cm ID, coiled to pass through a heat source. A convenient heat source is a water-bath heated from a steam line. The final nitrogen temperature should only be warm to the touch and not over 40 °C. Continue flowing nitrogen through the adsorbent until all the residual solvent is removed. The flow rate should be sufficient to gently agitate the particles but not so excessive as the cause the particles to fracture.
3.1.2.3 Quality Control Check. The adsorbent must be checked for residual toluene.
3.1.2.3.1 Extraction. Weigh 1.0 g sample of dried resin into a small vial, add 3 ml of toluene, cap the vial, and shake it well.
3.1.2.3.2 Analysis. Inject a 2 µl sample of the extract into a gas chromatograph operated under the following conditions:
Column: 6 ft × 1/8 in stainless steel containing 10 percent OV-101 on 100/120 Supelcoport. Carrier Gas: Helium at a rate of 30 ml/min. Detector: Flame ionization detector operated at a sensitivity of 4 × 10−11 A/mV. Injection Port Temperature: 250 °C. Detector Temperature: 305 °C. Oven Temperature: 30 °C for 4 min; programmed to rise at 40 °C/min until it reaches 250 °C; return to 30 °C after 17 minutes.Compare the results of the analysis to the results from the reference solution. Prepare the reference solution by injection 2.5 µl of methylene chloride into 100 ml of toluene. This corresponds to 100 µg of methylene chloride per g of adsorbent. The maximum acceptable concentration is 1000 µg/g of adsorbent. If the adsorbent exceeds this level, drying must be continued until the excess methylene chloride is removed.
3.1.2.4 Storage. The adsorbent must be used within 4 weeks of cleaning. After cleaning, it may be stored in a wide mouth amber glass container with a Teflon-lined cap or placed in one of the glass adsorbent modules tightly sealed with glass stoppers. If precleaned adsorbent is purchased in sealed containers, it must be used within 4 weeks after the seal is broken.
3.1.3 Glass Wool. Cleaned by sequential immersion in three aliquots of methylene chloride, dried in a 110 °C oven, and stored in a methylene chloride-washed glass jar with a Teflon-lined screw cap.
3.1.4 Water. Deionized distilled and stored in a methylene chloride-rinsed glass container with a Teflon-lined screw cap.
3.1.5 Silica Gel. Indicating type, 6 to 16 mesh. If previously used, dry at 175 °C (350 °F) for two hours. New silica gel may be used as received. Alternately other types of desiccants (equivalent or better) may be used, subject to the approval of the Administrator.
3.1.6 Chromic Acid Cleaning Solution. Dissolve 20 g of sodium dichromate in 15 ml of water, and then carefully add 400 ml of concentrated sulfuric acid.
3.2 Sample Recovery.
3.2.2 Acetone. Pesticide quality.
3.2.2 Methylene Chloride. Pesticide qualtity.
3.2.3 Toluene. Pesticide quality.
3.3 Analysis.
3.3.1 Potassium Hydroxide. ACS grade, 2-percent (weight/volume) in water.
3.3.2 Sodium Sulfate. Granulated, reagent grade. Purify prior to use by rinsing with methylene chloride and oven drying. Store the cleaned material in a glass container with a Teflon-lined screw cap.
3.3.3 Sulfuric Acid. Reagent grade.
3.3.4 Sodium Hydroxide. 1.0 N. Weigh 40 g of sodium hydroxide into a 1-liter volumetric flask. Dilute to 1 liter with water.
3.3.5 Hexane. Pesticide grade.
3.3.6 Methylene Chloride. Pesticide grade.
3.3.7 Benzene. Pesticide Grade.
3.3.8 Ethyl Acetate.
3.3.9 Methanol. Pesticide Grade.
3.3.10 Toluene. Pesticide Grade.
3.3.11 Nonane. Pesticide Grade.
3.3.12 Cyclohexane. Pesticide Grade.
3.3.13 Basic Alumina. Activity grade 1, 100-200 mesh. Prior to use, activate the alumina by heating for 16 hours at 130 °C before use. Store in a desiccator. Pre-activated alumina may be purchased from a supplier and may be used as received.
3.3.14 Silica Gel. Bio-Sil A, 100-200 mesh. Prior to use, activate the silica gel by heating for at least 30 minutes at 180 °C. After cooling, rinse the silica gel sequentially with methanol and methylene chloride. Heat the rinsed silica gel at 50 °C for 10 minutes, then increase the temperature gradually to 180 °C over 25 minutes and maintain it at this temperature for 90 minutes. Cool at room temperature and store in a glass container with a Teflon-lined screw cap.
3.3.15 Silica Gel Impregnated with Sulfuric Acid. Combine 100 g of silica gel with 44 g of concentrated sulfuric acid in a screw capped glass bottle and agitate thoroughly. Disperse the solids with a stirring rod until a uniform mixture is obtained. Store the mixture in a glass container with a Teflon-lined screw cap.
3.3.16 Silica Gel Impregnated with Sodium Hydroxide. Combine 39 g of 1 N sodium hydroxide with 100 g of silica gel in a screw capped glass bottle and agitate thoroughly. Disperse solids with a stirring rod until a uniform mixture is obtained. Store the mixture in glass container with a Teflon-lined screw cap.
3.3.17 Carbon/Celite. Combine 10.7 g of AX-21 carbon with 124 g of Celite 545 in a 250-ml glass bottle with a Teflon-lined screw cap. Agitate the mixture thoroughly until a uniform mixture is obtained. Store in the glass container.
3.3.18 Nitrogen. Ultra high purity.
3.3.19 Hydrogen. Ultra high purity.
3.3.20 Internal Standard Solution. Prepare a stock standard solution containing the isotopically labelled PCDD's and PCDF's at the concentrations shown in Table 1 under the heading “Internal Standards” in 10 ml of nonane.
3.3.21 Surrogate Standard Solution. Prepare a stock standard solution containing the isotopically labelled PCDD's and PCDF's at the concentrations shown in Table 1 under the heading “Surrogate Standards” in 10 ml of nonane.
3.3.22 Recovery Standard Solution. Prepare a stock standard solution containing the isotopically labelled PCDD's and PCDF's at the concentrations shown in Table 1 under the heading “Recovery Standards” in 10 ml of nonane.
4. Procedure4.1 Sampling. The complexity of this method is such that, in order to obtain reliable results, testers should be trained and experienced with the test procedures.
4.1.1 Pretest Preparation.
4.1.1.1 Cleaning Glassware. All glass components of the train upstream of and including the adsorbent module, shall be cleaned as described in section 3A of the “Manual of Analytical Methods for the Analysis of Pesticides in Human and Environmental Samples.” Special care shall be devoted to the removal of residual silicone grease sealants on ground glass connections of used glassware. Any residue shall be removed by soaking the glassware for several hours in a chromic acid cleaning solution prior to cleaning as described above.
4.1.1.2 Adsorbent Trap. The traps must be loaded in a clean area to avoid contamination. They may not be loaded in the field. Fill a trap with 20 to 40 g of XAD-2. Follow the XAD-2 with glass wool and tightly cap both ends of the trap. Add 100 µl of the surrogate standard solution (section 3.3.21) to each trap.
4.1.1.3 Sample Train. It is suggested that all components be maintained according to the procedure described in APTD-0576. Alternative mercury-free thermometers may be used if the thermometers are, at a minimum, equivalent in terms of performance or suitably effective for the specific temperature measurement application.
4.1.1.4 Silica Gel. Weigh several 200 to 300 g portions of silica gel in an air tight container to the nearest 0.5 g. Record the total weight of the silica gel plus container, on each container. As an alternative, the silica gel may be weighed directly in its impinger or sampling holder just prior to sampling.
4.1.1.5 Filter. Check each filter against light for irregularities and flaws or pinhole leaks. Pack the filters flat in a clean glass container.
4.1.2 Preliminary Determinations. Same as section 4.1.2 of Method 5.
4.1.3 Preparation of Collection Train.
4.1.3.1 During preparation and assembly of the sampling train, keep all train openings where contamination can enter, sealed until just prior to assembly or until sampling is about to begin.
Note:Do not use sealant grease in assembling the train.
4.1.3.2 Place approximately 100 ml of water in the second and third impingers, leave the first and fourth impingers empty, and transfer approximately 200 to 300 g of preweighed silica gel from its container to the fifth impinger.
4.1.3.3 Place the silica gel container in a clean place for later use in the sample recovery. Alternatively, the weight of the silica gel plus impinger may be determined to the nearest 0.5 g and recorded.
4.1.3.4 Assemble the train as shown in Figure 23-1.
4.1.3.5 Turn on the adsorbent module and condenser coil recirculating pump and begin monitoring the adsorbent module gas entry temperature. Ensure proper sorbent temperature gas entry temperature before proceeding and before sampling is initiated. It is extremely important that the XAD-2 adsorbent resin temperature never exceed 50 °C because thermal decomposition will occur. During testing, the XAD-2 temperature must not exceed 20 °C for efficient capture of the PCDD's and PCDF's.
4.1.4 Leak-Check Procedure. Same as Method 5, section 4.1.4.
4.1.5 Sample Train Operation. Same as Method 5, section 4.1.5.
4.2 Sample Recovery. Proper cleanup procedure begins as soon as the probe is removed from the stack at the end of the sampling period. Seal the nozzle end of the sampling probe with Teflon tape or aluminum foil.
When the probe can be safely handled, wipe off all external particulate matter near the tip of the probe. Remove the probe from the train and close off both ends with aluminum foil. Seal off the inlet to the train with Teflon tape, a ground glass cap, or aluminum foil.
Transfer the probe and impinger assembly to the cleanup area. This area shall be clean and enclosed so that the chances of losing or contaminating the sample are minimized. Smoking, which could contaminate the sample, shall not be allowed in the cleanup area.
Inspect the train prior to and during disassembly and note any abnormal conditions, e.g., broken filters, colored impinger liquid, etc. Treat the samples as follows:
4.2.1 Container No. 1. Either seal the filter holder or carefully remove the filter from the filter holder and place it in its identified container. Use a pair of cleaned tweezers to handle the filter. If it is necessary to fold the filter, do so such that the particulate cake is inside the fold. Carefully transfer to the container any particulate matter and filter fibers which adhere to the filter holder gasket, by using a dry inert bristle brush and a sharp-edged blade. Seal the container.
4.2.2 Adsorbent Module. Remove the module from the train, tightly cap both ends, label it, cover with aluminum foil, and store it on ice for transport to the laboratory.
4.2.3 Container No. 2. Quantitatively recover material deposited in the nozzle, probe transfer lines, the front half of the filter holder, and the cyclone, if used, first, by brushing while rinsing three times each with acetone and then, by rinsing the probe three times with methylene chloride. Collect all the rinses in Container No. 2.
Rinse the back half of the filter holder three times with acetone. Rinse the connecting line between the filter and the condenser three times with acetone. Soak the connecting line with three separate portions of methylene chloride for 5 minutes each. If using a separate condenser and adsorbent trap, rinse the condenser in the same manner as the connecting line. Collect all the rinses in Container No. 2 and mark the level of the liquid on the container.
4.2.4 Container No. 3. Repeat the methylene chloride-rinsing described in section 4.2.3 using toluene as the rinse solvent. Collect the rinses in Container No. 3 and mark the level of the liquid on the container.
4.2.5 Impinger Water. Measure the liquid in the first three impingers to within ±1 ml by using a graduated cylinder or by weighing it to within ±0.5 g by using a balance. Record the volume or weight of liquid present. This information is required to calculate the moisture content of the effluent gas.
Discard the liquid after measuring and recording the volume or weight.
4.2.7 Silica Gel. Note the color of the indicating silica gel to determine if it has been completely spent and make a mention of its condition. Transfer the silica gel from the fifth impinger to its original container and seal. If a moisture determination is made, follow the applicable procedures in sections 8.7.6.3 and 11.2.3 of Method 5 to handle and weigh the silica gel. If moisture is not measured, the silica gel may be disposed.
5. AnalysisAll glassware shall be cleaned as described in section 3A of the “Manual of Analytical Methods for the Analysis of Pesticides in Human and Environmental Samples.” All samples must be extracted within 30 days of collection and analyzed within 45 days of extraction.
5.1 Sample Extraction.
5.1.1 Extraction System. Place an extraction thimble (section 2.3.4), 1 g of silica gel, and a plug of glass wool into the Soxhlet apparatus, charge the apparatus with toluene, and reflux for a minimum of 3 hours. Remove the toluene and discard it, but retain the silica gel. Remove the extraction thimble from the extraction system and place it in a glass beaker to catch the solvent rinses.
5.1.2 Container No. 1 (Filter). Transfer the contents directly to the glass thimble of the extraction system and extract them simultaneously with the XAD-2 resin.
5.1.3 Adsorbent Cartridge. Suspend the adsorbent module directly over the extraction thimble in the beaker (See section 5.1.1). The glass frit of the module should be in the up position. Using a Teflon squeeze bottle containing toluene, flush the XAD-2 into the thimble onto the bed of cleaned silica gel. Thoroughly rinse the glass module catching the rinsings in the beaker containing the thimble. If the resin is wet, effective extraction can be accomplished by loosely packing the resin in the thimble. Add the XAD-2 glass wool plug into the thimble.
5.1.4 Container No. 2 (Acetone and Methylene Chloride). Concentrate the sample to a volume of about 1-5 ml using the rotary evaporator apparatus, at a temperature of less than 37 °C. Rinse the sample container three times with small portions of methylene chloride and add these to the concentrated solution and concentrate further to near dryness. This residue contains particulate matter removed in the rinse of the train probe and nozzle. Add the concentrate to the filter and the XAD-2 resin in the Soxhlet apparatus described in section 5.1.1.
5.1.5 Extraction. Add 100 µl of the internal standard solution (Section 3.3.20) to the extraction thimble containing the contents of the adsorbent cartridge, the contents of Container No. 1, and the concentrate from section 5.1.4. Cover the contents of the extraction thimble with the cleaned glass wool plug to prevent the XAD-2 resin from floating into the solvent reservoir of the extractor. Place the thimble in the extractor, and add the toluene contained in the beaker to the solvent reservoir. Pour additional toluene to fill the reservoir approximately 2/3 full. Add Teflon boiling chips and assemble the apparatus. Adjust the heat source to cause the extractor to cycle three times per hour. Extract the sample for 16 hours. After extraction, allow the Soxhlet to cool. Transfer the toluene extract and three 10-ml rinses to the rotary evaporator. Concentrate the extract to approximately 10 ml. At this point the analyst may choose to split the sample in half. If so, split the sample, store one half for future use, and analyze the other according to the procedures in sections 5.2 and 5.3. In either case, use a nitrogen evaporative concentrator to reduce the volume of the sample being analyzed to near dryness. Dissolve the residue in 5 ml of hexane.
5.1.6 Container No. 3 (Toluene Rinse). Add 100 µl of the Internal Standard solution (section 3.3.2) to the contents of the container. Concentrate the sample to a volume of about 1-5 ml using the rotary evaporator apparatus at a temperature of less than 37 °C. Rinse the sample container apparatus at a temperature of less than 37 °C. Rinse the sample container three times with small portions of toluene and add these to the concentrated solution and concentrate further to near dryness. Analyze the extract separately according to the procedures in sections 5.2 and 5.3, but concentrate the solution in a rotary evaporator apparatus rather than a nitrogen evaporative concentrator.
5.2 Sample Cleanup and Fractionation.
5.2.1 Silica Gel Column. Pack one end of a glass column, 20 mm × 230 mm, with glass wool. Add in sequence, 1 g silica gel, 2 g of sodium hydroxide impregnated silica gel, 1 g silica gel, 4 g of acid-modified silica gel, and 1 g of silica gel. Wash the column with 30 ml of hexane and discard it. Add the sample extract, dissolved in 5 ml of hexane to the column with two additional 5-ml rinses. Elute the column with an additional 90 ml of hexane and retain the entire eluate. Concentrate this solution to a volume of about 1 ml using the nitrogen evaporative concentrator (section 2.3.7).
5.2.2 Basic Alumina Column. Shorten a 25-ml disposable Pasteur pipette to about 16 ml. Pack the lower section with glass wool and 12 g of basic alumina. Transfer the concentrated extract from the silica gel column to the top of the basic alumina column and elute the column sequentially with 120 ml of 0.5 percent methylene chloride in hexane followed by 120 ml of 35 percent methylene chloride in hexane. Discard the first 120 ml of eluate. Collect the second 120 ml of eluate and concentrate it to about 0.5 ml using the nitrogen evaporative concentrator.
5.2.3 AX-21 Carbon/Celite 545 Column. Remove the botton 0.5 in. from the tip of a 9-ml disposable Pasteur pipette. Insert a glass fiber filter disk in the top of the pipette 2.5 cm from the constriction. Add sufficient carbon/celite mixture to form a 2 cm column. Top with a glass wool plug. In some cases AX-21 carbon fines may wash through the glass wool plug and enter the sample. This may be prevented by adding a celite plug to the exit end of the column. Rinse the column in sequence with 2 ml of 50 percent benzene in ethyl acetate, 1 ml of 50 percent methylene chloride in cyclohexane, and 2 ml of hexane. Discard these rinses. Transfer the concentrate in 1 ml of hexane from the basic alumina column to the carbon/celite column along with 1 ml of hexane rinse. Elute the column sequentially with 2 ml of 50 percent methylene chloride in hexane and 2 ml of 50 percent benzene in ethyl acetate and discard these eluates. Invert the column and elute in the reverse direction with 13 ml of toluene. Collect this eluate. Concentrate the eluate in a rotary evaporator at 50 °C to about 1 ml. Transfer the concentrate to a Reacti-vial using a toluene rinse and concentrate to a volume of 200 µl using a stream of N2. Store extracts at room temperature, shielded from light, until the analysis is performed.
5.3 Analysis. Analyze the sample with a gas chromatograph coupled to a mass spectrometer (GC/MS) using the instrumental parameters in sections 5.3.1 and 5.3.2. Immediately prior to analysis, add a 20 µl aliquot of the Recovery Standard solution from Table 1 to each sample. A 2 µl aliquot of the extract is injected into the GC. Sample extracts are first analyzed using the DB-5 capillary column to determine the concentration of each isomer of PCDD's and PCDF's (tetra-through octa-). If tetra-chlorinated dibenzofurans are detected in this analysis, then analyze another aliquot of the sample in a separate run, using the DB-225 column to measure the 2,3,7,8 tetra-chloro dibenzofuran isomer. Other column systems may be used, provided that the user is able to demonstrate using calibration and performance checks that the column system is able to meet the specifications of section 6.1.2.2.
5.3.1 Gas Chromatograph Operating Conditions.
5.3.1.1 Injector. Configured for capillary column, splitless, 250 °C.
5.3.1.2 Carrier Gas. Helium, 1-2 ml/min.
5.3.1.3 Oven. Initially at 150 °C. Raise by at least 40 °C/min to 190 °C and then at 3 °C/min up to 300 °C.
5.3.2 High Resolution Mass Spectrometer.
5.3.2.1 Resolution. 10000 m/e.
5.3.2.2 Ionization Mode. Electron impact.
5.3.2.3 Source Temperature 250 °C.
5.3.2.4 Monitoring Mode. Selected ion monitoring. A list of the various ions to be monitored is summarized in Table 3.
5.3.2.5 Identification Criteria. The following identification criteria shall be used for the characterization of polychlorinated dibenzodioxins and dibenzofurans.
1. The integrated ion-abundance ratio (M/M + 2 or M + 2/M + 4) shall be within 15 percent of the theoretical value. The acceptable ion-abundance ratio ranges for the identification of chlorine-containing compounds are given in Table 4.
2. The retention time for the analytes must be within 3 seconds of the corresponding 1 3 C-labeled internal standard, surrogate or alternate standard.
3. The monitored ions, shown in Table 3 for a given analyte, shall reach their maximum within 2 seconds of each other.
4. The identification of specific isomers that do not have corresponding 1 3 C-labeled standards is done by comparison of the relative retention time (RRT) of the analyte to the nearest internal standard retention time with reference (i.e., within 0.005 RRT units) to the comparable RRT's found in the continuing calibration.
5. The signal to noise ratio for all monitored ions must be greater than 2.5.
6. The confirmation of 2, 3, 7, 8-TCDD and 2, 3, 7, 8-TCDF shall satisfy all of the above identification criteria.
7. For the identification of PCDF's, no signal may be found in the corresponding PCDPE channels.
5.3.2.6 Quantification. The peak areas for the two ions monitored for each analyte are summed to yield the total response for each analyte. Each internal standard is used to quantify the indigenous PCDD's or PCDF's in its homologous series. For example, the 1 3 C 12-2,3,7,8-tetra chlorinated dibenzodioxin is used to calculate the concentrations of all other tetra chlorinated isomers. Recoveries of the tetra- and penta- internal standards are calculated using the 1 3 C 12-1,2,3,4-TCDD. Recoveries of the hexa- through octa- internal standards are calculated using 1 3 C 12-1,2,3,7,8,9-HxCDD. Recoveries of the surrogate standards are calculated using the corresponding homolog from the internal standard.
6. CalibrationSame as Method 5 with the following additions.
6.1 GC/MS System.
6.1.1 Initial Calibration. Calibrate the GC/MS system using the set of five standards shown in Table 2. The relative standard deviation for the mean response factor from each of the unlabeled analytes (Table 2) and of the internal, surrogate, and alternate standards shall be less than or equal to the values in Table 5. The signal to noise ratio for the GC signal present in every selected ion current profile shall be greater than or equal to 2.5. The ion abundance ratios shall be within the control limits in Table 4.
6.1.2 Daily Performance Check.
6.1.2.1 Calibration Check. Inject on µl of solution Number 3 from Table 2. Calculate the relative response factor (RRF) for each compound and compare each RRF to the corresponding mean RRF obtained during the initial calibration. The analyzer performance is acceptable if the measured RRF's for the labeled and unlabeled compounds for the daily run are within the limits of the mean values shown in Table 5. In addition, the ion-abundance ratios shall be within the allowable control limits shown in Table 4.
6.1.2.2 Column Separation Check. Inject a solution of a mixture of PCDD's and PCDF's that documents resolution between 2,3,7,8-TCDD and other TCDD isomers. Resolution is defined as a valley between peaks that is less than 25 percent of the lower of the two peaks. Identify and record the retention time windows for each homologous series.
Perform a similar resolution check on the confirmation column to document the resolution between 2,3,7,8 TCDF and other TCDF isomers.
6.2 Lock Channels. Set mass spectrometer lock channels as specified in Table 3. Monitor the quality control check channels specified in Table 3 to verify instrument stability during the analysis.
7. Quality Control7.1 Sampling Train Collection Efficiency Check. Add 100 µl of the surrogate standards in Table 1 to the absorbent cartridge of each train before collecting the field samples.
7.2 Internal Standard Percent Recoveries. A group of nine carbon labeled PCDD's and PCDF's representing, the tetra-through octachlorinated homologues, is added to every sample prior to extraction. The role of the internal standards is to quantify the native PCDD's and PCDF's present in the sample as well as to determine the overall method efficiency. Recoveries of the internal standards must be between 40 to 130 percent for the tetra-through hexachlorinated compounds while the range is 25 to 130 percent for the higher hepta- and octachlorinated homologues.
7.3 Surrogate Recoveries. The five surrogate compounds in Table 2 are added to the resin in the adsorbent sampling cartridge before the sample is collected. The surrogate recoveries are measured relative to the internal standards and are a measure of collection efficiency. They are not used to measure native PCDD's and PCDF's. All recoveries shall be between 70 and 130 percent. Poor recoveries for all the surrogates may be an indication of breakthrough in the sampling train. If the recovery of all standards is below 70 percent, the sampling runs must be repeated. As an alternative, the sampling runs do not have to be repeated if the final results are divided by the fraction of surrogate recovery. Poor recoveries of isolated surrogate compounds should not be grounds for rejecting an entire set of the samples.
7.4 Toluene QA Rinse. Report the results of the toluene QA rinse separately from the total sample catch. Do not add it to the total sample.
8.0 [Reserved] 9. CalculationsSame as Method 5, section 6 with the following additions.
9.1 Nomenclature.
Aai = Integrated ion current of the noise at the retention time of the analyte. A*ci = Integrated ion current of the two ions characteristic of the internal standard i in the calibration standard. Acij = Integrated ion current of the two ions characteristic of compound i in the jth calibration standard. A*cij = Integrated ion current of the two ions characteristic of the internal standard i in the jth calibration standard. Acsi = Integrated ion current of the two ions characteristic of surrogate compound i in the calibration standard. Ai = Integrated ion current of the two ions characteristic of compound i in the sample. A*i = Integrated ion current of the two ions characteristic of internal standard i in the sample. Ars = Integrated ion current of the two ions characteristic of the recovery standard. Asi = Integrated ion current of the two ions characteristic of surrogate compound i in the sample. Ci = Concentration of PCDD or PCDF i in the sample, pg/M 3. CT = Total concentration of PCDD's or PCDF's in the sample, pg/M 3. mci = Mass of compound i in the calibration standard injected into the analyzer, pg. mrs = Mass of recovery standard in the calibration standard injected into the analyzer, pg. msi = Mass of surrogate compound in the calibration standard, pg. RRFi = Relative response factor. RRFrs = Recovery standard response factor. RRFs = Surrogate compound response factor.9.2 Average Relative Response Factor.
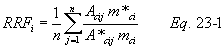
9.3 Concentration of the PCDD's and PCDF's.
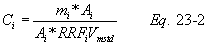
9.4 Recovery Standard Response Factor.
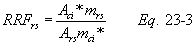
9.5 Recovery of Internal Standards (R*).

9.6 Surrogate Compound Response Factor.
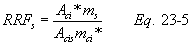
9.7 Recovery of Surrogate Compounds (Rs).

9.8 Minimum Detectable Limit (MDL).
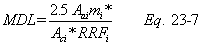
9.9 Total Concentration of PCDD's and PCDF's in the Sample.
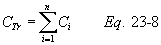
Any PCDD's or PCDF's that are reported as nondetected (below the MDL) shall be counted as zero for the purpose of calculating the total concentration of PCDD's and PCDF's in the sample.
10. Bibliography1. American Society of Mechanical Engineers. Sampling for the Determination of Chlorinated Organic Compounds in Stack Emissions. Prepared for U.S. Department of Energy and U.S. Environmental Protection Agency. Washington DC. December 1984. 25 p.
2. American Society of Mechanical Engineers. Analytical Procedures to Assay Stack Effluent Samples and Residual Combustion Products for Polychlorinated Dibenzo-p-Dioxins (PCDD) and Polychlorinated Dibenzofurans (PCDF). Prepared for the U.S. Department of Energy and U.S. Environmental Protection Agency. Washington, DC. December 1984. 23 p.
3. Thompson, J. R. (ed.). Analysis of Pesticide Residues in Human and Environmental Samples. U.S. Environmental Protection Agency. Research Triangle Park, NC. 1974.
4. Triangle Laboratories. Case Study: Analysis of Samples for the Presence of Tetra Through Octachloro-p-Dibenzodioxins and Dibenzofurans. Research Triangle Park, NC. 1988. 26 p.
5. U.S. Environmental Protection Agency. Method 8290 - The Analysis of Polychlorinated Dibenzo-p-dioxin and Polychlorinated Dibenzofurans by High-Resolution Gas Chromotography/High-Resolution Mass Spectrometry. In: Test Methods for Evaluating Solid Waste. Washington, DC. SW-846.
Table 1 - Composition of the Sample Fortification and Recovery Standards Solutions
Analyte | Concentration (pg/µl) |
---|---|
Internal Standards: | |
13 C12-2,3,7,8-TCDD | 100 |
13 C12-1,2,3,7,8-PeCDD | 100 |
13 C12-1,2,3,6,7,8-HxCDD | 100 |
13 C12-1,2,3,4,6,7,8-HpCDD | 100 |
13 C12-OCDD | 100 |
13 C12-2,3,7,8-TCDF | 100 |
13 C12-1,2,3,7,8-PeCDF | 100 |
13 C12-1,2,3,6,7,8-HxCDF | 100 |
13 C12-1,2,3,4,6,7,8-HpCDF | 100 |
Surrogate Standards: | |
37 Cl4-2,3,7,8-TCDD | 100 |
13 C12-1,2,3,4,7,8-HxCDD | 100 |
13 C12-2,3,4,7,8-PeCDF | 100 |
13 C12-1,2,3,4,7,8-HxCDF | 100 |
13 C12-1,2,3,4,7,8,9-HpCDF | 100 |
Recovery Standards: | |
13 C12-1,2,3,4-TCDD | 500 |
13 C12-1,2,3,7,8,9-HxCDD | 500 |
Table 2 - Composition of the Initial Calibration Solutions
Compound | Concentrations (pg/µL) | ||||
---|---|---|---|---|---|
Solution No. | |||||
1 | 2 | 3 | 4 | 5 | |
Alternate Standard: | |||||
13 C12-1,2,3,7,8,9-HxCDF | 2.5 | 5 | 25 | 250 | 500 |
Recovery Standards: | |||||
13 C12-1,2,3,4-TCDD | 100 | 100 | 100 | 100 | 100 |
13 C12-1,2,3,7,8,9-HxCDD | 100 | 100 | 100 | 100 | 100 |
Table 3 - Elemental Compositions and Exact Masses of the Ions Monitored by High Resolution Mass Spectrometry for PCDD's and PCDF's
Descriptor No. | Accurate mass | Ion type | Elemental composition | Analyte |
---|---|---|---|---|
2 | 292.9825 | LOCK | C7F11 | PFK |
303.9016 | M | C12H4 35Cl4O | TCDF | |
305.8987 | M + 2 | C12H4 35Cl 37O | TCDF | |
315.9419 | M | 13C12H4 35Cl4O | TCDF (S) | |
317.9389 | M + 2 | 13C12H4 35Cl3 37ClO | TCDF (S) | |
319.8965 | M | C12H4 35ClO2 | TCDD | |
321.8936 | M + 2 | C12H4 35Cl3 37ClO2 | TCDD | |
327.8847 | M | C12H4 37Cl4O2 | TCDD (S) | |
330.9792 | QC | C7F13 | PFK | |
331.9368 | M | 13C12H4 35Cl4O2 | TCDD (S) | |
333.9339 | M + 2 | 13C12H4 35Cl 37ClO2 | TCDD (S) | |
339.8597 | M + 2 | C12H3 35Cl4 37ClO | PECDF | |
341.8567 | M + 4 | C12H3 35Cl3 37Cl2O | PeCDF | |
351.9000 | M + 2 | 13C12H3 35Cl4 37ClO | PeCDF (S) | |
353.8970 | M + 4 | 13C12H3 35Cl 35 37Cl2O | PeCDF (S) | |
355.8546 | M + 2 | C12H3 35Cl337ClO2 | PeCDD | |
357.8516 | M + 4 | C12H3 35Cl3 37Cl2O2 | PeCDD | |
367.8949 | M + 2 | 13C12H3 35Cl4 37ClO2 | PeCDD (S) | |
369.8919 | M + 4 | 13C12H3 35Cl3 37 Cl2O2 | PeCDD (S) | |
375.8364 | M + 2 | C12H4 35Cl5 37ClO | HxCDPE | |
409.7974 | M + 2 | C12H3 35Cl6 37ClO | HpCPDE | |
3 | 373.8208 | M + 2 | C12H235Cl5 37ClO | HxCDF |
375.8178 | M + 4 | C12H2 35Cl4 37Cl2O | HxCDF | |
383.8639 | M | 13C12H2 35Cl6O | HxCDF (S) | |
385.8610 | M + 2 | 13C12H2 35Cl5 37ClO | HxCDF (S) | |
389.8157 | M + 2 | C12H2 35Cl5 37ClO2 | HxCDD | |
391.8127 | M + 4 | C12H2 35Cl4 37Cl2O2 | HxCDD | |
392.9760 | LOCK | C9F15 | PFK | |
401.8559 | M + 2 | 13C12H2 35Cl5 37ClO2 | HxCDD (S) | |
403.8529 | M + 4 | 13C12H2 35Cl4 37Cl2O | HxCDD (S) | |
445.7555 | M + 4 | C12H2 35Cl6 37Cl2O | OCDPE | |
430.9729 | QC | C9F17 | PFK | |
4 | 407.7818 | M + 2 | C12H 35Cl6 37ClO | HpCDF |
409.7789 | M + 4 | C12H 35Cl5 37Cl2O | HpCDF | |
417.8253 | M | 13C12H 35Cl7O | HpCDF (S) | |
419.8220 | M + 2 | 13C12H 35Cl6 37ClO | HpCDF (S) | |
423.7766 | M + 2 | C12H 35Cl6 37ClO2 | HpCDD | |
425.7737 | M + 4 | C12H 35Cl5 37Cl2O2 | HpCDD | |
435.8169 | M + 2 | 13C12H 35Cl6 37ClO2 | HpCDD (S) | |
437.8140 | M + 4 | 13C12H 35Cl5 37Cl2O2 | HpCDD (S) | |
479.7165 | M + 4 | C12H 35Cl7 37Cl2O | NCPDE | |
430.9729 | LOCK | C9F17 | PFK | |
441.7428 | M + 2 | C12 35Cl7 37ClO | OCDF | |
443.7399 | M + 4 | C12 35Cl6 37Cl2O | OCDF | |
457.7377 | M + 2 | C12 35Cl7 37ClO2 | OCDD | |
459.7348 | M + 4 | C12 35Cl6 37Cl2O2 | OCDD | |
469.7779 | M + 2 | 13C12 35Cl7 37ClO2 | OCDD (S) | |
471.7750 | M + 4 | 13C12 35Cl6 37Cl2O2 | OCDD (S) | |
513.6775 | M + 4 | C12 35Cl8 37Cl2O2 | DCDPE | |
442.9728 | QC | C10F17 | PFK |
(a) The following nuclidic masses were used:
H = 1.007825
C = 12.000000
13C = 13.003355
F = 18.9984
O = 15.994915
35Cl = 34.968853
37Cl = 36.965903
S = Labeled Standard
QC = Ion selected for monitoring instrument stability during the GC/MS analysis.
Table 4 - Acceptable Ranges for Ion-Abundance Ratios of PCDD's and PCDF's
No. of chlorine atoms | Ion type | Theoretical ratio | Control limits | |
---|---|---|---|---|
Lower | Upper | |||
4 | M/M + 2 | 0.77 | 0.65 | 0.89 |
5 | M + 2/M + 4 | 1.55 | 1.32 | 1.78 |
6 | M + 2/M + 4 | 1.24 | 1.05 | 1.43 |
6 a | M/M + 2 | 0.51 | 0.43 | 0.59 |
7 b | M/M + 2 | 0.44 | 0.37 | 0.51 |
7 | M + 2/M + 4 | 1.04 | 0.88 | 1.20 |
8 | M + 2/M + 4 | 0.89 | 0.76 | 1.02 |
a Used only for 13C-HxCDF.
b Used only for 13C-HpCDF.
Table 5 - Minimum Requirements for Initial and Daily Calibration Response Factors
Compound | Relative response factors | |
---|---|---|
Initial calibration RSD | Daily calibration % difference | |
Unlabeled Analytes: |
||
2,3,7,8-TCDD | 25 | 25 |
2,3,7,8-TCDF | 25 | 25 |
1,2,3,7,8-PeCDD | 25 | 25 |
1,2,3,7,8-PeCDF | 25 | 25 |
2,3,4,7,8-PeCDF | 25 | 25 |
1,2,4,5,7,8-HxCDD | 25 | 25 |
1,2,3,6,7,8-HxCDD | 25 | 25 |
1,2,3,7,8,9-HxCDD | 25 | 25 |
1,2,3,4,7,8-HxCDF | 25 | 25 |
1,2,3,6,7,8-HxCDF | 25 | 25 |
1,2,3,7,8,9-HxCDF | 25 | 25 |
2,3,4,6,7,8-HxCDF | 25 | 25 |
1,2,3,4,6,7,8-HpCDD | 25 | 25 |
1,2,3,4,6,7,8-HpCDF | 25 | 25 |
OCDD | 25 | 25 |
OCDF | 30 | 30 |
Internal Standards: |
||
13C12-2,3,7,8-TCDD | 25 | 25 |
13C12-1,2,3,7,8-PeCDD | 30 | 30 |
13C12-1,2,3,6,7,8-HxCDD | 25 | 25 |
13C12-1,2,3,4,6,7,8-HpCDD | 30 | 30 |
13C12-OCDD | 30 | 30 |
13C12-2,3,7,8-TCDF | 30 | 30 |
13C12-1,2,3,7,8-PeCDF | 30 | 30 |
13C12-1,2,3,6,7,8-HxCDF | 30 | 30 |
13C12-1,2,3,4,6,7,8-HpCDF | 30 | 30 |
Surrogate Standards: |
||
37Cl4-2,3,7,8-TCDD | 25 | 25 |
13C12-2,3,4,7,8-PeCDF | 25 | 25 |
13C12-1,2,3,4,7,8-HxCDD | 25 | 25 |
13C12-1,2,3,4,7,8-HxCDF | 25 | 25 |
13C12-1,2,3,4,7,8,9-HpCDF | 25 | 25 |
Alternate Standard: |
||
13C12-1,2,3,7,8,9-HxCDF | 25 | 25 |
1.1 Analytes.
Analyte | CAS No. |
---|---|
Volatile organic compounds Water | No CAS Number assigned 7732-18-5 |
1.2 Applicability. This method is applicable for the determination of volatile matter content, water content, density, volume solids, and weight solids of paint, varnish, lacquer, or other related surface coatings.
1.3 Precision and Bias. Intra-and inter-laboratory analytical precision statements are presented in section 13.1. No bias has been identified.
2.0 Summary of Method2.1 Standard methods are used to determine the volatile matter content, water content, density, volume solids, and weight solids of paint, varnish, lacquer, or other related surface coatings.
3.0 Definitions3.1 Waterborne coating means any coating which contains more than 5 percent water by weight in its volatile fraction.
3.2 Multicomponent coatings are coatings that are packaged in two or more parts, which are combined before application. Upon combination a coreactant from one part of the coating chemically reacts, at ambient conditions, with a coreactant from another part of the coating.
3.3 Ultraviolet (UV) radiation-cured coatings are coatings which contain unreacted monomers that are polymerized by exposure to ultraviolet light.
4.0 Interferences [Reserved] 5.0 Safety5.1 Disclaimer. This method may involve hazardous materials, operations, and equipment. This test method may not address all of the safety problems associated with its use. It is the responsibility of the user of this test method to establish appropriate safety and health practices and to determine the applicability of regulatory limitations prior to performing this test method.
5.2 Hazardous Components. Several of the compounds that may be contained in the coatings analyzed by this method may be irritating or corrosive to tissues (e.g., heptane) or may be toxic (e.g., benzene, methyl alcohol). Nearly all are fire hazards. Appropriate precautions can be found in reference documents, such as Reference 3 of section 16.0.
6.0 Equipment and SuppliesThe equipment and supplies specified in the ASTM methods listed in sections 6.1 through 6.6 (incorporated by reference - see § 60.17 for acceptable versions of the methods) are required:
6.1 ASTM D 1475-60, 80, or 90, Standard Test Method for Density of Paint, Varnish, Lacquer, and Related Products.
6.2 ASTM D 2369-81, 87, 90, 92, 93, 95, or 10. Standard Test Method for Volatile Content of Coatings.
6.3 ASTM D 3792-79 or 91, Standard Test Method for Water Content of Water Reducible Paints by Direct Injection into a Gas Chromatograph.
6.4 ASTM D 4017-81, 90, or 96a, Standard Test Method for Water in Paints and Paint Materials by the Karl Fischer Titration Method.
6.5 ASTM 4457-85 91, Standard Test Method for Determination of Dichloromethane and 1,1,1-Trichloroethane in Paints and Coatings by Direct Injection into a Gas Chromatograph.
6.6 ASTM D 5403-93, Standard Test Methods for Volatile Content of Radiation Curable Materials.
6.7 ASTM D 6419-00, Test Method for Volatile Content of Sheet-Fed and Coldset Web Offset Printing Inks.
7.0 Reagents and Standards7.1 The reagents and standards specified in the ASTM methods listed in sections 6.1 through 6.6 are required.
8.0 Sample Collection, Preservation, Storage, and Transport8.1 Follow the sample collection, preservation, storage, and transport procedures described in Reference 1 of section 16.0.
9.0 Quality Control9.1 Reproducibility
Note:Not applicable to UV radiation-cured coatings). The variety of coatings that may be subject to analysis makes it necessary to verify the ability of the analyst and the analytical procedures to obtain reproducible results for the coatings tested. Verification is accomplished by running duplicate analyses on each sample tested (Sections 11.2 through 11.4) and comparing the results with the intra-laboratory precision statements (Section 13.1) for each parameter.
9.2 Confidence Limits for Waterborne Coatings. Because of the inherent increased imprecision in the determination of the VOC content of waterborne coatings as the weight percent of water increases, measured parameters for waterborne coatings are replaced with appropriate confidence limits (Section 12.6). These confidence limits are based on measured parameters and inter-laboratory precision statements.
10.0 Calibration and Standardization10.1 Perform the calibration and standardization procedures specified in the ASTM methods listed in sections 6.1 through 6.6.
11.0 Analytical ProcedureAdditional guidance can be found in Reference 2 of section 16.0.
11.1 Non Thin-film Ultraviolet Radiation-cured (UV radiation-cured) Coatings.
11.1.1 Volatile Content. Use the procedure in ASTM D 5403 to determine the volatile matter content of the coating except the curing test described in NOTE 2 of ASTM D 5403 is required.
11.1.2 Water Content. To determine water content, follow section 11.3.2.
11.1.3 Coating Density. To determine coating density, follow section 11.3.3.
11.1.4 Solids Content. To determine solids content, follow section 11.3.4.
11.1.5 To determine if a coating or ink can be classified as a thin-film UV cured coating or ink, use the equation in section 12.2. If C is less than 0.2 g and A is greater than or equal to 225 cm 2 (35 in 2) then the coating or ink is considered a thin-film UV radiation-cured coating and ASTM D 5403 is not applicable.
Note:As noted in section 1.4 of ASTM D 5403, this method may not be applicable to radiation curable materials wherein the volatile material is water.
11.2 Multi-component Coatings.
11.2.1 Sample Preparation.
11.2.1.1 Prepare about 100 ml of sample by mixing the components in a storage container, such as a glass jar with a screw top or a metal can with a cap. The storage container should be just large enough to hold the mixture. Combine the components (by weight or volume) in the ratio recommended by the manufacturer. Tightly close the container between additions and during mixing to prevent loss of volatile materials. However, most manufacturers mixing instructions are by volume. Because of possible error caused by expansion of the liquid when measuring the volume, it is recommended that the components be combined by weight. When weight is used to combine the components and the manufacturer's recommended ratio is by volume, the density must be determined by section 11.3.3.
11.2.1.2 Immediately after mixing, take aliquots from this 100 ml sample for determination of the total volatile content, water content, and density.
11.2.2 Volatile Content. To determine total volatile content, use the apparatus and reagents described in ASTM D2369 (incorporated by reference; see § 60.17 for the approved versions of the standard), respectively, and use the following procedures:
11.2.2.1 Weigh and record the weight of an aluminum foil weighing dish. Add 3 ±1 ml of suitable solvent as specified in ASTM D2369 to the weighing dish. Using a syringe as specified in ASTM D2369, weigh to 1 mg, by difference, a sample of coating into the weighing dish. For coatings believed to have a volatile content less than 40 weight percent, a suitable size is 0.3 + 0.10 g, but for coatings believed to have a volatile content greater than 40 weight percent, a suitable size is 0.5 ±0.1 g.
Note:If the volatile content determined pursuant to section 12.4 is not in the range corresponding to the sample size chosen repeat the test with the appropriate sample size. Add the specimen dropwise, shaking (swirling) the dish to disperse the specimen completely in the solvent. If the material forms a lump that cannot be dispersed, discard the specimen and prepare a new one. Similarly, prepare a duplicate. The sample shall stand for a minimum of 1 hour, but no more than 24 hours prior to being oven cured at 110 ±5 °C (230 ±9 °F) for 1 hour.
11.2.2.2 Heat the aluminum foil dishes containing the dispersed specimens in the forced draft oven for 60 min at 110 ±5 °C (230 ±9 °F). Caution - provide adequate ventilation, consistent with accepted laboratory practice, to prevent solvent vapors from accumulating to a dangerous level.
11.2.2.3 Remove the dishes from the oven, place immediately in a desiccator, cool to ambient temperature, and weigh to within 1 mg.
11.2.2.4 Run analyses in pairs (duplicate sets) for each coating mixture until the criterion in section 11.4 is met. Calculate WV following Equation 24-2 and record the arithmetic average.
11.2.3 Water Content. To determine water content, follow section 11.3.2.
11.2.4 Coating Density. To determine coating density, follow section 11.3.3.
11.2.5 Solids Content. To determine solids content, follow section 11.3.4.
11.2.6 Exempt Solvent Content. To determine the exempt solvent content, follow section 11.3.5.
Note:For all other coatings (i.e., water-or solvent-borne coatings) not covered by multicomponent or UV radiation-cured coatings, analyze as shown below:
11.3 Water-or Solvent-borne coatings.
11.3.1 Volatile Content. Use the procedure in ASTM D 2369 to determine the volatile matter content (may include water) of the coating.
11.3.1.1 Record the following information:
W1 = weight of dish and sample before heating, g W2 = weight of dish and sample after heating, g W3 = sample weight, g.11.3.1.2 Calculate the weight fraction of the volatile matter (Wv) for each analysis as shown in section 12.3.
11.3.1.3 Run duplicate analyses until the difference between the two values in a set is less than or equal to the intra-laboratory precision statement in section 13.1.
11.3.1.4 Record the arithmetic average (Wv).
11.3.2 Water Content. For waterborne coatings only, determine the weight fraction of water (Ww) using either ASTM D 3792 or ASTM D 4017.
11.3.2.1 Run duplicate analyses until the difference between the two values in a set is less than or equal to the intra-laboratory precision statement in section 13.1.
11.3.2.2 Record the arithmetic average (ww).
11.3.3 Coating Density. Determine the density (Dc, kg/l) of the surface coating using the procedure in ASTM D 1475.
11.3.3.1 Run duplicate analyses until each value in a set deviates from the mean of the set by no more than the intra-laboratory precision statement in section 13.1.
11.3.3.2 Record the arithmetic average (Dc).
11.3.4 Solids Content. Determine the volume fraction (Vs) solids of the coating by calculation using the manufacturer's formulation.
11.3.5 Exempt Solvent Content. Determine the weight fraction of exempt solvents (WE) by using ASTM Method D4457. Run a duplicate set of determinations and record the arithmetic average (WE).
11.4 Sample Analysis Criteria. For Wv and Ww, run duplicate analyses until the difference between the two values in a set is less than or equal to the intra-laboratory precision statement for that parameter. For Dc, run duplicate analyses until each value in a set deviates from the mean of the set by no more than the intra-laboratory precision statement. If, after several attempts, it is concluded that the ASTM procedures cannot be used for the specific coating with the established intra-laboratory precision (excluding UV radiation-cured coatings), the U.S. Environmental Protection Agency (EPA) will assume responsibility for providing the necessary procedures for revising the method or precision statements upon written request to: Director, Emissions, Monitoring, and Analysis Division, MD-14, Office of Air Quality Planning and Standards, U.S. Environmental Protection Agency, Research Triangle Park, NC 27711.
12.0 Calculations and Data Analysis12.1 Nomenclature.
A = Area of substrate, cm 2, (in 2). C = Amount of coating or ink added to the substrate, g. Dc = Density of coating or ink, g/cm 3 (g/in 3). F = Manufacturer's recommended film thickness, cm (in). Wo = Weight fraction of nonaqueous volatile matter, g/g. Ws = Weight fraction of solids, g/g. Wv = Weight fraction of the volatile matter, g/g. Ww = Weight fraction of the water, g/g.12.2 To determine if a coating or ink can be classified as a thin-film UV cured coating or ink, use the following equation:
12.3 Calculate Wv for each analysis as shown below:
12.4 Nonaqueous Volatile Matter.
12.4.1 Solvent-borne Coatings.
12.4.2 Waterborne Coatings.
12.4.3 Coatings Containing Exempt Solvents.
12.5 Weight Fraction Solids.
12.6 Confidence Limit Calculations for Waterborne Coatings. To calculate the lower confidence limit, subtract the appropriate inter-laboratory precision value from the measured mean value for that parameter. To calculate the upper confidence limit, add the appropriate inter-laboratory precision value to the measured mean value for that parameter. For Wv and Dc, use the lower confidence limits; for Ww, use the upper confidence limit. Because Ws is calculated, there is no adjustment for this parameter.
13.0 Method Performance13.1 Analytical Precision Statements. The intra-and inter-laboratory precision statements are given in Table 24-1 in section 17.0.
14.0 Pollution Prevention [Reserved] 15.0 Waste Management [Reserved] 16.0 ReferencesSame as specified in section 6.0, with the addition of the following:
1. Standard Procedure for Collection of Coating and Ink Samples for Analysis by Reference Methods 24 and 24A. EPA-340/1-91-010. U.S. Environmental Protection Agency, Stationary Source Compliance Division, Washington, D.C. September 1991.
2. Standard Operating Procedure for Analysis of Coating and Ink Samples by Reference Methods 24 and 24A.
EPA-340/1-91-011. U.S. Environmental Protection Agency, Stationary Source Compliance Division, Washington, D.C. September 1991.
3. Handbook of Hazardous Materials: Fire, Safety, Health. Alliance of American Insurers. Schaumberg, IL. 1983.
17.0 Tables, Diagrams, Flowcharts, and Validation DataTable 24-1 - Analytical Precision Statements
Intra-laboratory | Inter-laboratory | |
---|---|---|
Volatile matter content, Wv | ±0.015 Wv | ±0.047 W v |
Water content, Ww | ±0.029 W w | ±0.075 Ww |
Density, Dc | ±0.001 kg/l | ±0.002 kg/l |
1.1 Analytes.
Analyte | CAS No. |
---|---|
Volatile organic compounds (VOC) | No CAS number assigned. |
1.2 Applicability. This method is applicable for the determination of the VOC content and density of solvent-borne (solvent-reducible) publication rotogravure inks and related publication rotogravure coatings.
2.0 Summary of Method2.1 Separate procedures are used to determine the VOC weight fraction and density of the ink or related coating and the density of the solvent in the ink or related coating. The VOC weight fraction is determined by measuring the weight loss of a known sample quantity which has been heated for a specified length of time at a specified temperature. The density of both the ink or related coating and solvent are measured by a standard procedure. From this information, the VOC volume fraction is calculated.
3.0 Definitions [Reserved] 4.0 Interferences [Reserved] 5.0 Safety5.1 Disclaimer. This method may involve hazardous materials, operations, and equipment. This test method does not purport to address all of the safety problems associated with its use. It is the responsibility of the user of this test method to establish appropriate safety and health practices and to determine the applicability of regulatory limitations prior to performing this test method.
5.2 Hazardous Components. Some of the compounds that may be contained in the inks or related coatings analyzed by this method may be irritating or corrosive to tissues or may be toxic. Nearly all are fire hazards. Appropriate precautions can be found in reference documents, such as Reference 6 of section 16.0.
6.0 Equipment and SuppliesThe following equipment and supplies are required for sample analysis:
6.1 Weighing Dishes. Aluminum foil, 58 mm (2.3 in.) in diameter by 18 mm (0.7 in.) high, with a flat bottom. There must be at least three weighing dishes per sample.
6.2 Disposable Syringe. 5 ml.
6.3 Analytical Balance. To measure to within 0.1 mg.
6.4 Oven. Vacuum oven capable of maintaining a temperature of 120 ±2 °C (248 ±4 °F) and an absolute pressure of 510 ±51 mm Hg (20 ±2 in. Hg) for 4 hours. Alternatively, a forced draft oven capable of maintaining a temperature of 120 ±2 °C (248 ±4 °F) for 24 hours.
6.5 The equipment and supplies specified in ASTM D 1475-60, 80, or 90 (incorporated by reference - see § 60.17).
7.0 Reagents and Standards7.1 The reagents and standards specified in ASTM D 1475-60, 80, or 90 are required.
8.0 Sample Collection, Preservation, Storage, and Transport8.1 Follow the sample collection, preservation, storage, and transport procedures described in Reference 4 of section 16.0.
9.0 Quality Control [Reserved] 10.0 Calibration and Standardization [Reserved] 11.0 Analytical ProcedureAdditional guidance can be found in Reference 5 of section 16.0.
11.1 VOC Weight Fraction. Shake or mix the ink or related coating sample thoroughly to assure that all the solids are completely suspended. Label and weigh to the nearest 0.1 mg a weighing dish and record this weight (Mx1). Using a 5 ml syringe, without a needle, extract an aliquot from the ink or related coating sample. Weigh the syringe and aliquot to the nearest 0.1 mg and record this weight (Mcy1). Transfer 1 to 3 g of the aliquot to the tared weighing dish. Reweigh the syringe and remaining aliquot to the nearest 0.1 mg and record this weight (Mcy2). Heat the weighing dish with the transferred aliquot in a vacuum oven at an absolute pressure of 510 ±51 mm Hg (20 ±2 in. Hg) and a temperature of 120 ±2 °C (248 ±4 °F) for 4 hours. Alternatively, heat the weighing dish with the transferred aliquot in a forced draft oven at a temperature of 120 ±2 °C for 24 hours. After the weighing dish has cooled, reweigh it to the nearest 0.1 mg and record the weight (Mx2). Repeat this procedure two times for each ink or related coating sample, for a total of three samples.
11.2 Ink or Related Coating Density. Determine the density of the ink or related coating (Dc) according to the procedure outlined in ASTM D 1475. Make a total of three determinations for each ink or related coating sample. Report the ink or related coating density as the arithmetic average (Dc) of the three determinations.
11.3 Solvent Density. Determine the density of the solvent (Do) according to the procedure outlined in ASTM D 1475. Make a total of three determinations for each ink or related coating sample. Report the solvent density as the arithmetic average (Do) of the three determinations.
12.0 Calculations and Data Analysis12.1 VOC Weight Fraction. For each determination, calculate the volatile organic content weight fraction (Wo) using the following equation:
Make a total of three determinations. Report the VOC weight fraction as the arithmetic average (W o) of the three determinations.12.2 VOC Volume Fraction. Calculate the volume fraction volatile organic content (Vo) using the following equation:
13.0 Method Performance [Reserved] 14.0 Pollution Prevention [Reserved] 15.0 Waste Management [Reserved] 16.0 References1. Standard Test Method for Density of Paint, Varnish, Lacquer, and Related Products. ASTM Designation D 1475.
2. Teleconversation. Wright, Chuck, Inmont Corporation with Reich, R., A., Radian Corporation. September 25, 1979, Gravure Ink Analysis.
3. Teleconversation. Oppenheimer, Robert, Gravure Research Institute with Burt, Rick, Radian Corporation, November 5, 1979, Gravure Ink Analysis.
4. Standard Procedure for Collection of Coating and Ink Samples for Analysis by Reference Methods 24 and 24A. EPA-340/1-91-010. U.S. Environmental Protection Agency, Stationary Source Compliance Division, Washington, D.C. September 1991.
5. Standard Operating Procedure for Analysis of Coating and Ink Samples by Reference Methods 24 and 24A. EPA-340/1-91-011. U.S. Environmental Protection Agency, Stationary Source Compliance Division, Washington, D.C. September 1991.
6. Handbook of Hazardous Materials: Fire, Safety, Health. Alliance of American Insurers. Schaumberg, IL. 1983.
17.0 Tables, Diagrams, Flowcharts, and Validation Data [Reserved] Method 25 - Determination of Total Gaseous Nonmethane Organic Emissions as Carbon 1.0 Scope and Application1.1 Analytes.
Analyte | CAS No. | Sensitivity |
---|---|---|
Total gaseous nonmethane organic compounds (TGNMO) | N/A | Dependent upon analytical equipment. |
1.2 Applicability.
1.2.1 This method is applicable for the determination of volatile organic compounds (VOC) (measured as total gaseous nonmethane organics (TGNMO) and reported as carbon) in stationary source emissions. This method is not applicable for the determination of organic particulate matter.
1.2.2 This method is not the only method that applies to the measurement of VOC. Costs, logistics, and other practicalities of source testing may make other test methods more desirable for measuring VOC contents of certain effluent streams. Proper judgment is required in determining the most applicable VOC test method. For example, depending upon the molecular composition of the organics in the effluent stream, a totally automated semicontinuous nonmethane organics (NMO) analyzer interfaced directly to the source may yield accurate results. This approach has the advantage of providing emission data semicontinuously over an extended time period.
1.2.3 Direct measurement of an effluent with a flame ionization detector (FID) analyzer may be appropriate with prior characterization of the gas stream and knowledge that the detector responds predictably to the organic compounds in the stream. If present, methane (CH4) will, of course, also be measured. The FID can be used under any of the following limited conditions: (1) Where only one compound is known to exist; (2) when the organic compounds consist of only hydrogen and carbon; (3) where the relative percentages of the compounds are known or can be determined, and the FID responses to the compounds are known; (4) where a consistent mixture of the compounds exists before and after emission control and only the relative concentrations are to be assessed; or (5) where the FID can be calibrated against mass standards of the compounds emitted (solvent emissions, for example).
1.2.4 Another example of the use of a direct FID is as a screening method. If there is enough information available to provide a rough estimate of the analyzer accuracy, the FID analyzer can be used to determine the VOC content of an uncharacterized gas stream. With a sufficient buffer to account for possible inaccuracies, the direct FID can be a useful tool to obtain the desired results without costly exact determination.
1.2.5 In situations where a qualitative/quantitative analysis of an effluent stream is desired or required, a gas chromatographic FID system may apply. However, for sources emitting numerous organics, the time and expense of this approach will be formidable.
2.0 Summary of Method2.1 An emission sample is withdrawn from the stack at a constant rate through a heated filter and a chilled condensate trap by means of an evacuated sample tank. After sampling is completed, the TGNMO are determined by independently analyzing the condensate trap and sample tank fractions and combining the analytical results. The organic content of the condensate trap fraction is determined by oxidizing the NMO to carbon dioxide (CO2) and quantitatively collecting in the effluent in an evacuated vessel; then a portion of the CO2 is reduced to CH4 and measured by an FID. The organic content of the sample tank fraction is measured by injecting a portion of the sample into a gas chromatographic column to separate the NMO from carbon monoxide (CO), CO2, and CH4; the NMO are oxidized to CO2, reduced to CH4, and measured by an FID. In this manner, the variable response of the FID associated with different types of organics is eliminated.
3.0 Definitions [Reserved] 4.0 Interferences4.1 Carbon Dioxide and Water Vapor. When carbon dioxide (CO2) and water vapor are present together in the stack, they can produce a positive bias in the sample. The magnitude of the bias depends on the concentrations of CO2 and water vapor. As a guideline, multiply the CO2 concentration, expressed as volume percent, times the water vapor concentration. If this product does not exceed 100, the bias can be considered insignificant. For example, the bias is not significant for a source having 10 percent CO2 and 10 percent water vapor, but it might be significant for a source having 10 percent CO2 and 20 percent water vapor.
4.2. Particulate Matter. Collection of organic particulate matter in the condensate trap would produce a positive bias. A filter is included in the sampling equipment to minimize this bias.
5.0 Safety5.1 Disclaimer. This method may involve hazardous materials, operations, and equipment. This test method may not address all of the safety problems associated with its use. It is the responsibility of the user of this test method to establish appropriate safety and health practices and determine the applicability of regulatory limitations prior to performing this test method.
6.0 Equipment and Supplies6.1 Sample Collection. The sampling system consists of a heated probe, heated filter, condensate trap, flow control system, and sample tank (see Figure 25-1). The TGNMO sampling equipment can be constructed from commercially available components and components fabricated in a machine shop. The following equipment is required:
6.1.1 Heated Probe. 6.4-mm ( 1/4-in.) OD stainless steel tubing with a heating system capable of maintaining a gas temperature at the exit end of at least 129 °C (265 °F). The probe shall be equipped with a temperature sensor at the exit end to monitor the gas temperature. A suitable probe is shown in Figure 25-1. The nozzle is an elbow fitting attached to the front end of the probe while the temperature sensor is inserted in the side arm of a tee fitting attached to the rear of the probe. The probe is wrapped with a suitable length of high temperature heating tape, and then covered with two layers of glass cloth insulation and one layer of aluminum foil or an equivalent wrapping.
Note:If it is not possible to use a heating system for safety reasons, an unheated system with an in-stack filter is a suitable alternative.
6.1.2 Filter Holder. 25-mm ( 15/16-in.) ID Gelman filter holder with 303 stainless steel body and 316 stainless steel support screen with the Viton O-ring replaced by a Teflon O-ring.
6.1.3 Filter Heating System.
6.1.3.1 A metal box consisting of an inner and an outer shell separated by insulating material with a heating element in the inner shell capable of maintaining a gas temperature at the filter of 121 ±3 °C (250 ±5 °F). The heating box shall include temperature sensors to monitor the gas temperature immediately upstream and immediately downstream of the filter.
6.1.3.2 A suitable heating box is shown in Figure 25-2. The outer shell is a metal box that measures 102 mm × 280 mm × 292 mm (4 in. × 11 in. × 11 1/2 in.), while the inner shell is a metal box measuring 76 mm × 229 mm × 241 mm (3 in. × 9 in. × 9 1/2 in.). The inner box is supported by 13-mm ( 1/2-in.) phenolic rods. The void space between the boxes is filled with ceramic fiber insulation which is sealed in place by means of a silicon rubber bead around the upper sides of the box. A removable lid made in a similar manner, with a 25-mm (1-in.) gap between the parts is used to cover the heating chamber. The inner box is heated with a 250-watt cartridge heater, shielded by a stainless steel shroud. The heater is regulated by a thermostatic temperature controller which is set to maintain a gas temperature of 121 °C (250 °F) as measured by the temperature sensor upstream of the filter.
Note:If it is not possible to use a heating system for safety reasons, an unheated system with an in-stack filter is a suitable alternative.
6.1.4 Condensate Trap. 9.5-mm ( 3/8-in.) OD 316 stainless steel tubing bent into a U-shape. Exact dimensions are shown in Figure 25-3. The tubing shall be packed with coarse quartz wool, to a density of approximately 0.11 g/cm 3 before bending. While the condensate trap is packed with dry ice in the Dewar, an ice bridge may form between the arms of the condensate trap making it difficult to remove the condensate trap. This problem can be prevented by attaching a steel plate between the arms of the condensate trap in the same plane as the arms to completely fill the intervening space.
6.1.5 Valve. Stainless steel control valve for starting and stopping sample flow.
6.1.6 Metering Valve. Stainless steel valve for regulating the sample flow rate through the sample train.
6.1.7 Rate Meter. Rotameter, or equivalent, capable of measuring sample flow in the range of 60 to 100 cm 3/min (0.13 to 0.21 ft 3/hr).
6.1.8 Sample Tank. Stainless steel or aluminum tank with a minimum volume of 4 liters (0.14 ft 3).
Note:Sample volumes greater than 4 liters may be required for sources with low organic concentrations.
6.1.9 Mercury Manometer. U-tube manometer or absolute pressure gauge capable of measuring pressure to within 1 mm Hg in the range of 0 to 900 mm.
6.1.10 Vacuum Pump. Capable of evacuating to an absolute pressure of 10 mm Hg.
6.2 Condensate Recovery. The system for the recovery of the organics captured in the condensate trap consists of a heat source, an oxidation catalyst, a nondispersive infrared (NDIR) analyzer, and an intermediate collection vessel (ICV). Figure 25-4 is a schematic of a typical system. The system shall be capable of proper oxidation and recovery, as specified in section 10.1.1. The following major components are required:
6.2.1 Heat Source. Sufficient to heat the condensate trap (including probe) to a temperature of 200 °C (390 °F). A system using both a heat gun and an electric tube furnace is recommended.
6.2.2 Heat Tape. Sufficient to heat the connecting tubing between the water trap and the oxidation catalyst to 100 °C (212 °F).
6.2.3 Oxidation Catalyst. A suitable length of 9.5 mm ( 3/8-in.) OD Inconel 600 tubing packed with 15 cm (6 in.) of 3.2 mm ( 3/8-in.) diameter 19 percent chromia on alumina pellets. The catalyst material is packed in the center of the catalyst tube with quartz wool packed on either end to hold it in place.
6.2.4 Water Trap. Leak-proof, capable of removing moisture from the gas stream.
6.2.5 Syringe Port. A 6.4-mm ( 1/4-in.) OD stainless steel tee fitting with a rubber septum placed in the side arm.
6.2.6 NDIR Detector. Capable of indicating CO2 concentration in the range of zero to 5 percent, to monitor the progress of combustion of the organic compounds from the condensate trap.
6.2.7 Flow-Control Valve. Stainless steel, to maintain the trap conditioning system near atmospheric pressure.
6.2.8 Intermediate Collection Vessel. Stainless steel or aluminum, equipped with a female quick connect. Tanks with nominal volumes of at least 6 liters (0.2 ft 3) are recommended.
6.2.9 Mercury Manometer. Same as described in section 6.1.9.
6.2.10 Syringe. 10-ml gas-tight glass syringe equipped with an appropriate needle.
6.2.11 Syringes. 10-µl and 50-µl liquid injection syringes.
6.2.12 Liquid Sample Injection Unit. 316 Stainless steel U-tube fitted with an injection septum (see Figure 25-7).
6.3 Analysis.
6.3.1 NMO Analyzer. The NMO analyzer is a gas chromatograph (GC) with backflush capability for NMO analysis and is equipped with an oxidation catalyst, reduction catalyst, and FID. Figures 25-5 and 25-6 are schematics of a typical NMO analyzer. This semicontinuous GC/FID analyzer shall be capable of: (1) Separating CO, CO2, and CH4 from NMO, (2) reducing the CO2 to CH4 and quantifying as CH4, and (3) oxidizing the NMO to CO2, reducing the CO2 to CH4 and quantifying as CH4, according to section 10.1.2. The analyzer consists of the following major components:
6.3.1.1 Oxidation Catalyst. A suitable length of 9.5-mm ( 3/8-in.) OD Inconel 600 tubing packed with 5.1 cm (2 in.) of 19 percent chromia on 3.2-mm ( 1/8-in.) alumina pellets. The catalyst material is packed in the center of the tube supported on either side by quartz wool. The catalyst tube must be mounted vertically in a 650 °C (1200 °F) furnace. Longer catalysts mounted horizontally may be used, provided they can meet the specifications of section 10.1.2.1.
6.3.1.2 Reduction Catalyst. A 7.6-cm (3-in.) length of 6.4-mm ( 1/4-in.) OD Inconel tubing fully packed with 100-mesh pure nickel powder. The catalyst tube must be mounted vertically in a 400 °C (750 °F) furnace.
6.3.1.3 Separation Column(s). A 30-cm (1-ft) length of 3.2-mm ( 1/8-in.) OD stainless steel tubing packed with 60/80 mesh Unibeads 1S followed by a 61-cm (2-ft) length of 3.2-mm ( 1/8-in.) OD stainless steel tubing packed with 60/80 mesh Carbosieve G. The Carbosieve and Unibeads columns must be baked separately at 200 °C (390 °F) with carrier gas flowing through them for 24 hours before initial use.
6.3.1.4 Sample Injection System. A single 10-port GC sample injection valve or a group of valves with sufficient ports fitted with a sample loop properly sized to interface with the NMO analyzer (1-cc loop recommended).
6.3.1.5 FID. An FID meeting the following specifications is required:
6.3.1.5.1 Linearity. A linear response (±5 percent) over the operating range as demonstrated by the procedures established in section 10.1.2.3.
6.3.1.5.2 Range. A full scale range of 10 to 50,000 ppm CH4. Signal attenuators shall be available to produce a minimum signal response of 10 percent of full scale.
6.3.1.6 Data Recording System. Analog strip chart recorder or digital integration system compatible with the FID for permanently recording the analytical results.
6.3.2 Barometer. Mercury, aneroid, or other barometer capable of measuring atmospheric pressure to within 1 mm Hg.
6.3.3 Temperature Sensor. Capable of measuring the laboratory temperature within 1 °C (2 °F).
6.3.4 Vacuum Pump. Capable of evacuating to an absolute pressure of 10 mm Hg.
7.0 Reagents and Standards7.1 Sample Collection. The following reagents are required for sample collection:
7.1.1 Dry Ice. Solid CO2, crushed.
7.1.2 Coarse Quartz Wool. 8 to 15 um.
7.1.3 Filters. Glass fiber filters, without organic binder, exhibiting at least 99.95 percent efficiency (<0.05 percent penetration) on 0.3 micron dioctyl phthalate smoke particles. The filter efficiency test shall be conducted in accordance with ASTM Method D2986-71, 78, or 95a (incorporated by reference - see § 60.17). Test data from the supplier's quality control program are sufficient for this purpose.
7.2 NMO Analysis. The following gases are required for NMO analysis:
7.2.1 Carrier Gases. Helium (He) and oxygen (O2) containing less than 1 ppm CO2 and less than 0.1 ppm hydrocarbon.
7.2.2 Fuel Gas. Hydrogen (H2), at least 99.999 percent pure.
7.2.3 Combustion Gas. Either air (less than 0.1 ppm total hydrocarbon content) or O2 (purity 99.99 percent or greater), as required by the detector.
7.3 Condensate Analysis. The following are required for condensate analysis:
7.3.1 Gases. Containing less than 1 ppm carbon.
7.3.1.1 Air.
7.3.1.2 Oxygen.
7.3.2 Liquids. To conform to the specifications established by the Committee on Analytical Reagents of the American Chemical Society.
7.3.2.1 Hexane.
7.3.2.2 Decane.
7.4 Calibration. For all calibration gases, the manufacturer must recommend a maximum shelf life for each cylinder (i.e., the length of time the gas concentration is not expected to change more than ±5 percent from its certified value). The date of gas cylinder preparation, certified organic concentration, and recommended maximum shelf life must be affixed to each cylinder before shipment from the gas manufacturer to the buyer. The following calibration gases are required:
7.4.1 Oxidation Catalyst Efficiency Check Calibration Gas. Gas mixture standard with nominal concentration of 1 percent methane in air.
7.4.2 FID Linearity and NMO Calibration Gases. Three gas mixture standards with nominal propane concentrations of 20 ppm, 200 ppm, and 3000 ppm, in air.
7.4.3 CO2 Calibration Gases. Three gas mixture standards with nominal CO2 concentrations of 50 ppm, 500 ppm, and 1 percent, in air.
Note:Total NMO less than 1 ppm required for 1 percent mixture.
7.4.4 NMO Analyzer System Check Calibration Gases. Four calibration gases are needed as follows:
7.4.4.1 Propane Mixture. Gas mixture standard containing (nominal) 50 ppm CO, 50 ppm CH4, 1 percent CO2, and 20 ppm C3H8, prepared in air.
7.4.4.2 Hexane. Gas mixture standard containing (nominal) 50 ppm hexane in air.
7.4.4.3 Toluene. Gas mixture standard containing (nominal) 20 ppm toluene in air.
7.4.4.4 Methanol. Gas mixture standard containing (nominal) 100 ppm methanol in air.
8.0 Sample Collection, Preservation, Transport, and Storage8.1 Sampling Equipment Preparation.
8.1.1 Condensate Trap Cleaning. Before its initial use and after each use, a condensate trap should be thoroughly cleaned and checked to ensure that it is not contaminated. Both cleaning and checking can be accomplished by installing the trap in the condensate recovery system and treating it as if it were a sample. The trap should be heated as described in section 11.1.3. A trap may be considered clean when the CO2 concentration in its effluent gas drops below 10 ppm. This check is optional for traps that most recently have been used to collect samples which were then recovered according to the procedure in section 11.1.3.
8.1.2 Sample Tank Evacuation and Leak-Check. Evacuate the sample tank to 10 mm Hg absolute pressure or less. Then close the sample tank valve, and allow the tank to sit for 60 minutes. The tank is acceptable if a change in tank vacuum of less than 1 mm Hg is noted. The evacuation and leak-check may be conducted either in the laboratory or the field.
8.1.3 Sampling Train Assembly. Just before assembly, measure the tank vacuum using a mercury manometer. Record this vacuum, the ambient temperature, and the barometric pressure at this time. Close the sample tank valve and assemble the sampling system as shown in Figure 25-1. Immerse the condensate trap body in dry ice at least 30 minutes before commencing sampling to improve collection efficiency. The point where the inlet tube joins the trap body should be 2.5 to 5 cm (1 to 2 in.) above the top of the dry ice.
8.1.4 Pretest Leak-Check. A pretest leak-check is required. Calculate or measure the approximate volume of the sampling train from the probe tip to the sample tank valve. After assembling the sampling train, plug the probe tip, and make certain that the sample tank valve is closed. Turn on the vacuum pump, and evacuate the sampling system from the probe tip to the sample tank valve to an absolute pressure of 10 mm Hg or less. Close the purge valve, turn off the pump, wait a minimum period of 10 minutes, and recheck the indicated vacuum. Calculate the maximum allowable pressure change based on a leak rate of 1 percent of the sampling rate using Equation 25-1, section 12.2. If the measured pressure change exceeds the allowable, correct the problem and repeat the leak-check before beginning sampling.
8.2 Sample Collection.
8.2.1 Unplug the probe tip, and place the probe into the stack such that the probe is perpendicular to the duct or stack axis; locate the probe tip at a single preselected point of average velocity facing away from the direction of gas flow. For stacks having a negative static pressure, seal the sample port sufficiently to prevent air in-leakage around the probe. Set the probe temperature controller to 129 °C (265 °F) and the filter temperature controller to 121 °C (250 °F). Allow the probe and filter to heat for about 30 minutes before purging the sample train.
8.2.2 Close the sample valve, open the purge valve, and start the vacuum pump. Set the flow rate between 60 and 100 cm 3/min (0.13 and 0.21 ft 3/hr), and purge the train with stack gas for at least 10 minutes.
8.2.3 When the temperatures at the exit ends of the probe and filter are within the corresponding specified ranges, check the dry ice level around the condensate trap, and add dry ice if necessary. Record the clock time. To begin sampling, close the purge valve and stop the pump. Open the sample valve and the sample tank valve. Using the flow control valve, set the flow through the sample train to the proper rate. Adjust the flow rate as necessary to maintain a constant rate (±10 percent) throughout the duration of the sampling period. Record the sample tank vacuum and flowmeter setting at 5-minute intervals. (See Figure 25-8.) Select a total sample time greater than or equal to the minimum sampling time specified in the applicable subpart of the regulations; end the sampling when this time period is reached or when a constant flow rate can no longer be maintained because of reduced sample tank vacuum.
Note:If sampling had to be stopped before obtaining the minimum sampling time (specified in the applicable subpart) because a constant flow rate could not be maintained, proceed as follows: After closing the sample tank valve, remove the used sample tank from the sampling train (without disconnecting other portions of the sampling train). Take another evacuated and leak-checked sample tank, measure and record the tank vacuum, and attach the new tank to the sampling train. After the new tank is attached to the sample train, proceed with the sampling until the required minimum sampling time has been exceeded.
8.3 Sample Recovery. After sampling is completed, close the flow control valve, and record the final tank vacuum; then record the tank temperature and barometric pressure. Close the sample tank valve, and disconnect the sample tank from the sample system. Disconnect the condensate trap at the inlet to the rate meter, and tightly seal both ends of the condensate trap. Do not include the probe from the stack to the filter as part of the condensate sample.
8.4 Sample Storage and Transport. Keep the trap packed in dry ice until the samples are returned to the laboratory for analysis. Ensure that run numbers are identified on the condensate trap and the sample tank(s).
9.0 Quality ControlSection | Quality control measure | Effect |
---|---|---|
10.1.1 | Initial performance check of condensate recovery apparatus | Ensure acceptable condensate recovery efficiency. |
10.1.2, 10.2 | NMO analyzer initial and daily performance checks | Ensure precision of analytical results. |
Maintain a record of performance of each item.
10.1 Initial Performance Checks.
10.1.1 Condensate Recovery Apparatus. Perform these tests before the system is first placed in operation, after any shutdown of 6 months or more, and after any major modification of the system, or at the frequency recommended by the manufacturer.
10.1.1.1 Carrier Gas and Auxiliary O2 Blank Check. Analyze each new tank of carrier gas or auxiliary O2 with the NMO analyzer to check for contamination. Treat the gas cylinders as noncondensible gas samples, and analyze according to the procedure in section 11.2.3. Add together any measured CH4, CO, CO2, or NMO. The total concentration must be less than 5 ppm.
10.1.1.2 Oxidation Catalyst Efficiency Check.
10.1.1.2.1 With a clean condensate trap installed in the recovery system or a 1/8″ stainless steel connector tube, replace the carrier gas cylinder with the high level methane standard gas cylinder (Section 7.4.1). Set the four-port valve to the recovery position, and attach an ICV to the recovery system. With the sample recovery valve in vent position and the flow-control and ICV valves fully open, evacuate the manometer or gauge, the connecting tubing, and the ICV to 10 mm Hg absolute pressure. Close the flow-control and vacuum pump valves.
10.1.1.2.2 After the NDIR response has stabilized, switch the sample recovery valve from vent to collect. When the manometer or pressure gauge begins to register a slight positive pressure, open the flow-control valve. Keep the flow adjusted such that the pressure in the system is maintained within 10 percent of atmospheric pressure. Continue collecting the sample in a normal manner until the ICV is filled to a nominal gauge pressure of 300 mm Hg. Close the ICV valve, and remove the ICV from the system. Place the sample recovery valve in the vent position, and return the recovery system to its normal carrier gas and normal operating conditions. Analyze the ICV for CO2 using the NMO analyzer; the catalyst efficiency is acceptable if the CO2 concentration is within 2 percent of the methane standard concentration.
10.1.1.3 System Performance Check. Construct a liquid sample injection unit similar in design to the unit shown in Figure 25-7. Insert this unit into the condensate recovery and conditioning system in place of a condensate trap, and set the carrier gas and auxiliary O2 flow rates to normal operating levels. Attach an evacuated ICV to the system, and switch from system vent to collect. With the carrier gas routed through the injection unit and the oxidation catalyst, inject a liquid sample (see sections 10.1.1.3.1 to 10.1.1.3.4) into the injection port. Operate the trap recovery system as described in section 11.1.3. Measure the final ICV pressure, and then analyze the vessel to determine the CO2 concentration. For each injection, calculate the percent recovery according to section 12.7. Calculate the relative standard deviation for each set of triplicate injections according to section 12.8. The performance test is acceptable if the average percent recovery is 100 ±5 percent and the relative standard deviation is less than 2 percent for each set of triplicate injections.
10.1.1.3.1 50 µl hexane.
10.1.1.3.2 10 µl hexane.
10.1.1.3.3 50 µl decane.
10.1.1.3.4 10 µl decane.
10.1.2 NMO Analyzer. Perform these tests before the system is first placed in operation, after any shutdown longer than 6 months, and after any major modification of the system.
10.1.2.1 Oxidation Catalyst Efficiency Check. Turn off or bypass the NMO analyzer reduction catalyst. Make triplicate injections of the high level methane standard (Section 7.4.1). The oxidation catalyst operation is acceptable if the FID response is less than 1 percent of the injected methane concentration.
10.1.2.2 Reduction Catalyst Efficiency Check. With the oxidation catalyst unheated or bypassed and the heated reduction catalyst bypassed, make triplicate injections of the high level methane standard (Section 7.4.1). Repeat this procedure with both catalysts operative. The reduction catalyst operation is acceptable if the responses under both conditions agree within 5 percent of their average.
10.1.2.3 NMO Analyzer Linearity Check Calibration. While operating both the oxidation and reduction catalysts, conduct a linearity check of the analyzer using the propane standards specified in section 7.4.2. Make triplicate injections of each calibration gas. For each gas (i.e., each set of triplicate injections), calculate the average response factor (area/ppm C) for each gas, as well as and the relative standard deviation (according to section 12.8). Then calculate the overall mean of the response factor values. The instrument linearity is acceptable if the average response factor of each calibration gas is within 2.5 percent of the overall mean value and if the relative standard deviation gas is less than 2 percent of the overall mean value. Record the overall mean of the propane response factor values as the NMO calibration response factor (RFNMO). Repeat the linearity check using the CO2 standards specified in section 7.4.3. Make triplicate injections of each gas, and then calculate the average response factor (area/ppm C) for each gas, as well as the overall mean of the response factor values. Record the overall mean of the response factor values as the CO2 calibration response factor (RFCO2). The RFCO2 must be within 10 percent of the RFNMO.
10.1.2.4 System Performance Check. Check the column separation and overall performance of the analyzer by making triplicate injections of the calibration gases listed in section 7.4.4. The analyzer performance is acceptable if the measured NMO value for each gas (average of triplicate injections) is within 5 percent of the expected value.
10.2 NMO Analyzer Daily Calibration. The following calibration procedures shall be performed before and immediately after the analysis of each set of samples, or on a daily basis, whichever is more stringent:
10.2.1 CO2 Response Factor. Inject triplicate samples of the high level CO2 calibration gas (Section 7.4.3), and calculate the average response factor. The system operation is adequate if the calculated response factor is within 5 percent of the RFCO2 calculated during the initial performance test (Section 10.1.2.3). Use the daily response factor (DRFCO2) for analyzer calibration and the calculation of measured CO2 concentrations in the ICV samples.
10.2.2 NMO Response Factors. Inject triplicate samples of the mixed propane calibration cylinder gas (Section 7.4.4.1), and calculate the average NMO response factor. The system operation is adequate if the calculated response factor is within 10 percent of the RFNMO calculated during the initial performance test (Section 10.1.2.4). Use the daily response factor (DRFNMO) for analyzer calibration and calculation of NMO concentrations in the sample tanks.
10.3 Sample Tank and ICV Volume. The volume of the gas sampling tanks used must be determined. Determine the tank and ICV volumes by weighing them empty and then filled with deionized distilled water; weigh to the nearest 5 g, and record the results. Alternatively, measure the volume of water used to fill them to the nearest 5 ml.
11.0 Analytical Procedure11.1 Condensate Recovery. See Figure 25-9. Set the carrier gas flow rate, and heat the catalyst to its operating temperature to condition the apparatus.
11.1.1 Daily Performance Checks. Each day before analyzing any samples, perform the following tests:
11.1.1.1 Leak-Check. With the carrier gas inlets and the sample recovery valve closed, install a clean condensate trap in the system, and evacuate the system to 10 mm Hg absolute pressure or less. Monitor the system pressure for 10 minutes. The system is acceptable if the pressure change is less than 2 mm Hg.
11.1.1.2 System Background Test. Adjust the carrier gas and auxiliary oxygen flow rate to their normal values of 100 cc/min and 150 cc/min, respectively, with the sample recovery valve in vent position. Using a 10-ml syringe, withdraw a sample from the system effluent through the syringe port. Inject this sample into the NMO analyzer, and measure the CO2 content. The system background is acceptable if the CO2 concentration is less than 10 ppm.
11.1.1.3 Oxidation Catalyst Efficiency Check. Conduct a catalyst efficiency test as specified in section 10.1.1.2. If the criterion of this test cannot be met, make the necessary repairs to the system before proceeding.
11.1.2 Condensate Trap CO2 Purge and Sample Tank Pressurization.
11.1.2.1 After sampling is completed, the condensate trap will contain condensed water and organics and a small volume of sampled gas. This gas from the stack may contain a significant amount of CO2 which must be removed from the condensate trap before the sample is recovered. This is accomplished by purging the condensate trap with zero air and collecting the purged gas in the original sample tank.
11.1.2.2 Begin with the sample tank and condensate trap from the test run to be analyzed. Set the four-port valve of the condensate recovery system in the CO2 purge position as shown in Figure 25-9. With the sample tank valve closed, attach the sample tank to the sample recovery system. With the sample recovery valve in the vent position and the flow control valve fully open, evacuate the manometer or pressure gauge to the vacuum of the sample tank. Next, close the vacuum pump valve, open the sample tank valve, and record the tank pressure.
11.1.2.3 Attach the dry ice-cooled condensate trap to the recovery system, and initiate the purge by switching the sample recovery valve from vent to collect position. Adjust the flow control valve to maintain atmospheric pressure in the recovery system. Continue the purge until the CO2 concentration of the trap effluent is less than 5 ppm. CO2 concentration in the trap effluent should be measured by extracting syringe samples from the recovery system and analyzing the samples with the NMO analyzer. This procedure should be used only after the NDIR response has reached a minimum level. Using a 10-ml syringe, extract a sample from the syringe port prior to the NDIR, and inject this sample into the NMO analyzer.
11.1.2.4 After the completion of the CO2 purge, use the carrier gas bypass valve to pressurize the sample tank to approximately 1,060 mm Hg absolute pressure with zero air.
11.1.3 Recovery of the Condensate Trap Sample (See Figure 25-10).
11.1.3.1 Attach the ICV to the sample recovery system. With the sample recovery valve in a closed position, between vent and collect, and the flow control and ICV valves fully open, evacuate the manometer or gauge, the connecting tubing, and the ICV to 10 mm Hg absolute pressure. Close the flow-control and vacuum pump valves.
11.1.3.2 Begin auxiliary oxygen flow to the oxidation catalyst at a rate of 150 cc/min, then switch the four-way valve to the trap recovery position and the sample recovery valve to collect position. The system should now be set up to operate as indicated in Figure 25-10. After the manometer or pressure gauge begins to register a slight positive pressure, open the flow control valve. Adjust the flow-control valve to maintain atmospheric pressure in the system within 10 percent.
11.1.3.3 Remove the condensate trap from the dry ice, and allow it to warm to ambient temperature while monitoring the NDIR response. If, after 5 minutes, the CO2 concentration of the catalyst effluent is below 10,000 ppm, discontinue the auxiliary oxygen flow to the oxidation catalyst. Begin heating the trap by placing it in a furnace preheated to 200 °C (390 °F). Once heating has begun, carefully monitor the NDIR response to ensure that the catalyst effluent concentration does not exceed 50,000 ppm. Whenever the CO2 concentration exceeds 50,000 ppm, supply auxiliary oxygen to the catalyst at the rate of 150 cc/min. Begin heating the tubing that connected the heated sample box to the condensate trap only after the CO2 concentration falls below 10,000 ppm. This tubing may be heated in the same oven as the condensate trap or with an auxiliary heat source such as a heat gun. Heating temperature must not exceed 200 °C (390 °F). If a heat gun is used, heat the tubing slowly along its entire length from the upstream end to the downstream end, and repeat the pattern for a total of three times. Continue the recovery until the CO2 concentration drops to less than 10 ppm as determined by syringe injection as described under the condensate trap CO2 purge procedure (Section 11.1.2).
11.1.3.4 After the sample recovery is completed, use the carrier gas bypass valve to pressurize the ICV to approximately 1060 mm Hg absolute pressure with zero air.
11.2 Analysis. Once the initial performance test of the NMO analyzer has been successfully completed (see section 10.1.2) and the daily CO2 and NMO response factors have been determined (see section 10.2), proceed with sample analysis as follows:
11.2.1 Operating Conditions. The carrier gas flow rate is 29.5 cc/min He and 2.2 cc/min O2. The column oven is heated to 85 °C (185 °F). The order of elution for the sample from the column is CO, CH4, CO2, and NMO.
11.2.2 Analysis of Recovered Condensate Sample. Purge the sample loop with sample, and then inject the sample. Under the specified operating conditions, the CO2 in the sample will elute in approximately 100 seconds. As soon as the detector response returns to baseline following the CO2 peak, switch the carrier gas flow to backflush, and raise the column oven temperature to 195 °C (380 °F) as rapidly as possible. A rate of 30 °C/min (90 °F) has been shown to be adequate. Record the value obtained for the condensible organic material (Ccm) measured as CO2 and any measured NMO. Return the column oven temperature to 85 °C (185 °F) in preparation for the next analysis. Analyze each sample in triplicate, and report the average Ccm.
11.2.3 Analysis of Sample Tank. Perform the analysis as described in section 11.2.2, but record only the value measured for NMO (Ctm).
12.0 Data Analysis and CalculationsCarry out the calculations, retaining at least one extra significant figure beyond that of the acquired data. Round off figures after final calculations. All equations are written using absolute pressure; absolute pressures are determined by adding the measured barometric pressure to the measured gauge or manometer pressure.
12.1 Nomenclature.
C = TGNMO concentration of the effluent, ppm C equivalent. Cc = Calculated condensible organic (condensate trap) concentration of the effluent, ppm C equivalent. Ccm = Measured concentration (NMO analyzer) for the condensate trap ICV, ppm CO2. Ct = Calculated noncondensible organic concentration (sample tank) of the effluent, ppm C equivalent. Ctm = Measured concentration (NMO analyzer) for the sample tank, ppm NMO. F = Sampling flow rate, cc/min. L = Volume of liquid injected, µl. M = Molecular weight of the liquid injected, g/g-mole. Mc = TGNMO mass concentration of the effluent, mg C/dsm 3. N = Carbon number of the liquid compound injected (N = 12 for decane, N = 6 for hexane). n = Number of data points. Pf = Final pressure of the intermediate collection vessel, mm Hg absolute. Pb = Barometric pressure, cm Hg. Pti = Gas sample tank pressure before sampling, mm Hg absolute. Pt = Gas sample tank pressure after sampling, but before pressurizing, mm Hg absolute. Ptf = Final gas sample tank pressure after pressurizing, mm Hg absolute. q = Total number of analyzer injections of intermediate collection vessel during analysis (where k = injection number, 1 * * * q). r = Total number of analyzer injections of sample tank during analysis (where j = injection number, 1 * * * r). r = Density of liquid injected, g/cc. Tf = Final temperature of intermediate collection vessel, °K. Tti = Sample tank temperature before sampling, °K. Tt = Sample tank temperature at completion of sampling, °K. Ttf = Sample tank temperature after pressurizing, °K. V = Sample tank volume, m 3. Vt = Sample train volume, cc. Vv = Intermediate collection vessel volume, m 3. Vs = Gas volume sampled, dsm 3. xi = Individual measurements. x = Mean value. ΔP = Allowable pressure change, cm Hg. Θ = Leak-check period, min.12.2 Allowable Pressure Change. For the pretest leak-check, calculate the allowable pressure change using Equation 25-1:
12.3 Sample Volume. For each test run, calculate the gas volume sampled using Equation 25-2:
12.4 Noncondensible Organics. For each sample tank, determine the concentration of nonmethane organics (ppm C) using Equation 25-3:
12.5 Condensible Organics. For each condensate trap determine the concentration of organics (ppm C) using Equation 25-4:
12.6 TGNMO Mass Concentration. Determine the TGNMO mass concentration as carbon for each test run, using Equation 25-5:
12.7 Percent Recovery. Calculate the percent recovery for the liquid injections to the condensate recovery and conditioning system using Equation 25-6:
where K = 1.604 (°K)(g-mole)(%)/(mm Hg)(ml)(m 3)(ppm).12.8 Relative Standard Deviation. Use Equation 25-7 to calculate the relative standard deviation (RSD) of percent recovery and analyzer linearity.
13.0 Method Performance13.1 Range. The minimum detectable limit of the method has been determined to be 50 parts per million by volume (ppm). No upper limit has been established.
14.0 Pollution Prevention [Reserved] 15.0 Waste Management [Reserved] 16.0 References1. Salo, A.E., S. Witz, and R.D. MacPhee. Determination of Solvent Vapor Concentrations by Total Combustion Analysis: A Comparison of Infrared with Flame Ionization Detectors. Paper No. 75-33.2. (Presented at the 68th Annual Meeting of the Air Pollution Control Association. Boston, MA. June 15-20, 1975.) 14 p.
2. Salo, A.E., W.L. Oaks, and R.D. MacPhee. Measuring the Organic Carbon Content of Source Emissions for Air Pollution Control. Paper No. 74-190. (Presented at the 67th Annual Meeting of the Air Pollution Control Association. Denver, CO. June 9-13, 1974.) 25 p.
17.0 Tables, Diagrams, Flowcharts, and Validation Data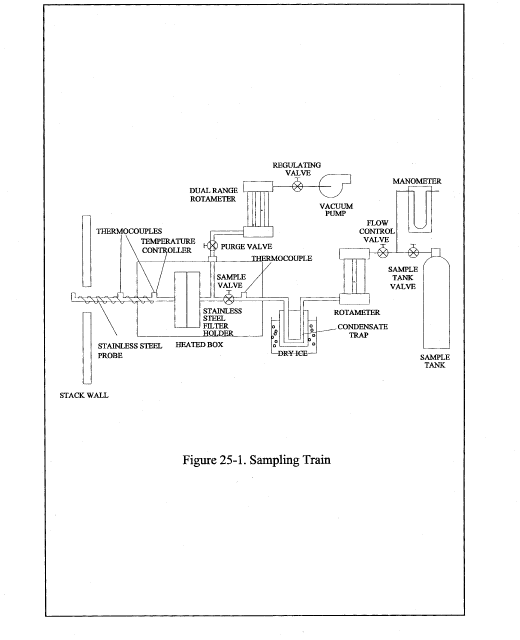
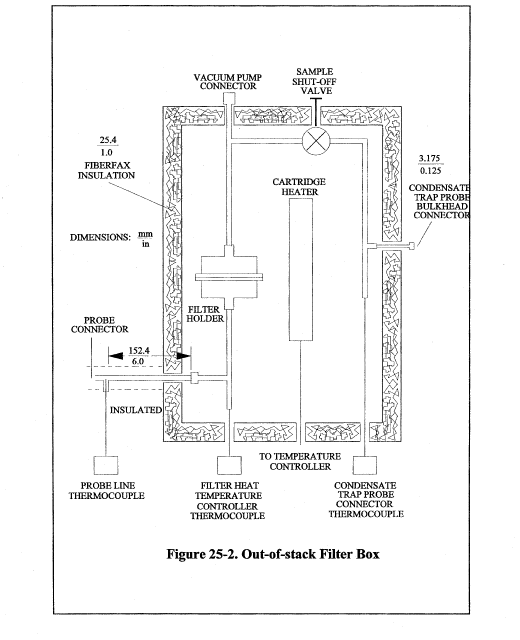
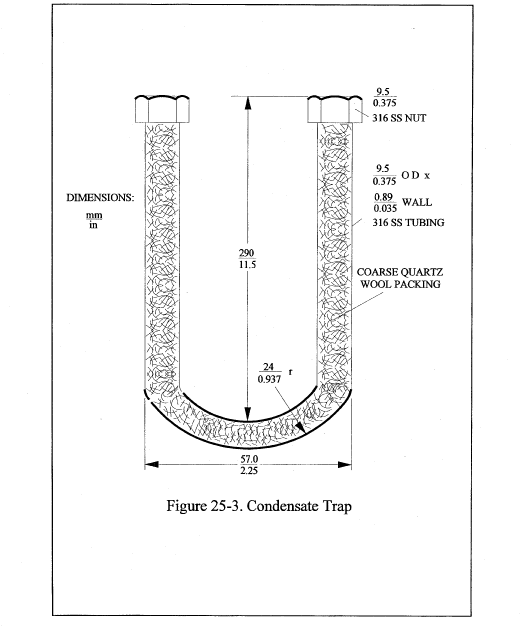
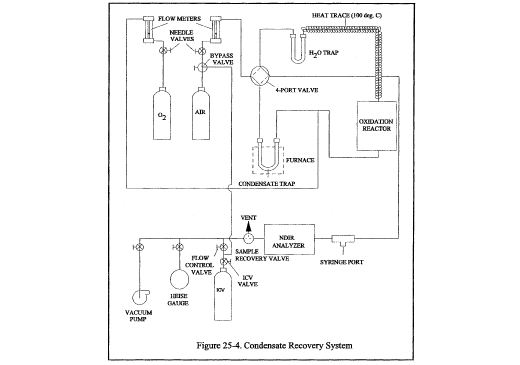
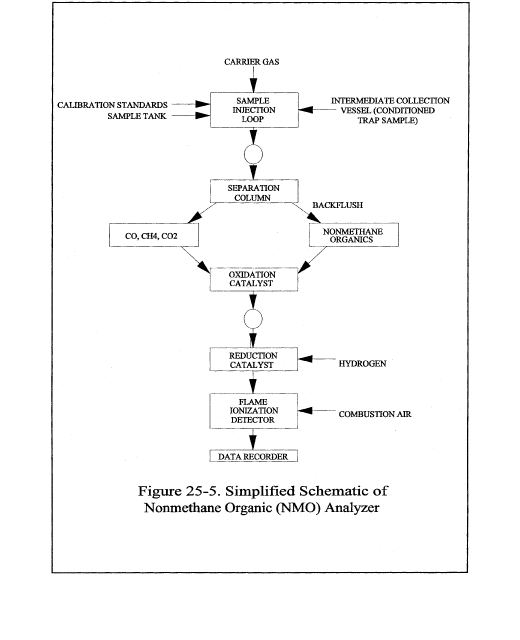
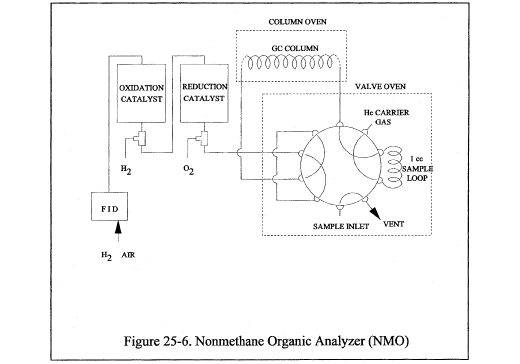
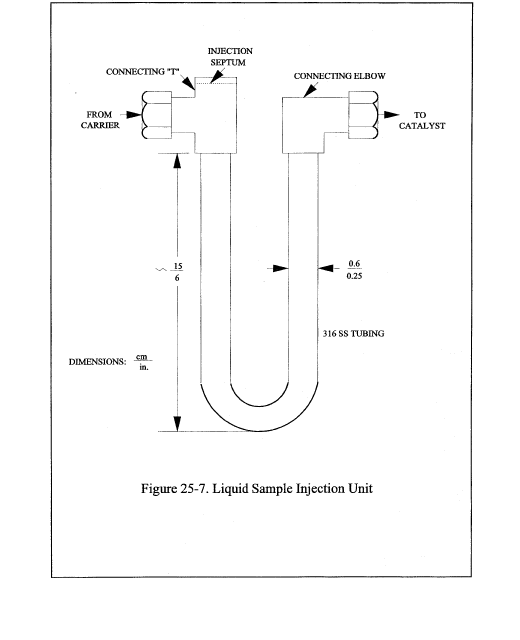
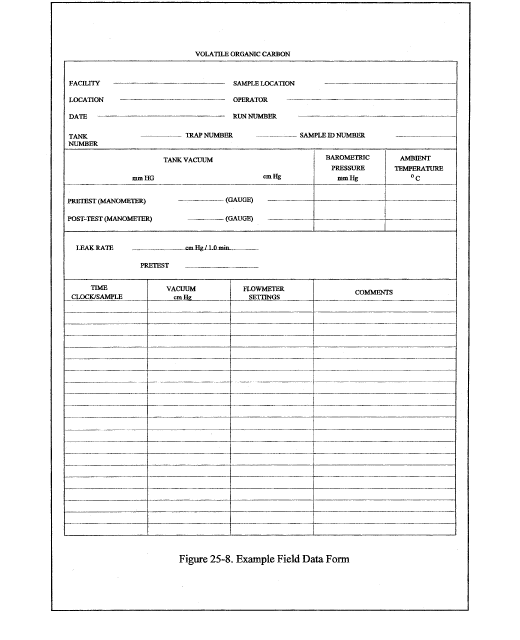
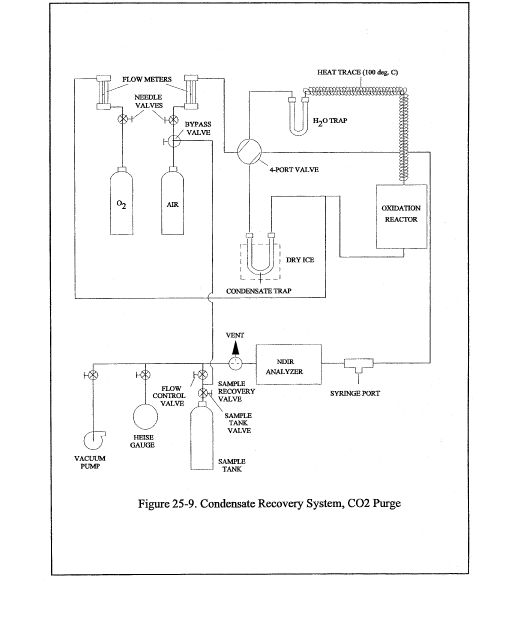
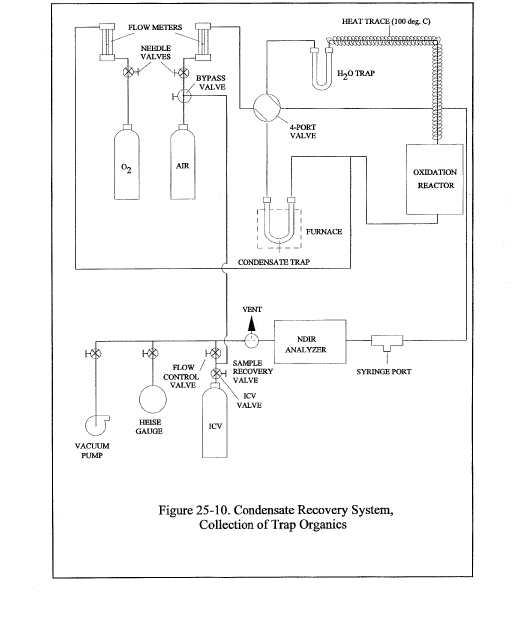
1.1 Analytes.
Analyte | CAS No. | Sensitivity |
---|---|---|
Total Organic Compounds | N/A | <2% of span. |
1.2 Applicability. This method is applicable for the determination of total gaseous organic concentration of vapors consisting primarily of alkanes, alkenes, and/or arenes (aromatic hydrocarbons). The concentration is expressed in terms of propane (or other appropriate organic calibration gas) or in terms of carbon.
1.3 Data Quality Objectives. Adherence to the requirements of this method will enhance the quality of the data obtained from air pollutant sampling methods.
2.0 Summary of Method2.1 A gas sample is extracted from the source through a heated sample line and glass fiber filter to a flame ionization analyzer (FIA). Results are reported as volume concentration equivalents of the calibration gas or as carbon equivalents.
3.0 Definitions3.1 Calibration drift means the difference in the measurement system response to a mid-level calibration gas before and after a stated period of operation during which no unscheduled maintenance, repair, or adjustment took place.
3.2 Calibration error means the difference between the gas concentration indicated by the measurement system and the know concentration of the calibration gas.
3.3 Calibration gas means a known concentration of a gas in an appropriate diluent gas.
3.4 Measurement system means the total equipment required for the determination of the gas concentration. The system consists of the following major subsystems:
3.4.1 Sample interface means that portion of a system used for one or more of the following: sample acquisition, sample transportation, sample conditioning, or protection of the analyzer(s) from the effects of the stack effluent.
3.4.2 Organic analyzer means that portion of the measurement system that senses the gas to be measured and generates an output proportional to its concentration.
3.5 Response time means the time interval from a step change in pollutant concentration at the inlet to the emission measurement system to the time at which 95 percent of the corresponding final value is reached as displayed on the recorder.
3.6 Span Value means the upper limit of a gas concentration measurement range that is specified for affected source categories in the applicable part of the regulations. The span value is established in the applicable regulation and is usually 1.5 to 2.5 times the applicable emission limit. If no span value is provided, use a span value equivalent to 1.5 to 2.5 times the expected concentration. For convenience, the span value should correspond to 100 percent of the recorder scale.
3.7 Zero drift means the difference in the measurement system response to a zero level calibration gas before or after a stated period of operation during which no unscheduled maintenance, repair, or adjustment took place.
4.0 Interferences [Reserved] 5.0 Safety5.1 Disclaimer. This method may involve hazardous materials, operations, and equipment. This test method may not address all of the safety problems associated with its use. It is the responsibility of the user of this test method to establish appropriate safety and health practices and determine the applicability of regulatory limitations prior to performing this test method. The analyzer users manual should be consulted for specific precautions to be taken with regard to the analytical procedure.
5.2 Explosive Atmosphere. This method is often applied in highly explosive areas. Caution and care should be exercised in choice of equipment and installation.
6.0 Equipment and Supplies6.1 Measurement System. Any measurement system for total organic concentration that meets the specifications of this method. A schematic of an acceptable measurement system is shown in Figure 25A-1. All sampling components leading to the analyzer shall be heated ≥110 °C (220 °F) throughout the sampling period, unless safety reasons are cited (Section 5.2) The essential components of the measurement system are described below:
6.1.1 Organic Concentration Analyzer. A flame ionization analyzer (FIA) capable of meeting or exceeding the specifications of this method. The flame ionization detector block shall be heated >120 °C (250 °F).
6.1.2 Sample Probe. Stainless steel, or equivalent, three-hole rake type. Sample holes shall be 4 mm (0.16-in.) in diameter or smaller and located at 16.7, 50, and 83.3 percent of the equivalent stack diameter. Alternatively, a single opening probe may be used so that a gas sample is collected from the centrally located 10 percent area of the stack cross-section.
6.1.3 Heated Sample Line. Stainless steel or Teflon” tubing to transport the sample gas to the analyzer. The sample line should be heated (≥110 °C) to prevent any condensation.
6.1.4 Calibration Valve Assembly. A three-way valve assembly to direct the zero and calibration gases to the analyzers is recommended. Other methods, such as quick-connect lines, to route calibration gas to the analyzers are applicable.
6.1.5 Particulate Filter. An in-stack or an out-of-stack glass fiber filter is recommended if exhaust gas particulate loading is significant. An out-of-stack filter should be heated to prevent any condensation.
6.1.6 Recorder. A strip-chart recorder, analog computer, or digital recorder for recording measurement data. The minimum data recording requirement is one measurement value per minute.
7.0 Reagents and Standards7.1 Calibration Gases. The calibration gases for the gas analyzer shall be propane in air or propane in nitrogen. Alternatively, organic compounds other than propane can be used; the appropriate corrections for response factor must be made. Calibration gases shall be prepared in accordance with the procedure listed in Citation 2 of section 16. Additionally, the manufacturer of the cylinder should provide a recommended shelf life for each calibration gas cylinder over which the concentration does not change more than ±2 percent from the certified value. For calibration gas values not generally available (i.e., organics between 1 and 10 percent by volume), alternative methods for preparing calibration gas mixtures, such as dilution systems (Test Method 205, 40 CFR Part 51, Appendix M), may be used with prior approval of the Administrator.
7.1.1 Fuel. A 40 percent H2/60 percent N2 gas mixture is recommended to avoid an oxygen synergism effect that reportedly occurs when oxygen concentration varies significantly from a mean value.
7.1.2 Zero Gas. High purity air with less than 0.1 part per million by volume (ppmv) of organic material (propane or carbon equivalent) or less than 0.1 percent of the span value, whichever is greater.
7.1.3 Low-level Calibration Gas. An organic calibration gas with a concentration equivalent to 25 to 35 percent of the applicable span value.
7.1.4 Mid-level Calibration Gas. An organic calibration gas with a concentration equivalent to 45 to 55 percent of the applicable span value.
7.1.5 High-level Calibration Gas. An organic calibration gas with a concentration equivalent to 80 to 90 percent of the applicable span value.
8.0 Sample Collection, Preservation, Storage, and Transport8.1 Selection of Sampling Site. The location of the sampling site is generally specified by the applicable regulation or purpose of the test (i.e., exhaust stack, inlet line, etc.). The sample port shall be located to meet the testing requirements of Method 1.
8.2 Location of Sample Probe. Install the sample probe so that the probe is centrally located in the stack, pipe, or duct and is sealed tightly at the stack port connection.
8.3 Measurement System Preparation. Prior to the emission test, assemble the measurement system by following the manufacturer's written instructions for preparing sample interface and the organic analyzer. Make the system operable (Section 10.1).
8.4 Calibration Error Test. Immediately prior to the test series (within 2 hours of the start of the test), introduce zero gas and high-level calibration gas at the calibration valve assembly. Adjust the analyzer output to the appropriate levels, if necessary. Calculate the predicted response for the low-level and mid-level gases based on a linear response line between the zero and high-level response. Then introduce low-level and mid-level calibration gases successively to the measurement system. Record the analyzer responses for low-level and mid-level calibration gases and determine the differences between the measurement system responses and the predicted responses. These differences must be less than 5 percent of the respective calibration gas value. If not, the measurement system is not acceptable and must be replaced or repaired prior to testing. No adjustments to the measurement system shall be conducted after the calibration and before the drift check (Section 8.6.2). If adjustments are necessary before the completion of the test series, perform the drift checks prior to the required adjustments and repeat the calibration following the adjustments. If multiple electronic ranges are to be used, each additional range must be checked with a mid-level calibration gas to verify the multiplication factor.
8.5 Response Time Test. Introduce zero gas into the measurement system at the calibration valve assembly. When the system output has stabilized, switch quickly to the high-level calibration gas. Record the time from the concentration change to the measurement system response equivalent to 95 percent of the step change. Repeat the test three times and average the results.
8.6 Emission Measurement Test Procedure.
8.6.1 Organic Measurement. Begin sampling at the start of the test period, recording time and any required process information as appropriate. In particulate, note on the recording chart, periods of process interruption or cyclic operation.
8.6.2 Drift Determination. Immediately following the completion of the test period and hourly during the test period, reintroduce the zero and mid-level calibration gases, one at a time, to the measurement system at the calibration valve assembly. (Make no adjustments to the measurement system until both the zero and calibration drift checks are made.) Record the analyzer response. If the drift values exceed the specified limits, invalidate the test results preceding the check and repeat the test following corrections to the measurement system. Alternatively, recalibrate the test measurement system as in section 8.4 and report the results using both sets of calibration data (i.e., data determined prior to the test period and data determined following the test period).
Note:Note on the recording chart periods of process interruption or cyclic operation.
9.0 Quality ControlMethod section | Quality control measure | Effect |
---|---|---|
8.4 | Zero and calibration drift tests | Ensures that bias introduced by drift in the measurement system output during the run is no greater than 3 percent of span. |
10.1 FIA equipment can be calibrated for almost any range of total organic concentrations. For high concentrations of organics (>1.0 percent by volume as propane), modifications to most commonly available analyzers are necessary. One accepted method of equipment modification is to decrease the size of the sample to the analyzer through the use of a smaller diameter sample capillary. Direct and continuous measurement of organic concentration is a necessary consideration when determining any modification design.
11.0 Analytical ProcedureThe sample collection and analysis are concurrent for this method (see section 8.0).
12.0 Calculations and Data Analysis12.1 Determine the average organic concentration in terms of ppmv as propane or other calibration gas. The average shall be determined by integration of the output recording over the period specified in the applicable regulation. If results are required in terms of ppmv as carbon, adjust measured concentrations using Equation 25A-1.
Where: Cc = Organic concentration as carbon, ppmv. Cmeas = Organic concentration as measured, ppmv. K = Carbon equivalent correction factor. = 2 for ethane. = 3 for propane. = 4 for butane. = Appropriate response factor for other organic calibration gases. 13.0 Method Performance13.1 Measurement System Performance Specifications.
13.1.1 Zero Drift. Less than ±3 percent of the span value.
13.1.2 Calibration Drift. Less than ±3 percent of span value.
13.1.3 Calibration Error. Less than ±5 percent of the calibration gas value.
14.0 Pollution Prevention [Reserved] 15.0 Waste Management [Reserved] 16.0 References1. Measurement of Volatile Organic Compounds - Guideline Series. U.S. Environmental Protection Agency. Research Triangle Park, NC. Publication No. EPA-450/2-78-041. June 1978. p. 46-54.
2. EPA Traceability Protocol for Assay and Certification of Gaseous Calibration Standards. U.S. Environmental Protection Agency, Quality Assurance and Technical Support Division. Research Triangle Park, N.C. September 1993.
3. Gasoline Vapor Emission Laboratory Evaluation - Part 2. U.S. Environmental Protection Agency, Office of Air Quality Planning and Standards. Research Triangle Park, NC. EMB Report No. 75-GAS-6. August 1975.
17.0 Tables, Diagrams, Flowcharts, and Validation Data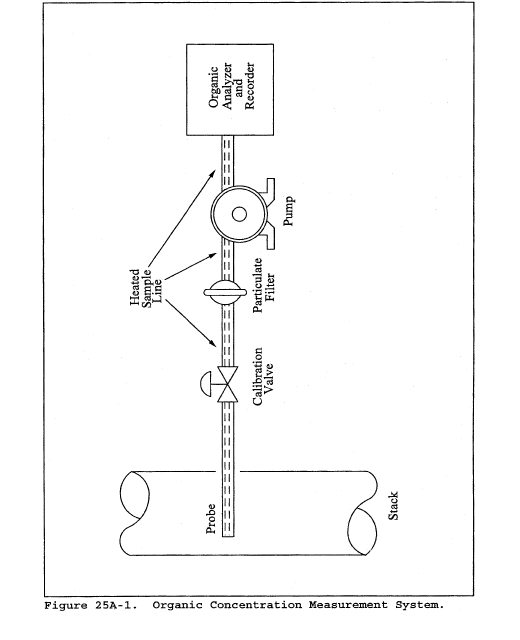
This method does not include all of the specifications (e.g., equipment and supplies) and procedures (e.g., sampling) essential to its performance. Some material is incorporated by reference from other methods in this part. Therefore, to obtain reliable results, persons using this method should have a thorough knowledge of at least the following additional test methods: Method 1, Method 6C, and Method 25A.
1.0 Scope and Application1.1 Analytes.
Analyte | CAS No. | Sensitivity |
---|---|---|
Total Organic Compounds | N/A | <2% of span. |
1.2 Applicability. This method is applicable for the determination of total gaseous organic concentration of vapors consisting primarily of alkanes. Other organic materials may be measured using the general procedure in this method, the appropriate calibration gas, and an analyzer set to the appropriate absorption band.
1.3 Data Quality Objectives. Adherence to the requirements of this method will enhance the quality of the data obtained from air pollutant sampling methods.
2.0 Summary of MethodA gas sample is extracted from the source through a heated sample line, if necessary, and glass fiber filter to a nondispersive infrared analyzer (NDIR). Results are reported as volume concentration equivalents of the calibration gas or as carbon equivalents.
3.0 DefinitionsSame as Method 25A, section 3.0.
4.0 Interferences [Reserved] 5.0 Safety5.1 Disclaimer. This method may involve hazardous materials, operations, and equipment. This test method may not address all of the safety problems associated with its use. It is the responsibility of the user of this test method to establish appropriate safety and health practices and determine the applicability of regulatory limitations prior to performing this test method. The analyzer users manual should be consulted for specific precautions to be taken with regard to the analytical procedure.
5.2 Explosive Atmosphere. This method is often applied in highly explosive areas. Caution and care should be exercised in choice of equipment and installation.
6.0 Equipment and SuppliesSame as Method 25A, section 6.0, with the exception of the following:
6.1 Organic Concentration Analyzer. A nondispersive infrared analyzer designed to measure alkane organics and capable of meeting or exceeding the specifications in this method.
7.0 Reagents and StandardsSame as Method 25A, section 7.1. No fuel gas is required for an NDIR.
8.0 Sample Collection, Preservation, Storage, and TransportSame as Method 25A, section 8.0.
9.0 Quality ControlSame as Method 25A, section 9.0.
10.0 Calibration and StandardizationSame as Method 25A, section 10.0.
11.0 Analytical ProcedureThe sample collection and analysis are concurrent for this method (see section 8.0).
12.0 Calculations and Data AnalysisSame as Method 25A, section 12.0.
13.0 Method Performance [Reserved] 14.0 Pollution Prevention [Reserved] 15.0 Waste Management [Reserved] 16.0 ReferencesSame as Method 25A, section 16.0.
17.0 Tables, Diagrams, Flowcharts, and Validation Data [Reserved] Method 25C - Determination of Nonmethane Organic Compounds (NMOC) in Landfill Gases Note:This method does not include all of the specifications (e.g., equipment and supplies) and procedures (e.g., sampling and analytical) essential to its performance. Some material is incorporated by reference from other methods in this part. Therefore, to obtain reliable results, persons using this method should also have a thorough knowledge of EPA Method 25.
1.0 Scope and Application1.1 Analytes.
Analyte | CAS No. |
---|---|
Nonmethane organic compounds (NMOC) | No CAS number assigned. |
1.2 Applicability. This method is applicable to the sampling and measurement of NMOC as carbon in landfill gases (LFG).
1.3 Data Quality Objectives. Adherence to the requirements of this method will enhance the quality of the data obtained from air pollutant sampling methods.
2.0 Summary of Method2.1 A sample probe that has been perforated at one end is driven or augured to a depth of 0.9 m (3 ft) below the bottom of the landfill cover. A sample of the landfill gas is extracted with an evacuated cylinder. The NMOC content of the gas is determined by injecting a portion of the gas into a gas chromatographic column to separate the NMOC from carbon monoxide (CO), carbon dioxide (CO2), and methane (CH4); the NMOC are oxidized to CO2, reduced to CH4, and measured by a flame ionization detector (FID). In this manner, the variable response of the FID associated with different types of organics is eliminated.
3.0 Definitions [Reserved] 4.0 Interferences [Reserved] 5.0 Safety5.1 Since this method is complex, only experienced personnel should perform this test. LFG contains methane, therefore explosive mixtures may exist on or near the landfill. It is advisable to take appropriate safety precautions when testing landfills, such as refraining from smoking and installing explosion-proof equipment.
6.0 Equipment and Supplies6.1 Sample Probe. Stainless steel, with the bottom third perforated. Teflon probe liners and sampling lines are also allowed. Non-perforated probes are allowed as long as they are withdrawn to create a gap equivalent to having the bottom third perforated. The sample probe must be capped at the bottom and must have a threaded cap with a sampling attachment at the top. The sample probe must be long enough to go through and extend no less than 0.9 m (3 ft) below the landfill cover. If the sample probe is to be driven into the landfill, the bottom cap should be designed to facilitate driving the probe into the landfill.
6.2 Sampling Train.
6.2.1 Rotameter with Flow Control Valve. Capable of measuring a sample flow rate of 100 ±10 ml/min. The control valve must be made of stainless steel.
6.2.2 Sampling Valve. Stainless steel.
6.2.3 Pressure Gauge. U-tube mercury manometer, or equivalent, capable of measuring pressure to within 1 mm Hg (0.5 in H2O) in the range of 0 to 1,100 mm Hg (0 to 590 in H2O).
6.2.4 Sample Tank. Stainless steel or aluminum cylinder, equipped with a stainless steel sample tank valve.
6.3 Vacuum Pump. Capable of evacuating to an absolute pressure of 10 mm Hg (5.4 in H2O).
6.4 Purging Pump. Portable, explosion proof, and suitable for sampling NMOC.
6.5 Pilot Probe Procedure. The following are needed only if the tester chooses to use the procedure described in section 8.2.1.
6.5.1 Pilot Probe. Tubing of sufficient strength to withstand being driven into the landfill by a post driver and an outside diameter of at least 6 mm (0.25 in.) smaller than the sample probe. The pilot probe shall be capped on both ends and long enough to go through the landfill cover and extend no less than 0.9 m (3 ft) into the landfill.
6.5.2 Post Driver and Compressor. Capable of driving the pilot probe and the sampling probe into the landfill. The Kitty Hawk portable post driver has been found to be acceptable.
6.6 Auger Procedure. The following are needed only if the tester chooses to use the procedure described in section 8.2.2.
6.6.1 Auger. Capable of drilling through the landfill cover and to a depth of no less than 0.9 m (3 ft) into the landfill.
6.6.2 Pea Gravel.
6.6.3 Bentonite.
6.7 NMOC Analyzer, Barometer, Thermometer, and Syringes. Same as in sections 6.3.1, 6.3.2, 6.33, and 6.2.10, respectively, of Method 25.
7.0 Reagents and Standards7.1 NMOC Analysis. Same as in Method 25, section 7.2.
7.2 Calibration. Same as in Method 25, section 7.4, except omit section 7.4.3.
8.0 Sample Collection, Preservation, Storage, and Transport8.1 Sample Tank Evacuation and Leak-Check. Conduct the sample tank evacuation and leak-check either in the laboratory or the field. Connect the pressure gauge and sampling valve to the sample tank. Evacuate the sample tank to 10 mm Hg (5.4 in H2O) absolute pressure or less. Close the sampling valve, and allow the tank to sit for 30 minutes. The tank is acceptable if no change more than ±2 mm is noted. Include the results of the leak-check in the test report.
8.2 Sample Probe Installation. The tester may use the procedure in section 8.2.1 or 8.2.2.
8.2.1 Pilot Probe Procedure. Use the post driver to drive the pilot probe at least 0.9 m (3 ft) below the landfill cover. Alternative procedures to drive the probe into the landfill may be used subject to the approval of the Administrator's designated representative.
8.2.1.1 Remove the pilot probe and drive the sample probe into the hole left by the pilot probe. The sample probe shall extend at least 0.9 m (3 ft) below the landfill cover and shall protrude about 0.3 m (1 ft) above the landfill cover. Seal around the sampling probe with bentonite and cap the sampling probe with the sampling probe cap.
8.2.2 Auger Procedure. Use an auger to drill a hole to at least 0.9 m (3 ft) below the landfill cover. Place the sample probe in the hole and backfill with pea gravel to a level 0.6 m (2 ft) from the surface. The sample probe shall protrude at least 0.3 m (1 ft) above the landfill cover. Seal the remaining area around the probe with bentonite. Allow 24 hours for the landfill gases to equilibrate inside the augured probe before sampling.
8.2.3 Driven Probes. Closed-point probes may be driven directly into the landfill in a single step. This method may not require backfilling if the probe is adequately sealed by its insertion. Unperforated probes that are inserted in this manner and withdrawn at a distance from a detachable tip to create an open space are also acceptable.
8.3 Sample Train Assembly. Just before assembling the sample train, measure the sample tank vacuum using the pressure gauge. Record the vacuum, the ambient temperature, and the barometric pressure at this time. Assemble the sampling probe purging system as shown in Figure 25C-1.
8.4 Sampling Procedure. Open the sampling valve and use the purge pump and the flow control valve to evacuate at least two sample probe volumes from the system at a flow rate of 500 ml/min or less. Close the sampling valve and replace the purge pump with the sample tank apparatus as shown in Figure 25C-2. Open the sampling valve and the sample tank valve and, using the flow control valve, sample at a flow rate of 500 ml/min or less until either a constant flow rate can no longer be maintained because of reduced sample tank vacuum or the appropriate composite volume is attained. Disconnect the sampling tank apparatus and pressurize the sample cylinder to approximately 1,060 mm Hg (567 in. H2O) absolute pressure with helium, and record the final pressure. Alternatively, the sample tank may be pressurized in the lab.
8.4.1 The following restrictions apply to compositing samples from different probe sites into a single cylinder: (1) Individual composite samples per cylinder must be of equal volume; this must be verified by recording the flow rate, sampling time, vacuum readings, or other appropriate volume measuring data, (2) individual composite samples must have a minimum volume of 1 liter unless data is provided showing smaller volumes can be accurately measured, and (3) composite samples must not be collected using the final cylinder vacuum as it diminishes to ambient pressure.
8.4.2 Use Method 3C to determine the percent N2 and O2 in each cylinder. The presence of N2 and O2 indicate either infiltration of ambient air into the landfill gas sample or an inappropriate testing site has been chosen where anaerobic decomposition has not begun. The landfill gas sample is acceptable if the concentration of N2 is less than 20 percent. Alternatively, the oxygen content of each cylinder must be less than 5 percent. Landfills with 3-year average annual rainfalls equal to or less than 20 inches annual rainfalls samples are acceptable when the N2 to O2 concentration ratio is greater than 3.71.
9.0 Quality Control9.1 Miscellaneous Quality Control Measures.
Section | Quality control measure | Effect |
---|---|---|
8.4.2 | If the 3-year average annual rainfall is greater than 20 inches, verify that landfill gas sample contains less than 20 percent N2 and 5 percent O2. Landfills with 3-year average annual rainfalls equal to or less than 20 inches annual rainfalls samples are acceptable when the N2 to O2 concentration ratio is greater than 3.71 | Ensures that ambient air was not drawn into the landfill gas sample and gas was sampled from an appropriate location. If outside of range, invalidate sample and repeat sample collection. |
10.1, 10.2 | NMOC analyzer initial and daily performance checks | Ensures precision of analytical results. |
Maintain a record of performance of each item.
10.1 Initial NMOC Analyzer Performance Test. Same as in Method 25, section 10.1, except omit the linearity checks for CO2 standards.
10.2 NMOC Analyzer Daily Calibration.
10.2.1 NMOC Response Factors. Same as in Method 25, section 10.2.2.
10.3 Sample Tank Volume. The volume of the gas sampling tanks must be determined. Determine the tank volumes by weighing them empty and then filled with deionized water; weigh to the nearest 5 g, and record the results. Alternatively, measure the volume of water used to fill them to the nearest 5 ml.
11.0 Analytical Procedures11.1 The oxidation, reduction, and measurement of NMOC's is similar to Method 25. Before putting the NMOC analyzer into routine operation, conduct an initial performance test. Start the analyzer, and perform all the necessary functions in order to put the analyzer into proper working order. Conduct the performance test according to the procedures established in section 10.1. Once the performance test has been successfully completed and the NMOC calibration response factor has been determined, proceed with sample analysis as follows:
11.1.1 Daily Operations and Calibration Checks. Before and immediately after the analysis of each set of samples or on a daily basis (whichever occurs first), conduct a calibration test according to the procedures established in section 10.2. If the criteria of the daily calibration test cannot be met, repeat the NMOC analyzer performance test (Section 10.1) before proceeding.
11.1.2 Operating Conditions. Same as in Method 25, section 11.2.1.
11.1.3 Analysis of Sample Tank. Purge the sample loop with sample, and then inject the sample. Under the specified operating conditions, the CO2 in the sample will elute in approximately 100 seconds. As soon as the detector response returns to baseline following the CO2 peak, switch the carrier gas flow to backflush, and raise the column oven temperature to 195 °C (383 °F) as rapidly as possible. A rate of 30 °C/min (54 °F/min) has been shown to be adequate. Record the value obtained for any measured NMOC. Return the column oven temperature to 85 °C (185 °F) in preparation for the next analysis. Analyze each sample in triplicate, and report the average as Ctm.
12.0 Data Analysis and Calculations Note:All equations are written using absolute pressure; absolute pressures are determined by adding the measured barometric pressure to the measured gauge or manometer pressure.
12.1 Nomenclature
Bw = Moisture content in the sample, fraction. CN2 = N2 concentration in the diluted sample gas. CmN2 = Measured N2 concentration, fraction in landfill gas. CmOx = Measured Oxygen concentration, fraction in landfill gas. COx = Oxygen concentration in the diluted sample gas. Ct = Calculated NMOC concentration, ppmv C equivalent. Ctm = Measured NMOC concentration, ppmv C equivalent. Pb = Barometric pressure, mm Hg. Pt = Gas sample tank pressure after sampling, but before pressurizing, mm Hg absolute. Ptf = Final gas sample tank pressure after pressurizing, mm Hg absolute. Pti = Gas sample tank pressure after evacuation, mm Hg absolute. Pw = Vapor pressure of H2O (from Table 25C-1), mm Hg. r = Total number of analyzer injections of sample tank during analysis (where j = injection number, 1 . . . r). Tt = Sample tank temperature at completion of sampling, °K. Tti = Sample tank temperature before sampling, °K. Ttf = Sample tank temperature after pressuring, °K.12.2 Water Correction. Use Table 25C-1 (Section 17.0), the LFG temperature, and barometric pressure at the sampling site to calculate Bw.
12.3 Nitrogen Concentration in the landfill gas. Use equation 25C-2 to calculate the measured concentration of nitrogen in the original landfill gas.

12.4 Oxygen Concentration in the landfill gas. Use equation 25C-3 to calculate the measured concentration of oxygen in the original landfill gas.

12.5 You must correct the NMOC Concentration for the concentration of nitrogen or oxygen based on which gas or gases passes the requirements in section 9.1 or based on the 3-year average annual rainfall based on the closest NOAA land-based station.
12.5.1 NMOC Concentration with nitrogen correction. Use Equation 25C-4 to calculate the concentration of NMOC for each sample tank when the nitrogen concentration is less than 20 percent.

12.5.2 NMOC Concentration with oxygen correction. Use Equation 25C-5 to calculate the concentration of NMOC for each sample tank if the landfill gas oxygen is less than 5 percent and the landfill gas nitrogen concentration is greater than 20 percent, or 3-year average annual rainfall based annual rainfall of less than 20 inches.

1. Salo, Albert E., Samuel Witz, and Robert D. MacPhee. Determination of Solvent Vapor Concentrations by Total Combustion Analysis: A Comparison of Infrared with Flame Ionization Detectors. Paper No. 75-33.2. (Presented at the 68th Annual Meeting of the Air Pollution Control Association. Boston, Massachusetts. June 15-20, 1975.) 14 p.
2. Salo, Albert E., William L. Oaks, and Robert D. MacPhee. Measuring the Organic Carbon Content of Source Emissions for Air Pollution Control. Paper No. 74-190. (Presented at the 67th Annual Meeting of the Air Pollution Control Association. Denver, Colorado. June 9-13, 1974.) 25 p.
17.0 Tables, Diagrams, Flowcharts, and Validation Data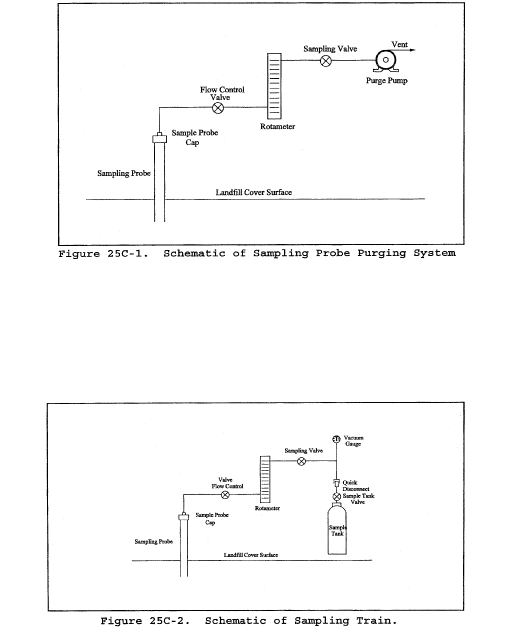
Table 25C-1 - Moisture Correction
Temperature, °C | Vapor Pressure of H2O, mm Hg | Temperature, °C | Vapor Pressure of H2O, mm Hg |
---|---|---|---|
4 | 6.1 | 18 | 15.5 |
6 | 7.0 | 20 | 17.5 |
8 | 8.0 | 22 | 19.8 |
10 | 9.2 | 24 | 22.4 |
12 | 10.5 | 26 | 25.2 |
14 | 12.0 | 28 | 28.3 |
16 | 13.6 | 30 | 31.8 |
Performance of this method should not be attempted by persons unfamiliar with the operation of a flame ionization detector (FID) or an electrolytic conductivity detector (ELCD) because knowledge beyond the scope of this presentation is required.
1.0 Scope and Application1.1 Analyte. Volatile Organic Compounds. No CAS No. assigned.
1.2 Applicability. This method is applicable for determining the volatile organic (VO) concentration of a waste sample.
2.0 Summary of Method2.1 Principle. A sample of waste is obtained at a point which is most representative of the unexposed waste (where the waste has had minimum opportunity to volatilize to the atmosphere). The sample is suspended in an organic/aqueous matrix, then heated and purged with nitrogen for 30 min. in order to separate certain organic compounds. Part of the sample is analyzed for carbon concentration, as methane, with an FID, and part of the sample is analyzed for chlorine concentration, as chloride, with an ELCD. The VO concentration is the sum of the carbon and chlorine content of the sample.
3.0 Definitions3.1 Well-mixed in the context of this method refers to turbulent flow which results in multiple-phase waste in effect behaving as single-phase waste due to good mixing.
4.0 Interferences [Reserved] 5.0 Safety5.1 Disclaimer. This method may involve hazardous materials, operations, and equipment. This test method may not address all of the safety problems associated with its use. It is the responsibility of the user of this test method to establish appropriate safety and health practices and to determine the applicability of regulatory limitations prior to performing this test method.
6.0 Equipment and Supplies Note:Mention of trade names or specific products does not constitute endorsement by the Environmental Protection Agency.
6.1 Sampling. The following equipment is required:
6.1.1 Sampling Tube. Flexible Teflon, 0.25 in. ID (6.35 mm).
6.1.2 Sample Container. Borosilicate glass, 40-mL, and a Teflon-lined screw cap capable of forming an air tight seal.
6.1.3 Cooling Coil. Fabricated from 0.25 in (6.35 mm). ID 304 stainless steel tubing with a thermocouple at the coil outlet.
6.2 Analysis. The following equipment is required.
6.2.1 Purging Apparatus. For separating the VO from the waste sample. A schematic of the system is shown in Figure 25D-1. The purging apparatus consists of the following major components.
6.2.1.1 Purging Flask. A glass container to hold the sample while it is heated and purged with dry nitrogen. The cap of the purging flask is equipped with three fittings: one for a purging lance (fitting with the #7 Ace-thread), one for the Teflon exit tubing (side fitting, also a #7 Ace-thread), and a third (a 50-mm Ace-thread) to attach the base of the purging flask as shown in Figure 25D-2. The base of the purging flask is a 50-mm ID (2 in) cylindrical glass tube. One end of the tube is open while the other end is sealed. Exact dimensions are shown in Figure 25D-2.
6.2.1.2 Purging Lance. Glass tube, 6-mm OD (0.2 in) by 30 cm (12 in) long. The purging end of the tube is fitted with a four-arm bubbler with each tip drawn to an opening 1 mm (0.04 in) in diameter. Details and exact dimensions are shown in Figure 25D-2.
6.2.1.3 Coalescing Filter. Porous fritted disc incorporated into a container with the same dimensions as the purging flask. The details of the design are shown in Figure 25D-3.
6.2.1.4 Constant Temperature Chamber. A forced draft oven capable of maintaining a uniform temperature around the purging flask and coalescing filter of 75 ±2 °C (167 ±3.6 °F).
6.2.1.5 Three-way Valve. Manually operated, stainless steel. To introduce calibration gas into system.
6.2.1.6 Flow Controllers. Two, adjustable. One capable of maintaining a purge gas flow rate of 6 ±0.06 L/min (0.2 ±0.002 ft 3/min) The other capable of maintaining a calibration gas flow rate of 1-100 mL/min (0.00004-0.004 ft 3/min).
6.2.1.7 Rotameter. For monitoring the air flow through the purging system (0-10 L/min)(0-0.4 ft 3/min).
6.2.1.8 Sample Splitters. Two heated flow restrictors (placed inside oven or heated to 120 ±10 °C (248 ±18 °F) ). At a purge rate of 6 L/min (0.2 ft 3/min), one will supply a constant flow to the first detector (the rest of the flow will be directed to the second sample splitter). The second splitter will split the analytical flow between the second detector and the flow restrictor. The approximate flow to the FID will be 40 mL/min (0.0014 ft 3/min) and to the ELCD will be 15 mL/min (0.0005 ft 3/min), but the exact flow must be adjusted to be compatible with the individual detector and to meet its linearity requirement. The two sample splitters will be connected to each other by 1/8′ OD (3.175 mm) stainless steel tubing.
6.2.1.9 Flow Restrictor. Stainless steel tubing, 1/8′ OD (3.175 mm), connecting the second sample splitter to the ice bath. Length is determined by the resulting pressure in the purging flask (as measured by the pressure gauge). The resulting pressure from the use of the flow restrictor shall be 6-7 psig.
6.2.1.10 Filter Flask. With one-hole stopper. Used to hold ice bath. Excess purge gas is vented through the flask to prevent condensation in the flowmeter and to trap volatile organic compounds.
6.2.1.11 Four-way Valve. Manually operated, stainless steel. Placed inside oven, used to bypass purging flask.
6.2.1.12 On/Off Valves. Two, stainless steel. One heat resistant up to 130 °C (266 °F) and placed between oven and ELCD. The other a toggle valve used to control purge gas flow.
6.2.1.13 Pressure Gauge. Range 0-40 psi. To monitor pressure in purging flask and coalescing filter.
6.2.1.14 Sample Lines. Teflon, 1/4′ OD (6.35 mm), used inside the oven to carry purge gas to and from purging chamber and to and from coalescing filter to four-way valve. Also used to carry sample from four-way valve to first sample splitter.
6.2.1.15 Detector Tubing. Stainless steel, 1/8′ OD (3.175 mm), heated to 120 ±10 °C (248 ±18 °F) . Used to carry sample gas from each sample splitter to a detector. Each piece of tubing must be wrapped with heat tape and insulating tape in order to insure that no cold spots exist. The tubing leading to the ELCD will also contain a heat-resistant on-off valve (Section 6.2.1.12) which shall also be wrapped with heat-tape and insulation.
6.2.2 Volatile Organic Measurement System. Consisting of an FID to measure the carbon concentration of the sample and an ELCD to measure the chlorine concentration.
6.2.2.1 FID. A heated FID meeting the following specifications is required.
6.2.2.1.1 Linearity. A linear response (±5 percent) over the operating range as demonstrated by the procedures established in section 10.1.1.
6.2.2.1.2 Range. A full scale range of 50 pg carbon/sec to 50 µg carbon/sec. Signal attenuators shall be available to produce a minimum signal response of 10 percent of full scale.
6.2.2.1.3 Data Recording System. A digital integration system compatible with the FID for permanently recording the output of the detector. The recorder shall have the capability to start and stop integration at points selected by the operator or it shall be capable of the “integration by slices” technique (this technique involves breaking down the chromatogram into smaller increments, integrating the area under the curve for each portion, subtracting the background for each portion, and then adding all of the areas together for the final area count).
6.2.2.2 ELCD. An ELCD meeting the following specifications is required. 1-propanol must be used as the electrolyte. The electrolyte flow through the conductivity cell shall be 1 to 2 mL/min (0.00004 to 0.00007 ft 3/min).
Note:A 1/4-in. ID (6.35 mm) quartz reactor tube is strongly recommended to reduce carbon buildup and the resulting detector maintenance.
6.2.2.2.1 Linearity. A linear response (±10 percent) over the response range as demonstrated by the procedures in section 10.1.2.
6.2.2.2.2 Range. A full scale range of 5.0 pg/sec to 500 ng/sec chloride. Signal attenuators shall be available to produce a minimum signal response of 10 percent of full scale.
6.2.2.2.3 Data Recording System. A digital integration system compatible with the output voltage range of the ELCD. The recorder must have the capability to start and stop integration at points selected by the operator or it shall be capable of performing the “integration by slices” technique.
7.0 Reagents and Standards7.1 Sampling.
7.1.1 Polyethylene Glycol (PEG). Ninety-eight percent pure with an average molecular weight of 400. Before using the PEG, remove any organic compounds that might be detected as volatile organics by heating it to 120 °C (248 °F) and purging it with nitrogen at a flow rate of 1 to 2 L/min (0.04 to 0.07 ft 3/min) for 2 hours. The cleaned PEG must be stored under a 1 to 2 L/min (0.04 to 0.07 ft 3/min) nitrogen purge until use. The purge apparatus is shown in Figure 25D-4.
7.2 Analysis.
7.2.1 Sample Separation. The following are required for the sample purging step.
7.2.1.1 PEG. Same as section 7.1.1.
7.2.1.2 Purge Gas. Zero grade nitrogen (N2), containing less than 1 ppm carbon.
7.2.2 Volatile Organics Measurement. The following are required for measuring the VO concentration.
7.2.2.1 Hydrogen (H2). Zero grade H2, 99.999 percent pure.
7.2.2.2 Combustion Gas. Zero grade air or oxygen as required by the FID.
7.2.2.3 Calibration Gas. Pressurized gas cylinder containing 10 percent propane and 1 percent 1,1-dichloroethylene by volume in nitrogen.
7.2.2.4 Water. Deionized distilled water that conforms to American Society for Testing and Materials Specification D 1193-74, Type 3, is required for analysis. At the option of the analyst, the KMnO4 test for oxidizable organic matter may be omitted when high concentrations are not expected to be present.
7.2.2.5 1-Propanol. ACS grade or better. Electrolyte Solution. For use in the ELCD.
8.0 Sample Collection, Preservation, Storage, and Transport8.1 Sampling.
8.1.1 Sampling Plan Design and Development. Use the procedures in chapter nine of Reference 1 in section 16 as guidance in developing a sampling plan.
8.1.2 Single Phase or Well-mixed Waste.
8.1.2.1 Install a sampling tap to obtain the sample at a point which is most representative of the unexposed waste (where the waste has had minimum opportunity to volatilize to the atmosphere). Assemble the sampling apparatus as shown in Figure 25D-5.
8.1.2.2 Prepare the sampling containers as follows: Pour 30 mL of clean PEG into the container. PEG will reduce but not eliminate the loss of organics during sample collection. Weigh the sample container with the screw cap, the PEG, and any labels to the nearest 0.01 g and record the weight (mst). Store the containers in an ice bath until 1 hour before sampling (PEG will solidify at ice bath temperatures; allow the containers to reach room temperature before sampling).
8.1.2.3 Begin sampling by purging the sample lines and cooling coil with at least four volumes of waste. Collect the purged material in a separate container and dispose of it properly.
8.1.2.4 After purging, stop the sample flow and direct the sampling tube to a preweighed sample container, prepared as described in section 8.1.2.2. Keep the tip of the tube below the surface of the PEG during sampling to minimize contact with the atmosphere. Sample at a flow rate such that the temperature of the waste is less than 10 °C (50 °F). Fill the sample container and immediately cap it (within 5 seconds) so that a minimum headspace exists in the container. Store immediately in a cooler and cover with ice.
8.1.3 Multiple-phase Waste. Collect a 10 g sample of each phase of waste generated using the procedures described in section 8.1.2 or 8.1.5. Each phase of the waste shall be analyzed as a separate sample. Calculate the weighted average VO concentration of the waste using Equation 25D-13 (Section 12.14).
8.1.4 Solid waste. Add approximately 10 g of the solid waste to a container prepared in the manner described in section 8.1.2.2, minimizing headspace. Cap and chill immediately.
8.1.5 Alternative to Tap Installation. If tap installation is impractical or impossible, fill a large, clean, empty container by submerging the container into the waste below the surface of the waste. Immediately fill a container prepared in the manner described in section 8.1.2.2 with approximately 10 g of the waste collected in the large container. Minimize headspace, cap and chill immediately.
8.1.6 Alternative sampling techniques may be used upon the approval of the Administrator.
8.2 Sample Recovery.
8.2.1 Assemble the purging apparatus as shown in Figures 25D-1 and 25D-2. The oven shall be heated to 75 ±2 °C (167 ±3.6 °F). The sampling lines leading from the oven to the detectors shall be heated to 120 ±10 °C (248 ±18 °F) with no cold spots. The flame ionization detector shall be operated with a heated block. Adjust the purging lance so that it reaches the bottom of the chamber.
8.2.2 Remove the sample container from the cooler, and wipe the exterior of the container to remove any extraneous ice, water, or other debris. Reweigh the sample container to the nearest 0.01 g, and record the weight (msf). Pour the contents of the sample container into the purging flask, rinse the sample container three times with a total of 20 mL of PEG (since the sample container originally held 30 mL of PEG, the total volume of PEG added to the purging flask will be 50 mL), transferring the rinsings to the purging flask after each rinse. Cap purging flask between rinses. The total volume of PEG in the purging flask shall be 50 mL. Add 50 mL of water to the purging flask.
9.0 Quality Control9.1 Quality Control Samples. If audit samples are not available, prepare and analyze the two types of quality control samples (QCS) listed in Sections 9.1.1 and 9.1.2. Before placing the system in operation, after a shutdown of greater than six months, and after any major modifications, analyze each QCS in triplicate. For each detector, calculate the percent recovery by dividing measured concentration by theoretical concentration and multiplying by 100. Determine the mean percent recovery for each detector for each QCS triplicate analysis. The RSD for any triplicate analysis shall be ≤10 percent. For QCS 1 (methylene chloride), the percent recovery shall be ≥90 percent for carbon as methane, and ≥55 percent for chlorine as chloride. For QCS 2 (1,3-dichloro-2-propanol), the percent recovery shall be ≤15 percent for carbon as methane, and ≤6 percent for chlorine as chloride. If the analytical system does not meet the above-mentioned criteria for both detectors, check the system parameters (temperature, system pressure, purge rate, etc.), correct the problem, and repeat the triplicate analysis of each QCS.
9.1.1 QCS 1, Methylene Chloride. Prepare a stock solution by weighing, to the nearest 0.1 mg, 55 µL of HPLC grade methylene chloride in a tared 5 mL volumetric flask. Record the weight in milligrams, dilute to 5 mL with cleaned PEG, and inject 100 µL of the stock solution into a sample prepared as a water blank (50 mL of cleaned PEG and 60 mL of water in the purging flask). Analyze the QCS according to the procedures described in sections 10.2 and 10.3, excluding section 10.2.2. To calculate the theoretical carbon concentration (in mg) in QCS 1, multiply mg of methylene chloride in the stock solution by 3.777 × 10−3. To calculate the theoretical chlorine concentration (in mg) in QCS 1, multiply mg of methylene chloride in the stock solution by 1.670 × 10−2.
9.1.2 QCS 2, 1,3-dichloro-2-propanol. Prepare a stock solution by weighing, to the nearest 0.1 mg, 60 µL of high purity grade 1,3-dichloro-2-propanol in a tared 5 mL volumetric flask. Record the weight in milligrams, dilute to 5 mL with cleaned PEG, and inject 100 µL of the stock solution into a sample prepared as a water blank (50 mL of cleaned PEG and 60 mL of water in the purging flask). Analyze the QCS according to the procedures described in sections 10.2 and 10.3, excluding section 10.2.2. To calculate the theoretical carbon concentration (in mg) in QCS 2, multiply mg of 1,3-dichloro-2-propanol in the stock solution by 7.461 × 10−3. To calculate the theoretical chlorine concentration (in mg) in QCS 2, multiply mg of 1,3-dichloro-2-propanol in the stock solution by 1.099 × 10−2.
9.1.3 Routine QCS Analysis. For each set of compliance samples (in this context, set is per facility, per compliance test), analyze one QCS 1 and one QCS 2 sample. The percent recovery for each sample for each detector shall be ±13 percent of the mean recovery established for the most recent set of QCS triplicate analysis (Section 9.4). If the sample does not meet this criteria, check the system components and analyze another QCS 1 and 2 until a single set of QCS meet the ±13 percent criteria.
10.0 Calibration and Standardization10.1 Initial Performance Check of Purging System. Before placing the system in operation, after a shutdown of greater than six months, after any major modifications, and at least once per month during continuous operation, conduct the linearity checks described in sections 10.1.1 and 10.1.2. Install calibration gas at the three-way calibration gas valve. See Figure 25D-1.
10.1.1 Linearity Check Procedure. Using the calibration standard described in section 7.2.2.3 and by varying the injection time, it is possible to calibrate at multiple concentration levels. Use Equation 25D-3 to calculate three sets of calibration gas flow rates and run times needed to introduce a total mass of carbon, as methane, (mc) of 1, 5, and 10 mg into the system (low, medium and high FID calibration, respectively). Use Equation 25D-4 to calculate three sets of calibration gas flow rates and run times needed to introduce a total chloride mass (mch) of 1, 5, and 10 mg into the system (low, medium and high ELCD calibration, respectively). With the system operating in standby mode, allow the FID and the ELCD to establish a stable baseline. Set the secondary pressure regulator of the calibration gas cylinder to the same pressure as the purge gas cylinder and set the proper flow rate with the calibration flow controller (see Figure 25D-1). The calibration gas flow rate can be measured with a flowmeter attached to the vent position of the calibration gas valve. Set the four-way bypass valve to standby position so that the calibration gas flows through the coalescing filter only. Inject the calibration gas by turning the calibration gas valve from vent position to inject position. Continue the calibration gas flow for the appropriate period of time before switching the calibration valve to vent position. Continue recording the response of the FID and the ELCD for 5 min after switching off calibration gas flow. Make triplicate injections of all six levels of calibration.
10.1.2 Linearity Criteria. Calculate the average response factor (Equations 25D-5 and 25D-6) and the relative standard deviation (RSD) (Equation 25D-10) at each level of the calibration curve for both detectors. Calculate the overall mean of the three response factor averages for each detector. The FID linearity is acceptable if each response factor is within 5 percent of the overall mean and if the RSD for each set of triplicate injections is less than 5 percent. The ELCD linearity is acceptable if each response factor is within 10 percent of the overall mean and if the RSD for each set of triplicate injections is less than 10 percent. Record the overall mean value of the response factors for the FID and the ELCD. If the calibration for either the FID or the ELCD does not meet the criteria, correct the detector/system problem and repeat sections 10.1.1 and 10.1.2.
10.2 Daily Calibrations.
10.2.1 Daily Linearity Check. Follow the procedures outlined in section 10.1.1 to analyze the medium level calibration for both the FID and the ELCD in duplicate at the start of the day. Calculate the response factors and the RSDs for each detector. For the FID, the calibration is acceptable if the average response factor is within 5 percent of the overall mean response factor (Section 10.1.2) and if the RSD for the duplicate injection is less than 5 percent. For the ELCD, the calibration is acceptable if the average response factor is within 10 percent of the overall mean response factor (Section 10.1.2) and if the RSD for the duplicate injection is less than 10 percent. If the calibration for either the FID or the ELCD does not meet the criteria, correct the detector/system problem and repeat sections 10.1.1 and 10.1.2.
10.2.2 Calibration Range Check.
10.2.2.1 If the waste concentration for either detector falls below the range of calibration for that detector, use the procedure outlined in section 10.1.1 to choose two calibration points that bracket the new target concentration. Analyze each of these points in triplicate (as outlined in section 10.1.1) and use the criteria in section 10.1.2 to determine the linearity of the detector in this “mini-calibration” range.
10.2.2.2 After the initial linearity check of the mini-calibration curve, it is only necessary to test one of the points in duplicate for the daily calibration check (in addition to the points specified in section 10.2.1). The average daily mini-calibration point should fit the linearity criteria specified in section 10.2.1. If the calibration for either the FID or the ELCD does not meet the criteria, correct the detector/system problem and repeat the calibration procedure mentioned in the first paragraph of section 10.2.2. A mini-calibration curve for waste concentrations above the calibration curve for either detector is optional.
10.3 Analytical Balance. Calibrate against standard weights.
11.0 Analysis11.1 Sample Analysis.
11.1.1 Turn on the constant temperature chamber and allow the temperature to equilibrate at 75 ±2 °C (167 ±3.6 °F). Turn the four-way valve so that the purge gas bypasses the purging flask, the purge gas flowing through the coalescing filter and to the detectors (standby mode). Turn on the purge gas. Allow both the FID and the ELCD to warm up until a stable baseline is achieved on each detector. Pack the filter flask with ice. Replace ice after each run and dispose of the waste water properly. When the temperature of the oven reaches 75 ±2 °C (167 ±3.6 °F), start both integrators and record baseline. After 1 min, turn the four-way valve so that the purge gas flows through the purging flask, to the coalescing filter and to the sample splitters (purge mode). Continue recording the response of the FID and the ELCD. Monitor the readings of the pressure gauge and the rotameter. If the readings fall below established setpoints, stop the purging, determine the source of the leak, and resolve the problem before resuming. Leaks detected during a sampling period invalidate that sample.
11.1.2 As the purging continues, monitor the output of the detectors to make certain that the analysis is proceeding correctly and that the results are being properly recorded. Every 10 minutes read and record the purge flow rate, the pressure and the chamber temperature. Continue the purging for 30 minutes.
11.1.3 For each detector output, integrate over the entire area of the peak starting at 1 minute and continuing until the end of the run. Subtract the established baseline area from the peak area. Record the corrected area of the peak. See Figure 25D-6 for an example integration.
11.2 Water Blank. A water blank shall be analyzed for each batch of cleaned PEG prepared. Transfer about 60 mL of water into the purging flask. Add 50 mL of the cleaned PEG to the purging flask. Treat the blank as described in sections 8.2 and 8.3, excluding section 8.2.2. Calculate the concentration of carbon and chlorine in the blank sample (assume 10 g of waste as the mass). A VO concentration equivalent to ≤10 percent of the applicable standard may be subtracted from the measured VO concentration of the waste samples. Include all blank results and documentation in the test report.
12.0 Data Analysis and Calculations12.1 Nomenclature.
Ab = Area under the water blank response curve, counts. Ac = Area under the calibration response curve, counts. As = Area under the sample response curve, counts. C = Concentration of volatile organics in the sample, ppmw. Cc = Concentration of carbon, as methane, in the calibration gas, mg/L. Cch = Concentration of chloride in the calibration gas, mg/L. Cj = VO concentration of phase j, ppmw. DRt = Average daily response factor of the FID, mg CH4/counts. Drth = Average daily response factor of the ELCD, mg Cl−/counts. Fj = Weight fraction of phase j present in the waste. mc = Mass of carbon, as methane, in a calibration run, mg. mch = Mass of chloride in a calibration run, mg. ms = Mass of the waste sample, g. msc = Mass of carbon, as methane, in the sample, mg. msf = Mass of sample container and waste sample, g. msh = Mass of chloride in the sample, mg. mst = Mass of sample container prior to sampling, g. mVO = Mass of volatile organics in the sample, mg. n = Total number of phases present in the waste. Pp = Percent propane in calibration gas (L/L). Pvc = Percent 1,1-dichloroethylene in calibration gas (L/L). Qc = Flow rate of calibration gas, L/min. tc = Length of time standard gas is delivered to the analyzer, min. W = Weighted average VO concentration, ppmw.12.2 Concentration of Carbon, as Methane, in the Calibration Gas.
12.3 Concentration of Chloride in the Calibration Gas.
12.4 Mass of Carbon, as Methane, in a Calibration Run.
12.5 Mass of Chloride in a Calibration Run.
12.6 FID Response Factor, mg/counts.
12.7 ELCD Response Factor, mg/counts.
12.8 Mass of Carbon in the Sample.
12.9 Mass of Chloride in the Sample.
12.10 Mass of Volatile Organics in the Sample.
12.11 Relative Standard Deviation.
12.12 Mass of Sample.
12.13 Concentration of Volatile Organics in Waste.
12.14 Weighted Average VO Concentration of Multi-phase Waste.
13.0 Method Performance [Reserved] 14.0 Pollution Prevention [Reserved] 15.0 Waste Management [Reserved] 16.0 References1. “Test Methods for Evaluating Solid Waste, Physical/Chemistry Methods”, U.S. Environmental Protection Agency. Publication SW-846, 3rd Edition, November 1986 as amended by Update I, November 1990.
17.0 Tables, Diagrams, Flowcharts, and Validation Data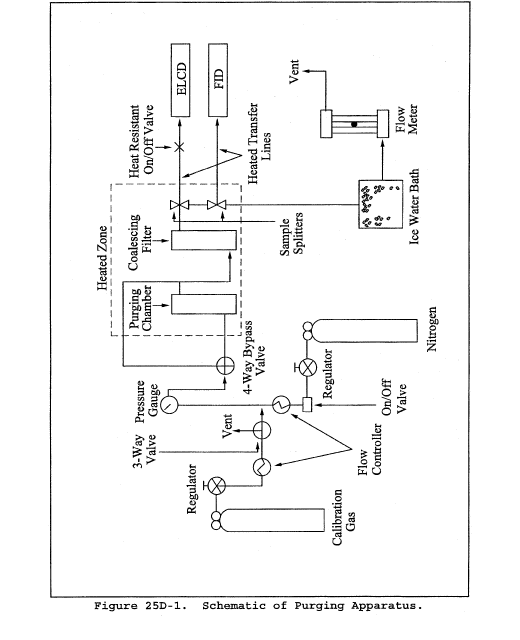
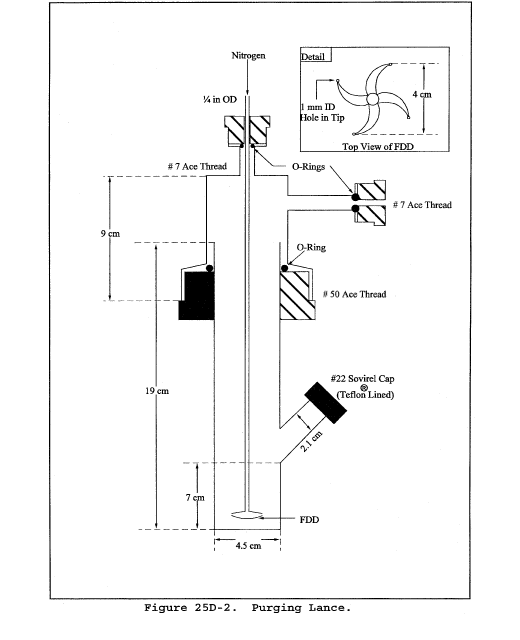
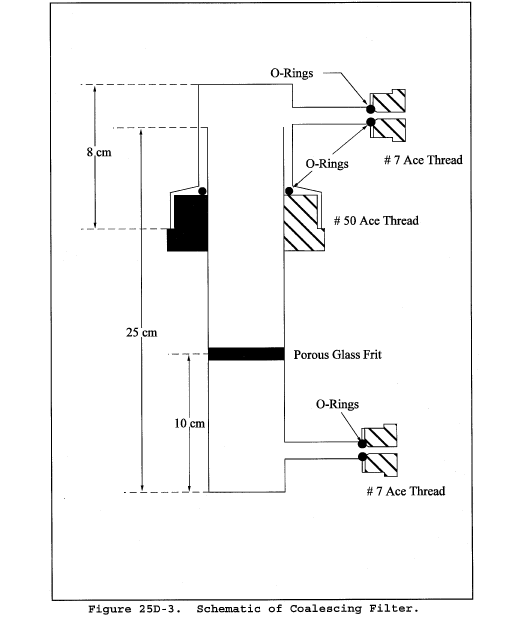
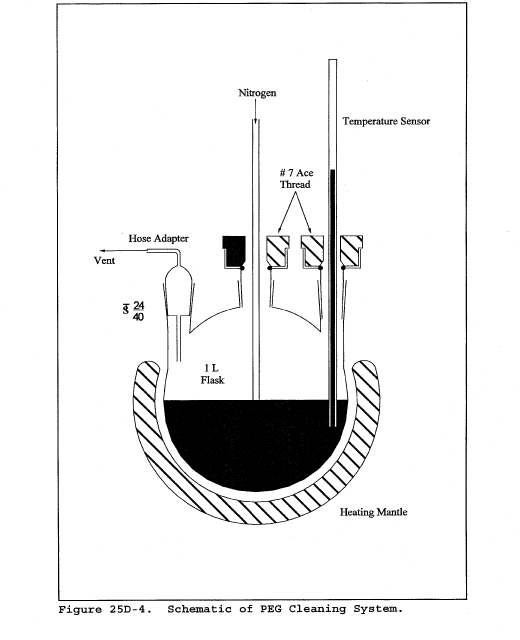
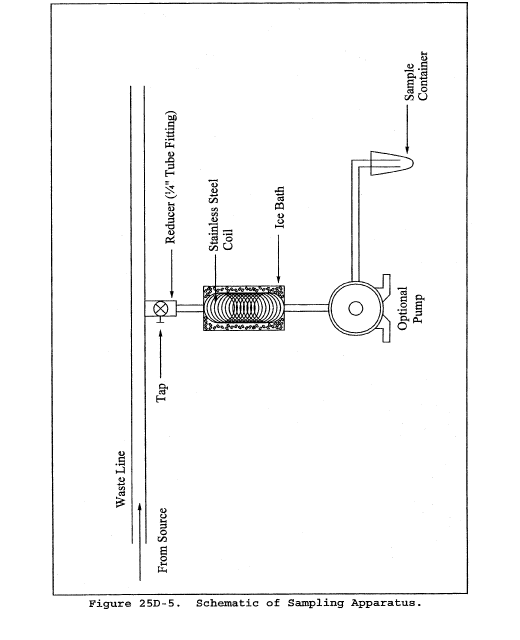
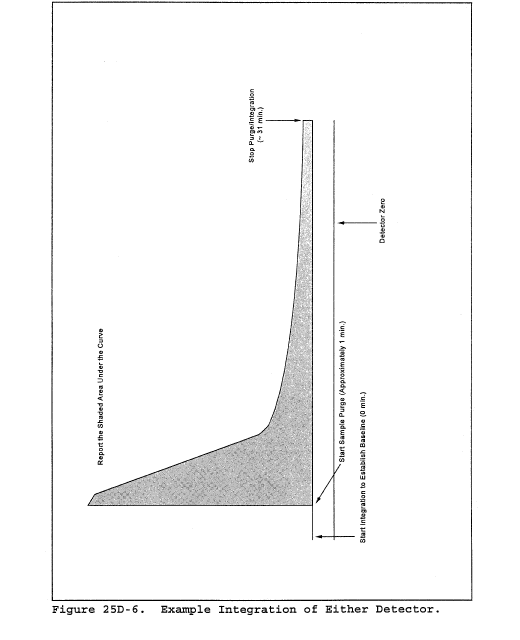
Performance of this method should not be attempted by persons unfamiliar with the operation of a flame ionization detector (FID) nor by those who are unfamiliar with source sampling because knowledge beyond the scope of this presentation is required. This method is not inclusive with respect to specifications (e.g., reagents and standards) and calibration procedures. Some material is incorporated by reference from other methods. Therefore, to obtain reliable results, persons using this method should have a thorough knowledge of at least the following additional test methods: Method 106, part 61, Appendix B, and Method 18, part 60, Appendix A.
1.0 Scope and Application1.1 Applicability. This method is applicable for determining the vapor pressure of waste cited by an applicable regulation.
1.2 Data Quality Objectives. Adherence to the requirements of this method will enhance the quality of the data obtained from air pollutant sampling methods.
2.0 Summary of Method2.1 The headspace vapor of the sample is analyzed for carbon content by a headspace analyzer, which uses an FID.
3.0 Definitions [Reserved] 4.0 Interferences4.1 The analyst shall select the operating parameters best suited to the requirements for a particular analysis. The analyst shall produce confirming data through an adequate supplemental analytical technique and have the data available for review by the Administrator.
5.0 Safety [Reserved] 6.0 Equipment and Supplies6.1 Sampling. The following equipment is required:
6.1.1 Sample Containers. Vials, glass, with butyl rubber septa, Perkin-Elmer Corporation Numbers 0105-0129 (glass vials), B001-0728 (gray butyl rubber septum, plug style), 0105-0131 (butyl rubber septa), or equivalent. The seal must be made from butyl rubber. Silicone rubber seals are not acceptable.
6.1.2 Vial Sealer. Perkin-Elmer Number 105-0106, or equivalent.
6.1.3 Gas-Tight Syringe. Perkin-Elmer Number 00230117, or equivalent.
6.1.4 The following equipment is required for sampling.
6.1.4.1 Tap.
6.1.4.2 Tubing. Teflon, 0.25-in. ID.
Note:Mention of trade names or specific products does not constitute endorsement by the Environmental Protection Agency.
6.1.4.3 Cooling Coil. Stainless steel (304), 0.25 in.-ID, equipped with a thermocouple at the coil outlet.
6.2 Analysis. The following equipment is required.
6.2.1 Balanced Pressure Headspace Sampler. Perkin-Elmer HS-6, HS-100, or equivalent, equipped with a glass bead column instead of a chromatographic column.
6.2.2 FID. An FID meeting the following specifications is required.
6.2.2.1 Linearity. A linear response (±5 percent) over the operating range as demonstrated by the procedures established in section 10.2.
6.2.2.2 Range. A full scale range of 1 to 10,000 parts per million (ppm) propane (C3H8). Signal attenuators shall be available to produce a minimum signal response of 10 percent of full scale.
6.2.3 Data Recording System. Analog strip chart recorder or digital integration system compatible with the FID for permanently recording the output of the detector.
6.2.4 Temperature Sensor. Capable of reading temperatures in the range of 30 to 60 °C (86 to 140 °F) with an accuracy of ±0.1 °C (±0.2 °F).
7.0 Reagents and Standards7.1 Analysis. The following items are required for analysis.
7.1.1 Hydrogen (H2). Zero grade hydrogen, as required by the FID.
7.1.2 Carrier Gas. Zero grade nitrogen, containing less than 1 ppm carbon (C) and less than 1 ppm carbon dioxide.
7.1.3 Combustion Gas. Zero grade air or oxygen as required by the FID.
7.2 Calibration and Linearity Check.
7.2.1 Stock Cylinder Gas Standard. 100 percent propane. The manufacturer shall: (a) Certify the gas composition to be accurate to ±3 percent or better (see section 7.2.1.1); (b) recommend a maximum shelf life over which the gas concentration does not change by greater than ±5 percent from the certified value; and (c) affix the date of gas cylinder preparation, certified propane concentration, and recommended maximum shelf life to the cylinder before shipment to the buyer.
7.2.1.1 Cylinder Standards Certification. The manufacturer shall certify the concentration of the calibration gas in the cylinder by (a) directly analyzing the cylinder and (b) calibrating his analytical procedure on the day of cylinder analysis. To calibrate his analytical procedure, the manufacturer shall use, as a minimum, a three-point calibration curve.
7.2.1.2 Verification of Manufacturer's Calibration Standards. Before using, the manufacturer shall verify each calibration standard by (a) comparing it to gas mixtures prepared in accordance with the procedure described in section 7.1 of Method 106 of Part 61, Appendix B, or by (b) calibrating it against Standard Reference Materials (SRM's) prepared by the National Bureau of Standards, if such SRM's are available. The agreement between the initially determined concentration value and the verification concentration value must be within ±5 percent. The manufacturer must reverify all calibration standards on a time interval consistent with the shelf life of the cylinder standards sold.
8.0 Sampling Collection, Preservation, Storage, and Transport8.1 Install a sampling tap to obtain a sample at a point which is most representative of the unexposed waste (where the waste has had minimum opportunity to volatilize to the atmosphere). Assemble the sampling apparatus as shown in Figure 25E-1.
8.2 Begin sampling by purging the sample lines and cooling coil with at least four volumes of waste. Collect the purged material in a separate container and dispose of it properly.
8.3 After purging, stop the sample flow and transfer the Teflon sampling tube to a sample container. Sample at a flow rate such that the temperature of the waste is <10 °C (<50 °F). Fill the sample container halfway (±5 percent) and cap it within 5 seconds. Store immediately in a cooler and cover with ice.
8.4 Alternative sampling techniques may be used upon the approval of the Administrator.
9.0 Quality Control9.1 Miscellaneous Quality Control Measures.
Section | Quality control measure | Effect |
---|---|---|
10.2, 10.3 | FID calibration and response check | Ensure precision of analytical results. |
Maintain a record of performance of each item.
10.1 Use the procedures in sections 10.2 to calibrate the headspace analyzer and FID and check for linearity before the system is first placed in operation, after any shutdown longer than 6 months, and after any modification of the system.
10.2 Calibration and Linearity. Use the procedures in section 10 of Method 18 of Part 60, Appendix A, to prepare the standards and calibrate the flowmeters, using propane as the standard gas. Fill the calibration standard vials halfway (±5 percent) with deionized water. Purge and fill the airspace with calibration standard. Prepare a minimum of three concentrations of calibration standards in triplicate at concentrations that will bracket the applicable cutoff. For a cutoff of 5.2 kPa (0.75 psi), prepare nominal concentrations of 30,000, 50,000, and 70,000 ppm as propane. For a cutoff of 27.6 kPa (4.0 psi), prepare nominal concentrations of 200,000, 300,000, and 400,000 ppm as propane.
10.2.1 Use the procedures in section 11.3 to measure the FID response of each standard. Use a linear regression analysis to calculate the values for the slope (k) and the y-intercept (b). Use the procedures in sections 12.3 and 12.2 to test the calibration and the linearity.
10.3 Daily FID Calibration Check. Check the calibration at the beginning and at the end of the daily runs by using the following procedures. Prepare 2 calibration standards at the nominal cutoff concentration using the procedures in section 10.2. Place one at the beginning and one at the end of the daily run. Measure the FID response of the daily calibration standard and use the values for k and b from the most recent calibration to calculate the concentration of the daily standard. Use an equation similar to 25E-2 to calculate the percent difference between the daily standard and Cs. If the difference is within 5 percent, then the previous values for k and b can be used. Otherwise, use the procedures in section 10.2 to recalibrate the FID.
11.0 Analytical Procedures11.1 Allow one hour for the headspace vials to equilibrate at the temperature specified in the regulation. Allow the FID to warm up until a stable baseline is achieved on the detector.
11.2 Check the calibration of the FID daily using the procedures in section 10.3.
11.3 Follow the manufacturer's recommended procedures for the normal operation of the headspace sampler and FID.
11.4 Use the procedures in sections 12.4 and 12.5 to calculate the vapor phase organic vapor pressure in the samples.
11.5 Monitor the output of the detector to make certain that the results are being properly recorded.
12.0 Data Analysis and Calculations12.1 Nomenclature.
A = Measurement of the area under the response curve, counts. b = y-intercept of the linear regression line. Ca = Measured vapor phase organic concentration of sample, ppm as propane. Cma = Average measured vapor phase organic concentration of standard, ppm as propane. Cm = Measured vapor phase organic concentration of standard, ppm as propane. Cs = Calculated standard concentration, ppm as propane. k = Slope of the linear regression line. Pbar = Atmospheric pressure at analysis conditions, mm Hg (in. Hg). P* = Organic vapor pressure in the sample, kPa (psi). PD = Percent difference between the average measured vapor phase organic concentration (Cm) and the calculated standard concentration (Cs). RSD = Relative standard deviation. β = 1.333 × 10−7 kPa/[(mm Hg)(ppm)], (4.91 × 10−7 psi/[(in. Hg)(ppm)])12.2 Linearity. Use the following equation to calculate the measured standard concentration for each standard vial.
12.2.1 Calculate the average measured standard concentration (Cma) for each set of triplicate standards and use the following equation to calculate PD between Cma and Cs. The instrument linearity is acceptable if the PD is within five for each standard.
12.3. Relative Standard Deviation (RSD). Use the following equation to calculate the RSD for each triplicate set of standards.
The calibration is acceptable if the RSD is within five for each standard concentration.12.4 Concentration of organics in the headspace. Use the following equation to calculate the concentration of vapor phase organics in each sample.
12.5 Vapor Pressure of Organics in the Headspace Sample. Use the following equation to calculate the vapor pressure of organics in the sample.
13.0 Method Performance [Reserved] 14.0 Pollution Prevention [Reserved] 15.0 Waste Management [Reserved] 16.0 References1. Salo, Albert E., Samuel Witz, and Robert D. MacPhee. “Determination of Solvent Vapor Concentrations by Total Combustion Analysis: a Comparison of Infared with Flame Ionization Detectors. Paper No. 75-33.2. (Presented at the 68th Annual Meeting of the Air Pollution Control Association. Boston, Massachusetts.
2. Salo, Albert E., William L. Oaks, and Robert D. MacPhee. “Measuring the Organic Carbon Content of Source Emissions for Air Pollution Control. Paper No. 74-190. (Presented at the 67th Annual Meeting of the Air Pollution Control Association. Denver, Colorado. June 9-13, 1974.) p. 25.
17.0 Tables, Diagrams, Flowcharts, and Validation Data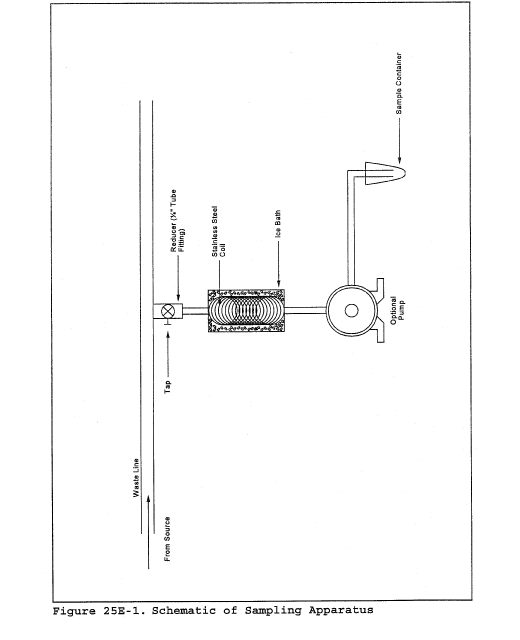
Appendix A-8 to Part 60 - Test Methods 26 through 30B
40:9.0.1.1.1.0.1.1.8 : Appendix A
Appendix A-8 to Part 60 - Test Methods 26 through 30B Method 26 - Determination of Hydrogen Chloride Emissions From Stationary Sources Method 26A - Determination of hydrogen halide and halogen emissions from stationary sources - isokinetic method Method 27 - Determination of vapor tightness of gasoline delivery tank using pressure-vacuum test Method 28 - Certification and auditing of wood heaters Method 28A - Measurement of air to fuel ratio and minimum achievable burn rates for wood-fired appliances Method 29 - Determination of metals emissions from stationary sourcesThe test methods in this appendix are referred to in § 60.8 (Performance Tests) and § 60.11 (Compliance With Standards and Maintenance Requirements) of 40 CFR part 60, subpart A (General Provisions). Specific uses of these test methods are described in the standards of performance contained in the subparts, beginning with Subpart D.
Within each standard of performance, a section title “Test Methods and Procedures” is provided to: (1) Identify the test methods to be used as reference methods to the facility subject to the respective standard and (2) identify any special instructions or conditions to be followed when applying a method to the respective facility. Such instructions (for example, establish sampling rates, volumes, or temperatures) are to be used either in addition to, or as a substitute for procedures in a test method. Similarly, for sources subject to emission monitoring requirements, specific instructions pertaining to any use of a test method as a reference method are provided in the subpart or in Appendix B.
Inclusion of methods in this appendix is not intended as an endorsement or denial of their applicability to sources that are not subject to standards of performance. The methods are potentially applicable to other sources; however, applicability should be confirmed by careful and appropriate evaluation of the conditions prevalent at such sources.
The approach followed in the formulation of the test methods involves specifications for equipment, procedures, and performance. In concept, a performance specification approach would be preferable in all methods because this allows the greatest flexibility to the user. In practice, however, this approach is impractical in most cases because performance specifications cannot be established. Most of the methods described herein, therefore, involve specific equipment specifications and procedures, and only a few methods in this appendix rely on performance criteria.
Minor changes in the test methods should not necessarily affect the validity of the results and it is recognized that alternative and equivalent methods exist. section 60.8 provides authority for the Administrator to specify or approve (1) equivalent methods, (2) alternative methods, and (3) minor changes in the methodology of the test methods. It should be clearly understood that unless otherwise identified all such methods and changes must have prior approval of the Administrator. An owner employing such methods or deviations from the test methods without obtaining prior approval does so at the risk of subsequent disapproval and retesting with approved methods.
Within the test methods, certain specific equipment or procedures are recognized as being acceptable or potentially acceptable and are specifically identified in the methods. The items identified as acceptable options may be used without approval but must be identified in the test report. The potentially approvable options are cited as “subject to the approval of the Administrator” or as “or equivalent.” Such potentially approvable techniques or alternatives may be used at the discretion of the owner without prior approval. However, detailed descriptions for applying these potentially approvable techniques or alternatives are not provided in the test methods. Also, the potentially approvable options are not necessarily acceptable in all applications. Therefore, an owner electing to use such potentially approvable techniques or alternatives is responsible for: (1) assuring that the techniques or alternatives are in fact applicable and are properly executed; (2) including a written description of the alternative method in the test report (the written method must be clear and must be capable of being performed without additional instruction, and the degree of detail should be similar to the detail contained in the test methods); and (3) providing any rationale or supporting data necessary to show the validity of the alternative in the particular application. Failure to meet these requirements can result in the Administrator's disapproval of the alternative.
Method 26 - Determination of Hydrogen Halide and Halogen Emissions From Stationary Sources Non-Isokinetic Method 1.0 Scope and Application1.1 Analytes.
Analytes | CAS No. |
---|---|
Hydrogen Chloride (HCl) | 7647-01-0 |
Hydrogen Bromide (HBr) | 10035-10-6 |
Hydrogen Fluoride (HF) | 7664-39-3 |
Chlorine (Cl2) | 7882-50-5 |
Bromine (Br2) | 7726-95-6 |
1.2 Applicability. This method is applicable for determining emissions of hydrogen halides (HX) (HCl, HBr, and HF) and halogens (X2) (Cl2 and Br2) from stationary sources when specified by the applicable subpart. Sources, such as those controlled by wet scrubbers, that emit acid particulate matter must be sampled using Method 26A.
1.3 Data Quality Objectives. Adherence to the requirements of this method will enhance the quality of the data obtained from air pollutant sampling methods.
2.0 Summary of Method2.1 An integrated sample is extracted from the source and passed through a prepurged heated probe and filter into dilute sulfuric acid and dilute sodium hydroxide solutions which collect the gaseous hydrogen halides and halogens, respectively. The filter collects particulate matter including halide salts but is not routinely recovered and analyzed. The hydrogen halides are solubilized in the acidic solution and form chloride (Cl−), bromide (Br−), and fluoride (F−) ions. The halogens have a very low solubility in the acidic solution and pass through to the alkaline solution where they are hydrolyzed to form a proton (H + ), the halide ion, and the hypohalous acid (HClO or HBrO). Sodium thiosulfate is added in excess to the alkaline solution to assure reaction with the hypohalous acid to form a second halide ion such that 2 halide ions are formed for each molecule of halogen gas. The halide ions in the separate solutions are measured by ion chromatography (IC).
3.0 Definitions [Reserved] 4.0 Interferences4.1 Volatile materials, such as chlorine dioxide (ClO2) and ammonium chloride (NH4Cl), which produce halide ions upon dissolution during sampling are potential interferents. Interferents for the halide measurements are the halogen gases which disproportionate to a hydrogen halide and a hydrohalous acid upon dissolution in water. However, the use of acidic rather than neutral or basic solutions for collection of the hydrogen halides greatly reduces the dissolution of any halogens passing through this solution.
4.2 The simultaneous presence of HBr and CL2 may cause a positive bias in the HCL result with a corresponding negative bias in the Cl2 result as well as affecting the HBr/Br2 split.
4.3 High concentrations of nitrogen oxides (NOX) may produce sufficient nitrate (NO3− to interfere with measurements of very low Br− levels.
4.4 A glass wool plug should not be used to remove particulate matter since a negative bias in the data could result.
4.5 There is anecdotal evidence that HF may be outgassed from new teflon components. If HF is a target analyte, then preconditioning of new teflon components, by heating should be considered.
5.0 Safety5.1 Disclaimer. This method may involve hazardous materials, operations, and equipment. This test method may not address all of the safety problems associated with its use. It is the responsibility of the user to establish appropriate safety and health practices and determine the applicability of regulatory limitations before performing this test method.
5.2 Corrosive Reagents. The following reagents are hazardous. Personal protective equipment and safe procedures are useful in preventing chemical splashes. If contact occurs, immediately flush with copious amounts of water for at least 15 minutes. Remove clothing under shower and decontaminate. Treat residual chemical burns as thermal burns.
5.2.1 Sodium Hydroxide (NaOH). Causes severe damage to eyes and skin. Inhalation causes irritation to nose, throat, and lungs. Reacts exothermically with limited amounts of water.
5.2.2 Sulfuric Acid (H2SO4). Rapidly destructive to body tissue. Will cause third degree burns. Eye damage may result in blindness. Inhalation may be fatal from spasm of the larynx, usually within 30 minutes. May cause lung tissue damage with edema. 1 mg/m 3 for 8 hours will cause lung damage or, in higher concentrations, death. Provide ventilation to limit inhalation. Reacts violently with metals and organics.
6.0 Equipment and Supplies Note:Mention of trade names or specific products does not constitute endorsement by the Environmental Protection Agency.
6.1 Sampling. The sampling train is shown in Figure 26-1, and component parts are discussed below.
6.1.1 Probe. Borosilicate glass, approximately 3/8-in. (9-mm) I.D. with a heating system capable of maintaining a probe gas temperature during sampling between 120 and 134 °C (248 and 273 °F) to prevent moisture condensation; or Teflon where stack probes are below 210 °C. If HF is a target analyte, then preconditioning of new teflon components by heating should be considered to prevent potential HF outgassing. A Teflon-glass filter in a mat configuration should be installed to remove particulate matter from the gas stream.
6.1.2 Three-way Stopcock. A borosilicate-glass three-way stopcock with a heating system to prevent moisture condensation. The heated stopcock should connect to the outlet of the heated filter and the inlet of the first impinger. The heating system should be capable of preventing condensation up to the inlet of the first impinger. Silicone grease may be used, if necessary, to prevent leakage.
6.1.3 Impingers. Four 30-ml midget impingers with leak-free glass connectors. Silicone grease may be used, if necessary, to prevent leakage. For sampling at high moisture sources or for sampling times greater than one hour, a midget impinger with a shortened stem (such that the gas sample does not bubble through the collected condensate) should be used in front of the first impinger.
6.1.4 Drying Tube or Impinger. Tube or impinger, of Mae West design, filled with 6- to 16-mesh indicating type silica gel, or equivalent, to dry the gas sample and to protect the dry gas meter and pump. If the silica gel has been used previously, dry at 175 °C (350 °F) for 2 hours. New silica gel may be used as received. Alternatively, other types of desiccants (equivalent or better) may be used.
6.1.5 Heating System. Any heating system capable of maintaining a temperature around the probe and filter holder between 120 and 134 °C (248 and 273 °F) during sampling, or such other temperature as specified by an applicable subpart of the standards or approved by the Administrator for a particular application.
6.1.6 Filter Holder and Support. The filter holder shall be made of Teflon or quartz. The filter support shall be made of Teflon. All Teflon filter holders and supports are available from Savillex Corp., 5325 Hwy 101, Minnetonka, MN 55345.
6.1.7 Sample Line. Leak-free, with compatible fittings to connect the last impinger to the needle valve.
6.1.8 Rate Meter. Rotameter, or equivalent, capable of measuring flow rate to within 2 percent of the selected flow rate of 2 liters/min (0.07 ft 3/min).
6.1.9 Purge Pump, Purge Line, Drying Tube, Needle Valve, and Rate Meter. Pump capable of purging the sampling probe at 2 liters/min, with drying tube, filled with silica gel or equivalent, to protect pump, and a rate meter capable of measuring 0 to 5 liters/min (0.2 ft 3/min).
6.1.10 Stopcock Grease, Valve, Pump, Volume Meter, Barometer, and Vacuum Gauge. Same as in Method 6, sections 6.1.1.4, 6.1.1.7, 6.1.1.8, 6.1.1.10, 6.1.2, and 6.1.3.
6.1.11 Temperature Measuring Devices. Temperature sensors to monitor the temperature of the probe and to monitor the temperature of the sampling system from the outlet of the probe to the inlet of the first impinger.
6.1.12 Ice Water Bath. To minimize loss of absorbing solution.
6.2 Sample Recovery.
6.2.1 Wash Bottles. Polyethylene or glass, 500-ml or larger, two.
6.2.2 Storage Containers. 100- or 250-ml, high-density polyethylene or glass sample storage containers with Teflon screw cap liners to store impinger samples.
6.3 Sample Preparation and Analysis. The materials required for volumetric dilution and chromatographic analysis of samples are described below.
6.3.1 Volumetric Flasks. Class A, 100-ml size.
6.3.2 Volumetric Pipets. Class A, assortment. To dilute samples to the calibration range of the ion chromatograph.
6.3.3 Ion Chromatograph (IC). Suppressed or non-suppressed, with a conductivity detector and electronic integrator operating in the peak area mode. Other detectors, strip chart recorders, and peak height measurements may be used.
7.0 Reagents and Standards Note:Unless otherwise indicated, all reagents must conform to the specifications established by the Committee on Analytical Reagents of the American Chemical Society (ACS reagent grade). When such specifications are not available, the best available grade shall be used.
7.1 Sampling.
7.1.1 Filter. A 25-mm (1 in) (or other size) Teflon glass mat, Pallflex TX40HI75 (Pallflex Inc., 125 Kennedy Drive, Putnam, CT 06260). This filter is in a mat configuration to prevent fine particulate matter from entering the sampling train. Its composition is 75% Teflon/25% borosilicate glass. Other filters may be used, but they must be in a mat (as opposed to a laminate) configuration and contain at least 75% Teflon. For practical rather than scientific reasons, when the stack gas temperature exceeds 210 °C (410 °F) and the HCl concentration is greater than 20 ppm, a quartz-fiber filter may be used since Teflon becomes unstable above this temperature.
7.1.2 Water. Deionized, distilled water that conforms to American Society of Testing and Materials (ASTM) Specification D 1193-77 or 91, Type 3 (incorporated by reference - see § 60.17).
7.1.3 Acidic Absorbing Solution, 0.1 N Sulfuric Acid (H2SO4). To prepare 100 ml of the absorbing solution for the front impinger pair, slowly add 0.28 ml of concentrated H2SO4 to about 90 ml of water while stirring, and adjust the final volume to 100 ml using additional water. Shake well to mix the solution.
7.1.4 Silica Gel. Indicating type, 6 to 16 mesh. If previously used, dry at 180 °C (350 °F) for 2 hours. New silica gel may be used as received. Alternatively, other types of desiccants may be used, subject to the approval of the Administrator.
7.1.5 Alkaline Adsorbing Solution, 0.1 N Sodium Hydroxide (NaOH). To prepare 100 ml of the scrubber solution for the third and fourth impinger, dissolve 0.40 g of solid NaOH in about 90 ml of water, and adjust the final solution volume to 100 ml using additional water. Shake well to mix the solution.
7.1.6 Sodium Thiosulfate (Na2S2O3 5 H2O)
7.2 Sample Preparation and Analysis.
7.2.1 Water. Same as in section 7.1.2.
7.2.2 Absorbing Solution Blanks. A separate blank solution of each absorbing reagent should be prepared for analysis with the field samples. Dilute 30 ml of each absorbing solution to approximately the same final volume as the field samples using the blank sample of rinse water.
7.2.3 Halide Salt Stock Standard Solutions. Prepare concentrated stock solutions from reagent grade sodium chloride (NaCl), sodium bromide (NaBr), and sodium fluoride (NaF). Each must be dried at 110 °C (230 °F) for two or more hours and then cooled to room temperature in a desiccator immediately before weighing. Accurately weigh 1.6 to 1.7 g of the dried NaCl to within 0.1 mg, dissolve in water, and dilute to 1 liter. Calculate the exact Cl− concentration using Equation 26-1 in section 12.2. In a similar manner, accurately weigh and solubilize 1.2 to 1.3 g of dried NaBr and 2.2 to 2.3 g of NaF to make 1-liter solutions. Use Equations 26-2 and 26-3 in section 12.2, to calculate the Br− and F− concentrations. Alternately, solutions containing a nominal certified concentration of 1000 mg/l NaCl are commercially available as convenient stock solutions from which standards can be made by appropriate volumetric dilution. Refrigerate the stock standard solutions and store no longer than one month.
7.2.4 Chromatographic Eluent. Effective eluents for nonsuppressed IC using a resin-or silica-based weak ion exchange column are a 4 mM potassium hydrogen phthalate solution, adjusted to pH 4.0 using a saturated sodium borate solution, and a 4 mM 4-hydroxy benzoate solution, adjusted to pH 8.6 using 1 N NaOH. An effective eluent for suppressed ion chromatography is a solution containing 3 mM sodium bicarbonate and 2.4 mM sodium carbonate. Other dilute solutions buffered to a similar pH and containing no interfering ions may be used. When using suppressed ion chromatography, if the “water dip” resulting from sample injection interferes with the chloride peak, use a 2 mM NaOH/2.4 mM sodium bicarbonate eluent.
8.0 Sample Collection, Preservation, Storage, and Transport Note:Because of the complexity of this method, testers and analyst should be trained and experienced with the procedure to ensure reliable results.
8.1 Sampling.
8.1.1 Preparation of Collection Train. Prepare the sampling train as follows: Pour 15 ml of the acidic absorbing solution into each one of the first pair of impingers, and 15 ml of the alkaline absorbing solution into each one of the second pair of impingers. Connect the impingers in series with the knockout impinger first, if used, followed by the two impingers containing the acidic absorbing solution and the two impingers containing the alkaline absorbing solution. Place a fresh charge of silica gel, or equivalent, in the drying tube or impinger at the end of the impinger train.
8.1.2 Adjust the probe temperature and the temperature of the filter and the stopcock (i.e., the heated area in Figure 26-1) to a temperature sufficient to prevent water condensation. This temperature must be maintained between 120 and 134 °C (248 and 273 °F). The temperature should be monitored throughout a sampling run to ensure that the desired temperature is maintained. It is important to maintain a temperature around the probe and filter in this range since it is extremely difficult to purge acid gases off these components. (These components are not quantitatively recovered and, hence, any collection of acid gases on these components would result in potential under reporting of these emissions. The applicable subparts may specify alternative higher temperatures.)
8.1.3 Leak-Check Procedure.
8.1.3.1 Sampling Train. A leak-check prior to the sampling run is optional; however, a leak-check after the sampling run is mandatory. The leak-check procedure is as follows: Temporarily attach a suitable [e.g., 0-40 cc/min (0-2.4 in 3/min)] rotameter to the outlet of the dry gas meter and place a vacuum gauge at or near the probe inlet. Plug the probe inlet, pull a vacuum of at least 250 mm Hg (10 in. Hg), and note the flow rate as indicated by the rotameter. A leakage rate not in excess of 2 percent of the average sampling rate is acceptable.
Note:Carefully release the probe inlet plug before turning off the pump.
8.1.3.2 Pump. It is suggested (not mandatory) that the pump be leak-checked separately, either prior to or after the sampling run. If done prior to the sampling run, the pump leak-check shall precede the leak-check of the sampling train described immediately above; if done after the sampling run, the pump leak-check shall follow the train leak-check. To leak-check the pump, proceed as follows: Disconnect the drying tube from the probe-impinger assembly. Place a vacuum gauge at the inlet to either the drying tube or pump, pull a vacuum of 250 mm (10 in) Hg, plug or pinch off the outlet of the flow meter, and then turn off the pump. The vacuum should remain stable for at least 30 sec. Other leak-check procedures may be used, subject to the approval of the Administrator, U.S. Environmental Protection Agency.
8.1.4 Purge Procedure. Immediately before sampling, connect the purge line to the stopcock, and turn the stopcock to permit the purge pump to purge the probe (see Figure 1A of Figure 26-1). Turn on the purge pump, and adjust the purge rate to 2 liters/min (0.07 ft 3/min). Purge for at least 5 minutes before sampling.
8.1.5 Sample Collection. Turn on the sampling pump, pull a slight vacuum of approximately 25 mm Hg (1 in Hg) on the impinger train, and turn the stopcock to permit stack gas to be pulled through the impinger train (see Figure 1C of Figure 26-1). Adjust the sampling rate to 2 liters/min, as indicated by the rate meter, and maintain this rate to within 10 percent during the entire sampling run. Take readings of the dry gas meter volume and temperature, rate meter, and vacuum gauge at least once every five minutes during the run. A sampling time of one hour is recommended. Shorter sampling times may introduce a significant negative bias in the HCl concentration. At the conclusion of the sampling run, remove the train from the stack, cool, and perform a leak-check as described in section 8.1.3.1.
8.2 Sample Recovery.
8.2.1 Disconnect the impingers after sampling. Quantitatively transfer the contents of the acid impingers and the knockout impinger, if used, to a leak-free storage bottle. Add the water rinses of each of these impingers and connecting glassware to the storage bottle.
8.2.2 Repeat this procedure for the alkaline impingers and connecting glassware using a separate storage bottle. Add 25 mg of sodium thiosulfate per the product of ppm of halogen anticipated to be in the stack gas times the volume (dscm) of stack gas sampled (0.7 mg per ppm-dscf).
Note:This amount of sodium thiosulfate includes a safety factor of approximately 5 to assure complete reaction with the hypohalous acid to form a second Cl− ion in the alkaline solution.
8.2.3 Save portions of the absorbing reagents (0.1 N H2SO4 and 0.1 N NaOH) equivalent to the amount used in the sampling train (these are the absorbing solution blanks described in section 7.2.2); dilute to the approximate volume of the corresponding samples using rinse water directly from the wash bottle being used. Add the same amount of sodium thiosulfate solution to the 0.1 N NaOH absorbing solution blank. Also, save a portion of the rinse water used to rinse the sampling train. Place each in a separate, prelabeled storage bottle. The sample storage bottles should be sealed, shaken to mix, and labeled. Mark the fluid level.
8.3 Sample Preparation for Analysis. Note the liquid levels in the storage bottles and confirm on the analysis sheet whether or not leakage occurred during transport. If a noticeable leakage has occurred, either void the sample or use methods, subject to the approval of the Administrator, to correct the final results. Quantitatively transfer the sample solutions to 100-ml volumetric flasks, and dilute to 100 ml with water.
9.0 Quality Control [Reserved] 10.0 Calibration and Standardization Note:Maintain a laboratory log of all calibrations.
10.1 Volume Metering System, Temperature Sensors, Rate Meter, and Barometer. Same as in Method 6, sections 10.1, 10.2, 10.3, and 10.4.
10.2 Ion Chromatograph.
10.2.1 To prepare the calibration standards, dilute given amounts (1.0 ml or greater) of the stock standard solutions to convenient volumes, using 0.1 N H2SO4 or 0.1 N NaOH, as appropriate. Prepare at least four calibration standards for each absorbing reagent containing the appropriate stock solutions such that they are within the linear range of the field samples.
10.2.2 Using one of the standards in each series, ensure adequate baseline separation for the peaks of interest.
10.2.3 Inject the appropriate series of calibration standards, starting with the lowest concentration standard first both before and after injection of the quality control check sample, reagent blanks, and field samples. This allows compensation for any instrument drift occurring during sample analysis. The values from duplicate injections of these calibration samples should agree within 5 percent of their mean for the analysis to be valid.
10.2.4 Determine the peak areas, or heights, for the standards and plot individual values versus halide ion concentrations in µg/ml.
10.2.5 Draw a smooth curve through the points. Use linear regression to calculate a formula describing the resulting linear curve.
11.0 Analytical Procedures11.1 Sample Analysis.
11.1.1 The IC conditions will depend upon analytical column type and whether suppressed or non-suppressed IC is used. An example chromatogram from a non-suppressed system using a 150-mm Hamilton PRP-X100 anion column, a 2 ml/min flow rate of a 4 mM 4-hydroxy benzoate solution adjusted to a pH of 8.6 using 1 N NaOH, a 50 µl sample loop, and a conductivity detector set on 1.0 µS full scale is shown in Figure 26-2.
11.1.2 Before sample analysis, establish a stable baseline. Next, inject a sample of water, and determine if any Cl−, Br−, or F− appears in the chromatogram. If any of these ions are present, repeat the load/injection procedure until they are no longer present. Analysis of the acid and alkaline absorbing solution samples requires separate standard calibration curves; prepare each according to section 10.2. Ensure adequate baseline separation of the analyses.
11.1.3 Between injections of the appropriate series of calibration standards, inject in duplicate the reagent blanks, quality control sample, and the field samples. Measure the areas or heights of the Cl−, Br−, and F− peaks. Use the mean response of the duplicate injections to determine the concentrations of the field samples and reagent blanks using the linear calibration curve. The values from duplicate injections should agree within 5 percent of their mean for the analysis to be valid. If the values of duplicate injections are not within 5 percent of the mean, the duplicate injections shall be repeated and all four values used to determine the average response. Dilute any sample and the blank with equal volumes of water if the concentration exceeds that of the highest standard.
12.0 Data Analysis and Calculations Note:Retain at least one extra decimal figure beyond those contained in the available data in intermediate calculations, and round off only the final answer appropriately.
12.1 Nomenclature.
BX− = Mass concentration of applicable absorbing solution blank, µg halide ion (Cl−, Br−, F−) /ml, not to exceed 1 µg/ml which is 10 times the published analytical detection limit of 0.1 µg/ml. C = Concentration of hydrogen halide (HX) or halogen (X2), dry basis, mg/dscm. K = 10−3 mg/µg. KHCl = 1.028 (µg HCl/µg-mole)/(µg Cl−/µg-mole). KHBr = 1.013 (µg HBr/µg-mole)/(µg Br−/µg-mole). KHF = 1.053 (µg HF/µg-mole)/(µg F−/µg-mole). mHX = Mass of HCl, HBr, or HF in sample, µg. mX2 = Mass of Cl2 or Br2 in sample, µg. SX− = Analysis of sample, µg halide ion (Cl−, Br−, F−)/ml. Vm(std) = Dry gas volume measured by the dry gas meter, corrected to standard conditions, dscm. Vs = Volume of filtered and diluted sample, ml.12.2 Calculate the exact Cl−, Br−, and F− concentration in the halide salt stock standard solutions using the following equations.
12.3 Sample Volume, Dry Basis, Corrected to Standard Conditions. Calculate the sample volume using Eq. 6-1 of Method 6.
12.4 Total µg HCl, HBr, or HF Per Sample.
12.5 Total µg Cl2 or Br2 Per Sample.
12.6 Concentration of Hydrogen Halide or Halogen in Flue Gas.
13.0 Method Performance13.1 Precision and Bias. The within-laboratory relative standard deviations are 6.2 and 3.2 percent at HCl concentrations of 3.9 and 15.3 ppm, respectively. The method does not exhibit a bias to Cl2 when sampling at concentrations less than 50 ppm.
13.2 Sample Stability. The collected Cl−samples can be stored for up to 4 weeks.
13.3 Detection Limit. A typical IC instrumental detection limit for Cl− is 0.2 µg/ml. Detection limits for the other analyses should be similar. Assuming 50 ml liquid recovered from both the acidified impingers, and the basic impingers, and 0.12 dscm (4.24 dscf) of stack gas sampled, then the analytical detection limit in the stack gas would be about 0.05 ppm for HCl and Cl2, respectively.
14.0 Pollution Prevention [Reserved] 15.0 Waste Management [Reserved] 16.0 Alternative ProceduresMethod 26A. Method 26A, which uses isokinetic sampling equipment, is an acceptable alternative to Method 26.
17.0 References1. Steinsberger, S. C. and J. H. Margeson, “Laboratory and Field Evaluation of a Methodology for Determination of Hydrogen Chloride Emissions from Municipal and Hazardous Waste Incinerators,” U.S. Environmental Protection Agency, Office of Research and Development, Report No. 600/3-89/064, April 1989. Available from the National Technical Information Service, Springfield, VA 22161 as PB89220586/AS.
2. State of California, Air Resources Board, Method 421, “Determination of Hydrochloric Acid Emissions from Stationary Sources,” March 18, 1987.
3. Cheney, J.L. and C.R. Fortune. Improvements in the Methodology for Measuring Hydrochloric Acid in Combustion Source Emissions. J. Environ. Sci. Health. A19(3): 337-350. 1984.
4. Stern, D. A., B. M. Myatt, J. F. Lachowski, and K. T. McGregor. Speciation of Halogen and Hydrogen Halide Compounds in Gaseous Emissions. In: Incineration and Treatment of Hazardous Waste: Proceedings of the 9th Annual Research Symposium, Cincinnati, Ohio, May 2-4, 1983. Publication No. 600/9-84-015. July 1984. Available from National Technical Information Service, Springfield, VA 22161 as PB84-234525.
5. Holm, R. D. and S. A. Barksdale. Analysis of Anions in Combustion Products. In: Ion Chromatographic Analysis of Environmental Pollutants. E. Sawicki, J. D. Mulik, and E. Wittgenstein (eds.). Ann Arbor, Michigan, Ann Arbor Science Publishers. 1978. pp. 99-110.
18.0 Tables, Diagrams, Flowcharts, and Validation Data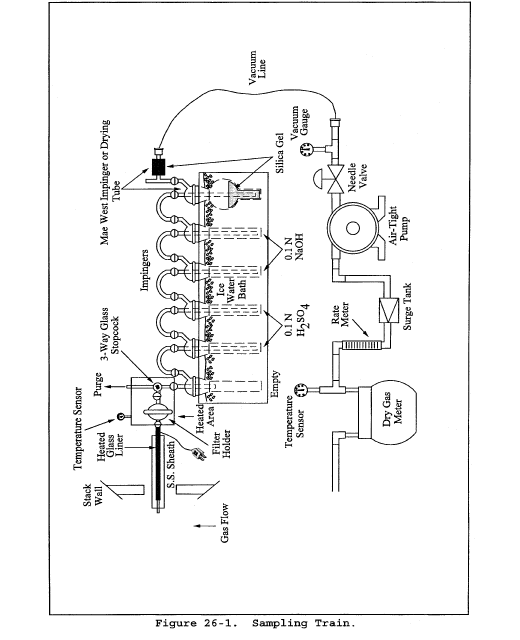
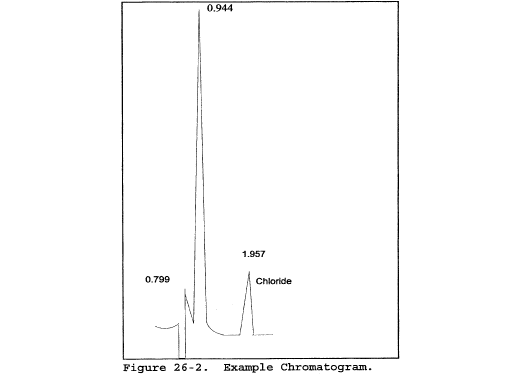
This method does not include all of the specifications (e.g., equipment and supplies) and procedures (e.g., sampling and analytical) essential to its performance. Some material is incorporated by reference from other methods in this part. Therefore, to obtain reliable results, persons using this method should have a thorough knowledge of at least the following additional test methods: Method 2, Method 5, and Method 26.
1.0 Scope and Application1.1 Analytes.
Analytes | CAS No. |
---|---|
Hydrogen Chloride (HCl) | 7647-01-0 |
Hydrogen Bromide (HBr) | 10035-10-6 |
Hydrogen Fluoride (HF) | 7664-39-3 |
Chlorine (Cl2) | 7882-50-5 |
Bromine (Br2) | 7726-95-6 |
1.2 This method is applicable for determining emissions of hydrogen halides (HX) [HCl, HBr, and HF] and halogens (X2) [Cl2 and Br2] from stationary sources when specified by the applicable subpart. This method collects the emission sample isokinetically and is therefore particularly suited for sampling at sources, such as those controlled by wet scrubbers, emitting acid particulate matter (e.g., hydrogen halides dissolved in water droplets).
1.3 Data Quality Objectives. Adherence to the requirements of this method will enhance the quality of the data obtained from air pollutant sampling methods.
2.0 Summary of Method2.1 Principle. Gaseous and particulate pollutants are withdrawn isokinetically from the source and collected in an optional cyclone, on a filter, and in absorbing solutions. The cyclone collects any liquid droplets and is not necessary if the source emissions do not contain them; however, it is preferable to include the cyclone in the sampling train to protect the filter from any liquid present. The filter collects particulate matter including halide salts but is not routinely recovered or analyzed. Acidic and alkaline absorbing solutions collect the gaseous hydrogen halides and halogens, respectively. Following sampling of emissions containing liquid droplets, any halides/halogens dissolved in the liquid in the cyclone and on the filter are vaporized to gas and collected in the impingers by pulling conditioned ambient air through the sampling train. The hydrogen halides are solubilized in the acidic solution and form chloride (Cl−), bromide (Br−), and fluoride (F−) ions. The halogens have a very low solubility in the acidic solution and pass through to the alkaline solution where they are hydrolyzed to form a proton (H + ), the halide ion, and the hypohalous acid (HClO or HBrO). Sodium thiosulfate is added to the alkaline solution to assure reaction with the hypohalous acid to form a second halide ion such that 2 halide ions are formed for each molecule of halogen gas. The halide ions in the separate solutions are measured by ion chromatography (IC). If desired, the particulate matter recovered from the filter and the probe is analyzed following the procedures in Method 5.
Note:If the tester intends to use this sampling arrangement to sample concurrently for particulate matter, the alternative Teflon probe liner, cyclone, and filter holder should not be used. The Teflon filter support must be used. The tester must also meet the probe and filter temperature requirements of both sampling trains.
3.0 Definitions [Reserved] 4.0 Interferences4.1 Volatile materials, such as chlorine dioxide (ClO2) and ammonium chloride (NH4Cl), which produce halide ions upon dissolution during sampling are potential interferents. Interferents for the halide measurements are the halogen gases which disproportionate to a hydrogen halide and a hypohalous acid upon dissolution in water. The use of acidic rather than neutral or basic solutions for collection of the hydrogen halides greatly reduces the dissolution of any halogens passing through this solution.
4.2 The simultaneous presence of both HBr and Cl2 may cause a positive bias in the HCl result with a corresponding negative bias in the Cl2 result as well as affecting the HBr/Br2 split.
4.3 High concentrations of nitrogen oxides (NOX) may produce sufficient nitrate (NO3−) to interfere with measurements of very low Br− levels. Dissociating chloride salts (e.g., ammonium chloride) at elevated temperatures interfere with halogen acid measurement in this method. Maintaining particulate probe/filter temperatures between 120 °C and 134 °C (248 °F and 273 °F) minimizes this interference.
4.4 There is anecdotal evidence that HF may be outgassed from new Teflon components. If HF is a target analyte then preconditioning of new Teflon components, by heating, should be considered.
5.0 Safety5.1 Disclaimer. This method may involve hazardous materials, operations, and equipment. This test method may not address all of the safety problems associated with its use. It is the responsibility of the user to establish appropriate safety and health practices and determine the applicability of regulatory limitations before performing this test method.
5.2 Corrosive Reagents. The following reagents are hazardous. Personal protective equipment and safe procedures are useful in preventing chemical splashes. If contact occurs, immediately flush with copious amounts of water for at least 15 minutes. Remove clothing under shower and decontaminate. Treat residual chemical burns as thermal burns.
5.2.1 Sodium Hydroxide (NaOH). Causes severe damage to eyes and skin. Inhalation causes irritation to nose, throat, and lungs. Reacts exothermically with limited amounts of water.
5.2.2 Sulfuric Acid (H2SO4). Rapidly destructive to body tissue. Will cause third degree burns. Eye damage may result in blindness. Inhalation may be fatal from spasm of the larynx, usually within 30 minutes. May cause lung tissue damage with edema. 1 mg/m 3 for 8 hours will cause lung damage or, in higher concentrations, death. Provide ventilation to limit inhalation. Reacts violently with metals and organics.
6.0. Equipment and Supplies Note:Mention of trade names or specific products does not constitute endorsement by the Environmental Protection Agency.
6.1 Sampling. The sampling train is shown in Figure 26A-1; the apparatus is similar to the Method 5 train where noted as follows:
6.1.1 Probe Nozzle. Borosilicate or quartz glass; constructed and calibrated according to Method 5, sections 6.1.1.1 and 10.1, and coupled to the probe liner using a Teflon union; a stainless steel nut is recommended for this union. When the stack temperature exceeds 210 °C (410 °F), a one-piece glass nozzle/liner assembly must be used.
6.1.2 Probe Liner. Same as Method 5, section 6.1.1.2, except metal liners shall not be used. Water-cooling of the stainless steel sheath is recommended at temperatures exceeding 500 °C (932 °F). Teflon may be used in limited applications where the minimum stack temperature exceeds 120 °C (250 °F) but never exceeds the temperature where Teflon is estimated to become unstable [approximately 210 °C (410 °F)].
6.1.3 Pitot Tube, Differential Pressure Gauge, Filter Heating System, Filter Temperature Sensor with a glass or Teflon encasement, Metering System, Barometer, Gas Density Determination Equipment. Same as Method 5, sections 6.1.1.3, 6.1.1.4, 6.1.1.6, 6.1.1.7, 6.1.1.9, 6.1.2, and 6.1.3.
6.1.4 Cyclone (Optional). Glass or Teflon. Use of the cyclone is required only when the sample gas stream is saturated with moisture; however, the cyclone is recommended to protect the filter from any liquid droplets present.
6.1.5 Filter Holder. Borosilicate or quartz glass, or Teflon filter holder, with a Teflon filter support and a sealing gasket. The sealing gasket shall be constructed of Teflon or equivalent materials. The holder design shall provide a positive seal against leakage at any point along the filter circumference. The holder shall be attached immediately to the outlet of the cyclone.
6.1.6 Impinger Train. The following system shall be used to determine the stack gas moisture content and to collect the hydrogen halides and halogens: five or six impingers connected in series with leak-free ground glass fittings or any similar leak-free noncontaminating fittings. The first impinger shown in Figure 26A-1 (knockout or condensate impinger) is optional and is recommended as a water knockout trap for use under high moisture conditions. If used, this impinger should be constructed as described below for the alkaline impingers, but with a shortened stem, and should contain 50 ml of 0.1 N H2SO4. The following two impingers (acid impingers which each contain 100 ml of 0.1 N H2SO4) shall be of the Greenburg-Smith design with the standard tip (Method 5, section 6.1.1.8). The next two impingers (alkaline impingers which each contain 100 ml of 0.1 N NaOH) and the last impinger (containing silica gel) shall be of the modified Greenburg-Smith design (Method 5, section 6.1.1.8). The condensate, acid, and alkaline impingers shall contain known quantities of the appropriate absorbing reagents. The last impinger shall contain a known weight of silica gel or equivalent desiccant. Teflon impingers are an acceptable alternative.
6.1.7 Heating System. Any heating system capable of maintaining a temperature around the probe and filter holder between 120 and 134 °C (248 to 273 °F) during sampling, or such other temperature as specified by an applicable subpart of the standards or approved by the Administrator for a particular application.
6.1.8 Ambient Air Conditioning Tube (Optional). Tube tightly packed with approximately 150 g of fresh 8 to 20 mesh sodium hydroxide-coated silica, or equivalent, (Ascarite II has been found suitable) to dry and remove acid gases from the ambient air used to remove moisture from the filter and cyclone, when the cyclone is used. The inlet and outlet ends of the tube should be packed with at least 1-cm thickness of glass wool or filter material suitable to prevent escape of fines. Fit one end with flexible tubing, etc. to allow connection to probe nozzle following the test run.
6.2 Sample Recovery.
6.2.1 Probe-Liner and Probe-Nozzle Brushes, Wash Bottles, Petri Dishes, Graduated Cylinder and/or Balance, and Rubber Policeman. Same as Method 5, sections 6.2.1, 6.2.2, 6.2.4, 6.2.5, and 6.2.7.
6.2.2 Plastic Storage Containers. Screw-cap polypropylene or polyethylene containers to store silica gel. High-density polyethylene bottles with Teflon screw cap liners to store impinger reagents, 1-liter.
6.2.3 Funnels. Glass or high-density polyethylene, to aid in sample recovery.
6.2.4 Sample Storage Containers. High-density polyethylene or glass sample storage containers with Teflon screw cap liners to store impinger samples.
6.3 Sample Preparation and Analysis.
6.3.1 Volumetric Flasks. Class A, various sizes.
6.3.2 Volumetric Pipettes. Class A, assortment. To dilute samples to calibration range of the ion chromatograph (IC).
6.3.3 Ion Chromatograph (IC). Suppressed or nonsuppressed, with a conductivity detector and electronic integrator operating in the peak area mode. Other detectors, a strip chart recorder, and peak heights may be used.
7.0 Reagents and Standards Note:Unless otherwise indicated, all reagents must conform to the specifications established by the Committee on Analytical Reagents of the American Chemical Society (ACS reagent grade). When such specifications are not available, the best available grade shall be used.
7.1 Sampling.
7.1.1 Filter. Teflon mat (e.g., Pallflex TX40HI45) filter. When the stack gas temperature exceeds 210 °C (410 °F) a quartz fiber filter may be used.
7.1.2 Water. Deionized, distilled water that conforms to American Society of Testing and Materials (ASTM) Specification D 1193-77 or 91, Type 3 (incorporated by reference - see § 60.17).
7.1.3 Acidic Absorbing Solution, 0.1 N Sulfuric Acid (H2SO4). To prepare 1 L, slowly add 2.80 ml of concentrated 17.9 M H2SO4 to about 900 ml of water while stirring, and adjust the final volume to 1 L using additional water. Shake well to mix the solution.
7.1.4 Silica Gel, Crushed Ice, and Stopcock Grease. Same as Method 5, sections 7.1.2, 7.1.4, and 7.1.5, respectively.
7.1.5 Alkaline Absorbing Solution, 0.1 N Sodium Hydroxide (NaOH). To prepare 1 L, dissolve 4.00 g of solid NaOH in about 900 ml of water and adjust the final volume to 1 L using additional water. Shake well to mix the solution.
7.1.6 Sodium Thiosulfate, (Na2S2O33.5 H2O).
7.2 Sample Preparation and Analysis.
7.2.1 Water. Same as in section 7.1.2.
7.2.2 Absorbing Solution Blanks. A separate blank solution of each absorbing reagent should be prepared for analysis with the field samples. Dilute 200 ml of each absorbing solution (250 ml of the acidic absorbing solution, if a condensate impinger is used) to the same final volume as the field samples using the blank sample of rinse water. If a particulate determination is conducted, collect a blank sample of acetone.
7.2.3 Halide Salt Stock Standard Solutions. Prepare concentrated stock solutions from reagent grade sodium chloride (NaCl), sodium bromide (NaBr), and sodium fluoride (NaF). Each must be dried at 110 °C (230 °F) for two or more hours and then cooled to room temperature in a desiccator immediately before weighing. Accurately weigh 1.6 to 1.7 g of the dried NaCl to within 0.1 mg, dissolve in water, and dilute to 1 liter. Calculate the exact Cl−concentration using Equation 26A-1 in section 12.2. In a similar manner, accurately weigh and solubilize 1.2 to 1.3 g of dried NaBr and 2.2 to 2.3 g of NaF to make 1-liter solutions. Use Equations 26A-2 and 26A-3 in section 12.2, to calculate the Br−and F−concentrations. Alternately, solutions containing a nominal certified concentration of 1000 mg/L NaCl are commercially available as convenient stock solutions from which standards can be made by appropriate volumetric dilution. Refrigerate the stock standard solutions and store no longer than one month.
7.2.4 Chromatographic Eluent. Same as Method 26, section 7.2.4.
7.2.5 Water. Same as section 7.1.1.
7.2.6 Acetone. Same as Method 5, section 7.2.
8.0 Sample Collection, Preservation, Storage, and Transport Note:Because of the complexity of this method, testers and analysts should be trained and experienced with the procedures to ensure reliable results.
8.1 Sampling.
8.1.1 Pretest Preparation. Follow the general procedure given in Method 5, section 8.1, except the filter need only be desiccated and weighed if a particulate determination will be conducted.
8.1.2 Preliminary Determinations. Same as Method 5, section 8.2.
8.1.3 Preparation of Sampling Train. Follow the general procedure given in Method 5, section 8.1.3, except for the following variations: Add 50 ml of 0.1 N H2SO4 to the condensate impinger, if used. Place 100 ml of 0.1 N H2SO4 in each of the next two impingers. Place 100 ml of 0.1 N NaOH in each of the following two impingers. Finally, transfer approximately 200-300 g of preweighed silica gel from its container to the last impinger. Set up the train as in Figure 26A-1. When used, the optional cyclone is inserted between the probe liner and filter holder and located in the heated filter box.
8.1.4 Leak-Check Procedures. Follow the leak-check procedures given in Method 5, sections 8.4.2 (Pretest Leak-Check), 8.4.3 (Leak-Checks During the Sample Run), and 8.4.4 (Post-Test Leak-Check).
8.1.5 Sampling Train Operation. Follow the general procedure given in Method 5, Section 8.5. It is important to maintain a temperature around the probe, filter (and cyclone, if used) between 120 and 134 °C (248 and 273 °F) since it is extremely difficult to purge acid gases off these components. (These components are not quantitatively recovered and hence any collection of acid gases on these components would result in potential under reporting these emissions. The applicable subparts may specify alternative higher temperatures.) For each run, record the data required on a data sheet such as the one shown in Method 5, Figure 5-3. If the condensate impinger becomes too full, it may be emptied, recharged with 50 ml of 0.1 N H2SO4, and replaced during the sample run. The condensate emptied must be saved and included in the measurement of the volume of moisture collected and included in the sample for analysis. The additional 50 ml of absorbing reagent must also be considered in calculating the moisture. Before the sampling train integrity is compromised by removing the impinger, conduct a leak-check as described in Method 5, section 8.4.2.
8.1.6 Post-Test Moisture Removal (Optional). When the optional cyclone is included in the sampling train or when liquid is visible on the filter at the end of a sample run even in the absence of a cyclone, perform the following procedure. Upon completion of the test run, connect the ambient air conditioning tube at the probe inlet and operate the train with the filter heating system between 120 and 134 °C (248 and 273 °F) at a low flow rate (e.g., ΔH = 1 in. H2O) to vaporize any liquid and hydrogen halides in the cyclone or on the filter and pull them through the train into the impingers. After 30 minutes, turn off the flow, remove the conditioning tube, and examine the cyclone and filter for any visible liquid. If liquid is visible, repeat this step for 15 minutes and observe again. Keep repeating until the cyclone is dry.
Note:It is critical that this procedure is repeated until the cyclone is completely dry.
8.2 Sample Recovery. Allow the probe to cool. When the probe can be handled safely, wipe off all the external surfaces of the tip of the probe nozzle and place a cap loosely over the tip to prevent gaining or losing particulate matter. Do not cap the probe tip tightly while the sampling train is cooling down because this will create a vacuum in the filter holder, drawing water from the impingers into the holder. Before moving the sampling train to the cleanup site, remove the probe from the sample train, wipe off any silicone grease, and cap the open outlet of the impinger train, being careful not to lose any condensate that might be present. Wipe off any silicone grease and cap the filter or cyclone inlet. Remove the umbilical cord from the last impinger and cap the impinger. If a flexible line is used between the first impinger and the filter holder, disconnect it at the filter holder and let any condensed water drain into the first impinger. Wipe off any silicone grease and cap the filter holder outlet and the impinger inlet. Ground glass stoppers, plastic caps, serum caps, Teflon tape, Parafilm, or aluminum foil may be used to close these openings. Transfer the probe and filter/impinger assembly to the cleanup area. This area should be clean and protected from the weather to minimize sample contamination or loss. Inspect the train prior to and during disassembly and note any abnormal conditions. Treat samples as follows:
8.2.1 Container No. 1 (Optional; Filter Catch for Particulate Determination). Same as Method 5, section 8.7.6.1, Container No. 1.
8.2.2 Container No. 2 (Optional; Front-Half Rinse for Particulate Determination). Same as Method 5, section 8.7.6.2, Container No. 2.
8.2.3 Container No. 3 (Knockout and Acid Impinger Catch for Moisture and Hydrogen Halide Determination). Disconnect the impingers. Measure the liquid in the acid and knockout impingers to ±1 ml by using a graduated cylinder or by weighing it to ±0.5 g by using a balance. Record the volume or weight of liquid present. This information is required to calculate the moisture content of the effluent gas. Quantitatively transfer this liquid to a leak-free sample storage container. Rinse these impingers and connecting glassware including the back portion of the filter holder (and flexible tubing, if used) with water and add these rinses to the storage container. Seal the container, shake to mix, and label. The fluid level should be marked so that if any sample is lost during transport, a correction proportional to the lost volume can be applied. Retain rinse water and acidic absorbing solution blanks to be analyzed with the samples.
8.2.4 Container No. 4 (Alkaline Impinger Catch for Halogen and Moisture Determination). Measure and record the liquid in the alkaline impingers as described in section 8.2.3. Quantitatively transfer this liquid to a leak-free sample storage container. Rinse these two impingers and connecting glassware with water and add these rinses to the container. Add 25 mg of sodium thiosulfate per ppm halogen anticipated to be in the stack gas multiplied by the volume (dscm) of stack gas sampled (0.7 mg/ppm-dscf). Seal the container, shake to mix, and label; mark the fluid level. Retain alkaline absorbing solution blank to be analyzed with the samples.
Note:25 mg per sodium thiosulfate per ppm halogen anticipated to be in the stack includes a safety factor of approximately 5 to assure complete reaction with the hypohalous acid to form a second Cl− ion in the alkaline solution.
8.2.5 Container No. 5 (Silica Gel for Moisture Determination). Same as Method 5, section 8.7.6.3, Container No. 3.
8.2.6 Container Nos. 6 through 9 (Reagent Blanks). Save portions of the absorbing reagents (0.1 N H2SO4 and 0.1 N NaOH) equivalent to the amount used in the sampling train; dilute to the approximate volume of the corresponding samples using rinse water directly from the wash bottle being used. Add the same ratio of sodium thiosulfate solution used in container No. 4 to the 0.1 N NaOH absorbing reagent blank. Also, save a portion of the rinse water alone and a portion of the acetone equivalent to the amount used to rinse the front half of the sampling train. Place each in a separate, prelabeled sample container.
8.2.7 Prior to shipment, recheck all sample containers to ensure that the caps are well-secured. Seal the lids of all containers around the circumference with Teflon tape. Ship all liquid samples upright and all particulate filters with the particulate catch facing upward.
9.0 Quality Control9.1 Miscellaneous Quality Control Measures.
Section | Quality control measure | Effect |
---|---|---|
8.1.4, 10.1 | Sampling equipment leak-check and calibration | Ensure accurate measurement of stack gas flow rate, sample volume. |
9.2 Volume Metering System Checks. Same as Method 5, section 9.2.
10.0 Calibration and Standardization Note:Maintain a laboratory log of all calibrations.
10.1 Probe Nozzle, Pitot Tube Assembly, Dry Gas Metering System, Probe Heater, Temperature Sensors, Leak-Check of Metering System, and Barometer. Same as Method 5, sections 10.1, 10.2, 10.3, 10.4, 10.5, 8.4.1, and 10.6, respectively.
10.2 Ion Chromatograph.
10.2.1 To prepare the calibration standards, dilute given amounts (1.0 ml or greater) of the stock standard solutions to convenient volumes, using 0.1 N H2SO4 or 0.1 N NaOH, as appropriate. Prepare at least four calibration standards for each absorbing reagent containing the three stock solutions such that they are within the linear range of the field samples.
10.2.2 Using one of the standards in each series, ensure adequate baseline separation for the peaks of interest.
10.2.3 Inject the appropriate series of calibration standards, starting with the lowest concentration standard first both before and after injection of the quality control check sample, reagent blanks, and field samples. This allows compensation for any instrument drift occurring during sample analysis. The values from duplicate injections of these calibration samples should agree within 5 percent of their mean for the analysis to be valid.
10.2.4 Determine the peak areas, or height, of the standards and plot individual values versus halide ion concentrations in µg/ml.
10.2.5 Draw a smooth curve through the points. Use linear regression to calculate a formula describing the resulting linear curve.
11.0 Analytical Procedures Note:The liquid levels in the sample containers and confirm on the analysis sheet whether or not leakage occurred during transport. If a noticeable leakage has occurred, either void the sample or use methods, subject to the approval of the Administrator, to correct the final results.
11.1 Sample Analysis.
11.1.1 The IC conditions will depend upon analytical column type and whether suppressed or non-suppressed IC is used. An example chromatogram from a non-suppressed system using a 150-mm Hamilton PRP-X100 anion column, a 2 ml/min flow rate of a 4 mM 4-hydroxy benzoate solution adjusted to a pH of 8.6 using 1 N NaOH, a 50 µl sample loop, and a conductivity detector set on 1.0 µS full scale is shown in Figure 26-2.
11.1.2 Before sample analysis, establish a stable baseline. Next, inject a sample of water, and determine if any Cl−, Br−, or F− appears in the chromatogram. If any of these ions are present, repeat the load/injection procedure until they are no longer present. Analysis of the acid and alkaline absorbing solution samples requires separate standard calibration curves; prepare each according to section 10.2. Ensure adequate baseline separation of the analyses.
11.1.3 Between injections of the appropriate series of calibration standards, inject in duplicate the reagent blanks, quality control sample, and the field samples. Measure the areas or heights of the Cl−, Br−, and F− peaks. Use the mean response of the duplicate injections to determine the concentrations of the field samples and reagent blanks using the linear calibration curve. The values from duplicate injections should agree within 5 percent of their mean for the analysis to be valid. If the values of duplicate injections are not within 5 percent of the mean, the duplicator injections shall be repeated and all four values used to determine the average response. Dilute any sample and the blank with equal volumes of water if the concentration exceeds that of the highest standard.
11.2 Container Nos. 1 and 2 and Acetone Blank (Optional; Particulate Determination). Same as Method 5, sections 11.2.1 and 11.2.2, respectively.
11.3 Container No. 5. Same as Method 5, section 11.2.3 for silica gel.
12.0 Data Analysis and Calculations Note:Retain at least one extra decimal figure beyond those contained in the available data in intermediate calculations, and round off only the final answer appropriately.
12.1 Nomenclature. Same as Method 5, section 12.1. In addition:
BX− = Mass concentration of applicable absorbing solution blank, µg halide ion (Cl−, Br−, F−)/ml, not to exceed 1 µg/ml which is 10 times the published analytical detection limit of 0.1 µg/ml. (It is also approximately 5 percent of the mass concentration anticipated to result from a one hour sample at 10 ppmv HCl.) C = Concentration of hydrogen halide (HX) or halogen (X2), dry basis, mg/dscm. K = 10−3 mg/µg. KHCl = 1.028 (µg HCl/µg-mole)/(µg Cl−/µg-mole). KHBr = 1.013 (µg HBr/µg-mole)/(µg Br−/µg-mole). KHF = 1.053 (µg HF/µg-mole)/(µg F−/µg-mole). mHX = Mass of HCl, HBr, or HF in sample, ug. mX2 = Mass of Cl2 or Br2 in sample, ug. SX− = Analysis of sample, ug halide ion (Cl−, Br−, F−)/ml. Vs = Volume of filtered and diluted sample, ml.12.2 Calculate the exact Cl−, Br−, and F− concentration in the halide salt stock standard solutions using the following equations.
12.3 Average Dry Gas Meter Temperature and Average Orifice Pressure Drop. See data sheet (Figure 5-3 of Method 5).
12.4 Dry Gas Volume. Calculate Vm(std) and adjust for leakage, if necessary, using the equation in section 12.3 of Method 5.
12.5 Volume of Water Vapor and Moisture Content. Calculate the volume of water vapor Vw(std) and moisture content Bws from the data obtained in this method (Figure 5-3 of Method 5); use Equations 5-2 and 5-3 of Method 5.
12.6 Isokinetic Variation and Acceptable Results. Use Method 5, section 12.11.
12.7 Acetone Blank Concentration, Acetone Wash Blank Residue Weight, Particulate Weight, and Particulate Concentration. For particulate determination.
12.8 Total µg HCl, HBr, or HF Per Sample.
12.9 Total µg Cl2 or Br2 Per Sample.
12.10 Concentration of Hydrogen Halide or Halogen in Flue Gas.
12.11 Stack Gas Velocity and Volumetric Flow Rate. Calculate the average stack gas velocity and volumetric flow rate, if needed, using data obtained in this method and the equations in sections 12.3 and 12.4 of Method 2.
13.0 Method Performance13.1 Precision and Bias. The method has a possible measurable negative bias below 20 ppm HCl perhaps due to reaction with small amounts of moisture in the probe and filter. Similar bias for the other hydrogen halides is possible.
13.2 Sample Stability. The collected Cl-samples can be stored for up to 4 weeks for analysis for HCl and Cl2.
13.3 Detection Limit. A typical analytical detection limit for HCl is 0.2 µg/ml. Detection limits for the other analyses should be similar. Assuming 300 ml of liquid recovered for the acidified impingers and a similar amounts recovered from the basic impingers, and 1 dscm of stack gas sampled, the analytical detection limits in the stack gas would be about 0.04 ppm for HCl and Cl2, respectively.
14.0 Pollution Prevention [Reserved] 15.0 Waste Management [Reserved] 16.0 References1. Steinsberger, S. C. and J. H. Margeson. Laboratory and Field Evaluation of a Methodology for Determination of Hydrogen Chloride Emissions from Municipal and Hazardous Waste Incinerators. U.S. Environmental Protection Agency, Office of Research and Development. Publication No. 600/3-89/064. April 1989. Available from National Technical Information Service, Springfield, VA 22161 as PB89220586/AS.
2. State of California Air Resources Board. Method 421 - Determination of Hydrochloric Acid Emissions from Stationary Sources. March 18, 1987.
3. Cheney, J.L. and C.R. Fortune. Improvements in the Methodology for Measuring Hydrochloric Acid in Combustion Source Emissions. J. Environ. Sci. Health. A19(3): 337-350. 1984.
4. Stern, D.A., B.M. Myatt, J.F. Lachowski, and K.T. McGregor. Speciation of Halogen and Hydrogen Halide Compounds in Gaseous Emissions. In: Incineration and Treatment of Hazardous Waste: Proceedings of the 9th Annual Research Symposium, Cincinnati, Ohio, May 2-4, 1983. Publication No. 600/9-84-015. July 1984. Available from National Technical Information Service, Springfield, VA 22161 as PB84-234525.
5. Holm, R.D. and S.A. Barksdale. Analysis of Anions in Combustion Products. In: Ion Chromatographic Analysis of Environmental Pollutants, E. Sawicki, J.D. Mulik, and E. Wittgenstein (eds.). Ann Arbor, Michigan, Ann Arbor Science Publishers. 1978. pp. 99-110.
17.0 Tables, Diagrams, Flowcharts, and Validation Data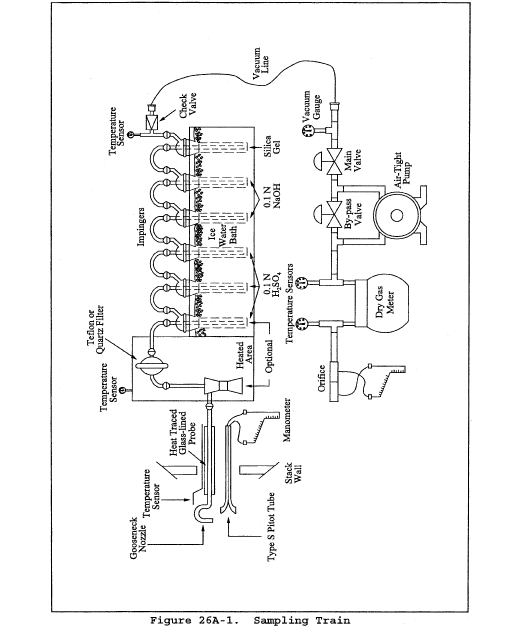
1.1 Applicability. This method is applicable for the determination of vapor tightness of a gasoline delivery collection equipment.
2.0 Summary of Method2.1 Pressure and vacuum are applied alternately to the compartments of a gasoline delivery tank and the change in pressure or vacuum is recorded after a specified period of time.
3.0 Definitions3.1 Allowable pressure change (Δp) means the allowable amount of decrease in pressure during the static pressure test, within the time period t, as specified in the appropriate regulation, in mm H2O.
3.2 Allowable vacuum change (Δv) means the allowable amount of decrease in vacuum during the static vacuum test, within the time period t, as specified in the appropriate regulation, in mm H2O.
3.3 Compartment means a liquid-tight division of a delivery tank.
3.4 Delivery tank means a container, including associated pipes and fittings, that is attached to or forms a part of any truck, trailer, or railcar used for the transport of gasoline.
3.5 Delivery tank vapor collection equipment means any piping, hoses, and devices on the delivery tank used to collect and route gasoline vapors either from the tank to a bulk terminal vapor control system or from a bulk plant or service station into the tank.
3.6 Gasoline means a petroleum distillate or petroleum distillate/alcohol blend having a Reid vapor pressure of 27.6 kilopascals or greater which is used as a fuel for internal combustion engines.
3.7 Initial pressure (Pi) means the pressure applied to the delivery tank at the beginning of the static pressure test, as specified in the appropriate regulation, in mm H2O.
3.8 Initial vacuum (Vi) means the vacuum applied to the delivery tank at the beginning of the static vacuum test, as specified in the appropriate regulation, in mm H3.
3.9 Time period of the pressure or vacuum test (t) means the time period of the test, as specified in the appropriate regulation, during which the change in pressure or vacuum is monitored, in minutes.
4.0 Interferences [Reserved] 5.0 Safety5.1 Gasoline contains several volatile organic compounds (e.g., benzene and hexane) which presents a potential for fire and/or explosions. It is advisable to take appropriate precautions when testing a gasoline vessel's vapor tightness, such as refraining from smoking and using explosion-proof equipment.
5.2 This method may involve hazardous materials, operations, and equipment. This test method may not address all of the safety problems associated with its use. It is the responsibility of the user of this test method to establish appropriate safety and health practices and determine the applicability of regulatory limitations prior to performing this test method
6.0 Equipment and SuppliesThe following equipment and supplies are required for testing:
6.1 Pressure Source. Pump or compressed gas cylinder of air or inert gas sufficient to pressurize the delivery tank to 500 mm (20 in.) H2O above atmospheric pressure.
6.2 Regulator. Low pressure regulator for controlling pressurization of the delivery tank.
6.3 Vacuum Source. Vacuum pump capable of evacuating the delivery tank to 250 mm (10 in.) H2O below atmospheric pressure.
6.4 Pressure-Vacuum Supply Hose.
6.5 Manometer. Liquid manometer, or equivalent instrument, capable of measuring up to 500 mm (20 in.) H2O gauge pressure with ±2.5 mm (0.1 in.) H2O precision.
6.6 Pressure-Vacuum Relief Valves. The test apparatus shall be equipped with an inline pressure-vacuum relief valve set to activate at 675 mm (26.6 in.) H2O above atmospheric pressure or 250 mm (10 in.) H2O below atmospheric pressure, with a capacity equal to the pressurizing or evacuating pumps.
6.7 Test Cap for Vapor Recovery Hose. This cap shall have a tap for manometer connection and a fitting with shut-off valve for connection to the pressure-vacuum supply hose.
6.8 Caps for Liquid Delivery Hoses.
7.0 Reagents and Standards [Reserved] 8.0 Sample Collection, Preservation, Storage, and Transport8.1 Pretest Preparations.
8.1.1 Summary. Testing problems may occur due to the presence of volatile vapors and/or temperature fluctuations inside the delivery tank. Under these conditions, it is often difficult to obtain a stable initial pressure at the beginning of a test, and erroneous test results may occur. To help prevent this, it is recommended that prior to testing, volatile vapors be removed from the tank and the temperature inside the tank be allowed to stabilize. Because it is not always possible to completely attain these pretest conditions, a provision to ensure reproducible results is included. The difference in results for two consecutive runs must meet the criteria in sections 8.2.2.5 and 8.2.3.5.
8.1.2 Emptying of Tank. The delivery tank shall be emptied of all liquid.
8.1.3 Purging of Vapor. As much as possible the delivery tank shall be purged of all volatile vapors by any safe, acceptable method. One method is to carry a load of non-volatile liquid fuel, such as diesel or heating oil, immediately prior to the test, thus flushing out all the volatile gasoline vapors. A second method is to remove the volatile vapors by blowing ambient air into each tank compartment for at least 20 minutes. This second method is usually not as effective and often causes stabilization problems, requiring a much longer time for stabilization during the testing.
8.1.4 Temperature Stabilization. As much as possible, the test shall be conducted under isothermal conditions. The temperature of the delivery tank should be allowed to equilibrate in the test environment. During the test, the tank should be protected from extreme environmental and temperature variability, such as direct sunlight.
8.2 Test Procedure.
8.2.1 Preparations.
8.2.1.1 Open and close each dome cover.
8.2.1.2 Connect static electrical ground connections to the tank. Attach the liquid delivery and vapor return hoses, remove the liquid delivery elbows, and plug the liquid delivery fittings.
Note:The purpose of testing the liquid delivery hoses is to detect tears or holes that would allow liquid leakage during a delivery. Liquid delivery hoses are not considered to be possible sources of vapor leakage, and thus, do not have to be attached for a vapor leakage test. Instead, a liquid delivery hose could be either visually inspected, or filled with water to detect any liquid leakage.
8.2.1.3 Attach the test cap to the end of the vapor recovery hose.
8.2.1.4 Connect the pressure-vacuum supply hose and the pressure-vacuum relief valve to the shut-off valve. Attach a manometer to the pressure tap.
8.2.1.5 Connect compartments of the tank internally to each other if possible. If not possible, each compartment must be tested separately, as if it were an individual delivery tank.
8.2.2 Pressure Test.
8.2.2.1 Connect the pressure source to the pressure-vacuum supply hose.
8.2.2.2 Open the shut-off valve in the vapor recovery hose cap. Apply air pressure slowly, pressurize the tank to Pi, the initial pressure specified in the regulation.
8.2.2.3 Close the shut-off and allow the pressure in the tank to stabilize, adjusting the pressure if necessary to maintain pressure of Pi. When the pressure stabilizes, record the time and initial pressure.
8.2.2.4 At the end of the time period (t) specified in the regulation, record the time and final pressure.
8.2.2.5 Repeat steps 8.2.2.2 through 8.2.2.4 until the change in pressure for two consecutive runs agrees within 12.5 mm (0.5 in.) H2O. Calculate the arithmetic average of the two results.
8.2.2.6 Compare the average measured change in pressure to the allowable pressure change, Δp, specified in the regulation. If the delivery tank does not satisfy the vapor tightness criterion specified in the regulation, repair the sources of leakage, and repeat the pressure test until the criterion is met.
8.2.2.7 Disconnect the pressure source from the pressure-vacuum supply hose, and slowly open the shut-off valve to bring the tank to atmospheric pressure.
8.2.3 Vacuum Test.
8.2.3.1 Connect the vacuum source to the pressure-vacuum supply hose.
8.2.3.2 Open the shut-off valve in the vapor recovery hose cap. Slowly evacuate the tank to Vi, the initial vacuum specified in the regulation.
8.2.3.3 Close the shut-off valve and allow the pressure in the tank to stabilize, adjusting the pressure if necessary to maintain a vacuum of Vi. When the pressure stabilizes, record the time and initial vacuum.
8.2.3.4 At the end of the time period specified in the regulation (t), record the time and final vacuum.
8.2.3.5 Repeat steps 8.2.3.2 through 8.2.3.4 until the change in vacuum for two consecutive runs agrees within 12.5 mm (0.5 in.) H2O. Calculate the arithmetic average of the two results.
8.2.3.6 Compare the average measured change in vacuum to the allowable vacuum change, Δv, as specified in the regulation. If the delivery tank does not satisfy the vapor tightness criterion specified in the regulation, repair the sources of leakage, and repeat the vacuum test until the criterion is met.
8.2.3.7 Disconnect the vacuum source from the pressure-vacuum supply hose, and slowly open the shut-off valve to bring the tank to atmospheric pressure.
8.2.4 Post-Test Clean-up. Disconnect all test equipment and return the delivery tank to its pretest condition.
9.0 Quality ControlSection(s) | Quality control measure | Effect |
---|---|---|
8.2.2.5, 8.3.3.5 | Repeat test procedures until change in pressure or vacuum for two consecutive runs agrees within ±12.5 mm (0.5 in.) H2O | Ensures data precision. |
13.1 Precision. The vapor tightness of a gasoline delivery tank under positive or negative pressure, as measured by this method, is precise within 12.5 mm (0.5 in.) H2O
13.2 Bias. No bias has been identified.
14.0 Pollution Prevention [Reserved] 15.0 Waste Management [Reserved] 16.0 Alternative Procedures16.1 The pumping of water into the bottom of a delivery tank is an acceptable alternative to the pressure source described above. Likewise, the draining of water out of the bottom of a delivery tank may be substituted for the vacuum source. Note that some of the specific step-by-step procedures in the method must be altered slightly to accommodate these different pressure and vacuum sources.
16.2 Techniques other than specified above may be used for purging and pressurizing a delivery tank, if prior approval is obtained from the Administrator. Such approval will be based upon demonstrated equivalency with the above method.
17.0 References [Reserved] 18.0 Tables, Diagrams, Flowcharts, and Validation Data [Reserved] Method 28 - Certification and Auditing of Wood Heaters Note:This method does not include all of the specifications (e.g., equipment and supplies) and procedures (e.g., sampling and analytical) essential to its performance. Some material is incorporated by reference from other methods in this part. Therefore, to obtain reliable results, persons using this method should have a thorough knowledge of at least the following additional test methods: Method 1, Method 2, Method 3, Method 4, Method 5, Method 5G, Method 5H, Method 6, Method 6C, and Method 16A.
1.0 Scope and Application1.1 Analyte. Particulate matter (PM). No CAS number assigned.
1.2 Applicability. This method is applicable for the certification and auditing of wood heaters, including pellet burning wood heaters.
1.3 Data Quality Objectives. Adherence to the requirements of this method will enhance the quality of the data obtained from air pollutant sampling methods.
2.0 Summary of Method2.1 Particulate matter emissions are measured from a wood heater burning a prepared test fuel crib in a test facility maintained at a set of prescribed conditions. Procedures for determining burn rates and particulate emission rates and for reducing data are provided.
3.0 Definitions3.1 2 × 4 or 4 × 4 means two inches by four inches or four inches by four inches (50 mm by 100 mm or 100 mm by 100 mm), as nominal dimensions for lumber.
3.2 Burn rate means the rate at which test fuel is consumed in a wood heater. Measured in kilograms or lbs of wood (dry basis) per hour (kg/hr or lb/hr).
3.3 Certification or audit test means a series of at least four test runs conducted for certification or audit purposes that meets the burn rate specifications in section 8.4.
3.4 Firebox means the chamber in the wood heater in which the test fuel charge is placed and combusted.
3.5 Height means the vertical distance extending above the loading door, if fuel could reasonably occupy that space, but not more than 2 inches above the top (peak height) of the loading door, to the floor of the firebox (i.e., below a permanent grate) if the grate allows a 1-inch diameter piece of wood to pass through the grate, or, if not, to the top of the grate. Firebox height is not necessarily uniform but must account for variations caused by internal baffles, air channels, or other permanent obstructions.
3.6 Length means the longest horizontal fire chamber dimension that is parallel to a wall of the chamber.
3.7 Pellet burning wood heater means a wood heater which meets the following criteria: (1) The manufacturer makes no reference to burning cord wood in advertising or other literature, (2) the unit is safety listed for pellet fuel only, (3) the unit operating and instruction manual must state that the use of cordwood is prohibited by law, and (4) the unit must be manufactured and sold including the hopper and auger combination as integral parts.
3.8 Secondary air supply means an air supply that introduces air to the wood heater such that the burn rate is not altered by more than 25 percent when the secondary air supply is adjusted during the test run. The wood heater manufacturer can document this through design drawings that show the secondary air is introduced only into a mixing chamber or secondary chamber outside the firebox.
3.9 Test facility means the area in which the wood heater is installed, operated, and sampled for emissions.
3.10 Test fuel charge means the collection of test fuel pieces placed in the wood heater at the start of the emission test run.
3.11 Test fuel crib means the arrangement of the test fuel charge with the proper spacing requirements between adjacent fuel pieces.
3.12 Test fuel loading density means the weight of the as-fired test fuel charge per unit volume of usable firebox.
3.13 Test fuel piece means the 2 × 4 or 4 × 4 wood piece cut to the length required for the test fuel charge and used to construct the test fuel crib.
3.14 Test run means an individual emission test which encompasses the time required to consume the mass of the test fuel charge.
3.15 Usable firebox volume means the volume of the firebox determined using its height, length, and width as defined in this section.
3.16 Width means the shortest horizontal fire chamber dimension that is parallel to a wall of the chamber.
3.17 Wood heater means an enclosed, woodburning appliance capable of and intended for space heating or domestic water heating, as defined in the applicable regulation.
4.0 Interferences [Reserved] 5.0 Safety5.1 Disclaimer. This method may involve hazardous materials, operations, and equipment. This test method may not address all of the safety problems associated with its use. It is the responsibility of the user of this test method to establish appropriate safety and health practices and to determine the applicability of regulatory limitations prior to performing this test method.
6.0 Equipment and SuppliesSame as section 6.0 of either Method 5G or Method 5H, with the addition of the following:
6.1 Insulated Solid Pack Chimney. For installation of wood heaters. Solid pack insulated chimneys shall have a minimum of 2.5 cm (1 in.) solid pack insulating material surrounding the entire flue and possess a label demonstrating conformance to U.L. 103 (incorporated by reference - see § 60.17).
6.2 Platform Scale and Monitor. For monitoring of fuel load weight change. The scale shall be capable of measuring weight to within 0.05 kg (0.1 lb) or 1 percent of the initial test fuel charge weight, whichever is greater.
6.3 Wood Heater Temperature Monitors. Seven, each capable of measuring temperature to within 1.5 percent of expected absolute temperatures.
6.4 Test Facility Temperature Monitor. A thermocouple located centrally in a vertically oriented 150 mm (6 in.) long, 50 mm (2 in.) diameter pipe shield that is open at both ends, capable of measuring temperature to within 1.5 percent of expected temperatures.
6.5 Balance (optional). Balance capable of weighing the test fuel charge to within 0.05 kg (0.1 lb).
6.6 Moisture Meter. Calibrated electrical resistance meter for measuring test fuel moisture to within 1 percent moisture content.
6.7 Anemometer. Device capable of detecting air velocities less than 0.10 m/sec (20 ft/min), for measuring air velocities near the test appliance.
6.8 Barometer. Mercury, aneroid or other barometer capable of measuring atmospheric pressure to within 2.5 mm Hg (0.1 in. Hg).
6.9 Draft Gauge. Electromanometer or other device for the determination of flue draft or static pressure readable to within 0.50 Pa (0.002 in. H2O).
6.10 Humidity Gauge. Psychrometer or hygrometer for measuring room humidity.
6.11 Wood Heater Flue.
6.11.1 Steel flue pipe extending to 2.6 ±0.15 m (8.5 ±0.5 ft) above the top of the platform scale, and above this level, insulated solid pack type chimney extending to 4.6 ±0.3 m (15 ±1 ft) above the platform scale, and of the size specified by the wood heater manufacturer. This applies to both freestanding and insert type wood heaters.
6.11.2 Other chimney types (e.g., solid pack insulated pipe) may be used in place of the steel flue pipe if the wood heater manufacturer's written appliance specifications require such chimney for home installation (e.g., zero clearance wood heater inserts). Such alternative chimney or flue pipe must remain and be sealed with the wood heater following the certification test.
6.12 Test Facility. The test facility shall meet the following requirements during testing:
6.12.1 The test facility temperature shall be maintained between 18 and 32 °C (65 and 90 °F) during each test run.
6.12.2 Air velocities within 0.6 m (2 ft) of the test appliance and exhaust system shall be less than 0.25 m/sec (50 ft/min) without fire in the unit.
6.12.3 The flue shall discharge into the same space or into a space freely communicating with the test facility. Any hood or similar device used to vent combustion products shall not induce a draft greater than 1.25 Pa (0.005 in. H2O) on the wood heater measured when the wood heater is not operating.
6.12.4 For test facilities with artificially induced barometric pressures (e.g., pressurized chambers), the barometric pressure in the test facility shall not exceed 775 mm Hg (30.5 in. Hg) during any test run.
7.0 Reagents and StandardsSame as section 6.0 of either Method 5G or Method 5H, with the addition of the following:
7.1 Test Fuel. The test fuel shall conform to the following requirements:
7.1.1 Fuel Species. Untreated, air-dried, Douglas fir lumber. Kiln-dried lumber is not permitted. The lumber shall be certified C grade (standard) or better Douglas fir by a lumber grader at the mill of origin as specified in the West Coast Lumber Inspection Bureau Standard No. 16 (incorporated by reference - see § 60.17).
7.1.2 Fuel Moisture. The test fuel shall have a moisture content range between 16 to 20 percent on a wet basis (19 to 25 percent dry basis). Addition of moisture to previously dried wood is not allowed. It is recommended that the test fuel be stored in a temperature and humidity-controlled room.
7.1.3 Fuel Temperature. The test fuel shall be at the test facility temperature of 18 to 32 °C (65 to 90 °F).
7.1.4 Fuel Dimensions. The dimensions of each test fuel piece shall conform to the nominal measurements of 2 × 4 and 4 × 4 lumber. Each piece of test fuel (not including spacers) shall be of equal length, except as necessary to meet requirements in section 8.8, and shall closely approximate 5/6 the dimensions of the length of the usable firebox. The fuel piece dimensions shall be determined in relation to the appliance's firebox volume according to guidelines listed below:
7.1.4.1 If the usable firebox volume is less than or equal to 0.043 m 3 (1.5 ft 3), use 2 × 4 lumber.
7.1.4.2 If the usable firebox volume is greater than 0.043 m 3 (1.5 ft 3) and less than or equal to 0.085 m 3 (3.0 ft 3), use 2 × 4 and 4 × 4 lumber. About half the weight of the test fuel charge shall be 2 × 4 lumber, and the remainder shall be 4 × 4 lumber.
7.1.4.3 If the usable firebox volume is greater than 0.085 m 3 (3.0 ft 3), use 4 × 4 lumber.
7.2 Test Fuel Spacers. Air-dried, Douglas fir lumber meeting the requirements outlined in sections 7.1.1 through 7.1.3. The spacers shall be 130 × 40 × 20 mm (5 × 1.5 × 0.75 in.).
8.0 Sample Collection, Preservation, Storage, and Transport8.1 Test Run Requirements.
8.1.1 Burn Rate Categories. One emission test run is required in each of the following burn rate categories:
Burn Rate Categories
[Average kg/hr (lb/hr), dry basis]
Category 1 | Category 2 | Category 3 | Category 4 |
---|---|---|---|
<0.80 | 0.80 to 1.25 | 1.25 to 1.90 | Maximum. |
(<1.76) | (1.76 to 2.76) | (2.76 to 4.19) | burn rate. |
8.1.1.1 Maximum Burn Rate. For Category 4, the wood heater shall be operated with the primary air supply inlet controls fully open (or, if thermostatically controlled, the thermostat shall be set at maximum heat output) during the entire test run, or the maximum burn rate setting specified by the manufacturer's written instructions.
8.1.1.2 Other Burn Rate Categories. For burn rates in Categories 1 through 3, the wood heater shall be operated with the primary air supply inlet control, or other mechanical control device, set at a predetermined position necessary to obtain the average burn rate required for the category.
8.1.1.3 Alternative Burn Rates for Burn Rate Categories 1 and 2.
8.1.1.3.1 If a wood heater cannot be operated at a burn rate below 0.80 kg/hr (1.76 lb/hr), two test runs shall be conducted with burn rates within Category 2. If a wood heater cannot be operated at a burn rate below 1.25 kg/hr (2.76 lb/hr), the flue shall be dampered or the air supply otherwise controlled in order to achieve two test runs within Category 2.
8.1.1.3.2 Evidence that a wood heater cannot be operated at a burn rate less than 0.80 kg/hr shall include documentation of two or more attempts to operate the wood heater in burn rate Category 1 and fuel combustion has stopped, or results of two or more test runs demonstrating that the burn rates were greater than 0.80 kg/hr when the air supply controls were adjusted to the lowest possible position or settings. Stopped fuel combustion is evidenced when an elapsed time of 30 minutes or more has occurred without a measurable (<0.05 kg (0.1 lb) or 1.0 percent, whichever is greater) weight change in the test fuel charge. See also section 8.8.3. Report the evidence and the reasoning used to determine that a test in burn rate Category 1 cannot be achieved; for example, two unsuccessful attempts to operate at a burn rate of 0.4 kg/hr are not sufficient evidence that burn rate Category 1 cannot be achieved.
Note:After July 1, 1990, if a wood heater cannot be operated at a burn rate less than 0.80 kg/hr, at least one test run with an average burn rate of 1.00 kg/hr or less shall be conducted. Additionally, if flue dampering must be used to achieve burn rates below 1.25 kg/hr (or 1.0 kg/hr), results from a test run conducted at burn rates below 0.90 kg/hr need not be reported or included in the test run average provided that such results are replaced with results from a test run meeting the criteria above.
8.2 Catalytic Combustor and Wood Heater Aging. The catalyst-equipped wood heater or a wood heater of any type shall be aged before the certification test begins. The aging procedure shall be conducted and documented by a testing laboratory accredited according to procedures in § 60.535 of 40 CFR part 60.
8.2.1 Catalyst-equipped Wood Heater. Operate the catalyst-equipped wood heater using fuel meeting the specifications outlined in sections 7.1.1 through 7.1.3, or cordwood with a moisture content between 15 and 25 percent on a wet basis. Operate the wood heater at a medium burn rate (Category 2 or 3) with a new catalytic combustor in place and in operation for at least 50 hours. Record and report hourly catalyst exit temperature data (Section 8.6.2) and the hours of operation.
8.2.2 Non-Catalyst Wood Heater. Operate the wood heater using the fuel described in section 8.4.1 at a medium burn rate for at least 10 hours. Record and report the hours of operation.
8.3 Pretest Recordkeeping. Record the test fuel charge dimensions and weights, and wood heater and catalyst descriptions as shown in the example in Figure 28-1.
8.4 Wood Heater Installation. Assemble the wood heater appliance and parts in conformance with the manufacturer's written installation instructions. Place the wood heater centrally on the platform scale and connect the wood heater to the flue described in section 6.11. Clean the flue with an appropriately sized, wire chimney brush before each certification test.
8.5 Wood Heater Temperature Monitors.
8.5.1 For catalyst-equipped wood heaters, locate a temperature monitor (optional) about 25 mm (1 in.) upstream of the catalyst at the centroid of the catalyst face area, and locate a temperature monitor (mandatory) that will indicate the catalyst exhaust temperature. This temperature monitor is centrally located within 25 mm (1 in.) downstream at the centroid of catalyst face area. Record these locations.
8.5.2 Locate wood heater surface temperature monitors at five locations on the wood heater firebox exterior surface. Position the temperature monitors centrally on the top surface, on two sidewall surfaces, and on the bottom and back surfaces. Position the monitor sensing tip on the firebox exterior surface inside of any heat shield, air circulation walls, or other wall or shield separated from the firebox exterior surface. Surface temperature locations for unusual design shapes (e.g., spherical, etc.) shall be positioned so that there are four surface temperature monitors in both the vertical and horizontal planes passing at right angles through the centroid of the firebox, not including the fuel loading door (total of five temperature monitors).
8.6 Test Facility Conditions.
8.6.1 Locate the test facility temperature monitor on the horizontal plane that includes the primary air intake opening for the wood heater. Locate the temperature monitor 1 to 2 m (3 to 6 ft) from the front of the wood heater in the 90° sector in front of the wood heater.
8.6.2 Use an anemometer to measure the air velocity. Measure and record the room air velocity before the pretest ignition period (Section 8.7) and once immediately following the test run completion.
8.6.3 Measure and record the test facility's ambient relative humidity, barometric pressure, and temperature before and after each test run.
8.6.4 Measure and record the flue draft or static pressure in the flue at a location no greater than 0.3 m (1 ft) above the flue connector at the wood heater exhaust during the test run at the recording intervals (Section 8.8.2).
8.7 Wood Heater Firebox Volume.
8.7.1 Determine the firebox volume using the definitions for height, width, and length in section 3. Volume adjustments due to presence of firebrick and other permanent fixtures may be necessary. Adjust width and length dimensions to extend to the metal wall of the wood heater above the firebrick or permanent obstruction if the firebrick or obstruction extending the length of the side(s) or back wall extends less than one-third of the usable firebox height. Use the width or length dimensions inside the firebrick if the firebrick extends more than one-third of the usable firebox height. If a log retainer or grate is a permanent fixture and the manufacturer recommends that no fuel be placed outside the retainer, the area outside of the retainer is excluded from the firebox volume calculations.
8.7.2 In general, exclude the area above the ash lip if that area is less than 10 percent of the usable firebox volume. Otherwise, take into account consumer loading practices. For instance, if fuel is to be loaded front-to-back, an ash lip may be considered usable firebox volume.
8.7.3 Include areas adjacent to and above a baffle (up to two inches above the fuel loading opening) if four inches or more horizontal space exist between the edge of the baffle and a vertical obstruction (e.g., sidewalls or air channels).
8.8 Test Fuel Charge.
8.8.1 Prepare the test fuel pieces in accordance with the specifications outlined in sections 7.1 and 7.2. Determine the test fuel moisture content with a calibrated electrical resistance meter or other equivalent performance meter. If necessary, convert fuel moisture content values from dry basis (%Md) to wet basis (%Mw) in section 12.2 using Equation 28-1. Determine fuel moisture for each fuel piece (not including spacers) by averaging at least three moisture meter readings, one from each of three sides, measured parallel to the wood grain. Average all the readings for all the fuel pieces in the test fuel charge. If an electrical resistance type meter is used, penetration of insulated electrodes shall be one-fourth the thickness of the test fuel piece or 19 mm (0.75 in.), whichever is greater. Measure the moisture content within a 4-hour period prior to the test run. Determine the fuel temperature by measuring the temperature of the room where the wood has been stored for at least 24 hours prior to the moisture determination.
8.8.2 Attach the spacers to the test fuel pieces with uncoated, ungalvanized nails or staples as illustrated in Figure 28-2. Attachment of spacers to the top of the test fuel piece(s) on top of the test fuel charge is optional.
8.8.3 To avoid stacking difficulties, or when a whole number of test fuel pieces does not result, all piece lengths shall be adjusted uniformly to remain within the specified loading density. The shape of the test fuel crib shall be geometrically similar to the shape of the firebox volume without resorting to special angular or round cuts on the individual fuel pieces.
8.8.4 The test fuel loading density shall be 112 ±11.2 kg/m 3 (7 ±0.7 lb/ft3) of usable firebox volume on a wet basis.
8.9 Sampling Equipment. Prepare the sampling equipment as defined by the selected method (i.e., either Method 5G or Method 5H). Collect one particulate emission sample for each test run.
8.10 Secondary Air Adjustment Validation.
8.10.1 If design drawings do not show the introduction of secondary air into a chamber outside the firebox (see “secondary air supply” under section 3.0, Definitions), conduct a separate test of the wood heater's secondary air supply. Operate the wood heater at a burn rate in Category 1 (Section 8.1.1) with the secondary air supply operated following the manufacturer's written instructions. Start the secondary air validation test run as described in section 8.8.1, except no emission sampling is necessary and burn rate data shall be recorded at 5-minute intervals.
8.10.2 After the start of the test run, operate the wood heater with the secondary air supply set as per the manufacturer's instructions, but with no adjustments to this setting. After 25 percent of the test fuel has been consumed, adjust the secondary air supply controls to another setting, as per the manufacturer's instructions. Record the burn rate data (5-minute intervals) for 20 minutes following the air supply adjustment.
8.10.3 Adjust the air supply control(s) to the original position(s), operate at this condition for at least 20 minutes, and repeat the air supply adjustment procedure above. Repeat the procedure three times at equal intervals over the entire burn period as defined in section 8.8. If the secondary air adjustment results in a burn rate change of more than an average of 25 percent between the 20-minute periods before and after the secondary adjustments, the secondary air supply shall be considered a primary air supply, and no adjustment to this air supply is allowed during the test run.
8.10.4 The example sequence below describes a typical secondary air adjustment validation check. The first cycle begins after at least 25 percent of the test fuel charge has been consumed.
Cycle 1 Part 1, sec air adjusted to final position - 20 min Part 2, sec air adjusted to final position - 20 min Part 3, sec air adjusted to final position - 20 min Cycle 2 Part 1, sec air adjusted to final position - 20 min Part 2, sec air adjusted to final position - 20 min Part 3, sec air adjusted to final position - 20 min Cycle 3 Part 1, sec air adjusted to final position - 20 min Part 2, sec air adjusted to final position - 20 min Part 3, sec air adjusted to final position - 20 min Note that the cycles may overlap; that is, Part 3 of Cycle 1 may coincide in part or in total with Part 1 of Cycle 2. The calculation of the secondary air percent effect for this example is as follows:8.11 Pretest Ignition. Build a fire in the wood heater in accordance with the manufacturer's written instructions.
8.11.1 Pretest Fuel Charge. Crumpled newspaper loaded with kindling may be used to help ignite the pretest fuel. The pretest fuel, used to sustain the fire, shall meet the same fuel requirements prescribed in section 7.1. The pretest fuel charge shall consist of whole 2 × 4's that are no less than 1/3 the length of the test fuel pieces. Pieces of 4 × 4 lumber in approximately the same weight ratio as for the test fuel charge may be added to the pretest fuel charge.
8.11.2 Wood Heater Operation and Adjustments. Set the air inlet supply controls at any position that will maintain combustion of the pretest fuel load. At least one hour before the start of the test run, set the air supply controls at the approximate positions necessary to achieve the burn rate desired for the test run. Adjustment of the air supply controls, fuel addition or subtractions, and coalbed raking shall be kept to a minimum but are allowed up to 15 minutes prior to the start of the test run. For the purposes of this method, coalbed raking is the use of a metal tool (poker) to stir coals, break burning fuel into smaller pieces, dislodge fuel pieces from positions of poor combustion, and check for the condition of uniform charcoalization. Record all adjustments made to the air supply controls, adjustments to and additions or subtractions of fuel, and any other changes to wood heater operations that occur during pretest ignition period. Record fuel weight data and wood heater temperature measurements at 10-minute intervals during the hour of the pretest ignition period preceding the start of the test run. During the 15-minute period prior to the start of the test run, the wood heater loading door shall not be open more than a total of 1 minute. Coalbed raking is the only adjustment allowed during this period.
Note:One purpose of the pretest ignition period is to achieve uniform charcoalization of the test fuel bed prior to loading the test fuel charge. Uniform charcoalization is a general condition of the test fuel bed evidenced by an absence of large pieces of burning wood in the coal bed and the remaining fuel pieces being brittle enough to be broken into smaller charcoal pieces with a metal poker. Manipulations to the fuel bed prior to the start of the test run should be done to achieve uniform charcoalization while maintaining the desired burn rate. In addition, some wood heaters (e.g., high mass units) may require extended pretest burn time and fuel additions to reach an initial average surface temperature sufficient to meet the thermal equilibrium criteria in section 8.3.
8.11.3 The weight of pretest fuel remaining at the start of the test run is determined as the difference between the weight of the wood heater with the remaining pretest fuel and the tare weight of the cleaned, dry wood heater with or without dry ash or sand added consistent with the manufacturer's instructions and the owner's manual. The tare weight of the wood heater must be determined with the wood heater (and ash, if added) in a dry condition.
8.12 Test Run. Complete a test run in each burn rate category, as follows:
8.12.1 Test Run Start.
8.12.1.1 When the kindling and pretest fuel have been consumed to leave a fuel weight between 20 and 25 percent of the weight of the test fuel charge, record the weight of the fuel remaining and start the test run. Record and report any other criteria, in addition to those specified in this section, used to determine the moment of the test run start (e.g., firebox or catalyst temperature), whether such criteria are specified by the wood heater manufacturer or the testing laboratory. Record all wood heater individual surface temperatures, catalyst temperatures, any initial sampling method measurement values, and begin the particulate emission sampling. Within 1 minute following the start of the test run, open the wood heater door, load the test fuel charge, and record the test fuel charge weight. Recording of average, rather than individual, surface temperatures is acceptable for tests conducted in accordance with § 60.533(o)(3)(i) of 40 CFR part 60.
8.12.1.2 Position the fuel charge so that the spacers are parallel to the floor of the firebox, with the spacer edges abutting each other. If loading difficulties result, some fuel pieces may be placed on edge. If the usable firebox volume is between 0.043 and 0.085 m 3 (1.5 and 3.0 ft 3), alternate the piece sizes in vertical stacking layers to the extent possible. For example, place 2 × 4's on the bottom layer in direct contact with the coal bed and 4 × 4's on the next layer, etc. (See Figure 28-3). Position the fuel pieces parallel to each other and parallel to the longest wall of the firebox to the extent possible within the specifications in section 8.8.
8.12.1.3 Load the test fuel in appliances having unusual or unconventional firebox design maintaining air space intervals between the test fuel pieces and in conformance with the manufacturer's written instructions. For any appliance that will not accommodate the loading arrangement specified in the paragraph above, the test facility personnel shall contact the Administrator for an alternative loading arrangement.
8.12.1.4 The wood heater door may remain open and the air supply controls adjusted up to five minutes after the start of the test run in order to make adjustments to the test fuel charge and to ensure ignition of the test fuel charge has occurred. Within the five minutes after the start of the test run, close the wood heater door and adjust the air supply controls to the position determined to produce the desired burn rate. No other adjustments to the air supply controls or the test fuel charge are allowed (except as specified in sections 8.12.3 and 8.12.4) after the first five minutes of the test run. Record the length of time the wood heater door remains open, the adjustments to the air supply controls, and any other operational adjustments.
8.12.2 Data Recording. Record on a data sheet similar to that shown in Figure 28-4, at intervals no greater than 10 minutes, fuel weight data, wood heater individual surface and catalyst temperature measurements, other wood heater operational data (e.g., draft), test facility temperature and sampling method data.
8.12.3 Test Fuel Charge Adjustment. The test fuel charge may be adjusted (i.e., repositioned) once during a test run if more than 60 percent of the initial test fuel charge weight has been consumed and more than 10 minutes have elapsed without a measurable (<0.05 kg (0.1 lb) or 1.0 percent, whichever is greater) weight change. The time used to make this adjustment shall be less than 15 seconds.
8.12.4 Air Supply Adjustment. Secondary air supply controls may be adjusted once during the test run following the manufacturer's written instructions (see section 8.10). No other air supply adjustments are allowed during the test run. Recording of wood heater flue draft during the test run is optional for tests conducted in accordance with § 60.533(o)(3)(i) of 40 CFR part 60.
8.12.5 Auxiliary Wood Heater Equipment Operation. Heat exchange blowers sold with the wood heater shall be operated during the test run following the manufacturer's written instructions. If no manufacturer's written instructions are available, operate the heat exchange blower in the “high” position. (Automatically operated blowers shall be operated as designed.) Shaker grates, by-pass controls, or other auxiliary equipment may be adjusted only one time during the test run following the manufacturer's written instructions.
Record all adjustments on a wood heater operational written record.
Note:If the wood heater is sold with a heat exchange blower as an option, test the wood heater with the heat exchange blower operating as described in sections 8.1 through 8.12 and report the results. As an alternative to repeating all test runs without the heat exchange blower operating, one additional test run may be without the blower operating as described in section 8.12.5 at a burn rate in Category 2 (Section 8.1.1). If the emission rate resulting from this test run without the blower operating is equal to or less than the emission rate plus 1.0 g/hr (0.0022 lb/hr) for the test run in burn rate Category 2 with the blower operating, the wood heater may be considered to have the same average emission rate with or without the blower operating. Additional test runs without the blower operating are unnecessary.
8.13 Test Run Completion. Continue emission sampling and wood heater operation for 2 hours. The test run is completed when the remaining weight of the test fuel charge is 0.00 kg (0.0 lb). End the test run when the scale has indicated a test fuel charge weight of 0.00 kg (0.0 lb) or less for 30 seconds. At the end of the test run, stop the particulate sampling, and record the final fuel weight, the run time, and all final measurement values.
8.14 Wood Heater Thermal Equilibrium. The average of the wood heater surface temperatures at the end of the test run shall agree with the average surface temperature at the start of the test run to within 70 °C (126 °F).
8.15 Consecutive Test Runs. Test runs on a wood heater may be conducted consecutively provided that a minimum one-hour interval occurs between test runs.
8.16 Additional Test Runs. The testing laboratory may conduct more than one test run in each of the burn rate categories specified in section 8.1.1. If more than one test run is conducted at a specified burn rate, the results from at least two-thirds of the test runs in that burn rate category shall be used in calculating the weighted average emission rate (see section 12.2). The measurement data and results of all test runs shall be reported regardless of which values are used in calculating the weighted average emission rate (see note in section 8.1).
9.0 Quality ControlSame as section 9.0 of either Method 5G or Method 5H.
10.0 Calibration and StandardizationsSame as section 10.0 of either Method 5G or Method 5H, with the addition of the following:
10.1 Platform Scale. Perform a multi-point calibration (at least five points spanning the operational range) of the platform scale before its initial use. The scale manufacturer's calibration results are sufficient for this purpose. Before each certification test, audit the scale with the wood heater in place by weighing at least one calibration weight (Class F) that corresponds to between 20 percent and 80 percent of the expected test fuel charge weight. If the scale cannot reproduce the value of the calibration weight within 0.05 kg (0.1 lb) or 1 percent of the expected test fuel charge weight, whichever is greater, recalibrate the scale before use with at least five calibration weights spanning the operational range of the scale.
10.2 Balance (optional). Calibrate as described in section 10.1.
10.3 Temperature Monitor. Calibrate as in Method 2, section 4.3, before the first certification test and semiannually thereafter.
10.4 Moisture Meter. Calibrate as per the manufacturer's instructions before each certification test.
10.5 Anemometer. Calibrate the anemometer as specified by the manufacturer's instructions before the first certification test and semiannually thereafter.
10.6 Barometer. Calibrate against a mercury barometer before the first certification test and semiannually thereafter.
10.7 Draft Gauge. Calibrate as per the manufacturer's instructions; a liquid manometer does not require calibration.
10.8 Humidity Gauge. Calibrate as per the manufacturer's instructions before the first certification test and semiannually thereafter.
11.0 Analytical ProceduresSame as section 11.0 of either Method 5G or Method 5H.
12.0 Data Analysis and CalculationsSame as section 12.0 of either Method 5G or Method 5H, with the addition of the following:
12.1 Nomenclature.
BR = Dry wood burn rate, kg/hr (lb/hr) Ei = Emission rate for test run, i, from Method 5G or 5H, g/hr (lb/hr) Ew = Weighted average emission rate, g/hr (lb/hr) ki = Test run weighting factor = Pi + 1 − Pi−1 %Md = Fuel moisture content, dry basis, percent. %Mw = Average moisture in test fuel charge, wet basis, percent. n = Total number of test runs. Pi = Probability for burn rate during test run, i, obtained from Table 28-1. Use linear interpolation to determine probability values for burn rates between those listed on the table. Wwd = Total mass of wood burned during the test run, kg (lb).12.2 Wet Basis Fuel Moisture Content.
12.3 Weighted Average Emission Rate. Calculate the weighted average emission rate (Ew) using Equation 28-1:
Note:Po always equals 0, P(n + 1) always equals 1, P1 corresponds to the probability of the lowest recorded burn rate, P2 corresponds to the probability of the next lowest burn rate, etc. An example calculation is in section 12.3.1.
12.3.1 Example Calculation of Weighted Average Emission Rate.
Burn rate category | Test No. |
Burn rate (Dry-kg/hr) |
Emissions (g/hr) |
---|---|---|---|
1 | 1 | 0.65 | 5.0 |
2 1 | 2 | 0.85 | 6.7 |
2 | 3 | 0.90 | 4.7 |
2 | 4 | 1.00 | 5.3 |
3 | 5 | 1.45 | 3.8 |
4 | 6 | 2.00 | 5.1 |
1 As permitted in section 6.6, this test run may be omitted from the calculation of the weighted average emission rate because three runs were conducted for this burn rate category.
Test No. | Burn rate | Pi | Ei | Ki |
---|---|---|---|---|
0 | 0.000 | |||
1 | 0.65 | 0.121 | 5.0 | 0.300 |
2 | 0.90 | 0.300 | 4.7 | 0.259 |
3 | 1.00 | 0.380 | 5.3 | 0.422 |
4 | 1.45 | 0.722 | 3.8 | 0.532 |
5 | 2.00 | 0.912 | 5.1 | 0.278 |
6 | 1.000 |
K1 = P2 − P0 = 0.300 − 0 = 0.300
K2 = P3 − P1 = 0.381 − 0.121 = 0.259
K3 = P4 − P2 = 0.722 − 0.300 = 0.422
K4 = P5 − P3 = 0.912 − 0.380 = 0.532
K5 = P6 − P4 = 1.000 − 0.722 = 0.278
12.4 Average Wood Heater Surface Temperatures. Calculate the average of the wood heater surface temperatures for the start of the test run (Section 8.12.1) and for the test run completion (Section 8.13). If the two average temperatures do not agree within 70 °C (125 °F), report the test run results, but do not include the test run results in the test average. Replace such test run results with results from another test run in the same burn rate category.
12.5 Burn Rate. Calculate the burn rate (BR) using Equation 28-3:
12.6 Reporting Criteria. Submit both raw and reduced test data for wood heater tests.
12.6.1 Suggested Test Report Format.
12.6.1.1 Introduction.
12.6.1.1.1 Purpose of test-certification, audit, efficiency, research and development.
12.6.1.1.2 Wood heater identification-manufacturer, model number, catalytic/noncatalytic, options.
12.6.1.1.3 Laboratory-name, location (altitude), participants.
12.6.1.1.4 Test information-date wood heater received, date of tests, sampling methods used, number of test runs.
12.6.1.2 Summary and Discussion of Results
12.6.1.2.1 Table of results (in order of increasing burn rate)-test run number, burn rate, particulate emission rate, efficiency (if determined), averages (indicate which test runs are used).
12.6.1.2.2 Summary of other data-test facility conditions, surface temperature averages, catalyst temperature averages, pretest fuel weights, test fuel charge weights, run times.
12.6.1.2.3 Discussion-Burn rate categories achieved, test run result selection, specific test run problems and solutions.
12.6.1.3 Process Description.
12.6.1.3.1 Wood heater dimensions-volume, height, width, lengths (or other linear dimensions), weight, volume adjustments.
12.6.1.3.2 Firebox configuration-air supply locations and operation, air supply introduction location, refractory location and dimensions, catalyst location, baffle and by-pass location and operation (include line drawings or photographs).
12.6.1.3.3 Process operation during test-air supply settings and adjustments, fuel bed adjustments, draft.
12.6.1.3.4 Test fuel-test fuel properties (moisture and temperature), test fuel crib description (include line drawing or photograph), test fuel loading density.
12.6.1.4 Sampling Locations.
12.6.1.4.1 Describe sampling location relative to wood heater. Include drawing or photograph.
12.6.1.5 Sampling and Analytical Procedures
12.6.1.5.1 Sampling methods-brief reference to operational and sampling procedures and optional and alternative procedures used.
12.6.1.5.2 Analytical methods-brief description of sample recovery and analysis procedures.
12.6.1.6 Quality Control and Assurance Procedures and Results
12.6.1.6.1 Calibration procedures and results-certification procedures, sampling and analysis procedures.
12.6.1.6.2 Test method quality control procedures-leak-checks, volume meter checks, stratification (velocity) checks, proportionality results.
12.6.1.7 Appendices
12.6.1.7.1 Results and Example Calculations. Complete summary tables and accompanying examples of all calculations.
12.6.1.7.2 Raw Data. Copies of all uncorrected data sheets for sampling measurements, temperature records and sample recovery data. Copies of all pretest burn rate and wood heater temperature data.
12.6.1.7.3 Sampling and Analytical Procedures. Detailed description of procedures followed by laboratory personnel in conducting the certification test, emphasizing particular parts of the procedures differing from the methods (e.g., approved alternatives).
12.6.1.7.4 Calibration Results. Summary of all calibrations, checks, and audits pertinent to certification test results with dates.
12.6.1.7.5 Participants. Test personnel, manufacturer representatives, and regulatory observers.
12.6.1.7.6 Sampling and Operation Records. Copies of uncorrected records of activities not included on raw data sheets (e.g., wood heater door open times and durations).
12.6.1.7.7 Additional Information. Wood heater manufacturer's written instructions for operation during the certification test.
12.6.2.1 Wood Heater Identification. Report wood heater identification information. An example data form is shown in Figure 28-4.
12.6.2.2 Test Facility Information. Report test facility temperature, air velocity, and humidity information. An example data form is shown on Figure 28-4.
12.6.2.3 Test Equipment Calibration and Audit Information. Report calibration and audit results for the platform scale, test fuel balance, test fuel moisture meter, and sampling equipment including volume metering systems and gaseous analyzers.
12.6.2.4 Pretest Procedure Description. Report all pretest procedures including pretest fuel weight, burn rates, wood heater temperatures, and air supply settings. An example data form is shown on Figure 28-4.
12.6.2.5 Particulate Emission Data. Report a summary of test results for all test runs and the weighted average emission rate. Submit copies of all data sheets and other records collected during the testing. Submit examples of all calculations.
13.0 Method Performance [Reserved] 14.0 Pollution Prevention [Reserved] 15.0 Waste Management [Reserved] 16.0 Alternative Procedures16.1 Pellet Burning Heaters. Certification testing requirements and procedures for pellet burning wood heaters are identical to those for other wood heaters, with the following exceptions:
16.1.1 Test Fuel Properties. The test fuel shall be all wood pellets with a moisture content no greater than 20 percent on a wet basis (25 percent on a dry basis). Determine the wood moisture content with either ASTM D 2016-74 or 83, (Method A), ASTM D 4444-92, or ASTM D 4442-84 or 92 (all noted ASTM standards are incorporated by reference - see § 60.17).
16.1.2 Test Fuel Charge Specifications. The test fuel charge size shall be as per the manufacturer's written instructions for maintaining the desired burn rate.
16.1.3 Wood Heater Firebox Volume. The firebox volume need not be measured or determined for establishing the test fuel charge size. The firebox dimensions and other heater specifications needed to identify the heater for certification purposes shall be reported.
16.1.4 Heater Installation. Arrange the heater with the fuel supply hopper on the platform scale as described in section 8.6.1.
16.1.5 Pretest Ignition. Start a fire in the heater as directed by the manufacturer's written instructions, and adjust the heater controls to achieve the desired burn rate. Operate the heater at the desired burn rate for at least 1 hour before the start of the test run.
16.1.6 Test Run. Complete a test run in each burn rate category as follows:
16.1.6.1 Test Run Start. When the wood heater has operated for at least 1 hour at the desired burn rate, add fuel to the supply hopper as necessary to complete the test run, record the weight of the fuel in the supply hopper (the wood heater weight), and start the test run. Add no additional fuel to the hopper during the test run.
Record all the wood heater surface temperatures, the initial sampling method measurement values, the time at the start of the test, and begin the emission sampling. Make no adjustments to the wood heater air supply or wood supply rate during the test run.
16.1.6.2 Data Recording. Record the fuel (wood heater) weight data, wood heater temperature and operational data, and emission sampling data as described in section 8.12.2.
16.1.6.3 Test Run Completion. Continue emission sampling and wood heater operation for 2 hours. At the end of the test run, stop the particulate sampling, and record the final fuel weight, the run time, and all final measurement values, including all wood heater individual surface temperatures.
16.1.7 Calculations. Determine the burn rate using the difference between the initial and final fuel (wood heater) weights and the procedures described in section 12.4. Complete the other calculations as described in section 12.0.
17.0 ReferencesSame as Method 5G, with the addition of the following:
1. Radian Corporation. OMNI Environmental Services, Inc., Cumulative Probability for a Given Burn Rate Based on Data Generated in the CONEG and BPA Studies. Package of materials submitted to the Fifth Session of the Regulatory Negotiation Committee, July 16-17, 1986.
18.0 Tables, Diagrams, Flowcharts, and Validation DataTable 28-1 - Burn Rate Weighted Probabilities for Calculating Weighted Average Emission Rates
Burn rate (kg/hr-dry) |
Cumulative probability (P) |
Burn rate (kg/hr-dry) |
Cumulative probability (P) |
Burn rate (kg/hr-dry) |
Cumulative probability (P) |
---|---|---|---|---|---|
0.00 | 0.000 | 1.70 | 0.840 | 3.40 | 0.989 |
0.05 | 0.002 | 1.75 | 0.857 | 3.45 | 0.989 |
0.10 | 0.007 | 1.80 | 0.875 | 3.50 | 0.990 |
0.15 | 0.012 | 1.85 | 0.882 | 3.55 | 0.991 |
0.20 | 0.016 | 1.90 | 0.895 | 3.60 | 0.991 |
0.25 | 0.021 | 1.95 | 0.906 | 3.65 | 0.992 |
0.30 | 0.028 | 2.00 | 0.912 | 3.70 | 0.992 |
0.35 | 0.033 | 2.05 | 0.920 | 3.75 | 0.992 |
0.40 | 0.041 | 2.10 | 0.925 | 3.80 | 0.993 |
0.45 | 0.054 | 2.15 | 0.932 | 3.85 | 0.994 |
0.50 | 0.065 | 2.20 | 0.936 | 3.90 | 0.994 |
0.55 | 0.086 | 2.25 | 0.940 | 3.95 | 0.994 |
0.60 | 0.100 | 2.30 | 0.945 | 4.00 | 0.994 |
0.65 | 0.121 | 2.35 | 0.951 | 4.05 | 0.995 |
0.70 | 0.150 | 2.40 | 0.956 | 4.10 | 0.995 |
0.75 | 0.185 | 2.45 | 0.959 | 4.15 | 0.995 |
0.80 | 0.220 | 2.50 | 0.964 | 4.20 | 0.995 |
0.85 | 0.254 | 2.55 | 0.968 | 4.25 | 0.995 |
0.90 | 0.300 | 2.60 | 0.972 | 4.30 | 0.996 |
0.95 | 0.328 | 2.65 | 0.975 | 4.35 | 0.996 |
1.00 | 0.380 | 2.70 | 0.977 | 4.40 | 0.996 |
1.05 | 0.407 | 2.75 | 0.979 | 4.45 | 0.996 |
1.10 | 0.460 | 2.80 | 0.980 | 4.50 | 0.996 |
1.15 | 0.490 | 2.85 | 0.981 | 4.55 | 0.996 |
1.20 | 0.550 | 2.90 | 0.982 | 4.60 | 0.996 |
1.25 | 0.572 | 2.95 | 0.984 | 4.65 | 0.996 |
1.30 | 0.620 | 3.00 | 0.984 | 4.70 | 0.996 |
1.35 | 0.654 | 3.05 | 0.985 | 4.75 | 0.997 |
1.40 | 0.695 | 3.10 | 0.986 | 4.80 | 0.997 |
1.45 | 0.722 | 3.15 | 0.987 | 4.85 | 0.997 |
1.50 | 0.750 | 3.20 | 0.987 | 4.90 | 0.997 |
1.55 | 0.779 | 3.25 | 0.988 | 4.95 | 0.997 |
1.60 | 0.800 | 3.30 | 0.988 | ≥5.00 | 1.000 |
1.65 | 0.825 | 3.35 | 0.989 |
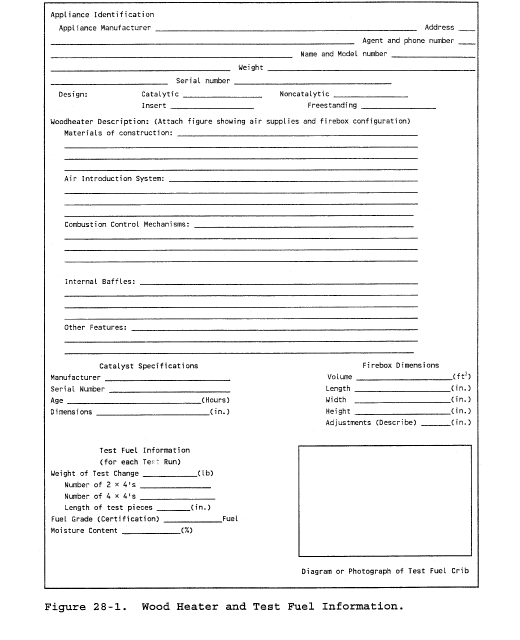
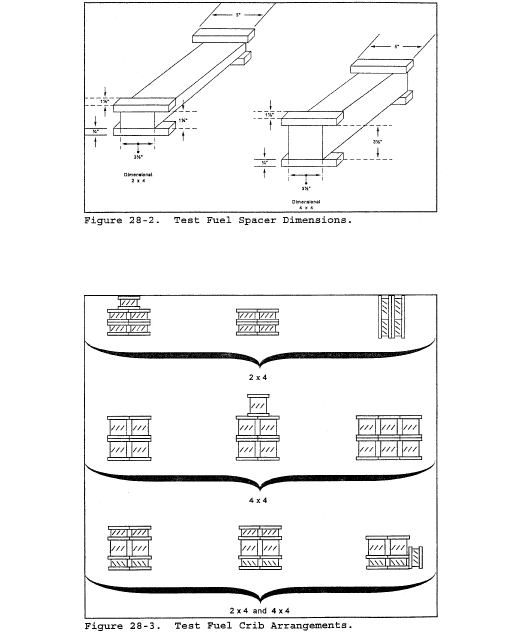
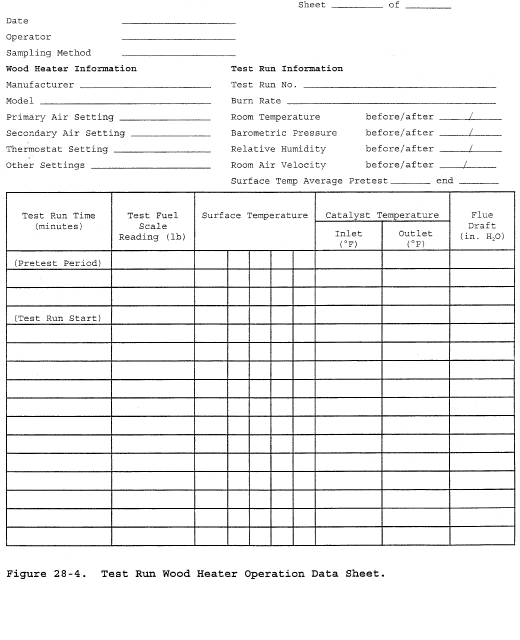
This method does not include all or the specifications (e.g., equipment and supplies) and procedures (e.g., sampling and analytical) essential to its performance. Some material is incorporated by reference from other methods in this part. Therefore, to obtain reliable results, persons using this method should also have a thorough knowledge of at least the following additional test methods: Method 3, Method 3A, Method 5H, Method 6C, and Method 28.
1.0 Scope and Application1.1 Analyte. Particulate matter (PM). No CAS number assigned.
1.2 Applicability. This method is applicable for the measurement of air-to-fuel ratios and minimum achievable burn rates, for determining whether a wood-fired appliance is an affected facility, as specified in 40 CFR 60.530.
1.3 Data Quality Objectives. Adherence to the requirements of this method will enhance the quality of the data obtained from air pollutant sampling methods.
2.0 Summary of Method2.1 A gas sample is extracted from a location in the stack of a wood-fired appliance while the appliance is operating at a prescribed set of conditions. The gas sample is analyzed for carbon dioxide (CO2), oxygen (O2), and carbon monoxide (CO). These stack gas components are measured for determining the dry molecular weight of the exhaust gas. Total moles of exhaust gas are determined stoichiometrically. Air-to-fuel ratio is determined by relating the mass of dry combustion air to the mass of dry fuel consumed.
3.0 DefinitionsSame as Method 28, section 3.0, with the addition of the following:
3.1 Air-to-fuel ratio means the ratio of the mass of dry combustion air introduced into the firebox to the mass of dry fuel consumed (grams of dry air per gram of dry wood burned).
4.0 Interferences [Reserved] 5.0 Safety5.1 Disclaimer. This method may involve hazardous materials, operations, and equipment. This test method may not address all of the safety problems associated with its use. It is the responsibility of the user of this test method to establish appropriate safety and health practices and to determine the applicability of regulatory limitations prior to performing this test method.
6.0 Equipment and Supplies6.1 Test Facility. Insulated Solid Pack Chimney, Platform Scale and Monitor, Test Facility Temperature Monitor, Balance, Moisture Meter, Anemometer, Barometer, Draft Gauge, Humidity Gauge, Wood Heater Flue, and Test Facility. Same as Method 28, sections 6.1, 6.2, and 6.4 to 6.12, respectively.
6.2 Sampling System. Probe, Condenser, Valve, Pump, Rate Meter, Flexible Bag, Pressure Gauge, and Vacuum Gauge. Same as Method 3, sections 6.2.1 to 6.2.8, respectively. Alternatively, the sampling system described in Method 5H, section 6.1 may be used.
6.3 Exhaust Gas Analysis. Use one or both of the following:
6.3.1 Orsat Analyzer. Same as Method 3, section 6.1.3
6.3.2 Instrumental Analyzers. Same as Method 5H, sections 6.1.3.4 and 6.1.3.5, for CO2 and CO analyzers, except use a CO analyzer with a range of 0 to 5 percent and use a CO2 analyzer with a range of 0 to 5 percent. Use an O2 analyzer capable of providing a measure of O2 in the range of 0 to 25 percent by volume at least once every 10 minutes.
7.0 Reagents and Standards7.1 Test Fuel and Test Fuel Spacers. Same as Method 28, sections 7.1 and 7.2, respectively.
7.2 Cylinder Gases. For each of the three analyzers, use the same concentration as specified in sections 7.2.1, 7.2.2, and 7.2.3 of Method 6C.
8.0 Sample Collection, Preservation, Storage, and Transport8.1 Wood Heater Air Supply Adjustments.
8.1.1 This section describes how dampers are to be set or adjusted and air inlet ports closed or sealed during Method 28A tests. The specifications in this section are intended to ensure that affected facility determinations are made on the facility configurations that could reasonably be expected to be employed by the user. They are also intended to prevent circumvention of the standard through the addition of an air port that would often be blocked off in actual use. These specifications are based on the assumption that consumers will remove such items as dampers or other closure mechanism stops if this can be done readily with household tools; that consumers will block air inlet passages not visible during normal operation of the appliance using aluminum tape or parts generally available at retail stores; and that consumers will cap off any threaded or flanged air inlets. They also assume that air leakage around glass doors, sheet metal joints or through inlet grilles visible during normal operation of the appliance would not be further blocked or taped off by a consumer.
8.1.2 It is not the intention of this section to cause an appliance that is clearly designed, intended, and, in most normal installations, used as a fireplace to be converted into a wood heater for purposes of applicability testing. Such a fireplace would be identifiable by such features as large or multiple glass doors or panels that are not gasketed, relatively unrestricted air inlets intended, in large part, to limit smoking and fogging of glass surfaces, and other aesthetic features not normally included in wood heaters.
8.1.3 Adjustable Air Supply Mechanisms. Any commercially available flue damper, other adjustment mechanism or other air inlet port that is designed, intended or otherwise reasonably expected to be adjusted or closed by consumers, installers, or dealers and which could restrict air into the firebox shall be set so as to achieve minimum air into the firebox (i.e., closed off or set in the most closed position).
8.1.3.1 Flue dampers, mechanisms and air inlet ports which could reasonably be expected to be adjusted or closed would include:
8.1.3.1.1 All internal or externally adjustable mechanisms (including adjustments that affect the tightness of door fittings) that are accessible either before and/or after installation.
8.1.3.1.2 All mechanisms, other inlet ports, or inlet port stops that are identified in the owner's manual or in any dealer literature as being adjustable or alterable. For example, an inlet port that could be used to provide access to an outside air duct but which is identified as being closable through use of additional materials whether or not they are supplied with the facility.
8.1.3.1.3 Any combustion air inlet port or commercially available flue damper or mechanism stop, which would readily lend itself to closure by consumers who are handy with household tools by the removal of parts or the addition of parts generally available at retail stores (e.g., addition of a pipe cap or plug, addition of a small metal plate to an inlet hole on a nondecorative sheet metal surface, or removal of riveted or screwed damper stops).
8.1.3.1.4 Any flue damper, other adjustment mechanisms or other air inlet ports that are found and documented in several (e.g., a number sufficient to reasonably conclude that the practice is not unique or uncommon) actual installations as having been adjusted to a more closed position, or closed by consumers, installers, or dealers.
8.1.4 Air Supply Adjustments During Test. The test shall be performed with all air inlets identified under this section in the closed or most closed position or in the configuration which otherwise achieves the lowest air inlet (i.e., greatest blockage).
Note:For the purposes of this section, air flow shall not be minimized beyond the point necessary to maintain combustion or beyond the point that forces smoke into the room.
8.1.5 Notwithstanding section 8.1.1, any flue damper, adjustment mechanism, or air inlet port (whether or not equipped with flue dampers or adjusting mechanisms) that is visible during normal operation of the appliance and which could not reasonably be closed further or blocked except through means that would significantly degrade the aesthetics of the facility (e.g., through use of duct tape) will not be closed further or blocked.
8.2 Sampling System.
8.2.1 Sampling Location. Same as Method 5H, section 8.1.2.
8.2.2 Sampling System Set Up. Set up the sampling equipment as described in Method 3, section 8.1.
8.3 Wood Heater Installation, Test Facility Conditions, Wood Heater Firebox Volume, and Test Fuel Charge. Same as Method 28, sections 8.4 and 8.6 to 8.8, respectively.
8.4 Pretest Ignition. Same as Method 28, section 8.11. Set the wood heater air supply settings to achieve a burn rate in Category 1 or the lowest achievable burn rate (see section 8.1).
8.5 Test Run. Same as Method 28, section 8.12. Begin sample collection at the start of the test run as defined in Method 28, section 8.12.1.
8.5.1 Gas Analysis.
8.5.1.1 If Method 3 is used, collect a minimum of two bag samples simultaneously at a constant sampling rate for the duration of the test run. A minimum sample volume of 30 liters (1.1 ft 3) per bag is recommended.
8.5.1.2 If instrumental gas concentration measurement procedures are used, conduct the gas measurement system performance tests, analyzer calibration, and analyzer calibration error check outlined in Method 6C, sections 8.2.3, 8.2.4, 8.5, and 10.0, respectively. Sample at a constant rate for the duration of the test run.
8.5.2 Data Recording. Record wood heater operational data, test facility temperature, sample train flow rate, and fuel weight data at intervals of no greater than 10 minutes.
8.5.3 Test Run Completion. Same as Method 28, section 8.13.
9.0 Quality Control9.1 Data Validation. The following quality control procedure is suggested to provide a check on the quality of the data.
9.1.1 Calculate a fuel factor, Fo, using Equation 28A-1 in section 12.2.
9.1.2 If CO is present in quantities measurable by this method, adjust the O2 and CO2 values before performing the calculation for Fo as shown in section 12.3 and 12.4.
9.1.3 Compare the calculated Fo factor with the expected Fo range for wood (1.000-1.120). Calculated Fo values beyond this acceptable range should be investigated before accepting the test results. For example, the strength of the solutions in the gas analyzer and the analyzing technique should be checked by sampling and analyzing a known concentration, such as air. If no detectable or correctable measurement error can be identified, the test should be repeated. Alternatively, determine a range of air-to-fuel ratio results that could include the correct value by using an Fo value of 1.05 and calculating a potential range of CO2 and O2 values. Acceptance of such results will be based on whether the calculated range includes the exemption limit and the judgment of the Administrator.
9.2 Method 3 Analyses. Compare the results of the analyses of the two bag samples. If all the gas components (O2, CO, and CO2) values for the two analyses agree within 0.5 percent (e.g., 6.0 percent O2 for bag 1 and 6.5 percent O2 for bag 2, agree within 0.5 percent), the results of the bag analyses may be averaged for the calculations in section 12. If the analysis results do not agree within 0.5 percent for each component, calculate the air-to-fuel ratio using both sets of analyses and report the results.
10.0 Calibration and Standardization [Reserved] 11.0 Analytical Procedures11.1 Method 3 Integrated Bag Samples. Within 4 hours after the sample collection, analyze each bag sample for percent CO2, O2, and CO using an Orsat analyzer as described in Method 3, section 11.0.
11.2 Instrumental Analyzers. Average the percent CO2, CO, and O2 values for the test run.
12.0 Data Analyses and CalculationsCarry out calculations, retaining at least one extra significant figure beyond that of the acquired data. Round off figure after the final calculation. Other forms of the equations may be used as long as they give equivalent results.
12.1 Nomenclature.
Md = Dry molecular weight, g/g-mole (lb/lb-mole). NT = Total gram-moles of dry exhaust gas per kg of wood burned (lb-moles/lb). %CO2 = Percent CO2 by volume (dry basis). %CO = Percent CO by volume (dry basis). %N2 = Percent N2 by volume (dry basis). %O2 = Percent O2 by volume (dry basis). YHC = Assumed mole fraction of HC (dry as CH4) = 0.0088 for catalytic wood heaters; = 0.0132 for noncatalytic wood heaters. = 0.0080 for pellet-fired wood heaters. YCO = Measured mole fraction of CO (e.g., 1 percent CO = .01 mole fraction), g/g-mole (lb/lb-mole). YCO2 = Measured mole fraction of COCO2 (e.g., 10 percent CO2 = .10 mole fraction), g/g-mole (lb/lb-mole). 0.280 = Molecular weight of N2 or CO, divided by 100. 0.320 = Molecular weight of O2 divided by 100. 0.440 = Molecular weight of CO2 divided by 100. 20.9 = Percent O2 by volume in ambient air. 42.5 = Gram-moles of carbon in 1 kg of dry wood assuming 51 percent carbon by weight dry basis (.0425 lb/lb-mole). 510 = Grams of carbon in exhaust gas per kg of wood burned. 1,000 = Grams in 1 kg.12.2 Fuel Factor. Use Equation 28A-1 to calculate the fuel factor.
12. 3 Adjusted %CO2. Use Equation 28A-2 to adjust CO2 values if measurable CO is present.
12.4 Adjusted %O2. Use Equation 28A-3 to adjust O2 value if measurable CO is present.
12.5 Dry Molecular Weight. Use Equation 28A-4 to calculate the dry molecular weight of the stack gas.
Note:The above equation does not consider argon in air (about 0.9 percent, molecular weight of 39.9). A negative error of about 0.4 percent is introduced. Argon may be included in the analysis using procedures subject to approval of the Administrator.
12.6 Dry Moles of Exhaust Gas. Use Equation 28A-5 to calculate the total moles of dry exhaust gas produced per kilogram of dry wood burned.
12.7 Air-to-Fuel Ratio. Use Equation 28A-6 to calculate the air-to-fuel ratio on a dry mass basis.
12.8 Burn Rate. Calculate the fuel burn rate as in Method 28, section 12.4.
13.0 Method Performance [Reserved] 14.0 Pollution Prevention [Reserved] 15.0 Waste Management [Reserved] 16.0 ReferencesSame as section 16.0 of Method 3 and section 17 of Method 5G.
17.0 Tables, Diagrams, Flowcharts, and Validation Data [Reserved] Test Method 28R for Certification and Auditing of Wood Heaters 1.0 Scope and Application1.1 This test method applies to certification and auditing of wood-fired room heaters and fireplace inserts.
1.2 The test method covers the fueling and operating protocol for measuring particulate emissions, as well as determining burn rates, heat output and efficiency.
1.3 Particulate emissions are measured by the dilution tunnel method as specified in ASTM E2515-11 Standard Test Method for Determination of Particulate Matter Emissions Collected in a Dilution Tunnel (IBR, see § 60.17). Upon request, four-inch filters may be used. Upon request, Teflon membrane filters or Teflon-coated glass fiber filters may be used.
2.0 Procedures2.1 This method incorporates the provisions of ASTM E2780-10 (IBR, see § 60.17) except as follows:
2.1.1 The burn rate categories, low burn rate requirement, and weightings in Method 28 shall be used.
2.1.2 The startup procedures shall be the same as in Method 28.
2.1.3 Manufacturers shall not specify a smaller volume of the firebox for testing than the full usable firebox.
2.1.4 Prior to testing, the heater must be operated for a minimum of 50 hours using a medium burn rate. The conditioning may be at the manufacturer's facility prior to the certification test. If the conditioning is at the certification test laboratory, the pre-burn for the first test can be included as part of the conditioning requirement.
2.2 Manufacturers may use ASTM E871-82 (reapproved 2013) (IBR, see § 60.17) as an alternative to the procedures in Method 5H or Method 28 for determining total weight basis moisture in the analysis sample of particulate wood fuel.
Test Method 28WHH for Measurement of Particulate Emissions and Heating Efficiency of Wood-Fired Hydronic Heating Appliances 1.0 Scope and Application1.1 This test method applies to wood-fired hydronic heating appliances. The units typically transfer heat through circulation of a liquid heat exchange media such as water or a water-antifreeze mixture.
1.2 The test method measures particulate emissions and delivered heating efficiency at specified heat output rates based on the appliance's rated heating capacity.
1.3 Particulate emissions are measured by the dilution tunnel method as specified in ASTM E2515-11 Standard Test Method for Determination of Particulate Matter Emissions Collected in a Dilution Tunnel (IBR, see § 60.17). Upon request, four-inch filters may be used. Upon request, Teflon membrane filters or Teflon-coated glass fiber filters may be used. Delivered efficiency is measured by determining the heat output through measurement of the flow rate and temperature change of water circulated through a heat exchanger external to the appliance and determining the input from the mass of dry wood fuel and its higher heating value. Delivered efficiency does not attempt to account for pipeline loss.
1.4 Products covered by this test method include both pressurized and non-pressurized heating appliances intended to be fired with wood. These products are wood-fired hydronic heating appliances that the manufacturer specifies for indoor or outdoor installation. They are often connected to a heat exchanger by insulated pipes and normally include a pump to circulate heated liquid. They are used to heat structures such as homes, barns and greenhouses and can heat domestic hot water, spas or swimming pools.
1.5 Distinguishing features of products covered by this standard include:
1.5.1 Manufacturer specifies for indoor or outdoor installation.
1.5.2 A firebox with an access door for hand loading of fuel.
1.5.3 Typically, an aquastat that controls combustion air supply to maintain the liquid in the appliance within a predetermined temperature range provided sufficient fuel is available in the firebox.
1.5.4 A chimney or vent that exhausts combustion products from the appliance.
1.6 The values stated are to be regarded as the standard whether in I-P or SI units. The values given in parentheses are for information only.
2.0 Summary of Method and References2.1 Particulate matter emissions are measured from a wood-fired hydronic heating appliance burning a prepared test fuel crib in a test facility maintained at a set of prescribed conditions. Procedures for determining burn rates, and particulate emissions rates and for reducing data are provided.
2.2 Referenced Documents
2.2.1 EPA Standards
2.2.1.1 Method 28 Certification and Auditing of Wood Heaters
2.2.2 Other Standards
2.2.2.1 ASTM E2515-11 - Standard Test Method for Determination of Particulate Matter Emissions Collected in a Dilution Tunnel (IBR, see § 60.17).
2.2.2.2 CSA-B415.1-10 Performance Testing of Solid-Fuel-Burning Heating Appliances (IBR, see § 60.17).
3.0 Terminology3.1 Definitions.
3.1.1 Hydronic Heating - A heating system in which a heat source supplies energy to a liquid heat exchange media such as water that is circulated to a heating load and returned to the heat source through pipes.
3.1.2 Aquastat - A control device that opens or closes a circuit to control the rate of fuel consumption in response to the temperature of the heating media in the heating appliance.
3.1.3 Delivered Efficiency - The percentage of heat available in a test fuel charge that is delivered to a simulated heating load as specified in this test method.
3.1.4 Manufacturer's Rated Heat Output Capacity - The value in Btu/hr (MJ/hr) that the manufacturer specifies that a particular model of hydronic heating appliance is capable of supplying at its design capacity as verified by testing, in accordance with Section 13.
3.1.5 Burn Rate - The rate at which test fuel is consumed in an appliance. Measured in pounds (lbs) or kilograms of wood (dry basis) per hour (lb/hr or kg/hr).
3.1.6 Firebox - The chamber in the appliance in which the test fuel charge is placed and combusted.
3.1.7 Test Fuel Charge - The collection of test fuel layers placed in the appliance at the start of the emission test run.
3.1.8 Test Fuel Layer - Horizontal arrangement of test fuel units.
3.1.9 Test Fuel Unit - One or more test fuel pieces with 3/4 inch (19 mm) spacers attached to the bottom and to one side. If composed of multiple test fuel pieces, the bottom spacer may be one continuous piece.
3.1.10 Test Fuel Piece - A single 4 × 4 (4 ±0.25 inches by 4 ±0.25 inches) [100 ±6 mm by 100 ±6 mm] white or red oak wood piece cut to the length required.
3.1.11 Test Run - An individual emission test that encompasses the time required to consume the mass of the test fuel charge.
3.1.12 Overall Efficiency (SLM) - The efficiency for each test run as determined using the CSA B415.1-10 (IBR, see § 60.17) stack loss method.
3.1.13 Thermopile - A device consisting of a number of thermocouples connected in series, used for measuring differential temperature.
4.0 Summary of Test Method4.1 Dilution Tunnel. Emissions are determined using the “dilution tunnel” method specified in ASTM E2515-11 Standard Test Method for Determination of Particulate Matter Emissions Collected in a Dilution Tunnel (IBR, see § 60.17). The flow rate in the dilution tunnel is maintained at a constant level throughout the test cycle and accurately measured. Samples of the dilution tunnel flow stream are extracted at a constant flow rate and drawn through high efficiency filters. The filters are dried and weighed before and after the test to determine the emissions catch and this value is multiplied by the ratio of tunnel flow to filter flow to determine the total particulate emissions produced in the test cycle.
4.2 Efficiency. The efficiency test procedure takes advantage of the fact that this type of appliance delivers heat through circulation of the heated liquid (water) from the appliance to a remote heat exchanger and back to the appliance. Measurements of the water temperature difference as it enters and exits the heat exchanger along with the measured flow rate allow for an accurate determination of the useful heat output of the appliance. The input is determined by weight of the test fuel charge, adjusted for moisture content, multiplied by the higher heating value. Additional measurements of the appliance weight and temperature at the beginning and end of a test cycle are used to correct for heat stored in the appliance. Overall efficiency (SLM) is determined using the CSA B415.1-10 (IBR, see § 60.17) stack loss method for data quality assurance purposes.
4.3 Operation. Appliance operation is conducted on a hot-to-hot test cycle meaning that the appliance is brought to operating temperature and a coal bed is established prior to the addition of the test fuel charge and measurements are made for each test fuel charge cycle. The measurements are made under constant heat draw conditions within predetermined ranges. No attempt is made to modulate the heat demand to simulate an indoor thermostat cycling on and off in response to changes in the indoor environment. Four test categories are used. These are:
4.3.1 Category I: A heat output of 15 percent or less of manufacturer's rated heat output capacity.
4.3.2 Category II: A heat output of 16 percent to 24 percent of manufacturer's rated heat output capacity.
4.3.3 Category III: A heat output of 25 percent to 50 percent of manufacturer's rated heat output capacity.
4.3.4 Category IV: Manufacturer's rated heat output capacity.
5.0 Significance and Use5.1 The measurement of particulate matter emission rates is an important test method widely used in the practice of air pollution control.
5.1.1 These measurements, when approved by state or federal agencies, are often required for the purpose of determining compliance with regulations and statutes.
5.1.2 The measurements made before and after design modifications are necessary to demonstrate the effectiveness of design changes in reducing emissions and make this standard an important tool in manufacturers' research and development programs.
5.2 Measurement of heating efficiency provides a uniform basis for comparison of product performance that is useful to the consumer. It is also required to relate emissions produced to the useful heat production.
5.3 This is a laboratory method and is not intended to be fully representative of all actual field use. It is recognized that users of hand-fired, wood-burning equipment have a great deal of influence over the performance of any wood-burning appliance. Some compromises in realism have been made in the interest of providing a reliable and repeatable test method.
6.0 Test Equipment6.1 Scale. A platform scale capable of weighing the appliance under test and associated parts and accessories when completely filled with water to an accuracy of ±1.0 pound (±0.5 kg).
6.2 Heat Exchanger. A water-to-water heat exchanger capable of dissipating the expected heat output from the system under test.
6.3 Water Temperature Difference Measurement. A Type - T 'special limits' thermopile with a minimum of 5 pairs of junctions shall be used to measure the temperature difference in water entering and leaving the heat exchanger. The temperature difference measurement uncertainty of this type of thermopile is equal to or less than ±0.50 °F (±0.25 °C). Other temperature measurement methods may be used if the temperature difference measurement uncertainty is equal to or less than ±0.50 °F (±0.25 °C).
6.4 Water Flow Meter. A water flow meter shall be installed in the inlet to the load side of the heat exchanger. The flow meter shall have an accuracy of ±1 percent of measured flow.
6.4.1 Optional - Appliance Side Water Flow Meter. A water flow meter with an accuracy of ±1 percent of the flow rate is recommended to monitor supply side water flow rate.
6.5 Optional Recirculation Pump. Circulating pump used during test to prevent stratification of liquid being heated.
6.6 Water Temperature Measurement - Thermocouples or other temperature sensors to measure the water temperature at the inlet and outlet of the load side of the heat exchanger. Must meet the calibration requirements specified in section 10.1.
6.7 Wood Moisture Meter - Calibrated electrical resistance meter capable of measuring test fuel moisture to within 1 percent moisture content. Must meet the calibration requirements specified in section 10.4.
6.8 Flue Gas Temperature Measurement - Must meet the requirements of CSA B415.1-10 (IBR, see § 60.17), clause 6.2.2.
6.9 Test Room Temperature Measurement - Must meet the requirements of CSA B415.1-10 (IBR, see § 60.17), clause 6.2.1.
6.10 Flue Gas Composition Measurement - Must meet the requirements of CSA B415.1-10 (IBR, see § 60.17), clauses 6.3.1 through 6.3.3.
7.0 Safety7.1 These tests involve combustion of wood fuel and substantial release of heat and products of combustion. The heating system also produces large quantities of very hot water and the potential for steam production and system pressurization. Appropriate precautions must be taken to protect personnel from burn hazards and respiration of products of combustion.
8.0 Sampling, Test Specimens and Test Appliances8.1 Test specimens shall be supplied as complete appliances including all controls and accessories necessary for installation in the test facility. A full set of specifications and design and assembly drawings shall be provided when the product is to be placed under certification of a third-party agency. The manufacturer's written installation and operating instructions are to be used as a guide in the set-up and testing of the appliance.
9.0 Preparation of Test Equipment9.1 The appliance is to be placed on a scale capable of weighing the appliance fully loaded with a resolution of ±1.0 lb (0.5 kg).
9.2 The appliance shall be fitted with the type of chimney recommended or provided by the manufacturer and extending to 15 ±0.5 feet (4.6 ±0.15 m) from the upper surface of the scale. If no flue or chimney system is recommended or provided by the manufacturer, connect the appliance to a flue of a diameter equal to the flue outlet of the appliance. The flue section from the appliance flue collar to 8 ±0.5 feet above the scale shall be single wall stove pipe and the remainder of the flue shall be double wall insulated class A chimney.
9.3 Optional Equipment Use
9.3.1 A recirculation pump may be installed between connections at the top and bottom of the appliance to minimize thermal stratification if specified by the manufacturer. The pump shall not be installed in such a way as to change or affect the flow rate between the appliance and the heat exchanger.
9.3.2 If the manufacturer specifies that a thermal control valve or other device be installed and set to control the return water temperature to a specific set point, the valve or other device shall be installed and set per the manufacturer's written instructions.
9.4 Prior to filling the tank, weigh and record the appliance mass.
9.5 Heat Exchanger
9.5.1 Plumb the unit to a water-to-water heat exchanger with sufficient capacity to draw off heat at the maximum rate anticipated. Route hoses, electrical cables, and instrument wires in a manner that does not influence the weighing accuracy of the scale as indicated by placing dead weights on the platform and verifying the scale's accuracy.
9.5.2 Locate thermocouples to measure the water temperature at the inlet and outlet of the load side of the heat exchanger.
9.5.3 Install a thermopile meeting the requirements of section 6.3 to measure the water temperature difference between the inlet and outlet of the load side of the heat exchanger.
9.5.4 Install a calibrated water flow meter in the heat exchanger load side supply line. The water flow meter is to be installed on the cooling water inlet side of the heat exchanger so that it will operate at the temperature at which it is calibrated.
9.5.5 Place the heat exchanger in a box with 2 in. (50 mm) of expanded polystyrene (EPS) foam insulation surrounding it to minimize heat losses from the heat exchanger.
9.5.6 The reported efficiency and heat output rate shall be based on measurements made on the load side of the heat exchanger.
9.5.7 Temperature instrumentation per section 6.6 shall be installed in the appliance outlet and return lines. The average of the outlet and return water temperature on the supply side of the system shall be considered the average appliance temperature for calculation of heat storage in the appliance (TFavg and TIavg). Installation of a water flow meter in the supply side of the system is optional.
9.6 Fill the system with water. Determine the total weight of the water in the appliance when the water is circulating. Verify that the scale indicates a stable weight under operating conditions. Make sure air is purged properly.
10.0 Calibration and Standardization10.1 Water Temperature Sensors. Temperature measuring equipment shall be calibrated before initial use and at least semi-annually thereafter. Calibrations shall be in compliance with National Institute of Standards and Technology (NIST) Monograph 175, Standard Limits of Error.
10.2 Heat Exchanger Load Side Water Flow Meter.
10.2.1 The heat exchanger load side water flow meter shall be calibrated within the flow range used for the test run using NIST traceable methods. Verify the calibration of the water flow meter before and after each test run and at least once during each test run by comparing the water flow rate indicated by the flow meter to the mass of water collected from the outlet of the heat exchanger over a timed interval. Volume of the collected water shall be determined based on the water density calculated from section 13, Eq. 8, using the water temperature measured at the flow meter. The uncertainty in the verification procedure used shall be 1 percent or less. The water flow rate determined by the collection and weighing method shall be within 1 percent of the flow rate indicated by the water flow meter.
10.3 Scales. The scales used to weigh the appliance and test fuel charge shall be calibrated using NIST traceable methods at least once every 6 months.
10.4 Moisture Meter. The moisture meter shall be calibrated per the manufacturer's instructions and checked before each use.
10.5 Flue Gas Analyzers - In accordance with CSA B415.1-10 (IBR, see § 60.17), clause 6.8.
11.0 Conditioning11.1 Prior to testing, the appliance is to be operated for a minimum of 50 hours using a medium heat draw rate. The conditioning may be at the manufacturer's facility prior to the certification test. If the conditioning is at the certification test laboratory, the pre-burn for the first test can be included as part of the conditioning requirement. If conditioning is included in pre-burn, then the appliance shall be aged with fuel meeting the specifications outlined in sections 12.2 with a moisture content between 19 and 25 percent on a dry basis. Operate the appliance at a medium burn rate (Category II or III) for at least 10 hours for noncatalytic appliances and 50 hours for catalytic appliances. Record and report hourly flue gas exit temperature data and the hours of operation. The aging procedure shall be conducted and documented by a testing laboratory.
12.0 Procedure12.1 Appliance Installation. Assemble the appliance and parts in conformance with the manufacturer's written installation instructions. Clean the flue with an appropriately sized, wire chimney brush before each certification test series.
12.2 Fuel. Test fuel charge fuel shall be red (Quercus ruba L.) or white (Quercus alba) oak 19 to 25 percent moisture content on a dry basis. Piece length shall be 80 percent of the firebox depth rounded down to the nearest 1 inch (25mm) increment. For example, if the firebox depth is 46 inches (1168mm) the 4 × 4 piece length would be 36 inches (46 inches × 0.8 = 36.8 inches rounded down to 36 inches). Pieces are to be placed in the firebox parallel to the longest firebox dimension. For fireboxes with sloped surfaces that create a non-uniform firebox length, the piece length shall be adjusted for each layer based on 80 percent of the length at the level where the layer is placed. Pieces are to be spaced 3/4 inches (19 mm) apart on all faces. The first fuel layer may be assembled using fuel units consisting of multiple 4 × 4s consisting of single pieces with bottom and side spacers of 3 or more pieces if needed for a stable layer. The second layer may consist of fuel units consisting of no more than two pieces with spacers attached on the bottom and side. The top two layers of the fuel charge must consist of single pieces unless the fuel charge is only three layers. In that instance only the top layer must consist of single units. Three-quarter inch (19 mm) by 1.5 inch (38 mm) spacers shall be attached to the bottom of piece to maintain a 3/4 inch (19 mm) separation. When a layer consists of two or more units of 4 × 4s an additional 3/4 inch (19 mm) thick by 1.5 inch (38 mm) wide spacer shall be attached to the vertical face of each end of one 4 × 4, such that the 3/4 inch (19 mm) space will be maintained when two 4 × 4 units or pieces are loaded side by side. In cases where a layer contains an odd number of 4 × 4s one piece shall not be attached, but shall have spacers attached in a manner that will provide for the 3/4 inch (19 mm) space to be maintained (See Figure 1). Spacers shall be attached perpendicular to the length of the 4 × 4s such that the edge of the spacer is 1 ± 0.25 inch from the end of the 4 × 4s in the previous layers. Spacers shall be red or white oak and will be attached with either nails (non-galvanized), brads or oak dowels. The use of kiln-dried wood is not allowed.
12.2.1 Using a fuel moisture meter as specified in section 6.7 of the test method, determine the fuel moisture for each test fuel piece used for the test fuel load by averaging at least five fuel moisture meter readings measured parallel to the wood grain. Penetration of the moisture meter insulated electrodes for all readings shall be 1/4 the thickness of the fuel piece or 19 mm ( 3/4 in.), whichever is lesser. One measurement from each of three sides shall be made at approximately 3 inches from each end and the center. Two additional measurements shall be made centered between the other three locations. Each individual moisture content reading shall be in the range of 18 to 28 percent on a dry basis. The average moisture content of each piece of test fuel shall be in the range of 19 to 25 percent. It is not required to measure the moisture content of the spacers. Moisture shall not be added to previously dried fuel pieces except by storage under high humidity conditions and temperature up to 100 °F. Fuel moisture shall be measured within 4 hours of using the fuel for a test.
12.2.2 Firebox Volume. Determine the firebox volume in cubic feet. Firebox volume shall include all areas accessible through the fuel loading door where firewood could reasonably be placed up to the horizontal plane defined by the top of the loading door. A drawing of the firebox showing front, side and plan views or an isometric view with interior dimensions shall be provided by the manufacturer and verified by the laboratory. Calculations for firebox volume from computer aided design (CAD) software programs are acceptable and shall be included in the test report if used. If the firebox volume is calculated by the laboratory the firebox drawings and calculations shall be included in the test report.
12.2.3 Test Fuel Charge. Test fuel charges shall be determined by multiplying the firebox volume by 10 pounds (4.54 kg) per ft 3 (28L), or a higher load density as recommended by the manufacturer's printed operating instructions, of wood (as used wet weight). Select the number of pieces of standard fuel that most nearly match this target weight. This is the standard fuel charge for all tests. For example, if the firebox loading area volume is 10 ft 3 (280L) and the firebox depth is 46 inches (1168 mm), test fuel charge target is 100 lbs (45 kg) minimum and the piece length is 36 inches (914 mm). If eight 4 × 4s, 36 inches long weigh 105 lbs (48 kg), use 8 pieces for each test fuel charge. All test fuel charges will be of the same configuration.
12.3 Sampling Equipment. Prepare the particulate emission sampling equipment as defined by ASTM E2515-11 Standard Test Method for Determination of Particulate Matter Emissions Collected in a Dilution Tunnel (IBR, see § 60.17). Upon request, four-inch filters may be used. Upon request, Teflon membrane filters or Teflon-coated glass fiber filters may be used.
12.4 Appliance Startup. The appliance shall be fired with wood fuel of any species, size and moisture content at the laboratories' discretion to bring it up to operating temperature. Operate the appliance until the water is heated to the upper operating control limit and has cycled at least two times. Then remove all unburned fuel, zero the scale and verify the scales accuracy using dead weights.
12.4.1 Pretest Burn Cycle. Reload appliance with oak wood and allow it to burn down to the specified coal bed weight. The pretest burn cycle fuel charge weight shall be within ±10 percent of the test fuel charge weight. Piece size and length shall be selected such that charcoalization is achieved by the time the fuel charge has burned down to the required coal bed weight. Pieces with a maximum thickness of approximately 2 inches have been found to be suitable. Charcoalization is a general condition of the test fuel bed evidenced by an absence of large pieces of burning wood in the coal bed and the remaining fuel pieces being brittle enough to be broken into smaller charcoal pieces with a metal poker. Manipulations to the fuel bed prior to the start of the test run are to be done to achieve charcoalization while maintaining the desired heat output rate. During the pre-test burn cycle and at least one hour prior to starting the test run, adjust water flow to the heat exchanger to establish the target heat draw for the test. For the first test run the heat draw rate shall be equal to the manufacturer's rated heat output capacity.
12.4.1.1 Allowable Adjustments. Fuel addition or subtractions, and coal bed raking shall be kept to a minimum but are allowed up to 15 minutes prior to the start of the test run. For the purposes of this method, coal bed raking is the use of a metal tool (poker) to stir coals, break burning fuel into smaller pieces, dislodge fuel pieces from positions of poor combustion, and check for the condition of charcoalization. Record all adjustments to and additions or subtractions of fuel, and any other changes to the appliance operations that occur during pretest ignition period. During the 15-minute period prior to the start of the test run, the wood heater loading door shall not be open more than a total of 1 minute. Coal bed raking is the only adjustment allowed during this period.
12.4.2 Coal Bed Weight. The appliance is to be loaded with the test fuel charge when the coal bed weight is between 10 percent and 20 percent of the test fuel charge weight. Coals may be raked as necessary to level the coal bed but may only be raked and stirred once between 15 to 20 minutes prior to the addition of the test fuel charge.
12.5 Test Runs. For all test runs, the return water temperature to the hydronic heater must be equal to or greater than 120 °F. Aquastat or other heater output control device settings that are adjustable shall be set using manufacturer specifications, either as factory set or in accordance with the owner's manual, and shall remain the same for all burn categories.
Complete a test run in each heat output rate category, as follows:
12.5.1 Test Run Start. Once the appliance is operating normally and the pretest coal bed weight has reached the target value per section 12.4.2, tare the scale and load the full test charge into the appliance. Time for loading shall not exceed 5 minutes. The actual weight of the test fuel charge shall be measured and recorded within 30 minutes prior to loading. Start all sampling systems.
12.5.1.1 Record all water temperatures, differential water temperatures and water flow rates at time intervals of one minute or less.
12.5.1.2 Record particulate emissions data per the requirements of ASTM E2515 (IBR, see § 60.17).
12.5.1.3 Record data needed to determine overall efficiency (SLM) per the requirements of CSA B415.1-10 (IBR, see § 60.17), clauses 6.2.1, 6.2.2, 6.3, 8.5.7, 10.4.3 (a), 10.4.3(f), and 13.7.9.3
12.5.1.3.1 Measure and record the test room air temperature in accordance with the requirements of CSA B415.1-10 (IBR, see § 60.17), clauses 6.2.1, 8.5.7 and 10.4.3 (g).
12.5.1.3.2 Measure and record the flue gas temperature in accordance with the requirements of CSA B415.1-10 (IBR, see § 60.17), clauses 6.2.2, 8.5.7 and 10.4.3 (f).
12.5.1.3.3 Determine and record the carbon monoxide (CO) and carbon dioxide (CO2) concentrations in the flue gas in accordance with CSA B415.1-10 (IBR, see § 60.17), clauses 6.3, 8.5.7 and 10.4.3 (i) and (j).
12.5.1.3.4 Measure and record the test fuel weight per the requirements of CSA B415.1-10 (IBR, see § 60.17), clauses 8.5.7 and 10.4.3 (h).
12.5.1.3.5 Record the test run time per the requirements of CSA B415.1-10 (IBR, see § 60.17), clauses 10.4.3 (a).
12.5.1.4 Monitor the average heat output rate on the load side of the heat exchanger. If the heat output rate gets close to the upper or lower limit of the target range (±5 percent) adjust the water flow through the heat exchanger to compensate. Make changes as infrequently as possible while maintaining the target heat output rate. The first test run shall be conducted at the Category IV heat output rate to validate that the appliance is capable of producing the manufacturer's rated heat output capacity.
12.5.2 Test Fuel Charge Adjustment. It is acceptable to adjust the test fuel charge (i.e., reposition) once during a test run if more than 60 percent of the initial test fuel charge weight has been consumed and more than 10 minutes have elapsed without a measurable (1 lb or 0. 5 kg) weight change while the operating control is in the demand mode. The time used to make this adjustment shall be less than 60 seconds.
12.5.3 Test Run Completion. The test run is completed when the remaining weight of the test fuel charge is 0.0 lb (0.0 kg). End the test run when the scale has indicated a test fuel charge weight of 0.0 lb (0.0 kg) or less for 30 seconds.
12.5.3.1 At the end of the test run, stop the particulate sampling train and overall efficiency (SLM) measurements, and record the run time, and all final measurement values.
12.5.4 Heat Output Capacity Validation. The first test run must produce a heat output rate that is within 10 percent of the manufacturer's rated heat output capacity (Category IV) throughout the test run and an average heat output rate within 5 percent of the manufacturer's rated heat output capacity. If the appliance is not capable of producing a heat output within these limits, the manufacturer's rated heat output capacity is considered not validated and testing is to be terminated. In such cases, the tests may be restarted using a lower heat output capacity if requested by the manufacturer.
12.5.5 Additional Test Runs. Using the manufacturer's rated heat output capacity as a basis, conduct a test for additional heat output categories as specified in section 4.3. It is not required to run these tests in any particular order.
12.5.6 Alternative Heat Output Rate for Category I. If an appliance cannot be operated in the Category I heat output range due to stopped combustion, two test runs shall be conducted at heat output rates within Category II, provided that the completed test run burn rate is no greater than the burn rate expected in home use. If this rate cannot be achieved, the test is not valid.
When the alternative heat output rate is used, the weightings for the weighted averages indicated in Table 2 shall be the average of the Category I and II weightings and shall be applied to both Category II results. The two completed runs in Category II will be deemed to meet the requirement for runs completed in both Category I and Category II. Appliances that are not capable of operation within Category II (<25 percent of maximum) cannot be evaluated by this test method. The test report must include full documentation and discussion of the attempted runs, completed rums and calculations.
12.5.6.1 Stopped Fuel Combustion. Evidence that an appliance cannot be operated at a Category I heat output rate due to stopped fuel combustion shall include documentation of two or more attempts to operate the appliance in burn rate Category I and fuel combustion has stopped prior to complete consumption of the test fuel charge. Stopped fuel combustion is evidenced when an elapsed time of 60 minutes or more has occurred without a measurable (1 lb or 0.5 kg) weight change in the test fuel charge while the appliance operating control is in the demand mode. Report the evidence and the reasoning used to determine that a test in burn rate Category I cannot be achieved. For example, two unsuccessful attempts to operate at an output rate of 10 percent of the rated output capacity are not sufficient evidence that burn rate Category I cannot be achieved. Note that section 12.5.6 requires that the completed test run burn rate can be no greater than the burn rate expected in home use. If this rate cannot be achieved, the test is not valid.
12.5.7 Appliance Overheating. Appliances shall be capable of operating in all heat output categories without overheating to be rated by this test method. Appliance overheating occurs when the rate of heat withdrawal from the appliance is lower than the rate of heat production when the unit control is in the idle mode. This condition results in the water in the appliance continuing to increase in temperature well above the upper limit setting of the operating control. Evidence of overheating includes: 1 hour or more of appliance water temperature increase above the upper temperature set-point of the operating control, exceeding the temperature limit of a safety control device (independent from the operating control), boiling water in a non-pressurized system or activation of a pressure or temperature relief valve in a pressurized system.
12.6 Additional Test Runs. The testing laboratory may conduct more than one test run in each of the heat output categories specified in section 4.3.1. If more than one test run is conducted at a specified heat output rate, the results from at least two-thirds of the test runs in that heat output rate category shall be used in calculating the weighted average emission rate (See section 14.1.14). The measurement data and results of all test runs shall be reported regardless of which values are used in calculating the weighted average emission rate.
13.0 Calculation of Results 13.1 Nomenclature ET - Total particulate emissions for the full test run as determined per ASTM E2515-11 (IBR, see § 60.17) in grams Eg/MJ - Emissions rate in grams per megajoule of heat output Elb/mmBtu output - Emissions rate in pounds per million Btu of heat output Eg/kg - Emissions factor in grams per kilogram of dry fuel burned Eg/hr - Emissions factor in grams per hour HHV - Higher heating value of fuel = 8600 Btu/lb (19.990 MJ/kg) LHV - Lower heating value of fuel = 7988 Btu/lb (18.567 MJ/kg) ΔT - Temperature difference between water entering and exiting the heat exchanger Qout - Total heat output in BTU's (megajoules) Qin - Total heat input available in test fuel charge in BTU (megajoules) M - Mass flow rate of water in lb/min (kg/min) Vi - Volume of water indicated by a totalizing flow meter at the ith reading in gallons (liters) Vf - Volumetric flow rate of water in heat exchange system in gallons per minute (liters/min) Θ - Total length of test run in hours ti - Data sampling interval in minutes ηdel - Delivered heating efficiency in percent Fi - Weighting factor for heat output category i (See Table 2) T1 - Temperature of water at the inlet on the supply side of the heat exchanger T2 - Temperature of the water at the outlet on the supply side of the heat exchanger T3 - Temperature of water at the inlet to the load side of the heat exchanger TIavg - Average temperature of the appliance and water at start of the test

13.2 After the test is completed, determine the particulate emissions ET in accordance with ASTM E2515-11 (IBR, see § 60.17).
13.3 Determine Average Fuel Load Moisture Content


The subscript (i) indicates the parameter value for sampling time interval ti.
Mi = Mass flow rate = gal/min × density of water (lb/gal) = lb/min




Vi is the total water volume at the end of interval i and Vi-1 is the total water volume at the beginning of the time interval. This calculation is necessary when a totalizing type water meter is used.
13.5.2 Determine heat output rate as:
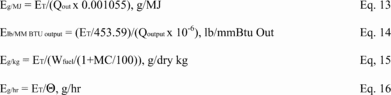

For determination of the average overall thermal efficiency (ηSLM) for the test run, use the data collected over the full test run and the calculations in accordance with CSA B415.1-10 (IBR, see § 60.17), clause 13.7 except for 13.7.2 (e), (f), (g), and (h), use the following average fuel properties for oak: percent C = 50.0, percent H = 6.6, percent O = 43.2, percent ash = 0.2 percent. The averaging period for determination of efficiency by the stack loss method allows averaging over 10 minute time periods for flue gas temperature, flue gas CO2, and flue gas CO for the determination of the efficiency. However, under some cycling conditions the “on” period may be short relative to this 10 minute period. For this reason, during cycling operation the averaging period for these parameters may not be longer than the burner on period divided by 10. The averaging period need not be shorter than one minute. During the off period, under cycling operation, the averaging periods specified may be used. Where short averaging times are used, however, the averaging period for fuel consumption may still be at 10 minutes. This average wood consumption rate shall be applied to all of the smaller time intervals included.
13.5.5.1 Whenever the CSA B415.1-10 (IBR, see § 60.17) overall efficiency is found to be lower than the overall efficiency based on load side measurements, as determined by Eq. 16 of this method, section 14.1.7 of the test report must include a discussion of the reasons for this result.
13.6 Weighted Average Emissions and Efficiency13.6.1 Determine the weighted average emission rate and delivered efficiency from the individual tests in the specified heat output categories. The weighting factors (Fi) are derived from an analysis of ASHRAE bin data which provides details of normal building heating requirements in terms of percent of design capacity and time in a particular capacity range - or “bin” - over the course of a heating season. The values used in this method represent an average of data from several cities located in the northern United States.

13.7 Average Heat Output (Qout-8hr) and Efficiency ((ηavg-8hr) for 8 hour burn time.
13.7.1 Units tested under this standard typically require infrequent fuelling, 8 to 12 hours intervals being typical. Rating unit's based on an average output sustainable over an 8 hour duration will assist consumers in appropriately sizing units to match the theoretical heat demand of their application.
13.7.2 Calculations:

13.7.2.1 Determine the test durations and actual load for each category as recorded in Table 1A.
13.7.2.2 Determine the data point that has the nearest duration greater than 8 hrs.
X1 = Actual load, Y1 = Test duration, and ηdel1 = Average delivered efficiency for this data point13.7.2.3 Determine the data point that has the nearest duration less than 8 hours.
X2 = Actual load, Y2 = Test duration, and ηdel2 = Average delivered efficiency for this data point13.7.2.4 Example:
Category Actual Load Duration
[Category Actual Load Duration ηdel]
(Btu/Hr) | (Hr) | (%) |
---|---|---|
1 15,000 | 10.2 | 70.0 |
2 26,000 | 8.4 | 75.5 |
3 50,000 | 6.4 | 80.1 |
4 100,000 | 4.7 | 80.9 |
Category 2 duration is just above 8 hours, therefore: X1 = 26,000 Btu/hr, ηdel1 = 75.5% and Y1 = 8.4 hrs
Category 3 duration is just below 8 hours, therefore: X2 = 50,000 Btu/hr, ηdel2 = 80.1% and Y2 = 6.4 hrs
Qout-8hr = 26,000 + {(8 - 8.4) × [(50,000 - 26,000)/(6.4 - 8.4)]} = 30,800 BTU/hr ηavg-8hr = 75.5 + {(8 - 8.4) × [(80.1 - 75.5)/(6.4 - 8.4)]} = 76.4% 13.8 Carbon Monoxide EmissionsFor each minute of the test period, the carbon monoxide emission rate shall be calculated as:

Total CO emissions for each of the three test periods (CO_1, CO_2, CO_3) shall be calculated as the sum of the emission rates for each of the 1 minute intervals.
Total CO emission for the test run, COT, shall be calculated as the sum of CO_1, CO_2, and CO_3.
14.0 Report14.1.1 The report shall include the following.
14.1.2 Name and location of the laboratory conducting the test.
14.1.3 A description of the appliance tested and its condition, date of receipt and dates of tests.
14.1.4 A statement that the test results apply only to the specific appliance tested.
14.1.5 A statement that the test report shall not be reproduced except in full, without the written approval of the laboratory.
14.1.6 A description of the test procedures and test equipment including a schematic or other drawing showing the location of all required test equipment. Also, a description of test fuel sourcing, handling and storage practices shall be included.
14.1.7 Details of deviations from, additions to or exclusions from the test method, and their data quality implications on the test results (if any), as well as information on specific test conditions, such as environmental conditions.
14.1.8 A list of participants and observers present for the tests.
14.1.9 Data and drawings indicating the fire box size and location of the fuel charge.
14.1.10 Drawings and calculations used to determine firebox volume.
14.1.11 Information for each test run fuel charge including piece size, moisture content, and weight.
14.1.12 All required data for each test run shall be provided in spreadsheet format. Formulae used for all calculations shall be accessible for review.
14.1.13 Test run duration for each test.
14.1.14 Calculated results for delivered efficiency at each burn rate and the weighted average emissions reported as total emissions in grams, pounds per mm Btu of delivered heat, grams per MJ of delivered heat, grams per kilogram of dry fuel and grams per hour. Results shall be reported for each heat output category and the weighted average.
14.1.15 Tables 1A, 1B, 1C and Table 2 must be used for presentation of results in test reports.
14.1.16 A statement of the estimated uncertainty of measurement of the emissions and efficiency test results.
14.1.17 Raw data, calibration records, and other relevant documentation shall be retained by the laboratory for a minimum of 7 years.
15.0 Precision and Bias15.1 Precision - It is not possible to specify the precision of the procedure in Method 28WHH because the appliance operation and fueling protocols and the appliances themselves produce variable amounts of emissions and cannot be used to determine reproducibility or repeatability of this measurement method.
15.2 Bias - No definitive information can be presented on the bias of the procedure in Method 28WHH for measuring solid fuel burning hydronic heater emissions because no material having an accepted reference value is available.
16.0 Keywords16.1 Solid fuel, hydronic heating appliances, wood-burning hydronic heaters.
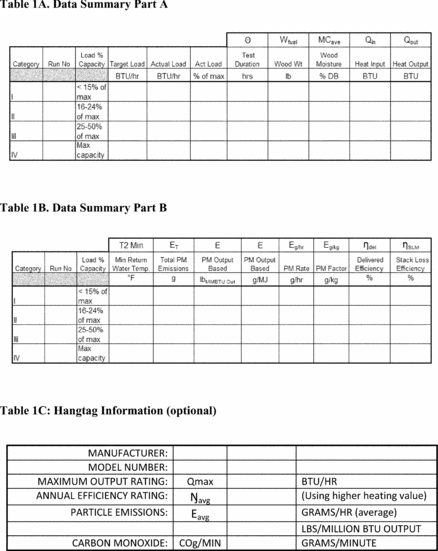
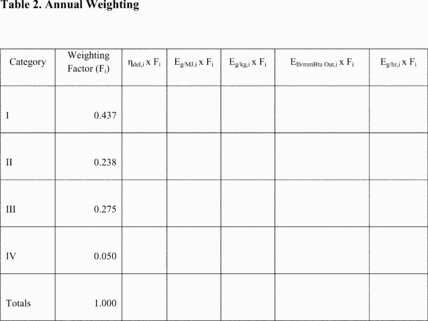
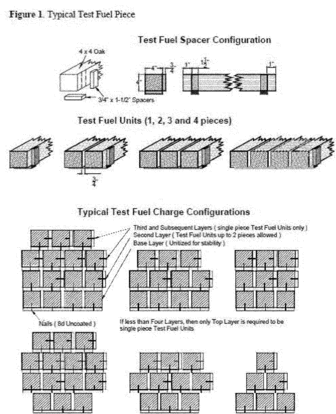
1.1 This test method applies to wood-fired hydronic heating appliances with heat storage external to the appliance. The units typically transfer heat through circulation of a liquid heat exchange media such as water or a water-antifreeze mixture. Throughout this document, the term “water” will be used to denote any of the heat transfer liquids approved for use by the manufacturer.
1.2 The test method measures PM and CO emissions and delivered heating efficiency at specified heat output rates referenced against the appliance's rated heating capacity as specified by the manufacturer and verified under this test method.
1.3 PM emissions are measured by the dilution tunnel method as specified in the EPA Method 28WHH and the standards referenced therein with the exceptions noted in section 12.5.9. Delivered efficiency is measured by determining the fuel energy input and appliance output. Heat output is determined through measurement of the flow rate and temperature change of water circulated through a heat exchanger external to the appliance and the increase in energy of the external storage. Heat input is determined from the mass of dry wood fuel and its higher heating value (HHV). Delivered efficiency does not attempt to account for pipeline loss.
1.4 Products covered by this test method include both pressurized and non-pressurized hydronic heating appliances intended to be fired with wood and for which the manufacturer specifies for indoor or outdoor installation. The system, which includes the heating appliance and external storage, is commonly connected to a heat exchanger by insulated pipes and normally includes a pump to circulate heated liquid. These systems are used to heat structures such as homes, barns and greenhouses. They also provide heat for domestic hot water, spas and swimming pools.
1.5 Distinguishing features of products covered by this standard include:
1.5.1 The manufacturer specifies the application for either indoor or outdoor installation.
1.5.2 A firebox with an access door for hand loading of fuel.
1.5.3 Typically an aquastat mounted as part of the appliance that controls combustion air supply to maintain the liquid in the appliance within a predetermined temperature range provided sufficient fuel is available in the firebox. The appliance may be equipped with other devices to control combustion.
1.5.4 A chimney or vent that exhausts combustion products from the appliance.
1.5.5 A liquid storage system, typically water, which is not large enough to accept all of the heat produced when a full load of wood is burned and the storage system starts a burn cycle at 125 °F.
1.5.6 The heating appliances require external thermal storage and these units will only be installed as part of a system which includes thermal storage. The manufacturer specifies the minimum amount of thermal storage required. However, the storage system shall be large enough to ensure that the boiler (heater) does not cycle, slumber, or go into an off-mode when operated in a Category III load condition (See section 4.3).
1.6 The values stated are to be regarded as the standard whether in I-P or SI units. The values given in parentheses are for information only.
2.0 Summary of Method and References2.1 PM and CO emissions are measured from a wood-fired hydronic heating appliance burning a prepared test fuel charge in a test facility maintained at a set of prescribed conditions. Procedures for determining heat output rates, PM and CO emissions, and efficiency and for reducing data are provided.
2.2 Referenced Documents2.2.1 EPA Standards
2.2.1.1 Method 28 Certification and Auditing of Wood Heaters
2.2.1.2 Method 28WHH Measurement of Particulate Emissions and Heating Efficiency of Wood-Fired Hydronic Heating Appliances and the Standards Referenced therein.
2.2.2 Other Standards
2.2.2.1 CSA-B415.1-10 Performance Testing of Solid-Fuel-Burning Heating Appliances
3.0 Terminology 3.1 Definitions3.1.1 Hydronic Heating - A heating system in which a heat source supplies energy to a liquid heat exchange media such as water that is circulated to a heating load and returned to the heat source through pipes.
3.1.2 Aquastat - A control device that opens or closes a circuit to control the rate of fuel consumption in response to the temperature of the heating media in the heating appliance.
3.1.3 Delivered Efficiency - The percentage of heat available in a test fuel charge that is delivered to a simulated heating load or the storage system as specified in this test method.
3.1.4 Emission Factor - The emission of a pollutant expressed in mass per unit of energy (typically) output from the boiler/heater.
3.1.5 Emission Index - The emission of a pollutant expressed in mass per unit mass of fuel used.
3.1.6 Emission Rate - The emission of a pollutant expressed in mass per unit time
3.1.7 Manufacturer's Rated Heat Output Capacity - The value in Btu/hr (MJ/hr) that the manufacturer specifies that a particular model of hydronic heating appliance is capable of supplying at its design capacity as verified by testing, in accordance with section 12.5.4.
3.1.8 Heat Output Rate - The average rate of energy output from the appliance during a specific test period in Btu/hr (MJ/hr).
3.1.9 Firebox - The chamber in the appliance in which the test fuel charge is placed and combusted.
3.1.10 NIST - National Institute of Standards and Technology.
3.1.11 Test Fuel Charge - The collection of test fuel placed in the appliance at the start of the emission test run.
3.1.12 Test Run - An individual emission test which encompasses the time required to consume the mass of the test fuel charge. The time of the test run also considers the time for the energy to be drawn from the thermal storage.
3.1.13 Test Run Under “Cold-to-Cold” Condition - Under this test condition the test fuel is added into an empty chamber along with kindling and ignition materials (paper). The boiler/heater at the start of this test is typically 125° to 130 °F.
3.1.14 Test Run Under “Hot-to-Hot” Condition - Under this test condition the test fuel is added onto a still-burning bed of charcoals produced in a pre-burn period. The boiler/heater water is near its operating control limit at the start of the test.
3.1.15 Overall Efficiency, also known as Stack Loss Efficiency - The efficiency for each test run as determined using the CSA B415.1-10 (IBR, see § 60.17) stack loss method (SLM).
3.1.16 Phases of a Burn Cycle - The “startup phase” is defined as the period from the start of the test until 15 percent of the test fuel charge is consumed. The “steady-state phase” is defined as the period from the end of the startup phase to a point at which 80 percent of the test fuel charge is consumed. The “end phase” is defined as the time from the end of the steady-state period to the end of the test.
3.1.17 Thermopile - A device consisting of a number of thermocouples connected in series, used for measuring differential temperature.
3.1.18 Slumber Mode - This is a mode in which the temperature of the water in the boiler/heater has exceeded the operating control limit and the control has changed the boiler/heater fan speed, dampers, and/or other operating parameters to minimize the heat output of the boiler/heater.
4.0 Summary of Test Method4.1 Dilution Tunnel. Emissions are determined using the “dilution tunnel” method specified in EPA Method 28WHH and the standards referenced therein. The flow rate in the dilution tunnel is maintained at a constant level throughout the test cycle and accurately measured. Samples of the dilution tunnel flow stream are extracted at a constant flow rate and drawn through high efficiency filters. The filters are dried and weighed before and after the test to determine the emissions collected and this value is multiplied by the ratio of tunnel flow to filter flow to determine the total particulate emissions produced in the test cycle.
4.2 Efficiency. The efficiency test procedure takes advantage of the fact that this type of system delivers heat through circulation of the heated liquid (water) from the system to a remote heat exchanger (e.g. baseboard radiators in a room) and back to the system. Measurements of the cooling water temperature difference as it enters and exits the test system heat exchanger along with the measured flow rate allow for an accurate determination of the useful heat output of the appliance. Also included in the heat output is the change in the energy content in the storage system during a test run. Energy input to the appliance during the test run is determined by weight of the test fuel charge, adjusted for moisture content, multiplied by the higher heating value. Additional measurements of the appliance weight and temperature at the beginning and end of a test cycle are used to correct for heat stored in the appliance. Overall efficiency (SLM) is determined using the CSA B415.1-10 (IBR, see § 60.17) stack loss method for data quality assurance purposes.
4.3 Operation. Four test categories are defined for use in this method. These are:
4.3.1 Category I: A heat output of 15 percent or less of manufacturer's rated heat output capacity.
4.3.2 Category II: A heat output of 16 percent to 24 percent of manufacturer's rated heat output capacity.
4.3.3 Category III: A heat output of 25 percent to 50 percent of manufacturer's rated heat output capacity.
4.3.4 Category IV: Manufacturer's Rated Heat Output Capacity. These heat output categories refer to the output from the system by way of the load heat exchanger installed for the test. The output from just the boiler/heater part of the system may be higher for all or part of a test, as part of this boiler/heater output goes to storage.
For the Category III and IV runs, appliance operation is conducted on a hot-to-hot test cycle meaning that the appliance is brought to operating temperature and a coal bed is established prior to the addition of the test fuel charge and measurements are made for each test fuel charge cycle. The measurements are made under constant heat draw conditions within pre-determined ranges. No attempt is made to modulate the heat demand to simulate an indoor thermostat cycling on and off in response to changes in the indoor environment.
For the Category I and II runs, the unit is tested with a “cold start.” At the manufacturer's option, the Category II and III runs may be waived and it may be assumed that the particulate emission values and efficiency values determined in the startup, steady-state, and end phases of Category I are applicable in Categories II and III for the purpose of determining the annual averages in lb/mmBtu and g/MJ (See section 13). For the annual average in g/hr, the length of time for stored heat to be drawn from thermal storage shall be determined for the test load requirements of the respective category.
All test operations and measurements shall be conducted by personnel of the laboratory responsible for the submission of the test report.
5.0 Significance and Use5.1 The measurement of particulate matter emission and CO rates is an important test method widely used in the practice of air pollution control.
5.1.1 These measurements, when approved by state or federal agencies, are often required for the purpose of determining compliance with regulations and statutes.
5.1.2 The measurements made before and after design modifications are necessary to demonstrate the effectiveness of design changes in reducing emissions and make this standard an important tool in manufacturers' research and development programs.
5.2 Measurement of heating efficiency provides a uniform basis for comparison of product performance that is useful to the consumer. It is also required to relate emissions produced to the useful heat production.
5.3 This is a laboratory method and is not intended to be fully representative of all actual field use. It is recognized that users of hand-fired, wood-burning equipment have a great deal of influence over the performance of any wood-burning appliance. Some compromises in realism have been made in the interest of providing a reliable and repeatable test method.
6.0 Test Equipment6.1 Scale. A platform scale capable of weighing the boiler/heater under test and associated parts and accessories when completely filled with water to an accuracy of ±1.0 pound (±0.5 kg) and a readout resolution of ±0.2 pound (±0.1 kg).
6.2 Heat Exchanger. A water-to-water heat exchanger capable of dissipating the expected heat output from the system under test.
6.3 Water Temperature Difference Measurement. A Type - T 'special limits' thermopile with a minimum of 5 pairs of junctions shall be used to measure the temperature difference in water entering and leaving the heat exchanger. The temperature difference measurement uncertainty of this type of thermopile is equal to or less than ±0.50 °F (±0.25 °C). Other temperature measurement methods may be used if the temperature difference measurement uncertainty is equal to or less than ±0.50 °F (±0.25 °C). This measurement uncertainty shall include the temperature sensor, sensor well arrangement, piping arrangements, lead wire, and measurement/recording system. The response time of the temperature measurement system shall be less than half of the time interval at which temperature measurements are recorded.
6.4 Water Flow Meter. A water flow meter shall be installed in the inlet to the load side of the heat exchanger. The flow meter shall have an accuracy of ±1 percent of measured flow.
6.4.1 Optional - Appliance Side Water Flow Meter. A water flow meter with an accuracy of ±1 percent of the flow rate is recommended to monitor supply side water flow rate.
6.5 Optional Recirculation Pump. Circulating pump used during test to prevent stratification, in the boiler/heater, of liquid being heated.
6.6 Water Temperature Measurement. Thermocouples or other temperature sensors to measure the water temperature at the inlet and outlet of the load side of the heat exchanger must meet the calibration requirements specified in 10.1 of this method.
6.7 Lab Scale. For measuring the moisture content of wood slices as part of the overall wood moisture determination. Accuracy of ±0.01 pounds.
6.8 Flue Gas Temperature Measurement. Must meet the requirements of CSA B415.1-10 (IBR, see § 60.17), clause 6.2.2.
6.9 Test Room Temperature Measurement. Must meet the requirements of CSA B415.1-10 (IBR, see § 60.17), clause 6.2.1.
6.10 Flue Gas Composition Measurement. Must meet the requirements of CSA B415.1-10 (IBR, see § 60.17), clauses 6.3.1 through 6.3.3.
6.11 Dilution Tunnel CO Measurement. In parallel with the flue gas composition measurements, the CO concentration in the dilution tunnel shall also be measured and reported at time intervals not to exceed one minute. This analyzer shall meet the zero and span drift requirements of CSA B415.1-10 (IBR, see § 60.17). In addition the measurement repeatability shall be better than ±15 ppm over the range of CO levels observed in the dilution tunnel.
7.0 Safety7.1 These tests involve combustion of wood fuel and substantial release of heat and products of combustion. The heating system also produces large quantities of very hot water and the potential for steam production and system pressurization. Appropriate precautions must be taken to protect personnel from burn hazards and respiration of products of combustion.
8.0 Sampling, Test Specimens and Test Appliances8.1 Test specimens shall be supplied as complete appliances, as described in marketing materials, including all controls and accessories necessary for installation in the test facility. A full set of specifications, installation and operating instructions, and design and assembly drawings shall be provided when the product is to be placed under certification of a third-party agency. The manufacturer's written installation and operating instructions are to be used as a guide in the set-up and testing of the appliance and shall be part of the test record.
8.2 The size, connection arrangement, and control arrangement for the thermal storage shall be as specified in the manufacturer's documentation. It is not necessary to use the specific storage system that the boiler/heater will be marketed with. However, the capacity of the system used in the test cannot be greater than that specified as the minimum allowable for the boiler/heater.
8.3 All system control settings shall be the as-shipped, default settings. These default settings shall be the same as those communicated in a document to the installer or end user. These control settings and the documentation of the control settings as to be provided to the installer or end user shall be part of the test record.
8.4 Where the manufacturer defines several alternatives for the connection and loading arrangement, one shall be defined in the appliance documentation as the default or standard installation. It is expected that this will be the configuration for use with a simple baseboard heating system. This is the configuration to be followed for these tests. The manufacturer's documentation shall define the other arrangements as optional or alternative arrangements.
9.0 Preparation of Test Equipment9.1 The appliance is to be placed on a scale capable of weighing the appliance fully loaded with a resolution of ±0.2 lb (0.1 kg).
9.2 The appliance shall be fitted with the type of chimney recommended or provided by the manufacturer and extending to 15 ±0.5 feet (4.6 ±0.15 m) from the upper surface of the scale. If no flue or chimney system is recommended or provided by the manufacturer, connect the appliance to a flue of a diameter equal to the flue outlet of the appliance. The flue section from the appliance flue collar to 8 ±0.5 feet above the scale shall be single wall stove pipe and the remainder of the flue shall be double wall insulated class A chimney.
9.3 Optional Equipment Use
9.3.1 A recirculation pump may be installed between connections at the top and bottom of the appliance to minimize thermal stratification if specified by the manufacturer. The pump shall not be installed in such a way as to change or affect the flow rate between the appliance and the heat exchanger.
9.3.2 If the manufacturer specifies that a thermal control valve or other device be installed and set to control the return water temperature to a specific set point, the valve or other device shall be installed and set per the manufacturer's written instructions.
9.4 Prior to filling the boiler/heater with water, weigh and record the appliance mass.
9.5 Heat Exchanger
9.5.1 Plumb the unit to a water-to-water heat exchanger with sufficient capacity to draw off heat at the maximum rate anticipated. Route hoses and electrical cables and instrument wires in a manner that does not influence the weighing accuracy of the scale as indicated by placing dead weights on the platform and verifying the scale's accuracy.
9.5.2 Locate thermocouples to measure the water temperature at the inlet and outlet of the load side of the heat exchanger.
9.5.3 Install a thermopile (or equivalent instrumentation) meeting the requirements of section 6.3 to measure the water temperature difference between the inlet and outlet of the load side of the heat exchanger
9.5.4 Install a calibrated water flow meter in the heat exchanger load side supply line. The water flow meter is to be installed on the cooling water inlet side of the heat exchanger so that it will operate at the temperature at which it is calibrated.
9.5.5 Place the heat exchanger in a box with 2 in. (50 mm) of expanded polystyrene (EPS) foam insulation surrounding it to minimize heat losses from the heat exchanger.
9.5.6 The reported efficiency and heat output rate shall be based on measurements made on the load side of the heat exchanger.
9.5.7 Temperature instrumentation per section 6.6 shall be installed in the appliance outlet and return lines. The average of the outlet and return water temperature on the supply side of the system shall be considered the average appliance temperature for calculation of heat storage in the appliance (TFavg and TIavg). Installation of a water flow meter in the supply side of the system is optional.
9.6 Storage Tank. The storage tank shall include a destratification pump as illustrated in Figure 1. The pump will draw from the bottom of the tank and return to the top as illustrated. Temperature sensors (TS1 and TS2 in Figure 1) shall be included to measure the temperature in the recirculation loop. The valve plan in Figure 1 allows the tank recirculation loop to operate and the boiler/heater-to-heat exchanger loop to operate at the same time but in isolation. This would typically be done before the start of a test or following completion of a test to determine the end of test average tank temperature. The nominal flow rate in the storage tank recirculation loop can be estimated based on pump manufacturers' performance curves and any significant restriction in the recirculation loop.
9.7 Fill the system with water. Determine the total weight of the water in the appliance when the water is circulating. Verify that the scale indicates a stable weight under operating conditions. Make sure air is purged properly.
10.0 Calibration and Standardization10.1 Water Temperature Sensors. Temperature measuring equipment shall be calibrated before initial use and at least semi-annually thereafter. Calibrations shall be in compliance with National Institute of Standards and Technology (NIST) Monograph 175, Standard Limits of Error.
10.2 Heat Exchanger Load Side Water Flow Meter.
10.2.1 The heat exchanger load side water flow meter shall be calibrated within the flow range used for the test run using NIST-traceable methods. Verify the calibration of the water flow meter before and after each test run and at least once during each test run by comparing the water flow rate indicated by the flow meter to the mass of water collected from the outlet of the heat exchanger over a timed interval. Volume of the collected water shall be determined based on the water density calculated from section 13, Eq. 12, using the water temperature measured at the flow meter. The uncertainty in the verification procedure used shall be 1 percent or less. The water flow rate determined by the collection and weighing method shall be within 1 percent of the flow rate indicated by the water flow meter.
10.3 Scales. The scales used to weigh the appliance and test fuel charge shall be calibrated using NIST-traceable methods at least once every 6 months.
10.4 Flue Gas Analyzers - In accordance with CSA B415.1-10 (IBR, see § 60.17), clause 6.8.
11.0 Conditioning11.1 Prior to testing, an appliance is to be operated for a minimum of 50 hours using a medium heat draw rate. The conditioning may be at the manufacturer's facility prior to the certification test. If the conditioning is at the certification test laboratory, the pre-burn for the first test can be included as part of the conditioning requirement. If conditioning is included in pre-burn, then the appliance shall be aged with fuel meeting the specifications outlined in section 12.2 with a moisture content between 19 and 25 percent on a dry basis. Operate the appliance at a medium heat output rate (Category II or III) for at least 10 hours for non-catalytic appliances and 50 hours for catalytic appliances. Record and report hourly flue gas exit temperature data and the hours of operation. The aging procedure shall be conducted and documented by a testing laboratory.
12.0 Procedure12.1 Appliance Installation. Assemble the appliance and parts in conformance with the manufacturer's written installation instructions. Clean the flue with an appropriately sized, wire chimney brush before each certification test series.
12.2 Fuel. Test fuel charge fuel shall be red (Quercus ruba L.) or white (Quercus Alba) oak 19 to 25 percent moisture content on a dry basis. Piece length shall be 80 percent of the firebox depth rounded down to the nearest 1 inch (25mm) increment. For example, if the firebox depth is 46 inches (1168mm) the piece length would be 36 inches (46 inches × 0.8 = 36.8 inches, rounded down to 36 inches). Pieces are to be placed in the firebox parallel to the longest firebox dimension. For fireboxes with sloped surfaces that create a non-uniform firebox length, the piece length shall be adjusted for each layer based on 80 percent of the length at the level where the layer is placed. The test fuel shall be cord wood with cross section dimensions and weight limits as defined in CSA B415.1-10 (IBR, see § 60.17), section 8.3, Table 4. The use of dimensional lumber is not allowed.
12.2.1 Select three pieces of cord wood from the same batch of wood as the test fuel and the same weight as the average weight of the pieces in the test load ±1.0 lb. From each of these three pieces, cut three slices. Each slice shall be 1/2 inch to 3/4 inch thick. One slice shall be cut across the center of the length of the piece. The other two slices shall be cut half way between the center and the end. Immediately measure the mass of each piece in pounds. Dry each slice in an oven at 220 °F for 24 hours or until no further weight change occurs. The slices shall be arranged in the oven so as to provide separation between faces. Remove from the oven and measure the mass of each piece again as soon as practical, in pounds.
The moisture content of each slice, on a dry basis, shall be calculated as:

The average moisture content of the entire test load (MC) shall be determined using Eq. 6. Each individual slice shall have a moisture content in the range of 18 percent to 28 percent on a dry basis. The average moisture content for the test fuel load shall be in the range of 19 percent to 25 percent. Moisture shall not be added to previously dried fuel pieces except by storage under high humidity conditions and temperature up to 100 °F. Fuel moisture measurement shall begin within 4 hours of using the fuel batch for a test. Use of a pin-type meter to estimate the moisture content prior to a test is recommended.
12.2.2 Firebox Volume. Determine the firebox volume in cubic feet. Firebox volume shall include all areas accessible through the fuel loading door where firewood could reasonably be placed up to the horizontal plane defined by the top of the loading door. A drawing of the firebox showing front, side and plan views or an isometric view with interior dimensions shall be provided by the manufacturer and verified by the laboratory. Calculations for firebox volume from computer aided design (CAD) software programs are acceptable and shall be included in the test report if used. If the firebox volume is calculated by the laboratory the firebox drawings and calculations shall be included in the test report.
12.2.3 Test Fuel charge. Test fuel charges shall be determined by multiplying the firebox volume by 10 pounds (4.54 kg) per ft 3 (28L), or a higher load density as recommended by the manufacturer's printed operating instructions, of wood (as used wet weight). Select the number of pieces of cord wood that most nearly match this target weight. However, the test fuel charge cannot be less than the target of 10 pounds (4.54 kg) per ft 3 (28L).
12.3 Sampling Equipment. Prepare the particulate emission sampling equipment as defined by EPA Method 28WHH and the standards referenced therein.
12.4 Appliance Startup. The appliance shall be fired with wood fuel of any species, size and moisture content, at the laboratory's discretion, to bring it up to operating temperature. Operate the appliance until the water is heated to the upper operating control limit and has cycled at least two times. Then remove all unburned fuel, zero the scale and verify the scales accuracy using dead weights.
12.4.1 Startup Procedure for Category III and IV Test Runs, “Hot-to-Hot.”
12.4.1.1 Pretest t Burn Cycle. Following appliance startup (section 12.4), reload appliance with oak cord wood and allow it to burn down to the specified coal bed weight. The pre-test burn cycle fuel charge weight shall be within ±10 percent of the test fuel charge weight. Piece size and length shall be selected such that charcoalization is achieved by the time the fuel charge has burned down to the required coal bed weight. Pieces with a maximum thickness of approximately 2 inches have been found to be suitable. Charcoalization is a general condition of the test fuel bed evidenced by an absence of large pieces of burning wood in the coal bed and the remaining fuel pieces being brittle enough to be broken into smaller charcoal pieces with a metal poker. Manipulations to the fuel bed prior to the start of the test run are to be done to achieve charcoalization while maintaining the desired heat output rate. During the pre-test burn cycle and at least one hour prior to starting the test run, adjust water flow to the heat exchanger to establish the target heat draw for the test. For the first test run the heat draw rate shall be equal to the manufacturer's rated heat output capacity.
12.4.1.2 Allowable Adjustments. Fuel addition or subtractions, and coal bed raking shall be kept to a minimum but are allowed up to 15 minutes prior to the start of the test run. For the purposes of this method, coal bed raking is the use of a metal tool (poker) to stir coals, break burning fuel into smaller pieces, dislodge fuel pieces from positions of poor combustion, and check for the condition of charcoalization. Record all adjustments to and additions or subtractions of fuel, and any other changes to the appliance operations that occur during pretest ignition period. During the 15-minute period prior to the start of the test run, the wood heater loading door shall not be open more than a total of 1 minute. Coal bed raking is the only adjustment allowed during this period.
12.4.1.3 Coal Bed Weight. The appliance is to be loaded with the test fuel charge when the coal bed weight is between 10 percent and 20 percent of the test fuel charge weight. Coals may be raked as necessary to level the coal bed but may only be raked and stirred once between 15 to 20 minutes prior to the addition of the test fuel charge.
12.4.1.4 Storage. The Category III and IV test runs may be done either with or without the thermal storage. If thermal storage is used, the initial temperature of the storage must be 125 °F or greater at the start of the test. The storage may be heated during the pre-test burn cycle or it may be heated by external means. If thermal storage is used, prior to the start of the test run, the storage tank destratification pump, shown in Figure 1, shall be operated until the total volume pumped exceeds 1.5 times the tank volume and the difference between the temperature at the top and bottom of the storage tank (TS1 and TS2) is less than 1 °F. These two temperatures shall then be recorded to determine the starting average tank temperature. The total volume pumped may be based on the nominal flow rate of the destratification pump (See section 9.6). If the Category III and IV runs are done with storage, it is recognized that during the last hour of the pre-burn cycle the storage tank must be mixed to achieve a uniform starting temperature and cannot receive heat from the boiler/heater during this time. During this time period, the boiler/heater might cycle or go into a steady reduced output mode. (Note - this would happen, for example, in a Category IV run if the actual maximum output of the boiler/heater exceed the manufacturer's rated output.) A second storage tank may be used temporarily to enable the boiler/heater to operate during this last hour of the pre-burn period as it will during the test period. The temperature of this second storage tank is not used in the calculations but the return water to the boiler/heater (after mixing device if used) must be 125 °F or greater.
12.4.2 Startup Procedure for Category I and II Test Runs, “Cold-to-Cold.”
12.4.2.1 Initial Temperatures. This test shall be started with both the boiler/heater and the storage at a minimum temperature of 125 °F. The boiler/heater maximum temperature at the start of this test shall be 135 °F. The boiler/heater and storage may be heated through a pre-burn or it may be heated by external means.
12.4.2.2 Firebox Condition at Test Start. Prior to the start of this test remove all ash and charcoal from the combustion chamber(s). The loading of the test fuel and kindling should follow the manufacturer's recommendations, subject to the following constraints: Up to 10 percent kindling and paper may be used which is in addition to the fuel load. Further, up to 10 percent of the fuel load (i.e., included in the 10 lb/ft 3) may be smaller than the main fuel. This startup fuel shall still be larger than 2 inches.
12.4.2.3 Storage. The Category I and II test runs shall be done with thermal storage. The initial temperature of the storage must be 125 °F or greater at the start of the test. The storage may be heated during the pre-test burn cycle or it may be heated by external means. Prior to the start of the test run, the storage tank destratification pump, shown in Figure 1, shall be operated until the total volume pumped exceeds 1.5 times the tank volume and the difference between the temperature at the top and bottom of the storage tank (TS1 and TS2) is less than 1 °F. These two temperatures shall then be recorded to determine the starting average tank temperature. The total volume pumped may be based on the nominal flow rate of the destratification pump (See section 9.6).
12.5 Test Runs. For all test runs, the return water temperature to the hydronic heater must be equal to or greater than 120 °F (this is lower than the initial tank temperature to allow for any pipeline losses). Where the storage system is used, flow of water from the boiler/heater shall be divided between the storage tank and the heat exchanger such that the temperature change of the circulating water across the heat exchanger shall be 30 ±5 °F, averaged over the entire test run. This is typically adjusted using the system valves.
Complete a test run in each heat output rate category, as follows:
12.5.1 Test Run Start. For Category III and IV runs: Once the appliance is operating normally and the pretest coal bed weight has reached the target value per section 12.4.1, tare the scale and load the full test charge into the appliance. Time for loading shall not exceed 5 minutes. The actual weight of the test fuel charge shall be measured and recorded within 30 minutes prior to loading. Start all sampling systems.
For Category I and II runs: Once the appliance has reached the starting temperature, tare the scale and load the full test charge, including kindling into the appliance. The actual weight of the test fuel charge shall be measured and recorded within 30 minutes prior to loading. Light the fire following the manufacturer's written normal startup procedure. Start all sampling systems.
12.5.1.1 Record all water temperatures, differential water temperatures and water flow rates at time intervals of one minute or less.
12.5.1.2 Record particulate emissions data per the requirements of EPA Method 28WHH and the standards referenced therein.
12.5.1.3 Record data needed to determine overall efficiency (SLM) per the requirements of CSA B415.1-10 (IBR, see § 60.17) clauses 6.2.1, 6.2.2, 6.3, 8.5.7, 10.4.3(a), 10.4.3(f), and 13.7.9.3
12.5.1.3.1 Measure and record the test room air temperature in accordance with the requirements of CSA B415.1-10 (IBR, see § 60.17), clauses 6.2.1, 8.5.7 and 10.4.3(g).
12.5.1.3.2 Measure and record the flue gas temperature in accordance with the requirements of CSA B415.1-10 (IBR, see § 60.17), clauses 6.2.2, 8.5.7 and 10.4.3(f).
12.5.1.3.3 Determine and record the carbon monoxide (CO) and carbon dioxide (CO2) concentrations in the flue gas in accordance with CSA B415.1-10 (IBR, see § 60.17), clauses 6.3, 8.5.7 and 10.4.3(i) and (j).
12.5.1.3.4 Measure and record the test fuel weight per the requirements of CSA B415.1-10 (IBR, see § 60.17), clauses 8.5.7 and 10.4.3(h).
12.5.1.3.5 Record the test run time per the requirements of CSA B415.1-10 (IBR, see § 60.17), clause 10.4.3(a).
12.5.1.3.6 Record and document all settings and adjustments, if any, made to the boiler/heater as recommended/required by manufacturer's instruction manual for different combustion conditions or heat loads. These may include temperature setpoints, under and over-fire air adjustment, or other adjustments that could be made by an operator to optimize or alter combustion. All such settings shall be included in the report for each test run.
12.5.1.4 Monitor the average heat output rate on the load side of the heat exchanger based on water temperatures and flow. If the heat output rate over a 10 minute averaging period gets close to the upper or lower limit of the target range (±5 percent), adjust the water flow through the heat exchanger to compensate. Make changes as infrequently as possible while maintaining the target heat output rate. The first test run shall be conducted at the Category IV heat output rate to validate that the appliance is capable of producing the manufacturer's rated heat output capacity.
12.5.2 Test Fuel Charge Adjustment. It is acceptable to adjust the test fuel charge (i.e., reposition) once during a test run if more than 60 percent of the initial test fuel charge weight has been consumed and more than 10 minutes have elapsed without a measurable (1 lb or 0.5 kg) weight change while the operating control is in the demand mode. The time used to make this adjustment shall be less than 60 seconds.
12.5.3 Test Run Completion. For the Category III and IV, “hot-to-hot” test runs, the test run is completed when the remaining weight of the test fuel charge is 0.0 lb (0.0 kg). (WFuelBurned = Wfuel) End the test run when the scale has indicated a test fuel charge weight of 0.0 lb (0.0 kg) or less for 30 seconds.
For the Category I and II “cold-to-cold” test runs, the test run is completed; and the end of a test is defined at the first occurrence of any one of the following:
(a) The remaining weight of the test fuel charge is less than 1 percent of the total test fuel weight (WFuelBurned > 0.99 · Wfuel);
(b) The automatic control system on the boiler/heater switches to an off mode. In this case, the boiler/heater fan (if used) is typically stopped and all air flow dampers are closed by the control system. Note that this off mode cannot be an “overheat” or emergency shutdown which typically requires a manual reset; or
(c) If the boiler/heater does not have an automatic off mode: After 90 percent of the fuel load has been consumed and the scale has indicated a rate of change of the test fuel charge of less than 1.0 lb/hr for a period of 10 minutes or longer. Note - this is not considered “stopped fuel combustion,” See section 12.5.6.1.
12.5.3.1 At the end of the test run, stop the particulate sampling train and overall efficiency (SLM) measurements, and record the run time, and all final measurement values.
12.5.3.2 At the end of the test run, continue to operate the storage tank destratification pump until the total volume pumped exceeds 1.5 times the tank volume. The maximum average of the top and bottom temperatures measured after this time may be taken as the average tank temperature at the end of the tests (TFSavg, See section 13.1). The total volume pumped may be based on the nominal flow rate of the destratification pump (See section 9.6).
12.5.3.3 For the Category I and II test runs, there is a need to determine the energy content of the unburned fuel remaining in the chamber if the remaining mass in the chamber is greater than 1 percent of the test fuel weight. Following the completion of the test, as soon as safely practical, this remaining fuel is removed from the chamber, separated from the remaining ash and weighed. This separation could be implemented with a slotted “scoop” or similar tool. A 1/4 inch opening size in the separation tool shall be used to separate the ash and charcoal. This separated char is assigned a heating value of 12,500 Btu/lb.
12.5.4 Heat Output Capacity Validation. The first test run must produce a heat output rate that is within 10 percent of the manufacturer's rated heat output capacity (Category IV) throughout the test run and an average heat output rate within 5 percent of the manufacturer's rated heat output capacity. If the appliance is not capable of producing a heat output within these limits, the manufacturer's rated heat output capacity is considered not validated and testing is to be terminated. In such cases, the tests may be restarted using a lower heat output capacity if requested by the manufacturer. Alternatively, during the Category IV run, if the rated output cannot be maintained for a 15 minute interval, the manufacturer may elect to reduce the rated output to match the test and complete the Category IV run on this basis. The target outputs for Categories I, II, and III shall then be recalculated based on this change in rated output capacity.
12.5.5 Additional Test Runs. Using the manufacturer's rated heat output capacity as a basis, conduct a test for additional heat output categories as specified in section 4.3. It is not required to run these tests in any particular order.
12.5.6 Alternative Heat Output Rate for Category I. If an appliance cannot be operated in the Category I heat output range due to stopped combustion, two test runs shall be conducted at heat output rates within Category II. When this is the case, the weightings for the weighted averages indicated in section 14.1.15 shall be the average of the Category I and II weighting's and shall be applied to both Category II results. Appliances that are not capable of operation within Category II (<25 percent of maximum) cannot be evaluated by this test method.
12.5.6.1 Stopped Fuel Combustion. Evidence that an appliance cannot be operated at a Category I heat output rate due to stopped fuel combustion shall include documentation of two or more attempts to operate the appliance in heat output rate Category I and fuel combustion has stopped prior to complete consumption of the test fuel charge. Stopped fuel combustion is evidenced when an elapsed time of 60 minutes or more has occurred without a measurable (1 lb or 0.5 kg) weight change in the test fuel charge while the appliance operating control is in the demand mode. Report the evidence and the reasoning used to determine that a test in heat output rate Category I cannot be achieved. For example, two unsuccessful attempts to operate at an output rate of 10 percent of the rated output capacity are not sufficient evidence that heat output rate Category I cannot be achieved.
12.5.7 Appliance Overheating. Appliances with their associated thermal storage shall be capable of operating in all heat output categories without overheating to be rated by this test method. Appliance overheating occurs when the rate of heat withdrawal from the appliance is lower than the rate of heat production when the unit control is in the idle mode. This condition results in the water in the appliance continuing to increase in temperature well above the upper limit setting of the operating control. Evidence of overheating includes: 1 hour or more of appliance water temperature increase above the upper temperature set-point of the operating control, exceeding the temperature limit of a safety control device (independent from the operating control - typically requires manual reset), boiling water in a non-pressurized system or activation of a pressure or temperature relief valve in a pressurized system.
12.5.8 Option to Eliminate Tests in Category II and III. Following successful completion of a test run in Category I, the manufacturer may eliminate the Category II and III tests. For the purpose of calculating the annual averages for particulates and efficiency, the values obtained in the Category I run shall be assumed to apply also to Category II and Category III. It is envisioned that this option would be applicable to systems which have sufficient thermal storage such that the fuel load in the Category I test can be completely consumed without the system reaching its upper operating temperature limit. In this case, the boiler/heater would likely be operating at maximum thermal output during the entire test and this output rate may be higher than the manufacturer's rated heat output capacity. The Category II and III runs would then be the same as the Category I run. It may be assumed that the particulate emission values and efficiency values determined in the startup, steady-state, and end phases of Category I are applicable in Categories II and III, for the purpose of determining the annual averages in lb/mmBtu and g/MJ (See section 13). For the annual average in g/hr, the length of time for stored heat to be drawn from thermal storage shall be determined for the test load requirements of the respective category.
12.5.9 Modification to Measurement Procedure in EPA Method 28WHH to Determine Emissions Separately During the Startup, Steady-State and End Phases. With one of the two particulate sampling trains used, filter changes shall be made at the end of the startup phase and the steady-state phase (See section 3.0). This shall be done to determine the particulate emission rate and particulate emission index for the startup, steady-state, and end phases individually. For this one train, the particulates measured during each of these three phases shall be added together to also determine the particulate emissions for the whole run.
12.5.10 Modification to Measurement Procedure in EPA Method 28WHH and the Standards Referenced therein on Averaging Period for Determination of Efficiency by the Stack Loss Method. The methods currently defined in Method 28WHH allow averaging over 10-minute time periods for flue gas temperature, flue gas CO2, and flue gas CO for the determination of the efficiency with the stack loss method. However, under some cycling conditions the “on” period may be short relative to this 10-minute period. For this reason, during cycling operation the averaging period for these parameters may not be longer than the burner on period divided by 10. The averaging period need not be shorter than one minute. During the off period, under cycling operation, averaging periods as specified in EPA Method 28WHH and the standards referenced therein, may be used. Where short averaging times are used, however, the averaging period for fuel consumption may still be at 10 minutes. This average wood consumption rate shall be applied to all of the smaller time intervals included.
12.6 Additional Test Runs. The testing laboratory may conduct more than one test run in each of the heat output categories specified in section 4.3. If more than one test run is conducted at a specified heat output rate, the results from at least two-thirds of the test runs in that heat output rate category shall be used in calculating the weighted average emission rate. The measurement data and results of all test runs shall be reported regardless of which values are used in calculating the weighted average emission rate.
13.0 Calculation of Results 13.1 Nomenclature COs - Carbon monoxide measured in the dilution tunnel at arbitrary time in ppm dry basis. COg/min - Carbon monoxide emission rate in g/min. COT - Total carbon monoxide emission for the full test run in grams. CO_1 - Startup period carbon monoxide emissions in grams. CO_2 - Steady-state period carbon monoxide emission in grams. CO_3 - End period carbon monoxide emission in grams. ET - Total particulate emissions for the full test run as determined per EPA Method 28WHH and the standards referenced therein in grams. E1 - Startup period particulate emissions in grams. E2 - Steady-state period particulate emissions in grams. E3 - End period particulate emissions in grams. E1_g/kg - Startup period particulate emission index in grams per kg fuel. E2_g/kg - Steady-state period particulate emission index in grams per kg fuel. E3_g/kg - End period particulate emission index in grams per kg fuel. E1_g/hr - Startup period particulate emission rate in grams per hour. E2_g/hr - Steady-state period particulate emission rate in grams per hour. E3_g/hr - End period particulate emission rate in grams per hour. Eg/MJ - Emission rate in grams per MJ of heat output. Elb/mmBtu output - Emissions rate in pounds per million Btu of heat output. Eg/kg - Emissions factor in grams per kilogram of dry fuel burned. Eg/hr - Emission factor in grams per hour. HHV - Higher heating value of fuel = 8600 Btu/lb (19.990 MJ/kg). LHV - Lower heating value of fuel = 7988 Btu/lb (18.567 MJ/kg). ΔT - Temperature difference between cooling water entering and exiting the heat exchanger. Qout - Total heat output in Btu (MJ). Qin - Total heat input available in test fuel charge in Btu's (MJ). Qstd - Volumetric flow rate in dilution tunnel in dscfm. M - Mass flow rate of water in lb/min (kg/min). Vi - Volume of water indicated by a totalizing flow meter at the ith reading in gallons (liters). Vf - Volumetric flow rate of water in heat exchange system in gallons per minute (liters/min). Θ - Total length of burn period in hours (Θ1 + Θ2 + Θ3). Θ1 - Length of time of the startup period in hours. Θ2 - Length of time of the steady-state period in hours. Θ3 - Length of time of the end period in hours. Θ4 - Length of time for stored heat to be used following a burn period in hours. ti - Data sampling interval in minutes. ηdel - Delivered heating efficiency in percent. Fi - Weighting factor for heat output category i. (See Table 2.) T1 - Temperature of water at the inlet on the supply side of the heat exchanger, °F. T2 - Temperature of the water at the outlet on the supply side of the heat exchanger, °F. T3 - Temperature of cooling water at the inlet to the load side of the heat exchanger, °F. T4 - Temperature of cooling water at the outlet of the load side of the heat exchanger, °F. T5 - Temperature of the hot water supply as it leaves the boiler/heater, °F. T6 - Temperature of return water as it enters the boiler/heater, °F. T7 - Temperature in the boiler/heater optional destratification loop at the top of the boiler/heater, °F. T8 - Temperature in the boiler/heater optional destratification loop at the bottom of the boiler/heater, °F. TIavg - Average temperature of the appliance and water at start of the test.



13.2 After the test is completed, determine the particulate emissions ET in accordance with EPA Method 28WHH and the standards referenced therein.
13.3 Determination of the weight of fuel that has been burned at an arbitrary time.
For the purpose of tracking the consumption of the test fuel load during a test run the following may be used to calculate the weight of fuel that burned since the start of the test:



13.5.1 Correction to Qin for the Category I and II tests, where there is greater than 1 percent of the test fuel charge in the chamber at the end of the test period.

13.6 Determine Heat Output, Efficiency, and Emissions.
13.6.1 Determine heat output as:
Qout = Σ [Heat output determined for each sampling time interval] + Change in heat stored in the appliance + Change in heat in storage tank.

The subscript (i) indicates the parameter value for sampling time interval ti.Mi = Mass flow rate = gal/min × density of water (lb/gal) = lb/min.


Vi is the total water volume at the end of interval i and Vi-1 is the total water volume at the beginning of the time interval. This calculation is necessary when a totalizing type water meter is used.
13.6.2 Determine Heat Output Rate Over Burn Period (Θ1 + Θ2 + Θ3) as:

13.6.3 Determine Emission Rates and Emission Factors as:
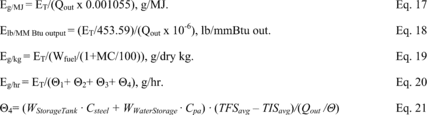
If thermal storage is not used in a Category III or IV run, then Θ4 = 0.
E1_g/kg = E1/(Wfuel_1/(1 + MC/100)), g/dry kg.
E2_g/kg = E2/(Wfuel_2/(1 + MC/100)), g/dry kg.
E3_g/kg = E3/(Wfuel_3/(1 + MC/100)), g/dry kg.
E1_g/hr = E1/Θ1, g/hr.
E2_g/hr = E2/Θ2, g/hr.
E3_g/hr = E3/Θ3, g/hr.
13.6.4 Determine delivered efficiency as:

13.6.5 Determine ηSLM - Overall Efficiency, also known as Stack Loss Efficiency, using stack loss method (SLM).
For determination of the average overall thermal efficiency (ηSLM) for the test run, use the data collected over the full test run and the calculations in accordance with CSA B415.1-10 (IBR, see § 60.17), clause 13.7 except for 13.7.2(e), (f), (g), and (h), use the following average fuel properties for oak: %C = 50.0, %H = 6.6, %O = 43.2, %Ash = 0.2.
13.6.5.1 Whenever the CSA B415.1-10 (IBR, see § 60.17) overall efficiency is found to be lower than the overall efficiency based on load side measurements, as determined by Eq. 22 of this method, section 14.1.7 of the test report must include a discussion of the reasons for this result. For a test where the CSA B415.1-10 overall efficiency SLM is less than 2 percentage points lower than the overall efficiency based on load side measurements, the efficiency based on load side measurements shall be considered invalid. [Note on the rationale for the 2 percentage points limit. The SLM method does not include boiler/heater jacket losses and, for this reason, should provide an efficiency which is actually higher than the efficiency based on the energy input and output measurements or “delivered efficiency.” A delivered efficiency that is higher than the efficiency based on the SLM could be considered suspect. A delivered efficiency greater than 2 percentage points higher than the efficiency based on the SLM, then, clearly indicates a measurement error.]
13.6.6 Carbon Monoxide Emissions
For each minute of the test period, the carbon monoxide emission rate shall be calculated as:

Total CO emissions for each of the three test periods (CO_1, CO_2, CO_3) shall be calculated as the sum of the emission rates for each of the 1-minute intervals. Total CO emission for the test run, COT, shall be calculated as the sum of CO_1, CO_2, and CO_3.
13.7 Weighted Average Emissions and Efficiency.
13.7.1 Determine the weighted average emission rate and delivered efficiency from the individual tests in the specified heat output categories. The weighting factors (Fi) are derived from an analysis of ASHRAE bin data which provides details of normal building heating requirements in terms of percent of design capacity and time in a particular capacity range - or “bin” - over the course of a heating season. The values used in this method represent an average of data from several cities located in the northern United States.

If, as discussed in section 12.5.8, the option to eliminate tests in Category II and III is elected, the values of efficiency and particulate emission rate as measured in Category I, shall be assigned also to Category II and III for the purpose of determining the annual averages.
14.0 Report14.1.1 The report shall include the following:
14.1.2 Name and location of the laboratory conducting the test.
14.1.3 A description of the appliance tested and its condition, date of receipt and dates of tests.
14.1.4 A description of the minimum amount of external thermal storage that is required for use with this system. This shall be specified both in terms of volume in gallons and stored energy content in Btu with a storage temperature ranging from 125 °F to the manufacturer's specified setpoint temperature.
14.1.5 A statement that the test results apply only to the specific appliance tested.
14.1.6 A statement that the test report shall not be reproduced except in full, without the written approval of the laboratory.
14.1.7 A description of the test procedures and test equipment including a schematic or other drawing showing the location of all required test equipment. Also, a description of test fuel sourcing, handling and storage practices shall be included.
14.1.8 Details of deviations from, additions to or exclusions from the test method, and their data quality implications on the test results (if any), as well as information on specific test conditions, such as environmental conditions.
14.1.9 A list of participants and their roles and observers present for the tests.
14.1.10 Data and drawings indicating the fire box size and location of the fuel charge.
14.1.11 Drawings and calculations used to determine firebox volume.
14.1.12 Information for each test run fuel charge including piece size, moisture content and weight.
14.1.13 All required data and applicable blanks for each test run shall be provided in spreadsheet format both in the printed report and in a computer file such that the data can be easily analyzed and calculations easily verified. Formulas used for all calculations shall be accessible for review.
14.1.14 For each test run, Θ1,Θ2, Θ3, the total CO and particulate emission for each of these three periods, and Θ4.
14.1.15 Calculated results for delivered efficiency at each heat output rate and the weighted average emissions reported as total emissions in grams, pounds per mm Btu of delivered heat, grams per MJ of delivered heat, grams per kilogram of dry fuel and grams per hour. Results shall be reported for each heat output category and the weighted average.
14.1.16 Tables 1A, 1B, 1C, 1D, 1E and Table 2 must be used for presentation of results in test reports.
14.1.17 A statement of the estimated uncertainty of measurement of the emissions and efficiency test results.
14.1.18 A plot of CO emission rate in grams/minute vs. time, based on 1 minute averages, for the entire test period, for each run.
14.1.19 A plot of estimated boiler/heater energy release rate in Btu/hr based on 10 minute averages, for the entire test period, for each run. This will be calculated from the fuel used, the wood heating value and moisture content, and the SLM efficiency during each 10 minute period.
14.1.20 Raw data, calibration records, and other relevant documentation shall be retained by the laboratory for a minimum of 7 years.
15.0 Precision and Bias15.1 Precision - It is not possible to specify the precision of the procedure in this test method because the appliance operation and fueling protocols and the appliances themselves produce variable amounts of emissions and cannot be used to determine reproducibility or repeatability of this test method.
15.2 Bias - No definitive information can be presented on the bias of the procedure in this test method for measuring solid fuel burning hydronic heater emissions because no material having an accepted reference value is available.
16.0 Keywords16.1 Solid fuel, hydronic heating appliances, wood-burning hydronic heaters, partial thermal storage.
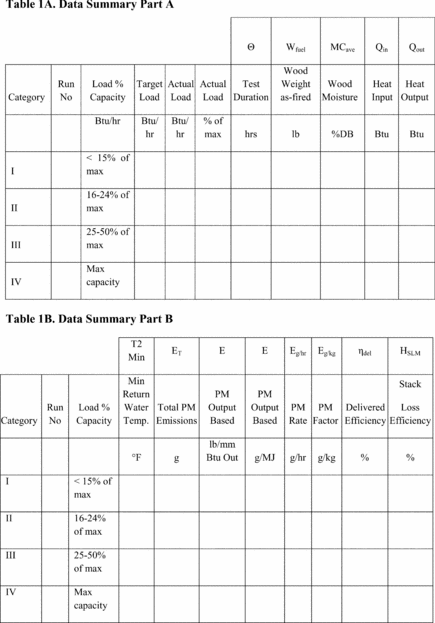
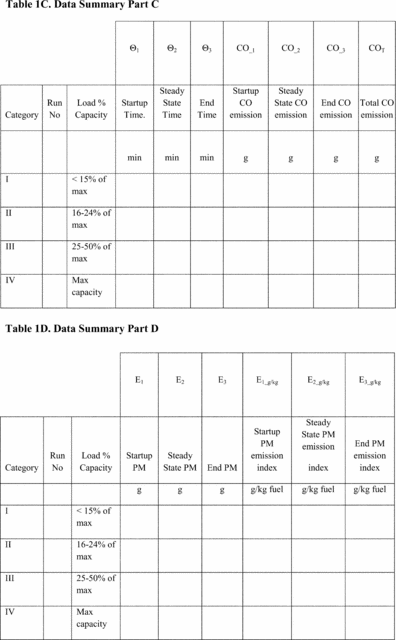
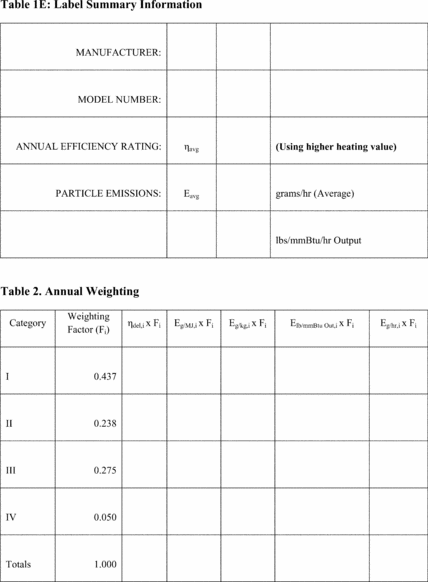
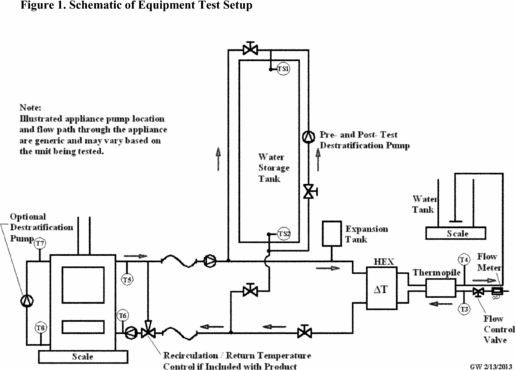
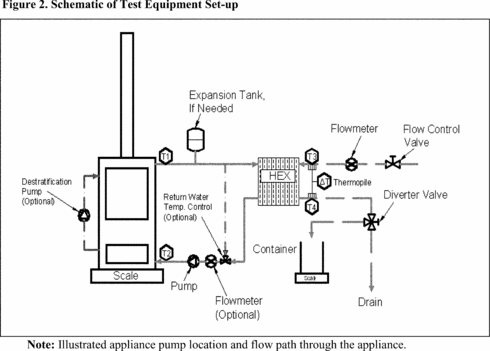
This method does not include all of the specifications (e.g., equipment and supplies) and procedures (e.g., sampling and analytical) essential to its performance. Some material is incorporated by reference from other methods in this part. Therefore, to obtain reliable results, persons using this method should have a thorough knowledge of at least the following additional test methods: Method 5 and Method 12.
1.0 Scope and Application1.1 Analytes.
Analyte | CAS No. |
---|---|
Antimony (Sb) | 7440-36-0 |
Arsenic (As) | 7440-38-2 |
Barium (Ba) | 7440-39-3 |
Beryllium (Be) | 7440-41-7 |
Cadmium (Cd) | 7440-43-9 |
Chromium (Cr) | 7440-47-3 |
Cobalt (Co) | 7440-48-4 |
Copper (Cu) | 7440-50-8 |
Lead (Pb) | 7439-92-1 |
Manganese (Mn) | 7439-96-5 |
Mercury (Hg) | 7439-97-6 |
Nickel (Ni) | 7440-02-0 |
Phosphorus (P) | 7723-14-0 |
Selenium (Se) | 7782-49-2 |
Silver (Ag) | 7440-22-4 |
Thallium (Tl) | 7440-28-0 |
Zinc (Zn) | 7440-66-6 |
1.2 Applicability. This method is applicable to the determination of metals emissions from stationary sources. This method may be used to determine particulate emissions in addition to the metals emissions if the prescribed procedures and precautions are followed.
1.2.1 Hg emissions can be measured, alternatively, using EPA Method 101A of Appendix B, 40 CFR Part 61. Method 101-A measures only Hg but it can be of special interest to sources which need to measure both Hg and Mn emissions.
2.0 Summary of Method2.1 Principle. A stack sample is withdrawn isokinetically from the source, particulate emissions are collected in the probe and on a heated filter, and gaseous emissions are then collected in an aqueous acidic solution of hydrogen peroxide (analyzed for all metals including Hg) and an aqueous acidic solution of potassium permanganate (analyzed only for Hg). The recovered samples are digested, and appropriate fractions are analyzed for Hg by cold vapor atomic absorption spectroscopy (CVAAS) and for Sb, As, Ba, Be, Cd, Cr, Co, Cu, Pb, Mn, Ni, P, Se, Ag, Tl, and Zn by inductively coupled argon plasma emission spectroscopy (ICAP) or atomic absorption spectroscopy (AAS). Graphite furnace atomic absorption spectroscopy (GFAAS) is used for analysis of Sb, As, Cd, Co, Pb, Se, and Tl if these elements require greater analytical sensitivity than can be obtained by ICAP. If one so chooses, AAS may be used for analysis of all listed metals if the resulting in-stack method detection limits meet the goal of the testing program. Similarly, inductively coupled plasma-mass spectroscopy (ICP-MS) may be used for analysis of Sb, As, Ba, Be, Cd, Cr, Co, Cu, Pb, Mn, Ni, Ag, Tl and Zn.
3.0 Definitions [Reserved] 4.0 Interferences4.1 Iron (Fe) can be a spectral interference during the analysis of As, Cr, and Cd by ICAP. Aluminum (Al) can be a spectral interference during the analysis of As and Pb by ICAP. Generally, these interferences can be reduced by diluting the analytical sample, but such dilution raises the in-stack detection limits. Background and overlap corrections may be used to adjust for spectral interferences. Refer to Method 6010 of Reference 2 in section 16.0 or the other analytical methods used for details on potential interferences to this method. For all GFAAS analyses, use matrix modifiers to limit interferences, and matrix match all standards.
5.0 Safety5.1 Disclaimer. This method may involve hazardous materials, operations, and equipment. This test method may not address all of the safety problems associated with its use. It is the responsibility of the user of this test method to establish appropriate safety and health practices and to determine the applicability of regulatory limitations prior to performing this test method.
5.2 Corrosive Reagents. The following reagents are hazardous. Personal protective equipment and safe procedures are useful in preventing chemical splashes. If contact occurs, immediately flush with copious amounts of water at least 15 minutes. Remove clothing under shower and decontaminate. Treat residual chemical burn as thermal burn.
5.2.1 Nitric Acid (HNO3). Highly corrosive to eyes, skin, nose, and lungs. Vapors cause bronchitis, pneumonia, or edema of lungs. Reaction to inhalation may be delayed as long as 30 hours and still be fatal. Provide ventilation to limit exposure. Strong oxidizer. Hazardous reaction may occur with organic materials such as solvents.
5.2.2 Sulfuric Acid (H2SO4). Rapidly destructive to body tissue. Will cause third degree burns. Eye damage may result in blindness. Inhalation may be fatal from spasm of the larynx, usually within 30 minutes. May cause lung tissue damage with edema. 1 mg/m 3 for 8 hours will cause lung damage or, in higher concentrations, death. Provide ventilation to limit inhalation. Reacts violently with metals and organics.
5.2.3 Hydrochloric Acid (HC1). Highly corrosive liquid with toxic vapors. Vapors are highly irritating to eyes, skin, nose, and lungs, causing severe damage. May cause bronchitis, pneumonia, or edema of lungs. Exposure to concentrations of 0.13 to 0.2 percent can be lethal to humans in a few minutes. Provide ventilation to limit exposure. Reacts with metals, producing hydrogen gas.
5.2.4 Hydrofluoric Acid (HF). Highly corrosive to eyes, skin, nose, throat, and lungs. Reaction to exposure may be delayed by 24 hours or more. Provide ventilation to limit exposure.
5.2.5 Hydrogen Peroxide (H2O2). Irritating to eyes, skin, nose, and lungs. 30% H2O2 is a strong oxidizing agent. Avoid contact with skin, eyes, and combustible material. Wear gloves when handling.
5.2.6 Potassium Permanganate (KMnO4). Caustic, strong oxidizer. Avoid bodily contact with.
5.2.7 Potassium Persulfate. Strong oxidizer. Avoid bodily contact with. Keep containers well closed and in a cool place.
5.3 Reaction Pressure. Due to the potential reaction of the potassium permanganate with the acid, there could be pressure buildup in the acidic KMnO4 absorbing solution storage bottle. Therefore these bottles shall not be fully filled and shall be vented to relieve excess pressure and prevent explosion potentials. Venting is required, but not in a manner that will allow contamination of the solution. A No. 70-72 hole drilled in the container cap and Teflon liner has been used.
6.0 Equipment and Supplies6.1 Sampling. A schematic of the sampling train is shown in Figure 29-1. It has general similarities to the Method 5 train.
6.1.1 Probe Nozzle (Probe Tip) and Borosilicate or Quartz Glass Probe Liner. Same as Method 5, sections 6.1.1.1 and 6.1.1.2, except that glass nozzles are required unless alternate tips are constructed of materials that are free from contamination and will not interfere with the sample. If a probe tip other than glass is used, no correction to the sample test results to compensate for the nozzle's effect on the sample is allowed. Probe fittings of plastic such as Teflon, polypropylene, etc. are recommended instead of metal fittings to prevent contamination. If one chooses to do so, a single glass piece consisting of a combined probe tip and probe liner may be used.
6.1.2 Pitot Tube and Differential Pressure Gauge. Same as Method 2, sections 6.1 and 6.2, respectively.
6.1.3 Filter Holder. Glass, same as Method 5, section 6.1.1.5, except use a Teflon filter support or other non-metallic, non-contaminating support in place of the glass frit.
6.1.4 Filter Heating System. Same as Method 5, section 6.1.1.6.
6.1.5 Condenser. Use the following system for condensing and collecting gaseous metals and determining the moisture content of the stack gas. The condensing system shall consist of four to seven impingers connected in series with leak-free ground glass fittings or other leak-free, non-contaminating fittings. Use the first impinger as a moisture trap. The second impinger (which is the first HNO3/H2O2 impinger) shall be identical to the first impinger in Method 5. The third impinger (which is the second HNO3/H2O2 impinger) shall be a Greenburg Smith impinger with the standard tip as described for the second impinger in Method 5, section 6.1.1.8. The fourth (empty) impinger and the fifth and sixth (both acidified KMnO4) impingers are the same as the first impinger in Method 5. Place a temperature sensor capable of measuring to within 1 °C (2 °F) at the outlet of the last impinger. If no Hg analysis is planned, then the fourth, fifth, and sixth impingers are not used.
6.1.6 Metering System, Barometer, and Gas Density Determination Equipment. Same as Method 5, sections 6.1.1.9, 6.1.2, and 6.1.3, respectively.
6.1.7 Teflon Tape. For capping openings and sealing connections, if necessary, on the sampling train.
6.2 Sample Recovery. Same as Method 5, sections 6.2.1 through 6.2.8 (Probe-Liner and Probe-Nozzle Brushes or Swabs, Wash Bottles, Sample Storage Containers, Petri Dishes, Glass Graduated Cylinder, Plastic Storage Containers, Funnel and Rubber Policeman, and Glass Funnel), respectively, with the following exceptions and additions:
6.2.1 Non-metallic Probe-Liner and Probe-Nozzle Brushes or Swabs. Use non-metallic probe-liner and probe-nozzle brushes or swabs for quantitative recovery of materials collected in the front-half of the sampling train.
6.2.2 Sample Storage Containers. Use glass bottles (see section 8.1 of this Method) with Teflon-lined caps that are non-reactive to the oxidizing solutions, with capacities of 1000- and 500-ml, for storage of acidified KMnO4 - containing samples and blanks. Glass or polyethylene bottles may be used for other sample types.
6.2.3 Graduated Cylinder. Glass or equivalent.
6.2.4 Funnel. Glass or equivalent.
6.2.5 Labels. For identifying samples.
6.2.6 Polypropylene Tweezers and/or Plastic Gloves. For recovery of the filter from the sampling train filter holder.
6.3 Sample Preparation and Analysis.
6.3.1 Volumetric Flasks, 100-ml, 250-ml, and 1000-ml. For preparation of standards and sample dilutions.
6.3.2 Graduated Cylinders. For preparation of reagents.
6.3.3 Parr Bombs or Microwave Pressure Relief Vessels with Capping Station (CEM Corporation model or equivalent). For sample digestion.
6.3.4 Beakers and Watch Glasses. 250-ml beakers, with watch glass covers, for sample digestion.
6.3.5 Ring Stands and Clamps. For securing equipment such as filtration apparatus.
6.3.6 Filter Funnels. For holding filter paper.
6.3.7 Disposable Pasteur Pipets and Bulbs.
6.3.8 Volumetric Pipets.
6.3.9 Analytical Balance. Accurate to within 0.1 mg.
6.3.10 Microwave or Conventional Oven. For heating samples at fixed power levels or temperatures, respectively.
6.3.11 Hot Plates.
6.3.12 Atomic Absorption Spectrometer (AAS). Equipped with a background corrector.
6.3.12.1 Graphite Furnace Attachment. With Sb, As, Cd, Co, Pb, Se, and Tl hollow cathode lamps (HCLs) or electrodeless discharge lamps (EDLs). Same as Reference 2 in section 16.0. Methods 7041 (Sb), 7060 (As), 7131 (Cd), 7201 (Co), 7421 (Pb), 7740 (Se), and 7841 (Tl).
6.3.12.2 Cold Vapor Mercury Attachment. With a mercury HCL or EDL, an air recirculation pump, a quartz cell, an aerator apparatus, and a heat lamp or desiccator tube. The heat lamp shall be capable of raising the temperature at the quartz cell by 10 °C above ambient, so that no condensation forms on the wall of the quartz cell. Same as Method 7470 in Reference 2 in section 16.0. See note 2: section 11.1.3 for other acceptable approaches for analysis of Hg in which analytical detection limits of 0.002 ng/ml were obtained.
6.3.13 Inductively Coupled Argon Plasma Spectrometer. With either a direct or sequential reader and an alumina torch. Same as EPA Method 6010 in Reference 2 in section 16.0.
6.3.14 Inductively Coupled Plasma-Mass Spectrometer.
Same as EPA Method 6020 in Reference 2 in section 16.0.
7.0 Reagents and Standards7.1 Unless otherwise indicated, it is intended that all reagents conform to the specifications established by the Committee on Analytical Reagents of the American Chemical Society, where such specifications are available. Otherwise, use the best available grade.
7.2 Sampling Reagents.
7.2.1 Sample Filters. Without organic binders. The filters shall contain less than 1.3 µg/in. 2 of each of the metals to be measured. Analytical results provided by filter manufacturers stating metals content of the filters are acceptable. However, if no such results are available, analyze filter blanks for each target metal prior to emission testing. Quartz fiber filters meeting these requirements are recommended. However, if glass fiber filters become available which meet these requirements, they may be used. Filter efficiencies and unreactiveness to sulfur dioxide (SO2) or sulfur trioxide (SO3) shall be as described in section 7.1.1 of Method 5.
7.2.2 Water. To conform to ASTM Specification D1193-77 or 91, Type II (incorporated by reference - see § 60.17). If necessary, analyze the water for all target metals prior to field use. All target metals should be less than 1 ng/ml.
7.2.3 HNO3, Concentrated. Baker Instra-analyzed or equivalent.
7.2.4 HCl, Concentrated. Baker Instra-analyzed or equivalent.
7.2.5 H2O2, 30 Percent (V/V).
7.2.6 KMnO4.
7.2.7 H2SO4, Concentrated.
7.2.8 Silica Gel and Crushed Ice. Same as Method 5, sections 7.1.2 and 7.1.4, respectively.
7.3 Pretest Preparation of Sampling Reagents.
7.3.1 HNO3/H2O2 Absorbing Solution, 5 Percent HNO3/10 Percent H2O2. Add carefully with stirring 50 ml of concentrated HNO3 to a 1000-ml volumetric flask containing approximately 500 ml of water, and then add carefully with stirring 333 ml of 30 percent H2O2. Dilute to volume with water. Mix well. This reagent shall contain less than 2 ng/ml of each target metal.
7.3.2 Acidic KMnO4 Absorbing Solution, 4 Percent KMnO4 (W/V), 10 Percent H2SO4 (V/V). Prepare fresh daily. Mix carefully, with stirring, 100 ml of concentrated H2SO4 into approximately 800 ml of water, and add water with stirring to make a volume of 1 liter: this solution is 10 percent H2SO4 (V/V). Dissolve, with stirring, 40 g of KMnO4 into 10 percent H2SO4 (V/V) and add 10 percent H2SO4 (V/V) with stirring to make a volume of 1 liter. Prepare and store in glass bottles to prevent degradation. This reagent shall contain less than 2 ng/ml of Hg.
Precaution: To prevent autocatalytic decomposition of the permanganate solution, filter the solution through Whatman 541 filter paper.
7.3.3 HNO3, 0.1 N. Add with stirring 6.3 ml of concentrated HNO3 (70 percent) to a flask containing approximately 900 ml of water. Dilute to 1000 ml with water. Mix well. This reagent shall contain less than 2 ng/ml of each target metal.
7.3.4 HCl, 8 N. Carefully add with stirring 690 ml of concentrated HCl to a flask containing 250 ml of water. Dilute to 1000 ml with water. Mix well. This reagent shall contain less than 2 ng/ml of Hg.
7.4 Glassware Cleaning Reagents.
7.4.1 HNO3, Concentrated. Fisher ACS grade or equivalent.
7.4.2 Water. To conform to ASTM Specifications D1193, Type II.
7.4.3 HNO3, 10 Percent (V/V). Add with stirring 500 ml of concentrated HNO3 to a flask containing approximately 4000 ml of water. Dilute to 5000 ml with water. Mix well. This reagent shall contain less than 2 ng/ml of each target metal.
7.5 Sample Digestion and Analysis Reagents. The metals standards, except Hg, may also be made from solid chemicals as described in Reference 3 in section 16.0. Refer to References 1, 2, or 5 in section 16.0 for additional information on Hg standards. The 1000 µg/ml Hg stock solution standard may be made according to section 7.2.7 of Method 101A.
7.5.1 HCl, Concentrated.
7.5.2 HF, Concentrated.
7.5.3 HNO3, Concentrated. Baker Instra-analyzed or equivalent.
7.5.4 HNO3, 50 Percent (V/V). Add with stirring 125 ml of concentrated HNO3 to 100 ml of water. Dilute to 250 ml with water. Mix well. This reagent shall contain less than 2 ng/ml of each target metal.
7.5.5 HNO3, 5 Percent (V/V). Add with stirring 50 ml of concentrated HNO3 to 800 ml of water. Dilute to 1000 ml with water. Mix well. This reagent shall contain less than 2 ng/ml of each target metal.
7.5.6 Water. To conform to ASTM Specifications D1193, Type II.
7.5.7 Hydroxylamine Hydrochloride and Sodium Chloride Solution. See Reference 2 In section 16.0 for preparation.
7.5.8 Stannous Chloride. See Reference 2 in section 16.0 for preparation.
7.5.9 KMnO4, 5 Percent (W/V). See Reference 2 in section 16.0 for preparation.
7.5.10 H2SO4, Concentrated.
7.5.11 Potassium Persulfate, 5 Percent (W/V). See Reference 2 in section 16.0 for preparation.
7.5.12 Nickel Nitrate, Ni(N03) 2 6H20.
7.5.13 Lanthanum Oxide, La203.
7.5.14 Hg Standard (AAS Grade), 1000 µg/ml.
7.5.15 Pb Standard (AAS Grade), 1000 µg/ml.
7.5.16 As Standard (AAS Grade), 1000 µg/ml.
7.5.17 Cd Standard (AAS Grade), 1000 µg/ml.
7.5.18 Cr Standard (AAS Grade), 1000 µg/ml.
7.5.19 Sb Standard (AAS Grade), 1000 µg/ml.
7.5.20 Ba Standard (AAS Grade), 1000 µg/ml.
7.5.21 Be Standard (AAS Grade), 1000 µg/ml.
7.5.22 Co Standard (AAS Grade), 1000 µg/ml.
7.5.23 Cu Standard (AAS Grade), 1000 µg/ml.
7.5.24 Mn Standard (AAS Grade), 1000 µg/ml.
7.5.25 Ni Standard (AAS Grade), 1000 µg/ml.
7.5.26 P Standard (AAS Grade), 1000 µg/ml.
7.5.27 Se Standard (AAS Grade), 1000 µg/ml.
7.5.28 Ag Standard (AAS Grade), 1000 µg/ml.
7.5.29 Tl Standard (AAS Grade), 1000 µg/ml.
7.5.30 Zn Standard (AAS Grade), 1000 µg/ml.
7.5.31 Al Standard (AAS Grade), 1000 µg/ml.
7.5.32 Fe Standard (AAS Grade), 1000 µg/ml.
7.5.33 Hg Standards and Quality Control Samples. Prepare fresh weekly a 10 µg/ml intermediate Hg standard by adding 5 ml of 1000 µg/ml Hg stock solution prepared according to Method 101A to a 500-ml volumetric flask; dilute with stirring to 500 ml by first carefully adding 20 ml of 15 percent HNO3 and then adding water to the 500-ml volume. Mix well. Prepare a 200 ng/ml working Hg standard solution fresh daily: add 5 ml of the 10 µg/ml intermediate standard to a 250-ml volumetric flask, and dilute to 250 ml with 5 ml of 4 percent KMnO4, 5 ml of 15 percent HNO3, and then water. Mix well. Use at least five separate aliquots of the working Hg standard solution and a blank to prepare the standard curve. These aliquots and blank shall contain 0.0, 1.0, 2.0, 3.0, 4.0, and 5.0 ml of the working standard solution containing 0, 200, 400, 600, 800, and 1000 ng Hg, respectively. Prepare quality control samples by making a separate 10 µg/ml standard and diluting until in the calibration range.
7.5.34 ICAP Standards and Quality Control Samples. Calibration standards for ICAP analysis can be combined into four different mixed standard solutions as follows:
Mixed Standard Solutions for ICAP Analysis
Solution | Elements |
---|---|
I | As, Be, Cd, Mn, Pb, Se, Zn. |
II | Ba, Co, Cu, Fe. |
III | Al, Cr, Ni. |
IV | Ag, P, Sb, Tl. |
Prepare these standards by combining and diluting the appropriate volumes of the 1000 µg/ml solutions with 5 percent HNO3. A minimum of one standard and a blank can be used to form each calibration curve. However, prepare a separate quality control sample spiked with known amounts of the target metals in quantities in the mid-range of the calibration curve. Suggested standard levels are 25 µg/ml for Al, Cr and Pb, 15 µg/ml for Fe, and 10 µg/ml for the remaining elements. Prepare any standards containing less than 1 µg/ml of metal on a daily basis. Standards containing greater than 1 µg/ml of metal should be stable for a minimum of 1 to 2 weeks. For ICP-MS, follow Method 6020 in EPA Publication SW-846 Third Edition (November 1986) including updates I, II, IIA, IIB and III, as incorporated by reference in § 60.17(i).
7.5.35 GFAAS Standards. Sb, As, Cd, Co, Pb, Se, and Tl. Prepare a 10 µg/ml standard by adding 1 ml of 1000 µg/ml standard to a 100-ml volumetric flask. Dilute with stirring to 100 ml with 10 percent HNO3. For GFAAS, matrix match the standards. Prepare a 100 ng/ml standard by adding 1 ml of the 10 µg/ml standard to a 100-ml volumetric flask, and dilute to 100 ml with the appropriate matrix solution. Prepare other standards by diluting the 100 ng/ml standards. Use at least five standards to make up the standard curve. Suggested levels are 0, 10, 50, 75, and 100 ng/ml. Prepare quality control samples by making a separate 10 µg/ml standard and diluting until it is in the range of the samples. Prepare any standards containing less than 1 µg/ml of metal on a daily basis. Standards containing greater than 1 µg/ml of metal should be stable for a minimum of 1 to 2 weeks.
7.5.36 Matrix Modifiers.
7.5.36.1 Nickel Nitrate, 1 Percent (V/V). Dissolve 4.956 g of Ni(N03)2·6H20 or other nickel compound suitable for preparation of this matrix modifier in approximately 50 ml of water in a 100-ml volumetric flask. Dilute to 100 ml with water.
7.5.36.2 Nickel Nitrate, 0.1 Percent (V/V). Dilute 10 ml of 1 percent nickel nitrate solution to 100 ml with water. Inject an equal amount of sample and this modifier into the graphite furnace during GFAAS analysis for As.
7.5.36.3 Lanthanum. Carefully dissolve 0.5864 g of La203 in 10 ml of concentrated HN03, and dilute the solution by adding it with stirring to approximately 50 ml of water. Dilute to 100 ml with water, and mix well. Inject an equal amount of sample and this modifier into the graphite furnace during GFAAS analysis for Pb.
7.5.37 Whatman 40 and 541 Filter Papers (or equivalent). For filtration of digested samples.
8.0 Sample Collection, Preservation, Transport, and Storage8.1 Sampling. The complexity of this method is such that, to obtain reliable results, both testers and analysts must be trained and experienced with the test procedures, including source sampling; reagent preparation and handling; sample handling; safety equipment and procedures; analytical calculations; reporting; and the specific procedural descriptions throughout this method.
8.1.1 Pretest Preparation. Follow the same general procedure given in Method 5, section 8.1, except that, unless particulate emissions are to be determined, the filter need not be desiccated or weighed. First, rinse all sampling train glassware with hot tap water and then wash in hot soapy water. Next, rinse glassware three times with tap water, followed by three additional rinses with water. Then soak all glassware in a 10 percent (V/V) nitric acid solution for a minimum of 4 hours, rinse three times with water, rinse a final time with acetone, and allow to air dry. Cover all glassware openings where contamination can occur until the sampling train is assembled for sampling.
8.1.2 Preliminary Determinations. Same as Method 5, section 8.1.2.
8.1.3 Preparation of Sampling Train.
8.1.3.1 Set up the sampling train as shown in Figure 29-1. Follow the same general procedures given in Method 5, section 8.3, except place 100 ml of the HNO3/H2O2 solution (Section 7.3.1 of this method) in each of the second and third impingers as shown in Figure 29-1. Place 100 ml of the acidic KMnO4 absorbing solution (Section 7.3.2 of this method) in each of the fifth and sixth impingers as shown in Figure 29-1, and transfer approximately 200 to 300 g of pre-weighed silica gel from its container to the last impinger. Alternatively, the silica gel may be weighed directly in the impinger just prior to final train assembly.
8.1.3.2 Based on the specific source sampling conditions, the use of an empty first impinger can be eliminated if the moisture to be collected in the impingers will be less than approximately 100 ml.
8.1.3.3 If Hg analysis will not be performed, the fourth, fifth, and sixth impingers as shown in Figure 29-1 are not required.
8.1.3.4 To insure leak-free sampling train connections and to prevent possible sample contamination problems, use Teflon tape or other non-contaminating material instead of silicone grease.
Precaution: Exercise extreme care to prevent contamination within the train. Prevent the acidic KMnO4 from contacting any glassware that contains sample material to be analyzed for Mn. Prevent acidic H2O2 from mixing with the acidic KMnO4.
8.1.4 Leak-Check Procedures. Follow the leak-check procedures given in Method 5, section 8.4.2 (Pretest Leak-Check), section 8.4.3 (Leak-Checks During the Sample Run), and section 8.4.4 (Post-Test Leak-Checks).
8.1.5 Sampling Train Operation. Follow the procedures given in Method 5, section 8.5. When sampling for Hg, use a procedure analogous to that described in section 8.1 of Method 101A, 40 CFR Part 61, Appendix B, if necessary to maintain the desired color in the last acidified permanganate impinger. For each run, record the data required on a data sheet such as the one shown in Figure 5-3 of Method 5.
8.1.6 Calculation of Percent Isokinetic. Same as Method 5, section 12.11.
8.2 Sample Recovery.
8.2.1 Begin cleanup procedures as soon as the probe is removed from the stack at the end of a sampling period. The probe should be allowed to cool prior to sample recovery. When it can be safely handled, wipe off all external particulate matter near the tip of the probe nozzle and place a rinsed, non-contaminating cap over the probe nozzle to prevent losing or gaining particulate matter. Do not cap the probe tip tightly while the sampling train is cooling; a vacuum can form in the filter holder with the undesired result of drawing liquid from the impingers onto the filter.
8.2.2 Before moving the sampling train to the cleanup site, remove the probe from the sampling train and cap the open outlet. Be careful not to lose any condensate that might be present. Cap the filter inlet where the probe was fastened. Remove the umbilical cord from the last impinger and cap the impinger. Cap the filter holder outlet and impinger inlet. Use non-contaminating caps, whether ground-glass stoppers, plastic caps, serum caps, or Teflon ® tape to close these openings.
8.2.3 Alternatively, the following procedure may be used to disassemble the train before the probe and filter holder/oven are completely cooled: Initially disconnect the filter holder outlet/impinger inlet and loosely cap the open ends. Then disconnect the probe from the filter holder or cyclone inlet and loosely cap the open ends. Cap the probe tip and remove the umbilical cord as previously described.
8.2.4 Transfer the probe and filter-impinger assembly to a cleanup area that is clean and protected from the wind and other potential causes of contamination or loss of sample. Inspect the train before and during disassembly and note any abnormal conditions. Take special precautions to assure that all the items necessary for recovery do not contaminate the samples. The sample is recovered and treated as follows (see schematic in Figures 29-2a and 29-2b):
8.2.5 Container No. 1 (Sample Filter). Carefully remove the filter from the filter holder and place it in its labeled petri dish container. To handle the filter, use either acid-washed polypropylene or Teflon coated tweezers or clean, disposable surgical gloves rinsed with water and dried. If it is necessary to fold the filter, make certain the particulate cake is inside the fold. Carefully transfer the filter and any particulate matter or filter fibers that adhere to the filter holder gasket to the petri dish by using a dry (acid-cleaned) nylon bristle brush. Do not use any metal-containing materials when recovering this train. Seal the labeled petri dish.
8.2.6 Container No. 2 (Acetone Rinse). Perform this procedure only if a determination of particulate emissions is to be made. Quantitatively recover particulate matter and any condensate from the probe nozzle, probe fitting, probe liner, and front half of the filter holder by washing these components with a total of 100 ml of acetone, while simultaneously taking great care to see that no dust on the outside of the probe or other surfaces gets in the sample. The use of exactly 100 ml is necessary for the subsequent blank correction procedures. Distilled water may be used instead of acetone when approved by the Administrator and shall be used when specified by the Administrator; in these cases, save a water blank and follow the Administrator's directions on analysis.
8.2.6.1 Carefully remove the probe nozzle, and clean the inside surface by rinsing with acetone from a wash bottle while brushing with a non-metallic brush. Brush until the acetone rinse shows no visible particles, then make a final rinse of the inside surface with acetone.
8.2.6.2 Brush and rinse the sample exposed inside parts of the probe fitting with acetone in a similar way until no visible particles remain. Rinse the probe liner with acetone by tilting and rotating the probe while squirting acetone into its upper end so that all inside surfaces will be wetted with acetone. Allow the acetone to drain from the lower end into the sample container. A funnel may be used to aid in transferring liquid washings to the container. Follow the acetone rinse with a non-metallic probe brush. Hold the probe in an inclined position, squirt acetone into the upper end as the probe brush is being pushed with a twisting action three times through the probe. Hold a sample container underneath the lower end of the probe, and catch any acetone and particulate matter which is brushed through the probe until no visible particulate matter is carried out with the acetone or until none remains in the probe liner on visual inspection. Rinse the brush with acetone, and quantitatively collect these washings in the sample container. After the brushing, make a final acetone rinse of the probe as described above.
8.2.6.3 It is recommended that two people clean the probe to minimize sample losses. Between sampling runs, keep brushes clean and protected from contamination. Clean the inside of the front-half of the filter holder by rubbing the surfaces with a non-metallic brush and rinsing with acetone. Rinse each surface three times or more if needed to remove visible particulate. Make a final rinse of the brush and filter holder. After all acetone washings and particulate matter have been collected in the sample container, tighten the lid so that acetone will not leak out when shipped to the laboratory. Mark the height of the fluid level to determine whether or not leakage occurred during transport. Clearly label the container to identify its contents.
8.2.7 Container No. 3 (Probe Rinse). Keep the probe assembly clean and free from contamination during the probe rinse. Rinse the probe nozzle and fitting, probe liner, and front-half of the filter holder thoroughly with a total of 100 ml of 0.1 N HNO3, and place the wash into a sample storage container. Perform the rinses as applicable and generally as described in Method 12, section 8.7.1. Record the volume of the rinses. Mark the height of the fluid level on the outside of the storage container and use this mark to determine if leakage occurs during transport. Seal the container, and clearly label the contents. Finally, rinse the nozzle, probe liner, and front-half of the filter holder with water followed by acetone, and discard these rinses.
Note:The use of a total of exactly 100 ml is necessary for the subsequent blank correction procedures.
8.2.8 Container No. 4 (Impingers 1 through 3, Moisture Knockout Impinger, when used, HNO3/H2O2 Impingers Contents and Rinses). Due to the potentially large quantity of liquid involved, the tester may place the impinger solutions from impingers 1 through 3 in more than one container, if necessary. Measure the liquid in the first three impingers to within 0.5 ml using a graduated cylinder. Record the volume. This information is required to calculate the moisture content of the sampled flue gas. Clean each of the first three impingers, the filter support, the back half of the filter housing, and connecting glassware by thoroughly rinsing with 100 ml of 0.1 N HNO3 using the procedure as applicable in Method 12, section 8.7.3.
Note:The use of exactly 100 ml of 0.1 N HNO3 rinse is necessary for the subsequent blank correction procedures. Combine the rinses and impinger solutions, measure and record the final total volume. Mark the height of the fluid level, seal the container, and clearly label the contents.
8.2.9 Container Nos. 5A (0.1 N HNO3), 5B (KMnO4/H2SO4 absorbing solution), and 5C (8 N HCl rinse and dilution).
8.2.9.1 When sampling for Hg, pour all the liquid from the impinger (normally impinger No. 4) that immediately preceded the two permanganate impingers into a graduated cylinder and measure the volume to within 0.5 ml. This information is required to calculate the moisture content of the sampled flue gas. Place the liquid in Container No. 5A. Rinse the impinger with exactly 100 ml of 0.1 N HNO3 and place this rinse in Container No. 5A.
8.2.9.2 Pour all the liquid from the two permanganate impingers into a graduated cylinder and measure the volume to within 0.5 ml. This information is required to calculate the moisture content of the sampled flue gas. Place this acidic KMnO4 solution into Container No. 5B. Using a total of exactly 100 ml of fresh acidified KMnO4 solution for all rinses (approximately 33 ml per rinse), rinse the two permanganate impingers and connecting glassware a minimum of three times. Pour the rinses into Container No. 5B, carefully assuring transfer of all loose precipitated materials from the two impingers. Similarly, using 100 ml total of water, rinse the permanganate impingers and connecting glass a minimum of three times, and pour the rinses into Container 5B, carefully assuring transfer of any loose precipitated material. Mark the height of the fluid level, and clearly label the contents. Read the Precaution: in section 7.3.2.
Note:Due to the potential reaction of KMnO4 with acid, pressure buildup can occur in the sample storage bottles. Do not fill these bottles completely and take precautions to relieve excess pressure. A No. 70-72 hole drilled in the container cap and Teflon liner has been used successfully.
8.2.9.3 Wash the two permanganate impingers with 25 ml of 8 N HCl, and place the wash in a separate sample container labeled No. 5C containing 200 ml of water. First, place 200 ml of water in the container. Then wash the impinger walls and stem with the 8 N HCl by turning the impinger on its side and rotating it so that the HCl contacts all inside surfaces. Use a total of only 25 ml of 8 N HCl for rinsing both permanganate impingers combined. Rinse the first impinger, then pour the actual rinse used for the first impinger into the second impinger for its rinse. Finally, pour the 25 ml of 8 N HCl rinse carefully into the container with the 200 ml of water. Mark the height of the fluid level on the outside of the container in order to determine if leakage occurs during transport.
8.2.10 Container No. 6 (Silica Gel). Note the color of the indicating silica gel to determine whether it has been completely spent and make a notation of its condition. Transfer the silica gel from its impinger to its original container and seal it. The tester may use a funnel to pour the silica gel and a rubber policeman to remove the silica gel from the impinger. The small amount of particles that might adhere to the impinger wall need not be removed. Do not use water or other liquids to transfer the silica gel since weight gained in the silica gel impinger is used for moisture calculations. Alternatively, if a balance is available in the field, record the weight of the spent silica gel (or silica gel plus impinger) to the nearest 0.5 g.
8.2.11 Container No. 7 (Acetone Blank). If particulate emissions are to be determined, at least once during each field test, place a 100-ml portion of the acetone used in the sample recovery process into a container labeled No. 7. Seal the container.
8.2.12 Container No. 8A (0.1 N HNO3 Blank). At least once during each field test, place 300 ml of the 0.1 N HNO3 solution used in the sample recovery process into a container labeled No. 8A. Seal the container.
8.2.13 Container No. 8B (Water Blank). At least once during each field test, place 100 ml of the water used in the sample recovery process into a container labeled No. 8B. Seal the container.
8.2.14 Container No. 9 (5 Percent HNO3/10 Percent H2O2 Blank). At least once during each field test, place 200 ml of the 5 Percent HNO3/10 Percent H2O2 solution used as the nitric acid impinger reagent into a container labeled No. 9. Seal the container.
8.2.15 Container No. 10 (Acidified KMnO4 Blank). At least once during each field test, place 100 ml of the acidified KMnO4 solution used as the impinger solution and in the sample recovery process into a container labeled No. 10. Prepare the container as described in section 8.2.9.2. Read the Precaution: in section 7.3.2 and read the note in section 8.2.9.2.
8.2.16 Container No. 11 (8 N HCl Blank). At least once during each field test, place 200 ml of water into a sample container labeled No. 11. Then carefully add with stirring 25 ml of 8 N HCl. Mix well and seal the container.
8.2.17 Container No. 12 (Sample Filter Blank). Once during each field test, place into a petri dish labeled No. 12 three unused blank filters from the same lot as the sampling filters. Seal the petri dish.
8.3 Sample Preparation. Note the level of the liquid in each of the containers and determine if any sample was lost during shipment. If a noticeable amount of leakage has occurred, either void the sample or use methods, subject to the approval of the Administrator, to correct the final results. A diagram illustrating sample preparation and analysis procedures for each of the sample train components is shown in Figure 29-3.
8.3.1 Container No. 1 (Sample Filter).
8.3.1.1 If particulate emissions are being determined, first desiccate the filter and filter catch without added heat (do not heat the filters to speed the drying) and weigh to a constant weight as described in section 11.2.1 of Method 5.
8.3.1.2 Following this procedure, or initially, if particulate emissions are not being determined in addition to metals analysis, divide the filter with its filter catch into portions containing approximately 0.5 g each. Place the pieces in the analyst's choice of either individual microwave pressure relief vessels or Parr Bombs. Add 6 ml of concentrated HNO3 and 4 ml of concentrated HF to each vessel. For microwave heating, microwave the samples for approximately 12 to 15 minutes total heating time as follows: heat for 2 to 3 minutes, then turn off the microwave for 2 to 3 minutes, then heat for 2 to 3 minutes, etc., continue this alternation until the 12 to 15 minutes total heating time are completed (this procedure should comprise approximately 24 to 30 minutes at 600 watts). Microwave heating times are approximate and are dependent upon the number of samples being digested simultaneously. Sufficient heating is evidenced by sorbent reflux within the vessel. For conventional heating, heat the Parr Bombs at 140 °C (285 °F) for 6 hours. Then cool the samples to room temperature, and combine with the acid digested probe rinse as required in section 8.3.3.
8.3.1.3 If the sampling train includes an optional glass cyclone in front of the filter, prepare and digest the cyclone catch by the procedures described in section 8.3.1.2 and then combine the digestate with the digested filter sample.
8.3.2 Container No. 2 (Acetone Rinse). Note the level of liquid in the container and confirm on the analysis sheet whether or not leakage occurred during transport. If a noticeable amount of leakage has occurred, either void the sample or use methods, subject to the approval of the Administrator, to correct the final results. Measure the liquid in this container either volumetrically within 1 ml or gravimetrically within 0.5 g. Transfer the contents to an acid-cleaned, tared 250-ml beaker and evaporate to dryness at ambient temperature and pressure. If particulate emissions are being determined, desiccate for 24 hours without added heat, weigh to a constant weight according to the procedures described in section 11.2.1 of Method 5, and report the results to the nearest 0.1 mg. Redissolve the residue with 10 ml of concentrated HNO3. Quantitatively combine the resultant sample, including all liquid and any particulate matter, with Container No. 3 before beginning section 8.3.3.
8.3.3 Container No. 3 (Probe Rinse). Verify that the pH of this sample is 2 or lower. If it is not, acidify the sample by careful addition with stirring of concentrated HNO3 to pH 2. Use water to rinse the sample into a beaker, and cover the beaker with a ribbed watch glass. Reduce the sample volume to approximately 20 ml by heating on a hot plate at a temperature just below boiling. Digest the sample in microwave vessels or Parr Bombs by quantitatively transferring the sample to the vessel or bomb, carefully adding the 6 ml of concentrated HNO3, 4 ml of concentrated HF, and then continuing to follow the procedures described in section 8.3.1.2. Then combine the resultant sample directly with the acid digested portions of the filter prepared previously in section 8.3.1.2. The resultant combined sample is referred to as “Sample Fraction 1”. Filter the combined sample using Whatman 541 filter paper. Dilute to 300 ml (or the appropriate volume for the expected metals concentration) with water. This diluted sample is “Analytical Fraction 1”. Measure and record the volume of Analytical Fraction 1 to within 0.1 ml. Quantitatively remove a 50-ml aliquot and label as “Analytical Fraction 1B”. Label the remaining 250-ml portion as “Analytical Fraction 1A”. Analytical Fraction 1A is used for ICAP or AAS analysis for all desired metals except Hg. Analytical Fraction 1B is used for the determination of front-half Hg.
8.3.4 Container No. 4 (Impingers 1-3). Measure and record the total volume of this sample to within 0.5 ml and label it “Sample Fraction 2”. Remove a 75- to 100-ml aliquot for Hg analysis and label the aliquot “Analytical Fraction 2B”. Label the remaining portion of Container No. 4 as “Sample Fraction 2A”. Sample Fraction 2A defines the volume of Analytical Fraction 2A prior to digestion. All of Sample Fraction 2A is digested to produce “Analytical Fraction 2A”. Analytical Fraction 2A defines the volume of Sample Fraction 2A after its digestion and the volume of Analytical Fraction 2A is normally 150 ml. Analytical Fraction 2A is analyzed for all metals except Hg. Verify that the pH of Sample Fraction 2A is 2 or lower. If necessary, use concentrated HNO3 by careful addition and stirring to lower Sample Fraction 2A to pH 2. Use water to rinse Sample Fraction 2A into a beaker and then cover the beaker with a ribbed watchglass. Reduce Sample Fraction 2A to approximately 20 ml by heating on a hot plate at a temperature just below boiling. Then follow either of the digestion procedures described in sections 8.3.4.1 or 8.3.4.2.
8.3.4.1 Conventional Digestion Procedure. Add 30 ml of 50 percent HNO3, and heat for 30 minutes on a hot plate to just below boiling. Add 10 ml of 3 percent H2O2 and heat for 10 more minutes. Add 50 ml of hot water, and heat the sample for an additional 20 minutes. Cool, filter the sample, and dilute to 150 ml (or the appropriate volume for the expected metals concentrations) with water. This dilution produces Analytical Fraction 2A. Measure and record the volume to within 0.1 ml.
8.3.4.2 Microwave Digestion Procedure. Add 10 ml of 50 percent HNO3 and heat for 6 minutes total heating time in alternations of 1 to 2 minutes at 600 Watts followed by 1 to 2 minutes with no power, etc., similar to the procedure described in section 8.3.1. Allow the sample to cool. Add 10 ml of 3 percent H2O2 and heat for 2 more minutes. Add 50 ml of hot water, and heat for an additional 5 minutes. Cool, filter the sample, and dilute to 150 ml (or the appropriate volume for the expected metals concentrations) with water. This dilution produces Analytical Fraction 2A. Measure and record the volume to within 0.1 ml.
Note:All microwave heating times given are approximate and are dependent upon the number of samples being digested at a time. Heating times as given above have been found acceptable for simultaneous digestion of up to 12 individual samples. Sufficient heating is evidenced by solvent reflux within the vessel.
8.3.5 Container No. 5A (Impinger 4), Container Nos. 5B and 5C (Impingers 5 and 6). Keep the samples in Containers Nos. 5A, 5B, and 5C separate from each other. Measure and record the volume of 5A to within 0.5 ml. Label the contents of Container No. 5A to be Analytical Fraction 3A. To remove any brown MnO2 precipitate from the contents of Container No. 5B, filter its contents through Whatman 40 filter paper into a 500 ml volumetric flask and dilute to volume with water. Save the filter for digestion of the brown MnO2 precipitate. Label the 500 ml filtrate from Container No. 5B to be Analytical Fraction 3B. Analyze Analytical Fraction 3B for Hg within 48 hours of the filtration step. Place the saved filter, which was used to remove the brown MnO2 precipitate, into an appropriately sized vented container, which will allow release of any gases including chlorine formed when the filter is digested. In a laboratory hood which will remove any gas produced by the digestion of the MnO2, add 25 ml of 8 N HCl to the filter and allow to digest for a minimum of 24 hours at room temperature. Filter the contents of Container No. 5C through a Whatman 40 filter into a 500-ml volumetric flask. Then filter the result of the digestion of the brown MnO2 from Container No. 5B through a Whatman 40 filter into the same 500-ml volumetric flask, and dilute and mix well to volume with water. Discard the Whatman 40 filter. Mark this combined 500-ml dilute HCl solution as Analytical Fraction 3C.
8.3.6 Container No. 6 (Silica Gel). Weigh the spent silica gel (or silica gel plus impinger) to the nearest 0.5 g using a balance.
9.0 Quality Control9.1 Field Reagent Blanks, if analyzed. Perform the digestion and analysis of the blanks in Container Nos. 7 through 12 that were produced in sections 8.2.11 through 8.2.17, respectively. For Hg field reagent blanks, use a 10 ml aliquot for digestion and analysis.
9.1.1 Digest and analyze one of the filters from Container No. 12 per section 8.3.1, 100 ml from Container No. 7 per section 8.3.2, and 100 ml from Container No. 8A per section 8.3.3. This step produces blanks for Analytical Fractions 1A and 1B.
9.1.2 Combine 100 ml of Container No. 8A with 200 ml from Container No. 9, and digest and analyze the resultant volume per section 8.3.4. This step produces blanks for Analytical Fractions 2A and 2B.
9.1.3 Digest and analyze a 100-ml portion of Container No. 8A to produce a blank for Analytical Fraction 3A.
9.1.4 Combine 100 ml from Container No. 10 with 33 ml from Container No. 8B to produce a blank for Analytical Fraction 3B. Filter the resultant 133 ml as described for Container No. 5B in section 8.3.5, except do not dilute the 133 ml. Analyze this blank for Hg within 48 hr of the filtration step, and use 400 ml as the blank volume when calculating the blank mass value. Use the actual volumes of the other analytical blanks when calculating their mass values.
9.1.5 Digest the filter that was used to remove any brown MnO2 precipitate from the blank for Analytical Fraction 3B by the same procedure as described in section 8.3.5 for the similar sample filter. Filter the digestate and the contents of Container No. 11 through Whatman 40 paper into a 500-ml volumetric flask, and dilute to volume with water. These steps produce a blank for Analytical Fraction 3C.
9.1.6 Analyze the blanks for Analytical Fraction Blanks 1A and 2A per section 11.1.1 and/or section 11.1.2. Analyze the blanks for Analytical Fractions 1B, 2B, 3A, 3B, and 3C per section 11.1.3. Analysis of the blank for Analytical Fraction 1A produces the front-half reagent blank correction values for the desired metals except for Hg; Analysis of the blank for Analytical Fraction 1B produces the front-half reagent blank correction value for Hg. Analysis of the blank for Analytical Fraction 2A produces the back-half reagent blank correction values for all of the desired metals except for Hg, while separate analyses of the blanks for Analytical Fractions 2B, 3A, 3B, and 3C produce the back-half reagent blank correction value for Hg.
9.2 Quality Control Samples. Analyze the following quality control samples.
9.2.1 ICAP and ICP-MS Analysis. Follow the respective quality control descriptions in section 8 of Methods 6010 and 6020 in EPA Publication SW-846 Third Edition (November 1986) including updates I, II, IIA, IIB and III, as incorporated by reference in § 60.17(i). For the purposes of a source test that consists of three sample runs, modify those requirements to include the following: two instrument check standard runs, two calibration blank runs, one interference check sample at the beginning of the analysis (analyze by Method of Standard Additions unless within 25 percent), one quality control sample to check the accuracy of the calibration standards (required to be within 25 percent of calibration), and one duplicate analysis (required to be within 20 percent of average or repeat all analyses).
9.2.2 Direct Aspiration AAS and/or GFAAS Analysis for Sb, As, Ba, Be, Cd, Cu, Cr, Co, Pb, Ni, Mn, Hg, P, Se, Ag, Tl, and Zn. Analyze all samples in duplicate. Perform a matrix spike on at least one front-half sample and one back-half sample, or one combined sample. If recoveries of less than 75 percent or greater than 125 percent are obtained for the matrix spike, analyze each sample by the Method of Standard Additions. Analyze a quality control sample to check the accuracy of the calibration standards. If the results are not within 20 percent, repeat the calibration.
9.2.3 CVAAS Analysis for Hg. Analyze all samples in duplicate. Analyze a quality control sample to check the accuracy of the calibration standards (if not within 15 percent, repeat calibration). Perform a matrix spike on one sample (if not within 25 percent, analyze all samples by the Method of Standard Additions). Additional information on quality control can be obtained from Method 7470 in EPA Publication SW-846 Third Edition (November 1986) including updates I, II, IIA, IIB and III, as incorporated by reference in § 60.17(i), or in Standard Methods for Water and Wastewater Method 303F.
10.0 Calibration and Standardization Note:Maintain a laboratory log of all calibrations.
10.1 Sampling Train Calibration. Calibrate the sampling train components according to the indicated sections of Method 5: Probe Nozzle (Section 10.1); Pitot Tube (Section 10.2); Metering System (Section 10.3); Probe Heater (Section 10.4); Temperature Sensors (Section 10.5); Leak-Check of the Metering System (Section 8.4.1); and Barometer (Section 10.6).
10.2 Inductively Coupled Argon Plasma Spectrometer Calibration. Prepare standards as outlined in section 7.5. Profile and calibrate the instrument according to the manufacturer's recommended procedures using those standards. Check the calibration once per hour. If the instrument does not reproduce the standard concentrations within 10 percent, perform the complete calibration procedures. Perform ICP-MS analysis by following Method 6020 in EPA Publication SW-846 Third Edition (November 1986) including updates I, II, IIA, IIB and III, as incorporated by reference in § 60.17(i).
10.3 Atomic Absorption Spectrometer - Direct Aspiration AAS, GFAAS, and CVAAS analyses. Prepare the standards as outlined in section 7.5 and use them to calibrate the spectrometer. Calibration procedures are also outlined in the EPA methods referred to in Table 29-2 and in Method 7470 in EPA Publication SW-846 Third Edition (November 1986) including updates I, II, IIA, IIB and III, as incorporated by reference in § 60.17(i), or in Standard Methods for Water and Wastewater Method 303F (for Hg). Run each standard curve in duplicate and use the mean values to calculate the calibration line. Recalibrate the instrument approximately once every 10 to 12 samples.
10.4 Field Balance Calibration Check. Check the calibration of the balance used to weigh impingers with a weight that is at least 500g or within 50g of a loaded impinger. The weight must be ASTM E617-13 “Standard Specification for Laboratory Weights and Precision Mass Standards” (incorporated by reference-see 40 CFR 60.17) Class 6 (or better). Daily before use, the field balance must measure the weight within ±0.5g of the certified mass. If the daily balance calibration check fails, perform corrective measures and repeat the check before using balance.
10.5 Analytical Balance Calibration. Perform a multipoint calibration (at least five points spanning the operational range) of the analytical balance before the first use, and semiannually thereafter. The calibration of the analytical balance must be conducted using ASTM E617-13 “Standard Specification for Laboratory Weights and Precision Mass Standards” (incorporated by reference - see 40 CFR 60.17) Class 2 (or better) tolerance weights. Audit the balance each day it is used for gravimetric measurements by weighing at least one ASTM E617-13 Class 2 tolerance (or better) calibration weight that corresponds to 50 to 150 percent of the weight of one filter or between 1g and 5g. If the scale cannot reproduce the value of the calibration weight to within 0.5 mg of the certified mass, perform corrective measures, and conduct the multipoint calibration before use.
11.0 Analytical Procedure11.1 Sample Analysis. For each sampling train sample run, seven individual analytical samples are generated; two for all desired metals except Hg, and five for Hg. A schematic identifying each sample container and the prescribed analytical preparation and analysis scheme is shown in Figure 29-3. The first two analytical samples, labeled Analytical Fractions 1A and 1B, consist of the digested samples from the front-half of the train. Analytical Fraction 1A is for ICAP, ICP-MS or AAS analysis as described in sections 11.1.1 and 11.1.2, respectively. Analytical Fraction 1B is for front-half Hg analysis as described in section 11.1.3. The contents of the back-half of the train are used to prepare the third through seventh analytical samples. The third and fourth analytical samples, labeled Analytical Fractions 2A and 2B, contain the samples from the moisture removal impinger No. 1, if used, and HNO3/H2O2 impingers Nos. 2 and 3. Analytical Fraction 2A is for ICAP, ICP-MS or AAS analysis for target metals, except Hg. Analytical Fraction 2B is for analysis for Hg. The fifth through seventh analytical samples, labeled Analytical Fractions 3A, 3B, and 3C, consist of the impinger contents and rinses from the empty impinger No. 4 and the H2SO4/KMnO4 Impingers Nos. 5 and 6. These analytical samples are for analysis for Hg as described in section 11.1.3. The total back-half Hg catch is determined from the sum of Analytical Fractions 2B, 3A, 3B, and 3C. Analytical Fractions 1A and 2A can be combined proportionally prior to analysis.
11.1.1 ICAP and ICP-MS Analysis. Analyze Analytical Fractions 1A and 2A by ICAP using Method 6010 or Method 200.7 (40 CFR 136, Appendix C). Calibrate the ICAP, and set up an analysis program as described in Method 6010 or Method 200.7. Follow the quality control procedures described in section 9.2.1. Recommended wavelengths for analysis are as shown in Table 29-2. These wavelengths represent the best combination of specificity and potential detection limit. Other wavelengths may be substituted if they can provide the needed specificity and detection limit, and are treated with the same corrective techniques for spectral interference. Initially, analyze all samples for the target metals (except Hg) plus Fe and Al. If Fe and Al are present, the sample might have to be diluted so that each of these elements is at a concentration of less than 50 ppm so as to reduce their spectral interferences on As, Cd, Cr, and Pb. Perform ICP-MS analysis by following Method 6020 in EPA Publication SW-846 Third Edition (November 1986) including updates I, II, IIA, IIB and III, as incorporated by reference in § 60.17(i).
Note:When analyzing samples in a HF matrix, an alumina torch should be used; since all front-half samples will contain HF, use an alumina torch.
11.1.2 AAS by Direct Aspiration and/or GFAAS. If analysis of metals in Analytical Fractions 1A and 2A by using GFAAS or direct aspiration AAS is needed, use Table 29-3 to determine which techniques and procedures to apply for each target metal. Use Table 29-3, if necessary, to determine techniques for minimization of interferences. Calibrate the instrument according to section 10.3 and follow the quality control procedures specified in section 9.2.2.
11.1.3 CVAAS Hg analysis. Analyze Analytical Fractions 1B, 2B, 3A, 3B, and 3C separately for Hg using CVAAS following the method outlined in Method 7470 in EPA Publication SW-846 Third Edition (November 1986) including updates I, II, IIA, IIB and III, as incorporated by reference in § 60.17(i), or in Standard Methods for Water and Wastewater Analysis, 15th Edition, Method 303F, or, optionally using note no. 2 at the end of this section. Set up the calibration curve (zero to 1000 ng) as described in Method 7470 or similar to Method 303F using 300-ml BOD bottles instead of Erlenmeyers. Perform the following for each Hg analysis. From each original sample, select and record an aliquot in the size range from 1 ml to 10 ml. If no prior knowledge of the expected amount of Hg in the sample exists, a 5 ml aliquot is suggested for the first dilution to 100 ml (see note no. 1 at end of this section). The total amount of Hg in the aliquot shall be less than 1 µg and within the range (zero to 1000 ng) of the calibration curve. Place the sample aliquot into a separate 300-ml BOD bottle, and add enough water to make a total volume of 100 ml. Next add to it sequentially the sample digestion solutions and perform the sample preparation described in the procedures of Method 7470 or Method 303F. (See note no. 2 at the end of this section). If the maximum readings are off-scale (because Hg in the aliquot exceeded the calibration range; including the situation where only a 1-ml aliquot of the original sample was digested), then dilute the original sample (or a portion of it) with 0.15 percent HNO3 (1.5 ml concentrated HNO3 per liter aqueous solution) so that when a 1- to 10-ml aliquot of the “0.15 HNO3 percent dilution of the original sample” is digested and analyzed by the procedures described above, it will yield an analysis within the range of the calibration curve.
Note No. 1:When Hg levels in the sample fractions are below the in-stack detection limit given in Table 29-1, select a 10 ml aliquot for digestion and analysis as described.
Note No. 2:Optionally, Hg can be analyzed by using the CVAAS analytical procedures given by some instrument manufacturer's directions. These include calibration and quality control procedures for the Leeman Model PS200, the Perkin Elmer FIAS systems, and similar models, if available, of other instrument manufacturers. For digestion and analyses by these instruments, perform the following two steps: (1), Digest the sample aliquot through the addition of the aqueous hydroxylamine hydrochloride/sodium chloride solution the same as described in this section: (The Leeman, Perkin Elmer, and similar instruments described in this note add automatically the necessary stannous chloride solution during the automated analysis of Hg.); (2), Upon completion of the digestion described in (1), analyze the sample according to the instrument manufacturer's directions. This approach allows multiple (including duplicate) automated analyses of a digested sample aliquot.
12.0 Data Analysis and Calculations12.1 Nomenclature.
A = Analytical detection limit, µg/ml. B = Liquid volume of digested sample prior to aliquotting for analysis, ml. C = Stack sample gas volume, dsm 3. Ca1 = Concentration of metal in Analytical Fraction 1A as read from the standard curve, µg/ml. Ca2 = Concentration of metal in Analytical Fraction 2A as read from the standard curve, (µg/ml). Cs = Concentration of a metal in the stack gas, mg/dscm. D = In-stack detection limit, µg/m 3. Fa = Aliquot factor, volume of Sample Fraction 2 divided by volume of Sample Fraction 2A (see section 8.3.4.) Fd = Dilution factor (Fd = the inverse of the fractional portion of the concentrated sample in the solution actually used in the instrument to produce the reading Ca1. For example, if a 2 ml aliquot of Analytical Fraction 1A is diluted to 10 ml to place it in the calibration range, Fd = 5). Hgbh = Total mass of Hg collected in the back-half of the sampling train, µg. Hgbh2 = Total mass of Hg collected in Sample Fraction 2, µg. Hgbh3(A,B,C) = Total mass of Hg collected separately in Fraction 3A, 3B, or 3C, µg. Hgbhb = Blank correction value for mass of Hg detected in back-half field reagent blanks, µg. Hgfh = Total mass of Hg collected in the front-half of the sampling train (Sample Fraction 1), µg. Hgfhb = Blank correction value for mass of Hg detected in front-half field reagent blank, µg. Hgt = Total mass of Hg collected in the sampling train, µg. Mbh = Total mass of each metal (except Hg) collected in the back-half of the sampling train (Sample Fraction 2), µg. Mbhb = Blank correction value for mass of metal detected in back-half field reagent blank, µg. Mfh = Total mass of each metal (except Hg) collected in the front half of the sampling train (Sample Fraction 1), µg. Mfhb = Blank correction value for mass of metal detected in front-half field reagent blank, µg. Mt = Total mass of each metal (separately stated for each metal) collected in the sampling train, µg. Mt = Total mass of that metal collected in the sampling train, µg; (substitute Hgt for Mt for the Hg calculation). Qbh2 = Quantity of Hg, µg, TOTAL in the ALIQUOT of Analytical Fraction 2B selected for digestion and analysis . Note:For example, if a 10 ml aliquot of Analytical Fraction 2B is taken and digested and analyzed (according to section 11.1.3 and its notes nos. 1 and 2), then calculate and use the total amount of Hg in the 10 ml aliquot for Qbh2.
Qbh3(A,B,C) = Quantity of Hg, µg, TOTAL, separately, in the ALIQUOT of Analytical Fraction 3A, 3B, or 3C selected for digestion and analysis (see notes in sections 12.7.1 and 12.7.2 describing the quantity “Q” and calculate similarly). Qfh = Quantity of Hg, µg, TOTAL in the ALIQUOT of Analytical Fraction 1B selected for digestion and analysis. Note:For example, if a 10 ml aliquot of Analytical Fraction 1B is taken and digested and analyzed (according to section 11.1.3 and its notes nos. 1 and 2), then calculate and use the total amount of Hg in the 10 ml aliquot for Qfh.
Va = Total volume of digested sample solution (Analytical Fraction 2A), ml (see section 8.3.4.1 or 8.3.4.2, as applicable). Vf1B = Volume of aliquot of Analytical Fraction 1B analyzed, ml. Note:For example, if a 1 ml aliquot of Analytical Fraction 1B was diluted to 50 ml with 0.15 percent HNO3 as described in section 11.1.3 to bring it into the proper analytical range, and then 1 ml of that 50-ml was digested according to section 11.1.3 and analyzed, Vf1B would be 0.02 ml.
Vf2B = Volume of Analytical Fraction 2B analyzed, ml. Note:For example, if 1 ml of Analytical Fraction 2B was diluted to 10 ml with 0.15 percent HNO3 as described in section 11.1.3 to bring it into the proper analytical range, and then 5 ml of that 10 ml was analyzed, Vf2B would be 0.5 ml.
Vf3(A,B,C) = Volume, separately, of Analytical Fraction 3A, 3B, or 3C analyzed, ml (see previous notes in sections 12.7.1 and 12.7.2, describing the quantity “V” and calculate similarly). Vm(std) = Volume of gas sample as measured by the dry gas meter, corrected to dry standard conditions, dscm. Vsoln,1 = Total volume of digested sample solution (Analytical Fraction 1), ml. Vsoln,1 = Total volume of Analytical Fraction 1, ml. Vsoln,2 = Total volume of Sample Fraction 2, ml.Vsoln,3(A,B,C) = Total volume, separately, of Analytical Fraction 3A, 3B, or 3C, ml.
K4 = 10−3 mg/µg.12.2 Dry Gas Volume. Using the data from this test, calculate Vm(std), the dry gas sample volume at standard conditions as outlined in section 12.3 of Method 5.
12.3 Volume of Water Vapor and Moisture Content. Using the total volume of condensate collected during the source sampling, calculate the volume of water vapor Vw(std) and the moisture content Bws of the stack gas. Use Equations 5-2 and 5-3 of Method 5.
12.4 Stack Gas Velocity. Using the data from this test and Equation 2-9 of Method 2, calculate the average stack gas velocity.
12.5 In-Stack Detection Limits. Calculate the in-stack method detection limits shown in Table 29-4 using the conditions described in section 13.3.1 as follows:
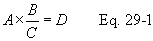
12.6 Metals (Except Hg) in Source Sample.
12.6.1 Analytical Fraction 1A, Front-Half, Metals (except Hg). Calculate separately the amount of each metal collected in Sample Fraction 1 of the sampling train using the following equation:

If Analytical Fractions 1A and 2A are combined, use proportional aliquots. Then make appropriate changes in Equations 29-2 through 29-4 to reflect this approach.
12.6.2 Analytical Fraction 2A, Back-Half, Metals (except Hg). Calculate separately the amount of each metal collected in Fraction 2 of the sampling train using the following equation:

12.6.3 Total Train, Metals (except Hg). Calculate the total amount of each of the quantified metals collected in the sampling train as follows:

If the measured blank value for the front half (Mfhb) is in the range 0.0 to “A” µg (where “A” µg equals the value determined by multiplying 1.4 µg/in.2 times the actual area in in.2 of the sample filter), use Mfhb to correct the emission sample value (Mfh); if Mfhb exceeds “A” µg, use the greater of I or II:
I. “A” µg.
II. The lesser of (a) Mfhb, or (b) 5 percent of Mfh. If the measured blank value for the back-half (Mbhb) is in the range 0.0 to 1 µg, use Mbhb to correct the emission sample value (Mbh); if Mbhb exceeds 1 µg, use the greater of I or II:
I. 1 µg.
II. The lesser of (a) Mbhb, or (b) 5 percent of Mbh.
12.7 Hg in Source Sample.
12.7.1 Analytical Fraction 1B; Front-Half Hg. Calculate the amount ofHg collected in the front-half, Sample Fraction 1, of the sampling train by using Equation 29-5:
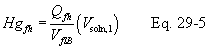
12.7.2 Analytical Fractions 2B, 3A, 3B, and 3C; Back Half Hg.
12.7.2.1 Calculate the amount of Hg collected in Sample Fraction 2 by using Equation 29-6:
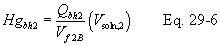
12.7.2.2 Calculate each of the back-half Hg values for Analytical Fractions 3A, 3B, and 3C by using Equation 29-7:

12.7.2.3 Calculate the total amount of Hg collected in the back-half of the sampling train by using Equation 29-8:

12.7.3 Total Train Hg Catch. Calculate the total amount of Hg collected in the sampling train by using Equation 29-9:

If the total of the measured blank values (Hgfhb + Hgbhb) is in the range of 0.0 to 0.6 µg, then use the total to correct the sample value (Hgfh + Hgbh); if it exceeds 0.6 µg, use the greater of I. or II:
I. 0.6 µg.
II. The lesser of (a) (Hgfhb + Hgbhb), or (b) 5 percent of the sample value (Hgfh + Hgbh).
12.8 Individual Metal Concentrations in Stack Gas. Calculate the concentration of each metal in the stack gas (dry basis, adjusted to standard conditions) by using Equation 29-10:
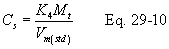
12.9 Isokinetic Variation and Acceptable Results. Same as Method 5, sections 12.11 and 12.12, respectively.
13.0 Method Performance13.1 Range. For the analysis described and for similar analyses, the ICAP response is linear over several orders of magnitude. Samples containing metal concentrations in the nanograms per ml (ng/ml) to micrograms per ml (µg/ml) range in the final analytical solution can be analyzed using this method. Samples containing greater than approximately 50 µg/ml As, Cr, or Pb should be diluted to that level or lower for final analysis. Samples containing greater than approximately 20 µg/ml of Cd should be diluted to that level before analysis.
13.2 Analytical Detection Limits.
Note:See section 13.3 for the description of in-stack detection limits.
13.2.1 ICAP analytical detection limits for the sample solutions (based on SW-846, Method 6010) are approximately as follows: Sb (32 ng/ml), As (53 ng/ml), Ba (2 ng/ml), Be (0.3 ng/ml), Cd (4 ng/ml), Cr (7 ng/ml), Co (7 ng/ml), Cu (6 ng/ml), Pb (42 ng/ml), Mn (2 ng/ml), Ni (15 ng/ml), P (75 ng/ml), Se (75 ng/ml), Ag (7 ng/ml), Tl (40 ng/ml), and Zn (2 ng/ml). ICP-MS analytical detection limits (based on SW-846, Method 6020) are lower generally by a factor of ten or more. Be is lower by a factor of three. The actual sample analytical detection limits are sample dependent and may vary due to the sample matrix.
13.2.2 The analytical detection limits for analysis by direct aspiration AAS (based on SW-846, Method 7000 series) are approximately as follows: Sb (200 ng/ml), As (2 ng/ml), Ba (100 ng/ml), Be (5 ng/ml), Cd (5 ng/ml), Cr (50 ng/ml), Co (50 ng/ml), Cu (20 ng/ml), Pb (100 ng/ml), Mn (10 ng/ml), Ni (40 ng/ml), Se (2 ng/ml), Ag (10 ng/ml), Tl (100 ng/ml), and Zn (5 ng/ml).
13.2.3 The detection limit for Hg by CVAAS (on the resultant volume of the digestion of the aliquots taken for Hg analyses) can be approximately 0.02 to 0.2 ng/ml, depending upon the type of CVAAS analytical instrument used. 13.2.4 The use of GFAAS can enhance the detection limits compared to direct aspiration AAS as follows: Sb (3 ng/ml), As (1 ng/ml), Be (0.2 ng/ml), Cd (0.1 ng/ml), Cr (1 ng/ml), Co (1 ng/ml), Pb (1 ng/ml), Se (2 ng/ml), and Tl (1 ng/ml).
13.3 In-stack Detection Limits.
13.3.1 For test planning purposes in-stack detection limits can be developed by using the following information: (1) The procedures described in this method, (2) the analytical detection limits described in section 13.2 and in SW-846,(3) the normal volumes of 300 ml (Analytical Fraction 1) for the front-half and 150 ml (Analytical Fraction 2A) for the back-half samples, and (4) a stack gas sample volume of 1.25 m 3. The resultant in-stack method detection limits for the above set of conditions are presented in Table 29-1 and were calculated by using Eq. 29-1 shown in section 12.5.
13.3.2 To ensure optimum precision/resolution in the analyses, the target concentrations of metals in the analytical solutions should be at least ten times their respective analytical detection limits. Under certain conditions, and with greater care in the analytical procedure, these concentrations can be as low as approximately three times the respective analytical detection limits without seriously impairing the precision of the analyses. On at least one sample run in the source test, and for each metal analyzed, perform either repetitive analyses, Method of Standard Additions, serial dilution, or matrix spike addition, etc., to document the quality of the data.
13.3.3 Actual in-stack method detection limits are based on actual source sampling parameters and analytical results as described above. If required, the method in-stack detection limits can be improved over those shown in Table 29-1 for a specific test by either increasing the sampled stack gas volume, reducing the total volume of the digested samples, improving the analytical detection limits, or any combination of the three. For extremely low levels of Hg only, the aliquot size selected for digestion and analysis can be increased to as much as 10 ml, thus improving the in-stack detection limit by a factor of ten compared to a 1 ml aliquot size.
13.3.3.1 A nominal one hour sampling run will collect a stack gas sampling volume of about 1.25 m 3. If the sampling time is increased to four hours and 5 m 3 are collected, the in-stack method detection limits would be improved by a factor of four compared to the values shown in Table 29-1.
13.3.3.2 The in-stack detection limits assume that all of the sample is digested and the final liquid volumes for analysis are the normal values of 300 ml for Analytical Fraction 1, and 150 ml for Analytical Fraction 2A. If the volume of Analytical Fraction 1 is reduced from 300 to 30 ml, the in-stack detection limits for that fraction of the sample would be improved by a factor of ten. If the volume of Analytical Fraction 2A is reduced from 150 to 25 ml, the in-stack detection limits for that fraction of the sample would be improved by a factor of six. Matrix effect checks are necessary on sample analyses and typically are of much greater significance for samples that have been concentrated to less than the normal original sample volume. Reduction of Analytical Fractions 1 and 2A to volumes of less than 30 and 25 ml, respectively, could interfere with the redissolving of the residue and could increase interference by other compounds to an intolerable level.
13.3.3.3 When both of the modifications described in sections 13.3.3.1 and 13.3.3.2 are used simultaneously on one sample, the resultant improvements are multiplicative. For example, an increase in stack gas volume by a factor of four and a reduction in the total liquid sample digested volume of both Analytical Fractions 1 and 2A by a factor of six would result in an improvement by a factor of twenty-four of the in-stack method detection limit.
13.4 Precision. The precision (relative standard deviation) for each metal detected in a method development test performed at a sewage sludge incinerator were found to be as follows:
Sb (12.7 percent), As (13.5 percent), Ba (20.6 percent), Cd (11.5 percent), Cr (11.2 percent), Cu (11.5 percent), Pb (11.6 percent), P (14.6 percent), Se (15.3 percent), Tl (12.3 percent), and Zn (11.8 percent). The precision for Ni was 7.7 percent for another test conducted at a source simulator. Be, Mn, and Ag were not detected in the tests. However, based on the analytical detection limits of the ICAP for these metals, their precisions could be similar to those for the other metals when detected at similar levels. 14.0 Pollution Prevention [Reserved] 15.0 Waste Management [Reserved] 16.0 Alternative Procedures16.1 Alternative Analyzer. Samples may also be analyzed by cold vapor atomic fluorescence spectrometry.
16.2 [Reserved]
17.0 References1. Method 303F in Standard Methods for the Examination of Water Wastewater, 15th Edition, 1980. Available from the American Public Health Association, 1015 18th Street N.W., Washington, D.C. 20036.
2. EPA Methods 6010, 6020, 7000, 7041, 7060, 7131, 7421, 7470, 7740, and 7841, Test Methods for Evaluating Solid Waste: Physical/Chemical Methods. SW-846, Third Edition, November 1986, with updates I, II, IIA, IIB and III. Office of Solid Waste and Emergency Response, U. S. Environmental Protection Agency, Washington, DC 20460.
3. EPA Method 200.7, Code of Federal Regulations, Title 40, Part 136, Appendix C. July 1, 1987.
4. EPA Methods 1 through 5, Code of Federal Regulations, Title 40, Part 60, Appendix A, July 1, 1991.
5. EPA Method 101A, Code of Federal Regulations, Title 40, Part 61, Appendix B, July 1, 1991.
18.0 Tables, Diagrams, Flowcharts, and Validation DataTable 29-1 - In Stack Method Detection Limits (ug/m 3) for the Front-Half, the Back Half, and the Total Sampling Train Using ICAP, GFAAS, and CVAAS
Metal | Front-half: probe and filter |
Back-half: impinters 1-3 | Back-half: impringers 4-6 a |
Total train |
---|---|---|---|---|
Antimony | 1 7.7 (0.7) | 1 3.8 (0.4) | 1 11.5 (1.1) | |
Arsenic | 1 12.7 (0.3) | 1 6.4 (0.1) | 1 19.1 (0.4) | |
Barium | 0.5 | 0.3 | 0.8 | |
Beryllium | 1 0.07 (0.05) | 1 0.04 (0.03) | 1 0.11 (0.08) | |
Cadmium | 1 1.0 (0.02) | 1 0.5 (0.01) | 1 1.5 (0.03) | |
Chromium | 1 1.7 (0.2) | 1 0.8 (0.1) | 1 2.5 (0.3) | |
Cobalt | 1 1.7 (0.2) | 1 0.8 (0.1) | 1 2.5 (0.3) | |
Copper | 1.4 | 0.7 | 2.1 | |
Lead | 1 10.1 (0.2) | 1 5.0 (0.1) | 1 15.1 (0.3) | |
Manganese | 1 0.5 (0.2) | 1 0.2 (0.1) | 1 0.7 (0.3) | |
Mercury | 2 0.06 | 2 0.3 | 2 0.2 | 2 0.56 |
Nickel | 3.6 | 1.8 | 5.4 | |
Phosphorus | 18 | 9 | 27 | |
Selenium | 1 18 (0.5) | 1 9 (0.3) | 1 27 (0.8) | |
Silver | 1.7 | 0.9 (0.7) | 2.6 | |
Thallium | 1 9.6 (0.2) | 1 4.8 (0.1) | 1 14.4 (0.3) | |
Zinc | 0.5 | 0.3 | 0.8 |
a Mercury analysis only.
1 Detection limit when analyzed by ICAP or GFAAS as shown in parentheses (see section 11.1.2).
2 Detection limit when anaylzed by CVAAS, estimated for Back-half and Total Train. See sections 13.2 and 11.1.3. Note: Actual method in-stack detection limits may vary from these values, as described in section 13.3.3.
Table 29-2 - Recommended Wavelengths for ICAP Analysis
Analyte | Wavelength (nm) |
---|---|
Aluminum (Al) | 308.215 |
Antimony (Sb) | 206.833 |
Arsenic (As) | 193.696 |
Barium (Ba) | 455.403 |
Beryllium (Be) | 313.042 |
Cadmium (Cd) | 226.502 |
Chromium (Cr) | 267.716 |
Cobalt (Co) | 228.616 |
Copper (Cu) | 328.754 |
Iron (Fe) | 259.940 |
Lead (Pb) | 220.353 |
Manganese (Mn) | 257.610 |
Nickel (Ni) | 231.604 |
Phosphorus (P) | 214.914 |
Selenium (Se) | 196.026 |
Silver (Ag) | 328.068 |
Thallium (T1) | 190,864 |
Zinc (Zn) | 213,856 |
Table 29-3 - Applicable Techniques, Methods and Minimization of Interferences for AAS Analysis
Metal | Technique | SW-846
1 Methods No. |
Wavelength (nm) |
Interferences | |
---|---|---|---|---|---|
Cause | Minimization | ||||
Fe | Aspiration | 7380 | 248.3 | Contamination | Great care taken to avoid contamination. |
Pb | Aspiration | 7420 | 283.3 | 217.0 nm alternate | Background correction required. |
Pb | Furnace | 7421 | 283.3 | Poor recoveries | Matrix modifier, add 10 µl of phosphorus acid to 1 ml of prepared sample in sampler cup. |
Mn | Aspiration | 7460 | 279.5 | 403.1 nm alternate | Background correction required. |
Ni | Aspiration | 7520 | 232.0 | 352.4 nm alternate Fe, Co, and
Cr Nonlinear response |
Background correction
required. Matrix matching or nitrous-oxide/acetylene flame Sample dilution or use 352.3 nm line |
Se | Furnace | 7740 | 196.0 | Volatility | Spike samples and reference materials and add nickel nitrate to minimize volatilization. |
Adsorption & scatter | Background correction is required and Zeeman background correction can be useful. | ||||
Ag | Aspiration | 7760 | 328.1 | Adsorption & scatter AgCl insoluble | Background correction is required. Avoid hydrochloric acid unless silver is in solution as a chloride complex. Sample and standards monitored for aspiration rate. |
Tl | Aspiration | 7840 | 276.8 | Background correction is required. Hydrochloric acid should not be used. | |
Tl | Furnace | 7841 | 276.8 | Hydrochloric acid or chloride | Background correction is required. Verify that losses are not occurring for volatilization by spiked samples or standard addition; Palladium is a suitable matrix modifier. |
Zn | Aspiration | 7950 | 213.9 | High Si, Cu, & P Contamination | Strontium removes Cu and
phosphate. Great care taken to avoid contamination. |
Sb | Aspiration | 7040 | 217.6 | 1000 mg/ml Pb, Ni, Cu, or acid | Use secondary wavelength of 231.1 nm; match sample & standards acid concentration or use nitrous oxide/acetylene flame. |
Sb | Furnace | 7041 | 217.6 | High Pb | Secondary wavelength or Zeeman correction. |
As | Furnace | 7060 | 193.7 | Arsenic Volatilization Aluminum | Spike samples and add nickel nitrate solution to digestates prior to analysis. Use Zeeman background correction. |
Ba | Aspiration | 7080 | 553.6 | ||
Calcium | |||||
Barium Ionization | High hollow cathode current
and narrow band set. 2 ml of KCl per 100 m1 of sample. |
||||
Be | Aspiration | 7090 | 234.9 | 500 ppm Al. High Mg and Si | Add 0.1% fluoride. |
Be | Furnace | 7091 | 234.9 | Be in optical path | Optimize parameters to minimize effects. |
Cd | Aspiration | 7130 | 228.8 | Absorption and light scattering | Background correction is required. |
Cd | Furnace | 7131 | 228.8 | As above Excess Chloride Pipet Tips |
As above. Ammonium phosphate used as a matrix modifier. Use cadmium-free tips. |
Cr | Aspiration | 7190 | 357.9 | Alkali metal | KCl ionization suppressant in samples and standards - Consult mfgs' literature. |
Co | Furnace | 7201 | 240.7 | Excess chloride | Use Method of Standard Additions. |
Cr | Furnace | 7191 | 357.9 | 200 mg/L Ca and P | All calcium nitrate for a know constant effect and to eliminate effect of phosphate. |
Cu | Aspiration | 7210 | 324.7 | Absorption and Scatter | Consult manufacturer's manual. |
1 Refer to EPA publication SW-846 (Reference 2 in section 16.0).
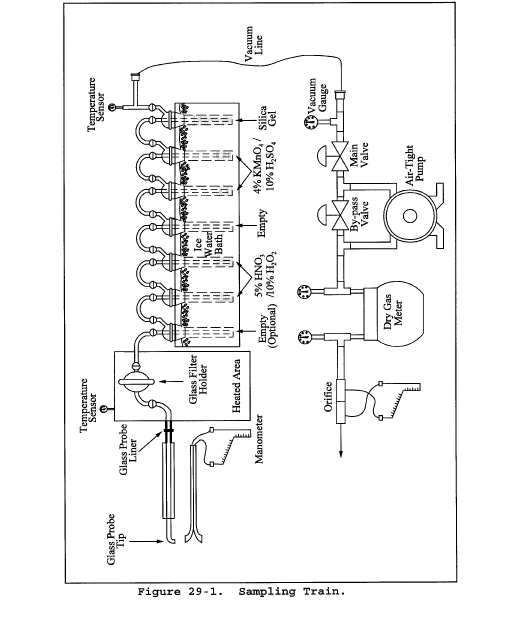
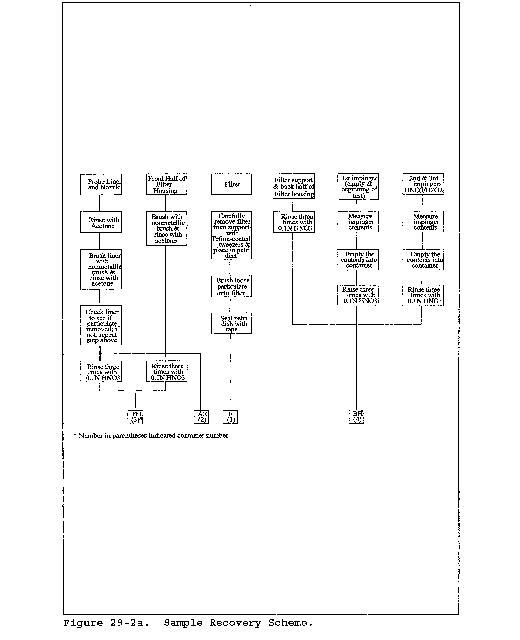
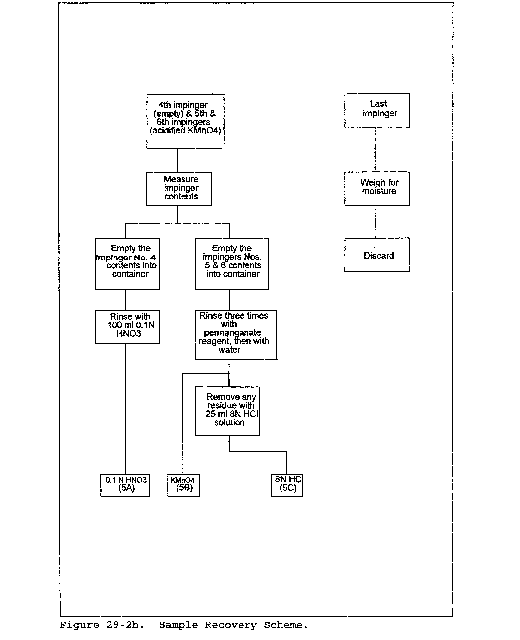
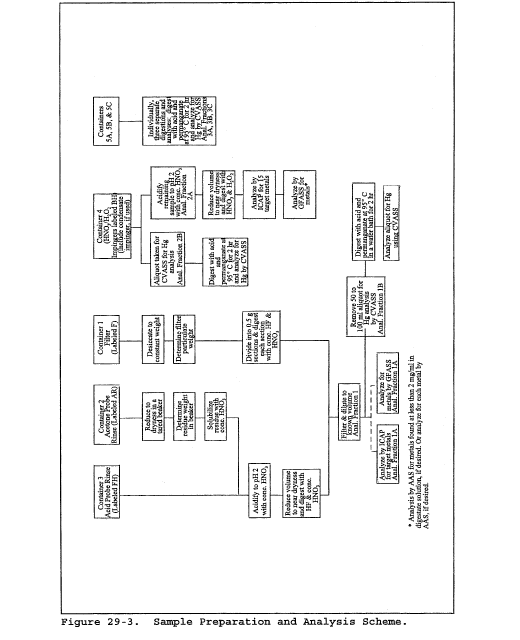
Method 30A is a procedure for measuring total vapor phase mercury (Hg) emissions from stationary sources using an instrumental analyzer. This method is particularly appropriate for performing emissions testing and for conducting relative accuracy test audits (RATAs) of mercury continuous emissions monitoring systems (Hg CEMS) and sorbent trap monitoring systems at coal-fired combustion sources. Quality assurance and quality control requirements are included to assure that you, the tester, collect data of known and acceptable quality for each testing site. This method does not completely describe all equipment, supplies, and sampling procedures and analytical procedures you will need but refers to other test methods for some of the details. Therefore, to obtain reliable results, you should also have a thorough knowledge of these additional methods which are also found in appendices A-1 and A-3 to this part:
(a) Method 1 - Sample and Velocity Traverses for Stationary Sources.
(b) Method 4 - Determination of Moisture Content in Stack Gases.
1.1 Analytes. What does this method determine? This method is designed to measure the mass concentration of total vapor phase Hg in flue gas, which represents the sum of elemental Hg (Hg 0) and oxidized forms of Hg (Hg+2), in mass concentration units of micrograms per cubic meter (µg/m 3).
Analyte | CAS No. | Sensitivity |
---|---|---|
Elemental Hg (Hg 0) | 7439-97-6 | Typically <2% of Calibration Span. |
Oxidized Hg (Hg+2) | (Same). |
1.2 Applicability. When is this method required? Method 30A is offered as a reference method for emission testing and for RATAs of Hg CEMS and sorbent trap monitoring systems at coal-fired boilers. Method 30A may also be specified for other source categories in the future, either by New Source Performance Standards (NSPS), National Emission Standards for Hazardous Air Pollutants (NESHAP), emissions trading programs, State Implementation Plans (SIP), or operating permits that require measurement of Hg concentrations in stationary source emissions to determine compliance with an applicable emission standard or limit, or to conduct RATAs of Hg CEMS and sorbent trap monitoring systems.
1.3 Data Quality Objectives (DQO). How good must my collected data be? Method 30A has been designed to provide data of high and known quality for Hg emission testing and for relative accuracy testing of Hg monitoring systems including Hg CEMS and sorbent trap monitoring systems. In these and other applications, the principle objective is to ensure the accuracy of the data at the actual emission levels encountered. To meet this objective, calibration standards prepared according to an EPA traceability protocol must be used and measurement system performance tests are required.
2.0 Summary of MethodIn this method, a sample of the effluent gas is continuously extracted and conveyed to an analyzer capable of measuring the total vapor phase Hg concentration. Elemental and oxidized mercury (i.e., Hg 0 and Hg+2) may be measured separately or simultaneously but, for purposes of this method, total vapor phase Hg is the sum of Hg 0 and Hg+2. You must meet the performance requirements of this method (i.e., system calibration, interference testing, dynamic spiking, and system integrity/drift checks) to validate your data. The dynamic spiking requirement is deferred until January 1, 2009.
3.0 Definitions3.1 Calibration Curve means the relationship between an analyzer's response to the injection of a series of calibration gases and the actual concentrations of those gases.
3.2 Calibration Gas means a gas standard containing Hg 0 or HgCl2 at a known concentration that is produced and certified in accordance with an EPA traceability protocol for certification of Hg calibration standards.
3.2.1 Zero Gas means a calibration gas with a concentration that is below the level detectable by the measurement system.
3.2.2 Low-Level Gas means a calibration gas with a concentration that is 10 to 30 percent of the calibration span.
3.2.3 Mid-Level Gas means a calibration gas with a concentration that is 40 to 60 percent of the calibration span.
3.2.4 High-Level Gas means a calibration gas whose concentration is equal to the calibration span.
3.3 Converter means a device that reduces oxidized mercury (Hg+2) to elemental mercury (Hg 0).
3.4 Calibration Span means the upper limit of valid instrument response during sampling. To the extent practicable the measured emissions are to be between 10 and 100 percent of the selected calibration span (i.e., the measured emissions should be within the calibrated range determined by the Low- and High-Level gas standards). It is recommended that the calibration span be at least twice the native concentration to accommodate the dynamic spiking procedure.
3.5 Centroidal Area means the central area that has the same shape as the stack or duct cross section and is no greater than one percent of the stack or duct total cross-sectional area.
3.6 Data Recorder means the equipment that permanently records the concentrations reported by the analyzer.
3.7 Drift Check means the test to determine the difference between the measurement system readings obtained in a post-run system integrity check and the prior pre-run system integrity check at a specific calibration gas concentration level (i.e., zero, mid-level, or high-level).
3.8 Dynamic Spiking means a procedure in which a known mass or concentration of vapor phase HgCl2 is injected into the probe sample gas stream at a known flow rate, in order to assess the effects of the flue gas matrix on the accuracy of the measurement system.
3.9 Gas Analyzer means the equipment that detects the total vapor phase Hg being measured and generates an output proportional to its concentration.
3.10 Interference Test means the test to detect analyzer responses to compounds other than Hg, usually gases present in the measured gas stream, that are not adequately accounted for in the calibration procedure and may cause measurement bias.
3.11 Measurement System means all of the equipment used to determine the Hg concentration. The measurement system may generally include the following major subsystems: sample acquisition, Hg+2 to Hg 0 converter, sample transport, sample conditioning, flow control/gas manifold, gas analyzer, and data recorder.
3.12 Native Concentration means the total vapor phase Hg concentration in the effluent gas stream.
3.13 NIST means the National Institute of Standards and Technology, located in Gaithersburg, Maryland.
3.14 Response Time means the time it takes for the measurement system, while operating normally at its target sample flow rate or dilution ratio, to respond to a known step change in gas concentration (from a low-level to a high-level gas) and to read within 5 percent of the stable high-level gas response.
3.15 Run means a series of gas samples taken successively from the stack or duct. A test normally consists of a specific number of runs.
3.16 System Calibration Error means the difference between the measured concentration of a low-, mid-, or high-level Hg 0 calibration gas and the certified concentration of the gas when it is introduced in system calibration mode.
3.17 System Calibration Mode means introducing the calibration gases into the measurement system at the probe, upstream of all sample conditioning components.
3.18 Test refers to the series of runs required by the applicable regulation.
4.0 InterferencesInterferences will vary among instruments and potential instrument-specific spectral and matrix interferences must be evaluated through the interference test and the dynamic spiking tests.
5.0 Safety What safety measures should I consider when using this method?This method may require you to work with hazardous materials and in hazardous conditions. You are encouraged to establish safety procedures before using the method. Among other precautions, you should become familiar with the safety recommendations in the gas analyzer user's manual. Occupational Safety and Health Administration (OSHA) regulations concerning use of compressed gas cylinders and noxious gases may apply.
6.0 Equipment and Supplies6.1 What do I need for the measurement system? This method is intended to be applicable to multiple instrumental technologies. You may use any equipment and supplies that meet the following specifications.
6.1.1 All wetted sampling system components, including probe components prior to the point at which the calibration gas is introduced, must be chemically inert to all Hg species. Materials such as perfluoroalkoxy (PFA) Teflon TM, quartz, treated stainless steel (SS) are examples of such materials. [Note: These materials of construction are required because components prior to the calibration gas injection point are not included in the system calibration error, system integrity, and interference tests.]
6.1.2 The interference, system calibration error, system integrity, drift and dynamic spiking test criteria must all be met by the system used.
6.1.3 The system must be capable of measuring and controlling sample flow rate.
6.1.4 All system components prior to the Hg+2 to Hg 0 converter must be maintained at a sample temperature above the acid gas dew point.
6.2 Measurement System Components. Figure 30A-1 in section 17.0 is an example schematic of a Method 30A measurement system.
6.2.1 Sample Probe. The probe must be made of the appropriate materials as noted in section 6.1.1, heated when necessary (see section 6.1.4), configured with ports for introduction of calibration and spiking gases, and of sufficient length to traverse all of the sample points.
6.2.2 Filter or Other Particulate Removal Device. The filter or other particulate removal device is considered to be a part of the measurement system, must be made of appropriate materials as noted in section 6.1.1, and must be included in all system tests.
6.2.3 Sample Line. The sample line that connects the probe to the converter, conditioning system and analyzer must be made of appropriate materials as noted in section 6.1.1.
6.2.4 Conditioning Equipment. For dry basis measurements, a condenser, dryer or other suitable device is required to remove moisture continuously from the sample gas. Any equipment needed to heat the probe, or sample line to avoid condensation prior to the moisture removal component is also required. For wet basis systems, you must keep the sample above its dew point either by: (1) Heating the sample line and all sample transport components up to the inlet of the analyzer (and, for hot-wet extractive systems, also heating the analyzer) or (2) by diluting the sample prior to analysis using a dilution probe system. The components required to do either of the above are considered to be conditioning equipment.
6.2.5 Sampling Pump. A pump is needed to push or pull the sample gas through the system at a flow rate sufficient to minimize the response time of the measurement system. If a mechanical sample pump is used and its surfaces are in contact with the sample gas prior to detection, the pump must be leak free and must be constructed of a material that is non-reactive to the gas being sampled (see section 6.1.1). For dilution-type measurement systems, an ejector pump (eductor) may be used to create a sufficient vacuum that sample gas will be drawn through a critical orifice at a constant rate. The ejector pump may be constructed of any material that is non-reactive to the gas being sampled.
6.2.6 Calibration Gas System(s). One or more systems may be needed to introduce calibration gases into the measurement system. A system should be able to flood the sampling probe sufficiently to prevent entry of gas from the effluent stream.
6.2.7 Dynamic Spiking Port. For the purposes of the dynamic spiking procedure described in section 8.2.7, the measurement system must be equipped with a port to allow introduction of the dynamic spike gas stream with the sample gas stream, at a point as close as possible to the inlet of the probe so as to ensure adequate mixing. The same port used for system calibrations and calibration error checks may be used for dynamic spiking purposes.
6.2.8 Sample Gas Delivery. The sample line may feed directly to a converter, to a by-pass valve (for speciating systems), or to a sample manifold. All valve and/or manifold components must be made of material that is non-reactive to the gas sampled and the calibration gas, and must be configured to safely discharge any excess gas.
6.2.9 Hg Analyzer. An instrument is required that continuously measures the total vapor phase Hg in the gas stream and meets the applicable specifications in section 13.0.
6.2.10 Data Recorder. A recorder, such as a computerized data acquisition and handling system (DAHS), digital recorder, strip chart, or data logger, is required for recording measurement data.
6.3 Moisture Measurement System. If correction of the measured Hg emissions for moisture is required (see section 8.5), either Method 4 in appendix A-3 to this part or other moisture measurement methods approved by the Administrator will be needed to measure stack gas moisture content.
7.0 Reagents and Standards7.1 Calibration Gases. What calibration gases do I need? You will need calibration gases of known concentrations of Hg 0 and HgCl2. Special reagents and equipment may be required to prepare the HgCl 2 gas standards (e.g., a NIST-traceable solution of HgCl2 and a gas generator equipped with mass flow controllers).
The following calibration gas concentrations are required:
7.1.1 High-Level Gas. Equal to the selected calibration span.
7.1.2 Mid-Level Gas. 40 to 60 percent of the calibration span.
7.1.3 Low-Level Gas. 10 to 30 percent of the calibration span.
7.1.4 Zero Gas. No detectable Hg.
7.1.5 Dynamic Spike Gas. The exact concentration of the HgCl2 calibration gas used to perform the pre-test dynamic spiking procedure described in section 8.2.7 depends on the native Hg concentration in the stack The spike gas must produce a spiked sample concentration above the native concentration, as specified in section 8.2.7.2.2.
7.2 Interference Test. What reagents do I need for the interference test? Use the appropriate test gases listed in Table 30A-3 in section 17.0 (i.e., the potential interferents for the source to be tested, as identified by the instrument manufacturer) to conduct the interference check. These gases need not be of protocol gas quality.
8.0 Sample Collection Emission Test ProcedureFigure 30A-2 in section 17.0 presents an overview of the test procedures required by this method. Since you may choose different options to comply with certain performance criteria, you must identify the specific options and associated frequencies you select and document your results in regard to the performance criteria.
8.1 Selection of Sampling Sites and Sampling Points. What sampling site and sampling points do I select?
8.1.1 When this method is used solely for Hg emission testing (e.g., to determine compliance with an emission standard or limit), use twelve sampling points located according to Table 1-1 or Table 1-2 of Method 1 in appendix A-1 to this part. Alternatively, you may conduct a stratification test as described in section 8.1.3 to determine the number and location of the sampling points.
8.1.2 When this method is used for relative accuracy testing of a Hg CEMS or sorbent trap monitoring system, follow the sampling site selection and sampling point layout procedures for gas monitor RATA testing described in the appropriate performance specification or applicable regulation (e.g., Performance Specification 2, section 8.1.3 of appendix B to this part or section 6.5.6 of appendix A to part 75 of this chapter), with one exception. If you elect to perform stratification testing as part of the sampling point selection process, perform the testing in accordance with section 8.1.3 of this method (see also “Summary Table of QA/QC Requirements” in section 9.0).
8.1.3 Determination of Stratification. If you elect to perform stratification testing as part of the sampling point selection process and the test results show your effluent gas stream to be unstratified or minimally stratified, you may be allowed to sample at fewer points or at different points than would otherwise be required.
8.1.3.1 Test Procedure. To test for stratification, use a probe of appropriate length to measure the total vapor phase Hg concentration at twelve traverse points located according to Table 1-1 or Table 1-2 of Method 1 in appendix A-1 to this part. Alternatively, for a sampling location where stratification is expected (e.g., after a wet scrubber or at a point where dissimilar gas streams are combined together), if a 12-point Hg stratification test has been previously performed at that location and the results of the test showed the location to be minimally stratified or unstratified according to the criteria in section 8.1.3.2, you may perform an abbreviated 3-point or 6-point Hg stratification test at the points specified in section 6.5.6.2(a) of appendix A to part 75 of this chapter in lieu of performing the 12-point test. Sample for a minimum of twice the system response time (see section 8.2.6) at each traverse point. Calculate the individual point and mean Hg concentrations.
8.1.3.2 Acceptance Criteria and Sampling Point Location.
8.1.3.2.1 If the Hg concentration at each traverse point differs from the mean concentration for all traverse points by no more than: (a) ±5 percent of the mean concentration; or (b) ±0.2 µg/m 3 (whichever is less restrictive), the gas stream is considered to be unstratified and you may collect samples from a single point that most closely matches the mean.
8.1.3.2.2 If the 5 percent or 0.2 µg/m 3 criterion in section 8.1.3.2.1 is not met, but the Hg concentration at each traverse point differs from the mean concentration for all traverse points by no more than: (a)±10 percent of the mean; or (b)±0.5 µg/m 3 (whichever is less restrictive), the gas stream is considered to be minimally stratified, and you may take samples from three points, provided the points are located on the measurement line exhibiting the highest average Hg concentration during the stratification test. If the stack diameter (or equivalent diameter, for a rectangular stack or duct) is greater than 2.4 meters (7.8 ft), locate the three sampling points at 0.4, 1.0, and 2.0 meters from the stack or duct wall. Alternatively, if a RATA required by part 75 of this chapter is being conducted, you may locate the three points at 4.4, 14.6, and 29.6 percent of the duct diameter, in accordance with Method 1 in appendix A-1 to this part. For stack or duct diameters of 2.4 meters (7.8 ft) or less, locate the three sampling points at 16.7, 50.0, and 83.3 percent of the measurement line.
8.1.3.2.3 If the gas stream is found to be stratified because the 10 percent or 0.5 µg/m 3 criterion in section 8.1.3.2.2 is not met, then either locate three sampling points at 16.7, 50.0, and 83.3 percent of the measurement line that exhibited the highest average Hg concentration during the stratification test, or locate twelve traverse points for the test in accordance with Table 1-1 or Table 1-2 of Method 1 in appendix A-1 to this part; or, if a RATA required by part 75 of this chapter is being conducted, locate six Method 1 points along the measurement line that exhibited the highest average Hg concentration.
8.1.3.3 Temporal Variations. Temporal variations in the source Hg concentration during a stratification test may complicate the determination of stratification. If temporal variations are a concern, you may use the following procedure to normalize the stratification test data. A second Hg measurement system, i.e., either an installed Hg CEMS or another Method 30A system, is required to perform this procedure. Position the sampling probe of the second Hg measurement system at a fixed point in the stack or duct, at least one meter from the stack or duct wall. Then, each time that the Hg concentration is measured at one of the stratification test points, make a concurrent measurement of Hg concentration at the fixed point. Normalize the Hg concentration measured at each traverse point, by multiplying it by the ratio of CF,avg to CF, where CF is the corresponding fixed-point Hg concentration measurement, and CF,avg is the average of all of the fixed-point measurements over the duration of the stratification test. Evaluate the results of the stratification test according to section 8.1.3.2, using the normalized Hg concentrations.
8.1.3.4 Stratification Testing Exemption. Stratification testing need not be performed at a test location where it would otherwise be required to justify using fewer sample points or different sample points, if the owner or operator documents that the Hg concentration in the stack gas is expected to be 3 µg/m 3 or less at the time of a Hg monitoring system RATA or an Hg emissions test. To demonstrate that a particular test location qualifies for the stratification testing exemption, representative Hg emissions data must be collected just prior to the RATA or emissions test. At least one hour of Hg concentration data is required for the demonstration. The data used for the demonstration shall be recorded at process operating conditions that closely approximate the operating conditions that will exist during the RATA or emissions test. It is recommended that collection of the demonstration data be integrated with the on-site pretest procedures required by the reference method being used for the RATA or emissions test (whether this method or another approved Hg reference method is used). Quality-assured data from an installed Hg monitoring system may also be used for the demonstration. If a particular test location qualifies for the stratification testing exemption, sampling shall be performed at three points, as described in section 8.1.3.2.2 of this method. The owner or operator shall fully document the method used to collect the demonstration data and shall keep this documentation on file with the data from the associated RATA or Hg emissions test.
8.1.3.5 Interim Alternative Stratification Test Procedures. In the time period between the effective date of this method and January 1, 2009, you may follow one of the following two procedures. Substitute a stratification test for sulfur dioxide (SO2) for the Hg stratification test described in section 8.1.3.1. If this option is chosen, follow the test procedures in section 6.5.6.1 of appendix A to part 75 of this chapter. Evaluate the test results and determine the sampling point locations according to section 6.5.6.3 of appendix A to part 75 of this chapter. If the sampling location is found to be minimally stratified or unstratified for SO2, it shall be considered minimally stratified or unstratified for Hg. Alternatively, you may forgo stratification testing, assume the gas stream is minimally stratified, and sample at three points as described in section 8.1.3.2.2 of this method.
8.2 Initial Measurement System Performance Tests. What initial performance criteria must my system meet before I begin sampling? Before measuring emissions, perform the following procedures:
(a) Interference Test;
(b) Calibration Gas Verification;
(c) Measurement System Preparation;
(d) 3-Point System Calibration Error Test;
(e) System Integrity Check;
(f) Measurement System Response Time Test; and
(g) Dynamic Spiking Test.
8.2.1 Interference Test (Optional). Your measurement system should be free of known interferences. It is recommended that you conduct this interference test of your measurement system prior to its initial use in the field to verify that the candidate test instrument is free from inherent biases or interferences resulting from common combustion emission constituents. If you have multiple measurement systems with components of the same make and model numbers, you need only perform this interference check on one system and you may also rely on an interference test conducted by the manufacturer on a system having components of the same make and model(s) of the system that you use. The interference test procedure is found in section 8.6 of this method.
8.2.2 Calibration Gas Verification. How must I verify the concentrations of my calibration gases?
8.2.2.1 Cylinder Gas Standards. When cylinder gas standards are used for Hg 0, obtain a certificate from the gas manufacturer and confirm that the documentation includes all information required by an EPA traceability protocol (see section 16). Confirm that the manufacturer certification is complete and current. Ensure that the calibration gas certifications have not expired.
8.2.2.2 Other Calibration Standards. All other calibration standards for HgCl2 and Hg 0, such as gas generators, must meet the requirements of an EPA traceability protocol (see section 16), and the certification procedures must be fully documented in the test report.
8.2.2.3 Calibration Span. Select the calibration span (i.e., high-level gas concentration) so that the measured source emissions are 10 to 100 percent of the calibration span. This requirement is waived for applications in which the Hg concentrations are consistently below 1 µg/m 3; however, the calibration span for these low-concentration applications shall not exceed 5 µg/m 3.
8.2.3 Measurement System Preparation. How do I prepare my measurement system for use? Assemble, prepare, and precondition the measurement system according to your standard operating procedure. Adjust the system to achieve the correct sampling rate or dilution ratio (as applicable). Then, conduct a 3-point system calibration error test using Hg 0 as described in section 8.2.4, an initial system integrity check using HgCl2 and a zero gas as described in section 8.2.5, and a pre-test dynamic spiking test as described in section 8.2.7.
8.2.4 System Calibration Error Test. Conduct a 3-point system calibration error test before the first test run. Use Hg 0 standards for this test. Introduce the low-, mid-, and high-level calibration gases in any order, in system calibration mode, unless you desire to determine the system response time during this test, in which case, inject the gases such that the high-level injection directly follows the low-level injection. For non-dilution systems, you may adjust the system to maintain the correct flow rate at the analyzer during the test, but you may not make adjustments for any other purpose. For dilution systems, you must operate the measurement system at the appropriate dilution ratio during all system calibration error checks, and you may make only the adjustments necessary to maintain the proper ratio. After each gas injection, wait until a stable response has been obtained. Record the analyzer's final, stable response to each calibration gas on a form similar to Table 30A-1 in section 17.0. For each calibration gas, calculate the system calibration error using Equation 30A-1 in section 12.2. The calibration error specification in section 13.1 must be met for the low-, mid-, and high-level gases. If the calibration error specification is not met for all three gases, take corrective action and repeat the test until an acceptable 3-point calibration is achieved.
8.2.5 System Integrity Check. Perform a two-point system integrity check before the first test run. Use the zero gas and either the mid- or high-level HgCl2 calibration gas for the check, whichever one best represents the total vapor phase Hg concentration levels in the stack. Record the data on a form similar to Table 30A-2 in section 17.0. The system integrity check specification in section 13.2 must be met for both the zero gas and the mid- or high-level gas. If the system integrity specification is not met for both gases, take corrective action and repeat the test until an acceptable system integrity check is achieved.
8.2.6 Measurement System Response Time. The measurement system response time is used to determine the minimum sampling time for each sampling point and is equal to the time that is required for the measured Hg concentration to increase from the stable low-level calibration gas response to a value within 5 percent of the stable high-level calibration gas response during the system calibration error test in section 8.2.4. Round off the measured system response time to the nearest minute.
8.2.7 Dynamic Spiking Test. You must perform dynamic spiking prior to the first test run to validate your test data. The purpose of this procedure is to demonstrate that the site-specific flue gas matrix does not adversely affect the accuracy of the measurement system. The specifications in section 13.5 must be met to validate your data. If these specifications are not met for the pre-test dynamic spiking, you may not proceed with the test until satisfactory results are obtained. For the time period between the effective date of this method and January 1, 2009, the dynamic spiking requirement is waived.
8.2.7.1 How do I perform dynamic spiking? Dynamic spiking is a gas phase application of the method of standard additions, which involves injecting a known quantity of Hg into the measurement system upstream of all sample conditioning components, similar to system calibration mode, except the probe is not flooded and the resulting sample stream includes both effluent gas and the spike gas. You must follow a written procedure that details how the spike is added to the system, how the spike dilution factor (DF) is measured, and how the Hg concentration data are collected and processed.
8.2.7.2 Spiking Procedure Requirements.
8.2.7.2.1 Spiking Gas Requirements. The spike gas must also be a HgCl2 calibration gas certified by an EPA traceability protocol. You must choose concentrations that can produce the target levels while being injected at a volumetric flow rate that is ≤20 percent of the total volumetric flow rate through the measurement system (i.e., sample flow rate plus spike gas flow rate).
8.2.7.2.2 Target Spiking Level. The target level for spiking must be 150 to 200 percent of the native Hg concentration; however, if the native Hg concentration is <1 µg/m 3, set the target level to add between 1 and 4 µg/m 3 Hg+2 to the native concentration. Use Equation 30A-5 in section 12.5 to calculate the acceptable range of spike gas concentrations at the target level. Then select a spike gas concentration in that range.
8.2.7.2.3 Spike Injections. You must inject spikes in such a manner that the spiking does not alter the total volumetric sample system flow rate and dilution ratio (if applicable). You must collect at least 3 data points, and the relative standard deviation (RSD) specification in section 13.5 must be met. Each data point represents a single spike injection, and pre- and post-injection measurements of the native Hg concentration (or diluted native concentration, as applicable) are required for each spike injection.
8.2.7.2.4 Spike Dilution Factor (DF). For each spike injection, DF, the dilution factor must be determined. DF is the ratio of the total volumetric flow rate of gas through the measurement system to the spike gas flow rate. This factor must be ≥5. The spiking mass balance calculation is directly dependent on the accuracy of the DF determination. As a result, high accuracy total volumetric flow rate and spike gas flowrate measurements are required. These flow rates may be determined by direct or indirect measurement. Calibrated flow meters, venturies, orifices or tracer gas measurements are examples of potential flow measurement techniques.
8.2.7.2.5 Concentrations. The measurement system must record total vapor phase Hg concentrations continuously during the dynamic spiking procedure. It is possible that dynamic spiking at a level close to 200 percent of the native Hg concentration may cause the measured Hg concentration to exceed the calibration span value. Avoid this by choosing a lower spiking level or by recalibration at a higher span. The measurements shall not exceed 120 percent of the calibration span. The “baseline” measurements made between spikes may represent the native Hg concentration (if spike gas flow is stopped between injections) or the native Hg concentration diluted by blank or carrier gas flowing at the same rate as the spike gas (if gas flow cannot be stopped between injections). Each baseline measurement must include at least 4 readings or 1 minute (whichever is greater) of stable responses. Use Equation 30A-10 or 30A-11 in section 12.10 (as applicable) to convert baseline measurements to native concentration.
8.2.7.2.6 Recovery. Calculate spike recoveries using Equation 30A-7 in section 12.7. Mass recoveries may be calculated from stable responses based on injected mass flows or from integrated response peaks based on total mass injected. Calculate the mean and RSD for the three (or more) spike injections and compare to the specifications in section 13.5.
8.2.7.2.7 Error Adjustment Option. You may adjust the measurement data collected during dynamic spiking for the system calibration error using Equation 30A-3 in section 12. To do this, perform the initial system integrity check prior to the dynamic spiking test, and perform another system integrity check following the dynamic spiking test and before the first test run. If you choose this option, you must apply Equation 30A-3 to both the spiked sample concentration measurement (Css) and the baseline or native concentration measurement (Cnative), each substituted in place of Cavg in the equation.
8.2.7.3 Example Spiking Procedure Using a Hot Vapor Calibration Source Generator.
(a) Introduce the spike gas into the probe using a hot vapor calibration source generator and a solution of HgCl2 in dilute HC1 and HNO3. The calibrator uses a mass flow controller (accurate within 2 percent) to measure the gas flow, and the solution feed is measured using a top-loading balance accurate to 0.01g. The challenges of injecting oxidized Hg may make it impractical to stop the flow of gas between spike injections. In this case, operate the hot vapor calibration source generator continuously during the spiking procedure, swapping blank solutions for HgCl2 solutions when switching between spiking and baseline measurements.
(b) If applicable, monitor the measurement system to make sure the total sampling system flow rate and the sample dilution ratio do not change during this procedure. Record all data on a data sheet similar to Table 30A-5 in section 17.0. If the Hg measurement system design makes it impractical to measure the total volumetric flow rate through the system, use a spike gas that includes a tracer for measuring the dilution factor, DF (see Equation 30A-9 in section 12.9). Allow the measurements to stabilize between each spike injection, average the pre- and post-injection baseline measurements, and calculate the native concentration. If this measurement shifts by more than 5 percent during any injection, it may be necessary to discard that data point and repeat the injection to achieve the required RSD among the injections. If the spikes persistently show poor repeatability, or if the recoveries are not within the range specified in section 13.5, take corrective action.
8.2.8 Run Validation. How do I confirm that each run I conduct is valid?
8.2.8.1 System Integrity Checks.
(a) Before and after each test run, perform a two-point system integrity check using the same procedure as the initial system integrity check described in section 8.2.5. You may use data from that initial system integrity check as the pre-run data for the first test run, provided it is the most recent system integrity check done before the first run. You may also use the results of a successful post-run system integrity check as the pre-run data for the next test run. Do not make any adjustments to the measurement system during these checks, other than to maintain the target calibration gas flow rate and the proper dilution ratio.
(b) As a time-saving alternative, you may, at the risk of invalidating multiple test runs, skip one or more integrity checks during a test day. Provided there have been no auto-calibrations or other instrument alterations, a single integrity check may suffice as a post-run check to validate (or invalidate) as many consecutive test runs as can be completed during a single test day. All subsequent test days must begin with a pre-run system integrity check subject to the same performance criteria and corrective action requirements as a post-run system integrity check.
(c) Each system integrity check must meet the criteria for system integrity checks in section 13.2. If a post-run system integrity check is failed, all test runs since the last passed system integrity check are invalid. If a post-run or a pre-run system integrity check is failed, you must take corrective action and pass another 3-point Hg 0 system calibration error test (Section 8.2.4) followed by another system integrity check before conducting any additional test runs. Record the results of the pre- and post-run system integrity checks on a form similar to Table 30A-2 in section 17.0.
8.2.8.2 Drift Check. Using the data from the successful pre- and post-run system integrity checks, calculate the zero and upscale drift, using Equation 30A-2 in section 12.3. Exceeding the section 13.3 specification does not invalidate the run, but corrective action must be taken and a new 3-point Hg 0 system calibration error test and a system integrity check must be passed before any more runs are made.
8.3 Dilution-Type Systems - Special Considerations. When a dilution-type measurement system is used, there are three important considerations that must be taken into account to ensure the quality of the emissions data. First, the critical orifice size and dilution ratio must be selected properly so that the sample dew point will be below the sample line and analyzer temperatures. Second, a high-quality, accurate dilution controller must be used to maintain the correct dilution ratio during sampling. The dilution controller should be capable of monitoring the dilution air pressure, orifice upstream pressure, eductor vacuum, and sample flow rates. Third, differences between the molecular weight of calibration gas mixtures, dilution air, and the stack gas molecular weight must be considered because these can affect the dilution ratio and introduce measurement bias.
8.4 Sampling.
(a) Position the probe at the first sampling point. Allow the system to flush and equilibrate for at least two times the measurement system response time before recording any data. Then, traverse and record measurements at all required sampling points. Sample at each traverse point for an equal length of time, maintaining the appropriate sample flow rate or dilution ratio (as applicable). For all Hg instrumental method systems, the minimum sampling time at each sampling point must be at least two times the system response time, but not less than 10 minutes. For concentrating systems, the minimum sampling time must also include at least 4 concentration measurement cycles.
(b) After recording data for the appropriate period of time at the first traverse point, you may move the sample probe to the next point and continue recording, omitting the requirement to allow the system to equilibrate for two times the system response time before recording data at the subsequent traverse points. You must, however, sample at this and all subsequent traverse points for the required minimum amount of time specified in this section. If you must remove the probe from the stack for any reason, you must again allow the sampling system to equilibrate for at least two times the system response time prior to resuming data recording.
(c) If at any point the measured Hg concentration exceeds the calibration span value, you must at a minimum identify and report this as a deviation from the method. Depending on the data quality objectives of the test, this event may require corrective action before proceeding. If the average Hg concentration for any run exceeds the calibration span value, the run is invalidated.
8.5 Moisture Correction. If the moisture basis (wet or dry) of the measurements made with this method is different from the moisture basis of either: (1) The applicable emission limit; or (2) a Hg CEMS or sorbent trap monitoring system being evaluated for relative accuracy, you must determine the moisture content of the flue gas and correct the measured gas concentrations to a dry basis using Method 4 in appendix A-3 of this part or other appropriate methods, subject to the approval of the Administrator.
8.6 Optional Interference Test Procedure.
(a) Select an appropriate calibration span that reflects the source(s) to be tested and perform the interference check at 40 percent of the lowest calibration span value anticipated, e.g., 10 µg/m 3. Alternatively, successfully conducting the interference test at an absolute Hg concentration of 2 µg/m 3 will demonstrate performance for an equivalent calibration span of 5 µg/m 3, the lowest calibration span allowed for Method 30A testing. Therefore, performing the interference test at the 2 µ/m 3 level will serve to demonstrate acceptable performance for all calibration spans greater than or equal to 5 µg/m 3.
(b) Introduce the interference test gases listed in Table 30A-3 in section 17.0 into the measurement system separately or as a mixture. The interference test gases HCl and NO must be introduced as a mixture. The interference test gases must be introduced into the sampling system at the probe such that the interference gas mixtures pass through all filters, scrubbers, conditioners, and other components as would be configured for normal sampling.
(c) The interference test must be performed using HgCl2, and each interference test gas (or gas mixture) must be evaluated in triplicate. This is accomplished by measuring the Hg response first with only the HgCl2 gas present and then when adding the interference test gas(es) while maintaining the HgCl2 concentration of the test stream constant. It is important that the equipment used to conduct the interference test be of sufficient quality so as to be capable of blending the HgCl2 and interference gases while maintaining the Hg concentration constant. Gas blending system or manifolds may be used.
(d) The duration of each test should be for a sufficient period of time to ensure the Hg measurement system surfaces are conditioned and a stable output is obtained. Measure the Hg response of the analyzer to these gases in µg/m3. Record the responses and determine the overall interference response using Table 30A-4 in section 17.0 and the equations presented in section 12.11. The specification in section 13.4 must be met.
(e) A copy of these data, including the date completed and a signed certification, must be included with each test report. The intent of this test is that the interference test results are intended to be valid for the life of the system. As a result, the Hg measurement system should be operated and tested in a configuration consistent with the configuration that will be used for field applications. However, if the system used for field testing is not consistent with the system that was interference-tested, the interference test must be repeated before it is used for any field applications. Examples of such conditions include, but are not limited to: major changes in dilution ratio (for dilution based systems), changes in catalyst materials, changes in filtering device design or materials, changes in probe design or configuration, and changes in gas conditioning materials or approaches.
9.0 Quality Control What quality control measures must I take?The table which follows is a summary of the mandatory, suggested, and alternative quality assurance and quality control measures and the associated frequency and acceptance criteria. All of the QC data, along with the run data, must be documented and included in the test report.
Summary Table of QA/QC Requirements
Status 1 | Process or element | QA/QC specification | Acceptance criteria | Checking frequency |
---|---|---|---|---|
S | Identify Data User | Regulatory Agency or other primary end user of data | Before designing test. | |
M | Analyzer Design | Analyzer range | Sufficiently >high-level gas to allow determination of system calibration error | |
S | Analyzer resolution or sensitivity | <2.0 % of full-scale range | Manufacturer design. | |
S | Interference response | Overall response ≤3% of
calibration span Alternatively, overall response ≤0.3 µg/m 3 |
||
M | Calibration Gases | Traceability protocol | Validation of concentration required | |
M | High-level Hg 0 gas | Equal to the calibration span | Each calibration error test. | |
M | Mid-level Hg 0 gas | 40 to 60% of calibration span | Each calibration error test. | |
M | Low-level Hg 0 gas | 10 to 30% of calibration span | Each calibration error test. | |
M | High-level HgCl2 gas | Equal to the calibration span | Each system integrity check (if it better represents Cnative than the mid level gas). | |
M | Mid-level HgCl2 | 40 to 60% of calibration span | Each system gas integrity check (if it better represents Cnative than the high level gas). | |
M | Zero gas | Each system integrity check. | ||
M | Dynamic spike gas (Cnative ≥1 µg/m 3) | A high-concentration HgCl2 gas, used to produce a spiked sample concentration that is 150 to 200% of the native concentration | Pre-test; dynamic spiking not required until 1/1/09. | |
M | Dynamic spike gas (Cnative <1 µg/m 3) | A high-concentration HgCl2 gas, used to produce a spiked sample concentration that is 1 to 2 µg/m 3 above the native concentration | Pre-test; dynamic spiking not required until 1/1/09. | |
S | Data Recorder Design | Data resolution | ≤0.5% of full-scale | Manufacturer design. |
M | Sample Extraction | Probe material | Inert to sample constituents (e.g., PFA Teflon, or quartz if stack >500 °F) | Each run. |
M | Sample Extraction | Probe, filter and sample line temperature | For dry-basis analyzers, keep
sample above the dew point, by heating prior to moisture
removal For wet-basis analyzers, keep sample above dew point at all times, by heating or dilution |
Each run. |
M | Sample Extraction | Calibration valve material | Inert to sample constituents (e.g., PFA Teflon or PFA Teflon coated) | Each test. |
S | Sample Extraction | Sample pump material | Inert to sample constituents | Each test. |
M | Sample Extraction | Manifold material | Inert to sample constituents | Each test. |
M | Particulate Removal | Filter inertness | Pass calibration error check | Each calibration error check. |
M | System Calibration Performance | System calibration error (CE) test | CE ≤5.0 % of the calibration
span for the low-, mid-or high-level Hg 0 calibration
gas Alternative specification: ≤0.5 µg/m 3 absolute difference between system response and reference value |
Before initial run and after a failed system integrity check or drift test. |
M | System Calibration Performance | System integrity check | Error ≤5.0% of the calibration
span for the zero and mid- or high-level HgCl2 calibration gas Alternative specification: ≤0.5 µg/m 3 absolute difference between system response and reference value |
Before initial run, after each run, at the beginning of subsequent test days, and after a failed system integrity check or drift test. |
M | System Performance | System response time | Used to determine minimum sampling time per point | During initial 3-point system calibration error test. |
M | System Performance | Drift | ≤3.0% of calibration span for
the zero and mid- or high-level gas Alternative specification: ≤0.3 µg/m 3 absolute difference between pre- and post-run system calibration error percentages. |
At least once per test day. |
M | System Performance | Minimum sampling time | The greater of two times the system response time or 10 minutes. Concentrating systems must also include at least 4 cycles | Each sampling point. |
M | System Performance | Percentage spike recovery and relative standard deviation | Percentage spike recovery, at
the target level: 100 ±10% Relative standard deviation: ≤5 percent Alternative specification: absolute difference between calculated and measured spike values ≤0.5 µg/m 3 |
Before initial run; dynamic spiking not required until 1/1/09. |
M | Sample Point Selection | Number and Location of Sample Points | For emission testing applications, use 12 points, located according to Method 1 in appendix A-1 to this part, unless the results of a stratification test allow fewer points to be used | Prior to first run. |
For Part 60 RATAs, follow the procedures in Performance Specification 2, section 8.1.3, and for Part 75 RATAs, follow the procedures in section 6.5.6 of appendix A to Part 75. That is: | ||||
• At any test location, you may use 3 sample points located at 16.7, 50.0, and 83.3% of a “long” measurement line passing through the centroidal area; or | ||||
• At any test location, you may use 6 sample points along a diameter, located according to Method 1 (Part 75 RATAs, only); or | ||||
• At a location where stratification is not expected and the measurement line is >2.4 m (7.8 ft), you may use 3 sample points located along a “short” measurement line at 0.4, 1.0, and 2.0 m from the stack or duct wall or, for Part 75 only, sample points may be located at 4.4, 14.6, and 29.6% of the measurement line; or | ||||
• After a wet scrubber or at a point where dissimilar gas streams are combined, either locate 3 sample points along the “long” measurement line or locate 6 Method 1 points along a diameter (Part 75, only), unless the results of a stratification test allow you to use a “short” 3-point measurement line or to sample at a single point | ||||
• If it can be demonstrated that stack gas concentration is ≤3 µg/m 3, then the test site is exempted from stratification testing. Use the 3-point “short” measurement line if the stack diameter is >2.4 m (7.8 ft) and the 3-point “long” line for stack diameters ≤2.4 m (7.8 ft) | ||||
A | Sample Point Selection | Stratification Test (See section 8.1.3). | If the Hg concentration
2 at each traverse point during the stratification test
is: • Within ±5% of mean, use 1-point sampling (at the point closest to the mean); or • Not within ±5% of mean, but is within ±10% of mean, use 3-point sampling. Locate points according to section 8.1.3.2.2 of this method. Alternatively, if the Hg concentration at each point is: • Within ±0.2 µg/m 3 of mean, use 1-point sampling (at the point closest to the mean); or • Not within ±0.2 µg/m 3 of mean, but is within ±0.5 µg/m 3 of mean, use 3-point sampling. Locate points according to section 8.1.3.2.2 of this method. |
Prior to first run. Prior to 1/1/09, you may (1) forgo stratification testing and use 3 sampling points (as per section 8.1.3.2.2) or (2) perform a SO2 stratification test (see sections 6.5.6.1 and 6.5.6.3 of appendix A to part 75), in lieu of a Hg stratification test. If the test location is unstratified or minimally stratified for SO2, it can be considered unstratified or minimally stratified for Hg also. |
M | Data Recording | Frequency | Once per cycle | During run. |
S | Data Parameters | Sample concentration and calibration span | All analyzer readings during each run within calibration span | Each run. |
M | Data Parameters | Sample concentration and calibration span | All analyzer readings during dynamic spiking tests within 120% of calibration span | Each spike injection. |
M | Data Parameters | Sample concentration and calibration span | Average Hg concentration for the run ≤calibration span | Each run. |
1 M = Mandatory; S = Suggested; A = Alternative.
2 These may either be the unadjusted Hg concentrations or concentrations normalized to account for temporal variations.
Your analyzer must be calibrated with Hg° standards. The initial 3-point system calibration error test described in section 8.2.4 is required before you start the test. Also, prior to and following test runs, the two-point system integrity checks described in sections 8.2.5 and 8.2.8 are required. On and after January 1, 2009, the pre-test dynamic spiking procedure described in section 8.2.7 is also required to verify that the accuracy of the measurement system is suitable and not adversely affected by the flue gas matrix.
11.0 Analytical ProceduresBecause sample collection and analysis are performed together (see section 8), additional discussion of the analytical procedure is not necessary.
12.0 Calculations and Data AnalysisYou must follow the procedures for calculations and data analysis listed in this section.
12.1 Nomenclature. The terms used in the equations are defined as follows:
Bws = Moisture content of sample gas as measured by Method 4 in Appendix A-3 to this part, percent/100. Cavg = Average unadjusted Hg concentration for the test run, as indicated by the data recorder µg/m 3. C baseline = Average Hg concentration measured before and after dynamic spiking injections, µg/m 3. Cd = Hg concentration, dry basis, µg/m 3. Cdif = Absolute value of the difference between the measured Hg concentrations of the reference HgCl2 calibration gas, with and without the individual or combined interference gases, µg/m 3. Cdif avg = Average of the 3 absolute values of the difference between the measured Hg concentrations of the reference HgCl2 calibration gas, with and without the individual or combined interference gases, µg/m 3. Cgas = Average Hg concentration in the effluent gas for the test run, adjusted for system calibration error, µg/m 3. Cint = Measured Hg concentration of the reference HgCl2 calibration gas plus the individual or combined interference gases, µg/m 3. Cm = Average of pre- and post-run system integrity check responses for the upscale (i.e., mid- or high-level) calibration gas, µg/m 3. Cma = Actual concentration of the upscale (i.e., mid- or high-level) calibration gas used for the system integrity checks, µg/m 3. C0 = Average of pre- and post-run system integrity check responses from the zero gas, µg/m 3. Cnative = Vapor phase Hg concentration in the source effluent, µg/m 3. Cref = Measured Hg concentration of the reference HgCl2 calibration gas alone, in the interference test, µg/m 3. Cs = Measured concentration of a calibration gas (zero-, low-, mid-, or high-level), when introduced in system calibration mode, µg/m 3. Cspike = Actual Hg concentration of the spike gas, µg/m 3. C*spike = Hg concentration of the spike gas required to achieve a certain target value for the spiked sample Hg concentration, µg/m 3. Css = Measured Hg concentration of the spiked sample at the target level, µg/m 3. C*ss = Expected Hg concentration of the spiked sample at the target level, µg/m 3. Ctarget = Target Hg concentration of the spiked sample, µg/m 3. CTnative = Measured tracer gas concentration present in native effluent gas, ppm. CTdir = Tracer gas concentration injected with spike gas, ppm. CTv = Diluted tracer gas concentration measured in a spiked sample, ppm. Cv = Certified Hg° or HgCl2 concentration of a calibration gas (zero, low, mid, or high), µg/m 3. Cw = Hg concentration measured under moist sample conditions, wet basis, µg/m 3. CS = Calibration span, µg/m 3. D = Zero or upscale drift, percent of calibration span. DF = Dilution factor of the spike gas, dimensionless. I = Interference response, percent of calibration span. Qprobe = Total flow rate of the stack gas sample plus the spike gas, liters/min. Qspike = Flow rate of the spike gas, liters/min. Ri = Individual injection spike recovery, %. R = Mean value of spike recoveries at a particular target level, %. RSD = Relative standard deviation, %;. SCE = System calibration error, percent of calibration span. SCEi = Pre-run system calibration error during the two-point system integrity check, percent of calibration span. SCEf = Post-run system calibration error during the two-point system integrity check, percent of calibration span.12.2 System Calibration Error. Use Equation 30A-1 to calculate the system calibration error. Equation 30A-1 applies to: 3-point system calibration error tests performed with Hg° standards; and pre- and post-run two-point system integrity checks performed with HgCl2.
12.3 Drift Assessment. Use Equation 30A-2 to separately calculate the zero and upscale drift for each test run.
12.3 Effluent Hg Concentration. For each test run, calculate Cavg, the arithmetic average of all valid Hg concentration values recorded during the run. Then, adjust the value of Cavg for system calibration error, using Equation 30A-3.
12.4 Moisture Correction. Use Equation 30A-4a if your measurements need to be corrected to a dry basis.
Use Equation 30A-4b if your measurements need to be corrected to a wet basis.
12.5 Dynamic Spike Gas Concentrations. Use Equation 30A-5 to determine the spike gas concentration needed to produce a spiked sample with a certain “target” Hg concentration.
12.6 Spiked Sample Concentration. Use Equation 30A-6 to determine the expected or theoretical Hg concentration of a spiked sample.
12.7 Spike Recovery. Use Equation 30A-7 to calculate the percentage recovery of each spike.
12.8 Relative Standard Deviation. Use Equation 30A-8 to calculate the relative standard deviation of the individual percentage spike recovery values from the mean.
12.9 Spike Dilution Factor. Use Equation 30A-9 to calculate the spike dilution factor, using either direct flow measurements or tracer gas measurements.
12.10 Native Concentration. For spiking procedures that inject blank or carrier gases (at the spiking flow rate, Qspike) between spikes, use Equation 30A-10 to calculate the native concentration.
For spiking procedures that halt all injections between spikes, the native concentration equals the average baseline concentration (see Equation 30A-11).
12.11 Overall Interference Response. Use equation 30A-12 to calculate the overall interference response.
Where, for each interference gas (or mixture):
13.0 Method Performance13.1 System Calibration Error Test. This specification applies to the 3-point system calibration error tests using Hg 0. At each calibration gas level tested (low-, mid-, or high-level), the calibration error must be within ±5.0 percent of the calibration span. Alternatively, the results are acceptable if | Cs − Cv | ≤0.5 µg/m 3.
13.2 System Integrity Checks. This specification applies to all pre- and post-run 2-point system integrity checks using HgCl2 and zero gas. At each calibration gas level tested (zero and mid- or high-level), the error must be within ±5.0 percent of the calibration span. Alternatively, the results are acceptable if | Cs − Cv | ≤0.5 µg/m 3.
13.3 Drift. For each run, the low-level and upscale drift must be less than or equal to 3.0 percent of the calibration span. The drift is also acceptable if the pre- and post-run system integrity check responses do not differ by more than 0.3 µg/m 3 (i.e., | Cs post-run − Cs pre-run | ≤0.3 µg/m 3).
13.4 Interference Test. Summarize the results following the format contained in Table 30A-4. For each interference gas (or mixture), calculate the mean difference between the measurement system responses with and without the interference test gas(es). The overall interference response for the analyzer that was used for the test (calculated according to Equation 30A-12), must not be greater than 3.0 percent of the calibration span used for the test (see section 8.6). The results of the interference test are also acceptable if the sum of the absolute average differences for all interference gases (i.e., Σ Cdif avg) does not exceed 0.3 µg/m 3.
13.5 Dynamic Spiking Test. For the pre-test dynamic spiking, the mean value of the percentage spike recovery must be 100 ±10 percent. In addition, the relative standard deviation (RSD) of the individual percentage spike recovery values from the mean must be ≤5.0 percent. Alternatively, if the mean percentage recovery is not met, the results are acceptable if the absolute difference between the theoretical spiked sample concentration (see section 12.6) and the actual average value of the spiked sample concentration is ≤0.5 µg/m 3.
14.0 Pollution Prevention [Reserved] 15.0 Waste Management [Reserved] 16.0 References1. EPA Traceability Protocol for Qualification and Certification of Elemental Mercury Gas Generators, expected publication date December 2008, see www.epa.gov/ttn/emc.
2. EPA Traceability Protocol for Qualification and Certification of Oxidized Mercury Gas Generators, expected publication date December 2008, see www.epa.gov/ttn/emc.
3. EPA Traceability Protocol for Assay and Certification of Gaseous Calibration Standards, expected revision publication date December 2008, see www.epa.gov/ttn/emc.
17.0 Figures and TablesTable 30A-3 - Interference Check Gas Concentrations
Potential interferent gas 1 | Concentration, tentative - (balance N2) |
---|---|
CO2 | 15% ±1% CO2 |
CO | 100 ±20 ppm |
HCl 2 | 100 ±20 ppm |
NO 2 | 250 ±50 ppm |
SO2 | 200 ±20 ppm |
O2 | 3% ±1% O2 |
H2O | 10% ±1% H2O |
Nitrogen | Balance |
Other |
1 Any of these specific gases can be tested at a lower level if the manufacturer has provided reliable means for limiting or scrubbing that gas to a specified level.
2 HCl and NO must be tested as a mixture.
Method 30B is a procedure for measuring total vapor phase mercury (Hg) emissions from coal-fired combustion sources using sorbent trap sampling and an extractive or thermal analytical technique. This method is only intended for use only under relatively low particulate conditions (e.g., sampling after all pollution control devices). Quality assurance and quality control requirements are included to assure that you, the tester, collect data of known and acceptable quality for each testing program. This method does not completely describe all equipment, supplies, and sampling and analytical procedures you will need, but instead refers to other test methods for some of the details. Therefore, to obtain reliable results, you should also have a thorough knowledge of these additional methods which are found in Appendices A-1 and A-3 to this part:
(a) Method 1 - Sample and Velocity Traverses for Stationary Sources.
(b) Method 4 - Determination of Moisture Content in Stack Gases.
(c) Method 5 - Determination of Particulate Matter Emissions from Stationary Sources
1.1 Analytes. What does this method determine? This method is designed to measure the mass concentration of total vapor phase Hg in flue gas, including elemental Hg (Hg 0) and oxidized forms of Hg (Hg+2), in micrograms per dry standard cubic meter (µg/dscm).
Analyte | CAS No. | Analytical range and sensitivity |
---|---|---|
Elemental Hg (Hg 0 ) | 7439-97-6 | Typically 0.1 µg/dscm to >50 µg/dscm. |
Oxidized Hg (Hg+2) | (Same) |
1.2 Applicability. When is this method required? Method 30B is a reference method for relative accuracy test audits (RATAs) of vapor phase Hg CEMS and sorbent trap monitoring systems installed at coal-fired boilers and is also appropriate for Hg emissions testing at such boilers. It is intended for use only under relatively low particulate conditions (i.e., sampling after all pollution control devices); in cases where significant amounts of particle-bound Hg may be present, an isokinetic sampling method for Hg should be used. Method 30B may also be specified by New Source Performance Standards (NSPS), National Emission Standards for Hazardous Air Pollutants (NESHAP), emissions trading programs, State Implementation Plans (SIPs), and operating permits that require measurement of Hg concentrations in stationary source emissions, either to determine compliance with an applicable emission standard or limit, or to conduct RATAs of Hg CEMS and sorbent trap monitoring systems.
1.3 Data Quality Objectives (DQO). How good must my collected data be? Method 30B has been designed to provide data of high and known quality for Hg emissions testing and for RATA testing of Hg monitoring systems, including CEMS and sorbent trap monitors. In these and other applications, the principal objective is to ensure the accuracy of the data at the actual emissions levels and in the actual emissions matrix encountered. To meet this objective, NIST-traceable calibration standards must be used and method performance tests are required.
2.0 Summary of MethodKnown volumes of flue gas are extracted from a stack or duct through paired, in-stack sorbent media traps at an appropriate flow rate. Collection of mercury on the sorbent media in the stack mitigates potential loss of mercury during transport through a probe/sample line. For each test run, paired train sampling is required to determine measurement precision and verify acceptability of the measured emissions data. A field recovery test which assesses recovery of an elemental Hg spike to determine measurement bias is also used to verify data acceptability. The sorbent traps are recovered from the sampling system, prepared for analysis as needed, and analyzed by any suitable determinative technique that can meet the performance criteria.
3.0 Definitions3.1 Analytical System is the combined equipment and apparatus used to perform sample analyses. This includes any associated sample preparation apparatus e.g., digestion equipment, spiking systems, reduction devices, etc., as well as analytical instrumentation such as UV AA and UV AF cold vapor analyzers.
3.2 Calibration Standards are the Hg containing solutions prepared from NIST traceable standards and are used to directly calibrate analytical systems.
3.3 Independent Calibration Standard is a NIST traceable standard obtained from a source or supplier independent of that for the calibration standards and is used to confirm the integrity of the calibration standards used.
3.4 Method Detection Limit (MDL) is the lowest mass of Hg greater than zero that can be estimated and reported by your candidate analytical technique. The MDL is statistically derived from replicate low level measurements near your analytical instrument's detection level.
3.5 NIST means the National Institute of Standards and Technology, located in Gaithersburg, Maryland.
3.6 Run means a series of gas samples taken successively from the stack or duct. A test normally consists of a specific number of runs.
3.7 Sorbent Trap means a cartridge or sleeve containing a sorbent media (typically activated carbon treated with iodine or some other halogen) with multiple sections separated by an inert material such as glass wool. These sorbent traps are optimized for the quantitative capture of elemental and oxidized forms of Hg and can be analyzed by multiple techniques.
3.8 Test refers to the series of runs required by the applicable regulation.
3.9 Thermal Analysis means an analytical technique where the contents of the sorbent traps are analyzed using a thermal technique (desorption or combustion) to release the captured Hg in a detectable form for quantification.
3.10 Wet Analysis means an analytical technique where the contents of the sorbent tube are first leached or digested to quantitatively transfer the captured Hg to liquid solution for subsequent analysis.
4.0 InterferencesInterferences may result from the sorbent trap material used as well as from the measurement environment itself. The iodine present on some sorbent traps may impart a negative measurement bias. High levels of sulfur trioxide (SO3) are also suspected to compromise the performance of sorbent trap Hg capture. These, and other, potential interferences are assessed by performing the analytical matrix interference, Hg 0 and HgCl2 analytical bias and field recovery tests.
5.0 SafetyWhat safety measures should I consider when using this method? This method may require you to work with hazardous materials and in hazardous conditions. You are encouraged to establish safety procedures before using the method. Among other precautions, you should become familiar with the safety recommendations in the gas analyzer user's manual. Occupational Safety and Health Administration (OSHA) regulations concerning use of compressed gas cylinders and noxious gases may apply.
5.1 Site Hazards. Prior to applying these procedures/specifications in the field, the potential hazards at the test site should be considered; advance coordination with the site is critical to understand the conditions and applicable safety policies. At a minimum, portions of the sampling system will be hot, requiring appropriate gloves, long sleeves, and caution in handling this equipment.
5.2 Laboratory Safety. Policies should be in place to minimize risk of chemical exposure and to properly handle waste disposal in the laboratory. Personnel shall wear appropriate laboratory attire according to a Chemical Hygiene Plan established by the laboratory.
5.3 Reagent Toxicity/Carcinogenicity. The toxicity and carcinogenicity of any reagents used must be considered. Depending upon the sampling and analytical technologies selected, this measurement may involve hazardous materials, operations, and equipment and this method does not address all of the safety problems associated with implementing this approach. It is the responsibility of the user to establish appropriate safety and health practices and determine the applicable regulatory limitations prior to performance. Any chemical should be regarded as a potential health hazard and exposure to these compounds should be minimized. Chemists should refer to the Material Safety Data Sheet (MSDS) for each chemical used.
5.4 Waste Disposal. Any waste generated by this procedure must be disposed of according to a hazardous materials management plan that details and tracks various waste streams and disposal procedures.
6.0 Equipment and SuppliesThe following list is presented as an example of key equipment and supplies likely required to measure vapor-phase Hg using a sorbent trap sampling system. It is recognized that additional equipment and supplies may be needed. Collection of paired samples is required.
6.1 Sorbent Trap Sampling System. A typical sorbent trap sampling system is shown in Figure 30B-1 in section 17.0. The sorbent trap sampling system shall include the following components:
6.1.1 Sorbent Traps. The sorbent media used to collect Hg must be configured in a trap with at least two distinct segments or sections, connected in series, that are amenable to separate analyses. section 1 is designated for primary capture of gaseous Hg. section 2 is designated as a backup section for determination of vapor phase Hg breakthrough. Each sorbent trap must be inscribed or otherwise permanently marked with a unique identification number, for tracking purposes. The sorbent media may be any collection material (e.g., carbon, chemically-treated filter, etc.) capable of quantitatively capturing and recovering for subsequent analysis, all gaseous forms of Hg in the emissions from the intended application. Selection of the sorbent media shall be based on the material's ability to achieve the performance criteria contained in this method as well as the sorbent's vapor phase Hg capture efficiency for the emissions matrix and the expected sampling duration at the test site. The sorbent media must be obtained from a source that can demonstrate their quality assurance and quality control (see section 7.2). The paired sorbent traps are supported on a probe (or probes) and inserted directly into the flue gas stream.
6.1.2 Sampling Probe Assembly. Each probe assembly shall have a leak-free attachment to the sorbent trap(s). Each sorbent trap must be mounted at the entrance of or within the probe such that the gas sampled enters the trap directly. Each probe/sorbent trap assembly must be heated to a temperature sufficient to prevent liquid condensation in the sorbent trap(s). Auxiliary heating is required only where the stack temperature is too low to prevent condensation. Use a calibrated thermocouple to monitor the stack temperature. A single probe capable of operating the paired sorbent traps may be used. Alternatively, individual probe/sorbent trap assemblies may be used, provided that the individual sorbent traps are co-located to ensure representative Hg monitoring.
6.1.3 Moisture Removal Device. A moisture removal device or system shall be used to remove water vapor from the gas stream prior to entering dry gas flow metering devices.
6.1.4 Vacuum Pump. Use a leak-tight, vacuum pump capable of operating within the system's flow range.
6.1.5 Gas Flow Meter. A gas flow meter (such as a dry gas meter, thermal mass flow meter, or other suitable measurement device) shall be used to determine the total sample volume on a dry basis, in units of standard cubic meters. The meter must be sufficiently accurate to measure the total sample volume to within 2 percent and must be calibrated at selected flow rates across the range of sample flow rates at which the sampling train will be operated. The gas flow meter shall be equipped with any necessary auxiliary measurement devices (e.g., temperature sensors, pressure measurement devices) needed to correct the sample volume to standard conditions.
6.1.6 Sample Flow Rate Meter and Controller. Use a flow rate indicator and controller for maintaining necessary sampling flow rates.
6.1.7 Temperature Sensor. Same as section 6.1.1.7 of Method 5 in Appendix A-3 to this part.
6.1.8 Barometer. Same as section 6.1.2 of Method 5 in Appendix A-3 to this part.
6.1.9 Data Logger (optional). Device for recording associated and necessary ancillary information (e.g., temperatures, pressures, flow, time, etc.).
6.2 Gaseous Hg 0 Sorbent Trap Spiking System. A known mass of gaseous Hg 0 must be either present on or spiked onto the first section of sorbent traps in order to perform the Hg 0 and HgCl2 analytical bias test and the field recovery study. Any approach capable of quantitatively delivering known masses of Hg 0 onto sorbent traps is acceptable. Several spiking technologies or devices are available to meet this objective. Their practicality is a function of Hg mass spike levels. For low levels, NIST-certified or NIST-traceable gas generators or tanks may be suitable. An alternative system, capable of delivering almost any mass required, makes use of NIST-certified or NIST-traceable Hg salt solutions (e.g., HgCl2, Hg(NO3)2). With this system, an aliquot of known volume and concentration is added to a reaction vessel containing a reducing agent (e.g., stannous chloride); the Hg salt solution is reduced to Hg 0 and purged onto the sorbent trap using an impinger sparging system. When available, information on example spiking systems will be posted at http://www.epa.gov/ttn/emc.
6.3 Sample Analysis Equipment. Any analytical system capable of quantitatively recovering and quantifying total Hg from the sorbent media selected is acceptable provided that the analysis can meet the performance criteria described in this method. Example recovery techniques include acid leaching, digestion, and thermal desorption/direct combustion. Example analytical techniques include, but are not limited to, ultraviolet atomic fluorescence (UV AF), ultraviolet atomic absorption (UV AA) with and without gold trapping, and X-ray fluorescence (XRF) analysis.
6.3 Moisture Measurement System. If correction of the measured Hg emissions for moisture is required (see section 8.3.3.7), either Method 4 in Appendix A-3 to this part or other moisture measurement methods approved by the Administrator will be needed to measure stack gas moisture content.
7.0 Reagents and Standards7.1 Reagents and Standards. Only NIST-certified or NIST-traceable calibration standards, standard reference materials, and reagents shall be used for the tests and procedures required by this method.
7.2 Sorbent Trap Media. The sorbent trap media shall be prepared such that the material used for testing is of known and acceptable quality. Sorbent supplier quality assurance/quality control measures to ensure appropriate and consistent performance such as sorptive capacity, uniformity of preparation treatments, and background levels shall be considered.
8.0 Sample Collection and HandlingThis section presents the sample collection and handling procedures along with the pretest and on-site performance tests required by this method. Since you may choose different options to comply with certain performance criteria, each test report must identify the specific options selected and document the results with respect to the performance criteria of this method.
8.1 Selection of Sampling Sites and Sampling Points. What sampling site and sampling points do I select? Same as section 8.1 of Method 30A of this appendix.
8.2 Measurement System Performance Tests. What performance criteria must my measurement system meet? The following laboratory and field procedures and associated criteria of this section are designed to ensure (1) selection of a sorbent and analytical technique combination capable of quantitative collection and analysis of gaseous Hg, (2) collection of an adequate amount of Hg on each sorbent trap during field tests, and (3) adequate performance of the method for each test program: The primary objectives of these performance tests are to characterize and verify the performance of your intended analytical system and associated sampling and analytical procedures, and to define the minimum amount of Hg (as the sample collection target) that can be quantified reliably.
(a) Analytical Matrix Interference Test;
(b) Determination of Minimum Sample Mass;
(c) Hg 0 and HgCl2 Analytical Bias Test;
(d) Determination of Nominal Sample Volume;
(e) Field Recovery Test.
8.2.1 Analytical Matrix Interference Test and Minimum Sample Dilution.
(a) The analytical matrix interference test is a laboratory procedure. It is required only if you elect to use a liquid digestion analytical approach and needs to be performed only once for each sorbent material used. The purpose of the test is to verify the presence or absence of known and potential analytical matrix interferences, including the potential negative bias associated with iodine common to many sorbent trap materials. The analytical matrix interference test determines the minimum dilution (if any) necessary to mitigate matrix effects on the sample digestate solutions.
(b) The result of the analytical matrix interference test, i.e., the minimum sample dilution required (if any) for all sample analyses, is used to establish the minimum sample mass needed for the Hg 0 and HgCl2 analytical bias test and to determine the nominal sample volume for a test run. The analytical matrix interference test is sorbent material-specific and shall be performed for each sorbent material you intend to use for field sampling and analysis. The test shall be performed using a mass of sorbent material comparable to the sorbent mass typically used in the first section of the trap for sampling. Similar sorbent materials from different sources of supply are considered to be different materials and must be tested individually. You must conduct the analytical matrix interference test for each sorbent material prior to the analysis of field samples.
8.2.1.1 Analytical Matrix Interference Test Procedures. Digest and prepare for analysis a representative mass of sorbent material (unsampled) according to your intended laboratory techniques for field samples. Analyze the digestate according to your intended analytical conditions at the least diluted level you intend to use for sample analysis (e.g., undiluted, 1 in 10 dilution, etc.). Determine the Hg concentration of the undiluted digestate solution. Prepare a series of solutions with a fixed final volume containing graduated aliquots of the sample digestate and, a fixed aliquot of a calibration standard (with the balance being Hg-free reagent or H20) to establish solutions of varied digestate dilution ratio (e.g., 1:2, 1:5, 1:10, 1:100, etc. - see example in section 8.2.1.3, below). One of these solutions should contain only the aliquot of the calibration standard in Hg-free reagent or H2O. This will result in a series of solutions where the amount of Hg is held relatively constant and only the volume of digestate diluted is varied. Analyze each of these solutions following intended sample analytical procedures and conditions, determining the concentration for each solution.
8.2.1.2 Analytical Matrix Interference Test Acceptance Criteria. Compare the measured concentration of each solution containing digestate to the measured concentration of the digestate-free solution. The lowest dilution ratio of any solution having a Hg concentration within ±5 percent of the digestate-free solution is the minimum dilution ratio required for analysis of all samples. If you desire to measure the digestate without dilution, the ±5 percent criterion must be met at a dilution ratio of at least 9:10 (i.e., ≥90% digestate).
8.2.1.3 Example Analytical Matrix Interference Test. An example analytical matrix interference test is presented below. Additional information on the conduct of the analytical matrix interference test will be posted at http://www.epa.gov/ttn/emc. Determine the most sensitive working range for the analyzer to be used. This will be a narrow range of concentrations. Digest and prepare for analysis a representative mass of sorbent material (unsampled) according to your intended laboratory techniques for sample preparation and analysis. Prepare a calibration curve for the most sensitive analytical region, e.g., 0.0, 0.5, 1.0, 3.0, 5.0, 10 ppb. Using the highest calibration standard, e.g., 10.0 ppb, prepare a series of solutions by adding successively smaller increments of the digestate to a fixed volume of the calibration standard and bringing each solution to a final fixed volume with mercury-free deionized water (diH2O). To 2.0 ml of the calibration standard add 18.0, 10.0, 4.0, 2.0, 1.0, 0.2, and 0.0 ml of the digestate. Bring the final volume of each solution to a total volume of 20 ml by adding 0.0, 8.0, 14.0, 16.0, 17.0, 17.8, and 18.0 ml of diH2O. This will yield solutions with dilution ratios of 9:10, 1:2, 1:5, 1:10, 1:20, 1:100, and 0:10, respectively. Determine the Hg concentration of each solution. The dilution ratio of any solution having a concentration that is within ±5 percent of the concentration of the solution containing 0.0 ml of digestate is an acceptable dilution ratio for analyzing field samples. If more than one solution meets this criterion, the one with the lowest dilution ratio is the minimum dilution required for analysis of field samples. If the 9:10 dilution meets this criterion, then no sample dilution is required.
8.2.2 Determination of Minimum Sample Mass. The minimum mass of Hg that must be collected per sample must be determined. This information is necessary in order to effectively perform the Hg 0 and HgCl2 Analytical Bias Test, to estimate target sample volumes/sample times for test runs, and to ensure the quality of the measurements. The determination of minimum sample mass is a direct function of analytical technique, measurement sensitivity, dilutions, etc. This determination is required for all analytical techniques. Based on the analytical approach you employ, you should determine the most sensitive calibration range. Based on a calibration point within that range, you must consider all sample treatments (e.g., dilutions) to determine the mass of sample that needs to be collected to ensure that all sample analyses fall within your calibration curve.
8.2.2.1 Determination of Minimum Calibration Concentration or Mass. Based on your instrument's sensitivity and linearity, determine the calibration concentrations or masses that make up a representative low level calibration range. Verify that you are able to meet the multipoint calibration performance criteria in section 11.0 of this method. Select a calibration concentration or mass that is no less than 2 times the lowest concentration or mass in your calibration curve. The lowest point in your calibration curve must be at least 5, and preferably 10, times the Method Detection Limit (MDL), which is the minimum amount of the analyte that can be detected and reported. The MDL must be determined at least once for the analytical system using an MDL study such as that found in section 15.0 to Method 301 of appendix A to part 63 of this chapter.
Note to section 8.2.2.1:While it might be desirable to base the minimum calibration concentration or mass on the lowest point in the calibration curve, selecting a higher concentration or mass is necessary to ensure that all analyses of the field samples will fall within the calibration curve. Therefore, it is strongly recommended that you select a minimum calibration concentration or mass that is sufficiently above the lowest point of the calibration curve (see examples in sections 8.2.2.2.1 and 8.2.2.2.2 below).
8.2.2.2 Determination of Minimum Sample Mass. Based on your minimum calibration concentration or mass and other sample treatments including, but not limited to, final digestate volume and minimum sample dilution, determine the minimum sample mass. Consideration should also be given to the Hg levels expected to be measured in section 2 of the sorbent traps and to the breakthrough criteria presented in Table 9-1.
8.2.2.2.1 Example Determination of Minimum Sample Mass for Thermal Desorption Analysis. A thermal analysis system has been calibrated at five Hg mass levels: 10 ng, 20 ng, 50 ng, 100 ng, 200 ng, and shown to meet the calibration performance criteria in this method. Based on 2 times the lowest point in the calibration curve, 20 ng is selected as the minimum calibration mass. Because the entire sample is analyzed and there are no dilutions involved, the minimum sample mass is also 20 ng.
Note:In this example, if the typical background (blank) Hg levels in section 2 were relatively high (e.g., 3 to 5 ng), a sample mass of 20 ng might not have been sufficient to ensure that the breakthrough criteria in Table 9-1 would be met, thereby necessitating the use of a higher point on the calibration curve (e.g., 50 ng) as the minimum calibration and sample mass.
8.2.2.2.2 Example Determination of Minimum Sample Mass for Acid Leachate/Digestate Analysis. A cold vapor analysis system has been calibrated at four Hg concentration levels: 2 ng/L, 5 ng, 10 ng/L, 20 ng/L, and shown to meet the calibration performance criteria in this method. Based on 2 times the lowest point in the calibration curve, 4 ng/L was selected as the minimum calibration concentration. The final sample volume of a digestate is nominally 50 ml (0.05 L) and the minimum dilution necessary was determined to be 1:100 by the Analytical Matrix Interference Test of section 8.2.1. The following calculation would be used to determine the minimum sample mass.
Minimum sample mass = (4 ng/L) × (0.05 L) × (100) = 20 ng Note:In this example, if the typical background (blank) Hg levels in section 2 were relatively high (e.g., 3 to 5 ng), a sample mass of 20 ng might not have been sufficient to ensure that the breakthrough criterion in Table 9-1 would be met, thereby necessitating the use of a higher point on the calibration curve (e.g., 10 ng/L) as the minimum calibration concentration.
8.2.3 Hg 0 and HgCl2 Analytical Bias Test. Before analyzing any field samples, the laboratory must demonstrate the ability to recover and accurately quantify Hg 0 and HgCl2 from the chosen sorbent media by performing the following analytical bias test for sorbent traps spiked with Hg 0 and HgCl2. The analytical bias test is performed at a minimum of two distinct sorbent trap Hg loadings that will: (1) Represent the lower and upper bound of sample Hg loadings for application of the analytical technique to the field samples, and (2) be used for data validation.
8.2.3.1 Hg 0 and HgCl2 Analytical Bias Test Procedures. Determine the lower and upper bound mass loadings. The minimum sample mass established in section 8.2.2.2 can be used for the lower bound Hg mass loading although lower Hg loading levels are acceptable. The upper bound Hg loading level should be an estimate of the greatest mass loading that may result as a function of stack concentration and volume sampled. As previously noted, this test defines the bounds that actual field samples must be within in order to be valid.
8.2.3.1.1 Hg 0 Analytical Bias Test. Analyze the front section of three sorbent traps containing Hg 0 at the lower bound mass loading level and the front section of three sorbent traps containing Hg 0 at the upper bound mass loading level. In other words, analyze each mass loading level in triplicate. You may refer to section 6.2 for spiking guidance. Prepare and analyze each spiked trap, using the same techniques that will be used to prepare and analyze the field samples. The average recovery for the three traps at each mass loading level must be between 90 and 110 percent. If multiple types of sorbent media are to be analyzed, a separate analytical bias test is required for each sorbent material.
8.2.3.1.2 HgCl2 Analytical Bias Test. Analyze the front section of three sorbent traps containing HgCl2 at the lower bound mass loading level and the front section of three traps containing HgCl2 at the upper bound mass loading level. HgCl2 can be spiked as a gas, or as a liquid solution containing HgCl2. However the liquid volume spiked must be <100 µL. Prepare and analyze each spiked trap, using the techniques that will be used to prepare and analyze the field samples. The average recovery for three traps at each spike concentration must be between 90 and 110 percent. Again, if multiple types of sorbent media are to be analyzed, a separate analytical bias test is required for each sorbent material.
8.2.4 Determination of Target Sample Volume. The target sample volume is an estimate of the sample volume needed to ensure that valid emissions data are collected (i.e., that sample mass Hg loadings fall within the analytical calibration curve and are within the upper and lower bounds set by the analytical bias tests). The target sample volume and minimum sample mass can also be determined by performing a diagnostic test run prior to initiation of formal testing.
Example:If the minimum sample mass is 50 ng and the concentration of mercury in the stack gas is estimated to be 2 µg/m 3 (ng/L) then the following calculation would be used to determine the target sample volume: Target Sample Volume = (50 ng) / (2 ng/L) = 25 L Note to section 8.2.4:For the purposes of relative accuracy testing of Hg monitoring systems under subpart UUUUU of part 63 of this chapter and Performance Specifications 12A and 12B in appendix B to this part, when the stack gas Hg concentration is expected to be very low (<0.5 µg/dscm), you may estimate the Hg concentration at 0.5 µg/dscm.
8.2.5 Determination of Sample Run Time. Sample run time will be a function of minimum sample mass (see section 8.2.2), target sample volume and nominal equipment sample flow rate. The minimum sample run time for conducting relative accuracy test audits of Hg monitoring systems is 30 minutes and for emissions testing to characterize an emission source is 1 hour. The target sample run time can be calculated using the following example.
Example:If the target sample volume has been determined to be 25 L, then the following formula would be used to determine the sampling time necessary to acquire 25 L of gas when sampling at a rate of 0.4 L/min. Sampling time (min) = 25 L / 0.4 L/min = 63 minutes8.2.6 Field Recovery Test. The field recovery test provides a test program-specific verification of the performance of the combined sampling and analytical approach. Three sets of paired samples, one of each pair which is spiked with a known level of Hg, are collected and analyzed and the average recovery of the spiked samples is used to verify performance of the measurement system under field conditions during that test program. The conduct of this test requires an estimate or confirmation of the stack Hg concentrations at the time of testing.
8.2.6.1 Calculation of Pre-sampling Spiking Level. Determine the sorbent trap spiking level for the field recovery test using estimates of the stack Hg concentration, the target sample flow rate, and the planned sample duration. First, determine the Hg mass expected to be collected in section 1 of the sorbent trap. The pre-sampling spike must be within 50 to 150 percent of this expected mass.
Example calculation:For an expected stack Hg concentration of 5 ug/m 3 (ng/L) a target sample rate of 0.40 liters/min, and a sample duration of 1 hour: (0.40 L/min) * (60 min) * (5ng/L) = 120 ngA Hg spike of 60 to 180 ng (50-150% of 120 ng) would be appropriate.
8.2.6.2 Procedures. Set up two identical sampling trains. One of the sampling trains shall be designated the spiked train and the other the unspiked train. Spike Hg 0 onto the front section of the sorbent trap in the spiked train before sampling. The mass of Hg spiked shall be 50 to 150 percent of the mass expected to be collected with the unspiked train. Sample the stack gas with the two trains simultaneously using the same procedures as for the field samples (see section 8.3). The total sample volume must be within ±20 percent of the target sample volume for the field sample test runs. Analyze the sorbent traps from the two trains utilizing the same analytical procedures and instrumentation as for the field samples (see section 11.0). Determine the fraction of spiked Hg recovered (R) using the equations in section 12.7. Repeat this procedure for a total of three runs. Report the individual R values in the test report; the average of the three R values must be between 85 and 115 percent.
Note to section 8.2.6.2:It is acceptable to perform the field recovery test concurrent with actual test runs (e.g., through the use of a quad probe). It is also acceptable to use the field recovery test runs as test runs for emissions testing or for the RATA of a Hg monitoring system under subpart UUUUU of part 63 of this chapter and Performance Specifications 12A and 12B in appendix B to this part, if certain conditions are met. To determine whether a particular field recovery test run may be used as a RATA run, subtract the mass of the Hg 0 spike from the total Hg mass collected in sections 1 and 2 of the spiked trap. The difference represents the mass of Hg in the stack gas sample. Divide this mass by the sample volume to obtain the Hg concentration in the effluent gas stream, as measured with the spiked trap. Compare this concentration to the corresponding Hg concentration measured with the unspiked trap. If the paired trains meet the relative deviation and other applicable data validation criteria in Table 9-1, then the average of the two Hg concentrations may be used as an emissions test run value or as the reference method value for a RATA run.
8.3 Sampling. This section describes the procedures and criteria for collecting the field samples for analysis. As noted in section 8.2.6, the field recovery test samples are also collected using these procedures.
8.3.1 Pre-test leak check. Perform a leak check of the sampling system with the sorbent traps in place. For each of the paired sampling trains, draw a vacuum in the train, and adjust the vacuum to ∼15″ Hg; and, using the gas flow meter, determine leak rate. The leak rate for an individual train must not exceed 4 percent of the target sampling rate. Once the leak check passes this criterion, carefully release the vacuum in the sample train, then seal the sorbent trap inlet until the probe is ready for insertion into the stack or duct.
8.3.2 Determination of Flue Gas Characteristics. Determine or measure the flue gas measurement environment characteristics (gas temperature, static pressure, gas velocity, stack moisture, etc.) in order to determine ancillary requirements such as probe heating requirements (if any), initial sampling rate, moisture management, etc.
8.3.3 Sample Collection
8.3.3.1 Remove the plug from the end of each sorbent trap and store each plug in a clean sorbent trap storage container. Remove the stack or duct port cap and insert the probe(s). Secure the probe(s) and ensure that no leakage occurs between the duct and environment.
8.3.3.2 Record initial data including the sorbent trap ID, date, and the run start time.
8.3.3.3 Record the initial gas flow meter reading, stack temperature, meter temperatures (if needed), and any other appropriate information, before beginning sampling. Begin sampling and target a sampling flow rate similar to that for the field recovery test. Then, at regular intervals (≤5 minutes) during the sampling period, record the date and time, the sample flow rate, the gas meter reading, the stack temperature, the flow meter temperatures (if using a dry gas meter), temperatures of heated equipment such as the vacuum lines and the probes (if heated), and the sampling system vacuum readings. Adjust the sampling flow rate as necessary to maintain the initial sample flow rate. Ensure that the total volume sampled for each run is within 20 percent of the total volume sampled for the field recovery test.
8.3.3.4 Data Recording. Obtain and record any essential operating data for the facility during the test period, e.g., the barometric pressure must be obtained for correcting sample volume to standard conditions when using a dry gas meter. At the end of the data collection period, record the final gas flow meter reading and the final values of all other essential parameters.
8.3.3.5 Post-Test Leak Check. When sampling is completed, turn off the sample pump, remove the probe(s) with sorbent traps from the port, and carefully seal the end of each sorbent trap. Perform another leak check of each sampling train with the sorbent trap in place, at the maximum vacuum reached during the sampling period. Record the leakage rates and vacuums. The leakage rate for each train must not exceed 4 percent of the average sampling rate for the data collection period. Following each leak check, carefully release the vacuum in the sample train.
8.3.3.6 Sample Recovery. Recover each sampled sorbent trap by removing it from the probe and sealing both ends. Wipe any deposited material from the outside of the sorbent trap. Place the sorbent trap into an appropriate sample storage container and store/preserve in appropriate manner (see section 8.3.3.8).
8.3.3.7 Stack Gas Moisture Determination. If the moisture basis of the measurements made with this method (dry) is different from the moisture basis of either: (1) the applicable emission limit; or (2) a Hg CEMS being evaluated for relative accuracy, you must determine the moisture content of the flue gas and correct for moisture using Method 4 in appendix A-3 to this part. If correction of the measured Hg concentrations for moisture is required, at least one Method 4 moisture determination shall be made during each test run.
8.3.3.8 Sample Handling, Preservation, Storage, and Transport. While the performance criteria of this approach provides for verification of appropriate sample handling, it is still important that the user consider, determine and plan for suitable sample preservation, storage, transport, and holding times for these measurements. Therefore, procedures in ASTM D6911-15 “Standard Guide for Packaging and Shipping Environmental Samples for Laboratory Analysis” (incorporated by reference-see 40 CFR 60.17) shall be followed for all samples, where appropriate. To avoid Hg contamination of the samples, special attention should be paid to cleanliness during transport, field handling, sampling, recovery, and laboratory analysis, as well as during preparation of the sorbent cartridges. Collection and analysis of blank samples (e.g., reagent, sorbent, field, etc.) is useful in verifying the absence or source of contaminant Hg.
8.3.3.9 Sample Custody. Proper procedures and documentation for sample chain of custody are critical to ensuring data integrity. The chain of custody procedures in ASTM D4840-99 “Standard Guide for Sampling Chain-of-Custody Procedures” shall be followed for all samples (including field samples and blanks).
9.0 Quality Assurance and Quality ControlTable 9-1 summarizes the QA/QC performance criteria that are used to validate the Hg emissions data from Method 30B sorbent trap measurement systems.
Table 9-1 - Quality Assurance/Quality Control Criteria for Method 30B
QA/QC test or specification | Acceptance criteria | Frequency | Consequences if not met |
---|---|---|---|
Gas flow meter calibration (At 3 settings or points) | Calibration factor (Yi) at each flow rate must be within ±2% of the average value (Y) | Prior to initial use and when post-test check is not within ±5% of Y | Recalibrate at 3 points until the acceptance criteria are met. |
Gas flow meter post-test calibration check (Single-point) | Calibration factor (Yi) must be within ±5% of the Y value from the most recent 3-point calibration | After each field test. For mass flow meters, must be done on-site, using stack gas | Recalibrate gas flow meter at 3 points to determine a new value of Y. For mass flow meters, must be done on-site, using stack gas. Apply the new Y value to the field test data. |
Temperature sensor calibration | Absolute temperature measures by sensor within ±1.5% of a reference sensor | Prior to initial use and before each test thereafter | Recalibrate; sensor may not be used until specification is met. |
Barometer calibration | Absolute pressure measured by instrument within ±10 mm Hg of reading with a mercury barometer or NIST traceable barometer | Prior to initial use and before each test thereafter | Recalibrate; instrument may not be used until specification is met. |
Pre-test leak check | ≤4% of target sampling rate | Prior to sampling | Sampling shall not commence until the leak check is passed. |
Post-test leak check | ≤4% of average sampling rate | After sampling | Sample invalidated.* |
Analytical matrix interference test (wet chemical analysis, only) | Establish minimum dilution (if any) needed to eliminate sorbent matrix interferences | Prior to analyzing any field samples; repeat for each type of sorbent used | Field sample results not validated. |
Analytical bias test | Average recovery between 90% and 110% for Hg 0 and HgCl2 at each of the 2 spike concentration levels | Prior to analyzing field samples and prior to use of new sorbent media | Field samples shall not be analyzed until the percent recovery criteria has been met. |
Multipoint analyzer calibration | Each analyzer reading within ±10% of true value and r 2≥0.99 | On the day of analysis, before analyzing any samples | Recalibrate until successful. |
Analysis of independent calibration standard | Within ±10% of true value | Following daily calibration, prior to analyzing field samples | Recalibrate and repeat independent standard analysis until successful. |
Analysis of continuing calibration verification standard (CCVS) | Within ±10% of true value | Following daily calibration, after analyzing ≤10 field samples, and at end of each set of analyses | Recalibrate and repeat independent standard analysis, reanalyze samples until successful, if possible; for destructive techniques, samples invalidated. |
Test run total sample volume | Within ±20% of total volume sampled during field recovery test | Each individual sample | Sample invalidated. |
Sorbent trap section 2 breakthrough | For compliance/emissions testing: | Every sample | Sample invalidated.* |
≤10% of section 1 Hg mass for Hg concentrations >1 µg/dscm; | |||
≤20% of section 1 Hg mass for Hg concentrations ≤1 µg/dscm | |||
≤50% of section 1 Hg mass if the stack Hg concentration is ≤30% of the Hg concentration that is equivalent to the applicable emission limit | |||
For relative accuracy testing: | |||
≤10% of section 1 Hg mass for Hg concentrations >1 µg/dscm; | |||
≤20% of section 1 Hg mass for Hg concentrations ≤1 µg/dscm and >0.5 µg/dscm; | |||
≤50% of section 1 Hg mass for Hg concentrations ≤0.5 µg/dscm >0.1 µg/dscm; | |||
no criterion for Hg concentrations ≤0.1 µg/dscm (must meet all other QA/QC specifications) | |||
Paired sorbent trap agreement | ≤10% Relative Deviation (RD) mass for Hg concentrations >1 µg/dscm; | Every run | Run invalidated.* |
≤20% RD or ≤0.2 µg/dscm absolute difference for Hg concentrations ≤1 µg/dscm | |||
Sample analysis | Within valid calibration range (within calibration curve) | All Section 1 samples where stack Hg concentration is ≥0.02 µg/dscm except in case where stack Hg concentration is ≤30% of the applicable emission limit | Reanalyze at more concentrated level if possible, samples invalidated if not within calibrated range. |
Sample analysis | Within bounds of Hg 0 and HgCl2 Analytical Bias Test | All Section 1 samples where stack Hg concentration is ≥0.5 µg/dscm | Expand bounds of Hg 0 and HgCl2 Analytical Bias Test; if not successful, samples invalidated. |
Field recovery test | Average recovery between 85% and 115% for Hg 0 | Once per field test | Field sample runs not validated without successful field recovery test. |
* And data from the pair of sorbent traps are also invalidated.
10.1 Only NIST-certified and NIST-traceable calibration standards (i.e., calibration gases, solutions, etc.) shall be used for the spiking and analytical procedures in this method.
10.2 Gas Flow Meter Calibration.
10.2.1 Preliminaries. The manufacturer or equipment supplier of the gas flow meter should perform all necessary set-up, testing, programming, etc., and should provide the end user with any necessary instructions, to ensure that the meter will give an accurate readout of dry gas volume in standard cubic meters for this method.
10.2.2 Initial Calibration. Prior to its initial use, a calibration of the gas flow meter shall be performed. The initial calibration may be done by the manufacturer, by the equipment supplier, or by the end user. If the flow meter is volumetric in nature (e.g., a dry gas meter), the manufacturer or end user may perform a direct volumetric calibration using any gas. For a mass flow meter, the manufacturer, equipment supplier, or end user may calibrate the meter using either: (1) A bottled gas mixture containing 12 ±0.5% CO2, 7 ±0.5% O2, and balance N2 (when this method is applied to coal-fired boilers); (2) a bottled gas mixture containing CO2, O2, and N2 in proportions representative of the expected stack gas composition; or (3) the actual stack gas.
10.2.2.1 Initial Calibration Procedures. Determine an average calibration factor (Y) for the gas flow meter by calibrating it at three sample flow rate settings covering the range of sample flow rates at which the sampling system will be operated. You may either follow the procedures in section 10.3.1 of Method 5 in appendix A-3 to this part or in section 16 of Method 5 in appendix A-3 to this part. If a dry gas meter is being calibrated, use at least five revolutions of the meter at each flow rate.
10.2.2.2 Alternative Initial Calibration Procedures. Alternatively, you may perform the initial calibration of the gas flow meter using a reference gas flow meter (RGFM). The RGFM may be: (1) A wet test meter calibrated according to section 10.3.1 of Method 5 in appendix A-3 to this part; (2) a gas flow metering device calibrated at multiple flow rates using the procedures in section 16 of Method 5 in appendix A-3 to this part; or (3) a NIST-traceable calibration device capable of measuring volumetric flow to an accuracy of 1 percent. To calibrate the gas flow meter using the RGFM, proceed as follows: While the Method 30B sampling system is sampling the actual stack gas or a compressed gas mixture that simulates the stack gas composition (as applicable), connect the RGFM to the discharge of the system. Care should be taken to minimize the dead volume between the gas flow meter being tested and the RGFM. Concurrently measure dry stack gas volume with the RGFM and the flow meter being calibrated for at least 10 minutes at each of three flow rates covering the typical range of operation of the sampling system. For each set of concurrent measurements, record the total sample volume, in units of dry standard cubic meters (dscm), measured by the RGFM and the gas flow meter being tested.
10.2.2.3 Initial Calibration Factor. Calculate an individual calibration factor Yi at each tested flow rate from section 10.2.2.1 or 10.2.2.2 of this method (as applicable) by taking the ratio of the reference sample volume to the sample volume recorded by the gas flow meter. Average the three Yi values, to determine Y, the calibration factor for the flow meter. Each of the three individual values of Yi must be within ±0.02 of Y. Except as otherwise provided in sections 10.2.2.4 and 10.2.2.5 of this method, use the average Y value from the initial 3-point calibration to adjust subsequent gas volume measurements made with the gas flow meter.
10.2.2.4 Pretest On-Site Calibration Check (Optional). For a mass flow meter, if the most recent 3-point calibration of the flow meter was performed using a compressed gas mixture, you may want to conduct the following on-site calibration check prior to testing, to ensure that the flow meter will accurately measure the volume of the stack gas: While sampling stack gas, check the calibration of the flow meter at one intermediate flow rate setting representative of normal operation of the sampling system. If the pretest calibration check shows that the value of Yi, the calibration factor at the tested flow rate, differs from the current value of Y by more than 5 percent, perform a full 3-point recalibration of the meter using stack gas to determine a new value of Y, and (except as otherwise provided in section 10.2.2.5 of this method) apply the new Y value to the data recorded during the field test.
10.2.2.5 Post-Test Calibration Check. Check the calibration of the gas flow meter following each field test at one intermediate flow rate setting, either at, or in close proximity to, the average sample flow rate during the field test. For dry gas meters, ensure at least three revolutions of the meter during the calibration check. For mass flow meters, this check must be performed before leaving the test site, while sampling stack gas. If a one-point calibration check shows that the value of Yi at the tested flow rate differs by more than 5 percent from the current value of Y, repeat the full 3-point calibration procedure to determine a new value of Y, and apply the new Y value to the gas volume measurements made with the gas flow meter during the field test that was just completed. For mass flow meters, perform the 3-point recalibration while sampling stack gas.
10.3 Thermocouples and Other Temperature Sensors. Use the procedures and criteria in Section 10.3 of Method 2 in appendix A-1 to this part to calibrate in-stack temperature sensors and thermocouples. Dial thermometers shall be calibrated against mercury-in-glass thermometers or equivalent. Calibrations must be performed prior to initial use and before each field test thereafter. At each calibration point, the absolute temperature measured by the temperature sensor must agree to within ±1.5 percent of the temperature measured with the reference sensor, otherwise the sensor may not continue to be used.
10.4 Barometer. Calibrate against a mercury barometer or other NIST-traceable barometer as per Section 10.6 of Method 5 in appendix A-3 to this part. Calibration must be performed prior to initial use and before each test program, and the absolute pressure measured by the barometer must agree to within ±10 mm Hg of the pressure measured by the mercury or other NIST-traceable barometer, otherwise the barometer may not continue to be used.
10.5 Other Sensors and Gauges. Calibrate all other sensors and gauges according to the procedures specified by the instrument manufacturer(s).
10.6 Analytical System Calibration. See section 11.1 of this method.
11.0 Analytical ProceduresThe analysis of Hg in the field and quality control samples may be conducted using any instrument or technology capable of quantifying total Hg from the sorbent media and meeting the performance criteria in this method. Because multiple analytical approaches, equipment and techniques are appropriate for the analysis of sorbent traps, it is not possible to provide detailed, technique-specific analytical procedures. As they become available, detailed procedures for a variety of candidate analytical approaches will be posted at http://www.epa.gov/ttn/emc.
11.1 Analytical System Calibration. Perform a multipoint calibration of the analyzer at three or more upscale points over the desired quantitative range (multiple calibration ranges shall be calibrated, if necessary). The field samples analyzed must fall within a calibrated, quantitative range and meet the performance criteria specified below. For samples suitable for aliquotting, a series of dilutions may be needed to ensure that the samples fall within a calibrated range. However, for sorbent media samples consumed during analysis (e.g., when using thermal desorption techniques), extra care must be taken to ensure that the analytical system is appropriately calibrated prior to sample analysis. The calibration curve range(s) should be determined such that the levels of Hg mass expected to be collected and measured will fall within the calibrated range. The calibration curve may be generated by directly introducing standard solutions into the analyzer or by spiking the standards onto the sorbent media and then introducing into the analyzer after preparing the sorbent/standard according to the particular analytical technique. For each calibration curve, the value of the square of the linear correlation coefficient, i.e., r 2, must be ≥0.99, and the analyzer response must be within ±10 percent of the reference value at each upscale calibration point. Calibrations must be performed on the day of the analysis, before analyzing any of the samples. Following calibration, an independent standard shall be analyzed. The measured value of the independently prepared standard must be within ±10 percent of the expected value.
11.2 Sample Preparation. Carefully separate the sections of each sorbent trap. Combine for analysis all materials associated with each section; any supporting substrate that the sample gas passes through prior to entering a media section (e.g., glass wool separators, acid gas traps, etc.) must be analyzed with that segment.
11.3 Field Sample Analyses. Analyze the sorbent trap samples following the same procedures that were used for conducting the Hg 0 and HgCl2 analytical bias tests. The individual sections of the sorbent trap and their respective components must be analyzed separately (i.e., section 1 and its components, then section 2 and its components). All sorbent trap section 1 sample analyses must be within the calibrated range of the analytical system as specified in Table 9-1. For wet analyses, the sample can simply be diluted to fall within the calibrated range. However, for the destructive thermal analyses, samples that are not within the calibrated range cannot be re-analyzed. As a result, the sample cannot be validated, and another sample must be collected. It is strongly suggested that the analytical system be calibrated over multiple ranges so that thermally analyzed samples fall within the calibrated range. The total mass of Hg measured in each sorbent trap section 1 must also fall within the lower and upper mass limits established during the initial Hg 0 and HgCl2 analytical bias test. If a sample is analyzed and found to fall outside of these limits, it is acceptable for an additional Hg 0 and HgCl2 analytical bias test to be performed that now includes this level. However, some samples (e.g., the mass collected in trap section 2), may have Hg levels so low that it may not be possible to quantify them in the analytical system's calibrated range. Because a reliable estimate of these low-level Hg measurements is necessary to fully validate the emissions data, the MDL (see section 8.2.2.1 of this method) is used to establish the minimum amount that can be detected and reported. If the measured mass or concentration is below the lowest point in the calibration curve and above the MDL, the analyst must estimate the mass or concentration of the sample based on the analytical instrument response relative to an additional calibration standard at a concentration or mass between the MDL and the lowest point in the calibration curve. This is accomplished by establishing a response factor (e.g., area counts per Hg mass or concentration) and estimating the amount of Hg present in the sample based on the analytical response and this response factor.
Example:The analysis of a particular sample results in a measured mass above the MDL, but below the lowest point in the calibration curve which is 10 ng. An MDL of 1.3 ng Hg has been established by the MDL study. A calibration standard containing 5 ng of Hg is analyzed and gives an analytical response of 6,170 area counts, which equates to a response factor of 1,234 area counts/ng Hg. The analytical response for the sample is 4,840 area counts. Dividing the analytical response for the sample (4,840 area counts) by the response factor gives 3.9 ng Hg, which is the estimated mass of Hg in the sample.11.4 Analysis of Continuing Calibration Verification Standard (CCVS). After no more than 10 samples and at the end of each set of analyses, a continuing calibration verification standard must be analyzed. The measured value of the continuing calibration standard must be within ±10 percent of the expected value.
11.5 Blanks. The analysis of blanks is optional. The analysis of blanks is useful to verify the absence of, or an acceptable level of, Hg contamination. Blank levels should be considered when quantifying low Hg levels and their potential contribution to meeting the sorbent trap section 2 breakthrough requirements; however, correcting sorbent trap results for blank levels is prohibited.
12.0 Calculations and Data AnalysisYou must follow the procedures for calculation and data analysis listed in this section.
12.1 Nomenclature. The terms used in the equations are defined as follows:
B = Breakthrough (%). Bws = Moisture content of sample gas as measured by Method 4, percent/100. Ca = Concentration of Hg for the sample collection period, for sorbent trap “a” (µg/dscm). Cb = Concentration of Hg for the sample collection period, for sorbent trap “b” (µg/dscm). Cd = Hg concentration, dry basis (µg/dscm). Crec = Concentration of spiked compound measured (µg/m 3). Cw = Hg concentration, wet basis (µg/m 3). m1 = Mass of Hg measured on sorbent trap section 1 (µg). m2 = Mass of Hg measured on sorbent trap section 2 (µg). mrecovered = Mass of spiked Hg recovered in Analytical Bias or Field Recovery Test (µg). ms = Total mass of Hg measured on spiked trap in Field Recovery Test (µg). mspiked = Mass of Hg spiked in Analytical Bias or Field Recovery Test (µg). mu = Total mass of Hg measured on unspiked trap in Field Recovery Test (µg). R = Percentage of spiked mass recovered (%). RD = Relative deviation between the Hg concentrations from traps “a” and “b” (%). vs = Volume of gas sampled, spiked trap in Field Recovery Test (dscm). Vt = Total volume of dry gas metered during the collection period (dscm); for the purposes of this method, standard temperature and pressure are defined as 20 °C and 760 mm Hg, respectively. vu = Volume of gas sampled, unspiked trap in Field Recovery Test (dscm).12.2 Calculation of Spike Recovery (Analytical Bias Test). Calculate the percent recovery of Hg 0 and HgCl2 using Equation 30B-1.
12.3 Calculation of Breakthrough. Use Equation 30B-2 to calculate the percent breakthrough to the second section of the sorbent trap.
12.4 Calculation of Hg Concentration. Calculate the Hg concentration measured with sorbent trap “a”, using Equation 30B-3.
For sorbent trap “b”, replace “Ca ” with “Cb ” in Equation 30B-3. Report the average concentration, i.e., 1/2 (Ca + Cb).
12.5 Moisture Correction. Use Equation 30B-4 if your measurements need to be corrected to a wet basis.
12.6 Calculation of Paired Trap Agreement. Calculate the relative deviation (RD) between the Hg concentrations measured with the paired sorbent traps using Equation 30B-5.
12.7 Calculation of Measured Spike Hg Concentration (Field Recovery Test). Calculate the measured spike concentration using Equation 30B-6.
Then calculate the spiked Hg recovery, R, using Equation 30B-7.
13.0 Method PerformanceHow do I validate my data? Measurement data are validated using initial, one-time laboratory tests coupled with test program-specific tests and procedures. The analytical matrix interference test and the Hg 0 and HgCl2 analytical bias test described in section 8.2 are used to verify the appropriateness of the selected analytical approach(es) as well as define the valid working ranges for sample analysis. The field recovery test serves to verify the performance of the combined sampling and analysis as applied for each test program. Field test samples are validated by meeting the above requirements as well as meeting specific sampling requirements (i.e., leak checks, paired train agreement, total sample volume agreement with field recovery test samples) and analytical requirements (i.e., valid calibration curve, continuing calibration performance, sample results within calibration curve and bounds of Hg 0 and HgCl2 analytical bias test). Complete data validation requirements are summarized in Table 9-1.
14.0 Pollution Prevention [Reserved] 15.0 Waste Management [Reserved] 16.0 References1. EPA Traceability Protocol for Qualification and Certification of Elemental Mercury Gas Generators, expected publication date December 2008, see www.epa.gov/ttn/emc.
2. EPA Traceability Protocol for Qualification and Certification of Oxidized Mercury Gas Generators, expected publication date December 2008, see www.epa.gov/ttn/emc.
3. EPA Traceability Protocol for Assay and Certification of Gaseous Calibration Standards, expected revision publication date December 2008, see www.epa.gov/ttn/emc.
17.0 Figures and Tables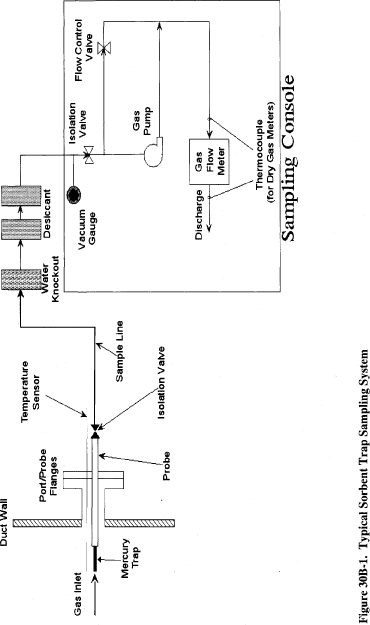
Appendix B to Part 60 - Performance Specifications
40:9.0.1.1.1.0.1.1.9 : Appendix B
Appendix B to Part 60 - Performance Specifications Performance Specification 1 - Specifications and test procedures for continuous opacity monitoring systems in stationary sources Performance Specification 2 - Specifications and Test Procedures for SO2 and NOX Continuous Emission Monitoring Systems in Stationary Sources Performance Specification 3 - Specifications and Test Procedures for O2 and CO2 Continuous Emission Monitoring Systems in Stationary Sources Performance Specification 4 - Specifications and Test Procedures for Carbon Monoxide Continuous Emission Monitoring Systems in Stationary Sources Performance Specification 4A - Specifications and Test Procedures for Carbon Monoxide Continuous Emission Monitoring Systems in Stationary Sources Performance Specification 4B - Specifications and Test Procedures for Carbon Monoxide and Oxygen Continuous Monitoring Systems in Stationary Sources Performance Specification 5 - Specifications and Test Procedures for TRS Continuous Emission Monitoring Systems in Stationary Sources Performance Specification 6 - Specifications and Test Procedures for Continuous Emission Rate Monitoring Systems in Stationary Sources Performance Specification 7 - Specifications and Test Procedures for Hydrogen Sulfide Continuous Emission Monitoring Systems in Stationary Sources Performance Specification 8 - Performance Specifications for Volatile Organic Compound Continuous Emission Monitoring Systems in Stationary Sources Performance Specification 8A - Specifications and Test Procedures for Total Hydrocarbon Continuous Monitoring Systems in Stationary Sources Performance Specification 9 - Specifications and Test Procedures for Gas Chromatographic Continuous Emission Monitoring Systems in Stationary Sources Performance Specification 11 - Specifications and Test Procedures for Particulate Matter Continuous Emission Monitoring Systems at Stationary Sources Performance Specification 12A - Specifications and Text Procedures for Total Vapor Phase Mercury Continuous Emission Monitoring Systems in Stationary Sources Performance Specification 12B - Specifications and Test Procedures for Monitoring Total Vapor Phase Mercury Emissions From Stationary Sources Using A Sorbent Trap Monitoring System Performance Specification 15 - Performance Specification for Extractive FTIR Continuous Emissions Monitor Systems in Stationary Sources Performance Specification 16 - Specifications and Test Procedures for Predictive Emission Monitoring Systems in Stationary Sources Performance Specification 17 [Reserved] Performance Specification 18 - Performance Specifications and Test Procedures for Gaseous Hydrogen Chloride (HCl) Continuous Emission Monitoring Systems at Stationary Sources PS-18 - Appendix A Standard Addition Procedures Performance Specification 1 - Specifications and Test Procedures for Continuous Opacity Monitoring Systems in Stationary Sources 1.0 What Is the Purpose and Applicability of Performance Specification 1?Performance Specification 1 (PS-1) provides (1) requirements for the design, performance, and installation of a continuous opacity monitoring system (COMS) and (2) data computation procedures for evaluating the acceptability of a COMS. It specifies activities for two groups (1) the owner or operator and (2) the opacity monitor manufacturer.
1.1 Measurement Parameter. PS-1 covers the instrumental measurement of opacity caused by attenuation of projected light due to absorption and scatter of the light by particulate matter in the effluent gas stream.
1.2 What COMS must comply with PS-1? If you are an owner or operator of a facility with a COMS as a result of this Part, then PS-1 applies to your COMS if one of the following is true:
(1) Your facility has a new COMS installed after February 6, 2001; or
(2) Your COMS is replaced, relocated, or substantially refurbished (in the opinion of the regulatory authority) after February 6, 2001; or
(3) Your COMS was installed before February 6, 2001 and is specifically required by regulatory action other than the promulgation of PS-1 to be recertified.
If you are an opacity monitor manufacturer, then paragraph 8.2 applies to you.
1.3 Does PS-1 apply to a facility with an applicable opacity limit less than 10 percent? If you are an owner or operator of a facility with a COMS as a result of this Part and the applicable opacity limit is less than 10 percent, then PS-1 applies to your COMS as described in section 1.2; taking into account (through statistical procedures or otherwise) the uncertainties associated with opacity measurements, and following the conditions for attenuators selection for low opacity applications as outlined in section 8.1(3)(ii). At your option, you, the source owner or operator, may select to establish a reduced full scale range of no less than 50 percent opacity instead of the 80 percent as prescribed in section 3.5, if the applicable opacity limit for your facility is less than 10 percent. The EPA recognizes that reducing the range of the analyzer to 50 percent does not necessarily result in any measurable improvement in measurement accuracy at opacity levels less than 10 percent; however, it may allow improved chart recorder interpretation.
1.4 What data uncertainty issues apply to COMS data? The measurement uncertainties associated with COMS data result from several design and performance factors including limitations on the availability of calibration attenuators for opacities less than about 6 percent (3 percent for single-pass instruments), calibration error tolerances, zero and upscale drift tolerances, and allowance for dust compensation that are significant relative to low opacity levels. The full scale requirements of this PS may also contribute to measurement uncertainty for opacity measurements where the applicable limits are below 10 percent opacity.
2.0 What Are the Basic Requirements of PS-1?PS-1 requires (1) opacity monitor manufacturers comply with a comprehensive series of design and performance specifications and test procedures to certify opacity monitoring equipment before shipment to the end user, (2) the owner or operator to follow installation guidelines, and (3) the owner or operator to conduct a set of field performance tests that confirm the acceptability of the COMS after it is installed.
2.1 ASTM D6216-12 (incorporated by reference, see § 60.17) is the reference for design specifications, manufacturer's performance specifications, and test procedures. The opacity monitor manufacturer must periodically select and test an opacity monitor, that is representative of a group of monitors produced during a specified period or lot, for conformance with the design specifications in ASTM D6216-12. The opacity monitor manufacturer must test each opacity monitor for conformance with the manufacturer's performance specifications in ASTM D6216-12. Note: If the initial certification of the opacity monitor occurred before November 14, 2018 using D6216-98, D6216-03, or D6216-07, it is not necessary to recertify using D6216-12.
2.2 section 8.1(2) provides guidance for locating an opacity monitor in vertical and horizontal ducts. You are encouraged to seek approval for the opacity monitor location from the appropriate regulatory authority prior to installation.
2.3 After the COMS is installed and calibrated, the owner or operator must test the COMS for conformance with the field performance specifications in PS-1.
3.0 What Special Definitions Apply to PS-1?3.1 All definitions and discussions from section 3 of ASTM D6216-12 are applicable to PS-1.
3.2 Centroid Area. A concentric area that is geometrically similar to the stack or duct cross-section and is no greater than 1 percent of the stack or duct cross-sectional area.
3.3 Data Recorder. That portion of the installed COMS that provides a permanent record of the opacity monitor output in terms of opacity. The data recorder may include automatic data reduction capabilities.
3.4 External Audit Device. The inherent design, equipment, or accommodation of the opacity monitor allowing the independent assessment of the COMS's calibration and operation.
3.5 Full Scale. The maximum data display output of the COMS. For purposes of recordkeeping and reporting, full scale will be greater than 80 percent opacity.
3.6 Operational Test Period. A period of time (168 hours) during which the COMS is expected to operate within the established performance specifications without any unscheduled maintenance, repair, or adjustment.
3.7 Primary Attenuators. Those devices (glass or grid filter that reduce the transmission of light) calibrated according to procedures in section 7.1.
3.8 Secondary Attenuators. Those devices (glass or grid filter that reduce the transmission of light) calibrated against primary attenuators according to procedures in section 7.2.
3.9 System Response Time. The amount of time the COMS takes to display 95 percent of a step change in opacity on the COMS data recorder.
4.0 Interferences. Water Droplets 5.0 What Do I Need To Know To Ensure the Safety of Persons Using PS-1?The procedures required under PS-1 may involve hazardous materials, operations, and equipment. PS-1 does not purport to address all of the safety problems associated with these procedures. Before performing these procedures, you must establish appropriate safety and health practices, and you must determine the applicable regulatory limitations. You should consult the COMS user's manual for specific precautions to take.
6.0 What Equipment and Supplies Do I Need?6.1 Continuous Opacity Monitoring System. You, as owner or operator, are responsible for purchasing an opacity monitor that meets the specifications of ASTM D6216-12, including a suitable data recorder or automated data acquisition handling system. Example data recorders include an analog strip chart recorder or more appropriately an electronic data acquisition and reporting system with an input signal range compatible with the analyzer output.
6.2 Calibration Attenuators. You, as owner or operator, are responsible for purchasing a minimum of three calibration attenuators that meet the requirements of PS-1. Calibration attenuators are optical filters with neutral spectral characteristics. Calibration attenuators must meet the requirements in section 7 and must be of sufficient size to attenuate the entire light beam received by the detector of the COMS. For transmissometers operating over a narrow bandwidth (e.g., laser), a calibration attenuator's value is determined for the actual operating wavelengths of the transmissometer. Some filters may not be uniform across the face. If errors result in the daily calibration drift or calibration error test, you may want to examine the across-face uniformity of the filter.
6.3 Calibration Spectrophotometer. Whoever calibrates the attenuators must have a spectrophotometer that meets the following minimum design specifications:
Parameter | Specification |
---|---|
Wavelength range | 300-800 nm. |
Detector angle of view | <10°. |
Accuracy | <0.5% transmittance, NIST traceable calibration. |
You will need to use attenuators (i.e., neutral density filters) to check the daily calibration drift and calibration error of a COMS. Attenuators are designated as either primary or secondary based on how they are calibrated.
7.1 Attenuators are designated primary in one of two ways:
(1) They are calibrated by NIST; or
(2) They are calibrated on a 6-month frequency through the assignment of a luminous transmittance value in the following manner:
(i) Use a spectrophotometer meeting the specifications of section 6.3 to calibrate the required filters. Verify the spectrophotometer calibration through use of a NIST 930D Standard Reference Material (SRM). A SRM 930D consists of three neutral density glass filters and a blank, each mounted in a cuvette. The wavelengths and temperature to be used in the calibration are listed on the NIST certificate that accompanies the reported values. Determine and record a transmittance of the SRM values at the NIST wavelengths (three filters at five wavelengths each for a total of 15 determinations). Calculate a percent difference between the NIST certified values and the spectrophotometer response. At least 12 of the 15 differences (in percent) must be within ±0.5 percent of the NIST SRM values. No difference can be greater than ±1.0 percent. Recalibrate the SRM or service the spectrophotometer if the calibration results fail the criteria.
(ii) Scan the filter to be tested and the NIST blank from wavelength 380 to 780 nm, and record the spectrophotometer percent transmittance responses at 10 nm intervals. Test in this sequence: blank filter, tested filter, tested filter rotated 90 degrees in the plane of the filter, blank filter. Calculate the average transmittance at each 10 nm interval. If any pair of the tested filter transmittance values (for the same filter and wavelength) differ by more than ±0.25 percent, rescan the tested filter. If the filter fails to achieve this tolerance, do not use the filter in the calibration tests of the COMS.
(iii) Correct the tested filter transmittance values by dividing the average tested filter transmittance by the average blank filter transmittance at each 10 nm interval.
(iv) Calculate the weighted (to the response of the human eye), tested filter transmittance by multiplying the transmittance value by the corresponding response factor shown in table 1-1, to obtain the Source C Human Eye Response.
(v) Recalibrate the primary attenuators semi-annually if they are used for the required calibration error test. Recalibrate the primary attenuators annually if they are used only for calibration of secondary attenuators.
7.2 Attenuators are designated secondary if the filter calibration is done using a laboratory-based transmissometer. Conduct the secondary attenuator calibration using a laboratory-based transmissometer calibrated as follows:
(i) Use at least three primary filters of nominal luminous transmittance 50, 70 and 90 percent, calibrated as specified in section 7.1(2)(i), to calibrate the laboratory-based transmissometer. Determine and record the slope of the calibration line using linear regression through zero opacity. The slope of the calibration line must be between 0.99 and 1.01, and the laboratory-based transmissometer reading for each primary filter must not deviate by more than ±2 percent from the linear regression line. If the calibration of the laboratory-based transmissometer yields a slope or individual readings outside the specified ranges, secondary filter calibrations cannot be performed. Determine the source of the variations (either transmissometer performance or changes in the primary filters) and repeat the transmissometer calibration before proceeding with the attenuator calibration.
(ii) Immediately following the laboratory-based transmissometer calibration, insert the secondary attenuators and determine and record the percent effective opacity value per secondary attenuator from the calibration curve (linear regression line).
(iii) Recalibrate the secondary attenuators semi-annually if they are used for the required calibration error test.
8.0 What Performance Procedures Are Required To Comply With PS-1?Procedures to verify the performance of the COMS are divided into those completed by the owner or operator and those completed by the opacity monitor manufacturer.
8.1 What procedures must I follow as the Owner or Operator?
(1) You must purchase an opacity monitor that complies with ASTM D6216-12 and obtain a certificate of conformance from the opacity monitor manufacturer.
(2) You must install the opacity monitor at a location where the opacity measurements are representative of the total emissions from the affected facility. You must meet this requirement by choosing a measurement location and a light beam path as follows:
(i) Measurement Location. Select a measurement location that is (1) at least 4 duct diameters downstream from all particulate control equipment or flow disturbance, (2) at least 2 duct diameters upstream of a flow disturbance, (3) where condensed water vapor is not present, and (4) accessible in order to permit maintenance. Alternatively, you may select a measurement location specified in paragraph 8.1(2)(ii) or 8.1(2)(iii).
(ii) Light Beam Path. Select a light beam path that passes through the centroidal area of the stack or duct. Also, you must follow these additional requirements or modifications for these measurement locations:
If your measurement location is in a: | And is: | Then use a light beam path that is: |
---|---|---|
1. Straight vertical section of stack or duct | Less than 4 equivalent diameters downstream from a bend | In the plane defined by the upstream bend (see figure 1-1). |
2. Straight vertical section of stack or duct | Less than 4 equivalent diameters upstream from a bend | In the plane defined by the downstream bend (see figure 1-2). |
3. Straight vertical section of stack or duct | Less than 4 equivalent diameters downstream and is also less than 1 diameter upstream from a bend | In the plane defined by the upstream bend (see figure 1-3). |
4. Horizontal section of stack or duct | At least 4 equivalent diameters downstream from a vertical bend | In the horizontal plane that is between 1/3 and 1/2 the distance up the vertical axis from the bottom of the duct (see figure 1-4). |
5. Horizontal section of duct | Less than 4 equivalent diameters downstream from a vertical bend | In the horizontal plane that is between 1/2 and 2/3 the distance up the vertical axis from the bottom of the duct for upward flow in the vertical section, and is between 1/3 and 1/2 the distance up the vertical axis from the bottom of the duct for downward flow (figure 1-5). |
(iii) Alternative Locations and Light Beam Paths. You may select locations and light beam paths, other than those cited above, if you demonstrate, to the satisfaction of the Administrator or delegated agent, that the average opacity measured at the alternative location or path is equivalent to the opacity as measured at a location meeting the criteria of sections 8.1(2)(i) and 8.1(2)(ii). The opacity at the alternative location is considered equivalent if (1) the average opacity value measured at the alternative location is within ±10 percent of the average opacity value measured at the location meeting the installation criteria, and (2) the difference between any two average opacity values is less than 2 percent opacity (absolute). You use the following procedure to conduct this demonstration: simultaneously measure the opacities at the two locations or paths for a minimum period of time (e.g., 180-minutes) covering the range of normal operating conditions and compare the results. The opacities of the two locations or paths may be measured at different times, but must represent the same process operating conditions. You may use alternative procedures for determining acceptable locations if those procedures are approved by the Administrator.
(3) Field Audit Performance Tests. After you install the COMS, you must perform the following procedures and tests on the COMS.
(i) Optical Alignment Assessment. Verify and record that all alignment indicator devices show proper alignment. A clear indication of alignment is one that is objectively apparent relative to reference marks or conditions.
(ii) Calibration Error Check. Conduct a three-point calibration error test using three calibration attenuators that produce outlet pathlength corrected, single-pass opacity values shown in ASTM D6216-12, section 7.5. If your applicable limit is less than 10 percent opacity, use attenuators as described in ASTM D6216-12, section 7.5 for applicable standards of 10 to 19 percent opacity. Confirm the external audit device produces the proper zero value on the COMS data recorder. Separately, insert each calibration attenuators (low, mid, and high-level) into the external audit device. While inserting each attenuator, (1) ensure that the entire light beam passes through the attenuator, (2) minimize interference from reflected light, and (3) leave the attenuator in place for at least two times the shortest recording interval on the COMS data recorder. Make a total of five nonconsecutive readings for each attenuator. At the end of the test, correlate each attenuator insertion to the corresponding value from the data recorder. Subtract the single-pass calibration attenuator values corrected to the stack exit conditions from the COMS responses. Calculate the arithmetic mean difference, standard deviation, and confidence coefficient of the five measurements value using equations 1-3, 1-4, and 1-5. Calculate the calibration error as the sum of the absolute value of the mean difference and the 95 percent confidence coefficient for each of the three test attenuators using equation 1-6. Report the calibration error test results for each of the three attenuators.
(iii) System Response Time Check. Using a high-level calibration attenuator, alternately insert the filter five times and remove it from the external audit device. For each filter insertion and removal, measure the amount of time required for the COMS to display 95 percent of the step change in opacity on the COMS data recorder. For the upscale response time, measure the time from insertion to display of 95 percent of the final, steady upscale reading. For the downscale response time, measure the time from removal to display 5 percent of the initial upscale reading. Calculate the mean of the five upscale response time measurements and the mean of the five downscale response time measurements. Report both the upscale and downscale response times.
(iv) Averaging Period Calculation and Recording Check. After the calibration error check, conduct a check of the averaging period calculation (e.g., 6-minute integrated average). Consecutively insert each of the calibration error check attenuators (low, mid, and high-level) into the external audit device for a period of two times the averaging period plus 1 minute (e.g., 13 minutes for a 6-minute averaging period). Compare the path length corrected opacity value of each attenuator to the valid average value calculated by the COMS data recording device for that attenuator.
(4) Operational Test Period. Before conducting the operational testing, you must have successfully completed the field audit tests described in sections 8.1(3)(i) through 8.1(3)(iv). Then, you operate the COMS for an initial 168-hour test period while the source is operating under normal operating conditions. If normal operations contain routine source shutdowns, include the source's down periods in the 168-hour operational test period. However, you must ensure that the following minimum source operating time is included in the operational test period: (1) For a batch operation, the operational test period must include at least one full cycle of batch operation during the 168-hour period unless the batch operation is longer than 168 hours or (2) for continuous operating processes, the unit must be operating for at least 50 percent of the 168-hour period. Except during times of instrument zero and upscale calibration drift checks, you must analyze the effluent gas for opacity and produce a permanent record of the COMS output. During this period, you may not perform unscheduled maintenance, repair, or adjustment to the COMS. Automatic zero and calibration adjustments (i.e., intrinsic adjustments), made by the COMS without operator intervention or initiation, are allowable at any time. At the end of the operational test period, verify and record that the COMS optical alignment is still correct. If the test period is interrupted because of COMS failure, record the time when the failure occurred. After the failure is corrected, you restart the 168-hour period and tests from the beginning (0-hour). During the operational test period, perform the following test procedures:
(i) Zero Calibration Drift Test. At the outset of the 168-hour operational test period and at each 24-hour interval, the automatic calibration check system must initiate the simulated zero device to allow the zero drift to be determined. Record the COMS response to the simulated zero device. After each 24-hour period, subtract the COMS zero reading from the nominal value of the simulated zero device to calculate the 24-hour zero drift (ZD). At the end of the 168-hour period, calculate the arithmetic mean, standard deviation, and confidence coefficient of the 24-hour ZDs using equations 1-3, 1-4, and 1-5. Calculate the sum of the absolute value of the mean and the absolute value of the confidence coefficient using equation 1-6, and report this value as the 24-hour ZD error.
(ii) Upscale Calibration Drift Test. At each 24-hour interval after the simulated zero device value has been checked, check and record the COMS response to the upscale calibration device. After each 24-hour period, subtract the COMS upscale reading from the nominal value of the upscale calibration device to calculate the 24-hour calibration drift (CD). At the end of the 168-hour period, calculate the arithmetic mean, standard deviation, and confidence coefficient of the 24-hour CD using equations 1-3, 1-4, and 1-5. Calculate the sum of the absolute value of the mean and the absolute value of the confidence coefficient using equation 1-6, and report this value as the 24-hour CD error.
(5) Retesting. If the COMS fails to meet the specifications for the tests conducted under the operational test period, make the necessary corrections and restart the operational test period. Depending on the opinion of the enforcing agency, you may have to repeat some or all of the field audit tests.
8.2 What are the responsibilities of the Opacity Monitor Manufacturer?
You, the manufacturer, must carry out the following activities:
(1) Conduct the verification procedures for design specifications in section 6 of ASTM D6216-12.
(2) Conduct the verification procedures for performance specifications in section 7 of ASTM D6216-12.
(3) Provide to the owner or operator, a report of the opacity monitor's conformance to the design and performance specifications required in sections 6 and 7 of ASTM D6216-12 in accordance with the reporting requirements of section 9 in ASTM D6216-12.
9.0 What quality control measures are required by PS-1?Opacity monitor manufacturers must initiate a quality program following the requirements of ASTM D6216-12, section 8. The quality program must include (1) a quality system and (2) a corrective action program.
10.0 Calibration and Standardization [Reserved] 11.0 Analytical Procedure [Reserved] 12.0 What Calculations Are Needed for PS-1?12.1 Desired Attenuator Values. Calculate the desired attenuator value corrected to the emission outlet pathlength as follows:
Where: OP1 = Nominal opacity value of required low-, mid-, or high-range calibration attenuators. OP2 = Desired attenuator opacity value from ASTM D6216-12, section 7.5 at the opacity limit required by the applicable subpart. L1 = Monitoring pathlength. L2 = Emission outlet pathlength.12.2 Luminous Transmittance Value of a Filter. Calculate the luminous transmittance of a filter as follows:
Where: LT = Luminous transmittance Ti = Weighted tested filter transmittance.12.3 Arithmetic Mean. Calculate the arithmetic mean of a data set as follows:
Where:12.4 Standard Deviation. Calculate the standard deviation as follows:
Where: Sd = Standard deviation of a data set.12.5 Confidence Coefficient. Calculate the 2.5 percent error confidence coefficient (one-tailed) as follows:
Where: CC = Confidence coefficient t0.975 = t − value (see table 1-2).12.6 Calibration Error. Calculate the error (calibration error, zero drift error, and calibration drift error) as follows:
Where: Er = Error.12.7 Conversion of Opacity Values for Monitor Pathlength to Emission Outlet Pathlength. When the monitor pathlength is different from the emission outlet pathlength, use either of the following equations to convert from one basis to the other (this conversion may be automatically calculated by the monitoring system):
Where: Op1 = Opacity of the effluent based upon L1. Op2 = Opacity of the effluent based upon L2. L1 = Monitor pathlength. L2 = Emission outlet pathlength. OD1 = Optical density of the effluent based upon L1. OD2 = Optical density of the effluent based upon L2.12.8 Mean Response Wavelength. Calculate the mean of the effective spectral response curve from the individual responses at the specified wavelength values as follows:
Where: L = mean of the effective spectral response curve Li = The specified wavelength at which the response gi is calculated at 20 nm intervals. gi = The individual response value at Li. 13.0 What Specifications Does a COMS Have to Meet for Certification?A COMS must meet the following design, manufacturer's performance, and field audit performance specifications:
Note: If the initial certification of the opacity monitor occurred before November 14, 2018 using D6216-98, D6216-03, or D6216-07, it is not necessary to recertify using D6216-12.A. COMS must meet the following design, manufacturer's performance, and field audit performance specifications.
13.1 Design Specifications. The opacity monitoring equipment must comply with the design specifications of ASTM D6216-12.
13.2 Manufacturer's Performance Specifications. The opacity monitor must comply with the manufacturer's performance specifications of ASTM D6216-12.
13.3 Field Audit Performance Specifications. The installed COMS must comply with the following performance specifications:
(1) Optical Alignment. Objectively indicate proper alignment relative to reference marks (e.g., bull's-eye) or conditions.
(2) Calibration Error. The calibration error must be ≤3 percent opacity for each of the three calibration attenuators.
(3) System Response Time. The COMS upscale and downscale response times must be ≤10 seconds as measured at the COMS data recorder.
(4) Averaging Period Calculation and Recording. The COMS data recorder must average and record each calibration attenuator value to within ±2 percent opacity of the certified value of the attenuator.
(5) Operational Test Period. The COMS must be able to measure and record opacity and to perform daily calibration drift assessments for 168 hours without unscheduled maintenance, repair, or adjustment.
(6) Zero and Upscale Calibration Drift Error. The COMS zero and upscale calibration drift error must not exceed 2 percent opacity over a 24 hour period.
14.0 Pollution Prevention [Reserved] 15.0 Waste Management [Reserved] 16.0 Which references are relevant to this method?1. Experimental Statistics. Department of Commerce. National Bureau of Standards Handbook 91. Paragraph 3-3.1.4. 1963. 3-31 p.
2. Performance Specifications for Stationary Source Monitoring Systems for Gases and Visible Emissions, EPA-650/2-74-013, January 1974, U. S. Environmental Protection Agency, Research Triangle Park, NC.
3. Koontz, E.C., Walton, J. Quality Assurance Programs for Visible Emission Evaluations. Tennessee Division of Air Pollution Control. Nashville, TN. 78th Meeting of the Air Pollution Control Association. Detroit, MI. June 16-21, 1985.
4. Evaluation of Opacity CEMS Reliability and Quality Assurance Procedures. Volume 1. U. S. Environmental Protection Agency. Research Triangle Park, NC. EPA-340/1-86-009a.
5. Nimeroff, I. “Colorimetry Precision Measurement and Calibration.” NBS Special Publication 300. Volume 9. June 1972.
6. Technical Assistance Document: Performance Audit Procedures for Opacity Monitors. U. S. Environmental Protection Agency. Research Triangle Park, NC. EPA-600/8-87-025. April 1987.
7. Technical Assistance Document: Performance Audit Procedures for Opacity Monitors. U. S. Environmental Protection Agency. Research Triangle Park, NC. EPA-450/4-92-010. April 1992.
8. ASTM D6216-12: Standard Practice for Opacity Monitor Manufacturers to Certify Conformance with Design and Performance Specifications. ASTM. October 2012.
17.0 What tables and diagrams are relevant to this method?17.1 Reference Tables.
Table 1-1 - Source C, Human Eye Response Factor
Wavelength nanometers |
Weighting factor a |
Wavelength nanometers |
Weighting factor a |
---|---|---|---|
380 | 0 | 590 | 6627 |
390 | 0 | 600 | 5316 |
400 | 2 | 610 | 4176 |
410 | 9 | 620 | 3153 |
420 | 37 | 630 | 2190 |
430 | 122 | 640 | 1443 |
440 | 262 | 650 | 886 |
450 | 443 | 660 | 504 |
460 | 694 | 670 | 259 |
470 | 1058 | 680 | 134 |
480 | 1618 | 690 | 62 |
490 | 2358 | 700 | 29 |
500 | 3401 | 720 | 14 |
510 | 4833 | 720 | 6 |
520 | 6462 | 730 | 3 |
530 | 7934 | 740 | 2 |
540 | 9194 | 750 | 1 |
550 | 9832 | 760 | 1 |
560 | 9841 | 770 | 0 |
570 | 9147 | 780 | 0 |
580 | 7992 |
1 Total of weighting factors = 100,000.
Table 1-2 T Values
n a | t 0.975 | n a | t 0.975 | n a | t 0.975 |
---|---|---|---|---|---|
2 | 12.706 | 7 | 2.447 | 12 | 2.201 |
3 | 4.303 | 8 | 2.365 | 13 | 2.179 |
4 | 3.182 | 9 | 2.306 | 14 | 2.160 |
5 | 2.776 | 10 | 2.262 | 15 | 2.145 |
6 | 2.571 | 11 | 2.228 | 16 | 2.131 |
a The values in this table are already corrected for n-1 degrees of freedom. Use n equal to the number of individual values.
17.2 Diagrams.
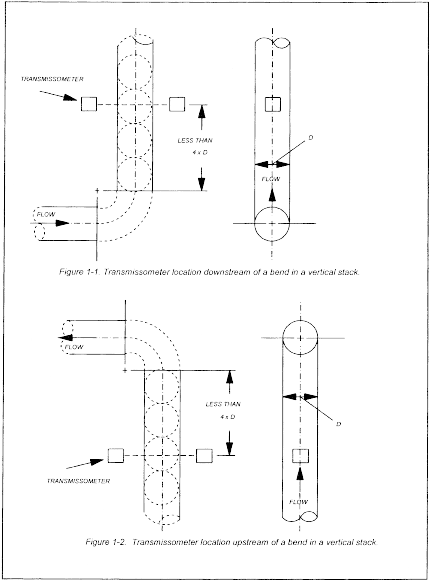
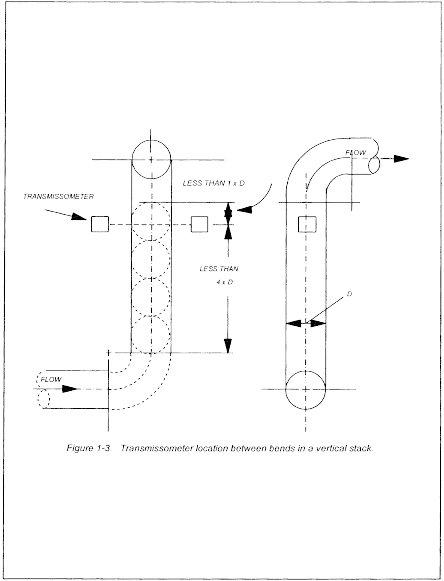
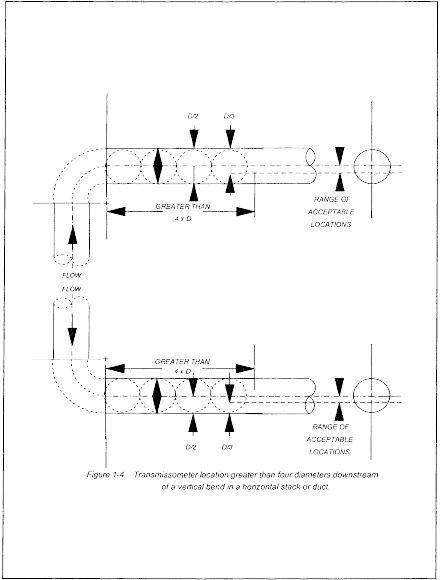
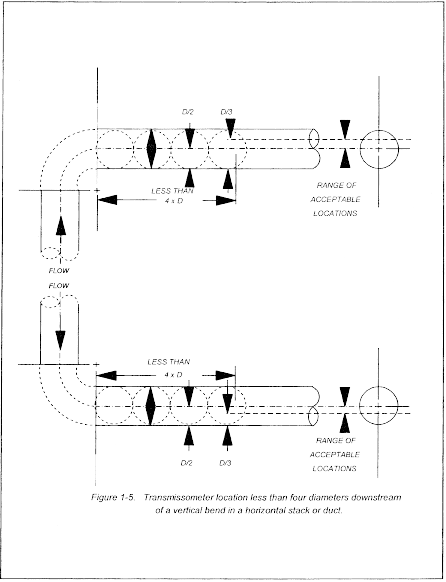
1.1 Analytes
Analyte | CAS Nos. |
---|---|
Sulfur Dioxide (SO2) | 7449-09-5 |
Nitrogen Oxides (NOX) | 10102-44-0 (NO2), 10024-97-2 (NO) |
1.2 Applicability.
1.2.1 This specification is for evaluating the acceptability of SO2 and NOX continuous emission monitoring systems (CEMS) at the time of installation or soon after and whenever specified in the regulations. The CEMS may include, for certain stationary sources, a diluent (O2 or CO2) monitor.
1.2.2 This specification is not designed to evaluate the installed CEMS performance over an extended period of time nor does it identify specific calibration techniques and other auxiliary procedures to assess the CEMS performance. The source owner or operator is responsible to calibrate, maintain, and operate the CEMS properly. The Administrator may require, under section 114 of the Act, the operator to conduct CEMS performance evaluations at other times besides the initial test to evaluate the CEMS performance. See 40 CFR Part 60, § 60.13(c).
2.0 Summary of Performance SpecificationProcedures for measuring CEMS relative accuracy and calibration drift are outlined. CEMS installation and measurement location specifications, equipment specifications, performance specifications, and data reduction procedures are included. Conformance of the CEMS with the Performance Specification is determined.
3.0 Definitions3.1 Calibration Drift (CD) means the difference in the CEMS output readings from the established reference value after a stated period of operation during which no unscheduled maintenance, repair, or adjustment took place.
3.2 Centroidal Area means a concentric area that is geometrically similar to the stack or duct cross section and is no greater than l percent of the stack or duct cross-sectional area.
3.3 Continuous Emission Monitoring System means the total equipment required for the determination of a gas concentration or emission rate. The sample interface, pollutant analyzer, diluent analyzer, and data recorder are the major subsystems of the CEMS.
3.4 Data Recorder means that portion of the CEMS that provides a permanent record of the analyzer output. The data recorder may include automatic data reduction capabilities.
3.5 Diluent Analyzer means that portion of the CEMS that senses the diluent gas (i.e., CO2 or O2) and generates an output proportional to the gas concentration.
3.6 Path CEMS means a CEMS that measures the gas concentration along a path greater than 10 percent of the equivalent diameter of the stack or duct cross section.
3.7 Point CEMS means a CEMS that measures the gas concentration either at a single point or along a path equal to or less than 10 percent of the equivalent diameter of the stack or duct cross section.
3.8 Pollutant Analyzer means that portion of the CEMS that senses the pollutant gas and generates an output proportional to the gas concentration.
3.9 Relative Accuracy (RA) means the absolute mean difference between the gas concentration or emission rate determined by the CEMS and the value determined by the reference method (RM), plus the 2.5 percent error confidence coefficient of a series of tests, divided by the mean of the RM tests or the applicable emission limit.
3.10 Sample Interface means that portion of the CEMS used for one or more of the following: sample acquisition, sample delivery, sample conditioning, or protection of the monitor from the effects of the stack effluent.
3.11 Span Value means the calibration portion of the measurement range as specified in the applicable regulation or other requirement. If the span is not specified in the applicable regulation or other requirement, then it must be a value approximately equivalent to two times the emission standard. For spans less than 500 ppm, the span value may either be rounded upward to the next highest multiple of 10 ppm, or to the next highest multiple of 100 ppm such that the equivalent emission concentration is not less than 30 percent of the selected span value.
4.0 Interferences [Reserved] 5.0 SafetyThe procedures required under this performance specification may involve hazardous materials, operations, and equipment. This performance specification may not address all of the safety problems associated with these procedures. It is the responsibility of the user to establish appropriate safety and health practices and determine the applicable regulatory limitations prior to performing these procedures. The CEMS user's manual and materials recommended by the reference method should be consulted for specific precautions to be taken.
6.0 Equipment and Supplies6.1 CEMS Equipment Specifications.
6.1.1 Data Recorder. The portion of the CEMS that provides a record of analyzer output. The data recorder may record other pertinent data such as effluent flow rates, various instrument temperatures or abnormal CEMS operation. The data recorder output range must include the full range of expected concentration values in the gas stream to be sampled including zero and span values.
6.1.2 The CEMS design should also allow the determination of calibration drift at the zero and span values. If this is not possible or practical, the design must allow these determinations to be conducted at a low-level value (zero to 20 percent of the span value) and at a value between 50 and 100 percent of the span value. In special cases, the Administrator may approve a single-point calibration drift determination.
6.2 Other equipment and supplies, as needed by the applicable reference method(s) (see section 8.4.2 of this Performance Specification), may be required.
7.0 Reagents and Standards7.1 Reference Gases, Gas Cells, or Optical Filters. As specified by the CEMS manufacturer for calibration of the CEMS (these need not be certified).
7.2 Reagents and Standards. May be required as needed by the applicable reference method(s) (see section 8.4.2 of this Performance Specification).
8.0 Performance Specification Test Procedure8.1 Installation and Measurement Location Specifications.
8.1.1 CEMS Installation. Install the CEMS at an accessible location where the pollutant concentration or emission rate measurements are directly representative or can be corrected so as to be representative of the total emissions from the affected facility or at the measurement location cross section. Then select representative measurement points or paths for monitoring in locations that the CEMS will pass the RA test (see section 8.4). If the cause of failure to meet the RA test is determined to be the measurement location and a satisfactory correction technique cannot be established, the Administrator may require the CEMS to be relocated. Suggested measurement locations and points or paths that are most likely to provide data that will meet the RA requirements are listed below.
8.1.2 CEMS Measurement Location. It is suggested that the measurement location be (1) at least two equivalent diameters downstream from the nearest control device, the point of pollutant generation, or other point at which a change in the pollutant concentration or emission rate may occur and (2) at least a half equivalent diameter upstream from the effluent exhaust or control device.
8.1.2.1 Point CEMS. It is suggested that the measurement point be (1) no less than 1.0 meter (3.3 ft) from the stack or duct wall or (2) within or centrally located over the centroidal area of the stack or duct cross section.
8.1.2.2 Path CEMS. It is suggested that the effective measurement path (1) be totally within the inner area bounded by a line 1.0 meter (3.3 ft) from the stack or duct wall, or (2) have at least 70 percent of the path within the inner 50 percent of the stack or duct cross-sectional area, or (3) be centrally located over any part of the centroidal area.
8.1.3 Reference Method Measurement Location and Traverse Points.
8.1.3.1 Select, as appropriate, an accessible RM measurement point at least two equivalent diameters downstream from the nearest control device, the point of pollutant generation, or other point at which a change in the pollutant concentration or emission rate may occur, and at least a half equivalent diameter upstream from the effluent exhaust or control device. When pollutant concentration changes are due solely to diluent leakage (e.g., air heater leakages) and pollutants and diluents are simultaneously measured at the same location, a half diameter may be used in lieu of two equivalent diameters. The CEMS and RM locations need not be the same.
8.1.3.2 Select traverse points that assure acquisition of representative samples over the stack or duct cross section. The minimum requirements are as follows: Establish a “measurement line” that passes through the centroidal area and in the direction of any expected stratification. If this line interferes with the CEMS measurements, displace the line up to 30 cm (12 in.) (or 5 percent of the equivalent diameter of the cross section, whichever is less) from the centroidal area. Locate three traverse points at 16.7, 50.0, and 83.3 percent of the measurement line. If the measurement line is longer than 2.4 meters (7.8 ft) and pollutant stratification is not expected, the three traverse points may be located on the line at 0.4, 1.2, and 2.0 meters from the stack or duct wall. This option must not be used after wet scrubbers or at points where two streams with different pollutant concentrations are combined. If stratification is suspected, the following procedure is suggested. For rectangular ducts, locate at least nine sample points in the cross section such that sample points are the centroids of similarly-shaped, equal area divisions of the cross section. Measure the pollutant concentration, and, if applicable, the diluent concentration at each point using appropriate reference methods or other appropriate instrument methods that give responses relative to pollutant concentrations. Then calculate the mean value for all sample points. For circular ducts, conduct a 12-point traverse (i.e., six points on each of the two perpendicular diameters) locating the sample points as described in 40 CFR 60, Appendix A, Method 1. Perform the measurements and calculations as described above. Determine if the mean pollutant concentration is more than 10% different from any single point. If so, the cross section is considered to be stratified, and the tester may not use the alternative traverse point locations (...0.4, 1.2, and 2.0 meters from the stack or duct wall.) but must use the three traverse points at 16.7, 50.0, and 83.3 percent of the entire measurement line. Other traverse points may be selected, provided that they can be shown to the satisfaction of the Administrator to provide a representative sample over the stack or duct cross section. Conduct all necessary RM tests within 3 cm (1.2 in.) of the traverse points, but no closer than 3 cm (1.2 in.) to the stack or duct wall.
8.2 Pretest Preparation. Install the CEMS, prepare the RM test site according to the specifications in section 8.1, and prepare the CEMS for operation according to the manufacturer's written instructions.
8.3 Calibration Drift Test Procedure.
8.3.1 CD Test Period. While the affected facility is operating, determine the magnitude of the CD once each day (at 24-hour intervals) for 7 consecutive calendar days according to the procedure given in sections 8.3.2 through 8.3.4. Alternatively, the CD test may be conducted over 7 consecutive unit operating days.
8.3.2 The purpose of the CD measurement is to verify the ability of the CEMS to conform to the established CEMS calibration used for determining the emission concentration or emission rate. Therefore, if periodic automatic or manual adjustments are made to the CEMS zero and calibration settings, conduct the CD test immediately before these adjustments, or conduct it in such a way that the CD can be determined.
8.3.3 Conduct the CD test at the two points specified in section 6.1.2. Introduce to the CEMS the reference gases, gas cells, or optical filters (these need not be certified). Record the CEMS response and subtract this value from the reference value (see example data sheet in Figure 2-1).
8.4 Relative Accuracy Test Procedure.
8.4.1 RA Test Period. Conduct the RA test according to the procedure given in sections 8.4.2 through 8.4.6 while the affected facility is operating at more than 50 percent of normal load, or as specified in an applicable subpart. The RA test may be conducted during the CD test period.
8.4.2 Reference Methods. Unless otherwise specified in an applicable subpart of the regulations, Methods 3B, 4, 6, and 7, or their approved alternatives, are the reference methods for diluent (O2 and CO2), moisture, SO2, and NOX, respectively.
8.4.3 Sampling Strategy for RM Tests. Conduct the RM tests in such a way that they will yield results representative of the emissions from the source and can be correlated to the CEMS data. It is preferable to conduct the diluent (if applicable), moisture (if needed), and pollutant measurements simultaneously. However, diluent and moisture measurements that are taken within an hour of the pollutant measurements may be used to calculate dry pollutant concentration and emission rates. In order to correlate the CEMS and RM data properly, note the beginning and end of each RM test period of each run (including the exact time of day) on the CEMS chart recordings or other permanent record of output. Use the following strategies for the RM tests:
8.4.3.1 For integrated samples (e.g., Methods 6 and Method 4), make a sample traverse of at least 21 minutes, sampling for an equal time at each traverse point (see section 8.1.3.2 for discussion of traverse points.
8.4.3.2 For grab samples (e.g., Method 7), take one sample at each traverse point, scheduling the grab samples so that they are taken simultaneously (within a 3-minute period) or at an equal interval of time apart over the span of time the CEM pollutant is measured. A test run for grab samples must be made up of at least three separate measurements.
Note:At times, CEMS RA tests are conducted during new source performance standards performance tests. In these cases, RM results obtained during CEMS RA tests may be used to determine compliance as long as the source and test conditions are consistent with the applicable regulations.
8.4.4 Number of RM Tests. Conduct a minimum of nine sets of all necessary RM test runs.
Note:More than nine sets of RM tests may be performed. If this option is chosen, a maximum of three sets of the test results may be rejected so long as the total number of test results used to determine the RA is greater than or equal to nine. However, all data must be reported, including the rejected data.
8.4.5 Correlation of RM and CEMS Data. Correlate the CEMS and the RM test data as to the time and duration by first determining from the CEMS final output (the one used for reporting) the integrated average pollutant concentration or emission rate for each pollutant RM test period. Consider system response time, if important, and confirm that the pair of results are on a consistent moisture, temperature, and diluent concentration basis. Then, compare each integrated CEMS value against the corresponding average RM value. Use the following guidelines to make these comparisons.
8.4.5.1 If the RM has an integrated sampling technique, make a direct comparison of the RM results and CEMS integrated average value.
8.4.5.2 If the RM has a grab sampling technique, first average the results from all grab samples taken during the test run, and then compare this average value against the integrated value obtained from the CEMS chart recording or output during the run. If the pollutant concentration is varying with time over the run, the arithmetic average of the CEMS value recorded at the time of each grab sample may be used.
8.4.6 Calculate the mean difference between the RM and CEMS values in the units of the emission standard, the standard deviation, the confidence coefficient, and the relative accuracy according to the procedures in section 12.0.
8.5 Reporting. At a minimum (check with the appropriate regional office, State, or Local agency for additional requirements, if any), summarize in tabular form the results of the CD tests and the RA tests or alternative RA procedure, as appropriate. Include all data sheets, calculations, charts (records of CEMS responses), cylinder gas concentration certifications, and calibration cell response certifications (if applicable) necessary to confirm that the performance of the CEMS met the performance specifications.
9.0 Quality Control [Reserved] 10.0 Calibration and Standardization [Reserved] 11.0 Analytical ProcedureSample collection and analysis are concurrent for this Performance Specification (see section 8.0). Refer to the RM for specific analytical procedures.
12.0 Calculations and Data AnalysisSummarize the results on a data sheet similar to that shown in Figure 2-2 (in section 18.0).
12.1 All data from the RM and CEMS must be on a consistent dry basis and, as applicable, on a consistent diluent basis and in the units of the emission standard. Correct the RM and CEMS data for moisture and diluent as follows:
12.1.1 Moisture Correction (as applicable). Correct each wet RM run for moisture with the corresponding Method 4 data; correct each wet CEMS run using the corresponding CEMS moisture monitor date using Equation 2-1.
12.1.2 Correction to Units of Standard (as applicable). Correct each dry RM run to the units of the emission standard with the corresponding Method 3B data; correct each dry CEMS run using the corresponding CEMS diluent monitor data as follows:
12.1.2.1 Correct to Diluent Basis. The following is an example of concentration (ppm) correction to 7% oxygen.
The following is an example of mass/gross calorific value (lbs/million Btu) correction.
lbs/MMBtu = Conc(dry) (F-factor) (20.9/20.9-%02)12.2 Arithmetic Mean. Calculate the arithmetic mean of the difference, d, of a data set as follows:
Where: n = Number of data points.12.3 Standard Deviation. Calculate the standard deviation, Sd, as follows:
12.4 Confidence Coefficient. Calculate the 2.5 percent error confidence coefficient (one-tailed), CC, as follows:
Where: t 0.975 = t-value (see Table 2-1).12.5 Relative Accuracy. Calculate the RA of a set of data as follows:
Where: |d | = Absolute value of the mean differences (from Equation 2-3). |CC| = Absolute value of the confidence coefficient (from Equation 2-3). RM = Average RM value. In cases where the average emissions for the test are less than 50 percent of the applicable standard, substitute the emission standard value in the denominator of Eq. 2-6 in place of RM. In all other cases, use RM. 13.0 Method Performance13.1 Calibration Drift Performance Specification. The CEMS calibration must not drift or deviate from the reference value of the gas cylinder, gas cell, or optical filter by more than 2.5 percent of the span value. If the CEMS includes pollutant and diluent monitors, the CD must be determined separately for each in terms of concentrations (See Performance Specification 3 for the diluent specifications), and none of the CDs may exceed the specification.
13.2 Relative Accuracy Performance Specification.
Calculate . . . | RA criteria (%) |
|
---|---|---|
If average emissions during the RATA are ≥50% of emission standard | Use Eq. 2-6, with RM in the denominator | ≤20.0 |
If average emissions during the RATA are <50% of emission standard | Use Eq. 2-6, emission standard in the denominator | ≤10.0 |
For SO2 emission standards ≤130 but ≥86 ng/J (0.30 and 0.20 lb/million Btu) | Use Eq. 2-6, emission standard in the denominator | ≤15.0 |
For SO2 emission standards <86 ng/J (0.20 lb/million Btu) | Use Eq. 2-6, emission standard in the denominator | ≤20.0 |
13.3 For instruments that use common components to measure more than one effluent gas constituent, all channels must simultaneously pass the RA requirement, unless it can be demonstrated that any adjustments made to one channel did not affect the others.
14.0 Pollution Prevention [Reserved] 15.0 Waste Management [Reserved] 16.0 Alternative ProceduresParagraphs 60.13(j)(1) and (2) of 40 CFR part 60 contain criteria for which the reference method procedure for determining relative accuracy (see section 8.4 of this Performance Specification) may be waived and the following procedure substituted.
16.1 Conduct a complete CEMS status check following the manufacturer's written instructions. The check should include operation of the light source, signal receiver, timing mechanism functions, data acquisition and data reduction functions, data recorders, mechanically operated functions (mirror movements, zero pipe operation, calibration gas valve operations, etc.), sample filters, sample line heaters, moisture traps, and other related functions of the CEMS, as applicable. All parts of the CEMS shall be functioning properly before proceeding to the alternative RA procedure.
16.2 Alternative RA Procedure.
16.2.1 Challenge each monitor (both pollutant and diluent, if applicable) with cylinder gases of known concentrations or calibration cells that produce known responses at two measurement points within the ranges shown in Table 2-2 (Section 18).
16.2.2 Use a separate cylinder gas (for point CEMS only) or calibration cell (for path CEMS or where compressed gas cylinders can not be used) for measurement points 1 and 2. Challenge the CEMS and record the responses three times at each measurement point. The Administrator may allow dilution of cylinder gas using the performance criteria in Test Method 205, 40 CFR Part 51, Appendix M. Use the average of the three responses in determining relative accuracy.
16.2.3 Operate each monitor in its normal sampling mode as nearly as possible. When using cylinder gases, pass the cylinder gas through all filters, scrubbers, conditioners, and other monitor components used during normal sampling and as much of the sampling probe as practical. When using calibration cells, the CEMS components used in the normal sampling mode should not be by-passed during the RA determination. These include light sources, lenses, detectors, and reference cells. The CEMS should be challenged at each measurement point for a sufficient period of time to assure adsorption-desorption reactions on the CEMS surfaces have stabilized.
16.2.4 Use cylinder gases that have been certified by comparison to National Institute of Standards and Technology (NIST) gaseous standard reference material (SRM) or NIST/EPA approved gas manufacturer's certified reference material (CRM) (See Reference 2 in section 17.0) following EPA Traceability Protocol Number 1 (See Reference 3 in section 17.0). As an alternative to Protocol Number 1 gases, CRM's may be used directly as alternative RA cylinder gases. A list of gas manufacturers that have prepared approved CRM's is available from EPA at the address shown in Reference 2. Procedures for preparation of CRM's are described in Reference 2.
16.2.5 Use calibration cells certified by the manufacturer to produce a known response in the CEMS. The cell certification procedure shall include determination of CEMS response produced by the calibration cell in direct comparison with measurement of gases of known concentration. This can be accomplished using SRM or CRM gases in a laboratory source simulator or through extended tests using reference methods at the CEMS location in the exhaust stack. These procedures are discussed in Reference 4 in section 17.0. The calibration cell certification procedure is subject to approval of the Administrator.
16.3 The differences between the known concentrations of the cylinder gases and the concentrations indicated by the CEMS are used to assess the accuracy of the CEMS. The calculations and limits of acceptable relative accuracy are as follows:
16.3.1 For pollutant CEMS:
Where: d = Average difference between responses and the concentration/responses (see section 16.2.2). AC = The known concentration/response of the cylinder gas or calibration cell.16.3.2 For diluent CEMS:
RA= d; ≤0.7 percent O2 or CO2, as applicable. Note:Waiver of the relative accuracy test in favor of the alternative RA procedure does not preclude the requirements to complete the CD tests nor any other requirements specified in an applicable subpart for reporting CEMS data and performing CEMS drift checks or audits.
17.0 References1. Department of Commerce. Experimental Statistics. Handbook 91. Washington, D.C. p. 3-31, paragraphs 3-3.1.4.
2. “A Procedure for Establishing Traceability of Gas Mixtures to Certain National Bureau of Standards Standard Reference Materials.” Joint publication by NBS and EPA. EPA 600/7-81-010. Available from U.S. Environmental Protection Agency, Quality Assurance Division (MD-77), Research Triangle Park, North Carolina 27711.
3. “Traceability Protocol for Establishing True Concentrations of Gases Used for Calibration and Audits of Continuous Source Emission Monitors. (Protocol Number 1).” June 1978. Protocol Number 1 is included in the Quality Assurance Handbook for Air Pollution Measurement Systems, Volume III, Stationary Source Specific Methods. EPA-600/4-77-027b. August 1977.
4. “Gaseous Continuous Emission Monitoring Systems - Performance Specification Guidelines for SO2, NOX, CO2, O2, and TRS.” EPA-450/3-82-026. Available from the U.S. EPA, Emission Measurement Center, Emission Monitoring and Data Analysis Division (MD-19), Research Triangle Park, North Carolina 27711.
18.0 Tables, Diagrams, Flowcharts, and Validation DataTable 2-1 - t-Values
n a | t0.975 | n a | t0.975 | n a | t0.975 |
---|---|---|---|---|---|
2 | 12.706 | 7 | 2.447 | 12 | 2.201 |
3 | 4.303 | 8 | 2.365 | 13 | 2.179 |
4 | 3.182 | 9 | 2.306 | 14 | 2.160 |
5 | 2.776 | 10 | 2.262 | 15 | 2.145 |
6 | 2.571 | 11 | 2.228 | 16 | 2.131 |
a The values in this table are already corrected for n−1 degrees of freedom. Use n equal to the number of individual values.
Table 2-2 - Measurement Range
Measurement point | Pollutant monitor | Diluent monitor for | |
---|---|---|---|
CO2 | O2 | ||
1 | 20-30% of span value | 5-8% by volume | 4-6% by volume. |
2 | 50-60% of span value | 10-14% by volume | 8-12% by volume. |
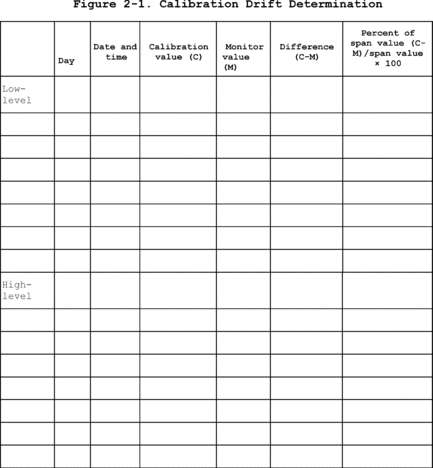
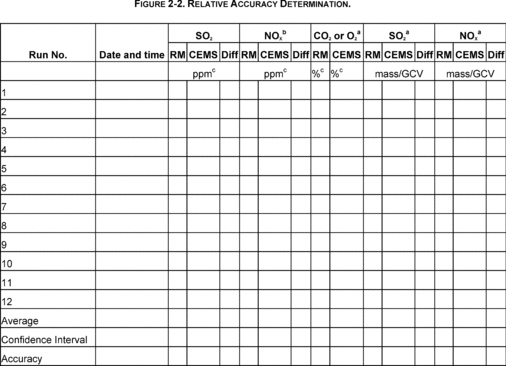
a For Steam generators.
b Average of three samples.
c Make sure that RM and CEMS data are on a consistent basis, either wet or dry.
1.1 Analytes.
Analytes | CAS No. |
---|---|
Carbon Dioxide (CO2) | 124-38-9 |
Oxygen (O2) | 7782-44-7 |
1.2 Applicability.
1.2.1 This specification is for evaluating acceptability of O2 and CO2 continuous emission monitoring systems (CEMS) at the time of installation or soon after and whenever specified in an applicable subpart of the regulations. This specification applies to O2 or CO2 monitors that are not included under Performance Specification 2 (PS 2).
1.2.2 This specification is not designed to evaluate the installed CEMS performance over an extended period of time, nor does it identify specific calibration techniques and other auxiliary procedures to assess the CEMS performance. The source owner or operator, is responsible to calibrate, maintain, and operate the CEMS properly. The Administrator may require, under section 114 of the Act, the operator to conduct CEMS performance evaluations at other times besides the initial test to evaluate the CEMS performance. See 40 CFR part 60, section 60.13(c).
1.2.3 The definitions, installation and measurement location specifications, calculations and data analysis, and references are the same as in PS 2, sections 3, 8.1, 12, and 17, respectively, and also apply to O2 and CO2 CEMS under this specification. The performance and equipment specifications and the relative accuracy (RA) test procedures for O2 and CO2 CEMS do not differ from those for SO2 and NOX CEMS (see PS 2), except as noted below.
2.0 Summary of Performance SpecificationThe RA and calibration drift (CD) tests are conducted to determine conformance of the CEMS to the specification.
3.0 DefinitionsSame as in section 3.0 of PS 2.
4.0 Interferences [Reserved] 5.0 SafetyThis performance specification may involve hazardous materials, operations, and equipment. This performance specification may not address all of the safety problems associated with its use. It is the responsibility of the user to establish appropriate safety and health practices and determine the applicable regulatory limitations prior to performing this performance specification. The CEMS users manual should be consulted for specific precautions to be taken with regard to the analytical procedures.
6.0 Equipment and SuppliesSame as section 6.0 of PS2.
7.0 Reagents and StandardsSame as section 7.0 of PS2.
8.0 Sample Collection, Preservation, Storage, and Transport8.1 Relative Accuracy Test Procedure. Sampling Strategy for reference method (RM) Tests, Correlation of RM and CEMS Data, and Number of RM Tests. Same as PS 2, sections 8.4.3, 8.4.5, and 8.4.4, respectively.
8.2 Reference Method. Unless otherwise specified in an applicable subpart of the regulations, Method 3B or other approved alternative is the RM for O2 or CO2.
9.0 Quality Control [Reserved] 10.0 Calibration and Standardization [Reserved] 11.0 Analytical ProcedureSample collection and analyses are concurrent for this performance specification (see section 8). Refer to the RM for specific analytical procedures.
12.0 Calculations and Data AnalysisCalculate the RA using equations 3-1 and 3-2. Summarize the results on a data sheet similar to that shown in Figure 2.2 of PS2.

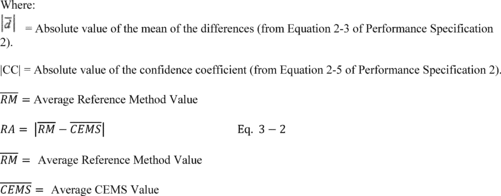
13.1 Calibration Drift Performance Specification. The CEMS calibration must not drift by more than 0.5 percent O2 or CO2 from the reference value of the gas, gas cell, or optical filter.
13.2 CEMS Relative Accuracy Performance Specification. The RA of the CEMS must be no greater than 20.0 percent of the mean value of the reference method (RM) data when calculated using equation 3-1. The results are also acceptable if the result of Equation 3-2 is less than or equal to 1.0 percent O2 (or CO2).
14.0 Pollution Prevention [Reserved] 15.0 Waste Management [Reserved] 16.0 ReferencesSame as in section 17.0 of PS 2.
17.0 Tables, Diagrams, Flowcharts, and Validation Data [Reserved] Performance Specification 4 - Specifications and Test Procedures for Carbon Monoxide Continuous Emission Monitoring Systems in Stationary Sources 1.0 Scope and Application1.1 Analytes.
Analyte | CAS No. |
---|---|
Carbon Monoxide (CO) | 630-08-0 |
1.2 Applicability.
1.2.1 This specification is for evaluating the acceptability of carbon monoxide (CO) continuous emission monitoring systems (CEMS) at the time of installation or soon after and whenever specified in an applicable subpart of the regulations. This specification was developed primarily for CEMS having span values of 1,000 ppmv CO.
1.2.2 This specification is not designed to evaluate the installed CEMS performance over an extended period of time nor does it identify specific calibration techniques and other auxiliary procedures to assess CEMS performance. The source owner or operator, is responsible to calibrate, maintain, and operate the CEMS. The Administrator may require, under section 114 of the Act, the source owner or operator to conduct CEMS performance evaluations at other times besides the initial test to evaluate the CEMS performance. See 40 CFR part 60, section 60.13(c).
1.2.3 The definitions, performance specification test procedures, calculations, and data analysis procedures for determining calibration drift (CD) and relative accuracy (RA) of Performance Specification 2 (PS 2), sections 3, 8.0, and 12, respectively, apply to this specification.
2.0 Summary of Performance SpecificationThe CD and RA tests are conducted to determine conformance of the CEMS to the specification.
3.0 DefinitionsSame as in section 3.0 of PS 2.
4.0 Interferences [Reserved] 5.0 SafetyThis performance specification may involve hazardous materials, operations, and equipment. This performance specification may not address all of the safety problems associated with its use. It is the responsibility of the user to establish appropriate safety and health practices and determine the applicable regulatory limitations prior to performing this performance specification. The CEMS users manual should be consulted for specific precautions to be taken with regard to the analytical procedures.
6.0 Equipment and SuppliesSame as section 6.0 of PS 2.
7.0 Reagents and StandardsSame as section 7.0 of PS 2.
8.0 Sample Collection, Preservation, Storage, and Transport8.1 Relative Accuracy Test Procedure. Sampling Strategy for reference method (RM) Tests, Number of RM Tests, and Correlation of RM and CEMS Data are the same as PS 2, sections 8.4.3, 8.4.4, and 8.4.5, respectively.
8.2 Reference Methods. Unless otherwise specified in an applicable subpart of the regulation, Method 10, 10A, 10B or other approved alternative are the RM for this PS.
9.0 Quality Control [Reserved] 10.0 Calibration and Standardization [Reserved] 11.0 Analytical ProcedureSample collection and analysis are concurrent for this performance specification (see section 8.0). Refer to the RM for specific analytical procedures.
12.0 Calculations and Data AnalysisSame as section 12.0 of PS 2.
13.0 Method Performance13.1 Calibration Drift. The CEMS calibration must not drift or deviate from the reference value of the calibration gas, gas cell, or optical filter by more than 5 percent of the established span value for 6 out of 7 test days (e.g., the established span value is 1000 ppm for Subpart J affected facilities).
13.2 Relative Accuracy. The RA of the CEMS must be no greater than 10 percent when the average RM value is used to calculate RA or 5 percent when the applicable emission standard is used to calculate RA.
14.0 Pollution Prevention [Reserved] 15.0 Waste Management [Reserved] 16.0 Alternative Procedures [Reserved] 17.0 References1. Ferguson, B.B., R.E. Lester, and W.J. Mitchell. Field Evaluation of Carbon Monoxide and Hydrogen Sulfide Continuous Emission Monitors at an Oil Refinery. U.S. Environmental Protection Agency. Research Triangle Park, N.C. Publication No. EPA-600/4-82-054. August 1982. 100 p.
2. “Gaseous Continuous Emission Monitoring Systems - Performance Specification Guidelines for SO2, NOX, CO2, O2, and TRS.” EPA-450/3-82-026. U.S. Environmental Protection Agency, Technical Support Division (MD-19), Research Triangle Park, NC 27711.
3. Repp, M. Evaluation of Continuous Monitors for Carbon Monoxide in Stationary Sources. U.S. Environmental Protection Agency. Research Triangle Park, N.C. Publication No. EPA-600/2-77-063. March 1977. 155 p.
4. Smith, F., D.E. Wagoner, and R.P. Donovan. Guidelines for Development of a Quality Assurance Program: Volume VIII - Determination of CO Emissions from Stationary Sources by NDIR Spectrometry. U.S. Environmental Protection Agency. Research Triangle Park, N.C. Publication No. EPA-650/4-74-005-h. February 1975. 96 p.
18.0 Tables, Diagrams, Flowcharts, and Validation DataSame as section 18.0 of PS 2.
Performance Specification 4A - Specifications and Test Procedures for Carbon Monoxide Continuous Emission Monitoring Systems in Stationary Sources 1.0 Scope and Application1.1 Analytes.
Analyte | CAS No. |
---|---|
Carbon Monoxide (CO) | 630-80-0 |
1.2 Applicability.
1.2.1 This specification is for evaluating the acceptability of carbon monoxide (CO) continuous emission monitoring systems (CEMS) at the time of installation or soon after and whenever specified in an applicable subpart of the regulations. This specification was developed primarily for CEMS that comply with low emission standards (less than 200 ppmv).
1.2.2 This specification is not designed to evaluate the installed CEMS performance over an extended period of time nor does it identify specific calibration techniques and other auxiliary procedures to assess CEMS performance. The source owner or operator is responsible to calibrate, maintain, and operate the CEMS. The Administrator may require, under section 114 of the Act, the source owner or operator to conduct CEMS performance evaluations at other times besides the initial test to evaluate CEMS performance. See 40 CFR Part 60, section 60.13(c).
1.2.3 The definitions, performance specification, test procedures, calculations and data analysis procedures for determining calibration drifts (CD) and relative accuracy (RA), of Performance Specification 2 (PS 2), sections 3, 8.0, and 12, respectively, apply to this specification.
2.0 Summary of Performance SpecificationThe CD and RA tests are conducted to determine conformance of the CEMS to the specification.
3.0 DefinitionsSame as in section 3.0 of PS 2.
4.0 Interferences [Reserved] 5.0 SafetyThis performance specification may involve hazardous materials, operations, and equipment. This performance specification may not address all of the safety problems associated with its use. It is the responsibility of the user to establish appropriate safety and health practices and determine the applicable regulatory limitations prior to performing this performance specification. The CEMS users manual should be consulted for specific precautions to be taken with regard to the analytical procedures.
6.0 Equipment and SuppliesSame as section 6.0 of PS 2 with the following additions.
6.1 Data Recorder Scale.
6.1.1 This specification is the same as section 6.1 of PS 2. The CEMS shall be capable of measuring emission levels under normal conditions and under periods of short-duration peaks of high concentrations. This dual-range capability may be met using two separate analyzers (one for each range) or by using dual-range units which have the capability of measuring both levels with a single unit. In the latter case, when the reading goes above the full-scale measurement value of the lower range, the higher-range operation shall be started automatically. The CEMS recorder range must include zero and a high-level value. Under applications of consistent low emissions, a single-range analyzer is allowed provided normal and spike emissions can be quantified. In this case, set an appropriate high-level value to include all emissions.
6.1.2 For the low-range scale of dual-range units, the high-level value shall be between 1.5 times the pollutant concentration corresponding to the emission standard level and the span value. For the high-range scale, the high-level value shall be set at 2000 ppm, as a minimum, and the range shall include the level of the span value. There shall be no concentration gap between the low-and high-range scales.
7.0 Reagents and StandardsSame as section 7.0 of PS 2.
8.0 Sample Collection, Preservation, Storage, and Transport8.1 Relative Accuracy Test Procedure. Sampling Strategy for reference method (RM) Tests, Number of RM Tests, and Correlation of RM and CEMS Data are the same as PS 2, sections 8.4.3, 8.4.4, and 8.4.5, respectively.
8.2 Reference Methods. Unless otherwise specified in an applicable subpart of the regulation, Methods 10, 10A, 10B, or other approved alternative is the RM for this PS. When evaluating nondispersive infrared CEMS using Method 10 as the RM, the alternative interference trap specified in section 16.0 of Method 10 shall be used.
8.3 Response Time Test Procedure. The response time test applies to all types of CEMS, but will generally have significance only for extractive systems. The entire system is checked with this procedure including applicable sample extraction and transport, sample conditioning, gas analyses, and data recording.
8.3.1 Introduce zero gas into the system. When the system output has stabilized (no change greater than 1 percent of full scale for 30 sec), introduce an upscale calibration gas and wait for a stable value. Record the time (upscale response time) required to reach 95 percent of the final stable value. Next, reintroduce the zero gas and wait for a stable reading before recording the response time (downscale response time). Repeat the entire procedure until you have three sets of data to determine the mean upscale and downscale response times. The slower or longer of the two means is the system response time.
8.4 Interference Check. The CEMS must be shown to be free from the effects of any interferences.
9.0 Quality Control [Reserved] 10.0 Calibration and Standardization [Reserved] 11.0 Analytical ProcedureSample collection and analysis are concurrent for this performance specification (see section 8.0). Refer to the RM for specific analytical procedures.
12.0 Calculations and Data Analysis. Same as section 12.0 of PS 2 13.0 Method Performance13.1 Calibration Drift. The CEMS calibration must not drift or deviate from the reference value of the calibration gas, gas cell, or optical filter by more than 5 percent of the established span value for 6 out of 7 test days.
13.2 Relative Accuracy. The RA of the CEMS must be no greater than 10 percent when the average RM value is used to calculate RA, 5 percent when the applicable emission standard is used to calculate RA, or within 5 ppmv when the RA is calculated as the absolute average difference between the RM and CEMS plus the 2.5 percent confidence coefficient.
13.3 Response Time. The CEMS response time shall not exceed 240 seconds to achieve 95 percent of the final stable value.
14.0 Pollution Prevention [Reserved] 15.0 Waste Management [Reserved] 16.0 Alternative Procedures16.1 Under conditions where the average CO emissions are less than 10 percent of the standard and this is verified by Method 10, a cylinder gas audit may be performed in place of the RA test to determine compliance with these limits. In this case, the cylinder gas shall contain CO in 12 percent carbon dioxide as an interference check. If this option is exercised, Method 10 must be used to verify that emission levels are less than 10 percent of the standard.
17.0 ReferencesSame as section 17 of PS 4.
18.0 Tables, Diagrams, Flowcharts, and Validation DataSame as section 18.0 of PS 2.
Performance Specification 4B - Specifications and Test Procedures for Carbon Monoxide and Oxygen Continuous Monitoring Systems in Stationary Sources a. Applicability and Principle1.1 Applicability. a. This specification is to be used for evaluating the acceptability of carbon monoxide (CO) and oxygen (O2) continuous emission monitoring systems (CEMS) at the time of or soon after installation and whenever specified in the regulations. The CEMS may include, for certain stationary sources, (a) flow monitoring equipment to allow measurement of the dry volume of stack effluent sampled, and (b) an automatic sampling system.
b. This specification is not designed to evaluate the installed CEMS' performance over an extended period of time nor does it identify specific calibration techniques and auxiliary procedures to assess the CEMS' performance. The source owner or operator, however, is responsible to properly calibrate, maintain, and operate the CEMS. To evaluate the CEMS' performance, the Administrator may require, under section 114 of the Act, the operator to conduct CEMS performance evaluations at times other than the initial test.
c. The definitions, installation and measurement location specifications, test procedures, data reduction procedures, reporting requirements, and bibliography are the same as in PS 3 (for O2) and PS 4A (for CO) except as otherwise noted below.
1.2 Principle. Installation and measurement location specifications, performance specifications, test procedures, and data reduction procedures are included in this specification. Reference method tests, calibration error tests, calibration drift tests, and interferant tests are conducted to determine conformance of the CEMS with the specification.
b. Definitions2.1 Continuous Emission Monitoring System (CEMS). This definition is the same as PS 2 section 2.1 with the following addition. A continuous monitor is one in which the sample to be analyzed passes the measurement section of the analyzer without interruption.
2.2 Response Time. The time interval between the start of a step change in the system input and when the pollutant analyzer output reaches 95 percent of the final value.
2.3 Calibration Error (CE). The difference between the concentration indicated by the CEMS and the known concentration generated by a calibration source when the entire CEMS, including the sampling interface is challenged. A CE test procedure is performed to document the accuracy and linearity of the CEMS over the entire measurement range.
3. Installation and Measurement Location Specifications3.1 The CEMS Installation and Measurement Location. This specification is the same as PS 2 section 3.1 with the following additions. Both the CO and O2 monitors should be installed at the same general location. If this is not possible, they may be installed at different locations if the effluent gases at both sample locations are not stratified and there is no in-leakage of air between sampling locations.
3.1.1 Measurement Location. Same as PS 2 section 3.1.1.
3.1.2 Point CEMS. The measurement point should be within or centrally located over the centroidal area of the stack or duct cross section.
3.1.3 Path CEMS. The effective measurement path should: (1) Have at least 70 percent of the path within the inner 50 percent of the stack or duct cross sectional area, or (2) be centrally located over any part of the centroidal area.
3.2 Reference Method (RM) Measurement Location and Traverse Points. This specification is the same as PS 2 section 3.2 with the following additions. When pollutant concentration changes are due solely to diluent leakage and CO and O2 are simultaneously measured at the same location, one half diameter may be used in place of two equivalent diameters.
3.3 Stratification Test Procedure. Stratification is defined as the difference in excess of 10 percent between the average concentration in the duct or stack and the concentration at any point more than 1.0 meter from the duct or stack wall. To determine whether effluent stratification exists, a dual probe system should be used to determine the average effluent concentration while measurements at each traverse point are being made. One probe, located at the stack or duct centroid, is used as a stationary reference point to indicate change in the effluent concentration over time. The second probe is used for sampling at the traverse points specified in Method 1 (40 CFR part 60 appendix A). The monitoring system samples sequentially at the reference and traverse points throughout the testing period for five minutes at each point.
d. Performance and Equipment Specifications4.1 Data Recorder Scale. For O2, same as specified in PS 3, except that the span must be 25 percent. The span of the O2 may be higher if the O2 concentration at the sampling point can be greater than 25 percent. For CO, same as specified in PS 4A, except that the low-range span must be 200 ppm and the high range span must be 3000 ppm. In addition, the scale for both CEMS must record all readings within a measurement range with a resolution of 0.5 percent.
4.2 Calibration Drift. For O2, same as specified in PS 3. For CO, the same as specified in PS 4A except that the CEMS calibration must not drift from the reference value of the calibration standard by more than 3 percent of the span value on either the high or low range.
4.3 Relative Accuracy (RA). For O2, same as specified in PS 3. For CO, the same as specified in PS 4A.
4.4 Calibration Error (CE). The mean difference between the CEMS and reference values at all three test points (see Table I) must be no greater than 5 percent of span value for CO monitors and 0.5 percent for O2 monitors.
4.5 Response Time. The response time for the CO or O2 monitor must not exceed 240 seconds.
e. Performance Specification Test Procedure5.1 Calibration Error Test and Response Time Test Periods. Conduct the CE and response time tests during the CD test period.
F. The CEMS Calibration Drift and Response Time Test ProceduresThe response time test procedure is given in PS 4A, and must be carried out for both the CO and O2 monitors.
7. Relative Accuracy and Calibration Error Test Procedures
7.1 Calibration Error Test Procedure. Challenge each monitor (both low and high range CO and O2) with zero gas and EPA Protocol 1 cylinder gases at three measurement points within the ranges specified in Table I.
Table I. Calibration Error Concentration Ranges
Measurement point | CO Low range (ppm) | CO High range (ppm) | O2 (%) |
---|---|---|---|
1 | 0-40 | 0-600 | 0-2 |
2 | 60-80 | 900-1200 | 8-10 |
3 | 140-160 | 2100-2400 | 14-16 |
7.1.1 Calculations. Summarize the results on a data sheet. Average the differences between the instrument response and the certified cylinder gas value for each gas. Calculate the CE results for the CO monitor according to:
CE = | d/FS | × 100 (1) Where d is the mean difference between the CEMS response and the known reference concentration, and FS is the span value. The CE for the O2 monitor is the average percent O2 difference between the O2 monitor and the certified cylinder gas value for each gas.7.2 Relative Accuracy Test Procedure. Follow the RA test procedures in PS 3 (for O2) section 3 and PS 4A (for CO) section 4.
7.3 Alternative RA Procedure. Under some operating conditions, it may not be possible to obtain meaningful results using the RA test procedure. This includes conditions where consistent, very low CO emission or low CO emissions interrupted periodically by short duration, high level spikes are observed. It may be appropriate in these circumstances to waive the RA test and substitute the following procedure.
Conduct a complete CEMS status check following the manufacturer's written instructions. The check should include operation of the light source, signal receiver, timing mechanism functions, data acquisition and data reduction functions, data recorders, mechanically operated functions, sample filters, sample line heaters, moisture traps, and other related functions of the CEMS, as applicable. All parts of the CEMS must be functioning properly before the RA requirement can be waived. The instrument must also successfully passed the CE and CD specifications. Substitution of the alternate procedure requires approval of the Regional Administrator.
8. Bibliography
1. 40 CFR Part 266, Appendix IX, section 2, “Performance Specifications for Continuous Emission Monitoring Systems.”
Performance Specification 5 - Specifications and Test Procedures for TRS Continuous Emission Monitoring Systems in Stationary Sources 1.0 Scope and Application1.1 Analytes.
Analyte | CAS No. |
---|---|
Total Reduced Sulfur (TRS) | NA |
1.2 Applicability. This specification is for evaluating the applicability of TRS continuous emission monitoring systems (CEMS) at the time of installation or soon after and whenever specified in an applicable subpart of the regulations. The CEMS may include oxygen monitors which are subject to Performance Specification 3 (PS 3).
1.3 The definitions, performance specification, test procedures, calculations and data analysis procedures for determining calibration drifts (CD) and relative accuracy (RA) of PS 2, sections 3.0, 8.0, and 12.0, respectively, apply to this specification.
2.0 Summary of Performance SpecificationThe CD and RA tests are conducted to determine conformance of the CEMS to the specification.
3.0 DefinitionsSame as in section 3.0 of PS 2.
4.0 Interferences [Reserved] 5.0 SafetyThis performance specification may involve hazardous materials, operations, and equipment. This performance specification may not address all of the safety problems associated with its use. It is the responsibility of the user to establish appropriate safety and health practices and determine the applicable regulatory limitations prior to performing this performance specification. The CEMS user's manual should be consulted for specific precautions to be taken with regard to the analytical procedures.
6.0 Equipment and SuppliesSame as section 6.0 of PS 2.
7.0 Reagents and StandardsSame as section 7.0 of PS 2.
8.0 Sample Collection, Preservation, Storage, and Transport8.1 Relative Accuracy Test Procedure. Sampling Strategy for reference method (RM) Tests, Number of RM Tests, and Correlation of RM and CEMS Data are the same as PS 2, sections 8.4.3, 8.4.4, and 8.4.5, respectively.
Note:For Method 16, a sample is made up of at least three separate injects equally spaced over time. For Method 16A, a sample is collected for at least 1 hour. For Method 16B, you must analyze a minimum of three aliquots spaced evenly over the test period.
Note:For Method 16, a sample is made up of at least three separate injects equally space over time. For Method 16A, a sample is collected for at least 1 hour.
8.2 Reference Methods. Unless otherwise specified in the applicable subpart of the regulations, Method 16, Method 16A, 16B or other approved alternative is the RM for TRS.
9.0 Quality Control [Reserved] 10.0 Calibration and Standardization [Reserved] 11.0 Analytical ProcedureSample collection and analysis are concurrent for this performance specification (see section 8.0). Refer to the reference method for specific analytical procedures.
12.0 Calculations and Data AnalysisSame as section 12.0 of PS 2.
13.0 Method Performance13.1 Calibration Drift. The CEMS detector calibration must not drift or deviate from the reference value of the calibration gas by more than 5 percent of the established span value for 6 out of 7 test days. This corresponds to 1.5 ppm drift for Subpart BB sources where the span value is 30 ppm. If the CEMS includes pollutant and diluent monitors, the CD must be determined separately for each in terms of concentrations (see PS 3 for the diluent specifications).
13.2 Relative Accuracy. The RA of the CEMS must be no greater than 20 percent when the average RM value is used to calculate RA or 10 percent when the applicable emission standard is used to calculate RA.
14.0 Pollution Prevention [Reserved] 15.0 Waste Management [Reserved] 16.0 Alternative Procedures [Reserved] 17.0 References1. Department of Commerce. Experimental Statistics, National Bureau of Standards, Handbook 91. 1963. Paragraphs 3-3.1.4, p. 3-31.
2. A Guide to the Design, Maintenance and Operation of TRS Monitoring Systems. National Council for Air and Stream Improvement Technical Bulletin No. 89. September 1977.
3. Observation of Field Performance of TRS Monitors on a Kraft Recovery Furnace. National Council for Air and Stream Improvement Technical Bulletin No. 91. January 1978.
18.0 Tables, Diagrams, Flowcharts, and Validation DataSame as section 18.0 of PS 2.
Performance Specification 6 - Specifications and Test Procedures for Continuous Emission Rate Monitoring Systems in Stationary Sources 1.0 Scope and Application1.1 Applicability. This specification is used for evaluating the acceptability of continuous emission rate monitoring systems (CERMSs).
1.2 The installation and measurement location specifications, performance specification test procedure, calculations, and data analysis procedures, of Performance Specifications (PS 2), sections 8.0 and 12, respectively, apply to this specification.
2.0 Summary of Performance SpecificationThe calibration drift (CD) and relative accuracy (RA) tests are conducted to determine conformance of the CERMS to the specification.
3.0 DefinitionsThe definitions are the same as in section 3 of PS 2, except this specification refers to the continuous emission rate monitoring system rather than the continuous emission monitoring system. The following definitions are added:
3.1 Continuous Emission Rate Monitoring System (CERMS). The total equipment required for the determining and recording the pollutant mass emission rate (in terms of mass per unit of time).
3.2 Flow Rate Sensor. That portion of the CERMS that senses the volumetric flow rate and generates an output proportional to that flow rate. The flow rate sensor shall have provisions to check the CD for each flow rate parameter that it measures individually (e.g., velocity, pressure).
4.0 Interferences [Reserved] 5.0 SafetyThis performance specification may involve hazardous materials, operations, and equipment. This performance specification may not address all of the safety problems associated with its use. It is the responsibility of the user to establish appropriate safety and health practices and determine the applicable regulatory limitations prior to performing this performance specification. The CERMS users manual should be consulted for specific precautions to be taken with regard to the analytical procedures.
6.0 Equipment and SuppliesSame as section 6.0 of PS 2.
7.0 Reagents and StandardsSame as section 7.0 of PS 2.
8.0 Sample Collection, Preservation, Storage, and Transport8.1 Calibration Drift Test Procedure.
8.1.1 The CD measurements are to verify the ability of the CERMS to conform to the established CERMS calibrations used for determining the emission rate. Therefore, if periodic automatic or manual adjustments are made to the CERMS zero and calibration settings, conduct the CD tests immediately before these adjustments, or conduct them in such a way that CD can be determined.
8.1.2 Conduct the CD tests for pollutant concentration at the two values specified in section 6.1.2 of PS 2. For other parameters that are selectively measured by the CERMS (e.g., velocity, pressure, flow rate), use two analogous values (e.g., Low: 0-20% of full scale, High: 50-100% of full scale). Introduce to the CERMS the reference signals (these need not be certified). Record the CERMS response to each and subtract this value from the respective reference value (see example data sheet in Figure 6-1).
8.2 Relative Accuracy Test Procedure.
8.2.1 Sampling Strategy for reference method (RM) Tests, Correlation of RM and CERMS Data, and Number of RM Tests are the same as PS 2, sections 8.4.3, 8.4.5, and 8.4.4, respectively. Summarize the results on a data sheet. An example is shown in Figure 6-1. The RA test may be conducted during the CD test period.
8.2.2 Reference Methods. Unless otherwise specified in the applicable subpart of the regulations, the RM for the pollutant gas is the Appendix A method that is cited for compliance test purposes, or its approved alternatives. Methods 2, 2A, 2B, 2C, or 2D, as applicable, are the RMs for the determination of volumetric flow rate.
9.0 Quality Control [Reserved] 10.0 Calibration and Standardization [Reserved] 11.0 Analytical ProcedureSame as section 11.0 of PS 2.
12.0 Calculations and Data AnalysisSame as section 12.0 of PS 2.
13.0 Method Performance13.1 Calibration Drift. Since the CERMS includes analyzers for several measurements, the CD shall be determined separately for each analyzer in terms of its specific measurement. The calibration for each analyzer associated with the measurement of flow rate shall not drift or deviate from each reference value of flow rate by more than 3 percent of the respective high-level reference value over the CD test period (e.g., seven-day) associated with the pollutant analyzer. The CD specification for each analyzer for which other PSs have been established (e.g., PS 2 for SO2 and NOX), shall be the same as in the applicable PS.
13.2 CERMS Relative Accuracy. Calculate the CERMS Relative Accuracy using Eq. 2-6 of section 12 of Performance Specification 2. The RA of the CERMS shall be no greater than 20 percent of the mean value of the RM's test data in terms of the units of the emission standard, or in cases where the average emissions for the test are less than 50 percent of the applicable standard, substitute the emission standard value in the denominator of Eq. 2-6 in place of the RM.
14.0 Pollution Prevention [Reserved] 15.0 Waste Management [Reserved] 16.0 Alternative ProceduresSame as in section 16.0 of PS 2.
17.0 References1. Brooks, E.F., E.C. Beder, C.A. Flegal, D.J. Luciani, and R. Williams. Continuous Measurement of Total Gas Flow Rate from Stationary Sources. U.S. Environmental Protection Agency. Research Triangle Park, North Carolina. Publication No. EPA-650/2-75-020. February 1975. 248 p.
18.0 Tables, Diagrams, Flowcharts, and Validation DataRun No. | Date and time | Emission rate (kg/hr) a | ||
---|---|---|---|---|
CERMS | RMs | Difference (RMs-CERMS) |
||
1 | ||||
2 | ||||
3 | ||||
4 | ||||
5 | ||||
6 | ||||
7 | ||||
8 | ||||
9 |
a The RMs and CERMS data as corrected to a consistent basis (i.e., moisture, temperature, and pressure conditions).
1.1 Analytes.
Analyte | CAS No. |
---|---|
Hydrogen Sulfide | 7783-06-4 |
1.2 Applicability.
1.2.1 This specification is to be used for evaluating the acceptability of hydrogen sulfide (H2S) continuous emission monitoring systems (CEMS) at the time of or soon after installation and whenever specified in an applicable subpart of the regulations.
1.2.2 This specification is not designed to evaluate the installed CEMS performance over an extended period of time nor does it identify specific calibration techniques and other auxiliary procedures to assess CEMS performance. The source owner or operator, however, is responsible to calibrate, maintain, and operate the CEMS. To evaluate CEMS performance, the Administrator may require, under section 114 of the Act, the source owner or operator to conduct CEMS performance evaluations at other times besides the initial test. See section 60.13(c).
2.0 SummaryCalibration drift (CD) and relative accuracy (RA) tests are conducted to determine that the CEMS conforms to the specification.
3.0 DefinitionsSame as section 3.0 of PS 2.
4.0 Interferences [Reserved] 5.0 SafetyThe procedures required under this performance specification may involve hazardous materials, operations, and equipment. This performance specification may not address all of the safety problems associated with these procedures. It is the responsibility of the user to establish appropriate safety problems associated with these procedures. It is the responsibility of the user to establish appropriate safety and health practices and determine the application regulatory limitations prior to performing these procedures. The CEMS user's manual and materials recommended by the reference method should be consulted for specific precautions to be taken.
6.0 Equipment and Supplies6.1 Instrument Zero and Span. This specification is the same as section 6.1 of PS 2.
6.2 Calibration Drift. The CEMS calibration must not drift or deviate from the reference value of the calibration gas or reference source by more than 5 percent of the established span value for 6 out of 7 test days (e.g., the established span value is 300 ppm for Subpart J fuel gas combustion devices).
6.3 Relative Accuracy. The RA of the CEMS must be no greater than 20 percent when the average reference method (RM) value is used to calculate RA or 10 percent when the applicable emission standard is used to calculate RA.
7.0 Reagents and StandardsSame as section 7.0 of PS 2.
8.0 Sample Collection, Preservation, Storage, and Transport.8.1 Installation and Measurement Location Specification. Same as section 8.1 of PS 2.
8.2 Pretest Preparation. Same as section 8.2 of PS 2.
8.3 Calibration Drift Test Procedure. Same as section 8.3 of PS 2.
8.4 Relative Accuracy Test Procedure.
8.4.1 Sampling Strategy for RM Tests, Number of RM Tests, Correlation of RM and CEMS Data, and Calculations. These are the same as that in PS-2, Sections 8.4.3 (except as specified below), 8.4.4, 8.4.5, and 8.4.6, respectively.
8.4.2 Reference Methods. Unless otherwise specified in an applicable subpart of the regulation, Methods 11, 15, and 16 may be used for the RM for this PS.
8.4.2.1 Sampling Time Per Run - Method 11. A sampling run, when Method 11 (integrated sampling) is used, shall consist of a single measurement for at least 10 minutes and 0.010 dscm (0.35 dscf). Each sample shall be taken at approximately 30-minute intervals.
8.4.2.2 Sampling Time Per Run - Methods 15 and 16. The sampling run shall consist of two injections equally spaced over a 30-minute period following the procedures described in the particular method. Note: Caution! Heater or non-approved electrical probes should not be used around explosive or flammable sources.
8.5 Reporting. Same as section 8.5 of PS 2.
9.0 Quality Control [Reserved] 10.0 Calibration and Standardizations [Reserved] 11.0 Analytical ProceduresSample Collection and analysis are concurrent for this PS (see section 8.0). Refer to the RM for specific analytical procedures.
12.0 Data Analysis and CalculationsSame as section 12.0 of PS 2.
13.0 Method Performance [Reserved] 14.0 Pollution Prevention [Reserved] 15.0 Waste Management [Reserved] 16.0 References1. U.S. Environmental Protection Agency. Standards of Performance for New Stationary Sources; Appendix B; Performance Specifications 2 and 3 for SO2, NOX, CO2, and O2 Continuous Emission Monitoring Systems; Final Rule. 48 CFR 23608. Washington, D.C. U.S. Government Printing Office. May 25, 1983.
2. U.S. Government Printing Office. Gaseous Continuous Emission Monitoring Systems - Performance Specification Guidelines for SO2, NOX, CO2, O2, and TRS. U.S. Environmental Protection Agency. Washington, D.C. EPA-450/3-82-026. October 1982. 26 p.
3. Maines, G.D., W.C. Kelly (Scott Environmental Technology, Inc.), and J.B. Homolya. Evaluation of Monitors for Measuring H2S in Refinery Gas. Prepared for the U.S. Environmental Protection Agency. Research Triangle Park, N.C. Contract No. 68-02-2707. 1978. 60 p.
4. Ferguson, B.B., R.E. Lester (Harmon Engineering and Testing), and W.J. Mitchell. Field Evaluation of Carbon Monoxide and Hydrogen Sulfide Continuous Emission Monitors at an Oil Refinery. Prepared for the U.S. Environmental Protection Agency. Research Triangle Park, N.C. Publication No. EPA-600/4-82-054. August 1982. 100 p.
5. Letter to RAMCON Environmental Corp. from Robert Kellam, December 27, 1992.
17.0 Tables, Diagrams, Flowcharts, and Validation DataSame as section 18.0 of PS 2.
Performance Specification 8 - Performance Specifications for Volatile Organic Compound Continuous Emission Monitoring Systems in Stationary Sources 1.0 Scope and Application1.1 Analytes. Volatile Organic Compounds (VOCs).
1.2 Applicability.
1.2.1 This specification is to be used for evaluating a continuous emission monitoring system (CEMS) that measures a mixture of VOC's and generates a single combined response value. The VOC detection principle may be flame ionization (FI), photoionization (PI), non-dispersive infrared absorption (NDIR), or any other detection principle that is appropriate for the VOC species present in the emission gases and that meets this performance specification. The performance specification includes procedures to evaluate the acceptability of the CEMS at the time of or soon after its installation and whenever specified in emission regulations or permits. This specification is not designed to evaluate the installed CEMS performance over an extended period of time, nor does it identify specific calibration techniques and other auxiliary procedures to assess the CEMS performance. The source owner or operator, however, is responsible to calibrate, maintain, and operate the CEMS properly. To evaluate the CEMS performance, the Administrator may require, under section 114 of the Act, the operator to conduct CEMS performance evaluations in addition to the initial test. See section 60.13(c).
1.2.2 In most emission circumstances, most VOC monitors can provide only a relative measure of the total mass or volume concentration of a mixture of organic gases, rather than an accurate quantification. This problem is removed when an emission standard is based on a total VOC measurement as obtained with a particular detection principle. In those situations where a true mass or volume VOC concentration is needed, the problem can be mitigated by using the VOC CEMS as a relative indicator of total VOC concentration if statistical analysis indicates that a sufficient margin of compliance exists for this approach to be acceptable. Otherwise, consideration can be given to calibrating the CEMS with a mixture of the same VOC's in the same proportions as they actually occur in the measured source. In those circumstances where only one organic species is present in the source, or where equal incremental amounts of each of the organic species present generate equal CEMS responses, the latter choice can be more easily achieved.
2.0 Summary of Performance Specification2.1 Calibration drift and relative accuracy tests are conducted to determine adherence of the CEMS with specifications given for those items. The performance specifications include criteria for installation and measurement location, equipment and performance, and procedures for testing and data reduction.
3.0 Definitions.Same as section 3.0 of PS 2.
4.0 Interferences [Reserved] 5.0 SafetyThe procedures required under this performance specification may involve hazardous materials, operations, and equipment. This performance specification may not address all of the safety problems associated with these procedures. It is the responsibility of the user to establish appropriate safety problems associated with these procedures. It is the responsibility of the user to establish appropriate safety and health practices and determine the application regulatory limitations prior to performing these procedures. The CEMS user's manual and materials recommended by the reference method should be consulted for specific precautions to be taken.
6.0 Equipment and Supplies6.1 VOC CEMS Selection. When possible, select a VOC CEMS with the detection principle of the reference method specified in the regulation or permit (usually either FI, NDIR, or PI). Otherwise, use knowledge of the source process chemistry, previous emission studies, or gas chromatographic analysis of the source gas to select an appropriate VOC CEMS. Exercise extreme caution in choosing and installing any CEMS in an area with explosive hazard potential.
6.2 Data Recorder Scale. Same as section 6.1 of PS 2.
7.0 Reagents and Standards [Reserved] 8.0 Sample Collection, Preservation, Storage, and Transport8.1 Installation and Measurement Location Specifications. Same as section 8.1 of PS 2.
8.2 Pretest Preparation. Same as section 8.2 of PS 2.
8.3 Calibration Drift Test Procedure. Same as section 8.3 of PS 2.
8.4 Reference Method (RM). Use the method specified in the applicable regulation or permit, or any approved alternative, as the RM.
8.5 Sampling Strategy for RM Tests, Correlation of RM and CEMS Data, and Number of RM Tests. Follow PS 2, sections 8.4.3, 8.4.5, and 8.4.4, respectively.
8.6 Reporting. Same as section 8.5 of PS 2.
9.0 Quality Control [Reserved] 10.0 Calibration and Standardization [Reserved] 11.0 Analytical ProcedureSample collection and analysis are concurrent for this PS (see section 8.0). Refer to the RM for specific analytical procedures.
12.0 Calculations and Data AnalysisSame as section 12.0 of PS 2.
13.0 Method Performance13.1 Calibration Drift. The CEMS calibration must not drift by more than 2.5 percent of the span value.
13.2 CEMS Relative Accuracy. Unless stated otherwise in the regulation or permit, the RA of the CEMS must not be greater than 20 percent of the mean value of the RM test data in terms of the units of the emission standard, or 10 percent of the applicable standard, whichever is greater.
14.0 Pollution Prevention [Reserved] 15.0 Waste Management [Reserved] 16.0 ReferencesSame as section 17.0 of PS 2.
17.0 Tables, Diagrams, Flowcharts, and Validation Data [Reserved] Performance Specification 8A - Specifications and Test Procedures for Total Hydrocarbon Continuous Monitoring Systems in Stationary Sources 1. Applicability and Principle1.1 Applicability. These performance specifications apply to hydrocarbon (HC) continuous emission monitoring systems (CEMS) installed on stationary sources. The specifications include procedures which are intended to be used to evaluate the acceptability of the CEMS at the time of its installation or whenever specified in regulations or permits. The procedures are not designed to evaluate CEMS performance over an extended period of time. The source owner or operator is responsible for the proper calibration, maintenance, and operation of the CEMS at all times.
1.2 Principle. A gas sample is extracted from the source through a heated sample line and heated filter to a flame ionization detector (FID). Results are reported as volume concentration equivalents of propane. Installation and measurement location specifications, performance and equipment specifications, test and data reduction procedures, and brief quality assurance guidelines are included in the specifications. Calibration drift, calibration error, and response time tests are conducted to determine conformance of the CEMS with the specifications.
2. Definitions2.1 Continuous Emission Monitoring System (CEMS). The total equipment used to acquire data, which includes sample extraction and transport hardware, analyzer, data recording and processing hardware, and software. The system consists of the following major subsystems:
2.1.1 Sample Interface. That portion of the system that is used for one or more of the following: Sample acquisition, sample transportation, sample conditioning, or protection of the analyzer from the effects of the stack effluent.
2.1.2 Organic Analyzer. That portion of the system that senses organic concentration and generates an output proportional to the gas concentration.
2.1.3 Data Recorder. That portion of the system that records a permanent record of the measurement values. The data recorder may include automatic data reduction capabilities.
2.2 Instrument Measurement Range. The difference between the minimum and maximum concentration that can be measured by a specific instrument. The minimum is often stated or assumed to be zero and the range expressed only as the maximum.
2.3 Span or Span Value. Full scale instrument measurement range. The span value must be documented by the CEMS manufacturer with laboratory data.
2.4 Calibration Gas. A known concentration of a gas in an appropriate diluent gas.
2.5 Calibration Drift (CD). The difference in the CEMS output readings from the established reference value after a stated period of operation during which no unscheduled maintenance, repair, or adjustment takes place. A CD test is performed to demonstrate the stability of the CEMS calibration over time.
2.6 Response Time. The time interval between the start of a step change in the system input (e.g., change of calibration gas) and the time when the data recorder displays 95 percent of the final value.
2.7 Accuracy. A measurement of agreement between a measured value and an accepted or true value, expressed as the percentage difference between the true and measured values relative to the true value. For these performance specifications, accuracy is checked by conducting a calibration error (CE) test.
2.8 Calibration Error (CE). The difference between the concentration indicated by the CEMS and the known concentration of the cylinder gas. A CE test procedure is performed to document the accuracy and linearity of the monitoring equipment over the entire measurement range.
2.9 Performance Specification Test (PST) Period. The period during which CD, CE, and response time tests are conducted.
2.10 Centroidal Area. A concentric area that is geometrically similar to the stack or duct cross section and is no greater than 1 percent of the stack or duct cross-sectional area.
3. Installation and Measurement Location Specifications3.1 CEMS Installation and Measurement Locations. The CEMS must be installed in a location in which measurements representative of the source's emissions can be obtained. The optimum location of the sample interface for the CEMS is determined by a number of factors, including ease of access for calibration and maintenance, the degree to which sample conditioning will be required, the degree to which it represents total emissions, and the degree to which it represents the combustion situation in the firebox (where applicable). The location should be as free from in-leakage influences as possible and reasonably free from severe flow disturbances. The sample location should be at least two equivalent duct diameters downstream from the nearest control device, point of pollutant generation, or other point at which a change in the pollutant concentration or emission rate occurs and at least 0.5 diameter upstream from the exhaust or control device. The equivalent duct diameter is calculated as per 40 CFR part 60, appendix A, method 1, section 2.1. If these criteria are not achievable or if the location is otherwise less than optimum, the possibility of stratification should be investigated as described in section 3.2. The measurement point must be within the centroidal area of the stack or duct cross section.
3.2 Stratification Test Procedure. Stratification is defined as a difference in excess of 10 percent between the average concentration in the duct or stack and the concentration at any point more than 1.0 meter from the duct or stack wall. To determine whether effluent stratification exists, a dual probe system should be used to determine the average effluent concentration while measurements at each traverse point are being made. One probe, located at the stack or duct centroid, is used as a stationary reference point to indicate the change in effluent concentration over time. The second probe is used for sampling at the traverse points specified in 40 CFR part 60 appendix A, method 1. The monitoring system samples sequentially at the reference and traverse points throughout the testing period for five minutes at each point.
4. CEMS Performance and Equipment SpecificationsIf this method is applied in highly explosive areas, caution and care must be exercised in choice of equipment and installation.
4.1 Flame Ionization Detector (FID) Analyzer. A heated FID analyzer capable of meeting or exceeding the requirements of these specifications. Heated systems must maintain the temperature of the sample gas between 150 °C (300 °F) and 175 °C (350 °F) throughout the system. This requires all system components such as the probe, calibration valve, filter, sample lines, pump, and the FID to be kept heated at all times such that no moisture is condensed out of the system. The essential components of the measurement system are described below:
4.1.1 Sample Probe. Stainless steel, or equivalent, to collect a gas sample from the centroidal area of the stack cross-section.
4.1.2 Sample Line. Stainless steel or Teflon tubing to transport the sample to the analyzer.
Note:Mention of trade names or specific products does not constitute endorsement by the Environmental Protection Agency.
4.1.3 Calibration Valve Assembly. A heated three-way valve assembly to direct the zero and calibration gases to the analyzer is recommended. Other methods, such as quick-connect lines, to route calibration gas to the analyzers are applicable.
4.1.4 Particulate Filter. An in-stack or out-of-stack sintered stainless steel filter is recommended if exhaust gas particulate loading is significant. An out-of-stack filter must be heated.
4.1.5 Fuel. The fuel specified by the manufacturer (e.g., 40 percent hydrogen/60 percent helium, 40 percent hydrogen/60 percent nitrogen gas mixtures, or pure hydrogen) should be used.
4.1.6 Zero Gas. High purity air with less than 0.1 parts per million by volume (ppm) HC as methane or carbon equivalent or less than 0.1 percent of the span value, whichever is greater.
4.1.7 Calibration Gases. Appropriate concentrations of propane gas (in air or nitrogen). Preparation of the calibration gases should be done according to the procedures in EPA Protocol 1. In addition, the manufacturer of the cylinder gas should provide a recommended shelf life for each calibration gas cylinder over which the concentration does not change by more than ±2 percent from the certified value.
4.2 CEMS Span Value. 100 ppm propane. The span value must be documented by the CEMS manufacturer with laboratory data.
4.3 Daily Calibration Gas Values. The owner or operator must choose calibration gas concentrations that include zero and high-level calibration values.
4.3.1 The zero level may be between zero and 0.1 ppm (zero and 0.1 percent of the span value).
4.3.2 The high-level concentration must be between 50 and 90 ppm (50 and 90 percent of the span value).
4.4 Data Recorder Scale. The strip chart recorder, computer, or digital recorder must be capable of recording all readings within the CEMS' measurement range and must have a resolution of 0.5 ppm (0.5 percent of span value).
4.5 Response Time. The response time for the CEMS must not exceed 2 minutes to achieve 95 percent of the final stable value.
4.6 Calibration Drift. The CEMS must allow the determination of CD at the zero and high-level values. The CEMS calibration response must not differ by more than ±3 ppm (±3 percent of the span value) after each 24-hour period of the 7-day test at both zero and high levels.
4.7 Calibration Error. The mean difference between the CEMS and reference values at all three test points listed below must be no greater than 5 ppm (±5 percent of the span value).
4.7.1 Zero Level. Zero to 0.1 ppm (0 to 0.1 percent of span value).
4.7.2 Mid-Level. 30 to 40 ppm (30 to 40 percent of span value).
4.7.3 High-Level. 70 to 80 ppm (70 to 80 percent of span value).
4.8 Measurement and Recording Frequency. The sample to be analyzed must pass through the measurement section of the analyzer without interruption. The detector must measure the sample concentration at least once every 15 seconds. An average emission rate must be computed and recorded at least once every 60 seconds.
4.9 Hourly Rolling Average Calculation. The CEMS must calculate every minute an hourly rolling average, which is the arithmetic mean of the 60 most recent 1-minute average values.
4.10 Retest. If the CEMS produces results within the specified criteria, the test is successful. If the CEMS does not meet one or more of the criteria, necessary corrections must be made and the performance tests repeated.
5. Performance Specification Test (PST) Periods5.1 Pretest Preparation Period. Install the CEMS, prepare the PTM test site according to the specifications in section 3, and prepare the CEMS for operation and calibration according to the manufacturer's written instructions. A pretest conditioning period similar to that of the 7-day CD test is recommended to verify the operational status of the CEMS.
5.2 Calibration Drift Test Period. While the facility is operating under normal conditions, determine the magnitude of the CD at 24-hour intervals for seven consecutive days according to the procedure given in section 6.1. All CD determinations must be made following a 24-hour period during which no unscheduled maintenance, repair, or adjustment takes place. If the combustion unit is taken out of service during the test period, record the onset and duration of the downtime and continue the CD test when the unit resumes operation.
5.3 Calibration Error Test and Response Time Test Periods. Conduct the CE and response time tests during the CD test period.
6. Performance Specification Test Procedures6.1 Relative Accuracy Test Audit (RATA) and Absolute Calibration Audits (ACA). The test procedures described in this section are in lieu of a RATA and ACA.
6.2 Calibration Drift Test.
6.2.1 Sampling Strategy. Conduct the CD test at 24-hour intervals for seven consecutive days using calibration gases at the two daily concentration levels specified in section 4.3. Introduce the two calibration gases into the sampling system as close to the sampling probe outlet as practical. The gas must pass through all CEM components used during normal sampling. If periodic automatic or manual adjustments are made to the CEMS zero and calibration settings, conduct the CD test immediately before these adjustments, or conduct it in such a way that the CD can be determined. Record the CEMS response and subtract this value from the reference (calibration gas) value. To meet the specification, none of the differences may exceed 3 percent of the span of the CEM.
6.2.2 Calculations. Summarize the results on a data sheet. An example is shown in Figure 1. Calculate the differences between the CEMS responses and the reference values.
6.3 Response Time. The entire system including sample extraction and transport, sample conditioning, gas analyses, and the data recording is checked with this procedure.
6.3.1 Introduce the calibration gases at the probe as near to the sample location as possible. Introduce the zero gas into the system. When the system output has stabilized (no change greater than 1 percent of full scale for 30 sec), switch to monitor stack effluent and wait for a stable value. Record the time (upscale response time) required to reach 95 percent of the final stable value.
6.3.2 Next, introduce a high-level calibration gas and repeat the above procedure. Repeat the entire procedure three times and determine the mean upscale and downscale response times. The longer of the two means is the system response time.
6.4 Calibration Error Test Procedure.
6.4.1 Sampling Strategy. Challenge the CEMS with zero gas and EPA Protocol 1 cylinder gases at measurement points within the ranges specified in section 4.7.
6.4.1.1 The daily calibration gases, if Protocol 1, may be used for this test.
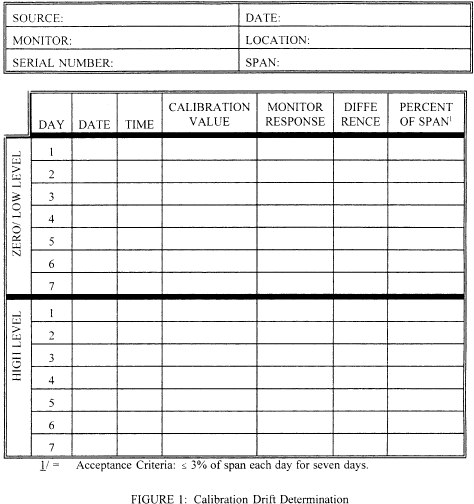
6.4.1.2 Operate the CEMS as nearly as possible in its normal sampling mode. The calibration gas should be injected into the sampling system as close to the sampling probe outlet as practical and must pass through all filters, scrubbers, conditioners, and other monitor components used during normal sampling. Challenge the CEMS three non-consecutive times at each measurement point and record the responses. The duration of each gas injection should be for a sufficient period of time to ensure that the CEMS surfaces are conditioned.
6.4.2 Calculations. Summarize the results on a data sheet. An example data sheet is shown in Figure 2. Average the differences between the instrument response and the certified cylinder gas value for each gas. Calculate three CE results according to Equation 1. No confidence coefficient is used in CE calculations.
7. EquationsCalibration Error. Calculate CE using Equation 1.

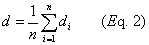
At a minimum, summarize in tabular form the results of the CD, response time, and CE test, as appropriate. Include all data sheets, calculations, CEMS data records, and cylinder gas or reference material certifications.
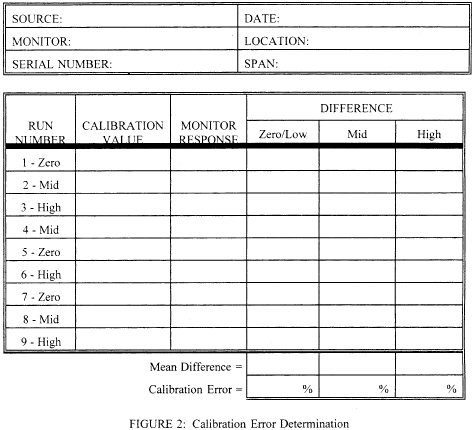
1. Measurement of Volatile Organic Compounds-Guideline Series. U.S. Environmental Protection Agency, Research Triangle Park, North Carolina, 27711, EPA-450/2-78-041, June 1978.
2. Traceability Protocol for Establishing True Concentrations of Gases Used for Calibration and Audits of Continuous Source Emission Monitors (Protocol No. 1). U.S. Environmental Protection Agency ORD/EMSL, Research Triangle Park, North Carolina, 27711, June 1978.
3. Gasoline Vapor Emission Laboratory Evaluation-Part 2. U.S. Environmental Protection Agency, OAQPS, Research Triangle Park, North Carolina, 27711, EMB Report No. 76-GAS-6, August 1975.
Performance Specification 9 - Specifications and Test Procedures for Gas Chromatographic Continuous Emission Monitoring Systems in Stationary Sources 1.0 Scope and Application1.1 Applicability. These requirements apply to continuous emission monitoring systems (CEMSs) that use gas chromatography (GC) to measure gaseous organic compound emissions. The requirements include procedures intended to evaluate the acceptability of the CEMS at the time of its installation and whenever specified in regulations or permits. Quality assurance procedures for calibrating, maintaining, and operating the CEMS properly at all times are also given in this procedure.
2.0 Summary of Performance Specification2.1 Calibration precision, calibration error, and performance audit tests are conducted to determine conformance of the CEMS with these specifications. Daily calibration and maintenance requirements are also specified.
3.0 Definitions3.1 Gas Chromatograph (GC). That portion of the system that separates and detects organic analytes and generates an output proportional to the gas concentration. The GC must be temperature controlled.
Note:The term temperature controlled refers to the ability to maintain a certain temperature around the column. Temperature-programmable GC is not required for this performance specification, as long as all other requirements for precision, linearity and accuracy listed in this performance specification are met. It should be noted that temperature programming a GC will speed up peak elution, thus allowing increased sampling frequency.
3.1.1 Column. Analytical column capable of separating the analytes of interest.
3.1.2 Detector. A detection system capable of detecting and quantifying all analytes of interest.
3.1.3 Integrator. That portion of the system that quantifies the area under a particular sample peak generated by the GC.
3.1.4 Data Recorder. A strip chart recorder, computer, or digital recorder capable of recording all readings within the instrument's calibration range.
3.2 Calibration Precision. The error between triplicate injections of each calibration standard.
4.0 Interferences [Reserved] 5.0 SafetyThe procedures required under this performance specification may involve hazardous materials, operations, and equipment. This performance specification does not purport to address all of the safety problems associated with these procedures. It is the responsibility of the user to establish appropriate safety problems associated with these procedures. It is the responsibility of the user to establish appropriate safety and health practices and determine the application regulatory limitations prior to performing these procedures. The CEMS user's manual and materials recommended by the reference method should be consulted for specific precautions to be taken.
6.0 Equipment and Supplies6.1 Presurvey Sample Analysis and GC Selection. Determine the pollutants to be monitored from the applicable regulation or permit and determine the approximate concentration of each pollutant (this information can be based on past compliance test results). Select an appropriate GC configuration to measure the organic compounds. The GC components should include a heated sample injection loop (or other sample introduction systems), separatory column, temperature-controlled oven, and detector. If the source chooses dual column and/or dual detector configurations, each column/detector is considered a separate instrument for the purpose of this performance specification and thus the procedures in this performance specification shall be carried out on each system. If this method is applied in highly explosive areas, caution should be exercised in selecting the equipment and method of installation.
6.2 Sampling System. The sampling system shall be heat traced and maintained at a minimum of 120 °C with no cold spots. All system components shall be heated, including the probe, calibration valve, sample lines, sampling loop (or sample introduction system), GC oven, and the detector block (when appropriate for the type of detector being utilized, e.g., flame ionization detector).
7.0 Reagents and Standards7.1 Calibration Gases. Obtain three concentrations of calibration gases certified by the manufacturer to be accurate to within 2 percent of the value on the label. A gas dilution system may be used to prepare the calibration gases from a high concentration certified standard if the gas dilution system meets the requirements specified in Test Method 205, 40 CFR Part 51, Appendix M. The performance test specified in Test Method 205 shall be repeated quarterly, and the results of the Method 205 test shall be included in the report. The calibration gas concentration of each target analyte shall be as follows (measured concentration is based on the presurvey concentration determined in section 6.1).
Note:If the low level calibration gas concentration falls at or below the limit of detection for the instrument for any target pollutant, a calibration gas with a concentration at 4 to 5 times the limit of detection for the instrument may be substituted for the low-level calibration gas listed in section 7.1.1.
7.1.1 Low-level. 40-60 percent of measured concentration.
7.1.2 Mid-level. 90-110 percent of measured concentration.
7.1.3 High-level. 140-160 percent of measured concentration, or select highest expected concentration.
7.2 Performance Audit Gas. Performance Audit Gas is an independent cylinder gas or cylinder gas mixture. A certified EPA audit gas shall be used, when possible. A gas mixture containing all the target compounds within the calibration range and certified by EPA's Traceability Protocol for Assay and Certification of Gaseous Calibration Standards may be used when EPA performance audit materials are not available. If a certified EPA audit gas or a traceability protocol gas is not available, use a gas manufacturer standard accurate to 2 percent.
8.0 Sample Collection, Preservation, Storage, and Transport8.1 Installation and Measurement Location Specifications. Install the CEMs in a location where the measurements are representative of the source emissions. Consider other factors, such as ease of access for calibration and maintenance purposes. The location should not be close to air in-leakages. The sampling location should be at least two equivalent duct diameters downstream from the nearest control device, point of pollutant generation, or other point at which a change in the pollutant concentration or emission rate occurs. The location should be at least 0.5 diameter upstream from the exhaust or control device. To calculate equivalent duct diameter, see section 12.2 of Method 1 (40 CFR Part 60, Appendix A). Sampling locations not conforming to the requirements in this section may be used if necessary upon approval of the Administrator.
8.2 Pretest Preparation Period. Using the procedures described in Method 18
(40 CFR Part 60, Appendix A), perform initial tests to determine GC conditions that provide good resolution and minimum analysis time for compounds of interest. Resolution interferences that may occur can be eliminated by appropriate GC column and detector choice or by shifting the retention times through changes in the column flow rate and the use of temperature programming.8.3 Seven (7)-Day Calibration Error (CE) Test Period. At the beginning of each 24-hour period, set the initial instrument set points by conducting a multi-point calibration for each compound. The multi-point calibration shall meet the requirements in sections 13.1, 13.2, and 13.3. Throughout the 24-hour period, sample and analyze the stack gas at the sampling intervals prescribed in the regulation or permit. At the end of the 24-hour period, inject the calibration gases at three concentrations for each compound in triplicate and determine the average instrument response. Determine the CE for each pollutant at each concentration using Equation 9-2. Each CE shall be ≤10 percent. Repeat this procedure six more times for a total of 7 consecutive days.
8.4 Performance Audit Test Periods. Conduct the performance audit once during the initial 7-day CE test and quarterly thereafter. Performance Audit Tests must be conducted through the entire sampling and analyzer system. Sample and analyze the EPA audit gas(es) (or the gas mixture) three times. Calculate the average instrument response. Results from the performance audit test must meet the requirements in sections 13.3 and 13.4.
8.5 Reporting. Follow the reporting requirements of the applicable regulation or permit. If the reporting requirements include the results of this performance specification, summarize in tabular form the results of the CE tests. Include all data sheets, calculations, CEMS data records, performance audit results, and calibration gas concentrations and certifications.
9.0 Quality Control [Reserved] 10.0 Calibration and Standardization10.1 Multi-Point Calibration. After initial startup of the GC, after routine maintenance or repair, or at least once per month, conduct a multi-point calibration of the GC for each target analyte. Calibration is performed at the instrument independent of the sample transport system. The multi-point calibration for each analyte shall meet the requirements in sections 13.1, 13.2, and 13.3.
10.2 Daily Calibration. Once every 24 hours, analyze the mid-level calibration standard for each analyte in triplicate. Calibration is performed at the instrument independent of the sample transport system. Calculate the average instrument response for each analyte. The average instrument response shall not vary by more than 10 percent from the certified concentration value of the cylinder for each analyte. If the difference between the analyzer response and the cylinder concentration for any target compound is greater than 10 percent, immediately inspect the instrument making any necessary adjustments, and conduct an initial multi-point calibration as described in section 10.1.
11.0 Analytical Procedure. Sample Collection and Analysis Are Concurrent for This Performance Specification (See section 8.0) 12.0 Calculations and Data Analysis12.1 Nomenclature.
Cm = average instrument response, ppm. Ca = cylinder gas value, ppm. F = Flow rate of stack gas through sampling system, in Liters/min. n = Number of measurement points. r 2 = Coefficient of determination. V = Sample system volume, in Liters, which is the volume inside the sample probe and tubing leading from the stack to the sampling loop. x = CEMS response. y = Actual value of calibration standard.12.2 Coefficient of Determination. Calculate r 2 using linear regression analysis and the average concentrations obtained at three calibration points as shown in Equation 9-1.
12.3 Calibration Error Determination. Determine the percent calibration error (CE) at each concentration for each pollutant using the following equation.
12.4 Sampling System Time Constant (T).
13.0 Method Performance13.1 Calibration Error (CE). The CEMS must allow the determination of CE at all three calibration levels. The average CEMS calibration response must not differ by more than 10 percent of calibration gas value at each level after each 24-hour period and after any triplicate calibration response check.
13.2 Calibration Precision and Linearity. For each triplicate injection at each concentration level for each target analyte, any one injection shall not deviate more than 5 percent from the average concentration measured at that level. When the CEMS response is evaluated over three concentration levels, the linear regression curve for each organic compound shall be determined using Equation 9-1 and must have an r 2 ≥0.995.
13.3 Measurement Frequency. The sample to be analyzed shall flow continuously through the sampling system. The sampling system time constant shall be ≤5 minutes or the sampling frequency specified in the applicable regulation, whichever is less. Use Equation 9-3 to determine T. The analytical system shall be capable of measuring the effluent stream at the frequency specified in the appropriate regulation or permit.
13.4 Audit Test Error. Determine the error for each average pollutant measurement using the Equation 9-2 in section 12.3. Each error shall be less than or equal to 10 percent of the cylinder gas certified value. Report the audit results including the average measured concentration, the error and the certified cylinder concentration of each pollutant as part of the reporting requirements in the appropriate regulation or permit.
14.0 Pollution Prevention [Reserved] 15.0 Waste Management [Reserved] 16.0 References [Reserved] 17.0 Tables, Diagrams, Flowcharts, and Validation Data [Reserved] Performance Specification 11 - Specifications and Test Procedures for Particulate Matter Continuous Emission Monitoring Systems at Stationary Sources 1.0 What Are the Purpose and Applicability of Performance Specification 11?The purpose of Performance Specification 11 (PS-11) is to establish the initial installation and performance procedures that are required for evaluating the acceptability of a particulate matter (PM) continuous emission monitoring system (CEMS); it is not to evaluate the ongoing performance of your PM CEMS over an extended period of time, nor to identify specific calibration techniques and auxiliary procedures to assess CEMS performance. You will find procedures for evaluating the ongoing performance of a PM CEMS in Procedure 2 of Appendix F - Quality Assurance Requirements for Particulate Matter Continuous Emission Monitoring Systems Used at Stationary Sources.
1.1 Under what conditions does PS-11 apply to my PM CEMS? The PS-11 applies to your PM CEMS if you are required by any provision of Title 40 of the Code of Federal Regulations (CFR) to install and operate PM CEMS.
1.2 When must I comply with PS-11? You must comply with PS-11 when directed by the applicable rule that requires you to install and operate a PM CEMS.
1.3 What other monitoring must I perform? To report your PM emissions in units of the emission standard, you may need to monitor additional parameters to correct the PM concentration reported by your PM CEMS. Your CEMS may include the components listed in paragraphs (1) through (3) of this section:
(1) A diluent monitor (i.e., O2, CO2, or other CEMS specified in the applicable regulation), which must meet its own performance specifications (also found in this appendix),
(2) Auxiliary monitoring equipment to allow measurement, determination, or input of the flue gas temperature, pressure, moisture content, and/or dry volume of stack effluent sampled, and
(3) An automatic sampling system. The performance of your PM CEMS and the establishment of its correlation to manual reference method measurements must be determined in units of mass concentration as measured by your PM CEMS (e.g., milligrams per actual cubic meter (mg/acm) or milligrams per dry standard cubic meter (mg/dscm)).
2.0 What Are the Basic Requirements of PS-11?The PS-11 requires you to perform initial installation and calibration procedures that confirm the acceptability of your CEMS when it is installed and placed into operation. You must develop a site-specific correlation of your PM CEMS response against manual gravimetric reference method measurements (including those made using EPA Methods 5, 5I, or 17).
2.1 What types of PM CEMS technologies are covered? Several different types of PM CEMS technologies (e.g., light scattering, Beta attenuation, etc.) can be designed with in-situ or extractive sample gas handling systems. Each PM CEMS technology and sample gas handling technology has certain site-specific advantages. You should select and install a PM CEMS that is appropriate for the flue gas conditions at your source.
2.2 How is PS-11 different from other performance specifications? The PS-11 is based on a technique of correlating PM CEMS responses relative to emission concentrations determined by the reference method. This technique is called “the correlation.” This differs from CEMS used to measure gaseous pollutants that have available calibration gases of known concentration. Because the type and characteristics of PM vary from source to source, a single PM correlation, applicable to all sources, is not possible.
2.3 How are the correlation data handled? You must carefully review your manual reference method data and your PM CEMS responses to include only valid, high-quality data. For the correlation, you must convert the manual reference method data to measurement conditions (e.g., wet or dry basis) that are consistent with your PM CEMS. Then, you must correlate the manual method and PM CEMS data in terms of the output as received from the monitor (e.g., milliamps). At the appropriate PM CEMS response specified in section 13.2 of this performance specification, you must calculate the confidence interval half range and tolerance interval half range as a percentage of the applicable PM concentration emission limit and compare the confidence interval and tolerance interval percentages with the performance criteria. Also, you must calculate the correlation coefficient and compare the correlation coefficient with the applicable performance criterion specified in section 13.2 of this performance specification.
Situations may arise where you will need two or more correlations. If you need multiple correlations, you must collect sufficient data for each correlation, and each correlation must satisfy the performance criteria specified in section 13.2 of this performance specification.
2.4 How do I design my PM CEMS correlation program? When planning your PM CEMS correlation effort, you must address each of the items in paragraphs (1) through (7) of this section to enhance the probability of success. You will find each of these elements further described in this performance specification or in the applicable reference method procedure.
(1) What type of PM CEMS should I select? You should select a PM CEMS that is appropriate for your source with technical consideration for potential factors such as interferences, site-specific configurations, installation location, flue gas conditions, PM concentration range, and other PM characteristics. You can find guidance on which technology is best suited for specific situations in our report “Current Knowledge of Particulate Matter (PM) Continuous Emission Monitoring” (PM CEMS Knowledge Document, see section 16.5).
(2) Where should I install my PM CEMS? Your PM CEMS must be installed in a location that is most representative of PM emissions, as determined by the reference method, such that the correlation between PM CEMS response and emissions determined by the reference method will meet these performance specifications. Care must be taken in selecting a location and measurement point to minimize problems due to flow disturbances, cyclonic flow, and varying PM stratification.
(3) How should I record my CEMS data? You need to ensure that your PM CEMS and data logger are set up to collect and record all normal emission levels and excursions. You must ensure that your data logger and PM CEMS have been properly programmed to accept and transfer status signals of valid monitor operation (e.g., flags for internal calibration, suspect data, or maintenance periods).
(4) What CEMS data should I review? You must review drift data daily to document proper operation. You must also ensure that any audit material is appropriate for the typical operating range of your PM CEMS.
(5) How long should I operate my PM CEMS before conducting the initial correlation test? You should allow sufficient time for your PM CEMS to operate for you to become familiar with your PM CEMS.
(i) You should observe PM CEMS response over time during normal and varying process conditions. This will ensure that your PM CEMS has been properly set up to operate at a range that is compatible with the concentrations and characteristics of PM emissions for your source. You should use this information to establish the range of operating conditions necessary to determine the correlations of PM CEMS data to manual reference method measurements over a wide operating range.
(ii) You must determine the types of process changes that will influence, on a definable and repeatable basis, flue gas PM concentrations and the resulting PM CEMS responses. You may find this period useful to make adjustments to your planned approach for operating your PM CEMS at your source. For instance, you may change the measurement range or batch sampling period to something other than those you initially planned to use.
(6) How do I conduct the initial correlation test? When conducting the initial correlation test of your PM CEMS response to PM emissions determined by the reference method, you must pay close attention to accuracy and details. Your PM CEMS must be operating properly. You must perform the manual reference method testing accurately, with attention to eliminating site-specific systemic errors. You must coordinate the timing of the manual reference method testing with the sampling cycle of your PM CEMS. You must complete a minimum of 15 manual reference method tests. You must perform the manual reference method testing over the full range of PM CEMS responses that correspond to normal operating conditions for your source and control device and will result in the widest range of emission concentrations.
(7) How should I perform the manual reference method testing? You must perform the manual reference method testing in accordance with specific rule requirements, coordinated closely with PM CEMS and process operations. It is highly recommended that you use paired trains for the manual reference method testing. You must perform the manual reference method testing over a suitable PM concentration range that corresponds to the full range of normal process and control device operating conditions. Because the manual reference method testing for this correlation test is not for compliance reporting purposes, you may conduct the reference method test runs for less than the typical minimum test run duration of 1 hour.
(8) What do I do with the manual reference method data and PM CEMS data? You must complete each of the activities in paragraphs (8)(i) through (v) of this section.
(i) Screen the manual reference method data for validity (e.g., isokinetics, leak checks), quality assurance, and quality control (e.g., outlier identification).
(ii) Screen your PM CEMS data for validity (e.g., daily drift check requirements) and quality assurance (e.g., flagged data).
(iii) Convert the manual reference method test data into measurement units (e.g., mg/acm) consistent with the measurement conditions of your PM CEMS.
(iv) Calculate the correlation equation(s) as specified in section 12.3.
(v) Calculate the correlation coefficient, confidence interval half range, and tolerance interval half range for the complete set of PM CEMS and reference method correlation data for comparison with the correlation performance criteria specified in section 13.2.
2.5 What other procedures must I perform? Before conducting the initial correlation test, you must successfully complete a 7-day drift test (See section 8.5).
3.0 What Special Definitions Apply to PS-11?3.1 “Appropriate Measurement Range of your PM CEMS” means a measurement range that is capable of recording readings over the complete range of your source's PM emission concentrations during routine operations. The appropriate range is determined during the pretest preparations as specified in section 8.4.
3.2 “Appropriate Data Range for PM CEMS Correlation” means the data range that reflects the full range of your source's PM emission concentrations recorded by your PM CEMS during the correlation test planning period or other normal operations as defined in the applicable regulations.
3.3 “Batch Sampling” means that gas is sampled on an intermittent basis and concentrated on a collection medium before intermittent analysis and follow-up reporting. Beta gauge PM CEMS are an example of batch sampling devices.
3.4 “Confidence Interval Half Range (CI)” is a statistical term and means one-half of the width of the 95 percent confidence interval around the predicted mean PM concentration (y value) calculated at the PM CEMS response value (x value) where the confidence interval is narrowest. Procedures for calculating CI are specified in section 12.3. The CI as a percent of the emission limit value (CI%) is calculated at the appropriate PM CEMS response value and must satisfy the criteria specified in section 13.2 (2).
3.5 “Continuous Emission Monitoring System (CEMS)” means all of the equipment required for determination of PM mass concentration in units of the emission standard. The sample interface, pollutant monitor, diluent monitor, other auxiliary data monitor(s), and data recorder are the major subsystems of your CEMS.
3.6 “Correlation” means the primary mathematical relationship for correlating the output from your PM CEMS to a PM concentration, as determined by the PM reference method. The correlation is expressed in the measurement units that are consistent with the measurement conditions (e.g., mg/dscm, mg/acm) of your PM CEMS.
3.7 “Correlation Coefficient (r)” means a quantitative measure of the association between your PM CEMS outputs and the reference method measurements. Equations for calculating the r value are provided in section 12.3(1)(iv) for linear correlations and in section 12.3(2)(iv) for polynomial correlations.
3.8 “Cycle Time” means the time required to complete one sampling, measurement, and reporting cycle. For a batch sampling PM CEMS, the cycle time would start when sample gas is first extracted from the stack/duct and end when the measurement of that batch sample is complete and a new result for that batch sample is produced on the data recorder.
3.9 “Data Recorder” means the portion of your CEMS that provides a permanent record of the monitor output in terms of response and status (flags). The data recorder may also provide automatic data reduction and CEMS control capabilities (see section 6.6).
3.10 “Diluent Monitor and Other Auxiliary Data Monitor(s) (if applicable)” means the portion of your CEMS that provides the diluent gas concentration (such as O2 or CO2, as specified by the applicable regulations), temperature, pressure, and/or moisture content, and generates an output proportional to the diluent gas concentration or gas property.
3.11 “Drift Check” means a check of the difference between your PM CEMS output readings and the established reference value of a reference standard or procedure after a stated period of operation during which no unscheduled maintenance, repair, or adjustment took place. The procedures used to determine drift are specific to the operating principles of your specific PM CEMS. A drift check includes both a zero drift check and an upscale drift check.
3.12 “Exponential Correlation” means an exponential equation used to define the relationship between your PM CEMS output and the reference method PM concentration, as indicated by Equation 11-37.
3.13 “Flagged Data” means data marked by your CEMS indicating that the response value(s) from one or more CEMS subsystems is suspect or invalid or that your PM CEMS is not in source-measurement operating mode.
3.14 “Linear Correlation” means a first-order mathematical relationship between your PM CEMS output and the reference method PM concentration that is linear in form, as indicated by Equation 11-3.
3.15 “Logarithmic Correlation” means a first-order mathematical relationship between the natural logarithm of your PM CEMS output and the reference method PM concentration that is linear in form, as indicated by Equation 11-34.
3.16 “Low-Emitting Source” means a source that operated at no more than 50 percent of the emission limit during the most recent performance test, and, based on the PM CEMS correlation, the daily average emissions for the source, measured in the units of the applicable emission limit, have not exceeded 50 percent of the emission limit for any day since the most recent performance test.
3.17 “Paired Trains” means two reference method trains that are used to conduct simultaneous measurements of PM concentrations. Guidance on the use of paired sampling trains can be found in the PM CEMS Knowledge Document (see section 16.5).
3.18 “Polynomial Correlation” means a second-order equation used to define the relationship between your PM CEMS output and reference method PM concentration, as indicated by Equation 11-16.
3.19 “Power Correlation” means an equation used to define a power function relationship between your PM CEMS output and the reference method concentration, as indicated by Equation 11-42.
3.20 “Reference Method” means the method defined in the applicable regulations, but commonly refers to those methods collectively known as EPA Methods 5, 5I, and 17 (for particulate matter), found in Appendix A of 40 CFR 60. Only the front half and dry filter catch portions of the reference method can be correlated to your PM CEMS output.
3.21 “Reference Standard” means a reference material or procedure that produces a known and unchanging response when presented to the pollutant monitor portion of your CEMS. You must use these standards to evaluate the overall operation of your PM CEMS, but not to develop a PM CEMS correlation.
3.22 “Response Time” means the time interval between the start of a step change in the system input and the time when the pollutant monitor output reaches 95 percent of the final value (see sections 6.5 and 13.3 for procedures and acceptance criteria).
3.23 “Sample Interface” means the portion of your CEMS used for one or more of the following: sample acquisition, sample delivery, sample conditioning, or protection of the monitor from the effects of the stack effluent.
3.24 “Sample Volume Check” means a check of the difference between your PM CEMS sample volume reading and the sample volume reference value.
3.25 “Tolerance Interval half range (TI)” means one-half of the width of the tolerance interval with upper and lower limits, within which a specified percentage of the future data population is contained with a given level of confidence, as defined by the respective tolerance interval half range equations in section 12.3(1)(iii) for linear correlations and in section 12.3(2)(iii) for polynomial correlations. The TI as a percent of the emission limit value (TI%) is calculated at the appropriate PM CEMS response value specified in section 13.2(3).
3.26 “Upscale Check Value” means the expected response to a reference standard or procedure used to check the upscale response of your PM CEMS.
3.27 “Upscale Drift (UD) Check” means a check of the difference between your PM CEMS output reading and the upscale check value.
3.28 “Zero Check Value” means the expected response to a reference standard or procedure used to check the response of your PM CEMS to particulate-free or low-particulate concentration conditions.
3.29 “Zero Drift (ZD) Check” means a check of the difference between your PM CEMS output reading and the zero check value.
3.30 “Zero Point Correlation Value” means a value added to PM CEMS correlation data to represent low or near zero PM concentration data (see section 8.6 for rationale and procedures).
4.0 Are There Any Potential Interferences for My PM CEMS?Yes, condensible water droplets or condensible acid gas aerosols (i.e., those with condensation temperatures above those specified by the reference method) at the measurement location can be interferences for your PM CEMS if the necessary precautions are not met.
4.1 Where are interferences likely to occur? Interferences may develop if your CEMS is installed downstream of a wet air pollution control system or any other conditions that produce flue gases, which, at your PM CEMS measurement point, normally or occasionally contain entrained water droplets or condensible salts before release to the atmosphere.
4.2 How do I deal with interferences? We recommend that you use a PM CEMS that extracts and heats representative samples of the flue gas for measurement to simulate results produced by the reference method for conditions such as those described in section 4.1. Independent of your PM CEMS measurement technology and extractive technique, you should have a configuration simulating the reference method to ensure that:
(1) No formation of new PM or deposition of PM occurs in sample delivery from the stack or duct; and
(2) No condensate accumulates in the sample flow measurement apparatus.
4.3 What PM CEMS measurement technologies should I use? You should use a PM CEMS measurement technology that is free of interferences from any condensible constituent in the flue gas.
5.0 What Do I Need To Know To Ensure the Safety of Persons Using PS-11?People using the procedures required under PS-11 may be exposed to hazardous materials, operations, site conditions, and equipment. This performance specification does not purport to address all of the safety issues associated with its use. It is your responsibility to establish appropriate safety and health practices and determine the applicable regulatory limitations before performing these procedures. You must consult your CEMS user's manual and other reference materials recommended by the reference method for specific precautions to be taken.
6.0 What Equipment and Supplies Do I Need?Different types of PM CEMS use different operating principles. You should select an appropriate PM CEMS based on your site-specific configurations, flue gas conditions, and PM characteristics.
(1) Your PM CEMS must sample the stack effluent continuously or, for batch sampling PM CEMS, intermittently.
(2) You must ensure that the averaging time, the number of measurements in an average, the minimum data availability, and the averaging procedure for your CEMS conform with those specified in the applicable emission regulation.
(3) Your PM CEMS must include, as a minimum, the equipment described in sections 6.1 through 6.7.
6.1 What equipment is needed for my PM CEMS's sample interface? Your PM CEMS's sample interface must be capable of delivering a representative sample of the flue gas to your PM CEMS. This subsystem may be required to heat the sample gas to avoid PM deposition or moisture condensation, provide dilution air, perform other gas conditioning to prepare the sample for analysis, or measure the sample volume or flow rate.
(1) If your PM CEMS is installed downstream of a wet air pollution control system such that the flue gases normally or occasionally contain entrained water droplets, we recommend that you select a sampling system that includes equipment to extract and heat a representative sample of the flue gas for measurement so that the pollutant monitor portion of your CEMS measures only dry PM. Heating should be sufficient to raise the temperature of the extracted flue gas above the water condensation temperature and should be maintained at all times and at all points in the sample line from where the flue gas is extracted, including the pollutant monitor and any sample flow measurement devices.
(2) You must consider the measured conditions of the sample gas stream to ensure that manual reference method test data are converted to units of PM concentration that are appropriate for the correlation calculations. Additionally, you must identify what, if any, additional auxiliary data from other monitoring and handling systems are necessary to convert your PM CEMS response into the units of the PM standard.
(3) If your PM CEMS is an extractive type and your source's flue gas volumetric flow rate varies by more than 10 percent from nominal, your PM CEMS should maintain an isokinetic sampling rate (within 10 percent of true isokinetic). If your extractive-type PM CEMS does not maintain an isokinetic sampling rate, you must use actual site-specific data or data from a similar installation to prove to us, the State, and/or local enforcement agency that isokinetic sampling is not necessary.
6.2 What type of equipment is needed for my PM CEMS? Your PM CEMS must be capable of providing an electronic output that can be correlated to the PM concentration.
(1) Your PM CEMS must be able to perform zero and upscale drift checks. You may perform these checks manually, but performing these checks automatically is preferred.
(2) We recommend that you select a PM CEMS that is capable of performing automatic diagnostic checks and sending instrument status signals (flags) to the data recorder.
(3) If your PM CEMS is an extractive type that measures the sample volume and uses the measured sample volume as part of calculating the output value, your PM CEMS must be able to perform a check of the sample volume to verify the accuracy of the sample volume measuring equipment. The sample volume check must be conducted daily and at the normal sampling rate of your PM CEMS.
6.3 What is the appropriate measurement range for my PM CEMS? Initially, your PM CEMS must be set up to measure over the expected range of your source's PM emission concentrations during routine operations. You may change the measurement range to a more appropriate range prior to correlation testing.
6.4 What if my PM CEMS does automatic range switching? Your PM CEMS may be equipped to perform automatic range switching so that it is operating in a range most sensitive to the detected concentrations. If your PM CEMS does automatic range switching, you must configure the data recorder to handle the recording of data values in multiple ranges during range-switching intervals.
6.5 What averaging time and sample intervals should be used? Your CEMS must sample the stack effluent such that the averaging time, the number of measurements in an average, the minimum sampling time, and the averaging procedure for reporting and determining compliance conform with those specified in the applicable regulation. Your PM CEMS must be designed to meet the specified response time and cycle time established in this performance specification (see section 13.3).
6.6 What type of equipment is needed for my data recorder? Your CEMS data recorder must be able to accept and record electronic signals from all the monitors associated with your PM CEMS.
(1) Your data recorder must record the signals from your PM CEMS that can be correlated to PM mass concentrations. If your PM CEMS uses multiple ranges, your data recorder must identify what range the measurement was made in and provide range-adjusted results.
(2) Your data recorder must accept and record monitor status signals (flagged data).
(3) Your data recorder must accept signals from auxiliary data monitors, as appropriate.
6.7 What other equipment and supplies might I need? You may need other supporting equipment as defined by the applicable reference method(s) (see section 7) or as specified by your CEMS manufacturer.
7.0 What Reagents and Standards Do I Need?You will need reference standards or procedures to perform the zero drift check, the upscale drift check, and the sample volume check.
7.1 What is the reference standard value for the zero drift check? You must use a zero check value that is no greater than 20 percent of the PM CEMS's response range. You must obtain documentation on the zero check value from your PM CEMS manufacturer.
7.2 What is the reference standard value for the upscale drift check? You must use an upscale check value that produces a response between 50 and 100 percent of the PM CEMS's response range. For a PM CEMS that produces output over a range of 4 mA to 20 mA, the upscale check value must produce a response in the range of 12 mA to 20 mA. You must obtain documentation on the upscale check value from your PM CEMS manufacturer.
7.3 What is the reference standard value for the sample volume check? You must use a reference standard value or procedure that produces a sample volume value equivalent to the normal sampling rate. You must obtain documentation on the sample volume value from your PM CEMS manufacturer.
8.0 What Performance Specification Test Procedure Do I Follow?You must complete each of the activities in sections 8.1 through 8.8 for your performance specification test.
8.1 How should I select and set up my equipment? You should select a PM CEMS that is appropriate for your source, giving consideration to potential factors such as flue gas conditions, interferences, site-specific configuration, installation location, PM concentration range, and other PM characteristics. Your PM CEMS must meet the equipment specifications in sections 6.1 and 6.2.
(1) You should select a PM CEMS that is appropriate for the flue gas conditions at your source. If your source's flue gas contains entrained water droplets, we recommend that your PM CEMS include a sample delivery and conditioning system that is capable of extracting and heating a representative sample.
(i) Your PM CEMS must maintain the sample at a temperature sufficient to prevent moisture condensation in the sample line before analysis of PM.
(ii) If condensible PM is an issue, we recommend that you operate your PM CEMS to maintain the sample gas temperature at the same temperature as the reference method filter.
(iii) Your PM CEMS must avoid condensation in the sample flow rate measurement lines.
(2) Some PM CEMS do not have a wide measurement range capability. Therefore, you must select a PM CEMS that is capable of measuring the full range of PM concentrations expected from your source from normal levels through the emission limit concentration.
(3) Some PM CEMS are sensitive to particle size changes, water droplets in the gas stream, particle charge, stack gas velocity changes, or other factors. Therefore, you should select a PM CEMS appropriate for the emission characteristics of your source.
(4) We recommend that you consult your PM CEMS vendor to obtain basic recommendations on the instrument capabilities and setup configuration. You are ultimately responsible for setup and operation of your PM CEMS.
8.2 Where do I install my PM CEMS? You must install your PM CEMS at an accessible location downstream of all pollution control equipment. You must perform your PM CEMS concentration measurements from a location considered representative or be able to provide data that can be corrected to be representative of the total PM emissions as determined by the manual reference method.
(1) You must select a measurement location that minimizes problems due to flow disturbances, cyclonic flow, and varying PM stratification (refer to Method 1 for guidance).
(2) If you plan to achieve higher emissions for correlation test purposes by adjusting the performance of the air pollution control device (per section 8.6(4)(i)), you must locate your PM CEMS and reference method sampling points well downstream of the control device (e.g., downstream of the induced draft fan), in order to minimize PM stratification that may be created in these cases.
8.3 How do I select the reference method measurement location and traverse points? You must follow EPA Method 1 for identifying manual reference method traverse points. Ideally, you should perform your manual reference method measurements at locations that satisfy the measurement site selection criteria specified in EPA Method 1 of at least eight duct diameters downstream and at least two duct diameters upstream of any flow disturbance. Where necessary, you may conduct testing at a location that is two diameters downstream and 0.5 diameters upstream of flow disturbances. If your location does not meet the minimum downstream and upstream requirements, you must obtain approval from us to test at your location.
8.4 What are my pretest preparation steps? You must install your CEMS and prepare the reference method test site according to the specifications in sections 8.2 and 8.3.
(1) After completing the initial field installation, we recommend that you operate your PM CEMS according to the manufacturer's instructions to familiarize yourself with its operation before you begin correlation testing.
(i) During this initial period of operation, we recommend that you conduct daily checks (zero and upscale drift and sample volume, as appropriate), and, when any check exceeds the daily specification (see section 13.1), make adjustments and perform any necessary maintenance to ensure reliable operation.
(2) When you are confident that your PM CEMS is operating properly, we recommend that you operate your CEMS over a correlation test planning period of sufficient duration to identify the full range of operating conditions and PM emissions to be used in your PM CEMS correlation test.
(i) During the correlation test planning period, you should operate the process and air pollution control equipment over the normal range of operating conditions, except when you attempt to produce higher emissions.
(ii) Your data recorder should record PM CEMS response during the full range of routine process operating conditions.
(iii) You should try to establish the relationships between operating conditions and PM CEMS response, especially those conditions that produce the highest PM CEMS response over 15-minute averaging periods, and the lowest PM CEMS response as well. The objective is to be able to reproduce the conditions for purposes of the actual correlation testing discussed in section 8.6.
(3) You must set the response range of your PM CEMS such that the instrument measures the full range of responses that correspond to the range of source operating conditions that you will implement during correlation testing.
(4) We recommend that you perform preliminary reference method testing after the correlation test planning period. During this preliminary testing, you should measure the PM emission concentration corresponding to the highest PM CEMS response observed during the full range of normal operation, when perturbing the control equipment, or as the result of PM spiking.
(5) Before performing correlation testing, you must perform a 7-day zero and upscale drift test (see section 8.5).
(6) You must not change the response range of the monitor once the response range has been set and the drift test successfully completed.
8.5 How do I perform the 7-day drift test? You must check the zero (or low-level value between 0 and 20 percent of the response range of the instrument) and upscale (between 50 and 100 percent of the instrument's response range) drift. You must perform this check at least once daily over 7 consecutive days. Your PM CEMS must quantify and record the zero and upscale measurements and the time of the measurements. If you make automatic or manual adjustments to your PM CEMS zero and upscale settings, you must conduct the drift test immediately before these adjustments, or conduct it in such a way that you can determine the amount of drift. You will find the calculation procedures for drift in section 12.1 and the acceptance criteria for allowable drift in section 13.1.
(1) What is the purpose of 7-day drift tests? The purpose of the 7-day drift test is to demonstrate that your system is capable of operating in a stable manner and maintaining its calibration for at least a 7-day period.
(2) How do I conduct the 7-day drift test? To conduct the 7-day drift test, you must determine the magnitude of the drift once each day, at 24-hour intervals, for 7 consecutive days while your source is operating normally.
(i) You must conduct the 7-day drift test at the two points specified in section 8.5. You may perform the 7-day drift tests automatically or manually by introducing to your PM CEMS suitable reference standards (these need not be certified) or by using other appropriate procedures.
(ii) You must record your PM CEMS zero and upscale response and evaluate them against the zero check value and upscale check value.
(3) When must I conduct the 7-day drift test? You must complete a valid 7-day drift test before attempting the correlation test.
8.6 How do I conduct my PM CEMS correlation test? You must conduct the correlation test according to the procedure given in paragraphs (1) through (5) of this section. If you need multiple correlations, you must conduct testing and collect at least 15 sets of reference method and PM CEMS data for calculating each separate correlation.
(1) You must use the reference method for PM (usually EPA Methods 5, 5I, or 17) that is prescribed by the applicable regulations. You may need to perform other reference methods or performance specifications (e.g., Method 3 for oxygen, Method 4 for moisture, etc.) depending on the units in which your PM CEMS reports PM concentration.
(i) We recommend that you use paired reference method trains when collecting manual PM data to identify and screen the reference method data for imprecision and bias. Procedures for checking reference method data for bias and precision can be found in the PM CEMS Knowledge Document (see section 16.5).
(ii) You may use test runs that are shorter than 60 minutes in duration (e.g., 20 or 30 minutes). You may perform your PM CEMS correlation tests during new source performance standards performance tests or other compliance tests subject to the Clean Air Act or other statutes, such as the Resource Conservation and Recovery Act. In these cases, your reference method results obtained during the PM CEMS correlation test may be used to determine compliance so long as your source and the test conditions and procedures (e.g., reference method sample run durations) are consistent with the applicable regulations and the reference method.
(iii) You must convert the reference method results to units consistent with the conditions of your PM CEMS measurements. For example, if your PM CEMS measures and reports PM emissions in the units of mass per actual volume of stack gas, you must convert your reference method results to those units (e.g., mg/acm). If your PM CEMS extracts and heats the sample gas to eliminate water droplets, then measures and reports PM emissions under those actual conditions, you must convert your reference method results to those same conditions (e.g., mg/acm at 160 °C).
(2) During each test run, you must coordinate process operations, reference method sampling, and PM CEMS operations. For example, you must ensure that the process is operating at the targeted conditions, both reference method trains are sampling simultaneously (if paired sampling trains are being used), and your PM CEMS and data logger are operating properly.
(i) You must coordinate the start and stop times of each run between the reference method sampling and PM CEMS operation. For a batch sampling PM CEMS, you must start the reference method at the same time as your PM CEMS sampling.
(ii) You must note the times for port changes (and other periods when the reference method sampling may be suspended) on the data sheets so that you can adjust your PM CEMS data accordingly, if necessary.
(iii) You must properly align the time periods for your PM CEMS and your reference method measurements to account for your PM CEMS response time.
(3) You must conduct a minimum of 15 valid runs each consisting of simultaneous PM CEMS and reference method measurement sets.
(i) You may conduct more than 15 sets of CEMS and reference method measurements. If you choose this option, you may reject certain test results so long as the total number of valid test results you use to determine the correlation is greater than or equal to 15.
(ii) You must report all data, including the rejected data.
(iii) You may reject the results of up to five test runs without explanation.
(iv) If you reject the results of more than five test runs, the basis for rejecting the results of the additional test runs must be explicitly stated in the reference method, this performance specification, Procedure 2 of appendix F, or your quality assurance plan.
(4) Simultaneous PM CEMS and reference method measurements must be performed in a manner to ensure that the range of data that will be used to establish the correlation for your PM CEMS is maximized. You must first attempt to maximize your correlation range by following the procedures described in paragraphs (4)(i) through (iv) of this section. If you cannot obtain the three levels as described in paragraphs (i) through (iv), then you must use the procedure described in section 8.6(5).
(i) You must attempt to obtain the three different levels of PM mass concentration by varying process operating conditions, varying PM control device conditions, or by means of PM spiking.
(ii) The three PM concentration levels you use in the correlation tests must be distributed over the complete operating range experienced by your source.
(iii) At least 20 percent of the minimum 15 measured data points you use should be contained in each of the following levels:
• Level 1: From no PM (zero concentration) emissions to 50 percent of the maximum PM concentration;
• Level 2: 25 to 75 percent of the maximum PM concentration; and
• Level 3: 50 to 100 percent of the maximum PM concentration.
(iv) Although the above levels overlap, you may only apply individual run data to one level.
(5) If you cannot obtain three distinct levels of PM concentration as described, you must perform correlation testing over the maximum range of PM concentrations that is practical for your PM CEMS. To ensure that the range of data used to establish the correlation for your PM CEMS is maximized, you must follow one or more of the steps in paragraphs (5)(i) through (iv) of this section.
(i) Zero point data for in-situ instruments should be obtained, to the extent possible, by removing the instrument from the stack and monitoring ambient air on a test bench.
(ii) Zero point data for extractive instruments should be obtained by removing the extractive probe from the stack and drawing in clean ambient air.
(iii) Zero point data also can be obtained by performing manual reference method measurements when the flue gas is free of PM emissions or contains very low PM concentrations (e.g., when your process is not operating, but the fans are operating or your source is combusting only natural gas).
(iv) If none of the steps in paragraphs (5)(i) through (iii) of this section are possible, you must estimate the monitor response when no PM is in the flue gas (e.g., 4 mA = 0 mg/acm).
8.7 What do I do with the initial correlation test data for my PM CEMS? You must calculate and report the results of the correlation testing, including the correlation coefficient, confidence interval, and tolerance interval for the PM CEMS response and reference method correlation data that are use to establish the correlation, as specified in section 12. You must include all data sheets, calculations, charts (records of PM CEMS responses), process data records including PM control equipment operating parameters, and reference media certifications necessary to confirm that your PM CEMS met the requirements of this performance specification. In addition, you must:
(1) Determine the integrated (arithmetic average) PM CEMS output over each reference method test period;
(2) Adjust your PM CEMS outputs and reference method test data to the same clock time (considering response time of your PM CEMS);
(3) Confirm that the reference method results are consistent with your PM CEMS response in terms of, where applicable, moisture, temperature, pressure, and diluent concentrations; and
(4) Determine whether any of the reference method test results do not meet the test method criteria.
8.8 What is the limitation on the range of my PM CEMS correlation? Although the data you collect during the correlation testing should be representative of the full range of normal operating conditions at your source, you must conduct additional correlation testing if either of the conditions specified in paragraphs (1) and (2) of this section occurs.
(1) If your source is a low-emitting source, as defined in section 3.16 of this specification, you must conduct additional correlation testing if either of the events specified in paragraphs (1)(i) or (ii) of this section occurs while your source is operating under normal conditions.
(i) Your source generates 24 consecutive hourly average PM CEMS responses that are greater than 125 percent of the highest PM CEMS response (e.g., mA reading) used for the correlation curve or are greater than the PM CEMS response that corresponds to 50 percent of the emission limit, whichever is greater, or
(ii) The cumulative hourly average PM CEMS responses generated by your source are greater than 125 percent of the highest PM CEMS response used for the correlation curve or are greater than the PM CEMS response that corresponds to 50 percent of the emission limit, whichever is greater, for more than 5 percent of your PM CEMS operating hours for the previous 30-day period.
(2) If your source is not a low-emitting source, as defined in section 3.16 of this specification, you must conduct additional correlation testing if either of the events specified in paragraph (i) or (ii) of this section occurs while your source is operating under normal conditions.
(i) Your source generates 24 consecutive hourly average PM CEMS responses that are greater than 125 percent of the highest PM CEMS response (e.g., mA reading) used for the correlation curve, or
(ii) The cumulative hourly average PM CEMS responses generated by your source are greater than 125 percent of the highest PM CEMS response used for the correlation curve for more than 5 percent of your PM CEMS operating hours for the previous 30-day period.
(3) If additional correlation testing is required, you must conduct at least three additional test runs under the conditions that caused the higher PM CEMS response.
(i) You must complete the additional testing and use the resulting new data along with the previous data to calculate a revised correlation equation within 60 days after the occurrence of the event that requires additional testing, as specified in paragraphs 8.8(1) and (2).
(4) If your source generates consecutive PM CEMS hourly responses that are greater than 125 percent of the highest PM CEMS response used to develop the correlation curve for 24 hours or for a cumulative period that amounts to more than 5 percent of the PM CEMS operating hours for the previous 30-day period, you must report the reason for the higher PM CEMS responses.
9.0 What Quality Control Measures Are Required?Quality control measures for PM CEMS are specified in 40 CFR 60, Appendix F, Procedure 2.
10.0 What Calibration and Standardization Procedures Must I Perform? [Reserved] 11.0 What Analytical Procedures Apply to This Procedure?Specific analytical procedures are outlined in the applicable reference method(s).
12.0 What Calculations and Data Analyses Are Needed?You must determine the primary relationship for correlating the output from your PM CEMS to a PM concentration, typically in units of mg/acm or mg/dscm of flue gas, using the calculations and data analysis process in sections 12.2 and 12.3. You develop the correlation by performing an appropriate regression analysis between your PM CEMS response and your reference method data.
12.1 How do I calculate upscale drift and zero drift? You must determine the difference in your PM CEMS output readings from the established reference values (zero and upscale check values) after a stated period of operation during which you performed no unscheduled maintenance, repair or adjustment.
(1) Calculate the upscale drift (UD) using Equation 11-1:

(2) Calculate the zero drift (ZD) using Equation 11-2:

(3) Summarize the results on a data sheet similar to that shown in Table 2 (see section 17).
12.2 How do I perform the regression analysis? You must couple each reference method PM concentration measurement, y, in the appropriate units, with an average PM CEMS response, x, over corresponding time periods. You must complete your PM CEMS correlation calculations using data deemed acceptable by quality control procedures identified in 40 CFR 60, Appendix F, Procedure 2.
(1) You must evaluate all flagged or suspect data produced during measurement periods and determine whether they should be excluded from your PM CEMS's average.
(2) You must assure that the reference method and PM CEMS results are on a consistent moisture, temperature, and diluent basis. You must convert the reference method PM concentration measurements (dry standard conditions) to the units of your PM CEMS measurement conditions. The conditions of your PM CEMS measurement are monitor-specific. You must obtain from your PM CEMS vendor or instrument manufacturer the conditions and units of measurement for your PM CEMS.
(i) If your sample gas contains entrained water droplets and your PM CEMS is an extractive system that measures at actual conditions (i.e., wet basis), you must use the measured moisture content determined from the impinger analysis when converting your reference method PM data to PM CEMS conditions; do not use the moisture content calculated from a psychrometric chart based on saturated conditions.
12.3 How do I determine my PM CEMS correlation? To predict PM concentrations from PM CEMS responses, you must use the calculation method of least squares presented in paragraphs (1) through (5) of this section. When performing the calculations, each reference method PM concentration measurement must be treated as a discrete data point; if using paired sampling trains, do not average reference method data pairs for any test run.
This performance specification describes procedures for evaluating five types of correlation models: linear, polynomial, logarithmic, exponential, and power. Procedures for selecting the most appropriate correlation model are presented in section 12.4 of this specification.
(1) How do I evaluate a linear correlation for my correlation test data? To evaluate a linear correlation, follow the procedures described in paragraphs (1)(i) through (iv) of this section.
(i) Calculate the linear correlation equation, which gives the predicted PM concentration () as a function of the PM CEMS response (x), as indicated by Equation 11-3:
Where: y = the predicted PM concentration, b0 = the intercept for the correlation curve, as calculated using Equation 11-4, b1 = the slope of the correlation curve, as calculated using Equation 11-6, and x = the PM CEMS response value.Calculate the y intercept (b0) of the correlation curve using Equation 11-4:
Where: x = the mean value of the PM CEMS response data, as calculated using Equation 11-5, and y = the mean value of the PM concentration data, as calculated using Equation 11-5: Where: xi = the PM CEMS response value for run i, yi = the PM concentration value for run i, and n = the number of data points.Calculate the slope (b1) of the correlation curve using Equation 11-6:
Where: Sxx, Sxy = as calculated using Equation 11-7:(ii) Calculate the half range of the 95 percent confidence interval (CI) for the predicted PM concentration () at the mean value of x, using Equation 11-8:
Where: CI = the half range of the 95 percent confidence interval for the predicted PM concentration at the mean x value, tdf,1-a/2 = the value for the t statistic provided in Table 1 for df = (n - 2), and SL = the scatter or deviation of values about the correlation curve, which is determined using Equation 11-9: Calculate the confidence interval half range for the predicted PM concentration () at the mean x value as a percentage of the emission limit (CI%) using Equation 11-10: Where: CI = the half range of the 95 percent confidence interval for the predicted PM concentration at the mean x value, and EL = PM emission limit, as described in section 13.2.(iii) Calculate the half range of the tolerance interval (TI) for the predicted PM concentration () at the mean x value using Equation 11-11:
Where: TI = the half range of the tolerance interval for the predicted PM concentration () at the mean x value, kT = as calculated using Equation 11-12, and SL = as calculated using Equation 11-9: Where: n′ = the number of test runs (n), un′ = the tolerance factor for 75 percent coverage at 95 percent confidence provided in Table 1 for df = (n−2), and vdf = the value from Table 1 for df = (n−2).Calculate the half range of the tolerance interval for the predicted PM concentration () at the mean x value as a percentage of the emission limit (TI%) using Equation 11-13:
Where: TI = the half range of the tolerance interval for the predicted PM concentration () at the mean x value, and EL = PM emission limit, as described in section 13.2.(iv) Calculate the linear correlation coefficient (r) using Equation 11-14:
Where: SL = as calculated using Equation 11-9, and Sy = as calculated using Equation 11-15:(2) How do I evaluate a polynomial correlation for my correlation test data? To evaluate a polynomial correlation, follow the procedures described in paragraphs (2)(i) through (iv) of this section.
(i) Calculate the polynomial correlation equation, which is indicated by Equation 11-16, using Equations 11-17 through 11-22:
Where: = the PM CEMS concentration predicted by the polynomial correlation equation, and b0, b1, b2 = the coefficients determined from the solution to the matrix equation Ab = B Where: Where: Xi = the PM CEMS response for run i, Yi = the reference method PM concentration for run i, and n = the number of test runs.Calculate the polynomial correlation curve coefficients (b0, b1, and b2) using Equations 11-19 through 11-21, respectively:
Where:(ii) Calculate the 95 percent confidence interval half range (CI) by first calculating the C coefficients (Co to C5) using Equations 11-23 and 11-24:
Where: Calculate Δ using Equation 11-25 for each x value: Determine the x value that corresponds to the minimum value of Δ (Δmin). Determine the scatter or deviation of values about the polynomial correlation curve (SP) using Equation 11-26: Calculate the half range of the 95 percent confidence interval (CI) for the predicted PM concentration () at the x value that corresponds to Δmin using Equation 11-27: Where: df = (n-3), and tdf = as listed in Table 1 (see section 17). Calculate the half range of the 95 percent confidence interval for the predicted PM concentration at the x value that corresponds to Δmin as a percentage of the emission limit (CI%) using Equation 11-28: Where: CI = the half range of the 95 percent confidence interval for the predicted PM concentration at the x value that corresponds to Δmin, and EL = PM emission limit, as described in section 13.2.(iii) Calculate the tolerance interval half range (TI) for the predicted PM concentration at the x value that corresponds to Δmin, as indicated in Equation 11-29 for the polynomial correlation, using Equations 11-30 and 11-31:
Where: un′ = the value indicated in Table 1 for df = (n′-3), and vdf = the value indicated in Table 1 for df = (n′ - 3). Calculate the tolerance interval half range for the predicted PM concentration at the x value that corresponds to Δmin as a percentage of the emission limit (TI%) using Equation 11-32: Where: TI = the tolerance interval half range for the predicted PM concentration at the x value that corresponds to Δmin, and EL = PM emission limit, as described in section 13.2.(iv) Calculate the polynomial correlation coefficient (r) using Equation 11-33:
Where: SP = as calculated using Equation 11-26, and Sy = as calculated using Equation 11-15.(3) How do I evaluate a logarithmic correlation for my correlation test data? To evaluate a logarithmic correlation, which has the form indicated by Equation 11-34, follow the procedures described in paragraphs (3)(i) through (iii) of this section.
(i) Perform a logarithmic transformation of each PM CEMS response value (x values) using Equation 11-35:
Where: xi′ = is the transformed value of xi, and Ln(xi) = the natural logarithm of the PM CEMS response for run i.(ii) Using the values for xi′ in place of the values for xi, perform the same procedures used to develop the linear correlation equation described in paragraph (1)(i) of this section. The resulting equation has the form indicated by Equation 11-36:
Where: x′ = the natural logarithm of the PM CEMS response, and the variables , b0, and b1 are as defined in paragraph (1)(i) of this section.(iii) Using the values for xi′ in place of the values for xi, calculate the confidence interval half range at the mean x′ value as a percentage of the emission limit (CI%), the tolerance interval half range at the mean x′ value as a percentage of the emission limit (TI%), and the correlation coefficient (r) using the procedures described in paragraphs (1)(ii) through (iv) of this section.
(4) How do I evaluate an exponential correlation for my correlation test data? To evaluate an exponential correlation, which has the form indicated by Equation 11-37, follow the procedures described in paragraphs (4)(i) through (v) of this section:
(i) Perform a logarithmic transformation of each PM concentration measurement (y values) using Equation 11-38:
Where: y′i = is the transformed value of yi, and Ln(yi) = the natural logarithm of the PM concentration measurement for run i.(ii) Using the values for y′i in place of the values for yi, perform the same procedures used to develop the linear correlation equation described in paragraph (1)(i) of this section. The resulting equation will have the form indicated by Equation 11-39.
Where: ′ = the predicted log PM concentration value, b′0 = the natural logarithm of b0, and the variables b0, b1, and x are as defined in paragraph (1)(i) of this section.(iii) Using the values for y″i in place of the values for yi, calculate the half range of the 95 percent confidence interval (CI′), as described in paragraph (1)(ii) of this section for CI. Note that CI′ is on the log scale. Next, calculate the upper and lower 95 percent confidence limits for the mean value y′ using Equations 11-40 and 11-41:



(iv) Using the values for y′i in place of the values for yi, calculate the half range tolerance interval (TI′), as described in paragraph (1)(iii) of this section for TI. Note that TI′ is on the log scale. Next, calculate the half range tolerance limits for the mean value y′ using Equations 11-43 and 11-44:



(v) Using the values for y″ i in place of the values for yi, calculate the correlation coefficient (r) using the procedure described in paragraph (1)(iv) of this section.
(5) How do I evaluate a power correlation for my correlation test data? To evaluate a power correlation, which has the form indicated by Equation 11-46, follow the procedures described in paragraphs (5)(i) through (v) of this section.

(i) Perform logarithmic transformations of each PM CEMS response (x values) and each PM concentration measurement (y values) using Equations 11-35 and 11-38, respectively.
(ii) Using the values for x″i in place of the values for xi, and the values for y″i in place of the values for yi, perform the same procedures used to develop the linear correlation equation described in paragraph (1)(i) of this section. The resulting equation will have the form indicated by Equation 11-47:

(iii) Using the same procedure described for exponential models in paragraph (4)(iii) of this section, calculate the half range of the 95 percent confidence interval for the predicted PM concentration corresponding to the mean value of x′ as a percentage of the emission limit.
(iv) Using the same procedure described for exponential models in paragraph (4)(iv) of this section, calculate the tolerance interval half range for the predicted PM concentration corresponding to the mean value of x′ as a percentage of the emission limit.
(v) Using the values for y′i in place of the values for yi, calculate the correlation coefficient (r) using the procedure described in paragraph (1)(iv) of this section.
Note: PS-11 does not address the application of correlation equations to calculate PM emission concentrations using PM CEMS response data during normal operations of a PM CEMS. However, we will provide guidance on the use of specific correlation models (i.e., logarithmic, exponential, and power models) to calculate PM concentrations in an operating PM CEMS in situations when the PM CEMS response values are equal to or less than zero, and the correlation model is undefined.
12.4 Which correlation model should I use? Follow the procedures described in paragraphs (1) through (4) of this section to determine which correlation model you should use.
(1) For each correlation model that you develop using the procedures described in section 12.3 of this specification, compare the confidence interval half range percentage, tolerance interval half range percentage, and correlation coefficient to the performance criteria specified in section 13.2 of this specification. You can use the linear, logarithmic, exponential, or power correlation model if the model satisfies all of the performance criteria specified in section 13.2 of this specification. However, to use the polynomial model you first must check that the polynomial correlation curve satisfies the criteria for minimum and maximum values specified in paragraph (3) of this section.
(2) If you develop more than one correlation curve that satisfy the performance criteria specified in section 13.2 of this specification, you should use the correlation curve with the greatest correlation coefficient. If the polynomial model has the greatest correlation coefficient, you first must check that the polynomial correlation curve satisfies the criteria for minimum and maximum values specified in paragraph (3) of this section.
(3) You can use the polynomial model that you develop using the procedures described in section 12.3(2) if the model satisfies the performance criteria specified in section 13.2 of this specification, and the minimum or maximum value of the polynomial correlation curve does not occur within the expanded data range. The minimum or maximum value of the polynomial correlation curve is the point where the slope of the curve equals zero. To determine if the minimum or maximum value occurs within the expanded data range, follow the procedure described in paragraphs (3)(i) through (iv) of this section.
(i) Determine if your polynomial correlation curve has a minimum or maximum point by comparing the polynomial coefficient b2 to zero. If b2 is less than zero, the curve has a maximum value. If b2 is greater than zero, the curve has a minimum value. (Note: If b2 equals zero, the correlation curve is linear.)
(ii) Calculate the minimum value using Equation 11-48.
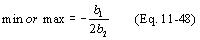
(iii) If your polynomial correlation curve has a minimum point, you must compare the minimum value to the minimum PM CEMS response used to develop the correlation curve. If the correlation curve minimum value is less than or equal to the minimum PM CEMS response value, you can use the polynomial correlation curve, provided the correlation curve also satisfies all of the performance criteria specified in section 13.2 of this specification. If the correlation curve minimum value is greater than the minimum PM CEMS response value, you cannot use the polynomial correlation curve to predict PM concentrations.
(iv) If your polynomial correlation curve has a maximum, the maximum value must be greater than the allowable extrapolation limit. If your source is not a low-emitting source, as defined in section 3.16 of this specification, the allowable extrapolation limit is 125 percent of the highest PM CEMS response used to develop the correlation curve. If your source is a low-emitting source, the allowable extrapolation limit is 125 percent of the highest PM CEMS response used to develop the correlation curve or the PM CEMS response that corresponds to 50 percent of the emission limit, whichever is greater. If the polynomial correlation curve maximum value is greater than the extrapolation limit, and the correlation curve satisfies all of the performance criteria specified in section 13.2 of this specification, you can use the polynomial correlation curve to predict PM concentrations. If the correlation curve maximum value is less than the extrapolation limit, you cannot use the polynomial correlation curve to predict PM concentrations.
(4) You may petition the Administrator for alternative solutions or sampling recommendations if the correlation models described in section 12.3 of this specification do not satisfy the performance criteria specified in section 13.2 of this specification.
13.0 What Are the Performance Criteria for My PM CEMS?You must evaluate your PM CEMS based on the 7-day drift check, the accuracy of the correlation, and the sampling periods and cycle/response time.
13.1 What is the 7-day drift check performance specification? Your daily PM CEMS internal drift checks must demonstrate that the daily drift of your PM CEMS does not deviate from the value of the reference light, optical filter, Beta attenuation signal, or other technology-suitable reference standard by more than 2 percent of the response range. If your CEMS includes diluent and/or auxiliary monitors (for temperature, pressure, and/or moisture) that are employed as a necessary part of this performance specification, you must determine the calibration drift separately for each ancillary monitor in terms of its respective output (see the appropriate performance specification for the diluent CEMS specification). None of the calibration drifts may exceed their individual specification.
13.2 What performance criteria must my PM CEMS correlation satisfy? Your PM CEMS correlation must meet each of the minimum specifications in paragraphs (1), (2), and (3) of this section. Before confidence and tolerance interval half range percentage calculations are made, you must convert the emission limit to the appropriate units of your PM CEMS measurement conditions using the average of emissions gas property values (e.g., diluent concentration, temperature, pressure, and moisture) measured during the correlation test.
(1) The correlation coefficient must satisfy the criterion specified in paragraph (1)(i) or (ii), whichever applies.
(i) If your source is not a low-emitting source, as defined in section 3.16 of this specification, the correlation coefficient (r) must be greater than or equal to 0.85.
(ii) If your source is a low-emitting source, as defined in section 3.16 of this specification, the correlation coefficient (r) must be greater than or equal to 0.75.
(2) The confidence interval half range must satisfy the applicable criterion specified in paragraph (2)(i), (ii), or (iii) of this section, based on the type of correlation model.
(i) For linear or logarithmic correlations, the 95 percent confidence interval half range at the mean PM CEMS response value from the correlation test must be within 10 percent of the PM emission limit value specified in the applicable regulation. Therefore, the CI% calculated using Equation 11-10 must be less than or equal to 10 percent.
(ii) For polynomial correlations, the 95 percent confidence interval half range at the PM CEMS response value from the correlation test that corresponds to the minimum value for Δ must be within 10 percent of the PM emission limit value specified in the applicable regulation. Therefore, the CI% calculated using Equation 11-28 must be less than or equal to 10 percent.
(iii) For exponential or power correlations, the 95 percent confidence interval half range at the mean of the logarithm of the PM CEMS response values from the correlation test must be within 10 percent of the PM emission limit value specified in the applicable regulation. Therefore, the CI% calculated using Equation 11-10 must be less than or equal to 10 percent.
(3) The tolerance interval half range must satisfy the applicable criterion specified in paragraph (3)(i), (ii), or (iii) of this section, based on the type of correlation model.
(i) For linear or logarithmic correlations, the half range tolerance interval with 95 percent confidence and 75 percent coverage at the mean PM CEMS response value from the correlation test must be within 25 percent of the PM emission limit value specified in the applicable regulation. Therefore, the TI% calculated using Equation 11-13 must be less than or equal to 25 percent.
(ii) For polynomial correlations, the half range tolerance interval with 95 percent confidence and 75 percent coverage at the PM CEMS response value from the correlation test that corresponds to the minimum value for Δ must be within 25 percent of the PM emission limit value specified in the applicable regulation. Therefore, the TI% calculated using Equation 11-32 must be less than or equal to 25 percent.
(iii) For exponential or power correlations, the half range tolerance interval with 95 percent confidence and 75 percent coverage at the mean of the logarithm of the PM CEMS response values from the correlation test must be within 25 percent of the PM emission limit value specified in the applicable regulation. Therefore, the TI% calculated using Equation 11-13 must be less than or equal to 25 percent.
13.3 What are the sampling periods and cycle/response time? You must document and maintain the response time and any changes in the response time following installation.
(1) If you have a batch sampling PM CEMS, you must evaluate the limits presented in paragraphs (1)(i) and (ii) of this section.
(i) The response time of your PM CEMS, which is equivalent to the cycle time, must be no longer than 15 minutes. In addition, the delay between the end of the sampling time and reporting of the sample analysis must be no greater than 3 minutes. You must document any changes in the response time following installation.
(ii) The sampling time of your PM CEMS must be no less than 30 percent of the cycle time. If you have a batch sampling PM CEMS, sampling must be continuous except during pauses when the collected pollutant on the capture media is being analyzed and the next capture medium starts collecting a new sample.
13.4 What PM compliance monitoring must I do? You must report your CEMS measurements in the units of the standard expressed in the regulations (e.g., mg/dscm @ 7 percent oxygen, pounds per million Btu (lb/mmBtu), etc.). You may need to install auxiliary data monitoring equipment to convert the units reported by your PM CEMS into units of the PM emission standard.
14.0 Pollution Prevention [Reserved] 15.0 Waste Management [Reserved] 16.0 Which References Are Relevant to This Performance Specification?16.1 Technical Guidance Document: Compliance Assurance Monitoring. U.S. Environmental Protection Agency Office of Air Quality Planning and Standards Emission Measurement Center. August 1998.
16.2 40 CFR 60, Appendix B, “Performance Specification 2 - Specifications and Test Procedures for SO2, and NOX, Continuous Emission Monitoring Systems in Stationary Sources.”
16.3 40 CFR 60, Appendix B, “Performance Specification 1 - Specification and Test Procedures for Opacity Continuous Emission Monitoring Systems in Stationary Sources.”
16.4 40 CFR 60, Appendix A, “Method 1 - Sample and Velocity Traverses for Stationary Sources.”
16.5 “Current Knowledge of Particulate Matter (PM) Continuous Emission Monitoring.” EPA-454/R-00-039. U.S. Environmental Protection Agency, Research Triangle Park, NC. September 2000.
16.6 40 CFR 266, Appendix IX, section 2, “Performance Specifications for Continuous Emission Monitoring Systems.”
16.7 ISO 10155, “Stationary Source Emissions - Automated Monitoring of Mass Concentrations of Particles: Performance Characteristics, Test Procedures, and Specifications.” American National Standards Institute, New York City. 1995.
16.8 Snedecor, George W. and Cochran, William G. (1989), Statistical Methods, Eighth Edition, Iowa State University Press.
16.9 Wallis, W. A. (1951) “Tolerance Intervals for Linear Regression,” in Second Berkeley Symposium on Mathematical Statistics and Probability, ed. J. Neyman, Berkeley: University of California Press, pp. 43-51.
17.0 What Reference Tables and Validation Data Are Relevant to PS-11?Use the information in Table 1 for determining the confidence and tolerance interval half ranges. Use Table 2 to record your 7-day drift test data.
Table 1 - Factors for Calculation of Confidence and Tolerance Interval Half Ranges
df | Student's t, tdf | Tolerance interval with 75% coverage and 95% confidence level | ||
---|---|---|---|---|
vdf (95%) | un′ (75%) | kT | ||
3 | 3.182 | 2.920 | 1.266 | 3.697 |
4 | 2.776 | 2.372 | 1.247 | 2.958 |
5 | 2.571 | 2.089 | 1.233 | 2.576 |
6 | 2.447 | 1.915 | 1.223 | 2.342 |
7 | 2.365 | 1.797 | 1.214 | 2.183 |
8 | 2.306 | 1.711 | 1.208 | 2.067 |
9 | 2.262 | 1.645 | 1.203 | 1.979 |
10 | 2.228 | 1.593 | 1.198 | 1.909 |
11 | 2.201 | 1.551 | 1.195 | 1.853 |
12 | 2.179 | 1.515 | 1.192 | 1.806 |
13 | 2.160 | 1.485 | 1.189 | 1.766 |
14 | 2.145 | 1.460 | 1.186 | 1.732 |
15 | 2.131 | 1.437 | 1.184 | 1.702 |
16 | 2.120 | 1.418 | 1.182 | 1.676 |
17 | 2.110 | 1.400 | 1.181 | 1.653 |
18 | 2.101 | 1.384 | 1.179 | 1.633 |
19 | 2.093 | 1.370 | 1.178 | 1.614 |
20 | 2.086 | 1.358 | 1.177 | 1.597 |
21 | 2.080 | 1.346 | 1.175 | 1.582 |
22 | 2.074 | 1.335 | 1.174 | 1.568 |
23 | 2.069 | 1.326 | 1.173 | 1.555 |
24 | 2.064 | 1.316 | 1.172 | 1.544 |
25 | 2.060 | 1.308 | 1.172 | 1.533 |
26 | 2.056 | 1.300 | 1.171 | 1.522 |
27 | 2.052 | 1.293 | 1.170 | 1.513 |
28 | 2.048 | 1.286 | 1.170 | 1.504 |
29 | 2.045 | 1.280 | 1.169 | 1.496 |
30 | 2.042 | 1.274 | 1.168 | 1.488 |
31 | 2.040 | 1.268 | 1.168 | 1.481 |
32 | 2.037 | 1.263 | 1.167 | 1.474 |
33 | 2.035 | 1.258 | 1.167 | 1.467 |
34 | 2.032 | 1.253 | 1.166 | 1.461 |
35 | 2.030 | 1.248 | 1.166 | 1.455 |
36 | 2.028 | 1.244 | 1.165 | 1.450 |
37 | 2.026 | 1.240 | 1.165 | 1.444 |
38 | 2.024 | 1.236 | 1.165 | 1.439 |
39 | 2.023 | 1.232 | 1.164 | 1.435 |
40 | 2.021 | 1.228 | 1.164 | 1.430 |
41 | 2.020 | 1.225 | 1.164 | 1.425 |
42 | 2.018 | 1.222 | 1.163 | 1.421 |
43 | 2.017 | 1.218 | 1.163 | 1.417 |
44 | 2.015 | 1.215 | 1.163 | 1.413 |
45 | 2.014 | 1.212 | 1.163 | 1.410 |
46 | 2.013 | 1.210 | 1.162 | 1.406 |
47 | 2.012 | 1.207 | 1.162 | 1.403 |
48 | 2.011 | 1.204 | 1.162 | 1.399 |
49 | 2.010 | 1.202 | 1.162 | 1.396 |
50 | 2.009 | 1.199 | 1.161 | 1.393 |
51 | 2.008 | 1.197 | 1.161 | 1.390 |
52 | 2.007 | 1.195 | 1.161 | 1.387 |
53 | 2.006 | 1.192 | 1.161 | 1.384 |
54 | 2.005 | 1.190 | 1.161 | 1.381 |
55 | 2.004 | 1.188 | 1.160 | 1.379 |
56 | 2.003 | 1.186 | 1.160 | 1.376 |
57 | 2.002 | 1.184 | 1.160 | 1.374 |
58 | 2.002 | 1.182 | 1.160 | 1.371 |
59 | 2.001 | 1.180 | 1.160 | 1.369 |
60 | 2.000 | 1.179 | 1.160 | 1.367 |
References 16.8 (t values) and 16.9 (vdf and un′ values).
Table 2 - 7-Day Drift Test Data
Zero drift day # | Date and time |
Zero check value (RL) |
PM CEMS response (RCEMS) |
Difference (RCEMS−RL) |
Zero drift ((RCEMS−RL) /RU) × 100 |
---|---|---|---|---|---|
1 | |||||
2 | |||||
3 | |||||
4 | |||||
5 | |||||
6 | |||||
7 |
Upscale drift day # | Date and time |
Upscale check value (RU) |
PM CEMS response (RCEMS) |
Difference (RCEMS−RU) |
Upscale drift ((RCEMS−RU)/RU) × 100% |
---|---|---|---|---|---|
1 | |||||
2 | |||||
3 | |||||
4 | |||||
5 | |||||
6 | |||||
7 |
1.1 Analyte. The analyte measured by these procedures and specifications is total vapor phase mercury (Hg) in the flue gas, which represents the sum of elemental Hg (Hg°, CAS Number 7439-97-6) and oxidized forms of gaseous Hg (Hg+2), in concentration units of micrograms per cubic meter (µg/m 3).
1.2 Applicability.
1.2.1 This specification is for evaluating the acceptability of total vapor phase Hg continuous emission monitoring systems (CEMS) installed at stationary sources at the time of or soon after installation and whenever specified in the regulations. The Hg CEMS must be capable of measuring the total concentration in µg/m 3 of vapor phase Hg, regardless of speciation, and recording that concentration at standard conditions on a wet or dry basis. These specifications do not address measurement of particle bound Hg.
1.2.2 This specification is not designed to evaluate an installed CEMS's performance over an extended period of time nor does it identify specific calibration techniques and auxiliary procedures to assess the CEMS's performance. The source owner or operator, however, is responsible to calibrate, maintain, and operate the CEMS properly. The Administrator may require, under section 114 of the Clean Air Act, the operator to conduct CEMS performance evaluations at other times besides the initial performance evaluation test. See §§ 60.13(c) and 63.8(e)(1).
1.2.3 Mercury monitoring approaches not entirely suited to these specifications may be approvable under the alternative monitoring or alternative test method provisions of § 60.13(i) and § 63.8(f) or § 60.8(b)(3) and § 63.7(f), respectively.
2.0 Summary of Performance SpecificationProcedures for determining CEMS relative accuracy, linearity, and calibration drift are outlined. CEMS installation and measurement location specifications, data reduction procedures, and performance criteria are included.
3.0 Definitions3.1 Continuous Emission Monitoring System (CEMS) means the total equipment required to measure a pollutant concentration. The system generally consists of the following three major subsystems:
3.2 Sample Interface means that portion of the CEMS used for one or more of the following: sample acquisition, sample transport, sample conditioning, and protection of the monitor from the effects of the stack effluent.
3.3 Hg Analyzer means that portion of the Hg CEMS that measures the total vapor phase Hg mass concentration and generates a proportional output.
3.4 Data Recorder means that portion of the CEMS that provides a permanent electronic record of the analyzer output. The data recorder may provide automatic data reduction and CEMS control capabilities.
3.5 Span Value means the measurement range as specified in the applicable regulation or other requirement. If the span is not specified in the applicable regulation or other requirement, then it must be a value approximately equivalent to two times the emission standard. Unless otherwise specified, the span value may be rounded up to the nearest multiple of 10.
3.6 Measurement Error Test means a test procedure in which the accuracy of the concentrations measured by a CEMS at three or more points over its measurement range is evaluated using reference gases. For Hg CEMS, elemental and oxidized Hg (Hg 0 and mercuric chloride, HgCl2) gas standards of known concentration are used for this procedure.
3.7 Measurement Error (ME) means the absolute value of the difference between the concentration indicated by the CEMS and the known concentration of a reference gas, expressed as a percentage of the span value, when the entire CEMS, including the sampling interface, is challenged.
3.8 Calibration Drift (CD) means the absolute value of the difference between the CEMS output response and either an upscale Hg reference gas or a zero-level Hg reference gas, expressed as a percentage of the span value, when the entire CEMS, including the sampling interface, is challenged after a stated period of operation during which no unscheduled maintenance or repair took place.
3.9 Relative Accuracy Test Procedure means a test procedure consisting of at least nine test runs, in which the accuracy of the concentrations measured by a CEMS is evaluated by comparison against concurrent measurements made with a reference method (RM). Relative accuracy tests repeated on a regular, on-going basis are referred to as relative accuracy test audits or RATAs.
3.10 Relative Accuracy (RA) means the absolute mean difference between the pollutant concentrations determined by the CEMS and the values determined by the RM plus the 2.5 percent error confidence coefficient of a series of tests divided by the mean of the RM tests. Alternatively, for sources with an average RM concentration less than 5.0 micrograms per standard cubic meter (µg/scm), the RA may be expressed as the absolute value of the difference between the mean CEMS and RM values.
4.0 Interferences [Reserved] 5.0 SafetyThe procedures required under this performance specification may involve hazardous materials, operations, and equipment. This performance specification may not address all of the safety problems associated with these procedures. It is the responsibility of the user to establish appropriate safety and health practices and determine the applicable regulatory limitations prior to performing these procedures. The CEMS user's manual and materials recommended by the RM should be consulted for specific precautions to be taken.
6.0 Equipment and Supplies6.1 CEMS Equipment Specifications.
6.1.1 Data Recorder Scale. The Hg CEMS data recorder output range must include the full range of expected Hg concentration values in the gas stream to be sampled including zero and the span value.
6.1.2 The Hg CEMS design should also provide for the determination of CD and ME at a zero value (zero to 20 percent of the span value) and at upscale values (between 50 and 100 percent of the span value). The Hg CEMS must be constructed to permit the introduction of known concentrations of Hg and HgCl2 separately into the sampling system of the CEMS immediately preceding the sample extraction filtration system such that the entire CEMS can be challenged.
6.2 Reference Gas Delivery System. The reference gas delivery system must be designed so that the flowrate exceeds the sampling system flow requirements of the CEMS and that the gas is delivered to the CEMS at atmospheric pressure.
6.3 Other equipment and supplies, as needed by the reference method used for the Relative Accuracy Test Procedure. See section 8.6.2.
7.0 Reagents and Standards7.1 Reference Gases. Reference gas standards are required for both elemental and oxidized Hg (Hg and mercuric chloride, HgCl2). The use of National Institute of Standards and Technology (NIST)-traceable standards and reagents is required. The following gas concentrations are required.
7.1.1 Zero-level. 0 to 20 percent of the span value.
7.1.2 Mid-level. 50 to 60 percent of the span value.
7.1.3 High-level. 80 to 100 percent of the span value.
7.2 Reference gas standards may also be required for the reference methods. See section 8.6.2.
8.0 Performance Specification Test Procedure8.1 Installation and Measurement Location Specifications.
8.1.1 CEMS Installation. Install the CEMS at an accessible location downstream of all pollution control equipment. Place the probe outlet or other sampling interface at a point or location in the stack (or vent) representative of the stack gas concentration of Hg. Since the Hg CEMS sample system normally extracts gas from a single point in the stack, a location that has been shown to be free of stratification for Hg or, alternatively, SO2 is recommended. If the cause of failure to meet the RA test requirement is determined to be the measurement location and a satisfactory correction technique cannot be established, the Administrator may require the CEMS to be relocated. Measurement locations and points or paths that are most likely to provide data that will meet the RA requirements are described in sections 8.1.2 and 8.1.3 below.
8.1.2 Measurement Location. The measurement location should be (1) at least two equivalent diameters downstream of the nearest control device, point of pollutant generation or other point at which a change of pollutant concentration may occur, and (2) at least half an equivalent diameter upstream from the effluent exhaust. The equivalent duct diameter is calculated according to Method 1 in appendix A-1 to this part.
8.1.3 Hg CEMS Sample Extraction Point. Use a sample extraction point either (1) no less than 1.0 meter from the stack or duct wall, or (2) within the centroidal velocity traverse area of the stack or duct cross section. This does not apply to cross-stack, in-situ measurement systems.
8.2 Measurement Error (ME) Test Procedure. Sequentially inject each of at least three elemental Hg reference gases (zero, mid-level, and high level, as defined in section 7.1), three times each for a total of nine injections. Inject the gases in such a manner that the entire CEMS is challenged. Do not inject the same gas concentration twice in succession. At each reference gas concentration, determine the average of the three CEMS responses and subtract the average response from the reference gas value. Calculate the measurement error (ME) using Equation 12-1 by expressing the absolute value of the difference between the average CEMS response (A) and the reference gas value (R) as a percentage of the span (see example data sheet in Figure 12A-1). For each elemental Hg reference gas, the absolute value of the difference between the CEMS response and the reference value must not exceed 5 percent of the span value. If this specification is not met, identify and correct the problem before proceeding. Repeat the measurement error test procedure using oxidized Hg reference gases. For each oxidized Hg reference gas, the absolute value of the difference between the CEMS response and the reference value shall not exceed 10 percent of the span value. If this specification is not met, identify and correct the problem before proceeding.
8.3 Seven-Day Calibration Drift (CD) Test Procedure.
8.3.1 CD Test Period. While the affected facility is operating normally, or as specified in an applicable regulation, determine the magnitude of the CD once each day (at 24-hour intervals, to the extent practicable) for 7 consecutive unit operating days according to the procedures in sections 8.3.2 and 8.3.3. The 7 consecutive unit operating days need not be 7 consecutive calendar days. Use either Hg° or HgCl2 standards for this test.
8.3.2 The purpose of the CD measurement is to verify the ability of the CEMS to conform to the established CEMS response used for determining emission concentrations or emission rates. Therefore, if periodic automatic or manual adjustments are made to the CEMS zero and upscale response settings, conduct the CD test immediately before these adjustments, or conduct it in such a way that the CD can be determined.
8.3.3 Conduct the CD test using the zero gas specified and either the mid-level or high-level gas as specified in section 7.1. Sequentially introduce the reference gases to the CEMS at the sampling system of the CEMS immediately preceding the sample extraction filtration system. Record the CEMS response (A) for each reference gas and, using Equation 12A-2, subtract the corresponding reference value (R) from the CEMS value, and express the absolute value of the difference as a percentage of the span value (see also example data sheet in Figure 12A-2). For each reference gas, the absolute value of the difference between the CEMS response and the reference value must not exceed 5 percent of the span value. If these specifications are not met, identify and correct the problem before proceeding.
8.4 Relative Accuracy (RA) Test Procedure.
8.4.1 RA Test Period. Conduct the RA test according to the procedure given in sections 8.4.2 through 8.4.6 while the affected facility is operating normally, or as specified in an applicable subpart. The RA test may be conducted during the CD test period.
8.4.2 Reference Methods (RM). Unless otherwise specified in an applicable subpart of the regulations, use Method 29, Method 30A, or Method 30B in appendix A-8 to this part or American Society of Testing and Materials (ASTM) Method D6784-02 (incorporated by reference, see § 60.17) as the RM for Hg concentration. For Method 29 and ASTM Method D6784-02 only, the filterable portion of the sample need not be included when making comparisons to the CEMS results. When Method 29, Method 30B, or ASTM D6784-02 is used, conduct the RM test runs with paired or duplicate sampling systems and use the average of the vapor phase Hg concentrations measured by the two trains. When Method 30A is used, paired sampling systems are not required. If the RM and CEMS measure on a different moisture basis, data derived with Method 4 in appendix A-3 to this part must also be obtained during the RA test.
8.4.3 Sampling Strategy for RM Tests. Conduct the RM tests in such a way that they will yield results representative of the emissions from the source and can be compared to the CEMS data. The RM and CEMS locations need not be immediately adjacent. Locate the RM measurement points in accordance with section 8.1.3 of Performance Specification 2 (PS 2) in this appendix. It is preferable to conduct moisture measurements (if needed) and Hg measurements simultaneously, although moisture measurements that are taken within an hour of the Hg measurements may be used to adjust the Hg concentrations to a consistent moisture basis. In order to correlate the CEMS and RM data properly, note the beginning and end of each RM test period for each paired RM run (including the exact time of day) on the CEMS chart recordings or other permanent record of output.
8.4.4 Number and Length of RM Test Runs. Conduct a minimum of nine RM test runs. When Method 29, Method 30B, or ASTM D6784-02 is used, only test runs for which the paired RM trains meet the relative deviation criteria (RD) of this PS must be used in the RA calculations. In addition, for Method 29 and ASTM D6784-02, use a minimum sample time of 2 hours and for Methods 30A and 30B use a minimum sample time of 30 minutes.
Note:More than nine sets of RM test runs may be performed. If this option is chosen, RM test run results may be excluded so long as the total number of RM test run results used to determine the CEMS RA is greater than or equal to nine. However, all data must be reported including the excluded test run data.
8.4.5 Correlation of RM and CEMS Data. Correlate the CEMS and the RM test data as to the time and duration by first determining from the CEMS final output (the one used for reporting) the integrated average pollutant concentration for each RM test period. Consider system response time, if important, and confirm that the results are on a consistent moisture basis with the RM test. Then, compare each integrated CEMS value against the corresponding RM value. When Method 29, Method 30B, or ASTM D6784-02 is used, compare each CEMS value against the corresponding average of the paired RM values.
8.4.6 Paired RM Outliers.
8.4.6.1 When Method 29, Method 30B, or ASTM D6784-02 is used, outliers are identified through the determination of relative deviation (RD) of the paired RM tests. Data that do not meet the RD criteria must be flagged as a data quality problem and may not be used in the calculation of RA. The primary reason for performing paired RM sampling is to ensure the quality of the RM data. The percent RD of paired data is the parameter used to quantify data quality. Determine RD for paired data points as follows:
Where: Ca and Cb are the Hg concentration values determined from the paired samples.8.4.6.2 The minimum performance criteria for RM Hg data is that RD for any data pair must be ≤10 percent as long as the mean Hg concentration is greater than 1.0 µg/m 3. If the mean Hg concentration is less than or equal to 1.0 µg/m 3, the RD must be ≤20 percent or ≤0.2 µg/m 3 absolute difference. Pairs of RM data exceeding these RD criteria should be eliminated from the data set used to develop a Hg CEMS correlation or to assess CEMS RA.
8.4.7 Calculate the mean difference between the RM and CEMS values in the units of micrograms per cubic meter (µg/m 3), the standard deviation, the confidence coefficient, and the RA according to the procedures in section 12.0.
8.5 Reporting. At a minimum (check with the appropriate EPA Regional Office, State or local Agency for additional requirements, if any), summarize in tabular form the results of the CD tests, the linearity tests, and the RA test or alternative RA procedure, as appropriate. Include all data sheets, calculations, charts (records of CEMS responses), reference gas concentration certifications, and any other information necessary to confirm that the CEMS meets the performance criteria.
9.0 Quality Control [Reserved] 10.0 Calibration and Standardization [Reserved] 11.0 Analytical ProcedureFor Method 30A, sample collection and analysis are concurrent. For the other RM, post-run sample analyses are performed. Refer to the RM employed for specific analytical procedures.
12.0 Calculations and Data AnalysisCalculate and summarize the RA test results on a data sheet similar to Figure 12A-3.
12.1 Consistent Basis. All data from the RM and CEMS must be compared in units of micrograms per standard cubic meter (µg/scm), on a consistent and identified moisture basis. The values must be standardized to 20 °C, 760 mm Hg.
12.1.1 Moisture Correction (as applicable). If the RM and CEMS measure Hg on a different moisture basis, they will need to be corrected to a consistent basis. Use Equation 12A-4a to correct data from a wet basis to a dry basis.
Use Equation 12A-4b to correct data from a dry basis to a wet basis.
Where: Bws is the moisture content of the flue gas from Method 4, expressed as a decimal fraction (e.g., for 8.0 percent H2O, Bws= 0.08).12.2 Arithmetic Mean. Calculate d , the arithmetic mean of the differences (di) of a data set as follows:
Where: n = Number of data points.12.3 Standard Deviation. Calculate the standard deviation, Sd, as follows:
12.3 Confidence Coefficient (CC). Calculate the 2.5 percent error confidence coefficient (one-tailed), CC, as follows:
12.4 Relative Accuracy. Calculate the RA of a set of data as follows:
Where: |d | = Absolute value of the mean of the differences (from Equation 12A-5) |CC| = Absolute value of the confidence coefficient (from Equation 12A-7) RM = Average reference method value 13.0 Method Performance13.1 Measurement Error (ME). For Hg 0, the ME must not exceed 5 percent of the span value at the zero-, mid-, and high-level reference gas concentrations. For HgCl2, the ME must not exceed 10 percent of the span value at the zero-, mid-, and high-level reference gas concentrations.
13.2 Calibration Drift (CD). The CD must not exceed 5 percent of the span value on any of the 7 days of the CD test.
13.3 Relative Accuracy (RA). The RA of the CEMS must be no greater than 20 percent of the mean value of the RM test data in terms of units of µg/scm. Alternatively, if the mean RM is less than 5.0 µg/scm, the results are acceptable if the absolute value of the difference between the mean RM and CEMS values does not exceed 1.0 µg/scm.
14.0 Pollution Prevention [Reserved] 15.0 Waste Management [Reserved] 16.0 Alternative Procedures [Reserved] 17.0 Bibliography17.1 40 CFR part 60, appendix B, “Performance Specification 2 - Specifications and Test Procedures for SO2 and NOX Continuous Emission Monitoring Systems in Stationary Sources.”
17.2 40 CFR part 60, appendix A, “Method 29 - Determination of Metals Emissions from Stationary Sources.”
17.3 40 CFR part 60, appendix A, “Method 30A - Determination of Total Vapor Phase Mercury Emissions From Stationary Sources (Instrumental Analyzer Procedure).
17.4 40 CFR part 60, appendix A, “Method 30B - Determination of Total Vapor Phase Mercury Emissions From Coal-Fired Combustion Sources Using Carbon Sorbent Traps.”
17.5 ASTM Method D6784-02, “Standard Test Method for Elemental, Oxidized, Particle-Bound and Total Mercury in Flue Gas Generated from Coal-Fired Stationary Sources (Ontario Hydro Method).”
18.0 Tables and FiguresTable 12A-1 - T-Values
n a | t0.975 | n a | t0.975 | n a | t0.975 |
---|---|---|---|---|---|
2 | 12.706 | 7 | 2.447 | 12 | 2.201 |
3 | 4.303 | 8 | 2.365 | 13 | 2.179 |
4 | 3.182 | 9 | 2.306 | 14 | 2.160 |
5 | 2.776 | 10 | 2.262 | 15 | 2.145 |
6 | 2.571 | 11 | 2.228 | 16 | 2.131 |
a The values in this table are already corrected for n-1 degrees of freedom. Use n equal to the number of individual values.
Figure 12A-1 - ME Determination
Date | Time | Reference gas value (µg/m 3) |
CEMS measured value (µg/m 3) |
Absolute difference (µg/m 3) |
ME (% of span value) |
|
---|---|---|---|---|---|---|
Zero level | ||||||
Average | ||||||
Mid level | ||||||
Average | ||||||
High level | ||||||
Average |
Figure 12A-2 - 7-Day Calibration Drift Determination
Date | Time | Reference gas value (µg/m 3) |
CEMS measured value (µg/m 3) |
Absolute difference (µg/m 3) |
CD (% of span value) |
|
---|---|---|---|---|---|---|
Zero level | ||||||
Upscale (Mid or High) |
||||||
Figure 12A-3 - Relative Accuracy Test Data
Run No. | Date | Begin time | End time | RM value (µg/m 3) | CEMS value (µg/m 3) | Difference (µg/m 3) |
Run used? (Yes/No) | RD 1 |
---|---|---|---|---|---|---|---|---|
1 | ||||||||
2 | ||||||||
3 | ||||||||
4 | ||||||||
5 | ||||||||
6 | ||||||||
7 | ||||||||
8 | ||||||||
9 | ||||||||
10 | ||||||||
11 | ||||||||
12 | ||||||||
Average Values | ||||||||
Arithmetic Mean Difference: | ||||||||
Standard Deviation: | ||||||||
Confidence Coefficient: | ||||||||
T-Value: | ||||||||
% Relative Accuracy: | ||||||||
| (RM)avg − (CEMS)avg | : |
1 Calculate the RD only if paired samples are taken using RM 30B, RM 29, or ASTM 6784-08. Express RD as a percentage or, for very low RM concentrations (≤1.0 µg/m 3), as the absolute difference between Ca and Cb.
The purpose of Performance Specification 12B (PS 12B) is to establish performance benchmarks for, and to evaluate the acceptability of, sorbent trap monitoring systems used to monitor total vapor-phase mercury (Hg) emissions in stationary source flue gas streams. These monitoring systems involve continuous repetitive in-stack sampling using paired sorbent media traps with periodic analysis of the time-integrated samples. Persons using PS 12B should have a thorough working knowledge of Methods 1, 2, 3, 4, 5 and 30B in appendices A-1 through A-3 and A-8 to this part.
1.1 Analyte. The analyte measured by these procedures and specifications is total vapor phase Hg in the flue gas, which represents the sum of elemental Hg (Hg 0, CAS Number 7439-97-6) and gaseous forms of oxidized Hg (i.e., Hg+2) in mass concentration units of micrograms per dry standard cubic meter (µg/dscm).
1.2 Applicability1.2.1 These procedures are only intended for use under relatively low particulate conditions (e.g., monitoring after all pollution control devices). This specification is for evaluating the acceptability of total vapor phase Hg sorbent trap monitoring systems installed at stationary sources at the time of, or soon after, installation and whenever specified in the regulations. The Hg monitoring system must be capable of measuring the total concentration of vapor phase Hg (regardless of speciation), in units of µg/dscm.
1.2.2 This specification contains routine procedures and specifications designed to evaluate an installed sorbent trap monitoring system's performance over time; Procedure 5 of appendix F to this part contains additional procedures and specifications which may be required for long term operation. In addition, the source owner or operator is responsible to calibrate, maintain, and operate the monitoring system properly. The Administrator may require the owner or operator, under section 114 of the Clean Air Act, to conduct performance evaluations at other times besides the initial test to evaluate the CEMS performance. See § 60.13(c) and 63.8(e)(1).
2.0 PrincipleKnown volumes of flue gas are continuously extracted from a stack or duct through paired, in-stack, pre-spiked sorbent media traps at appropriate nominal flow rates. The sorbent traps in the sampling system are periodically exchanged with new ones, prepared for analysis as needed, and analyzed by any technique that can meet the performance criteria. For quality-assurance purposes, a section of each sorbent trap is spiked with Hg 0 prior to sampling. Following sampling, this section is analyzed separately and a specified minimum percentage of the spike must be recovered. Paired train sampling is required to determine method precision.
3.0 Definitions3.1 Sorbent Trap Monitoring System means the total equipment required for the collection of gaseous Hg samples using paired three-partition sorbent traps.
3.2 Relative Accuracy Test Procedure means a test procedure consisting of at least nine runs, in which the accuracy of the total vapor phase Hg concentrations measured by the sorbent trap monitoring system is evaluated by comparison against concurrent measurements made with a reference method (RM). Relative accuracy tests repeated on a regular, on-going basis are referred to as relative accuracy test audits or RATAs.
3.3 Relative Accuracy (RA) means the absolute mean difference between the pollutant (Hg) concentrations determined by the sorbent trap monitoring system and the values determined by the reference method (RM) plus the 2.5 percent error confidence coefficient of a series of tests divided by the mean of the RM tests. Alternatively, for low concentration sources, the RA may be expressed as the absolute value of the difference between the mean sorbent trap monitoring system and RM values.
3.4 Relative Deviation (RD) means the absolute difference of the Hg concentration values obtained with a pair of sorbent traps divided by the sum of those concentrations, expressed as a percentage. RD is used to assess the precision of the sorbent trap monitoring system.
3.5 Spike Recovery means the mass of Hg recovered from the spiked trap section, expressed as a percentage of the amount spiked. Spike recovery is used to assess sample matrix interference.
4.0 Interferences [Reserved] 5.0 SafetyThe procedures required under this performance specification may involve hazardous materials, operations, and equipment. This performance specification may not address all of the safety problems associated with these procedures. It is the responsibility of the user to establish appropriate safety and health practices and determine the applicable regulatory limitations prior to performing these procedures.
6.0 Equipment and Supplies6.1 Sorbent Trap Monitoring System Equipment Specifications.
6.1.1 Monitoring System. The equipment described in Method 30B in appendix A-8 to this part must be used to continuously sample for Hg emissions, with the substitution of three-section traps in place of two-section traps, as described below. A typical sorbent trap monitoring system is shown in Figure 12B-1.
6.1.2 Three-Section Sorbent Traps. The sorbent media used to collect Hg must be configured in traps with three distinct and identical segments or sections, connected in series, to be separately analyzed. section 1 is designated for primary capture of gaseous Hg. section 2 is designated as a backup section for determination of vapor-phase Hg breakthrough. section 3 is designated for quality assurance/quality control (QA/QC) purposes. section 3 must be spiked with a known amount of gaseous Hg 0 prior to sampling and later analyzed to determine the spike (and hence sample) recovery efficiency.
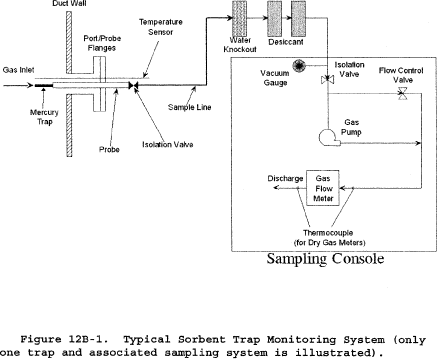
6.1.3 Gaseous Hg 0 Sorbent Trap Spiking System. A known mass of gaseous Hg 0 must be spiked onto section 3 of each sorbent trap prior to sampling. Any approach capable of quantitatively delivering known masses of Hg 0 onto sorbent traps is acceptable. Several technologies or devices are available to meet this objective. Their practicality is a function of Hg mass spike levels. For low levels, NIST-certified or NIST-traceable gas generators or tanks may be suitable, but will likely require long preparation times. A more practical, alternative system, capable of delivering almost any mass required, employs NIST-certified or NIST-traceable Hg salt solutions (e.g., Hg(NO3)2). With this system, an aliquot of known volume and concentration is added to a reaction vessel containing a reducing agent (e.g., stannous chloride); the Hg salt solution is reduced to Hg 0 and purged onto section 3 of the sorbent trap by using an impinger sparging system.
6.1.4 Sample Analysis Equipment. Any analytical system capable of quantitatively recovering and quantifying total gaseous Hg from sorbent media is acceptable provided that the analysis can meet the performance criteria in Table 12B-1 in section 9 of this performance specification. Candidate recovery techniques include leaching, digestion, and thermal desorption. Candidate analytical techniques include ultraviolet atomic fluorescence (UV AF); ultraviolet atomic absorption (UV AA), with and without gold trapping; and in-situ X-ray fluorescence (XRF).
7.0 Reagents and StandardsOnly NIST-certified or NIST-traceable calibration gas standards and reagents must be used for the tests and procedures required under this performance specification. The sorbent media may be any collection material (e.g., carbon, chemically treated filter, etc.) capable of quantitatively capturing and recovering for subsequent analysis, all gaseous forms of Hg in the emissions from the intended application. Selection of the sorbent media must be based on the material's ability to achieve the performance criteria contained in this method as well as the sorbent's vapor phase Hg capture efficiency for the emissions matrix and the expected sampling duration at the test site.
8.0 Performance Specification Test Procedure8.1 Installation and Measurement Location Specifications.
8.1.1 Selection of Monitoring Site. Sampling site information should be obtained in accordance with Method 1 in appendix A-1 to this part. Place the probe inlet at a point or location in the stack (or vent) downstream of all pollution control equipment and representative of the stack gas concentration of Hg. A location that has been shown to be free of stratification for Hg or, alternatively, SO2 is recommended. An estimation of the expected stack Hg concentration is required to establish a target sample flow rate, total gas sample volume, and the mass of Hg 0 to be spiked onto section 3 of each sorbent trap.
8.1.2 Pre-sampling Spiking of Sorbent Traps. Based on the estimated Hg concentration in the stack, the target sample rate and the target sampling duration, calculate the expected mass loading for section 1 of each sorbent trap (see section 12.1 of this performance specification). The pre-sampling spike to be added to section 3 of each sorbent trap must be within ±50 percent of the expected section 1 mass loading. Spike section 3 of each sorbent trap at this level, as described in section 6.1.3 of this performance specification. For each sorbent trap, keep a record of the mass of Hg 0 added to section 3. This record must include, at a minimum, the identification number of the trap, the date and time of the spike, the name of the analyst performing the procedure, the method of spiking, the mass of Hg 0 added to section 3 of the trap (µg), and the supporting calculations.
8.1.3 Pre-monitoring Leak Check. Perform a leak check with the sorbent traps in place in the sampling system. Draw a vacuum in each sample train. Adjust the vacuum in each sample train to ∼15″ Hg. Use the gas flow meter to determine leak rate. The leakage rate must not exceed 4 percent of the target sampling rate. Once the leak check passes this criterion, carefully release the vacuum in the sample train, then seal the sorbent trap inlet until the probe is ready for insertion into the stack or duct.
8.1.4 Determination of Flue Gas Characteristics. Determine or measure the flue gas measurement environment characteristics (gas temperature, static pressure, gas velocity, stack moisture, etc.) in order to determine ancillary requirements such as probe heating requirements (if any), sampling rate, proportional sampling conditions, moisture management, etc.
8.2 Monitoring.
8.2.1 System Preparation and Initial Data Recording. Remove the plug from the end of each sorbent trap and store each plug in a clean sorbent trap storage container. Remove the stack or duct port cap and insert the probe(s) with the inlet(s) aligned perpendicular to the stack gas flow. Secure the probe(s) and ensure that no leakage occurs between the duct and environment. Record initial data including the sorbent trap ID, start time, starting gas flow meter readings, initial temperatures, set points, and any other appropriate information.
8.2.2 Flow Rate Control. Set the initial sample flow rate at the target value from section 8.1.1 of this performance specification. Then, for every operating hour during the sampling period, record the date and time, the sample flow rate, the gas flow meter reading, the stack temperature (if needed), the flow meter temperatures (if needed), temperatures of heated equipment such as the vacuum lines and the probes (if heated), and the sampling system vacuum readings. Also, record the stack gas flow rate and the ratio of the stack gas flow rate to the sample flow rate. Adjust the sampling flow rate to maintain proportional sampling, i.e., keep the ratio of the stack gas flow rate to sample flow rate within ±25 percent of the reference ratio from the first hour of the data collection period (see section 12.2 of this performance specification). The sample flow rate through a sorbent trap monitoring system during any hour (or portion of an hour) that the unit is not operating must be zero.
8.2.3 Stack Gas Moisture Determination. If data from the sorbent trap monitoring system will be used to calculate Hg mass emissions, determine the stack gas moisture content using a continuous moisture monitoring system or other means acceptable to the Administrator, such as the ones described in § 75.11(b) of this chapter. Alternatively, for combustion of coal, wood, or natural gas in boilers only, a default moisture percentage from § 75.11(b) of this chapter may be used.
8.2.4 Essential Operating Data. Obtain and record any essential operating data for the facility during the test period, e.g., the barometric pressure for correcting the sample volume measured by a dry gas meter to standard conditions. At the end of the data collection period, record the final gas flow meter reading and the final values of all other essential parameters.
8.2.5 Post-monitoring Leak Check. When the monitoring period is completed, turn off the sample pump, remove the probe/sorbent trap from the port and carefully re-plug the end of each sorbent trap. Perform a leak check with the sorbent traps in place, at the maximum vacuum reached during the monitoring period. Use the same general approach described in section 8.1.3 of this performance specification. Record the leakage rate and vacuum. The leakage rate must not exceed 4 percent of the average sampling rate for the monitoring period. Following the leak check, carefully release the vacuum in the sample train.
8.2.6 Sample Recovery. Recover each sampled sorbent trap by removing it from the probe and seal both ends. Wipe any deposited material from the outside of the sorbent trap. Place the sorbent trap into an appropriate sample storage container and store/preserve it in an appropriate manner.
8.2.7 Sample Preservation, Storage, and Transport. While the performance criteria of this approach provide for verification of appropriate sample handling, it is still important that the user consider, determine, and plan for suitable sample preservation, storage, transport, and holding times for these measurements. Therefore, procedures in recognized voluntary consensus standards such as those in ASTM D6911-03 “Standard Guide for Packaging and Shipping Environmental Samples for Laboratory Analysis” should be followed for all samples.
8.2.8 Sample Custody. Proper procedures and documentation for sample chain of custody are critical to ensuring data integrity. Chain of custody procedures in recognized voluntary consensus standards such as those in ASTM D4840-99 “Standard Guide for Sample Chain-of-Custody Procedures” should be followed for all samples (including field samples and blanks).
8.3 Relative Accuracy (RA) Test Procedure
8.3.1 For the initial certification of a sorbent trap monitoring system, a RA Test is required. Follow the basic RA test procedures and calculation methodology described in sections 8.4.1 through 8.4.7 and 12.4 of PS 12A in this appendix, replacing the term “CEMS” with “sorbent trap monitoring system”.
8.3.2 Special Considerations. The type of sorbent material used in the traps must be the same as that used for daily operation of the monitoring system; however, the size of the traps used for the RA test may be smaller than the traps used for daily operation of the system. Spike the third section of each sorbent trap with elemental Hg, as described in section 8.1.2 of this performance specification. Install a new pair of sorbent traps prior to each test run. For each run, the sorbent trap data must be validated according to the quality assurance criteria in Table 12B-1 in section 9.0, below.
8.3.3 Acceptance Criteria. The RA of the sorbent trap monitoring system must be no greater than 20 percent of the mean value of the RM test data in terms of units of µg/scm. Alternatively, if the RM concentration is less than or equal to 5.0 µg/scm, then the RA results are acceptable if the absolute difference between the means of the RM and sorbent trap monitoring system values does not exceed 1.0 µg/scm.
9.0 Quality Assurance and Quality Control (QA/QC)Table 12B-1 summarizes the QA/QC performance criteria that are used to validate the Hg emissions data from a sorbent trap monitoring system. Failure to achieve these performance criteria will result in invalidation of Hg emissions data, except where otherwise noted.
Table 12B-1 - QA/QC Criteria for Sorbent Trap Monitoring Systems
QA/QC test or specification |
Acceptance criteria | Frequency | Consequences if not met |
---|---|---|---|
Pre-test leak check | ≤4% of target sampling rate | Prior to monitoring | Monitoring must not commence until the leak check is passed. |
Post-test leak check | ≤4% of average sampling rate | After monitoring | Invalidate the data from the paired traps or, if certain conditions are met, report adjusted data from a single trap (see Section 12.8.3). |
Ratio of stack gas flow rate to sample flow rate | No more than 5% of the hourly ratios or 5 hourly ratios (whichever is less restrictive) may deviate from the reference ratio by more than ±25% | Every hour throughout monitoring period | Invalidate the data from the paired traps or, if certain conditions are met, report adjusted data from a single trap (see Section 12.8.3). |
Sorbent trap section 2 breakthrough | ≤5% of Section 1 Hg mass ≤10% of Section 1 Hg mass if average Hg concentration is ≤0.5 µg/scm |
Every sample | Invalidate the data from the paired traps or, if certain conditions are met, report adjusted data from a single trap (see Section 12.8.3). |
No criterion when Hg concentration for trap less than 10% of the applicable emission limit (must meet all other QA/QC specifications) | |||
Paired sorbent trap agreement | ≤10% Relative Deviation (RD)
if the average concentration is > 1.0 µg/m 3 ≤20% RD if the average concentration is ≤1.0 µg/m 3 |
Every sample | Either invalidate the data from the paired traps or report the results from the trap with the higher Hg concentration. |
Results also acceptable if absolute difference between concentrations from paired traps is ≤ 0.03 µg/m 3 | |||
Spike Recovery Study | Average recovery between 85% and 115% for each of the 3 spike concentration levels | Prior to analyzing field samples and prior to use of new sorbent media | Field samples must not be analyzed until the percent recovery criteria have been met. |
Multipoint analyzer calibration | Each analyzer reading within ±10% of true value and r 2 ≥ 0.99 | On the day of analysis, before analyzing any samples | Recalibrate until successful. |
Analysis of independent calibration standard | Within ±10% of true value | Following daily calibration, prior to analyzing field samples | Recalibrate and repeat independent standard analysis until successful. |
Spike recovery from section 3 of both sorbent traps | 75-125% of spike amount | Every sample | Invalidate the data from the paired traps or, if certain conditions are met, report adjusted data from a single trap (see Section 12.8.3). |
Relative Accuracy | RA ≤ 20.0% of RM mean value; or if RM mean value ≤5.0 µg/scm, absolute difference between RM and sorbent trap monitoring system mean values ≤1.0 µg/scm | RA specification must be met for initial certification | Data from the system are invalid until a RA test is passed. |
Gas flow meter calibration | An initial calibration factor (Y) has been determined at 3 settings; for mass flow meters, initial calibration with stack gas has been performed. For subsequent calibrations, Y within ±5% of average value from the most recent 3-point calibration | At 3 settings prior to initial use and at least quarterly at one setting thereafter | Recalibrate meter at 3 settings to determine a new value of Y. |
Temperature sensor calibration | Absolute temperature measured by sensor within ±1.5% of a reference sensor | Prior to initial use and at least quarterly thereafter | Recalibrate; sensor may not be used until specification is met. |
Barometer calibration | Absolute pressure measured by instrument within ±10 mm Hg of reading with a NIST-traceable barometer | Prior to initial use and at least quarterly thereafter | Recalibrate; instrument may not be used until specification is met. |
10.1 Gaseous and Liquid Standards. Only NIST certified or NIST-traceable calibration standards (i.e., calibration gases, solutions, etc.) must be used for the spiking and analytical procedures in this performance specification.
10.2 Gas Flow Meter Calibration. The manufacturer or supplier of the gas flow meter should perform all necessary set-up, testing, programming, etc., and should provide the end user with any necessary instructions, to ensure that the meter will give an accurate readout of dry gas volume in standard cubic meters for the particular field application.
10.2.1 Initial Calibration. Prior to its initial use, a calibration of the flow meter must be performed. The initial calibration may be done by the manufacturer, by the equipment supplier, or by the end user. If the flow meter is volumetric in nature (e.g., a dry gas meter), the manufacturer, equipment supplier, or end user may perform a direct volumetric calibration using any gas. For a mass flow meter, the manufacturer, equipment supplier, or end user may calibrate the meter using a bottled gas mixture containing 12 ±0.5% CO2, 7 ±0.5% O2, and balance N2, or these same gases in proportions more representative of the expected stack gas composition. Mass flow meters may also be initially calibrated on-site, using actual stack gas.
10.2.1.1 Initial Calibration Procedures. Determine an average calibration factor (Y) for the gas flow meter, by calibrating it at three sample flow rate settings covering the range of sample flow rates at which the sorbent trap monitoring system typically operates. Either the procedures in section 10.3.1 of Method 5 in appendix A-3 to this part or the procedures in section 16 of Method 5 in appendix A-3 to this part may be followed. If a dry gas meter is being calibrated, use at least five revolutions of the meter at each flow rate.
10.2.1.2 Alternative Initial Calibration Procedures. Alternatively, the initial calibration of the gas flow meter may be performed using a reference gas flow meter (RGFM). The RGFM may be either: (1) A wet test meter calibrated according to section 10.3.1 of Method 5 in appendix A-3 to this part; (2) A gas flow metering device calibrated at multiple flow rates using the procedures in section 16 of Method 5 in appendix A-3 to this part; or (3) A NIST-traceable calibration device capable of measuring volumetric flow to an accuracy of 1 percent. To calibrate the gas flow meter using the RGFM, proceed as follows: While the sorbent trap monitoring system is sampling the actual stack gas or a compressed gas mixture that simulates the stack gas composition (as applicable), connect the RGFM to the discharge of the system. Care should be taken to minimize the dead volume between the sample flow meter being tested and the RGFM. Concurrently measure dry gas volume with the RGFM and the flow meter being calibrated for a minimum of 10 minutes at each of three flow rates covering the typical range of operation of the sorbent trap monitoring system. For each 10-minute (or longer) data collection period, record the total sample volume, in units of dry standard cubic meters (dscm), measured by the RGFM and the gas flow meter being tested.
10.2.1.3 Initial Calibration Factor. Calculate an individual calibration factor Yi at each tested flow rate from section 10.2.1.1 or 10.2.1.2 of this performance specification (as applicable), by taking the ratio of the reference sample volume to the sample volume recorded by the gas flow meter. Average the three Yi values, to determine Y, the calibration factor for the flow meter. Each of the three individual values of Yi must be within ±0.02 of Y. Except as otherwise provided in sections 10.2.1.4 and 10.2.1.5 of this performance specification, use the average Y value from the three level calibration to adjust all subsequent gas volume measurements made with the gas flow meter.
10.2.2 Initial On-Site Calibration Check. For a mass flow meter that was initially calibrated using a compressed gas mixture, an on-site calibration check must be performed before using the flow meter to provide data. While sampling stack gas, check the calibration of the flow meter at one intermediate flow rate typical of normal operation of the monitoring system. Follow the basic procedures in section 10.2.1.1 or 10.2.1.2 of this performance specification. If the onsite calibration check shows that the value of Yi, the calibration factor at the tested flow rate, differs by more than 5 percent from the value of Y obtained in the initial calibration of the meter, repeat the full 3-level calibration of the meter using stack gas to determine a new value of Y, and apply the new Y value to all subsequent gas volume measurements made with the gas flow meter.
10.2.3 Ongoing Quality Control. Recalibrate the gas flow meter quarterly at one intermediate flow rate setting representative of normal operation of the monitoring system. Follow the basic procedures in section 10.2.1.1 or 10.2.1.2 of this performance specification. If a quarterly recalibration shows that the value of Yi, the calibration factor at the tested flow rate, differs from the current value of Y by more than 5 percent, repeat the full 3-level calibration of the meter to determine a new value of Y, and apply the new Y value to all subsequent gas volume measurements made with the gas flow meter.
10.3 Calibration of Thermocouples and Other Temperature Sensors. Use the procedures and criteria in section 10.3 of Method 2 in appendix A-1 to this part to calibrate in-stack temperature sensors and thermocouples. Calibrations must be performed prior to initial use and at least quarterly thereafter. At each calibration point, the absolute temperature measured by the temperature sensor must agree to within ±1.5 percent of the temperature measured with the reference sensor, otherwise the sensor may not continue to be used.
10.4 Barometer Calibration. Calibrate the barometer against another barometer that has a NIST-traceable calibration. This calibration must be performed prior to initial use and at least quarterly thereafter. At each calibration point, the absolute pressure measured by the barometer must agree to within ±10 mm Hg of the pressure measured by the NIST-traceable barometer, otherwise the barometer may not continue to be used.
10.5 Calibration of Other Sensors and Gauges. Calibrate all other sensors and gauges according to the procedures specified by the instrument manufacturer(s).
10.6 Analytical System Calibration. See section 11.1 of this performance specification.
11.0 Analytical ProceduresThe analysis of the Hg samples may be conducted using any instrument or technology capable of quantifying total Hg from the sorbent media and meeting the performance criteria in section 9 of this performance specification.
11.1 Analyzer System Calibration. Perform a multipoint calibration of the analyzer at three or more upscale points over the desired quantitative range (multiple calibration ranges must be calibrated, if necessary). The field samples analyzed must fall within a calibrated, quantitative range and meet the necessary performance criteria. For samples that are suitable for aliquotting, a series of dilutions may be needed to ensure that the samples fall within a calibrated range. However, for sorbent media samples that are consumed during analysis (e.g., thermal desorption techniques), extra care must be taken to ensure that the analytical system is appropriately calibrated prior to sample analysis. The calibration curve range(s) should be determined based on the anticipated level of Hg mass on the sorbent media. Knowledge of estimated stack Hg concentrations and total sample volume may be required prior to analysis. The calibration curve for use with the various analytical techniques (e.g., UV AA, UV AF, and XRF) can be generated by directly introducing standard solutions into the analyzer or by spiking the standards onto the sorbent media and then introducing into the analyzer after preparing the sorbent/standard according to the particular analytical technique. For each calibration curve, the value of the square of the linear correlation coefficient, i.e., r 2, must be ≥0.99, and the analyzer response must be within ±10 percent of reference value at each upscale calibration point. Calibrations must be performed on the day of the analysis, before analyzing any of the samples. Following calibration, an independently prepared standard (not from same calibration stock solution) must be analyzed. The measured value of the independently prepared standard must be within ±10 percent of the expected value.
11.2 Sample Preparation. Carefully separate the three sections of each sorbent trap. Combine for analysis all materials associated with each section, i.e., any supporting substrate that the sample gas passes through prior to entering a media section (e.g., glass wool, polyurethane foam, etc.) must be analyzed with that segment.
11.3 Spike Recovery Study. Before analyzing any field samples, the laboratory must demonstrate the ability to recover and quantify Hg from the sorbent media by performing the following spike recovery study for sorbent media traps spiked with elemental mercury. Using the procedures described in sections 6.2 and 12.1 of this performance specification, spike the third section of nine sorbent traps with gaseous Hg 0, i.e., three traps at each of three different mass loadings, representing the range of masses anticipated in the field samples. This will yield a 3 × 3 sample matrix. Prepare and analyze the third section of each spiked trap, using the techniques that will be used to prepare and analyze the field samples. The average recovery for each spike concentration must be between 85 and 115 percent. If multiple types of sorbent media are to be analyzed, a separate spike recovery study is required for each sorbent material. If multiple ranges are calibrated, a separate spike recovery study is required for each range.
11.4 Field Sample Analyses. Analyze the sorbent trap samples following the same procedures that were used for conducting the spike recovery study. The three sections of each sorbent trap must be analyzed separately (i.e., section 1, then section 2, then section 3). Quantify the total mass of Hg for each section based on analytical system response and the calibration curve from section 11.1 of this performance specification. Determine the spike recovery from sorbent trap section 3. The spike recovery must be no less than 75 percent and no greater than 125 percent. To report the final Hg mass for each trap, add together the Hg masses collected in trap sections 1 and 2.
12.0 Calculations, Data Reduction, and Data Analysis12.1 Calculation of Pre-Sampling Spiking Level. Determine sorbent trap section 3 spiking level using estimates of the stack Hg concentration, the target sample flow rate, and the expected monitoring period. Calculate Mexp, the expected Hg mass that will be collected in section 1 of the trap, using Equation 12B-1. The pre-sampling spike must be within ±50 percent of this mass.
Where: Mexp = Expected sample mass (µg) Qs = Sample flow rate (L/min) ts = Expected monitoring period (min) Cest = Estimated Hg concentration in stack gas (µg/m 3) 10−3 = Conversion factor (m 3/L) Example calculation:For an estimated stack Hg concentration of 5 µg/m 3, a target sample rate of 0.30 L/min, and a monitoring period of 5 days: Mexp = (0.30 L/min)(1440 min/day)(5 days)(10−3 m 3/L)(5 µg/m 3) = 10.8 µgA pre-sampling spike of 10.8 µg ±50 percent is, therefore, appropriate.
12.2 Calculations for Flow-Proportional Sampling. For the first hour of the data collection period, determine the reference ratio of the stack gas volumetric flow rate to the sample flow rate, as follows:
Where: Rref = Reference ratio of hourly stack gas flow rate to hourly sample flow rate Qref = Average stack gas volumetric flow rate for first hour of collection period (scfh) Fref = Average sample flow rate for first hour of the collection period, in appropriate units (e.g., liters/min, cc/min, dscm/min) K = Power of ten multiplier, to keep the value of Rref between 1 and 100. The appropriate K value will depend on the selected units of measure for the sample flow rate.Then, for each subsequent hour of the data collection period, calculate ratio of the stack gas flow rate to the sample flow rate using Equation 12B-3:
Where: Rh = Ratio of hourly stack gas flow rate to hourly sample flow rate Qh = Average stack gas volumetric flow rate for the hour (scfh) Fh = Average sample flow rate for the hour, in appropriate units (e.g., liters/min, cc/min, dscm/min) K = Power of ten multiplier, to keep the value of Rh between 1 and 100. The appropriate K value will depend on the selected units of measure for the sample flow rate and the range of expected stack gas flow rates.Maintain the value of Rh within ±25 percent of Rref throughout the data collection period.
12.3 Calculation of Spike Recovery. Calculate the percent recovery of each section 3 spike, as follows:
Where: %R = Percentage recovery of the pre-sampling spike M3 = Mass of Hg recovered from section 3 of the sorbent trap, (µg) Ms = Calculated Hg mass of the pre-sampling spike, from section 8.1.2 of this performance specification, (µg)12.4 Calculation of Breakthrough. Calculate the percent breakthrough to the second section of the sorbent trap, as follows:
Where: %B = Percent breakthrough M2 = Mass of Hg recovered from section 2 of the sorbent trap, (µg) M1 = Mass of Hg recovered from section 1 of the sorbent trap, (µg)12.5 Calculation of Hg Concentration. Calculate the Hg concentration for each sorbent trap, using the following equation:
Where: C = Concentration of Hg for the collection period, (µg/dscm) M* = Total mass of Hg recovered from sections 1 and 2 of the sorbent trap, (µg) Vt = Total volume of dry gas metered during the collection period, (dscm). For the purposes of this performance specification, standard temperature and pressure are defined as 20 °C and 760 mm Hg, respectively.12.6 Calculation of Paired Trap Agreement. Calculate the relative deviation (RD) between the Hg concentrations measured with the paired sorbent traps:
Where: RD = Relative deviation between the Hg concentrations from traps “a” and “b” (percent) Ca = Concentration of Hg for the collection period, for sorbent trap “a” (µg/dscm) Cb = Concentration of Hg for the collection period, for sorbent trap “b” (µg/dscm)12.7 Calculation of Relative Accuracy. Calculate the relative accuracy as described in section 12.4 of PS 12A in this appendix.
12.8 Data Reduction. Typical monitoring periods for normal, day-to-day operation of a sorbent trap monitoring system range from about 24 hours to 168 hours. For the required RA tests of the system, smaller sorbent traps are often used, and the “monitoring period” or time per run is considerably shorter (e.g., 1 hour or less). Generally speaking, to validate sorbent trap monitoring system data, the acceptance criteria for the following five QC specifications in Table 12B-1 above must be met for both traps: (a) the post-monitoring leak check; (b) the ratio of stack gas flow rate to sample flow rate; (c) section 2 breakthrough; (d) paired trap agreement; and (e) section 3 spike recovery.
12.8.1 For routine day-to-day operation of a sorbent trap monitoring system, when both traps meet the acceptance criteria for all five QC specifications, the two measured Hg concentrations must be averaged arithmetically and the average value must be applied to each hour of the data collection period.
12.8.2 To validate a RA test run, both traps must meet the acceptance criteria for all five QC specifications. However, as specified in section 12.8.3 below, for routine day-to-day operation of the monitoring system, a monitoring period may, in certain instances, be validated based on the results from one trap.
12.8.3 For the routine, day-to-day operation of the monitoring system, when one of the two sorbent trap samples or sampling systems either: (a) Fails the post-monitoring leak check; or (b) has excessive section 2 breakthrough; or (c) fails to maintain the proper stack flow-to-sample flow ratio; or (d) fails to achieve the required section 3 spike recovery; or (e) is lost, broken, or damaged, provided that the other trap meets the acceptance criteria for all four of these QC specifications, the Hg concentration measured by the valid trap may be multiplied by a factor of 1.111 and then used for reporting purposes. Further, if both traps meet the acceptance criteria for all four of these QC specifications, but the acceptance criterion for paired trap agreement is not met, the owner or operator may report the higher of the two Hg concentrations measured by the traps, in lieu of invalidating the data from the paired traps.
12.8.4 Whenever the data from a pair of sorbent traps must be invalidated and no quality-assured data from a certified backup Hg monitoring system or Hg reference method are available to cover the hours in the data collection period, treat those hours in the manner specified in the applicable regulation (i.e., use missing data substitution procedures or count the hours as monitoring system down time, as appropriate).
13.0 Monitoring System PerformanceThese monitoring criteria and procedures have been successfully applied to coal-fired utility boilers (including units with post-combustion emission controls), having vapor-phase Hg concentrations ranging from 0.03 µg/dscm to approximately 100 µg/dscm.
14.0 Pollution Prevention [Reserved] 15.0 Waste Management [Reserved] 16.0 Alternative Procedures [Reserved] 17.0 Bibliography17.1 40 CFR Part 60, Appendix B, “Performance Specification 2 - Specifications and Test Procedures for SO2 and NOX Continuous Emission Monitoring Systems in Stationary Sources.”
17.2 40 CFR Part 60, Appendix B, “Performance Specification 12A - Specifications and Test Procedures for Total Vapor Phase Mercury Continuous Emission Monitoring Systems in Stationary Sources.”
Performance Specification 15 - Performance Specification for Extractive FTIR Continuous Emissions Monitor Systems in Stationary Sources 1.0 Scope and Application1.1 Analytes. This performance specification is applicable for measuring all hazardous air pollutants (HAPs) which absorb in the infrared region and can be quantified using Fourier Transform Infrared Spectroscopy (FTIR), as long as the performance criteria of this performance specification are met. This specification is to be used for evaluating FTIR continuous emission monitoring systems for measuring HAPs regulated under Title III of the 1990 Clean Air Act Amendments. This specification also applies to the use of FTIR CEMs for measuring other volatile organic or inorganic species.
1.2 Applicability. A source which can demonstrate that the extractive FTIR system meets the criteria of this performance specification for each regulated pollutant may use the FTIR system to continuously monitor for the regulated pollutants.
2.0 Summary of Performance SpecificationFor compound-specific sampling requirements refer to FTIR sampling methods (e.g., reference 1). For data reduction procedures and requirements refer to the EPA FTIR Protocol (reference 2), hereafter referred to as the “FTIR Protocol.” This specification describes sampling and analytical procedures for quality assurance. The infrared spectrum of any absorbing compound provides a distinct signature. The infrared spectrum of a mixture contains the superimposed spectra of each mixture component. Thus, an FTIR CEM provides the capability to continuously measure multiple components in a sample using a single analyzer. The number of compounds that can be speciated in a single spectrum depends, in practice, on the specific compounds present and the test conditions.
3.0 DefinitionsFor a list of definitions related to FTIR spectroscopy refer to Appendix A of the FTIR Protocol. Unless otherwise specified, spectroscopic terms, symbols and equations in this performance specification are taken from the FTIR Protocol or from documents cited in the Protocol. Additional definitions are given below.
3.1 FTIR Continuous Emission Monitoring System (FTIR CEM).
3.1.1 FTIR System. Instrument to measure spectra in the mid-infrared spectral region (500 to 4000 cm−1). It contains an infrared source, interferometer, sample gas containment cell, infrared detector, and computer. The interferometer consists of a beam splitter that divides the beam into two paths, one path a fixed distance and the other a variable distance. The computer is equipped with software to run the interferometer and store the raw digitized signal from the detector (interferogram). The software performs the mathematical conversion (the Fourier transform) of the interferogram into a spectrum showing the frequency dependent sample absorbance. All spectral data can be stored on computer media.
3.1.2 Gas Cell. A gas containment cell that can be evacuated. It contains the sample as the infrared beam passes from the interferometer, through the sample, and to the detector. The gas cell may have multi-pass mirrors depending on the required detection limit(s) for the application.
3.1.3 Sampling System. Equipment used to extract sample from the test location and transport the gas to the FTIR analyzer. Sampling system components include probe, heated line, heated non-reactive pump, gas distribution manifold and valves, flow measurement devices and any sample conditioning systems.
3.2 Reference CEM. An FTIR CEM, with sampling system, that can be used for comparison measurements.
3.3 Infrared Band (also Absorbance Band or Band). Collection of lines arising from rotational transitions superimposed on a vibrational transition. An infrared absorbance band is analyzed to determine the analyte concentration.
3.4 Sample Analysis. Interpreting infrared band shapes, frequencies, and intensities to obtain sample component concentrations. This is usually performed by a software routine using a classical least squares (cls), partial least squares (pls), or K- or P- matrix method.
3.5 (Target) Analyte. A compound whose measurement is required, usually to some established limit of detection and analytical uncertainty.
3.6 Interferant. A compound in the sample matrix whose infrared spectrum overlaps at least part of an analyte spectrum complicating the analyte measurement. The interferant may not prevent the analyte measurement, but could increase the analytical uncertainty in the measured concentration. Reference spectra of interferants are used to distinguish the interferant bands from the analyte bands. An interferant for one analyte may not be an interferant for other analytes.
3.7 Reference Spectrum. Infrared spectra of an analyte, or interferant, prepared under controlled, documented, and reproducible laboratory conditions (see section 4.6 of the FTIR Protocol). A suitable library of reference spectra can be used to measure target analytes in gas samples.
3.8 Calibration Spectrum. Infrared spectrum of a compound suitable for characterizing the FTIR instrument configuration (Section 4.5 in the FTIR Protocol).
3.9 One hundred percent line. A double beam transmittance spectrum obtained by combining two successive background single beam spectra. Ideally, this line is equal to 100 percent transmittance (or zero absorbance) at every point in the spectrum. The zero absorbance line is used to measure the RMS noise of the system.
3.10 Background Deviation. Any deviation (from 100 percent) in the one hundred percent line (or from zero absorbance). Deviations greater than ±5 percent in any analytical region are unacceptable. Such deviations indicate a change in the instrument throughput relative to the single-beam background.
3.11 Batch Sampling. A gas cell is alternately filled and evacuated. A Spectrum of each filled cell (one discreet sample) is collected and saved.
3.12 Continuous Sampling. Sample is continuously flowing through a gas cell. Spectra of the flowing sample are collected at regular intervals.
3.13 Continuous Operation. In continuous operation an FTIR CEM system, without user intervention, samples flue gas, records spectra of samples, saves the spectra to a disk, analyzes the spectra for the target analytes, and prints concentrations of target analytes to a computer file. User intervention is permitted for initial set-up of sampling system, initial calibrations, and periodic maintenance.
3.14 Sampling Time. In batch sampling - the time required to fill the cell with flue gas. In continuous sampling - the time required to collect the infrared spectrum of the sample gas.
3.15 PPM-Meters. Sample concentration expressed as the concentration-path length product, ppm (molar) concentration multiplied by the path length of the FTIR gas cell. Expressing concentration in these units provides a way to directly compare measurements made using systems with different optical configurations. Another useful expression is (ppm-meters)/K, where K is the absolute temperature of the sample in the gas cell.
3.16 CEM Measurement Time Constant. The Time Constant (TC, minutes for one cell volume to flow through the cell) determines the minimum interval for complete removal of an analyte from the FTIR cell. It depends on the sampling rate (Rs in Lpm), the FTIR cell volume (Vcell in L) and the chemical and physical properties of an analyte.
For example, if the sample flow rate (through the FTIR cell) is 5 Lpm and the cell volume is 7 liters, then TC is equal to 1.4 minutes (0.71 cell volumes per minute). This performance specification defines 5 * TC as the minimum interval between independent samples.3.17 Independent Measurement. Two independent measurements are spectra of two independent samples. Two independent samples are separated by, at least 5 cell volumes. The interval between independent measurements depends on the cell volume and the sample flow rate (through the cell). There is no mixing of gas between two independent samples. Alternatively, estimate the analyte residence time empirically: (1) Fill cell to ambient pressure with a (known analyte concentration) gas standard, (2) measure the spectrum of the gas standard, (3) purge the cell with zero gas at the sampling rate and collect a spectrum every minute until the analyte standard is no longer detected spectroscopically. If the measured time corresponds to less than 5 cell volumes, use 5 * TC as the minimum interval between independent measurements. If the measured time is greater than 5 * TC, then use this time as the minimum interval between independent measurements.
3.18 Test Condition. A period of sampling where all process, and sampling conditions, and emissions remain constant and during which a single sampling technique and a single analytical program are used. One Run may include results for more than one test condition. Constant emissions means that the composition of the emissions remains approximately stable so that a single analytical program is suitable for analyzing all of the sample spectra. A greater than two-fold change in analyte or interferant concentrations or the appearance of additional compounds in the emissions, may constitute a new test condition and may require modification of the analytical program.
3.19 Run. A single Run consists of spectra (one spectrum each) of at least 10 independent samples over a minimum of one hour. The concentration results from the spectra can be averaged together to give a run average for each analyte measured in the test run.
4.0 InterferencesSeveral compounds, including water, carbon monoxide, and carbon dioxide, are known interferences in the infrared region in which the FTIR instrument operates. Follow the procedures in the FTIR protocol for subtracting or otherwise dealing with these and other interferences.
5.0 SafetyThe procedures required under this performance specification may involve hazardous materials, operations, and equipment. This performance specification may not address all of the safety problems associated with these procedures. It is the responsibility of the user to establish appropriate safety and health practices and determine the applicable regulatory limitations prior to performing these procedures. The CEMS users manual and materials recommended by this performance specification should be consulted for specific precautions to be taken.
6.0 Equipment and Supplies6.1 Installation of sampling equipment should follow requirements of FTIR test Methods such as references 1 and 3 and the EPA FTIR Protocol (reference 2). Select test points where the gas stream composition is representative of the process emissions. If comparing to a reference method, the probe tips for the FTIR CEM and the RM should be positioned close together using the same sample port if possible.
6.2 FTIR Specifications. The FTIR CEM must be equipped with reference spectra bracketing the range of path length-concentrations (absorbance intensities) to be measured for each analyte. The effective concentration range of the analyzer can be adjusted by changing the path length of the gas cell or by diluting the sample. The optical configuration of the FTIR system must be such that maximum absorbance of any target analyte is no greater than 1.0 and the minimum absorbance of any target analyte is at least 10 times the RMSD noise in the analytical region. For example, if the measured RMSD in an analytical region is equal to 10−3, then the peak analyte absorbance is required to be at least 0.01. Adequate measurement of all of the target analytes may require changing path lengths during a run, conducting separate runs for different analytes, diluting the sample, or using more than one gas cell.
6.3 Data Storage Requirements. The system must have sufficient capacity to store all data collected in one week of routine sampling. Data must be stored to a write-protected medium, such as write-once-read-many (WORM) optical storage medium or to a password protected remote storage location. A back-up copy of all data can be temporarily saved to the computer hard drive. The following items must be stored during testing.
• At least one sample interferogram per sampling Run or one interferogram per hour, whichever is greater. This assumes that no sampling or analytical conditions have changed during the run.
• All sample absorbance spectra (about 12 per hr, 288 per day).
• All background spectra and interferograms (variable, but about 5 per day).
• All CTS spectra and interferograms (at least 2 each 24 hour period).
• Documentation showing a record of resolution, path length, apodization, sampling time, sampling conditions, and test conditions for all sample, CTS, calibration, and background spectra.
Using a resolution of 0.5 cm−1, with analytical range of 3500 cm−1, assuming about 65 Kbytes per spectrum and 130 Kb per interferogram, the storage requirement is about 164 Mb for one week of continuous sampling. Lower spectral resolution requires less storage capacity. All of the above data must be stored for at least two weeks. After two weeks, storage requirements include: (1) all analytical results (calculated concentrations), (2) at least 1 sample spectrum with corresponding background and sample interferograms for each test condition, (3) CTS and calibration spectra with at least one interferogram for CTS and all interferograms for calibrations, (4) a record of analytical input used to produce results, and (5) all other documentation. These data must be stored according to the requirements of the applicable regulation.
7.0 Reagents and Standards [Reserved] 8.0 Sample Collection, Preservation, Storage, and Transport [Reserved] 9.0 Quality ControlThese procedures shall be used for periodic quarterly or semiannual QA/QC checks on the operation of the FTIR CEM. Some procedures test only the analytical program and are not intended as a test of the sampling system.
9.1 Audit Sample. This can serve as a check on both the sampling system and the analytical program.
9.1.1 Sample Requirements. The audit sample can be a mixture or a single component. It must contain target analyte(s) at approximately the expected flue gas concentration(s). If possible, each mixture component concentration should be NIST traceable (±2 percent accuracy). If a cylinder mixture standard(s) cannot be obtained, then, alternatively, a gas phase standard can be generated from a condensed phase analyte sample. Audit sample contents and concentrations are not revealed to the FTIR CEM operator until after successful completion of procedures in 5.3.2.
9.1.2 Test Procedure. Spike the audit sample using the analyte spike procedure in section 11. The audit sample is measured directly by the FTIR system (undiluted) and then spiked into the effluent at a known dilution ratio. Measure a series of spiked and unspiked samples using the same procedures as those used to analyze the stack gas. Analyze the results using sections 12.1 and 12.2. The measured concentration of each analyte must be within ±5 percent of the expected concentration (plus the uncertainty), i.e., the calculated correction factor must be within 0.93 and 1.07 for an audit with an analyte uncertainty of ±2 percent.
9.2 Audit Spectra. Audit spectra can be used to test the analytical program of the FTIR CEM, but provide no test of the sampling system.
9.2.1 Definition and Requirements. Audit spectra are absorbance spectra that; (1) have been well characterized, and (2) contain absorbance bands of target analyte(s) and potential interferants at intensities equivalent to what is expected in the source effluent. Audit spectra are provided by the administrator without identifying information. Methods of preparing Audit spectra include; (1) mathematically adding sample spectra or adding reference and interferant spectra, (2) obtaining sample spectra of mixtures prepared in the laboratory, or (3) they may be sample spectra collected previously at a similar source. In the last case it must be demonstrated that the analytical results are correct and reproducible. A record associated with each Audit spectrum documents its method of preparation. The documentation must be sufficient to enable an independent analyst to reproduce the Audit spectra.
9.2.2 Test Procedure. Audit spectra concentrations are measured using the FTIR CEM analytical program. Analytical results must be within ±5 percent of the certified audit concentration for each analyte (plus the uncertainty in the audit concentration). If the condition is not met, demonstrate how the audit spectra are unrepresentative of the sample spectra. If the audit spectra are representative, modify the FTIR CEM analytical program until the test requirement is met. Use the new analytical program in subsequent FTIR CEM analyses of effluent samples.
9.3 Submit Spectra For Independent Analysis. This procedure tests only the analytical program and not the FTIR CEM sampling system. The analyst can submit FTIR CEM spectra for independent analysis by EPA. Requirements for submission include; (1) three representative absorbance spectra (and stored interferograms) for each test period to be reviewed, (2) corresponding CTS spectra, (3) corresponding background spectra and interferograms, (4) spectra of associated spiked samples if applicable, and (5) analytical results for these sample spectra. The analyst will also submit documentation of process times and conditions, sampling conditions associated with each spectrum, file names and sampling times, method of analysis and reference spectra used, optical configuration of FTIR CEM including cell path length and temperature, spectral resolution and apodization used for every spectrum. Independent analysis can also be performed on site in conjunction with the FTIR CEM sampling and analysis. Sample spectra are stored on the independent analytical system as they are collected by the FTIR CEM system. The FTIR CEM and the independent analyses are then performed separately. The two analyses will agree to within ±120 percent for each analyte using the procedure in section 12.3. This assumes both analytical routines have properly accounted for differences in optical path length, resolution, and temperature between the sample spectra and the reference spectra.
10.0 Calibration and Standardization10.1 Calibration Transfer Standards. For CTS requirements see section 4.5 of the FTIR Protocol. A well characterized absorbance band in the CTS gas is used to measure the path length and line resolution of the instrument. The CTS measurements made at the beginning of every 24 hour period must agree to within ±5 percent after correction for differences in pressure.
Verify that the frequency response of the instrument and CTS absorbance intensity are correct by comparing to other CTS spectra or by referring to the literature.
10.2 Analyte Calibration. If EPA library reference spectra are not available, use calibration standards to prepare reference spectra according to section 6 of the FTIR Protocol. A suitable set of analyte reference data includes spectra of at least 2 independent samples at each of at least 2 different concentrations. The concentrations bracket a range that includes the expected analyte absorbance intensities. The linear fit of the reference analyte band areas must have a fractional calibration uncertainty (FCU in Appendix F of the FTIR Protocol) of no greater than 10 percent. For requirements of analyte standards refer to section 4.6 of the FTIR Protocol.
10.3 System Calibration. The calibration standard is introduced at a point on the sampling probe. The sampling system is purged with the calibration standard to verify that the absorbance measured in this way is equal to the absorbance in the analyte calibration. Note that the system calibration gives no indication of the ability of the sampling system to transport the target analyte(s) under the test conditions.
10.4 Analyte Spike. The target analyte(s) is spiked at the outlet of the sampling probe, upstream of the particulate filter, and combined with effluent at a ratio of about 1 part spike to 9 parts effluent. The measured absorbance of the spike is compared to the expected absorbance of the spike plus the analyte concentration already in the effluent. This measures sampling system bias, if any, as distinguished from analyzer bias. It is important that spiked sample pass through all of the sampling system components before analysis.
10.5 Signal-to-Noise Ratio (S/N). The measure of S/N in this performance specification is the root-mean-square (RMS) noise level as given in Appendix C of the FTIR Protocol. The RMS noise level of a contiguous segment of a spectrum is defined as the RMS difference (RMSD) between the n contiguous absorbance values (Ai) which form the segment and the mean value (AM) of that segment.
A decrease in the S/N may indicate a loss in optical throughput, or detector or interferometer malfunction.10.6 Background Deviation. The 100 percent baseline must be between 95 and 105 percent transmittance (absorbance of 0.02 to −0.02) in every analytical region. When background deviation exceeds this range, a new background spectrum must be collected using nitrogen or other zero gas.
10.7 Detector Linearity. Measure the background and CTS at three instrument aperture settings; one at the aperture setting to be used in the testing, and one each at settings one half and twice the test aperture setting. Compare the three CTS spectra. CTS band areas should agree to within the uncertainty of the cylinder standard. If test aperture is the maximum aperture, collect CTS spectrum at maximum aperture, then close the aperture to reduce the IR through-put by half. Collect a second background and CTS at the smaller aperture setting and compare the spectra as above. Instead of changing the aperture neutral density filters can be used to attenuate the infrared beam. Set up the FTIR system as it will be used in the test measurements. Collect a CTS spectrum. Use a neutral density filter to attenuate the infrared beam (either immediately after the source or the interferometer) to approximately 1/2 its original intensity. Collect a second CTS spectrum. Use another filter to attenuate the infrared beam to approximately 1/4 its original intensity. Collect a third background and CTS spectrum. Compare the CTS spectra as above. Another check on linearity is to observe the single beam background in frequency regions where the optical configuration is known to have a zero response. Verify that the detector response is “flat” and equal to zero in these regions. If detector response is not linear, decrease aperture, or attenuate the infrared beam. Repeat the linearity check until system passes the requirement.
11.0 Analytical Procedure11.1 Initial Certification. First, perform the evaluation procedures in section 6.0 of the FTIR Protocol. The performance of an FTIR CEM can be certified upon installation using EPA Method 301 type validation (40 CFR, Part 63, Appendix A), or by comparison to a reference Method if one exists for the target analyte(s). Details of each procedure are given below. Validation testing is used for initial certification upon installation of a new system. Subsequent performance checks can be performed with more limited analyte spiking. Performance of the analytical program is checked initially, and periodically as required by EPA, by analyzing audit spectra or audit gases.
11.1.1 Validation. Use EPA Method 301 type sampling (reference 4, section 5.3 of Method 301) to validate the FTIR CEM for measuring the target analytes. The analyte spike procedure is as follows: (1) a known concentration of analyte is mixed with a known concentration of a non-reactive tracer gas, (2) the undiluted spike gas is sent directly to the FTIR cell and a spectrum of this sample is collected, (3) pre-heat the spiked gas to at least the sample line temperature, (4) introduce spike gas at the back of the sample probe upstream of the particulate filter, (5) spiked effluent is carried through all sampling components downstream of the probe, (6) spike at a ratio of roughly 1 part spike to 9 parts flue gas (or more dilute), (7) the spike-to-flue gas ratio is estimated by comparing the spike flow to the total sample flow, and (8) the spike ratio is verified by comparing the tracer concentration in spiked flue gas to the tracer concentration in undiluted spike gas. The analyte flue gas concentration is unimportant as long as the spiked component can be measured and the sample matrix (including interferences) is similar to its composition under test conditions. Validation can be performed using a single FTIR CEM analyzing sample spectra collected sequentially. Since flue gas analyte (unspiked) concentrations can vary, it is recommended that two separate sampling lines (and pumps) are used; one line to carry unspiked flue gas and the other line to carry spiked flue gas. Even with two sampling lines the variation in unspiked concentration may be fast compared to the interval between consecutive measurements. Alternatively, two FTIR CEMs can be operated side-by-side, one measuring spiked sample, the other unspiked sample. In this arrangement spiked and unspiked measurements can be synchronized to minimize the affect of temporal variation in the unspiked analyte concentration. In either sampling arrangement, the interval between measured concentrations used in the statistical analysis should be, at least, 5 cell volumes (5 * TC in equation 1). A validation run consists of, at least, 24 independent analytical results, 12 spiked and 12 unspiked samples. See section 3.17 for definition of an “independent” analytical result. The results are analyzed using sections 12.1 and 12.2 to determine if the measurements passed the validation requirements. Several analytes can be spiked and measured in the same sampling run, but a separate statistical analysis is performed for each analyte. In lieu of 24 independent measurements, averaged results can be used in the statistical analysis. In this procedure, a series of consecutive spiked measurements are combined over a sampling period to give a single average result. The related unspiked measurements are averaged in the same way. The minimum 12 spiked and 12 unspiked result averages are obtained by averaging measurements over subsequent sampling periods of equal duration. The averaged results are grouped together and statistically analyzed using section 12.2.
11.1.1.1 Validation with a Single Analyzer and Sampling Line. If one sampling line is used, connect the sampling system components and purge the entire sampling system and cell with at least 10 cell volumes of sample gas. Begin sampling by collecting spectra of 2 independent unspiked samples. Introduce the spike gas into the back of the probe, upstream of the particulate filter. Allow 10 cell volumes of spiked flue gas to purge the cell and sampling system. Collect spectra of 2 independent spiked samples. Turn off the spike flow and allow 10 cell volumes of unspiked flue gas to purge the FTIR cell and sampling system. Repeat this procedure 6 times until the 24 samples are collected. Spiked and unspiked samples can also be measured in groups of 4 instead of in pairs. Analyze the results using sections 12.1 and 12.2. If the statistical analysis passes the validation criteria, then the validation is completed. If the results do not pass the validation, the cause may be that temporal variations in the analyte sample gas concentration are fast relative to the interval between measurements. The difficulty may be avoided by: (1) Averaging the measurements over long sampling periods and using the averaged results in the statistical analysis, (2) modifying the sampling system to reduce TC by, for example, using a smaller volume cell or increasing the sample flow rate, (3) using two sample lines (4) use two analyzers to perform synchronized measurements. This performance specification permits modifications in the sampling system to minimize TC if the other requirements of the validation sampling procedure are met.
11.1.1.2 Validation With a Single Analyzer and Two Sampling Lines. An alternative sampling procedure uses two separate sample lines, one carrying spiked flue gas, the other carrying unspiked gas. A valve in the gas distribution manifold allows the operator to choose either sample. A short heated line connects the FTIR cell to the 3-way valve in the manifold. Both sampling lines are continuously purged. Each sample line has a rotameter and a bypass vent line after the rotameter, immediately upstream of the valve, so that the spike and unspiked sample flows can each be continuously monitored. Begin sampling by collecting spectra of 2 independent unspiked samples. Turn the sampling valve to close off the unspiked gas flow and allow the spiked flue gas to enter the FTIR cell. Isolate and evacuate the cell and fill with the spiked sample to ambient pressure. (While the evacuated cell is filling, prevent air leaks into the cell by making sure that the spike sample rotameter always indicates that a portion of the flow is directed out the by-pass vent.) Open the cell outlet valve to allow spiked sample to continuously flow through the cell. Measure spectra of 2 independent spiked samples. Repeat this procedure until at least 24 samples are collected.
11.1.1.3 Synchronized Measurements With Two Analyzers. Use two FTIR analyzers, each with its own cell, to perform synchronized spiked and unspiked measurements. If possible, use a similar optical configuration for both systems. The optical configurations are compared by measuring the same CTS gas with both analyzers. Each FTIR system uses its own sampling system including a separate sampling probe and sampling line. A common gas distribution manifold can be used if the samples are never mixed. One sampling system and analyzer measures spiked effluent. The other sampling system and analyzer measures unspiked flue gas. The two systems are synchronized so that each measures spectra at approximately the same times. The sample flow rates are also synchronized so that both sampling rates are approximately the same (TC1 ∼ TC2 in equation 1). Start both systems at the same time. Collect spectra of at least 12 independent samples with each (spiked and unspiked) system to obtain the minimum 24 measurements. Analyze the analytical results using sections 12.1 and 12.2. Run averages can be used in the statistical analysis instead of individual measurements.
11.1.1.4 Compare to a Reference Method (RM). Obtain EPA approval that the method qualifies as an RM for the analyte(s) and the source to be tested. Follow the published procedures for the RM in preparing and setting up equipment and sampling system, performing measurements, and reporting results. Since FTIR CEMS have multicomponent capability, it is possible to perform more than one RM simultaneously, one for each target analyte. Conduct at least 9 runs where the FTIR CEM and the RM are sampling simultaneously. Each Run is at least 30 minutes long and consists of spectra of at least 5 independent FTIR CEM samples and the corresponding RM measurements. If more than 9 runs are conducted, the analyst may eliminate up to 3 runs from the analysis if at least 9 runs are used.
11.1.1.4.1 RMs Using Integrated Sampling. Perform the RM and FTIR CEM sampling simultaneously. The FTIR CEM can measure spectra as frequently as the analyst chooses (and should obtain measurements as frequently as possible) provided that the measurements include spectra of at least 5 independent measurements every 30 minutes. Concentration results from all of the FTIR CEM spectra within a run may be averaged for use in the statistical comparison even if all of the measurements are not independent. When averaging the FTIR CEM concentrations within a run, it is permitted to exclude some measurements from the average provided the minimum of 5 independent measurements every 30 minutes are included: The Run average of the FTIR CEM measurements depends on both the sample flow rate and the measurement frequency (MF). The run average of the RM using the integrated sampling method depends primarily on its sampling rate. If the target analyte concentration fluctuates significantly, the contribution to the run average of a large fluctuation depends on the sampling rate and measurement frequency, and on the duration and magnitude of the fluctuation. It is, therefore, important to carefully select the sampling rate for both the FTIR CEM and the RM and the measurement frequency for the FTIR CEM. The minimum of 9 run averages can be compared according to the relative accuracy test procedure in Performance Specification 2 for SO2 and NOX CEMs (40 CFR, Part 60, App. B).
11.1.1.4.2 RMs Using a Grab Sampling Technique. Synchronize the RM and FTIR CEM measurements as closely as possible. For a grab sampling RM, record the volume collected and the exact sampling period for each sample. Synchronize the FTIR CEM so that the FTIR measures a spectrum of a similar cell volume at the same time as the RM grab sample was collected. Measure at least five independent samples with both the FTIR CEM and the RM for each of the minimum nine runs. Compare the run concentration averages by using the relative accuracy analysis procedure in Performance Specification 2 of appendix B of 40 CFR part 60.
11.1.1.4.3 Continuous Emission Monitors as RMs. If the RM is a CEM, synchronize the sampling flow rates of the RM and the FTIR CEM. Each run is at least 1 hour long and consists of at least 10 FTIR CEM measurements and the corresponding 10 RM measurements (or averages). For the statistical comparison, use the relative accuracy analysis procedure in Performance Specification 2 of appendix B of 40 CFR part 60. If the RM time constant is < 1/2 the FTIR CEM time constant, brief fluctuations in analyte concentrations that are not adequately measured with the slower FTIR CEM time constant can be excluded from the run average along with the corresponding RM measurements. However, the FTIR CEM run average must still include at least 10 measurements over a 1-hour period.
12.0 Calculations and Data Analysis12.1 Spike Dilution Ratio, Expected Concentration. The Method 301 bias is calculated as follows.
Where: B = Bias at the spike level Sm = Mean of the observed spiked sample concentrations Mm = Mean of the observed unspiked sample concentrations CS = Expected value of the spiked concentration.The CS is determined by comparing the SF6 tracer concentration in undiluted spike gas to the SF6 tracer concentrations in the spiked samples;
The expected concentration (CS) is the measured concentration of the analyte in undiluted spike gas divided by the dilution factor Where: [anal]dir = The analyte concentration in undiluted spike gas measured directly by filling the FTIR cell with the spike gas. If the bias is statistically significant (Section 12.2), Method 301 requires that a correction factor, CF, be multiplied by the analytical results, and that 0.7 ≤CF ≤1.3.12.2 Statistical Analysis of Validation Measurements. Arrange the independent measurements (or measurement averages) as in Table 1. More than 12 pairs of measurements can be analyzed. The statistical analysis follows EPA Method 301, section 6.3. section 12.1 of this performance specification shows the calculations for the bias, expected spike concentration, and correction factor. This section shows the determination of the statistical significance of the bias. Determine the statistical significance of the bias at the 95 percent confidence level by calculating the t-value for the set of measurements. First, calculate the differences, di, for each pair of spiked and each pair of unspiked measurements. Then calculate the standard deviation of the spiked pairs of measurements.
Where: di = The differences between pairs of spiked measurements. SDs = The standard deviation in the di values. n = The number of spiked pairs, 2n = 12 for the minimum of 12 spiked and 12 unspiked measurements. Calculate the relative standard deviation, RSD, using SDs and the mean of the spiked concentrations, Sm. The RSD must be ≤50%. Repeat the calculations in equations 7 and 8 to determine SDu and RSD, respectively, for the unspiked samples. Calculate the standard deviation of the mean using SDs and SDu from equation 7. The t-statistic is calculated as follows to test the bias for statistical significance; where the bias, B, and the correction factor, CF, are given in section 12.1. For 11 degrees of freedom, and a one-tailed distribution, Method 301 requires that t ≤2.201. If the t-statistic indicates the bias is statistically significant, then analytical measurements must be multiplied by the correction factor. There is no limitation on the number of measurements, but there must be at least 12 independent spiked and 12 independent unspiked measurements. Refer to the t-distribution (Table 2) at the 95 percent confidence level and appropriate degrees of freedom for the critical t-value. 13.0 Method Performance [Reserved] 14.0 Pollution Prevention [Reserved] 15.0 Waste Management [Reserved] 16.0 References1. Method 318, 40 CFR, Part 63, Appendix A (Draft), “Measurement of Gaseous Formaldehyde, Phenol and Methanol Emissions by FTIR Spectroscopy,” EPA Contract No. 68D20163, Work Assignment 2-18, February, 1995.
2. “EPA Protocol for the Use of Extractive Fourier Transform Infrared (FTIR) Spectrometry in Analyses of Gaseous Emissions from Stationary Industrial Sources,” February, 1995.
3. “Measurement of Gaseous Organic and Inorganic Emissions by Extractive FTIR Spectroscopy,” EPA Contract No. 68-D2-0165, Work Assignment 3-08.
4. “Method 301 - Field Validation of Pollutant Measurement Methods from Various Waste Media,” 40 CFR 63, App A.
17.0 Tables, Diagrams, Flowcharts, and Validation DataTable 1 - Arrangement of Validation Measurements for Statistical Analysis
Measurement (or average) |
Time | Spiked (ppm) |
di spiked | Unspiked (ppm) |
di unspiked |
---|---|---|---|---|---|
1 | S1 | U1 | |||
2 | S2 | S2−S1 | U2 | U2−U1 | |
3 | S3 | U3 | |||
4 | S4 | S4−S3 | U4 | U4−U3 | |
5 | S5 | U5 | |||
6 | S6 | S6−S5 | U6 | U6−U5 | |
7 | S7 | U7 | |||
8 | S8 | S8−S7 | U8 | U8−U7 | |
9 | S9 | U9 | |||
10 | S10 | S10−S9 | U10 | U10−U9 | |
11 | S11 | U11 | |||
12 | S12 | S12−S11 | U12 | U12−U11 | |
Average −> | Sm | Mm |
Table 2 - t = Values
n−1 a | t−value | n−1 a | t−value | n−1 a | t−value | n−1 a | t−value |
---|---|---|---|---|---|---|---|
11 | 2.201 | 17 | 2.110 | 23 | 2.069 | 29 | 2.045 |
12 | 2.179 | 18 | 2.101 | 24 | 2.064 | 30 | 2.042 |
13 | 2.160 | 19 | 2.093 | 25 | 2.060 | 40 | 2.021 |
14 | 2.145 | 20 | 2.086 | 26 | 2.056 | 60 | 2.000 |
15 | 2.131 | 21 | 2.080 | 27 | 2.052 | 120 | 1.980 |
16 | 2.120 | 22 | 2.074 | 28 | 2.048 | 8 | 1.960 |
a n is the number of independent pairs of measurements (a pair consists of one spiked and its corresponding unspiked measurement). Either discreet (independent) measurements in a single run, or run averages can be used.
1.1 Does this performance specification apply to me? If you, the source owner or operator, intend to use (with any necessary approvals) a predictive emission monitoring system (PEMS) to show compliance with your emission limitation under 40 CFR 60, 61, or 63, you must use the procedures in this performance specification (PS) to determine whether your PEMS is acceptable for use in demonstrating compliance with applicable requirements. Use these procedures to certify your PEMS after initial installation and periodically thereafter to ensure the PEMS is operating properly. If your PEMS contains a diluent (O2 or CO2) measuring component and your emissions limitation is in units that require a diluent measurement (e.g. lbs/mm Btu), the diluent component must be tested as well. These specifications apply to PEMS that are installed under 40 CFR 60, 61, and 63 after the effective date of this performance specification. These specifications do not apply to parametric monitoring systems, these are covered under PS-17.
1.1.1 How do I certify my PEMS after it is installed? PEMS must pass a relative accuracy (RA) test and accompanying statistical tests in the initial certification test to be acceptable for use in demonstrating compliance with applicable requirements. Ongoing quality assurance tests also must be conducted to ensure the PEMS is operating properly. An ongoing sensor evaluation procedure must be in place before the PEMS certification is complete. The amount of testing and data validation that is required depends upon the regulatory needs, i.e., whether precise quantification of emissions will be needed or whether indication of exceedances of some regulatory threshold will suffice. Performance criteria are more rigorous for PEMS used in determining continual compliance with an emission limit than those used to measure excess emissions. You must perform the initial certification test on your PEMS before reporting any PEMS data as quality-assured.
1.1.2 Is other testing required after certification? After you initially certify your PEMS, you must pass additional periodic performance checks to ensure the long-term quality of data. These periodic checks are listed in the table in section 9. You are always responsible for properly maintaining and operating your PEMS.
2.0 Summary of Performance SpecificationThe following performance tests are required in addition to other equipment and measurement location requirements.
2.1 Initial PEMS Certification.
2.1.1 Excess Emissions PEMS. For a PEMS that is used for excess emission reporting, the owner or operator must perform a minimum 9-run, 3-level (3 runs at each level) RA test (see section 8.2).
2.1.2 Compliance PEMS. For a PEMS that is used for continual compliance standards, the owner or operator must perform a minimum 27-run, 3-level (9 runs at each level) RA test (see section 8.2). Additionally, the data must be evaluated for bias and by F-test and correlation analysis.
2.2 Periodic Quality Assurance (QA) Assessments. Owners and operators of all PEMS are required to conduct quarterly relative accuracy audits (RAA) and yearly relative accuracy test audits (RATA) to assess ongoing PEMS operation. The frequency of these periodic assessments may be shortened by successful operation during a prior year.
3.0 DefinitionsThe following definitions apply:
3.1 Centroidal Area means that area in the center of the stack (or duct) comprising no more than 1 percent of the stack cross-sectional area and having the same geometric shape as the stack.
3.2 Data Recorder means the equipment that provides a permanent record of the PEMS output. The data recorder may include automatic data reduction capabilities and may include electronic data records, paper records, or a combination of electronic data and paper records.
3.3 Defective sensor means a sensor that is responsible for PEMS malfunction or that operates outside the approved operating envelope. A defective sensor may be functioning properly, but because it is operating outside the approved operating envelope, the resulting predicted emission is not validated.
3.4 Diluent PEMS means the total equipment required to predict a diluent gas concentration or emission rate.
3.5 Operating envelope means the defined range of a parameter input that is established during PEMS development. Emission data generated from parameter inputs that are beyond the operating envelope are not considered quality assured and are therefore unacceptable.
3.6 PEMS means all of the equipment required to predict an emission concentration or emission rate. The system may consist of any of the following major subsystems: sensors and sensor interfaces, emission model, algorithm, or equation that uses process data to generate an output that is proportional to the emission concentration or emission rate, diluent emission model, data recorder, and sensor evaluation system. Systems that use fewer than 3 variables do not qualify as PEMS unless the system has been specifically approved by the Administrator for use as a PEMS. A PEMS may predict emissions data that are corrected for diluent if the relative accuracy and relevant QA tests are passed in the emission units corrected for diluent. Parametric monitoring systems that serve as indicators of compliance and have parametric limits but do not predict emissions to comply with an emissions limit are not included in this definition.
3.7 PEMS training means the process of developing or confirming the operation of the PEMS against a reference method under specified conditions.
3.8 Quarter means a quarter of a calendar year in which there are at least 168 unit operating hours.
3.9 Reconciled Process Data means substitute data that are generated by a sensor evaluation system to replace that of a failed sensor. Reconciled process data may not be used without approval from the Administrator.
3.10 Relative Accuracy means the accuracy of the PEMS when compared to a reference method (RM) at the source. The RA is the average difference between the pollutant PEMS and RM data for a specified number of comparison runs plus a 2.5 percent confidence coefficient, divided by the average of the RM tests. For a diluent PEMS, the RA may be expressed as a percentage of absolute difference between the PEMS and RM. Alternative specifications are given for units that have very low emissions.
3.11 Relative Accuracy Audit means a quarterly audit of the PEMS against a portable analyzer meeting the requirements of ASTM D6522-00 or a RM for a specified number of runs. A RM may be used in place of the portable analyzer for the RAA.
3.12 Relative Accuracy Test Audit means a RA test that is performed at least once every four calendar quarters after the initial certification test while the PEMS is operating at the normal operating level.
3.13 Reference Value means a PEMS baseline value that may be established by RM testing under conditions when all sensors are functioning properly. This reference value may then be used in the sensor evaluation system or in adjusting new sensors.
3.14 Sensor Evaluation System means the equipment or procedure used to periodically assess the quality of sensor input data. This system may be a sub-model that periodically cross-checks sensor inputs among themselves or any other procedure that checks sensor integrity at least daily (when operated for more than one hour in any calendar day).
3.15 Sensors and Sensor Interface means the equipment that measures the process input signals and transports them to the emission prediction system.
4.0 Interferences [Reserved] 5.0 Safety [Reserved] 6.0 Equipment and Supplies6.1 PEMS Design. You must detail the design of your PEMS and make this available in reports and for on-site inspection. You must also establish the following, as applicable:
6.1.1 Number of Input Parameters. An acceptable PEMS will normally use three or more input parameters. You must obtain the Administrator's permission on a case-by-case basis if you desire to use a PEMS having fewer than three input parameters.
6.1.2 Parameter Operating Envelopes. Before you evaluate your PEMS through the certification test, you must specify the input parameters your PEMS uses, define their range of minimum and maximum values (operating envelope), and demonstrate the integrity of the parameter operating envelope using graphs and data from the PEMS development process, vendor information, or engineering calculations, as appropriate. If you operate the PEMS beyond these envelopes at any time after the certification test, the data generated during this condition will not be acceptable for use in demonstrating compliance with applicable requirements. If these parameter operating envelopes are not clearly defined and supported by development data, the PEMS operation will be limited to the range of parameter inputs encountered during the certification test until the PEMS has a new operating envelope established.
6.1.3 Source-Specific Operating Conditions. Identify any source-specific operating conditions, such as fuel type, that affect the output of your PEMS. You may only use the PEMS under the source-specific operating conditions it was certified for.
6.1.4 Ambient Conditions. You must explain whether and how ambient conditions and seasonal changes affect your PEMS. Some parameters such as absolute ambient humidity cannot be manipulated during a test. The effect of ambient conditions such as humidity on the pollutant concentration must be determined and this effect extrapolated to include future anticipated conditions. Seasonal changes and their effects on the PEMS must be evaluated unless you can show that such effects are negligible.
6.1.5 PEMS Principle of Operation. If your PEMS is developed on the basis of known physical principles, you must identify the specific physical assumptions or mathematical manipulations that support its operation. If your PEMS is developed on the basis of linear or nonlinear regression analysis, you must make available the paired data (preferably in graphic form) used to develop or train the model.
6.1.6 Data Recorder Scale. If you are not using a digital recorder, you must choose a recorder scale that accurately captures the desired range of potential emissions. The lower limit of your data recorder's range must be no greater than 20 percent of the applicable emission standard (if subject to an emission standard). The upper limit of your data recorder's range must be determined using the following table. If you obtain approval first, you may use other lower and upper recorder limits.
If PEMS is measuring. . . | And if. . . | Then your upper limit. . . |
---|---|---|
Uncontrolled emissions, such as NOX at the stack of a natural gas-fired boiler | No other regulation sets an upper limit for the data recorder's range | Must be 1.25 to 2 times the average potential emission level |
Uncontrolled emissions, such as NOX at the stack of a natural gas-fired boiler | Another regulation sets an upper limit for the data recorder's range | Must follow the other regulation |
Controlled emissions | Must be 1.5 to 2.0 times concentration of the emission standard that applies to your emission unit | |
Continual compliance emissions for an applicable regulation | Must be 1.1 to 1.5 times the concentration of the emission standard that applies to your emission unit |
6.1.7 Sensor Location and Repair. We recommend you install sensors in an accessible location in order to perform repairs and replacements. Permanently-installed platforms or ladders may not be needed. If you install sensors in an area that is not accessible, you may be required to shut down the emissions unit to repair or replace a sensor. Conduct a new RATA after replacing a sensor that supplies a critical PEMS parameter if the new sensor provides a different output or scaling or changes the historical training dataset of the PEMS. Replacement of a non-critical sensor that does not cause an impact in the accuracy of the PEMS does not trigger a RATA. All sensors must be calibrated as often as needed but at least as often as recommended by the manufacturers.
6.1.8 Sensor Evaluation System. Your PEMS must be designed to perform automatic or manual determination of defective sensors on at least a daily basis. This sensor evaluation system may consist of a sensor validation sub-model, a comparison of redundant sensors, a spot check of sensor input readings at a reference value, operation, or emission level, or other procedure that detects faulty or failed sensors. Some sensor evaluation systems generate substitute values (reconciled data) that are used when a sensor is perceived to have failed. You must obtain prior approval before using reconciled data.
6.1.9 Parameter Envelope Exceedances. Your PEMS must include a plan to detect and notify the operator of parameter envelope exceedances. Emission data collected outside the ranges of the sensor envelopes will not be considered quality assured.
6.2 Recordkeeping. All valid data recorded by the PEMS must be used to calculate the emission value.
7.0 Reagents and Standards [Reserved] 8.0 Sample Collection, Preservation, Storage, and Transport8.1 Initial Certification. Use the following procedure to certify your PEMS. Complete all PEMS training before the certification begins.
8.2 Relative Accuracy Test.
8.2.1 Reference Methods. Unless otherwise specified in the applicable regulations, you must use the test methods in appendix A of this part for the RM test. Conduct the RM tests at three operating levels. The RM tests shall be performed at a low-load (or production) level between the minimum safe, stable load and 50 percent of the maximum level load, at the mid-load level (an intermediary level between the low and high levels), and at a high-load level between 80 percent and the maximum load. Alternatively, if practicable, you may test at three levels of the key operating parameter (e.g. selected based on a covariance analysis between each parameter and the PEMS output) equally spaced within the normal range of the parameter.
8.2.2 Number of RM Tests for Excess Emission PEMS. For PEMS used for excess emission reporting, conduct at least the following number of RM tests at the following key parameter operating levels:
(1) Three at a low level.
(2) Three at a mid level.
(3) Three at a high level.
You may choose to perform more than nine total RM tests. If you perform more than nine tests, you may reject a maximum of three tests as long as the total number of test results used to determine the RA is nine or greater and each operating level has at least three tests. You must report all data, including the rejected data.
8.2.3 Number of RM Tests for Continual Compliance PEMS. For PEMS used to determine compliance, conduct at least the following number of RM tests at the following key parameter operating levels:
(1) Nine at a low level.
(2) Nine at a mid level.
(3) Nine at a high level.
You may choose to perform more than 9 RM runs at each operating level. If you perform more than 9 runs, you may reject a maximum of three runs per level as long as the total number of runs used to determine the RA at each operating level is 9 or greater.
8.2.4 Reference Method Measurement Location. Select an accessible measurement point for the RM that will ensure you measure emissions representatively. Ensure the location is at least two equivalent stack diameters downstream and half an equivalent diameter upstream from the nearest flow disturbance such as the control device, point of pollutant generation, or other place where the pollutant concentration or emission rate can change. You may use a half diameter downstream instead of the two diameters if you meet both of the following conditions:
(1) Changes in the pollutant concentration are caused solely by diluent leakage, such as leaks from air heaters.
(2) You measure pollutants and diluents simultaneously at the same locations.
8.2.5 Traverse Points. Select traverse points that ensure representative samples. Conduct all RM tests within 3 cm of each selected traverse point but no closer than 3 cm to the stack or duct wall. The minimum requirement for traverse points are as follows:
(1) Establish a measurement line across the stack that passes through the center and in the direction of any expected stratification.
(2) Locate a minimum of three traverse points on the line at 16.7, 50.0, and 83.3 percent of the stack inside diameter.
(3) Alternatively, if the stack inside diameter is greater than 2.4 meters, you may locate the three traverse points on the line at 0.4, 1.2, and 2.0 meters from the stack or duct wall. You may not use this alternative option after wet scrubbers or at points where two streams with different pollutant concentrations are combined. You may select different traverse points if you demonstrate and provide verification that it provides a representative sample. You may also use the traverse point specifications given the RM.
8.2.6 Relative Accuracy Procedure. Perform the number of RA tests at the levels required in sections 8.2.2 and 8.2.3. For integrated samples (e.g., Method 3A or 7E), make a sample traverse of at least 21 minutes, sampling for 7 minutes at each traverse point. For grab samples (e.g., Method 3 or 7), take one sample at each traverse point, scheduling the grab samples so that they are taken simultaneously (within a 3-minute period) or at an equal interval of time apart over a 21-minute period. A test run for grab samples must be made up of at least three separate measurements. Where multiple fuels are used in the monitored unit and the fuel type affects the predicted emissions, determine a RA for each fuel unless the effects of the alternative fuel on predicted emissions or diluent were addressed in the model training process. The unit may only use fuels that have been evaluated this way.
8.2.7 Correlation of RM and PEMS Data. Mark the beginning and end of each RM test run (including the exact time of day) on the permanent record of PEMS output. Correlate the PEMS and the RM test data by the time and duration using the following steps:
A. Determine the integrated pollutant concentration for the PEMS for each corresponding RM test period.
B. Consider system response time, if important, and confirm that the pair of results is on a consistent moisture, temperature, and diluent concentration basis.
C. Compare each average PEMS value to the corresponding average RM value. Use the following guidelines to make these comparisons.
If . . . | Then . . . | And then . . . |
---|---|---|
The RM has an instrumental or integrated non-instrumental sampling technique | Directly compare RM and PEMS results | |
The RM has a grab sampling technique | Average the results from all grab samples taken during the test run. The test run must include ≥3 separate grab measurements | Compare this average RM result with the PEMS result obtained during the run. |
Use the paired PEMS and RM data and the equations in section 12.2 to calculate the RA in the units of the applicable emission standard. For this 3-level RA test, calculate the RA at each operation level.
8.3 Statistical Tests for PEMS that are Used for Continual Compliance. In addition to the RA determination, evaluate the paired RA and PEMS data using the following statistical tests.
8.3.1 Bias Test. From the RA data taken at the mid-level, determine if a bias exists between the RM and PEMS. Use the equations in section 12.3.1.
8.3.2 F-test. Perform a separate F-test for the RA paired data from each operating level to determine if the RM and PEMS variances differ by more than might be expected from chance. Use the equations in section 12.3.2.
8.3.3 Correlation Analysis. Perform a correlation analysis using the RA paired data from all operating levels combined to determine how well the RM and PEMS correlate. Use the equations in section 12.3.3. The correlation is waived if the process cannot be varied to produce a concentration change sufficient for a successful correlation test because of its technical design. In such cases, should a subsequent RATA identify a variation in the RM measured values by more than 30 percent, the waiver will not apply, and a correlation analysis test must be performed at the next RATA.
8.4 Reporting. Summarize in tabular form the results of the RA and statistical tests. Include all data sheets, calculations, and charts (records of PEMS responses) necessary to verify that your PEMS meets the performance specifications. Include in the report the documentation used to establish your PEMS parameter envelopes.
8.5 Reevaluating Your PEMS After a Failed Test, Change in Operations, or Change in Critical PEMS Parameter. After initial certification, if your PEMS fails to pass a quarterly RAA or yearly RATA, or if changes occur or are made that could result in a significant change in the emission rate (e.g., turbine aging, process modification, new process operating modes, or changes to emission controls), your PEMS must be recertified using the tests and procedures in section 8.1. For example, if you initially developed your PEMS for the emissions unit operating at 80-100 percent of its range, you would have performed the initial test under these conditions. Later, if you wanted to operate the emission unit at 50-100 percent of its range, you must conduct another RA test and statistical tests, as applicable, to verify that the new conditions of 50-100 percent of range are functional. These tests must demonstrate that your PEMS provides acceptable data when operating in the new range or with the new critical PEMS parameter(s). The requirements of section 8.1 must be completed by the earlier of 60 unit operating days or 180 calendar days after the failed RATA or after the change that caused a significant change in emission rate.
9.0 Quality ControlYou must incorporate a QA plan beyond the initial PEMS certification test to verify that your system is generating quality-assured data. The QA plan must include the components of this section.
9.1 QA/QC Summary. Conduct the applicable ongoing tests listed below.
Ongoing Quality Assurance Tests
Test | PEMS regulatory purpose |
Acceptability | Frequency |
---|---|---|---|
Sensor Evaluation | All | Daily. | |
RAA | Compliance | 3-test avg ≤10% of simultaneous analyzer or RM average | Each quarter except quarter when RATA performed. |
RATA | All | Same as for RA in Sec. 13.1 | Yearly in quarter when RAA not performed. |
Bias Correction | All | If davg ≤ |cc| | Bias test passed (no correction factor needed). |
PEMS Training | All | If Fcritical ≥F r ≥0.8 |
Optional after initial and subsequent RATAs. |
Sensor Evaluation Alert Test (optional) | All | See Section 6.1.8 | After each PEMS training. |
9.2 Daily Sensor Evaluation Check. Your sensor evaluation system must check the integrity of each PEMS input at least daily.
9.3 Quarterly Relative Accuracy Audits. In the first year of operation after the initial certification, perform a RAA consisting of at least three 30-minute portable analyzer or RM determinations each quarter a RATA is not performed. To conduct a RAA, follow the procedures in Section 8.2 for the relative accuracy test, except that only three sets of measurement data are required, and the statistical tests are not required. The average of the three or more portable analyzer or RM determinations must not exceed the limits given in Section 13.5. Report the data from all sets of measurement data. If a PEMS passes all quarterly RAAs in the first year and also passes the subsequent yearly RATA in the second year, you may elect to perform a single mid-year RAA in the second year in place of the quarterly RAAs. This option may be repeated, but only until the PEMS fails either a mid-year RAA or a yearly RATA. When such a failure occurs, you must resume quarterly RAAs in the quarter following the failure and continue conducting quarterly RAAs until the PEMS successfully passes both a year of quarterly RAAs and a subsequent RATA.
9.4 Yearly Relative Accuracy Test. Perform a minimum 9-run RATA at the normal operating level on a yearly basis in the quarter that the RAA is not performed. The statistical tests in Section 8.3 are not required for the yearly RATA.
10.0 Calibration and Standardization [Reserved] 11.0 Analytical Procedure [Reserved] 12.0 Calculations and Data Analysis 12.1 Nomenclature B = PEMS bias adjustment factor. cc = Confidence coefficient. di = Difference between each RM and PEMS run. d = Arithmetic mean of differences for all runs. ei = Individual measurement provided by the PEMS or RM at a particular level. em = Mean of the PEMS or RM measurements at a particular level. ep = Individual measurement provided by the PEMS. ev = Individual measurement provided by the RM. F = Calculated F-value. n = Number of RM runs. PEMSi = Individual measurement provided by the PEMS. PEMSiAdjusted = Individual measurement provided by the PEMS adjusted for bias. PEMS = Mean of the values provided by the PEMS at the normal operating range during the bias test. r = Coefficient of correlation. RA = Relative accuracy. RAA = Relative accuracy audit. RM = Average RM value (or in the case of the RAA, the average portable analyzer value). In cases where the average emissions for the test are less than 50 percent of the applicable standard, substitute the emission standard value here in place of the average RM value. Sd = Standard deviation of differences. S 2 = Variance of your PEMS or RM. t0.025 = t-value for a one-sided, 97.5 percent confidence interval (see Table 16-1).12.2 Relative Accuracy Calculations. Calculate the mean of the RM values. Calculate the differences between the pairs of observations for the RM and the PEMS output sets. Finally, calculate the mean of the differences, standard deviation, confidence coefficient, and PEMS RA, using Equations 16-1, 16-2, 16-3, and 16-4, respectively. For compliance PEMS, calculate the RA at each test level. The PEMS must pass the RA criterion at each test level.
12.2.1 Arithmetic Mean. Calculate the arithmetic mean of the differences between paired RM and PEMS observations using Equation 16-1.
12.2.2 Standard Deviation. Calculate the standard deviation of the differences using Equation 16-2 (positive square root).
12.2.3 Confidence Coefficient. Calculate the confidence coefficient using Equation 16-3 and Table 16-1 for n−1 degrees of freedom.
12.2.4 Relative Accuracy. Calculate the RA of your data using Equation 16-4.
12.3 Compliance PEMS Statistical Tests. If your PEMS will be used for continual compliance purposes, conduct the following tests using the information obtained during the RA tests. For the pollutant measurements at any one test level, if the mean value of the RM is less than either 10 ppm or 5 percent of the emission standard, all statistical tests are waived at that specific test level. For diluent measurements at any one test level, if the mean value of the RM is less than 3 percent of span, all statistical tests are waived for that specific test level.
12.3.1 Bias Test. Conduct a bias test to determine if your PEMS is biased relative to the RM. Determine the PEMS bias by comparing the confidence coefficient obtained from Equation 16-3 to the arithmetic mean of the differences determined in Equation 16-1. If the arithmetic mean of the differences (d ) is greater than the absolute value of the confidence coefficient (cc), your PEMS must incorporate a bias factor to adjust future PEMS values as in Equation 16-5.
Where:12.3.2 F-test. Conduct an F-test for each of the three RA data sets collected at different test levels. Calculate the variances of the PEMS and the RM using Equation 16-6.
Determine if the variance of the PEMS data is significantly different from that of the RM data at each level by calculating the F-value using Equation 16-7. Compare the calculated F-value with the critical value of F at the 95 percent confidence level with n-1 degrees of freedom. The critical value is obtained from Table 16-2 or a similar table for F-distribution. If the calculated F-value is greater than the critical value at any level, your proposed PEMS is unacceptable. For pollutant PEMS measurements, if the standard deviation of the RM is less than either 3 percent of the span or 5 ppm, use a RM standard deviation of either 5 ppm or 3 percent of span. For diluent PEMS measurements, if the standard deviation of the reference method is less than 3 percent of span, use a RM standard deviation of 3 percent of span.12.3.3 Correlation Analysis. Calculate the correlation coefficient either manually using Eq. 16-8, on a graph, or by computer using all of the paired data points from all operating levels. Your PEMS correlation must be 0.8 or greater to be acceptable. If during the initial certification test, your PEMS data are determined to be auto-correlated according to the procedures in 40 CFR 75.41(b)(2), or if the signal-to-noise ratio of the data is less than 4, then the correlation analysis is permanently waived.
12.4 Relative Accuracy Audit. Calculate the quarterly RAA using Equation 16-9.

13.1 PEMS Relative Accuracy. The RA must not exceed 10 percent if the PEMS measurements are greater than 100 ppm or 0.2 lbs/mm Btu. The RA must not exceed 20 percent if the PEMS measurements are between 100 ppm (or 0.2 lb/mm Btu) and 10 ppm (or 0.05 lb/mm Btu). For measurements below 10 ppm, the absolute mean difference between the PEMS measurements and the RM measurements must not exceed 2 pppm. For diluent PEMS, an alternative criterion of ±1 percent absolute difference between the PEMS and RM may be used if less stringent.
13.2 PEMS Bias. Your PEMS data is considered biased and must be adjusted if the arithmetic mean (d) is greater than the absolute value of the confidence coefficient (cc) in Equations 16.1 and 16.3. In such cases, a bias factor must be used to correct your PEMS data.
13.3 PEMS Variance. Your calculated F-value must not be greater than the critical F-value at the 95-percent confidence level for your PEMS to be acceptable.
13.4 PEMS Correlation. Your calculated r-value must be greater than or equal to 0.8 for your PEMS to be acceptable.
13.5 Relative Accuracy Audits. The average of the three portable analyzer or RM determinations must not differ from the simultaneous PEMS average value by more than 10 percent of the analyzer or RM for concentrations greater than 100 ppm or 20 percent for concentrations between 100 and 20 ppm, or the test is failed. For measurements at 20 ppm or less, this difference must not exceed 2 ppm for a pollutant PEMS and 1 percent absolute for a diluents PEMS.
14.0 Pollution Prevention [Reserved] 15.0 Waste Management [Reserved] 16.0 References [Reserved] 17.0 Tables, Diagrams, Flowcharts, and Validation DataTable 16-1 - t-Values for One-sided, 97.5 Percent Confidence Intervals for Selected Sample Sizes *
n−1 * | t-value | n−1 | t-value |
---|---|---|---|
1 | 12.706 | 15 | 2.131 |
2 | 4.303 | 16 | 2.120 |
3 | 3.182 | 17 | 2.110 |
4 | 2.776 | 18 | 2.101 |
5 | 2.571 | 19 | 2.093 |
6 | 2.447 | 20 | 2.086 |
7 | 2.365 | 21 | 2.080 |
8 | 2.306 | 22 | 2.074 |
9 | 2.262 | 23 | 2.069 |
10 | 2.228 | 24 | 2.064 |
11 | 2.201 | 25 | 2.060 |
12 | 2.179 | 26 | 2.056 |
13 | 2.160 | 27 | 2.052 |
14 | 2.145 | >28 | t-Table |
* The value n is the number of RM runs; n−1 equals the degrees of freedom.
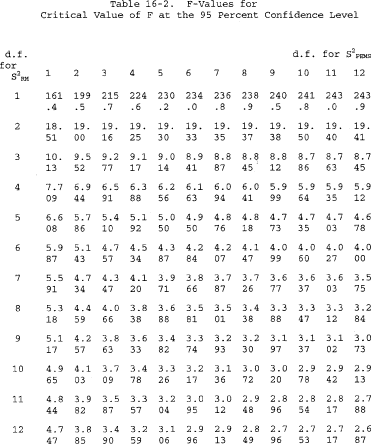
1.1 Analyte. This performance specification (PS) is applicable for measuring gaseous concentrations of hydrogen chloride (HCl), CAS: 7647-01-0, on a continuous basis in the units of the applicable standard or in units that can be converted to units of the applicable standard(s).
1.2 Applicability.
1.2.1 This specification is used to evaluate the acceptability of HCl continuous emission monitoring systems (CEMS) at the time of installation or soon after and whenever specified in the regulations. The specification includes requirements for initial acceptance including instrument accuracy and stability assessments and use of audit samples if they are available.
1.2.2 The Administrator may require the operator, under section 114 of the Clean Air Act, to conduct CEMS performance evaluations at other times besides the initial test to evaluate the CEMS performance. See 40 CFR part 60, §§ 60.13(c) and 63.8(e)(1).
1.2.3 A source that demonstrates their CEMS meets the criteria of this PS may use the system to continuously monitor gaseous HCl under any regulation or permit that requires compliance with this PS. If your CEMS is capable of reporting the HCl concentration in the units of the applicable standard, no additional CEMS components are necessary. If your CEMS does not report concentrations in the units of the existing standard, then other CEMS components (e.g., oxygen (O2), temperature, stack gas flow, moisture and pressure) may be necessary to convert the units reported by your CEMS to the units of the standard.
1.2.4 These specification test results are intended to be valid for the life of the system. As a result, the HCl measurement system must be tested and operated in a configuration consistent with the configuration that will be used for ongoing continuous emissions monitoring.
1.2.5 Substantive changes to the system configuration require retesting according to this PS. Examples of such conditions include, but are not limited to: major changes in dilution ratio (for dilution based systems); changes in sample conditioning and transport, if used, such as filtering device design or materials; changes in probe design or configuration and changes in materials of construction. Changes consistent with instrument manufacturer upgrade that fall under manufacturer's certification do not require additional field verification. Manufacturer's upgrades require recertification by the manufacturer for those requirements allowed by this PS, including interference, level of detection (LOD), and light intensity qualification.
1.2.6 This specification is not designed to evaluate the ongoing CEMS performance nor does it identify specific calibration techniques and auxiliary procedures to assess CEMS performance over an extended period of time. The requirements in appendix F, Procedure 6 are designed to provide a way to assess CEMS performance over an extended period of time. The source owner or operator is responsible to calibrate, maintain, and operate the CEMS properly.
2.0 Summary of Performance Specification2.1 This specification covers the procedures that each CEMS must meet during the performance evaluation test. Installation and measurement location specifications, data reduction procedures, and performance criteria are included.
2.2 The technology used to measure gaseous HCl must provide a distinct response and address any appropriate interference correction(s). It must accurately measure gaseous HCl in a representative sample (path or point sampling) of stack effluent.
2.3 The relative accuracy (RA) must be established against a reference method (RM) (e.g., Method 26A, Method 320, ASTM International (ASTM) D6348-12, including mandatory annexes, or Method 321 for Portland cement plants as specified by the applicable regulation or, if not specified, as appropriate for the source concentration and category). Method 26 may be approved as a RM by the Administrator on a case-by-case basis if not otherwise allowed or denied in an applicable regulation.
2.4 A standard addition (SA) procedure using a reference standard is included in appendix A to this performance specification for use in verifying LOD. For extractive CEMS, where the SA is done by dynamic spiking (DS), the appendix A procedure is allowed as an option for assessing calibration drift and is also referenced by Procedure 6 of appendix F to this part for ongoing quality control tests.
3.0 Definitions3.1 Beam attenuation is the reduction in electromagnetic radiation (light) throughput from the maximum beam intensity experienced during site specific CEMS operation.
3.2 Beam intensity is the electromagnetic radiation (light) throughput for an IP-CEMS instrument measured following manufacturers specifications.
3.3 Calibration cell means a gas containment cell used with cross stack or integrated path (IP) CEMS for calibration and to perform many of the test procedures required by this performance specification. The cell may be a removable sealed cell or an evacuated and/or purged cell capable of exchanging reference and other calibration gases as well as zero gas standards. When charged, it contains a known concentration of HCl and/or interference gases. The calibration cell is filled with zero gas or removed from the optical path during stack gas measurement.
3.4 Calibration drift (CD) means the absolute value of the difference between the CEMS output response and an upscale reference gas or a zero-level gas, expressed as a percentage of the span value, when the CEMS is challenged after a stated period of operation during which no unscheduled adjustments, maintenance or repairs took place.
3.5 Centroidal area means a central area that is geometrically similar to the stack or duct cross section and is no greater than 10 percent of the stack or duct cross-sectional area.
3.6 Continuous Emission Monitoring System (CEMS) means the total equipment required to measure the pollutant concentration or emission rate continuously. The system generally consists of the following three major subsystems:
3.6.1 Sample interface means that portion of the CEMS used for one or more of the following: Sample acquisition, sample transport, sample conditioning, defining the optical measurement path, and protection of the monitor from the effects of the stack effluent.
3.6.2 HCl analyzer means that portion of the HCl CEMS that measures the total vapor phase HCl concentration and generates a proportional output.
3.6.3 Data recorder means that portion of the CEMS that provides a permanent electronic record of the analyzer output. The data recorder may record other pertinent data such as effluent flow rates, various instrument temperatures or abnormal CEMS operation. The data recorder may also include automatic data reduction capabilities and CEMS control capabilities.
3.7 Diluent gas means a major gaseous constituent in a gaseous pollutant mixture. For combustion sources, either carbon dioxide (CO2) or oxygen (O2) or a combination of these two gases are the major gaseous diluents of interest.
3.8 Dynamic spiking (DS) means the procedure where a known concentration of HCl gas is injected into the probe sample gas stream for extractive CEMS at a known flow rate to assess the performance of the measurement system in the presence of potential interference from the flue gas sample matrix.
3.9 Independent measurement(s) means the series of CEMS data values taken during sample gas analysis separated by two times the procedure specific response time (RT) of the CEMS.
3.10 Integrated path CEMS (IP-CEMS) means an in-situ CEMS that measures the gas concentration along an optical path in the stack or duct cross section.
3.11 Interference means a compound or material in the sample matrix other than HCl whose characteristics may bias the CEMS measurement (positively or negatively). The interference may not prevent the sample measurement, but could increase the analytical uncertainty in the measured HCl concentration through reaction with HCl or by changing the electronic signal generated during HCl measurement.
3.12 Interference test means the test to detect CEMS responses to interferences that are not adequately accounted for in the calibration procedure and may cause measurement bias.
3.13 Level of detection (LOD) means the lowest level of pollutant that the CEMS can detect in the presence of the source gas matrix interferents with 99 percent confidence.
3.14 Liquid evaporative standard means a reference gas produced by vaporizing National Institute of Standards and Technology (NIST) traceable liquid standards of known HCl concentration and quantitatively diluting the resultant vapor with a carrier gas.
3.15 Measurement error (ME) is the mean difference between the concentration measured by the CEMS and the known concentration of a reference gas standard, divided by the span, when the entire CEMS, including the sampling interface, is challenged.
3.16 Optical path means the route light travels from the light source to the receiver used to make sample measurements.
3.17 Path length means, for an extractive optical CEMS, the distance in meters of the optical path within a gas measurement cell. For an IP-CEMS, path length means the distance in meters of the optical path that passes through the source gas in the stack or duct.
3.18 Point CEMS means a CEMS that measures the source gas concentration, either at a single point at the sampling probe tip or over a path length for IP-CEMS less than 10 percent of the equivalent diameter of the stack or duct cross section.
3.19 Stack pressure measurement device means a NIST-traceable gauge or monitor that measures absolute pressure and conforms to the design requirements of ASME B40.100-2010, “Pressure Gauges and Gauge Attachments” (incorporated by reference - see § 60.17).
3.20 Reference gas standard means a NIST-traceable gas standard containing a known concentration of HCl certified in accordance with an EPA traceability protocol in section 7.1 of this PS.
3.21 Relative accuracy (RA) means the absolute mean difference between the gas concentration or the emission rate determined by the CEMS and the value determined by the RM, plus the confidence coefficient of a series of nine test runs, divided by the average of the RM or the applicable emission standard.
3.22 Response time (RT) means the time it takes for the measurement system, while operating normally at its target sample flow rate, dilution ratio, or data collection rate to respond to a known step change in gas concentration, either from a low- or zero-level to a high-level gas concentration or from a high-level to a low or zero-level gas concentration, and to read 95 percent of the change to the stable instrument response. There may be several RTs for an instrument related to different functions or procedures (e.g., DS, LOD, and ME).
3.23 Span value means an HCl concentration approximately equal to two times the concentration equivalent to the emission standard unless otherwise specified in the applicable regulation, permit or other requirement. Unless otherwise specified, the span may be rounded up to the nearest multiple of 5.
3.24 Standard addition means the addition of known amounts of HCl gas (either statically or dynamically) to the actual measurement path or measured sample gas stream.
3.25 Zero gas means a gas or liquid with an HCl concentration that is below the LOD of the measurement system.
4.0 InterferencesSample gas interferences will vary depending on the instrument or technology used to make the measurement. Interferences must be evaluated through the interference test in this PS. Several compounds including carbon dioxide (CO2), carbon monoxide (CO), formaldehyde (CH2O), methane (CH4), and water (H2O) are potential optical interferences with certain types of HCl monitoring technology. Ammonia is a potential chemical interference with HCl.
5.0 SafetyThe procedures required under this PS may involve hazardous materials, operations, and equipment. This PS may not address all of the safety issues associated with these procedures. It is the responsibility of the user to establish appropriate safety and health practices and determine the applicable regulatory limitations prior to performing these procedures. The CEMS user's manual and materials recommended by the RM should be consulted for specific precautions to be taken.
6.0 Equipment and SuppliesEquipment and supplies for CEMS will vary depending on the measurement technology and equipment vendors. This section provides a description of the equipment and supplies typically found in one or more types of CEMS.
6.1 Sample Extraction System. The portion of an extractive CEMS that collects and transports the sample to the pressure regulation and sample conditioning module. The extraction system must deliver a representative sample to the measurement instrument. The sample extraction system typically consists of a sample probe and a heated umbilical line.
6.2 Sample Conditioning Module. The portion of an extractive CEMS that removes particulate matter and moisture from the gas stream and provides a sample gas stream to the CEMS analysis module or analyzer. You must keep the particle-free gas sample above the dew point temperature of its components.
6.3 HClAnalyzer. The portion of the CEMS that detects, quantifies and generates an output proportional to the sample gas HCl concentration.
6.4 System Controller. The portion of the CEMS that provides control of the analyzer and other sub-systems (e.g., sample extraction, sample conditioning, reference gas) as necessary for continuous operation and periodic maintenance/QC activities.
6.5 Data Recorder. The portion of the CEMS that provides a record of analyzer output. The data recorder may record other pertinent data such as effluent flow rates, various instrument temperatures or abnormal CEMS operation. The data recorder output range must include the full range of expected HCl concentration values in the gas stream to be sampled including zero and span value.
6.6 Reference Gas System(s). Gas handling system(s) needed to introduce reference and other gases into the measurement system. For extractive CEMS, the system must be able to introduce gas flow sufficient to flood the sampling probe and prevent entry of gas from the effluent stream. For IP-CEMS, the system must be able to introduce a known concentration of HCl, at known cell length, pressure and temperature, into the optical path used to measure HCl gas concentration.
6.7 Moisture Measurement System. If correction of the measured HCl emissions for moisture is required, you must install, operate, maintain, and quality assure a continuous moisture monitoring system for measuring and recording the moisture content of the flue gases. The following continuous moisture monitoring systems are acceptable: An FTIR system validated according to Method 301 or section 13.0 of Method 320 in appendix A to part 63 of this chapter; a continuous moisture sensor; an oxygen analyzer (or analyzers) capable of measuring O2 both on a wet basis and on a dry basis; a stack temperature sensor and a moisture look-up table, i.e., a psychrometric chart (for saturated gas streams following wet scrubbers or other demonstrably saturated gas streams, only); or other continuous moisture measurement methods approved by the Administrator. Alternatively, for any type of fuel, you may determine an appropriate site-specific default moisture value (or values), using measurements made with Method 4 - Determination of Moisture Content In Stack Gases, in appendix A-3 to of this part. If this option is selected, the site-specific moisture default value(s) must represent the fuel(s) or fuel blends that are combusted in the unit during normal, stable operation, and must account for any distinct difference(s) in the stack gas moisture content associated with different process operating conditions. At least nine Method 4 runs are required for determining each site-specific default moisture percentage. Calculate each site-specific default moisture value by taking the arithmetic average of the Method 4 runs. Each site-specific moisture default value shall be updated whenever the current value is non-representative, due to changes in unit or process operation, but in any event no less frequently than annually.
7.0 Reagents and Standards7.1 Reference Gases. Reference gases (e.g., cylinder gases or liquid evaporative standards) used to meet the requirements of this PS must be NIST certified or NIST-traceable and vendor certified to ±5.0 percent accuracy. HCl cylinder gases must be certified according to Reference 5 in section 16 of this PS through a documented unbroken chain of comparisons each contributing to the reported uncertainty. Liquid evaporative standards must be certified using the gravimetrically-based procedures of the latest version of the EPA Traceability Protocol for Qualification and Certification of Evaporative HCl Gas Standards and Humidification of HCl Gas Standards from Cylinders (see EPA-HQ-OAR-2013-0696-0026.pdf).
7.2 Cylinder gas and/or liquid evaporative standards must be used within their certification periods.
7.3 High concentration cylinder gas or liquid evaporative HCl standards may be diluted for use in this specification. You must document the quantitative introduction of HCl standards into the system using Method 205, found in 40 CFR part 51, appendix M, or other procedure approved by the Administrator.
8.0 CEMS Measurement Location Specifications and Pretest Preparation8.1 Prior to the start of your initial PS tests, you must ensure that the CEMS is installed according to the manufacturer's specifications and the requirements in this section. You may use either point or IP sampling technology.
8.2 CEMS Installation. Install the CEMS at an accessible location where the pollutant concentration or emission rate measurements are directly representative of the HCl emissions or can be corrected so as to be representative of the total emissions from the affected facility. The CEMS need not be installed at the same location as the relative accuracy test location. If you fail the RA requirements in this specification due to the CEMS measurement location and a satisfactory correction technique cannot be established, the Administrator may require the CEMS to be relocated.
8.2.1 Single point sample gas extraction should be (1) no less than 1.0 m (3.3 ft.) from the stack or duct wall or (2) within the centroidal area of the stack or duct cross section.
8.2.2 IP-CEMS measurements should (1) be conducted totally within the inner area bounded by a line 1.0 m (3.3 ft.) from the stack or duct wall, (2) have at least 70 percent of the path within the inner 50 percent of the stack or duct cross-sectional area, or (3) be located over any part of the centroidal area.
8.2.2.1 You must measure the IP-CEMS path length from the inner flange of the sampling ports or the inner end of the instrument insertion into the stack cavity using a laser tape measure, mechanical measurement tape, or similar device accurate to ±1.5 mm (0.059 in).
8.2.2.2 You must ensure that any purge flow used to protect IP-CEMS instrument windows from stack gas does not alter the measurement path length. Purge flow of less than or equal to 10 percent of the gas velocity in the duct meets this requirement.
8.2.3 CEMS and Data Recorder Scale Check. After CEMS installation, record and document the measurement range of the HCl CEMS. The CEMS operating range and the range of the data recording device must encompass all potential and expected HCl concentrations, including the concentration equivalent to the applicable emission limit and the span value.
9.0 Quality Control [Reserved] 10.0 Calibration and Standardization [Reserved] 11.0 Performance Specification Test ProcedureAfter completing the CEMS installation, setup and calibration, you must complete the PS test procedures in this section. You must perform the following procedures and meet the performance requirements for the initial demonstration of your CEMS:
a. Interference Test;
b. Beam Intensity Test (IP-CEMS only);
c. Temperature Verification Procedure (IP-CEMS only);
d. Pressure Verification Procedure (IP-CEMS only);
e. Level of Detection Determination;
f. Response Time Test;
g. Measurement Error Test;
h. Calibration Drift Test; and
i. Relative Accuracy Test.
11.1 Interference Test11.1.1 Prior to its initial use in the field, you must demonstrate that your monitoring system meets the performance requirements of the interference test in section 13.5 to verify that the candidate system measures HCl accurately in the presence of common interferences in emission matrices.
11.1.2 Your interference test must be conducted in a controlled environment. The equipment you test for interference must include the combination of the analyzer, related analysis software, and any sample conditioning equipment (e.g., dilution module, moisture removal equipment or other interferent scrubber) used to control interferents.
11.1.3 If you own multiple measurement systems with components of the same make and model numbers, you need only perform this interference test on one analyzer and associated interference conditioning equipment combination. You may also rely on an interference test conducted by the manufacturer or a continuous measurement system integrator on a system having components of the same make and model(s) of the system that you use.
11.1.4 Perform the interference check using an HCl reference gas concentration of approximately five times the LOD.
11.1.5 Introduce the interference test gases listed in Table 1 in section 17.0 of this PS to the analyzer/conditioning system separately or in any combination. The interference test gases need not be of reference gas quality.
11.1.5.1 For extractive CEMS, the interference test gases may be introduced directly into the inlet to the analyzer/conditioning system after the probe extension coupling.
11.1.5.2 For IP-CEMS, the interference test gases may be added with the HCl in a calibration cell or separately in a temperature-controlled cell. The effective concentration of the gas in the cell must meet the requirements in Table 1 corrected for absolute pressure, temperature and the nominal stack sampling path length of the CEMS.
11.1.6 The interference test must be performed by combining an HCl reference gas with each interference test gas (or gas mixture). You must measure the baseline HCl response, followed by the response after adding the interference test gas(es) while maintaining a constant HCl concentration. You must perform each interference gas injection and evaluation in triplicate.
Note:The baseline HCl gas may include interference gases at concentrations typical of ambient air (e.g., 21 percent O2, 400 parts per million (ppm) CO2, 2 percent H2O), but these concentrations must be brought to the concentrations listed in Table 1 when their interference effects are being evaluated.
11.1.7 You should document the gas volume/rate, temperature, and pressure used to conduct the interference test. A gas blending system or manifold may be used.
11.1.8 Ensure the duration of each interference test is sufficient to condition the HCl measurement system surfaces before a stable measurement is obtained.
11.1.9 Measure the HCl response of the analyzer/sample conditioning system combination to the test gases in ppmv. Record the responses and determine the overall interference response using Table 2 in section 17.0.
11.1.10 For each interference gas (or mixture), calculate the mean difference (ΔMCavg) between the measurement system responses with and without the interference test gas(es) using Equation 1 in section 12.2. Summarize the results following the format contained in Table 2 in section 17.
11.1.11 Calculate the percent interference (I) for the gas runs using Equation 2 in section 12.2.
11.1.12 The total interference response (i.e., the sum of the interference responses of all tested gaseous components) must not exceed the criteria set forth in section 13.5 of this PS.
11.2 Beam Intensity Test for IP-CEMS11.2.1 For IP-CEMS, you must establish the tolerance of your system to beam intensity attenuation.
11.2.1.1 Your beam intensity test may be conducted in either a controlled environment or on-site during initial setup and demonstration of your CEMS.
11.2.1.2 If you have multiple measurement systems with components of the same make and model numbers, you need only perform this attenuation check on one system and you may also rely on an attenuation test conducted by the manufacturer on a system having components of the same make and model(s) of the system that you use.
11.2.2 Insert one or more neutral density filter(s) or otherwise attenuate the beam intensity by a known percentage (e.g., 90 percent of the beam intensity).
11.2.3 Perform a high-level HCl reference gas measurement.
11.2.4 Record and report the attenuated beam intensity, the measured HCl calibration gas concentration at full beam intensity, the measured HCl gas concentration with attenuated beam intensity, and the percent difference between the two HCl measurements with and without attenuation of the beam intensity. The percent difference must not exceed the criteria set forth in section 13.6 of this PS.
11.2.5 In the future, you may not operate your IP-CEMS at a beam intensity lower than that established based on the attenuation used during this test. However, you may repeat the test to establish a lower beam intensity limit or level.
11.3 Temperature Measurement Verification Procedure for IP-CEMS11.3.1 Any measurement instrument or device that is used as a reference in verification of temperature measurement must have an accuracy that is traceable to NIST.
11.3.2 You must verify the temperature sensor used in IP-CEMS measurements on-site as part of the initial installation and verification procedures.
11.3.3 Comparison to Calibrated Temperature Measurement Device.
11.3.3.1 Place the sensor of a calibrated temperature reference device adjacent to the sensor used to measure stack temperature for your IP-CEMS. The calibrated temperature reference device must satisfy the accuracy requirements specified in Table 3 of this PS. The calibrated temperature reference device must also have a range equal to or greater than the range of your IP-CEMS temperature sensor.
11.3.3.2 Allow sufficient time for the response of the calibrated temperature reference device to reach equilibrium. With the process and control device operating under normal conditions, concurrently record the temperatures measured by your IP-CEMS system (Mt) and the calibrated temperature reference device (Vt). You must meet the accuracy requirements specified in section 13.7 of this PS.
11.3.3.3 If your IP-CEMS temperature sensor does not satisfy the accuracy requirement of this PS, check all system components and take any corrective action that is necessary to achieve the required minimum accuracy. Repeat this verification procedure until the accuracy requirement of this specification is satisfied.
11.4 Pressure Measurement Verification Procedure for IP-CEMS11.4.1 For stack pressure measurement verification, you must select a NIST-traceable gauge or monitor that conforms to the design requirements of ASME B40.100-2010, “Pressure Gauges and Gauge Attachments,” (incorporated by reference - see § 60.17) as a reference device.
11.4.2 As an alternative for a calibrated pressure reference device with NIST-traceable accuracy, you may use a water-in-glass U-tube manometer to verify your IP-CEMS pressure measurement equipment, provided there is also an accurate measurement of absolute atmospheric pressure at the manometer location.
11.4.3 Allow sufficient time for the response of the reference pressure measurement device to reach equilibrium. With the process and control device operating under normal conditions, concurrently record the pressures measured by your IP-CEMS system (MP) and the pressure reference device (Vp). You must meet the accuracy requirements specified in section 13.8 of this PS.
11.4.4 If your IP-CEMS pressure sensor does not satisfy the accuracy requirement of this PS, check all system components and take any corrective action that is necessary to achieve the required minimum accuracy. Repeat this verification procedure until the accuracy requirement of this specification is satisfied.
11.5 Level of Detection Determination11.5.1 You must determine the minimum amount of HCl that can be detected above the background in a representative gas matrix.
11.5.2 You must perform the LOD determination in a controlled environment such as a laboratory or manufacturer's facility.
11.5.3 You must add interference gases listed in Table 1 of this PS to a constant concentration of HCl reference gas.
11.5.3.1 You may not use an effective reference HCl gas concentration greater than five times the estimated instrument LOD.
11.5.3.2 For extractive CEMS, inject the HCl and interferents described in section 11.1.5 directly into the inlet to the analyzer.
11.5.3.3 For IP-CEMS, the HCl and interference test gases may be added to a calibration cell or separately in a temperature-controlled cell that is part of the measurement path. The effective concentration of the gas in the cell must meet the requirements in Table 1 corrected for absolute pressure, temperature and the nominal stack sampling path length of the CEMS.
11.5.4 Collect seven or more consecutive measurements separated by twice the RT (described in section 11.6) to determine the LOD.
11.5.5 Calculate the standard deviation of the measured values and define the LOD as three times the standard deviation of these measurements.
11.5.5.1 The LOD for extractive units must be determined and reported in ppmv.
11.5.5.2 The LOD for IP units must be determined and reported on a ppm-meter basis and the site- or installation-specific LOD must be calculated based on the actual measurement path length and gas density of the emissions at the specific site installation in ppmv.
11.5.6 You must verify the controlled environment LOD of section 11.5.2 of this PS for your CEMS during initial setup and field certification testing. You must use the SA procedure in appendix A of this PS with the following exceptions:
11.5.6.1 For the LOD verification in the field, you must make three independent SA measurements spiking the native source concentration by no more than three times the controlled environment LOD concentration determined in section 11.5.5.
11.5.6.2 For extractive CEMS, you must perform the SA as a dynamic spike by passing the spiked source gas sample through all filters, scrubbers, conditioners and other monitoring system components used during normal sampling, and as much of the sampling probe as practical. For IP-CEMS, you must perform the SA procedure by adding or passing a known concentration reference gas into a calibration cell in the optical path of the CEMS; you must also include the source measurement optical path while performing the SA measurement.
11.5.6.3 The amount detected, or standard addition response (SAR), is based on the average difference of the native HCl concentration in the stack or duct relative to the native stack concentration plus the SA. You must be able to detect the effective spike addition (ESA) above the native HCl present in the stack gas matrix. For extractive CEMS, the ESA is calculated using Equation A7 in appendix A of this PS. For IP-CEMS, the ESA is calculated as Ci,eff using Equation 4 of this PS.
11.5.6.4 For extractive CEMS, calculate the SAR using Equation A4 in appendix A of this PS. For IP-CEMS, calculate the SAR using Equation A8.
11.5.6.5 If your system LOD field verification does not demonstrate a SAR greater than or equal to your initial controlled environment LOD, you must increase the SA concentration incrementally and repeat the field verification procedure until the SAR is equal to or greater than LOD. The site-specific standard addition detection level (SADL) is equal to the standard addition needed to achieve the acceptable SAR, and SADL replaces the controlled environment LOD. For extractive CEMS, the SADL is calculated as the ESA using Equation A7 in appendix A of this PS. For IP-CEMS, the SADL is the SA calculated using Equation A8 in appendix A of this PS. As described in section 13.1 of this PS, the LOD or the SADL that replaces an LOD must be less than 20 percent of the applicable emission limit.
11.6 Response Time Determination. You must determine ME-, LOD- and SA-RT11.6.1 For ME- or LOD-RT, start the upscale RT determination by injecting zero gas into the measurement system as required by the procedures in section 11.7 or 11.5, respectively. You may use humidified zero gas. For standard addition RT, start the upscale RT determination by measuring the native stack gas concentration of HCl.
11.6.1.1 For extractive CEMS measuring ME- or LOD-RT, the output has stabilized when there is no change greater than 1.0 percent of full scale for 30 seconds.
11.6.1.2 For standard addition RT that includes the stack gas matrix the final stable response may continue to vary by more than 1 percent, but may be considered stable if the variability is random and not continuously rising or falling.
11.6.2 When the CEMS output has stabilized, record the response in ppmv and introduce an upscale (high level) or spike reference gas as required by the relevant procedure.
11.6.3 Record the time (upscale RT) required to reach 95 percent of the change to the final stable value.
11.6.4 Next, for ME or LOD RT, reintroduce the zero gas and record the time required to reach 95 percent of the change to the stable instrument response at the zero gas reading. For SA RT, introduce zero gas to the IP-CEMS cell or stop the spike gas flow to the extractive CEMS as required by the specified procedure and record the time required to reach 95 percent of the change to the stable instrument response of the native gas reading. This time is the downscale RT.
(Note: For CEMS that perform a series of operations (purge, blow back, sample integration, analyze, etc.), you must start adding reference or zero gas immediately after these procedures are complete.)
11.6.5 Repeat the entire procedure until you have three sets of data, then determine the mean upscale and mean downscale RTs for each relevant procedure. Report the greater of the average upscale or average downscale RTs as the RT for the system.
11.7 Measurement Error (ME) Test11.7.1 On the same day and as close in time as practicable to when the ME test is conducted, perform and meet requirements for a calibration drift (CD) test using a zero gas as used in the Seven-Day Drift Test (see section 11.8) and document and report the results. To meet this requirement, the ME test may be conducted during the Seven-Day CD Test.
11.7.2 Extractive CEMS ME Test.
11.7.2.1 Introduce reference gases to the CEMS probe, prior to the sample conditioning and filtration system.
11.7.2.2 Measure three upscale HCl reference gas concentrations in the range shown in Table 4 of this PS.
11.7.2.3 Introduce the gases into the sampling probe with sufficient flow rate to replace the entire source gas sample.
11.7.2.4 Continue to add the reference gas until the response is stable as evidenced when the difference between two consecutive measurements is less than the LOD or within five percent of each other.
11.7.2.5 Make triplicate measurements for each reference gas for a total of nine measurements. Introduce different reference gas concentrations in any order but do not introduce the same gas concentration twice in succession.
11.7.2.6 At each reference gas concentration, determine the average of the three CEMS responses (MCl). Calculate the ME using Equation 3A in section 12.3.
11.7.2.7 If you desire to determine the system RT during this test, you must inject zero gas immediately before and after each injection of the high-level gas standard.
11.7.2.8 For non-dilution systems, you may adjust the system to maintain the correct flow rate at the analyzer during the test, but you may not make adjustments for any other purpose. For dilution systems, you must operate the measurement system at the appropriate dilution ratio during all system ME checks, and you may make only the adjustments necessary to maintain the proper ratio.
11.7.3 IP-CEMS ME Test.
11.7.3.1 Conduct a 3-level system ME test by individually adding the known concentrations of HCl reference gases into a calibration cell of known volume, temperature, pressure and path length.
Note: The optical path used for IP-CEMS ME checks must include the native HCl measurement path. You must also collect native stack concentration HCl measurements before and after each HCl standard measurement. Bracketing HCl reference gas measurements with native stack HCl measurements must be used in the calculations in Equation 5 in section 12.4.2 to correct the upscale measurements for stack gas HCl concentration changes.
11.7.3.2 Introduce HCl reference gas into your calibration cell in a range of concentrations that produce responses equivalent to the source concentrations shown in Table 4 of this PS for your path length.
11.7.3.3 Make triplicate measurements for each reference gas standard for a total of nine measurements. Introduce different calibration concentrations in any order but do not introduce the same reference gas concentration twice in succession.
11.7.3.4 You must calculate the effective concentration (Ci,eff) of the HCl reference gas equivalent to the stack concentration by correcting for calibration cell temperature, pressure, path length, line strength factor (LSF) and, if necessary, the native stack gas HCl concentration using Equation 4 in section 12.0.
11.7.3.5 You may use the LSF provided by your instrument manufacturer or determine an instrument-specific LSF as a function of temperature using a heated gas cell and equivalent concentrations (Ci,eff) between 50 and 150 percent of the emission limit.
11.7.3.6 At each reference gas concentration, average the three independent CEMS measurement responses corrected for native HCl stack concentration. Calculate the ME using Equation 6A in section 12.4.3.
11.7.4 You may use Figure 1 in section 17.0 to record and report your ME test results.
11.7.5 If the ME specification in section 13.3 is not met for all three reference gas concentrations, take corrective action and repeat the test until an acceptable 3-level ME test is achieved.
11.8 Seven-Day Calibration Drift (CD) Test11.8.1 The CD Test Period. Prior to the start of the RA tests, you must perform a seven-day CD test. The purpose of the seven-day CD test is to verify the ability of the CEMS to maintain calibration for each of seven consecutive unit operating days as specified in section 11.8.5 of this PS.
11.8.2 The CD tests must be performed using the zero gas and mid-level reference gas standards as defined in Table 4 of this PS.
11.8.3 Conduct the CD test on each day during continuous operation of the CEMS and normal facility operations following the procedures in section 11.7 of this PS, except that the zero gas and mid-level gas need only be introduced to the measurement system once each.
11.8.4 If periodic automatic or manual adjustments are made to the CEMS zero and upscale response factor settings, conduct the CD test immediately before these adjustments.
Note:Automatic signal or mathematical processing of all measurement data to determine emission results may be performed throughout the entire CD process.
11.8.5 Determine the magnitude of the CD at approximately 24-hour intervals, for 7 consecutive unit operating days. The 7 consecutive unit operating days need not be 7 consecutive calendar days.
11.8.6 Record the CEMS response for single measurements of zero gas and mid-level reference gas. You may use Figure 2 in section 17 of this PS to record and report the results of your 7-day CD test.
11.8.6.1 For extractive CEMS, calculate the CD using Equation 3B in section 12.3. Report the absolute value of the differences as a percentage of the span value.
11.8.6.2 For IP-CEMS, you must include the source measurement optical path while performing the upscale CD measurement; you may exclude the source measurement optical path when determining the zero gas concentration. Calculate the CD for IP CEMS using equations 4, 5, 6B, and 7 in section 12.4.
11.8.7 The zero-level and mid-level CD for each day must be less than 5.0 percent of the span value as specified in section 13.2 of this PS. You must meet this criterion for 7 consecutive operating days.
11.8.8 Dynamic Spiking Option for Seven-Day CD Test. For extractive CEMS, you have the option to conduct a mid-level dynamic spiking procedure for each of the 7 days in lieu of the mid-level reference gas injection described in sections 11.8.2 and 11.8.3. If this option is selected, the daily zero CD check is still required.
11.8.8.1 To conduct each of the seven daily mid-level dynamic spikes, you must use the DS procedure described in appendix A of this PS using a single spike of the mid-level reference gas (see Table 4).
11.8.8.2 You must perform the dynamic spike procedure by passing the spiked source gas sample through all filters, scrubbers, conditioners and other monitoring system components used during normal sampling, and as much of the sampling probe as practical.
11.8.8.3 Calculate the mid-level CD as a percent of span using Equation A6 of appendix A to this PS and calculate the zero drift using Equation 3B in section 12.3. Record and report the results as described in sections 11.8.6 and 11.8.7.
11.9 Relative Accuracy Test11.9.1 Unless otherwise specified in an applicable regulation, use Method 26A in 40 CFR part 60, appendix A-8, Method 320 in 40 CFR part 63, appendix A, or ASTM D6348-12 including all annexes, as applicable, as the RMs for HCl measurement. Obtain and analyze RM audit samples, if they are available, concurrently with RM test samples according to the same procedure specified for performance tests in the general provisions of the applicable part. If Method 26 is not specified in an applicable subpart of the regulations, you may request approval to use Method 26 in appendix A-8 to this part as the RM on a site-specific basis under §§ 63.7(f) or 60.8(b). Other RMs for moisture, O2, etc., may be necessary. Conduct the RM tests in such a way that they will yield results representative of the emissions from the source and can be compared to the CEMS data.
11.9.1.1 When Method 26A is used as the RM, you must sample sufficient gas to reach three times your method detection limit for Method 26A in 40 CFR part 60, appendix A-8, or for a minimum of one hour, whichever is greater.
11.9.1.2 When Method 320 or Method 321, both found in 40 CFR part 63, appendix A, or ASTM D6348-12, are used as the RM, you must collect gas samples that are at stack conditions (hot and wet) and you must traverse as required in section 11.9.3.
11.9.2 Conduct the diluent (if applicable), moisture (if needed), and pollutant measurements simultaneously. However, diluent and moisture measurements that are taken within an hour of the pollutant measurements may be used to calculate dry pollutant concentration and emission rates.
11.9.3 Reference Method Measurement Location and Traverse Point(s) Selection.
11.9.3.1 Measurement Location. Select, as appropriate, an accessible RM measurement location at least two equivalent diameters downstream from the nearest control device, point of pollutant generation, or other point at which a change in the pollutant concentration or emission rate may occur, and at least one half equivalent diameter upstream from the effluent exhaust or a control device. When pollutant concentration changes are due solely to diluent leakage (e.g., air heater leakages) and pollutants and diluents are simultaneously measured at the same location, a half diameter may be used in lieu of two equivalent diameters. The equivalent duct diameter is calculated according to Method 1 in appendix A-1 to this part. The CEMS and RM sampling locations need not be the same.
11.9.3.2 Traverse Point Selection. Select traverse points that assure acquisition of representative RM samples over the stack or duct cross section according to one of the following options: (a) sample at twelve traverse points located according to section 11.3 of Method 1 in appendix A-1 to this part, (b) sample at 6 Method 1 traverse points according to section 6.5.6(b)(1) of appendix A to part 75 of this chapter, or (c) sample at three points on a measurement line (“3-point long line”) that passes through the centroidal area of the duct in the direction of any potential stratification. If this line interferes with the CEMS measurements, you may displace the line up to 20 cm (12 in.) or 5.0 percent of the equivalent diameter of the cross section, whichever is less, from the centroidal area. Locate the three traverse points at 16.7, 50.0, and 83.3 percent of the measurement line. Alternatively, you may conduct a stratification test following the procedures in sections 11.9.3.2.1 through 11.9.3.2.4 to justify sampling at a single point or three points located on the measurement line at 0.4, 1.2, and 2.0 m from the stack wall (“3-point short line”). Stratification testing must be conducted at the sampling location to be used for the RM measurements during the RA test and must be made during normal facility operating conditions. You must evaluate the stratification by measuring the gas on the same moisture basis as the HCl CEMS (wet or dry). Stratification testing must be repeated for each RA test program to justify single point or “3-point short line” sampling.
11.9.3.2.1 Use a probe of appropriate length to measure the HCl concentration or an alternative analyte, as described in this section, using 12 traverse points located according to section 11.3 of Method 1 in appendix A-1 to 40 CFR part 60 for a circular stack or nine points at the centroids of similarly-shaped, equal area divisions of the cross section of a rectangular stack.
11.9.3.2.2 You may substitute a stratification test for SO2 for the HCl stratification test. If you select this option, you must follow the test procedures in Method 6C of appendix A-4 to 40 CFR part 60 or Method 320 of appendix A of 40 CFR part 63.
11.9.3.2.3 Calculate the mean measured concentration for all sampling points (MNavg).
11.9.3.2.4 Calculate the percent stratification (St) of each traverse point using Equation 8 in section 12.5.
11.9.3.2.5 The gas stream is considered to be unstratified and you may perform the RA testing at a single point that most closely matches the mean if the concentration at each traverse point differs from the mean concentration for all traverse points by: (a) No more than 5.0 percent of the mean concentration; or (b) 0.2 ppm (for HCl) or 3 ppm (for SO2) absolute, whichever is less restrictive.
11.9.3.2.6 If the criterion for single point sampling (5.0 percent, 0.2 ppm for HCl or 3 ppm for SO2 are not met, but the concentration at each traverse point differs from the mean concentration for all traverse points by no more than 10.0 percent of the mean, the gas stream is considered to be minimally stratified, and you may take RA samples using the “3-point short line”. Alternatively, you may use the 3-point short line if each traverse point differs from the mean value by no more than 0.4 ppm (for HCl) or 5 ppm (for SO2).
11.9.3.2.7 If the concentration at any traverse point differs from the mean concentration by more than 10 percent, the gas stream is considered stratified and you must sample using one of the options in section 11.9.3.2 above.
11.9.3.3 Conduct all necessary RM tests within 3 cm (1.2 in.) of the traverse points, but no closer than 3 cm (1.2 in.) to the stack or duct wall.
11.9.4 In order to correlate the CEMS and RM data properly, record the beginning and end of each RM run (including the time of day in hours, minutes, and seconds) using a clock synchronized with the CEM clock used to create a permanent time record with the CEMS output.
11.9.5 You must conduct the RATA during representative process and control operating conditions or as specified in an applicable regulation, permit or subpart.
11.9.6 Conduct a minimum of nine RM test runs. NOTE: More than nine RM test runs may be performed. If this option is chosen, up to three test run results may be excluded so long as the total number of test run results used to determine the CEMS RA is greater than or equal to nine. However, all data must be reported including the excluded test runs.
11.9.7 Analyze the results from the RM test runs using Equations 9-14 in section 12.6. Calculate the RA between the CEMS results and the RM.
11.10 Record Keeping and Reporting11.10.1 For systems that use a liquid evaporative standard generator to deliver HCl reference gas standards, record supporting data for these devices, including liquid feed calibrations, liquid standard concentration(s) and NIST-traceability, feed rate and gas flow calibrations for all diluent and HCl gas flows. All calibrations must include a stated uncertainty, and the combined uncertainty of the delivered HCl reference gas concentration must be calculated and reported.
11.10.2 Record the results of the CD test, the RT test, the ME test, the RA test, and for IP-CEMS, the results of the beam intensity, temperature and pressure verification procedures. Also keep records of the RM and CEMS field data, calculations, and reference gas certifications necessary to confirm that the performance of the CEMS met the performance specifications.
11.10.3 For systems that use Method 205 to prepare HCl reference gas standards, record results of Method 205 performance test field evaluation, reference gas certifications, and gas dilution system calibration.
11.10.4 Record the LOD for the CEMS. For extractive CEMS, record the LOD in ppmv. For IP-CEMS, record the LOD on a ppm-meter basis along with a calculation of the installation specific LOD in ppmv. For both CEMS types, you must also record the field verified SADL.
11.10.5 Record the results of the interference test.
11.10.6 Report the results of all certification tests to the appropriate regulatory agency (or agencies), in hardcopy and/or electronic format, as required by the applicable regulation or permit.
12.0 Calculations and Data Analysis 12.1 Nomenclature Ci = Zero or HCl reference gas concentration used for test i (ppmv); Ci,eff = Equivalent concentration of the reference gas value, Ci, at the specified conditions (ppmv); CC = Confidence coefficient (ppmv); CDextractive = Calibration drift for extractive CEMS (percent); CDIP = Calibration drift for IP-CEMS (percent); CD0 = Calibration drift at zero HCl concentrations for an IP-CEMS (percent); davg = Mean difference between CEMS response and the reference gas (ppmv); di = Difference of CEMS response and the RM value (ppmv); I = Total interference from major matrix stack gases, (percent); LSF = Line strength factor for IP-CEMS instrument specific correction for temperature and gas matrix effects derived from the HITRAN and/or manufacturer specific database (unitless); ΔMCavg = Average of the 3 absolute values of the difference between the measured HCl calibration gas concentrations with and without interference from selected stack gases (ppmv); MCi = Measured HCl reference gas concentration i (ppmv); MCi = Average of the measured HCl reference gas concentration i (ppmv); MCint = Measured HCl concentration of the HCl reference gas plus the individual or combined interference gases (ppmv); MEextractive = Measurement error for extractive CEMS (percent); MEIP = Measurement error for IP-CEMS (percent); MNavg = Average concentration at all sampling points (ppmv); MNbi = Measured native concentration bracketing each calibration check measurement (ppmv); MNi = Measured native concentration for test or run I (ppmv); n = Number of measurements in an average value; Pstack = Absolute stack pressure (mm Hg) Preference = Absolute pressure of the calibration cell for IP-CEMS (mm Hg) PLCell = Path length of IP-CEMS calibration cell (m); PLStack = Path length of IP-CEMS stack optical path (m); RA = Relative accuracy of CEMS compared to a RM (percent); RMi = RM concentration for test run i (ppmv); RMavg = Mean measured RM value (ppmv); S = Span value (ppmv); Sd = Standard deviation of the differences (ppmv); Sti = Stratification at traverse point i (percent); SADL = Standard addition detection level (ppmv); t0.975 = One-sided t-value at the 97.5th percentile obtained from Table 5 in section 17.0 for n-1 measurements; Treference = Temperature of the calibration cell for IP-CEMS (degrees Kelvin); Tstack = Temperature of the stack at the monitoring location for IP-CEM (degrees Kelvin).12.2 Calculate the difference between the measured HCl concentration with and without interferents for each interference gas (or mixture) for your CEMS as:

Calculate the total percent interference as:

12.2.1 Calculate the equivalent concentration Ci,eff using Equation 4:



12.4.1 Calculate the equivalent concentration Ci,eff using Equation 4:

12.4.2 Calculate the average native concentration before and after each calibration check measurement as:

12.4.3 Calculate the ME or CD at concentration i for an IP-CEM as:
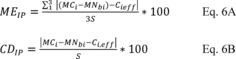

12.4.4 Calculate the zero CD as a percent of span for an IP-CEMS as:


12.6.1 Determine the CEMS final integrated minute average pollutant concentration or emission rate for each RM test period. Consider system RT, if important, and confirm that the results have been corrected to the same moisture, temperature and diluent concentration basis.
12.6.2 When Method 26A (or if approved for use, Method 26), found in 40 CFR part 60, appendix A-8 of this part, is used as the RM, compare each CEMS integrated average value against the corresponding RM value for identical test periods. Make these comparisons on the same basis (e.g., wet, dry, ppmv, or units of the standard). To convert results generate by Method 26A or 26 in mg/DSCM to ppmv, use the conversion factor 0.662 ppm/(mg/DSCM).
12.6.3 If the RM is Method 320 or Method 321, found in 40 CFR part 63, appendix A, or ASTM D6348-12, make a direct comparison of the average RM results and CEMS average value for identical test periods.
12.6.4 For each test run, calculate the arithmetic difference of the RM and CEMS results using Equation 9.

12.6.5 Calculate the standard deviation of the differences (Sd) of the CEMS measured and RM results using Equation 10.

12.6.6 Calculate the confidence coefficient (CC) for the RATA using Equation 11.

12.6.7 Calculate the mean difference (davg) between the RM and CEMS values in the units of ppmv or the emission standard using Equation 12.

12.6.8 Calculate the average RM value using Equation 13.

12.6.9 Calculate RA of the CEMS using Equation 14.

13.1 Level of Detection. You may not use a CEMS whose LOD or SADL is greater than 20 percent of the applicable regulatory limit or other action level for the intended use of the data.
13.2 Calibration Drift. The zero- and mid-level calibration drift for the CEMS must not exceed 5.0 percent of the span value for 7 consecutive operating days.
13.3 Measurement Error. The ME must be less than or equal to 5.0 percent of the span value at the low-, mid-, and high-level reference gas concentrations.
13.4 Relative Accuracy. Unless otherwise specified in an applicable regulation or permit, the RA of the CEMS, whether calculated in units of HCl concentration or in units of the emission standard, must be less than or equal to 20.0 percent of the RM when RMavg is used in the denominator of Equation 14.
13.4.1 In cases where the RA is calculated on a concentration (ppmv) basis, if the average RM emission level for the test is less than 75 percent of the HCl concentration equivalent to the emission standard, you may substitute the HCl concentration equivalent to the standard in the denominator of Equation 14 in place of RMavg.
13.4.2 Similarly, if the RA is calculated in units of the emission standard and the HCl emission level measured by the RMs is less than 75 percent of the emission standard, you may substitute the emission standard in the denominator of Equation 14 in place of RMavg.
13.4.3 The alternative calculated RA in paragraph 13.4.1 or 13.4.2 must be less than or equal to 15.0 percent.
13.5 Interference Test.
13.5.1 The sum of the interference response(s) from Equation 2 must not be greater than 2.5 percent of the calibration span or ±3.0 percent of the equivalent HCl concentration used for the interference test, whichever is less restrictive. The results are also acceptable if the sum of the interference response(s) does not exceed six times the LOD or 0.5 ppmv for a calibration span of 5 to 10 ppm, or 0.2 ppmv for a calibration span of less than 5 ppmv.
13.6 IP-CEMS Beam Intensity Test. For IP-CEMS, the percent difference between the measured concentration with and without attenuation of the light source must not exceed ±3.0 percent.
13.7 IP-CEMS Temperature Measurement Verification. Your temperature sensor satisfies the accuracy required if the absolute relative difference between measured value of stack temperature (Mt) and the temperature value from the calibrated temperature reference device (Vt) is ≤1.0 percent or if the absolute difference between Mt and Vt is ≤2.8 °C (5.0 °F), whichever is less restrictive.
13.8 IP-CEMS Pressure Sensor Measurement Verification. Your pressure sensor satisfies the accuracy required if the absolute relative difference between the measured value of stack pressure (MP) and the pressure value from the calibrated pressure reference device (VP) is ≤5.0 percent or if the absolute difference between Mp and VP is ≤0.12 kilopascals (0.5 inches of water column), whichever is less restrictive.
14.0 Pollution Prevention [Reserved] 15.0 Waste Management [Reserved] 16.0 Bibliography1. Method 318 - Extractive FTIR Method for the Measurement of Emissions From the Mineral Wool and Wool Fiberglass Industries, 40 CFR, part 63, subpart HHHHHHH, appendix A.
2. “EPA Protocol for the Use of Extractive Fourier Transform Infrared (FTIR) Spectrometry in Analyses of Gaseous Emissions from Stationary Industrial Sources,” February, 1995.
3. “Measurement of Gaseous Organic and Inorganic Emissions by Extractive FTIR Spectroscopy,” EPA Contract No. 68-D2-0165, Work Assignment 3-08.
4. “Method 301 - Field Validation of Pollutant Measurement Methods from Various Waste Media,” 40 CFR part 63, appendix A.
5. EPA Traceability Protocol for Assay and Certification of Gaseous Calibration Standards, U.S. Environmental Protection Agency office of Research and Development, EPA/600/R-12/531, May 2012.
17.0 Tables, Diagrams, Flowcharts, and Validation DataTable 1 - Interference Test Gas Concentrations
Potential interferent gas 1 | Approximate concentration (balance N2) |
---|---|
CO2 | 15% ± 1% CO2. 2 |
CO | 100 ± 20 ppm. |
CH2O | 20 ± 5 ppm. |
CH4 | 100 ± 20 ppm. |
NH3 | 10 ± 5 ppm (extractive CEMS only). |
NO | 250 ± 50 ppm. |
SO2 | 200 ± 20 ppm. |
O2 | 3% ± 1% O2. 2 |
H2O | 10% ± 1% H2O. 2 |
N2 | Balance. 2 |
1 Any of these specific gases can be tested at a lower level if the manufacturer has provided reliable means for limiting or scrubbing that gas to a specified level in CEMS field installations.
2 Gases for short path IP cell interference tests cannot be added above 100 percent stack equivalent concentration. Add these gases at the indicated percentages to make up the remaining cell volume.
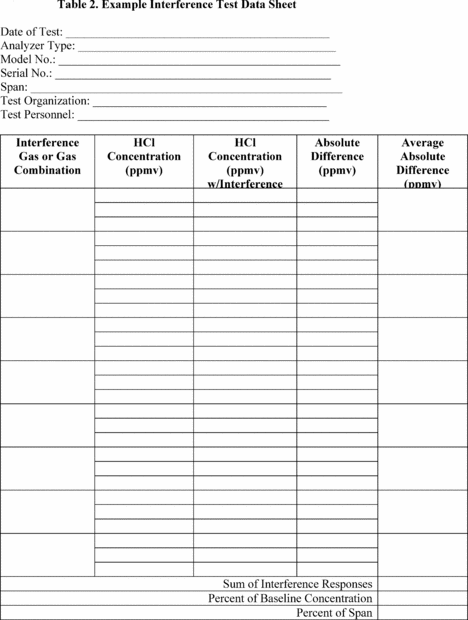
Table 3 - Design Standards for Temperature Sensors
If the sensor is a . . . | You can use the following design standards as guidance in selecting a sensor for your IP-CEMS |
---|---|
1. Thermocouple | a. ASTM E235-88 (1996), “Specification for Thermocouples, Sheathed, Type K, for Nuclear or Other High-Reliability Applications.” |
b. ASTM E585/E585M-04, “Specification for Compacted Mineral-Insulated, Metal-Sheathed, Base Metal Thermocouple Cable.” | |
c. ASTM E608/E608M-06, “Specification for Mineral-Insulated, Metal-Sheathed Base Metal Thermocouples.” | |
d. ASTM E696-07, “Specification for Tungsten-Rhenium Alloy Thermocouple Wire.” | |
e. ASTM E1129/E1129M-98 (2002), “Standard Specification for Thermocouple Connectors.” | |
f. ASTM E1159-98 (2003), “Specification for Thermocouple Materials, Platinum-Rhodium Alloys, and Platinum.” | |
g. ISA-MC96.1-1982, “Temperature Measurement Thermocouples.” | |
2. Resistance temperature detector | ASTM E1137/E1137M-04, “Standard Specification for Industrial Platinum Resistance Thermometers.” |
Table 4 - Performance Specification Test Zero and Reference Gas Ranges
Test | Units | HCl Zero and Reference Gas Concentrations in Terms of Percent of Span a | Section | |||
---|---|---|---|---|---|---|
Zero | Low Level | Mid Level | High Level | |||
Calibration Drift | % of Span | <LOD | NA | 50-60 b | NA | 11.8 |
Measurement Error | % of Span | NA | 20-30 | 50-60 | 80-100 | 11.7 |
a Reference gas concentration must be NIST traceable. (see section 7.1)
b Mid-level is required. For DS calibration drift option, choose a concentration that yields a value in this range at the analyzer.
Table 5 - Student's t-Values
n-1 a | t-value | n-1 a | t-value | n-1 a | t-value |
---|---|---|---|---|---|
1 | 12.71 | 11 | 2.201 | 21 | 2.080 |
2 | 4.303 | 12 | 2.179 | 22 | 2.074 |
3 | 3.182 | 13 | 2.160 | 23 | 2.069 |
4 | 2.776 | 14 | 2.145 | 24 | 2.064 |
5 | 2.571 | 15 | 2.131 | 25 | 2.060 |
6 | 2.447 | 16 | 2.120 | 26 | 2.056 |
7 | 2.365 | 17 | 2.110 | 27 | 2.052 |
8 | 2.306 | 18 | 2.101 | 28 | 2.048 |
9 | 2.262 | 19 | 2.093 | 29 | 2.045 |
10 | 2.228 | 20 | 2.086 | 30 | 2.042 |
a The value n is the number of independent pairs of measurements. Either discrete (independent) measurements in a single run, or run averages can be used.
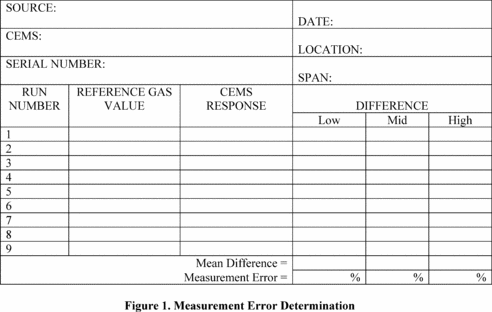
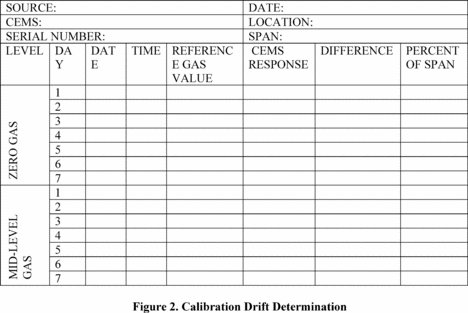
1.1 This appendix to Performance Specification (PS) 18 describes the procedure and performance requirements for standard addition (SA) as a quality check for hydrogen chloride (HCl) continuous emission monitoring systems (CEMS).
1.2 This appendix is applicable to quality checks of both extractive and integrated path (IP) technologies used to measure HCl emissions.
1.3 For extractive CEMS, this procedure must be used, as a level of detection (LOD) verification of all field-installed CEMS. Additionally, it is allowed by Procedure 6 in appendix F to this part as an alternative to upscale calibration drift (CD) tests, cylinder gas audits and relative accuracy audits (RAAs), and may be used for quality assurance purposes under other applicable regulations or permits that require HCl monitoring.
1.4 For IP-CEMS, this procedure must be used as a LOD verification of all field-installed CEMS.
2.0 Summary of the Appendix for Standard AdditionAs used here, SA is a gas phase method of standard additions (either static or dynamic) used to verify the accuracy of CEMS measurements in the presence of the sample matrix. For extractive CEMS, it consists of spiking a known quantity of HCl dynamically into the measurement system as an addition to the native HCl and the native source gas matrix. For IP-CEMS, this procedure consists of introducing a known quantity of HCl into the optical path that also includes the native source gas.
3.0 Definitions. (See PS-18 and Procedure 6 of Appendix F to Part 60 for the Definitions Used in This Appendix.) 4.0 Interferences. Interferences are discussed in PS-18, section 4.05.0 Safety. The procedures required under this appendix may involve hazardous materials, operations and equipment. This procedure may not address all of the safety problems associated with these procedures. You as the facility or operator must establish appropriate safety and health practices and determine the applicable regulatory limitations prior to performing these procedures. As the CEMS user, you should consult instrument operation manuals, material safety data sheets, compressed gas safety requirements, and other Occupational Safety and Health Administration regulations for specific precautions to be taken.
6.0 Equipment and Supplies. An example of equipment and supplies is described in section 6 of PS-18.
7.0 Reagents and Standards. SA materials must meet the requirements defined for reference gases in section 7 of PS-18 to perform this procedure with the following exception. You may use gases certified by the gas vendor to ±5 percent to perform the daily calibration drift assessment in section 4.1 of Procedure 6 in appendix F of this part.
Note:For extractive CEMS the concentrations of reference gases required for SA are likely to be significantly higher than the concentration of reference gases associated with PS-18 requirements.
8.0 Standard Addition and Dynamic Spiking Procedure. The standard addition procedure consists of measuring the native source gas concentration, addition of reference gas, and measurement of the resulting SA elevated source gas concentration. For extractive CEMS, HCl is spiked dynamically and thus, one must account for the dilution of sample gas from the addition of the HCl reference gas. For IP-CEMS, standard addition of an HCl reference gas is made by either adding an HCl reference gas to a flow through cell or inserting a sealed reference gas cell into the measurement path of the CEMS. The enclosed cell or a fixed cell must contain an HCl concentration that accounts for the difference in path length of the cell used for SA relative to the measurement path.
8.1 SA Concentration and Measurement Replicates.
8.1.1 You must inject HCl gas to create a measured concentration based on the requirements of the particular performance test (e.g., LOD verification, CD, DSA).
8.1.2 Each dynamic spike (DS) or standard addition (SA) replicate consists of a measurement of the source emissions concentration of HCl (native stack concentration) with and without the addition of HCl. With a single CEMS, you must alternate the measurement of the native and SA-elevated source gas so that each measurement of SA-elevated source gas is immediately preceded and followed by a measurement of native stack gas. Introduce the SA gases in such a manner that the entire CEMS is challenged. Alternatively, you may use an independent continuous HCl monitor to measure the native source concentration before and after each standard addition as described in section 8.1.4.
8.1.3 Unless specified otherwise by an applicable rule, your SA-elevated concentration may not exceed 100 percent of span when the SA and native HCl concentration are combined.
8.1.4 As an alternative to making background measurements pre- and post-SA, you may use an independent continuous HCl monitor as a temporary unit to measure native stack HCl concentration while simultaneously using the CEMS to measure the SA-elevated source concentration. If you use an independent continuous HCl monitor you must make one concurrent background or native HCl measurement using both the installed CEMS and the independent continuous HCl monitor, immediately before the SA procedure in section 8.2 or 8.3 begins, to confirm that the independent monitoring system measures the same background concentration as the CEMS being qualified with this PS.
8.2 SA Procedure for Extractive CEMS (Dynamic Spiking)
8.2.1 Your HCl spike addition must not alter the total volumetric sample system flow rate or basic dilution ratio of your CEMS (if applicable).
8.2.2 Your spike gas flow rate must not contribute more than 10 percent of the total volumetric flow rate through the CEMS.
8.2.3 You must determine a dilution factor (DF) or relative concentration of HCl for each dynamic spike. Calibrated, NIST-traceable flow meters accurate to within 2.0 percent or highly accurate tracer gas measurements are required to make the necessary DF determinations at the accuracy required for this PS. Calibrated, NIST-traceable flow meters (e.g., venturi, orifice) accurate to within 2.0 percent should be recertified against an NIST-traceable flow meter annually. Note: Since the spiking mass balance calculation is directly dependent on the accuracy of the DF determination, the accuracy of measurements required to determine the total volumetric gas flow rate, spike gas flow rate, or tracer gas standard addition concentration is critical to your ability to accurately perform the DS procedure and calculate the results.
8.2.4 You must monitor and record the total sampling system flow rate and sample dilution factor (DF) for the spiking and stack gas sampling systems to ensure they are known and do not change during the spiking procedure. Record all data on a data sheet similar to Table A1 in section 13 of this appendix.
8.2.4.1 You may either measure the spike gas flow and the total flow with calibrated flow meters capable of NIST traceable accuracy to ±2.0 percent or calculate the flow using a stable tracer gas included in your spike gas standard.
8.2.4.2 If you use flow measurements to determine the spike dilution, then use Equation A1 in section 11.2.1 of this appendix to calculate the DF. Determination of the spike dilution requires measurement of HCl spike flow (Qspike) and total flow through the CEM sampling system (Qprobe).
8.2.4.3 If your CEMS is capable of measuring an independent stable tracer gas, you may use a spike gas that includes the tracer to determine the DF using Equation A2 or A3 (sections 11.2.2 and 11.2.3 of this appendix) depending on whether the tracer gas is also present in the native source emissions.
8.2.4.4 For extractive CEMS, you must correct the background measurements of HCl for the dilution caused by the addition of the spike gas standard. For spiking systems that alternate between addition of HCl and zero gas at a constant DF, the background measurements between spikes will not be equal to the native source concentration.
8.2.5 Begin by collecting unspiked sample measurements of HCl. You must use the average of two unspiked sample measurements as your pre-spike background.
Note:Measurements should agree within 5.0 percent or three times the level of detection to avoid biasing the spike results.
8.2.5.1 Introduce the HCl gas spike into the permanent CEMS probe, upstream of the particulate filter or sample conditioning system and as close to the sampling inlet as practical.
8.2.5.2 Maintain the HCl gas spike for at least twice the DS response time of your CEMS or until the consecutive measurements agree within 5.0 percent. Collect two independent measurements of the native plus spiked HCl concentration.
8.2.5.3 Stop the flow of spike gas for at least twice the DS response time of your CEMS or until the consecutive measurements agree within 5.0 percent. Collect two independent measurements of the native HCl concentration.
8.2.6 Repeat the collection of sample measurements in section 8.2.5 until you have data for each spike concentration including a final set of unspiked sample measurements according to section 8.2.5.3.
8.2.7 Verify that the CEMS responded as expected for each spike gas injection, and that the data quality is not impacted by large shifts in the native source concentration. Discard and repeat any spike injections as necessary to generate a complete set of the required replicate spike measurements.
8.2.8 Calculate the standard addition response (SAR) for extractive CEMS, using Equation A4 in section 11.2, of this appendix.
8.2.9 If the DS results do not meet the specifications for the appropriate performance test in PS-18 or Procedure 6 of appendix F of this part, you must take corrective action and repeat the DS procedure.
8.3 SA Procedure for IP-CEMS (Static Spiking).
8.3.1 For IP-CEMS, you must make measurements of native source gas HCl concentration and an HCl standard addition using a calibration cell added to the optical measurement path.
8.3.2 Introduce zero gas into a calibration cell located in the optical measurement path of the instrument. Continue to flush the zero gas into the cell for at least the SA response time of your CEMS or until two consecutive measurements taken are within 5.0 percent, then collect two independent measurements. Alternatively you may measure native concentrations without the calibration cell in the optical path.
8.3.3 Introduce the HCl spike gas into the calibration cell. Continue to flush the spike gas into the cell for at least the SA response time of your CEMS or until two consecutive measurements taken are within 5.0 percent of one another. Then collect two independent measurements of the SA addition to the native concentration. Alternatively you may insert a sealed calibration cell, containing HCl at the appropriate concentration, into the optical path to measure the SA addition to the native concentration.
8.3.4 Repeat the collection of SA-elevated and native HCl measurements in sections 8.3.2 and 8.3.3 until you have data for each SA concentration. Then, make a final native HCl measurement. The measured concentrations must be corrected for calibration cell and stack temperature, pressure and stack measurement path length.
8.3.5 Calculate the standard addition response (SAR) for an IP-CEMS, using Equation A8 in section 11.3 of this appendix.
8.3.6 If the SA results do not meet the specifications for the appropriate performance test in PS-18 or Procedure 6 of appendix F of this part, you must take corrective action and repeat the SA procedure.
9.0 Quality Control [Reserved] 10.0 Calibration and Standardization [Reserved]11.0 Calculations and Data Analysis. Calculate the SA response for each measurement and its associated native HCl measurement(s), using equations in this section. (Note: For cases where the emission standard is expressed in units of lb/MMBtu or corrected to a specified O2 or CO2 concentration, an absolute accuracy specification based on a span at stack conditions may be calculated using the average concentration and applicable conversion factors. The appropriate procedures for use in cases where a percent removal standard is more restrictive than the emission standard are the same as in 40 CFR part 60, PS-2, sections 12 and 13.)
11.1 Nomenclature.
Cspike = Actual HCl reference gas concentration spiked (e.g., bottle or reference gas concentration) ppmv; Ctracer spiked = Tracer gas concentration injected with spike gas (“reference concentration”) ppmv; DF = Spiked gas dilution factor; DSCD = Calibration drift determined using DS procedure (percent); DSE = Dynamic spike error (ppmv); ESA = Effective spike addition (ppmv); MCSA = Measured SA-elevated source gas concentration (ppmv); MCspiked = Measured HCl reference gas concentration i (ppmv); MCnative = Average measured concentration of the native HCl (ppmv); Mnative tracer = Measured tracer gas concentration present in native effluent gas (ppmv); Mspiked tracer = Measured diluted tracer gas concentration in a spiked sample (ppmv); Qspike = Flow rate of the dynamic spike gas (Lpm); Qprobe = Average total stack sample flow through the system (Lpm); S = Span (ppmv); SAR = Standard addition response (ppmv)11.2 Calculating Dynamic Spike Response and Error for Extractive CEMS.
11.2.1 If you determine your spike DF using spike gas and stack sample flow measurements, calculate the DF using equation A1:

11.2.2 If you determine your spike DF using an independent stable tracer gas that is not present in the native source emissions, calculate the DF for DS using equation A2:

11.2.3 If you determine your spike dilution factor using an independent stable tracer that is present in the native source emissions, calculate the dilution factor for dynamic spiking using equation A3:

11.2.4 Calculate the SA response using Equation A4:

11.2.5 Calculate the DS error using Equation A5.

11.2.6 Calculating CD using DS. When using the DS option for determining mid-level CD, calculate the CD as a percent of span using equation A6:

11.2.7 The effective spike addition (ESA) is the expected increase in the measured concentration as a result of injecting a spike. Calculate ESA using Equation A7:

11.3 Standard Addition Response for IP-CEMS. If you use an IP-CEMS and a calibration cell, calculate the SA response using Equation A8.

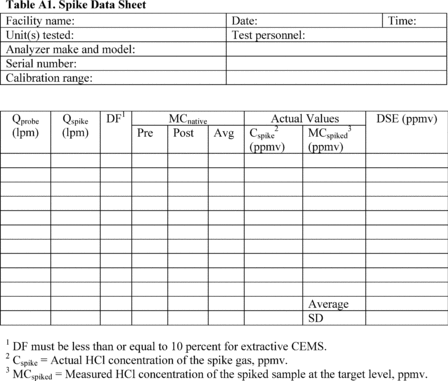
Appendix C to Part 60 - Determination of Emission Rate Change
40:9.0.1.1.1.0.1.1.10 : Appendix C
Appendix C to Part 60 - Determination of Emission Rate Change 1. Introduction1.1 The following method shall be used to determine whether a physical or operational change to an existing facility resulted in an increase in the emission rate to the atmosphere. The method used is the Student's t test, commonly used to make inferences from small samples.
2. Data2.1 Each emission test shall consist of n runs (usually three) which produce n emission rates. Thus two sets of emission rates are generated, one before and one after the change, the two sets being of equal size.
2.2 When using manual emission tests, except as provided in § 60.8(b) of this part, the reference methods of appendix A to this part shall be used in accordance with the procedures specified in the applicable subpart both before and after the change to obtain the data.
2.3 When using continuous monitors, the facility shall be operated as if a manual emission test were being performed. Valid data using the averaging time which would be required if a manual emission test were being conducted shall be used.
3. Procedure3.1 Subscripts a and b denote prechange and postchange respectively.
3.2 Calculate the arithmetic mean emission rate, E, for each set of data using Equation 1.
Where: Ei = Emission rate for the i th run. n = number of runs.3.3 Calculate the sample variance, S2, for each set of data using Equation 2.
3.4 Calculate the pooled estimate, Sp, using Equation 3.
3.5 Calculate the test statistic, t, using Equation 4.
4. Results4.1 If Eb>,Ea and t>t′, where t′ is the critical value of t obtained from Table 1, then with 95% confidence the difference between Eb and Ea is significant, and an increase in emission rate to the atmosphere has occurred.
Table 1
Degrees of freedom (na=nb−2) | t′ (95 percent confidence level) |
---|---|
2 | 2.920 |
3 | 2.353 |
4 | 2.132 |
5 | 2.015 |
6 | 1.943 |
7 | 1.895 |
8 | 1.860 |
5.1 Assume the two performance tests produced the following set of data:
Test a | Test b |
---|---|
Run 1. 100 | 115 |
Run 2. 95 | 120 |
Run 3. 110 | 125 |
5.2 Using Equation 1 -
Ea = 100 + 95 + 110/3 = 102 Eb = 115 + 120 + 125/3 = 1205.3 Using Equation 2 -
Sa2 = (100−102) 2 + (95−102) 2 + (110−102) 2/3−1 = 58.5 Sb2 = (115−120) 2 + (120−120) 2 + (125−120) 2/3−1 = 255.4 Using Equation 3 -
Sp = [(3 − 1)(58.5) + (3 + 1)(25) / 3 + 3 − 2] 1/2 = 6.465.5 Using Equation 4 -
5.6 Since (n 1 + n 2 − 2) = 4, t′ = 2.132 (from Table 1). Thus since t>t′ the difference in the values of Ea and Eb is significant, and there has been an increase in emission rate to the atmosphere.
6. Continuous Monitoring Data6.1 Hourly averages from continuous monitoring devices, where available, should be used as data points and the above procedure followed.
[40 FR 58420, Dec. 16, 1975]Appendix D to Part 60 - Required Emission Inventory Information
40:9.0.1.1.1.0.1.1.11 : Appendix D
Appendix D to Part 60 - Required Emission Inventory Information(a) Completed NEDS point source form(s) for the entire plant containing the designated facility, including information on the applicable criteria pollutants. If data concerning the plant are already in NEDS, only that information must be submitted which is necessary to update the existing NEDS record for that plant. Plant and point identification codes for NEDS records shall correspond to those previously assigned in NEDS; for plants not in NEDS, these codes shall be obtained from the appropriate Regional Office.
(b) Accompanying the basic NEDS information shall be the following information on each designated facility:
(1) The state and county identification codes, as well as the complete plant and point identification codes of the designated facility in NEDS. (The codes are needed to match these data with the NEDS data.)
(2) A description of the designated facility including, where appropriate:
(i) Process name.
(ii) Description and quantity of each product (maximum per hour and average per year).
(iii) Description and quantity of raw materials handled for each product (maximum per hour and average per year).
(iv) Types of fuels burned, quantities and characteristics (maximum and average quantities per hour, average per year).
(v) Description and quantity of solid wastes generated (per year) and method of disposal.
(3) A description of the air pollution control equipment in use or proposed to control the designated pollutant, including:
(i) Verbal description of equipment.
(ii) Optimum control efficiency, in percent. This shall be a combined efficiency when more than one device operates in series. The method of control efficiency determination shall be indicated (e.g., design efficiency, measured efficiency, estimated efficiency).
(iii) Annual average control efficiency, in percent, taking into account control equipment down time. This shall be a combined efficiency when more than one device operates in series.
(4) An estimate of the designated pollutant emissions from the designated facility (maximum per hour and average per year). The method of emission determination shall also be specified (e.g., stack test, material balance, emission factor).
[40 FR 53349, Nov. 17, 1975]Appendix E to Part 60 [Reserved]
40:9.0.1.1.1.0.1.1.12 : Appendix E
Appendix E to Part 60 [Reserved]Appendix F to Part 60 - Quality Assurance Procedures
40:9.0.1.1.1.0.1.1.13 : Appendix F
Appendix F to Part 60 - Quality Assurance Procedures Procedure 1. Quality Assurance Requirements for Gas Continuous Emission Monitoring Systems Used for Compliance Determination 1. Applicability and Principle1.1 Applicability. Procedure 1 is used to evaluate the effectiveness of quality control (QC) and quality assurance (QA) procedures and the quality of data produced by any continuous emission monitoring system (CEMS) that is used for determining compliance with the emission standards on a continuous basis as specified in the applicable regulation. The CEMS may include pollutant (e.g., S02 and N0x) and diluent (e.g., 02 or C02) monitors.
This procedure specifies the minimum QA requirements necessary for the control and assessment of the quality of CEMS data submitted to the Environmental Protection Agency (EPA). Source owners and operators responsible for one or more CEMS's used for compliance monitoring must meet these minimum requirements and are encouraged to develop and implement a more extensive QA program or to continue such programs where they already exist.
Data collected as a result of QA and QC measures required in this procedure are to be submitted to the Agency. These data are to be used by both the Agency and the CEMS operator in assessing the effectiveness of the CEMS QC and QA procedures in the maintenance of acceptable CEMS operation and valid emission data.
Appendix F, Procedure 1 is applicable December 4, 1987. The first CEMS accuracy assessment shall be a relative accuracy test audit (RATA) (see section 5) and shall be completed by March 4, 1988 or the date of the initial performance test required by the applicable regulation, whichever is later.
1.2 Principle. The QA procedures consist of two distinct and equally important functions. One function is the assessment of the quality of the CEMS data by estimating accuracy. The other function is the control and improvement of the quality of the CEMS data by implementing QC policies and corrective actions. These two functions form a control loop: When the assessment function indicates that the data quality is inadequate, the control effort must be increased until the data quality is acceptable. In order to provide uniformity in the assessment and reporting of data quality, this procedure explicitly specifies the assessment methods for response drift and accuracy. The methods are based on procedures included in the applicable performance specifications (PS's) in appendix B of 40 CFR part 60. Procedure 1 also requires the analysis of the EPA audit samples concurrent with certain reference method (RM) analyses as specified in the applicable RM's.
Because the control and corrective action function encompasses a variety of policies, specifications, standards, and corrective measures, this procedure treats QC requirements in general terms to allow each source owner or operator to develop a QC system that is most effective and efficient for the circumstances.
2. Definitions2.1 Continuous Emission Monitoring System. The total equipment required for the determination of a gas concentration or emission rate.
2.2 Diluent Gas. A major gaseous constituent in a gaseous pollutant mixture. For combustion sources, CO2 and O2 are the major gaseous constituents of interest.
2.3 Span Value. The upper limit of a gas concentration measurement range that is specified for affected source categories in the applicable subpart of the regulation.
2.4 Zero, Low-Level, and High-Level Values. The CEMS response values related to the source specific span value. Determination of zero, low-level, and high-level values is defined in the appropriate PS in appendix B of this part.
2.5 Calibration Drift (CD). The difference in the CEMS output reading from a reference value after a period of operation during which no unscheduled maintenance, repair or adjustment took place. The reference value may be supplied by a cylinder gas, gas cell, or optical filter and need not be certified.
2.6 Relative Accuracy (RA). The absolute mean difference between the gas concentration or emission rate determined by the CEMS and the value determined by the RM's plus the 2.5 percent error confidence coefficient of a series of tests divided by the mean of the RM tests or the applicable emission limit.
3. QC RequirementsEach source owner or operator must develop and implement a QC program. As a minimum, each QC program must include written procedures which should describe in detail, complete, step-by-step procedures and operations for each of the following activities:
1. Calibration of CEMS.
2. CD determination and adjustment of CEMS.
3. Preventive maintenance of CEMS (including spare parts inventory).
4. Data recording, calculations, and reporting.
5. Accuracy audit procedures including sampling and analysis methods.
6. Program of corrective action for malfunctioning CEMS.
As described in section 5.2, whenever excessive inaccuracies occur for two consecutive quarters, the source owner or operator must revise the current written procedures or modify or replace the CEMS to correct the deficiency causing the excessive inaccuracies.
These written procedures must be kept on record and available for inspection by the enforcement agency.
4. CD Assessment4.1 CD Requirement. As described in 40 CFR 60.13(d), source owners and operators of CEMS must check, record, and quantify the CD at two concentration values at least once daily (approximately 24 hours) in accordance with the method prescribed by the manufacturer. The CEMS calibration must, as minimum, be adjusted whenever the daily zero (or low-level) CD or the daily high-level CD exceeds two times the limits of the applicable PS's in appendix B of this regulation.
4.2 Recording Requirement for Automatic CD Adjusting Monitors. Monitors that automatically adjust the data to the corrected calibration values (e.g., microprocessor control) must be programmed to record the unadjusted concentration measured in the CD prior to resetting the calibration, if performed, or record the amount of adjustment.
4.3 Criteria for Excessive CD. If either the zero (or low-level) or high-level CD result exceeds twice the applicable drift specification in appendix B for five, consecutive, daily periods, the CEMS is out-of-control. If either the zero (or low-level) or high-level CD result exceeds four times the applicable drift specification in appendix B during any CD check, the CEMS is out-of-control. If the CEMS is out-of-control, take necessary corrective action. Following corrective action, repeat the CD checks.
4.3.1 Out-Of-Control Period Definition. The beginning of the out-of-control period is the time corresponding to the completion of the fifth, consecutive, daily CD check with a CD in excess of two times the allowable limit, or the time corresponding to the completion of the daily CD check preceding the daily CD check that results in a CD in excess of four times the allowable limit. The end of the out-of-control period is the time corresponding to the completion of the CD check following corrective action that results in the CD's at both the zero (or low-level) and high-level measurement points being within the corresponding allowable CD limit (i.e., either two times or four times the allowable limit in appendix B).
4.3.2 CEMS Data Status During Out-of-Control Period. During the period the CEMS is out-of-control, the CEMS data may not be used in calculating emission compliance nor be counted towards meeting minimum data availability as required and described in the applicable subpart [e.g., § 60.47a(f)].
4.4 Data Recording and Reporting. As required in § 60.7(d) of this regulation (40 CFR part 60), all measurements from the CEMS must be retained on file by the source owner for at least 2 years. However, emission data obtained on each successive day while the CEMS is out-of-control may not be included as part of the minimum daily data requirement of the applicable subpart [e.g., § 60.47a(f)] nor be used in the calculation of reported emissions for that period.
5. Data Accuracy Assessment5.1 Auditing Requirements. Each CEMS must be audited at least once each calendar quarter. Successive quarterly audits shall occur no closer than 2 months. The audits shall be conducted as follows:
5.1.1 Relative Accuracy Test Audit (RATA). The RATA must be conducted at least once every four calendar quarters, except as otherwise noted in section 5.1.4 of this appendix. Conduct the RATA as described for the RA test procedure in the applicable PS in appendix B (e.g., PS 2 for SO2 and NOX). In addition, analyze the appropriate performance audit samples received from EPA as described in the applicable sampling methods (e.g., Methods 6 and 7).
5.1.2 Cylinder Gas Audit (CGA). If applicable, a CGA may be conducted in three of four calendar quarters, but in no more than three quarters in succession.
To conduct a CGA: (1) Challenge the CEMS (both pollutant and diluent portions of the CEMS, if applicable) with an audit gas of known concentration at two points within the following ranges:
Audit point | Audit range | ||
---|---|---|---|
Pollutant monitors | Diluent monitors for - | ||
CO2 | O2 | ||
1 | 20 to 30% of span value | 5 to 8% by volume | 4 to 6% by volume. |
2 | 50 to 60% of span value | 10 to 14% by volume | 8 to 12% by volume. |
Introduce each of the audit gases, three times each for a total of six challenges. Introduce the gases in such a manner that the entire CEMS is challenged. Do not introduce the same gas concentration twice in succession.
Use of separate audit gas cylinder for audit points 1 and 2. Do not dilute gas from audit cylinder when challenging the CEMS.
The monitor should be challenged at each audit point for a sufficient period of time to assure adsorption-desorption of the CEMS sample transport surfaces has stabilized.
(2) Operate each monitor in its normal sampling mode, i.e., pass the audit gas through all filters, scrubbers, conditioners, and other monitor components used during normal sampling, and as much of the sampling probe as is practical. At a minimum, the audit gas should be introduced at the connection between the probe and the sample line.
(3) Use Certified Reference Materials (CRM's) (See Citation 1) audit gases that have been certified by comparison to National Institute of Standards and Technology (NIST) Standard Reference Materials (SRM's) or EPA Protocol Gases following the most recent edition of the EPA Traceability Protocol for Assay and Certification of Gaseous Calibration Standards (See Citation 2). Procedures for preparation of CRM's are described in Citation 1. Procedures for preparation of EPA Protocol Gases are described in Citation 2. In the case that a suitable audit gas level is not commercially available, Method 205 (See Citation 3) may be used to dilute CRM's or EPA Protocol Gases to the needed level. The difference between the actual concentration of the audit gas and the concentration indicated by the monitor is used to assess the accuracy of the CEMS.
5.1.3 Relative Accuracy Audit (RAA). The RAA may be conducted three of four calendar quarters, but in no more than three quarters in succession. To conduct a RAA, follow the procedure described in the applicable PS in appendix B for the relative accuracy test, except that only three sets of measurement data are required. Analyses of EPA performance audit samples are also required.
The relative difference between the mean of the RM values and the mean of the CEMS responses will be used to assess the accuracy of the CEMS.
5.1.4 Other Alternative Audits. Other alternative audit procedures may be used as approved by the Administrator for three of four calendar quarters. One RATA is required at least every four calendar quarters, except in the case where the affected facility is off-line (does not operate) in the fourth calendar quarter since the quarter of the previous RATA. In that case, the RATA shall be performed in the quarter in which the unit recommences operation. Also, cylinder gas audits are not be required for calendar quarters in which the affected facility does not operate.
5.2 Excessive Audit Inaccuracy. If the RA, using the RATA, CGA, or RAA exceeds the criteria in section 5.2.3, the CEMS is out-of-control. If the CEMS is out-of-control, take necessary corrective action to eliminate the problem. Following corrective action, the source owner or operator must audit the CEMS with a RATA, CGA, or RAA to determine if the CEMS is operating within the specifications. A RATA must always be used following an out-of-control period resulting from a RATA. The audit following corrective action does not require analysis of EPA performance audit samples. If audit results show the CEMS to be out-of-control, the CEMS operator shall report both the audit showing the CEMS to be out-of-control and the results of the audit following corrective action showing the CEMS to be operating within specifications.
5.2.1 Out-Of-Control Period Definition. The beginning of the out-of-control period is the time corresponding to the completion of the sampling for the RATA, RAA, or CGA. The end of the out-of-control period is the time corresponding to the completion of the sampling of the subsequent successful audit.
5.2.2 CEMS Data Status During Out-Of-Control Period. During the period the monitor is out-of-control, the CEMS data may not be used in calculating emission compliance nor be counted towards meeting minimum data availabilty as required and described in the applicable subpart [e.g., § 60.47a(f)].
5.2.3 Criteria for Excessive Audit Inaccuracy. Unless specified otherwise in the applicable subpart, the criteria for excessive inaccuracy are:
(1) For the RATA, the allowable RA in the applicable PS in appendix B.
(2) For the CGA, ±15 percent of the average audit value or ±5 ppm, whichever is greater; for diluent monitors, ±15 percent of the average audit value.
(3) For the RAA, ±15 percent of the three run average or ±7.5 percent of the applicable standard, whichever is greater.
5.3 Criteria for Acceptable QC Procedure. Repeated excessive inaccuracies (i.e., out-of-control conditions resulting from the quarterly audits) indicates the QC procedures are inadequate or that the CEMS is incapable of providing quality data. Therefore, whenever excessive inaccuracies occur for two consective quarters, the source owner or operator must revise the QC procedures (see section 3) or modify or replace the CEMS.
6. Calculations for CEMS Data Accuracy6.1 RATA RA Calculation. Follow the equations described in section 8 of appendix B, PS 2 to calculate the RA for the RATA. The RATA must be calculated in units of the applicable emission standard (e.g., ng/J).
6.2 RAA Accuracy Calculation. Use the calculation procedure in the relevant performance specification to calculate the accuracy for the RAA. The RAA must be calculated in the units of the applicable emission standard.
6.3 CGA Accuracy Calculation. Use Equation 1-1 to calculate the accuracy for the CGA, which is calculated in units of the appropriate concentration (e.g., ppm SO2 or percent O2). Each component of the CEMS must meet the acceptable accuracy requirement.
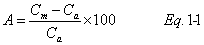
A = Accuracy of the CEMS, percent.
Cm = Average CEMS response during audit in units of applicable standard or appropriate concentration.
Ca = Average audit value (CGA certified value or three-run average for RAA) in units of applicable standard or appropriate concentration.
6.4 Example Accuracy Calculations. Example calculations for the RATA, RAA, and CGA are available in Citation 3.
7. Reporting RequirementsAt the reporting interval specified in the applicable regulation, report for each CEMS the accuracy results from section 6 and the CD assessment results from section 4. Report the drift and accuracy information as a Data Assessment Report (DAR), and include one copy of this DAR for each quarterly audit with the report of emissions required under the applicable subparts of this part.
As a minimum, the DAR must contain the following information:
1. Source owner or operator name and address.
2. Identification and location of monitors in the CEMS.
3. Manufacturer and model number of each monitor in the CEMS.
4. Assessment of CEMS data accuracy and date of assessment as determined by a RATA, RAA, or CGA described in section 5 including the RA for the RATA, the A for the RAA or CGA, the RM results, the cylinder gases certified values, the CEMS responses, and the calculations results as defined in section 6. If the accuracy audit results show the CEMS to be out-of-control, the CEMS operator shall report both the audit results showing the CEMS to be out-of-control and the results of the audit following corrective action showing the CEMS to be operating within specifications.
5. Results from EPA performance audit samples described in section 5 and the applicable RM's.
6. Summary of all corrective actions taken when CEMS was determined out-of-control, as described in sections 4 and 5.
An example of a DAR format is shown in Figure 1.
8. Bibliography1. “A Procedure for Establishing Traceability of Gas Mixtures to Certain National Bureau of Standards Standard Reference Materials.” Joint publication by NBS and EPA-600/7-81-010, Revised 1989. Available from the U.S. Environmental Protection Agency. Quality Assurance Division (MD-77). Research Triangle Park, NC 27711.
2. “EPA Traceability Protocol For Assay And Certification Of Gaseous Calibration Standards.” EPA-600/R-97/121, September 1997. Available from EPA's Emission Measurement Center at http://www.epa.gov/ttn/emc.
3. Method 205, “Verification of Gas Dilution Systems for Field Instrument Calibrations,” 40 CFR 51, appendix M.
Figure 1 - Example Format for Data Assessment Report Period ending date Year Company name Plant name Source unit no. CEMS manufacturer Model no. CEMS serial no. CEMS type (e.g., in situ) CEMS sampling location (e.g., control device outlet) CEMS span values as per the applicable regulation: ______ (e.g., SO2 ____ ppm, NOX ____ ppm). ________I. Accuracy assessment results (Complete A, B, or C below for each CEMS or for each pollutant and diluent analyzer, as applicable.) If the quarterly audit results show the CEMS to be out-of-control, report the results of both the quarterly audit and the audit following corrective action showing the CEMS to be operating properly.
A. Relative accuracy test audit (RATA) for ____ (e.g., SO2 in ng/J).
1. Date of audit ____.
2. Reference methods (RM's) used ____ (e.g., Methods 3 and 6).
3. Average RM value ____ (e.g., ng/J, mg/dsm 3, or percent volume).
4. Average CEMS value ____.
5. Absolute value of mean difference [d] ____.
6. Confidence coefficient [CC] ____.
7. Percent relative accuracy (RA) ____ percent.
8. EPA performance audit results:
a. Audit lot number (1) ____ (2) ____
b. Audit sample number (1) ____ (2) ____
c. Results (mg/dsm 3) (1) ____ (2) ____
d. Actual value (mg/dsm 3)* (1) ____ (2) ____
e. Relative error* (1) ____ (2) ____
B. Cylinder gas audit (CGA) for ____ (e.g., SO2 in ppm).
Audit point 1 | Audit point 2 | ||
---|---|---|---|
1. Date of audit | |||
2. Cylinder ID number | |||
3. Date of certification | |||
4. Type of certification | (e.g., EPA Protocol 1 or CRM). | ||
5. Certified audit value | (e.g., ppm). | ||
6. CEMS response value | (e.g., ppm). | ||
7. Accuracy | percent. |
C. Relative accuracy audit (RAA) for ____ (e.g., SO2 in ng/J).
1. Date of audit ____.
2. Reference methods (RM's) used ____ (e.g., Methods 3 and 6).
3. Average RM value ____ (e.g., ng/J).
4. Average CEMS value ____.
5. Accuracy ____ percent.
6. EPA performance audit results:
a. Audit lot number (1) ____ (2) ____
b. Audit sample number (1) ____ (2) ____
c. Results (mg/dsm 3) (1) ____ (2) ____
d. Actual value (mg/dsm 3) *(1) ____ (2)
e. Relative error* (1) ____ (2) ____
* To be completed by the Agency.
D. Corrective action for excessive inaccuracy.
1. Out-of-control periods.
a. Date(s) ____.
b. Number of days ____.
2. Corrective action taken3. Results of audit following corrective action. (Use format of A, B, or C above, as applicable.)
II. Calibration drift assessment.
A. Out-of-control periods.
1. Date(s) ____.
2. Number of days ____.
B. Corrective action taken Procedure 2 - Quality Assurance Requirements for Particulate Matter Continuous Emission Monitoring Systems at Stationary Sources 1.0 What Are the Purpose and Applicability of Procedure 2?The purpose of Procedure 2 is to establish the minimum requirements for evaluating the effectiveness of quality control (QC) and quality assurance (QA) procedures and the quality of data produced by your particulate matter (PM) continuous emission monitoring system (CEMS). Procedure 2 applies to PM CEMS used for continuously determining compliance with emission standards or operating permit limits as specified in an applicable regulation or permit. Other QC procedures may apply to diluent (e.g., O2) monitors and other auxiliary monitoring equipment included with your CEMS to facilitate PM measurement or determination of PM concentration in units specified in an applicable regulation.
1.1 What measurement parameter does Procedure 2 address? Procedure 2 covers the instrumental measurement of PM as defined by your source's applicable reference method (no Chemical Abstract Service number assigned).
1.2 For what types of devices must I comply with Procedure 2? You must comply with Procedure 2 for the total equipment that:
(1) We require you to install and operate on a continuous basis under the applicable regulation, and
(2) You use to monitor the PM mass concentration associated with the operation of a process or emission control device.
1.3 What are the data quality objectives (DQOs) of Procedure 2? The overall DQO of Procedure 2 is the generation of valid, representative data that can be transferred into useful information for determining PM CEMS concentrations averaged over a prescribed interval. Procedure 2 is also closely associated with Performance Specification 11 (PS-11).
(1) Procedure 2 specifies the minimum requirements for controlling and assessing the quality of PM CEMS data submitted to us or the delegated permitting authority.
(2) You must meet these minimum requirements if you are responsible for one or more PM CEMS used for compliance monitoring. We encourage you to develop and implement a more extensive QA program or to continue such programs where they already exist.
1.4 What is the intent of the QA/QC procedures specified in Procedure 2? Procedure 2 is intended to establish the minimum QA/QC requirements for PM CEMS and is presented in general terms to allow you to develop a program that is most effective for your circumstances. You may adopt QA/QC procedures that go beyond these minimum requirements to ensure compliance with applicable regulations.
1.5 When must I comply with Procedure 2? You must comply with the basic requirements of Procedure 2 immediately following successful completion of the initial correlation test of PS-11.
2.0 What Are the Basic Requirements of Procedure 2?Procedure 2 requires you to perform periodic evaluations of PM CEMS performance and to develop and implement QA/QC programs to ensure that PM CEMS data quality is maintained.
2.1 What are the basic functions of Procedure 2?
(1) Assessment of the quality of your PM CEMS data by estimating measurement accuracy;
(2) Control and improvement of the quality of your PM CEMS data by implementing QC requirements and corrective actions until the data quality is acceptable; and
(3) Specification of requirements for daily instrument zero and upscale drift checks and daily sample volume checks, as well as routine response correlation audits, absolute correlation audits, sample volume audits, and relative response audits.
3.0 What Special Definitions Apply to Procedure 2?The definitions in Procedure 2 include those provided in PS-11 of Appendix B, with the following additions:
3.1 “Absolute Correlation Audit (ACA)” means an evaluation of your PM CEMS response to a series of reference standards covering the full measurement range of the instrument (e.g., 4 mA to 20 mA).
3.2 “Correlation Range” means the range of PM CEMS responses used in the complete set of correlation test data.
3.3 “PM CEMS Correlation” means the site-specific relationship (i.e., a regression equation) between the output from your PM CEMS (e.g., mA) and the particulate concentration, as determined by the reference method. The PM CEMS correlation is expressed in the same units as the PM concentration measured by your PM CEMS (e.g., mg/acm). You must derive this relation from PM CEMS response data and manual reference method data that were gathered simultaneously. These data must be representative of the full range of source and control device operating conditions that you expect to occur. You must develop the correlation by performing the steps presented in sections 12.2 and 12.3 of PS-11.
3.4 “Reference Method Sampling Location” means the location in your source's exhaust duct from which you collect manual reference method data for developing your PM CEMS correlation and for performing relative response audits (RRAs) and response correlation audits (RCAs).
3.5 “Response Correlation Audit (RCA)” means the series of tests specified in section 10.3(8) of this procedure that you conduct to ensure the continued validity of your PM CEMS correlation.
3.6 “Relative Response Audit (RRA)” means the brief series of tests specified in section 10.3(6) of this procedure that you conduct between consecutive RCAs to ensure the continued validity of your PM CEMS correlation.
3.7 “Sample Volume Audit (SVA)” means an evaluation of your PM CEMS measurement of sample volume if your PM CEMS determines PM concentration based on a measure of PM mass in an extracted sample volume and an independent determination of sample volume.
4.0 Interferences [Reserved] 5.0 What Do I Need To Know To Ensure the Safety of Persons Using Procedure 2?People using Procedure 2 may be exposed to hazardous materials, operations, and equipment. Procedure 2 does not purport to address all of the safety issues associated with its use. It is your responsibility to establish appropriate safety and health practices and determine the applicable regulatory limitations before performing this procedure. You must consult your CEMS user's manual for specific precautions to be taken with regard to your PM CEMS procedures.
6.0 What Equipment and Supplies Do I Need? [Reserved] 7.0 What Reagents and Standards Do I Need?You will need reference standards or procedures to perform the zero drift check, the upscale drift check, and the sample volume check.
7.1 What is the reference standard value for the zero drift check? You must use a zero check value that is no greater than 20 percent of the PM CEMS's response range. You must obtain documentation on the zero check value from your PM CEMS manufacturer.
7.2 What is the reference standard value for the upscale drift check? You must use an upscale check value that produces a response between 50 and 100 percent of the PM CEMS's response range. For a PM CEMS that produces output over a range of 4 mA to 20 mA, the upscale check value must produce a response in the range of 12 mA to 20 mA. You must obtain documentation on the upscale check value from your PM CEMS manufacturer.
7.3 What is the reference standard value for the sample volume check? You must use a reference standard value or procedure that produces a sample volume value equivalent to the normal sampling rate. You must obtain documentation on the sample volume value from your PM CEMS manufacturer.
8.0 What Sample Collection, Preservation, Storage, and Transport Are Relevant to This Procedure? [Reserved] 9.0 What Quality Control Measures Are Required by This Procedure for My PM CEMS?You must develop and implement a QC program for your PM CEMS. Your QC program must, at a minimum, include written procedures that describe, in detail, complete step-by-step procedures and operations for the activities in paragraphs (1) through (8) of this section.
(1) Procedures for performing drift checks, including both zero drift and upscale drift and the sample volume check (see sections 10.2(1), (2), and (5)).
(2) Methods for adjustment of PM CEMS based on the results of drift checks, sample volume checks (if applicable), and the periodic audits specified in this procedure.
(3) Preventative maintenance of PM CEMS (including spare parts inventory and sampling probe integrity).
(4) Data recording, calculations, and reporting.
(5) RCA and RRA procedures, including sampling and analysis methods, sampling strategy, and structuring test conditions over the prescribed range of PM concentrations.
(6) Procedures for performing ACAs and SVAs and methods for adjusting your PM CEMS response based on ACA and SVA results.
(7) Program of corrective action for malfunctioning PM CEMS, including flagged data periods.
(8) For extractive PM CEMS, procedures for checking extractive system ducts for material accumulation.
9.1 What QA/QC documentation must I have? You are required to keep the written QA/QC procedures on record and available for inspection by us, the State, and/or local enforcement agency for the life of your CEMS or until you are no longer subject to the requirements of this procedure.
9.2 How do I know if I have acceptable QC procedures for my PM CEMS? Your QC procedures are inadequate or your PM CEMS is incapable of providing quality data if you fail two consecutive QC audits (i.e., out-of-control conditions resulting from the annual audits, quarterly audits, or daily checks). Therefore, if you fail the same two consecutive audits, you must revise your QC procedures or modify or replace your PM CEMS to correct the deficiencies causing the excessive inaccuracies (see section 10.4 for limits for excessive audit inaccuracy).
10.0 What Calibration/Correlation and Standardization Procedures Must I Perform for My PM CEMS?You must generate a site-specific correlation for each of your PM CEMS installation(s) relating response from your PM CEMS to results from simultaneous PM reference method testing. The PS-11 defines procedures for developing the correlation and defines a series of statistical parameters for assessing acceptability of the correlation. However, a critical component of your PM CEMS correlation process is ensuring the accuracy and precision of reference method data. The activities listed in sections 10.1 through 10.10 assure the quality of the correlation.
10.1 When should I use paired trains for reference method testing? Although not required, we recommend that you should use paired-train reference method testing to generate data used to develop your PM CEMS correlation and for RCA testing. Guidance on the use of paired sampling trains can be found in the PM CEMS Knowledge Document (see section 16.5 of PS-11).
10.2 What routine system checks must I perform on my PM CEMS? You must perform routine checks to ensure proper operation of system electronics and optics, light and radiation sources and detectors, and electric or electro-mechanical systems. Necessary components of the routine system checks will depend on design details of your PM CEMS. As a minimum, you must verify the system operating parameters listed in paragraphs (1) through (5) of this section on a daily basis. Some PM CEMS may perform one or more of these functions automatically or as an integral portion of unit operations; for other PM CEMS, you must initiate or perform one or more of these functions manually.
(1) You must check the zero drift to ensure stability of your PM CEMS response to the zero check value. You must determine system output on the most sensitive measurement range when the PM CEMS is challenged with a zero reference standard or procedure. You must, at a minimum, adjust your PM CEMS whenever the daily zero drift exceeds 4 percent.
(2) You must check the upscale drift to ensure stability of your PM CEMS response to the upscale check value. You must determine system output when the PM CEMS is challenged with a reference standard or procedure corresponding to the upscale check value. You must, at a minimum, adjust your PM CEMS whenever the daily upscale drift check exceeds 4 percent.
(3) For light-scattering and extinction-type PM CEMS, you must check the system optics to ensure that system response has not been altered by the condition of optical components, such as fogging of lens and performance of light monitoring devices.
(4) You must record data from your automatic drift-adjusting PM CEMS before any adjustment is made. If your PM CEMS automatically adjusts its response to the corrected calibration values (e.g., microprocessor control), you must program your PM CEMS to record the unadjusted concentration measured in the drift check before resetting the calibration. Alternately, you may program your PM CEMS to record the amount of adjustment.
(5) For extractive PM CEMS that measure the sample volume and use the measured sample volume as part of calculating the output value, you must check the sample volume on a daily basis to verify the accuracy of the sample volume measuring equipment. This sample volume check must be done at the normal sampling rate of your PM CEMS. You must adjust your PM CEMS sample volume measurement whenever the daily sample volume check error exceeds 10 percent.
10.3 What are the auditing requirements for my PM CEMS? You must subject your PM CEMS to an ACA and an SVA, as applicable, at least once each calendar quarter. Successive quarterly audits must occur no closer than 2 months apart. You must conduct an RCA and an RRA at the frequencies specified in the applicable regulation or facility operating permit. An RRA or RCA conducted during any calendar quarter can take the place of the ACA required for that calendar quarter. An RCA conducted during the period in which an RRA is required can take the place of the RRA for that period.
(1) When must I perform an ACA? You must perform an ACA each quarter unless you conduct an RRA or RCA during that same quarter.
(2) How do I perform an ACA? You perform an ACA according to the procedure specified in paragraphs (2)(i) through (v) of this section.
(i) You must challenge your PM CEMS with an audit standard or an equivalent audit reference to reproduce the PM CEMS's measurement at three points within the following ranges:
Audit point | Audit range |
---|---|
1 | 0 to 20 percent of measurement range |
2 | 40 to 60 percent of measurement range |
3 | 70 to 100 percent of measurement range |
(ii) You must then challenge your PM CEMS three times at each audit point and use the average of the three responses in determining accuracy at each audit point. Use a separate audit standard for audit points 1, 2, and 3. Challenge the PM CEMS at each audit point for a sufficient period of time to ensure that your PM CEMS response has stabilized.
(iii) Operate your PM CEMS in the mode, manner, and range specified by the manufacturer.
(iv) Store, maintain, and use audit standards as recommended by the manufacturer.
(v) Use the difference between the actual known value of the audit standard and the response of your PM CEMS to assess the accuracy of your PM CEMS.
(3) When must I perform an SVA? You must perform an audit of the measured sample volume (e.g., the sampling flow rate for a known time) once per quarter for applicable PM CEMS with an extractive sampling system. Also, you must perform and pass an SVA prior to initiation of any of the reference method data collection runs for an RCA or RRA.
(4) How do I perform an SVA? You perform an SVA according to the procedure specified in paragraphs (4)(i) through (iii) of this section.
(i) You perform an SVA by independently measuring the volume of sample gas extracted from the stack or duct over each batch cycle or time period with a calibrated device. You may make this measurement either at the inlet or outlet of your PM CEMS, so long as it measures the sample gas volume without including any dilution or recycle air. Compare the measured volume with the volume reported by your PM CEMS for the same cycle or time period to calculate sample volume accuracy.
(ii) You must make measurements during three sampling cycles for batch extractive monitors (e.g., Beta-gauge) or during three periods of at least 20 minutes for continuous extractive PM CEMS.
(iii) You may need to condense, collect, and measure moisture from the sample gas prior to the calibrated measurement device (e.g., dry gas meter) and correct the results for moisture content. In any case, the volumes measured by the calibrated device and your PM CEMS must be on a consistent temperature, pressure, and moisture basis.
(5) How often must I perform an RRA? You must perform an RRA at the frequency specified in the applicable regulation or facility operating permit. You may conduct an RCA instead of an RRA during the period when the RRA is required.
(6) How do I perform an RRA? You must perform the RRA according to the procedure specified in paragraphs (6)(i) and (ii) of this section.
(i) You perform an RRA by collecting three simultaneous reference method PM concentration measurements and PM CEMS measurements at the as-found source operating conditions and PM concentration.
(ii) We recommend that you use paired trains for reference method sampling. Guidance on the use of paired sampling trains can be found in the PM CEMS Knowledge Document (see section 16.5 of PS-11).
(7) How often must I perform an RCA? You must perform an RCA at the frequency specified in the applicable regulation or facility operating permit.
(8) How do I perform an RCA? You must perform the RCA according to the procedures for the PM CEMS correlation test described in PS-11, section 8.6, except that the minimum number of runs required is 12 in the RCA instead of 15 as specified in PS-11.
(9) What other alternative audits can I use? You can use other alternative audit procedures as approved by us, the State, or local agency for the quarters when you would conduct ACAs.
10.4 What are my limits for excessive audit inaccuracy? Unless specified otherwise in the applicable subpart, the criteria for excessive audit inaccuracy are listed in paragraphs (1) through (6) of this section.
(1) What are the criteria for excessive zero or upscale drift? Your PM CEMS is out of control if the zero drift check or upscale drift check either exceeds 4 percent for five consecutive daily periods or exceeds 8 percent for any one day.
(2) What are the criteria for excessive sample volume measurement error? Your PM CEMS is out of control if sample volume check error exceeds 10 percent for five consecutive daily periods or exceeds 20 percent for any one day.
(3) What are the criteria for excessive ACA error? Your PM CEMS is out of control if the results of any ACA exceed ±10 percent of the average audit value, as calculated using Equation 2-1a, or 7.5 percent of the applicable standard, as calculated using Equation 2-1b, whichever is greater.
(4) What is the criterion for excessive SVA error? Your PM CEMS is out of control if results exceed ±5 percent of the average sample volume audit value.
(5) What are the criteria for passing a RCA? To pass a RCA, you must meet the criteria specified in paragraphs (5)(i) and (ii) of this section. If your PM CEMS fails to meet these RCA criteria, it is out of control.
(i) For all 12 data points, the PM CEMS response value can be no greater than the greatest PM CEMS response value used to develop your correlation curve.
(ii) At least 75 percent of a minimum number of 12 sets of PM CEMS and reference method measurements must fall within a specified area on a graph of the correlation regression line. The specified area on the graph of the correlation regression line is defined by two lines parallel to the correlation regression line, offset at a distance of ±25 percent of the numerical emission limit value from the correlation regression line. If any of the PM CEMS response values resulting from your RCA are lower than the lowest PM CEMS response value of your existing correlation curve, you may extend your correlation regression line to the point corresponding to the lowest PM CEMS response value obtained during the RCA. This extended correlation regression line must then be used to determine if the RCA data meets this criterion.
(6) What are the criteria to pass a RRA? To pass a RRA, you must meet the criteria specified in paragraphs (6)(i) and (ii) of this section. If your PM CEMS fails to meet these RRA criteria, it is out of control.
(i) For all three data points, the PM CEMS response value can be no greater than the greatest PM CEMS response value used to develop your correlation curve.
(ii) At least two of the three sets of PM CEMS and reference method measurements must fall within the same specified area on a graph of the correlation regression line as required for the RCA and described in paragraph (5)(ii) of this section.
10.5 What do I do if my PM CEMS is out of control? If your PM CEMS is out of control, you must take the actions listed in paragraphs (1) and (2) of this section.
(1) You must take necessary corrective action to eliminate the problem and perform tests, as appropriate, to ensure that the corrective action was successful.
(i) Following corrective action, you must repeat the previously failed audit to confirm that your PM CEMS is operating within the specifications.
(ii) If your PM CEMS failed an RRA, you must take corrective action until your PM CEMS passes the RRA criteria. If the RRA criteria cannot be achieved, you must perform an RCA.
(iii) If your PM CEMS failed an RCA, you must follow procedures specified in section 10.6 of this procedure.
(2) You must report both the audit showing your PM CEMS to be out of control and the results of the audit following corrective action showing your PM CEMS to be operating within specifications.
10.6 What do I do if my PM CEMS fails an RCA? After an RCA failure, you must take all applicable actions listed in paragraphs (1) through (3) of this section.
(1) Combine RCA data with data from the active PM CEMS correlation and perform the mathematical evaluations defined in PS-11 for development of a PM CEMS correlation, including examination of alternate correlation models (i.e., linear, polynomial, logarithmic, exponential, and power). If the expanded data base and revised correlation meet PS-11 statistical criteria, use the revised correlation.
(2) If the criteria specified in paragraph (1) of this section are not achieved, you must develop a new PM CEMS correlation based on revised data. The revised data set must consist of the test results from only the RCA. The new data must meet all requirements of PS-11 to develop a revised PM CEMS correlation, except that the minimum number of sets of PM CEMS and reference method measurements is 12 instead of the minimum of 15 sets required by PS-11. Your PM CEMS is considered to be back in controlled status when the revised correlation meets all of the performance criteria specified in section 13.2 of PS-11.
(3) If the actions in paragraphs (1) and (2) of this section do not result in an acceptable correlation, you must evaluate the cause(s) and comply with the actions listed in paragraphs (3)(i) through (iv) of this section within 90 days after the completion of the failed RCA.
(i) Completely inspect your PM CEMS for mechanical or operational problems. If you find a mechanical or operational problem, repair your PM CEMS and repeat the RCA.
(ii) You may need to relocate your PM CEMS to a more appropriate measurement location. If you relocate your PM CEMS, you must perform a new correlation test according to the procedures specified in PS-11.
(iii) The characteristics of the PM or gas in your source's flue gas stream may have changed such that your PM CEMS measurement technology is no longer appropriate. If this is the case, you must install a PM CEMS with measurement technology that is appropriate for your source's flue gas characteristics. You must perform a new correlation test according to the procedures specified in PS-11.
(iv) If the corrective actions in paragraphs (3)(i) through (iii) of this section were not successful, you must petition us, the State, or local agency for approval of alternative criteria or an alternative for continuous PM monitoring.
10.7 When does the out-of-control period begin and end? The out-of-control period begins immediately after the last test run or check of an unsuccessful RCA, RRA, ACA, SVA, drift check, or sample volume check. The out-of-control period ends immediately after the last test run or check of the subsequent successful audit or drift check.
10.8 Can I use the data recorded by my PM CEMS during out-of-control periods? During any period when your PM CEMS is out of control, you may not use your PM CEMS data to calculate emission compliance or to meet minimum data availability requirements described in the applicable regulation.
10.9 What are the QA/QC reporting requirements for my PM CEMS? You must report the accuracy results for your PM CEMS, specified in section 10.4 of this procedure, at the interval specified in the applicable regulation. Report the drift and accuracy information as a Data Assessment Report (DAR), and include one copy of this DAR for each quarterly audit with the report of emissions required under the applicable regulation. An example DAR is provided in Procedure 1, Appendix F of this part.
10.10 What minimum information must I include in my DAR? As a minimum, you must include the information listed in paragraphs (1) through (5) of this section in the DAR:
(1) Your name and address.
(2) Identification and location of monitors in your CEMS.
(3) Manufacturer and model number of each monitor in your CEMS.
(4) Assessment of PM CEMS data accuracy/acceptability, and date of assessment, as determined by an RCA, RRA, ACA, or SVA described in section 10, including the acceptability determination for the RCA or RRA, the accuracy for the ACA or SVA, the reference method results, the audit standards, your PM CEMS responses, and the calculation results as defined in section 12. If the accuracy audit results show your PM CEMS to be out of control, you must report both the audit results showing your PM CEMS to be out of control and the results of the audit following corrective action showing your PM CEMS to be operating within specifications.
(5) Summary of all corrective actions you took when you determined your PM CEMS to be out of control, as described in section 10.5, or after failing on RCA, as described in section 10.6.
10.7 Where and how long must I retain the QA data that this procedure requires me to record for my PM CEMS? You must keep the records required by this procedure for your PM CEMS onsite and available for inspection by us, the State, and/or local enforcement agency for a period of 5 years.
11.0 What Analytical Procedures Apply to This Procedure?Sample collection and analysis are concurrent for this procedure. You must refer to the appropriate reference method for the specific analytical procedures.
12.0 What Calculations and Data Analysis Must I Perform for my PM CEMS?(1) How do I determine RCA and RRA acceptability? You must plot each of your PM CEMS and reference method data sets from an RCA or RRA on a graph based on your PM CEMS correlation line to determine if the criteria in paragraphs 10.4(5) or (6), respectively, are met.
(2) How do I calculate ACA accuracy? You must use either Equation 2-1a or 2-1b to calculate ACA accuracy for each of the three audit points. However, when calculating ACA accuracy for the first audit point (0 to 20 percent of measurement range), you must use Equation 2-1b to calculate ACA accuracy if the reference standard value (Rv) equals zero.
Where: ACA Accuracy = The ACA accuracy at each audit point, in percent, RCEM = Your PM CEMS response to the reference standard, and RV = The reference standard value. Where: ACA Accuracy = The ACA accuracy at each audit point, in percent, CCEM = The PM concentration that corresponds to your PM CEMS response to the reference standard, as calculated using the correlation equation for your PM CEMS, CRV = The PM concentration that corresponds to the reference standard value in units consistent with CCEM, and Cs = The PM concentration that corresponds to the applicable emission limit in units consistent with CCEM.(3) How do I calculate daily upscale and zero drift? You must calculate the upscale drift using Equation 2-2 and the zero drift using Equation 2-3:


(4) How do I calculate SVA accuracy? You must use Equation 2-4 to calculate the accuracy, in percent, for each of the three SVA tests or the daily sample volume check:

Before calculating SVA accuracy, you must correct the sample gas volumes measured by your PM CEMS and the independent calibrated reference device to the same basis of temperature, pressure, and moisture content. You must document all data and calculations.
13.0 Method Performance [Reserved] 14.0 Pollution Prevention [Reserved] 15.0 Waste Management [Reserved] 16.0 Which References are Relevant to This Method? [Reserved] 17.0 What Tables, Diagrams, Flowcharts, and Validation Data Are Relevant to This Method? [Reserved] Procedure 3 - Quality Assurance Requirements for Continuous Opacity Monitoring Systems at Stationary Sources 1.0 What are the purpose and applicability of Procedure 3?The purpose of Procedure 3 is to establish quality assurance and quality control (QA/QC) procedures for continuous opacity monitoring systems (COMS). Procedure 3 applies to COMS used to demonstrate continuous compliance with opacity standards specified in new source performance standards (NSPS) promulgated by EPA pursuant to section 111(b) of the Clean Air Act, 42 U.S.C. 7411(b) - Standards of Performance for New Stationary Sources.
1.1 What are the data quality objectives of Procedure 3? The overall data quality objective (DQO) of Procedure 3 is the generation of valid and representative opacity data. Procedure 3 specifies the minimum requirements for controlling and assessing the quality of COMS data submitted to us or the delegated regulatory agency. Procedure 3 requires you to perform periodic evaluations of a COMS performance and to develop and implement QA/QC programs to ensure that COMS data quality is maintained.
1.2 What is the intent of the QA/QC procedures specified in Procedure 3? Procedure 3 is intended to establish the minimum QA/QC requirements to verify and maintain an acceptable level of quality of the data produced by COMS. It is presented in general terms to allow you to develop a program that is most effective for your circumstances.
1.3 When must I comply with Procedure 3? You must comply with Procedure 3 no later than November 12, 2014.
2.0 What are the basic functions of Procedure 3?The basic functions of Procedure 3 are assessment of the quality of your COMS data and control and improvement of the quality of the data by implementing QC requirements and corrective actions. Procedure 3 provides requirements for:
(1) Daily instrument zero and upscale drift checks and status indicators checks;
(2) Quarterly performance audits which include the following assessments:
(i) Optical alignment,
(ii) Calibration error, and
(iii) Zero compensation.
Sources that achieve quality assured data for four consecutive quarters may reduce their auditing frequency to semi-annual. If a performance audit is failed, the source must resume quarterly testing for that audit requirement until it again demonstrates successful performance over four consecutive quarters.(3) Annual zero alignment.
3.0 What special definitions apply to Procedure 3?The definitions in Procedure 3 include those provided in Performance Specification 1 (PS-1) of Appendix B of this part and ASTM D6216-12 and the following additional definitions.
3.1 Out-of-control periods. Out-of-control periods mean that one or more COMS parameters falls outside of the acceptable limits established by this rule.
(1) Daily Assessments. Whenever the calibration drift (CD) exceeds twice the specification of PS-1, the COMS is out-of-control. The beginning of the out-of-control period is the time corresponding to the completion of the daily calibration drift check. The end of the out-of-control period is the time corresponding to the completion of appropriate adjustment and subsequent successful CD assessment.
(2) Quarterly and Annual Assessments. Whenever an annual zero alignment or quarterly performance audit fails to meet the criteria established in paragraphs (2) and (3) of section 10.4, the COMS is out-of-control. The beginning of the out-of-control period is the time corresponding to the completion of the performance audit indicating the failure to meet these established criteria. The end of the out-of-control period is the time corresponding to the completion of appropriate corrective actions and the subsequent successful audit (or, if applicable, partial audit).
4.0 What interferences must I avoid?Opacity cannot be measured accurately in the presence of condensed water vapor. Thus, COMS opacity compliance determinations cannot be made when condensed water vapor is present, such as downstream of a wet scrubber without a reheater or at other saturated flue gas locations. Therefore, COMS must be located where condensed water vapor is not present.
5.0 What do I need to know to ensure the safety of persons using Procedure 3?Those implementing Procedure 3 may be exposed to hazardous materials, operations and equipment. Procedure 3 does not purport to address all of the safety issues associated with its use. It is your responsibility to establish appropriate health and safety practices and determine the applicable regulatory limitations before performing this procedure. You should consult the COMS user's manual for specific precautions to take.
6.0 What equipment and supplies do I need?The equipment and supplies that you need are specified in PS-1. You are not required to purchase a new COMS if your existing COMS meets the requirements specified in Procedure 3.
7.0 What reagents and standards do I need?The reagents and standards that you need are specified in PS-1. You are not required to purchase a new COMS if your existing COMS meets the requirements specified in Procedure 3.
8.0 What sample collection, preservation, storage, and transport are relevant to this procedure? [Reserved] 9.0 What quality control measures are required by this procedure for my COMS?You must develop and implement a QC program for your COMS. Your QC program must, at a minimum, include written procedures which describe in detail complete step-by-step procedures and operations for the activities in paragraphs (1) through (4):
(1) Procedures for performing drift checks, including both zero and upscale drift and the status indicators check,
(2) Procedures for performing quarterly performance audits,
(3) A means of checking the zero alignment of the COMS, and
(4) A program of corrective action for a malfunctioning COMS. The corrective action must include, at a minimum, the requirements specified in section 10.5.
9.1 What QA/QC documentation must I have? You are required to keep the QA/QC written procedures required in section 9.0 on site and available for inspection by us, the state, and/or local enforcement agencies.
9.2 What actions must I take if I fail QC audits? If you fail two consecutive annual audits, two consecutive quarterly audits, or five consecutive daily checks, you must either revise your QC procedures or determine if your COMS is malfunctioning. If you determine that your COMS is malfunctioning, you must take the necessary corrective action as specified in section 10.5. If you determine that your COMS requires extensive repairs, you may use a substitute COMS provided the substitute meets the requirements in section 10.6.
10.0 What calibration and standardization procedures must I perform for my COMS?(1) You must perform daily system checks to ensure proper operation of system electronics and optics, light and radiation sources and detectors, electric or electro-mechanical systems, and general stability of the system calibration. Daily is defined as any portion of a calendar day in which a unit operates.
(2) You must subject your COMS to a performance audit to include checks of the individual COMS components and factors affecting the accuracy of the monitoring data at least once per QA operating quarter. A QA operating quarter is a calendar quarter in which a unit operates at least 168 hours.
(3) At least annually, you must perform a zero alignment by comparing the COMS simulated zero to the actual clear path zero. Annually is defined as a period wherein the unit is operating at least 28 days in a calendar year. The simulated zero device produces a simulated clear path condition or low-level opacity condition, where the energy reaching the detector is between 90 and 110 percent of the energy reaching the detector under actual clear path conditions.
10.1 What daily system checks must I perform on my COMS? The specific components required to undergo daily system checks will depend on the design details of your COMS. At a minimum, you must verify the system operating parameters listed in paragraphs (1) through (3) of this section. Some COMS may perform one or more of these functions automatically or as an integral portion of unit operations; other COMS may perform one or more of these functions manually.
(1) You must check the zero drift to ensure stability of your COMS response to the simulated zero device. The simulated zero device, an automated mechanism within the transmissometer that produces a simulated clear path condition or low-level opacity condition, is used to check the zero drift. You must, at a minimum, take corrective action on your COMS whenever the daily zero drift exceeds twice the applicable drift specification in section 13.3(6) of PS-1.
(2) You must check the upscale drift to ensure stability of your COMS response to the upscale drift value. The upscale calibration device, an automated mechanism (employing an attenuator or reduced reflectance device) within the transmissometer that produces an upscale opacity value is used to check the upscale drift. You must, at a minimum, take corrective action on your COMS whenever the daily upscale drift check exceeds twice the applicable drift specification in section 13.3(6) of PS-1.
(3) You must, at a minimum, check the status indicators, data acquisition system error messages, and other system self-diagnostic indicators. You must take appropriate corrective action based on the manufacturer's recommendations when the COMS is operating outside preset limits.
10.2 What are the quarterly auditing requirements for my COMS? At a minimum, the parameters listed in paragraphs (1) through (3) of this section must be included in the performance audit conducted on a quarterly basis as defined in section 10.0(2).
(1) For units with automatic zero compensation, you must determine the zero compensation for the COMS. The value of the zero compensation applied at the time of the audit must be calculated as equivalent opacity and corrected to stack exit conditions according to the procedures specified by the manufacturer. The compensation applied to the effluent by the monitor system must be recorded.
(2) You must conduct a three-point calibration error test of the COMS. Three calibration attenuators, either primary or secondary must meet the requirements of PS-1, with one exception. Instead of recalibrating the attenuators semi-annually, they must be recalibrated annually. If two annual calibrations agree within 0.5 percent opacity, the attenuators may then be calibrated once every five years. The three attenuators must be placed in the COMS light beam path for at least three nonconsecutive readings. All monitor responses must then be independently recorded from the COMS permanent data recorder. Additional guidance for conducting this test is included in section 8.1(3)(ii) of PS-1. The low-, mid-, and high-range calibration error results must be computed as the mean difference and 95 percent confidence interval for the difference between the expected and actual responses of the monitor as corrected to stack exit conditions. The equations necessary to perform the calculations are found in section 12.0 of PS-1. For the calibration error test method, you must use the external audit device. When the external audit device is installed, with no calibration attenuator inserted, the COMS measurement reading must be less than or equal to one percent opacity. You must also document procedures for properly handling and storing the external audit device and calibration attenuators within your written QC program.
(3) You must check the optical alignment of the COMS in accordance with the instrument manufacturer's recommendations. If the optical alignment varies with stack temperature, perform the optical alignment test when the unit is operating.
10.3 What are the annual auditing requirements for my COMS?
(1) You must perform the primary zero alignment method under clear path conditions. The COMS must be removed from its installation and set up under clear path conditions. There must be no adjustments to the monitor other than the establishment of the proper monitor path length and correct optical alignment of the COMS components. You must record the COMS response to a clear condition and to the COMS's simulated zero condition as percent opacity corrected to stack exit conditions. For a COMS with automatic zero compensation, you must disconnect or disable the zero compensation mechanism or record the amount of correction applied to the COMS's simulated zero condition. The response difference in percent opacity to the clear path and simulated zero conditions must be recorded as the zero alignment error. You must adjust the COMS's simulated zero device to provide the same response as the clear path condition as specified in paragraph (3) of section 10.0.
(2) As an alternative, monitors capable of allowing the installation of an external zero device may use the device for the zero alignment provided that: (1) The external zero device setting has been established for the monitor path length and recorded for the specific COMS by comparison of the COMS responses to the installed external zero device and to the clear path condition, and (2) the external zero device is demonstrated to be capable of producing a consistent zero response when it is repeatedly (i.e., three consecutive installations and removals prior to conducting the final zero alignment check) installed on the COMS. This can be demonstrated by either the manufacturer's certificate of conformance (MCOC) or actual on-site performance. The external zero device setting must be permanently set at the time of initial zeroing to the clear path zero value and protected when not in use to ensure that the setting equivalent to zero opacity does not change. The external zero device response must be checked and recorded prior to initiating the zero alignment. If the external zero device setting has changed, you must remove the COMS from the stack in order to reset the external zero device. If you employ an external zero device, you must perform the zero alignment audits with the COMS off the stack at least every three years. If the external zero device is adjusted within the three-year period, you must perform the zero alignment with the COMS off the stack no later than three years from the date of adjustment.
(3) The procedure in section 6.8 of ASTM D6216-12 is allowed.
10.4 What are my limits for excessive audit inaccuracy? Unless specified otherwise in the applicable subpart, the criteria for excessive inaccuracy are listed in paragraphs (1) through (4).
(1) What is the criterion for excessive zero or upscale drift? Your COMS is out-of-control if either the zero drift check or upscale drift check exceeds twice the applicable drift specification in PS-1 for any one day.
(2) What is the criterion for excessive zero alignment? Your COMS is out-of-control if the zero alignment error exceeds 2 percent opacity.
(3) What is the criterion to pass the quarterly performance audit? Your COMS is out-of-control if the results of a quarterly performance audit indicate noncompliance with the following criteria:
(i) The optical alignment indicator does not show proper alignment (i.e., does not fall within a specific reference mark or condition).
(ii) The zero compensation exceeds 4 percent opacity, or
(iii) The calibration error exceeds 3 percent opacity.
(4) What is the criterion for data capture? You must adhere to the data capture criterion specified in the applicable subpart.
10.5 What corrective action must I take if my COMS is malfunctioning? You must have a corrective action program in place to address the repair and/or maintenance of your COMS. The corrective action program must address routine/preventative maintenance and various types of analyzer repairs. The corrective action program must establish what diagnostic testing must be performed after each type of activity to ensure that the COMS is collecting valid, quality-assured data. Recommended maintenance and repair procedures and diagnostic testing after repairs may be found in an associated guidance document.
10.6 What requirements must I meet if I use a temporary opacity monitor?
(1) In the event that your certified opacity monitor has to be removed for extended service, you may install a temporary replacement monitor to obtain required opacity emissions data provided that:
(i) The temporary monitor has been certified according to ASTM D6216-12 for which a MCOC has been provided;
(ii) The use of the temporary monitor does not exceed 1080 hours (45 days) of operation per year as a replacement for a fully certified opacity monitor. After that time, the analyzer must complete a full certification according to PS-1 prior to further use as a temporary replacement monitor. Once a temporary replacement monitor has been installed and required testing and adjustments have been successfully completed, it cannot be replaced by another temporary replacement monitor to avoid the full PS-1 certification testing required after 1080 hours (45 days) of use;
(iii) The temporary monitor has been installed and successfully completed an optical alignment assessment and status indicator assessment;
(iv) The temporary monitor has successfully completed an off-stack clear path zero assessment and zero calibration value adjustment procedure;
(v) The temporary monitor has successfully completed an abbreviated zero and upscale drift check consisting of seven zero and upscale calibration value drift checks which may be conducted within a 24-hour period with not more than one calibration drift check every three hours and not less than one calibration drift check every 25 hours. Calculated zero and upscale drift requirements are the same as specified for the normal PS-1 certification;
(vi) The temporary monitor has successfully completed a three-point calibration error test;
(vii) The upscale reference calibration check value of the new monitor has been updated in the associated data recording equipment;
(viii) The overall calibration of the monitor and data recording equipment has been verified; and
(ix) The user has documented all of the above in the maintenance log.
(2) Data generated by the temporary monitor is considered valid when paragraphs (i) through (ix) in this section have been met.
10.7 When do out-of-control periods begin and end? The out-of-control periods are as specified in section 3.1.
10.8 What are the limitations on the use of my COMS data collected during out-of-control periods? During the period your COMS is out-of-control, you may not use your COMS data to calculate emission compliance or to meet minimum data capture requirements in this procedure or the applicable regulation.
10.9 What are the QA/QC reporting requirements for my COMS? You must report in a Data Assessment Report (DAR) the information required by sections 10.0, 10.1, 10.2, and 10.3 for your COMS at the interval specified in the applicable regulation.
10.10 What minimum information must I include in my DAR? At a minimum, you must include the information listed in paragraphs (1) through (5) of this section in the DAR.
(1) Name of person completing the report and facility address,
(2) Identification and location of your COMS(s),
(3) Manufacturer, model, and serial number of your COMS(s),
(4) Assessment of COMS data accuracy/acceptability and date of assessment as determined by a performance audit described in section 10.0. If the accuracy audit results show your COMS to be out-of-control, you must report both the audit results showing your COMS to be out-of-control and the results of the audit following corrective action showing your COMS to be operating within specifications, and
(5) Summary of all corrective actions you took when you determined your COMS was out-of-control.
10.11 Where and how long must I retain the QA data that this procedure requires me to record for my COMS? You must keep the records required by this procedure for your COMS on site and available for inspection by us, the state, and/or the local enforcement agency for the period specified in the regulations requiring the use of COMS.
11.0 What analytical procedures apply to this procedure? [Reserved] 12.0 What calculations and data analysis must I perform for my COMS? The calculations required for the quarterly performance audit are in section 12.0 of PS-1. 13.0 Method Performance [Reserved] 14.0 Pollution Prevention [Reserved] 15.0 Waste Management [Reserved] 16.0 References16.1 Performance Specification 1-Specifications and Test Procedures for Continuous Opacity Monitoring Systems in Stationary Sources, 40 CFR part 60, Appendix B.
16.2 ASTM D6216-12-Standard Practice for Opacity Monitor Manufacturers to Certify Conformance with Design and Performance Specifications, American Society for Testing and Materials (ASTM).
17.0 What tables, diagrams, flowcharts, and validation data are relevant to this procedure? [Reserved] Procedure 4. [Reserved] Procedure 5. Quality Assurance Requirements for Vapor Phase Mercury Continuous Emissions Monitoring Systems and Sorbent Trap Monitoring Systems Used for Compliance Determination at Stationary Sources 1.0 Applicability and Principle1.1 Applicability. The purpose of Procedure 5 is to establish the minimum requirements for evaluating the effectiveness of quality control (QC) and quality assurance (QA) procedures as well as the quality of data produced by vapor phase mercury (Hg) continuous emissions monitoring systems (CEMS) and sorbent trap monitoring systems. Procedure 5 applies to Hg CEMS and sorbent trap monitoring systems used for continuously determining compliance with emission standards or operating permit limits as specified in an applicable regulation or permit. Other QA/QC procedures may apply to other auxiliary monitoring equipment that may be needed to determine Hg emissions in the units of measure specified in an applicable permit or regulation.
Procedure 5 covers the measurement of Hg emissions as defined in Performance Specification 12A (PS 12A) and Performance Specification 12B (PS 12B) in appendix B to this part, i.e., total vapor phase Hg representing the sum of the elemental (Hg°, CAS Number 7439-97-6) and oxidized (Hg+2) forms of gaseous Hg.
Procedure 5 specifies the minimum requirements for controlling and assessing the quality of Hg CEMS and sorbent trap monitoring system data submitted to EPA or a delegated permitting authority. You must meet these minimum requirements if you are responsible for one or more Hg CEMS or sorbent trap monitoring systems used for compliance monitoring. We encourage you to develop and implement a more extensive QA program or to continue such programs where they already exist.
You must comply with the basic requirements of Procedure 5 immediately following successful completion of the initial performance test described in PS 12A or PS 12B in appendix B to this part (as applicable).
1.2 Principle. The QA procedures consist of two distinct and equally important functions. One function is the assessment of the quality of the Hg CEMS or sorbent trap monitoring system data by estimating accuracy. The other function is the control and improvement of the quality of the CEMS or sorbent trap monitoring system data by implementing QC policies and corrective actions. These two functions form a control loop: When the assessment function indicates that the data quality is inadequate, the quality control effort must be increased until the data quality is acceptable. In order to provide uniformity in the assessment and reporting of data quality, this procedure explicitly specifies assessment methods for calibration drift, system integrity, and accuracy. Several of the procedures are based on those of PS 12A and PS 12B in appendix B to this part. Because the control and corrective action function encompasses a variety of policies, specifications, standards, and corrective measures, this procedure treats QC requirements in general terms to allow each source owner or operator to develop a QC system that is most effective and efficient for the circumstances.
2.0 Definitions2.1 Mercury Continuous Emission Monitoring System (Hg CEMS) means the equipment required for the determination of the total vapor phase Hg concentration in the stack effluent. The Hg CEMS consists of the following major subsystems:
2.1.1 Sample Interface means that portion of the CEMS used for one or more of the following: sample acquisition, sample transport, sample conditioning, and protection of the monitor from the effects of the stack effluent.
2.1.2 Hg Analyzer means that portion of the Hg CEMS that measures the total vapor phase Hg concentration and generates a proportional output.
2.1.3 Data Recorder means that portion of the CEMS that provides a permanent electronic record of the analyzer output. The data recorder may provide automatic data reduction and CEMS control capabilities.
2.2 Sorbent Trap Monitoring System means the total equipment required for the collection of gaseous Hg samples using paired three-partition sorbent traps as described in PS 12B in appendix B to this part.
2.3 Span Value means the measurement range as specified for the affected source category in the applicable regulation and/or monitoring performance specification.
2.4 Zero, Mid-Level, and High Level Values means the reference gas concentrations used for calibration drift assessments and system integrity checks on a Hg CEMS, expressed as percentages of the span value (see section 7.1 of PS 12A in appendix B to this part).
2.5 Calibration Drift (CD) means the absolute value of the difference between the CEMS output response and either the upscale Hg reference gas or the zero-level Hg reference gas, expressed as a percentage of the span value, when the entire CEMS, including the sampling interface, is challenged after a stated period of operation during which no unscheduled maintenance, repair, or adjustment took place.
2.6 System Integrity (SI) Check means a test procedure assessing transport and measurement of oxidized Hg by a Hg CEMS. In particular, system integrity is expressed as the absolute value of the difference between the CEMS output response and the reference value of either a mid- or high-level mercuric chloride (HgCl2) reference gas, as a percentage of span, when the entire CEMS, including the sampling interface, is challenged.
2.7 Relative Accuracy (RA) means the absolute mean difference between the pollutant concentrations determined by a continuous monitoring system (e.g., Hg CEMS or sorbent trap monitoring system) and the values determined by a reference method (RM) plus the 2.5 percent error confidence coefficient of a series of tests divided by the mean of the RM tests. Alternatively, for sources with an average RM concentration less than 5.0 micrograms per standard cubic meter (µg/scm), the RA may be expressed as the absolute value of the difference between the mean CEMS and RM values.
2.8 Relative Accuracy Test Audit (RATA) means an audit test procedure consisting of at least nine runs, in which the accuracy of the total vapor phase Hg concentrations measured by a CEMS or sorbent trap monitoring system is evaluated by comparison against concurrent measurements made with a reference test method.
2.9 Quarterly Gas Audit (QGA) means an audit procedure in which the accuracy of the total vapor phase Hg concentrations measured by a CEMS is evaluated by challenging the CEMS with a zero and two upscale reference gases.
3.0 QC Requirements3.1 Each source owner or operator must develop and implement a QC program. At a minimum, each QC program must include written procedures which should describe in detail, complete, step-by-step procedures and operations for each of the following activities (as applicable):
(a) Calibration drift (CD) checks of Hg CEMS.
(b) CD determination and adjustment of Hg CEMS.
(c) Weekly system integrity check procedures for Hg CEMS.
(d) Routine operation, maintenance, and QA/QC procedures for sorbent trap monitoring systems.
(e) Routine and preventive maintenance procedures for Hg CEMS (including spare parts inventory).
(f) Data recording, calculations, and reporting.
(g) Accuracy audit procedures for Hg CEMS and sorbent trap monitoring systems including sampling and analysis methods.
(h) Program of corrective action for malfunctioning Hg CEMS and sorbent trap monitoring systems.
These written procedures must be kept on record and available for inspection by the responsible enforcement agency. Also, as noted in section 5.2.4, below, whenever excessive inaccuracies of a Hg CEMS occur for two consecutive quarters, the source owner or operator must revise the current written procedures or modify or replace the CEMS or sorbent trap monitoring system to correct the deficiency causing the excessive inaccuracies.
4.0 Calibration Drift (CD) Assessment4.1 CD Requirement. As described in 40 CFR 60.13(d) and 63.8(c), source owners and operators of Hg CEMS must check, record, and quantify the CD at two concentration values at least once daily (approximately 24 hours) in accordance with the method prescribed by the manufacturer. The Hg CEMS calibration must, as minimum, be adjusted whenever the daily zero (or low-level) CD or the daily high-level CD exceeds two times the limits of the applicable PS in appendix B of this part.
4.2 Recording Requirement for Automatic CD Adjusting CEMS. CEMS that automatically adjust the data to the corrected calibration values (e.g., microprocessor control) must either be programmed to record the unadjusted concentration measured in the CD prior to resetting the calibration, if performed, or to record the amount of adjustment.
4.3 Criteria for Excessive CD. If either the zero (or low-level) or high-level CD result exceeds twice the applicable drift specification in section 13.2 of PS 12A in appendix B to this part for five, consecutive, daily periods, the CEMS is out-of-control. If either the zero (or low-level) or high-level CD result exceeds four times the applicable drift specification in PS 12A during any CD check, the CEMS is out-of-control. If the CEMS is out-of-control, take necessary corrective action. Following corrective action, repeat the CD checks.
4.3.1 Out-Of-Control Period Definition. The beginning of the out-of-control period is the time corresponding to the completion of the fifth, consecutive, daily CD check with a CD in excess of two times the allowable limit, or the time corresponding to the completion of the daily CD check preceding the daily CD check that results in a CD in excess of four times the allowable limit. The end of the out-of-control period is the time corresponding to the completion of the CD check following corrective action that results in the CD's at both the zero (or low-level) and high-level measurement points being within the corresponding allowable CD limit (i.e., either two times or four times the allowable limit in the applicable PS in appendix B).
4.3.2 CEMS Data Status During Out-of-Control Period. During the period the CEMS is out-of-control, the CEMS data may not be used either to determine compliance with an emission limit or to meet a minimum data availability requirement specified in an applicable regulation or permit.
5.0 Data Accuracy Assessment5.1 Hg CEMS Audit Requirements. For each Hg CEMS, an accuracy audit must be performed at least once each calendar quarter. Successive quarterly audits must, to the extent practicable, be performed no less than 2 months apart. The audits must be conducted as follows:
5.1.1 Relative Accuracy Test Audit (RATA). A RATA of the Hg CEMS must be conducted at least once every four calendar quarters, except as otherwise noted in section 5.1.4 of this appendix. Perform the RATA as described in section 8.5 of PS 12A in appendix B to this part. Calculate the results according to section 12.4 of PS 12A.
5.1.2 Quarterly Gas Audit. A quarterly gas audit (QGA) may be conducted in three of four calendar quarters, but in no more than three quarters in succession. To perform a QGA, challenge the CEMS with a zero-level and two upscale level audit gases of known concentrations, first of elemental Hg and then of oxidized Hg, within the following ranges:
Audit point | Audit range |
---|---|
1 | 20 to 30% of span value. |
2 | 50 to 60% of span value. |
Sequentially inject each of the three audit gases (zero and two upscale), three times each for a total of nine injections. Inject the gases in such a manner that the entire CEMS is challenged. Do not inject the same gas concentration twice in succession.
Use elemental Hg and oxidized Hg (mercuric chloride, HgCl2) audit gases that are National Institute of Standards and Technology (NIST)-certified or NIST-traceable following an EPA Traceability Protocol. If audit gas cylinders are used, do not dilute gas when challenging the Hg CEMS. For each reference gas concentration, determine the average of the three CEMS responses and subtract the average response from the reference gas value. Calculate the measurement error at each gas level using Equation 12A-1 in section 8.2 of PS 12A.
5.1.3 Relative Accuracy Audit (RAA). As an alternative to the QGA, a RAA may be conducted in three of four calendar quarters, but in no more than three quarters in succession. To conduct a RAA, follow the RATA test procedures in section 8.5 of PS 12A in appendix B to this part, except that only three test runs are required.
5.1.4 Alternative Quarterly Audits. Alternative quarterly audit procedures may be used as approved by the Administrator for three of four calendar quarters. One RATA is required at least every four calendar quarters, except in the case where the affected facility is off-line (does not operate) in the fourth calendar quarter since the quarter of the previous RATA. In that case, the RATA must be performed in the quarter in which the unit recommences operation. Also, quarterly gas audits (or RAAs, if applicable) are not required for calendar quarters in which the affected facility does not operate.
5.2 Sorbent Trap Monitoring System Audit Requirements. For each sorbent trap monitoring system, a RATA must be conducted at least once every four calendar quarters, except as otherwise noted in section 5.1.4 of this appendix. Perform the RATA as described in section 8.3 of PS 12B in appendix B to this part. Calculate the results according to section 12.4 of PS 12A.
5.3 Excessive Audit Inaccuracy. If the results of a RATA, QGA, or RAA exceed the applicable criteria in section 5.3.3, the Hg CEMS or sorbent trap monitoring system is out-of-control. If the Hg CEMS or sorbent trap monitoring system is out-of-control, take necessary corrective action to eliminate the problem. Following corrective action, the source owner or operator must audit the CEMS or sorbent trap monitoring system using the same type of test that failed to meet the accuracy criterion. For instance, a RATA must always be performed following an out-of-control period resulting from a failed RATA. Whenever audit results show the Hg CEMS or sorbent trap monitoring system to be out-of-control, the owner or operator must report both the results of the failed test and the results of the retest following corrective action showing the CEMS to be operating within specifications.
5.3.1 Out-Of-Control Period Definition. The beginning of the out-of-control period is the hour immediately following the completion of a RATA, RAA, QGA or system integrity check that fails to meet the applicable performance criteria in section 5.3.3, below. The end of the out-of-control period is the time corresponding to the completion of a subsequent successful test of the same type.
5.3.2 Monitoring Data Status During Out-Of-Control Period. During the period the monitor is out-of-control, the monitoring data may not be used to determine compliance with an applicable emission limit or to meet a minimum data availability requirement in an applicable regulation or permit.
5.3.3 Criteria for Excessive Audit Inaccuracy. Unless specified otherwise in an applicable regulation or permit, the criteria for excessive inaccuracy are:
(a) For the RATA, the allowable RA in the applicable PS in appendix B (e.g., PS 12A or PS 12B).
(b) For the QGA, ±15 percent of the average audit value or ±0.5 µg/m 3, whichever is greater.
(c) For the RAA, ±20 percent of the three run average or ±10 percent of the applicable standard, whichever is greater.
5.3.4 Criteria for Acceptable QC Procedures. Repeated excessive inaccuracies (i.e., out-of-control conditions resulting from the quarterly audits) indicates the QC procedures are inadequate or that the CEMS or sorbent trap monitoring system is incapable of providing quality data. Therefore, whenever excessive inaccuracies occur for two consecutive quarters, the source owner or operator must revise the QC procedures (see section 3) or modify, repair, or replace the CEMS or sorbent trap monitoring system.
6.0 Reporting Requirements6.1 Data Assessment Report. At the reporting interval specified in the applicable regulation or permit, report for each Hg CEMS and/or sorbent trap monitoring system the accuracy assessment results from section 5, above. For Hg CEMS, also report the CD assessment results from section 4, above. Report this information as a Data Assessment Report (DAR), and include the appropriate DAR(s) with the emissions report required under the applicable regulation or permit.
6.2 Contents of the DAR. At a minimum, the DAR must contain the following information:
6.2.1 Facility name and address including identification of source owner/operator.
6.2.2 Identification and location of each Hg CEMS and/or sorbent trap monitoring system.
6.2.3 Manufacturer, model, and serial number of each Hg CEMS and/or sorbent trap monitoring system.
6.2.4 CD Assessment for each Hg CEMS, including the identification of out-of-control periods.
6.2.5 System integrity check data for each Hg CEMS.
6.2.6 Accuracy assessment for each Hg CEMS and/or sorbent trap monitoring system, including the identification of out-of-control periods. The results of all required RATAs, QGAs, RAAs, and audits of auxiliary equipment must be reported. If an accuracy audit shows a CEMS or sorbent trap monitoring system to be out-of-control, report both the audit results that caused the out-of-control period and the results of the retest following corrective action, showing the monitoring system to be operating within specifications.
6.2.7 Summary of all corrective actions taken when the Hg CEMS and/or sorbent trap monitoring system was determined to be out-of-control.
6.3 Data Retention. As required in 40 CFR 60.7(d) and 63.10(b), all measurements from CEMS and sorbent trap monitoring systems, including the quality assurance data required by this procedure, must be retained by the source owner for at least 5 years.
7.0 Bibliography7.1 Calculation and Interpretation of Accuracy for Continuous Emission Monitoring Systems (CEMS). section 3.0.7 of the Quality Assurance Handbook for Air Pollution Measurement Systems, Volume III, Stationary Source Specific Methods. EPA-600/4-77-027b. August 1977. U.S. Environmental Protection Agency. Office of Research and Development Publications, 26 West St. Clair Street, Cincinnati, OH 45268.
Procedure 6. Quality Assurance Requirements for Gaseous Hydrogen Chloride (HCl) Continuous Emission Monitoring Systems Used for Compliance Determination at Stationary Sources 1.0 Applicability and Principle1.1 Applicability. Procedure 6 is used to evaluate the effectiveness of quality control (QC) and quality assurance (QA) procedures and evaluate the quality of data produced by any hydrogen chloride (HCl) gas, CAS: 7647-01-0, continuous emission monitoring system (CEMS) that is used for determining compliance with emission standards for HCl on a continuous basis as specified in an applicable permit or regulation.
1.1.1 This procedure specifies the minimum QA requirements necessary for the control and assessment of the quality of CEMS data submitted to the Environmental Protection Agency (EPA) or a delegated authority. If you are responsible for one or more CEMS used for HCl compliance monitoring you must meet these minimum requirements and you are encouraged to develop and implement a more extensive QA program or to continue such programs where they already exist.
1.1.2 Data collected as a result of QA and QC measures required in this procedure are to be submitted to the EPA or the delegated authority in accordance with the applicable regulation or permit. These data are to be used by both the delegated authority and you, as the CEMS operator, in assessing the effectiveness of the CEMS QC and QA procedures in the maintenance of acceptable CEMS operation and valid emission data.
1.2 Principle1.2.1 The QA procedures consist of two distinct and equally important functions. One function is the assessment of the quality of the CEMS data by estimating accuracy. The other function is the control and improvement of the quality of the CEMS data by implementing QC policies and corrective actions. These two functions form an iterative control loop. When the assessment function indicates that the data quality is inadequate, the control effort must be increased until the data quality is acceptable. In order to provide uniformity in the assessment and reporting of data quality, this procedure specifies the assessment procedures to evaluate response drift and accuracy. The procedures specified are based on Performance Specification 18 (PS-18) in appendix B to this part.
(Note: Because the control and corrective action function encompasses a variety of policies, specifications, standards and corrective measures, this procedure treats QC requirements in general terms to allow you, as source owner or operator to develop the most effective and efficient QC system for your circumstances.)
2.0 DefinitionsSee PS-18 of this subpart for the primary definitions used in this Procedure.
3.0 QC Requirements3.1 You, as a source owner or operator, must develop and implement a QC program. At a minimum, each QC program must include written procedures and/or manufacturer's information which should describe in detail, complete, step-by-step procedures and operations for each of the following activities:
(a) Calibration Drift (CD) checks of CEMS;
(b) CD determination and adjustment of CEMS;
(c) Integrated Path (IP) CEMS temperature and pressure sensor accuracy checks;
(d) IP CEMS beam intensity checks;
(e) Routine and preventative maintenance of CEMS (including spare parts inventory);
(f) Data recording, calculations, and reporting;
(g) Accuracy audit procedures for CEMS including reference method(s); and
(h) Program of corrective action for malfunctioning CEMS.
3.2 These written procedures must be kept on site and available for inspection by the delegated authority. As described in section 5.4, whenever excessive inaccuracies occur for two consecutive quarters, you must revise the current written procedures, or modify or replace the CEMS to correct the deficiency causing the excessive inaccuracies.
4.0 Daily Data Quality Requirements and Measurement Standardization Procedures4.1 CD Assessment. An upscale gas, used to meet a requirement in this section must be either a NIST-traceable reference gas or a gas certified by the gas vendor to ±5.0 percent accuracy.
4.1.1 CD Requirement. Consistent with 40 CFR 60.13(d) and 63.8(c), you, as source owners or operators of CEMS must check, record, and quantify the CD at two levels, using a zero gas and mid-level gas at least once daily (approximately every 24 hours). Perform the CD check in accordance with the procedure in applicable performance specification (e.g., section 11.8 of PS-18 in appendix B of this part). The daily zero- and mid-level CD must not exceed two times the drift limits specified in the applicable performance specification (e.g., section 13.2 of PS-18 in appendix B to this part.)
4.1.2 Recording Requirement for CD Corrective action. Corrective actions taken to bring a CEMS back in control after exceeding a CD limit must be recorded and reported with the associated CEMS data. Reporting corrective action must include the unadjusted concentration measured prior to resetting the calibration and the adjusted value after resetting the calibration to bring the CEMS back into control.
4.1.3 Dynamic Spiking Option for Mid-level CD. For extractive CEMS, you have the option to conduct a daily dynamic spiking procedure found in section 11.8.8 of PS-18 of appendix B of this part in lieu of the daily mid-level CD check. If this option is selected, the daily zero CD check is still required.
4.1.4 Out of Control Criteria for Excessive CD. As specified in § 63.8(c)(7)(i)(A), a CEMS is out of control if the zero or mid-level CD exceeds two times the applicable CD specification in the applicable PS or in the relevant standard. When a CEMS is out of control, you as owner or operator of the affected source must take the necessary corrective actions and repeat the tests that caused the system to go out of control (in this case, the failed CD check) until the applicable performance requirements are met.
4.1.5 Additional Quality Assurance for Data above Span. This procedure must be used when required by an applicable regulation and may be used when significant data above span are being collected. Furthermore, the terms of this procedure do not apply to the extent that alternate terms are otherwise specified in an applicable rule or permit.
4.1.5.1 Any time the average measured concentration of HCl exceeds 150 percent of the span value for two consecutive one-hour averages, conduct the following 'above span' CEMS response check.
4.1.5.1.1 Within a period of 24 hours (before or after) of the 'above span' period, introduce a higher, 'above span' HCl reference gas standard to the CEMS. Use 'above span' reference gas that meets the requirements of section 7.0 of PS-18 and target a concentration level between 75 and 125 percent of the highest hourly concentration measured during the period of measurements above span.
4.1.5.1.2 Introduce the reference gas at the probe for extractive CEMS or for IP-CEMS as an equivalent path length corrected concentration in the instrument calibration cell.
4.1.5.1.3 At no time may the 'above span' concentration exceed the analyzer full-scale range.
4.1.5.2 Record and report the results of this procedure as you would for a daily calibration. The 'above span' response check is successful if the value measured by the CEMS is within 20 percent of the certified value of the reference gas.
4.1.5.3 If the 'above span' response check is conducted during the period when measured emissions are above span and there is a failure to collect at least one data point in an hour due to the response check duration, then determine the emissions average for that missed hour as the average of hourly averages for the hour preceding the missed hour and the hour following the missed hour.
4.1.5.4 In the event that the 'above span' response check is not successful (i.e., the CEMS measured value is not within 20 percent of the certified value of the reference gas), then you must normalize the one-hour average stack gas values measured above the span during the 24-hour period preceding or following the 'above span' response check for reporting based on the CEMS response to the reference gas as shown in Eq. 6-1:

4.2.1 Beam Intensity Measurement. If you use a HCl IP-CEMS, you must quantify and record the beam intensity of the IP-CEMS in appropriate units at least once daily (approximately 24 hours apart) according to manufacturer's specifications and procedures.
4.2.2 Out of Control Criteria for Excessive Beam Intensity Loss. If the beam intensity falls below the level established for the operation range determined following the procedures in section 11.2 of PS-18 of this part, then your CEMS is out-of-control. This quality check is independent of whether the CEMS daily CD is acceptable. If your CEMS is out-of-control, take necessary corrective action. You have the option to repeat the beam intensity test procedures in section 11.2 of PS-18 to expand the acceptable range of acceptable beam intensity. Following corrective action, repeat the beam intensity check.
4.3 Out Of Control Period Duration for Daily Assessments. The beginning of the out-of-control period is the hour in which the owner or operator conducts a daily performance check (e.g., calibration drift or beam intensity check) that indicates an exceedance of the performance requirements established under this procedure. The end of the out-of-control period is the completion of daily assessment of the same type following corrective actions, which shows that the applicable performance requirements have been met.
4.4 CEMS Data Status During Out-of-Control Period. During the period the CEMS is out-of-control, the CEMS data may not be used in calculating compliance with an emissions limit nor be counted towards meeting minimum data availability as required and described in the applicable regulation or permit.
5.0 Data Accuracy AssessmentYou must audit your CEMS for the accuracy of HCl measurement on a regular basis at the frequency described in this section, unless otherwise specified in an applicable regulation or permit. Quarterly audits are performed at least once each calendar quarter. Successive quarterly audits, to the extent practicable, shall occur no closer than 2 months apart. Annual audits are performed at least once every four consecutive calendar quarters.
5.1 Temperature and Pressure Accuracy Assessment for IP CEMS.5.1.1 Stack or source gas temperature measurement audits for HCl IP-CEMS must be conducted and recorded at least annually in accordance with the procedure described in section 11.3 of PS-18 in appendix B to this part. As an alternative, temperature measurement devices may be replaced with certified instruments on an annual basis. Units removed from service may be bench tested against an NIST traceable sensor and reused during subsequent years. Any measurement instrument or device that is used to conduct ongoing verification of temperature measurement must have an accuracy that is traceable to NIST.
5.1.2 Stack or source gas pressure measurement audits for HCl IP-CEMS must be conducted and recorded at least annually in accordance with the procedure described in section 11.4 of PS-18 in appendix B of this part. As an alternative, pressure measurement devices may be replaced with certified instruments on an annual basis. Units removed from service may be bench tested against an NIST traceable sensor and reused during subsequent years. Any measurement instrument or device that is used to conduct ongoing verification of pressure measurement must have an accuracy that is traceable to NIST.
5.1.3 Out of Control Criteria for Excessive Parameter Verification Inaccuracy. If the temperature or pressure verification audit exceeds the criteria in sections 5.3.4.5 and 5.3.4.6, respectively, the CEMS is out-of-control. If the CEMS is out-of-control, take necessary corrective action to eliminate the problem. Following corrective action, you must repeat the failed verification audit until the temperature or pressure measurement device is operating within the applicable specifications, at which point the out-of-control period ends.
5.2 Concentration Accuracy Auditing Requirements. Unless otherwise specified in an applicable rule or permit, you must audit the HCl measurement accuracy of each CEMS at least once each calendar quarter, except in the case where the affected facility is off-line (does not operate). In that case, the audit must be performed as soon as is practicable in the quarter in which the unit recommences operation. Successive quarterly audits must, to the extent practicable, be performed no less than 2 months apart. The accuracy audits shall be conducted as follows:
5.2.1 Relative Accuracy Test Audit. A RATA must be conducted at least once every four calendar quarters, except as otherwise noted in sections 5.2.5 or 5.5 of this procedure. Perform the RATA as described in section 11.9 of PS-18 in appendix B to this part. If the HCl concentration measured by the RM during a RATA (in ppmv) is less than or equal to 20 percent of the concentration equivalent to the applicable emission standard, you must perform a Cylinder Gas Audit (CGA) or a Dynamic Spike Audit (DSA) for at least one subsequent (one of the following three) quarterly accuracy audits.
5.2.2 Quarterly Relative Accuracy Audit (RAA). A quarterly RAA may be conducted as an option to conducting a RATA in three of four calendar quarters, but in no more than three quarters in succession. To conduct an RAA, follow the test procedures in section 11.9 of PS-18 in appendix B to this part, except that only three test runs are required. The difference between the mean of the RM values and the mean of the CEMS responses relative to the mean of the RM values (or alternatively the emission standard) is used to assess the accuracy of the CEMS. Calculate the RAA results as described in section 6.2. As an alternative to an RAA, a cylinder gas audit or a dynamic spiking audit may be conducted.
5.2.3 Cylinder Gas Audit. A quarterly CGA may be conducted as an option to conducting a RATA in three of four calendar quarters, but in no more than three consecutive quarters. To perform a CGA, challenge the CEMS with a zero-level and two upscale level audit gases of known concentrations within the following ranges:
Audit point | Audit range |
---|---|
1 (Mid-Level) | 50 to 60% of span value. |
2 (High-Level) | 80 to 100% of span value. |
5.2.3.1 Inject each of the three audit gases (zero and two upscale) three times each for a total of nine injections. Inject the gases in such a manner that the entire CEMS is challenged. Do not inject the same gas concentration twice in succession.
5.2.3.2 Use HCl audit gases that meet the requirements of section 7 of PS-18 in appendix B to this part.
5.2.3.3 Calculate results as described in section 6.3.
5.2.4 Dynamic Spiking Audit. For extractive CEMS, a quarterly DSA may be conducted as an option to conducting a RATA in three of four calendar quarters, but in no more than three quarters in succession.
5.2.4.1 To conduct a DSA, you must challenge the entire HCl CEMS with a zero gas in accordance with the procedure in section 11.8 of PS-18 in appendix B of this part. You must also conduct the DS procedure as described in appendix A to PS-18 of appendix B to this part. You must conduct three spike injections with each of two upscale level audit gases. The upscale level gases must meet the requirements of section 7 of PS-18 in appendix B to this part and must be chosen to yield concentrations at the analyzer of 50 to 60 percent of span and 80 to 100 percent of span. Do not inject the same gas concentration twice in succession.
5.2.4.2 Calculate results as described in section 6.4. To determine CEMS accuracy, you must calculate the dynamic spiking error (DSE) for each of the two upscale audit gases using Equation A5 in appendix A to PS-18 and Equation 6-3 in section 6.4 of Procedure 6 in appendix B to this part.
5.2.5 Other Alternative Quarterly Audits. Other alternative audit procedures, as approved by the Administrator, may be used for three of four calendar quarters.
5.3 Out of Control Criteria for Excessive Audit Inaccuracy. If the results of the RATA, RAA, CGA, or DSA do not meet the applicable performance criteria in section 5.3.4, the CEMS is out-of-control. If the CEMS is out-of-control, take necessary corrective action to eliminate the problem. Following corrective action, the CEMS must pass a test of the same type that resulted in the out-of-control period to determine if the CEMS is operating within the specifications (e.g., a RATA must always follow an out-of-control period resulting from a RATA).
5.3.1 If the audit results show the CEMS to be out-of-control, you must report both the results of the audit showing the CEMS to be out-of-control and the results of the audit following corrective action showing the CEMS to be operating within specifications.
5.3.2 Out-Of-Control Period Duration for Excessive Audit Inaccuracy. The beginning of the out-of-control period is the time corresponding to the completion of the sampling for the failed RATA, RAA, CGA or DSA. The end of the out-of-control period is the time corresponding to the completion of the sampling of the subsequent successful audit.
5.3.3 CEMS Data Status During Out-Of-Control Period. During the period the CEMS is out-of-control, the CEMS data may not be used in calculating emission compliance nor be counted towards meeting minimum data availability as required and described in the applicable regulation or permit.
5.3.4 Criteria for Excessive Quarterly and Yearly Audit Inaccuracy. Unless specified otherwise in the applicable regulation or permit, the criteria for excessive inaccuracy are:
5.3.4.1 For the RATA, the CEMS must meet the RA specifications in section 13.4 of PS-18 in appendix B to this part.
5.3.4.2 For the CGA, the accuracy must not exceed 5.0 percent of the span value at the zero gas and the mid- and high-level reference gas concentrations.
5.3.4.3 For the RAA, the RA must not exceed 20.0 percent of the RMavg as calculated using Equation 6-2 in section 6.2 of this procedure whether calculated in units of HCl concentration or in units of the emission standard. In cases where the RA is calculated on a concentration (ppmv) basis, if the average HCl concentration measured by the RM during the test is less than 75 percent of the HCl concentration equivalent to the applicable standard, you may substitute the equivalent emission standard value (in ppmvw) in the denominator of Equation 6-2 in the place of RMavg and the result of this alternative calculation of RA must not exceed 15.0 percent.
5.3.4.4 For DSA, the accuracy must not exceed 5.0 percent of the span value at the zero gas and the mid- and high-level reference gas concentrations or 20.0 percent of the applicable emission standard, whichever is greater.
5.3.4.5 For the gas temperature measurement audit, the CEMS must satisfy the requirements in section 13.7 in PS-18 of appendix B to this part.
5.3.4.6 For the gas pressure measurement audit, the CEMS must satisfy the requirements in section 13.8 in PS-18 of appendix B to this part.
5.4 Criteria for Acceptable QC Procedures. Repeated excessive inaccuracies (i.e., out-of-control conditions resulting from the quarterly or yearly audits) indicate that the QC procedures are inadequate or that the CEMS is incapable of providing quality data. Therefore, whenever excessive inaccuracies occur for two consecutive quarters, you must revise the QC procedures (see section 3.0) or modify or replace the CEMS.
5.5 Criteria for Optional QA Test Frequency. If all the quality criteria are met in sections 4 and 5 of this procedure, the CEMS is in-control.
5.5.1 Unless otherwise specified in an applicable rule or permit, if the CEMS is in-control and if your source emits ≤75 percent of the HCl emission limit for each averaging period as specified in the relevant standard for eight consecutive quarters that include a minimum of two RATAs, you may revise your auditing procedures to use CGA, RAA or DSA each quarter for seven subsequent quarters following a RATA.
5.5.2 You must perform at least one RATA that meets the acceptance criteria every 2 years.
5.5.3 If you fail a RATA, RAA, CGA, or DSA, then the audit schedule in section 5.2 must be followed until the audit results meet the criteria in section 5.3.4 to start requalifying for the optional QA test frequency in section 5.5.
6.0 Calculations for CEMS Data Accuracy6.1 RATA RA Calculation. Follow Equations 9 through 14 in section 12 of PS-18 in appendix B to this part to calculate the RA for the RATA. The RATA must be calculated either in units of the applicable emission standard or in concentration units (ppmv).
6.2 RAA Accuracy Calculation. Use Equation 6-2 to calculate the accuracy for the RAA. The RA may be calculated in concentration units (ppmv) or in the units of the applicable emission standard.

6.3 CGA Accuracy Calculation. For each gas concentration, determine the average of the three CEMS responses and subtract the average response from the audit gas value. For extractive CEMS, calculate the ME at each gas level using Equation 3A in section 12.3 of PS-18 in appendix B to this part. For IP-CEMS, calculate the ME at each gas level using Equation 6A in section 12.4.3 of PS-18 in appendix B to this part.
6.4 DSA Accuracy Calculation. DSA accuracy is calculated as a percent of span. To calculate the DSA accuracy for each upscale spike concentration, first calculate the DSE using Equation A5 in appendix A of PS-18 in appendix B to this part. Then use Equation 6-3 to calculate the average DSA accuracy for each upscale spike concentration. To calculate DSA accuracy at the zero level, use equation 3A in section 12.3 of PS-18 in appendix B to this part.

At the reporting interval specified in the applicable regulation or permit, report for each CEMS the quarterly and annual accuracy audit results from section 6 and the daily assessment results from section 4. Unless otherwise specified in the applicable regulation or permit, include all data sheets, calculations, CEMS data records (i.e., charts, records of CEMS responses), reference gas certifications and reference method results necessary to confirm that the performance of the CEMS met the performance specifications.
7.1 Unless otherwise specified in the applicable regulations or permit, report the daily assessments (CD and beam intensity) and accuracy audit information at the interval for emissions reporting required under the applicable regulations or permits.
7.1.1 At a minimum, the daily assessments and accuracy audit information reporting must contain the following information:
a. Company name and address.
b. Identification and location of monitors in the CEMS.
c. Manufacturer and model number of each monitor in the CEMS.
d. Assessment of CEMS data accuracy and date of assessment as determined by a RATA, RAA, CGA or DSA described in section 5 including:
i. The RA for the RATA;
ii. The accuracy for the CGA, RAA, or DSA;
iiii. Temperature and pressure sensor audit results for IP-CEMS;
iv. The RM results, the reference gas certified values;
v. The CEMS responses;
vi. The calculation results as defined in section 6; and
vii. Results from the performance audit samples described in section 5 and the applicable RMs.
e. Summary of all out-of-control periods including corrective actions taken when CEMS was determined out-of-control, as described in sections 4 and 5.
7.1.2 If the accuracy audit results show the CEMS to be out-of-control, you must report both the audit results showing the CEMS to be out-of-control and the results of the audit following corrective action showing the CEMS to be operating within specifications.
8.0 Bibliography1. EPA Traceability Protocol for Assay and Certification of Gaseous Calibration Standards, U.S. Environmental Protection Agency office of Research and Development, EPA/600/R-12/531, May 2012.
2. Method 205, “Verification of Gas Dilution Systems for Field Instrument Calibrations,” 40 CFR part 51, appendix M.
9.0 Tables, Diagrams, Flowcharts [Reserved] [52 FR 21008, June 4, 1987; 52 FR 27612, July 22, 1987, as amended at 56 FR 5527, Feb. 11, 1991; 69 FR 1816, Jan. 12, 2004; 72 FR 32768, June 13, 2007; 74 FR 12590, Mar. 25, 2009; 75 FR 55040, Sept. 9, 2010; 79 FR 11274, Feb. 27, 2014; 79 FR 28441, May 16, 2014; 80 FR 38649, July 7, 2015; 81 FR 59824, Aug. 30, 2016; 82 FR 37824, Aug. 14, 2017; 82 FR 44108, Sept. 21, 2017; 83 FR 56725, Nov. 14, 2018; 85 FR 63418, Oct. 7, 2020]Appendix G to Part 60 - Provisions for an Alternative Method of Demonstrating Compliance With 40 CFR 60.43 for the Newton Power Station of Central Illinois Public Service Company
40:9.0.1.1.1.0.1.1.14 : Appendix G
Appendix G to Part 60 - Provisions for an Alternative Method of Demonstrating Compliance With 40 CFR 60.43 for the Newton Power Station of Central Illinois Public Service Company1. Designation of Affected Facilities
1.1 The affected facilities to which this alternative compliance method applies are the Unit 1 and 2 coal-fired steam generating units located at the Central Illinois Public Service Company's (CIPS) Newton Power Station in Jasper County, Illinois. Each of these units is subject to the Standards of Performance for Fossil-Fuel-Fired Steam Generators for Which Construction Commenced After August 17, 1971 (subpart D).
2. Definitions
2.1 All definitions in subparts D and Da of part 60 apply to this provision except that:
24-hour period means the period of time between 12:00 midnight and the following midnight.
Boiler operating day means a 24-hour period during which any fossil is combusted in either the Unit 1 or Unit 2 steam generating unit and during which the provisions of § 60.43(e) are applicable.
CEMs means continuous emission monitoring system.
Coal bunker means a single or group of coal trailers, hoppers, silos or other containers that:
(1) are physically attached to the affected facility; and
(2) provide coal to the coal pulverizers.
DAFGDS means the dual alkali flue gas desulfurization system for the Newton Unit 1 steam generating unit.
3. Compliance Provisions
3.1 If the owner or operator of the affected facility elects to comply with the 470 ng/J (1.1 lbs/MMBTU) of combined heat input emission limit under § 60.43(e), he shall notify the Regional Administrator, of the United States Environmental Protection Agency (USEPA), Region 5 and the Director, of the Illinois Environmental Protection Agency (IEPA) at least 30 days in advance of the date such election is to take effect, stating the date such operation is to commence. When the owner or operator elects to comply with this limit after one or more periods of reverting to the 520 ng/J heat input (1.2 lbs/MMBTU) limit of § 60.43(a)(2), as provided under 3.4, he shall notify the Regional Administrator of the USEPA, Region 5 and the Director of the (IEPA) in writing at least ten (10) days in advance of the date such election is to take effect.
3.2 Compliance with the sulfur dioxide emission limit under § 60.43(e) is determined on a continuous basis by performance testing using CEMs. Within 60 days after the initial operation of Units 1 and 2 subject to the combined emission limit in § 60.43(e), the owner or operator shall conduct an initial performance test, as required by § 60.8, to determine compliance with the combined emission limit. This initial performance test is to be scheduled so that the thirtieth boiler operating day of the 30 successive boiler operating days is completed within 60 days after initial operation subject to the 470 ng/J (1.1 lbs/MMBTU) combined emission limit. Following the initial performance test, a separate performance test is completed at the end of each boiler operating day Unit 1 and Unit 2 are subject to § 60.43(e), and a new 30 day average emission rate calculated.
3.2.1 Following the initial performance test, a new 30 day average emission rate is calculated for each boiler operating day the affected facility is subject to § 60.43(e). If the owner or operator of the affected facility elects to comply with § 60.43(e) after one or more periods of reverting to the 520 ng/J heat input (1.2 lbs/MMBTU) limit under § 60.43(a)(2), as provided under 3.4, the 30 day average emission rate under § 60.43(e) is calculated using emissions data of the current boiler operating day and data for the previous 29 boiler operating days when the affected facility was subject to § 60.43(e). Periods of operation of the affected facility under § 60.43(a)(2) are not considered boiler operating days. Emissions data collected during operation under § 60.43(a)(2) are not considered relative to 4.6 and emissions data are not included in calculations of emission under § 60.43(e).
3.2.2 When the affected facility is operated under the provisions of § 60.43(e), the Unit 1 DAFGDS bypass damper must be fully closed. The DAFGDS bypass may be opened only during periods of DAFGDS startup, shutdown, malfunction or testing as described under sections 3.5.1, 3.5.2, 3.5.3, 3.5.4, and 4.8.2.
3.3 Compliance with the sulfur dioxide emission limit set forth in § 60.43(e) is based on the average combined hourly emission rate from Units 1 and 2 for 30 successive boiler operating days determined as follows:
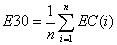
3.3.1 The average hourly combined emission rate for Units 1 and 2for each hour of operation of either Unit 1 or 2, or both, is determined as follows:
EC=[(E1) + (E2)]/[H1 + H2] where: EC = the hourly combined SO2 emission rate, lbs/MMBTU, from Units 1 and 2 when Units 1 and 2 are subject to § 60.43(e). E1 = the hourly SO2 mass emission, lb/hr, from Unit 1 as determined from CEMs data using the calculation procedures in section 4 of this appendix. E2 = the hourly SO2 mass emission, lb/hr, from Unit 2 as determined from CEMs data using the calculation procedures in section 4 of this appendix. H1 = the hourly heat input, MMBTU/HR to Unit 1 as determined in section 4 of this appendix. H2 = the hourly heat input, MMBTU/HR, to Unit 2 as determined by section 4 of this appendix.3.3.2 If data for any of the four hourly parameters (E1, E2, H1and H2, under 3.3.1 are unavailable during an hourly period, the combined emission rate (EC) is not calculated and the period is counted as missing data under 4.6.1., except as provided under 3.5. and 4.4.2.
3.4 After the date of initial operation subject to the combined emission limit, Units 1 and 2 shall remain subject to the combined emission limit and the owner or operator shall remain subject to the requirements of this Appendix until the initial performance test as required by 3.2 is completed and the owner or operator of the affected facility elects and provides notice to revert on a certain date to the 520 ng/J heat input (1.2 lbs/MMBTU) limit of § 60.43(a)(2) applicable separately at each unit. The Regional Administrator of the USEPA, Region 5 and the Director, of the IEPA shall be given written notification from CIPS as soon as possible of CIPs' decision to revert to the 520 ng/J heat input (1.2 lbs/MMBTU) limit of § 60.43(a)(2) separately at each unit, but no later than 10 days in advance of the date such election is to take effect.
3.5 Emission monitoring data for Unit 1 may be excluded from calculations of the 30 day rolling average only during the following times:
3.5.1 Periods of DAFGDS startup.
3.5.2 Periods of DAFGDS shutdown.
3.5.3 Periods of DAFGDS malfunction during system emergencies as defined in § 60.41a.
3.5.4 The first 250 hours per calendar year of DAFGDS malfunctions of Unit 1 DAFGDS provided that efforts are made to minimize emissions from Unit 1 in accordance with § 60.11(d), and if, after 16 hours but not more than 24 hours of DAFGDS malfunction, the owner or operator of the affected facility begins (following the customary loading procedures) loading into the Unit 1 coal bunker, coal with a potential SO2 emission rate equal to or less than the emission rate of Unit 2 recorded at the beginning of the DAFGDS malfunction. Malfunction periods under 3.5.3 are not counted toward the 250 hour/yr limit under this section.
3.5.4.1 The malfunction exemption in 3.5.4 is limited to the first 250 hours per calendar year of DAFGDS malfunction.
3.5.4.2 For malfunctions of the DAFGDS after the 250 hours per calendar year limit (cumulative), other than those defined in 3.5.3, the owner or operator of the affected facility shall combust lower sulfur coal or use any other method to comply with the 470 ng/J (1.1 lbs/MMBTU) combined emission limit.
3.5.4.3 During the first 250 hours of DAFGDS malfunction per year or during periods of DAFGDS startup, or DAFGDS shutdown, CEMs emissions data from Unit 2 shall continue to be included in the daily calculation of the combined 30 day rolling average emission rate; that is, the load on Unit 1 is assumed to be zero (H1 and E1 = O; EC = E2/H2).
3.5.5-3.5.7 [Reserved]
3.6 The provision for excluding CEMs data from Unit 1 during the first 250 hours of DAFGDS malfunctions from combined hourly emissions calculations supersedes the provisions of § 60.11(d). However, the general purpose contained in § 60.11(d) (i.e., following good control practices to minimize air pollution emission during malfunctions) has not been superseded.
4. Continuous Emission Monitoring4.1 The CEMs required under section 3.2 are operated and data are recorded for all periods of operation of the affected facility including periods of the DAFGDS startup, shutdown and malfunction except for CEMs breakdowns, repairs, calibration checks, and zero and span adjustment. All provisions of § 60.45 apply except as follows:
4.2 The owner or operator shall install, calibrate, maintain, and operate CEMs and monitoring devices for measuring the following:
4.2.1 For Unit 1:
4.2.1.1 Sulfur dioxide, oxygen or carbon dioxide, and volumetric flow rate for the Unit 1 DAFGDS stack.
4.2.1.2 Sulfur dioxide, oxygen or carbon dioxide, and volumetric flow rate for the Unit 1 DAFGDS bypass stack.
4.2.1.3 Moisture content of the flue gas must be determined continuously for the Unit 1 DAFGDS stack and the Unit 1 DAFGDS bypass stack, if the sulfur dioxide concentration in each stack is measured on a dry basis.
4.2.2 For Unit 2, sulfur dioxide, oxygen or carbon dioxide, and volumetric flow rate.
4.2.2.1 Moisture content of the flue gas must be determined continuously for the Unit 2 stack, if the sulfur dioxide concentration in the stack is measured on a dry basis.
4.2.3 For Units 1 and 2, the hourly heat input, the hourly steam production rate, or the hourly gross electrical power output from each unit.
4.3 For the Unit 1 bypass stack and the Unit 2 stack, the span value of the sulfur dioxide analyzer shall be equivalent to 200 percent of the maximum estimated hourly potential sulfur dioxide emissions of the fuel fired in parts per million sulfur dioxide. For the Unit 1 DAFGDS stack, the span value of the sulfur dioxide analyzer shall be equivalent to 100 percent of the maximum estimated hourly potential emissions of the fuel fired in parts per million sulfur dioxide. The span value for volumetric flow monitors shall be equivalent to 125 percent of the maximum estimated hourly flow in standard cubic meters/minute (standard cubic feet per minute). The span value of the continuous moisture monitors, if required by 4.2.1.3 and 4.2.2.1, shall be equivalent to 100 percent by volume. The span value of the oxygen or carbon dioxide analyzers shall be equivalent to 25 percent by volume.
4.3.1-4.3.2 [Reserved]
4.4 The monitoring devices required in 4.2 shall be installed, calibrated, and maintained as follows:
4.4.1 Each volumetric flow rate monitoring device specified in 4.2 shall be installed at approximately the same location as the sulfur dioxide emission monitoring sample location.
4.4.2 Hourly steam production rate and hourly electrical power output monitoring devices for Unit 1 and Unit 2 shall be calibrated and maintained according to manufacturer's specifications. The data from either of these devices may be used in the calculation of the combined emission rate in section 3.3.1, only when the hourly heat input for Unit 1 (H1) or the hourly heat input for Unit 2 (H2) cannot be determined from CEM data, and the hourly heat input to steam production or hourly heat input to electrical power output efficiency over a given segment of each boiler or generator operating range, respectively, varies by less than 5 percent within the specified operating range, or the efficiencies of the boiler/generator units differ by less than 5 percent. The hourly heat input for Unit 1 (H1) or the hourly heat input for Unit 2 (H2) in section 3.3.1 may also be calculated based on the fuel firing rates and fuel analysis.
4.4.3-4.4.5 [Reserved]
4.5 The hourly mass emissions from Unit 1 (E1) and Unit 2 (E2) and the hourly heat inputs from Unit 1 (H1) and Unit 2 (H2) used to determine the hourly combined emission rate for Units 1 and 2 (EC) in section 3.3.1 are calculated using CEM data for each respective stack as follows:
4.5.1 The hourly SO2 mass emission from each respective stack is determined as follows:
E = (C) (F) (D) (K) Where: E = SO2 mass emission from the respective stack in lb per hour C = SO2 concentration from the respective stack ppm F = flue gas flow rate from the respective stack in scfm D = density of SO2 in lb per standard cubic feet K = time conversion, 60 mins./hr4.5.2 The hourly heat input from each respective stack is determined as follows:
H=[(F) (C) (K)/(Fc) where: H = heat input from the respective stack in MMBTU per hour C = CO2 or O2 concentration from the respective stack as a decimal F = flue gas flow rate from the respective stack in scfm K = time conversion, 60 mins./hr Fc = fuel constant for the appropriate diluent in scf/MMBTU as per §§ 60.45(f) (4) and (5)4.5.3 The hourly SO2 mass emission for Unit 1 in pounds per hour (E1) is calculated as follows, when leakage or diversion of any DAFGDS inlet gas to the bypass stack occurs:
E1 = (EF) + (EB) Where: EF = Hourly SO2 mass emission measured in DAFGDS stack, lb/hr, using the calculation in section 4.5.1. EB = Hourly SO2 mass emission measured in bypass stack, lb/hr, using the calculation in section 4.5.1. Other than during conditions under 3.5.1, 3.5.2, 3.5.3, 3.5.4, or 4.8.2, the DAFGDS bypass damper must be fully closed and any leakage will be indicated by the bypass stack volumetric flow and SO2 measurements, and when no leakage through the bypass damper is indicated: E1 = EF4.5.4 The hourly heat input for Unit 1 in MMBTU per hour (H1) is calculated as follows, when leakage or diversion of any DAFGDS inlet gas to the bypass stack occurs:
H1 = (HF) + (HB) where: HF = Hourly heat input as determined from the DAFGDS stack CEMs, in MMBTU per hour, using the calculation in section 4.5.2 HB = Hourly heat input as determined from the DAFGDS bypass stack CEMs, in MMBTU per hour, using the calculation in section 4.5.24.6 For the CEMs required for Unit 1 and Unit 2, the owner or operator of the affected facility shall maintain and operate the CEMs and obtain combined emission data values (EC) for at least 75 percent of the boiler operting hours per day for at least 26 out of each 30 successive boiler operating days.
4.6.1 When hourly SO2 emission data are not obtained by the CEMs because of CEMs breakdowns, repairs, calibration checks and zero and span adjustment, hourly emission data required by 4.6 are obtained by using Methods 6 or 6C and 3 or 3A, 6A, or 8 and 3, or by other alternative methods approved by the Regional Administrator of the USEPA, Region 5 and the Director, of the IEPA. Failure to obtain the minimum data requirements of 4.6 by CEMs, or by CEMs supplemented with alternative methods of this section, is a violation of performance testing requirements.
4.6.2 Independent of complying with the minimum data requirements of 4.6, all valid emissions data collected are used to calculate combined hourly emission rates (EC) and 30-day rolling average emission rates (E30) are calculated and used to judge compliance with 60.43(e).
4.7 For each continuous emission monitoring system, a quality control plan shall be prepared by CIPS and submitted to the Regional Administrator of the USEPA, Region 5 and the Director, of the IEPA. The plan is to be submitted to the Regional Administrator of the USEPA, Region 5 and the Director, of the IEPA 45 days before initiation of the initial performance test. At a minimum, the plan shall contain the following quality control elements:
4.7.1 Calibration of continuous emission monitoring systems (CEMs) and volumetric flow measurement devices.
4.7.2 Calibration drift determination and adjustment of CEMs and volumetric flow measurement devices.
4.7.3 Periodic CEMs, volumetric flow measurement devices and relative accuracy determinations.
4.7.4 Preventive maintenance of CEMs and volumetric flow measurement devices (including spare parts inventory).
4.7.5 Data recording and reporting.
4.7.6 Program of corrective action for malfunctioning CEMs and volumetric flow measurement devices.
4.7.7 Criteria for determining when the CEMs and volumetric flow measurement devices are not producing valid data.
4.7.8 Calibration and periodic checks of monitoring devices identified in 4.4.2.
4.8 For the purpose of conducting the continuous emission monitoring system performance specification tests as required by § 60.13 and appendix B, the following conditions apply:
4.8.1 The calibration drift specification of Performance Specification 2, appendix B shall be determined separately for each of the Unit 1 SO2 CEMs and the Unit 2 SO2 CEMs. The calibration drift specification of Performance Specification 3, appendix B shall be determined separately for each of the Unit 1 diluent CEMs and Unit 2 diluent CEMs.
4.8.2 The relative accuracy of the combined SO2 emission rate for Unit 1 and Unit 2, as calculated from CEMs and volumetric flow data using the procedures in 3.3.1, 4.5.1, 4.5.2 and 4.5.3 shall be no greater than 20 percent of the mean value of the combined emission rate, as determined from testing conducted simultaneously on the DAFGDS stack, the DAFGDS bypass stack and the Unit 2 stack using reference methods 2, 3, or 3A and 6 or 6C, or shall be no greater than 10 percent of the emission limit in § 60.43(e), whichever criteria is less stringent. The relative accuracy shall be computed from at least nine comparisons of the combined emission rate values using the procedures in section 7 and the equations in section 8, Performance Specification 2, appendix B. Throughout, but only during, the relative accuracy test period the DAFGDS bypass damper shall be partially opened such that there is a detectable flow.
4.8.3-4.8.3.4 [Reserved]
4.9 The total monitoring system required by 4.2 shall be subject only to an annual relative accuracy test audit (RATA) in accordance with the quality assurance requirements of section 5.1.1 of 40 CFR part 60, appendix F. Each SO2 and diluent CEMs shall be subject to cylinder gas audits (OGA) in accordance with the quality assurance requirements of section 5.1.2 of appendix F with the exception that any SO2 or diluent CEMs without any type of probe or sample line shall be exempt from the OGA requirements.
5. Recordkeeping Requirements5.1 The plant owner or operator shall keep a record of each hourly emission rate, each hourly SO2 CEMs value and hourly flow rate value, and each hourly Btu heat input rate, hourly steam rate, or hourly electrical power output, and a record of each hourly weighted average emission rate. These records shall be kept for all periods of operation of Unit 1 or 2 under provisions of § 60.43(e), including operations of Unit 1 (E1) during periods of DAFGDS startup, shutdown, and malfunction when H1 and E1 are assumed to be zero (0) (see 4.5).
5.2 The plant owner or operator shall keep a record of each hourly gas flow rate through the DAFGDS stack, each hourly stack gas flow rate through the bypass stack during any periods that the DAFGDS bypass damper is opened or flow is indicated, and reason for bypass operation.
6. Reporting Requirements6.1 The owner or operator of any affected facility shall submit the written reports required under 6.2 of this section and subpart A to the Regional Administrator of the USEPA, Region 5 and the Director, of the IEPA for every calendar quarter. All quarterly reports shall be submitted by the 30th day following the end of each calendar quarter.
6.2 For sulfur dioxide, the following data resubmitted to the Regional Administrator of the USEPA, Region 5 and the Director, of the IEPA for each 24-hour period:
6.2.1 Calendar date
6.2.2 The combined average sulfur dioxide emission rate (ng/J or lb/million Btu) for the past 30 successive boiler operating days (ending with the last 30-day period in the quarter); and, for any noncompliance periods, reasons for noncompliance with the emission standards and description of corrective action taken.
6.2.3 Identification of the boiler operating days for which valid sulfur dioxide emissions data required by 4.6 have not been obtained for 75 percent of the boiler operating hours; reasons for not obtaining sufficient data; and description of corrective actions taken to prevent recurrence.
6.2.4 Identification of the time periods (hours) when Unit 1 or Unit 2 were operated but combined hourly emission rates (EC) were not calculated because of the unavailability of parameters E1, E2, H1, or H2 as described in 3.2.
6.2.5 Identification of the time periods (hours) when Unit 1 and Unit 2 were operated and where the combined hourly emission rate (EC) equalled Unit 2 (E2/H2) emissions because of the Unit 1 malfunction provisions under 3.5.3, and 3.5.4.
6.2.6 Identification of the time periods (hours) when emissions from the Unit 1 DAFGDS have been excluded from the calculation of average sulfur dioxide emission rates because of Unit 1 DAFGDS startup, shutdown, malfunction, or other reasons; and justification for excluding data for reasons other than startup or shutdown. Reporting of hourly emission rate of Unit 1 (E1/H2) during each hour of the DAFGDS startup, malfunction under 3.5.1, 3.5.2, 3.5.3, and 3.5.4 (see 4.5).
6.2.7 Identification of the number of days in the calendar quarter that the affected facility was operated (any fuel fired).
6.2.8 Identify any periods where Unit 1 DAFGDS malfunctions occurred and the cumulative hours of Unit 1 DAFGDS malfunction for the quarter.
6.2.9 Identify any periods of time that any exhaust gases were discharged to the DAFGDS bypass stack and the hourly gas flow rate through the DAFGDS stack and through the DAFGDS bypass stack during such periods and reason for bypass operation.
6.2.10 [Reserved]
[52 FR 28955, Aug. 4, 1987, as amended at 58 FR 28785, May 17, 1993; 59 FR 8135, Feb. 18, 1994]Appendix H to Part 60 [Reserved]
40:9.0.1.1.1.0.1.1.15 : Appendix H
Appendix H to Part 60 [Reserved]Appendix I to Part 60 - Owner's Manuals and Temporary Labels for Wood Heaters Subject to Subparts AAA and QQQQ of Part 60
40:9.0.1.1.1.0.1.1.16 : Appendix I
Appendix I to Part 60 - Owner's Manuals and Temporary Labels for Wood Heaters Subject to Subparts AAA and QQQQ of Part 60 1. IntroductionThe purpose of this appendix is to provide specific instructions and examples to manufacturers for compliance with the owner's manual provisions of subparts AAA and QQQQ of this part.
2. Instructions for Preparation of Wood Heater Owner's Manuals2.1 Introduction
Although the owner's manuals do not require premarket approval, EPA will monitor the contents to ensure that sufficient information is included to provide heater proper operation and maintenance information affecting emissions to consumers. The manufacturer must make current and historical owner's manuals available on the company Web site and upon request to the EPA. The purpose of this section is to provide instructions to manufacturers for compliance with the owner's manual provisions of § 60.536(g) of subpart AAA that applies to wood heaters and § 60.5478(f) of subpart QQQQ that applies to hydronic heaters and forced-air furnaces. A checklist of topics and illustrative language is provided as instructions. Owner's manuals should be tailored to specific wood heater models, as appropriate.
2.2 Topics Required To Be Addressed in Owner's Manual(a) Wood heater description and compliance status;
(b) Tamper warnings;
(c) Overall heater warranty information and catalyst information and warranty (if catalyst-equipped);
(d) Fuel selection;
(e) Achieving and maintaining catalyst light-off (if catalyst-equipped);
(f) Catalyst monitoring (if catalyst-equipped);
(g) Troubleshooting catalytic-equipped heaters (if catalyst-equipped);
(h) Catalyst replacement (if catalyst-equipped);
(i) Wood heater proper operation and maintenance, including minimizing visible emissions;
(j) Wood heater proper installation, including location, stack height and achieving proper draft;
(k) Use of smoke detectors and carbon monoxide monitors; and
(l) Efficiency.
2.3 Sample Text/Descriptions(a) The following are example texts and/or further descriptions illustrating the topics identified above. Although the regulation requires manufacturers to address (where applicable) the 10 topics identified above, the exact language is not specified. Manuals should be written specific to the model and design of the wood heater. The following instructions are composed of generic descriptions and texts.
(b) If manufacturers choose to use the language provided in the example, the portion in italics should be revised as appropriate. Any manufacturer electing to use the EPA example language will be considered to be in compliance with owner's manual requirements provided that the particular language is printed in full with only such changes as are necessary to ensure accuracy.
Example language is not provided for certain topics, since these areas are generally heater specific. For these topics, manufacturers should develop text that is specific to the proper operation and maintenance of their particular products.
2.3.1 Wood Heater Description and Compliance StatusOwner's manuals must include:
(a) Manufacturer and model;
(b) Compliance status (2015 standard, 2016 standard, 2017 standard, 2020 standard, crib wood standard or cord wood alternative standard, last allowable sell date, etc.); and
(c) Heat output range.
Exhibit 1 - Example Text covering 2.3.1(a), (b), and (c) of this appendix:
“This manual describes the installation and operation of the Brand X, Model 0 catalytic equipped wood heater. This heater meets the 2015 U.S. Environmental Protection Agency's crib wood emission limits for wood heaters sold after May 15, 2015. Under specific test conditions this heater has been shown to deliver heat at rates ranging from 8,000 to 35,000 Btu/hr.”
2.3.2 Tamper Warnings(a) The following statement must be included in the owner's manual for all units:
“This wood heater has a manufacturer-set minimum low burn rate that must not be altered. It is against federal regulations to alter this setting or otherwise operate this wood heater in a manner inconsistent with operating instructions in this manual.”
(b) The following statement must be included in the owner's manual for catalyst-equipped units:
“This wood heater contains a catalytic combustor, which needs periodic inspection and replacement for proper operation. It is against federal regulations to operate this wood heater in a manner inconsistent with operating instructions in this manual, or if the catalytic element is deactivated or removed.”
2.3.3 Overall Heater Warranty Information and Catalyst Information and Warranty (if catalyst-equipped)The following information must be included with or supplied in the owner's and warranty manuals:
(a) Manufacturer and model, including catalyst if catalyst-equipped;
(b) Warranty details, including catalyst if catalyst-equipped; and
(c) Instructions for warranty claims.
Exhibit 2 - Example Text covering 2.3.3(a), (b), and (c) of this appendix for catalysts:
“The combustor supplied with this heater is a Brand Z, Long Life Combustor. Consult the catalytic combustor warranty also supplied with this wood heater. Warranty claims should be addressed to:
Stove or Catalyst Manufacturer Address Phone #______________”2.3.3.1 This section should also provide clear instructions on how to exercise the warranty (how to package parts for return shipment, etc.).
2.3.4 Fuel Selection
Owner's manuals must include:
(a) Instructions on acceptable fuels;
(b) Warning against inappropriate fuels; and
(c) How to determine seasoned wood compared to unseasoned wood, how to use moisture meters and other techniques and the importance of seasoned wood.
Exhibit 3 - Example Text covering 2.3.4(a) and (b) of this appendix:
“This heater is designed to burn natural wood only. Higher efficiencies and lower emissions generally result when burning air dried seasoned hardwoods, as compared to softwoods or to green or freshly cut hardwoods. DO NOT BURN:
(1) Garbage;
(2) Lawn clippings or yard waste;
(3) Materials containing rubber, including tires;
(4) Materials containing plastic;
(5) Waste petroleum products, paints or paint thinners, or asphalt products;
(6) Materials containing asbestos;
(7) Construction or demolition debris;
(8) Railroad ties or pressure-treated wood;
(9) Manure or animal remains;
(10) Salt water driftwood or other previously salt water saturated materials;
(11) Unseasoned wood; or
(12) Paper products, cardboard, plywood, or particleboard. The prohibition against burning these materials does not prohibit the use of fire starters made from paper, cardboard, saw dust, wax and similar substances for the purpose of starting a fire in an affected wood heater.
Burning these materials may result in release of toxic fumes or render the heater ineffective and cause smoke.”
2.3.5 Achieving and Maintaining Catalyst Light-OffOwner's manuals must describe in detail proper procedures for:
(a) Operation of catalyst bypass (stove specific);
(b) Achieving catalyst light-off from a cold start; and
(c) Achieving catalyst light-off when refueling.
2.3.5.1 No example text is supplied for describing operation of catalyst bypass mechanisms (Item 2.3.5(a) of this appendix) since these are typically stove-specific. Manufacturers must provide instructions specific to their model describing:
(1) Bypass position during startup;
(2) Bypass position during normal operation; and
(3) Bypass position during reloading.
Exhibit 4 - Example Text for Item 2.3.5(b) of this appendix:
“The temperature in the stove and the gases entering the combustor must be raised to between 500° to 700 °F for catalytic activity to be initiated. During the startup of a cold stove, a medium to high firing rate must be maintained for about 20 minutes. This ensures that the stove, catalyst, and fuel are all stabilized at proper operating temperatures. Even though it is possible to have gas temperatures reach 600 °F within 2 to 3 minutes after a fire is started, if the fire is allowed to die down immediately, it may go out or the combustor may stop working. Once the combustor starts working, heat generated in it by burning the smoke will keep it working.”
Exhibit 5 - Example Text for Item 2.3.5(c) of this appendix:
“REFUELING: During the refueling and rekindling of a cool fire, or a fire that has burned down to the charcoal phase, operate the stove at a medium to high firing rate for about 10 minutes to ensure that the catalyst reaches approximately 600 °F.”
2.3.6 Catalyst MonitoringOwner's manuals must include:
(a) Recommendation to visually inspect combustor at least three times during the heating season;
(b) Discussion on expected combustor temperatures for monitor-equipped units; and
(c) Suggested monitoring and inspection techniques and importance of ensuring catalyst is operating properly.
Exhibit 6 - Example Text covering 2.3.6(a), (b) and (c) of this appendix:
“It is important to periodically monitor the operation of the catalytic combustor to ensure that it is functioning properly and to determine when it needs to be replaced. A non-functioning combustor will result in a loss of heating efficiency, and an increase in creosote and emissions. Following is a list of items that should be checked on a periodic basis:
• Combustors should be visually inspected at least three times during the heating season to determine if physical degradation has occurred. Actual removal of the combustor is not recommended unless more detailed inspection is warranted because of decreased performance. If any of these conditions exists, refer to Catalyst Troubleshooting section of this owner's manual.
• This catalytic (or hybrid) heater is equipped with a temperature probe to monitor catalyst operation. Properly functioning combustors typically maintain temperatures in excess of 500 °F, and often reach temperatures in excess of 1,000 °F. If catalyst temperatures are not in excess of 500 °F, refer to Catalyst Troubleshooting section of this owner's manual.
• You can get an indication of whether the catalyst is working by comparing the amount of smoke leaving the chimney when the smoke is going through the combustor and catalyst light-off has been achieved, to the amount of smoke leaving the chimney when the smoke is not routed through the combustor (bypass mode).
Step 1 - Light stove in accordance with instructions in section 3.3.5.
Step 2 - With smoke routed through the catalyst, go outside and observe the emissions leaving the chimney.
Step 3 - Engage the bypass mechanism and again observe the emissions leaving the chimney.
Significantly more smoke will be seen when the exhaust is not routed through the combustor (bypass mode).”
2.3.7 Catalyst TroubleshootingThe owner's manual must provide clear descriptions of symptoms and remedies to common combustor problems and importance. It is recommended that photographs of catalyst peeling, plugging, thermal cracking, mechanical cracking, and masking be included in the manual to aid the consumer in identifying problems and to provide direction for corrective action.
2.3.8 Catalyst ReplacementThe owner's manual must provide clear step-by-step instructions on how to remove and replace the catalytic combustor. The section should include diagrams and/or photographs.
2.3.9 Wood Heater Proper Operation and MaintenanceThe owner's manual must provide clear descriptions of symptoms and remedies to common heater problems and importance. The owner's manual information must be adequate to enable consumers to achieve optimal emissions performance. Such information must be consistent with the operating instructions provided by the manufacturer to the approved test laboratory for operating the wood heater during certification testing, except for details of the certification test that would not be relevant to the user.
Owner's manual must include:
(a) Recommendations about building and maintaining a fire, especially for cold starts and the effectiveness of the top-down approach for starting fires;
(b) Instruction on proper use of air controls, including how to establish good combustion and how to ensure good combustion at the lowest burn rate for which the heater is warranted;
(c) Ash removal and disposal;
(d) Instruction replacement of gaskets, air tubes and other parts that are critical to the emissions performance of the unit, and other maintenance and repair instructions;
(e) Warning against overfiring; and
(f) Suggested monitoring and inspection techniques and importance of ensuring heater is operating properly, including ensuring visible emissions are minimized.
2.3.9.1 No example text is supplied for 2.3.9(a), (b), (d) and (f) of this appendix since these items are model specific. Manufacturers should provide detailed instructions on building and maintaining a fire including selection of fuel pieces, fuel quantity and stacking arrangement. Manufacturers should also provide instruction on proper air settings (both primary and secondary) for attaining minimum and maximum heat outputs and any special instructions for operating thermostatic controls. Step-by-step instructions on inspection and replacement of gaskets should also be included. Manufacturers should provide diagrams and/or photographs to assist the consumer. Gasket type and size should be specified.
Exhibit 7 - Example Text for Item 2.3.9(c) of this appendix:
“Whenever ashes get 3 to 4 inches deep in your firebox or ash pan, and when the fire has burned down and cooled, remove excess ashes. Leave an ash bed approximately 1 inch deep on the firebox bottom to help maintain a hot charcoal bed.”
“Ashes should be placed in a metal container with a tight-fitting lid. The closed container of ashes should be placed on a noncombustible floor or on the ground, away from all combustible materials, pending final disposal. The ashes should be retained in the closed container until all cinders have thoroughly cooled.”
Exhibit 8 - Example Text covering Item 2.3.9(e) of this appendix:
“DO NOT OVERFIRE THIS HEATER”“Attempts to achieve heat output rates that exceed heater design specifications can result in permanent damage to the heater and to the catalytic combustor if so equipped.”
2.3.10 Wood Heater Installation, Including Stack Height, Heater Locations and Achieving Proper DraftOwner's manual must include:
(a) Importance of proper draft;
(b) Conditions indicating inadequate draft;
(c) Conditions indicating excessive draft; and
(d) Guidance on proper stack height and proper heater locations, i.e., not too close to neighbors or in valleys that would cause unhealthy air quality or nuisance conditions.
2.3.10.1 No example text is supplied for (d) because state, local and tribal requirements are model and location specific.
Exhibit 9 - Example Text for Item (a):
“Draft is the force which moves air from the appliance up through the chimney. The amount of draft in your chimney depends on the length of the chimney, local geography, nearby obstructions and other factors. Too much draft may cause excessive temperatures in the appliance and may damage the catalytic combustor. Inadequate draft may cause backpuffing into the room and 'plugging' of the chimney or the catalyst.”
Exhibit 10 - Example Text for Item (b):
“Inadequate draft will cause the appliance to leak smoke into the room through appliance and chimney connector joints.”
Exhibit 11 - Example Text for Item (c):
“An uncontrollable burn or excessive temperature indicates excessive draft.”
2.3.11 EfficiencyOwner's manual must include:
(a) Description of how the efficiency was determined, e.g., use higher heating value of the fuel instead of lower heating value of the fuel, discuss sweet spot versus annual average versus annual fuel usage efficiency (AFUE);
(b) How operation and fuels affect efficiency, e.g., seasoned wood versus high moisture fuel; operation at sweet spot versus low-burn rates; and
(c) How location affects the efficiency, e.g., in main living area versus basement versus outdoors in sub-freezing temperatures.
2.3.12 Smoke and Carbon Monoxide Emissions and MonitorsOwner's manual must include:
(a) Discussion of smoke and carbon monoxide (CO) emissions, including the CO data submitted in the certification application and expected variations for different operating conditions;
(b) Recommendation to have smoke monitors; and
(c) Recommendation to have monitors for areas that are expected to generate CO, e.g., heater fueling areas, pellet fuel bulk storage areas, sheds containing hydronic heaters.
3. Instructions for Preparation of Wood Heater Temporary Labels3.1 Temporary labels that show the values for emissions, efficiency, recommended heating area and the compliance status may (voluntarily) be affixed by the manufacturer to wood heaters that meet the 2020 particulate matter emission standards early or that meet the cord wood alternative compliance options in subparts AAA and QQQQ of this part.
3.2 The seller of each heater covered by section 3.1 may ensure that the temporary label remains affixed until each heater is purchased by the end user.
3.3 The temporary label option for the 2020 particulate matter emission standards end as of May 15, 2020.
3.4 The template for the temporary labels will be supplied by the Administrator upon request.
[80 FR 13751, Mar. 16, 2015]