Appendix A-1 to Part 50 - Reference Measurement Principle and Calibration Procedure for the Measurement of Sulfur Dioxide in the Atmosphere (Ultraviolet Fluorescence Method)
40:2.0.1.1.1.0.1.20.1 : Appendix A
Appendix A-1 to Part 50 - Reference Measurement Principle and
Calibration Procedure for the Measurement of Sulfur Dioxide in the
Atmosphere (Ultraviolet Fluorescence Method) 1.0 Applicability
1.1 This ultraviolet fluorescence (UVF) method provides a
measurement of the concentration of sulfur dioxide (SO2) in ambient
air for determining compliance with the national primary and
secondary ambient air quality standards for sulfur oxides (sulfur
dioxide) as specified in § 50.4, § 50.5, and § 50.17 of this
chapter. The method is applicable to the measurement of ambient SO2
concentrations using continuous (real-time) sampling. Additional
quality assurance procedures and guidance are provided in part 58,
appendix A, of this chapter and in Reference 3.
2.0 Principle
2.1 This reference method is based on automated measurement of
the intensity of the characteristic fluorescence released by SO2 in
an ambient air sample contained in a measurement cell of an
analyzer when the air sample is irradiated by ultraviolet (UV)
light passed through the cell. The fluorescent light released by
the SO2 is also in the ultraviolet region, but at longer
wavelengths than the excitation light. Typically, optimum
instrumental measurement of SO2 concentrations is obtained with an
excitation wavelength in a band between approximately 190 to 230
nm, and measurement of the SO2 fluorescence in a broad band around
320 nm, but these wavelengths are not necessarily constraints of
this reference method. Generally, the measurement system (analyzer)
also requires means to reduce the effects of aromatic hydrocarbon
species, and possibly other compounds, in the air sample to control
measurement interferences from these compounds, which may be
present in the ambient air. References 1 and 2 describe UVF
method.
2.2 The measurement system is calibrated by referencing the
instrumental fluorescence measurements to SO2 standard
concentrations traceable to a National Institute of Standards and
Technology (NIST) primary standard for SO2 (see Calibration
Procedure below).
2.3 An analyzer implementing this measurement principle is shown
schematically in Figure 1. Designs should include a measurement
cell, a UV light source of appropriate wavelength, a UV detector
system with appropriate wave length sensitivity, a pump and flow
control system for sampling the ambient air and moving it into the
measurement cell, sample air conditioning components as necessary
to minimize measurement interferences, suitable control and
measurement processing capability, and other apparatus as may be
necessary. The analyzer must be designed to provide accurate,
repeatable, and continuous measurements of SO2 concentrations in
ambient air, with measurement performance as specified in Subpart B
of Part 53 of this chapter.
2.4 Sampling considerations: The use of a particle filter
on the sample inlet line of a UVF SO2 analyzer is required to
prevent interference, malfunction, or damage due to particles in
the sampled air.
3.0 Interferences
3.1 The effects of the principal potential interferences may
need to be mitigated to meet the interference equivalent
requirements of part 53 of this chapter. Aromatic hydrocarbons such
as xylene and naphthalene can fluoresce and act as strong positive
interferences. These gases can be removed by using a permeation
type scrubber (hydrocarbon “kicker”). Nitrogen oxide (NO) in high
concentrations can also fluoresce and cause positive interference.
Optical filtering can be employed to improve the rejection of
interference from high NO. Ozone can absorb UV light given off by
the SO2 molecule and cause a measurement offset. This effect can be
reduced by minimizing the measurement path length between the area
where SO2 fluorescence occurs and the photomultiplier tube detector
(e.g., <5 cm). A hydrocarbon scrubber, optical filter and
appropriate distancing of the measurement path length may be
required method components to reduce interference.
4.0 Calibration Procedure
Atmospheres containing accurately known concentrations of sulfur
dioxide are prepared using a compressed gas transfer standard
diluted with accurately metered clean air flow rates.
4.1 Apparatus: Figure 2 shows a typical generic system
suitable for diluting a SO2 gas cylinder concentration standard
with clean air through a mixing chamber to produce the desired
calibration concentration standards. A valve may be used to
conveniently divert the SO2 from the sampling manifold to provide
clean zero air at the output manifold for zero adjustment. The
system may be made up using common laboratory components, or it may
be a commercially manufactured system. In either case, the
principle components are as follows:
4.1.1 SO2 standard gas flow control and measurement devices (or
a combined device) capable of regulating and maintaining the
standard gas flow rate constant to within ±2 percent and measuring
the gas flow rate accurate to within ±2, properly calibrated to a
NIST-traceable standard.
4.1.2 Dilution air flow control and measurement devices (or a
combined device) capable of regulating and maintaining the air flow
rate constant to within ±2 percent and measuring the air flow rate
accurate to within ±2, properly calibrated to a NIST-traceable
standard.
4.1.3 Mixing chamber, of an inert material such as glass and of
proper design to provide thorough mixing of pollutant gas and
diluent air streams.
4.1.4 Sampling manifold, constructed of glass,
polytetrafluoroethylene (PTFE Teflon TM), or other suitably inert
material and of sufficient diameter to insure a minimum pressure
drop at the analyzer connection, with a vent designed to insure a
minimum over-pressure (relative to ambient air pressure) at the
analyzer connection and to prevent ambient air from entering the
manifold.
4.1.5 Standard gas pressure regulator, of clean stainless steel
with a stainless steel diaphragm, suitable for use with a high
pressure SO2 gas cylinder.
4.1.6 Reagents
4.1.6.1 SO2 gas concentration transfer standard having a
certified SO2 concentration of not less than 10 ppm, in N2,
traceable to a NIST Standard Reference Material (SRM).
4.1.6.2 Clean zero air, free of contaminants that could cause a
detectable response or a change in sensitivity of the analyzer.
Since ultraviolet fluorescence analyzers may be sensitive to
aromatic hydrocarbons and O2-to-N2 ratios, it is important that the
clean zero air contains less than 0.1 ppm aromatic hydrocarbons and
O2 and N2 percentages approximately the same as in ambient air. A
procedure for generating zero air is given in reference 1.
4.2 Procedure
4.2.1 Obtain a suitable calibration apparatus, such as the one
shown schematically in Figure 1, and verify that all materials in
contact with the pollutant are of glass, Teflon TM, or other
suitably inert material and completely clean.
4.2.2 Purge the SO2 standard gas lines and pressure regulator to
remove any residual air.
4.2.3 Ensure that there are no leaks in the system and that the
flow measuring devices are properly and accurately calibrated under
the conditions of use against a reliable volume or flow rate
standard such as a soap-bubble meter or a wet-test meter traceable
to a NIST standard. All volumetric flow rates should be corrected
to the same reference temperature and pressure by using the formula
below:
Where:
Fc = corrected flow rate (L/min
at 25 °C and 760 mm Hg),
Fm = measured flow rate, (at
temperature, Tm and pressure, Pm),
Pm = measured pressure in
mm Hg, (absolute), and
Tm = measured temperature in degrees
Celsius.
4.2.4 Allow the SO2 analyzer under calibration to sample zero
air until a stable response is obtained, then make the proper zero
adjustment.
4.2.5 Adjust the airflow to provide an SO2 concentration of
approximately 80 percent of the upper measurement range limit of
the SO2 instrument and verify that the total air flow of the
calibration system exceeds the demand of all analyzers sampling
from the output manifold (with the excess vented).
4.2.6 Calculate the actual SO2 calibration concentration
standard as:
Where:
C = the concentration of the SO2
gas standard
Fp = the flow rate of SO2 gas standard
Ft = the total air flow rate of pollutant and diluent gases
4.2.7 When the analyzer response has stabilized, adjust the SO2
span control to obtain the desired response equivalent to the
calculated standard concentration. If substantial adjustment of the
span control is needed, it may be necessary to re-check the zero
and span adjustments by repeating steps 4.2.4 through 4.2.7 until
no further adjustments are needed.
4.2.8 Adjust the flow rate(s) to provide several other SO2
calibration concentrations over the analyzer's measurement range.
At least five different concentrations evenly spaced throughout the
analyzer's range are suggested.
4.2.9 Plot the analyzer response (vertical or Y-axis) versus SO2
concentration (horizontal or X-axis). Compute the linear regression
slope and intercept and plot the regression line to verify that no
point deviates from this line by more than 2 percent of the maximum
concentration tested.
Note:
Additional information on calibration and pollutant standards is
provided in Section 12 of Reference 3.
5.0 Frequency of Calibration
The frequency of calibration, as well as the number of points
necessary to establish the calibration curve and the frequency of
other performance checking will vary by analyzer; however, the
minimum frequency, acceptance criteria, and subsequent actions are
specified in Reference 3, Appendix D: Measurement Quality
Objectives and Validation Template for SO2 (page 9 of 30). The
user's quality control program should provide guidelines for
initial establishment of these variables and for subsequent
alteration as operational experience is accumulated. Manufacturers
of analyzers should include in their instruction/operation manuals
information and guidance as to these variables and on other matters
of operation, calibration, routine maintenance, and quality
control.
6.0 References for SO2 Method 1. H. Okabe, P. L. Splitstone, and J.
J. Ball, “Ambient and Source SO2 Detector Based on a Fluorescence
Method”,
Journal of the Air Control Pollution Association,
vol. 23, p. 514-516 (1973). 2. F. P. Schwarz, H. Okabe, and J. K.
Whittaker, “Fluorescence Detection of Sulfur Dioxide in Air at the
Parts per Billion Level,”
Analytical Chemistry, vol. 46, pp.
1024-1028 (1974). 3.
QA Handbook for Air Pollution Measurement
Systems - Volume II. Ambient Air Quality Monitoring Programs.
U.S.
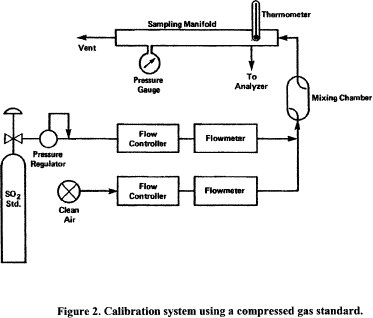
[75 FR
35593, June 22, 2010]
Appendix A-2 to Part 50 - Reference Method for the Determination of Sulfur Dioxide in the Atmosphere (Pararosaniline Method)
40:2.0.1.1.1.0.1.20.2 : Appendix A
Appendix A-2 to Part 50 - Reference Method for the Determination of
Sulfur Dioxide in the Atmosphere (Pararosaniline Method)
1.0 Applicability.
1.1 This method provides a measurement of the concentration of
sulfur dioxide (SO2) in ambient air for determining compliance with
the primary and secondary national ambient air quality standards
for sulfur oxides (sulfur dioxide) as specified in § 50.4 and §
50.5 of this chapter. The method is applicable to the measurement
of ambient SO2 concentrations using sampling periods ranging from
30 minutes to 24 hours. Additional quality assurance procedures and
guidance are provided in part 58, appendixes A and B, of this
chapter and in references 1 and 2.
2.0 Principle.
2.1 A measured volume of air is bubbled through a solution of
0.04 M potassium tetrachloromercurate (TCM). The SO2 present in the
air stream reacts with the TCM solution to form a stable
monochlorosulfonatomercurate(3) complex. Once formed, this
complex resists air oxidation(4, 5) and is stable in the
presence of strong oxidants such as ozone and oxides of nitrogen.
During subsequent analysis, the complex is reacted with
acid-bleached pararosaniline dye and formaldehyde to form an
intensely colored pararosaniline methyl sulfonic acid.
(6) The optical density of this species is determined
spectrophotometrically at 548 nm and is directly related to the
amount of SO2 collected. The total volume of air sampled, corrected
to EPA reference conditions (25 °C, 760 mm Hg [101 kPa]), is
determined from the measured flow rate and the sampling time. The
concentration of SO2 in the ambient air is computed and expressed
in micrograms per standard cubic meter (µg/std m 3).
3.0 Range.
3.1 The lower limit of detection of SO2 in 10 mL of TCM is 0.75
µg (based on collaborative test results).(7) This represents
a concentration of 25 µg SO2/m 3 (0.01 ppm) in an air sample of 30
standard liters (short-term sampling) and a concentration of 13 µg
SO2/m 3 (0.005 ppm) in an air sample of 288 standard liters
(long-term sampling). Concentrations less than 25 µg SO2/m 3 can be
measured by sampling larger volumes of ambient air; however, the
collection efficiency falls off rapidly at low
concentrations.(8, 9) Beer's law is adhered to up to 34 µg
of SO2 in 25 mL of final solution. This upper limit of the analysis
range represents a concentration of 1,130 µg SO2/m 3 (0.43 ppm) in
an air sample of 30 standard liters and a concentration of 590 µg
SO2/m 3 (0.23 ppm) in an air sample of 288 standard liters. Higher
concentrations can be measured by collecting a smaller volume of
air, by increasing the volume of absorbing solution, or by diluting
a suitable portion of the collected sample with absorbing solution
prior to analysis.
4.0 Interferences.
4.1 The effects of the principal potential interferences have
been minimized or eliminated in the following manner: Nitrogen
oxides by the addition of sulfamic acid,(10, 11) heavy
metals by the addition of ethylenediamine tetracetic acid disodium
salt (EDTA) and phosphoric acid,(10, 12) and ozone by time
delay.(10) Up to 60 µg Fe (III), 22 µg V (V), 10 µg Cu (II),
10 µg Mn (II), and 10 µg Cr (III) in 10 mL absorbing reagent can be
tolerated in the procedure.(10) No significant interference
has been encountered with 2.3 µg NH3.(13)
5.0 Precision and Accuracy.
5.1 The precision of the analysis is 4.6 percent (at the 95
percent confidence level) based on the analysis of standard sulfite
samples.(10)
5.2 Collaborative test results (14) based on the analysis
of synthetic test atmospheres (SO2 in scrubbed air) using the
24-hour sampling procedure and the sulfite-TCM calibration
procedure show that:
• The replication error varies linearly with concentration from
±2.5 µg/m 3 at concentrations of 100 µg/m 3 to ±7 µg/m 3 at
concentrations of 400 µg/m 3. • The day-to-day variability within
an individual laboratory (repeatability) varies linearly with
concentration from ±18.1 µg/m 3 at levels of 100 µg/m 3 to ±50.9
µg/m 3 at levels of 400 µg/m 3. • The day-to-day variability
between two or more laboratories (reproducibility) varies linearly
with concentration from ±36.9 µg/m 3 at levels of 100 µg/m 3 to
±103.5 µ g/m 3 at levels of 400 µg/m 3. • The method has a
concentration-dependent bias, which becomes significant at the 95
percent confidence level at the high concentration level. Observed
values tend to be lower than the expected SO2 concentration level.
6.0 Stability.
6.1 By sampling in a controlled temperature environment of 15°
±10 °C, greater than 98.9 percent of the SO2-TCM complex is
retained at the completion of sampling. (15) If kept at 5 °C
following the completion of sampling, the collected sample has been
found to be stable for up to 30 days. (10) The presence of
EDTA enhances the stability of SO2 in the TCM solution and the rate
of decay is independent of the concentration of SO2.
(16)
7.0 Apparatus.
7.1 Sampling.
7.1.1 Sample probe: A sample probe meeting the
requirements of section 7 of 40 CFR part 58, appendix E (Teflon ®
or glass with residence time less than 20 sec.) is used to
transport ambient air to the sampling train location. The end of
the probe should be designed or oriented to preclude the sampling
of precipitation, large particles, etc. A suitable probe can be
constructed from Teflon ® tubing connected to an inverted
funnel.
7.1.2 Absorber - short-term sampling: An all glass midget
impinger having a solution capacity of 30 mL and a stem clearance
of 4 ±1 mm from the bottom of the vessel is used for sampling
periods of 30 minutes and 1 hour (or any period considerably less
than 24 hours). Such an impinger is shown in Figure 1. These
impingers are commercially available from distributors such as Ace
Glass, Incorporated.
7.1.3 Absorber - 24-hour sampling: A polypropylene tube
32 mm in diameter and 164 mm long (available from Bel Art Products,
Pequammock, NJ) is used as the absorber. The cap of the absorber
must be a polypropylene cap with two ports (rubber stoppers are
unacceptable because the absorbing reagent can react with the
stopper to yield erroneously high SO2 concentrations). A glass
impinger stem, 6 mm in diameter and 158 mm long, is inserted into
one port of the absorber cap. The tip of the stem is tapered to a
small diameter orifice (0.4 ±0.1 mm) such that a No. 79 jeweler's
drill bit will pass through the opening but a No. 78 drill bit will
not. Clearance from the bottom of the absorber to the tip of the
stem must be 6 ±2 mm. Glass stems can be fabricated by any
reputable glass blower or can be obtained from a scientific supply
firm. Upon receipt, the orifice test should be performed to verify
the orifice size. The 50 mL volume level should be permanently
marked on the absorber. The assembled absorber is shown in Figure
2.
7.1.4 Moisture trap: A moisture trap constructed of a
glass trap as shown in Figure 1 or a polypropylene tube as shown in
Figure 2 is placed between the absorber tube and flow control
device to prevent entrained liquid from reaching the flow control
device. The tube is packed with indicating silica gel as shown in
Figure 2. Glass wool may be substituted for silica gel when
collecting short-term samples (1 hour or less) as shown in Figure
1, or for long term (24 hour) samples if flow changes are not
routinely encountered.
7.1.5 Cap seals: The absorber and moisture trap caps must
seal securely to prevent leaks during use. Heat-shrink material as
shown in Figure 2 can be used to retain the cap seals if there is
any chance of the caps coming loose during sampling, shipment, or
storage.
7.1.6 Flow control device: A calibrated rotameter and
needle valve combination capable of maintaining and measuring air
flow to within ±2 percent is suitable for short-term sampling but
may not be used for long-term sampling. A critical orifice can be
used for regulating flow rate for both long-term and short-term
sampling. A 22-gauge hypodermic needle 25 mm long may be used as a
critical orifice to yield a flow rate of approximately 1 L/min for
a 30-minute sampling period. When sampling for 1 hour, a 23-gauge
hypodermic needle 16 mm in length will provide a flow rate of
approximately 0.5 L/min. Flow control for a 24-hour sample may be
provided by a 27-gauge hypodermic needle critical orifice that is
9.5 mm in length. The flow rate should be in the range of 0.18 to
0.22 L/min.
7.1.7 Flow measurement device: Device calibrated as
specified in 9.4.1 and used to measure sample flow rate at the
monitoring site.
7.1.8 Membrane particle filter: A membrane filter of 0.8
to 2 µm porosity is used to protect the flow controller from
particles during long-term sampling. This item is optional for
short-term sampling.
7.1.9 Vacuum pump: A vacuum pump equipped with a vacuum
gauge and capable of maintaining at least 70 kPa (0.7 atm) vacuum
differential across the flow control device at the specified flow
rate is required for sampling.
7.1.10 Temperature control device: The temperature of the
absorbing solution during sampling must be maintained at 15° ±10
°C. As soon as possible following sampling and until analysis, the
temperature of the collected sample must be maintained at 5° ±5 °C.
Where an extended period of time may elapse before the collected
sample can be moved to the lower storage temperature, a collection
temperature near the lower limit of the 15 ±10 °C range should be
used to minimize losses during this period. Thermoelectric coolers
specifically designed for this temperature control are available
commercially and normally operate in the range of 5° to 15 °C.
Small refrigerators can be modified to provide the required
temperature control; however, inlet lines must be insulated from
the lower temperatures to prevent condensation when sampling under
humid conditions. A small heating pad may be necessary when
sampling at low temperatures (<7 °C) to prevent the absorbing
solution from freezing.(17)
7.1.11 Sampling train container: The absorbing solution
must be shielded from light during and after sampling. Most
commercially available sampler trains are enclosed in a light-proof
box.
7.1.12 Timer: A timer is recommended to initiate and to
stop sampling for the 24-hour period. The timer is not a required
piece of equipment; however, without the timer a technician would
be required to start and stop the sampling manually. An elapsed
time meter is also recommended to determine the duration of the
sampling period.
7.2 Shipping.
7.2.1 Shipping container: A shipping container that can
maintain a temperature of 5° ±5 °C is used for transporting the
sample from the collection site to the analytical laboratory. Ice
coolers or refrigerated shipping containers have been found to be
satisfactory. The use of eutectic cold packs instead of ice will
give a more stable temperature control. Such equipment is available
from Cole-Parmer Company, 7425 North Oak Park Avenue, Chicago, IL
60648.
7.3 Analysis.
7.3.1 Spectrophotometer: A spectrophotometer suitable for
measurement of absorbances at 548 nm with an effective spectral
bandwidth of less than 15 nm is required for analysis. If the
spectrophotometer reads out in transmittance, convert to absorbance
as follows:
where: A = absorbance, and T = transmittance
(0<≥T<1).
A standard wavelength filter traceable to the National Bureau of
Standards is used to verify the wavelength calibration according to
the procedure enclosed with the filter. The wavelength calibration
must be verified upon initial receipt of the instrument and after
each 160 hours of normal use or every 6 months, whichever occurs
first.
7.3.2 Spectrophotometer cells: A set of 1-cm path length
cells suitable for use in the visible region is used during
analysis. If the cells are unmatched, a matching correction factor
must be determined according to Section 10.1.
7.3.3 Temperature control device: The color development
step during analysis must be conducted in an environment that is in
the range of 20° to 30 °C and controlled to ±1 °C. Both calibration
and sample analysis must be performed under identical conditions
(within 1 °C). Adequate temperature control may be obtained by
means of constant temperature baths, water baths with manual
temperature control, or temperature controlled rooms.
7.3.4 Glassware: Class A volumetric glassware of various
capacities is required for preparing and standardizing reagents and
standards and for dispensing solutions during analysis. These
included pipets, volumetric flasks, and burets.
7.3.5 TCM waste receptacle: A glass waste receptacle is
required for the storage of spent TCM solution. This vessel should
be stoppered and stored in a hood at all times.
8.0 Reagents.
8.1 Sampling.
8.1.1 Distilled water: Purity of distilled water must be
verified by the following procedure:(18)
• Place 0.20 mL of potassium permanganate solution (0.316 g/L), 500
mL of distilled water, and 1mL of concentrated sulfuric acid in a
chemically resistant glass bottle, stopper the bottle, and allow to
stand. • If the permanganate color (pink) does not disappear
completely after a period of 1 hour at room temperature, the water
is suitable for use. • If the permanganate color does disappear,
the water can be purified by redistilling with one crystal each of
barium hydroxide and potassium permanganate in an all glass still.
8.1.2 Absorbing reagent (0.04 M potassium
tetrachloromercurate [TCM]): Dissolve 10.86 g mercuric chloride,
0.066 g EDTA, and 6.0 g potassium chloride in distilled water and
dilute to volume with distilled water in a 1,000-mL volumetric
flask. (Caution: Mercuric chloride is highly poisonous. If
spilled on skin, flush with water immediately.) The pH of this
reagent should be between 3.0 and 5.0 (10) Check the pH of
the absorbing solution by using pH indicating paper or a pH meter.
If the pH of the solution is not between 3.0 and 5.0, dispose of
the solution according to one of the disposal techniques described
in Section 13.0. The absorbing reagent is normally stable for 6
months. If a precipitate forms, dispose of the reagent according to
one of the procedures described in Section 13.0.
8.2 Analysis.
8.2.1 Sulfamic acid (0.6%): Dissolve 0.6 g sulfamic acid
in 100 mL distilled water. Perpare fresh daily.
8.2.2 Formaldehyde (0.2%): Dilute 5 mL formaldehyde
solution (36 to 38 percent) to 1,000 mL with distilled water.
Prepare fresh daily.
8.2.3 Stock iodine solution (0.1 N): Place 12.7 g
resublimed iodine in a 250-mL beaker and add 40 g potassium iodide
and 25 mL water. Stir until dissolved, transfer to a 1,000 mL
volumetric flask and dilute to volume with distilled water.
8.2.4 Iodine solution (0.01 N): Prepare approximately
0.01 N iodine solution by diluting 50 mL of stock iodine solution
(Section 8.2.3) to 500 mL with distilled water.
8.2.5 Starch indicator solution: Triturate 0.4 g soluble
starch and 0.002 g mercuric iodide (preservative) with enough
distilled water to form a paste. Add the paste slowly to 200 mL of
boiling distilled water and continue boiling until clear. Cool and
transfer the solution to a glass stopperd bottle.
8.2.6 1 N hydrochloric acid: Slowly and while stirring,
add 86 mL of concentrated hydrochloric acid to 500 mL of distilled
water. Allow to cool and dilute to 1,000 mL with distilled
water.
8.2.7 Potassium iodate solution: Accurately weigh to the
nearest 0.1 mg, 1.5 g (record weight) of primary standard grade
potassium iodate that has been previously dried at 180 °C for at
least 3 hours and cooled in a dessicator. Dissolve, then dilute to
volume in a 500-mL volumetric flask with distilled water.
8.2.8 Stock sodium thiosulfate solution (0.1 N): Prepare
a stock solution by dissolving 25 g sodium thiosulfate (Na2 S2 O3 ÷
5H2 O) in 1,000 mL freshly boiled, cooled, distilled water and
adding 0.1 g sodium carbonate to the solution. Allow the solution
to stand at least 1 day before standardizing. To standardize,
accurately pipet 50 mL of potassium iodate solution (Section 8.2.7)
into a 500-mL iodine flask and add 2.0 g of potassium iodide and 10
mL of 1 N HCl. Stopper the flask and allow to stand for 5 minutes.
Titrate the solution with stock sodium thiosulfate solution
(Section 8.2.8) to a pale yellow color. Add 5 mL of starch solution
(Section 8.2.5) and titrate until the blue color just disappears.
Calculate the normality (Ns) of the stock sodium thiosulfate
solution as follows:
where: M = volume of thiosulfate required in
mL, and W = weight of potassium iodate in g (recorded weight in
Section 8.2.7).
8.2.9 Working sodium thiosulfate titrant (0.01 N):
Accurately pipet 100 mL of stock sodium thiosulfate solution
(Section 8.2.8) into a 1,000-mL volumetric flask and dilute to
volume with freshly boiled, cooled, distilled water. Calculate the
normality of the working sodium thiosulfate titrant (NT) as
follows:
8.2.10 Standardized sulfite solution for the preparation of
working sulfite-TCM solution: Dissolve 0.30 g sodium
metabisulfite (Na2 S2 O5) or 0.40 g sodium sulfite (Na2 SO3) in 500
mL of recently boiled, cooled, distilled water. (Sulfite solution
is unstable; it is therefore important to use water of the highest
purity to minimize this instability.) This solution contains the
equivalent of 320 to 400 µg SO2/mL. The actual concentration of the
solution is determined by adding excess iodine and back-titrating
with standard sodium thiosulfate solution. To back-titrate, pipet
50 mL of the 0.01 N iodine solution (Section 8.2.4) into each of
two 500-mL iodine flasks (A and B). To flask A (blank) add 25 mL
distilled water, and to flask B (sample) pipet 25 mL sulfite
solution. Stopper the flasks and allow to stand for 5 minutes.
Prepare the working sulfite-TCM solution (Section 8.2.11)
immediately prior to adding the iodine solution to the flasks.
Using a buret containing standardized 0.01 N thiosulfate titrant
(Section 8.2.9), titrate the solution in each flask to a pale
yellow color. Then add 5 mL starch solution (Section 8.2.5) and
continue the titration until the blue color just disappears.
8.2.11 Working sulfite-TCM solution: Accurately pipet 5
mL of the standard sulfite solution (Section 8.2.10) into a 250-mL
volumetric flask and dilute to volume with 0.04 M TCM. Calculate
the concentration of sulfur dioxide in the working solution as
follows:
where: A = volume of thiosulfate titrant
required for the blank, mL; B = volume of thiosulfate titrant
required for the sample, mL; NT = normality of the thiosulfate
titrant, from equation (3); 32,000 = milliequivalent weight of SO2,
µg; 25 = volume of standard sulfite solution, mL; and 0.02 =
dilution factor.
This solution is stable for 30 days if kept at 5 °C. (16) If not
kept at 5 °C, prepare fresh daily.
8.2.12 Purified pararosaniline (PRA) stock solution (0.2%
nominal):
8.2.12.1 Dye specifications -
• The dye must have a maximum absorbance at a wavelength of 540 nm
when assayed in a buffered solution of 0.1 M sodium acetate-acetic
acid; • The absorbance of the reagent blank, which is temperature
sensitive (0.015 absorbance unit/ °C), must not exceed 0.170 at 22
°C with a 1-cm optical path length when the blank is prepared
according to the specified procedure; • The calibration curve
(Section 10.0) must have a slope equal to 0.030 ±0.002 absorbance
unit/µg SO2 with a 1-cm optical path length when the dye is pure
and the sulfite solution is properly standardized.
8.2.12.2 Preparation of stock PRA solution - A specially
purified (99 to 100 percent pure) solution of pararosaniline, which
meets the above specifications, is commercially available in the
required 0.20 percent concentration (Harleco Co.). Alternatively,
the dye may be purified, a stock solution prepared, and then
assayed according to the procedure as described
below.(10)
8.2.12.3 Purification procedure for PRA -
1. Place 100 mL each of 1-butanol and 1 N HCl in a large
separatory funnel (250-mL) and allow to equilibrate. Note: Certain
batches of 1-butanol contain oxidants that create an SO2 demand.
Before using, check by placing 20 mL of 1-butanol and 5 mL of 20
percent potassium iodide (KI) solution in a 50-mL separatory funnel
and shake thoroughly. If a yellow color appears in the alcohol
phase, redistill the 1-butanol from silver oxide and collect the
middle fraction or purchase a new supply of 1-butanol.
2. Weigh 100 mg of pararosaniline hydrochloride dye (PRA) in a
small beaker. Add 50 mL of the equilibrated acid (drain in acid
from the bottom of the separatory funnel in 1.) to the beaker and
let stand for several minutes. Discard the remaining acid phase in
the separatory funnel.
3. To a 125-mL separatory funnel, add 50 mL of the equilibrated
1-butanol (draw the 1-butanol from the top of the separatory funnel
in 1.). Transfer the acid solution (from 2.) containing the dye to
the funnel and shake carefully to extract. The violet impurity will
transfer to the organic phase.
4. Transfer the lower aqueous phase into another separatory
funnel, add 20 mL of equilibrated 1-butanol, and extract again.
5. Repeat the extraction procedure with three more 10-mL
portions of equilibrated 1-butanol.
6. After the final extraction, filter the acid phase through a
cotton plug into a 50-mL volumetric flask and bring to volume with
1 N HCl. This stock reagent will be a yellowish red.
7. To check the purity of the PRA, perform the assay and
adjustment of concentration (Section 8.2.12.4) and prepare a
reagent blank (Section 11.2); the absorbance of this reagent blank
at 540 nm should be less than 0.170 at 22 °C. If the absorbance is
greater than 0.170 under these conditions, further extractions
should be performed.
8.2.12.4 PRA assay procedure - The concentration of
pararosaniline hydrochloride (PRA) need be assayed only once after
purification. It is also recommended that commercial solutions of
pararosaniline be assayed when first purchased. The assay procedure
is as follows:(10)
1. Prepare 1 M acetate-acetic acid buffer stock solution with a
pH of 4.79 by dissolving 13.61 g of sodium acetate trihydrate in
distilled water in a 100-mL volumetric flask. Add 5.70 mL of
glacial acetic acid and dilute to volume with distilled water.
2. Pipet 1 mL of the stock PRA solution obtained from the
purification process or from a commercial source into a 100-mL
volumetric flask and dilute to volume with distilled water.
3. Transfer a 5-mL aliquot of the diluted PRA solution from 2.
into a 50-mL volumetric flask. Add 5mL of 1 M acetate-acetic acid
buffer solution from 1. and dilute the mixture to volume with
distilled water. Let the mixture stand for 1 hour.
4. Measure the absorbance of the above solution at 540 nm with a
spectrophotometer against a distilled water reference. Compute the
percentage of nominal concentration of PRA by
where: A = measured absorbance of the final
mixture (absorbance units); W = weight in grams of the PRA dye used
in the assay to prepare 50 mL of stock solution (for example, 0.100
g of dye was used to prepare 50 mL of solution in the purification
procedure; when obtained from commercial sources, use the stated
concentration to compute W; for 98% PRA, W = .098 g.); and K = 21.3
for spectrophotometers having a spectral bandwidth of less than 15
nm and a path length of 1 cm.
8.2.13 Pararosaniline reagent: To a 250-mL volumetric
flask, add 20 mL of stock PRA solution. Add an additional 0.2 mL of
stock solution for each percentage that the stock assays below 100
percent. Then add 25 mL of 3 M phosphoric acid and dilute to volume
with distilled water. The reagent is stable for at least 9 months.
Store away from heat and light.
9.0 Sampling Procedure.
9.1 General Considerations. Procedures are described for
short-term sampling (30-minute and 1-hour) and for long-term
sampling (24-hour). Different combinations of absorbing reagent
volume, sampling rate, and sampling time can be selected to meet
special needs. For combinations other than those specifically
described, the conditions must be adjusted so that linearity is
maintained between absorbance and concentration over the dynamic
range. Absorbing reagent volumes less than 10 mL are not
recommended. The collection efficiency is above 98 percent for the
conditions described; however, the efficiency may be substantially
lower when sampling concentrations below 25 µγSO2/m
3.(8,9)
9.2 30-Minute and 1-Hour Sampling. Place 10 mL of TCM
absorbing reagent in a midget impinger and seal the impinger with a
thin film of silicon stopcock grease (around the ground glass
joint). Insert the sealed impinger into the sampling train as shown
in Figure 1, making sure that all connections between the various
components are leak tight. Greaseless ball joint fittings, heat
shrinkable Teflon ® tubing, or Teflon ® tube fittings may be used
to attain leakfree conditions for portions of the sampling train
that come into contact with air containing SO2. Shield the
absorbing reagent from direct sunlight by covering the impinger
with aluminum foil or by enclosing the sampling train in a
light-proof box. Determine the flow rate according to Section
9.4.2. Collect the sample at 1 ±0.10 L/min for 30-minute sampling
or 0.500 ±0.05 L/min for 1-hour sampling. Record the exact sampling
time in minutes, as the sample volume will later be determined
using the sampling flow rate and the sampling time. Record the
atmospheric pressure and temperature.
9.3 24-Hour Sampling. Place 50 mL of TCM absorbing
solution in a large absorber, close the cap, and, if needed, apply
the heat shrink material as shown in Figure 3. Verify that the
reagent level is at the 50 mL mark on the absorber. Insert the
sealed absorber into the sampling train as shown in Figure 2. At
this time verify that the absorber temperature is controlled to 15
±10 °C. During sampling, the absorber temperature must be
controlled to prevent decomposition of the collected complex. From
the onset of sampling until analysis, the absorbing solution must
be protected from direct sunlight. Determine the flow rate
according to Section 9.4.2. Collect the sample for 24 hours from
midnight to midnight at a flow rate of 0.200 ±0.020 L/min. A
start/stop timer is helpful for initiating and stopping sampling
and an elapsed time meter will be useful for determining the
sampling time.
9.4 Flow Measurement.
9.4.1 Calibration: Flow measuring devices used for the
on-site flow measurements required in 9.4.2 must be calibrated
against a reliable flow or volume standard such as an NBS traceable
bubble flowmeter or calibrated wet test meter. Rotameters or
critical orifices used in the sampling train may be calibrated, if
desired, as a quality control check, but such calibration shall not
replace the on-site flow measurements required by 9.4.2. In-line
rotameters, if they are to be calibrated, should be calibrated in
situ, with the appropriate volume of solution in the absorber.
9.4.2 Determination of flow rate at sampling site: For
short-term samples, the standard flow rate is determined at the
sampling site at the initiation and completion of sample collection
with a calibrated flow measuring device connected to the inlet of
the absorber. For 24-hour samples, the standard flow rate is
determined at the time the absorber is placed in the sampling train
and again when the absorber is removed from the train for shipment
to the analytical laboratory with a calibrated flow measuring
device connected to the inlet of the sampling train. The flow rate
determination must be made with all components of the sampling
system in operation (e.g., the absorber temperature controller and
any sample box heaters must also be operating). Equation 6 may be
used to determine the standard flow rate when a calibrated positive
displacement meter is used as the flow measuring device. Other
types of calibrated flow measuring devices may also be used to
determine the flow rate at the sampling site provided that the user
applies any appropriate corrections to devices for which output is
dependent on temperature or pressure.
where: Qstd = flow rate at standard conditions,
std L/min (25 °C and 760 mm Hg); Qact = flow rate at monitoring
site conditions, L/min; Pb = barometric pressure at monitoring site
conditions, mm Hg or kPa; RH = fractional relative humidity of the
air being measured; PH2O = vapor pressure of water at the
temperature of the air in the flow or volume standard, in the same
units as Pb, (for wet volume standards only, i.e., bubble flowmeter
or wet test meter; for dry standards, i.e., dry test meter, PH2O =
0); Pstd = standard barometric pressure, in the same units as Pb
(760 mm Hg or 101 kPa); and Tmeter = temperature of the air in the
flow or volume standard, °C (e.g., bubble flowmeter).
If a barometer is not available, the following equation may be
used to determine the barometric pressure:
where: H = sampling site elevation above sea
level in meters.
If the initial flow rate (Qi) differs from the flow rate of the
critical orifice or the flow rate indicated by the flowmeter in the
sampling train (Qc) by more than 5 percent as determined by
equation (8), check for leaks and redetermine Qi.
Invalidate the sample if the difference between the initial (Qi)
and final (Qf) flow rates is more than 5 percent as determined by
equation (9):
9.5 Sample Storage and Shipment. Remove the impinger or
absorber from the sampling train and stopper immediately. Verify
that the temperature of the absorber is not above 25 °C. Mark the
level of the solution with a temporary (e.g., grease pencil) mark.
If the sample will not be analyzed within 12 hours of sampling, it
must be stored at 5° ±5 °C until analysis. Analysis must occur
within 30 days. If the sample is transported or shipped for a
period exceeding 12 hours, it is recommended that thermal coolers
using eutectic ice packs, refrigerated shipping containers, etc.,
be used for periods up to 48 hours. (17) Measure the
temperature of the absorber solution when the shipment is received.
Invalidate the sample if the temperature is above 10 °C. Store the
sample at 5° ±5 °C until it is analyzed.
10.0 Analytical Calibration.
10.1 Spectrophotometer Cell Matching. If unmatched
spectrophotometer cells are used, an absorbance correction factor
must be determined as follows:
1. Fill all cells with distilled water and designate the one
that has the lowest absorbance at 548 nm as the reference. (This
reference cell should be marked as such and continually used for
this purpose throughout all future analyses.)
2. Zero the spectrophotometer with the reference cell.
3. Determine the absorbance of the remaining cells (Ac) in
relation to the reference cell and record these values for future
use. Mark all cells in a manner that adequately identifies the
correction.
The corrected absorbance during future analyses using each cell
is determining as follows:
where: A = corrected absorbance, Aobs =
uncorrected absorbance, and Ac = cell correction.
10.2 Static Calibration Procedure (Option 1). Prepare a
dilute working sulfite-TCM solution by diluting 10 mL of the
working sulfite-TCM solution (Section 8.2.11) to 100 mL with TCM
absorbing reagent. Following the table below, accurately pipet the
indicated volumes of the sulfite-TCM solutions into a series of
25-mL volumetric flasks. Add TCM absorbing reagent as indicated to
bring the volume in each flask to 10 mL.
Sulfite-TCM solution |
Volume of sulfite-TCM
solution |
Volume of TCM, mL |
Total µg SO2 (approx.* |
Working |
4.0 |
6.0 |
28.8 |
Working |
3.0 |
7.0 |
21.6 |
Working |
2.0 |
8.0 |
14.4 |
Dilute
working |
10.0 |
0.0 |
7.2 |
Dilute
working |
5.0 |
5.0 |
3.6 |
|
0.0 |
10.0 |
0.0 |
To each volumetric flask, add 1 mL 0.6% sulfamic acid (Section
8.2.1), accurately pipet 2 mL 0.2% formaldehyde solution (Section
8.2.2), then add 5 mL pararosaniline solution (Section 8.2.13).
Start a laboratory timer that has been set for 30 minutes. Bring
all flasks to volume with recently boiled and cooled distilled
water and mix thoroughly. The color must be developed (during the
30-minute period) in a temperature environment in the range of 20°
to 30 °C, which is controlled to ±1 °C. For increased precision, a
constant temperature bath is recommended during the color
development step. After 30 minutes, determine the corrected
absorbance of each standard at 548 nm against a distilled water
reference (Section 10.1). Denote this absorbance as (A). Distilled
water is used in the reference cell rather than the reagant blank
because of the temperature sensitivity of the reagent blank.
Calculate the total micrograms SO2 in each solution:
where: VTCM/SO2 = volume of sulfite-TCM
solution used, mL; CTCM/SO2 = concentration of sulfur dioxide in
the working sulfite-TCM, µg SO2/mL (from equation 4); and D =
dilution factor (D = 1 for the working sulfite-TCM solution; D =
0.1 for the diluted working sulfite-TCM solution).
A calibration equation is determined using the method of linear
least squares (Section 12.1). The total micrograms SO2 contained in
each solution is the x variable, and the corrected absorbance (eq.
10) associated with each solution is the y variable. For the
calibration to be valid, the slope must be in the range of 0.030
±0.002 absorbance unit/µg SO2, the intercept as determined by the
least squares method must be equal to or less than 0.170 absorbance
unit when the color is developed at 22 °C (add 0.015 to this 0.170
specification for each °C above 22 °C) and the correlation
coefficient must be greater than 0.998. If these criteria are not
met, it may be the result of an impure dye and/or an improperly
standardized sulfite-TCM solution. A calibration factor (Bs) is
determined by calculating the reciprocal of the slope and is
subsequently used for calculating the sample concentration (Section
12.3).
10.3 Dynamic Calibration Procedures (Option 2).
Atmospheres containing accurately known concentrations of sulfur
dioxide are prepared using permeation devices. In the systems for
generating these atmospheres, the permeation device emits gaseous
SO2 at a known, low, constant rate, provided the temperature of the
device is held constant (±0.1 °C) and the device has been
accurately calibrated at the temperature of use. The SO2 permeating
from the device is carried by a low flow of dry carrier gas to a
mixing chamber where it is diluted with SO2-free air to the desired
concentration and supplied to a vented manifold. A typical system
is shown schematically in Figure 4 and this system and other
similar systems have been described in detail by O'Keeffe and
Ortman; (19) Scaringelli, Frey, and Saltzman, (20)
and Scaringelli, O'Keeffe, Rosenberg, and Bell. (21)
Permeation devices may be prepared or purchased and in both cases
must be traceable either to a National Bureau of Standards (NBS)
Standard Reference Material (SRM 1625, SRM 1626, SRM 1627) or to an
NBS/EPA-approved commercially available Certified Reference
Material (CRM). CRM's are described in Reference 22, and a list of
CRM sources is available from the address shown for Reference 22. A
recommended protocol for certifying a permeation device to an NBS
SRM or CRM is given in Section 2.0.7 of Reference 2. Device
permeation rates of 0.2 to 0.4 µg/min, inert gas flows of about 50
mL/min, and dilution air flow rates from 1.1 to 15 L/min
conveniently yield standard atmospheres in the range of 25 to 600
µg SO2/m 3 (0.010 to 0.230 ppm).
10.3.1 Calibration Option 2A (30-minute and 1-hour
samples): Generate a series of six standard atmospheres of SO2
(e.g., 0, 50, 100, 200, 350, 500, 750 µg/m 3) by adjusting the
dilution flow rates appropriately. The concentration of SO2 in each
atmosphere is calculated as follows:
where: Ca = concentration of SO2 at standard
conditions, µg/m 3; Pr = permeation rate, µg/min; Qd = flow rate of
dilution air, std L/min; and Qp = flow rate of carrier gas across
permeation device, std L/min.
Be sure that the total flow rate of the standard exceeds the
flow demand of the sample train, with the excess flow vented at
atmospheric pressure. Sample each atmosphere using similar
apparatus as shown in Figure 1 and under the same conditions as
field sampling (i.e., use same absorbing reagent volume and
sample same volume of air at an equivalent flow rate). Due to the
length of the sampling periods required, this method is not
recommended for 24-hour sampling. At the completion of sampling,
quantitatively transfer the contents of each impinger to one of a
series of 25-mL volumetric flasks (if 10 mL of absorbing solution
was used) using small amounts of distilled water for rinse
(<5mL). If >10 mL of absorbing solution was used, bring the
absorber solution in each impinger to orginal volume with distilled
H2 O and pipet 10-mL portions from each impinger into a series of
25-mL volumetric flasks. If the color development steps are not to
be started within 12 hours of sampling, store the solutions at 5°
±5 °C. Calculate the total micrograms SO2 in each solution as
follows:
where: Ca = concentration of SO2 in the
standard atmosphere, µg/m 3; Os = sampling flow rate, std L/min; t
= sampling time, min; Va = volume of absorbing solution used for
color development (10 mL); and Vb = volume of absorbing solution
used for sampling, mL.
Add the remaining reagents for color development in the same
manner as in Section 10.2 for static solutions. Calculate a
calibration equation and a calibration factor (Bg) according to
Section 10.2, adhering to all the specified criteria.
10.3.2 Calibration Option 2B (24-hour samples): Generate a
standard atmosphere containing approximately 1,050 µg SO2/m 3 and
calculate the exact concentration according to equation 12. Set up
a series of six absorbers according to Figure 2 and connect to a
common manifold for sampling the standard atmosphere. Be sure that
the total flow rate of the standard exceeds the flow demand at the
sample manifold, with the excess flow vented at atmospheric
pressure. The absorbers are then allowed to sample the atmosphere
for varying time periods to yield solutions containing 0, 0.2, 0.6,
1.0, 1.4, 1.8, and 2.2 µg SO2/mL solution. The sampling times
required to attain these solution concentrations are calculated as
follows:
where: t = sampling time, min; Vb = volume of
absorbing solution used for sampling (50 mL); Cs = desired
concentration of SO2 in the absorbing solution, µg/mL; Ca =
concentration of the standard atmosphere calculated according to
equation 12, µg/m 3; and Qs = sampling flow rate, std L/min.
At the completion of sampling, bring the absorber solutions to
original volume with distilled water. Pipet a 10-mL portion from
each absorber into one of a series of 25-mL volumetric flasks. If
the color development steps are not to be started within 12 hours
of sampling, store the solutions at 5° ±5 °C. Add the remaining
reagents for color development in the same manner as in Section
10.2 for static solutions. Calculate the total µg SO2 in each
standard as follows:
where: Va = volume of absorbing solution used
for color development (10 mL). All other parameters are defined in
equation 14.
Calculate a calibration equation and a calibration factor (Bt)
according to Section 10.2 adhering to all the specified
criteria.
11.0 Sample Preparation and Analysis.
11.1 Sample Preparation. Remove the samples from the
shipping container. If the shipment period exceeded 12 hours from
the completion of sampling, verify that the temperature is below 10
°C. Also, compare the solution level to the temporary level mark on
the absorber. If either the temperature is above 10 °C or there was
significant loss (more than 10 mL) of the sample during shipping,
make an appropriate notation in the record and invalidate the
sample. Prepare the samples for analysis as follows:
1. For 30-minute or 1-hour samples: Quantitatively transfer the
entire 10 mL amount of absorbing solution to a 25-mL volumetric
flask and rinse with a small amount (<5 mL) of distilled
water.
2. For 24-hour samples: If the volume of the sample is less than
the original 50-mL volume (permanent mark on the absorber), adjust
the volume back to the original volume with distilled water to
compensate for water lost to evaporation during sampling. If the
final volume is greater than the original volume, the volume must
be measured using a graduated cylinder. To analyze, pipet 10 mL of
the solution into a 25-mL volumetric flask.
11.2 Sample Analysis. For each set of determinations,
prepare a reagent blank by adding 10 mL TCM absorbing solution to a
25-mL volumetric flask, and two control standards containing
approximately 5 and 15 µg SO2, respectively. The control standards
are prepared according to Section 10.2 or 10.3. The analysis is
carried out as follows:
1. Allow the sample to stand 20 minutes after the completion of
sampling to allow any ozone to decompose (if applicable).
2. To each 25-mL volumetric flask containing reagent blank,
sample, or control standard, add 1 mL of 0.6% sulfamic acid
(Section 8.2.1) and allow to react for 10 min.
3. Accurately pipet 2 mL of 0.2% formaldehyde solution (Section
8.2.2) and then 5 mL of pararosaniline solution (Section 8.2.13)
into each flask. Start a laboratory timer set at 30 minutes.
4. Bring each flask to volume with recently boiled and cooled
distilled water and mix thoroughly.
5. During the 30 minutes, the solutions must be in a temperature
controlled environment in the range of 20° to 30 °C maintained to
±1 °C. This temperature must also be within 1 °C of that used
during calibration.
6. After 30 minutes and before 60 minutes, determine the
corrected absorbances (equation 10) of each solution at 548 nm
using 1-cm optical path length cells against a distilled water
reference (Section 10.1). (Distilled water is used as a
reference instead of the reagent blank because of the sensitivity
of the reagent blank to temperature.)
7. Do not allow the colored solution to stand in the cells
because a film may be deposited. Clean the cells with isopropyl
alcohol after use.
8. The reagent blank must be within 0.03 absorbance units of the
intercept of the calibration equation determined in Section 10.
11.3 Absorbance range. If the absorbance of the sample
solution ranges between 1.0 and 2.0, the sample can be diluted 1:1
with a portion of the reagent blank and the absorbance redetermined
within 5 minutes. Solutions with higher absorbances can be diluted
up to sixfold with the reagent blank in order to obtain scale
readings of less than 1.0 absorbance unit. However, it is
recommended that a smaller portion (<10 mL) of the original
sample be reanalyzed (if possible) if the sample requires a
dilution greater than 1:1.
11.4 Reagent disposal. All reagents containing mercury
compounds must be stored and disposed of using one of the
procedures contained in Section 13. Until disposal, the discarded
solutions can be stored in closed glass containers and should be
left in a fume hood.
12.0 Calculations.
12.1 Calibration Slope, Intercept, and Correlation
Coefficient. The method of least squares is used to calculate a
calibration equation in the form of:
where: y = corrected absorbance, m = slope,
absorbance unit/µg SO2, x = micrograms of SO2, b = y intercept
(absorbance units).
The slope (m), intercept (b), and correlation coefficient (r)
are calculated as follows:
where n
is the number of calibration points.
A data form (Figure 5) is supplied for easily organizing
calibration data when the slope, intercept, and correlation
coefficient are calculated by hand.
12.2 Total Sample Volume. Determine the sampling volume
at standard conditions as follows:
where: Vstd = sampling volume in std L, Qi =
standard flow rate determined at the initiation of sampling in std
L/min, Qf = standard flow rate determined at the completion of
sampling is std L/min, and t = total sampling time, min.
12.3 Sulfur Dioxide Concentration. Calculate and report
the concentration of each sample as follows:
where: A = corrected absorbance of the sample
solution, from equation (10); Ao = corrected absorbance of the
reagent blank, using equation (10); BX = calibration factor equal
to Bs, Bg, or Bt depending on the calibration procedure used, the
reciprocal of the slope of the calibration equation; Va = volume of
absorber solution analyzed, mL; Vb = total volume of solution in
absorber (see 11.1-2), mL; and Vstd = standard air volume sampled,
std L (from Section 12.2).
Data Form
[For hand calculations]
Calibration point no. |
Micro- grams So2 |
Absor- bance units |
|
|
|
|
(x) |
(y) |
x 2 |
xy |
y 2 |
1 |
|
|
|
|
|
2 |
|
|
|
|
|
3 |
|
|
|
|
|
4 |
|
|
|
|
|
5 |
|
|
|
|
|
6 |
|
|
|
|
|
Σ x=___ Σ y=___ Σ x 2=___ Σxy___ Σy 2___ n=___ (number of pairs of
coordinates.) Figure 5. Data form for hand calculations.
12.4 Control Standards. Calculate the analyzed micrograms of SO2
in each control standard as follows:
where: Cq = analyzed µg SO2 in each control
standard, A = corrected absorbance of the control standard, and Ao
= corrected absorbance of the reagent blank.
The difference between the true and analyzed values of the
control standards must not be greater than 1 µg. If the difference
is greater than 1 µg, the source of the discrepancy must be
identified and corrected.
12.5 Conversion of µg/m 3 to ppm (v/v). If desired, the
concentration of sulfur dioxide at reference conditions can be
converted to ppm SO2 (v/v) as follows:
13.0 The TCM absorbing solution and any reagents containing
mercury compounds must be treated and disposed of by one of the
methods discussed below. Both methods remove greater than 99.99
percent of the mercury.
13.1 Disposal of Mercury-Containing Solutions.
13.2 Method for Forming an Amalgam.
1. Place the waste solution in an uncapped vessel in a hood.
2. For each liter of waste solution, add approximately 10 g of
sodium carbonate until neutralization has occurred (NaOH may have
to be used).
3. Following neutralization, add 10 g of granular zinc or
magnesium.
4. Stir the solution in a hood for 24 hours. Caution must be
exercised as hydrogen gas is evolved by this treatment process.
5. After 24 hours, allow the solution to stand without stirring
to allow the mercury amalgam (solid black material) to settle to
the bottom of the waste receptacle.
6. Upon settling, decant and discard the supernatant liquid.
7. Quantitatively transfer the solid material to a container and
allow to dry.
8. The solid material can be sent to a mercury reclaiming plant.
It must not be discarded.
13.3 Method Using Aluminum Foil Strips.
1. Place the waste solution in an uncapped vessel in a hood.
2. For each liter of waste solution, add approximately 10 g of
aluminum foil strips. If all the aluminum is consumed and no gas is
evolved, add an additional 10 g of foil. Repeat until the foil is
no longer consumed and allow the gas to evolve for 24 hours.
3. Decant the supernatant liquid and discard.
4. Transfer the elemental mercury that has settled to the bottom
of the vessel to a storage container.
5. The mercury can be sent to a mercury reclaiming plant. It
must not be discarded.
14.0 References for SO2 Method.
1. Quality Assurance Handbook for Air Pollution Measurement
Systems, Volume I, Principles. EPA-600/9-76-005, U.S. Environmental
Protection Agency, Research Triangle Park, NC 27711, 1976.
2. Quality Assurance Handbook for Air Pollution Measurement
Systems, Volume II, Ambient Air Specific Methods.
EPA-600/4-77-027a, U.S. Environmental Protection Agency, Research
Triangle Park, NC 27711, 1977.
3. Dasqupta, P. K., and K. B. DeCesare. Stability of Sulfur
Dioxide in Formaldehyde and Its Anomalous Behavior in
Tetrachloromercurate (II). Submitted for publication in
Atmospheric Environment, 1982.
4. West, P. W., and G. C. Gaeke. Fixation of Sulfur Dioxide as
Disulfitomercurate (II) and Subsequent Colorimetric Estimation.
Anal. Chem., 28:1816, 1956.
5. Ephraim, F. Inorganic Chemistry. P. C. L. Thorne and E. R.
Roberts, Eds., 5th Edition, Interscience, 1948, p. 562.
6. Lyles, G. R., F. B. Dowling, and V. J. Blanchard.
Quantitative Determination of Formaldehyde in the Parts Per Hundred
Million Concentration Level. J. Air. Poll. Cont. Assoc., Vol.
15(106), 1965.
7. McKee, H. C., R. E. Childers, and O. Saenz, Jr. Collaborative
Study of Reference Method for Determination of Sulfur Dioxide in
the Atmosphere (Pararosaniline Method). EPA-APTD-0903, U.S.
Environmental Protection Agency, Research Triangle Park, NC 27711,
September 1971.
8. Urone, P., J. B. Evans, and C. M. Noyes. Tracer Techniques in
Sulfur - Air Pollution Studies Apparatus and Studies of Sulfur
Dioxide Colorimetric and Conductometric Methods. Anal. Chem., 37:
1104, 1965.
9. Bostrom, C. E. The Absorption of Sulfur Dioxide at Low
Concentrations (pphm) Studied by an Isotopic Tracer Method. Intern.
J. Air Water Poll., 9:333, 1965.
10. Scaringelli, F. P., B. E. Saltzman, and S. A. Frey.
Spectrophotometric Determination of Atmospheric Sulfur Dioxide.
Anal. Chem., 39: 1709, 1967.
11. Pate, J. B., B. E. Ammons, G. A. Swanson, and J. P. Lodge,
Jr. Nitrite Interference in Spectrophotometric Determination of
Atmospheric Sulfur Dioxide. Anal. Chem., 37:942, 1965.
12. Zurlo, N., and A. M. Griffini. Measurement of the Sulfur
Dioxide Content of the Air in the Presence of Oxides of Nitrogen
and Heavy Metals. Medicina Lavoro, 53:330, 1962.
13. Rehme, K. A., and F. P. Scaringelli. Effect of Ammonia on
the Spectrophotometric Determination of Atmospheric Concentrations
of Sulfur Dioxide. Anal. Chem., 47:2474, 1975.
14. McCoy, R. A., D. E. Camann, and H. C. McKee. Collaborative
Study of Reference Method for Determination of Sulfur Dioxide in
the Atmosphere (Pararosaniline Method) (24-Hour Sampling).
EPA-650/4-74-027, U.S. Environmental Protection Agency, Research
Triangle Park, NC 27711, December 1973.
15. Fuerst, R. G. Improved Temperature Stability of Sulfur
Dioxide Samples Collected by the Federal Reference Method.
EPA-600/4-78-018, U.S. Environmental Protection Agency, Research
Triangle Park, NC 27711, April 1978.
16. Scaringelli, F. P., L. Elfers, D. Norris, and S. Hochheiser.
Enhanced Stability of Sulfur Dioxide in Solution. Anal. Chem.,
42:1818, 1970.
17. Martin, B. E. Sulfur Dioxide Bubbler Temperature Study.
EPA-600/4-77-040, U.S. Environmental Protection Agency, Research
Triangle Park, NC 27711, August 1977.
18. American Society for Testing and Materials. ASTM Standards,
Water; Atmospheric Analysis. Part 23. Philadelphia, PA, October
1968, p. 226.
19. O'Keeffe, A. E., and G. C. Ortman. Primary Standards for
Trace Gas Analysis. Anal. Chem., 38:760, 1966.
20. Scaringelli, F. P., S. A. Frey, and B. E. Saltzman.
Evaluation of Teflon Permeation Tubes for Use with Sulfur Dioxide.
Amer. Ind. Hygiene Assoc. J., 28:260, 1967.
21. Scaringelli, F. P., A. E. O'Keeffe, E. Rosenberg, and J. P.
Bell, Preparation of Known Concentrations of Gases and Vapors With
Permeation Devices Calibrated Gravimetrically. Anal. Chem., 42:871,
1970.
22. A Procedure for Establishing Traceability of Gas Mixtures to
Certain National Bureau of Standards Standard Reference Materials.
EPA-600/7-81-010, U.S. Environmental Protection Agency,
Environmental Monitoring Systems Laboratory (MD-77), Research
Triangle Park, NC 27711, January 1981.
[47 FR 54899, Dec. 6, 1982; 48 FR 17355, Apr. 22, 1983.
Redesignated at 75 FR 35595, June 22, 2010]