Title 29
SECTION 1910.241
1910.241 Definitions.
§ 1910.241 Definitions.As used in this subpart:
(a) Explosive-actuated fastening tool terms - (1) Hammer-operated piston tool - low-velocity type. A tool which, by means of a heavy mass hammer supplemented by a load, moves a piston designed to be captive to drive a stud, pin, or fastener into a work surface, always starting the fastener at rest and in contact with the work surface. It shall be so designed that when used with any load that accurately chambers in it and that is commercially available at the time the tool is submitted for approval, it will not cause such stud, pin, or fastener to have a mean velocity in excess of 300 feet per second when measured 6.5 feet from the muzzle end of the barrel.
(2) High-velocity tool. A tool or machine which, when used with a load, propels or discharges a stud, pin, or fastener, at velocities in excess of 300 feet per second when measured 6.5 feet from the muzzle end of the barrel, for the purpose of impinging it upon, affixing it to, or penetrating another object or material.
(3) Low-velocity piston tool. A tool that utilizes a piston designed to be captive to drive a stud, pin, or fastener into a work surface. It shall be so designed that when used with any load that accurately chambers in it and that is commercially available at the time the tool is submitted for approval, it will not cause such stud, pin, or fastener to have a mean velocity in excess of 300 feet per second when measured 6.5 feet from the muzzle end of the barrel.
(4) Stud, pin, or fastener. A fastening device specifically designed and manufactured for use in explosive-actuated fastening tools.
(5) To chamber. To fit properly without the use of excess force, the case being duly supported.
(6) Explosive powerload, also known as load. Any substance in any form capable of producing a propellant force.
(7) Tool. An explosive-actuated fastening tool, unless otherwise indicated, and all accessories pertaining thereto.
(8) Protective shield or guard. A device or guard attached to the muzzle end of the tool, which is designed to confine flying particles.
(b) Abrasive wheel terms - (1) Mounted wheels. Mounted wheels, usually 2-inch diameter or smaller, and of various shapes, may be either organic or inorganic bonded abrasive wheels. They are secured to plain or threaded steel mandrels.
(2) Tuck pointing. Removal, by grinding, of cement, mortar, or other nonmetallic jointing material.
(3) Tuck pointing wheels. Tuck pointing wheels, usually Type 1, reinforced organic bonded wheels have diameter, thickness and hole size dimension. They are subject to the same limitations of use and mounting as Type 1 wheels defined in subparagraph (10) of this paragraph.
Limitation: Wheels used for tuck pointing should be reinforced, organic bonded. (See § 1910.243(c)(1)(ii)(c.))
(4) Portable grinding. A grinding operation where the grinding machine is designed to be hand held and may be easily moved from one location to another.
(5) Organic bonded wheels. Organic wheels are wheels which are bonded by means of an organic material such as resin, rubber, shellac, or other similar bonding agent.
(6) Safety guard. A safety guard is an enclosure designed to restrain the pieces of the grinding wheel and furnish all possible protection in the event that the wheel is broken in operation.
(7) Reinforced wheels. The term reinforced as applied to grinding wheels shall define a class of organic wheels which contain strengthening fabric or filament. The term reinforced does not cover wheels using such mechanical additions as steel rings, steel cup backs or wire or tape winding.
(8) Type 11 flaring cup wheels. Type 11 flaring cup wheels have double diameter dimensions D and J, and in addition have thickness, hole size, rim and back thickness dimensions. Grinding is always performed on rim face, W dimension. Type 11 wheels are subject to all limitations of use and mounting listed for Type 6 straight sided cup wheels definition in subparagraph (9) of this paragraph.
Type 11 Flaring Cup Wheels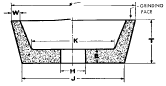
Limitation: Minimum back thickness, E dimension, should not be less than one-fourth T dimension. In addition when unthreaded hole wheels are specified the inside flat, K dimension, shall be large enough to accommodate a suitable flange.
(9) Type 6 straight cup wheels. Type 6 cup wheels have diameter, thickness, hole size, rim thickness, and back thickness dimensions. Grinding is always performed on rim face, W dimension.
Limitation: Minimum back thickness, E dimension, should not be less than one-fourth T dimension. In addition, when unthreaded hole wheels are specified, the inside flat, K dimension, must be large enough to accommodate a suitable flange.
Type 6 Straight Cup Wheels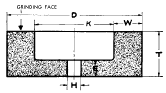
(10) Type 1 straight wheels. Type 1 straight wheels have diameter, thickness, and hole size dimensions and should be used only on the periphery. Type 1 wheels shall be mounted between flanges.
Limitation: Hole dimension (H) should not be greater than two-thirds of wheel diameter dimension (D) for precision, cylindrical, centerless, or surface grinding applications. Maximum hole size for all other applications should not exceed one-half wheel diameter.
Type 1 Straight Wheels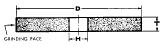
(c) [Reserved]
(d) Jack terms - (1) Jack. A jack is an appliance for lifting and lowering or moving horizontally a load by application of a pushing force.
Note:Jacks may be of the following types: Lever and ratchet, screw and hydraulic.
(2) Rating. The rating of a jack is the maximum working load for which it is designed to lift safely that load throughout its specified amount of travel.
Note:To raise the rated load of a jack, the point of application of the load, the applied force, and the length of lever arm should be those designated by the manufacturer for the particular jack considered.
[39 FR 23502, June 27, 1974, as amended at 43 FR 49750, Oct. 24, 1978]