Title 19
PART 190 APPENDIX A
Imported merchandise or drawback products 1 to be designated as the basis for drawback on the exported products | Duty-paid, duty-free, or domestic merchandise classifiable under the same 8-digit HTSUS subheading number as that designated which will be used in the production of the exported products. |
Component parts identified by individual part numbers and 8-digit HTSUS subheading number | Component parts classifiable under the same 8-digit HTSUS subheading number and identified with the same individual part numbers as those in the column immediately to the left. |
The designated components must be manufactured in accordance with the same specifications and from the same materials, and must be identified by the same 8-digit HTSUS classification and part number as the substituted components. Further, the designated and substituted components are used interchangeably in the manufacture of the exported articles upon which drawback will be claimed. Specifications or drawings will be maintained and made available for review by CBP Officials.
1 Drawback products are those produced in the United States in accordance with the drawback law and regulations. Such products have “dual status” under section 1313(b). They may be designated as the basis for drawback and also may be deemed to be domestic merchandise.
B. Exported Articles on Which Drawback Will Be ClaimedThe exported articles will have been manufactured in the United States using components described in the Parallel Columns above.
C. General StatementThe manufacturer or producer manufactures or produces for its own account. The manufacturer or producer may manufacture or produce articles for the account of another or another manufacturer or producer may manufacture or produce for the account of the manufacturer or producer under contract within the principal and agency relationship outlined in T.D.s 55027(2) and 55207(1) (see § 190.9).
D. Process of Manufacture or ProductionThe components described in the Parallel Columns will be used to manufacture or produce articles in accordance with § 190.2.
E. Multiple ProductsNot applicable.
F. WasteNo drawback is payable on any waste which results from the manufacturing operation. Unless the claim for drawback is based on the quantity of components appearing in the exported articles, records will be maintained to establish the value (or the lack of value), quantity, and disposition of any waste that results from manufacturing the exported articles. If no waste results, records will be maintained to establish that fact.
G. [Reserved] H. Procedures and Records MaintainedRecords, which may include records kept in the normal course of business, will be maintained to establish:
1. The identity and 8-digit HTSUS classification of the designated merchandise;
2. The quantity of merchandise classifiable under the same 8-digit HTSUS classification as the designated merchandise 2 used to produce the exported articles;
2 If claims are to be made on an “appearing in” basis, the remainder of this sentence should read “appearing in the exported articles produced.”
3. That, within 5 years after the date of importation of the designated merchandise, the manufacturer or producer used the merchandise to produce articles. During the same 5-year period, the manufacturer or producer produced 3 the exported articles. To obtain drawback the claimant must establish that the completed articles were exported within 5 years after the importation of the imported merchandise. Records establishing compliance with these requirements will be available for audit by CBP during business hours. Drawback is not payable without proof of compliance.
3 The date of production is the date an article is completed.
I. Inventory ProceduresThe inventory records of the manufacturer or producer must show how the drawback recordkeeping requirements set forth in 19 U.S.C. 1313(b) and part 190 of the CBP Regulations will be met, as discussed under the heading “Procedures and Records Maintained”. If those records do not establish satisfaction of all legal requirements, drawback cannot be paid.
J. Basis of Claim for DrawbackDrawback will be claimed on the quantity of eligible components used in producing the exported articles only if there is no waste or valueless or unrecovered waste in the manufacturing operation. Drawback may be claimed on the quantity of eligible components that appear in the exported articles, regardless of whether there is waste, and no records of waste need be maintained. If there is valuable waste recovered from the manufacturing operation and records are kept which show the quantity and value of the waste, drawback may be claimed on the quantity of eligible components used to produce the exported articles less the amount of those components which the value of the waste would replace.
K. General RequirementsThe manufacturer or producer will:
1. Comply fully with the terms of this general ruling when claiming drawback;
2. Open its factory and records for examination at all reasonable hours by authorized Government officers;
3. Keep its drawback related records and supporting data for at least 3 years from the date of liquidation of any drawback claim predicated in whole or in part upon this general ruling;
4. Keep its letter of notification of intent to operate under this general ruling current by reporting promptly to the drawback office which liquidates its claims any changes in the information required by the General Instructions of this Appendix (I. General Instructions, 1 through 10), the corporate name, or corporate organization by succession or reincorporation;
5. Keep a copy of this general ruling on file for ready reference by employees and require all officials and employees concerned to familiarize themselves with the provisions of this general ruling; and
6. Issue instructions to insure proper compliance with title 19, United States Code, section 1313, part 190 of the CBP Regulations and this general ruling.
VI. General Manufacturing Drawback Ruling Under 19 U.S.C. 1313(a) for Flaxseed (T.D. 83-80)Drawback may be allowed under the provision of 19 U.S.C. 1313(a) upon the exportation of linseed oil, linseed oil cake, and linseed oil meal, manufactured or produced with the use of imported flaxseed, subject to the following special requirements:
A. Imported Merchandise or Drawback Products 1 Used1 Drawback products are those produced in the United States in accordance with the drawback law and regulations.
Imported merchandise or drawback products (flaxseed) are used in the manufacture of the exported articles upon which drawback claims will be based.
B. Exported Articles on Which Drawback Will Be ClaimedExported articles on which drawback will be claimed must be manufactured in the United States using imported merchandise or drawback products.
C. General StatementThe manufacturer or producer manufactures or produces for its own account. The manufacturer or producer may manufacture or produce articles for the account of another or another manufacturer or producer may manufacture or produce for the account of the manufacturer or producer under contract within the principal and agency relationship outlined in T.D.s 55027(2) and 55207(1) (see § 190.9).
D. Process of Manufacture or ProductionThe imported merchandise or drawback products will be used to manufacture or produce articles in accordance with § 190.2.
E. Multiple ProductsDrawback law mandates the assignment of relative values when two or more products necessarily are produced concurrently in the same operation. If multiple products are produced records will be maintained of the market value of each product at the time it is first separated in the manufacturing process (when a claim covers a manufacturing period, the entire period covered by the claim is the time of separation of the products and the value per unit of product is the market value for the period (see §§ 190.2, 190.22(e)). The “appearing in” basis may not be used if multiple products are produced.
F. Loss or GainRecords will be maintained showing the extent of any loss or gain in net weight or measurement of the imported merchandise, caused by atmospheric conditions, chemical reactions, or other factors.
G. WasteNo drawback is payable on any waste which results from the manufacturing operation. Unless the claim for drawback is based on the quantity of merchandise appearing in the exported articles, records will be maintained to establish the value, quantity, and disposition of any waste that results from manufacturing the exported articles. If no waste results, records will be maintained to establish that fact.
H. Procedures and Records MaintainedRecords, which may include records kept in the normal course of business, will be maintained to establish:
1. That the exported articles on which drawback is claimed were produced with the use of the imported merchandise; and
2. The quantity of imported merchandise 2 used in producing the exported articles.
2 If claims are to be made on an “appearing in” basis, the remainder of the sentence should read “appearing in the exported articles.”
To obtain drawback the claimant must establish that the completed articles were exported within 5 years after importation of the imported merchandise. Records establishing compliance with these requirements will be available for audit by CBP during business hours. Drawback is not payable without proof of compliance.
I. Inventory ProceduresThe inventory records of the manufacturer or producer must show how the drawback recordkeeping requirements set forth in 19 U.S.C. 1313(a) and part 190 of the CBP Regulations will be met, as discussed under the heading “Procedures and Records Maintained”. If those records do not establish satisfaction of all legal requirements, drawback cannot be paid.
The inventory records of the manufacturer or producer will show: The inclusive dates of manufacture; the quantity, identity, value, and 8-digit HTSUS classification of the imported flaxseed or screenings, scalpings, chaff, or scourings used; the quantity by actual weight and value, if any, of the material removed from the foregoing by screening prior to crushing; the quantity and kind of domestic merchandise added, if any; the quantity by actual weight or gauge and value of the oil, cake, and meal obtained; and the quantity and value, if any, of the waste incurred. The quantity of imported flaxseed, screenings, scalpings, chaff, or scourings used or of material removed will not be estimated nor computed on the basis of the quantity of finished products obtained, but will be determined by actually weighing the said flaxseed, screenings, scalpings, chaff, scourings, or other material; or, at the option of the crusher, the quantities of imported materials used may be determined from CBP weights, as shown by the import entry covering such imported materials, and the Government weight certificate of analysis issued at the time of entry. The entire period covered by an abstract will be deemed the time of separation of the oil and cake covered thereby.
If the records of the manufacturer or producer do not show the quantity of oil cake used in the manufacture or production of the exported oil meal, and the quantity of oil meal obtained, the net weight of the oil meal exported will be regarded as the weight of the oil cake used in the manufacture thereof.
If various tanks are used for the storage of imported flaxseed, the mill records must establish the tank or tanks in which each lot or cargo is stored. If raw or processed oil manufactured or produced during different periods of manufacture is intermixed in storage, a record must be maintained showing the quantity, identity, and 8-digit HTSUS classification of oil so intermixed. The identity of the merchandise or articles in either instance must be in accordance with § 190.14.
J. Basis of Claim for DrawbackDrawback will be claimed on the quantity of merchandise used in producing the exported articles only if there is no waste or valueless or unrecovered waste in the manufacturing operation. Drawback may be claimed on the quantity of eligible merchandise that appears in the exported articles, regardless of whether there is waste, and no records of waste need be maintained. If there is valuable waste recovered from the manufacturing operation and records are kept which show the quantity and value of the waste, drawback may be claimed on the quantity of eligible material used to produce the exported articles, less the amount of that merchandise which the value of the waste would replace.
K. General RequirementsThe manufacturer or producer will:
1. Comply fully with the terms of this general ruling when claiming drawback;
2. Open its factory and records for examination at all reasonable hours by authorized Government officers;
3. Keep its drawback related records and supporting data for at least 3 years from the date of liquidation of any drawback claim predicated in whole or in part upon this general ruling;
4. Keep its letter of notification of intent to operate under this general ruling current by reporting promptly to the drawback office which liquidates its claims any changes in the information required by the General Instructions of this Appendix (I. General Instructions, 1 through 10), the corporate name, or corporate organization by succession or reincorporation.
5. Keep a copy of this general ruling on file for ready reference by employees and require all officials and employees concerned to familiarize themselves with the provisions of this general ruling; and
6. Issue instructions to insure proper compliance with 19, United States Code, § 1313, part 190 of the CBP Regulations and this general ruling.
VII. General Manufacturing Drawback Ruling Under 19 U.S.C. 1313(a) for Fur Skins or Fur Skin Articles (T.D. 83-77)Drawback may be allowed under 19 U.S.C. 1313(a) upon the exportation of dressed, redressed, dyed, redyed, bleached, blended, or striped fur skins or fur skin articles manufactured or produced by any one, or a combination, of the foregoing processes, with the use of fur skins or fur skin articles, such as plates, mats, sacs, strips, and crosses, imported in a raw, dressed, or dyed condition, subject to the following special requirements:
A. Imported Merchandise or Drawback Products 1 Used1 Drawback products are those produced in the United States in accordance with the drawback law and regulations.
Imported merchandise or drawback products (fur skins or fur skin articles) are used in the manufacture of the exported articles upon which drawback claims will be based.
B. Exported Articles on Which Drawback Will Be ClaimedExported articles on which drawback will be claimed must be manufactured in the United States using imported merchandise or drawback products.
C. General StatementThe manufacturer or producer manufactures or produces for its own account. The manufacturer or producer may manufacture or produce articles for the account of another or another manufacturer or producer may manufacture or produce for the account of the manufacturer or producer under contract within the principal and agency relationship outlined in T.D.s 55027(2) and 55207(1) (see § 190.9).
D. Process of Manufacture or ProductionThe imported merchandise or drawback products will be used to manufacture or produce articles in accordance with § 190.2.
Drawback will not be allowed under this general manufacturing drawback ruling when the process performed results only in the restoration of the merchandise to its condition at the time of importation.
E. Multiple ProductsNot applicable.
F. Loss or GainRecords will be maintained showing the extent of any loss or gain in net weight or measurement of the imported merchandise, caused by atmospheric conditions, chemical reactions, or other factors.
G. WasteNo drawback is payable on any waste which results from the manufacturing operation. Unless the claim for drawback is based on the quantity of merchandise appearing in the exported articles, records will be maintained to establish the value, quantity, and disposition of any waste that results from manufacturing the exported articles. If no waste results, records will be maintained to establish that fact.
H. Procedures and Records MaintainedRecords, which may include records kept in the normal course of business, will be maintained to establish:
1. That the exported articles on which drawback is claimed were produced with the use of the imported merchandise; and
2. The quantity of imported merchandise 2 used in producing the exported articles.
2 If claims are to be made on an “appearing in” basis, the remainder of the sentence should read “appearing in the exported articles.”
To obtain drawback the claimant must establish that the completed articles were exported within 5 years after importation of the imported merchandise. Records establishing compliance with these requirements will be available for audit by CBP during business hours. Drawback is not payable without proof of compliance.
I. Inventory ProceduresThe inventory records of the manufacturer or producer must show how the drawback recordkeeping requirements set forth in 19 U.S.C. 1313(a) and part 190 of the CBP Regulations will be met, as discussed under the heading “Procedures and Records Maintained”. If those records do not establish satisfaction of all legal requirements, drawback cannot be paid.
The records of the manufacturer or producer must show, as to each lot of fur skins and/or fur skin articles used in the manufacture or production of articles for exportation with benefit of drawback, the lot number and date or inclusive dates of manufacture or production, the quantity, identity, description, and 8-digit HTSUS classification of the imported merchandise used, the condition in which imported, the process or processes applied thereto, the quantity, description, and 8-digit HTSUS classification of the finished articles obtained, and the quantity of imported pieces rejected, if any, or spoiled in manufacture or production.
J. Basis of Claim for DrawbackDrawback will be claimed on the quantity of merchandise used in producing the exported articles only if there is no waste or valueless or unrecovered waste in the manufacturing operation. Drawback may be claimed on the quantity of eligible merchandise that appears in the exported articles, regardless of whether there is waste, and no records of waste need be maintained. If there is valuable waste recovered from the manufacturing operation and records are kept which show the quantity and value of the waste, drawback may be claimed on the quantity of eligible material used to produce the exported articles, less the amount of that merchandise which the value of the waste would replace. (If rejects and/or spoilage are incurred, the quantity of imported merchandise used will be determined by deducting from the quantity of fur skins or fur skin articles put into manufacture or production the quantity of such rejects and/or spoilage.)
K. General RequirementsThe manufacturer or producer will:
1. Comply fully with the terms of this general ruling when claiming drawback;
2. Open its factory and records for examination at all reasonable hours by authorized Government officers;
3. Keep its drawback related records and supporting data for at least 3 years from the date of liquidation of any drawback claim predicated in whole or in part upon this general ruling;
4. Keep its letter of notification of intent to operate under this general ruling current by reporting promptly to the drawback office which liquidates its claims any changes in the information required by the General Instructions of this Appendix (I. General Instructions, 1 through 10), the corporate name, or corporate organization by succession or reincorporation.
5. Keep a copy of this general ruling on file for ready reference by employees and require all officials and employees concerned to familiarize themselves with the provisions of this general ruling; and
6. Issue instructions to insure proper compliance with 19, United States Code, § 1313, part 190 of the CBP Regulations and this general ruling.
VIII. General Manufacturing Drawback Ruling Under 19 U.S.C. 1313(b) for Orange Juice (T.D. 85-110) A. Same 8-Digit HTSUS Classification (Parallel Columns)Imported merchandise or drawback products 1 to be designated as the basis for drawback on the exported products | Duty-paid, duty-free, or domestic merchandise, classifiable under the same 8-digit HTSUS subheading number as that designated which will be used in the production of the exported products. |
Concentrated orange juice for manufacturing (of not less than 55° Brix), as defined in the standard of identity of the Food and Drug Administration (21 CFR 146.53), which meets the Grade A standard of the U.S. Dept. of Agriculture (7 CFR 52.1557, Table IV) | Concentrated orange juice for manufacturing as described in the left-hand parallel column. |
The imported merchandise designated on drawback claims must be classifiable under the same 8-digit HTSUS classification as the merchandise used in producing the exported articles on which drawback is claimed.
1 Drawback products are those produced in the United States in accordance with the drawback law and regulations. Such products have “dual status” under section 1313(b). They may be designated as the basis for drawback and also may be deemed to be domestic merchandise.
B. Exported Articles on Which Drawback Will Be Claimed1. Orange juice from concentrate (reconstituted juice).
2. Frozen concentrated orange juice.
3. Bulk concentrated orange juice.
C. General StatementThe manufacturer or producer manufactures or produces for its own account. The manufacturer or producer may manufacture or produce articles for the account of another or another manufacturer or producer may manufacture or produce for the account of the manufacturer or producer under contract within the principal and agency relationship outlined in T.D.s 55027(2) and 55207(1) (see § 190.9).
D. Process of Manufacture or Production1. Orange juice from concentrate (reconstituted juice). Concentrated orange juice for manufacturing is reduced to a desired 11.8° Brix by a blending process to produce orange juice from concentrate. The following optional blending processes may be used:
i. The concentrate is blended with fresh orange juice (single strength juice); or
ii. The concentrate is blended with essential oils, flavoring components, and water; or
iii. The concentrate is blended with water and is heat treated to reduce the enzymatic activity and the number of viable microorganisms.
2. Frozen concentrated orange juice. Concentrated orange juice for manufacturing is reduced to a desired degree Brix of not less than 41.8° Brix by the following optional blending processes:
i. The concentrate is blended with fresh orange juice (single strength juice); or
ii. The concentrate is blended with essential oils and flavoring components and water.
3. Bulk concentrated orange juice. Concentrated orange juice for manufacturing is blended with essential oils and flavoring components which would enable another processor such as a dairy to prepare finished frozen concentrated orange juice or orange juice from concentrate by merely adding water to the (intermediate) bulk concentrated orange juice.
E. Multiple Products, Waste, Loss or GainNot applicable.
F. [Reserved] G. Procedures and Records MaintainedRecords, which may include records kept in the normal course of business, will be maintained to establish:
1. The 8-digit HTSUS classification and identity of the designated merchandise;
2. The quantity of merchandise classifiable under the same 8-digit HTSUS classification as the designated merchandise 2 used to produce the exported articles;
2 If claims are to be made on an “appearing in” basis, the remainder of this sentence should read “appearing in the exported articles produced.”
3. That, within 5 years after the date of importation of the designated merchandise, the manufacturer or producer used the designated merchandise to produce articles. During the same 5-year period, the manufacturer or producer produced 3 the exported articles.
3 The date of production is the date an article is completed.
To obtain drawback it must be established that the completed articles were exported within 5 years after the importation of the imported merchandise. Records establishing compliance with these requirements must be available for audit by CBP during business hours. No drawback is payable without proof of compliance.
H. Inventory ProceduresThe inventory records of the manufacturer or producer must show how the drawback recordkeeping requirements set forth in 19 U.S.C. 1313(b) and part 190 of the CBP Regulations will be met, as discussed under the heading “Procedures and Records Maintained”, and will show what components were blended with the concentrated orange juice for manufacturing. If those records do not establish satisfaction of all legal requirements drawback cannot be paid.
I. Basis of Claim for DrawbackThe basis of claim for drawback will be the quantity of concentrated orange juice for manufacturing used in the production of the exported articles. It is understood that when fresh orange juice is used as “cutback”, it will not be included in the “pound solids” when computing the drawback due.
J. General RequirementsThe manufacturer or producer will:
1. Comply fully with the terms of this general ruling when claiming drawback;
2. Open its factory and records for examination at all reasonable hours by authorized Government officers;
3. Keep its drawback related records and supporting data for at least 3 years from the date of liquidation of any drawback claim predicated in whole or in part upon this general ruling;
4. Keep its letter of notification of intent to operate under this general ruling current by reporting promptly to the drawback office which liquidates its claims any changes in the information required by the General Instructions of this Appendix (I. General Instructions, 1 through 10), the corporate name, or corporate organization by succession or reincorporation;
5. Keep a copy of this general ruling on file for ready reference by employees and require all officials and employees concerned to familiarize themselves with the provisions of this general ruling; and
6. Issue instructions to insure proper compliance with title 19, United States Code, section 1313, part 190 of the CBP Regulations and this general ruling.
IX. General Manufacturing Drawback Ruling Under 19 U.S.C. 1313(b) for Petroleum or Petroleum Derivatives (T.D. 84-49) A. Same 8-Digit HTSUS Classification (Parallel Columns)Imported merchandise or drawback products 1 to be designated as the basis for drawback on the exported products | Duty-paid, duty-free, or domestic merchandise, classifiable under the same 8-digit HTSUS subheading number as that designated which will be used in the production of the exported products. |
1 Drawback products are those produced in the United States in accordance with the drawback law and regulations. Such products have “dual status” under section 1313(b). They may be designated as the basis for drawback and also may be deemed to be domestic merchandise.
1. Motor Gasoline 2. Aviation Gasoline 3. Special Naphthas 4. Jet Fuel 5. Kerosene & Range Oils 6. Distillate Oils 7. Residual Oils 8. Lubricating Oils 9. Paraffin Wax 10. Petroleum Coke 11. Asphalt 12. Road Oil 13. Still Gas 14. Liquified Petroleum Gas 15. Petrochemical Synthetic Rubber 16. Petrochemical Plastics & Resins 17. All Other Petrochemical Products C. Exported Articles on Which Drawback Will Be ClaimedSee the General Instructions, I.A.7., for this general drawback ruling. Each article to be exported must be named. When the identity of the product is not clearly evident by its name, there must be a statement as to what the product is, e.g., a herbicide.
D. General StatementThe manufacturer or producer manufactures or produces for its own account. The manufacturer or producer may manufacture or produce articles for the account of another or another manufacturer or producer may manufacture or produce for the account of the manufacturer or producer under contract within the principal and agency relationship outlined in T.D.s 55027(2) and 55207(1) (see § 190.9).
E. Process of Manufacture or ProductionHeated crude oil is charged to an atmospheric distillation tower where it is subjected to fractionation. The charge to the distillation tower consists of a single crude oil, or of commingled crudes which are fed to the tower simultaneously or after blending in a tank. During fractionation, components of different boiling ranges are separated.
F. Multiple Products 1. Relative ValuesFractionation results in 17 products. In order to insure proper distribution of drawback to each of these products, the manufacturer or producer agrees to record the relative values at the time of separation. The entire period covered by an abstract is to be treated as the time of separation. The value per unit of each product will be the average market value for the abstract period.
2. ProducibilityThe manufacturer or producer can vary the proportionate quantity of each product. The manufacturer or producer understands that drawback is payable on exported products only to the extent that these products could have been produced from the designated merchandise. The records of the manufacturer or producer must show that all of the products exported, for which drawback will be claimed under this general manufacturing drawback ruling could, have been produced concurrently on a practical operating basis from the designated merchandise.
The manufacturer or producer agrees to establish the amount to be designated by reference to the Industry Standards of Potential Production published in T.D. 66-16. 2
2 A manufacturer who proposes to use standards other than those in T.D. 66-16 must state the proposed standards and provide sufficient information to CBP in order for those proposed standards to be verified in accordance with T.D. 84-49.
There are no valuable wastes as a result of the processing.
G. Loss or GainBecause the manufacturer or producer keeps records on a volume basis rather than a weight basis, it is anticipated that the material balance will show a volume gain. For the same reason, it is possible that occasionally the material balance will show a volume loss. Fluctuations in type of crude used, together with the type of finished product desired make an estimate of an average volume gain meaningless. However, records will be kept to show the amount of loss or gain with respect to the production of export products.
H. ExchangeThe use of any domestic merchandise acquired in exchange for imported merchandise that meets the same kind and quality specifications contained in the Parallel Columns of this general ruling shall be treated as use of the imported merchandise.
I. Procedures and Records MaintainedRecords, which may include records kept in the normal course of business, will be maintained to establish:
1. The identity, and 8-digit HTSUS classification of the merchandise designated;
2. The quantity of merchandise classifiable under the same 8-digit HTSUS classification as the designated merchandise used to produce the exported articles.
3. That, within 5 years after importation, the manufacturer or producer used the designated merchandise to produce articles. During the same 5-year period, the manufacturer or producer produced the exported articles.
4(a). The manufacturer or producer agrees to use a 28-31 day period (monthly) abstract period for each refinery covered by this general manufacturing drawback ruling, or
(b). The manufacturer or producer agrees to use an abstract period (not to exceed 1 year) for each refinery covered by this general manufacturing drawback ruling. The manufacturer or producer certifies that if it were to file abstracts covering each manufacturing period, of not less than 28 days and not more than 31 days (monthly) within the longer period, in no such monthly abstract would the quantity of designated merchandise exceed the material introduced into the manufacturing process during that monthly period. (Select (a) or (b), and state which is selected in the application, and, if (b) is selected, specify the length of the particular abstract period chosen (not to exceed 1 year (see General Instruction I.A.7.)).)
5. On each abstract of production the manufacturer or producer agrees to show the value per barrel to five decimal places.
6. The manufacturer or producer agrees to file claims in the format set forth in exhibits A through F which are attached to this general manufacturing drawback ruling. The manufacturer or producer realizes that to obtain drawback the claimant must establish that the completed articles were exported within 5 years after importation of the imported merchandise. Records establishing compliance with these requirements will be available for audit by CBP during business hours. It is understood that drawback is not payable without proof of compliance. Records will be kept in accordance with T.D. 84-49, as amended by T.D. 95-61.
J. Residual RightsIt is understood that the refiner can reserve as the basis for future payment the right to drawback only on the number of barrels of raw material computed by subtracting from Line E the larger of Lines A or B, of a given Exhibit E. It is further understood that this right to future payment can be claimed only against products concurrently producible with the products listed in Column 21, in the quantities shown in Column 22 of such Exhibit E. Such residual right can be transferred to another refinery of the same refiner only when Line B of Exhibit E is larger than Line A. Unless the number of residual barrels is specifically computed, and rights thereto are expressly reserved on Exhibit E, such residual rights will be deemed waived. The procedure the manufacturer or producer must follow in preparing drawback entries claiming this residual right is illustrated in the attached sample Exhibit E-1. It is understood that claims involving residual rights must be filed only at the port where the Exhibit E reserving such right was filed.
K. Inventory ProceduresThe manufacturer or producer realizes that inventory control is of major importance. In accordance with the normal accounting procedures of the manufacturer or producer, each refinery prepares a monthly stock and yield report, which accounts for inventories, production, and disposals, from time of receipt to time of disposition. This provides an audit trail of all products.
The above-noted records will provide the required audit trail from the initial source documents to the drawback claims of the manufacturer or producer and will support adherence with the requirements discussed under the heading Procedures and Records Maintained.
L. Basis of Claim for DrawbackThe amount of raw material on which drawback may be based will be computed by multiplying the quantity of each product exported by the drawback factor for that product. The amount of raw material which may be designated as the basis for drawback on the exported products produced at a given refinery and covered by a drawback entry must not exceed the quantity of such raw material used at the refinery during the abstract period or periods from which the exported products were produced. The quantity of raw material to be designated as the basis for drawback on exported products must be at least as great as the quantity of raw material which would be required to produce the exported products in the quantities exported.
M. AgreementsThe manufacturer or producer specifically agrees that it will:
1. Comply fully with the terms of this general ruling when claiming drawback;
2. Open its refinery and records for examination at all reasonable hours by authorized Government officers;
3. Keep its drawback related records and supporting data for at least 3 years from the date of liquidation of any drawback claim predicated in whole or in part upon this application;
4. Keep this application current by reporting promptly to the drawback office which liquidates its claims any changes in the information required by the General Instructions of this Appendix (I. General Instructions, 1 through 10), the corporate name, or corporate organization by succession or reincorporation;
5. Keep a copy of this general ruling on file for ready reference by employees and require all officials and employees concerned to familiarize themselves with the provisions of this general ruling; and
6. Issue instructions to insure proper compliance with title 19, United States Code, section 1313, part 190 of the CBP Regulations and this general ruling.
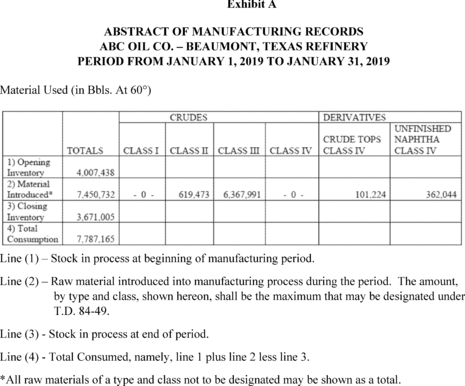
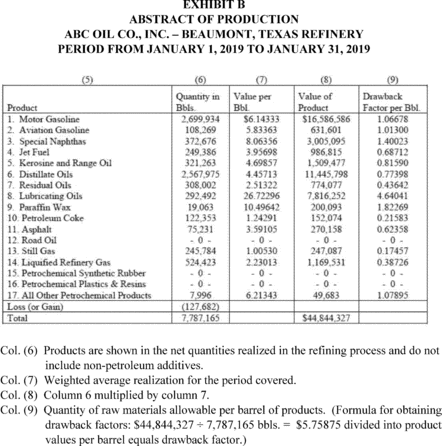
Exhibit C - Inventory Control Sheet: ABC Oil Co., Inc.; Beaumont, Texas Refinery,
Period From January 1, 2019 to January 31, 2019
[All quantities exclude non-petroleum additives]
Aviation gasoline | Residual oils | Lubricating oils | Petrochemicals, all other | |||||
---|---|---|---|---|---|---|---|---|
Bbls. | Drawback factor |
Bbls. | Drawback factor |
Bbls. | Drawback factor |
Bbls. | Drawback factor |
|
(10) Opening Inventory | 11,218 | 1.00126 | 21,221 | .45962 | 9,242 | 4.52178 | 891 | 1.00244 |
(11) Production | 108,269 | 1.01300 | 308,002 | .43642 | 292,492 | 4.64041 | 7,996 | 1.07895 |
(11-A) Receipts | ||||||||
(12) Exports | 11,218 176 |
1.00126 1.01300 |
21,221 104,397 |
.45962 .43642 |
8,774 | 4.52178 | 195 | 1.00244 |
(13) Drawback Deliveries | 696 319 |
1.00244 1.07895 |
||||||
(14) Domestic Shipments | 97,863 | 1.01300 | 180,957 | .43642 | 468 278,286 |
4.52178 4.64041 |
6,867 | 1.07895 |
(15) Closing Inventory | 10,230 | 1.01300 | 22,648 | .43642 | 14,206 | 4.64041 | 810 | 1.07895 |
Line (10) - Opening inventory from previous period's closing inventory.
Line (11) - From production period under consideration.
Line (11-A) - Product received from other sources.
Line (12) - From earliest on hand (inventory or production). Totals from drawback entry or entries recapitulated (see column 18).
Line (13) - Deliveries for export or for designation against further manufacture - earliest on hand after exports are deducted.
Line (14) - From earliest on hand after lines (12) and (13) are deducted.
Line (15) - Balance on hand.
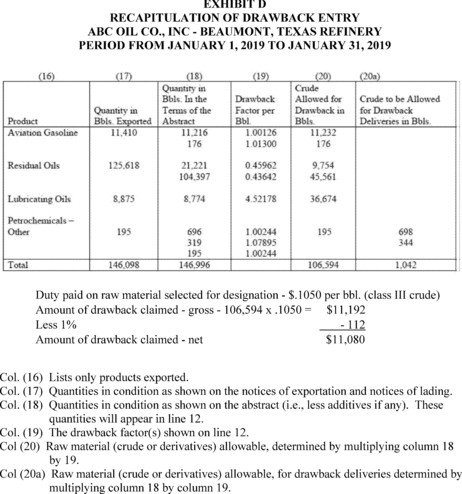
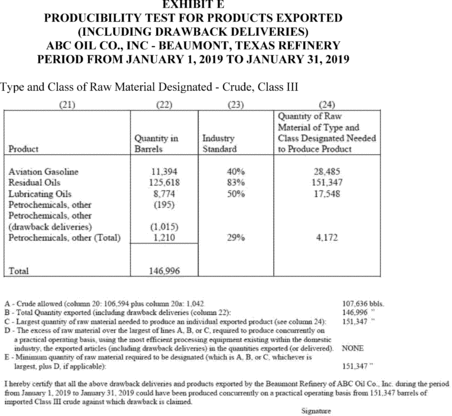
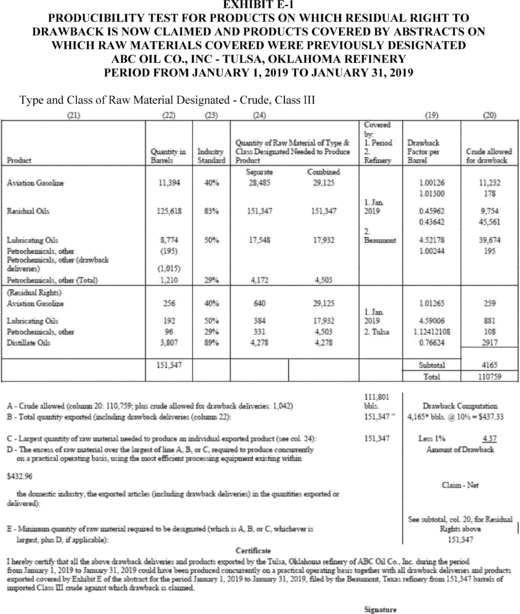
Exhibit E (Combination) - Producibility Test for Products Exported (Including Drawback Deliveries) ABC Oil Co., Inc.; Beaumont, Texas Refinery, Period from January 1, 2019 to January 31, 2019
[Type and class of raw material designated - Crude, Class III]
Product | Quantity in barrels | Industry standard (%) |
Quantity of raw material of type and class designated needed to produce product per barrel |
Drawback factor |
Crude allowed for drawback |
---|---|---|---|---|---|
(21) | (22) | (23) | (24) | (19) | (20) |
Aviation Gasoline 1 | 1 11,218 1176 |
40 40 |
28,045 440 |
1.00126 1.01300 |
11,232 178 |
Residual Oils 1 | 1 21,221 1 104,397 |
83 83 |
25,567 125,780 |
.45962 .43642 |
9,754 45,561 |
Lubricating Oils 1 | 1 8,774 | 50 | 17,548 | 4.52178 | 39,674 |
Petrochemicals, Other 1 | 1 195 | 29 | 672 | 1.00244 | 195 |
Petrochemicals, Other 2 | 2 696 | 29 | 2,400 | 1.00244 | 698 |
Petrochemicals, Other 2 | 2 319 | 29 | 1,100 | 1.07895 | 344 |
Total | 146,996 | 107,636 |
1 Exports.
2 Drawback deliveries.
A - Crude allowed (column 20: 107,636 bbls. (106,594 for export, plus 1,042 for drawback deliveries)).
B - Total quantity exported (including drawback deliveries) (column 22): 146,996.
C - Largest quantity of raw material needed to produce an individual exported product (see column 24): 151,347.
D - The excess of raw material over the largest of lines A, B, or C, required to produce concurrently on a practical operating basis, using the most efficient processing equipment existing within the domestic industry, the exported articles (including drawback deliveries) in the quantities exported (or delivered): None.
E - Minimum quantity of raw material required to be designated (which is A, B, or C, whichever is largest, plus D, if applicable): 151,347 bbs.
I hereby certify that all the above drawback deliveries and products exported by the Beaumont refinery of ABC Oil Co., Inc. during the period from January 1, 2019 to January 31, 2019, could have been produced concurrently on a practical operating basis from 151,347 barrels of imported Class III crude against which drawback is claimed.
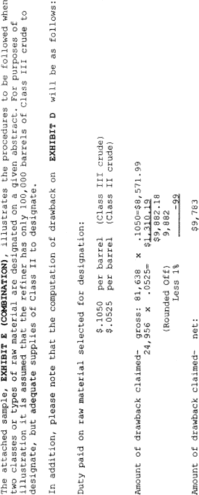
Exhibit F - Designations for Drawback Claim, ABC Oil Co., Inc.; Beaumont, Texas Refinery
[Period from January 1, 2019 to January 31, 2019]
Entry No. | Date of importation |
Kind of materials | Quantity of materials in barrels | Date received | Date consumed | Rate of duty |
---|---|---|---|---|---|---|
26192 | 04/13/17 | Class III Crude | 75,125 | 04/13/17 | May 2017 | $.1050 |
23990 | 08/04/18 | ......do | 37,240 | 08/04/18 | Oct. 2018 | .1050 |
22517 | 10/05/18 | ......do | 38,982 | 10/05/18 | Nov. 2018 | .1050 |
Imported merchandise or drawback products 1 to be designated as the basis for drawback on the exported products. | Duty-paid, duty-free or domestic merchandise classifiable under the same 8-digit HTSUS subheading number as that designated which will be used in the production of the exported products. |
Piece goods. | Piece goods. |
The piece goods used in manufacture will be classifiable under the same 8-digit HTSUS classification as the piece goods designated as the basis of claim for drawback, and are used interchangeably without change in manufacturing processes or resultant products (including, if applicable, multiple products), or wastes. Some tolerances between imported-designated piece goods and the used-exported piece goods will be permitted to accommodate variations which are normally found in piece goods. These tolerances are no greater than the tolerances generally allowed in the industry for piece goods classifiable under the same 8-digit HTSUS classification as follows:
1 Drawback products are those produced in the United States in accordance with the drawback law and regulations. Such products have “dual status” under 19 U.S.C. 1313(b). They may be designated as the basis for drawback and also may be deemed to be domestic merchandise.
1. A 4% weight tolerance so that the piece goods used in manufacture will be not more than 4% lighter or heavier than the imported piece goods which will be designated;
2. A tolerance of 4% in the aggregate thread count per square inch so that the piece goods used in manufacture will have an aggregate thread count within 4%, more or less of the aggregate thread count of the imported piece goods which will be designated. In each case, the average yarn number of the domestic piece goods will be the same or greater than the average yarn number of the imported piece goods designated, and in each case, the substitution and tolerance will be employed only within the same family of fabrics, i.e., print cloth for print cloth, gingham for gingham, greige for greige, dyed for dyed, bleached for bleached, etc. The piece goods used in manufacture of the exported articles will be designated as containing the identical percentage of identical fibers as the piece goods designated as the basis for allowance of drawback; for example, piece goods containing 65% cotton and 35% dacron will be designated against the use of piece goods shown to contain 65% cotton and 35% dacron. The actual fiber composition may vary slightly from that described on the invoice or other acceptance of the fabric as having the composition described on documents in accordance with trade practices.
B. Exported Articles on Which Drawback Will Be ClaimedFinished piece goods.
C. General StatementThe manufacturer or producer manufactures or produces for its own account. The manufacturer or producer may manufacture or produce articles for the account of another or another manufacturer or producer may manufacture or produce for the account of the manufacturer or producer under contract within the principal and agency relationship outlined in T.D.s. 55027(2) and 55207(1) (see § 190.9).
D. Process of Manufacture or ProductionPiece goods are subject to any one of the following finishing productions:
1. Bleaching,
2. Mercerizing,
3. Dyeing,
4. Printing,
5. A combination of the above, or
6. Any additional finishing processes.
E. Multiple ProductsNot applicable.
F. WasteRag waste may be incurred. No drawback is payable on any waste which results from the manufacturing operation. Unless the claim for drawback is based on the quantity of merchandise appearing in the exported articles, the records of the manufacturer or producer must show the quantity of rag waste, if any, and its value. In instances where rag waste occurs and it is impractical to account for the actual quantity of rag waste incurred, it may be assumed that such rag waste constituted 2% of the piece goods put into the finishing processes. If necessary to establish the quantity of merchandise (eligible piece goods) appearing in the exported articles, such waste records must also be kept.
G. Shrinkage, Gain, and SpoilageUnless the claim for drawback is based on the quantity of merchandise appearing in the exported articles, the records of the manufacturer or producer must show the yardage lost by shrinkage or gained by stretching during manufacture or production, and the quantity of remnants resulting and of spoilage incurred, if any. If necessary to establish the quantity of merchandise (eligible piece goods) appearing in the exported articles, such records for shrinkage, gain and spoilage will also be kept.
H. [Reserved] I. Procedures and Records MaintainedRecords, which may include records kept in the normal course of business, will be maintained to establish:
1. The identity and 8-digit HTSUS classification of the designated merchandise;
2. The quantity of merchandise classifiable under the same 8-digit HTSUS classification as the designated merchandise 2 used to produce the exported articles;
2 If claims are to be made on an “appearing in” basis, the remainder of this sentence should read “appearing in the exported articles produced.”
3. That, within 5 years after the date of importation of the designated merchandise, the manufacturer or producer used the merchandise to produce articles. During the same 5-year period, the manufacturer or producer produced 3 the exported articles.
3 The date of production is the date an article is completed.
To obtain drawback the claimant must establish that the completed articles were exported within 5 years after the importation of the imported merchandise. Records establishing compliance with these requirements will be available for audit by CBP during business hours. Drawback is not payable without proof of compliance.
J. Inventory ProceduresThe inventory records of the manufacturer or producer must show how the drawback recordkeeping requirements set forth in 19 U.S.C. 1313(b) and part 190 of the CBP Regulations will be met, as discussed under the heading “Procedures and Records Maintained”. If those records do not establish satisfaction of all legal requirements, drawback cannot be paid.
K. Basis of Claim for DrawbackDrawback will be claimed on the quantity of eligible piece goods used in producing the exported articles only if there is no waste or valueless or unrecovered waste in the manufacturing operation. Drawback may be claimed on the quantity of eligible piece goods that appears in the exported articles, regardless of whether there is waste, and no records of waste need be maintained. If there is valuable waste recovered from the manufacturing operation and records are kept which show the quantity and value of the waste from each lot of piece goods, drawback may be claimed on the quantity of eligible piece goods used to produce the exported articles less the amount of piece goods which the value of the waste would replace.
L. General RequirementsThe manufacturer or producer will:
1. Comply fully with the terms of this general ruling when claiming drawback;
2. Open its factory and records for examination at all reasonable hours by authorized Government officers;
3. Keep its drawback related records and supporting data for at least 3 years from the date of liquidation of any drawback claim predicated in whole or in part upon this general ruling;
4. Keep its letter of notification of intent to operate under this general ruling current by reporting promptly to the drawback office which liquidates its claims any changes in the information required by the General Instructions of this Appendix (I. General Instructions, 1 through 10), the corporate name, or corporate organization by succession or reincorporation;
5. Keep a copy of this general ruling on file for ready reference by employees and require all officials and employees concerned to familiarize themselves with the provisions of this general ruling; and
6. Issue instructions to insure proper compliance with title 19, United States Code, section 1313, part 190 of the CBP Regulations and this general ruling.
XI. General Manufacturing Drawback Ruling Under 19 U.S.C. 1313(b) for Raw Sugar (T.D. 83-59)Drawback may be allowed under 19 U.S.C. 1313(b) upon the exportation of hard or soft refined sugars and sirups manufactured from raw sugar, subject to the following special requirements:
A. The drawback allowance must not exceed an amount calculated pursuant to regulations prescribed by the Secretary of the Treasury, of the duties, taxes, and fees paid on a quantity of raw sugar designated by the refiner which contains a quantity of sucrose not in excess of the quantity required to manufacture the exported sugar or sirup, ascertained as provided in this general rule.
B. The refined sugars and sirups must have been manufactured with the use of duty-paid, duty-free, or domestic sugar, or combinations thereof, within 5 years after the date of importation, and must have been exported within 5 years from the date of importation of the designated sugar.
C. All granulated sugar testing by the polariscope 99.5 [degrees] and over will be deemed hard refined sugar. All refined sugar testing by the polariscope less than 99.5 [degrees] will be deemed soft refined sugar. All “blackstrap,” “unfiltered sirup,” and “final molasses” will be deemed sirup.
D. The imported duty-paid sugar selected by the refiner as the basis for the drawback claim (designated sugar) must be classifiable under the same 8-digit HTSUS classification as that used in the manufacture of the exported refined sugar or sirup and must have been used within 5 years after the date of importation. Duty-paid sugar which has been used at a plant of a refiner within 5 years after the date on which it was imported by such refiner may be designated as the basis for the allowance of drawback on refined sugars or sirups manufactured at another plant of the same refiner.
E. For the purpose of distributing the drawback, relative values must be established between hard refined (granulated) sugar, soft refined (various grades) sugar, and sirups at the time of separation. The entire period covered by an abstract will be deemed the time of separation of the sugars and sirups covered by such abstract.
F. The sucrose allowance per pound on hard refined (granulated) sugar established by an abstract, as provided for in this general ruling, will be applied to hard refined sugar commercially known as loaf, cut loaf, cube, pressed, crushed, or powdered sugar manufactured from the granulated sugar covered by the abstract.
G. The sucrose allowance per gallon on sirup established by an abstract, as provided for in this general ruling, will be applied to sirup further advanced in value by filtration or otherwise, unless such sirup is the subject of a special manufacturing drawback ruling.
H. As to each lot of imported or domestic sugar used in the manufacture of refined sugar or sirup on which drawback is to be claimed, the raw stock records must show the refiner's raw lot number, the number and character of the packages, the settlement weight in pounds, the settlement polarization, and the 8-digit HTSUS classification. Such records covering imported sugar must show, in addition to the foregoing, the import entry number, date of importation, name of importing carrier, country of origin, the Government weight, and the Government polarization.
I. The melt records must show the date of melting, the number of pounds of each lot of raw sugar melted, and the full analysis at melting.
J. There must be kept a daily record of final products boiled showing the date of the melt, the date of boiling, the magma filling serial number, the number of the vacuum pan or crystallizer filling, the date worked off, and the sirup filling serial number.
K. The sirup manufacture records must show the date of boiling, the period of the melt, the sirup filling serial number, the number of barrels in the filling, the magma filling serial number, the quantity of sirup, its disposition in tanks or barrels and the refinery serial manufacture number.
L. The refined sugar stock records must show the refinery serial manufacture number, the period of the melt, the date of manufacture, the grade of sugar produced, its polarization, the number and kind of packages, and the net weight. When soft sugars are manufactured, the commercial grade number and quantity of each must be shown.
M. Each lot of hard or soft refined sugar and each lot of sirup manufactured, regardless of the character of the containers or vessels in which it is packed or stored, must be marked immediately with the date of manufacture and the refinery manufacture number applied to it in the refinery records provided for and shown in the abstract, as provided for in this general ruling, from such records. If all the sugar or sirup contained in any lot manufactured is not intended for exportation, only such of the packages as are intended for exportation need be marked as prescribed above, provided there is filed with the drawback office immediately after such marking a statement showing the date of manufacture, the refinery manufacture number, the number of packages marked, and the quantity of sugar or sirup contained therein. No drawback will be allowed in such case on any sugar or sirup in excess of the quantity shown on the statement as having been marked. If any packages of sugar or sirup so marked are repacked into other containers, the new containers must be marked with the marks which appeared on the original containers and a revised statement covering such repacking and remarking must be filed with the drawback office. If sirups from more than one lot are stored in the same tank, the refinery records must show the refinery manufacture number and the quantity of sirup from each lot contained in such tank.
N. An abstract from the foregoing records covering manufacturing periods of not less than 1 month nor more than 3 months, unless a different period will have been authorized, must be filed when drawback is to be claimed on any part of the refined sugar or sirup manufactured during such period. Such abstract must be filed by each refiner with the drawback office where drawback claims are filed on the basis of this general ruling. Such abstract must consist of: (1) A raw stock record (accounting for Refiner's raw lot No., Import entry No., Packages No. and kind, Pounds, Polarization, By whom imported or withdrawn, Date of importation, Date of receipt by refiner, Date of melt, Importing carrier, Country of origin); (2) A melt record [number of pounds in each lot melted] (accounting for Lot No. Pounds, and Polarization degrees and pounds sucrose); (3) Sirup stock records (accounting for Date of boiling, Refinery serial manufacture No., Quantity of sirup in gallons, and Pounds sucrose contained therein); (4) Refined sugar stock record (accounting for Refinery serial production No., Date of manufacture, Hard or soft refined, Polarization and No., Net weight in pounds); (5) Recapitulation (consisting of (in pounds): (a) Sucrose in process at beginning of period, (b) sucrose melted during period, (c) sucrose in process at end of period, (d) sucrose used in manufacture, and (e) sucrose contained in manufacture, in which item (a) plus item (b), minus item (c), should equal item (d)); and (6) A statement as follows:
I, ____, the ____ refiner at the ____ refinery of ____, located at ____, do solemnly and truly declare that each of the statements contained in the foregoing abstract is true to the best of my knowledge and belief and can be verified by the refinery records, which have been kept in accordance with Treasury Decision 83-59 and Appendix A of 19 CFR part 190 and which are at all times open to the inspection of CBP.
Date SignatureO. The refiner must file with each abstract a statement, showing the average market values of the products specified in the abstract and including a statement as follows: I, ____, (Official capacity) of the ____ (Refinery), do solemnly and truly declare that the values shown above are true to the best of my knowledge and belief, and can be verified by our records.
Date SignatureP. At the end of each calendar month the refiner must furnish to the drawback office a statement showing the actual sales of sirup and the average market values of refined sugars for the calendar month.
Q. The sucrose allowance to be applied to the various products based on the abstract and statement provided for in this general ruling will be in accordance with the example set forth in Treasury Decision 83-59.
R. [Reserved]
S. Drawback entries under this general ruling must state the polarization in degrees and the sucrose in pounds for the designated imported sugar. Drawback claims under this general ruling must include a statement as follows:
I, ____, the ____ of ____, located at ____ declare that the sugar (or sirup) described in this entry, was manufactured by said company at its refinery at ____ and is part of the sugar (or sirup) covered by abstract No. __, filed at the port of ____; that, subject to 19 U.S.C. 1508 and 1313(t), the refinery and other records of the company verifying the statements contained in said abstract are now and at all times hereafter will be open to inspection by CBP. I further declare that the above-designated imported sugar (upon which the duties have been paid) was received by said company on ____ and was used in the manufacture of sugar and sirup during the period covered by abstract No. __, CBP No. __, on file with the port director at ____. I further declare that the sugar or sirup specified therein was exported as stated in the entry.
Date SignatureT. General Statement. The refiner manufactures or produces for its own account. The refiner may manufacture or produce articles for the account of another or another manufacturer or producer may manufacture or produce for the refiner's account under contract within the principal and agency relationship outlined in T.D.s 55027(2) and 55207(1) (see § 190.9).
U. Waste. No drawback is payable on any waste which results from the manufacturing operation. Unless drawback claims are based on the “appearing in” method, records will be maintained to establish the value (or the lack of value), quantity, and disposition of any waste that results from manufacturing the exported articles. If no waste results, records to establish that fact will be maintained.
V. Loss or Gain. The refiner will maintain records showing the extent of any loss or gain in net weight or measurement of the sugar caused by atmospheric conditions, chemical reactions, or other factors.
W. [Reserved]
X. Procedures and Records Maintained.
Records, which may include records kept in the normal course of business, will be maintained to establish:
1. The identity and 8-digit HTSUS classification of the designated merchandise;
2. The quantity of merchandise classifiable under the same 8-digit HTSUS classification as the designated merchandise 1 used to produce the exported articles; and
1 If claims are to be made on an “appearing in” basis, the remainder of this sentence should read “appearing in the exported articles produced.”
3. That, within 5 years of the date of importation of the designated merchandise, the refiner used the designated merchandise to produce articles. During the same 5-year period, the refiner produced 2 the exported articles.
2 The date of production is the date an article is completed.
To obtain drawback the claimant must establish that the completed articles were exported within 5 years after the importation of the imported merchandise. Records establishing compliance with these requirements will be available for audit by CBP during business hours. Drawback is not payable without proof of compliance.
Y. General requirements. The refiner will:
1. Comply fully with the terms of this general ruling when claiming drawback;
2. Open its factory and records for examination at all reasonable hours by authorized Government officers;
3. Keep its drawback related records and supporting data for at least 3 years from the date of liquidation of any drawback claim predicated in whole or in part upon this general ruling;
4. Keep its letter of notification of intent to operate under this general ruling current by reporting promptly to the drawback office which liquidates its claims any changes in the information required by the General Instructions of this Appendix (I. General Instructions, 1 through 10), the corporate name, or corporate organization by succession or reincorporation;
5. Keep a copy of this general ruling on file for ready reference by employees and require all officials and employees concerned to familiarize themselves with the provisions of this general ruling; and
6. Issue instructions to insure proper compliance with title 19, United States Code, section 1313, part 190 of the CBP Regulations and this general ruling.
XII. General Manufacturing Drawback Ruling Under 19 U.S.C. 1313(b) for Steel (T.D. 81-74) A. Same 8-Digit HTSUS Classification (Parallel Columns)Imported merchandise or drawback products 1 to be designated as the basis for drawback on the exported products. | Duty-paid, duty-free or domestic merchandise classifiable under the same 8-digit HTSUS subheading number as that designated which will be used in the production of the exported products. |
Steel of one general class, e.g., an ingot, falling within on SAE, AISI, or ASTM 2 specification and, if the specification contains one or more grades, falling within one grade of the specification. | Steel of the same general class, specification, and grade as the steel in the column immediately to the left hereof. |
1. The duty-paid, duty-free, or domestic steel used instead of the imported, duty-paid steel (or drawback products) will be interchangeable for manufacturing purposes with the duty-paid steel. To be interchangeable a steel must be able to be used in place of the substituted steel without any additional processing step in the manufacture of the article on which drawback is to be claimed.
1 Drawback products are those produced in the United States in accordance with the drawback law and regulations. Such products have “dual status” under section 1313(b). They may be designated as the basis for drawback and also may be deemed to be domestic merchandise.
2 Standards set by the Society of Automotive Engineers (SAE), the American Iron and Steel Institute (AISI), or the American Society for Testing and Materials (ASTM).
2. Because the duty-paid steel (or drawback products) that is to be designated as the basis for drawback is dutiable according to its value, the amount of duty can vary with its size (gauge, width, or length) or composition (e.g., chrome content). If such variances occur, designation will be by “price extra,” and in no case will drawback be claimed in a greater amount than that which would have accrued to that steel used in manufacture of or appearing in the exported articles. Price extra is not available for coated or plated steel, covered in paragraph 4, infra, insofar as the coating or plating is concerned.
3. If the steel is coated or plated with a base metal, in addition to meeting the requirements for uncoated or unplated steel set forth in the Parallel Columns, the base-metal coating or plating on the duty-paid, duty-free, or domestic steel used in place of the duty-paid steel (or drawback products) will have the same composition and thickness as the coating or plating on the duty-paid steel. If the coated or plated duty-paid steel is within an SAE, AISI, ASTM specification, then any duty-paid, duty-free, or domestic coated or plated steel must be covered by the same specification and grade (if two or more grades are in the specification).
B. Exported Articles on Which Drawback Will Be ClaimedThe exported articles will have been manufactured in the United States using steels described in the Parallel Columns above.
C. General StatementThe manufacturer or producer manufactures or produces for its own account.
The manufacturer or producer may manufacture or produce articles for the account of another or another manufacturer or producer may manufacture or produce for the account of the manufacturer or producer under contract within the principal and agency relationship outlined in T.D.s 55027(2) and 55207(1) (see § 190.9).
D. Process of Manufacture or ProductionThe steel described in the Parallel Columns will be used to manufacture or produce articles in accordance with § 190.2.
E. Multiple ProductsNot applicable.
F. WasteNo drawback is payable on any waste which results from the manufacturing operation. Unless the claim for drawback is based on the quantity of steel appearing in the exported articles, records will be maintained to establish the value (or the lack of value), quantity, and disposition of any waste that results from manufacturing the exported articles. If no waste results, records to establish that fact will be maintained.
G. Loss or GainThe manufacturer or producer will maintain records showing the extent of any loss or gain in net weight or measurement of the steel caused by atmospheric conditions, chemical reactions, or other factors.
H. [Reserved] I. Procedures and Records MaintainedRecords, which may include records kept in the normal course of business, will be maintained to establish:
1. The identity and 8-digit HTSUS classification of the designated merchandise;
2. The quantity of merchandise of the designated merchandise 3 used to produce the exported articles;
3 If claims are to be made on an “appearing in” basis, the remainder of this sentence should read “appearing in the exported articles produced.”
3. That, within 5 years of the date of importation of the designated merchandise, the manufacturer or producer used the merchandise to produce articles. During the same 5-year period, the manufacturer or producer produced 4 the exported articles.
4 The date of production is the date an article is completed.
To obtain drawback the claimant must establish that the completed articles were exported within 5 years after the importation of the imported merchandise. Records establishing compliance with these requirements will be available for audit by CBP during business hours. Drawback is not payable without proof of compliance.
J. Inventory ProceduresThe inventory records of the manufacturer or producer must show how the drawback recordkeeping requirements set forth in 19 U.S.C. 1313(b) and part 190 of the CBP Regulations will be met, as discussed under the heading “Procedures and Records Maintained.” If those records do not establish satisfaction of all legal requirements, drawback cannot be paid.
K. Basis of Claim for DrawbackDrawback will be claimed on the quantity of steel used in producing the exported articles only if there is no waste or valueless or unrecovered waste in the manufacturing operation. Drawback may be claimed on the quantity of eligible steel that appears in the exported articles, regardless of whether there is waste, and no records of waste need be maintained. If there is valuable waste recovered from the manufacturing operation and records are kept which show the quantity and value of the waste from each lot of steel, drawback may be claimed on the quantity of eligible steel used to produce the exported articles less the amount of that steel which the value of the waste would replace.
L. General RequirementsThe manufacturer or producer will:
1. Comply fully with the terms of this general ruling when claiming drawback;
2. Open its factory and records for examination at all reasonable hours by authorized Government officers;
3. Keep its drawback related records and supporting data for at least 3 years from the date of liquidation of any drawback claim predicated in whole or in part upon this general ruling;
4. Keep its letter of notification to operate under this general ruling current by reporting promptly to the drawback office which liquidates its claims any changes in the information required by the General Instructions of this Appendix (I. General Instructions, 1 through 10), the corporate name, or corporate organization by succession or reincorporation;
5. Keep a copy of this general ruling on file for ready reference by employees and require all officials and employees concerned to familiarize themselves with the provisions of this general ruling; and
6. Issue instructions to insure proper compliance with title 19, United States Code, section 1313, part 190 of the CBP Regulations and this general ruling.
XIII. General Manufacturing Drawback Ruling Under 19 U.S.C. 1313(b) for Sugar (T.D. 81-92) A. Same 8-Digit HTSUS Classification (Parallel Columns)Imported merchandise or drawback products 1 to be designated as the basis for drawback on the exported products. | Duty-paid, duty-free or domestic merchandise classifiable under the same 8-digit HTSUS subheading number as that designated which will be used in the production of the exported products. |
1. Granulated or liquid sugar for manufacturing, containing sugar solids of not less than 99.5 sugar degrees. | 1. Granulated or liquid sugar for manufacturing, containing sugar solids of less than 99.5 sugar degrees. |
2. Granulated or liquid sugar for manufacturing, containing sugar solids of not less than 99.5 sugar degrees. | 2. Granulated or liquid sugar for manufacturing, containing sugar solids of less than 99.5 sugar degrees. |
The sugars listed above test within three-tenths of a degree on the polariscope. Sugars in each column are completely interchangeable with the sugars directly opposite and designation will be made on this basis only. The designated sugar on which claims for drawback will be based will be classifiable under the same 8-digit HTSUS classification.
1 Drawback products are those produced in the United States in accordance with the drawback law and regulations. Such products have “dual status” under section 1313(b). They may be designated as the basis for drawback and also may be deemed to be domestic merchandise.
B. Exported Articles on Which Drawback Will Be ClaimedEdible substances (including confectionery) and/or beverages and/or ingredients therefor.
C. General StatementThe manufacturer or producer manufactures or produces for its own account. The manufacturer or producer may manufacture or produce articles for the account of another or another manufacturer or producer may manufacture or produce for the account of the manufacturer or producer under contract within the principal and agency relationship outlined in T.D.s 55027(2) and 55207(1) (see § 190.9).
D. Process of Manufacture or ProductionThe sugars are subjected to one or more of the following operations to form the desired product(s):
1. Mixing with other substances,
2. Cooking with other substances,
3. Boiling with other substances,
4. Baking with other substances,
5. Additional similar processes.
E. Multiple ProductsNot applicable.
F. WasteNo drawback is payable on any waste which results from the manufacturing operation. Unless the claim for drawback is based on the quantity of sugar appearing in the exported articles, records will be maintained to establish the value (or the lack of value), quantity, disposition of any waste that results from manufacturing the exported articles. If no waste results, records to establish that fact will be maintained.
G. Loss or GainThe manufacturer or producer will maintain records showing the extent of any loss or gain in net weight or measurement of the sugar caused by atmospheric conditions, chemical reactions, or other factors.
H. [Reserved] I. Procedures and Records MaintainedRecords, which may include records kept in the normal course of business, will be maintained to establish:
1. The identity and 8-digit HTSUS classification of the designated merchandise;
2. The quantity of merchandise classifiable under the same 8-digit HTSUS classification as the designated merchandise 2 used to produce the exported articles;
2 If claims are to be made on an “appearing in” basis, the remainder of this sentence should read “appearing in the exported articles produced.”
3. That, within 5 years of the date of importation of the designated merchandise, the manufacturer or producer used the merchandise to produce articles. During the same 5-year period, the manufacturer or producer produced 3 the exported articles.
3 The date of production is the date an article is completed.
To obtain drawback the claimant must establish that the completed articles were exported within 5 years after the importation of the imported merchandise. Records establishing compliance with these requirements will be available for audit by CBP during business hours. Drawback is not payable without proof of compliance.
J. Inventory ProceduresThe inventory records of the manufacturer or producer, will show how the drawback recordkeeping requirements set forth in 19 U.S.C. 1313(b) and part 190 of the CBP Regulations will be met, as discussed under the heading “Procedures and Records Maintained.” If those records do not establish satisfaction of all legal requirements, drawback cannot be paid.
K. Basis of Claim for DrawbackDrawback will be claimed on the quantity of sugar used in producing the exported articles only if there is no waste or valueless or unrecovered waste in the manufacturing operation. Drawback may be claimed on the quantity of eligible sugar that appears in the exported articles regardless of whether there is waste, and no records of waste need be maintained. If there is valuable waste recovered from the manufacturing operation and records are kept which show the quantity and value of the waste, drawback may be claimed on the quantity of eligible material used to produce the exported articles less the amount of that sugar which the value of the waste would replace.
L. General RequirementsThe manufacturer or producer will:
1. Comply fully with the terms of this general ruling when claiming drawback;
2. Open its factory and records for examination at all reasonable hours by authorized Government officers;
3. Keep its drawback related records and supporting data for at least 3 years from the date of liquidation of any drawback claim predicated in whole or in part upon this general ruling;
4. Keep its letter of notification of intent to operate under this general ruling current by reporting promptly to the drawback office which liquidates its claims any changes in the information required by the General Instructions of this Appendix (I. General Instructions, 1 through 10), the corporate name, or corporate organization by succession or reincorporation;
5. Keep a copy of this general ruling on file for ready reference by employees and require all officials and employees concerned to familiarize themselves with the provisions of this general ruling; and
6. Issue instructions to insure proper compliance with title 19, United States Code, section 1313, part 190 of the CBP Regulations and this general ruling.
XIV. General Manufacturing Drawback Ruling Under 19 U.S.C. 1313(a) for Woven Piece Goods (T.D. 83-84)Drawback may be allowed under 19 U.S.C. 1313(a) upon the exportation of bleached, mercerized, printed, dyed, or redyed piece goods manufactured or produced by any one or a combination of the foregoing processes with the use of imported woven piece goods, subject to the following special requirements:
A. Imported Merchandise or Drawback Products 1 Used1 Drawback products are those produced in the United States in accordance with the drawback law and regulations.
Imported merchandise or drawback products (woven piece goods) are used in the manufacture of the exported articles upon which drawback claims will be based.
B. Exported Articles on Which Drawback Will Be ClaimedExported articles on which drawback will be claimed must be manufactured in the United States using imported merchandise or drawback products.
C. General StatementThe manufacturer or producer manufactures or produces for its own account. The manufacturer or producer may manufacture or produce articles for the account of another or another manufacturer or producer may manufacture or produce for the account of the manufacturer or producer under contract within the principal and agency relationship outlined in T.D.s 55027(2) and 55207(1) (see § 190.9).
D. Process of Manufacture or ProductionThe imported merchandise or drawback products will be used to manufacture or produce articles in accordance with § 190.2.
The piece goods used in manufacture or production under this general manufacturing drawback ruling may also be subjected to one or more finishing processes. Drawback will not be allowed under this general manufacturing drawback ruling when the process performed results only in the restoration of the merchandise to its condition at the time of importation.
E. Multiple ProductsNot applicable.
F. WasteRag waste may be incurred. No drawback is payable on any waste which results from the manufacturing operation. Unless the claim for drawback is based on the quantity of merchandise appearing in the exported articles, the records of the manufacturer or producer must show the quantity of rag waste, if any, its value, and its disposition. If no waste results, records will be maintained to establish that fact. In instances where rag waste occurs and it is impractical to account for the actual quantity of rag waste incurred, it may be assumed that such rag waste constituted 2% of the woven piece goods put into process. If necessary to establish the quantity of merchandise (eligible piece goods) appearing in the exported articles, such waste records will also be kept.
G. Shrinkage, Gain, and SpoilageUnless the claim for drawback is based on the quantity of merchandise appearing in the exported articles, the records of the manufacturer or producer must show the yardage lost by shrinkage or gained by stretching during manufacture, and the quantity of remnants resulting and of spoilage incurred, if any. If necessary to establish the quantity of merchandise (eligible piece goods) appearing in the exported articles, such records for shrinkage, gain, and spoilage will also be kept.
H. Procedures and Records MaintainedRecords, which may include records kept in the normal course of business, will be maintained to establish:
1. That the exported articles on which drawback is claimed were produced with the use of the imported merchandise; and
2. The quantity of imported merchandise 2 used in producing the exported articles.
2 If claims are to be made on an “appearing in” basis, the remainder of the sentence should read “appearing in the exported articles.”
To obtain drawback the claimant must establish that the completed articles were exported within 5 years after importation of the imported merchandise. Records establishing compliance with these requirements will be available for audit by CBP during business hours. Drawback is not payable without proof of compliance.
I. Inventory ProceduresThe inventory records of the manufacturer or producer must show how the drawback recordkeeping requirements set forth in 19 U.S.C. 1313(a) and part 190 of the CBP Regulations will be met, as discussed under the heading “Procedures and Records Maintained”. If those records do not establish satisfaction of all legal requirements, drawback cannot be paid.
The records of the manufacturer or producer must show, as to each lot of piece goods manufactured or produced for exportation with benefit of drawback, the lot number and the date or inclusive dates of manufacture or production, the quantity, identity, value, and 8-digit HTSUS classification of the imported (or drawback product) piece goods used, the condition in which imported or received (whether in the gray, bleached, dyed, or mercerized), the working allowance specified in the contract under which they are received, the process or processes applied thereto, and the quantity and description of the piece goods obtained. The records must also show the yardage lost by shrinkage or gained by stretching during manufacture or production, and the quantity of remnants resulting and of spoilage incurred.
J. Basis of Claim for DrawbackDrawback will be claimed on the quantity of merchandise used in producing the exported articles only if there is no waste or valueless or unrecovered waste in the manufacturing operation. Drawback may be claimed on the quantity of eligible merchandise that appears in the exported articles, regardless of whether there is waste, and no records of waste need be maintained. If there is valuable waste recovered from the manufacturing operation and records are kept which show the quantity and value of the waste, drawback may be claimed on the quantity of eligible material used to produce the exported articles, less the amount of that merchandise which the value of the waste would replace. (If remnants and/or spoilage occur during manufacture or production, the quantity of imported merchandise used will be determined by deducting from the quantity of piece goods received and put into manufacture or production the quantity of such remnants and/or spoilage. The remaining quantity will be reduced by the quantity thereof which the value of the rag waste, if any, would replace.)
K. General RequirementsThe manufacturer or producer will:
1. Comply fully with the terms of this general ruling when claiming drawback;
2. Open its factory and records for examination at all reasonable hours by authorized Government officers;
3. Keep its drawback related records and supporting data for at least 3 years from the date of liquidation of any drawback claim predicated in whole or in part upon this general ruling;
4. Keep its letter of notification of intent to operate under this general ruling current by reporting promptly to the drawback office which liquidates its claims any changes in the information required by the General Instructions of this Appendix (I. General Instructions, 1 through 10), the corporate name, or corporate organization by succession or reincorporation.
5. Keep a copy of this general ruling on file for ready reference by employees and require all officials and employees concerned to familiarize themselves with the provisions of this general ruling; and
6. Issue instructions to insure proper compliance with 19 U.S.C. 1313, part 190 of the CBP Regulations and this general ruling.