Title 10
PART 431 APPENDIX C
Motor horsepower/standard kilowatt equivalent | Least efficient
basic model - (model numbers(s)) Nominal full-load efficiency |
|||||||
---|---|---|---|---|---|---|---|---|
Open motors (number of poles) |
Enclosed
motors (number of poles) |
|||||||
8 | 6 | 4 | 2 | 8 | 6 | 4 | 2 | |
1/.75 | ___ | ___ | ___ | ___ | ___ | ___ | ___ | ___ |
___ | ___ | ___ | ___ | ___ | ___ | ___ | ___ | |
1.5/1.1 | ___ | ___ | ___ | ___ | ___ | ___ | ___ | ___ |
___ | ___ | ___ | ___ | ___ | ___ | ___ | ___ | |
2/1.5 | ___ | ___ | ___ | ___ | ___ | ___ | ___ | ___ |
___ | ___ | ___ | ___ | ___ | ___ | ___ | ___ | |
3/2.2 | ___ | ___ | ___ | ___ | ___ | ___ | ___ | ___ |
___ | ___ | ___ | ___ | ___ | ___ | ___ | ___ | |
5/3.7 | ___ | ___ | ___ | ___ | ___ | ___ | ___ | ___ |
___ | ___ | ___ | ___ | ___ | ___ | ___ | ___ | |
___ | ___ | ___ | ___ | ___ | ___ | ___ | ___ | |
___ | ___ | ___ | ___ | ___ | ___ | ___ | ___ | |
Etc | ___ | ___ | ___ | ___ | ___ | ___ | ___ | ___ |
___ | ___ | ___ | ___ | ___ | ___ | ___ | ___ |
Note: Place an asterisk beside each reported nominal full load efficiency that is determined by actual testing rather than by application of an alternative efficiency determination method. Also list below additional basic models that were subjected to actual testing.
Basic Model means all units of a given type of electric motor (or class thereof) manufactured by a single manufacturer, and which (i) have the same rating, (ii) have electrical design characteristics that are essentially identical, and (iii) do not have any differing physical or functional characteristics that affect energy consumption or efficiency.
Rating means one of the combinations of an electric motor's horsepower (or standard kilowatt equivalent), number of poles, motor type, and open or enclosed construction, with respect to which § 431.25 of 10 CFR Part 431 prescribes nominal full load efficiency standards.
Models Actually Tested and Not Previously Identified
Motor horsepower/standard kilowatt equivalent | Least efficient
basic model - (model numbers(s)) Nominal full-load efficiency |
|||||||
---|---|---|---|---|---|---|---|---|
Open motors (number of poles) |
Enclosed
motors (number of poles) |
|||||||
8 | 6 | 4 | 2 | 8 | 6 | 4 | 2 | |
___ | ___ | ___ | ___ | ___ | ___ | ___ | ___ | ___ |
___ | ___ | ___ | ___ | ___ | ___ | ___ | ___ | |
___ | ___ | ___ | ___ | ___ | ___ | ___ | ___ | ___ |
___ | ___ | ___ | ___ | ___ | ___ | ___ | ___ | |
___ | ___ | ___ | ___ | ___ | ___ | ___ | ___ | ___ |
___ | ___ | ___ | ___ | ___ | ___ | ___ | ___ | |
___ | ___ | ___ | ___ | ___ | ___ | ___ | ___ | ___ |
___ | ___ | ___ | ___ | ___ | ___ | ___ | ___ | |
___ | ___ | ___ | ___ | ___ | ___ | ___ | ___ | ___ |
___ | ___ | ___ | ___ | ___ | ___ | ___ | ___ | |
___ | ___ | ___ | ___ | ___ | ___ | ___ | ___ | ___ |
___ | ___ | ___ | ___ | ___ | ___ | ___ | ___ | |
Etc | ___ | ___ | ___ | ___ | ___ | ___ | ___ | ___ |
___ | ___ | ___ | ___ | ___ | ___ | ___ | ___ |
Appendix C to Subpart G of Part 431 - Uniform Test Method for the Measurement of Thermal Efficiency and Standby Loss of Gas-Fired and Oil-Fired Instantaneous Water Heaters and Hot Water Supply Boilers (Other Than Storage-Type Instantaneous Water Heaters)
10:3.0.1.4.19.7.64.6.53 : Appendix C
Appendix C to Subpart G of Part 431 - Uniform Test Method for the Measurement of Thermal Efficiency and Standby Loss of Gas-Fired and Oil-Fired Instantaneous Water Heaters and Hot Water Supply Boilers (Other Than Storage-Type Instantaneous Water Heaters) Note:Prior to November 6, 2017, manufacturers must make any representations with respect to the energy use or efficiency of the subject commercial water heating equipment in accordance with the results of testing pursuant to this appendix or the procedures in 10 CFR 431.106 that were in place on January 1, 2016. On and after November 6, 2017, manufacturers must make any representations with respect to energy use or efficiency of gas-fired and oil-fired instantaneous water heaters and hot water supply boilers (other than storage-type instantaneous water heaters) in accordance with the results of testing pursuant to this appendix to demonstrate compliance with the energy conservation standards at 10 CFR 431.110.
1. GeneralDetermine the thermal efficiency and standby loss (as applicable) in accordance with the following sections of this appendix. Certain sections reference sections of Annex E.1 of ANSI Z21.10.3-2015 (incorporated by reference; see § 431.105). Where the instructions contained in the sections below conflict with instructions in Annex E.1 of ANSI Z21.10.3-2015, the instructions contained in this appendix control.
2. Test Set-Up2.1. Placement of Water Heater. A water heater for installation on combustible floors must be placed on a 3/4-inch plywood platform supported by three 2 x 4-inch runners. If the water heater is for installation on noncombustible floors, suitable noncombustible material must be placed on the platform. When the use of the platform for a large water heater is not practical, the water heater may be placed on any suitable flooring. A wall-mounted water heater must be mounted on a simulated wall section.
2.2. Test Configuration. If the instantaneous water heater or hot water supply boiler is not required to be tested using a recirculating loop, then set up the unit in accordance with Figures 2.1, 2.2, or 2.3 of this appendix (as applicable). If the unit is required to be tested using a recirculating loop, then set up the unit as per Figure 2.4 of this appendix.
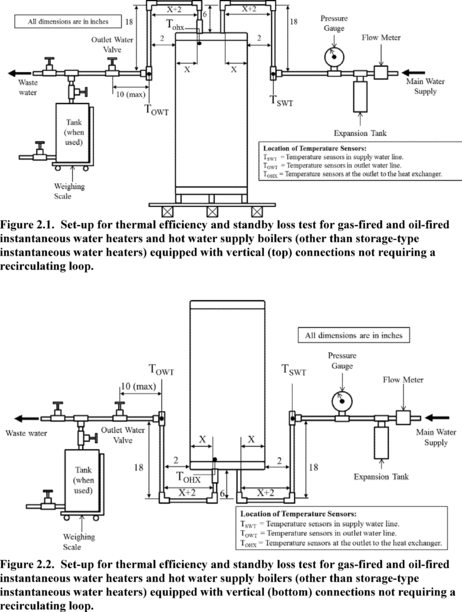
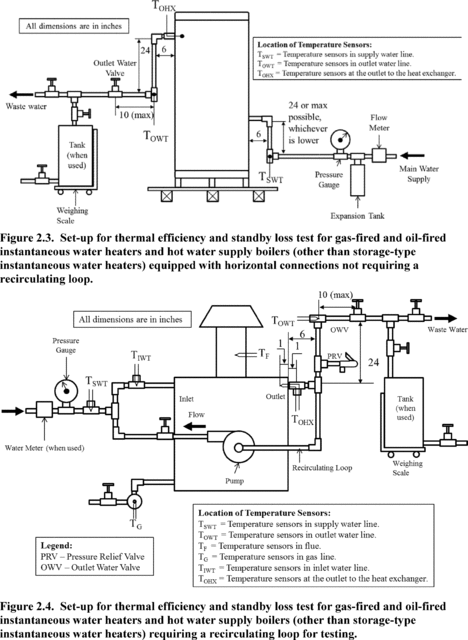
2.2.1. If the instantaneous water heater or hot water supply boiler does not have any external piping, install an outlet water valve within 10 inches of piping length of the water heater jacket or enclosure. If the instantaneous water heater or hot water supply boiler includes external piping assembled at the manufacturer's premises prior to shipment, install water valves in the outlet piping within 5 inches of the end of the piping supplied with the unit.
2.2.2. If the water heater is not able to achieve an outlet water temperature of 70 °F ± 2 °F (TOWT) above the supply water temperature at full firing rate, a recirculating loop with pump as shown in Figure 2.4 of this appendix must be used.
2.2.2.1. If a recirculating loop with a pump is used, then ensure that the inlet water temperature labeled as TIWT in Figure 2.4 of this appendix, is greater than or equal to 70 °F and less than or equal to 120 °F at all times during the thermal efficiency test and steady-state verification period (as applicable).
2.3. Installation of Temperature Sensors2.3.1. Without Recirculating Loop.
2.3.1.1. Vertical Connections. Use Figure 2.1 (for top connections) and 2.2 (for bottom connections) of this appendix.
2.3.1.2. Horizontal Connections. Use Figure 2.3 of this appendix.
2.3.2. With Recirculating Loop. Set up the recirculating loop as shown in Figure 2.4 of this appendix.
2.3.3. For water heaters with multiple outlet water connections leaving the water heater jacket that are required to be operated to achieve the rated input, temperature sensors must be installed for each outlet water connection leaving the water heater jacket or enclosure that is used during testing, in accordance with the provisions in sections 2.3.1 and 2.3.2 of this appendix (as applicable).
2.4. Piping Insulation. Insulate all water piping external to the water heater jacket or enclosure, including piping that is installed by the manufacturer or shipped with the unit, for at least 4 ft of piping length from the connection at the appliance with material having an R-value not less than 4 °F·ft 2·h/Btu. Ensure that the insulation does not contact any appliance surface except at the location where the pipe connections penetrate the appliance jacket or enclosure.
2.5. Temperature and Pressure Relief Valve Insulation. If the manufacturer has not provided a temperature and pressure relief valve, one shall be installed and insulated as specified in section 2.4 of this appendix. The temperature and pressure relief valve must be installed in the outlet water piping, between the unit being tested and the outlet water valve.
2.6. Vent Requirements. Follow the requirements for venting arrangements specified in paragraph c of Annex E.1 of ANSI Z21.10.3-2015 (incorporated by reference; see § 431.105).
2.7. Energy Consumption. Install equipment that determines, within ± 1 percent:
2.7.1. The quantity and rate of fuel consumed.
2.7.2. The quantity of electricity consumed by factory-supplied water heater components, and of the test loop recirculating pump, if used.
3. Test Conditions 3.1. Water Supply3.1.1. Water Supply Pressure. The pressure of the water supply must be maintained between 40 psi and the maximum pressure specified by the manufacturer of the unit being tested. The accuracy of the pressure-measuring devices must be within ± 1.0 psi.
3.1.2. Water Supply Temperature. During the thermal efficiency test and steady-state verification period (as applicable), the temperature of the supply water (TSWT) must be maintained at 70 °F ± 2 °F.
3.2. Gas Pressure for Gas-Fired Equipment. The supply gas pressure must be within the range specified by the manufacturer on the nameplate of the unit being tested. The difference between the outlet pressure of the gas appliance pressure regulator and the value specified by the manufacturer on the nameplate of the unit being tested must not exceed the greater of: ± 10 percent of the nameplate value or ± 0.2 inches water column (in. w.c.). Obtain the higher heating value of the gas burned.
3.3. Ambient Room Temperature. Maintain the ambient room temperature at 75 °F ± 10 °F at all times during the steady-state verification period, the thermal efficiency test, and the standby loss test (as applicable). Measure the ambient room temperature at 1-minute intervals during these periods. Measure the ambient room temperature at the vertical mid-point of the water heater and approximately 2 feet from the water heater jacket or enclosure. Shield the sensor against radiation. Calculate the average ambient room temperature separately for the thermal efficiency test and the standby loss test. During the thermal efficiency and standby loss tests, the ambient room temperature must not vary by more than ± 5.0 °F at any reading from the average ambient room temperature.
3.4. Test Air Temperature. During the steady-state verification period, the thermal efficiency test, and the standby loss test (as applicable), the test air temperature must not vary by more than ± 5 °F from the ambient room temperature at any reading. Measure the test air temperature at 1-minute intervals during these periods and at a location within two feet of the air inlet of the water heater or the combustion air intake vent, as applicable. Shield the sensor against radiation. For units with multiple air inlets, measure the test air temperature at each air inlet, and maintain the specified tolerance on deviation from the ambient room temperature at each air inlet. For units without a dedicated air inlet, measure the test air temperature within two feet of any location on the water heater where combustion air is drawn.
3.5. Maximum Air Draft. During the steady-state verification period, the thermal efficiency test, and the standby loss test (as applicable), the water heater must be located in an area protected from drafts of more than 50 ft/min. Prior to beginning the steady-state verification period and the standby loss test, measure the air draft within three feet of the jacket or enclosure of the water heater to ensure this condition is met. Ensure that no other changes that would increase the air draft are made to the test set-up or conditions during the conduct of the tests.
3.6. Primary Control3.6.1. Thermostatically-Activated Water Heaters With an Internal Thermostat. Before starting the thermal efficiency test and the standby loss test (unless the thermostat is already set before the thermal efficiency test), the thermostat setting must be obtained. Set the thermostat to ensure:
3.6.1.1. With supply water temperature set as per section 3.1.2 of this appendix (i.e., 70 °F ± 2 °F) the water flow rate can be varied so that the outlet water temperature is constant at 70 °F ± 2 °F above the supply water temperature, while the burner is firing at full firing rate; and
3.6.1.2. After the water supply is turned off and the thermostat reduces the fuel supply to a minimum, the maximum heat exchanger outlet water temperature (TOHX) is 140 °F ± 5 °F.
3.6.1.3. If the water heater includes a built-in safety mechanism that prevents it from achieving a heat exchanger outlet water temperature of 140 °F ± 5 °F, adjust the thermostat to its maximum setting.
3.6.2. Flow-Activated Instantaneous Water Heaters and Thermostatically-Activated Instantaneous Water Heaters With an External Thermostat. Energize the primary control such that it is always calling for heating and the burner is firing at the full firing rate. Maintain the supply water temperature as per section 3.1.2 of this appendix (i.e., 70 °F ± 2 °F). Set the control so that the outlet water temperature (TOWT) is 140 °F ± 5 °F. If the water heater includes a built-in safety mechanism that prevents it from achieving a heat exchanger outlet water temperature of 140 °F ± 5 °F, adjust the control to its maximum setting.
3.7. Units With Multiple Outlet Water Connections3.7.1. For each connection leaving the water heater that is required for the unit to achieve the rated input, the outlet water temperature must not differ from that of any other outlet water connection by more than 2 °F during the steady-state verification period and thermal efficiency test.
3.7.2. Determine the outlet water temperature representative for the entire unit at every required measurement interval by calculating the average of the outlet water temperatures measured at each connection leaving the water heater jacket or enclosure that is used during testing. Use the outlet water temperature representative for the entire unit in all calculations for the thermal efficiency and standby loss tests, as applicable.
3.8. Additional Requirements for Oil-Fired Equipment.
3.8.1. Venting Requirements. Connect a vertical length of flue pipe to the flue gas outlet of sufficient height so as to meet the minimum draft specified by the manufacturer.
3.8.2. Oil Supply. Adjust the burner rate so that the following conditions are met:
3.8.2.1. The CO2 reading is within the range specified by the manufacturer;
3.8.2.2. The fuel pump pressure is within ± 10 percent of manufacturer's specifications;
3.8.2.3. If either the fuel pump pressure or range for CO2 reading are not specified by the manufacturer on the nameplate of the unit, in literature shipped with the unit, or in supplemental test report instructions included with a certification report, then a default value of 100 psig is to be used for fuel pump pressure, and a default range of 9-12 percent is to be used for CO2 reading; and
3.8.2.4. Smoke in the flue does not exceed No. 1 smoke as measured by the procedure in ASTM D2156-09 (Reapproved 2013) (incorporated by reference, see § 431.105). To determine the smoke spot number, the smoke measuring device shall be connected to an open-ended tube. This tube must project into the flue 1/4 to 1/2 of the pipe diameter.
3.8.2.5. If no settings on the water heater have been changed and the water heater has not been turned off since the end of a previously run thermal efficiency (or standby loss test for thermostatically-activated instantaneous water heaters with an internal thermostat), measurement of the CO2 reading and conduct of the smoke spot test are not required prior to beginning a test. Otherwise, measure the CO2 reading and determine the smoke spot number, with the burner firing, before beginning measurements for the steady-state verification period (prior to beginning the thermal efficiency test or standby loss test, as applicable). However, measurement of the CO2 reading and conduct of the smoke spot test are not required for the standby loss test for thermostatically-activated instantaneous water heaters with an external thermostat and flow-activated instantaneous water heaters.
3.9. Data Collection Intervals. Follow the data recording intervals specified in the following sections.
3.9.1. Steady-State Verification Period and Thermal Efficiency Test. For the steady-state verification period and the thermal efficiency test, follow the data recording intervals specified in Table 3.1 of this appendix. These data recording intervals must also be followed if conducting a steady-state verification period prior to conducting the standby loss test.
Table 3.1 - Data To Be Recorded Before and During the Steady-State Verification Period and Thermal Efficiency Test
Item recorded | Before steady-state verification period |
Every 1 minute a |
Every 10 minutes |
---|---|---|---|
Gas supply pressure, in w.c. | X | ||
Gas outlet pressure, in w.c. | X | ||
Barometric pressure, in Hg | X | ||
Fuel higher heating value, Btu/ft 3 (gas) or Btu/lb (oil) | X | ||
Oil pump pressure, psig (oil only) | X | ||
CO2 reading, % (oil only) | X b | ||
Oil smoke spot reading (oil only) | X b | ||
Air draft, ft/min | X | ||
Time, minutes/seconds | X | ||
Fuel weight or volume, lb (oil) or ft 3 (gas) | X c | ||
Supply water temperature (TSWT), °F | X | ||
Inlet water temperature (TIWT), °F | X d | ||
Outlet water temperature (TOWT), °F | X | ||
Ambient room temperature, °F | X | ||
Test air temperature, °F | X | ||
Water flow rate, gpm | X |
Notes:
a These measurements are to be recorded at the start and end of both the steady-state verification period and the thermal efficiency test, as well as every minute during both periods.
b The smoke spot test and CO2 reading are not required prior to beginning the steady-state verification period if no settings on the water heater have been changed and the water heater has not been turned off since the end of a previously-run efficiency test (i.e., thermal efficiency or standby loss).
c Fuel and electricity consumption over the course of the entire thermal efficiency test must be measured and used in calculation of thermal efficiency.
d Only measured when a recirculating loop is used.
3.9.2. Standby Loss Test. For the standby loss test, follow the data recording intervals specified in Table 3.2 of this appendix. (Follow the data recording intervals specified in Table 3.1 of this appendix of the steady-state verification period, if conducted prior to the standby loss test.) Additionally, the fuel and electricity consumption over the course of the entire test must be measured and used in calculation of standby loss.
Table 3.2 - Data To Be Recorded Before and During the Standby Loss Test
Item recorded | Before test | Every 1 minute a |
|
---|---|---|---|
Gas supply pressure, in w.c. | X | ||
Gas outlet pressure, in w.c. | X | ||
Barometric pressure, in Hg | X | ||
Fuel higher heating value, Btu/ft 3 (gas) or Btu/lb (oil) | X | ||
Oil pump pressure, psig (oil only) | X | ||
Air draft, ft/min | X | ||
Time, minutes/seconds | X | ||
Heat exchanger outlet water temperature (TOHX), °F | X | ||
Ambient room temperature, °F | X | ||
Test air temperature, °F | X | ||
Water flow rate, gpm | X b | ||
Inlet water temperature (TIWT), °F | X b |
Notes:
a These measurements are to be recorded at the start and end of the test, as well as every minute during the test.
b The water flow rate and supply water temperature and inlet water temperature (if a recirculating loop is used) must be measured during the steady-state verification period at 1-minute intervals. After the steady-state verification period ends, flow rate, supply water temperature, and inlet water temperature (if measured) are not required to be measured during the standby loss test, as there is no flow occurring during the standby loss test.
4. Determination of Storage Volume. Determine the storage volume by subtracting the tare weight, measured while the system is dry and empty, from the weight of the system when filled with water and dividing the resulting net weight of water by the density of water at the measured water temperature. The volume of water contained in the water heater must be computed in gallons.
5. Fuel Input Rate5.1. Determination of Fuel Input Rate. During the steady-state verification period and thermal efficiency test, as applicable, record the fuel consumption at 10-minute intervals. Calculate the fuel input rate for each 10-minute period using the equations in section 5.2 of this appendix. The measured fuel input rates for these 10-minute periods must not vary by more than ± 2 percent between any two readings. Determine the overall fuel input rate using the fuel consumption for the entire duration of the thermal efficiency test.
5.2. Fuel Input Rate Calculation. To calculate the fuel input rate, use the following equation:

6. Thermal Efficiency Test. Before beginning the steady-state verification period, record the applicable parameters as specified in section 3.9.1 of this appendix. Begin drawing water from the unit by opening the main supply and outlet water valve, and adjust the water flow rate to achieve an outlet water temperature of 70 °F ± 2 °F above supply water temperature. The thermal efficiency test shall be deemed complete when there is a continuous, one-hour-long period where the steady-state conditions specified in section 6.1 of this appendix have been met, as confirmed by consecutive readings of the relevant parameters at 1-minute intervals (except for fuel input rate, which is determined at 10-minute intervals, as specified in section 5.1 of this appendix). During the one-hour-long period, the water heater must fire continuously at its full firing rate (i.e., no modulation or cut-outs) and no settings can be changed on the unit being tested at any time. The first 30 minutes of the one-hour-period where the steady-state conditions in section 6.1 of this appendix are met is the steady-state verification period. The final 30 minutes of the one-hour-period where the steady-state conditions in section 6.1 of this appendix are met is the thermal efficiency test. The last reading of the steady-state verification period must be the first reading of the thermal efficiency test (i.e., the thermal efficiency test starts immediately once the steady-state verification period ends).
6.1. Steady-State Conditions. The following conditions must be met at consecutive readings taken at 1-minute intervals (except for fuel input rate, for which measurements are taken at 10-minute intervals) to verify the water heater has achieved steady-state operation during the steady-state verification period and the thermal efficiency test.
6.1.1. The water flow rate must be maintained within ± 0.25 gallons per minute (gpm) of the initial reading at the start of the steady-state verification period.
6.1.2. Outlet water temperature must be maintained at 70 °F ± 2 °F above supply water temperature.
6.1.3. Fuel input rate must be maintained within ± 2 percent of the rated input certified by the manufacturer.
6.1.4. The supply water temperature (TSWT) (or inlet water temperature (TIWT) if a recirculating loop is used) must be maintained within ± 0.50 °F of the initial reading at the start of the steady-state verification period.
6.1.5. The rise between supply (or inlet if a recirculating loop is used) and outlet water temperatures must be maintained within ± 0.50 °F of its initial value taken at the start of the steady-state verification period for units with rated input less than 500,000 Btu/h, and maintained within ± 1.00 °F of its initial value for units with rated input greater than or equal to 500,000 Btu/h.
6.2. Water Flow Measurement. Measure the total weight of water heated during the 30-minute thermal efficiency test with either a scale or a water flow meter. With either method, the error of measurement of weight of water heated must not exceed 1 percent of the weight of the total draw.
6.3. Thermal Efficiency Calculation. Thermal efficiency must be calculated using data from the 30-minute thermal efficiency test. Calculate thermal efficiency, Et, using the following equation:
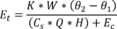
7. Standby Loss Test. If the standby loss test is conducted immediately after a thermal efficiency test and no settings or conditions have been changed since the completion of the thermal efficiency test, then skip to section 7.2 or 7.3 of this appendix (as applicable). Otherwise, perform the steady-state verification in section 7.1 of this appendix. For thermostatically-activated instantaneous water heaters with an internal thermostat, use section 7.2 of this appendix to conduct the standby loss test, and for flow-activated and/or thermostatically-activated instantaneous water heaters with an external thermostat use section 7.3 of this appendix to conduct the standby loss test.
7.1. Steady-State Verification Period. For water heaters where the standby loss test is not conducted immediately following the thermal efficiency test, the steady-state verification period must be conducted before starting the standby loss test. Set the primary control in accordance with section 3.6 of this appendix, such that the primary control is always calling for heat and the water heater is firing continuously at the full firing rate (i.e., no modulation or cut-outs). Begin drawing water from the unit by opening the main supply and the outlet water valve, and adjust the water flow rate to achieve an outlet water temperature of 70 °F ± 2 °F above supply water temperature. The steady-state verification period is complete when there is a continuous 30-minute period where the steady-state conditions specified in section 7.1.1 of this appendix are met, as confirmed by consecutive readings of the relevant parameters recorded at 1-minute intervals (except for fuel input rate, which is determined at 10-minute intervals, as specified in section 5.1 of this appendix).
7.1.1. Steady-State Conditions. The following conditions must be met at consecutive readings taken at 1-minute intervals (except for fuel input rate, for which measurements are taken at 10-minute intervals) to verify the water heater has achieved steady-state operation during the steady-state verification period prior to conducting the standby loss test.
7.1.1.1. The water flow rate must be maintained within ± 0.25 gallons per minute (gpm) of the initial reading at the start of the steady-state verification period;
7.1.1.2. Fuel input rate must be maintained within ± 2 percent of the rated input certified by the manufacturer;
7.1.1.3. The supply water temperature (TSWT) (or inlet water temperature (TIWT) if a recirculating loop is used) must be maintained within ± 0.50 °F of the initial reading at the start of the steady-state verification period; and
7.1.1.4. The rise between the supply (or inlet if a recirculating loop is used) and outlet water temperatures must be maintained within ± 0.50 °F of its initial value taken at the start of the steady-state verification period for units with rated input less than 500,000 Btu/h, and maintained within ± 1.00 °F of its initial value for units with rated input greater than or equal to 500,000 Btu/h.
7.2. Thermostatically-Activated Instantaneous Water Heaters with an Internal Thermostat. For water heaters that will experience cut-in based on a temperature-activated control that is internal to the water heater, use the following steps to conduct the standby loss test.
7.2.1. Immediately after the thermal efficiency test or the steady-state verification period (as applicable), turn off the outlet water valve(s) (installed as per the provisions in section 2.2 of this appendix), and the water pump (if applicable) simultaneously and ensure that there is no flow of water through the water heater.
7.2.2. After the first cut-out following the end of the thermal efficiency test or steady-state verification period (as applicable), allow the water heater to remain in standby mode. Do not change any settings on the water heater at any point until measurements for the standby loss test are finished. Begin recording the applicable parameters specified in section 3.9.2 of this appendix.
7.2.3. At the second cut-out, record the time and ambient room temperature, and begin measuring the fuel and electricity consumption. Record the initial heat exchanger outlet water temperature (TOHX) and initial ambient room temperature. For the remainder of the test, continue recording the applicable parameters specified in section 3.9.2 of this appendix.
7.2.4. Stop the test after the first cut-out that occurs after 24 hours, or at 48 hours, whichever comes first.
7.2.5. Immediately after conclusion of the standby loss test, record the total fuel flow and electrical energy consumption, the final ambient room temperature, the duration of the standby loss test, and if the test ends at 48 hours without a cut-out, the final heat exchanger outlet temperature, or if the test ends after a cut-out, the maximum heat exchanger outlet temperature that occurs after the cut-out. Calculate the average of the recorded values of the heat exchanger outlet water temperature and the ambient room temperature taken at each measurement interval, including the initial and final values.
7.2.6. Standby Loss Calculation. To calculate the standby loss, follow the steps below:
7.2.6.1. The standby loss expressed as a percentage (per hour) of the heat content of the stored water above room temperature must be calculated using the following equation:

7.2.6.2. The standby loss expressed in Btu per hour must be calculated as follows:
SL (Btu per hour) = S (% per hour) × 8.25 (Btu/gal- °F) × Measured Volume (gal) × 70 ( °F).
Where, SL refers to the standby loss of the water heater, defined as the amount of energy required to maintain the stored water temperature expressed in Btu per hour.
7.3. Flow-Activated and Thermostatically-Activated Instantaneous Water Heaters with an External Thermostat. For water heaters that are either flow-activated or thermostatically-activated with an external thermostat, use the following steps to conduct the standby loss test.
7.3.1. Immediately after the thermal efficiency test or the steady-state verification period (as applicable), de-energize the primary control to end the call for heating. If the main burners do not cut out, then turn off the fuel supply.
7.3.1.1. If the unit does not have an integral pump purge functionality, then turn off the outlet water valve and water pump at this time.
7.3.1.2. If the unit has an integral pump purge functionality, allow the pump purge operation to continue. After the pump purge operation is complete, immediately turn off the outlet water valve and water pump and continue recording the required parameters for the remainder of the test.
7.3.2. Recording Data7.3.2.1. For units with pump purge functionality, record the initial heat exchanger outlet water temperature (TOHX), and ambient room temperature when the main burner(s) cut-out or the fuel supply is turned off. After the pump purge operation is complete, record the time as t = 0 and the initial electricity meter reading. Continue to monitor and record the heat exchanger outlet water temperature (TOHX) and time elapsed from the start of the test, and the electricity consumption as per the requirements in section 3.9.2 of this appendix.
7.3.2.2. For units not equipped with pump purge functionality, begin recording the measurements as per the requirements of section 3.9.2 of this appendix when the main burner(s) cut-out or the fuel supply is turned off. Specifically, record the time as t = 0, and record the initial heat exchanger outlet water temperature (TOHX), ambient room temperature, and electricity meter readings. Continue to monitor and record the heat exchanger outlet water temperature (TOHX) and the time elapsed from the start of the test as per the requirements in section 3.9.2 of this appendix.
7.3.3. Stopping Criteria. Stop the test when one of the following occurs:
7.3.3.1. The heat exchanger outlet water temperature (TOHX) decreases by 35 °F from its value recorded immediately after the main burner(s) has cut-out, and the pump purge operation (if applicable) is complete; or
7.3.3.2. 24 hours have elapsed from the start of the test.
7.3.4. At the end of the test, record the final heat exchanger outlet water temperature (TOHX), fuel consumed, electricity consumed from time t=0, and the time elapsed from the start of the test.
7.3.5. Standby Loss Calculation7.3.5.1. Once the test is complete, use the following equation to calculate the standby loss as a percentage (per hour) of the heat content of the stored water above room temperature:
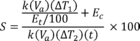
7.3.5.2. The standby loss expressed in terms of Btu per hour must be calculated as follows:
SL (Btu per hour) = S (% per hour) × 8.25 (Btu/gal- °F) × Measured Volume (gal) × 70 ( °F)
Where, SL refers to the standby loss of the water heater, defined as the amount of energy required to maintain the stored water temperature expressed in Btu per hour.
[81 FR 79332, Nov. 10, 2016]Appendix C to Subpart R of Part 431 - Uniform Test Method for the Measurement of Net Capacity and AWEF of Walk-In Cooler and Walk-In Freezer Refrigeration Systems
10:3.0.1.4.19.18.85.7.61 : Appendix C
Appendix C to Subpart R of Part 431 - Uniform Test Method for the Measurement of Net Capacity and AWEF of Walk-In Cooler and Walk-In Freezer Refrigeration Systems 1.0 ScopeThis appendix covers the test requirements used to determine the net capacity and the AWEF of the refrigeration system of a walk-in cooler or walk-in freezer.
2.0 DefinitionsThe definitions contained in § 431.302 and AHRI 1250-2009 (incorporated by reference; see § 431.303) apply to this appendix. When definitions in standards incorporated by reference are in conflict or when they conflict with this section, the hierarchy of precedence shall be in the following order: § 431.302, AHRI 1250-2009, and then either AHRI 420-2008 (incorporated by reference; see § 431.303) for unit coolers or ASHRAE 23.1-2010 (incorporated by reference; see § 431.303) for dedicated condensing units.
3.0 Test Methods, Measurements, and CalculationsDetermine the Annual Walk-in Energy Factor (AWEF) and net capacity of walk-in cooler and walk-in freezer refrigeration systems by conducting the test procedure set forth in AHRI 1250-2009 (incorporated by reference; see § 431.303), with the modifications to that test procedure provided in this section. When standards that are incorporated by reference are in conflict or when they conflict with this section, the hierarchy of precedence shall be in the following order: § 431.302, AHRI 1250-2009, and then either AHRI 420-2008 (incorporated by reference; see § 431.303) or ASHRAE 23.1-2010 (incorporated by reference; see § 431.303).
3.1. General modifications: Test Conditions and Tolerances.
When conducting testing in accordance with AHRI 1250-2009 (incorporated by reference; see § 431.303), the following modifications must be made.
3.1.1. In Table 1, Instrumentation Accuracy, refrigerant temperature measurements shall have a tolerance of ±0.5 F for unit cooler in/out, ±1.0 F for all other temperature measurements.
3.1.2. In Table 2, Test Operating and Test Condition Tolerances for Steady-State Test, electrical power frequency shall have a Test Condition Tolerance of 1 percent.
3.1.3. In Table 2, the Test Operating Tolerances and Test Condition Tolerances for Air Leaving Temperatures shall be deleted.
3.1.4. In Tables 2 through 14, the Test Condition Outdoor Wet Bulb Temperature requirement and its associated tolerance apply only to units with evaporative cooling.
3.1.5. Tables 15 and 16 shall be modified to read as follows:
Table 15 - Refrigerator Unit Cooler
Test description |
Unit cooler air entering dry-bulb, °F |
Unit cooler air entering relative humidity, % |
Saturated suction temp, °F |
Liquid inlet saturation temp, °F | Liquid inlet subcooling temp, °F | Compressor capacity |
Test objective |
---|---|---|---|---|---|---|---|
Off Cycle Fan Power | 35 | <50 | - | - | - | Compressor Off | Measure fan input power during compressor off cycle. |
Refrigeration Capacity Suction A | 35 | <50 | 25 | 105 | 9 | Compressor On | Determine Net Refrigeration Capacity of Unit Cooler. |
Refrigeration Capacity Suction B | 35 | <50 | 20 | 105 | 9 | Compressor On | Determine Net Refrigeration Capacity of Unit Cooler. |
Note: Superheat to be set according to equipment specification in equipment or installation manual. If no superheat specification is given, a default superheat value of 6.5 °F shall be used. The superheat setting used in the test shall be reported as part of the standard rating.
Table 16 - Freezer Unit Cooler
Test description |
Unit cooler air entering dry-bulb, °F |
Unit cooler air entering relative humidity, % |
Saturated suction temp, °F |
Liquid inlet saturation temp, °F | Liquid inlet subcooling temp, °F | Compressor capacity |
Test objective |
---|---|---|---|---|---|---|---|
Off Cycle Fan Power | −10 | <50 | - | - | - | Compressor Off | Measure fan input power during compressor off cycle. |
Refrigeration Capacity Suction A | −10 | <50 | −20 | 105 | 9 | Compressor On | Determine Net Refrigeration Capacity of Unit Cooler. |
Refrigeration Capacity Suction B | −10 | <50 | −26 | 105 | 9 | Compressor On | Determine Net Refrigeration Capacity of Unit Cooler. |
Defrost | −10 | Various | - | - | - | Compressor Off | Test according to Appendix C Section C11. |
Note: Superheat to be set according to equipment specification in equipment or installation manual. If no superheat specification is given, a default superheat value of 6.5 °F shall be used. The superheat setting used in the test shall be reported as part of the standard rating.
When conducting testing in accordance with appendix C of AHRI 1250-2009 (incorporated by reference; see § 431.303), the following modifications must be made.
3.2.1. In appendix C, section C3.1.6, any refrigerant temperature measurements upstream and downstream of the unit cooler may use sheathed sensors immersed in the flowing refrigerant instead of thermometer wells.
3.2.2. It is not necessary to perform composition analysis of refrigerant (appendix C, section C3.3.6) or refrigerant oil concentration testing (appendix C, section C3.4.6).
3.2.3. In appendix C, section C3.4.5, for verification of sub-cooling downstream of mass flow meters, only the sight glass and a temperature sensor located on the tube surface under the insulation are required.
3.2.4. In appendix C, section C3.5, regarding unit cooler fan power measurements, for a given motor winding configuration, the total power input shall be measured at the highest nameplate voltage. For three-phase power, voltage imbalances shall be no more than 2 percent from phase to phase.
3.2.5. In the test setup (appendix C, section C8.3), the liquid line and suction line shall be constructed of pipes of the manufacturer-specified size. The pipe lines shall be insulated with a minimum total thermal resistance equivalent to 1/2-inch thick insulation having a flat-surface R-Value of 3.7 ft 2- °F-hr/Btu per inch or greater. Flow meters need not be insulated but must not be in contact with the floor. The lengths of the connected liquid line and suction line shall be 25 feet ± 3 inches, not including the requisite flow meters, each. Of this length, no more than 15 feet shall be in the conditioned space. Where there are multiple branches of piping, the maximum length of piping applies to each branch individually as opposed to the total length of the piping.
3.3. Matched systems, single-package dedicated systems, and unit coolers tested alone: Use the test method in AHRI 1250-2009 (incorporated by reference; see § 431.303), appendix C as the method of test for matched refrigeration systems, single-package dedicated systems, or unit coolers tested alone, with the following modifications:
3.3.1. For unit coolers tested alone, use test procedures described in AHRI 1250-2009 (incorporated by reference; see § 431.303) for testing unit coolers for use in mix-match system ratings, except that for the test conditions in Tables 15 and 16, use the Suction A saturation condition test points only. Also for unit coolers tested alone, use the calculations in section 7.9 to determine AWEF and net capacity described in AHRI 1250-2009 for unit coolers matched to parallel rack systems.
3.3.2. In appendix C, section C.13, the version of AHRI Standard 420 used for test methods, requirements, and procedures shall be AHRI 420-2008 (incorporated by reference; see § 431.303).
3.3.3. Use appendix C, section C10 of AHRI 1250-2009 for off-cycle evaporator fan testing, with the exception that evaporator fan controls using periodic stir cycles shall be adjusted so that the greater of a 50% duty cycle (rather than a 25% duty cycle) or the manufacturer default is used for measuring off-cycle fan energy. For adjustable-speed controls, the greater of 50% fan speed (rather than 25% fan speed) or the manufacturer's default fan speed shall be used for measuring off-cycle fan energy. Also, a two-speed or multi-speed fan control may be used as the qualifying evaporator fan control. For such a control, a fan speed no less than 50% of the speed used in the maximum capacity tests shall be used for measuring off-cycle fan energy.
3.3.4. Use appendix C, section C11 of AHRI 1250-2009 (incorporated by reference, see § 431.303) for defrost testing. The Frost Load Condition Defrost Test (C11.1.1) is optional.
3.3.4.1. If the frost load condition defrost test is performed:
3.3.4.1.1 Operate the unit cooler at the dry coil conditions as specified in appendix C, section C11.1 to obtain dry coil defrost energy, DFd, in W-h.
3.3.4.1.2 Operate the unit cooler at the frost load conditions as specified in appendix C, sections C11.1 and C11.1.1 to obtain frosted coil defrost energy, DFf, in W-h.
3.3.4.1.3 The number of defrosts per day, NDF, shall be calculated from the time interval between successive defrosts from the start of one defrost to the start of the next defrost at the frost load conditions.
3.3.4.1.4 Use appendix C, equations C13 and C14 in section C11.3 to calculate, respectively, the daily average defrost energy, DF, in W-h and the daily contribution of the load attributed to defrost QDF in Btu.
3.3.4.1.5 The defrost adequacy requirements in appendix C, section C11.3 shall apply.
3.3.4.2 If the frost load test is not performed:
3.3.4.2.1 Operate the unit cooler at the dry coil conditions as specified in appendix C, section C11.1 to obtain dry coil defrost energy, DFd, in W-h.
3.3.4.2.2 The frost load defrost energy, DFf, in W-h shall be equal to 1.05 multiplied by the dry coil energy consumption, DFd, measured using the dry coil condition test in appendix C, section C11.1.
3.3.4.2.3 The number of defrosts per day NDF used in subsequent calculations shall be 4.
3.3.4.2.4 Use appendix C, equation C13 in section C11.3 to calculate the daily average defrost energy, DF, in W-h.
3.3.4.2.5 The daily contribution of the load attributed to defrost QDF in Btu shall be calculated as follows:

3.3.5. If a unit has adaptive defrost, use appendix C, section C11.2 of AHRI 1250-2009 as follows:
3.3.5.1. When testing to certify to the energy conservation standards in § 431.306, do not perform the optional test for adaptive or demand defrost in appendix C, section C11.2.
3.3.5.2. When determining the represented value of the calculated benefit for the inclusion of adaptive defrost, conduct the optional test for adaptive or demand defrost in appendix C, section C11.2 to establish the maximum time interval allowed between dry coil defrosts. If this time is greater than 24 hours, set its value to 24 hours. Then, calculate NDF (the number of defrosts per day) by averaging the time in hours between successive defrosts for the dry coil condition with the time in hours between successive defrosts for the frosted coil condition, and dividing 24 by this average time. (The time between successive defrosts for the frosted coil condition is found as specified in section 3.3.4 of this appendix C of AHRI 1250-2009: That is, if the optional frosted coil test was performed, the time between successive defrosts for the frosted coil condition is found by performing the frosted coil test as specified in section 3.3.4.1 of this appendix; and if the optional frosted coil test was not performed, the time between successive defrosts for the frosted coil condition shall be set to 4 as specified in section 3.3.4.2. of this appendix) Use this new value of NDF in subsequent calculations.
3.3.6. For matched refrigeration systems and single-package dedicated systems, calculate the AWEF using the calculations in AHRI 1250-2009 (incorporated by reference; see § 431.303), section 7.4, 7.5, 7.6, or 7.7, as applicable.
3.3.7. For unit coolers tested alone, calculate the AWEF and net capacity using the calculations in AHRI 1250-2009, (incorporated by reference; see § 431.303), section 7.9. If the unit cooler has variable-speed evaporator fans that vary fan speed in response to load, then:
3.3.7.1. When testing to certify compliance with the energy conservation standards in § 431.306, fans shall operate at full speed during on-cycle operation. Do not conduct the calculations in AHRI 1250-2009, section 7.9.3. Instead, use AHRI 1250-2009, section 7.9.2 to determine the system's AWEF.
3.3.7.2. When calculating the benefit for the inclusion of variable-speed evaporator fans that modulate fan speed in response to load for the purposes of making representations of efficiency, use AHRI 1250-2009, section 7.9.3 to determine the system AWEF.
3.4. Dedicated condensing units that are not matched for testing and are not single-package dedicated systems3.4.1. Refer to appendix C, section C.12 of AHRI 1250-2009 (incorporated by reference; see § 431.303), for the method of test for dedicated condensing units. The version of ASHRAE Standard 23 used for test methods, requirements, and procedures shall be ANSI/ASHRAE Standard 23.1-2010 (incorporated by reference; see § 431.303). When applying this test method, use the applicable test method modifications listed in sections 3.1 and 3.2 of this appendix. For the test conditions in AHRI 1250-2009, Tables 11, 12, 13, and 14, use the Suction A condition test points only.
3.4.2. Calculate the AWEF and net capacity for dedicated condensing units using the calculations in AHRI 1250-2009 (incorporated by reference; see § 431.303) section 7.8. Use the following modifications to the calculations in lieu of unit cooler test data:
3.4.2.1. For calculating enthalpy leaving the unit cooler to calculate gross capacity, (a) The saturated refrigerant temperature (dew point) at the unit cooler coil exit, Tevap, shall be 25 °F for medium-temperature systems (coolers) and −20 °F for low-temperature systems (freezers), and (b) the refrigerant temperature at the unit cooler exit shall be 35 °F for medium-temperature systems (coolers) and −14 °F for low-temperature systems (freezers). For calculating gross capacity, the measured enthalpy at the condensing unit exit shall be used as the enthalpy entering the unit cooler.
3.4.2.2. The on-cycle evaporator fan power in watts, EFcomp,on, shall be calculated as follows:
For medium-temperature systems (coolers), EFcomp,on = 0.013 × qmix,cd
For low-temperature systems (freezers), EFcomp,on = 0.016 × qmix,cd
Where: qmix,cd is the gross cooling capacity of the system in Btu/h, found by a single test at the Capacity A, Suction A condition for outdoor units and the Suction A condition for indoor units.3.4.2.3. The off-cycle evaporator fan power in watts, EFcomp,off, shall be calculated as follows:
EFcomp,off = 0.2 × EFcomp,on
Where: EF comp,on is the on-cycle evaporator fan power in watts.3.4.2.4. The daily defrost energy use in watt-hours, DF, shall be calculated as follows:
For medium-temperature systems (coolers), DF = 0
For low-temperature systems (freezers), DF = 8.5 × 10−3 × qmix,cd 1.27 × NDF
Where: qmix,cd is the gross cooling capacity of the system in Btu/h, found by a single test at the Capacity A, Suction A condition for outdoor units and the Suction A condition for indoor units, and NDF is the number of defrosts per day, equal to 4.3.4.2.5. The daily defrost heat load contribution in Btu, QDF, shall be calculated as follows:
For medium-temperature systems (coolers), QDF = 0
For low-temperature systems (freezers), QDF = 0.95 × DF × 3.412
Where: DF is the daily defrost energy use in watt-hours. 3.5 Hot Gas Defrost Refrigeration SystemsFor all hot gas defrost refrigeration systems, remove the hot gas defrost mechanical components and disconnect all such components from electrical power.
3.5.1 Hot Gas Defrost Dedicated Condensing Units Tested Alone: Test these units as described in section 3.4 of this appendix for electric defrost dedicated condensing units that are not matched for testing and are not single-package dedicated systems.
3.5.2 Hot Gas Defrost Matched Systems, Single-package Dedicated Systems, and Unit Coolers Tested Alone: Test these units as described in section 3.3 of this appendix for electric defrost matched systems, single-package dedicated systems, and unit coolers tested alone, but do not conduct defrost tests as described in sections 3.3.4 and 3.3.5 of this appendix. Calculate daily defrost energy use as described in section 3.4.2.4 of this appendix. Calculate daily defrost heat contribution as described in section 3.4.2.5 of this appendix.
[81 FR 95803, Dec. 28, 2016]Appendix C to Subpart Y of Part 431 - Uniform Test Method for the Measurement of Energy Efficiency of Dedicated-Purpose Pool Pumps
10:3.0.1.4.19.25.89.7.66 : Appendix C
Appendix C to Subpart Y of Part 431 - Uniform Test Method for the Measurement of Energy Efficiency of Dedicated-Purpose Pool Pumps Note:Any representations made on or after July 19, 2021, with respect to the energy use or efficiency of dedicated-purpose pool pumps subject to testing pursuant to 10 CFR 431.464(b) must be made in accordance with the results of testing pursuant to this appendix.
I. Test Procedure for Dedicated-Purpose Pool Pumps A. GeneralA.1 Test Method. To determine the weighted energy factor (WEF) for dedicated-purpose pool pumps, perform “wire-to-water” testing in accordance with HI 40.6-2014-B, except section 40.6.4.1, “Vertically suspended pumps”; section 40.6.4.2, “Submersible pumps”; section 40.6.5.3, “Test report”; section 40.6.5.5, “Test conditions”; section 40.6.5.5.2, “Speed of rotation during testing”; section 40.6.6.1, “Translation of test results to rated speed of rotation”; section 40.6.6.2, “Pump efficiency”; section 40.6.6.3, “Performance curve”; section A.7, “Testing at temperatures exceeding 30 °C (86 °F)”; and appendix B, “Reporting of test results”; (incorporated by reference, see § 431.463) with the modifications and additions as noted throughout the provisions below. Do not use the test points specified in section 40.6.5.5.1, “Test procedure” of HI 40.6-2014-B and instead use those test points specified in section D.3 of this appendix for the applicable dedicated-purpose pool pump variety and speed configuration. When determining overall efficiency, best efficiency point, or other applicable pump energy performance information, section 40.6.5.5.1, “Test procedure”; section 40.6.6.2, “Pump efficiency”; and section 40.6.6.3, “Performance curve” must be used, as applicable. For the purposes of applying this appendix, the term “volume per unit time,” as defined in section 40.6.2, “Terms and definitions,” of HI 40.6-2014-B shall be deemed to be synonymous with the term “flow rate” used throughout that standard and this appendix .
A.2 Calculations and Rounding. All terms and quantities refer to values determined in accordance with the procedures set forth in this appendix for the rated pump. Perform all calculations using raw measured values without rounding. Round WEF, maximum head, vertical lift, and true priming time values to the tenths place (i.e., 0.1) and rated hydraulic horsepower to the thousandths place (i.e., 0.001). Round all other reported values to the hundredths place unless otherwise specified.
B. Measurement EquipmentB.1 For the purposes of measuring flow rate, speed of rotation, temperature, and pump power output, the equipment specified in HI 40.6-2014-B Appendix C (incorporated by reference, see § 431.463) necessary to measure head, speed of rotation, flow rate, and temperature must be used and must comply with the stated accuracy requirements in HI 40.6-2014-B Table 40.6.3.2.3, except as specified in sections B.1.1 and B.1.2 of this appendix. When more than one instrument is used to measure a given parameter, the combined accuracy, calculated as the root sum of squares of individual instrument accuracies, must meet the specified accuracy requirements.
B.1.1 Electrical measurement equipment for determining the driver power input to the motor or controls must be capable of measuring true root mean squared (RMS) current, true RMS voltage, and real power up to the 40th harmonic of fundamental supply source frequency, and have a combined accuracy of ±2.0 percent of the measured value at the fundamental supply source frequency.
B.1.2 Instruments for measuring distance (e.g., height above the reference plane or water level) must be accurate to and have a resolution of at least ±0.1 inch.
B.2 Calibration. Calibration requirements for instrumentation are specified in appendix D of HI 40.6-2014-B (incorporated by reference, see § 431.463). Historical calibration data may be used to justify time periods up to three times longer than those specified in table D.1 of HI 40.6-2014-B provided the supporting historical data shows maintenance of calibration of the given instrument up to the selected extended calibration interval on at least two unique occasions, based on the interval specified in HI 40.6-2014-B.
C. Test Conditions and TolerancesC.1 Pump Specifications. Conduct testing at full impeller diameter in accordance with the test conditions, stabilization requirements, and specifications of HI 40.6-2014-B section 40.6.3, “Pump efficiency testing”; section 40.6.4, “Considerations when determining the efficiency of a pump”; section 40.6.5.4 (including appendix A), “Test arrangements”; and section 40.6.5.5, “Test conditions” (incorporated by reference, see § 431.463).
C.2 Power Supply Requirements. The following conditions also apply to the mains power supplied to the DPPP motor or controls, if any:
(1) Maintain the voltage within ±5 percent of the rated value of the motor,
(2) Maintain the frequency within ±1 percent of the rated value of the motor,
(3) Maintain the voltage unbalance of the power supply within ±3 percent of the value with which the motor was rated, and
(4) Maintain total harmonic distortion below 12 percent throughout the test.
C.3 Test Conditions. Testing must be carried out with water that is between 50 and 107 °F with less than or equal to 15 nephelometric turbidity units (NTU).
C.4 Tolerances. For waterfall pumps, multi-speed self-priming and non-self-priming pool filter pumps, and variable-speed self-priming and non-self-priming pool filter pumps all measured load points must be within ±2.5 percent of the specified head value and comply with any specified flow values or thresholds. For all other dedicated-purpose pool pumps, all measured load points must be within the greater of ±2.5 percent of the specified flow rate values or ±0.5 gpm and comply with any specified head values or thresholds.
D. Data Collection and StabilizationD.1 Damping Devices. Use of damping devices, as described in section 40.6.3.2.2 of HI 40.6-2014-B (incorporated by reference, see § 431.463), are only permitted to integrate up to the data collection interval used during testing.
D.2 Stabilization. Record data at any tested load point only under stabilized conditions, as defined in HI 40.6-2014-B section 40.6.5.5.1 (incorporated by reference, see § 431.463), where a minimum of two measurements are used to determine stabilization.
D.3 Test Points. Measure the flow rate in gpm, pump total head in ft, the driver power input in W, and the speed of rotation in rpm at each load point specified in Table 1 of this appendix for each DPPP variety and speed configuration:
Table 1 - Load Points (i) and Weights (wi) for Each DPPP Variety and Speed Configuration
DPPP varieties | Speed configuration(s) | Number of load
points (n) |
Load point (i) |
Test points | ||
---|---|---|---|---|---|---|
Flow rate (Q) (GPM) |
Head (H) (ft) |
Speed (rpm) |
||||
Self-Priming Pool Filter Pumps And Non-Self-Priming Pool Filter Pumps | Single-speed dedicated-purpose pool pumps and all self-priming and non-self-priming pool filter pumps not meeting the definition of two-*, multi-, or variable-speed dedicated-purpose pool pump | 1 | High | Qhigh (gpm) = Qmax_speed@C ** | H = 0.0082 × Qhigh 2 | Maximum speed. |
Two-speed dedicated-purpose pool pumps * | 2 | Low | Qlow (gpm) = Flow rate
associated with specified head and speed that is not below: • 31.1 gpm if rated hydraulic horsepower is >0.75 or • 24.7 gpm if rated hydraulic horsepower is ≤0.75 |
H = 0.0082 × Qlow 2 | Lowest speed capable of meeting the specified flow and head values, if any. *** | |
High | Qhigh (gpm) = Qmax_speed@C ** | H = 0.0082 × Qlow 2 | Maximum speed. | |||
Multi-speed and variable-speed dedicated-purpose pool pumps | 2 | Low | Qlow (gpm) = • If rated hydraulic horsepower is >0.75, then Qlow ≥31.1 gpm • If rated hydraulic horsepower is ≤0.75, then Qlow ≥24.7 gpm |
H = 0.0082 × Qlow 2 | Lowest speed capable of meeting the specified flow and head values. | |
High | Qhigh (gpm) ≥0.8 × Qmax_speed@C ** | H = 0.0082 × Qhigh 2 | Lowest speed capable of meeting the specified flow and head values. | |||
Waterfall Pumps | Single-speed dedicated-purpose pool pumps | 1 | High | Qlow (gpm) = Flow corresponding to specified head | 17.0 ft | Maximum speed. |
Pressure Cleaner Booster Pumps | Any | 1 | High | 10.0 gpm | ≥60.0 ft | Lowest speed capable of meeting the specified flow and head values. |
* In order to apply the test points for two-speed self-priming and non-self-priming pool filter pumps, self-priming pool filter pumps that are greater than or equal to 0.711 rated hydraulic horsepower that are two-speed dedicated-purpose pool pumps must also be distributed in commerce either: (1) With a pool pump control (variable speed drive and user interface or switch) that changes the speed in response to pre-programmed user preferences and allows the user to select the duration of each speed and/or the on/off times or (2) without a pool pump control that has such capability, but without which the pump is unable to operate. Two-speed self-priming pool filter pumps greater than or equal to 0.711 rated hydraulic horsepower that do not meet these requirements must be tested using the load point for single-speed self-priming or non-self-priming pool filter pumps, as appropriate.
** Qmax_speed@C = Flow at max speed on curve C (gpm).
*** If a two-speed pump has a low speed that results in a flow rate below the specified values, the low speed of that pump shall not be tested.
E.1 Determination of Weighted Energy Factor. Determine the WEF as a ratio of the measured flow and driver power input to the dedicated-purpose pool pump in accordance with the following equation:
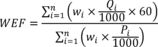
E.2 Weights. When determining WEF, apply the weights specified in Table 2 of this appendix for the applicable load points, DPPP varieties, and speed configurations:
Table 2 - Load Point Weights (wi)
DPPP varieties | Speed configuration(s) | Load point(s) i |
|
---|---|---|---|
Low flow | High flow | ||
Self-Priming Pool Filter Pumps and Non-Self-Priming Pool Filter Pumps | Single-speed dedicated-purpose pool pumps and all self-priming and non-self-priming pool filter pumps not meeting the definition of two-*, multi-, or variable-speed dedicated-purpose pool pump | 1.0 | |
Two-speed dedicated-purpose pool pumps * | 0.80 | 0.20 | |
Multi-speed and variable-speed dedicated-purpose pool pumps | 0.80 | 0.20 | |
Waterfall Pumps | Single-speed dedicated-purpose pool pumps | 1.0 | |
Pressure Cleaner Booster Pump | Any | 1.0 |
* In order to apply the test points for two-speed self-priming and non-self-priming pool filter pumps, self-priming pool filter pumps that are greater than or equal to 0.711 rated hydraulic horsepower that are two-speed dedicated-purpose pool pumps must also be distributed in commerce either: (1) With a pool pump control (variable speed drive and user interface or switch) that changes the speed in response to pre-programmed user preferences and allows the user to select the duration of each speed and/or the on/off times or (2) without a pool pump control that has such capability, but without which the pump is unable to operate. Two-speed self-priming pool filter pumps greater than or equal to 0.711 rated hydraulic horsepower that do not meet these requirements must be tested using the load point for single-speed self-priming or non-self-priming pool filter pumps, as appropriate.
E.3 Determination of Horsepower and True Power Factor Metrics
E.3.1 Determine the pump power output at any load point i using the following equation:

E.3.1.1 Determine the rated hydraulic horsepower as the pump power output measured on the reference curve at maximum rotating speed and full impeller diameter for the rated pump.
E.3.2 For dedicated-purpose pool pumps with single-phase AC motors or DC motors, determine the dedicated-purpose pool pump nominal motor horsepower as the product of the measured full load speed and torque, adjusted to the appropriate units, as shown in the following equation:

Full-load speed and torque shall be determined based on the maximum continuous duty motor power output rating allowable for the motor's nameplate ambient rating and insulation class.
E.3.2.1 For single-phase AC motors, determine the measured speed and torque at full load according to either section E.3.2.1.1 or E.3.2.1.2 of this appendix.
E.3.2.1.1 Use the procedures in section 3.2, “Tests with load”; section 4 “Testing facilities”; section 5.2 “Mechanical measurements”; section 5.3 “Temperature measurements”; and section 6 “Tests” of IEEE 114-2010 (incorporated by reference, see § 431.463), or
E.3.2.1.2 Use the applicable procedures in section 5, “General test requirements” and section 6, “Tests” of CSA C747-2009 (RA 2014); except in section 6.4(b) the conversion factor shall be 5252, only measurements at full load are required in section 6.5, and section 6.6 shall be disregarded (incorporated by reference, see § 431.463).
E.3.2.2 For DC motors, determine the measured speed and torque at full load according to either section E.3.2.2.1 or E.3.2.2.2 of this appendix.
E.3.2.2.1 Use the procedures in section 3.1, “Instrument Selection Factors”; section 3.4 “Power Measurement”: Section 3.5 “Power Sources”; section 4.1.2 “Ambient Air”; section 4.1.4 “Direction of Rotation”; section 5.4.1 “Reference Conditions”; and section 5.4.3.2 “Dynomometer or Torquemeter Method” of IEEE 113-1985 (incorporated by reference, see § 431.463), or
E.3.2.2.2 Use the applicable procedures in section 5, “General test requirements” and section 6, “Tests” of CSA C747-2009 (RA 2014); except in section 6.4(b) the conversion factor shall be 5252, only measurements at full load are required in section 6.5, and section 6.6 shall be disregarded (incorporated by reference, see § 431.463).
E.3.3 For dedicated-purpose pool pumps with single-phase AC motors or DC motors, the dedicated-purpose pool pump service factor is equal to 1.0.
E.3.4 Determine the dedicated-purpose pool pump motor total horsepower according to section E.3.4.1 of this appendix for dedicated-purpose pool pumps with single-phase AC motors or DC motors and section E.3.4.2 of this appendix for dedicated-purpose pool pumps with polyphase AC motors.
E.3.4.1 For dedicated-purpose pool pumps with single-phase AC motors or DC motors, determine the dedicated-purpose pool pump motor total horsepower as the product of the dedicated-purpose pool pump nominal motor horsepower, determined in accordance with section E.3.2 of this appendix, and the dedicated-purpose pool pump service factor, determined in accordance with section E.3.3 of this appendix.
E.3.4.2 For dedicated-purpose pool pumps with polyphase AC induction motors, determine the dedicated-purpose pool pump motor total horsepower as the product of the rated nominal motor horsepower and the rated service factor of the motor.
E.3.5 Determine the true power factor at each applicable load point specified in Table 1 of this appendix for each DPPP variety and speed configuration as a ratio of driver power input to the motor (or controls, if present) (Pi), in watts, divided by the product of the voltage in volts and the current in amps at each load point i, as shown in the following equation:

E.4 Determination of Maximum Head. Determine the maximum head for self-priming pool filter pumps, non-self-priming pool filter pumps, and waterfall pumps by measuring the head at maximum speed and the minimum flow rate at which the pump is designed to operate continuously or safely, where the minimum flow rate is assumed to be zero unless stated otherwise in the manufacturer literature.
F. Determination of Self-Priming CapabilityF.1 Test Method. Determine the vertical lift and true priming time of non-self-priming pool filter pumps and self-priming pool filter pumps that are not already certified as self-priming under NSF/ANSI 50-2015 (incorporated by reference, see § 431.463) by testing such pumps pursuant to section C.3 of appendix C of NSF/ANSI 50-2015, except for the modifications and exceptions listed in the following sections F.1.1 through F.1.5 of this appendix:
F.1.1 Where section C.3.2, “Apparatus,” and section C.3.4, “Self-priming capability test method,” of NSF/ANSI 50-2015 (incorporated by reference, see § 431.463) state that the “suction line must be essentially as shown in annex C, figure C.1;” the phrase “essentially as shown in Annex C, figure C.1” means:
(1) The centerline of the pump impeller shaft is situated a vertical distance equivalent to the specified vertical lift (VL), calculated in accordance with section F.1.1.1. of this appendix, above the water level of a water tank of sufficient volume as to maintain a constant water surface level for the duration of the test;
(2) The pump draws water from the water tank with a riser pipe that extends below the water level a distance of at least 3 times the riser pipe diameter (i.e., 3 pipe diameters);
(3) The suction inlet of the pump is at least 5 pipe diameters from any obstructions, 90° bends, valves, or fittings; and
(4) The riser pipe is of the same pipe diameter as the pump suction inlet.
F.1.1.1 The vertical lift (VL) must be normalized to 5.0 feet at an atmospheric pressure of 14.7 psia and a water density of 62.4 lb/ft 3 in accordance with the following equation:
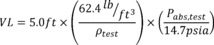
F.1.2 The equipment accuracy requirements specified in section B, “Measurement Equipment,” of this appendix also apply to this section F, as applicable.
F.1.2.1 All measurements of head (gauge pressure), flow, and water temperature must be taken at the pump suction inlet and all head measurements must be normalized back to the centerline of the pump impeller shaft in accordance with section A.3.1.3.1 of HI 40.6-2014-B (incorporated by reference, see § 431.463).
F.1.3 All tests must be conducted with clear water that meets the requirements adopted in section C.3 of this appendix.
F.1.4 In section C.3.4, “Self-priming capability test method,” of NSF/ANSI 50-2015 (incorporated by reference, see § 431.463), “the elapsed time to steady discharge gauge reading or full discharge flow” is determined when the changes in head and flow, respectively, are within the tolerance values specified in table 40.6.3.2.2, “Permissible amplitude of fluctuation as a percentage of mean value of quantity being measured at any test point,” of HI 40.6-2014-B (incorporated by reference, see § 431.463). The measured priming time (MPT) is determined as the point in time when the stabilized load point is first achieved, not when stabilization is determined. In addition, the true priming time (TPT) is equivalent to the MPT.
F.1.5 The maximum true priming time for each test run must not exceed 10.0 minutes. Disregard section C.3.5 of NSF/ANSI 50-2015 (incorporated by reference, see § 431.463).
G. Optional Testing and CalculationsG.1 Replacement Dedicated-Purpose Pool Pump Motors. To determine the WEF for replacement DPPP motors, test each replacement DPPP motor paired with each dedicated-purpose pool pump bare pump for which the replacement DPPP motor is advertised to be paired, as stated in the manufacturer's literature for that replacement DPPP motor model, according to the testing and calculations described in sections A, B, C, D, and E of this appendix. Alternatively, each replacement DPPP motor may be tested with the most consumptive dedicated-purpose pool pump bare pump for which it is advertised to be paired, as stated in the manufacturer's literature for that replacement DPPP motor model. If a replacement DPPP motor is not advertised to be paired with any specific dedicated-purpose pool pump bare pumps, test with the most consumptive dedicated-purpose pool pump bare pump available.
[82 FR 36924, Aug. 7, 2017]