Title 10
PART 431 APPENDIX A
Category | Test procedure | Integrated average temperature |
---|---|---|
(i) Refrigerator with Solid Door(s) | ARI Standard 1200-2006 1 |
38 °F (±2 °F). |
(ii) Refrigerator with Transparent Door(s) | ARI Standard 1200-2006 1 |
38 °F (±2 °F). |
(iii) Freezer with Solid Door(s) | ARI Standard 1200-2006 1 |
0 °F (±2 °F). |
(iv) Freezer with Transparent Door(s) | ARI Standard 1200-2006 1 |
0 °F (±2 °F). |
(v) Refrigerator-Freezer with Solid Door(s) | ARI Standard 1200-2006 1 |
38 °F (±2 °F) for refrigerator compartment. 0 °F (±2 °F) for freezer compartment. |
(vi) Commercial Refrigerator with a Self-Contained Condensing Unit Designed for Pull-Down Temperature Applications and Transparent Doors | ARI Standard 1200-2006 1 |
38 °F (±2 °F). |
(vii) Ice-Cream Freezer | ARI Standard 1200-2006 1 |
−15.0 °F (±2 °F). |
(viii) Commercial Refrigerator, Freezer, and Refrigerator-Freezer with a Self-Contained Condensing Unit and without Doors | ARI Standard 1200-2006 1 |
(A) 0 °F (±2 °F) for low
temperature applications. (B) 38 °F (±2 °F) for medium temperature applications. |
(ix) Commercial Refrigerator, Freezer, and Refrigerator-Freezer with a Remote Condensing Unit | ARI Standard 1200-2006 1 |
(A) 0 °F (±2 °F) for low
temperature applications. (B) 38 °F (±2 °F) for medium temperature applications. |
1 Incorporated by reference, see § 431.63.
2.2. Lowest Application Product Temperature. If a unit of commercial refrigeration equipment is not able to be operated at the integrated average temperature specified in the table in paragraph 2.1, test the unit at the lowest application product temperature (LAPT), as defined in § 431.62. For units equipped with a thermostat, LAPT is the lowest thermostat setting. For remote condensing equipment without a thermostat or other means of controlling temperature at the case, the lowest application product temperature is the temperature achieved with the dew point temperature (as defined in AHRI Standard 1200 (I-P)-2010 (incorporated by reference see § 431.63)) set to 5 degrees colder than that required to maintain the manufacturer's lowest specified operating temperature.
2.3. Testing at NSF Test Conditions. For commercial refrigeration equipment that is also tested in accordance with NSF test procedures (Type I and Type II), integrated average temperatures and ambient conditions used for NSF testing may be used in place of the DOE-prescribed integrated average temperatures and ambient conditions provided they result in a more stringent test. That is, the measured daily energy consumption of the same unit, when tested at the rating temperatures and/or ambient conditions specified in the DOE test procedure, must be lower than or equal to the measured daily energy consumption of the unit when tested with the rating temperatures or ambient conditions used for NSF testing. The integrated average temperature measured during the test may be lower than the range specified by the DOE applicable temperature specification provided in paragraph 2.1 of this appendix, but may not exceed the upper value of the specified range. Ambient temperatures and/or humidity values may be higher than those specified in the DOE test procedure.
3. Volume and Total Display Area3.1. Determination of Volume. Determine the volume of a commercial refrigerator, freezer, refrigerator-freezer, or ice-cream freezer using the method set forth in the ANSI/AHAM HRF-1-2004, “Energy, Performance and Capacity of Household Refrigerators, Refrigerator-Freezers and Freezers” (incorporated by reference, see § 431.63), section 3.21, “Volume,” sections 4.1 through 4.3, “Method for Computing Total Refrigerated Volume and Total Shelf Area of Household Refrigerators and Household Wine Chillers,” and sections 5.1 through 5.3, “Method for Computing Total Refrigerated Volume and Total Shelf Area of Household Freezers.”
3.2. Determination of Total Display Area. Determine the total display area of a commercial refrigerator, freezer, refrigerator-freezer, or ice-cream freezer using the method set forth in ARI Standard 1200-2006 (incorporated by reference, see § 431.63), but disregarding the specification that “transparent material (≥65% light transmittance) in Appendix D. Specifically, total display area shall be the sum of the projected area(s) of visible product, expressed in ft 2 (i.e., portions through which product can be viewed from an angle normal, or perpendicular, to the transparent area). Determine L as the interior length of the CRE model, provided no more than 10 percent of that length consists of non-transparent material. For those cases with greater than 10 percent of non-transparent area, L shall be determined as the projected linear dimension(s) of visible product plus 10 percent of non-transparent area.
See Figures A3.1, A3.2, A3.3, A3.4, and A3.5 as examples of how to calculate the dimensions associated with calculation of total display area. In the diagrams, Dh and L represent the dimensions of the projected visible product.
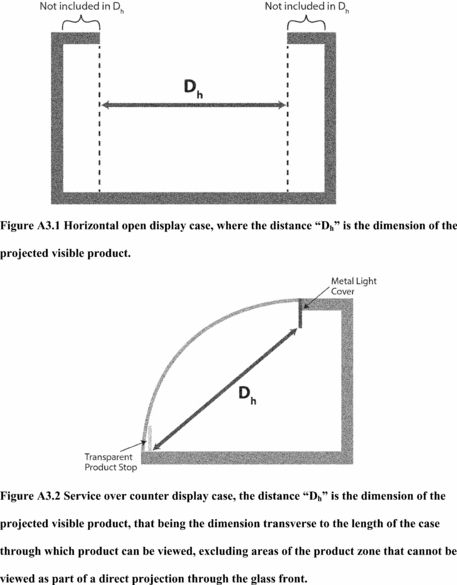
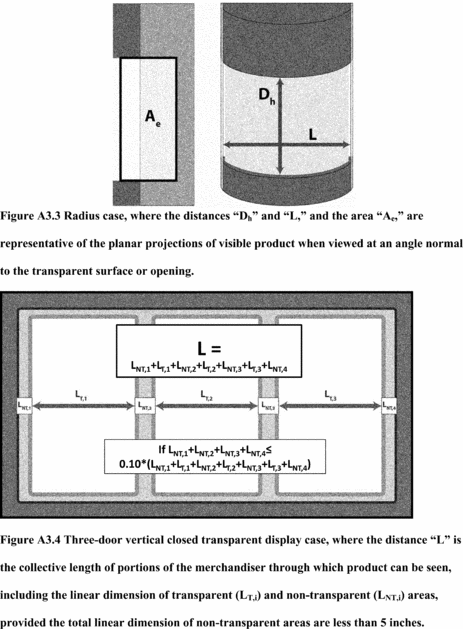
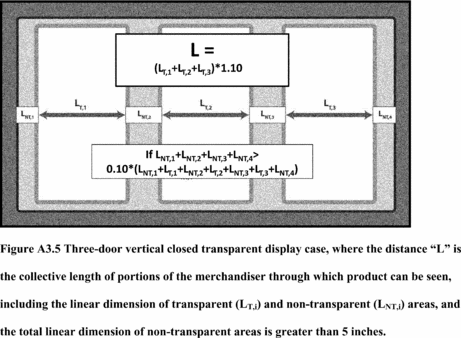
Appendix A to Subpart E of Part 431 - Uniform Test Method for the Measurement of Thermal Efficiency and Combustion Efficiency of Commercial Packaged Boilers
10:3.0.1.4.19.5.60.6.49 : Appendix A
Appendix A to Subpart E of Part 431 - Uniform Test Method for the Measurement of Thermal Efficiency and Combustion Efficiency of Commercial Packaged Boilers Note:Prior to December 4, 2017, manufacturers must make any representations with respect to the energy use or efficiency of commercial packaged boilers in accordance with the results of testing pursuant to this Appendix or the test procedures as they appeared in 10 CFR 431.86 revised as of January 1, 2016. On and after December 4, 2017, manufacturers must make any representations with respect to energy use or efficiency in accordance with the results of testing pursuant to this appendix.
1. Definitions.
For purposes of this appendix, the Department of Energy incorporates by reference the definitions established in section 3 of the American National Standards Institute (ANSI) and Air-Conditioning, Heating, and Refrigeration Institute (AHRI) Standard 1500, “2015 Standard for Performance Rating of Commercial Space Heating Boilers,” beginning with 3.1 and ending with 3.35 (incorporated by reference, see § 431.85; hereafter “ANSI/AHRI Standard 1500-2015”), excluding the introductory text to section 3, the introductory text to section 3.2, “Boiler”; 3.2.4, “Heating Boiler”; 3.2.7, “Packaged Boiler”; 3.6, “Combustion Efficiency”; 3.12, “Efficiency, Combustion”; 3.13, “Efficiency, Thermal”; 3.20, “Gross Output”; 3.23, “Input Rating”; 3.24, “Net Rating”; 3.26, “Published Rating”; 3.26.1, “Standard Rating”; 3.27, “Rating Conditions”; 3.27.1, “Standard Rating Conditions”; and 3.31, “Thermal Efficiency.” In cases where there is a conflict, the language of the test procedure in this appendix takes precedence over ANSI/AHRI Standard 1500-2015.
1.1. In all incorporated sections of ANSI/AHRI Standard 1500-2015, references to the manufacturer's “specifications,” “recommendations,” “directions,” or “requests” mean the manufacturer's instructions in the installation and operation manual shipped with the commercial packaged boiler being tested or in supplemental instructions provided by the manufacturer pursuant to § 429.60(b)(4) of this chapter. For parameters or considerations not specified in this appendix, refer to the manual shipped with the commercial packaged boiler. Should the manual shipped with the commercial packaged boiler not provide the necessary information, refer to the supplemental instructions for the basic model pursuant to § 429.60(b)(4) of this chapter. The supplemental instructions provided pursuant to § 429.60(b)(4) of this chapter do not replace or alter any requirements in this appendix nor do they override the manual shipped with the commercial packaged boiler. In cases where these supplemental instructions conflict with any instructions or provisions provided in the manual shipped with the commercial packaged boiler, use the manual shipped with the commercial packaged boiler.
1.2. Unless otherwise noted, in all incorporated sections of ANSI/AHRI Standard 1500-2015, the term “boiler” means a commercial packaged boiler as defined in § 431.82.
1.3. Unless otherwise noted, in all incorporated sections of ANSI/AHRI Standard 1500-2015, the term “input rating” means “rated input” as defined in § 431.82.
2. Thermal Efficiency Test.
2.1. Test Setup.
2.1.1. Instrumentation. Use instrumentation meeting the minimum requirements found in Table C1 of Appendix C of ANSI/AHRI Standard 1500-2015 (incorporated by reference, see § 431.85).
2.1.2. Data collection and sampling. Record all test data in accordance with Table 2.1 and Table 2.2. Do not use Section C5 and Table C4 of Appendix C of ANSI/AHRI Standard 1500-2015.
Table 2.1 - Data To Be Recorded Before Testing
Item recorded | Additional instruction |
---|---|
Date of Test | None. |
Manufacturer | None. |
Commercial Packaged Boiler Model Number | None. |
Burner Model Number & Manufacturer | None. |
Nozzle description and oil pressure | None. |
Oil Analysis - H, C, API Gravity, lb/gal and Btu/lb | None. |
Gas Manifold Pressure | Record at start and end of test. |
Gas line pressure at meter | Measurement may be made manually. |
Gas temperature | Measurement may be made manually. |
Barometric Pressure (Steam and Natural Gas Only) | Measurement may be made manually. |
Gas Heating Value, Btu/ft 3* | Record at start and end of test. |
* Multiplied by correction factors, as applicable, in accordance with Appendix E of ANSI/AHRI Standard 1500-2015.
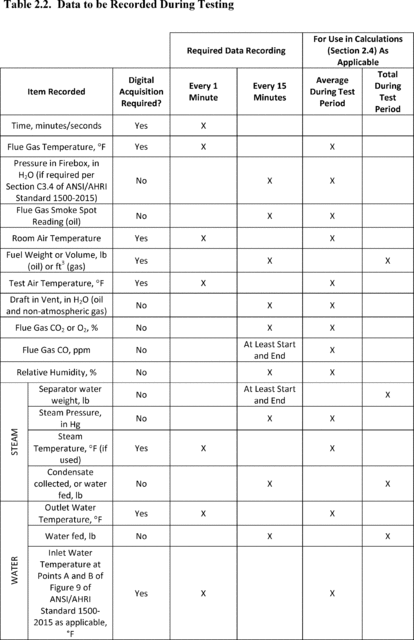
2.1.3. Instrument Calibration. Instruments must be calibrated at least once per year and a calibration record, containing at least the date of calibration and the method of calibration, must be kept as part of the data underlying each basic model certification, pursuant to § 429.71 of this chapter.
2.1.4. Test Setup and Apparatus. Set up the commercial packaged boiler for thermal efficiency testing according to the provisions of Section C2 (except section C2.1) of Appendix C of ANSI/AHRI Standard 1500-2015 (incorporated by reference, see § 431.85).
2.1.4.1. For tests of oil-fired commercial packaged boilers, determine the weight of fuel consumed using one of the methods specified in the following sections 2.1.4.1.1. or 2.1.4.1.2. of this appendix:
2.1.4.1.1. If using a scale, determine the weight of fuel consumed as the difference between the weight of the oil vessel before and after each measurement period, as specified in sections 2.1.4.1.3.1. or 2.1.4.1.3.2. of this appendix, determined using a scale meeting the accuracy requirements of Table C1 of Appendix C of ANSI/AHRI Standard 1500-2015.
2.1.4.1.2. If using a flow meter, first determine the volume of fuel consumed as the total volume over the applicable measurement period as specified in 2.1.4.1.3.1. or 2.1.4.1.3.2. of this appendix and as measured by a flow meter meeting the accuracy requirements of Table C1 of Appendix C of ANSI/AHRI Standard 1500-2015 upstream of the oil inlet port of the commercial packaged boiler. Then determine the weight of fuel consumed by multiplying the total volume of fuel over the applicable measurement period by the density of oil as determined pursuant to C3.2.1.1.3. of Appendix C of ANSI/AHRI Standard 1500-2015.
2.1.4.1.3. The applicable measurement period for the purposes of determining fuel input rate must be as specified in section 2.1.4.1.3.1. of this appendix for the “Warm-Up Period” or section 2.1.4.1.3.2. of this appendix for the “Test Period.”
2.1.4.1.3.1. For the purposes of confirming steady-state operation during the “Warm-Up Period,” the measurement period must be 15 minutes and tT in Equation C2 in Section C7.2.3.1 of Appendix C of ANSI/AHRI Standard 1500-2015 must be 0.25 hours to determine fuel input rate.
2.1.4.1.3.2. For the purposes of determining thermal efficiency during the “Test Period,” the measurement period and tT are as specified in sections 2.3.4 and 2.3.5 of this appendix.
2.1.4.2 For tests of gas-fired commercial packaged boilers, install a volumetric gas meter meeting the accuracy requirements of Table C1 of Appendix C of ANSI/AHRI Standard 1500-2015 upstream of the gas inlet port of the commercial packaged boiler. Record the accumulated gas volume consumed for each applicable measurement period. Use Equation C7.2.3.2. of Appendix C of ANSI/AHRI Standard 1500-2015 to calculate fuel input rate.
2.1.4.2.1. The applicable measurement period for the purposes of determining fuel input rate must be as specified in section 2.1.4.2.1.1. of this appendix for the “Warm-Up Period” and 2.1.4.2.1.2. of this appendix for the “Test Period.”
2.1.4.2.1.1. For the purposes of confirming steady-state operation during the “Warm-Up Period,” the measurement period must be 15 minutes and tT in Equation C2 in Section C7.2.3.1 of Appendix C of ANSI/AHRI Standard 1500-2015 must be 0.25 hours to determine fuel input rate.
2.1.4.2.1.2. For the purposes of determining thermal efficiency during the “Test Period,” the measurement period and tT are as specified in sections 2.3.4 and 2.3.5 of this appendix.
2.1.4.3 In addition to the provisions of Section C2.2.1.2 of ANSI/AHRI Standard 1500-2015, vent gases may alternatively be discharged vertically into a straight stack section without elbows. R-7 minimum insulation must extend 6 stack diameters above the flue collar, the thermocouple grid must be located at a vertical distance of 3 stack diameters above the flue collar, and the sampling tubes for flue gases must be installed within 1 stack diameter beyond the thermocouple grid. If dilution air is introduced into the flue gases before the plane of the thermocouple and flue gas sampling points, utilize an alternate plane of thermocouple grid and flue gas sampling point located downstream from the heat exchanger and upstream from the point of dilution air introduction.
2.1.5. Additional Requirements for Outdoor Commercial Packaged Boilers. If the manufacturer provides more than one outdoor venting arrangement, the outdoor commercial packaged boiler (as defined in Section 3.2.6 of ANSI/AHRI Standard 1500-2015; incorporated by reference, see § 431.85) must be tested with the shortest total venting arrangement as measured by adding the straight lengths of venting supplied with the equipment. If the manufacturer does not provide an outdoor venting arrangement, install the outdoor commercial packaged boiler venting consistent with the procedure specified in Section C2.2 of Appendix C of ANSI/AHRI Standard 1500-2015.
2.1.6. Additional Requirements for Steam Tests. In addition to the provisions of Section C2 of Appendix C of ANSI/AHRI Standard 1500-2015 (incorporated by reference, see § 431.85), the following requirements apply for steam tests.
2.1.6.1. Insulate all steam piping from the commercial packaged boiler to the steam separator, and extend insulation at least one foot (1 ft.) beyond the steam separator, using insulation meeting the requirements specified in Table 2.3 of this appendix.
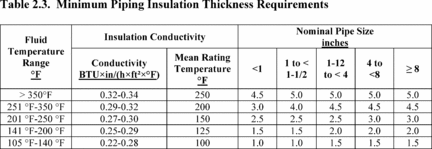
2.1.6.2. A temperature sensing device must be installed in the insulated steam piping prior to the water separator if the commercial packaged boiler produces superheated steam.
2.1.6.3. Water entrained in the steam and water condensing within the steam piping must be collected and used to calculate the quality of steam during the “Test Period.” Steam condensate must be collected and measured using either a cumulative (totalizing) flow rate or by measuring the mass of the steam condensate. Instrumentation used to determine the amount of steam condensate must meet the requirements identified in Table C1 in Appendix C of ANSI/AHRI Standard 1500-2015.
2.1.7. Additional Requirements for Water Tests. In addition to the provisions of section C2 of Appendix C of ANSI/AHRI Standard 1500-2015 (incorporated by reference, see § 431.85), the following requirements apply for water tests.
2.1.7.1. Insulate all water piping between the commercial packaged boiler and the location of the temperature measuring equipment, including one foot (1 ft.) beyond the sensor, using insulation meeting the requirements specified in Table 2.3 of this appendix.
2.1.7.2. Install a temperature measuring device at Point B of Figure C9 of ANSI/AHRI Standard 1500-2015 (incorporated by reference, see § 431.85). Water entering the commercial packaged boiler must first enter the run of a tee and exit from the top outlet of the tee. The remaining connection of the tee must be plugged. Measure the inlet water temperature at Point B in the run of a second tee located 12 ± 2 pipe diameters downstream from the first tee and no more than the greater of 12 inches or 6 pipe diameters from the inlet of the commercial packaged boiler. The temperature measuring device shall extend into the water flow at the point of exit from the side outlet of the second tee. All inlet piping between the temperature measuring device and the inlet of the commercial packaged boilers must be wrapped with R-7 insulation.
2.1.7.3. Do not use Section C2.7.2.2.2 or its subsections of ANSI/AHRI Standard 1500-2015 for water meter calibration.
2.1.8. Flue Gas Sampling. In section C2.5.2 of Appendix C of ANSI/AHRI Standard 1500-2015, replace the last sentence with the following: When taking flue gas samples from a rectangular plane, collect samples at 1/4, 1/2, and 3/4 the distance from one side of the rectangular plane in the longer dimension and along the centerline midway between the edges of the plane in the shorter dimension and use the average of the three samples. The tolerance in each dimension for each measurement location is ± 1 inch.
2.2. Test Conditions.
2.2.1. General. Use the test conditions from Section 5 and Section C3 of Appendix C of ANSI/AHRI Standard 1500-2015 (incorporated by reference, see § 431.85) for thermal efficiency testing but do not use the following sections:
(1) 5.3 Introductory text (2) 5.3.5 (and subsections; see sections 2.2.3. and 2.2.4. of this appendix) (3) 5.3.8 (see section 2.2.5. of this appendix) (4) 5.3.9 (see section 2.2.6. of this appendix) (5) C3.1.3 (and subsections) (6) C3.5 (including Table C2; see section 2.2.7. of this appendix) (7) C3.6 (see section 2.2.5. of this appendix) (8) C3.7 (see section 2.2.6. of this appendix)2.2.2. Burners for Oil-Fired Commercial Packaged Boilers. In addition to section C3.3 of Appendix C of ANSI/AHRI Standard 1500-2015, the following applies: For oil-fired commercial packaged boilers, test the unit with the particular make and model of burner as certified (or to be certified) by the manufacturer. If multiple burners are specified in the certification report for that basic model, then use any of the listed burners for testing.
2.2.3. Water Temperatures. Maintain the outlet temperature measured at Point C in Figure C9 of Appendix C of ANSI/AHRI Standard 1500-2015 at 180 °F ± 2 °F and maintain the inlet temperature measured at Point B at 80 °F ± 5 °F during the “Warm-up Period” and “Test Period” as indicated by 1-minute interval data pursuant to Table 2.2 of this appendix. Each reading must meet these temperature requirements. Use the inlet temperature and flow rate measured at Point B in Figure C9 of Appendix C of ANSI/AHRI Standard 1500-2015 for calculation of thermal efficiency.
2.2.4 Exceptions to Water Temperature Requirements. For commercial packaged boilers that require a higher flow rate than that resulting from the water temperature requirements of sections 2.2.3 of this appendix to prevent boiling, use a recirculating loop and maintain the inlet temperature at Point B of Figure C9 of Appendix C of ANSI/AHRI Standard 1500-2015 at 140 °F ± 5 °F during the “Warm-up Period” and “Test Period” as indicated by 1-minute interval data pursuant to Table 2.2 of this appendix. Each reading must meet these temperature requirements. Use the inlet temperature and flow rate measured at Point A in Figure C9 of Appendix C of ANSI/AHRI Standard 1500-2015 for calculation of thermal efficiency.
2.2.5 Air Temperature. For tests of non-condensing boilers, maintain ambient room temperature between 65 °F and 100 °F at all times during the “Warm-up Period” and “Test Period” (as described in Section C4 of Appendix C of ANSI/AHRI Standard 1500-2015) as indicated by 1-minute interval data pursuant to Table 2.2 of this appendix. For tests of condensing boilers, maintain ambient room temperature between 65 °F and 85 °F at all times during the “Warm-up Period” and “Test Period” (as described in Section C4 of Appendix C of ANSI/AHRI Standard 1500-2015) as indicated by 1-minute interval data pursuant to Table 2.2 of this appendix. The ambient room temperature may not differ by more than ± 5 °F from the average ambient room temperature during the entire “Test Period” at any reading. Measure the room ambient temperature within 6 feet of the front of the unit at mid height. The test air temperature, measured at the air inlet of the commercial packaged boiler, must be within ± 5 °F of the room ambient temperature when recorded at the 1-minute interval defined by Table 2.2 of this appendix.
2.2.6. Ambient Humidity. For condensing boilers, maintain ambient room relative humidity below 80-percent at all times during both the “Warm-up Period” and “Test Period” (as described in Section C4 of Appendix C of ANSI/AHRI Standard 1500-2015) pursuant to Table 2.2 of this appendix. Measure the ambient humidity in the same location as ambient air temperature in section 2.2.5 of this appendix.
2.2.7. Flue Gas Temperature. The flue gas temperature during the test must not vary from the flue gas temperature measured at the start of the Test Period (as defined in Section C4 of ANSI/AHRI Standard 1500-2015) when recorded at the interval defined in Table 2.2 of this appendix by more than the limits prescribed in Table 2.4 of this appendix.
Table 2.4 - Flue Gas Temperature Variation Limits During Test Period
Fuel type | Non-condensing | Condensing |
---|---|---|
Gas | ± 2 percent | Greater of ± 3 percent and ± 5 °F |
Light Oil | ± 2 percent | |
Heavy Oil | Greater of ± 3 percent and ± 5 °F |
2.3. Test Method.
2.3.1. General. Conduct the thermal efficiency test as prescribed in Section C4 “Test Procedure” of Appendix C of ANSI/AHRI Standard 1500-2015 (incorporated by reference, see § 431.85) excluding sections:
(1) C4.1.1.1.2 (see section 2.3.1.1 of this appendix) (2) C4.1.1.2.3 (see 2.3.4 of this appendix) (3) C4.1.2.1.5 (see section 2.3.2. of this appendix) (4) C4.1.2.2.2 (5) C4.1.2.2.3 (see 2.3.5 of this appendix) (6) C4.2 (7) C4.2.1 (8) C4.2.22.3.1.1. Adjust oil or non-atmospheric gas to produce the required firebox pressure and CO2 or O2 concentration in the flue gas, as described in Section 5.3.1 of ANSI/AHRI Standard 1500-2015. Conduct steam tests with steam pressure at the pressure specified in the manufacturer literature shipped with the commercial packaged boiler or in the manufacturer's supplemental testing instructions pursuant to § 429.60(b)(4) of this chapter, but not exceeding 15 psig. If no pressure is specified in the manufacturer literature shipped with the commercial packaged boiler or in the manufacturer's supplemental testing instructions (pursuant to § 429.60(b)(4) of this chapter), or if a range of operating pressures is specified, conduct testing at a steam pressure equal to atmospheric pressure. If necessary to maintain steam quality as required by Section 5.3.7 of ANSI/AHRI Standard 1500-2015, increase steam pressure in 1 psig increments by throttling with a valve beyond the separator until the test is completed and the steam quality requirements have been satisfied, but do not increase the steam pressure to greater than 15 psig.
2.3.2. Water Test Steady-State. Ensure that a steady-state is reached by confirming that three consecutive readings have been recorded at 15-minute intervals pursuant to Table 2.2 of this appendix that indicate that the measured fuel input rate is within ± 2-percent of the rated input. Water temperatures must meet the conditions specified in sections 2.2.3 and 2.2.4 of this appendix as applicable.
2.3.3. Condensate Collection for Condensing Commercial Packaged Boilers. Collect condensate in a covered vessel so as to prevent evaporation.
2.3.4. Steam Test Duration. Replace Section C4.1.1.2.3 of ANSI/AHRI Standard 1500-2015 with the following: The test period is one hour in duration if the steam condensate is measured or two hours if feedwater is measured. The test period must end with a 15-minute reading (steam condensate or feedwater and separator weight reading) pursuant to Table 2.2 of this appendix. When feedwater is measured, the water line at the end of the test must be within 0.25 inches of the starting level.
2.3.5. Water Test Duration. Replace Section C4.1.2.2.3 of ANSI/AHRI Standard 1500-2015 with the following: The test period is one hour for condensing commercial packaged boilers and 30 minutes for non-condensing commercial packaged boilers, and ends with a 15-minute interval reading pursuant to Table 2.2 of this appendix.
2.4. Calculations.
2.4.1. General. To determine the thermal efficiency of commercial packaged boilers, use the variables in section C6 of Appendix C of ANSI/AHRI Standard 1500-2015 and calculation procedure for the thermal efficiency test specified in section C7.2 of Appendix C of ANSI/AHRI Standard 1500-2015, excluding sections C7.2.12 and C7.2.20.
2.4.2. Use of Steam Properties Table. If the average measured temperature of the steam is higher than the value in Table D1 in Appendix D of ANSI/AHRI Standard 1500-2015 that corresponds to the average measured steam pressure, then use Table 2.5 of this appendix to determine the latent heat of superheated steam in (Btu/lb). Use linear interpolation for determining the latent heat of steam in Btu/lb if the measured steam pressure is between two values listed in Table D1 in Appendix D of ANSI/AHRI Standard 1500-2015 or in Table 2.5 of this appendix.
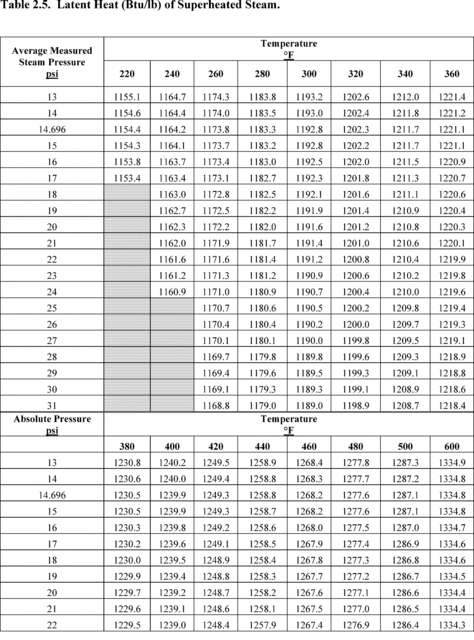
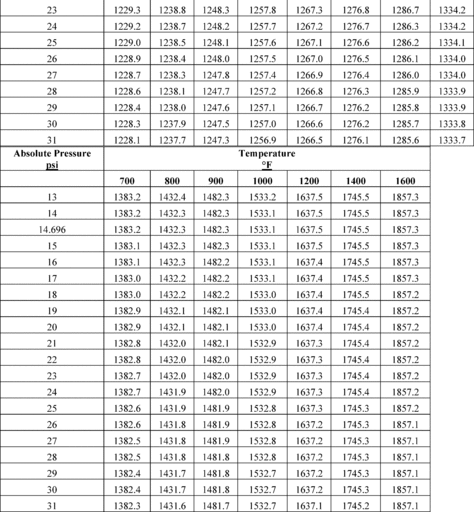
2.4.3. Alternative Thermal Efficiency Calculation for Large Steam Commercial Packaged Boilers. To determine the thermal efficiency of commercial packaged boilers with a fuel input rate greater than 5,000,000 Btu/h according to the steam test pursuant to Section C4.1.1 of ANSI/AHRI Standard 1500-2015, either:
2.4.3.1. Calculate the thermal efficiency of commercial packaged boiler models in steam mode in accordance with the provisions of section 2.4.1 of this appendix, or
2.4.3.2. Measure and calculate combustion efficiency Effyss in steam mode according to Section 3. Combustion Efficiency Test of this appendix and convert to thermal efficiency using the following equation:
EffyT = Effyss − 2.0 where EffyT is the thermal efficiency and EFFYss is the combustion efficiency as defined in C6 of ANSI/AHRI Standard 1500-2015. The combustion efficiency Effyss is as calculated in Section C7.2.14 of ANSI/AHRI Standard 1500-2015.2.4.4. Rounding. Round the final thermal efficiency value to nearest one tenth of one percent.
3. Combustion Efficiency Test.
3.1. Test Setup.
3.1.1. Instrumentation. Use instrumentation meeting the minimum requirements found in Table C1 of ANSI/AHRI Standard 1500-2015 (incorporated by reference, see § 431.85).
3.1.2. Data collection and sampling. Record all test data in accordance with Table 3.1 and Table 3.2 of this appendix. Do not use Section C5 and Table C4 of Appendix C in ANSI/AHRI Standard 1500-2015.
Table 3.1 - Data To Be Recorded Before Testing
Item recorded | Additional instruction |
---|---|
Date of Test | None. |
Manufacturer | None. |
Commercial Packaged Boiler Model Number | None. |
Burner Model Number & Manufacturer | None. |
Nozzle description and oil pressure | None. |
Oil Analysis - H, C, API Gravity, lb/gal and Btu/lb | None. |
Gas Manifold Pressure | Record at start and end of test. |
Gas line pressure at meter | Measurement may be made manually. |
Gas temperature | Measurement may be made manually. |
Barometric Pressure (Steam and Natural Gas Only) | Measurement may be made manually. |
Gas Heating Value, Btu/ft 3 * | Record at start and end of test. |
* Multiplied by correction factors, as applicable, in accordance with Appendix E of ANSI/AHRI Standard 1500-2015.
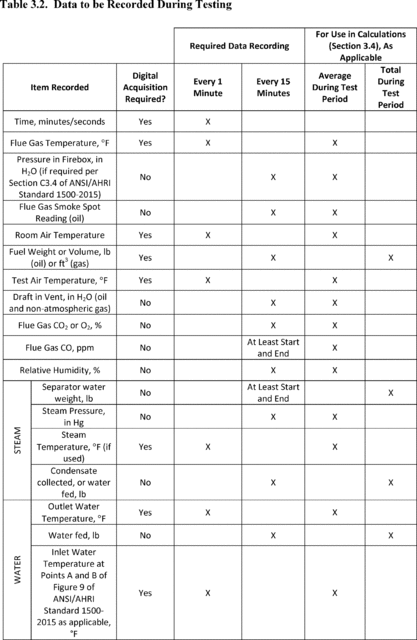
3.1.3. Instrument Calibration. Instruments must be calibrated at least once per year and a calibration record, containing at least the date of calibration and the method of calibration, must be kept as part of the data underlying each basic model certification, pursuant to § 429.71 of this chapter.
3.1.4. Test Setup and Apparatus. Set up the commercial packaged boiler for combustion efficiency testing according to the provisions of Section C2 (except section C2.1) of Appendix C of ANSI/AHRI Standard 1500-2015.
3.1.4.1. For tests of oil-fired commercial packaged boilers, determine the weight of fuel consumed using one of the methods specified in sections 3.1.4.1.1. or 3.1.4.1.2. of this appendix:
3.1.4.1.1. If using a scale, determine the weight of fuel consumed as the difference between the weight of the oil vessel before and after each measurement period, as specified in sections 3.1.4.1.3.1. or 3.1.4.1.3.2. of this appendix, determined using a scale meeting the accuracy requirements of Table C1 of ANSI/AHRI Standard 1500-2015.
3.1.4.1.2. If using a flow meter, first determine the volume of fuel consumed as the total volume over the applicable measurement period, as specified in sections 3.1.4.1.3.1. or 3.1.4.1.3.2. of this appendix, and as measured by a flow meter meeting the accuracy requirements of Table C1 of ANSI/AHRI Standard 1500-2015 upstream of the oil inlet port of the commercial packaged boiler. Then determine the weight of fuel consumed by multiplying the total volume of fuel over the applicable measurement period by the density of oil, in pounds per gallon, as determined pursuant to Section C3.2.1.1.3. of ANSI/AHRI Standard 1500-2015.
3.1.4.1.3. The applicable measurement period for the purposes of determining fuel input rate must be as specified in section 3.1.4.1.3.1. of this appendix for the “Warm-Up Period” or 3.1.4.1.3.2. of this appendix for the “Test Period.”
3.1.4.1.3.1. For the purposes of confirming steady-state operation during the “Warm-Up Period,” the measurement period must be 15 minutes and tT in Equation C2 in Section C7.2.3.1 of ANSI/AHRI Standard 1500-2015 must be 0.25 hours to determine fuel input rate.
3.1.4.1.3.2. For the purposes of determining combustion efficiency during the “Test Period,” the measurement period and tT are 0.5 hours pursuant to section 3.3.1.1. of this appendix.
3.1.4.2 For tests of gas-fired commercial packaged boilers, install a volumetric gas meter meeting the accuracy requirements of Table C1 of ANSI/AHRI Standard 1500-2015 upstream of the gas inlet port of the commercial packaged boiler. Record the accumulated gas volume consumed for each applicable measurement period. Use Equation C7.2.3.2. of ANSI/AHRI Standard 1500-2015 to calculate fuel input rate.
3.1.4.2.1. The applicable measurement period for the purposes of determining fuel input rate must be as specified in section 3.1.4.2.1.1. of this appendix for the “Warm-Up Period” and 3.1.4.2.1.2. of this appendix for the “Test Period.”
3.1.4.2.1.1. For the purposes of confirming steady-state operation during the “Warm-Up Period,” the measurement period must be 15 minutes and tT in Equation C2 in Section C7.2.3.1 of ANSI/AHRI Standard 1500-2015 must be 0.25 hour to determine fuel input rate.
3.1.4.2.1.2. For the purposes of determining combustion efficiency during the “Test Period,” the measurement period and tT are 0.5 hour pursuant to section 3.3.1.1. of this appendix.
3.1.4.3. In addition to the provisions of Section C2.2.1.2 of ANSI/AHRI Standard 1500-2015, vent gases may alternatively be discharged vertically into a straight stack section without elbows. R-7 minimum insulation must extend 6 stack diameters above the flue collar, the thermocouple grid must be located at a vertical distance of 3 stack diameters above the flue collar, and the sampling tubes for flue gases must be installed within 1 stack diameter beyond the thermocouple grid. If dilution air is introduced into the flue gases before the plane of the thermocouple and flue gas sampling points, utilize an alternate plane of thermocouple grid and flue gas sampling point located downstream from the heat exchanger and upstream from the point of dilution air introduction.
3.1.5. Additional Requirements for Outdoor Commercial Packaged Boilers. If the manufacturer provides more than one outdoor venting arrangement, the outdoor commercial packaged boiler (as defined in section 3.2.6 of ANSI/AHRI Standard 1500-2015 (incorporated by reference, see § 431.85) must be tested with the shortest total venting arrangement as measured by adding the straight lengths of venting supplied with the equipment. If the manufacturer does not provide an outdoor venting arrangement, install the outdoor commercial packaged boiler venting consistent with the procedure specified in Section C2.2 of Appendix C of ANSI/AHRI Standard 1500-2015.
3.1.6. Additional Requirements for Field Tests.
3.1.6.1 Field tests are exempt from the requirements of Section C2.2 of Appendix C of ANSI/AHRI Standard 1500-2015. Measure the flue gas temperature according to Section C2.5.1 of Appendix C of ANSI/AHRI Standard 1500-2015 and the thermocouple grids identified in Figure C12 of ANSI/AHRI Standard 1500-2015, with the following modification: the thermocouple grid may be staggered vertically by up to 1.5 inches to allow the use of instrumented rods to be inserted through holes drilled in the venting.
3.1.6.2. Field tests are exempt from the requirements of Section C2.6.3 of Appendix C of ANSI/AHRI Standard 1500-2015.
3.1.7. Additional Requirements for Water Tests. In addition to the provisions of Section C2 of Appendix C of ANSI/AHRI Standard 1500-2015 (incorporated by reference, see § 431.85) the following requirements apply for water tests:
3.1.7.1. Insulate all water piping between the commercial packaged boiler and the location of the temperature measuring equipment, including one foot (1 ft.) beyond the sensor, using insulation meeting the requirements specified in Table 2.3 of this appendix.
3.1.7.2. Install a temperature measuring device at Point B of Figure C9 of ANSI/AHRI Standard 1500-2015. Water entering the commercial packaged boiler must first enter the run of a tee and exit from the top outlet of the tee. The remaining connection of the tee must be plugged. Measure the inlet water temperature at Point B in the run of a second tee located 12 ± 2 pipe diameters downstream from the first tee and no more than the greater of 12 inches or 6 pipe diameters from the inlet of the commercial packaged boiler. The temperature measuring device shall extend into the water flow at the point of exit from the side outlet of the second tee. All inlet piping between the temperature measuring device and the inlet of the commercial packaged boilers must be wrapped with R-7 insulation. Field tests must also measure the inlet water temperature at Point B in Figure C9, however they are not required to use the temperature measurement piping described in this section 3.1.7. of this appendix.
3.1.7.3. Do not use Section C2.7.2.2.2 or its subsections of ANSI/AHRI Standard 1500-2015 for water meter calibration.
3.1.8. Flue Gas Sampling. In section C2.5.2 of Appendix C of ANSI/AHRI Standard 1500-2015, replace the last sentence with the following: When taking flue gas samples from a rectangular plane, collect samples at 1/4, 1/2, and 3/4 the distance from one side of the rectangular plane in the longer dimension and along the centerline midway between the edges of the plane in the shorter dimension and use the average of the three samples. The tolerance in each dimension for each measurement location is ± 1 inch.
3.2. Test Conditions.
3.2.1. General. Use the test conditions from Sections 5 and C3 of Appendix C of ANSI/AHRI Standard 1500-2015 (incorporated by reference; see § 431.85) for combustion efficiency testing but do not use the following sections:
(1) 5.3 Introductory text (2) 5.3.5 (and subsections; see sections 3.2.3, 3.2.3.1, and 3.2.3.2 of this appendix) (3) 5.3.7 (excluded for field tests only) (4) 5.3.8 (see section 3.2.4 of this appendix) (5) 5.3.9 (see section 3.2.5 of this appendix) (6) C3.1.3 (and subsections) (7) C3.5 (including Table C2; see section 3.2.6 of this appendix) (8) C3.6 (see section 3.2.4 of this appendix) (9) C3.7 (see section 3.2.5 of this appendix)3.2.2. Burners for Oil-Fired Commercial Packaged Boilers. In addition to Section C3.3 of Appendix C of ANSI/AHRI Standard 1500-2015, the following applies: for oil-fired commercial packaged boilers, test the unit with the particular make and model of burner as certified (or to be certified) by the manufacturer. If multiple burners are specified in the certification report for that basic model, then use any of the listed burners for testing.
3.2.3. Water Temperatures. Maintain the outlet temperature measured at Point C in Figure C9 at 180 °F ± 2 °F and maintain the inlet temperature measured at Point B at 80 °F ± 5 °F during the “Warm-up Period” and “Test Period” as indicated by 1-minute interval data pursuant to Table 3.2 of this appendix. Each reading must meet these temperature requirements. Field tests are exempt from this requirement and instead must comply with the requirements of section 3.2.3.1 of this appendix.
3.2.3.1. For field tests, the inlet temperature measured at Point A and Point B in Figure C9 and the outlet temperature measured and Point C in Figure C9 of ANSI/AHRI Standard 1500-2015 must be recorded in the data underlying that model's certification pursuant to § 429.71 of this chapter, and the difference between the inlet (measured at Point B) and outlet temperature (measured at Point C) must not be less than 20 °F at any point during the “Warm-up Period” and “Test Period,” after stabilization has been achieved, as indicated by 1-minute interval data pursuant to Table 3.2 of this appendix.
3.2.3.2 For commercial packaged boilers that require a higher flow rate than that resulting from the water temperature requirements of sections 3.2.3 of this appendix to prevent boiling, use a recirculating loop and maintain the inlet temperature at Point B of Figure C9 of ANSI/AHRI Standard 1500-2015 at 140 °F ± 5 °F during the “Warm-up Period” and “Test Period” as indicated by 1-minute interval data pursuant to Table 3.2 of this appendix. Each reading must meet these temperature requirements.
3.2.4. Air Temperature. For tests of non-condensing boilers (except during field tests), maintain ambient room temperature between 65 °F and 100 °F at all times during the “Warm-up Period” and “Test Period” (as described in Section C4 of Appendix C of ANSI/AHRI Standard 1500-2015) as indicated by 1-minute interval data pursuant to Table 3.2 of this appendix. For tests of condensing boilers (except during field tests), maintain ambient room temperature between 65 °F and 85 °F at all times during the “Warm-up Period” and “Test Period” (as described in Section C4 of Appendix C of ANSI/AHRI Standard 1500-2015) as indicated by 1-minute interval data pursuant to Table 3.2 of this appendix. The ambient room temperature may not differ by more than ± 5 °F from the average ambient room temperature during the entire “Test Period” at any 1-minute interval reading. Measure the room ambient temperature within 6 feet of the front of the unit at mid height. The test air temperature, measured at the air inlet of the commercial packaged boiler, must be within ± 5 °F of the room ambient temperature when recorded at the 1-minute interval defined by Table 3.2 of this appendix. For field tests, record the ambient room temperature at 1-minute intervals in accordance with Table 3.2 of this appendix.
3.2.5. Ambient Humidity. For condensing boilers (except during field tests), maintain ambient room relative humidity below 80-percent relative humidity at all times during both the “Warm-up Period” and “Test Period” (as described in Section C4 of Appendix C of ANSI/AHRI Standard 1500-2015) pursuant to Table 3.2 of this appendix. Measure the ambient humidity in the same location as ambient air temperature. For field tests of condensing boilers, record the ambient room relative humidity in accordance with Table 3.2 of this appendix.
3.2.6. Flue Gas Temperature. The flue gas temperature during the test must not vary from the flue gas temperature measured at the start of the Test Period (as defined in Section C4 of ANSI/AHRI Standard 1500-2015) when recorded at the interval defined in Table 3.2 by more than the limits prescribed in Table 3.3 of this appendix. For field tests, flue gas temperature does not need to be within the limits in Table 3.3 of this appendix but must be recorded at the interval specified in Table 3.2 of this appendix.
Table 3.3 - Flue Gas Temperature Variation Limits During Test Period
Fuel type | Non-condensing | Condensing |
---|---|---|
Gas | ± 2 percent | Greater of ± 3 percent and ± 5 °F. |
Light Oil | ± 2 percent | |
Heavy Oil | Greater of ± 3 percent and ± 5 °F |
3.3. Test Method.
3.3.1. General. Conduct the combustion efficiency test using the test method prescribed in Section C4 “Test Procedure” of Appendix C of ANSI/AHRI Standard 1500-2015 excluding sections:
(1) C4.1.1.1.2 (see section 3.3.1.2 of this appendix) (2) C4.1.1.2.3 (3) C4.1.2.1.5 (see section 3.3.2 of this appendix) (4) C4.1.2.2.2 (5) C4.1.2.2.3 (6) C4.2 (7) C4.2.1 (8) C4.2.23.3.1.1. The duration of the “Test Period” for combustion efficiency outlined in sections C4.1.1.2 of Appendix C of ANSI/AHRI Standard 1500-2015 (incorporated by reference, see § 431.85) and C4.1.2.2 of Appendix C of ANSI/AHRI Standard 1500-2015 is 30 minutes. For condensing commercial packaged boilers, condensate must be collected for the 30 minute Test Period.
3.3.1.2. Adjust oil or non-atmospheric gas to produce the required firebox pressure and CO2 or O2 concentration in the flue gas, as described in section 5.3.1 of ANSI/AHRI Standard 1500-2015. Conduct steam tests with steam pressure at the pressure specified in the manufacturer literature shipped with the commercial packaged boiler or in the manufacturer's supplemental testing instructions pursuant to § 429.60(b)(4) of this chapter, but not exceeding 15 psig. If no pressure is specified in the manufacturer literature shipped with the commercial packaged boiler or in the manufacturer's supplemental testing instructions (pursuant to § 429.60(b)(4)) of this chapter, or if a range of operating pressures is specified, conduct testing at a steam pressure equal to atmospheric pressure. If necessary to maintain steam quality as required by section 5.3.7 of ANSI/AHRI Standard 1500-2015, increase steam pressure in 1 psig increments by throttling with a valve beyond the separator until the test is completed and the steam quality requirements have been satisfied, but do not increase the steam pressure to greater than 15 psig.
3.3.2. Water Test Steady-State. Ensure that a steady-state is reached by confirming that three consecutive readings have been recorded at 15-minute intervals that indicate that the measured fuel input rate is within ± 2-percent of the rated input. Water temperatures must meet the conditions specified in sections 3.2.3, 3.2.3.1, and 3.2.3.2 of this appendix as applicable.
3.3.3. Procedure for the Measurement of Condensate for a Condensing Commercial Packaged Boiler. Collect flue condensate using a covered vessel so as to prevent evaporation. Measure the condensate from the flue gas during the “Test Period.” Flue condensate mass must be measured within 5 minutes after the end of the “Test Period” (defined in C4.1.1.2 and C4.1.2.2 of ANSI/AHRI Standard 1500-2015) to prevent evaporation loss from the sample. Determine the mass of flue condensate for the “Test Period” by subtracting the tare container weight from the total weight of the container and flue condensate measured at the end of the ”Warm-up Period.”
3.4. Calculations.
3.4.1. General. To determine the combustion efficiency of commercial packaged boilers, use the variables in Section C6 and calculation procedure for the combustion efficiency test specified in Section C7.3 of Appendix C (including the specified subsections of C7.2) of ANSI/AHRI Standard 1500-2015 (incorporated by reference, see § 431.85).
3.4.2. Rounding. Round the final combustion efficiency value to nearest one tenth of a percent.
[81 FR 89306, Dec. 9, 2016]Appendix A to Subpart F of Part 431 - Uniform Test Method for the Measurement of Energy Consumption of Air-Cooled Small (≥65,000 Btu/h), Large, and Very Large Commercial Package Air Conditioning and Heating Equipment
10:3.0.1.4.19.6.62.6.50 : Appendix A
Appendix A to Subpart F of Part 431 - Uniform Test Method for the Measurement of Energy Consumption of Air-Cooled Small (≥65,000 Btu/h), Large, and Very Large Commercial Package Air Conditioning and Heating EquipmentNote: Prior to December 19, 2016, representations with respect to the energy use or efficiency of air-cooled small, large, and very large commercial package air conditioning and heating equipment, including compliance certifications, must be based on testing conducted in accordance with either Table 1 to § 431.96 as it now appears or Table 1 to § 431.96 as it appeared in subpart F of this part, in the 10 CFR parts 200 through 499 edition revised as of January 1, 2015. After December 19, 2016, representations with respect to energy use or efficiency of air-cooled small, large, and very large commercial package air conditioning and heating equipment, including compliance certifications, must be based on testing conducted in accordance with Table 1 to § 431.96 as it now appears.
(1) Cooling mode test method. The test method for cooling mode consists of the methods and conditions in AHRI 340/360-2007 sections 3, 4, and 6 (omitting section 6.3) (incorporated by reference; see § 431.95), and in ANSI/ASHRAE 37-2009 (incorporated by reference; see § 431.95). In case of a conflict between AHRI 340/360-2007 or ANSI/ASHRAE 37-2009 and the CFR, the CFR provisions control.
(2) Heating mode test method. The test method for heating mode consists of the methods and conditions in AHRI 340/360-2007 sections 3, 4, and 6 (omitting section 6.3) (incorporated by reference; see § 431.95), and in ANSI/ASHRAE 37-2009 (incorporated by reference; see § 431.95). In case of a conflict between AHRI 340/360-2007 or ANSI/ASHRAE 37-2009 and the CFR, the CFR provisions control.
(3) Minimum external static pressure. Use the certified cooling capacity for the basic model to choose the minimum external static pressure found in table 5 of section 6 of AHRI 340/360-2007 (incorporated by reference; see § 431.95) for testing.
(4) Optional break-in period. Manufacturers may optionally specify a “break-in” period, not to exceed 20 hours, to operate the equipment under test prior to conducting the test method in appendix A of this part. A manufacturer who elects to use an optional compressor break-in period in its certification testing must record this information (including the duration) as part of the information in the supplemental testing instructions under 10 CFR 429.43.
(5) Additional provisions for equipment set-up. The only additional specifications that may be used in setting up a unit for test are those set forth in the installation and operation manual shipped with the unit. Each unit should be set up for test in accordance with the manufacturer installation and operation manuals. Paragraphs (5)(i) through (ii) of this section provide specifications for addressing key information typically found in the installation and operation manuals.
(i) If a manufacturer specifies a range of superheat, sub-cooling, and/or refrigerant pressure in its installation and operation manual for a given basic model, any value(s) within that range may be used to determine refrigerant charge or mass of refrigerant, unless the manufacturer clearly specifies a rating value in its installation and operation manual, in which case the specified rating value shall be used.
(ii) The airflow rate used for testing must be that set forth in the installation and operation manuals being shipped to the customer with the basic model and clearly identified as that used to generate the DOE performance ratings. If a certified airflow value for testing is not clearly identified, a value of 400 standard cubic feet per minute (scfm) per ton shall be used.
(6) Indoor airflow testing and adjustment. (i) When testing full-capacity cooling operation at the required external static pressure condition, the full-load indoor airflow rate must be within ± 3 percent of the certified-rated airflow at full-capacity cooling operation. If the indoor airflow rate at the required minimum external pressure is outside the ± 3-percent tolerance, the unit and/or test setup must be adjusted such that both the airflow and ESP are within the required tolerances. This process may include, but is not limited to, adjusting any adjustable motor sheaves, adjusting variable drive settings, or adjusting the code tester fan.
(ii) When testing other than full-capacity cooling operation using the full-load indoor airflow rate (e.g., full-load heating), the full-load indoor airflow rate must be within ± 3 percent of the certified-rated full-load cooling airflow (without regard to the resulting external static pressure), unless the unit is designed to operate at a different airflow for cooling and heating mode. If necessary, a test facility setup may be made in order to maintain airflow within the required tolerance; however, no adjustments to the unit under test may be made.
(7) Condenser head pressure controls. Condenser head pressure controls, if typically shipped with units of the basic model by the manufacturer or available as an option to the basic model, must be active during testing.
(8) Standard CFM. In the referenced sections of AHRI 340/360-2007 (incorporated by reference; see § 431.95), all instances of CFM refer to standard CFM (SCFM). Likewise, all references to airflow or air quantity refer to standard airflow and standard air quantity.
(9) Capacity rating at part-load. When testing to determine EER for the part-load rating points (i.e. 75-percent load, 50-percent load, and 25-percent load), if the measured capacity expressed as a percent of full-load capacity for a given part-load test is within three percent above or below the target part-load percentage, the EER calculated for the test may be used without any interpolation to determine IEER.
(10) Condenser air inlet temperature for part-load testing. When testing to determine EER for the part-load rating points (i.e. 75-percent load, 50-percent load, and 25-percent load), the condenser air inlet temperature shall be calculated (using the equation in Table 6 of AHRI 340/360-2007; incorporated by reference; see § 431.95) for the target percent load rather than for the percent load measured in the test. Table 1 of this appendix shows the condenser air inlet temperature corresponding with each target percent load, as calculated using the equation in Table 6 of AHRI 340/360-2007.
Table 1 to Appendix A to Subpart F of Part 431 - Condenser Air Inlet Temperatures for Part-Load Tests
Target percent load (%) |
Condenser air inlet
temperature ( °F) |
---|---|
25 | 65 |
50 | 68 |
75 | 81.5 |
Appendix A to Subpart G of Part 431 - Uniform Test Method for the Measurement of Thermal Efficiency and Standby Loss of Gas-Fired and Oil-Fired Storage Water Heaters and Storage-Type Instantaneous Water Heaters
10:3.0.1.4.19.7.64.6.51 : Appendix A
Appendix A to Subpart G of Part 431 - Uniform Test Method for the Measurement of Thermal Efficiency and Standby Loss of Gas-Fired and Oil-Fired Storage Water Heaters and Storage-Type Instantaneous Water HeatersNote: Prior to November 6, 2017, manufacturers must make any representations with respect to the energy use or efficiency of the subject commercial water heating equipment in accordance with the results of testing pursuant to this appendix or the procedures in 10 CFR 431.106 that were in place on January 1, 2016. On and after November 6, 2017, manufacturers must make any representations with respect to energy use or efficiency of gas-fired and oil-fired storage water heaters and storage-type instantaneous water heaters in accordance with the results of testing pursuant to this appendix to demonstrate compliance with the energy conservation standards at 10 CFR 431.110.
1. GeneralDetermine the thermal efficiency and standby loss (as applicable) in accordance with the following sections of this appendix. Certain sections reference sections of Annex E.1 of ANSI Z21.10.3-2015 (incorporated by reference; see § 431.105). Where the instructions contained in the sections below conflict with instructions in Annex E.1 of ANSI Z21.10.3-2015, the instructions contained in this appendix control.
2. Test Set-Up2.1. Placement of Water Heater. A water heater for installation on combustible floors must be placed on a 3/4-inch plywood platform supported by three 2 x 4-inch runners. If the water heater is for installation on noncombustible floors, suitable noncombustible material must be placed on the platform. When the use of the platform for a large water heater is not practical, the water heater may be placed on any suitable flooring. A wall-mounted water heater must be mounted on a simulated wall section.
2.2. Installation of Temperature Sensors. Inlet and outlet water piping must be turned vertically downward from the connections on the water heater so as to form heat traps. Temperature sensors for measuring supply and outlet water temperatures must be installed upstream from the inlet heat trap piping and downstream from the outlet heat trap piping, respectively, in accordance with Figure 2.1, 2.2, or 2.3 (as applicable based on the location of inlet and outlet piping connections) of this section.
The water heater must meet the requirements shown in Figure 2.1, 2.2, or 2.3 (as applicable) at all times during the conduct of the thermal efficiency and standby loss tests. Any factory-supplied heat traps must be installed per the installation instructions while ensuring the requirements in Figure 2.1, 2.2, or 2.3 are met. All dimensions specified in Figure 2.1, 2.2, and 2.3 and in this section are measured from the outer surface of the pipes and water heater outer casing (as applicable).
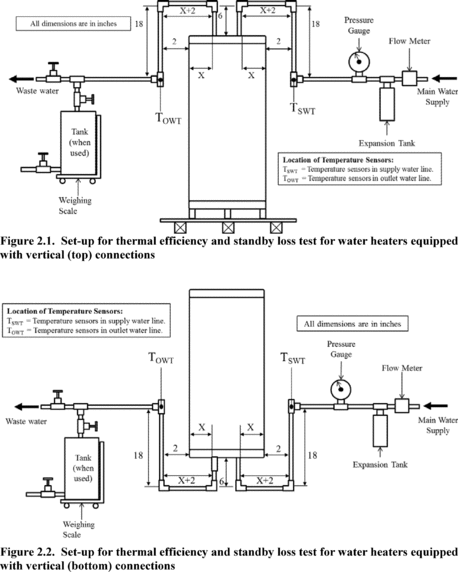
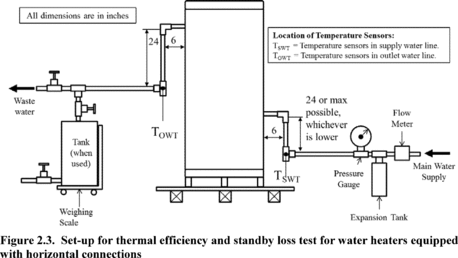
2.3 Installation of Temperature Sensors for Measurement of Mean Tank Temperature. Install temperature sensors inside the tank for measurement of mean tank temperature according to the instructions in paragraph f of Annex E.1 of ANSI Z21.10.3-2015 (incorporated by reference; see § 431.105). Calculate the mean tank temperature as the average of the six installed temperature sensors.
2.4. Piping Insulation. Insulate all water piping external to the water heater jacket, including heat traps and piping that are installed by the manufacturer or shipped with the unit, for at least 4 ft of piping length from the connection at the appliance, with material having an R-value not less than 4 °F·ft 2·h/Btu. Ensure that the insulation does not contact any appliance surface except at the location where the pipe connections penetrate the appliance jacket or enclosure.
2.5. Temperature and Pressure Relief Valve Insulation. If the manufacturer has not provided a temperature and pressure relief valve, one shall be installed and insulated as specified in section 2.4 of this appendix.
2.6. Vent Requirements. Follow the requirements for venting arrangements specified in paragraph c of Annex E.1 of ANSI Z21.10.3-2015 (incorporated by reference; see § 431.105).
2.7. Energy Consumption. Install equipment that determines, within ± 1 percent:
2.7.1. The quantity and rate of fuel consumed.
2.7.2. The quantity of electricity consumed by factory-supplied water heater components.
3. Test Conditions3.1. Water Supply
3.1.1. Water Supply Pressure. The pressure of the water supply must be maintained between 40 psi and the maximum pressure specified by the manufacturer of the unit being tested. The accuracy of the pressure-measuring devices must be within ± 1.0 pounds per square inch (psi).
3.1.2. Water Supply Temperature. During the steady-state verification period and the thermal efficiency test, the temperature of the supply water must be maintained at 70 °F ± 2 °F.
3.1.3. Isolate the water heater using a shutoff valve in the supply line with an expansion tank installed in the supply line downstream of the shutoff valve. There must be no shutoff means between the expansion tank and the appliance inlet.
3.2. Gas Pressure for Gas-Fired Equipment. The supply gas pressure must be within the range specified by the manufacturer on the nameplate of the unit being tested. The difference between the outlet pressure of the gas appliance pressure regulator and the value specified by the manufacturer on the nameplate of the unit being tested must not exceed the greater of: ± 10 percent of the nameplate value or ± 0.2 inches water column (in. w.c.). Obtain the higher heating value of the gas burned.
3.3. Ambient Room Temperature. During the soak-in period (as applicable), the steady-state verification period, the thermal efficiency test, and the standby loss test, maintain the ambient room temperature at 75 °F ± 10 °F at all times. Measure the ambient room temperature at 1-minute intervals during these periods, except for the soak-in period. Measure the ambient room temperature once before beginning the soak-in period, and ensure no actions are taken during the soak-in period that would cause the ambient room temperature to deviate from the allowable range. Measure the ambient room temperature at the vertical mid-point of the water heater and approximately 2 feet from the water heater jacket. Shield the sensor against radiation. Calculate the average ambient room temperature separately for the thermal efficiency test and standby loss test. During the thermal efficiency and standby loss tests, the ambient room temperature must not vary by more than ± 5.0 °F at any reading from the average ambient room temperature.
3.4. Test Air Temperature. During the steady-state verification period, the thermal efficiency test, and the standby loss test, the test air temperature must not vary by more than ± 5 °F from the ambient room temperature at any reading. Measure the test air temperature at 1-minute intervals during these periods and at a location within two feet of the air inlet of the water heater or the combustion air intake vent, as applicable. Shield the sensor against radiation. For units with multiple air inlets, measure the test air temperature at each air inlet, and maintain the specified tolerance on deviation from the ambient room temperature at each air inlet. For units without a dedicated air inlet, measure the test air temperature within two feet of any location on the water heater where combustion air is drawn.
3.5. Maximum Air Draft. During the steady-state verification period, the thermal efficiency test, and the standby loss test, the water heater must be located in an area protected from drafts of more than 50 ft/min. Prior to beginning the steady-state verification period and the standby loss test, measure the air draft within three feet of the jacket or enclosure of the water heater to ensure this condition is met. Ensure that no other changes that would increase the air draft are made to the test set-up or conditions during the conduct of the tests.
3.6. Setting the Tank Thermostat. Before starting the steady-state verification period (as applicable) or before the soak-in period (as applicable), the thermostat setting must first be obtained by starting with the water in the system at 70 °F ± 2 °F. Set the thermostat to ensure:
3.6.1. With the supply water temperature set as per section 3.1.2 of this appendix (i.e., 70 °F ± 2 °F), the water flow rate can be varied so that the outlet water temperature is constant at 70 °F ± 2 °F above the supply water temperature while the burner is firing at full firing rate; and
3.6.2. After the water supply is turned off and the thermostat reduces the fuel supply to a minimum, the maximum water temperature measured by the topmost tank temperature sensor (i.e., the highest of the 6 temperature sensors used for calculating mean tank temperature, as required by section 2.3 of this appendix) is 140 °F ± 5 °F.
3.7. Additional Requirements for Oil-Fired Equipment.
3.7.1. Venting Requirements. Connect a vertical length of flue pipe to the flue gas outlet of sufficient height so as to meet the minimum draft specified by the manufacturer.
3.7.2. Oil Supply. Adjust the burner rate so that the following conditions are met:
3.7.2.1. The CO2 reading is within the range specified by the manufacturer;
3.7.2.2. The fuel pump pressure is within ± 10 percent of manufacturer's specifications;
3.7.2.3. If either the fuel pump pressure or range for CO2 reading are not specified by the manufacturer on the nameplate of the unit, in literature shipped with the unit, or in supplemental test report instructions included with a certification report, then a default value of 100 psig is to be used for fuel pump pressure, and a default range of 9-12 percent is to be used for CO2 reading; and
3.7.2.4. Smoke in the flue does not exceed No. 1 smoke as measured by the procedure in ASTM D2156-09 (Reapproved 2013) (incorporated by reference, see § 431.105). To determine the smoke spot number, connect the smoke measuring device to an open-ended tube. This tube must project into the flue 1/4 to 1/2 of the pipe diameter.
3.7.2.5. If no settings on the water heater have been changed and the water heater has not been turned off since the end of a previously run thermal efficiency or standby loss test, measurement of the CO2 reading and conduct of the smoke spot test are not required prior to beginning a test. Otherwise, measure the CO2 reading and determine the smoke spot number, with the burner firing, before the beginning of the steady-state verification period prior to the thermal efficiency test, and prior to beginning the standby loss test.
3.8. Data Collection Intervals. Follow the data recording intervals specified in the following sections.
3.8.1. Soak-In Period. For units that require a soak-in period, measure the ambient room temperature, in °F, prior to beginning the soak-in period.
3.8.2. Steady-State Verification Period and Thermal Efficiency Test. For the steady-state verification period and the thermal efficiency test, follow the data recording intervals specified in Table 3.1 of this appendix.
Table 3.1 - Data To Be Recorded Before and During the Steady-State Verification Period and Thermal Efficiency Test
Item recorded | Before steady-state verification period |
Every 1 minute a |
Every 10 minutes |
---|---|---|---|
Gas supply pressure, in w.c. | X | ||
Gas outlet pressure, in w.c. | X | ||
Barometric pressure, in Hg | X | ||
Fuel higher heating value, Btu/ft 3 (gas) or Btu/lb (oil) | X | ||
Oil pump pressure, psig (oil only) | X | ||
CO2 reading, % (oil only) | X b | ||
Oil smoke spot reading (oil only) | X b | ||
Air draft, ft/min | X | ||
Time, minutes/seconds | X | ||
Fuel weight or volume, lb (oil) or ft 3 (gas) | X c | ||
Supply water temperature (TSWT), °F | X | ||
Outlet water temperature (TOWT), °F | X | ||
Ambient room temperature, °F | X | ||
Test air temperature, °F | X | ||
Water flow rate, (gpm) | X |
Notes:
a These measurements are to be recorded at the start of the steady-state verification period and the end of the thermal efficiency test, as well as every minute during both periods.
b The smoke spot test and CO2 reading are not required prior to beginning the steady-state verification period if no settings on the water heater have been changed and the water heater has not been turned off since the end of a previously-run efficiency test (i.e., thermal efficiency or standby loss).
c Fuel and electricity consumption over the course of the entire thermal efficiency test must be measured and used in calculation of thermal efficiency.
3.8.3. Standby Loss Test. For the standby loss test, follow the data recording intervals specified in Table 3.2 of this appendix. Additionally, the fuel and electricity consumption over the course of the entire test must be measured and used in calculation of standby loss.
Table 3.2 - Data To Be Recorded Before and During the Standby Loss Test
Item recorded | Before test | Every 1 minute a |
---|---|---|
Gas supply pressure, in w.c. | X | |
Gas outlet pressure, in w.c. | X | |
Barometric pressure, in Hg | X | |
Fuel higher heating value, Btu/ft 3 (gas) or Btu/lb (oil) | X | |
Oil pump pressure, psig (oil only) | X | |
CO2 reading, % (oil only) | X b | |
Oil smoke spot reading (oil only) | X b | |
Air draft, ft/min | X | |
Time, minutes/seconds | X | |
Mean tank temperature, °F | X c | |
Ambient room temperature, °F | X | |
Test air temperature, °F | X |
Notes:
a These measurements are to be recorded at the start and end of the test, as well as every minute during the test.
b The smoke spot test and CO2 reading are not required prior to beginning the standby loss test if no settings on the water heater have been changed and the water heater has not been turned off since the end of a previously-run efficiency test (i.e., thermal efficiency or standby loss).
c Mean tank temperature is calculated as the average of the 6 tank temperature sensors, installed per section 2.3 of this appendix.
4. Determination of Storage Volume. Determine the storage volume by subtracting the tare weight, measured while the system is dry and empty, from the weight of the system when filled with water and dividing the resulting net weight of water by the density of water at the measured water temperature. The volume of the water contained in the water heater must be computed in gallons.
5. Thermal Efficiency Test. Before beginning the steady-state verification period, record the applicable parameters as specified in section 3.8.2 of this appendix. Begin drawing water from the unit by opening the main supply, and adjust the water flow rate to achieve an outlet water temperature of 70 °F ± 2 °F above supply water temperature. The thermal efficiency test shall be deemed complete when there is a continuous, one-hour-long period where the steady-state conditions specified in section 5.1 of this appendix have been met, as confirmed by consecutive readings of the relevant parameters recorded at 1-minute intervals (except for fuel input rate, which is determined at 10-minute intervals, as specified in section 5.4 of this appendix). During the one-hour-long period, the water heater must fire continuously at its full firing rate (i.e., no modulations or cut-outs) and no settings can be changed on the unit being tested at any time. The first 30 minutes of the one-hour-period where the steady-state conditions in section 5.1 of this appendix are met is the steady-state verification period. The final 30 minutes of the one-hour-period where the steady-state conditions in section 5.1 of this appendix are met is the thermal efficiency test. The last reading of the steady-state verification period must be the first reading of the thermal efficiency test (i.e., the thermal efficiency test starts immediately once the steady-state verification period ends).
5.1. Steady-State Conditions. The following conditions must be met at consecutive readings taken at 1-minute intervals (except for fuel input rate, for which measurements are taken at 10-minute intervals) to verify the water heater has achieved steady-state operation during the steady-state verification period and thermal efficiency test.
5.1.1. The water flow rate must be maintained within ± 0.25 gallons per minute (gpm) of the initial reading at the start of the steady-state verification period;
5.1.2. Outlet water temperature must be maintained at 70 °F ± 2 °F above supply water temperature;
5.1.3. Fuel input rate must be maintained within ± 2 percent of the rated input certified by the manufacturer;
5.1.4. The supply water temperature must be maintained within ± 0.50 °F of the initial reading at the start of the steady-state verification period; and
5.1.5. The rise between the supply and outlet water temperatures must be maintained within ± 0.50 °F of its initial value taken at the start of the steady-state verification period for units with rated input less than 500,000 Btu/h, and maintained within ± 1.00 °F of its initial value for units with rated input greater than or equal to 500,000 Btu/h.
5.2. Water Flow Measurement. Measure the total weight of water heated during the 30-minute thermal efficiency test with either a scale or a water flow meter. With either method, the error of measurement of weight of water heated must not exceed 1 percent of the weight of the total draw.
5.3. Determination of Fuel Input Rate. During the steady-state verification period and the thermal efficiency test, record the fuel consumed at 10-minute intervals. Calculate the fuel input rate over each 10-minute period using the equations in section 5.4 of this appendix. The measured fuel input rates for these 10-minute periods must not vary by more than ± 2 percent between any two readings. Determine the overall fuel input rate using the fuel consumption for the entire duration of the thermal efficiency test.
5.4. Fuel Input Rate Calculation. To calculate the fuel input rate, use the following equation:

5.5. Thermal Efficiency Calculation. Thermal efficiency must be calculated using data from the 30-minute thermal efficiency test. Calculate thermal efficiency, Et, using the following equation:
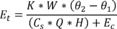
6.1. If no settings on the water heater have changed and the water heater has not been turned off since a previously run thermal efficiency or standby loss test, skip to section 6.3 of this appendix. Otherwise, conduct the soak-in period according to section 6.2 of this appendix.
6.2. Soak-In Period. Conduct a soak-in period, in which the water heater must sit without any draws taking place for at least 12 hours. Begin the soak-in period after setting the tank thermostat as specified in section 3.6 of this appendix, and maintain these thermostat settings throughout the soak-in period.
6.3. Begin the standby loss test at the first cut-out following the end of the soak-in period (if applicable); or at a cut-out following the previous thermal efficiency or standby loss test (if applicable). Allow the water heater to remain in standby mode. Do not change any settings on the water heater at any point until measurements for the standby loss test are finished. Begin recording the applicable parameters specified in section 3.8.3 of this appendix.
6.4. At the second cut-out, record the time and ambient room temperature, and begin measuring the fuel and electricity consumption. Record the initial mean tank temperature and initial ambient room temperature. For the remainder of the test, continue recording the applicable parameters specified in section 3.8.3 of this appendix.
6.5. Stop the test after the first cut-out that occurs after 24 hours, or at 48 hours, whichever comes first.
6.6. Immediately after conclusion of the standby loss test, record the total fuel flow and electrical energy consumption, the final ambient room temperature, the duration of the standby loss test, and if the test ends at 48 hours without a cut-out, the final mean tank temperature, or if the test ends after a cut-out, the maximum mean tank temperature that occurs after the cut-out. Calculate the average of the recorded values of the mean tank temperature and of the ambient room temperature taken at each measurement interval, including the initial and final values.
6.7. Standby Loss Calculation. To calculate the standby loss, follow the steps below:
6.7.1. The standby loss expressed as a percentage (per hour) of the heat content of the stored water above room temperature must be calculated using the following equation:

6.7.2. The standby loss expressed in Btu per hour must be calculated as follows:
SL (Btu per hour) = S (% per hour) × 8.25 (Btu/gal- °F) × Measured Volume (gal) × 70 ( °F).
Where, SL refers to the standby loss of the water heater, defined as the amount of energy required to maintain the stored water temperature expressed in Btu per hour
[81 FR 79323, Nov. 10, 2016]Appendix A to Subpart K of Part 431 - Uniform Test Method for Measuring the Energy Consumption of Distribution Transformers
10:3.0.1.4.19.11.71.5.56 : Appendix A
Appendix A to Subpart K of Part 431 - Uniform Test Method for Measuring the Energy Consumption of Distribution Transformers 1.0 Definitions.The definitions contained in §§ 431.2 and 431.192 are applicable to this appendix A.
2.0 Accuracy Requirements.(a) Equipment and methods for loss measurement shall be sufficiently accurate that measurement error will be limited to the values shown in Table 2.1.
Table 2.1 - Test System Accuracy Requirements for Each Measured Quantity
Measured quantity | Test system accuracy |
---|---|
Power Losses | ±3.0% |
Voltage | ±0.5% |
Current | ±0.5% |
Resistance | ±0.5% |
Temperature | ±1.0 °C |
(b) Only instrument transformers meeting the 0.3 metering accuracy class, or better, may be used under this test method.
3.0 Resistance Measurements3.1 General Considerations
(a) Measure or establish the winding temperature at the time of the winding resistance measurement.
(b) Measure the direct current resistance (Rdc) of transformer windings by one of the methods outlined in section 3.3. The methods of section 3.5 must be used to correct load losses to the applicable reference temperature from the temperature at which they are measured. Observe precautions while taking measurements, such as those in section 3.4, in order to maintain measurement uncertainty limits specified in Table 2.1.
3.2 Temperature Determination of Windings and Pre-conditions for Resistance Measurement.
Make temperature measurements in protected areas where the air temperature is stable and there are no drafts. Determine the winding temperature (Tdc) for liquid-immersed and dry-type distribution transformers by the methods described in sections 3.2.1 and 3.2.2, respectively.
3.2.1 Liquid-Immersed Distribution Transformers.
3.2.1.1 MethodsRecord the winding temperature (Tdc) of liquid-immersed transformers as the average of either of the following:
(a) The measurements from two temperature sensing devices (for example, thermocouples) applied to the outside of the transformer tank and thermally insulated from the surrounding environment, with one located at the level of the oil and the other located near the tank bottom or at the lower radiator header if applicable; or
(b) The measurements from two temperature sensing devices immersed in the transformer liquid, with one located directly above the winding and other located directly below the winding.
3.2.1.2 ConditionsMake this determination under either of the following conditions:
(a) The windings have been under insulating liquid with no excitation and no current in the windings for four hours before the dc resistance is measured; or
(b) The temperature of the insulating liquid has stabilized, and the difference between the top and bottom temperature does not exceed 5 °C.
3.2.2 Dry-Type Distribution Transformers.
Record the winding temperature (Tdc) of dry-type transformers as either of the following:
(a) For ventilated dry-type units, use the average of readings of four or more thermometers, thermocouples, or other suitable temperature sensors inserted within the coils. Place the sensing points of the measuring devices as close as possible to the winding conductors. For sealed units, such as epoxy-coated or epoxy-encapsulated units, use the average of four or more temperature sensors located on the enclosure and/or cover, as close to different parts of the winding assemblies as possible; or
(b) For both ventilated and sealed units, use the ambient temperature of the test area, under the following conditions:
(1) All internal temperatures measured by the internal temperature sensors must not differ from the test area ambient temperature by more than 2 °C.
(2) Enclosure surface temperatures for sealed units must not differ from the test area ambient temperature by more than 2 °C.
(3) Test area ambient temperature should not have changed by more than 3 °C for 3 hours before the test.
(4) Neither voltage nor current has been applied to the unit under test for 24 hours. In addition, increase this initial 24 hour period by any added amount of time necessary for the temperature of the transformer windings to stabilize at the level of the ambient temperature. However, this additional amount of time need not exceed 24 hours.
3.3 Resistance Measurement Methods.
Make resistance measurements using either the resistance bridge method, the voltmeter-ammeter method or a resistance meter. In each instance when this Uniform Test Method is used to test more than one unit of a basic model to determine the efficiency of that basic model, the resistance of the units being tested may be determined from making resistance measurements on only one of the units.
3.3.1 Resistance Bridge Methods.
If the resistance bridge method is selected, use either the Wheatstone or Kelvin bridge circuit (or the equivalent of either).
3.3.1.1 Wheatstone Bridge(a) This bridge is best suited for measuring resistances larger than ten ohms. A schematic diagram of a Wheatstone bridge with a representative transformer under test is shown in Figure 3.1.
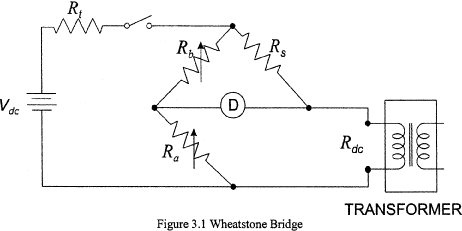
(b) In the measurement process, turn on the source (Vdc), and adjust the resistance ratio (Ra/Rb) to produce zero signal at the detector (D). Determine the winding resistance by using equation 3-1 as follows:
3.3.1.2 Kelvin Bridge(a) This bridge separates the resistance of the connecting conductors to the transformer winding being measured from the resistance of the winding, and therefore is best suited for measuring resistances of ten ohms and smaller. A schematic diagram of a Kelvin bridge with a representative transformer under test is shown in Figure 3.2.
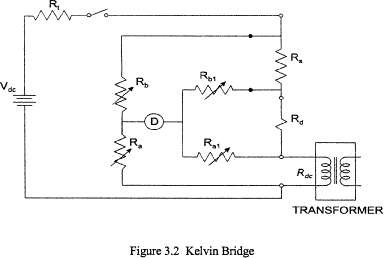
(b) The Kelvin Bridge has seven of the same type of components as in the Wheatstone Bridge. It has two more resistors than the Wheatstone bridge, Ra1 and Rb1. At least one of these resistors must have adjustable resistance. In the measurement process, the source is turned on, two resistance ratios (Ra/Rb) and (Ra1/Rb1) are adjusted to be equal, and then the two ratios are adjusted together to balance the bridge producing zero signal at the detector. Determine the winding resistance by using equation 3-2 as follows:
as with the Wheatstone bridge, with an additional condition that:(c) The Kelvin bridge provides two sets of leads, current-carrying and voltage-sensing, to the transformer terminals and the standard resistor, thus eliminating voltage drops from the measurement in the current-carrying leads as represented by Rd.
3.3.2 Voltmeter-Ammeter Method.
(a) Employ the voltmeter-ammeter method only if the rated current of the winding is greater than one ampere and the test current is limited to 15 percent of the winding current. Connect the transformer winding under test to the circuit shown in Figure 3.3.
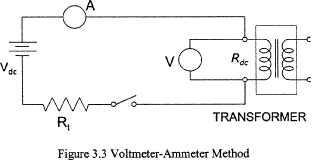
(b) To perform the measurement, turn on the source to produce current no larger than 15 percent of the rated current for the winding. Wait until the current and voltage readings have stabilized and then take simultaneous readings of voltage and current. Determine the winding resistance Rdc by using equation 3-4 as follows:

(c) As shown in Figure 3.3, separate current and voltage leads must be brought to the transformer terminals. (This eliminates the errors due to lead and contact resistance.)
3.3.3 Resistance Meters.
Resistance meters may be based on voltmeter-ammeter, or resistance bridge, or some other operating principle. Any meter used to measure a transformer's winding resistance must have specifications for resistance range, current range, and ability to measure highly inductive resistors that cover the characteristics of the transformer being tested. Also the meter's specifications for accuracy must meet the applicable criteria of Table 2.1 in section 2.0.
3.4 Precautions in Measuring Winding Resistance.
3.4.1 Required actions.
The following guidelines must be observed when making resistance measurements:
(a) Use separate current and voltage leads when measuring small (<10 ohms) resistance.
(b) Use null detectors in bridge circuits, and measuring instruments in voltmeter-ammeter circuits, that have sensitivity and resolution sufficient to enable observation of at least 0.1 percent change in the measured resistance.
(c) Maintain the dc test current at or below 15 percent of the rated winding current.
(d) Inclusion of a stabilizing resistor Rt (see section 3.4.2) will require higher source voltage.
(e) Disconnect the null detector (if a bridge circuit is used) and voltmeter from the circuit before the current is switched off, and switch off current by a suitable insulated switch.
3.4.2 Guideline for Time Constant.
(a) The following guideline is suggested for the tester as a means to facilitate the measurement of resistance in accordance with the accuracy requirements of section 2.0:
(b) The accurate reading of resistance Rdc may be facilitated by shortening the time constant. This is done by introducing a resistor Rt in series with the winding under test in both the bridge and voltmeter-ammeter circuits as shown in Figures 3.1 to 3.3. The relationship for the time constant is:

(c) Because Rtc is in the denominator of the expression for the time constant, increasing the resistance Rtc will decrease the time constant. If the time constant in a given test circuit is too long for the resistance readings to be stable, then a higher resistance can be substituted for the existing Rtc, and successive replacements can be made until adequate stability is reached.
3.5 Conversion of Resistance Measurements.
(a) Resistance measurements must be corrected, from the temperature at which the winding resistance measurements were made, to the reference temperature. As specified in these test procedures, the reference temperature for liquid-immersed transformers loaded at 50 percent of the rated load is 55 °C. For medium-voltage, dry-type transformers loaded at 50 percent of the rated load, and for low-voltage, dry-type transformers loaded at 35 percent of the rated load, the reference temperature is 75 °C.
(b) Correct the measured resistance to the resistance at the reference temperature using equation 3-6 as follows:

4.1 General Considerations.
The efficiency of a transformer is computed from the total transformer losses, which are determined from the measured value of the no-load loss and load loss power components. Each of these two power loss components is measured separately using test sets that are identical, except that shorting straps are added for the load-loss test. The measured quantities will need correction for instrumentation losses and may need corrections for known phase angle errors in measuring equipment and for the waveform distortion in the test voltage. Any power loss not measured at the applicable reference temperature must be adjusted to that reference temperature. The measured load loss must also be adjusted to a specified output loading level if not measured at the specified output loading level. Test distribution transformers designed for harmonic currents using a sinusoidal waveform (k = 1).
4.2 Measurement of Power Losses.
4.2.1 No-Load Loss.
Measure the no-load loss and apply corrections as described in section 4.4, using the appropriate test set as described in section 4.3.
4.2.2 Load Loss.
Measure the load loss and apply corrections as described in section 4.5, using the appropriate test set as described in section 4.3.
4.3 Test Sets.
(a) The same test set may be used for both the no-load loss and load loss measurements provided the range of the test set encompasses the test requirements of both tests. Calibrate the test set to national standards to meet the tolerances in Table 2.1 in section 2.0. In addition, the wattmeter, current measuring system and voltage measuring system must be calibrated separately if the overall test set calibration is outside the tolerance as specified in section 2.0 or the individual phase angle error exceeds the values specified in section 4.5.3.
(b) A test set based on the wattmeter-voltmeter-ammeter principle may be used to measure the power loss and the applied voltage and current of a transformer where the transformer's test current and voltage are within the measurement capability of the measuring instruments. Current and voltage transformers, known collectively as instrument transformers, or other scaling devices such as resistive or capacitive dividers for voltage, may be used in the above circumstance, and must be used together with instruments to measure current, voltage, or power where the current or voltage of the transformer under test exceeds the measurement capability of such instruments. Thus, a test set may include a combination of measuring instruments and instrument transformers (or other scaling devices), so long as the current or voltage of the transformer under test does not exceed the measurement capability of any of the instruments.
4.3.1 Single-Phase Test Sets.
Use these for testing single-phase distribution transformers.
4.3.1.1 Without Instrument Transformers.
(a) A single-phase test set without an instrument transformer is shown in Figure 4.1.
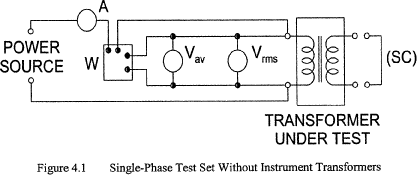
(b) Either the primary or the secondary winding can be connected to the test set. However, more compatible voltage and current levels for the measuring instruments are available if for no-load loss measurements the secondary (low voltage) winding is connected to the test set, and for load loss measurements the primary winding is connected to the test set. Use the average-sensing voltmeter, Vav, only in no-load loss measurements.
4.3.1.2 With Instrument Transformers.
A single-phase test set with instrument transformers is shown in Figure 4.2. This circuit has the same four measuring instruments as that in Figure 4.1. The current and voltage transformers, designated as (CT) and (VT), respectively, are added.
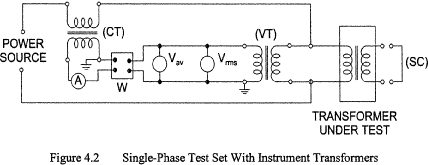
4.3.2 Three-Phase Test Sets.
Use these for testing three-phase distribution transformers. Use in a four-wire, three-wattmeter test circuit.
4.3.2.1 Without Instrument Transformers.
(a) A three-phase test set without instrument transformers is shown in Figure 4.3. This test set is essentially the same circuit shown in Figure 4.1 repeated three times, and the instruments are individual devices as shown. As an alternative, the entire instrumentation system of a three-phase test set without transformers may consist of a multi-function analyzer.
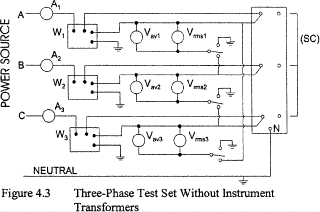
(b) Either group of windings, the primary or the secondary, can be connected in wye or delta configuration. If both groups of windings are connected in the wye configuration for the no-load test, the neutral of the winding connected to the test set must be connected to the neutral of the source to provide a return path for the neutral current.
(c) In the no-load loss measurement, the voltage on the winding must be measured. Therefore a provision must be made to switch the voltmeters for line-to-neutral measurements for wye-connected windings and for line-to-line measurements for delta-connected windings.
4.3.2.2 With Instrument Transformers.
A three-phase test set with instrument transformers is shown in Figure 4.4. This test set is essentially the same circuit shown in Figure 4.2 repeated three times. Provision must be made to switch the voltmeters for line-to-neutral and line-to-line measurements as in section 4.3.2.1. The voltage sensors (“coils”) of the wattmeters must always be connected in the line-to-neutral configuration.
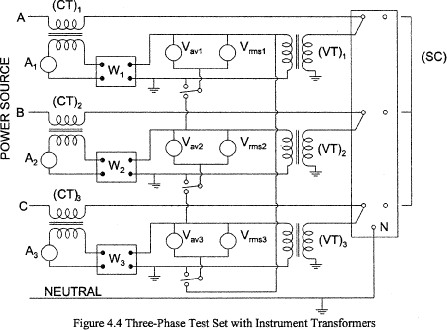
4.3.2.3 Test Set Neutrals.
If the power source in the test circuit is wye-connected, ground the neutral. If the power source in the test circuit is delta-connected, use a grounding transformer to obtain neutral and ground for the test.
4.4 No-Load Losses: Measurement and Calculations.
4.4.1 General Considerations.
Measurement corrections are permitted but not required for instrumentation losses and for losses from auxiliary devices. Measurement corrections are required:
(a) When the waveform of the applied voltage is non-sinusoidal; and
(b) When the core temperature or liquid temperature is outside the 20 °C ±10 °C range.
4.4.2 No-Load Loss Test.
(a) The purpose of the no-load loss test is to measure no-load losses at a specified excitation voltage and a specified frequency. The no-load loss determination must be based on a sine-wave voltage corrected to the reference temperature. Connect either of the transformer windings, primary or secondary, to the appropriate test set of Figures 4.1 to 4.4, giving consideration to section 4.4.2(a)(2). Leave the unconnected winding(s) open circuited. Apply the rated voltage at rated frequency, as measured by the average-sensing voltmeter, to the transformer. Take the readings of the wattmeter(s) and the average-sensing and true rms voltmeters. Observe the following precautions:
(1) Voltmeter connections. When correcting to a sine-wave basis using the average-voltmeter method, the voltmeter connections must be such that the waveform applied to the voltmeters is the same as the waveform across the energized windings.
(2) Energized windings. Energize either the high voltage or the low voltage winding of the transformer under test.
(3) Voltage and frequency. The no-load loss test must be conducted with rated voltage impressed across the transformer terminals using a voltage source at a frequency equal to the rated frequency of the transformer under test.
(b) Adjust the voltage to the specified value as indicated by the average-sensing voltmeter. Record the values of rms voltage, rms current, electrical power, and average voltage as close to simultaneously as possible. For a three-phase transformer, take all of the readings on one phase before proceeding to the next, and record the average of the three rms voltmeter readings as the rms voltage value.
Note:When the tester uses a power supply that is not synchronized with an electric utility grid, such as a dc/ac motor-generator set, check the frequency and maintain it within ±0.5 percent of the rated frequency of the transformer under test. A power source that is directly connected to, or synchronized with, an electric utility grid need not be monitored for frequency.
4.4.3 Corrections.
4.4.3.1 Correction for Instrumentation Losses.
Measured losses attributable to the voltmeters and wattmeter voltage circuit, and to voltage transformers if they are used, may be deducted from the total no-load losses measured during testing.
4.4.3.2 Correction for Non-Sinusoidal Applied Voltage.
(a) The measured value of no-load loss must be corrected to a sinusoidal voltage, except when waveform distortion in the test voltage causes the magnitude of the correction to be less than 1 percent. In such a case, no correction is required.
(b) To make a correction where the distortion requires a correction of 5 percent or less, use equation 4-1. If the distortion requires a correction to be greater than 5 percent, improve the test voltage and re-test. Repeat until the distortion requires a correction of 5 percent or less.
(c) Determine the no-load losses of the transformer corrected for sine-wave basis from the measured value by using equation 4-1 as follows:
Where: Pncl is the no-load loss corrected to a sine-wave basis at the temperature (Tnm) at which no-load loss is measured, Pnm is the measured no-load loss at temperature Tnm, P1 is the per unit hysteresis loss, P2 is the per unit eddy-current loss, P1 + P2 = 1, Vr(nm) is the test voltage measured by rms voltmeter, and Va(nm) is the test voltage measured by average-voltage voltmeter.(d) The two loss components (P1 and P2) are assumed equal in value, each assigned a value of 0.5 per unit, unless the actual measurement-based values of hysteresis and eddy-current losses are available (in per unit form), in which case the actual measurements apply.
4.4.3.3 Correction of No-Load Loss to Reference Temperature.
After correcting the measured no-load loss for waveform distortion, correct the loss to the reference temperature of 20 °C. If the no-load loss measurements were made between 10 °C and 30 °C, this correction is not required. If the correction to reference temperature is applied, then the core temperature of the transformer during no-load loss measurement (Tnm) must be determined within ±10 °C of the true average core temperature. Correct the no-load loss to the reference temperature by using equation 4-2 as follows:
Where: Pnc is the no-load losses corrected for waveform distortion and then to the reference temperature of 20 °C, Pnc1 is the no-load losses, corrected for waveform distortion, at temperature Tnm, Tnm is the core temperature during the measurement of no-load losses, and Tnr is the reference temperature, 20 °C.4.5 Load Losses: Measurement and Calculations.
4.5.1 General Considerations.
(a) The load losses of a transformer are those losses incident to a specified load carried by the transformer. Load losses consist of ohmic loss in the windings due to the load current and stray losses due to the eddy currents induced by the leakage flux in the windings, core clamps, magnetic shields, tank walls, and other conducting parts. The ohmic loss of a transformer varies directly with temperature, whereas the stray losses vary inversely with temperature.
(b) For a transformer with a tap changer, conduct the test at the rated current and rated-voltage tap position. For a transformer that has a configuration of windings which allows for more than one nominal rated voltage, determine its load losses either in the winding configuration in which the highest losses occur or in each winding configuration in which the transformer can operate.
4.5.2 Tests for Measuring Load Losses.
(a) Connect the transformer with either the high-voltage or low-voltage windings to the appropriate test set. Then short-circuit the winding that was not connected to the test set. Apply a voltage at the rated frequency (of the transformer under test) to the connected windings to produce the rated current in the transformer. Take the readings of the wattmeter(s), the ammeters(s), and rms voltmeter(s).
(b) Regardless of the test set selected, the following preparatory requirements must be satisfied for accurate test results:
(1) Determine the temperature of the windings using the applicable method in section 3.2.1 or section 3.2.2.
(2) The conductors used to short-circuit the windings must have a cross-sectional area equal to, or greater than, the corresponding transformer leads, or, if the tester uses a different method to short-circuit the windings, the losses in the short-circuiting conductor assembly must be less than 10 percent of the transformer's load losses.
(3) When the tester uses a power supply that is not synchronized with an electric utility grid, such as a dc/ac motor-generator set, follow the provisions of the “Note” in section 4.4.2.
4.5.3 Corrections.
4.5.3.1 Correction for Losses from Instrumentation and Auxiliary Devices.
4.5.3.1.1 Instrumentation Losses.
Measured losses attributable to the voltmeters, wattmeter voltage circuit and short-circuiting conductor (SC), and to the voltage transformers if they are used, may be deducted from the total load losses measured during testing.
4.5.3.1.2 Losses from Auxiliary Devices.
Measured losses attributable to auxiliary devices (e.g., circuit breakers, fuses, switches) installed in the transformer, if any, that are not part of the winding and core assembly, may be excluded from load losses measured during testing. To exclude these losses, either (1) measure transformer losses without the auxiliary devices by removing or by-passing them, or (2) measure transformer losses with the auxiliary devices connected, determine the losses associated with the auxiliary devices, and deduct these losses from the load losses measured during testing.
4.5.3.2 Correction for Phase Angle Errors.
(a) Corrections for phase angle errors are not required if the instrumentation is calibrated over the entire range of power factors and phase angle errors. Otherwise, determine whether to correct for phase angle errors from the magnitude of the normalized per unit correction, βn, obtained by using equation 4-3 as follows:
(b) The correction must be applied if βn is outside the limits of ±0.01. If βn is within the limits of ±0.01, the correction is permitted but not required.
(c) If the correction for phase angle errors is to be applied, first examine the total system phase angle (βw − βv + βc). Where the total system phase angle is equal to or less than ±12 milliradians (±41 minutes), use either equation 4-4 or 4-5 to correct the measured load loss power for phase angle errors, and where the total system phase angle exceeds ±12 milliradians (±41 minutes) use equation 4-5, as follows:
(d) The symbols in this section (4.5.3.2) have the following meanings:
Plc1 is the corrected wattmeter reading for phase angle errors, Plm is the actual wattmeter reading, Vlm is the measured voltage at the transformer winding, Ilm is the measured rms current in the transformer winding, is the measured phase angle between Vlm and Ilm, βw is the phase angle error (in radians) of the wattmeter; the error is positive if the phase angle between the voltage and current phasors as sensed by the wattmeter is smaller than the true phase angle, thus effectively increasing the measured power, βv is the phase angle error (in radians) of the voltage transformer; the error is positive if the secondary voltage leads the primary voltage, and βc is the phase angle error (in radians) of the current transformer; the error is positive if the secondary current leads the primary current.(e) The instrumentation phase angle errors used in the correction equations must be specific for the test conditions involved.
4.5.3.3 Temperature Correction of Load Loss.
(a) When the measurement of load loss is made at a temperature Tlm that is different from the reference temperature, use the procedure summarized in the equations 4-6 to 4-10 to correct the measured load loss to the reference temperature. The symbols used in these equations are defined at the end of this section.
(b) Calculate the ohmic loss (Pe) by using equation 4-6 as follows:
(c) Obtain the stray loss by subtracting the calculated ohmic loss from the measured load loss, by using equation 4-7 as follows:
(d) Correct the ohmic and stray losses to the reference temperature for the load loss by using equations 4-8 and 4-9, respectively, as follows:
(e) Add the ohmic and stray losses, corrected to the reference temperature, to give the load loss, Plc2, at the reference temperature, by using equation 4-10 as follows:
(f) The symbols in this section (4.5.3.3) have the following meanings:
Ilm(p) is the primary current in amperes, Ilm(s) is the secondary current in amperes, Pe is the ohmic loss in the transformer in watts at the temperature Tlm, Pe(p) is the ohmic loss in watts in the primary winding at the temperature Tlm, Pe(s) is the ohmic loss in watts in the secondary winding at the temperature Tlm, Per is the ohmic loss in watts corrected to the reference temperature, Plc1 is the measured load loss in watts, corrected for phase angle error, at the temperature Tlm, Plc2 is the load loss at the reference temperature, Ps is the stray loss in watts at the temperature Tlm, Psr is the stray loss in watts corrected to the reference temperature, Rdc(p) is the measured dc primary winding resistance in ohms, Rdc(s) is the measured dc secondary winding resistance in ohms, Tk is the critical temperature in degrees Celsius for the material of the transformer windings. Where copper is used in both primary and secondary windings, Tk is 234.5 °C; where aluminum is used in both primary and secondary windings, Tk is 225 °C; where both copper and aluminum are used in the same transformer, the value of 229 °C is used for Tk, Tk(p) is the critical temperature in degrees Celsius for the material of the primary winding: 234.5 °C if copper and 225 °C if aluminum, Tk(s) is the critical temperature in degrees Celsius for the material of the secondary winding: 234.5 °C if copper and 225 °C if aluminum, Tlm is the temperature in degrees Celsius at which the load loss is measured, Tlr is the reference temperature for the load loss in degrees Celsius, Tdc is the temperature in degrees Celsius at which the resistance values are measured, and N1/N2 is the ratio of the number of turns in the primary winding (N1) to the number of turns in the secondary winding (N2); for a primary winding with taps, N1 is the number of turns used when the voltage applied to the primary winding is the rated primary voltage. 5.0 Determining the Efficiency Value of the TransformerThis section presents the equations to use in determining the efficiency value of the transformer at the required reference conditions and at the specified loading level. The details of measurements are described in sections 3.0 and 4.0. For a transformer that has a configuration of windings which allows for more than one nominal rated voltage, determine its efficiency either at the voltage at which the highest losses occur or at each voltage at which the transformer is rated to operate.
5.1 Output Loading Level Adjustment.
If the output loading level for energy efficiency is different from the level at which the load loss power measurements were made, then adjust the corrected load loss power, Plc2, by using equation 5-1 as follows:
Where: Plc is the adjusted load loss power to the specified energy efficiency load level, Plc2 is as calculated in section 4.5.3.3, Por is the rated transformer apparent power (name plate), Pos is the specified energy efficiency load level, where Pos = PorL, and L is the per unit load level, e.g., if the load level is 50 percent then “L” will be 0.5.5.2 Total Loss Power Calculation.
Calculate the corrected total loss power by using equation 5-2 as follows:
Where: Pts is the corrected total loss power adjusted for the transformer output loading specified by the standard, Pnc is as calculated in section 4.4.3.3, and Plc is as calculated in section 5.1.5.3 Energy Efficiency Calculation.
Calculate efficiency (η) in percent at specified energy efficiency load level, Pos, by using equation 5-3 as follows:
Where: Pos is as described and calculated in section 5.1, and Pts is as described and calculated in section 5.2.5.4 Significant Figures in Power Loss and Efficiency Data.
In measured and calculated data, retain enough significant figures to provide at least 1 percent resolution in power loss data and 0.01 percent resolution in efficiency data.
6.0 Test Equipment Calibration and CertificationMaintain and calibrate test equipment and measuring instruments, maintain calibration records, and perform other test and measurement quality assurance procedures according to the following sections. The calibration of the test set must confirm the accuracy of the test set to that specified in section 2.0, Table 2.1.
6.1 Test Equipment.
The party performing the tests shall control, calibrate and maintain measuring and test equipment, whether or not it owns the equipment, has the equipment on loan, or the equipment is provided by another party. Equipment shall be used in a manner which assures that measurement uncertainty is known and is consistent with the required measurement capability.
6.2 Calibration and Certification.
The party performing the tests must:
(a) Identify the measurements to be made, the accuracy required (section 2.0) and select the appropriate measurement and test equipment;
(b) At prescribed intervals, or prior to use, identify, check and calibrate, if needed, all measuring and test equipment systems or devices that affect test accuracy, against certified equipment having a known valid relationship to nationally recognized standards; where no such standards exist, the basis used for calibration must be documented;
(c) Establish, document and maintain calibration procedures, including details of equipment type, identification number, location, frequency of checks, check method, acceptance criteria and action to be taken when results are unsatisfactory;
(d) Ensure that the measuring and test equipment is capable of the accuracy and precision necessary, taking into account the voltage, current and power factor of the transformer under test;
(e) Identify measuring and test equipment with a suitable indicator or approved identification record to show the calibration status;
(f) Maintain calibration records for measuring and test equipment;
(g) Assess and document the validity of previous test results when measuring and test equipment is found to be out of calibration;
(h) Ensure that the environmental conditions are suitable for the calibrations, measurements and tests being carried out;
(i) Ensure that the handling, preservation and storage of measuring and test equipment is such that the accuracy and fitness for use is maintained; and
(j) Safeguard measuring and test facilities, including both test hardware and test software, from adjustments which would invalidate the calibration setting.
[71 FR 24999, Apr. 27, 2006, as amended at 71 FR 60662, Oct. 16, 2006] Effective Date Note:At 71 FR 24999, Apr. 27, 2006, appendix A to subpart K of part 431 was added. Section 6.2(f) contains information collection requirements and will not become effective until approval has been given by the Office of Management and Budget.Appendix A to Subpart Q of Part 431 - Uniform Test Method for the Measurement of Energy Consumption of Refrigerated Bottled or Canned Beverage Vending Machines
10:3.0.1.4.19.17.83.6.57 : Appendix A
Appendix A to Subpart Q of Part 431 - Uniform Test Method for the Measurement of Energy Consumption of Refrigerated Bottled or Canned Beverage Vending Machines Note:Prior to January 27, 2016, manufacturers must make any representations with respect to the energy use or efficiency of refrigerated bottled or canned beverage vending machines in accordance with the results of testing pursuant to this Appendix A or the procedures in 10 CFR 431.294 as it appeared in the edition of 10 CFR parts 200 to 499 revised as of January 1, 2015. Any representations made with respect to the energy use or efficiency of such refrigerated beverage vending machines must be in accordance with whichever version is selected. On or after January 27, 2016, manufacturers must make any representations with respect to energy use or efficiency in accordance with the results of testing pursuant to this Appendix A to demonstrate compliance with the energy conservation standards at 10 CFR 431.296, for which compliance was required as of August 31, 2012.
1. General. Section 3, “Definitions”; section 4, “Instruments”; section 5, “Vendible Capacity”; section 6, “Test Conditions”; section 7.1, “Test Procedures - General Requirements”; and section 7.2, “Energy Consumption Test” of ANSI/ASHRAE 32.1 (incorporated by reference; see § 431.293) apply to this appendix except as noted throughout this appendix. In cases where there is a conflict, the language of the test procedure in this appendix takes precedence over ANSI/ASHRAE 32.1.
1.1. Instruments. In addition to the instrument accuracy requirements in section 4, “Instruments,” of ANSI/ASHRAE 32.1 (incorporated by reference, see § 431.293), humidity shall be measured with a calibrated instrument accurate to ±2 percent RH at the specified ambient relative humidity condition specified in section 2.1.2 of this appendix.
1.2. Definitions. In addition to the definitions specified in section 3, “Definitions,” of ANSI/ASHRAE 32.1 (incorporated by reference, see § 431.293), the following definition is also applicable to this appendix.
External accessory standby mode means the mode of operation in which any external, integral customer display signs, lighting, or digital screens:
(1) Are connected to mains power;
(2) Do not produce the intended illumination, display, or interaction functionality; and
(3) Can be switched into another mode automatically with only a remote user-generated or an internal signal.
Instantaneous average next-to-vend beverage temperature means the spatial average of all standard test packages in the next-to-vend beverages positions at a given time.
Integrated average temperature means the average temperature of all standard test package measurements in the next-to-vend beverage positions taken over the duration of the test, expressed in degrees Fahrenheit ( °F).
Lowest application product temperature means the lowest integrated average temperature a given basic model is capable of maintaining so as to comply with the temperature stabilization requirements specified in section 7.2.2.2 of ANSI/ASHRAE 32.1 (incorporated by reference, see § 431.293).
2. Test Procedure.
2.1. Test Conditions. The test conditions specified in section 6, “Test Conditions,” of ANSI/ASHRAE 32.1 (incorporated by reference, see § 431.293) apply to this appendix except that in section 6.1, “Voltage and Frequency,” of ANSI/ASHRAE 32.1, the voltage and frequency tolerances specified in section 6.1.a of ANSI/ASHRAE 32.1 also apply equivalently to section 6.1.b of ANSI/ASHRAE 32.1 for equipment with dual nameplate voltages.
2.1.1. Average Beverage Temperature. The integrated average temperature measured during the test must be within ±1 °F of the value specified in Table A.1 of this appendix or the lowest application product temperature for models tested in accordance with paragraph 2.1.3 of this appendix. The measurement of integrated average temperature must begin after temperature stabilization has been achieved and continue for the following 24 consecutive hours. All references to “Table 1” in ANSI/ASHRAE 32.1 (incorporated by reference, see § 431.293) shall instead be interpreted as references to Table A.1 of this appendix and all references to “average beverage temperature” in ANSI/ASHRAE 32.1 shall instead be interpreted as references to the integrated average temperature as defined in section 1.2 of this appendix of this subpart, except as noted in section 2.1.1.1 of this appendix.
2.1.1.1. Temperature Stabilization. Temperature stabilization shall be determined in accordance with section 7.2.2.2 of ANSI/ASHRAE 32.1 (incorporated by reference § 431.293), except that the reference to “average beverage temperature” shall instead refer to the “instantaneous average next-to-vend beverage temperature,” as defined in section 1.2 of this appendix, and the reference to “Table 1” shall instead refer to Table A.1 of this appendix. That is, temperature stabilization is considered to be achieved 24 hours after the instantaneous average next-to-vend beverage temperature reaches the specified value (see Table A.1) and energy consumption for two successive 6 hour periods are within 2 percent of each other.
2.1.2. Ambient Test Conditions. The refrigerated bottled or canned beverage vending machine must be tested at the test conditions and tolerances specified in the following Table A.1 of this appendix. The specified ambient temperature and humidity conditions shall be maintained within the ranges specified for each recorded measurement. All references to “Table 1” in ANSI/ASHRAE 32.1 (incorporated by reference, see § 431.293) shall instead be interpreted as references to Table A.1 of this appendix. In contrast to the requirements of section 6.1 and Table 1 of ANSI/ASHRAE 32.1, conduct testing only one time at the conditions referenced in Table A.1 of this appendix. Testing at alternate ambient conditions is not required or permitted.
Table A.1 - Ambient Temperature and Relative Humidity Specified Value and Tolerance
Test and pretest condition | Value | Tolerance | Acceptable range (based on value and tolerance) |
---|---|---|---|
Instantaneous Average Next-to-Vend Temperature | 36 °F | ±1 °F | 35-37 °F. |
Integrated Average Temperature | 36 °F | ±1 °F | N/A (value is averaged throughout test). |
Ambient Temperature | 75 °F | ±2 °F | 73-77 °F. |
Relative Humidity | 45 percent RH | ±5 percent RH | 40-50 percent RH. |
2.1.3. Lowest Application Product Temperature. If a refrigerated bottled or canned beverage vending machine is not capable of maintaining an integrated average temperature of 36 °F (±1 °F) during the 24 hour test period, the unit must be tested at the lowest application product temperature, as defined in section 1.2 of this appendix. For refrigerated bottled or canned beverage vending machines equipped with a thermostat, the lowest application product temperature is the integrated average temperature achieved at the lowest thermostat setting.
2.2. Equipment Installation and Test Set Up. Except as provided in this appendix, the test procedure for energy consumption of refrigerated bottled or canned beverage vending machines shall be conducted in accordance with the methods specified in sections 7.1 through 7.2.2.3 under “Test Procedures” of ANSI/ASHRAE 32.1 (incorporated by reference, see § 431.293).
2.2.1. Equipment Loading. Configure refrigerated bottled or canned beverage vending machines to hold the maximum number of standard products in the refrigerated compartment(s) and place standard test packages as specified in section 2.2.1.1 or 2.2.1.2 of this appendix.
2.2.1.1. Placement of Standard Test Packages for Equipment with Products Arranged Horizontally. For refrigerated bottled or canned beverage vending machines with products arranged horizontally (e.g., on shelves or in product spirals), place standard test packages in the refrigerated compartment(s) in the following locations, as shown in Figure A.1:
(a) For odd-number shelves, when counting starting from the bottom shelf, standard test packages shall be placed at:
(1) The left-most next-to-vend product location,
(2) The right-most next-to-vend product location, and
(3) For equipment with greater than or equal to five next-to-vend product locations on each shelf, either:
(A) The next-to-vend product location in the center of the shelf (i.e., equidistant from the left-most and right-most next-to-vend product locations) if there are an odd number of next-to-vend products on the shelf or
(B) The next-to-vend product location immediately to the right and the left of the center position if there are an even number of next-to-vend products on the shelf.
(b) For even-numbered shelves, when counting from the bottom shelf, standard test packages shall be places at either:
(1) For equipment with less than or equal to six next-to-vend product locations on each shelf, the next-to-vend product location(s):
(A) One location towards the center from the left-most next-to-vend product location; and
(B) One location towards to the center from the right-most next-to-vend product location, or
(2) For equipment with greater than six next-to-vend product locations on each shelf, the next-to-vend product locations
(A) Two locations towards the center from the left-most next-to-vend product location; and
(B) Two locations towards to the center from the right-most next-to-vend product location.
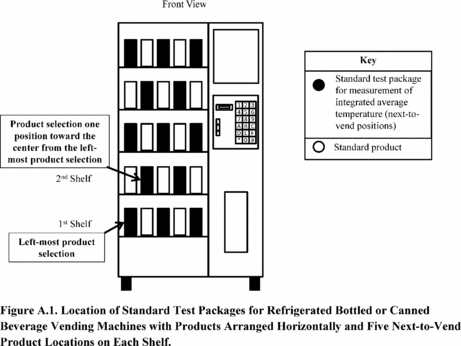
2.2.1.2. Placement of Standard Test Packages for Equipment with Products Arranged Vertically. For refrigerated bottled or canned beverage vending machines with products arranged vertically (e.g., in stacks), place standard test packages in the refrigerated compartment(s) in each next-to-vend product location.
2.2.1.3. Loading of Combination Vending Machines. For combination vending machines, the non-refrigerated compartment(s) must not be loaded with any standard products, test packages, or other vendible merchandise.
2.2.1.4. Standard Products. The standard product shall be standard 12-ounce aluminum beverage cans filled with a liquid with a density of 1.0 grams per milliliter (g/mL) ± 0.1 g/mL at 36 °F. For product storage racks that are not capable of vending 12-ounce cans, but are capable of vending 20-ounce bottles, the standard product shall be 20-ounce plastic bottles filled with a liquid with a density of 1.0 g/mL ± 0.1 g/mL at 36 °F. For product storage racks that are not capable of vending 12-ounce cans or 20-ounce bottles, the standard product shall be the packaging and contents specified by the manufacturer in product literature as the standard product (i.e., the specific merchandise the refrigerated bottled or canned beverage vending machine is designed to vend).
2.2.1.5. Standard Test Packages. A standard test package is a standard product, as specified in 2.2.1.4 of this appendix, altered to include a temperature-measuring instrument at its center of mass.
2.2.2. Sensor Placement. The integrated average temperature of next-to-vend beverages shall be measured in standard test packages in the next-to-vend product locations specified in section 2.2.1.1 of this appendix. Do not run the thermocouple wire and other measurement apparatus through the dispensing door; the thermocouple wire and other measurement apparatus must be configured and sealed so as to minimize air flow between the interior refrigerated volume and the ambient room air. If a manufacturer chooses to employ a method other than routing thermocouple and sensor wires through the door gasket and ensuring the gasket is compressed around the wire to ensure a good seal, then it must maintain a record of the method used in the data underlying that basic model's certification pursuant to 10 CFR 429.71.
2.2.3. Accessories. (a) All standard components that would be used during normal operation of the model in the field and are necessary to provide sufficient functionality for cooling and vending products in field installations (i.e., product inventory, temperature management, product merchandising (including, e.g., lighting or signage), product selection, and product transport and delivery) shall be in place during testing and shall be set to the maximum energy-consuming setting if manually adjustable, except that the specific components and accessories listed in the subsequent sections shall be operated as stated. Components not necessary for the inventory, temperature management, product merchandising (e.g., lighting or signage), product selection, and or product transport and delivery shall be de-energized. If systems not required for the primary functionality of the machine as stated in this section cannot be de-energized without preventing the operation of the machine, then they shall be placed in the lowest energy consuming state.
(b) Instead of testing pursuant to section 7.2.2.4 of ANSI/ASHRAE 32.1 (incorporated by reference, see § 431.293), provide, if necessary, any physical stimuli or other input to the machine needed to prevent automatic activation of energy management systems that can be adjusted by the machine operator during the test period. Automatic energy management systems that cannot be adjusted by the machine operator may be enabled, as specified by section 7.2.1 of ANSI/ASHRAE 32.1.
2.2.3.1. Payment Mechanisms. Refrigerated bottled or canned beverage vending machines shall be tested with no payment mechanism in place, the payment mechanism in place but de-energized, or the payment mechanism in place but set to the lowest energy consuming state, if it cannot be de-energized. A default payment mechanism energy consumption value of 0.20 kWh/day shall be added to the primary rated energy consumption per day, as required in section 2.3 of this appendix.
2.2.3.2. Internal Lighting. All lighting that is contained within or is part of the internal physical boundary of the refrigerated bottled or canned beverage vending machine, as established by the top, bottom, and side panels of the equipment, shall be placed in its maximum energy consuming state.
2.2.3.3. External Customer Display Signs, Lights, and Digital Screens. All external customer display signs, lights, and digital screens that are independent from the refrigeration or vending performance of the refrigerated bottled or canned beverage vending machine must be disconnected, disabled, or otherwise de-energized for the duration of testing. Customer display signs, lighting, and digital screens that are integrated into the beverage vending machine cabinet or controls such that they cannot be de-energized without disabling the refrigeration or vending functions of the refrigerated bottled or canned beverage vending machine or modifying the circuitry must be placed in external accessory standby mode, if available, or their lowest energy-consuming state. Digital displays that also serve a vending or money processing function must be placed in the lowest energy-consuming state that still allows the money processing feature to function.
2.2.3.4. Anti-sweat and Other Electric Resistance Heaters. Anti-sweat and other electric resistance heaters must be operational during the entirety of the test procedure. Units with a user-selectable setting must have the heaters energized and set to the most energy-consumptive position. Units featuring an automatic, non-user-adjustable controller that turns on or off based on environmental conditions must be operating in the automatic state. Units that are not shipped with a controller from the point of manufacture, but are intended to be used with a controller, must be equipped with an appropriate controller when tested.
2.2.3.5. Condensate Pan Heaters and Pumps. All electric resistance condensate heaters and condensate pumps must be installed and operational during the test. Prior to the start of the test, including the 24 hour period used to determine temperature stabilization, as described in ANSI/ASHRAE 32.1 section 7.2.2.2 (incorporated by reference, see § 431.293), the condensate pan must be dry. For the duration of the test, including the 24 hour time period necessary for temperature stabilization, allow any condensate moisture generated to accumulate in the pan. Do not manually add or remove water from the condensate pan at any time during the test.
2.2.3.6. Illuminated Temperature Displays. All illuminated temperature displays must be energized and operated during the test the same way they would be energized and operated during normal field operation, as recommended in manufacturer product literature, including manuals.
2.2.3.7. Condenser Filters. Remove any nonpermanent filters provided to prevent particulates from blocking a model's condenser coil.
2.2.3.8. Security Covers. Remove any devices used to secure the model from theft or tampering.
2.2.3.9. General Purpose Outlets. During the test, do not connect any external load to any general purpose outlets available on a unit.
2.2.3.10. Crankcase Heaters and Other Electric Resistance Heaters for Cold Weather. Crankcase heaters and other electric resistance heaters for cold weather must be operational during the test. If a control system, such as a thermostat or electronic controller, is used to modulate the operation of the heater, it must be activated during the test and operated in accordance with the manufacturer's instructions.
2.2.4. Sampling and Recording of Data. Record the data listed in section 7.2.2.3 of ANSI/ASHRAE 32.1 (incorporated by reference, see § 431.293) at least every 1 minute. For the purpose of this subsection, “average beverage temperature,” listed in section 7.2.2.3 of ANSI/ASHRAE 32.1, means “instantaneous average next-to-vend beverage temperature.”
2.3. Determination of Daily Energy Consumption. Determine the daily energy consumption of each tested refrigerated bottled or canned beverage vending machine as the sum of:
(a) The default payment mechanism energy consumption value from section 2.2.3.1 of this appendix and
(b) The primary rated energy consumption per day (ED), in kWh, and determined in accordance with the calculation procedure in section 7.2.3.1, “Calculation of Daily Energy Consumption,” of ANSI/ASHRAE 32.1 (incorporated by reference, see § 431.293).
2.3.1. Calculations and Rounding. In all cases, the primary rated energy consumption per day (ED) must be calculated with raw measured values and rounded to units of 0.01 kWh/day.
3. Determination of Refrigerated Volume, Vendible Capacity, and Surface Area.
3.1. Refrigerated Volume. Determine the “refrigerated volume” of refrigerated bottled or canned beverage vending machines in accordance with appendix C, “Measurement of Volume,” of ANSI/ASHRAE 32.1 (incorporated by reference, see § 431.293). For combination vending machines, the “refrigerated volume” does not include any non-refrigerated compartments.
3.2. Vendible Capacity. Determine the “vendible capacity” of refrigerated bottled or canned beverage vending machines in accordance with the first paragraph of section 5, “Vending Machine Capacity,” of ANSI/ASHRAE 32.1, (incorporated by reference, see § 431.293). For combination vending machines, the “vendible capacity” includes only the capacity of any portion of the refrigerated bottled or canned beverage vending machine that is refrigerated and does not include the capacity of the non-refrigerated compartment(s).
[80 FR 45793, July 31, 2015]Appendix A to Subpart R of Part 431 - Uniform Test Method for the Measurement of Energy Consumption of the Components of Envelopes of Walk-In Coolers and Walk-In Freezers
10:3.0.1.4.19.18.85.7.59 : Appendix A
Appendix A to Subpart R of Part 431 - Uniform Test Method for the Measurement of Energy Consumption of the Components of Envelopes of Walk-In Coolers and Walk-In Freezers 1.0 ScopeThis appendix covers the test requirements used to measure the energy consumption of the components that make up the envelope of a walk-in cooler or walk-in freezer.
2.0 DefinitionsThe definitions contained in § 431.302 are applicable to this appendix.
3.0 Additional Definitions3.1 Automatic door opener/closer means a device or control system that “automatically” opens and closes doors without direct user contact, such as a motion sensor that senses when a forklift is approaching the entrance to a door and opens it, and then closes the door after the forklift has passed.
3.2-3.3 [Reserved]
3.4 Surface area means the area of the surface of the walk-in component that would be external to the walk-in cooler or walk-in freezer as appropriate.
3.5 Rated power means the electricity consuming device's power as specified on the device's nameplate. If the device does not have a nameplate or such nameplate does not list the device's power, then the rated power must be read from the device's product data sheet.
3.6 Rating conditions means, unless explicitly stated otherwise, all conditions shown in Table A.1 of this section.
3.7 Percent time off (PTO) means the percent of time that an electrical device is assumed to be off.
Table A.1 - Temperature Conditions
Internal Temperatures (cooled space within the envelope) | |
Cooler Dry Bulb Temperature | 35 °F |
Freezer Dry Bulb Temperature | −10 °F |
External Temperatures (space external to the envelope) | |
Freezer and Cooler Dry Bulb Temperatures | 75 °F. |
4.1 Display Panels
(a) Calculate the U-factor of the display panel in accordance with section 5.3 of this appendix, Btu/h-ft 2- °F.
(b) Calculate the display panel surface area, as defined in section 3.4 of this appendix, Adp, ft 2, with standard geometric formulas or engineering software.
(c) Calculate the temperature differential, ΔTdp, °F, for the display panel, as follows:

(d) Calculate the conduction load through the display panel, Qcond-dp, Btu/h, as follows:

(e) Select Energy Efficiency Ratio (EER), as follows:
(1) For coolers, use EER = 12.4 Btu/W-h
(2) For freezers, use EER = 6.3 Btu/W-h
(f) Calculate the total daily energy consumption, Edp, kWh/day, as follows:

4.2 [Reserved]
4.3 [Reserved]
4.4 Display Doors 4.4.1 Conduction Through Display Doors(a) Calculate the U-factor of the door in accordance with section 5.3 of this appendix, Btu/h-ft 2- °F
(b) Calculate the surface area, as defined in section 3.4 of this appendix, of the display door, Add, ft 2, with standard geometric formulas or engineering software.
(c) Calculate the temperature differential, ΔTdd, °F, for the display door as follows:

(d) Calculate the conduction load through the display doors, Qcond-dd, Btu/h, as follows:

Electrical components associated with display doors could include, but are not limited to: heater wire (for anti-sweat or anti-freeze application); lights (including display door lighting systems); control system units; and sensors.
(a) Select the required value for percent time off (PTO) for each type of electricity consuming device, PTOt (%)
(1) For lights without timers, control system or other demand-based control, PTO = 25 percent. For lighting with timers, control system or other demand-based control, PTO = 50 percent.
(2) For anti-sweat heaters on coolers (if included): Without timers, control system or other demand-based control, PTO = 0 percent. With timers, control system or other demand-based control, PTO = 75 percent. For anti-sweat heaters on freezers (if included): Without timers, control system or other auto-shut-off systems, PTO = 0 percent. With timers, control system or other demand-based control, PTO = 50 percent.
(3) For all other electricity consuming devices: Without timers, control system, or other auto-shut-off systems, PTO = 0 percent. If it can be demonstrated that the device is controlled by a preinstalled timer, control system or other auto-shut-off system, PTO = 25 percent.
(b) Calculate the power usage for each type of electricity consuming device, Pdd-comp,u,t, kWh/day, as follows:

(c) Calculate the total electrical energy consumption for interior and exterior power, Pdd-tot, int (kWh/day) and Pdd-tot, ext (kWh/day), respectively, as follows:
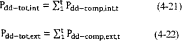
(d) Calculate the total electrical energy consumption, Pdd-tot, (kWh/day), as follows:

(a) Select Energy Efficiency Ratio (EER), as follows:
(1) For coolers, use EER = 12.4 Btu/Wh
(2) For freezers, use EER = 6.3 Btu/Wh
(b) Calculate the additional refrigeration energy consumption due to thermal output from electrical components sited inside the display door, Cdd-load, kWh/day, as follows:

(a) Select Energy Efficiency Ratio (EER), as follows:
(1) For coolers, use EER = 12.4 Btu/W-h
(2) For freezers, use EER = 6.3 Btu/W-h
(b) Calculate the total daily energy consumption due to conduction thermal load, Edd, thermal, kWh/day, as follows:

(c) Calculate the total energy, Edd,tot, kWh/day,

(a) Calculate the surface area, as defined in section 3.4 of this appendix, of the non-display door, And, ft 2, with standard geometric formulas or with engineering software.
(b) Calculate the temperature differential of the non-display door, ΔTnd, °F, as follows:

(c) Calculate the conduction load through the non-display door: Qcond-nd, Btu/h,

Electrical components associated with a walk-in non-display door comprise any components that are on the non-display door and that directly consume electrical energy. This includes, but is not limited to, heater wire (for anti-sweat or anti-freeze application), control system units, and sensors.
(a) Select the required value for percent time off for each type of electricity consuming device, PTOt (%)
(1) For lighting without timers, control system or other demand-based control, PTO = 25 percent. For lighting with timers, control system or other demand-based control, PTO = 50 percent.
(2) For anti-sweat heaters on coolers (if included): Without timers, control system or other demand-based control, PTO = 0 percent. With timers, control system or other demand-based control, PTO = 75 percent. For anti-sweat heaters on freezers (if included): Without timers, control system or other auto-shut-off systems, PTO = 0 percent. With timers, control system or other demand-based control, PTO = 50 percent.
(3) For all other electricity consuming devices: Without timers, control system, or other auto-shut-off systems, PTO = 0 percent. If it can be demonstrated that the device is controlled by a preinstalled timer, control system or other auto-shut-off system, PTO = 25 percent.
(b) Calculate the power usage for each type of electricity consuming device, Pnd-comp,u,t, kWh/day, as follows:

(c) Calculate the total electrical energy consumption for interior and exterior power, Pnd-tot, int (kWh/day) and Pnd-tot, ext (kWh/day), respectively, as follows:
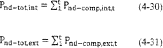
(d) Calculate the total electrical energy consumption, Pnd-tot, kWh/day, as follows:

(a) Select Energy Efficiency Ratio (EER), as follows:
(1) For coolers, use EER = 12.4 Btu/Wh
(2) For freezers, use EER = 6.3 Btu/Wh
(b) Calculate the additional refrigeration energy consumption due to thermal output from electrical components associated with the non-display door, Cnd-load, kWh/day, as follows:

(a) Select Energy Efficiency Ratio (EER), as follows:
(1) For coolers, use EER = 12.4 Btu/W-h
(2) For freezers, use EER = 6.3 Btu/W-h
(b) Calculate the total daily energy consumption due to thermal load, End, thermal, kWh/day, as follows:

(c) Calculate the total energy, End,tot, kWh/day, as follows:

5.1-5.2 [Reserved]
5.3 U-factor of Doors and Display Panels(a) Follow the procedure in NFRC 100, (incorporated by reference; see § 431.303), exactly, with these exceptions:
(1) The average surface heat transfer coefficient on the cold-side of the apparatus shall be 30 Watts per square-meter-Kelvin (W/m 2*K) ±5%. The average surface heat transfer coefficient on the warm-side of the apparatus shall be 7.7 Watts per square-meter-Kelvin (W/m 2*K) ±5%.
(2) Cold-side conditions:
(i) Air temperature of 35 °F (1.7 °C) for cooler doors and −10 °F (−23.3 °C) for freezer doors
(ii) Mean inside radiant temperature must be the same as shown in section 5.3(a)(2)(i), above.
(3) Warm-side conditions
(i) Air temperature of 75 °F (23.9 °C)
(ii) Mean outside radiant temperature must be the same as section 5.3(a)(3)(i), above.
(4) Direct solar irradiance = 0 W/m 2 (Btu/h-ft 2).
(b) Required Test Measurements
(i) Display Doors and Display Panels
1. Thermal Transmittance: Udd
(ii) Non-Display Door
1. Thermal Transmittance: Und
[76 FR 21606, Apr. 15, 2011, as amended at 76 FR 31796, June 2, 2011; 76 FR 33632, June 9, 2011; 79 FR 27414, May 13, 2014; 81 FR 95803, Dec. 28, 2016]Appendix A to Subpart T of Part 431 - Uniform Test Method for Certain Air Compressors
10:3.0.1.4.19.20.87.7.62 : Appendix A
Appendix A to Subpart T of Part 431 - Uniform Test Method for Certain Air Compressors Note:Starting on July 3, 2017, any representations made with respect to the energy use or efficiency of compressors subject to testing pursuant to 10 CFR 431.344 must be made in accordance with the results of testing pursuant to this appendix.
I. Measurements, Test Conditions, and Equipment Configuration A. Measurement EquipmentA.1. For the purposes of measuring air compressor performance, the equipment necessary to measure volume flow rate, inlet and discharge pressure, temperature, condensate, and packaged compressor power input must comply with the equipment and accuracy requirements specified in ISO 1217:2009(E) sections 5.2, 5.3, 5.4, 5.6, 5.9, and Annex C, sections C.2.3 and C.2.4 (incorporated by reference, see § 431.343).
A.2. Electrical measurement equipment must be capable of measuring true root mean square (RMS) current, true RMS voltage, and real power up to the 40th harmonic of fundamental supply source frequency.
A.3. Any instruments used to measure a particular parameter specified in paragraph (A.1.) must have a combined accuracy of ±2.0 percent of the measured value at the fundamental supply source frequency, where combined accuracy is the square root of the sum of the squares of individual instrument accuracies.
A.4. Any instruments used to directly measure the density of air must have an accuracy of ±1.0 percent of the measured value.
A.5. Any pressure measurement equipment used in a calculation of another variable (e.g., actual volume flow rate) must also meet all accuracy and measurement requirements of section 5.2 of ISO 1217:2009(E) (incorporated by reference, see § 431.343).
A.6. Any temperature measurement equipment used in a calculation of another variable (e.g., actual volume flow rate) must also meet all accuracy and measurement requirements of section 5.3 of ISO 1217:2009(E) (incorporated by reference, see § 431.343).
A.7. Where ISO 1217:2009(E) refers to “corrected volume flow rate,” the term is deemed synonymous with the term “actual volume flow rate,” as defined in section 3.4.1 of ISO 1217:2009(E) (incorporated by reference, see § 431.343).
B. Test Conditions and Configuration of Unit Under TestB.1. For both fixed-speed and variable-speed compressors, conduct testing in accordance with the test conditions, unit configuration, and specifications of ISO 1217:2009(E), Section 6.2 paragraphs (g) and (h) and Annex C, sections C.1.1, C.2.2, C.2.3, C.2.4, C.4.1, C.4.2.1, C.4.2.3, and C.4.3.2 (incorporated by reference, see § 431.343).
B.2. The power supply must:
(1) Maintain the voltage greater than or equal to 95 percent and less than or equal to 110 percent of the rated value of the motor,
(2) Maintain the frequency within ±5 percent of the rated value of the motor,
(3) Maintain the voltage unbalance of the power supply within ±3 percent of the rated values of the motor, and
(4) Maintain total harmonic distortion below 12 percent throughout the test.
B.3. Ambient Conditions. The ambient air temperature must be greater than or equal to 68 °F and less than or equal to 90 °F for the duration of testing. There are no ambient condition requirements for inlet pressure or relative humidity.
B.4. All equipment indicated in Table 1 of this appendix must be present and installed for all tests specified in this appendix. If the compressor is distributed in commerce without an item from Table 1 of this appendix, the manufacturer must provide an appropriate item to be installed for the test. Additional ancillary equipment may be installed for the test, if distributed in commerce with the compressor, but this additional ancillary equipment is not required. If any of the equipment listed in Table 2 of this appendix is distributed in commerce with units of the compressor basic model, it must be present and installed for all tests specified in this appendix.
Table 1 - Equipment Required During Test
Equipment | Fixed-speed rotary air compressors |
Variable-speed rotary air compressors |
---|---|---|
Driver | Yes | Yes. |
Bare compressors | Yes | Yes. |
Inlet filter | Yes | Yes. |
Inlet valve | Yes | Yes. |
Minimum pressure check valve/backflow check valve | Yes | Yes. |
Lubricant separator | Yes | Yes. |
Air piping | Yes | Yes. |
Lubricant piping | Yes | Yes. |
Lubricant filter | Yes | Yes. |
Lubricant cooler | Yes | Yes. |
Thermostatic valve | Yes | Yes. |
Electrical switchgear or frequency converter for the driver | Yes | Not applicable. 1 |
Device to control the speed of the driver (e.g., variable speed drive) | Not applicable 2 | Yes. |
Compressed air cooler(s) | Yes | Yes. |
Pressure switch, pressure transducer, or similar pressure control device | Yes | Yes. |
Moisture separator and drain | Yes | Yes. |
1 This category is not applicable to variable-speed rotary air compressors.
2 This category is not applicable to fixed-speed rotary air compressors.
Table 2 - Equipment Required During Test, if Distributed in Commerce With the Basic Model
Equipment | Fixed-speed rotary air compressors |
Variable-speed rotary air compressors |
---|---|---|
Cooling fan(s) and motors | Yes | Yes. |
Mechanical equipment | Yes | Yes. |
Lubricant pump | Yes | Yes. |
Interstage cooler | Yes | Yes. |
Electronic or electrical controls and user interface | Yes | Yes. |
All protective and safety devices | Yes | Yes. |
B.5. The inlet of the compressor under test must be open to the atmosphere and take in ambient air for all tests specified in this appendix.
B.6. The compressor under test must be set up according to all manufacturer instructions for normal operation (e.g., verify lubricant level, connect all loose electrical connections, close off bottom of unit to floor, cover forklift holes).
B.7. The piping connected to the discharge orifice of the compressor must be of a diameter at least equal to that of the compressor discharge orifice to which it is connected. The piping must be straight with a length of at least 6 inches.
B.8. Transducers used to record compressor discharge pressure must be located on the discharge piping between 2 inches and 6 inches, inclusive, from the discharge orifice of the compressor. The pressure tap for transducers must be located at the highest point of the pipe's cross section.
II. Determination of Package Isentropic Efficiency, Package Specific Power, and Pressure Ratio at Full-Load Operating Pressure A. Data Collection and AnalysisA.1. Stabilization. Record data at each load point under steady-state conditions. Steady-state conditions are achieved when a set of two consecutive readings taken at least 10 seconds apart and no more than 60 seconds apart are within the maximum permissible fluctuation from the average (of the two consecutive readings), as specified in Table 1 of ISO 1217:2009(E) (incorporated by reference, see § 431.343) for -
(1) Discharge pressure;
(2) Temperature at the nozzle or orifice plate, measured per section 5.3 of ISO 1217:2009(E) (incorporated by reference, see § 431.343); and
(3) Differential pressure over the nozzle or orifice plate, measured per section 5.2 of ISO 1217:2009(E) (incorporated by reference, see § 431.343).
A.2. Data Sampling and Frequency. At each load point, record a minimum set of 16 unique readings, collected over a minimum time of 15 minutes. Each consecutive reading must be no more than 60 seconds apart, and not less than 10 seconds apart. All readings at each load point must be within the maximum permissible fluctuation from average specified in Table 1 of ISO 1217:2009(E) (incorporated by reference, see § 431.343) for -
(1) Discharge pressure;
(2) Temperature at the nozzle or orifice plate, measured per section 5.3 of ISO 1217:2009(E) (incorporated by reference, see § 431.343); and
(3) Differential pressure over the nozzle or orifice plate, measured per section 5.2 of ISO 1217:2009(E) (incorporated by reference, see § 431.343).
If one or more readings do not meet the requirements, then all previous readings must be disregarded and a new set of at least 16 new unique readings must be collected over a minimum time of 15 minutes. Average the readings to determine the value of each parameter to be used in subsequent calculations.
A.3. Calculations and Rounding. Perform all calculations using raw measured values. Round the final result for package isentropic efficiency to the thousandth (i.e., 0.001), for package specific power in kilowatts per 100 cubic feet per minute to the nearest hundredth (i.e., 0.01), for pressure ratio at full-load operating pressure to the nearest tenth (i.e., 0.1), for full-load actual volume flow rate in cubic feet per minute to the nearest tenth (i.e., 0.1), and for full-load operating pressure in pounds per square inch gauge (psig) to the nearest integer (i.e., 1). All terms and quantities refer to values determined in accordance with the procedures set forth in this appendix for the tested unit.
B. Full-Load Operating Pressure and Full-Load Actual Volume Flow RateDetermine the full-load operating pressure and full-load actual volume flow rate (referenced throughout this appendix) in accordance with the procedures prescribed in section III of this appendix.
C. Full-Load Package Isentropic Efficiency for Fixed- and Variable-Speed Air CompressorsUse this test method to test fixed-speed air compressors and variable-speed air compressors.
C.1. Test unit at full-load operating pressure and full-load volume flow rate according to the requirements established in sections I, II.A, and II.B of this appendix. Measure volume flow rate and calculate actual volume flow rate in accordance with section C.4.2.1 of Annex C of ISO 1217:2009(E) (incorporated by reference, see § 431.343) with no corrections made for shaft speed. Measure discharge gauge pressure and packaged compressor power input. Measured discharge gauge pressure and calculated actual volume flow rate must be within the deviation limits for discharge pressure and volume flow rate specified in Tables C.1 and C.2 of Annex C of ISO 1217:2009(E) (incorporated by reference, see § 431.343), where full-load operating pressure and full-load actual volume flow rate (as determined in section III of this appendix) are the targeted values.
C.2. Calculate the package isentropic efficiency at full-load operating pressure and full-load actual volume flow rate (full-load package isentropic efficiency, ηisen,FL) using the equation for isentropic efficiency in section 3.6.1 of ISO 1217:2009(E) as modified by ISO 1217:2009/Amd.1:2016(E) (incorporated by reference, see § 431.343). For Pisen, use the isentropic power required for compression at full-load operating pressure and full-load actual volume flow rate, as determined in section II.C.2.1 of this appendix. For Preal, use the real packaged compressor power input at full-load operating pressure and full-load actual volume flow rate, as determined in section II.C.2.2 of this appendix.
C.2.1. Calculate the isentropic power required for compression at full-load operating pressure and full-load actual volume flow rate using equation (H.6) of Annex H of ISO 1217:2009/Amd.1:2016(E) (incorporated by reference, see § 431.343). For qV1, use the actual volume flow rate (cubic meters per second) calculated in section II.C.1 of this appendix. For p1, use 100 kPa. For p2, use the sum of (a) 100 kPa, and (b) the measured discharge gauge pressure (Pa) from section II.C.1 of this appendix. For K, use the isentropic exponent (ratio of specific heats) of air, which, for the purposes of this test procedure, is 1.400.
C.2.2. Calculate real packaged compressor power input at full-load operating pressure and full-load actual volume flow rate using the following equation:
Preal,100% = K5 · PPR,100% Where: K5 = correction factor for inlet pressure, as determined in section C.4.3.2 of Annex C to ISO 1217:2009(E) (incorporated by reference, see § 431.343). For calculations of this variable use a value of 100 kPa for contractual inlet pressure; and PPR,100% = packaged compressor power input reading at full-load operating pressure and full-load actual volume flow rate measured in section II.C.1 of this appendix (W). D. Part-Load Package Isentropic Efficiency for Variable-Speed Air CompressorsUse this test method to test variable-speed air compressors.
D.1. Test unit at two load points: (1) Full-load operating pressure and 70 percent of full-load actual volume flow rate and (2) full-load operating pressure and 40 percent of full-load actual volume flow rate, according to the requirements established in sections I, II.A, and II.B of this appendix. To reach each specified load point, adjust the speed of the driver and the backpressure of the system. For each load point, measure volume flow rate and calculate actual volume flow rate in accordance with section C.4.2.1 of Annex C of ISO 1217:2009(E) (incorporated by reference, see § 431.343), with no corrections made for shaft speed. For each load point, measure discharge gauge pressure and packaged compressor power input. Measured discharge gauge pressure and calculated actual volume flow rate must be within the deviation limits for discharge pressure and volume flow rate specified in Tables C.1 and C.2 of Annex C of ISO 1217:2009(E), where the targeted values are as specified in the beginning of this section.
D.2. For variable-speed compressors, calculate the part-load package isentropic efficiency using the following equation:
ηisen,PL = ω40% × ηisen,40% + ω70% × ηisen,70% + ω100% × ηisen,100% Where: ηisen,PL = part-load package isentropic efficiency for a variable-speed compressor; ηisen,100% = package isentropic efficiency at full-load operating pressure and 100 percent of full-load actual volume flow rate, as determined in section II.C.2 of this appendix; ηisen,70% = package isentropic efficiency at full-load operating pressure and 70 percent of full-load actual volume flow rate, as determined in section II.D.3 of this appendix; ηisen,40% = package isentropic efficiency at full-load operating pressure and 40 percent of full-load actual volume flow rate, as determined in section II.D.4 of this appendix; ω40% = weighting at 40 percent of full-load actual volume flow rate and is 0.25; ω70% = weighting at 70 percent of full-load actual volume flow rate and is 0.50; and ω100% = weighting at 100 percent of full-load actual volume flow rate and is 0.25.D.3. Calculate package isentropic efficiency at full-load operating pressure and 70 percent of full-load actual volume flow rate using the equation for isentropic efficiency in section 3.6.1 of ISO 1217:2009(E) as modified by ISO 1217:2009/Amd.1:2016(E) (incorporated by reference, see § 431.343). For Pisen, use the isentropic power required for compression at full-load operating pressure and 70 percent of full-load actual volume flow rate, as determined in section II.D.3.1 of this appendix. For Preal, use the real packaged compressor power input at full-load operating pressure and 70 percent of full-load actual volume flow rate, as determined in section II.D.3.2 of this appendix.
D.3.1. Calculate the isentropic power required for compression at full-load operating pressure and 70 percent of full-load actual volume flow rate using equation (H.6) of Annex H of ISO 1217:2009/Amd.1:2016(E) (incorporated by reference, see § 431.343). For qV1, use actual volume flow rate (cubic meters per second) at full-load operating pressure and 70 percent of full-load actual volume flow rate, as calculated in section II.D.1 of this appendix. For p1, use 100 kPa. For p2, use the sum of (a) 100 kPa, and (b) discharge gauge pressure (Pa) at full-load operating pressure and 70 percent of full-load actual volume flow rate, as calculated in section II.D.1 of this appendix. For K, use the isentropic exponent (ratio of specific heats) of air, which, for the purposes of this test procedure, is 1.400.
D.3.2. Calculate real packaged compressor power input at full-load operating pressure and 70 percent of full-load actual volume flow rate using the following equation:
Preal,70% = K5 · PPR,70% Where: K5 = correction factor for inlet pressure, as determined in section C.4.3.2 of Annex C to ISO 1217:2009(E) (incorporated by reference, see § 431.343). For calculations of this variable use a value of 100 kPa for contractual inlet pressure; and PPR,70% = packaged compressor power input reading at full-load operating pressure and 70 percent of full-load actual volume flow rate, as measured in section II.D.1 of this appendix (W).D.4. Calculate package isentropic efficiency at full-load operating pressure and 40 percent of full-load actual volume flow rate using the equation for isentropic efficiency in section 3.6.1 of ISO 1217:2009(E) as modified by ISO 1217:2009/Amd.1:2016(E) (incorporated by reference, see § 431.343). For Pisen, use the isentropic power required for compression at full-load operating pressure and 40 percent of full-load actual volume flow rate, as determined in section II.D.4.1 of this appendix. For Preal, use the real packaged compressor power input at full-load operating pressure and 40 percent of full-load actual volume flow rate, as determined in section II.D.4.2 of this appendix.
D.4.1. Calculate the isentropic power required for compression at full-load operating pressure and 40 percent of full-load actual volume flow rate using equation (H.6) of Annex H of ISO 1217:2009/Amd.1:2016(E) (incorporated by reference, see § 431.343). For qV1, use actual volume flow rate (cubic meters per second) at full-load operating pressure and 40 percent of full-load actual volume flow rate, as calculated in section II.D.1 of this appendix. For p1, use 100 kPa. For p2, use the sum of (a) 100 kPa, and (b) discharge gauge pressure (Pa) at full-load operating pressure and 40 percent of full-load actual volume flow rate, as calculated in section II.D.1 of this appendix. For K, use the isentropic exponent (ratio of specific heats) of air, which, for the purposes of this test procedure, is 1.400.
D.4.2. Calculate real packaged compressor power input at full-load operating pressure and 40 percent of full-load actual volume flow rate using the following equation:
Preal,40% = K5 · PPR,40% Where: K5 = correction factor for inlet pressure, as determined in section C.4.3.2 of Annex C to ISO 1217:2009(E) (incorporated by reference, see § 431.343). For calculations of this variable use a value of 100 kPa for contractual inlet pressure; and PPR,40% = packaged compressor power input reading at full-load operating pressure and 40 percent of full-load actual volume flow rate, as measured in section II.D.1 of this appendix (W). E. Determination of Package Specific PowerFor both fixed and variable-speed air compressors, determine the package specific power, at any load point, using the equation for specific energy consumption in section C.4.4 of Annex C of ISO 1217:2009(E) (incorporated by reference, see § 431.343) and other values measured pursuant to this appendix, with no correction for shaft speed. Calculate PPcorr in section C.4.4 of Annex C of ISO 1217:2009(E) (incorporated by reference, see § 431.343) using the following equation:
PPcorr = K5 · PPR Where: K5 = correction factor for inlet pressure, as determined in section C.4.3.2 of Annex C to ISO 1217:2009(E) (incorporated by reference, see § 431.343). For calculations of this variable use a value of 100 kPa for contractual inlet pressure; and PPR = packaged compressor power input reading (W), as determined in section C.2.4 of Annex C to ISO 1217:2009(E) (incorporated by reference, see § 431.343). F. Determination of Pressure Ratio at Full-Load Operating PressurePressure ratio at full-load operating pressure, as defined in § 431.342, is calculated using the following equation:

The principal strategy of this method is to incrementally increase discharge pressure by 2 psig relative to a starting point, and identify the maximum full-flow operating pressure at which the compressor is capable of operating. The maximum discharge pressure achieved is the maximum full-flow operating pressure. The full-load operating pressure and full-load actual volume flow rate are determined based on the maximum full-flow operating pressure.
B. Pre-test Instructions B.1. SafetyFor the method presented in section III.C.1 of this appendix, only test discharge pressure within the safe operating range of the compressor, as specified by the manufacturer in the installation and operation manual shipped with the unit. Make no changes to safety limits or equipment. Do not violate any manufacturer-provided motor operational guidelines for normal use, including any restriction on instantaneous and continuous input power draw and output shaft power (e.g., electrical rating and service factor limits).
B.2. Adjustment of Discharge PressureB.2.1. If the air compressor is not equipped, as distributed in commerce by the manufacturer, with any mechanism to adjust the maximum discharge pressure output limit, proceed to section III.B.3 of this appendix.
B.2.2. If the air compressor is equipped, as distributed in commerce by the manufacturer, with any mechanism to adjust the maximum discharge pressure output limit, then adjust this mechanism to the maximum pressure allowed, according to the manufacturer's operating instructions for these mechanisms. Mechanisms to adjust discharge pressure may include, but are not limited to, onboard digital or analog controls, and user-adjustable inlet valves.
B.3. Driver speedIf the unit under test is a variable-speed compressor, maintain maximum driver speed throughout the test. If the unit under test is a fixed-speed compressor with a multi-speed driver, maintain driver speed at the maximum speed throughout the test.
B.4. Measurements and Tolerances B.4.1. RecordingRecord data by electronic means such that the requirements of section B.4.5 of section III of this appendix are met.
B.4.2. Discharge PressureMeasure discharge pressure in accordance with section 5.2 of ISO 1217:2009(E) (incorporated by reference, see § 431.343). Express compressor discharge pressure in psig in reference to ambient conditions, and record it to the nearest integer. Specify targeted discharge pressure points in integer values only. The maximum allowable measured deviation from the targeted discharge pressure at each tested point is ±1 psig.
B.4.3. Actual Volume Flow RateMeasure actual volume flow rate in accordance with section C.4.2.1 of Annex C of ISO 1217:2009(E) (incorporated by reference, see § 431.343) (where it is called “corrected volume flow rate”) with no corrections made for shaft speed. Express compressor actual volume flow rate in cubic feet per minute at inlet conditions (cfm).
B.4.4. StabilizationRecord data at each tested load point under steady-state conditions, as determined in section II.A.1 of this appendix.
B.4.5. Data Sampling and FrequencyAt each load point, record a set of at least of two readings, collected at a minimum of 10 seconds apart. All readings at each load point must be within the maximum permissible fluctuation from the average (of the two consecutive readings), as specified in II.A.2 of this appendix. Average the measurements to determine the value of each parameter to be used in subsequent calculations.
B.5. Adjusting System BackpressureSet up the unit under test so that backpressure on the unit can be adjusted (e.g., by valves) incrementally, causing the measured discharge pressure to change, until the compressor is in an unloaded condition.
B.6. Unloaded ConditionA unit is considered to be in an unloaded condition if capacity controls on the unit automatically reduce the actual volume flow rate from the compressor (e.g., shutting the motor off, or unloading by adjusting valves).
C. Test InstructionsC.1. Adjust the backpressure of the system so the measured discharge pressure is 90 percent of the expected maximum full-flow operating pressure, rounded to the nearest integer, in psig. If the expected maximum full-flow operating pressure is not known, then adjust the backpressure of the system so that the measured discharge pressure is 65 psig. Allow the unit to remain at this setting for 15 minutes to allow the unit to thermally stabilize. Then measure and record discharge pressure and actual volume flow rate at the starting pressure.
C.2. Adjust the backpressure of the system to increase the discharge pressure by 2 psig from the previous value, allow the unit to remain at this setting for a minimum of 2 minutes, and proceed to section III.C.3 of this appendix.
C.3. If the unit is now in an unloaded condition, end the test and proceed to section III.C.4 of this appendix. If the unit is not in an unloaded condition, measure discharge pressure and actual volume flow rate, and repeat section III.C.2 of this appendix.
C.4. Of the discharge pressures recorded under stabilized conditions in sections III.C.1 through III.C.3 of this appendix, identify the largest. This is the maximum full-flow operating pressure. Determine the full-load operating pressure as a self-declared value greater than or equal to the lesser of (A) 90 percent of the maximum full-flow operating pressure, or (B) 10 psig less than the maximum full-flow operating pressure.
C.5. The full-load actual volume flow rate is the actual volume flow rate measured at the full-load operating pressure. If the self-declared full-load operating pressure falls on a previously tested value of discharge pressure, then use the previously measured actual volume flow rate as the full-load actual volume flow rate. If the self-declared full-load operating pressure does not fall on a previously tested value of discharge pressure, then adjust the backpressure of the system to the self-declared full-load operating pressure and allow the unit to remain at this setting for a minimum of 2 minutes. The measured actual volume flow rate at this setting is the full-load actual volume flow rate.
[82 FR 1102, Jan. 4, 2017]Appendix A to Subpart U of Part 431 - Sampling Plan for Enforcement Testing of Electric Motors
10:3.0.1.4.19.21.87.8.63 : Appendix A
Appendix A to Subpart U of Part 431 - Sampling Plan for Enforcement Testing of Electric MotorsStep 1. The first sample size (n1) must be five or more units.
Step 2. Compute the mean (X 1 of the measured energy performance of the n1 units in the first sample as follows:
where Xi is the measured full-load efficiency of unit i.Step 3. Compute the sample standard deviation (S1) of the measured full-load efficiency of the n1 units in the first sample as follows:
Step 4. Compute the standard error (SE(X 1)) of the mean full-load efficiency of the first sample as follows:
Step 5. Compute the lower control limit (LCL1) for the mean of the first sample using RE as the desired mean as follows:
where: RE is the applicable EPCA nominal full-load efficiency when the test is to determine compliance with the applicable statutory standard, or is the labeled nominal full-load efficiency when the test is to determine compliance with the labeled efficiency value, and t is the 2.5th percentile of a t-distribution for a sample size of n1, which yields a 97.5 percent confidence level for a one-tailed t-test.Step 6. Compare the mean of the first sample (X 1) with the lower control limit (LCL1) to determine one of the following:
(i) If the mean of the first sample is below the lower control limit, then the basic model is in non-compliance and testing is at an end.
(ii) If the mean is equal to or greater than the lower control limit, no final determination of compliance or non-compliance can be made; proceed to Step 7.
Step 7. Determine the recommended sample size (n) as follows:
where S1, RE and t have the values used in Steps 3 and 5, respectively. The factor is based on a 20 percent tolerance in the total power loss at full-load and fixed output power.Given the value of n, determine one of the following:
(i) If the value of n is less than or equal to n1 and if the mean energy efficiency of the first sample (X 1) is equal to or greater than the lower control limit (LCL1), the basic model is in compliance and testing is at an end.
(ii) If the value of n is greater than n1, the basic model is in non-compliance. The size of a second sample n2 is determined to be the smallest integer equal to or greater than the difference n−n1. If the value of n2 so calculated is greater than 20−n1, set n2 equal to 20−n1.
Step 8. Compute the combined (X 2) mean of the measured energy performance of the n1 and n2 units of the combined first and second samples as follows:
Step 9. Compute the standard error (SE(X 2)) of the mean full-load efficiency of the n1 and n2 units in the combined first and second samples as follows:
(Note that S1 is the value obtained above in Step 3.)Step 10. Set the lower control limit (LCL2) to,
where t has the value obtained in Step 5, and compare the combined sample mean (X 2) to the lower control limit (LCL2) to find one of the following:(i) If the mean of the combined sample (X 2) is less than the lower control limit (LCL2), the basic model is in non-compliance and testing is at an end.
(ii) If the mean of the combined sample (X 2) is equal to or greater than the lower control limit (LCL2), the basic model is in compliance and testing is at an end.
Manufacturer-Option TestingIf a determination of non-compliance is made in Steps 6, 7 or 10, of this appendix A, the manufacturer may request that additional testing be conducted, in accordance with the following procedures.
Step A. The manufacturer requests that an additional number, n3, of units be tested, with n3 chosen such that n1 + n2 + n3 does not exceed 20.
Step B. Compute the mean full-load efficiency, standard error, and lower control limit of the new combined sample in accordance with the procedures prescribed in Steps 8, 9, and 10, of this appendix A.
Step C. Compare the mean performance of the new combined sample to the lower control limit (LCL2) to determine one of the following:
(a) If the new combined sample mean is equal to or greater than the lower control limit, the basic model is in compliance and testing is at an end.
(b) If the new combined sample mean is less than the lower control limit and the value of n1 + n2 + n3 is less than 20, the manufacturer may request that additional units be tested. The total of all units tested may not exceed 20. Steps A, B, and C are then repeated.
(c) Otherwise, the basic model is determined to be in non-compliance.
Appendix A to Subpart Y of Part 431 - Uniform Test Method for the Measurement of Energy Consumption of Pumps
10:3.0.1.4.19.25.89.7.64 : Appendix A
Appendix A to Subpart Y of Part 431 - Uniform Test Method for the Measurement of Energy Consumption of Pumps Note:Starting on July 25, 2016, any representations made with respect to the energy use or efficiency of pumps subject to testing pursuant to 10 CFR 431.464(a) must be made in accordance with the results of testing pursuant to this appendix.
I. Test Procedure for PumpsA. General. To determine the constant load pump energy index (PEICL) for bare pumps and pumps sold with electric motors or the variable load pump energy index (PEIVL) for pumps sold with electric motors and continuous or non-continuous controls, perform testing in accordance with HI 40.6-2014, except section 40.6.5.3, “Test report;” section A.7, “Testing at temperatures exceeding 30 °C (86 °F);” and appendix B, “Reporting of test results;” (incorporated by reference, see § 431.463) with the modifications and additions as noted throughout the provisions below. Where HI 40.6-2014 refers to “pump,” the term refers to the “bare pump,” as defined in § 431.462. Also, for the purposes of applying this appendix, the term “volume per unit time,” as defined in section 40.6.2, “Terms and definitions,” of HI 40.6-2014 shall be deemed to be synonymous with the term “flow rate” used throughout that standard and this appendix. In addition, the specifications of section 40.6.4.1 of HI 40.6-2014 do not apply to ST pumps and the performance of ST bare pumps considers the bowl performance only.
A.1 Scope. Section II of this appendix is applicable to all pumps and describes how to calculate the pump energy index (section II.A) based on the pump energy rating for the minimally compliant reference pump (PERSTD; section II.B) and the constant load pump energy rating (PERCL) or variable load pump energy rating (PERVL) determined in accordance with one of sections III through VII of this appendix, based on the configuration in which the pump is distributed in commerce and the applicable testing method specified in sections III through VII and as described in Table 1 of this appendix.
Table 1 - Applicability of Calculation-Based and Testing-Based Test Procedure Options Based on Pump Configuration
Pump configuration |
Pump sub-configuration | Applicable test methods |
---|---|---|
Bare Pump | Bare Pump OR Pump + Single-Phase Induction Motor OR Pump + Driver Other Than Electric Motor |
Section III: Test Procedure for Bare Pumps. |
Pump + Motor * | Pump + Polyphase Motor Covered
by DOE's Electric Motor Energy Conservation Standards ** OR Pump + Submersible Motor |
Section IV: Testing-Based
Approach for Pumps Sold with Motors OR Section V: Calculation-Based Approach for Pumps Sold with Motors. |
Pump + Motor Not Covered by DOE's Electric Motor Energy Conservation Standards (Except Submersible Motors) ** *** | Section IV: Testing-Based Approach for Pumps Sold with Motors. | |
Pump + Motor +
Continuous Controls OR Pump + Motor + Non-Continuous Controls |
Pump + Polyphase Motor Covered
by DOE's Electric Motor Energy Conservation Standards** +
Continuous Control OR Pump + Submersible Motor + Continuous Control |
Section VI: Testing-Based
Approach for Pumps Sold with Motors and Controls OR Section VII: Calculation-Based Approach for Pumps Sold with Motors Controls. |
Pump + Polyphase Motor Covered
by DOE's Electric Motor Energy Conservation Standards** +
Non-Continuous Control OR Pump + Submersible Motor + Non-Continuous Control |
Section VI: Testing-Based Approach for Pumps Sold with Motors and Controls. | |
Pump + Motor Not Covered by DOE's Electric Motor Energy Conservation Standards (Except Submersible Motors) ** *** + Continuous or Non-Continuous Controls | Section VI: Testing-Based Approach for Pumps Sold with Motors and Controls. |
* Also applies if unit is sold with controls other than continuous or non-continuous controls (e.g., ON/OFF switches).
** All references to “Motors Covered by DOE's Electric Motor Energy Conservation Standards” refer to those listed at § 431.25(g) of this chapter.
*** Includes pumps sold with single-phase induction motors.
A.2 Section III of this appendix addresses the test procedure applicable to bare pumps. This test procedure also applies to pumps sold with drivers other than motors and pumps sold with single-phase induction motors.
A.3 Section IV of this appendix addresses the testing-based approach for pumps sold with motors, which is applicable to all pumps sold with electric motors, including single-phase induction motors. This test procedure also applies to pumps sold with controls other than continuous or non-continuous controls (e.g., on/off switches).
A.4 Section V of this appendix addresses the calculation-based approach for pumps sold with motors, which applies to:
(1) Pumps sold with polyphase electric motors regulated by DOE's energy conservation standards for electric motors at § 431.25(g), and
(2) Pumps sold with submersible motors.
A.5 Section VI of this appendix addresses the testing-based approach for pumps sold with motors and controls, which is applicable to all pumps sold with electric motors (including single-phase induction motors) and continuous or non-continuous controls.
A.6 Section VII of this appendix discusses the calculation-based approach for pumps sold with motors and controls, which applies to:
(1) Pumps sold with polyphase electric motors regulated by DOE's energy conservation standards for electric motors at § 431.25(g) and continuous controls and
(2) Pumps sold with submersible motors and continuous controls.
B. Measurement Equipment. For the purposes of measuring pump power input, driver power input to the motor or controls, and pump power output, the equipment specified in HI 40.6-2014 Appendix C (incorporated by reference, see § 431.463) necessary to measure head, speed of rotation, flow rate, temperature, torque, and electrical power must be used and must comply with the stated accuracy requirements in HI 40.6-2014 Table 40.6.3.2.3 except as noted in sections III.B, IV.B, V.B, VI.B, and VII.B of this appendix. When more than one instrument is used to measure a given parameter, the combined accuracy, calculated as the root sum of squares of individual instrument accuracies, must meet the specified accuracy requirements.
C. Test Conditions. Conduct testing at full impeller diameter in accordance with the test conditions, stabilization requirements, and specifications of HI 40.6-2014 (incorporated by reference, see § 431.463) section 40.6.3, “Pump efficiency testing;” section 40.6.4, “Considerations when determining the efficiency of a pump;” section 40.6.5.4 (including appendix A), “Test arrangements;” and section 40.6.5.5, “Test conditions.”. For ST pumps, head measurements must be based on the bowl assembly total head as described in section A.5 of 40.6-2014 and the pump power input or driver power input, as applicable, must be based on the measured input power to the driver or bare pump, respectively; section 40.6.4.1, “vertically suspended pumps,” does not apply to ST pumps.
C.1 Nominal Speed of Rotation. Determine the nominal speed of rotation based on the range of speeds of rotation at which the pump is designed to operate, in accordance with sections I.C.1.1, I.C.1.2, I.C.1.3, I.C.1.4, or I.C.1.5 of this appendix, as applicable. When determining the range of speeds at which the pump is designed to operate, DOE will refer to published data, marketing literature, and other publically-available information about the pump model and motor, as applicable.
C.1.1 For pumps sold without motors, select the nominal speed of rotation based on the speed for which the pump is designed. For bare pumps designed for speeds of rotation including 2,880 to 4,320 revolutions per minute (rpm), the nominal speed of rotation shall be 3,600 rpm. For bare pumps designed for speeds of rotation including 1,440 to 2,160 rpm, the nominal speed of rotation shall be 1,800 rpm.
C.1.2 For pumps sold with 4-pole induction motors, the nominal speed of rotation shall be 1,800 rpm.
C.1.3 For pumps sold with 2-pole induction motors, the nominal speed of rotation shall be 3,600 rpm.
C.1.4 For pumps sold with non-induction motors where the operating range of the pump and motor includes speeds of rotation between 2,880 and 4,320 rpm, the nominal speed of rotation shall be 3,600 rpm.
C.1.5 For pumps sold with non-induction motors where the operating range of the pump and motor includes speeds of rotation between 1,440 and 2,160 rpm, the nominal speed of rotation shall be 1,800 rpm.
C.2 Multi-stage Pumps. For RSV and ST pumps, perform testing on the pump with three stages for RSV pumps and nine stages for ST pumps. If the basic model of pump being tested is only available with fewer than the required number of stages, test the pump with the maximum number of stages with which the basic model is distributed in commerce in the United States. If the basic model of pump being tested is only available with greater than the required number of stages, test the pump with the lowest number of stages with which the basic model is distributed in commerce in the United States. If the basic model of pump being tested is available with both fewer and greater than the required number of stages, but not the required number of stages, test the pump with the number of stages closest to the required number of stages. If both the next lower and next higher number of stages are equivalently close to the required number of stages, test the pump with the next higher number of stages.
C.3 Twin Head Pumps. For twin head pumps, perform testing on an equivalent single impeller IL pump, constructed by incorporating one of the driver and impeller assemblies of the twin head pump being rated into an adequate, IL style, single impeller volute and casing. An adequate, IL style, single impeller volute and casing means a volute and casing for which any physical and functional characteristics that affect energy consumption and energy efficiency are the same to their corresponding characteristics for a single impeller in the twin head pump volute and casing.
D. Data Collection and AnalysisD.1 Damping Devices. Use of damping devices, as described in section 40.6.3.2.2 of HI 40.6−2014 (incorporated by reference, see § 431.463), are only permitted to integrate up to the data collection interval used during testing.
D.2 Stabilization. Record data at any tested load point only under stabilized conditions, as defined in HI 40.6-2014 section 40.6.5.5.1 (incorporated by reference, see § 431.463), where a minimum of two measurements are used to determine stabilization.
D.3 Calculations and Rounding. Normalize all measured data to the nominal speed of rotation of 3,600 or 1,800 rpm based on the nominal speed of rotation selected for the pump in section I.C.1 of this appendix, in accordance with the procedures specified in section 40.6.6.1.1 of HI 40.6-2014 (incorporated by reference, see § 431.463). Except for the “expected BEP flow rate,” all terms and quantities refer to values determined in accordance with the procedures set forth in this appendix for the rated pump. Perform all calculations using raw measured values without rounding. Round PERCL and PERVL to three significant digits, and round PEICL, and PEIVL values, as applicable, to the hundredths place (i.e., 0.01).
D.4 Pumps with BEP at Run Out.
Test pumps for which the expected BEP corresponds to a volume rate of flow that is within 20 percent of the expected maximum flow rate at which the pump is designed to operate continuously or safely (i.e., pumps with BEP at run-out) in accordance with the test procedure specified in this appendix, but with the following exceptions:
(1) Use the following seven flow points for determination of BEP in sections III.D, IV.D, V.D, VI.D, and VII.D of this appendix instead of those specified in those sections: 40, 50, 60, 70, 80, 90, and 100 percent of the expected.
(2) Use flow points of 60, 70, 80, 90, and 100 percent of the expected maximum flow rate of the pump to determine pump power input or driver power input at the specified load points in section III.E.1.1, IV.E.1, V.E.1.1, VI.E.1, and VII.E.1.1 of this appendix instead of those specified in those sections.
(3) To determine of PERCL and PERSTD, use load points of 65, 90, and 100 percent of the BEP flow rate determined with the modified flow points specified in this section I.D.4 of this appendix instead of 75, 100, and 110 percent of BEP flow.
II. Calculation of the Pump Energy IndexA. Determine the PEI of each tested pump based on the configuration in which it is sold, as follows:
A.1. For pumps rated as bare pumps or pumps sold with motors, determine the PEICL using the following equation:

A.2 For pumps rated as pumps sold with motors and continuous controls or non-continuous controls, determine the PEIVL using the following equation:

B. Determine the pump energy rating for the minimally compliant reference pump (PERSTD), according to the following equation:

B.1. Determine the driver power input at each load point corresponding to 75, 100, or 110 percent of the BEP flow rate as follows:

B.1.1. Determine the pump power input to the minimally compliant pump at each load point corresponding to 75, 100, or 110 percent of the BEP flow rate as follows:
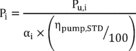
B.1.1.1 Calculate the minimally compliant pump efficiency based on the following equation:
ηpump,STD = −0.8500 × ln(Q100%) 2 −0.3800 × ln(Ns) × ln(Q100%) − 11.480 × ln(Ns) 2 + 17.800 × ln(Q100%) + 179.80 × ln(Ns) − (C + 555.60 Where: ηpump,STD = minimally compliant pump efficiency (%), Q100% = the BEP flow rate of the tested pump at full impeller and nominal speed of rotation (gpm), Ns = specific speed of the tested pump determined in accordance with section II.B.1.1.1.1 of this appendix, and C = the appropriate C-value for the category and nominal speed of rotation of the tested pump, as listed at § 431.466.B.1.1.1.1 Determine the specific speed of the rated pump using the following equation:

B.1.1.2 Determine the pump power output at each load point corresponding to 75, 100, or 110 percent of the BEP flow rate using the following equation:

B.1.2 Determine the motor part load losses at each load point corresponding to 75, 100, or 110 percent of the BEP flow rate as follows:
Li = Lfull × yi Where: Li = part load motor losses at load point i (hp), Lfull = motor losses at full load (hp), as determined in accordance with section II.B.1.2.1 of this appendix, yi = part load loss factor at load point i determined in accordance with section II.B.1.2.2 of this appendix, and i = load point corresponding to 75, 100, or 110 percent of the BEP flow rate.B.1.2.1 Determine the full load motor losses using the appropriate motor efficiency value and horsepower as shown in the following equation:
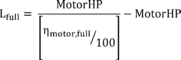
B.1.2.1.1 Determine the motor horsepower as follows:
• For bare pumps other than ST pumps, the motor horsepower is determined as the horsepower rating listed in Table 2 of this appendix that is either equivalent to, or the next highest horsepower greater than, the pump power input to the bare pump at 120 percent of the BEP flow rate of the tested pump.
• For ST bare pumps, the motor horsepower is determined as the horsepower rating listed in Table 2 of this appendix that, is either equivalent to, or the next highest horsepower greater than, the pump power input to the bare pump at 120 percent of the BEP flow rate of the tested pump divided by a service factor of 1.15.
• For pumps sold with motors, pumps sold with motors and continuous controls, or pumps sold with motors and non-continuous controls, the motor horsepower is the rated horsepower of the motor with which the pump is being tested.
B.1.2.1.2 Determine the default nominal full load motor efficiency as described in section II.B.1.2.1.2.1 of this appendix for pumps other than ST pumps or II.B.1.2.1.2.2 of this appendix for ST pumps.
B.1.2.1.2.1. For pumps other than ST pumps, the default nominal full load motor efficiency is the minimum of the nominal full load motor efficiency standards (open or enclosed) from the table containing the current energy conservation standards for NEMA Design B motors at § 431.25, with the number of poles relevant to the speed at which the pump is being tested (see section I.C.1 of this appendix) and the motor horsepower determined in section II.B.1.2.1.1 of this appendix.
B.1.2.1.2.2. For ST pumps, the default nominal full load motor efficiency is the default nominal full load submersible motor efficiency listed in Table 2 of this appendix, with the number of poles relevant to the speed at which the pump is being tested (see section I.C.1 of this appendix) and the motor horsepower determined in section II.B.1.2.1.1 of this appendix.
B.1.2.2 Determine the part load loss factor at each load point corresponding to 75, 100, or 110 percent of the BEP flow rate as follows:


A. Scope. This section III applies only to:
(1) Bare pumps,
(2) Pumps sold with drivers other than electric motors, and
(3) Pumps sold with single-phase induction motors.
B. Measurement Equipment. The requirements regarding measurement equipment presented in section I.B of this appendix apply to this section III, and in addition, when testing pumps using a calibrated motor:
(1) Electrical measurement equipment must be capable of measuring true RMS current, true RMS voltage, and real power up to the 40th harmonic of fundamental supply source frequency, and
(2) Any instruments used to measure a particular parameter specified in paragraph (1) must have a combined accuracy of ±2.0 percent of the measured value at the fundamental supply source frequency, where combined accuracy is the root sum of squares of individual instrument accuracies.
C. Test Conditions. The requirements regarding test conditions presented in section I.C of this appendix apply to this section III. When testing pumps using a calibrated motor the following conditions also apply to the mains power supplied to the motor:
(1) Maintain the voltage within ±5 percent of the rated value of the motor,
(2) Maintain the frequency within ±1 percent of the rated value of the motor,
(3) Maintain the voltage unbalance of the power supply within ±3 percent of the rated values of the motor, and
(2) Maintain total harmonic distortion below 12 percent throughout the test.
D. Testing BEP for the Pump. Determine the best efficiency point (BEP) of the pump as follows:
D.1. Adjust the flow by throttling the pump without changing the speed of rotation of the pump and conduct the test at a minimum of the following seven flow points: 40, 60, 75, 90, 100, 110, and 120 percent of the expected BEP flow rate of the pump at the nominal speed of rotation, as specified in HI 40.6-2014, except section 40.6.5.3, section A.7, and appendix B (incorporated by reference, see § 431.463).
D.2. Determine the BEP flow rate as the flow rate at the operating point of maximum pump efficiency on the pump efficiency curve, as determined in accordance with section 40.6.6.3 of HI 40.6-2014 (incorporated by reference, see § 431.463), where the pump efficiency is the ratio of the pump power output divided by the pump power input, as specified in Table 40.6.2.1 of HI 40.6-2014, disregarding the calculations provided in section 40.6.6.2.
E. Calculating the Constant Load Pump Energy Rating. Determine the PERCL of each tested pump using the following equation:

E.1 Determine the driver power input at each load point corresponding to 75, 100, or 110 percent of the BEP flow rate as follows:

E.1.1 Determine the pump power input at 75, 100, 110, and 120 percent of the BEP flow rate by employing a least squares regression to determine a linear relationship between the pump power input at the nominal speed of rotation of the pump and the measured flow rate at the following load points: 60, 75, 90, 100, 110, and 120 percent of the expected BEP flow rate. Use the linear relationship to determine the pump power input at the nominal speed of rotation for the load points of 75, 100, 110, and 120 percent of the BEP flow rate.
E.1.2 Determine the motor part load losses at each load point corresponding to 75, 100, or 110 percent of the BEP flow rate as follows:
Li = Lfull × yi Where: Li = motor losses at load point i (hp), Lfull = motor losses at full load (hp), as determined in accordance with section III.E.1.2.1 of this appendix, yi = loss factor at load point i as determined in accordance with section III.E.1.2.2 of this appendix, and i = load point corresponding to 75, 100, or 110 percent of the BEP flow rate.E.1.2.1 Determine the full load motor losses using the appropriate motor efficiency value and horsepower as shown in the following equation:
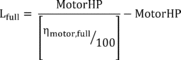
E.1.2.1.1 Determine the motor horsepower as follows:
• For bare pumps other than ST pumps, determine the motor horsepower by selecting the horsepower rating listed in Table 2 of this appendix that is either equivalent to, or the next highest horsepower greater than, the pump power input to the bare pump at 120 percent of the BEP flow rate of the tested pump.
• For ST bare pumps, determine the motor horsepower by selecting the horsepower rating listed in Table 2 of this appendix that, is either equivalent to, or the next highest horsepower greater than, the pump power input to the bare pump at 120 percent of the BEP flow rate of the tested pump divided by a service factor of 1.15.
• For pumps sold with motors, pumps sold with motors and continuous controls, or pumps sold with motors and non-continuous controls, the motor horsepower is the rated horsepower of the motor with which the pump is being tested.
E.1.2.1.2 Determine the default nominal full load motor efficiency as described in section III.E.1.2.1.2.1 of this appendix for pumps other than ST pumps or III.E.1.2.1.2.2. of this appendix for ST pumps.
E.1.2.1.2.1. For pumps other than ST pumps, the default nominal full load motor efficiency is the minimum of the nominal full load motor efficiency standards (open or enclosed) from the table containing the current energy conservation standards for NEMA Design B motors at § 431.25, with the number of poles relevant to the speed at which the pump is being tested (see section I.C.1 of this appendix) and the motor horsepower determined in section III.E.1.2.1.1 of this appendix.
E.1.2.1.2.2. For ST pumps, the default nominal full load motor efficiency is the default nominal full load submersible motor efficiency listed in Table 2 of this appendix, with the number of poles relevant to the speed at which the pump is being tested (see section I.C.1 of this appendix) and the motor horsepower determined in section III.E.1.2.1.1 of this appendix;
E.1.2.2 Determine the loss factor at each load point corresponding to 75, 100, or 110 percent of the BEP flow rate as follows:

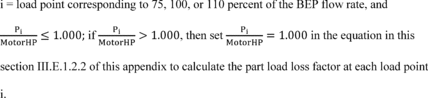
A. Scope. This section IV applies only to pumps sold with electric motors, including single-phase induction motors.
B. Measurement Equipment. The requirements regarding measurement equipment presented in section I.B of this appendix apply to this section IV, and in addition, the electrical measurement equipment must:
(1) Be capable of measuring true RMS current, true RMS voltage, and real power up to the 40th harmonic of fundamental supply source frequency, and
(2) For all instruments used to measure a given parameter, have a combined accuracy of ±2.0 percent of the measured value at the fundamental supply source frequency, where combined accuracy is the root sum of squares of individual instrument accuracies.
C. Test Conditions. The requirements regarding test conditions presented in section I.C of this appendix apply to this section IV. The following conditions also apply to the mains power supplied to the motor:
(1) Maintain the voltage within ±5 percent of the rated value of the motor,
(2) Maintain the frequency within ±1 percent of the rated value of the motor,
(3) Maintain the voltage unbalance of the power supply within ±3 percent of the rated values of the motor, and
(4) Maintain total harmonic distortion below 12 percent throughout the test.
D. Testing BEP for the Pump. Determine the BEP of the pump as follows:
D.1 Adjust the flow by throttling the pump without changing the speed of rotation of the pump to a minimum of seven flow points: 40, 60, 75, 90, 100, 110, and 120 percent of the expected BEP flow rate of the pump at the nominal speed of rotation, as specified in HI 40.6-2014, except section 40.6.5.3, section A.7, and appendix B (incorporated by reference, see § 431.463).
D.2. Determine the BEP flow rate as the flow rate at the operating point of maximum overall efficiency on the pump efficiency curve, as determined in accordance with section 40.6.6.3 of HI 40.6-2014 (incorporated by reference, see § 431.463), where the overall efficiency is the ratio of the pump power output divided by the driver power input, as specified in Table 40.6.2.1 of HI 40.6-2014, disregarding the calculations provided in section 40.6.6.2.
E. Calculating the Constant Load Pump Energy Rating. Determine the PERCL of each tested pump using the following equation:

E.1 Determine the driver power input at 75, 100, and 110 percent of the BEP flow rate by employing a least squares regression to determine a linear relationship between the driver power input at the nominal speed of rotation of the pump and the measured flow rate at the following load points: 60, 75, 90, 100, 110, and 120 percent of the expected BEP flow rate. Use the linear relationship to determine the driver power input at the nominal speed of rotation for the load points of 75, 100, and 110 percent of the BEP flow rate.
V. Calculation-Based Approach for Pumps Sold With MotorsA. Scope. This section V can only be used in lieu of the test method in section IV of this appendix to calculate the index for pumps sold with motors listed in section V.A.1 or V.A.2 of this appendix.
A.1 Pumps sold with motors subject to DOE's energy conservation standards for polyphase electric motors at § 431.25(g), and
A.2. Pumps sold with submersible motors.
A.3. Pumps sold with motors not listed in sections V.A.1 or V.A.2 of this appendix cannot use this section V and must apply the test method in section IV of this appendix.
B. Measurement Equipment. The requirements regarding measurement equipment presented in section I.B of this appendix apply to this section V, and in addition, when testing pumps using a calibrated motor electrical measurement equipment must:
(1) Be capable of measuring true RMS current, true RMS voltage, and real power up to the 40th harmonic of fundamental supply source frequency, and
(2) For all instruments used to measure a given parameter, have a combined accuracy of ±2.0 percent of the measured value at the fundamental supply source frequency, where combined accuracy is the root sum of squares of individual instrument accuracies.
C. Test Conditions. The requirements regarding test conditions presented in section I.C of this appendix apply to this section V. When testing pumps using a calibrated motor the following conditions also apply to the mains power supplied to the motor:
(1) Maintain the voltage within ±5 percent of the rated value of the motor,
(2) Maintain the frequency within ±1 percent of the rated value of the motor,
(3) Maintain the voltage unbalance of the power supply within ±3 percent of the rated values of the motor, and
(4) Maintain total harmonic distortion below 12 percent throughout the test.
D. Testing BEP for the Bare Pump. Determine the best efficiency point (BEP) of the pump as follows:
D.1 Adjust the flow by throttling the pump without changing the speed of rotation of the pump to a minimum of seven flow points: 40, 60, 75, 90, 100, 110, and 120 percent of the expected BEP flow rate of the pump at the nominal speed of rotation, as specified in HI 40.6-2014, except section 40.6.5.3, section A.7, and appendix B (incorporated by reference, see § 431.463).
D.2. Determine the BEP flow rate as the flow rate at the operating point of maximum pump efficiency on the pump efficiency curve, as determined in accordance with section 40.6.6.3 of HI 40.6-2014 (incorporated by reference, see § 431.463), where pump efficiency is the ratio of the pump power output divided by the pump power input, as specified in Table 40.6.2.1 of HI 40.6-2014 and the calculations provided in section 40.6.6.2 are to be disregarded.
E. Calculating the Constant Load Pump Energy Rating. Determine the PERCL of each tested pump using the following equation:

E.1 Determine the driver power input at each load point corresponding to 75, 100, or 110 percent of the BEP flow rate as follows:

E.1.1 Determine the pump power input at 75, 100, 110, and 120 percent of the BEP flow rate by employing a least squares regression to determine a linear relationship between the pump power input at the nominal speed of rotation of the pump and the measured flow rate at the following load points: 60, 75, 90, 100, 110, and 120 percent of the expected BEP flow rate. Use the linear relationship to determine the pump power input at the nominal speed of rotation for the load points of 75, 100, 110, and 120 percent of the BEP flow rate.
E.1.2 Determine the motor part load losses at each load point corresponding to 75, 100, or 110 percent of the BEP flow rate as follows:
Li = Lfull × Yi Where: Li = motor losses at load point i (hp), Lfull = motor losses at full load as determined in accordance with section V.E.1.2.1 of this appendix (hp), yi = part load loss factor at load point i as determined in accordance with section V.E.1.2.2 of this appendix, and i = load point corresponding to 75, 100, or 110 percent of the BEP flow rate.E.1.2.1 Determine the full load motor losses using the appropriate motor efficiency value and horsepower as shown in the following equation:
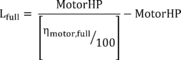
E.1.2.1.1 For pumps sold with motors other than submersible motors, determine the represented nominal full load motor efficiency as described in section V.E.1.2.1.1.1 of this appendix. For pumps sold with submersible motors determine the default nominal full load submersible motor efficiency as described in section V.E.1.2.1.1.2 of this appendix.
E.1.2.1.1.1. For pumps sold with motors other than submersible motors, the represented nominal full load motor efficiency is that of the motor with which the given pump model is being tested, as determined in accordance with the DOE test procedure for electric motors at § 431.16 and applicable representation procedures in parts 429 and 430.
E.1.2.1.1.2. For pumps sold with submersible motors, the default nominal full load submersible motor efficiency is that listed in Table 2 of this appendix, with the number of poles relevant to the speed at which the pump is being tested (see section I.C.1 of this appendix) and the motor horsepower of the pump being tested.
E.1.2.2 Determine the loss factor at each load point corresponding to 75, 100, or 110 percent of the BEP flow rate as follows:

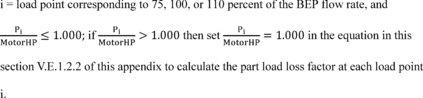
A. Scope. This section VI applies only to pumps sold with electric motors, including single-phase induction motors, and continuous or non-continuous controls. For the purposes of this section VI, all references to “driver input power” in this section VI or HI 40.6-2014 (incorporated by reference, see § 431.463) refer to the input power to the continuous or non-continuous controls.
B. Measurement Equipment. The requirements regarding measurement equipment presented in section I.B of this appendix apply to this section VI, and in addition electrical measurement equipment must:
(1) Be capable of measuring true RMS current, true RMS voltage, and real power up to the 40th harmonic of fundamental supply source frequency, and
(2) For all instruments used to measure a given parameter, have a combined accuracy of ±2.0 percent of the measured value at the fundamental supply source frequency, where combined accuracy is the root sum of squares of individual instrument accuracies.
C. Test Conditions. The requirements regarding test conditions presented in section I.C of this appendix apply to this section VI. The following conditions also apply to the mains power supplied to the continuous or non-continuous control:
(1) Maintain the voltage within ±5 percent of the rated value of the motor,
(2) Maintain the frequency within ±1 percent of the rated value of the motor,
(3) Maintain the voltage unbalance of the power supply within ±3 percent of the rated values of the motor, and
(4) Maintain total harmonic distortion below 12 percent throughout the test.
D. Testing BEP for the Pump. Determine the BEP of the pump as follows:
D.1. Adjust the flow by throttling the pump without changing the speed of rotation of the pump to a minimum of seven flow points: 40, 60, 75, 90, 100, 110, and 120 percent of the expected BEP flow rate of the pump at the nominal speed of rotation, as specified in HI 40.6-2014, except section 40.6.5.3, section A.7, and appendix B (incorporated by reference, see § 431.463).
D.2. Determine the BEP flow rate as the flow rate at the operating point of maximum overall efficiency on the pump efficiency curve, as determined in accordance with section 40.6.6.3 of HI 40.6-2014 (incorporated by reference, see § 431.463), where overall efficiency is the ratio of the pump power output divided by the driver power input, as specified in Table 40.6.2.1 of HI 40.6-2014 and the calculations provided in section 40.6.6.2 are to be disregarded.
E. Calculating the Variable Load Pump Energy Rating. Determine the PERVL of each tested pump using the following equation:

E.1. Determine the driver power input at 100 percent of the measured BEP flow rate of the tested pump by employing a least squares regression to determine a linear relationship between the measured driver power input at the nominal speed of rotation of the pump and the measured flow rate, using the following load points: 60, 75, 90, 100, 110, and 120 percent of the expected BEP flow rate. Use the linear relationship to determine the driver power input at the nominal speed of rotation for the load point of 100 percent of the measured BEP flow rate of the tested pump.
E.2 Determine the driver power input at 25, 50, and 75 percent of the BEP flow rate by measuring the driver power input at the load points defined by:
(1) Those flow rates, and
(2) The associated head points calculated according to the following reference system curve equation:

E.2.1. For pumps sold with motors and continuous controls, the specific head and flow points must be achieved within 10 percent of the calculated values and the measured driver power input must be corrected to the exact intended head and flow conditions using the following equation:
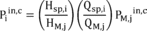
E.2.2. For pumps sold with motors and non-continuous controls, the head associated with each of the specified flow points shall be no lower than 10 percent below that defined by the reference system curve equation in section VI.E.2 of this appendix. Only the measured flow points must be achieved within 10 percent of the calculated values. Correct for flow and head as described in section VI.E.2.1, except do not correct measured head values that are higher than the reference system curve at the same flow rate; only correct flow rate and head values lower than the reference system curve at the same flow rate. For head values higher than the system curve, use the measured head points directly to calculate PEIVL.
VII. Calculation-Based Approach for Pumps Sold With Motors and ControlsA. Scope. This section VII can only be used in lieu of the test method in section VI of this appendix to calculate the index for pumps listed in section VII.A.1 or VII.A.2 of this appendix.
A.1. Pumps sold with motors regulated by DOE's energy conservation standards for polyphase NEMA Design B electric motors at § 431.25(g) and continuous controls, and
A.2. Pumps sold with submersible motors and continuous controls.
A.3. Pumps sold with motors not listed in VII.A.1 or VII.A.2 of this appendix and pumps sold without continuous controls, including pumps sold with non-continuous controls, cannot use this section and must apply the test method in section VI of this appendix.
B. Measurement Equipment. The requirements regarding measurement equipment presented in section I.B of this appendix apply to this section VII, and in addition, when testing pumps using a calibrated motor electrical measurement equipment must:
(1) Be capable of measuring true RMS current, true RMS voltage, and real power up to the 40th harmonic of fundamental supply source frequency, and
(2) For all instruments used to measure a given parameter, have a combined accuracy of ±2.0 percent of the measured value at the fundamental supply source frequency, where combined accuracy is the root sum of squares of individual instrument accuracies.
C. Test Conditions. The requirements regarding test conditions presented in section I.C of this appendix apply to this section VII. When testing pumps using a calibrated motor the following conditions also apply to the mains power supplied to the motor:
(1) Maintain the voltage within ±5 percent of the rated value of the motor,
(2) Maintain the frequency within ±1 percent of the rated value of the motor,
(3) Maintain the voltage unbalance of the power supply within ±3 percent of the rated values of the motor, and
(4) Maintain total harmonic distortion below 12 percent throughout the test.
D. Testing BEP for the Bare Pump. Determine the BEP of the pump as follows:
D.1. Adjust the flow by throttling the pump without changing the speed of rotation of the pump to a minimum of seven flow points: 40, 60, 75, 90, 100, 110, and 120 percent of the expected BEP flow rate of the pump at the nominal speed of rotation, as specified in HI 40.6-2014, except section 40.6.5.3, section A.7, and appendix B (incorporated by reference, see § 431.463).
D.2. Determine the BEP flow rate as the flow rate at the operating point of maximum pump efficiency on the pump efficiency curve, as determined in accordance with section 40.6.6.3 of HI 40.6-2014 (incorporated by reference, see § 431.463), where pump efficiency is the ratio of the pump power output divided by the pump power input, as specified in Table 40.6.2.1 of HI 40.6-2014 and the calculations provided in section 40.6.6.2 are to be disregarded.
E. Calculating the Variable Load Pump Energy Rating. Determine the PERVL of each tested pump using the following equation:

E.1 Determine the driver power input at each load point corresponding to 25, 50, 75, or 100 percent of the BEP flow rate as follows:

E.1.1 Determine the pump power input at 100 percent of the measured BEP flow rate of the tested pump by employing a least squares regression to determine a linear relationship between the measured pump power input at the nominal speed of rotation and the measured flow rate at the following load points: 60, 75, 90, 100, 110, and 120 percent of the expected BEP flow rate. Use the linear relationship to determine the pump power input at the nominal speed of rotation for the load point of 100 percent of the BEP flow rate.
E.1.1.1 Determine the pump power input at 25, 50, and 75 percent of the BEP flow rate based on the measured pump power input at 100 percent of the BEP flow rate and using with the following equation:

E.1.2 Calculate the motor and control part load losses at each load point corresponding to 25, 50, 75, and 100 percent of the BEP flow rate as follows:
Li = Lfull × zi Where: Li = motor and control losses at load point i (hp), Lfull = motor losses at full load as determined in accordance with section VII.E.1.2.1 of this appendix (hp), zi = part load loss factor at load point i as determined in accordance with section VII.E.1.2.2 of this appendix, and i = load point corresponding to 25, 50, 75, or 100 percent of the BEP flow rate.E.1.2.1 Determine the full load motor losses using the appropriate motor efficiency value and horsepower as shown in the following equation:
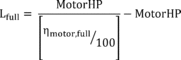
E.1.2.1.1 For pumps sold with motors other than submersible motors, determine the represented nominal full load motor efficiency as described in section VII.E.1.2.1.1.1 of this appendix. For pumps sold with submersible motors, determine the default nominal full load submersible motor efficiency as described in section VII.E.1.2.1.1.2 of this appendix.
E.1.2.1.1.1 For pumps sold with motors other than submersible motors, the represented nominal full load motor efficiency is that of the motor with which the given pump model is being tested, as determined in accordance with the DOE test procedure for electric motors at § 431.16 and applicable representation procedures in parts 429 and 430.
E.1.2.1.1.2 For pumps sold with submersible motors, the default nominal full load submersible motor efficiency is that listed in Table 2 of this appendix, with the number of poles relevant to the speed at which the pump is being tested (see section I.C.1 of this appendix) and the motor horsepower of the pump being tested.
E.1.2.2 For load points corresponding to 25, 50, 75, and 100 percent of the BEP flow rate, determine the part load loss factor at each load point as follows:


Table 2 - Default Nominal Full Load Submersible Motor Efficiency by Motor Horsepower and Pole
Motor
horsepower (hp) |
Default nominal
full load submersible motor efficiency |
|
---|---|---|
2 poles | 4 poles | |
1 | 55 | 68 |
1.5 | 66 | 70 |
2 | 68 | 70 |
3 | 70 | 75.5 |
5 | 74 | 75.5 |
7.5 | 68 | 74 |
10 | 70 | 74 |
15 | 72 | 75.5 |
20 | 72 | 77 |
25 | 74 | 78.5 |
30 | 77 | 80 |
40 | 78.5 | 81.5 |
50 | 80 | 82.5 |
60 | 81.5 | 84 |
75 | 81.5 | 85.5 |
100 | 81.5 | 84 |
125 | 84 | 84 |
150 | 84 | 85.5 |
200 | 85.5 | 86.5 |
250 | 86.5 | 86.5 |
Table 3 - Nominal Full Load Motor Efficiency Values
Nominal full load motor efficiency* |
---|
50.5 |
52.5 |
55.0 |
57.5 |
59.5 |
62.0 |
64.0 |
66.0 |
68.0 |
70.0 |
72.0 |
74.0 |
75.5 |
77.0 |
78.5 |
80.0 |
81.5 |
82.5 |
84.0 |
85.5 |
86.5 |
87.5 |
88.5 |
89.5 |
90.2 |
91.0 |
91.7 |
92.4 |
93.0 |
93.6 |
94.1 |
94.5 |
95.0 |
95.4 |
95.8 |
96.2 |
96.5 |
96.8 |
97.1 |
97.4 |
97.6 |
97.8 |
98.0 |
98.2 |
98.4 |
98.5 |
98.6 |
98.7 |
98.8 |
98.9 |
99.0 |
* Note: Each consecutive incremental value of nominal efficiency represents one band.
Table 4 - Motor and Control Part Load Loss Factor Equation Coefficients for Section VII.E.1.2.2 of This Appendix A
Motor
horsepower (hp) |
Coefficients for
Motor and Control Part Load Loss Factor (zi) |
||
---|---|---|---|
a | b | c | |
≤5 | − 0.4658 | 1.4965 | 0.5303 |
>5 and ≤20 | − 1.3198 | 2.9551 | 0.1052 |
>20 and ≤50 | − 1.5122 | 3.0777 | 0.1847 |
>50 | − 0.8914 | 2.8846 | 0.2625 |