Appendix O to Subpart B of Part 430 - Uniform Test Method for Measuring the Energy Consumption of Vented Home Heating Equipment
10:3.0.1.4.18.3.13.6.25 : Appendix O
Appendix O to Subpart B of Part 430 - Uniform Test Method for
Measuring the Energy Consumption of Vented Home Heating Equipment
Note:
On and after July 6, 2015, any representations made with respect
to the energy use or efficiency of vented home heating equipment
must be made in accordance with the results of testing pursuant to
this appendix. On and after this date, if a manufacturer makes
representations of standby mode and off mode energy consumption,
then testing must also include the provisions of this appendix
related to standby mode and off mode energy consumption. Until July
6, 2015, manufacturers must test vented home heating equipment in
accordance with this appendix or appendix O as it appeared at 10
CFR part 430, subpart B revised as of January 1, 2014. Any
representations made with respect to the energy use or efficiency
of such vented home heating equipment must be made in accordance
with whichever version is selected. DOE notes that, because testing
under this appendix O is required as of July 6, 2015, manufacturers
may wish to begin using this test procedure immediately.
1.0 Definitions
1.1 “Active mode” means the condition during the heating season
in which the vented heater is connected to the power source, and
either the burner or any electrical auxiliary is activated.
1.2 “Air shutter” means an adjustable device for varying the
size of the primary air inlet(s) to the combustion chamber power
burner.
1.3 “Air tube” means a tube which carries combustion air from
the burner fan to the burner nozzle for combustion.
1.4 “Barometic draft regulator or barometric damper” means a
mechanical device designed to maintain a constant draft in a vented
heater.
1.5 “Condensing vented heater” means a vented heater that,
during the laboratory tests prescribed in this appendix, condenses
part of the water vapor in the flue gases.
1.6 “Draft hood” means an external device which performs the
same function as an integral draft diverter, as defined in section
1.17 of this appendix.
1.7 “Electro-mechanical stack damper” means a type of stack
damper which is operated by electrical and/or mechanical means.
1.8 “Excess air” means air which passes through the combustion
chamber and the vented heater flues in excess of that which is
theoretically required for complete combustion.
1.9 “Flue” means a conduit between the flue outlet of a vented
heater and the integral draft diverter, draft hood, barometric
damper or vent terminal through which the flue gases pass prior to
the point of draft relief.
1.10 “Flue damper” means a device installed between the furnace
and the integral draft diverter, draft hood, barometric draft
regulator, or vent terminal which is not equipped with a draft
control device, designed to open the venting system when the
appliance is in operation and to close the venting system when the
appliance is in a standby condition.
1.11 “Flue gases” means reaction products resulting from the
combustion of a fuel with the oxygen of the air, including the
inerts and any excess air.
1.12 “Flue losses” means the sum of sensible and latent heat
losses above room temperature of the flue gases leaving a vented
heater.
1.13 “Flue outlet” means the opening provided in a vented heater
for the exhaust of the flue gases from the combustion chamber.
1.14 “Heat input” (Qin) means the rate of energy supplied in a
fuel to a vented heater operating under steady-state conditions,
expressed in Btu's per hour. It includes any input energy to the
pilot light and is obtained by multiplying the measured rate of
fuel consumption by the measured higher heating value of the
fuel.
1.15 “Heating capacity” (Qout) means the rate of useful heat
output from a vented heater, operating under steady-state
conditions, expressed in Btu's per hour. For room and wall heaters,
it is obtained by multiplying the “heat input” (Qin) by the
steady-state efficency (ηss) divided by 100. For floor furnaces, it
is obtained by multiplying (A) the “heat input” (Qin) by (B) the
steady-state efficiency divided by 100, minus the quantity (2.8)
(Lj) divided by 100, where Lj is the jacket loss as determined in
section 3.2 of this appendix.
1.16 “Higher heating value” (HHV) means the heat produced per
unit of fuel when complete combustion takes place at constant
pressure and the products of combustion are cooled to the initial
temperature of the fuel and air and when the water vapor formed
during combustion is condensed. The higher heating value is usually
expressed in Btu's per pound, Btu's per cubic foot for gaseous
fuel, or Btu's per gallon for liquid fuel.
1.17 “IEC 62301 (Second Edition)” means the test standard
published by the International Electrotechnical Commission, titled
“Household electrical appliances - Measurement of standby power,”
Publication 62301 Edition 2.0 2011-01 (incorporated by reference;
see § 430.3).
1.18 “Induced draft” means a method of drawing air into the
combustion chamber by mechanical means.
1.19 “Infiltration parameter” means that portion of
unconditioned outside air drawn into the heated space as a
consequence of loss of conditioned air through the exhaust system
of a vented heater.
1.20 “Integral draft diverter” means a device which is an
integral part of a vented heater, designed to: (1) Provide for the
exhaust of the products of combustion in the event of no draft,
back draft, or stoppage beyond the draft diverter, (2) prevent a
back draft from entering the vented heater, and (3) neutralize the
stack action of the chimney or gas vent upon the operation of the
vented heater.
1.21 “Manually controlled vented heaters” means either gas or
oil fueled vented heaters equipped without thermostats.
1.22 “Modulating control” means either a step-modulating or
two-stage control.
1.23 “Off mode” means the condition during the non-heating
season in which the vented heater is connected to the power source,
and neither the burner nor any electrical auxiliary is
activated.
1.24 “Power burner” means a vented heater burner which supplies
air for combustion at a pressure exceeding atmospheric pressure, or
a burner which depends on the draft induced by a fan incorporated
in the furnace for proper operation.
1.25 “Reduced heat input rate” means the factory adjusted lowest
reduced heat input rate for vented home heating equipment equipped
with either two stage thermostats or step-modulating
thermostats.
1.26 “Seasonal off switch” means the control device, such as a
lever or toggle, on the vented heater that affects a difference in
off mode energy consumption as compared to standby mode
consumption.
1.27 “Single-stage thermostat” means a thermostat that cycles a
burner at the maximum heat input rate and off.
1.28 “Stack” means the portion of the exhaust system downstream
of the integral draft diverter, draft hood or barometric draft
regulator.
1.29 “Stack damper” means a device installed downstream of the
integral draft diverter, draft hood, or barometric draft regulator,
designed to open the venting system when the appliance is in
operation and to close off the venting system when the appliance is
in the standby condition.
1.30 “Stack gases” means the flue gases combined with dilution
air that enters at the integral draft diverter, draft hood or
barometric draft regulator.
1.31 “Standby mode” means the condition during the heating
season in which the vented heater is connected to the power source,
and neither the burner nor any electrical auxiliary is
activated.
1.32 “Steady-state conditions for vented home heating equipment”
means equilibrium conditions as indicated by temperature variations
of not more than 5 °F (2.8C) in the flue gas temperature for units
equipped with draft hoods, barometric draft regulators or direct
vent systems, in three successive readings taken 15 minutes apart
or not more than 3 °F (1.7C) in the stack gas temperature for units
equipped with integral draft diverters in three successive readings
taken 15 minutes apart.
1.33 “Step-modulating control” means a control that either
cycles off and on at the low input if the heating load is light, or
gradually, increases the heat input to meet any higher heating load
that cannot be met with the low firing rate.
1.34 “Thermal stack damper” means a type of stack damper which
is dependent for operation exclusively upon the direct conversion
of thermal energy of the stack gases into movement of the damper
plate.
1.35 “Two stage control” means a control that either cycles a
burner at the reduced heat input rate and off or cycles a burner at
the maximum heat input rate and off.
1.36 “Vaporizing-type oil burner” means a device with an oil
vaporizing bowl or other receptacle designed to operate by
vaporizing liquid fuel oil by the heat of combustion and mixing the
vaporized fuel with air.
1.37 “Vent/air intake terminal” means a device which is located
on the outside of a building and is connected to a vented heater by
a system of conduits. It is composed of an air intake terminal
through which the air for combustion is taken from the outside
atmosphere and a vent terminal from which flue gases are
discharged.
1.38 “Vent limiter” means a device which limits the flow of air
from the atmospheric diaphragm chamber of a gas pressure regulator
to the atmosphere. A vent limiter may be a limiting orifice or
other limiting device.
1.39 “Vent pipe” means the passages and conduits in a direct
vent system through which gases pass from the combustion chamber to
the outdoor air.
2.0 Testing conditions.
2.1 Installation of test unit.
2.1.1 Vented wall furnaces (including direct vent
systems). Install non-direct vent gas fueled vented wall
furnaces as specified in section 8.1.3 and figure 7 or figure 10 of
ANSI Z21.86 (incorporated by reference, see § 430.3). Install
direct vent gas fueled vented wall furnaces as specified in section
6.1.3 and figure 6 of ANSI Z21.86 (incorporated by reference, see §
430.3). Install oil fueled vented wall furnaces as specified in
section 36.1 of UL 730 (incorporated by reference, see §
430.3).
2.1.2 Vented floor furnaces. Install vented floor
furnaces for test as specified in section 38.1 of UL 729
(incorporated by reference, see § 430.3).
2.1.3 Vented room heaters. Install vented room heaters
for test in accordance with the manufacturer's installation and
operations (I&O) manual provided with the unit.
2.2 Flue and stack requirements.
2.2.1 Gas fueled vented home heating equipment employing
integral draft diverters and draft hoods (excluding direct vent
systems). Attach to, and vertically above the outlet of gas
fueled vented home heating equipment employing draft diverters or
draft hoods with vertically discharging outlets, a five (5) foot
long test stack having a cross sectional area the same size as the
draft diverter outlet.
Attach to the outlet of vented heaters having a horizontally
discharging draft diverter or draft hood outlet a 90 degree elbow,
and a five (5) foot long vertical test stack. A horizontal section
of pipe may be used on the floor furnace between the diverter and
the elbow if necessary to clear any framing used in the
installation. Use the minimum length of pipe possible for this
section. Use stack, elbow, and horizontal section with same cross
sectional area as the diverter outlet.
2.2.2 Oil fueled vented home heating equipment (excluding
direct vent systems). Use flue connections for oil fueled
vented floor furnaces as specified in section 38.2 of UL 729,
sections 36.2 of UL 730 for oil fueled vented wall furnaces, and
sections 37.1.2 and 37.1.3 of UL 896 (all incorporated by
reference, see § 430.3) for oil fueled vented room heaters.
2.2.3 Direct vent systems. Have the exhaust/air intake
system supplied by the manufacturer in place during all tests. Test
units intended for installation with a variety of vent pipe lengths
with the minimum length recommended by the manufacturer. Do not
connect a heater employing a direct vent system to a chimney or
induced draft source. Vent the gas solely on the provision for
venting incorporated in the heater and the vent/air intake system
supplied with it.
2.2.4 Condensing vented heater, additional flue
requirements. The flue pipe installation must not allow
condensate formed in the flue pipe to flow back into the unit. An
initial downward slope from the unit's exit, an offset with a drip
leg, annular collection rings, or drain holes must be included in
the flue pipe installation without disturbing normal flue gas flow.
Flue gases should not flow out of the drain with the condensate.
For condensing vented heaters that do not include means for
collection of condensate, a means to collect condensate must be
supplied by the test lab for the purposes of testing.
2.3 Fuel supply.
2.3.1 Natural gas. For a gas fueled vented heater,
maintain the gas supply to the unit under test at a normal inlet
test pressure immediately ahead of all controls at 7 to 10 inches
water column. Maintain the regulator outlet pressure at normal test
pressure approximately at that recommended by the manufacturer. Use
natural gas having a specific gravity of approximately 0.65 and a
higher heating value within ±5 percent of 1,025 Btu's per standard
cubic foot. Determine the actual higher heating value in Btu's per
standard cubic foot for the natural gas to be used in the test with
an error no greater than one percent.
2.3.2 Propane gas. For a propane-gas fueled vented
heater, maintain the gas supply to the unit under test at a normal
inlet pressure of 11 to 13 inches water column and a specific
gravity of approximately 1.53. Maintain the regulator outlet
pressure, on units so equipped, approximately at that recommended
by the manufacturer. Use propane having a specific gravity of
approximately 1.53 and a higher heating value within ±5 percent of
2,500 Btu's per standard cubic foot. Determine the actual higher
heating value in Btu's per standard cubic foot for the propane to
be used in the test
2.3.3 Other test gas. Use other test gases with
characteristics as described in Table 4 of ANSI Z21.86
(incorporated by reference, see § 430.3). Use gases with a measured
higher heating value within ±5 percent of the values specified in
the Tables section of ANSIZ21.86. Determine the actual higher
heating value of the gas used in the test with an error no greater
than one percent.
2.3.4 Oil supply. For an oil fueled vented heater, use
No. 1 fuel oil (kerosene) for vaporizing-type burners and either
No. 1 or No. 2 fuel oil, as specified by the manufacturer in the
I&O manual provided with the unit, for mechanical atomizing
type burners. Use test fuel conforming to the specifications given
in Tables 2 and 3 of ASHRAE 103-2007 (incorporated by reference,
see § 430.3). Measure the higher heating value of the test fuel
within ±1 percent.
2.3.5 Electrical supply. For auxiliary electric
components of a vented heater, maintain the electrical supply to
the test unit within one percent of the nameplate voltage for the
entire test cycle. If a voltage range is used for nameplate
voltage, maintain the electrical supply within one percent of the
mid-point of the nameplate voltage range.
2.4 Burner adjustments.
2.4.1 Gas burner adjustments. Adjust the burners of gas
fueled vented heaters to their maximum Btu ratings at the test
pressure specified in section 2.3 of this appendix. Correct the
burner volumetric flow rate to 60 °F (15.6C) and 30 inches of
mercury barometric pressure, set the fuel flow rate to obtain a
heat rate of within ±2 percent of the hourly Btu rating specified
by the manufacturer as measured after 15 minutes of operation
starting with all parts of the vented heater at room temperature.
Set the primary air shutters in accordance with the manufacturer's
recommendations to give a good flame at this adjustment. Do not
allow the deposit of carbon during any test specified herein.
If a vent limiting means is provided on a gas pressure
regulator, have it in place during all tests.
For gas fueled heaters with modulating controls adjust the
controls to operate the heater at the maximum fuel input rate. Set
the thermostat control to the maximum setting. Start the heater by
turning the safety control valve to the “on” position. In order to
prevent modulation of the burner at maximum input, place the
thermostat sensing element in a temperature control bath which is
held at a temperature below the maximum set point temperature of
the control.
For gas fueled heaters with modulating controls adjust the
controls to operate the heater at the reduced fuel input rate. Set
the thermostat control to the minimum setting. Start the heater by
turning the safety control valve to the “on” position. If ambient
test room temperature is above the lowest control set point
temperature, initiate burner operation by placing the thermostat
sensing element in a temperature control bath that is held at a
temperature below the minimum set point temperature of the
control.
2.4.2 Oil burner adjustments. Adjust the burners of oil
fueled vented heaters to give the CO2 reading recommended by the
manufacturer and an hourly Btu input, during the steady-state
performance test described below, which is within ±2 percent of the
heater manufacturer's specified normal hourly Btu input rating. On
units employing a power burner, do not allow smoke in the flue to
exceed a No. 1 smoke during the steady-state performance test as
measured by the procedure in ASTM D2156 (incorporated by reference,
see § 430.3). If, on units employing a power burner, the smoke in
the flue exceeds a No. 1 smoke during the steady-state test,
readjust the burner to give a lower smoke reading, and, if
necessary a lower CO2 reading, and start all tests over. Maintain
the average draft over the fire and in the flue during the
steady-state performance test at that recommended by the
manufacturer within ±0.005 inches of water gauge. Do not make
additional adjustments to the burner during the required series of
performance tests. The instruments and measuring apparatus for this
test are described in section 6 and shown in Figure 8 of ASHRAE
103-2007 (incorporated by reference, see § 430.3).
2.5 Circulating air adjustments.
2.5.1 Forced air vented wall furnaces (including direct vent
systems). During testing, maintain the air flow through the
heater as specified by the manufacturer in the I&O manual
provided with the unit and operate the vented heater with the
outlet air temperature between 80 °F and 130 °F above room
temperature. If adjustable air discharge registers are provided,
adjust them so as to provide the maximum possible air restriction.
Measure air discharge temperature as specified in section 8.7 of
ANSI Z21.86 (incorporated by reference, see § 430.3).
2.5.2 Fan type vented room heaters and floor furnaces.
During tests on fan type furnaces and heaters, adjust the air flow
through the heater as specified by the manufacturer. If adjustable
air discharge registers are provided, adjust them to provide the
maximum possible air restriction.
2.6 Location of temperature measuring
instrumentation.
2.6.1 Gas fueled vented home heating equipment (including
direct vent systems). For units employing an integral draft
diverter, install nine thermocouples, wired in parallel, in a
horizontal plane in the five foot test stack located one foot from
the test stack inlet. Equalize the length of all thermocouple leads
before paralleling. Locate one thermocouple in the center of the
stack. Locate eight thermocouples along imaginary lines
intersecting at right angles in this horizontal plane at points one
third and two thirds of the distance between the center of the
stack and the stack wall.
For units which employ a direct vent system, locate at least one
thermocouple at the center of each flue way exiting the heat
exchanger. Provide radiation shields if the thermocouples are
exposed to burner radiation.
For units which employ a draft hood or units which employ a
direct vent system which does not significantly preheat the
incoming combustion air, install nine thermocouples, wired in
parallel, in a horizontal plane located within 12 inches (304.8 mm)
of the heater outlet and upstream of the draft hood on units so
equipped. Locate one thermocouple in the center of the pipe and
eight thermocouples along imaginary lines intersecting at right
angles in this horizontal plane at points one third and two thirds
of the distance between the center of the pipe and the pipe
wall.
For units which employ direct vent systems that significantly
preheat the incoming combustion air, install nine thermocouples,
wired in parallel, in a plane parallel to and located within 6
inches (152.4 mm) of the vent/air intake terminal. Equalize the
length of all thermocouple leads before paralleling. Locate one
thermocouple in the center of the vent pipe and eight thermocouples
along imaginary lines intersecting at right angles in this plane at
points one third and two thirds of the distance between the center
of the flue pipe and the pipe wall.
Use bead-type thermocouples having wire size not greater than
No. 24 American Wire Gauge (AWG). If there is a possibility that
the thermocouples could receive direct radiation from the fire,
install radiation shields on the fire side of the thermocouples
only and position the shields so that they do not touch the
thermocouple junctions.
Install thermocouples for measuring conditioned warm air
temperature as described in Part VIII section 8.7 of ANSI Z21.86
(incorporated by reference, see § 430.3). Establish the temperature
of the inlet air by means of single No. 24 AWG bead-type
thermocouple, suitably shielded from direct radiation and located
in the center of the plane of each inlet air opening.
2.6.2 Oil fueled vented home heating equipment (including
direct vent systems). Install nine thermocouples, wired in
parallel and having equal length leads, in a plane perpendicular to
the axis of the flue pipe. Locate this plane at the position shown
in Figure 36.4 of UL 730, or Figure 38.1 and 38.2 of UL 729
(incorporated by reference, see § 430.3) for a single thermocouple,
except that on direct vent systems which significantly preheat the
incoming combustion air, it shall be located within 6 inches (152.5
mm) of the outlet of the vent/air intake terminal. Locate one
thermocouple in the center of the flue pipe and eight thermocouples
along imaginary lines intersecting at right angles in this plane at
points one third and two thirds of the distance between the center
of the pipe and pipe wall.
Use bead-type thermocouples having a wire size not greater than
No. 24 AWG. If there is a possibility that the thermocouples could
receive direct radiation from the fire, install radiation shields
on the fire side of the thermocouples only and position the shields
so that they do not touch the thermocouple junctions.
Install thermocouples for measuring the conditioned warm air
temperature as described in sections 37.5.8 through 37.5.18 of UL
730 (incorporated by reference, see § 430.3). Establish the
temperature of the inlet air by means of a single No. 24 AWG
bead-type thermocouple, suitably shielded from direct radiation and
located in the center of the plane of each inlet air opening.
2.7 Combustion measurement instrumentation. Analyze the
samples of stack and flue gases for vented heaters to determine the
concentration by volume of carbon dioxide present in the dry gas
with instrumentation which will result in a reading having an
accuracy of ±0.1 percentage points.
2.8 Energy flow instrumentation. Install one or more
instruments, which measure the rate of gas flow or fuel oil
supplied to the vented heater, and if appropriate, the electrical
energy with an error no greater than one percent.
2.9 Room ambient temperature. The room ambient
temperature shall be the arithmetic average temperature of the test
area, determined by measurement with four No. 24 AWG bead-type
thermocouples with junctions shielded against radiation, located
approximately at 90-degree positions on a circle circumscribing the
heater or heater enclosure under test, in a horizontal plane
approximately at the vertical midpoint of the appliance or test
enclosure, and with the junctions approximately 24 inches from
sides of the heater or test enclosure and located so as not to be
affected by other than room air.
The value TRA is the room ambient temperature measured at the
last of the three successive readings taken 15 minutes apart
described in section 3.1.1 or 3.1.2 as applicable. During the time
period required to perform all the testing and measurement
procedures specified in section 3.0 of this appendix, maintain the
room ambient temperature within ±5 °F (±2.8 C) of the value TRA. At
no time during these tests shall the room ambient temperature
exceed 100 °F (37.8 C) or fall below 65 °F (18.3 C).
Locate a thermocouple at each elevation of draft relief inlet
opening and combustion air inlet opening at a distance of
approximately 24 inches from the inlet openings. The temperature of
the air for combustion and the air for draft relief shall not
differ more than ±5 °F from the room ambient temperature as
measured above at any point in time. This requirement for
combustion air inlet temperature does not need to be met once the
burner is shut off during the testing described in sections 3.3 and
3.6 of this appendix.
2.10 Equipment used to measure mass flow rate in flue and
stack. The tracer gas chosen for this task should have a
density which is less than or approximately equal to the density of
air. Use a gas unreactive with the environment to be encountered.
Using instrumentation of either the batch or continuous type,
measure the concentration of tracer gas with an error no greater
than 2 percent of the value of the concentration measured.
2.11 Equipment with multiple control modes. For equipment
that has both manual and automatic thermostat control modes, test
the unit according to the procedure for its automatic control mode,
i.e. single-stage, two stage, or step-modulating.
3.0 Testing and measurements.
3.1 Steady-state testing.
3.1.1 Gas fueled vented home heating equipment (including
direct vent systems). Set up the vented heater as specified in
sections 2.1, 2.2, and 2.3 of this appendix. The draft diverter
shall be in the normal open condition and the stack shall not be
insulated. (Insulation of the stack is no longer required for the
vented heater test.) Begin the steady-state performance test by
operating the burner and the circulating air blower, on units so
equipped, with the adjustments specified by sections 2.4.1 and 2.5
of this appendix, until steady-state conditions are attained as
indicated by three successive readings taken 15 minutes apart with
a temperature variation of not more than ±3 °F (1.7 C) in the stack
gas temperature for vented heaters equipped with draft diverters or
±5 °F (2.8 C) in the flue gas temperature for vented heaters
equipped with either draft hoods or direct vent systems. The
measurements described in this section are to coincide with the
last of these 15 minute readings.
On units employing draft diverters, measure the room temperature
(TRA) as described in section 2.9 of this appendix and measure the
steady-state stack gas temperature (TS,SS) using the nine
thermocouples located in the 5 foot test stack as specified in
section 2.6.1 of this appendix. Secure a sample of the stack gases
in the plane where TS,SS is measured or within 3.5 feet downstream
of this plane. Determine the concentration by volume of carbon
dioxide (XCO2S) present in the dry stack gas. If the location of
the gas sampling differs from the temperature measurement plane,
there shall be no air leaks through the stack between these two
locations.
On units employing draft hoods or direct vent systems, measure
the room temperature (TRA) as described in section 2.9 of this
appendix and measure the steady-state flue gas temperature (TF,SS),
using the nine thermocouples located in the flue pipe as described
in section 2.6.1 of this appendix. Secure a sample of the flue gas
in the plane of temperature measurement and determine the
concentration by volume of CO2 (XCO2F) present in dry flue gas. In
addition, for units employing draft hoods, secure a sample of the
stack gas in a horizontal plane in the five foot test stack located
one foot from the test stack inlet; and determine the concentration
by volume of CO2 (XCO2S) present in dry stack gas.
Determine the steady-state heat input rate (Qin) including pilot
gas by multiplying the measured higher heating value of the test
gas by the steady-state gas input rate corrected to standard
conditions of 60 °F and 30 inches of mercury. Use measured values
of gas temperature and pressure at the meter and the barometric
pressure to correct the metered gas flow rate to standard
conditions.
After the above test measurements have been completed on units
employing draft diverters, secure a sample of the flue gases at the
exit of the heat exchanger(s) and determine the concentration of
CO2 (XCO2F) present. In obtaining this sample of flue gas, move the
sampling probe around or use a sample probe with multiple sampling
ports in order to assure that an average value is obtained for the
CO2 concentration. For units with multiple heat exchanger outlets,
measure the CO2 concentration in a sample from each outlet to
obtain the average CO2 concentration for the unit. A manifold
(parallel connected sampling tubes) may be used to obtain this
sample.
For heaters with single-stage thermostat control (wall mounted
electric thermostats), determine the steady-state efficiency at the
maximum fuel input rate as specified in section 2.4 of this
appendix.
For gas fueled vented heaters equipped with either two stage
control or step-modulating control, determine the steady-state
efficiency at the maximum fuel input rate and at the reduced fuel
input rate, as specified in section 2.4.1 of this appendix.
For manually controlled gas fueled vented heaters with various
input rates, determine the steady-state efficiency at a fuel input
rate that is within ±5 percent of 50 percent of the maximum rated
fuel input rate as indicated on the nameplate of the unit or in the
manufacturer's installation and operation manual shipped with the
unit. If the heater is designed to use a control that precludes
operation at other than maximum rated fuel input rate (single
firing rate) determine the steady state efficiency at the maximum
rated fuel input rate only.
3.1.2 Oil fueled vented home heating equipment (including
direct vent systems). Set up and adjust the vented heater as
specified in sections 2.1, 2.2, and 2.3.4 of this appendix. Begin
the steady-state performance test by operating the burner and the
circulating air blower, on units so equipped, with the adjustments
specified by sections 2.4.2 and 2.5 of this appendix, until
steady-state conditions are attained as indicated by a temperature
variation of not more than ±5 °F (2.8 C) in the flue gas
temperature in three successive readings taken 15 minutes apart.
The measurements described in this section are to coincide with the
last of these 15 minutes readings.
For units equipped with power burners, do not allow smoke in the
flue to exceed a No. 1 smoke during the steady-state performance
test as measured by the procedure described in ASTM D2156
(incorporated by reference, see § 430.3). Maintain the average
draft over the fire and in the breeching during the steady-state
performance test at that recommended by the manufacturer ±0.005
inches of water gauge.
Measure the room temperature (TRA) as described in section 2.9
of this appendix. Measure the steady-state flue gas temperature
(TF,SS) using nine thermocouples located in the flue pipe as
described in section 2.6.2 of this appendix. From the plane where
TF,SS was measured, collect a sample of the flue gas and determine
the concentration by volume of CO2 (XCO2F) present in dry flue gas.
Measure and record the steady-state heat input rate (Qin).
For manually controlled oil fueled vented heaters, determine the
steady-state efficiency at a fuel input rate that is within ±5
percent of 50 percent of the maximum fuel input rate; or, if the
design of the heater is such that the fuel input rate cannot be set
to ±5 percent of 50 percent of the maximum rated fuel input rate,
determine the steady-state efficiency at the minimum rated fuel
input rate as measured in section 3.1.2 of this appendix for
manually controlled oil fueled vented heaters.
3.1.3 Auxiliary Electric Power Measurement. Allow the
auxiliary electrical system of a gas or oil vented heater to
operate for at least five minutes before recording the maximum
auxiliary electric power measurement from the wattmeter. Record the
maximum electric power (PE) expressed in kilowatts. For vented
heaters with modulating controls, the recorded (PE) shall be
maximum measured electric power multiplied by the following factor
(R). For two stage controls, R = 1.3. For step modulating controls,
R = 1.4 when the ratio of minimum-to-maximum fuel input is greater
than or equal to 0.7, R = 1.7 when the ratio of minimum-to-maximum
fuel input is less than 0.7 and greater than or equal to 0.5, and R
= 2.2 when the ratio of minimum-to-maximum fuel input is less than
0.5.
3.2 Jacket loss measurement. Conduct a jacket loss test
for vented floor furnaces. Measure the jacket loss (Lj) in
accordance with ASHRAE 103-2007 section 8.6 (incorporated by
reference, see § 430.3), applying the provisions for furnaces and
not the provisions for boilers.
3.3 Measurement of the off-cycle losses for vented heaters
equipped with thermal stack dampers. Unless specified
otherwise, the thermal stack damper should be at the draft diverter
exit collar. Attach a five foot length of bare stack to the outlet
of the damper. Install thermocouples as specified in section 2.6.1
of this appendix.
For vented heaters equipped with single-stage thermostats,
measure the off-cycle losses at the maximum fuel input rate. For
vented heaters equipped with two stage thermostats, measure the
off-cycle losses at the maximum fuel input rate and at the reduced
fuel input rate. For vented heaters equipped with step-modulating
thermostats, measure the off-cycle losses at the reduced fuel input
rate.
Allow the vented heater to heat up to a steady-state condition.
Feed a tracer gas at a constant metered rate into the stack
directly above and within one foot above the stack damper. Record
tracer gas flow rate and temperature. Measure the tracer gas
concentration in the stack at several locations in a horizontal
plane through a cross-section of the stack at a point sufficiently
above the stack damper to ensure that the tracer gas is well mixed
in the stack.
Continuously measure the tracer gas concentration and
temperature during a 10-minute cool-down period. Shut the burner
off and immediately begin measuring tracer gas concentration in the
stack, stack temperature, room temperature, and barometric
pressure. Record these values as the midpoint of each one-minute
interval between burner shut-down and ten minutes after burner
shut-down. Meter response time and sampling delay time shall be
considered in timing these measurements.
3.4 Measurement of the effectiveness of electro-mechanical
stack dampers. For vented heaters equipped with
electro-mechanical stack dampers, measure the cross sectional area
of the stack (As), the net area of the damper plate (Ao), and the
angle that the damper plate makes when closed with a plane
perpendicular to the axis of the stack (Ω). The net area of the
damper plate means the area of the damper plate minus the area of
any holes through the damper plate.
3.5 Pilot light measurement.
3.5.1 Measure the energy input rate to the pilot light (QP) with
an error no greater than 3 percent for vented heaters so
equipped.
3.5.2 For manually controlled heaters where the pilot light is
designed to be turned off by the user when the heater is not in
use, that is, turning the control to the OFF position will shut off
the gas supply to the burner(s) and to the pilot light, the
measurement of QP is not needed. This provision applies only if an
instruction to turn off the unit is provided on the heater near the
gas control valve (e.g. by label) by the manufacturer.
3.6 Optional procedure for determining Dp′ DF′ and Ds
for systems for all types of vented heaters. For all types
of vented heaters, Dp′ DF′ and DS can be measured by the following
optional cool down test.
Conduct a cool down test by letting the unit heat up until
steady-state conditions are reached, as indicated by temperature
variation of not more than 5 °F (2.8 °C) in the flue gas
temperature in three successive readings taken 15 minutes apart,
and then shutting the unit off with the stack or flue damper
controls by-passed or adjusted so that the stack or flue damper
remains open during the resulting cool down period. If a draft was
maintained on oil fueled units in the flue pipe during the
steady-state performance test described in section 3.1 of this
appendix, maintain the same draft (within a range of −.001 to +
.005 inches of water gauge of the average steady-state draft)
during this cool down period.
Measure the flue gas mass flow rate (mF,OFF) during the cool
down test described above at a specific off-period flue gas
temperature and corrected to obtain its value at the steady-state
flue gas temperature (TF,SS), using the procedure described
below.
Within one minute after the unit is shut off to start the cool
down test for determining DF, begin feeding a tracer gas into the
combustion chamber at a constant flow rate of VT, and at a point
which will allow for the best possible mixing with the air flowing
through the chamber. (On units equipped with an oil fired power
burner, the best location for injecting this tracer gas appears to
be through a hole drilled in the air tube.) Periodically measure
the value of VT with an instantaneously reading flow meter having
an accuracy of ±3 percent of the quantity measured. Maintain VT at
less than 1 percent of the air flow rate through the furnace. If a
combustible tracer gas is used, there should be a delay period
between the time the burner gas is shut off and the time the tracer
gas is first injected to prevent ignition of the tracer gas.
Between 5 and 6 minutes after the unit is shut off to start the
cool down test, measure at the exit of the heat exchanger the
average flue gas temperature, T*F,Off. At the same instant the flue
gas temperature is measured, also measure the percent volumetric
concentration of tracer gas CT in the flue gas in the same plane
where T*F,Off is determined. Obtain the concentration of tracer gas
using an instrument which will result in an accuracy of ±2 percent
in the value of CT measured. If use of a continuous reading type
instrument results in a delay time between drawing of a sample and
its analysis, this delay should be taken into account so that the
temperature measurement and the measurement of tracer gas
concentration coincide. In addition, determine the temperature of
the tracer gas entering the flow meter (TT) and the barometric
pressure (PB).
The rate of the flue gas mass flow through the vented heater and
the factors DP, DF, and DS are calculated by the equations in
sections 4.5.1 through 4.5.3 of this appendix.
3.6.1 Procedure for determining (DF and DP) of vented
home heating equipment with no measurable airflow. On units
whose design is such that there is no measurable airflow through
the combustion chamber and heat exchanger when the burner(s) is off
(as determined by the test procedure in section 3.6.2 of this
appendix), DF and DP may be set equal to 0.05.
3.6.2 Test Method to Determine Whether the Use of the Default
Draft Factors (DF and DP) of 0.05 is Allowed.
Manufacturers may use the following test protocol to determine
whether air flows through the combustion chamber and heat exchanger
when the burner(s) is off using a smoke stick device. The default
draft factor of 0.05 (as allowed per section 3.6.1 of this
appendix) may be used only for units determined pursuant to this
protocol to have no air flow through the combustion chamber and
heat exchanger.
3.6.2.1 Test Conditions. Wait for two minutes following
the termination of the vented heater's on-cycle.
3.6.2.2 Location of Test Apparatus
3.6.2.2.1 After all air currents and drafts in the test chamber
have been minimized, position the operable smoke stick/pencil as
specified, based on the following equipment configuration: for
horizontal combustion air intakes, approximately 4 inches from the
vertical plane at the termination of the intake vent and 4 inches
below the bottom edge of the combustion air intake, or for vertical
combustion air intakes, approximately 4 inches horizontal from vent
perimeter at the termination of the intake vent and 4 inches down
(parallel to the vertical axis of the vent). In the instance where
the boiler combustion air intake is closer than 4 inches to the
floor, place the smoke device directly on the floor without
impeding the flow of smoke.
3.6.2.2.2 Monitor the presence and the direction of the smoke
flow.
3.6.2.3 Duration of Test. Continue monitoring the release
of smoke for no less than 30 seconds.
3.6.2.4 Test Results
3.6.2.4.1 During visual assessment, determine whether there is
any draw of smoke into the combustion air intake.
3.6.2.4.2 If absolutely no smoke is drawn into the combustion
air intake, the vented heater meets the requirements to allow use
of the default draft factor of 0.05 pursuant to Section 8.8.3
and/or 9.10 of ASHRAE 103-2007 (incorporated by reference, see §
430.3).
3.6.2.4.3 If there is any smoke drawn into the intake, use of
default draft factor of 0.05 is prohibited. Proceed with the
methods of testing as prescribed in section 3.6 of this appendix,
or select the appropriate default draft factor from Table 1.
3.7 Measurement of electrical standby mode and off mode
power.
3.7.1 Standby power measurements. With all electrical
auxiliaries of the vented heater not activated, measure the standby
power (PW,SB) in accordance with the procedures in IEC 62301
(Second Edition) (incorporated by reference, see § 430.3), except
that section 2.9, Room ambient temperature, and the voltage
provision of section 2.3.5, Electrical supply, of this
appendix shall apply in lieu of the IEC 62301 (Second Edition)
corresponding sections 4.2, Test room, and 4.3, Power
supply. Clarifying further, the IEC 62301 (Second Edition)
sections 4.4, Power measuring instruments, and section 5,
Measurements, shall apply in lieu of section 2.8, Energy
flow instrumentation, of this appendix. Measure the wattage so
that all possible standby mode wattage for the entire appliance is
recorded, not just the standby mode wattage of a single auxiliary.
The recorded standby power (PW,SB) shall be rounded to the second
decimal place, and for loads greater than or equal to 10W, at least
three significant figures shall be reported.
3.7.2 Off mode power measurement. If the unit is equipped
with a seasonal off switch or there is an expected difference
between off mode power and standby mode power, measure off mode
power (PW,OFF) in accordance with the standby power procedures in
IEC 62301 (Second Edition) (incorporated by reference, see §
430.3), except that section 2.9, Room ambient temperature,
and the voltage provision of section 2.3.5, Electrical
supply, of this appendix shall apply in lieu of the IEC 62301
(Second Edition) corresponding sections 4.2, Test room, and
4.3, Power supply. Clarifying further, the IEC 62301 (Second
Edition) sections 4.4, Power measuring instruments, and
section 5, Measurements, shall apply in lieu of section 2.8,
Energy flow instrumentation, of this appendix. Measure the
wattage so that all possible off mode wattage for the entire
appliance is recorded, not just the off mode wattage of a single
auxiliary. If there is no expected difference in off mode power and
standby mode power, let PW,OFF = PW,SB, in which case no separate
measurement of off mode power is necessary. The recorded off mode
power (PW,OFF) shall be rounded to the second decimal place, and
for loads greater than or equal to 10W, at least three significant
figures shall be reported.
3.8 Condensing vented heaters - measurement of condensate
under steady-state and cyclic conditions. Attach condensate
drain lines to the vented heater as specified in the manufacturer's
I&O manual provided with the unit. The test unit shall be level
prior to all testing. A continuous downward slope of drain lines
from the unit shall be maintained. The drain lines must facilitate
uninterrupted flow of condensate during the test. The condensate
collection container must be glass or polished stainless steel to
facilitate removal of interior deposits. The collection container
shall have a vent opening to the atmosphere, be dried prior to each
use, and be at room ambient temperature. The humidity of the room
air shall at no time exceed 80 percent relative humidity. For
condensing units not designed for collecting and draining
condensate, drain lines must be provided during testing that meet
the criteria set forth in this section 3.8. Units employing manual
controls and units not tested under the optional tracer gas
procedures of sections 3.3 and 3.6 of this appendix shall only
conduct the steady-state condensate collection test.
3.8.1 Steady-state condensate collection test. Begin
steady-state condensate collection concurrently with or immediately
after completion of the steady-state testing of section 3.1 of this
appendix. The steady-state condensate collection period shall be 30
minutes. Condensate mass shall be measured immediately at the end
of the collection period to minimize evaporation loss from the
sample. Record fuel input during the 30-minute condensate
collection steady-state test period. Measure and record fuel higher
heating value (HHV), temperature, and pressures necessary for
determining fuel energy input (Qc,ss). The fuel quantity and HHV
shall be measured with errors no greater than ±1 percent. Determine
the mass of condensate for the steady-state test (Mc,ss) in pounds
by subtracting the tare container weight from the total container
and condensate weight measured at the end of the 30-minute
condensate collection test period. The error associated with the
mass measurement instruments shall not exceed ±0.5 percent of the
quantity measured.
For units with step-modulating or two stage controls, the
steady-state condensate collection test shall be conducted at both
the maximum and reduced input rates.
3.8.2 Cyclic condensate collection tests. If existing
controls do not allow for cyclical operation of the tested unit,
control devices shall be installed to allow cyclical operation of
the vented heater. Run three consecutive test cycles. For each
cycle, operate the unit until flue gas temperatures at the end of
each on-cycle, rounded to the nearest whole number, are within 5 °F
of each other for two consecutive cycles. On-cycle and off-cycle
times are 4 minutes and 13 minutes respectively. Control of ON and
OFF operation actions shall be within ±6 seconds of the scheduled
time. For fan-type vented heaters, maintain circulating air
adjustments as specified in section 2.5 of this appendix. Begin
condensate collection at one minute before the on-cycle period of
the first test cycle. Remove the container one minute before the
end of each off-cycle period. Measure condensate mass for each
test-cycle. The error associated with the mass measurement
instruments shall not exceed ±0.5 percent of the quantity
measured.
Fuel input shall be recorded during the entire test period
starting at the beginning of the on-time period of the first cycle
to the beginning of the on-time period of the second cycle, from
the beginning of the on-time period of the second cycle to the
beginning of the on-time period of the third cycle, etc., for each
of the test cycles. Fuel HHV, temperature, and pressure necessary
for determining fuel energy input, Qc, shall be recorded. Determine
the mass of condensate for each cycle, Mc, in pounds. If at the end
of three cycles, the sample standard deviation is within 20 percent
of the mean value for three cycles, use total condensate collected
in the three cycles as Mc; if not, continue collection for an
additional three cycles and use the total condensate collected for
the six cycles as Mc. Determine the fuel energy input, Qc, during
the three or six test cycles, expressed in Btu.
4.0 Calculations.
4.1 Annual fuel utilization efficiency for gas fueled or oil
fueled vented home heating equipment equipped without manual
controls or with multiple control modes as per 2.11 and without
thermal stack dampers. The following procedure determines the
annual fuel utilization efficiency for gas fueled or oil fueled
vented home heating equipment equipped without manual controls and
without thermal stack dampers.
4.1.1 System number. Obtain the system number from Table
1 of this appendix.
4.1.2 Off-cycle flue gas draft factor. Based on the
system number, determine the off-cycle flue gas draft factor (DF)
from Table 1 of this appendix or the test method and calculations
of sections 3.6 and 4.5 of this appendix.
4.1.3 Off-cycle stack gas draft factor. Based on the
system number, determine the off-cycle stack gas draft factor (Ds)
from Table 1 of this appendix or from the test method and
calculations of sections 3.6 and 4.5 of this appendix,.
4.1.4 Pilot fraction. Calculate the pilot fraction (PF)
expressed as a decimal and defined as:
PF = QP/Qin where: QP = as defined in 3.5 of this appendix Qin = as
defined in 3.1 of this appendix at the maximum fuel input rate
4.1.5 Jacket loss for floor furnaces. Determine the
jacket loss (Lj) expressed as a percent and measured in accordance
with section 3.2 of this appendix. For other vented heaters Lj =
0.0.
4.1.6 Latent heat loss. For non-condensing vented
heaters, obtain the latent heat loss (LL,A) from Table 2 of this
appendix. For condensing vented heaters, calculate a modified
latent heat loss (LL,A*) as follows:
For steady-state conditions:
LL,A*= LL,A−LG,SS + LC,SS where: LL,A = Latent heat loss, based on
fuel type, from Table 2 of this appendix, LG,SS = Steady-state
latent heat gain due to condensation as determined in section
4.1.6.1 of this appendix, and LC,SS = Steady-state heat loss due to
hot condensate going down the drain as determined in 4.1.6.2 of
this appendix. For cyclic conditions: (only for vented heaters
tested under the optional tracer gas procedures of section 3.3 or
3.6) LL,A*= LL,A−LG + LC where: LL,A = Latent heat loss, based on
fuel type, from Table 2 of this appendix, LG = Latent heat gain due
to condensation under cyclic conditions as determined in section
4.1.6.3 of this appendix, and LC = Heat loss due to hot condensate
going down the drain under cyclic conditions as determined in
section 4.1.6.4 of this appendix.
4.1.6.1 Latent heat gain due to condensation under
steady-state conditions. Calculate the latent heat gain (LG,SS)
expressed as a percent and defined as:
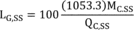
where:
100 = conversion factor to express a decimal as a percent, 1053.3 =
latent heat of vaporization of water, Btu per pound, Mc,ss = mass
of condensate for the steady-state test as determined in section
3.8.1 of this appendix, pounds, and Qc,ss = fuel energy input for
steady-state test as determined in section 3.8.1 of this appendix,
Btu.
4.1.6.2 Heat loss due to hot condensate going down the drain
under steady-state conditions. Calculate the steady-state heat
loss due to hot condensate going down the drain (LC,SS) expressed
as a percent and defined as:

where:
LG,SS = Latent heat gain due to condensation under steady-state
conditions as defined in section 4.1.6.1 of this appendix, 1.0 =
specific heat of water, Btu/lb− °F, TF,SS = Flue (or stack) gas
temperature as defined in section 3.1 of this appendix, °F, 70 =
assumed indoor temperature, °F, 0.45 = specific heat of water
vapor, Btu/lb− °F, and 45 = average outdoor temperature for vented
heaters, °F.
4.1.6.3 Latent heat gain due to condensation under cyclic
conditions. (only for vented heaters tested under the optional
tracer gas procedures of section 3.3 or 3.6 of this appendix)
Calculate the latent heat gain (LG) expressed as a percent and
defined as:
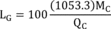
where:
100 = conversion factor to express a decimal as a percent, 1053.3 =
latent heat of vaporization of water, Btu per pound, Mc = mass of
condensate for the cyclic test as determined in 3.8.2 of this
appendix, pounds, and Qc = fuel energy input for cyclic test as
determined in 3.8.2 of this appendix, Btu.
4.1.6.4 Heat loss due to hot condensate going down the drain
under cyclic conditions. (only for vented heaters tested under the
optional tracer gas procedures of section 3.3 or 3.6 of this
appendix) Calculate the cyclic heat loss due to hot condensate
going down the drain (LC) expressed as a percent and defined
as:

where: LG
= Latent heat gain due to condensation under cyclic conditions as
defined in section 4.1.6.3 of this appendix, 1.0 = specific heat of
water, Btu/lb− °F, TF,SS = Flue (or stack) gas temperature as
defined in section 3.1 of this appendix, 70 = assumed indoor
temperature, °F, 0.45 = specific heat of water vapor, Btu/lb− °F,
and 45 = average outdoor temperature for vented heaters, °F.
4.1.7 Ratio of combustion air mass flow rate to
stoichiometric air mass flow rate. Determine the ratio of
combustion air mass flow rate to stoichiometric air mass flow rate
(RT,F), and defined as:
RT,F = A + B/XCO2F where: A = as determined from Table 2 of this
appendix B = as determined from Table 2 of this appendix XCO2F = as
defined in 3.1 of this appendix
4.1.8 Ratio of combustion and relief air mass flow rate to
stoichiometric air mass flow rate. For vented heaters equipped
with either an integral draft diverter or a draft hood, determine
the ratio of combustion and relief air mass flow rate to
stoichiometric air mass flow rate (RT,S), and defined as:
RT,S = A + [B/XCO2S] where: A = as determined from Table 2 of this
appendix, B = as determined from Table 2 of this appendix, and
XCO2S = as defined in section 3.1 of this appendix.
4.1.9 Sensible heat loss at steady-state operation. For
vented heaters equipped with either an integral draft diverter or a
draft hood, determine the sensible heat loss at steady-state
operation (LS,SS,A) expressed as a percent and defined as:
where: LS,SS,A = C(RT,S + D)(TS,SS−TRA) C = as determined from
Table 2 of this appendix RT,S = as defined in 4.1.8 of this
appendix D = as determined from Table 2 of this appendix TS,SS = as
defined in 3.1 of this appendix TRA = as defined in 2.9 of this
appendix
For vented heaters equipped without an integral draft diverter,
determine (LS,SS,A) expressed as a percent and defined as:
LS,SS,A = C(RT,F + D)(TF,SS−TRA) where: C = as determined from
Table 2 of this appendix RT,F = as defined in 4.1.7 of this
appendix D = as determined from Table 2 of this appendix TF,SS = as
defined in 3.1 of this appendix TRA = as defined in 2.9 of this
appendix
4.1.10 Steady-state efficiency. For vented heaters
equipped with single-stage thermostats, calculate the steady-state
efficiency (excluding jacket loss), ηSS, expressed in percent and
defined as:
ηSS = 100−LL,A−LS,SS,A where: LL,A = latent heat loss, as defined
in section 4.1.6 of this appendix (for condensing vented heaters
LL,A* for steady-state conditions), and LS,SS,A = sensible heat
loss at steady-state operation, as defined in section 4.1.9 of this
appendix.
For vented heaters equipped with either two stage controls or
with step-modulating controls, calculate the steady-state
efficiency at the reduced fuel input rate, ηSS−L, expressed in
percent and defined as:
ηSS−L = 100−LL,A−LS,SS,A where: LL,A = latent heat loss, as defined
in section 4.1.6 of this appendix (for condensing vented heaters
LL,A* for steady-state conditions at the reduced firing rate), and
LS,SS,A = sensible heat loss at steady-state operation, as defined
in section 4.1.9 of this appendix, in which LS,SS,A is determined
at the reduced fuel input rate.
For vented heaters equipped with two stage controls, calculate
the steady-state efficiency at the maximum fuel input rate, ηSS−H,
expressed in percent and defined as:
ηSS−H = 100−LL,A−LS,SS,A where: LL,A = latent heat loss, as defined
in section 4.1.6 of this appendix (for condensing vented heaters
LL,A* for steady-state conditions at the maximum fuel input rate),
and LS,SS,A = sensible heat loss at steady-state operation, as
defined in section 4.1.9 of this appendix, in which LS,SS,A is
measured at the maximum fuel input rate.
For vented heaters equipped with step-modulating thermostats,
calculate the weighted-average steady-state efficiency in the
modulating mode, ηSS−MOD, expressed in percent and defined as:

where:
ηSS-H = steady-state efficiency at the maximum fuel input rate, as
defined in section 4.1.10 of this appendix, ηSS-L = steady-state
efficiency at the reduced fuel input rate, as defined in section
4.1.10 of this appendix, TOA* = average outdoor temperature for
vented heaters with step-modulating thermostats operating in the
modulating mode and is obtained from Table 3 or Figure 1 of this
appendix, and TC = balance point temperature which represents a
temperature used to apportion the annual heating load between the
reduced input cycling mode and either the modulating mode or
maximum input cycling mode and is obtained either from Table 3 of
this appendix or calculated by the following equation: TC =
65−[(65−15)R] where: 65 = average outdoor temperature at which a
vented heater starts operating, 15 = national average outdoor
design temperature for vented heaters, and R = ratio of reduced to
maximum heat output rates, as defined in section 4.1.13 of this
appendix.
4.1.11 Reduced heat output rate. For vented heaters
equipped with either two stage thermostats or step-modulating
thermostats, calculate the reduced heat output rate
(Qred-out) defined as: Qred-out = ηSS-L Qred-in where: ηSS-L = as
defined in 4.1.10 of this appendix Qred-in = the reduced fuel input
rate
4.1.12 Maximum heat output rate. For vented heaters
equipped with either two stage thermostats or step-modulating
thermostas, calculate the maximum heat output rate (Qmax-out)
defined as:
Qmax,out = hSS,H Qmax,in where: ηSS-H = as defined in 4.1.10 of
this appendix Qmax-in = the maximum fuel input rate
4.1.13 Ratio of reduced to maximum heat output rates. For
vented heaters equipped with either two stage thermostats or
step-modulating thermostats, calculate the ratio of reduced to
maximum heat output rates (R) expressed as a decimal and defined
as:
R = Qred-out/Qmax-out where: Qred-out = as defined in 4.1.11 of
this appendix Qmax-out = as defined in 4.1.12 of this appendix
4.1.14 Fraction of heating load at reduced operating
mode. For vented heaters equipped with either two stage
thermostats or step-modulating thermostats, determine the fraction
of heating load at the reduced operating mode (X1) expressed as a
decimal and listed in Table 3 of this appendix or obtained from
Figure 2 of this appendix.
4.1.15 Fraction of heating load at maximum operating mode or
noncycling mode. For vented heaters equipped with either two
stage thermostats or step-modulating thermostats, determine the
fraction of heating load at the maximum operating mode or
noncycling mode (X2) expressed as a decimal and listed in Table 3
of this appendix or obtained from Figure 2 of this appendix.
4.1.16 Weighted-average steady-state efficiency. For
vented heaters equipped with single-stage thermostats, the
weighted-average steady-state efficiency (ηSS-WT) is equal to ηSS,
as defined in section 4.1.10 of this appendix. For vented heaters
equipped with two stage thermostats, ηSS-WT is defined as:
ηSS-WT = X1ηSS-L + X2ηSS-H where: X1 = as defined in section 4.1.14
of this appendix ηSS-L = as defined in section 4.1.10 of this
appendix X2 = as defined in section 4.1.15 of this appendix ηSS-H =
as defined in section 4.1.10 of this appendix
For vented heaters equipped with step-modulating controls,
ηSS-WT is defined as:
ηSS-WT = X1ηSS-L + X2ηSS-MOD where: X1 = as defined in section
4.1.14 of this appendix ηSS-L = as defined in section 4.1.10 of
this appendix X2 = as defined in section 4.1.15 of this appendix
ηSS-MOD = as defined in section 4.1.10 of this appendix
4.1.17 Annual fuel utilization efficiency. Calculate the
annual fuel utilization efficiency (AFUE) expressed as percent and
defined as:
AFUE=[0.968ηSS − WT] − 1.78DF − 1.89DS − 129PF − 2.8 LJ + 1.81
where: ηSS-WT = as defined in 4.1.16 of this appendix DF = as
defined in 4.1.2 of this appendix DS = as defined in 4.1.3 of this
appendix PF = as defined in 4.1.4 of this appendix LJ = as defined
in 4.1.5 of this appendix
4.2 Annual fuel utilization efficiency for gas or oil fueled
vented home heating equipment equipped with manual controls.
The following procedure determines the annual fuel utilization
efficiency for gas or oil fueled vented home heating equipment
equipped with manual controls.
4.2.1 Average ratio of stack gas mass flow rate to flue gas
mass flow rate at steady-state operation. For vented heaters
equipped with either direct vents or direct exhaust or that are
outdoor units, the average ratio of stack gas mass flow rate to
flue gas mass flow rate at steady-state operation (S/F) shall be
equal to unity. (S/F = 1) For all other types of vented heaters,
calculate (S/F) defined as:

where:
RT,S = as defined in section 4.1.8 of this appendix with XCO2s as
measured in section 3.1. of this appendix RT,F = as defined in
section 4.1.7 of this appendix with XCO2F as measured in section
3.1. of this appendix
4.2.2 Multiplication factor for infiltration loss during
burner on-cycle. Calculate the multiplication factor for
infiltration loss during burner on-cycle (KI,ON) defined as:

where:
100 = converts a decimal fraction into a percent 0.24 = specific
heat of air A/F = stoichiometric air/fuel ratio, determined in
accordance with Table 2 of this appendix S/F = as defined in
section 4.2.1 of this appendix 0.7 = infiltration parameter RT,F =
as defined in section 4.1.7 of this appendix HHVA = average higher
heating value of the test fuel, determined in accordance with Table
2 of this appendix
4.2.3 On-cycle infiltration heat loss. Calculate the
on-cycle infiltration heat loss (LI,ON) expressed as a percent and
defined as:
LI,ON = KI,ON (70-45) where: KI,ON = as defined in 4.2.2 of this
appendix 70 = average indoor temperature 45 = average outdoor
temperature
4.2.4 Weighted-average steady-state efficiency.
4.2.4.1 For manually controlled heaters with various input rates
the weighted average steady-state efficiency (ηSS−WT), is
determined as follows:
ηSS-WT = 100−LL,A−LS,SS,A where: LL,A = latent heat loss, as
defined in section 4.1.6 of this appendix (for condensing vented
heaters, LL,A* for steady-state conditions), and LS,SS,A =
steady-state efficiency at the reduced fuel input rate, as defined
in section 4.1.9 of this appendix and where LL,A and LS,SS,A are
determined:
(1) at 50 percent of the maximum fuel input rate as measured in
either section 3.1.1 of this appendix for manually controlled gas
vented heaters or section 3.1.2 of this appendix for manually
controlled oil vented heaters, or
(2) at the minimum fuel input rate as measured in either section
3.1.1 of this appendix for manually controlled gas vented heaters
or section 3.1.2 of this appendix for manually controlled oil
vented heaters if the design of the heater is such that the ±5
percent of 50 percent of the maximum fuel input rate cannot be set,
provided this minimum rate is no greater than 2/3 of the maximum
input rate of the heater.
4.2.4.2 For manually controlled heater with one single firing
rate the weighted average steady-state efficiency is the
steady-state efficiency measured at the single firing rate.
4.2.5 Part-load fuel utilization efficiency. Calculate
the part-load fuel utilization efficiency (ηu) expressed as a
percent and defined as:
ηu = ηSS-WT−LI,ON where: ηSS-WT = as defined in 4.2.4 of this
appendix LI,ON = as defined in 4.2.3 of this appendix
4.2.6 Annual Fuel Utilization Efficiency.
4.2.6.1 For manually controlled vented heaters, calculate the
AFUE expressed as a percent and defined as:
where: 2,950 = average number of heating degree
days ηSS = as defined as ηSS−WT in 4.2.4 of this appendix ηu = as
defined in 4.2.5 of this appendix Qin−max = as defined as Qin at
the maximum fuel input rate, as defined in 3.1 of this appendix
4,600 = average number of non-heating season hours per year QP = as
defined in 3.5 of this appendix 2.083 = (65 − 15) / 24 = 50 / 24 65
= degree day base temperature, °F 15 = national average outdoor
design temperature for vented heaters as defined in section 4.1.10
of this appendix 24 = number of hours in a day
4.2.6.2 For manually controlled vented heaters where the pilot
light can be turned off by the user when the heater is not in use
as described in section 3.5.2, calculate the AFUE expressed as a
percent and defined as:
AFUE=ηu where: ηu = as defined in section 4.2.5 of this appendix
4.3 Annual fuel utilization efficiency by the tracer gas
method. The annual fuel utilization efficiency shall be
determined by the following tracer gas method for all vented
heaters equipped with thermal stack dampers.
4.3.1 On-cycle sensible heat loss. For vented heaters
equipped with single-stage thermostats, calculate the on-cycle
sensible heat loss (LS,ON) expressed as a percent and defined
as:
LS,ON = LS,SS,A where: LS,SS,A = as defined in section 4.1.9 of
this appendix For vented heaters equipped with two stage
thermostats, calculate LS,ON defined as: LS,ON = X1LS,SS,A-red +
X2LS,SS,A-max where: X1 = as defined in section 4.1.14 of this
appendix LS,SS,A-red = as defined as LS,SS,A in section 4.1.9 of
this appendix at the reduced fuel input rate X2 = as defined in
section 4.1.15 of this appendix LS,SS,A-max = as defined as LS,SS,A
in section 4.1.9 of this appendix at the maximum fuel input rate
For vented heaters with step-modulating controls, calculate
LS,ON defined as:
LS,ON = X1LS,SS,A-red + X2LS,SS,A-avg where: X1 = as defined in
section 4.1.14 of this appendix LLS,SS,A-red = as defined in
section 4.3.1 of this appendix X2 = as defined in section 4.1.15 of
this appendix LS,SS,A-avg = average sensible heat loss for
step-modulating vented heaters operating in the modulating mode

where:
LS,SS,A-avg = as defined in section 4.3.1 of this appendix TC = as
defined in section 4.1.10 of this appendix TOA* = as defined in
section 4.1.10 of this appendix 15 = as defined in section 4.1.10
of this appendix
4.3.2 On-cycle infiltration heat loss. For vented heaters
equipped with single-stage thermostats, calculate the on-cycle
infiltration heat loss (LI,ON) expressed as a percent and defined
as:
LI,ON = KI,ON(70−45) where: KI,ON = as defined in section 4.2.2 of
this appendix 70 = as defined in section 4.2.3 of this appendix 45
= as defined in section 4.2.3 of this appendix
For vented heaters equipped with two stage thermostats,
calculate LI,ON defined as:
LI,ON = X1KI,ON-Max(70−TOA*) + X2KI,ON,red(70−TOA) where: X1 = as
defined in section 4.1.14 of this appendix KI,ON-max = as defined
as KI,ON in section 4.2.2 of this appendix at the maximum heat
input rate 70 = as defined in section 4.2.3 of this appendix TOA* =
as defined in section 4.3.4 of this appendix KI,ON,red = as defined
as KI,ON in section 4.2.2 of this appendix at the minimum heat
input rate TOA = as defined in section 4.3.4 of this appendix X2 =
as defined in section 4.1.15 of this appendix
For vented heaters equipped with step-modulating thermostats,
calculate LI,ON defined as:
LI,ON = X1KI,ON-avg(70−TOA*) + X2KI,ON,red(70−TOA) where: X1 = as
defined in section 4.1.14 of this appendix

70 = as defined in
section 4.2.3 of this appendix TOA* = as defined in section 4.3.4
of this appendix X2 = as defined in section 4.1.15 of this appendix
TOA = as defined in section 4.3.4 of this appendix
4.3.3 Off-cycle sensible heat loss. For vented heaters
equipped with single-stage thermostats, calculate the off-cycle
sensible heat loss (LS,OFF) at the maximum fuel input rate. For
vented heaters equipped with step-modulating thermostats, calculate
LS,OFF defined as:
LS,OFF = X1 LS,OFF,red where: X1 = as defined in section 4.1.14 of
this appendix, and LS,OFF,red = as defined as LS,OFF in section
4.3.3 of this appendix at the reduced fuel input rate.
For vented heaters equipped with two stage controls, calculate
LS,OFF defined as:
LS,OFF = X1 LS,OFF,red + X2 LS,OFF,Max where: X1 = as defined in
section 4.1.14 of this appendix, LS,OFF,red = as defined as LS,OFF
in section 4.3.3 of this appendix at the reduced fuel input rate,
X2 = as defined in section 4.1.15 of this appendix, and LS,OFF,Max
= as defined as LS,OFF in section 4.3.3 of this appendix at the
maximum fuel input rate.
Calculate the off-cycle sensible heat loss (LS,OFF) expressed as
a percent and defined as:

where:
100 = conversion factor for percent, 0.24 = specific heat of air in
Btu per pound - °F, Qin = fuel input rate, as defined in section
3.1 of this appendix in Btu per minute (as appropriate for the
firing rate), ton = average burner on-time per cycle and is 20
minutes, Σ mS,OFF (TS,OFF −TRA) = summation of the ten values (for
single-stage or step-modulating models) or twenty values (for two
tage models) of the quantity, mS,OFF (TS,OFF −TRA), measured in
accordance with section 3.3 of this appendix, and mS,OFF = stack
gas mass flow rate pounds per minute.

TS,OFF = stack gas
temperature measured in accordance with section 3.3 of this
appendix, TRA = average room temperature measured in accordance
with section 3.3 of this appendix, PB = barometric pressure in
inches of mercury, VT = flow rate of the tracer gas through the
stack in cubic feet per minute, CT* = concentration by volume of
the active tracer gas in the mixture in percent and is 100 when the
tracer gas is a single component gas, CT = concentration by volume
of the active tracer gas in the diluted stack gas in percent, TT =
temperature of the tracer gas entering the flow meter in degrees
Fahrenheit, and (TT + 460) = absolute temperature of the tracer gas
entering the flow meter in degrees Rankine.
4.3.4 Average outdoor temperature. For vented heaters
equipped with single-stage thermostats, the average outdoor
temperature (TOA) is 45 °F. For vented heaters equipped with either
two stage thermostats or step-modulating thermostats, TOA during
the reduced operating mode is obtained from Table 3 or Figure 1 of
this appendix. For vented heaters equipped with two stage
thermostats, TOA* during the maximum operating mode is obtained
from Table 3 or Figure 1 of this appendix.
4.3.5 Off-cycle infiltration heat loss. For vented
heaters equipped with single stage thermostats, calculate the
off-cycle infiltration heat loss (LI,OFF) at the maximum fuel input
rate. For vented heaters equipped with step-modulating thermostats,
calculate LI,OFF defined as:
LI,OFF = X1LI,OFF,red where: X1 = as defined in section 4.1.14 of
this appendix LI,OFF,red = as defined in LI,OFF in section 4.3.5 of
this appendix at the reduced fuel input rate
For vented heaters equipped with two stage thermostats,
calculate LI,OFF defined as:
LI,OFF = X1LI,OFF,red + X2LI,OFF,max where: X1 = as defined in
section 4.1.14 of this appendix LI,OFF,red = as defined as LI,OFF
in section 4.3.5 of this appendix at the reduced fuel input rate X2
= as defined in section 4.1.15 of this appendix LI,OFF,Max = as
defined as LI,OFF in section 4.3.5 of this appendix at the maximum
fuel input rate
Calculate the off-cycle infiltration heat loss (LI,OFF)
expressed as a percent and defined as:

where:
100 = conversion factor for percent 0.24 = specific heat of air in
Btu per pound - °F 1.3 = dimensionless factor for converting
laboratory measured stack flow to typical field conditions 0.7 =
infiltration parameter 70 = assumed average indoor air temperature,
°F TOA = average outdoor temperature as defined in section 4.3.4 of
this appendix Qin = fuel input rate, as defined in section 3.1 of
this appendix in Btu per minute (as appropriate for the firing
rate) ton = average burner on-time per cycle and is 20 minutes Σ
mS,OFF = summation of the twenty values of the quantity, mS,OFF,
measured in accordance with section 3.3 of this appendix mS,OFF =
as defined in section 4.3.3 of this appendix
4.3.6 Part-load fuel utilization efficiency. Calculate
the part-load fuel utilization efficiency (ηu) expressed as a
percent and defined as:

where: Cj
= 2.8, adjustment factor, Lj = jacket loss as defined in section
4.1.5, LL,A = Latent heat loss, as defined in section 4.1.6 of this
appendix (for condensing vented heaters LL,A* for cyclic
conditions), ton = Average burner on time which is 20 minutes,
LS,ON = On-cycle sensible heat loss, as defined in section 4.3.1 of
this appendix, LS,OFF = Off-cycle sensible heat loss, as defined in
section 4.3.3 of this appendix, LI,ON = On-cycle infiltration heat
loss, as defined in section 4.3.2 of this appendix, LI,OFF =
Off-cycle infiltration heat loss, as defined in section 4.3.5 of
this appendix, PF = Pilot fraction, as defined in section 4.1.4 of
this appendix, and tOFF = average burner off-time per cycle, which
is 20 minutes.
4.3.7 Annual Fuel Utilization Efficiency.
Calculate the AFUE expressed as a percent and defined as:
where: 2,950 = average number of heating degree
days ηSS-WT = as defined in 4.1.16 of this appendix ηu = as defined
in 4.3.6 of this appendix Qin−max = as defined in 4.2.6 of this
appendix 4,600 = as specified in 4.2.6 of this appendix QP = as
defined in 3.5 of this appendix 2.083 = as specified in 4.2.6 of
this appendix
4.4 Stack damper effectiveness for vented heaters equipped
with electro-mechanical stack dampers. Determine the stack
damper effectiveness for vented heaters equipped with
electro-mechanical stack dampers (Do), defined as:
Do = 1.62 [1 - AD cos Ω/AS] where: AD = as defined in 3.4 of this
appendix Ω = as defined in 3.4 of this appendix AS = as defined in
3.4 of this appendix
4.5 Addition requirements for vented home heating equipment
using indoor air for combustion and draft control. For vented
home heating equipment using indoor air for combustion and draft
control, DF, as described in section 4.1.2 of this appendix, and
DS, as described in section 4.1.3 of this appendix, shall be
determined from Table 1 of this appendix.
4.5.1 Optional procedure for determining DP for vented
home heating equipment. Calculate the ratio (DP) of the rate of
flue gas mass through the vented heater during the off-period,
MF,OFF(TF,SS), to the rate of flue gas mass flow during the
on-period, MF,SS(TF,SS), and defined as:
DP = MF,OFF(TF,SS)/MF,SS(TF,SS)
For vented heaters in which no draft is maintained during the
steady-state or cool down tests, MF,OFF(TF,SS) is defined as:
For oil fueled vented heaters in which an imposed draft is
maintained, as described in section 3.6 of this appendix,
MF,OFF(TF,SS) is defined as:
MF,OFF(TF,SS) = MF,OFF(T*F,OFF) where: TF,SS = as defined in
section 3.1.1 of this appendix, T*F,OFF = flue gas temperature
during the off-period measured in accordance with section 3.6 of
this appendix in degrees Fahrenheit, and TRA = as defined in
section 2.9 of this appendix.

PB = barometric
pressure measured in accordance with section 3.6 of this appendix
in inches of mercury, VT = flow rate of tracer gas through the
vented heater measured in accordance with section 3.6 of this
appendix in cubic feet per minute, CT = concentration by volume of
tracer gas present in the flue gas sample measured in accordance
with section 3.6 of this appendix in percent, CT* = concentration
by volume of the active tracer gas in the mixture in percent and is
100 when the tracer gas is a single component gas, TT = the
temperature of the tracer gas entering the flow meter measured in
accordance with section 3.6 of this appendix in degrees Fahrenheit,
and (TT + 460) = absolute temperature of the tracer gas entering
the flow meter in degrees Rankine. MF,SS(TF,SS) = Qin[RT,F(A/F) +
1]/[60HHVA] Qin = as defined in section 3.1 of this appendix, RT,F
= as defined in section 4.1.7 of this appendix, A/F = as defined in
section 4.2.2 of this appendix, and HHVA = as defined in section
4.2.2 of this appendix.
4.5.2 Optional procedure for determining off-cycle draft
factor for flue gas flow for vented heaters. For systems
numbered 1 through 10, calculate the off-cycle draft factor for
flue gas flow (DF) defined as:
DF = DP For systems numbered 11 or 12: DF = DP DO For systems
complying with section 3.6.1 or 3.6.2, DF = 0.05 Where: DP = as
defined in section 4.5.1. of this appendix, and DO = as defined in
section 4.4 of this appendix.
4.5.3 Optional procedure for determining off-cycle draft
factor for stack gas flow for vented heaters. Calculate the
off-cycle draft factor for stack gas flow (DS) defined as:
For systems numbered 1 or 2: DS = 1.0 For systems numbered 3 or 4:
DS = (DP + 0.79)/1.4 For systems numbered 5 or 6: DS = DO For
systems numbered 7 or 8 and if DO(S/F)<1:DS = DO DP For systems
numbered 7 or 8 and if DO(S/F)>1: DS = DO DP + [0.85−DO DP]
[DO(S/F)−1]/[S/F−1] where: DP = as defined in section 4.5.1 or
3.6.1 of this appendix, as applicable DO = as defined in section
4.4 of this appendix
4.6 Annual energy consumption.
4.6.1 National average number of burner operating hours.
For vented heaters equipped with single stage controls or manual
controls, the national average number of burner operating hours
(BOH) is defined as:
BOHSS = 1,416AFA DHR−1,416 B where: 1,416 = national average
heating load hours for vented heaters based on 2,950 degree days
and 15 °F outdoor design temperature AF = 0.7067, adjustment factor
to adjust the calculated design heating requirement and heating
load hours to the actual heating load experienced by the heating
system DHR = typical design heating requirements based on QOUT,
from Table 4 of this appendix. QOUT = [(ηSS/100)−Cj (Lj/100)] Qin
Lj = jacket loss as defined in 4.1.5 of this appendix Cj = 2.8,
adjustment factor as defined in 4.3.6 of this appendix ηSS =
steady-state efficiency as defined in 4.1.10 of this appendix,
percent Qin = as defined in 3.1 of this appendix at the maximum
fuel input rate A = 100,000/[341,300PE + (Qin−QP)ηu] B = 2.938(QP)
ηu A/100,000 100,000 = factor that accounts for percent and kBtu PE
= as defined in 3.1.3 of this appendix QP = as defined in 3.5 of
this appendix ηu = as defined in 4.3.6 of this appendix for vented
heaters using the tracer gas method, percent = as defined in 4.2.5
of this appendix for manually controlled vented heaters, percent =
2,950 AFUEηSS Qin/[2,950 ηSS Qin - AFUE(2.083)(4,600)QP], for
vented heaters equipped without manual controls and without thermal
stack dampers and not using the optional tracer gas method, where:
AFUE = as defined in 4.1.17 of this appendix, percent 2,950 =
average number of heating degree days as defined in 4.2.6 of this
appendix 4,600 = average number of non-heating season hours per
year as defined in 4.2.6 of this appendix 2.938 = (4,160/1,416) =
ratio of the average length of the heating season in hours to the
average heating load hours 2.083 = as specified in 4.2.6 of this
appendix
4.6.1.1 For vented heaters equipped with two stage or step
modulating controls the national average number of burner operating
hours at the reduced operating mode is defined as:
BOHR = X1EM/Qred-in where: X1 = as defined in 4.1.14 of this
appendix Qred-in = as defined in 4.1.11 of this appendix EM =
average annual energy used during the heating season =
(Qin−QP)BOHSS + (8,760−4,600)QP Qin = as defined in 3.1 of this
appendix at the maximum fuel input rate QP = as defined in 3.5 of
this appendix BOHSS = as defined in 4.6.1 of this appendix, in
which the term PE in the factor A is increased by the factor R,
which is defined in 3.1.3 of this appendix as: R = 1.3 for two
stage controls = 1.4 for step modulating controls when the ratio of
minimum-to-maximum fuel input is greater than or equal to 0.7 = 1.7
for step modulating controls when the ratio of minimum-to-maximum
fuel input is less than 0.7 and greater than or equal to 0.5 = 2.2
for step modulating controls when the ratio of minimum-to-maximum
fuel input is less than 0.5 A = 100,000/[341,300 PE R + (Qin −
QP)ηu] 8,760 = total number of hours per year 4,600 = as specified
in 4.2.6 of this appendix
4.6.1.2 For vented heaters equipped with two stage or step
modulating controls the national average number of burner operating
hours at the maximum operating mode (BOHH) is defined as:
BOHH = X2EM/Qin where: X2 = as defined in 4.1.15 of this appendix
EM = average annual energy used during the heating season =
(Qin−QP)BOHSS + (8,760−4,600)QP Qin = as defined in 3.1 of this
appendix at the maximum fuel input rate
4.6.2 Average annual fuel energy for gas or oil fueled vented
heaters. For vented heaters equipped with single stage controls
or manual controls, the average annual fuel energy consumption (EF)
is expressed in Btu per year and defined as:
EF = BOHSS (Qin−QP) + 8,760 QP where: BOHSS = as defined in 4.6.1
of this appendix Qin = as defined in 3.1 of this appendix QP = as
defined in 3.5 of this appendix 8,760 = as specified in 4.6.1 of
this appendix
4.6.2.1 For vented heaters equipped with either two stage or
step modulating controls EF is defined as:
EF = EM + 4,600QP where: EM = as defined in 4.6.1.2 of this
appendix 4,600 = as specified 4.2.6 of this appendix QP = as
defined in 3.5 of this appendix
4.6.3 Average annual auxiliary electrical energy consumption
for vented heaters. For vented heaters with single-stage
controls or manual controls, the average annual auxiliary
electrical consumption (EAE) is expressed in kilowatt-hours and
defined as:
EAE = BOHSSPE + ESO Where: BOHSS = as defined in 4.6.1 of this
appendix PE = as defined in 3.1.3 of this appendix ESO = as defined
in 4.7 of this appendix
4.6.3.1 For vented heaters with two-stage or modulating
controls, EAE is defined as:
EAE = (BOHR + BOHH)PE + ESO Where: BOHR = as defined in 4.6.1 of
this appendix BOHH = as defined in 4.6.1 of this appendix PE = as
defined in 3.1.3 of this appendix ESO = as defined in 4.7 of this
appendix
4.6.4 Average annual energy consumption for vented heaters
located in a different geographic region of the United States and
in buildings with different design heating requirements.
4.6.4.1 Average annual fuel energy consumption for gas or oil
fueled vented home heaters located in a different geographic region
of the United States and in buildings with different design heating
requirements. For gas or oil fueled vented heaters the average
annual fuel energy consumption for a specific geographic region and
a specific typical design heating requirement (EFR) is expressed in
Btu per year and defined as:
EFR = (EF−8,760 QP)(HLH/1,416) + 8,760QP where: EF = as defined in
4.6.2 of this appendix 8,760 = as specified in 4.6.1 of this
appendix QP = as defined in 3.5 of this appendix HLH = heating load
hours for a specific geographic region determined from the heating
load hour map in Figure 3 of this appendix 1,416 = as specified in
4.6.1 of this appendix
4.6.4.2 Average annual auxiliary electrical energy
consumption for gas or oil fueled vented home heaters located in a
different geographic region of the United States and in buildings
with different design heating requirements. For gas or oil
fueled vented home heaters the average annual auxiliary electrical
energy consumption for a specific geographic region and a specific
typical design heating requirement (EAER) is expressed in
kilowatt-hours and defined as:
EAER = EAE HLH/1,416 where: EAE = as defined in 4.6.3 of this
appendix HLH = as defined in 4.6.4.1 of this appendix 1,416 = as
specified in 4.6.1 of this appendix
Table 1 - Off-Cycle Draft Factors for Flue
Gas Flow (DF) and for Stack Gas Flow (DS) for Vented Home Heating
Equipment Equipped Without Thermal Stack Dampers
System number |
(DF) |
(DS) |
Burner type |
Venting system type
1 |
1 |
1.0 |
1.0 |
Atmospheric |
Draft hood or diverter. |
2 |
0.4 |
1.0 |
Power |
Draft hood or diverter. |
3 |
1.0 |
1.0 |
Atmospheric |
Barometric draft
regulator. |
4 |
0.4 |
0.85 |
Power |
Barometric draft
regulator. |
5 |
1.0 |
DO |
Atmospheric |
Draft hood or diverter with
damper. |
6 |
0.4 |
DO |
Power |
Draft hood or diverter with
damper. |
7 |
1.0 |
DO |
Atmospheric |
Barometric draft regulator
with damper. |
8 |
0.4 |
DODP |
Power |
Barometric draft regulator
with damper. |
9 |
1.0 |
0 |
Atmospheric |
Direct vent. |
10 |
0.4 |
0 |
Power |
Direct vent. |
11 |
DO |
0 |
Atmospheric |
Direct vent with damper. |
12 |
0.4 DO |
0 |
Power |
Direct vent with damper. |
Table 2 - Values of Higher Heating Value
(HHV(A), Stoichiometric Air/Fuel (A/F), Latent Heat Loss (LL,A) and
Fuel-Specified Parameters (A, B, C, and D) for Typical Fuels
Fuels |
HHVA (Btu/lb) |
A/F |
LL,A |
A |
B |
C |
D |
No. 1 oil |
19,800 |
14.56 |
6.55 |
0.0679 |
14.22 |
0.0179 |
0.167 |
No. 2 oil |
19,500 |
14.49 |
6.50 |
0.0667 |
14.34 |
0.0181 |
0.167 |
Natural gas |
20,120 |
14.45 |
9.55 |
0.0919 |
10.96 |
0.0175 |
0.171 |
Manufactured
gas |
18,500 |
11.81 |
10.14 |
0.0965 |
10.10 |
0.0155 |
0.235 |
Propane |
21,500 |
15.58 |
7.99 |
0.0841 |
12.60 |
0.0177 |
0.151 |
Butane |
20,000 |
15.36 |
7.79 |
0.0808 |
12.93 |
0.0180 |
0.143 |
Table 3 - Fraction of Heating Load at
Reduced Operating Mode (X1) and at Maximum Operating Mode (X2),
Average Outdoor Temperatures (TOA and TOA*), and Balance Point
Temperature (TC) for Vented Heaters Equipped With Either Two-Stage
Thermostats or Step-Modulating Thermostats
Heat output ratio
a |
X1 |
X2 |
TOA |
TOA* |
TC |
0.20 to 0.24 |
.12 |
.88 |
57 |
40 |
53 |
0.25 to 0.29 |
.16 |
.84 |
56 |
39 |
51 |
0.30 to 0.34 |
.20 |
.80 |
54 |
38 |
49 |
0.35 to 0.39 |
.30 |
.70 |
53 |
36 |
46 |
0.40 to 0.44 |
.36 |
.64 |
52 |
35 |
44 |
0.45 to 0.49 |
.43 |
.57 |
51 |
34 |
42 |
0.50 to 0.54 |
.52 |
.48 |
50 |
32 |
39 |
0.55 to 0.59 |
.60 |
.40 |
49 |
30 |
37 |
0.60 to 0.64 |
.70 |
.30 |
48 |
29 |
34 |
0.65 to 0.69 |
.76 |
.24 |
47 |
27 |
32 |
0.70 to 0.74 |
.84 |
.16 |
46 |
25 |
29 |
0.75 to 0.79 |
.88 |
.12 |
46 |
22 |
27 |
0.80 to 0.84 |
.94 |
.06 |
45 |
20 |
23 |
0.85 to 0.89 |
.96 |
.04 |
45 |
18 |
21 |
0.90 to 0.94 |
.98 |
.02 |
44 |
16 |
19 |
0.95 to 0.99 |
.99 |
.01 |
44 |
13 |
17 |
Table 4 - Average Design Heating
Requirements for Vented Heaters With Different Output
Capacities
Vented heaters output
capacity Qout - (Btu/hr) |
Average design heating
requirements (kBtu/hr) |
5,000-7,499 |
5.0 |
7,500-10,499 |
7.5 |
10,500-13,499 |
10.0 |
13,500-16,499 |
12.5 |
16,500-19,499 |
15.0 |
19,500-22,499 |
17.5 |
22,500-26,499 |
20.5 |
26,500-30,499 |
23.5 |
30,500-34,499 |
26.5 |
34,500-38,499 |
30.0 |
38,500-42,499 |
33.5 |
42,500-46,499 |
36.5 |
46,500-51,499 |
40.0 |
51,500-56,499 |
44.0 |
56,500-61,499 |
48.0 |
61,500-66,499 |
52.0 |
66,500-71,499 |
56.0 |
71,500-76,500 |
60.0 |
4.7 Average annual electric standby mode and off mode energy
consumption.
Calculate the annual electric standby mode and off mode energy
consumption, ESO, defined as, in kilowatt-hours:
ESO = ((PW,SB * (4160 - BOH)) + (PW,OFF * 4600)) * K Where: PW,SB =
vented heater standby mode power, in watts, as measured in section
3.7 of this appendix 4160 = average heating season hours per year
PW,OFF = vented heater off mode power, in watts, as measured in
section 3.7 of this appendix 4600 = average non-heating season
hours per year K = 0.001 kWh/Wh, conversion factor for watt-hours
to kilowatt-hours BOH = burner operating hours as calculated in
section 4.6.1 of this appendix where for single-stage controls or
manual controls vented heaters BOH = BOHSS and for vented heaters
equipped with two-stage or modulating controls BOH = (BOHR + BOHH).
[49 FR 12169, Mar. 28, 1984, as amended at 62 FR 26162, May 12,
1997; 77 FR 74571, Dec. 17, 2012; 80 FR 806, Jan. 6, 2015]